Remembering Joseph Juran And His Impact on Quality PDF
VerifiedAdded on 2022/01/19
|50
|8139
|48
AI Summary
Contribute Materials
Your contribution can guide someone’s learning journey. Share your
documents today.
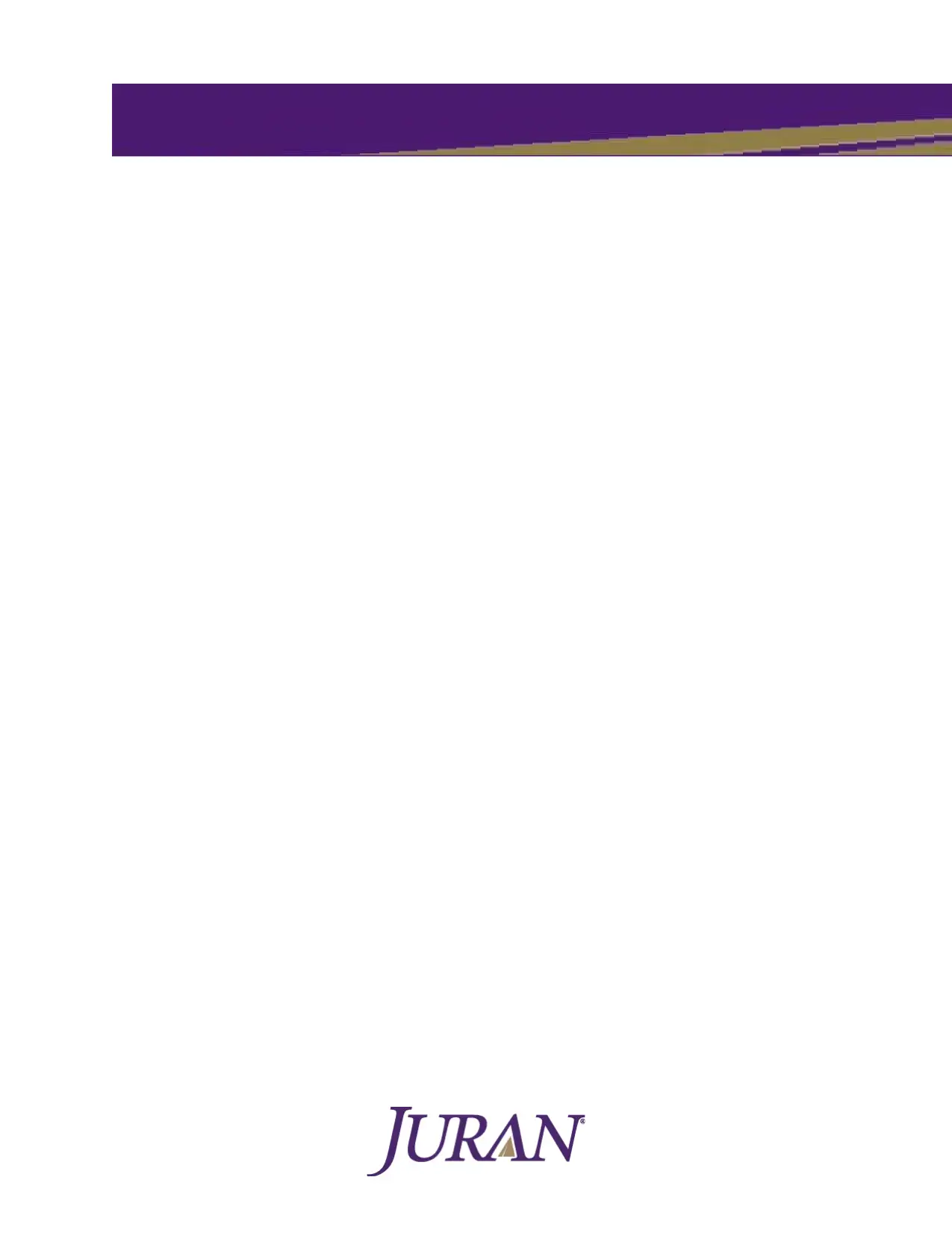
A DMAIC Six Sigma
Improvement Story
Improvement Story
Secure Best Marks with AI Grader
Need help grading? Try our AI Grader for instant feedback on your assignments.

About Juran Institute
Juran Institute is a benchmarking, consulting and training
firm founded in 1979 by Dr. Joseph M. Juran. Dr. Juran is
one of the most internationally recognized pioneers and
visionaries in attaining business results by managing
quality. By concentrating on clients' needs over the years,
Juran has offered professional consulting services and
developed training and education materials in a wide
variety of Operational Excellence methods and tools.
Juran offers best-in-class assessment, benchmarking,
consulting, and training services to implement your
operational excellence programs aimed at improving your
business results. Our services include assessment tools
that benchmark you against international best practices
and training programs to deploy operational excellence,
change management, and quality management.
Contact Juran Institute at info@juran.com
Inventory #6009
Juran Institute, Inc. holds the copyright for this material. Unless otherwise specified,
this book may not be copied, reproduced, or transmitted in any form or by any means,
electronic or otherwise, including but not limited to photocopying, recording,
digital transmission, or printing without written permission of Juran Institute, Inc.
Information from other sources, if included in this material, is used with
permission from the originator and is indicated as such. Juran Institute, Inc.
does not advocate exclusive use of any products used within this workshop.
Instructors have no proprietary interest in any materials used in this workshop.
Juran Institute is a benchmarking, consulting and training
firm founded in 1979 by Dr. Joseph M. Juran. Dr. Juran is
one of the most internationally recognized pioneers and
visionaries in attaining business results by managing
quality. By concentrating on clients' needs over the years,
Juran has offered professional consulting services and
developed training and education materials in a wide
variety of Operational Excellence methods and tools.
Juran offers best-in-class assessment, benchmarking,
consulting, and training services to implement your
operational excellence programs aimed at improving your
business results. Our services include assessment tools
that benchmark you against international best practices
and training programs to deploy operational excellence,
change management, and quality management.
Contact Juran Institute at info@juran.com
Inventory #6009
Juran Institute, Inc. holds the copyright for this material. Unless otherwise specified,
this book may not be copied, reproduced, or transmitted in any form or by any means,
electronic or otherwise, including but not limited to photocopying, recording,
digital transmission, or printing without written permission of Juran Institute, Inc.
Information from other sources, if included in this material, is used with
permission from the originator and is indicated as such. Juran Institute, Inc.
does not advocate exclusive use of any products used within this workshop.
Instructors have no proprietary interest in any materials used in this workshop.
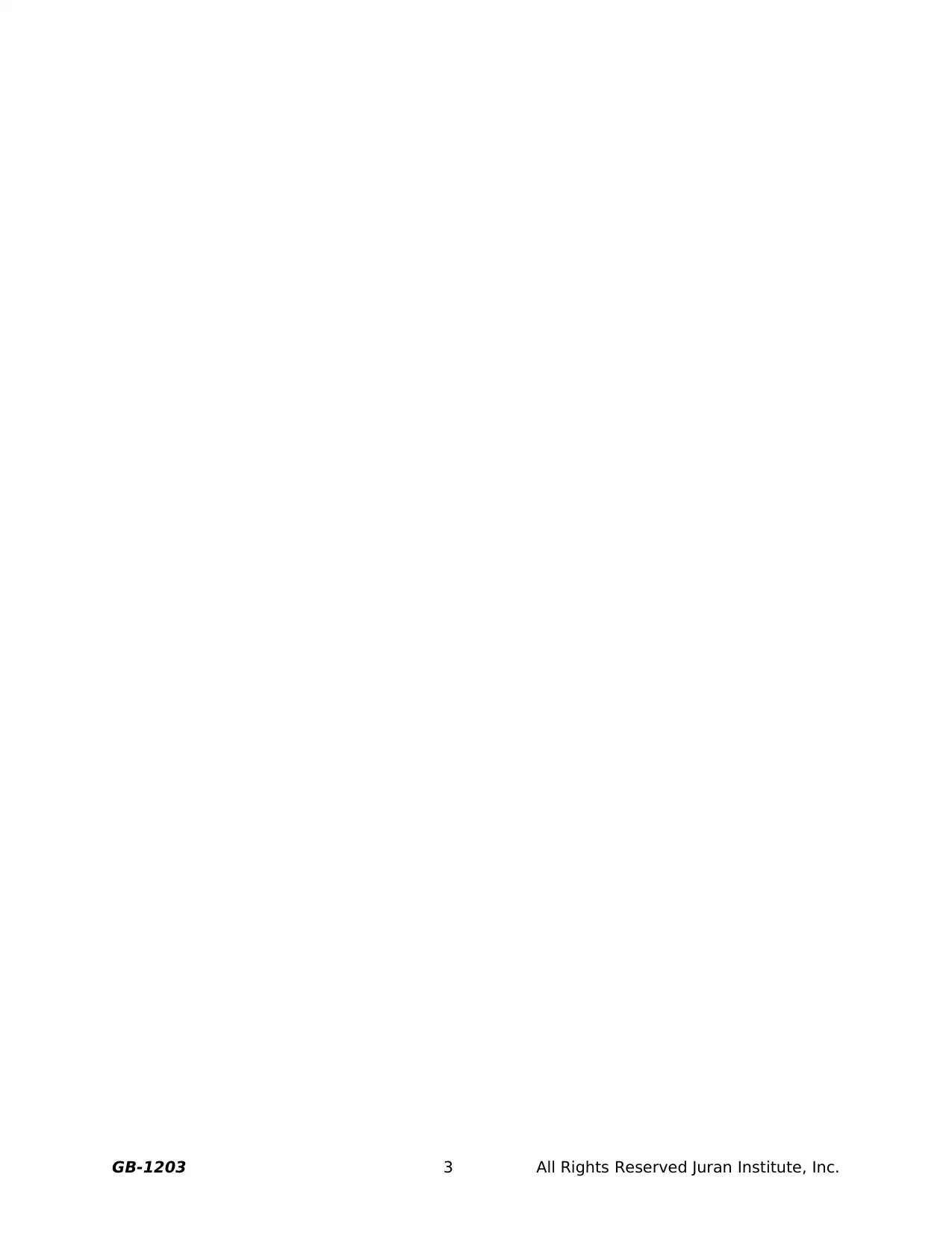
GB-1203 3 All Rights Reserved Juran Institute, Inc.
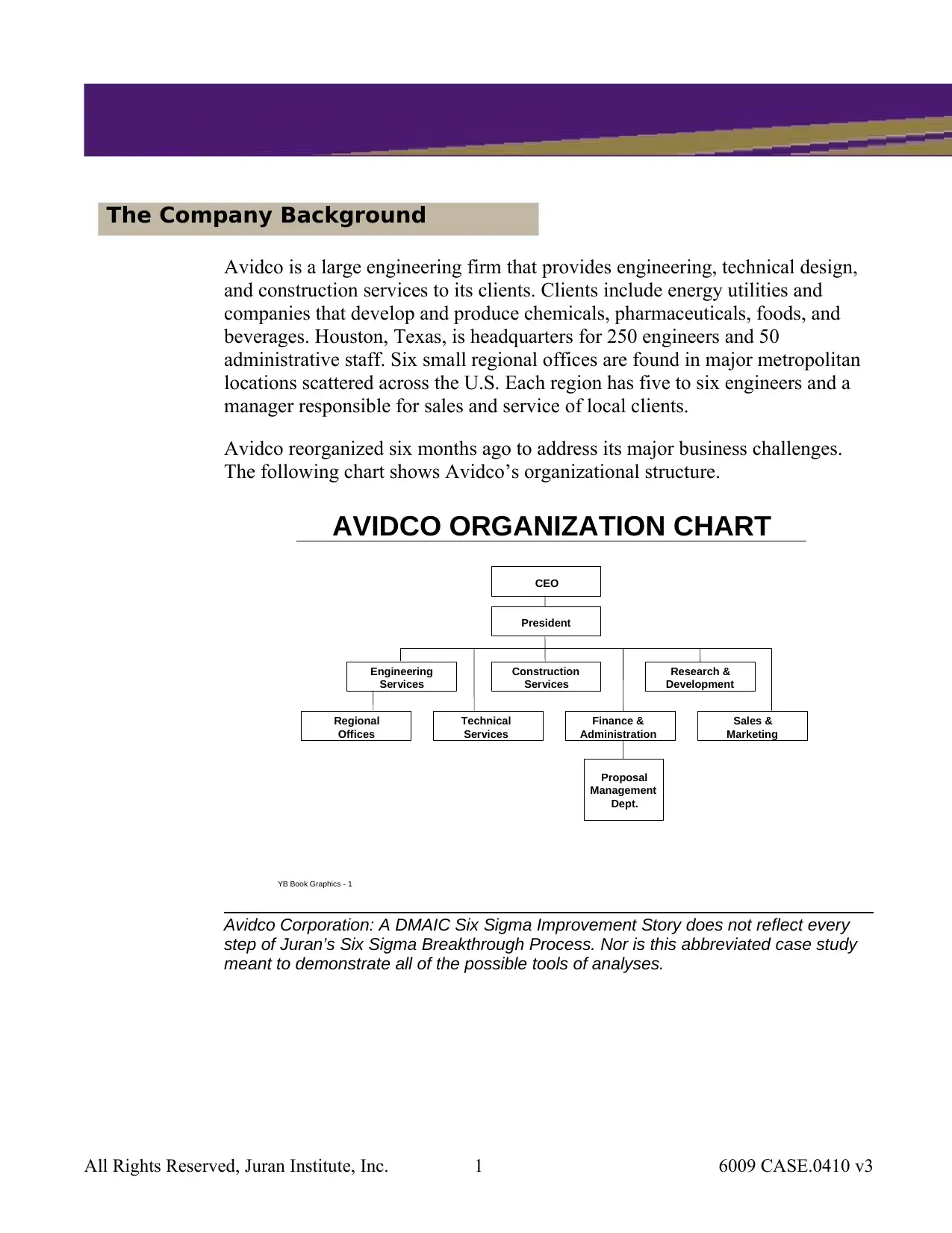
A DMAIC Six Sigma
Improvement Story
The Company Background
Avidco is a large engineering firm that provides engineering, technical design,
and construction services to its clients. Clients include energy utilities and
companies that develop and produce chemicals, pharmaceuticals, foods, and
beverages. Houston, Texas, is headquarters for 250 engineers and 50
administrative staff. Six small regional offices are found in major metropolitan
locations scattered across the U.S. Each region has five to six engineers and a
manager responsible for sales and service of local clients.
Avidco reorganized six months ago to address its major business challenges.
The following chart shows Avidco’s organizational structure.
YB Book Graphics - 1 All Rights Reserved, Juran Institute, Inc.
AVIDCO ORGANIZATION CHART
CEO
President
Engineering
Services
Construction
Services
Research &
Development
Regional
Offices
Technical
Services
Finance &
Administration
Sales &
Marketing
Proposal
Management
Dept.
Avidco Corporation: A DMAIC Six Sigma Improvement Story does not reflect every
step of Juran’s Six Sigma Breakthrough Process. Nor is this abbreviated case study
meant to demonstrate all of the possible tools of analyses.
All Rights Reserved, Juran Institute, Inc. 1 6009 CASE.0410 v3
Improvement Story
The Company Background
Avidco is a large engineering firm that provides engineering, technical design,
and construction services to its clients. Clients include energy utilities and
companies that develop and produce chemicals, pharmaceuticals, foods, and
beverages. Houston, Texas, is headquarters for 250 engineers and 50
administrative staff. Six small regional offices are found in major metropolitan
locations scattered across the U.S. Each region has five to six engineers and a
manager responsible for sales and service of local clients.
Avidco reorganized six months ago to address its major business challenges.
The following chart shows Avidco’s organizational structure.
YB Book Graphics - 1 All Rights Reserved, Juran Institute, Inc.
AVIDCO ORGANIZATION CHART
CEO
President
Engineering
Services
Construction
Services
Research &
Development
Regional
Offices
Technical
Services
Finance &
Administration
Sales &
Marketing
Proposal
Management
Dept.
Avidco Corporation: A DMAIC Six Sigma Improvement Story does not reflect every
step of Juran’s Six Sigma Breakthrough Process. Nor is this abbreviated case study
meant to demonstrate all of the possible tools of analyses.
All Rights Reserved, Juran Institute, Inc. 1 6009 CASE.0410 v3
Secure Best Marks with AI Grader
Need help grading? Try our AI Grader for instant feedback on your assignments.
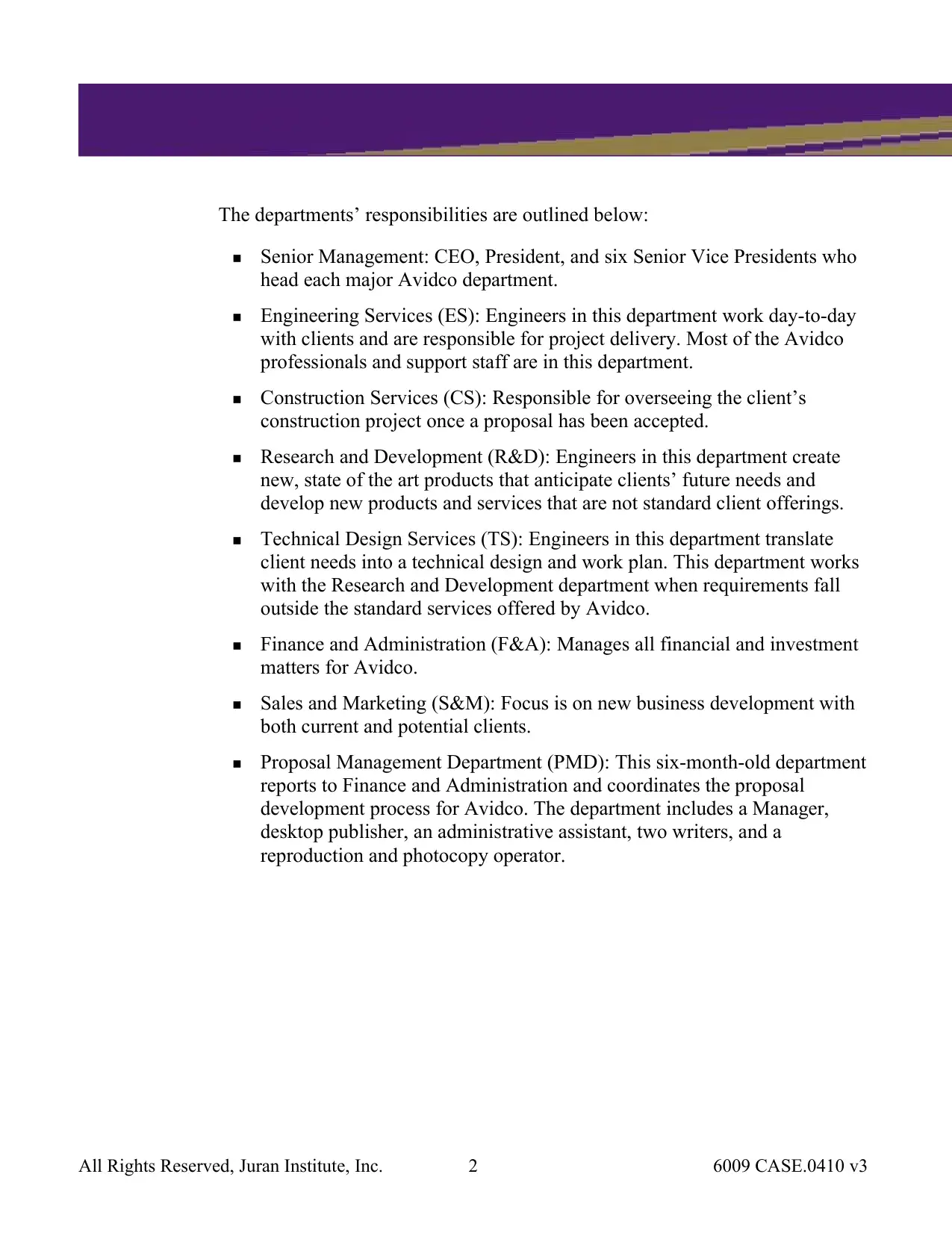
A DMAIC Six Sigma
Improvement Story
The departments’ responsibilities are outlined below:
Senior Management: CEO, President, and six Senior Vice Presidents who
head each major Avidco department.
Engineering Services (ES): Engineers in this department work day-to-day
with clients and are responsible for project delivery. Most of the Avidco
professionals and support staff are in this department.
Construction Services (CS): Responsible for overseeing the client’s
construction project once a proposal has been accepted.
Research and Development (R&D): Engineers in this department create
new, state of the art products that anticipate clients’ future needs and
develop new products and services that are not standard client offerings.
Technical Design Services (TS): Engineers in this department translate
client needs into a technical design and work plan. This department works
with the Research and Development department when requirements fall
outside the standard services offered by Avidco.
Finance and Administration (F&A): Manages all financial and investment
matters for Avidco.
Sales and Marketing (S&M): Focus is on new business development with
both current and potential clients.
Proposal Management Department (PMD): This six-month-old department
reports to Finance and Administration and coordinates the proposal
development process for Avidco. The department includes a Manager,
desktop publisher, an administrative assistant, two writers, and a
reproduction and photocopy operator.
All Rights Reserved, Juran Institute, Inc. 2 6009 CASE.0410 v3
Improvement Story
The departments’ responsibilities are outlined below:
Senior Management: CEO, President, and six Senior Vice Presidents who
head each major Avidco department.
Engineering Services (ES): Engineers in this department work day-to-day
with clients and are responsible for project delivery. Most of the Avidco
professionals and support staff are in this department.
Construction Services (CS): Responsible for overseeing the client’s
construction project once a proposal has been accepted.
Research and Development (R&D): Engineers in this department create
new, state of the art products that anticipate clients’ future needs and
develop new products and services that are not standard client offerings.
Technical Design Services (TS): Engineers in this department translate
client needs into a technical design and work plan. This department works
with the Research and Development department when requirements fall
outside the standard services offered by Avidco.
Finance and Administration (F&A): Manages all financial and investment
matters for Avidco.
Sales and Marketing (S&M): Focus is on new business development with
both current and potential clients.
Proposal Management Department (PMD): This six-month-old department
reports to Finance and Administration and coordinates the proposal
development process for Avidco. The department includes a Manager,
desktop publisher, an administrative assistant, two writers, and a
reproduction and photocopy operator.
All Rights Reserved, Juran Institute, Inc. 2 6009 CASE.0410 v3
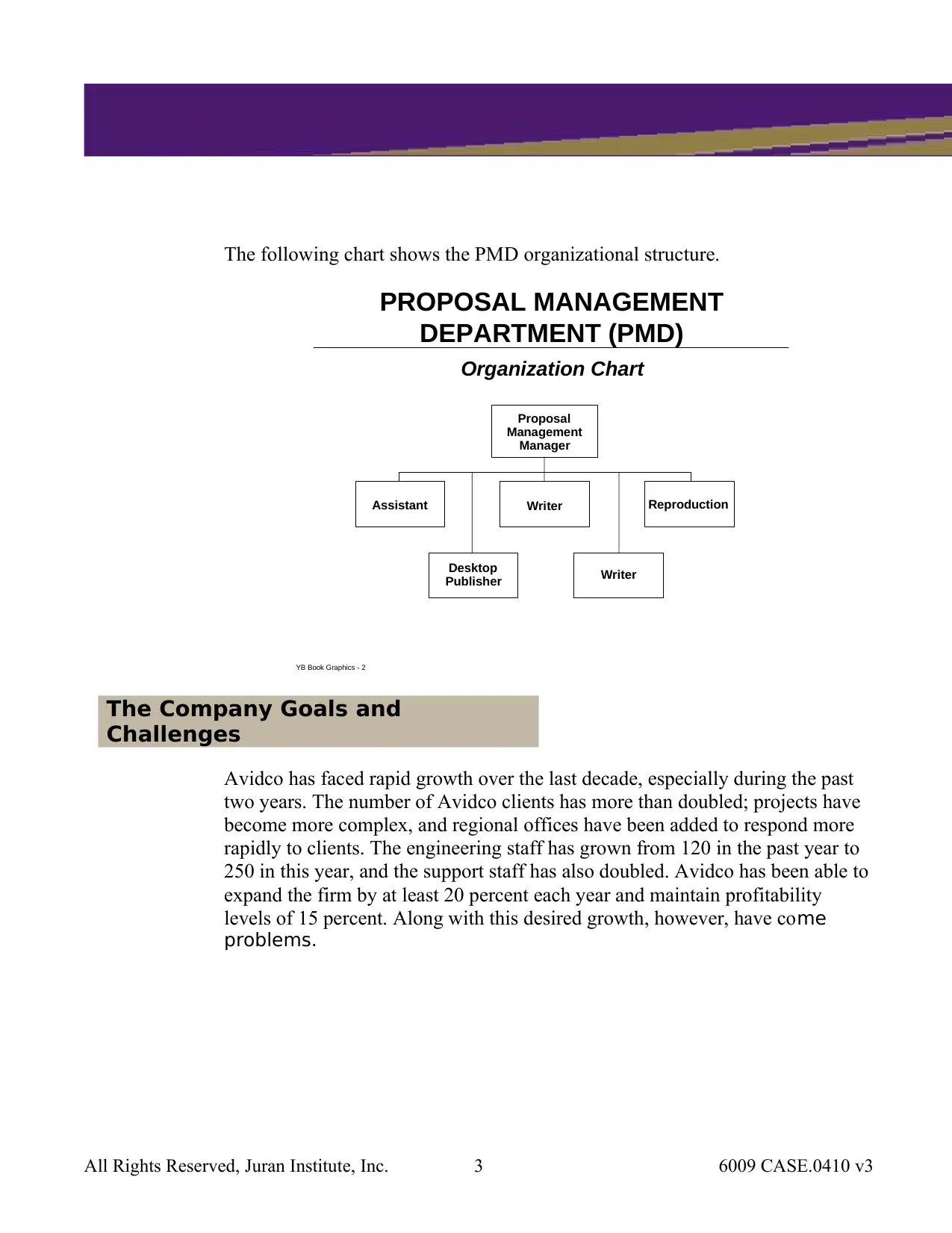
A DMAIC Six Sigma
Improvement Story
The following chart shows the PMD organizational structure.
YB Book Graphics - 2 All Rights Reserved, Juran Institute, Inc.
PROPOSAL MANAGEMENT
DEPARTMENT (PMD)
Organization Chart
Proposal
Management
Manager
Desktop
Publisher
ReproductionWriterAssistant
Writer
The Company Goals and
Challenges
Avidco has faced rapid growth over the last decade, especially during the past
two years. The number of Avidco clients has more than doubled; projects have
become more complex, and regional offices have been added to respond more
rapidly to clients. The engineering staff has grown from 120 in the past year to
250 in this year, and the support staff has also doubled. Avidco has been able to
expand the firm by at least 20 percent each year and maintain profitability
levels of 15 percent. Along with this desired growth, however, have come
problems.
All Rights Reserved, Juran Institute, Inc. 3 6009 CASE.0410 v3
Improvement Story
The following chart shows the PMD organizational structure.
YB Book Graphics - 2 All Rights Reserved, Juran Institute, Inc.
PROPOSAL MANAGEMENT
DEPARTMENT (PMD)
Organization Chart
Proposal
Management
Manager
Desktop
Publisher
ReproductionWriterAssistant
Writer
The Company Goals and
Challenges
Avidco has faced rapid growth over the last decade, especially during the past
two years. The number of Avidco clients has more than doubled; projects have
become more complex, and regional offices have been added to respond more
rapidly to clients. The engineering staff has grown from 120 in the past year to
250 in this year, and the support staff has also doubled. Avidco has been able to
expand the firm by at least 20 percent each year and maintain profitability
levels of 15 percent. Along with this desired growth, however, have come
problems.
All Rights Reserved, Juran Institute, Inc. 3 6009 CASE.0410 v3
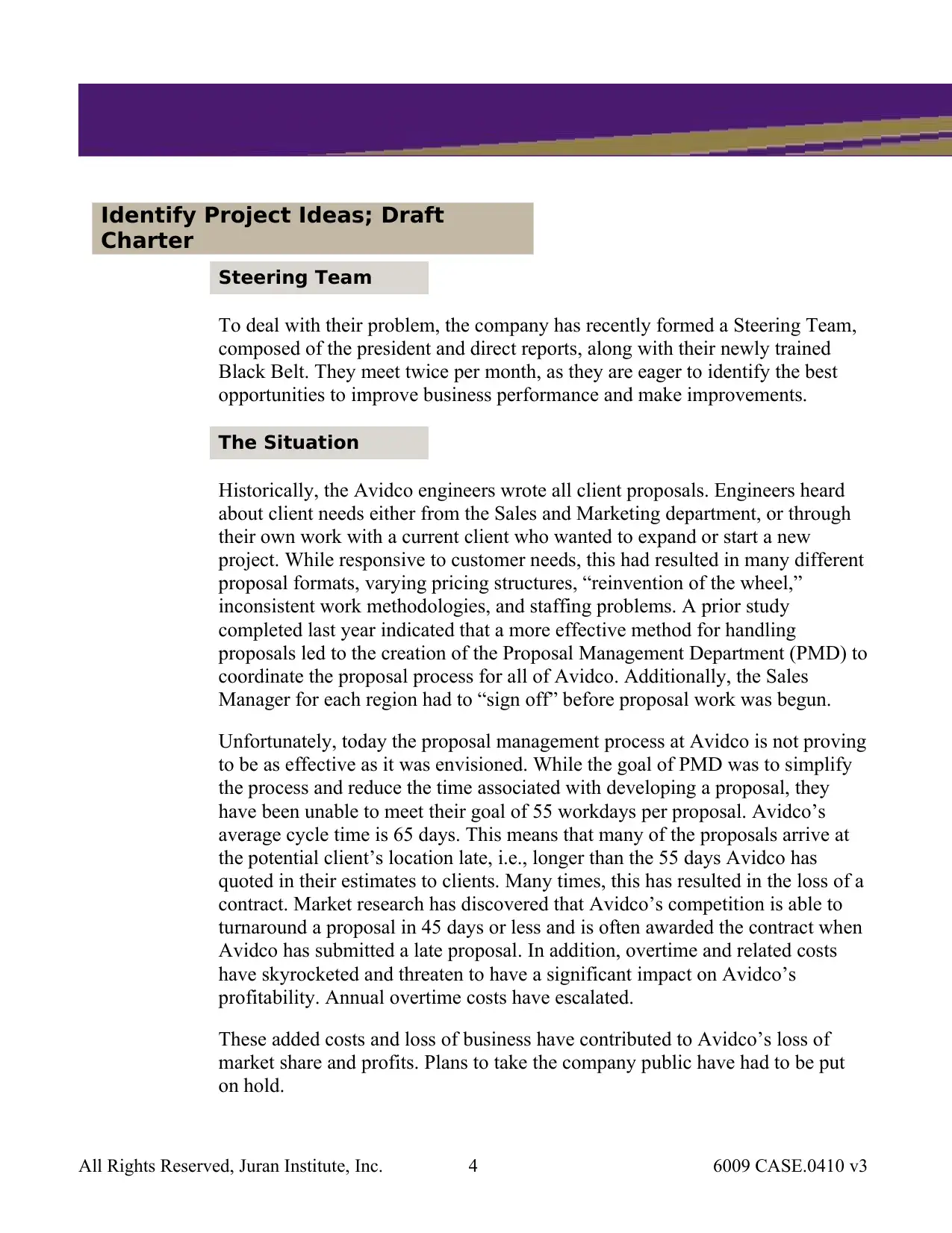
A DMAIC Six Sigma
Improvement Story
Identify Project Ideas; Draft
Charter
Steering Team
To deal with their problem, the company has recently formed a Steering Team,
composed of the president and direct reports, along with their newly trained
Black Belt. They meet twice per month, as they are eager to identify the best
opportunities to improve business performance and make improvements.
The Situation
Historically, the Avidco engineers wrote all client proposals. Engineers heard
about client needs either from the Sales and Marketing department, or through
their own work with a current client who wanted to expand or start a new
project. While responsive to customer needs, this had resulted in many different
proposal formats, varying pricing structures, “reinvention of the wheel,”
inconsistent work methodologies, and staffing problems. A prior study
completed last year indicated that a more effective method for handling
proposals led to the creation of the Proposal Management Department (PMD) to
coordinate the proposal process for all of Avidco. Additionally, the Sales
Manager for each region had to “sign off” before proposal work was begun.
Unfortunately, today the proposal management process at Avidco is not proving
to be as effective as it was envisioned. While the goal of PMD was to simplify
the process and reduce the time associated with developing a proposal, they
have been unable to meet their goal of 55 workdays per proposal. Avidco’s
average cycle time is 65 days. This means that many of the proposals arrive at
the potential client’s location late, i.e., longer than the 55 days Avidco has
quoted in their estimates to clients. Many times, this has resulted in the loss of a
contract. Market research has discovered that Avidco’s competition is able to
turnaround a proposal in 45 days or less and is often awarded the contract when
Avidco has submitted a late proposal. In addition, overtime and related costs
have skyrocketed and threaten to have a significant impact on Avidco’s
profitability. Annual overtime costs have escalated.
These added costs and loss of business have contributed to Avidco’s loss of
market share and profits. Plans to take the company public have had to be put
on hold.
All Rights Reserved, Juran Institute, Inc. 4 6009 CASE.0410 v3
Improvement Story
Identify Project Ideas; Draft
Charter
Steering Team
To deal with their problem, the company has recently formed a Steering Team,
composed of the president and direct reports, along with their newly trained
Black Belt. They meet twice per month, as they are eager to identify the best
opportunities to improve business performance and make improvements.
