Toyota's Operation Management: A Comprehensive Analysis of Strategies
VerifiedAdded on 2021/02/22
|10
|2948
|107
Report
AI Summary
This report offers a detailed analysis of Toyota's operation management, focusing on key strategies such as Six Sigma, TQM, JIT, and Kaizen. It explores the importance of operational management, including controlling distribution systems, transforming raw materials, and managing capacity. The report examines the role of leaders and managers in implementing these strategies, emphasizing their involvement in training, resource allocation, and employee support. Furthermore, it investigates how Toyota enhances efficiency through regular training, employee empowerment, and customer service. The analysis highlights Toyota's focus on employee productivity, incentive programs, and logistics management. The report concludes with insights into how Toyota prioritizes client satisfaction and the implementation of the Toyota Production System (TPS) to achieve lean manufacturing and continuous improvement.
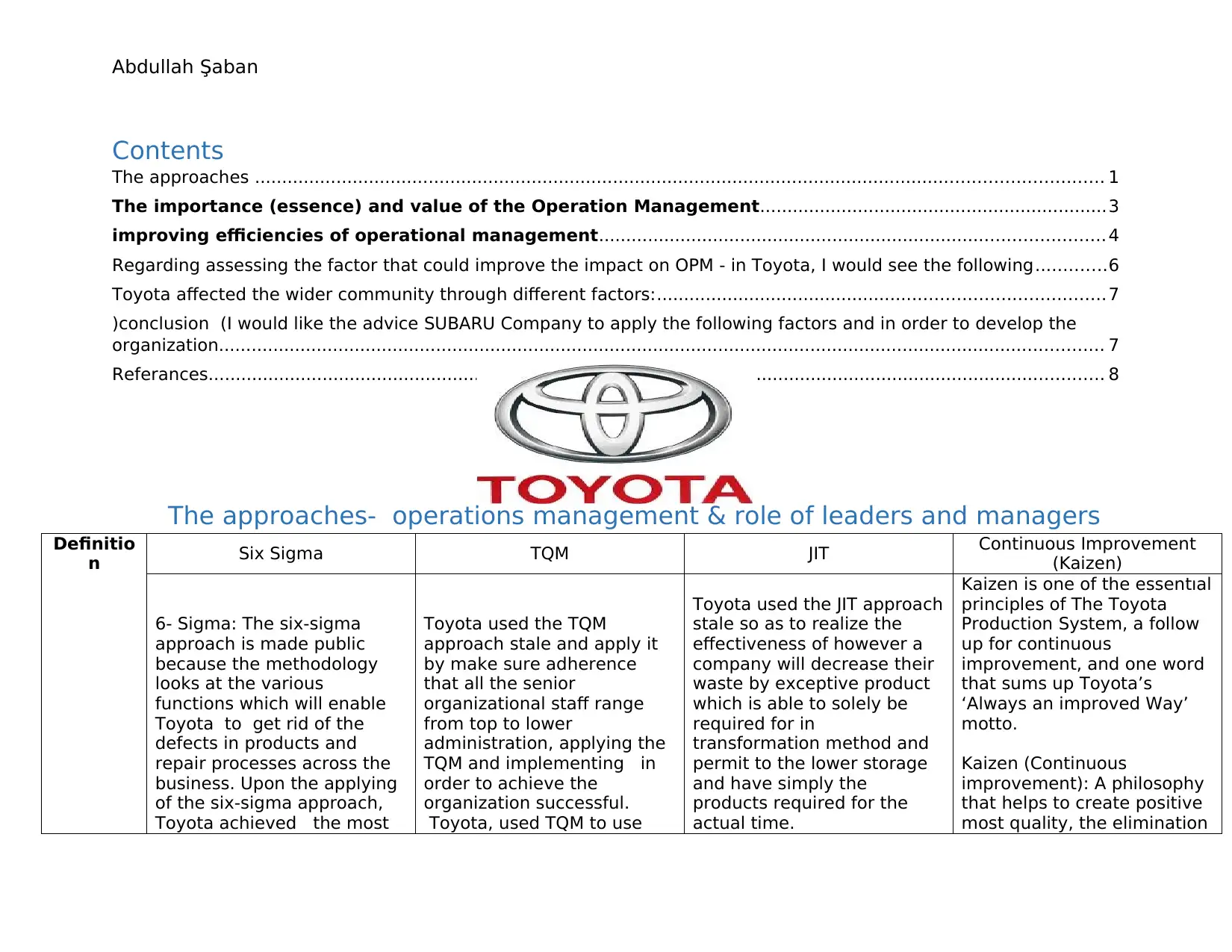
Abdullah Şaban
Contents
The approaches ............................................................................................................................................................ 1
The importance (essence) and value of the Operation Management................................................................3
improving efficiencies of operational management............................................................................................. 4
Regarding assessing the factor that could improve the impact on OPM - in Toyota, I would see the following.............6
Toyota affected the wider community through different factors:..................................................................................7
)conclusion (I would like the advice SUBARU Company to apply the following factors and in order to develop the
organization................................................................................................................................................................... 7
Referances..................................................................................................................................................................... 8
The approaches- operations management & role of leaders and managers
Definitio
n Six Sigma TQM JIT Continuous Improvement
(Kaizen)
6- Sigma: The six-sigma
approach is made public
because the methodology
looks at the various
functions which will enable
Toyota to get rid of the
defects in products and
repair processes across the
business. Upon the applying
of the six-sigma approach,
Toyota achieved the most
Toyota used the TQM
approach stale and apply it
by make sure adherence
that all the senior
organizational staff range
from top to lower
administration, applying the
TQM and implementing in
order to achieve the
organization successful.
Toyota, used TQM to use
Toyota used the JIT approach
stale so as to realize the
effectiveness of however a
company will decrease their
waste by exceptive product
which is able to solely be
required for in
transformation method and
permit to the lower storage
and have simply the
products required for the
actual time.
Kaizen is one of the essentıal
principles of The Toyota
Production System, a follow
up for continuous
improvement, and one word
that sums up Toyota’s
‘Always an improved Way’
motto.
Kaizen (Continuous
improvement): A philosophy
that helps to create positive
most quality, the elimination
Contents
The approaches ............................................................................................................................................................ 1
The importance (essence) and value of the Operation Management................................................................3
improving efficiencies of operational management............................................................................................. 4
Regarding assessing the factor that could improve the impact on OPM - in Toyota, I would see the following.............6
Toyota affected the wider community through different factors:..................................................................................7
)conclusion (I would like the advice SUBARU Company to apply the following factors and in order to develop the
organization................................................................................................................................................................... 7
Referances..................................................................................................................................................................... 8
The approaches- operations management & role of leaders and managers
Definitio
n Six Sigma TQM JIT Continuous Improvement
(Kaizen)
6- Sigma: The six-sigma
approach is made public
because the methodology
looks at the various
functions which will enable
Toyota to get rid of the
defects in products and
repair processes across the
business. Upon the applying
of the six-sigma approach,
Toyota achieved the most
Toyota used the TQM
approach stale and apply it
by make sure adherence
that all the senior
organizational staff range
from top to lower
administration, applying the
TQM and implementing in
order to achieve the
organization successful.
Toyota, used TQM to use
Toyota used the JIT approach
stale so as to realize the
effectiveness of however a
company will decrease their
waste by exceptive product
which is able to solely be
required for in
transformation method and
permit to the lower storage
and have simply the
products required for the
actual time.
Kaizen is one of the essentıal
principles of The Toyota
Production System, a follow
up for continuous
improvement, and one word
that sums up Toyota’s
‘Always an improved Way’
motto.
