Permanent Magnet Wind Turbine Generator System: Analysis and Control
VerifiedAdded on 2021/04/21
|30
|6367
|78
Report
AI Summary
This report provides a comprehensive analysis of permanent magnet wind turbine generator systems, focusing on their integration with the grid and energy conversion efficiency. It discusses the use of Buck-Boost converters for permanent magnet synchronous generators in variable speed applications and explores the benefits of five-level diode-clamped multilevel converters. The report covers various aspects, including synchronous generators, modeling of wind turbine-generators (aerodynamic, drivetrain, and power converters), and control strategies. It delves into different generator types such as synchronous generators, squirrel-cage induction generators, and double-fed induction generators, along with their respective advantages and disadvantages. The research design, results, and conclusions are presented to provide insights into the performance and efficiency of these systems, aiming to achieve highly efficient, simple, and robust wind energy conversion systems. The report also emphasizes the importance of renewable energy sources to minimize environmental pollution and meet growing power demands. The report also covers literature review, introduction and conclusion.

1
PERMANENT MAGNET WIND TURBINE GENERATOR
Student’s Name
Institution
City, Date
PERMANENT MAGNET WIND TURBINE GENERATOR
Student’s Name
Institution
City, Date
Paraphrase This Document
Need a fresh take? Get an instant paraphrase of this document with our AI Paraphraser

2
Abstract
This article talks about system of control, modelling and analysing the permanent magnet
generator wind turbine based attached to the grind, converting energy wind by use of Buck-
Boost converter for permanent magnet synchronous generator in relation to the speed variable,
wind energy conversion system has been preferred whereby it is integrated by use of the five-
level diode-clamped multilevel converter with the grind. Converters that are highly efficient are
important for systems of energy that can be renewed particularly, those connected with grind
applications of wind. The adoption of systems of renewing energy for electric power sources
generation is getting relevance so as to minimize pollution of the environment and global
warming additionally, achieving the power escalating by consumer demand. Generation of
power from wind generally, either uses turbines of variable speed or speed which is fixed and the
major converters and generators configurations are applied in the connected grind variable wind
power system are [1]. The goal is to achieve a system that is highly efficient, simple,
maintenance free and robust where the five-level diode-clamped multilevel that was proposed
had in 3 stages of the system of wind energy being applied of which the outcome was several
benefits that were promising. It is important to understand the systems of power, applications and
machines of electronic power converters and schemes of control together put on a platform that
is common.
Abstract
This article talks about system of control, modelling and analysing the permanent magnet
generator wind turbine based attached to the grind, converting energy wind by use of Buck-
Boost converter for permanent magnet synchronous generator in relation to the speed variable,
wind energy conversion system has been preferred whereby it is integrated by use of the five-
level diode-clamped multilevel converter with the grind. Converters that are highly efficient are
important for systems of energy that can be renewed particularly, those connected with grind
applications of wind. The adoption of systems of renewing energy for electric power sources
generation is getting relevance so as to minimize pollution of the environment and global
warming additionally, achieving the power escalating by consumer demand. Generation of
power from wind generally, either uses turbines of variable speed or speed which is fixed and the
major converters and generators configurations are applied in the connected grind variable wind
power system are [1]. The goal is to achieve a system that is highly efficient, simple,
maintenance free and robust where the five-level diode-clamped multilevel that was proposed
had in 3 stages of the system of wind energy being applied of which the outcome was several
benefits that were promising. It is important to understand the systems of power, applications and
machines of electronic power converters and schemes of control together put on a platform that
is common.

3
Contents
1. Introduction.........................................................................................................................................4
2. Literature Review................................................................................................................................5
2.1. Synchronous generators run by a turbine with a fixed speed...........................................................5
2.2. Modelling Systems of Wind Turbine-Generators............................................................................9
2.3. Systems of Wind Turbine-Generator Control Strategies................................................................12
2.4. Topologies of Power Converters in Systems of Wind Turbine Generators....................................14
3. RESEARCH DESIGN.......................................................................................................................18
4. Result and Analysis...........................................................................................................................21
5. Conclusion.........................................................................................................................................25
References.................................................................................................................................................27
Contents
1. Introduction.........................................................................................................................................4
2. Literature Review................................................................................................................................5
2.1. Synchronous generators run by a turbine with a fixed speed...........................................................5
2.2. Modelling Systems of Wind Turbine-Generators............................................................................9
2.3. Systems of Wind Turbine-Generator Control Strategies................................................................12
2.4. Topologies of Power Converters in Systems of Wind Turbine Generators....................................14
3. RESEARCH DESIGN.......................................................................................................................18
4. Result and Analysis...........................................................................................................................21
5. Conclusion.........................................................................................................................................25
References.................................................................................................................................................27
⊘ This is a preview!⊘
Do you want full access?
Subscribe today to unlock all pages.

Trusted by 1+ million students worldwide

4
1. Introduction
The power used on a large scale is electricity as an energy source in places of work, homes and
industries hence the growth of industries and population have significantly caused the increase in
consumption of power for over 3 years that have past. Resources that are natural such as coal,
gas and petroleum which runs plants, vehicles and industries for many years are depleting at a
rate that is fast, and this has led to countries all over the world to come up with alternative
sources of energy to that conserve the natural resources which are inexhaustible. Stable
advancements in technology invented over fifteen years ago have impacted wind plants and more
of this developments has been done in the components in the relation of integration of wind,
converters of power, the capability to control and machines that are electrical [2].