The Situation
Historically, the Avidco engineers wrote all client proposals. Engineers heard
about client needs either from the Sales and Marketing department, or through
their own work with a current client who wanted to expand or start a new
project. While responsive to customer needs, this had resulted in many different
proposal formats, varying pricing structures, “reinvention of the wheel,”
inconsistent work methodologies, and staffing problems. A prior study
completed last year indicated that a more effective method for handling
proposals led to the creation of the Proposal Management Department (PMD) to
coordinate the proposal process for all of Avidco. Additionally, the Sales
Manager for each region had to “sign off” before proposal work was begun.
Unfortunately, today the proposal management process at Avidco is not proving
to be as effective as it was envisioned. While the goal of PMD was to simplify
the process and reduce the time associated with developing a proposal, they
have been unable to meet their goal of 55 workdays per proposal. Avidco’s
average cycle time is 65 days. This means that many of the proposals arrive at
the potential client’s location late, i.e., longer than the 55 days Avidco has
quoted in their estimates to clients. Many times, this has resulted in the loss of a
contract. Market research has discovered that Avidco’s competition is able to
turnaround a proposal in 45 days or less and is often awarded the contract when
Avidco has submitted a late proposal. In addition, overtime and related costs
have skyrocketed and threaten to have a significant impact on Avidco’s
profitability. Annual overtime costs have escalated.
These added costs and loss of business have contributed to Avidco’s loss of
market share and profits. Plans to take the company public have had to be put
on hold.
All Rights Reserved, Juran Institute, Inc. 4 6009 CASE.0410 v3
Paraphrase This Document
Need a fresh take? Get an instant paraphrase of this document with our AI Paraphraser
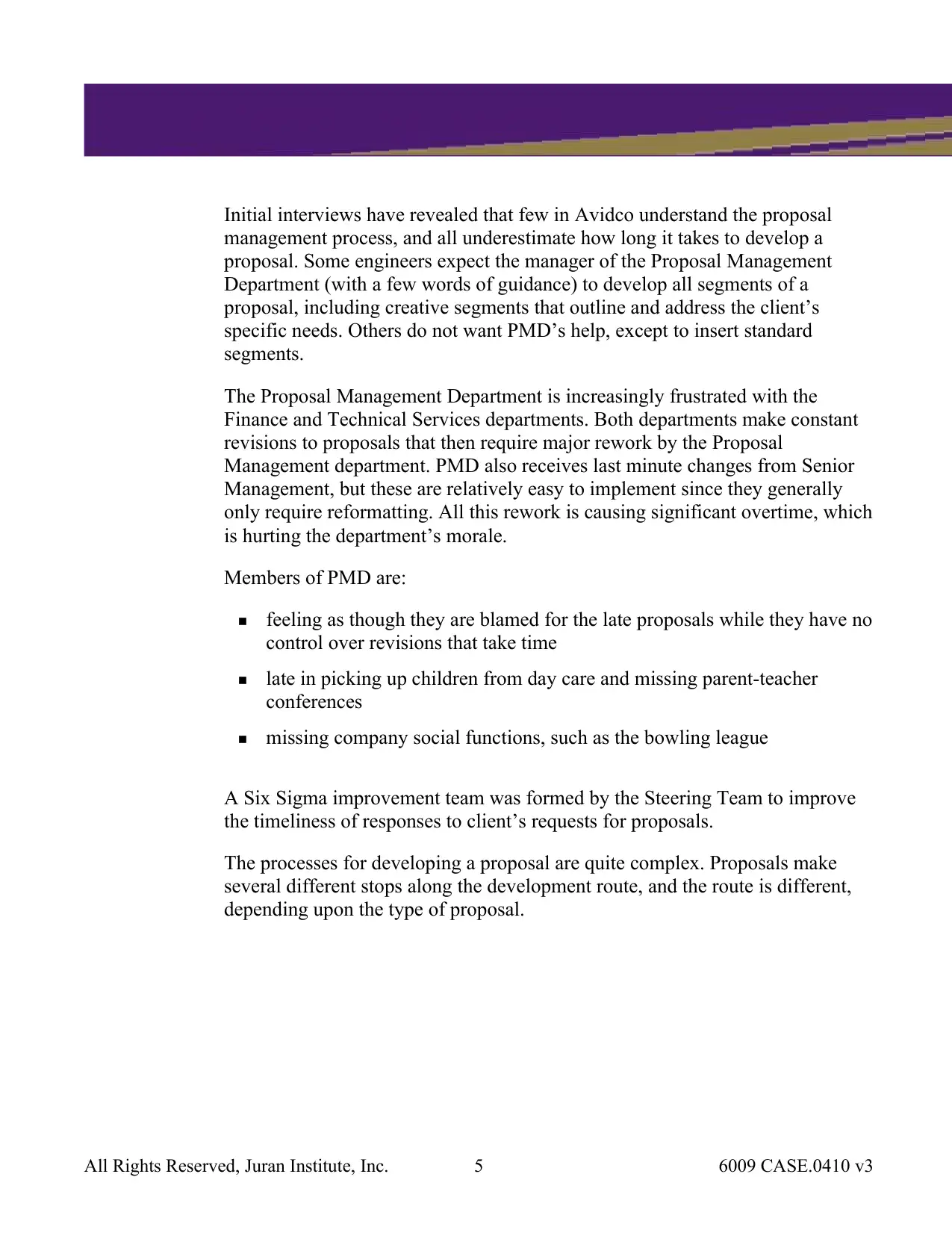
A DMAIC Six Sigma
Improvement Story
Initial interviews have revealed that few in Avidco understand the proposal
management process, and all underestimate how long it takes to develop a
proposal. Some engineers expect the manager of the Proposal Management
Department (with a few words of guidance) to develop all segments of a
proposal, including creative segments that outline and address the client’s
specific needs. Others do not want PMD’s help, except to insert standard
segments.
The Proposal Management Department is increasingly frustrated with the
Finance and Technical Services departments. Both departments make constant
revisions to proposals that then require major rework by the Proposal
Management department. PMD also receives last minute changes from Senior
Management, but these are relatively easy to implement since they generally
only require reformatting. All this rework is causing significant overtime, which
is hurting the department’s morale.
Members of PMD are:
feeling as though they are blamed for the late proposals while they have no
control over revisions that take time
late in picking up children from day care and missing parent-teacher
conferences
missing company social functions, such as the bowling league
A Six Sigma improvement team was formed by the Steering Team to improve
the timeliness of responses to client’s requests for proposals.
The processes for developing a proposal are quite complex. Proposals make
several different stops along the development route, and the route is different,
depending upon the type of proposal.
All Rights Reserved, Juran Institute, Inc. 5 6009 CASE.0410 v3
Improvement Story
Initial interviews have revealed that few in Avidco understand the proposal
management process, and all underestimate how long it takes to develop a
proposal. Some engineers expect the manager of the Proposal Management
Department (with a few words of guidance) to develop all segments of a
proposal, including creative segments that outline and address the client’s
specific needs. Others do not want PMD’s help, except to insert standard
segments.
The Proposal Management Department is increasingly frustrated with the
Finance and Technical Services departments. Both departments make constant
revisions to proposals that then require major rework by the Proposal
Management department. PMD also receives last minute changes from Senior
Management, but these are relatively easy to implement since they generally
only require reformatting. All this rework is causing significant overtime, which
is hurting the department’s morale.
Members of PMD are:
feeling as though they are blamed for the late proposals while they have no
control over revisions that take time
late in picking up children from day care and missing parent-teacher
conferences
missing company social functions, such as the bowling league
A Six Sigma improvement team was formed by the Steering Team to improve
the timeliness of responses to client’s requests for proposals.
The processes for developing a proposal are quite complex. Proposals make
several different stops along the development route, and the route is different,
depending upon the type of proposal.
All Rights Reserved, Juran Institute, Inc. 5 6009 CASE.0410 v3
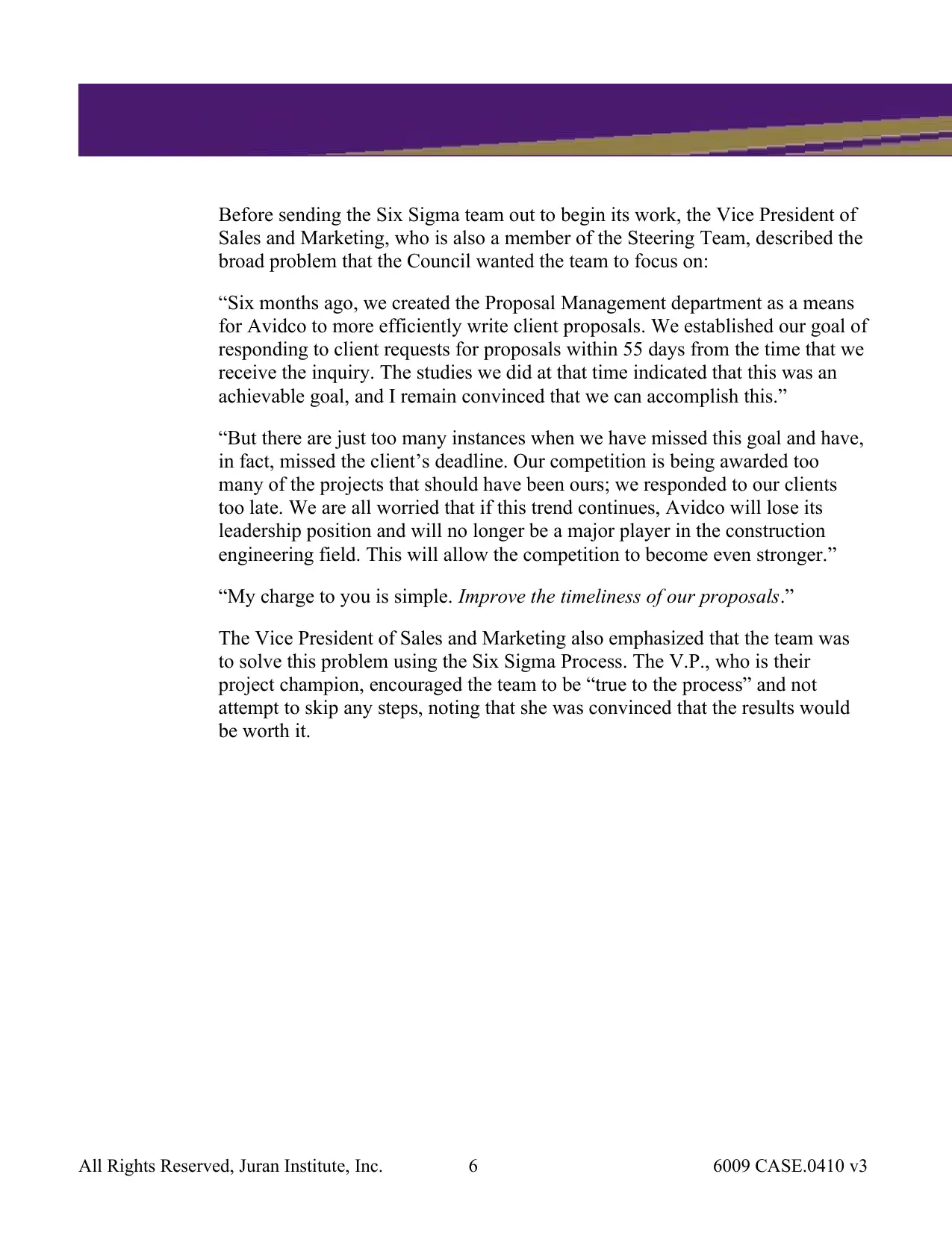
A DMAIC Six Sigma
Improvement Story
Before sending the Six Sigma team out to begin its work, the Vice President of
Sales and Marketing, who is also a member of the Steering Team, described the
broad problem that the Council wanted the team to focus on:
“Six months ago, we created the Proposal Management department as a means
for Avidco to more efficiently write client proposals. We established our goal of
responding to client requests for proposals within 55 days from the time that we
receive the inquiry. The studies we did at that time indicated that this was an
achievable goal, and I remain convinced that we can accomplish this.”
“But there are just too many instances when we have missed this goal and have,
in fact, missed the client’s deadline. Our competition is being awarded too
many of the projects that should have been ours; we responded to our clients
too late. We are all worried that if this trend continues, Avidco will lose its
leadership position and will no longer be a major player in the construction
engineering field. This will allow the competition to become even stronger.”
“My charge to you is simple. Improve the timeliness of our proposals.”
The Vice President of Sales and Marketing also emphasized that the team was
to solve this problem using the Six Sigma Process. The V.P., who is their
project champion, encouraged the team to be “true to the process” and not
attempt to skip any steps, noting that she was convinced that the results would
be worth it.
All Rights Reserved, Juran Institute, Inc. 6 6009 CASE.0410 v3
Improvement Story
Before sending the Six Sigma team out to begin its work, the Vice President of
Sales and Marketing, who is also a member of the Steering Team, described the
broad problem that the Council wanted the team to focus on:
“Six months ago, we created the Proposal Management department as a means
for Avidco to more efficiently write client proposals. We established our goal of
responding to client requests for proposals within 55 days from the time that we
receive the inquiry. The studies we did at that time indicated that this was an
achievable goal, and I remain convinced that we can accomplish this.”
“But there are just too many instances when we have missed this goal and have,
in fact, missed the client’s deadline. Our competition is being awarded too
many of the projects that should have been ours; we responded to our clients
too late. We are all worried that if this trend continues, Avidco will lose its
leadership position and will no longer be a major player in the construction
engineering field. This will allow the competition to become even stronger.”
“My charge to you is simple. Improve the timeliness of our proposals.”
The Vice President of Sales and Marketing also emphasized that the team was
to solve this problem using the Six Sigma Process. The V.P., who is their
project champion, encouraged the team to be “true to the process” and not
attempt to skip any steps, noting that she was convinced that the results would
be worth it.
All Rights Reserved, Juran Institute, Inc. 6 6009 CASE.0410 v3
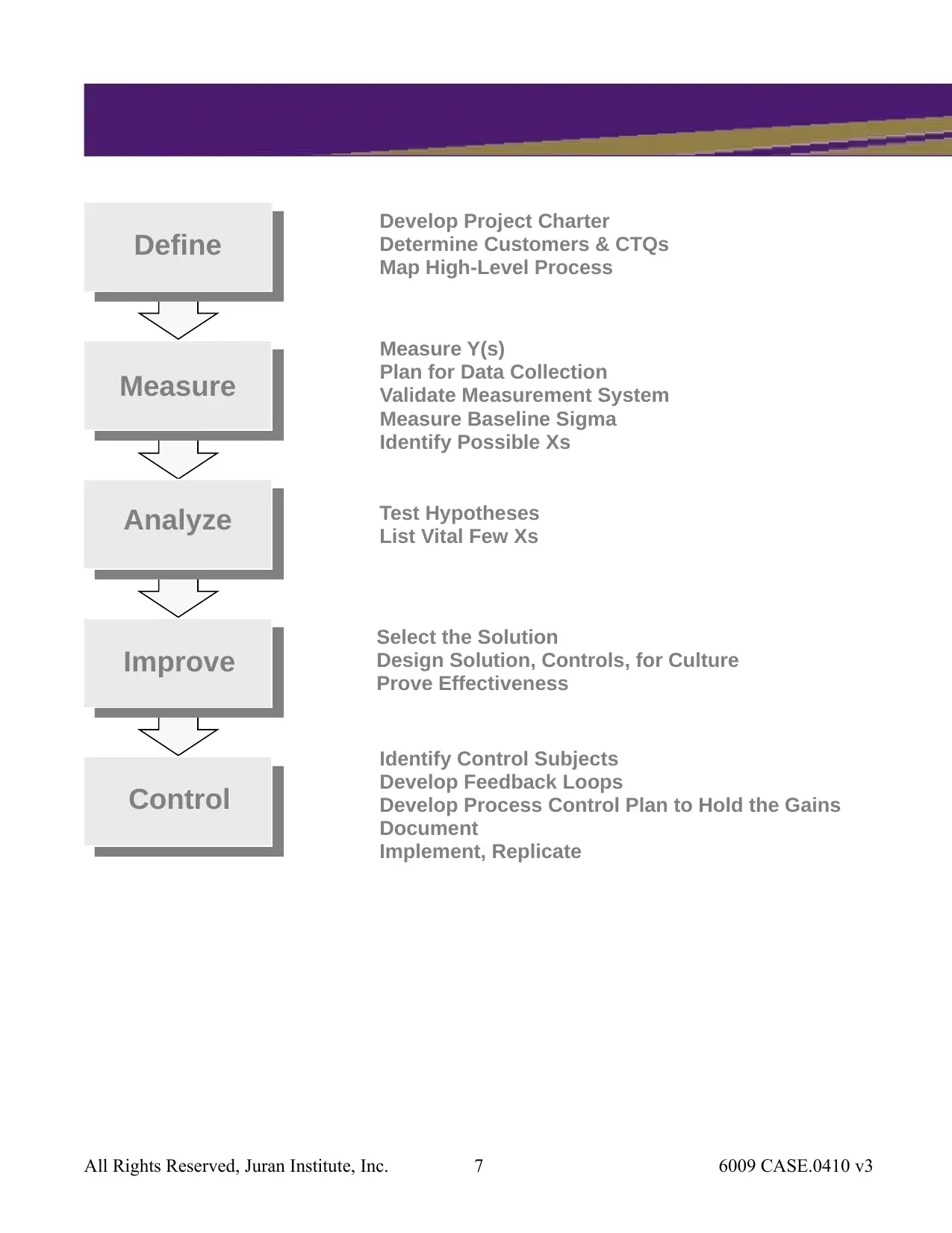
A DMAIC Six Sigma
Improvement Story
All Rights Reserved, Juran Institute, Inc. 7 6009 CASE.0410 v3
Test Hypotheses
List Vital Few Xs
Identify Control Subjects
Develop Feedback Loops
Develop Process Control Plan to Hold the Gains
Document
Implement, Replicate
Select the Solution
Design Solution, Controls, for Culture
Prove Effectiveness
Develop Project Charter
Determine Customers & CTQs
Map High-Level Process
Control
Improve
Analyze
Measure
Define
Measure Y(s)
Plan for Data Collection
Validate Measurement System
Measure Baseline Sigma
Identify Possible Xs
Improvement Story
All Rights Reserved, Juran Institute, Inc. 7 6009 CASE.0410 v3
Test Hypotheses
List Vital Few Xs
Identify Control Subjects
Develop Feedback Loops
Develop Process Control Plan to Hold the Gains
Document
Implement, Replicate
Select the Solution
Design Solution, Controls, for Culture
Prove Effectiveness
Develop Project Charter
Determine Customers & CTQs
Map High-Level Process
Control
Improve
Analyze
Measure
Define
Measure Y(s)
Plan for Data Collection
Validate Measurement System
Measure Baseline Sigma
Identify Possible Xs
Secure Best Marks with AI Grader
Need help grading? Try our AI Grader for instant feedback on your assignments.
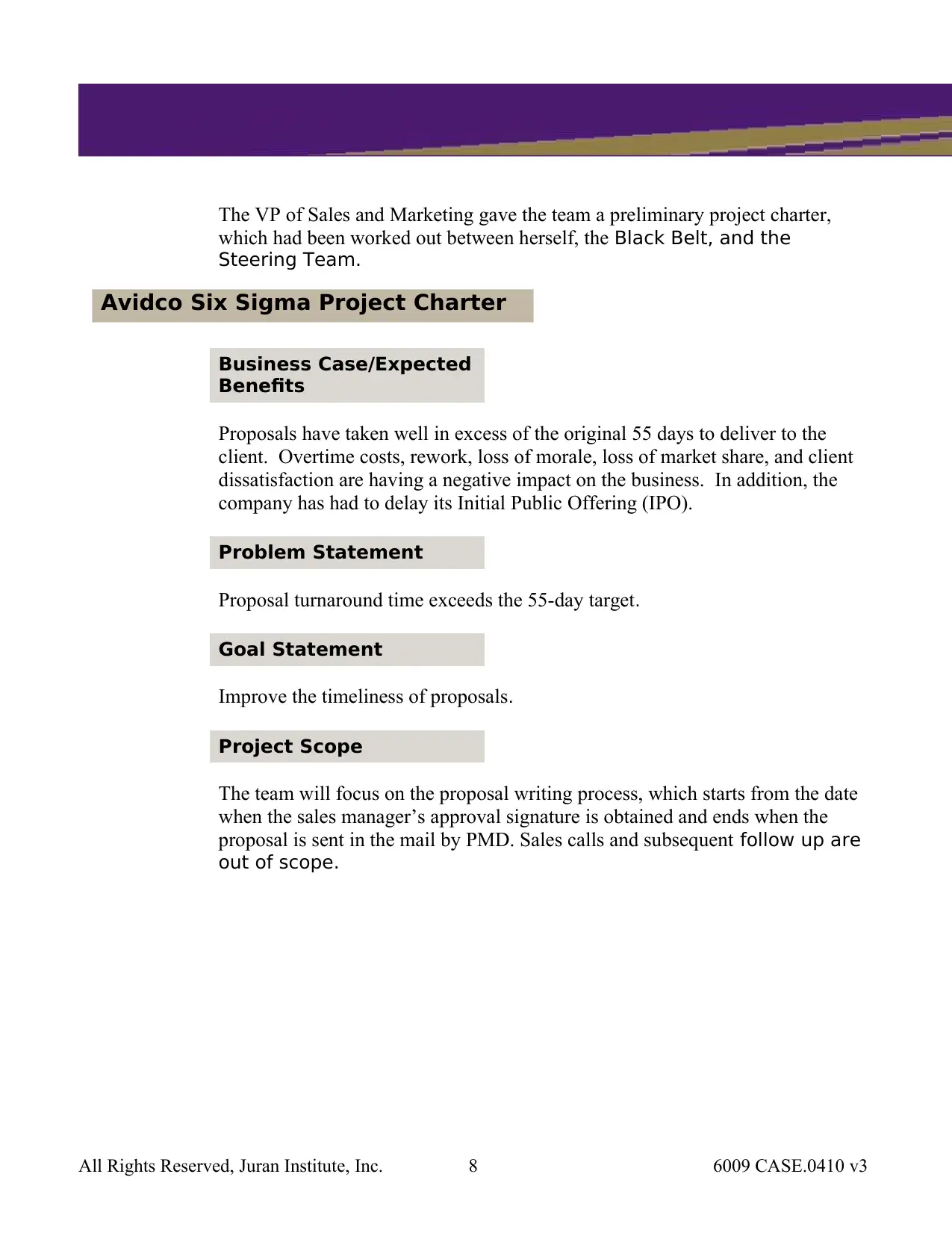
A DMAIC Six Sigma
Improvement Story
The VP of Sales and Marketing gave the team a preliminary project charter,
which had been worked out between herself, the Black Belt, and the
Steering Team.
Avidco Six Sigma Project Charter
Business Case/Expected
Benefits
Proposals have taken well in excess of the original 55 days to deliver to the
client. Overtime costs, rework, loss of morale, loss of market share, and client
dissatisfaction are having a negative impact on the business. In addition, the
company has had to delay its Initial Public Offering (IPO).
Problem Statement
Proposal turnaround time exceeds the 55-day target.
Goal Statement
Improve the timeliness of proposals.
Project Scope
The team will focus on the proposal writing process, which starts from the date
when the sales manager’s approval signature is obtained and ends when the
proposal is sent in the mail by PMD. Sales calls and subsequent follow up are
out of scope.
All Rights Reserved, Juran Institute, Inc. 8 6009 CASE.0410 v3
Improvement Story
The VP of Sales and Marketing gave the team a preliminary project charter,
which had been worked out between herself, the Black Belt, and the
Steering Team.
Avidco Six Sigma Project Charter
Business Case/Expected
Benefits
Proposals have taken well in excess of the original 55 days to deliver to the
client. Overtime costs, rework, loss of morale, loss of market share, and client
dissatisfaction are having a negative impact on the business. In addition, the
company has had to delay its Initial Public Offering (IPO).
Problem Statement
Proposal turnaround time exceeds the 55-day target.
Goal Statement
Improve the timeliness of proposals.
Project Scope
The team will focus on the proposal writing process, which starts from the date
when the sales manager’s approval signature is obtained and ends when the
proposal is sent in the mail by PMD. Sales calls and subsequent follow up are
out of scope.
All Rights Reserved, Juran Institute, Inc. 8 6009 CASE.0410 v3
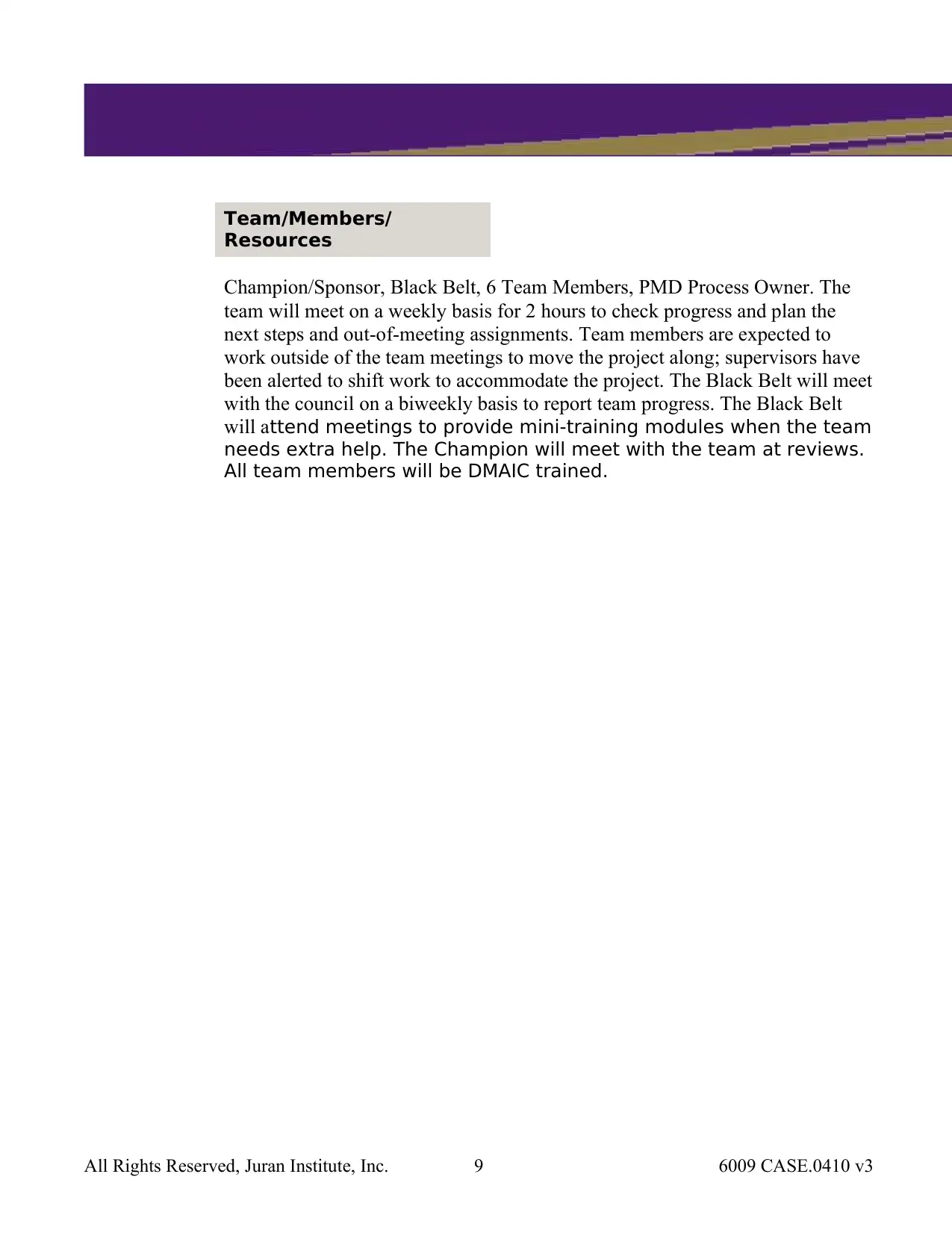
A DMAIC Six Sigma
Improvement Story
Team/Members/
Resources
Champion/Sponsor, Black Belt, 6 Team Members, PMD Process Owner. The
team will meet on a weekly basis for 2 hours to check progress and plan the
next steps and out-of-meeting assignments. Team members are expected to
work outside of the team meetings to move the project along; supervisors have
been alerted to shift work to accommodate the project. The Black Belt will meet
with the council on a biweekly basis to report team progress. The Black Belt
will attend meetings to provide mini-training modules when the team
needs extra help. The Champion will meet with the team at reviews.
All team members will be DMAIC trained.
All Rights Reserved, Juran Institute, Inc. 9 6009 CASE.0410 v3
Improvement Story
Team/Members/
Resources
Champion/Sponsor, Black Belt, 6 Team Members, PMD Process Owner. The
team will meet on a weekly basis for 2 hours to check progress and plan the
next steps and out-of-meeting assignments. Team members are expected to
work outside of the team meetings to move the project along; supervisors have
been alerted to shift work to accommodate the project. The Black Belt will meet
with the council on a biweekly basis to report team progress. The Black Belt
will attend meetings to provide mini-training modules when the team
needs extra help. The Champion will meet with the team at reviews.
All team members will be DMAIC trained.
All Rights Reserved, Juran Institute, Inc. 9 6009 CASE.0410 v3
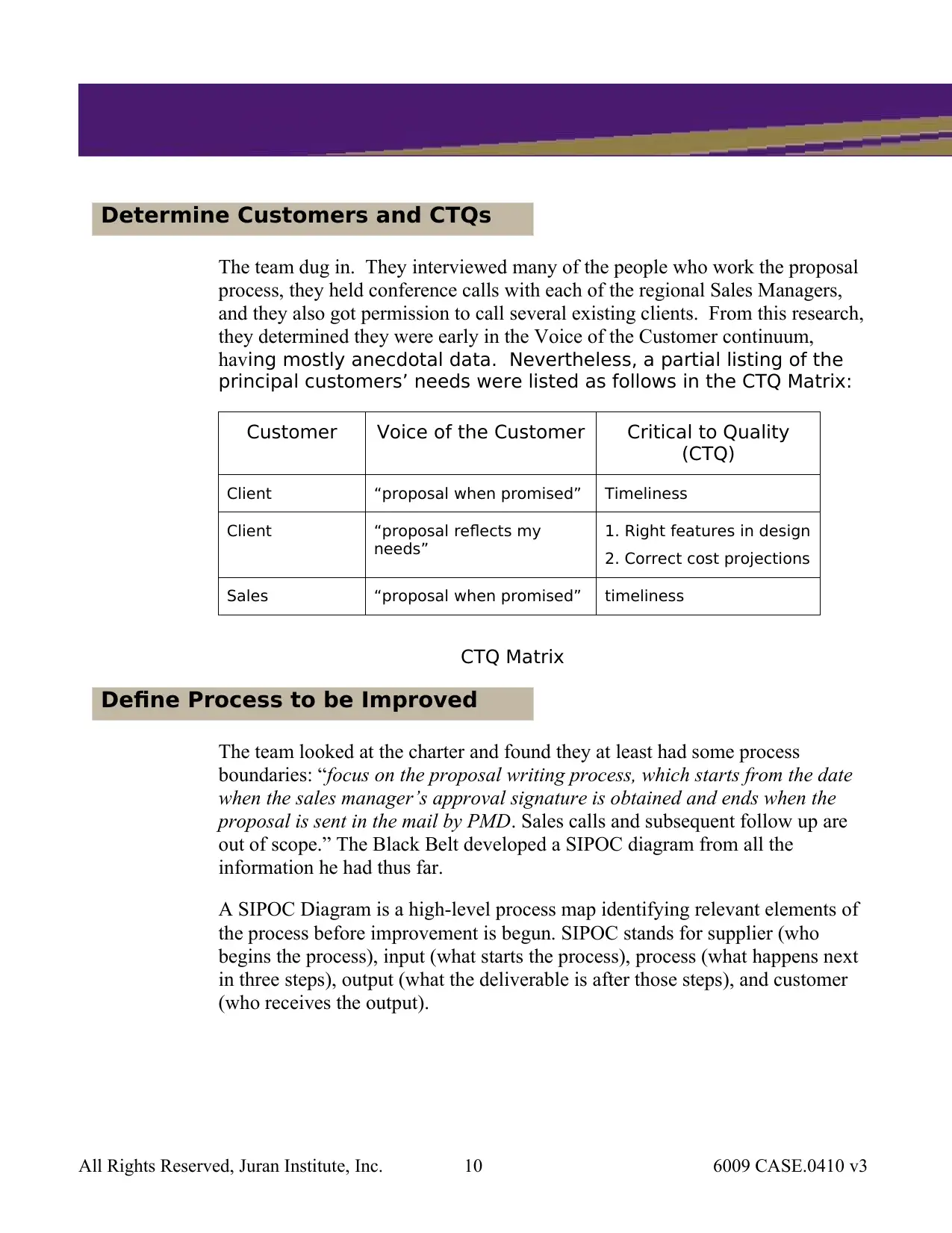
A DMAIC Six Sigma
Improvement Story
Determine Customers and CTQs
The team dug in. They interviewed many of the people who work the proposal
process, they held conference calls with each of the regional Sales Managers,
and they also got permission to call several existing clients. From this research,
they determined they were early in the Voice of the Customer continuum,
having mostly anecdotal data. Nevertheless, a partial listing of the
principal customers’ needs were listed as follows in the CTQ Matrix:
Customer Voice of the Customer Critical to Quality
(CTQ)
Client “proposal when promised” Timeliness
Client “proposal reflects my
needs”
1. Right features in design
2. Correct cost projections
Sales “proposal when promised” timeliness
CTQ Matrix
Define Process to be Improved
The team looked at the charter and found they at least had some process
boundaries: “focus on the proposal writing process, which starts from the date
when the sales manager’s approval signature is obtained and ends when the
proposal is sent in the mail by PMD. Sales calls and subsequent follow up are
out of scope.” The Black Belt developed a SIPOC diagram from all the
information he had thus far.
A SIPOC Diagram is a high-level process map identifying relevant elements of
the process before improvement is begun. SIPOC stands for supplier (who
begins the process), input (what starts the process), process (what happens next
in three steps), output (what the deliverable is after those steps), and customer
(who receives the output).
