Managerial Accounting: Activity Based Costing at Angelo Ltd (MBA)
VerifiedAdded on 2023/06/04
|17
|3841
|397
Report
AI Summary
This report provides a detailed analysis of Activity Based Costing (ABC) and its advantages over traditional costing methods, using Angelo Ltd as a case study. It begins with an explanation of ABC, highlighting its ability to allocate overhead costs based on actual resource consumption. The report t...
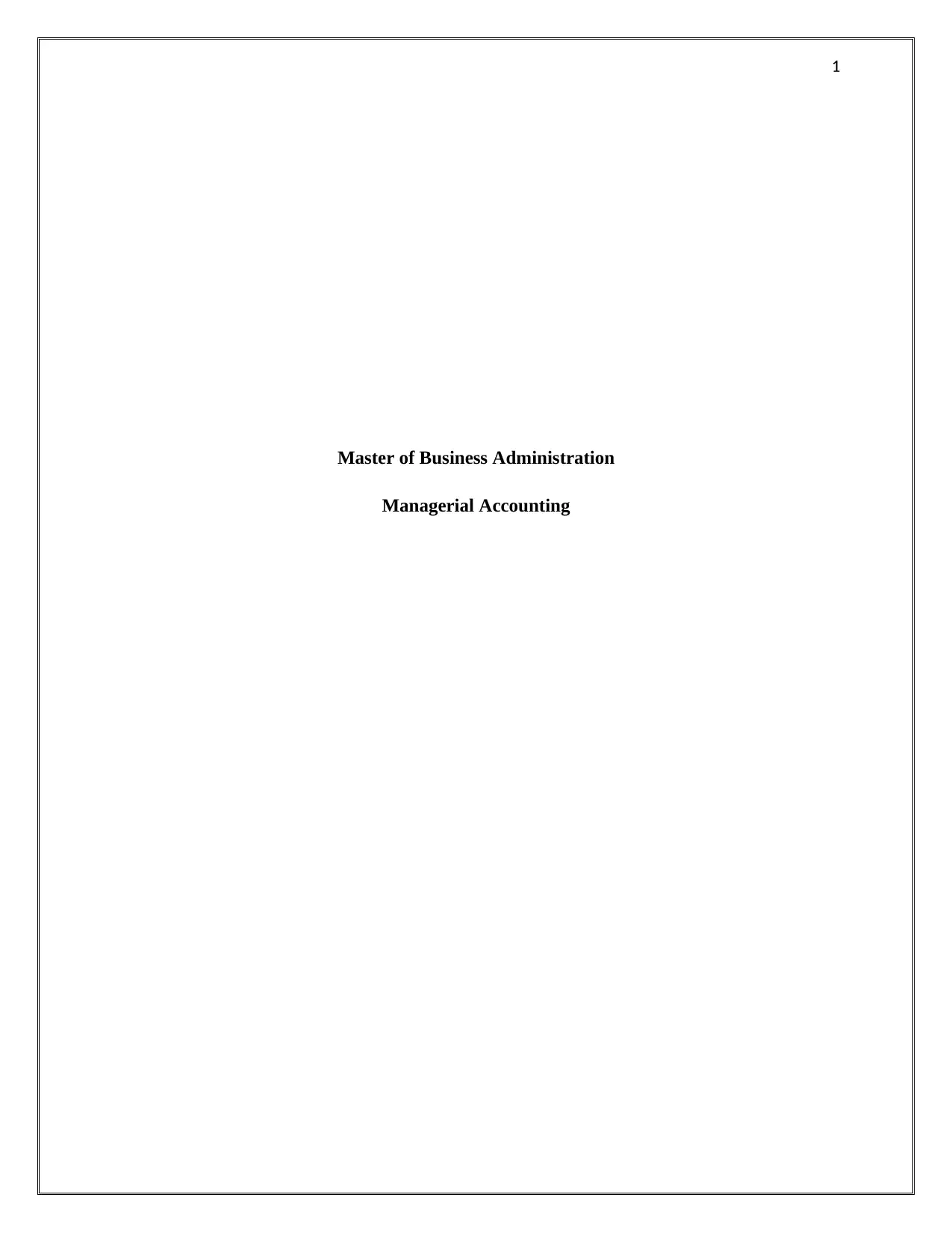
1
Master of Business Administration
Managerial Accounting
Master of Business Administration
Managerial Accounting
Paraphrase This Document
Need a fresh take? Get an instant paraphrase of this document with our AI Paraphraser
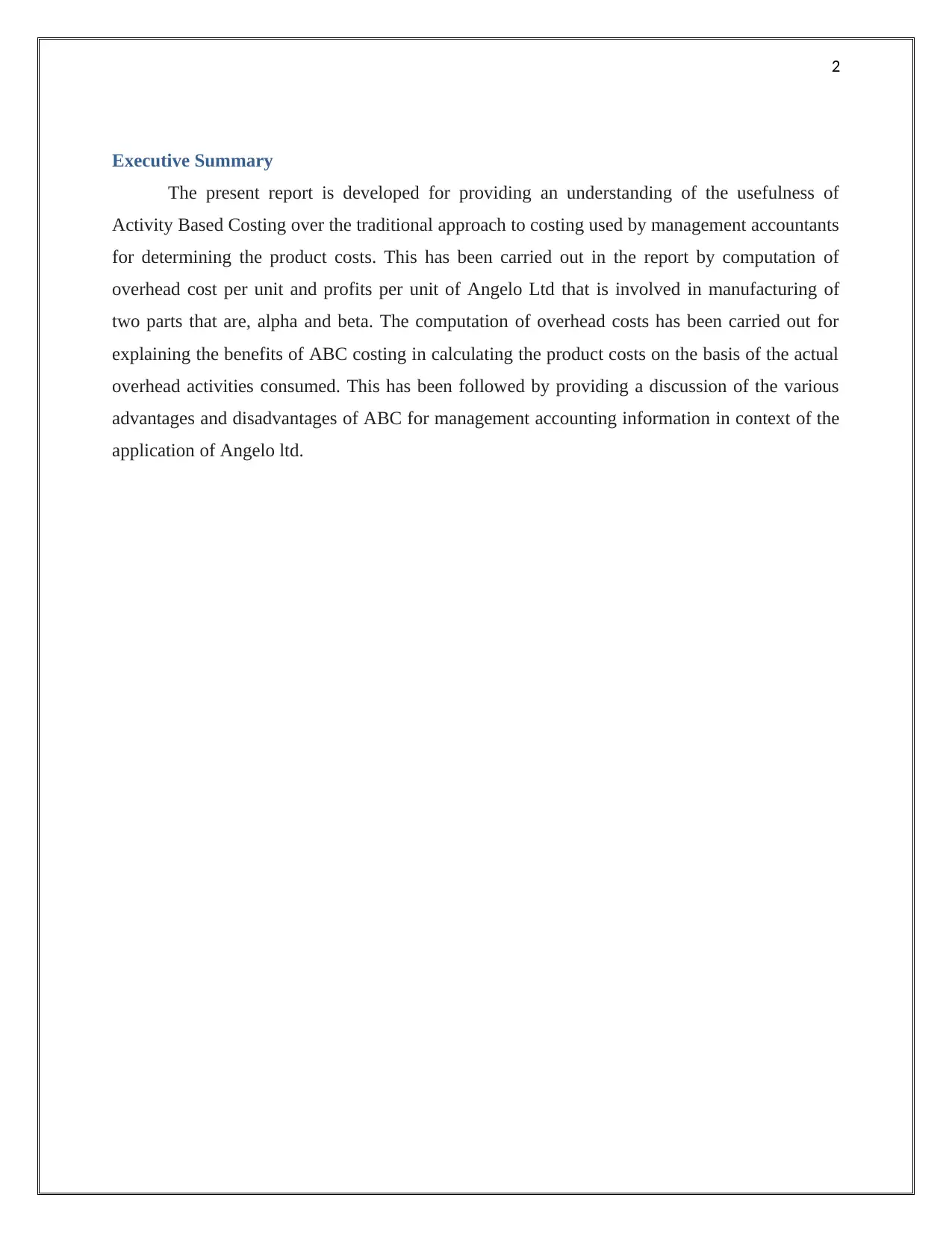
2
Executive Summary
The present report is developed for providing an understanding of the usefulness of
Activity Based Costing over the traditional approach to costing used by management accountants
for determining the product costs. This has been carried out in the report by computation of
overhead cost per unit and profits per unit of Angelo Ltd that is involved in manufacturing of
two parts that are, alpha and beta. The computation of overhead costs has been carried out for
explaining the benefits of ABC costing in calculating the product costs on the basis of the actual
overhead activities consumed. This has been followed by providing a discussion of the various
advantages and disadvantages of ABC for management accounting information in context of the
application of Angelo ltd.
Executive Summary
The present report is developed for providing an understanding of the usefulness of
Activity Based Costing over the traditional approach to costing used by management accountants
for determining the product costs. This has been carried out in the report by computation of
overhead cost per unit and profits per unit of Angelo Ltd that is involved in manufacturing of
two parts that are, alpha and beta. The computation of overhead costs has been carried out for
explaining the benefits of ABC costing in calculating the product costs on the basis of the actual
overhead activities consumed. This has been followed by providing a discussion of the various
advantages and disadvantages of ABC for management accounting information in context of the
application of Angelo ltd.
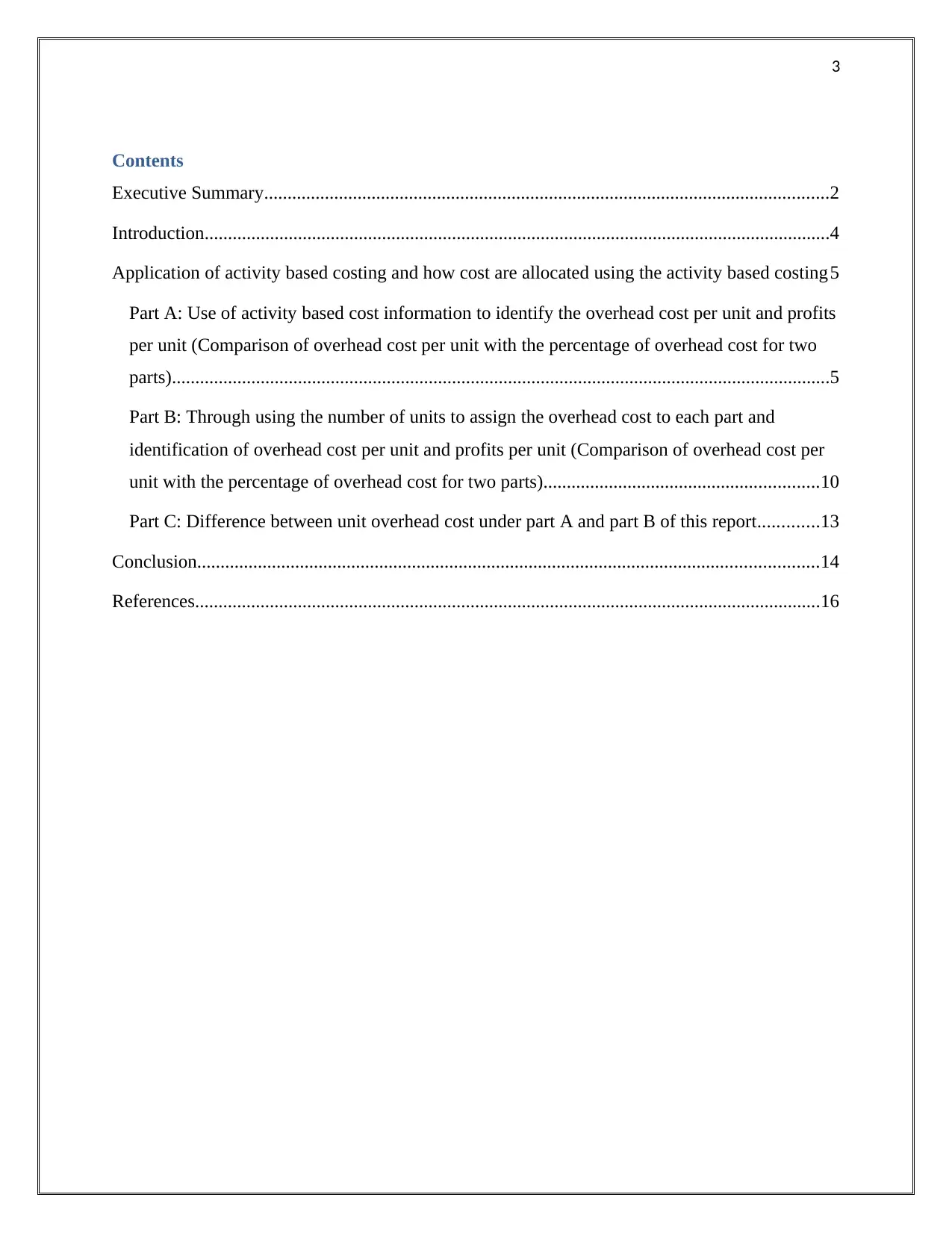
3
Contents
Executive Summary.........................................................................................................................2
Introduction......................................................................................................................................4
Application of activity based costing and how cost are allocated using the activity based costing5
Part A: Use of activity based cost information to identify the overhead cost per unit and profits
per unit (Comparison of overhead cost per unit with the percentage of overhead cost for two
parts).............................................................................................................................................5
Part B: Through using the number of units to assign the overhead cost to each part and
identification of overhead cost per unit and profits per unit (Comparison of overhead cost per
unit with the percentage of overhead cost for two parts)...........................................................10
Part C: Difference between unit overhead cost under part A and part B of this report.............13
Conclusion.....................................................................................................................................14
References......................................................................................................................................16
Contents
Executive Summary.........................................................................................................................2
Introduction......................................................................................................................................4
Application of activity based costing and how cost are allocated using the activity based costing5
Part A: Use of activity based cost information to identify the overhead cost per unit and profits
per unit (Comparison of overhead cost per unit with the percentage of overhead cost for two
parts).............................................................................................................................................5
Part B: Through using the number of units to assign the overhead cost to each part and
identification of overhead cost per unit and profits per unit (Comparison of overhead cost per
unit with the percentage of overhead cost for two parts)...........................................................10
Part C: Difference between unit overhead cost under part A and part B of this report.............13
Conclusion.....................................................................................................................................14
References......................................................................................................................................16
⊘ This is a preview!⊘
Do you want full access?
