Industrial Training Report: CECB and Quantity Surveying Experience
VerifiedAdded on 2021/10/01
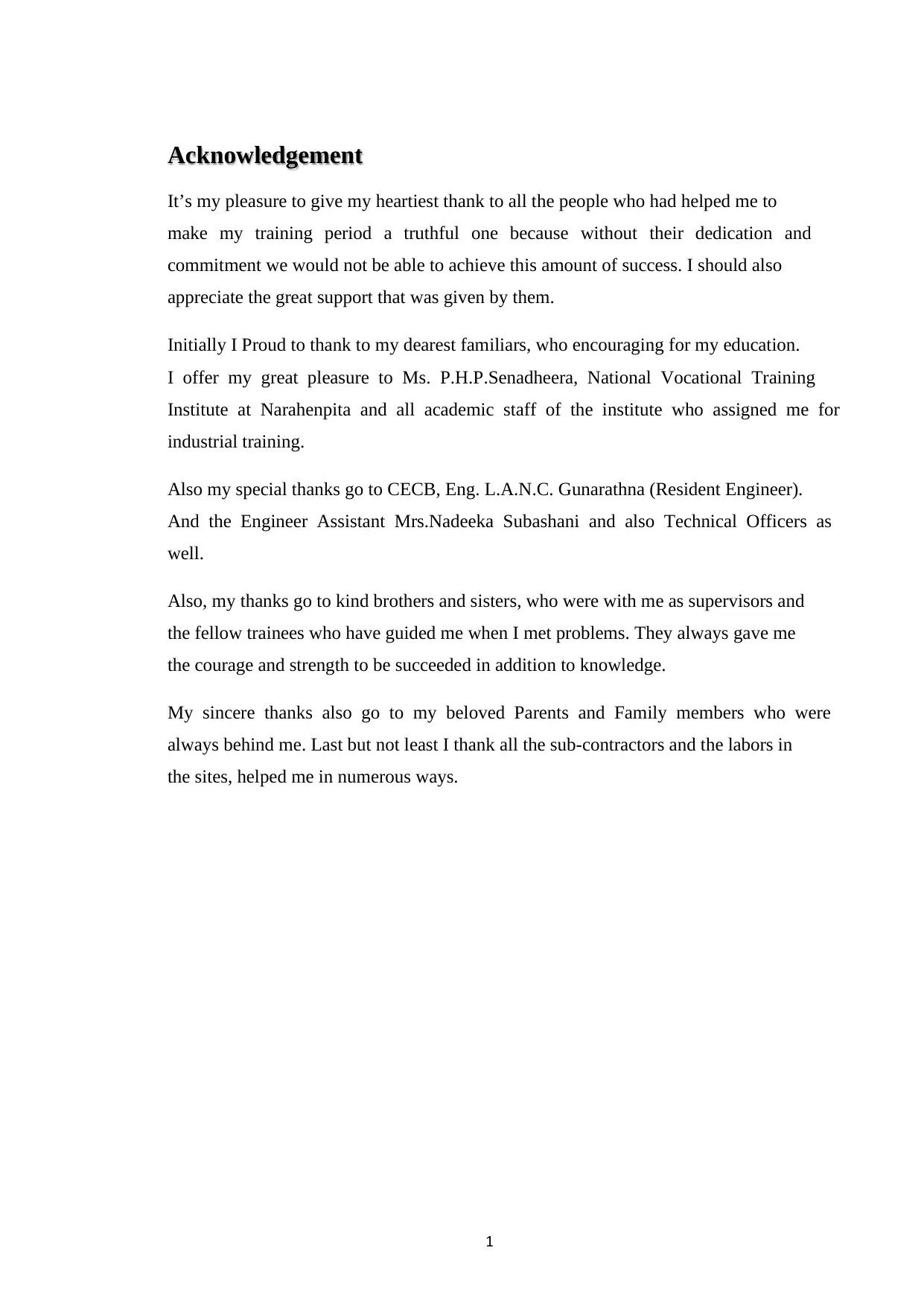
Acknowledgement
It’s my pleasure to give my heartiest thank to all the people who had helped me to
make my training period a truthful one because without their dedication and
commitment we would not be able to achieve this amount of success. I should also
appreciate the great support that was given by them.
Initially I Proud to thank to my dearest familiars, who encouraging for my education.
I offer my great pleasure to Ms. P.H.P.Senadheera, National Vocational Training
Institute at Narahenpita and all academic staff of the institute who assigned me for
industrial training.
Also my special thanks go to CECB, Eng. L.A.N.C. Gunarathna (Resident Engineer).
And the Engineer Assistant Mrs.Nadeeka Subashani and also Technical Officers as
well.
Also, my thanks go to kind brothers and sisters, who were with me as supervisors and
the fellow trainees who have guided me when I met problems. They always gave me
the courage and strength to be succeeded in addition to knowledge.
My sincere thanks also go to my beloved Parents and Family members who were
always behind me. Last but not least I thank all the sub-contractors and the labors in
the sites, helped me in numerous ways.
Paraphrase This Document
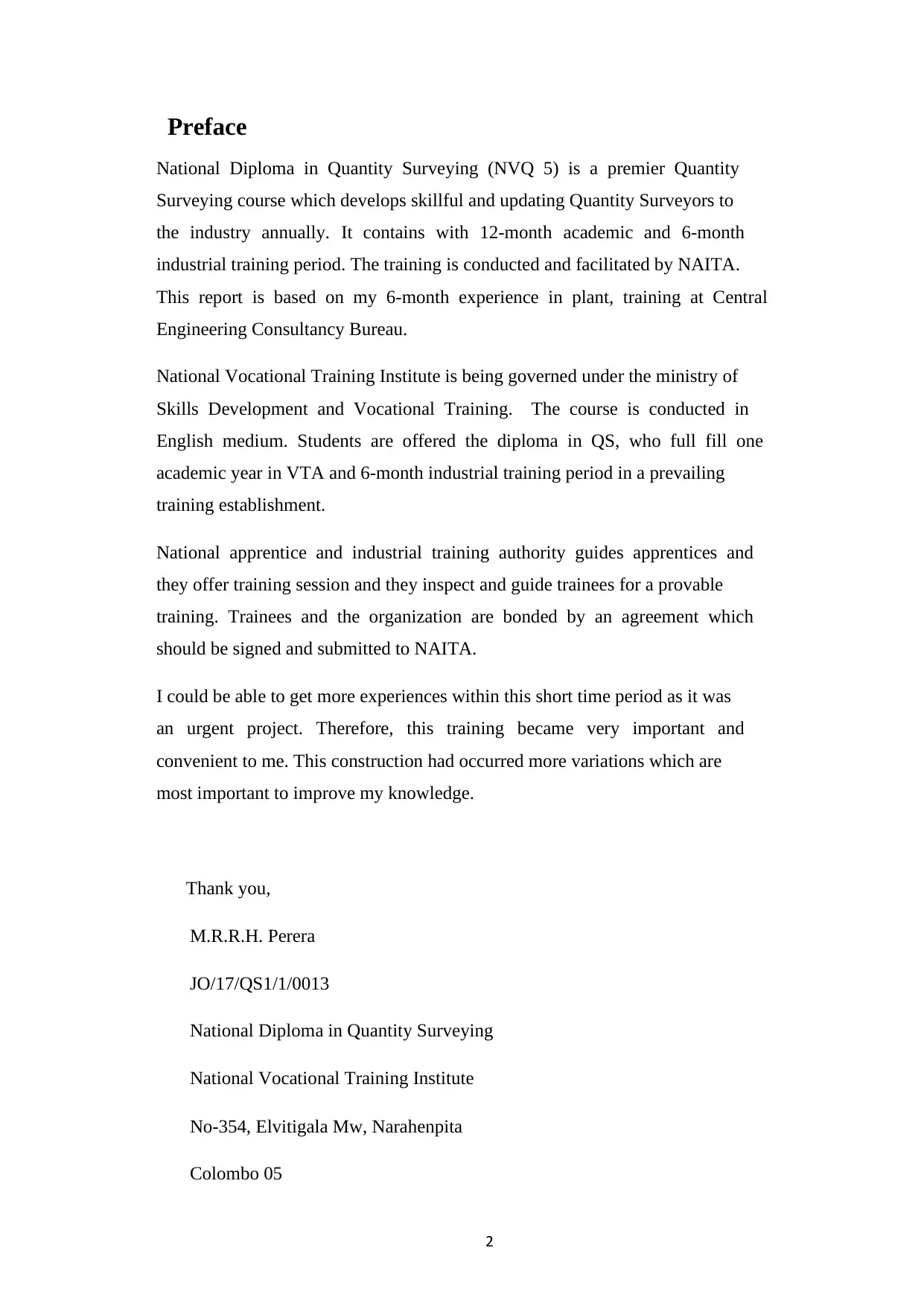
Preface
National Diploma in Quantity Surveying (NVQ 5) is a premier Quantity
Surveying course which develops skillful and updating Quantity Surveyors to
the industry annually. It contains with 12-month academic and 6-month
industrial training period. The training is conducted and facilitated by NAITA.
This report is based on my 6-month experience in plant, training at Central
Engineering Consultancy Bureau.
National Vocational Training Institute is being governed under the ministry of
Skills Development and Vocational Training. The course is conducted in
English medium. Students are offered the diploma in QS, who full fill one
academic year in VTA and 6-month industrial training period in a prevailing
training establishment.
National apprentice and industrial training authority guides apprentices and
they offer training session and they inspect and guide trainees for a provable
training. Trainees and the organization are bonded by an agreement which
should be signed and submitted to NAITA.
I could be able to get more experiences within this short time period as it was
an urgent project. Therefore, this training became very important and
convenient to me. This construction had occurred more variations which are
most important to improve my knowledge.
Thank you,
M.R.R.H. Perera
JO/17/QS1/1/0013
National Diploma in Quantity Surveying
National Vocational Training Institute
No-354, Elvitigala Mw, Narahenpita
Colombo 05
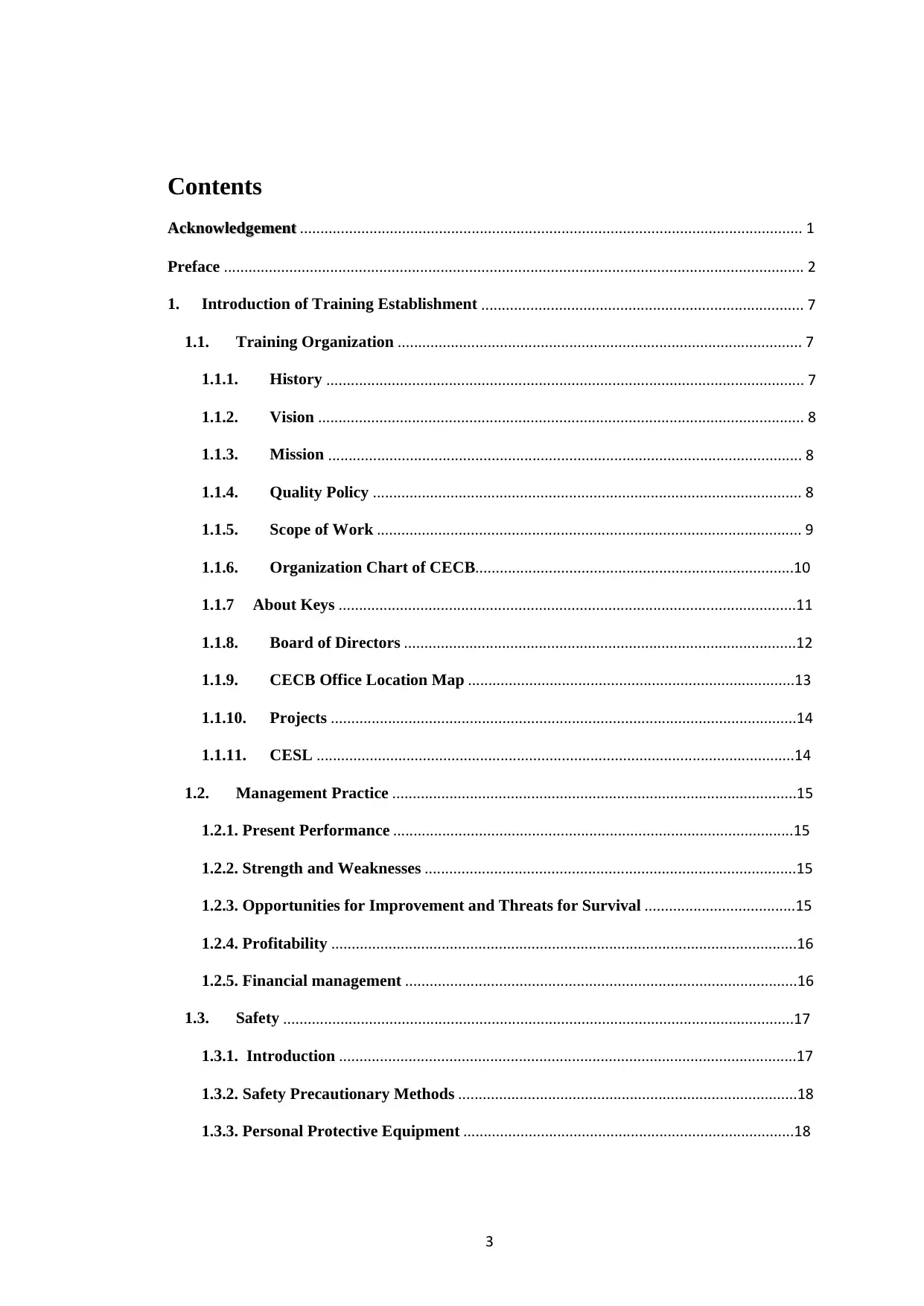
Contents
Acknowledgement ........................................................................................................................... 1
Preface .............................................................................................................................................. 2
1. Introduction of Training Establishment ............................................................................... 7
1.1. Training Organization ................................................................................................... 7
1.1.1. History ..................................................................................................................... 7
1.1.2. Vision ....................................................................................................................... 8
1.1.3. Mission .................................................................................................................... 8
1.1.4. Quality Policy ......................................................................................................... 8
1.1.5. Scope of Work ........................................................................................................ 9
1.1.6. Organization Chart of CECB..............................................................................10
1.1.7 About Keys ................................................................................................................11
1.1.8. Board of Directors ................................................................................................12
1.1.9. CECB Office Location Map ................................................................................13
1.1.10. Projects ..................................................................................................................14
1.1.11. CESL .....................................................................................................................14
1.2. Management Practice ...................................................................................................15
1.2.1. Present Performance ..................................................................................................15
1.2.2. Strength and Weaknesses ...........................................................................................15
1.2.3. Opportunities for Improvement and Threats for Survival .....................................15
1.2.4. Profitability ..................................................................................................................16
1.2.5. Financial management ................................................................................................16
1.3. Safety .............................................................................................................................17
1.3.1. Introduction ................................................................................................................17
1.3.2. Safety Precautionary Methods ...................................................................................18
1.3.3. Personal Protective Equipment .................................................................................18
⊘ This is a preview!⊘
Do you want full access?
Subscribe today to unlock all pages.

Trusted by 1+ million students worldwide
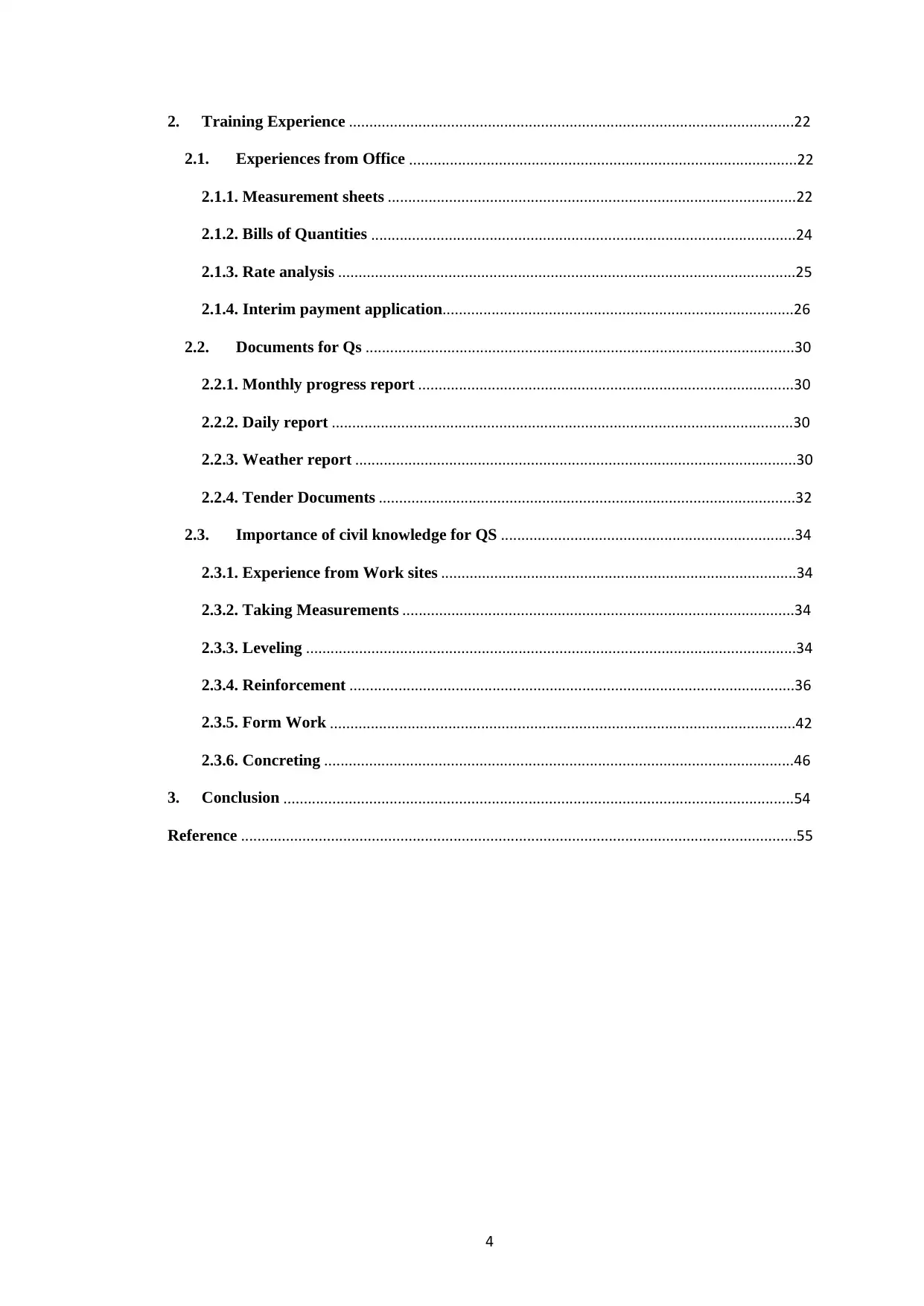
2. Training Experience .............................................................................................................22
2.1. Experiences from Office ...............................................................................................22
2.1.1. Measurement sheets ....................................................................................................22
2.1.2. Bills of Quantities ........................................................................................................24
2.1.3. Rate analysis ................................................................................................................25
2.1.4. Interim payment application......................................................................................26
2.2. Documents for Qs .........................................................................................................30
2.2.1. Monthly progress report ............................................................................................30
2.2.2. Daily report .................................................................................................................30
2.2.3. Weather report ............................................................................................................30
2.2.4. Tender Documents ......................................................................................................32
2.3. Importance of civil knowledge for QS ........................................................................34
2.3.1. Experience from Work sites .......................................................................................34
2.3.2. Taking Measurements ................................................................................................34
2.3.3. Leveling ........................................................................................................................34
2.3.4. Reinforcement .............................................................................................................36
2.3.5. Form Work ..................................................................................................................42
2.3.6. Concreting ...................................................................................................................46
3. Conclusion .............................................................................................................................54
Reference ........................................................................................................................................55
Paraphrase This Document
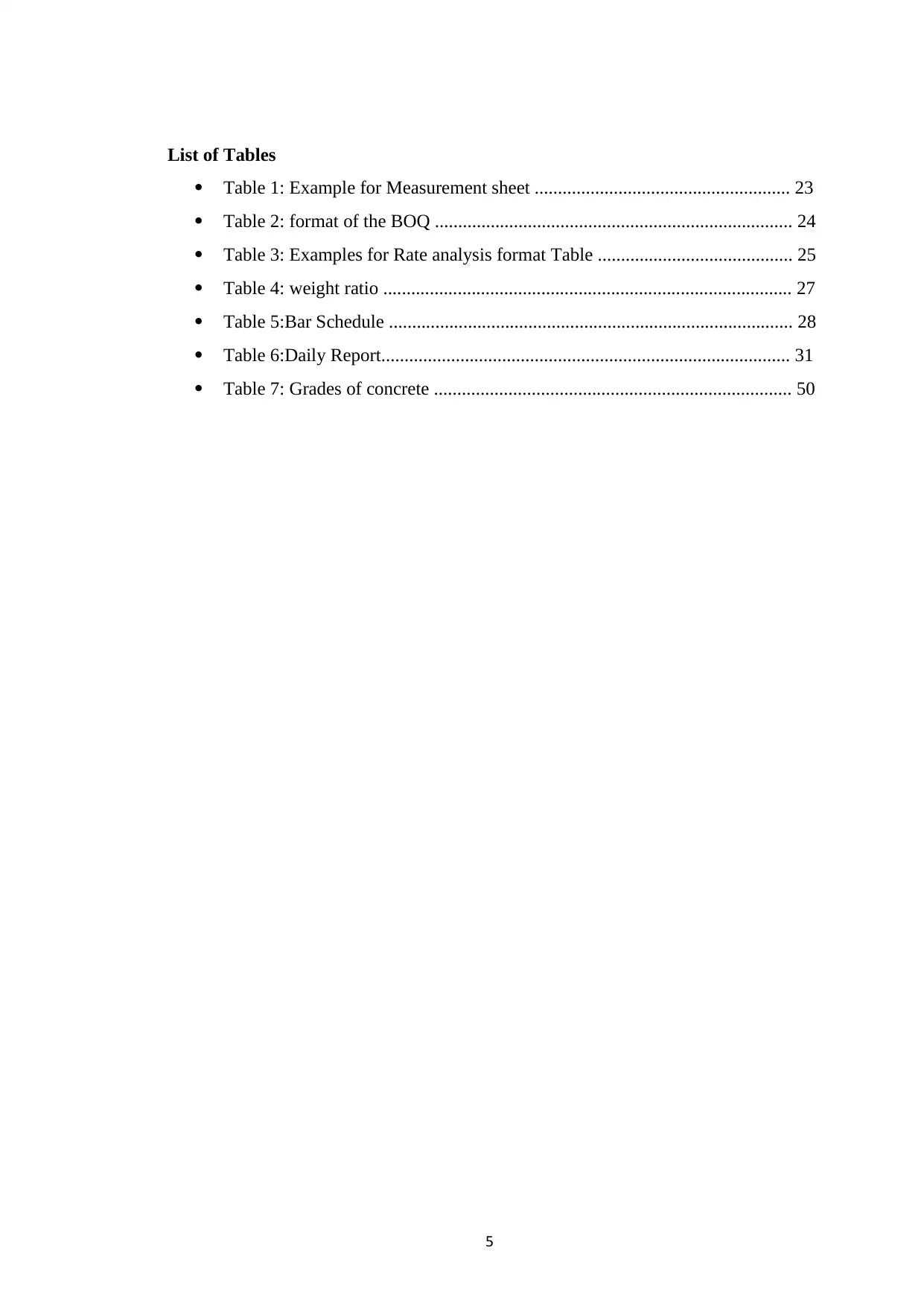
List of Tables
Table 1: Example for Measurement sheet ....................................................... 23
Table 2: format of the BOQ ............................................................................. 24
Table 3: Examples for Rate analysis format Table .......................................... 25
Table 4: weight ratio ........................................................................................ 27
Table 5:Bar Schedule ....................................................................................... 28
Table 6:Daily Report........................................................................................ 31
Table 7: Grades of concrete ............................................................................. 50
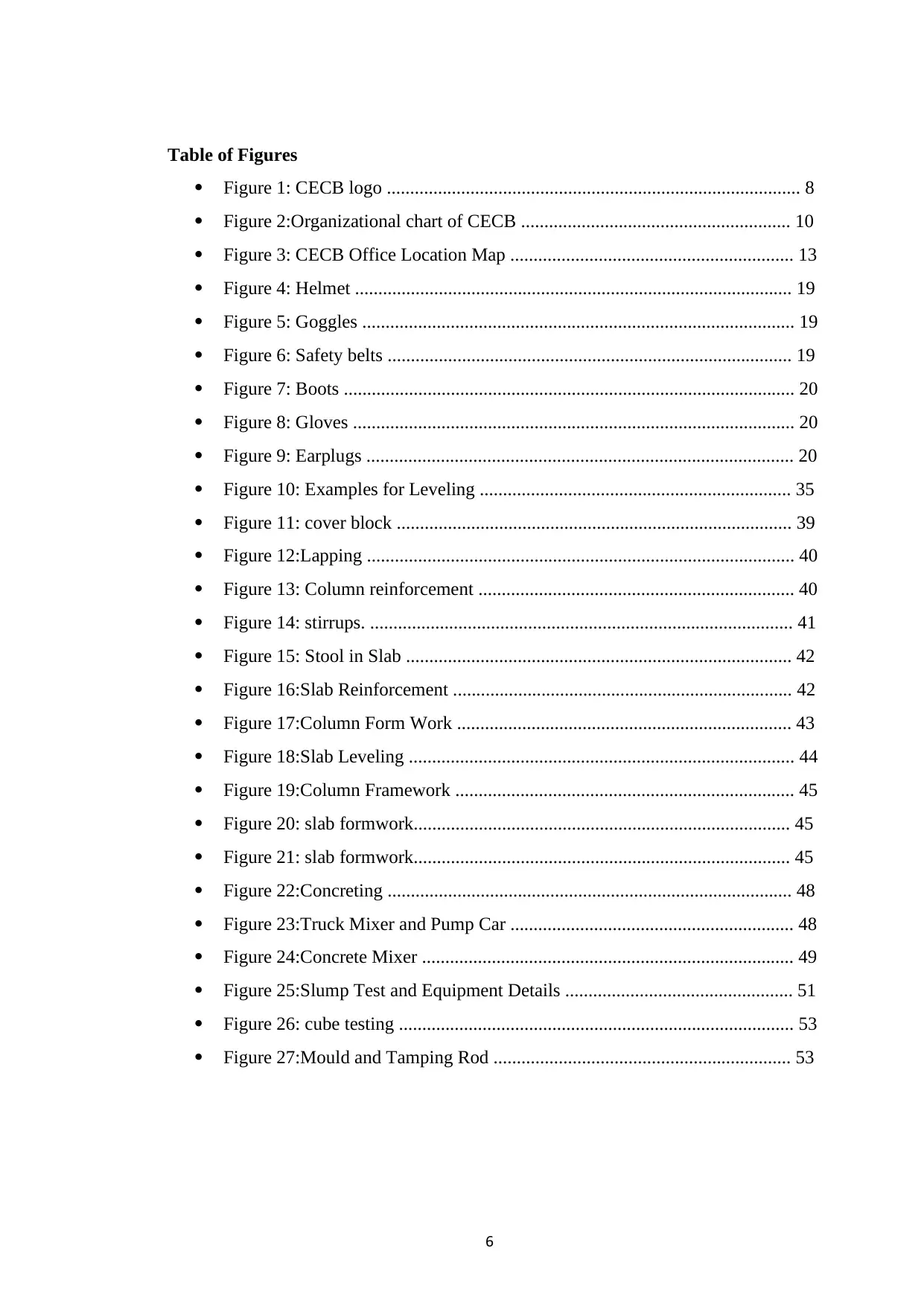
Table of Figures
Figure 1: CECB logo ......................................................................................... 8
Figure 2:Organizational chart of CECB .......................................................... 10
Figure 3: CECB Office Location Map ............................................................. 13
Figure 4: Helmet .............................................................................................. 19
Figure 5: Goggles ............................................................................................. 19
Figure 6: Safety belts ....................................................................................... 19
Figure 7: Boots ................................................................................................. 20
Figure 8: Gloves ............................................................................................... 20
Figure 9: Earplugs ............................................................................................ 20
Figure 10: Examples for Leveling ................................................................... 35
Figure 11: cover block ..................................................................................... 39
Figure 12:Lapping ............................................................................................ 40
Figure 13: Column reinforcement .................................................................... 40
Figure 14: stirrups. ........................................................................................... 41
Figure 15: Stool in Slab ................................................................................... 42
Figure 16:Slab Reinforcement ......................................................................... 42
Figure 17:Column Form Work ........................................................................ 43
Figure 18:Slab Leveling ................................................................................... 44
Figure 19:Column Framework ......................................................................... 45
Figure 20: slab formwork................................................................................. 45
Figure 21: slab formwork................................................................................. 45
Figure 22:Concreting ....................................................................................... 48
Figure 23:Truck Mixer and Pump Car ............................................................. 48
Figure 24:Concrete Mixer ................................................................................ 49
Figure 25:Slump Test and Equipment Details ................................................. 51
Figure 26: cube testing ..................................................................................... 53
Figure 27:Mould and Tamping Rod ................................................................ 53
⊘ This is a preview!⊘
Do you want full access?
Subscribe today to unlock all pages.

