Advanced Modelling, Simulation and Control of Dynamic Systems
VerifiedAdded on 2023/06/03
|40
|5928
|106
AI Summary
This text discusses the analysis of vehicle dynamics using finite element, dynamical substructure and multi-body system models. It covers the design and customization of features such as 4WD and payload variations, and delves into the mathematical modelling of mechanical systems, control theory and the role of engineering assumptions. The text also explores the limitations of mathematical models and the identification and evaluation of engineering uncertainty.
Contribute Materials
Your contribution can guide someone’s learning journey. Share your
documents today.
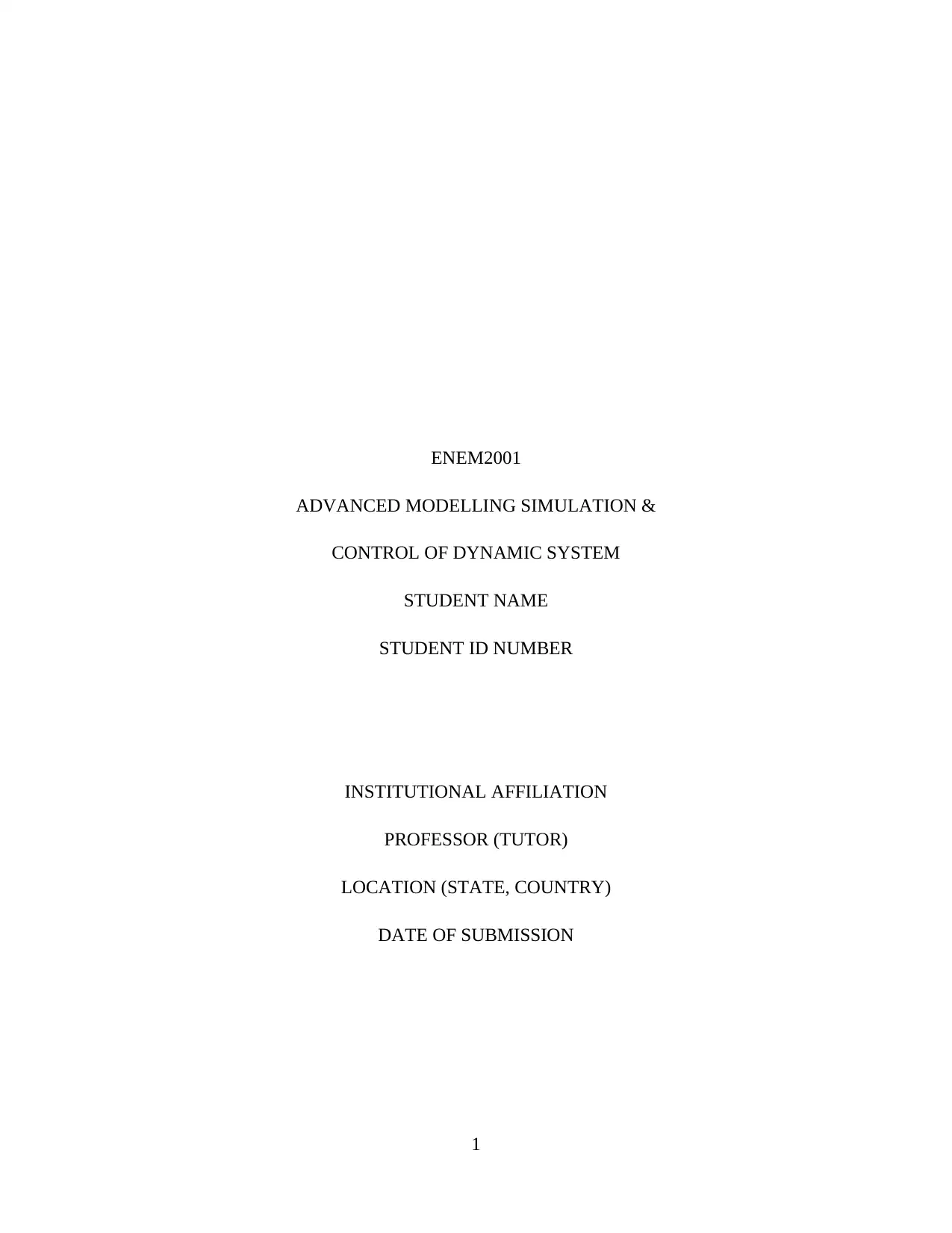
ENEM2001
ADVANCED MODELLING SIMULATION &
CONTROL OF DYNAMIC SYSTEM
STUDENT NAME
STUDENT ID NUMBER
INSTITUTIONAL AFFILIATION
PROFESSOR (TUTOR)
LOCATION (STATE, COUNTRY)
DATE OF SUBMISSION
1
ADVANCED MODELLING SIMULATION &
CONTROL OF DYNAMIC SYSTEM
STUDENT NAME
STUDENT ID NUMBER
INSTITUTIONAL AFFILIATION
PROFESSOR (TUTOR)
LOCATION (STATE, COUNTRY)
DATE OF SUBMISSION
1
Secure Best Marks with AI Grader
Need help grading? Try our AI Grader for instant feedback on your assignments.
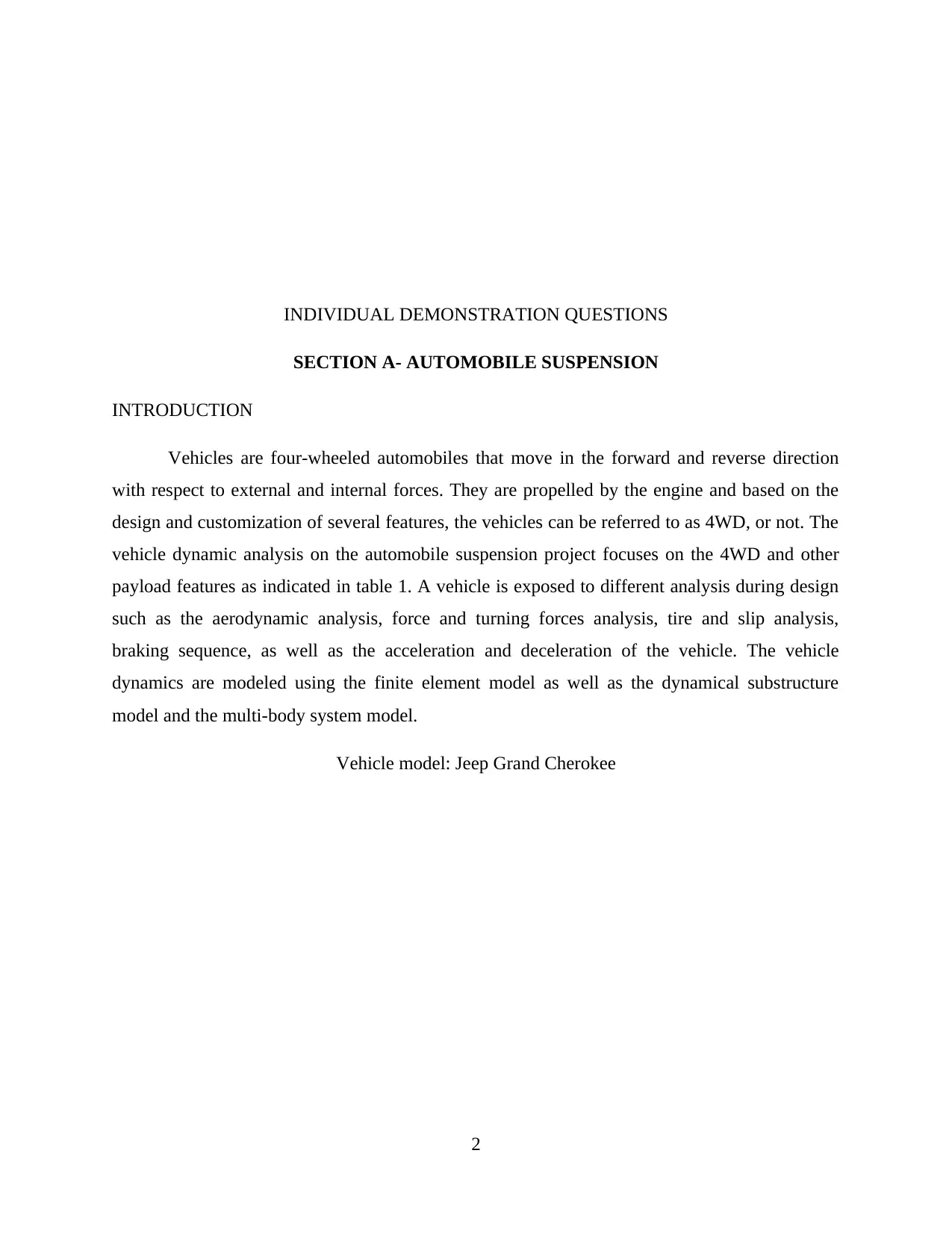
INDIVIDUAL DEMONSTRATION QUESTIONS
SECTION A- AUTOMOBILE SUSPENSION
INTRODUCTION
Vehicles are four-wheeled automobiles that move in the forward and reverse direction
with respect to external and internal forces. They are propelled by the engine and based on the
design and customization of several features, the vehicles can be referred to as 4WD, or not. The
vehicle dynamic analysis on the automobile suspension project focuses on the 4WD and other
payload features as indicated in table 1. A vehicle is exposed to different analysis during design
such as the aerodynamic analysis, force and turning forces analysis, tire and slip analysis,
braking sequence, as well as the acceleration and deceleration of the vehicle. The vehicle
dynamics are modeled using the finite element model as well as the dynamical substructure
model and the multi-body system model.
Vehicle model: Jeep Grand Cherokee
2
SECTION A- AUTOMOBILE SUSPENSION
INTRODUCTION
Vehicles are four-wheeled automobiles that move in the forward and reverse direction
with respect to external and internal forces. They are propelled by the engine and based on the
design and customization of several features, the vehicles can be referred to as 4WD, or not. The
vehicle dynamic analysis on the automobile suspension project focuses on the 4WD and other
payload features as indicated in table 1. A vehicle is exposed to different analysis during design
such as the aerodynamic analysis, force and turning forces analysis, tire and slip analysis,
braking sequence, as well as the acceleration and deceleration of the vehicle. The vehicle
dynamics are modeled using the finite element model as well as the dynamical substructure
model and the multi-body system model.
Vehicle model: Jeep Grand Cherokee
2
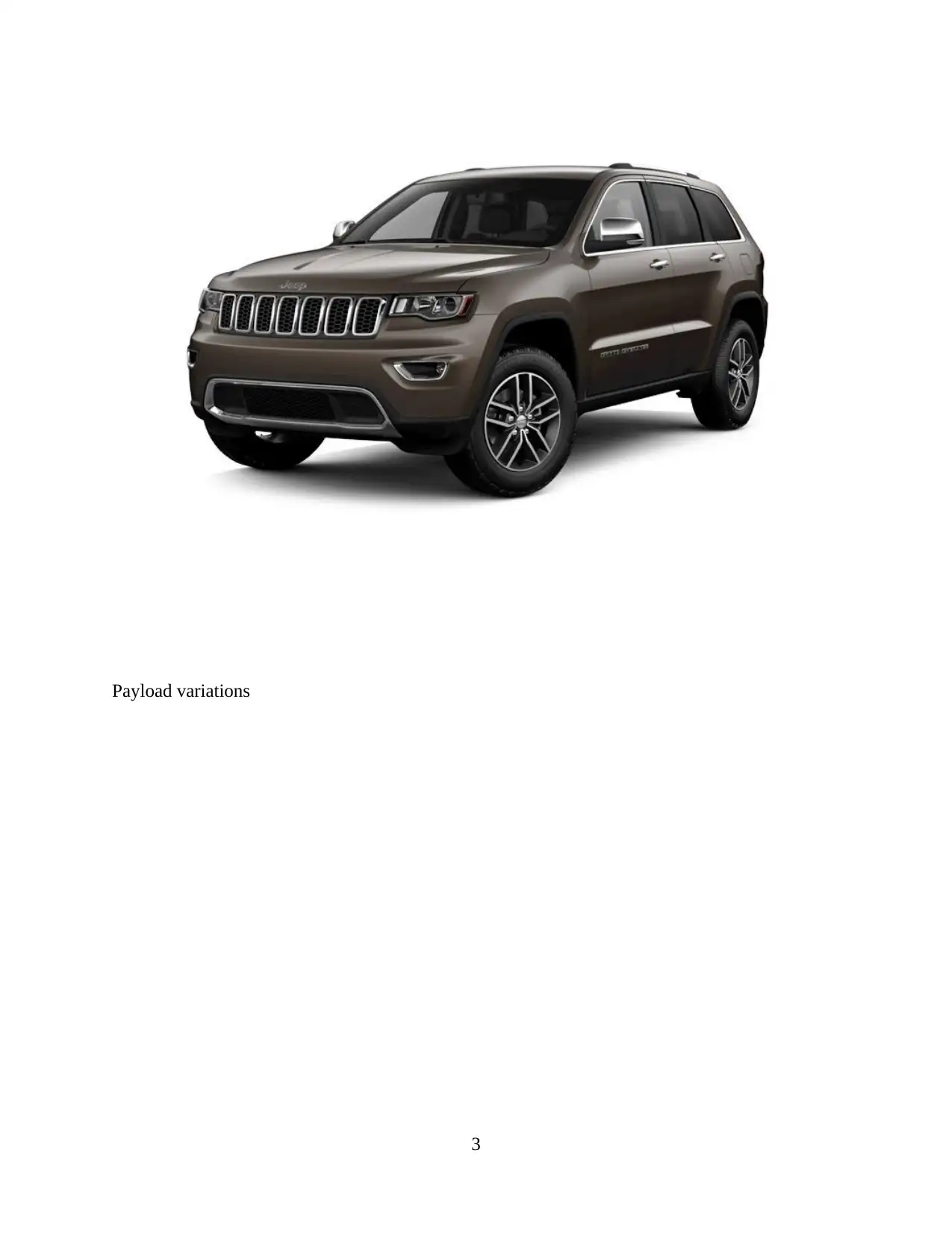
Payload variations
3
3
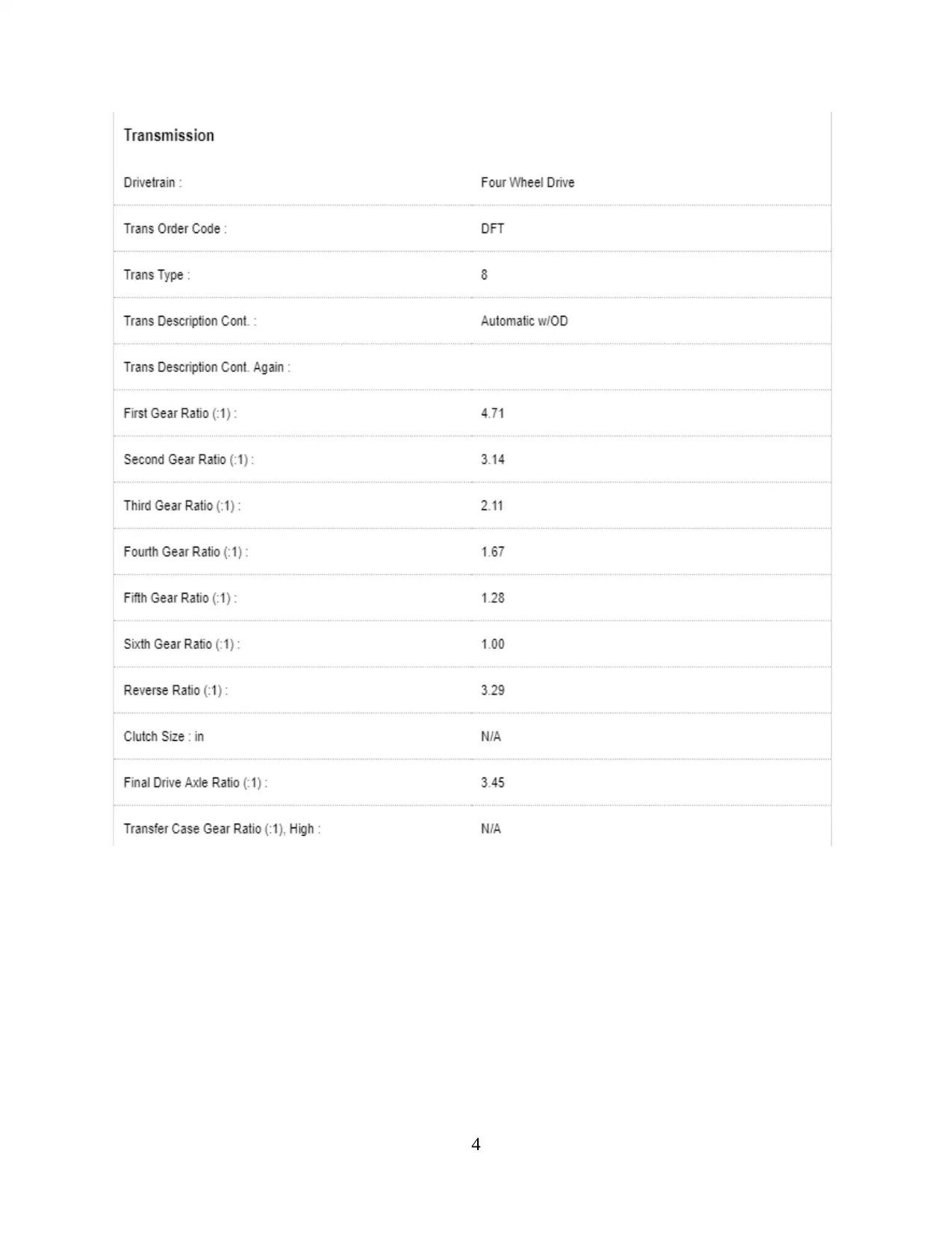
4
Secure Best Marks with AI Grader
Need help grading? Try our AI Grader for instant feedback on your assignments.
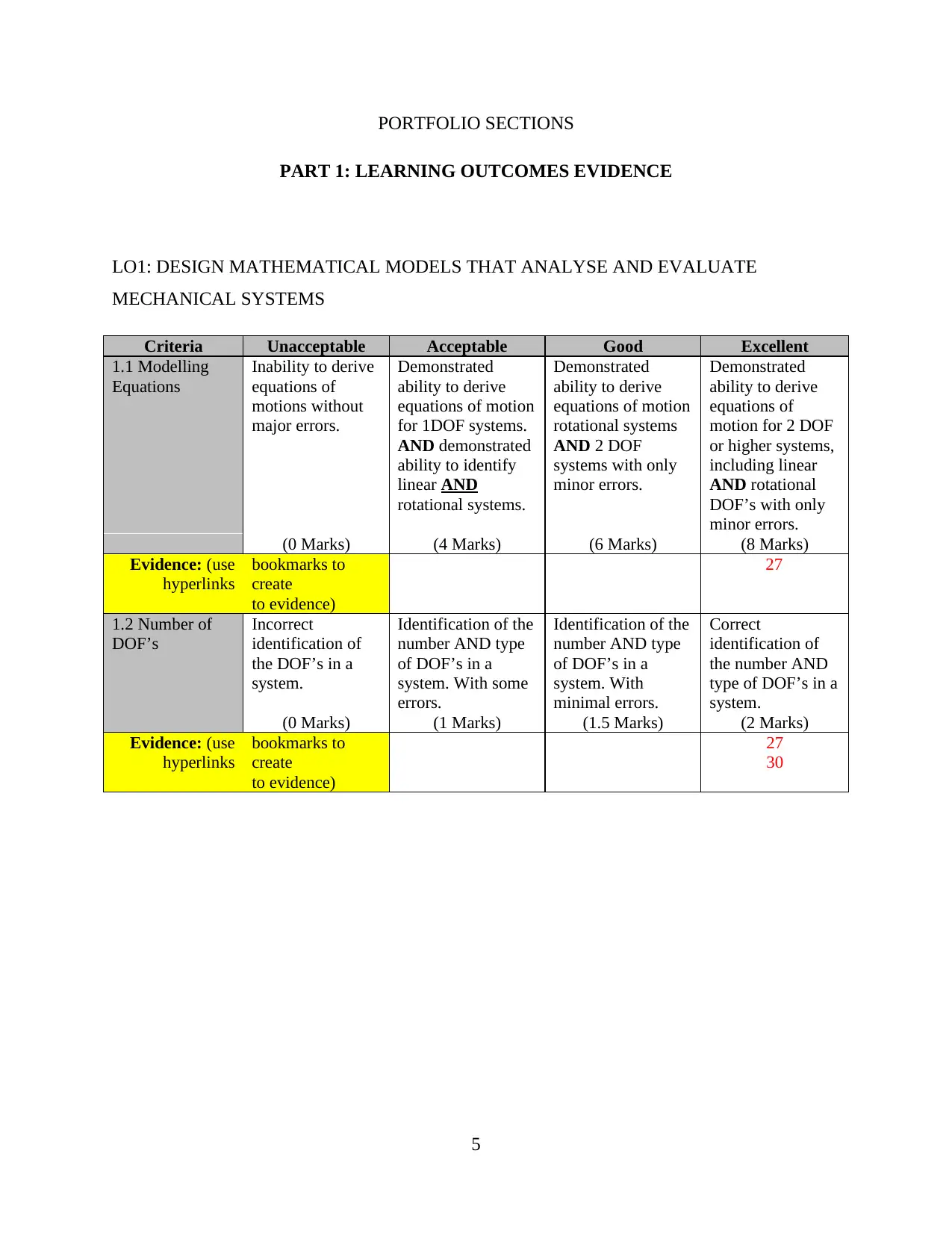
PORTFOLIO SECTIONS
PART 1: LEARNING OUTCOMES EVIDENCE
LO1: DESIGN MATHEMATICAL MODELS THAT ANALYSE AND EVALUATE
MECHANICAL SYSTEMS
Criteria Unacceptable Acceptable Good Excellent
1.1 Modelling
Equations
Inability to derive
equations of
motions without
major errors.
Demonstrated
ability to derive
equations of motion
for 1DOF systems.
AND demonstrated
ability to identify
linear AND
rotational systems.
Demonstrated
ability to derive
equations of motion
rotational systems
AND 2 DOF
systems with only
minor errors.
Demonstrated
ability to derive
equations of
motion for 2 DOF
or higher systems,
including linear
AND rotational
DOF’s with only
minor errors.
(0 Marks) (4 Marks) (6 Marks) (8 Marks)
Evidence: (use
hyperlinks
bookmarks to
create
to evidence)
27
1.2 Number of
DOF’s
Incorrect
identification of
the DOF’s in a
system.
Identification of the
number AND type
of DOF’s in a
system. With some
errors.
Identification of the
number AND type
of DOF’s in a
system. With
minimal errors.
Correct
identification of
the number AND
type of DOF’s in a
system.
(0 Marks) (1 Marks) (1.5 Marks) (2 Marks)
Evidence: (use
hyperlinks
bookmarks to
create
to evidence)
27
30
5
PART 1: LEARNING OUTCOMES EVIDENCE
LO1: DESIGN MATHEMATICAL MODELS THAT ANALYSE AND EVALUATE
MECHANICAL SYSTEMS
Criteria Unacceptable Acceptable Good Excellent
1.1 Modelling
Equations
Inability to derive
equations of
motions without
major errors.
Demonstrated
ability to derive
equations of motion
for 1DOF systems.
AND demonstrated
ability to identify
linear AND
rotational systems.
