Fluid and particle dynamics in laser powder bed fusion
VerifiedAdded on 2023/04/05
|14
|11136
|392
AI Summary
This article discusses the fluid and particle dynamics in laser powder bed fusion (LPBF) process and its implications on the heat, mass, and momentum transfer. It also highlights the importance of understanding fluid dynamic phenomena in preventing defects in additively manufactured parts.
Contribute Materials
Your contribution can guide someone’s learning journey. Share your
documents today.
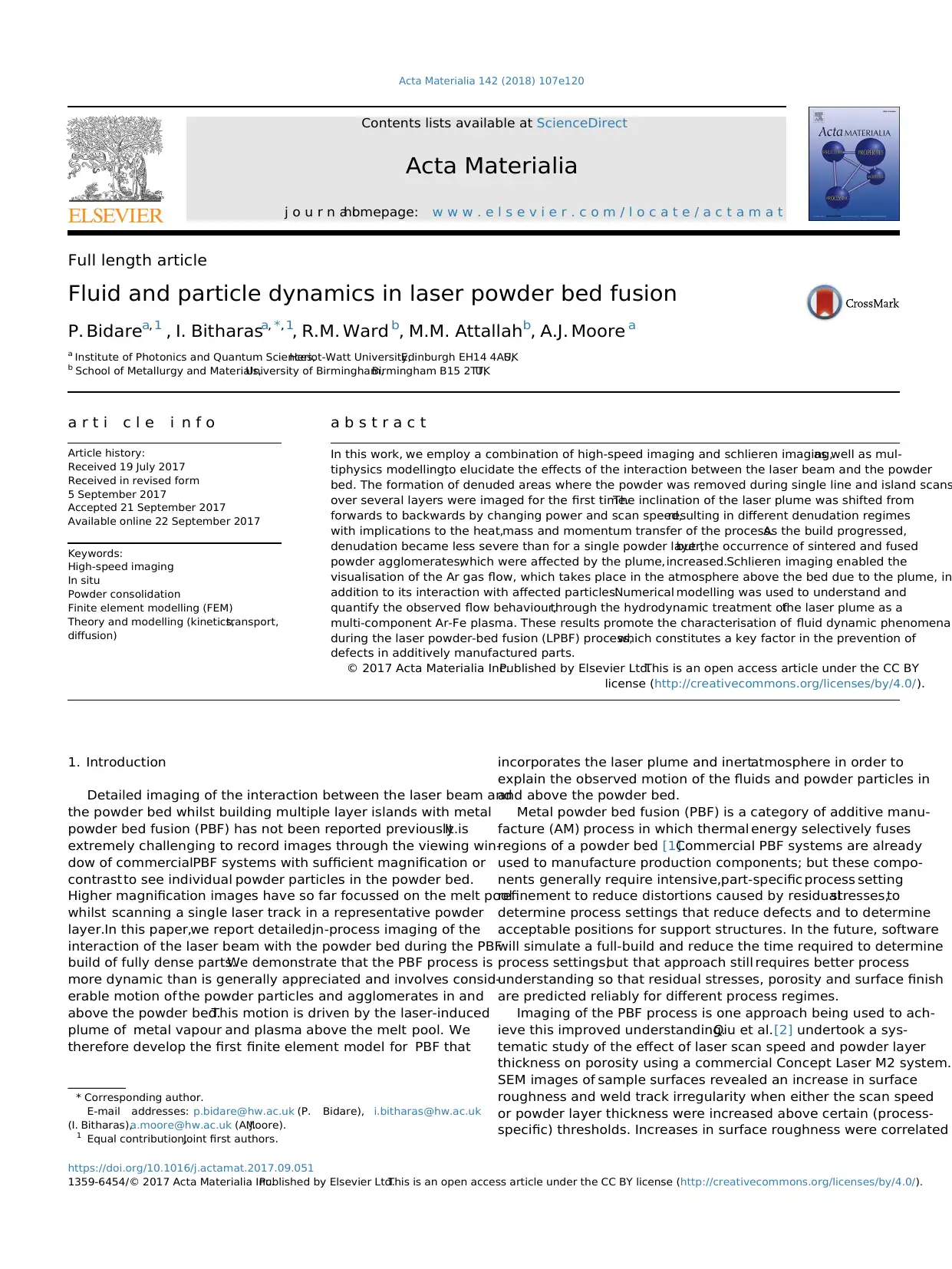
Full length article
Fluid and particle dynamics in laser powder bed fusion
P. Bidarea, 1 , I. Bitharasa, *, 1
, R.M. Ward b
, M.M. Attallah b
, A.J. Moore a
a Institute of Photonics and Quantum Sciences,Heriot-Watt University,Edinburgh EH14 4AS,UK
b School of Metallurgy and Materials,University of Birmingham,Birmingham B15 2TT,UK
a r t i c l e i n f o
Article history:
Received 19 July 2017
Received in revised form
5 September 2017
Accepted 21 September 2017
Available online 22 September 2017
Keywords:
High-speed imaging
In situ
Powder consolidation
Finite element modelling (FEM)
Theory and modelling (kinetics,transport,
diffusion)
a b s t r a c t
In this work, we employ a combination of high-speed imaging and schlieren imaging,as well as mul-
tiphysics modelling,to elucidate the effects of the interaction between the laser beam and the powder
bed. The formation of denuded areas where the powder was removed during single line and island scans
over several layers were imaged for the first time.The inclination of the laser plume was shifted from
forwards to backwards by changing power and scan speed,resulting in different denudation regimes
with implications to the heat,mass and momentum transfer of the process.As the build progressed,
denudation became less severe than for a single powder layer,but the occurrence of sintered and fused
powder agglomerates,which were affected by the plume,increased.Schlieren imaging enabled the
visualisation of the Ar gas flow, which takes place in the atmosphere above the bed due to the plume, in
addition to its interaction with affected particles.Numerical modelling was used to understand and
quantify the observed flow behaviour,through the hydrodynamic treatment ofthe laser plume as a
multi-component Ar-Fe plasma. These results promote the characterisation of fluid dynamic phenomena
during the laser powder-bed fusion (LPBF) process,which constitutes a key factor in the prevention of
defects in additively manufactured parts.
© 2017 Acta Materialia Inc.Published by Elsevier Ltd.This is an open access article under the CC BY
license (http://creativecommons.org/licenses/by/4.0/).
1. Introduction
Detailed imaging of the interaction between the laser beam and
the powder bed whilst building multiple layer islands with metal
powder bed fusion (PBF) has not been reported previously.It is
extremely challenging to record images through the viewing win-
dow of commercialPBF systems with sufficient magnification or
contrastto see individual powder particles in the powder bed.
Higher magnification images have so far focussed on the melt pool
whilst scanning a single laser track in a representative powder
layer.In this paper,we report detailed,in-process imaging of the
interaction of the laser beam with the powder bed during the PBF
build of fully dense parts.We demonstrate that the PBF process is
more dynamic than is generally appreciated and involves consid-
erable motion of the powder particles and agglomerates in and
above the powder bed.This motion is driven by the laser-induced
plume of metal vapour and plasma above the melt pool. We
therefore develop the first finite element model for PBF that
incorporates the laser plume and inertatmosphere in order to
explain the observed motion of the fluids and powder particles in
and above the powder bed.
Metal powder bed fusion (PBF) is a category of additive manu-
facture (AM) process in which thermal energy selectively fuses
regions of a powder bed [1].Commercial PBF systems are already
used to manufacture production components; but these compo-
nents generally require intensive,part-specific process setting
refinement to reduce distortions caused by residualstresses,to
determine process settings that reduce defects and to determine
acceptable positions for support structures. In the future, software
will simulate a full-build and reduce the time required to determine
process settings,but that approach still requires better process
understanding so that residual stresses, porosity and surface finish
are predicted reliably for different process regimes.
Imaging of the PBF process is one approach being used to ach-
ieve this improved understanding.Qiu et al.[2] undertook a sys-
tematic study of the effect of laser scan speed and powder layer
thickness on porosity using a commercial Concept Laser M2 system.
SEM images of sample surfaces revealed an increase in surface
roughness and weld track irregularity when either the scan speed
or powder layer thickness were increased above certain (process-
specific) thresholds. Increases in surface roughness were correlated
* Corresponding author.
E-mail addresses: p.bidare@hw.ac.uk (P. Bidare), i.bitharas@hw.ac.uk
(I. Bitharas),a.moore@hw.ac.uk (A.J.Moore).
1 Equal contribution,Joint first authors.
Contents lists available at ScienceDirect
Acta Materialia
j o u r n a lhomepage: w w w . e l s e v i e r . c o m / l o c a t e / a c t a m a t
https://doi.org/10.1016/j.actamat.2017.09.051
1359-6454/© 2017 Acta Materialia Inc.Published by Elsevier Ltd.This is an open access article under the CC BY license (http://creativecommons.org/licenses/by/4.0/).
Acta Materialia 142 (2018) 107e120
Fluid and particle dynamics in laser powder bed fusion
P. Bidarea, 1 , I. Bitharasa, *, 1
, R.M. Ward b
, M.M. Attallah b
, A.J. Moore a
a Institute of Photonics and Quantum Sciences,Heriot-Watt University,Edinburgh EH14 4AS,UK
b School of Metallurgy and Materials,University of Birmingham,Birmingham B15 2TT,UK
a r t i c l e i n f o
Article history:
Received 19 July 2017
Received in revised form
5 September 2017
Accepted 21 September 2017
Available online 22 September 2017
Keywords:
High-speed imaging
In situ
Powder consolidation
Finite element modelling (FEM)
Theory and modelling (kinetics,transport,
diffusion)
a b s t r a c t
In this work, we employ a combination of high-speed imaging and schlieren imaging,as well as mul-
tiphysics modelling,to elucidate the effects of the interaction between the laser beam and the powder
bed. The formation of denuded areas where the powder was removed during single line and island scans
over several layers were imaged for the first time.The inclination of the laser plume was shifted from
forwards to backwards by changing power and scan speed,resulting in different denudation regimes
with implications to the heat,mass and momentum transfer of the process.As the build progressed,
denudation became less severe than for a single powder layer,but the occurrence of sintered and fused
powder agglomerates,which were affected by the plume,increased.Schlieren imaging enabled the
visualisation of the Ar gas flow, which takes place in the atmosphere above the bed due to the plume, in
addition to its interaction with affected particles.Numerical modelling was used to understand and
quantify the observed flow behaviour,through the hydrodynamic treatment ofthe laser plume as a
multi-component Ar-Fe plasma. These results promote the characterisation of fluid dynamic phenomena
during the laser powder-bed fusion (LPBF) process,which constitutes a key factor in the prevention of
defects in additively manufactured parts.
© 2017 Acta Materialia Inc.Published by Elsevier Ltd.This is an open access article under the CC BY
license (http://creativecommons.org/licenses/by/4.0/).
1. Introduction
Detailed imaging of the interaction between the laser beam and
the powder bed whilst building multiple layer islands with metal
powder bed fusion (PBF) has not been reported previously.It is
extremely challenging to record images through the viewing win-
dow of commercialPBF systems with sufficient magnification or
contrastto see individual powder particles in the powder bed.
Higher magnification images have so far focussed on the melt pool
whilst scanning a single laser track in a representative powder
layer.In this paper,we report detailed,in-process imaging of the
interaction of the laser beam with the powder bed during the PBF
build of fully dense parts.We demonstrate that the PBF process is
more dynamic than is generally appreciated and involves consid-
erable motion of the powder particles and agglomerates in and
above the powder bed.This motion is driven by the laser-induced
plume of metal vapour and plasma above the melt pool. We
therefore develop the first finite element model for PBF that
incorporates the laser plume and inertatmosphere in order to
explain the observed motion of the fluids and powder particles in
and above the powder bed.
Metal powder bed fusion (PBF) is a category of additive manu-
facture (AM) process in which thermal energy selectively fuses
regions of a powder bed [1].Commercial PBF systems are already
used to manufacture production components; but these compo-
nents generally require intensive,part-specific process setting
refinement to reduce distortions caused by residualstresses,to
determine process settings that reduce defects and to determine
acceptable positions for support structures. In the future, software
will simulate a full-build and reduce the time required to determine
process settings,but that approach still requires better process
understanding so that residual stresses, porosity and surface finish
are predicted reliably for different process regimes.
Imaging of the PBF process is one approach being used to ach-
ieve this improved understanding.Qiu et al.[2] undertook a sys-
tematic study of the effect of laser scan speed and powder layer
thickness on porosity using a commercial Concept Laser M2 system.
SEM images of sample surfaces revealed an increase in surface
roughness and weld track irregularity when either the scan speed
or powder layer thickness were increased above certain (process-
specific) thresholds. Increases in surface roughness were correlated
* Corresponding author.
E-mail addresses: p.bidare@hw.ac.uk (P. Bidare), i.bitharas@hw.ac.uk
(I. Bitharas),a.moore@hw.ac.uk (A.J.Moore).
1 Equal contribution,Joint first authors.
Contents lists available at ScienceDirect
Acta Materialia
j o u r n a lhomepage: w w w . e l s e v i e r . c o m / l o c a t e / a c t a m a t
https://doi.org/10.1016/j.actamat.2017.09.051
1359-6454/© 2017 Acta Materialia Inc.Published by Elsevier Ltd.This is an open access article under the CC BY license (http://creativecommons.org/licenses/by/4.0/).
Acta Materialia 142 (2018) 107e120
Secure Best Marks with AI Grader
Need help grading? Try our AI Grader for instant feedback on your assignments.
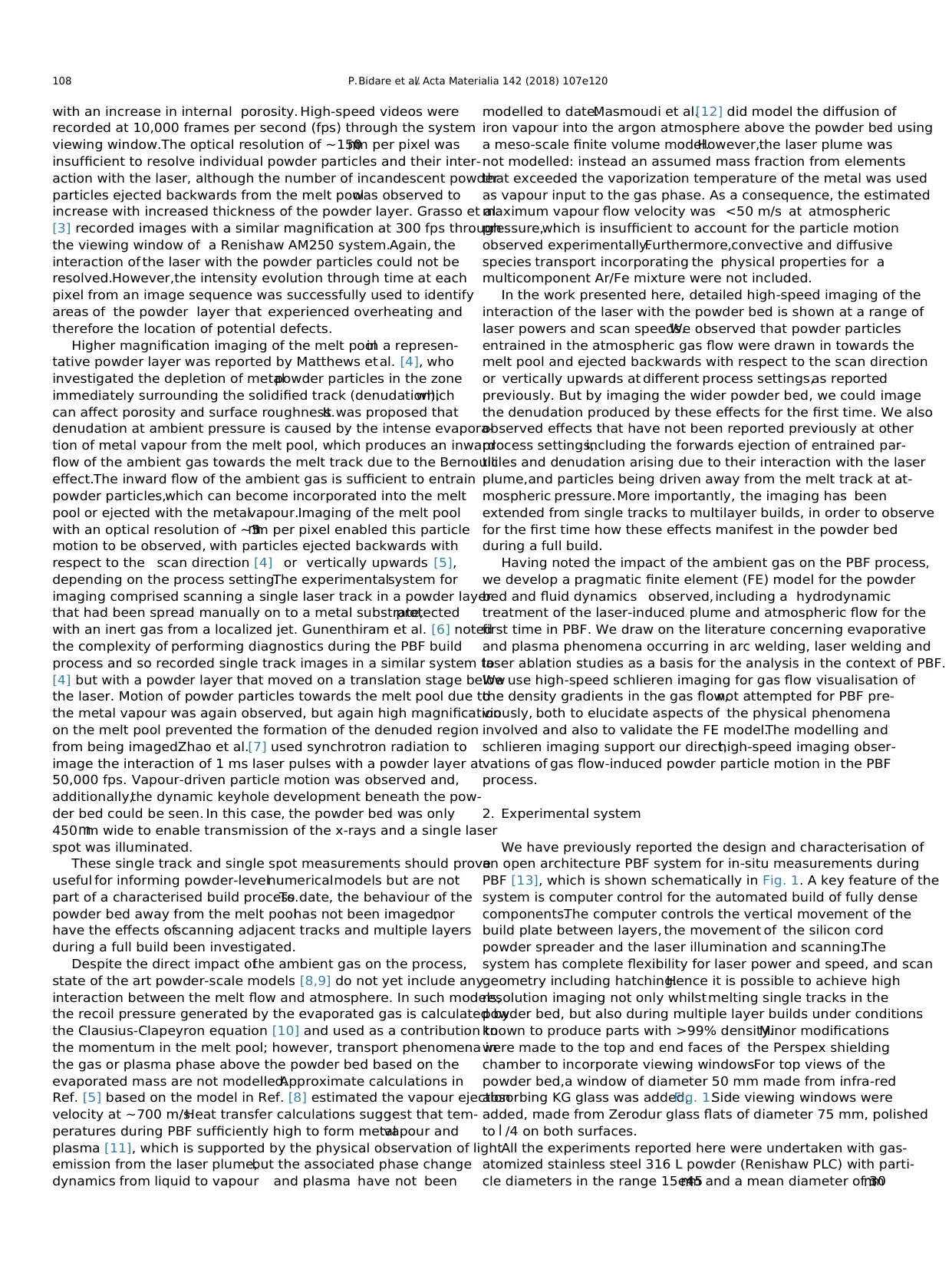
with an increase in internal porosity. High-speed videos were
recorded at 10,000 frames per second (fps) through the system
viewing window.The optical resolution of ~150mm per pixel was
insufficient to resolve individual powder particles and their inter-
action with the laser, although the number of incandescent powder
particles ejected backwards from the melt poolwas observed to
increase with increased thickness of the powder layer. Grasso et al.
[3] recorded images with a similar magnification at 300 fps through
the viewing window of a Renishaw AM250 system.Again, the
interaction of the laser with the powder particles could not be
resolved.However,the intensity evolution through time at each
pixel from an image sequence was successfully used to identify
areas of the powder layer that experienced overheating and
therefore the location of potential defects.
Higher magnification imaging of the melt poolin a represen-
tative powder layer was reported by Matthews et al. [4], who
investigated the depletion of metalpowder particles in the zone
immediately surrounding the solidified track (denudation),which
can affect porosity and surface roughness.It was proposed that
denudation at ambient pressure is caused by the intense evapora-
tion of metal vapour from the melt pool, which produces an inward
flow of the ambient gas towards the melt track due to the Bernoulli
effect.The inward flow of the ambient gas is sufficient to entrain
powder particles,which can become incorporated into the melt
pool or ejected with the metalvapour.Imaging of the melt pool
with an optical resolution of ~5mm per pixel enabled this particle
motion to be observed, with particles ejected backwards with
respect to the scan direction [4] or vertically upwards [5],
depending on the process setting.The experimentalsystem for
imaging comprised scanning a single laser track in a powder layer
that had been spread manually on to a metal substrate,protected
with an inert gas from a localized jet. Gunenthiram et al. [6] noted
the complexity of performing diagnostics during the PBF build
process and so recorded single track images in a similar system to
[4] but with a powder layer that moved on a translation stage below
the laser. Motion of powder particles towards the melt pool due to
the metal vapour was again observed, but again high magnification
on the melt pool prevented the formation of the denuded region
from being imaged.Zhao et al.[7] used synchrotron radiation to
image the interaction of 1 ms laser pulses with a powder layer at
50,000 fps. Vapour-driven particle motion was observed and,
additionally,the dynamic keyhole development beneath the pow-
der bed could be seen. In this case, the powder bed was only
450 mm wide to enable transmission of the x-rays and a single laser
spot was illuminated.
These single track and single spot measurements should prove
useful for informing powder-levelnumericalmodels but are not
part of a characterised build process.To date, the behaviour of the
powder bed away from the melt poolhas not been imaged,nor
have the effects ofscanning adjacent tracks and multiple layers
during a full build been investigated.
Despite the direct impact ofthe ambient gas on the process,
state of the art powder-scale models [8,9] do not yet include any
interaction between the melt flow and atmosphere. In such models,
the recoil pressure generated by the evaporated gas is calculated by
the Clausius-Clapeyron equation [10] and used as a contribution to
the momentum in the melt pool; however, transport phenomena in
the gas or plasma phase above the powder bed based on the
evaporated mass are not modelled.Approximate calculations in
Ref. [5] based on the model in Ref. [8] estimated the vapour ejection
velocity at ~700 m/s.Heat transfer calculations suggest that tem-
peratures during PBF sufficiently high to form metalvapour and
plasma [11], which is supported by the physical observation of light
emission from the laser plume,but the associated phase change
dynamics from liquid to vapour and plasma have not been
modelled to date.Masmoudi et al.[12] did model the diffusion of
iron vapour into the argon atmosphere above the powder bed using
a meso-scale finite volume model.However,the laser plume was
not modelled: instead an assumed mass fraction from elements
that exceeded the vaporization temperature of the metal was used
as vapour input to the gas phase. As a consequence, the estimated
maximum vapour flow velocity was <50 m/s at atmospheric
pressure,which is insufficient to account for the particle motion
observed experimentally.Furthermore,convective and diffusive
species transport incorporating the physical properties for a
multicomponent Ar/Fe mixture were not included.
