Case Study on CFD Heat Transfer from Fins
VerifiedAdded on 2023/04/03
|21
|2757
|52
AI Summary
This case study focuses on the heat transfer from fins using Computational Fluid Dynamics (CFD). It explores different configurations of the inlet and outlet ducts to determine the best cooling effect on the fins. The study also investigates the impact of fin orientation on temperature distribution. ANSYS software is used for modeling and analysis, with the governing equations of mass, momentum, and heat transfer. The results show the minimum and maximum temperatures for each configuration.
Contribute Materials
Your contribution can guide someone’s learning journey. Share your
documents today.
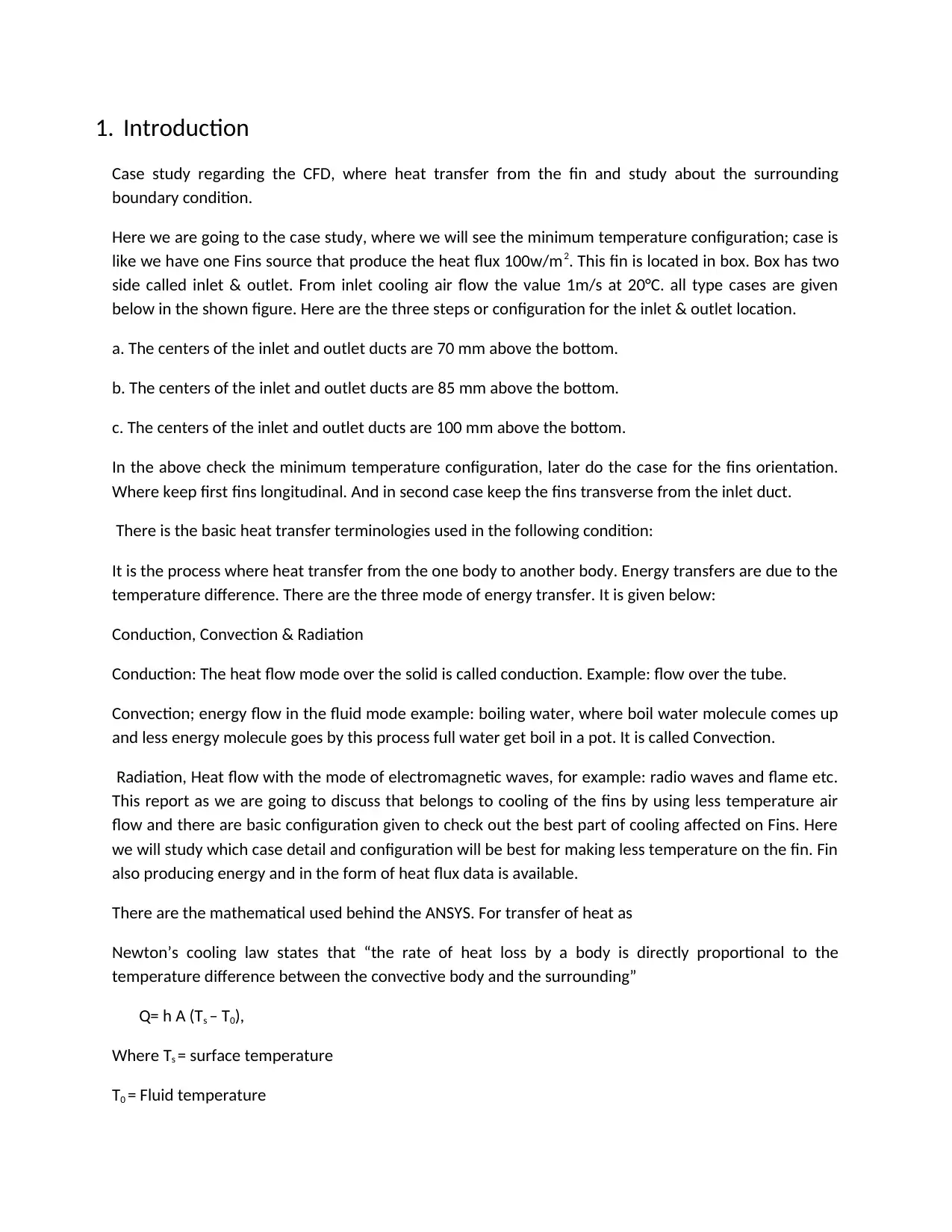
1. Introduction
Case study regarding the CFD, where heat transfer from the fin and study about the surrounding
boundary condition.
Here we are going to the case study, where we will see the minimum temperature configuration; case is
like we have one Fins source that produce the heat flux 100w/m2. This fin is located in box. Box has two
side called inlet & outlet. From inlet cooling air flow the value 1m/s at 20°C. all type cases are given
below in the shown figure. Here are the three steps or configuration for the inlet & outlet location.
a. The centers of the inlet and outlet ducts are 70 mm above the bottom.
b. The centers of the inlet and outlet ducts are 85 mm above the bottom.
c. The centers of the inlet and outlet ducts are 100 mm above the bottom.
In the above check the minimum temperature configuration, later do the case for the fins orientation.
Where keep first fins longitudinal. And in second case keep the fins transverse from the inlet duct.
There is the basic heat transfer terminologies used in the following condition:
It is the process where heat transfer from the one body to another body. Energy transfers are due to the
temperature difference. There are the three mode of energy transfer. It is given below:
Conduction, Convection & Radiation
Conduction: The heat flow mode over the solid is called conduction. Example: flow over the tube.
Convection; energy flow in the fluid mode example: boiling water, where boil water molecule comes up
and less energy molecule goes by this process full water get boil in a pot. It is called Convection.
Radiation, Heat flow with the mode of electromagnetic waves, for example: radio waves and flame etc.
This report as we are going to discuss that belongs to cooling of the fins by using less temperature air
flow and there are basic configuration given to check out the best part of cooling affected on Fins. Here
we will study which case detail and configuration will be best for making less temperature on the fin. Fin
also producing energy and in the form of heat flux data is available.
There are the mathematical used behind the ANSYS. For transfer of heat as
Newton’s cooling law states that “the rate of heat loss by a body is directly proportional to the
temperature difference between the convective body and the surrounding”
Q= h A (Ts – T0),
Where Ts = surface temperature
T0 = Fluid temperature
Case study regarding the CFD, where heat transfer from the fin and study about the surrounding
boundary condition.
Here we are going to the case study, where we will see the minimum temperature configuration; case is
like we have one Fins source that produce the heat flux 100w/m2. This fin is located in box. Box has two
side called inlet & outlet. From inlet cooling air flow the value 1m/s at 20°C. all type cases are given
below in the shown figure. Here are the three steps or configuration for the inlet & outlet location.
a. The centers of the inlet and outlet ducts are 70 mm above the bottom.
b. The centers of the inlet and outlet ducts are 85 mm above the bottom.
c. The centers of the inlet and outlet ducts are 100 mm above the bottom.
In the above check the minimum temperature configuration, later do the case for the fins orientation.
Where keep first fins longitudinal. And in second case keep the fins transverse from the inlet duct.
There is the basic heat transfer terminologies used in the following condition:
It is the process where heat transfer from the one body to another body. Energy transfers are due to the
temperature difference. There are the three mode of energy transfer. It is given below:
Conduction, Convection & Radiation
Conduction: The heat flow mode over the solid is called conduction. Example: flow over the tube.
Convection; energy flow in the fluid mode example: boiling water, where boil water molecule comes up
and less energy molecule goes by this process full water get boil in a pot. It is called Convection.
Radiation, Heat flow with the mode of electromagnetic waves, for example: radio waves and flame etc.
This report as we are going to discuss that belongs to cooling of the fins by using less temperature air
flow and there are basic configuration given to check out the best part of cooling affected on Fins. Here
we will study which case detail and configuration will be best for making less temperature on the fin. Fin
also producing energy and in the form of heat flux data is available.
There are the mathematical used behind the ANSYS. For transfer of heat as
Newton’s cooling law states that “the rate of heat loss by a body is directly proportional to the
temperature difference between the convective body and the surrounding”
Q= h A (Ts – T0),
Where Ts = surface temperature
T0 = Fluid temperature
Secure Best Marks with AI Grader
Need help grading? Try our AI Grader for instant feedback on your assignments.
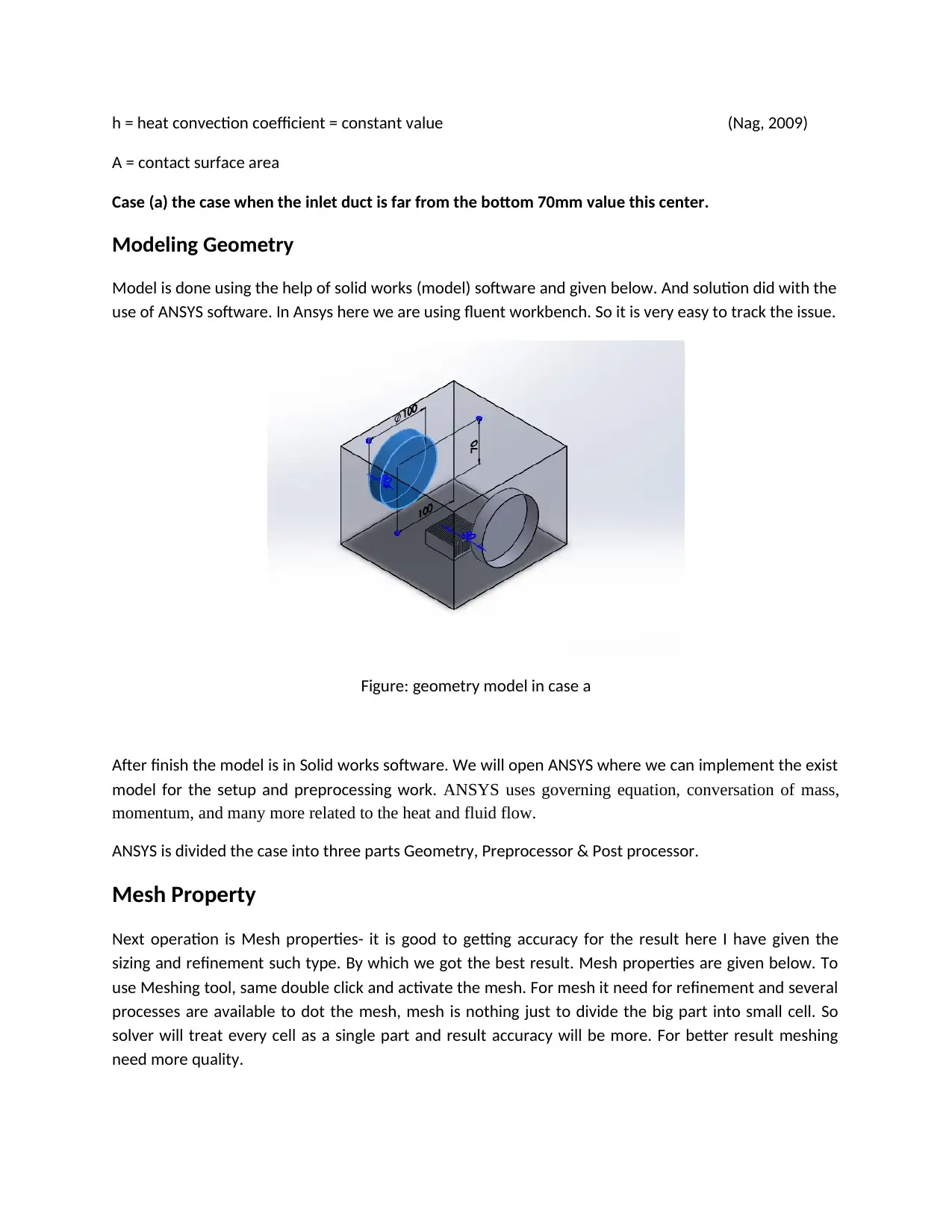
h = heat convection coefficient = constant value (Nag, 2009)
A = contact surface area
Case (a) the case when the inlet duct is far from the bottom 70mm value this center.
Modeling Geometry
Model is done using the help of solid works (model) software and given below. And solution did with the
use of ANSYS software. In Ansys here we are using fluent workbench. So it is very easy to track the issue.