Long gone are machines that simply inducted with a start that is soft because there is an
enhancement of real and power reactivated machines power output limit and speed and voltage
control. A lot of research has been conducted worldwide on this aspect and developments on the
technology that gives a capability deal that is great thus a variety of reasons for applying wind
turbine with variable speed;
Much power is generated from the generator with variable speed as compared to other
counterparts with speed that is constant systems.
Availability of simplified control of pitch with costs that are feasible.
The compensator of power that is reactive and omission of starter soft system due to the
existence of electronic power devices.
Minimized pulsation of torque improves the quality of power by power variation
elimination and minimizing flickers.
1. Introduction
The power used on a large scale is electricity as an energy source in places of work, homes and
industries hence the growth of industries and population have significantly caused the increase in
consumption of power for over 3 years that have past. Resources that are natural such as coal,
gas and petroleum which runs plants, vehicles and industries for many years are depleting at a
rate that is fast, and this has led to countries all over the world to come up with alternative
sources of energy to that conserve the natural resources which are inexhaustible. Stable
advancements in technology invented over fifteen years ago have impacted wind plants and more
of this developments has been done in the components in the relation of integration of wind,
converters of power, the capability to control and machines that are electrical [2].
Long gone are machines that simply inducted with a start that is soft because there is an
enhancement of real and power reactivated machines power output limit and speed and voltage
control. A lot of research has been conducted worldwide on this aspect and developments on the
technology that gives a capability deal that is great thus a variety of reasons for applying wind
turbine with variable speed;
Much power is generated from the generator with variable speed as compared to other
counterparts with speed that is constant systems.
Availability of simplified control of pitch with costs that are feasible.
The compensator of power that is reactive and omission of starter soft system due to the
existence of electronic power devices.
Minimized pulsation of torque improves the quality of power by power variation
elimination and minimizing flickers.
Paraphrase This Document
Need a fresh take? Get an instant paraphrase of this document with our AI Paraphraser
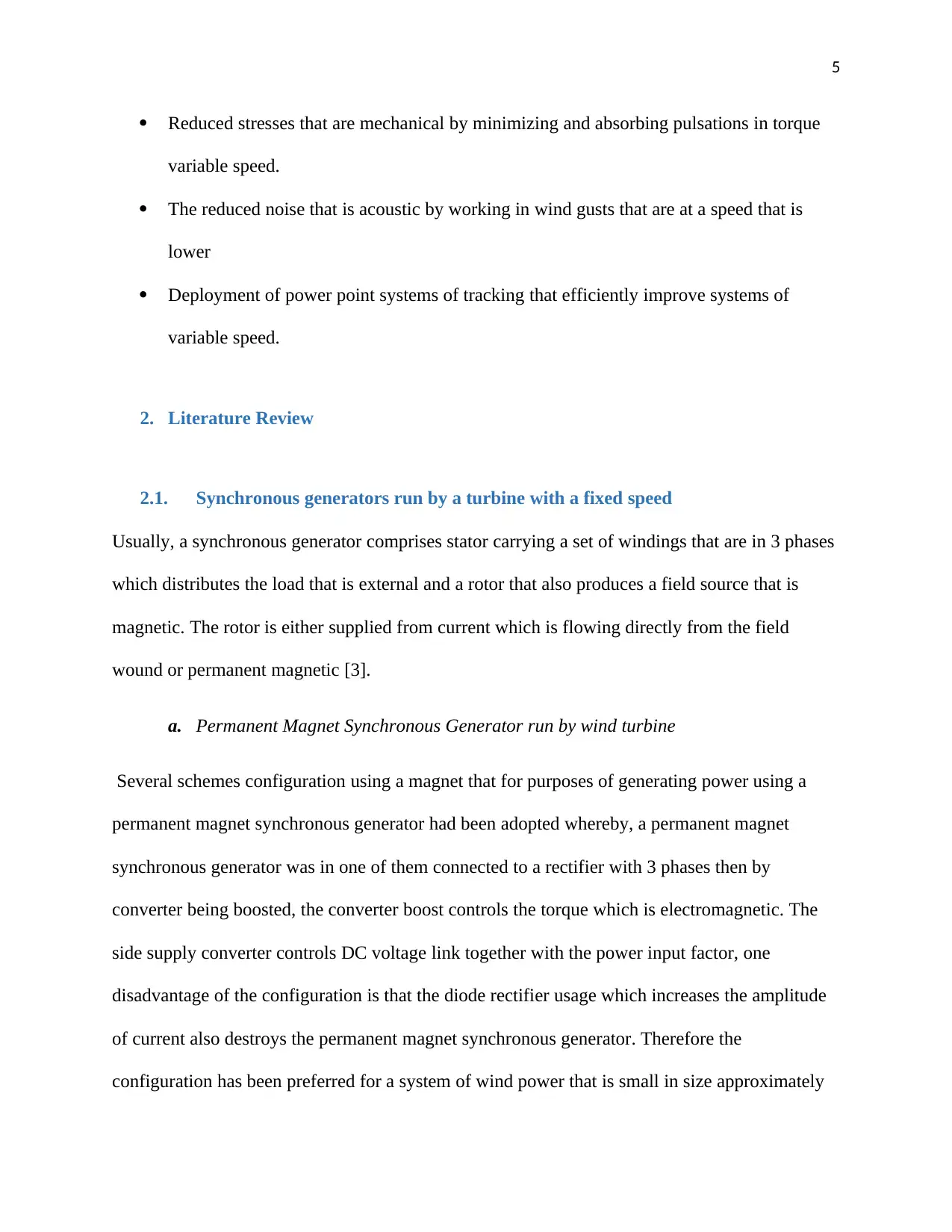
5
Reduced stresses that are mechanical by minimizing and absorbing pulsations in torque
variable speed.