Demonstrated
ability to derive
equations of motion
rotational systems
AND 2 DOF
systems with only
minor errors.
Demonstrated
ability to derive
equations of
motion for 2 DOF
or higher systems,
including linear
AND rotational
DOF’s with only
minor errors.
(0 Marks) (4 Marks) (6 Marks) (8 Marks)
Evidence: (use
hyperlinks
bookmarks to
create
to evidence)
27
1.2 Number of
DOF’s
Incorrect
identification of
the DOF’s in a
system.
Identification of the
number AND type
of DOF’s in a
system. With some
errors.
Identification of the
number AND type
of DOF’s in a
system. With
minimal errors.
Correct
identification of
the number AND
type of DOF’s in a
system.
(0 Marks) (1 Marks) (1.5 Marks) (2 Marks)
Evidence: (use
hyperlinks
bookmarks to
create
to evidence)
27
30
5
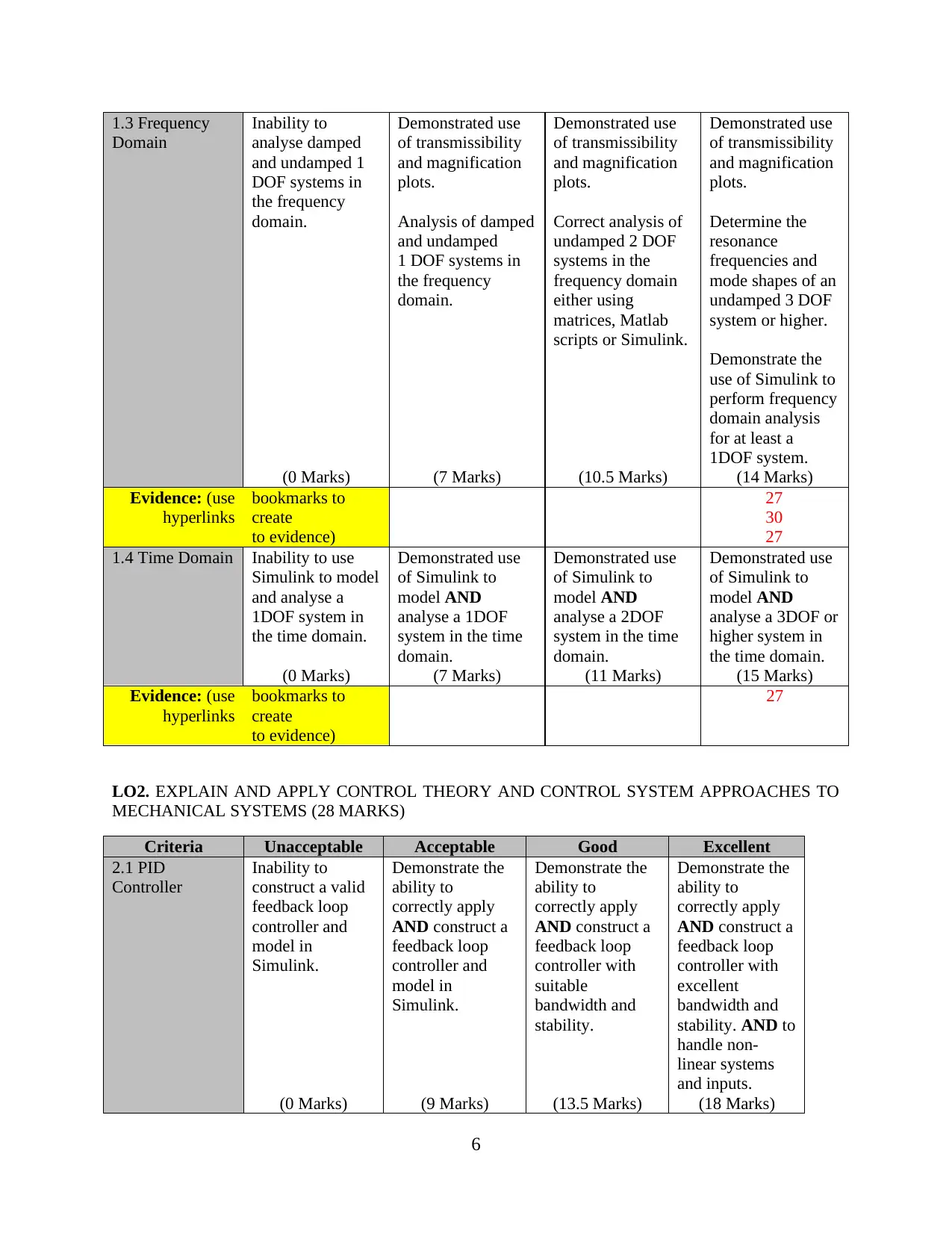
1.3 Frequency
Domain
Inability to
analyse damped
and undamped 1
DOF systems in
the frequency
domain.
Demonstrated use
of transmissibility
and magnification
plots.
Analysis of damped
and undamped
1 DOF systems in
the frequency
domain.
Demonstrated use
of transmissibility
and magnification
plots.
Correct analysis of
undamped 2 DOF
systems in the
frequency domain
either using
matrices, Matlab
scripts or Simulink.
Demonstrated use
of transmissibility
and magnification
plots.
Determine the
resonance
frequencies and
mode shapes of an
undamped 3 DOF
system or higher.
Demonstrate the
use of Simulink to
perform frequency
domain analysis
for at least a
1DOF system.
(0 Marks) (7 Marks) (10.5 Marks) (14 Marks)
Evidence: (use
hyperlinks
bookmarks to
create
to evidence)
27
30
27
1.4 Time Domain Inability to use
Simulink to model
and analyse a
1DOF system in
the time domain.
Demonstrated use
of Simulink to
model AND
analyse a 1DOF
system in the time
domain.
Demonstrated use
of Simulink to
model AND
analyse a 2DOF
system in the time
domain.
Demonstrated use
of Simulink to
model AND
analyse a 3DOF or
higher system in
the time domain.
(0 Marks) (7 Marks) (11 Marks) (15 Marks)
Evidence: (use
hyperlinks
bookmarks to
create
to evidence)
27
LO2. EXPLAIN AND APPLY CONTROL THEORY AND CONTROL SYSTEM APPROACHES TO
MECHANICAL SYSTEMS (28 MARKS)
Criteria Unacceptable Acceptable Good Excellent
2.1 PID
Controller
Inability to
construct a valid
feedback loop
controller and
model in
Simulink.
Demonstrate the
ability to
correctly apply
AND construct a
feedback loop
controller and
model in
Simulink.
Demonstrate the
ability to
correctly apply
AND construct a
feedback loop
controller with
suitable
bandwidth and
stability.
Demonstrate the
ability to
correctly apply
AND construct a
feedback loop
controller with
excellent
bandwidth and
stability. AND to
handle non-
linear systems
and inputs.
(0 Marks) (9 Marks) (13.5 Marks) (18 Marks)
6
Domain
Inability to
analyse damped
and undamped 1
DOF systems in
the frequency
domain.
Demonstrated use
of transmissibility
and magnification
plots.
Analysis of damped
and undamped
1 DOF systems in
the frequency
domain.
Demonstrated use
of transmissibility
and magnification
plots.
Correct analysis of
undamped 2 DOF
systems in the
frequency domain
either using
matrices, Matlab
scripts or Simulink.
Demonstrated use
of transmissibility
and magnification
plots.
Determine the
resonance
frequencies and
mode shapes of an
undamped 3 DOF
system or higher.
Demonstrate the
use of Simulink to
perform frequency
domain analysis
for at least a
1DOF system.
(0 Marks) (7 Marks) (10.5 Marks) (14 Marks)
Evidence: (use
hyperlinks
bookmarks to
create
to evidence)
27
30
27
1.4 Time Domain Inability to use
Simulink to model
and analyse a
1DOF system in
the time domain.
Demonstrated use
of Simulink to
model AND
analyse a 1DOF
system in the time
domain.
Demonstrated use
of Simulink to
model AND
analyse a 2DOF
system in the time
domain.
Demonstrated use
of Simulink to
model AND
analyse a 3DOF or
higher system in
the time domain.
(0 Marks) (7 Marks) (11 Marks) (15 Marks)
Evidence: (use
hyperlinks
bookmarks to
create
to evidence)
27
LO2. EXPLAIN AND APPLY CONTROL THEORY AND CONTROL SYSTEM APPROACHES TO
MECHANICAL SYSTEMS (28 MARKS)
Criteria Unacceptable Acceptable Good Excellent
2.1 PID
Controller
Inability to
construct a valid
feedback loop
controller and
model in
Simulink.
Demonstrate the
ability to
correctly apply
AND construct a
feedback loop
controller and
model in
Simulink.
Demonstrate the
ability to
correctly apply
AND construct a
feedback loop
controller with
suitable
bandwidth and
stability.
Demonstrate the
ability to
correctly apply
AND construct a
feedback loop
controller with
excellent
bandwidth and
stability. AND to
handle non-
linear systems
and inputs.
(0 Marks) (9 Marks) (13.5 Marks) (18 Marks)
6
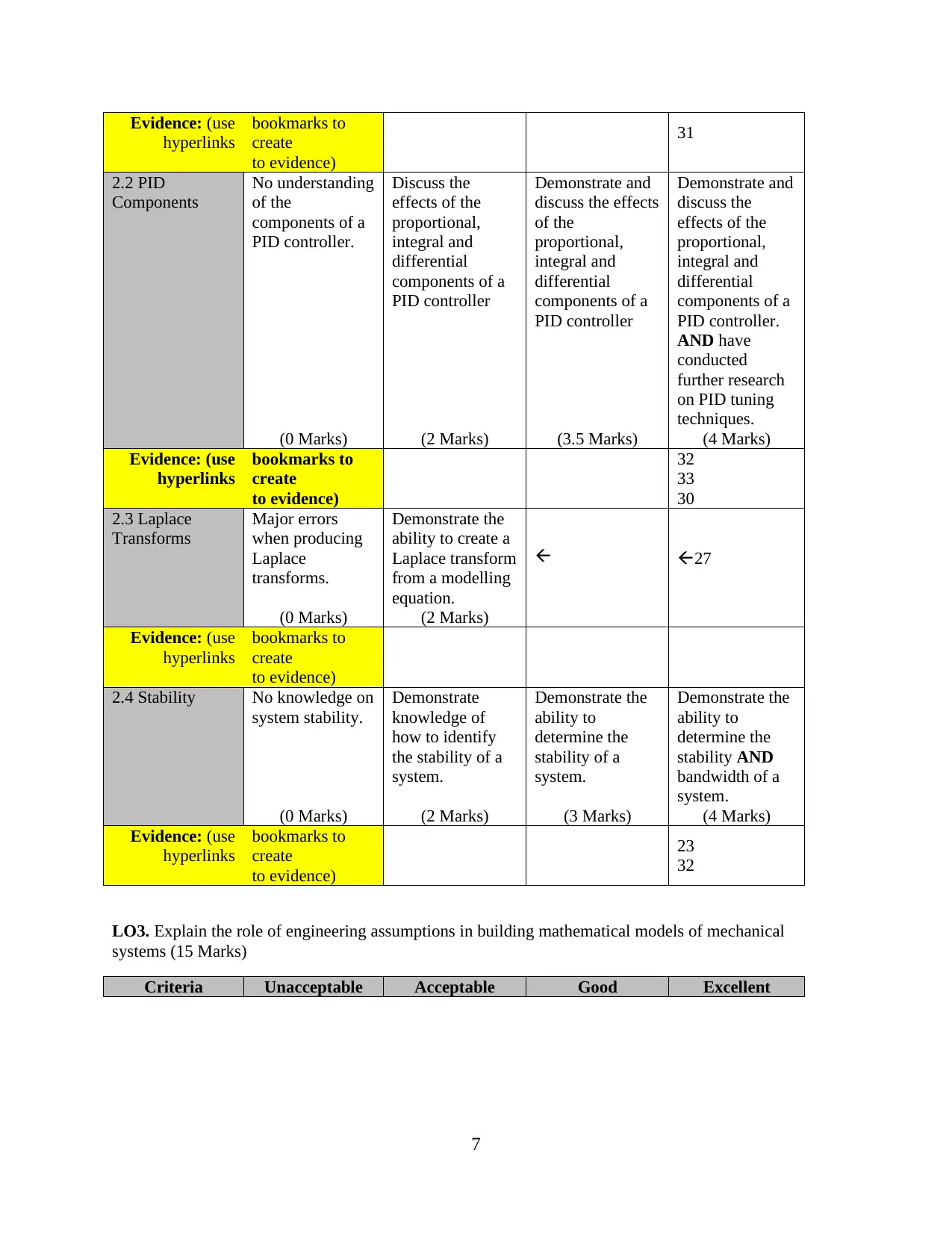
Evidence: (use
hyperlinks
bookmarks to
create
to evidence)
31
2.2 PID
Components
No understanding
of the
components of a
PID controller.
Discuss the
effects of the
proportional,
integral and
differential
components of a
PID controller
Demonstrate and
discuss the effects
of the
proportional,
integral and
differential
components of a
PID controller
Demonstrate and
discuss the
effects of the
proportional,
integral and
differential
components of a
PID controller.
AND have
conducted
further research
on PID tuning
techniques.
(0 Marks) (2 Marks) (3.5 Marks) (4 Marks)
Evidence: (use
hyperlinks
bookmarks to
create
to evidence)
32
33
30
2.3 Laplace
Transforms
Major errors
when producing
Laplace
transforms.
Demonstrate the
ability to create a
Laplace transform
from a modelling
equation.
27
(0 Marks) (2 Marks)
Evidence: (use
hyperlinks
bookmarks to
create
to evidence)
2.4 Stability No knowledge on
system stability.
Demonstrate
knowledge of
how to identify
the stability of a
system.
Demonstrate the
ability to
determine the
stability of a
system.
Demonstrate the
ability to
determine the
stability AND
bandwidth of a
system.
(0 Marks) (2 Marks) (3 Marks) (4 Marks)
Evidence: (use
hyperlinks
bookmarks to
create
to evidence)
23
32
LO3. Explain the role of engineering assumptions in building mathematical models of mechanical
systems (15 Marks)
Criteria Unacceptable Acceptable Good Excellent
7
hyperlinks
bookmarks to
create
to evidence)
31
2.2 PID
Components
No understanding
of the
components of a
PID controller.
Discuss the
effects of the
proportional,
integral and
differential
components of a
PID controller
Demonstrate and
discuss the effects
of the
proportional,
integral and
differential
components of a
PID controller
Demonstrate and
discuss the
effects of the
proportional,
integral and
differential
components of a
PID controller.
AND have
conducted
further research
on PID tuning
techniques.
(0 Marks) (2 Marks) (3.5 Marks) (4 Marks)
Evidence: (use
hyperlinks
bookmarks to
create
to evidence)
32
33
30
2.3 Laplace
Transforms
Major errors
when producing
Laplace
transforms.
Demonstrate the
ability to create a
Laplace transform
from a modelling
equation.
27
(0 Marks) (2 Marks)
Evidence: (use
hyperlinks
bookmarks to
create
to evidence)
2.4 Stability No knowledge on
system stability.
Demonstrate
knowledge of
how to identify
the stability of a
system.
Demonstrate the
ability to
determine the
stability of a
system.
Demonstrate the
ability to
determine the
stability AND
bandwidth of a
system.
(0 Marks) (2 Marks) (3 Marks) (4 Marks)
Evidence: (use
hyperlinks
bookmarks to
create
to evidence)
23
32
LO3. Explain the role of engineering assumptions in building mathematical models of mechanical
systems (15 Marks)
Criteria Unacceptable Acceptable Good Excellent
7
Paraphrase This Document
Need a fresh take? Get an instant paraphrase of this document with our AI Paraphraser
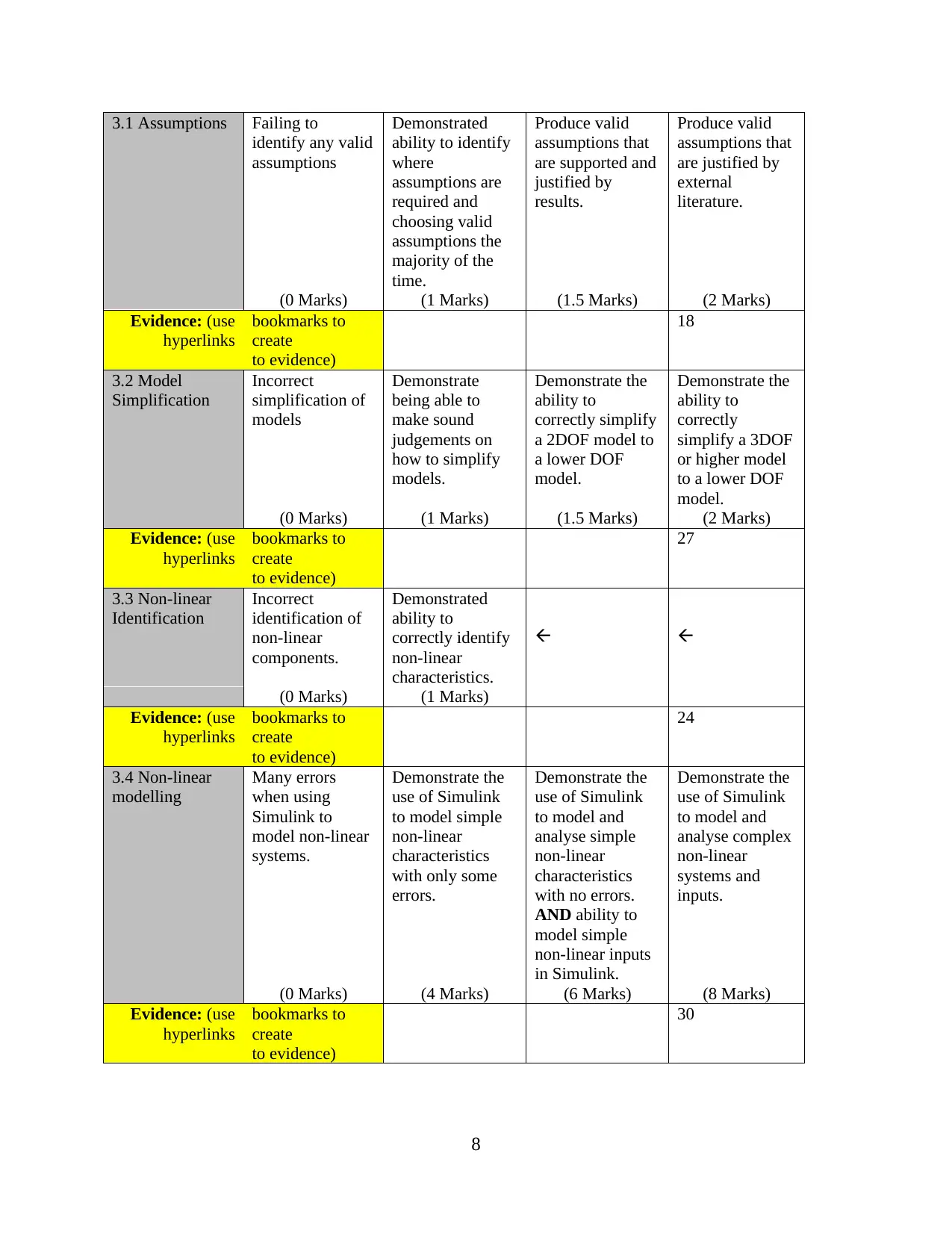
3.1 Assumptions Failing to
identify any valid
assumptions
Demonstrated
ability to identify
where
assumptions are
required and
choosing valid
assumptions the
majority of the
time.
Produce valid
assumptions that
are supported and
justified by
results.
Produce valid
assumptions that
are justified by
external
literature.
(0 Marks) (1 Marks) (1.5 Marks) (2 Marks)
Evidence: (use
hyperlinks
bookmarks to
create
to evidence)
18
3.2 Model
Simplification
Incorrect
simplification of
models
Demonstrate
being able to
make sound
judgements on
how to simplify
models.
Demonstrate the
ability to
correctly simplify
a 2DOF model to
a lower DOF
model.
Demonstrate the
ability to
correctly
simplify a 3DOF
or higher model
to a lower DOF
model.
(0 Marks) (1 Marks) (1.5 Marks) (2 Marks)
Evidence: (use
hyperlinks
bookmarks to
create
to evidence)
27
3.3 Non-linear
Identification
Incorrect
identification of
non-linear
components.
Demonstrated
ability to
correctly identify
non-linear
characteristics.
(0 Marks) (1 Marks)
Evidence: (use
hyperlinks
bookmarks to
create
to evidence)
24
3.4 Non-linear
modelling
Many errors
when using
Simulink to
model non-linear
systems.
Demonstrate the
use of Simulink
to model simple
non-linear
characteristics
with only some
errors.
Demonstrate the
use of Simulink
to model and
analyse simple
non-linear
characteristics
with no errors.
AND ability to
model simple
non-linear inputs
in Simulink.
Demonstrate the
use of Simulink
to model and
analyse complex
non-linear
systems and
inputs.
(0 Marks) (4 Marks) (6 Marks) (8 Marks)
Evidence: (use
hyperlinks
bookmarks to
create
to evidence)
30
8
identify any valid
assumptions
Demonstrated
ability to identify
where
assumptions are
required and
choosing valid
assumptions the
majority of the
time.
Produce valid
assumptions that
are supported and
justified by
results.
Produce valid
assumptions that
are justified by
external
literature.
(0 Marks) (1 Marks) (1.5 Marks) (2 Marks)
Evidence: (use
hyperlinks
bookmarks to
create
to evidence)
18
3.2 Model
Simplification
Incorrect
simplification of
models
Demonstrate
being able to
make sound
judgements on
how to simplify
models.
Demonstrate the
ability to
correctly simplify
a 2DOF model to
a lower DOF
model.
Demonstrate the
ability to
correctly
simplify a 3DOF
or higher model
to a lower DOF
model.
(0 Marks) (1 Marks) (1.5 Marks) (2 Marks)
Evidence: (use
hyperlinks
bookmarks to
create
to evidence)
27
3.3 Non-linear
Identification
Incorrect
identification of
non-linear
components.
Demonstrated
ability to
correctly identify
non-linear
characteristics.
(0 Marks) (1 Marks)
Evidence: (use
hyperlinks
bookmarks to
create
to evidence)
24
3.4 Non-linear
modelling
Many errors
when using
Simulink to
model non-linear
systems.
Demonstrate the
use of Simulink
to model simple
non-linear
characteristics
with only some
errors.
Demonstrate the
use of Simulink
to model and
analyse simple
non-linear
characteristics
with no errors.
AND ability to
model simple
non-linear inputs
in Simulink.
Demonstrate the
use of Simulink
to model and
analyse complex
non-linear
systems and
inputs.
