Fluid and particle dynamics in laser powder bed fusion
Perform a literature search on one of the provided topics in the field of advanced materials and processes.
14 Pages11136 Words392 Views
Added on 2023-04-05
About This Document
This article discusses the fluid and particle dynamics in laser powder bed fusion (LPBF) process and its implications on the heat, mass, and momentum transfer. It also highlights the importance of understanding fluid dynamic phenomena in preventing defects in additively manufactured parts.
Fluid and particle dynamics in laser powder bed fusion
Perform a literature search on one of the provided topics in the field of advanced materials and processes.
Added on 2023-04-05
ShareRelated Documents
Full length article
Fluid and particle dynamics in laser powder bed fusion
P. Bidare a, 1 , I. Bitharas a, *, 1
, R.M. Ward b
, M.M. Attallah b
, A.J. Moore a
a Institute of Photonics and Quantum Sciences, Heriot-Watt University, Edinburgh EH14 4AS, UK
b School of Metallurgy and Materials, University of Birmingham, Birmingham B15 2TT, UK
a r t i c l e i n f o
Article history:
Received 19 July 2017
Received in revised form
5 September 2017
Accepted 21 September 2017
Available online 22 September 2017
Keywords:
High-speed imaging
In situ
Powder consolidation
Finite element modelling (FEM)
Theory and modelling (kinetics, transport,
diffusion)
a b s t r a c t
In this work, we employ a combination of high-speed imaging and schlieren imaging, as well as mul-
tiphysics modelling, to elucidate the effects of the interaction between the laser beam and the powder
bed. The formation of denuded areas where the powder was removed during single line and island scans
over several layers were imaged for the first time. The inclination of the laser plume was shifted from
forwards to backwards by changing power and scan speed, resulting in different denudation regimes
with implications to the heat, mass and momentum transfer of the process. As the build progressed,
denudation became less severe than for a single powder layer, but the occurrence of sintered and fused
powder agglomerates, which were affected by the plume, increased. Schlieren imaging enabled the
visualisation of the Ar gas flow, which takes place in the atmosphere above the bed due to the plume, in
addition to its interaction with affected particles. Numerical modelling was used to understand and
quantify the observed flow behaviour, through the hydrodynamic treatment of the laser plume as a
multi-component Ar-Fe plasma. These results promote the characterisation of fluid dynamic phenomena
during the laser powder-bed fusion (LPBF) process, which constitutes a key factor in the prevention of
defects in additively manufactured parts.
© 2017 Acta Materialia Inc. Published by Elsevier Ltd. This is an open access article under the CC BY
license (http://creativecommons.org/licenses/by/4.0/).
1. Introduction
Detailed imaging of the interaction between the laser beam and
the powder bed whilst building multiple layer islands with metal
powder bed fusion (PBF) has not been reported previously. It is
extremely challenging to record images through the viewing win-
dow of commercial PBF systems with sufficient magnification or
contrast to see individual powder particles in the powder bed.
Higher magnification images have so far focussed on the melt pool
whilst scanning a single laser track in a representative powder
layer. In this paper, we report detailed, in-process imaging of the
interaction of the laser beam with the powder bed during the PBF
build of fully dense parts. We demonstrate that the PBF process is
more dynamic than is generally appreciated and involves consid-
erable motion of the powder particles and agglomerates in and
above the powder bed. This motion is driven by the laser-induced
plume of metal vapour and plasma above the melt pool. We
therefore develop the first finite element model for PBF that
incorporates the laser plume and inert atmosphere in order to
explain the observed motion of the fluids and powder particles in
and above the powder bed.
Metal powder bed fusion (PBF) is a category of additive manu-
facture (AM) process in which thermal energy selectively fuses
regions of a powder bed [1]. Commercial PBF systems are already
used to manufacture production components; but these compo-
nents generally require intensive, part-specific process setting
refinement to reduce distortions caused by residual stresses, to
determine process settings that reduce defects and to determine
acceptable positions for support structures. In the future, software
will simulate a full-build and reduce the time required to determine
process settings, but that approach still requires better process
understanding so that residual stresses, porosity and surface finish
are predicted reliably for different process regimes.
Imaging of the PBF process is one approach being used to ach-
ieve this improved understanding. Qiu et al. [2] undertook a sys-
tematic study of the effect of laser scan speed and powder layer
thickness on porosity using a commercial Concept Laser M2 system.
SEM images of sample surfaces revealed an increase in surface
roughness and weld track irregularity when either the scan speed
or powder layer thickness were increased above certain (process-
specific) thresholds. Increases in surface roughness were correlated
* Corresponding author.
E-mail addresses: p.bidare@hw.ac.uk (P. Bidare), i.bitharas@hw.ac.uk
(I. Bitharas), a.moore@hw.ac.uk (A.J. Moore).
1 Equal contribution, Joint first authors.
Contents lists available at ScienceDirect
Acta Materialia
j o u r n a l h o m e p a g e : w w w . e l s e v i e r . c o m / l o c a t e / a c t a m a t
https://doi.org/10.1016/j.actamat.2017.09.051
1359-6454/© 2017 Acta Materialia Inc. Published by Elsevier Ltd. This is an open access article under the CC BY license (http://creativecommons.org/licenses/by/4.0/).
Acta Materialia 142 (2018) 107e120
Fluid and particle dynamics in laser powder bed fusion
P. Bidare a, 1 , I. Bitharas a, *, 1
, R.M. Ward b
, M.M. Attallah b
, A.J. Moore a
a Institute of Photonics and Quantum Sciences, Heriot-Watt University, Edinburgh EH14 4AS, UK
b School of Metallurgy and Materials, University of Birmingham, Birmingham B15 2TT, UK
a r t i c l e i n f o
Article history:
Received 19 July 2017
Received in revised form
5 September 2017
Accepted 21 September 2017
Available online 22 September 2017
Keywords:
High-speed imaging
In situ
Powder consolidation
Finite element modelling (FEM)
Theory and modelling (kinetics, transport,
diffusion)
a b s t r a c t
In this work, we employ a combination of high-speed imaging and schlieren imaging, as well as mul-
tiphysics modelling, to elucidate the effects of the interaction between the laser beam and the powder
bed. The formation of denuded areas where the powder was removed during single line and island scans
over several layers were imaged for the first time. The inclination of the laser plume was shifted from
forwards to backwards by changing power and scan speed, resulting in different denudation regimes
with implications to the heat, mass and momentum transfer of the process. As the build progressed,
denudation became less severe than for a single powder layer, but the occurrence of sintered and fused
powder agglomerates, which were affected by the plume, increased. Schlieren imaging enabled the
visualisation of the Ar gas flow, which takes place in the atmosphere above the bed due to the plume, in
addition to its interaction with affected particles. Numerical modelling was used to understand and
quantify the observed flow behaviour, through the hydrodynamic treatment of the laser plume as a
multi-component Ar-Fe plasma. These results promote the characterisation of fluid dynamic phenomena
during the laser powder-bed fusion (LPBF) process, which constitutes a key factor in the prevention of
defects in additively manufactured parts.
