AC4410 - Evaluating Costing Methods for Product Decisions
VerifiedAdded on 2023/06/15
|9
|1634
|390
Essay
AI Summary
This essay discusses various product costing methods, including the traditional model, marginal costing, and activity-based costing (ABC). It explains how to calculate the cost of an individual product, service, or activity using relevant examples for each method. The traditional method is criticized for it...
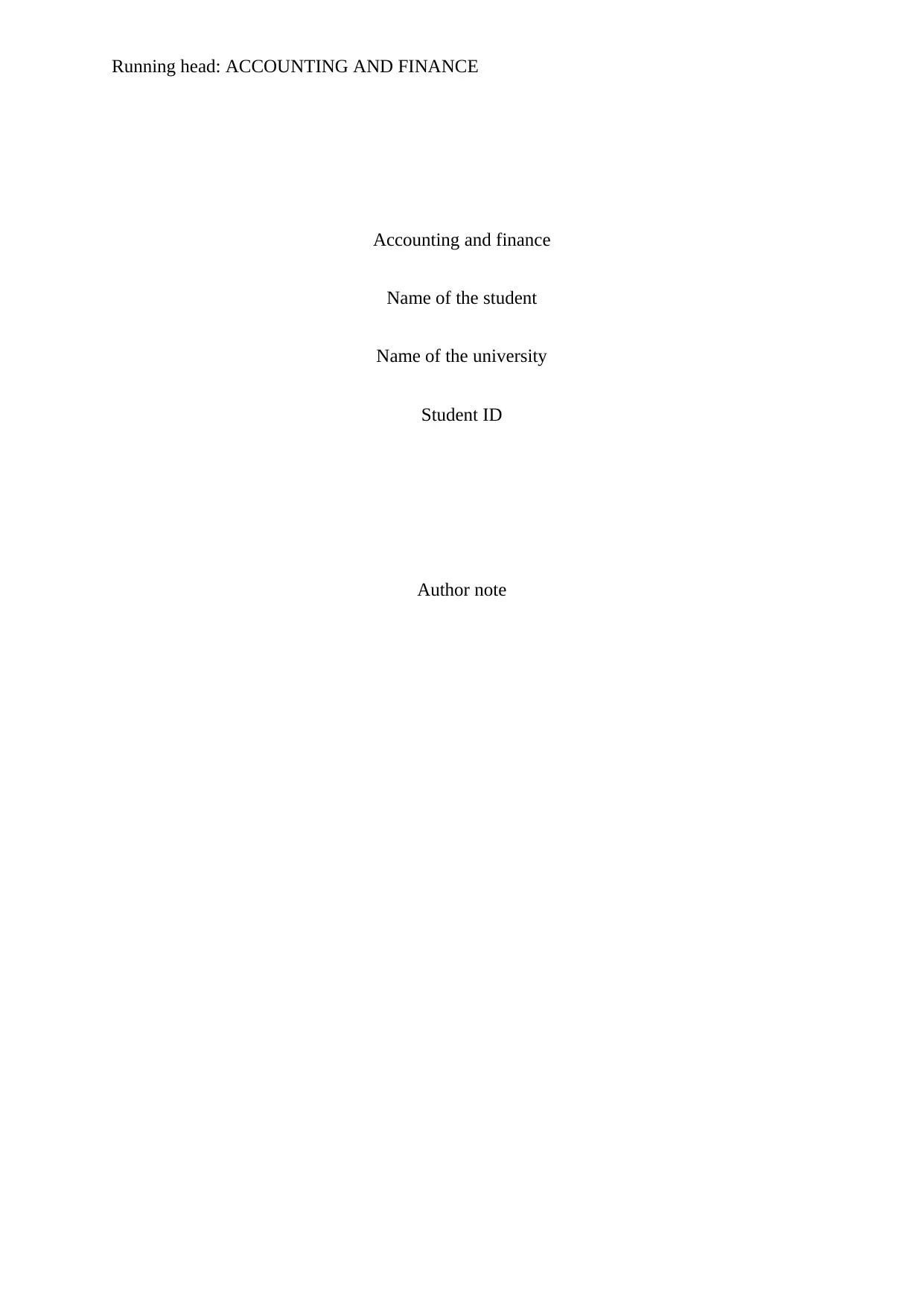
Running head: ACCOUNTING AND FINANCE
Accounting and finance
Name of the student
Name of the university
Student ID
Author note
Accounting and finance
Name of the student
Name of the university
Student ID
Author note
Paraphrase This Document
Need a fresh take? Get an instant paraphrase of this document with our AI Paraphraser
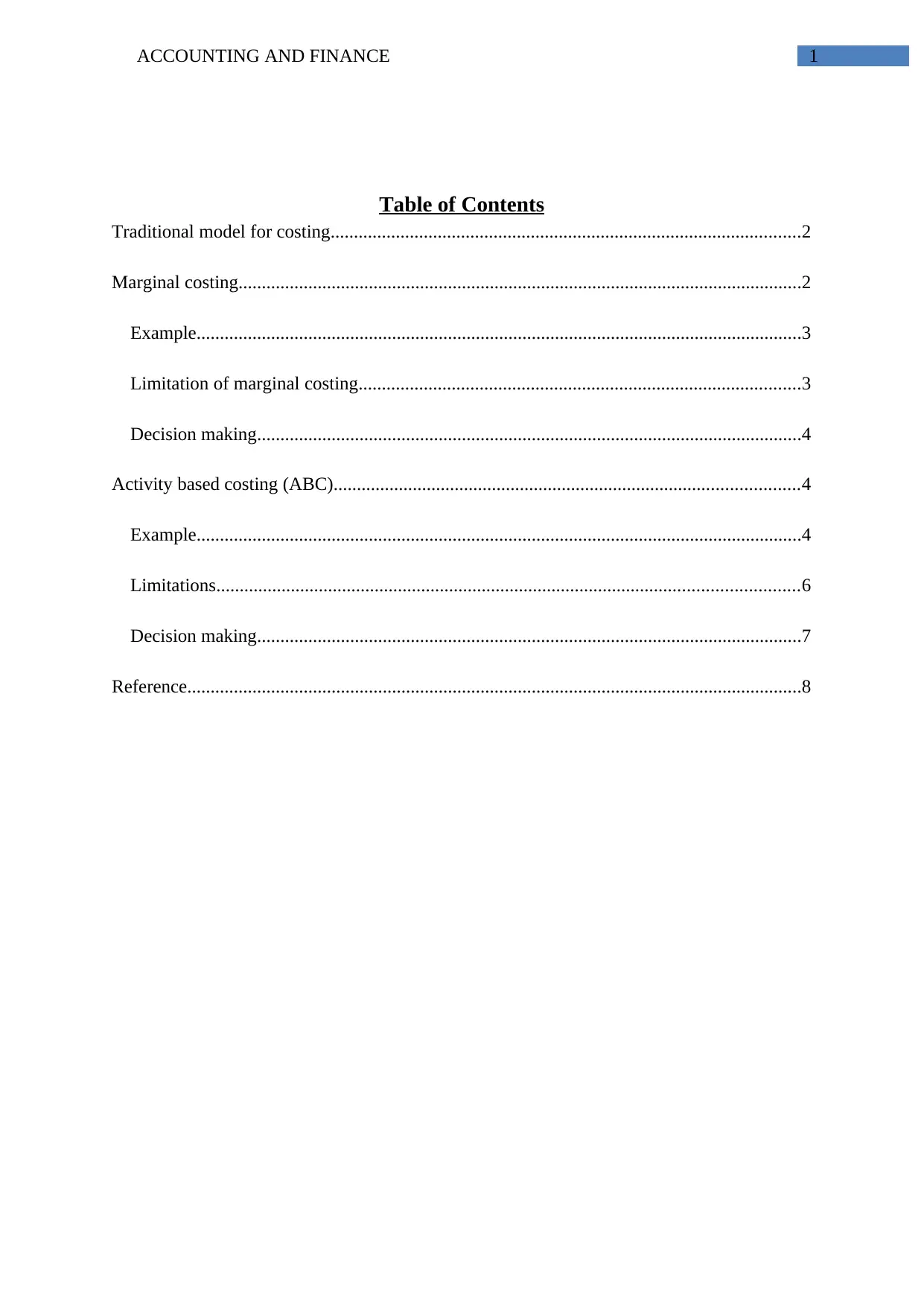
ACCOUNTING AND FINANCE 1
Table of Contents
Traditional model for costing.....................................................................................................2
Marginal costing.........................................................................................................................2
Example..................................................................................................................................3
Limitation of marginal costing...............................................................................................3
Decision making.....................................................................................................................4
Activity based costing (ABC)....................................................................................................4
Example..................................................................................................................................4
Limitations.............................................................................................................................6
Decision making.....................................................................................................................7
Reference....................................................................................................................................8
Table of Contents
Traditional model for costing.....................................................................................................2
