Additive Manufacturing of Polymer-Based Composites Reinforced with Nano Particle
VerifiedAdded on 2022/11/26
|3
|1374
|125
AI Summary
This article discusses the process of additive manufacturing of polymer-based composites reinforced with nano particles. It explores the benefits of this manufacturing method, the materials used, and the relationship between microstructure and mechanical properties. The article also provides references for further reading.
Contribute Materials
Your contribution can guide someone’s learning journey. Share your
documents today.
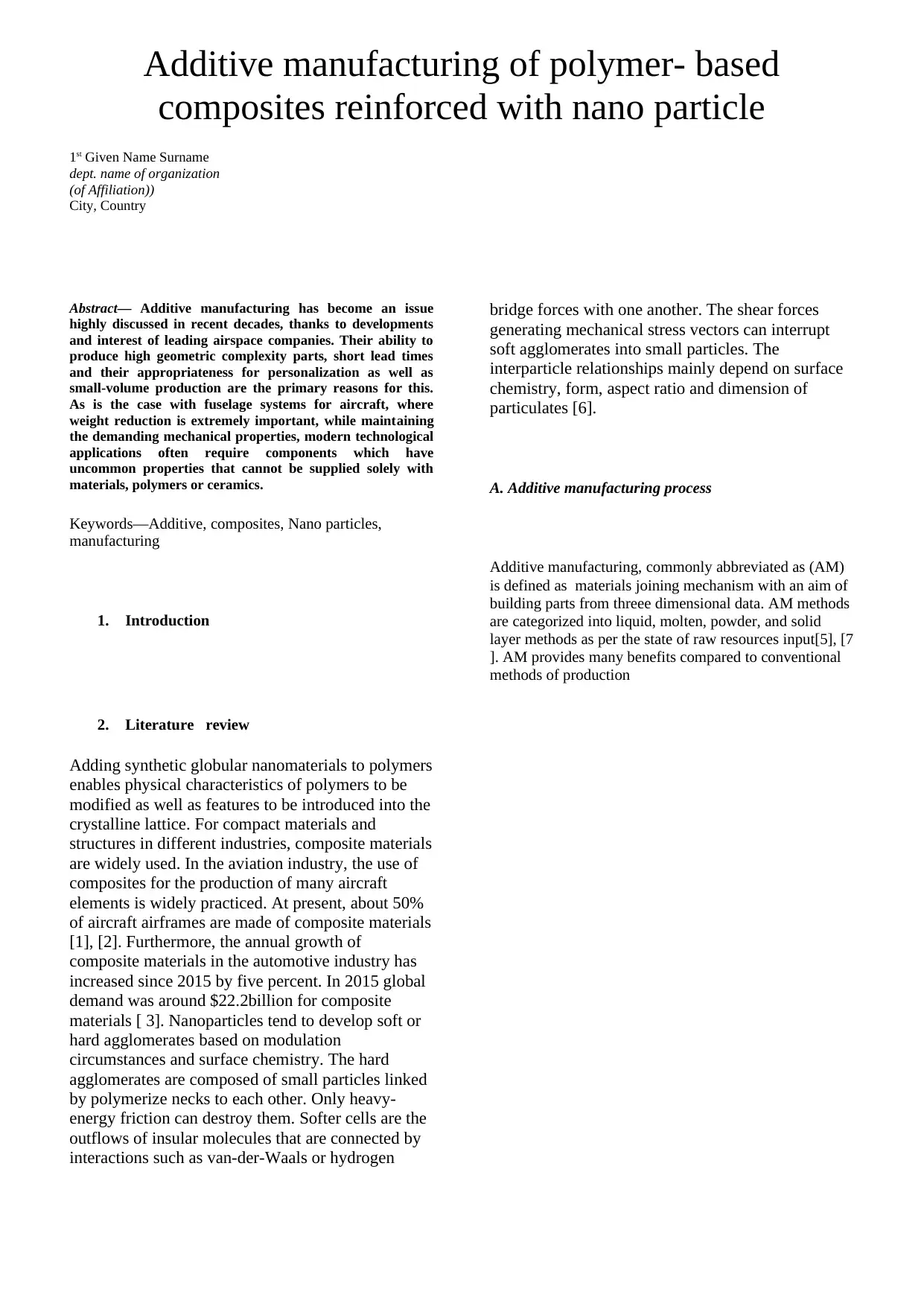
Additive manufacturing of polymer- based
composites reinforced with nano particle
1st Given Name Surname
dept. name of organization
(of Affiliation))
City, Country
Abstract— Additive manufacturing has become an issue
highly discussed in recent decades, thanks to developments
and interest of leading airspace companies. Their ability to
produce high geometric complexity parts, short lead times
and their appropriateness for personalization as well as
small-volume production are the primary reasons for this.