Trusted by 1+ million students worldwide
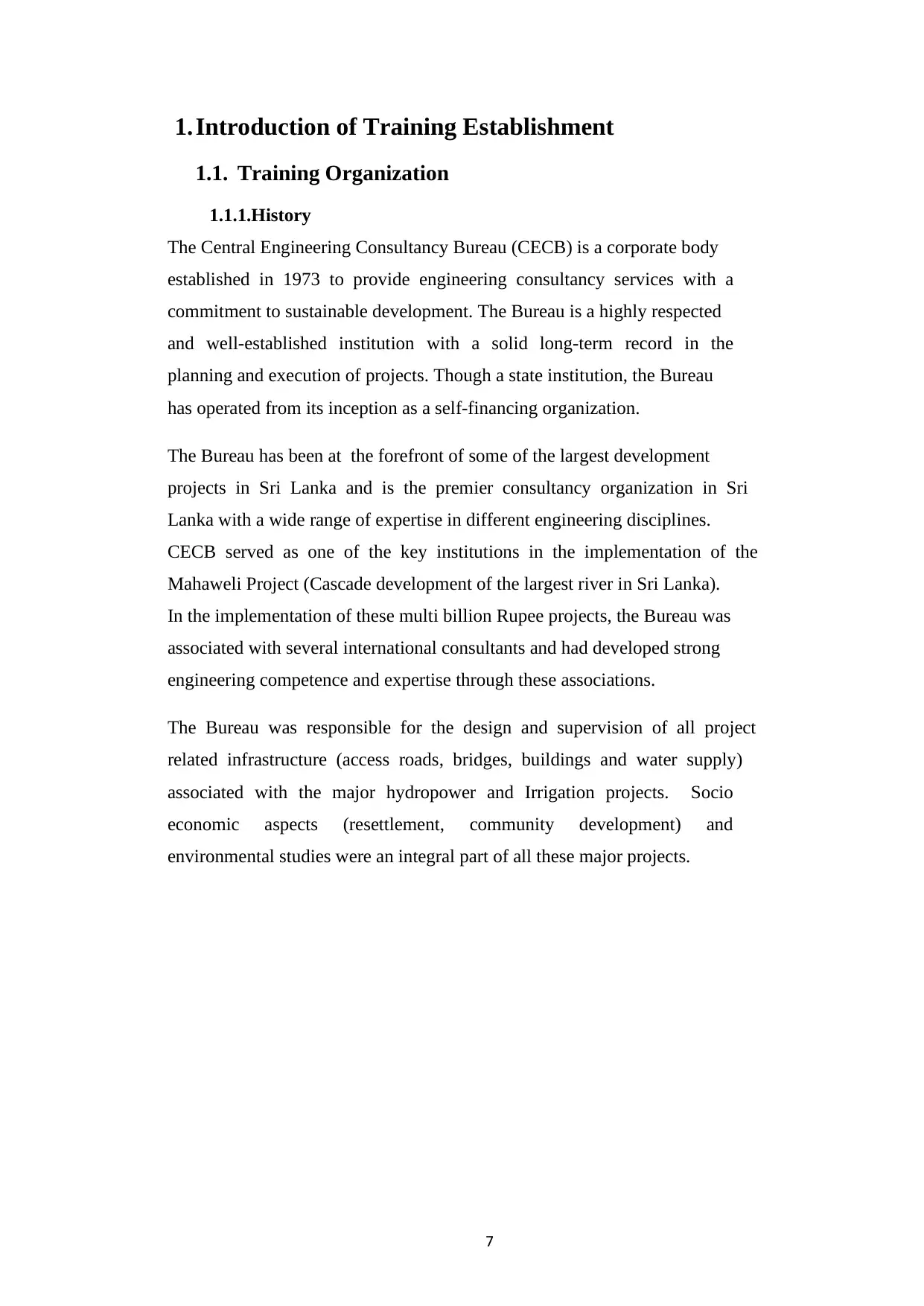
1. Introduction of Training Establishment
1.1. Training Organization
1.1.1.History
The Central Engineering Consultancy Bureau (CECB) is a corporate body
established in 1973 to provide engineering consultancy services with a
commitment to sustainable development. The Bureau is a highly respected
and well-established institution with a solid long-term record in the
planning and execution of projects. Though a state institution, the Bureau
has operated from its inception as a self-financing organization.
The Bureau has been at the forefront of some of the largest development
projects in Sri Lanka and is the premier consultancy organization in Sri
Lanka with a wide range of expertise in different engineering disciplines.
CECB served as one of the key institutions in the implementation of the
Mahaweli Project (Cascade development of the largest river in Sri Lanka).
In the implementation of these multi billion Rupee projects, the Bureau was
associated with several international consultants and had developed strong
engineering competence and expertise through these associations.
The Bureau was responsible for the design and supervision of all project
related infrastructure (access roads, bridges, buildings and water supply)
associated with the major hydropower and Irrigation projects. Socio
economic aspects (resettlement, community development) and
environmental studies were an integral part of all these major projects.
Paraphrase This Document
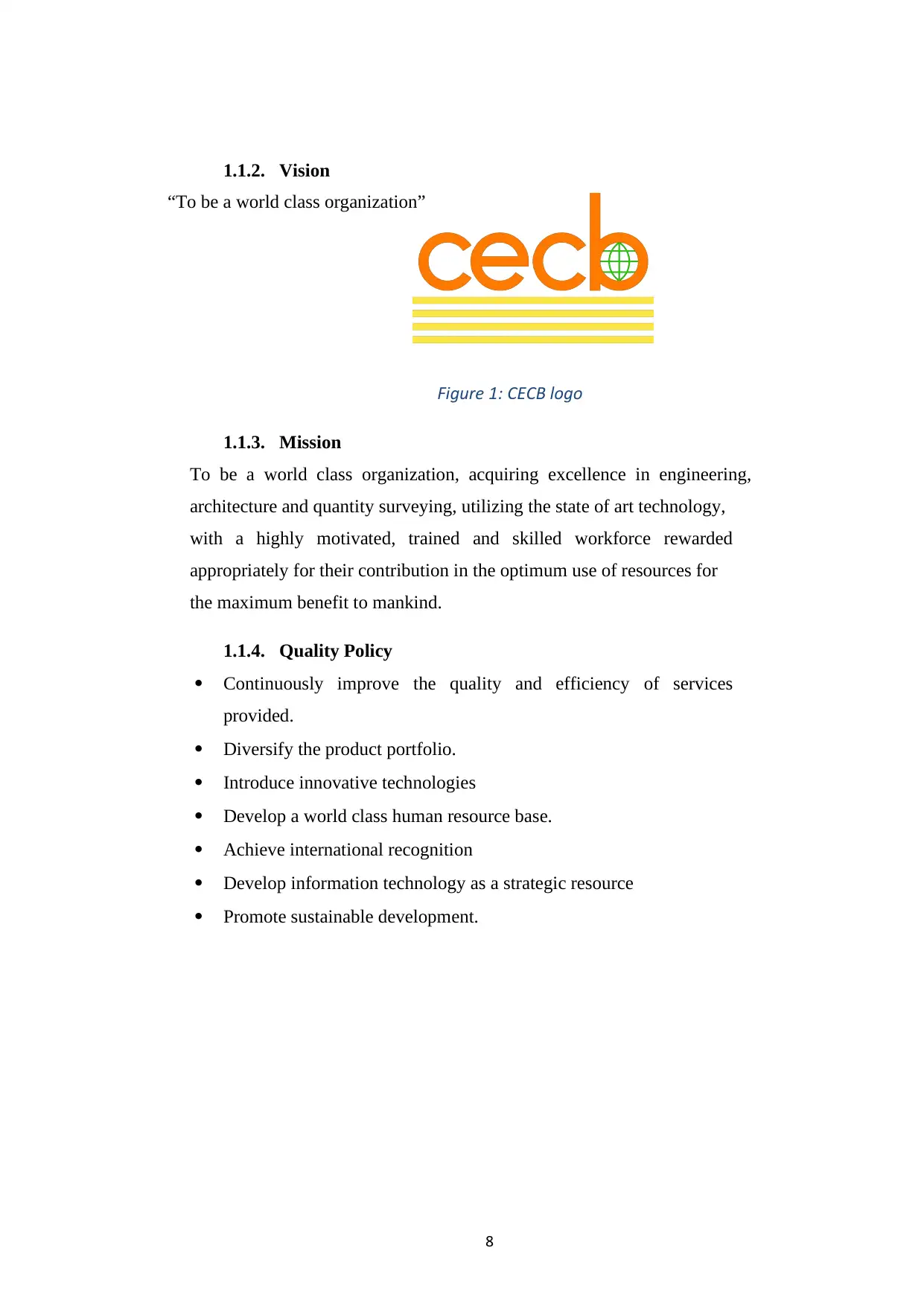
1.1.2. Vision
“To be a world class organization”
Figure 1: CECB logo
1.1.3. Mission
To be a world class organization, acquiring excellence in engineering,
architecture and quantity surveying, utilizing the state of art technology,
with a highly motivated, trained and skilled workforce rewarded
appropriately for their contribution in the optimum use of resources for
the maximum benefit to mankind.
1.1.4. Quality Policy
Continuously improve the quality and efficiency of services
provided.
Diversify the product portfolio.
Introduce innovative technologies
Develop a world class human resource base.
Achieve international recognition
Develop information technology as a strategic resource
Promote sustainable development.
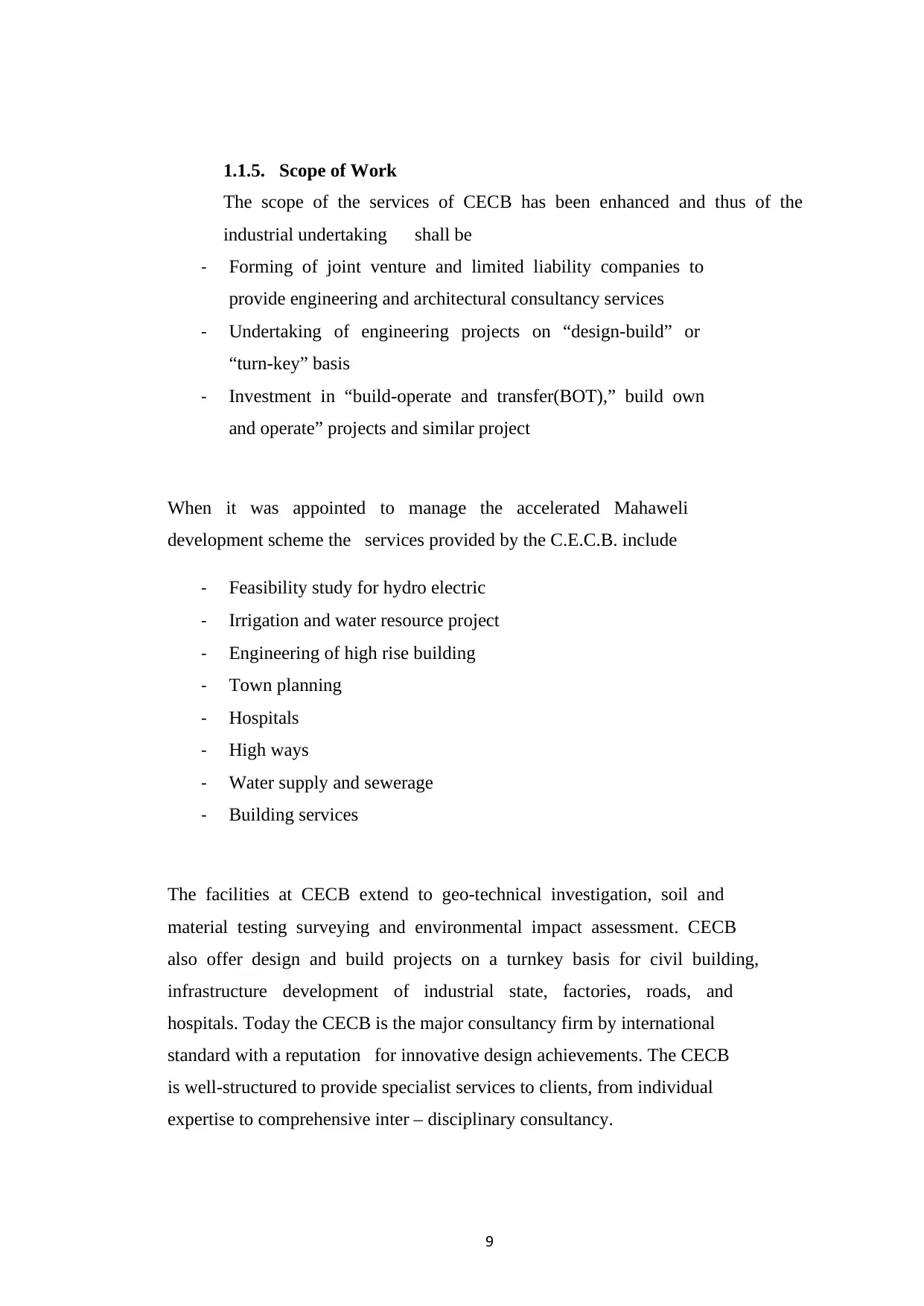
1.1.5. Scope of Work
The scope of the services of CECB has been enhanced and thus of the
industrial undertaking shall be
- Forming of joint venture and limited liability companies to
provide engineering and architectural consultancy services
- Undertaking of engineering projects on “design-build” or
“turn-key” basis
- Investment in “build-operate and transfer(BOT),” build own
and operate” projects and similar project
When it was appointed to manage the accelerated Mahaweli
development scheme the services provided by the C.E.C.B. include
- Feasibility study for hydro electric
- Irrigation and water resource project
- Engineering of high rise building
- Town planning
- Hospitals
- High ways
- Water supply and sewerage
- Building services
The facilities at CECB extend to geo-technical investigation, soil and
material testing surveying and environmental impact assessment. CECB
also offer design and build projects on a turnkey basis for civil building,
infrastructure development of industrial state, factories, roads, and
hospitals. Today the CECB is the major consultancy firm by international
standard with a reputation for innovative design achievements. The CECB
is well-structured to provide specialist services to clients, from individual
expertise to comprehensive inter – disciplinary consultancy.
⊘ This is a preview!⊘
Do you want full access?
Subscribe today to unlock all pages.

Trusted by 1+ million students worldwide
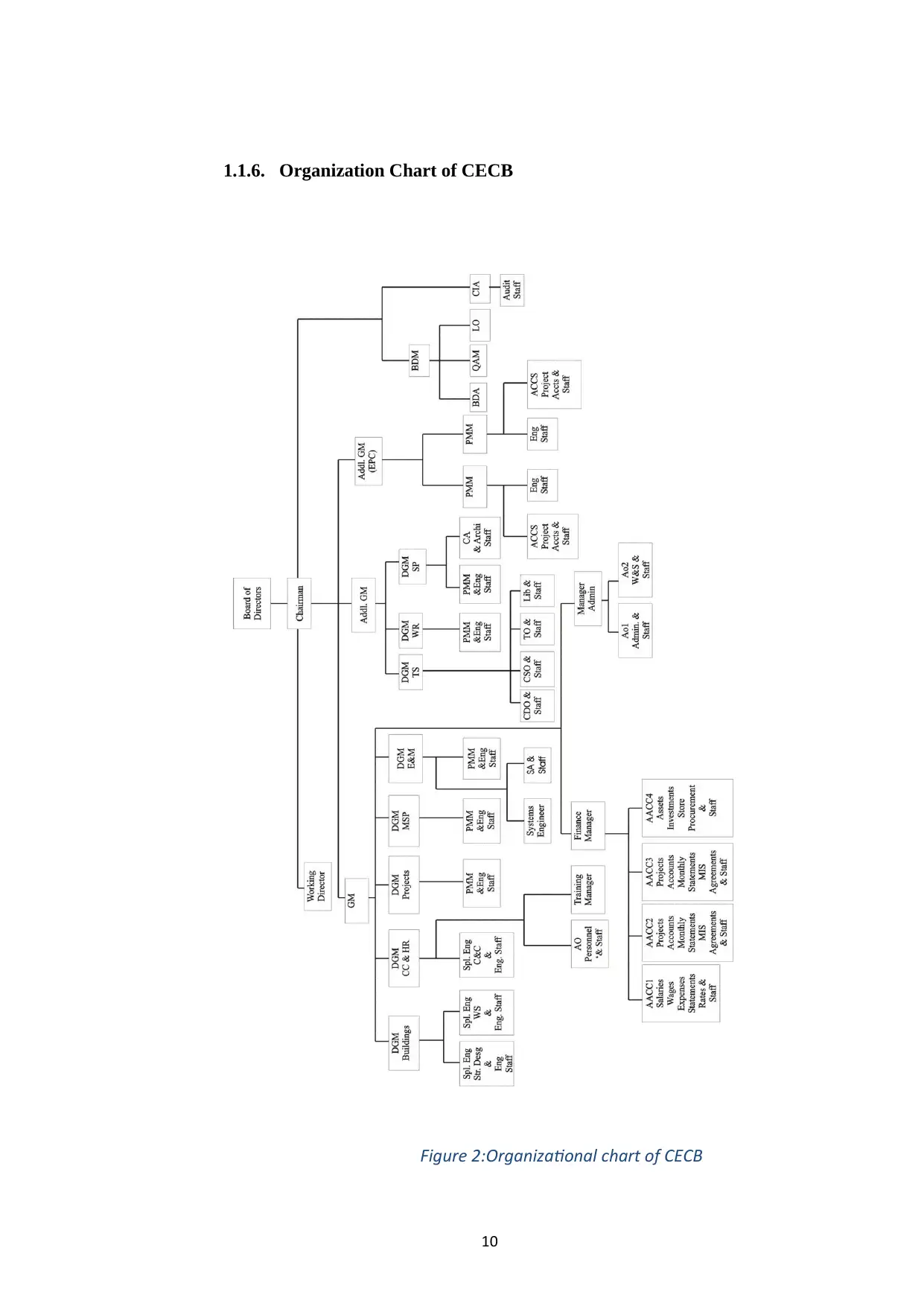
1.1.6. Organization Chart of CECB
Figure 2:Organizational chart of CECB
Paraphrase This Document
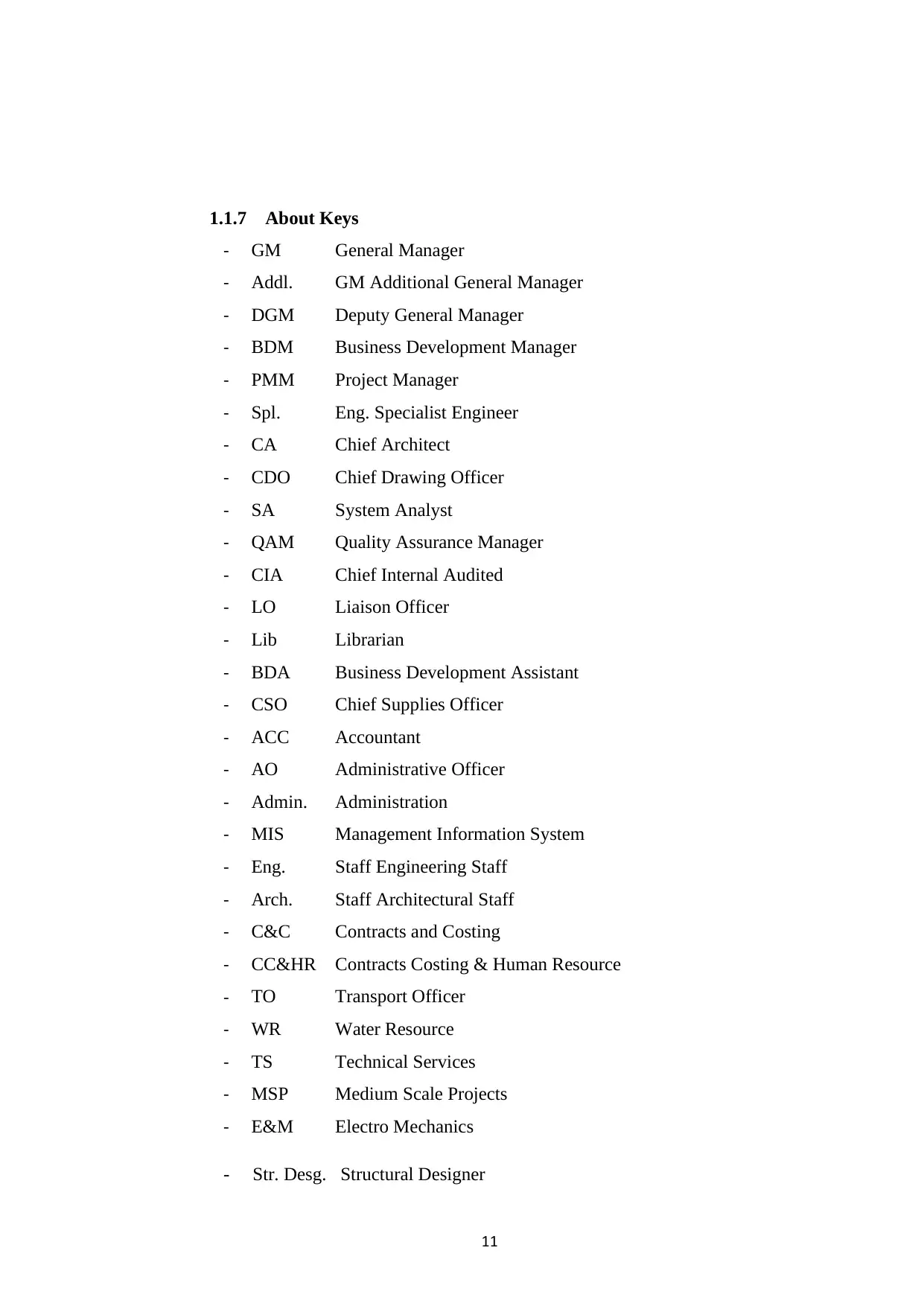
1.1.7 About Keys
- GM General Manager
- Addl. GM Additional General Manager
- DGM Deputy General Manager
- BDM Business Development Manager
- PMM Project Manager
- Spl. Eng. Specialist Engineer
- CA Chief Architect
- CDO Chief Drawing Officer
- SA System Analyst
- QAM Quality Assurance Manager
- CIA Chief Internal Audited
- LO Liaison Officer
- Lib Librarian
- BDA Business Development Assistant
- CSO Chief Supplies Officer
- ACC Accountant
- AO Administrative Officer
- Admin. Administration
- MIS Management Information System
- Eng. Staff Engineering Staff
- Arch. Staff Architectural Staff
- C&C Contracts and Costing
- CC&HR Contracts Costing & Human Resource
- TO Transport Officer
- WR Water Resource
- TS Technical Services
- MSP Medium Scale Projects
- E&M Electro Mechanics
- Str. Desg. Structural Designer
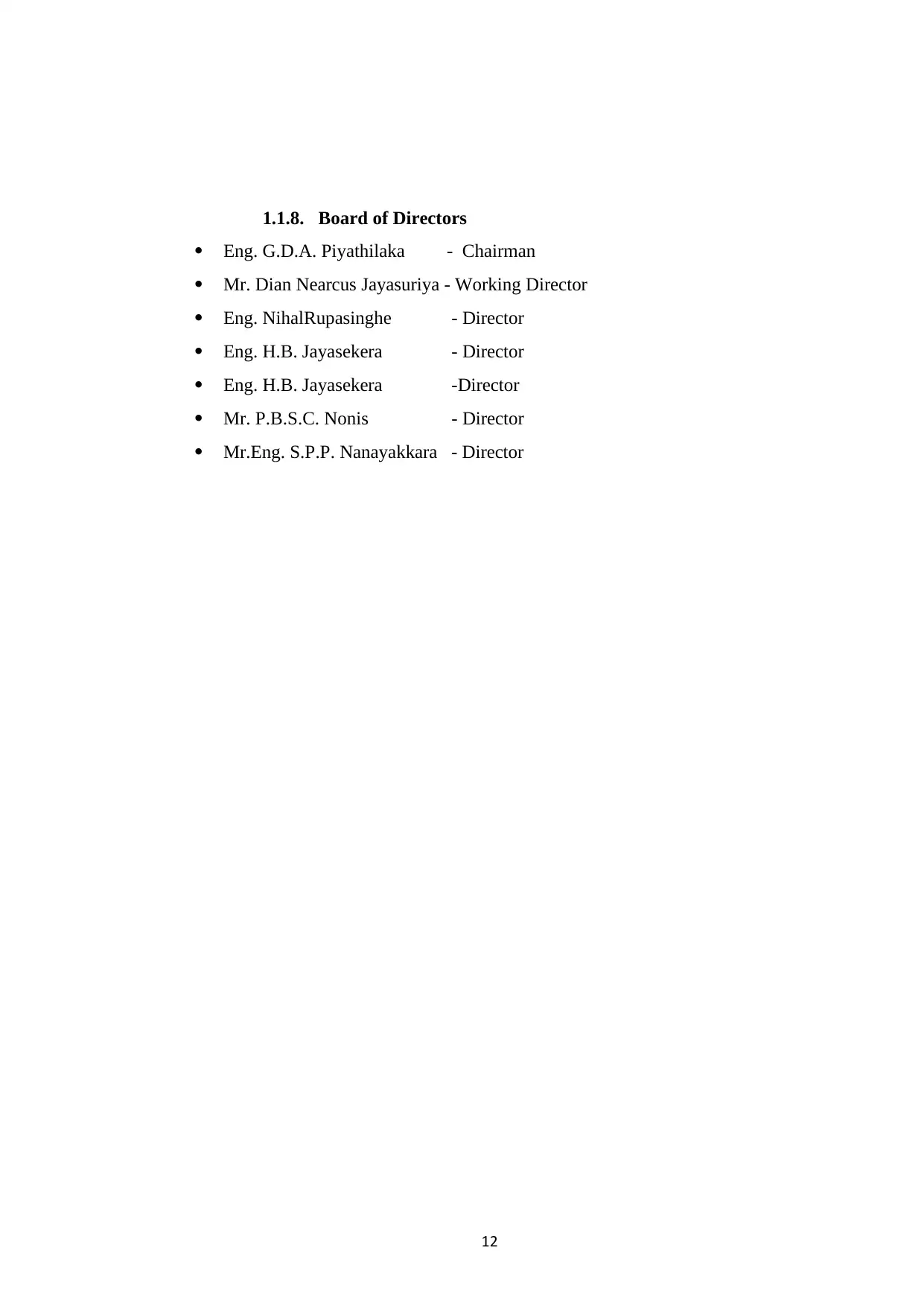
1.1.8. Board of Directors
Eng. G.D.A. Piyathilaka - Chairman
Mr. Dian Nearcus Jayasuriya - Working Director
Eng. NihalRupasinghe - Director
Eng. H.B. Jayasekera - Director
Eng. H.B. Jayasekera -Director
Mr. P.B.S.C. Nonis - Director
Mr.Eng. S.P.P. Nanayakkara - Director
⊘ This is a preview!⊘
Do you want full access?
Subscribe today to unlock all pages.

Trusted by 1+ million students worldwide
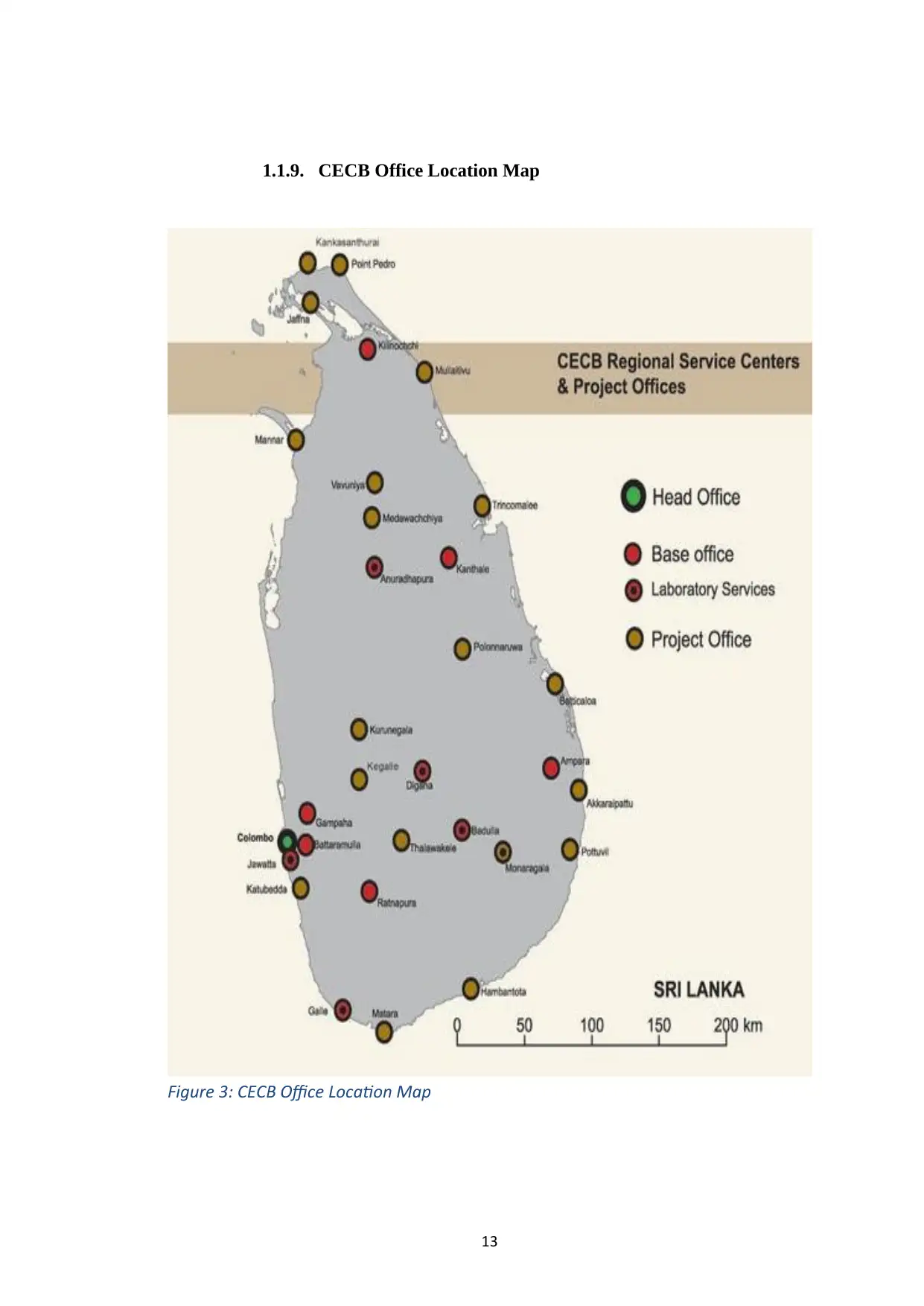
1.1.9. CECB Office Location Map
Figure 3: CECB Office Location Map
Paraphrase This Document
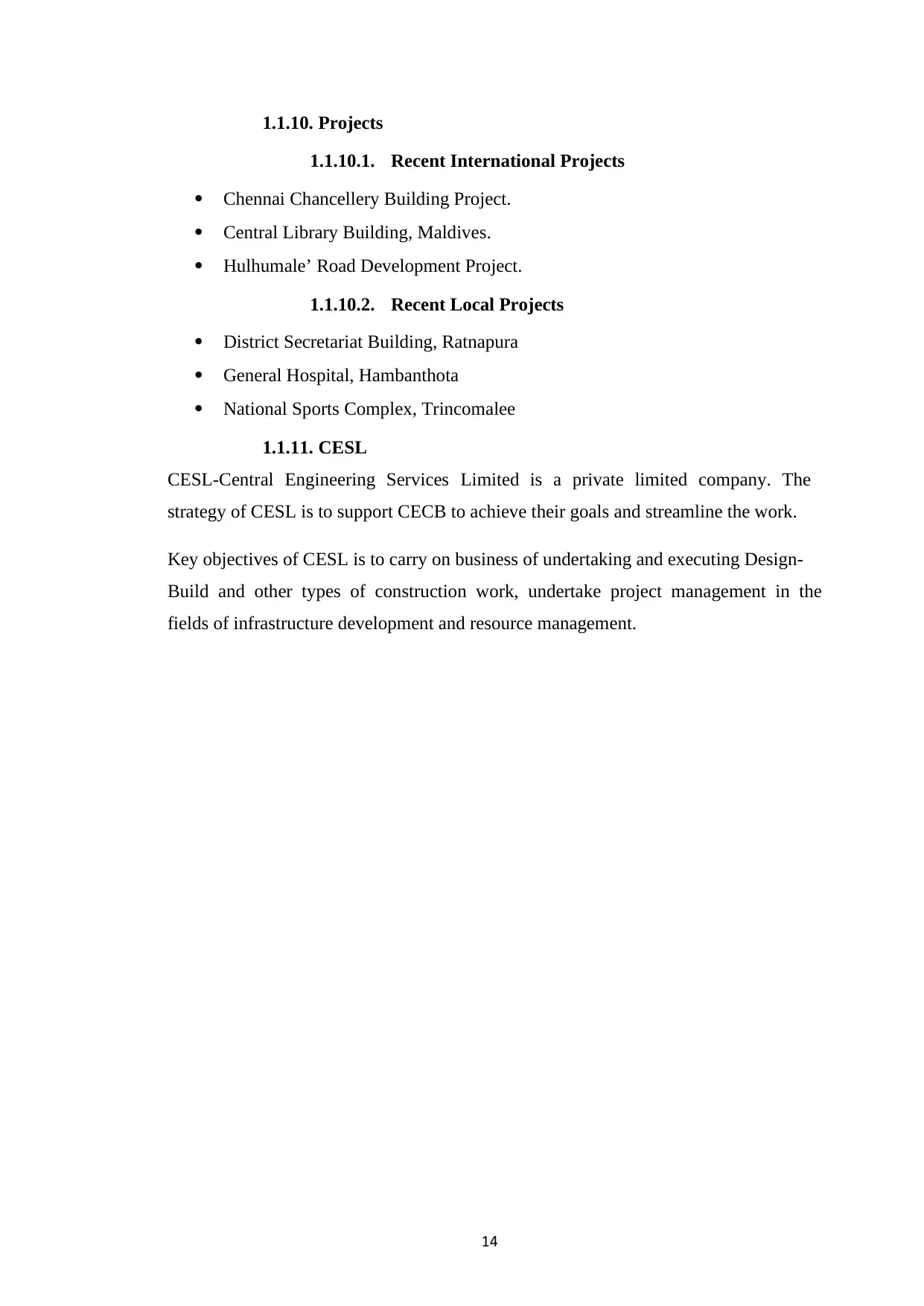
1.1.10. Projects
1.1.10.1. Recent International Projects
Chennai Chancellery Building Project.
Central Library Building, Maldives.
Hulhumale’ Road Development Project.
1.1.10.2. Recent Local Projects
District Secretariat Building, Ratnapura
General Hospital, Hambanthota
National Sports Complex, Trincomalee
1.1.11. CESL
CESL-Central Engineering Services Limited is a private limited company. The
strategy of CESL is to support CECB to achieve their goals and streamline the work.
Key objectives of CESL is to carry on business of undertaking and executing Design-
Build and other types of construction work, undertake project management in the
fields of infrastructure development and resource management.
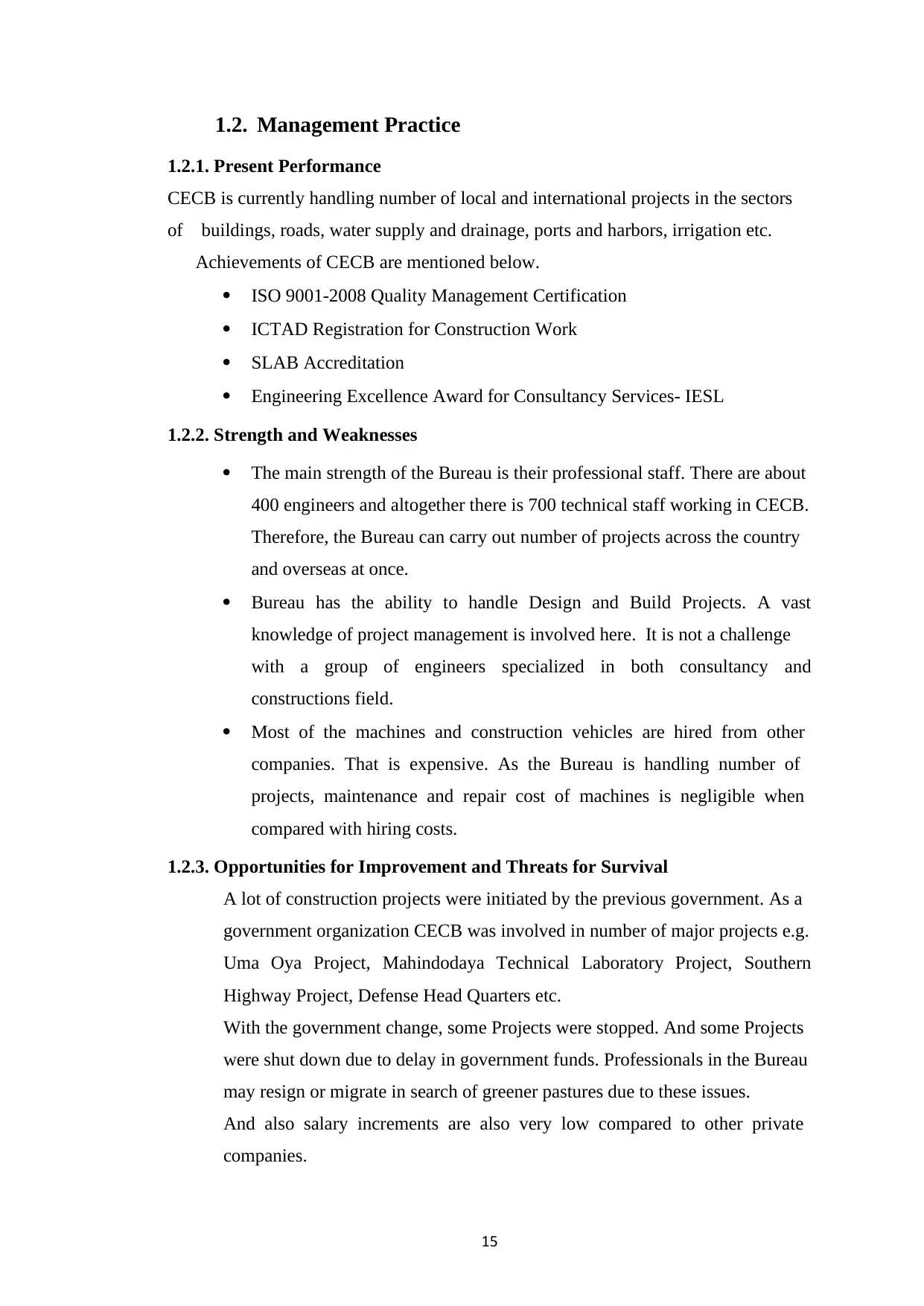
1.2. Management Practice
1.2.1. Present Performance
CECB is currently handling number of local and international projects in the sectors
of buildings, roads, water supply and drainage, ports and harbors, irrigation etc.
Achievements of CECB are mentioned below.
ISO 9001-2008 Quality Management Certification
ICTAD Registration for Construction Work
SLAB Accreditation
Engineering Excellence Award for Consultancy Services- IESL
1.2.2. Strength and Weaknesses
The main strength of the Bureau is their professional staff. There are about
400 engineers and altogether there is 700 technical staff working in CECB.
Therefore, the Bureau can carry out number of projects across the country
and overseas at once.
Bureau has the ability to handle Design and Build Projects. A vast
knowledge of project management is involved here. It is not a challenge
with a group of engineers specialized in both consultancy and
constructions field.
Most of the machines and construction vehicles are hired from other
companies. That is expensive. As the Bureau is handling number of
projects, maintenance and repair cost of machines is negligible when
compared with hiring costs.
1.2.3. Opportunities for Improvement and Threats for Survival
A lot of construction projects were initiated by the previous government. As a
government organization CECB was involved in number of major projects e.g.
Uma Oya Project, Mahindodaya Technical Laboratory Project, Southern
Highway Project, Defense Head Quarters etc.
With the government change, some Projects were stopped. And some Projects
were shut down due to delay in government funds. Professionals in the Bureau
may resign or migrate in search of greener pastures due to these issues.
And also salary increments are also very low compared to other private
companies.
⊘ This is a preview!⊘
Do you want full access?
Subscribe today to unlock all pages.

