Application of 3D Printing Technology for Designing Light-weight Unmanned Aerial Vehicle Wing Structures
This assignment is designed to develop a portfolio of resources that you can use during your degree.
6 Pages5293 Words334 Views
Added on 2023-06-12
About This Document
This research investigates the use of 3D printing technology for designing light-weight unmanned aerial vehicle (UAV) wing structures. The objective is to develop adaptive design technologies by investigating current design methods and knowledge of deployable technologies in the area of engineering design and manufacturing. The proposed lattice structure designs are fabricated using an Objet 350 3D printer while the material chosen is a polypropylene-like photopolymer called Objet DurusWhite RGD430. Based on compression testing, the proposed inflatable wing design will combine the advantages of compliant mechanisms and deployable structures to maximize flexibilities of movement in UAV design and development.
Application of 3D Printing Technology for Designing Light-weight Unmanned Aerial Vehicle Wing Structures
This assignment is designed to develop a portfolio of resources that you can use during your degree.
Added on 2023-06-12
ShareRelated Documents
INTERNATIONAL JOURNAL OF PRECISION ENGINEERING AND MANUFACTURING-GREEN TECHNOLOGY Vol. 1, No. 3, pp. 223-228 JULY 2014 / 223
© KSPE and Springer 2014
Application of 3D Printing Technology for Designing
Light-weight Unmanned Aerial Vehicle Wing Structures
Seung Ki Moon1, Yu En Tan1, Jihong Hwang2, and Yong-Jin Yoon1,#
1 School of Mechanical and Aerospace Engineering, NTU Additive Manufacturing Centre, Nanyang Technological University, 50 Nanyang Avenue, Singapore 639798
2 Department of Mechanical System Design Eng., Seoul Nat’l Univ. of Sci. & Tech., 233 Gongreung-ro, Nowon-gu, Seoul, Korea, 139-743
# Corresponding Author / E-mail: yongjiny@ntu.edu.sg, TEL: +65-6790-5033, FAX: +65-6792-4062
KEYWORDS: 3D Printing, Additive manufacturing, Deployable wing design, Light-weight structures, Unmanned aerial vehicles
Unmanned Aerial Vehicles (UAVs) have been developed to perform various military and civilian applications, such as reconnaissance,
attack missions, surveillance of pipelines, and interplanetary exploration. The present research is motivated by the need to develop
a fast adaptable UAV design technologies for agile, fuel efficient, and flexible structures that are capable of adapting and operating
in any environments. The objective of this research is to develop adaptive design technologies by investigating current design methods
and knowledge of deployable technologies in the area of engineering design and manufacturing. More specifically, this research seeks
to identify one truss lattice with the optimal elastic performance for deployable UAV wing design according to the Hashin &
Shtrikman theoretical bounds. We propose three lattice designs - 3D Kagome structure, 3D pyramidal structure and the hexagonal
diamond structure. The proposed lattice structure designs are fabricated using an Objet 350 3D printer while the material chosen
is a polypropylene-like photopolymer called Objet DurusWhite RGD430. Based on compression testing, the proposed inflatable wing
design will combine the advantages of compliant mechanisms and deployable structures to maximize flexibilities of movement in UAV
design and development.
