3D PRINTER About 3D printer and its working 3D printing
VerifiedAdded on 2023/04/23
|17
|5709
|186
AI Summary
Contribute Materials
Your contribution can guide someone’s learning journey. Share your
documents today.
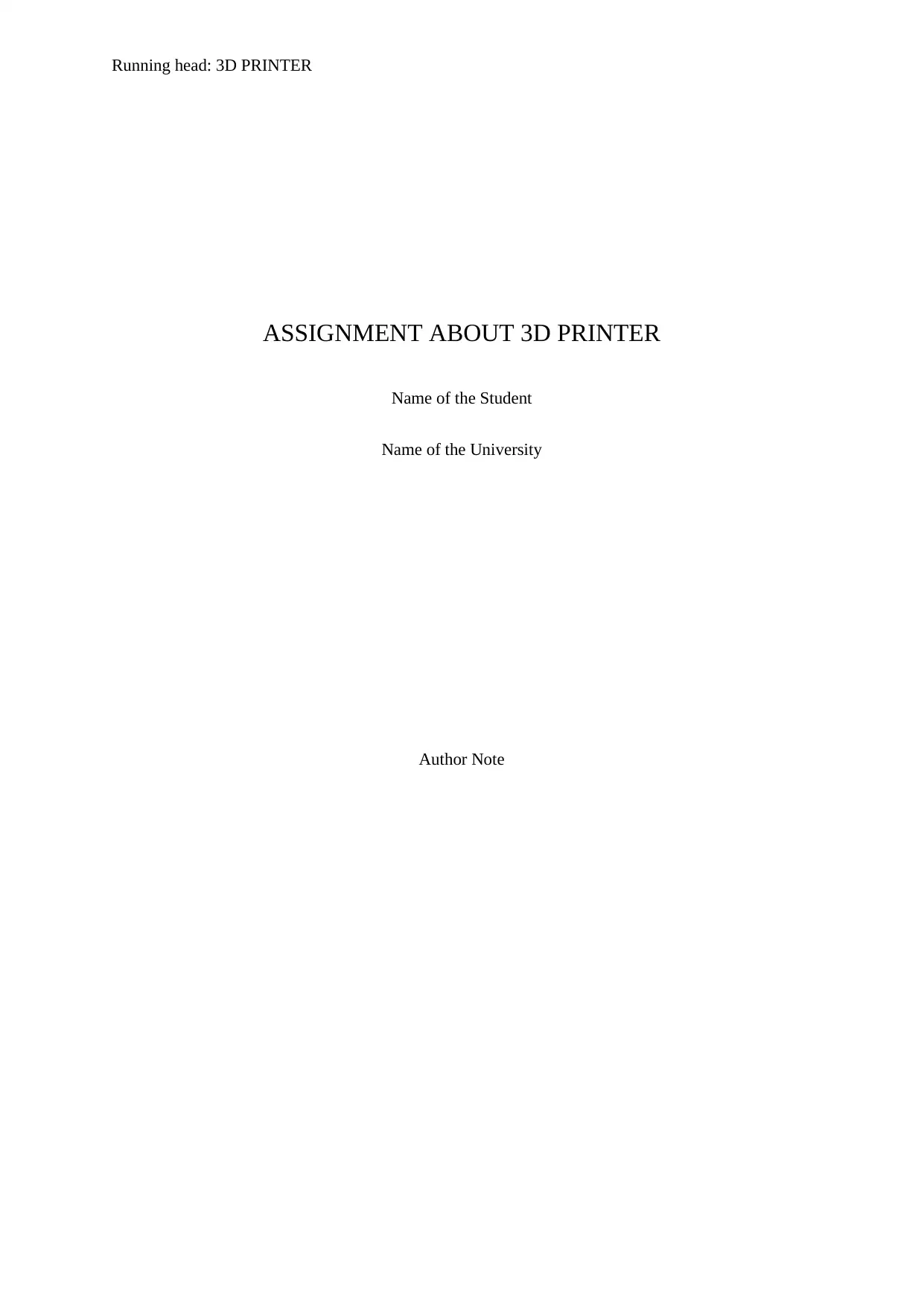
Running head: 3D PRINTER
ASSIGNMENT ABOUT 3D PRINTER
Name of the Student
Name of the University
Author Note
ASSIGNMENT ABOUT 3D PRINTER
Name of the Student
Name of the University
Author Note
Secure Best Marks with AI Grader
Need help grading? Try our AI Grader for instant feedback on your assignments.
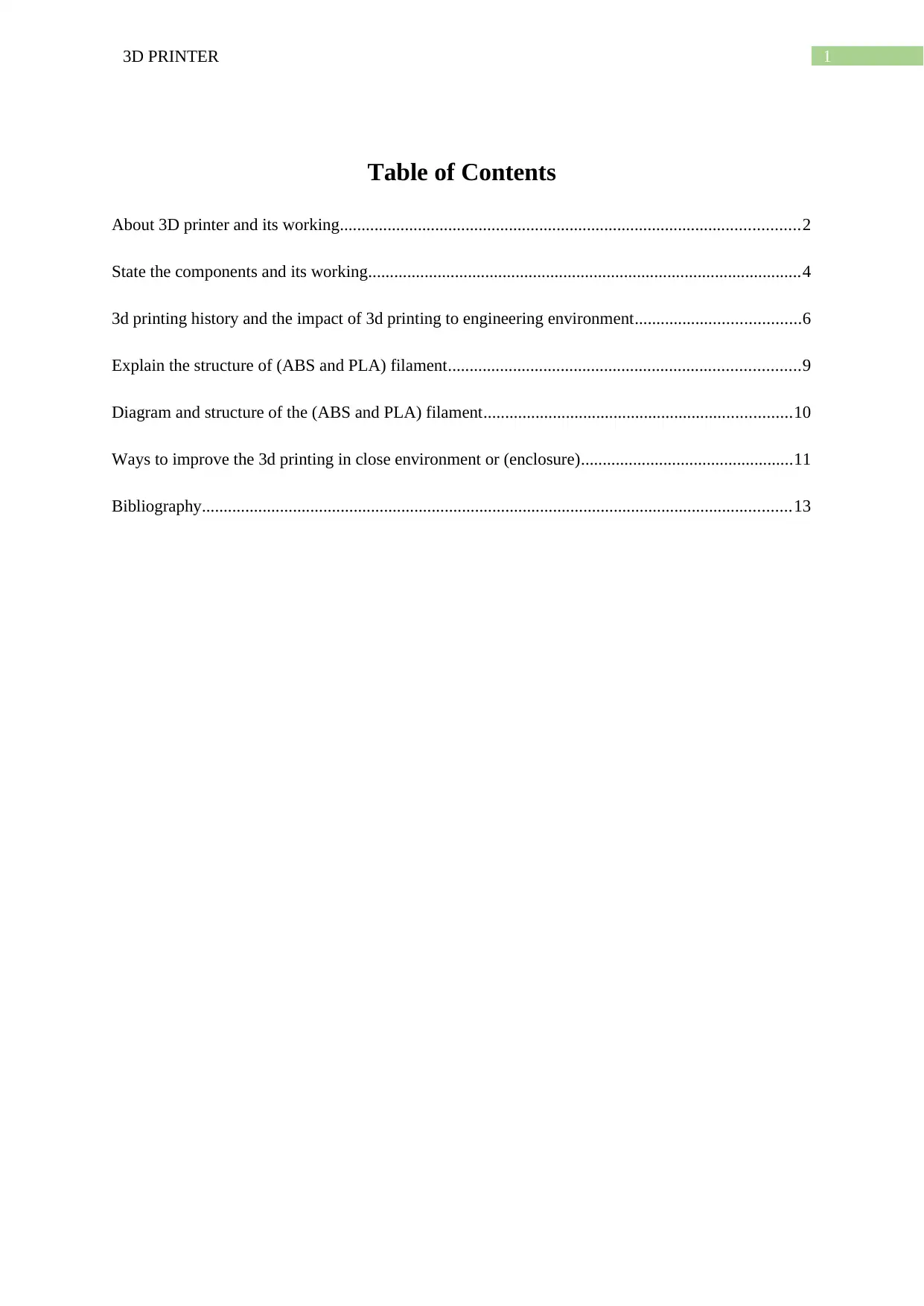
13D PRINTER
Table of Contents
About 3D printer and its working..........................................................................................................2
State the components and its working....................................................................................................4
3d printing history and the impact of 3d printing to engineering environment......................................6
Explain the structure of (ABS and PLA) filament.................................................................................9
Diagram and structure of the (ABS and PLA) filament.......................................................................10
Ways to improve the 3d printing in close environment or (enclosure).................................................11
Bibliography........................................................................................................................................13
Table of Contents
About 3D printer and its working..........................................................................................................2
State the components and its working....................................................................................................4
3d printing history and the impact of 3d printing to engineering environment......................................6
Explain the structure of (ABS and PLA) filament.................................................................................9
Diagram and structure of the (ABS and PLA) filament.......................................................................10
Ways to improve the 3d printing in close environment or (enclosure).................................................11
Bibliography........................................................................................................................................13
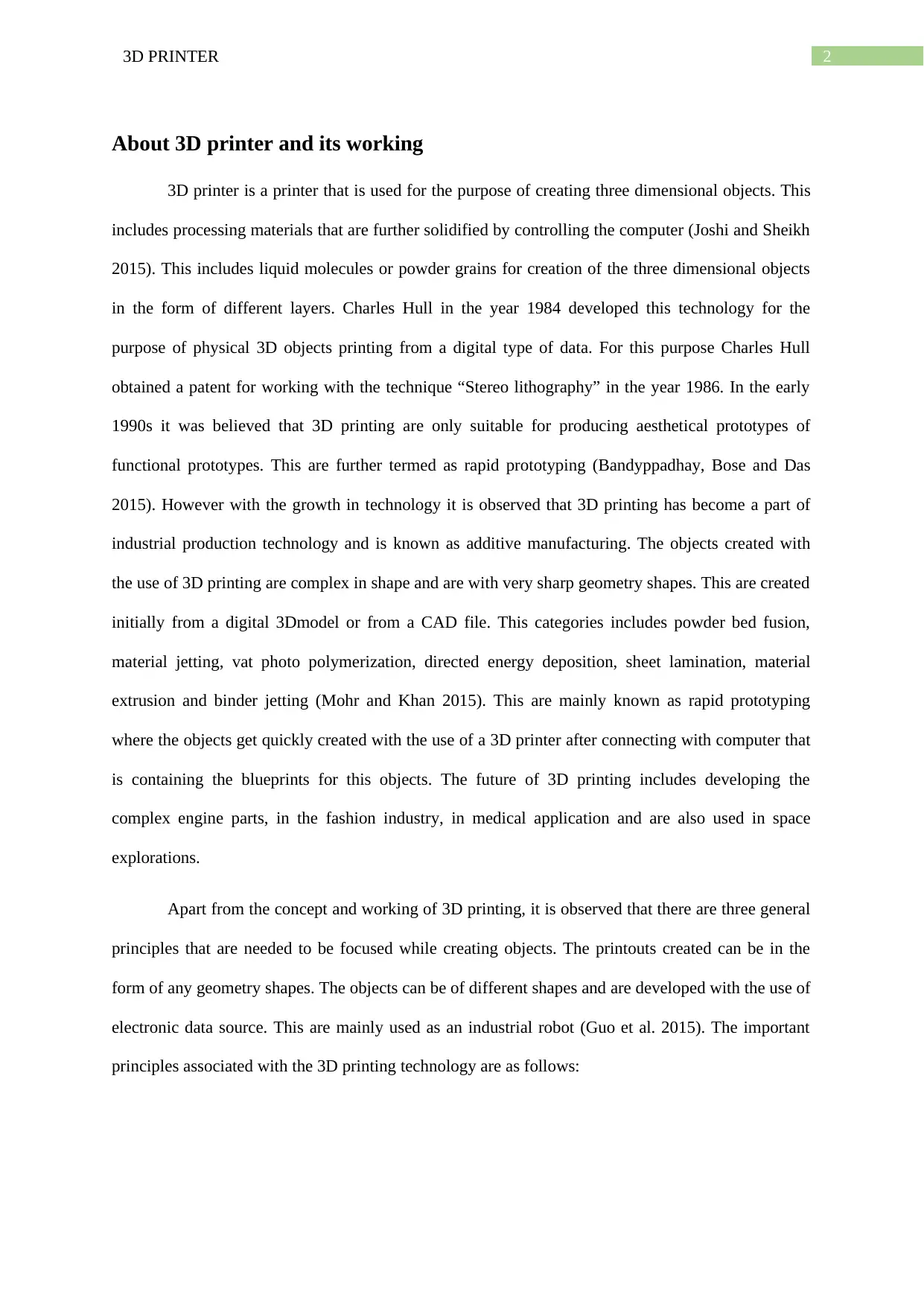
23D PRINTER
About 3D printer and its working
3D printer is a printer that is used for the purpose of creating three dimensional objects. This
includes processing materials that are further solidified by controlling the computer (Joshi and Sheikh
2015). This includes liquid molecules or powder grains for creation of the three dimensional objects
in the form of different layers. Charles Hull in the year 1984 developed this technology for the
purpose of physical 3D objects printing from a digital type of data. For this purpose Charles Hull
obtained a patent for working with the technique “Stereo lithography” in the year 1986. In the early
1990s it was believed that 3D printing are only suitable for producing aesthetical prototypes of
functional prototypes. This are further termed as rapid prototyping (Bandyppadhay, Bose and Das
2015). However with the growth in technology it is observed that 3D printing has become a part of
industrial production technology and is known as additive manufacturing. The objects created with
the use of 3D printing are complex in shape and are with very sharp geometry shapes. This are created
initially from a digital 3Dmodel or from a CAD file. This categories includes powder bed fusion,
material jetting, vat photo polymerization, directed energy deposition, sheet lamination, material
extrusion and binder jetting (Mohr and Khan 2015). This are mainly known as rapid prototyping
where the objects get quickly created with the use of a 3D printer after connecting with computer that
is containing the blueprints for this objects. The future of 3D printing includes developing the
complex engine parts, in the fashion industry, in medical application and are also used in space
explorations.
