Importance of Value Chain Management in Business Operations
VerifiedAdded on 2023/01/17
|11
|1877
|28
AI Summary
This document discusses the concept of value chain management (VCM) and its importance in improving business operations. It explains how VCM helps companies streamline their operations, manage resources, and integrate information across the supply chain. The document also highlights the benefits of effective VCM, such as improved sales, better product planning, standardized processes, and reduced costs.
Contribute Materials
Your contribution can guide someone’s learning journey. Share your
documents today.
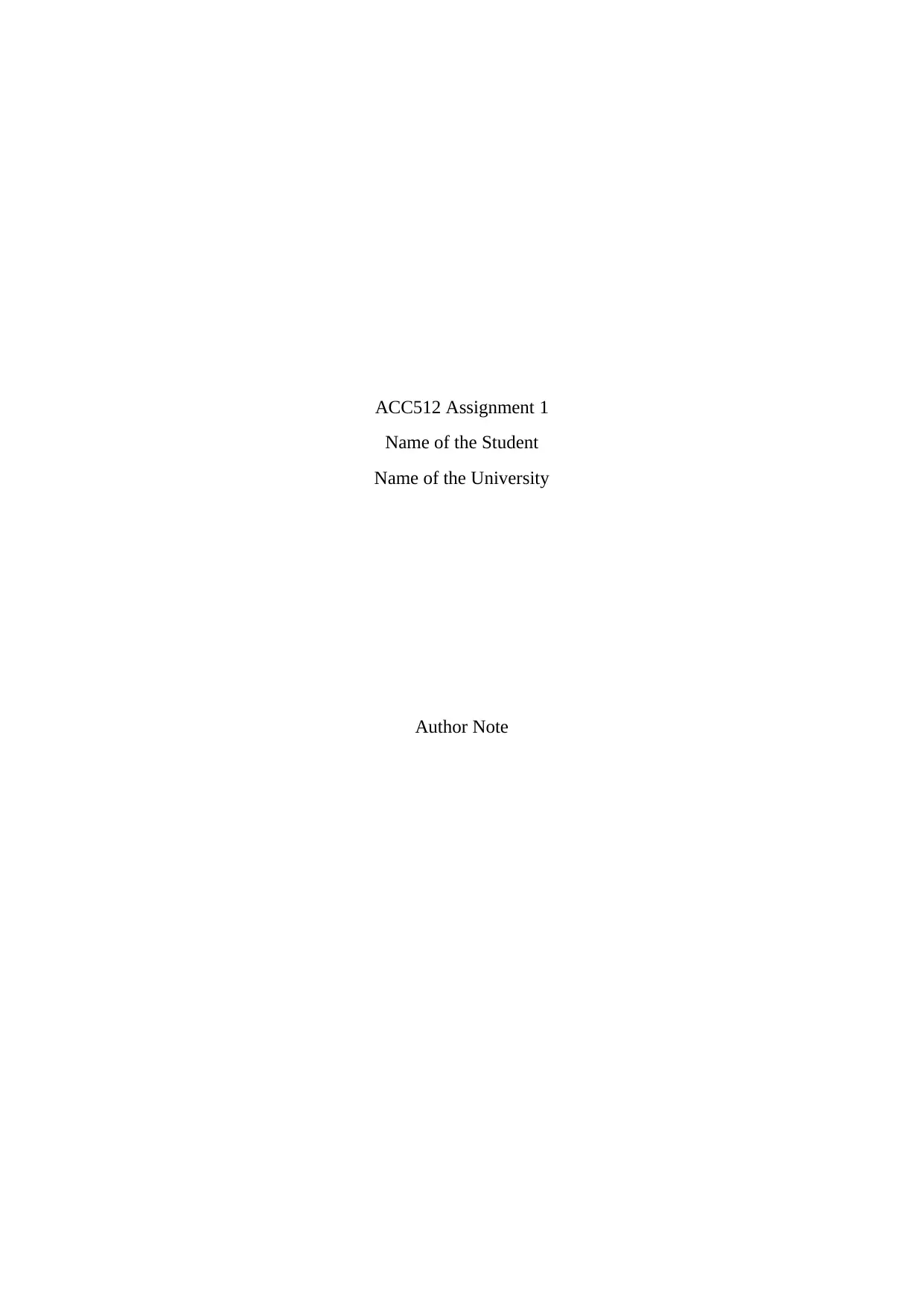
ACC512 Assignment 1
Name of the Student
Name of the University
Author Note
Name of the Student
Name of the University
Author Note
Secure Best Marks with AI Grader
Need help grading? Try our AI Grader for instant feedback on your assignments.
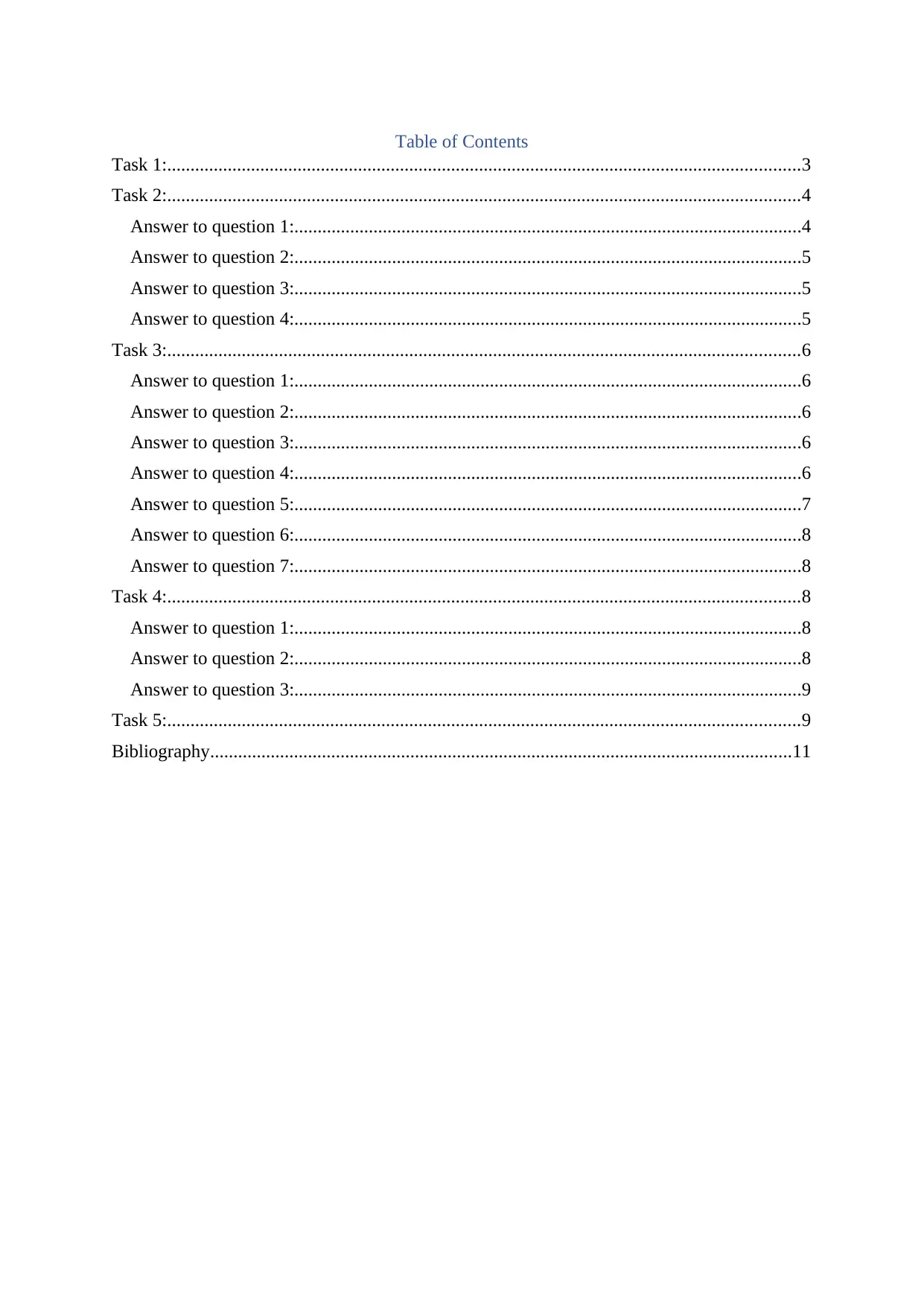
Table of Contents
Task 1:........................................................................................................................................3
Task 2:........................................................................................................................................4
Answer to question 1:.............................................................................................................4
Answer to question 2:.............................................................................................................5
Answer to question 3:.............................................................................................................5
Answer to question 4:.............................................................................................................5
Task 3:........................................................................................................................................6
Answer to question 1:.............................................................................................................6
Answer to question 2:.............................................................................................................6
Answer to question 3:.............................................................................................................6
Answer to question 4:.............................................................................................................6
Answer to question 5:.............................................................................................................7
Answer to question 6:.............................................................................................................8
Answer to question 7:.............................................................................................................8
Task 4:........................................................................................................................................8
Answer to question 1:.............................................................................................................8
Answer to question 2:.............................................................................................................8
Answer to question 3:.............................................................................................................9