The reduced noise that is acoustic by working in wind gusts that are at a speed that is
lower
Deployment of power point systems of tracking that efficiently improve systems of
variable speed.
2. Literature Review
2.1. Synchronous generators run by a turbine with a fixed speed
Usually, a synchronous generator comprises stator carrying a set of windings that are in 3 phases
which distributes the load that is external and a rotor that also produces a field source that is
magnetic. The rotor is either supplied from current which is flowing directly from the field
wound or permanent magnetic [3].
a. Permanent Magnet Synchronous Generator run by wind turbine
Several schemes configuration using a magnet that for purposes of generating power using a
permanent magnet synchronous generator had been adopted whereby, a permanent magnet
synchronous generator was in one of them connected to a rectifier with 3 phases then by
converter being boosted, the converter boost controls the torque which is electromagnetic. The
side supply converter controls DC voltage link together with the power input factor, one
disadvantage of the configuration is that the diode rectifier usage which increases the amplitude
of current also destroys the permanent magnet synchronous generator. Therefore the
configuration has been preferred for a system of wind power that is small in size approximately
Reduced stresses that are mechanical by minimizing and absorbing pulsations in torque
variable speed.
The reduced noise that is acoustic by working in wind gusts that are at a speed that is
lower
Deployment of power point systems of tracking that efficiently improve systems of
variable speed.
2. Literature Review
2.1. Synchronous generators run by a turbine with a fixed speed
Usually, a synchronous generator comprises stator carrying a set of windings that are in 3 phases
which distributes the load that is external and a rotor that also produces a field source that is
magnetic. The rotor is either supplied from current which is flowing directly from the field
wound or permanent magnetic [3].
a. Permanent Magnet Synchronous Generator run by wind turbine
Several schemes configuration using a magnet that for purposes of generating power using a
permanent magnet synchronous generator had been adopted whereby, a permanent magnet
synchronous generator was in one of them connected to a rectifier with 3 phases then by
converter being boosted, the converter boost controls the torque which is electromagnetic. The
side supply converter controls DC voltage link together with the power input factor, one
disadvantage of the configuration is that the diode rectifier usage which increases the amplitude
of current also destroys the permanent magnet synchronous generator. Therefore the
configuration has been preferred for a system of wind power that is small in size approximately

6
smaller than 50KW whereas in other schemes that use a permanent magnet synchronous
generator the rectifier PWM is in between the link DC and the generator placed and another
PWM converter connected to the network [4].
The importance of this system in relation to the usage of field-orientation control, is that the
generator is allowed to operate almost to the working point that is optimal so as to lower losses
in the electronic power circuit and the generator, however, performance relies on the knowledge
that is good on the parameter of the generator which changes with frequency and temperature.
The main disadvantage of the permanent magnet synchronous generator is that it’s cost increases
in price which also affects machine and demagnetizing of the material that is permanently
magnetic which makes it difficult to control the machine’s factor of power.
b. Wound field synchronous generator driven by a wind turbine
The winding stator is connected to the network by a converter of power which is a four-quadrant
and consists of two sinusoidal PWM that is back to back while the converter side machine
controls the torque electromagnetic and the side grid converter controls the reactive and real
power the WPS delivers to the utility. Advantages of the wound field synchronous generator are
high efficiency as it wholly involves the stator current for production of torque electromagnetic
however the main advantage of adopting wound field synchronous generator with a pole that is
salient, it enables direct regulation of the machine power factor thereby also minimizing the
current stator at any operational conditions. The presence of a circuit in winding in the rotor is a
setback than with a permanent magnet synchronous generator additionally, for reactive and
active generated power to be regulated, the converter must be typically sized 1.2 of the WPS
power that is rated [3].
smaller than 50KW whereas in other schemes that use a permanent magnet synchronous
generator the rectifier PWM is in between the link DC and the generator placed and another
PWM converter connected to the network [4].
The importance of this system in relation to the usage of field-orientation control, is that the
generator is allowed to operate almost to the working point that is optimal so as to lower losses
in the electronic power circuit and the generator, however, performance relies on the knowledge
that is good on the parameter of the generator which changes with frequency and temperature.
The main disadvantage of the permanent magnet synchronous generator is that it’s cost increases
in price which also affects machine and demagnetizing of the material that is permanently
magnetic which makes it difficult to control the machine’s factor of power.
b. Wound field synchronous generator driven by a wind turbine
The winding stator is connected to the network by a converter of power which is a four-quadrant
and consists of two sinusoidal PWM that is back to back while the converter side machine
controls the torque electromagnetic and the side grid converter controls the reactive and real
power the WPS delivers to the utility. Advantages of the wound field synchronous generator are
high efficiency as it wholly involves the stator current for production of torque electromagnetic
however the main advantage of adopting wound field synchronous generator with a pole that is
salient, it enables direct regulation of the machine power factor thereby also minimizing the
current stator at any operational conditions. The presence of a circuit in winding in the rotor is a
setback than with a permanent magnet synchronous generator additionally, for reactive and
active generated power to be regulated, the converter must be typically sized 1.2 of the WPS
power that is rated [3].
⊘ This is a preview!⊘
Do you want full access?
Subscribe today to unlock all pages.