Marginal costing.........................................................................................................................2
Example..................................................................................................................................3
Limitation of marginal costing...............................................................................................3
Decision making.....................................................................................................................4
Activity based costing (ABC)....................................................................................................4
Example..................................................................................................................................4
Limitations.............................................................................................................................6
Decision making.....................................................................................................................7
Reference....................................................................................................................................8
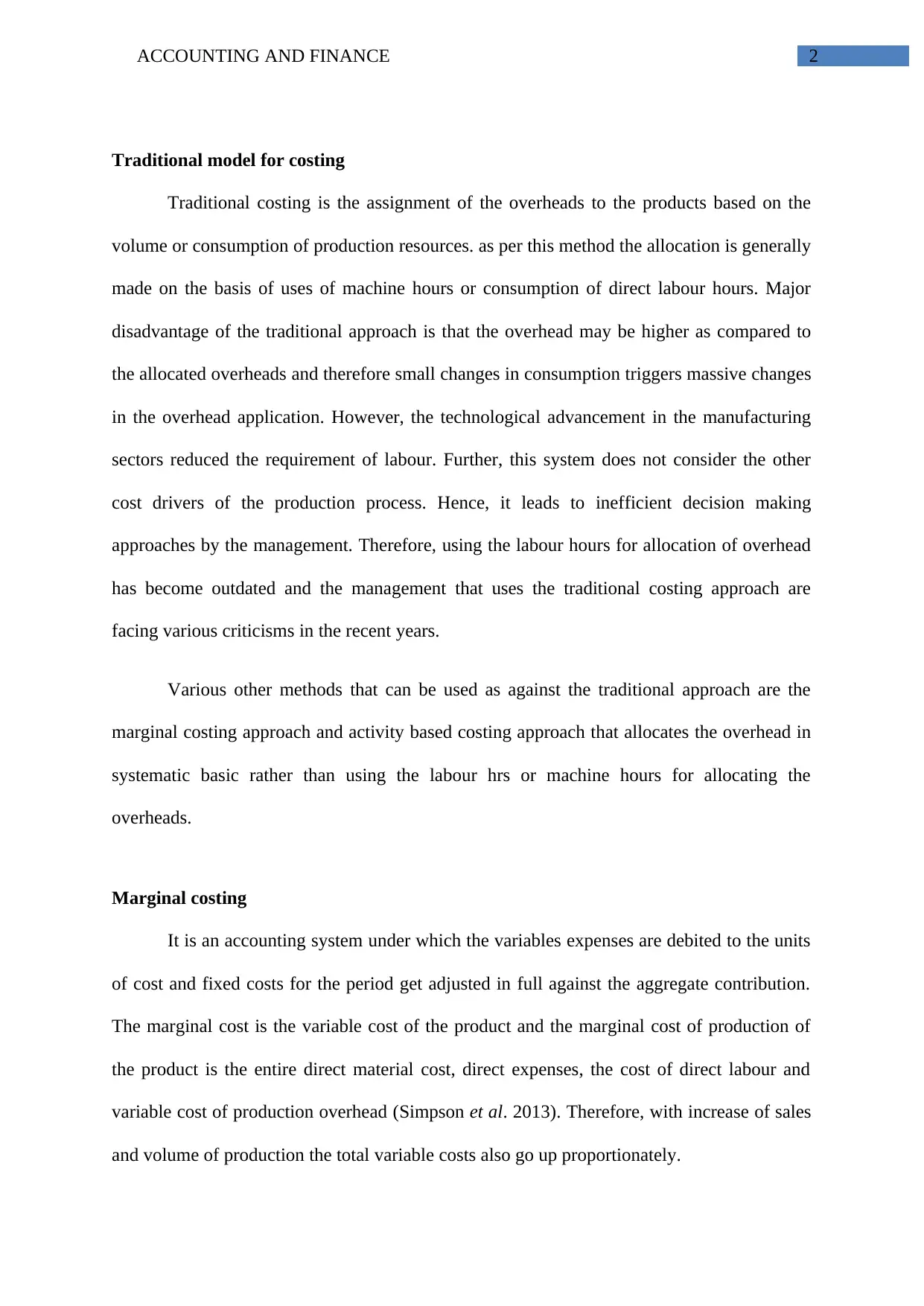
ACCOUNTING AND FINANCE 2
Traditional model for costing
Traditional costing is the assignment of the overheads to the products based on the
volume or consumption of production resources. as per this method the allocation is generally
made on the basis of uses of machine hours or consumption of direct labour hours. Major
disadvantage of the traditional approach is that the overhead may be higher as compared to
the allocated overheads and therefore small changes in consumption triggers massive changes
in the overhead application. However, the technological advancement in the manufacturing
sectors reduced the requirement of labour. Further, this system does not consider the other
cost drivers of the production process. Hence, it leads to inefficient decision making
approaches by the management. Therefore, using the labour hours for allocation of overhead
has become outdated and the management that uses the traditional costing approach are
facing various criticisms in the recent years.