Figure: geometry model in case a
After finish the model is in Solid works software. We will open ANSYS where we can implement the exist
model for the setup and preprocessing work. ANSYS uses governing equation, conversation of mass,
momentum, and many more related to the heat and fluid flow.
ANSYS is divided the case into three parts Geometry, Preprocessor & Post processor.
Mesh Property
Next operation is Mesh properties- it is good to getting accuracy for the result here I have given the
sizing and refinement such type. By which we got the best result. Mesh properties are given below. To
use Meshing tool, same double click and activate the mesh. For mesh it need for refinement and several
processes are available to dot the mesh, mesh is nothing just to divide the big part into small cell. So
solver will treat every cell as a single part and result accuracy will be more. For better result meshing
need more quality.
A = contact surface area
Case (a) the case when the inlet duct is far from the bottom 70mm value this center.
Modeling Geometry
Model is done using the help of solid works (model) software and given below. And solution did with the
use of ANSYS software. In Ansys here we are using fluent workbench. So it is very easy to track the issue.
Figure: geometry model in case a
After finish the model is in Solid works software. We will open ANSYS where we can implement the exist
model for the setup and preprocessing work. ANSYS uses governing equation, conversation of mass,
momentum, and many more related to the heat and fluid flow.
ANSYS is divided the case into three parts Geometry, Preprocessor & Post processor.
Mesh Property
Next operation is Mesh properties- it is good to getting accuracy for the result here I have given the
sizing and refinement such type. By which we got the best result. Mesh properties are given below. To
use Meshing tool, same double click and activate the mesh. For mesh it need for refinement and several
processes are available to dot the mesh, mesh is nothing just to divide the big part into small cell. So
solver will treat every cell as a single part and result accuracy will be more. For better result meshing
need more quality.
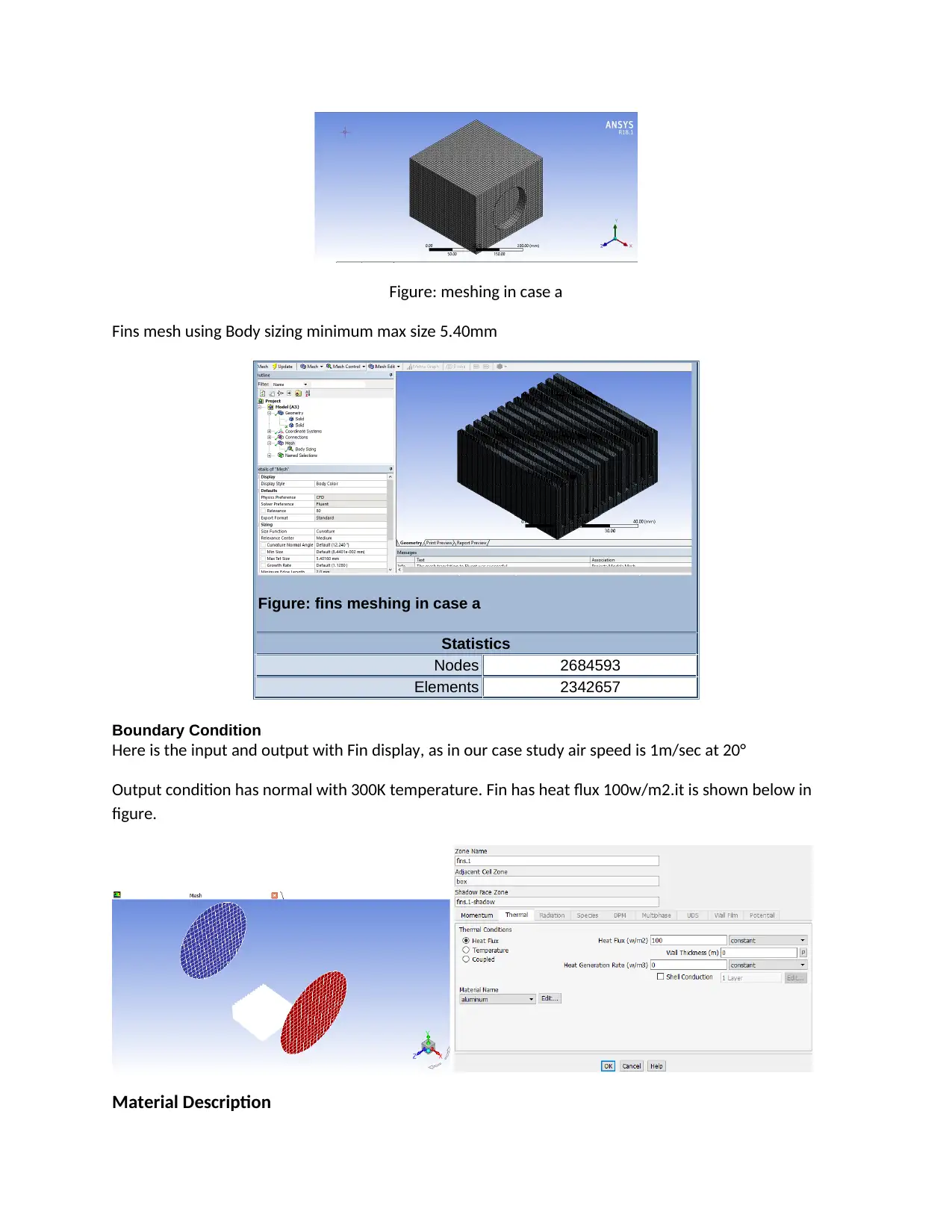
Figure: meshing in case a
Fins mesh using Body sizing minimum max size 5.40mm
Figure: fins meshing in case a
Statistics
Nodes 2684593
Elements 2342657
Boundary Condition
Here is the input and output with Fin display, as in our case study air speed is 1m/sec at 20°
Output condition has normal with 300K temperature. Fin has heat flux 100w/m2.it is shown below in
figure.
Material Description
Fins mesh using Body sizing minimum max size 5.40mm
Figure: fins meshing in case a
Statistics
Nodes 2684593
Elements 2342657
Boundary Condition
Here is the input and output with Fin display, as in our case study air speed is 1m/sec at 20°
Output condition has normal with 300K temperature. Fin has heat flux 100w/m2.it is shown below in
figure.
Material Description
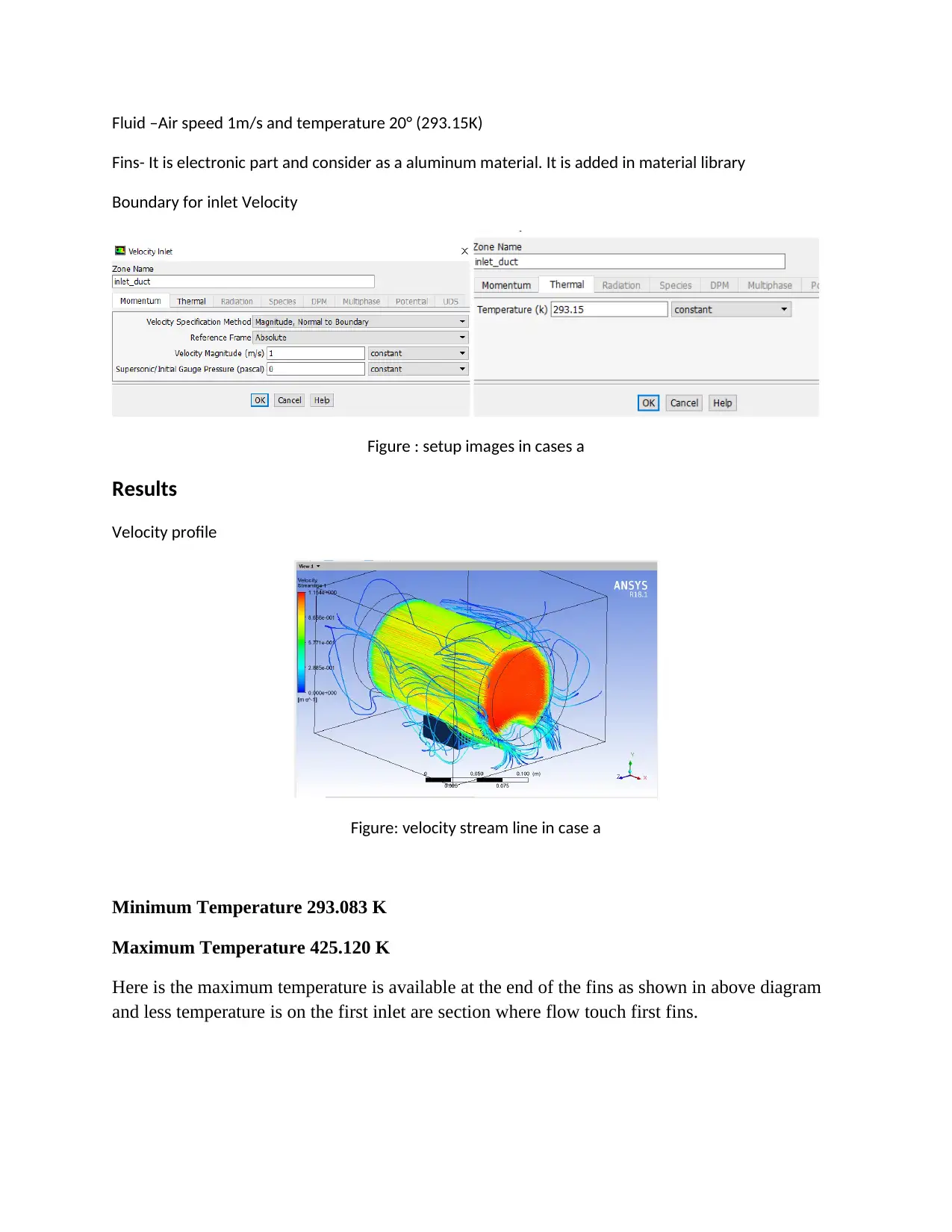
Fluid –Air speed 1m/s and temperature 20° (293.15K)
Fins- It is electronic part and consider as a aluminum material. It is added in material library
Boundary for inlet Velocity
Figure : setup images in cases a
Results
Velocity profile
Figure: velocity stream line in case a
Minimum Temperature 293.083 K
Maximum Temperature 425.120 K
Here is the maximum temperature is available at the end of the fins as shown in above diagram
and less temperature is on the first inlet are section where flow touch first fins.
Fins- It is electronic part and consider as a aluminum material. It is added in material library
Boundary for inlet Velocity
Figure : setup images in cases a
Results
Velocity profile
Figure: velocity stream line in case a
Minimum Temperature 293.083 K
Maximum Temperature 425.120 K
Here is the maximum temperature is available at the end of the fins as shown in above diagram
and less temperature is on the first inlet are section where flow touch first fins.
Secure Best Marks with AI Grader
Need help grading? Try our AI Grader for instant feedback on your assignments.