Manuscript received: March 21, 2014 / Revised: April 22, 2014 / Accepted: April 28, 2014 (Invited Paper)
1. Introduction
Unmanned Aerial Vehicles (UAVs) have been developed to perform
various military and civilian applications, such as reconnaissance,
attack missions, surveillance of pipelines, and interplanetary
exploration. Recently, small and deployable UAVs have gained
attention due to a wide range of potential applications with
sophisticated operations and increased flexibilities for smaller
transportation enclosures and storage. The idea of incorporating
inflatable structures into flight has existed for a long time, but it was
only in the last few decades that inflatable wing technology was
properly developed. One of the earliest successful demonstrations was
the Goodyear inflatoplane developed during the 1950s. During this
period, Goodyear Aerospace designed and manufactured numerous
aircraft prototypes equipped with inflatable components. One of their
final designs was the GA-468 Inflatoplane.1 The inflatoplane was
developed as a military rescue plane that can be dropped behind enemy
lines near downed pilots to help them escape. More recently, NASA’s
Dryden research center developed the I2000 micro UAV that was
designed with wings made of inflatable tubes surrounded with
crushable foam. During its test flight, the UAV was launched from a
larger UAV “mother ship” at an altitude of around 300 meters and its
inflatable wings deployed from a compacted state in about one-third of
a second. The wings were developed by Vertigo, Inc. for the US Navy
as a gun-launched observation vehicle. Compared with the inflatoplane,
the I2000 is much smaller and has a wingspan of 1.63 m and a chord
length of 0.18 m.2 By changing the wings of a UAV from a rigid
NOMENCLATURE
σB Flexural modulus
σT Tensile strength
σY Yeild strength
σU Flexural strength
E Modulus of elasticity
H Height
∆ Change
DOI: 10.1007/s40684-014-0028-x
© KSPE and Springer 2014
Application of 3D Printing Technology for Designing
Light-weight Unmanned Aerial Vehicle Wing Structures
Seung Ki Moon1, Yu En Tan1, Jihong Hwang2, and Yong-Jin Yoon1,#
1 School of Mechanical and Aerospace Engineering, NTU Additive Manufacturing Centre, Nanyang Technological University, 50 Nanyang Avenue, Singapore 639798
2 Department of Mechanical System Design Eng., Seoul Nat’l Univ. of Sci. & Tech., 233 Gongreung-ro, Nowon-gu, Seoul, Korea, 139-743
# Corresponding Author / E-mail: yongjiny@ntu.edu.sg, TEL: +65-6790-5033, FAX: +65-6792-4062
KEYWORDS: 3D Printing, Additive manufacturing, Deployable wing design, Light-weight structures, Unmanned aerial vehicles
Unmanned Aerial Vehicles (UAVs) have been developed to perform various military and civilian applications, such as reconnaissance,
attack missions, surveillance of pipelines, and interplanetary exploration. The present research is motivated by the need to develop
a fast adaptable UAV design technologies for agile, fuel efficient, and flexible structures that are capable of adapting and operating
in any environments. The objective of this research is to develop adaptive design technologies by investigating current design methods
and knowledge of deployable technologies in the area of engineering design and manufacturing. More specifically, this research seeks
to identify one truss lattice with the optimal elastic performance for deployable UAV wing design according to the Hashin &
Shtrikman theoretical bounds. We propose three lattice designs - 3D Kagome structure, 3D pyramidal structure and the hexagonal
diamond structure. The proposed lattice structure designs are fabricated using an Objet 350 3D printer while the material chosen
is a polypropylene-like photopolymer called Objet DurusWhite RGD430. Based on compression testing, the proposed inflatable wing
design will combine the advantages of compliant mechanisms and deployable structures to maximize flexibilities of movement in UAV
design and development.
Manuscript received: March 21, 2014 / Revised: April 22, 2014 / Accepted: April 28, 2014 (Invited Paper)
1. Introduction
Unmanned Aerial Vehicles (UAVs) have been developed to perform
various military and civilian applications, such as reconnaissance,
attack missions, surveillance of pipelines, and interplanetary
exploration. Recently, small and deployable UAVs have gained