Trusted by 1+ million students worldwide
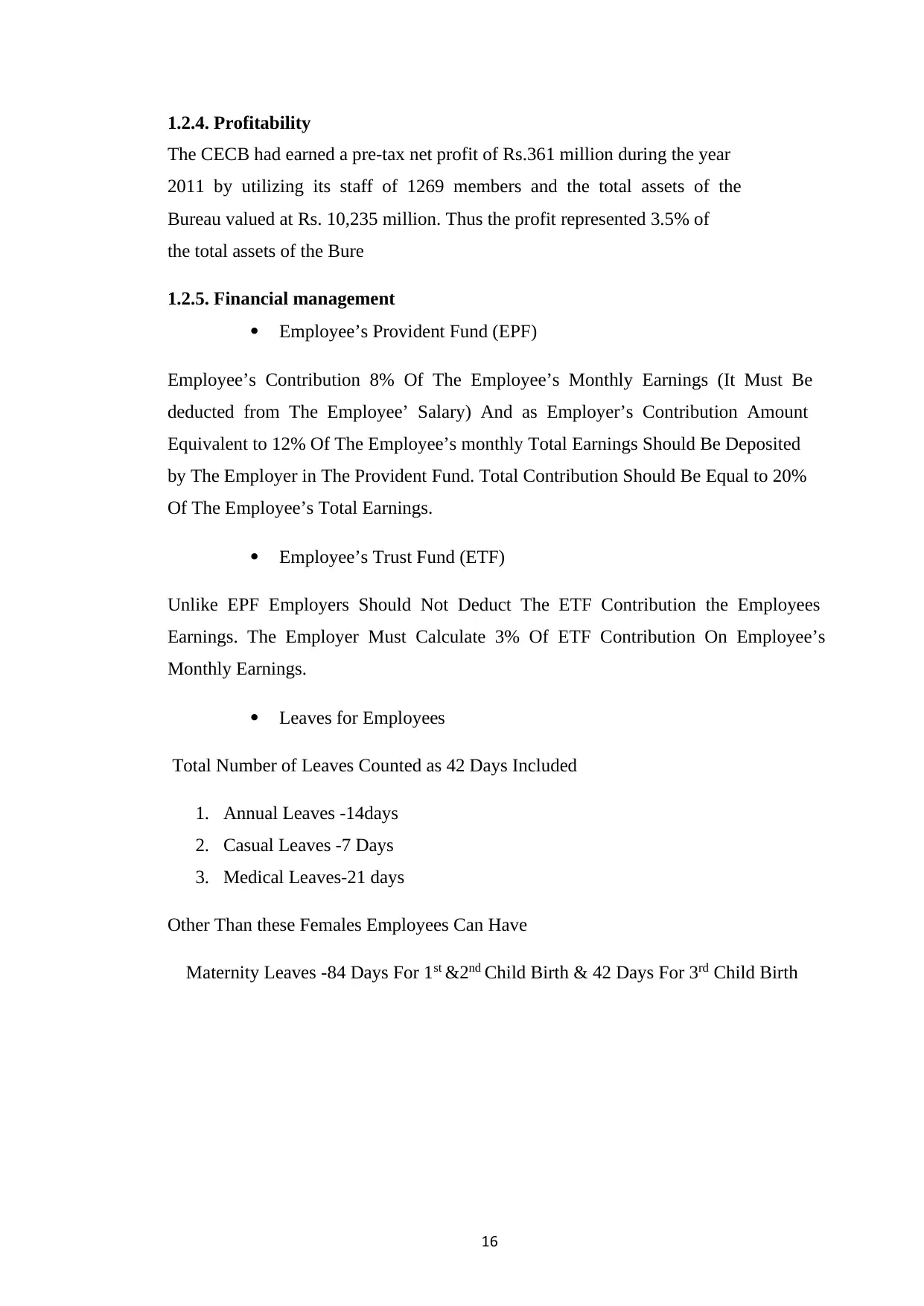
1.2.4. Profitability
The CECB had earned a pre-tax net profit of Rs.361 million during the year
2011 by utilizing its staff of 1269 members and the total assets of the
Bureau valued at Rs. 10,235 million. Thus the profit represented 3.5% of
the total assets of the Bure
1.2.5. Financial management
Employee’s Provident Fund (EPF)
Employee’s Contribution 8% Of The Employee’s Monthly Earnings (It Must Be
deducted from The Employee’ Salary) And as Employer’s Contribution Amount
Equivalent to 12% Of The Employee’s monthly Total Earnings Should Be Deposited
by The Employer in The Provident Fund. Total Contribution Should Be Equal to 20%
Of The Employee’s Total Earnings.
Employee’s Trust Fund (ETF)
Unlike EPF Employers Should Not Deduct The ETF Contribution the Employees
Earnings. The Employer Must Calculate 3% Of ETF Contribution On Employee’s
Monthly Earnings.
Leaves for Employees
Total Number of Leaves Counted as 42 Days Included
1. Annual Leaves -14days
2. Casual Leaves -7 Days
3. Medical Leaves-21 days
Other Than these Females Employees Can Have
Maternity Leaves -84 Days For 1st &2nd Child Birth & 42 Days For 3rd Child Birth
Paraphrase This Document
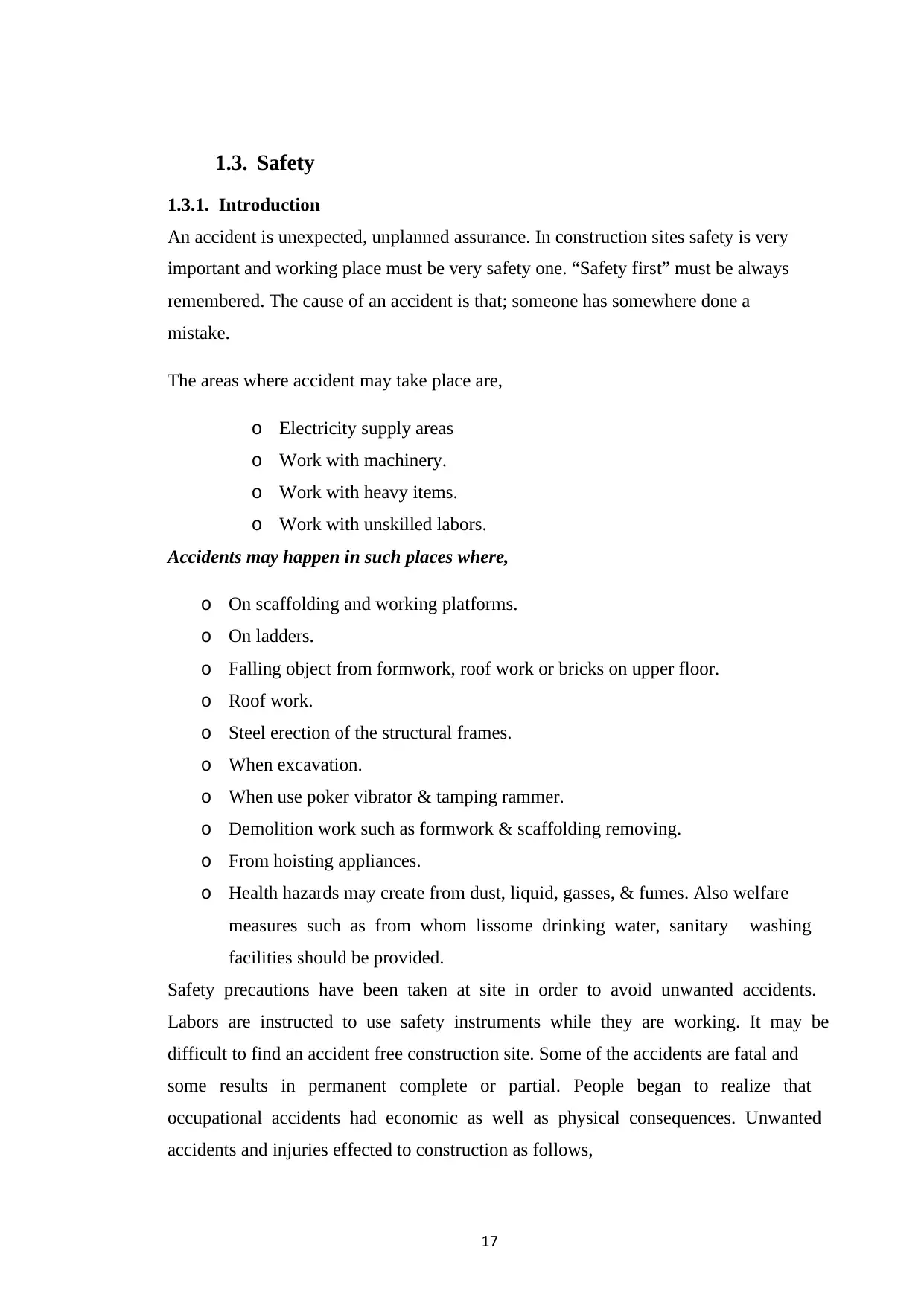
1.3. Safety
1.3.1. Introduction
An accident is unexpected, unplanned assurance. In construction sites safety is very
important and working place must be very safety one. “Safety first” must be always
remembered. The cause of an accident is that; someone has somewhere done a
mistake.
The areas where accident may take place are,
o Electricity supply areas
o Work with machinery.
o Work with heavy items.
o Work with unskilled labors.
Accidents may happen in such places where,
o On scaffolding and working platforms.
o On ladders.
o Falling object from formwork, roof work or bricks on upper floor.
o Roof work.
o Steel erection of the structural frames.
o When excavation.
o When use poker vibrator & tamping rammer.
o Demolition work such as formwork & scaffolding removing.
o From hoisting appliances.
o Health hazards may create from dust, liquid, gasses, & fumes. Also welfare
measures such as from whom lissome drinking water, sanitary washing
facilities should be provided.
Safety precautions have been taken at site in order to avoid unwanted accidents.
Labors are instructed to use safety instruments while they are working. It may be
difficult to find an accident free construction site. Some of the accidents are fatal and
some results in permanent complete or partial. People began to realize that
occupational accidents had economic as well as physical consequences. Unwanted
accidents and injuries effected to construction as follows,
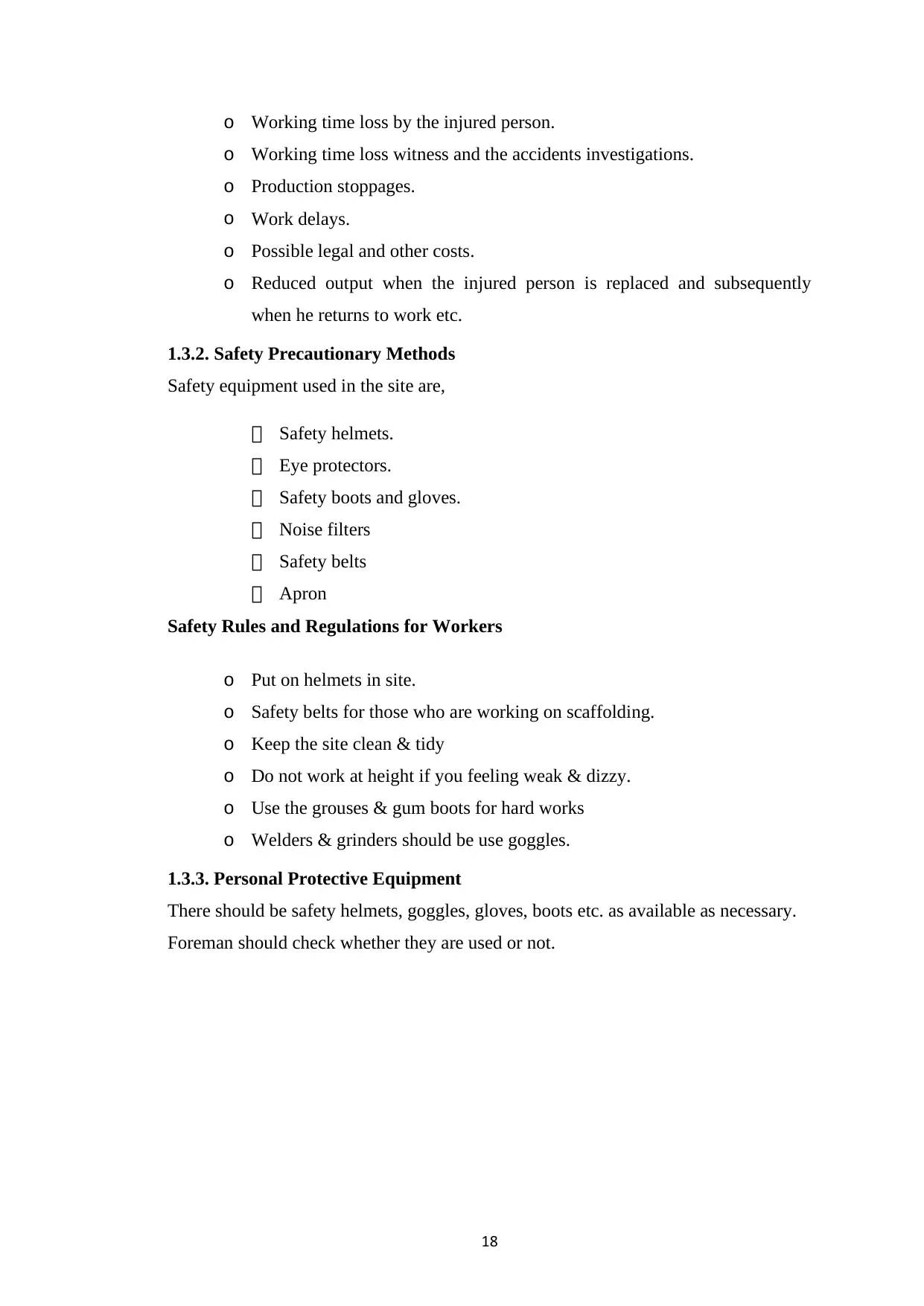
o Working time loss by the injured person.
o Working time loss witness and the accidents investigations.
o Production stoppages.
o Work delays.
o Possible legal and other costs.
o Reduced output when the injured person is replaced and subsequently
when he returns to work etc.
1.3.2. Safety Precautionary Methods
Safety equipment used in the site are,
Safety helmets.
Eye protectors.
Safety boots and gloves.
Noise filters
Safety belts
Apron
Safety Rules and Regulations for Workers
o Put on helmets in site.
o Safety belts for those who are working on scaffolding.
o Keep the site clean & tidy
o Do not work at height if you feeling weak & dizzy.
o Use the grouses & gum boots for hard works
o Welders & grinders should be use goggles.
1.3.3. Personal Protective Equipment
There should be safety helmets, goggles, gloves, boots etc. as available as necessary.
Foreman should check whether they are used or not.
⊘ This is a preview!⊘
Do you want full access?
Subscribe today to unlock all pages.

Trusted by 1+ million students worldwide
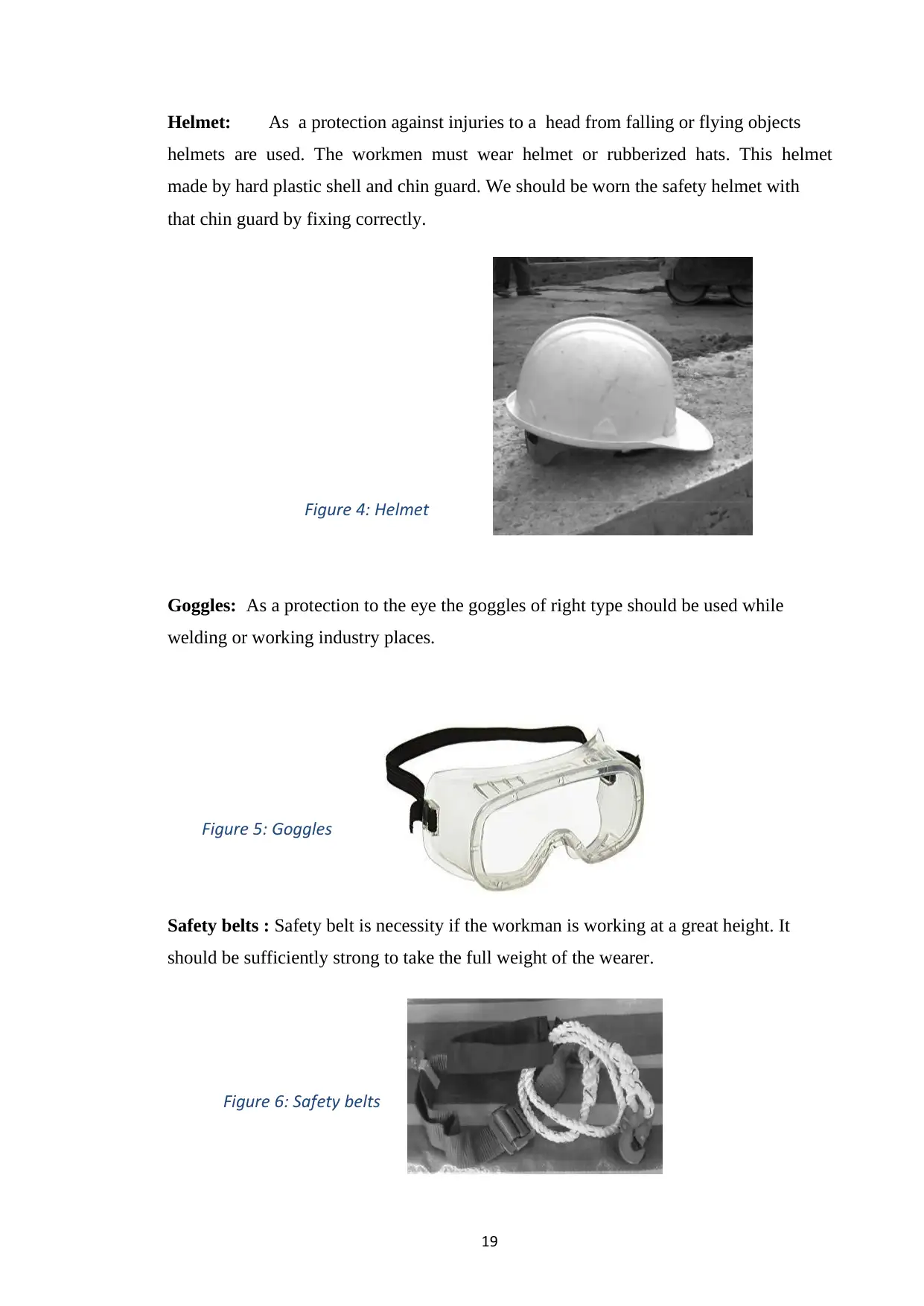
Helmet: As a protection against injuries to a head from falling or flying objects
helmets are used. The workmen must wear helmet or rubberized hats. This helmet
made by hard plastic shell and chin guard. We should be worn the safety helmet with
that chin guard by fixing correctly.
Figure 4: Helmet
Goggles: As a protection to the eye the goggles of right type should be used while
welding or working industry places.
Figure 5: Goggles
Safety belts : Safety belt is necessity if the workman is working at a great height. It
should be sufficiently strong to take the full weight of the wearer.
Figure 6: Safety belts
Paraphrase This Document
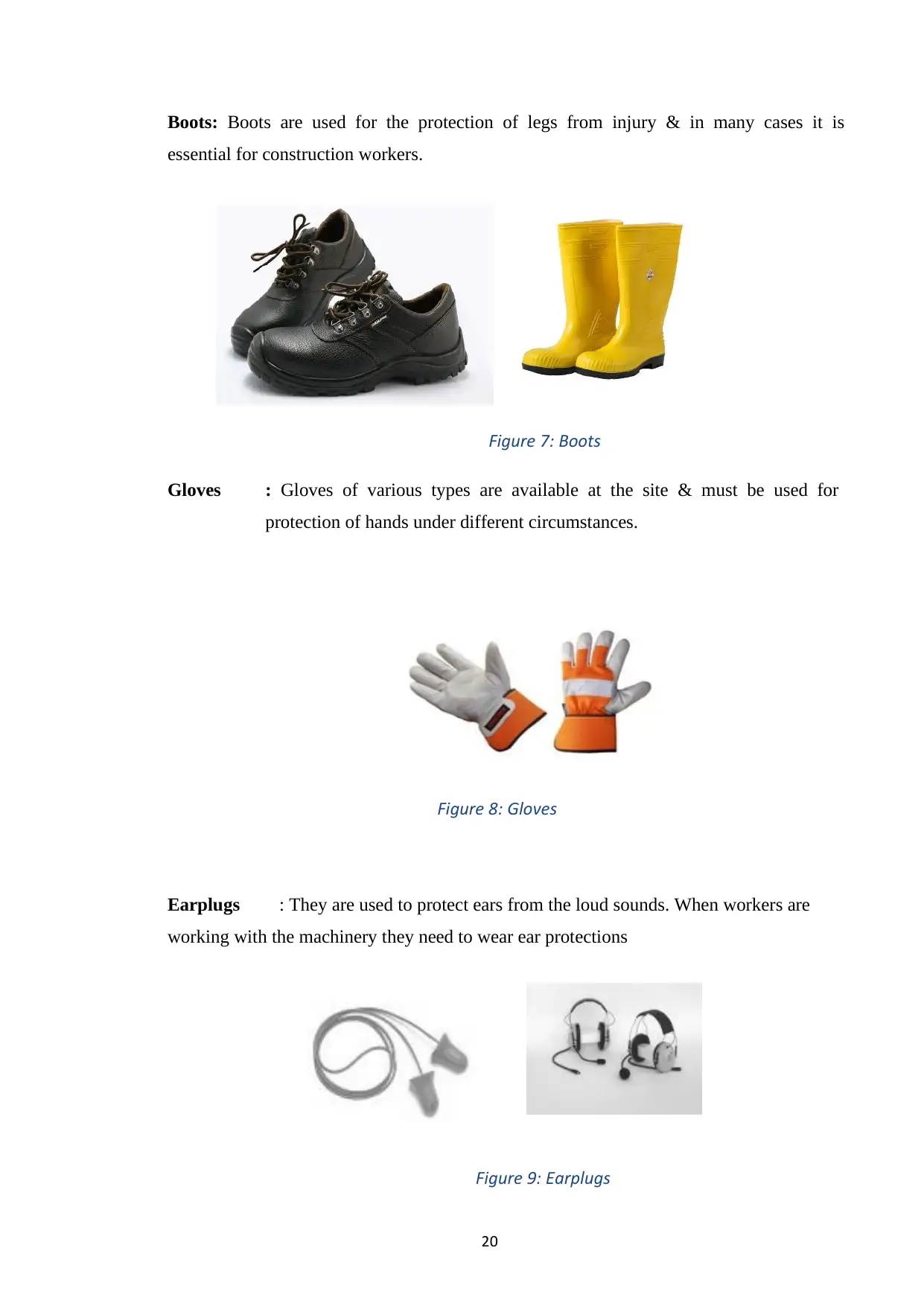
Boots: Boots are used for the protection of legs from injury & in many cases it is
essential for construction workers.
Figure 7: Boots
Gloves : Gloves of various types are available at the site & must be used for
protection of hands under different circumstances.
Figure 8: Gloves
Earplugs : They are used to protect ears from the loud sounds. When workers are
working with the machinery they need to wear ear protections
Figure 9: Earplugs
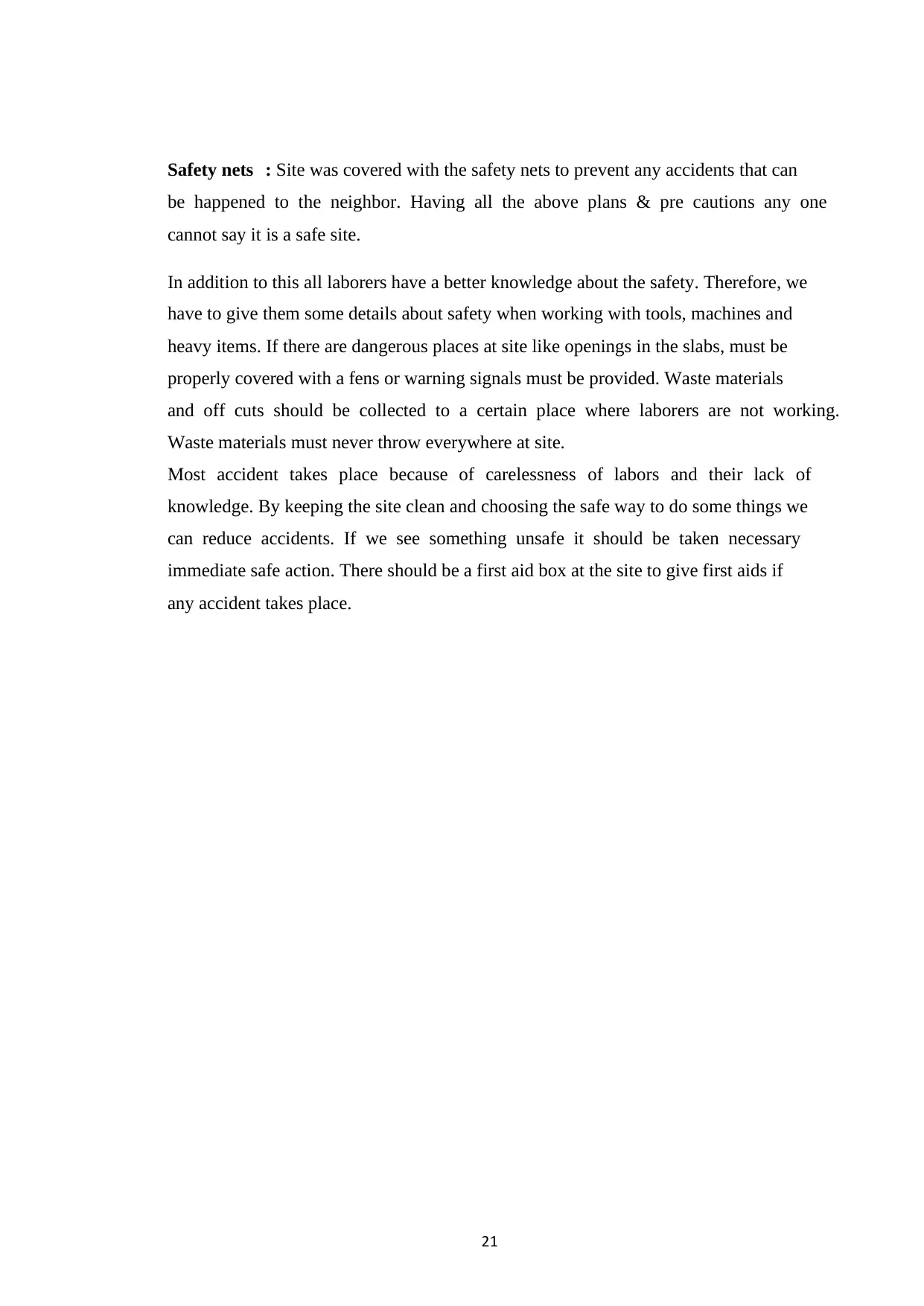
Safety nets : Site was covered with the safety nets to prevent any accidents that can
be happened to the neighbor. Having all the above plans & pre cautions any one
cannot say it is a safe site.
In addition to this all laborers have a better knowledge about the safety. Therefore, we
have to give them some details about safety when working with tools, machines and
heavy items. If there are dangerous places at site like openings in the slabs, must be
properly covered with a fens or warning signals must be provided. Waste materials
and off cuts should be collected to a certain place where laborers are not working.
Waste materials must never throw everywhere at site.
Most accident takes place because of carelessness of labors and their lack of
knowledge. By keeping the site clean and choosing the safe way to do some things we
can reduce accidents. If we see something unsafe it should be taken necessary
immediate safe action. There should be a first aid box at the site to give first aids if
any accident takes place.
⊘ This is a preview!⊘
Do you want full access?
Subscribe today to unlock all pages.