Kaizen (Continuous
improvement): A philosophy
that helps to create positive
most quality, the elimination
Paraphrase This Document
Need a fresh take? Get an instant paraphrase of this document with our AI Paraphraser
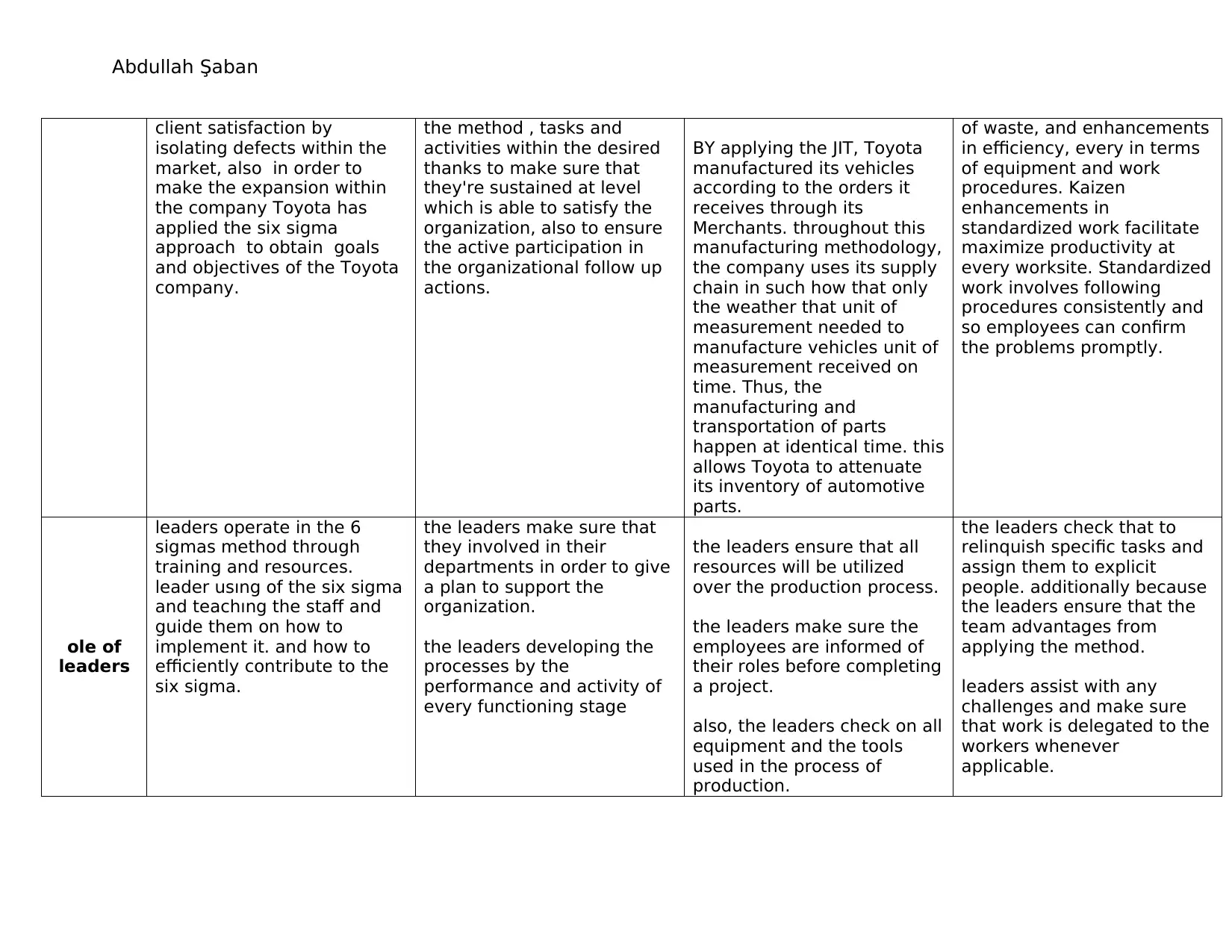
Abdullah Şaban
client satisfaction by
isolating defects within the
market, also in order to
make the expansion within
the company Toyota has
applied the six sigma
approach to obtain goals
and objectives of the Toyota
company.
the method , tasks and
activities within the desired
thanks to make sure that
they're sustained at level
which is able to satisfy the
organization, also to ensure
the active participation in
the organizational follow up
actions.
BY applying the JIT, Toyota
manufactured its vehicles
according to the orders it
receives through its
Merchants. throughout this
manufacturing methodology,
the company uses its supply
chain in such how that only
the weather that unit of
measurement needed to
manufacture vehicles unit of
measurement received on
time. Thus, the
manufacturing and
transportation of parts
happen at identical time. this
allows Toyota to attenuate
its inventory of automotive
parts.
of waste, and enhancements
in efficiency, every in terms
of equipment and work
procedures. Kaizen
enhancements in
standardized work facilitate
maximize productivity at
every worksite. Standardized
work involves following
procedures consistently and
so employees can confirm
the problems promptly.
ole of
leaders
leaders operate in the 6
sigmas method through
training and resources.
leader usıng of the six sigma
and teachıng the staff and
guide them on how to
implement it. and how to
efficiently contribute to the
six sigma.
the leaders make sure that
they involved in their
departments in order to give
a plan to support the
organization.
the leaders developing the
processes by the
performance and activity of
every functioning stage
the leaders ensure that all
resources will be utilized
over the production process.
the leaders make sure the
employees are informed of
their roles before completing
a project.
also, the leaders check on all
equipment and the tools
used in the process of
production.
the leaders check that to
relinquish specific tasks and
assign them to explicit
people. additionally because
the leaders ensure that the
team advantages from
applying the method.
leaders assist with any
challenges and make sure
that work is delegated to the
workers whenever
applicable.
client satisfaction by
isolating defects within the
market, also in order to
make the expansion within
the company Toyota has
applied the six sigma
approach to obtain goals
and objectives of the Toyota
company.
the method , tasks and
activities within the desired
thanks to make sure that
they're sustained at level
which is able to satisfy the
organization, also to ensure
the active participation in
the organizational follow up
actions.
BY applying the JIT, Toyota
manufactured its vehicles
according to the orders it
receives through its
Merchants. throughout this
manufacturing methodology,
the company uses its supply
chain in such how that only
the weather that unit of
measurement needed to
manufacture vehicles unit of
measurement received on
time. Thus, the
manufacturing and
transportation of parts
happen at identical time. this
allows Toyota to attenuate
its inventory of automotive
parts.
of waste, and enhancements
in efficiency, every in terms
of equipment and work
procedures. Kaizen
enhancements in
standardized work facilitate
maximize productivity at
every worksite. Standardized
work involves following
procedures consistently and
so employees can confirm
the problems promptly.
ole of
leaders
leaders operate in the 6
sigmas method through
training and resources.
leader usıng of the six sigma
and teachıng the staff and
guide them on how to
implement it. and how to
efficiently contribute to the
six sigma.
the leaders make sure that
they involved in their
departments in order to give
a plan to support the
organization.
the leaders developing the
processes by the
performance and activity of
every functioning stage
the leaders ensure that all
resources will be utilized
over the production process.
the leaders make sure the
employees are informed of
their roles before completing
a project.
also, the leaders check on all
equipment and the tools
used in the process of
production.
the leaders check that to
relinquish specific tasks and
assign them to explicit
people. additionally because
the leaders ensure that the
team advantages from
applying the method.
leaders assist with any
challenges and make sure
that work is delegated to the
workers whenever
applicable.