Trusted by 1+ million students worldwide
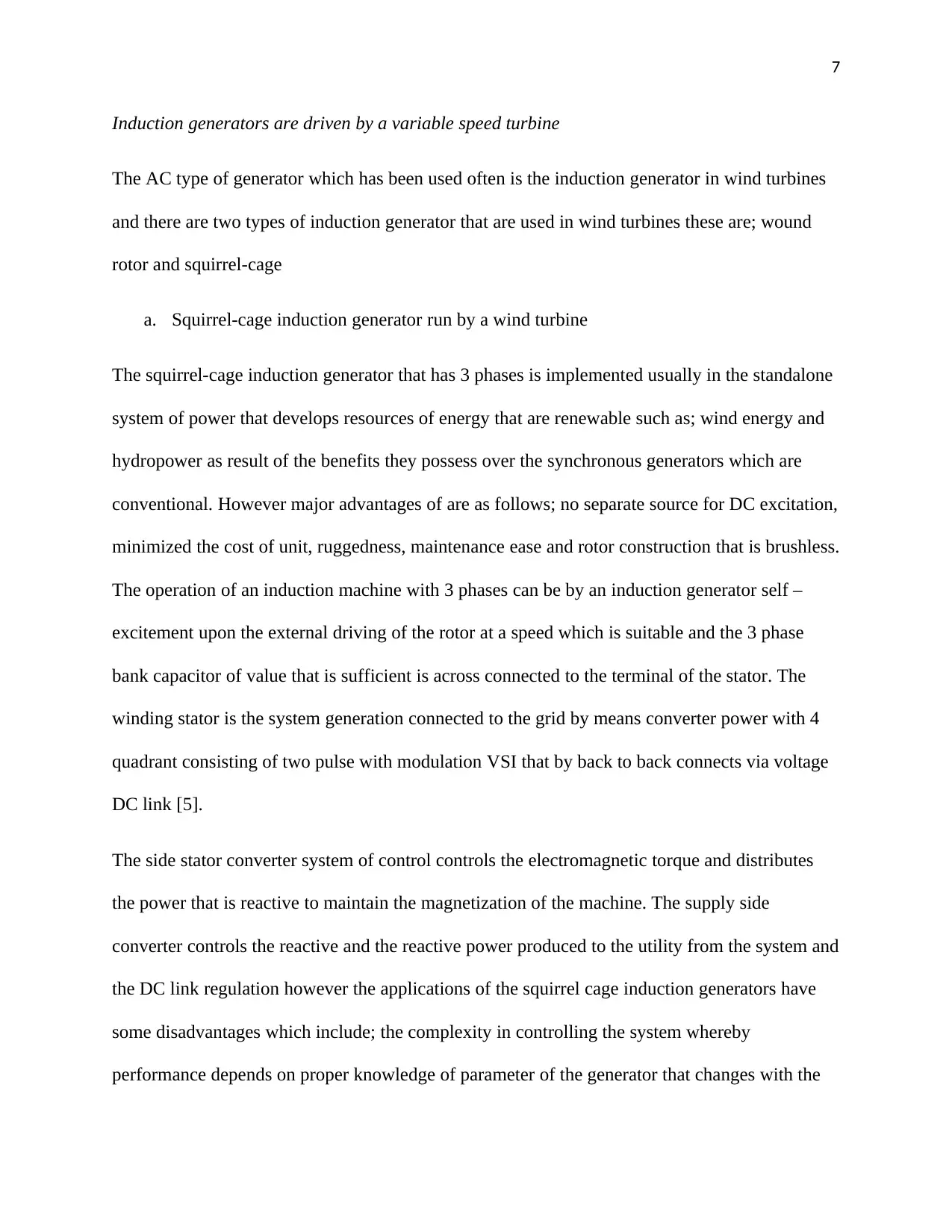
7
Induction generators are driven by a variable speed turbine
The AC type of generator which has been used often is the induction generator in wind turbines
and there are two types of induction generator that are used in wind turbines these are; wound
rotor and squirrel-cage
a. Squirrel-cage induction generator run by a wind turbine
The squirrel-cage induction generator that has 3 phases is implemented usually in the standalone
system of power that develops resources of energy that are renewable such as; wind energy and
hydropower as result of the benefits they possess over the synchronous generators which are
conventional. However major advantages of are as follows; no separate source for DC excitation,
minimized the cost of unit, ruggedness, maintenance ease and rotor construction that is brushless.
The operation of an induction machine with 3 phases can be by an induction generator self –
excitement upon the external driving of the rotor at a speed which is suitable and the 3 phase
bank capacitor of value that is sufficient is across connected to the terminal of the stator. The
winding stator is the system generation connected to the grid by means converter power with 4
quadrant consisting of two pulse with modulation VSI that by back to back connects via voltage
DC link [5].
The side stator converter system of control controls the electromagnetic torque and distributes
the power that is reactive to maintain the magnetization of the machine. The supply side
converter controls the reactive and the reactive power produced to the utility from the system and
the DC link regulation however the applications of the squirrel cage induction generators have
some disadvantages which include; the complexity in controlling the system whereby
performance depends on proper knowledge of parameter of the generator that changes with the
Induction generators are driven by a variable speed turbine
The AC type of generator which has been used often is the induction generator in wind turbines
and there are two types of induction generator that are used in wind turbines these are; wound
rotor and squirrel-cage
a. Squirrel-cage induction generator run by a wind turbine
The squirrel-cage induction generator that has 3 phases is implemented usually in the standalone
system of power that develops resources of energy that are renewable such as; wind energy and
hydropower as result of the benefits they possess over the synchronous generators which are
conventional. However major advantages of are as follows; no separate source for DC excitation,
minimized the cost of unit, ruggedness, maintenance ease and rotor construction that is brushless.
