Advanced Engineering Materials - Metal Foams
VerifiedAdded on 2023/03/17
|20
|1042
|82
Presentation
AI Summary
This presentation provides an in-depth overview of advanced engineering materials, specifically metal foams. It covers the types of composites and metal foams, their properties, and various modeling methods. The presentation also discusses the applications of metal foams and the mathematical models used to calculate their properties. References are provided for further reading.
Contribute Materials
Your contribution can guide someone’s learning journey. Share your
documents today.
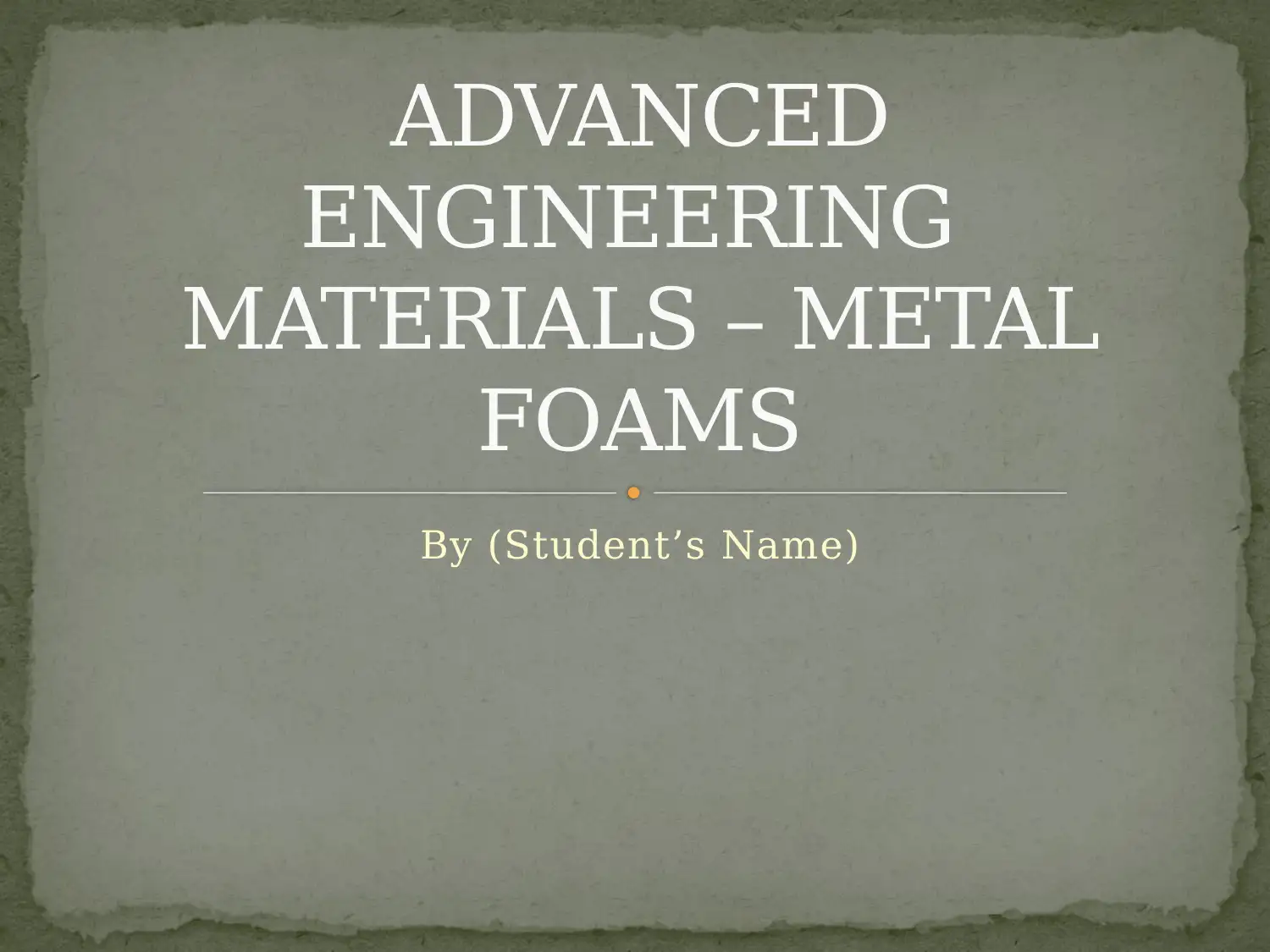
By (Student’s Name)
ADVANCED
ENGINEERING
MATERIALS – METAL
FOAMS
ADVANCED
ENGINEERING
MATERIALS – METAL
FOAMS
Secure Best Marks with AI Grader
Need help grading? Try our AI Grader for instant feedback on your assignments.
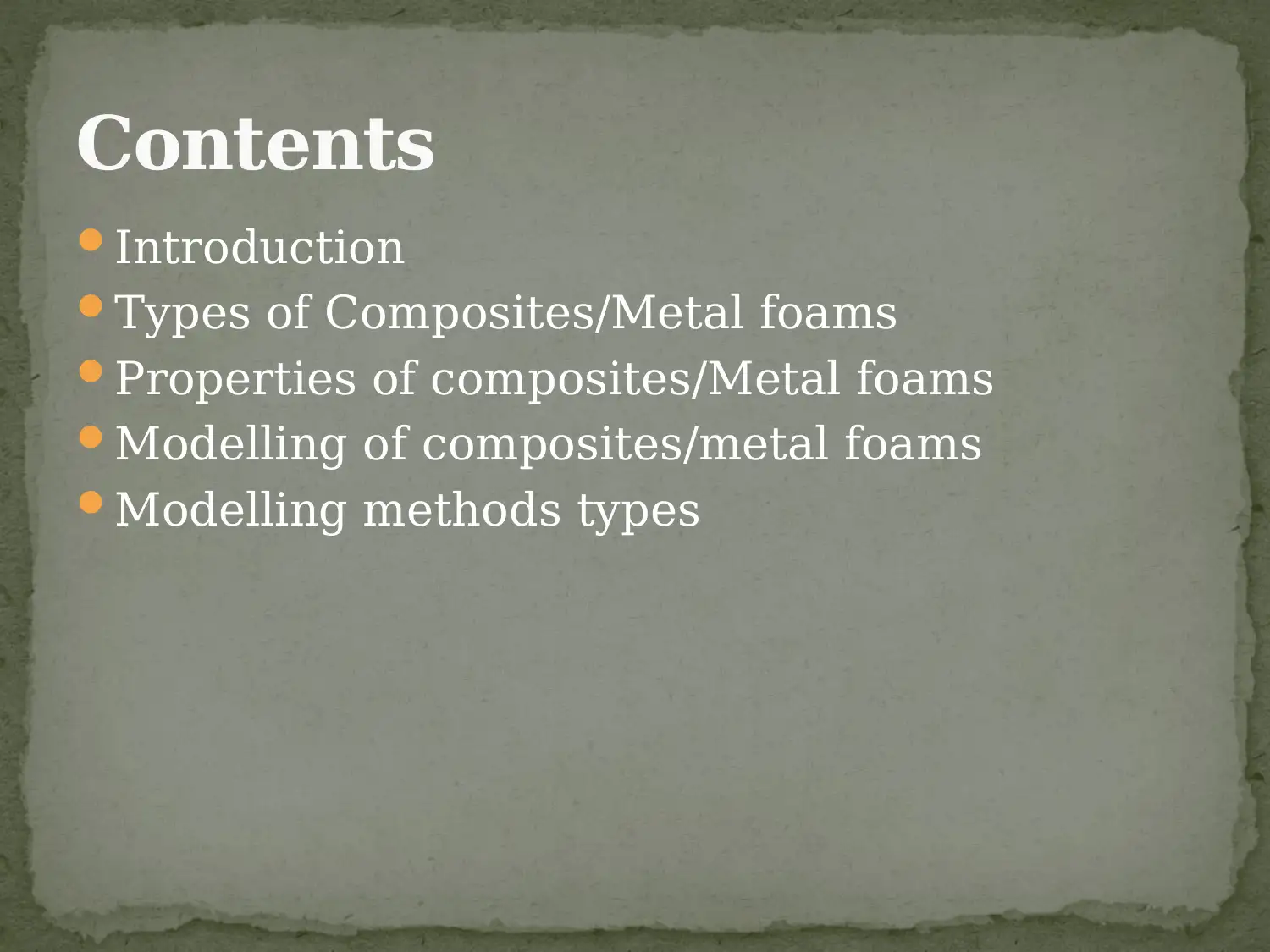
Introduction
Types of Composites/Metal foams
Properties of composites/Metal foams
Modelling of composites/metal foams
Modelling methods types
Contents
Types of Composites/Metal foams
Properties of composites/Metal foams
Modelling of composites/metal foams
Modelling methods types
Contents
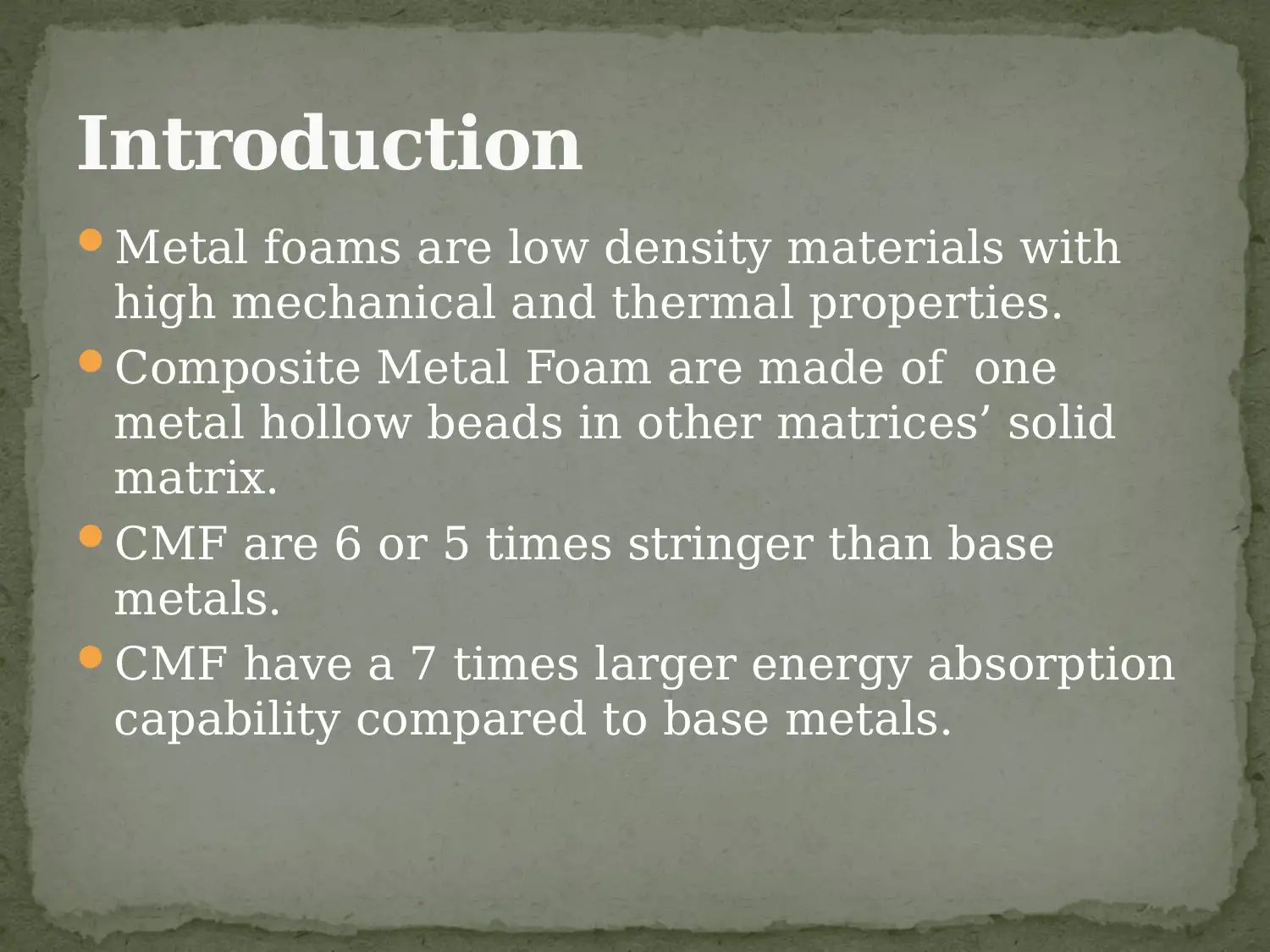
Metal foams are low density materials with
high mechanical and thermal properties.