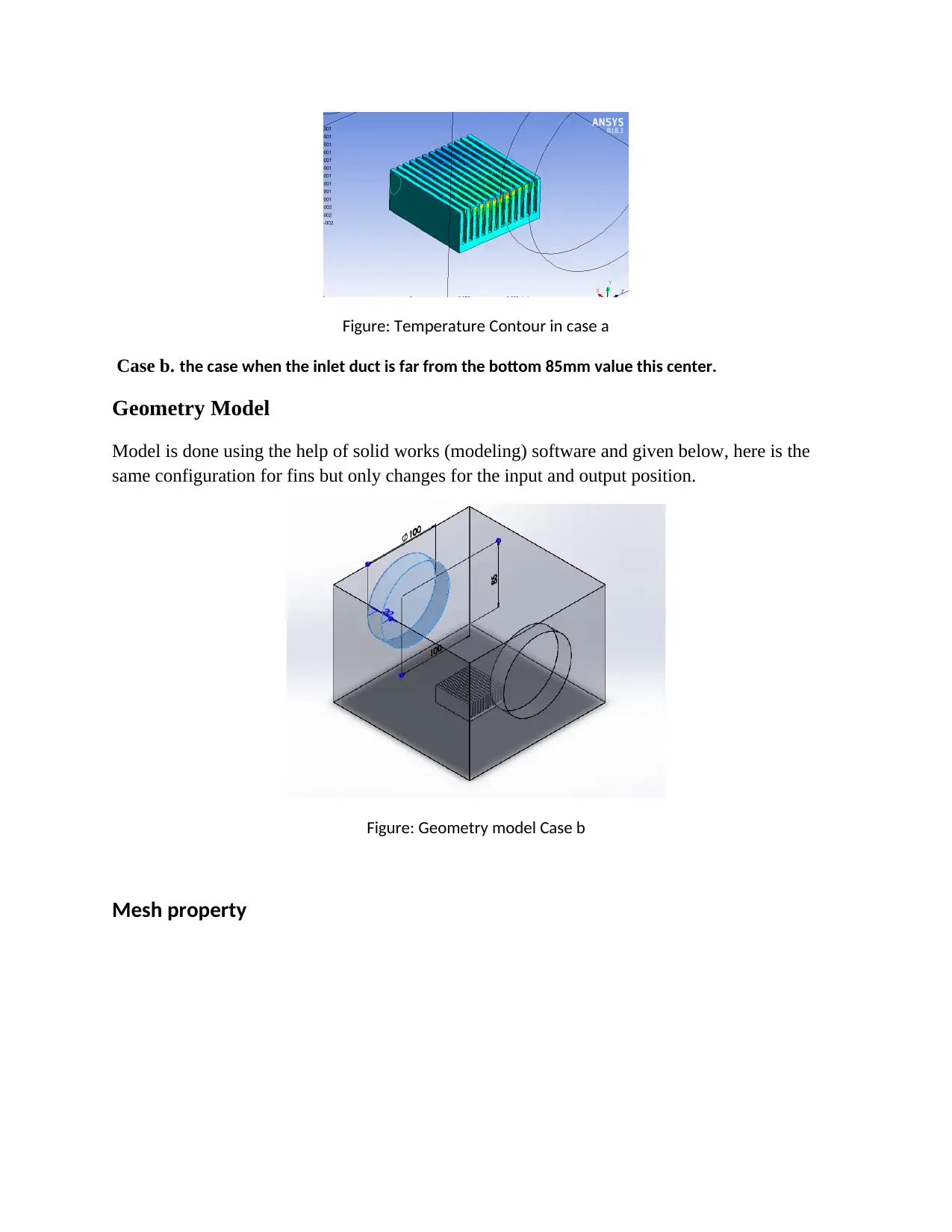
Figure: Temperature Contour in case a
Case b. the case when the inlet duct is far from the bottom 85mm value this center.
Geometry Model
Model is done using the help of solid works (modeling) software and given below, here is the
same configuration for fins but only changes for the input and output position.
Figure: Geometry model Case b
Mesh property
Case b. the case when the inlet duct is far from the bottom 85mm value this center.
Geometry Model
Model is done using the help of solid works (modeling) software and given below, here is the
same configuration for fins but only changes for the input and output position.
Figure: Geometry model Case b
Mesh property
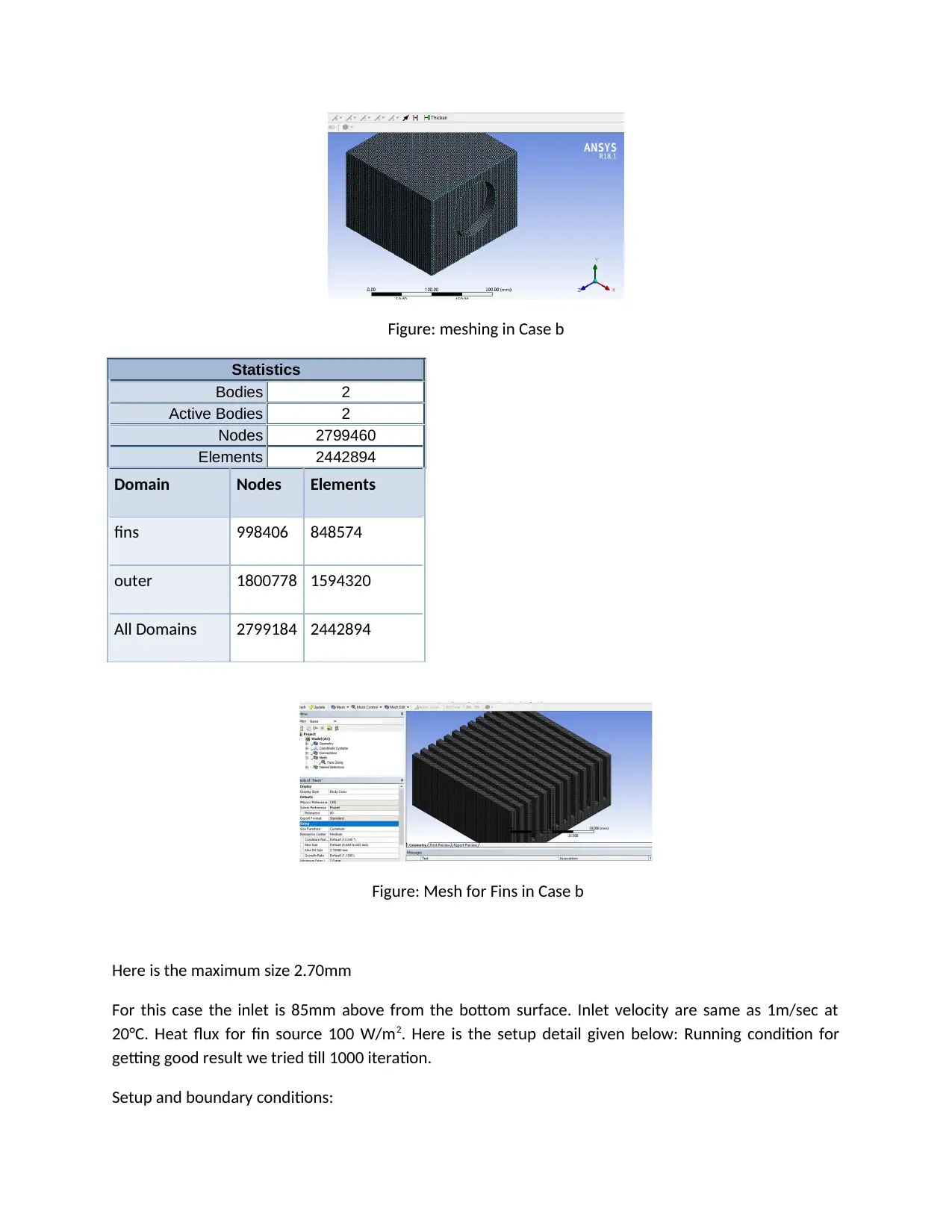
Figure: meshing in Case b
Statistics
Bodies 2
Active Bodies 2
Nodes 2799460
Elements 2442894
Domain Nodes Elements
fins 998406 848574
outer 1800778 1594320
All Domains 2799184 2442894
Figure: Mesh for Fins in Case b
Here is the maximum size 2.70mm
For this case the inlet is 85mm above from the bottom surface. Inlet velocity are same as 1m/sec at
20°C. Heat flux for fin source 100 W/m2. Here is the setup detail given below: Running condition for
getting good result we tried till 1000 iteration.
Setup and boundary conditions:
Statistics
Bodies 2
Active Bodies 2
Nodes 2799460
Elements 2442894
Domain Nodes Elements
fins 998406 848574
outer 1800778 1594320
All Domains 2799184 2442894
Figure: Mesh for Fins in Case b
Here is the maximum size 2.70mm
For this case the inlet is 85mm above from the bottom surface. Inlet velocity are same as 1m/sec at
20°C. Heat flux for fin source 100 W/m2. Here is the setup detail given below: Running condition for
getting good result we tried till 1000 iteration.
Setup and boundary conditions:
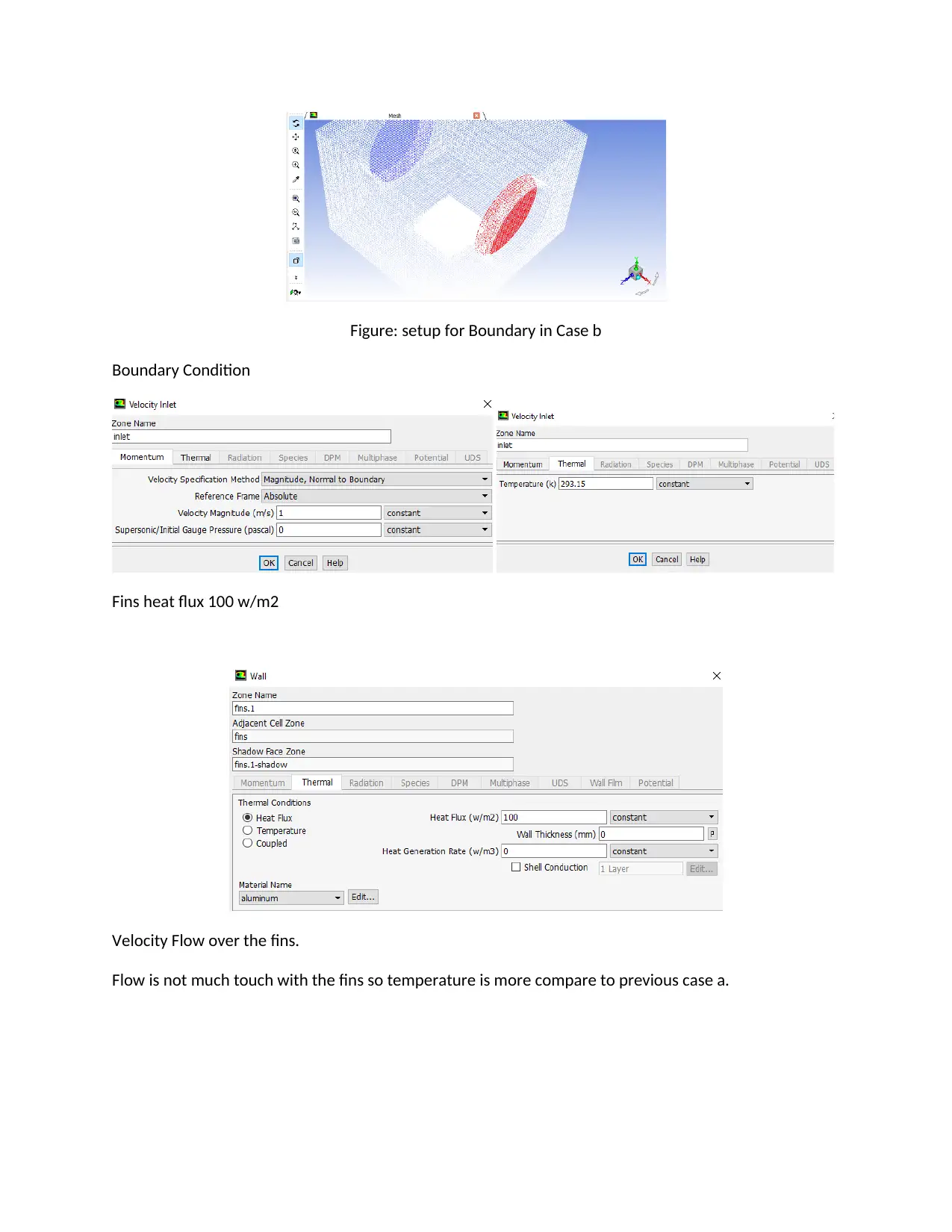
Figure: setup for Boundary in Case b
Boundary Condition
Fins heat flux 100 w/m2
Velocity Flow over the fins.
Flow is not much touch with the fins so temperature is more compare to previous case a.
Boundary Condition
Fins heat flux 100 w/m2
Velocity Flow over the fins.
Flow is not much touch with the fins so temperature is more compare to previous case a.