Various other methods that can be used as against the traditional approach are the
marginal costing approach and activity based costing approach that allocates the overhead in
systematic basic rather than using the labour hrs or machine hours for allocating the
overheads.
Marginal costing
It is an accounting system under which the variables expenses are debited to the units
of cost and fixed costs for the period get adjusted in full against the aggregate contribution.
The marginal cost is the variable cost of the product and the marginal cost of production of
the product is the entire direct material cost, direct expenses, the cost of direct labour and
variable cost of production overhead (Simpson et al. 2013). Therefore, with increase of sales
and volume of production the total variable costs also go up proportionately.
Traditional model for costing
Traditional costing is the assignment of the overheads to the products based on the
volume or consumption of production resources. as per this method the allocation is generally
made on the basis of uses of machine hours or consumption of direct labour hours. Major
disadvantage of the traditional approach is that the overhead may be higher as compared to
the allocated overheads and therefore small changes in consumption triggers massive changes
in the overhead application. However, the technological advancement in the manufacturing
sectors reduced the requirement of labour. Further, this system does not consider the other
cost drivers of the production process. Hence, it leads to inefficient decision making
approaches by the management. Therefore, using the labour hours for allocation of overhead
has become outdated and the management that uses the traditional costing approach are
facing various criticisms in the recent years.
Various other methods that can be used as against the traditional approach are the
marginal costing approach and activity based costing approach that allocates the overhead in
systematic basic rather than using the labour hrs or machine hours for allocating the
overheads.
Marginal costing
It is an accounting system under which the variables expenses are debited to the units
of cost and fixed costs for the period get adjusted in full against the aggregate contribution.
The marginal cost is the variable cost of the product and the marginal cost of production of
the product is the entire direct material cost, direct expenses, the cost of direct labour and
variable cost of production overhead (Simpson et al. 2013). Therefore, with increase of sales
and volume of production the total variable costs also go up proportionately.
⊘ This is a preview!⊘
Do you want full access?
Subscribe today to unlock all pages.

Trusted by 1+ million students worldwide
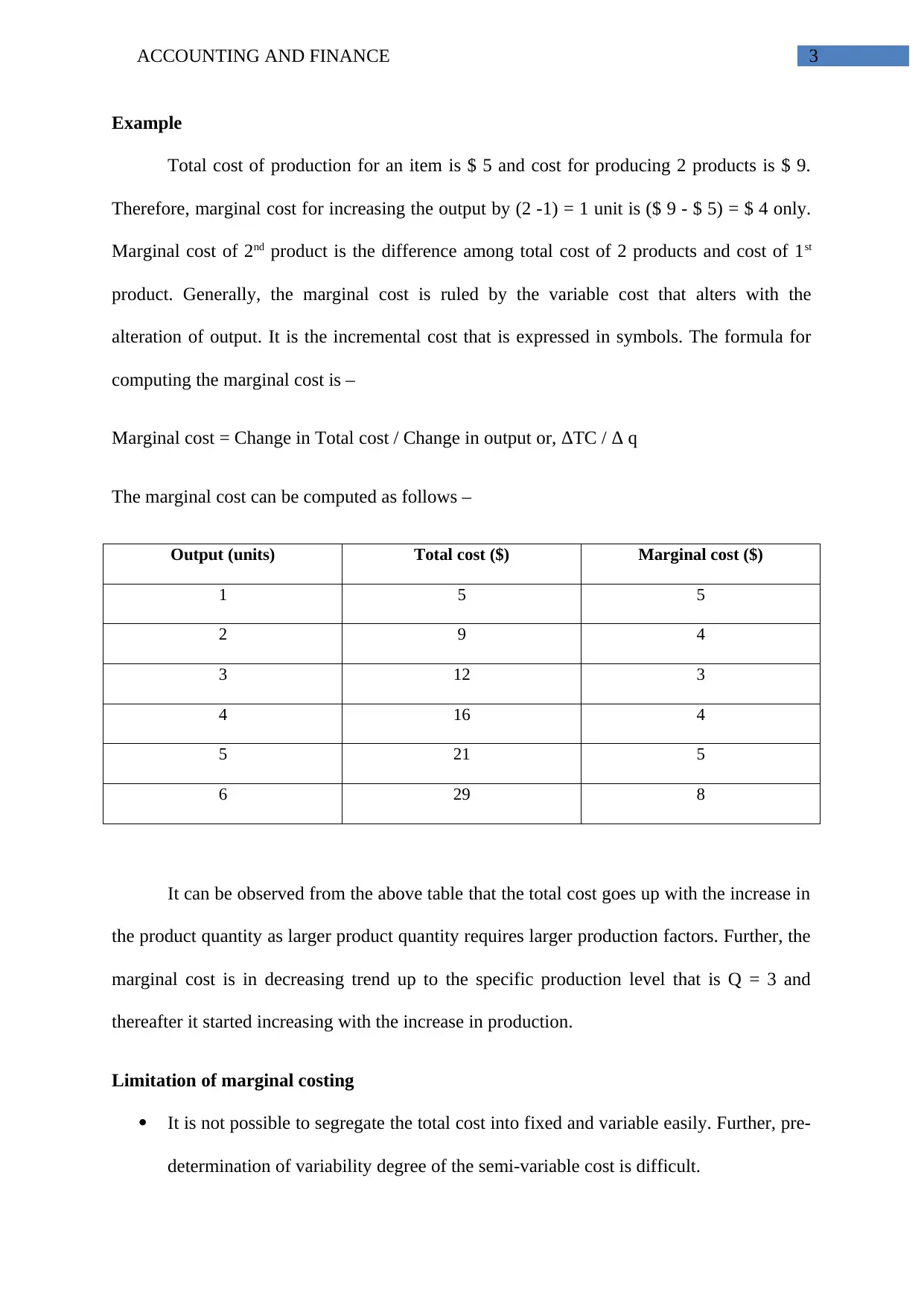
ACCOUNTING AND FINANCE 3
Example
Total cost of production for an item is $ 5 and cost for producing 2 products is $ 9.