As is the case with fuselage systems for aircraft, where
weight reduction is extremely important, while maintaining
the demanding mechanical properties, modern technological
applications often require components which have
uncommon properties that cannot be supplied solely with
materials, polymers or ceramics.
Keywords—Additive, composites, Nano particles,
manufacturing
1. Introduction
2. Literature review
Adding synthetic globular nanomaterials to polymers
enables physical characteristics of polymers to be
modified as well as features to be introduced into the
crystalline lattice. For compact materials and
structures in different industries, composite materials
are widely used. In the aviation industry, the use of
composites for the production of many aircraft
elements is widely practiced. At present, about 50%
of aircraft airframes are made of composite materials
[1], [2]. Furthermore, the annual growth of
composite materials in the automotive industry has
increased since 2015 by five percent. In 2015 global
demand was around $22.2billion for composite
materials [ 3]. Nanoparticles tend to develop soft or
hard agglomerates based on modulation
circumstances and surface chemistry. The hard
agglomerates are composed of small particles linked
by polymerize necks to each other. Only heavy-
energy friction can destroy them. Softer cells are the
outflows of insular molecules that are connected by
interactions such as van-der-Waals or hydrogen
bridge forces with one another. The shear forces
generating mechanical stress vectors can interrupt
soft agglomerates into small particles. The
interparticle relationships mainly depend on surface
chemistry, form, aspect ratio and dimension of
particulates [6].
A. Additive manufacturing process
Additive manufacturing, commonly abbreviated as (AM)
is defined as materials joining mechanism with an aim of
building parts from threee dimensional data. AM methods
are categorized into liquid, molten, powder, and solid
layer methods as per the state of raw resources input[5], [7
]. AM provides many benefits compared to conventional
methods of production
composites reinforced with nano particle
1st Given Name Surname
dept. name of organization
(of Affiliation))
City, Country
Abstract— Additive manufacturing has become an issue
highly discussed in recent decades, thanks to developments
and interest of leading airspace companies. Their ability to
produce high geometric complexity parts, short lead times
and their appropriateness for personalization as well as
small-volume production are the primary reasons for this.
As is the case with fuselage systems for aircraft, where
weight reduction is extremely important, while maintaining
the demanding mechanical properties, modern technological
applications often require components which have
uncommon properties that cannot be supplied solely with
materials, polymers or ceramics.
Keywords—Additive, composites, Nano particles,
manufacturing
1. Introduction
2. Literature review
Adding synthetic globular nanomaterials to polymers
enables physical characteristics of polymers to be
modified as well as features to be introduced into the
crystalline lattice. For compact materials and
structures in different industries, composite materials
are widely used. In the aviation industry, the use of
composites for the production of many aircraft
elements is widely practiced. At present, about 50%
of aircraft airframes are made of composite materials
[1], [2]. Furthermore, the annual growth of
composite materials in the automotive industry has
increased since 2015 by five percent. In 2015 global
demand was around $22.2billion for composite
materials [ 3]. Nanoparticles tend to develop soft or
hard agglomerates based on modulation
circumstances and surface chemistry. The hard
agglomerates are composed of small particles linked
by polymerize necks to each other. Only heavy-
energy friction can destroy them. Softer cells are the
outflows of insular molecules that are connected by
interactions such as van-der-Waals or hydrogen
bridge forces with one another. The shear forces
generating mechanical stress vectors can interrupt
soft agglomerates into small particles. The
interparticle relationships mainly depend on surface
chemistry, form, aspect ratio and dimension of
particulates [6].
A. Additive manufacturing process
Additive manufacturing, commonly abbreviated as (AM)
is defined as materials joining mechanism with an aim of
building parts from threee dimensional data. AM methods
are categorized into liquid, molten, powder, and solid
layer methods as per the state of raw resources input[5], [7
]. AM provides many benefits compared to conventional
methods of production
Secure Best Marks with AI Grader
Need help grading? Try our AI Grader for instant feedback on your assignments.