Trusted by 1+ million students worldwide

2. Training Experience
2.1. Experiences from Office
I was attached to the maintenance office Kegalle hospital under the CECB during my
24 weeks. I was the first trainee to had six months (24 weeks) training in the field of
Quantity Surveying at Earlier the maintenance office Kegalle hospital were few other
trainees in difference fields. I had to be prepared lot of estimates and checked bills for
whether those are correct. And also I had to be drawn any plans, sketches using by
AutoCAD. I could be able to lot of gains from this office.
2.1.1. Measurement sheets
I start working as a Quantity Surveyor, all my measurements and calculations
required to be presented on a special format. It is called as a measurement sheet or
TDS sheet. Standard for Time sing, Dimension and Squaring in that order and adding
description column we will be got a TDS sheet.
The importance of measurement sheet
Measurements are calculated in the measurements sheet before the quantities
are taken to the BOQ
Measurements & calculations can be shown as very clearly and correctly in
TDS sheets.
When we want to measure or calculate quantity of a structure, we must follow
a recognized standard.
If we don’t follow, one officer can calculate the quantity his own way, at the
same time another officer can calculate the quantity his own way.
When we are comparing above both results we may be different results. Therefore,
this purpose we use the standard method of measurements internally.
The format of Measurement sheet is given below.
Paraphrase This Document
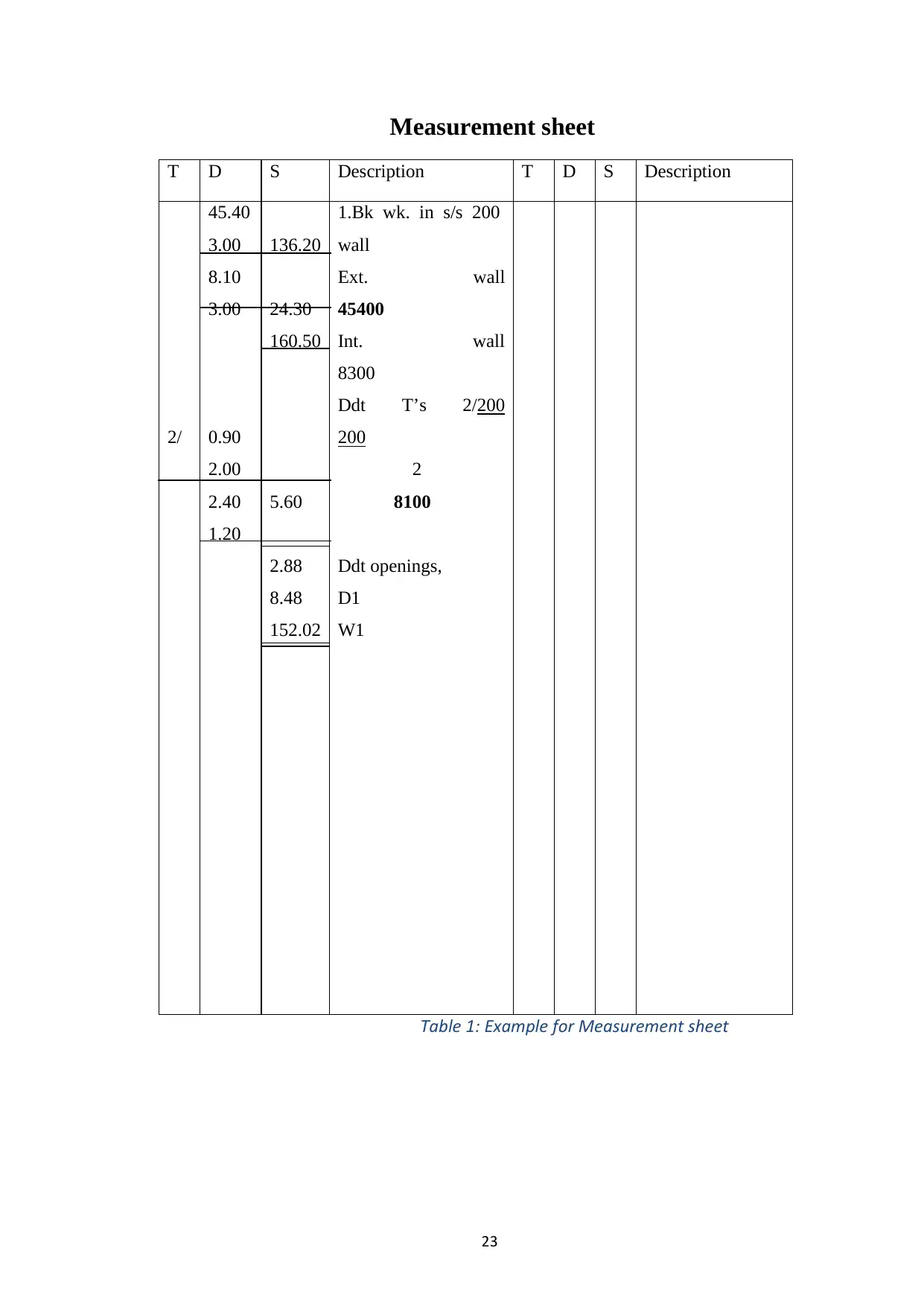
Measurement sheet
Table 1: Example for Measurement sheet
T D S Description T D S Description
2/
45.40
3.00
8.10
3.00
0.90
2.00
2.40
1.20
136.20
24.30
160.50
5.60
2.88
8.48
152.02
1.Bk wk. in s/s 200
wall
Ext. wall
45400
Int. wall
8300
Ddt T’s 2/200
200
2
8100
Ddt openings,
D1
W1
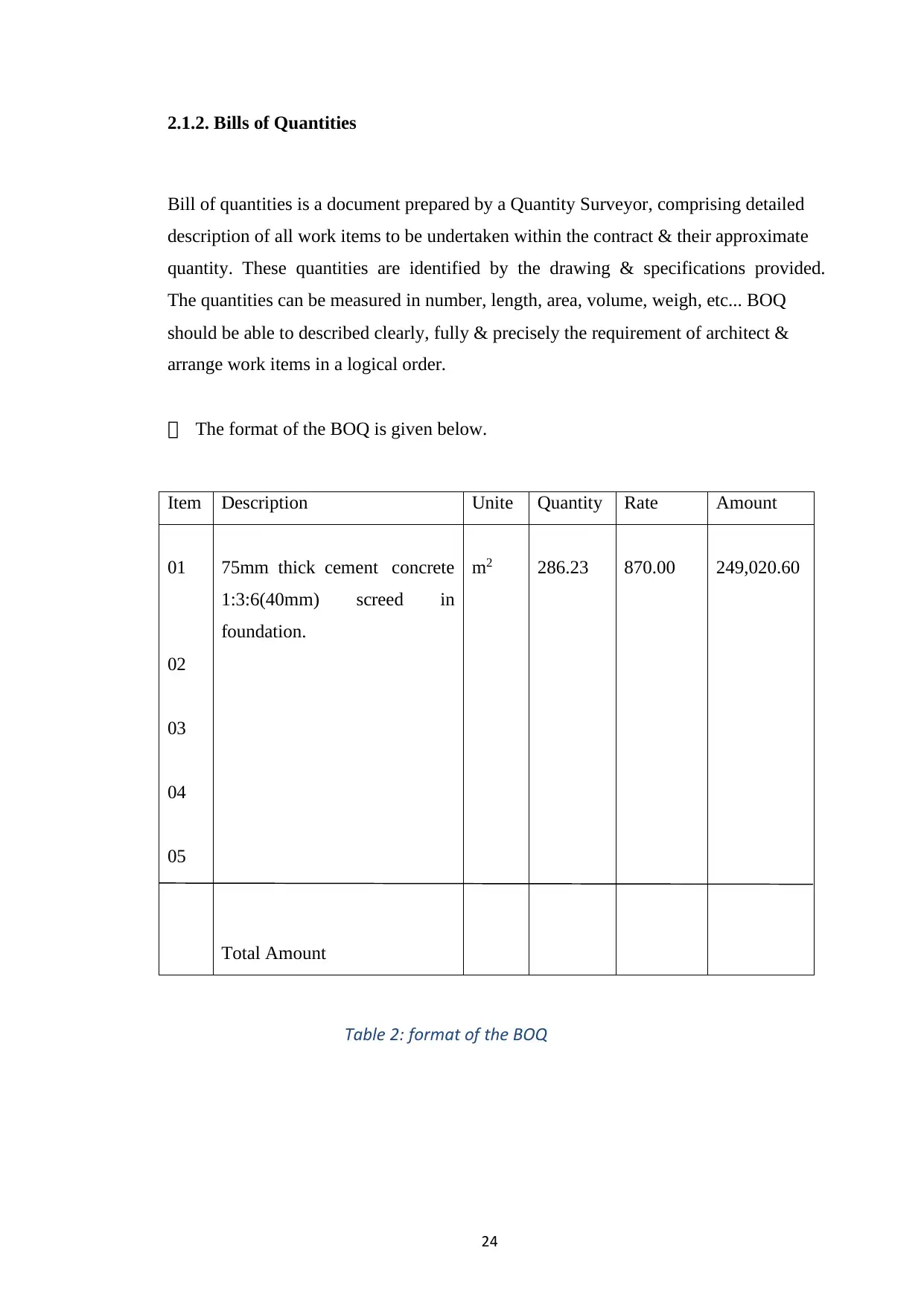
2.1.2. Bills of Quantities
Bill of quantities is a document prepared by a Quantity Surveyor, comprising detailed
description of all work items to be undertaken within the contract & their approximate
quantity. These quantities are identified by the drawing & specifications provided.
The quantities can be measured in number, length, area, volume, weigh, etc... BOQ
should be able to described clearly, fully & precisely the requirement of architect &
arrange work items in a logical order.
The format of the BOQ is given below.
Table 2: format of the BOQ
Item Description Unite Quantity Rate Amount
01
02
03
04
05
75mm thick cement concrete
1:3:6(40mm) screed in
foundation.
Total Amount
m2 286.23 870.00 249,020.60
⊘ This is a preview!⊘
Do you want full access?
Subscribe today to unlock all pages.

Trusted by 1+ million students worldwide
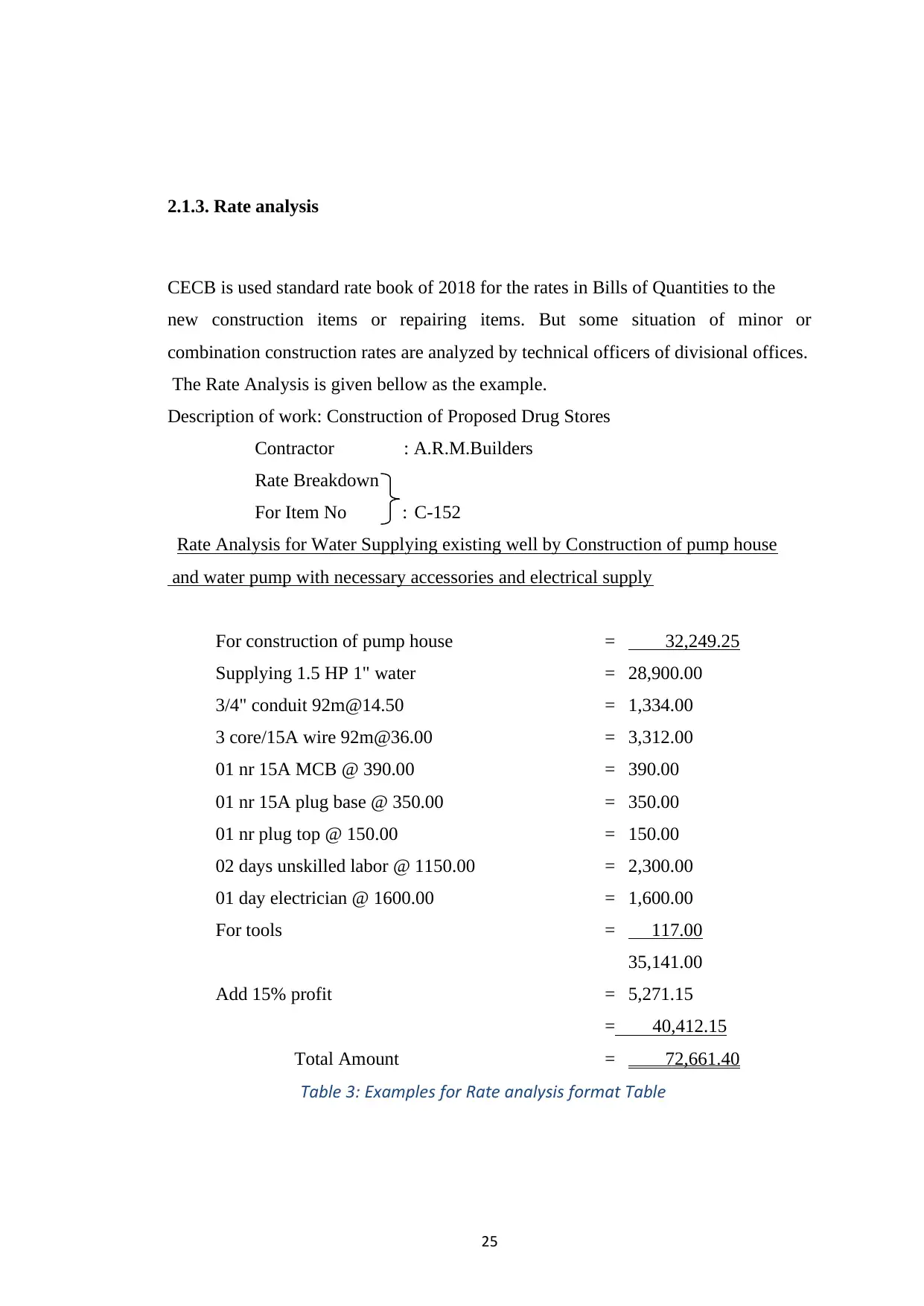
2.1.3. Rate analysis
CECB is used standard rate book of 2018 for the rates in Bills of Quantities to the
new construction items or repairing items. But some situation of minor or
combination construction rates are analyzed by technical officers of divisional offices.
The Rate Analysis is given bellow as the example.
Description of work: Construction of Proposed Drug Stores
Contractor : A.R.M.Builders
Rate Breakdown
For Item No : C-152
Rate Analysis for Water Supplying existing well by Construction of pump house
and water pump with necessary accessories and electrical supply
For construction of pump house = 32,249.25
Supplying 1.5 HP 1" water = 28,900.00
3/4" conduit 92m@14.50 = 1,334.00
3 core/15A wire 92m@36.00 = 3,312.00
01 nr 15A MCB @ 390.00 = 390.00
01 nr 15A plug base @ 350.00 = 350.00
01 nr plug top @ 150.00 = 150.00
02 days unskilled labor @ 1150.00 = 2,300.00
01 day electrician @ 1600.00 = 1,600.00
For tools = 117.00
35,141.00
Add 15% profit = 5,271.15
= 40,412.15
Total Amount = 72,661.40
Table 3: Examples for Rate analysis format Table
Paraphrase This Document
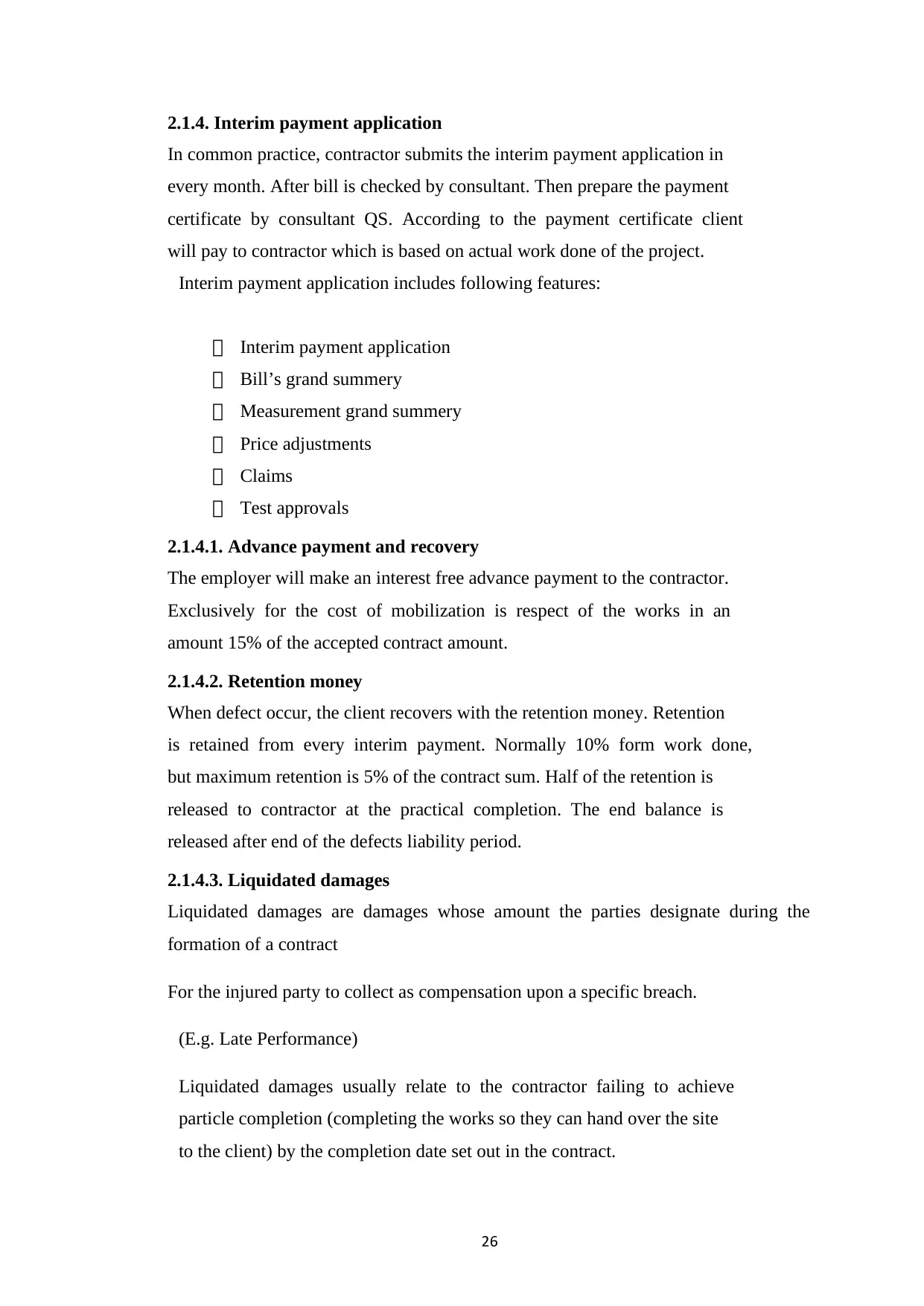
2.1.4. Interim payment application
In common practice, contractor submits the interim payment application in
every month. After bill is checked by consultant. Then prepare the payment
certificate by consultant QS. According to the payment certificate client
will pay to contractor which is based on actual work done of the project.
Interim payment application includes following features:
Interim payment application
Bill’s grand summery
Measurement grand summery
Price adjustments
Claims
Test approvals
2.1.4.1. Advance payment and recovery
The employer will make an interest free advance payment to the contractor.
Exclusively for the cost of mobilization is respect of the works in an
amount 15% of the accepted contract amount.
2.1.4.2. Retention money
When defect occur, the client recovers with the retention money. Retention
is retained from every interim payment. Normally 10% form work done,
but maximum retention is 5% of the contract sum. Half of the retention is
released to contractor at the practical completion. The end balance is
released after end of the defects liability period.
2.1.4.3. Liquidated damages
Liquidated damages are damages whose amount the parties designate during the
formation of a contract
For the injured party to collect as compensation upon a specific breach.
(E.g. Late Performance)
Liquidated damages usually relate to the contractor failing to achieve
particle completion (completing the works so they can hand over the site
to the client) by the completion date set out in the contract.
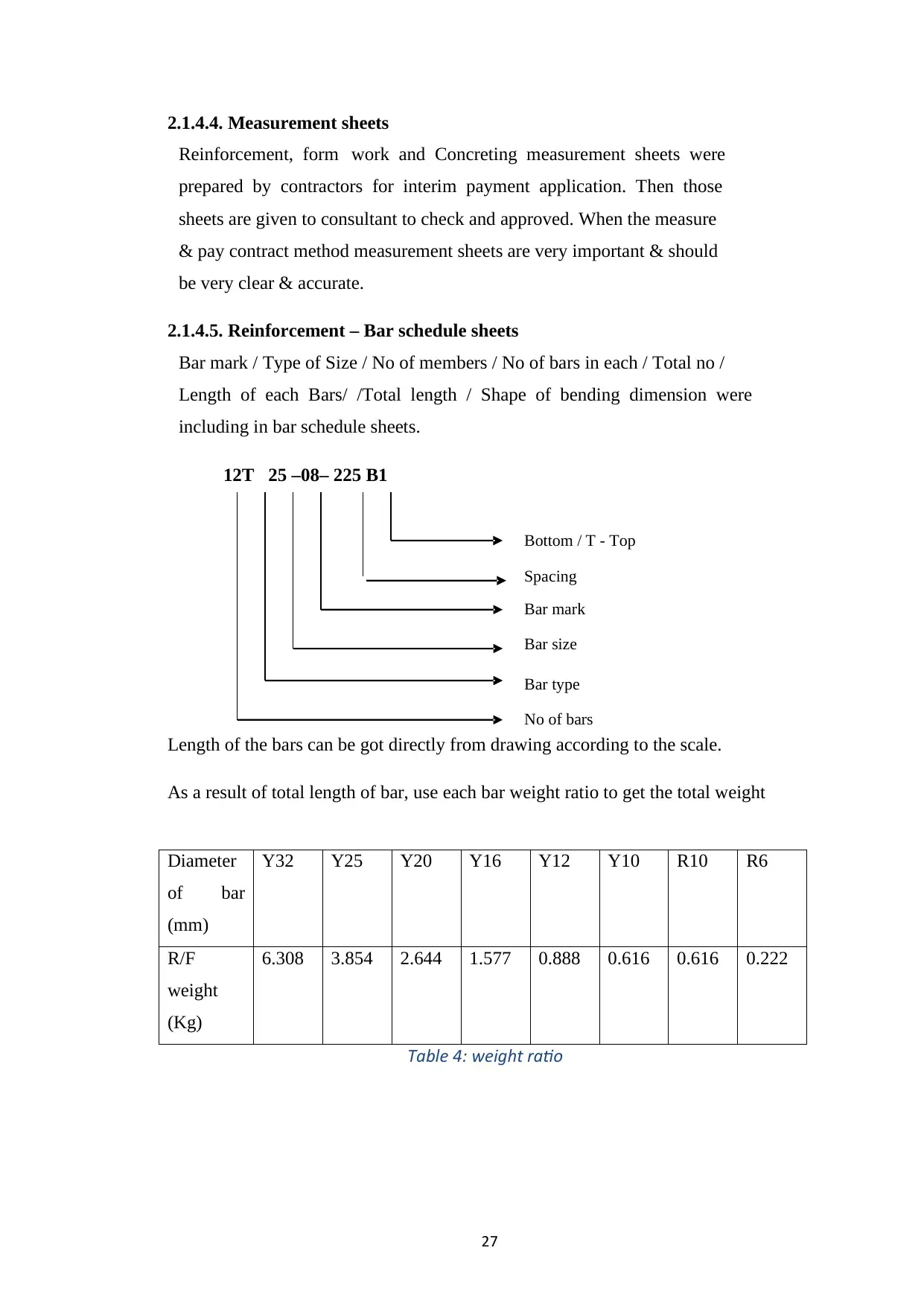
2.1.4.4. Measurement sheets
Reinforcement, form work and Concreting measurement sheets were
prepared by contractors for interim payment application. Then those
sheets are given to consultant to check and approved. When the measure
& pay contract method measurement sheets are very important & should
be very clear & accurate.
2.1.4.5. Reinforcement – Bar schedule sheets
Bar mark / Type of Size / No of members / No of bars in each / Total no /
Length of each Bars/ /Total length / Shape of bending dimension were
including in bar schedule sheets.
12T 25 –08– 225 B1
Length of the bars can be got directly from drawing according to the scale.
As a result of total length of bar, use each bar weight ratio to get the total weight
Table 4: weight ratio
Diameter
of bar
(mm)
Y32 Y25 Y20 Y16 Y12 Y10 R10 R6
R/F
weight
(Kg)
6.308 3.854 2.644 1.577 0.888 0.616 0.616 0.222
Spacing
Bar mark
Bar size
Bar type
No of bars
Bottom / T - Top
⊘ This is a preview!⊘
Do you want full access?
Subscribe today to unlock all pages.