All Rights Reserved, Juran Institute, Inc. 10 6009 CASE.0410 v3
Improvement Story
Determine Customers and CTQs
The team dug in. They interviewed many of the people who work the proposal
process, they held conference calls with each of the regional Sales Managers,
and they also got permission to call several existing clients. From this research,
they determined they were early in the Voice of the Customer continuum,
having mostly anecdotal data. Nevertheless, a partial listing of the
principal customers’ needs were listed as follows in the CTQ Matrix:
Customer Voice of the Customer Critical to Quality
(CTQ)
Client “proposal when promised” Timeliness
Client “proposal reflects my
needs”
1. Right features in design
2. Correct cost projections
Sales “proposal when promised” timeliness
CTQ Matrix
Define Process to be Improved
The team looked at the charter and found they at least had some process
boundaries: “focus on the proposal writing process, which starts from the date
when the sales manager’s approval signature is obtained and ends when the
proposal is sent in the mail by PMD. Sales calls and subsequent follow up are
out of scope.” The Black Belt developed a SIPOC diagram from all the
information he had thus far.
A SIPOC Diagram is a high-level process map identifying relevant elements of
the process before improvement is begun. SIPOC stands for supplier (who
begins the process), input (what starts the process), process (what happens next
in three steps), output (what the deliverable is after those steps), and customer
(who receives the output).
All Rights Reserved, Juran Institute, Inc. 10 6009 CASE.0410 v3
Paraphrase This Document
Need a fresh take? Get an instant paraphrase of this document with our AI Paraphraser
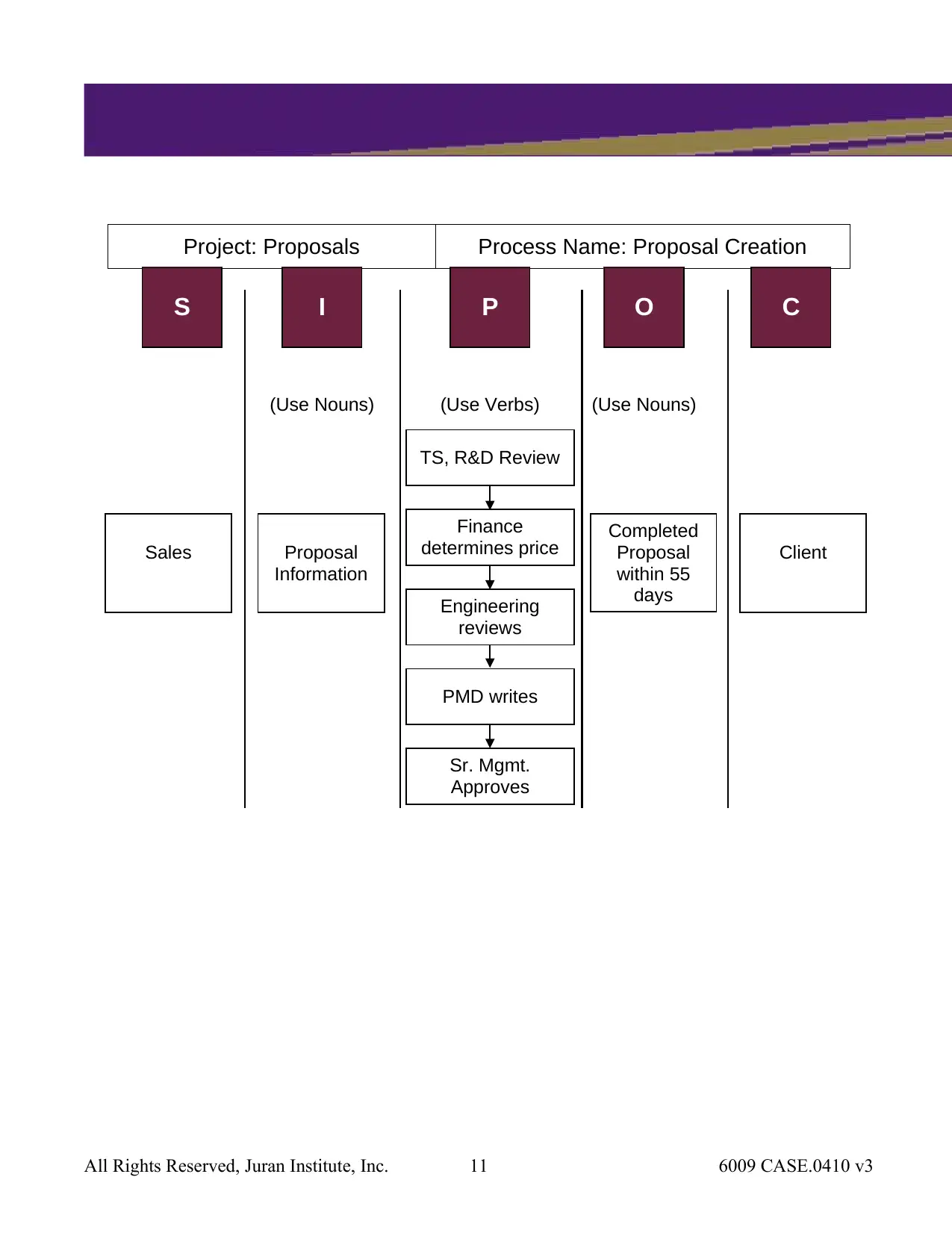
A DMAIC Six Sigma
Improvement Story
Project: Proposals Process Name: Proposal Creation
All Rights Reserved, Juran Institute, Inc. 11 6009 CASE.0410 v3
S I P O C
Sales
(Use Nouns)
TS, R&D Review
(Use Verbs)
Sr. Mgmt.
Approves
PMD writes
Engineering
reviews
Finance
determines price Completed
Proposal
within 55
days
Client
(Use Nouns)
Proposal
Information
Improvement Story
Project: Proposals Process Name: Proposal Creation
All Rights Reserved, Juran Institute, Inc. 11 6009 CASE.0410 v3
S I P O C
Sales
(Use Nouns)
TS, R&D Review
(Use Verbs)
Sr. Mgmt.
Approves
PMD writes
Engineering
reviews
Finance
determines price Completed
Proposal
within 55
days
Client
(Use Nouns)
Proposal
Information
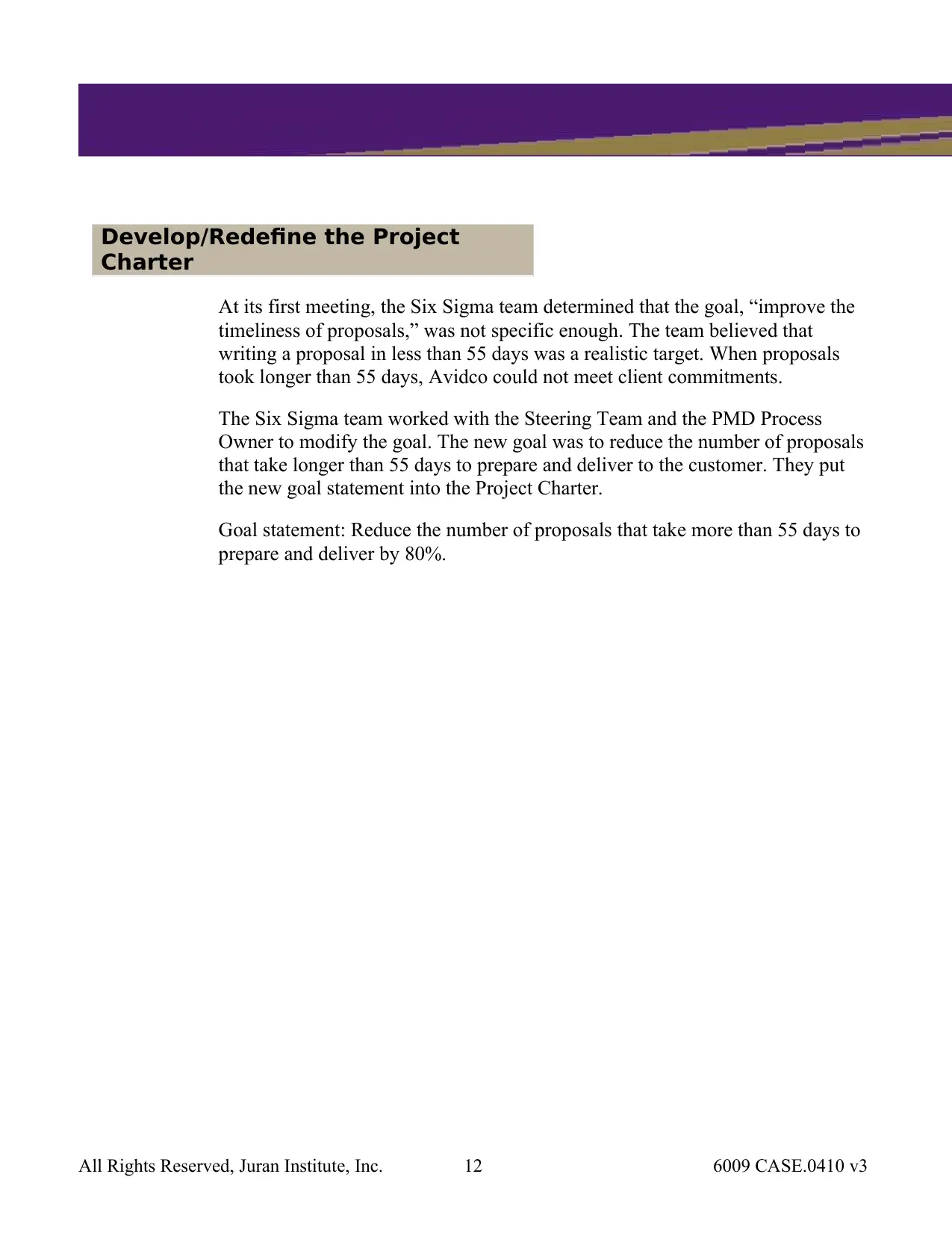
A DMAIC Six Sigma
Improvement Story
Develop/Redefine the Project
Charter
At its first meeting, the Six Sigma team determined that the goal, “improve the
timeliness of proposals,” was not specific enough. The team believed that
writing a proposal in less than 55 days was a realistic target. When proposals
took longer than 55 days, Avidco could not meet client commitments.
The Six Sigma team worked with the Steering Team and the PMD Process
Owner to modify the goal. The new goal was to reduce the number of proposals
that take longer than 55 days to prepare and deliver to the customer. They put
the new goal statement into the Project Charter.
Goal statement: Reduce the number of proposals that take more than 55 days to
prepare and deliver by 80%.
All Rights Reserved, Juran Institute, Inc. 12 6009 CASE.0410 v3
Improvement Story
Develop/Redefine the Project
Charter
At its first meeting, the Six Sigma team determined that the goal, “improve the
timeliness of proposals,” was not specific enough. The team believed that
writing a proposal in less than 55 days was a realistic target. When proposals
took longer than 55 days, Avidco could not meet client commitments.
The Six Sigma team worked with the Steering Team and the PMD Process
Owner to modify the goal. The new goal was to reduce the number of proposals
that take longer than 55 days to prepare and deliver to the customer. They put
the new goal statement into the Project Charter.
Goal statement: Reduce the number of proposals that take more than 55 days to
prepare and deliver by 80%.
All Rights Reserved, Juran Institute, Inc. 12 6009 CASE.0410 v3
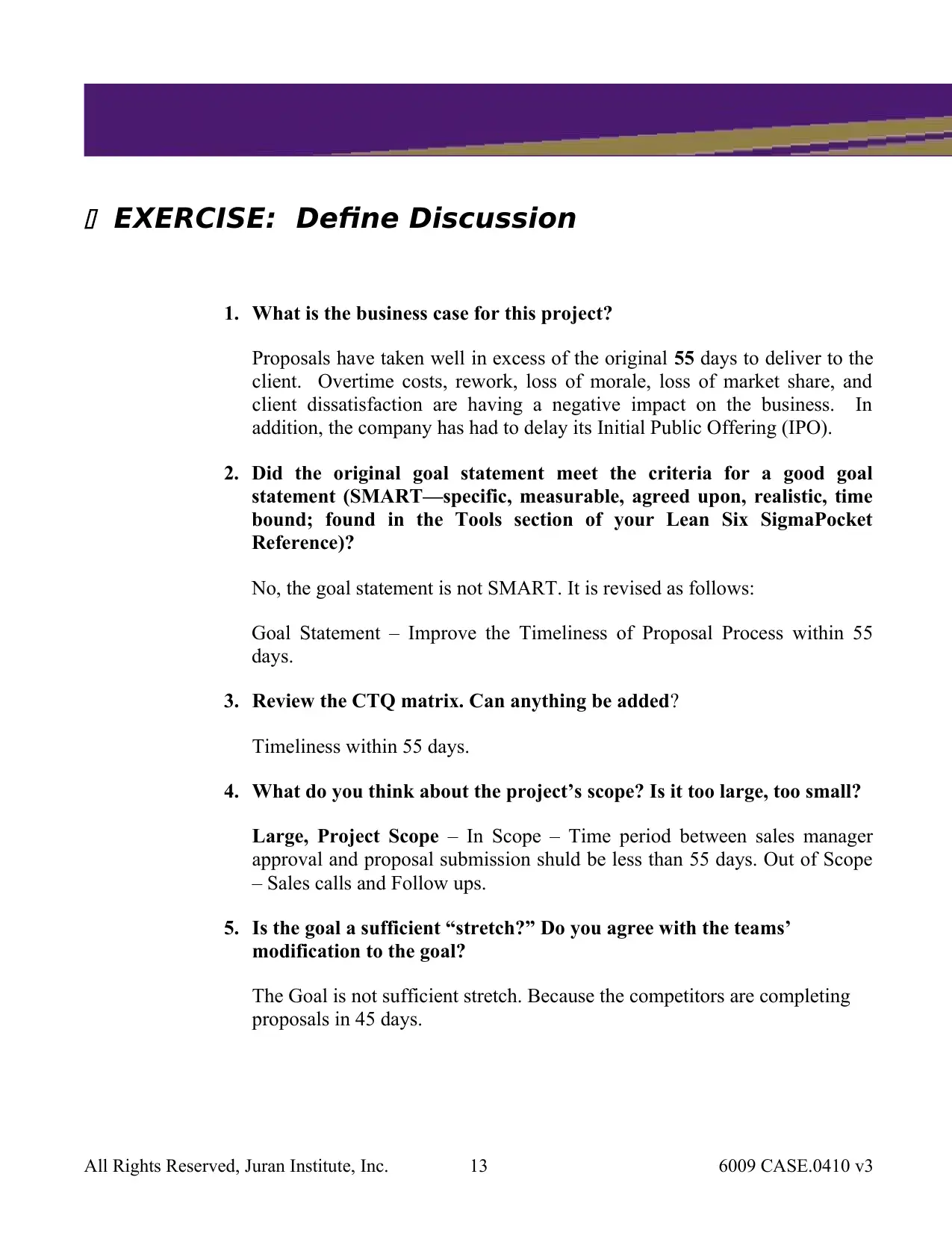
A DMAIC Six Sigma
Improvement Story
EXERCISE: Define Discussion
1. What is the business case for this project?
Proposals have taken well in excess of the original 55 days to deliver to the
client. Overtime costs, rework, loss of morale, loss of market share, and
client dissatisfaction are having a negative impact on the business. In
addition, the company has had to delay its Initial Public Offering (IPO).
2. Did the original goal statement meet the criteria for a good goal
statement (SMART—specific, measurable, agreed upon, realistic, time
bound; found in the Tools section of your Lean Six SigmaPocket
Reference)?
No, the goal statement is not SMART. It is revised as follows:
Goal Statement – Improve the Timeliness of Proposal Process within 55
days.
3. Review the CTQ matrix. Can anything be added?
Timeliness within 55 days.
4. What do you think about the project’s scope? Is it too large, too small?
Large, Project Scope – In Scope – Time period between sales manager
approval and proposal submission shuld be less than 55 days. Out of Scope
– Sales calls and Follow ups.
5. Is the goal a sufficient “stretch?” Do you agree with the teams’
modification to the goal?
The Goal is not sufficient stretch. Because the competitors are completing
proposals in 45 days.
All Rights Reserved, Juran Institute, Inc. 13 6009 CASE.0410 v3
Improvement Story
EXERCISE: Define Discussion
1. What is the business case for this project?
Proposals have taken well in excess of the original 55 days to deliver to the
client. Overtime costs, rework, loss of morale, loss of market share, and
client dissatisfaction are having a negative impact on the business. In
addition, the company has had to delay its Initial Public Offering (IPO).
2. Did the original goal statement meet the criteria for a good goal
statement (SMART—specific, measurable, agreed upon, realistic, time
bound; found in the Tools section of your Lean Six SigmaPocket
Reference)?
No, the goal statement is not SMART. It is revised as follows:
Goal Statement – Improve the Timeliness of Proposal Process within 55
days.
3. Review the CTQ matrix. Can anything be added?
Timeliness within 55 days.
4. What do you think about the project’s scope? Is it too large, too small?
Large, Project Scope – In Scope – Time period between sales manager
approval and proposal submission shuld be less than 55 days. Out of Scope
– Sales calls and Follow ups.
5. Is the goal a sufficient “stretch?” Do you agree with the teams’
modification to the goal?
The Goal is not sufficient stretch. Because the competitors are completing
proposals in 45 days.
All Rights Reserved, Juran Institute, Inc. 13 6009 CASE.0410 v3
Secure Best Marks with AI Grader
Need help grading? Try our AI Grader for instant feedback on your assignments.
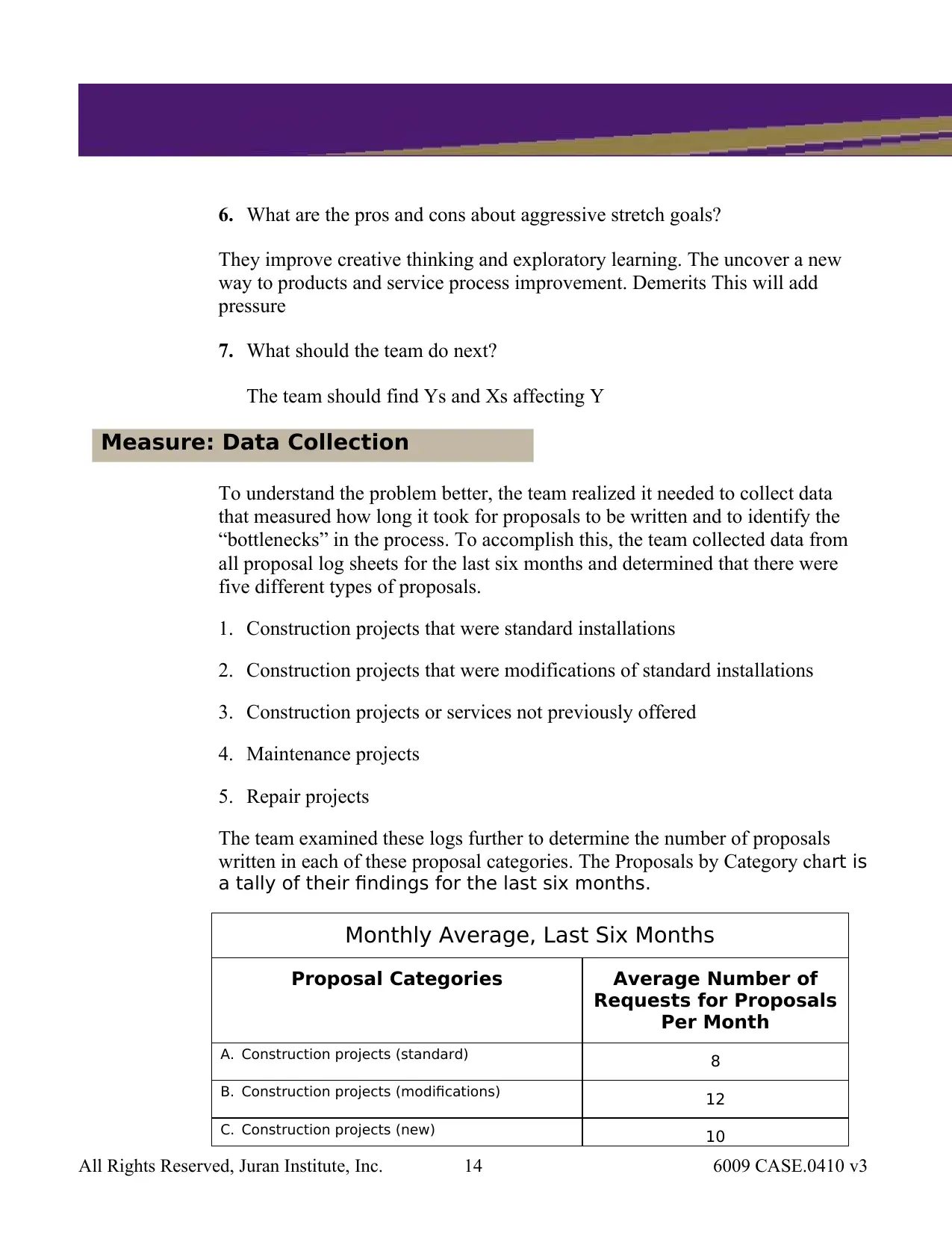
A DMAIC Six Sigma
Improvement Story
6. What are the pros and cons about aggressive stretch goals?
They improve creative thinking and exploratory learning. The uncover a new
way to products and service process improvement. Demerits This will add
pressure
7. What should the team do next?
The team should find Ys and Xs affecting Y
Measure: Data Collection
To understand the problem better, the team realized it needed to collect data
that measured how long it took for proposals to be written and to identify the
“bottlenecks” in the process. To accomplish this, the team collected data from
all proposal log sheets for the last six months and determined that there were
five different types of proposals.
1. Construction projects that were standard installations
2. Construction projects that were modifications of standard installations
3. Construction projects or services not previously offered
4. Maintenance projects
5. Repair projects
The team examined these logs further to determine the number of proposals
written in each of these proposal categories. The Proposals by Category chart is
a tally of their findings for the last six months.
Monthly Average, Last Six Months
Proposal Categories Average Number of
Requests for Proposals
Per Month
A. Construction projects (standard) 8
B. Construction projects (modifications) 12
C. Construction projects (new) 10
All Rights Reserved, Juran Institute, Inc. 14 6009 CASE.0410 v3
Improvement Story
6. What are the pros and cons about aggressive stretch goals?
They improve creative thinking and exploratory learning. The uncover a new
way to products and service process improvement. Demerits This will add
pressure
7. What should the team do next?
The team should find Ys and Xs affecting Y
Measure: Data Collection
To understand the problem better, the team realized it needed to collect data
that measured how long it took for proposals to be written and to identify the
“bottlenecks” in the process. To accomplish this, the team collected data from
all proposal log sheets for the last six months and determined that there were
five different types of proposals.
1. Construction projects that were standard installations
2. Construction projects that were modifications of standard installations
3. Construction projects or services not previously offered
4. Maintenance projects
5. Repair projects
The team examined these logs further to determine the number of proposals
written in each of these proposal categories. The Proposals by Category chart is
a tally of their findings for the last six months.
Monthly Average, Last Six Months
Proposal Categories Average Number of
Requests for Proposals
Per Month
A. Construction projects (standard) 8
B. Construction projects (modifications) 12
C. Construction projects (new) 10
All Rights Reserved, Juran Institute, Inc. 14 6009 CASE.0410 v3
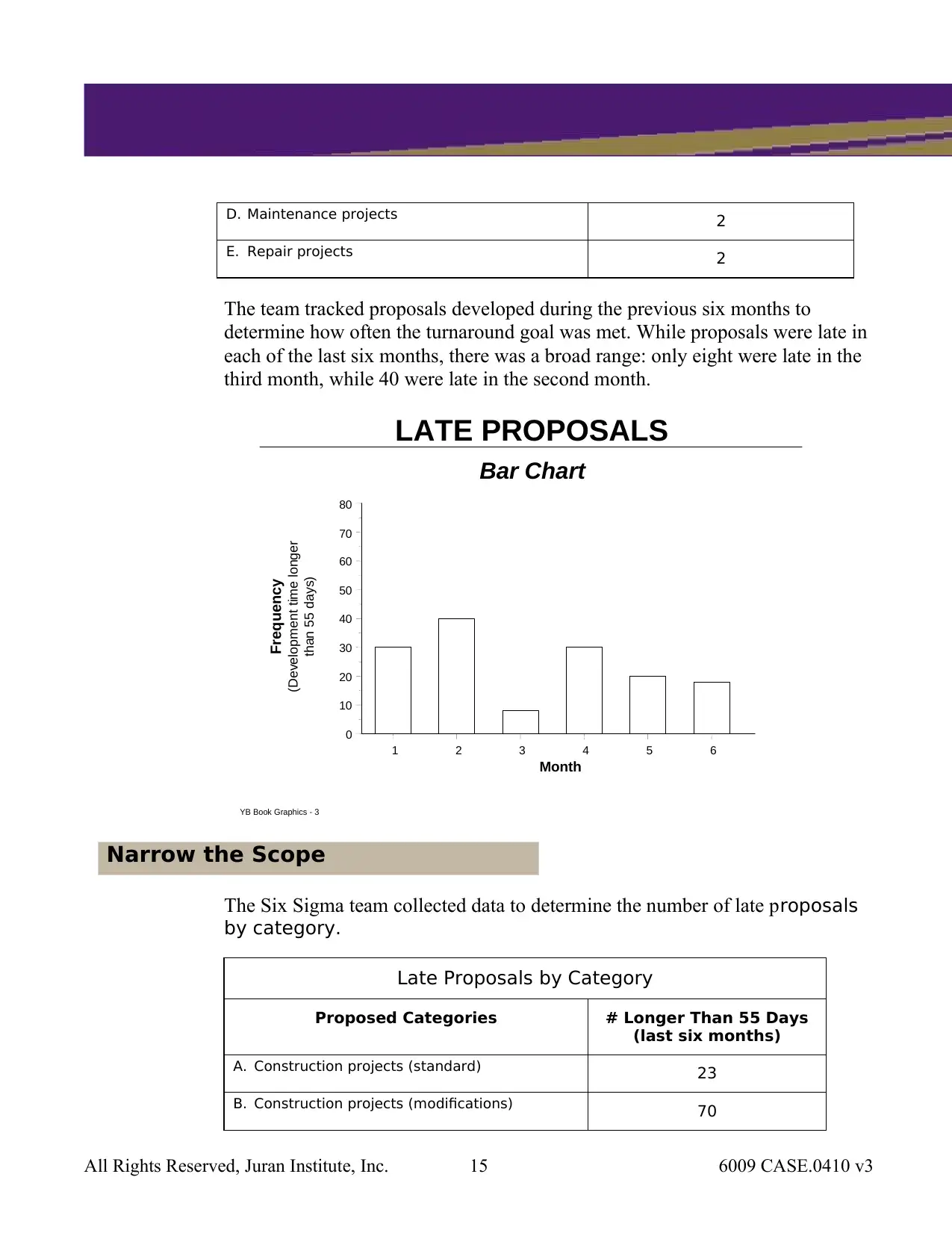
A DMAIC Six Sigma
Improvement Story
D. Maintenance projects 2
E. Repair projects 2
The team tracked proposals developed during the previous six months to
determine how often the turnaround goal was met. While proposals were late in
each of the last six months, there was a broad range: only eight were late in the
third month, while 40 were late in the second month.
YB Book Graphics - 3 All Rights Reserved, Juran Institute, Inc.
LATE PROPOSALS
Bar Chart
1 2 3 4 5 6
0
10
20
30
40
50
60
70
80
Month
Frequency
(Development time longer
than 55 days)
Narrow the Scope
The Six Sigma team collected data to determine the number of late proposals
by category.
Late Proposals by Category
Proposed Categories # Longer Than 55 Days
(last six months)
A. Construction projects (standard) 23
B. Construction projects (modifications) 70
All Rights Reserved, Juran Institute, Inc. 15 6009 CASE.0410 v3
Improvement Story
D. Maintenance projects 2
E. Repair projects 2
The team tracked proposals developed during the previous six months to
determine how often the turnaround goal was met. While proposals were late in
each of the last six months, there was a broad range: only eight were late in the
third month, while 40 were late in the second month.
YB Book Graphics - 3 All Rights Reserved, Juran Institute, Inc.
LATE PROPOSALS
Bar Chart
1 2 3 4 5 6
0
10
20
30
40
50
60
70
80
Month
Frequency
(Development time longer
than 55 days)
Narrow the Scope
The Six Sigma team collected data to determine the number of late proposals
by category.
Late Proposals by Category
Proposed Categories # Longer Than 55 Days
(last six months)
A. Construction projects (standard) 23
B. Construction projects (modifications) 70
All Rights Reserved, Juran Institute, Inc. 15 6009 CASE.0410 v3
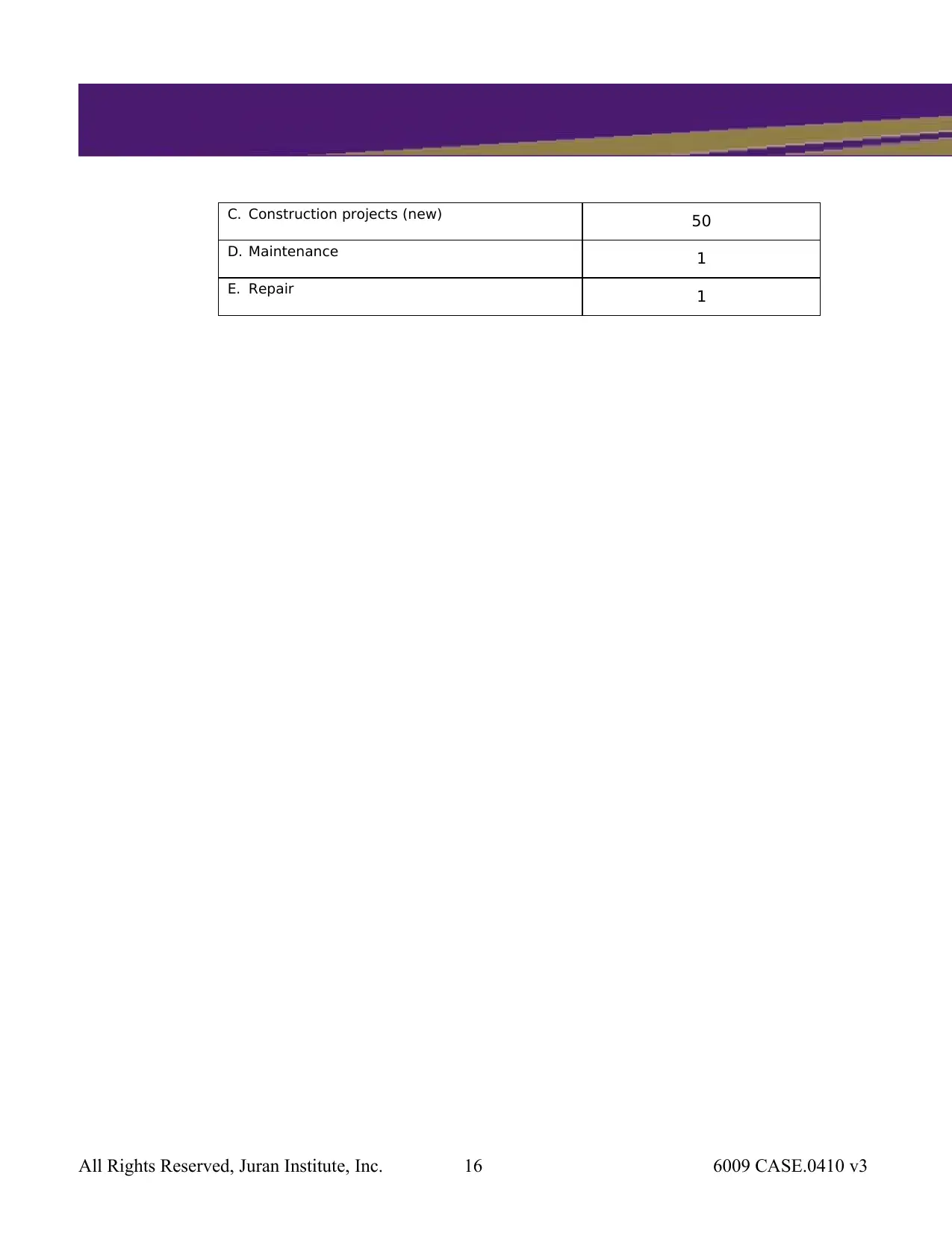
A DMAIC Six Sigma
Improvement Story
C. Construction projects (new) 50
D. Maintenance 1
E. Repair 1
All Rights Reserved, Juran Institute, Inc. 16 6009 CASE.0410 v3
Improvement Story
C. Construction projects (new) 50
D. Maintenance 1
E. Repair 1
All Rights Reserved, Juran Institute, Inc. 16 6009 CASE.0410 v3
Paraphrase This Document
Need a fresh take? Get an instant paraphrase of this document with our AI Paraphraser
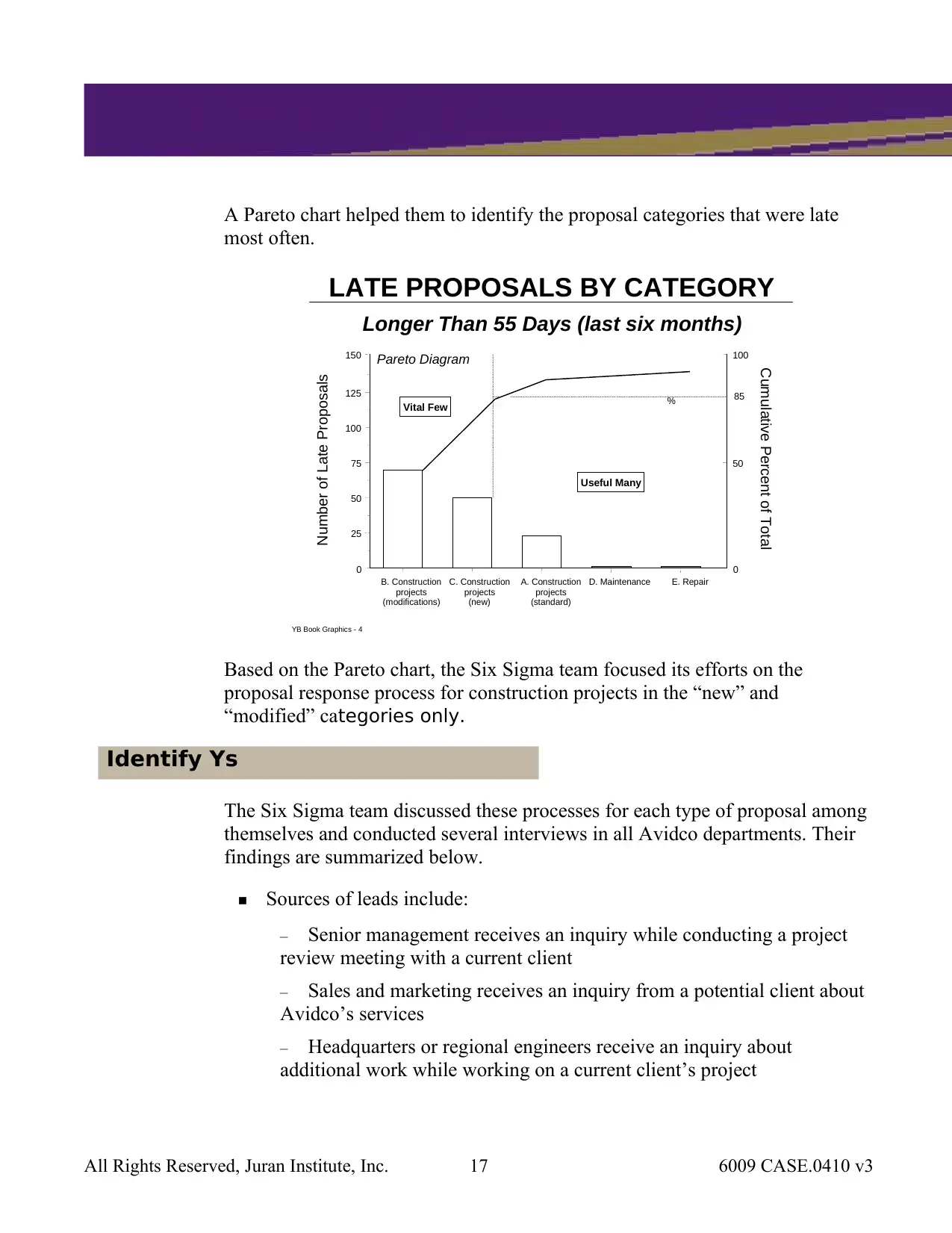
A DMAIC Six Sigma
Improvement Story
A Pareto chart helped them to identify the proposal categories that were late
most often.