Task 5:........................................................................................................................................9
Bibliography.............................................................................................................................11
Task 1:........................................................................................................................................3
Task 2:........................................................................................................................................4
Answer to question 1:.............................................................................................................4
Answer to question 2:.............................................................................................................5
Answer to question 3:.............................................................................................................5
Answer to question 4:.............................................................................................................5
Task 3:........................................................................................................................................6
Answer to question 1:.............................................................................................................6
Answer to question 2:.............................................................................................................6
Answer to question 3:.............................................................................................................6
Answer to question 4:.............................................................................................................6
Answer to question 5:.............................................................................................................7
Answer to question 6:.............................................................................................................8
Answer to question 7:.............................................................................................................8
Task 4:........................................................................................................................................8
Answer to question 1:.............................................................................................................8
Answer to question 2:.............................................................................................................8
Answer to question 3:.............................................................................................................9
Task 5:........................................................................................................................................9
Bibliography.............................................................................................................................11
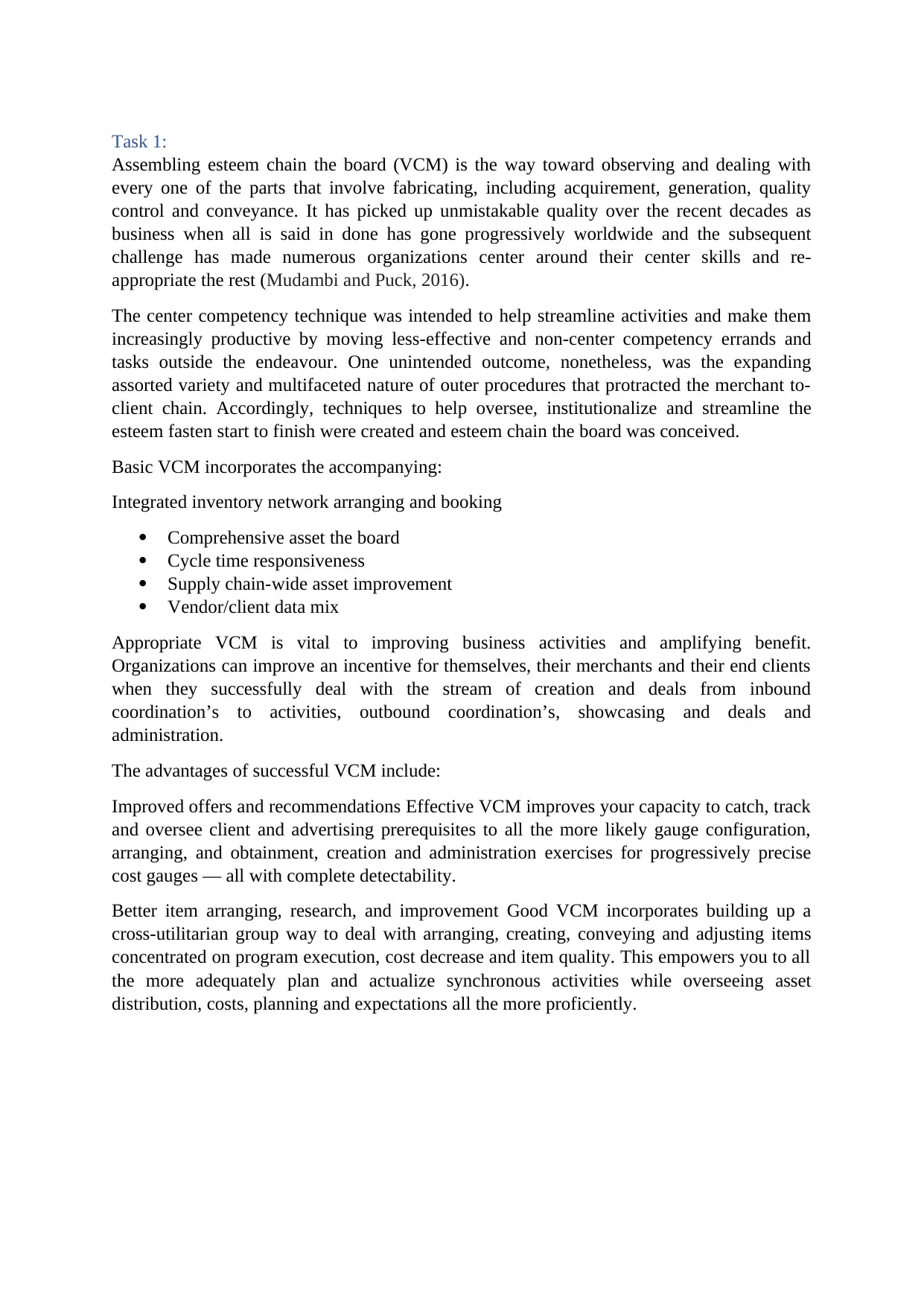
Task 1:
Assembling esteem chain the board (VCM) is the way toward observing and dealing with
every one of the parts that involve fabricating, including acquirement, generation, quality
control and conveyance. It has picked up unmistakable quality over the recent decades as
business when all is said in done has gone progressively worldwide and the subsequent
challenge has made numerous organizations center around their center skills and re-
appropriate the rest (Mudambi and Puck, 2016).