© 2017 Acta Materialia Inc. Published by Elsevier Ltd. This is an open access article under the CC BY
license (http://creativecommons.org/licenses/by/4.0/).
1. Introduction
Detailed imaging of the interaction between the laser beam and
the powder bed whilst building multiple layer islands with metal
powder bed fusion (PBF) has not been reported previously. It is
extremely challenging to record images through the viewing win-
dow of commercial PBF systems with sufficient magnification or
contrast to see individual powder particles in the powder bed.
Higher magnification images have so far focussed on the melt pool
whilst scanning a single laser track in a representative powder
layer. In this paper, we report detailed, in-process imaging of the
interaction of the laser beam with the powder bed during the PBF
build of fully dense parts. We demonstrate that the PBF process is
more dynamic than is generally appreciated and involves consid-
erable motion of the powder particles and agglomerates in and
above the powder bed. This motion is driven by the laser-induced
plume of metal vapour and plasma above the melt pool. We
therefore develop the first finite element model for PBF that
incorporates the laser plume and inert atmosphere in order to
explain the observed motion of the fluids and powder particles in
and above the powder bed.
Metal powder bed fusion (PBF) is a category of additive manu-
facture (AM) process in which thermal energy selectively fuses
regions of a powder bed [1]. Commercial PBF systems are already
used to manufacture production components; but these compo-
nents generally require intensive, part-specific process setting
refinement to reduce distortions caused by residual stresses, to
determine process settings that reduce defects and to determine
acceptable positions for support structures. In the future, software
will simulate a full-build and reduce the time required to determine
process settings, but that approach still requires better process
understanding so that residual stresses, porosity and surface finish
are predicted reliably for different process regimes.
Imaging of the PBF process is one approach being used to ach-
ieve this improved understanding. Qiu et al. [2] undertook a sys-
tematic study of the effect of laser scan speed and powder layer
thickness on porosity using a commercial Concept Laser M2 system.
SEM images of sample surfaces revealed an increase in surface
roughness and weld track irregularity when either the scan speed
or powder layer thickness were increased above certain (process-
specific) thresholds. Increases in surface roughness were correlated
* Corresponding author.
E-mail addresses: p.bidare@hw.ac.uk (P. Bidare), i.bitharas@hw.ac.uk
(I. Bitharas), a.moore@hw.ac.uk (A.J. Moore).
1 Equal contribution, Joint first authors.
Contents lists available at ScienceDirect
Acta Materialia
j o u r n a l h o m e p a g e : w w w . e l s e v i e r . c o m / l o c a t e / a c t a m a t
https://doi.org/10.1016/j.actamat.2017.09.051
1359-6454/© 2017 Acta Materialia Inc. Published by Elsevier Ltd. This is an open access article under the CC BY license (http://creativecommons.org/licenses/by/4.0/).
Acta Materialia 142 (2018) 107e120
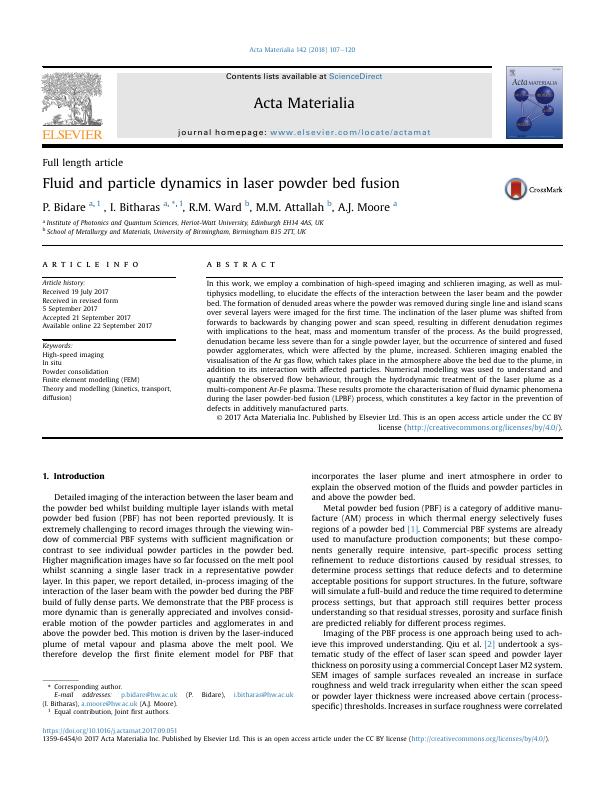
with an increase in internal porosity. High-speed videos were
recorded at 10,000 frames per second (fps) through the system
viewing window. The optical resolution of ~150 mm per pixel was
insufficient to resolve individual powder particles and their inter-
action with the laser, although the number of incandescent powder
particles ejected backwards from the melt pool was observed to
increase with increased thickness of the powder layer. Grasso et al.
[3] recorded images with a similar magnification at 300 fps through
the viewing window of a Renishaw AM250 system. Again, the
interaction of the laser with the powder particles could not be
resolved. However, the intensity evolution through time at each
pixel from an image sequence was successfully used to identify
areas of the powder layer that experienced overheating and
therefore the location of potential defects.
Higher magnification imaging of the melt pool in a represen-
tative powder layer was reported by Matthews et al. [4], who
investigated the depletion of metal powder particles in the zone
immediately surrounding the solidified track (denudation), which
can affect porosity and surface roughness. It was proposed that
denudation at ambient pressure is caused by the intense evapora-
tion of metal vapour from the melt pool, which produces an inward
flow of the ambient gas towards the melt track due to the Bernoulli
effect. The inward flow of the ambient gas is sufficient to entrain
powder particles, which can become incorporated into the melt
pool or ejected with the metal vapour. Imaging of the melt pool
with an optical resolution of ~5 mm per pixel enabled this particle
motion to be observed, with particles ejected backwards with
respect to the scan direction [4] or vertically upwards [5],
depending on the process setting. The experimental system for
imaging comprised scanning a single laser track in a powder layer
that had been spread manually on to a metal substrate, protected
with an inert gas from a localized jet. Gunenthiram et al. [6] noted
the complexity of performing diagnostics during the PBF build
process and so recorded single track images in a similar system to
[4] but with a powder layer that moved on a translation stage below
the laser. Motion of powder particles towards the melt pool due to
the metal vapour was again observed, but again high magnification
on the melt pool prevented the formation of the denuded region
from being imaged. Zhao et al. [7] used synchrotron radiation to
image the interaction of 1 ms laser pulses with a powder layer at
50,000 fps. Vapour-driven particle motion was observed and,
additionally, the dynamic keyhole development beneath the pow-
der bed could be seen. In this case, the powder bed was only
450 mm wide to enable transmission of the x-rays and a single laser
spot was illuminated.