(0 Marks) (4 Marks) (6 Marks) (8 Marks)
Evidence: (use
hyperlinks
bookmarks to
create
to evidence)
30
8
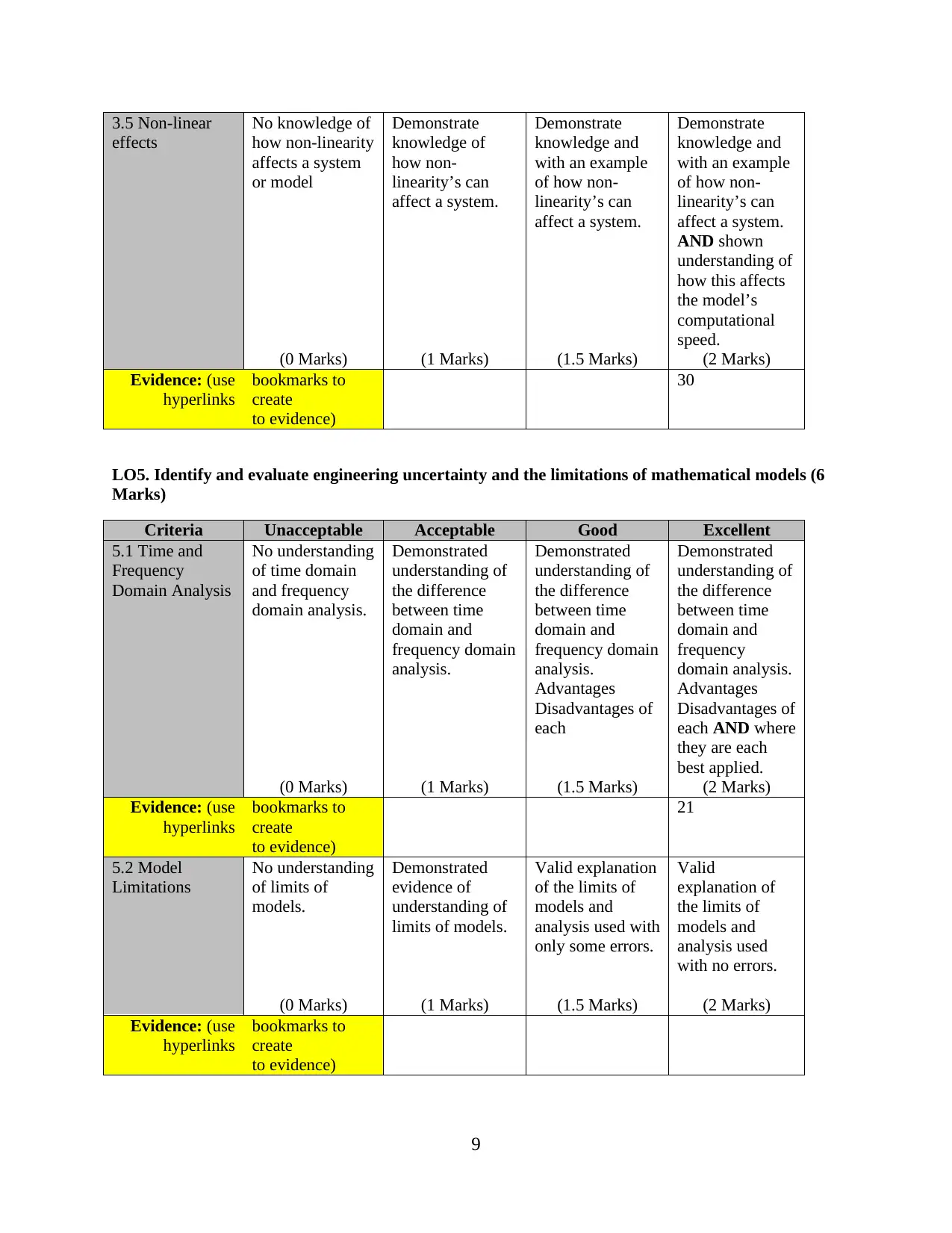
3.5 Non-linear
effects
No knowledge of
how non-linearity
affects a system
or model
Demonstrate
knowledge of
how non-
linearity’s can
affect a system.
Demonstrate
knowledge and
with an example
of how non-
linearity’s can
affect a system.
Demonstrate
knowledge and
with an example
of how non-
linearity’s can
affect a system.
AND shown
understanding of
how this affects
the model’s
computational
speed.
(0 Marks) (1 Marks) (1.5 Marks) (2 Marks)
Evidence: (use
hyperlinks
bookmarks to
create
to evidence)
30
LO5. Identify and evaluate engineering uncertainty and the limitations of mathematical models (6
Marks)
Criteria Unacceptable Acceptable Good Excellent
5.1 Time and
Frequency
Domain Analysis
No understanding
of time domain
and frequency
domain analysis.
Demonstrated
understanding of
the difference
between time
domain and
frequency domain
analysis.
Demonstrated
understanding of
the difference
between time
domain and
frequency domain
analysis.
Advantages
Disadvantages of
each
Demonstrated
understanding of
the difference
between time
domain and
frequency
domain analysis.
Advantages
Disadvantages of
each AND where
they are each
best applied.
(0 Marks) (1 Marks) (1.5 Marks) (2 Marks)
Evidence: (use
hyperlinks
bookmarks to
create
to evidence)
21
5.2 Model
Limitations
No understanding
of limits of
models.
Demonstrated
evidence of
understanding of
limits of models.
Valid explanation
of the limits of
models and
analysis used with
only some errors.
Valid
explanation of
the limits of
models and
analysis used
with no errors.
(0 Marks) (1 Marks) (1.5 Marks) (2 Marks)
Evidence: (use
hyperlinks
bookmarks to
create
to evidence)
9
effects
No knowledge of
how non-linearity
affects a system
or model
Demonstrate
knowledge of
how non-
linearity’s can
affect a system.
Demonstrate
knowledge and
with an example
of how non-
linearity’s can
affect a system.
Demonstrate
knowledge and
with an example
of how non-
linearity’s can
affect a system.
AND shown
understanding of
how this affects
the model’s
computational
speed.
(0 Marks) (1 Marks) (1.5 Marks) (2 Marks)
Evidence: (use
hyperlinks
bookmarks to
create
to evidence)
30
LO5. Identify and evaluate engineering uncertainty and the limitations of mathematical models (6
Marks)
Criteria Unacceptable Acceptable Good Excellent
5.1 Time and
Frequency
Domain Analysis
No understanding
of time domain
and frequency
domain analysis.
Demonstrated
understanding of
the difference
between time
domain and
frequency domain
analysis.
Demonstrated
understanding of
the difference
between time
domain and
frequency domain
analysis.
Advantages
Disadvantages of
each
Demonstrated
understanding of
the difference
between time
domain and
frequency
domain analysis.
Advantages
Disadvantages of
each AND where
they are each
best applied.
(0 Marks) (1 Marks) (1.5 Marks) (2 Marks)
Evidence: (use
hyperlinks
bookmarks to
create
to evidence)
21
5.2 Model
Limitations
No understanding
of limits of
models.
Demonstrated
evidence of
understanding of
limits of models.
Valid explanation
of the limits of
models and
analysis used with
only some errors.
Valid
explanation of
the limits of
models and
analysis used
with no errors.
(0 Marks) (1 Marks) (1.5 Marks) (2 Marks)
Evidence: (use
hyperlinks
bookmarks to
create
to evidence)
9
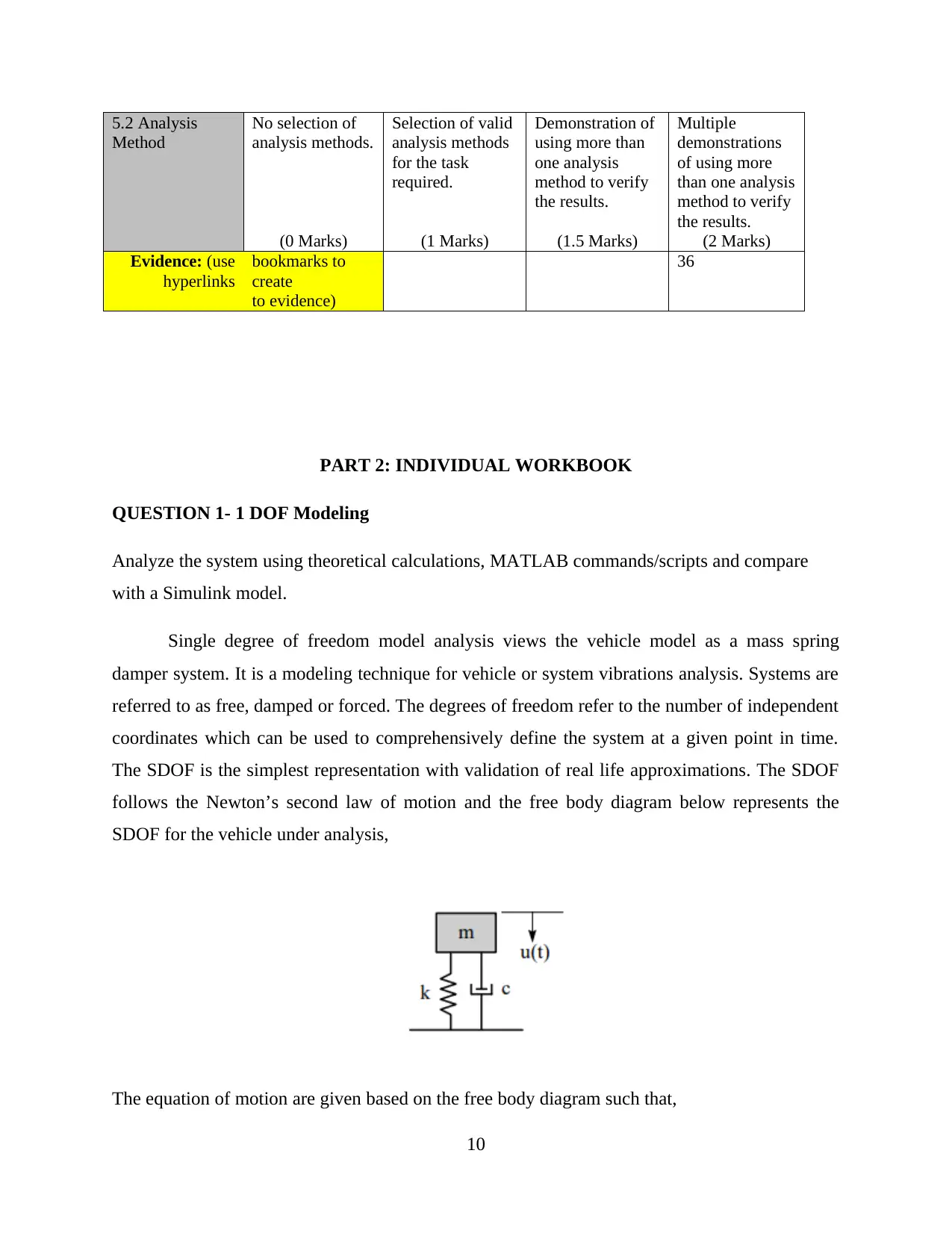
5.2 Analysis
Method
No selection of
analysis methods.
Selection of valid
analysis methods
for the task
required.
Demonstration of
using more than
one analysis
method to verify
the results.
Multiple
demonstrations
of using more
than one analysis
method to verify
the results.
(0 Marks) (1 Marks) (1.5 Marks) (2 Marks)
Evidence: (use
hyperlinks
bookmarks to
create
to evidence)
36
PART 2: INDIVIDUAL WORKBOOK
QUESTION 1- 1 DOF Modeling
Analyze the system using theoretical calculations, MATLAB commands/scripts and compare
with a Simulink model.
Single degree of freedom model analysis views the vehicle model as a mass spring
damper system. It is a modeling technique for vehicle or system vibrations analysis. Systems are
referred to as free, damped or forced. The degrees of freedom refer to the number of independent
coordinates which can be used to comprehensively define the system at a given point in time.
The SDOF is the simplest representation with validation of real life approximations. The SDOF
follows the Newton’s second law of motion and the free body diagram below represents the
SDOF for the vehicle under analysis,
The equation of motion are given based on the free body diagram such that,
10
Method
No selection of
analysis methods.
Selection of valid
analysis methods
for the task
required.
Demonstration of
using more than
one analysis
method to verify
the results.
Multiple
demonstrations
of using more
than one analysis
method to verify
the results.
(0 Marks) (1 Marks) (1.5 Marks) (2 Marks)
Evidence: (use
hyperlinks
bookmarks to
create
to evidence)
36
PART 2: INDIVIDUAL WORKBOOK
QUESTION 1- 1 DOF Modeling
Analyze the system using theoretical calculations, MATLAB commands/scripts and compare
with a Simulink model.
Single degree of freedom model analysis views the vehicle model as a mass spring
damper system. It is a modeling technique for vehicle or system vibrations analysis. Systems are
referred to as free, damped or forced. The degrees of freedom refer to the number of independent
coordinates which can be used to comprehensively define the system at a given point in time.
The SDOF is the simplest representation with validation of real life approximations. The SDOF
follows the Newton’s second law of motion and the free body diagram below represents the
SDOF for the vehicle under analysis,
The equation of motion are given based on the free body diagram such that,
10
Secure Best Marks with AI Grader
Need help grading? Try our AI Grader for instant feedback on your assignments.
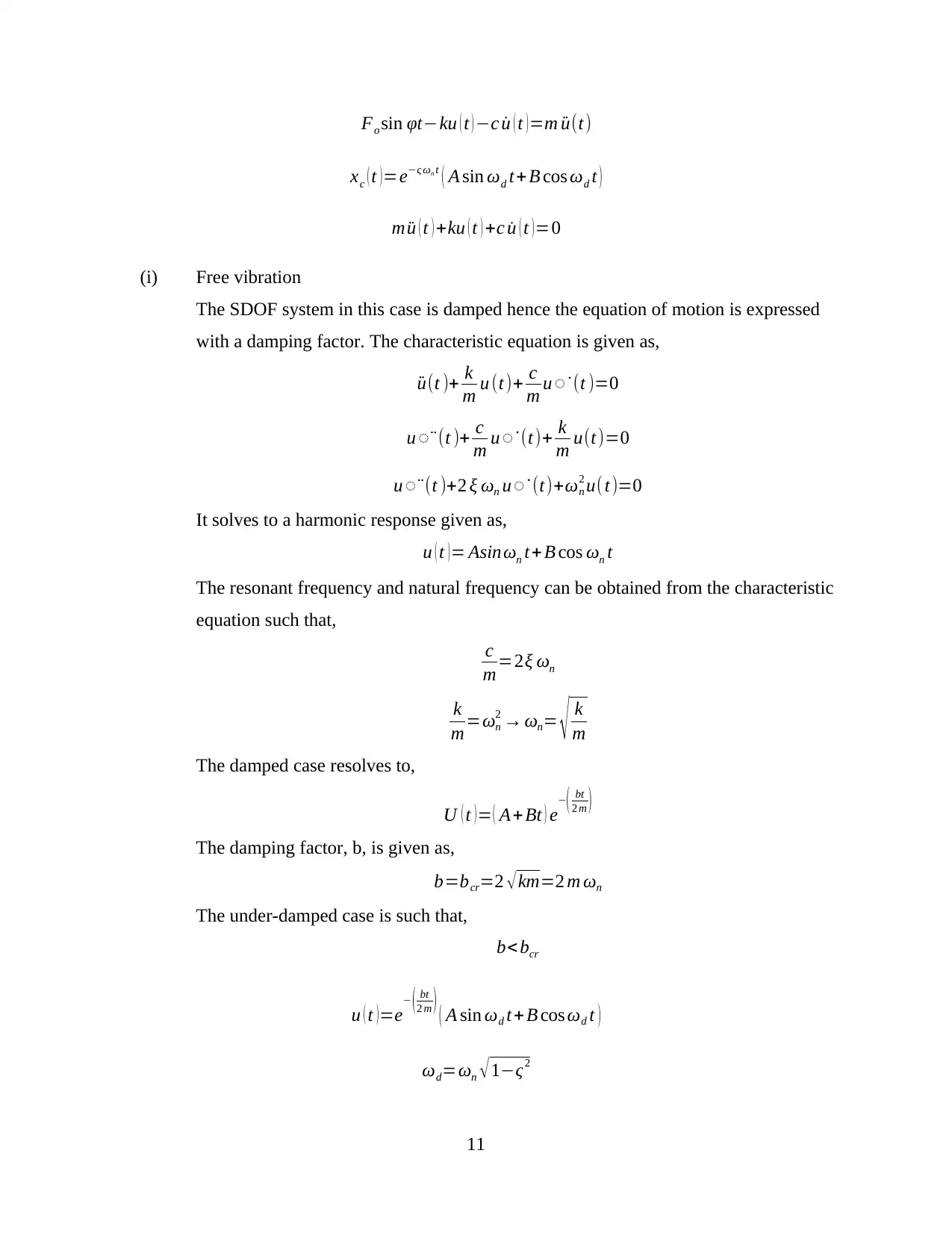
Fo sin φt−ku ( t ) −c ˙u ( t )=m ¨u(t)
xc ( t )=e−ς ωn t ( A sin ωd t+B cos ωd t )
m ¨u ( t ) +ku ( t ) +c ˙u ( t ) =0
(i) Free vibration
The SDOF system in this case is damped hence the equation of motion is expressed
with a damping factor. The characteristic equation is given as,
¨u(t )+ k
m u (t)+ c
m u̇ (t )=0
u̇ (t )+ c
m u̇ (t)+ k
m u(t)=0
u̇ (t )+2 ξ ωn u̇ (t)+ωn
2 u(t )=0
It solves to a harmonic response given as,
u ( t ) = Asin ωn t+ B cos ωn t
The resonant frequency and natural frequency can be obtained from the characteristic
equation such that,
c
m=2ξ ωn
k
m=ωn
2 → ωn= √ k
m
The damped case resolves to,
U ( t )= ( A+Bt ) e−( bt
2 m )
The damping factor, b, is given as,
b=bcr=2 √km=2 m ωn
The under-damped case is such that,
b< bcr
u ( t )=e− ( bt
2 m ) ( A sin ωd t +B cos ωd t )
ωd=ωn √ 1−ς2
11
xc ( t )=e−ς ωn t ( A sin ωd t+B cos ωd t )
m ¨u ( t ) +ku ( t ) +c ˙u ( t ) =0
(i) Free vibration
The SDOF system in this case is damped hence the equation of motion is expressed
with a damping factor. The characteristic equation is given as,
¨u(t )+ k
m u (t)+ c
m u̇ (t )=0
u̇ (t )+ c
m u̇ (t)+ k
m u(t)=0
u̇ (t )+2 ξ ωn u̇ (t)+ωn
2 u(t )=0
It solves to a harmonic response given as,
u ( t ) = Asin ωn t+ B cos ωn t
The resonant frequency and natural frequency can be obtained from the characteristic
equation such that,
c
m=2ξ ωn
k
m=ωn
2 → ωn= √ k
m
The damped case resolves to,
U ( t )= ( A+Bt ) e−( bt
2 m )
The damping factor, b, is given as,
b=bcr=2 √km=2 m ωn
The under-damped case is such that,
b< bcr
u ( t )=e− ( bt
2 m ) ( A sin ωd t +B cos ωd t )
ωd=ωn √ 1−ς2
11
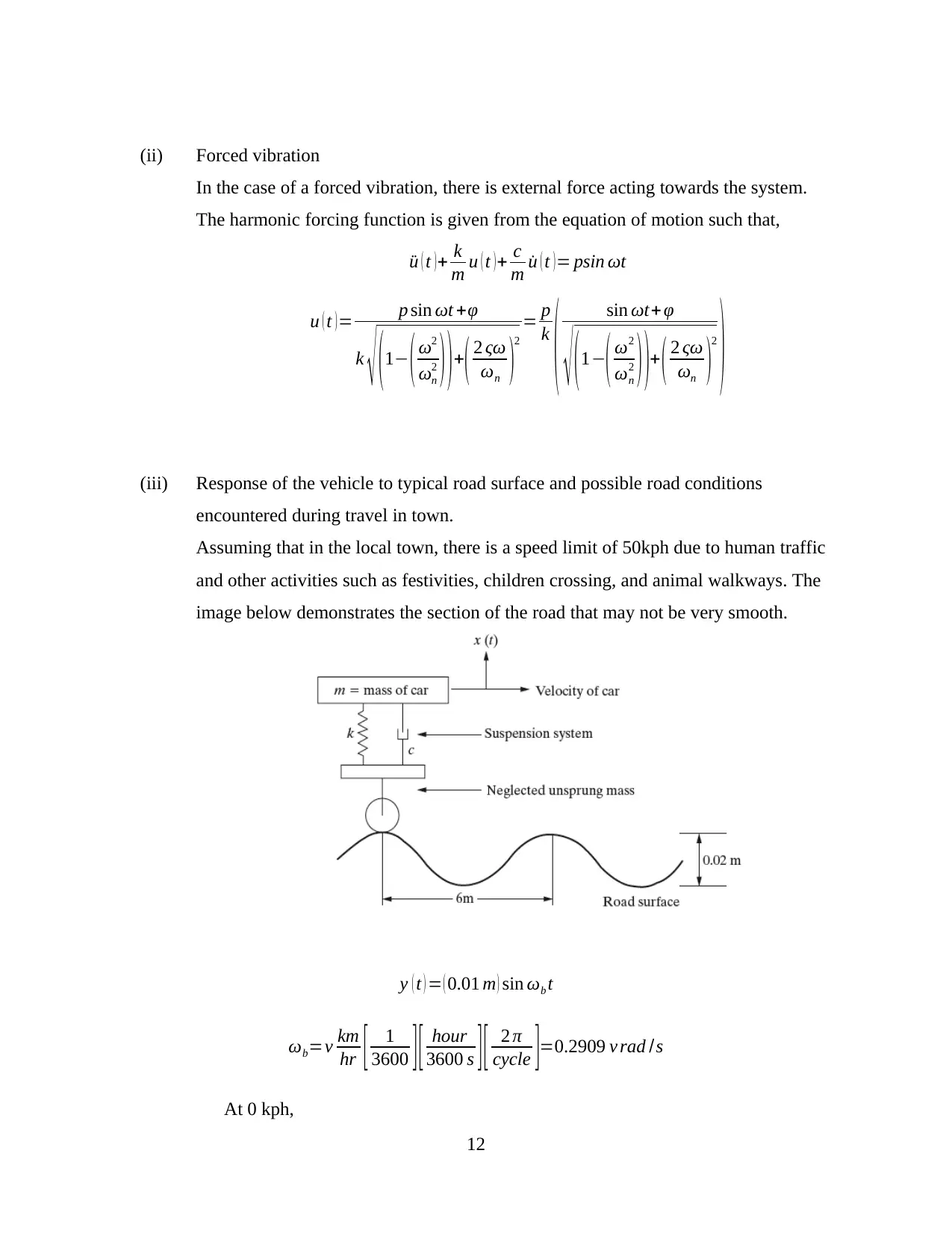
(ii) Forced vibration
In the case of a forced vibration, there is external force acting towards the system.
The harmonic forcing function is given from the equation of motion such that,
¨u ( t )+ k
m u ( t )+ c
m ˙u ( t )= psin ωt
u ( t ) = p sin ωt +φ
k
√ ( 1− ( ω2
ωn
2 ) ) +
( 2 ςω
ωn )
2
= p
k
( sin ωt+ φ
√ ( 1−
( ω2
ωn
2 ) )+ ( 2 ςω
ωn )
2
)
(iii) Response of the vehicle to typical road surface and possible road conditions
encountered during travel in town.
Assuming that in the local town, there is a speed limit of 50kph due to human traffic
and other activities such as festivities, children crossing, and animal walkways. The
image below demonstrates the section of the road that may not be very smooth.
y ( t ) = ( 0.01 m ) sin ωb t
ωb=v km
hr [ 1
3600 ][ hour
3600 s ][ 2 π
cycle ]=0.2909 v rad /s
At 0 kph,
12
In the case of a forced vibration, there is external force acting towards the system.