Apart from the concept and working of 3D printing, it is observed that there are three general
principles that are needed to be focused while creating objects. The printouts created can be in the
form of any geometry shapes. The objects can be of different shapes and are developed with the use of
electronic data source. This are mainly used as an industrial robot (Guo et al. 2015). The important
principles associated with the 3D printing technology are as follows:
About 3D printer and its working
3D printer is a printer that is used for the purpose of creating three dimensional objects. This
includes processing materials that are further solidified by controlling the computer (Joshi and Sheikh
2015). This includes liquid molecules or powder grains for creation of the three dimensional objects
in the form of different layers. Charles Hull in the year 1984 developed this technology for the
purpose of physical 3D objects printing from a digital type of data. For this purpose Charles Hull
obtained a patent for working with the technique “Stereo lithography” in the year 1986. In the early
1990s it was believed that 3D printing are only suitable for producing aesthetical prototypes of
functional prototypes. This are further termed as rapid prototyping (Bandyppadhay, Bose and Das
2015). However with the growth in technology it is observed that 3D printing has become a part of
industrial production technology and is known as additive manufacturing. The objects created with
the use of 3D printing are complex in shape and are with very sharp geometry shapes. This are created
initially from a digital 3Dmodel or from a CAD file. This categories includes powder bed fusion,
material jetting, vat photo polymerization, directed energy deposition, sheet lamination, material
extrusion and binder jetting (Mohr and Khan 2015). This are mainly known as rapid prototyping
where the objects get quickly created with the use of a 3D printer after connecting with computer that
is containing the blueprints for this objects. The future of 3D printing includes developing the
complex engine parts, in the fashion industry, in medical application and are also used in space
explorations.
Apart from the concept and working of 3D printing, it is observed that there are three general
principles that are needed to be focused while creating objects. The printouts created can be in the
form of any geometry shapes. The objects can be of different shapes and are developed with the use of
electronic data source. This are mainly used as an industrial robot (Guo et al. 2015). The important
principles associated with the 3D printing technology are as follows:
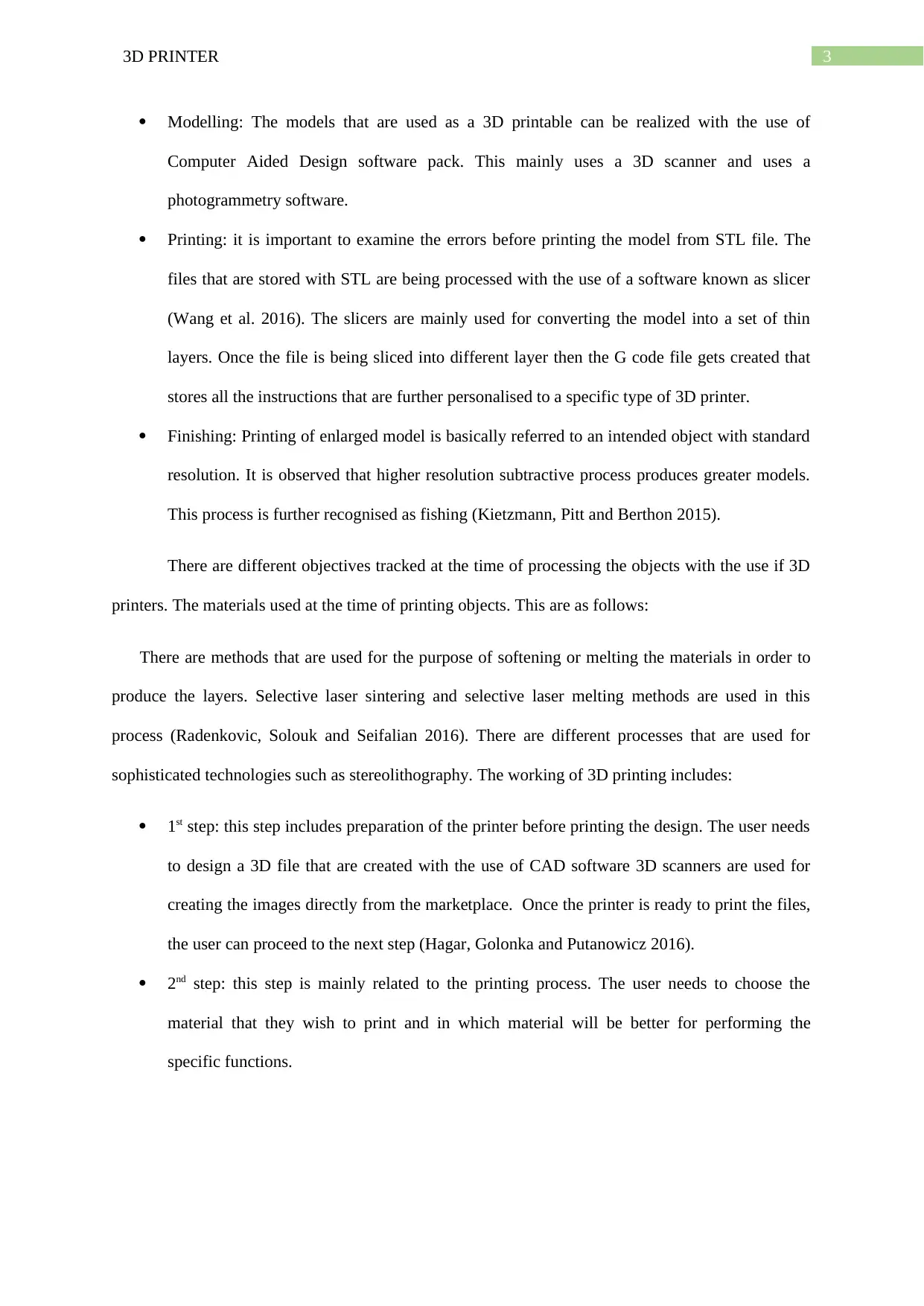
33D PRINTER
Modelling: The models that are used as a 3D printable can be realized with the use of
Computer Aided Design software pack. This mainly uses a 3D scanner and uses a
photogrammetry software.
Printing: it is important to examine the errors before printing the model from STL file. The
files that are stored with STL are being processed with the use of a software known as slicer
(Wang et al. 2016). The slicers are mainly used for converting the model into a set of thin
layers. Once the file is being sliced into different layer then the G code file gets created that
stores all the instructions that are further personalised to a specific type of 3D printer.
Finishing: Printing of enlarged model is basically referred to an intended object with standard
resolution. It is observed that higher resolution subtractive process produces greater models.
This process is further recognised as fishing (Kietzmann, Pitt and Berthon 2015).
There are different objectives tracked at the time of processing the objects with the use if 3D
printers. The materials used at the time of printing objects. This are as follows:
There are methods that are used for the purpose of softening or melting the materials in order to
produce the layers. Selective laser sintering and selective laser melting methods are used in this
process (Radenkovic, Solouk and Seifalian 2016). There are different processes that are used for
sophisticated technologies such as stereolithography. The working of 3D printing includes:
1st step: this step includes preparation of the printer before printing the design. The user needs
to design a 3D file that are created with the use of CAD software 3D scanners are used for
creating the images directly from the marketplace. Once the printer is ready to print the files,
the user can proceed to the next step (Hagar, Golonka and Putanowicz 2016).
2nd step: this step is mainly related to the printing process. The user needs to choose the
material that they wish to print and in which material will be better for performing the
specific functions.
Modelling: The models that are used as a 3D printable can be realized with the use of
Computer Aided Design software pack. This mainly uses a 3D scanner and uses a
photogrammetry software.
Printing: it is important to examine the errors before printing the model from STL file. The
files that are stored with STL are being processed with the use of a software known as slicer
(Wang et al. 2016). The slicers are mainly used for converting the model into a set of thin
layers. Once the file is being sliced into different layer then the G code file gets created that
stores all the instructions that are further personalised to a specific type of 3D printer.
Finishing: Printing of enlarged model is basically referred to an intended object with standard
resolution. It is observed that higher resolution subtractive process produces greater models.
This process is further recognised as fishing (Kietzmann, Pitt and Berthon 2015).
There are different objectives tracked at the time of processing the objects with the use if 3D
printers. The materials used at the time of printing objects. This are as follows:
There are methods that are used for the purpose of softening or melting the materials in order to
produce the layers. Selective laser sintering and selective laser melting methods are used in this
process (Radenkovic, Solouk and Seifalian 2016). There are different processes that are used for
sophisticated technologies such as stereolithography. The working of 3D printing includes:
1st step: this step includes preparation of the printer before printing the design. The user needs
to design a 3D file that are created with the use of CAD software 3D scanners are used for
creating the images directly from the marketplace. Once the printer is ready to print the files,
the user can proceed to the next step (Hagar, Golonka and Putanowicz 2016).
2nd step: this step is mainly related to the printing process. The user needs to choose the
material that they wish to print and in which material will be better for performing the
specific functions.
Secure Best Marks with AI Grader
Need help grading? Try our AI Grader for instant feedback on your assignments.
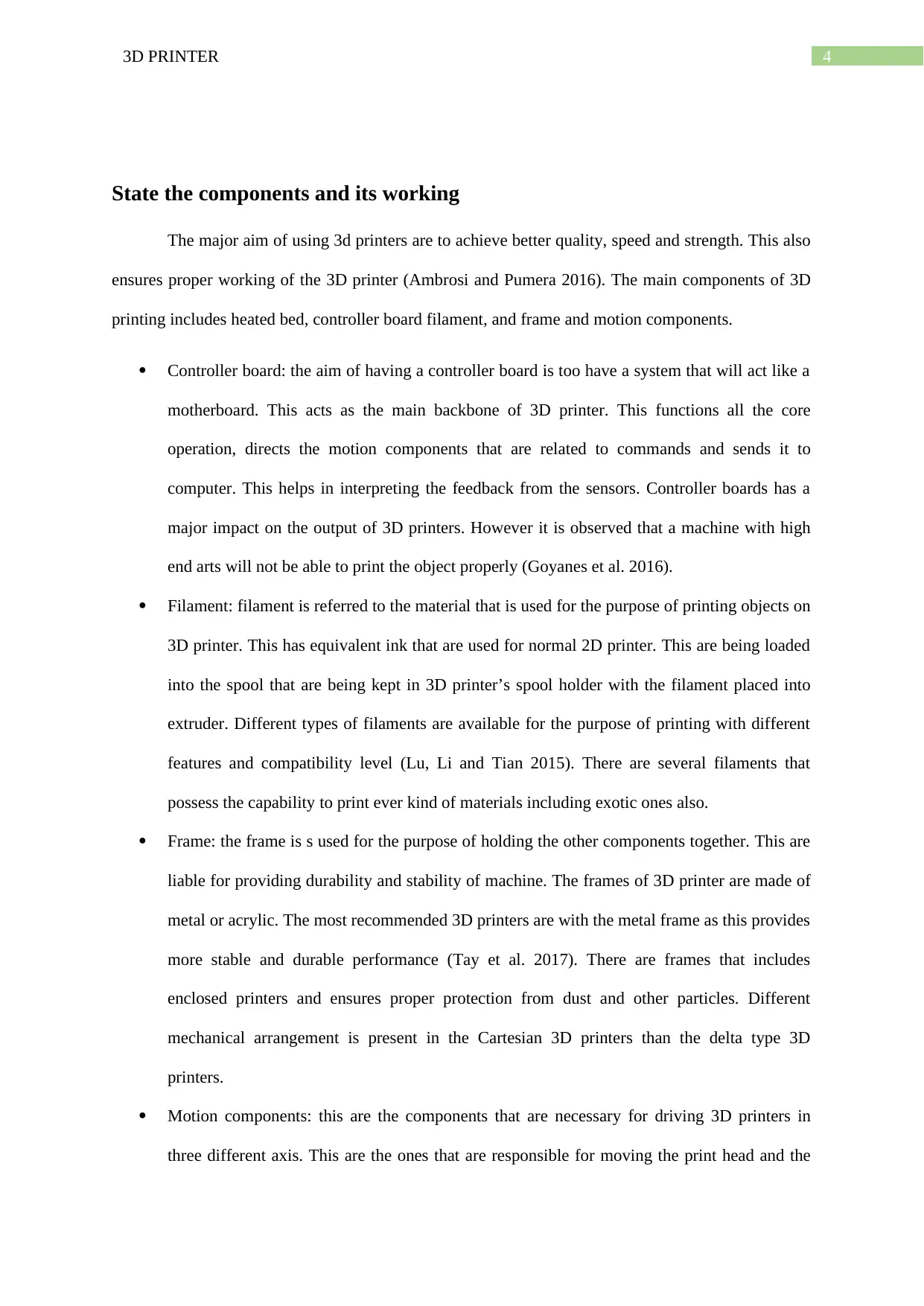
43D PRINTER
State the components and its working
The major aim of using 3d printers are to achieve better quality, speed and strength. This also
ensures proper working of the 3D printer (Ambrosi and Pumera 2016). The main components of 3D
printing includes heated bed, controller board filament, and frame and motion components.
Controller board: the aim of having a controller board is too have a system that will act like a
motherboard. This acts as the main backbone of 3D printer. This functions all the core
operation, directs the motion components that are related to commands and sends it to
computer. This helps in interpreting the feedback from the sensors. Controller boards has a
major impact on the output of 3D printers. However it is observed that a machine with high
end arts will not be able to print the object properly (Goyanes et al. 2016).
Filament: filament is referred to the material that is used for the purpose of printing objects on
3D printer. This has equivalent ink that are used for normal 2D printer. This are being loaded
into the spool that are being kept in 3D printer’s spool holder with the filament placed into
extruder. Different types of filaments are available for the purpose of printing with different
features and compatibility level (Lu, Li and Tian 2015). There are several filaments that
possess the capability to print ever kind of materials including exotic ones also.
Frame: the frame is s used for the purpose of holding the other components together. This are
liable for providing durability and stability of machine. The frames of 3D printer are made of
metal or acrylic. The most recommended 3D printers are with the metal frame as this provides
more stable and durable performance (Tay et al. 2017). There are frames that includes
enclosed printers and ensures proper protection from dust and other particles. Different
mechanical arrangement is present in the Cartesian 3D printers than the delta type 3D
printers.
Motion components: this are the components that are necessary for driving 3D printers in
three different axis. This are the ones that are responsible for moving the print head and the
State the components and its working
The major aim of using 3d printers are to achieve better quality, speed and strength. This also
ensures proper working of the 3D printer (Ambrosi and Pumera 2016). The main components of 3D
printing includes heated bed, controller board filament, and frame and motion components.
Controller board: the aim of having a controller board is too have a system that will act like a
motherboard. This acts as the main backbone of 3D printer. This functions all the core
operation, directs the motion components that are related to commands and sends it to
computer. This helps in interpreting the feedback from the sensors. Controller boards has a
major impact on the output of 3D printers. However it is observed that a machine with high
end arts will not be able to print the object properly (Goyanes et al. 2016).