These single track and single spot measurements should prove
useful for informing powder-level numerical models but are not
part of a characterised build process. To date, the behaviour of the
powder bed away from the melt pool has not been imaged, nor
have the effects of scanning adjacent tracks and multiple layers
during a full build been investigated.
Despite the direct impact of the ambient gas on the process,
state of the art powder-scale models [8,9] do not yet include any
interaction between the melt flow and atmosphere. In such models,
the recoil pressure generated by the evaporated gas is calculated by
the Clausius-Clapeyron equation [10] and used as a contribution to
the momentum in the melt pool; however, transport phenomena in
the gas or plasma phase above the powder bed based on the
evaporated mass are not modelled. Approximate calculations in
Ref. [5] based on the model in Ref. [8] estimated the vapour ejection
velocity at ~700 m/s. Heat transfer calculations suggest that tem-
peratures during PBF sufficiently high to form metal vapour and
plasma [11], which is supported by the physical observation of light
emission from the laser plume, but the associated phase change
dynamics from liquid to vapour and plasma have not been
modelled to date. Masmoudi et al. [12] did model the diffusion of
iron vapour into the argon atmosphere above the powder bed using
a meso-scale finite volume model. However, the laser plume was
not modelled: instead an assumed mass fraction from elements
that exceeded the vaporization temperature of the metal was used
as vapour input to the gas phase. As a consequence, the estimated
maximum vapour flow velocity was <50 m/s at atmospheric
pressure, which is insufficient to account for the particle motion
observed experimentally. Furthermore, convective and diffusive
species transport incorporating the physical properties for a
multicomponent Ar/Fe mixture were not included.
In the work presented here, detailed high-speed imaging of the
interaction of the laser with the powder bed is shown at a range of
laser powers and scan speeds. We observed that powder particles
entrained in the atmospheric gas flow were drawn in towards the
melt pool and ejected backwards with respect to the scan direction
or vertically upwards at different process settings, as reported
previously. But by imaging the wider powder bed, we could image
the denudation produced by these effects for the first time. We also
observed effects that have not been reported previously at other
process settings, including the forwards ejection of entrained par-
ticles and denudation arising due to their interaction with the laser
plume, and particles being driven away from the melt track at at-
mospheric pressure. More importantly, the imaging has been
extended from single tracks to multilayer builds, in order to observe
for the first time how these effects manifest in the powder bed
during a full build.
Having noted the impact of the ambient gas on the PBF process,
we develop a pragmatic finite element (FE) model for the powder
bed and fluid dynamics observed, including a hydrodynamic
treatment of the laser-induced plume and atmospheric flow for the
first time in PBF. We draw on the literature concerning evaporative
and plasma phenomena occurring in arc welding, laser welding and
laser ablation studies as a basis for the analysis in the context of PBF.
We use high-speed schlieren imaging for gas flow visualisation of
the density gradients in the gas flow, not attempted for PBF pre-
viously, both to elucidate aspects of the physical phenomena
involved and also to validate the FE model. The modelling and
schlieren imaging support our direct, high-speed imaging obser-
vations of gas flow-induced powder particle motion in the PBF
process.
2. Experimental system
We have previously reported the design and characterisation of
an open architecture PBF system for in-situ measurements during
PBF [13], which is shown schematically in Fig. 1. A key feature of the
system is computer control for the automated build of fully dense
components. The computer controls the vertical movement of the
build plate between layers, the movement of the silicon cord
powder spreader and the laser illumination and scanning. The
system has complete flexibility for laser power and speed, and scan
geometry including hatching. Hence it is possible to achieve high
resolution imaging not only whilst melting single tracks in the
powder bed, but also during multiple layer builds under conditions
known to produce parts with >99% density. Minor modifications
were made to the top and end faces of the Perspex shielding
chamber to incorporate viewing windows. For top views of the
powder bed, a window of diameter 50 mm made from infra-red
absorbing KG glass was added, Fig. 1. Side viewing windows were
added, made from Zerodur glass flats of diameter 75 mm, polished
to l/4 on both surfaces.
All the experiments reported here were undertaken with gas-
atomized stainless steel 316 L powder (Renishaw PLC) with parti-
cle diameters in the range 15e45 mm and a mean diameter of 30 mm
P. Bidare et al. / Acta Materialia 142 (2018) 107e120108
recorded at 10,000 frames per second (fps) through the system
viewing window. The optical resolution of ~150 mm per pixel was
insufficient to resolve individual powder particles and their inter-
action with the laser, although the number of incandescent powder
particles ejected backwards from the melt pool was observed to
increase with increased thickness of the powder layer. Grasso et al.
[3] recorded images with a similar magnification at 300 fps through
the viewing window of a Renishaw AM250 system. Again, the
interaction of the laser with the powder particles could not be
resolved. However, the intensity evolution through time at each
pixel from an image sequence was successfully used to identify
areas of the powder layer that experienced overheating and
therefore the location of potential defects.
Higher magnification imaging of the melt pool in a represen-
tative powder layer was reported by Matthews et al. [4], who
investigated the depletion of metal powder particles in the zone
immediately surrounding the solidified track (denudation), which
can affect porosity and surface roughness. It was proposed that
denudation at ambient pressure is caused by the intense evapora-
tion of metal vapour from the melt pool, which produces an inward
flow of the ambient gas towards the melt track due to the Bernoulli
effect. The inward flow of the ambient gas is sufficient to entrain
powder particles, which can become incorporated into the melt
pool or ejected with the metal vapour. Imaging of the melt pool
with an optical resolution of ~5 mm per pixel enabled this particle
motion to be observed, with particles ejected backwards with
respect to the scan direction [4] or vertically upwards [5],
depending on the process setting. The experimental system for
imaging comprised scanning a single laser track in a powder layer
that had been spread manually on to a metal substrate, protected
with an inert gas from a localized jet. Gunenthiram et al. [6] noted
the complexity of performing diagnostics during the PBF build
process and so recorded single track images in a similar system to
[4] but with a powder layer that moved on a translation stage below
the laser. Motion of powder particles towards the melt pool due to
the metal vapour was again observed, but again high magnification
on the melt pool prevented the formation of the denuded region
from being imaged. Zhao et al. [7] used synchrotron radiation to
image the interaction of 1 ms laser pulses with a powder layer at
50,000 fps. Vapour-driven particle motion was observed and,
additionally, the dynamic keyhole development beneath the pow-
der bed could be seen. In this case, the powder bed was only
450 mm wide to enable transmission of the x-rays and a single laser
spot was illuminated.