Composite Metal Foam are made of one
metal hollow beads in other matrices’ solid
matrix.
CMF are 6 or 5 times stringer than base
metals.
CMF have a 7 times larger energy absorption
capability compared to base metals.
Introduction
high mechanical and thermal properties.
Composite Metal Foam are made of one
metal hollow beads in other matrices’ solid
matrix.
CMF are 6 or 5 times stringer than base
metals.
CMF have a 7 times larger energy absorption
capability compared to base metals.
Introduction
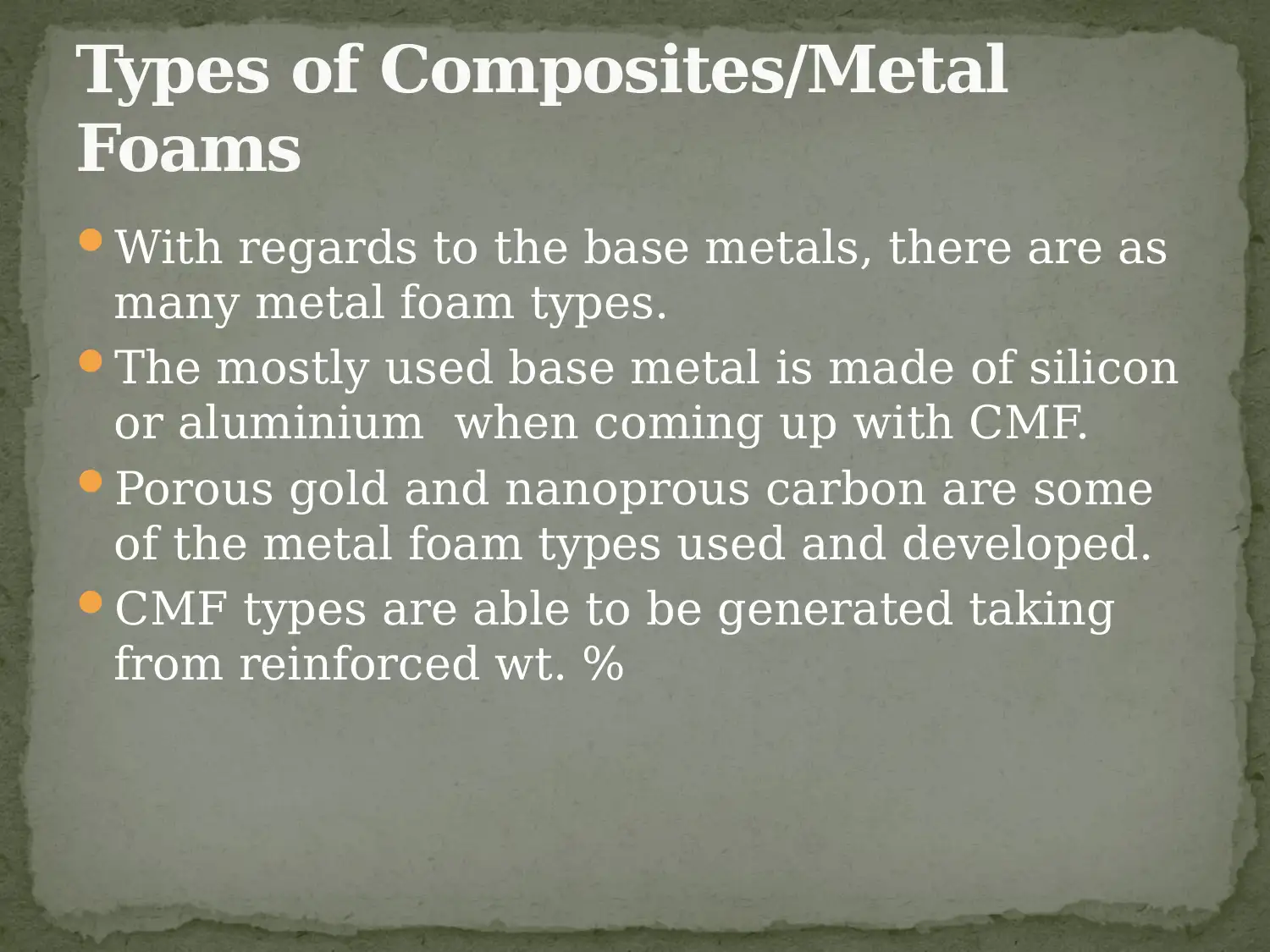
With regards to the base metals, there are as
many metal foam types.
The mostly used base metal is made of silicon
or aluminium when coming up with CMF.
Porous gold and nanoprous carbon are some
of the metal foam types used and developed.
CMF types are able to be generated taking
from reinforced wt. %
Types of Composites/Metal
Foams
many metal foam types.
The mostly used base metal is made of silicon
or aluminium when coming up with CMF.
Porous gold and nanoprous carbon are some
of the metal foam types used and developed.
CMF types are able to be generated taking
from reinforced wt. %
Types of Composites/Metal
Foams
Secure Best Marks with AI Grader
Need help grading? Try our AI Grader for instant feedback on your assignments.
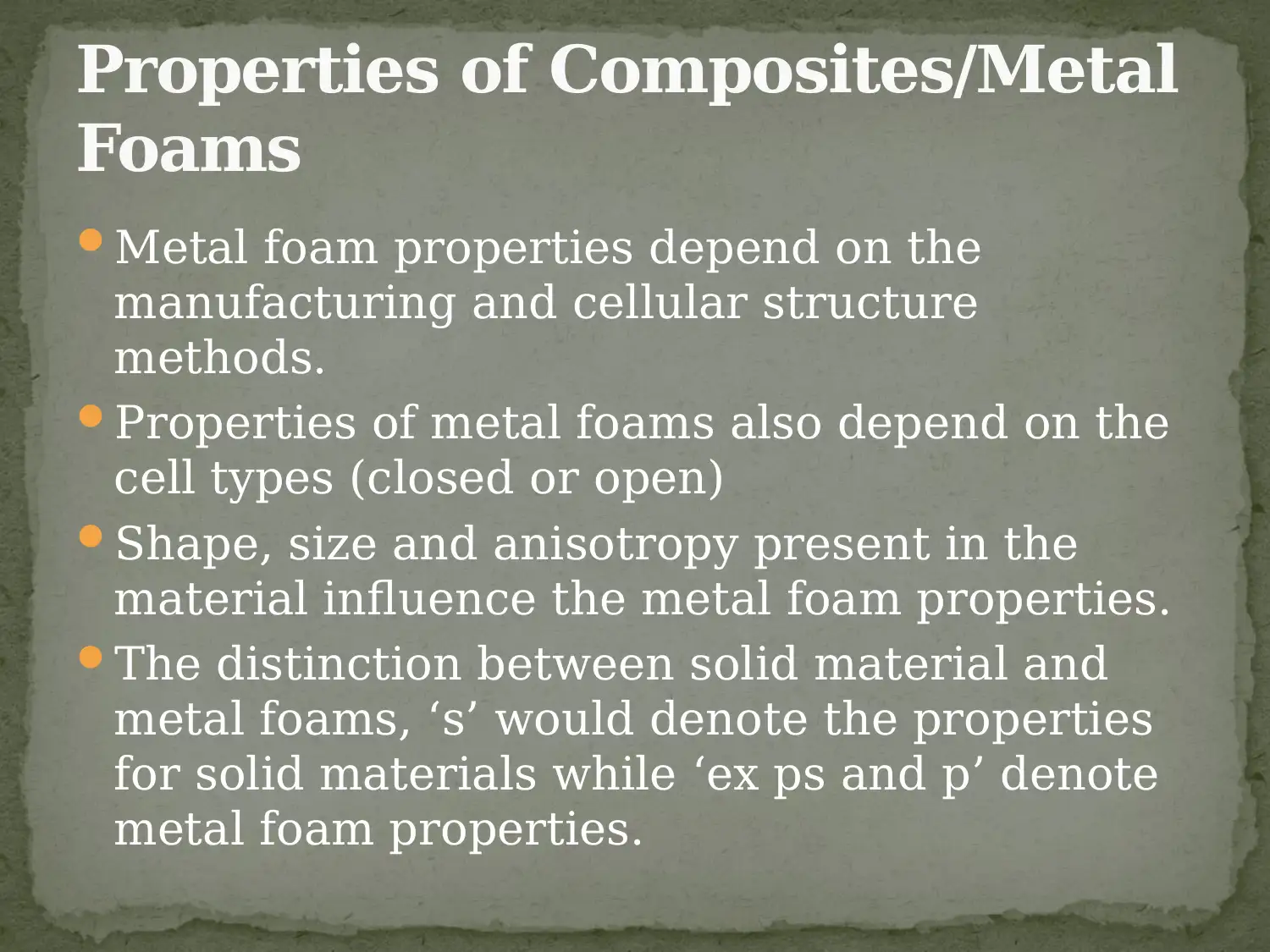
Metal foam properties depend on the
manufacturing and cellular structure
methods.
Properties of metal foams also depend on the
cell types (closed or open)
Shape, size and anisotropy present in the
material influence the metal foam properties.
The distinction between solid material and
metal foams, ‘s’ would denote the properties
for solid materials while ‘ex ps and p’ denote
metal foam properties.
Properties of Composites/Metal
Foams
manufacturing and cellular structure
methods.
Properties of metal foams also depend on the
cell types (closed or open)
Shape, size and anisotropy present in the
material influence the metal foam properties.
The distinction between solid material and
metal foams, ‘s’ would denote the properties
for solid materials while ‘ex ps and p’ denote
metal foam properties.