Filament: filament is referred to the material that is used for the purpose of printing objects on
3D printer. This has equivalent ink that are used for normal 2D printer. This are being loaded
into the spool that are being kept in 3D printer’s spool holder with the filament placed into
extruder. Different types of filaments are available for the purpose of printing with different
features and compatibility level (Lu, Li and Tian 2015). There are several filaments that
possess the capability to print ever kind of materials including exotic ones also.
Frame: the frame is s used for the purpose of holding the other components together. This are
liable for providing durability and stability of machine. The frames of 3D printer are made of
metal or acrylic. The most recommended 3D printers are with the metal frame as this provides
more stable and durable performance (Tay et al. 2017). There are frames that includes
enclosed printers and ensures proper protection from dust and other particles. Different
mechanical arrangement is present in the Cartesian 3D printers than the delta type 3D
printers.
Motion components: this are the components that are necessary for driving 3D printers in
three different axis. This are the ones that are responsible for moving the print head and the
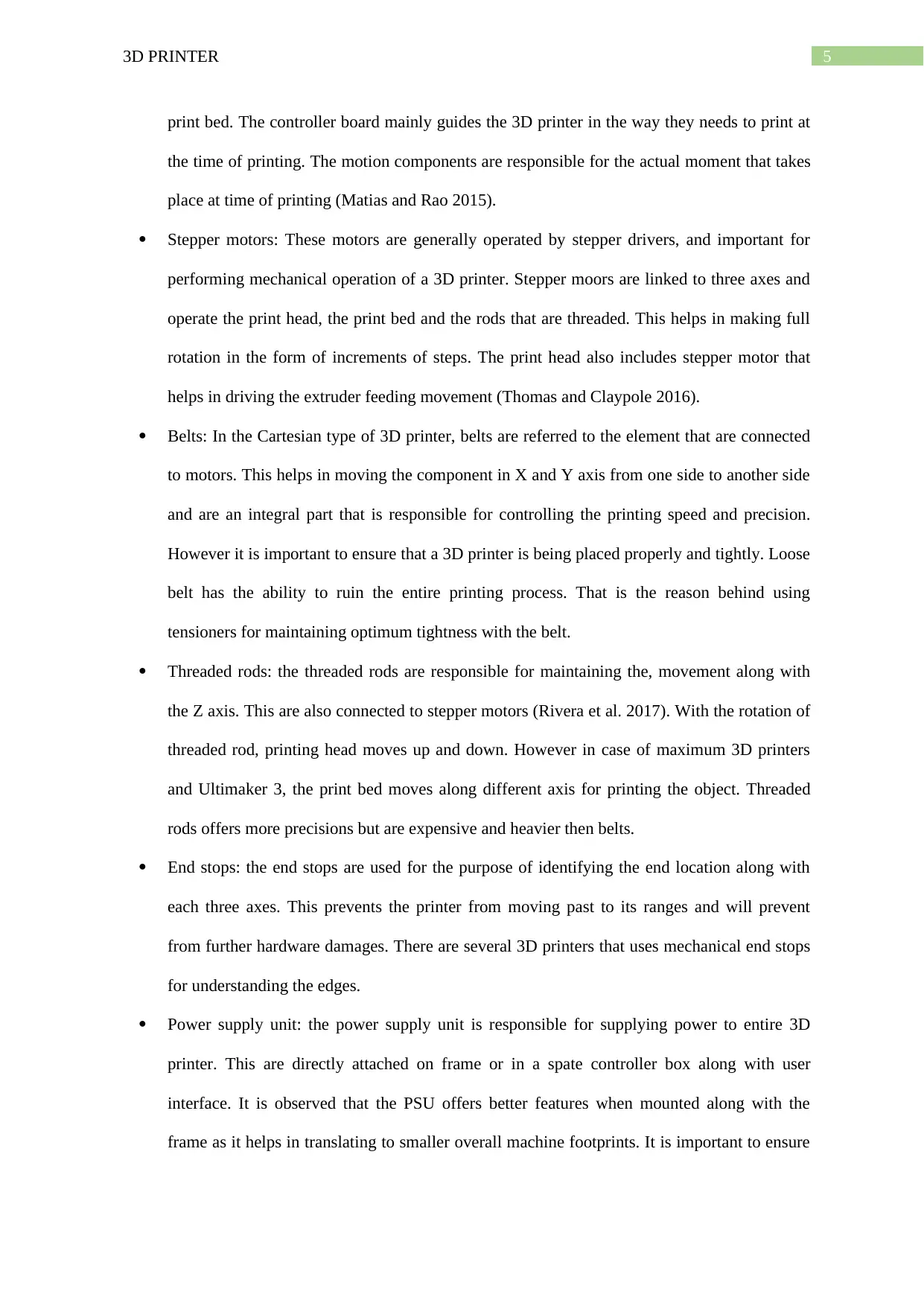
53D PRINTER
print bed. The controller board mainly guides the 3D printer in the way they needs to print at
the time of printing. The motion components are responsible for the actual moment that takes
place at time of printing (Matias and Rao 2015).
Stepper motors: These motors are generally operated by stepper drivers, and important for
performing mechanical operation of a 3D printer. Stepper moors are linked to three axes and
operate the print head, the print bed and the rods that are threaded. This helps in making full
rotation in the form of increments of steps. The print head also includes stepper motor that
helps in driving the extruder feeding movement (Thomas and Claypole 2016).
Belts: In the Cartesian type of 3D printer, belts are referred to the element that are connected
to motors. This helps in moving the component in X and Y axis from one side to another side
and are an integral part that is responsible for controlling the printing speed and precision.
However it is important to ensure that a 3D printer is being placed properly and tightly. Loose
belt has the ability to ruin the entire printing process. That is the reason behind using
tensioners for maintaining optimum tightness with the belt.
Threaded rods: the threaded rods are responsible for maintaining the, movement along with
the Z axis. This are also connected to stepper motors (Rivera et al. 2017). With the rotation of
threaded rod, printing head moves up and down. However in case of maximum 3D printers
and Ultimaker 3, the print bed moves along different axis for printing the object. Threaded
rods offers more precisions but are expensive and heavier then belts.
End stops: the end stops are used for the purpose of identifying the end location along with
each three axes. This prevents the printer from moving past to its ranges and will prevent
from further hardware damages. There are several 3D printers that uses mechanical end stops
for understanding the edges.
Power supply unit: the power supply unit is responsible for supplying power to entire 3D
printer. This are directly attached on frame or in a spate controller box along with user
interface. It is observed that the PSU offers better features when mounted along with the
frame as it helps in translating to smaller overall machine footprints. It is important to ensure
print bed. The controller board mainly guides the 3D printer in the way they needs to print at
the time of printing. The motion components are responsible for the actual moment that takes
place at time of printing (Matias and Rao 2015).
Stepper motors: These motors are generally operated by stepper drivers, and important for
performing mechanical operation of a 3D printer. Stepper moors are linked to three axes and
operate the print head, the print bed and the rods that are threaded. This helps in making full
rotation in the form of increments of steps. The print head also includes stepper motor that
helps in driving the extruder feeding movement (Thomas and Claypole 2016).
Belts: In the Cartesian type of 3D printer, belts are referred to the element that are connected
to motors. This helps in moving the component in X and Y axis from one side to another side
and are an integral part that is responsible for controlling the printing speed and precision.
However it is important to ensure that a 3D printer is being placed properly and tightly. Loose
belt has the ability to ruin the entire printing process. That is the reason behind using
tensioners for maintaining optimum tightness with the belt.
Threaded rods: the threaded rods are responsible for maintaining the, movement along with
the Z axis. This are also connected to stepper motors (Rivera et al. 2017). With the rotation of
threaded rod, printing head moves up and down. However in case of maximum 3D printers
and Ultimaker 3, the print bed moves along different axis for printing the object. Threaded
rods offers more precisions but are expensive and heavier then belts.
End stops: the end stops are used for the purpose of identifying the end location along with
each three axes. This prevents the printer from moving past to its ranges and will prevent
from further hardware damages. There are several 3D printers that uses mechanical end stops
for understanding the edges.
Power supply unit: the power supply unit is responsible for supplying power to entire 3D
printer. This are directly attached on frame or in a spate controller box along with user
interface. It is observed that the PSU offers better features when mounted along with the
frame as it helps in translating to smaller overall machine footprints. It is important to ensure
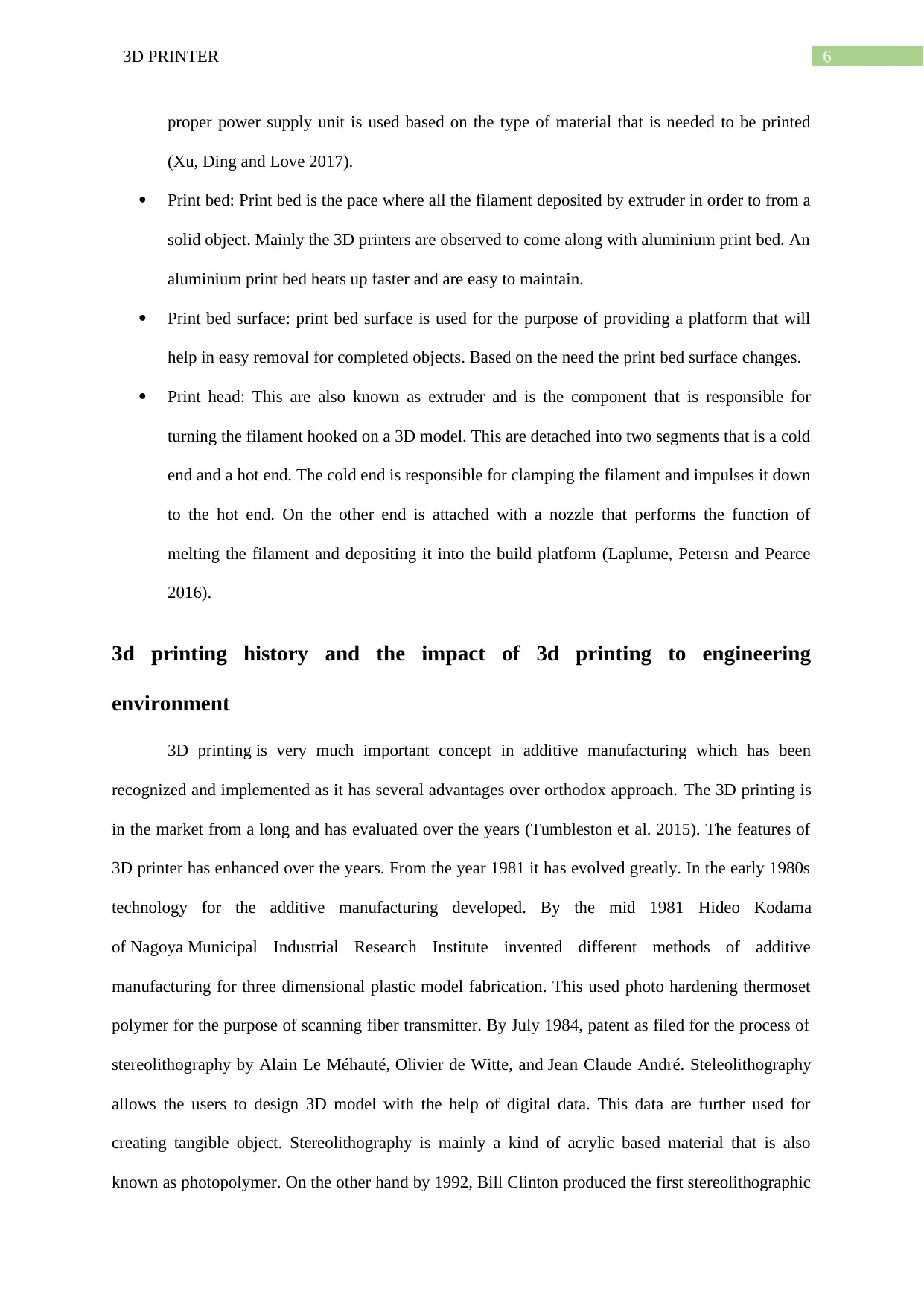
63D PRINTER
proper power supply unit is used based on the type of material that is needed to be printed
(Xu, Ding and Love 2017).
Print bed: Print bed is the pace where all the filament deposited by extruder in order to from a
solid object. Mainly the 3D printers are observed to come along with aluminium print bed. An
aluminium print bed heats up faster and are easy to maintain.
Print bed surface: print bed surface is used for the purpose of providing a platform that will
help in easy removal for completed objects. Based on the need the print bed surface changes.
Print head: This are also known as extruder and is the component that is responsible for
turning the filament hooked on a 3D model. This are detached into two segments that is a cold
end and a hot end. The cold end is responsible for clamping the filament and impulses it down
to the hot end. On the other end is attached with a nozzle that performs the function of
melting the filament and depositing it into the build platform (Laplume, Petersn and Pearce
2016).
3d printing history and the impact of 3d printing to engineering
environment
3D printing is very much important concept in additive manufacturing which has been
recognized and implemented as it has several advantages over orthodox approach. The 3D printing is
in the market from a long and has evaluated over the years (Tumbleston et al. 2015). The features of
3D printer has enhanced over the years. From the year 1981 it has evolved greatly. In the early 1980s
technology for the additive manufacturing developed. By the mid 1981 Hideo Kodama
of Nagoya Municipal Industrial Research Institute invented different methods of additive
manufacturing for three dimensional plastic model fabrication. This used photo hardening thermoset
polymer for the purpose of scanning fiber transmitter. By July 1984, patent as filed for the process of
stereolithography by Alain Le Méhauté, Olivier de Witte, and Jean Claude André. Steleolithography
allows the users to design 3D model with the help of digital data. This data are further used for
creating tangible object. Stereolithography is mainly a kind of acrylic based material that is also
known as photopolymer. On the other hand by 1992, Bill Clinton produced the first stereolithographic
proper power supply unit is used based on the type of material that is needed to be printed
(Xu, Ding and Love 2017).
Print bed: Print bed is the pace where all the filament deposited by extruder in order to from a
solid object. Mainly the 3D printers are observed to come along with aluminium print bed. An
aluminium print bed heats up faster and are easy to maintain.
Print bed surface: print bed surface is used for the purpose of providing a platform that will
help in easy removal for completed objects. Based on the need the print bed surface changes.
Print head: This are also known as extruder and is the component that is responsible for
turning the filament hooked on a 3D model. This are detached into two segments that is a cold
end and a hot end. The cold end is responsible for clamping the filament and impulses it down
to the hot end. On the other end is attached with a nozzle that performs the function of
melting the filament and depositing it into the build platform (Laplume, Petersn and Pearce
2016).