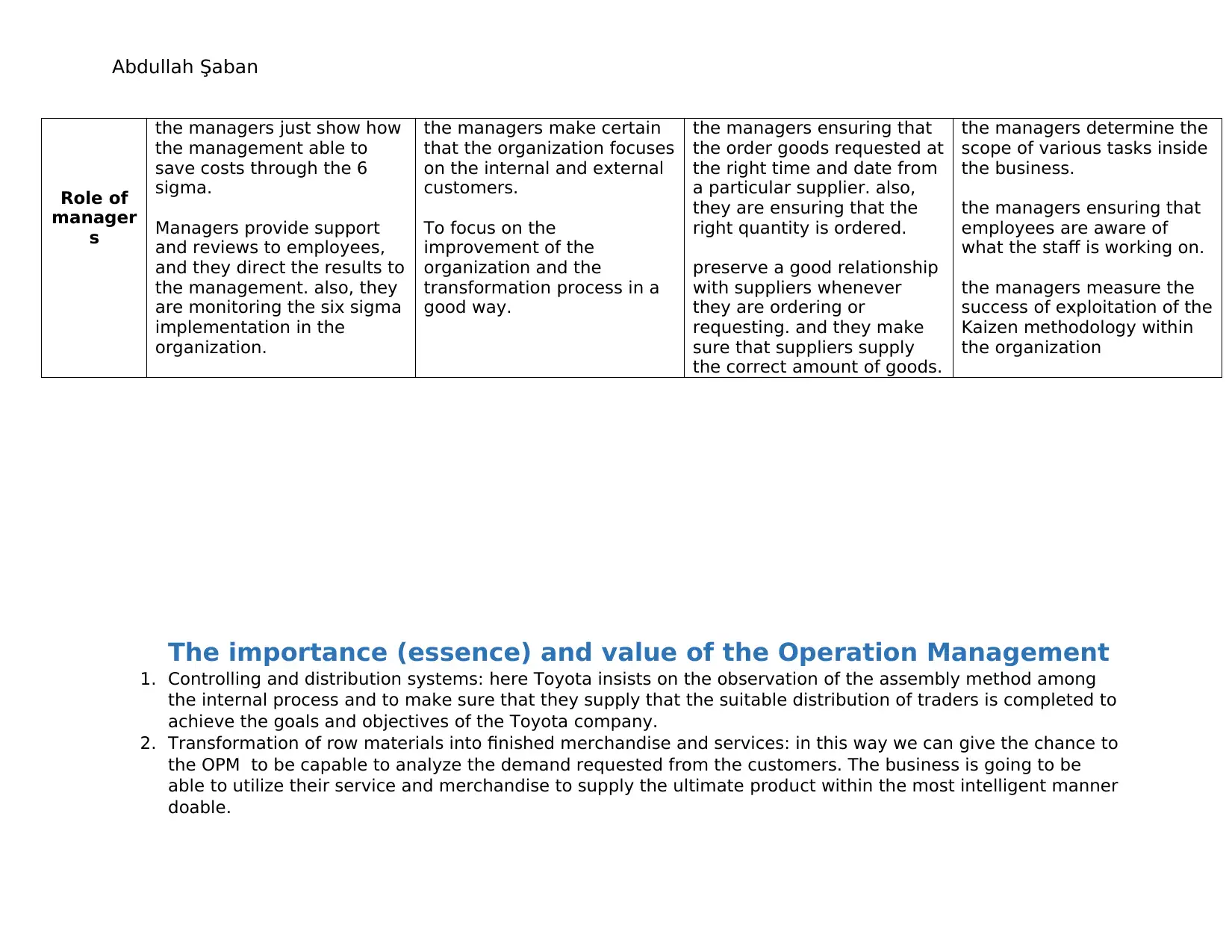
Abdullah Şaban
Role of
manager
s
the managers just show how
the management able to
save costs through the 6
sigma.
Managers provide support
and reviews to employees,
and they direct the results to
the management. also, they
are monitoring the six sigma
implementation in the
organization.
the managers make certain
that the organization focuses
on the internal and external
customers.
To focus on the
improvement of the
organization and the
transformation process in a
good way.
the managers ensuring that
the order goods requested at
the right time and date from
a particular supplier. also,
they are ensuring that the
right quantity is ordered.
preserve a good relationship
with suppliers whenever
they are ordering or
requesting. and they make
sure that suppliers supply
the correct amount of goods.
the managers determine the
scope of various tasks inside
the business.
the managers ensuring that
employees are aware of
what the staff is working on.
the managers measure the
success of exploitation of the
Kaizen methodology within
the organization
The importance (essence) and value of the Operation Management
1. Controlling and distribution systems: here Toyota insists on the observation of the assembly method among
the internal process and to make sure that they supply that the suitable distribution of traders is completed to
achieve the goals and objectives of the Toyota company.
2. Transformation of row materials into finished merchandise and services: in this way we can give the chance to
the OPM to be capable to analyze the demand requested from the customers. The business is going to be
able to utilize their service and merchandise to supply the ultimate product within the most intelligent manner
doable.
Role of
manager
s
the managers just show how
the management able to
save costs through the 6
sigma.
Managers provide support
and reviews to employees,
and they direct the results to
the management. also, they
are monitoring the six sigma
implementation in the
organization.
the managers make certain
that the organization focuses
on the internal and external
customers.
To focus on the
improvement of the
organization and the
transformation process in a
good way.
the managers ensuring that
the order goods requested at
the right time and date from
a particular supplier. also,
they are ensuring that the
right quantity is ordered.
preserve a good relationship
with suppliers whenever
they are ordering or
requesting. and they make
sure that suppliers supply
the correct amount of goods.
the managers determine the
scope of various tasks inside
the business.
the managers ensuring that
employees are aware of
what the staff is working on.
the managers measure the
success of exploitation of the
Kaizen methodology within
the organization
The importance (essence) and value of the Operation Management
1. Controlling and distribution systems: here Toyota insists on the observation of the assembly method among
the internal process and to make sure that they supply that the suitable distribution of traders is completed to
achieve the goals and objectives of the Toyota company.
2. Transformation of row materials into finished merchandise and services: in this way we can give the chance to
the OPM to be capable to analyze the demand requested from the customers. The business is going to be
able to utilize their service and merchandise to supply the ultimate product within the most intelligent manner
doable.
⊘ This is a preview!⊘
Do you want full access?
Subscribe today to unlock all pages.

Trusted by 1+ million students worldwide
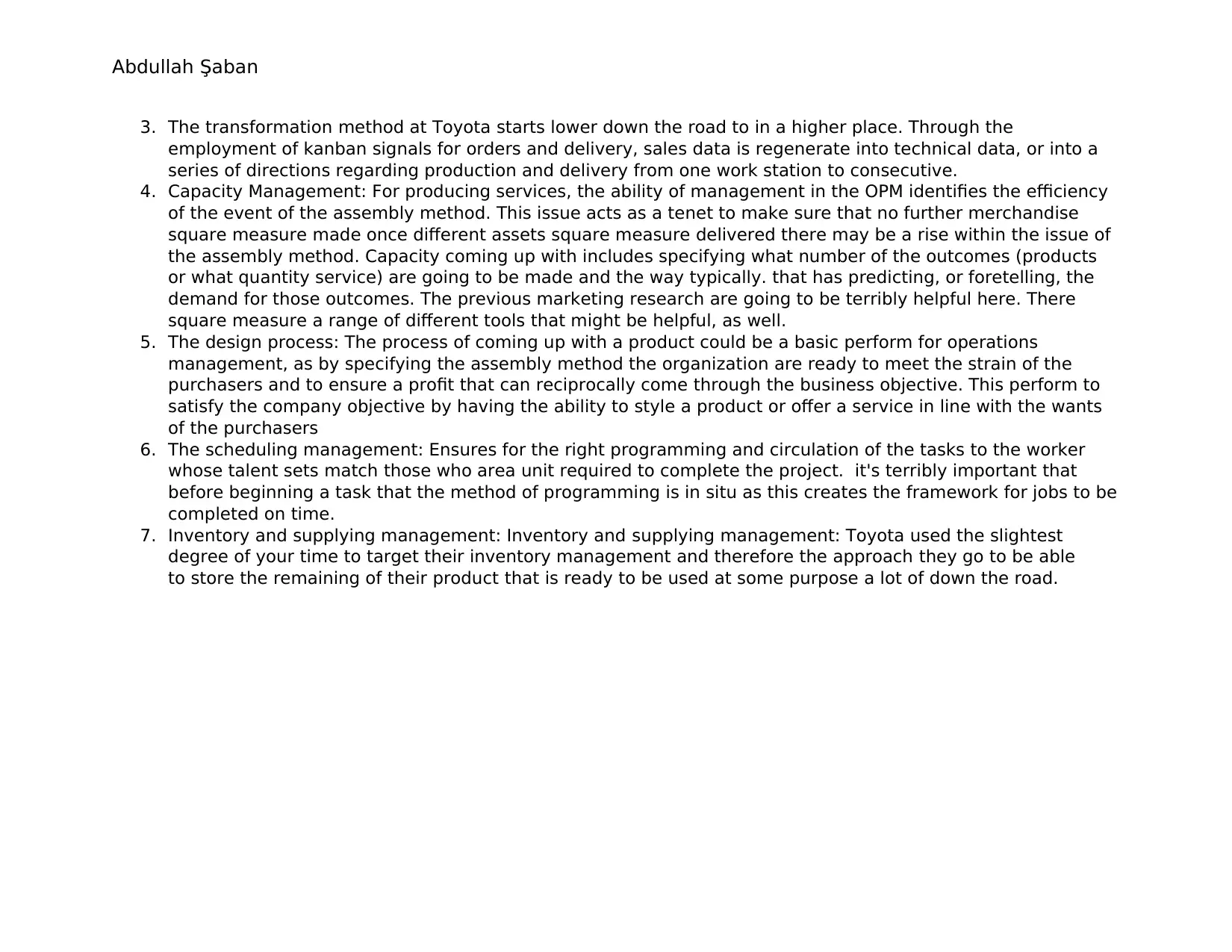
Abdullah Şaban
3. The transformation method at Toyota starts lower down the road to in a higher place. Through the
employment of kanban signals for orders and delivery, sales data is regenerate into technical data, or into a
series of directions regarding production and delivery from one work station to consecutive.