attention due to a wide range of potential applications with
sophisticated operations and increased flexibilities for smaller
transportation enclosures and storage. The idea of incorporating
inflatable structures into flight has existed for a long time, but it was
only in the last few decades that inflatable wing technology was
properly developed. One of the earliest successful demonstrations was
the Goodyear inflatoplane developed during the 1950s. During this
period, Goodyear Aerospace designed and manufactured numerous
aircraft prototypes equipped with inflatable components. One of their
final designs was the GA-468 Inflatoplane.1 The inflatoplane was
developed as a military rescue plane that can be dropped behind enemy
lines near downed pilots to help them escape. More recently, NASA’s
Dryden research center developed the I2000 micro UAV that was
designed with wings made of inflatable tubes surrounded with
crushable foam. During its test flight, the UAV was launched from a
larger UAV “mother ship” at an altitude of around 300 meters and its
inflatable wings deployed from a compacted state in about one-third of
a second. The wings were developed by Vertigo, Inc. for the US Navy
as a gun-launched observation vehicle. Compared with the inflatoplane,
the I2000 is much smaller and has a wingspan of 1.63 m and a chord
length of 0.18 m.2 By changing the wings of a UAV from a rigid
NOMENCLATURE
σB Flexural modulus
σT Tensile strength
σY Yeild strength
σU Flexural strength
E Modulus of elasticity
H Height
∆ Change
DOI: 10.1007/s40684-014-0028-x
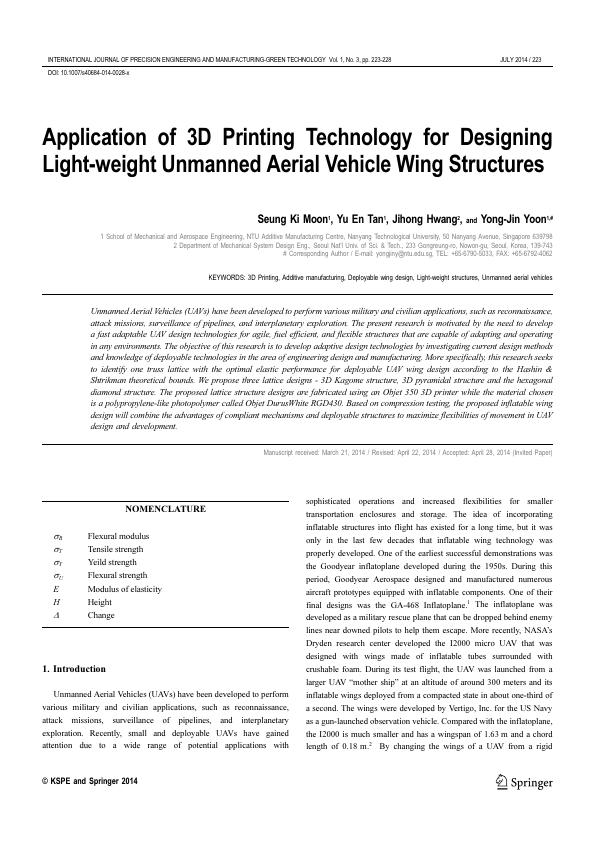
224 / JULY 2014 INTERNATIONAL JOURNAL OF PRECISION ENGINEERING AND MANUFACTURING-GREEN TECHNOLOGY Vol. 1, No. 3
design to an inflatable one, improved portability through reduced
volume/weight ratio is one possible advantage that can be obtained. A
second possible advantage of using an inflatable wing is that the
geometry of the wing can be easily changed from, for example, the
standard wing spans to a high-aspect ratio designs to suit mission
requirements.
High-strength light-weight materials have relatively high stiffness
and yield strength that are achievable at low density. They play a
significant role in achieving fuel efficiency goals for the aerospace and
automotive industries among others.3,4 Honeycombs, foams, and truss
lattice structures are examples of the high-strength light-weight
materials. The three structures have been extensively developed and
optimized to provide unique performance benefits in various
applications.5-7
Based on the results from literatures, it can be seen that 3D truss
lattices are superior to both metal foams and honeycombs in terms of
elastic modulus. Moreover, in contrast to closed cell metal foams and
honeycombs which are open only from one direction, truss lattices has
the added advantage of an open structure for multi-functional
applications such as heat transfer roles. The objective of this research
is to develop adaptive design technologies by investigating current
design methods and knowledge of deployable technologies in the area
of engineering design and manufacturing. More specifically, we
investigate the apparent strengths of truss lattices to identify the truss
lattice with the optimal elastic performance. We compare the
compressive strength of three lattice structures that have high values in
elastic performance for deployable UAV wing design. We propose
three lattice designs, such as 3D Kagome structure, 3D pyramidal
structure and the hexagonal diamond structure, for compression testing.
The proposed lattice structure designs are fabricated using an Objet 350
3D printer while the material chosen is a polypropylene-like
photopolymer called Objet DurusWhite RGD430. Based on the
compression testing, the proposed inflatable wing design will combine
the advantages of compliant mechanisms and deployable structures to
maximize flexibilities of movement in UAV development.
The remainder of this paper is organized as follows. Section 2
reviews related literature and background in lattice structures. Section
3 describes the proposed method for fabricating the proposed three
structures. Section 4 gives experiments for a compression test. Results,
discussion, and applications are described in Section 5. Closing
remarks and future work are presented in Section 6.