Subscribe today to unlock all pages.

Trusted by 1+ million students worldwide
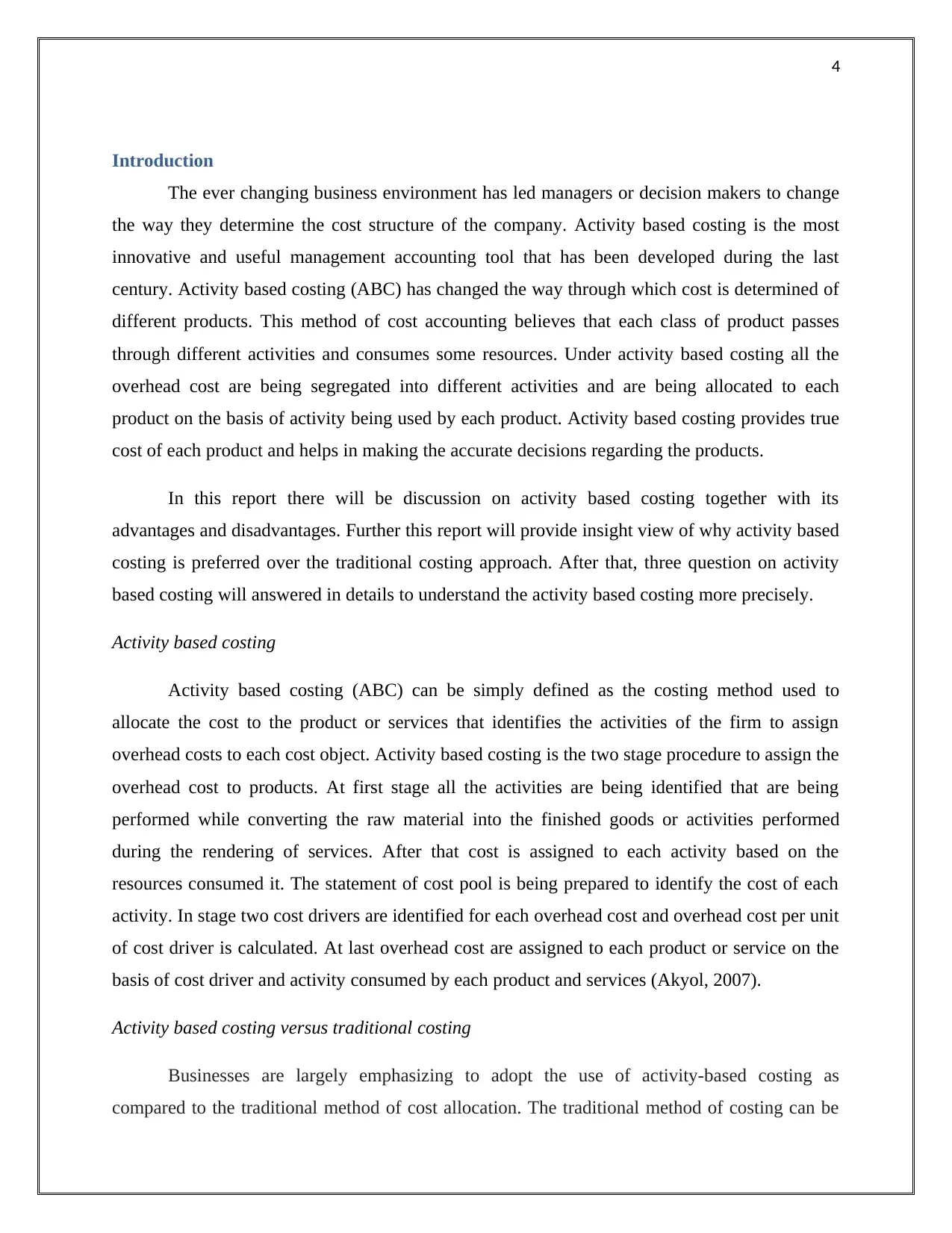
4
Introduction
The ever changing business environment has led managers or decision makers to change
the way they determine the cost structure of the company. Activity based costing is the most
innovative and useful management accounting tool that has been developed during the last
century. Activity based costing (ABC) has changed the way through which cost is determined of
different products. This method of cost accounting believes that each class of product passes
through different activities and consumes some resources. Under activity based costing all the
overhead cost are being segregated into different activities and are being allocated to each
product on the basis of activity being used by each product. Activity based costing provides true
cost of each product and helps in making the accurate decisions regarding the products.
In this report there will be discussion on activity based costing together with its
advantages and disadvantages. Further this report will provide insight view of why activity based
costing is preferred over the traditional costing approach. After that, three question on activity
based costing will answered in details to understand the activity based costing more precisely.
Activity based costing
Activity based costing (ABC) can be simply defined as the costing method used to
allocate the cost to the product or services that identifies the activities of the firm to assign
overhead costs to each cost object. Activity based costing is the two stage procedure to assign the
overhead cost to products. At first stage all the activities are being identified that are being
performed while converting the raw material into the finished goods or activities performed
during the rendering of services. After that cost is assigned to each activity based on the
resources consumed it. The statement of cost pool is being prepared to identify the cost of each
activity. In stage two cost drivers are identified for each overhead cost and overhead cost per unit
of cost driver is calculated. At last overhead cost are assigned to each product or service on the
basis of cost driver and activity consumed by each product and services (Akyol, 2007).
Activity based costing versus traditional costing
Businesses are largely emphasizing to adopt the use of activity-based costing as
compared to the traditional method of cost allocation. The traditional method of costing can be
Introduction
The ever changing business environment has led managers or decision makers to change
the way they determine the cost structure of the company. Activity based costing is the most
innovative and useful management accounting tool that has been developed during the last
century. Activity based costing (ABC) has changed the way through which cost is determined of
different products. This method of cost accounting believes that each class of product passes
through different activities and consumes some resources. Under activity based costing all the
overhead cost are being segregated into different activities and are being allocated to each
product on the basis of activity being used by each product. Activity based costing provides true
cost of each product and helps in making the accurate decisions regarding the products.
In this report there will be discussion on activity based costing together with its
advantages and disadvantages. Further this report will provide insight view of why activity based
costing is preferred over the traditional costing approach. After that, three question on activity
based costing will answered in details to understand the activity based costing more precisely.
Activity based costing
Activity based costing (ABC) can be simply defined as the costing method used to
allocate the cost to the product or services that identifies the activities of the firm to assign
overhead costs to each cost object. Activity based costing is the two stage procedure to assign the
overhead cost to products. At first stage all the activities are being identified that are being
performed while converting the raw material into the finished goods or activities performed
during the rendering of services. After that cost is assigned to each activity based on the
resources consumed it. The statement of cost pool is being prepared to identify the cost of each
activity. In stage two cost drivers are identified for each overhead cost and overhead cost per unit
of cost driver is calculated. At last overhead cost are assigned to each product or service on the
basis of cost driver and activity consumed by each product and services (Akyol, 2007).
Activity based costing versus traditional costing
Businesses are largely emphasizing to adopt the use of activity-based costing as
compared to the traditional method of cost allocation. The traditional method of costing can be
Paraphrase This Document
Need a fresh take? Get an instant paraphrase of this document with our AI Paraphraser
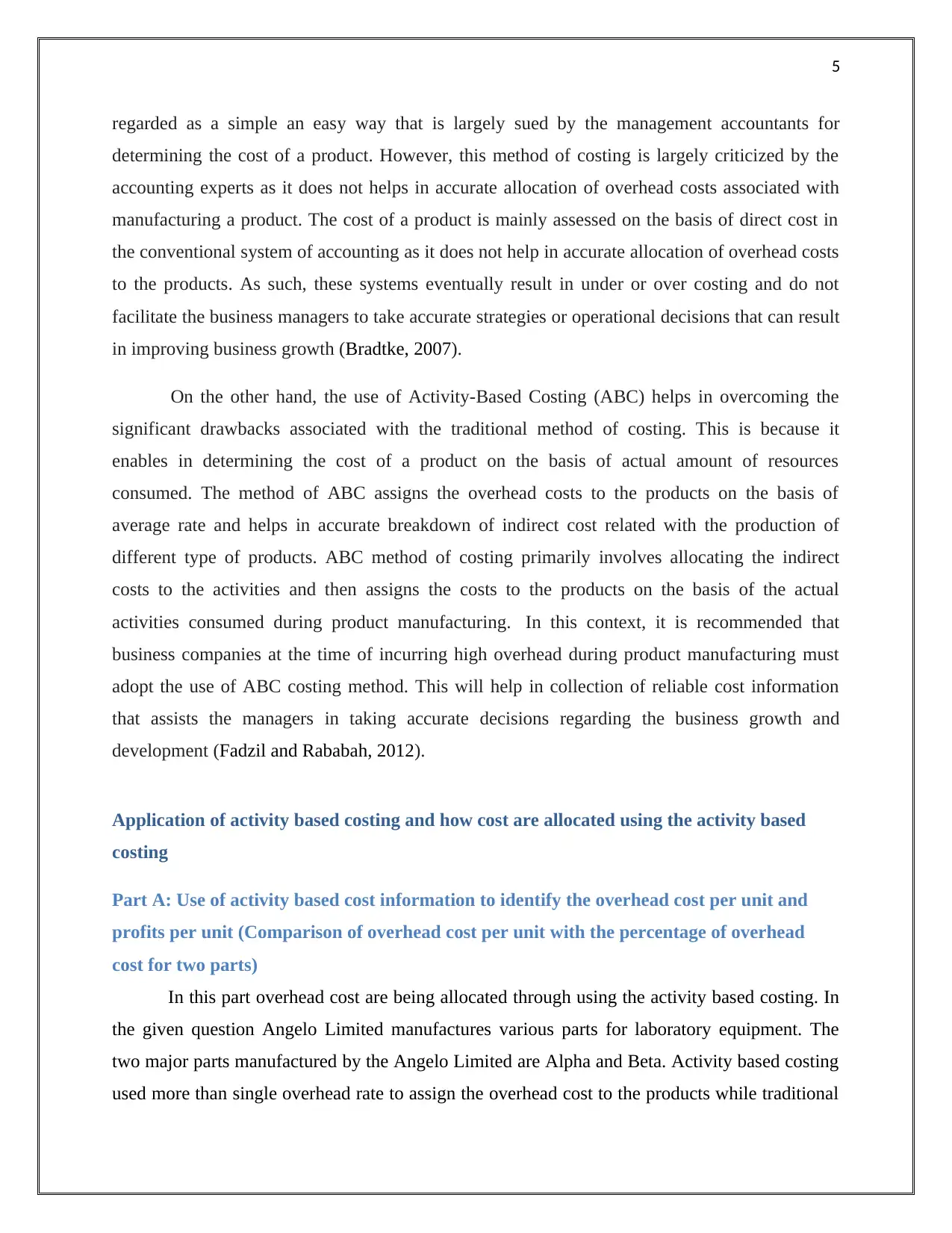
5
regarded as a simple an easy way that is largely sued by the management accountants for
determining the cost of a product. However, this method of costing is largely criticized by the
accounting experts as it does not helps in accurate allocation of overhead costs associated with
manufacturing a product. The cost of a product is mainly assessed on the basis of direct cost in
the conventional system of accounting as it does not help in accurate allocation of overhead costs
to the products. As such, these systems eventually result in under or over costing and do not
facilitate the business managers to take accurate strategies or operational decisions that can result
in improving business growth (Bradtke, 2007).