In the work presented here, detailed high-speed imaging of the
interaction of the laser with the powder bed is shown at a range of
laser powers and scan speeds.We observed that powder particles
entrained in the atmospheric gas flow were drawn in towards the
melt pool and ejected backwards with respect to the scan direction
or vertically upwards at different process settings,as reported
previously. But by imaging the wider powder bed, we could image
the denudation produced by these effects for the first time. We also
observed effects that have not been reported previously at other
process settings,including the forwards ejection of entrained par-
ticles and denudation arising due to their interaction with the laser
plume,and particles being driven away from the melt track at at-
mospheric pressure.More importantly, the imaging has been
extended from single tracks to multilayer builds, in order to observe
for the first time how these effects manifest in the powder bed
during a full build.
Having noted the impact of the ambient gas on the PBF process,
we develop a pragmatic finite element (FE) model for the powder
bed and fluid dynamics observed, including a hydrodynamic
treatment of the laser-induced plume and atmospheric flow for the
first time in PBF. We draw on the literature concerning evaporative
and plasma phenomena occurring in arc welding, laser welding and
laser ablation studies as a basis for the analysis in the context of PBF.
We use high-speed schlieren imaging for gas flow visualisation of
the density gradients in the gas flow,not attempted for PBF pre-
viously, both to elucidate aspects of the physical phenomena
involved and also to validate the FE model.The modelling and
schlieren imaging support our direct,high-speed imaging obser-
vations of gas flow-induced powder particle motion in the PBF
process.
2. Experimental system
We have previously reported the design and characterisation of
an open architecture PBF system for in-situ measurements during
PBF [13], which is shown schematically in Fig. 1. A key feature of the
system is computer control for the automated build of fully dense
components.The computer controls the vertical movement of the
build plate between layers, the movement of the silicon cord
powder spreader and the laser illumination and scanning.The
system has complete flexibility for laser power and speed, and scan
geometry including hatching.Hence it is possible to achieve high
resolution imaging not only whilst melting single tracks in the
powder bed, but also during multiple layer builds under conditions
known to produce parts with >99% density.Minor modifications
were made to the top and end faces of the Perspex shielding
chamber to incorporate viewing windows.For top views of the
powder bed,a window of diameter 50 mm made from infra-red
absorbing KG glass was added,Fig. 1.Side viewing windows were
added, made from Zerodur glass flats of diameter 75 mm, polished
to l /4 on both surfaces.
All the experiments reported here were undertaken with gas-
atomized stainless steel 316 L powder (Renishaw PLC) with parti-
cle diameters in the range 15e45mm and a mean diameter of 30mm
P. Bidare et al./ Acta Materialia 142 (2018) 107e120108
recorded at 10,000 frames per second (fps) through the system
viewing window.The optical resolution of ~150mm per pixel was
insufficient to resolve individual powder particles and their inter-
action with the laser, although the number of incandescent powder
particles ejected backwards from the melt poolwas observed to
increase with increased thickness of the powder layer. Grasso et al.
[3] recorded images with a similar magnification at 300 fps through
the viewing window of a Renishaw AM250 system.Again, the
interaction of the laser with the powder particles could not be
resolved.However,the intensity evolution through time at each
pixel from an image sequence was successfully used to identify
areas of the powder layer that experienced overheating and
therefore the location of potential defects.
Higher magnification imaging of the melt poolin a represen-
tative powder layer was reported by Matthews et al. [4], who
investigated the depletion of metalpowder particles in the zone
immediately surrounding the solidified track (denudation),which
can affect porosity and surface roughness.It was proposed that
denudation at ambient pressure is caused by the intense evapora-
tion of metal vapour from the melt pool, which produces an inward
flow of the ambient gas towards the melt track due to the Bernoulli
effect.The inward flow of the ambient gas is sufficient to entrain
powder particles,which can become incorporated into the melt
pool or ejected with the metalvapour.Imaging of the melt pool
with an optical resolution of ~5mm per pixel enabled this particle
motion to be observed, with particles ejected backwards with
respect to the scan direction [4] or vertically upwards [5],
depending on the process setting.The experimentalsystem for
imaging comprised scanning a single laser track in a powder layer
that had been spread manually on to a metal substrate,protected
with an inert gas from a localized jet. Gunenthiram et al. [6] noted
the complexity of performing diagnostics during the PBF build
process and so recorded single track images in a similar system to
[4] but with a powder layer that moved on a translation stage below
the laser. Motion of powder particles towards the melt pool due to
the metal vapour was again observed, but again high magnification
on the melt pool prevented the formation of the denuded region
from being imaged.Zhao et al.[7] used synchrotron radiation to
image the interaction of 1 ms laser pulses with a powder layer at
50,000 fps. Vapour-driven particle motion was observed and,
additionally,the dynamic keyhole development beneath the pow-
der bed could be seen. In this case, the powder bed was only
450 mm wide to enable transmission of the x-rays and a single laser
spot was illuminated.
These single track and single spot measurements should prove
useful for informing powder-levelnumericalmodels but are not
part of a characterised build process.To date, the behaviour of the
powder bed away from the melt poolhas not been imaged,nor
have the effects ofscanning adjacent tracks and multiple layers
during a full build been investigated.
Despite the direct impact ofthe ambient gas on the process,
state of the art powder-scale models [8,9] do not yet include any
interaction between the melt flow and atmosphere. In such models,
the recoil pressure generated by the evaporated gas is calculated by
the Clausius-Clapeyron equation [10] and used as a contribution to
the momentum in the melt pool; however, transport phenomena in
the gas or plasma phase above the powder bed based on the
evaporated mass are not modelled.Approximate calculations in
Ref. [5] based on the model in Ref. [8] estimated the vapour ejection
velocity at ~700 m/s.Heat transfer calculations suggest that tem-
peratures during PBF sufficiently high to form metalvapour and
plasma [11], which is supported by the physical observation of light
emission from the laser plume,but the associated phase change
dynamics from liquid to vapour and plasma have not been
modelled to date.Masmoudi et al.[12] did model the diffusion of
iron vapour into the argon atmosphere above the powder bed using
a meso-scale finite volume model.However,the laser plume was
not modelled: instead an assumed mass fraction from elements
that exceeded the vaporization temperature of the metal was used
as vapour input to the gas phase. As a consequence, the estimated
maximum vapour flow velocity was <50 m/s at atmospheric
pressure,which is insufficient to account for the particle motion
observed experimentally.Furthermore,convective and diffusive
species transport incorporating the physical properties for a
multicomponent Ar/Fe mixture were not included.
In the work presented here, detailed high-speed imaging of the
interaction of the laser with the powder bed is shown at a range of
laser powers and scan speeds.We observed that powder particles
entrained in the atmospheric gas flow were drawn in towards the
melt pool and ejected backwards with respect to the scan direction
or vertically upwards at different process settings,as reported
previously. But by imaging the wider powder bed, we could image
the denudation produced by these effects for the first time. We also
observed effects that have not been reported previously at other
process settings,including the forwards ejection of entrained par-
ticles and denudation arising due to their interaction with the laser
plume,and particles being driven away from the melt track at at-
mospheric pressure.More importantly, the imaging has been
extended from single tracks to multilayer builds, in order to observe
for the first time how these effects manifest in the powder bed
during a full build.
Having noted the impact of the ambient gas on the PBF process,
we develop a pragmatic finite element (FE) model for the powder
bed and fluid dynamics observed, including a hydrodynamic
treatment of the laser-induced plume and atmospheric flow for the
first time in PBF. We draw on the literature concerning evaporative
and plasma phenomena occurring in arc welding, laser welding and
laser ablation studies as a basis for the analysis in the context of PBF.
We use high-speed schlieren imaging for gas flow visualisation of
the density gradients in the gas flow,not attempted for PBF pre-
viously, both to elucidate aspects of the physical phenomena
involved and also to validate the FE model.The modelling and
schlieren imaging support our direct,high-speed imaging obser-
vations of gas flow-induced powder particle motion in the PBF
process.
2. Experimental system
We have previously reported the design and characterisation of
an open architecture PBF system for in-situ measurements during
PBF [13], which is shown schematically in Fig. 1. A key feature of the
system is computer control for the automated build of fully dense
components.The computer controls the vertical movement of the
build plate between layers, the movement of the silicon cord
powder spreader and the laser illumination and scanning.The
system has complete flexibility for laser power and speed, and scan
geometry including hatching.Hence it is possible to achieve high
resolution imaging not only whilst melting single tracks in the
powder bed, but also during multiple layer builds under conditions
known to produce parts with >99% density.Minor modifications
were made to the top and end faces of the Perspex shielding
chamber to incorporate viewing windows.For top views of the
powder bed,a window of diameter 50 mm made from infra-red
absorbing KG glass was added,Fig. 1.Side viewing windows were
added, made from Zerodur glass flats of diameter 75 mm, polished
to l /4 on both surfaces.
All the experiments reported here were undertaken with gas-
atomized stainless steel 316 L powder (Renishaw PLC) with parti-
cle diameters in the range 15e45mm and a mean diameter of 30mm
P. Bidare et al./ Acta Materialia 142 (2018) 107e120108
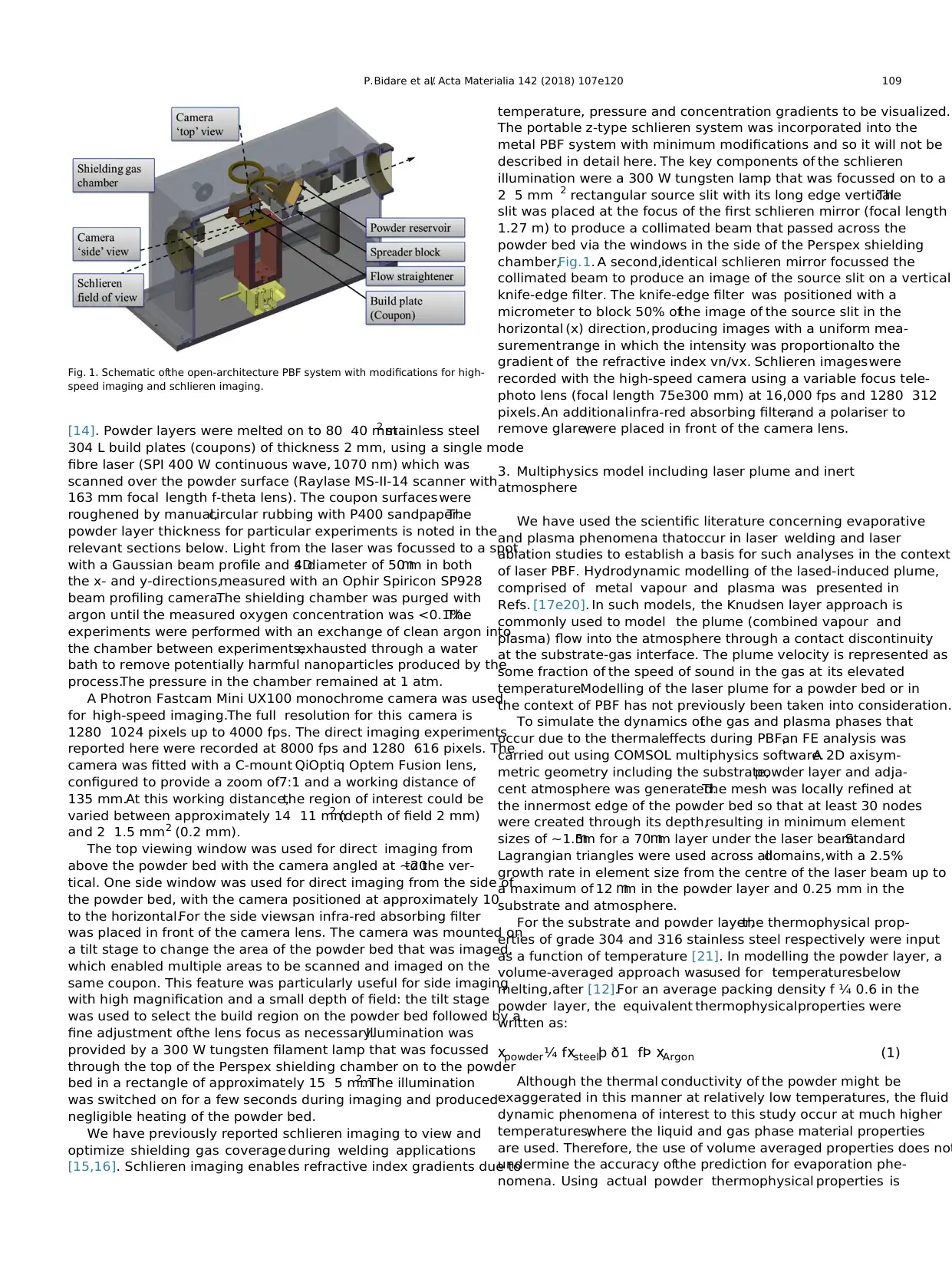
[14]. Powder layers were melted on to 80 40 mm2 stainless steel
304 L build plates (coupons) of thickness 2 mm, using a single mode
fibre laser (SPI 400 W continuous wave, 1070 nm) which was
scanned over the powder surface (Raylase MS-II-14 scanner with
163 mm focal length f-theta lens). The coupon surfaceswere
roughened by manual,circular rubbing with P400 sandpaper.The
powder layer thickness for particular experiments is noted in the
relevant sections below. Light from the laser was focussed to a spot
with a Gaussian beam profile and 4Ds diameter of 50mm in both
the x- and y-directions,measured with an Ophir Spiricon SP928
beam profiling camera.The shielding chamber was purged with
argon until the measured oxygen concentration was <0.1%.The
experiments were performed with an exchange of clean argon into
the chamber between experiments,exhausted through a water
bath to remove potentially harmful nanoparticles produced by the
process.The pressure in the chamber remained at 1 atm.
A Photron Fastcam Mini UX100 monochrome camera was used
for high-speed imaging.The full resolution for this camera is
1280 1024 pixels up to 4000 fps. The direct imaging experiments
reported here were recorded at 8000 fps and 1280 616 pixels. The
camera was fitted with a C-mount QiOptiq Optem Fusion lens,
configured to provide a zoom of7:1 and a working distance of
135 mm.At this working distance,the region of interest could be
varied between approximately 14 11 mm2 (depth of field 2 mm)
and 2 1.5 mm 2 (0.2 mm).
The top viewing window was used for direct imaging from
above the powder bed with the camera angled at ~20to the ver-
tical. One side window was used for direct imaging from the side of
the powder bed, with the camera positioned at approximately 10
to the horizontal.For the side views,an infra-red absorbing filter
was placed in front of the camera lens. The camera was mounted on
a tilt stage to change the area of the powder bed that was imaged,
which enabled multiple areas to be scanned and imaged on the
same coupon. This feature was particularly useful for side imaging
with high magnification and a small depth of field: the tilt stage
was used to select the build region on the powder bed followed by a
fine adjustment ofthe lens focus as necessary.Illumination was
provided by a 300 W tungsten filament lamp that was focussed
through the top of the Perspex shielding chamber on to the powder
bed in a rectangle of approximately 15 5 mm2
. The illumination
was switched on for a few seconds during imaging and produced
negligible heating of the powder bed.
We have previously reported schlieren imaging to view and
optimize shielding gas coverage during welding applications
[15,16]. Schlieren imaging enables refractive index gradients due to
temperature, pressure and concentration gradients to be visualized.
The portable z-type schlieren system was incorporated into the
metal PBF system with minimum modifications and so it will not be
described in detail here. The key components of the schlieren
illumination were a 300 W tungsten lamp that was focussed on to a
2 5 mm 2 rectangular source slit with its long edge vertical.The
slit was placed at the focus of the first schlieren mirror (focal length
1.27 m) to produce a collimated beam that passed across the
powder bed via the windows in the side of the Perspex shielding
chamber,Fig.1. A second,identical schlieren mirror focussed the
collimated beam to produce an image of the source slit on a vertical,
knife-edge filter. The knife-edge filter was positioned with a
micrometer to block 50% ofthe image of the source slit in the
horizontal (x) direction,producing images with a uniform mea-
surementrange in which the intensity was proportionalto the
gradient of the refractive index vn/vx. Schlieren imageswere
recorded with the high-speed camera using a variable focus tele-
photo lens (focal length 75e300 mm) at 16,000 fps and 1280 312
pixels.An additionalinfra-red absorbing filter,and a polariser to
remove glare,were placed in front of the camera lens.
3. Multiphysics model including laser plume and inert
atmosphere
We have used the scientific literature concerning evaporative
and plasma phenomena thatoccur in laser welding and laser
ablation studies to establish a basis for such analyses in the context
of laser PBF. Hydrodynamic modelling of the lased-induced plume,
comprised of metal vapour and plasma was presented in
Refs. [17e20]. In such models, the Knudsen layer approach is
commonly used to model the plume (combined vapour and
plasma) flow into the atmosphere through a contact discontinuity
at the substrate-gas interface. The plume velocity is represented as
some fraction of the speed of sound in the gas at its elevated
temperature.Modelling of the laser plume for a powder bed or in
the context of PBF has not previously been taken into consideration.
To simulate the dynamics ofthe gas and plasma phases that
occur due to the thermaleffects during PBF,an FE analysis was
carried out using COMSOL multiphysics software.A 2D axisym-
metric geometry including the substrate,powder layer and adja-
cent atmosphere was generated.The mesh was locally refined at
the innermost edge of the powder bed so that at least 30 nodes
were created through its depth,resulting in minimum element
sizes of ~1.5mm for a 70mm layer under the laser beam.Standard
Lagrangian triangles were used across alldomains,with a 2.5%
growth rate in element size from the centre of the laser beam up to
a maximum of 12 mm in the powder layer and 0.25 mm in the
substrate and atmosphere.
For the substrate and powder layer,the thermophysical prop-
erties of grade 304 and 316 stainless steel respectively were input
as a function of temperature [21]. In modelling the powder layer, a
volume-averaged approach wasused for temperaturesbelow
melting,after [12].For an average packing density f ¼ 0.6 in the
powder layer, the equivalent thermophysicalproperties were
written as:
xpowder ¼ f xsteelþ ð1 fÞ xArgon (1)
Although the thermal conductivity of the powder might be
exaggerated in this manner at relatively low temperatures, the fluid
dynamic phenomena of interest to this study occur at much higher
temperatures,where the liquid and gas phase material properties
are used. Therefore, the use of volume averaged properties does not
undermine the accuracy ofthe prediction for evaporation phe-
nomena. Using actual powder thermophysical properties is
Fig. 1. Schematic ofthe open-architecture PBF system with modifications for high-
speed imaging and schlieren imaging.
P.Bidare et al./ Acta Materialia 142 (2018) 107e120 109
304 L build plates (coupons) of thickness 2 mm, using a single mode
fibre laser (SPI 400 W continuous wave, 1070 nm) which was
scanned over the powder surface (Raylase MS-II-14 scanner with
163 mm focal length f-theta lens). The coupon surfaceswere
roughened by manual,circular rubbing with P400 sandpaper.The
powder layer thickness for particular experiments is noted in the
relevant sections below. Light from the laser was focussed to a spot
with a Gaussian beam profile and 4Ds diameter of 50mm in both
the x- and y-directions,measured with an Ophir Spiricon SP928
beam profiling camera.The shielding chamber was purged with
argon until the measured oxygen concentration was <0.1%.The
experiments were performed with an exchange of clean argon into
the chamber between experiments,exhausted through a water
bath to remove potentially harmful nanoparticles produced by the
process.The pressure in the chamber remained at 1 atm.
A Photron Fastcam Mini UX100 monochrome camera was used
for high-speed imaging.The full resolution for this camera is
1280 1024 pixels up to 4000 fps. The direct imaging experiments
reported here were recorded at 8000 fps and 1280 616 pixels. The
camera was fitted with a C-mount QiOptiq Optem Fusion lens,
configured to provide a zoom of7:1 and a working distance of
135 mm.At this working distance,the region of interest could be
varied between approximately 14 11 mm2 (depth of field 2 mm)
and 2 1.5 mm 2 (0.2 mm).
The top viewing window was used for direct imaging from
above the powder bed with the camera angled at ~20to the ver-
tical. One side window was used for direct imaging from the side of
the powder bed, with the camera positioned at approximately 10
to the horizontal.For the side views,an infra-red absorbing filter
was placed in front of the camera lens. The camera was mounted on
a tilt stage to change the area of the powder bed that was imaged,
which enabled multiple areas to be scanned and imaged on the
same coupon. This feature was particularly useful for side imaging
with high magnification and a small depth of field: the tilt stage
was used to select the build region on the powder bed followed by a
fine adjustment ofthe lens focus as necessary.Illumination was
provided by a 300 W tungsten filament lamp that was focussed
through the top of the Perspex shielding chamber on to the powder
bed in a rectangle of approximately 15 5 mm2
. The illumination
was switched on for a few seconds during imaging and produced
negligible heating of the powder bed.
We have previously reported schlieren imaging to view and
optimize shielding gas coverage during welding applications
[15,16]. Schlieren imaging enables refractive index gradients due to
temperature, pressure and concentration gradients to be visualized.
The portable z-type schlieren system was incorporated into the
metal PBF system with minimum modifications and so it will not be
described in detail here. The key components of the schlieren
illumination were a 300 W tungsten lamp that was focussed on to a
2 5 mm 2 rectangular source slit with its long edge vertical.The
slit was placed at the focus of the first schlieren mirror (focal length
1.27 m) to produce a collimated beam that passed across the
powder bed via the windows in the side of the Perspex shielding
chamber,Fig.1. A second,identical schlieren mirror focussed the
collimated beam to produce an image of the source slit on a vertical,
knife-edge filter. The knife-edge filter was positioned with a
micrometer to block 50% ofthe image of the source slit in the
horizontal (x) direction,producing images with a uniform mea-
surementrange in which the intensity was proportionalto the
gradient of the refractive index vn/vx. Schlieren imageswere
recorded with the high-speed camera using a variable focus tele-
photo lens (focal length 75e300 mm) at 16,000 fps and 1280 312
pixels.An additionalinfra-red absorbing filter,and a polariser to
remove glare,were placed in front of the camera lens.