2. Literature Reviews and Background
2.1 Additive Manufacturing
Additive manufacturing (AM) is an umbrella term referring to a
group of technologies used for building physical models, prototypes,
patterns, tooling components, and final production parts from computer
data, three dimensional scanning systems, or video games.8 AM forms
objects layer by layer through the joining of liquid, powder, or sheet
materials as opposed to traditional manufacturing techniques like
machining which are subtractive in nature. AM is used to produce parts
that are difficult or impossible to fabricate using other techniques.9
Some of these technologies include stereolithography, selective
laser melting (SLM), three dimensional printing (3DP), and fused
deposition modeling (FDM). Each technology has its own strengths
and weaknesses. The number of AM technologies is consistently
growing as awareness, acceptance and application of these technologies
by designers, engineers and other professionals increase.
2.2 Structures for High-strength Light-weight Materials
A honeycomb consists of an array of hollow cells separated by thin
vertical walls. The cells are normally columnar and hexagonal in shape
although rectangular and triangular shapes are also possible. A
common application of honeycomb is in sandwich composite panels
for use in aircraft structures.5
Metal foams are sponge-like materials that are manufactured by
injecting inert gas into molten metal. The resulting structure is a solid
filled with voids that have varying sizes and shape. If individual voids
are fully encapsulated by the solid, the structure formed is a closed cell
metal foam. Similarly, if the voids overlap and form an interconnected
network, then the structure formed is an open cell metal foam.6
Lattice structures consist of repeating units of identical skeleton
structures of geometric three dimensional shapes such as a polyhedron
arranged in a regular pattern. New manufacturing processes have
enabled lattice structures to be more easily fabricated than before. The
methods devised permit entire lattice structures of unit cells ranging
from millimeters to centimeters to be produced.7 The mechanical
properties of honeycombs, metal foams and truss lattices have been
studied extensively and numerous publications on this subject can be
found. From literatures, the elastic moduli of honeycombs, metal
foams, and truss lattices are compared against the Hashin-Shtrikman
(HS) bounds. In others, honeycombs are compared with foams and
truss lattices are compared with honeycombs etc. The HS upper bound
represents the maximum values for the effective elastic moduli of
isotropic two-phase composites for a given phase volume fraction.10 In
3D applications, rank-6 laminates are known to attain the HS bounds
on the bulk and shear moduli.11 Rank laminates are obtained by a
sequential process where at each stage the previous laminate is
laminated again with a single lamina in a new direction. However, a
rank laminate is a multi-length-scale structure and therefore not
manufacturable. Thus, there is a need to find a single-length-scale
substitute in honeycombs, foams or truss lattices with the optimal
microstructure.
Among relevant research, one study indicated that closed cell foams
can be superior to honeycombs with respect to shear strength and shear
modulus. Also, closed cell foams provide compressive strengths which
are isotropic and yet can be comparable to the compressive strengths of
honeycombs in the thickness direction.12 However, the study does not
indicate whether closed cell foams attain the HS upper bounds. The
bulk and shear moduli of an octet-truss lattice material having single-
length-scale microstructure were evaluated against the HS upper bound
and found to be about half the attainable values.13 The study also
compared the stiffness and strength of the octet-truss lattice to those of
metal foams and found that the lattice is 3 to 10 times stiffer.
2.3 Description of 3D Lattice Structures
3D Kagome lattice structure - 2D Kagome structure originated as a
traditional bamboo basket weave pattern and was identified by
design to an inflatable one, improved portability through reduced
volume/weight ratio is one possible advantage that can be obtained. A
second possible advantage of using an inflatable wing is that the
geometry of the wing can be easily changed from, for example, the
standard wing spans to a high-aspect ratio designs to suit mission
requirements.