The operation of an induction machine with 3 phases can be by an induction generator self –
excitement upon the external driving of the rotor at a speed which is suitable and the 3 phase
bank capacitor of value that is sufficient is across connected to the terminal of the stator. The
winding stator is the system generation connected to the grid by means converter power with 4
quadrant consisting of two pulse with modulation VSI that by back to back connects via voltage
DC link [5].
The side stator converter system of control controls the electromagnetic torque and distributes
the power that is reactive to maintain the magnetization of the machine. The supply side
converter controls the reactive and the reactive power produced to the utility from the system and
the DC link regulation however the applications of the squirrel cage induction generators have
some disadvantages which include; the complexity in controlling the system whereby
performance depends on proper knowledge of parameter of the generator that changes with the
Paraphrase This Document
Need a fresh take? Get an instant paraphrase of this document with our AI Paraphraser

8
saturation of the magnet, frequency and temperature. The side stator converter is important to be
sized over 30- 50% in regards to the power rated so as to supply requirements for magnetizing
the machine.
b. Double fed induction generator is driven by a wind turbine
The wind system of power in the figure below comprises of a doubly fed induction generator
where the winding stator is connected directly to the network and the winding rotor to the
network also connected via four quadrant converter of power consisting of two back to back
sinusoidal pulse with modulation and the side thyristor converter may as well be used though, the
performance is limited. The rotor side converter controller usually, controls the electromagnetic
torque and distributes part of the power which is reactive for maintenance of the machine
magnetization alternatively, the grid side converter’s controller controls the voltage of the DC
link [5].
[5]
Above: Squirrel cage induction generator wind driven turbine
[5]
Above; doubly fed induction
generator wind driven turbine
saturation of the magnet, frequency and temperature. The side stator converter is important to be
sized over 30- 50% in regards to the power rated so as to supply requirements for magnetizing
the machine.
b. Double fed induction generator is driven by a wind turbine
The wind system of power in the figure below comprises of a doubly fed induction generator
where the winding stator is connected directly to the network and the winding rotor to the
network also connected via four quadrant converter of power consisting of two back to back
sinusoidal pulse with modulation and the side thyristor converter may as well be used though, the
performance is limited. The rotor side converter controller usually, controls the electromagnetic
torque and distributes part of the power which is reactive for maintenance of the machine
magnetization alternatively, the grid side converter’s controller controls the voltage of the DC
link [5].
[5]
Above: Squirrel cage induction generator wind driven turbine
[5]
Above; doubly fed induction
generator wind driven turbine

9
Advantages of the doubly fed inducted generator as compared to the synchronous generator are
as follows;
Lower costs of the converter filter as filters rated 0.25 per unit total power system and
converter harmonics stands for a fraction that is smaller of the total harmonics system
Minimal costs of converter due to rating of converter typically 25% of the total power
system which is due to the converters only require to regulate rotor’s slip power.
The response that is stable and robustness of the machine undergoing disturbances that
are external
2.2. Modelling Systems of Wind Turbine-Generators
The modelling of wind turbine-generators includes aerodynamic modelling, DFIG modelling,
modelling of drivetrain systems and modelling of power converters. Therefore, this
documentation puts its focus on modelling such as system [5].
a) Aerodynamic modelling
In [1]there is a deduction of the highest possible energy to be gotten from systems of wind
turbines from the air system from conditions that are ideal. In [2]the source derives the existing
relationship the speed of passing wind and mechanical power input through the rotor plane
turbine. This was able to be expressed in the turbine’s power coefficient. There exists three
commonly used simulation methods for obtaining the coefficients of power which are provided
by the manufacturer of the wind turbine. The two methods that come first are found in [3]while
the third method is known as the lookup table method provided in [4]
b) Drive Train Modelling
Advantages of the doubly fed inducted generator as compared to the synchronous generator are
as follows;
Lower costs of the converter filter as filters rated 0.25 per unit total power system and
converter harmonics stands for a fraction that is smaller of the total harmonics system
Minimal costs of converter due to rating of converter typically 25% of the total power
system which is due to the converters only require to regulate rotor’s slip power.
The response that is stable and robustness of the machine undergoing disturbances that
are external
2.2. Modelling Systems of Wind Turbine-Generators
The modelling of wind turbine-generators includes aerodynamic modelling, DFIG modelling,
modelling of drivetrain systems and modelling of power converters. Therefore, this
documentation puts its focus on modelling such as system [5].
a) Aerodynamic modelling
In [1]there is a deduction of the highest possible energy to be gotten from systems of wind
turbines from the air system from conditions that are ideal. In [2]the source derives the existing
relationship the speed of passing wind and mechanical power input through the rotor plane
turbine. This was able to be expressed in the turbine’s power coefficient. There exists three
commonly used simulation methods for obtaining the coefficients of power which are provided
by the manufacturer of the wind turbine. The two methods that come first are found in [3]while
the third method is known as the lookup table method provided in [4]
b) Drive Train Modelling
⊘ This is a preview!⊘
Do you want full access?
Subscribe today to unlock all pages.