These single track and single spot measurements should prove
useful for informing powder-level numerical models but are not
part of a characterised build process. To date, the behaviour of the
powder bed away from the melt pool has not been imaged, nor
have the effects of scanning adjacent tracks and multiple layers
during a full build been investigated.
Despite the direct impact of the ambient gas on the process,
state of the art powder-scale models [8,9] do not yet include any
interaction between the melt flow and atmosphere. In such models,
the recoil pressure generated by the evaporated gas is calculated by
the Clausius-Clapeyron equation [10] and used as a contribution to
the momentum in the melt pool; however, transport phenomena in
the gas or plasma phase above the powder bed based on the
evaporated mass are not modelled. Approximate calculations in
Ref. [5] based on the model in Ref. [8] estimated the vapour ejection
velocity at ~700 m/s. Heat transfer calculations suggest that tem-
peratures during PBF sufficiently high to form metal vapour and
plasma [11], which is supported by the physical observation of light
emission from the laser plume, but the associated phase change
dynamics from liquid to vapour and plasma have not been
modelled to date. Masmoudi et al. [12] did model the diffusion of
iron vapour into the argon atmosphere above the powder bed using
a meso-scale finite volume model. However, the laser plume was
not modelled: instead an assumed mass fraction from elements
that exceeded the vaporization temperature of the metal was used
as vapour input to the gas phase. As a consequence, the estimated
maximum vapour flow velocity was <50 m/s at atmospheric
pressure, which is insufficient to account for the particle motion
observed experimentally. Furthermore, convective and diffusive
species transport incorporating the physical properties for a
multicomponent Ar/Fe mixture were not included.
In the work presented here, detailed high-speed imaging of the
interaction of the laser with the powder bed is shown at a range of
laser powers and scan speeds. We observed that powder particles
entrained in the atmospheric gas flow were drawn in towards the
melt pool and ejected backwards with respect to the scan direction
or vertically upwards at different process settings, as reported
previously. But by imaging the wider powder bed, we could image
the denudation produced by these effects for the first time. We also
observed effects that have not been reported previously at other
process settings, including the forwards ejection of entrained par-
ticles and denudation arising due to their interaction with the laser
plume, and particles being driven away from the melt track at at-
mospheric pressure. More importantly, the imaging has been
extended from single tracks to multilayer builds, in order to observe
for the first time how these effects manifest in the powder bed
during a full build.
Having noted the impact of the ambient gas on the PBF process,
we develop a pragmatic finite element (FE) model for the powder
bed and fluid dynamics observed, including a hydrodynamic
treatment of the laser-induced plume and atmospheric flow for the
first time in PBF. We draw on the literature concerning evaporative
and plasma phenomena occurring in arc welding, laser welding and
laser ablation studies as a basis for the analysis in the context of PBF.
We use high-speed schlieren imaging for gas flow visualisation of
the density gradients in the gas flow, not attempted for PBF pre-
viously, both to elucidate aspects of the physical phenomena
involved and also to validate the FE model. The modelling and
schlieren imaging support our direct, high-speed imaging obser-
vations of gas flow-induced powder particle motion in the PBF
process.
2. Experimental system
We have previously reported the design and characterisation of
an open architecture PBF system for in-situ measurements during
PBF [13], which is shown schematically in Fig. 1. A key feature of the
system is computer control for the automated build of fully dense
components. The computer controls the vertical movement of the
build plate between layers, the movement of the silicon cord
powder spreader and the laser illumination and scanning. The
system has complete flexibility for laser power and speed, and scan
geometry including hatching. Hence it is possible to achieve high
resolution imaging not only whilst melting single tracks in the
powder bed, but also during multiple layer builds under conditions
known to produce parts with >99% density. Minor modifications
were made to the top and end faces of the Perspex shielding
chamber to incorporate viewing windows. For top views of the
powder bed, a window of diameter 50 mm made from infra-red
absorbing KG glass was added, Fig. 1. Side viewing windows were
added, made from Zerodur glass flats of diameter 75 mm, polished
to l/4 on both surfaces.
All the experiments reported here were undertaken with gas-
atomized stainless steel 316 L powder (Renishaw PLC) with parti-
cle diameters in the range 15e45 mm and a mean diameter of 30 mm
P. Bidare et al. / Acta Materialia 142 (2018) 107e120108

[14]. Powder layers were melted on to 80 40 mm 2 stainless steel
304 L build plates (coupons) of thickness 2 mm, using a single mode
fibre laser (SPI 400 W continuous wave, 1070 nm) which was
scanned over the powder surface (Raylase MS-II-14 scanner with
163 mm focal length f-theta lens). The coupon surfaces were
roughened by manual, circular rubbing with P400 sandpaper. The
powder layer thickness for particular experiments is noted in the
relevant sections below. Light from the laser was focussed to a spot
with a Gaussian beam profile and 4Ds diameter of 50 mm in both
the x- and y-directions, measured with an Ophir Spiricon SP928
beam profiling camera. The shielding chamber was purged with
argon until the measured oxygen concentration was <0.1%. The
experiments were performed with an exchange of clean argon into
the chamber between experiments, exhausted through a water
bath to remove potentially harmful nanoparticles produced by the
process. The pressure in the chamber remained at 1 atm.
A Photron Fastcam Mini UX100 monochrome camera was used
for high-speed imaging. The full resolution for this camera is
1280 1024 pixels up to 4000 fps. The direct imaging experiments
reported here were recorded at 8000 fps and 1280 616 pixels. The
camera was fitted with a C-mount QiOptiq Optem Fusion lens,
configured to provide a zoom of 7:1 and a working distance of
135 mm. At this working distance, the region of interest could be
varied between approximately 14 11 mm 2 (depth of field 2 mm)
and 2 1.5 mm2 (0.2 mm).