Properties of Composites/Metal
Foams
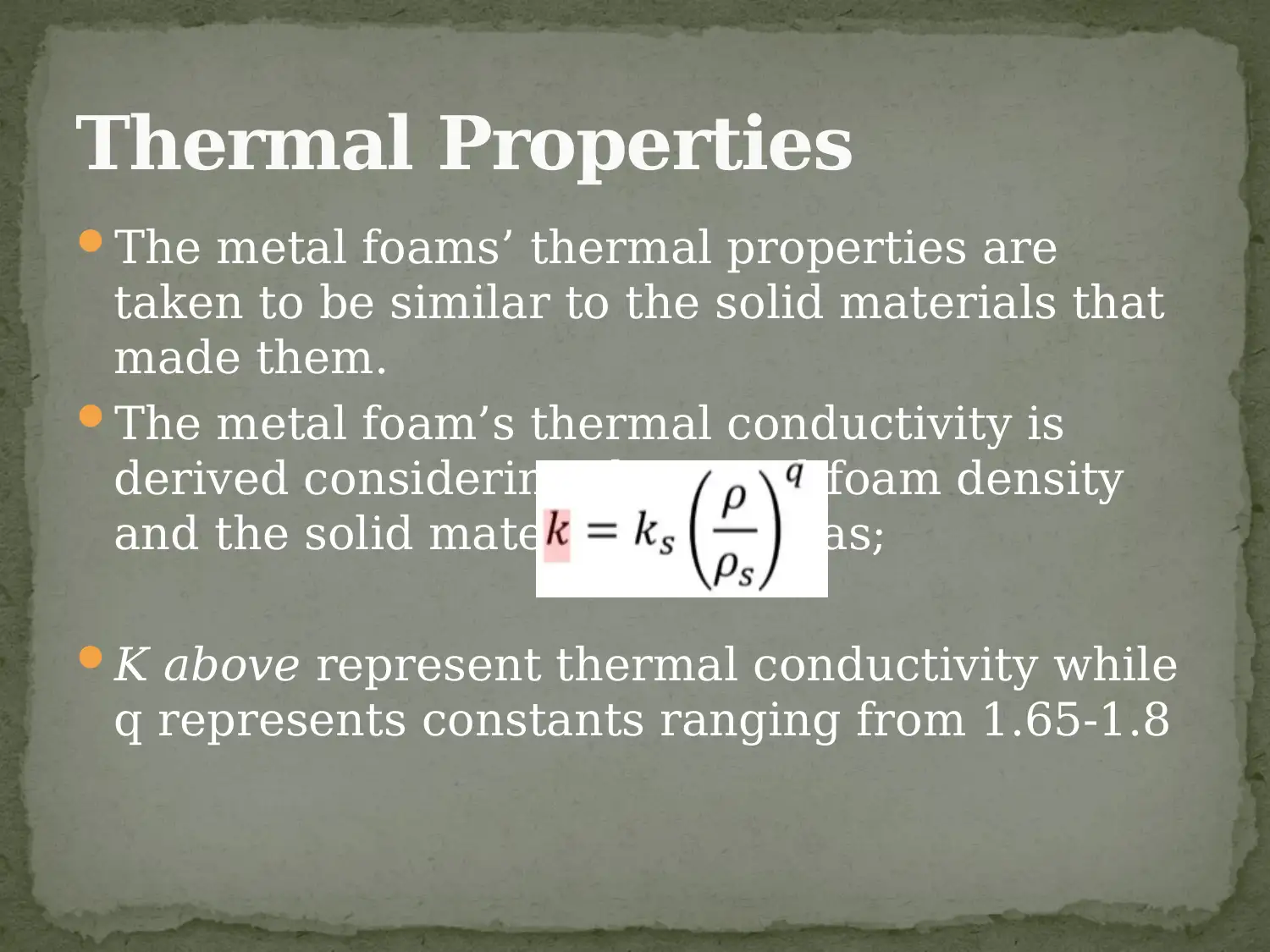
The metal foams’ thermal properties are
taken to be similar to the solid materials that
made them.
The metal foam’s thermal conductivity is
derived considering the metal foam density
and the solid material density as;
K above represent thermal conductivity while
q represents constants ranging from 1.65-1.8
Thermal Properties
taken to be similar to the solid materials that
made them.
The metal foam’s thermal conductivity is
derived considering the metal foam density
and the solid material density as;
K above represent thermal conductivity while
q represents constants ranging from 1.65-1.8
Thermal Properties
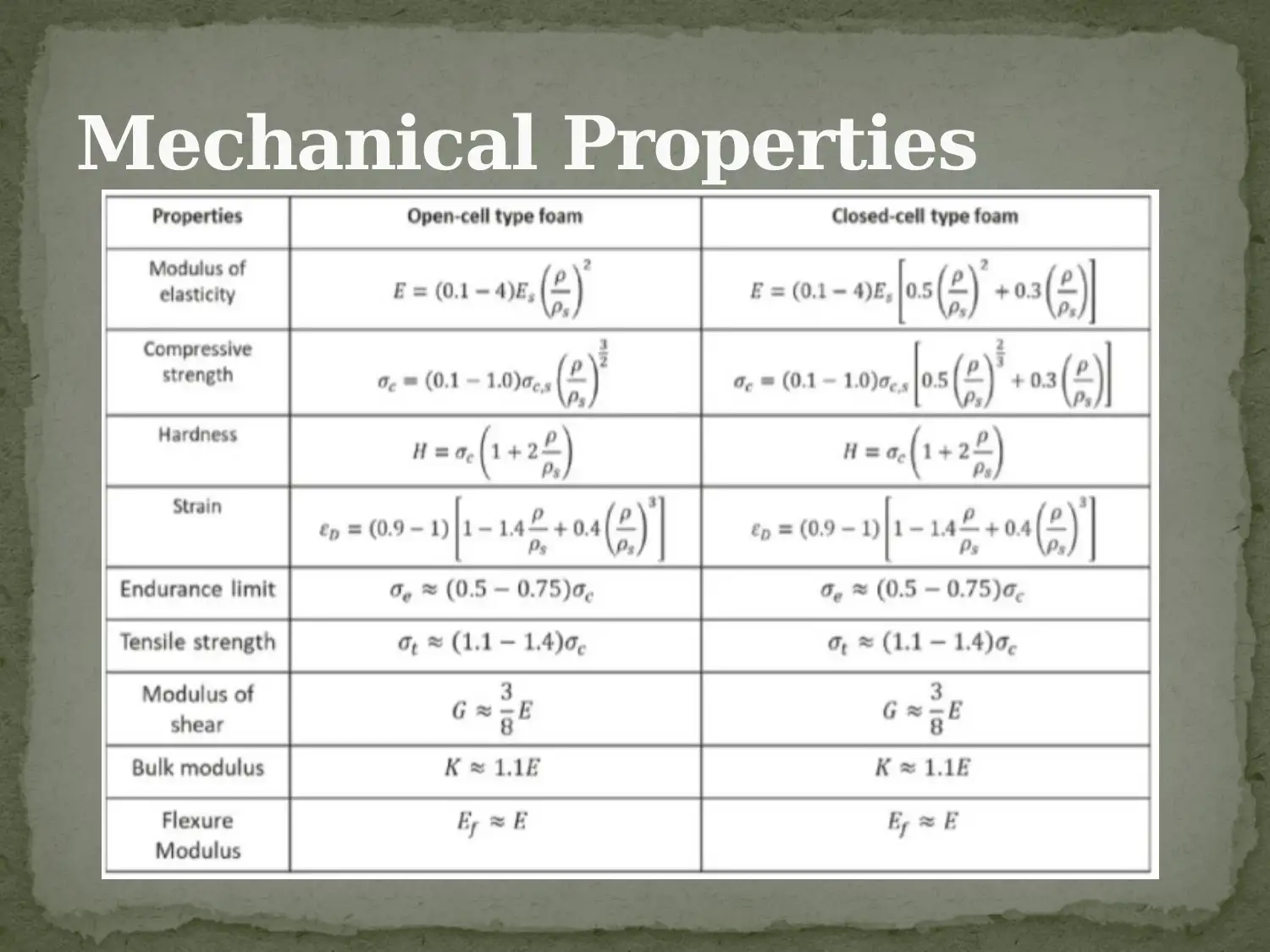
Mechanical Properties
Paraphrase This Document
Need a fresh take? Get an instant paraphrase of this document with our AI Paraphraser
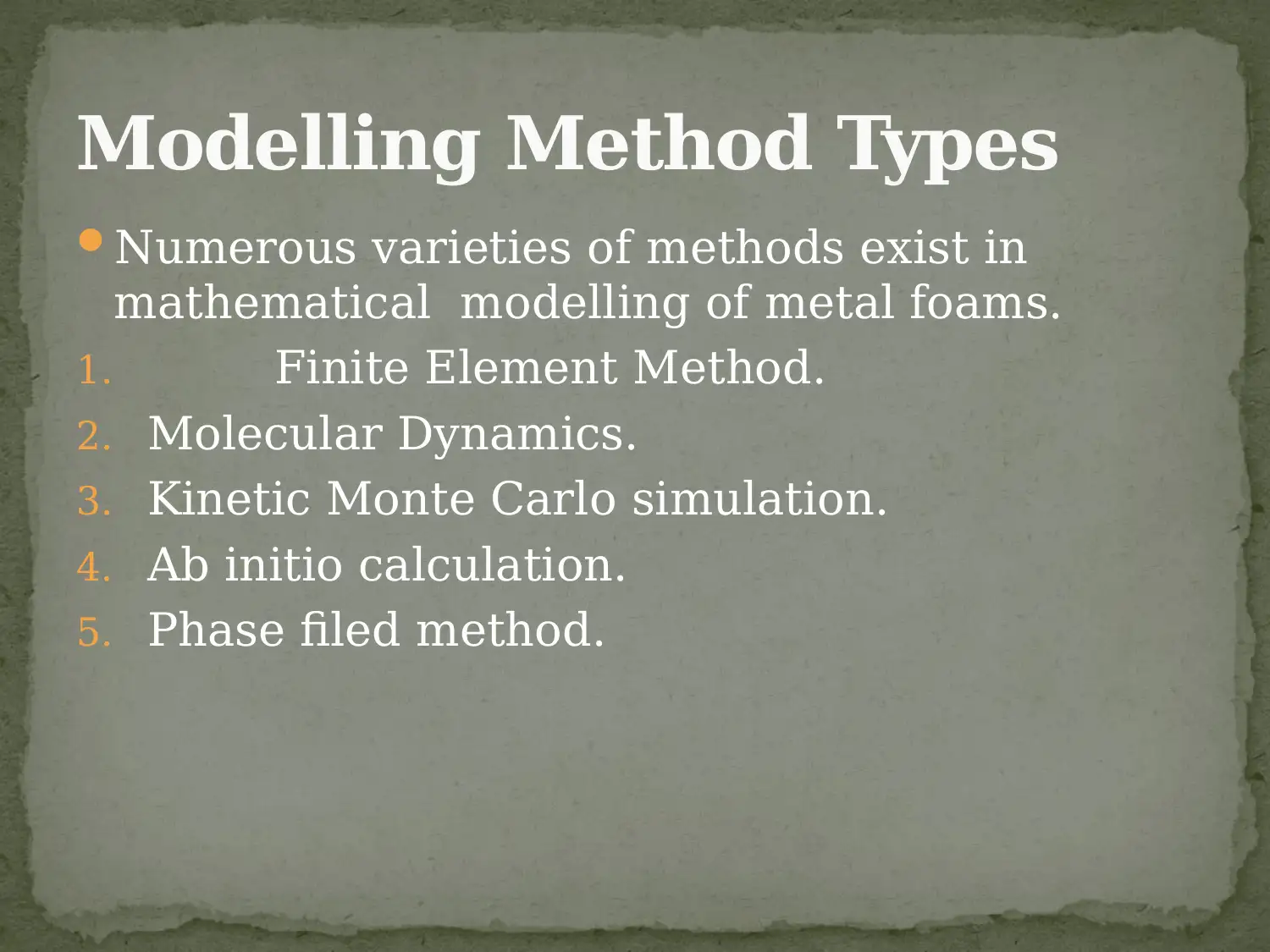
Modelling Method Types
Numerous varieties of methods exist in
mathematical modelling of metal foams.