4. Capacity Management: For producing services, the ability of management in the OPM identifies the efficiency
of the event of the assembly method. This issue acts as a tenet to make sure that no further merchandise
square measure made once different assets square measure delivered there may be a rise within the issue of
the assembly method. Capacity coming up with includes specifying what number of the outcomes (products
or what quantity service) are going to be made and the way typically. that has predicting, or foretelling, the
demand for those outcomes. The previous marketing research are going to be terribly helpful here. There
square measure a range of different tools that might be helpful, as well.
5. The design process: The process of coming up with a product could be a basic perform for operations
management, as by specifying the assembly method the organization are ready to meet the strain of the
purchasers and to ensure a profit that can reciprocally come through the business objective. This perform to
satisfy the company objective by having the ability to style a product or offer a service in line with the wants
of the purchasers
6. The scheduling management: Ensures for the right programming and circulation of the tasks to the worker
whose talent sets match those who area unit required to complete the project. it's terribly important that
before beginning a task that the method of programming is in situ as this creates the framework for jobs to be
completed on time.
7. Inventory and supplying management: Inventory and supplying management: Toyota used the slightest
degree of your time to target their inventory management and therefore the approach they go to be able
to store the remaining of their product that is ready to be used at some purpose a lot of down the road.
3. The transformation method at Toyota starts lower down the road to in a higher place. Through the
employment of kanban signals for orders and delivery, sales data is regenerate into technical data, or into a
series of directions regarding production and delivery from one work station to consecutive.
4. Capacity Management: For producing services, the ability of management in the OPM identifies the efficiency
of the event of the assembly method. This issue acts as a tenet to make sure that no further merchandise
square measure made once different assets square measure delivered there may be a rise within the issue of
the assembly method. Capacity coming up with includes specifying what number of the outcomes (products
or what quantity service) are going to be made and the way typically. that has predicting, or foretelling, the
demand for those outcomes. The previous marketing research are going to be terribly helpful here. There
square measure a range of different tools that might be helpful, as well.
5. The design process: The process of coming up with a product could be a basic perform for operations
management, as by specifying the assembly method the organization are ready to meet the strain of the
purchasers and to ensure a profit that can reciprocally come through the business objective. This perform to
satisfy the company objective by having the ability to style a product or offer a service in line with the wants
of the purchasers
6. The scheduling management: Ensures for the right programming and circulation of the tasks to the worker
whose talent sets match those who area unit required to complete the project. it's terribly important that
before beginning a task that the method of programming is in situ as this creates the framework for jobs to be
completed on time.
7. Inventory and supplying management: Inventory and supplying management: Toyota used the slightest
degree of your time to target their inventory management and therefore the approach they go to be able
to store the remaining of their product that is ready to be used at some purpose a lot of down the road.
Paraphrase This Document
Need a fresh take? Get an instant paraphrase of this document with our AI Paraphraser
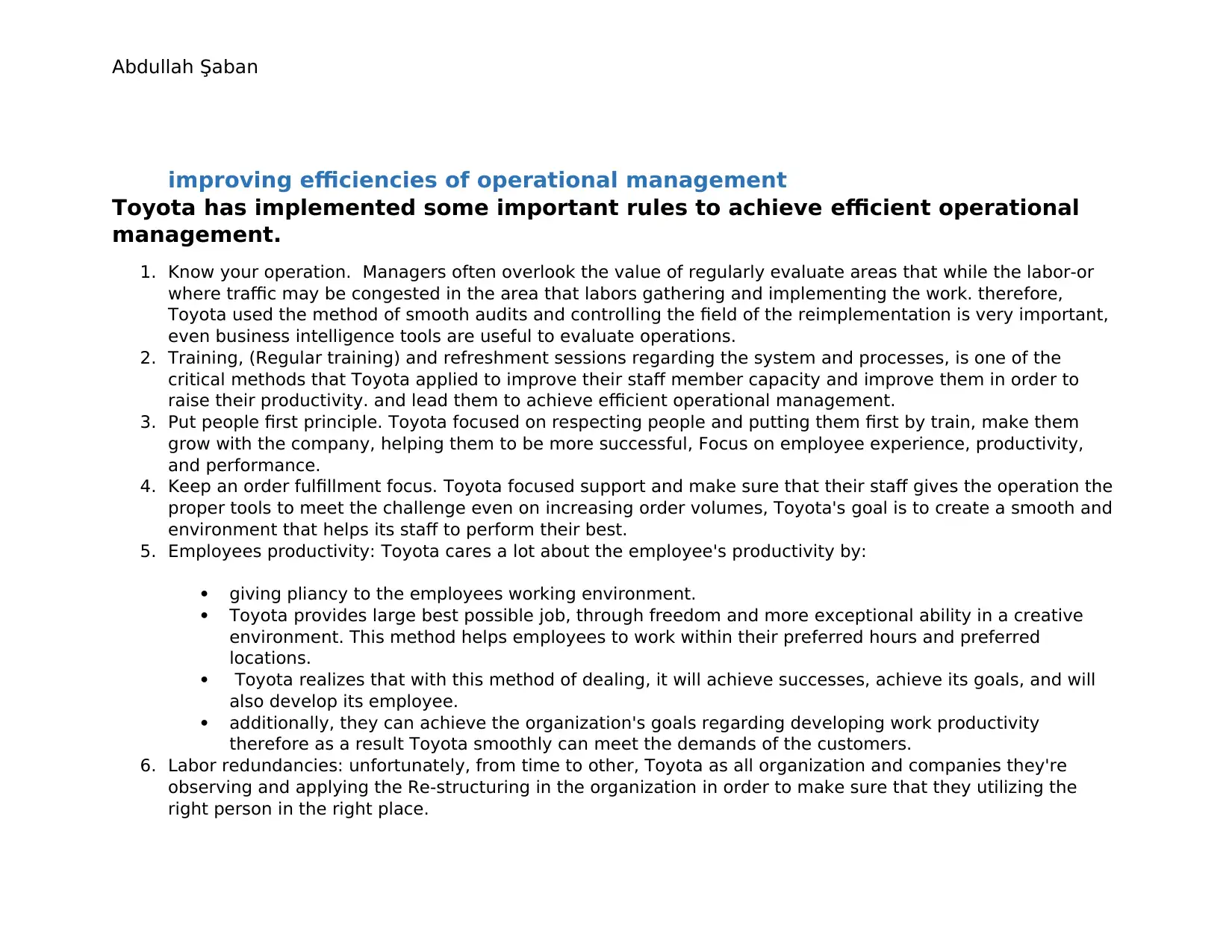
Abdullah Şaban
improving efficiencies of operational management
Toyota has implemented some important rules to achieve efficient operational
management.
1. Know your operation. Managers often overlook the value of regularly evaluate areas that while the labor-or
where traffic may be congested in the area that labors gathering and implementing the work. therefore,
Toyota used the method of smooth audits and controlling the field of the reimplementation is very important,
even business intelligence tools are useful to evaluate operations.
2. Training, (Regular training) and refreshment sessions regarding the system and processes, is one of the
critical methods that Toyota applied to improve their staff member capacity and improve them in order to
raise their productivity. and lead them to achieve efficient operational management.
3. Put people first principle. Toyota focused on respecting people and putting them first by train, make them
grow with the company, helping them to be more successful, Focus on employee experience, productivity,
and performance.