The center competency technique was intended to help streamline activities and make them
increasingly productive by moving less-effective and non-center competency errands and
tasks outside the endeavour. One unintended outcome, nonetheless, was the expanding
assorted variety and multifaceted nature of outer procedures that protracted the merchant to-
client chain. Accordingly, techniques to help oversee, institutionalize and streamline the
esteem fasten start to finish were created and esteem chain the board was conceived.
Basic VCM incorporates the accompanying:
Integrated inventory network arranging and booking
Comprehensive asset the board
Cycle time responsiveness
Supply chain-wide asset improvement
Vendor/client data mix
Appropriate VCM is vital to improving business activities and amplifying benefit.
Organizations can improve an incentive for themselves, their merchants and their end clients
when they successfully deal with the stream of creation and deals from inbound
coordination’s to activities, outbound coordination’s, showcasing and deals and
administration.
The advantages of successful VCM include:
Improved offers and recommendations Effective VCM improves your capacity to catch, track
and oversee client and advertising prerequisites to all the more likely gauge configuration,
arranging, and obtainment, creation and administration exercises for progressively precise
cost gauges — all with complete detectability.
Better item arranging, research, and improvement Good VCM incorporates building up a
cross-utilitarian group way to deal with arranging, creating, conveying and adjusting items
concentrated on program execution, cost decrease and item quality. This empowers you to all
the more adequately plan and actualize synchronous activities while overseeing asset
distribution, costs, planning and expectations all the more proficiently.
Assembling esteem chain the board (VCM) is the way toward observing and dealing with
every one of the parts that involve fabricating, including acquirement, generation, quality
control and conveyance. It has picked up unmistakable quality over the recent decades as
business when all is said in done has gone progressively worldwide and the subsequent
challenge has made numerous organizations center around their center skills and re-
appropriate the rest (Mudambi and Puck, 2016).
The center competency technique was intended to help streamline activities and make them
increasingly productive by moving less-effective and non-center competency errands and
tasks outside the endeavour. One unintended outcome, nonetheless, was the expanding
assorted variety and multifaceted nature of outer procedures that protracted the merchant to-
client chain. Accordingly, techniques to help oversee, institutionalize and streamline the
esteem fasten start to finish were created and esteem chain the board was conceived.
Basic VCM incorporates the accompanying:
Integrated inventory network arranging and booking
Comprehensive asset the board
Cycle time responsiveness
Supply chain-wide asset improvement
Vendor/client data mix
Appropriate VCM is vital to improving business activities and amplifying benefit.
Organizations can improve an incentive for themselves, their merchants and their end clients
when they successfully deal with the stream of creation and deals from inbound
coordination’s to activities, outbound coordination’s, showcasing and deals and
administration.
The advantages of successful VCM include:
Improved offers and recommendations Effective VCM improves your capacity to catch, track
and oversee client and advertising prerequisites to all the more likely gauge configuration,
arranging, and obtainment, creation and administration exercises for progressively precise
cost gauges — all with complete detectability.
Better item arranging, research, and improvement Good VCM incorporates building up a
cross-utilitarian group way to deal with arranging, creating, conveying and adjusting items
concentrated on program execution, cost decrease and item quality. This empowers you to all
the more adequately plan and actualize synchronous activities while overseeing asset
distribution, costs, planning and expectations all the more proficiently.

Institutionalized procedures VCM calls for repeatable and quantifiable business procedures to
all the more likely deal with the item ace information to guarantee that client desires and
responsibilities are met. Dynamic VCM empowers discharge and change procedures to be
better overseen from idea to execution. Standard, dependable and repeatable procedures
contribute essentially to diminishing generally operational wasteful aspects and waste.
Improved merchant the executives Synchronizing structure and sourcing groups with sellers
guarantees that re-appropriated segments and subsystems are figured out how to meet
execution, quality, calendar and cost necessities while maintaining a strategic distance from
configuration imperfections, abundance stock and waste. Through VCM, you're ready to all
the more likely oversee and track in-administration item design changes composed among
field administration, client backing and building assets.
Decreased expenses Optimizing all the esteem chain segments recorded above can result in
generous start to finish cost investment funds from streamlined procedures, diminished
wasteful aspects and waste, better stock control and improved item quality. A definitive
consequence of a far reaching and strong VCM program is upgraded incomes and better net
revenues, adding to more noteworthy generally achievement.
Task 2:
Answer to question 1:
Portland Precision Engineering Co Ltd
As on 31st December 2018
Particulars Amount
Direct materials
Raw Material Opening Inventory $67,200.00
+Purchases $1,94,600.00
+Freight Inwards $2,800.00
all the more likely deal with the item ace information to guarantee that client desires and
responsibilities are met. Dynamic VCM empowers discharge and change procedures to be
better overseen from idea to execution. Standard, dependable and repeatable procedures
contribute essentially to diminishing generally operational wasteful aspects and waste.
Improved merchant the executives Synchronizing structure and sourcing groups with sellers
guarantees that re-appropriated segments and subsystems are figured out how to meet
execution, quality, calendar and cost necessities while maintaining a strategic distance from
configuration imperfections, abundance stock and waste. Through VCM, you're ready to all
the more likely oversee and track in-administration item design changes composed among
field administration, client backing and building assets.
Decreased expenses Optimizing all the esteem chain segments recorded above can result in
generous start to finish cost investment funds from streamlined procedures, diminished
wasteful aspects and waste, better stock control and improved item quality. A definitive
consequence of a far reaching and strong VCM program is upgraded incomes and better net
revenues, adding to more noteworthy generally achievement.
Task 2:
Answer to question 1:
Portland Precision Engineering Co Ltd
As on 31st December 2018
Particulars Amount
Direct materials
Raw Material Opening Inventory $67,200.00
+Purchases $1,94,600.00
+Freight Inwards $2,800.00
Secure Best Marks with AI Grader
Need help grading? Try our AI Grader for instant feedback on your assignments.