1. Finite Element Method.
2. Molecular Dynamics.
3. Kinetic Monte Carlo simulation.
4. Ab initio calculation.
5. Phase filed method.
Numerous varieties of methods exist in
mathematical modelling of metal foams.
1. Finite Element Method.
2. Molecular Dynamics.
3. Kinetic Monte Carlo simulation.
4. Ab initio calculation.
5. Phase filed method.
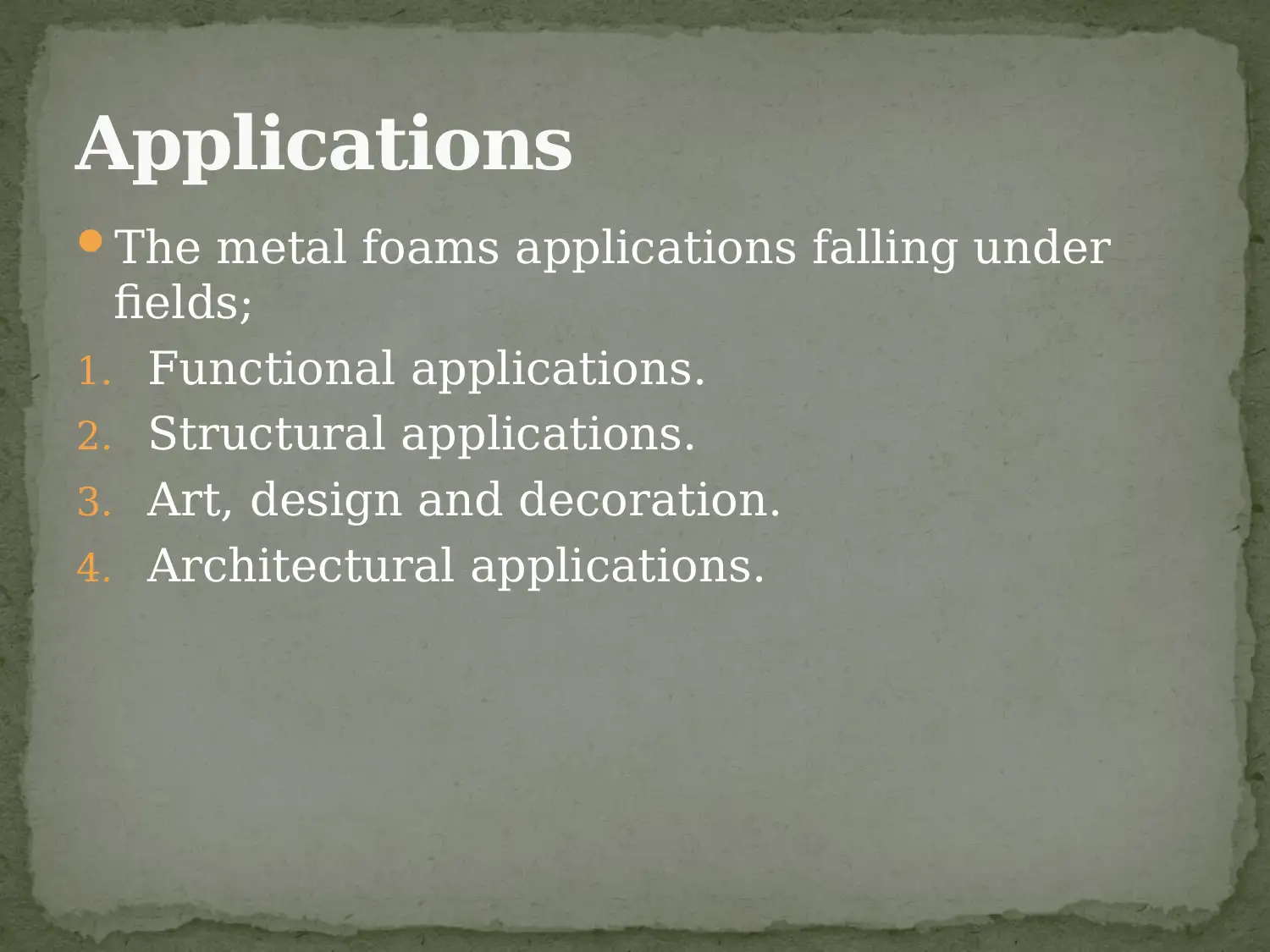
Applications
The metal foams applications falling under
fields;
1. Functional applications.
2. Structural applications.
3. Art, design and decoration.
4. Architectural applications.
The metal foams applications falling under
fields;
1. Functional applications.
2. Structural applications.
3. Art, design and decoration.
4. Architectural applications.
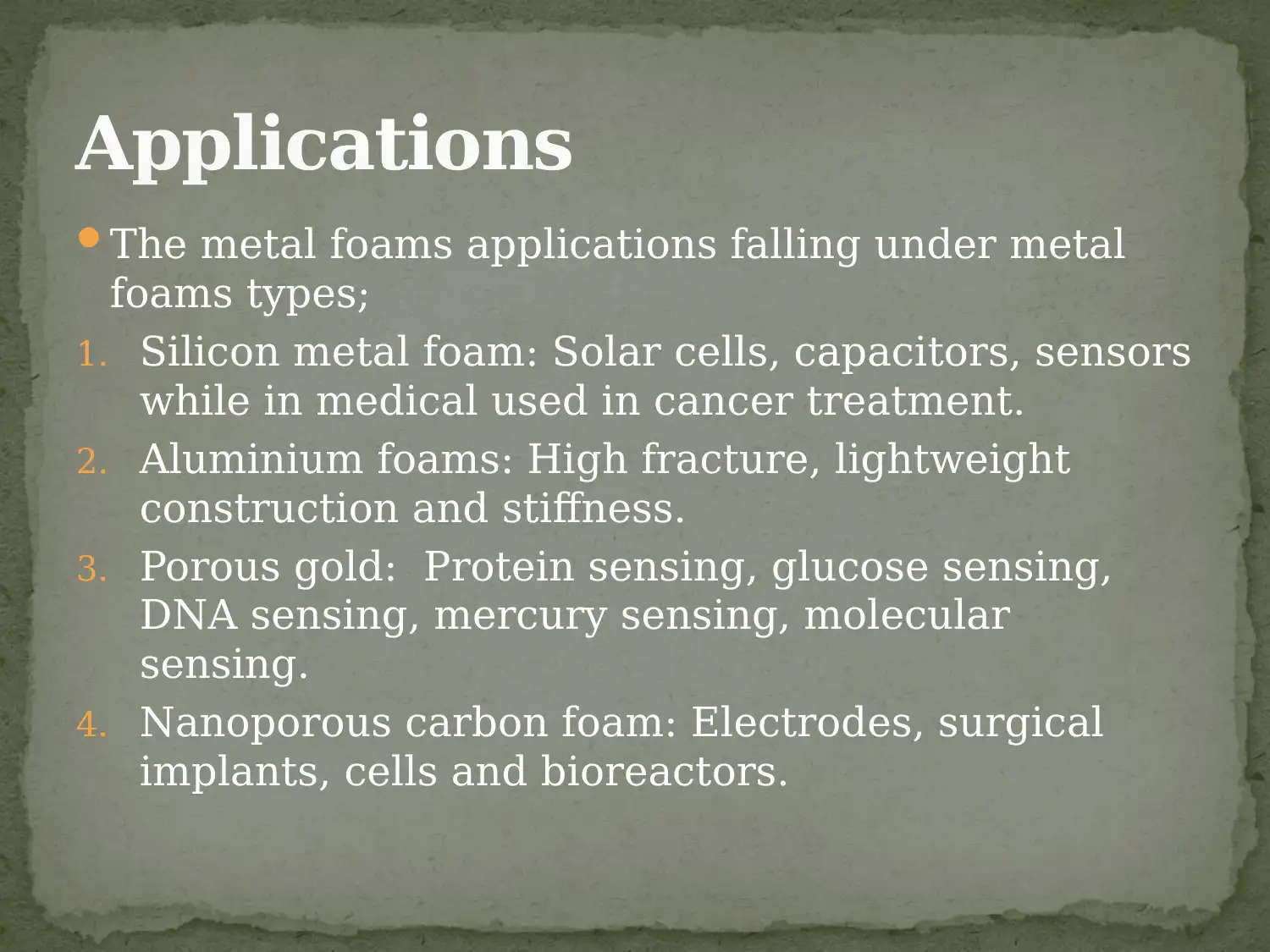
Applications
The metal foams applications falling under metal
foams types;
1. Silicon metal foam: Solar cells, capacitors, sensors
while in medical used in cancer treatment.
2. Aluminium foams: High fracture, lightweight
construction and stiffness.
3. Porous gold: Protein sensing, glucose sensing,
DNA sensing, mercury sensing, molecular
sensing.
4. Nanoporous carbon foam: Electrodes, surgical
implants, cells and bioreactors.
The metal foams applications falling under metal
foams types;
1. Silicon metal foam: Solar cells, capacitors, sensors
while in medical used in cancer treatment.
2. Aluminium foams: High fracture, lightweight
construction and stiffness.
3. Porous gold: Protein sensing, glucose sensing,
DNA sensing, mercury sensing, molecular
sensing.
4. Nanoporous carbon foam: Electrodes, surgical
implants, cells and bioreactors.
Secure Best Marks with AI Grader
Need help grading? Try our AI Grader for instant feedback on your assignments.