Trusted by 1+ million students worldwide
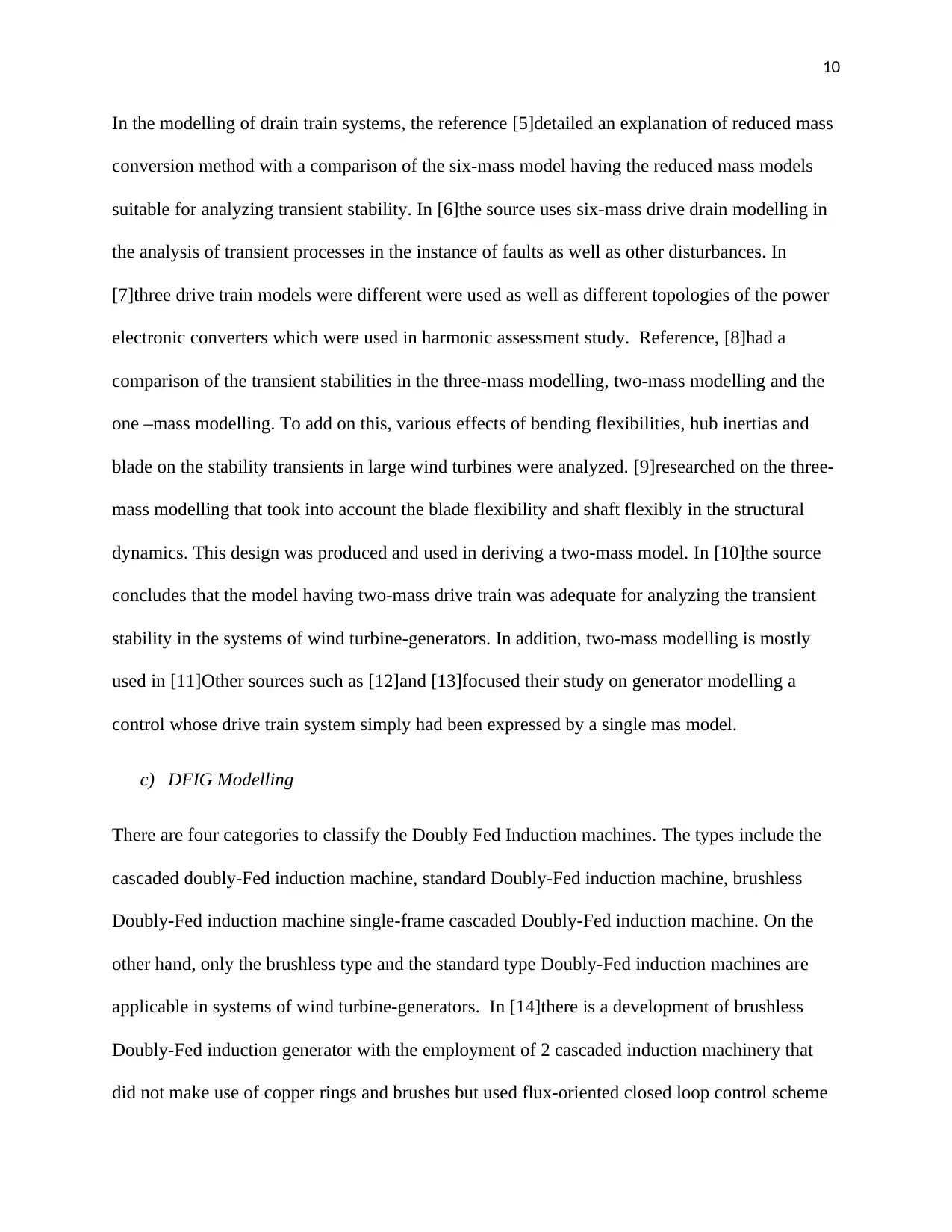
10
In the modelling of drain train systems, the reference [5]detailed an explanation of reduced mass
conversion method with a comparison of the six-mass model having the reduced mass models
suitable for analyzing transient stability. In [6]the source uses six-mass drive drain modelling in
the analysis of transient processes in the instance of faults as well as other disturbances. In
[7]three drive train models were different were used as well as different topologies of the power
electronic converters which were used in harmonic assessment study. Reference, [8]had a
comparison of the transient stabilities in the three-mass modelling, two-mass modelling and the
one –mass modelling. To add on this, various effects of bending flexibilities, hub inertias and
blade on the stability transients in large wind turbines were analyzed. [9]researched on the three-
mass modelling that took into account the blade flexibility and shaft flexibly in the structural
dynamics. This design was produced and used in deriving a two-mass model. In [10]the source
concludes that the model having two-mass drive train was adequate for analyzing the transient
stability in the systems of wind turbine-generators. In addition, two-mass modelling is mostly
used in [11]Other sources such as [12]and [13]focused their study on generator modelling a
control whose drive train system simply had been expressed by a single mas model.
c) DFIG Modelling
There are four categories to classify the Doubly Fed Induction machines. The types include the
cascaded doubly-Fed induction machine, standard Doubly-Fed induction machine, brushless
Doubly-Fed induction machine single-frame cascaded Doubly-Fed induction machine. On the
other hand, only the brushless type and the standard type Doubly-Fed induction machines are
applicable in systems of wind turbine-generators. In [14]there is a development of brushless
Doubly-Fed induction generator with the employment of 2 cascaded induction machinery that
did not make use of copper rings and brushes but used flux-oriented closed loop control scheme
In the modelling of drain train systems, the reference [5]detailed an explanation of reduced mass
conversion method with a comparison of the six-mass model having the reduced mass models
suitable for analyzing transient stability. In [6]the source uses six-mass drive drain modelling in
the analysis of transient processes in the instance of faults as well as other disturbances. In
[7]three drive train models were different were used as well as different topologies of the power
electronic converters which were used in harmonic assessment study. Reference, [8]had a
comparison of the transient stabilities in the three-mass modelling, two-mass modelling and the
one –mass modelling. To add on this, various effects of bending flexibilities, hub inertias and
blade on the stability transients in large wind turbines were analyzed. [9]researched on the three-
mass modelling that took into account the blade flexibility and shaft flexibly in the structural
dynamics. This design was produced and used in deriving a two-mass model. In [10]the source
concludes that the model having two-mass drive train was adequate for analyzing the transient
stability in the systems of wind turbine-generators. In addition, two-mass modelling is mostly
used in [11]Other sources such as [12]and [13]focused their study on generator modelling a
control whose drive train system simply had been expressed by a single mas model.