The harmonic forcing function is given from the equation of motion such that,
¨u ( t )+ k
m u ( t )+ c
m ˙u ( t )= psin ωt
u ( t ) = p sin ωt +φ
k
√ ( 1− ( ω2
ωn
2 ) ) +
( 2 ςω
ωn )
2
= p
k
( sin ωt+ φ
√ ( 1−
( ω2
ωn
2 ) )+ ( 2 ςω
ωn )
2
)
(iii) Response of the vehicle to typical road surface and possible road conditions
encountered during travel in town.
Assuming that in the local town, there is a speed limit of 50kph due to human traffic
and other activities such as festivities, children crossing, and animal walkways. The
image below demonstrates the section of the road that may not be very smooth.
y ( t ) = ( 0.01 m ) sin ωb t
ωb=v km
hr [ 1
3600 ][ hour
3600 s ][ 2 π
cycle ]=0.2909 v rad /s
At 0 kph,
12
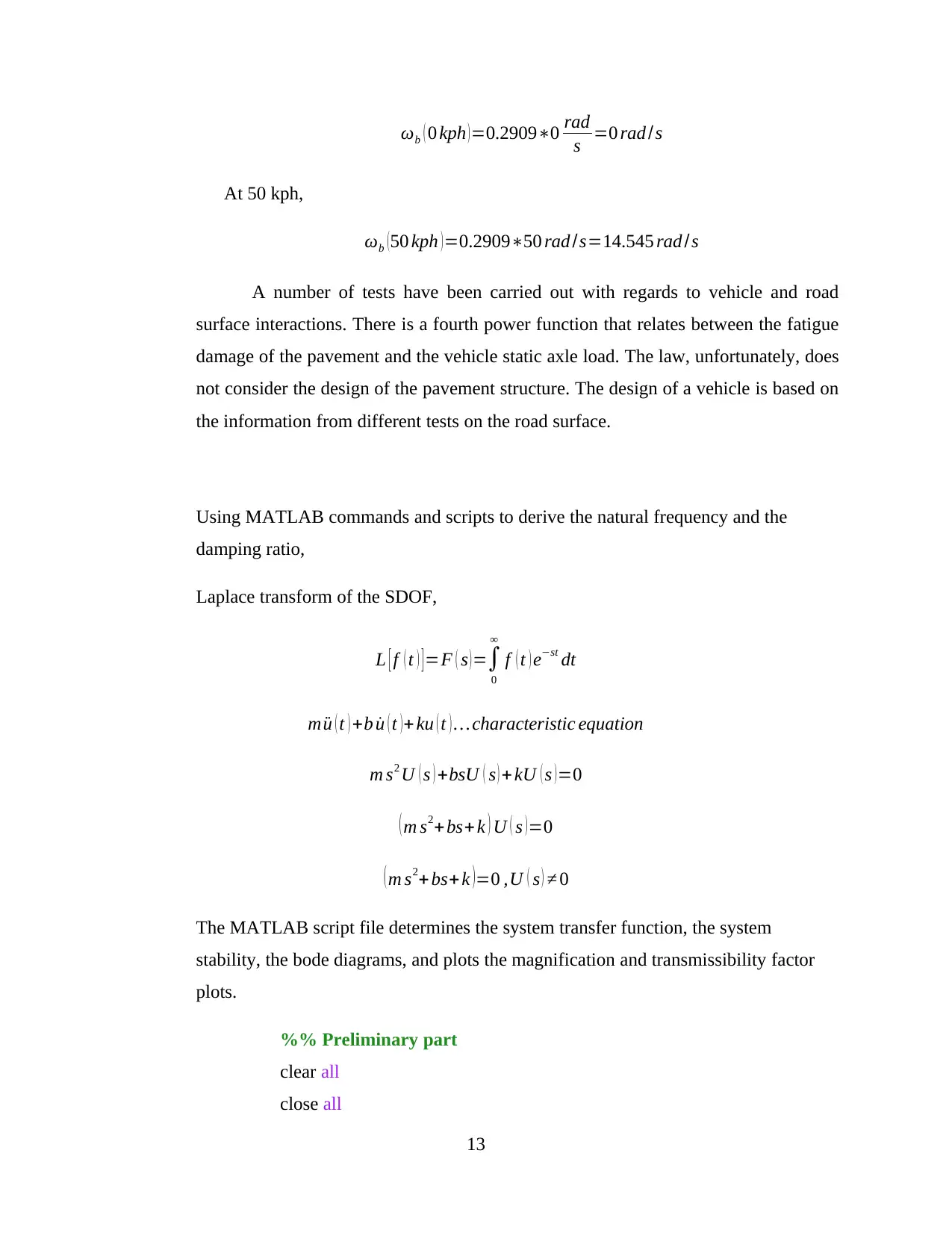
ωb ( 0 kph )=0.2909∗0 rad
s =0 rad /s
At 50 kph,
ωb ( 50 kph ) =0.2909∗50 rad /s=14.545 rad /s
A number of tests have been carried out with regards to vehicle and road
surface interactions. There is a fourth power function that relates between the fatigue
damage of the pavement and the vehicle static axle load. The law, unfortunately, does
not consider the design of the pavement structure. The design of a vehicle is based on
the information from different tests on the road surface.
Using MATLAB commands and scripts to derive the natural frequency and the
damping ratio,
Laplace transform of the SDOF,
L [ f ( t ) ]=F ( s )=∫
0
∞
f ( t ) e−st dt
m ¨u ( t ) +b ˙u ( t ) + ku ( t ) … characteristic equation
m s2 U ( s ) +bsU ( s ) + kU ( s ) =0
( m s2+bs+ k ) U ( s )=0
( m s2+ bs+ k )=0 ,U ( s ) ≠ 0
The MATLAB script file determines the system transfer function, the system
stability, the bode diagrams, and plots the magnification and transmissibility factor
plots.
%% Preliminary part
clear all
close all
13
s =0 rad /s
At 50 kph,
ωb ( 50 kph ) =0.2909∗50 rad /s=14.545 rad /s
A number of tests have been carried out with regards to vehicle and road
surface interactions. There is a fourth power function that relates between the fatigue
damage of the pavement and the vehicle static axle load. The law, unfortunately, does
not consider the design of the pavement structure. The design of a vehicle is based on
the information from different tests on the road surface.
Using MATLAB commands and scripts to derive the natural frequency and the
damping ratio,
Laplace transform of the SDOF,
L [ f ( t ) ]=F ( s )=∫
0
∞
f ( t ) e−st dt
m ¨u ( t ) +b ˙u ( t ) + ku ( t ) … characteristic equation
m s2 U ( s ) +bsU ( s ) + kU ( s ) =0
( m s2+bs+ k ) U ( s )=0
( m s2+ bs+ k )=0 ,U ( s ) ≠ 0
The MATLAB script file determines the system transfer function, the system
stability, the bode diagrams, and plots the magnification and transmissibility factor
plots.
%% Preliminary part
clear all
close all
13
Paraphrase This Document
Need a fresh take? Get an instant paraphrase of this document with our AI Paraphraser
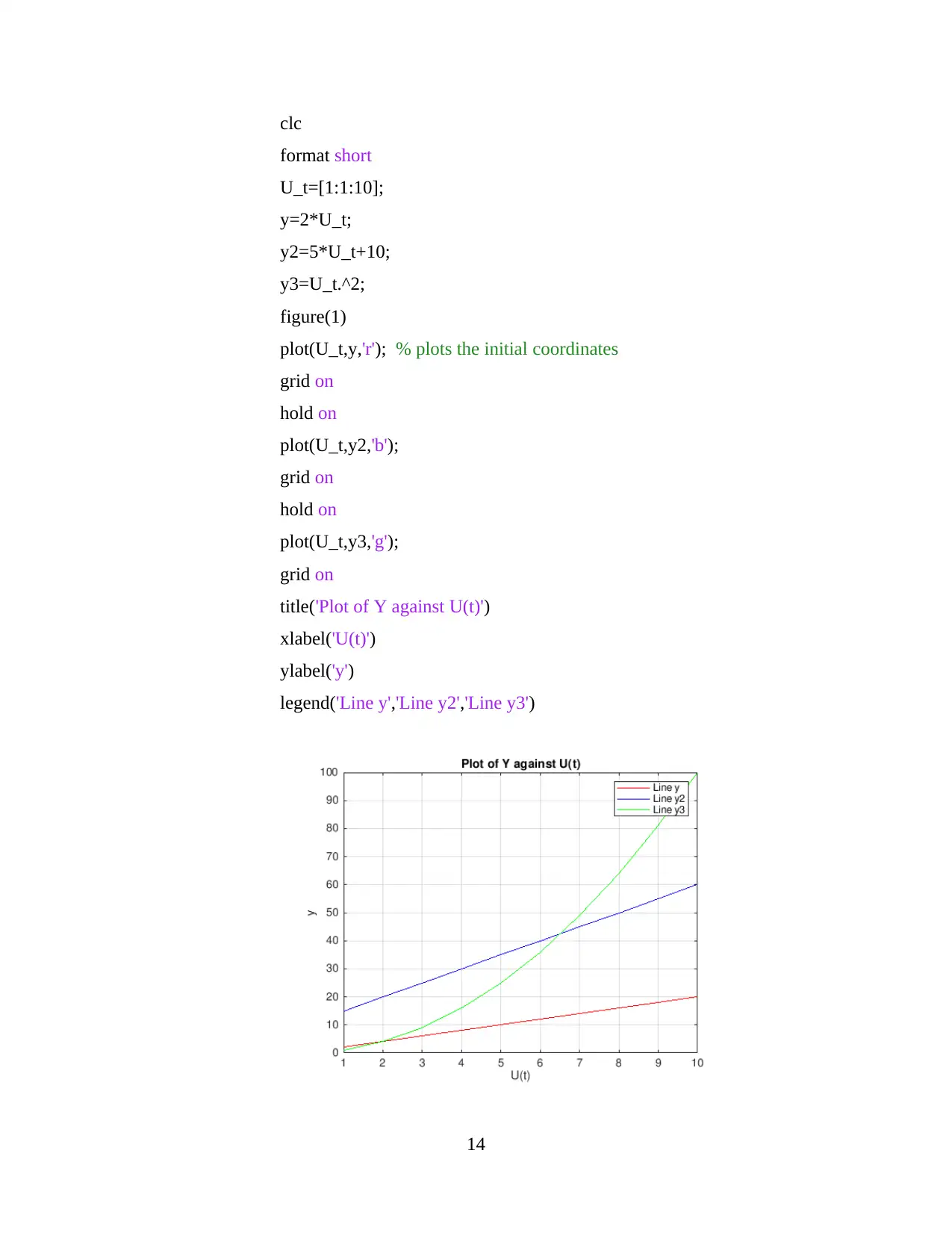
clc
format short
U_t=[1:1:10];
y=2*U_t;
y2=5*U_t+10;
y3=U_t.^2;
figure(1)
plot(U_t,y,'r'); % plots the initial coordinates
grid on
hold on
plot(U_t,y2,'b');
grid on
hold on
plot(U_t,y3,'g');
grid on
title('Plot of Y against U(t)')
xlabel('U(t)')
ylabel('y')
legend('Line y','Line y2','Line y3')
14
format short
U_t=[1:1:10];
y=2*U_t;
y2=5*U_t+10;
y3=U_t.^2;
figure(1)
plot(U_t,y,'r'); % plots the initial coordinates
grid on
hold on
plot(U_t,y2,'b');
grid on
hold on
plot(U_t,y3,'g');
grid on
title('Plot of Y against U(t)')
xlabel('U(t)')
ylabel('y')
legend('Line y','Line y2','Line y3')
14
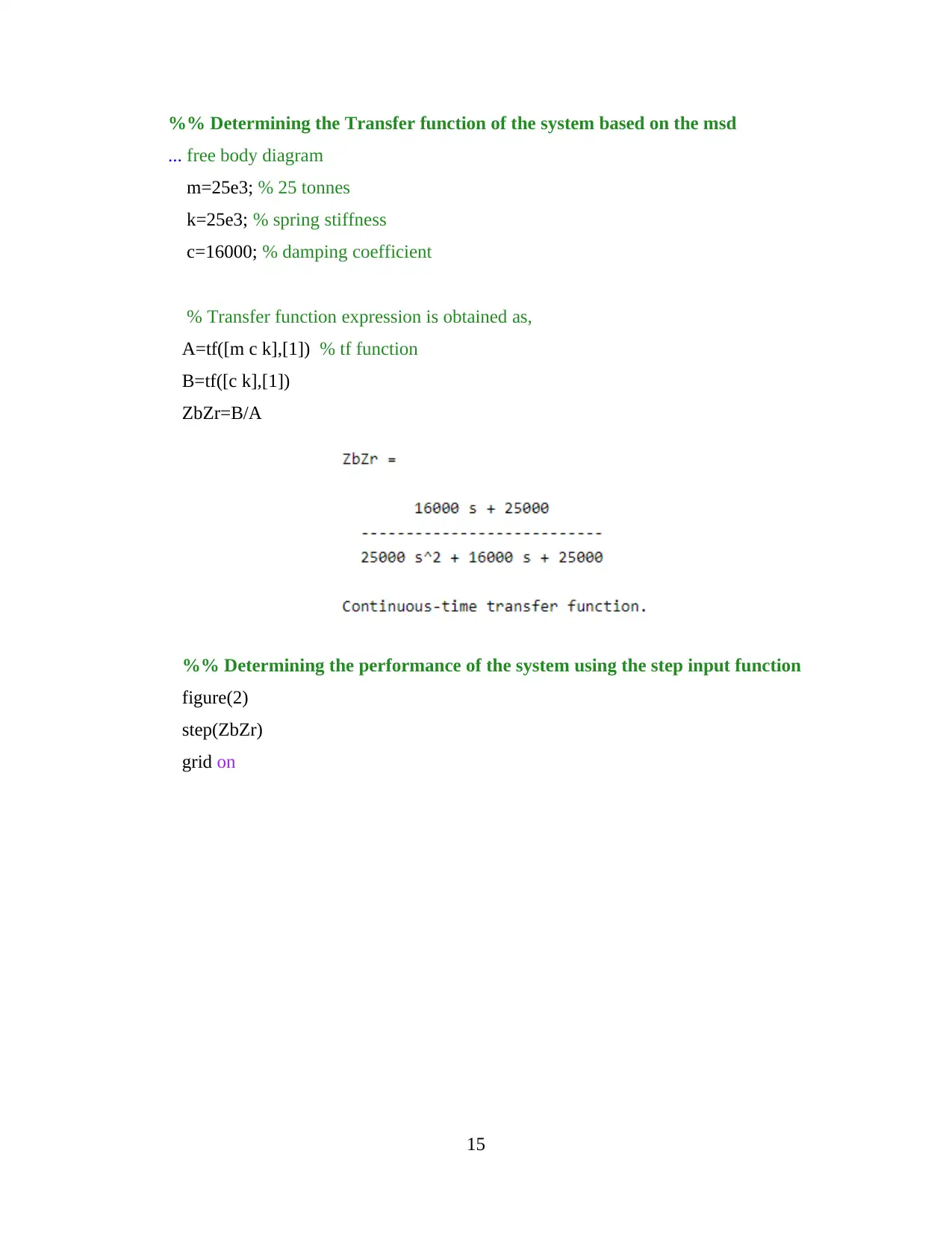
%% Determining the Transfer function of the system based on the msd
... free body diagram
m=25e3; % 25 tonnes
k=25e3; % spring stiffness
c=16000; % damping coefficient
% Transfer function expression is obtained as,
A=tf([m c k],[1]) % tf function
B=tf([c k],[1])
ZbZr=B/A
%% Determining the performance of the system using the step input function
figure(2)
step(ZbZr)
grid on
15
... free body diagram
m=25e3; % 25 tonnes
k=25e3; % spring stiffness
c=16000; % damping coefficient
% Transfer function expression is obtained as,
A=tf([m c k],[1]) % tf function
B=tf([c k],[1])
ZbZr=B/A
%% Determining the performance of the system using the step input function
figure(2)
step(ZbZr)
grid on
15
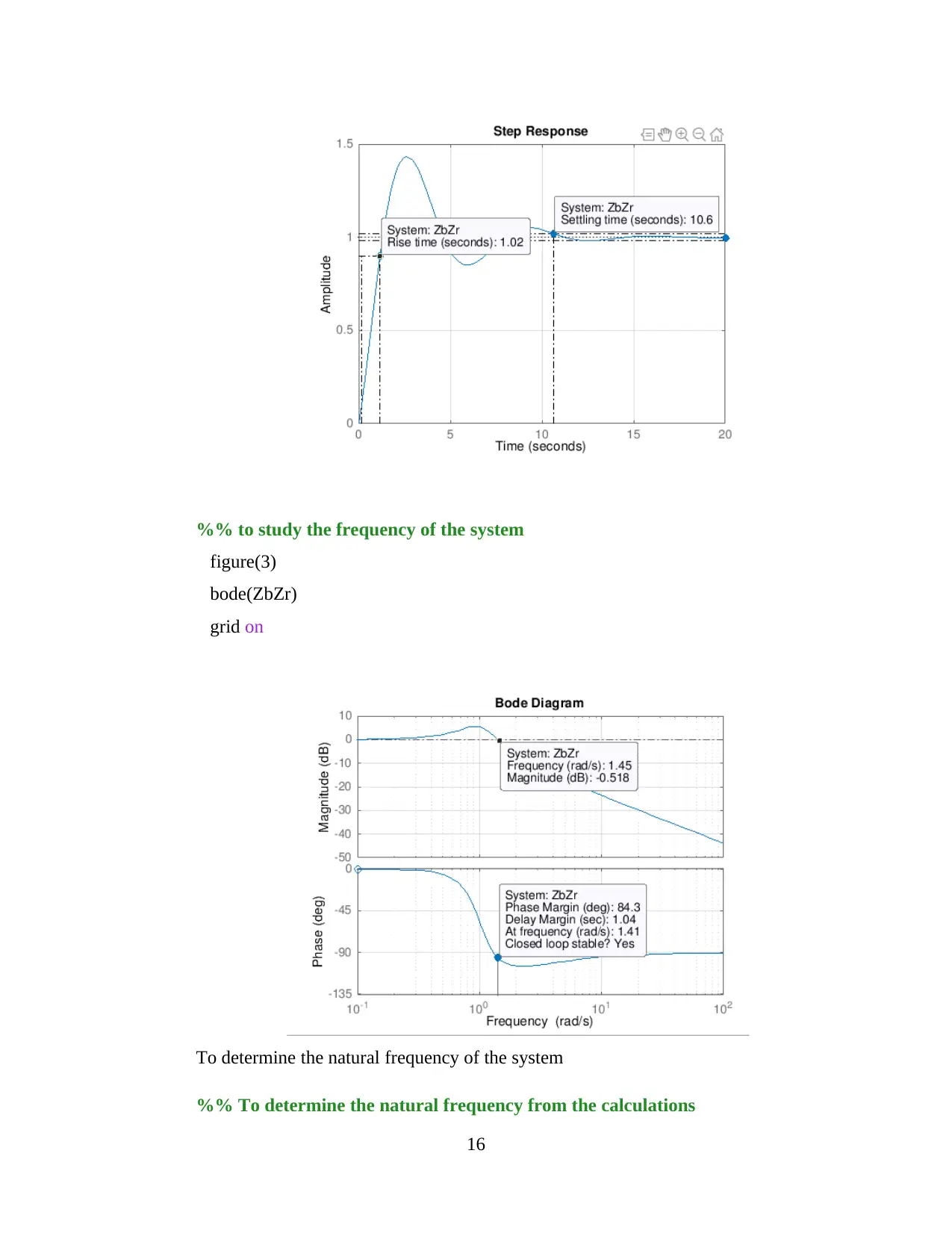
%% to study the frequency of the system
figure(3)
bode(ZbZr)
grid on
To determine the natural frequency of the system
%% To determine the natural frequency from the calculations
16
figure(3)
bode(ZbZr)
grid on
To determine the natural frequency of the system
%% To determine the natural frequency from the calculations
16
Secure Best Marks with AI Grader
Need help grading? Try our AI Grader for instant feedback on your assignments.