Total Available Raw Material $2,64,600.00
-Raw Material Ending Inventory -$71,500.00
Direct materials $1,93,100.00
Direct labour $4,90,000.00
Manufacturing Overhead
Indirect labour costs incurred $77,200.00
+Council rates $90,000.00
+Depreciation on factory machinery $10,750.00
+Indirect material used $8,726.00
+Depreciation on factory fittings $6,400.00
+Factory rent expense $39,270.00
+Other manufacturing expenses $5,600.00
+Sales salaries expense $1,21,520.00
+Electricity for factory $58,800.00
+Insurance on factory and equipment $22,120.00
Total Manufacturing Overhead $4,40,386.00
Total Manufacturing Cost $11,23,486.00
Work in Progress Opening Inventory $49,000.00
Work in Progress Ending Inventory -$50,700.00
Cost Goods Manufactured $11,21,786.00
Answer to question 2:
Portland Precision Engineering Co Ltd
As on 31st December 2018
Particulars Amount
Cost of Goods Manufactured $11,21,786.00
+Finished Goods Opening Inventory $21,000.00
Finished Goods Available for sale $11,42,786.00
Finished Goods Ending Inventory -$2,01,500.00
Cost of Goods Sold $9,41,286.00
Answer to question 3:
Portland Precision Engineering Co Ltd
As on 31st December 2018
Particulars Amount
Revenues $14,00,000.00
Cost of Goods Sold -$9,41,286.00
Gross Margin $4,58,714.00
Answer to question 4:
Portland Precision Engineering Co Ltd
As on 31st December 2018
Particulars Amount
Gross Margin $4,58,714.00
Selling and Administrative expenses -$22,880.00
-Raw Material Ending Inventory -$71,500.00
Direct materials $1,93,100.00
Direct labour $4,90,000.00
Manufacturing Overhead
Indirect labour costs incurred $77,200.00
+Council rates $90,000.00
+Depreciation on factory machinery $10,750.00
+Indirect material used $8,726.00
+Depreciation on factory fittings $6,400.00
+Factory rent expense $39,270.00
+Other manufacturing expenses $5,600.00
+Sales salaries expense $1,21,520.00
+Electricity for factory $58,800.00
+Insurance on factory and equipment $22,120.00
Total Manufacturing Overhead $4,40,386.00
Total Manufacturing Cost $11,23,486.00
Work in Progress Opening Inventory $49,000.00
Work in Progress Ending Inventory -$50,700.00
Cost Goods Manufactured $11,21,786.00
Answer to question 2:
Portland Precision Engineering Co Ltd
As on 31st December 2018
Particulars Amount
Cost of Goods Manufactured $11,21,786.00
+Finished Goods Opening Inventory $21,000.00
Finished Goods Available for sale $11,42,786.00
Finished Goods Ending Inventory -$2,01,500.00
Cost of Goods Sold $9,41,286.00
Answer to question 3:
Portland Precision Engineering Co Ltd
As on 31st December 2018
Particulars Amount
Revenues $14,00,000.00
Cost of Goods Sold -$9,41,286.00
Gross Margin $4,58,714.00
Answer to question 4:
Portland Precision Engineering Co Ltd
As on 31st December 2018
Particulars Amount
Gross Margin $4,58,714.00
Selling and Administrative expenses -$22,880.00
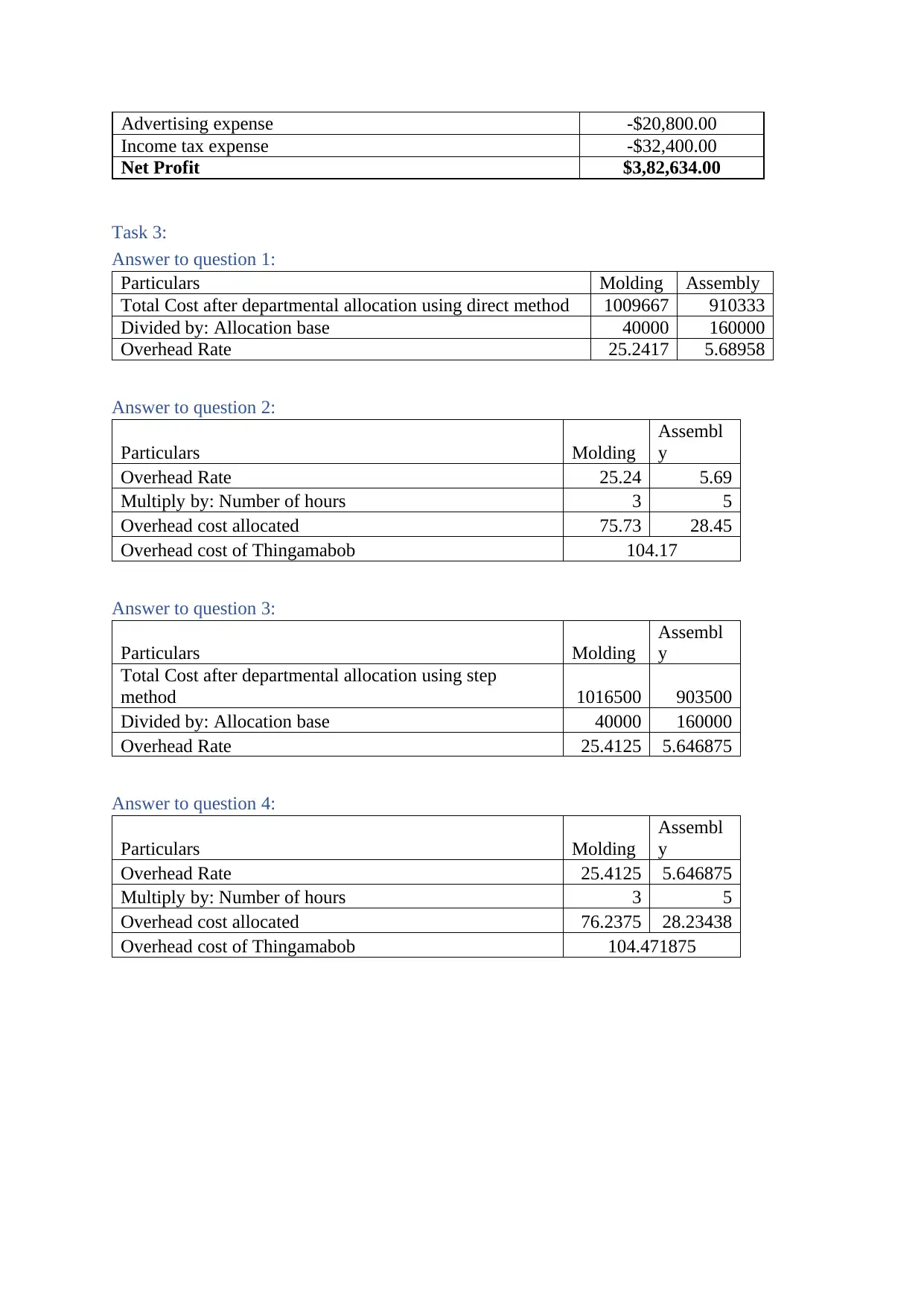
Advertising expense -$20,800.00
Income tax expense -$32,400.00
Net Profit $3,82,634.00
Task 3:
Answer to question 1:
Particulars Molding Assembly
Total Cost after departmental allocation using direct method 1009667 910333
Divided by: Allocation base 40000 160000
Overhead Rate 25.2417 5.68958
Answer to question 2:
Particulars Molding
Assembl
y
Overhead Rate 25.24 5.69
Multiply by: Number of hours 3 5
Overhead cost allocated 75.73 28.45
Overhead cost of Thingamabob 104.17
Answer to question 3:
Particulars Molding
Assembl
y
Total Cost after departmental allocation using step