On the other hand, the use of Activity-Based Costing (ABC) helps in overcoming the
significant drawbacks associated with the traditional method of costing. This is because it
enables in determining the cost of a product on the basis of actual amount of resources
consumed. The method of ABC assigns the overhead costs to the products on the basis of
average rate and helps in accurate breakdown of indirect cost related with the production of
different type of products. ABC method of costing primarily involves allocating the indirect
costs to the activities and then assigns the costs to the products on the basis of the actual
activities consumed during product manufacturing. In this context, it is recommended that
business companies at the time of incurring high overhead during product manufacturing must
adopt the use of ABC costing method. This will help in collection of reliable cost information
that assists the managers in taking accurate decisions regarding the business growth and
development (Fadzil and Rababah, 2012).
Application of activity based costing and how cost are allocated using the activity based
costing
Part A: Use of activity based cost information to identify the overhead cost per unit and
profits per unit (Comparison of overhead cost per unit with the percentage of overhead
cost for two parts)
In this part overhead cost are being allocated through using the activity based costing. In
the given question Angelo Limited manufactures various parts for laboratory equipment. The
two major parts manufactured by the Angelo Limited are Alpha and Beta. Activity based costing
used more than single overhead rate to assign the overhead cost to the products while traditional
regarded as a simple an easy way that is largely sued by the management accountants for
determining the cost of a product. However, this method of costing is largely criticized by the
accounting experts as it does not helps in accurate allocation of overhead costs associated with
manufacturing a product. The cost of a product is mainly assessed on the basis of direct cost in
the conventional system of accounting as it does not help in accurate allocation of overhead costs
to the products. As such, these systems eventually result in under or over costing and do not
facilitate the business managers to take accurate strategies or operational decisions that can result
in improving business growth (Bradtke, 2007).
On the other hand, the use of Activity-Based Costing (ABC) helps in overcoming the
significant drawbacks associated with the traditional method of costing. This is because it
enables in determining the cost of a product on the basis of actual amount of resources
consumed. The method of ABC assigns the overhead costs to the products on the basis of
average rate and helps in accurate breakdown of indirect cost related with the production of
different type of products. ABC method of costing primarily involves allocating the indirect
costs to the activities and then assigns the costs to the products on the basis of the actual
activities consumed during product manufacturing. In this context, it is recommended that
business companies at the time of incurring high overhead during product manufacturing must
adopt the use of ABC costing method. This will help in collection of reliable cost information
that assists the managers in taking accurate decisions regarding the business growth and
development (Fadzil and Rababah, 2012).
Application of activity based costing and how cost are allocated using the activity based
costing
Part A: Use of activity based cost information to identify the overhead cost per unit and
profits per unit (Comparison of overhead cost per unit with the percentage of overhead
cost for two parts)
In this part overhead cost are being allocated through using the activity based costing. In
the given question Angelo Limited manufactures various parts for laboratory equipment. The
two major parts manufactured by the Angelo Limited are Alpha and Beta. Activity based costing
used more than single overhead rate to assign the overhead cost to the products while traditional
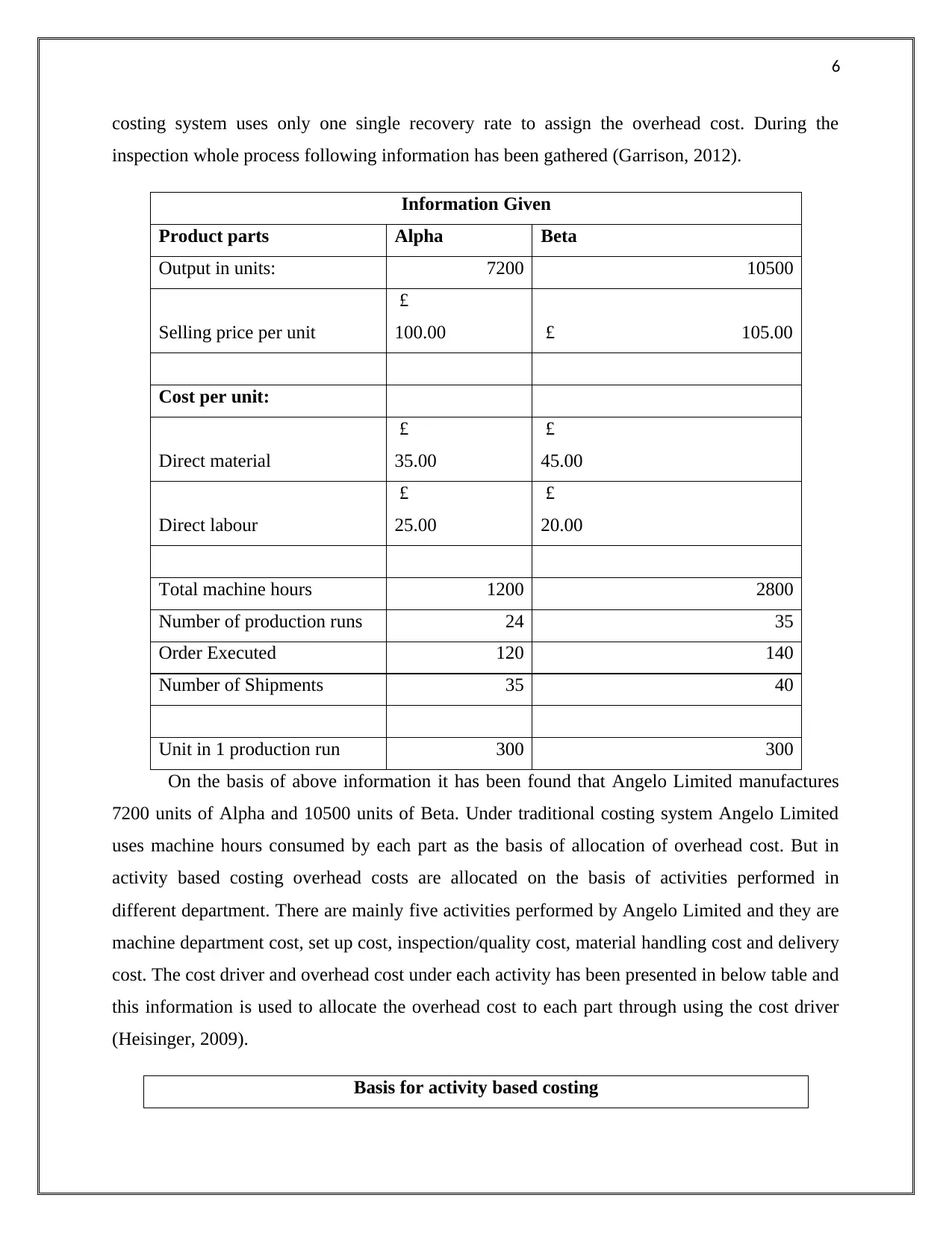
6
costing system uses only one single recovery rate to assign the overhead cost. During the
inspection whole process following information has been gathered (Garrison, 2012).
Information Given
Product parts Alpha Beta
Output in units: 7200 10500
Selling price per unit
£
100.00 £ 105.00
Cost per unit:
Direct material
£
35.00
£
45.00
Direct labour
£
25.00
£
20.00
Total machine hours 1200 2800
Number of production runs 24 35
Order Executed 120 140
Number of Shipments 35 40
Unit in 1 production run 300 300
On the basis of above information it has been found that Angelo Limited manufactures
7200 units of Alpha and 10500 units of Beta. Under traditional costing system Angelo Limited
uses machine hours consumed by each part as the basis of allocation of overhead cost. But in
activity based costing overhead costs are allocated on the basis of activities performed in
different department. There are mainly five activities performed by Angelo Limited and they are
machine department cost, set up cost, inspection/quality cost, material handling cost and delivery
cost. The cost driver and overhead cost under each activity has been presented in below table and
this information is used to allocate the overhead cost to each part through using the cost driver
(Heisinger, 2009).
Basis for activity based costing
costing system uses only one single recovery rate to assign the overhead cost. During the
inspection whole process following information has been gathered (Garrison, 2012).
Information Given
Product parts Alpha Beta
Output in units: 7200 10500
Selling price per unit
£
100.00 £ 105.00
Cost per unit:
Direct material
£
35.00
£
45.00
Direct labour
£
25.00
£
20.00
Total machine hours 1200 2800
Number of production runs 24 35
Order Executed 120 140
Number of Shipments 35 40
Unit in 1 production run 300 300
On the basis of above information it has been found that Angelo Limited manufactures
7200 units of Alpha and 10500 units of Beta. Under traditional costing system Angelo Limited
uses machine hours consumed by each part as the basis of allocation of overhead cost. But in
activity based costing overhead costs are allocated on the basis of activities performed in
different department. There are mainly five activities performed by Angelo Limited and they are
machine department cost, set up cost, inspection/quality cost, material handling cost and delivery
cost. The cost driver and overhead cost under each activity has been presented in below table and
this information is used to allocate the overhead cost to each part through using the cost driver
(Heisinger, 2009).
Basis for activity based costing
⊘ This is a preview!⊘
Do you want full access?
Subscribe today to unlock all pages.

Trusted by 1+ million students worldwide
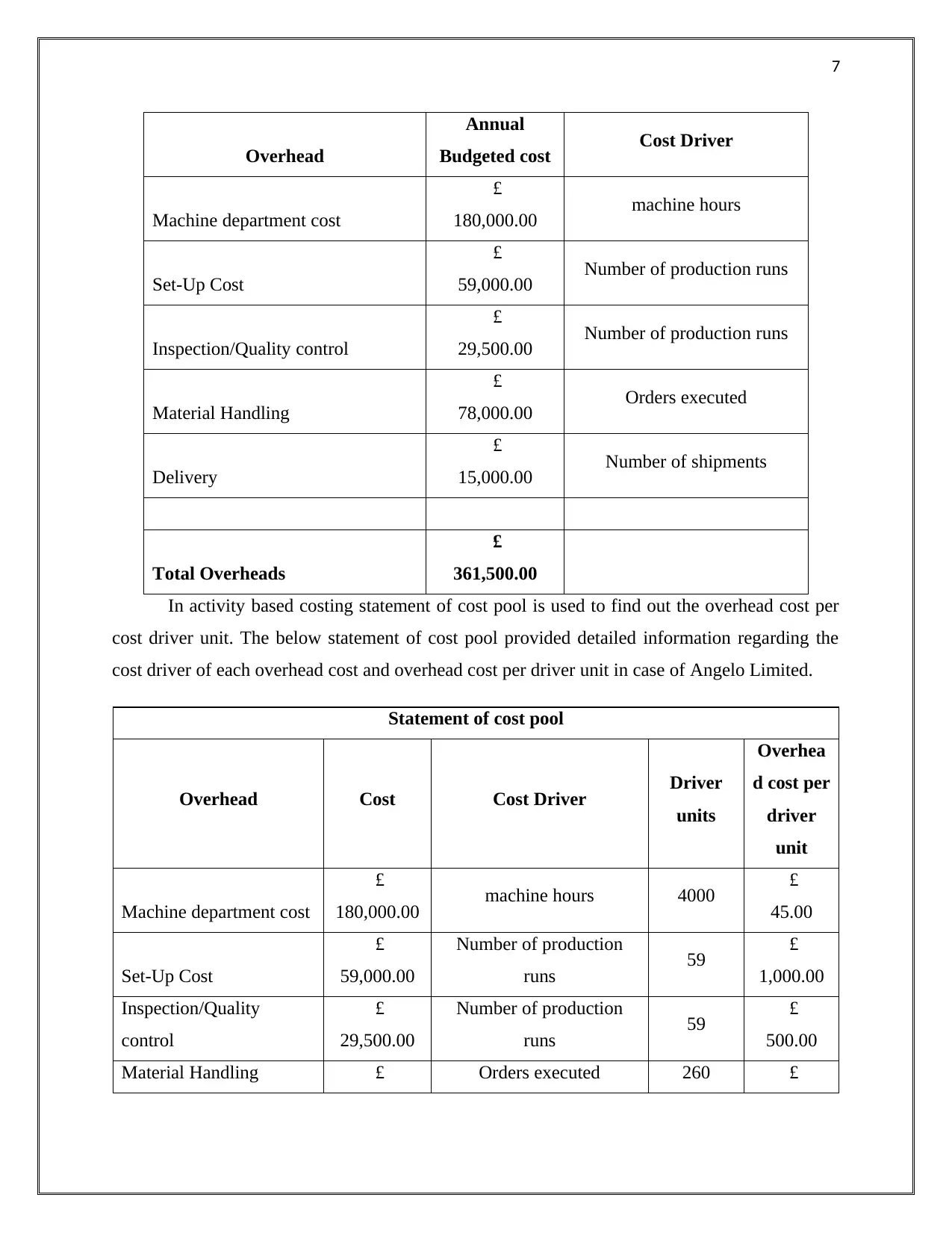
7
Overhead
Annual
Budgeted cost Cost Driver
Machine department cost
£
180,000.00 machine hours
Set-Up Cost
£
59,000.00 Number of production runs
Inspection/Quality control
£
29,500.00 Number of production runs
Material Handling
£
78,000.00 Orders executed
Delivery
£
15,000.00 Number of shipments
Total Overheads
£
361,500.00
In activity based costing statement of cost pool is used to find out the overhead cost per
cost driver unit. The below statement of cost pool provided detailed information regarding the
cost driver of each overhead cost and overhead cost per driver unit in case of Angelo Limited.