Therefore, marginal cost for increasing the output by (2 -1) = 1 unit is ($ 9 - $ 5) = $ 4 only.
Marginal cost of 2nd product is the difference among total cost of 2 products and cost of 1st
product. Generally, the marginal cost is ruled by the variable cost that alters with the
alteration of output. It is the incremental cost that is expressed in symbols. The formula for
computing the marginal cost is –
Marginal cost = Change in Total cost / Change in output or, ΔTC / Δ q
The marginal cost can be computed as follows –
Output (units) Total cost ($) Marginal cost ($)
1 5 5
2 9 4
3 12 3
4 16 4
5 21 5
6 29 8
It can be observed from the above table that the total cost goes up with the increase in
the product quantity as larger product quantity requires larger production factors. Further, the
marginal cost is in decreasing trend up to the specific production level that is Q = 3 and
thereafter it started increasing with the increase in production.
Limitation of marginal costing
It is not possible to segregate the total cost into fixed and variable easily. Further, pre-
determination of variability degree of the semi-variable cost is difficult.
Example
Total cost of production for an item is $ 5 and cost for producing 2 products is $ 9.
Therefore, marginal cost for increasing the output by (2 -1) = 1 unit is ($ 9 - $ 5) = $ 4 only.
Marginal cost of 2nd product is the difference among total cost of 2 products and cost of 1st
product. Generally, the marginal cost is ruled by the variable cost that alters with the
alteration of output. It is the incremental cost that is expressed in symbols. The formula for
computing the marginal cost is –
Marginal cost = Change in Total cost / Change in output or, ΔTC / Δ q
The marginal cost can be computed as follows –
Output (units) Total cost ($) Marginal cost ($)
1 5 5
2 9 4
3 12 3
4 16 4
5 21 5
6 29 8
It can be observed from the above table that the total cost goes up with the increase in
the product quantity as larger product quantity requires larger production factors. Further, the
marginal cost is in decreasing trend up to the specific production level that is Q = 3 and
thereafter it started increasing with the increase in production.
Limitation of marginal costing
It is not possible to segregate the total cost into fixed and variable easily. Further, pre-
determination of variability degree of the semi-variable cost is difficult.
Paraphrase This Document
Need a fresh take? Get an instant paraphrase of this document with our AI Paraphraser
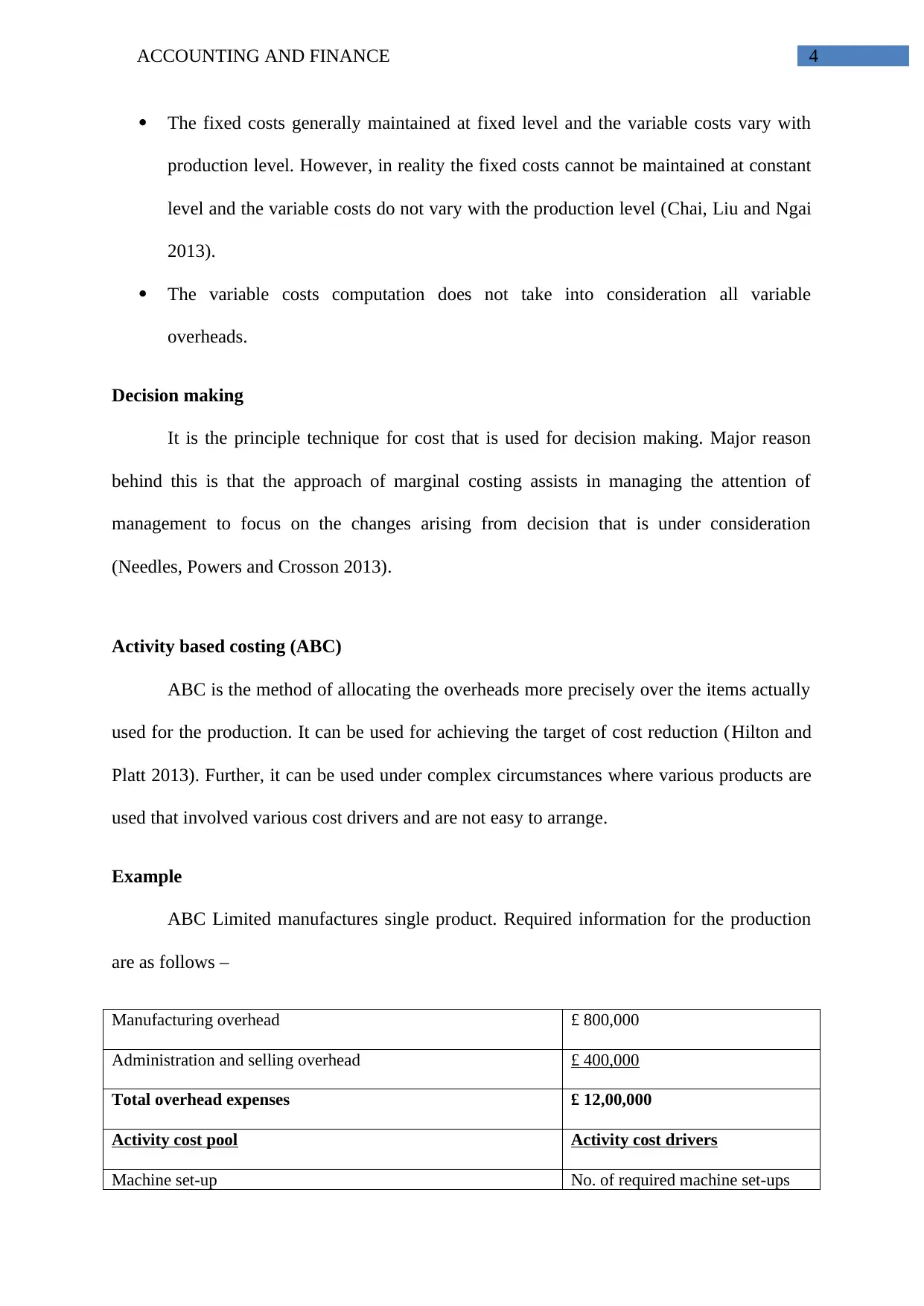
ACCOUNTING AND FINANCE 4
The fixed costs generally maintained at fixed level and the variable costs vary with
production level. However, in reality the fixed costs cannot be maintained at constant
level and the variable costs do not vary with the production level (Chai, Liu and Ngai
2013).