High-strength light-weight materials have relatively high stiffness
and yield strength that are achievable at low density. They play a
significant role in achieving fuel efficiency goals for the aerospace and
automotive industries among others.3,4 Honeycombs, foams, and truss
lattice structures are examples of the high-strength light-weight
materials. The three structures have been extensively developed and
optimized to provide unique performance benefits in various
applications.5-7
Based on the results from literatures, it can be seen that 3D truss
lattices are superior to both metal foams and honeycombs in terms of
elastic modulus. Moreover, in contrast to closed cell metal foams and
honeycombs which are open only from one direction, truss lattices has
the added advantage of an open structure for multi-functional
applications such as heat transfer roles. The objective of this research
is to develop adaptive design technologies by investigating current
design methods and knowledge of deployable technologies in the area
of engineering design and manufacturing. More specifically, we
investigate the apparent strengths of truss lattices to identify the truss
lattice with the optimal elastic performance. We compare the
compressive strength of three lattice structures that have high values in
elastic performance for deployable UAV wing design. We propose
three lattice designs, such as 3D Kagome structure, 3D pyramidal
structure and the hexagonal diamond structure, for compression testing.
The proposed lattice structure designs are fabricated using an Objet 350
3D printer while the material chosen is a polypropylene-like
photopolymer called Objet DurusWhite RGD430. Based on the
compression testing, the proposed inflatable wing design will combine
the advantages of compliant mechanisms and deployable structures to
maximize flexibilities of movement in UAV development.
The remainder of this paper is organized as follows. Section 2
reviews related literature and background in lattice structures. Section
3 describes the proposed method for fabricating the proposed three
structures. Section 4 gives experiments for a compression test. Results,
discussion, and applications are described in Section 5. Closing
remarks and future work are presented in Section 6.
2. Literature Reviews and Background
2.1 Additive Manufacturing
Additive manufacturing (AM) is an umbrella term referring to a
group of technologies used for building physical models, prototypes,
patterns, tooling components, and final production parts from computer
data, three dimensional scanning systems, or video games.8 AM forms
objects layer by layer through the joining of liquid, powder, or sheet
materials as opposed to traditional manufacturing techniques like
machining which are subtractive in nature. AM is used to produce parts
that are difficult or impossible to fabricate using other techniques.9
Some of these technologies include stereolithography, selective
laser melting (SLM), three dimensional printing (3DP), and fused
deposition modeling (FDM). Each technology has its own strengths
and weaknesses. The number of AM technologies is consistently
growing as awareness, acceptance and application of these technologies
by designers, engineers and other professionals increase.
2.2 Structures for High-strength Light-weight Materials
A honeycomb consists of an array of hollow cells separated by thin
vertical walls. The cells are normally columnar and hexagonal in shape
although rectangular and triangular shapes are also possible. A
common application of honeycomb is in sandwich composite panels
for use in aircraft structures.5
Metal foams are sponge-like materials that are manufactured by
injecting inert gas into molten metal. The resulting structure is a solid
filled with voids that have varying sizes and shape. If individual voids
are fully encapsulated by the solid, the structure formed is a closed cell
metal foam. Similarly, if the voids overlap and form an interconnected
network, then the structure formed is an open cell metal foam.6
Lattice structures consist of repeating units of identical skeleton
structures of geometric three dimensional shapes such as a polyhedron
arranged in a regular pattern. New manufacturing processes have
enabled lattice structures to be more easily fabricated than before. The
methods devised permit entire lattice structures of unit cells ranging
from millimeters to centimeters to be produced.7 The mechanical
properties of honeycombs, metal foams and truss lattices have been
studied extensively and numerous publications on this subject can be
found. From literatures, the elastic moduli of honeycombs, metal
foams, and truss lattices are compared against the Hashin-Shtrikman
(HS) bounds. In others, honeycombs are compared with foams and
truss lattices are compared with honeycombs etc. The HS upper bound
represents the maximum values for the effective elastic moduli of
isotropic two-phase composites for a given phase volume fraction.10 In
3D applications, rank-6 laminates are known to attain the HS bounds
on the bulk and shear moduli.11 Rank laminates are obtained by a
sequential process where at each stage the previous laminate is
laminated again with a single lamina in a new direction. However, a
rank laminate is a multi-length-scale structure and therefore not
manufacturable. Thus, there is a need to find a single-length-scale
substitute in honeycombs, foams or truss lattices with the optimal
microstructure.