method 1016500 903500
Divided by: Allocation base 40000 160000
Overhead Rate 25.4125 5.646875
Answer to question 4:
Particulars Molding
Assembl
y
Overhead Rate 25.4125 5.646875
Multiply by: Number of hours 3 5
Overhead cost allocated 76.2375 28.23438
Overhead cost of Thingamabob 104.471875
Income tax expense -$32,400.00
Net Profit $3,82,634.00
Task 3:
Answer to question 1:
Particulars Molding Assembly
Total Cost after departmental allocation using direct method 1009667 910333
Divided by: Allocation base 40000 160000
Overhead Rate 25.2417 5.68958
Answer to question 2:
Particulars Molding
Assembl
y
Overhead Rate 25.24 5.69
Multiply by: Number of hours 3 5
Overhead cost allocated 75.73 28.45
Overhead cost of Thingamabob 104.17
Answer to question 3:
Particulars Molding
Assembl
y
Total Cost after departmental allocation using step
method 1016500 903500
Divided by: Allocation base 40000 160000
Overhead Rate 25.4125 5.646875
Answer to question 4:
Particulars Molding
Assembl
y
Overhead Rate 25.4125 5.646875
Multiply by: Number of hours 3 5
Overhead cost allocated 76.2375 28.23438
Overhead cost of Thingamabob 104.471875
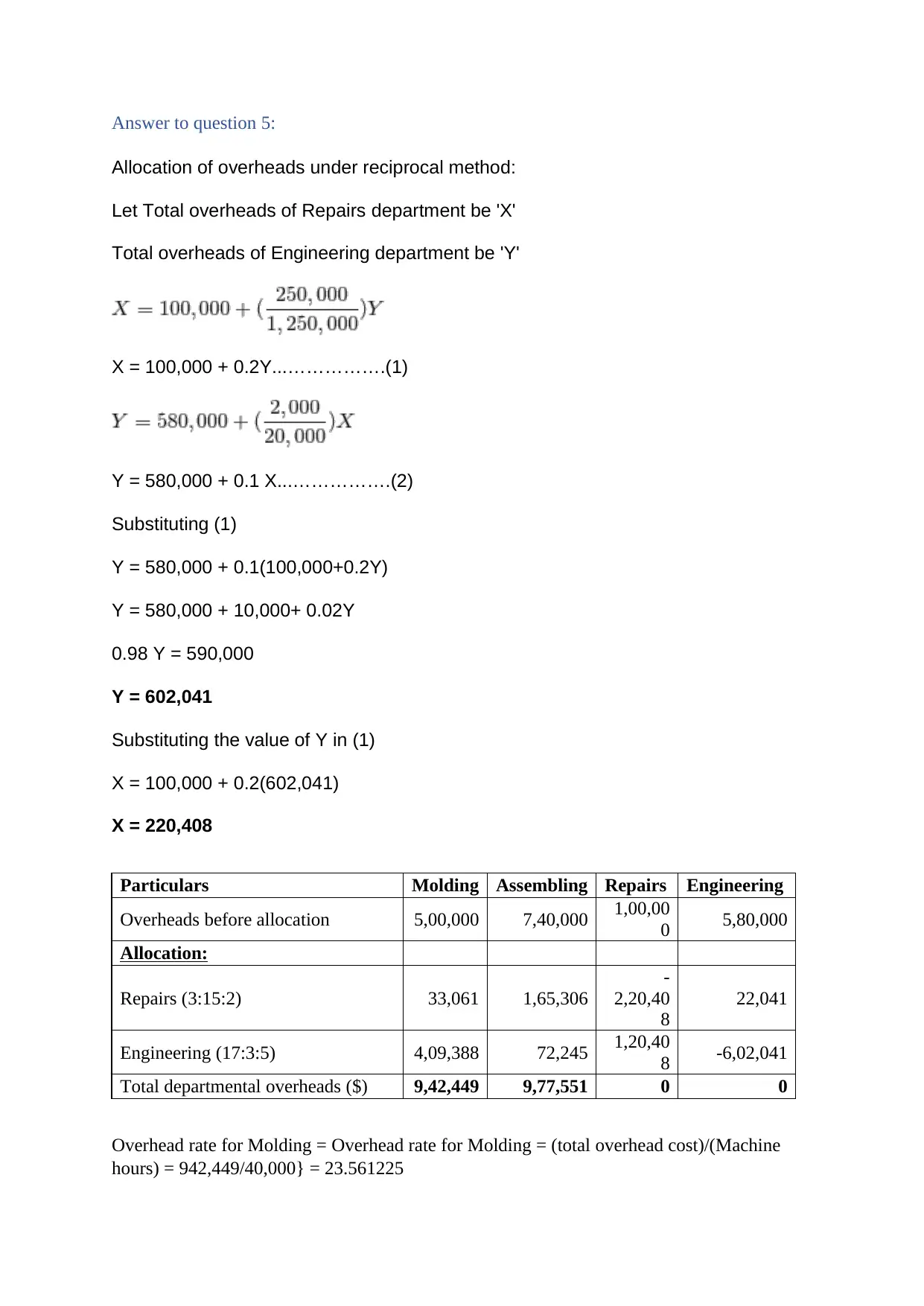
Answer to question 5:
Allocation of overheads under reciprocal method:
Let Total overheads of Repairs department be 'X'
Total overheads of Engineering department be 'Y'
X = 100,000 + 0.2Y...…………….(1)
Y = 580,000 + 0.1 X...…………….(2)
Substituting (1)
Y = 580,000 + 0.1(100,000+0.2Y)
Y = 580,000 + 10,000+ 0.02Y
0.98 Y = 590,000
Y = 602,041
Substituting the value of Y in (1)
X = 100,000 + 0.2(602,041)
X = 220,408
Particulars Molding Assembling Repairs Engineering
Overheads before allocation 5,00,000 7,40,000 1,00,00
0 5,80,000
Allocation:
Repairs (3:15:2) 33,061 1,65,306
-
2,20,40
8
22,041
Engineering (17:3:5) 4,09,388 72,245 1,20,40
8 -6,02,041
Total departmental overheads ($) 9,42,449 9,77,551 0 0
Overhead rate for Molding = Overhead rate for Molding = (total overhead cost)/(Machine
hours) = 942,449/40,000} = 23.561225
Allocation of overheads under reciprocal method:
Let Total overheads of Repairs department be 'X'
Total overheads of Engineering department be 'Y'
X = 100,000 + 0.2Y...…………….(1)
Y = 580,000 + 0.1 X...…………….(2)
Substituting (1)
Y = 580,000 + 0.1(100,000+0.2Y)
Y = 580,000 + 10,000+ 0.02Y
0.98 Y = 590,000
Y = 602,041
Substituting the value of Y in (1)
X = 100,000 + 0.2(602,041)
X = 220,408
Particulars Molding Assembling Repairs Engineering
Overheads before allocation 5,00,000 7,40,000 1,00,00
0 5,80,000
Allocation:
Repairs (3:15:2) 33,061 1,65,306
-
2,20,40
8
22,041
Engineering (17:3:5) 4,09,388 72,245 1,20,40
8 -6,02,041
Total departmental overheads ($) 9,42,449 9,77,551 0 0
Overhead rate for Molding = Overhead rate for Molding = (total overhead cost)/(Machine
hours) = 942,449/40,000} = 23.561225
Paraphrase This Document
Need a fresh take? Get an instant paraphrase of this document with our AI Paraphraser

Overhead rate for Assembling = Total overhead cost/Labour hours
= 977,551/160,000
= 6.10969
Answer to question 6:
Total Overhead cost of Thingamabob
= (23.561225*3) + (6.10969*5)
= 70.68 + 30.55
= 101.23
Answer to question 7:
Reciprocal method is the most appropriate method of departmental cost allocations. It
considers the interdepartmental services between service departments where in case of direct
method and step method service department costs are allocated only for production
departments. Hence it is considered as most accurate method.