The variable costs computation does not take into consideration all variable
overheads.
Decision making
It is the principle technique for cost that is used for decision making. Major reason
behind this is that the approach of marginal costing assists in managing the attention of
management to focus on the changes arising from decision that is under consideration
(Needles, Powers and Crosson 2013).
Activity based costing (ABC)
ABC is the method of allocating the overheads more precisely over the items actually
used for the production. It can be used for achieving the target of cost reduction (Hilton and
Platt 2013). Further, it can be used under complex circumstances where various products are
used that involved various cost drivers and are not easy to arrange.
Example
ABC Limited manufactures single product. Required information for the production
are as follows –
Manufacturing overhead £ 800,000
Administration and selling overhead £ 400,000
Total overhead expenses £ 12,00,000
Activity cost pool Activity cost drivers
Machine set-up No. of required machine set-ups
The fixed costs generally maintained at fixed level and the variable costs vary with
production level. However, in reality the fixed costs cannot be maintained at constant
level and the variable costs do not vary with the production level (Chai, Liu and Ngai
2013).
The variable costs computation does not take into consideration all variable
overheads.
Decision making
It is the principle technique for cost that is used for decision making. Major reason
behind this is that the approach of marginal costing assists in managing the attention of
management to focus on the changes arising from decision that is under consideration
(Needles, Powers and Crosson 2013).
Activity based costing (ABC)
ABC is the method of allocating the overheads more precisely over the items actually
used for the production. It can be used for achieving the target of cost reduction (Hilton and
Platt 2013). Further, it can be used under complex circumstances where various products are
used that involved various cost drivers and are not easy to arrange.
Example
ABC Limited manufactures single product. Required information for the production
are as follows –
Manufacturing overhead £ 800,000
Administration and selling overhead £ 400,000
Total overhead expenses £ 12,00,000
Activity cost pool Activity cost drivers
Machine set-up No. of required machine set-ups
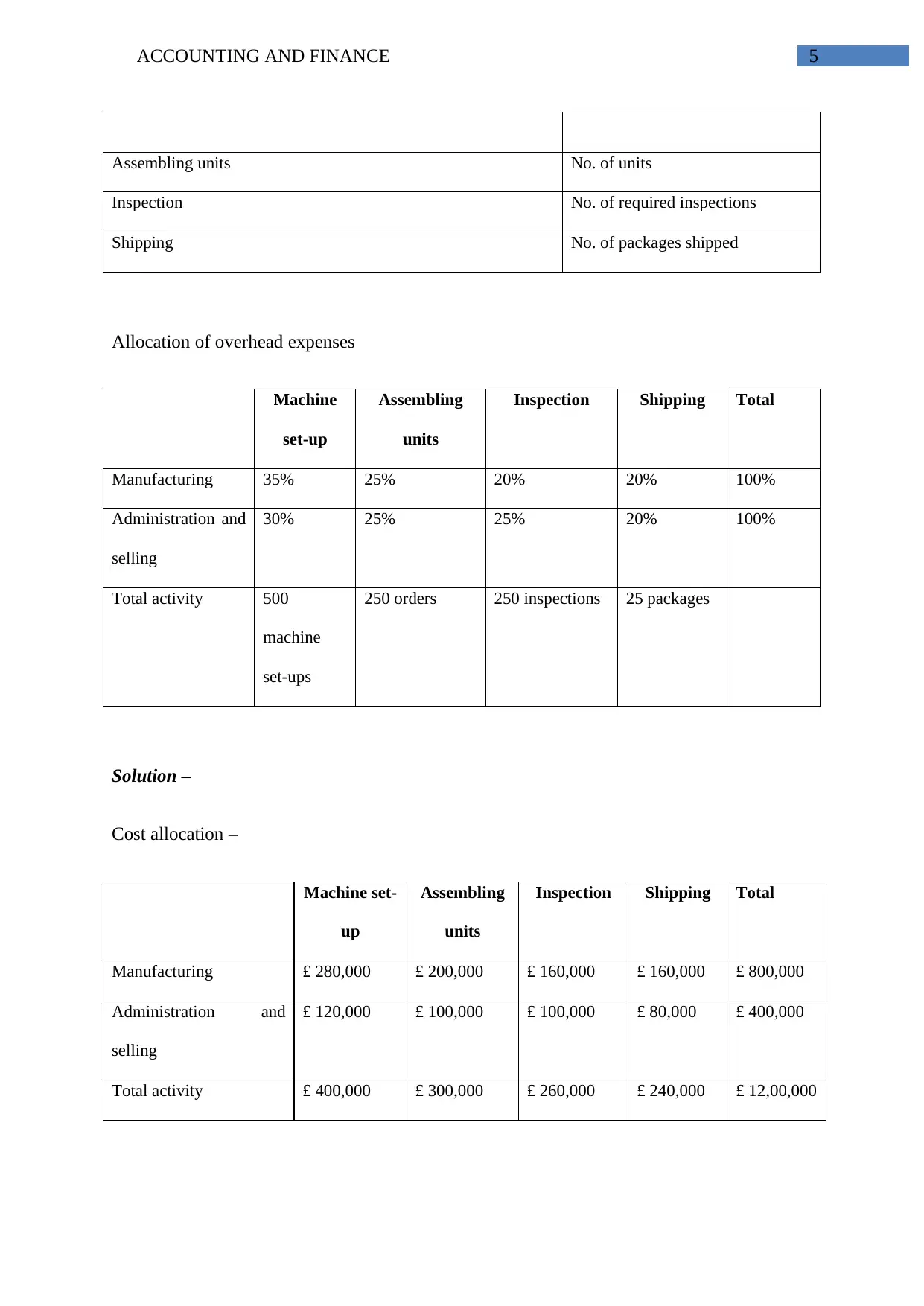
ACCOUNTING AND FINANCE 5
Assembling units No. of units
Inspection No. of required inspections
Shipping No. of packages shipped
Allocation of overhead expenses
Machine
set-up
Assembling
units
Inspection Shipping Total
Manufacturing 35% 25% 20% 20% 100%
Administration and
selling
30% 25% 25% 20% 100%
Total activity 500
machine
set-ups
250 orders 250 inspections 25 packages
Solution –
Cost allocation –
Machine set-
up
Assembling
units
Inspection Shipping Total
Manufacturing £ 280,000 £ 200,000 £ 160,000 £ 160,000 £ 800,000
Administration and
selling
£ 120,000 £ 100,000 £ 100,000 £ 80,000 £ 400,000
Total activity £ 400,000 £ 300,000 £ 260,000 £ 240,000 £ 12,00,000
Assembling units No. of units
Inspection No. of required inspections
Shipping No. of packages shipped
Allocation of overhead expenses
Machine
set-up
Assembling
units
Inspection Shipping Total
Manufacturing 35% 25% 20% 20% 100%
Administration and
selling
30% 25% 25% 20% 100%
Total activity 500
machine
set-ups
250 orders 250 inspections 25 packages
Solution –
Cost allocation –
Machine set-
up
Assembling
units
Inspection Shipping Total
Manufacturing £ 280,000 £ 200,000 £ 160,000 £ 160,000 £ 800,000
Administration and
selling
£ 120,000 £ 100,000 £ 100,000 £ 80,000 £ 400,000
Total activity £ 400,000 £ 300,000 £ 260,000 £ 240,000 £ 12,00,000
⊘ This is a preview!⊘
Do you want full access?