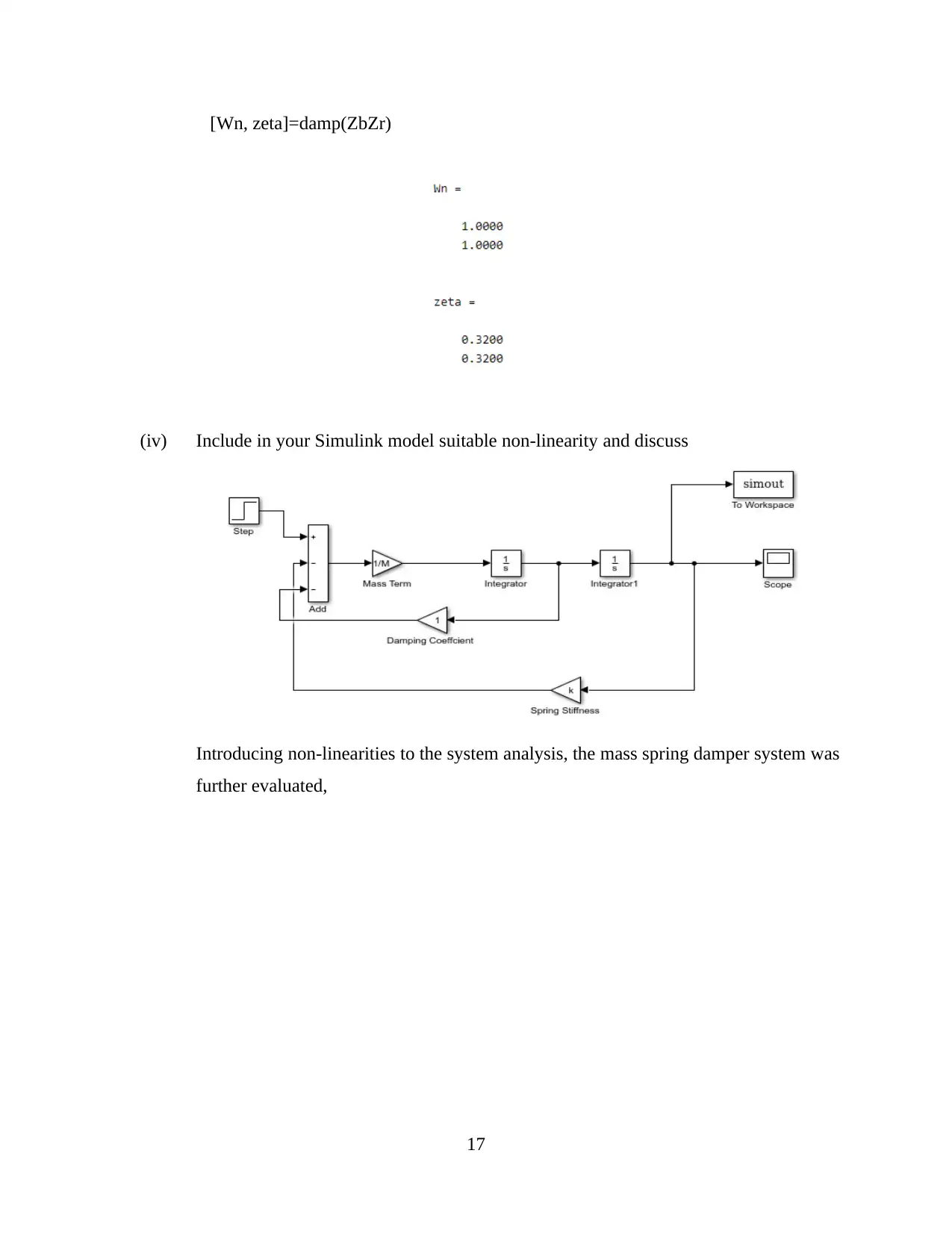
[Wn, zeta]=damp(ZbZr)
(iv) Include in your Simulink model suitable non-linearity and discuss
Introducing non-linearities to the system analysis, the mass spring damper system was
further evaluated,
17
(iv) Include in your Simulink model suitable non-linearity and discuss
Introducing non-linearities to the system analysis, the mass spring damper system was
further evaluated,
17
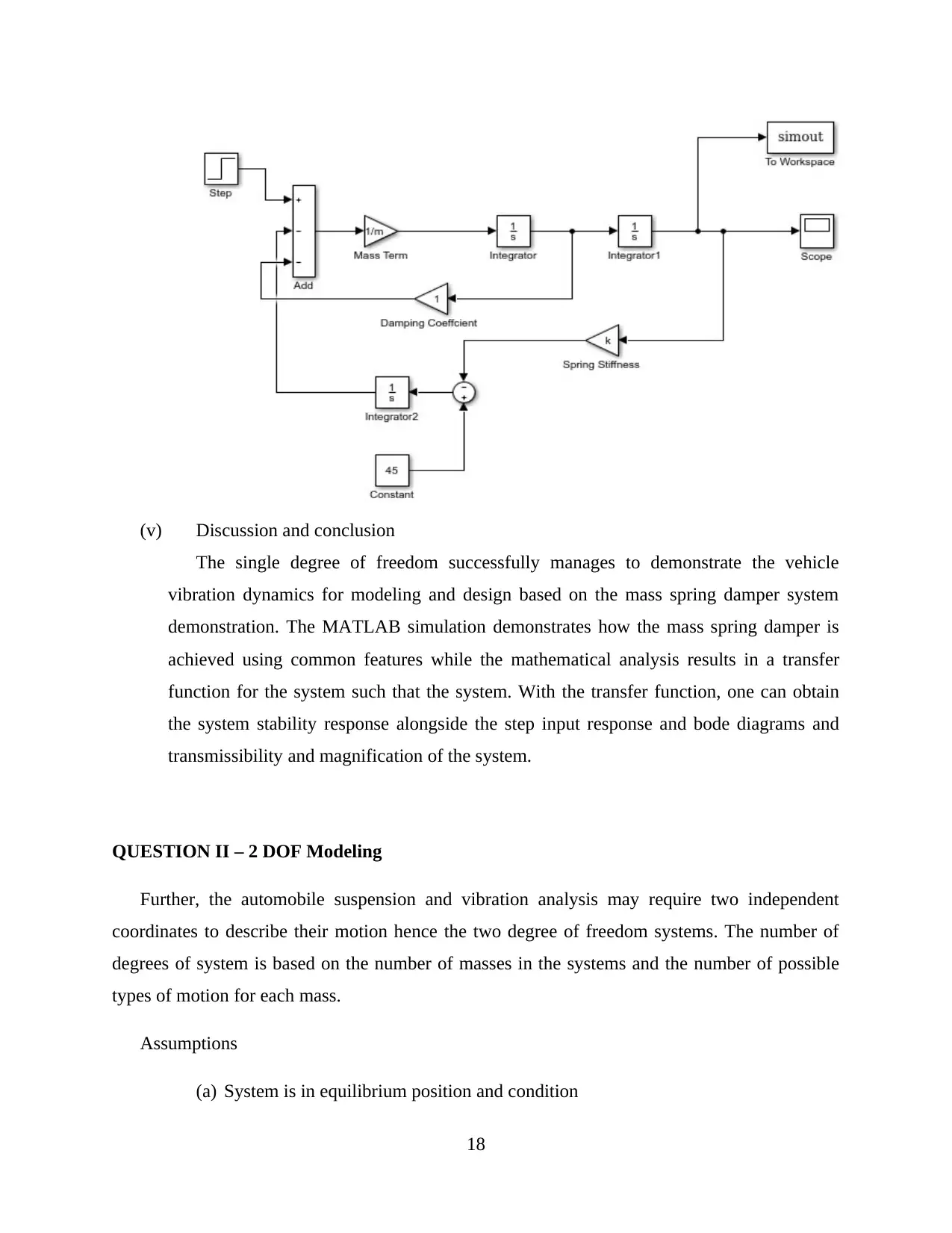
(v) Discussion and conclusion
The single degree of freedom successfully manages to demonstrate the vehicle
vibration dynamics for modeling and design based on the mass spring damper system
demonstration. The MATLAB simulation demonstrates how the mass spring damper is
achieved using common features while the mathematical analysis results in a transfer
function for the system such that the system. With the transfer function, one can obtain
the system stability response alongside the step input response and bode diagrams and
transmissibility and magnification of the system.
QUESTION II – 2 DOF Modeling
Further, the automobile suspension and vibration analysis may require two independent
coordinates to describe their motion hence the two degree of freedom systems. The number of
degrees of system is based on the number of masses in the systems and the number of possible
types of motion for each mass.
Assumptions
(a) System is in equilibrium position and condition
18
The single degree of freedom successfully manages to demonstrate the vehicle
vibration dynamics for modeling and design based on the mass spring damper system
demonstration. The MATLAB simulation demonstrates how the mass spring damper is
achieved using common features while the mathematical analysis results in a transfer
function for the system such that the system. With the transfer function, one can obtain
the system stability response alongside the step input response and bode diagrams and
transmissibility and magnification of the system.
QUESTION II – 2 DOF Modeling
Further, the automobile suspension and vibration analysis may require two independent
coordinates to describe their motion hence the two degree of freedom systems. The number of
degrees of system is based on the number of masses in the systems and the number of possible
types of motion for each mass.
Assumptions
(a) System is in equilibrium position and condition
18
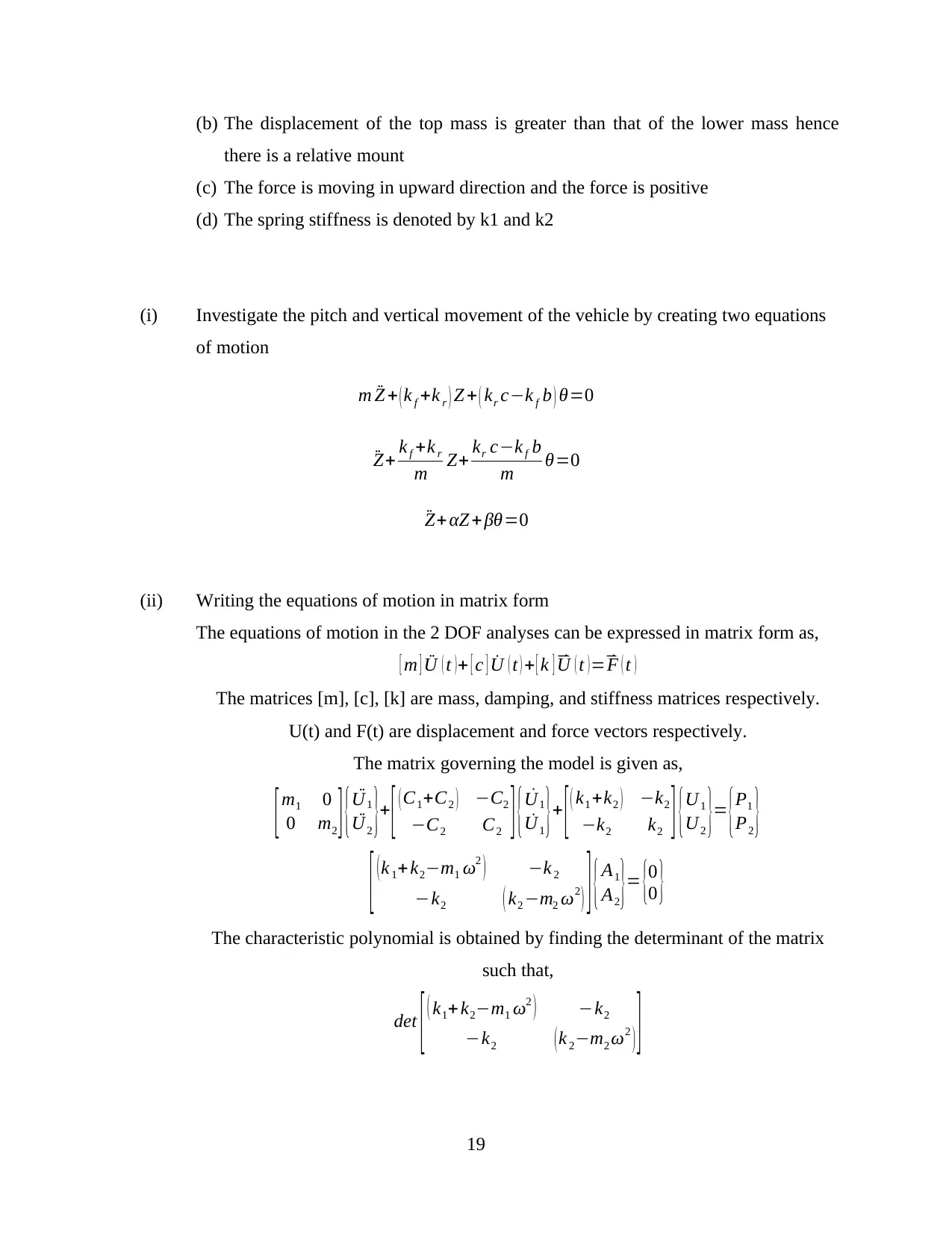
(b) The displacement of the top mass is greater than that of the lower mass hence
there is a relative mount
(c) The force is moving in upward direction and the force is positive
(d) The spring stiffness is denoted by k1 and k2
(i) Investigate the pitch and vertical movement of the vehicle by creating two equations
of motion
m ¨Z + ( k f +k r ) Z + ( kr c−k f b ) θ=0
¨Z+ k f +k r
m Z+ kr c−k f b
m θ=0
¨Z+ αZ +βθ=0
(ii) Writing the equations of motion in matrix form
The equations of motion in the 2 DOF analyses can be expressed in matrix form as,
[ m ] ¨U ( t )+ [ c ] ˙U ( t ) + [ k ]⃑ U ( t )=⃑ F ( t )
The matrices [m], [c], [k] are mass, damping, and stiffness matrices respectively.
U(t) and F(t) are displacement and force vectors respectively.
The matrix governing the model is given as,
[ m1 0
0 m2 ] { ¨U1
¨U2 }+ [ ( C1+C2 ) −C2
−C2 C2 ] { ˙U1
˙U1 }+ [ ( k1 +k2 ) −k2
−k2 k2 ] {U1
U2 }= {P1
P2 }
[ (k 1+ k2−m1 ω2 ) −k 2
−k2 ( k2 −m2 ω2
) ] {A1
A2 }= {0
0 }
The characteristic polynomial is obtained by finding the determinant of the matrix
such that,
det [ ( k1+ k2−m1 ω2 ) −k2
−k2 ( k 2−m2 ω2
) ]
19
there is a relative mount
(c) The force is moving in upward direction and the force is positive
(d) The spring stiffness is denoted by k1 and k2
(i) Investigate the pitch and vertical movement of the vehicle by creating two equations
of motion
m ¨Z + ( k f +k r ) Z + ( kr c−k f b ) θ=0
¨Z+ k f +k r
m Z+ kr c−k f b
m θ=0
¨Z+ αZ +βθ=0
(ii) Writing the equations of motion in matrix form
The equations of motion in the 2 DOF analyses can be expressed in matrix form as,
[ m ] ¨U ( t )+ [ c ] ˙U ( t ) + [ k ]⃑ U ( t )=⃑ F ( t )
The matrices [m], [c], [k] are mass, damping, and stiffness matrices respectively.
U(t) and F(t) are displacement and force vectors respectively.
The matrix governing the model is given as,
[ m1 0
0 m2 ] { ¨U1
¨U2 }+ [ ( C1+C2 ) −C2
−C2 C2 ] { ˙U1
˙U1 }+ [ ( k1 +k2 ) −k2
−k2 k2 ] {U1
U2 }= {P1
P2 }
[ (k 1+ k2−m1 ω2 ) −k 2
−k2 ( k2 −m2 ω2
) ] {A1
A2 }= {0
0 }
The characteristic polynomial is obtained by finding the determinant of the matrix
such that,
det [ ( k1+ k2−m1 ω2 ) −k2
−k2 ( k 2−m2 ω2
) ]
19
Paraphrase This Document
Need a fresh take? Get an instant paraphrase of this document with our AI Paraphraser
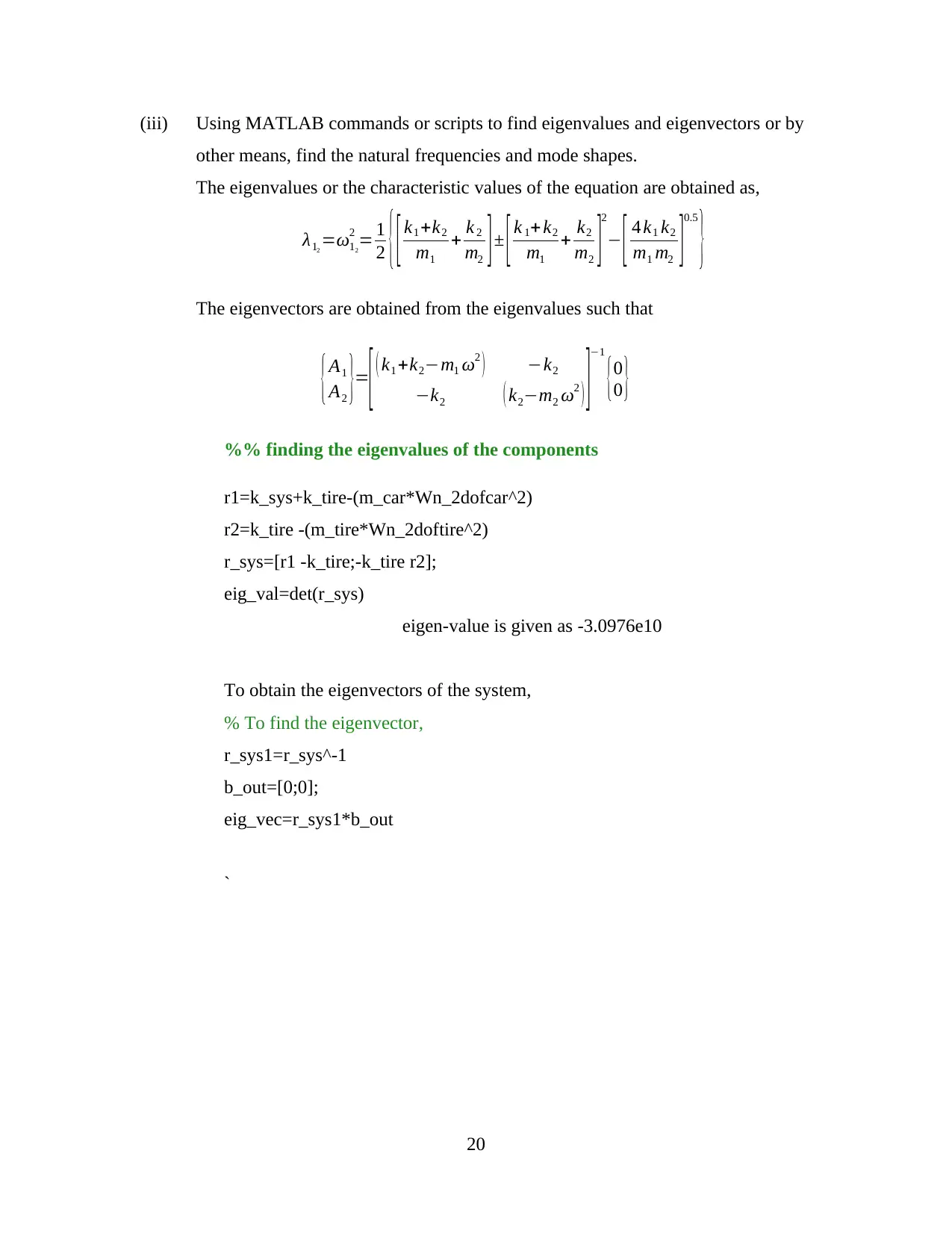
(iii) Using MATLAB commands or scripts to find eigenvalues and eigenvectors or by
other means, find the natural frequencies and mode shapes.
The eigenvalues or the characteristic values of the equation are obtained as,
λ12
=ω12
2 = 1
2 {[ k1 +k2
m1
+ k 2
m2 ]± [ k 1+ k2
m1
+ k2
m2 ]2
− [ 4 k1 k2
m1 m2 ]0.5
}
The eigenvectors are obtained from the eigenvalues such that
{ A1
A2 }=
[ ( k1 +k2−m1 ω2 ) −k2
−k2 ( k2−m2 ω2 ) ]
−1
{0
0 }
%% finding the eigenvalues of the components
r1=k_sys+k_tire-(m_car*Wn_2dofcar^2)
r2=k_tire -(m_tire*Wn_2doftire^2)
r_sys=[r1 -k_tire;-k_tire r2];
eig_val=det(r_sys)
eigen-value is given as -3.0976e10
To obtain the eigenvectors of the system,
% To find the eigenvector,
r_sys1=r_sys^-1
b_out=[0;0];
eig_vec=r_sys1*b_out
`
20
other means, find the natural frequencies and mode shapes.
The eigenvalues or the characteristic values of the equation are obtained as,
λ12
=ω12
2 = 1
2 {[ k1 +k2
m1
+ k 2
m2 ]± [ k 1+ k2
m1
+ k2
m2 ]2
− [ 4 k1 k2
m1 m2 ]0.5
}
The eigenvectors are obtained from the eigenvalues such that
{ A1
A2 }=
[ ( k1 +k2−m1 ω2 ) −k2
−k2 ( k2−m2 ω2 ) ]
−1
{0
0 }
%% finding the eigenvalues of the components
r1=k_sys+k_tire-(m_car*Wn_2dofcar^2)
r2=k_tire -(m_tire*Wn_2doftire^2)
r_sys=[r1 -k_tire;-k_tire r2];
eig_val=det(r_sys)
eigen-value is given as -3.0976e10
To obtain the eigenvectors of the system,
% To find the eigenvector,
r_sys1=r_sys^-1
b_out=[0;0];
eig_vec=r_sys1*b_out
`
20
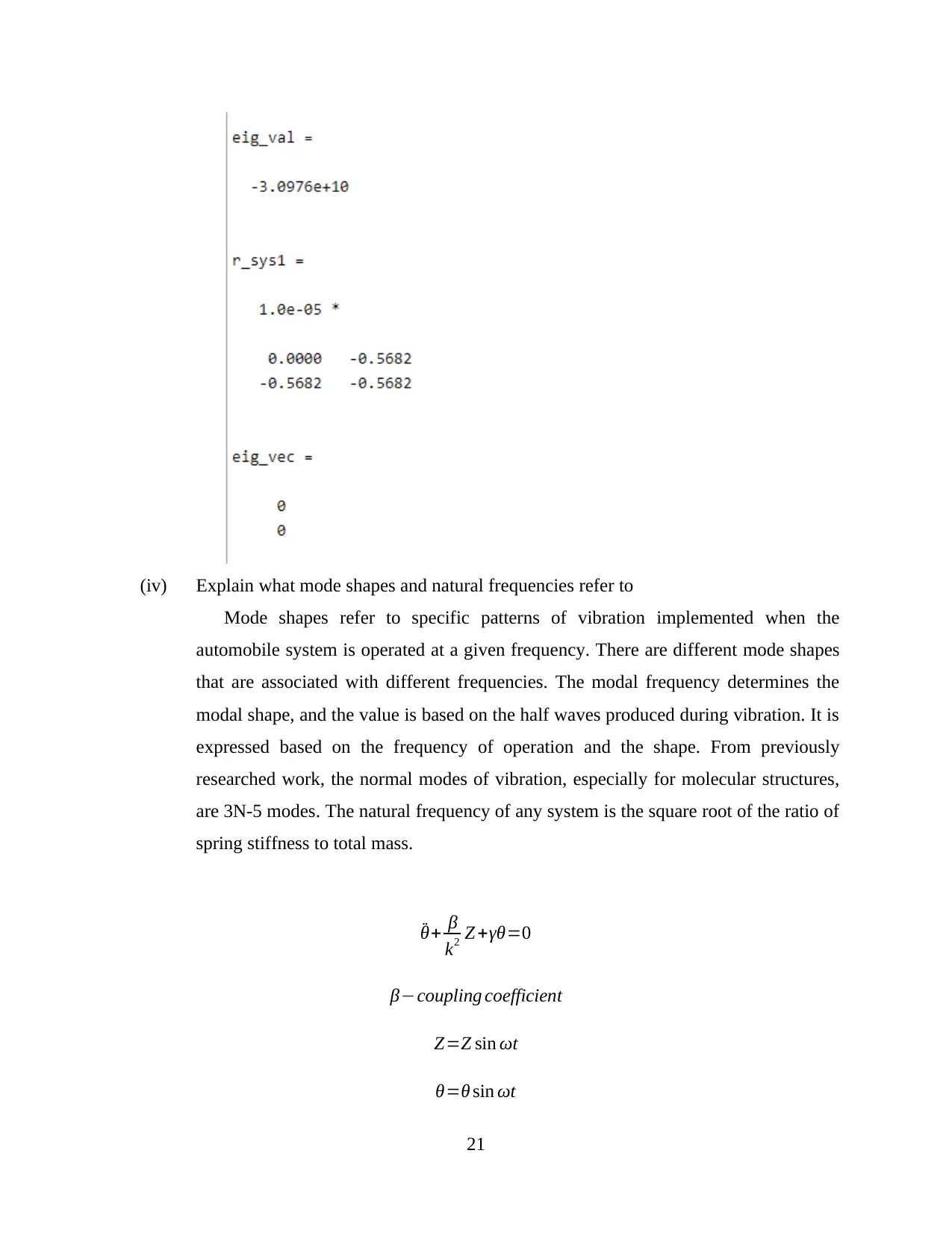
(iv) Explain what mode shapes and natural frequencies refer to
Mode shapes refer to specific patterns of vibration implemented when the
automobile system is operated at a given frequency. There are different mode shapes
that are associated with different frequencies. The modal frequency determines the
modal shape, and the value is based on the half waves produced during vibration. It is
expressed based on the frequency of operation and the shape. From previously
researched work, the normal modes of vibration, especially for molecular structures,
are 3N-5 modes. The natural frequency of any system is the square root of the ratio of
spring stiffness to total mass.
¨θ+ β
k2 Z +γθ=0
β−coupling coefficient
Z=Z sin ωt
θ=θ sin ωt
21
Mode shapes refer to specific patterns of vibration implemented when the
automobile system is operated at a given frequency. There are different mode shapes
that are associated with different frequencies. The modal frequency determines the
modal shape, and the value is based on the half waves produced during vibration. It is
expressed based on the frequency of operation and the shape. From previously
researched work, the normal modes of vibration, especially for molecular structures,
are 3N-5 modes. The natural frequency of any system is the square root of the ratio of
spring stiffness to total mass.