YB Book Graphics - 4 All Rights Reserved, Juran Institute, Inc.
LATE PROPOSALS BY CATEGORY
Longer Than 55 Days (last six months)
0
25
50
75
100
125
150
0
50
100
Number of Late Proposals
Cumulative Percent of Total
% 85
B. Construction
projects
(modifications)
C. Construction
projects
(new)
A. Construction
projects
(standard)
D. Maintenance E. Repair
Pareto Diagram
Vital Few
Useful Many
Based on the Pareto chart, the Six Sigma team focused its efforts on the
proposal response process for construction projects in the “new” and
“modified” categories only.
Identify Ys
The Six Sigma team discussed these processes for each type of proposal among
themselves and conducted several interviews in all Avidco departments. Their
findings are summarized below.
Sources of leads include:
– Senior management receives an inquiry while conducting a project
review meeting with a current client
– Sales and marketing receives an inquiry from a potential client about
Avidco’s services
– Headquarters or regional engineers receive an inquiry about
additional work while working on a current client’s project
All Rights Reserved, Juran Institute, Inc. 17 6009 CASE.0410 v3
Improvement Story
A Pareto chart helped them to identify the proposal categories that were late
most often.
YB Book Graphics - 4 All Rights Reserved, Juran Institute, Inc.
LATE PROPOSALS BY CATEGORY
Longer Than 55 Days (last six months)
0
25
50
75
100
125
150
0
50
100
Number of Late Proposals
Cumulative Percent of Total
% 85
B. Construction
projects
(modifications)
C. Construction
projects
(new)
A. Construction
projects
(standard)
D. Maintenance E. Repair
Pareto Diagram
Vital Few
Useful Many
Based on the Pareto chart, the Six Sigma team focused its efforts on the
proposal response process for construction projects in the “new” and
“modified” categories only.
Identify Ys
The Six Sigma team discussed these processes for each type of proposal among
themselves and conducted several interviews in all Avidco departments. Their
findings are summarized below.
Sources of leads include:
– Senior management receives an inquiry while conducting a project
review meeting with a current client
– Sales and marketing receives an inquiry from a potential client about
Avidco’s services
– Headquarters or regional engineers receive an inquiry about
additional work while working on a current client’s project
All Rights Reserved, Juran Institute, Inc. 17 6009 CASE.0410 v3
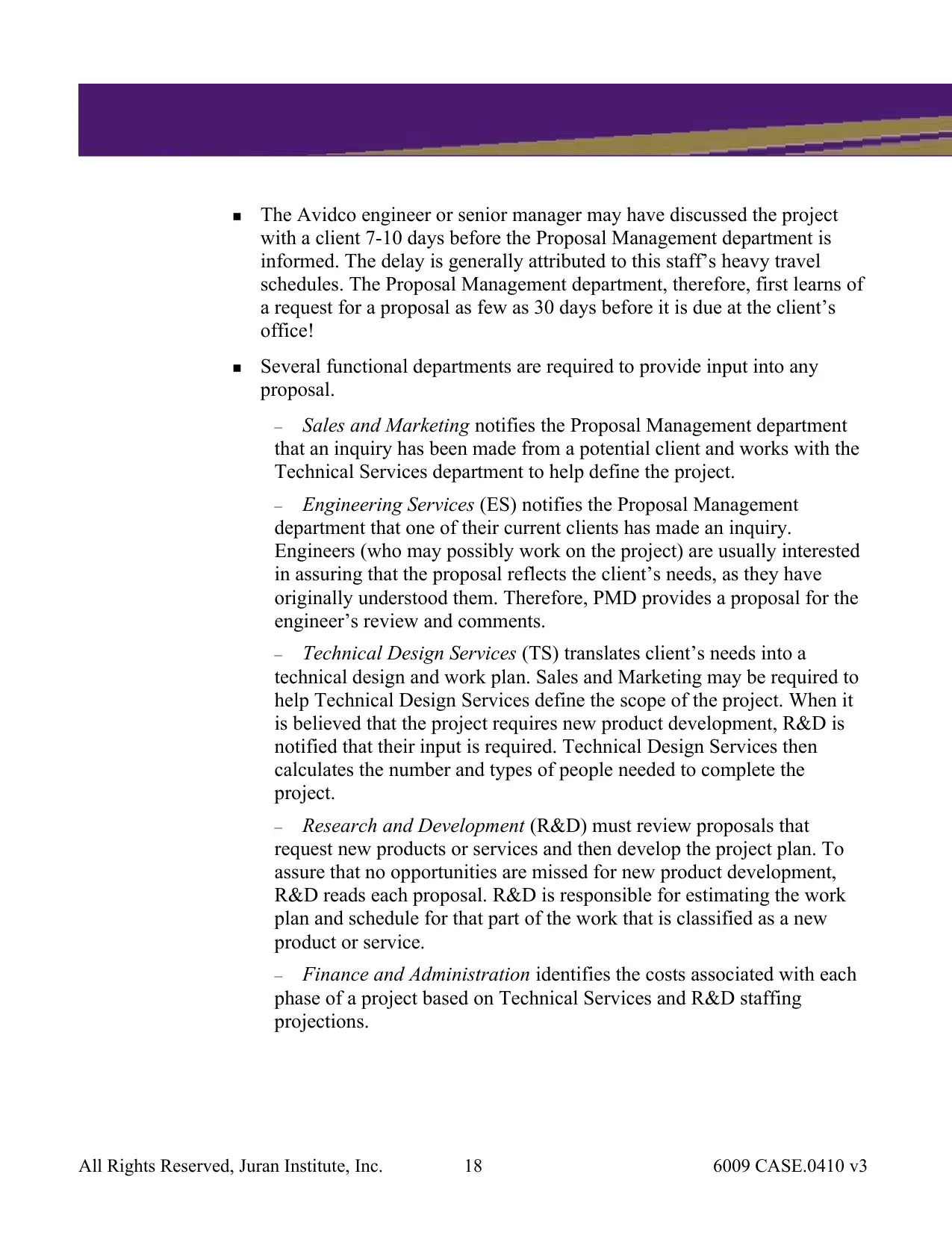
A DMAIC Six Sigma
Improvement Story
The Avidco engineer or senior manager may have discussed the project
with a client 7-10 days before the Proposal Management department is
informed. The delay is generally attributed to this staff’s heavy travel
schedules. The Proposal Management department, therefore, first learns of
a request for a proposal as few as 30 days before it is due at the client’s
office!
Several functional departments are required to provide input into any
proposal.
– Sales and Marketing notifies the Proposal Management department
that an inquiry has been made from a potential client and works with the
Technical Services department to help define the project.
– Engineering Services (ES) notifies the Proposal Management
department that one of their current clients has made an inquiry.
Engineers (who may possibly work on the project) are usually interested
in assuring that the proposal reflects the client’s needs, as they have
originally understood them. Therefore, PMD provides a proposal for the
engineer’s review and comments.
– Technical Design Services (TS) translates client’s needs into a
technical design and work plan. Sales and Marketing may be required to
help Technical Design Services define the scope of the project. When it
is believed that the project requires new product development, R&D is
notified that their input is required. Technical Design Services then
calculates the number and types of people needed to complete the
project.
– Research and Development (R&D) must review proposals that
request new products or services and then develop the project plan. To
assure that no opportunities are missed for new product development,
R&D reads each proposal. R&D is responsible for estimating the work
plan and schedule for that part of the work that is classified as a new
product or service.
– Finance and Administration identifies the costs associated with each
phase of a project based on Technical Services and R&D staffing
projections.
All Rights Reserved, Juran Institute, Inc. 18 6009 CASE.0410 v3
Improvement Story
The Avidco engineer or senior manager may have discussed the project
with a client 7-10 days before the Proposal Management department is
informed. The delay is generally attributed to this staff’s heavy travel
schedules. The Proposal Management department, therefore, first learns of
a request for a proposal as few as 30 days before it is due at the client’s
office!
Several functional departments are required to provide input into any
proposal.
– Sales and Marketing notifies the Proposal Management department
that an inquiry has been made from a potential client and works with the
Technical Services department to help define the project.
– Engineering Services (ES) notifies the Proposal Management
department that one of their current clients has made an inquiry.
Engineers (who may possibly work on the project) are usually interested
in assuring that the proposal reflects the client’s needs, as they have
originally understood them. Therefore, PMD provides a proposal for the
engineer’s review and comments.
– Technical Design Services (TS) translates client’s needs into a
technical design and work plan. Sales and Marketing may be required to
help Technical Design Services define the scope of the project. When it
is believed that the project requires new product development, R&D is
notified that their input is required. Technical Design Services then
calculates the number and types of people needed to complete the
project.
– Research and Development (R&D) must review proposals that
request new products or services and then develop the project plan. To
assure that no opportunities are missed for new product development,
R&D reads each proposal. R&D is responsible for estimating the work
plan and schedule for that part of the work that is classified as a new
product or service.
– Finance and Administration identifies the costs associated with each
phase of a project based on Technical Services and R&D staffing
projections.
All Rights Reserved, Juran Institute, Inc. 18 6009 CASE.0410 v3
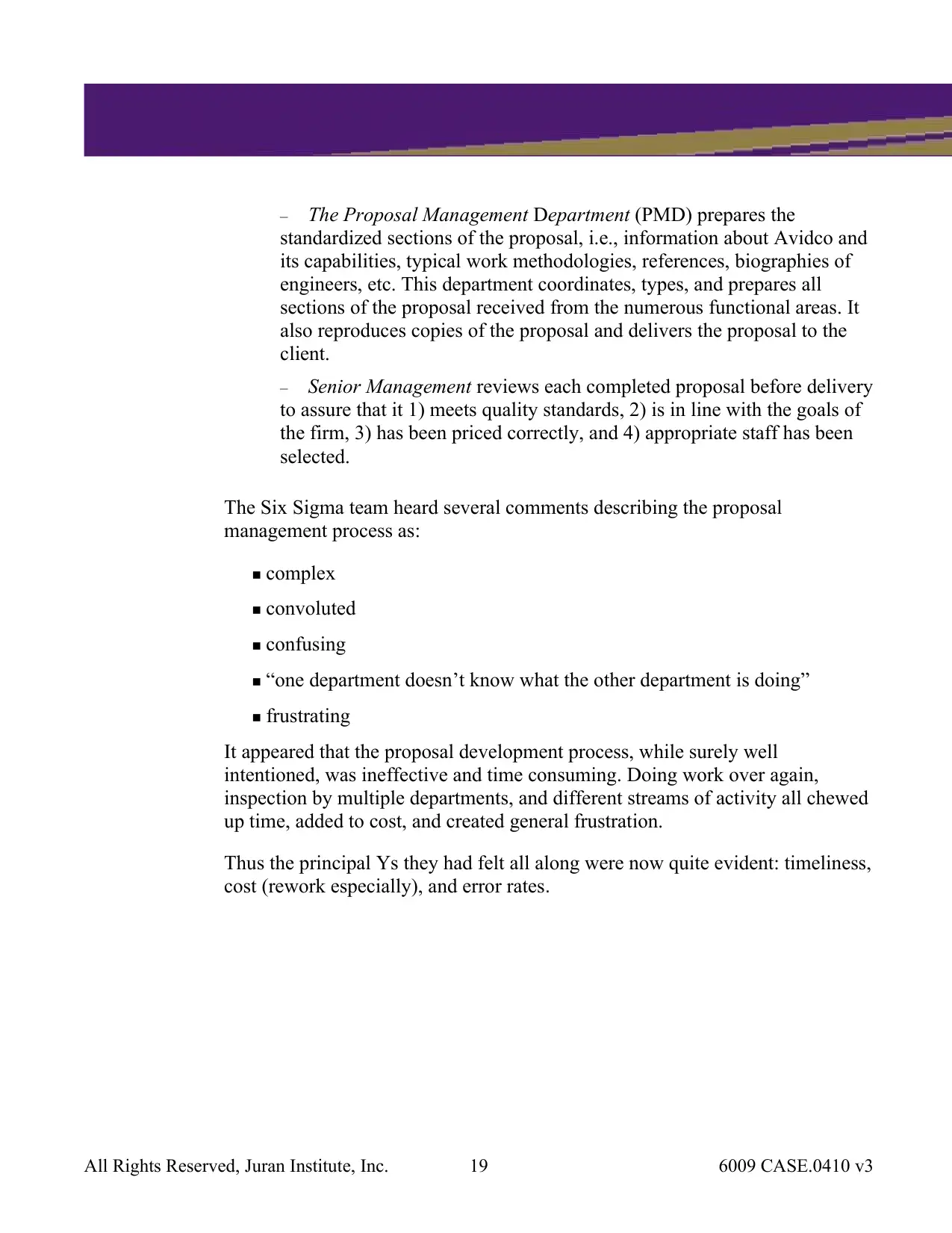
A DMAIC Six Sigma
Improvement Story
– The Proposal Management Department (PMD) prepares the
standardized sections of the proposal, i.e., information about Avidco and
its capabilities, typical work methodologies, references, biographies of
engineers, etc. This department coordinates, types, and prepares all
sections of the proposal received from the numerous functional areas. It
also reproduces copies of the proposal and delivers the proposal to the
client.
– Senior Management reviews each completed proposal before delivery
to assure that it 1) meets quality standards, 2) is in line with the goals of
the firm, 3) has been priced correctly, and 4) appropriate staff has been
selected.
The Six Sigma team heard several comments describing the proposal
management process as:
complex
convoluted
confusing
“one department doesn’t know what the other department is doing”
frustrating
It appeared that the proposal development process, while surely well
intentioned, was ineffective and time consuming. Doing work over again,
inspection by multiple departments, and different streams of activity all chewed
up time, added to cost, and created general frustration.
Thus the principal Ys they had felt all along were now quite evident: timeliness,
cost (rework especially), and error rates.
All Rights Reserved, Juran Institute, Inc. 19 6009 CASE.0410 v3
Improvement Story
– The Proposal Management Department (PMD) prepares the
standardized sections of the proposal, i.e., information about Avidco and
its capabilities, typical work methodologies, references, biographies of
engineers, etc. This department coordinates, types, and prepares all
sections of the proposal received from the numerous functional areas. It
also reproduces copies of the proposal and delivers the proposal to the
client.
– Senior Management reviews each completed proposal before delivery
to assure that it 1) meets quality standards, 2) is in line with the goals of
the firm, 3) has been priced correctly, and 4) appropriate staff has been
selected.
The Six Sigma team heard several comments describing the proposal
management process as:
complex
convoluted
confusing
“one department doesn’t know what the other department is doing”
frustrating
It appeared that the proposal development process, while surely well
intentioned, was ineffective and time consuming. Doing work over again,
inspection by multiple departments, and different streams of activity all chewed
up time, added to cost, and created general frustration.
Thus the principal Ys they had felt all along were now quite evident: timeliness,
cost (rework especially), and error rates.
All Rights Reserved, Juran Institute, Inc. 19 6009 CASE.0410 v3
Secure Best Marks with AI Grader
Need help grading? Try our AI Grader for instant feedback on your assignments.
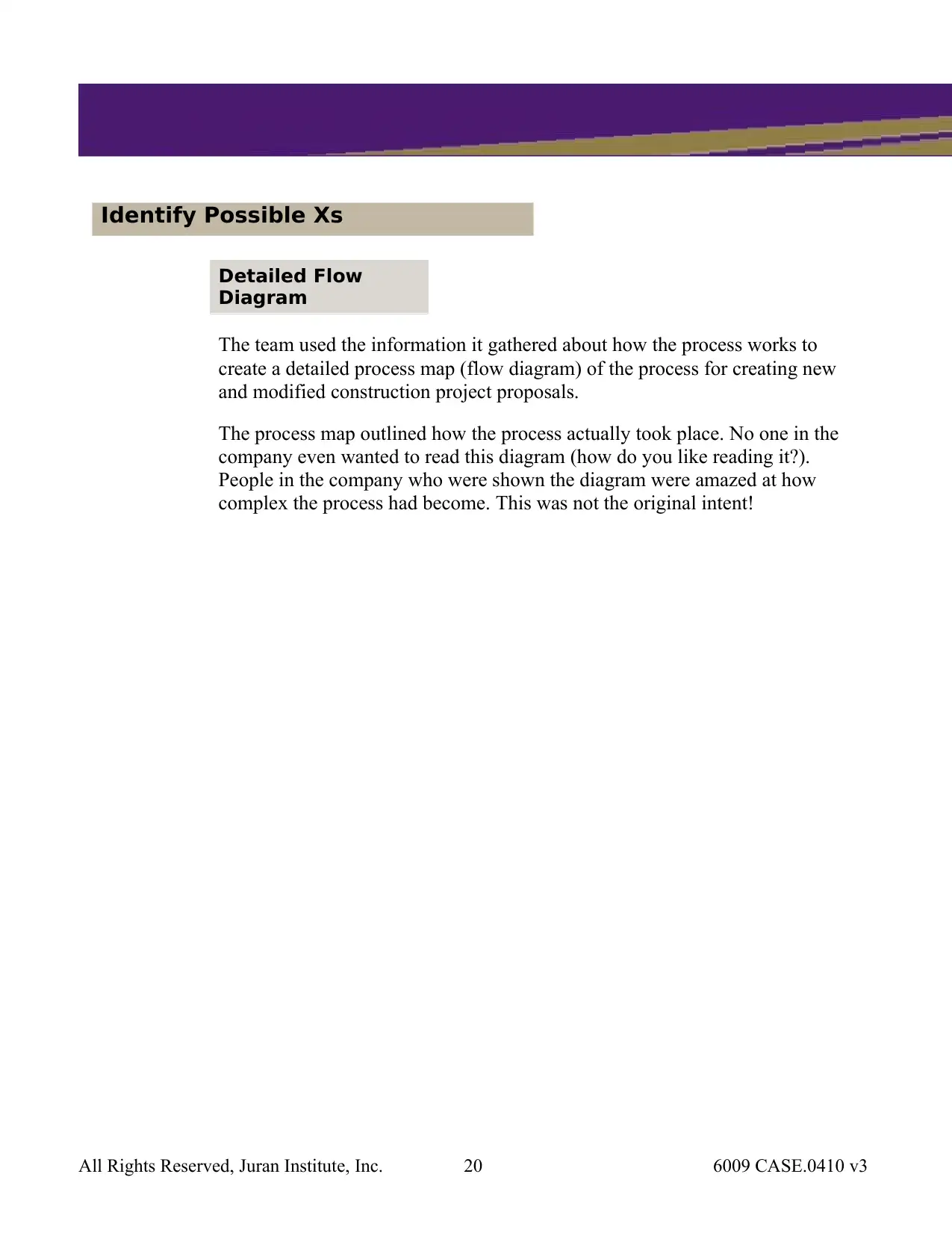
A DMAIC Six Sigma
Improvement Story
Identify Possible Xs
Detailed Flow
Diagram
The team used the information it gathered about how the process works to
create a detailed process map (flow diagram) of the process for creating new
and modified construction project proposals.
The process map outlined how the process actually took place. No one in the
company even wanted to read this diagram (how do you like reading it?).
People in the company who were shown the diagram were amazed at how
complex the process had become. This was not the original intent!
All Rights Reserved, Juran Institute, Inc. 20 6009 CASE.0410 v3
Improvement Story
Identify Possible Xs
Detailed Flow
Diagram
The team used the information it gathered about how the process works to
create a detailed process map (flow diagram) of the process for creating new
and modified construction project proposals.
The process map outlined how the process actually took place. No one in the
company even wanted to read this diagram (how do you like reading it?).
People in the company who were shown the diagram were amazed at how
complex the process had become. This was not the original intent!
All Rights Reserved, Juran Institute, Inc. 20 6009 CASE.0410 v3
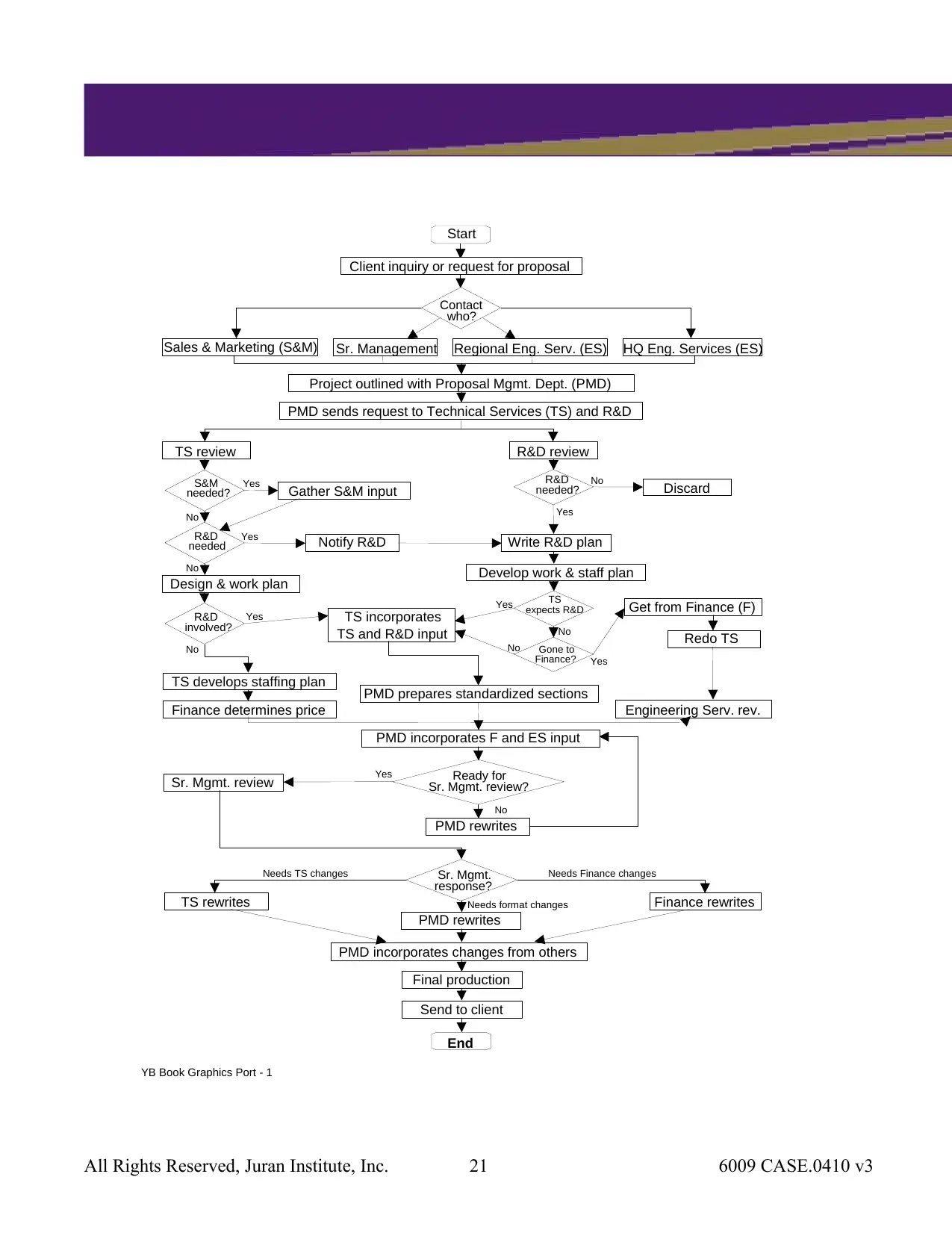
A DMAIC Six Sigma
Improvement Story
YB Book Graphics Port - 1
Start
Client inquiry or request for proposal
Contact
who?
Sales & Marketing (S&M) Regional Eng. Serv. (ES) HQ Eng. Services (ES)Sr. Management
PMD sends request to Technical Services (TS) and R&D
Project outlined with Proposal Mgmt. Dept. (PMD)
TS review R&D review
S&M
needed?
R&D
needed
Design & work plan
R&D
involved?
Finance determines price
TS develops staffing plan
Engineering Serv. rev.
PMD prepares standardized sections
R&D
needed? Discard
Write R&D plan
Develop work & staff plan
Gone to
Finance?
TS
expects R&D
Notify R&D
Gather S&M input
TS incorporates
TS and R&D input
Get from Finance (F)
Redo TS
PMD incorporates F and ES input
Ready for
Sr. Mgmt. review?
PMD rewrites
Sr. Mgmt. review
Finance rewritesTS rewrites
Sr. Mgmt.
response?
PMD incorporates changes from others
Send to client
Final production
PMD rewrites
End
Needs TS changes Needs Finance changes
Needs format changes
Yes
No
Yes
No
No
Yes
Yes
No
No
No
Yes
Yes No
Yes
All Rights Reserved, Juran Institute, Inc. 21 6009 CASE.0410 v3
Improvement Story
YB Book Graphics Port - 1
Start
Client inquiry or request for proposal
Contact
who?
Sales & Marketing (S&M) Regional Eng. Serv. (ES) HQ Eng. Services (ES)Sr. Management
PMD sends request to Technical Services (TS) and R&D
Project outlined with Proposal Mgmt. Dept. (PMD)
TS review R&D review
S&M
needed?
R&D
needed
Design & work plan
R&D
involved?
Finance determines price
TS develops staffing plan
Engineering Serv. rev.
PMD prepares standardized sections
R&D
needed? Discard
Write R&D plan
Develop work & staff plan
Gone to
Finance?
TS
expects R&D
Notify R&D
Gather S&M input
TS incorporates
TS and R&D input
Get from Finance (F)
Redo TS
PMD incorporates F and ES input
Ready for
Sr. Mgmt. review?
PMD rewrites
Sr. Mgmt. review
Finance rewritesTS rewrites
Sr. Mgmt.
response?
PMD incorporates changes from others
Send to client
Final production
PMD rewrites
End
Needs TS changes Needs Finance changes
Needs format changes
Yes
No
Yes
No
No
Yes
Yes
No
No
No
Yes
Yes No
Yes
All Rights Reserved, Juran Institute, Inc. 21 6009 CASE.0410 v3
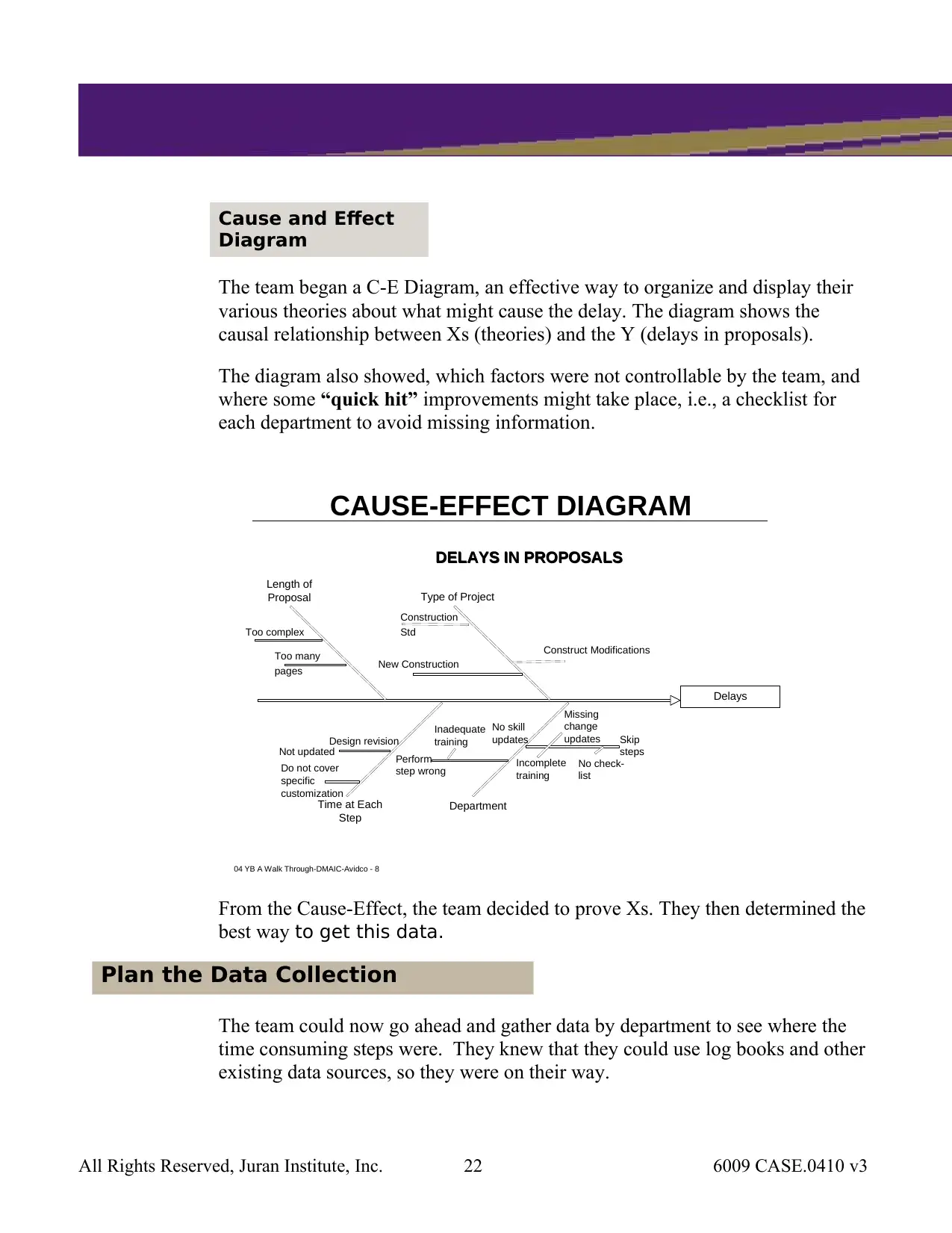
A DMAIC Six Sigma
Improvement Story
Cause and Effect
Diagram
The team began a C-E Diagram, an effective way to organize and display their
various theories about what might cause the delay. The diagram shows the
causal relationship between Xs (theories) and the Y (delays in proposals).
The diagram also showed, which factors were not controllable by the team, and
where some “quick hit” improvements might take place, i.e., a checklist for
each department to avoid missing information.
04 YB A Walk Through-DMAIC-Avidco - 8 All Rights Reserved, Juran Institute, Inc.
Length of
Proposal Type of Project
Time at Each
Step
Department
Too complex
Too many
pages
Construction
Std
Do not cover
specific
customization
Not updated Perform
step wrong
Inadequate
training
New Construction
Construct Modifications
Design revision
No skill
updates
Missing
change
updates
Incomplete
training
No check-
list
Skip
steps
DELAYS IN PROPOSALSDELAYS IN PROPOSALS
Delays
CAUSE-EFFECT DIAGRAM
From the Cause-Effect, the team decided to prove Xs. They then determined the
best way to get this data.
Plan the Data Collection
The team could now go ahead and gather data by department to see where the
time consuming steps were. They knew that they could use log books and other
existing data sources, so they were on their way.