Subscribe today to unlock all pages.

Trusted by 1+ million students worldwide
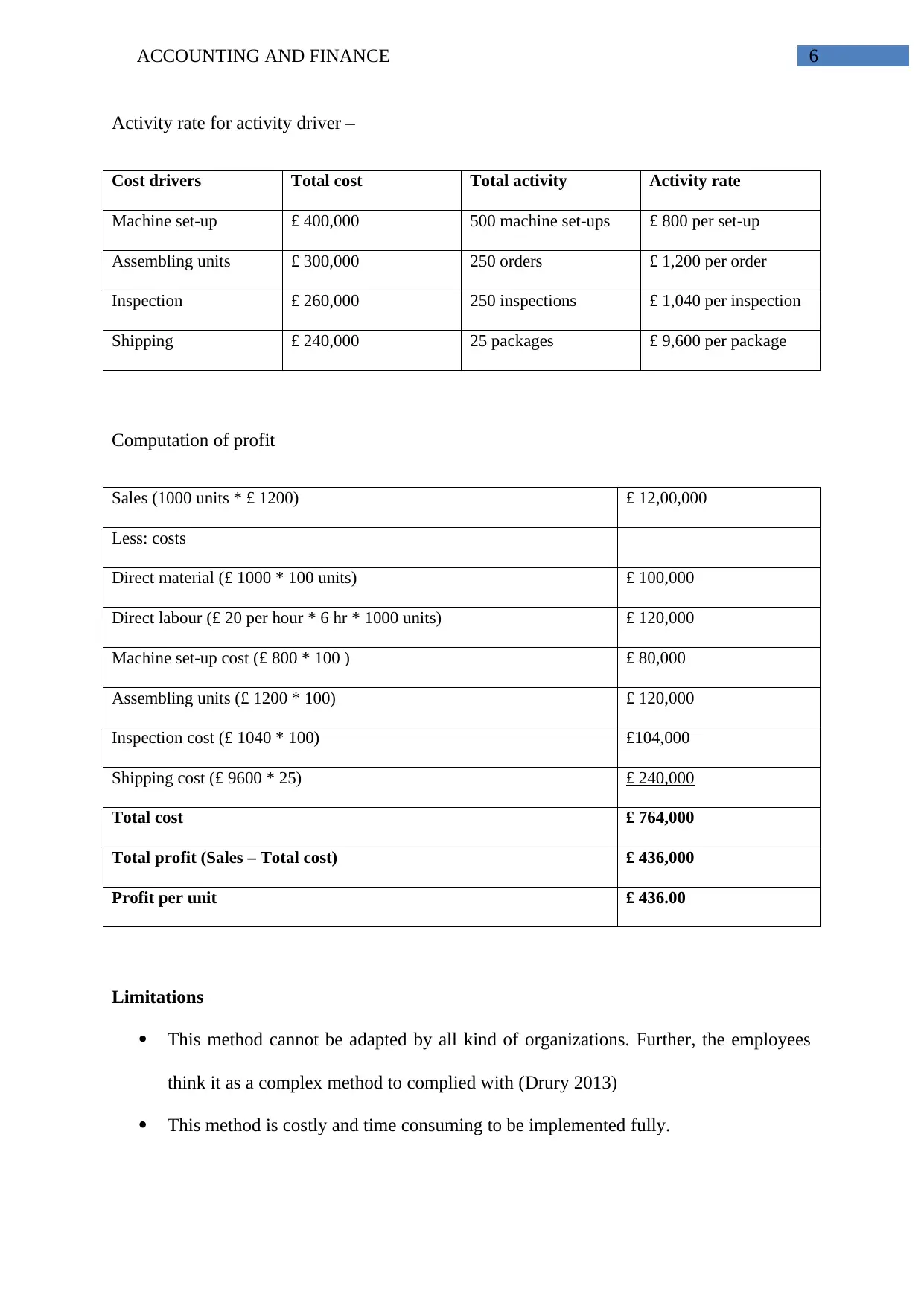
ACCOUNTING AND FINANCE 6
Activity rate for activity driver –
Cost drivers Total cost Total activity Activity rate
Machine set-up £ 400,000 500 machine set-ups £ 800 per set-up
Assembling units £ 300,000 250 orders £ 1,200 per order
Inspection £ 260,000 250 inspections £ 1,040 per inspection
Shipping £ 240,000 25 packages £ 9,600 per package
Computation of profit
Sales (1000 units * £ 1200) £ 12,00,000
Less: costs
Direct material (£ 1000 * 100 units) £ 100,000
Direct labour (£ 20 per hour * 6 hr * 1000 units) £ 120,000
Machine set-up cost (£ 800 * 100 ) £ 80,000
Assembling units (£ 1200 * 100) £ 120,000
Inspection cost (£ 1040 * 100) £104,000
Shipping cost (£ 9600 * 25) £ 240,000
Total cost £ 764,000
Total profit (Sales – Total cost) £ 436,000
Profit per unit £ 436.00
Limitations
This method cannot be adapted by all kind of organizations. Further, the employees
think it as a complex method to complied with (Drury 2013)
This method is costly and time consuming to be implemented fully.
Activity rate for activity driver –
Cost drivers Total cost Total activity Activity rate
Machine set-up £ 400,000 500 machine set-ups £ 800 per set-up
Assembling units £ 300,000 250 orders £ 1,200 per order
Inspection £ 260,000 250 inspections £ 1,040 per inspection
Shipping £ 240,000 25 packages £ 9,600 per package
Computation of profit
Sales (1000 units * £ 1200) £ 12,00,000
Less: costs
Direct material (£ 1000 * 100 units) £ 100,000
Direct labour (£ 20 per hour * 6 hr * 1000 units) £ 120,000
Machine set-up cost (£ 800 * 100 ) £ 80,000
Assembling units (£ 1200 * 100) £ 120,000
Inspection cost (£ 1040 * 100) £104,000
Shipping cost (£ 9600 * 25) £ 240,000
Total cost £ 764,000
Total profit (Sales – Total cost) £ 436,000
Profit per unit £ 436.00
Limitations
This method cannot be adapted by all kind of organizations. Further, the employees
think it as a complex method to complied with (Drury 2013)
This method is costly and time consuming to be implemented fully.