Statement of cost pool
Overhead Cost Cost Driver Driver
units
Overhea
d cost per
driver
unit
Machine department cost
£
180,000.00 machine hours 4000 £
45.00
Set-Up Cost
£
59,000.00
Number of production
runs 59 £
1,000.00
Inspection/Quality
control
£
29,500.00
Number of production
runs 59 £
500.00
Material Handling £ Orders executed 260 £
Overhead
Annual
Budgeted cost Cost Driver
Machine department cost
£
180,000.00 machine hours
Set-Up Cost
£
59,000.00 Number of production runs
Inspection/Quality control
£
29,500.00 Number of production runs
Material Handling
£
78,000.00 Orders executed
Delivery
£
15,000.00 Number of shipments
Total Overheads
£
361,500.00
In activity based costing statement of cost pool is used to find out the overhead cost per
cost driver unit. The below statement of cost pool provided detailed information regarding the
cost driver of each overhead cost and overhead cost per driver unit in case of Angelo Limited.
Statement of cost pool
Overhead Cost Cost Driver Driver
units
Overhea
d cost per
driver
unit
Machine department cost
£
180,000.00 machine hours 4000 £
45.00
Set-Up Cost
£
59,000.00
Number of production
runs 59 £
1,000.00
Inspection/Quality
control
£
29,500.00
Number of production
runs 59 £
500.00
Material Handling £ Orders executed 260 £
Paraphrase This Document
Need a fresh take? Get an instant paraphrase of this document with our AI Paraphraser
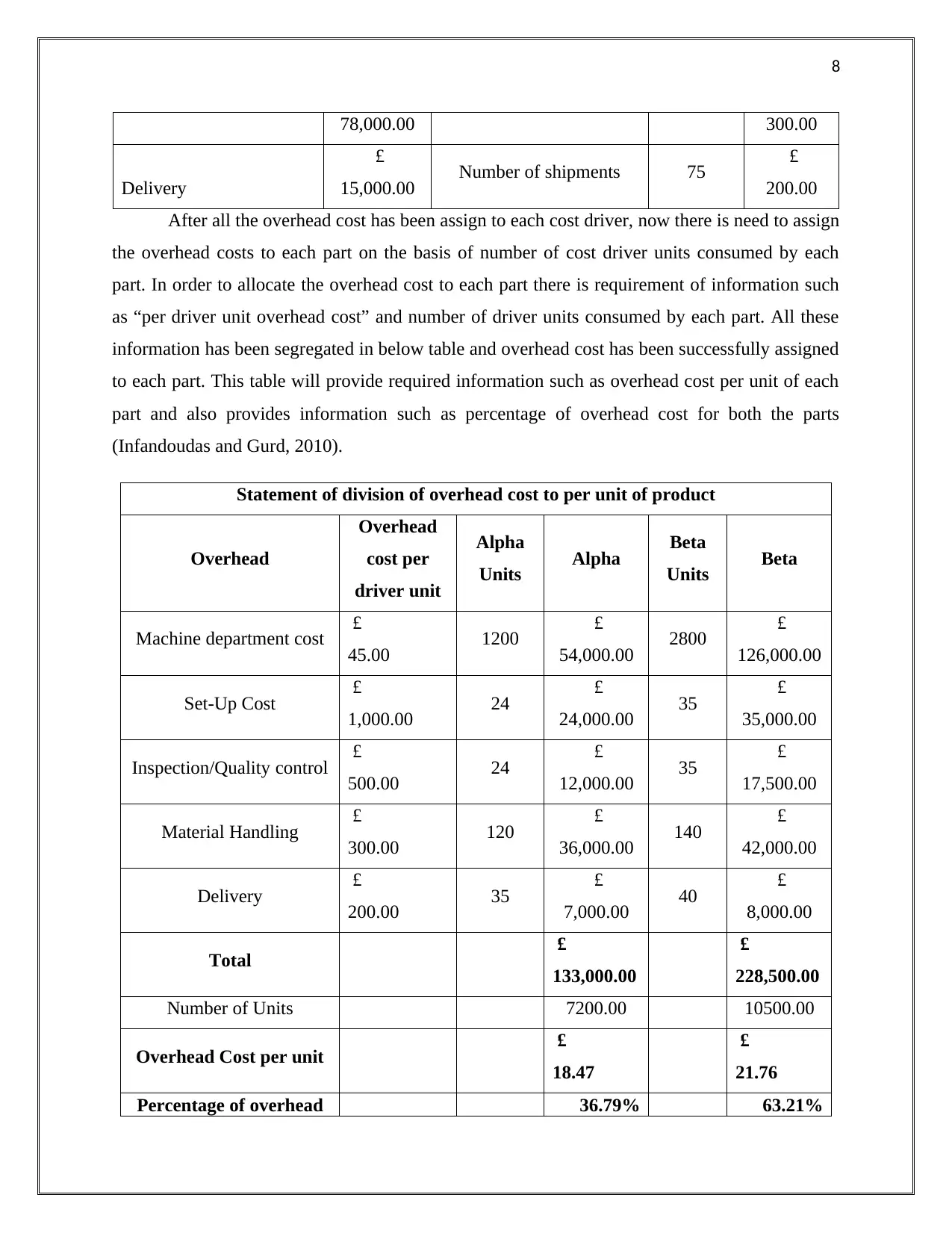
8
78,000.00 300.00
Delivery
£
15,000.00 Number of shipments 75 £
200.00
After all the overhead cost has been assign to each cost driver, now there is need to assign
the overhead costs to each part on the basis of number of cost driver units consumed by each
part. In order to allocate the overhead cost to each part there is requirement of information such
as “per driver unit overhead cost” and number of driver units consumed by each part. All these
information has been segregated in below table and overhead cost has been successfully assigned
to each part. This table will provide required information such as overhead cost per unit of each
part and also provides information such as percentage of overhead cost for both the parts
(Infandoudas and Gurd, 2010).
Statement of division of overhead cost to per unit of product
Overhead
Overhead
cost per
driver unit
Alpha
Units Alpha Beta
Units Beta
Machine department cost £
45.00 1200 £
54,000.00 2800 £
126,000.00
Set-Up Cost £
1,000.00 24 £
24,000.00 35 £
35,000.00
Inspection/Quality control £
500.00 24 £
12,000.00 35 £
17,500.00
Material Handling £
300.00 120 £
36,000.00 140 £
42,000.00
Delivery £
200.00 35 £
7,000.00 40 £
8,000.00
Total £
133,000.00
£
228,500.00
Number of Units 7200.00 10500.00
Overhead Cost per unit £
18.47
£
21.76
Percentage of overhead 36.79% 63.21%
78,000.00 300.00
Delivery
£
15,000.00 Number of shipments 75 £
200.00
After all the overhead cost has been assign to each cost driver, now there is need to assign
the overhead costs to each part on the basis of number of cost driver units consumed by each
part. In order to allocate the overhead cost to each part there is requirement of information such
as “per driver unit overhead cost” and number of driver units consumed by each part. All these
information has been segregated in below table and overhead cost has been successfully assigned
to each part. This table will provide required information such as overhead cost per unit of each
part and also provides information such as percentage of overhead cost for both the parts
(Infandoudas and Gurd, 2010).
Statement of division of overhead cost to per unit of product
Overhead
Overhead
cost per
driver unit
Alpha
Units Alpha Beta
Units Beta
Machine department cost £
45.00 1200 £
54,000.00 2800 £
126,000.00
Set-Up Cost £
1,000.00 24 £
24,000.00 35 £
35,000.00
Inspection/Quality control £
500.00 24 £
12,000.00 35 £
17,500.00
Material Handling £
300.00 120 £
36,000.00 140 £
42,000.00
Delivery £
200.00 35 £
7,000.00 40 £
8,000.00
Total £
133,000.00
£
228,500.00
Number of Units 7200.00 10500.00
Overhead Cost per unit £
18.47
£
21.76
Percentage of overhead 36.79% 63.21%
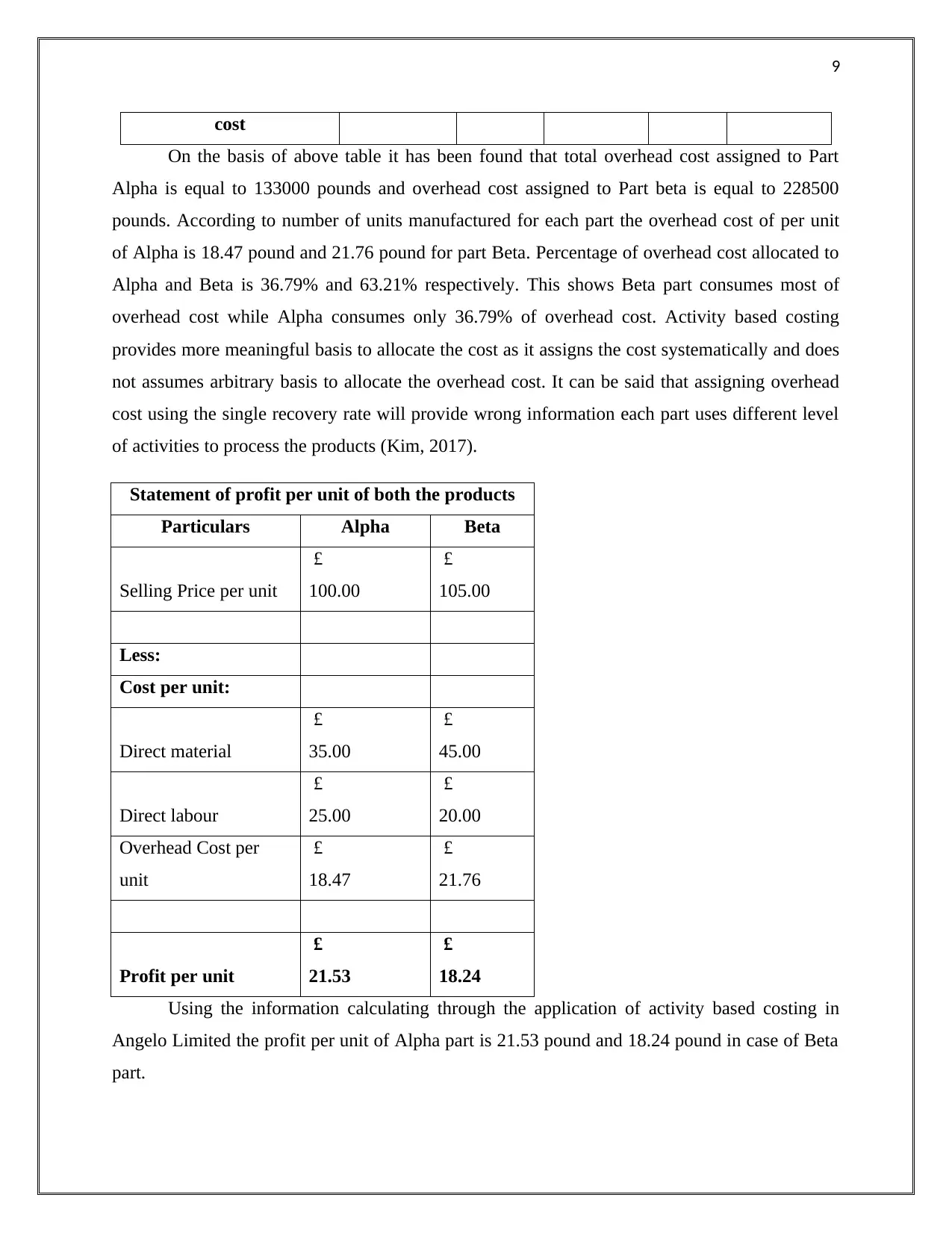
9
cost
On the basis of above table it has been found that total overhead cost assigned to Part
Alpha is equal to 133000 pounds and overhead cost assigned to Part beta is equal to 228500
pounds. According to number of units manufactured for each part the overhead cost of per unit
of Alpha is 18.47 pound and 21.76 pound for part Beta. Percentage of overhead cost allocated to
Alpha and Beta is 36.79% and 63.21% respectively. This shows Beta part consumes most of
overhead cost while Alpha consumes only 36.79% of overhead cost. Activity based costing
provides more meaningful basis to allocate the cost as it assigns the cost systematically and does
not assumes arbitrary basis to allocate the overhead cost. It can be said that assigning overhead
cost using the single recovery rate will provide wrong information each part uses different level
of activities to process the products (Kim, 2017).