Paraphrase This Document
Need a fresh take? Get an instant paraphrase of this document with our AI Paraphraser
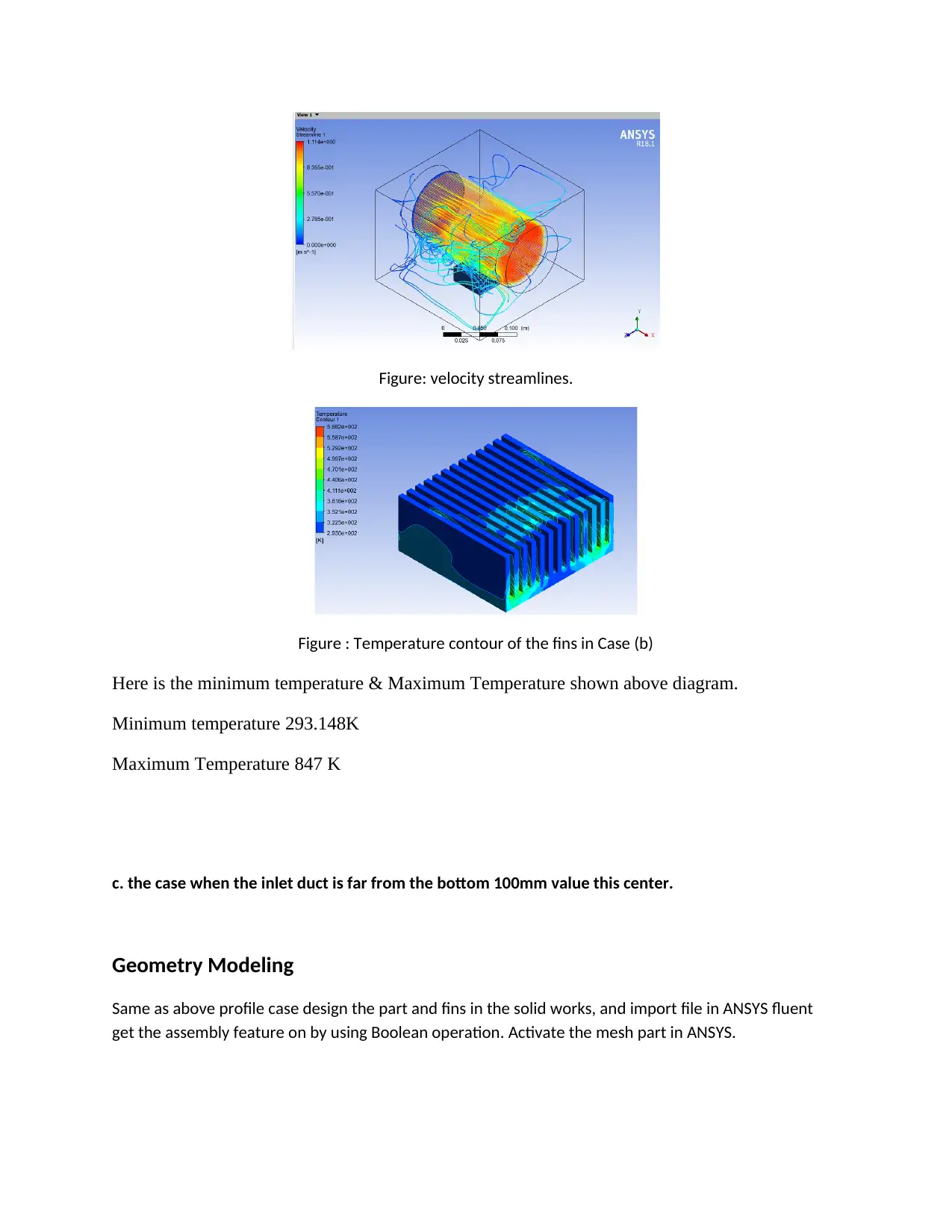
Figure: velocity streamlines.
Figure : Temperature contour of the fins in Case (b)
Here is the minimum temperature & Maximum Temperature shown above diagram.
Minimum temperature 293.148K
Maximum Temperature 847 K
c. the case when the inlet duct is far from the bottom 100mm value this center.
Geometry Modeling
Same as above profile case design the part and fins in the solid works, and import file in ANSYS fluent
get the assembly feature on by using Boolean operation. Activate the mesh part in ANSYS.
Figure : Temperature contour of the fins in Case (b)
Here is the minimum temperature & Maximum Temperature shown above diagram.
Minimum temperature 293.148K
Maximum Temperature 847 K
c. the case when the inlet duct is far from the bottom 100mm value this center.
Geometry Modeling
Same as above profile case design the part and fins in the solid works, and import file in ANSYS fluent
get the assembly feature on by using Boolean operation. Activate the mesh part in ANSYS.
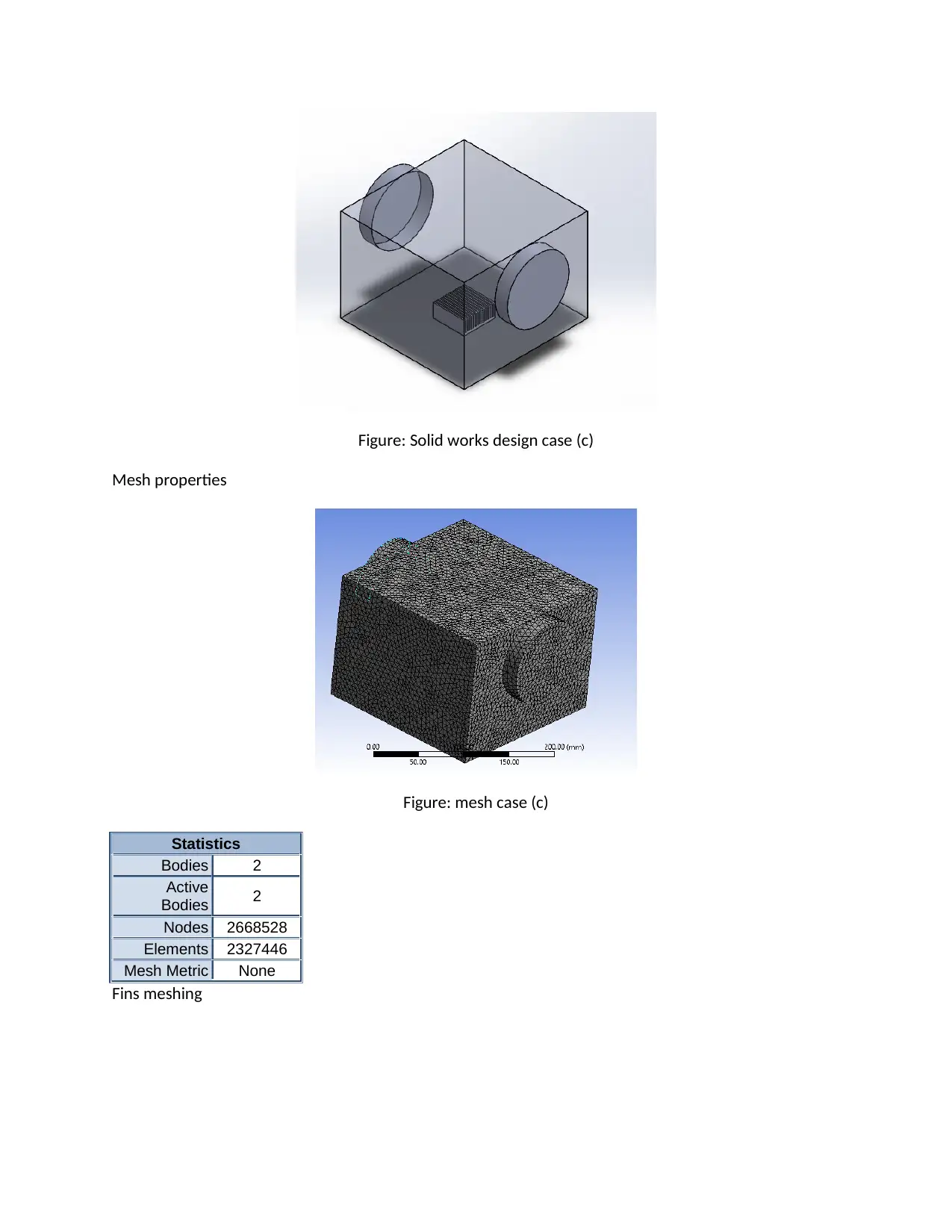
Figure: Solid works design case (c)
Mesh properties
Figure: mesh case (c)
Statistics
Bodies 2
Active
Bodies 2
Nodes 2668528
Elements 2327446
Mesh Metric None
Fins meshing
Mesh properties
Figure: mesh case (c)
Statistics
Bodies 2
Active
Bodies 2
Nodes 2668528
Elements 2327446
Mesh Metric None
Fins meshing
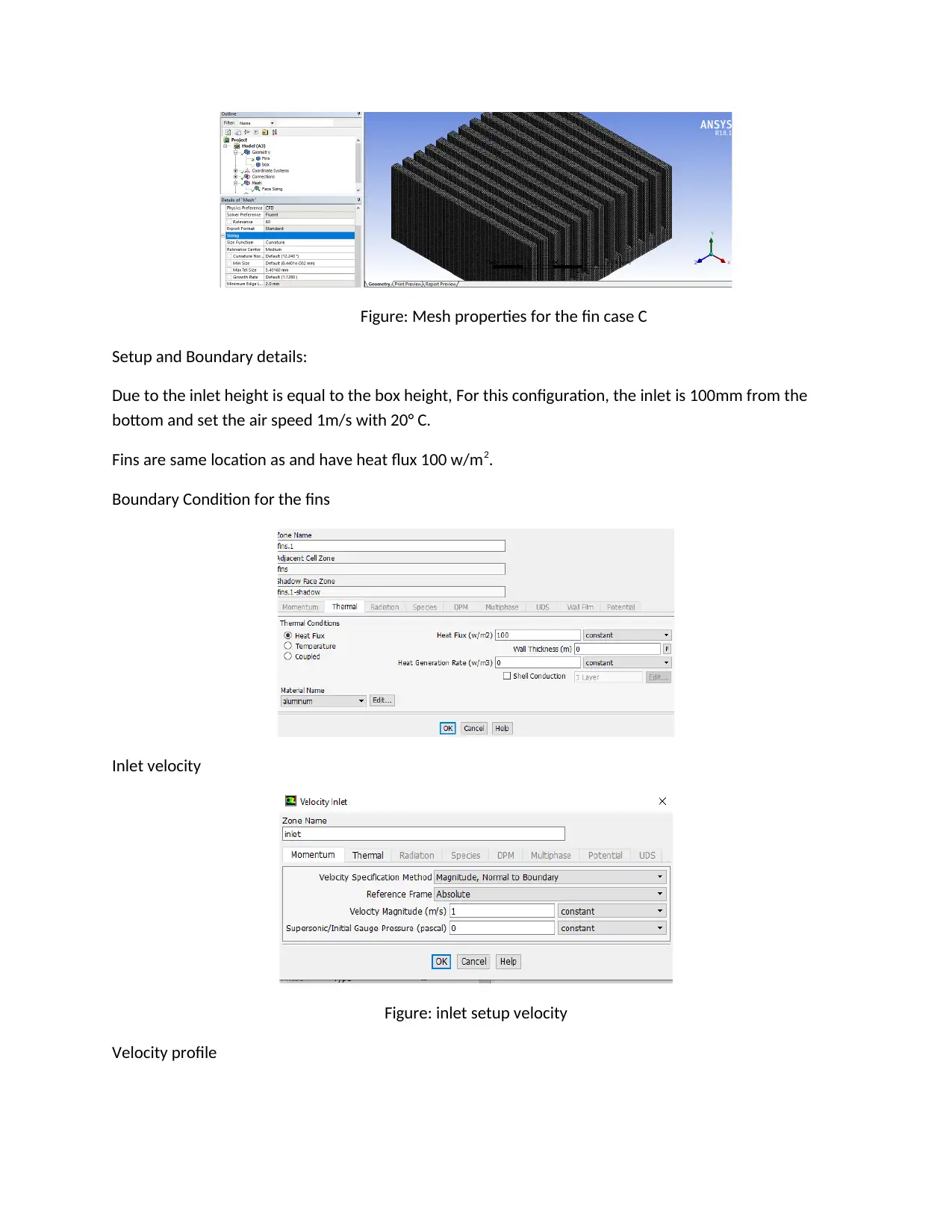
Figure: Mesh properties for the fin case C
Setup and Boundary details:
Due to the inlet height is equal to the box height, For this configuration, the inlet is 100mm from the
bottom and set the air speed 1m/s with 20° C.
Fins are same location as and have heat flux 100 w/m2.