All Rights Reserved, Juran Institute, Inc. 22 6009 CASE.0410 v3
Improvement Story
Cause and Effect
Diagram
The team began a C-E Diagram, an effective way to organize and display their
various theories about what might cause the delay. The diagram shows the
causal relationship between Xs (theories) and the Y (delays in proposals).
The diagram also showed, which factors were not controllable by the team, and
where some “quick hit” improvements might take place, i.e., a checklist for
each department to avoid missing information.
04 YB A Walk Through-DMAIC-Avidco - 8 All Rights Reserved, Juran Institute, Inc.
Length of
Proposal Type of Project
Time at Each
Step
Department
Too complex
Too many
pages
Construction
Std
Do not cover
specific
customization
Not updated Perform
step wrong
Inadequate
training
New Construction
Construct Modifications
Design revision
No skill
updates
Missing
change
updates
Incomplete
training
No check-
list
Skip
steps
DELAYS IN PROPOSALSDELAYS IN PROPOSALS
Delays
CAUSE-EFFECT DIAGRAM
From the Cause-Effect, the team decided to prove Xs. They then determined the
best way to get this data.
Plan the Data Collection
The team could now go ahead and gather data by department to see where the
time consuming steps were. They knew that they could use log books and other
existing data sources, so they were on their way.
All Rights Reserved, Juran Institute, Inc. 22 6009 CASE.0410 v3
Paraphrase This Document
Need a fresh take? Get an instant paraphrase of this document with our AI Paraphraser
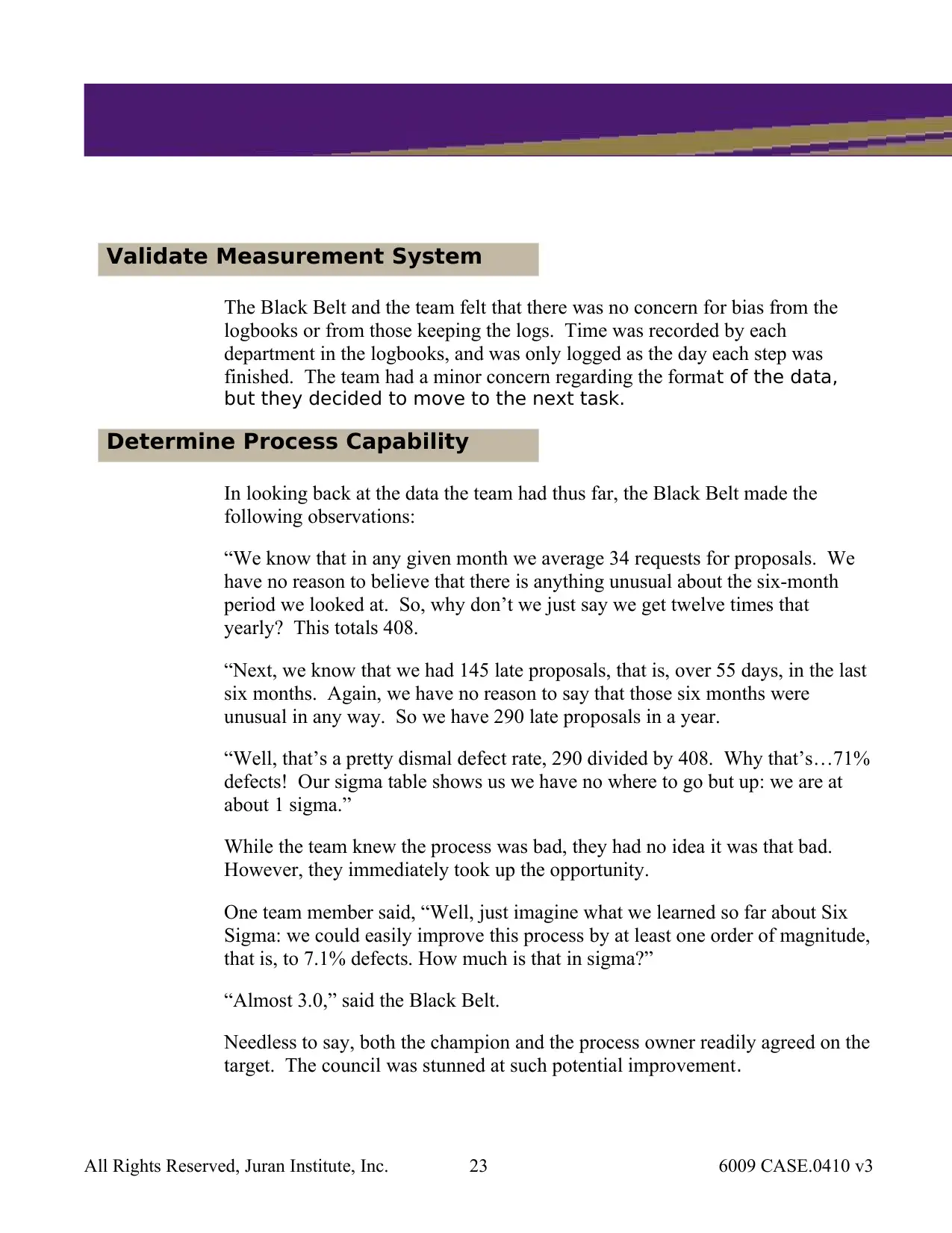
A DMAIC Six Sigma
Improvement Story
Validate Measurement System
The Black Belt and the team felt that there was no concern for bias from the
logbooks or from those keeping the logs. Time was recorded by each
department in the logbooks, and was only logged as the day each step was
finished. The team had a minor concern regarding the format of the data,
but they decided to move to the next task.
Determine Process Capability
In looking back at the data the team had thus far, the Black Belt made the
following observations:
“We know that in any given month we average 34 requests for proposals. We
have no reason to believe that there is anything unusual about the six-month
period we looked at. So, why don’t we just say we get twelve times that
yearly? This totals 408.
“Next, we know that we had 145 late proposals, that is, over 55 days, in the last
six months. Again, we have no reason to say that those six months were
unusual in any way. So we have 290 late proposals in a year.
“Well, that’s a pretty dismal defect rate, 290 divided by 408. Why that’s…71%
defects! Our sigma table shows us we have no where to go but up: we are at
about 1 sigma.”
While the team knew the process was bad, they had no idea it was that bad.
However, they immediately took up the opportunity.
One team member said, “Well, just imagine what we learned so far about Six
Sigma: we could easily improve this process by at least one order of magnitude,
that is, to 7.1% defects. How much is that in sigma?”
“Almost 3.0,” said the Black Belt.
Needless to say, both the champion and the process owner readily agreed on the
target. The council was stunned at such potential improvement.
All Rights Reserved, Juran Institute, Inc. 23 6009 CASE.0410 v3
Improvement Story
Validate Measurement System
The Black Belt and the team felt that there was no concern for bias from the
logbooks or from those keeping the logs. Time was recorded by each
department in the logbooks, and was only logged as the day each step was
finished. The team had a minor concern regarding the format of the data,
but they decided to move to the next task.
Determine Process Capability
In looking back at the data the team had thus far, the Black Belt made the
following observations:
“We know that in any given month we average 34 requests for proposals. We
have no reason to believe that there is anything unusual about the six-month
period we looked at. So, why don’t we just say we get twelve times that
yearly? This totals 408.
“Next, we know that we had 145 late proposals, that is, over 55 days, in the last
six months. Again, we have no reason to say that those six months were
unusual in any way. So we have 290 late proposals in a year.
“Well, that’s a pretty dismal defect rate, 290 divided by 408. Why that’s…71%
defects! Our sigma table shows us we have no where to go but up: we are at
about 1 sigma.”
While the team knew the process was bad, they had no idea it was that bad.
However, they immediately took up the opportunity.
One team member said, “Well, just imagine what we learned so far about Six
Sigma: we could easily improve this process by at least one order of magnitude,
that is, to 7.1% defects. How much is that in sigma?”
“Almost 3.0,” said the Black Belt.
Needless to say, both the champion and the process owner readily agreed on the
target. The council was stunned at such potential improvement.
All Rights Reserved, Juran Institute, Inc. 23 6009 CASE.0410 v3
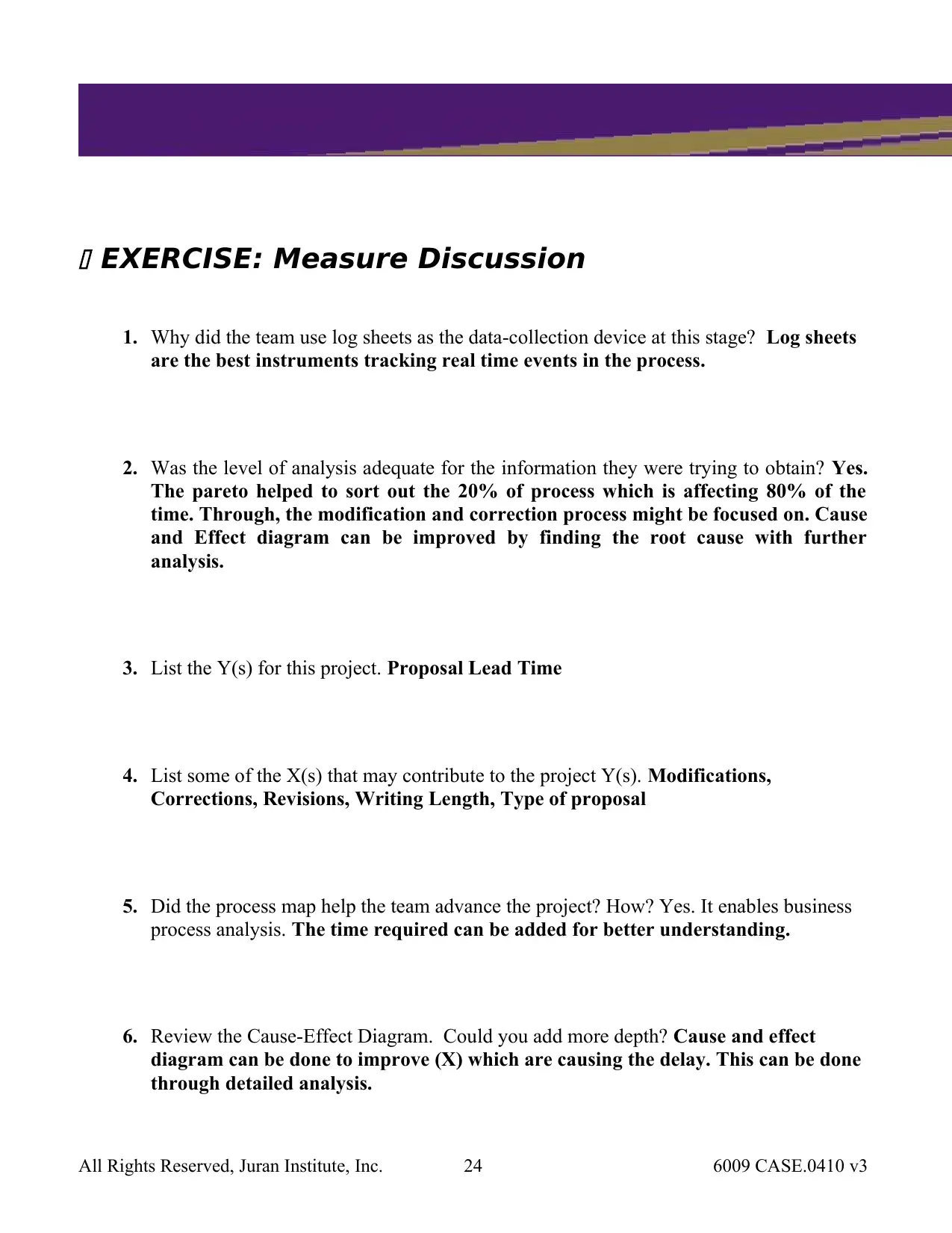
A DMAIC Six Sigma
Improvement Story
EXERCISE: Measure Discussion
1. Why did the team use log sheets as the data-collection device at this stage? Log sheets
are the best instruments tracking real time events in the process.
2. Was the level of analysis adequate for the information they were trying to obtain? Yes.
The pareto helped to sort out the 20% of process which is affecting 80% of the
time. Through, the modification and correction process might be focused on. Cause
and Effect diagram can be improved by finding the root cause with further
analysis.
3. List the Y(s) for this project. Proposal Lead Time
4. List some of the X(s) that may contribute to the project Y(s). Modifications,
Corrections, Revisions, Writing Length, Type of proposal
5. Did the process map help the team advance the project? How? Yes. It enables business
process analysis. The time required can be added for better understanding.
6. Review the Cause-Effect Diagram. Could you add more depth? Cause and effect
diagram can be done to improve (X) which are causing the delay. This can be done
through detailed analysis.
All Rights Reserved, Juran Institute, Inc. 24 6009 CASE.0410 v3
Improvement Story
EXERCISE: Measure Discussion
1. Why did the team use log sheets as the data-collection device at this stage? Log sheets
are the best instruments tracking real time events in the process.
2. Was the level of analysis adequate for the information they were trying to obtain? Yes.
The pareto helped to sort out the 20% of process which is affecting 80% of the
time. Through, the modification and correction process might be focused on. Cause
and Effect diagram can be improved by finding the root cause with further
analysis.
3. List the Y(s) for this project. Proposal Lead Time
4. List some of the X(s) that may contribute to the project Y(s). Modifications,
Corrections, Revisions, Writing Length, Type of proposal
5. Did the process map help the team advance the project? How? Yes. It enables business
process analysis. The time required can be added for better understanding.
6. Review the Cause-Effect Diagram. Could you add more depth? Cause and effect
diagram can be done to improve (X) which are causing the delay. This can be done
through detailed analysis.
All Rights Reserved, Juran Institute, Inc. 24 6009 CASE.0410 v3
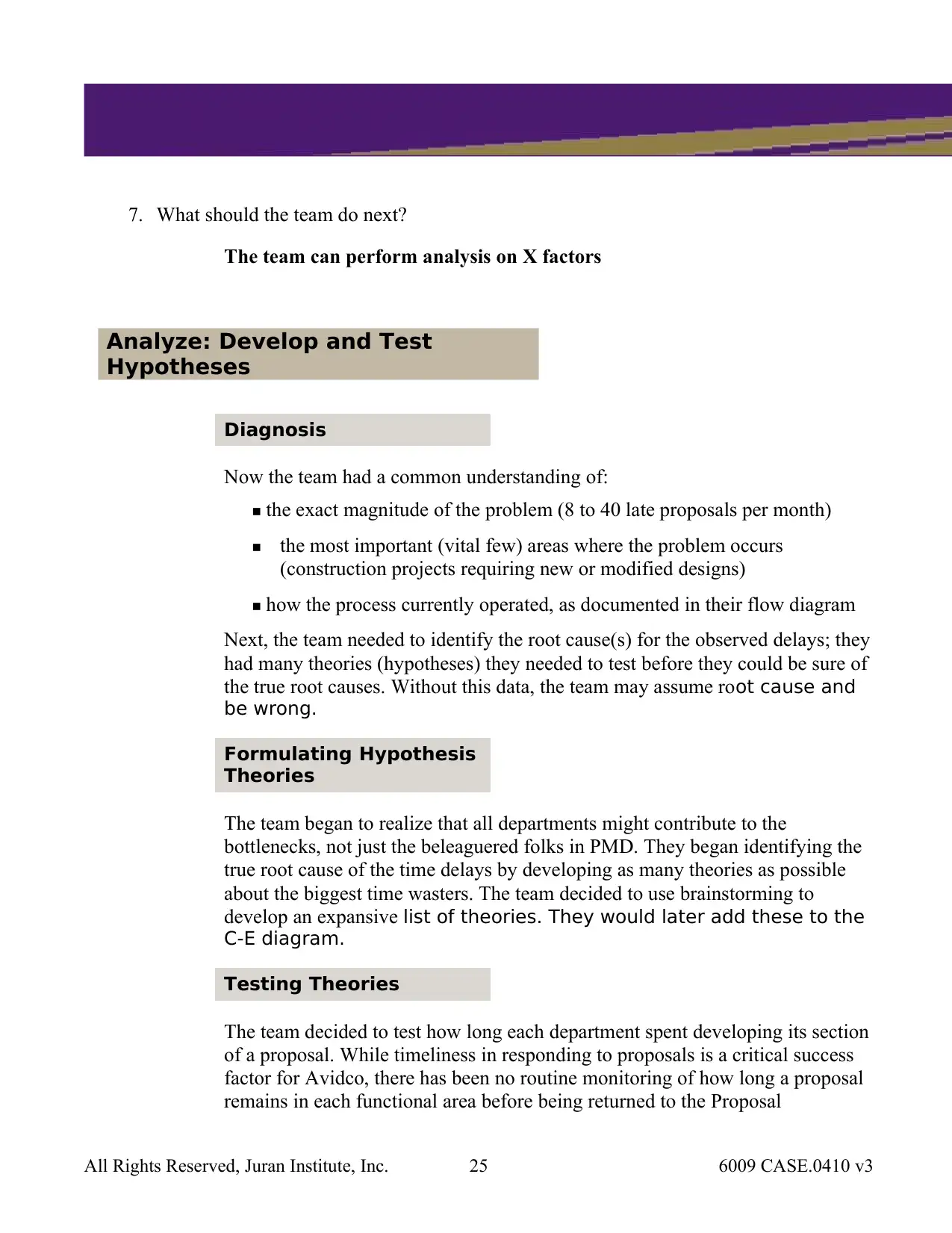
A DMAIC Six Sigma
Improvement Story
7. What should the team do next?
The team can perform analysis on X factors
Analyze: Develop and Test
Hypotheses
Diagnosis
Now the team had a common understanding of:
the exact magnitude of the problem (8 to 40 late proposals per month)
the most important (vital few) areas where the problem occurs
(construction projects requiring new or modified designs)
how the process currently operated, as documented in their flow diagram
Next, the team needed to identify the root cause(s) for the observed delays; they
had many theories (hypotheses) they needed to test before they could be sure of
the true root causes. Without this data, the team may assume root cause and
be wrong.
Formulating Hypothesis
Theories
The team began to realize that all departments might contribute to the
bottlenecks, not just the beleaguered folks in PMD. They began identifying the
true root cause of the time delays by developing as many theories as possible
about the biggest time wasters. The team decided to use brainstorming to
develop an expansive list of theories. They would later add these to the
C-E diagram.
Testing Theories
The team decided to test how long each department spent developing its section
of a proposal. While timeliness in responding to proposals is a critical success
factor for Avidco, there has been no routine monitoring of how long a proposal
remains in each functional area before being returned to the Proposal
All Rights Reserved, Juran Institute, Inc. 25 6009 CASE.0410 v3
Improvement Story
7. What should the team do next?
The team can perform analysis on X factors
Analyze: Develop and Test
Hypotheses
Diagnosis
Now the team had a common understanding of:
the exact magnitude of the problem (8 to 40 late proposals per month)
the most important (vital few) areas where the problem occurs
(construction projects requiring new or modified designs)
how the process currently operated, as documented in their flow diagram
Next, the team needed to identify the root cause(s) for the observed delays; they
had many theories (hypotheses) they needed to test before they could be sure of
the true root causes. Without this data, the team may assume root cause and
be wrong.
Formulating Hypothesis
Theories
The team began to realize that all departments might contribute to the
bottlenecks, not just the beleaguered folks in PMD. They began identifying the
true root cause of the time delays by developing as many theories as possible
about the biggest time wasters. The team decided to use brainstorming to
develop an expansive list of theories. They would later add these to the
C-E diagram.
Testing Theories
The team decided to test how long each department spent developing its section
of a proposal. While timeliness in responding to proposals is a critical success
factor for Avidco, there has been no routine monitoring of how long a proposal
remains in each functional area before being returned to the Proposal
All Rights Reserved, Juran Institute, Inc. 25 6009 CASE.0410 v3
Secure Best Marks with AI Grader
Need help grading? Try our AI Grader for instant feedback on your assignments.
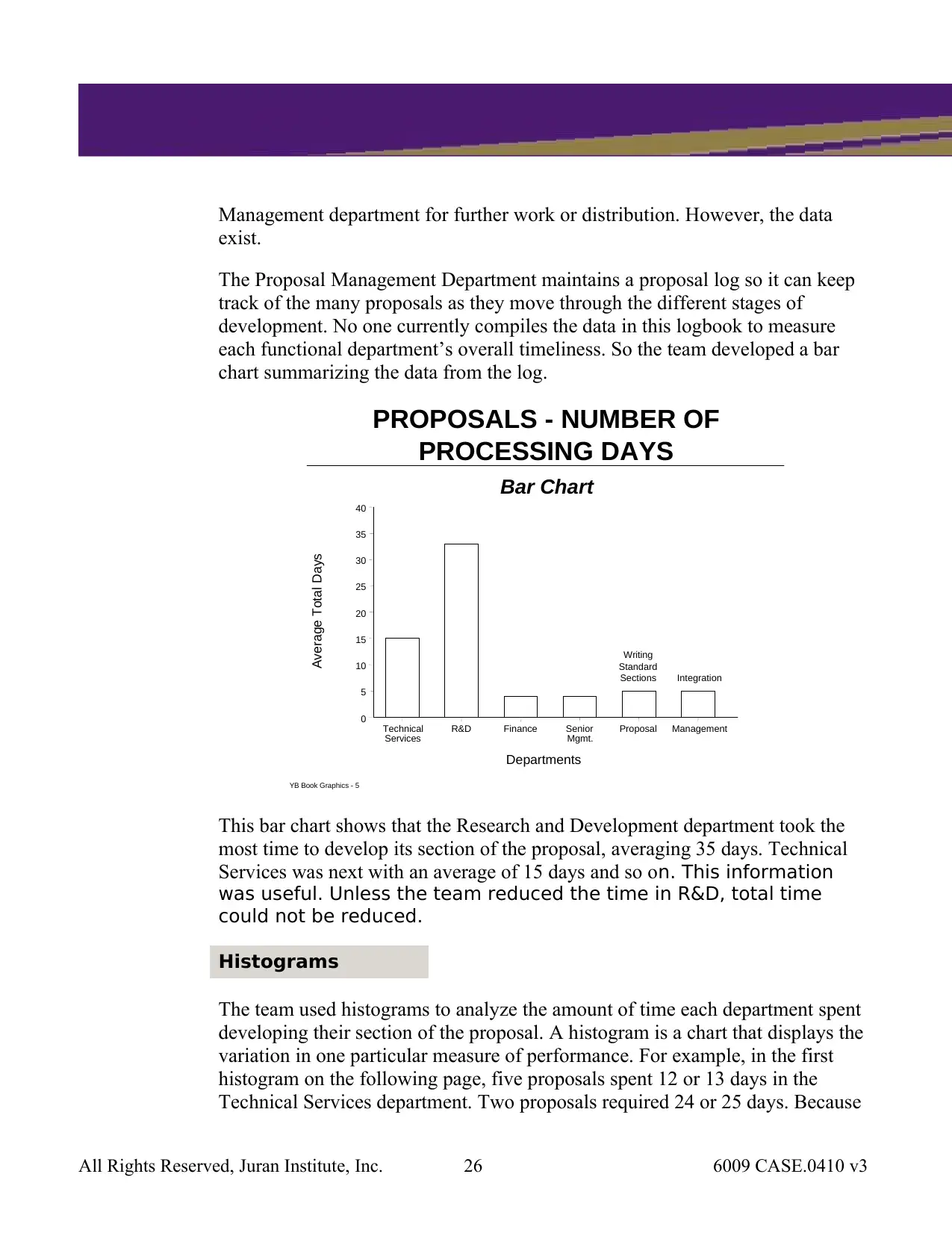
A DMAIC Six Sigma
Improvement Story
Management department for further work or distribution. However, the data
exist.
The Proposal Management Department maintains a proposal log so it can keep
track of the many proposals as they move through the different stages of
development. No one currently compiles the data in this logbook to measure
each functional department’s overall timeliness. So the team developed a bar
chart summarizing the data from the log.
YB Book Graphics - 5 All Rights Reserved, Juran Institute, Inc.
PROPOSALS - NUMBER OF
PROCESSING DAYS
Bar Chart
0
5
10
15
20
25
30
35
40
Average Total Days
Departments
Technical
Services
Finance Senior
Mgmt.
Proposal ManagementR&D
Writing
Standard
Sections Integration
This bar chart shows that the Research and Development department took the
most time to develop its section of the proposal, averaging 35 days. Technical
Services was next with an average of 15 days and so on. This information
was useful. Unless the team reduced the time in R&D, total time
could not be reduced.
Histograms
The team used histograms to analyze the amount of time each department spent
developing their section of the proposal. A histogram is a chart that displays the
variation in one particular measure of performance. For example, in the first
histogram on the following page, five proposals spent 12 or 13 days in the
Technical Services department. Two proposals required 24 or 25 days. Because
All Rights Reserved, Juran Institute, Inc. 26 6009 CASE.0410 v3
Improvement Story
Management department for further work or distribution. However, the data
exist.
The Proposal Management Department maintains a proposal log so it can keep
track of the many proposals as they move through the different stages of
development. No one currently compiles the data in this logbook to measure
each functional department’s overall timeliness. So the team developed a bar
chart summarizing the data from the log.
YB Book Graphics - 5 All Rights Reserved, Juran Institute, Inc.
PROPOSALS - NUMBER OF
PROCESSING DAYS
Bar Chart
0
5
10
15
20
25
30
35
40
Average Total Days
Departments
Technical
Services
Finance Senior
Mgmt.
Proposal ManagementR&D
Writing
Standard
Sections Integration
This bar chart shows that the Research and Development department took the
most time to develop its section of the proposal, averaging 35 days. Technical
Services was next with an average of 15 days and so on. This information
was useful. Unless the team reduced the time in R&D, total time
could not be reduced.
Histograms
The team used histograms to analyze the amount of time each department spent
developing their section of the proposal. A histogram is a chart that displays the
variation in one particular measure of performance. For example, in the first
histogram on the following page, five proposals spent 12 or 13 days in the
Technical Services department. Two proposals required 24 or 25 days. Because
All Rights Reserved, Juran Institute, Inc. 26 6009 CASE.0410 v3
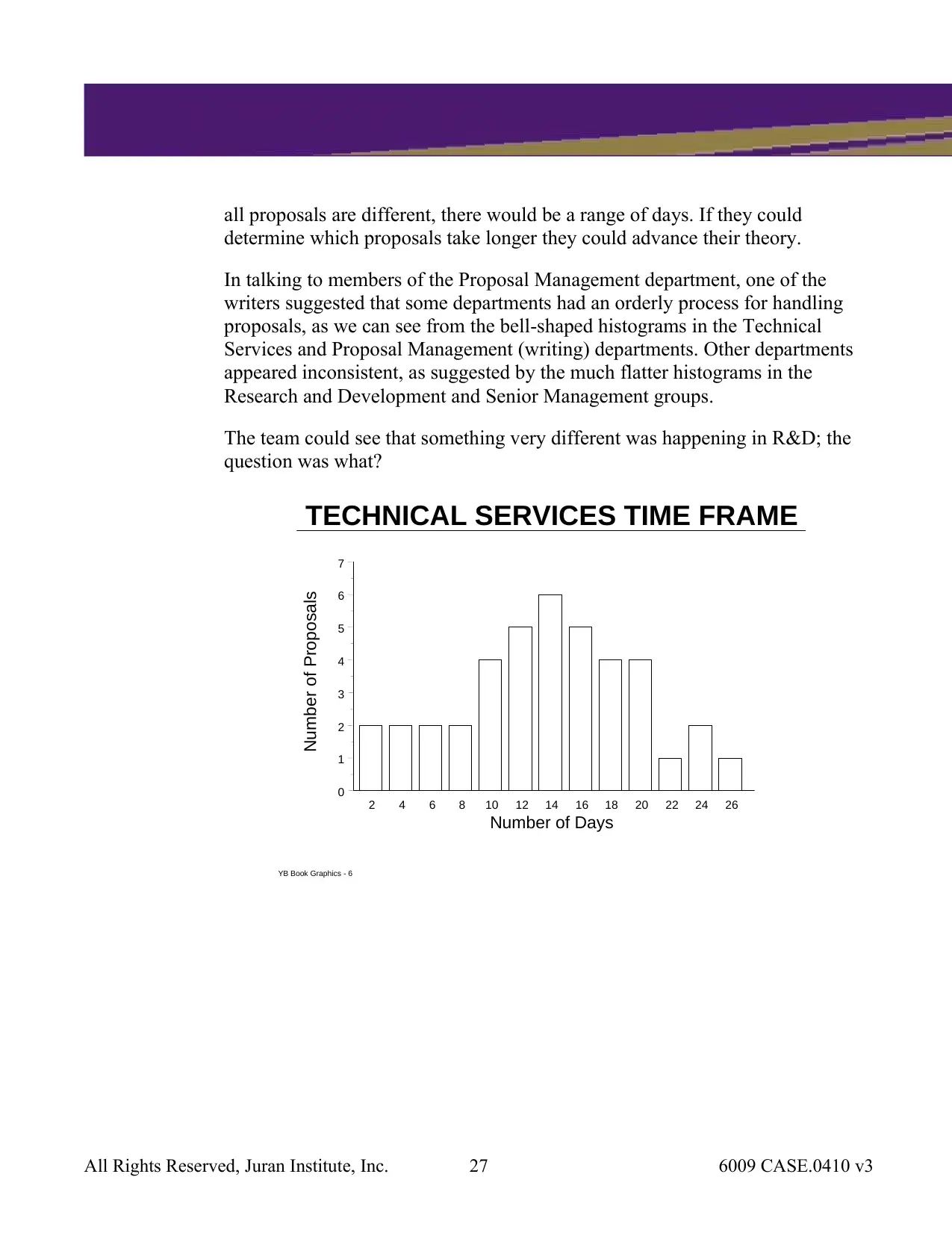
A DMAIC Six Sigma
Improvement Story
all proposals are different, there would be a range of days. If they could
determine which proposals take longer they could advance their theory.
In talking to members of the Proposal Management department, one of the
writers suggested that some departments had an orderly process for handling
proposals, as we can see from the bell-shaped histograms in the Technical
Services and Proposal Management (writing) departments. Other departments
appeared inconsistent, as suggested by the much flatter histograms in the
Research and Development and Senior Management groups.
The team could see that something very different was happening in R&D; the
question was what?
YB Book Graphics - 6 All Rights Reserved, Juran Institute, Inc.
TECHNICAL SERVICES TIME FRAME
2 4 6 8 10 12 14 16 18 20 22 24 26
0
1
2
3
4
5
6
7
Number of Days
Number of Proposals
All Rights Reserved, Juran Institute, Inc. 27 6009 CASE.0410 v3
Improvement Story
all proposals are different, there would be a range of days. If they could
determine which proposals take longer they could advance their theory.
In talking to members of the Proposal Management department, one of the
writers suggested that some departments had an orderly process for handling
proposals, as we can see from the bell-shaped histograms in the Technical
Services and Proposal Management (writing) departments. Other departments
appeared inconsistent, as suggested by the much flatter histograms in the
Research and Development and Senior Management groups.
The team could see that something very different was happening in R&D; the
question was what?
YB Book Graphics - 6 All Rights Reserved, Juran Institute, Inc.
TECHNICAL SERVICES TIME FRAME
2 4 6 8 10 12 14 16 18 20 22 24 26
0
1
2
3
4
5
6
7
Number of Days
Number of Proposals
All Rights Reserved, Juran Institute, Inc. 27 6009 CASE.0410 v3
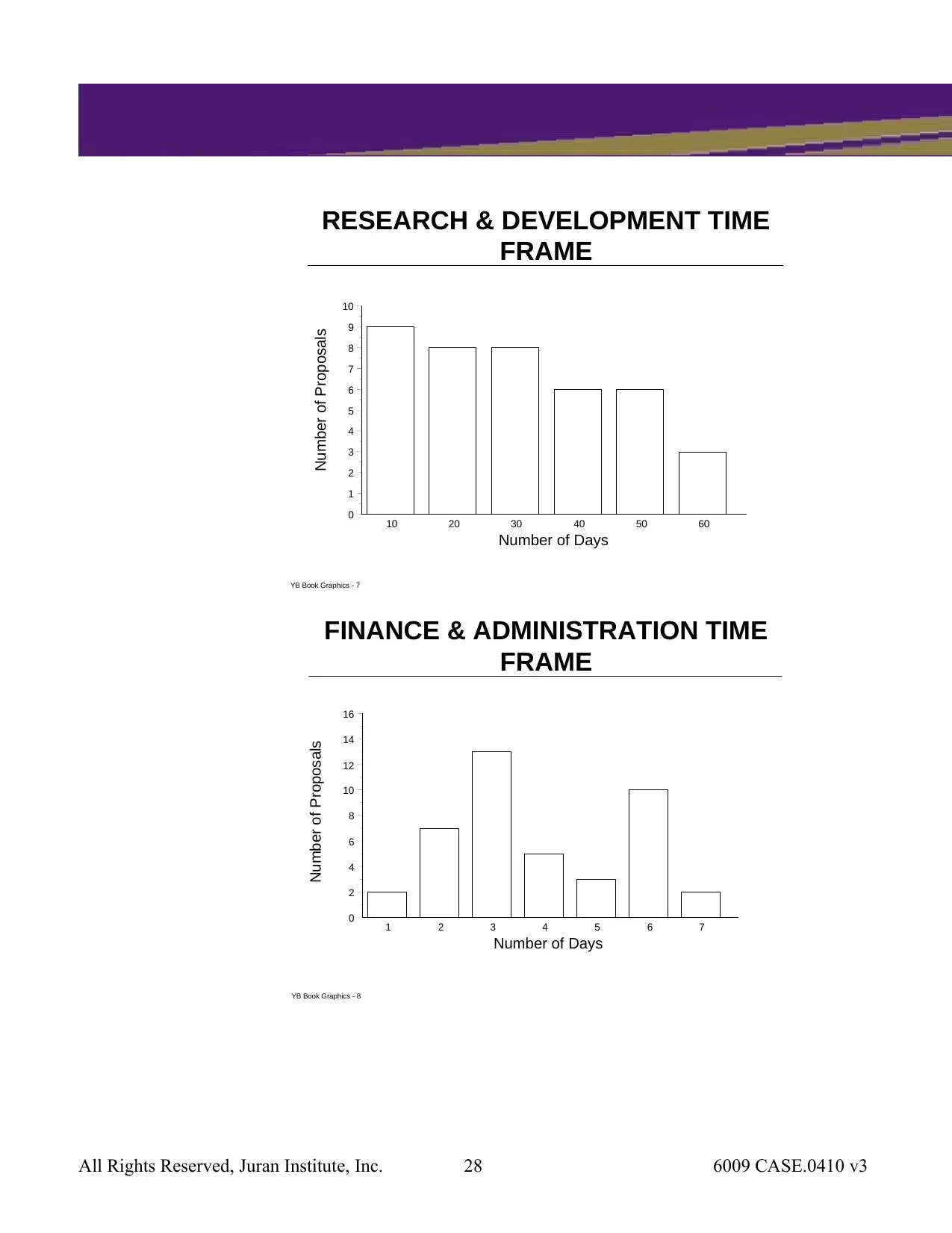
A DMAIC Six Sigma
Improvement Story
YB Book Graphics - 7 All Rights Reserved, Juran Institute, Inc.