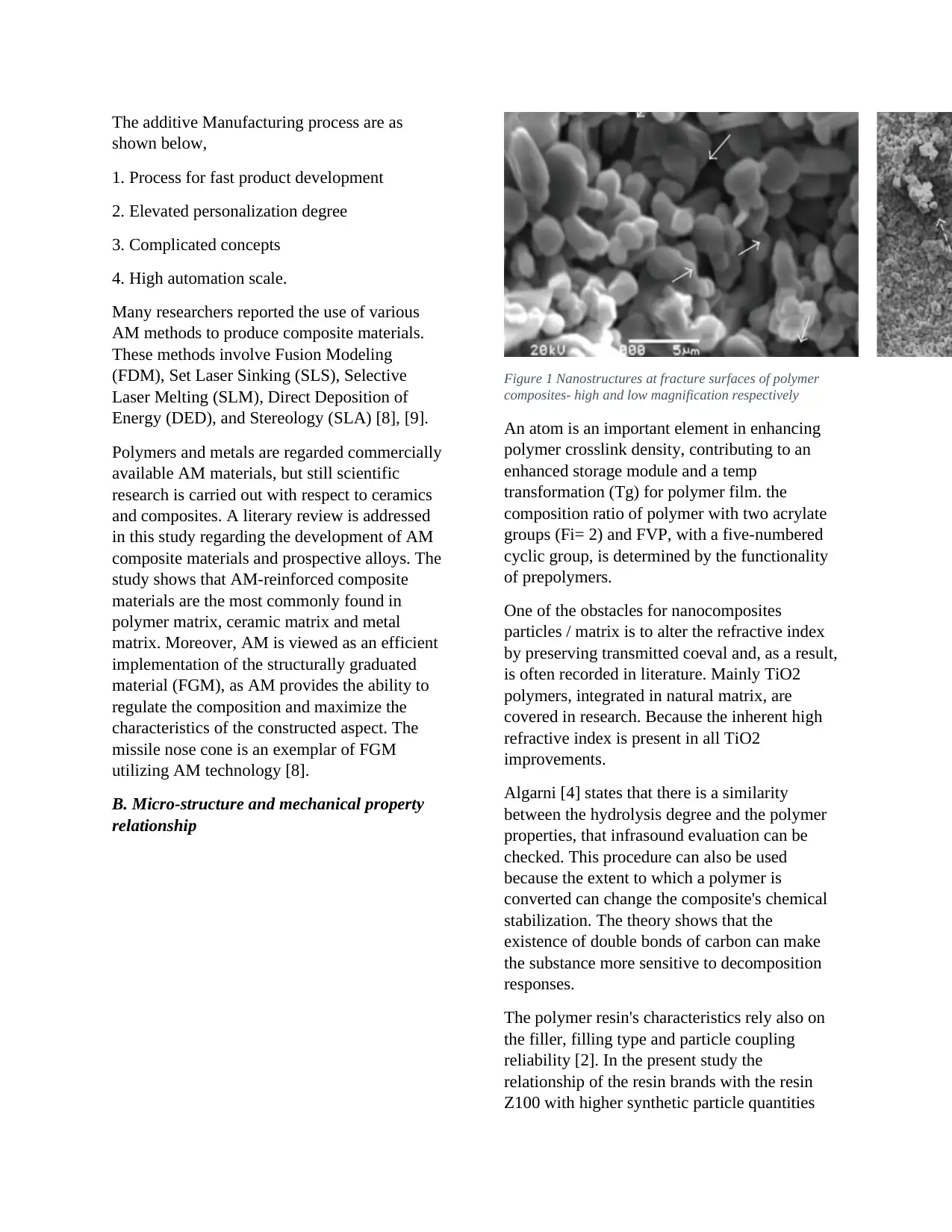
The additive Manufacturing process are as
shown below,
1. Process for fast product development
2. Elevated personalization degree
3. Complicated concepts
4. High automation scale.
Many researchers reported the use of various
AM methods to produce composite materials.
These methods involve Fusion Modeling
(FDM), Set Laser Sinking (SLS), Selective
Laser Melting (SLM), Direct Deposition of
Energy (DED), and Stereology (SLA) [8], [9]. ⠀
Polymers and metals are regarded commercially
available AM materials, but still scientific
research is carried out with respect to ceramics
and composites. A literary review is addressed
in this study regarding the development of AM
composite materials and prospective alloys. The
study shows that AM-reinforced composite
materials are the most commonly found in
polymer matrix, ceramic matrix and metal
matrix. Moreover, AM is viewed as an efficient
implementation of the structurally graduated
material (FGM), as AM provides the ability to
regulate the composition and maximize the
characteristics of the constructed aspect. The
missile nose cone is an exemplar of FGM
utilizing AM technology [8].