Boundary Condition for the fins
Inlet velocity
Figure: inlet setup velocity
Velocity profile
Setup and Boundary details:
Due to the inlet height is equal to the box height, For this configuration, the inlet is 100mm from the
bottom and set the air speed 1m/s with 20° C.
Fins are same location as and have heat flux 100 w/m2.
Boundary Condition for the fins
Inlet velocity
Figure: inlet setup velocity
Velocity profile
Secure Best Marks with AI Grader
Need help grading? Try our AI Grader for instant feedback on your assignments.
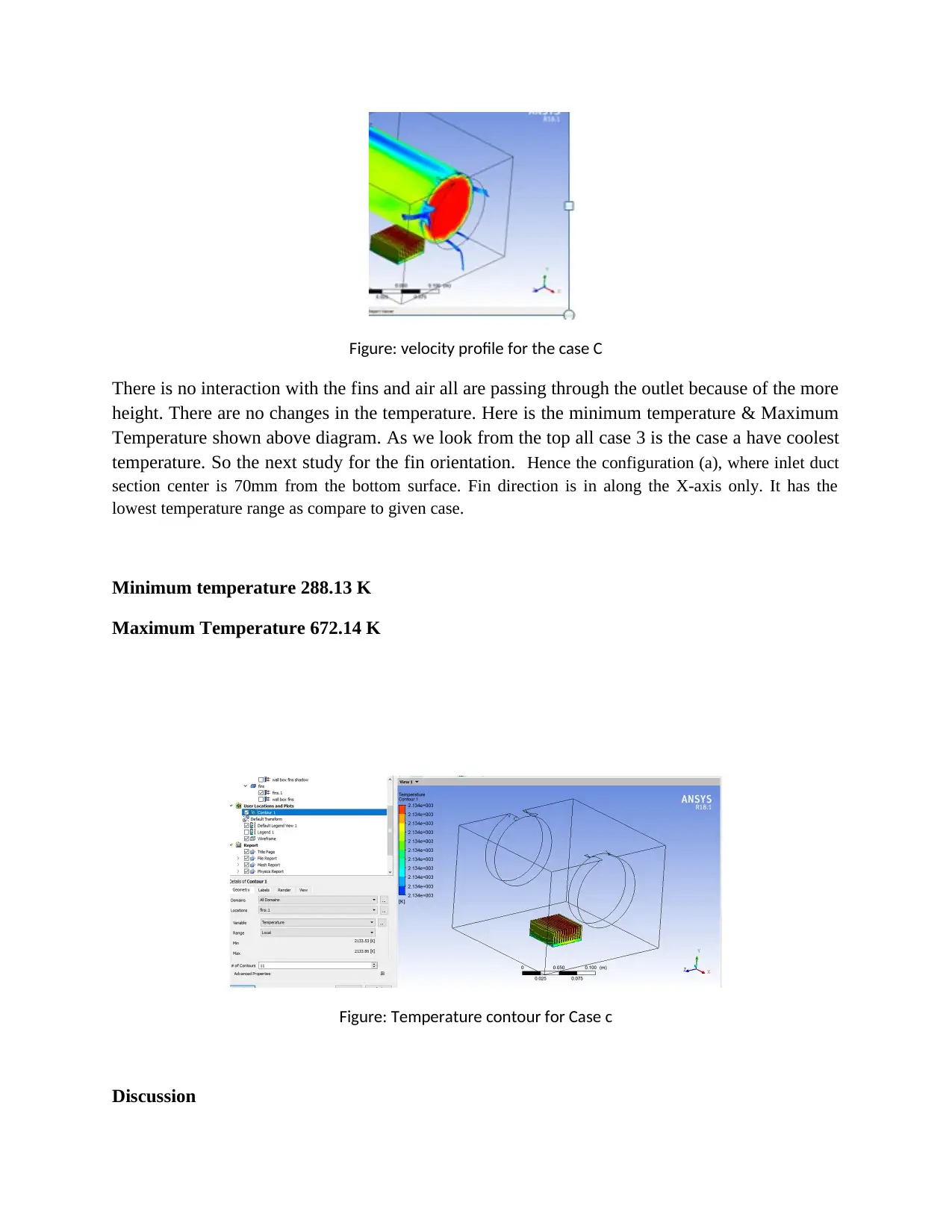
Figure: velocity profile for the case C
There is no interaction with the fins and air all are passing through the outlet because of the more
height. There are no changes in the temperature. Here is the minimum temperature & Maximum
Temperature shown above diagram. As we look from the top all case 3 is the case a have coolest
temperature. So the next study for the fin orientation. Hence the configuration (a), where inlet duct
section center is 70mm from the bottom surface. Fin direction is in along the X-axis only. It has the
lowest temperature range as compare to given case.
Minimum temperature 288.13 K
Maximum Temperature 672.14 K
Figure: Temperature contour for Case c
Discussion
There is no interaction with the fins and air all are passing through the outlet because of the more
height. There are no changes in the temperature. Here is the minimum temperature & Maximum
Temperature shown above diagram. As we look from the top all case 3 is the case a have coolest
temperature. So the next study for the fin orientation. Hence the configuration (a), where inlet duct
section center is 70mm from the bottom surface. Fin direction is in along the X-axis only. It has the
lowest temperature range as compare to given case.
Minimum temperature 288.13 K
Maximum Temperature 672.14 K
Figure: Temperature contour for Case c
Discussion
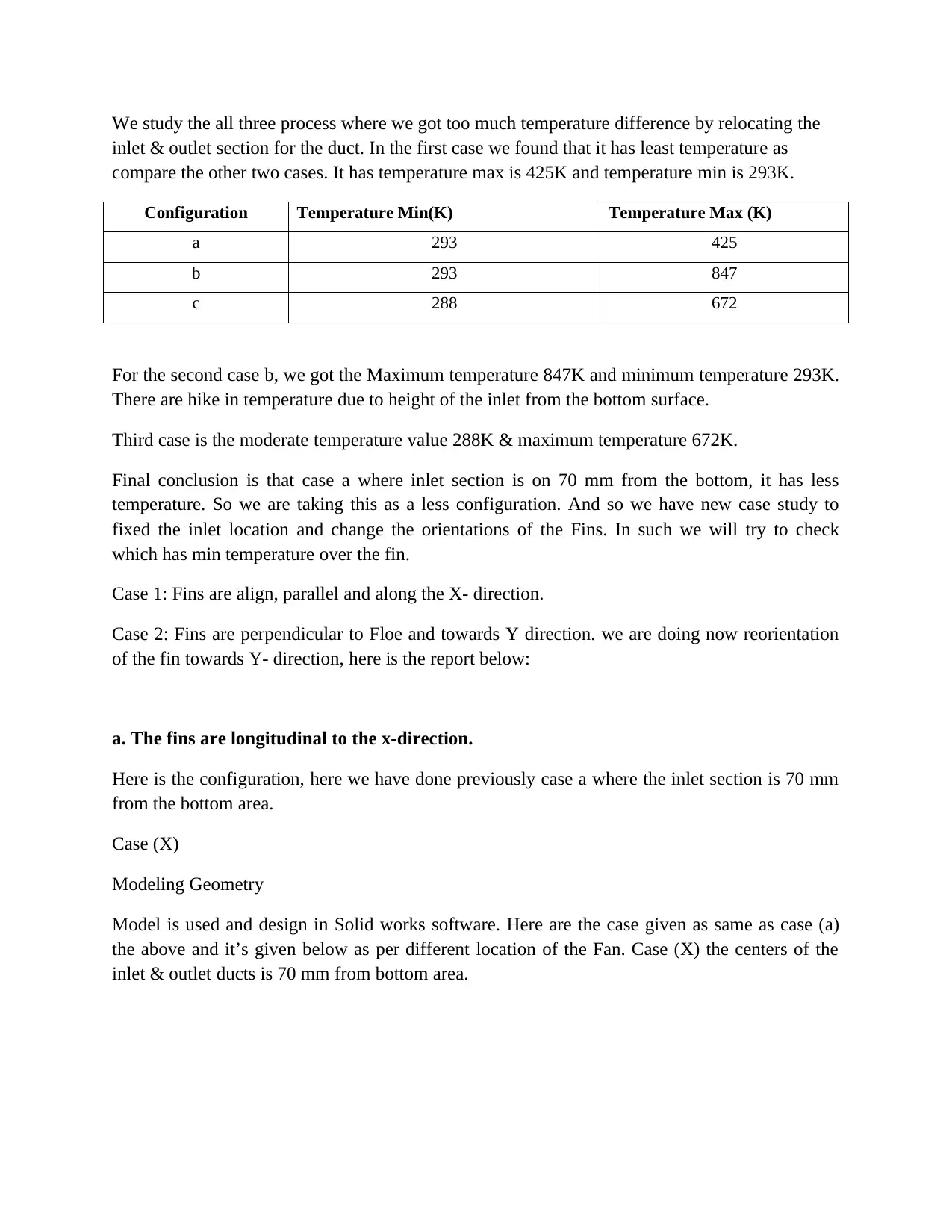
We study the all three process where we got too much temperature difference by relocating the
inlet & outlet section for the duct. In the first case we found that it has least temperature as
compare the other two cases. It has temperature max is 425K and temperature min is 293K.
Configuration Temperature Min(K) Temperature Max (K)
a 293 425
b 293 847
c 288 672
For the second case b, we got the Maximum temperature 847K and minimum temperature 293K.
There are hike in temperature due to height of the inlet from the bottom surface.
Third case is the moderate temperature value 288K & maximum temperature 672K.
Final conclusion is that case a where inlet section is on 70 mm from the bottom, it has less
temperature. So we are taking this as a less configuration. And so we have new case study to
fixed the inlet location and change the orientations of the Fins. In such we will try to check
which has min temperature over the fin.
Case 1: Fins are align, parallel and along the X- direction.
Case 2: Fins are perpendicular to Floe and towards Y direction. we are doing now reorientation
of the fin towards Y- direction, here is the report below:
a. The fins are longitudinal to the x-direction.
Here is the configuration, here we have done previously case a where the inlet section is 70 mm
from the bottom area.
Case (X)
Modeling Geometry
Model is used and design in Solid works software. Here are the case given as same as case (a)
the above and it’s given below as per different location of the Fan. Case (X) the centers of the
inlet & outlet ducts is 70 mm from bottom area.
inlet & outlet section for the duct. In the first case we found that it has least temperature as
compare the other two cases. It has temperature max is 425K and temperature min is 293K.
Configuration Temperature Min(K) Temperature Max (K)
a 293 425
b 293 847
c 288 672
For the second case b, we got the Maximum temperature 847K and minimum temperature 293K.
There are hike in temperature due to height of the inlet from the bottom surface.
Third case is the moderate temperature value 288K & maximum temperature 672K.
Final conclusion is that case a where inlet section is on 70 mm from the bottom, it has less
temperature. So we are taking this as a less configuration. And so we have new case study to
fixed the inlet location and change the orientations of the Fins. In such we will try to check
which has min temperature over the fin.
Case 1: Fins are align, parallel and along the X- direction.
Case 2: Fins are perpendicular to Floe and towards Y direction. we are doing now reorientation
of the fin towards Y- direction, here is the report below:
a. The fins are longitudinal to the x-direction.
Here is the configuration, here we have done previously case a where the inlet section is 70 mm
from the bottom area.
Case (X)
Modeling Geometry
Model is used and design in Solid works software. Here are the case given as same as case (a)
the above and it’s given below as per different location of the Fan. Case (X) the centers of the
inlet & outlet ducts is 70 mm from bottom area.