c) DFIG Modelling
There are four categories to classify the Doubly Fed Induction machines. The types include the
cascaded doubly-Fed induction machine, standard Doubly-Fed induction machine, brushless
Doubly-Fed induction machine single-frame cascaded Doubly-Fed induction machine. On the
other hand, only the brushless type and the standard type Doubly-Fed induction machines are
applicable in systems of wind turbine-generators. In [14]there is a development of brushless
Doubly-Fed induction generator with the employment of 2 cascaded induction machinery that
did not make use of copper rings and brushes but used flux-oriented closed loop control scheme
Paraphrase This Document
Need a fresh take? Get an instant paraphrase of this document with our AI Paraphraser
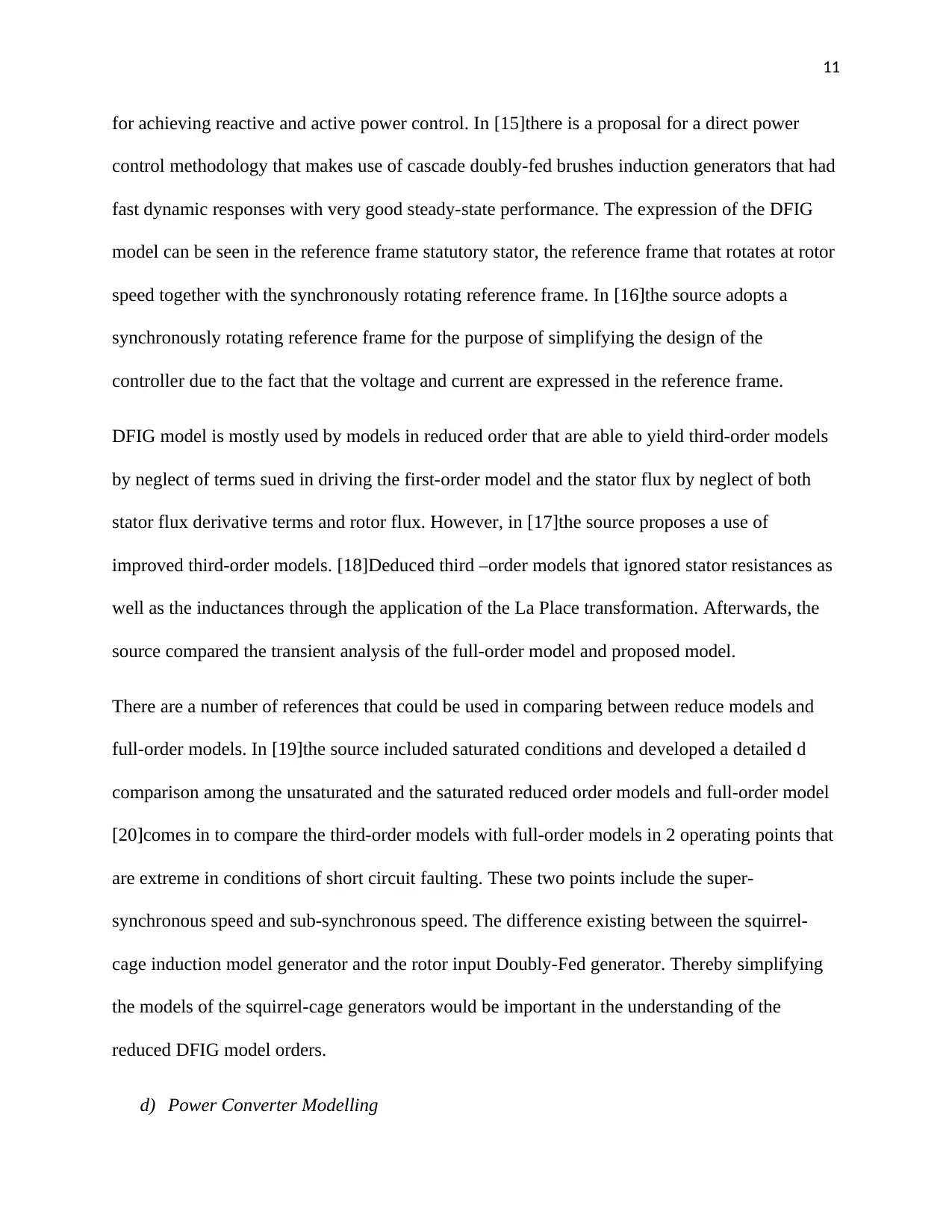
11
for achieving reactive and active power control. In [15]there is a proposal for a direct power
control methodology that makes use of cascade doubly-fed brushes induction generators that had
fast dynamic responses with very good steady-state performance. The expression of the DFIG
model can be seen in the reference frame statutory stator, the reference frame that rotates at rotor
speed together with the synchronously rotating reference frame. In [16]the source adopts a
synchronously rotating reference frame for the purpose of simplifying the design of the
controller due to the fact that the voltage and current are expressed in the reference frame.