RESEARCH & DEVELOPMENT TIME
FRAME
10 20 30 40 50 60
0
1
2
3
4
5
6
7
8
9
10
Number of Days
Number of Proposals
YB Book Graphics - 8 All Rights Reserved, Juran Institute, Inc.
FINANCE & ADMINISTRATION TIME
FRAME
1 2 3 4 5 6 7
0
2
4
6
8
10
12
14
16
Number of Days
Number of Proposals
All Rights Reserved, Juran Institute, Inc. 28 6009 CASE.0410 v3
Improvement Story
YB Book Graphics - 7 All Rights Reserved, Juran Institute, Inc.
RESEARCH & DEVELOPMENT TIME
FRAME
10 20 30 40 50 60
0
1
2
3
4
5
6
7
8
9
10
Number of Days
Number of Proposals
YB Book Graphics - 8 All Rights Reserved, Juran Institute, Inc.
FINANCE & ADMINISTRATION TIME
FRAME
1 2 3 4 5 6 7
0
2
4
6
8
10
12
14
16
Number of Days
Number of Proposals
All Rights Reserved, Juran Institute, Inc. 28 6009 CASE.0410 v3
Paraphrase This Document
Need a fresh take? Get an instant paraphrase of this document with our AI Paraphraser
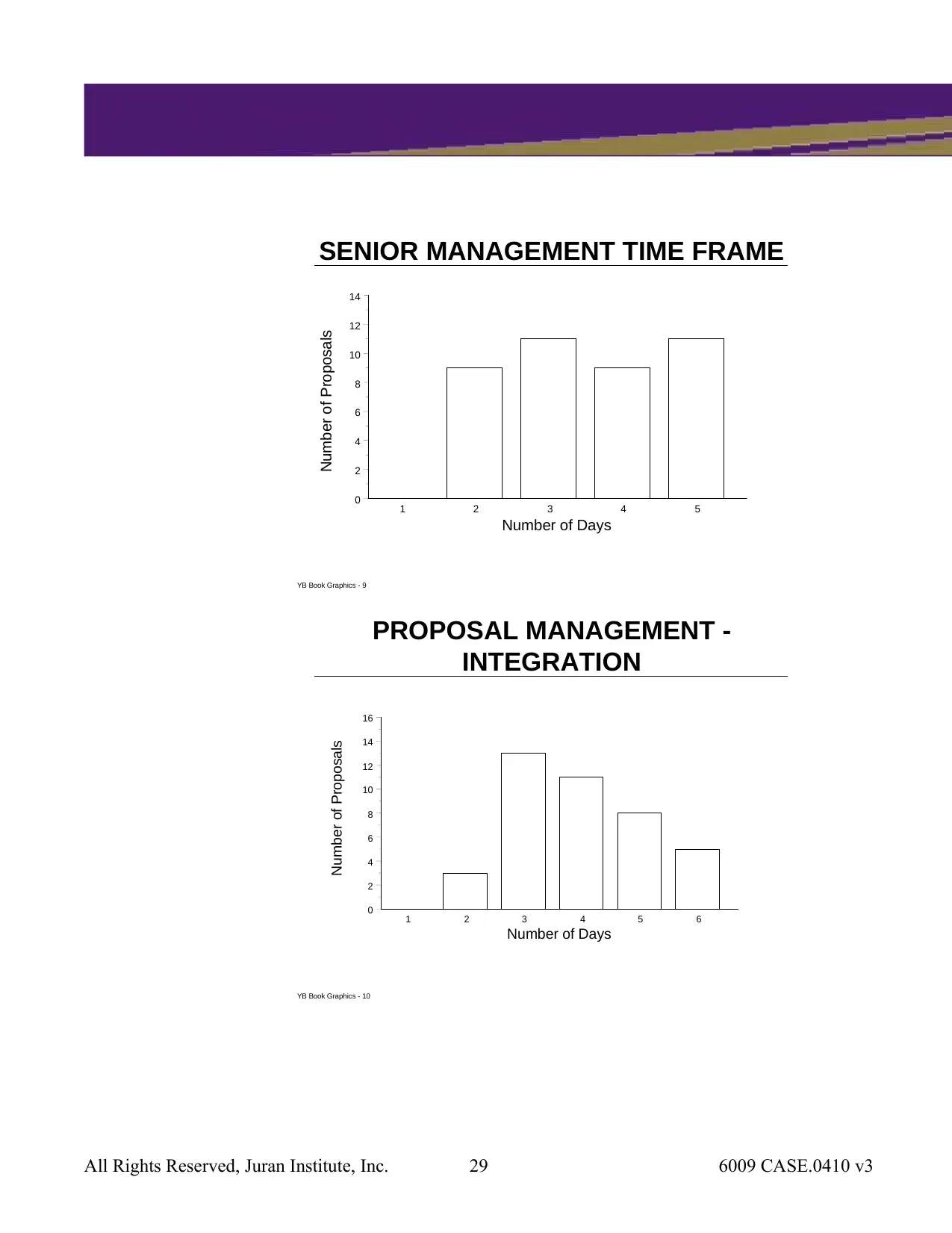
A DMAIC Six Sigma
Improvement Story
YB Book Graphics - 9 All Rights Reserved, Juran Institute, Inc.
SENIOR MANAGEMENT TIME FRAME
1 2 3 4 5
0
2
4
6
8
10
12
14
Number of Days
Number of Proposals
YB Book Graphics - 10 All Rights Reserved, Juran Institute, Inc.
PROPOSAL MANAGEMENT -
INTEGRATION
1 2 3 4 5 6
0
2
4
6
8
10
12
14
16
Number of Days
Number of Proposals
All Rights Reserved, Juran Institute, Inc. 29 6009 CASE.0410 v3
Improvement Story
YB Book Graphics - 9 All Rights Reserved, Juran Institute, Inc.
SENIOR MANAGEMENT TIME FRAME
1 2 3 4 5
0
2
4
6
8
10
12
14
Number of Days
Number of Proposals
YB Book Graphics - 10 All Rights Reserved, Juran Institute, Inc.
PROPOSAL MANAGEMENT -
INTEGRATION
1 2 3 4 5 6
0
2
4
6
8
10
12
14
16
Number of Days
Number of Proposals
All Rights Reserved, Juran Institute, Inc. 29 6009 CASE.0410 v3
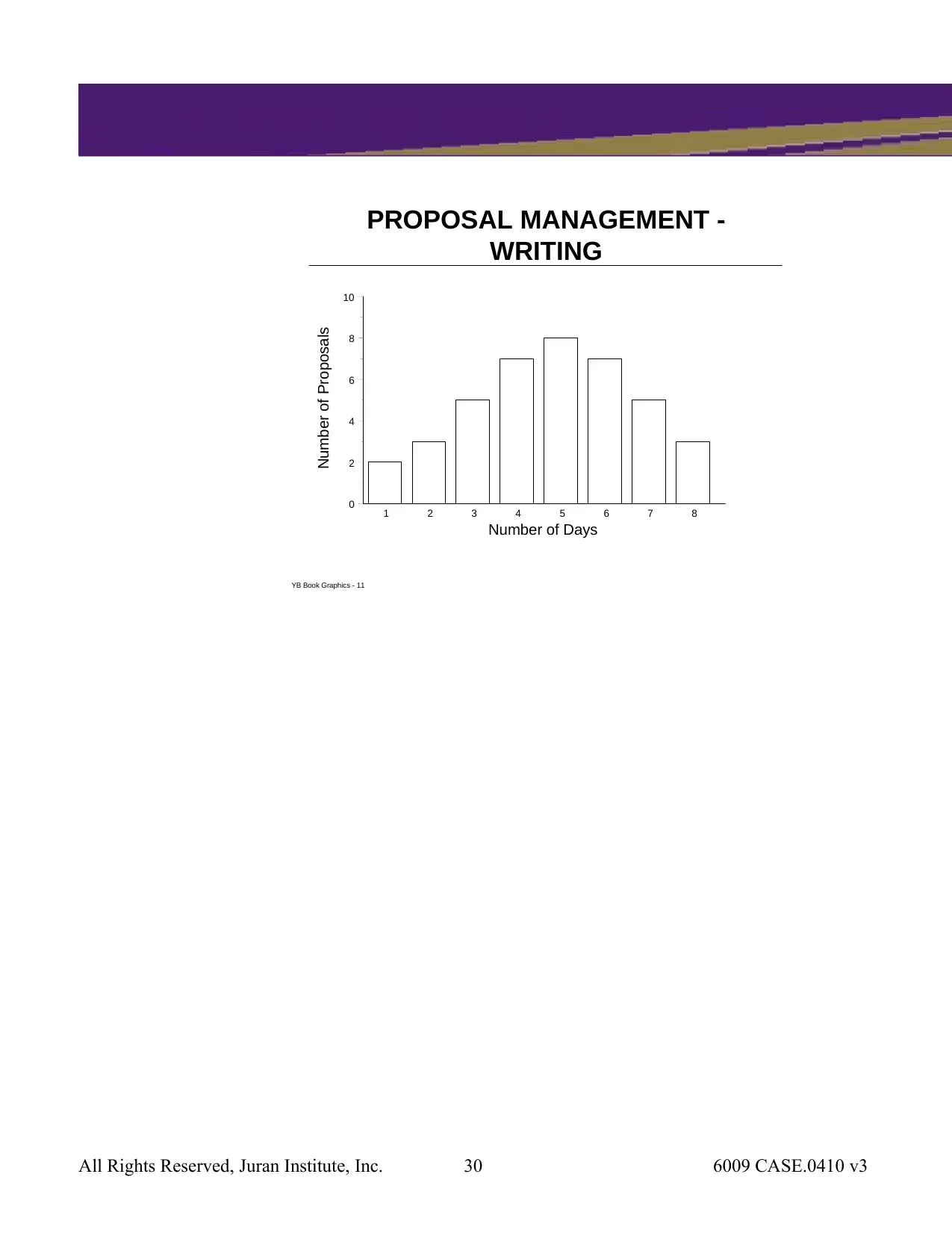
A DMAIC Six Sigma
Improvement Story
YB Book Graphics - 11 All Rights Reserved, Juran Institute, Inc.
PROPOSAL MANAGEMENT -
WRITING
1 2 3 4 5 6 7 8
0
2
4
6
8
10
Number of Days
Number of Proposals
All Rights Reserved, Juran Institute, Inc. 30 6009 CASE.0410 v3
Improvement Story
YB Book Graphics - 11 All Rights Reserved, Juran Institute, Inc.
PROPOSAL MANAGEMENT -
WRITING
1 2 3 4 5 6 7 8
0
2
4
6
8
10
Number of Days
Number of Proposals
All Rights Reserved, Juran Institute, Inc. 30 6009 CASE.0410 v3
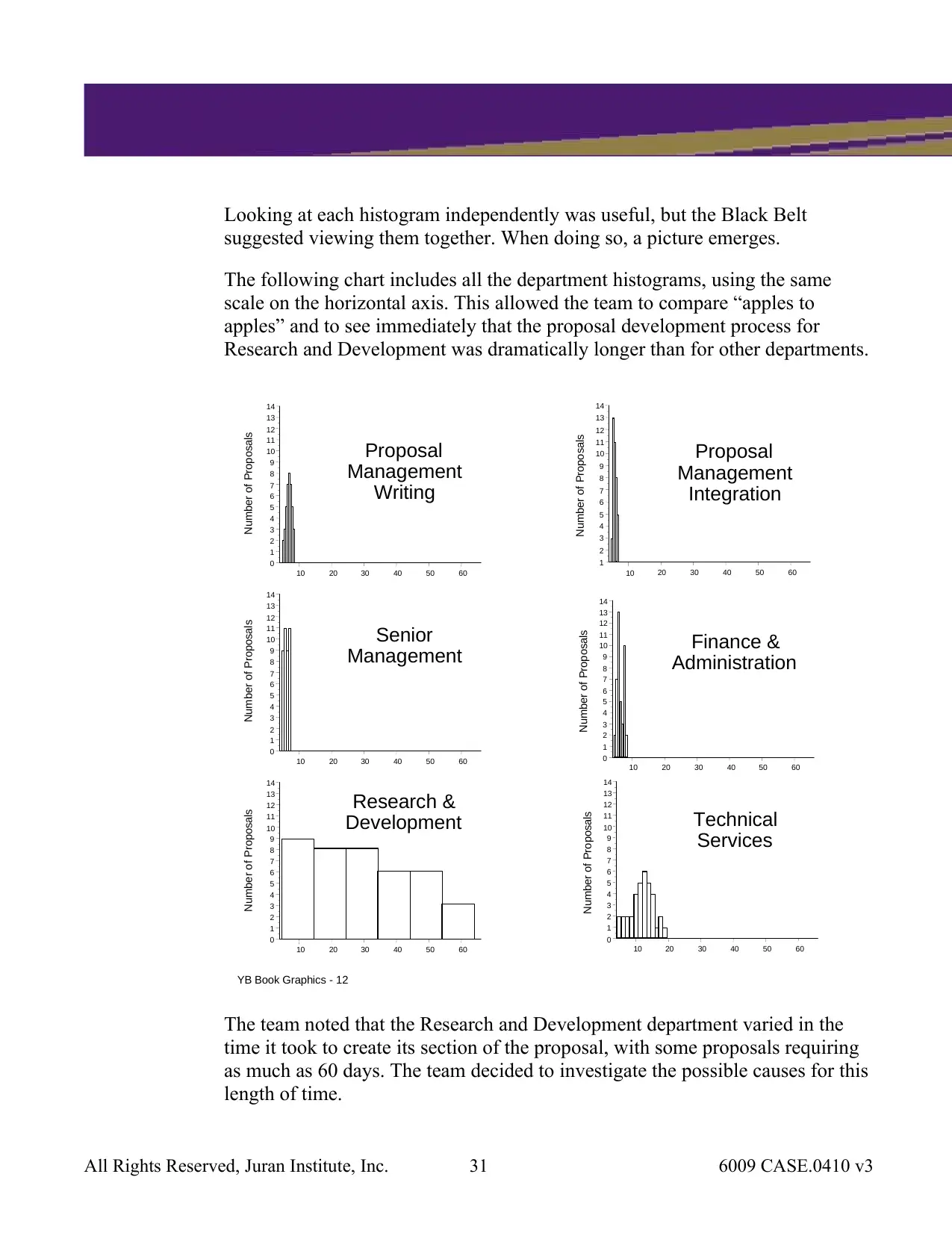
A DMAIC Six Sigma
Improvement Story
Looking at each histogram independently was useful, but the Black Belt
suggested viewing them together. When doing so, a picture emerges.
The following chart includes all the department histograms, using the same
scale on the horizontal axis. This allowed the team to compare “apples to
apples” and to see immediately that the proposal development process for
Research and Development was dramatically longer than for other departments.
YB Book Graphics - 12 All Rights Reserved, Juran Inst
10 20 30 40 50 60
0
1
2
3
4
5
6
7
8
9
10
11
12
13
14
Number of Proposals
Proposal
Management
Writing
10 20 30 40 50 60
0
1
2
3
4
5
6
7
8
9
10
11
12
13
14
Number of Proposals
Senior
Management
10 20 30 40 50 60
0
1
2
3
4
5
6
7
8
9
10
11
12
13
14
Number of Proposals Research &
Development
10 20 30 40 50 60
1
2
3
4
5
6
7
8
9
10
11
12
13
14
Number of Proposals
Proposal
Management
Integration
10 20 30 40 50 60
0
1
2
3
4
5
6
7
8
9
10
11
12
13
14
Number of Proposals
Finance &
Administration
10 20 30 40 50 60
0
1
2
3
4
5
6
7
8
9
10
11
12
13
14
Number of Proposals
Technical
Services
The team noted that the Research and Development department varied in the
time it took to create its section of the proposal, with some proposals requiring
as much as 60 days. The team decided to investigate the possible causes for this
length of time.
All Rights Reserved, Juran Institute, Inc. 31 6009 CASE.0410 v3
Improvement Story
Looking at each histogram independently was useful, but the Black Belt
suggested viewing them together. When doing so, a picture emerges.
The following chart includes all the department histograms, using the same
scale on the horizontal axis. This allowed the team to compare “apples to
apples” and to see immediately that the proposal development process for
Research and Development was dramatically longer than for other departments.
YB Book Graphics - 12 All Rights Reserved, Juran Inst
10 20 30 40 50 60
0
1
2
3
4
5
6
7
8
9
10
11
12
13
14
Number of Proposals
Proposal
Management
Writing
10 20 30 40 50 60
0
1
2
3
4
5
6
7
8
9
10
11
12
13
14
Number of Proposals
Senior
Management
10 20 30 40 50 60
0
1
2
3
4
5
6
7
8
9
10
11
12
13
14
Number of Proposals Research &
Development
10 20 30 40 50 60
1
2
3
4
5
6
7
8
9
10
11
12
13
14
Number of Proposals
Proposal
Management
Integration
10 20 30 40 50 60
0
1
2
3
4
5
6
7
8
9
10
11
12
13
14
Number of Proposals
Finance &
Administration
10 20 30 40 50 60
0
1
2
3
4
5
6
7
8
9
10
11
12
13
14
Number of Proposals
Technical
Services
The team noted that the Research and Development department varied in the
time it took to create its section of the proposal, with some proposals requiring
as much as 60 days. The team decided to investigate the possible causes for this
length of time.
All Rights Reserved, Juran Institute, Inc. 31 6009 CASE.0410 v3
Secure Best Marks with AI Grader
Need help grading? Try our AI Grader for instant feedback on your assignments.
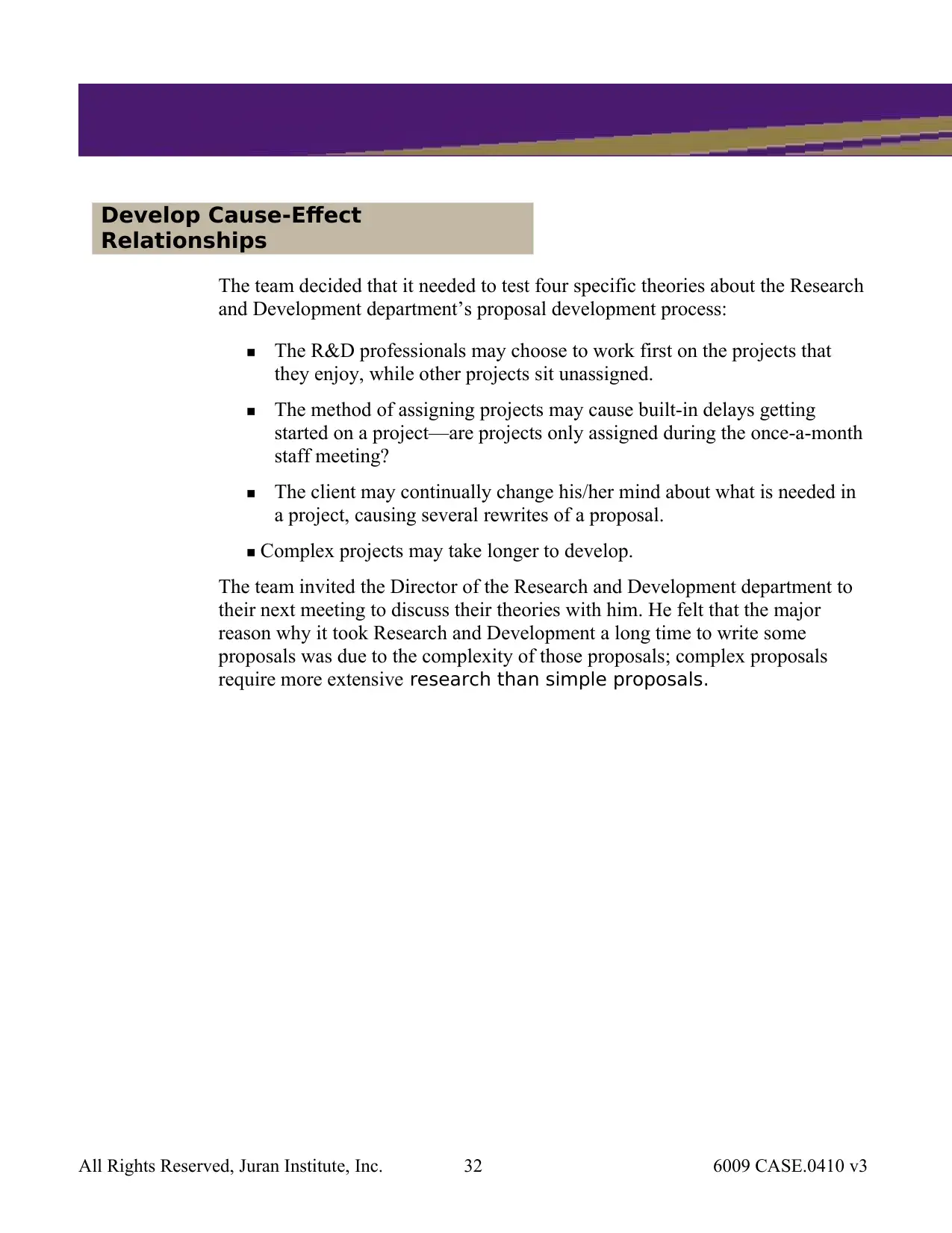
A DMAIC Six Sigma
Improvement Story
Develop Cause-Effect
Relationships
The team decided that it needed to test four specific theories about the Research
and Development department’s proposal development process:
The R&D professionals may choose to work first on the projects that
they enjoy, while other projects sit unassigned.
The method of assigning projects may cause built-in delays getting
started on a project—are projects only assigned during the once-a-month
staff meeting?
The client may continually change his/her mind about what is needed in
a project, causing several rewrites of a proposal.
Complex projects may take longer to develop.
The team invited the Director of the Research and Development department to
their next meeting to discuss their theories with him. He felt that the major
reason why it took Research and Development a long time to write some
proposals was due to the complexity of those proposals; complex proposals
require more extensive research than simple proposals.
All Rights Reserved, Juran Institute, Inc. 32 6009 CASE.0410 v3
Improvement Story
Develop Cause-Effect
Relationships
The team decided that it needed to test four specific theories about the Research
and Development department’s proposal development process:
The R&D professionals may choose to work first on the projects that
they enjoy, while other projects sit unassigned.
The method of assigning projects may cause built-in delays getting
started on a project—are projects only assigned during the once-a-month
staff meeting?
The client may continually change his/her mind about what is needed in
a project, causing several rewrites of a proposal.
Complex projects may take longer to develop.
The team invited the Director of the Research and Development department to
their next meeting to discuss their theories with him. He felt that the major
reason why it took Research and Development a long time to write some
proposals was due to the complexity of those proposals; complex proposals
require more extensive research than simple proposals.
All Rights Reserved, Juran Institute, Inc. 32 6009 CASE.0410 v3
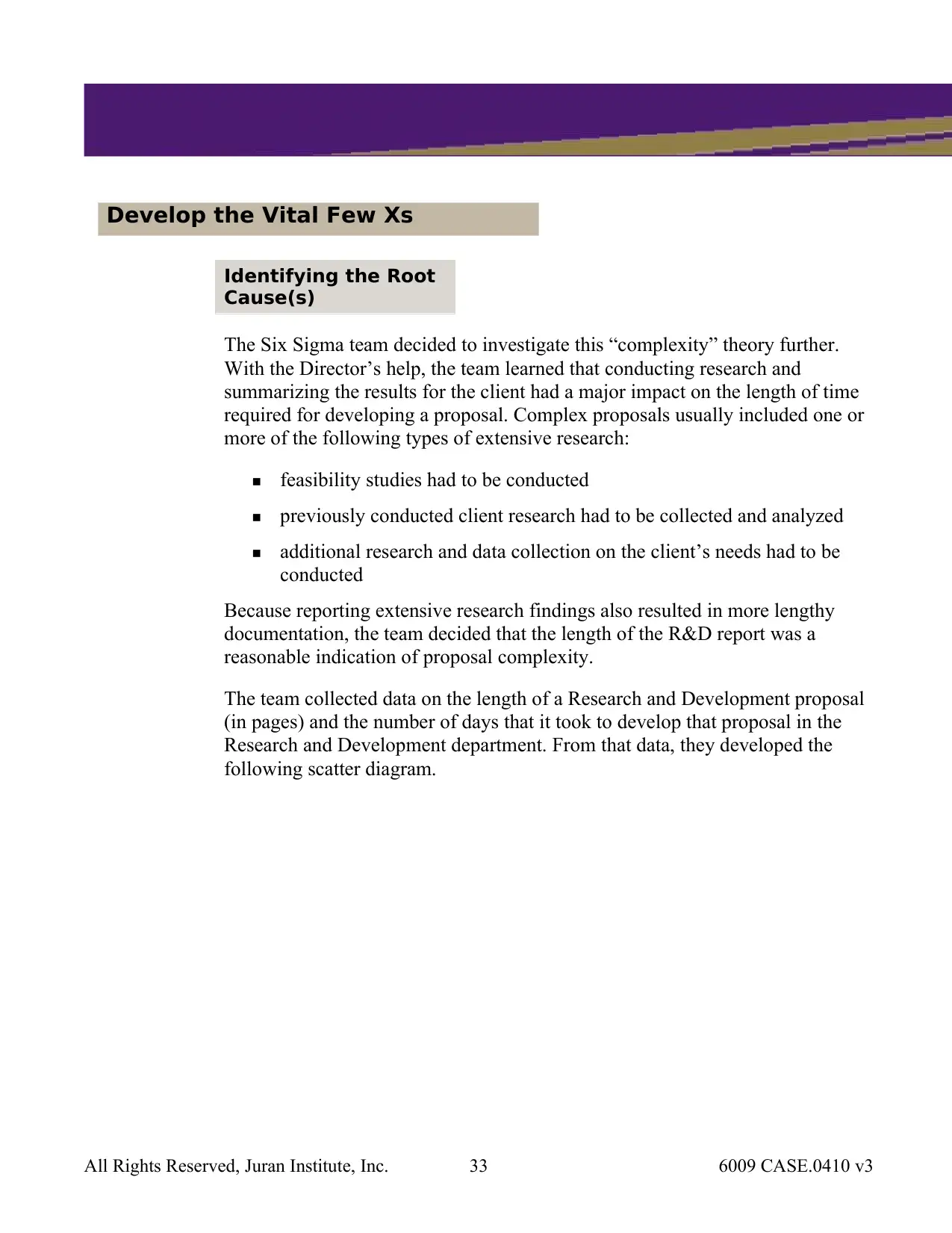
A DMAIC Six Sigma
Improvement Story
Develop the Vital Few Xs
Identifying the Root
Cause(s)
The Six Sigma team decided to investigate this “complexity” theory further.
With the Director’s help, the team learned that conducting research and
summarizing the results for the client had a major impact on the length of time
required for developing a proposal. Complex proposals usually included one or
more of the following types of extensive research:
feasibility studies had to be conducted
previously conducted client research had to be collected and analyzed
additional research and data collection on the client’s needs had to be
conducted
Because reporting extensive research findings also resulted in more lengthy
documentation, the team decided that the length of the R&D report was a
reasonable indication of proposal complexity.
The team collected data on the length of a Research and Development proposal
(in pages) and the number of days that it took to develop that proposal in the
Research and Development department. From that data, they developed the
following scatter diagram.
All Rights Reserved, Juran Institute, Inc. 33 6009 CASE.0410 v3
Improvement Story
Develop the Vital Few Xs
Identifying the Root
Cause(s)
The Six Sigma team decided to investigate this “complexity” theory further.
With the Director’s help, the team learned that conducting research and
summarizing the results for the client had a major impact on the length of time
required for developing a proposal. Complex proposals usually included one or
more of the following types of extensive research:
feasibility studies had to be conducted
previously conducted client research had to be collected and analyzed
additional research and data collection on the client’s needs had to be
conducted
Because reporting extensive research findings also resulted in more lengthy
documentation, the team decided that the length of the R&D report was a
reasonable indication of proposal complexity.
The team collected data on the length of a Research and Development proposal
(in pages) and the number of days that it took to develop that proposal in the
Research and Development department. From that data, they developed the
following scatter diagram.
All Rights Reserved, Juran Institute, Inc. 33 6009 CASE.0410 v3
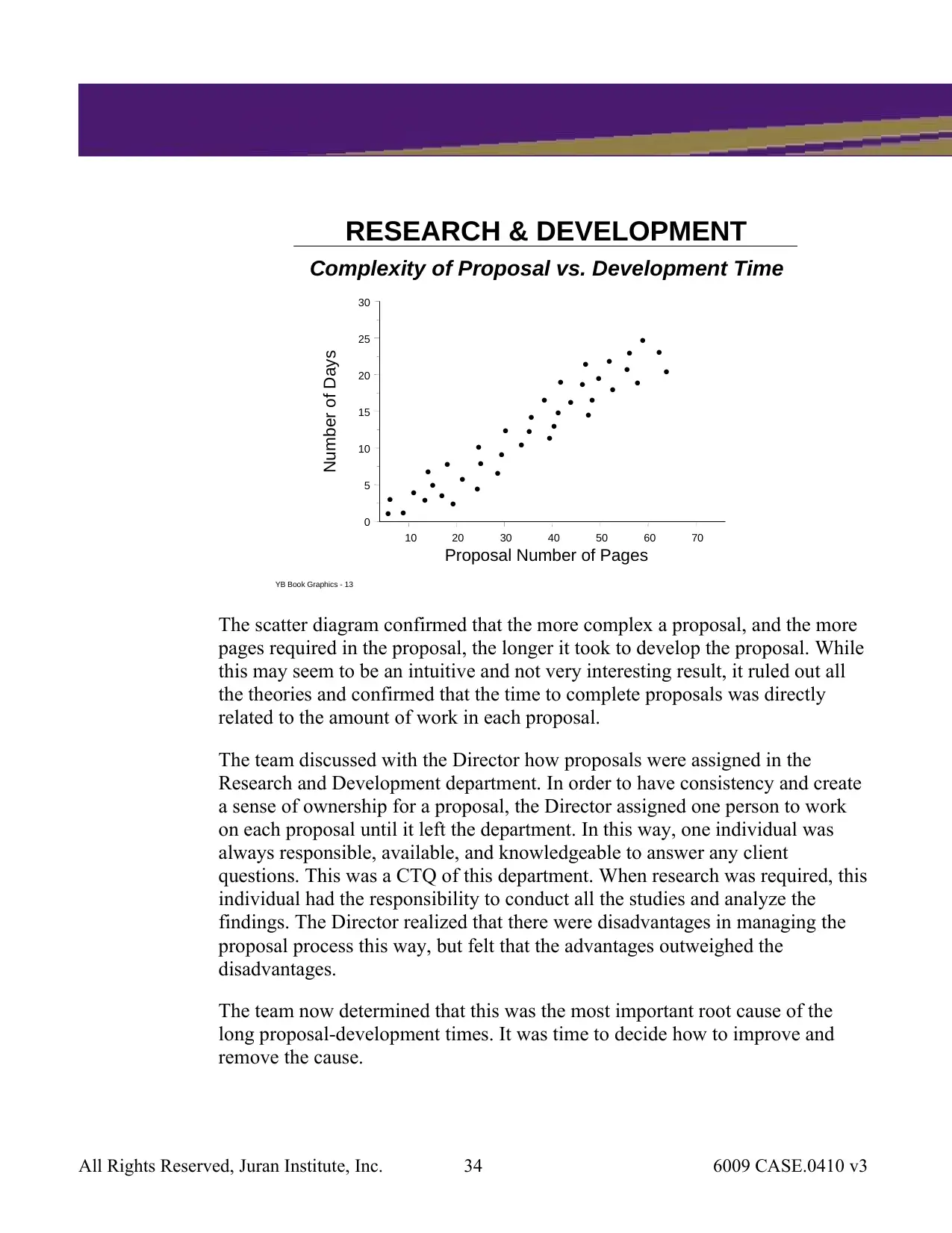
A DMAIC Six Sigma
Improvement Story
YB Book Graphics - 13 All Rights Reserved, Juran Institute, Inc.
RESEARCH & DEVELOPMENT
Complexity of Proposal vs. Development Time
10 20 30 40 50 60 70
0
5
10
15
20
25
30
Proposal Number of Pages
Number of Days
The scatter diagram confirmed that the more complex a proposal, and the more
pages required in the proposal, the longer it took to develop the proposal. While
this may seem to be an intuitive and not very interesting result, it ruled out all
the theories and confirmed that the time to complete proposals was directly
related to the amount of work in each proposal.