Trusted by 1+ million students worldwide
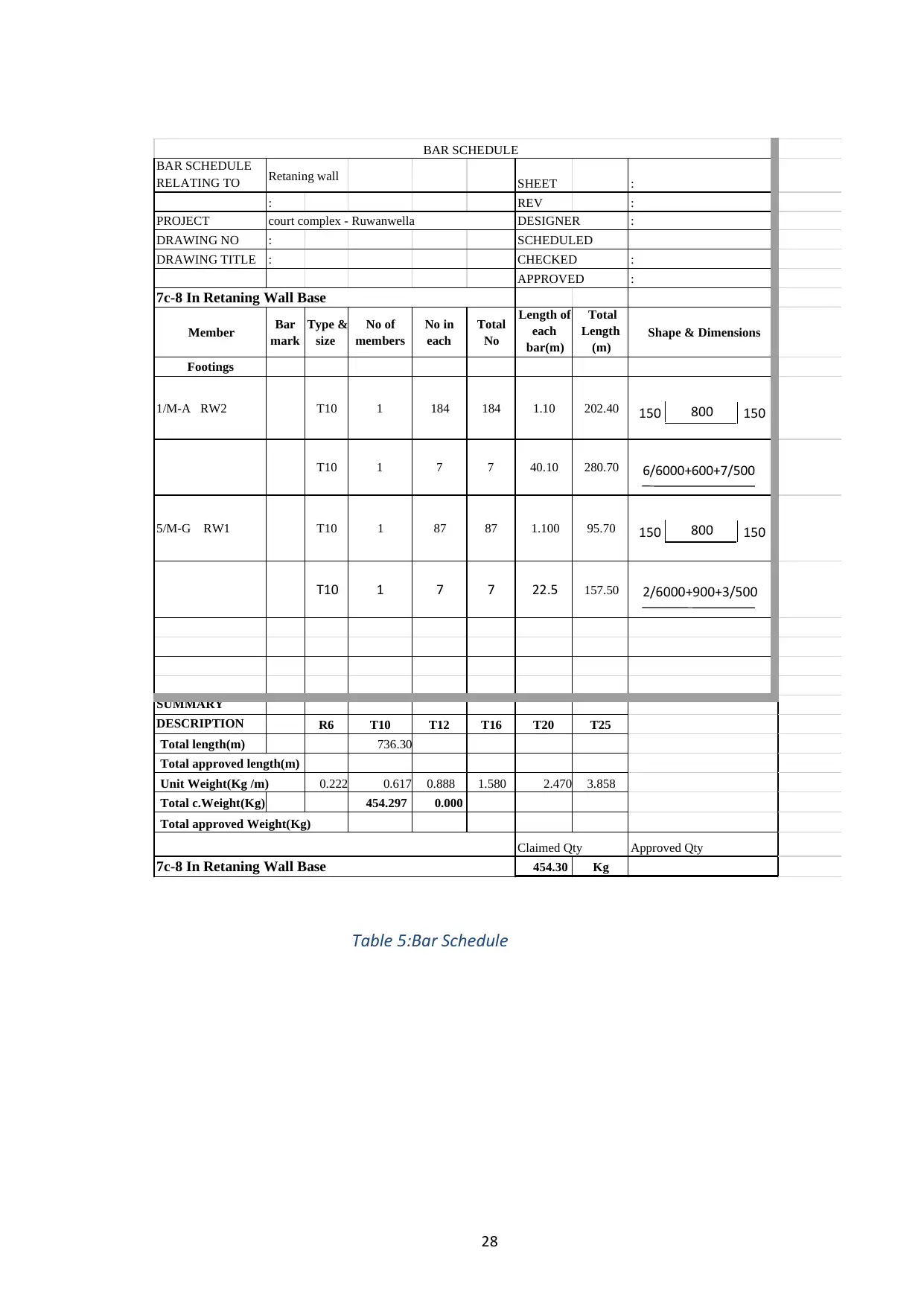
Table 5:Bar Schedule
BAR SCHEDULE
RELATING TO Retaning wall SHEET :
: REV :
PROJECT DESIGNER :
DRAWING NO : SCHEDULED
DRAWING TITLE : CHECKED :
APPROVED :
Member Bar
mark
Type &
size
No of
members
No in
each
Total
No
Length of
each
bar(m)
Total
Length
(m)
Shape & Dimensions
Footings
1/M-A RW2 T10 1 184 184 1.10 202.40
T10 1 7 7 40.10 280.70
5/M-G RW1 T10 1 87 87 1.100 95.70
T10 1 7 7 22.5 157.50
SUMMARY
DESCRIPTION R6 T10 T12 T16 T20 T25
Total length(m) 736.30
Total approved length(m)
Unit Weight(Kg /m) 0.222 0.617 0.888 1.580 2.470 3.858
Total c.Weight(Kg) 454.297 0.000
Total approved Weight(Kg)
Claimed Qty Approved Qty
454.30 Kg
BAR SCHEDULE
court complex - Ruwanwella
7c-8 In Retaning Wall Base
7c-8 In Retaning Wall Base
150 800
6/6000+600+7/500
150
150 800 150
2/6000+900+3/500
Paraphrase This Document
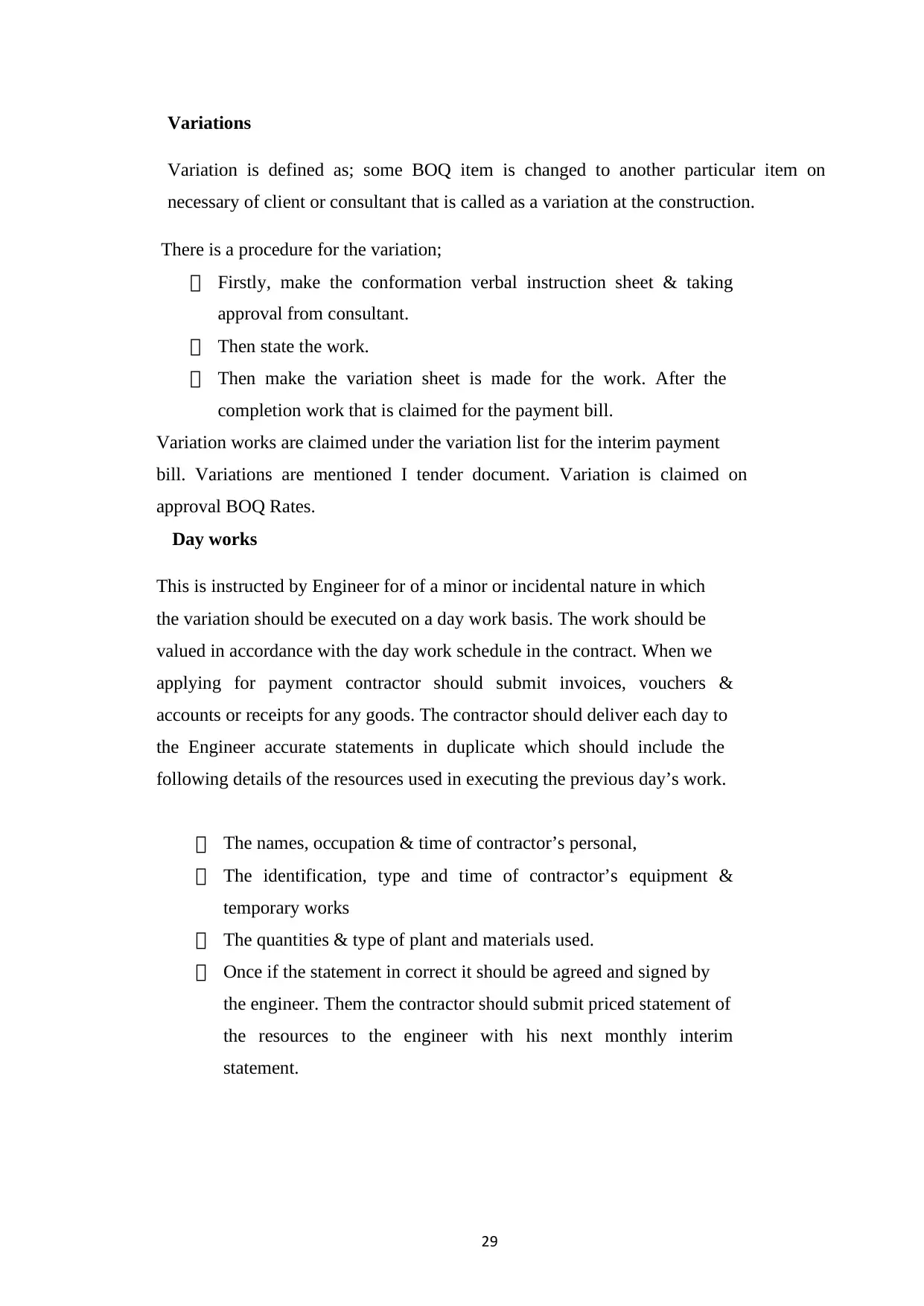
Variations
Variation is defined as; some BOQ item is changed to another particular item on
necessary of client or consultant that is called as a variation at the construction.
There is a procedure for the variation;
Firstly, make the conformation verbal instruction sheet & taking
approval from consultant.
Then state the work.
Then make the variation sheet is made for the work. After the
completion work that is claimed for the payment bill.
Variation works are claimed under the variation list for the interim payment
bill. Variations are mentioned I tender document. Variation is claimed on
approval BOQ Rates.
Day works
This is instructed by Engineer for of a minor or incidental nature in which
the variation should be executed on a day work basis. The work should be
valued in accordance with the day work schedule in the contract. When we
applying for payment contractor should submit invoices, vouchers &
accounts or receipts for any goods. The contractor should deliver each day to
the Engineer accurate statements in duplicate which should include the
following details of the resources used in executing the previous day’s work.
The names, occupation & time of contractor’s personal,
The identification, type and time of contractor’s equipment &
temporary works
The quantities & type of plant and materials used.
Once if the statement in correct it should be agreed and signed by
the engineer. Them the contractor should submit priced statement of
the resources to the engineer with his next monthly interim
statement.
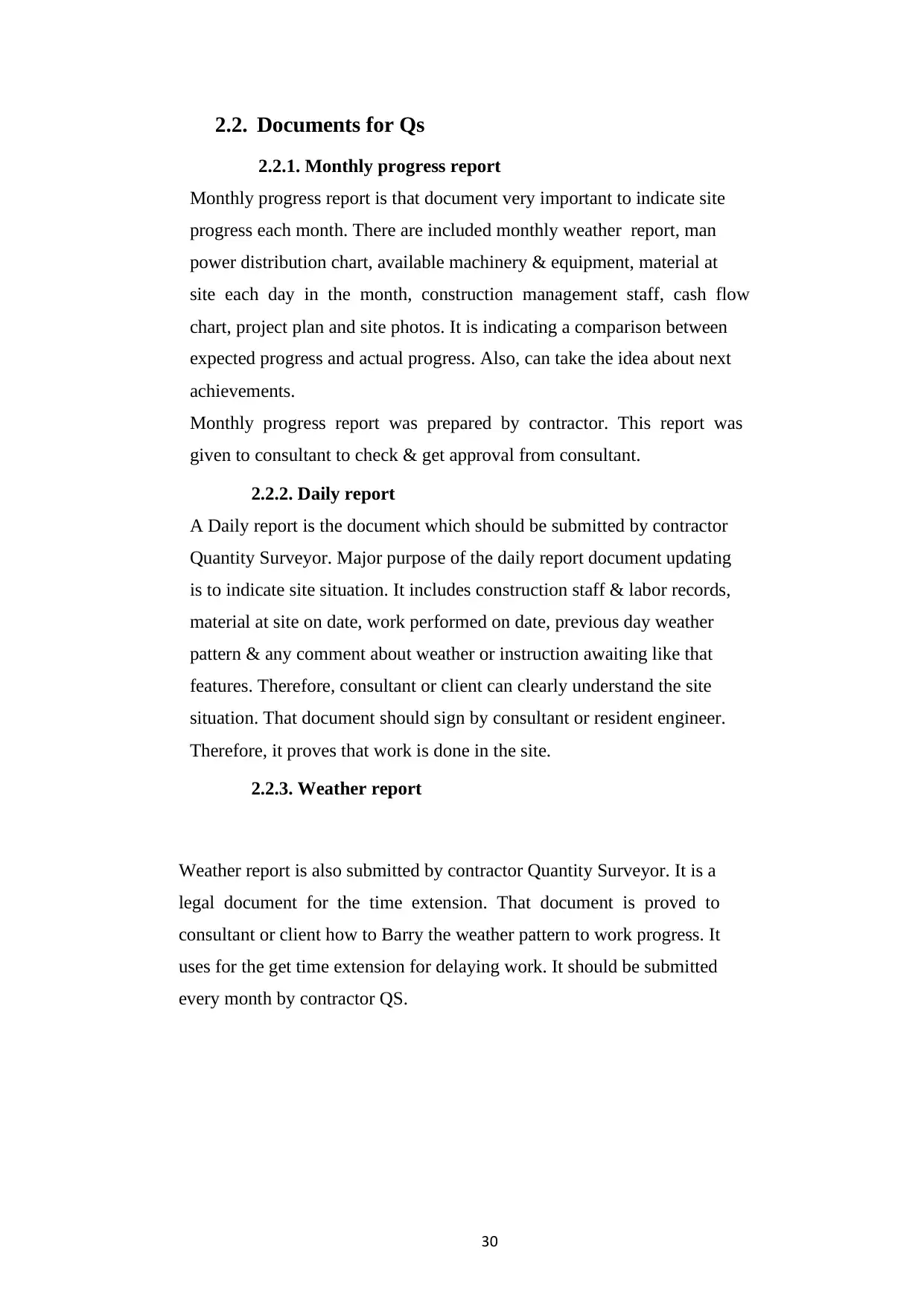
2.2. Documents for Qs
2.2.1. Monthly progress report
Monthly progress report is that document very important to indicate site
progress each month. There are included monthly weather report, man
power distribution chart, available machinery & equipment, material at
site each day in the month, construction management staff, cash flow
chart, project plan and site photos. It is indicating a comparison between
expected progress and actual progress. Also, can take the idea about next
achievements.
Monthly progress report was prepared by contractor. This report was
given to consultant to check & get approval from consultant.
2.2.2. Daily report
A Daily report is the document which should be submitted by contractor
Quantity Surveyor. Major purpose of the daily report document updating
is to indicate site situation. It includes construction staff & labor records,
material at site on date, work performed on date, previous day weather
pattern & any comment about weather or instruction awaiting like that
features. Therefore, consultant or client can clearly understand the site
situation. That document should sign by consultant or resident engineer.
Therefore, it proves that work is done in the site.
2.2.3. Weather report
Weather report is also submitted by contractor Quantity Surveyor. It is a
legal document for the time extension. That document is proved to
consultant or client how to Barry the weather pattern to work progress. It
uses for the get time extension for delaying work. It should be submitted
every month by contractor QS.
⊘ This is a preview!⊘
Do you want full access?
Subscribe today to unlock all pages.

Trusted by 1+ million students worldwide
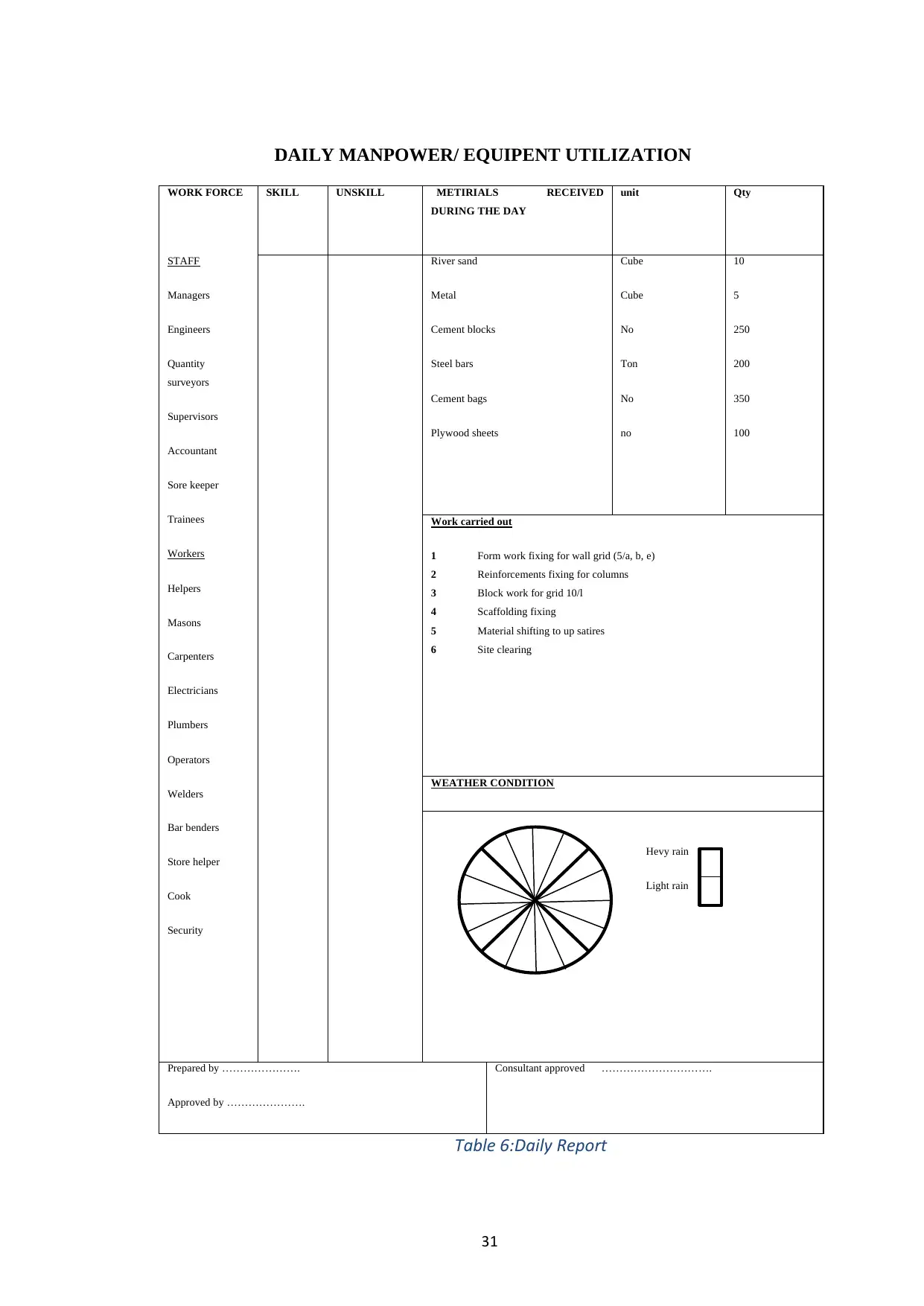
DAILY MANPOWER/ EQUIPENT UTILIZATION
Table 6:Daily Report
WORK FORCE SKILL UNSKILL METIRIALS RECEIVED
DURING THE DAY
unit Qty
STAFF
Managers
Engineers
Quantity
surveyors
Supervisors
Accountant
Sore keeper
Trainees
Workers
Helpers
Masons
Carpenters
Electricians
Plumbers
Operators
Welders
Bar benders
Store helper
Cook
Security
River sand
Metal
Cement blocks
Steel bars
Cement bags
Plywood sheets
Cube
Cube
No
Ton
No
no
10
5
250
200
350
100
Work carried out
1 Form work fixing for wall grid (5/a, b, e)
2 Reinforcements fixing for columns
3 Block work for grid 10/l
4 Scaffolding fixing
5 Material shifting to up satires
6 Site clearing
WEATHER CONDITION
Hevy rain
Light rain
Prepared by ………………….
Approved by ………………….
Consultant approved ………………………….
Paraphrase This Document
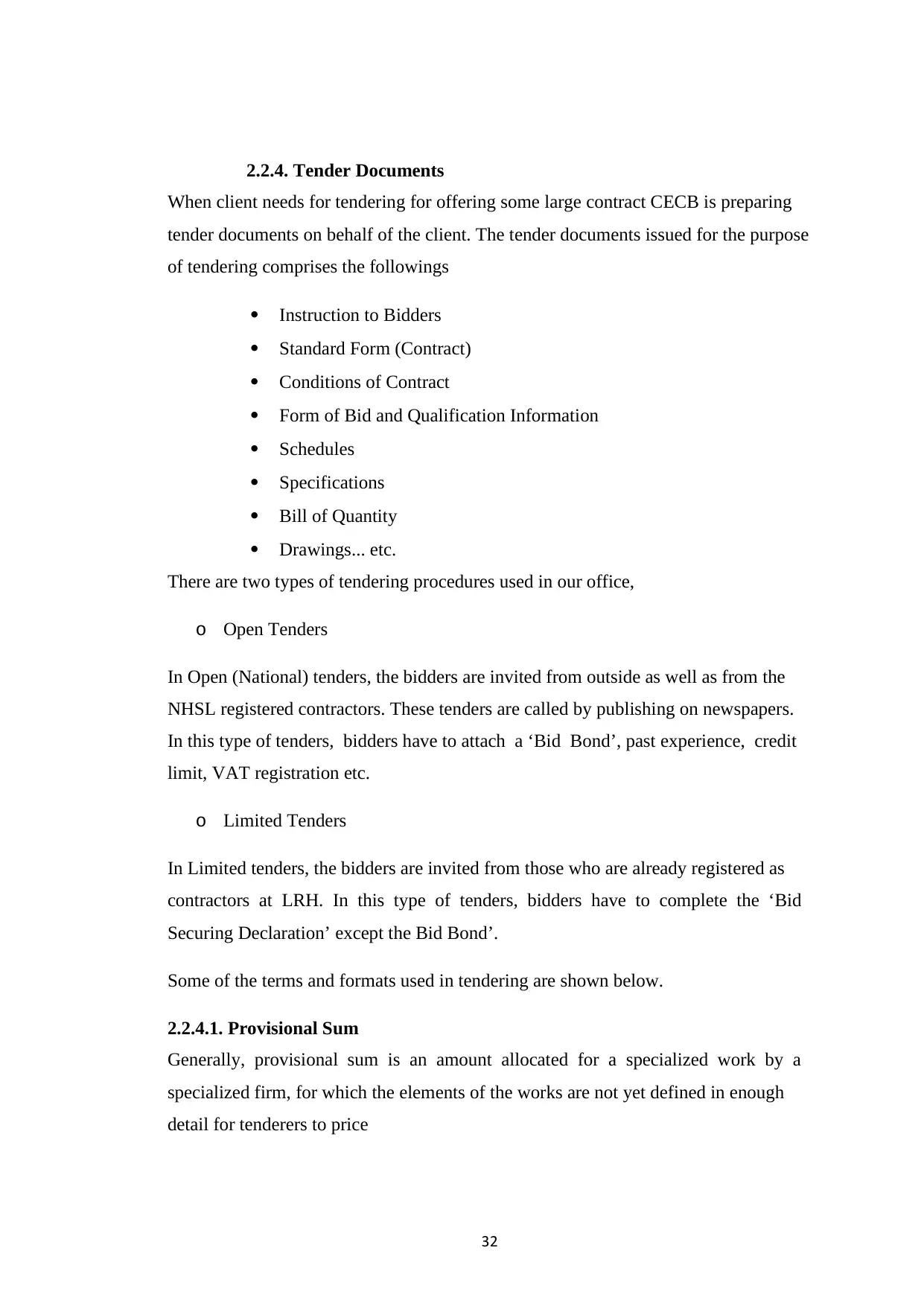
2.2.4. Tender Documents
When client needs for tendering for offering some large contract CECB is preparing
tender documents on behalf of the client. The tender documents issued for the purpose
of tendering comprises the followings
Instruction to Bidders
Standard Form (Contract)
Conditions of Contract
Form of Bid and Qualification Information
Schedules
Specifications
Bill of Quantity
Drawings... etc.
There are two types of tendering procedures used in our office,
o Open Tenders
In Open (National) tenders, the bidders are invited from outside as well as from the
NHSL registered contractors. These tenders are called by publishing on newspapers.
In this type of tenders, bidders have to attach a ‘Bid Bond’, past experience, credit
limit, VAT registration etc.
o Limited Tenders
In Limited tenders, the bidders are invited from those who are already registered as
contractors at LRH. In this type of tenders, bidders have to complete the ‘Bid
Securing Declaration’ except the Bid Bond’.
Some of the terms and formats used in tendering are shown below.
2.2.4.1. Provisional Sum
Generally, provisional sum is an amount allocated for a specialized work by a
specialized firm, for which the elements of the works are not yet defined in enough
detail for tenderers to price
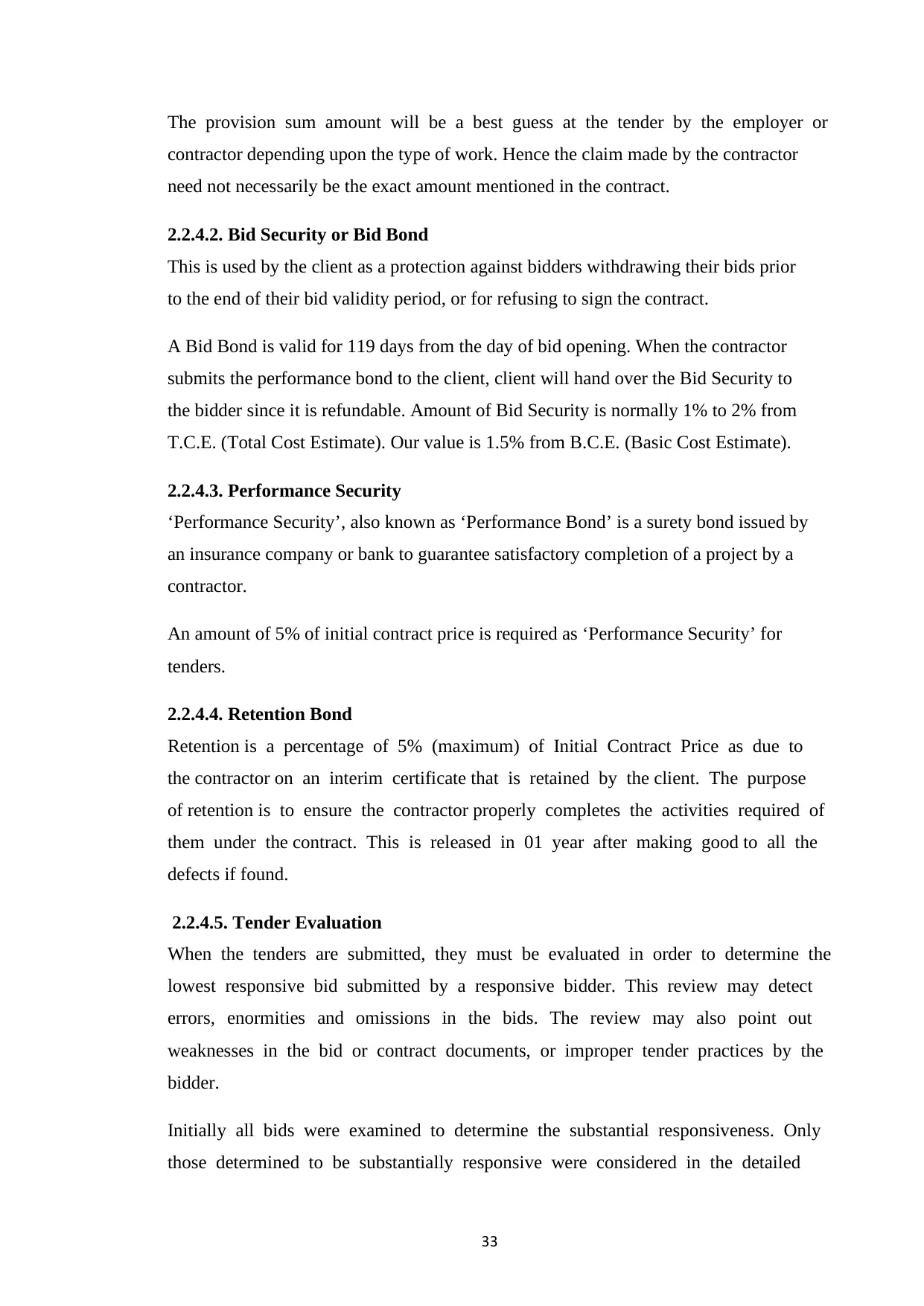
The provision sum amount will be a best guess at the tender by the employer or
contractor depending upon the type of work. Hence the claim made by the contractor
need not necessarily be the exact amount mentioned in the contract.
2.2.4.2. Bid Security or Bid Bond
This is used by the client as a protection against bidders withdrawing their bids prior
to the end of their bid validity period, or for refusing to sign the contract.
A Bid Bond is valid for 119 days from the day of bid opening. When the contractor
submits the performance bond to the client, client will hand over the Bid Security to
the bidder since it is refundable. Amount of Bid Security is normally 1% to 2% from
T.C.E. (Total Cost Estimate). Our value is 1.5% from B.C.E. (Basic Cost Estimate).
2.2.4.3. Performance Security
‘Performance Security’, also known as ‘Performance Bond’ is a surety bond issued by
an insurance company or bank to guarantee satisfactory completion of a project by a
contractor.
An amount of 5% of initial contract price is required as ‘Performance Security’ for
tenders.
2.2.4.4. Retention Bond
Retention is a percentage of 5% (maximum) of Initial Contract Price as due to
the contractor on an interim certificate that is retained by the client. The purpose
of retention is to ensure the contractor properly completes the activities required of
them under the contract. This is released in 01 year after making good to all the
defects if found.
2.2.4.5. Tender Evaluation
When the tenders are submitted, they must be evaluated in order to determine the
lowest responsive bid submitted by a responsive bidder. This review may detect
errors, enormities and omissions in the bids. The review may also point out
weaknesses in the bid or contract documents, or improper tender practices by the
bidder.
Initially all bids were examined to determine the substantial responsiveness. Only
those determined to be substantially responsive were considered in the detailed
⊘ This is a preview!⊘
Do you want full access?
Subscribe today to unlock all pages.