Statement of profit per unit of both the products
Particulars Alpha Beta
Selling Price per unit
£
100.00
£
105.00
Less:
Cost per unit:
Direct material
£
35.00
£
45.00
Direct labour
£
25.00
£
20.00
Overhead Cost per
unit
£
18.47
£
21.76
Profit per unit
£
21.53
£
18.24
Using the information calculating through the application of activity based costing in
Angelo Limited the profit per unit of Alpha part is 21.53 pound and 18.24 pound in case of Beta
part.
cost
On the basis of above table it has been found that total overhead cost assigned to Part
Alpha is equal to 133000 pounds and overhead cost assigned to Part beta is equal to 228500
pounds. According to number of units manufactured for each part the overhead cost of per unit
of Alpha is 18.47 pound and 21.76 pound for part Beta. Percentage of overhead cost allocated to
Alpha and Beta is 36.79% and 63.21% respectively. This shows Beta part consumes most of
overhead cost while Alpha consumes only 36.79% of overhead cost. Activity based costing
provides more meaningful basis to allocate the cost as it assigns the cost systematically and does
not assumes arbitrary basis to allocate the overhead cost. It can be said that assigning overhead
cost using the single recovery rate will provide wrong information each part uses different level
of activities to process the products (Kim, 2017).
Statement of profit per unit of both the products
Particulars Alpha Beta
Selling Price per unit
£
100.00
£
105.00
Less:
Cost per unit:
Direct material
£
35.00
£
45.00
Direct labour
£
25.00
£
20.00
Overhead Cost per
unit
£
18.47
£
21.76
Profit per unit
£
21.53
£
18.24
Using the information calculating through the application of activity based costing in
Angelo Limited the profit per unit of Alpha part is 21.53 pound and 18.24 pound in case of Beta
part.
⊘ This is a preview!⊘
Do you want full access?
Subscribe today to unlock all pages.

Trusted by 1+ million students worldwide
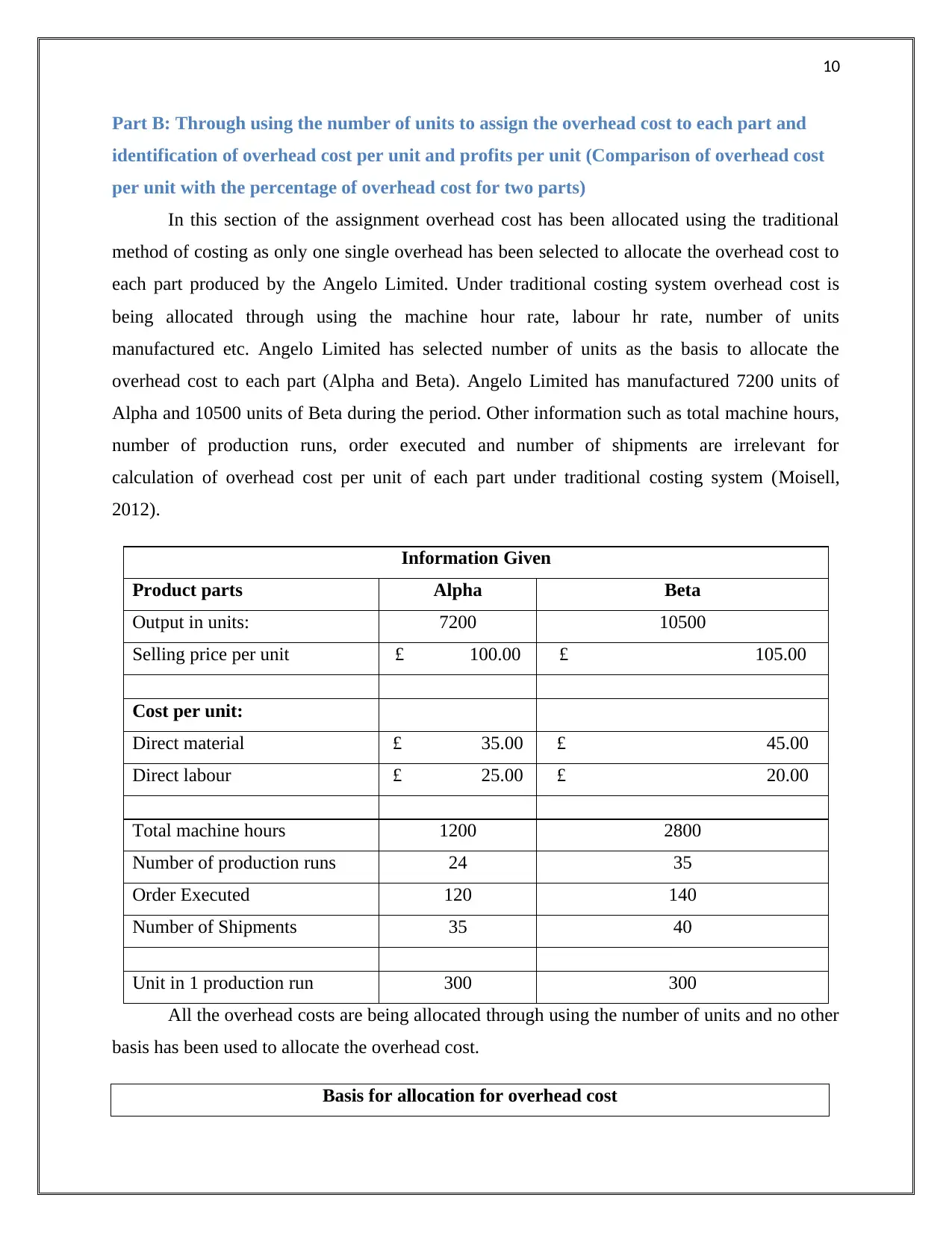
10
Part B: Through using the number of units to assign the overhead cost to each part and
identification of overhead cost per unit and profits per unit (Comparison of overhead cost
per unit with the percentage of overhead cost for two parts)
In this section of the assignment overhead cost has been allocated using the traditional
method of costing as only one single overhead has been selected to allocate the overhead cost to
each part produced by the Angelo Limited. Under traditional costing system overhead cost is
being allocated through using the machine hour rate, labour hr rate, number of units
manufactured etc. Angelo Limited has selected number of units as the basis to allocate the
overhead cost to each part (Alpha and Beta). Angelo Limited has manufactured 7200 units of
Alpha and 10500 units of Beta during the period. Other information such as total machine hours,
number of production runs, order executed and number of shipments are irrelevant for
calculation of overhead cost per unit of each part under traditional costing system (Moisell,
2012).
Information Given
Product parts Alpha Beta
Output in units: 7200 10500
Selling price per unit £ 100.00 £ 105.00
Cost per unit:
Direct material £ 35.00 £ 45.00
Direct labour £ 25.00 £ 20.00
Total machine hours 1200 2800
Number of production runs 24 35
Order Executed 120 140
Number of Shipments 35 40
Unit in 1 production run 300 300
All the overhead costs are being allocated through using the number of units and no other
basis has been used to allocate the overhead cost.
Basis for allocation for overhead cost
Part B: Through using the number of units to assign the overhead cost to each part and
identification of overhead cost per unit and profits per unit (Comparison of overhead cost
per unit with the percentage of overhead cost for two parts)
In this section of the assignment overhead cost has been allocated using the traditional
method of costing as only one single overhead has been selected to allocate the overhead cost to
each part produced by the Angelo Limited. Under traditional costing system overhead cost is
being allocated through using the machine hour rate, labour hr rate, number of units
manufactured etc. Angelo Limited has selected number of units as the basis to allocate the
overhead cost to each part (Alpha and Beta). Angelo Limited has manufactured 7200 units of
Alpha and 10500 units of Beta during the period. Other information such as total machine hours,
number of production runs, order executed and number of shipments are irrelevant for
calculation of overhead cost per unit of each part under traditional costing system (Moisell,
2012).
Information Given
Product parts Alpha Beta
Output in units: 7200 10500
Selling price per unit £ 100.00 £ 105.00
Cost per unit:
Direct material £ 35.00 £ 45.00
Direct labour £ 25.00 £ 20.00
Total machine hours 1200 2800
Number of production runs 24 35
Order Executed 120 140
Number of Shipments 35 40
Unit in 1 production run 300 300
All the overhead costs are being allocated through using the number of units and no other
basis has been used to allocate the overhead cost.
Basis for allocation for overhead cost
Paraphrase This Document
Need a fresh take? Get an instant paraphrase of this document with our AI Paraphraser
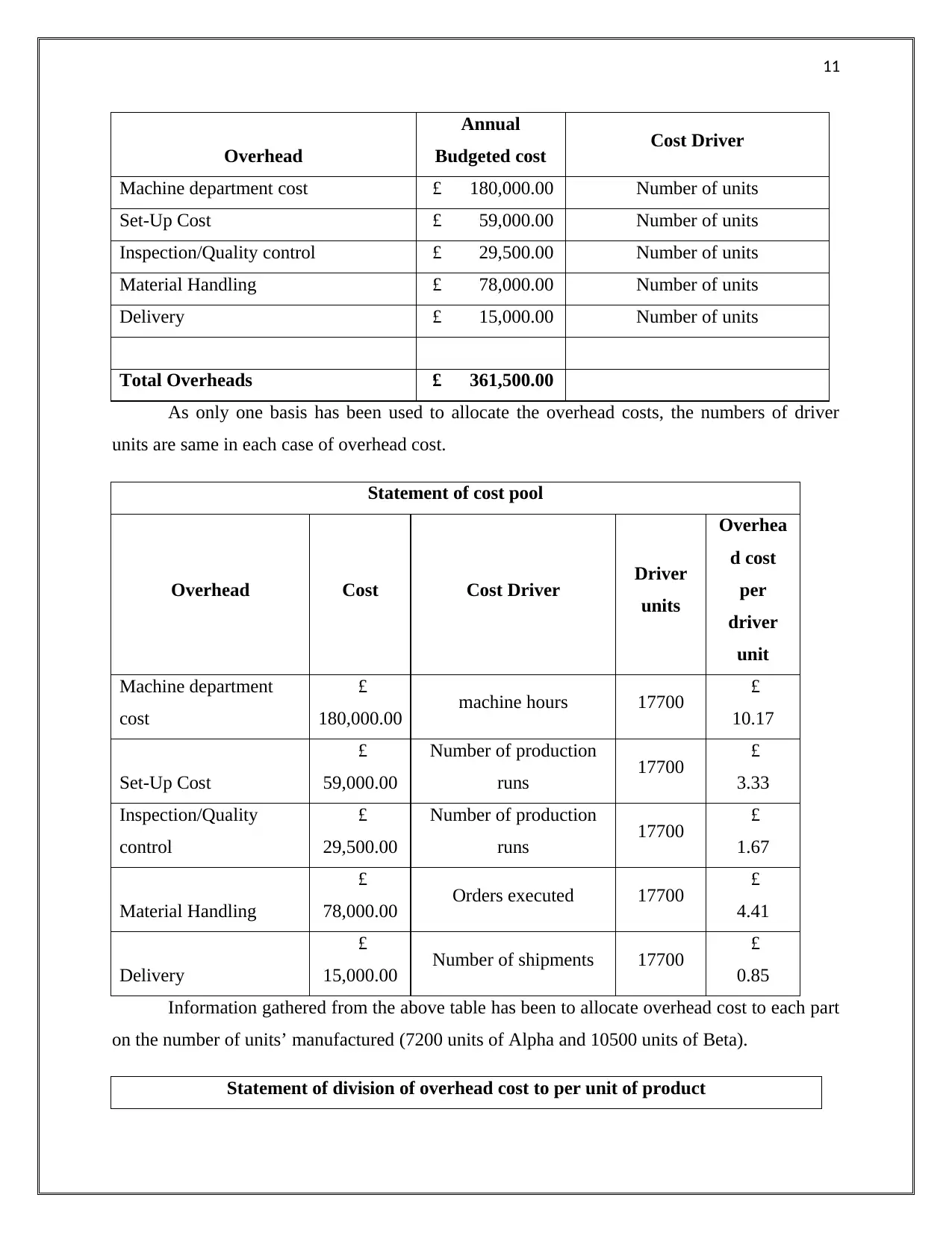
11
Overhead
Annual
Budgeted cost Cost Driver
Machine department cost £ 180,000.00 Number of units
Set-Up Cost £ 59,000.00 Number of units
Inspection/Quality control £ 29,500.00 Number of units
Material Handling £ 78,000.00 Number of units
Delivery £ 15,000.00 Number of units
Total Overheads £ 361,500.00
As only one basis has been used to allocate the overhead costs, the numbers of driver
units are same in each case of overhead cost.