Task 4:
Answer to question 1:
Calculation of Predetermined Overhead rate:
Preparation department = Total Overhead / Total Machine hours
= 285600 / 6800
=$42 per machine hour
Finishing Department = Total Overhead / Total Labour cost
= 684000/380000
=$1.8 per $ of labour cost
Answer to question 2:
Total Cost of Job 842:
Particulars $ $
[a] Direct Material requisition
[i] Preparation Department 1300
[ii] Finishing Department 1420 2720
[b] Direct labour cost
[i] Preparation Department 1640
[ii] Finishing Department 1800 3440
[c] Manufacturing Overhead [working 1]
[i] Preparation Department 1680
[ii] Finishing Department 3240 4920
= 977,551/160,000
= 6.10969
Answer to question 6:
Total Overhead cost of Thingamabob
= (23.561225*3) + (6.10969*5)
= 70.68 + 30.55
= 101.23
Answer to question 7:
Reciprocal method is the most appropriate method of departmental cost allocations. It
considers the interdepartmental services between service departments where in case of direct
method and step method service department costs are allocated only for production
departments. Hence it is considered as most accurate method.
Task 4:
Answer to question 1:
Calculation of Predetermined Overhead rate:
Preparation department = Total Overhead / Total Machine hours
= 285600 / 6800
=$42 per machine hour
Finishing Department = Total Overhead / Total Labour cost
= 684000/380000
=$1.8 per $ of labour cost
Answer to question 2:
Total Cost of Job 842:
Particulars $ $
[a] Direct Material requisition
[i] Preparation Department 1300
[ii] Finishing Department 1420 2720
[b] Direct labour cost
[i] Preparation Department 1640
[ii] Finishing Department 1800 3440
[c] Manufacturing Overhead [working 1]
[i] Preparation Department 1680
[ii] Finishing Department 3240 4920
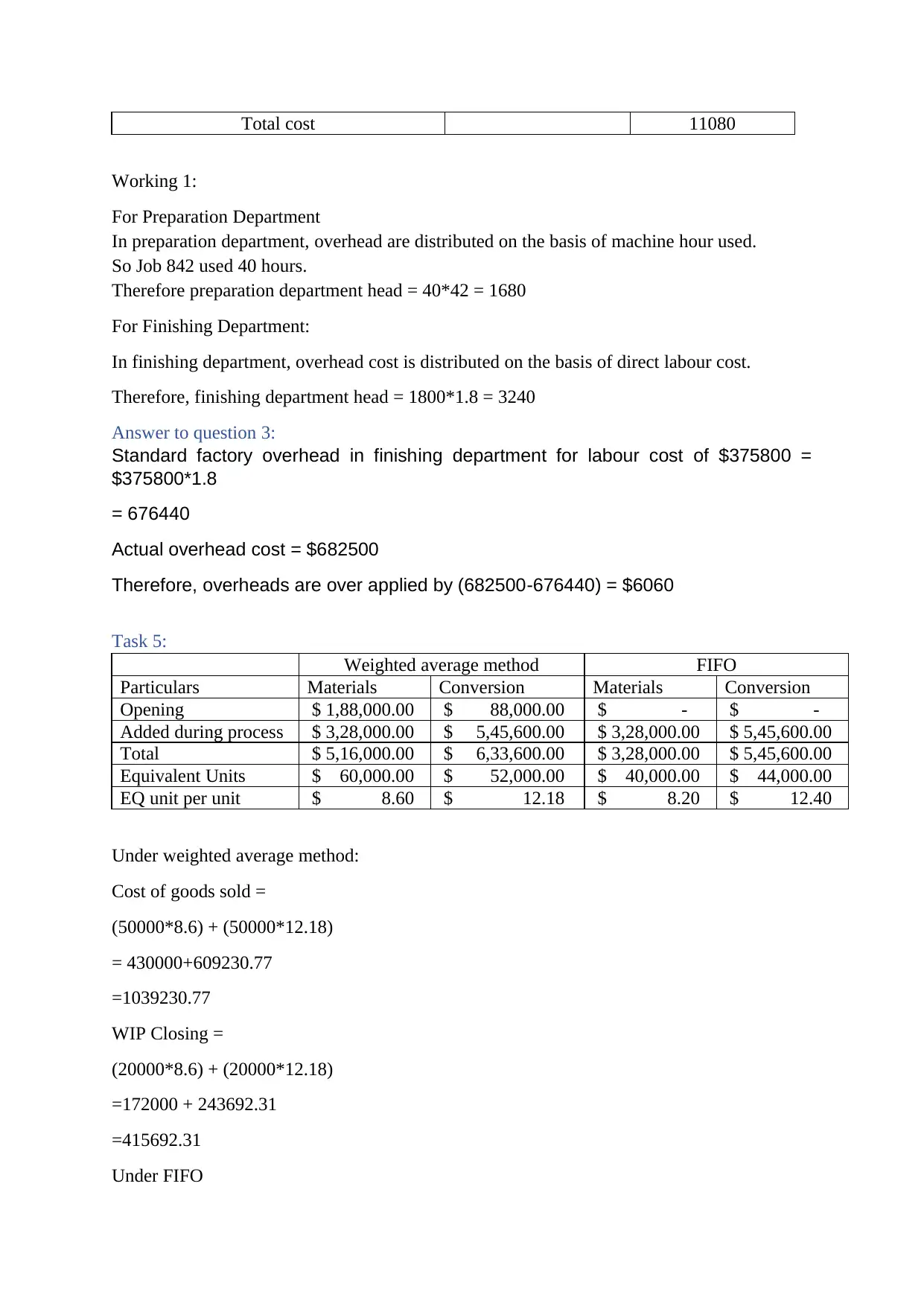
Total cost 11080
Working 1:
For Preparation Department
In preparation department, overhead are distributed on the basis of machine hour used.