The top viewing window was used for direct imaging from
above the powder bed with the camera angled at ~20 to the ver-
tical. One side window was used for direct imaging from the side of
the powder bed, with the camera positioned at approximately 10
to the horizontal. For the side views, an infra-red absorbing filter
was placed in front of the camera lens. The camera was mounted on
a tilt stage to change the area of the powder bed that was imaged,
which enabled multiple areas to be scanned and imaged on the
same coupon. This feature was particularly useful for side imaging
with high magnification and a small depth of field: the tilt stage
was used to select the build region on the powder bed followed by a
fine adjustment of the lens focus as necessary. Illumination was
provided by a 300 W tungsten filament lamp that was focussed
through the top of the Perspex shielding chamber on to the powder
bed in a rectangle of approximately 15 5 mm2 . The illumination
was switched on for a few seconds during imaging and produced
negligible heating of the powder bed.
We have previously reported schlieren imaging to view and
optimize shielding gas coverage during welding applications
[15,16]. Schlieren imaging enables refractive index gradients due to
temperature, pressure and concentration gradients to be visualized.
The portable z-type schlieren system was incorporated into the
metal PBF system with minimum modifications and so it will not be
described in detail here. The key components of the schlieren
illumination were a 300 W tungsten lamp that was focussed on to a
2 5 mm2 rectangular source slit with its long edge vertical. The
slit was placed at the focus of the first schlieren mirror (focal length
1.27 m) to produce a collimated beam that passed across the
powder bed via the windows in the side of the Perspex shielding
chamber, Fig. 1. A second, identical schlieren mirror focussed the
collimated beam to produce an image of the source slit on a vertical,
knife-edge filter. The knife-edge filter was positioned with a
micrometer to block 50% of the image of the source slit in the
horizontal (x) direction, producing images with a uniform mea-
surement range in which the intensity was proportional to the
gradient of the refractive index vn/vx. Schlieren images were
recorded with the high-speed camera using a variable focus tele-
photo lens (focal length 75e300 mm) at 16,000 fps and 1280 312
pixels. An additional infra-red absorbing filter, and a polariser to
remove glare, were placed in front of the camera lens.
3. Multiphysics model including laser plume and inert
atmosphere
We have used the scientific literature concerning evaporative
and plasma phenomena that occur in laser welding and laser
ablation studies to establish a basis for such analyses in the context
of laser PBF. Hydrodynamic modelling of the lased-induced plume,
comprised of metal vapour and plasma was presented in
Refs. [17e20]. In such models, the Knudsen layer approach is
commonly used to model the plume (combined vapour and
plasma) flow into the atmosphere through a contact discontinuity
at the substrate-gas interface. The plume velocity is represented as
some fraction of the speed of sound in the gas at its elevated
temperature. Modelling of the laser plume for a powder bed or in
the context of PBF has not previously been taken into consideration.
To simulate the dynamics of the gas and plasma phases that
occur due to the thermal effects during PBF, an FE analysis was
carried out using COMSOL multiphysics software. A 2D axisym-
metric geometry including the substrate, powder layer and adja-
cent atmosphere was generated. The mesh was locally refined at
the innermost edge of the powder bed so that at least 30 nodes
were created through its depth, resulting in minimum element
sizes of ~1.5 mm for a 70 mm layer under the laser beam. Standard
Lagrangian triangles were used across all domains, with a 2.5%
growth rate in element size from the centre of the laser beam up to
a maximum of 12 mm in the powder layer and 0.25 mm in the
substrate and atmosphere.
For the substrate and powder layer, the thermophysical prop-
erties of grade 304 and 316 stainless steel respectively were input
as a function of temperature [21]. In modelling the powder layer, a
volume-averaged approach was used for temperatures below
melting, after [12]. For an average packing density f ¼ 0.6 in the
powder layer, the equivalent thermophysical properties were
written as:
xpowder ¼ fxsteel þ ð1 fÞxArgon (1)
Although the thermal conductivity of the powder might be
exaggerated in this manner at relatively low temperatures, the fluid
dynamic phenomena of interest to this study occur at much higher
temperatures, where the liquid and gas phase material properties
are used. Therefore, the use of volume averaged properties does not
undermine the accuracy of the prediction for evaporation phe-
nomena. Using actual powder thermophysical properties is
Fig. 1. Schematic of the open-architecture PBF system with modifications for high-
speed imaging and schlieren imaging.
P. Bidare et al. / Acta Materialia 142 (2018) 107e120 109
304 L build plates (coupons) of thickness 2 mm, using a single mode
fibre laser (SPI 400 W continuous wave, 1070 nm) which was
scanned over the powder surface (Raylase MS-II-14 scanner with
163 mm focal length f-theta lens). The coupon surfaces were
roughened by manual, circular rubbing with P400 sandpaper. The
powder layer thickness for particular experiments is noted in the
relevant sections below. Light from the laser was focussed to a spot
with a Gaussian beam profile and 4Ds diameter of 50 mm in both
the x- and y-directions, measured with an Ophir Spiricon SP928
beam profiling camera. The shielding chamber was purged with
argon until the measured oxygen concentration was <0.1%. The
experiments were performed with an exchange of clean argon into
the chamber between experiments, exhausted through a water
bath to remove potentially harmful nanoparticles produced by the
process. The pressure in the chamber remained at 1 atm.
A Photron Fastcam Mini UX100 monochrome camera was used
for high-speed imaging. The full resolution for this camera is
1280 1024 pixels up to 4000 fps. The direct imaging experiments
reported here were recorded at 8000 fps and 1280 616 pixels. The
camera was fitted with a C-mount QiOptiq Optem Fusion lens,
configured to provide a zoom of 7:1 and a working distance of
135 mm. At this working distance, the region of interest could be
varied between approximately 14 11 mm 2 (depth of field 2 mm)
and 2 1.5 mm2 (0.2 mm).
The top viewing window was used for direct imaging from
above the powder bed with the camera angled at ~20 to the ver-
tical. One side window was used for direct imaging from the side of
the powder bed, with the camera positioned at approximately 10
to the horizontal. For the side views, an infra-red absorbing filter
was placed in front of the camera lens. The camera was mounted on
a tilt stage to change the area of the powder bed that was imaged,
which enabled multiple areas to be scanned and imaged on the
same coupon. This feature was particularly useful for side imaging
with high magnification and a small depth of field: the tilt stage
was used to select the build region on the powder bed followed by a
fine adjustment of the lens focus as necessary. Illumination was
provided by a 300 W tungsten filament lamp that was focussed
through the top of the Perspex shielding chamber on to the powder
bed in a rectangle of approximately 15 5 mm2 . The illumination
was switched on for a few seconds during imaging and produced
negligible heating of the powder bed.