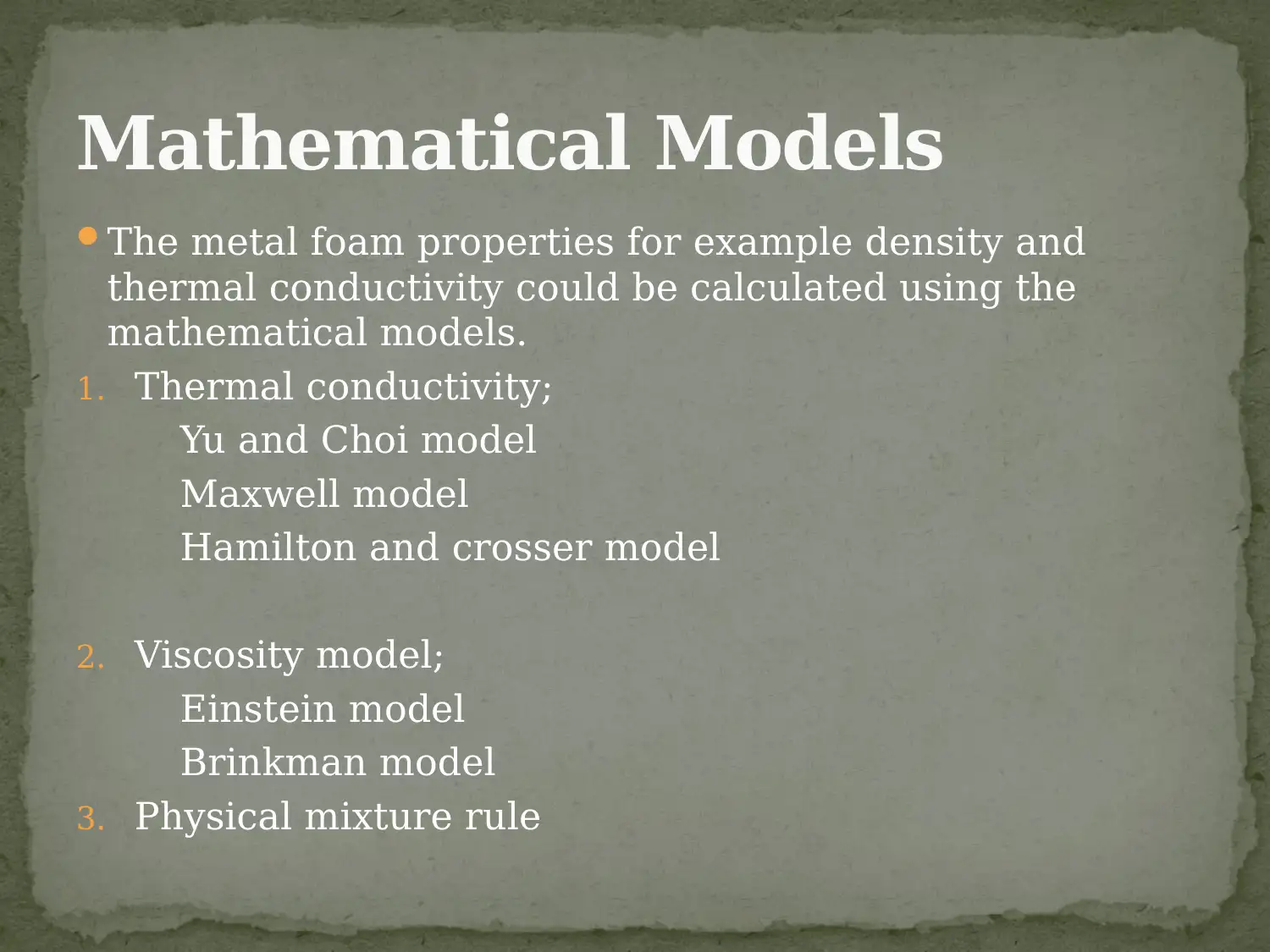
Mathematical Models
The metal foam properties for example density and
thermal conductivity could be calculated using the
mathematical models.
1. Thermal conductivity;
Yu and Choi model
Maxwell model
Hamilton and crosser model
2. Viscosity model;
Einstein model
Brinkman model
3. Physical mixture rule
The metal foam properties for example density and
thermal conductivity could be calculated using the
mathematical models.
1. Thermal conductivity;
Yu and Choi model
Maxwell model
Hamilton and crosser model
2. Viscosity model;
Einstein model
Brinkman model
3. Physical mixture rule
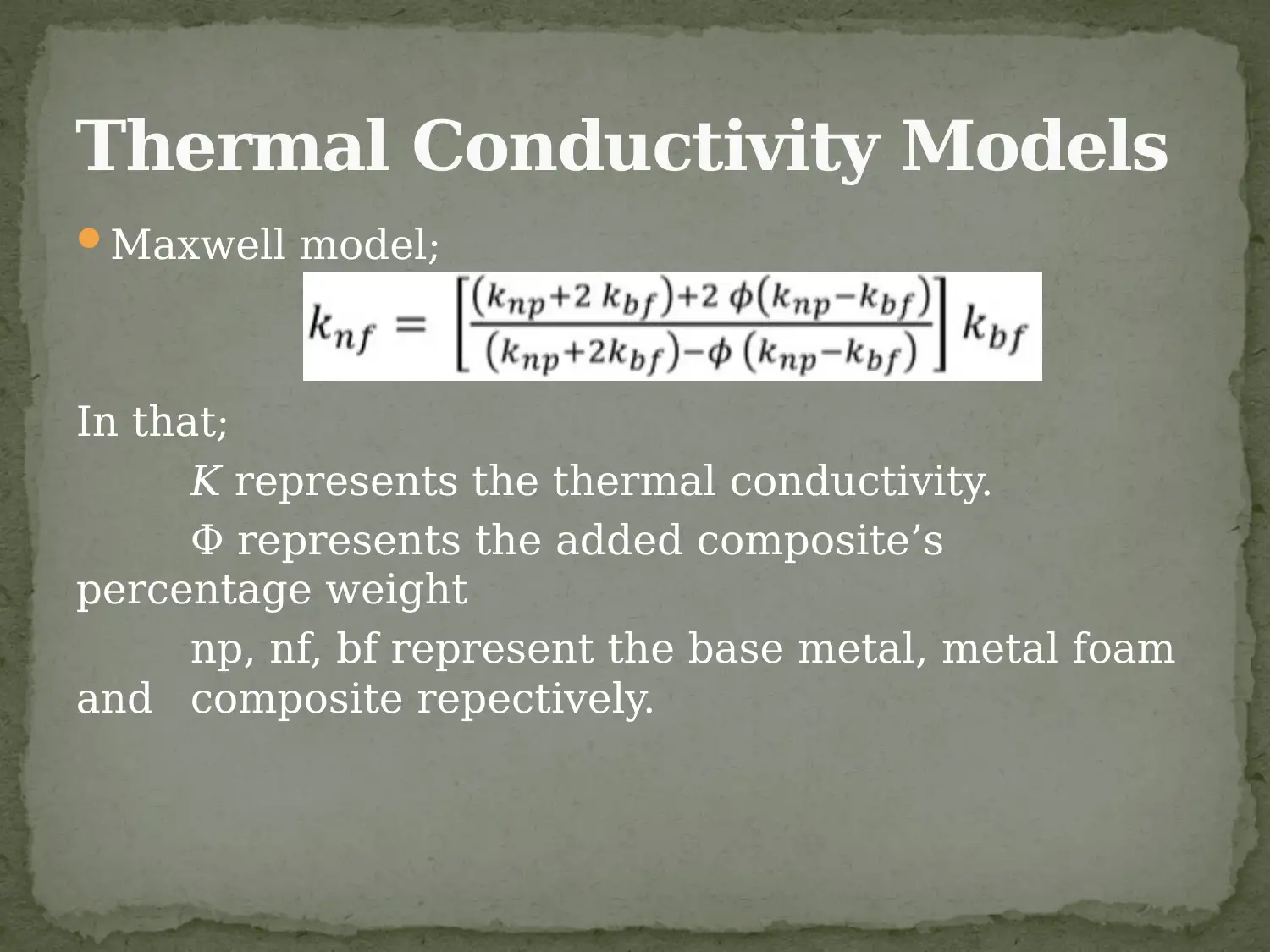
Thermal Conductivity Models
Maxwell model;
In that;
K represents the thermal conductivity.
Φ represents the added composite’s
percentage weight
np, nf, bf represent the base metal, metal foam
and composite repectively.
Maxwell model;
In that;
K represents the thermal conductivity.
Φ represents the added composite’s
percentage weight
np, nf, bf represent the base metal, metal foam
and composite repectively.
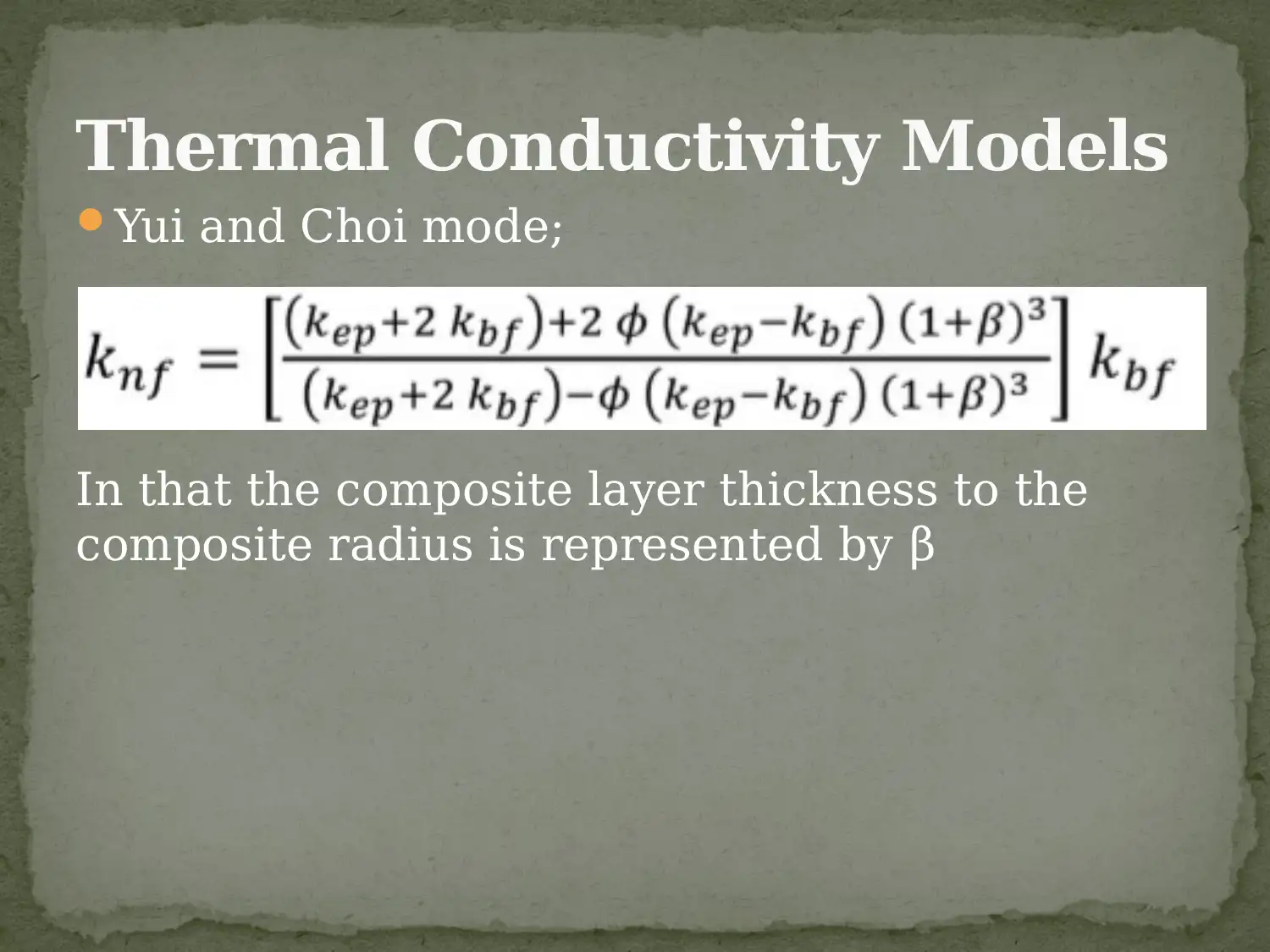
Thermal Conductivity Models
Yui and Choi mode;
In that the composite layer thickness to the