3d printing history and the impact of 3d printing to engineering
environment
3D printing is very much important concept in additive manufacturing which has been
recognized and implemented as it has several advantages over orthodox approach. The 3D printing is
in the market from a long and has evaluated over the years (Tumbleston et al. 2015). The features of
3D printer has enhanced over the years. From the year 1981 it has evolved greatly. In the early 1980s
technology for the additive manufacturing developed. By the mid 1981 Hideo Kodama
of Nagoya Municipal Industrial Research Institute invented different methods of additive
manufacturing for three dimensional plastic model fabrication. This used photo hardening thermoset
polymer for the purpose of scanning fiber transmitter. By July 1984, patent as filed for the process of
stereolithography by Alain Le Méhauté, Olivier de Witte, and Jean Claude André. Steleolithography
allows the users to design 3D model with the help of digital data. This data are further used for
creating tangible object. Stereolithography is mainly a kind of acrylic based material that is also
known as photopolymer. On the other hand by 1992, Bill Clinton produced the first stereolithographic
Paraphrase This Document
Need a fresh take? Get an instant paraphrase of this document with our AI Paraphraser
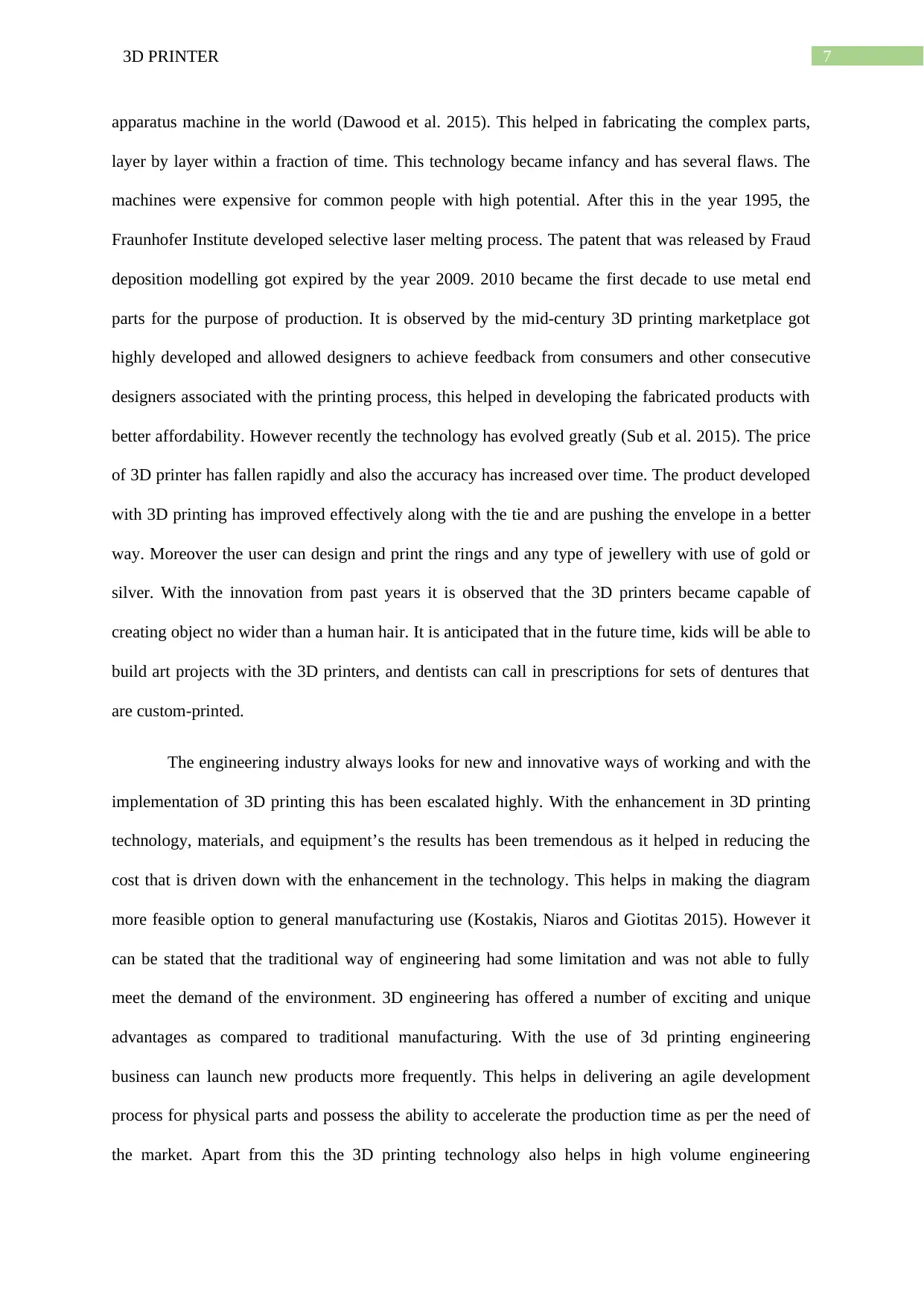
73D PRINTER
apparatus machine in the world (Dawood et al. 2015). This helped in fabricating the complex parts,
layer by layer within a fraction of time. This technology became infancy and has several flaws. The
machines were expensive for common people with high potential. After this in the year 1995, the
Fraunhofer Institute developed selective laser melting process. The patent that was released by Fraud
deposition modelling got expired by the year 2009. 2010 became the first decade to use metal end
parts for the purpose of production. It is observed by the mid-century 3D printing marketplace got
highly developed and allowed designers to achieve feedback from consumers and other consecutive
designers associated with the printing process, this helped in developing the fabricated products with
better affordability. However recently the technology has evolved greatly (Sub et al. 2015). The price
of 3D printer has fallen rapidly and also the accuracy has increased over time. The product developed
with 3D printing has improved effectively along with the tie and are pushing the envelope in a better
way. Moreover the user can design and print the rings and any type of jewellery with use of gold or
silver. With the innovation from past years it is observed that the 3D printers became capable of
creating object no wider than a human hair. It is anticipated that in the future time, kids will be able to
build art projects with the 3D printers, and dentists can call in prescriptions for sets of dentures that
are custom-printed.
The engineering industry always looks for new and innovative ways of working and with the
implementation of 3D printing this has been escalated highly. With the enhancement in 3D printing
technology, materials, and equipment’s the results has been tremendous as it helped in reducing the
cost that is driven down with the enhancement in the technology. This helps in making the diagram
more feasible option to general manufacturing use (Kostakis, Niaros and Giotitas 2015). However it
can be stated that the traditional way of engineering had some limitation and was not able to fully
meet the demand of the environment. 3D engineering has offered a number of exciting and unique
advantages as compared to traditional manufacturing. With the use of 3d printing engineering
business can launch new products more frequently. This helps in delivering an agile development
process for physical parts and possess the ability to accelerate the production time as per the need of
the market. Apart from this the 3D printing technology also helps in high volume engineering
apparatus machine in the world (Dawood et al. 2015). This helped in fabricating the complex parts,
layer by layer within a fraction of time. This technology became infancy and has several flaws. The
machines were expensive for common people with high potential. After this in the year 1995, the
Fraunhofer Institute developed selective laser melting process. The patent that was released by Fraud
deposition modelling got expired by the year 2009. 2010 became the first decade to use metal end
parts for the purpose of production. It is observed by the mid-century 3D printing marketplace got
highly developed and allowed designers to achieve feedback from consumers and other consecutive
designers associated with the printing process, this helped in developing the fabricated products with
better affordability. However recently the technology has evolved greatly (Sub et al. 2015). The price
of 3D printer has fallen rapidly and also the accuracy has increased over time. The product developed
with 3D printing has improved effectively along with the tie and are pushing the envelope in a better
way. Moreover the user can design and print the rings and any type of jewellery with use of gold or
silver. With the innovation from past years it is observed that the 3D printers became capable of
creating object no wider than a human hair. It is anticipated that in the future time, kids will be able to
build art projects with the 3D printers, and dentists can call in prescriptions for sets of dentures that
are custom-printed.
The engineering industry always looks for new and innovative ways of working and with the
implementation of 3D printing this has been escalated highly. With the enhancement in 3D printing
technology, materials, and equipment’s the results has been tremendous as it helped in reducing the
cost that is driven down with the enhancement in the technology. This helps in making the diagram
more feasible option to general manufacturing use (Kostakis, Niaros and Giotitas 2015). However it
can be stated that the traditional way of engineering had some limitation and was not able to fully
meet the demand of the environment. 3D engineering has offered a number of exciting and unique
advantages as compared to traditional manufacturing. With the use of 3d printing engineering
business can launch new products more frequently. This helps in delivering an agile development
process for physical parts and possess the ability to accelerate the production time as per the need of
the market. Apart from this the 3D printing technology also helps in high volume engineering
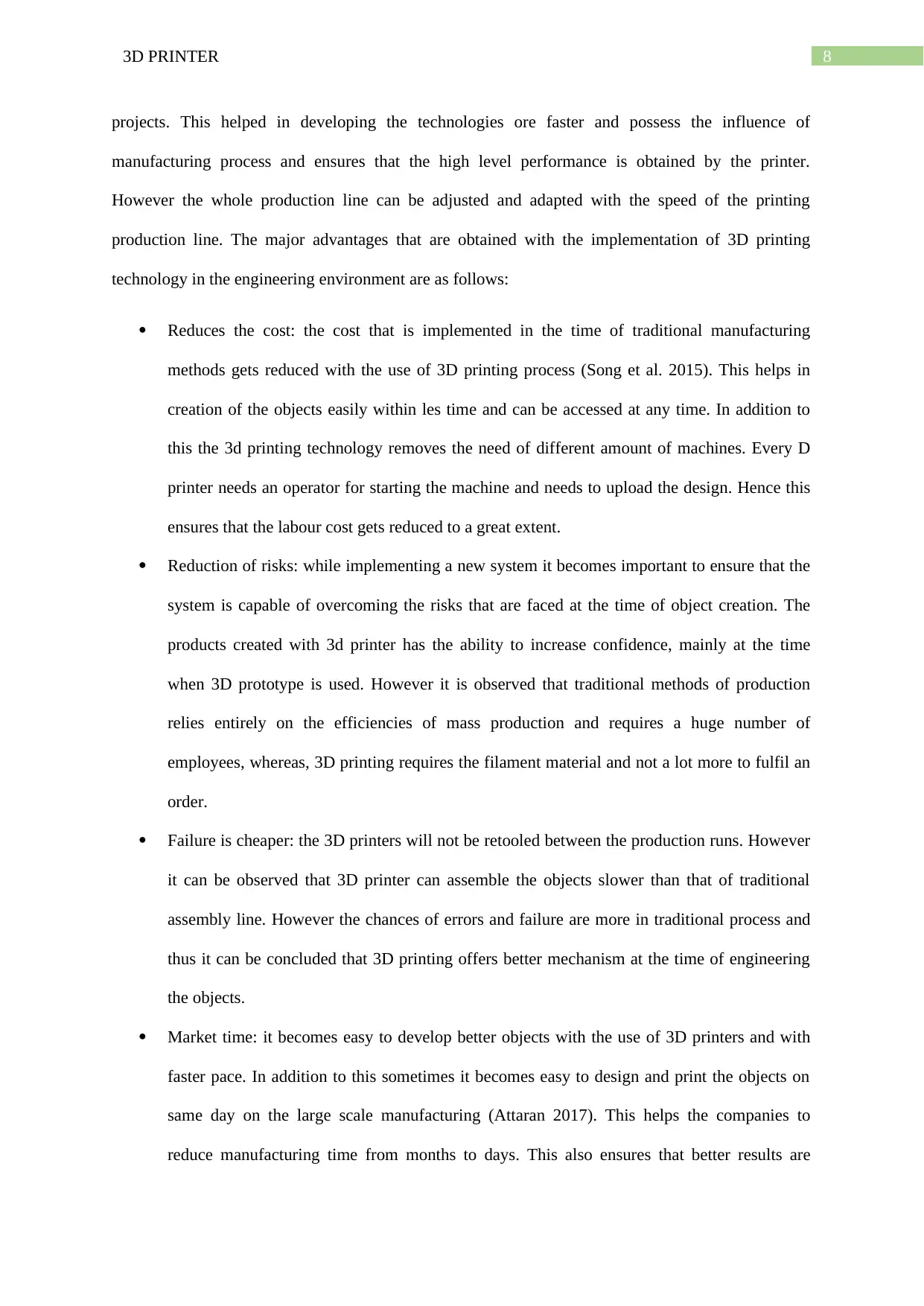
83D PRINTER
projects. This helped in developing the technologies ore faster and possess the influence of
manufacturing process and ensures that the high level performance is obtained by the printer.
However the whole production line can be adjusted and adapted with the speed of the printing
production line. The major advantages that are obtained with the implementation of 3D printing
technology in the engineering environment are as follows:
Reduces the cost: the cost that is implemented in the time of traditional manufacturing
methods gets reduced with the use of 3D printing process (Song et al. 2015). This helps in
creation of the objects easily within les time and can be accessed at any time. In addition to
this the 3d printing technology removes the need of different amount of machines. Every D
printer needs an operator for starting the machine and needs to upload the design. Hence this
ensures that the labour cost gets reduced to a great extent.
Reduction of risks: while implementing a new system it becomes important to ensure that the
system is capable of overcoming the risks that are faced at the time of object creation. The
products created with 3d printer has the ability to increase confidence, mainly at the time
when 3D prototype is used. However it is observed that traditional methods of production
relies entirely on the efficiencies of mass production and requires a huge number of
employees, whereas, 3D printing requires the filament material and not a lot more to fulfil an
order.
Failure is cheaper: the 3D printers will not be retooled between the production runs. However
it can be observed that 3D printer can assemble the objects slower than that of traditional
assembly line. However the chances of errors and failure are more in traditional process and
thus it can be concluded that 3D printing offers better mechanism at the time of engineering
the objects.
Market time: it becomes easy to develop better objects with the use of 3D printers and with
faster pace. In addition to this sometimes it becomes easy to design and print the objects on
same day on the large scale manufacturing (Attaran 2017). This helps the companies to
reduce manufacturing time from months to days. This also ensures that better results are
projects. This helped in developing the technologies ore faster and possess the influence of
manufacturing process and ensures that the high level performance is obtained by the printer.
However the whole production line can be adjusted and adapted with the speed of the printing
production line. The major advantages that are obtained with the implementation of 3D printing
technology in the engineering environment are as follows:
Reduces the cost: the cost that is implemented in the time of traditional manufacturing
methods gets reduced with the use of 3D printing process (Song et al. 2015). This helps in
creation of the objects easily within les time and can be accessed at any time. In addition to
this the 3d printing technology removes the need of different amount of machines. Every D
printer needs an operator for starting the machine and needs to upload the design. Hence this
ensures that the labour cost gets reduced to a great extent.