We have previously reported schlieren imaging to view and
optimize shielding gas coverage during welding applications
[15,16]. Schlieren imaging enables refractive index gradients due to
temperature, pressure and concentration gradients to be visualized.
The portable z-type schlieren system was incorporated into the
metal PBF system with minimum modifications and so it will not be
described in detail here. The key components of the schlieren
illumination were a 300 W tungsten lamp that was focussed on to a
2 5 mm2 rectangular source slit with its long edge vertical. The
slit was placed at the focus of the first schlieren mirror (focal length
1.27 m) to produce a collimated beam that passed across the
powder bed via the windows in the side of the Perspex shielding
chamber, Fig. 1. A second, identical schlieren mirror focussed the
collimated beam to produce an image of the source slit on a vertical,
knife-edge filter. The knife-edge filter was positioned with a
micrometer to block 50% of the image of the source slit in the
horizontal (x) direction, producing images with a uniform mea-
surement range in which the intensity was proportional to the
gradient of the refractive index vn/vx. Schlieren images were
recorded with the high-speed camera using a variable focus tele-
photo lens (focal length 75e300 mm) at 16,000 fps and 1280 312
pixels. An additional infra-red absorbing filter, and a polariser to
remove glare, were placed in front of the camera lens.
3. Multiphysics model including laser plume and inert
atmosphere
We have used the scientific literature concerning evaporative
and plasma phenomena that occur in laser welding and laser
ablation studies to establish a basis for such analyses in the context
of laser PBF. Hydrodynamic modelling of the lased-induced plume,
comprised of metal vapour and plasma was presented in
Refs. [17e20]. In such models, the Knudsen layer approach is
commonly used to model the plume (combined vapour and
plasma) flow into the atmosphere through a contact discontinuity
at the substrate-gas interface. The plume velocity is represented as
some fraction of the speed of sound in the gas at its elevated
temperature. Modelling of the laser plume for a powder bed or in
the context of PBF has not previously been taken into consideration.
To simulate the dynamics of the gas and plasma phases that
occur due to the thermal effects during PBF, an FE analysis was
carried out using COMSOL multiphysics software. A 2D axisym-
metric geometry including the substrate, powder layer and adja-
cent atmosphere was generated. The mesh was locally refined at
the innermost edge of the powder bed so that at least 30 nodes
were created through its depth, resulting in minimum element
sizes of ~1.5 mm for a 70 mm layer under the laser beam. Standard
Lagrangian triangles were used across all domains, with a 2.5%
growth rate in element size from the centre of the laser beam up to
a maximum of 12 mm in the powder layer and 0.25 mm in the
substrate and atmosphere.
For the substrate and powder layer, the thermophysical prop-
erties of grade 304 and 316 stainless steel respectively were input
as a function of temperature [21]. In modelling the powder layer, a
volume-averaged approach was used for temperatures below
melting, after [12]. For an average packing density f ¼ 0.6 in the
powder layer, the equivalent thermophysical properties were
written as:
xpowder ¼ fxsteel þ ð1 fÞxArgon (1)
Although the thermal conductivity of the powder might be
exaggerated in this manner at relatively low temperatures, the fluid
dynamic phenomena of interest to this study occur at much higher
temperatures, where the liquid and gas phase material properties
are used. Therefore, the use of volume averaged properties does not
undermine the accuracy of the prediction for evaporation phe-
nomena. Using actual powder thermophysical properties is
Fig. 1. Schematic of the open-architecture PBF system with modifications for high-
speed imaging and schlieren imaging.
P. Bidare et al. / Acta Materialia 142 (2018) 107e120 109
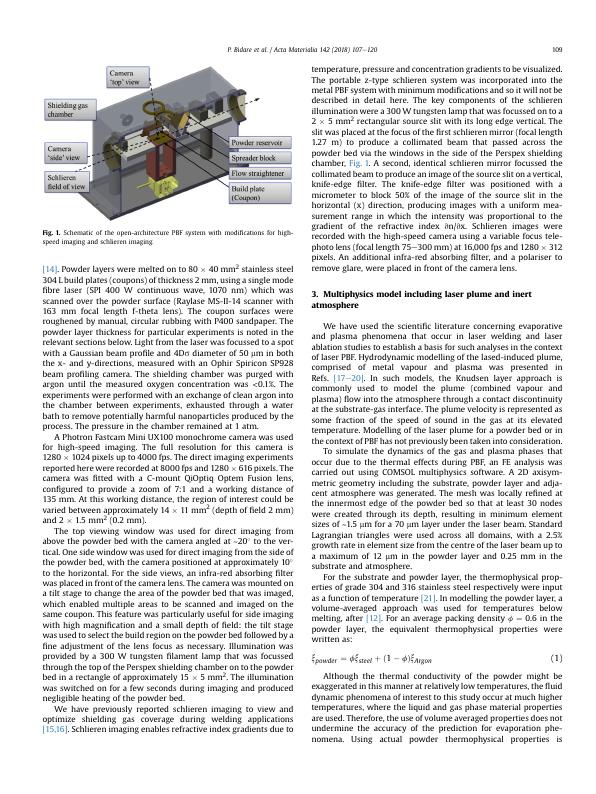
however essential for simulations investigating the melt pool size
or residual stress development. The properties used in the fluid
domain above the powder bed were those of an Ar-Fe gas/plasma
mixture in local thermodynamic equilibrium (LTE). The values were
therefore input as a function of temperature and Fe mass fraction,
taken from Ref. [22].
The partial differential equations (PDEs) used in the model are
given below using vector notation. Vectors are represented in bold,
while constitutive properties used as a function of temperature and
Fe mass fraction are in italics. For fluid flow, the compressible
Navier-Stokes equations for momentum (2) and mass (3) conser-
vation were used:
rðu$VuÞ ¼ V$
h
p þ m
Vu þ ðVuÞTi
þ rg (2)
V$ðruÞ ¼ 0 (3)
where r is the density, u the flow velocity, p the pressure, m the
dynamic viscosity and g the acceleration due to gravity. In order to
better capture the turbulence due to the laser plume, but also to
expand the stable solution space of the model, the RANS SST tur-
bulence model was used.