Paraphrase This Document
Need a fresh take? Get an instant paraphrase of this document with our AI Paraphraser
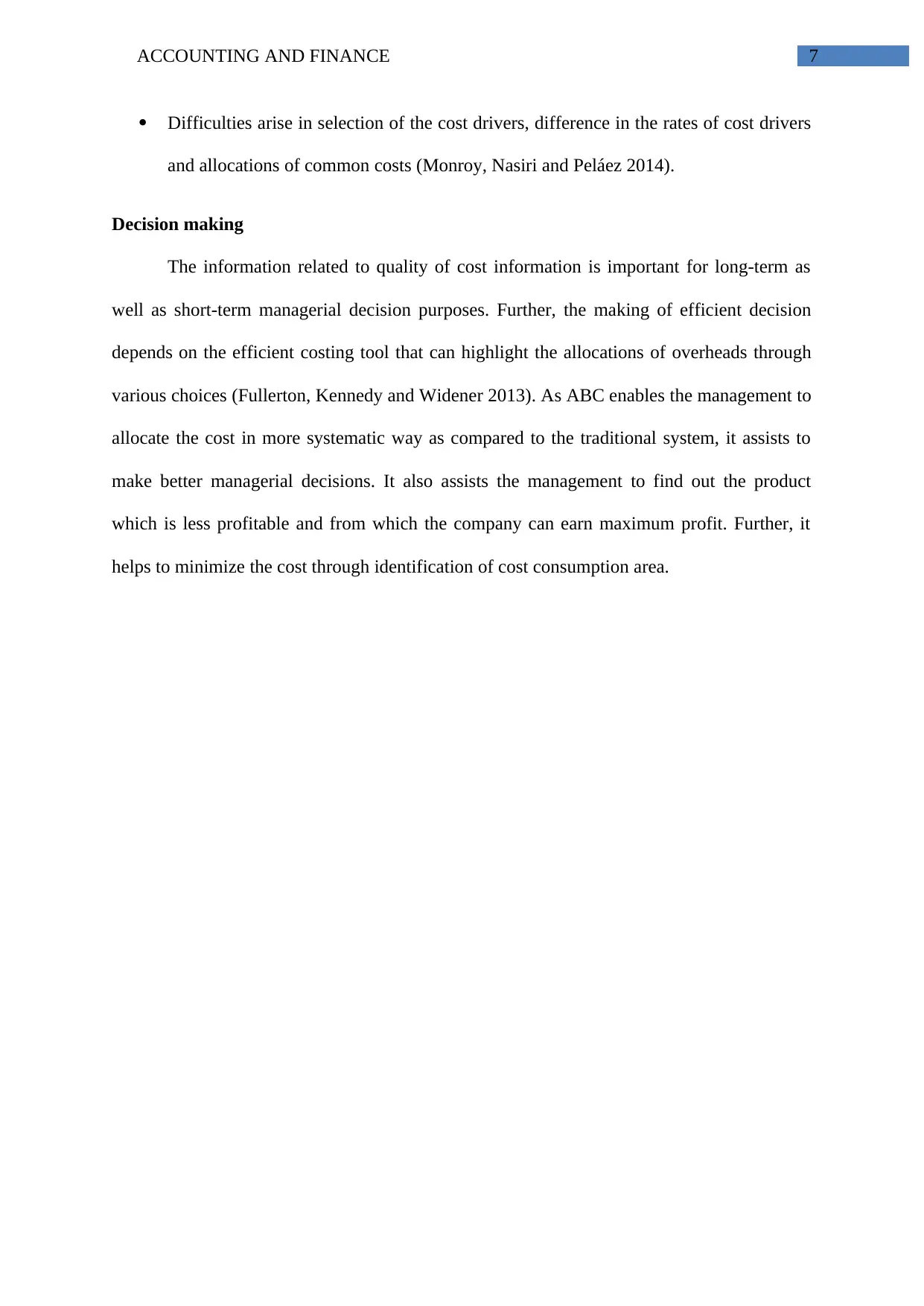
ACCOUNTING AND FINANCE 7
Difficulties arise in selection of the cost drivers, difference in the rates of cost drivers
and allocations of common costs (Monroy, Nasiri and Peláez 2014).
Decision making
The information related to quality of cost information is important for long-term as
well as short-term managerial decision purposes. Further, the making of efficient decision
depends on the efficient costing tool that can highlight the allocations of overheads through
various choices (Fullerton, Kennedy and Widener 2013). As ABC enables the management to
allocate the cost in more systematic way as compared to the traditional system, it assists to
make better managerial decisions. It also assists the management to find out the product
which is less profitable and from which the company can earn maximum profit. Further, it
helps to minimize the cost through identification of cost consumption area.
Difficulties arise in selection of the cost drivers, difference in the rates of cost drivers
and allocations of common costs (Monroy, Nasiri and Peláez 2014).
Decision making
The information related to quality of cost information is important for long-term as
well as short-term managerial decision purposes. Further, the making of efficient decision
depends on the efficient costing tool that can highlight the allocations of overheads through
various choices (Fullerton, Kennedy and Widener 2013). As ABC enables the management to
allocate the cost in more systematic way as compared to the traditional system, it assists to
make better managerial decisions. It also assists the management to find out the product
which is less profitable and from which the company can earn maximum profit. Further, it
helps to minimize the cost through identification of cost consumption area.