Trusted by 1+ million students worldwide
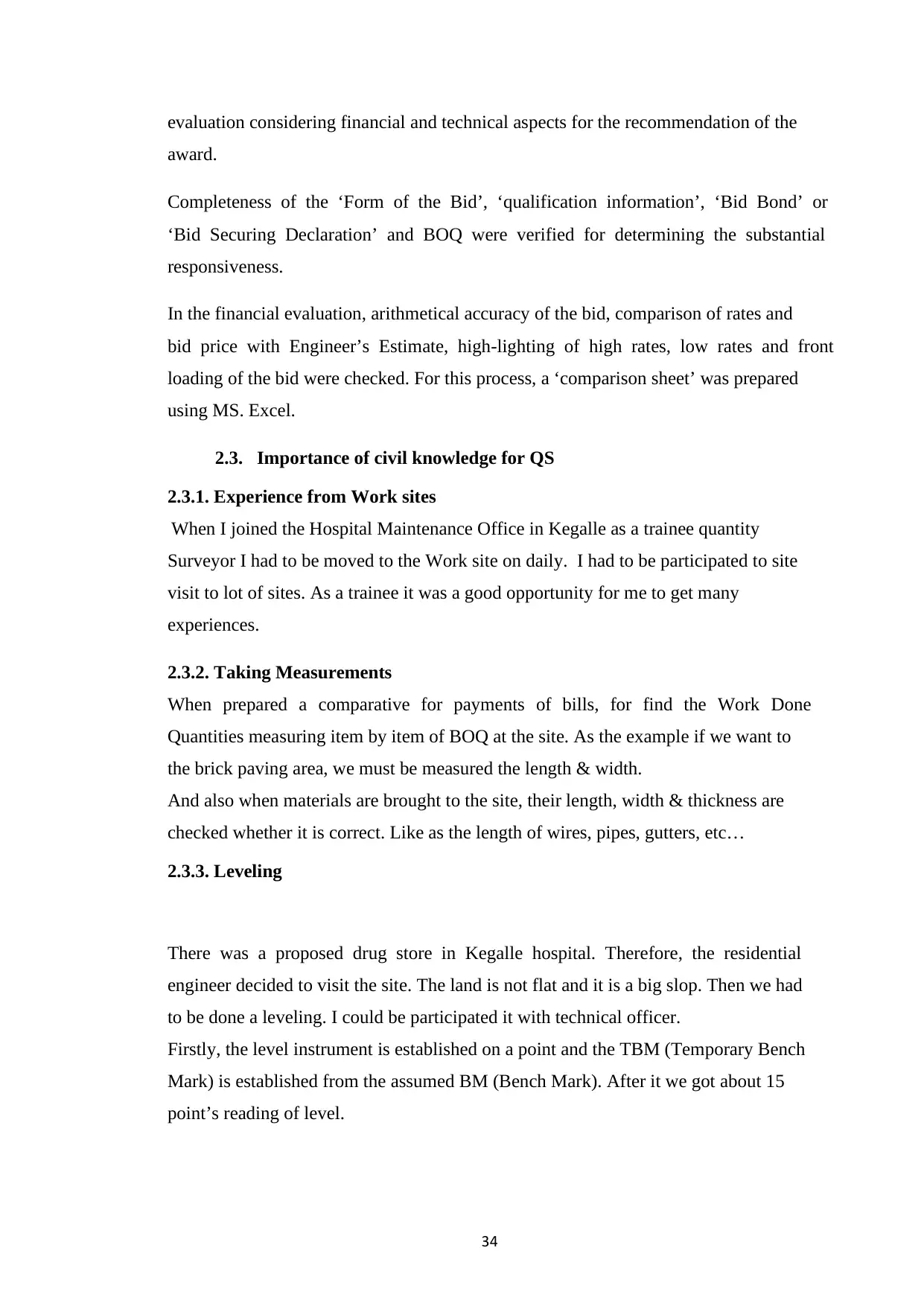
evaluation considering financial and technical aspects for the recommendation of the
award.
Completeness of the ‘Form of the Bid’, ‘qualification information’, ‘Bid Bond’ or
‘Bid Securing Declaration’ and BOQ were verified for determining the substantial
responsiveness.
In the financial evaluation, arithmetical accuracy of the bid, comparison of rates and
bid price with Engineer’s Estimate, high-lighting of high rates, low rates and front
loading of the bid were checked. For this process, a ‘comparison sheet’ was prepared
using MS. Excel.
2.3. Importance of civil knowledge for QS
2.3.1. Experience from Work sites
When I joined the Hospital Maintenance Office in Kegalle as a trainee quantity
Surveyor I had to be moved to the Work site on daily. I had to be participated to site
visit to lot of sites. As a trainee it was a good opportunity for me to get many
experiences.
2.3.2. Taking Measurements
When prepared a comparative for payments of bills, for find the Work Done
Quantities measuring item by item of BOQ at the site. As the example if we want to
the brick paving area, we must be measured the length & width.
And also when materials are brought to the site, their length, width & thickness are
checked whether it is correct. Like as the length of wires, pipes, gutters, etc…
2.3.3. Leveling
There was a proposed drug store in Kegalle hospital. Therefore, the residential
engineer decided to visit the site. The land is not flat and it is a big slop. Then we had
to be done a leveling. I could be participated it with technical officer.
Firstly, the level instrument is established on a point and the TBM (Temporary Bench
Mark) is established from the assumed BM (Bench Mark). After it we got about 15
point’s reading of level.
Paraphrase This Document
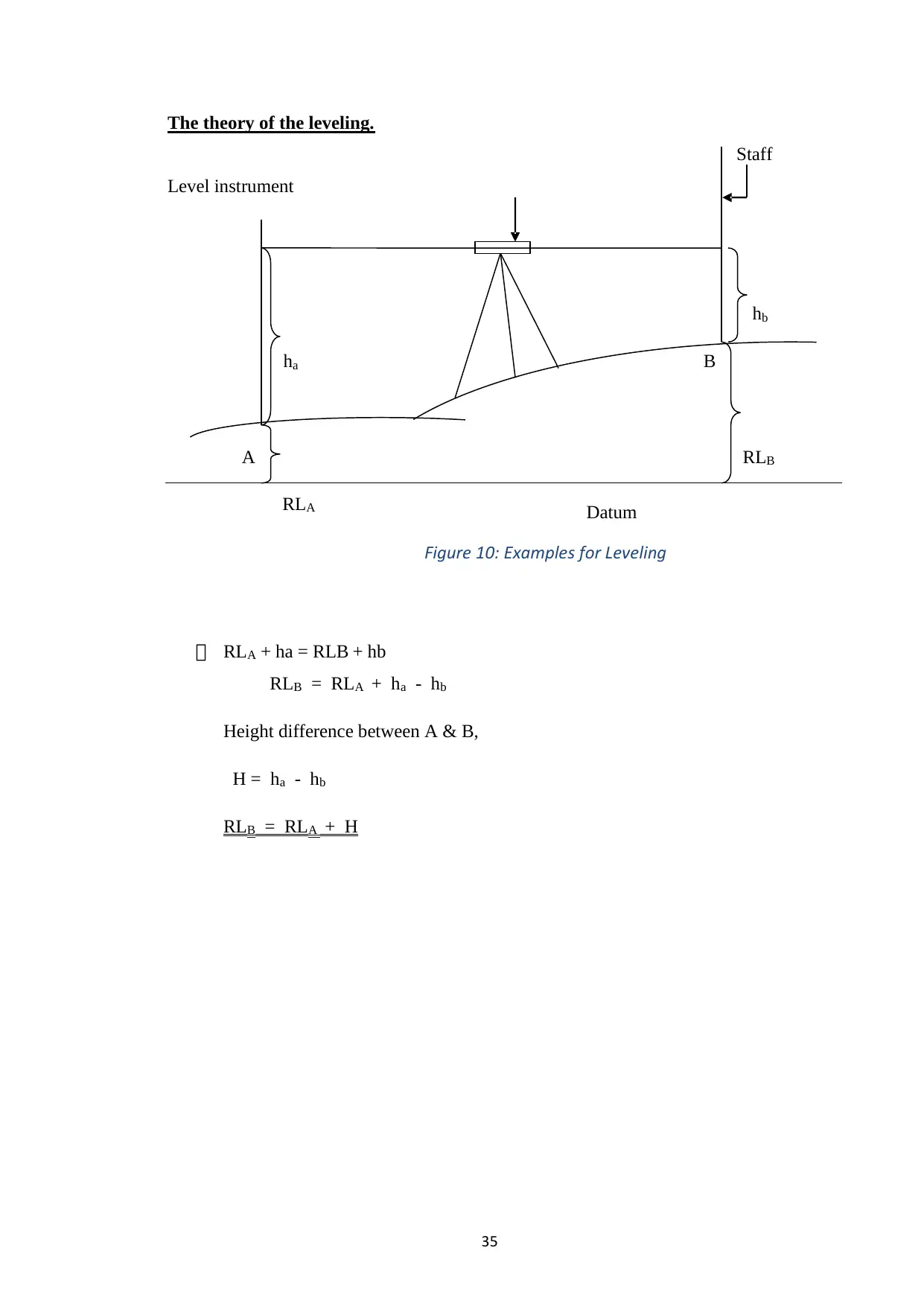
The theory of the leveling.
Staff
Level instrument
hb
ha B
A RLB
RLA
Figure 10: Examples for Leveling
RLA + ha = RLB + hb
RLB = RLA + ha - hb
Height difference between A & B,
H = ha - hb
RLB = RLA + H
Datum
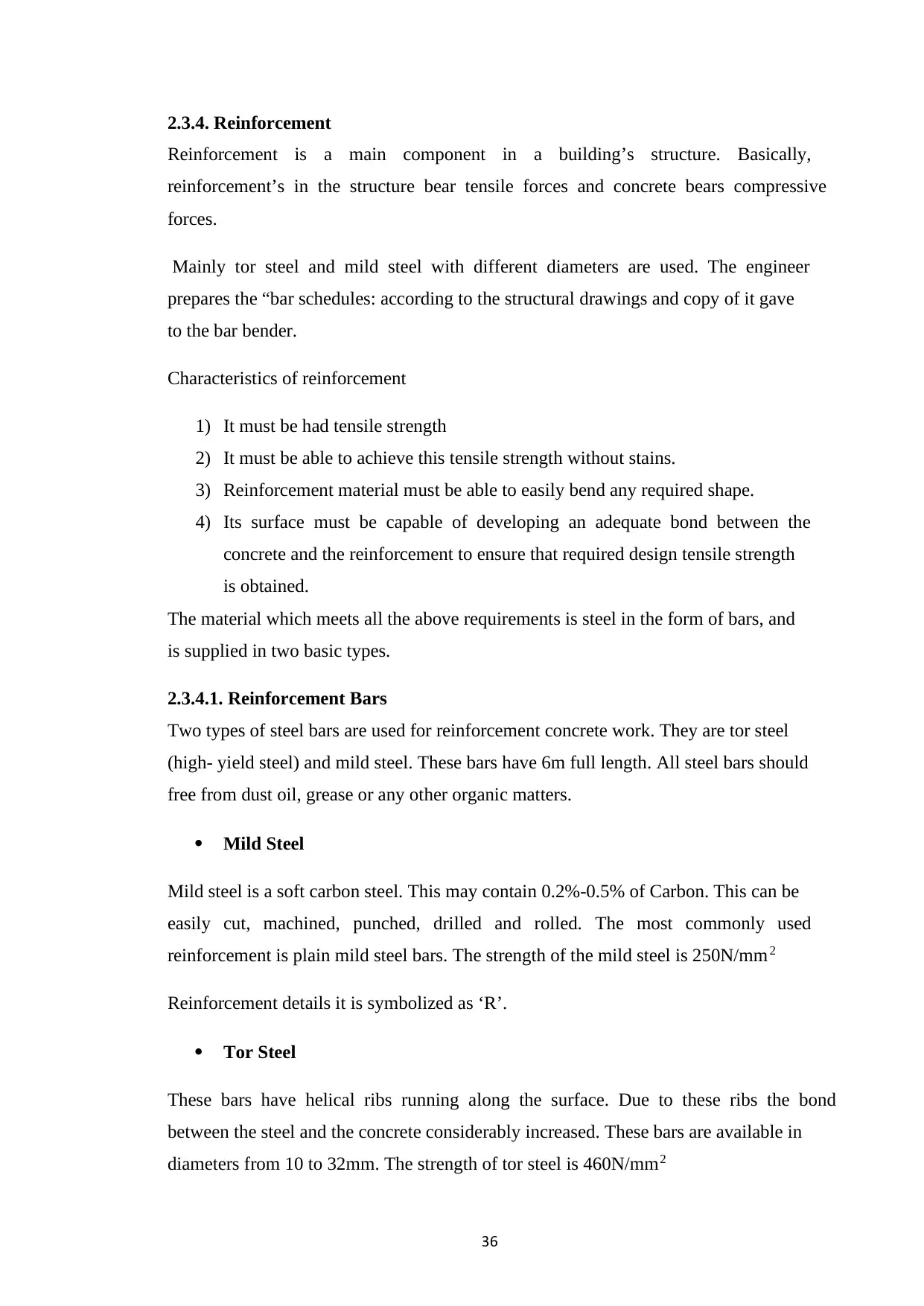
2.3.4. Reinforcement
Reinforcement is a main component in a building’s structure. Basically,
reinforcement’s in the structure bear tensile forces and concrete bears compressive
forces.
Mainly tor steel and mild steel with different diameters are used. The engineer
prepares the “bar schedules: according to the structural drawings and copy of it gave
to the bar bender.
Characteristics of reinforcement
1) It must be had tensile strength
2) It must be able to achieve this tensile strength without stains.
3) Reinforcement material must be able to easily bend any required shape.
4) Its surface must be capable of developing an adequate bond between the
concrete and the reinforcement to ensure that required design tensile strength
is obtained.
The material which meets all the above requirements is steel in the form of bars, and
is supplied in two basic types.
2.3.4.1. Reinforcement Bars
Two types of steel bars are used for reinforcement concrete work. They are tor steel
(high- yield steel) and mild steel. These bars have 6m full length. All steel bars should
free from dust oil, grease or any other organic matters.
Mild Steel
Mild steel is a soft carbon steel. This may contain 0.2%-0.5% of Carbon. This can be
easily cut, machined, punched, drilled and rolled. The most commonly used
reinforcement is plain mild steel bars. The strength of the mild steel is 250N/mm2
Reinforcement details it is symbolized as ‘R’.
Tor Steel
These bars have helical ribs running along the surface. Due to these ribs the bond
between the steel and the concrete considerably increased. These bars are available in
diameters from 10 to 32mm. The strength of tor steel is 460N/mm2
⊘ This is a preview!⊘
Do you want full access?
Subscribe today to unlock all pages.

Trusted by 1+ million students worldwide
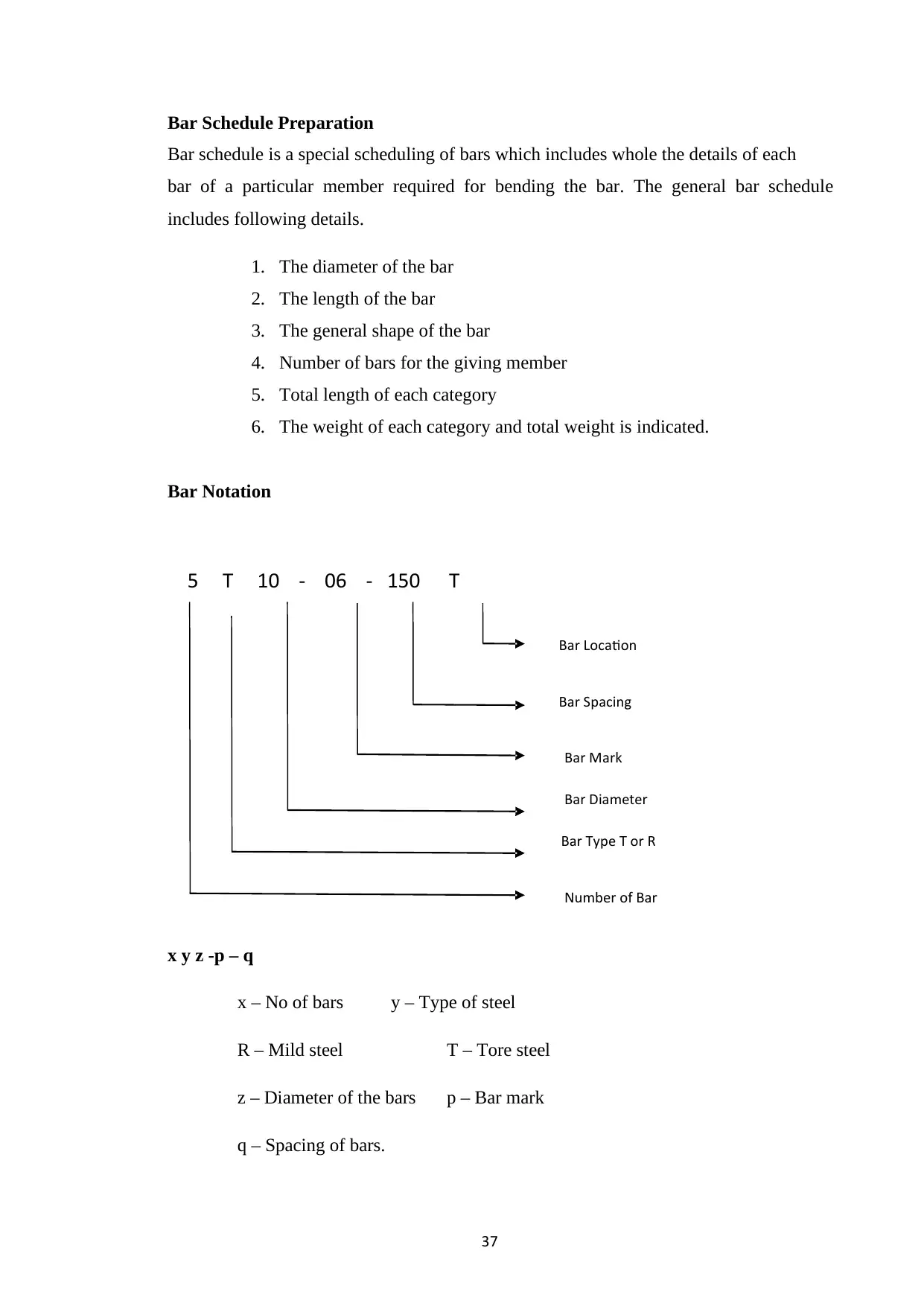
Bar Schedule Preparation
Bar schedule is a special scheduling of bars which includes whole the details of each
bar of a particular member required for bending the bar. The general bar schedule
includes following details.
1. The diameter of the bar
2. The length of the bar
3. The general shape of the bar
4. Number of bars for the giving member
5. Total length of each category
6. The weight of each category and total weight is indicated.
Bar Notation
x y z -p – q
x – No of bars y – Type of steel
R – Mild steel T – Tore steel
z – Diameter of the bars p – Bar mark
q – Spacing of bars.
5 T 10 - 06 - 150 T
Bar Mark
Bar Diameter
Bar Type T or R
Number of Bar
Bar Spacing
Bar Location
Paraphrase This Document
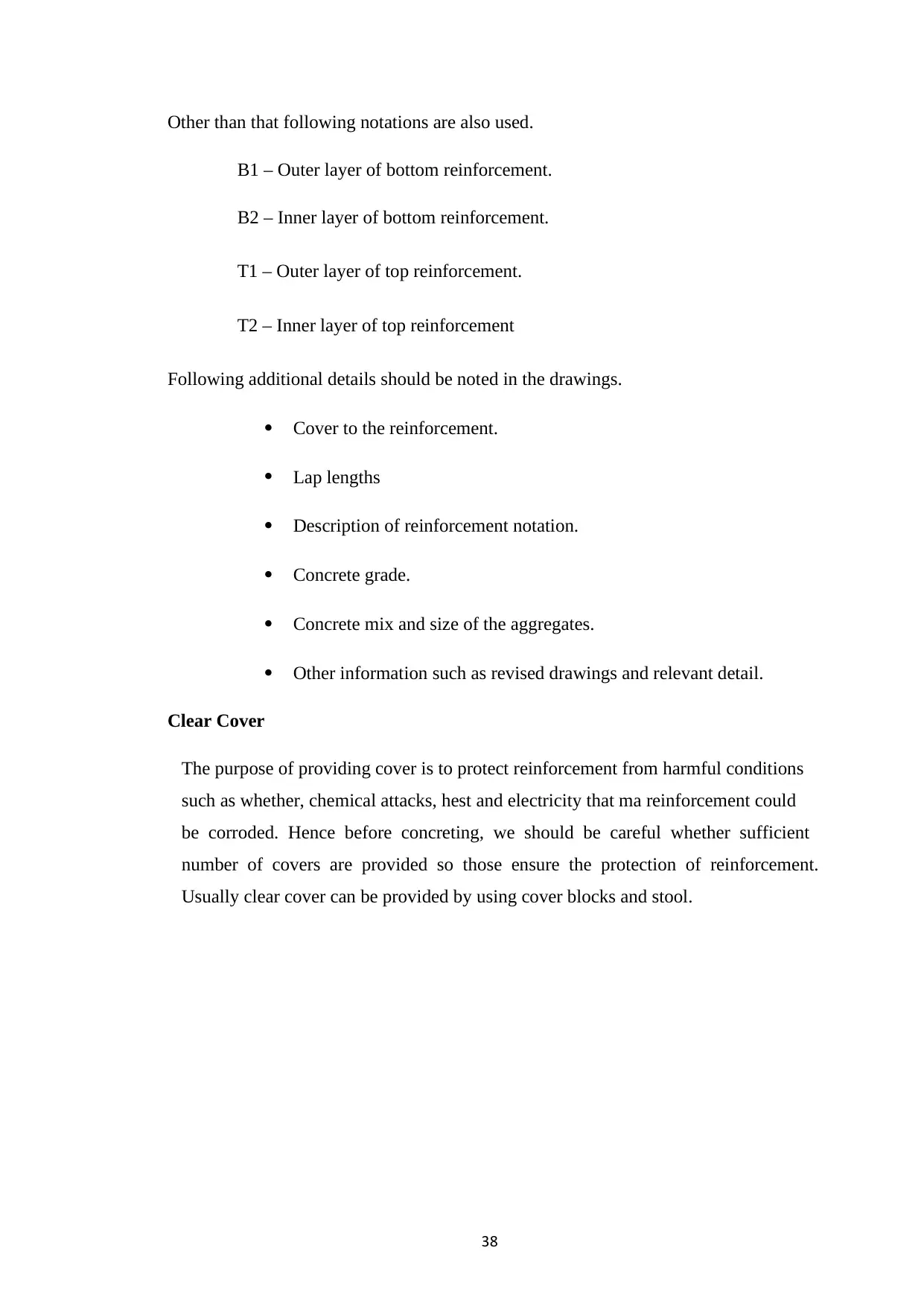
Other than that following notations are also used.
B1 – Outer layer of bottom reinforcement.
B2 – Inner layer of bottom reinforcement.
T1 – Outer layer of top reinforcement.
T2 – Inner layer of top reinforcement
Following additional details should be noted in the drawings.
Cover to the reinforcement.
Lap lengths
Description of reinforcement notation.
Concrete grade.
Concrete mix and size of the aggregates.
Other information such as revised drawings and relevant detail.
Clear Cover
The purpose of providing cover is to protect reinforcement from harmful conditions
such as whether, chemical attacks, hest and electricity that ma reinforcement could
be corroded. Hence before concreting, we should be careful whether sufficient
number of covers are provided so those ensure the protection of reinforcement.
Usually clear cover can be provided by using cover blocks and stool.
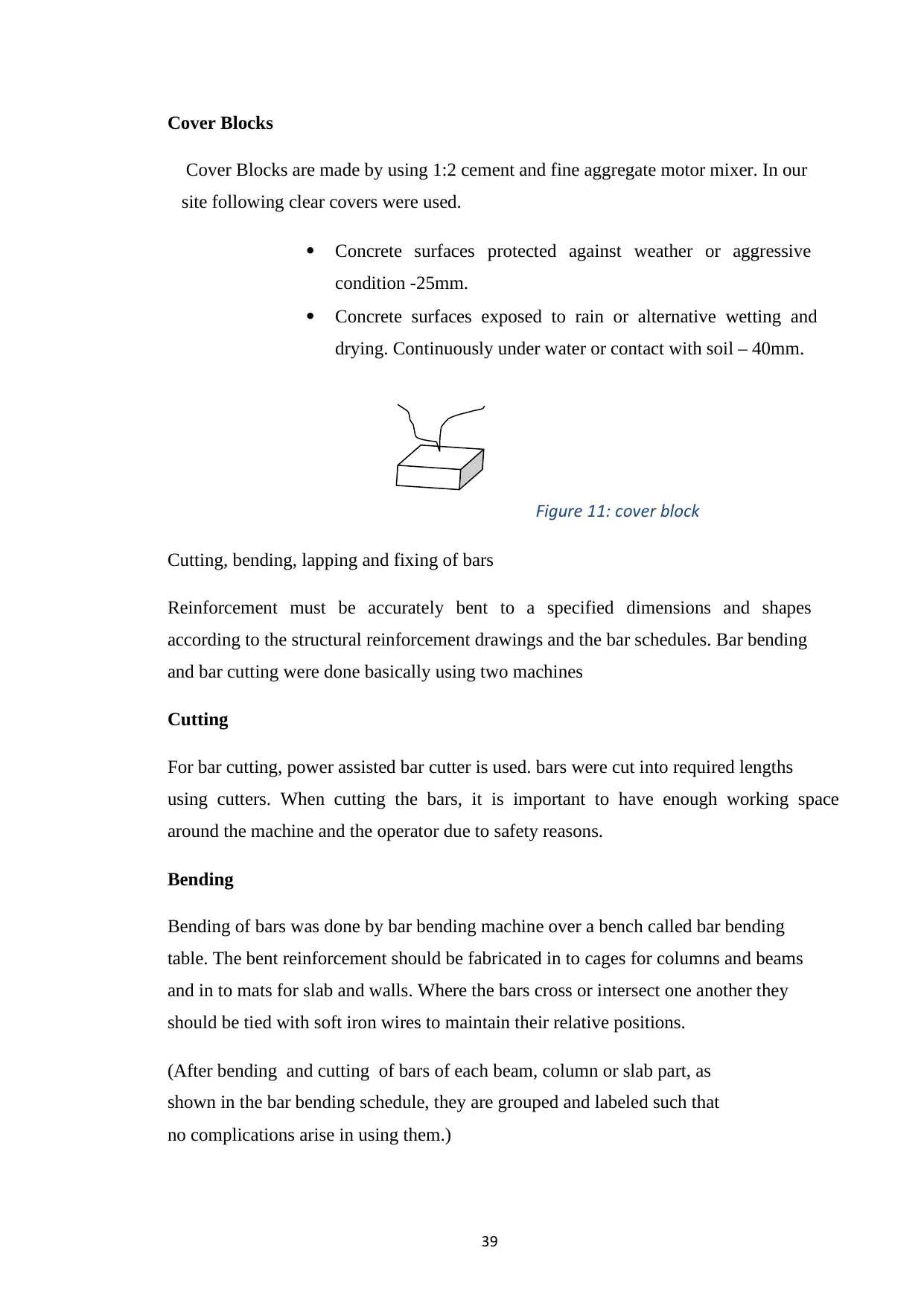
Cover Blocks
Cover Blocks are made by using 1:2 cement and fine aggregate motor mixer. In our
site following clear covers were used.
Concrete surfaces protected against weather or aggressive
condition -25mm.
Concrete surfaces exposed to rain or alternative wetting and
drying. Continuously under water or contact with soil – 40mm.
Figure 11: cover block
Cutting, bending, lapping and fixing of bars
Reinforcement must be accurately bent to a specified dimensions and shapes
according to the structural reinforcement drawings and the bar schedules. Bar bending
and bar cutting were done basically using two machines
Cutting
For bar cutting, power assisted bar cutter is used. bars were cut into required lengths
using cutters. When cutting the bars, it is important to have enough working space
around the machine and the operator due to safety reasons.
Bending
Bending of bars was done by bar bending machine over a bench called bar bending
table. The bent reinforcement should be fabricated in to cages for columns and beams
and in to mats for slab and walls. Where the bars cross or intersect one another they
should be tied with soft iron wires to maintain their relative positions.
(After bending and cutting of bars of each beam, column or slab part, as
shown in the bar bending schedule, they are grouped and labeled such that
no complications arise in using them.)
⊘ This is a preview!⊘
Do you want full access?
Subscribe today to unlock all pages.

Trusted by 1+ million students worldwide
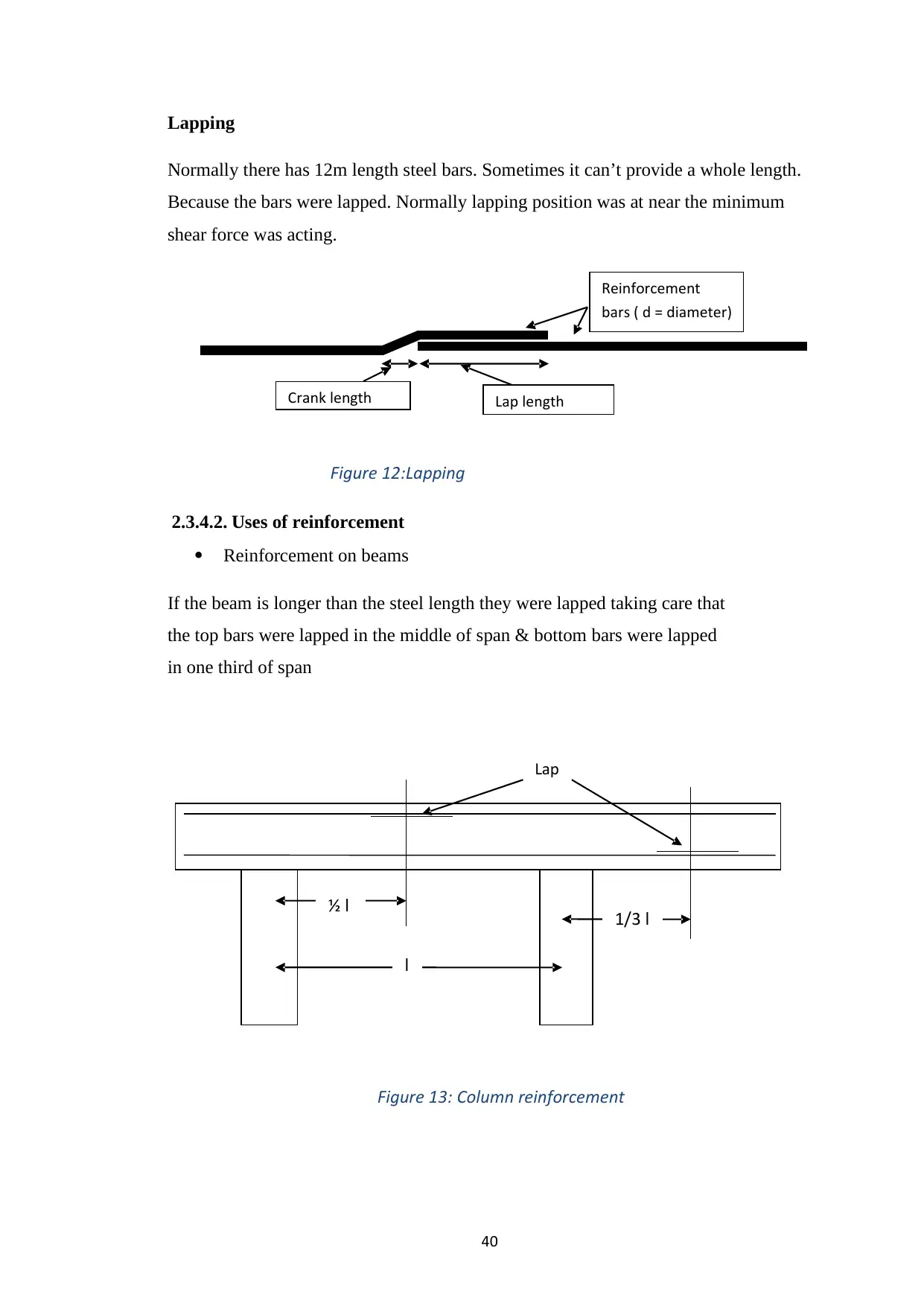
Lapping
Normally there has 12m length steel bars. Sometimes it can’t provide a whole length.
Because the bars were lapped. Normally lapping position was at near the minimum
shear force was acting.
Figure 12:Lapping
2.3.4.2. Uses of reinforcement
Reinforcement on beams
If the beam is longer than the steel length they were lapped taking care that
the top bars were lapped in the middle of span & bottom bars were lapped
in one third of span
Figure 13: Column reinforcement
Crank length Lap length
Reinforcement
bars ( d = diameter)
½ l 1/3 l
l
Lap
Paraphrase This Document
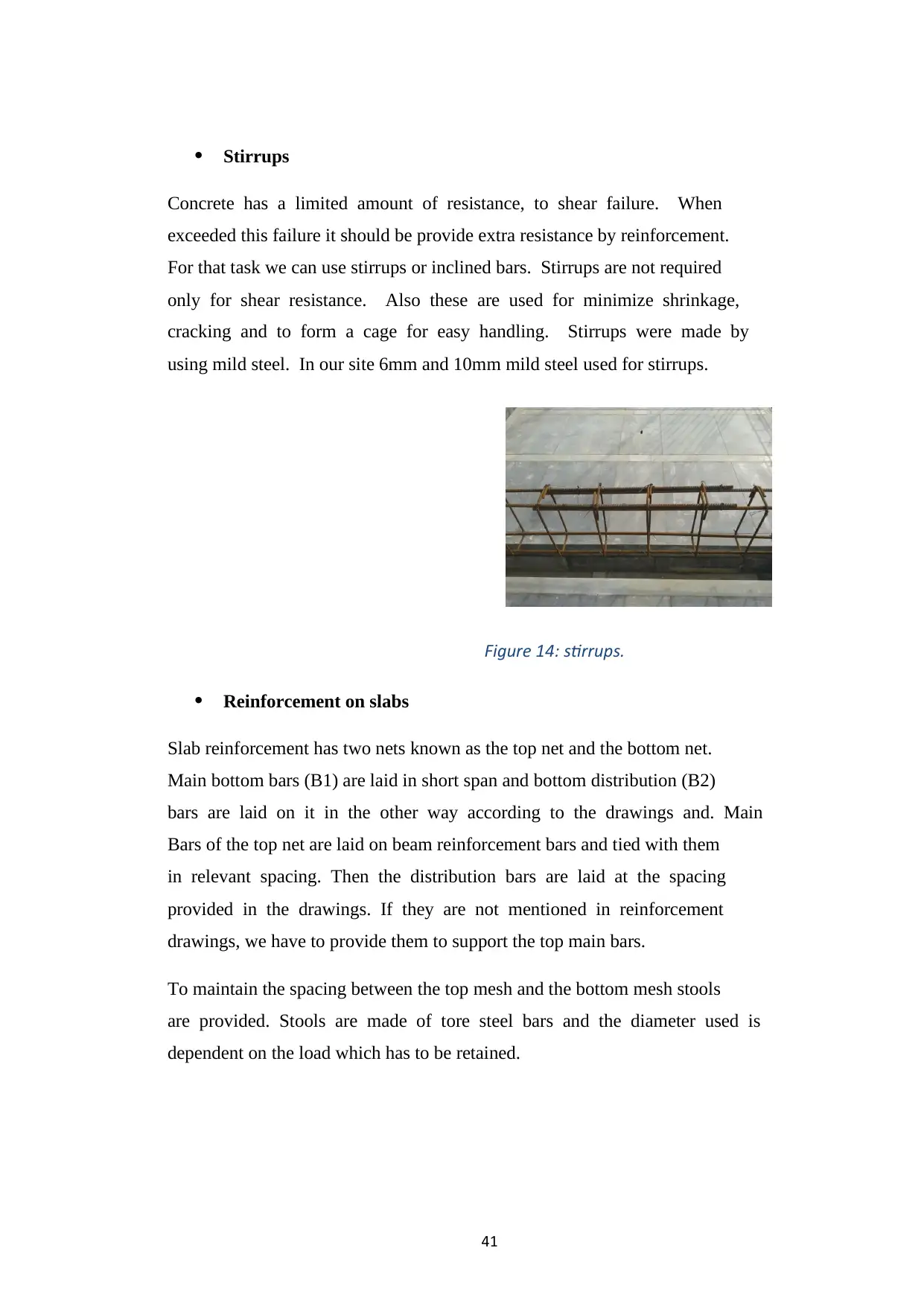
Stirrups
Concrete has a limited amount of resistance, to shear failure. When
exceeded this failure it should be provide extra resistance by reinforcement.
For that task we can use stirrups or inclined bars. Stirrups are not required
only for shear resistance. Also these are used for minimize shrinkage,
cracking and to form a cage for easy handling. Stirrups were made by
using mild steel. In our site 6mm and 10mm mild steel used for stirrups.
Figure 14: stirrups.
Reinforcement on slabs
Slab reinforcement has two nets known as the top net and the bottom net.
Main bottom bars (B1) are laid in short span and bottom distribution (B2)
bars are laid on it in the other way according to the drawings and. Main
Bars of the top net are laid on beam reinforcement bars and tied with them
in relevant spacing. Then the distribution bars are laid at the spacing
provided in the drawings. If they are not mentioned in reinforcement
drawings, we have to provide them to support the top main bars.
To maintain the spacing between the top mesh and the bottom mesh stools
are provided. Stools are made of tore steel bars and the diameter used is
dependent on the load which has to be retained.
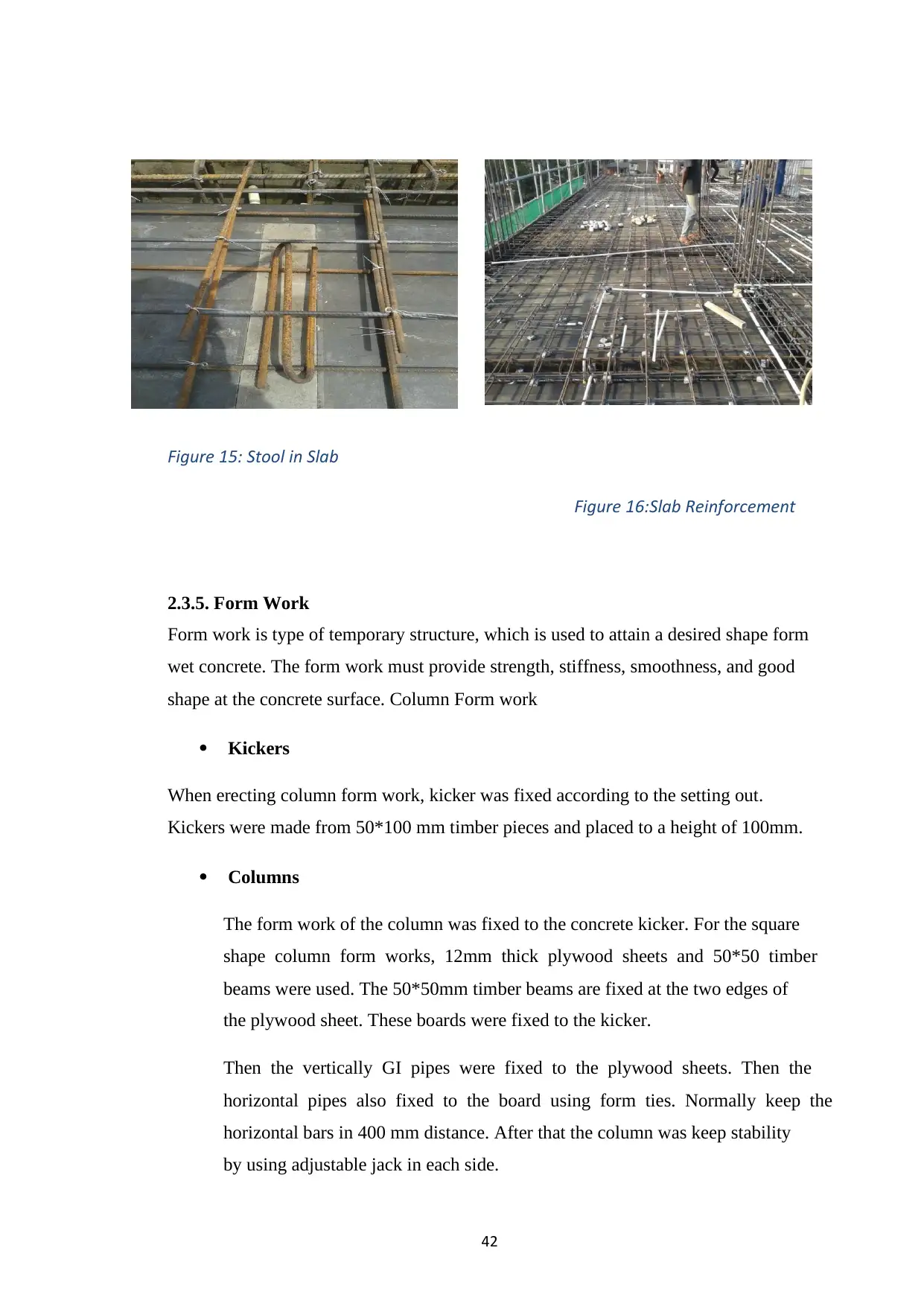
Figure 15: Stool in Slab
Figure 16:Slab Reinforcement
2.3.5. Form Work
Form work is type of temporary structure, which is used to attain a desired shape form
wet concrete. The form work must provide strength, stiffness, smoothness, and good
shape at the concrete surface. Column Form work
Kickers
When erecting column form work, kicker was fixed according to the setting out.
Kickers were made from 50*100 mm timber pieces and placed to a height of 100mm.
Columns
The form work of the column was fixed to the concrete kicker. For the square
shape column form works, 12mm thick plywood sheets and 50*50 timber
beams were used. The 50*50mm timber beams are fixed at the two edges of
the plywood sheet. These boards were fixed to the kicker.
Then the vertically GI pipes were fixed to the plywood sheets. Then the
horizontal pipes also fixed to the board using form ties. Normally keep the
horizontal bars in 400 mm distance. After that the column was keep stability
by using adjustable jack in each side.
⊘ This is a preview!⊘
Do you want full access?
Subscribe today to unlock all pages.