composite radius is represented by β
Yui and Choi mode;
In that the composite layer thickness to the
composite radius is represented by β
Paraphrase This Document
Need a fresh take? Get an instant paraphrase of this document with our AI Paraphraser
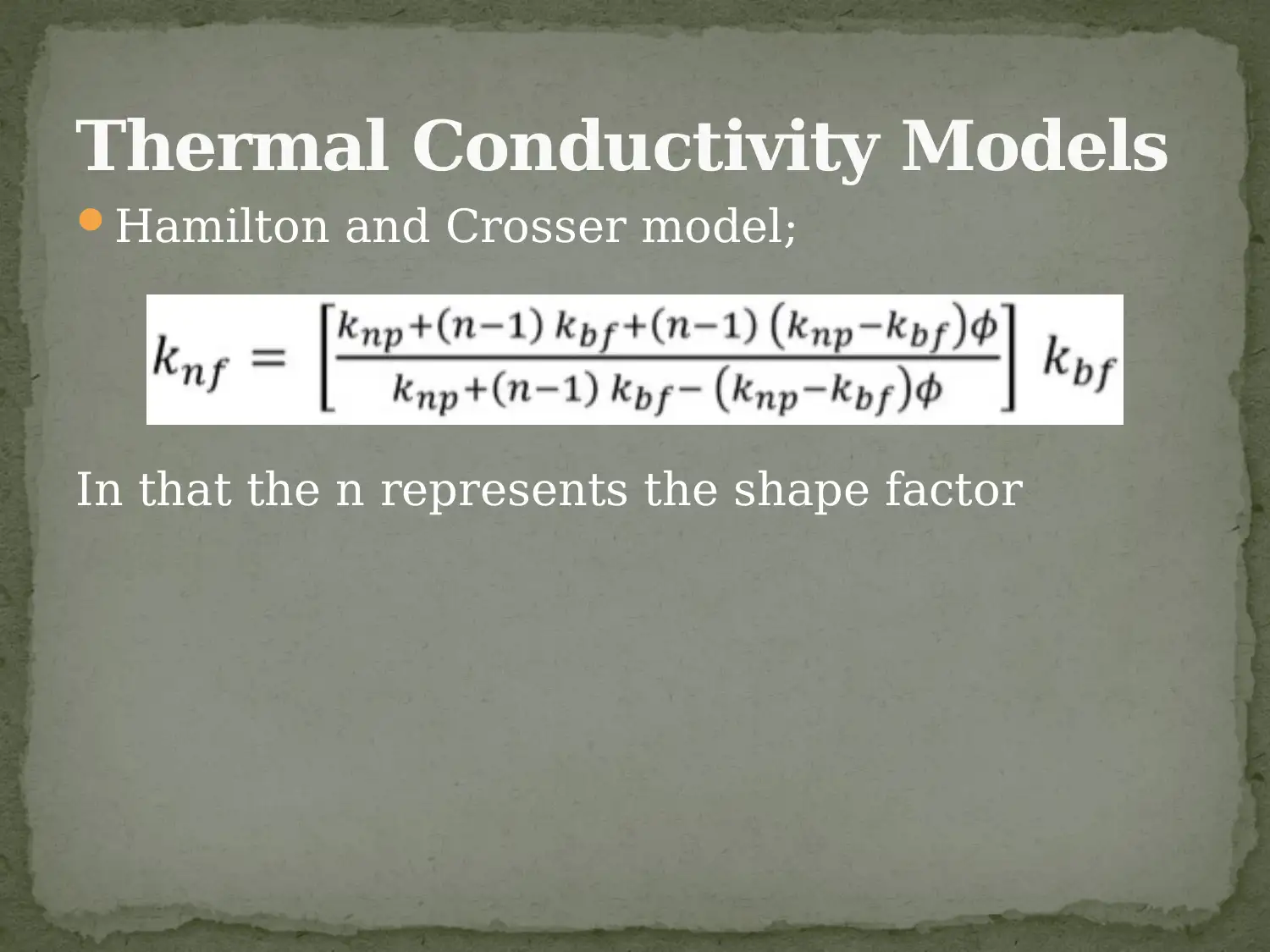
Thermal Conductivity Models
Hamilton and Crosser model;
In that the n represents the shape factor
Hamilton and Crosser model;
In that the n represents the shape factor
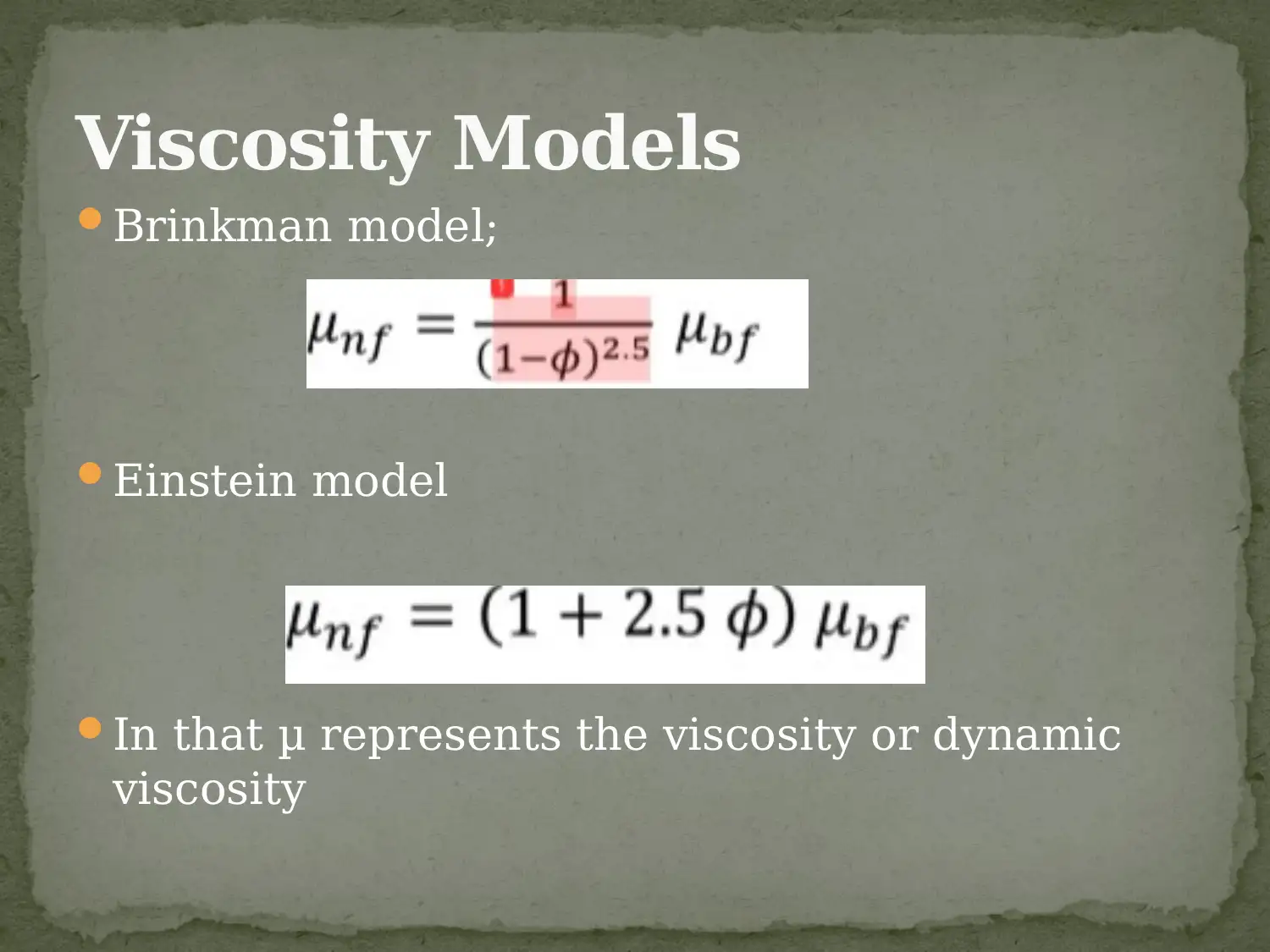
Viscosity Models
Brinkman model;
Einstein model
In that μ represents the viscosity or dynamic
viscosity
Brinkman model;
Einstein model
In that μ represents the viscosity or dynamic
viscosity
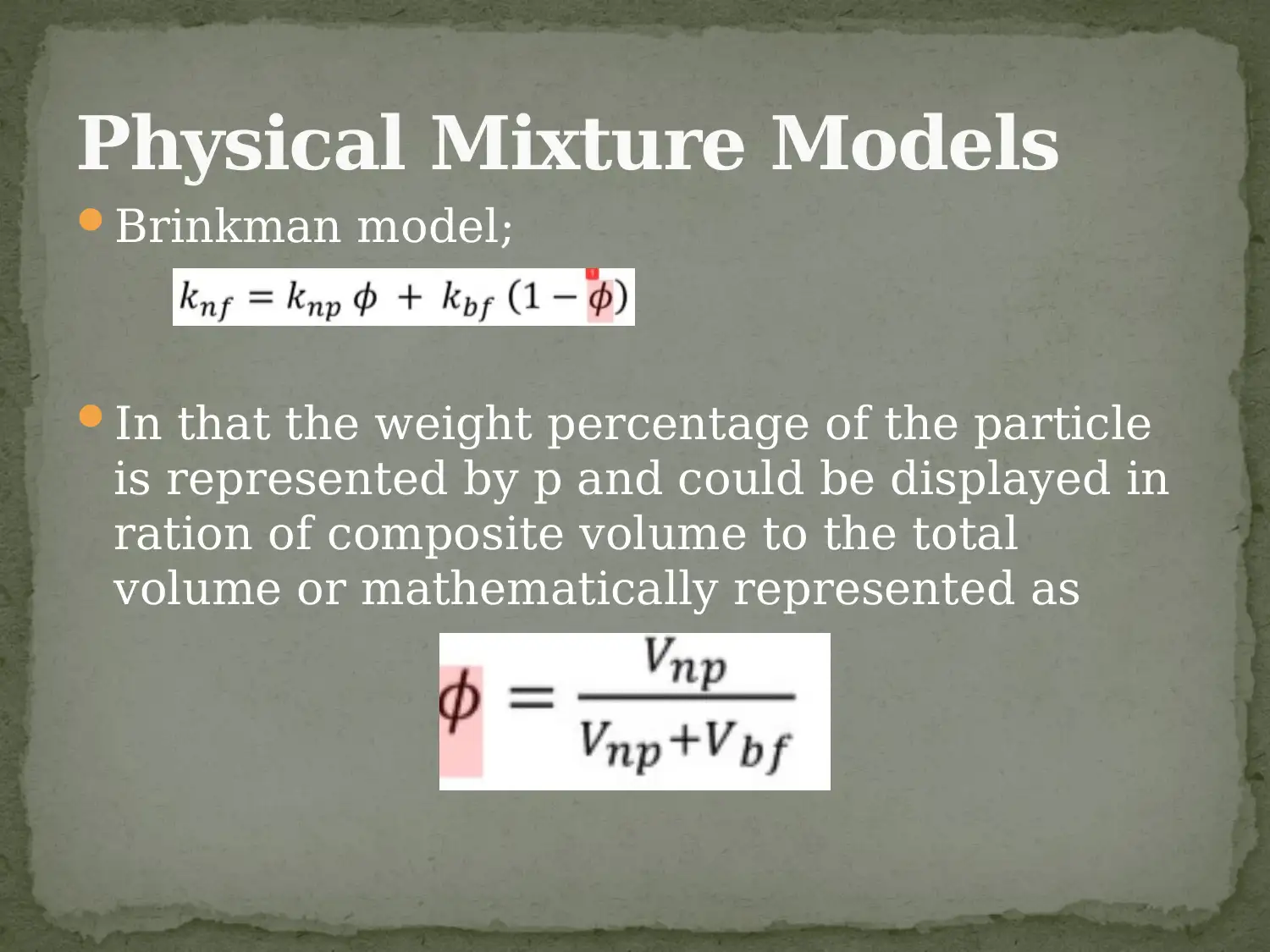
Physical Mixture Models
Brinkman model;
In that the weight percentage of the particle
is represented by p and could be displayed in
ration of composite volume to the total
volume or mathematically represented as
Brinkman model;
In that the weight percentage of the particle
is represented by p and could be displayed in
ration of composite volume to the total
volume or mathematically represented as
Secure Best Marks with AI Grader
Need help grading? Try our AI Grader for instant feedback on your assignments.