3. Multiphysics model including laser plume and inert
atmosphere
We have used the scientific literature concerning evaporative
and plasma phenomena thatoccur in laser welding and laser
ablation studies to establish a basis for such analyses in the context
of laser PBF. Hydrodynamic modelling of the lased-induced plume,
comprised of metal vapour and plasma was presented in
Refs. [17e20]. In such models, the Knudsen layer approach is
commonly used to model the plume (combined vapour and
plasma) flow into the atmosphere through a contact discontinuity
at the substrate-gas interface. The plume velocity is represented as
some fraction of the speed of sound in the gas at its elevated
temperature.Modelling of the laser plume for a powder bed or in
the context of PBF has not previously been taken into consideration.
To simulate the dynamics ofthe gas and plasma phases that
occur due to the thermaleffects during PBF,an FE analysis was
carried out using COMSOL multiphysics software.A 2D axisym-
metric geometry including the substrate,powder layer and adja-
cent atmosphere was generated.The mesh was locally refined at
the innermost edge of the powder bed so that at least 30 nodes
were created through its depth,resulting in minimum element
sizes of ~1.5mm for a 70mm layer under the laser beam.Standard
Lagrangian triangles were used across alldomains,with a 2.5%
growth rate in element size from the centre of the laser beam up to
a maximum of 12 mm in the powder layer and 0.25 mm in the
substrate and atmosphere.
For the substrate and powder layer,the thermophysical prop-
erties of grade 304 and 316 stainless steel respectively were input
as a function of temperature [21]. In modelling the powder layer, a
volume-averaged approach wasused for temperaturesbelow
melting,after [12].For an average packing density f ¼ 0.6 in the
powder layer, the equivalent thermophysicalproperties were
written as:
xpowder ¼ f xsteelþ ð1 fÞ xArgon (1)
Although the thermal conductivity of the powder might be
exaggerated in this manner at relatively low temperatures, the fluid
dynamic phenomena of interest to this study occur at much higher
temperatures,where the liquid and gas phase material properties
are used. Therefore, the use of volume averaged properties does not
undermine the accuracy ofthe prediction for evaporation phe-
nomena. Using actual powder thermophysical properties is
Fig. 1. Schematic ofthe open-architecture PBF system with modifications for high-
speed imaging and schlieren imaging.
P.Bidare et al./ Acta Materialia 142 (2018) 107e120 109

however essential for simulations investigating the melt pool size
or residual stress development.The properties used in the fluid
domain above the powder bed were those of an Ar-Fe gas/plasma
mixture in local thermodynamic equilibrium (LTE). The values were
therefore input as a function of temperature and Fe mass fraction,
taken from Ref. [22].
The partial differential equations (PDEs) used in the model are
given below using vector notation. Vectors are represented in bold,
while constitutive properties used as a function of temperature and
Fe mass fraction are in italics.For fluid flow, the compressible
Navier-Stokes equations for momentum (2) and mass (3) conser-
vation were used:
r ðu$VuÞ ¼ V$
h
p þ m Vu þ ðVuÞT i
þ r g (2)
V$ðr uÞ ¼ 0 (3)
where r is the density,u the flow velocity,p the pressure,mthe
dynamic viscosity and g the acceleration due to gravity. In order to
better capture the turbulence due to the laser plume,but also to
expand the stable solution space of the model,the RANS SST tur-
bulence model was used.
The Knudsen layer approach gives the velocity magnitude of the
laser plume normal to the powder bed surface based on the local
sound speed:
juj ¼ M
ffiffiffiffiffiffiffiffiffiffiffiffiffiffiffiffiffiffiffiffiffiffiffiffiffiffiffiffiffiffiffiffiffiffiffi
gKT
u 1 mAr þ u 2 mFe
s
(4)
where M is the Mach number,g ¼ 5/3 is the heat capacity ratio for a
monoatomic gas, K is the Boltzmann constant and mAr ; mFe are the
atomic masses andu 1 ; u 2 the mass fractions of Ar and Fe,respec-
tively. The Mach number was assumed to vary linearly based on the
incident laser radiation, from M ¼ 0.01 at an intensity of 105 W/cm2
,
to M ¼ 1 for a flux of 107 W/cm2 [23]. On the outer flow boundaries,
an outflow condition was specified by setting the normal diffusive
flux equal to 0 at atmospheric pressure.
Extending an approach employed in state-of-the-art arc weld-
ing simulations [10,24], an additional set of conservation equations
were added to model the convective and diffusive modes of
transport of the vaporized gas.The mass fraction of the i-th con-
stituentu i is given by:
V$ r Do
i Vu i þ ru i Do
i
VM n
M n
þ DT
i
VT
T þ r ðu$VÞu i ¼ 0 (5)
where Do
i is the ordinary diffusion coefficient and DT
i is the thermal
diffusion coefficient while Mn is the sum of the molar masses of all
the constituents. Equation (5) was solved for speciesu 2 (Fe) and the
remaining mass was assigned to speciesu 1 (Ar). An additional
contribution DiT ¼ mT =ScT to the diffusion coefficient of each spe-
cies was added to account for turbulent mixing ofsmall eddies,
where mT is the Reynolds-averaged turbulent kinematic viscosity
and ScT ¼ 0.7 is the turbulent Schmidt number. The Fe mass fraction
at the powder surface was defined based on the vapour pressure
and molar masses of Ar and Fe as [24]:
u 2 ¼ PvapM Fe
PvapM Fe þ Patm P vap M Ar
(6)
For the process thermodynamics, an energy balance was used to
account for conductive, convective and radiative heat transfer.
r cpðu$VTÞ ¼ V$ðkVTÞ 4p εN (7)
The last term of equation (7) is solved only within the gas/
plasma domain,and accounts for the total radiative loss from the
Ar-Fe plasma across all wavelengths. The plasma was assumed to be
optically thin,and the net radiative emission coefficient εN was
taken as a function of both temperature and mass fraction from
Ref.[25].Based on the literature [20,26],as well as in-house nu-
merical solutions of the Saha equation and calculation of the rele-
vant absorption coefficients, inverse bremsstrahlung absorption of
the incident laser beam at 1070 nm for temperatures < 10,000 K is
negligible and therefore was not included in the model.For the
substrate and powder layer,no convection term was used as the
melt pool motion was omitted for this study and translational
motion cannot be conveyed in axisymmetric models.
The laser radiation reaching the powder layer was modelled as a
Gaussian heat source with intensity:
I ¼2AP
p R2 exp 2r 2
R2 (8)
where A ¼ 0.6 is the absorption of the powder layer [33],P is the
laser power and R is the beam radius. The heat lost from the metal
surface due to evaporation is given by q ¼_mvapLvap, where Lvap is
the heat of vaporization and_mvap is the Fe vapour mass flowrate,
based on the vapour pressure Pvap and temperature,written as
[21,27]:
log _mvap ¼ 2:52 þ logPvap 0:5logðTÞ (9)
log Pvap ¼ 6:121 þ
18836
T (10)
Gray-body radiative energy losses were prescribed for all solid
surfaces, including the powder-substrateboundary, given by
q ¼ ε s ðT4
amb T 4 Þ, where ε ¼ 0.4 is the emissivity ofstainless
steel ands is the Stefan-Boltzmann constant.The temperature at
the outer boundaries of the powder and substrate was set at 300 K.
To account for ambient convection,the total losses at the gas/
plasma outer boundaries were prescribed as q ¼ hðTamb TÞ. A
convective heat transfer coefficient of h ¼ 50 W/m2 was used.
4. Results
The high-speed direct imaging results are divided into single
track and multilayer builds in the following sections.These are
followed by sections for the results of high-speed schlieren imaging
and finite element modelling.All the results in this section were
recorded without a flow of shielding gas across the powder bed in
order to focus attention on the gas movement due to the laser's
interaction with the powder bed. The effect of an additional flow of
shielding gas across the powder bed is introduced in the Discussion
section.
4.1.High-speed imaging: single tracks
Fig. 2 and Videos Fig. 2(a)-2(f) show high-speed imaging for side
and top views of the powder bed during laser scans of individual
tracks.Three different laser power and scan speed combinations
are shown: 50 W and 0.1 m/s, 100 W and 0.5 m/s,and 200 W and
1 m/s.The 100 and 200 W laser power conditions have the same
line energy (laser power divided by scan speed) at 200 J/m while
the 50 W condition has a line energy of 500 J/m.The 50 W and
100 W laser power conditions have been shown to build parts with
>99% density [13].These results are for the first powder layer of
thickness 50mm spread on the coupon. We had access to only one
high-speed camera and so the side and top views were recorded in
P. Bidare et al./ Acta Materialia 142 (2018) 107e120110
or residual stress development.The properties used in the fluid
domain above the powder bed were those of an Ar-Fe gas/plasma
mixture in local thermodynamic equilibrium (LTE). The values were
therefore input as a function of temperature and Fe mass fraction,
taken from Ref. [22].
The partial differential equations (PDEs) used in the model are
given below using vector notation. Vectors are represented in bold,
while constitutive properties used as a function of temperature and
Fe mass fraction are in italics.For fluid flow, the compressible
Navier-Stokes equations for momentum (2) and mass (3) conser-
vation were used:
r ðu$VuÞ ¼ V$
h
p þ m Vu þ ðVuÞT i
þ r g (2)
V$ðr uÞ ¼ 0 (3)
where r is the density,u the flow velocity,p the pressure,mthe
dynamic viscosity and g the acceleration due to gravity. In order to
better capture the turbulence due to the laser plume,but also to
expand the stable solution space of the model,the RANS SST tur-
bulence model was used.
The Knudsen layer approach gives the velocity magnitude of the
laser plume normal to the powder bed surface based on the local
sound speed:
juj ¼ M
ffiffiffiffiffiffiffiffiffiffiffiffiffiffiffiffiffiffiffiffiffiffiffiffiffiffiffiffiffiffiffiffiffiffiffi
gKT
u 1 mAr þ u 2 mFe
s
(4)
where M is the Mach number,g ¼ 5/3 is the heat capacity ratio for a
monoatomic gas, K is the Boltzmann constant and mAr ; mFe are the
atomic masses andu 1 ; u 2 the mass fractions of Ar and Fe,respec-
tively. The Mach number was assumed to vary linearly based on the
incident laser radiation, from M ¼ 0.01 at an intensity of 105 W/cm2
,
to M ¼ 1 for a flux of 107 W/cm2 [23]. On the outer flow boundaries,
an outflow condition was specified by setting the normal diffusive
flux equal to 0 at atmospheric pressure.
Extending an approach employed in state-of-the-art arc weld-
ing simulations [10,24], an additional set of conservation equations
were added to model the convective and diffusive modes of
transport of the vaporized gas.The mass fraction of the i-th con-
stituentu i is given by:
V$ r Do
i Vu i þ ru i Do
i
VM n
M n
þ DT
i
VT
T þ r ðu$VÞu i ¼ 0 (5)
where Do
i is the ordinary diffusion coefficient and DT
i is the thermal
diffusion coefficient while Mn is the sum of the molar masses of all
the constituents. Equation (5) was solved for speciesu 2 (Fe) and the
remaining mass was assigned to speciesu 1 (Ar). An additional
contribution DiT ¼ mT =ScT to the diffusion coefficient of each spe-
cies was added to account for turbulent mixing ofsmall eddies,
where mT is the Reynolds-averaged turbulent kinematic viscosity
and ScT ¼ 0.7 is the turbulent Schmidt number. The Fe mass fraction
at the powder surface was defined based on the vapour pressure
and molar masses of Ar and Fe as [24]:
u 2 ¼ PvapM Fe
PvapM Fe þ Patm P vap M Ar
(6)
For the process thermodynamics, an energy balance was used to
account for conductive, convective and radiative heat transfer.
r cpðu$VTÞ ¼ V$ðkVTÞ 4p εN (7)
The last term of equation (7) is solved only within the gas/
plasma domain,and accounts for the total radiative loss from the
Ar-Fe plasma across all wavelengths. The plasma was assumed to be
optically thin,and the net radiative emission coefficient εN was
taken as a function of both temperature and mass fraction from
Ref.[25].Based on the literature [20,26],as well as in-house nu-
merical solutions of the Saha equation and calculation of the rele-
vant absorption coefficients, inverse bremsstrahlung absorption of
the incident laser beam at 1070 nm for temperatures < 10,000 K is
negligible and therefore was not included in the model.For the
substrate and powder layer,no convection term was used as the
melt pool motion was omitted for this study and translational
motion cannot be conveyed in axisymmetric models.
The laser radiation reaching the powder layer was modelled as a
Gaussian heat source with intensity:
I ¼2AP
p R2 exp 2r 2
R2 (8)
where A ¼ 0.6 is the absorption of the powder layer [33],P is the
laser power and R is the beam radius. The heat lost from the metal
surface due to evaporation is given by q ¼_mvapLvap, where Lvap is
the heat of vaporization and_mvap is the Fe vapour mass flowrate,
based on the vapour pressure Pvap and temperature,written as
[21,27]:
log _mvap ¼ 2:52 þ logPvap 0:5logðTÞ (9)
log Pvap ¼ 6:121 þ
18836
T (10)
Gray-body radiative energy losses were prescribed for all solid
surfaces, including the powder-substrateboundary, given by
q ¼ ε s ðT4
amb T 4 Þ, where ε ¼ 0.4 is the emissivity ofstainless
steel ands is the Stefan-Boltzmann constant.The temperature at
the outer boundaries of the powder and substrate was set at 300 K.
To account for ambient convection,the total losses at the gas/
plasma outer boundaries were prescribed as q ¼ hðTamb TÞ. A
convective heat transfer coefficient of h ¼ 50 W/m2 was used.
4. Results
The high-speed direct imaging results are divided into single
track and multilayer builds in the following sections.These are
followed by sections for the results of high-speed schlieren imaging
and finite element modelling.All the results in this section were
recorded without a flow of shielding gas across the powder bed in
order to focus attention on the gas movement due to the laser's
interaction with the powder bed. The effect of an additional flow of
shielding gas across the powder bed is introduced in the Discussion
section.
4.1.High-speed imaging: single tracks
Fig. 2 and Videos Fig. 2(a)-2(f) show high-speed imaging for side
and top views of the powder bed during laser scans of individual
tracks.Three different laser power and scan speed combinations
are shown: 50 W and 0.1 m/s, 100 W and 0.5 m/s,and 200 W and
1 m/s.The 100 and 200 W laser power conditions have the same
line energy (laser power divided by scan speed) at 200 J/m while
the 50 W condition has a line energy of 500 J/m.The 50 W and
100 W laser power conditions have been shown to build parts with
>99% density [13].These results are for the first powder layer of
thickness 50mm spread on the coupon. We had access to only one
high-speed camera and so the side and top views were recorded in
P. Bidare et al./ Acta Materialia 142 (2018) 107e120110
Secure Best Marks with AI Grader
Need help grading? Try our AI Grader for instant feedback on your assignments.
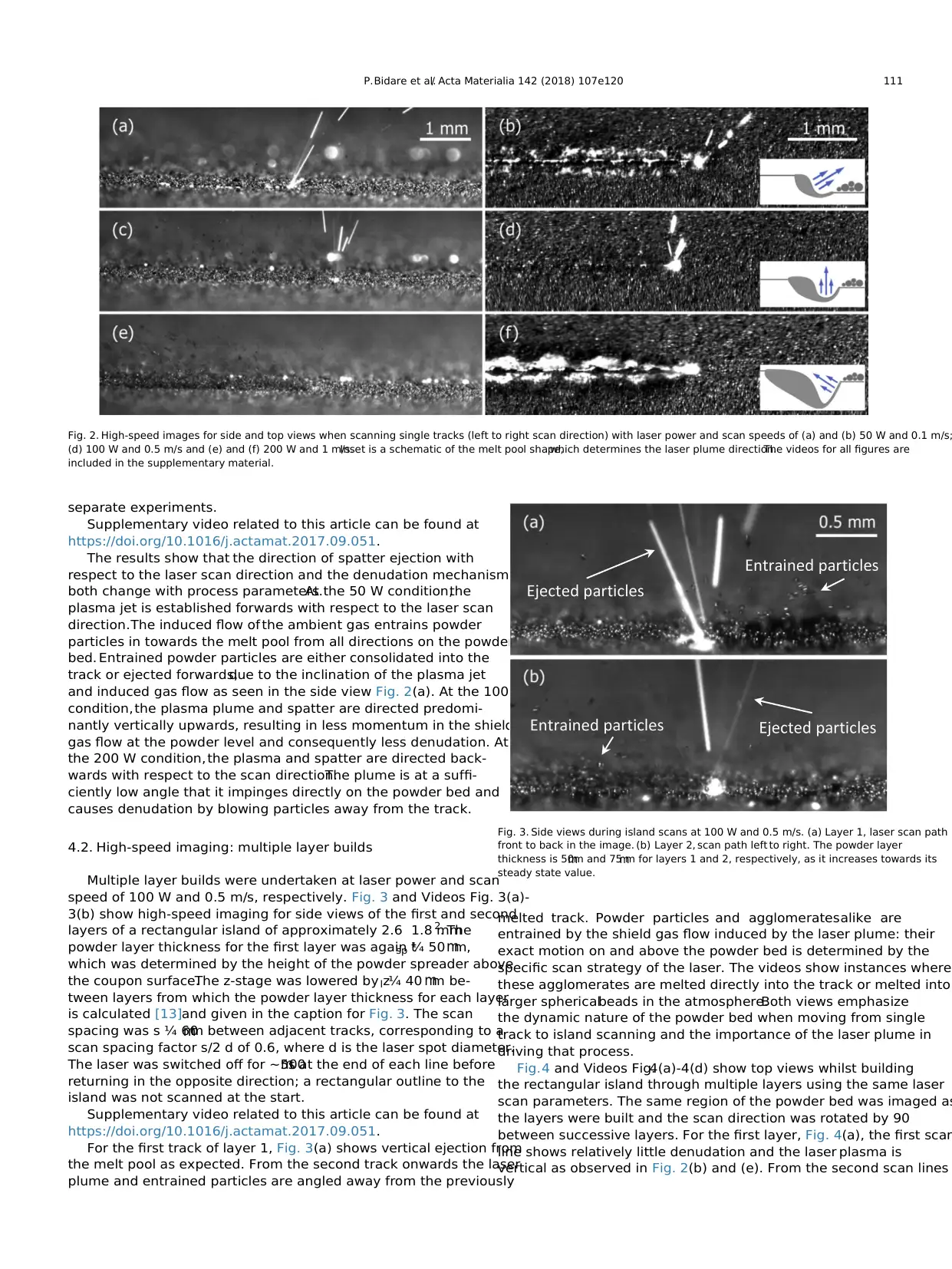
separate experiments.
Supplementary video related to this article can be found at
https://doi.org/10.1016/j.actamat.2017.09.051.
The results show that the direction of spatter ejection with
respect to the laser scan direction and the denudation mechanism
both change with process parameters.At the 50 W condition,the
plasma jet is established forwards with respect to the laser scan
direction.The induced flow of the ambient gas entrains powder
particles in towards the melt pool from all directions on the powder
bed. Entrained powder particles are either consolidated into the
track or ejected forwards,due to the inclination of the plasma jet
and induced gas flow as seen in the side view Fig. 2(a). At the 100 W
condition,the plasma plume and spatter are directed predomi-
nantly vertically upwards, resulting in less momentum in the shield
gas flow at the powder level and consequently less denudation. At
the 200 W condition, the plasma and spatter are directed back-
wards with respect to the scan direction.The plume is at a suffi-
ciently low angle that it impinges directly on the powder bed and
causes denudation by blowing particles away from the track.
4.2. High-speed imaging: multiple layer builds
Multiple layer builds were undertaken at laser power and scan
speed of 100 W and 0.5 m/s, respectively. Fig. 3 and Videos Fig. 3(a)-
3(b) show high-speed imaging for side views of the first and second
layers of a rectangular island of approximately 2.6 1.8 mm2
. The
powder layer thickness for the first layer was again tsp ¼ 50 mm,
which was determined by the height of the powder spreader above
the coupon surface.The z-stage was lowered by zl ¼ 40 mm be-
tween layers from which the powder layer thickness for each layer
is calculated [13]and given in the caption for Fig. 3. The scan
spacing was s ¼ 60mm between adjacent tracks, corresponding to a
scan spacing factor s/2 d of 0.6, where d is the laser spot diameter.
The laser was switched off for ~500ms at the end of each line before
returning in the opposite direction; a rectangular outline to the
island was not scanned at the start.
Supplementary video related to this article can be found at
https://doi.org/10.1016/j.actamat.2017.09.051.
For the first track of layer 1, Fig. 3(a) shows vertical ejection from
the melt pool as expected. From the second track onwards the laser
plume and entrained particles are angled away from the previously
melted track. Powder particles and agglomeratesalike are
entrained by the shield gas flow induced by the laser plume: their
exact motion on and above the powder bed is determined by the
specific scan strategy of the laser. The videos show instances where
these agglomerates are melted directly into the track or melted into
larger sphericalbeads in the atmosphere.Both views emphasize
the dynamic nature of the powder bed when moving from single
track to island scanning and the importance of the laser plume in
driving that process.