¨θ+ β
k2 Z +γθ=0
β−coupling coefficient
Z=Z sin ωt
θ=θ sin ωt
21
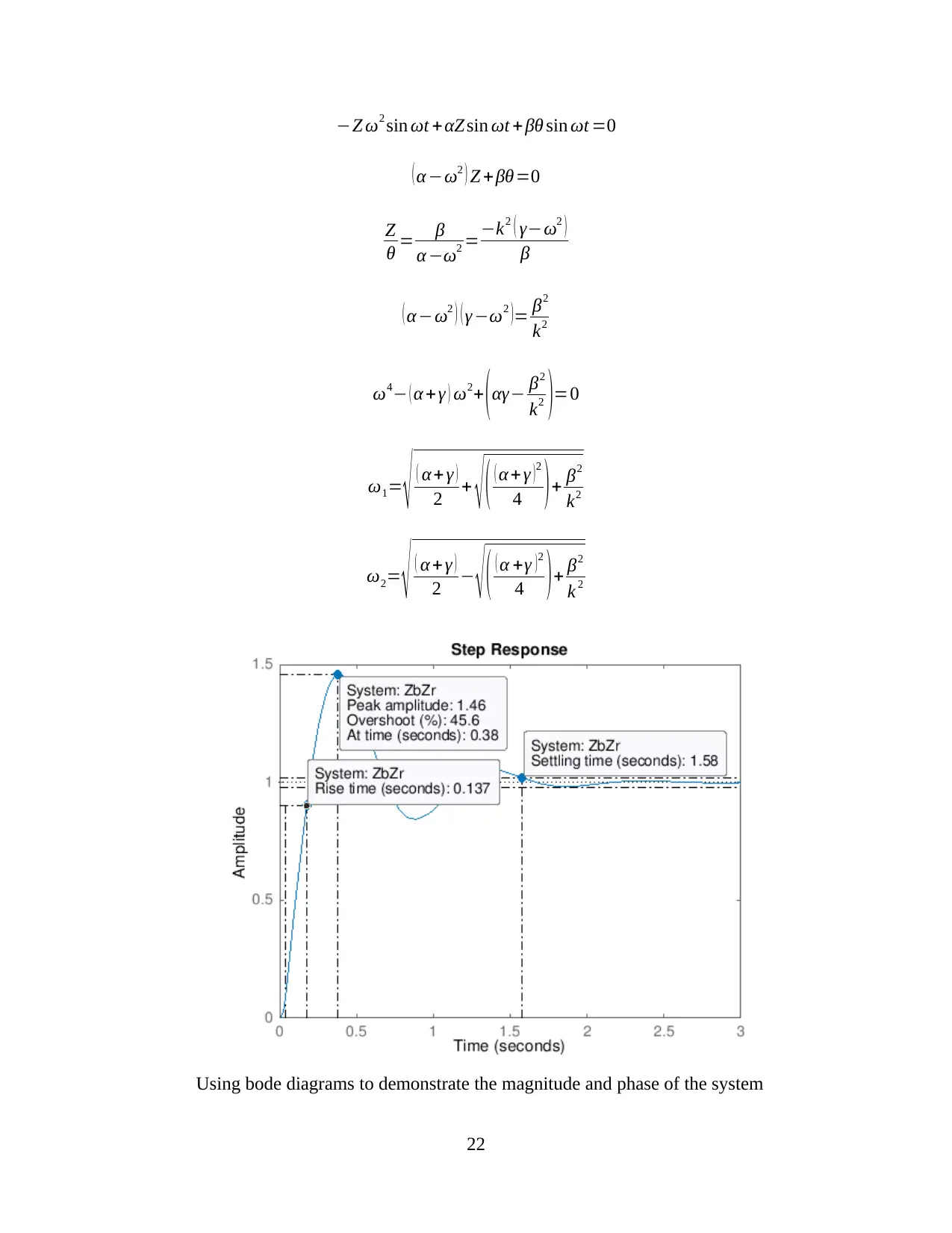
−Z ω2 sin ωt +αZ sin ωt + βθ sin ωt =0
( α−ω2 ) Z +βθ=0
Z
θ = β
α −ω2 =−k2 ( γ−ω2 )
β
( α −ω2 ) ( γ−ω2 )= β2
k2
ω4− ( α + γ ) ω2+ ( αγ− β2
k2 )=0
ω1= √ ( α+ γ )
2 + √ ( ( α + γ ) 2
4 ) + β2
k2
ω2= √ ( α + γ )
2 − √ ( ( α +γ )2
4 )+ β2
k 2
Using bode diagrams to demonstrate the magnitude and phase of the system
22
( α−ω2 ) Z +βθ=0
Z
θ = β
α −ω2 =−k2 ( γ−ω2 )
β
( α −ω2 ) ( γ−ω2 )= β2
k2
ω4− ( α + γ ) ω2+ ( αγ− β2
k2 )=0
ω1= √ ( α+ γ )
2 + √ ( ( α + γ ) 2
4 ) + β2
k2
ω2= √ ( α + γ )
2 − √ ( ( α +γ )2
4 )+ β2
k 2
Using bode diagrams to demonstrate the magnitude and phase of the system
22
Secure Best Marks with AI Grader
Need help grading? Try our AI Grader for instant feedback on your assignments.
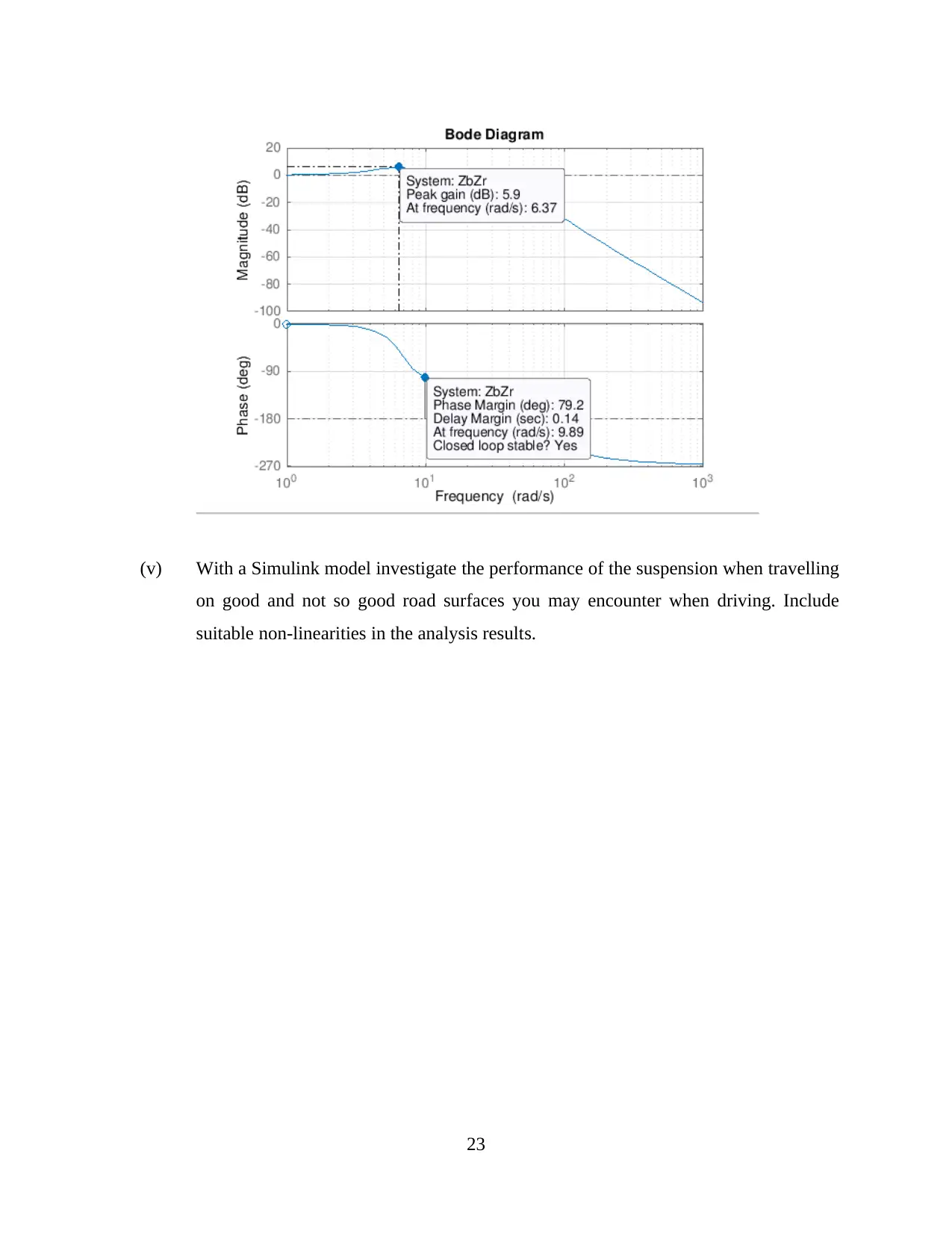
(v) With a Simulink model investigate the performance of the suspension when travelling
on good and not so good road surfaces you may encounter when driving. Include
suitable non-linearities in the analysis results.
23
on good and not so good road surfaces you may encounter when driving. Include
suitable non-linearities in the analysis results.
23
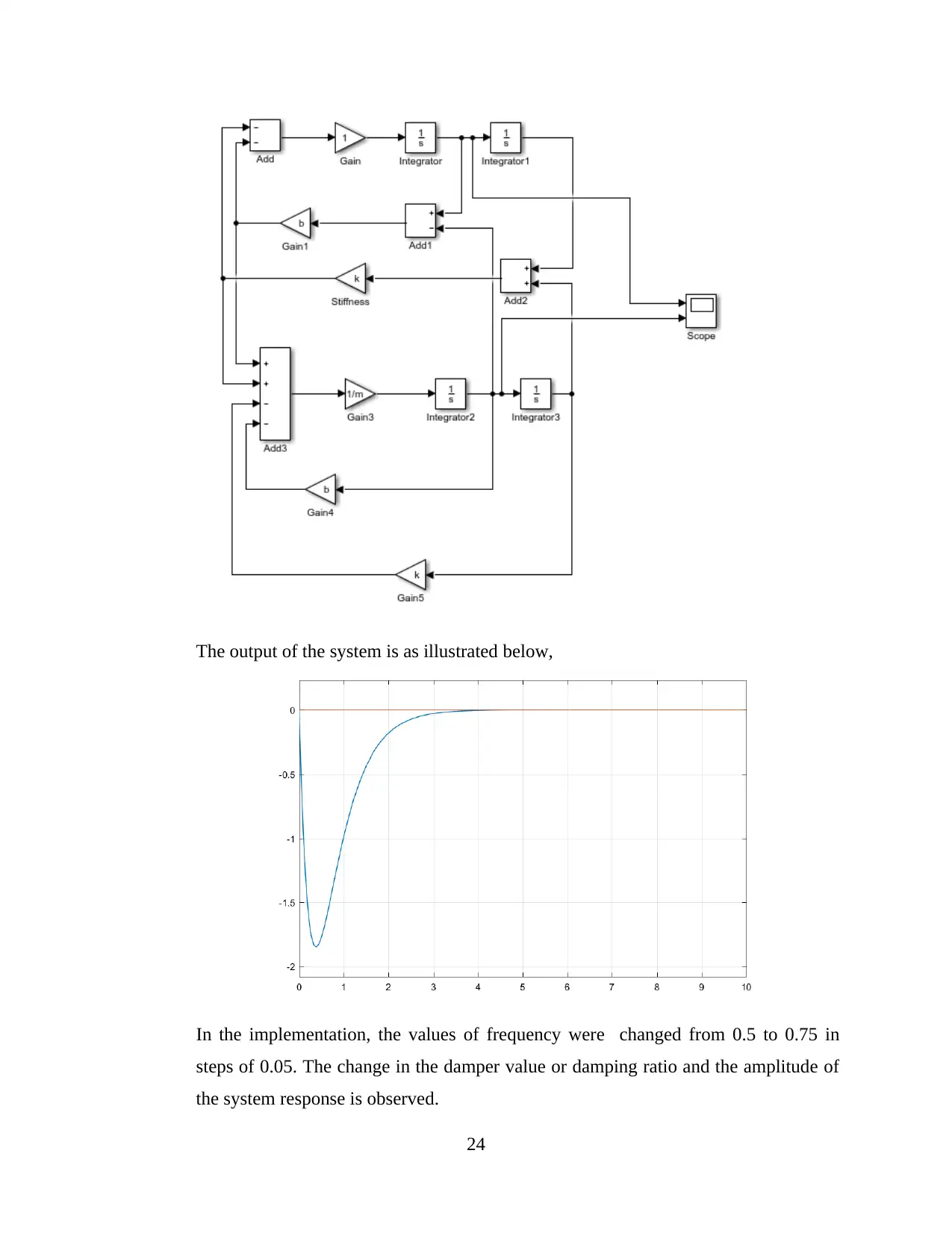
The output of the system is as illustrated below,
In the implementation, the values of frequency were changed from 0.5 to 0.75 in
steps of 0.05. The change in the damper value or damping ratio and the amplitude of
the system response is observed.
24
In the implementation, the values of frequency were changed from 0.5 to 0.75 in
steps of 0.05. The change in the damper value or damping ratio and the amplitude of
the system response is observed.
24
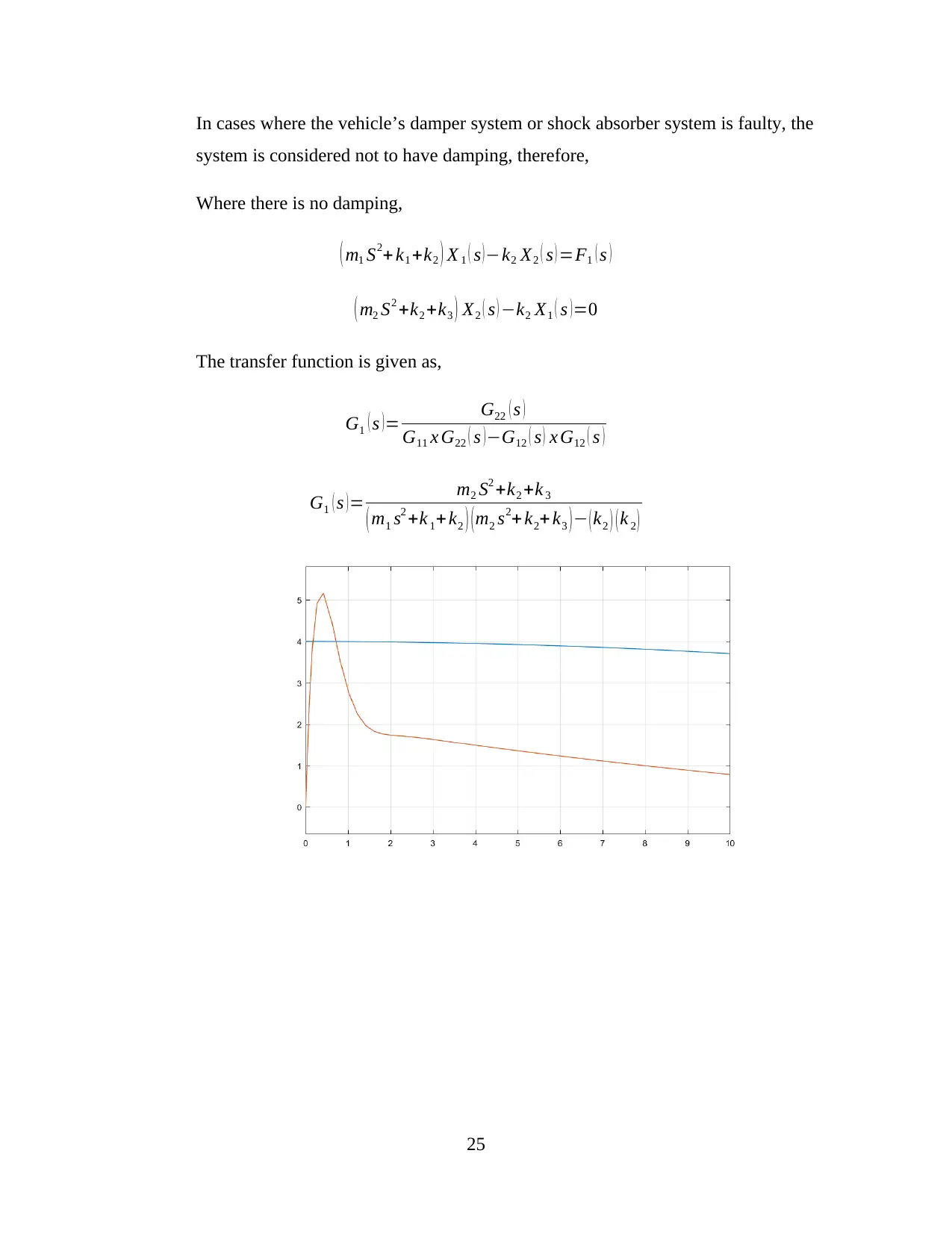
In cases where the vehicle’s damper system or shock absorber system is faulty, the
system is considered not to have damping, therefore,
Where there is no damping,
( m1 S2+ k1 +k2 ) X 1 ( s )−k2 X2 ( s ) =F1 ( s )
( m2 S2 +k2 +k3 ) X2 ( s ) −k2 X1 ( s ) =0
The transfer function is given as,
G1 ( s )= G22 ( s )
G11 x G22 ( s )−G12 ( s ) x G12 ( s )
G1 ( s )= m2 S2 +k2 +k 3
( m1 s2 +k 1+ k2 ) (m2 s2+ k2+ k3 )− (k2 ) ( k 2 )
25
system is considered not to have damping, therefore,
Where there is no damping,
( m1 S2+ k1 +k2 ) X 1 ( s )−k2 X2 ( s ) =F1 ( s )
( m2 S2 +k2 +k3 ) X2 ( s ) −k2 X1 ( s ) =0
The transfer function is given as,
G1 ( s )= G22 ( s )
G11 x G22 ( s )−G12 ( s ) x G12 ( s )
G1 ( s )= m2 S2 +k2 +k 3
( m1 s2 +k 1+ k2 ) (m2 s2+ k2+ k3 )− (k2 ) ( k 2 )
25
Paraphrase This Document
Need a fresh take? Get an instant paraphrase of this document with our AI Paraphraser
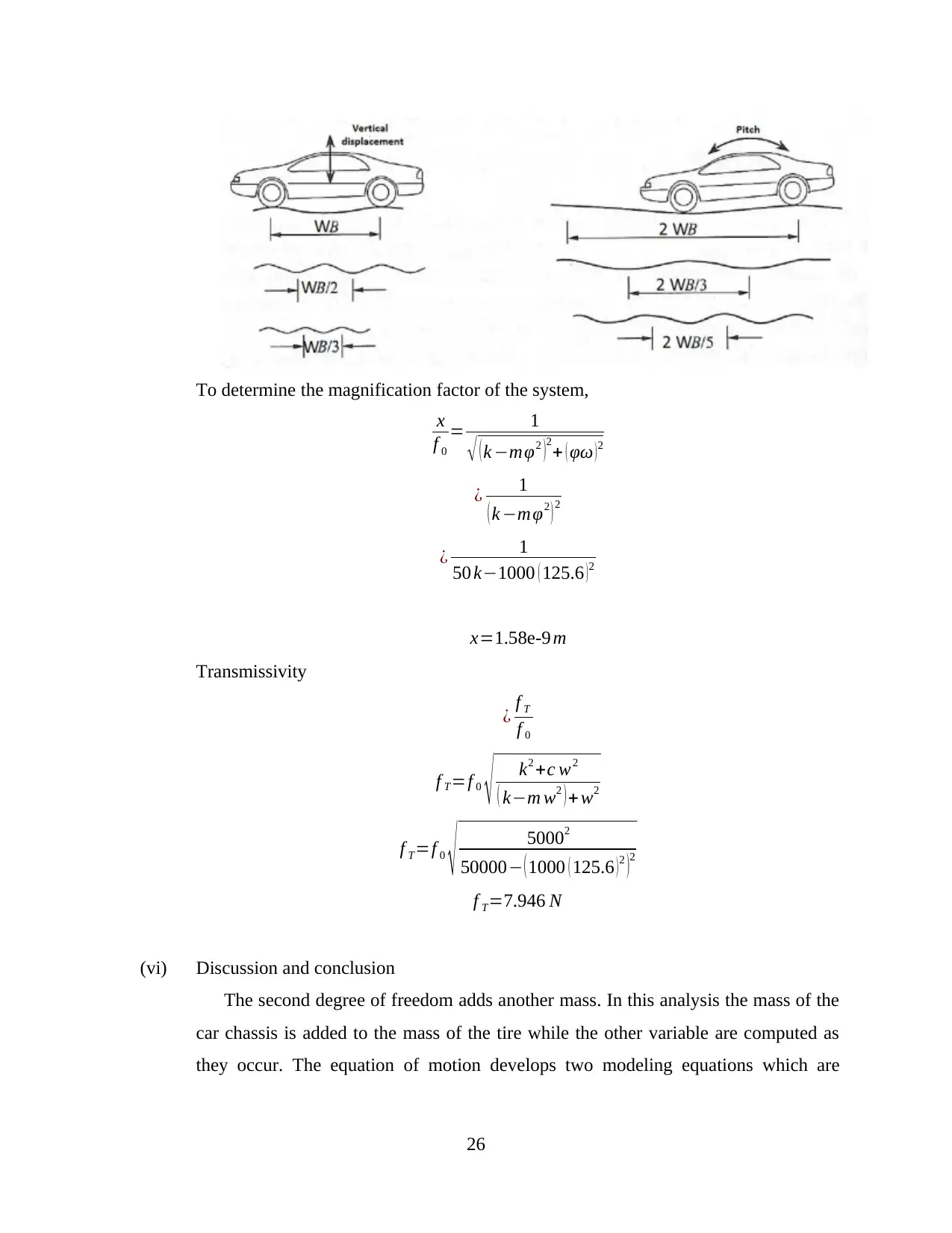
To determine the magnification factor of the system,
x
f 0
= 1
√ ( k −mφ2 )2
+ ( φω )2
¿ 1
( k −mφ2 ) 2
¿ 1
50 k−1000 ( 125.6 )2
x=1.58e-9 m
Transmissivity
¿ f T
f 0
f T=f 0
√ k2 +c w2
( k−m w2 ) + w2
f T=f 0
√ 50002
50000− ( 1000 ( 125.6 ) 2 )
2
f T=7.946 N
(vi) Discussion and conclusion
The second degree of freedom adds another mass. In this analysis the mass of the
car chassis is added to the mass of the tire while the other variable are computed as
they occur. The equation of motion develops two modeling equations which are
26
x
f 0
= 1
√ ( k −mφ2 )2
+ ( φω )2
¿ 1
( k −mφ2 ) 2
¿ 1
50 k−1000 ( 125.6 )2
x=1.58e-9 m
Transmissivity
¿ f T
f 0
f T=f 0
√ k2 +c w2
( k−m w2 ) + w2
f T=f 0
√ 50002
50000− ( 1000 ( 125.6 ) 2 )
2
f T=7.946 N
(vi) Discussion and conclusion
The second degree of freedom adds another mass. In this analysis the mass of the
car chassis is added to the mass of the tire while the other variable are computed as
they occur. The equation of motion develops two modeling equations which are
26
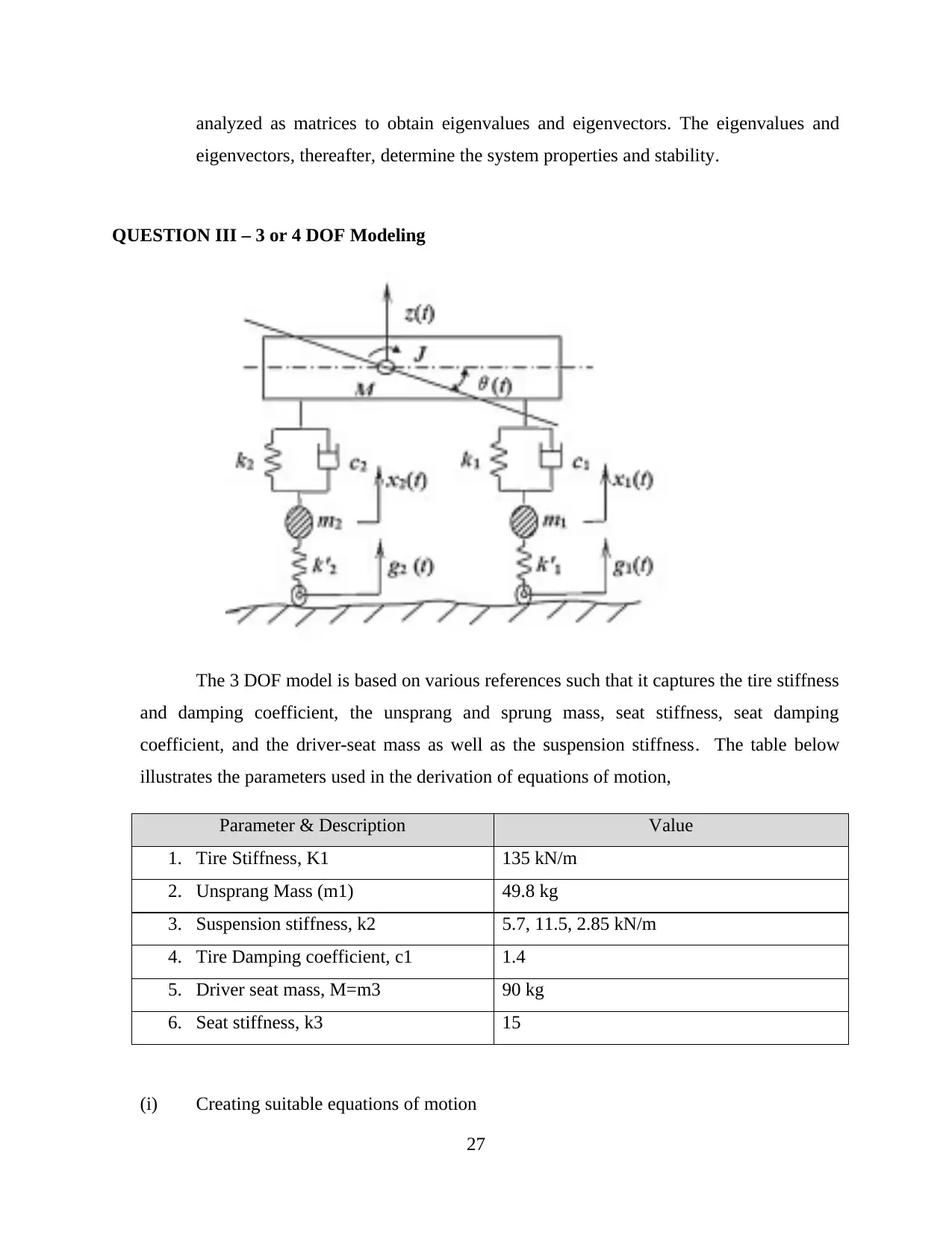
analyzed as matrices to obtain eigenvalues and eigenvectors. The eigenvalues and
eigenvectors, thereafter, determine the system properties and stability.