4. Keep an order fulfillment focus. Toyota focused support and make sure that their staff gives the operation the
proper tools to meet the challenge even on increasing order volumes, Toyota's goal is to create a smooth and
environment that helps its staff to perform their best.
5. Employees productivity: Toyota cares a lot about the employee's productivity by:
giving pliancy to the employees working environment.
Toyota provides large best possible job, through freedom and more exceptional ability in a creative
environment. This method helps employees to work within their preferred hours and preferred
locations.
Toyota realizes that with this method of dealing, it will achieve successes, achieve its goals, and will
also develop its employee.
additionally, they can achieve the organization's goals regarding developing work productivity
therefore as a result Toyota smoothly can meet the demands of the customers.
6. Labor redundancies: unfortunately, from time to other, Toyota as all organization and companies they're
observing and applying the Re-structuring in the organization in order to make sure that they utilizing the
right person in the right place.
improving efficiencies of operational management
Toyota has implemented some important rules to achieve efficient operational
management.
1. Know your operation. Managers often overlook the value of regularly evaluate areas that while the labor-or
where traffic may be congested in the area that labors gathering and implementing the work. therefore,
Toyota used the method of smooth audits and controlling the field of the reimplementation is very important,
even business intelligence tools are useful to evaluate operations.
2. Training, (Regular training) and refreshment sessions regarding the system and processes, is one of the
critical methods that Toyota applied to improve their staff member capacity and improve them in order to
raise their productivity. and lead them to achieve efficient operational management.
3. Put people first principle. Toyota focused on respecting people and putting them first by train, make them
grow with the company, helping them to be more successful, Focus on employee experience, productivity,
and performance.
4. Keep an order fulfillment focus. Toyota focused support and make sure that their staff gives the operation the
proper tools to meet the challenge even on increasing order volumes, Toyota's goal is to create a smooth and
environment that helps its staff to perform their best.
5. Employees productivity: Toyota cares a lot about the employee's productivity by:
giving pliancy to the employees working environment.
Toyota provides large best possible job, through freedom and more exceptional ability in a creative
environment. This method helps employees to work within their preferred hours and preferred
locations.
Toyota realizes that with this method of dealing, it will achieve successes, achieve its goals, and will
also develop its employee.
additionally, they can achieve the organization's goals regarding developing work productivity
therefore as a result Toyota smoothly can meet the demands of the customers.
6. Labor redundancies: unfortunately, from time to other, Toyota as all organization and companies they're
observing and applying the Re-structuring in the organization in order to make sure that they utilizing the
right person in the right place.
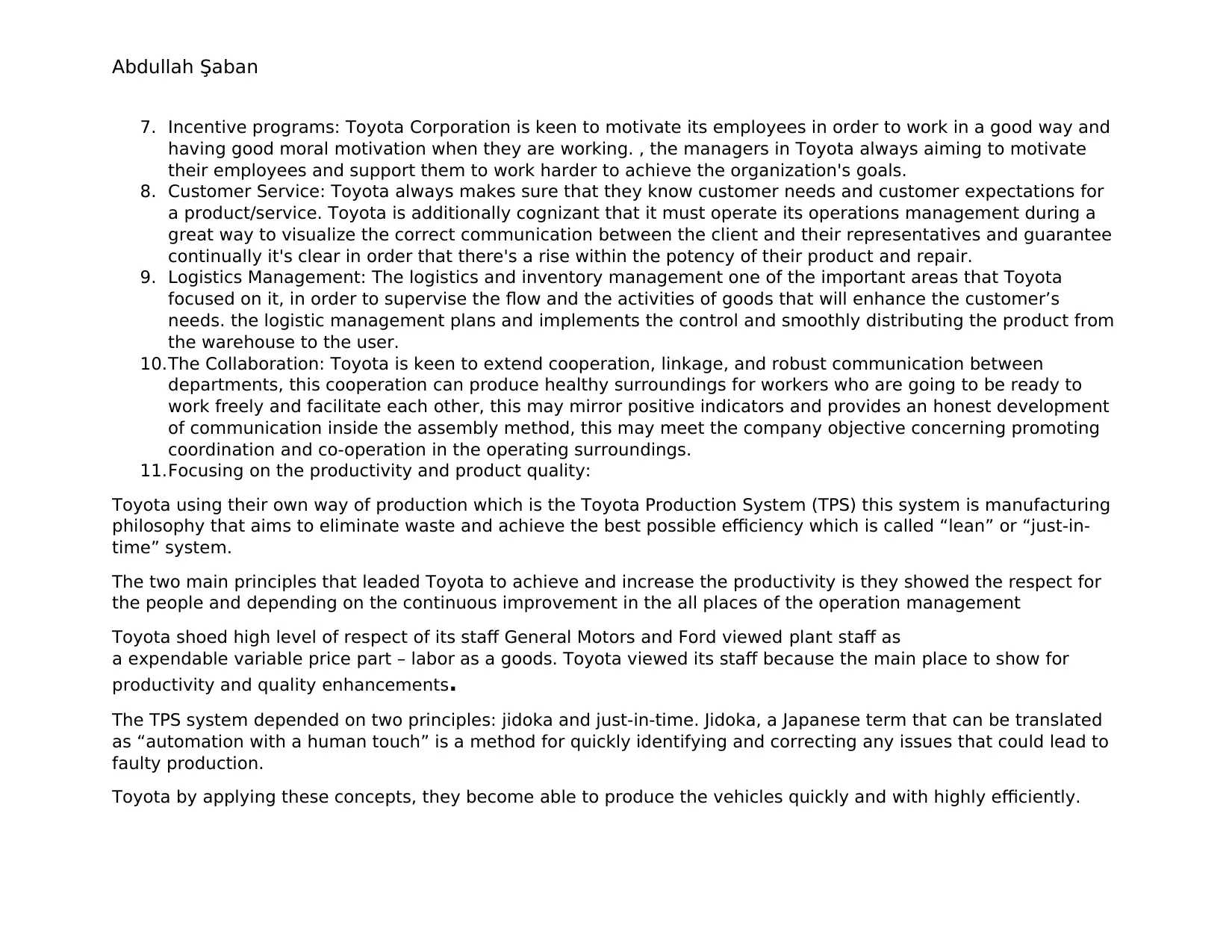
Abdullah Şaban
7. Incentive programs: Toyota Corporation is keen to motivate its employees in order to work in a good way and
having good moral motivation when they are working. , the managers in Toyota always aiming to motivate
their employees and support them to work harder to achieve the organization's goals.
8. Customer Service: Toyota always makes sure that they know customer needs and customer expectations for
a product/service. Toyota is additionally cognizant that it must operate its operations management during a
great way to visualize the correct communication between the client and their representatives and guarantee
continually it's clear in order that there's a rise within the potency of their product and repair.
9. Logistics Management: The logistics and inventory management one of the important areas that Toyota
focused on it, in order to supervise the flow and the activities of goods that will enhance the customer’s
needs. the logistic management plans and implements the control and smoothly distributing the product from
the warehouse to the user.
10.The Collaboration: Toyota is keen to extend cooperation, linkage, and robust communication between
departments, this cooperation can produce healthy surroundings for workers who are going to be ready to
work freely and facilitate each other, this may mirror positive indicators and provides an honest development
of communication inside the assembly method, this may meet the company objective concerning promoting
coordination and co-operation in the operating surroundings.
11.Focusing on the productivity and product quality:
Toyota using their own way of production which is the Toyota Production System (TPS) this system is manufacturing
philosophy that aims to eliminate waste and achieve the best possible efficiency which is called “lean” or “just-in-
time” system.
The two main principles that leaded Toyota to achieve and increase the productivity is they showed the respect for
the people and depending on the continuous improvement in the all places of the operation management
Toyota shoed high level of respect of its staff General Motors and Ford viewed plant staff as
a expendable variable price part – labor as a goods. Toyota viewed its staff because the main place to show for
productivity and quality enhancements.
The TPS system depended on two principles: jidoka and just-in-time. Jidoka, a Japanese term that can be translated
as “automation with a human touch” is a method for quickly identifying and correcting any issues that could lead to
faulty production.