B. Micro-structure and mechanical property
relationship
Figure 1 Nanostructures at fracture surfaces of polymer
composites- high and low magnification respectively
An atom is an important element in enhancing
polymer crosslink density, contributing to an
enhanced storage module and a temp
transformation (Tg) for polymer film. the
composition ratio of polymer with two acrylate
groups (Fi= 2) and FVP, with a five-numbered
cyclic group, is determined by the functionality
of prepolymers.
One of the obstacles for nanocomposites
particles / matrix is to alter the refractive index
by preserving transmitted coeval and, as a result,
is often recorded in literature. Mainly TiO2
polymers, integrated in natural matrix, are
covered in research. Because the inherent high
refractive index is present in all TiO2
improvements.
Algarni [4] states that there is a similarity
between the hydrolysis degree and the polymer
properties, that infrasound evaluation can be
checked. This procedure can also be used
because the extent to which a polymer is
converted can change the composite's chemical
stabilization. The theory shows that the
existence of double bonds of carbon can make
the substance more sensitive to decomposition
responses.
The polymer resin's characteristics rely also on
the filler, filling type and particle coupling
reliability [2]. In the present study the
relationship of the resin brands with the resin
Z100 with higher synthetic particle quantities
shown below,
1. Process for fast product development
2. Elevated personalization degree
3. Complicated concepts
4. High automation scale.
Many researchers reported the use of various
AM methods to produce composite materials.
These methods involve Fusion Modeling
(FDM), Set Laser Sinking (SLS), Selective
Laser Melting (SLM), Direct Deposition of
Energy (DED), and Stereology (SLA) [8], [9]. ⠀
Polymers and metals are regarded commercially
available AM materials, but still scientific
research is carried out with respect to ceramics
and composites. A literary review is addressed
in this study regarding the development of AM
composite materials and prospective alloys. The
study shows that AM-reinforced composite
materials are the most commonly found in
polymer matrix, ceramic matrix and metal
matrix. Moreover, AM is viewed as an efficient
implementation of the structurally graduated
material (FGM), as AM provides the ability to
regulate the composition and maximize the
characteristics of the constructed aspect. The
missile nose cone is an exemplar of FGM
utilizing AM technology [8].
B. Micro-structure and mechanical property
relationship
Figure 1 Nanostructures at fracture surfaces of polymer
composites- high and low magnification respectively
An atom is an important element in enhancing
polymer crosslink density, contributing to an
enhanced storage module and a temp
transformation (Tg) for polymer film. the
composition ratio of polymer with two acrylate
groups (Fi= 2) and FVP, with a five-numbered
cyclic group, is determined by the functionality
of prepolymers.
One of the obstacles for nanocomposites
particles / matrix is to alter the refractive index
by preserving transmitted coeval and, as a result,
is often recorded in literature. Mainly TiO2
polymers, integrated in natural matrix, are
covered in research. Because the inherent high
refractive index is present in all TiO2
improvements.
Algarni [4] states that there is a similarity
between the hydrolysis degree and the polymer
properties, that infrasound evaluation can be
checked. This procedure can also be used
because the extent to which a polymer is
converted can change the composite's chemical
stabilization. The theory shows that the
existence of double bonds of carbon can make
the substance more sensitive to decomposition
responses.