Reduction of risks: while implementing a new system it becomes important to ensure that the
system is capable of overcoming the risks that are faced at the time of object creation. The
products created with 3d printer has the ability to increase confidence, mainly at the time
when 3D prototype is used. However it is observed that traditional methods of production
relies entirely on the efficiencies of mass production and requires a huge number of
employees, whereas, 3D printing requires the filament material and not a lot more to fulfil an
order.
Failure is cheaper: the 3D printers will not be retooled between the production runs. However
it can be observed that 3D printer can assemble the objects slower than that of traditional
assembly line. However the chances of errors and failure are more in traditional process and
thus it can be concluded that 3D printing offers better mechanism at the time of engineering
the objects.
Market time: it becomes easy to develop better objects with the use of 3D printers and with
faster pace. In addition to this sometimes it becomes easy to design and print the objects on
same day on the large scale manufacturing (Attaran 2017). This helps the companies to
reduce manufacturing time from months to days. This also ensures that better results are
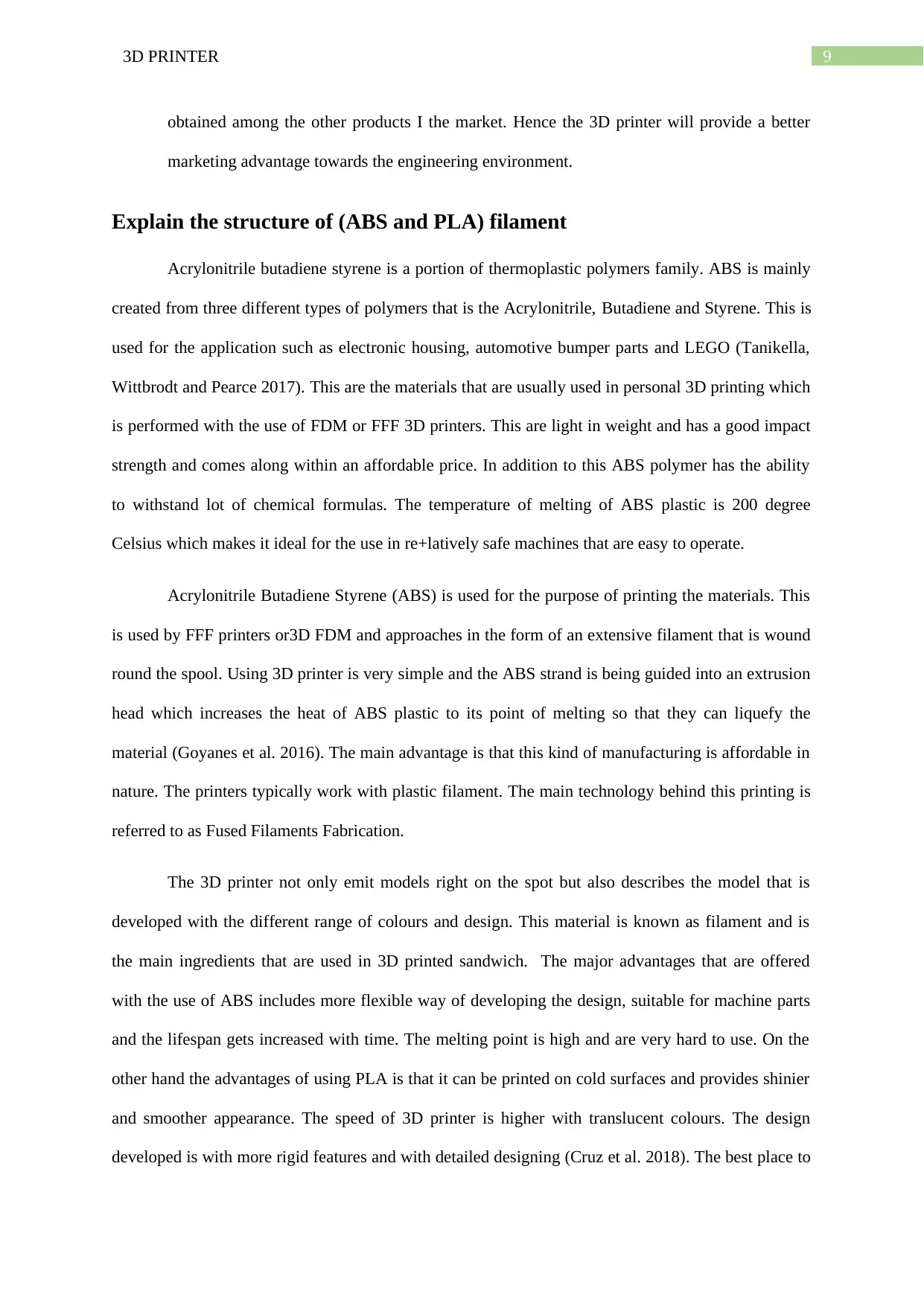
93D PRINTER
obtained among the other products I the market. Hence the 3D printer will provide a better
marketing advantage towards the engineering environment.
Explain the structure of (ABS and PLA) filament
Acrylonitrile butadiene styrene is a portion of thermoplastic polymers family. ABS is mainly
created from three different types of polymers that is the Acrylonitrile, Butadiene and Styrene. This is
used for the application such as electronic housing, automotive bumper parts and LEGO (Tanikella,
Wittbrodt and Pearce 2017). This are the materials that are usually used in personal 3D printing which
is performed with the use of FDM or FFF 3D printers. This are light in weight and has a good impact
strength and comes along within an affordable price. In addition to this ABS polymer has the ability
to withstand lot of chemical formulas. The temperature of melting of ABS plastic is 200 degree
Celsius which makes it ideal for the use in re+latively safe machines that are easy to operate.
Acrylonitrile Butadiene Styrene (ABS) is used for the purpose of printing the materials. This
is used by FFF printers or3D FDM and approaches in the form of an extensive filament that is wound
round the spool. Using 3D printer is very simple and the ABS strand is being guided into an extrusion
head which increases the heat of ABS plastic to its point of melting so that they can liquefy the
material (Goyanes et al. 2016). The main advantage is that this kind of manufacturing is affordable in
nature. The printers typically work with plastic filament. The main technology behind this printing is
referred to as Fused Filaments Fabrication.
The 3D printer not only emit models right on the spot but also describes the model that is
developed with the different range of colours and design. This material is known as filament and is
the main ingredients that are used in 3D printed sandwich. The major advantages that are offered
with the use of ABS includes more flexible way of developing the design, suitable for machine parts
and the lifespan gets increased with time. The melting point is high and are very hard to use. On the
other hand the advantages of using PLA is that it can be printed on cold surfaces and provides shinier
and smoother appearance. The speed of 3D printer is higher with translucent colours. The design
developed is with more rigid features and with detailed designing (Cruz et al. 2018). The best place to
obtained among the other products I the market. Hence the 3D printer will provide a better
marketing advantage towards the engineering environment.
Explain the structure of (ABS and PLA) filament
Acrylonitrile butadiene styrene is a portion of thermoplastic polymers family. ABS is mainly
created from three different types of polymers that is the Acrylonitrile, Butadiene and Styrene. This is
used for the application such as electronic housing, automotive bumper parts and LEGO (Tanikella,
Wittbrodt and Pearce 2017). This are the materials that are usually used in personal 3D printing which
is performed with the use of FDM or FFF 3D printers. This are light in weight and has a good impact
strength and comes along within an affordable price. In addition to this ABS polymer has the ability
to withstand lot of chemical formulas. The temperature of melting of ABS plastic is 200 degree
Celsius which makes it ideal for the use in re+latively safe machines that are easy to operate.
Acrylonitrile Butadiene Styrene (ABS) is used for the purpose of printing the materials. This
is used by FFF printers or3D FDM and approaches in the form of an extensive filament that is wound
round the spool. Using 3D printer is very simple and the ABS strand is being guided into an extrusion
head which increases the heat of ABS plastic to its point of melting so that they can liquefy the
material (Goyanes et al. 2016). The main advantage is that this kind of manufacturing is affordable in
nature. The printers typically work with plastic filament. The main technology behind this printing is
referred to as Fused Filaments Fabrication.
The 3D printer not only emit models right on the spot but also describes the model that is
developed with the different range of colours and design. This material is known as filament and is
the main ingredients that are used in 3D printed sandwich. The major advantages that are offered
with the use of ABS includes more flexible way of developing the design, suitable for machine parts
and the lifespan gets increased with time. The melting point is high and are very hard to use. On the
other hand the advantages of using PLA is that it can be printed on cold surfaces and provides shinier
and smoother appearance. The speed of 3D printer is higher with translucent colours. The design
developed is with more rigid features and with detailed designing (Cruz et al. 2018). The best place to
Secure Best Marks with AI Grader
Need help grading? Try our AI Grader for instant feedback on your assignments.
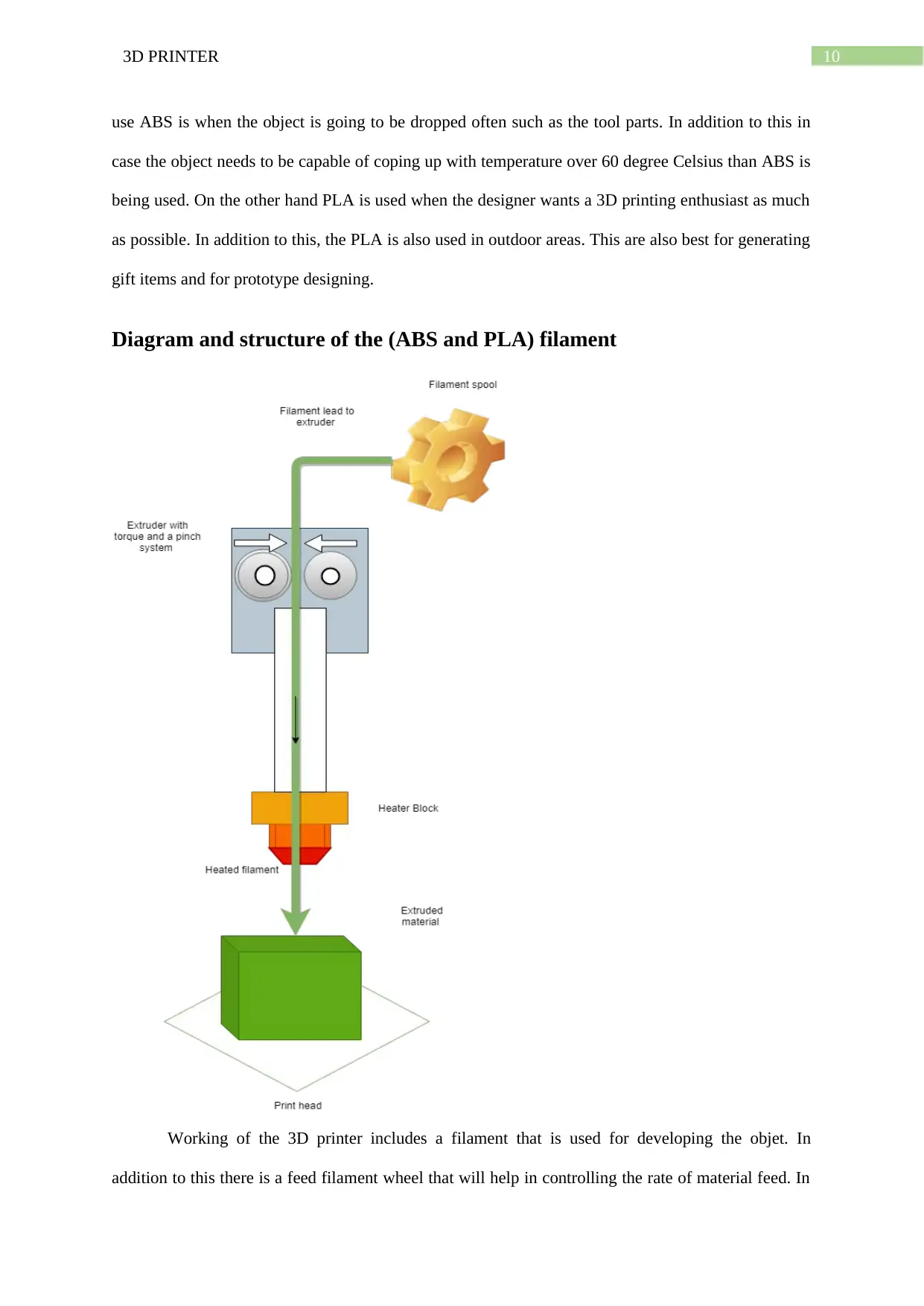
103D PRINTER
use ABS is when the object is going to be dropped often such as the tool parts. In addition to this in
case the object needs to be capable of coping up with temperature over 60 degree Celsius than ABS is
being used. On the other hand PLA is used when the designer wants a 3D printing enthusiast as much
as possible. In addition to this, the PLA is also used in outdoor areas. This are also best for generating
gift items and for prototype designing.
Diagram and structure of the (ABS and PLA) filament
Working of the 3D printer includes a filament that is used for developing the objet. In
addition to this there is a feed filament wheel that will help in controlling the rate of material feed. In
use ABS is when the object is going to be dropped often such as the tool parts. In addition to this in
case the object needs to be capable of coping up with temperature over 60 degree Celsius than ABS is
being used. On the other hand PLA is used when the designer wants a 3D printing enthusiast as much
as possible. In addition to this, the PLA is also used in outdoor areas. This are also best for generating
gift items and for prototype designing.