Among relevant research, one study indicated that closed cell foams
can be superior to honeycombs with respect to shear strength and shear
modulus. Also, closed cell foams provide compressive strengths which
are isotropic and yet can be comparable to the compressive strengths of
honeycombs in the thickness direction.12 However, the study does not
indicate whether closed cell foams attain the HS upper bounds. The
bulk and shear moduli of an octet-truss lattice material having single-
length-scale microstructure were evaluated against the HS upper bound
and found to be about half the attainable values.13 The study also
compared the stiffness and strength of the octet-truss lattice to those of
metal foams and found that the lattice is 3 to 10 times stiffer.
2.3 Description of 3D Lattice Structures
3D Kagome lattice structure - 2D Kagome structure originated as a
traditional bamboo basket weave pattern and was identified by
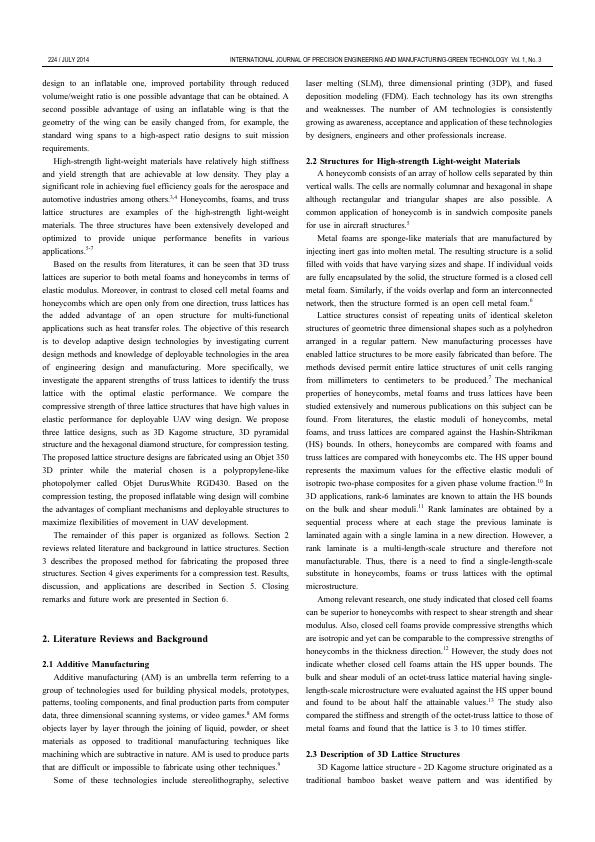
INTERNATIONAL JOURNAL OF PRECISION ENGINEERING AND MANUFACTURING-GREEN TECHNOLOGY Vol. 1, No. 3 JULY 2014 / 225
topology optimization as an optimal structure based on its elastic
modulus for a range of fraction volumes.13 The 3D variant was
proposed by a recent research investigating if the superior properties
observed in the 2D variant are carried over.14 3D Kagome core panels
were found to be superior to both tetrahedral and pyramidal truss core
panels. Both analytical and empirical studies attributed the greater load
carrying capacity and lower softening rate beyond the peak load to the
3D variant’s diminished sensitivity to plastic buckling.15,16 In this
experiment, the 3D Kagome structure is tested as a truss core panel
sandwiched between two solid face sheets as shown in Fig. 1. This is
identical to the configuration used in earlier experiments.16 The 3D
Kagome structure is formed by having pairs of tetrahedrons vertically
inverted and rotationally offset from each other by 60o.
Hexagonal diamond structure - The hexagonal diamond is a
hexagonal modification of the cubic diamond structure. It has been
found embedded in meteorites17 and synthesized in the laboratory using
high temperatures and pressures.18 This structure may also be present
in carbon films grown using chemical vapor deposition that is found to
contain a high density of (111) microtwins and stacking faults.
The local atomic arrangements of the hexagonal and cubic diamond
are similar. Both have covalent tetrahedral bonds and contain six-
membered rings of bonds. The main difference is the alignment of their
(111) atomic layers (each pair labeled as A, B or C). In the cubic
diamond, each successive layer is displaced sideways from the
previous with the fourth layer returning to the same position as the first
leading to a stacking sequence ABCABC.... The stacking sequence of
hexagonal diamond, in contrast, is of the type ABAB....