Trusted by 1+ million students worldwide
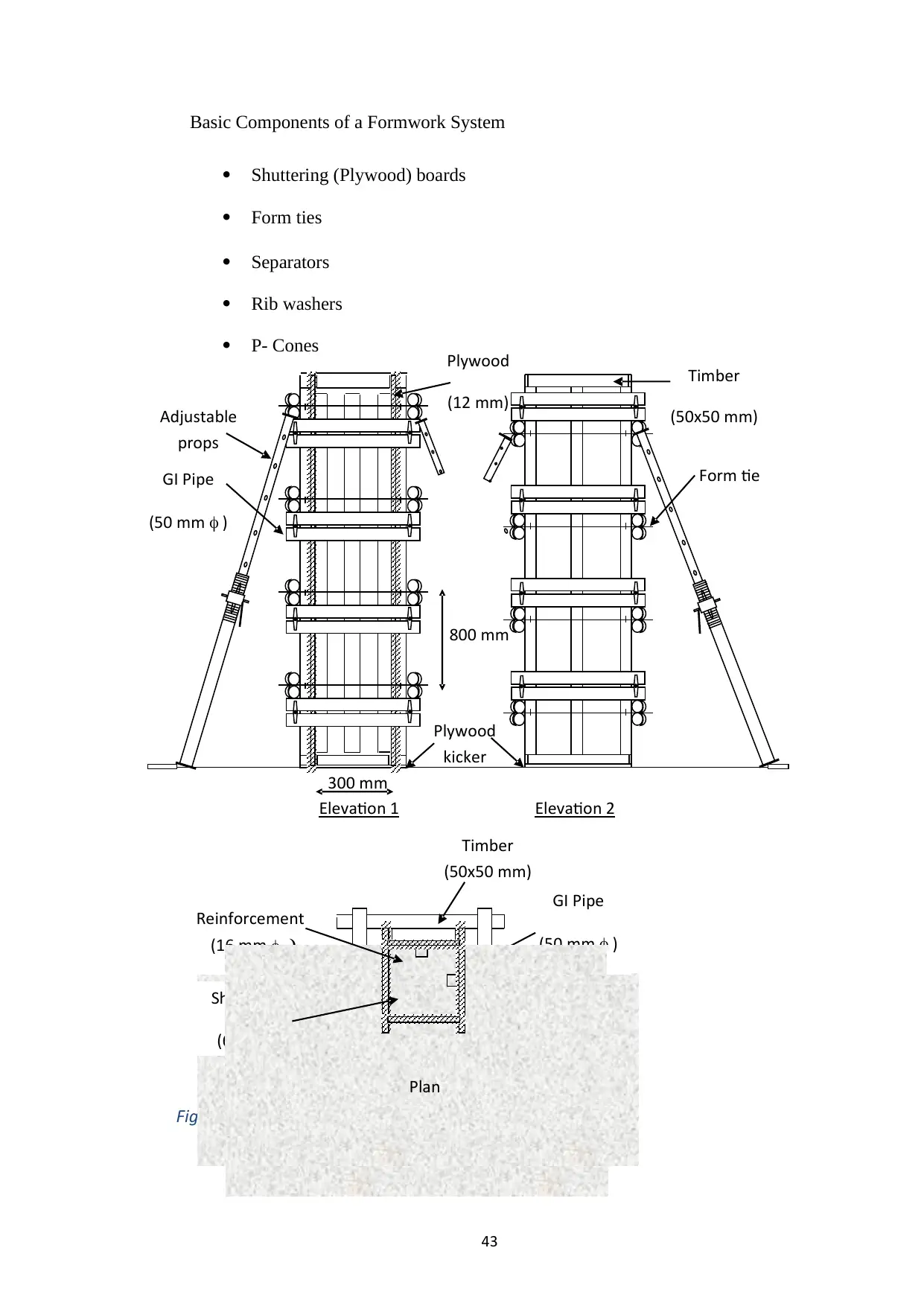
Basic Components of a Formwork System
Shuttering (Plywood) boards
Form ties
Separators
Rib washers
P- Cones
Figure 17:Column Form Work
Plywood
(12 mm)
Elevation 1 Elevation 2
300 mm
800 mm
Adjustable
props
Form tie
Timber
(50x50 mm)
GI Pipe
(50 mm )
Plywood
kicker
Timber
(50x50 mm)
GI Pipe
(50 mm )
Plywood
(12 mm)
Cover
blocks
Shear links
(6 mm
Reinforcement
(16 mm
Plan
Paraphrase This Document
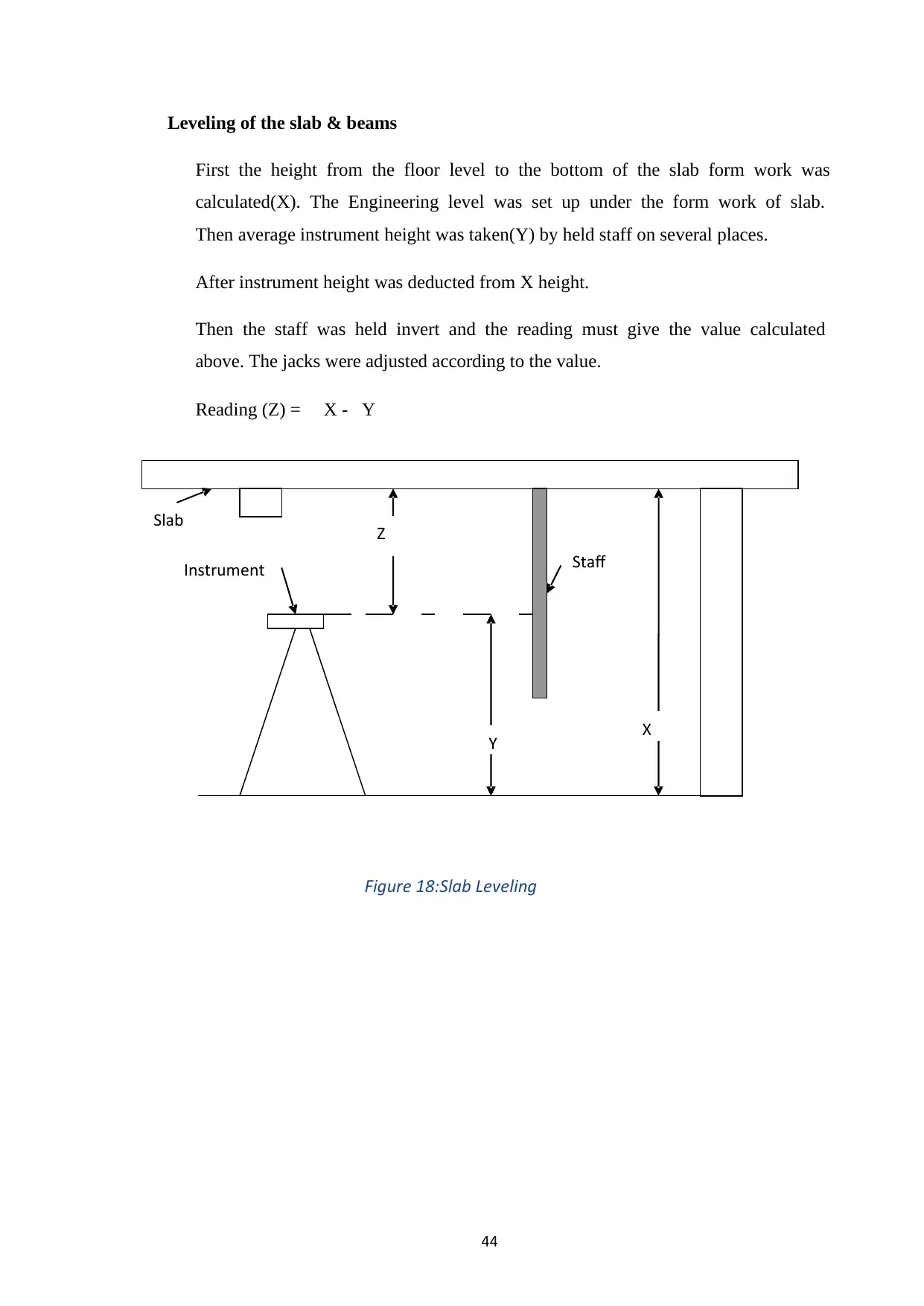
Leveling of the slab & beams
First the height from the floor level to the bottom of the slab form work was
calculated(X). The Engineering level was set up under the form work of slab.
Then average instrument height was taken(Y) by held staff on several places.
After instrument height was deducted from X height.
Then the staff was held invert and the reading must give the value calculated
above. The jacks were adjusted according to the value.
Reading (Z) = X - Y
Figure 18:Slab Leveling
Z
Y X
Staff
Slab
Instrument
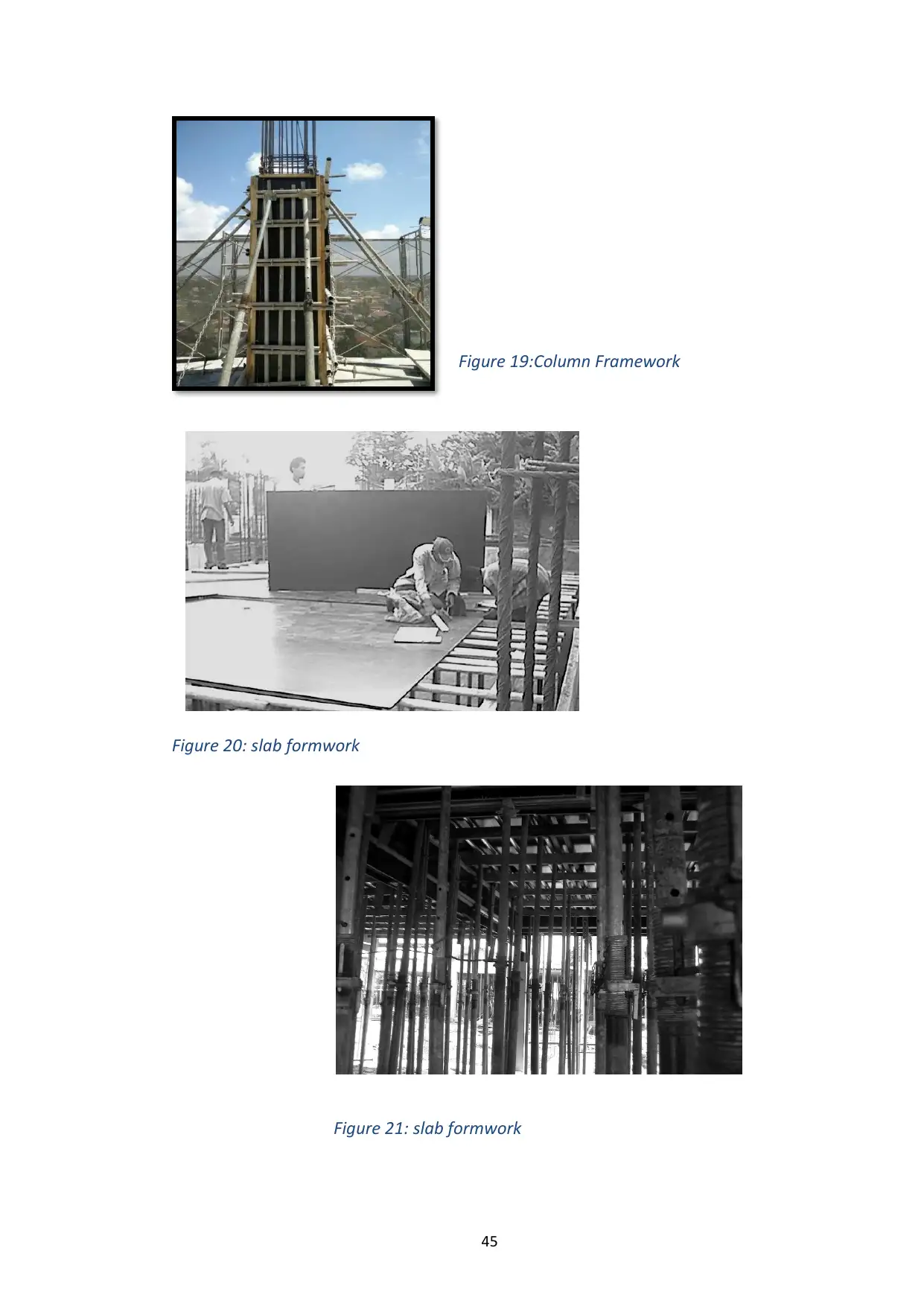
Figure 19:Column Framework
Figure 20: slab formwork
Figure 21: slab formwork
⊘ This is a preview!⊘
Do you want full access?
Subscribe today to unlock all pages.

Trusted by 1+ million students worldwide
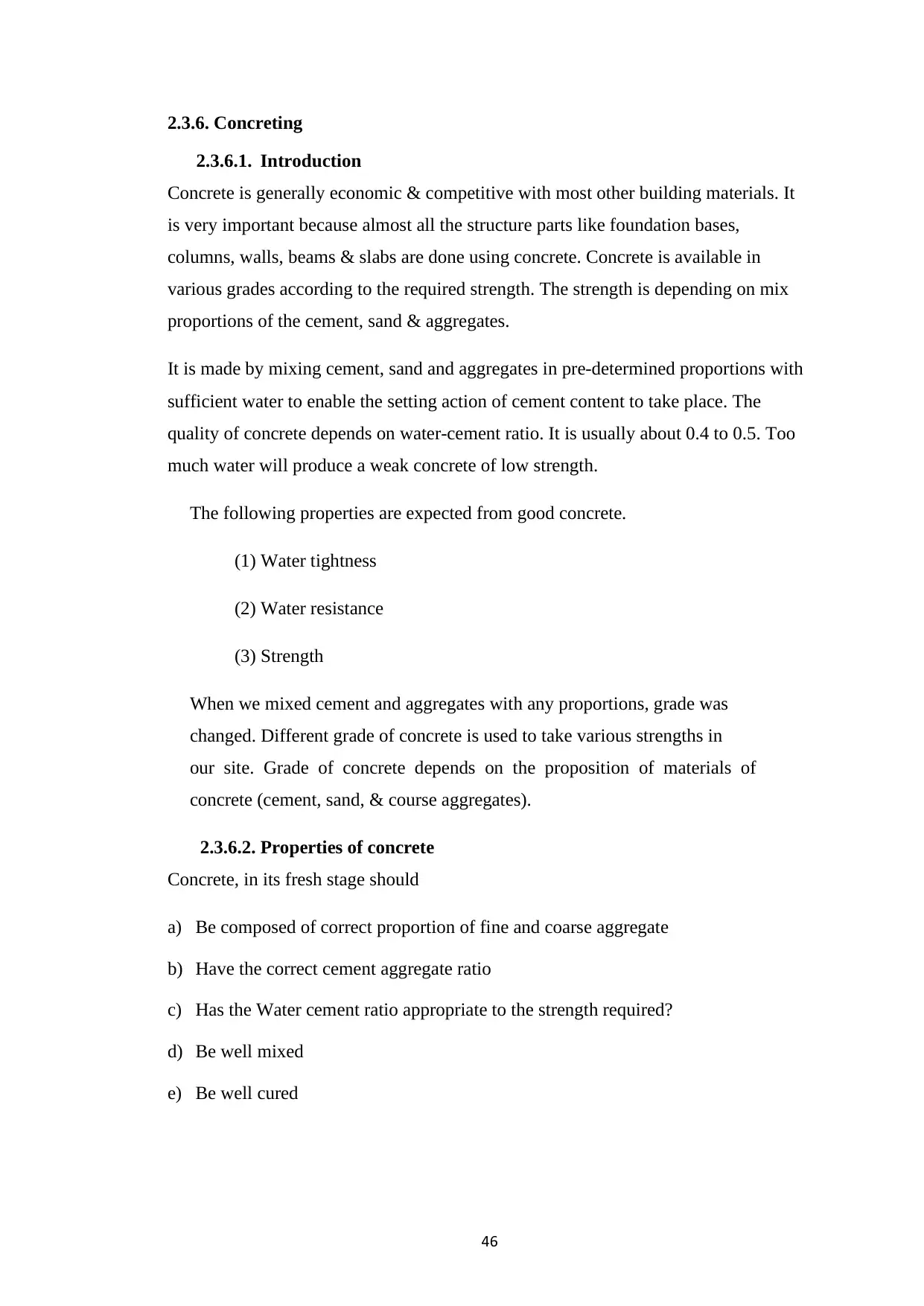
2.3.6. Concreting
2.3.6.1. Introduction
Concrete is generally economic & competitive with most other building materials. It
is very important because almost all the structure parts like foundation bases,
columns, walls, beams & slabs are done using concrete. Concrete is available in
various grades according to the required strength. The strength is depending on mix
proportions of the cement, sand & aggregates.
It is made by mixing cement, sand and aggregates in pre-determined proportions with
sufficient water to enable the setting action of cement content to take place. The
quality of concrete depends on water-cement ratio. It is usually about 0.4 to 0.5. Too
much water will produce a weak concrete of low strength.
The following properties are expected from good concrete.
(1) Water tightness
(2) Water resistance
(3) Strength
When we mixed cement and aggregates with any proportions, grade was
changed. Different grade of concrete is used to take various strengths in
our site. Grade of concrete depends on the proposition of materials of
concrete (cement, sand, & course aggregates).
2.3.6.2. Properties of concrete
Concrete, in its fresh stage should
a) Be composed of correct proportion of fine and coarse aggregate
b) Have the correct cement aggregate ratio
c) Has the Water cement ratio appropriate to the strength required?
d) Be well mixed
e) Be well cured
Paraphrase This Document
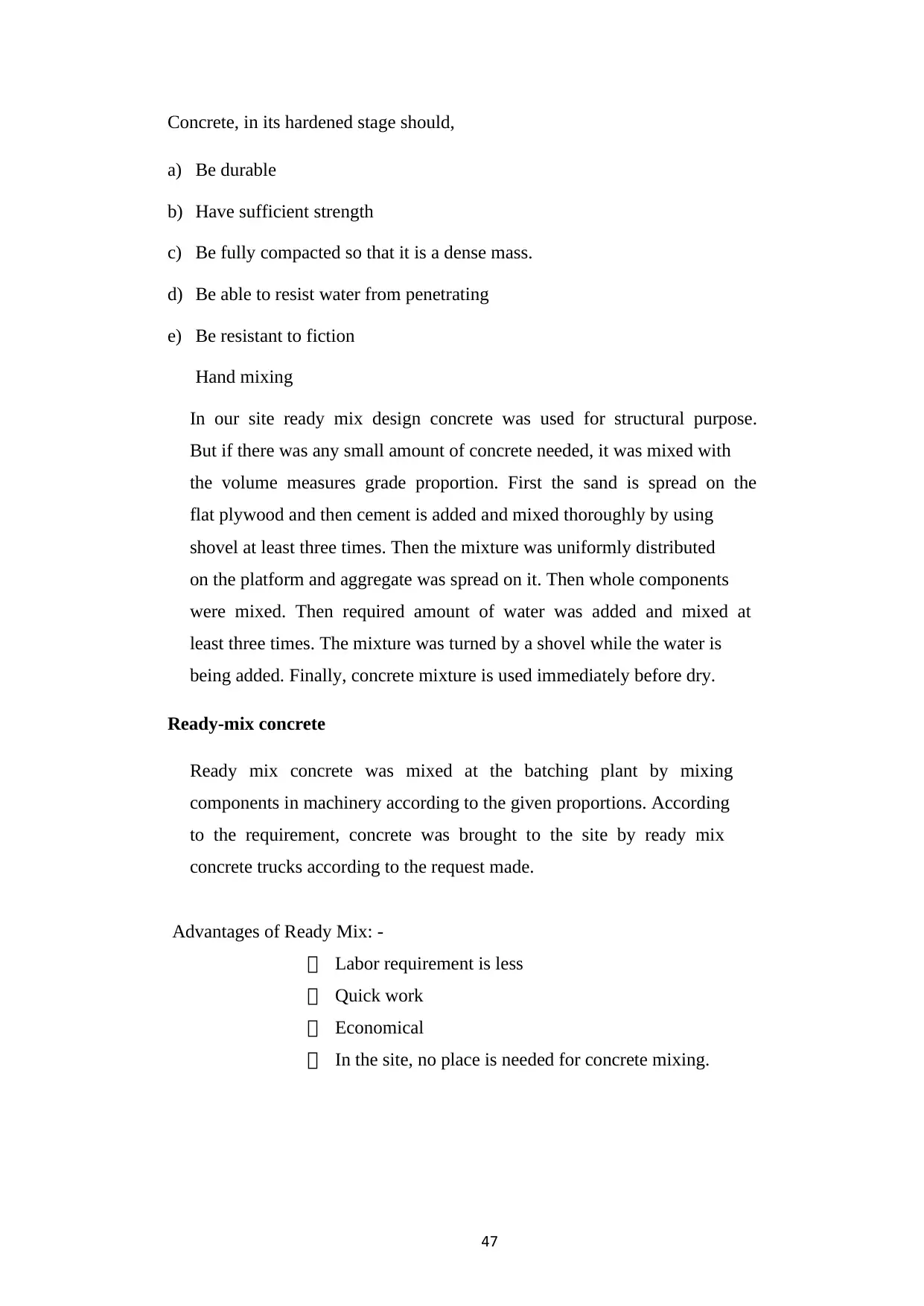
Concrete, in its hardened stage should,
a) Be durable
b) Have sufficient strength
c) Be fully compacted so that it is a dense mass.
d) Be able to resist water from penetrating
e) Be resistant to fiction
Hand mixing
In our site ready mix design concrete was used for structural purpose.
But if there was any small amount of concrete needed, it was mixed with
the volume measures grade proportion. First the sand is spread on the
flat plywood and then cement is added and mixed thoroughly by using
shovel at least three times. Then the mixture was uniformly distributed
on the platform and aggregate was spread on it. Then whole components
were mixed. Then required amount of water was added and mixed at
least three times. The mixture was turned by a shovel while the water is
being added. Finally, concrete mixture is used immediately before dry.
Ready-mix concrete
Ready mix concrete was mixed at the batching plant by mixing
components in machinery according to the given proportions. According
to the requirement, concrete was brought to the site by ready mix
concrete trucks according to the request made.
Advantages of Ready Mix: -
Labor requirement is less
Quick work
Economical
In the site, no place is needed for concrete mixing.
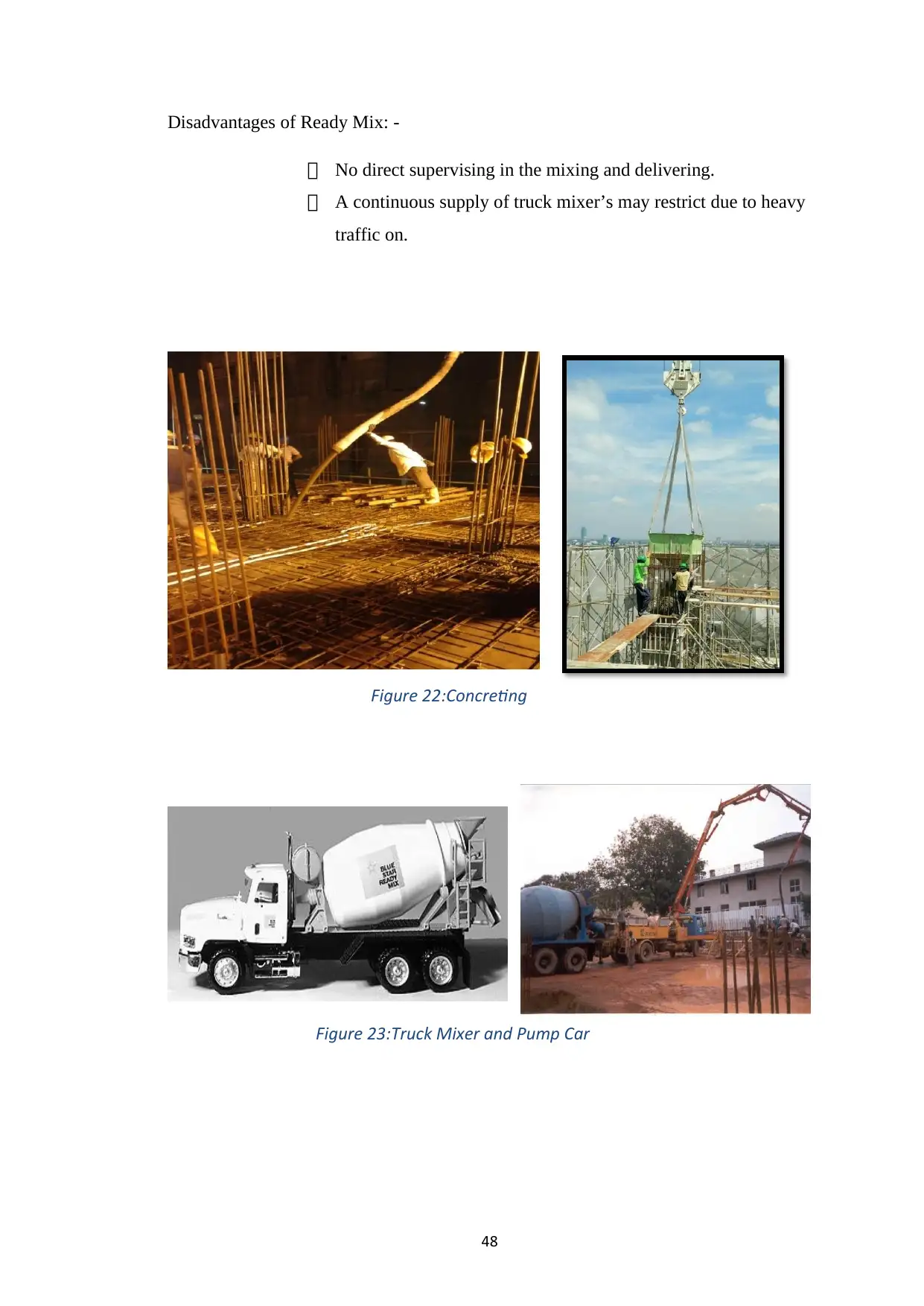
Disadvantages of Ready Mix: -
No direct supervising in the mixing and delivering.
A continuous supply of truck mixer’s may restrict due to heavy
traffic on.
Figure 22:Concreting
Figure 23:Truck Mixer and Pump Car
⊘ This is a preview!⊘
Do you want full access?
Subscribe today to unlock all pages.