Diagram and structure of the (ABS and PLA) filament
Working of the 3D printer includes a filament that is used for developing the objet. In
addition to this there is a feed filament wheel that will help in controlling the rate of material feed. In
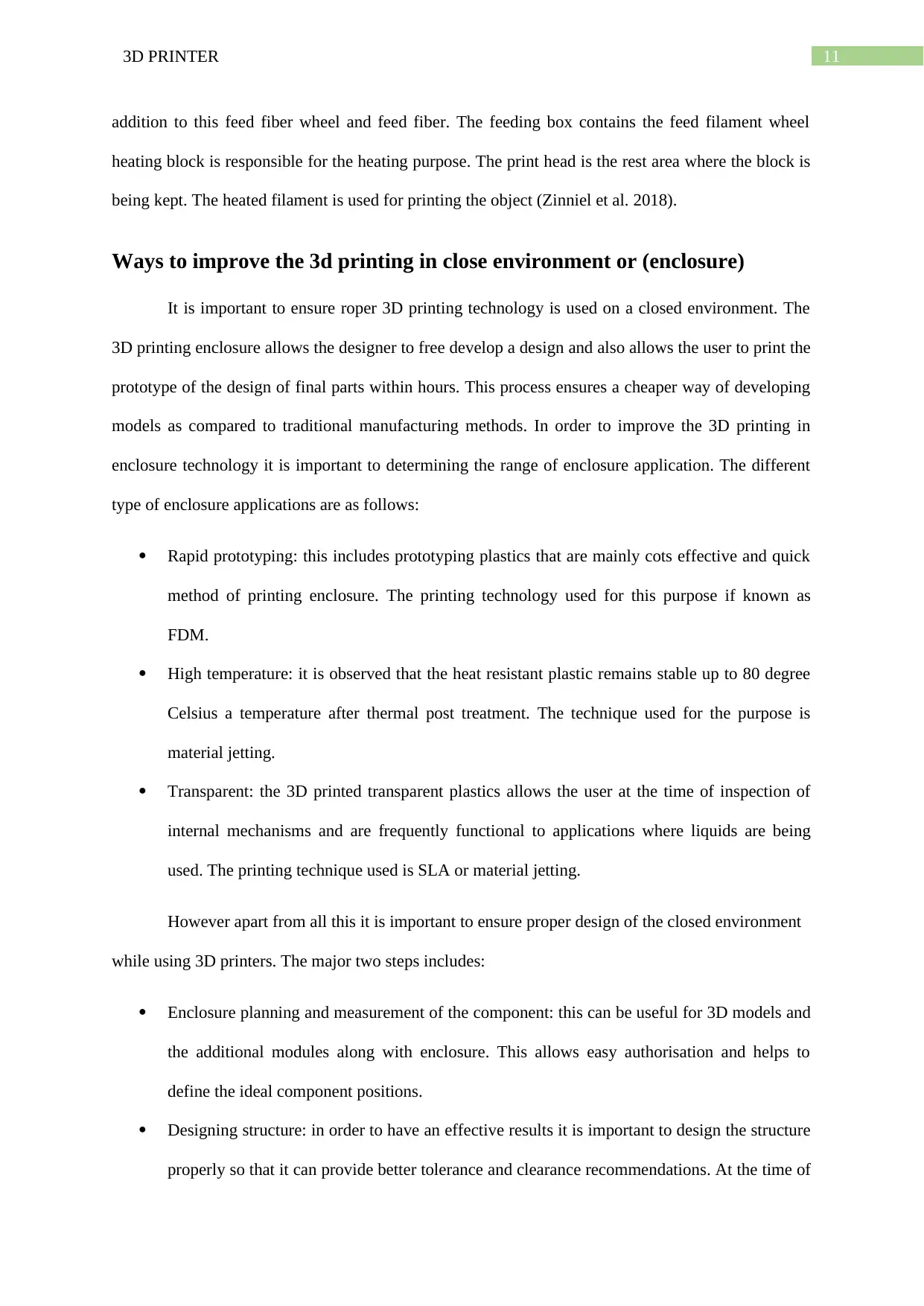
113D PRINTER
addition to this feed fiber wheel and feed fiber. The feeding box contains the feed filament wheel
heating block is responsible for the heating purpose. The print head is the rest area where the block is
being kept. The heated filament is used for printing the object (Zinniel et al. 2018).
Ways to improve the 3d printing in close environment or (enclosure)
It is important to ensure roper 3D printing technology is used on a closed environment. The
3D printing enclosure allows the designer to free develop a design and also allows the user to print the
prototype of the design of final parts within hours. This process ensures a cheaper way of developing
models as compared to traditional manufacturing methods. In order to improve the 3D printing in
enclosure technology it is important to determining the range of enclosure application. The different
type of enclosure applications are as follows:
Rapid prototyping: this includes prototyping plastics that are mainly cots effective and quick
method of printing enclosure. The printing technology used for this purpose if known as
FDM.
High temperature: it is observed that the heat resistant plastic remains stable up to 80 degree
Celsius a temperature after thermal post treatment. The technique used for the purpose is
material jetting.
Transparent: the 3D printed transparent plastics allows the user at the time of inspection of
internal mechanisms and are frequently functional to applications where liquids are being
used. The printing technique used is SLA or material jetting.
However apart from all this it is important to ensure proper design of the closed environment
while using 3D printers. The major two steps includes:
Enclosure planning and measurement of the component: this can be useful for 3D models and
the additional modules along with enclosure. This allows easy authorisation and helps to
define the ideal component positions.
Designing structure: in order to have an effective results it is important to design the structure
properly so that it can provide better tolerance and clearance recommendations. At the time of
addition to this feed fiber wheel and feed fiber. The feeding box contains the feed filament wheel
heating block is responsible for the heating purpose. The print head is the rest area where the block is
being kept. The heated filament is used for printing the object (Zinniel et al. 2018).
Ways to improve the 3d printing in close environment or (enclosure)
It is important to ensure roper 3D printing technology is used on a closed environment. The
3D printing enclosure allows the designer to free develop a design and also allows the user to print the
prototype of the design of final parts within hours. This process ensures a cheaper way of developing
models as compared to traditional manufacturing methods. In order to improve the 3D printing in
enclosure technology it is important to determining the range of enclosure application. The different
type of enclosure applications are as follows:
Rapid prototyping: this includes prototyping plastics that are mainly cots effective and quick
method of printing enclosure. The printing technology used for this purpose if known as
FDM.
High temperature: it is observed that the heat resistant plastic remains stable up to 80 degree
Celsius a temperature after thermal post treatment. The technique used for the purpose is
material jetting.
Transparent: the 3D printed transparent plastics allows the user at the time of inspection of
internal mechanisms and are frequently functional to applications where liquids are being
used. The printing technique used is SLA or material jetting.
However apart from all this it is important to ensure proper design of the closed environment
while using 3D printers. The major two steps includes:
Enclosure planning and measurement of the component: this can be useful for 3D models and
the additional modules along with enclosure. This allows easy authorisation and helps to
define the ideal component positions.
Designing structure: in order to have an effective results it is important to design the structure
properly so that it can provide better tolerance and clearance recommendations. At the time of
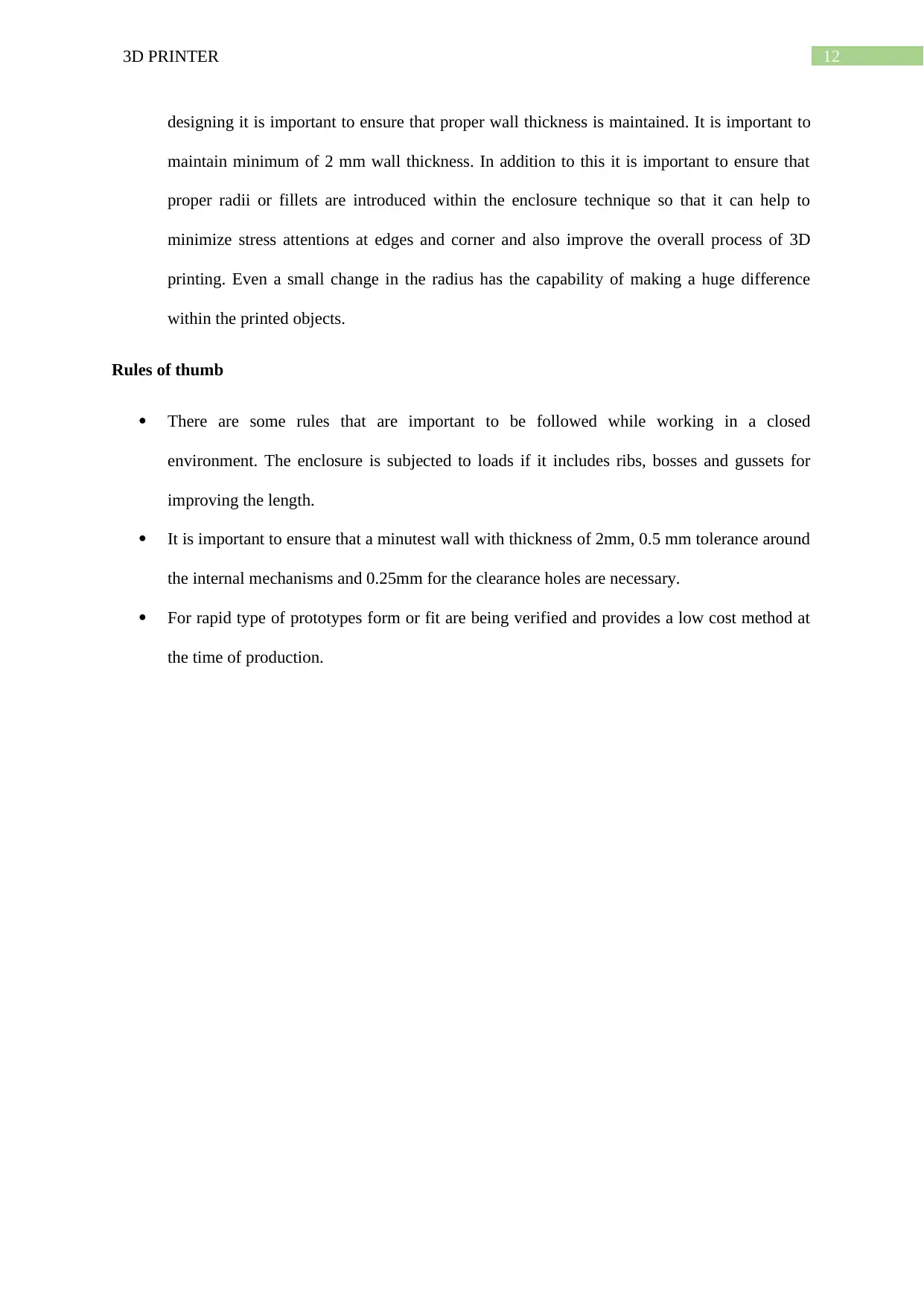
123D PRINTER
designing it is important to ensure that proper wall thickness is maintained. It is important to
maintain minimum of 2 mm wall thickness. In addition to this it is important to ensure that
proper radii or fillets are introduced within the enclosure technique so that it can help to
minimize stress attentions at edges and corner and also improve the overall process of 3D
printing. Even a small change in the radius has the capability of making a huge difference
within the printed objects.
Rules of thumb
There are some rules that are important to be followed while working in a closed
environment. The enclosure is subjected to loads if it includes ribs, bosses and gussets for
improving the length.
It is important to ensure that a minutest wall with thickness of 2mm, 0.5 mm tolerance around
the internal mechanisms and 0.25mm for the clearance holes are necessary.
For rapid type of prototypes form or fit are being verified and provides a low cost method at
the time of production.
designing it is important to ensure that proper wall thickness is maintained. It is important to
maintain minimum of 2 mm wall thickness. In addition to this it is important to ensure that
proper radii or fillets are introduced within the enclosure technique so that it can help to
minimize stress attentions at edges and corner and also improve the overall process of 3D
printing. Even a small change in the radius has the capability of making a huge difference
within the printed objects.
Rules of thumb
There are some rules that are important to be followed while working in a closed
environment. The enclosure is subjected to loads if it includes ribs, bosses and gussets for
improving the length.
It is important to ensure that a minutest wall with thickness of 2mm, 0.5 mm tolerance around
the internal mechanisms and 0.25mm for the clearance holes are necessary.
For rapid type of prototypes form or fit are being verified and provides a low cost method at
the time of production.
Paraphrase This Document
Need a fresh take? Get an instant paraphrase of this document with our AI Paraphraser
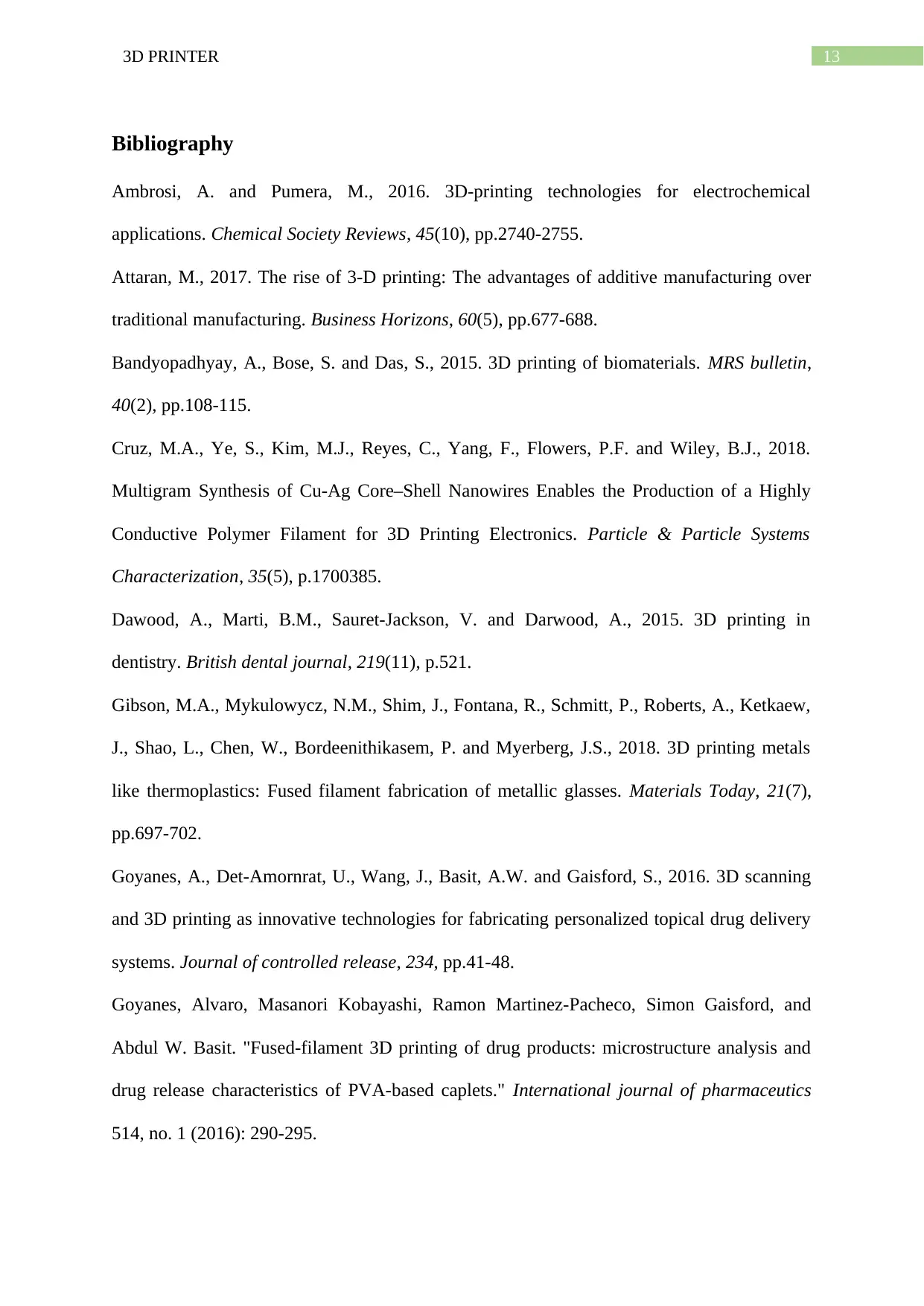
133D PRINTER
Bibliography
Ambrosi, A. and Pumera, M., 2016. 3D-printing technologies for electrochemical
applications. Chemical Society Reviews, 45(10), pp.2740-2755.