Statement of cost pool
Overhead Cost Cost Driver Driver
units
Overhea
d cost
per
driver
unit
Machine department
cost
£
180,000.00 machine hours 17700 £
10.17
Set-Up Cost
£
59,000.00
Number of production
runs 17700 £
3.33
Inspection/Quality
control
£
29,500.00
Number of production
runs 17700 £
1.67
Material Handling
£
78,000.00 Orders executed 17700 £
4.41
Delivery
£
15,000.00 Number of shipments 17700 £
0.85
Information gathered from the above table has been to allocate overhead cost to each part
on the number of units’ manufactured (7200 units of Alpha and 10500 units of Beta).
Statement of division of overhead cost to per unit of product
Overhead
Annual
Budgeted cost Cost Driver
Machine department cost £ 180,000.00 Number of units
Set-Up Cost £ 59,000.00 Number of units
Inspection/Quality control £ 29,500.00 Number of units
Material Handling £ 78,000.00 Number of units
Delivery £ 15,000.00 Number of units
Total Overheads £ 361,500.00
As only one basis has been used to allocate the overhead costs, the numbers of driver
units are same in each case of overhead cost.
Statement of cost pool
Overhead Cost Cost Driver Driver
units
Overhea
d cost
per
driver
unit
Machine department
cost
£
180,000.00 machine hours 17700 £
10.17
Set-Up Cost
£
59,000.00
Number of production
runs 17700 £
3.33
Inspection/Quality
control
£
29,500.00
Number of production
runs 17700 £
1.67
Material Handling
£
78,000.00 Orders executed 17700 £
4.41
Delivery
£
15,000.00 Number of shipments 17700 £
0.85
Information gathered from the above table has been to allocate overhead cost to each part
on the number of units’ manufactured (7200 units of Alpha and 10500 units of Beta).
Statement of division of overhead cost to per unit of product
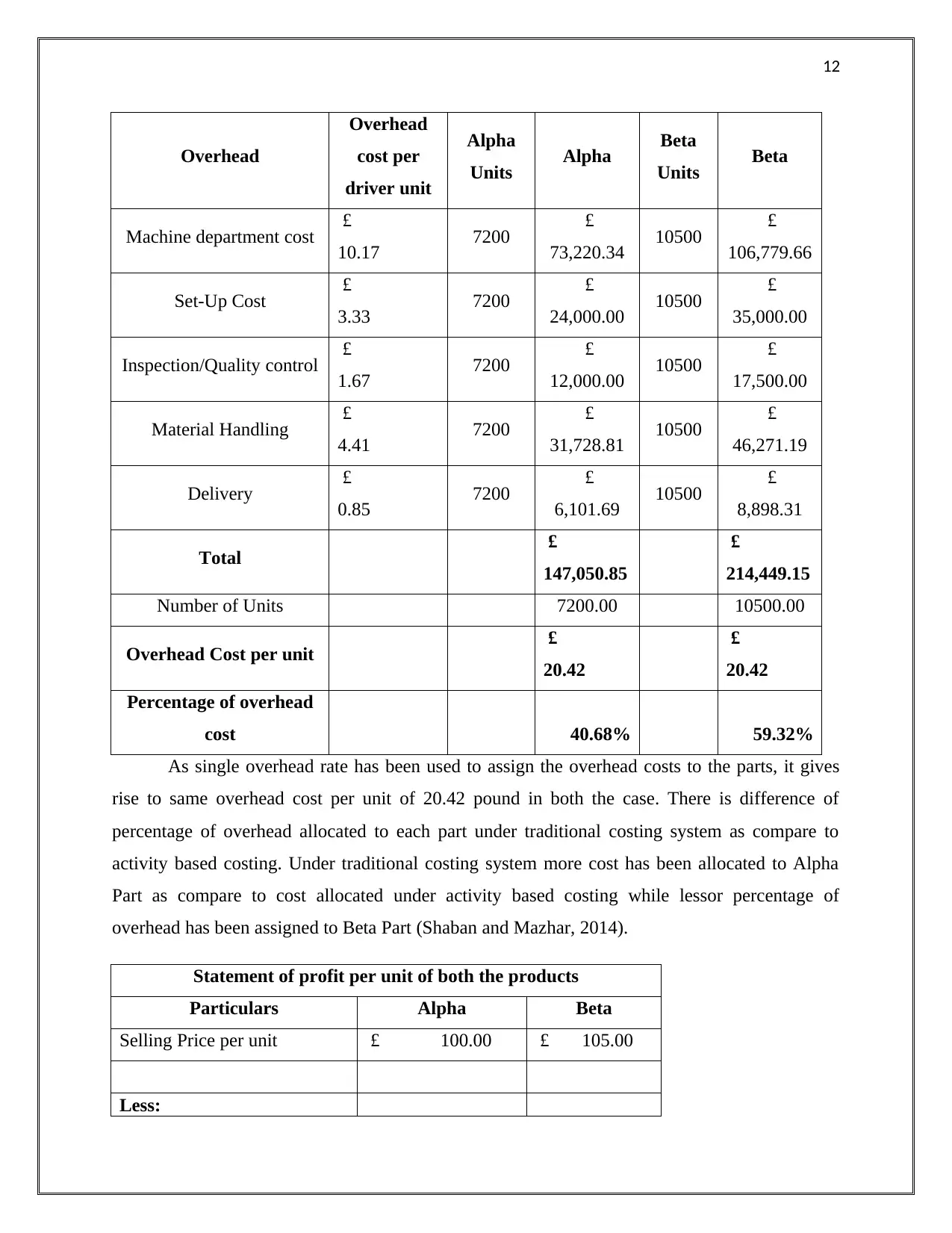
12
Overhead
Overhead
cost per
driver unit
Alpha
Units Alpha Beta
Units Beta
Machine department cost £
10.17 7200 £
73,220.34 10500 £
106,779.66
Set-Up Cost £
3.33 7200 £
24,000.00 10500 £
35,000.00
Inspection/Quality control £
1.67 7200 £
12,000.00 10500 £
17,500.00
Material Handling £
4.41 7200 £
31,728.81 10500 £
46,271.19
Delivery £
0.85 7200 £
6,101.69 10500 £
8,898.31
Total £
147,050.85
£
214,449.15
Number of Units 7200.00 10500.00
Overhead Cost per unit £
20.42
£
20.42
Percentage of overhead
cost 40.68% 59.32%
As single overhead rate has been used to assign the overhead costs to the parts, it gives
rise to same overhead cost per unit of 20.42 pound in both the case. There is difference of
percentage of overhead allocated to each part under traditional costing system as compare to
activity based costing. Under traditional costing system more cost has been allocated to Alpha
Part as compare to cost allocated under activity based costing while lessor percentage of
overhead has been assigned to Beta Part (Shaban and Mazhar, 2014).
Statement of profit per unit of both the products
Particulars Alpha Beta
Selling Price per unit £ 100.00 £ 105.00
Less:
Overhead
Overhead
cost per
driver unit
Alpha
Units Alpha Beta
Units Beta
Machine department cost £
10.17 7200 £
73,220.34 10500 £
106,779.66
Set-Up Cost £
3.33 7200 £
24,000.00 10500 £
35,000.00
Inspection/Quality control £
1.67 7200 £
12,000.00 10500 £
17,500.00
Material Handling £
4.41 7200 £
31,728.81 10500 £
46,271.19
Delivery £
0.85 7200 £
6,101.69 10500 £
8,898.31
Total £
147,050.85
£
214,449.15
Number of Units 7200.00 10500.00
Overhead Cost per unit £
20.42
£
20.42
Percentage of overhead
cost 40.68% 59.32%
As single overhead rate has been used to assign the overhead costs to the parts, it gives
rise to same overhead cost per unit of 20.42 pound in both the case. There is difference of
percentage of overhead allocated to each part under traditional costing system as compare to
activity based costing. Under traditional costing system more cost has been allocated to Alpha
Part as compare to cost allocated under activity based costing while lessor percentage of
overhead has been assigned to Beta Part (Shaban and Mazhar, 2014).
Statement of profit per unit of both the products
Particulars Alpha Beta
Selling Price per unit £ 100.00 £ 105.00
Less:
⊘ This is a preview!⊘
Do you want full access?
Subscribe today to unlock all pages.

Trusted by 1+ million students worldwide
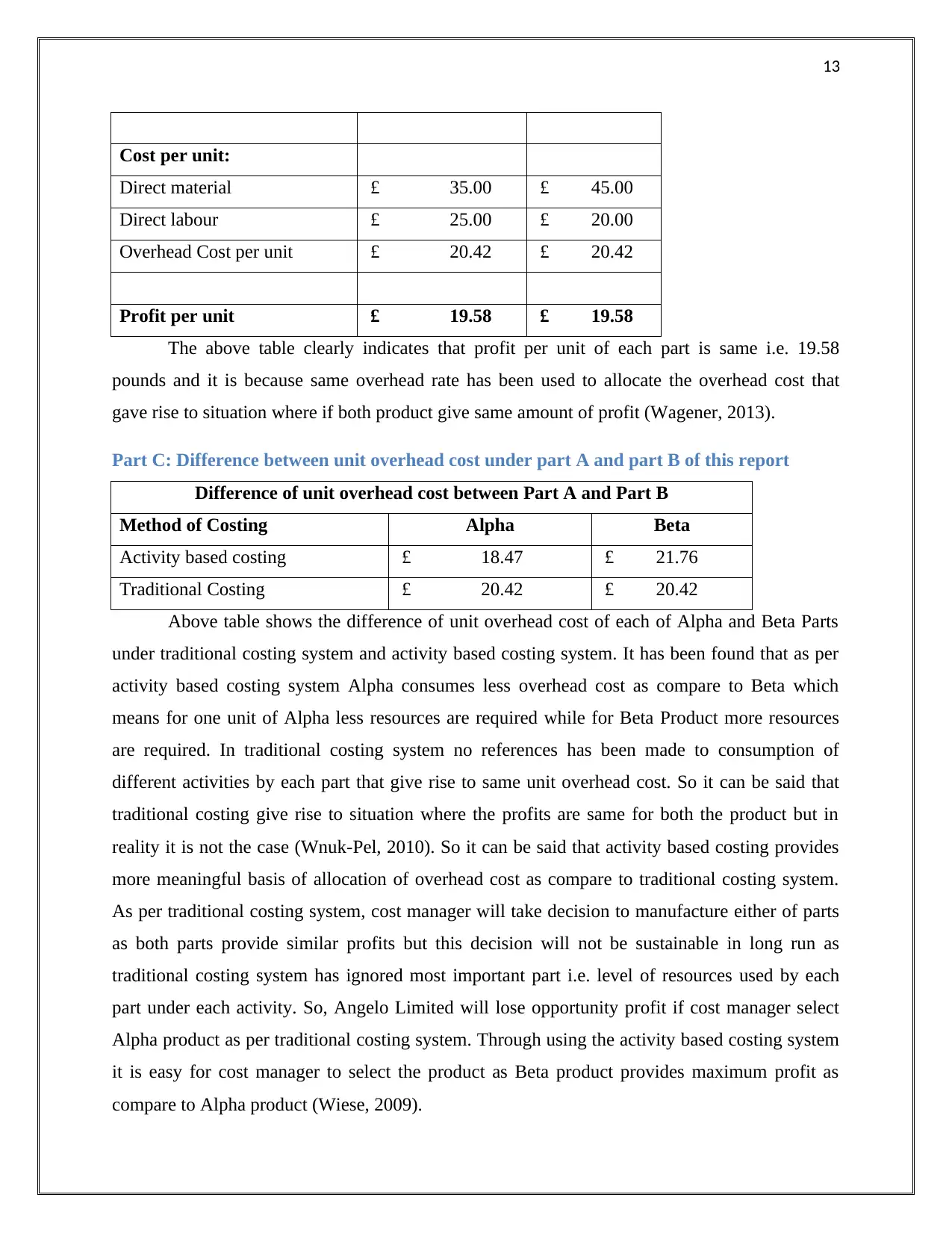
13
Cost per unit:
Direct material £ 35.00 £ 45.00
Direct labour £ 25.00 £ 20.00
Overhead Cost per unit £ 20.42 £ 20.42
Profit per unit £ 19.58 £ 19.58
The above table clearly indicates that profit per unit of each part is same i.e. 19.58
pounds and it is because same overhead rate has been used to allocate the overhead cost that
gave rise to situation where if both product give same amount of profit (Wagener, 2013).
Part C: Difference between unit overhead cost under part A and part B of this report
Difference of unit overhead cost between Part A and Part B
Method of Costing Alpha Beta
Activity based costing £ 18.47 £ 21.76
Traditional Costing £ 20.42 £ 20.42
Above table shows the difference of unit overhead cost of each of Alpha and Beta Parts
under traditional costing system and activity based costing system. It has been found that as per
activity based costing system Alpha consumes less overhead cost as compare to Beta which
means for one unit of Alpha less resources are required while for Beta Product more resources
are required. In traditional costing system no references has been made to consumption of
different activities by each part that give rise to same unit overhead cost. So it can be said that
traditional costing give rise to situation where the profits are same for both the product but in
reality it is not the case (Wnuk-Pel, 2010). So it can be said that activity based costing provides
more meaningful basis of allocation of overhead cost as compare to traditional costing system.