More importantly, research has shown that the hexagonal diamond
is around 58% harder than cubic diamond and is able to resist up to 152
GPA of indentation pressure.19 Given the unique properties of
hexagonal diamond, we are interested in evaluating the performance of
this structure as a macro-sized lattice structure. The unit cell structure
of the hexagonal diamond is shown in Fig. 2.
Cross pyramidal structure - A pyramidal lattice structure consists of
four inclined trusses meeting at a sheet node. The advantage of this
design is that the incline of the trusses can be altered to support larger
amount of compressive stress or shear stress depending on the
requirements of the structure.
In order to obtain a design that can be more easily converted into
a multi-layered structure, we modified the original design and derived
an alternate structure formed by having two pyramidal structures
placed against each other. The alternate design is shown in Fig. 3.
3. 3D Printing Method
Numerous options exist for the mass production of lattice structures
but they become limited for the production of one-offs or small
quantities. The problem becomes even more acute for complex designs
with undercuts and overhanging features since very few conventional
manufacturing techniques can produce them. For testing purposes,
multiple variants may be required for different geometric parameters of
the design e.g. truss diameter, size of unit cell, density of structure
which mean more tooling are needed.
AM offers a less expensive and more flexible design and
manufacturing option as the layer-by-layer approach allows arbitrary
shapes, including lattice structures, to be easily produced directly from
computer-aided design (CAD) files.20 Also, the per-unit cost of an AM
part is the same regardless whether the machine makes one part or
hundreds of parts.
The method chosen is commercialized by Objet Geometries Ltd. It
combines ink-jet technologies with the use of photopolymers as raw
materials to produce 3D parts. The system chosen was the Objet 350
3D printer while the photopolymer selected is a polypropylene-like
material called Objet DurusWhite RGD430. Its properties are listed in
Table 1.
According to at least one U.S. patent document assigned to the
company, the printer works by depositing liquid photopolymer in the
shape of 3D objects and then exposing the liquid to ultra-violet
radiation to harden it.21-23
The CAD model of the various structures is prepared according to
Fig. 1 3D Kagome truss core panel and unit cell of 3D Kagome
structure16
Fig. 2 Hexagonal diamond structure
Fig. 3 Cross pyramidal structure
Table 1 Properties of objet duruswhite
Symbol Units Metric
Tensile strength σT MPa 20-30
Modulus of elasticity E MPa 1000-1200
Flexural strength σU MPa 30-40
Flexural modulus σB MPa 1200-1600
topology optimization as an optimal structure based on its elastic
modulus for a range of fraction volumes.13 The 3D variant was
proposed by a recent research investigating if the superior properties
observed in the 2D variant are carried over.14 3D Kagome core panels
were found to be superior to both tetrahedral and pyramidal truss core
panels. Both analytical and empirical studies attributed the greater load
carrying capacity and lower softening rate beyond the peak load to the
3D variant’s diminished sensitivity to plastic buckling.15,16 In this
experiment, the 3D Kagome structure is tested as a truss core panel
sandwiched between two solid face sheets as shown in Fig. 1. This is
identical to the configuration used in earlier experiments.16 The 3D
Kagome structure is formed by having pairs of tetrahedrons vertically
inverted and rotationally offset from each other by 60o.
Hexagonal diamond structure - The hexagonal diamond is a
hexagonal modification of the cubic diamond structure. It has been
found embedded in meteorites17 and synthesized in the laboratory using
high temperatures and pressures.18 This structure may also be present
in carbon films grown using chemical vapor deposition that is found to
contain a high density of (111) microtwins and stacking faults.
The local atomic arrangements of the hexagonal and cubic diamond
are similar. Both have covalent tetrahedral bonds and contain six-
membered rings of bonds. The main difference is the alignment of their
(111) atomic layers (each pair labeled as A, B or C). In the cubic
diamond, each successive layer is displaced sideways from the
previous with the fourth layer returning to the same position as the first
leading to a stacking sequence ABCABC.... The stacking sequence of
hexagonal diamond, in contrast, is of the type ABAB....
More importantly, research has shown that the hexagonal diamond
is around 58% harder than cubic diamond and is able to resist up to 152
GPA of indentation pressure.19 Given the unique properties of
hexagonal diamond, we are interested in evaluating the performance of
this structure as a macro-sized lattice structure. The unit cell structure
of the hexagonal diamond is shown in Fig. 2.