The team discussed with the Director how proposals were assigned in the
Research and Development department. In order to have consistency and create
a sense of ownership for a proposal, the Director assigned one person to work
on each proposal until it left the department. In this way, one individual was
always responsible, available, and knowledgeable to answer any client
questions. This was a CTQ of this department. When research was required, this
individual had the responsibility to conduct all the studies and analyze the
findings. The Director realized that there were disadvantages in managing the
proposal process this way, but felt that the advantages outweighed the
disadvantages.
The team now determined that this was the most important root cause of the
long proposal-development times. It was time to decide how to improve and
remove the cause.
All Rights Reserved, Juran Institute, Inc. 34 6009 CASE.0410 v3
Improvement Story
YB Book Graphics - 13 All Rights Reserved, Juran Institute, Inc.
RESEARCH & DEVELOPMENT
Complexity of Proposal vs. Development Time
10 20 30 40 50 60 70
0
5
10
15
20
25
30
Proposal Number of Pages
Number of Days
The scatter diagram confirmed that the more complex a proposal, and the more
pages required in the proposal, the longer it took to develop the proposal. While
this may seem to be an intuitive and not very interesting result, it ruled out all
the theories and confirmed that the time to complete proposals was directly
related to the amount of work in each proposal.
The team discussed with the Director how proposals were assigned in the
Research and Development department. In order to have consistency and create
a sense of ownership for a proposal, the Director assigned one person to work
on each proposal until it left the department. In this way, one individual was
always responsible, available, and knowledgeable to answer any client
questions. This was a CTQ of this department. When research was required, this
individual had the responsibility to conduct all the studies and analyze the
findings. The Director realized that there were disadvantages in managing the
proposal process this way, but felt that the advantages outweighed the
disadvantages.
The team now determined that this was the most important root cause of the
long proposal-development times. It was time to decide how to improve and
remove the cause.
All Rights Reserved, Juran Institute, Inc. 34 6009 CASE.0410 v3
Paraphrase This Document
Need a fresh take? Get an instant paraphrase of this document with our AI Paraphraser
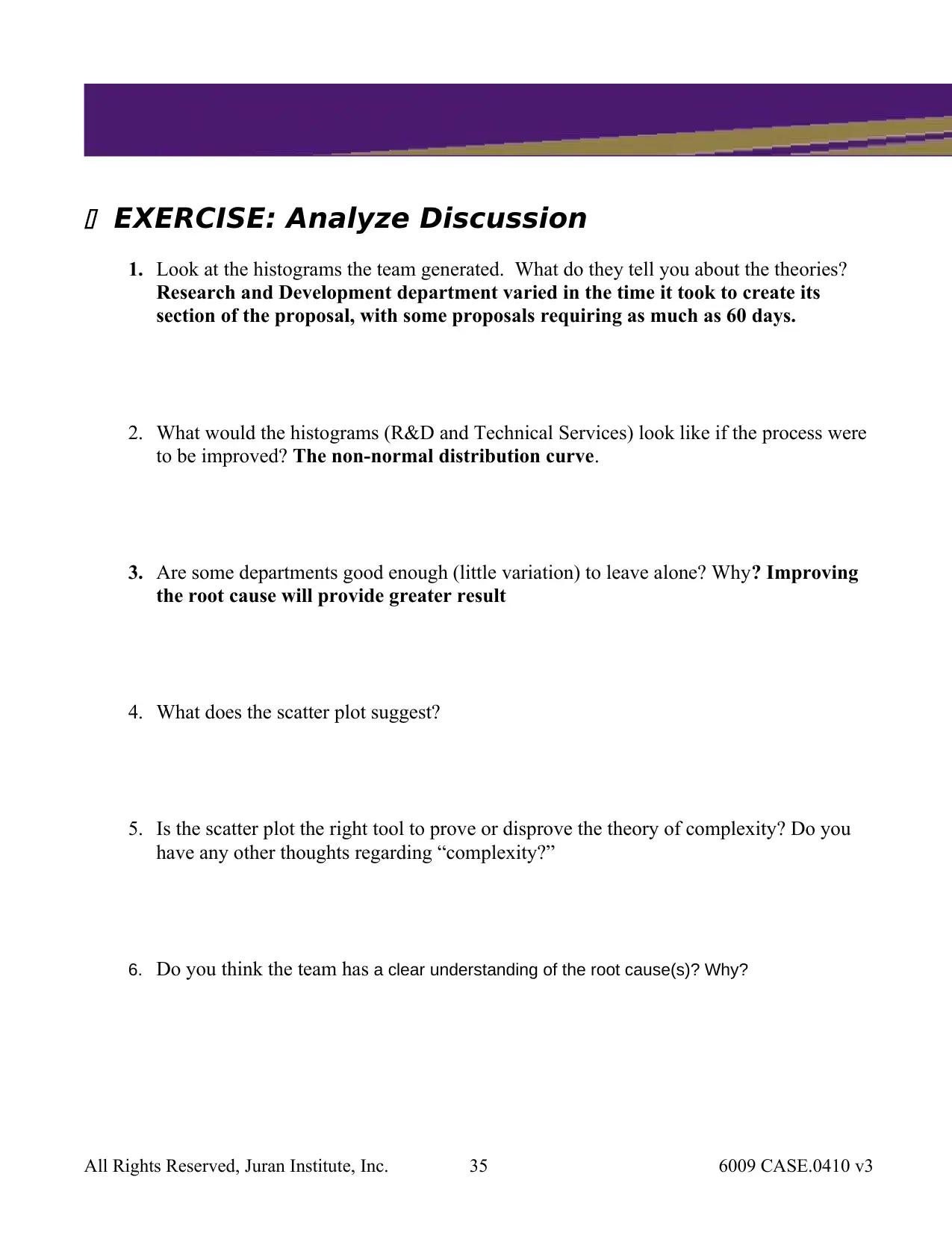
A DMAIC Six Sigma
Improvement Story
EXERCISE: Analyze Discussion
1. Look at the histograms the team generated. What do they tell you about the theories?
Research and Development department varied in the time it took to create its
section of the proposal, with some proposals requiring as much as 60 days.
2. What would the histograms (R&D and Technical Services) look like if the process were
to be improved? The non-normal distribution curve.
3. Are some departments good enough (little variation) to leave alone? Why? Improving
the root cause will provide greater result
4. What does the scatter plot suggest?
5. Is the scatter plot the right tool to prove or disprove the theory of complexity? Do you
have any other thoughts regarding “complexity?”
6. Do you think the team has a clear understanding of the root cause(s)? Why?
All Rights Reserved, Juran Institute, Inc. 35 6009 CASE.0410 v3
Improvement Story
EXERCISE: Analyze Discussion
1. Look at the histograms the team generated. What do they tell you about the theories?
Research and Development department varied in the time it took to create its
section of the proposal, with some proposals requiring as much as 60 days.
2. What would the histograms (R&D and Technical Services) look like if the process were
to be improved? The non-normal distribution curve.
3. Are some departments good enough (little variation) to leave alone? Why? Improving
the root cause will provide greater result
4. What does the scatter plot suggest?
5. Is the scatter plot the right tool to prove or disprove the theory of complexity? Do you
have any other thoughts regarding “complexity?”
6. Do you think the team has a clear understanding of the root cause(s)? Why?
All Rights Reserved, Juran Institute, Inc. 35 6009 CASE.0410 v3
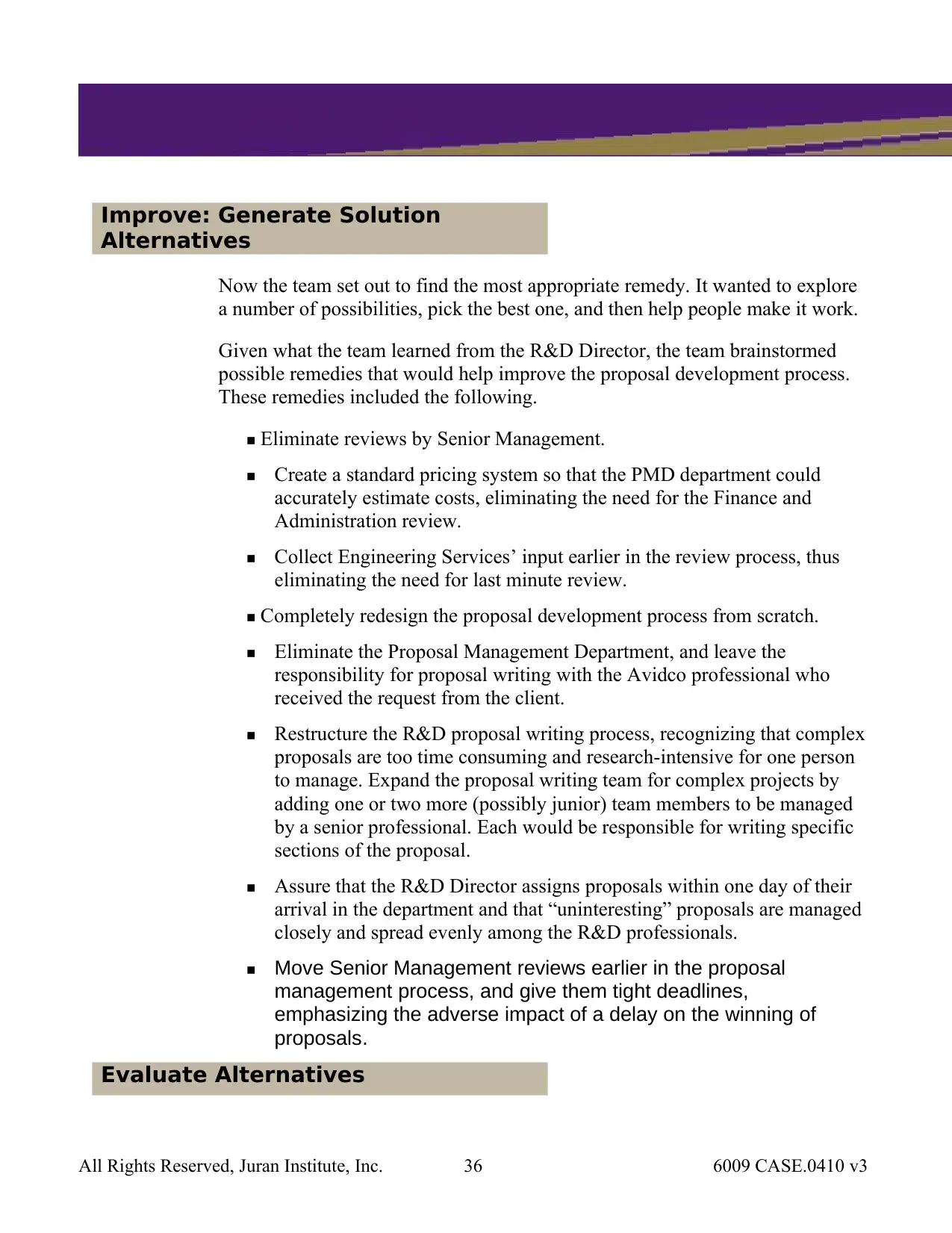
A DMAIC Six Sigma
Improvement Story
Improve: Generate Solution
Alternatives
Now the team set out to find the most appropriate remedy. It wanted to explore
a number of possibilities, pick the best one, and then help people make it work.
Given what the team learned from the R&D Director, the team brainstormed
possible remedies that would help improve the proposal development process.
These remedies included the following.
Eliminate reviews by Senior Management.
Create a standard pricing system so that the PMD department could
accurately estimate costs, eliminating the need for the Finance and
Administration review.
Collect Engineering Services’ input earlier in the review process, thus
eliminating the need for last minute review.
Completely redesign the proposal development process from scratch.
Eliminate the Proposal Management Department, and leave the
responsibility for proposal writing with the Avidco professional who
received the request from the client.
Restructure the R&D proposal writing process, recognizing that complex
proposals are too time consuming and research-intensive for one person
to manage. Expand the proposal writing team for complex projects by
adding one or two more (possibly junior) team members to be managed
by a senior professional. Each would be responsible for writing specific
sections of the proposal.
Assure that the R&D Director assigns proposals within one day of their
arrival in the department and that “uninteresting” proposals are managed
closely and spread evenly among the R&D professionals.
Move Senior Management reviews earlier in the proposal
management process, and give them tight deadlines,
emphasizing the adverse impact of a delay on the winning of
proposals.
Evaluate Alternatives
All Rights Reserved, Juran Institute, Inc. 36 6009 CASE.0410 v3
Improvement Story
Improve: Generate Solution
Alternatives
Now the team set out to find the most appropriate remedy. It wanted to explore
a number of possibilities, pick the best one, and then help people make it work.
Given what the team learned from the R&D Director, the team brainstormed
possible remedies that would help improve the proposal development process.
These remedies included the following.
Eliminate reviews by Senior Management.
Create a standard pricing system so that the PMD department could
accurately estimate costs, eliminating the need for the Finance and
Administration review.
Collect Engineering Services’ input earlier in the review process, thus
eliminating the need for last minute review.
Completely redesign the proposal development process from scratch.
Eliminate the Proposal Management Department, and leave the
responsibility for proposal writing with the Avidco professional who
received the request from the client.
Restructure the R&D proposal writing process, recognizing that complex
proposals are too time consuming and research-intensive for one person
to manage. Expand the proposal writing team for complex projects by
adding one or two more (possibly junior) team members to be managed
by a senior professional. Each would be responsible for writing specific
sections of the proposal.
Assure that the R&D Director assigns proposals within one day of their
arrival in the department and that “uninteresting” proposals are managed
closely and spread evenly among the R&D professionals.
Move Senior Management reviews earlier in the proposal
management process, and give them tight deadlines,
emphasizing the adverse impact of a delay on the winning of
proposals.
Evaluate Alternatives
All Rights Reserved, Juran Institute, Inc. 36 6009 CASE.0410 v3
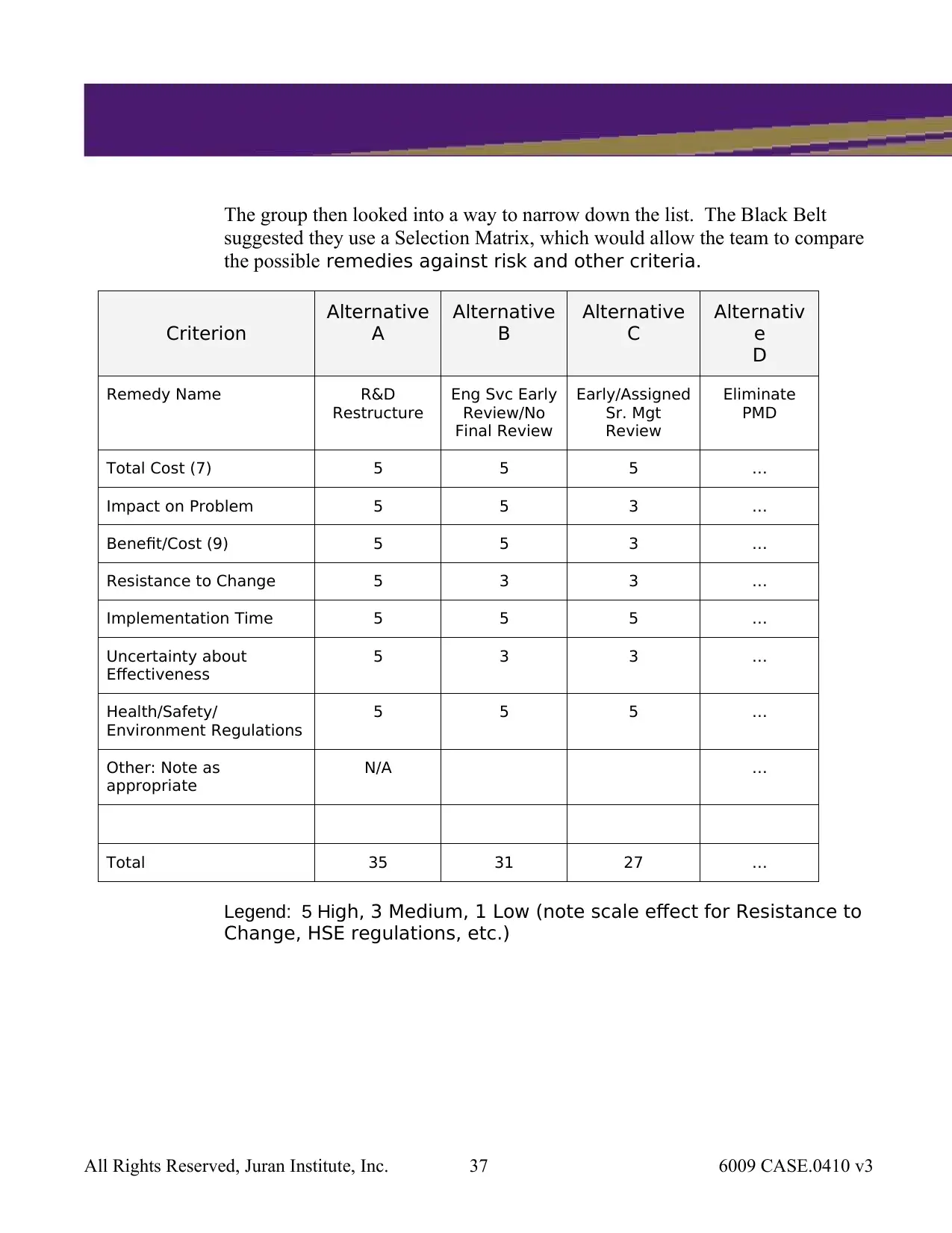
A DMAIC Six Sigma
Improvement Story
The group then looked into a way to narrow down the list. The Black Belt
suggested they use a Selection Matrix, which would allow the team to compare
the possible remedies against risk and other criteria.
Criterion
Alternative
A
Alternative
B
Alternative
C
Alternativ
e
D
Remedy Name R&D
Restructure
Eng Svc Early
Review/No
Final Review
Early/Assigned
Sr. Mgt
Review
Eliminate
PMD
Total Cost (7) 5 5 5 …
Impact on Problem 5 5 3 …
Benefit/Cost (9) 5 5 3 …
Resistance to Change 5 3 3 …
Implementation Time 5 5 5 …
Uncertainty about
Effectiveness
5 3 3 …
Health/Safety/
Environment Regulations
5 5 5 …
Other: Note as
appropriate
N/A …
Total 35 31 27 …
Legend: 5 High, 3 Medium, 1 Low (note scale effect for Resistance to
Change, HSE regulations, etc.)
All Rights Reserved, Juran Institute, Inc. 37 6009 CASE.0410 v3
Improvement Story
The group then looked into a way to narrow down the list. The Black Belt
suggested they use a Selection Matrix, which would allow the team to compare
the possible remedies against risk and other criteria.
Criterion
Alternative
A
Alternative
B
Alternative
C
Alternativ
e
D
Remedy Name R&D
Restructure
Eng Svc Early
Review/No
Final Review
Early/Assigned
Sr. Mgt
Review
Eliminate
PMD
Total Cost (7) 5 5 5 …
Impact on Problem 5 5 3 …
Benefit/Cost (9) 5 5 3 …
Resistance to Change 5 3 3 …
Implementation Time 5 5 5 …
Uncertainty about
Effectiveness
5 3 3 …
Health/Safety/
Environment Regulations
5 5 5 …
Other: Note as
appropriate
N/A …
Total 35 31 27 …
Legend: 5 High, 3 Medium, 1 Low (note scale effect for Resistance to
Change, HSE regulations, etc.)
All Rights Reserved, Juran Institute, Inc. 37 6009 CASE.0410 v3
Secure Best Marks with AI Grader
Need help grading? Try our AI Grader for instant feedback on your assignments.
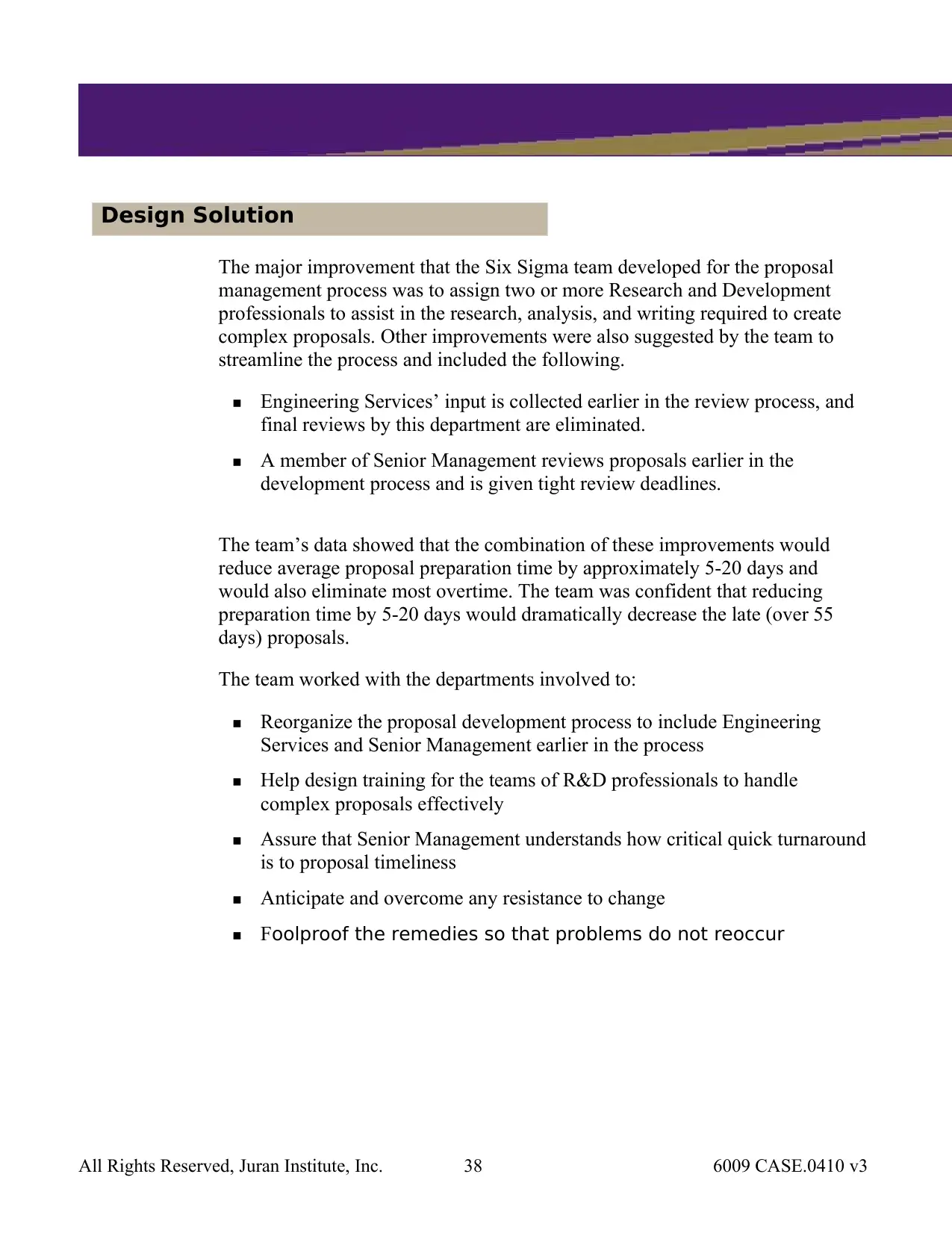
A DMAIC Six Sigma
Improvement Story
Design Solution
The major improvement that the Six Sigma team developed for the proposal
management process was to assign two or more Research and Development
professionals to assist in the research, analysis, and writing required to create
complex proposals. Other improvements were also suggested by the team to
streamline the process and included the following.
Engineering Services’ input is collected earlier in the review process, and
final reviews by this department are eliminated.
A member of Senior Management reviews proposals earlier in the
development process and is given tight review deadlines.
The team’s data showed that the combination of these improvements would
reduce average proposal preparation time by approximately 5-20 days and
would also eliminate most overtime. The team was confident that reducing
preparation time by 5-20 days would dramatically decrease the late (over 55
days) proposals.
The team worked with the departments involved to:
Reorganize the proposal development process to include Engineering
Services and Senior Management earlier in the process
Help design training for the teams of R&D professionals to handle
complex proposals effectively
Assure that Senior Management understands how critical quick turnaround
is to proposal timeliness
Anticipate and overcome any resistance to change
Foolproof the remedies so that problems do not reoccur
All Rights Reserved, Juran Institute, Inc. 38 6009 CASE.0410 v3
Improvement Story
Design Solution
The major improvement that the Six Sigma team developed for the proposal
management process was to assign two or more Research and Development
professionals to assist in the research, analysis, and writing required to create
complex proposals. Other improvements were also suggested by the team to
streamline the process and included the following.
Engineering Services’ input is collected earlier in the review process, and
final reviews by this department are eliminated.
A member of Senior Management reviews proposals earlier in the
development process and is given tight review deadlines.
The team’s data showed that the combination of these improvements would
reduce average proposal preparation time by approximately 5-20 days and
would also eliminate most overtime. The team was confident that reducing
preparation time by 5-20 days would dramatically decrease the late (over 55
days) proposals.
The team worked with the departments involved to:
Reorganize the proposal development process to include Engineering
Services and Senior Management earlier in the process
Help design training for the teams of R&D professionals to handle
complex proposals effectively
Assure that Senior Management understands how critical quick turnaround
is to proposal timeliness
Anticipate and overcome any resistance to change
Foolproof the remedies so that problems do not reoccur
All Rights Reserved, Juran Institute, Inc. 38 6009 CASE.0410 v3
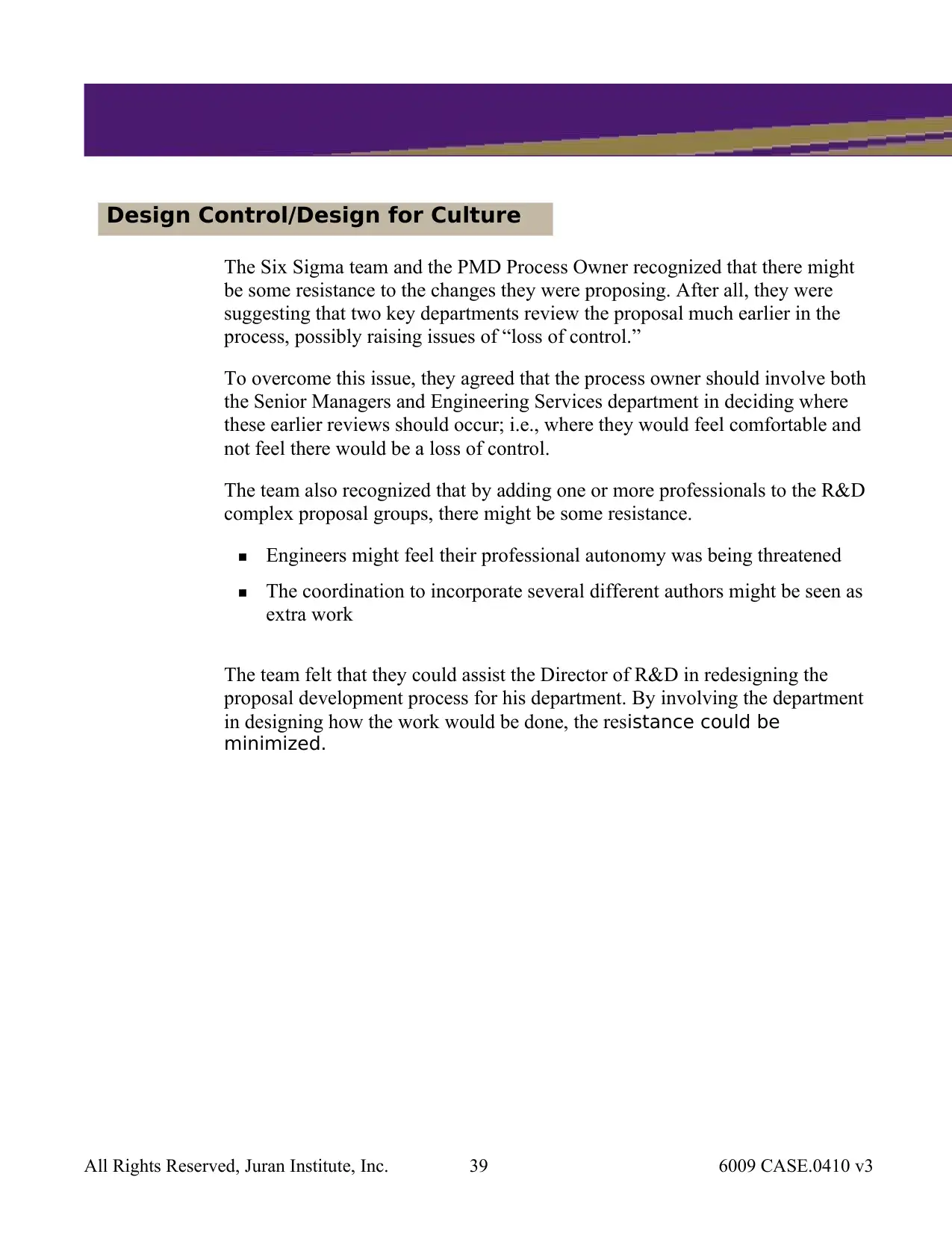
A DMAIC Six Sigma
Improvement Story
Design Control/Design for Culture
The Six Sigma team and the PMD Process Owner recognized that there might
be some resistance to the changes they were proposing. After all, they were
suggesting that two key departments review the proposal much earlier in the
process, possibly raising issues of “loss of control.”
To overcome this issue, they agreed that the process owner should involve both
the Senior Managers and Engineering Services department in deciding where
these earlier reviews should occur; i.e., where they would feel comfortable and
not feel there would be a loss of control.
The team also recognized that by adding one or more professionals to the R&D
complex proposal groups, there might be some resistance.
Engineers might feel their professional autonomy was being threatened
The coordination to incorporate several different authors might be seen as
extra work
The team felt that they could assist the Director of R&D in redesigning the
proposal development process for his department. By involving the department
in designing how the work would be done, the resistance could be
minimized.
All Rights Reserved, Juran Institute, Inc. 39 6009 CASE.0410 v3
Improvement Story
Design Control/Design for Culture
The Six Sigma team and the PMD Process Owner recognized that there might
be some resistance to the changes they were proposing. After all, they were
suggesting that two key departments review the proposal much earlier in the
process, possibly raising issues of “loss of control.”
To overcome this issue, they agreed that the process owner should involve both
the Senior Managers and Engineering Services department in deciding where
these earlier reviews should occur; i.e., where they would feel comfortable and
not feel there would be a loss of control.
The team also recognized that by adding one or more professionals to the R&D
complex proposal groups, there might be some resistance.
Engineers might feel their professional autonomy was being threatened
The coordination to incorporate several different authors might be seen as
extra work
The team felt that they could assist the Director of R&D in redesigning the
proposal development process for his department. By involving the department
in designing how the work would be done, the resistance could be
minimized.
All Rights Reserved, Juran Institute, Inc. 39 6009 CASE.0410 v3
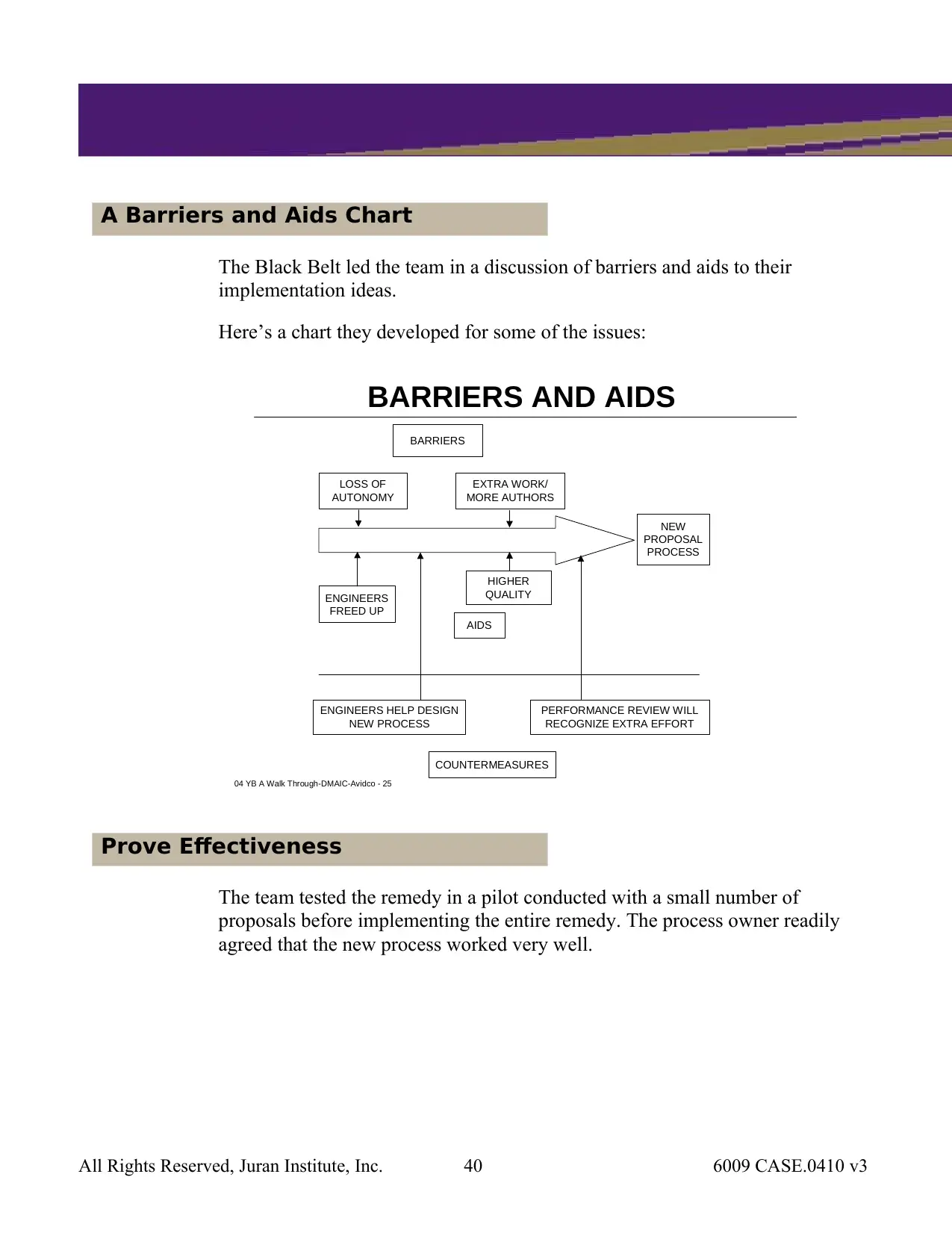
A DMAIC Six Sigma
Improvement Story
A Barriers and Aids Chart
The Black Belt led the team in a discussion of barriers and aids to their
implementation ideas.