Toyota by applying these concepts, they become able to produce the vehicles quickly and with highly efficiently.
7. Incentive programs: Toyota Corporation is keen to motivate its employees in order to work in a good way and
having good moral motivation when they are working. , the managers in Toyota always aiming to motivate
their employees and support them to work harder to achieve the organization's goals.
8. Customer Service: Toyota always makes sure that they know customer needs and customer expectations for
a product/service. Toyota is additionally cognizant that it must operate its operations management during a
great way to visualize the correct communication between the client and their representatives and guarantee
continually it's clear in order that there's a rise within the potency of their product and repair.
9. Logistics Management: The logistics and inventory management one of the important areas that Toyota
focused on it, in order to supervise the flow and the activities of goods that will enhance the customer’s
needs. the logistic management plans and implements the control and smoothly distributing the product from
the warehouse to the user.
10.The Collaboration: Toyota is keen to extend cooperation, linkage, and robust communication between
departments, this cooperation can produce healthy surroundings for workers who are going to be ready to
work freely and facilitate each other, this may mirror positive indicators and provides an honest development
of communication inside the assembly method, this may meet the company objective concerning promoting
coordination and co-operation in the operating surroundings.
11.Focusing on the productivity and product quality:
Toyota using their own way of production which is the Toyota Production System (TPS) this system is manufacturing
philosophy that aims to eliminate waste and achieve the best possible efficiency which is called “lean” or “just-in-
time” system.
The two main principles that leaded Toyota to achieve and increase the productivity is they showed the respect for
the people and depending on the continuous improvement in the all places of the operation management
Toyota shoed high level of respect of its staff General Motors and Ford viewed plant staff as
a expendable variable price part – labor as a goods. Toyota viewed its staff because the main place to show for
productivity and quality enhancements.
The TPS system depended on two principles: jidoka and just-in-time. Jidoka, a Japanese term that can be translated
as “automation with a human touch” is a method for quickly identifying and correcting any issues that could lead to
faulty production.
Toyota by applying these concepts, they become able to produce the vehicles quickly and with highly efficiently.
⊘ This is a preview!⊘
Do you want full access?
Subscribe today to unlock all pages.

Trusted by 1+ million students worldwide
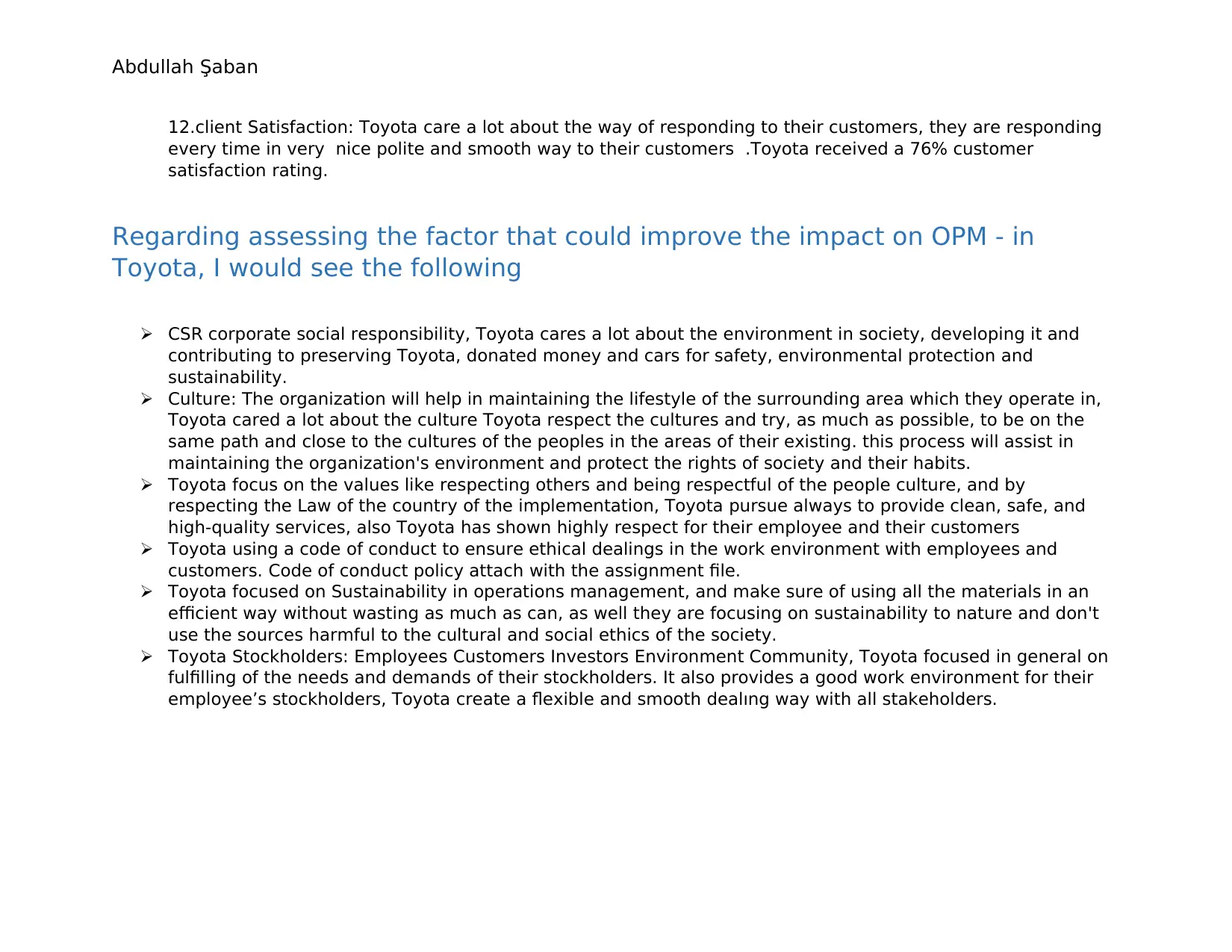
Abdullah Şaban
12.client Satisfaction: Toyota care a lot about the way of responding to their customers, they are responding
every time in very nice polite and smooth way to their customers .Toyota received a 76% customer
satisfaction rating.
Regarding assessing the factor that could improve the impact on OPM - in
Toyota, I would see the following
CSR corporate social responsibility, Toyota cares a lot about the environment in society, developing it and
contributing to preserving Toyota, donated money and cars for safety, environmental protection and
sustainability.
Culture: The organization will help in maintaining the lifestyle of the surrounding area which they operate in,
Toyota cared a lot about the culture Toyota respect the cultures and try, as much as possible, to be on the
same path and close to the cultures of the peoples in the areas of their existing. this process will assist in
maintaining the organization's environment and protect the rights of society and their habits.
Toyota focus on the values like respecting others and being respectful of the people culture, and by
respecting the Law of the country of the implementation, Toyota pursue always to provide clean, safe, and
high-quality services, also Toyota has shown highly respect for their employee and their customers
Toyota using a code of conduct to ensure ethical dealings in the work environment with employees and
customers. Code of conduct policy attach with the assignment file.
Toyota focused on Sustainability in operations management, and make sure of using all the materials in an
efficient way without wasting as much as can, as well they are focusing on sustainability to nature and don't
use the sources harmful to the cultural and social ethics of the society.
Toyota Stockholders: Employees Customers Investors Environment Community, Toyota focused in general on
fulfilling of the needs and demands of their stockholders. It also provides a good work environment for their
employee’s stockholders, Toyota create a flexible and smooth dealıng way with all stakeholders.
12.client Satisfaction: Toyota care a lot about the way of responding to their customers, they are responding
every time in very nice polite and smooth way to their customers .Toyota received a 76% customer
satisfaction rating.
Regarding assessing the factor that could improve the impact on OPM - in
Toyota, I would see the following
CSR corporate social responsibility, Toyota cares a lot about the environment in society, developing it and
contributing to preserving Toyota, donated money and cars for safety, environmental protection and
sustainability.
Culture: The organization will help in maintaining the lifestyle of the surrounding area which they operate in,
Toyota cared a lot about the culture Toyota respect the cultures and try, as much as possible, to be on the
same path and close to the cultures of the peoples in the areas of their existing. this process will assist in
maintaining the organization's environment and protect the rights of society and their habits.