Fig.4 and Videos Fig.4(a)-4(d) show top views whilst building
the rectangular island through multiple layers using the same laser
scan parameters. The same region of the powder bed was imaged as
the layers were built and the scan direction was rotated by 90
between successive layers. For the first layer, Fig. 4(a), the first scan
line shows relatively little denudation and the laser plasma is
vertical as observed in Fig. 2(b) and (e). From the second scan lines
Fig. 2. High-speed images for side and top views when scanning single tracks (left to right scan direction) with laser power and scan speeds of (a) and (b) 50 W and 0.1 m/s;
(d) 100 W and 0.5 m/s and (e) and (f) 200 W and 1 m/s.Inset is a schematic of the melt pool shape,which determines the laser plume direction.The videos for all figures are
included in the supplementary material.
Fig. 3. Side views during island scans at 100 W and 0.5 m/s. (a) Layer 1, laser scan path
front to back in the image. (b) Layer 2, scan path left to right. The powder layer
thickness is 50mm and 75mm for layers 1 and 2, respectively, as it increases towards its
steady state value.
P.Bidare et al./ Acta Materialia 142 (2018) 107e120 111
Supplementary video related to this article can be found at
https://doi.org/10.1016/j.actamat.2017.09.051.
The results show that the direction of spatter ejection with
respect to the laser scan direction and the denudation mechanism
both change with process parameters.At the 50 W condition,the
plasma jet is established forwards with respect to the laser scan
direction.The induced flow of the ambient gas entrains powder
particles in towards the melt pool from all directions on the powder
bed. Entrained powder particles are either consolidated into the
track or ejected forwards,due to the inclination of the plasma jet
and induced gas flow as seen in the side view Fig. 2(a). At the 100 W
condition,the plasma plume and spatter are directed predomi-
nantly vertically upwards, resulting in less momentum in the shield
gas flow at the powder level and consequently less denudation. At
the 200 W condition, the plasma and spatter are directed back-
wards with respect to the scan direction.The plume is at a suffi-
ciently low angle that it impinges directly on the powder bed and
causes denudation by blowing particles away from the track.
4.2. High-speed imaging: multiple layer builds
Multiple layer builds were undertaken at laser power and scan
speed of 100 W and 0.5 m/s, respectively. Fig. 3 and Videos Fig. 3(a)-
3(b) show high-speed imaging for side views of the first and second
layers of a rectangular island of approximately 2.6 1.8 mm2
. The
powder layer thickness for the first layer was again tsp ¼ 50 mm,
which was determined by the height of the powder spreader above
the coupon surface.The z-stage was lowered by zl ¼ 40 mm be-
tween layers from which the powder layer thickness for each layer
is calculated [13]and given in the caption for Fig. 3. The scan
spacing was s ¼ 60mm between adjacent tracks, corresponding to a
scan spacing factor s/2 d of 0.6, where d is the laser spot diameter.
The laser was switched off for ~500ms at the end of each line before
returning in the opposite direction; a rectangular outline to the
island was not scanned at the start.
Supplementary video related to this article can be found at
https://doi.org/10.1016/j.actamat.2017.09.051.
For the first track of layer 1, Fig. 3(a) shows vertical ejection from
the melt pool as expected. From the second track onwards the laser
plume and entrained particles are angled away from the previously
melted track. Powder particles and agglomeratesalike are
entrained by the shield gas flow induced by the laser plume: their
exact motion on and above the powder bed is determined by the
specific scan strategy of the laser. The videos show instances where
these agglomerates are melted directly into the track or melted into
larger sphericalbeads in the atmosphere.Both views emphasize
the dynamic nature of the powder bed when moving from single
track to island scanning and the importance of the laser plume in
driving that process.
Fig.4 and Videos Fig.4(a)-4(d) show top views whilst building
the rectangular island through multiple layers using the same laser
scan parameters. The same region of the powder bed was imaged as
the layers were built and the scan direction was rotated by 90
between successive layers. For the first layer, Fig. 4(a), the first scan
line shows relatively little denudation and the laser plasma is
vertical as observed in Fig. 2(b) and (e). From the second scan lines
Fig. 2. High-speed images for side and top views when scanning single tracks (left to right scan direction) with laser power and scan speeds of (a) and (b) 50 W and 0.1 m/s;
(d) 100 W and 0.5 m/s and (e) and (f) 200 W and 1 m/s.Inset is a schematic of the melt pool shape,which determines the laser plume direction.The videos for all figures are
included in the supplementary material.
Fig. 3. Side views during island scans at 100 W and 0.5 m/s. (a) Layer 1, laser scan path
front to back in the image. (b) Layer 2, scan path left to right. The powder layer
thickness is 50mm and 75mm for layers 1 and 2, respectively, as it increases towards its
steady state value.
P.Bidare et al./ Acta Materialia 142 (2018) 107e120 111
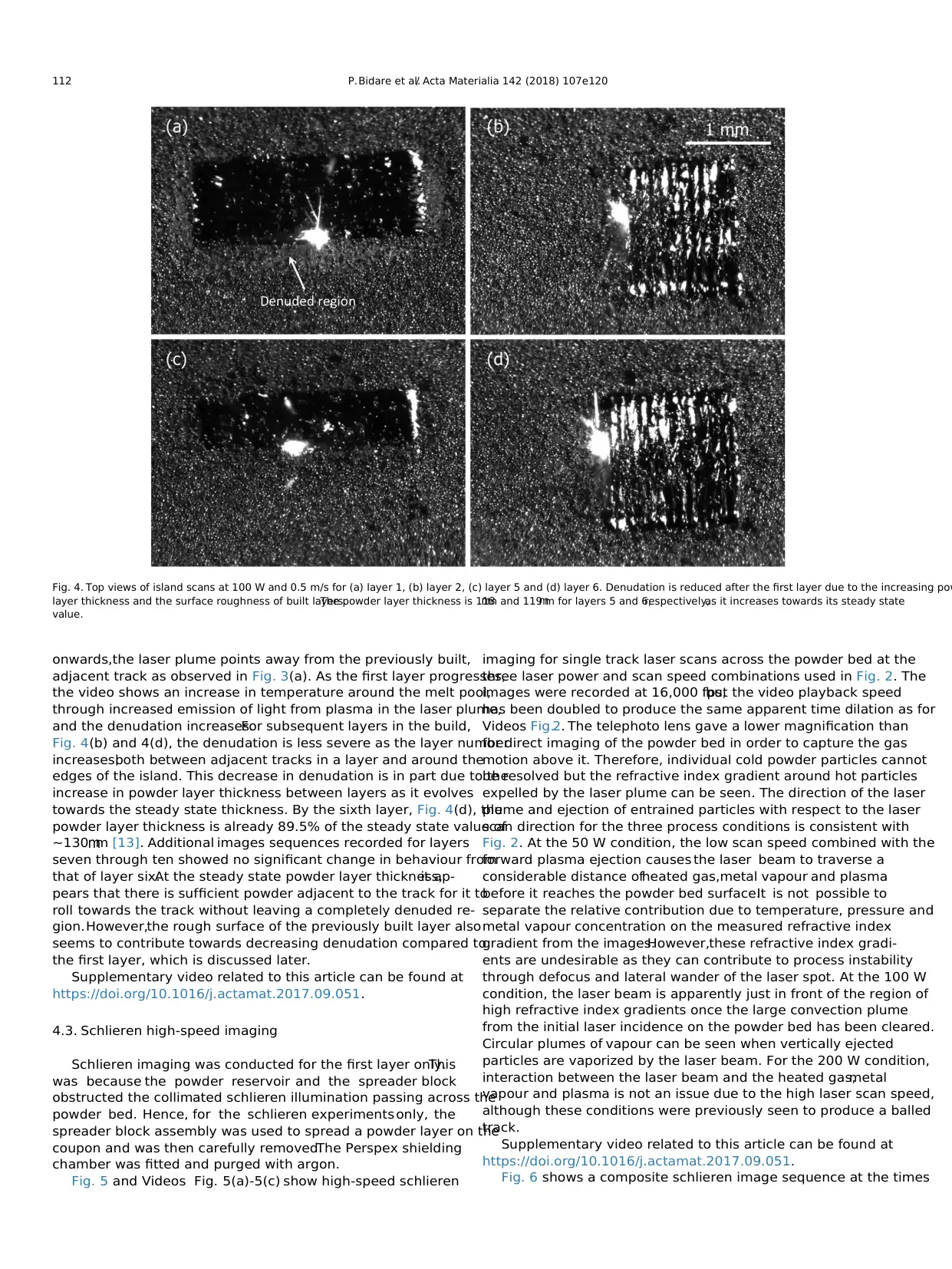
onwards,the laser plume points away from the previously built,
adjacent track as observed in Fig. 3(a). As the first layer progresses,
the video shows an increase in temperature around the melt pool,
through increased emission of light from plasma in the laser plume,
and the denudation increases.For subsequent layers in the build,
Fig. 4(b) and 4(d), the denudation is less severe as the layer number
increases,both between adjacent tracks in a layer and around the
edges of the island. This decrease in denudation is in part due to the
increase in powder layer thickness between layers as it evolves
towards the steady state thickness. By the sixth layer, Fig. 4(d), the
powder layer thickness is already 89.5% of the steady state value of
~130mm [13]. Additional images sequences recorded for layers
seven through ten showed no significant change in behaviour from
that of layer six.At the steady state powder layer thickness,it ap-
pears that there is sufficient powder adjacent to the track for it to
roll towards the track without leaving a completely denuded re-
gion.However,the rough surface of the previously built layer also
seems to contribute towards decreasing denudation compared to
the first layer, which is discussed later.
Supplementary video related to this article can be found at
https://doi.org/10.1016/j.actamat.2017.09.051.
4.3. Schlieren high-speed imaging
Schlieren imaging was conducted for the first layer only.This
was because the powder reservoir and the spreader block
obstructed the collimated schlieren illumination passing across the
powder bed. Hence, for the schlieren experiments only, the
spreader block assembly was used to spread a powder layer on the
coupon and was then carefully removed.The Perspex shielding
chamber was fitted and purged with argon.
Fig. 5 and Videos Fig. 5(a)-5(c) show high-speed schlieren
imaging for single track laser scans across the powder bed at the
three laser power and scan speed combinations used in Fig. 2. The
images were recorded at 16,000 fps,but the video playback speed
has been doubled to produce the same apparent time dilation as for
Videos Fig.2. The telephoto lens gave a lower magnification than
for direct imaging of the powder bed in order to capture the gas
motion above it. Therefore, individual cold powder particles cannot
be resolved but the refractive index gradient around hot particles
expelled by the laser plume can be seen. The direction of the laser
plume and ejection of entrained particles with respect to the laser
scan direction for the three process conditions is consistent with
Fig. 2. At the 50 W condition, the low scan speed combined with the
forward plasma ejection causes the laser beam to traverse a
considerable distance ofheated gas,metal vapour and plasma
before it reaches the powder bed surface.It is not possible to
separate the relative contribution due to temperature, pressure and
metal vapour concentration on the measured refractive index
gradient from the images.However,these refractive index gradi-
ents are undesirable as they can contribute to process instability
through defocus and lateral wander of the laser spot. At the 100 W
condition, the laser beam is apparently just in front of the region of
high refractive index gradients once the large convection plume
from the initial laser incidence on the powder bed has been cleared.
Circular plumes of vapour can be seen when vertically ejected
particles are vaporized by the laser beam. For the 200 W condition,
interaction between the laser beam and the heated gas,metal
vapour and plasma is not an issue due to the high laser scan speed,
although these conditions were previously seen to produce a balled
track.
Supplementary video related to this article can be found at
https://doi.org/10.1016/j.actamat.2017.09.051.
Fig. 6 shows a composite schlieren image sequence at the times
Fig. 4. Top views of island scans at 100 W and 0.5 m/s for (a) layer 1, (b) layer 2, (c) layer 5 and (d) layer 6. Denudation is reduced after the first layer due to the increasing pow
layer thickness and the surface roughness of built layers.The powder layer thickness is 113mm and 119mm for layers 5 and 6,respectively,as it increases towards its steady state
value.
P. Bidare et al./ Acta Materialia 142 (2018) 107e120112
adjacent track as observed in Fig. 3(a). As the first layer progresses,
the video shows an increase in temperature around the melt pool,
through increased emission of light from plasma in the laser plume,
and the denudation increases.For subsequent layers in the build,
Fig. 4(b) and 4(d), the denudation is less severe as the layer number
increases,both between adjacent tracks in a layer and around the
edges of the island. This decrease in denudation is in part due to the
increase in powder layer thickness between layers as it evolves
towards the steady state thickness. By the sixth layer, Fig. 4(d), the
powder layer thickness is already 89.5% of the steady state value of
~130mm [13]. Additional images sequences recorded for layers
seven through ten showed no significant change in behaviour from
that of layer six.At the steady state powder layer thickness,it ap-
pears that there is sufficient powder adjacent to the track for it to
roll towards the track without leaving a completely denuded re-
gion.However,the rough surface of the previously built layer also
seems to contribute towards decreasing denudation compared to
the first layer, which is discussed later.
Supplementary video related to this article can be found at
https://doi.org/10.1016/j.actamat.2017.09.051.
4.3. Schlieren high-speed imaging
Schlieren imaging was conducted for the first layer only.This
was because the powder reservoir and the spreader block
obstructed the collimated schlieren illumination passing across the
powder bed. Hence, for the schlieren experiments only, the
spreader block assembly was used to spread a powder layer on the
coupon and was then carefully removed.The Perspex shielding
chamber was fitted and purged with argon.
Fig. 5 and Videos Fig. 5(a)-5(c) show high-speed schlieren
imaging for single track laser scans across the powder bed at the
three laser power and scan speed combinations used in Fig. 2. The
images were recorded at 16,000 fps,but the video playback speed
has been doubled to produce the same apparent time dilation as for
Videos Fig.2. The telephoto lens gave a lower magnification than
for direct imaging of the powder bed in order to capture the gas
motion above it. Therefore, individual cold powder particles cannot
be resolved but the refractive index gradient around hot particles
expelled by the laser plume can be seen. The direction of the laser
plume and ejection of entrained particles with respect to the laser
scan direction for the three process conditions is consistent with
Fig. 2. At the 50 W condition, the low scan speed combined with the
forward plasma ejection causes the laser beam to traverse a
considerable distance ofheated gas,metal vapour and plasma
before it reaches the powder bed surface.It is not possible to
separate the relative contribution due to temperature, pressure and
metal vapour concentration on the measured refractive index
gradient from the images.However,these refractive index gradi-
ents are undesirable as they can contribute to process instability
through defocus and lateral wander of the laser spot. At the 100 W
condition, the laser beam is apparently just in front of the region of
high refractive index gradients once the large convection plume
from the initial laser incidence on the powder bed has been cleared.
Circular plumes of vapour can be seen when vertically ejected
particles are vaporized by the laser beam. For the 200 W condition,
interaction between the laser beam and the heated gas,metal
vapour and plasma is not an issue due to the high laser scan speed,
although these conditions were previously seen to produce a balled
track.
Supplementary video related to this article can be found at
https://doi.org/10.1016/j.actamat.2017.09.051.
Fig. 6 shows a composite schlieren image sequence at the times
Fig. 4. Top views of island scans at 100 W and 0.5 m/s for (a) layer 1, (b) layer 2, (c) layer 5 and (d) layer 6. Denudation is reduced after the first layer due to the increasing pow
layer thickness and the surface roughness of built layers.The powder layer thickness is 113mm and 119mm for layers 5 and 6,respectively,as it increases towards its steady state
value.
P. Bidare et al./ Acta Materialia 142 (2018) 107e120112
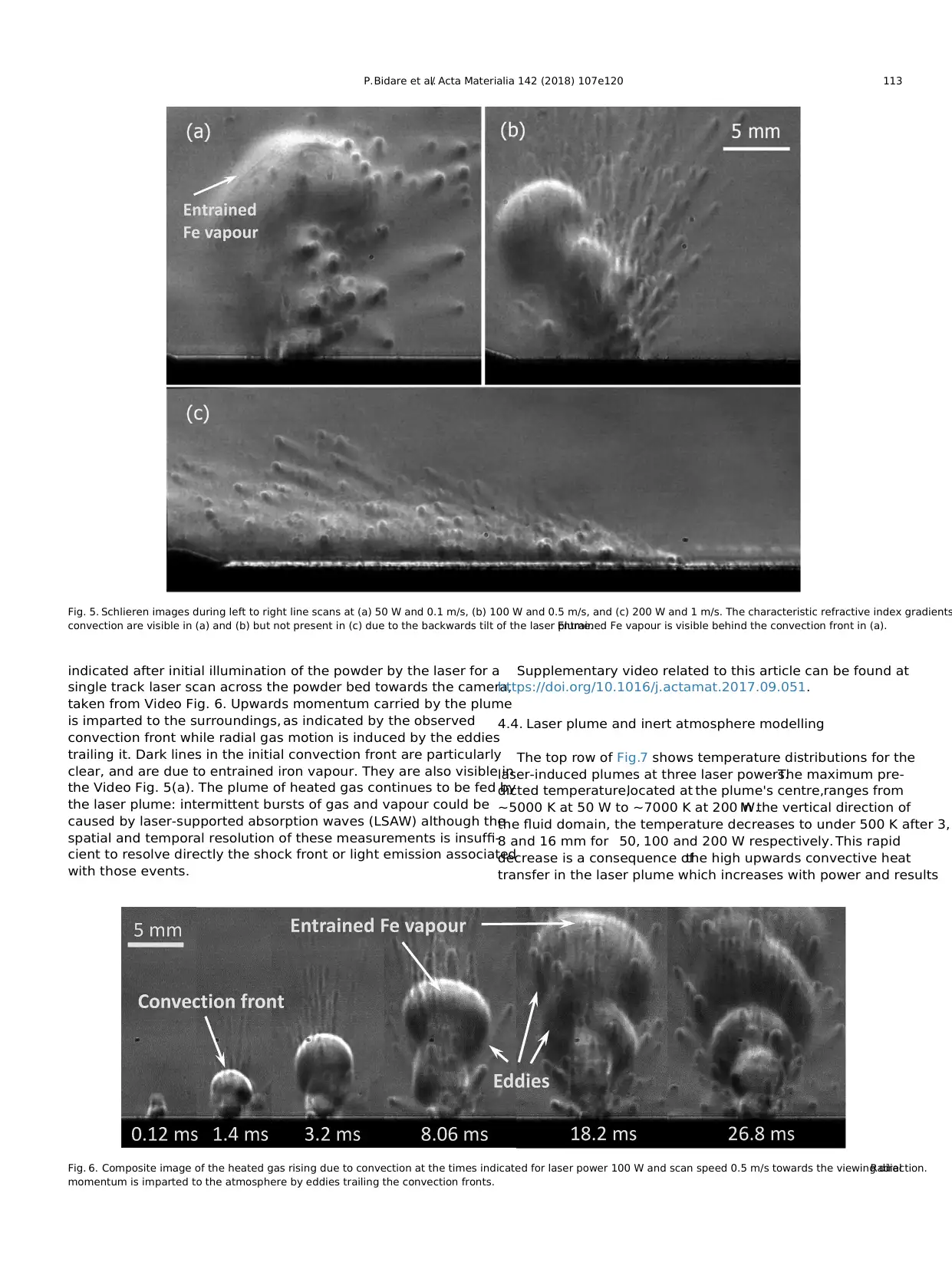
indicated after initial illumination of the powder by the laser for a
single track laser scan across the powder bed towards the camera,
taken from Video Fig. 6. Upwards momentum carried by the plume
is imparted to the surroundings, as indicated by the observed
convection front while radial gas motion is induced by the eddies
trailing it. Dark lines in the initial convection front are particularly
clear, and are due to entrained iron vapour. They are also visible in
the Video Fig. 5(a). The plume of heated gas continues to be fed by
the laser plume: intermittent bursts of gas and vapour could be
caused by laser-supported absorption waves (LSAW) although the
spatial and temporal resolution of these measurements is insuffi-
cient to resolve directly the shock front or light emission associated
with those events.
Supplementary video related to this article can be found at
https://doi.org/10.1016/j.actamat.2017.09.051.
4.4. Laser plume and inert atmosphere modelling
The top row of Fig.7 shows temperature distributions for the
laser-induced plumes at three laser powers.The maximum pre-
dicted temperature,located at the plume's centre,ranges from
~5000 K at 50 W to ~7000 K at 200 W.In the vertical direction of
the fluid domain, the temperature decreases to under 500 K after 3,
8 and 16 mm for 50, 100 and 200 W respectively. This rapid
decrease is a consequence ofthe high upwards convective heat
transfer in the laser plume which increases with power and results
Fig. 5. Schlieren images during left to right line scans at (a) 50 W and 0.1 m/s, (b) 100 W and 0.5 m/s, and (c) 200 W and 1 m/s. The characteristic refractive index gradients
convection are visible in (a) and (b) but not present in (c) due to the backwards tilt of the laser plume.Entrained Fe vapour is visible behind the convection front in (a).
Fig. 6. Composite image of the heated gas rising due to convection at the times indicated for laser power 100 W and scan speed 0.5 m/s towards the viewing direction.Radial
momentum is imparted to the atmosphere by eddies trailing the convection fronts.