Here’s a chart they developed for some of the issues:
04 YB A Walk Through-DMAIC-Avidco - 25 All Rights Reserved, Juran Institute, Inc.
BARRIERS AND AIDS
NEW
PROPOSAL
PROCESS
LOSS OF
AUTONOMY
AIDS
COUNTERMEASURES
ENGINEERS
FREED UP
ENGINEERS HELP DESIGN
NEW PROCESS
EXTRA WORK/
MORE AUTHORS
HIGHER
QUALITY
PERFORMANCE REVIEW WILL
RECOGNIZE EXTRA EFFORT
BARRIERS
Prove Effectiveness
The team tested the remedy in a pilot conducted with a small number of
proposals before implementing the entire remedy. The process owner readily
agreed that the new process worked very well.
All Rights Reserved, Juran Institute, Inc. 40 6009 CASE.0410 v3
Improvement Story
A Barriers and Aids Chart
The Black Belt led the team in a discussion of barriers and aids to their
implementation ideas.
Here’s a chart they developed for some of the issues:
04 YB A Walk Through-DMAIC-Avidco - 25 All Rights Reserved, Juran Institute, Inc.
BARRIERS AND AIDS
NEW
PROPOSAL
PROCESS
LOSS OF
AUTONOMY
AIDS
COUNTERMEASURES
ENGINEERS
FREED UP
ENGINEERS HELP DESIGN
NEW PROCESS
EXTRA WORK/
MORE AUTHORS
HIGHER
QUALITY
PERFORMANCE REVIEW WILL
RECOGNIZE EXTRA EFFORT
BARRIERS
Prove Effectiveness
The team tested the remedy in a pilot conducted with a small number of
proposals before implementing the entire remedy. The process owner readily
agreed that the new process worked very well.
All Rights Reserved, Juran Institute, Inc. 40 6009 CASE.0410 v3
Paraphrase This Document
Need a fresh take? Get an instant paraphrase of this document with our AI Paraphraser
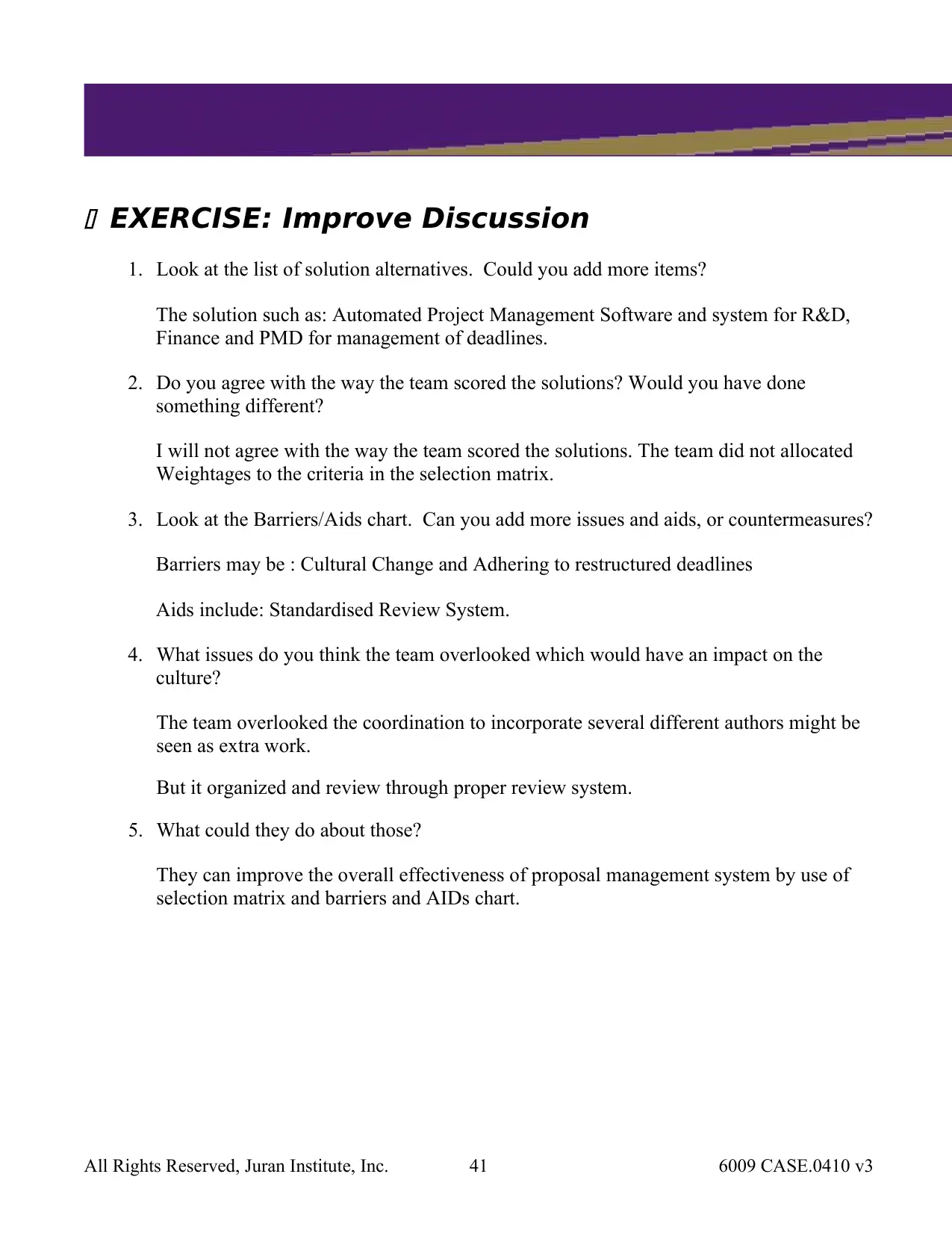
A DMAIC Six Sigma
Improvement Story
EXERCISE: Improve Discussion
1. Look at the list of solution alternatives. Could you add more items?
The solution such as: Automated Project Management Software and system for R&D,
Finance and PMD for management of deadlines.
2. Do you agree with the way the team scored the solutions? Would you have done
something different?
I will not agree with the way the team scored the solutions. The team did not allocated
Weightages to the criteria in the selection matrix.
3. Look at the Barriers/Aids chart. Can you add more issues and aids, or countermeasures?
Barriers may be : Cultural Change and Adhering to restructured deadlines
Aids include: Standardised Review System.
4. What issues do you think the team overlooked which would have an impact on the
culture?
The team overlooked the coordination to incorporate several different authors might be
seen as extra work.
But it organized and review through proper review system.
5. What could they do about those?
They can improve the overall effectiveness of proposal management system by use of
selection matrix and barriers and AIDs chart.
All Rights Reserved, Juran Institute, Inc. 41 6009 CASE.0410 v3
Improvement Story
EXERCISE: Improve Discussion
1. Look at the list of solution alternatives. Could you add more items?
The solution such as: Automated Project Management Software and system for R&D,
Finance and PMD for management of deadlines.
2. Do you agree with the way the team scored the solutions? Would you have done
something different?
I will not agree with the way the team scored the solutions. The team did not allocated
Weightages to the criteria in the selection matrix.
3. Look at the Barriers/Aids chart. Can you add more issues and aids, or countermeasures?
Barriers may be : Cultural Change and Adhering to restructured deadlines
Aids include: Standardised Review System.
4. What issues do you think the team overlooked which would have an impact on the
culture?
The team overlooked the coordination to incorporate several different authors might be
seen as extra work.
But it organized and review through proper review system.
5. What could they do about those?
They can improve the overall effectiveness of proposal management system by use of
selection matrix and barriers and AIDs chart.
All Rights Reserved, Juran Institute, Inc. 41 6009 CASE.0410 v3
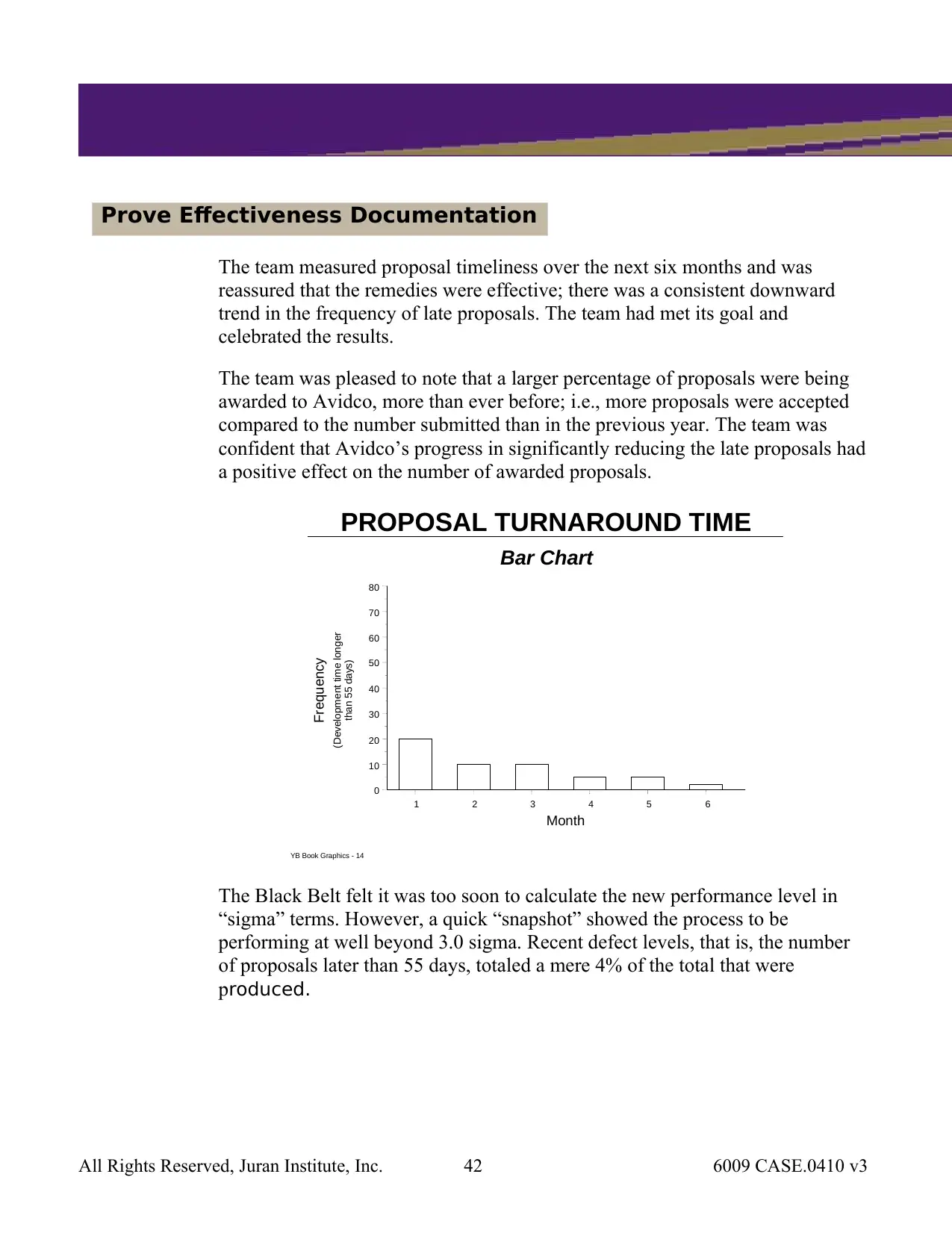
A DMAIC Six Sigma
Improvement Story
Prove Effectiveness Documentation
The team measured proposal timeliness over the next six months and was
reassured that the remedies were effective; there was a consistent downward
trend in the frequency of late proposals. The team had met its goal and
celebrated the results.
The team was pleased to note that a larger percentage of proposals were being
awarded to Avidco, more than ever before; i.e., more proposals were accepted
compared to the number submitted than in the previous year. The team was
confident that Avidco’s progress in significantly reducing the late proposals had
a positive effect on the number of awarded proposals.
YB Book Graphics - 14 All Rights Reserved, Juran Institute, Inc.
PROPOSAL TURNAROUND TIME
Bar Chart
1 2 3 4 5 6
0
10
20
30
40
50
60
70
80
Month
Frequency
(Development time longer
than 55 days)
The Black Belt felt it was too soon to calculate the new performance level in
“sigma” terms. However, a quick “snapshot” showed the process to be
performing at well beyond 3.0 sigma. Recent defect levels, that is, the number
of proposals later than 55 days, totaled a mere 4% of the total that were
produced.
All Rights Reserved, Juran Institute, Inc. 42 6009 CASE.0410 v3
Improvement Story
Prove Effectiveness Documentation
The team measured proposal timeliness over the next six months and was
reassured that the remedies were effective; there was a consistent downward
trend in the frequency of late proposals. The team had met its goal and
celebrated the results.
The team was pleased to note that a larger percentage of proposals were being
awarded to Avidco, more than ever before; i.e., more proposals were accepted
compared to the number submitted than in the previous year. The team was
confident that Avidco’s progress in significantly reducing the late proposals had
a positive effect on the number of awarded proposals.
YB Book Graphics - 14 All Rights Reserved, Juran Institute, Inc.
PROPOSAL TURNAROUND TIME
Bar Chart
1 2 3 4 5 6
0
10
20
30
40
50
60
70
80
Month
Frequency
(Development time longer
than 55 days)
The Black Belt felt it was too soon to calculate the new performance level in
“sigma” terms. However, a quick “snapshot” showed the process to be
performing at well beyond 3.0 sigma. Recent defect levels, that is, the number
of proposals later than 55 days, totaled a mere 4% of the total that were
produced.
All Rights Reserved, Juran Institute, Inc. 42 6009 CASE.0410 v3
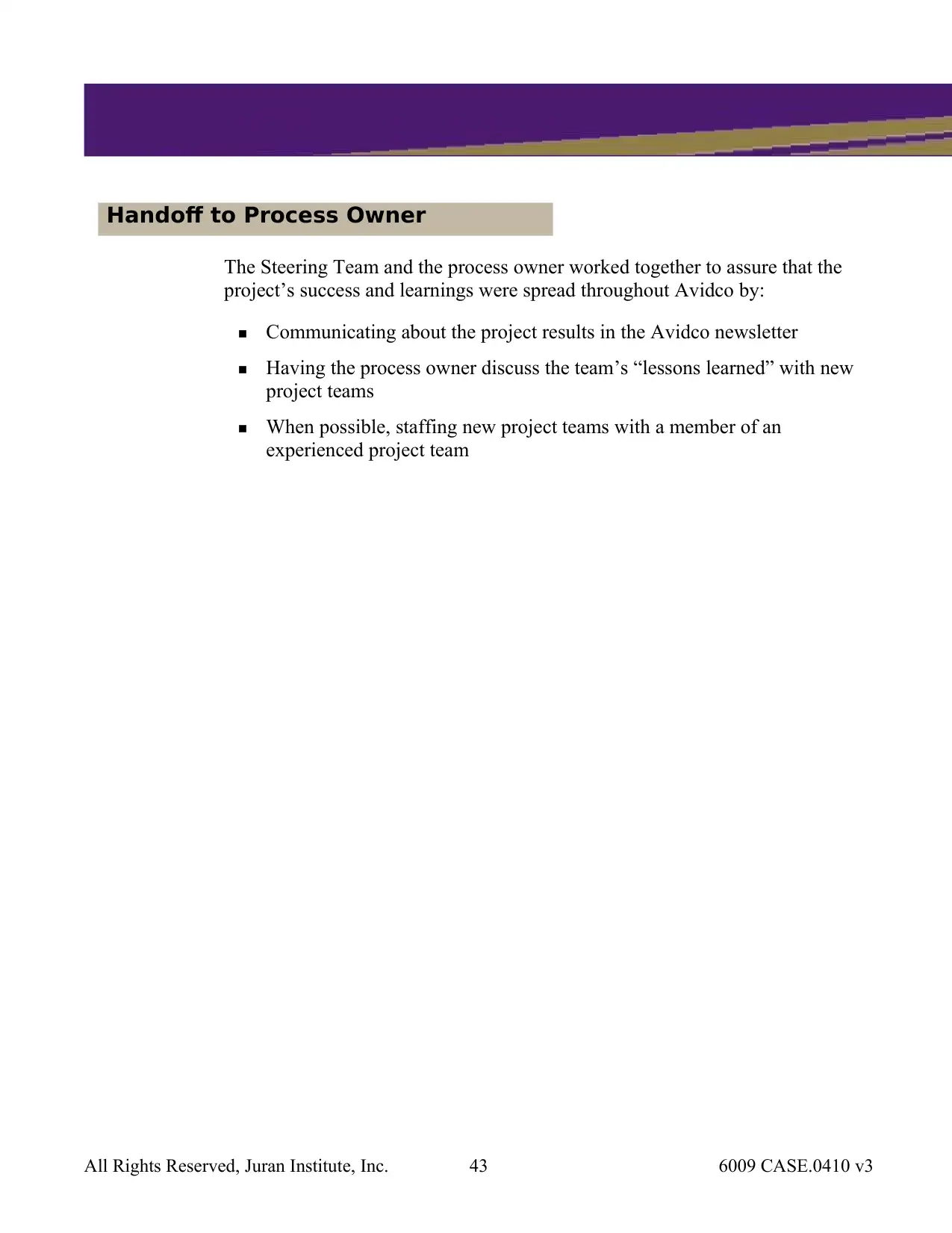
A DMAIC Six Sigma
Improvement Story
Handoff to Process Owner
The Steering Team and the process owner worked together to assure that the
project’s success and learnings were spread throughout Avidco by:
Communicating about the project results in the Avidco newsletter
Having the process owner discuss the team’s “lessons learned” with new
project teams
When possible, staffing new project teams with a member of an
experienced project team
All Rights Reserved, Juran Institute, Inc. 43 6009 CASE.0410 v3
Improvement Story
Handoff to Process Owner
The Steering Team and the process owner worked together to assure that the
project’s success and learnings were spread throughout Avidco by:
Communicating about the project results in the Avidco newsletter
Having the process owner discuss the team’s “lessons learned” with new
project teams
When possible, staffing new project teams with a member of an
experienced project team
All Rights Reserved, Juran Institute, Inc. 43 6009 CASE.0410 v3
Secure Best Marks with AI Grader
Need help grading? Try our AI Grader for instant feedback on your assignments.
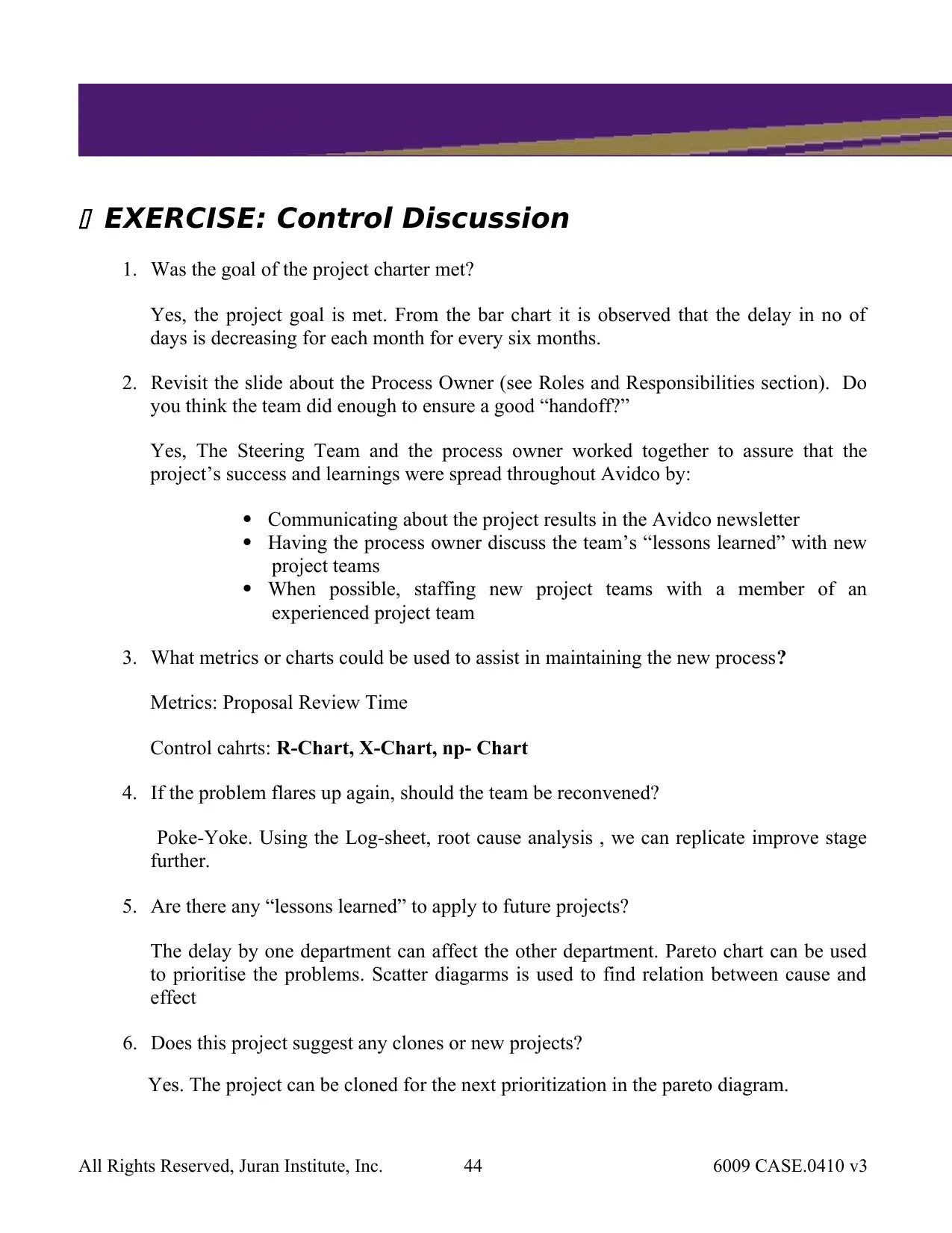
A DMAIC Six Sigma
Improvement Story
EXERCISE: Control Discussion
1. Was the goal of the project charter met?
Yes, the project goal is met. From the bar chart it is observed that the delay in no of
days is decreasing for each month for every six months.
2. Revisit the slide about the Process Owner (see Roles and Responsibilities section). Do
you think the team did enough to ensure a good “handoff?”
Yes, The Steering Team and the process owner worked together to assure that the
project’s success and learnings were spread throughout Avidco by:
Communicating about the project results in the Avidco newsletter
Having the process owner discuss the team’s “lessons learned” with new
project teams
When possible, staffing new project teams with a member of an
experienced project team
3. What metrics or charts could be used to assist in maintaining the new process?
Metrics: Proposal Review Time
Control cahrts: R-Chart, X-Chart, np- Chart
4. If the problem flares up again, should the team be reconvened?
Poke-Yoke. Using the Log-sheet, root cause analysis , we can replicate improve stage
further.
5. Are there any “lessons learned” to apply to future projects?
The delay by one department can affect the other department. Pareto chart can be used
to prioritise the problems. Scatter diagarms is used to find relation between cause and
effect
6. Does this project suggest any clones or new projects?
Yes. The project can be cloned for the next prioritization in the pareto diagram.
All Rights Reserved, Juran Institute, Inc. 44 6009 CASE.0410 v3
Improvement Story
EXERCISE: Control Discussion
1. Was the goal of the project charter met?
Yes, the project goal is met. From the bar chart it is observed that the delay in no of
days is decreasing for each month for every six months.
2. Revisit the slide about the Process Owner (see Roles and Responsibilities section). Do
you think the team did enough to ensure a good “handoff?”
Yes, The Steering Team and the process owner worked together to assure that the
project’s success and learnings were spread throughout Avidco by:
Communicating about the project results in the Avidco newsletter
Having the process owner discuss the team’s “lessons learned” with new
project teams
When possible, staffing new project teams with a member of an
experienced project team
3. What metrics or charts could be used to assist in maintaining the new process?
Metrics: Proposal Review Time
Control cahrts: R-Chart, X-Chart, np- Chart
4. If the problem flares up again, should the team be reconvened?
Poke-Yoke. Using the Log-sheet, root cause analysis , we can replicate improve stage
further.
5. Are there any “lessons learned” to apply to future projects?
The delay by one department can affect the other department. Pareto chart can be used
to prioritise the problems. Scatter diagarms is used to find relation between cause and
effect
6. Does this project suggest any clones or new projects?
Yes. The project can be cloned for the next prioritization in the pareto diagram.
All Rights Reserved, Juran Institute, Inc. 44 6009 CASE.0410 v3

A DMAIC Six Sigma
Improvement Story
All Rights Reserved, Juran Institute, Inc. 45 6009 CASE.0410 v3
Improvement Story
All Rights Reserved, Juran Institute, Inc. 45 6009 CASE.0410 v3
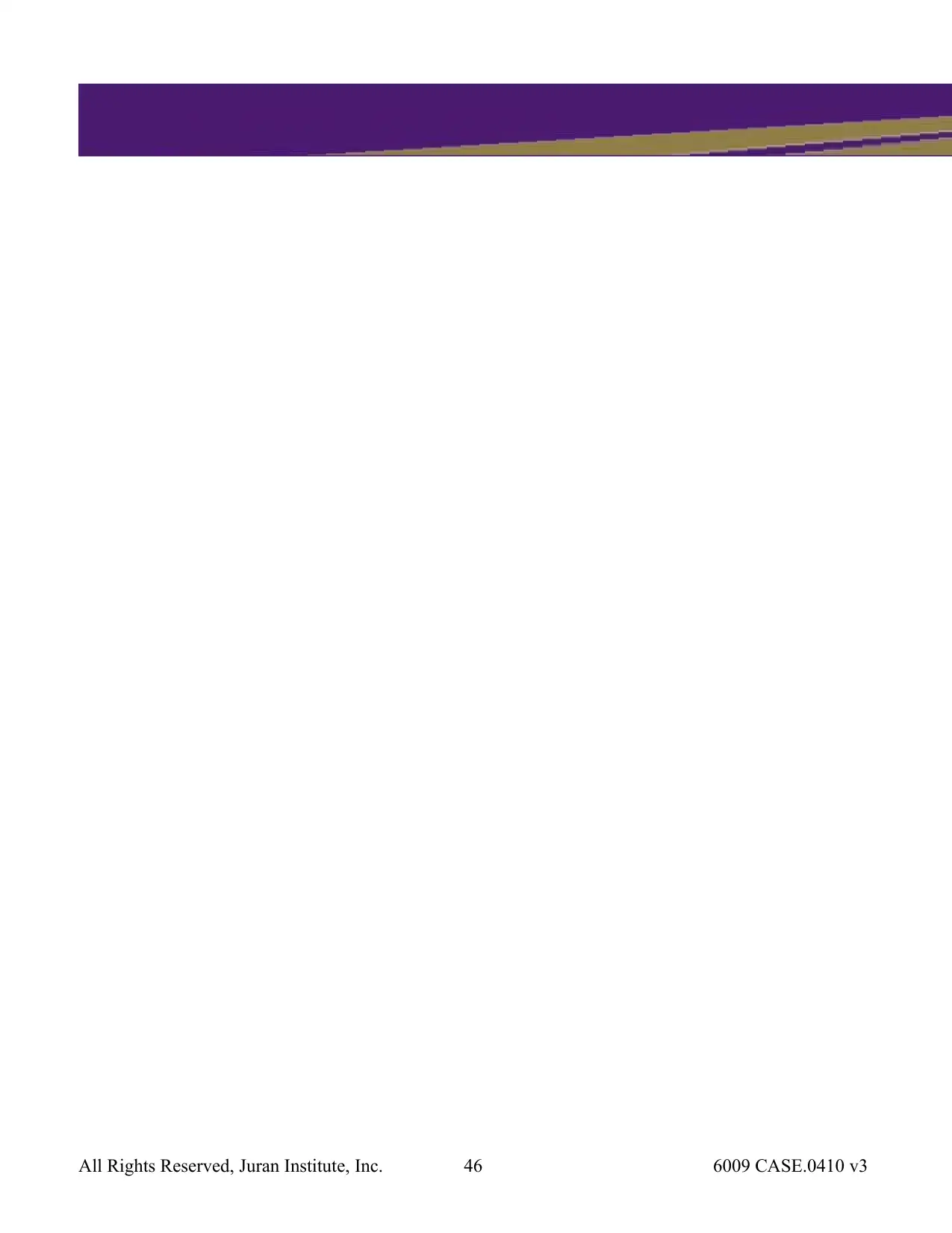
A DMAIC Six Sigma
Improvement Story
All Rights Reserved, Juran Institute, Inc. 46 6009 CASE.0410 v3
Improvement Story
All Rights Reserved, Juran Institute, Inc. 46 6009 CASE.0410 v3
Paraphrase This Document
Need a fresh take? Get an instant paraphrase of this document with our AI Paraphraser
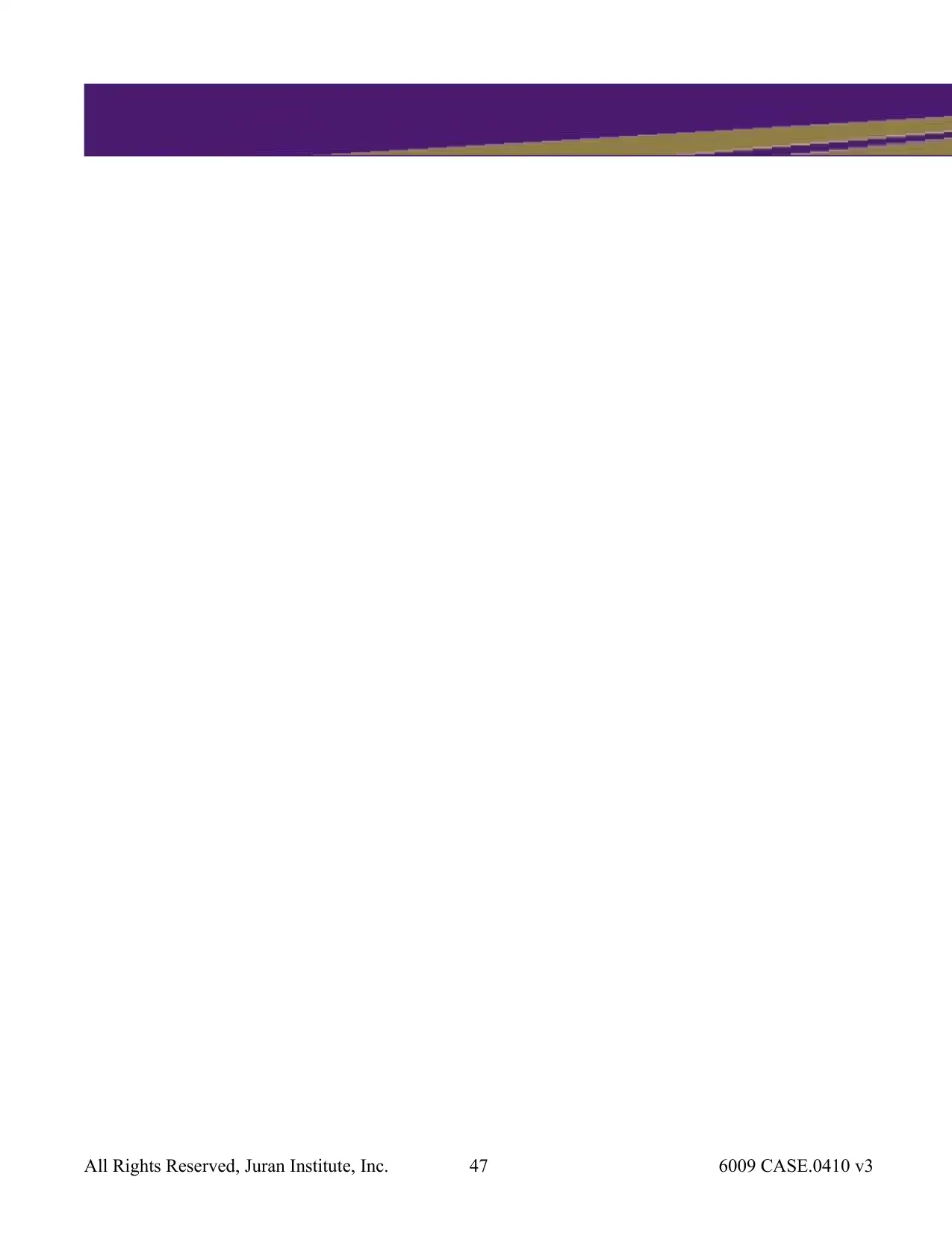
A DMAIC Six Sigma
Improvement Story
All Rights Reserved, Juran Institute, Inc. 47 6009 CASE.0410 v3
Improvement Story
All Rights Reserved, Juran Institute, Inc. 47 6009 CASE.0410 v3
1 out of 50
![[object Object]](/_next/image/?url=%2F_next%2Fstatic%2Fmedia%2Flogo.6d15ce61.png&w=640&q=75)
Your All-in-One AI-Powered Toolkit for Academic Success.
+13062052269
info@desklib.com
Available 24*7 on WhatsApp / Email
Unlock your academic potential
© 2024 | Zucol Services PVT LTD | All rights reserved.