As per traditional costing system, cost manager will take decision to manufacture either of parts
as both parts provide similar profits but this decision will not be sustainable in long run as
traditional costing system has ignored most important part i.e. level of resources used by each
part under each activity. So, Angelo Limited will lose opportunity profit if cost manager select
Alpha product as per traditional costing system. Through using the activity based costing system
it is easy for cost manager to select the product as Beta product provides maximum profit as
compare to Alpha product (Wiese, 2009).
Cost per unit:
Direct material £ 35.00 £ 45.00
Direct labour £ 25.00 £ 20.00
Overhead Cost per unit £ 20.42 £ 20.42
Profit per unit £ 19.58 £ 19.58
The above table clearly indicates that profit per unit of each part is same i.e. 19.58
pounds and it is because same overhead rate has been used to allocate the overhead cost that
gave rise to situation where if both product give same amount of profit (Wagener, 2013).
Part C: Difference between unit overhead cost under part A and part B of this report
Difference of unit overhead cost between Part A and Part B
Method of Costing Alpha Beta
Activity based costing £ 18.47 £ 21.76
Traditional Costing £ 20.42 £ 20.42
Above table shows the difference of unit overhead cost of each of Alpha and Beta Parts
under traditional costing system and activity based costing system. It has been found that as per
activity based costing system Alpha consumes less overhead cost as compare to Beta which
means for one unit of Alpha less resources are required while for Beta Product more resources
are required. In traditional costing system no references has been made to consumption of
different activities by each part that give rise to same unit overhead cost. So it can be said that
traditional costing give rise to situation where the profits are same for both the product but in
reality it is not the case (Wnuk-Pel, 2010). So it can be said that activity based costing provides
more meaningful basis of allocation of overhead cost as compare to traditional costing system.
As per traditional costing system, cost manager will take decision to manufacture either of parts
as both parts provide similar profits but this decision will not be sustainable in long run as
traditional costing system has ignored most important part i.e. level of resources used by each
part under each activity. So, Angelo Limited will lose opportunity profit if cost manager select
Alpha product as per traditional costing system. Through using the activity based costing system
it is easy for cost manager to select the product as Beta product provides maximum profit as
compare to Alpha product (Wiese, 2009).
Paraphrase This Document
Need a fresh take? Get an instant paraphrase of this document with our AI Paraphraser
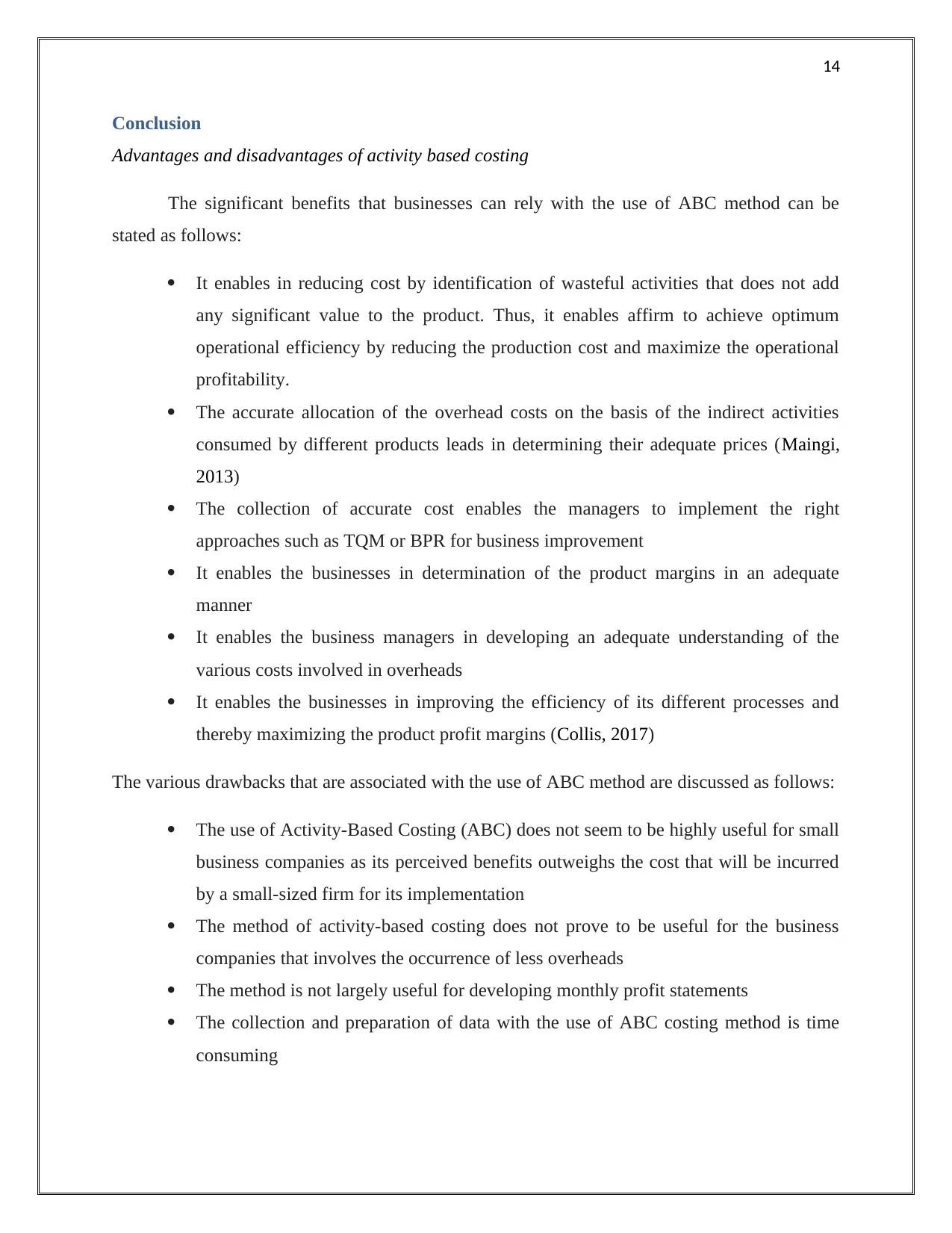
14
Conclusion
Advantages and disadvantages of activity based costing
The significant benefits that businesses can rely with the use of ABC method can be
stated as follows:
It enables in reducing cost by identification of wasteful activities that does not add
any significant value to the product. Thus, it enables affirm to achieve optimum
operational efficiency by reducing the production cost and maximize the operational
profitability.
The accurate allocation of the overhead costs on the basis of the indirect activities
consumed by different products leads in determining their adequate prices (Maingi,
2013)
The collection of accurate cost enables the managers to implement the right
approaches such as TQM or BPR for business improvement
It enables the businesses in determination of the product margins in an adequate
manner
It enables the business managers in developing an adequate understanding of the
various costs involved in overheads
It enables the businesses in improving the efficiency of its different processes and
thereby maximizing the product profit margins (Collis, 2017)
The various drawbacks that are associated with the use of ABC method are discussed as follows:
The use of Activity-Based Costing (ABC) does not seem to be highly useful for small
business companies as its perceived benefits outweighs the cost that will be incurred
by a small-sized firm for its implementation
The method of activity-based costing does not prove to be useful for the business
companies that involves the occurrence of less overheads
The method is not largely useful for developing monthly profit statements
The collection and preparation of data with the use of ABC costing method is time
consuming
Conclusion
Advantages and disadvantages of activity based costing
The significant benefits that businesses can rely with the use of ABC method can be
stated as follows:
It enables in reducing cost by identification of wasteful activities that does not add
any significant value to the product. Thus, it enables affirm to achieve optimum
operational efficiency by reducing the production cost and maximize the operational
profitability.
The accurate allocation of the overhead costs on the basis of the indirect activities
consumed by different products leads in determining their adequate prices (Maingi,
2013)
The collection of accurate cost enables the managers to implement the right
approaches such as TQM or BPR for business improvement
It enables the businesses in determination of the product margins in an adequate
manner
It enables the business managers in developing an adequate understanding of the
various costs involved in overheads
It enables the businesses in improving the efficiency of its different processes and
thereby maximizing the product profit margins (Collis, 2017)
The various drawbacks that are associated with the use of ABC method are discussed as follows:
The use of Activity-Based Costing (ABC) does not seem to be highly useful for small
business companies as its perceived benefits outweighs the cost that will be incurred
by a small-sized firm for its implementation
The method of activity-based costing does not prove to be useful for the business
companies that involves the occurrence of less overheads
The method is not largely useful for developing monthly profit statements
The collection and preparation of data with the use of ABC costing method is time
consuming
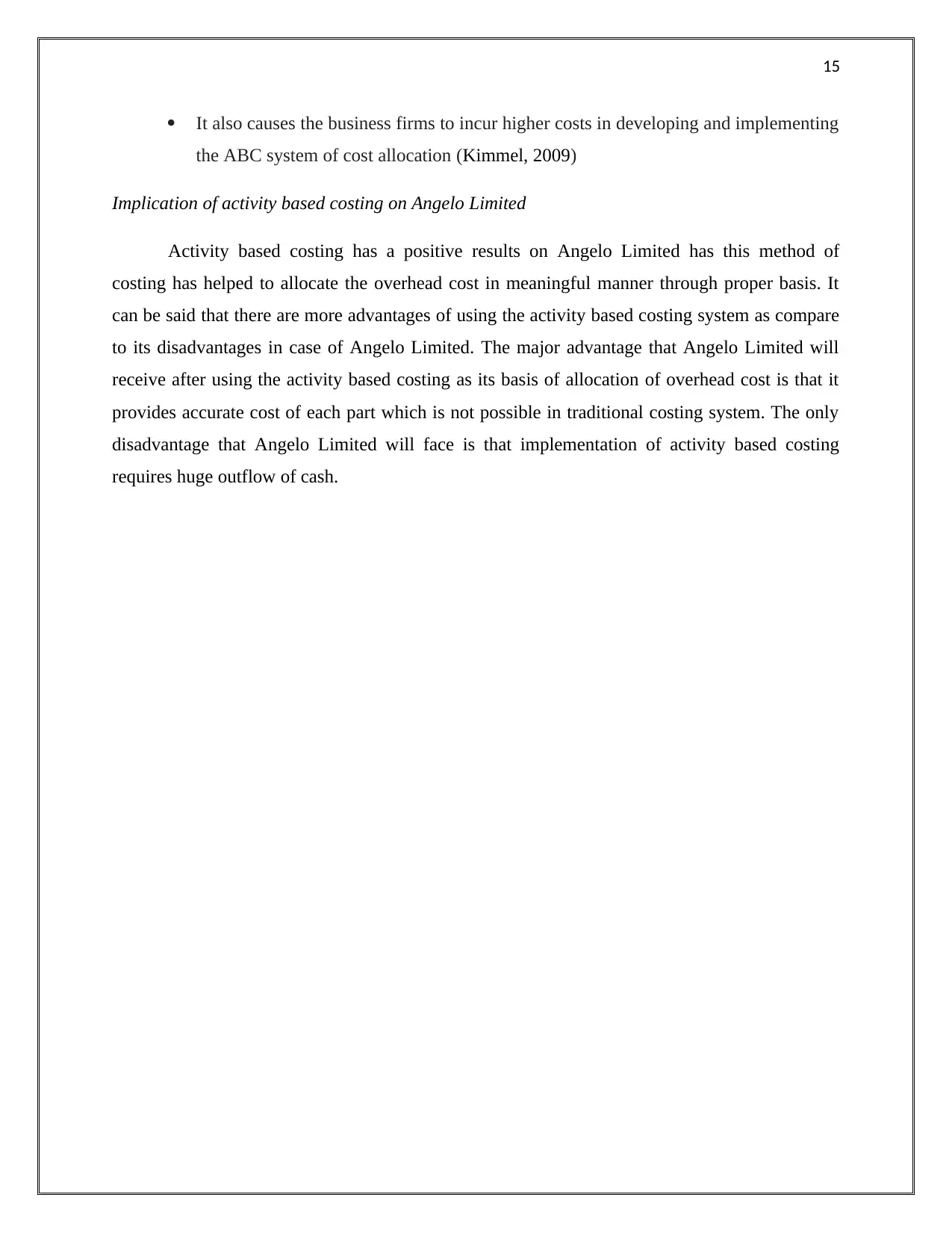
15
It also causes the business firms to incur higher costs in developing and implementing
the ABC system of cost allocation (Kimmel, 2009)
Implication of activity based costing on Angelo Limited
Activity based costing has a positive results on Angelo Limited has this method of
costing has helped to allocate the overhead cost in meaningful manner through proper basis. It
can be said that there are more advantages of using the activity based costing system as compare
to its disadvantages in case of Angelo Limited. The major advantage that Angelo Limited will
receive after using the activity based costing as its basis of allocation of overhead cost is that it
provides accurate cost of each part which is not possible in traditional costing system. The only
disadvantage that Angelo Limited will face is that implementation of activity based costing
requires huge outflow of cash.