P.Bidare et al./ Acta Materialia 142 (2018) 107e120 113
single track laser scan across the powder bed towards the camera,
taken from Video Fig. 6. Upwards momentum carried by the plume
is imparted to the surroundings, as indicated by the observed
convection front while radial gas motion is induced by the eddies
trailing it. Dark lines in the initial convection front are particularly
clear, and are due to entrained iron vapour. They are also visible in
the Video Fig. 5(a). The plume of heated gas continues to be fed by
the laser plume: intermittent bursts of gas and vapour could be
caused by laser-supported absorption waves (LSAW) although the
spatial and temporal resolution of these measurements is insuffi-
cient to resolve directly the shock front or light emission associated
with those events.
Supplementary video related to this article can be found at
https://doi.org/10.1016/j.actamat.2017.09.051.
4.4. Laser plume and inert atmosphere modelling
The top row of Fig.7 shows temperature distributions for the
laser-induced plumes at three laser powers.The maximum pre-
dicted temperature,located at the plume's centre,ranges from
~5000 K at 50 W to ~7000 K at 200 W.In the vertical direction of
the fluid domain, the temperature decreases to under 500 K after 3,
8 and 16 mm for 50, 100 and 200 W respectively. This rapid
decrease is a consequence ofthe high upwards convective heat
transfer in the laser plume which increases with power and results
Fig. 5. Schlieren images during left to right line scans at (a) 50 W and 0.1 m/s, (b) 100 W and 0.5 m/s, and (c) 200 W and 1 m/s. The characteristic refractive index gradients
convection are visible in (a) and (b) but not present in (c) due to the backwards tilt of the laser plume.Entrained Fe vapour is visible behind the convection front in (a).
Fig. 6. Composite image of the heated gas rising due to convection at the times indicated for laser power 100 W and scan speed 0.5 m/s towards the viewing direction.Radial
momentum is imparted to the atmosphere by eddies trailing the convection fronts.
P.Bidare et al./ Acta Materialia 142 (2018) 107e120 113
Paraphrase This Document
Need a fresh take? Get an instant paraphrase of this document with our AI Paraphraser
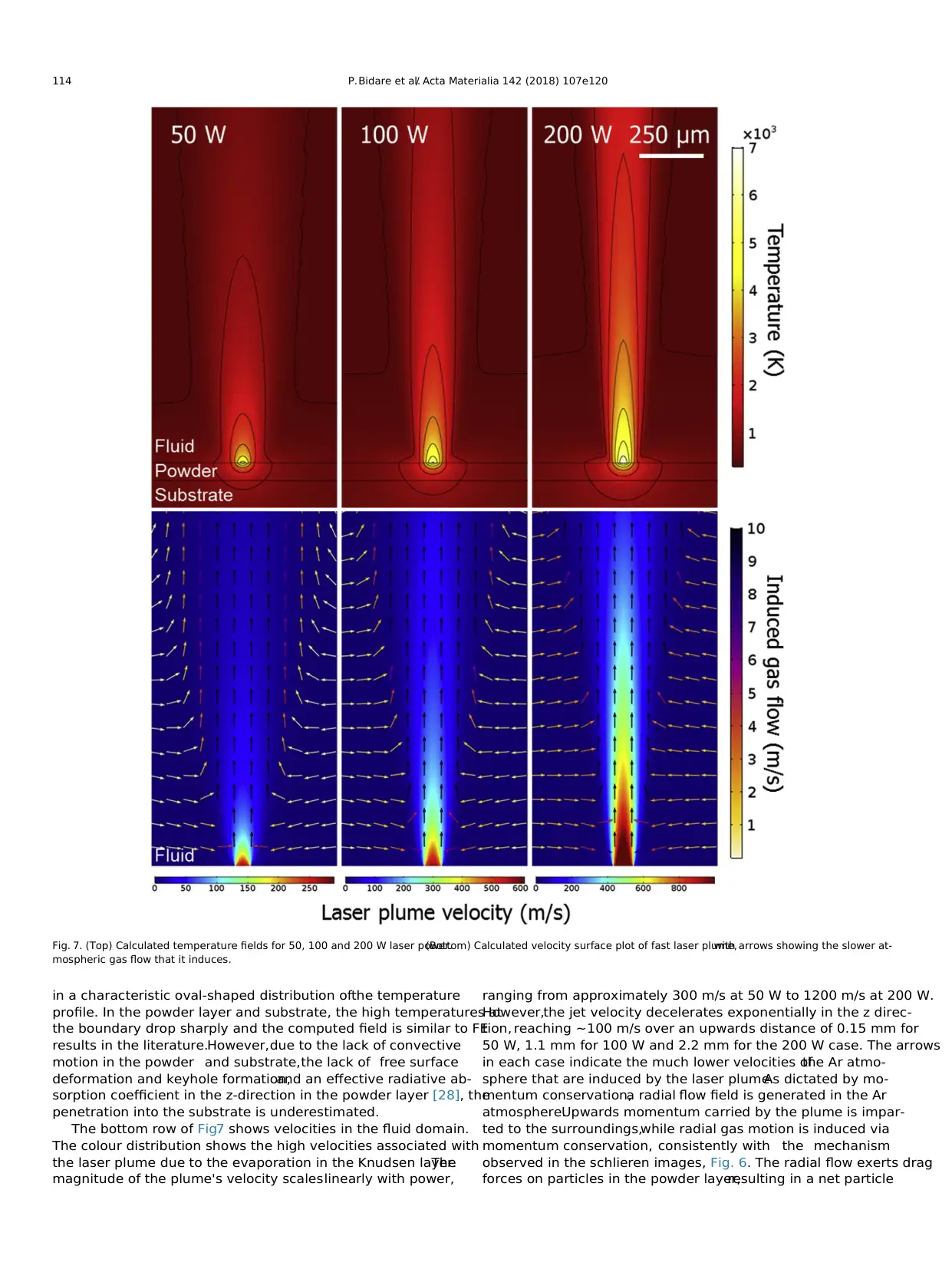
in a characteristic oval-shaped distribution ofthe temperature
profile. In the powder layer and substrate, the high temperatures at
the boundary drop sharply and the computed field is similar to FE
results in the literature.However,due to the lack of convective
motion in the powder and substrate,the lack of free surface
deformation and keyhole formation,and an effective radiative ab-
sorption coefficient in the z-direction in the powder layer [28], the
penetration into the substrate is underestimated.
The bottom row of Fig.7 shows velocities in the fluid domain.
The colour distribution shows the high velocities associated with
the laser plume due to the evaporation in the Knudsen layer.The
magnitude of the plume's velocity scaleslinearly with power,
ranging from approximately 300 m/s at 50 W to 1200 m/s at 200 W.
However,the jet velocity decelerates exponentially in the z direc-
tion, reaching ~100 m/s over an upwards distance of 0.15 mm for
50 W, 1.1 mm for 100 W and 2.2 mm for the 200 W case. The arrows
in each case indicate the much lower velocities ofthe Ar atmo-
sphere that are induced by the laser plume.As dictated by mo-
mentum conservation,a radial flow field is generated in the Ar
atmosphere.Upwards momentum carried by the plume is impar-
ted to the surroundings,while radial gas motion is induced via
momentum conservation, consistently with the mechanism
observed in the schlieren images, Fig. 6. The radial flow exerts drag
forces on particles in the powder layer,resulting in a net particle
Fig. 7. (Top) Calculated temperature fields for 50, 100 and 200 W laser power.(Bottom) Calculated velocity surface plot of fast laser plume,with arrows showing the slower at-
mospheric gas flow that it induces.
P. Bidare et al./ Acta Materialia 142 (2018) 107e120114
profile. In the powder layer and substrate, the high temperatures at
the boundary drop sharply and the computed field is similar to FE
results in the literature.However,due to the lack of convective
motion in the powder and substrate,the lack of free surface
deformation and keyhole formation,and an effective radiative ab-
sorption coefficient in the z-direction in the powder layer [28], the
penetration into the substrate is underestimated.
The bottom row of Fig.7 shows velocities in the fluid domain.
The colour distribution shows the high velocities associated with
the laser plume due to the evaporation in the Knudsen layer.The
magnitude of the plume's velocity scaleslinearly with power,
ranging from approximately 300 m/s at 50 W to 1200 m/s at 200 W.
However,the jet velocity decelerates exponentially in the z direc-
tion, reaching ~100 m/s over an upwards distance of 0.15 mm for
50 W, 1.1 mm for 100 W and 2.2 mm for the 200 W case. The arrows
in each case indicate the much lower velocities ofthe Ar atmo-
sphere that are induced by the laser plume.As dictated by mo-
mentum conservation,a radial flow field is generated in the Ar
atmosphere.Upwards momentum carried by the plume is impar-
ted to the surroundings,while radial gas motion is induced via
momentum conservation, consistently with the mechanism
observed in the schlieren images, Fig. 6. The radial flow exerts drag
forces on particles in the powder layer,resulting in a net particle
Fig. 7. (Top) Calculated temperature fields for 50, 100 and 200 W laser power.(Bottom) Calculated velocity surface plot of fast laser plume,with arrows showing the slower at-
mospheric gas flow that it induces.
P. Bidare et al./ Acta Materialia 142 (2018) 107e120114
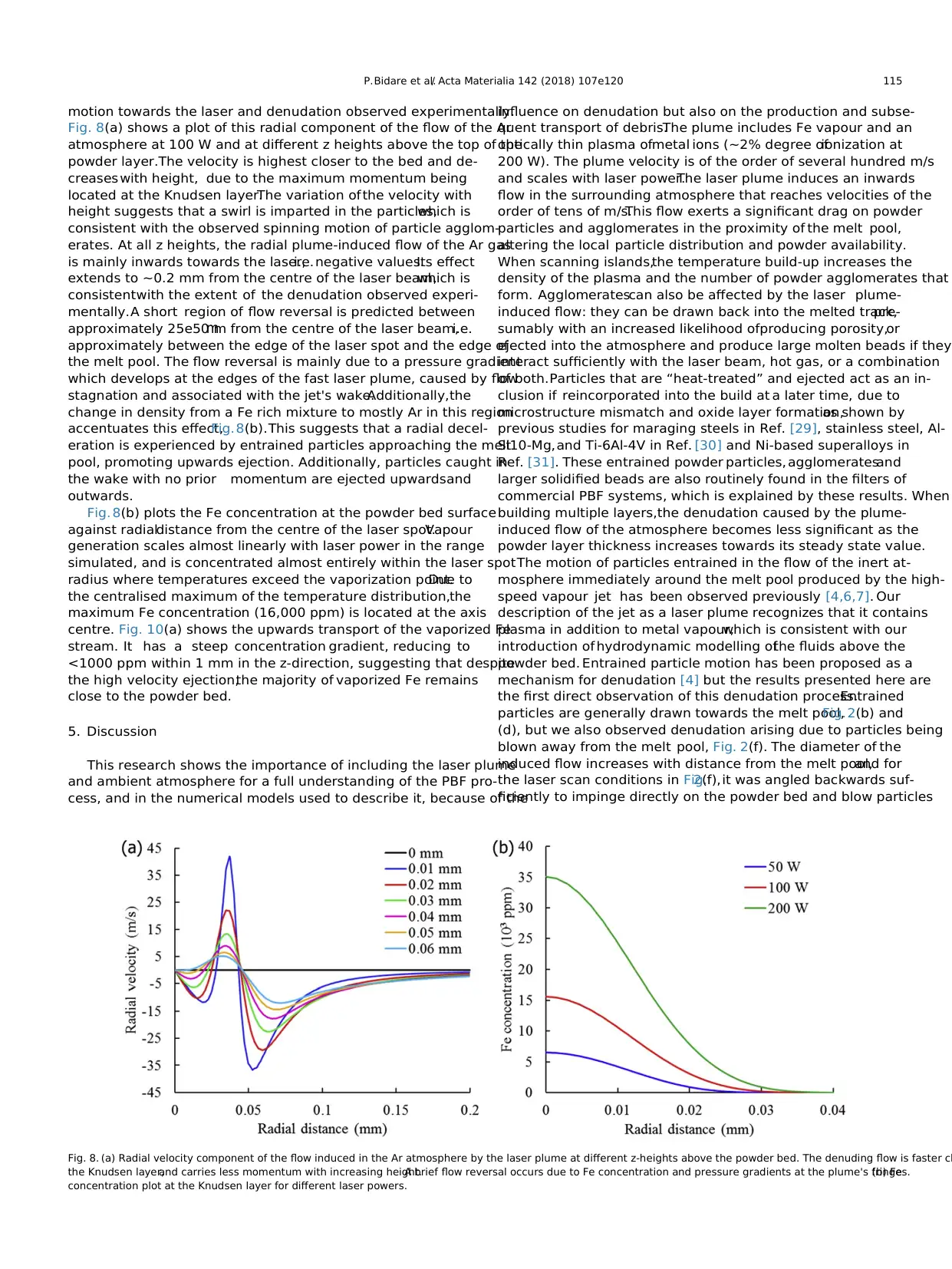
motion towards the laser and denudation observed experimentally.
Fig. 8(a) shows a plot of this radial component of the flow of the Ar
atmosphere at 100 W and at different z heights above the top of the
powder layer.The velocity is highest closer to the bed and de-
creases with height, due to the maximum momentum being
located at the Knudsen layer.The variation ofthe velocity with
height suggests that a swirl is imparted in the particles,which is
consistent with the observed spinning motion of particle agglom-
erates. At all z heights, the radial plume-induced flow of the Ar gas
is mainly inwards towards the laser,i.e. negative values.Its effect
extends to ~0.2 mm from the centre of the laser beam,which is
consistentwith the extent of the denudation observed experi-
mentally.A short region of flow reversal is predicted between
approximately 25e50mm from the centre of the laser beam,i.e.
approximately between the edge of the laser spot and the edge of
the melt pool. The flow reversal is mainly due to a pressure gradient
which develops at the edges of the fast laser plume, caused by flow
stagnation and associated with the jet's wake.Additionally,the
change in density from a Fe rich mixture to mostly Ar in this region
accentuates this effect,Fig.8(b).This suggests that a radial decel-
eration is experienced by entrained particles approaching the melt
pool, promoting upwards ejection. Additionally, particles caught in
the wake with no prior momentum are ejected upwardsand
outwards.
Fig. 8(b) plots the Fe concentration at the powder bed surface
against radialdistance from the centre of the laser spot.Vapour
generation scales almost linearly with laser power in the range
simulated, and is concentrated almost entirely within the laser spot
radius where temperatures exceed the vaporization point.Due to
the centralised maximum of the temperature distribution,the
maximum Fe concentration (16,000 ppm) is located at the axis
centre. Fig. 10(a) shows the upwards transport of the vaporized Fe
stream. It has a steep concentration gradient, reducing to
<1000 ppm within 1 mm in the z-direction, suggesting that despite
the high velocity ejection,the majority of vaporized Fe remains
close to the powder bed.
5. Discussion
This research shows the importance of including the laser plume
and ambient atmosphere for a full understanding of the PBF pro-
cess, and in the numerical models used to describe it, because of the
influence on denudation but also on the production and subse-
quent transport of debris.The plume includes Fe vapour and an
optically thin plasma ofmetal ions (~2% degree ofionization at
200 W). The plume velocity is of the order of several hundred m/s
and scales with laser power.The laser plume induces an inwards
flow in the surrounding atmosphere that reaches velocities of the
order of tens of m/s.This flow exerts a significant drag on powder
particles and agglomerates in the proximity of the melt pool,
altering the local particle distribution and powder availability.
When scanning islands,the temperature build-up increases the
density of the plasma and the number of powder agglomerates that
form. Agglomeratescan also be affected by the laser plume-
induced flow: they can be drawn back into the melted track,pre-
sumably with an increased likelihood ofproducing porosity,or
ejected into the atmosphere and produce large molten beads if they
interact sufficiently with the laser beam, hot gas, or a combination
of both.Particles that are “heat-treated” and ejected act as an in-
clusion if reincorporated into the build at a later time, due to
microstructure mismatch and oxide layer formation,as shown by
previous studies for maraging steels in Ref. [29], stainless steel, Al-
Si10-Mg,and Ti-6Al-4V in Ref. [30] and Ni-based superalloys in
Ref. [31]. These entrained powder particles, agglomeratesand
larger solidified beads are also routinely found in the filters of
commercial PBF systems, which is explained by these results. When
building multiple layers,the denudation caused by the plume-
induced flow of the atmosphere becomes less significant as the
powder layer thickness increases towards its steady state value.
The motion of particles entrained in the flow of the inert at-
mosphere immediately around the melt pool produced by the high-
speed vapour jet has been observed previously [4,6,7]. Our
description of the jet as a laser plume recognizes that it contains
plasma in addition to metal vapour,which is consistent with our
introduction of hydrodynamic modelling ofthe fluids above the
powder bed. Entrained particle motion has been proposed as a
mechanism for denudation [4] but the results presented here are
the first direct observation of this denudation process.Entrained
particles are generally drawn towards the melt pool,Fig.2(b) and
(d), but we also observed denudation arising due to particles being
blown away from the melt pool, Fig. 2(f). The diameter of the
induced flow increases with distance from the melt pool,and for
the laser scan conditions in Fig.2(f),it was angled backwards suf-
ficiently to impinge directly on the powder bed and blow particles
Fig. 8. (a) Radial velocity component of the flow induced in the Ar atmosphere by the laser plume at different z-heights above the powder bed. The denuding flow is faster cl
the Knudsen layer,and carries less momentum with increasing height.A brief flow reversal occurs due to Fe concentration and pressure gradients at the plume's fringes.(b) Fe
concentration plot at the Knudsen layer for different laser powers.
P.Bidare et al./ Acta Materialia 142 (2018) 107e120 115
Fig. 8(a) shows a plot of this radial component of the flow of the Ar
atmosphere at 100 W and at different z heights above the top of the
powder layer.The velocity is highest closer to the bed and de-
creases with height, due to the maximum momentum being
located at the Knudsen layer.The variation ofthe velocity with
height suggests that a swirl is imparted in the particles,which is
consistent with the observed spinning motion of particle agglom-
erates. At all z heights, the radial plume-induced flow of the Ar gas
is mainly inwards towards the laser,i.e. negative values.Its effect
extends to ~0.2 mm from the centre of the laser beam,which is
consistentwith the extent of the denudation observed experi-
mentally.A short region of flow reversal is predicted between
approximately 25e50mm from the centre of the laser beam,i.e.
approximately between the edge of the laser spot and the edge of
the melt pool. The flow reversal is mainly due to a pressure gradient
which develops at the edges of the fast laser plume, caused by flow
stagnation and associated with the jet's wake.Additionally,the
change in density from a Fe rich mixture to mostly Ar in this region
accentuates this effect,Fig.8(b).This suggests that a radial decel-
eration is experienced by entrained particles approaching the melt
pool, promoting upwards ejection. Additionally, particles caught in
the wake with no prior momentum are ejected upwardsand
outwards.
Fig. 8(b) plots the Fe concentration at the powder bed surface
against radialdistance from the centre of the laser spot.Vapour
generation scales almost linearly with laser power in the range
simulated, and is concentrated almost entirely within the laser spot
radius where temperatures exceed the vaporization point.Due to
the centralised maximum of the temperature distribution,the
maximum Fe concentration (16,000 ppm) is located at the axis
centre. Fig. 10(a) shows the upwards transport of the vaporized Fe
stream. It has a steep concentration gradient, reducing to
<1000 ppm within 1 mm in the z-direction, suggesting that despite
the high velocity ejection,the majority of vaporized Fe remains
close to the powder bed.
5. Discussion
This research shows the importance of including the laser plume
and ambient atmosphere for a full understanding of the PBF pro-
cess, and in the numerical models used to describe it, because of the
influence on denudation but also on the production and subse-
quent transport of debris.The plume includes Fe vapour and an
optically thin plasma ofmetal ions (~2% degree ofionization at
200 W). The plume velocity is of the order of several hundred m/s
and scales with laser power.The laser plume induces an inwards
flow in the surrounding atmosphere that reaches velocities of the
order of tens of m/s.This flow exerts a significant drag on powder
particles and agglomerates in the proximity of the melt pool,
altering the local particle distribution and powder availability.
When scanning islands,the temperature build-up increases the
density of the plasma and the number of powder agglomerates that
form. Agglomeratescan also be affected by the laser plume-
induced flow: they can be drawn back into the melted track,pre-
sumably with an increased likelihood ofproducing porosity,or
ejected into the atmosphere and produce large molten beads if they
interact sufficiently with the laser beam, hot gas, or a combination
of both.Particles that are “heat-treated” and ejected act as an in-
clusion if reincorporated into the build at a later time, due to
microstructure mismatch and oxide layer formation,as shown by
previous studies for maraging steels in Ref. [29], stainless steel, Al-
Si10-Mg,and Ti-6Al-4V in Ref. [30] and Ni-based superalloys in
Ref. [31]. These entrained powder particles, agglomeratesand
larger solidified beads are also routinely found in the filters of
commercial PBF systems, which is explained by these results. When
building multiple layers,the denudation caused by the plume-
induced flow of the atmosphere becomes less significant as the
powder layer thickness increases towards its steady state value.