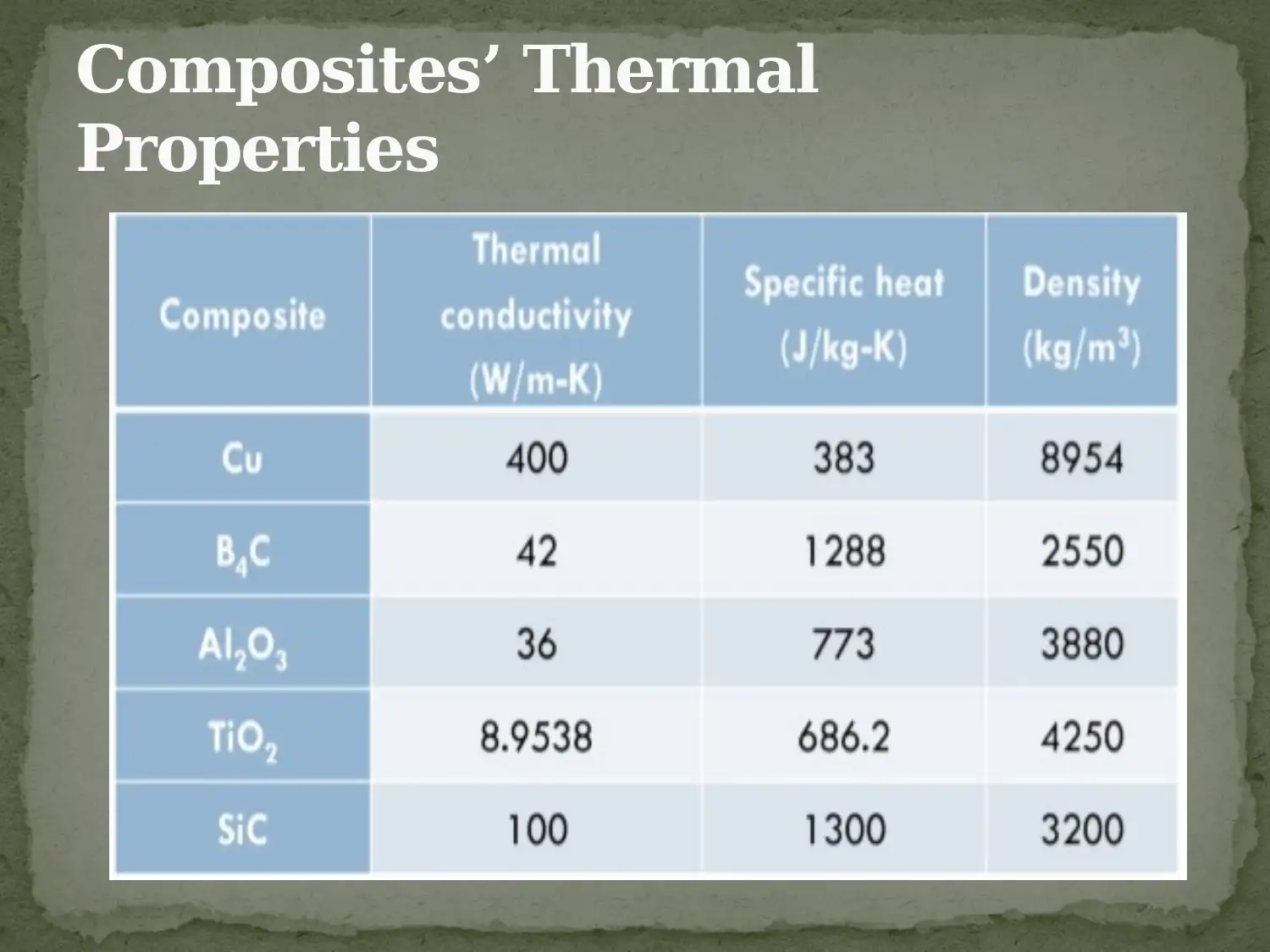
Composites’ Thermal
Properties
Properties
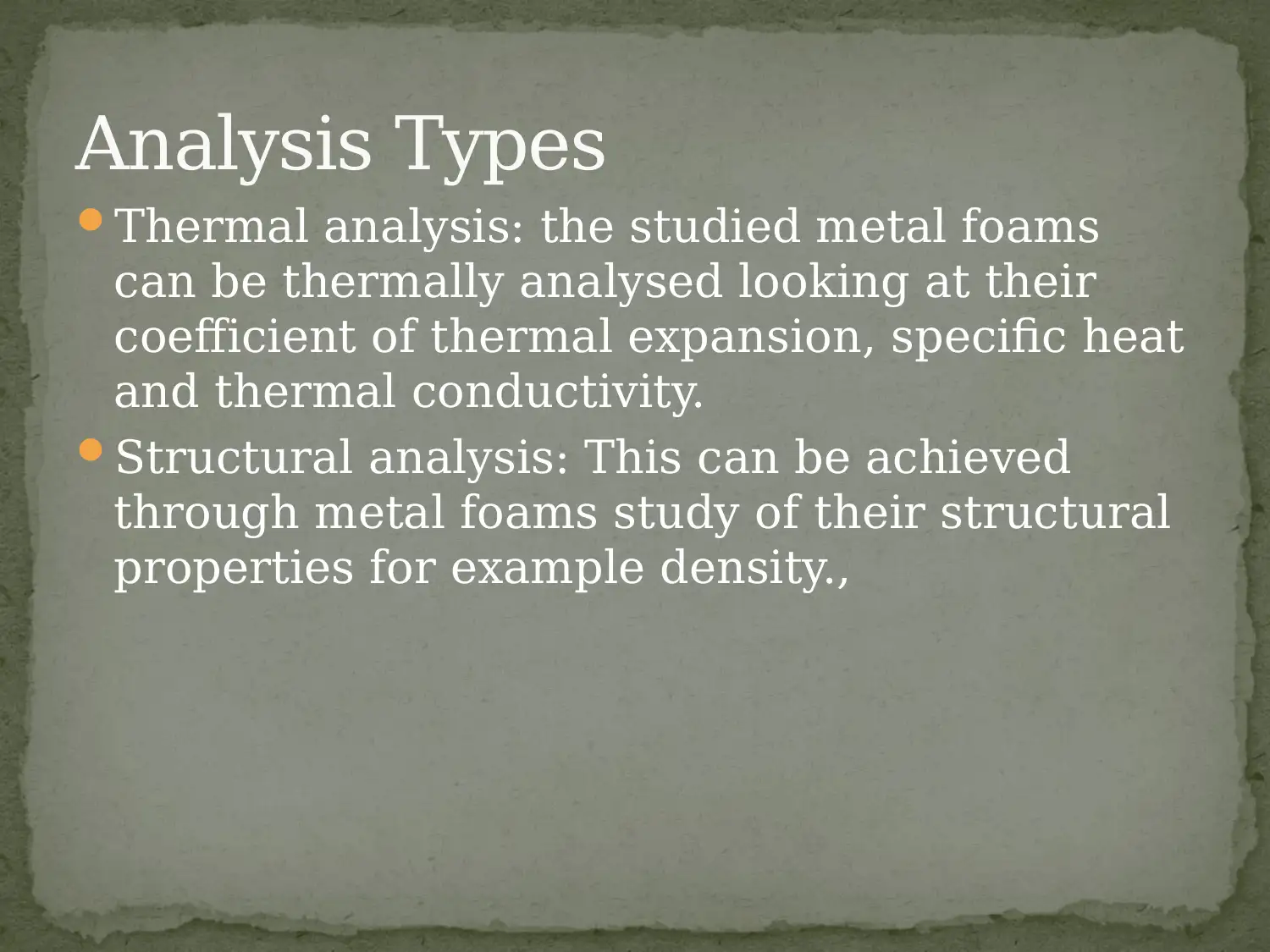
Analysis Types
Thermal analysis: the studied metal foams
can be thermally analysed looking at their
coefficient of thermal expansion, specific heat
and thermal conductivity.
Structural analysis: This can be achieved
through metal foams study of their structural
properties for example density.,
Thermal analysis: the studied metal foams
can be thermally analysed looking at their
coefficient of thermal expansion, specific heat
and thermal conductivity.