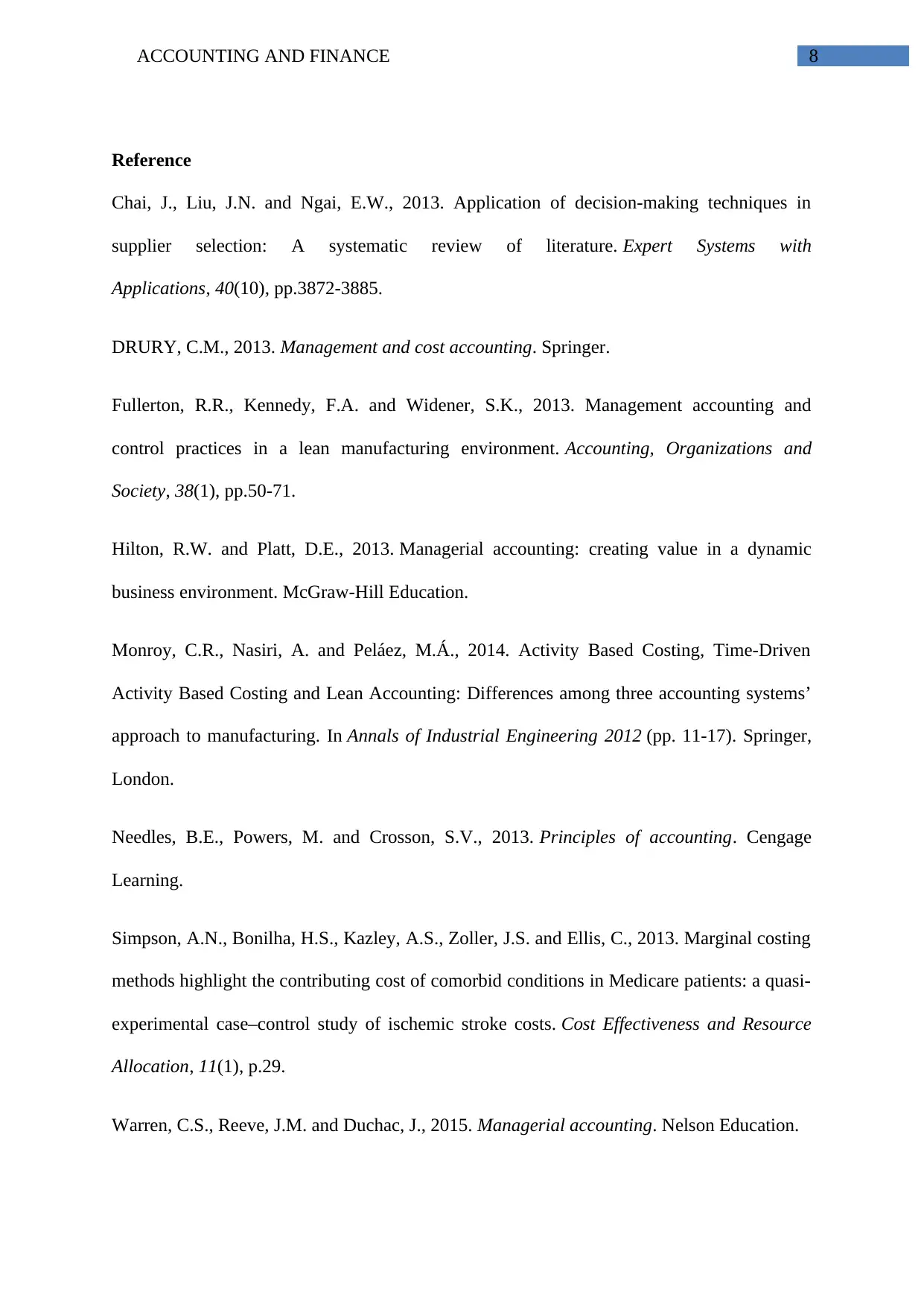
ACCOUNTING AND FINANCE 8
Reference
Chai, J., Liu, J.N. and Ngai, E.W., 2013. Application of decision-making techniques in
supplier selection: A systematic review of literature. Expert Systems with
Applications, 40(10), pp.3872-3885.
DRURY, C.M., 2013. Management and cost accounting. Springer.
Fullerton, R.R., Kennedy, F.A. and Widener, S.K., 2013. Management accounting and
control practices in a lean manufacturing environment. Accounting, Organizations and
Society, 38(1), pp.50-71.
Hilton, R.W. and Platt, D.E., 2013. Managerial accounting: creating value in a dynamic
business environment. McGraw-Hill Education.
Monroy, C.R., Nasiri, A. and Peláez, M.Á., 2014. Activity Based Costing, Time-Driven
Activity Based Costing and Lean Accounting: Differences among three accounting systems’
approach to manufacturing. In Annals of Industrial Engineering 2012 (pp. 11-17). Springer,
London.
Needles, B.E., Powers, M. and Crosson, S.V., 2013. Principles of accounting. Cengage
Learning.
Simpson, A.N., Bonilha, H.S., Kazley, A.S., Zoller, J.S. and Ellis, C., 2013. Marginal costing
methods highlight the contributing cost of comorbid conditions in Medicare patients: a quasi-
experimental case–control study of ischemic stroke costs. Cost Effectiveness and Resource
Allocation, 11(1), p.29.
Warren, C.S., Reeve, J.M. and Duchac, J., 2015. Managerial accounting. Nelson Education.
Reference
Chai, J., Liu, J.N. and Ngai, E.W., 2013. Application of decision-making techniques in
supplier selection: A systematic review of literature. Expert Systems with
Applications, 40(10), pp.3872-3885.
DRURY, C.M., 2013. Management and cost accounting. Springer.
Fullerton, R.R., Kennedy, F.A. and Widener, S.K., 2013. Management accounting and
control practices in a lean manufacturing environment. Accounting, Organizations and
Society, 38(1), pp.50-71.
Hilton, R.W. and Platt, D.E., 2013. Managerial accounting: creating value in a dynamic
business environment. McGraw-Hill Education.
Monroy, C.R., Nasiri, A. and Peláez, M.Á., 2014. Activity Based Costing, Time-Driven
Activity Based Costing and Lean Accounting: Differences among three accounting systems’
approach to manufacturing. In Annals of Industrial Engineering 2012 (pp. 11-17). Springer,
London.
Needles, B.E., Powers, M. and Crosson, S.V., 2013. Principles of accounting. Cengage
Learning.
Simpson, A.N., Bonilha, H.S., Kazley, A.S., Zoller, J.S. and Ellis, C., 2013. Marginal costing
methods highlight the contributing cost of comorbid conditions in Medicare patients: a quasi-
experimental case–control study of ischemic stroke costs. Cost Effectiveness and Resource
Allocation, 11(1), p.29.
Warren, C.S., Reeve, J.M. and Duchac, J., 2015. Managerial accounting. Nelson Education.
⊘ This is a preview!⊘
Do you want full access?
Subscribe today to unlock all pages.

Trusted by 1+ million students worldwide
1 out of 9
Related Documents

Your All-in-One AI-Powered Toolkit for Academic Success.
+13062052269
info@desklib.com
Available 24*7 on WhatsApp / Email
Unlock your academic potential
© 2024 | Zucol Services PVT LTD | All rights reserved.