The motion of particles entrained in the flow of the inert at-
mosphere immediately around the melt pool produced by the high-
speed vapour jet has been observed previously [4,6,7]. Our
description of the jet as a laser plume recognizes that it contains
plasma in addition to metal vapour,which is consistent with our
introduction of hydrodynamic modelling ofthe fluids above the
powder bed. Entrained particle motion has been proposed as a
mechanism for denudation [4] but the results presented here are
the first direct observation of this denudation process.Entrained
particles are generally drawn towards the melt pool,Fig.2(b) and
(d), but we also observed denudation arising due to particles being
blown away from the melt pool, Fig. 2(f). The diameter of the
induced flow increases with distance from the melt pool,and for
the laser scan conditions in Fig.2(f),it was angled backwards suf-
ficiently to impinge directly on the powder bed and blow particles
Fig. 8. (a) Radial velocity component of the flow induced in the Ar atmosphere by the laser plume at different z-heights above the powder bed. The denuding flow is faster cl
the Knudsen layer,and carries less momentum with increasing height.A brief flow reversal occurs due to Fe concentration and pressure gradients at the plume's fringes.(b) Fe
concentration plot at the Knudsen layer for different laser powers.
P.Bidare et al./ Acta Materialia 142 (2018) 107e120 115
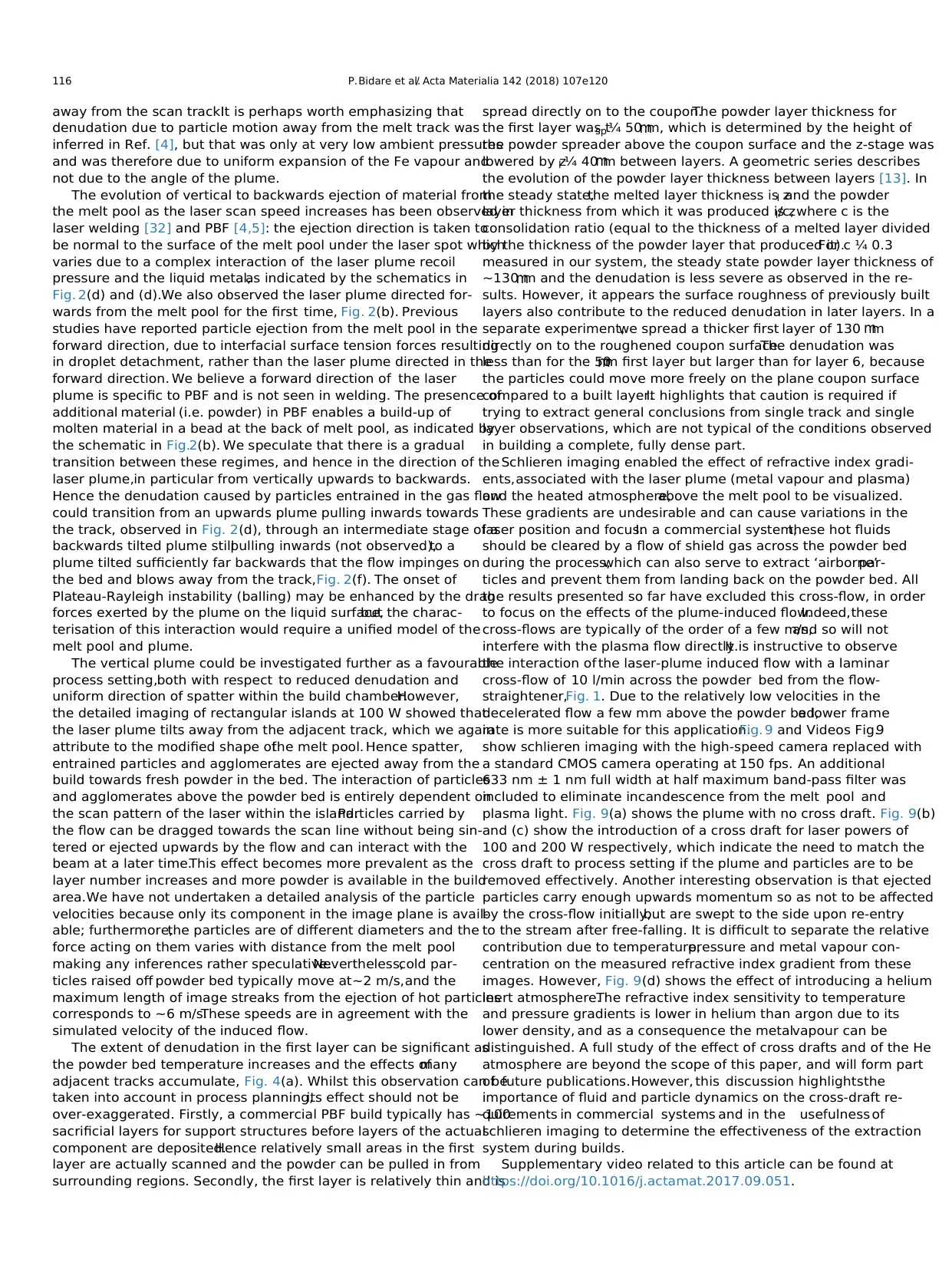
away from the scan track.It is perhaps worth emphasizing that
denudation due to particle motion away from the melt track was
inferred in Ref. [4], but that was only at very low ambient pressures
and was therefore due to uniform expansion of the Fe vapour and
not due to the angle of the plume.
The evolution of vertical to backwards ejection of material from
the melt pool as the laser scan speed increases has been observed in
laser welding [32] and PBF [4,5]: the ejection direction is taken to
be normal to the surface of the melt pool under the laser spot which
varies due to a complex interaction of the laser plume recoil
pressure and the liquid metal,as indicated by the schematics in
Fig. 2(d) and (d).We also observed the laser plume directed for-
wards from the melt pool for the first time, Fig. 2(b). Previous
studies have reported particle ejection from the melt pool in the
forward direction, due to interfacial surface tension forces resulting
in droplet detachment, rather than the laser plume directed in the
forward direction. We believe a forward direction of the laser
plume is specific to PBF and is not seen in welding. The presence of
additional material (i.e. powder) in PBF enables a build-up of
molten material in a bead at the back of melt pool, as indicated by
the schematic in Fig.2(b). We speculate that there is a gradual
transition between these regimes, and hence in the direction of the
laser plume,in particular from vertically upwards to backwards.
Hence the denudation caused by particles entrained in the gas flow
could transition from an upwards plume pulling inwards towards
the track, observed in Fig. 2(d), through an intermediate stage of a
backwards tilted plume stillpulling inwards (not observed),to a
plume tilted sufficiently far backwards that the flow impinges on
the bed and blows away from the track,Fig. 2(f). The onset of
Plateau-Rayleigh instability (balling) may be enhanced by the drag
forces exerted by the plume on the liquid surface,but the charac-
terisation of this interaction would require a unified model of the
melt pool and plume.
The vertical plume could be investigated further as a favourable
process setting,both with respect to reduced denudation and
uniform direction of spatter within the build chamber.However,
the detailed imaging of rectangular islands at 100 W showed that
the laser plume tilts away from the adjacent track, which we again
attribute to the modified shape ofthe melt pool. Hence spatter,
entrained particles and agglomerates are ejected away from the
build towards fresh powder in the bed. The interaction of particles
and agglomerates above the powder bed is entirely dependent on
the scan pattern of the laser within the island.Particles carried by
the flow can be dragged towards the scan line without being sin-
tered or ejected upwards by the flow and can interact with the
beam at a later time.This effect becomes more prevalent as the
layer number increases and more powder is available in the build
area.We have not undertaken a detailed analysis of the particle
velocities because only its component in the image plane is avail-
able; furthermore,the particles are of different diameters and the
force acting on them varies with distance from the melt pool
making any inferences rather speculative.Nevertheless,cold par-
ticles raised off powder bed typically move at~2 m/s,and the
maximum length of image streaks from the ejection of hot particles
corresponds to ~6 m/s.These speeds are in agreement with the
simulated velocity of the induced flow.
The extent of denudation in the first layer can be significant as
the powder bed temperature increases and the effects ofmany
adjacent tracks accumulate, Fig. 4(a). Whilst this observation can be
taken into account in process planning,its effect should not be
over-exaggerated. Firstly, a commercial PBF build typically has ~100
sacrificial layers for support structures before layers of the actual
component are deposited.Hence relatively small areas in the first
layer are actually scanned and the powder can be pulled in from
surrounding regions. Secondly, the first layer is relatively thin and is
spread directly on to the coupon.The powder layer thickness for
the first layer was tsp ¼ 50mm, which is determined by the height of
the powder spreader above the coupon surface and the z-stage was
lowered by zl ¼ 40mm between layers. A geometric series describes
the evolution of the powder layer thickness between layers [13]. In
the steady state,the melted layer thickness is zl and the powder
layer thickness from which it was produced is zl /c, where c is the
consolidation ratio (equal to the thickness of a melted layer divided
by the thickness of the powder layer that produced it).For c ¼ 0.3
measured in our system, the steady state powder layer thickness of
~130mm and the denudation is less severe as observed in the re-
sults. However, it appears the surface roughness of previously built
layers also contribute to the reduced denudation in later layers. In a
separate experiment,we spread a thicker first layer of 130 mm
directly on to the roughened coupon surface.The denudation was
less than for the 50mm first layer but larger than for layer 6, because
the particles could move more freely on the plane coupon surface
compared to a built layer.It highlights that caution is required if
trying to extract general conclusions from single track and single
layer observations, which are not typical of the conditions observed
in building a complete, fully dense part.
Schlieren imaging enabled the effect of refractive index gradi-
ents,associated with the laser plume (metal vapour and plasma)
and the heated atmosphere,above the melt pool to be visualized.
These gradients are undesirable and can cause variations in the
laser position and focus.In a commercial system,these hot fluids
should be cleared by a flow of shield gas across the powder bed
during the process,which can also serve to extract ‘airborne’par-
ticles and prevent them from landing back on the powder bed. All
the results presented so far have excluded this cross-flow, in order
to focus on the effects of the plume-induced flow.Indeed,these
cross-flows are typically of the order of a few m/s,and so will not
interfere with the plasma flow directly.It is instructive to observe
the interaction of the laser-plume induced flow with a laminar
cross-flow of 10 l/min across the powder bed from the flow-
straightener,Fig. 1. Due to the relatively low velocities in the
decelerated flow a few mm above the powder bed,a lower frame
rate is more suitable for this application.Fig. 9 and Videos Fig.9
show schlieren imaging with the high-speed camera replaced with
a standard CMOS camera operating at 150 fps. An additional
633 nm ± 1 nm full width at half maximum band-pass filter was
included to eliminate incandescence from the melt pool and
plasma light. Fig. 9(a) shows the plume with no cross draft. Fig. 9(b)
and (c) show the introduction of a cross draft for laser powers of
100 and 200 W respectively, which indicate the need to match the
cross draft to process setting if the plume and particles are to be
removed effectively. Another interesting observation is that ejected
particles carry enough upwards momentum so as not to be affected
by the cross-flow initially,but are swept to the side upon re-entry
to the stream after free-falling. It is difficult to separate the relative
contribution due to temperature,pressure and metal vapour con-
centration on the measured refractive index gradient from these
images. However, Fig. 9(d) shows the effect of introducing a helium
inert atmosphere.The refractive index sensitivity to temperature
and pressure gradients is lower in helium than argon due to its
lower density, and as a consequence the metalvapour can be
distinguished. A full study of the effect of cross drafts and of the He
atmosphere are beyond the scope of this paper, and will form part
of future publications.However, this discussion highlightsthe
importance of fluid and particle dynamics on the cross-draft re-
quirements in commercial systems and in the usefulness of
schlieren imaging to determine the effectiveness of the extraction
system during builds.
Supplementary video related to this article can be found at
https://doi.org/10.1016/j.actamat.2017.09.051.
P. Bidare et al./ Acta Materialia 142 (2018) 107e120116
denudation due to particle motion away from the melt track was
inferred in Ref. [4], but that was only at very low ambient pressures
and was therefore due to uniform expansion of the Fe vapour and
not due to the angle of the plume.
The evolution of vertical to backwards ejection of material from
the melt pool as the laser scan speed increases has been observed in
laser welding [32] and PBF [4,5]: the ejection direction is taken to
be normal to the surface of the melt pool under the laser spot which
varies due to a complex interaction of the laser plume recoil
pressure and the liquid metal,as indicated by the schematics in
Fig. 2(d) and (d).We also observed the laser plume directed for-
wards from the melt pool for the first time, Fig. 2(b). Previous
studies have reported particle ejection from the melt pool in the
forward direction, due to interfacial surface tension forces resulting
in droplet detachment, rather than the laser plume directed in the
forward direction. We believe a forward direction of the laser
plume is specific to PBF and is not seen in welding. The presence of
additional material (i.e. powder) in PBF enables a build-up of
molten material in a bead at the back of melt pool, as indicated by
the schematic in Fig.2(b). We speculate that there is a gradual
transition between these regimes, and hence in the direction of the
laser plume,in particular from vertically upwards to backwards.
Hence the denudation caused by particles entrained in the gas flow
could transition from an upwards plume pulling inwards towards
the track, observed in Fig. 2(d), through an intermediate stage of a
backwards tilted plume stillpulling inwards (not observed),to a
plume tilted sufficiently far backwards that the flow impinges on
the bed and blows away from the track,Fig. 2(f). The onset of
Plateau-Rayleigh instability (balling) may be enhanced by the drag
forces exerted by the plume on the liquid surface,but the charac-
terisation of this interaction would require a unified model of the
melt pool and plume.
The vertical plume could be investigated further as a favourable
process setting,both with respect to reduced denudation and
uniform direction of spatter within the build chamber.However,
the detailed imaging of rectangular islands at 100 W showed that
the laser plume tilts away from the adjacent track, which we again
attribute to the modified shape ofthe melt pool. Hence spatter,
entrained particles and agglomerates are ejected away from the
build towards fresh powder in the bed. The interaction of particles
and agglomerates above the powder bed is entirely dependent on
the scan pattern of the laser within the island.Particles carried by
the flow can be dragged towards the scan line without being sin-
tered or ejected upwards by the flow and can interact with the
beam at a later time.This effect becomes more prevalent as the
layer number increases and more powder is available in the build
area.We have not undertaken a detailed analysis of the particle
velocities because only its component in the image plane is avail-
able; furthermore,the particles are of different diameters and the
force acting on them varies with distance from the melt pool
making any inferences rather speculative.Nevertheless,cold par-
ticles raised off powder bed typically move at~2 m/s,and the
maximum length of image streaks from the ejection of hot particles
corresponds to ~6 m/s.These speeds are in agreement with the
simulated velocity of the induced flow.
The extent of denudation in the first layer can be significant as
the powder bed temperature increases and the effects ofmany
adjacent tracks accumulate, Fig. 4(a). Whilst this observation can be
taken into account in process planning,its effect should not be
over-exaggerated. Firstly, a commercial PBF build typically has ~100
sacrificial layers for support structures before layers of the actual
component are deposited.Hence relatively small areas in the first
layer are actually scanned and the powder can be pulled in from
surrounding regions. Secondly, the first layer is relatively thin and is
spread directly on to the coupon.The powder layer thickness for
the first layer was tsp ¼ 50mm, which is determined by the height of
the powder spreader above the coupon surface and the z-stage was
lowered by zl ¼ 40mm between layers. A geometric series describes
the evolution of the powder layer thickness between layers [13]. In
the steady state,the melted layer thickness is zl and the powder
layer thickness from which it was produced is zl /c, where c is the
consolidation ratio (equal to the thickness of a melted layer divided
by the thickness of the powder layer that produced it).For c ¼ 0.3
measured in our system, the steady state powder layer thickness of
~130mm and the denudation is less severe as observed in the re-
sults. However, it appears the surface roughness of previously built
layers also contribute to the reduced denudation in later layers. In a
separate experiment,we spread a thicker first layer of 130 mm
directly on to the roughened coupon surface.The denudation was
less than for the 50mm first layer but larger than for layer 6, because
the particles could move more freely on the plane coupon surface
compared to a built layer.It highlights that caution is required if
trying to extract general conclusions from single track and single
layer observations, which are not typical of the conditions observed
in building a complete, fully dense part.
Schlieren imaging enabled the effect of refractive index gradi-
ents,associated with the laser plume (metal vapour and plasma)
and the heated atmosphere,above the melt pool to be visualized.
These gradients are undesirable and can cause variations in the
laser position and focus.In a commercial system,these hot fluids
should be cleared by a flow of shield gas across the powder bed
during the process,which can also serve to extract ‘airborne’par-
ticles and prevent them from landing back on the powder bed. All
the results presented so far have excluded this cross-flow, in order
to focus on the effects of the plume-induced flow.Indeed,these
cross-flows are typically of the order of a few m/s,and so will not
interfere with the plasma flow directly.It is instructive to observe
the interaction of the laser-plume induced flow with a laminar
cross-flow of 10 l/min across the powder bed from the flow-
straightener,Fig. 1. Due to the relatively low velocities in the
decelerated flow a few mm above the powder bed,a lower frame
rate is more suitable for this application.Fig. 9 and Videos Fig.9
show schlieren imaging with the high-speed camera replaced with
a standard CMOS camera operating at 150 fps. An additional
633 nm ± 1 nm full width at half maximum band-pass filter was
included to eliminate incandescence from the melt pool and
plasma light. Fig. 9(a) shows the plume with no cross draft. Fig. 9(b)
and (c) show the introduction of a cross draft for laser powers of
100 and 200 W respectively, which indicate the need to match the
cross draft to process setting if the plume and particles are to be
removed effectively. Another interesting observation is that ejected
particles carry enough upwards momentum so as not to be affected
by the cross-flow initially,but are swept to the side upon re-entry
to the stream after free-falling. It is difficult to separate the relative
contribution due to temperature,pressure and metal vapour con-
centration on the measured refractive index gradient from these
images. However, Fig. 9(d) shows the effect of introducing a helium
inert atmosphere.The refractive index sensitivity to temperature
and pressure gradients is lower in helium than argon due to its
lower density, and as a consequence the metalvapour can be
distinguished. A full study of the effect of cross drafts and of the He
atmosphere are beyond the scope of this paper, and will form part
of future publications.However, this discussion highlightsthe
importance of fluid and particle dynamics on the cross-draft re-
quirements in commercial systems and in the usefulness of
schlieren imaging to determine the effectiveness of the extraction
system during builds.
Supplementary video related to this article can be found at
https://doi.org/10.1016/j.actamat.2017.09.051.
P. Bidare et al./ Acta Materialia 142 (2018) 107e120116
Secure Best Marks with AI Grader
Need help grading? Try our AI Grader for instant feedback on your assignments.
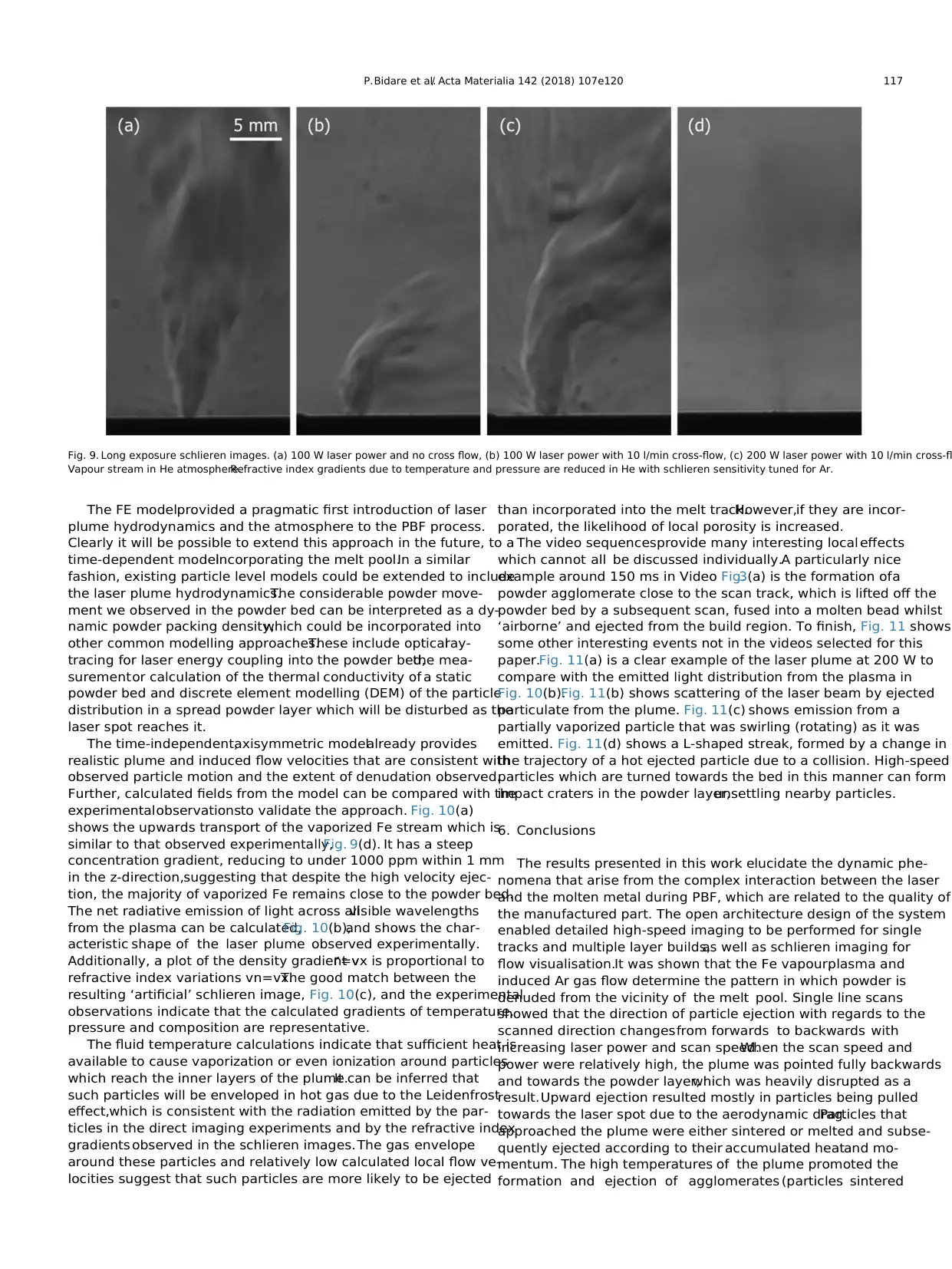
The FE modelprovided a pragmatic first introduction of laser
plume hydrodynamics and the atmosphere to the PBF process.