The polymer resin's characteristics rely also on
the filler, filling type and particle coupling
reliability [2]. In the present study the
relationship of the resin brands with the resin
Z100 with higher synthetic particle quantities
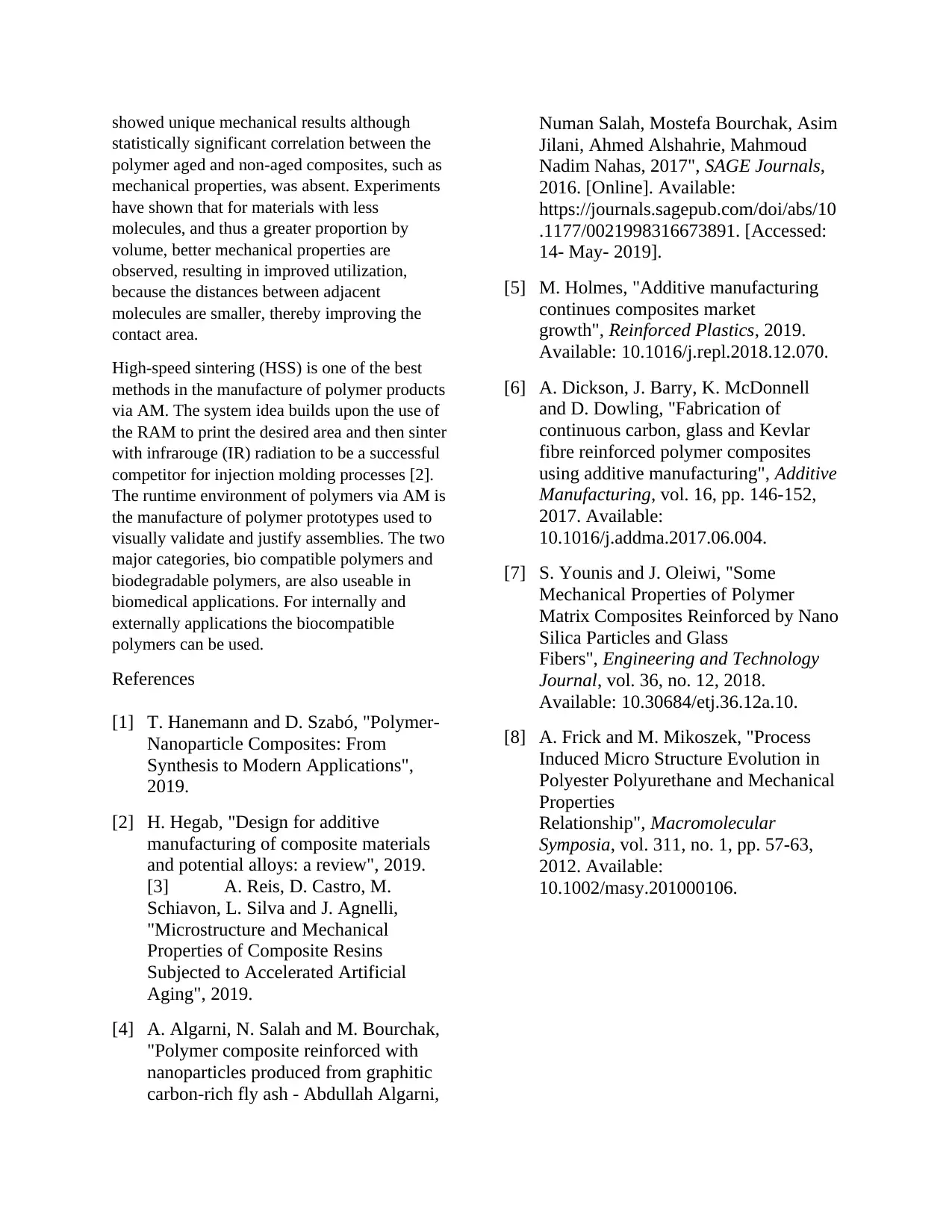
showed unique mechanical results although
statistically significant correlation between the
polymer aged and non-aged composites, such as
mechanical properties, was absent. Experiments
have shown that for materials with less
molecules, and thus a greater proportion by
volume, better mechanical properties are
observed, resulting in improved utilization,
because the distances between adjacent
molecules are smaller, thereby improving the
contact area.
High-speed sintering (HSS) is one of the best
methods in the manufacture of polymer products
via AM. The system idea builds upon the use of
the RAM to print the desired area and then sinter
with infrarouge (IR) radiation to be a successful
competitor for injection molding processes [2].
The runtime environment of polymers via AM is
the manufacture of polymer prototypes used to
visually validate and justify assemblies. The two
major categories, bio compatible polymers and
biodegradable polymers, are also useable in
biomedical applications. For internally and
externally applications the biocompatible
polymers can be used.
References
[1] T. Hanemann and D. Szabó, "Polymer-
Nanoparticle Composites: From
Synthesis to Modern Applications",
2019.
[2] H. Hegab, "Design for additive
manufacturing of composite materials
and potential alloys: a review", 2019.
[3] A. Reis, D. Castro, M.
Schiavon, L. Silva and J. Agnelli,
"Microstructure and Mechanical
Properties of Composite Resins
Subjected to Accelerated Artificial
Aging", 2019.
[4] A. Algarni, N. Salah and M. Bourchak,
"Polymer composite reinforced with
nanoparticles produced from graphitic
carbon-rich fly ash - Abdullah Algarni,
Numan Salah, Mostefa Bourchak, Asim
Jilani, Ahmed Alshahrie, Mahmoud
Nadim Nahas, 2017", SAGE Journals,
2016. [Online]. Available:
https://journals.sagepub.com/doi/abs/10
.1177/0021998316673891. [Accessed:
14- May- 2019].