So Job 842 used 40 hours.
Therefore preparation department head = 40*42 = 1680
For Finishing Department:
In finishing department, overhead cost is distributed on the basis of direct labour cost.
Therefore, finishing department head = 1800*1.8 = 3240
Answer to question 3:
Standard factory overhead in finishing department for labour cost of $375800 =
$375800*1.8
= 676440
Actual overhead cost = $682500
Therefore, overheads are over applied by (682500-676440) = $6060
Task 5:
Weighted average method FIFO
Particulars Materials Conversion Materials Conversion
Opening $ 1,88,000.00 $ 88,000.00 $ - $ -
Added during process $ 3,28,000.00 $ 5,45,600.00 $ 3,28,000.00 $ 5,45,600.00
Total $ 5,16,000.00 $ 6,33,600.00 $ 3,28,000.00 $ 5,45,600.00
Equivalent Units $ 60,000.00 $ 52,000.00 $ 40,000.00 $ 44,000.00
EQ unit per unit $ 8.60 $ 12.18 $ 8.20 $ 12.40
Under weighted average method:
Cost of goods sold =
(50000*8.6) + (50000*12.18)
= 430000+609230.77
=1039230.77
WIP Closing =
(20000*8.6) + (20000*12.18)
=172000 + 243692.31
=415692.31
Under FIFO
Working 1:
For Preparation Department
In preparation department, overhead are distributed on the basis of machine hour used.
So Job 842 used 40 hours.
Therefore preparation department head = 40*42 = 1680
For Finishing Department:
In finishing department, overhead cost is distributed on the basis of direct labour cost.
Therefore, finishing department head = 1800*1.8 = 3240
Answer to question 3:
Standard factory overhead in finishing department for labour cost of $375800 =
$375800*1.8
= 676440
Actual overhead cost = $682500
Therefore, overheads are over applied by (682500-676440) = $6060
Task 5:
Weighted average method FIFO
Particulars Materials Conversion Materials Conversion
Opening $ 1,88,000.00 $ 88,000.00 $ - $ -
Added during process $ 3,28,000.00 $ 5,45,600.00 $ 3,28,000.00 $ 5,45,600.00
Total $ 5,16,000.00 $ 6,33,600.00 $ 3,28,000.00 $ 5,45,600.00
Equivalent Units $ 60,000.00 $ 52,000.00 $ 40,000.00 $ 44,000.00
EQ unit per unit $ 8.60 $ 12.18 $ 8.20 $ 12.40
Under weighted average method:
Cost of goods sold =
(50000*8.6) + (50000*12.18)
= 430000+609230.77
=1039230.77
WIP Closing =
(20000*8.6) + (20000*12.18)
=172000 + 243692.31
=415692.31
Under FIFO
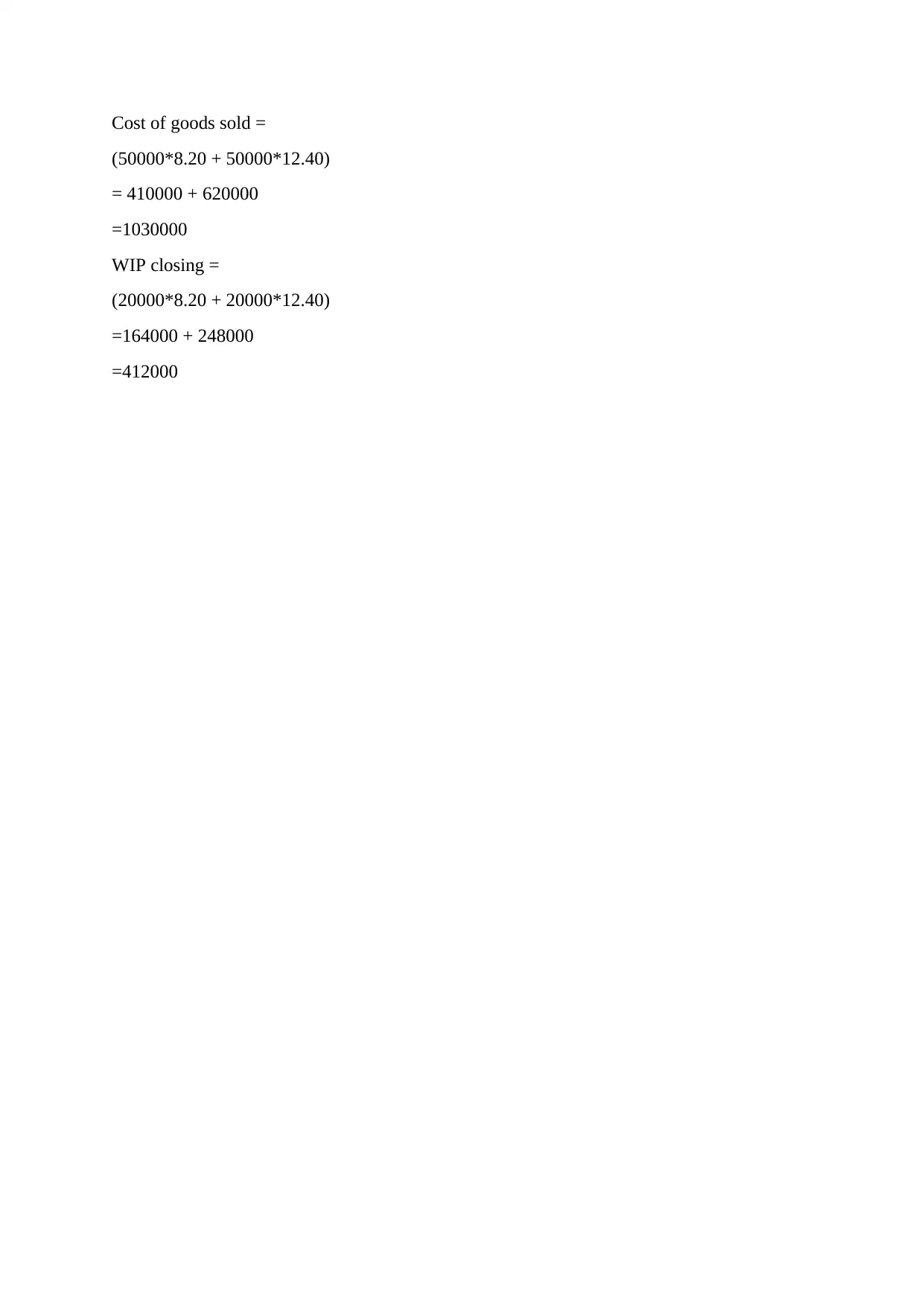
Cost of goods sold =
(50000*8.20 + 50000*12.40)
= 410000 + 620000
=1030000
WIP closing =
(20000*8.20 + 20000*12.40)
=164000 + 248000
=412000
(50000*8.20 + 50000*12.40)
= 410000 + 620000
=1030000
WIP closing =
(20000*8.20 + 20000*12.40)
=164000 + 248000
=412000
Secure Best Marks with AI Grader
Need help grading? Try our AI Grader for instant feedback on your assignments.