Clearly it will be possible to extend this approach in the future, to a
time-dependent modelincorporating the melt pool.In a similar
fashion, existing particle level models could be extended to include
the laser plume hydrodynamics.The considerable powder move-
ment we observed in the powder bed can be interpreted as a dy-
namic powder packing density,which could be incorporated into
other common modelling approaches.These include opticalray-
tracing for laser energy coupling into the powder bed,the mea-
surementor calculation of the thermal conductivity of a static
powder bed and discrete element modelling (DEM) of the particle
distribution in a spread powder layer which will be disturbed as the
laser spot reaches it.
The time-independent,axisymmetric modelalready provides
realistic plume and induced flow velocities that are consistent with
observed particle motion and the extent of denudation observed.
Further, calculated fields from the model can be compared with the
experimentalobservationsto validate the approach. Fig. 10(a)
shows the upwards transport of the vaporized Fe stream which is
similar to that observed experimentally,Fig. 9(d). It has a steep
concentration gradient, reducing to under 1000 ppm within 1 mm
in the z-direction,suggesting that despite the high velocity ejec-
tion, the majority of vaporized Fe remains close to the powder bed.
The net radiative emission of light across allvisible wavelengths
from the plasma can be calculated,Fig. 10(b),and shows the char-
acteristic shape of the laser plume observed experimentally.
Additionally, a plot of the density gradient vr =vx is proportional to
refractive index variations vn=vx.The good match between the
resulting ‘artificial’ schlieren image, Fig. 10(c), and the experimental
observations indicate that the calculated gradients of temperature,
pressure and composition are representative.
The fluid temperature calculations indicate that sufficient heat is
available to cause vaporization or even ionization around particles
which reach the inner layers of the plume.It can be inferred that
such particles will be enveloped in hot gas due to the Leidenfrost
effect,which is consistent with the radiation emitted by the par-
ticles in the direct imaging experiments and by the refractive index
gradients observed in the schlieren images. The gas envelope
around these particles and relatively low calculated local flow ve-
locities suggest that such particles are more likely to be ejected
than incorporated into the melt track.However,if they are incor-
porated, the likelihood of local porosity is increased.
The video sequencesprovide many interesting local effects
which cannot all be discussed individually.A particularly nice
example around 150 ms in Video Fig.3(a) is the formation ofa
powder agglomerate close to the scan track, which is lifted off the
powder bed by a subsequent scan, fused into a molten bead whilst
‘airborne’ and ejected from the build region. To finish, Fig. 11 shows
some other interesting events not in the videos selected for this
paper.Fig. 11(a) is a clear example of the laser plume at 200 W to
compare with the emitted light distribution from the plasma in
Fig. 10(b).Fig. 11(b) shows scattering of the laser beam by ejected
particulate from the plume. Fig. 11(c) shows emission from a
partially vaporized particle that was swirling (rotating) as it was
emitted. Fig. 11(d) shows a L-shaped streak, formed by a change in
the trajectory of a hot ejected particle due to a collision. High-speed
particles which are turned towards the bed in this manner can form
impact craters in the powder layer,unsettling nearby particles.
6. Conclusions
The results presented in this work elucidate the dynamic phe-
nomena that arise from the complex interaction between the laser
and the molten metal during PBF, which are related to the quality of
the manufactured part. The open architecture design of the system
enabled detailed high-speed imaging to be performed for single
tracks and multiple layer builds,as well as schlieren imaging for
flow visualisation.It was shown that the Fe vapour,plasma and
induced Ar gas flow determine the pattern in which powder is
denuded from the vicinity of the melt pool. Single line scans
showed that the direction of particle ejection with regards to the
scanned direction changesfrom forwards to backwards with
increasing laser power and scan speed.When the scan speed and
power were relatively high, the plume was pointed fully backwards
and towards the powder layer,which was heavily disrupted as a
result.Upward ejection resulted mostly in particles being pulled
towards the laser spot due to the aerodynamic drag.Particles that
approached the plume were either sintered or melted and subse-
quently ejected according to their accumulated heatand mo-
mentum. The high temperatures of the plume promoted the
formation and ejection of agglomerates (particles sintered
Fig. 9. Long exposure schlieren images. (a) 100 W laser power and no cross flow, (b) 100 W laser power with 10 l/min cross-flow, (c) 200 W laser power with 10 l/min cross-fl
Vapour stream in He atmosphere.Refractive index gradients due to temperature and pressure are reduced in He with schlieren sensitivity tuned for Ar.
P.Bidare et al./ Acta Materialia 142 (2018) 107e120 117
plume hydrodynamics and the atmosphere to the PBF process.
Clearly it will be possible to extend this approach in the future, to a
time-dependent modelincorporating the melt pool.In a similar
fashion, existing particle level models could be extended to include
the laser plume hydrodynamics.The considerable powder move-
ment we observed in the powder bed can be interpreted as a dy-
namic powder packing density,which could be incorporated into
other common modelling approaches.These include opticalray-
tracing for laser energy coupling into the powder bed,the mea-
surementor calculation of the thermal conductivity of a static
powder bed and discrete element modelling (DEM) of the particle
distribution in a spread powder layer which will be disturbed as the
laser spot reaches it.
The time-independent,axisymmetric modelalready provides
realistic plume and induced flow velocities that are consistent with
observed particle motion and the extent of denudation observed.
Further, calculated fields from the model can be compared with the
experimentalobservationsto validate the approach. Fig. 10(a)
shows the upwards transport of the vaporized Fe stream which is
similar to that observed experimentally,Fig. 9(d). It has a steep
concentration gradient, reducing to under 1000 ppm within 1 mm
in the z-direction,suggesting that despite the high velocity ejec-
tion, the majority of vaporized Fe remains close to the powder bed.
The net radiative emission of light across allvisible wavelengths
from the plasma can be calculated,Fig. 10(b),and shows the char-
acteristic shape of the laser plume observed experimentally.
Additionally, a plot of the density gradient vr =vx is proportional to
refractive index variations vn=vx.The good match between the
resulting ‘artificial’ schlieren image, Fig. 10(c), and the experimental
observations indicate that the calculated gradients of temperature,
pressure and composition are representative.
The fluid temperature calculations indicate that sufficient heat is
available to cause vaporization or even ionization around particles
which reach the inner layers of the plume.It can be inferred that
such particles will be enveloped in hot gas due to the Leidenfrost
effect,which is consistent with the radiation emitted by the par-
ticles in the direct imaging experiments and by the refractive index
gradients observed in the schlieren images. The gas envelope
around these particles and relatively low calculated local flow ve-
locities suggest that such particles are more likely to be ejected
than incorporated into the melt track.However,if they are incor-
porated, the likelihood of local porosity is increased.
The video sequencesprovide many interesting local effects
which cannot all be discussed individually.A particularly nice
example around 150 ms in Video Fig.3(a) is the formation ofa
powder agglomerate close to the scan track, which is lifted off the
powder bed by a subsequent scan, fused into a molten bead whilst
‘airborne’ and ejected from the build region. To finish, Fig. 11 shows
some other interesting events not in the videos selected for this
paper.Fig. 11(a) is a clear example of the laser plume at 200 W to
compare with the emitted light distribution from the plasma in
Fig. 10(b).Fig. 11(b) shows scattering of the laser beam by ejected
particulate from the plume. Fig. 11(c) shows emission from a
partially vaporized particle that was swirling (rotating) as it was
emitted. Fig. 11(d) shows a L-shaped streak, formed by a change in
the trajectory of a hot ejected particle due to a collision. High-speed
particles which are turned towards the bed in this manner can form
impact craters in the powder layer,unsettling nearby particles.
6. Conclusions
The results presented in this work elucidate the dynamic phe-
nomena that arise from the complex interaction between the laser
and the molten metal during PBF, which are related to the quality of
the manufactured part. The open architecture design of the system
enabled detailed high-speed imaging to be performed for single
tracks and multiple layer builds,as well as schlieren imaging for
flow visualisation.It was shown that the Fe vapour,plasma and
induced Ar gas flow determine the pattern in which powder is
denuded from the vicinity of the melt pool. Single line scans
showed that the direction of particle ejection with regards to the
scanned direction changesfrom forwards to backwards with
increasing laser power and scan speed.When the scan speed and
power were relatively high, the plume was pointed fully backwards
and towards the powder layer,which was heavily disrupted as a
result.Upward ejection resulted mostly in particles being pulled
towards the laser spot due to the aerodynamic drag.Particles that
approached the plume were either sintered or melted and subse-
quently ejected according to their accumulated heatand mo-
mentum. The high temperatures of the plume promoted the
formation and ejection of agglomerates (particles sintered
Fig. 9. Long exposure schlieren images. (a) 100 W laser power and no cross flow, (b) 100 W laser power with 10 l/min cross-flow, (c) 200 W laser power with 10 l/min cross-fl
Vapour stream in He atmosphere.Refractive index gradients due to temperature and pressure are reduced in He with schlieren sensitivity tuned for Ar.
P.Bidare et al./ Acta Materialia 142 (2018) 107e120 117

Fig. 11.(a) Laser plume radiation during an island scan at 200 W and 0.5 m/s,where surface temperature is increased. (b) Scattering of the laser beam by ejected particulate from
the plume.(c) Swirling hot particle ejection (d) Ejection of hot particle followed by collision,deflecting the particle back towards the bed.
Fig. 10.Simulation outputs at 100 W.(a) Fe concentration plot,showing localized dissipation of generated vapour.(b) Plot of the net radiative emission coefficient term 4pεN. (c)
Artificial schlieren,generated by plotting the vr=vr density gradient.
P. Bidare et al./ Acta Materialia 142 (2018) 107e120118
the plume.(c) Swirling hot particle ejection (d) Ejection of hot particle followed by collision,deflecting the particle back towards the bed.
Fig. 10.Simulation outputs at 100 W.(a) Fe concentration plot,showing localized dissipation of generated vapour.(b) Plot of the net radiative emission coefficient term 4pεN. (c)
Artificial schlieren,generated by plotting the vr=vr density gradient.
P. Bidare et al./ Acta Materialia 142 (2018) 107e120118
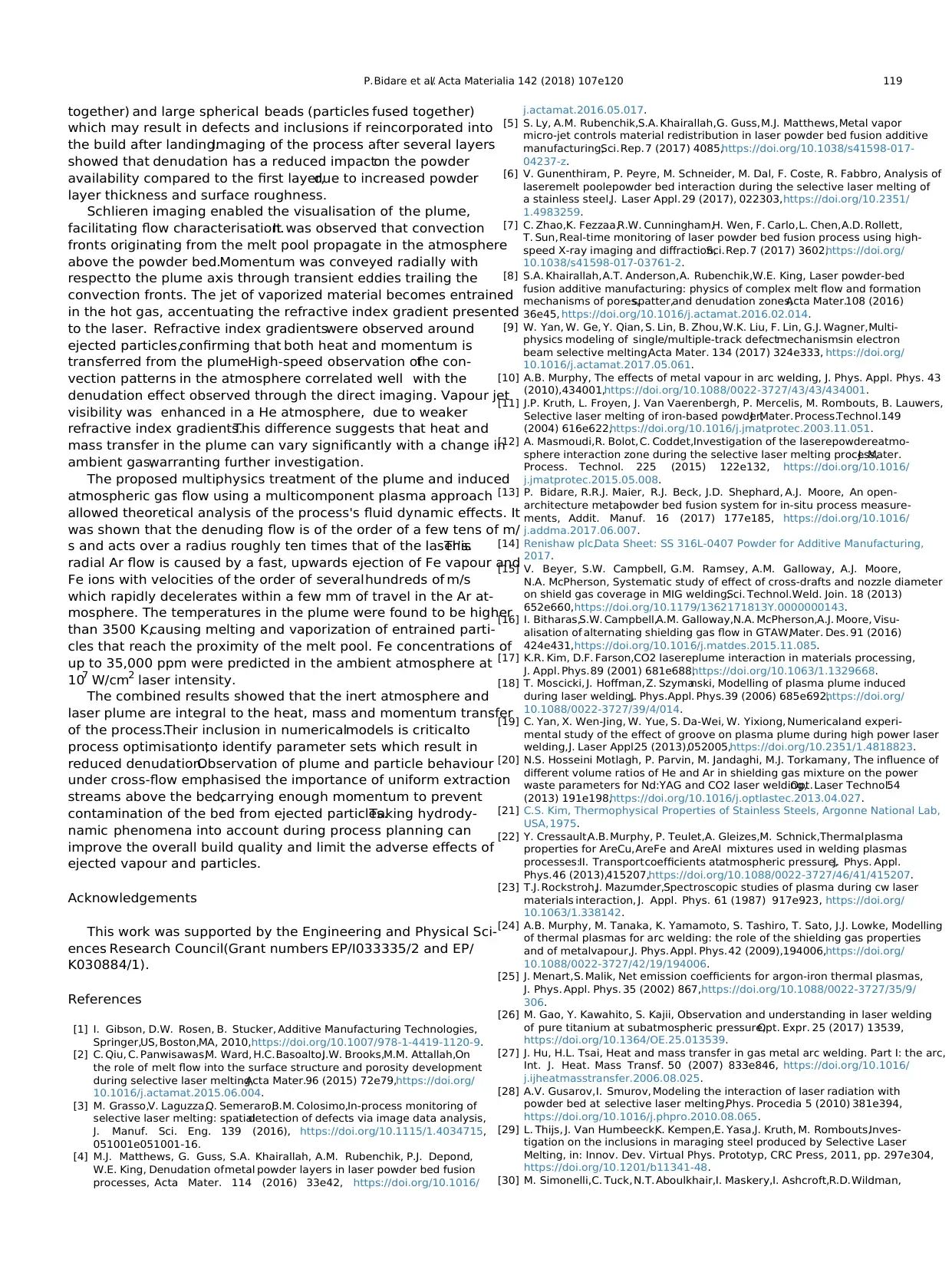
together) and large spherical beads (particles fused together)
which may result in defects and inclusions if reincorporated into
the build after landing.Imaging of the process after several layers
showed that denudation has a reduced impacton the powder
availability compared to the first layer,due to increased powder
layer thickness and surface roughness.
Schlieren imaging enabled the visualisation of the plume,
facilitating flow characterisation.It was observed that convection
fronts originating from the melt pool propagate in the atmosphere
above the powder bed.Momentum was conveyed radially with
respectto the plume axis through transient eddies trailing the
convection fronts. The jet of vaporized material becomes entrained
in the hot gas, accentuating the refractive index gradient presented
to the laser. Refractive index gradientswere observed around
ejected particles,confirming that both heat and momentum is
transferred from the plume.High-speed observation ofthe con-
vection patterns in the atmosphere correlated well with the
denudation effect observed through the direct imaging. Vapour jet
visibility was enhanced in a He atmosphere, due to weaker
refractive index gradients.This difference suggests that heat and
mass transfer in the plume can vary significantly with a change in
ambient gas,warranting further investigation.
The proposed multiphysics treatment of the plume and induced
atmospheric gas flow using a multicomponent plasma approach
allowed theoretical analysis of the process's fluid dynamic effects. It
was shown that the denuding flow is of the order of a few tens of m/
s and acts over a radius roughly ten times that of the laser's.This
radial Ar flow is caused by a fast, upwards ejection of Fe vapour and
Fe ions with velocities of the order of severalhundreds of m/s
which rapidly decelerates within a few mm of travel in the Ar at-
mosphere. The temperatures in the plume were found to be higher
than 3500 K,causing melting and vaporization of entrained parti-
cles that reach the proximity of the melt pool. Fe concentrations of
up to 35,000 ppm were predicted in the ambient atmosphere at
107 W/cm2 laser intensity.
The combined results showed that the inert atmosphere and
laser plume are integral to the heat, mass and momentum transfer
of the process.Their inclusion in numericalmodels is criticalto
process optimisation,to identify parameter sets which result in
reduced denudation.Observation of plume and particle behaviour
under cross-flow emphasised the importance of uniform extraction
streams above the bed,carrying enough momentum to prevent
contamination of the bed from ejected particles.Taking hydrody-
namic phenomena into account during process planning can
improve the overall build quality and limit the adverse effects of
ejected vapour and particles.
Acknowledgements
This work was supported by the Engineering and Physical Sci-
ences Research Council(Grant numbers EP/I033335/2 and EP/
K030884/1).
References
[1] I. Gibson, D.W. Rosen, B. Stucker, Additive Manufacturing Technologies,
Springer,US, Boston,MA, 2010,https://doi.org/10.1007/978-1-4419-1120-9.
[2] C. Qiu, C. Panwisawas,M. Ward, H.C.Basoalto,J.W. Brooks,M.M. Attallah,On
the role of melt flow into the surface structure and porosity development
during selective laser melting,Acta Mater.96 (2015) 72e79,https://doi.org/
10.1016/j.actamat.2015.06.004.
[3] M. Grasso,V. Laguzza,Q. Semeraro,B.M. Colosimo,In-process monitoring of
selective laser melting: spatialdetection of defects via image data analysis,
J. Manuf. Sci. Eng. 139 (2016), https://doi.org/10.1115/1.4034715,
051001e051001-16.
[4] M.J. Matthews, G. Guss, S.A. Khairallah, A.M. Rubenchik, P.J. Depond,
W.E. King, Denudation ofmetal powder layers in laser powder bed fusion
processes, Acta Mater. 114 (2016) 33e42, https://doi.org/10.1016/
j.actamat.2016.05.017.
[5] S. Ly, A.M. Rubenchik,S.A. Khairallah,G. Guss,M.J. Matthews,Metal vapor
micro-jet controls material redistribution in laser powder bed fusion additive
manufacturing,Sci.Rep.7 (2017) 4085,https://doi.org/10.1038/s41598-017-
04237-z.
[6] V. Gunenthiram, P. Peyre, M. Schneider, M. Dal, F. Coste, R. Fabbro, Analysis of
laseremelt poolepowder bed interaction during the selective laser melting of
a stainless steel,J. Laser Appl. 29 (2017), 022303,https://doi.org/10.2351/
1.4983259.
[7] C. Zhao,K. Fezzaa,R.W. Cunningham,H. Wen, F. Carlo,L. Chen,A.D. Rollett,
T. Sun,Real-time monitoring of laser powder bed fusion process using high-
speed X-ray imaging and diffraction,Sci.Rep.7 (2017) 3602,https://doi.org/
10.1038/s41598-017-03761-2.
[8] S.A. Khairallah,A.T. Anderson,A. Rubenchik,W.E. King, Laser powder-bed
fusion additive manufacturing: physics of complex melt flow and formation
mechanisms of pores,spatter,and denudation zones,Acta Mater.108 (2016)
36e45, https://doi.org/10.1016/j.actamat.2016.02.014.
[9] W. Yan, W. Ge, Y. Qian, S. Lin, B. Zhou,W.K. Liu, F. Lin, G.J. Wagner,Multi-
physics modeling of single/multiple-track defectmechanismsin electron
beam selective melting,Acta Mater. 134 (2017) 324e333, https://doi.org/
10.1016/j.actamat.2017.05.061.
[10] A.B. Murphy, The effects of metal vapour in arc welding, J. Phys. Appl. Phys. 43
(2010),434001,https://doi.org/10.1088/0022-3727/43/43/434001.
[11] J.P. Kruth, L. Froyen, J. Van Vaerenbergh, P. Mercelis, M. Rombouts, B. Lauwers,
Selective laser melting of iron-based powder,J. Mater.Process.Technol.149
(2004) 616e622,https://doi.org/10.1016/j.jmatprotec.2003.11.051.
[12] A. Masmoudi,R. Bolot,C. Coddet,Investigation of the laserepowdereatmo-
sphere interaction zone during the selective laser melting process,J. Mater.
Process. Technol. 225 (2015) 122e132, https://doi.org/10.1016/
j.jmatprotec.2015.05.008.
[13] P. Bidare, R.R.J. Maier, R.J. Beck, J.D. Shephard, A.J. Moore, An open-
architecture metalpowder bed fusion system for in-situ process measure-
ments, Addit. Manuf. 16 (2017) 177e185, https://doi.org/10.1016/
j.addma.2017.06.007.
[14] Renishaw plc,Data Sheet: SS 316L-0407 Powder for Additive Manufacturing,
2017.
[15] V. Beyer, S.W. Campbell, G.M. Ramsey, A.M. Galloway, A.J. Moore,
N.A. McPherson, Systematic study of effect of cross-drafts and nozzle diameter
on shield gas coverage in MIG welding,Sci. Technol.Weld. Join. 18 (2013)
652e660,https://doi.org/10.1179/1362171813Y.0000000143.
[16] I. Bitharas,S.W. Campbell,A.M. Galloway,N.A. McPherson,A.J. Moore, Visu-
alisation of alternating shielding gas flow in GTAW,Mater. Des. 91 (2016)
424e431,https://doi.org/10.1016/j.matdes.2015.11.085.