QUESTION III – 3 or 4 DOF Modeling
The 3 DOF model is based on various references such that it captures the tire stiffness
and damping coefficient, the unsprang and sprung mass, seat stiffness, seat damping
coefficient, and the driver-seat mass as well as the suspension stiffness. The table below
illustrates the parameters used in the derivation of equations of motion,
Parameter & Description Value
1. Tire Stiffness, K1 135 kN/m
2. Unsprang Mass (m1) 49.8 kg
3. Suspension stiffness, k2 5.7, 11.5, 2.85 kN/m
4. Tire Damping coefficient, c1 1.4
5. Driver seat mass, M=m3 90 kg
6. Seat stiffness, k3 15
(i) Creating suitable equations of motion
27
eigenvectors, thereafter, determine the system properties and stability.
QUESTION III – 3 or 4 DOF Modeling
The 3 DOF model is based on various references such that it captures the tire stiffness
and damping coefficient, the unsprang and sprung mass, seat stiffness, seat damping
coefficient, and the driver-seat mass as well as the suspension stiffness. The table below
illustrates the parameters used in the derivation of equations of motion,
Parameter & Description Value
1. Tire Stiffness, K1 135 kN/m
2. Unsprang Mass (m1) 49.8 kg
3. Suspension stiffness, k2 5.7, 11.5, 2.85 kN/m
4. Tire Damping coefficient, c1 1.4
5. Driver seat mass, M=m3 90 kg
6. Seat stiffness, k3 15
(i) Creating suitable equations of motion
27
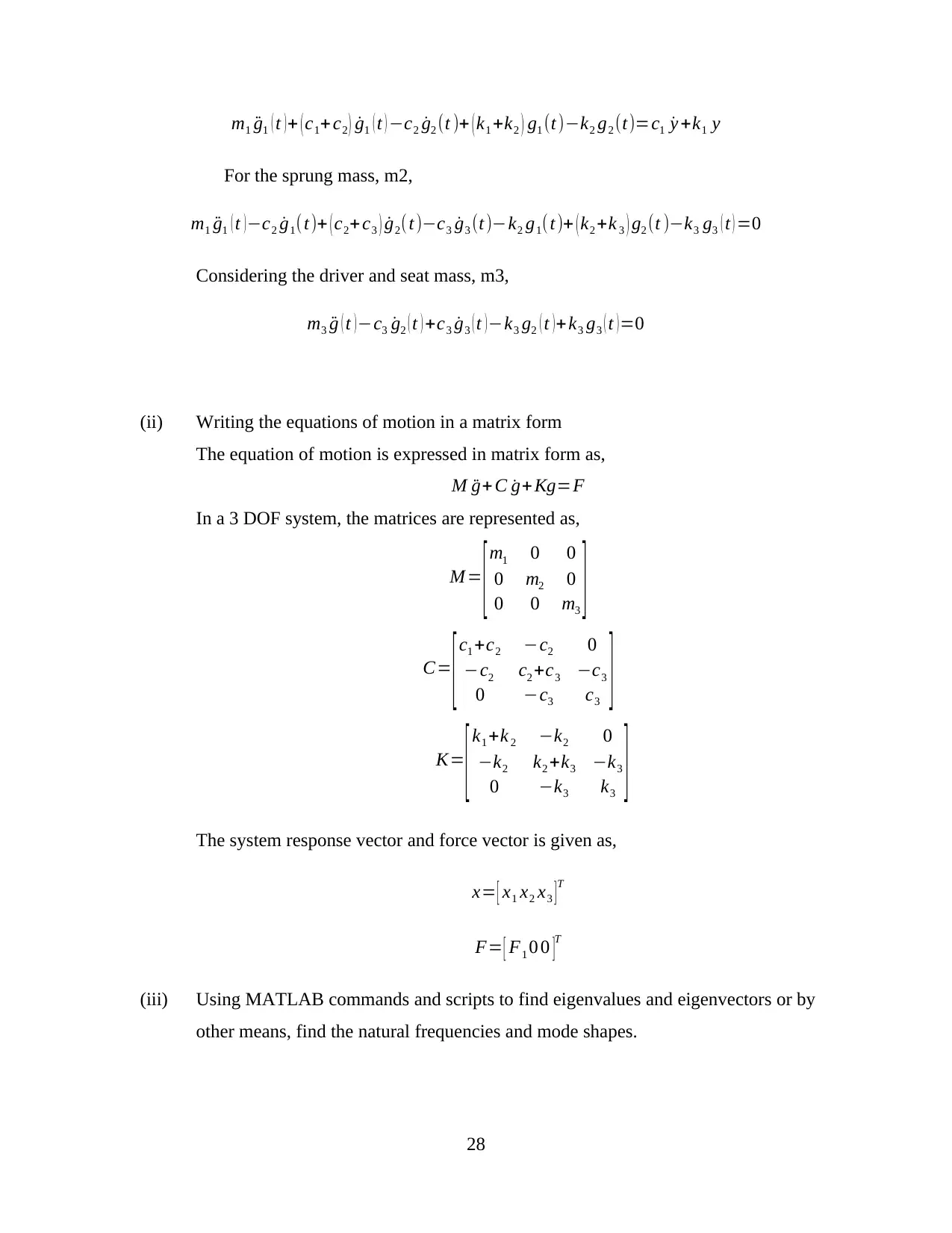
m1 ¨g1 ( t )+ ( c1+ c2 ) ˙g1 ( t ) −c2 ˙g2 (t )+ ( k1 +k2 ) g1 (t)−k2 g2 (t)=c1 ˙y +k1 y
For the sprung mass, m2,
m1 ¨g1 ( t ) −c2 ˙g1(t)+ ( c2+c3 ) ˙g2(t)−c3 ˙g3 (t)−k2 g1(t)+ ( k2 +k 3 ) g2 (t )−k3 g3 ( t ) =0
Considering the driver and seat mass, m3,
m3 ¨g ( t )−c3 ˙g2 ( t ) +c3 ˙g3 ( t )−k3 g2 ( t )+k3 g3 ( t )=0
(ii) Writing the equations of motion in a matrix form
The equation of motion is expressed in matrix form as,
M ¨g+ C ˙g+ Kg=F
In a 3 DOF system, the matrices are represented as,
M =
[ m1 0 0
0 m2 0
0 0 m3 ]
C=
[c1 +c2 −c2 0
−c2 c2 +c3 −c3
0 −c3 c3 ]
K=
[ k1 +k 2 −k2 0
−k2 k2 +k3 −k3
0 −k3 k3 ]
The system response vector and force vector is given as,
x= [ x1 x2 x3 ] T
F= [ F1 0 0 ]T
(iii) Using MATLAB commands and scripts to find eigenvalues and eigenvectors or by
other means, find the natural frequencies and mode shapes.
28
For the sprung mass, m2,
m1 ¨g1 ( t ) −c2 ˙g1(t)+ ( c2+c3 ) ˙g2(t)−c3 ˙g3 (t)−k2 g1(t)+ ( k2 +k 3 ) g2 (t )−k3 g3 ( t ) =0
Considering the driver and seat mass, m3,
m3 ¨g ( t )−c3 ˙g2 ( t ) +c3 ˙g3 ( t )−k3 g2 ( t )+k3 g3 ( t )=0
(ii) Writing the equations of motion in a matrix form
The equation of motion is expressed in matrix form as,
M ¨g+ C ˙g+ Kg=F
In a 3 DOF system, the matrices are represented as,
M =
[ m1 0 0
0 m2 0
0 0 m3 ]
C=
[c1 +c2 −c2 0
−c2 c2 +c3 −c3
0 −c3 c3 ]
K=
[ k1 +k 2 −k2 0
−k2 k2 +k3 −k3
0 −k3 k3 ]
The system response vector and force vector is given as,
x= [ x1 x2 x3 ] T
F= [ F1 0 0 ]T
(iii) Using MATLAB commands and scripts to find eigenvalues and eigenvectors or by
other means, find the natural frequencies and mode shapes.
28
Secure Best Marks with AI Grader
Need help grading? Try our AI Grader for instant feedback on your assignments.
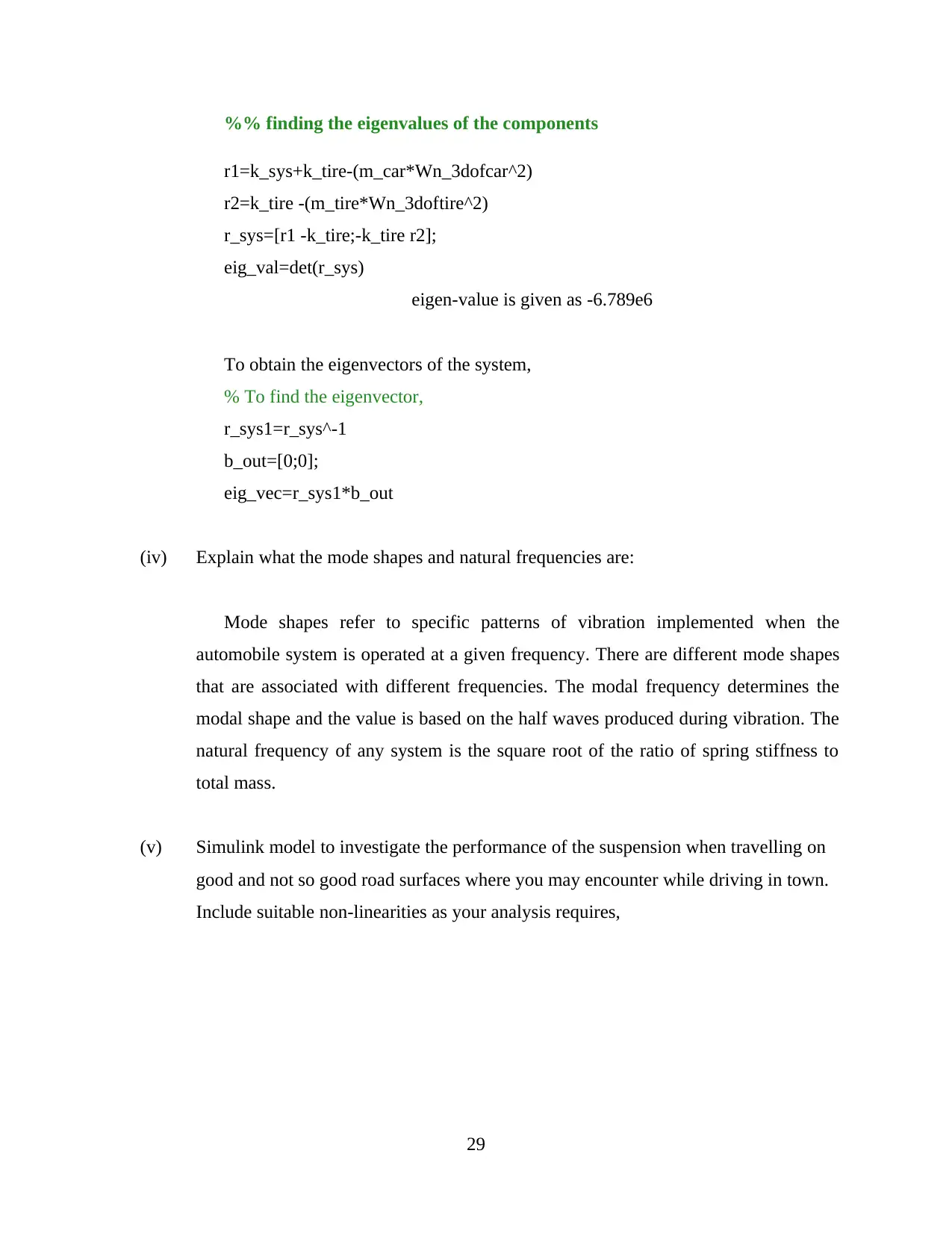
%% finding the eigenvalues of the components
r1=k_sys+k_tire-(m_car*Wn_3dofcar^2)
r2=k_tire -(m_tire*Wn_3doftire^2)
r_sys=[r1 -k_tire;-k_tire r2];
eig_val=det(r_sys)
eigen-value is given as -6.789e6
To obtain the eigenvectors of the system,
% To find the eigenvector,
r_sys1=r_sys^-1
b_out=[0;0];
eig_vec=r_sys1*b_out
(iv) Explain what the mode shapes and natural frequencies are:
Mode shapes refer to specific patterns of vibration implemented when the
automobile system is operated at a given frequency. There are different mode shapes
that are associated with different frequencies. The modal frequency determines the
modal shape and the value is based on the half waves produced during vibration. The
natural frequency of any system is the square root of the ratio of spring stiffness to
total mass.
(v) Simulink model to investigate the performance of the suspension when travelling on
good and not so good road surfaces where you may encounter while driving in town.
Include suitable non-linearities as your analysis requires,
29
r1=k_sys+k_tire-(m_car*Wn_3dofcar^2)
r2=k_tire -(m_tire*Wn_3doftire^2)
r_sys=[r1 -k_tire;-k_tire r2];
eig_val=det(r_sys)
eigen-value is given as -6.789e6
To obtain the eigenvectors of the system,
% To find the eigenvector,
r_sys1=r_sys^-1
b_out=[0;0];
eig_vec=r_sys1*b_out
(iv) Explain what the mode shapes and natural frequencies are:
Mode shapes refer to specific patterns of vibration implemented when the
automobile system is operated at a given frequency. There are different mode shapes
that are associated with different frequencies. The modal frequency determines the
modal shape and the value is based on the half waves produced during vibration. The
natural frequency of any system is the square root of the ratio of spring stiffness to
total mass.
(v) Simulink model to investigate the performance of the suspension when travelling on
good and not so good road surfaces where you may encounter while driving in town.
Include suitable non-linearities as your analysis requires,
29
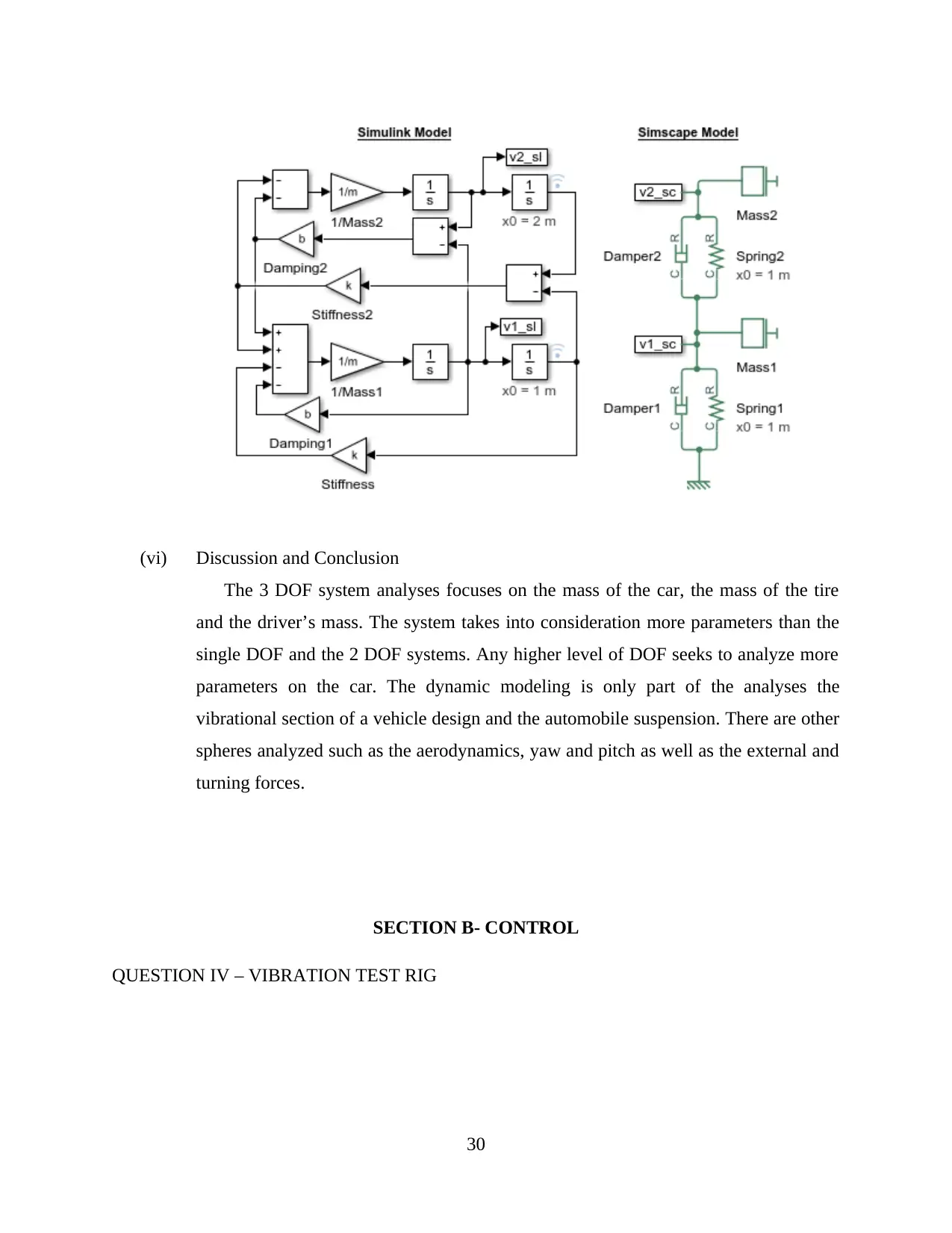
(vi) Discussion and Conclusion
The 3 DOF system analyses focuses on the mass of the car, the mass of the tire
and the driver’s mass. The system takes into consideration more parameters than the
single DOF and the 2 DOF systems. Any higher level of DOF seeks to analyze more
parameters on the car. The dynamic modeling is only part of the analyses the
vibrational section of a vehicle design and the automobile suspension. There are other
spheres analyzed such as the aerodynamics, yaw and pitch as well as the external and
turning forces.
SECTION B- CONTROL
QUESTION IV – VIBRATION TEST RIG
30
The 3 DOF system analyses focuses on the mass of the car, the mass of the tire
and the driver’s mass. The system takes into consideration more parameters than the
single DOF and the 2 DOF systems. Any higher level of DOF seeks to analyze more
parameters on the car. The dynamic modeling is only part of the analyses the
vibrational section of a vehicle design and the automobile suspension. There are other
spheres analyzed such as the aerodynamics, yaw and pitch as well as the external and
turning forces.