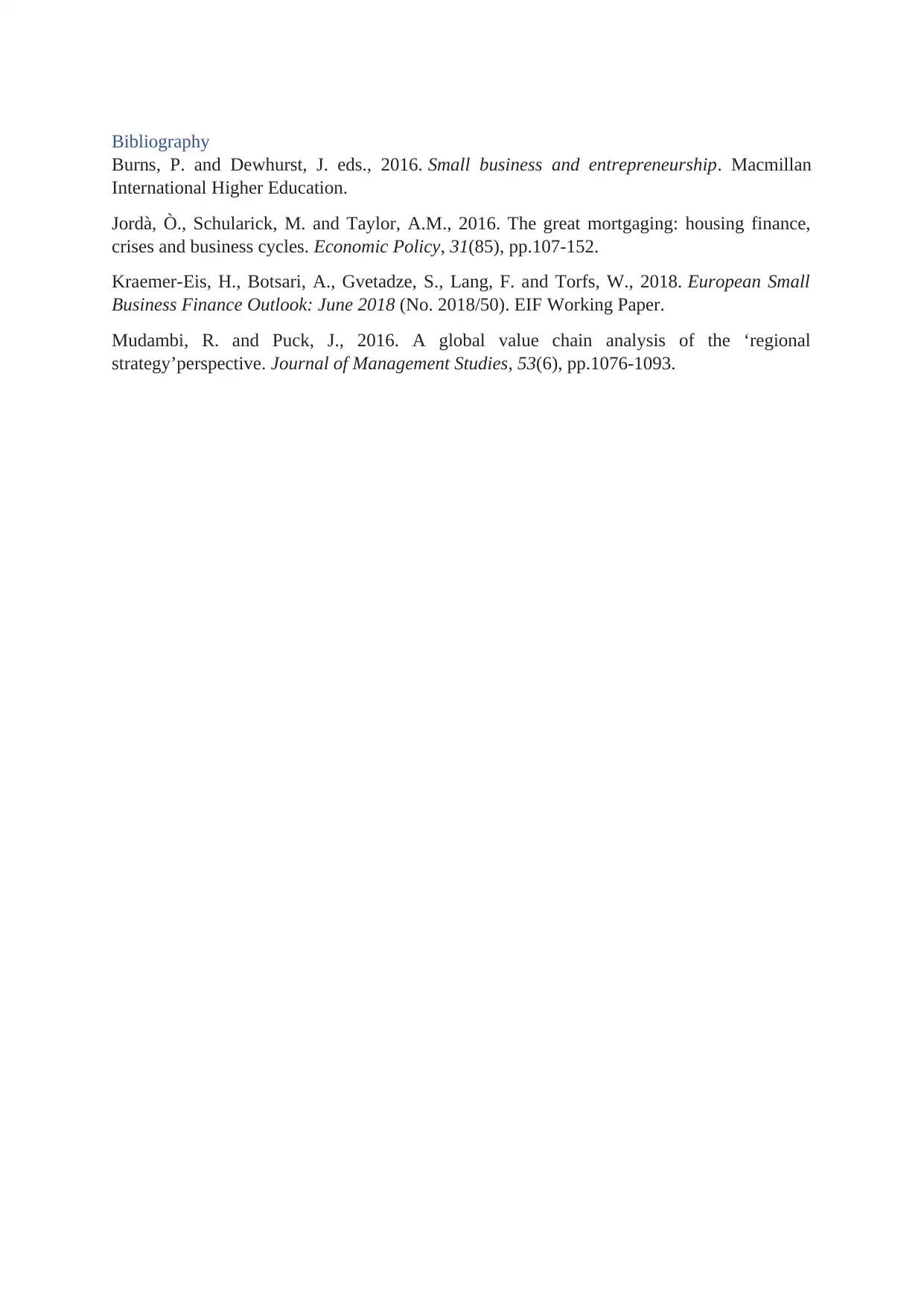
Bibliography
Burns, P. and Dewhurst, J. eds., 2016. Small business and entrepreneurship. Macmillan
International Higher Education.
Jordà, Ò., Schularick, M. and Taylor, A.M., 2016. The great mortgaging: housing finance,
crises and business cycles. Economic Policy, 31(85), pp.107-152.
Kraemer-Eis, H., Botsari, A., Gvetadze, S., Lang, F. and Torfs, W., 2018. European Small
Business Finance Outlook: June 2018 (No. 2018/50). EIF Working Paper.
Mudambi, R. and Puck, J., 2016. A global value chain analysis of the ‘regional
strategy’perspective. Journal of Management Studies, 53(6), pp.1076-1093.
Burns, P. and Dewhurst, J. eds., 2016. Small business and entrepreneurship. Macmillan
International Higher Education.
Jordà, Ò., Schularick, M. and Taylor, A.M., 2016. The great mortgaging: housing finance,
crises and business cycles. Economic Policy, 31(85), pp.107-152.
Kraemer-Eis, H., Botsari, A., Gvetadze, S., Lang, F. and Torfs, W., 2018. European Small
Business Finance Outlook: June 2018 (No. 2018/50). EIF Working Paper.
Mudambi, R. and Puck, J., 2016. A global value chain analysis of the ‘regional
strategy’perspective. Journal of Management Studies, 53(6), pp.1076-1093.
1 out of 11
Related Documents
![[object Object]](/_next/image/?url=%2F_next%2Fstatic%2Fmedia%2Flogo.6d15ce61.png&w=640&q=75)
Your All-in-One AI-Powered Toolkit for Academic Success.
+13062052269
info@desklib.com
Available 24*7 on WhatsApp / Email
Unlock your academic potential
© 2024 | Zucol Services PVT LTD | All rights reserved.