The Knudsen layer approach gives the velocity magnitude of the
laser plume normal to the powder bed surface based on the local
sound speed:
juj ¼ M
ffiffiffiffiffiffiffiffiffiffiffiffiffiffiffiffiffiffiffiffiffiffiffiffiffiffiffiffiffiffiffiffiffiffiffi
gKT
u1 m Ar þ u2 mFe
s
(4)
where M is the Mach number, g ¼ 5/3 is the heat capacity ratio for a
monoatomic gas, K is the Boltzmann constant and m Ar; m Fe are the
atomic masses and u1; u2 the mass fractions of Ar and Fe, respec-
tively. The Mach number was assumed to vary linearly based on the
incident laser radiation, from M ¼ 0.01 at an intensity of 10 5 W/cm2 ,
to M ¼ 1 for a flux of 107 W/cm 2 [23]. On the outer flow boundaries,
an outflow condition was specified by setting the normal diffusive
flux equal to 0 at atmospheric pressure.
Extending an approach employed in state-of-the-art arc weld-
ing simulations [10,24], an additional set of conservation equations
were added to model the convective and diffusive modes of
transport of the vaporized gas. The mass fraction of the i-th con-
stituent ui is given by:
V$
rD o
i Vui þ ruiDo
i
VM n
Mn
þ DT
i
VT
T
þ rðu$VÞui ¼ 0 (5)
where Do
i is the ordinary diffusion coefficient and D T
i is the thermal
diffusion coefficient while Mn is the sum of the molar masses of all
the constituents. Equation (5) was solved for species u2 (Fe) and the
remaining mass was assigned to species u1 (Ar). An additional
contribution DiT ¼ mT=Sc T to the diffusion coefficient of each spe-
cies was added to account for turbulent mixing of small eddies,
where mT is the Reynolds-averaged turbulent kinematic viscosity
and Sc T ¼ 0.7 is the turbulent Schmidt number. The Fe mass fraction
at the powder surface was defined based on the vapour pressure
and molar masses of Ar and Fe as [24]:
u2 ¼ Pvap MFe
Pvap MFe þ Patm Pvap
MAr
(6)
For the process thermodynamics, an energy balance was used to
account for conductive, convective and radiative heat transfer.
rc pðu$VTÞ ¼ V$ðkVTÞ 4pεN (7)
The last term of equation (7) is solved only within the gas/
plasma domain, and accounts for the total radiative loss from the
Ar-Fe plasma across all wavelengths. The plasma was assumed to be
optically thin, and the net radiative emission coefficient εN was
taken as a function of both temperature and mass fraction from
Ref. [25]. Based on the literature [20,26], as well as in-house nu-
merical solutions of the Saha equation and calculation of the rele-
vant absorption coefficients, inverse bremsstrahlung absorption of
the incident laser beam at 1070 nm for temperatures < 10,000 K is
negligible and therefore was not included in the model. For the
substrate and powder layer, no convection term was used as the
melt pool motion was omitted for this study and translational
motion cannot be conveyed in axisymmetric models.
The laser radiation reaching the powder layer was modelled as a
Gaussian heat source with intensity:
I ¼ 2AP
pR 2 exp
2r 2
R 2
(8)
where A ¼ 0.6 is the absorption of the powder layer [33], P is the
laser power and R is the beam radius. The heat lost from the metal
surface due to evaporation is given by q ¼ _m vap L vap , where L vap is
the heat of vaporization and _m vap is the Fe vapour mass flowrate,
based on the vapour pressure Pvap and temperature, written as
[21,27]:
log _m vap
¼ 2:52 þ logPvap
0:5logðTÞ (9)
logPvap
¼ 6:121 þ 18836
T (10)
Gray-body radiative energy losses were prescribed for all solid
surfaces, including the powder-substrate boundary, given by
q ¼ εsðT 4
amb T4Þ, where ε ¼ 0.4 is the emissivity of stainless
steel and s is the Stefan-Boltzmann constant. The temperature at
the outer boundaries of the powder and substrate was set at 300 K.
To account for ambient convection, the total losses at the gas/
plasma outer boundaries were prescribed as q ¼ hðTamb TÞ. A
convective heat transfer coefficient of h ¼ 50 W/m2 was used.
4. Results
The high-speed direct imaging results are divided into single
track and multilayer builds in the following sections. These are
followed by sections for the results of high-speed schlieren imaging
and finite element modelling. All the results in this section were
recorded without a flow of shielding gas across the powder bed in
order to focus attention on the gas movement due to the laser's
interaction with the powder bed. The effect of an additional flow of
shielding gas across the powder bed is introduced in the Discussion
section.
4.1. High-speed imaging: single tracks
Fig. 2 and Videos Fig. 2(a)-2(f) show high-speed imaging for side
and top views of the powder bed during laser scans of individual
tracks. Three different laser power and scan speed combinations
are shown: 50 W and 0.1 m/s, 100 W and 0.5 m/s, and 200 W and
1 m/s. The 100 and 200 W laser power conditions have the same
line energy (laser power divided by scan speed) at 200 J/m while
the 50 W condition has a line energy of 500 J/m. The 50 W and
100 W laser power conditions have been shown to build parts with
>99% density [13]. These results are for the first powder layer of
thickness 50 mm spread on the coupon. We had access to only one
high-speed camera and so the side and top views were recorded in
P. Bidare et al. / Acta Materialia 142 (2018) 107e120110
or residual stress development. The properties used in the fluid
domain above the powder bed were those of an Ar-Fe gas/plasma
mixture in local thermodynamic equilibrium (LTE). The values were
therefore input as a function of temperature and Fe mass fraction,
taken from Ref. [22].
The partial differential equations (PDEs) used in the model are
given below using vector notation. Vectors are represented in bold,
while constitutive properties used as a function of temperature and
Fe mass fraction are in italics. For fluid flow, the compressible
Navier-Stokes equations for momentum (2) and mass (3) conser-
vation were used:
rðu$VuÞ ¼ V$
h
p þ m
Vu þ ðVuÞTi
þ rg (2)
V$ðruÞ ¼ 0 (3)
where r is the density, u the flow velocity, p the pressure, m the
dynamic viscosity and g the acceleration due to gravity. In order to
better capture the turbulence due to the laser plume, but also to
expand the stable solution space of the model, the RANS SST tur-
bulence model was used.
The Knudsen layer approach gives the velocity magnitude of the
laser plume normal to the powder bed surface based on the local
sound speed:
juj ¼ M
ffiffiffiffiffiffiffiffiffiffiffiffiffiffiffiffiffiffiffiffiffiffiffiffiffiffiffiffiffiffiffiffiffiffiffi
gKT
u1 m Ar þ u2 mFe
s
(4)
where M is the Mach number, g ¼ 5/3 is the heat capacity ratio for a
monoatomic gas, K is the Boltzmann constant and m Ar; m Fe are the
atomic masses and u1; u2 the mass fractions of Ar and Fe, respec-
tively. The Mach number was assumed to vary linearly based on the
incident laser radiation, from M ¼ 0.01 at an intensity of 10 5 W/cm2 ,
to M ¼ 1 for a flux of 107 W/cm 2 [23]. On the outer flow boundaries,
an outflow condition was specified by setting the normal diffusive
flux equal to 0 at atmospheric pressure.