[5] M. Holmes, "Additive manufacturing
continues composites market
growth", Reinforced Plastics, 2019.
Available: 10.1016/j.repl.2018.12.070.
[6] A. Dickson, J. Barry, K. McDonnell
and D. Dowling, "Fabrication of
continuous carbon, glass and Kevlar
fibre reinforced polymer composites
using additive manufacturing", Additive
Manufacturing, vol. 16, pp. 146-152,
2017. Available:
10.1016/j.addma.2017.06.004.
[7] S. Younis and J. Oleiwi, "Some
Mechanical Properties of Polymer
Matrix Composites Reinforced by Nano
Silica Particles and Glass
Fibers", Engineering and Technology
Journal, vol. 36, no. 12, 2018.
Available: 10.30684/etj.36.12a.10.
[8] A. Frick and M. Mikoszek, "Process
Induced Micro Structure Evolution in
Polyester Polyurethane and Mechanical
Properties
Relationship", Macromolecular
Symposia, vol. 311, no. 1, pp. 57-63,
2012. Available:
10.1002/masy.201000106.
statistically significant correlation between the
polymer aged and non-aged composites, such as
mechanical properties, was absent. Experiments
have shown that for materials with less
molecules, and thus a greater proportion by
volume, better mechanical properties are
observed, resulting in improved utilization,
because the distances between adjacent
molecules are smaller, thereby improving the
contact area.
High-speed sintering (HSS) is one of the best
methods in the manufacture of polymer products
via AM. The system idea builds upon the use of
the RAM to print the desired area and then sinter
with infrarouge (IR) radiation to be a successful
competitor for injection molding processes [2].
The runtime environment of polymers via AM is
the manufacture of polymer prototypes used to
visually validate and justify assemblies. The two
major categories, bio compatible polymers and
biodegradable polymers, are also useable in
biomedical applications. For internally and
externally applications the biocompatible
polymers can be used.
References
[1] T. Hanemann and D. Szabó, "Polymer-
Nanoparticle Composites: From
Synthesis to Modern Applications",
2019.
[2] H. Hegab, "Design for additive
manufacturing of composite materials
and potential alloys: a review", 2019.
[3] A. Reis, D. Castro, M.
Schiavon, L. Silva and J. Agnelli,
"Microstructure and Mechanical
Properties of Composite Resins
Subjected to Accelerated Artificial
Aging", 2019.
[4] A. Algarni, N. Salah and M. Bourchak,
"Polymer composite reinforced with
nanoparticles produced from graphitic
carbon-rich fly ash - Abdullah Algarni,
Numan Salah, Mostefa Bourchak, Asim
Jilani, Ahmed Alshahrie, Mahmoud
Nadim Nahas, 2017", SAGE Journals,
2016. [Online]. Available:
https://journals.sagepub.com/doi/abs/10
.1177/0021998316673891. [Accessed:
14- May- 2019].
[5] M. Holmes, "Additive manufacturing
continues composites market
growth", Reinforced Plastics, 2019.
Available: 10.1016/j.repl.2018.12.070.
[6] A. Dickson, J. Barry, K. McDonnell
and D. Dowling, "Fabrication of
continuous carbon, glass and Kevlar
fibre reinforced polymer composites
using additive manufacturing", Additive
Manufacturing, vol. 16, pp. 146-152,
2017. Available:
10.1016/j.addma.2017.06.004.
[7] S. Younis and J. Oleiwi, "Some
Mechanical Properties of Polymer
Matrix Composites Reinforced by Nano
Silica Particles and Glass
Fibers", Engineering and Technology
Journal, vol. 36, no. 12, 2018.
Available: 10.30684/etj.36.12a.10.
[8] A. Frick and M. Mikoszek, "Process
Induced Micro Structure Evolution in
Polyester Polyurethane and Mechanical
Properties
Relationship", Macromolecular
Symposia, vol. 311, no. 1, pp. 57-63,
2012. Available:
10.1002/masy.201000106.
1 out of 3
Related Documents
![[object Object]](/_next/image/?url=%2F_next%2Fstatic%2Fmedia%2Flogo.6d15ce61.png&w=640&q=75)
Your All-in-One AI-Powered Toolkit for Academic Success.
+13062052269
info@desklib.com
Available 24*7 on WhatsApp / Email
Unlock your academic potential
© 2024 | Zucol Services PVT LTD | All rights reserved.