Attaran, M., 2017. The rise of 3-D printing: The advantages of additive manufacturing over
traditional manufacturing. Business Horizons, 60(5), pp.677-688.
Bandyopadhyay, A., Bose, S. and Das, S., 2015. 3D printing of biomaterials. MRS bulletin,
40(2), pp.108-115.
Cruz, M.A., Ye, S., Kim, M.J., Reyes, C., Yang, F., Flowers, P.F. and Wiley, B.J., 2018.
Multigram Synthesis of Cu‐Ag Core–Shell Nanowires Enables the Production of a Highly
Conductive Polymer Filament for 3D Printing Electronics. Particle & Particle Systems
Characterization, 35(5), p.1700385.
Dawood, A., Marti, B.M., Sauret-Jackson, V. and Darwood, A., 2015. 3D printing in
dentistry. British dental journal, 219(11), p.521.
Gibson, M.A., Mykulowycz, N.M., Shim, J., Fontana, R., Schmitt, P., Roberts, A., Ketkaew,
J., Shao, L., Chen, W., Bordeenithikasem, P. and Myerberg, J.S., 2018. 3D printing metals
like thermoplastics: Fused filament fabrication of metallic glasses. Materials Today, 21(7),
pp.697-702.
Goyanes, A., Det-Amornrat, U., Wang, J., Basit, A.W. and Gaisford, S., 2016. 3D scanning
and 3D printing as innovative technologies for fabricating personalized topical drug delivery
systems. Journal of controlled release, 234, pp.41-48.
Goyanes, Alvaro, Masanori Kobayashi, Ramon Martinez-Pacheco, Simon Gaisford, and
Abdul W. Basit. "Fused-filament 3D printing of drug products: microstructure analysis and
drug release characteristics of PVA-based caplets." International journal of pharmaceutics
514, no. 1 (2016): 290-295.
Bibliography
Ambrosi, A. and Pumera, M., 2016. 3D-printing technologies for electrochemical
applications. Chemical Society Reviews, 45(10), pp.2740-2755.
Attaran, M., 2017. The rise of 3-D printing: The advantages of additive manufacturing over
traditional manufacturing. Business Horizons, 60(5), pp.677-688.
Bandyopadhyay, A., Bose, S. and Das, S., 2015. 3D printing of biomaterials. MRS bulletin,
40(2), pp.108-115.
Cruz, M.A., Ye, S., Kim, M.J., Reyes, C., Yang, F., Flowers, P.F. and Wiley, B.J., 2018.
Multigram Synthesis of Cu‐Ag Core–Shell Nanowires Enables the Production of a Highly
Conductive Polymer Filament for 3D Printing Electronics. Particle & Particle Systems
Characterization, 35(5), p.1700385.
Dawood, A., Marti, B.M., Sauret-Jackson, V. and Darwood, A., 2015. 3D printing in
dentistry. British dental journal, 219(11), p.521.
Gibson, M.A., Mykulowycz, N.M., Shim, J., Fontana, R., Schmitt, P., Roberts, A., Ketkaew,
J., Shao, L., Chen, W., Bordeenithikasem, P. and Myerberg, J.S., 2018. 3D printing metals
like thermoplastics: Fused filament fabrication of metallic glasses. Materials Today, 21(7),
pp.697-702.
Goyanes, A., Det-Amornrat, U., Wang, J., Basit, A.W. and Gaisford, S., 2016. 3D scanning
and 3D printing as innovative technologies for fabricating personalized topical drug delivery
systems. Journal of controlled release, 234, pp.41-48.
Goyanes, Alvaro, Masanori Kobayashi, Ramon Martinez-Pacheco, Simon Gaisford, and
Abdul W. Basit. "Fused-filament 3D printing of drug products: microstructure analysis and
drug release characteristics of PVA-based caplets." International journal of pharmaceutics
514, no. 1 (2016): 290-295.
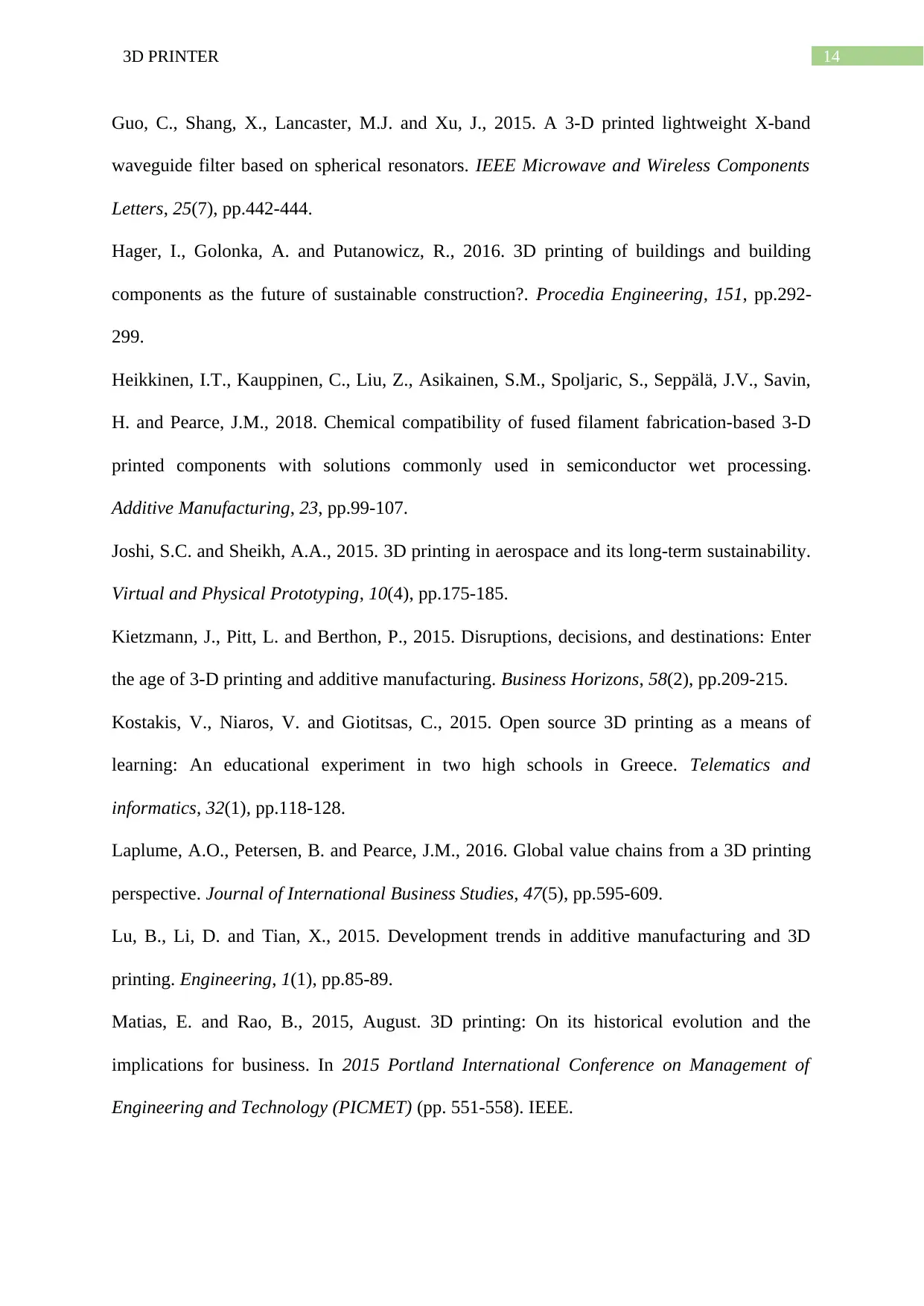
143D PRINTER
Guo, C., Shang, X., Lancaster, M.J. and Xu, J., 2015. A 3-D printed lightweight X-band
waveguide filter based on spherical resonators. IEEE Microwave and Wireless Components
Letters, 25(7), pp.442-444.
Hager, I., Golonka, A. and Putanowicz, R., 2016. 3D printing of buildings and building
components as the future of sustainable construction?. Procedia Engineering, 151, pp.292-
299.
Heikkinen, I.T., Kauppinen, C., Liu, Z., Asikainen, S.M., Spoljaric, S., Seppälä, J.V., Savin,
H. and Pearce, J.M., 2018. Chemical compatibility of fused filament fabrication-based 3-D
printed components with solutions commonly used in semiconductor wet processing.
Additive Manufacturing, 23, pp.99-107.
Joshi, S.C. and Sheikh, A.A., 2015. 3D printing in aerospace and its long-term sustainability.
Virtual and Physical Prototyping, 10(4), pp.175-185.
Kietzmann, J., Pitt, L. and Berthon, P., 2015. Disruptions, decisions, and destinations: Enter
the age of 3-D printing and additive manufacturing. Business Horizons, 58(2), pp.209-215.
Kostakis, V., Niaros, V. and Giotitsas, C., 2015. Open source 3D printing as a means of
learning: An educational experiment in two high schools in Greece. Telematics and
informatics, 32(1), pp.118-128.
Laplume, A.O., Petersen, B. and Pearce, J.M., 2016. Global value chains from a 3D printing
perspective. Journal of International Business Studies, 47(5), pp.595-609.
Lu, B., Li, D. and Tian, X., 2015. Development trends in additive manufacturing and 3D
printing. Engineering, 1(1), pp.85-89.
Matias, E. and Rao, B., 2015, August. 3D printing: On its historical evolution and the
implications for business. In 2015 Portland International Conference on Management of
Engineering and Technology (PICMET) (pp. 551-558). IEEE.
Guo, C., Shang, X., Lancaster, M.J. and Xu, J., 2015. A 3-D printed lightweight X-band
waveguide filter based on spherical resonators. IEEE Microwave and Wireless Components
Letters, 25(7), pp.442-444.
Hager, I., Golonka, A. and Putanowicz, R., 2016. 3D printing of buildings and building
components as the future of sustainable construction?. Procedia Engineering, 151, pp.292-
299.
Heikkinen, I.T., Kauppinen, C., Liu, Z., Asikainen, S.M., Spoljaric, S., Seppälä, J.V., Savin,
H. and Pearce, J.M., 2018. Chemical compatibility of fused filament fabrication-based 3-D
printed components with solutions commonly used in semiconductor wet processing.
Additive Manufacturing, 23, pp.99-107.
Joshi, S.C. and Sheikh, A.A., 2015. 3D printing in aerospace and its long-term sustainability.
Virtual and Physical Prototyping, 10(4), pp.175-185.
Kietzmann, J., Pitt, L. and Berthon, P., 2015. Disruptions, decisions, and destinations: Enter
the age of 3-D printing and additive manufacturing. Business Horizons, 58(2), pp.209-215.
Kostakis, V., Niaros, V. and Giotitsas, C., 2015. Open source 3D printing as a means of
learning: An educational experiment in two high schools in Greece. Telematics and
informatics, 32(1), pp.118-128.
Laplume, A.O., Petersen, B. and Pearce, J.M., 2016. Global value chains from a 3D printing
perspective. Journal of International Business Studies, 47(5), pp.595-609.
Lu, B., Li, D. and Tian, X., 2015. Development trends in additive manufacturing and 3D
printing. Engineering, 1(1), pp.85-89.
Matias, E. and Rao, B., 2015, August. 3D printing: On its historical evolution and the
implications for business. In 2015 Portland International Conference on Management of
Engineering and Technology (PICMET) (pp. 551-558). IEEE.
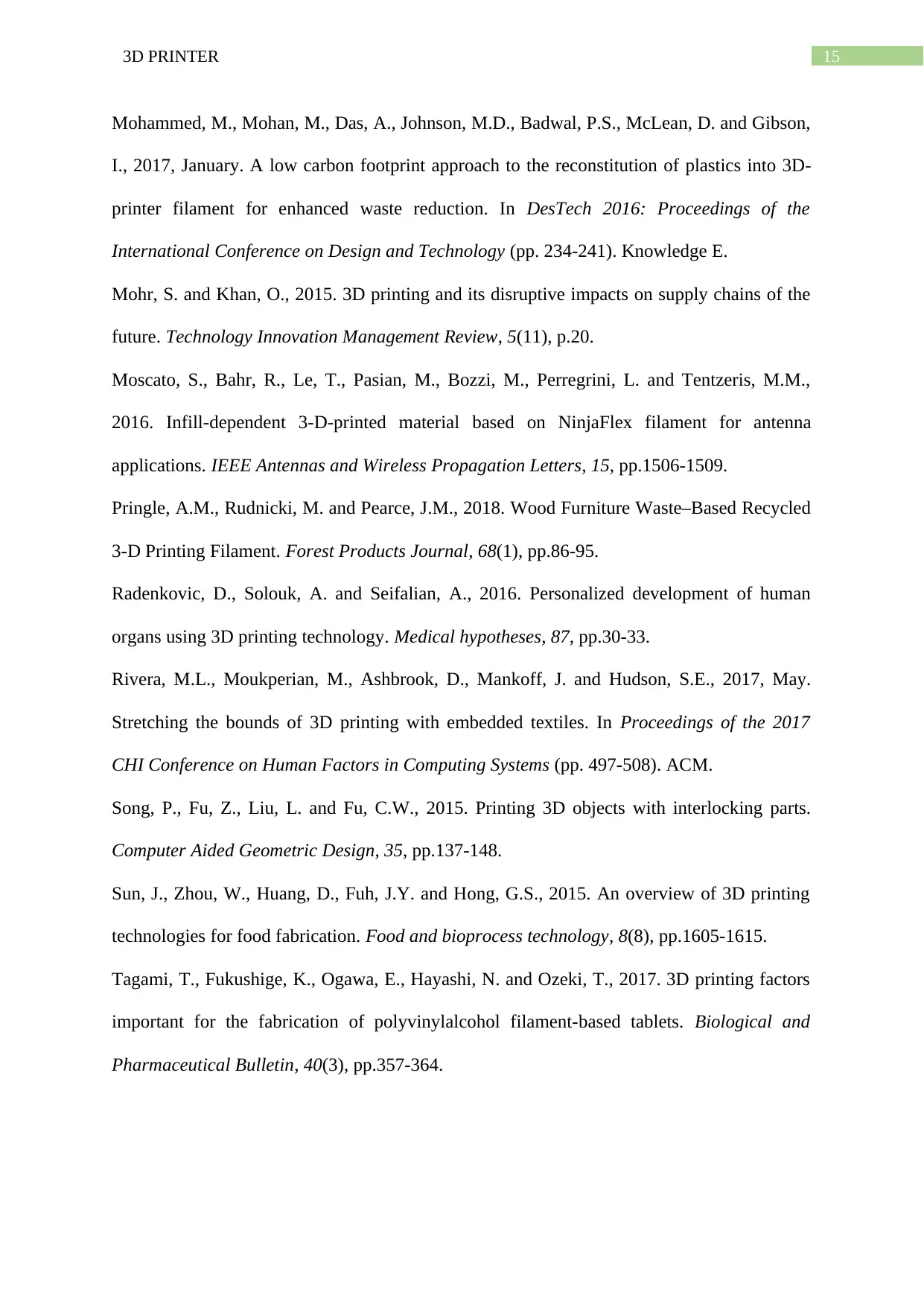
153D PRINTER
Mohammed, M., Mohan, M., Das, A., Johnson, M.D., Badwal, P.S., McLean, D. and Gibson,
I., 2017, January. A low carbon footprint approach to the reconstitution of plastics into 3D-
printer filament for enhanced waste reduction. In DesTech 2016: Proceedings of the
International Conference on Design and Technology (pp. 234-241). Knowledge E.