Toyota focus on the values like respecting others and being respectful of the people culture, and by
respecting the Law of the country of the implementation, Toyota pursue always to provide clean, safe, and
high-quality services, also Toyota has shown highly respect for their employee and their customers
Toyota using a code of conduct to ensure ethical dealings in the work environment with employees and
customers. Code of conduct policy attach with the assignment file.
Toyota focused on Sustainability in operations management, and make sure of using all the materials in an
efficient way without wasting as much as can, as well they are focusing on sustainability to nature and don't
use the sources harmful to the cultural and social ethics of the society.
Toyota Stockholders: Employees Customers Investors Environment Community, Toyota focused in general on
fulfilling of the needs and demands of their stockholders. It also provides a good work environment for their
employee’s stockholders, Toyota create a flexible and smooth dealıng way with all stakeholders.
Paraphrase This Document
Need a fresh take? Get an instant paraphrase of this document with our AI Paraphraser
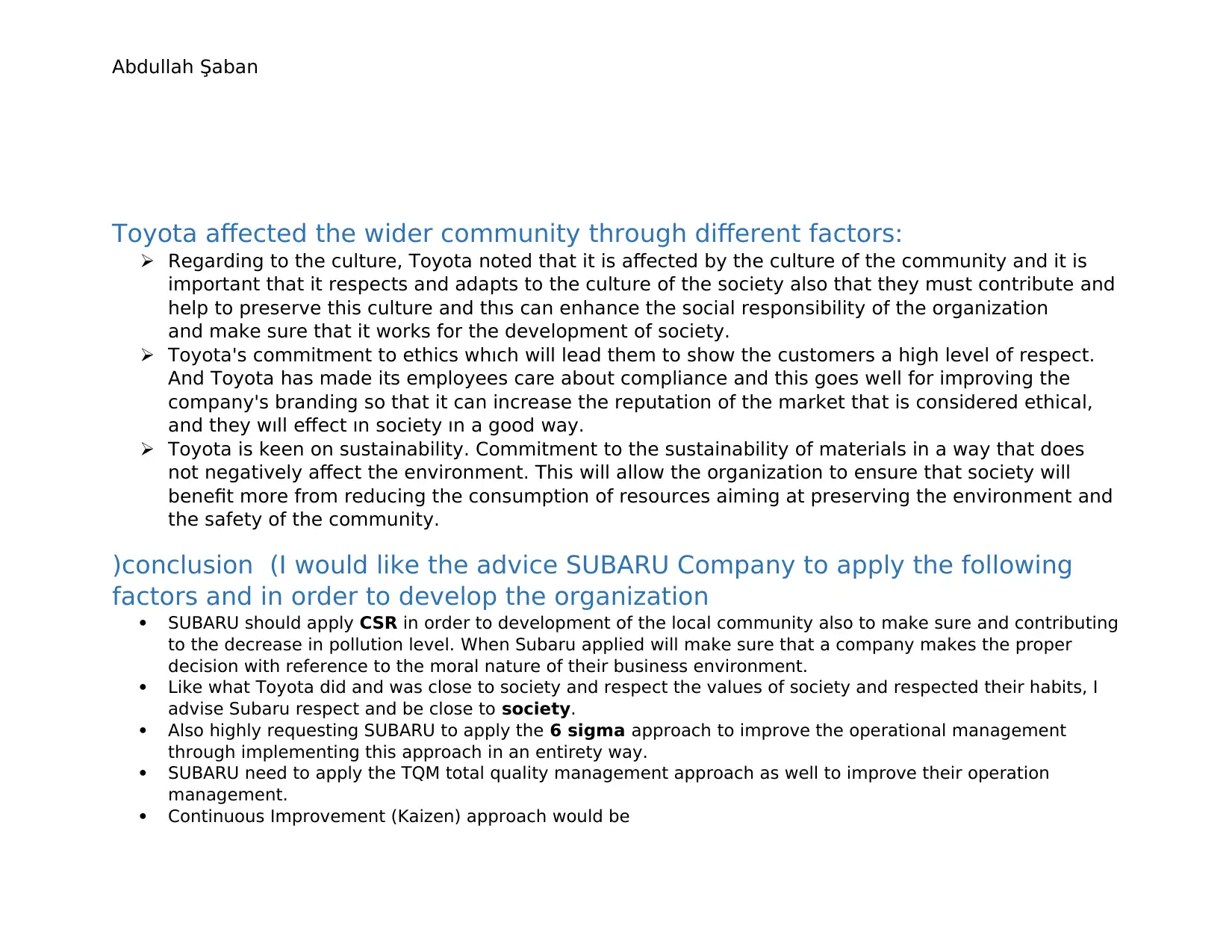
Abdullah Şaban
Toyota affected the wider community through different factors:
Regarding to the culture, Toyota noted that it is affected by the culture of the community and it is
important that it respects and adapts to the culture of the society also that they must contribute and
help to preserve this culture and thıs can enhance the social responsibility of the organization
and make sure that it works for the development of society.
Toyota's commitment to ethics whıch will lead them to show the customers a high level of respect.
And Toyota has made its employees care about compliance and this goes well for improving the
company's branding so that it can increase the reputation of the market that is considered ethical,
and they wıll effect ın society ın a good way.
Toyota is keen on sustainability. Commitment to the sustainability of materials in a way that does
not negatively affect the environment. This will allow the organization to ensure that society will
benefit more from reducing the consumption of resources aiming at preserving the environment and
the safety of the community.
)conclusion (I would like the advice SUBARU Company to apply the following
factors and in order to develop the organization
SUBARU should apply CSR in order to development of the local community also to make sure and contributing
to the decrease in pollution level. When Subaru applied will make sure that a company makes the proper
decision with reference to the moral nature of their business environment.
Like what Toyota did and was close to society and respect the values of society and respected their habits, I
advise Subaru respect and be close to society.
Also highly requesting SUBARU to apply the 6 sigma approach to improve the operational management
through implementing this approach in an entirety way.
SUBARU need to apply the TQM total quality management approach as well to improve their operation
management.
Continuous Improvement (Kaizen) approach would be
Toyota affected the wider community through different factors:
Regarding to the culture, Toyota noted that it is affected by the culture of the community and it is
important that it respects and adapts to the culture of the society also that they must contribute and
help to preserve this culture and thıs can enhance the social responsibility of the organization
and make sure that it works for the development of society.
Toyota's commitment to ethics whıch will lead them to show the customers a high level of respect.
And Toyota has made its employees care about compliance and this goes well for improving the
company's branding so that it can increase the reputation of the market that is considered ethical,
and they wıll effect ın society ın a good way.
Toyota is keen on sustainability. Commitment to the sustainability of materials in a way that does
not negatively affect the environment. This will allow the organization to ensure that society will
benefit more from reducing the consumption of resources aiming at preserving the environment and
the safety of the community.
)conclusion (I would like the advice SUBARU Company to apply the following
factors and in order to develop the organization
SUBARU should apply CSR in order to development of the local community also to make sure and contributing
to the decrease in pollution level. When Subaru applied will make sure that a company makes the proper
decision with reference to the moral nature of their business environment.
Like what Toyota did and was close to society and respect the values of society and respected their habits, I
advise Subaru respect and be close to society.
Also highly requesting SUBARU to apply the 6 sigma approach to improve the operational management
through implementing this approach in an entirety way.
SUBARU need to apply the TQM total quality management approach as well to improve their operation
management.