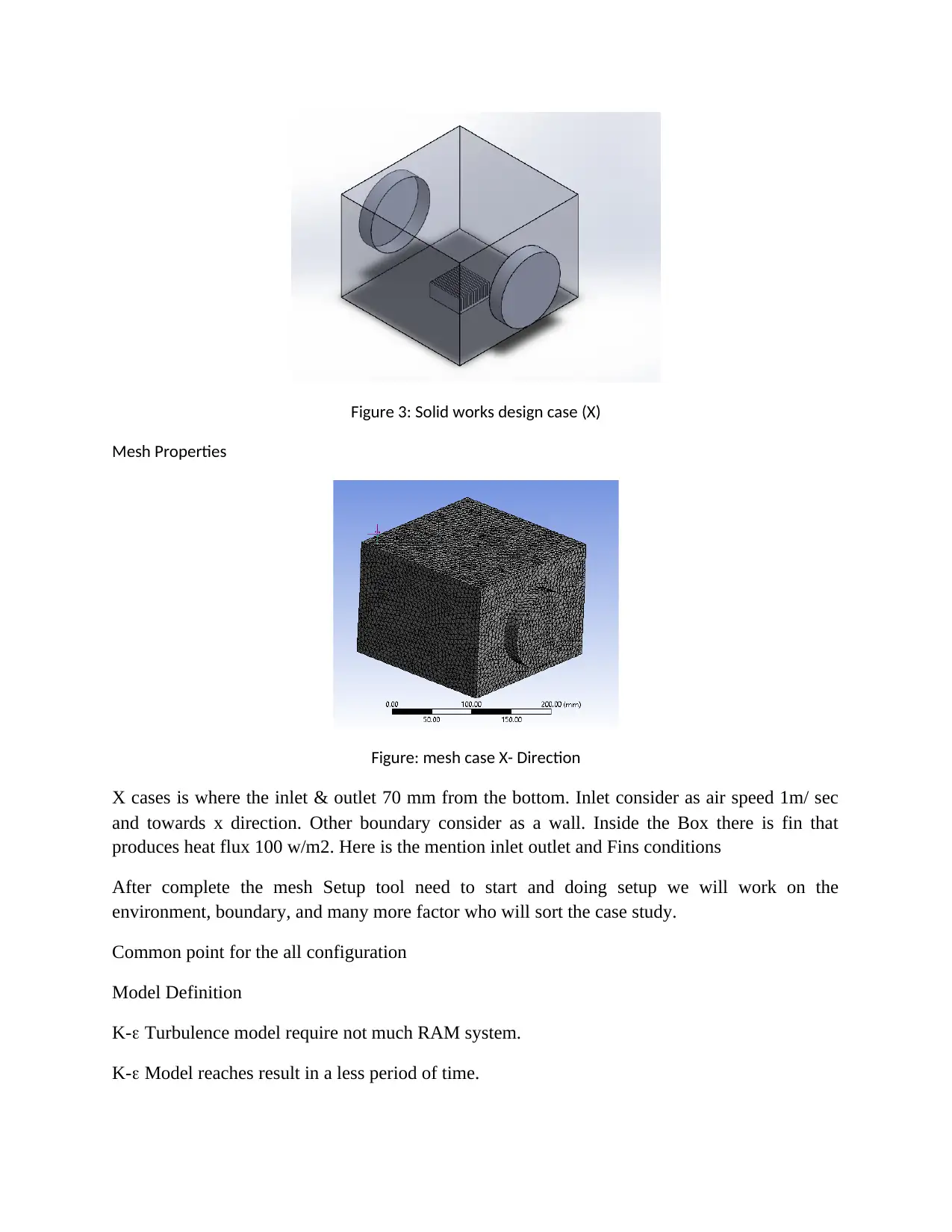
Figure 3: Solid works design case (X)
Mesh Properties
Figure: mesh case X- Direction
X cases is where the inlet & outlet 70 mm from the bottom. Inlet consider as air speed 1m/ sec
and towards x direction. Other boundary consider as a wall. Inside the Box there is fin that
produces heat flux 100 w/m2. Here is the mention inlet outlet and Fins conditions
After complete the mesh Setup tool need to start and doing setup we will work on the
environment, boundary, and many more factor who will sort the case study.
Common point for the all configuration
Model Definition
K- Turbulence model require not much RAM system.
K- Model reaches result in a less period of time.
Mesh Properties
Figure: mesh case X- Direction
X cases is where the inlet & outlet 70 mm from the bottom. Inlet consider as air speed 1m/ sec
and towards x direction. Other boundary consider as a wall. Inside the Box there is fin that
produces heat flux 100 w/m2. Here is the mention inlet outlet and Fins conditions
After complete the mesh Setup tool need to start and doing setup we will work on the
environment, boundary, and many more factor who will sort the case study.
Common point for the all configuration
Model Definition
K- Turbulence model require not much RAM system.
K- Model reaches result in a less period of time.
Paraphrase This Document
Need a fresh take? Get an instant paraphrase of this document with our AI Paraphraser
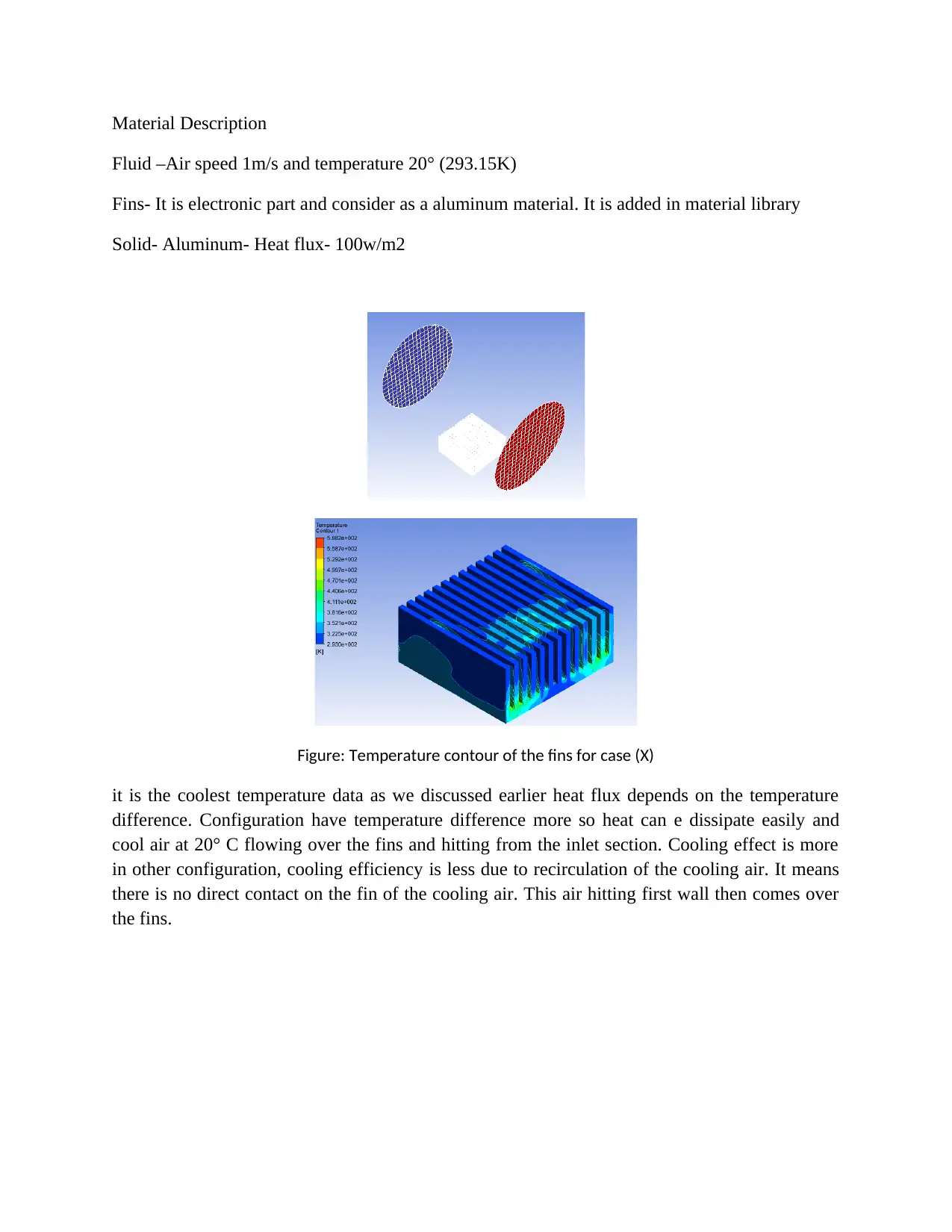
Material Description
Fluid –Air speed 1m/s and temperature 20° (293.15K)
Fins- It is electronic part and consider as a aluminum material. It is added in material library
Solid- Aluminum- Heat flux- 100w/m2
Figure: Temperature contour of the fins for case (X)
it is the coolest temperature data as we discussed earlier heat flux depends on the temperature
difference. Configuration have temperature difference more so heat can e dissipate easily and
cool air at 20° C flowing over the fins and hitting from the inlet section. Cooling effect is more
in other configuration, cooling efficiency is less due to recirculation of the cooling air. It means
there is no direct contact on the fin of the cooling air. This air hitting first wall then comes over
the fins.
Fluid –Air speed 1m/s and temperature 20° (293.15K)
Fins- It is electronic part and consider as a aluminum material. It is added in material library
Solid- Aluminum- Heat flux- 100w/m2
Figure: Temperature contour of the fins for case (X)
it is the coolest temperature data as we discussed earlier heat flux depends on the temperature
difference. Configuration have temperature difference more so heat can e dissipate easily and
cool air at 20° C flowing over the fins and hitting from the inlet section. Cooling effect is more
in other configuration, cooling efficiency is less due to recirculation of the cooling air. It means
there is no direct contact on the fin of the cooling air. This air hitting first wall then comes over
the fins.
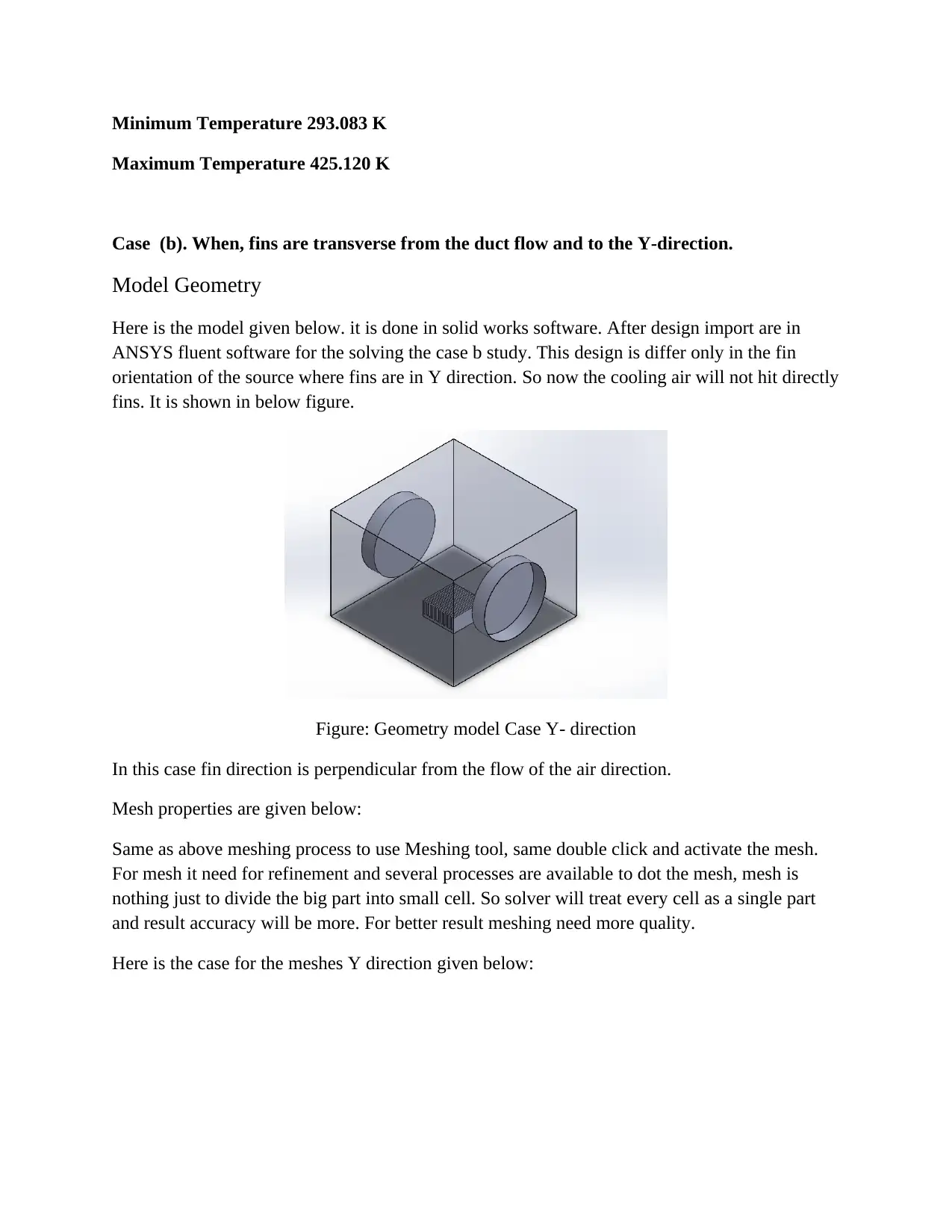
Minimum Temperature 293.083 K
Maximum Temperature 425.120 K
Case (b). When, fins are transverse from the duct flow and to the Y-direction.