DFIG model is mostly used by models in reduced order that are able to yield third-order models
by neglect of terms sued in driving the first-order model and the stator flux by neglect of both
stator flux derivative terms and rotor flux. However, in [17]the source proposes a use of
improved third-order models. [18]Deduced third –order models that ignored stator resistances as
well as the inductances through the application of the La Place transformation. Afterwards, the
source compared the transient analysis of the full-order model and proposed model.
There are a number of references that could be used in comparing between reduce models and
full-order models. In [19]the source included saturated conditions and developed a detailed d
comparison among the unsaturated and the saturated reduced order models and full-order model
[20]comes in to compare the third-order models with full-order models in 2 operating points that
are extreme in conditions of short circuit faulting. These two points include the super-
synchronous speed and sub-synchronous speed. The difference existing between the squirrel-
cage induction model generator and the rotor input Doubly-Fed generator. Thereby simplifying
the models of the squirrel-cage generators would be important in the understanding of the
reduced DFIG model orders.
d) Power Converter Modelling
for achieving reactive and active power control. In [15]there is a proposal for a direct power
control methodology that makes use of cascade doubly-fed brushes induction generators that had
fast dynamic responses with very good steady-state performance. The expression of the DFIG
model can be seen in the reference frame statutory stator, the reference frame that rotates at rotor
speed together with the synchronously rotating reference frame. In [16]the source adopts a
synchronously rotating reference frame for the purpose of simplifying the design of the
controller due to the fact that the voltage and current are expressed in the reference frame.
DFIG model is mostly used by models in reduced order that are able to yield third-order models
by neglect of terms sued in driving the first-order model and the stator flux by neglect of both
stator flux derivative terms and rotor flux. However, in [17]the source proposes a use of
improved third-order models. [18]Deduced third –order models that ignored stator resistances as
well as the inductances through the application of the La Place transformation. Afterwards, the
source compared the transient analysis of the full-order model and proposed model.
There are a number of references that could be used in comparing between reduce models and
full-order models. In [19]the source included saturated conditions and developed a detailed d
comparison among the unsaturated and the saturated reduced order models and full-order model
[20]comes in to compare the third-order models with full-order models in 2 operating points that
are extreme in conditions of short circuit faulting. These two points include the super-
synchronous speed and sub-synchronous speed. The difference existing between the squirrel-
cage induction model generator and the rotor input Doubly-Fed generator. Thereby simplifying
the models of the squirrel-cage generators would be important in the understanding of the
reduced DFIG model orders.
d) Power Converter Modelling

12
A power converter that is traditional to make use of systems of wind turbine-generators which
have back-to-back two-level PWM converters. The source of the three-phase PWM model
converter could be described in the reference frame made of abc with the reference frame having
the d-q synchronization being deduced for control purposes. The mathematical model bases its
space vectors described in the abc reference frame shown in [21]In [22]authors produced
detailed description of the study on the transformation of the model with PWM converter to the
d-q synchronization and abc reference frame.
In applications purposed for wind turbines, some researchers produced presented simple power
converter model that employs the equal AC voltage for the generation of the fundamental
frequency. [23]produced detail of the description of the working principles, comparisons and
control strategies for the three-phase sources of current and voltage for PWM converters.
2.3. Systems of Wind Turbine-Generator Control Strategies
The scheme control for systems of wind turbine-generator system includes DFIG control, pitch
angel control and maximum power tracking point control. The traditionally used method of
control technique, as well as the advanced techniques of control for wind turbine-generators, will
be reviewed in this subtopic.
Pitch Angle Control
This control method is mechanically used in the control of the blade angle as it moves in the
wind turbine when it captures power form t hind exceeding the rated value or the speed of wind
exceeding the rated value.in this manner, this type of control is enabled to control the maximum
output power being equal to the power that is rated, hence protecting the generator when the
speed of wind goes through gusts. Only at high speed of wind would the controller be activated.
A power converter that is traditional to make use of systems of wind turbine-generators which
have back-to-back two-level PWM converters. The source of the three-phase PWM model
converter could be described in the reference frame made of abc with the reference frame having
the d-q synchronization being deduced for control purposes. The mathematical model bases its
space vectors described in the abc reference frame shown in [21]In [22]authors produced
detailed description of the study on the transformation of the model with PWM converter to the
d-q synchronization and abc reference frame.
In applications purposed for wind turbines, some researchers produced presented simple power
converter model that employs the equal AC voltage for the generation of the fundamental
frequency. [23]produced detail of the description of the working principles, comparisons and
control strategies for the three-phase sources of current and voltage for PWM converters.
2.3. Systems of Wind Turbine-Generator Control Strategies
The scheme control for systems of wind turbine-generator system includes DFIG control, pitch
angel control and maximum power tracking point control. The traditionally used method of
control technique, as well as the advanced techniques of control for wind turbine-generators, will
be reviewed in this subtopic.
Pitch Angle Control
This control method is mechanically used in the control of the blade angle as it moves in the
wind turbine when it captures power form t hind exceeding the rated value or the speed of wind
exceeding the rated value.in this manner, this type of control is enabled to control the maximum
output power being equal to the power that is rated, hence protecting the generator when the
speed of wind goes through gusts. Only at high speed of wind would the controller be activated.
⊘ This is a preview!⊘
Do you want full access?
Subscribe today to unlock all pages.

Trusted by 1+ million students worldwide
1 out of 30