Continuous Improvement (Kaizen) approach would be
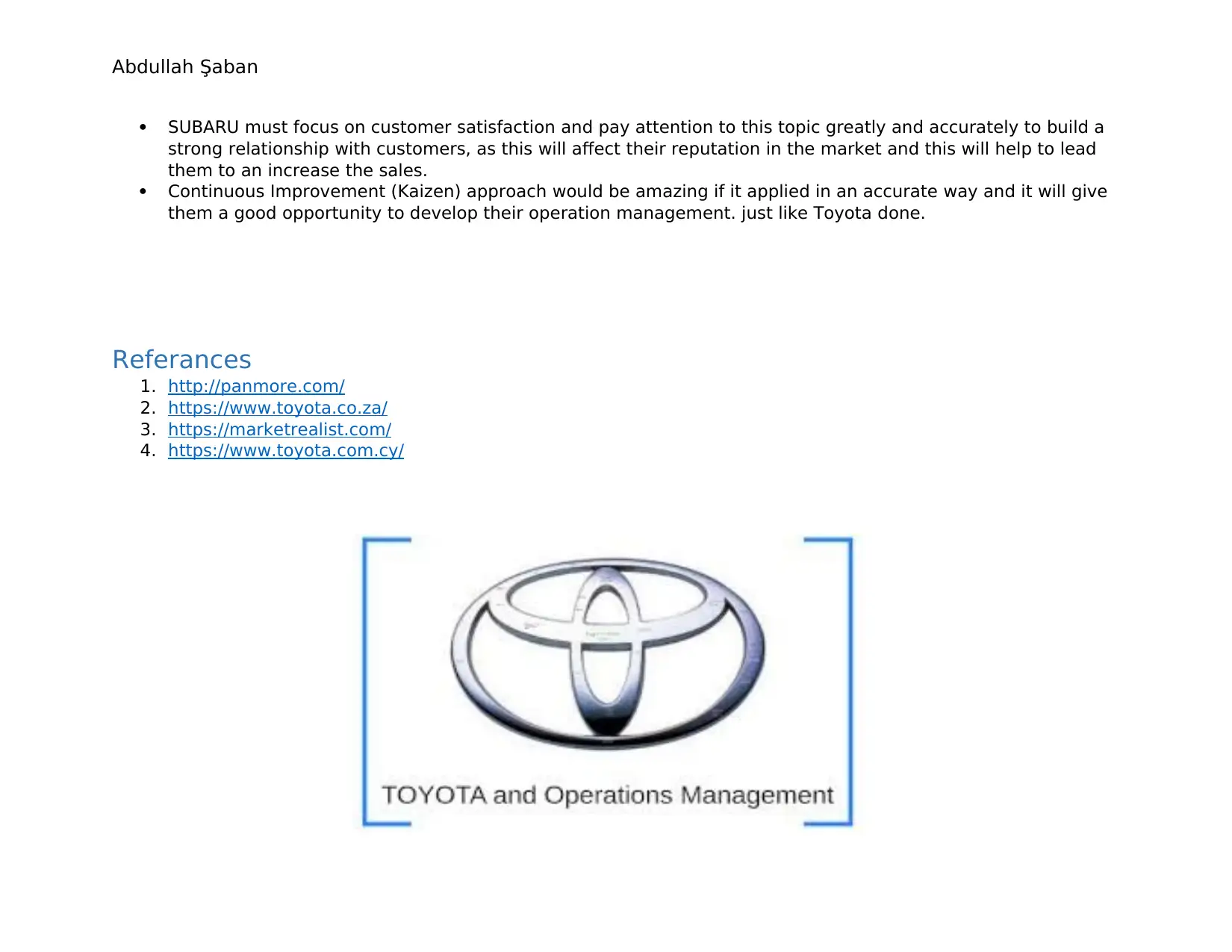
Abdullah Şaban
SUBARU must focus on customer satisfaction and pay attention to this topic greatly and accurately to build a
strong relationship with customers, as this will affect their reputation in the market and this will help to lead
them to an increase the sales.
Continuous Improvement (Kaizen) approach would be amazing if it applied in an accurate way and it will give
them a good opportunity to develop their operation management. just like Toyota done.
Referances
1. http://panmore.com/
2. https://www.toyota.co.za/
3. https://marketrealist.com/
4. https://www.toyota.com.cy/
SUBARU must focus on customer satisfaction and pay attention to this topic greatly and accurately to build a
strong relationship with customers, as this will affect their reputation in the market and this will help to lead
them to an increase the sales.
Continuous Improvement (Kaizen) approach would be amazing if it applied in an accurate way and it will give
them a good opportunity to develop their operation management. just like Toyota done.
Referances
1. http://panmore.com/
2. https://www.toyota.co.za/
3. https://marketrealist.com/
4. https://www.toyota.com.cy/
⊘ This is a preview!⊘
Do you want full access?
Subscribe today to unlock all pages.

Trusted by 1+ million students worldwide
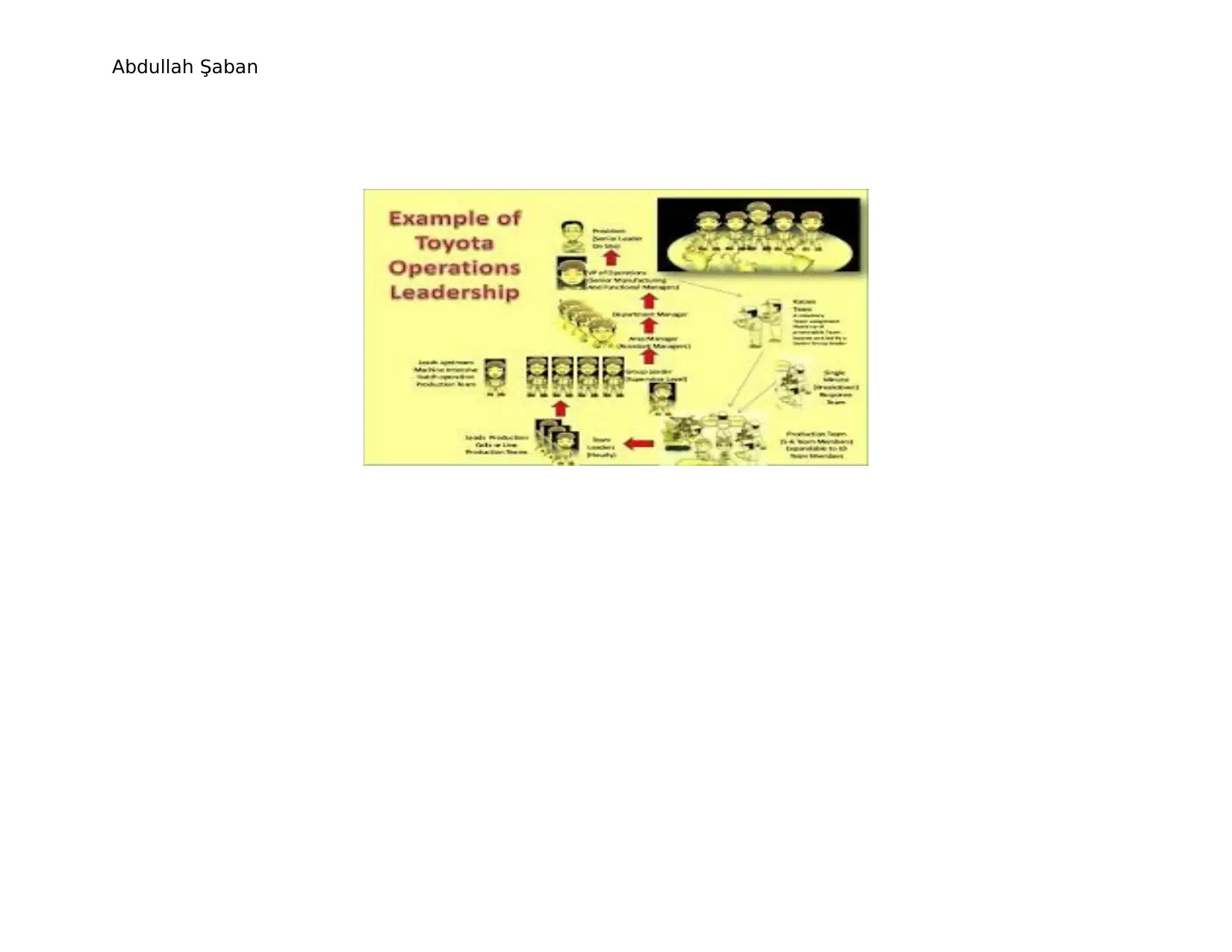
Abdullah Şaban
1 out of 10
Related Documents

Your All-in-One AI-Powered Toolkit for Academic Success.
+13062052269
info@desklib.com
Available 24*7 on WhatsApp / Email
Unlock your academic potential
© 2024 | Zucol Services PVT LTD | All rights reserved.