Cross pyramidal structure - A pyramidal lattice structure consists of
four inclined trusses meeting at a sheet node. The advantage of this
design is that the incline of the trusses can be altered to support larger
amount of compressive stress or shear stress depending on the
requirements of the structure.
In order to obtain a design that can be more easily converted into
a multi-layered structure, we modified the original design and derived
an alternate structure formed by having two pyramidal structures
placed against each other. The alternate design is shown in Fig. 3.
3. 3D Printing Method
Numerous options exist for the mass production of lattice structures
but they become limited for the production of one-offs or small
quantities. The problem becomes even more acute for complex designs
with undercuts and overhanging features since very few conventional
manufacturing techniques can produce them. For testing purposes,
multiple variants may be required for different geometric parameters of
the design e.g. truss diameter, size of unit cell, density of structure
which mean more tooling are needed.
AM offers a less expensive and more flexible design and
manufacturing option as the layer-by-layer approach allows arbitrary
shapes, including lattice structures, to be easily produced directly from
computer-aided design (CAD) files.20 Also, the per-unit cost of an AM
part is the same regardless whether the machine makes one part or
hundreds of parts.
The method chosen is commercialized by Objet Geometries Ltd. It
combines ink-jet technologies with the use of photopolymers as raw
materials to produce 3D parts. The system chosen was the Objet 350
3D printer while the photopolymer selected is a polypropylene-like
material called Objet DurusWhite RGD430. Its properties are listed in
Table 1.
According to at least one U.S. patent document assigned to the
company, the printer works by depositing liquid photopolymer in the
shape of 3D objects and then exposing the liquid to ultra-violet
radiation to harden it.21-23
The CAD model of the various structures is prepared according to
Fig. 1 3D Kagome truss core panel and unit cell of 3D Kagome
structure16
Fig. 2 Hexagonal diamond structure
Fig. 3 Cross pyramidal structure
Table 1 Properties of objet duruswhite
Symbol Units Metric
Tensile strength σT MPa 20-30
Modulus of elasticity E MPa 1000-1200
Flexural strength σU MPa 30-40
Flexural modulus σB MPa 1200-1600
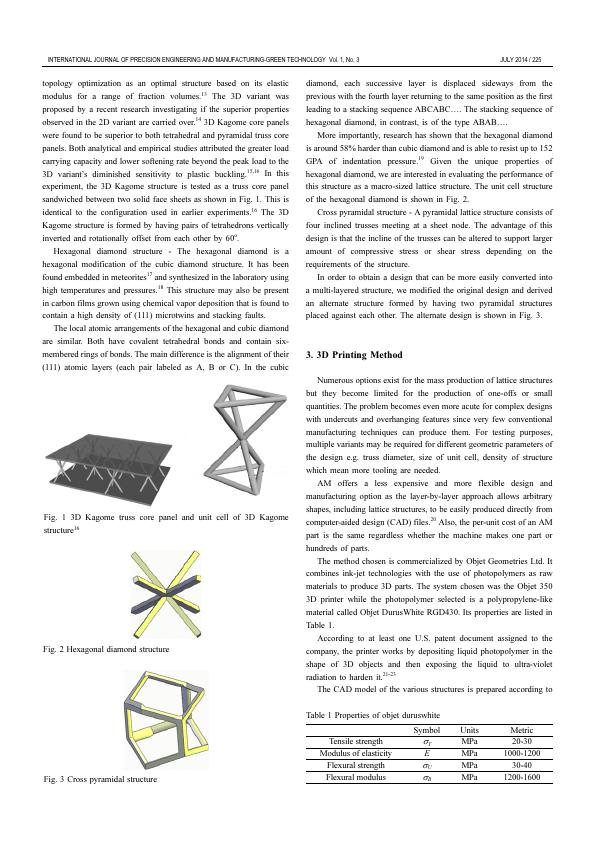
End of preview
Want to access all the pages? Upload your documents or become a member.
Related Documents
Application of 3D printing technology for designing light-weight unmanned aerial vehicle wing structureslg...
|4
|758
|383