Extending an approach employed in state-of-the-art arc weld-
ing simulations [10,24], an additional set of conservation equations
were added to model the convective and diffusive modes of
transport of the vaporized gas. The mass fraction of the i-th con-
stituent ui is given by:
V$
rD o
i Vui þ ruiDo
i
VM n
Mn
þ DT
i
VT
T
þ rðu$VÞui ¼ 0 (5)
where Do
i is the ordinary diffusion coefficient and D T
i is the thermal
diffusion coefficient while Mn is the sum of the molar masses of all
the constituents. Equation (5) was solved for species u2 (Fe) and the
remaining mass was assigned to species u1 (Ar). An additional
contribution DiT ¼ mT=Sc T to the diffusion coefficient of each spe-
cies was added to account for turbulent mixing of small eddies,
where mT is the Reynolds-averaged turbulent kinematic viscosity
and Sc T ¼ 0.7 is the turbulent Schmidt number. The Fe mass fraction
at the powder surface was defined based on the vapour pressure
and molar masses of Ar and Fe as [24]:
u2 ¼ Pvap MFe
Pvap MFe þ Patm Pvap
MAr
(6)
For the process thermodynamics, an energy balance was used to
account for conductive, convective and radiative heat transfer.
rc pðu$VTÞ ¼ V$ðkVTÞ 4pεN (7)
The last term of equation (7) is solved only within the gas/
plasma domain, and accounts for the total radiative loss from the
Ar-Fe plasma across all wavelengths. The plasma was assumed to be
optically thin, and the net radiative emission coefficient εN was
taken as a function of both temperature and mass fraction from
Ref. [25]. Based on the literature [20,26], as well as in-house nu-
merical solutions of the Saha equation and calculation of the rele-
vant absorption coefficients, inverse bremsstrahlung absorption of
the incident laser beam at 1070 nm for temperatures < 10,000 K is
negligible and therefore was not included in the model. For the
substrate and powder layer, no convection term was used as the
melt pool motion was omitted for this study and translational
motion cannot be conveyed in axisymmetric models.
The laser radiation reaching the powder layer was modelled as a
Gaussian heat source with intensity:
I ¼ 2AP
pR 2 exp
2r 2
R 2
(8)
where A ¼ 0.6 is the absorption of the powder layer [33], P is the
laser power and R is the beam radius. The heat lost from the metal
surface due to evaporation is given by q ¼ _m vap L vap , where L vap is
the heat of vaporization and _m vap is the Fe vapour mass flowrate,
based on the vapour pressure Pvap and temperature, written as
[21,27]:
log _m vap
¼ 2:52 þ logPvap
0:5logðTÞ (9)
logPvap
¼ 6:121 þ 18836
T (10)
Gray-body radiative energy losses were prescribed for all solid
surfaces, including the powder-substrate boundary, given by
q ¼ εsðT 4
amb T4Þ, where ε ¼ 0.4 is the emissivity of stainless
steel and s is the Stefan-Boltzmann constant. The temperature at
the outer boundaries of the powder and substrate was set at 300 K.
To account for ambient convection, the total losses at the gas/
plasma outer boundaries were prescribed as q ¼ hðTamb TÞ. A
convective heat transfer coefficient of h ¼ 50 W/m2 was used.
4. Results
The high-speed direct imaging results are divided into single
track and multilayer builds in the following sections. These are
followed by sections for the results of high-speed schlieren imaging
and finite element modelling. All the results in this section were
recorded without a flow of shielding gas across the powder bed in
order to focus attention on the gas movement due to the laser's
interaction with the powder bed. The effect of an additional flow of
shielding gas across the powder bed is introduced in the Discussion
section.
4.1. High-speed imaging: single tracks
Fig. 2 and Videos Fig. 2(a)-2(f) show high-speed imaging for side
and top views of the powder bed during laser scans of individual
tracks. Three different laser power and scan speed combinations
are shown: 50 W and 0.1 m/s, 100 W and 0.5 m/s, and 200 W and
1 m/s. The 100 and 200 W laser power conditions have the same
line energy (laser power divided by scan speed) at 200 J/m while
the 50 W condition has a line energy of 500 J/m. The 50 W and
100 W laser power conditions have been shown to build parts with
>99% density [13]. These results are for the first powder layer of
thickness 50 mm spread on the coupon. We had access to only one
high-speed camera and so the side and top views were recorded in
P. Bidare et al. / Acta Materialia 142 (2018) 107e120110
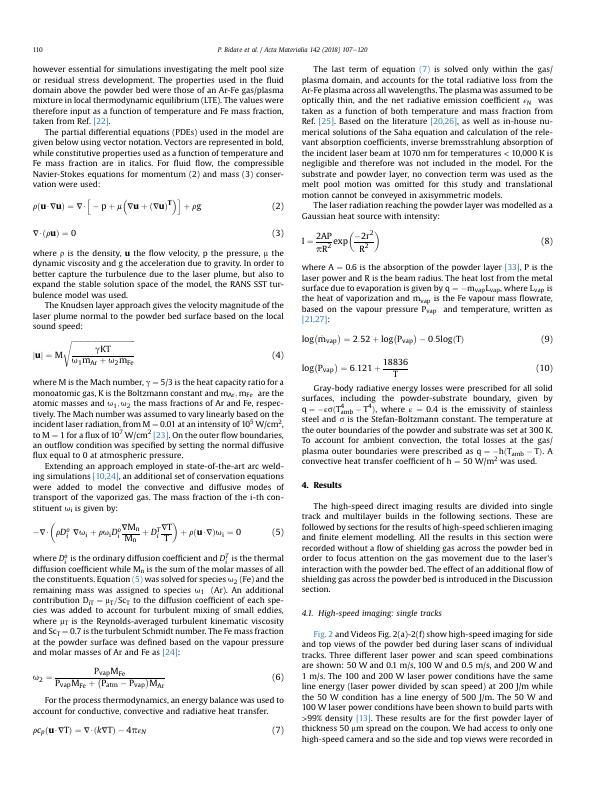
End of preview
Want to access all the pages? Upload your documents or become a member.