Structural analysis: This can be achieved
through metal foams study of their structural
properties for example density.,
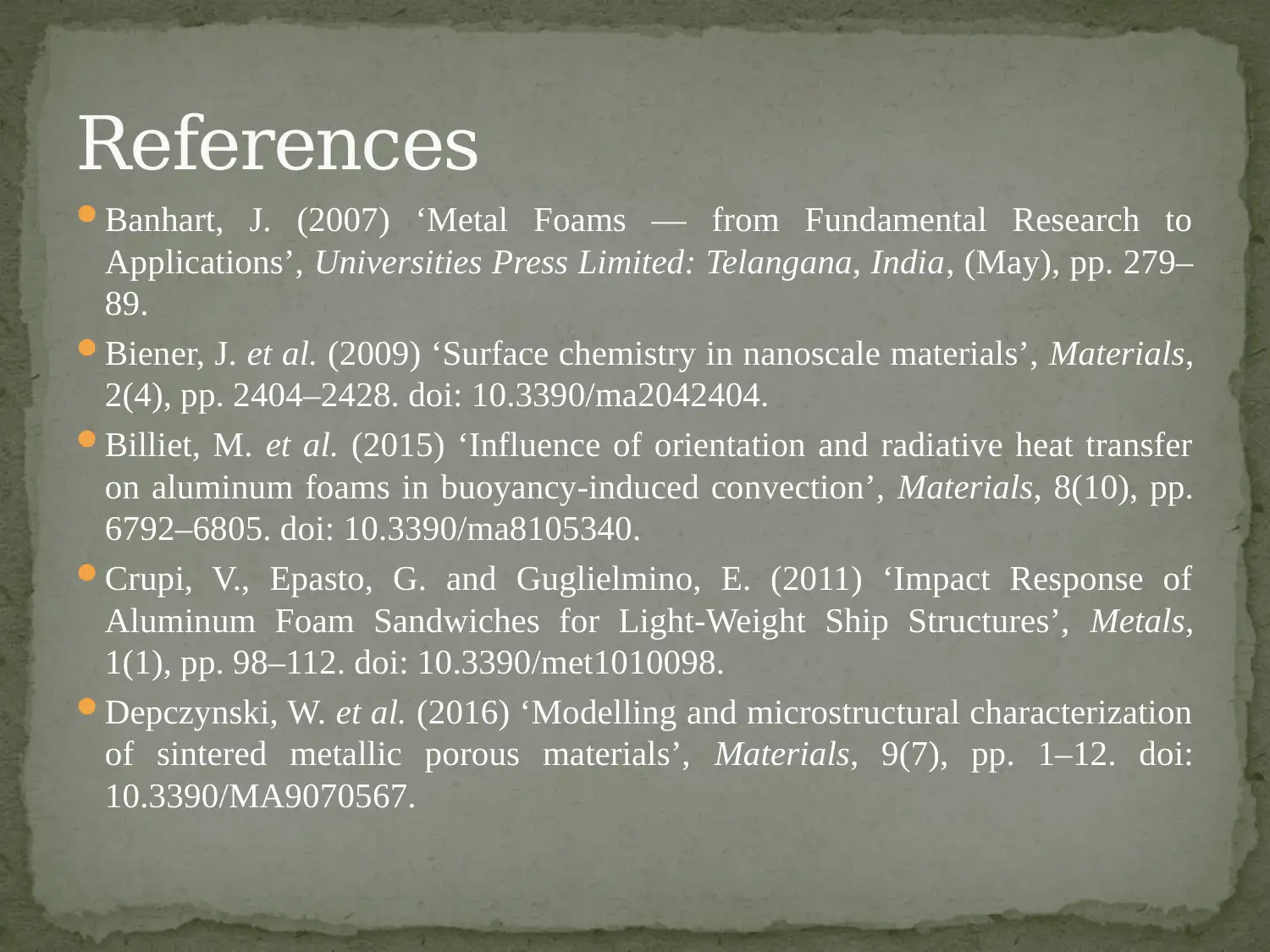
References
Banhart, J. (2007) ‘Metal Foams — from Fundamental Research to
Applications’, Universities Press Limited: Telangana, India, (May), pp. 279–
89.
Biener, J. et al. (2009) ‘Surface chemistry in nanoscale materials’, Materials,
2(4), pp. 2404–2428. doi: 10.3390/ma2042404.
Billiet, M. et al. (2015) ‘Influence of orientation and radiative heat transfer
on aluminum foams in buoyancy-induced convection’, Materials, 8(10), pp.
6792–6805. doi: 10.3390/ma8105340.
Crupi, V., Epasto, G. and Guglielmino, E. (2011) ‘Impact Response of
Aluminum Foam Sandwiches for Light-Weight Ship Structures’, Metals,
1(1), pp. 98–112. doi: 10.3390/met1010098.
Depczynski, W. et al. (2016) ‘Modelling and microstructural characterization
of sintered metallic porous materials’, Materials, 9(7), pp. 1–12. doi:
10.3390/MA9070567.
Banhart, J. (2007) ‘Metal Foams — from Fundamental Research to
Applications’, Universities Press Limited: Telangana, India, (May), pp. 279–
89.
Biener, J. et al. (2009) ‘Surface chemistry in nanoscale materials’, Materials,
2(4), pp. 2404–2428. doi: 10.3390/ma2042404.
Billiet, M. et al. (2015) ‘Influence of orientation and radiative heat transfer
on aluminum foams in buoyancy-induced convection’, Materials, 8(10), pp.
6792–6805. doi: 10.3390/ma8105340.
Crupi, V., Epasto, G. and Guglielmino, E. (2011) ‘Impact Response of
Aluminum Foam Sandwiches for Light-Weight Ship Structures’, Metals,
1(1), pp. 98–112. doi: 10.3390/met1010098.
Depczynski, W. et al. (2016) ‘Modelling and microstructural characterization
of sintered metallic porous materials’, Materials, 9(7), pp. 1–12. doi:
10.3390/MA9070567.
Paraphrase This Document
Need a fresh take? Get an instant paraphrase of this document with our AI Paraphraser
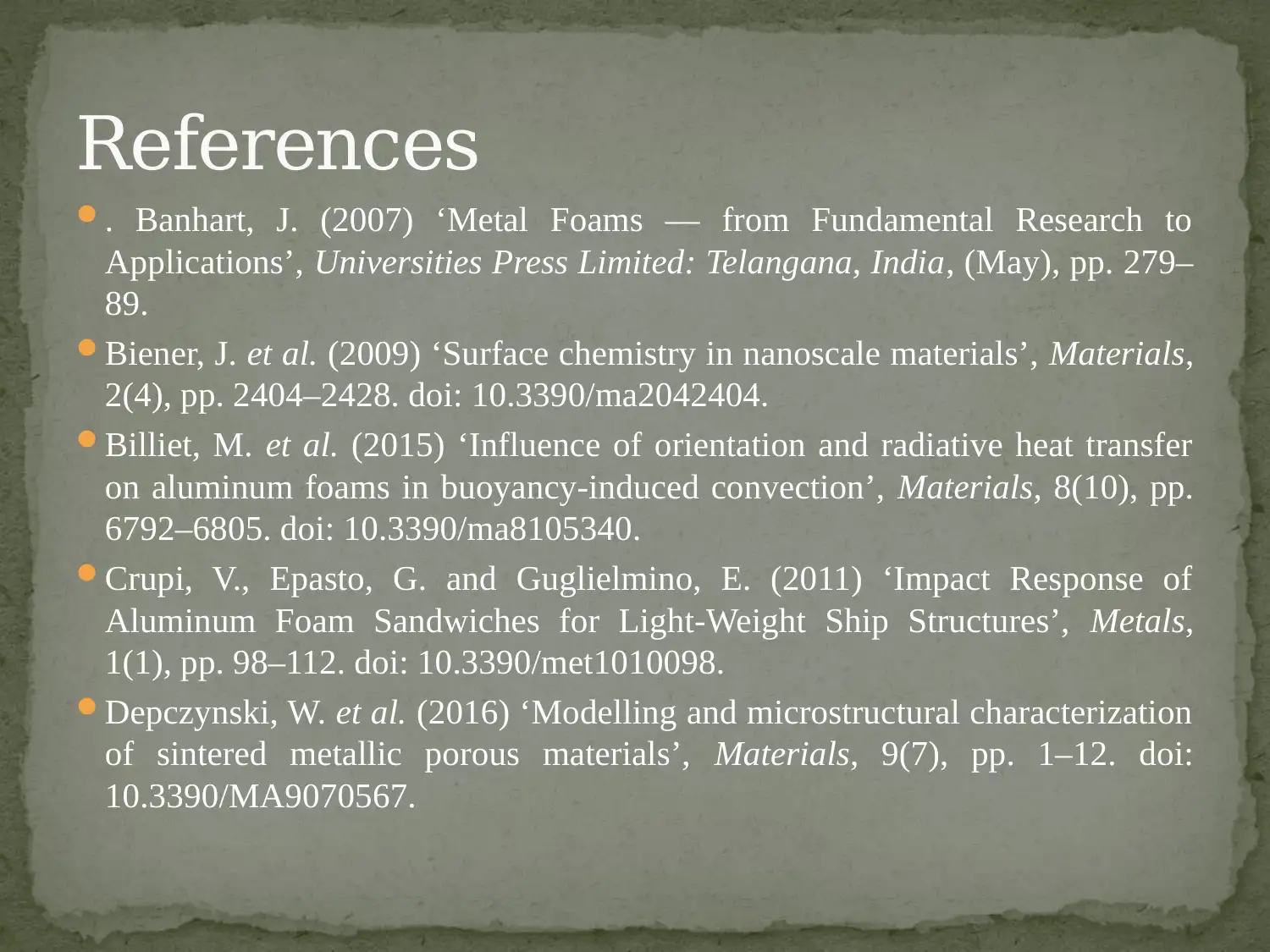
References
. Banhart, J. (2007) ‘Metal Foams — from Fundamental Research to
Applications’, Universities Press Limited: Telangana, India, (May), pp. 279–
89.
Biener, J. et al. (2009) ‘Surface chemistry in nanoscale materials’, Materials,
2(4), pp. 2404–2428. doi: 10.3390/ma2042404.
Billiet, M. et al. (2015) ‘Influence of orientation and radiative heat transfer
on aluminum foams in buoyancy-induced convection’, Materials, 8(10), pp.
6792–6805. doi: 10.3390/ma8105340.
Crupi, V., Epasto, G. and Guglielmino, E. (2011) ‘Impact Response of
Aluminum Foam Sandwiches for Light-Weight Ship Structures’, Metals,
1(1), pp. 98–112. doi: 10.3390/met1010098.
Depczynski, W. et al. (2016) ‘Modelling and microstructural characterization
of sintered metallic porous materials’, Materials, 9(7), pp. 1–12. doi:
10.3390/MA9070567.
. Banhart, J. (2007) ‘Metal Foams — from Fundamental Research to
Applications’, Universities Press Limited: Telangana, India, (May), pp. 279–
89.
Biener, J. et al. (2009) ‘Surface chemistry in nanoscale materials’, Materials,
2(4), pp. 2404–2428. doi: 10.3390/ma2042404.
Billiet, M. et al. (2015) ‘Influence of orientation and radiative heat transfer
on aluminum foams in buoyancy-induced convection’, Materials, 8(10), pp.
6792–6805. doi: 10.3390/ma8105340.
Crupi, V., Epasto, G. and Guglielmino, E. (2011) ‘Impact Response of
Aluminum Foam Sandwiches for Light-Weight Ship Structures’, Metals,
1(1), pp. 98–112. doi: 10.3390/met1010098.
Depczynski, W. et al. (2016) ‘Modelling and microstructural characterization
of sintered metallic porous materials’, Materials, 9(7), pp. 1–12. doi:
10.3390/MA9070567.
1 out of 20
Related Documents
![[object Object]](/_next/image/?url=%2F_next%2Fstatic%2Fmedia%2Flogo.6d15ce61.png&w=640&q=75)
Your All-in-One AI-Powered Toolkit for Academic Success.
+13062052269
info@desklib.com
Available 24*7 on WhatsApp / Email
Unlock your academic potential
© 2024 | Zucol Services PVT LTD | All rights reserved.