Trusted by 1+ million students worldwide
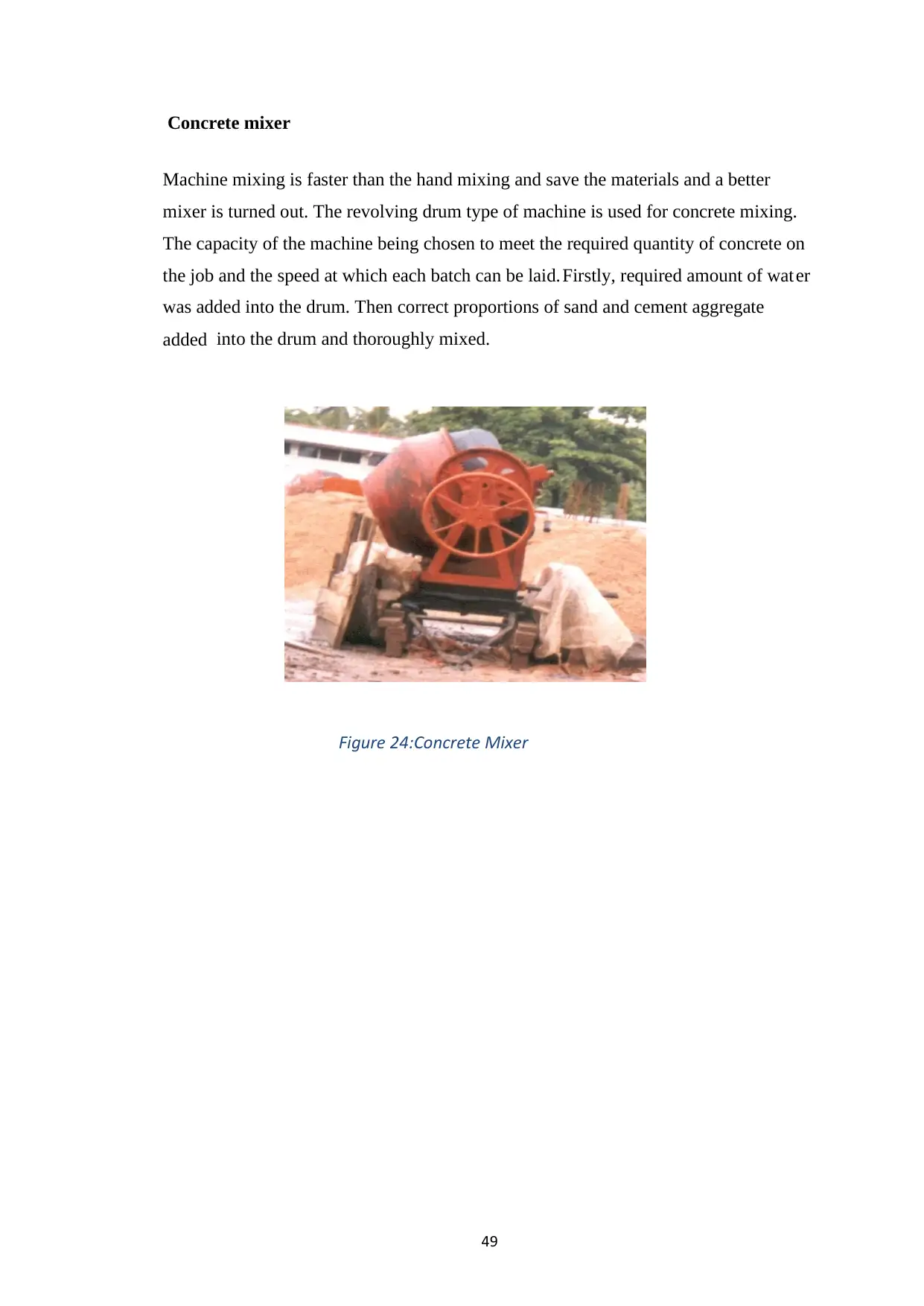
Concrete mixer
Figure 24:Concrete Mixer
Machine mixing is faster than the hand mixing and save the materials and a better
mixer is turned out. The revolving drum type of machine is used for concrete mixing.
The capacity of the machine being chosen to meet the required quantity of concrete on
the job and the speed at which each batch can be laid.Firstly, required amount of wat er
was added into the drum. Then correct proportions of sand and cement aggregate
added into the drum and thoroughly mixed.
Paraphrase This Document
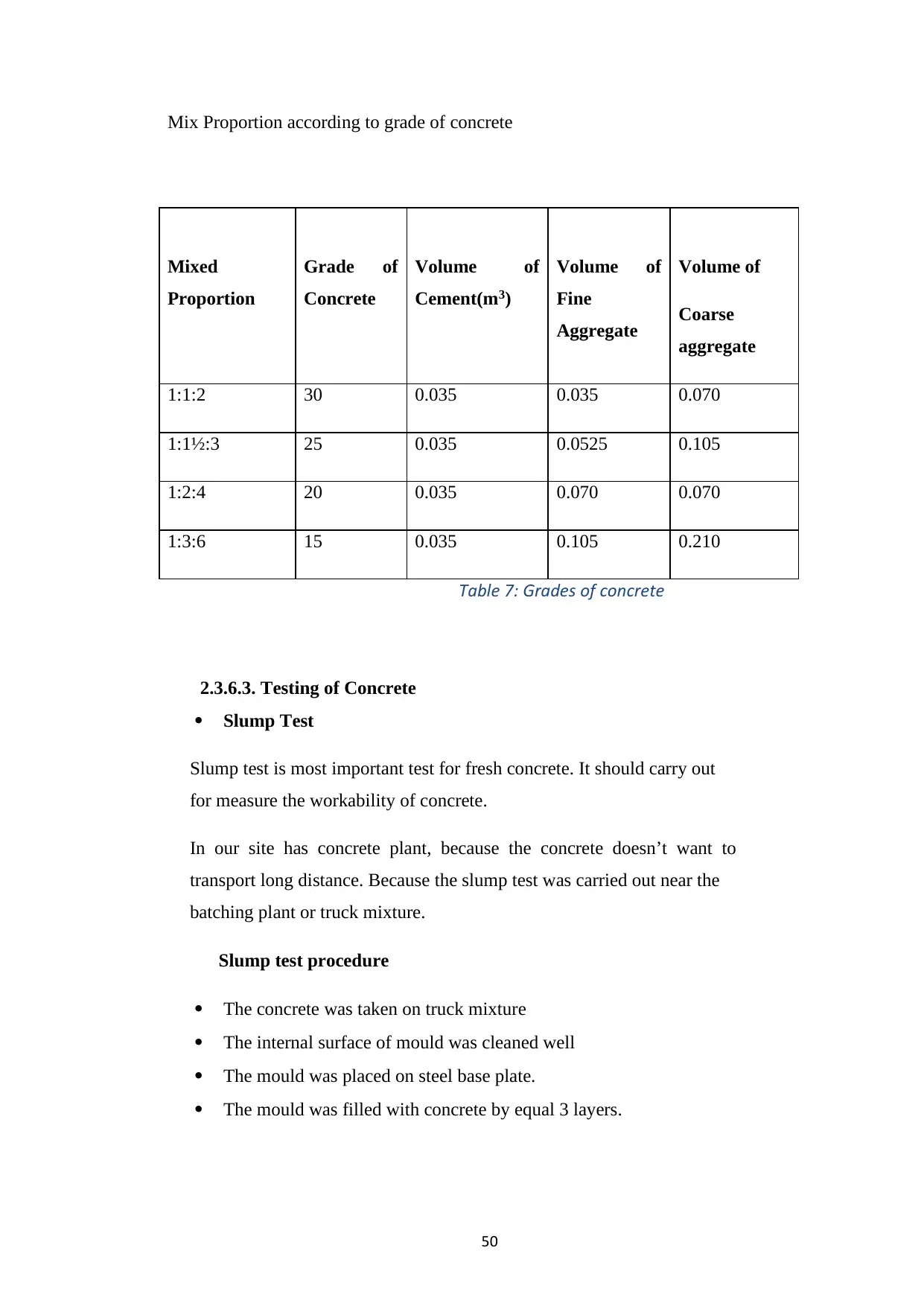
Mix Proportion according to grade of concrete
Mixed
Proportion
Grade of
Concrete
Volume of
Cement(m3)
Volume of
Fine
Aggregate
Volume of
Coarse
aggregate
1:1:2 30 0.035 0.035 0.070
1:1½:3 25 0.035 0.0525 0.105
1:2:4 20 0.035 0.070 0.070
1:3:6 15 0.035 0.105 0.210
Table 7: Grades of concrete
2.3.6.3. Testing of Concrete
Slump Test
Slump test is most important test for fresh concrete. It should carry out
for measure the workability of concrete.
In our site has concrete plant, because the concrete doesn’t want to
transport long distance. Because the slump test was carried out near the
batching plant or truck mixture.
Slump test procedure
The concrete was taken on truck mixture
The internal surface of mould was cleaned well
The mould was placed on steel base plate.
The mould was filled with concrete by equal 3 layers.
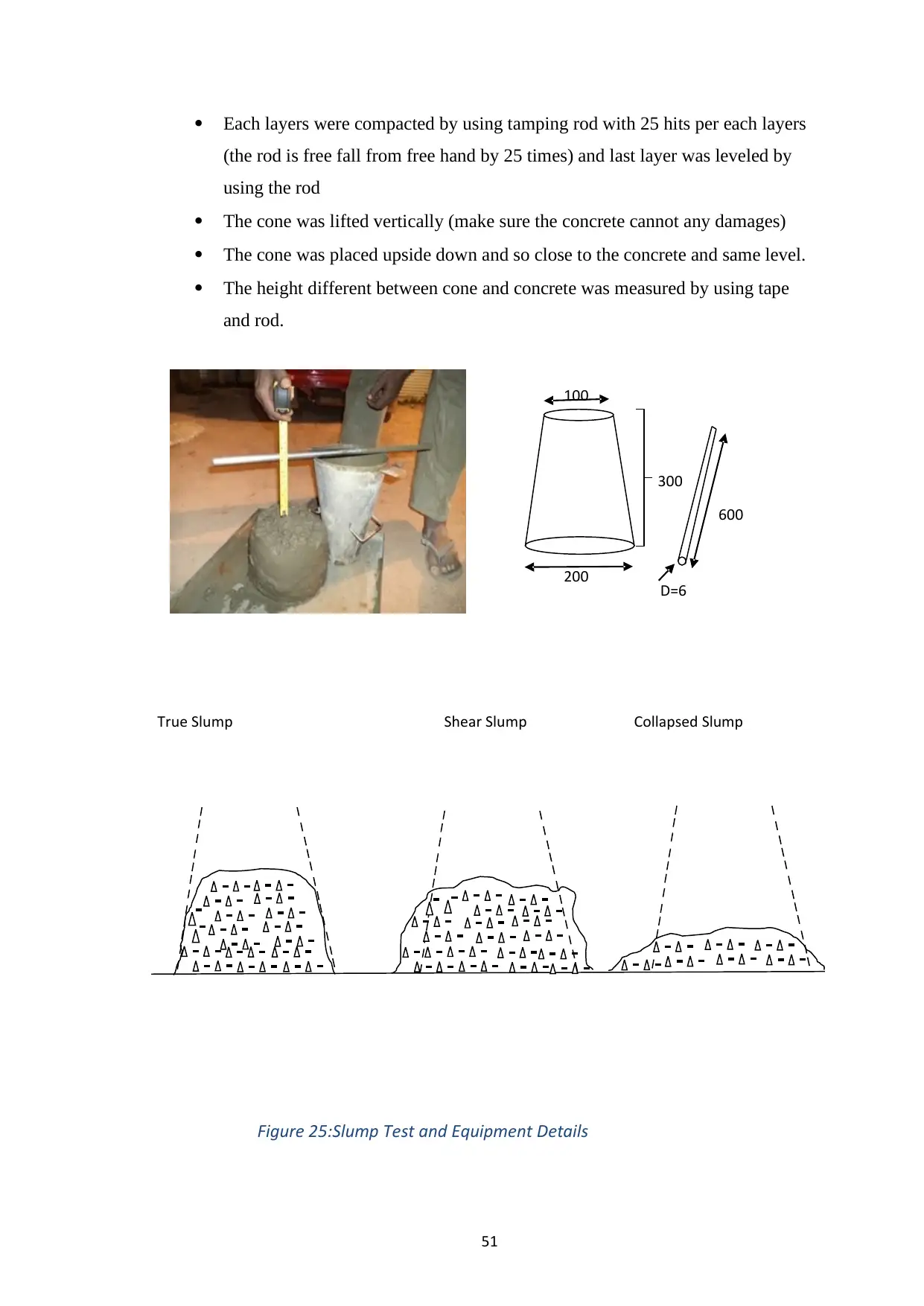
Each layers were compacted by using tamping rod with 25 hits per each layers
(the rod is free fall from free hand by 25 times) and last layer was leveled by
using the rod
The cone was lifted vertically (make sure the concrete cannot any damages)
The cone was placed upside down and so close to the concrete and same level.
The height different between cone and concrete was measured by using tape
and rod.
Figure 25:Slump Test and Equipment Details
300
100
200
600
D=6
True Slump Shear Slump Collapsed Slump
⊘ This is a preview!⊘
Do you want full access?
Subscribe today to unlock all pages.

Trusted by 1+ million students worldwide
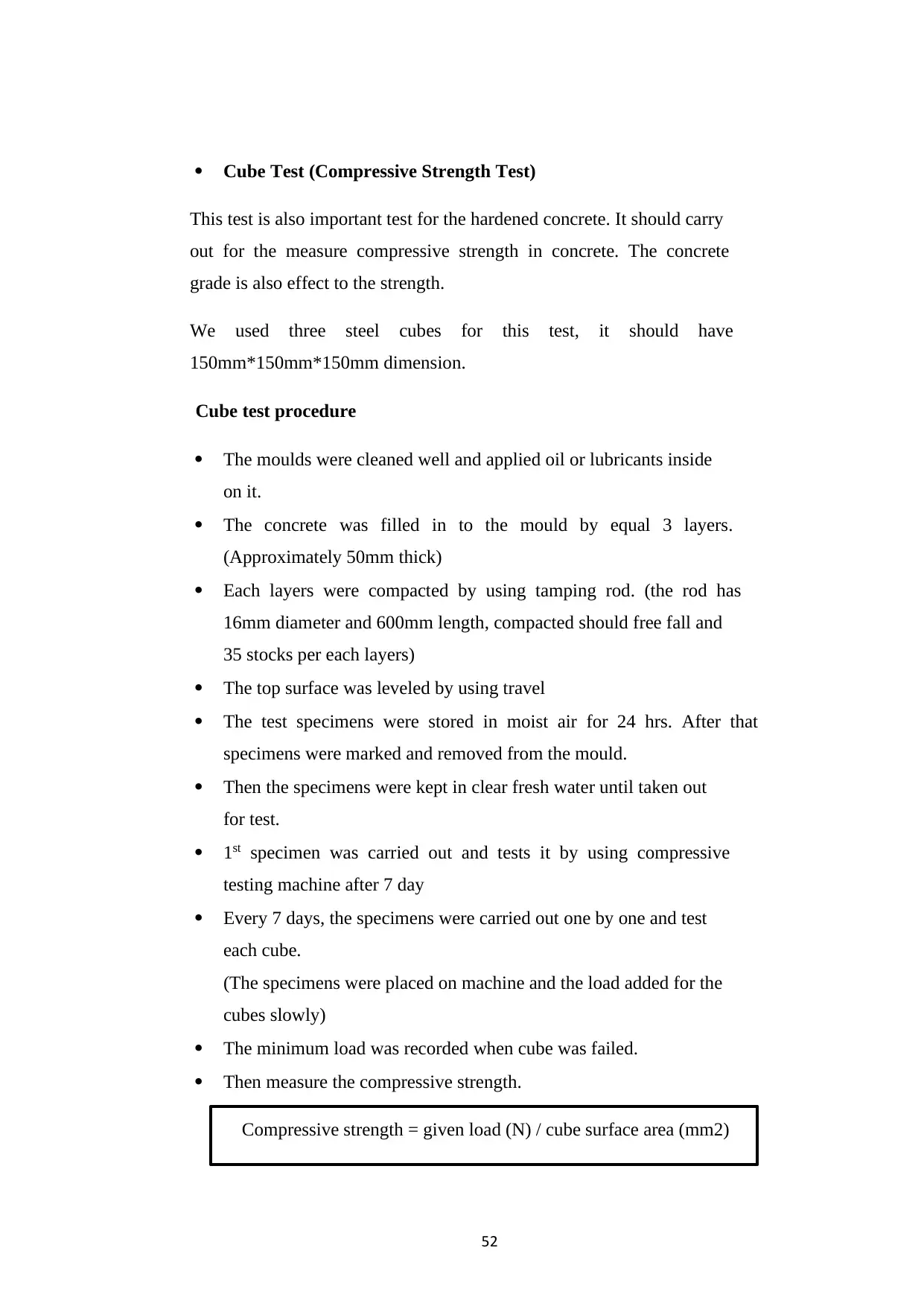
Cube Test (Compressive Strength Test)
This test is also important test for the hardened concrete. It should carry
out for the measure compressive strength in concrete. The concrete
grade is also effect to the strength.
We used three steel cubes for this test, it should have
150mm*150mm*150mm dimension.
Cube test procedure
The moulds were cleaned well and applied oil or lubricants inside
on it.
The concrete was filled in to the mould by equal 3 layers.
(Approximately 50mm thick)
Each layers were compacted by using tamping rod. (the rod has
16mm diameter and 600mm length, compacted should free fall and
35 stocks per each layers)
The top surface was leveled by using travel
The test specimens were stored in moist air for 24 hrs. After that
specimens were marked and removed from the mould.
Then the specimens were kept in clear fresh water until taken out
for test.
1st specimen was carried out and tests it by using compressive
testing machine after 7 day
Every 7 days, the specimens were carried out one by one and test
each cube.
(The specimens were placed on machine and the load added for the
cubes slowly)
The minimum load was recorded when cube was failed.
Then measure the compressive strength.
Compressive strength = given load (N) / cube surface area (mm2)
Paraphrase This Document
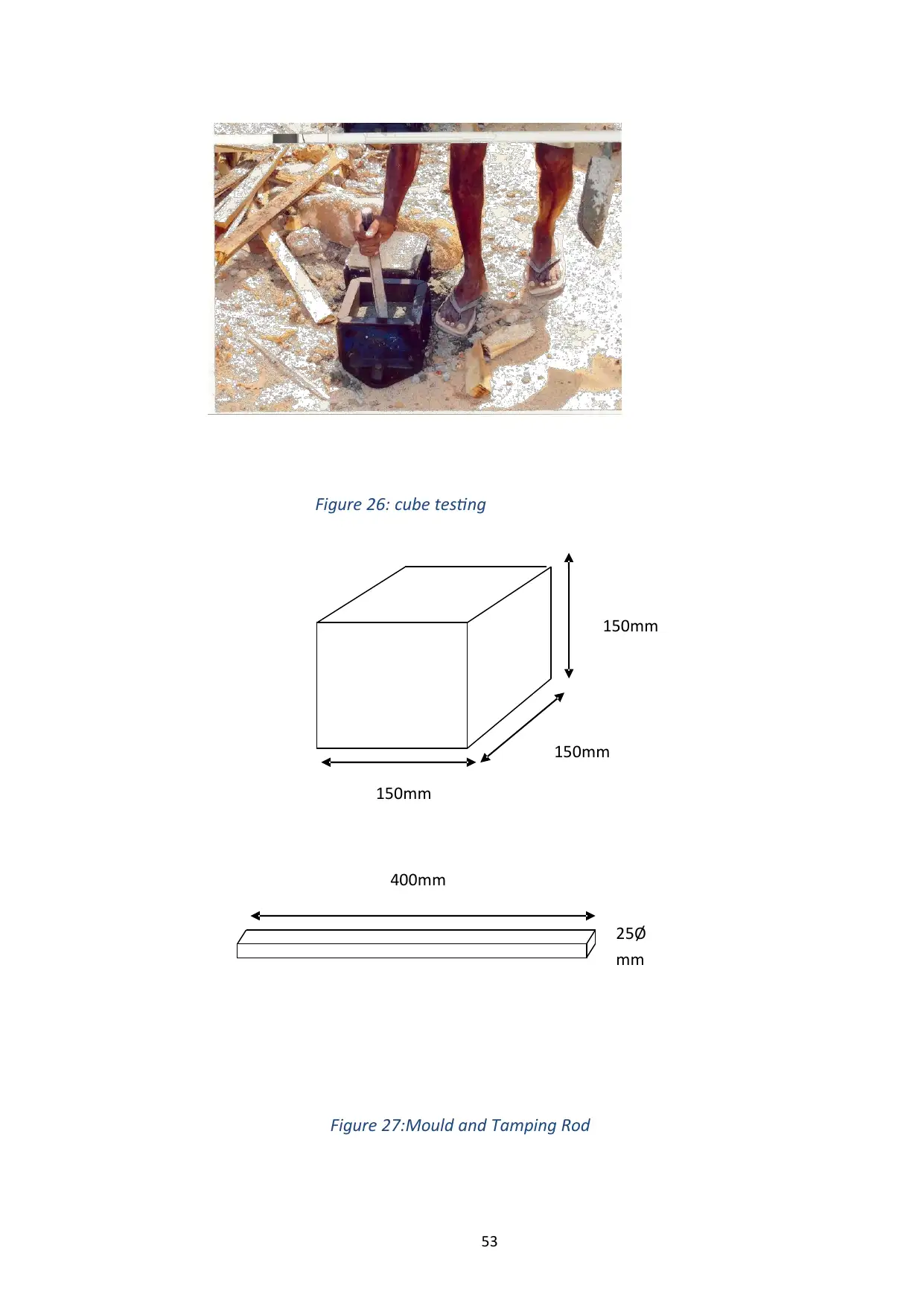
Figure 26: cube testing
Figure 27:Mould and Tamping Rod
150mm
150mm
150mm
400mm
25Ø
mm
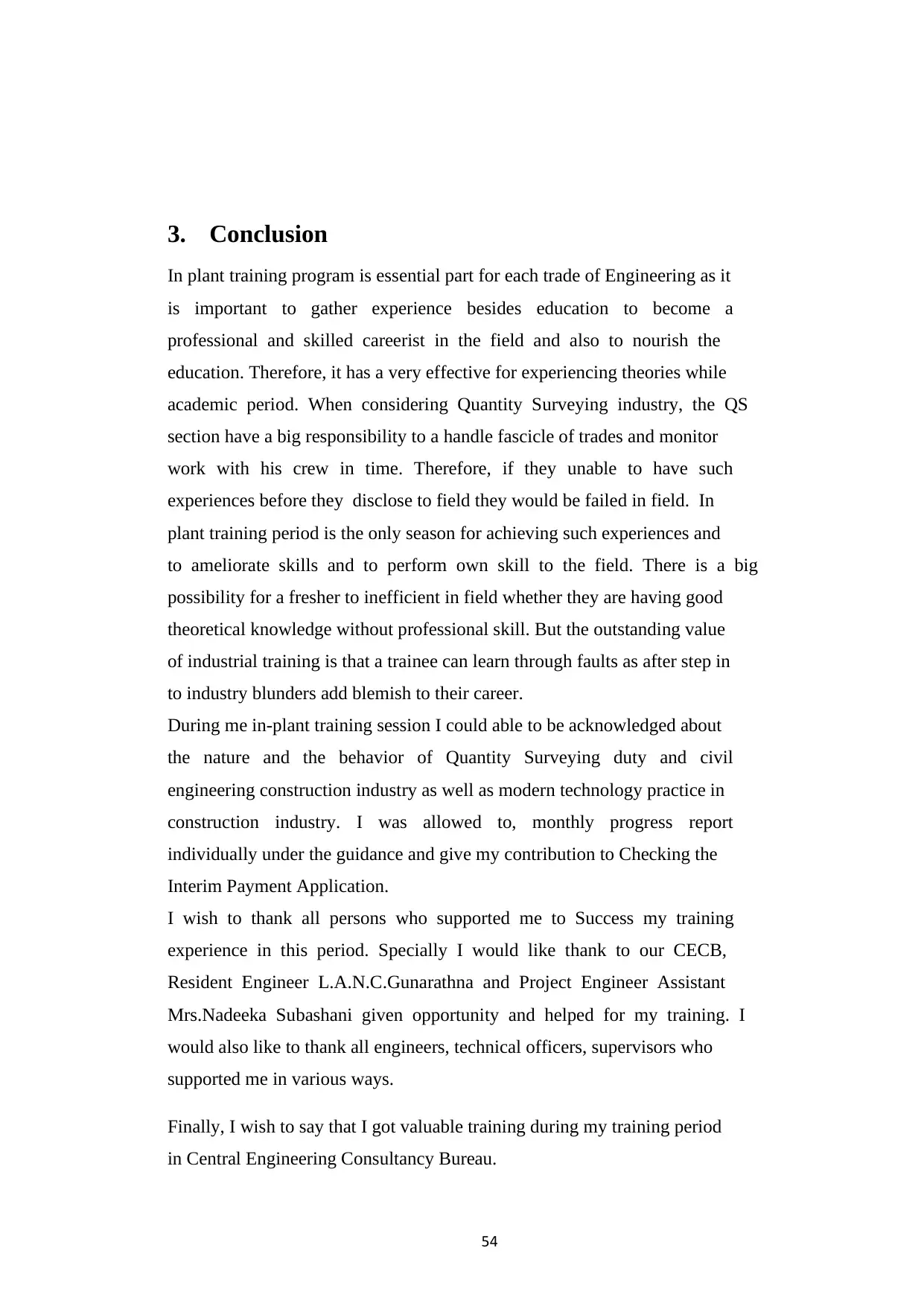
3. Conclusion
In plant training program is essential part for each trade of Engineering as it
is important to gather experience besides education to become a
professional and skilled careerist in the field and also to nourish the
education. Therefore, it has a very effective for experiencing theories while
academic period. When considering Quantity Surveying industry, the QS
section have a big responsibility to a handle fascicle of trades and monitor
work with his crew in time. Therefore, if they unable to have such
experiences before they disclose to field they would be failed in field. In
plant training period is the only season for achieving such experiences and
to ameliorate skills and to perform own skill to the field. There is a big
possibility for a fresher to inefficient in field whether they are having good
theoretical knowledge without professional skill. But the outstanding value
of industrial training is that a trainee can learn through faults as after step in
to industry blunders add blemish to their career.
During me in-plant training session I could able to be acknowledged about
the nature and the behavior of Quantity Surveying duty and civil
engineering construction industry as well as modern technology practice in
construction industry. I was allowed to, monthly progress report
individually under the guidance and give my contribution to Checking the
Interim Payment Application.
I wish to thank all persons who supported me to Success my training
experience in this period. Specially I would like thank to our CECB,
Resident Engineer L.A.N.C.Gunarathna and Project Engineer Assistant
Mrs.Nadeeka Subashani given opportunity and helped for my training. I
would also like to thank all engineers, technical officers, supervisors who
supported me in various ways.
Finally, I wish to say that I got valuable training during my training period
in Central Engineering Consultancy Bureau.
⊘ This is a preview!⊘
Do you want full access?
Subscribe today to unlock all pages.

Trusted by 1+ million students worldwide
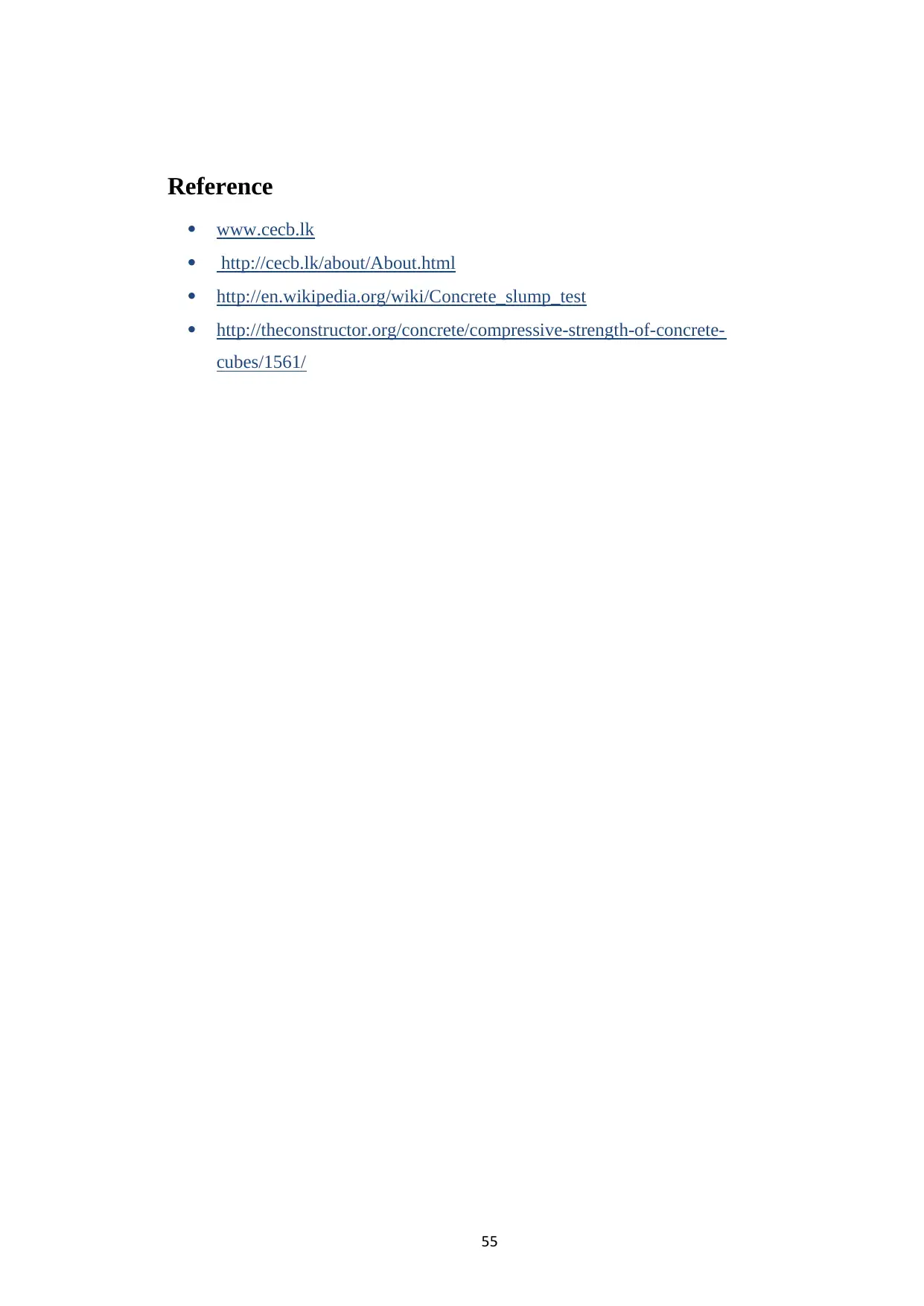
Reference
www.cecb.lk
http://cecb.lk/about/About.html
http://en.wikipedia.org/wiki/Concrete_slump_test
http://theconstructor.org/concrete/compressive-strength-of-concrete-
cubes/1561/
Paraphrase This Document

Related Documents

Your All-in-One AI-Powered Toolkit for Academic Success.
+13062052269
info@desklib.com
Available 24*7 on WhatsApp / Email
© 2024 | Zucol Services PVT LTD | All rights reserved.