Mohr, S. and Khan, O., 2015. 3D printing and its disruptive impacts on supply chains of the
future. Technology Innovation Management Review, 5(11), p.20.
Moscato, S., Bahr, R., Le, T., Pasian, M., Bozzi, M., Perregrini, L. and Tentzeris, M.M.,
2016. Infill-dependent 3-D-printed material based on NinjaFlex filament for antenna
applications. IEEE Antennas and Wireless Propagation Letters, 15, pp.1506-1509.
Pringle, A.M., Rudnicki, M. and Pearce, J.M., 2018. Wood Furniture Waste–Based Recycled
3-D Printing Filament. Forest Products Journal, 68(1), pp.86-95.
Radenkovic, D., Solouk, A. and Seifalian, A., 2016. Personalized development of human
organs using 3D printing technology. Medical hypotheses, 87, pp.30-33.
Rivera, M.L., Moukperian, M., Ashbrook, D., Mankoff, J. and Hudson, S.E., 2017, May.
Stretching the bounds of 3D printing with embedded textiles. In Proceedings of the 2017
CHI Conference on Human Factors in Computing Systems (pp. 497-508). ACM.
Song, P., Fu, Z., Liu, L. and Fu, C.W., 2015. Printing 3D objects with interlocking parts.
Computer Aided Geometric Design, 35, pp.137-148.
Sun, J., Zhou, W., Huang, D., Fuh, J.Y. and Hong, G.S., 2015. An overview of 3D printing
technologies for food fabrication. Food and bioprocess technology, 8(8), pp.1605-1615.
Tagami, T., Fukushige, K., Ogawa, E., Hayashi, N. and Ozeki, T., 2017. 3D printing factors
important for the fabrication of polyvinylalcohol filament-based tablets. Biological and
Pharmaceutical Bulletin, 40(3), pp.357-364.
Mohammed, M., Mohan, M., Das, A., Johnson, M.D., Badwal, P.S., McLean, D. and Gibson,
I., 2017, January. A low carbon footprint approach to the reconstitution of plastics into 3D-
printer filament for enhanced waste reduction. In DesTech 2016: Proceedings of the
International Conference on Design and Technology (pp. 234-241). Knowledge E.
Mohr, S. and Khan, O., 2015. 3D printing and its disruptive impacts on supply chains of the
future. Technology Innovation Management Review, 5(11), p.20.
Moscato, S., Bahr, R., Le, T., Pasian, M., Bozzi, M., Perregrini, L. and Tentzeris, M.M.,
2016. Infill-dependent 3-D-printed material based on NinjaFlex filament for antenna
applications. IEEE Antennas and Wireless Propagation Letters, 15, pp.1506-1509.
Pringle, A.M., Rudnicki, M. and Pearce, J.M., 2018. Wood Furniture Waste–Based Recycled
3-D Printing Filament. Forest Products Journal, 68(1), pp.86-95.
Radenkovic, D., Solouk, A. and Seifalian, A., 2016. Personalized development of human
organs using 3D printing technology. Medical hypotheses, 87, pp.30-33.
Rivera, M.L., Moukperian, M., Ashbrook, D., Mankoff, J. and Hudson, S.E., 2017, May.
Stretching the bounds of 3D printing with embedded textiles. In Proceedings of the 2017
CHI Conference on Human Factors in Computing Systems (pp. 497-508). ACM.
Song, P., Fu, Z., Liu, L. and Fu, C.W., 2015. Printing 3D objects with interlocking parts.
Computer Aided Geometric Design, 35, pp.137-148.
Sun, J., Zhou, W., Huang, D., Fuh, J.Y. and Hong, G.S., 2015. An overview of 3D printing
technologies for food fabrication. Food and bioprocess technology, 8(8), pp.1605-1615.
Tagami, T., Fukushige, K., Ogawa, E., Hayashi, N. and Ozeki, T., 2017. 3D printing factors
important for the fabrication of polyvinylalcohol filament-based tablets. Biological and
Pharmaceutical Bulletin, 40(3), pp.357-364.
Secure Best Marks with AI Grader
Need help grading? Try our AI Grader for instant feedback on your assignments.
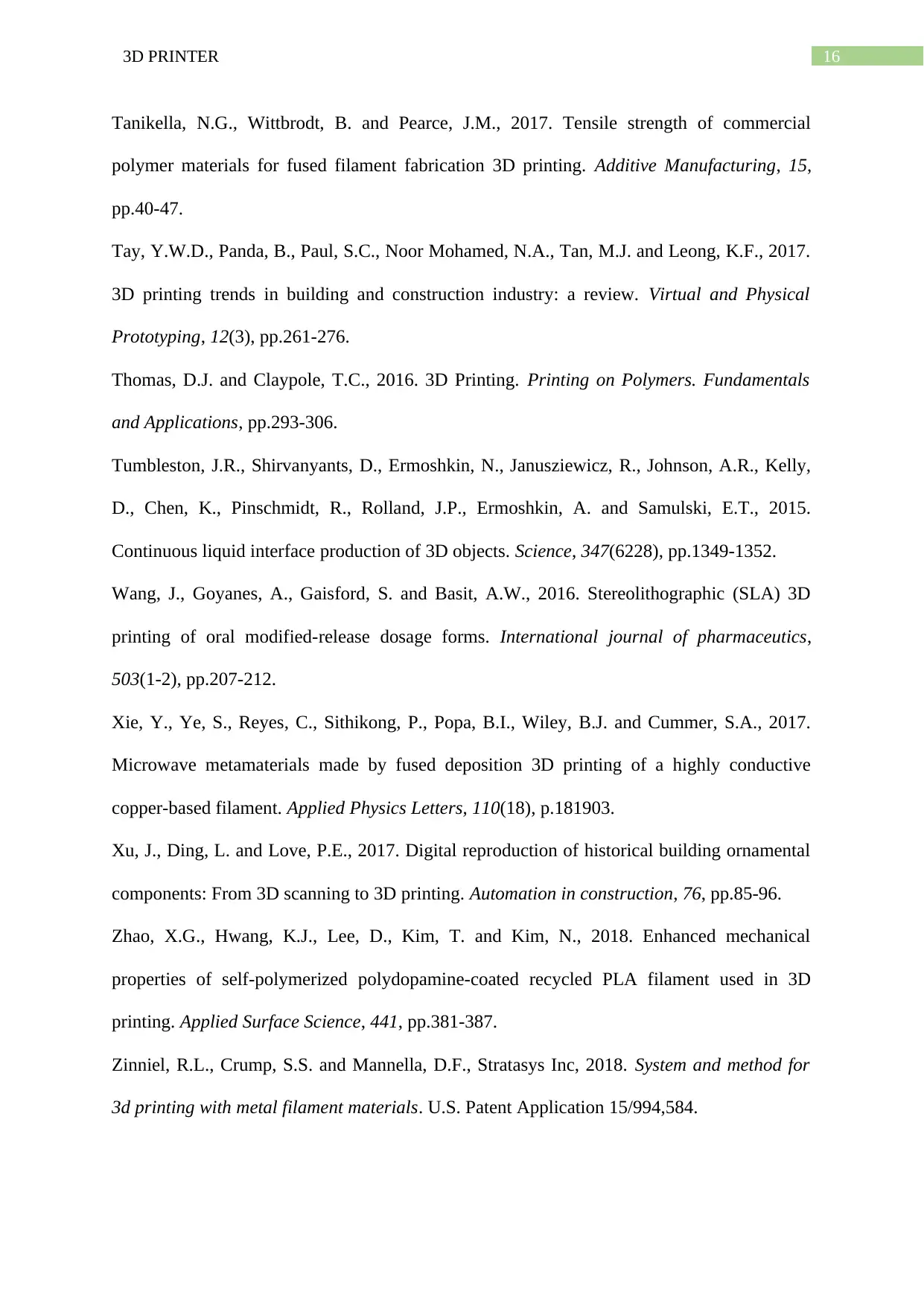
163D PRINTER
Tanikella, N.G., Wittbrodt, B. and Pearce, J.M., 2017. Tensile strength of commercial
polymer materials for fused filament fabrication 3D printing. Additive Manufacturing, 15,
pp.40-47.
Tay, Y.W.D., Panda, B., Paul, S.C., Noor Mohamed, N.A., Tan, M.J. and Leong, K.F., 2017.
3D printing trends in building and construction industry: a review. Virtual and Physical
Prototyping, 12(3), pp.261-276.
Thomas, D.J. and Claypole, T.C., 2016. 3D Printing. Printing on Polymers. Fundamentals
and Applications, pp.293-306.
Tumbleston, J.R., Shirvanyants, D., Ermoshkin, N., Janusziewicz, R., Johnson, A.R., Kelly,
D., Chen, K., Pinschmidt, R., Rolland, J.P., Ermoshkin, A. and Samulski, E.T., 2015.
Continuous liquid interface production of 3D objects. Science, 347(6228), pp.1349-1352.
Wang, J., Goyanes, A., Gaisford, S. and Basit, A.W., 2016. Stereolithographic (SLA) 3D
printing of oral modified-release dosage forms. International journal of pharmaceutics,
503(1-2), pp.207-212.
Xie, Y., Ye, S., Reyes, C., Sithikong, P., Popa, B.I., Wiley, B.J. and Cummer, S.A., 2017.
Microwave metamaterials made by fused deposition 3D printing of a highly conductive
copper-based filament. Applied Physics Letters, 110(18), p.181903.
Xu, J., Ding, L. and Love, P.E., 2017. Digital reproduction of historical building ornamental
components: From 3D scanning to 3D printing. Automation in construction, 76, pp.85-96.
Zhao, X.G., Hwang, K.J., Lee, D., Kim, T. and Kim, N., 2018. Enhanced mechanical
properties of self-polymerized polydopamine-coated recycled PLA filament used in 3D
printing. Applied Surface Science, 441, pp.381-387.
Zinniel, R.L., Crump, S.S. and Mannella, D.F., Stratasys Inc, 2018. System and method for
3d printing with metal filament materials. U.S. Patent Application 15/994,584.
Tanikella, N.G., Wittbrodt, B. and Pearce, J.M., 2017. Tensile strength of commercial
polymer materials for fused filament fabrication 3D printing. Additive Manufacturing, 15,
pp.40-47.
Tay, Y.W.D., Panda, B., Paul, S.C., Noor Mohamed, N.A., Tan, M.J. and Leong, K.F., 2017.
3D printing trends in building and construction industry: a review. Virtual and Physical
Prototyping, 12(3), pp.261-276.
Thomas, D.J. and Claypole, T.C., 2016. 3D Printing. Printing on Polymers. Fundamentals
and Applications, pp.293-306.
Tumbleston, J.R., Shirvanyants, D., Ermoshkin, N., Janusziewicz, R., Johnson, A.R., Kelly,
D., Chen, K., Pinschmidt, R., Rolland, J.P., Ermoshkin, A. and Samulski, E.T., 2015.
Continuous liquid interface production of 3D objects. Science, 347(6228), pp.1349-1352.
Wang, J., Goyanes, A., Gaisford, S. and Basit, A.W., 2016. Stereolithographic (SLA) 3D
printing of oral modified-release dosage forms. International journal of pharmaceutics,
503(1-2), pp.207-212.
Xie, Y., Ye, S., Reyes, C., Sithikong, P., Popa, B.I., Wiley, B.J. and Cummer, S.A., 2017.
Microwave metamaterials made by fused deposition 3D printing of a highly conductive
copper-based filament. Applied Physics Letters, 110(18), p.181903.
Xu, J., Ding, L. and Love, P.E., 2017. Digital reproduction of historical building ornamental
components: From 3D scanning to 3D printing. Automation in construction, 76, pp.85-96.
Zhao, X.G., Hwang, K.J., Lee, D., Kim, T. and Kim, N., 2018. Enhanced mechanical
properties of self-polymerized polydopamine-coated recycled PLA filament used in 3D
printing. Applied Surface Science, 441, pp.381-387.
Zinniel, R.L., Crump, S.S. and Mannella, D.F., Stratasys Inc, 2018. System and method for
3d printing with metal filament materials. U.S. Patent Application 15/994,584.
1 out of 17
Related Documents
![[object Object]](/_next/image/?url=%2F_next%2Fstatic%2Fmedia%2Flogo.6d15ce61.png&w=640&q=75)
Your All-in-One AI-Powered Toolkit for Academic Success.
+13062052269
info@desklib.com
Available 24*7 on WhatsApp / Email
Unlock your academic potential
© 2024 | Zucol Services PVT LTD | All rights reserved.