It also causes the business firms to incur higher costs in developing and implementing
the ABC system of cost allocation (Kimmel, 2009)
Implication of activity based costing on Angelo Limited
Activity based costing has a positive results on Angelo Limited has this method of
costing has helped to allocate the overhead cost in meaningful manner through proper basis. It
can be said that there are more advantages of using the activity based costing system as compare
to its disadvantages in case of Angelo Limited. The major advantage that Angelo Limited will
receive after using the activity based costing as its basis of allocation of overhead cost is that it
provides accurate cost of each part which is not possible in traditional costing system. The only
disadvantage that Angelo Limited will face is that implementation of activity based costing
requires huge outflow of cash.
⊘ This is a preview!⊘
Do you want full access?
Subscribe today to unlock all pages.

Trusted by 1+ million students worldwide
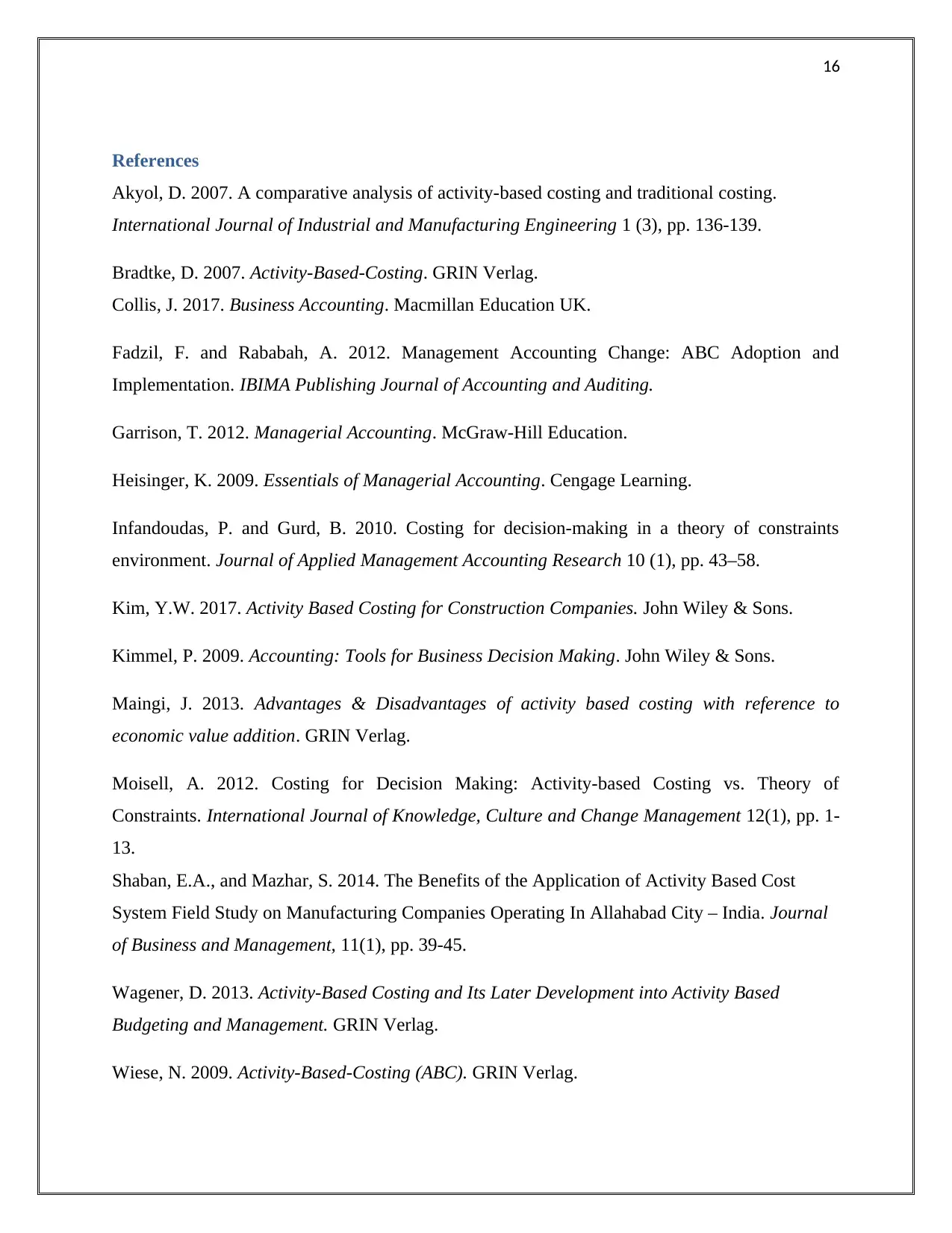
16
References
Akyol, D. 2007. A comparative analysis of activity-based costing and traditional costing.
International Journal of Industrial and Manufacturing Engineering 1 (3), pp. 136-139.
Bradtke, D. 2007. Activity-Based-Costing. GRIN Verlag.
Collis, J. 2017. Business Accounting. Macmillan Education UK.
Fadzil, F. and Rababah, A. 2012. Management Accounting Change: ABC Adoption and
Implementation. IBIMA Publishing Journal of Accounting and Auditing.
Garrison, T. 2012. Managerial Accounting. McGraw-Hill Education.
Heisinger, K. 2009. Essentials of Managerial Accounting. Cengage Learning.
Infandoudas, P. and Gurd, B. 2010. Costing for decision-making in a theory of constraints
environment. Journal of Applied Management Accounting Research 10 (1), pp. 43–58.
Kim, Y.W. 2017. Activity Based Costing for Construction Companies. John Wiley & Sons.
Kimmel, P. 2009. Accounting: Tools for Business Decision Making. John Wiley & Sons.
Maingi, J. 2013. Advantages & Disadvantages of activity based costing with reference to
economic value addition. GRIN Verlag.
Moisell, A. 2012. Costing for Decision Making: Activity-based Costing vs. Theory of
Constraints. International Journal of Knowledge, Culture and Change Management 12(1), pp. 1-
13.
Shaban, E.A., and Mazhar, S. 2014. The Benefits of the Application of Activity Based Cost
System Field Study on Manufacturing Companies Operating In Allahabad City – India. Journal
of Business and Management, 11(1), pp. 39-45.
Wagener, D. 2013. Activity-Based Costing and Its Later Development into Activity Based
Budgeting and Management. GRIN Verlag.
Wiese, N. 2009. Activity-Based-Costing (ABC). GRIN Verlag.
References
Akyol, D. 2007. A comparative analysis of activity-based costing and traditional costing.
International Journal of Industrial and Manufacturing Engineering 1 (3), pp. 136-139.
Bradtke, D. 2007. Activity-Based-Costing. GRIN Verlag.
Collis, J. 2017. Business Accounting. Macmillan Education UK.
Fadzil, F. and Rababah, A. 2012. Management Accounting Change: ABC Adoption and
Implementation. IBIMA Publishing Journal of Accounting and Auditing.
Garrison, T. 2012. Managerial Accounting. McGraw-Hill Education.
Heisinger, K. 2009. Essentials of Managerial Accounting. Cengage Learning.
Infandoudas, P. and Gurd, B. 2010. Costing for decision-making in a theory of constraints
environment. Journal of Applied Management Accounting Research 10 (1), pp. 43–58.
Kim, Y.W. 2017. Activity Based Costing for Construction Companies. John Wiley & Sons.
Kimmel, P. 2009. Accounting: Tools for Business Decision Making. John Wiley & Sons.
Maingi, J. 2013. Advantages & Disadvantages of activity based costing with reference to
economic value addition. GRIN Verlag.
Moisell, A. 2012. Costing for Decision Making: Activity-based Costing vs. Theory of
Constraints. International Journal of Knowledge, Culture and Change Management 12(1), pp. 1-
13.
Shaban, E.A., and Mazhar, S. 2014. The Benefits of the Application of Activity Based Cost
System Field Study on Manufacturing Companies Operating In Allahabad City – India. Journal
of Business and Management, 11(1), pp. 39-45.
Wagener, D. 2013. Activity-Based Costing and Its Later Development into Activity Based
Budgeting and Management. GRIN Verlag.
Wiese, N. 2009. Activity-Based-Costing (ABC). GRIN Verlag.
Paraphrase This Document
Need a fresh take? Get an instant paraphrase of this document with our AI Paraphraser
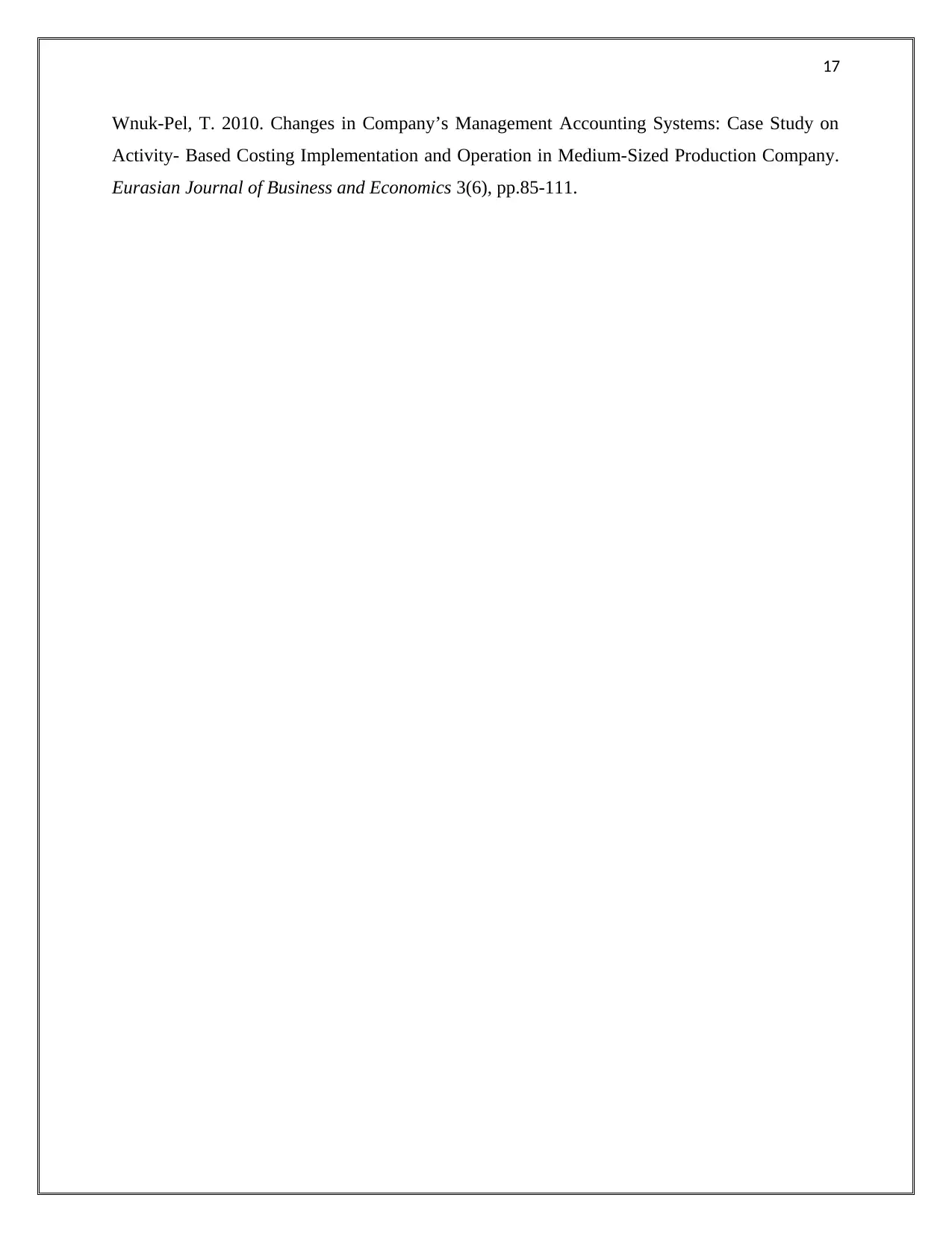
17
Wnuk-Pel, T. 2010. Changes in Company’s Management Accounting Systems: Case Study on
Activity- Based Costing Implementation and Operation in Medium-Sized Production Company.
Eurasian Journal of Business and Economics 3(6), pp.85-111.
Wnuk-Pel, T. 2010. Changes in Company’s Management Accounting Systems: Case Study on
Activity- Based Costing Implementation and Operation in Medium-Sized Production Company.
Eurasian Journal of Business and Economics 3(6), pp.85-111.
1 out of 17
Related Documents

Your All-in-One AI-Powered Toolkit for Academic Success.
+13062052269
info@desklib.com
Available 24*7 on WhatsApp / Email
Unlock your academic potential
© 2024 | Zucol Services PVT LTD | All rights reserved.