Model Geometry
Here is the model given below. it is done in solid works software. After design import are in
ANSYS fluent software for the solving the case b study. This design is differ only in the fin
orientation of the source where fins are in Y direction. So now the cooling air will not hit directly
fins. It is shown in below figure.
Figure: Geometry model Case Y- direction
In this case fin direction is perpendicular from the flow of the air direction.
Mesh properties are given below:
Same as above meshing process to use Meshing tool, same double click and activate the mesh.
For mesh it need for refinement and several processes are available to dot the mesh, mesh is
nothing just to divide the big part into small cell. So solver will treat every cell as a single part
and result accuracy will be more. For better result meshing need more quality.
Here is the case for the meshes Y direction given below:
Maximum Temperature 425.120 K
Case (b). When, fins are transverse from the duct flow and to the Y-direction.
Model Geometry
Here is the model given below. it is done in solid works software. After design import are in
ANSYS fluent software for the solving the case b study. This design is differ only in the fin
orientation of the source where fins are in Y direction. So now the cooling air will not hit directly
fins. It is shown in below figure.
Figure: Geometry model Case Y- direction
In this case fin direction is perpendicular from the flow of the air direction.
Mesh properties are given below:
Same as above meshing process to use Meshing tool, same double click and activate the mesh.
For mesh it need for refinement and several processes are available to dot the mesh, mesh is
nothing just to divide the big part into small cell. So solver will treat every cell as a single part
and result accuracy will be more. For better result meshing need more quality.
Here is the case for the meshes Y direction given below:
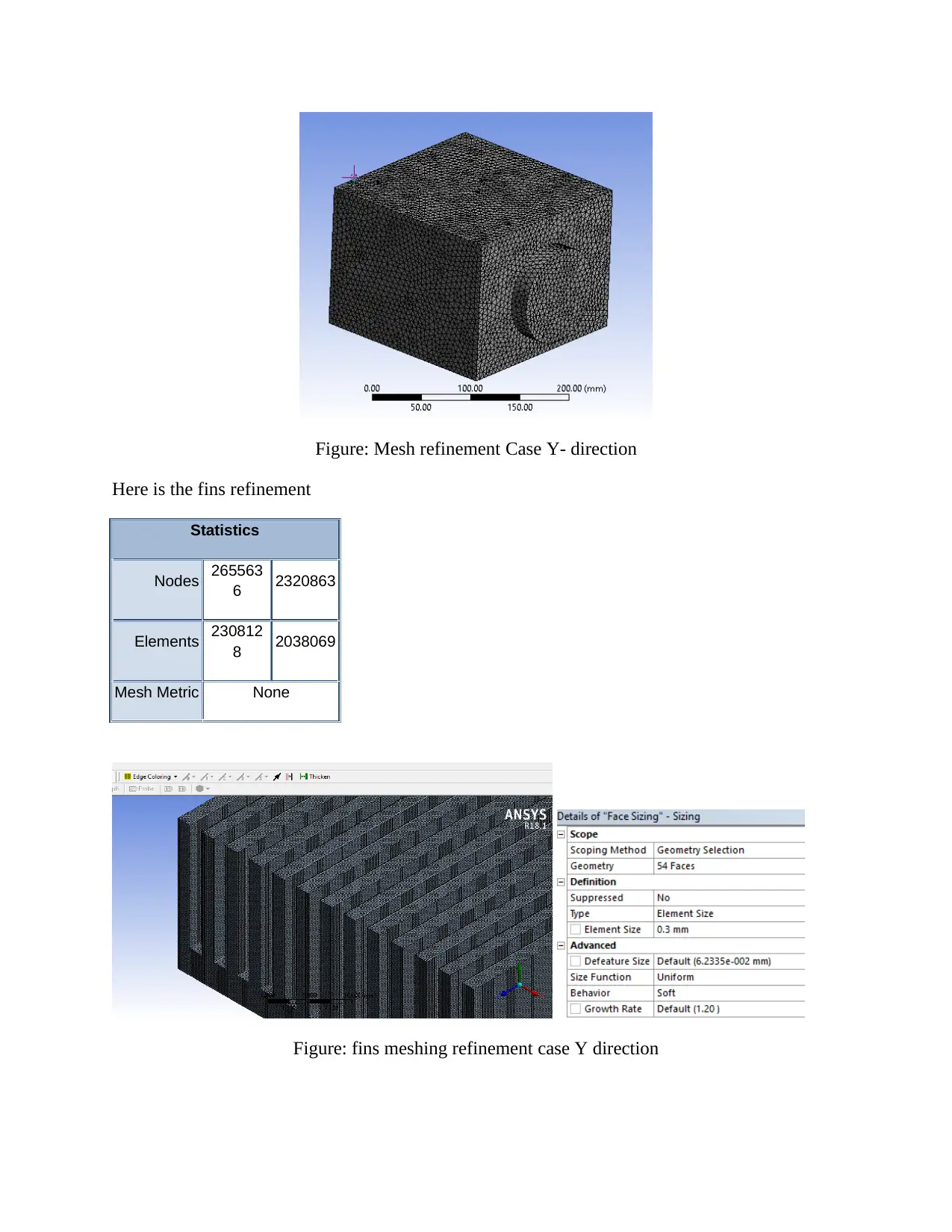
Figure: Mesh refinement Case Y- direction
Here is the fins refinement
Statistics
Nodes 265563
6 2320863
Elements 230812
8 2038069
Mesh Metric None
Figure: fins meshing refinement case Y direction
Here is the fins refinement
Statistics
Nodes 265563
6 2320863
Elements 230812
8 2038069
Mesh Metric None
Figure: fins meshing refinement case Y direction
Secure Best Marks with AI Grader
Need help grading? Try our AI Grader for instant feedback on your assignments.
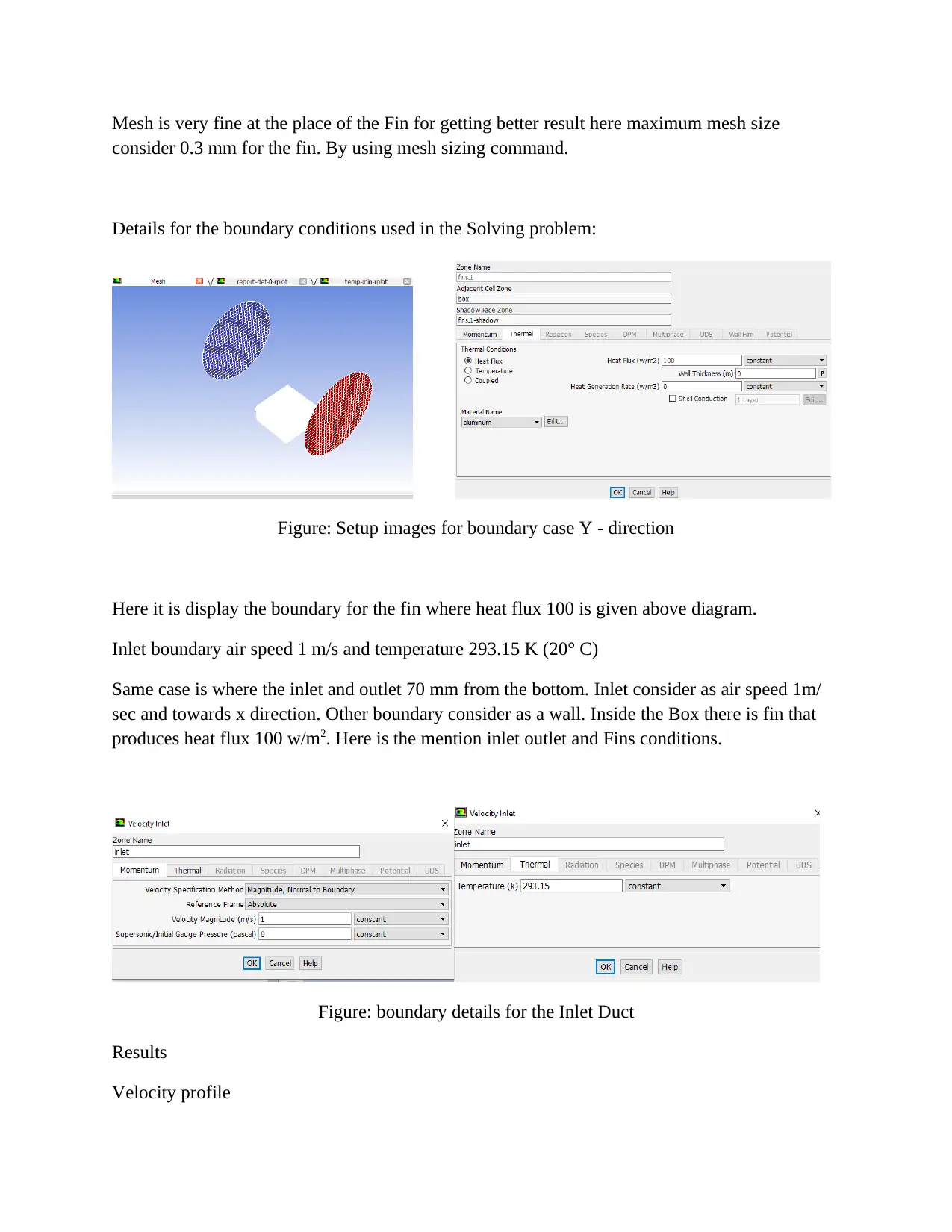
Mesh is very fine at the place of the Fin for getting better result here maximum mesh size
consider 0.3 mm for the fin. By using mesh sizing command.
Details for the boundary conditions used in the Solving problem:
Figure: Setup images for boundary case Y - direction
Here it is display the boundary for the fin where heat flux 100 is given above diagram.
Inlet boundary air speed 1 m/s and temperature 293.15 K (20° C)
Same case is where the inlet and outlet 70 mm from the bottom. Inlet consider as air speed 1m/
sec and towards x direction. Other boundary consider as a wall. Inside the Box there is fin that
produces heat flux 100 w/m2. Here is the mention inlet outlet and Fins conditions.
Figure: boundary details for the Inlet Duct
Results
Velocity profile
consider 0.3 mm for the fin. By using mesh sizing command.
Details for the boundary conditions used in the Solving problem:
Figure: Setup images for boundary case Y - direction
Here it is display the boundary for the fin where heat flux 100 is given above diagram.
Inlet boundary air speed 1 m/s and temperature 293.15 K (20° C)
Same case is where the inlet and outlet 70 mm from the bottom. Inlet consider as air speed 1m/
sec and towards x direction. Other boundary consider as a wall. Inside the Box there is fin that
produces heat flux 100 w/m2. Here is the mention inlet outlet and Fins conditions.