[17] K.R. Kim, D.F. Farson,CO2 lasereplume interaction in materials processing,
J. Appl. Phys.89 (2001) 681e688,https://doi.org/10.1063/1.1329668.
[18] T. Moscicki, J. Hoffman,Z. Szymanski, Modelling of plasma plume induced
during laser welding,J. Phys.Appl. Phys.39 (2006) 685e692,https://doi.org/
10.1088/0022-3727/39/4/014.
[19] C. Yan, X. Wen-Jing, W. Yue, S. Da-Wei, W. Yixiong, Numericaland experi-
mental study of the effect of groove on plasma plume during high power laser
welding,J. Laser Appl.25 (2013),052005,https://doi.org/10.2351/1.4818823.
[20] N.S. Hosseini Motlagh, P. Parvin, M. Jandaghi, M.J. Torkamany, The influence of
different volume ratios of He and Ar in shielding gas mixture on the power
waste parameters for Nd:YAG and CO2 laser welding,Opt.Laser Technol.54
(2013) 191e198,https://doi.org/10.1016/j.optlastec.2013.04.027.
[21] C.S. Kim, Thermophysical Properties of Stainless Steels, Argonne National Lab,
USA,1975.
[22] Y. Cressault,A.B.Murphy, P. Teulet,A. Gleizes,M. Schnick,Thermalplasma
properties for AreCu,AreFe and AreAl mixtures used in welding plasmas
processes:II. Transportcoefficients atatmospheric pressure,J. Phys. Appl.
Phys.46 (2013),415207,https://doi.org/10.1088/0022-3727/46/41/415207.
[23] T.J. Rockstroh,J. Mazumder,Spectroscopic studies of plasma during cw laser
materials interaction, J. Appl. Phys. 61 (1987) 917e923, https://doi.org/
10.1063/1.338142.
[24] A.B. Murphy, M. Tanaka, K. Yamamoto, S. Tashiro, T. Sato, J.J. Lowke, Modelling
of thermal plasmas for arc welding: the role of the shielding gas properties
and of metalvapour,J. Phys.Appl. Phys.42 (2009),194006,https://doi.org/
10.1088/0022-3727/42/19/194006.
[25] J. Menart,S. Malik, Net emission coefficients for argon-iron thermal plasmas,
J. Phys. Appl. Phys. 35 (2002) 867,https://doi.org/10.1088/0022-3727/35/9/
306.
[26] M. Gao, Y. Kawahito, S. Kajii, Observation and understanding in laser welding
of pure titanium at subatmospheric pressure,Opt. Expr. 25 (2017) 13539,
https://doi.org/10.1364/OE.25.013539.
[27] J. Hu, H.L. Tsai, Heat and mass transfer in gas metal arc welding. Part I: the arc,
Int. J. Heat. Mass Transf. 50 (2007) 833e846, https://doi.org/10.1016/
j.ijheatmasstransfer.2006.08.025.
[28] A.V. Gusarov,I. Smurov, Modeling the interaction of laser radiation with
powder bed at selective laser melting,Phys. Procedia 5 (2010) 381e394,
https://doi.org/10.1016/j.phpro.2010.08.065.
[29] L. Thijs, J. Van Humbeeck,K. Kempen,E. Yasa,J. Kruth, M. Rombouts,Inves-
tigation on the inclusions in maraging steel produced by Selective Laser
Melting, in: Innov. Dev. Virtual Phys. Prototyp, CRC Press, 2011, pp. 297e304,
https://doi.org/10.1201/b11341-48.
[30] M. Simonelli,C. Tuck,N.T. Aboulkhair,I. Maskery,I. Ashcroft,R.D.Wildman,
P.Bidare et al./ Acta Materialia 142 (2018) 107e120 119
which may result in defects and inclusions if reincorporated into
the build after landing.Imaging of the process after several layers
showed that denudation has a reduced impacton the powder
availability compared to the first layer,due to increased powder
layer thickness and surface roughness.
Schlieren imaging enabled the visualisation of the plume,
facilitating flow characterisation.It was observed that convection
fronts originating from the melt pool propagate in the atmosphere
above the powder bed.Momentum was conveyed radially with
respectto the plume axis through transient eddies trailing the
convection fronts. The jet of vaporized material becomes entrained
in the hot gas, accentuating the refractive index gradient presented
to the laser. Refractive index gradientswere observed around
ejected particles,confirming that both heat and momentum is
transferred from the plume.High-speed observation ofthe con-
vection patterns in the atmosphere correlated well with the
denudation effect observed through the direct imaging. Vapour jet
visibility was enhanced in a He atmosphere, due to weaker
refractive index gradients.This difference suggests that heat and
mass transfer in the plume can vary significantly with a change in
ambient gas,warranting further investigation.
The proposed multiphysics treatment of the plume and induced
atmospheric gas flow using a multicomponent plasma approach
allowed theoretical analysis of the process's fluid dynamic effects. It
was shown that the denuding flow is of the order of a few tens of m/
s and acts over a radius roughly ten times that of the laser's.This
radial Ar flow is caused by a fast, upwards ejection of Fe vapour and
Fe ions with velocities of the order of severalhundreds of m/s
which rapidly decelerates within a few mm of travel in the Ar at-
mosphere. The temperatures in the plume were found to be higher
than 3500 K,causing melting and vaporization of entrained parti-
cles that reach the proximity of the melt pool. Fe concentrations of
up to 35,000 ppm were predicted in the ambient atmosphere at
107 W/cm2 laser intensity.
The combined results showed that the inert atmosphere and
laser plume are integral to the heat, mass and momentum transfer
of the process.Their inclusion in numericalmodels is criticalto
process optimisation,to identify parameter sets which result in
reduced denudation.Observation of plume and particle behaviour
under cross-flow emphasised the importance of uniform extraction
streams above the bed,carrying enough momentum to prevent
contamination of the bed from ejected particles.Taking hydrody-
namic phenomena into account during process planning can
improve the overall build quality and limit the adverse effects of
ejected vapour and particles.
Acknowledgements
This work was supported by the Engineering and Physical Sci-
ences Research Council(Grant numbers EP/I033335/2 and EP/
K030884/1).
References
[1] I. Gibson, D.W. Rosen, B. Stucker, Additive Manufacturing Technologies,
Springer,US, Boston,MA, 2010,https://doi.org/10.1007/978-1-4419-1120-9.
[2] C. Qiu, C. Panwisawas,M. Ward, H.C.Basoalto,J.W. Brooks,M.M. Attallah,On
the role of melt flow into the surface structure and porosity development
during selective laser melting,Acta Mater.96 (2015) 72e79,https://doi.org/
10.1016/j.actamat.2015.06.004.
[3] M. Grasso,V. Laguzza,Q. Semeraro,B.M. Colosimo,In-process monitoring of
selective laser melting: spatialdetection of defects via image data analysis,
J. Manuf. Sci. Eng. 139 (2016), https://doi.org/10.1115/1.4034715,
051001e051001-16.
[4] M.J. Matthews, G. Guss, S.A. Khairallah, A.M. Rubenchik, P.J. Depond,
W.E. King, Denudation ofmetal powder layers in laser powder bed fusion
processes, Acta Mater. 114 (2016) 33e42, https://doi.org/10.1016/
j.actamat.2016.05.017.
[5] S. Ly, A.M. Rubenchik,S.A. Khairallah,G. Guss,M.J. Matthews,Metal vapor
micro-jet controls material redistribution in laser powder bed fusion additive
manufacturing,Sci.Rep.7 (2017) 4085,https://doi.org/10.1038/s41598-017-
04237-z.
[6] V. Gunenthiram, P. Peyre, M. Schneider, M. Dal, F. Coste, R. Fabbro, Analysis of
laseremelt poolepowder bed interaction during the selective laser melting of
a stainless steel,J. Laser Appl. 29 (2017), 022303,https://doi.org/10.2351/
1.4983259.
[7] C. Zhao,K. Fezzaa,R.W. Cunningham,H. Wen, F. Carlo,L. Chen,A.D. Rollett,
T. Sun,Real-time monitoring of laser powder bed fusion process using high-
speed X-ray imaging and diffraction,Sci.Rep.7 (2017) 3602,https://doi.org/
10.1038/s41598-017-03761-2.
[8] S.A. Khairallah,A.T. Anderson,A. Rubenchik,W.E. King, Laser powder-bed
fusion additive manufacturing: physics of complex melt flow and formation
mechanisms of pores,spatter,and denudation zones,Acta Mater.108 (2016)
36e45, https://doi.org/10.1016/j.actamat.2016.02.014.
[9] W. Yan, W. Ge, Y. Qian, S. Lin, B. Zhou,W.K. Liu, F. Lin, G.J. Wagner,Multi-
physics modeling of single/multiple-track defectmechanismsin electron
beam selective melting,Acta Mater. 134 (2017) 324e333, https://doi.org/
10.1016/j.actamat.2017.05.061.
[10] A.B. Murphy, The effects of metal vapour in arc welding, J. Phys. Appl. Phys. 43
(2010),434001,https://doi.org/10.1088/0022-3727/43/43/434001.
[11] J.P. Kruth, L. Froyen, J. Van Vaerenbergh, P. Mercelis, M. Rombouts, B. Lauwers,
Selective laser melting of iron-based powder,J. Mater.Process.Technol.149
(2004) 616e622,https://doi.org/10.1016/j.jmatprotec.2003.11.051.
[12] A. Masmoudi,R. Bolot,C. Coddet,Investigation of the laserepowdereatmo-
sphere interaction zone during the selective laser melting process,J. Mater.
Process. Technol. 225 (2015) 122e132, https://doi.org/10.1016/
j.jmatprotec.2015.05.008.
[13] P. Bidare, R.R.J. Maier, R.J. Beck, J.D. Shephard, A.J. Moore, An open-
architecture metalpowder bed fusion system for in-situ process measure-
ments, Addit. Manuf. 16 (2017) 177e185, https://doi.org/10.1016/
j.addma.2017.06.007.
[14] Renishaw plc,Data Sheet: SS 316L-0407 Powder for Additive Manufacturing,
2017.
[15] V. Beyer, S.W. Campbell, G.M. Ramsey, A.M. Galloway, A.J. Moore,
N.A. McPherson, Systematic study of effect of cross-drafts and nozzle diameter
on shield gas coverage in MIG welding,Sci. Technol.Weld. Join. 18 (2013)
652e660,https://doi.org/10.1179/1362171813Y.0000000143.
[16] I. Bitharas,S.W. Campbell,A.M. Galloway,N.A. McPherson,A.J. Moore, Visu-
alisation of alternating shielding gas flow in GTAW,Mater. Des. 91 (2016)
424e431,https://doi.org/10.1016/j.matdes.2015.11.085.
[17] K.R. Kim, D.F. Farson,CO2 lasereplume interaction in materials processing,
J. Appl. Phys.89 (2001) 681e688,https://doi.org/10.1063/1.1329668.
[18] T. Moscicki, J. Hoffman,Z. Szymanski, Modelling of plasma plume induced
during laser welding,J. Phys.Appl. Phys.39 (2006) 685e692,https://doi.org/
10.1088/0022-3727/39/4/014.
[19] C. Yan, X. Wen-Jing, W. Yue, S. Da-Wei, W. Yixiong, Numericaland experi-
mental study of the effect of groove on plasma plume during high power laser
welding,J. Laser Appl.25 (2013),052005,https://doi.org/10.2351/1.4818823.
[20] N.S. Hosseini Motlagh, P. Parvin, M. Jandaghi, M.J. Torkamany, The influence of
different volume ratios of He and Ar in shielding gas mixture on the power
waste parameters for Nd:YAG and CO2 laser welding,Opt.Laser Technol.54
(2013) 191e198,https://doi.org/10.1016/j.optlastec.2013.04.027.
[21] C.S. Kim, Thermophysical Properties of Stainless Steels, Argonne National Lab,
USA,1975.
[22] Y. Cressault,A.B.Murphy, P. Teulet,A. Gleizes,M. Schnick,Thermalplasma
properties for AreCu,AreFe and AreAl mixtures used in welding plasmas
processes:II. Transportcoefficients atatmospheric pressure,J. Phys. Appl.
Phys.46 (2013),415207,https://doi.org/10.1088/0022-3727/46/41/415207.
[23] T.J. Rockstroh,J. Mazumder,Spectroscopic studies of plasma during cw laser
materials interaction, J. Appl. Phys. 61 (1987) 917e923, https://doi.org/
10.1063/1.338142.
[24] A.B. Murphy, M. Tanaka, K. Yamamoto, S. Tashiro, T. Sato, J.J. Lowke, Modelling
of thermal plasmas for arc welding: the role of the shielding gas properties
and of metalvapour,J. Phys.Appl. Phys.42 (2009),194006,https://doi.org/
10.1088/0022-3727/42/19/194006.
[25] J. Menart,S. Malik, Net emission coefficients for argon-iron thermal plasmas,
J. Phys. Appl. Phys. 35 (2002) 867,https://doi.org/10.1088/0022-3727/35/9/
306.
[26] M. Gao, Y. Kawahito, S. Kajii, Observation and understanding in laser welding
of pure titanium at subatmospheric pressure,Opt. Expr. 25 (2017) 13539,
https://doi.org/10.1364/OE.25.013539.
[27] J. Hu, H.L. Tsai, Heat and mass transfer in gas metal arc welding. Part I: the arc,
Int. J. Heat. Mass Transf. 50 (2007) 833e846, https://doi.org/10.1016/
j.ijheatmasstransfer.2006.08.025.
[28] A.V. Gusarov,I. Smurov, Modeling the interaction of laser radiation with
powder bed at selective laser melting,Phys. Procedia 5 (2010) 381e394,
https://doi.org/10.1016/j.phpro.2010.08.065.
[29] L. Thijs, J. Van Humbeeck,K. Kempen,E. Yasa,J. Kruth, M. Rombouts,Inves-
tigation on the inclusions in maraging steel produced by Selective Laser
Melting, in: Innov. Dev. Virtual Phys. Prototyp, CRC Press, 2011, pp. 297e304,
https://doi.org/10.1201/b11341-48.
[30] M. Simonelli,C. Tuck,N.T. Aboulkhair,I. Maskery,I. Ashcroft,R.D.Wildman,
P.Bidare et al./ Acta Materialia 142 (2018) 107e120 119
Paraphrase This Document
Need a fresh take? Get an instant paraphrase of this document with our AI Paraphraser
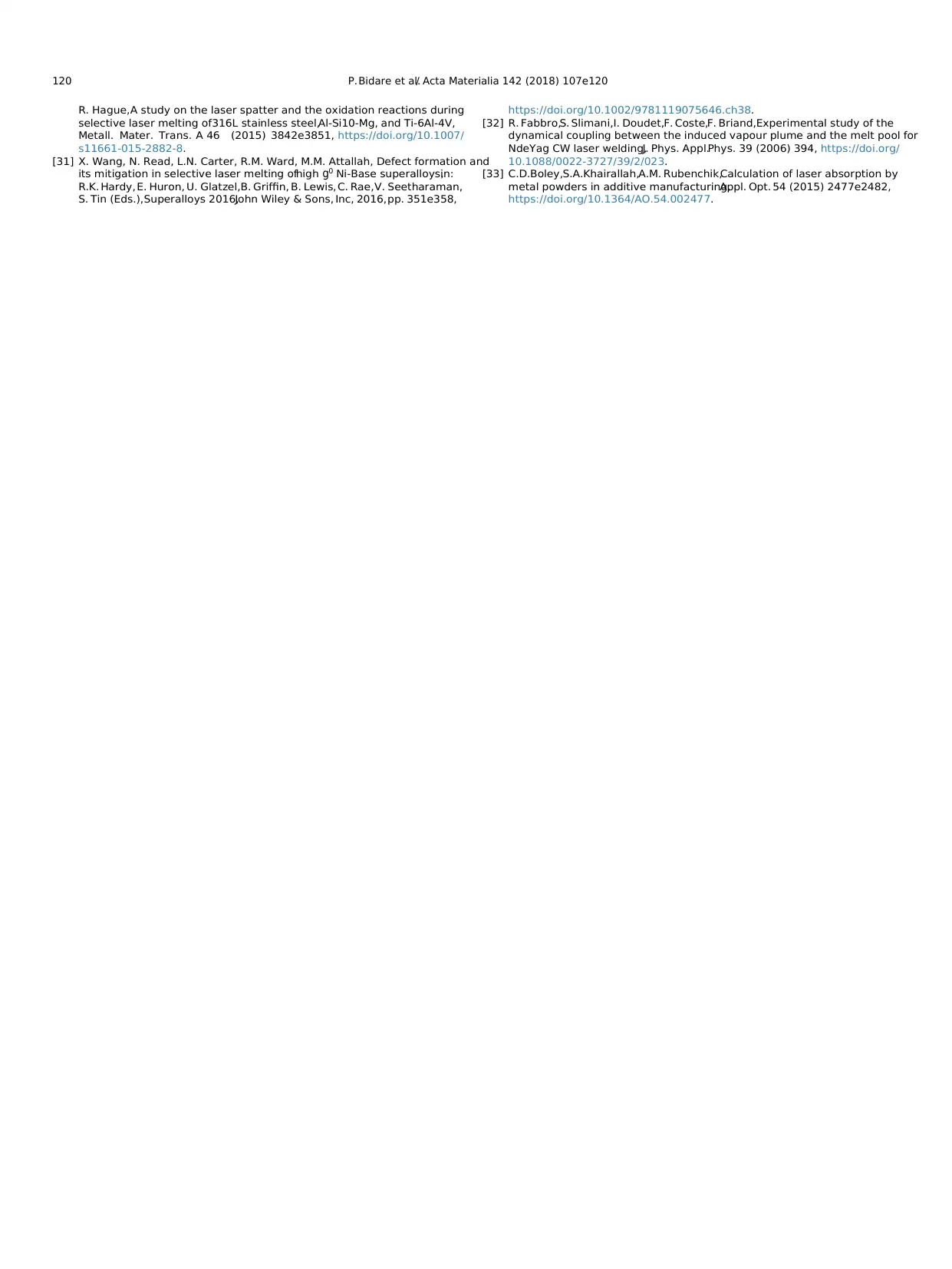
R. Hague,A study on the laser spatter and the oxidation reactions during
selective laser melting of316L stainless steel,Al-Si10-Mg, and Ti-6Al-4V,
Metall. Mater. Trans. A 46 (2015) 3842e3851, https://doi.org/10.1007/
s11661-015-2882-8.
[31] X. Wang, N. Read, L.N. Carter, R.M. Ward, M.M. Attallah, Defect formation and
its mitigation in selective laser melting ofhigh g0 Ni-Base superalloys,in:
R.K. Hardy,E. Huron, U. Glatzel,B. Griffin, B. Lewis, C. Rae,V. Seetharaman,
S. Tin (Eds.),Superalloys 2016,John Wiley & Sons, Inc, 2016,pp. 351e358,
https://doi.org/10.1002/9781119075646.ch38.
[32] R. Fabbro,S. Slimani,I. Doudet,F. Coste,F. Briand,Experimental study of the
dynamical coupling between the induced vapour plume and the melt pool for
NdeYag CW laser welding,J. Phys. Appl.Phys. 39 (2006) 394, https://doi.org/
10.1088/0022-3727/39/2/023.
[33] C.D.Boley,S.A.Khairallah,A.M. Rubenchik,Calculation of laser absorption by
metal powders in additive manufacturing,Appl. Opt. 54 (2015) 2477e2482,
https://doi.org/10.1364/AO.54.002477.
P. Bidare et al./ Acta Materialia 142 (2018) 107e120120
selective laser melting of316L stainless steel,Al-Si10-Mg, and Ti-6Al-4V,
Metall. Mater. Trans. A 46 (2015) 3842e3851, https://doi.org/10.1007/
s11661-015-2882-8.
[31] X. Wang, N. Read, L.N. Carter, R.M. Ward, M.M. Attallah, Defect formation and
its mitigation in selective laser melting ofhigh g0 Ni-Base superalloys,in:
R.K. Hardy,E. Huron, U. Glatzel,B. Griffin, B. Lewis, C. Rae,V. Seetharaman,
S. Tin (Eds.),Superalloys 2016,John Wiley & Sons, Inc, 2016,pp. 351e358,
https://doi.org/10.1002/9781119075646.ch38.
[32] R. Fabbro,S. Slimani,I. Doudet,F. Coste,F. Briand,Experimental study of the
dynamical coupling between the induced vapour plume and the melt pool for
NdeYag CW laser welding,J. Phys. Appl.Phys. 39 (2006) 394, https://doi.org/
10.1088/0022-3727/39/2/023.
[33] C.D.Boley,S.A.Khairallah,A.M. Rubenchik,Calculation of laser absorption by
metal powders in additive manufacturing,Appl. Opt. 54 (2015) 2477e2482,
https://doi.org/10.1364/AO.54.002477.
P. Bidare et al./ Acta Materialia 142 (2018) 107e120120
1 out of 14
![[object Object]](/_next/image/?url=%2F_next%2Fstatic%2Fmedia%2Flogo.6d15ce61.png&w=640&q=75)
Your All-in-One AI-Powered Toolkit for Academic Success.
+13062052269
info@desklib.com
Available 24*7 on WhatsApp / Email
Unlock your academic potential
© 2024 | Zucol Services PVT LTD | All rights reserved.