Figure: boundary details for the Inlet Duct
Results
Velocity profile
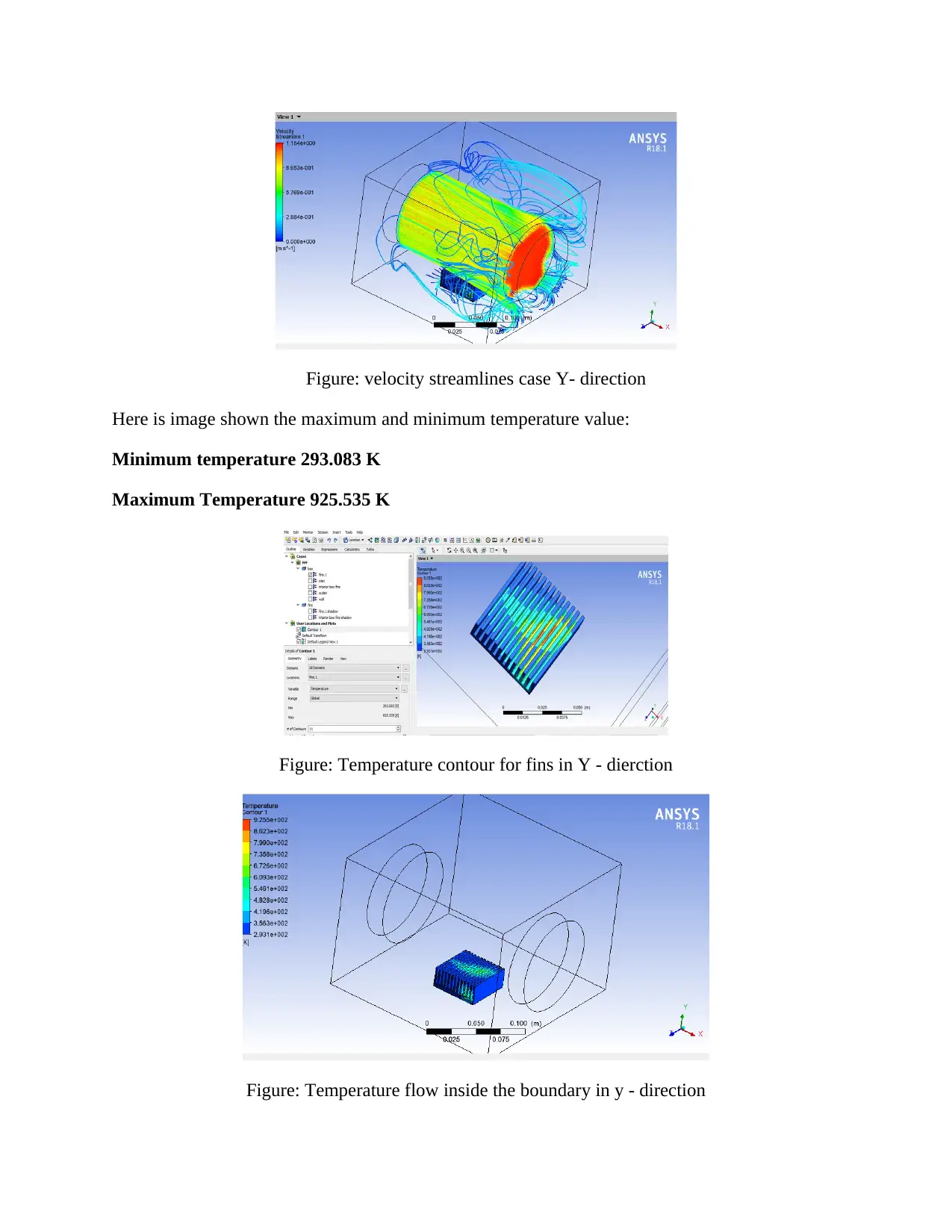
Figure: velocity streamlines case Y- direction
Here is image shown the maximum and minimum temperature value:
Minimum temperature 293.083 K
Maximum Temperature 925.535 K
Figure: Temperature contour for fins in Y - dierction
Figure: Temperature flow inside the boundary in y - direction
Here is image shown the maximum and minimum temperature value:
Minimum temperature 293.083 K
Maximum Temperature 925.535 K
Figure: Temperature contour for fins in Y - dierction
Figure: Temperature flow inside the boundary in y - direction

Here is the final conclusion on above case as we were doing the case on the 70 mm inlet above
the bottom level. Only the changes are in the fins orientation.
Configuration Minimum Temperature (K) Maximum Temperature (K)
A 293 425
B 293.08 925
Conclusion:
In the conclusion as we have discussed about the temperature. We did all analysis using the help of
ANSYS software where ANSYS fluent is provided the accurate result. ANSYS has the some percentage
error or differ from the theoretical value. Final line of this report, after completing first three case we
found the lowest and maximum temperature over the fins by using ANSYS Fluent workbench. There
were little changes in mesh volume, parameters and setup variation. We found that who has lowest and
near to fins inlet that is configuration a. It is numerical technique based part. In the first case a where the
inlet is in 70mm far from the bottom. It has lowest temperature. As we discussed that the increase contact
are increase the heat flux value same case here/ cooling air is directly hitting on the front side of the fins
so it getting cool very easily and here Maximum temperature found in the between fins on the bottom
side.
Second case b where temperature is more as per the height increase there is no direct link over the cooling
air and fins. Fir cooling air hit the wall area and then it come in contacts of the fins surface because of that
cooling efficiency getting reduced. This is the reason we got more temperature as compare to the case a.
Similar case for case c as in the “b” case air is not direct contact with the fins so getting cooling
efficiency down, here is more height as compare first and second case. After finalizing the case is for the
lowest temperature. We took the fins orientation towards Y direction. Here we got the part (fins) are not
fully in contact. So the front area towards the inlet is getting cool easily but far side there are temperature
more and between the fins on the bottom side temperature are more.
In this case we are trying to understand the flow parallel to Fins and perpendicular to fins. as we got to
know that if flow is perpendicular on fins there is much more temperature exist (877.5 K). It is more as
compare to flow by X-direction. There is reason of high temperature in Y direction. Flow is not going
directly between the fins and transverse direction need to take so flow over fins is getting divert. So,
Cooling Efficiency is getting reduced.
the bottom level. Only the changes are in the fins orientation.
Configuration Minimum Temperature (K) Maximum Temperature (K)
A 293 425
B 293.08 925
Conclusion:
In the conclusion as we have discussed about the temperature. We did all analysis using the help of
ANSYS software where ANSYS fluent is provided the accurate result. ANSYS has the some percentage
error or differ from the theoretical value. Final line of this report, after completing first three case we
found the lowest and maximum temperature over the fins by using ANSYS Fluent workbench. There
were little changes in mesh volume, parameters and setup variation. We found that who has lowest and
near to fins inlet that is configuration a. It is numerical technique based part. In the first case a where the
inlet is in 70mm far from the bottom. It has lowest temperature. As we discussed that the increase contact
are increase the heat flux value same case here/ cooling air is directly hitting on the front side of the fins
so it getting cool very easily and here Maximum temperature found in the between fins on the bottom
side.
Second case b where temperature is more as per the height increase there is no direct link over the cooling
air and fins. Fir cooling air hit the wall area and then it come in contacts of the fins surface because of that
cooling efficiency getting reduced. This is the reason we got more temperature as compare to the case a.
Similar case for case c as in the “b” case air is not direct contact with the fins so getting cooling
efficiency down, here is more height as compare first and second case. After finalizing the case is for the
lowest temperature. We took the fins orientation towards Y direction. Here we got the part (fins) are not
fully in contact. So the front area towards the inlet is getting cool easily but far side there are temperature
more and between the fins on the bottom side temperature are more.
In this case we are trying to understand the flow parallel to Fins and perpendicular to fins. as we got to
know that if flow is perpendicular on fins there is much more temperature exist (877.5 K). It is more as
compare to flow by X-direction. There is reason of high temperature in Y direction. Flow is not going
directly between the fins and transverse direction need to take so flow over fins is getting divert. So,
Cooling Efficiency is getting reduced.
Paraphrase This Document
Need a fresh take? Get an instant paraphrase of this document with our AI Paraphraser
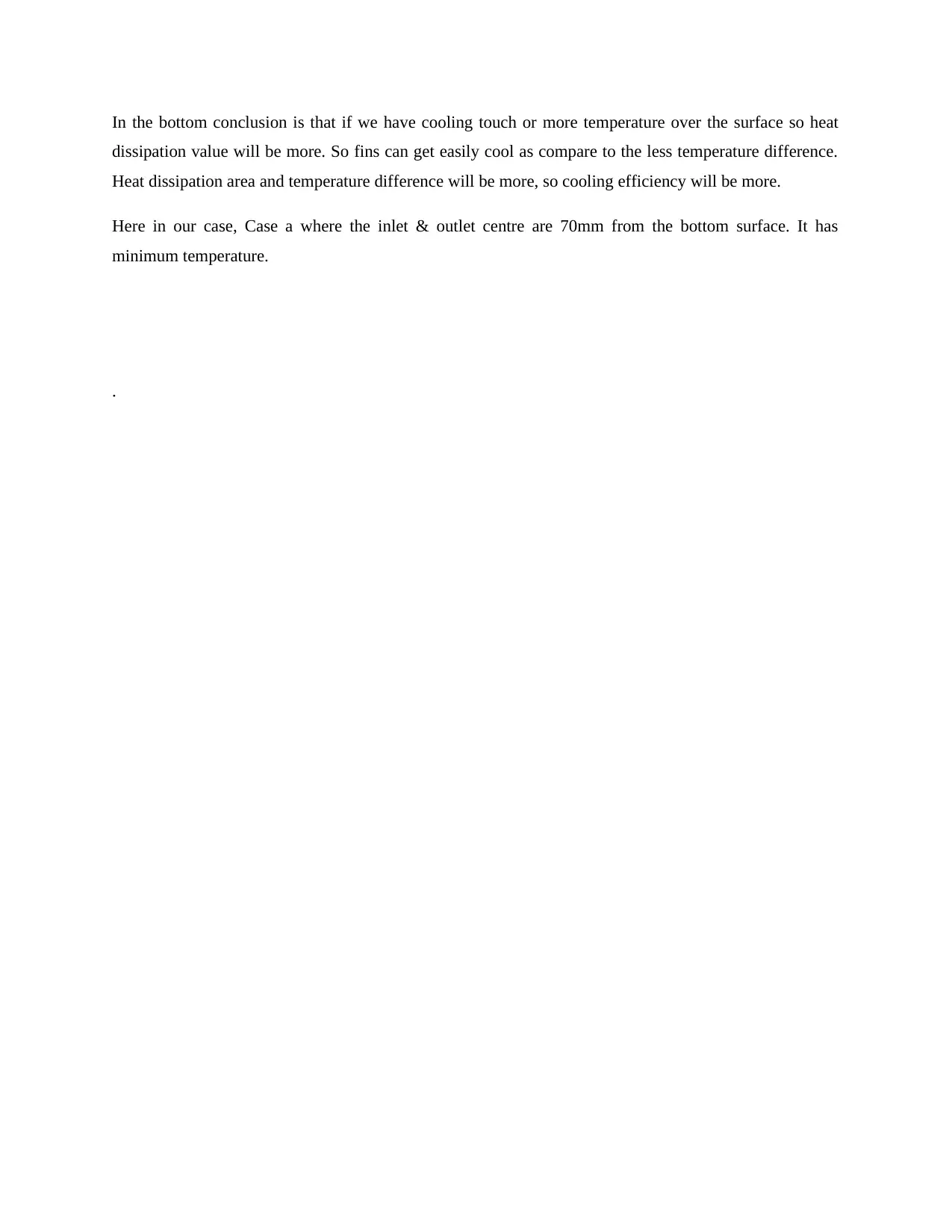
In the bottom conclusion is that if we have cooling touch or more temperature over the surface so heat
dissipation value will be more. So fins can get easily cool as compare to the less temperature difference.
Heat dissipation area and temperature difference will be more, so cooling efficiency will be more.
Here in our case, Case a where the inlet & outlet centre are 70mm from the bottom surface. It has
minimum temperature.
.
dissipation value will be more. So fins can get easily cool as compare to the less temperature difference.
Heat dissipation area and temperature difference will be more, so cooling efficiency will be more.
Here in our case, Case a where the inlet & outlet centre are 70mm from the bottom surface. It has
minimum temperature.
.

Reference
Nag, P. K. (2009), Engineering Thermodynamics, Tata McGraw-Hill Education, New Delhi
Nag, P. K. (2009), Engineering Thermodynamics, Tata McGraw-Hill Education, New Delhi
1 out of 21
Related Documents

Your All-in-One AI-Powered Toolkit for Academic Success.
+13062052269
info@desklib.com
Available 24*7 on WhatsApp / Email
Unlock your academic potential
© 2024 | Zucol Services PVT LTD | All rights reserved.