SECTION B- CONTROL
QUESTION IV – VIBRATION TEST RIG
30
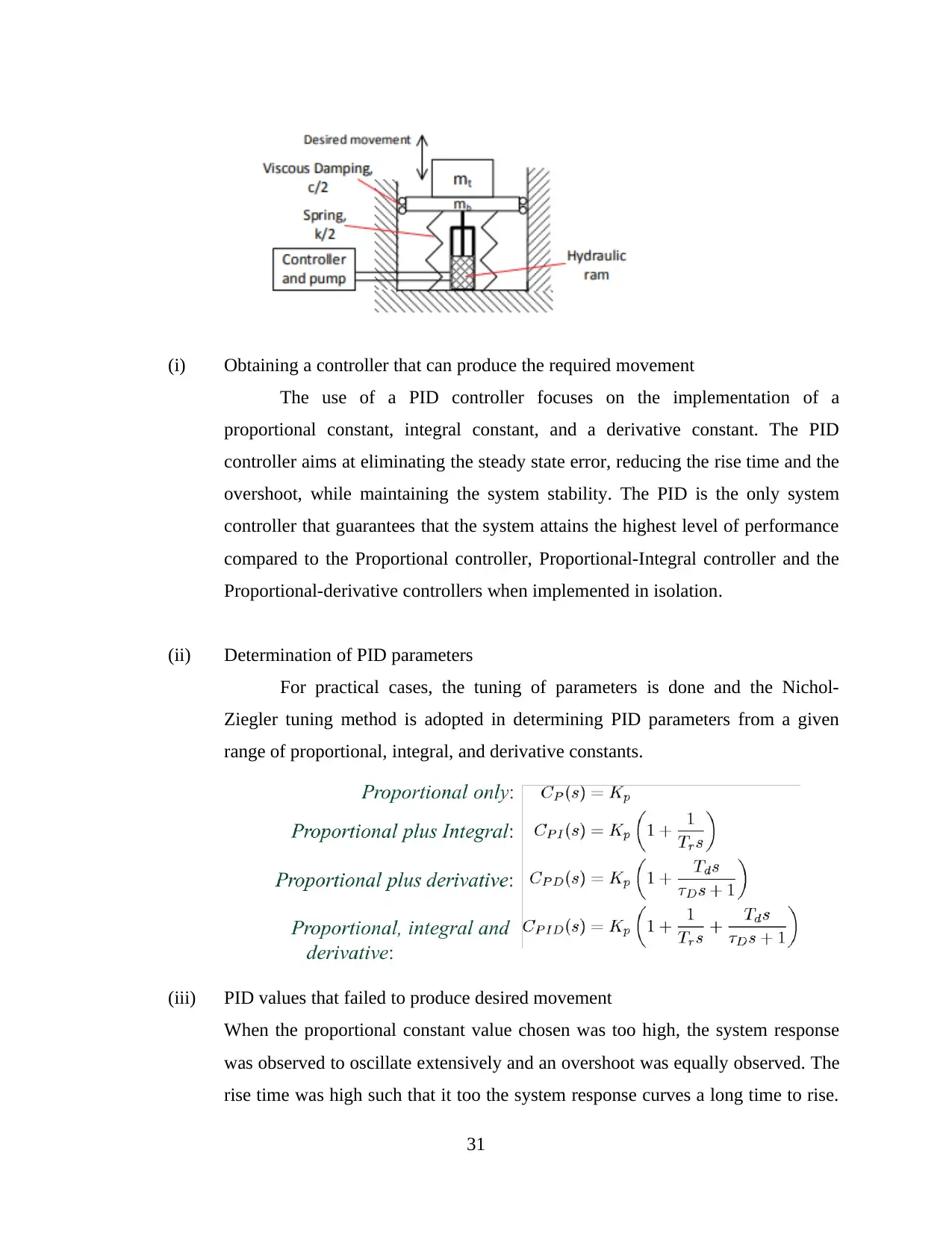
(i) Obtaining a controller that can produce the required movement
The use of a PID controller focuses on the implementation of a
proportional constant, integral constant, and a derivative constant. The PID
controller aims at eliminating the steady state error, reducing the rise time and the
overshoot, while maintaining the system stability. The PID is the only system
controller that guarantees that the system attains the highest level of performance
compared to the Proportional controller, Proportional-Integral controller and the
Proportional-derivative controllers when implemented in isolation.
(ii) Determination of PID parameters
For practical cases, the tuning of parameters is done and the Nichol-
Ziegler tuning method is adopted in determining PID parameters from a given
range of proportional, integral, and derivative constants.
(iii) PID values that failed to produce desired movement
When the proportional constant value chosen was too high, the system response
was observed to oscillate extensively and an overshoot was equally observed. The
rise time was high such that it too the system response curves a long time to rise.
31
The use of a PID controller focuses on the implementation of a
proportional constant, integral constant, and a derivative constant. The PID
controller aims at eliminating the steady state error, reducing the rise time and the
overshoot, while maintaining the system stability. The PID is the only system
controller that guarantees that the system attains the highest level of performance
compared to the Proportional controller, Proportional-Integral controller and the
Proportional-derivative controllers when implemented in isolation.
(ii) Determination of PID parameters
For practical cases, the tuning of parameters is done and the Nichol-
Ziegler tuning method is adopted in determining PID parameters from a given
range of proportional, integral, and derivative constants.
(iii) PID values that failed to produce desired movement
When the proportional constant value chosen was too high, the system response
was observed to oscillate extensively and an overshoot was equally observed. The
rise time was high such that it too the system response curves a long time to rise.
31
Paraphrase This Document
Need a fresh take? Get an instant paraphrase of this document with our AI Paraphraser

This prompted the designer to moderate the PID parameter values using the
Nichols-Ziegler tuning method which ensured that the steady state error was
eliminated, and the parameter values used were reasonable to avoid making the
system unstable while performing inefficiently.
(1) Ziegler-Nichols Oscillation method
(2) Ziegler-Nichols Reaction curve method
(3) Cohen-Coon Reaction curve method
Kp Tr Td
P 0.50 Kc
PI 0.45 Kc Pc
1.2
PID 0.60 Kc 0.5Pc Pc
8
(iv) Determine the maximum force required from the hydraulic ram
U ( t )
f ( t ) = 1
s2+ 10 s+50
At S=0
1
02 +10(0)+50
¿ 1
50 =0.02 kN
(v) Simulink model
%% Vibration test rig
clear all
close all
clc
format short
32
Nichols-Ziegler tuning method which ensured that the steady state error was
eliminated, and the parameter values used were reasonable to avoid making the
system unstable while performing inefficiently.
(1) Ziegler-Nichols Oscillation method
(2) Ziegler-Nichols Reaction curve method
(3) Cohen-Coon Reaction curve method
Kp Tr Td
P 0.50 Kc
PI 0.45 Kc Pc
1.2
PID 0.60 Kc 0.5Pc Pc
8
(iv) Determine the maximum force required from the hydraulic ram
U ( t )
f ( t ) = 1
s2+ 10 s+50
At S=0
1
02 +10(0)+50
¿ 1
50 =0.02 kN
(v) Simulink model
%% Vibration test rig
clear all
close all
clc
format short
32
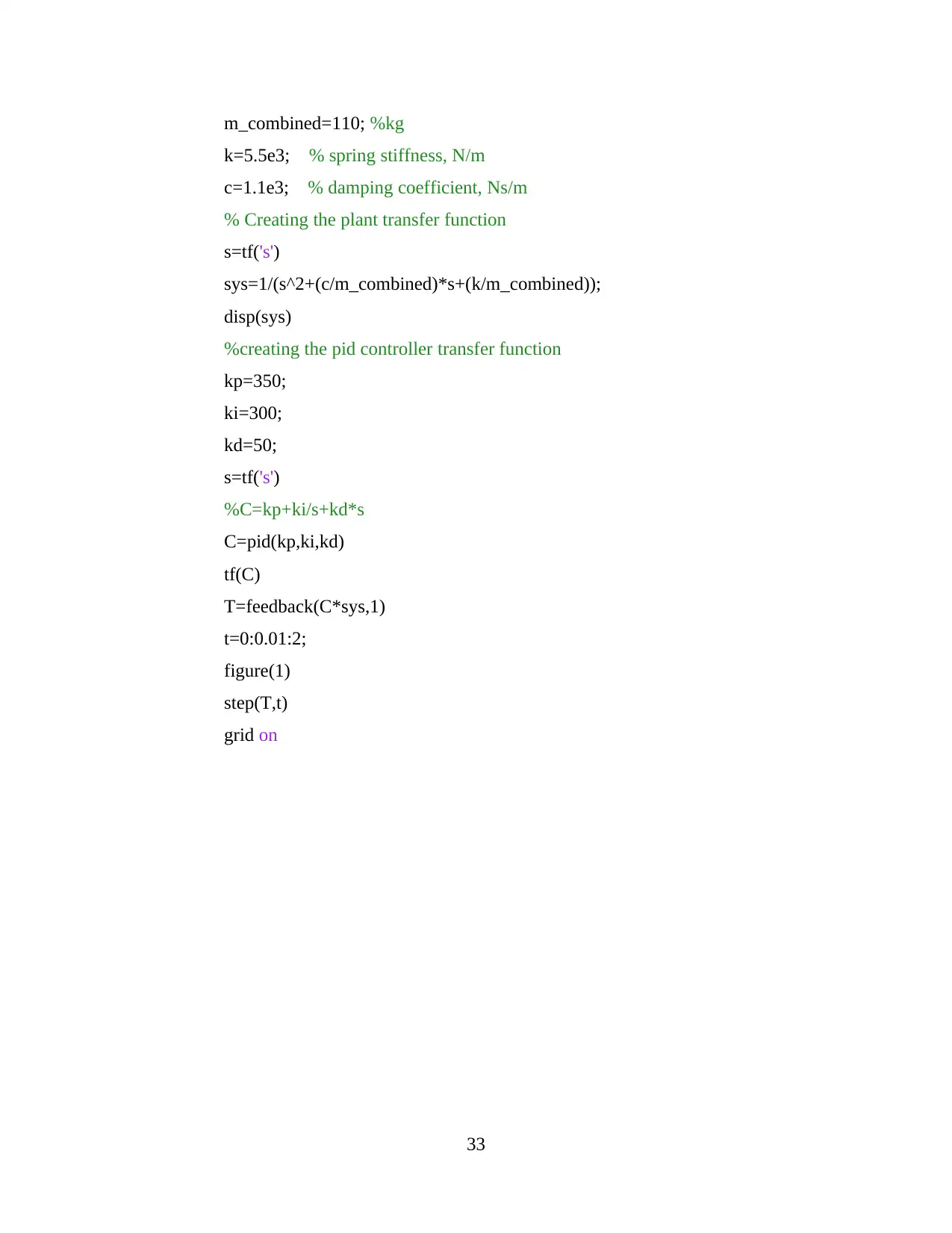
m_combined=110; %kg
k=5.5e3; % spring stiffness, N/m
c=1.1e3; % damping coefficient, Ns/m
% Creating the plant transfer function
s=tf('s')
sys=1/(s^2+(c/m_combined)*s+(k/m_combined));
disp(sys)
%creating the pid controller transfer function
kp=350;
ki=300;
kd=50;
s=tf('s')
%C=kp+ki/s+kd*s
C=pid(kp,ki,kd)
tf(C)
T=feedback(C*sys,1)
t=0:0.01:2;
figure(1)
step(T,t)
grid on
33
k=5.5e3; % spring stiffness, N/m
c=1.1e3; % damping coefficient, Ns/m
% Creating the plant transfer function
s=tf('s')
sys=1/(s^2+(c/m_combined)*s+(k/m_combined));
disp(sys)
%creating the pid controller transfer function
kp=350;
ki=300;
kd=50;
s=tf('s')
%C=kp+ki/s+kd*s
C=pid(kp,ki,kd)
tf(C)
T=feedback(C*sys,1)
t=0:0.01:2;
figure(1)
step(T,t)
grid on
33
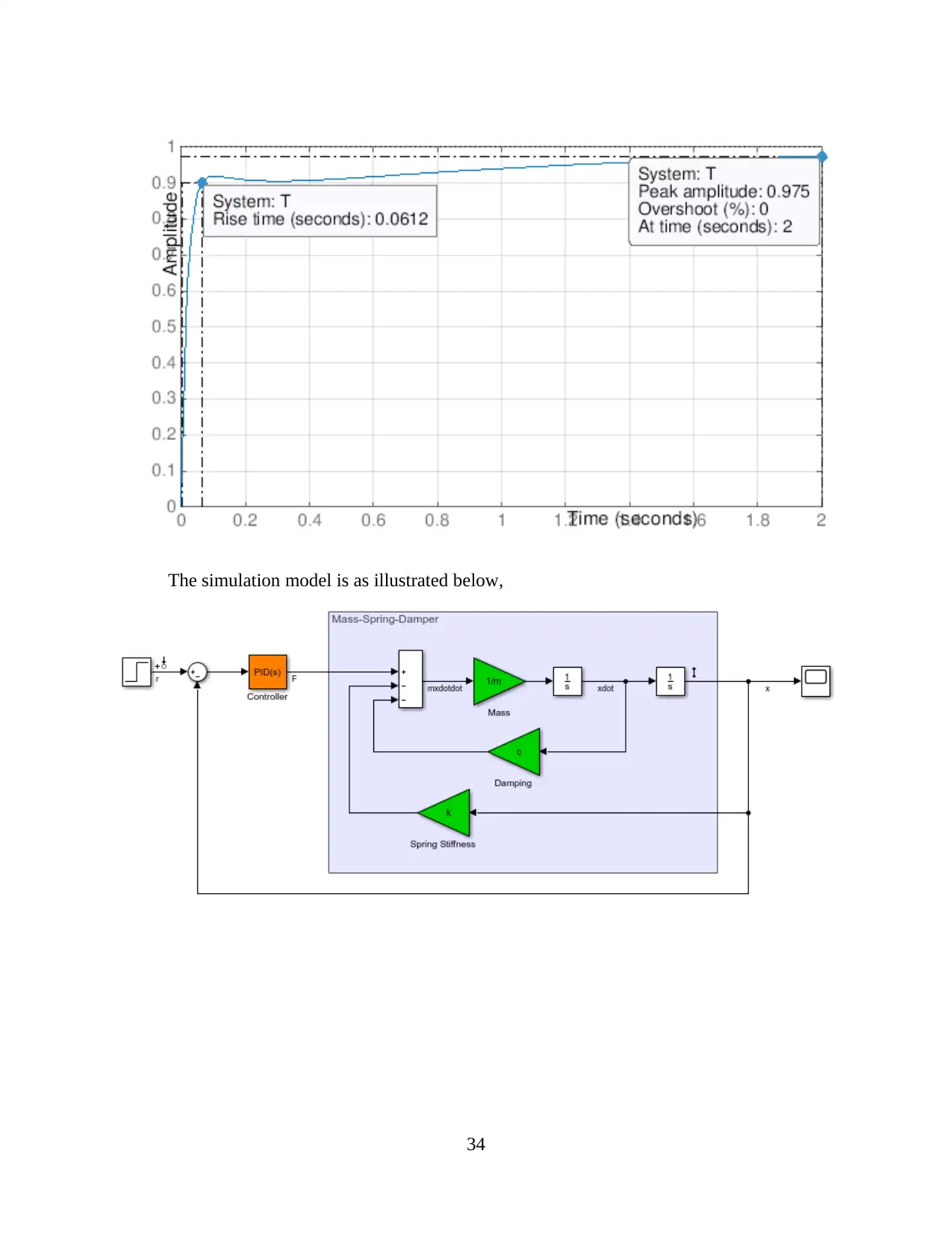
The simulation model is as illustrated below,
34
34
Secure Best Marks with AI Grader
Need help grading? Try our AI Grader for instant feedback on your assignments.
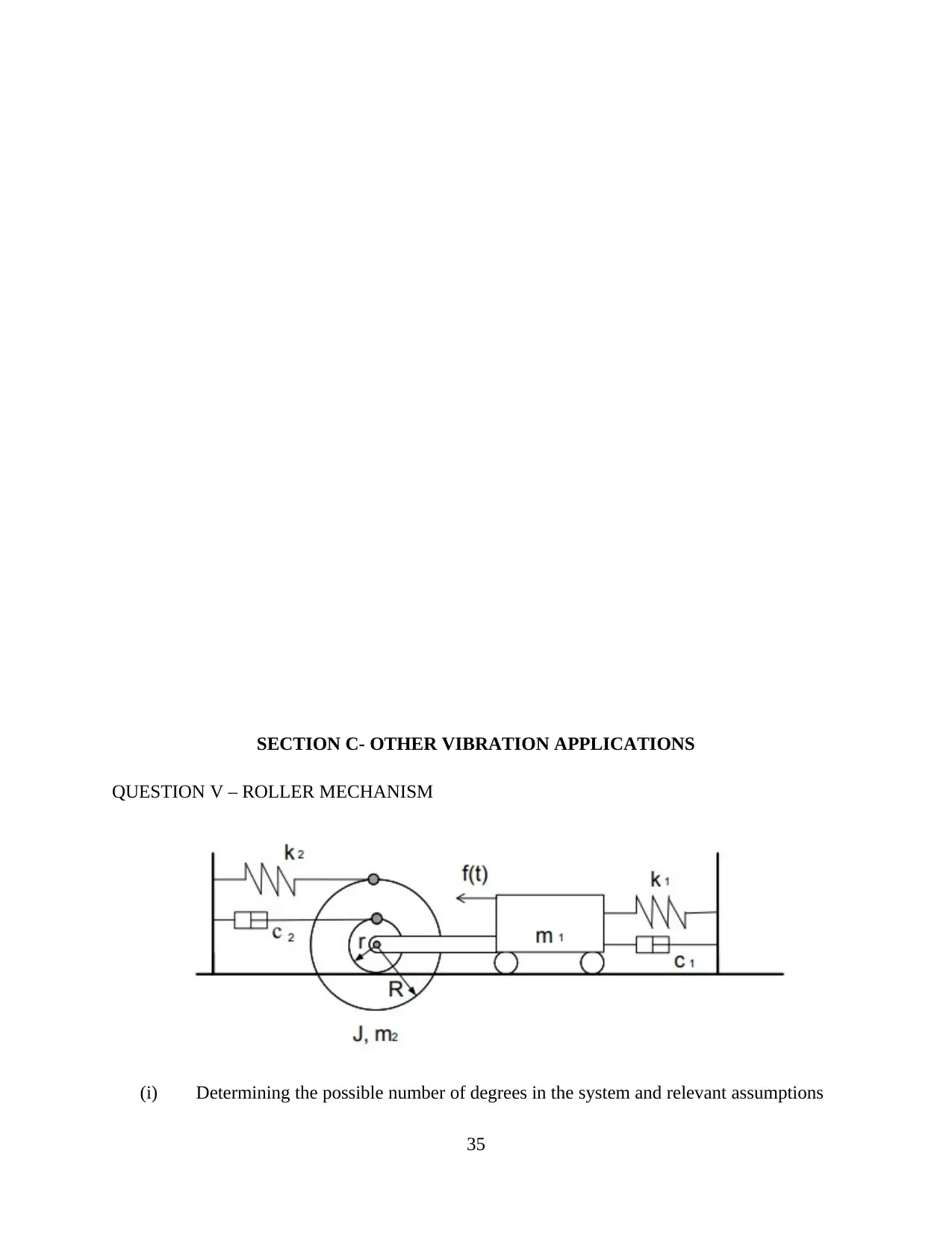
SECTION C- OTHER VIBRATION APPLICATIONS
QUESTION V – ROLLER MECHANISM
(i) Determining the possible number of degrees in the system and relevant assumptions
35
QUESTION V – ROLLER MECHANISM
(i) Determining the possible number of degrees in the system and relevant assumptions
35
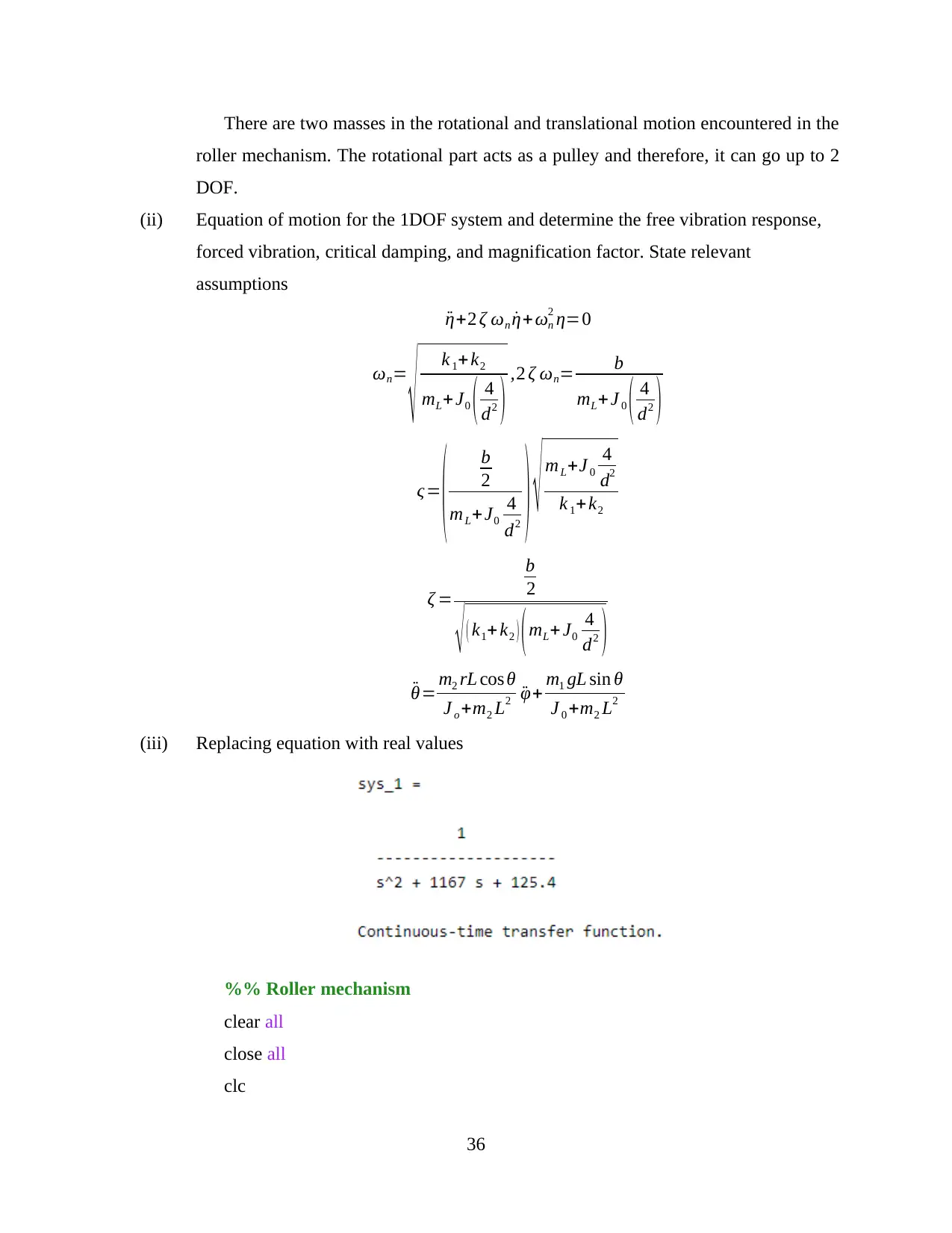
There are two masses in the rotational and translational motion encountered in the
roller mechanism. The rotational part acts as a pulley and therefore, it can go up to 2
DOF.
(ii) Equation of motion for the 1DOF system and determine the free vibration response,
forced vibration, critical damping, and magnification factor. State relevant
assumptions
¨η+2 ζ ωn ˙η+ωn
2 η=0
ωn=
√ k 1+ k2
mL+ J0 ( 4
d2 ) ,2 ζ ωn= b
mL+ J 0 ( 4
d2 )
ς=
( b
2
mL+J0
4
d2 ) √ mL+J 0
4
d2
k 1+k2
ζ =
b
2
√ ( k1+ k2 ) ( mL+ J0
4
d2 )
¨θ= m2 rL cos θ
J o +m2 L2 ¨φ+ m1 gL sin θ
J 0 +m2 L2
(iii) Replacing equation with real values
%% Roller mechanism
clear all
close all
clc
36
roller mechanism. The rotational part acts as a pulley and therefore, it can go up to 2
DOF.
(ii) Equation of motion for the 1DOF system and determine the free vibration response,
forced vibration, critical damping, and magnification factor. State relevant
assumptions
¨η+2 ζ ωn ˙η+ωn
2 η=0
ωn=
√ k 1+ k2
mL+ J0 ( 4
d2 ) ,2 ζ ωn= b
mL+ J 0 ( 4
d2 )
ς=
( b
2
mL+J0
4
d2 ) √ mL+J 0
4
d2
k 1+k2
ζ =
b
2
√ ( k1+ k2 ) ( mL+ J0
4
d2 )
¨θ= m2 rL cos θ
J o +m2 L2 ¨φ+ m1 gL sin θ
J 0 +m2 L2
(iii) Replacing equation with real values
%% Roller mechanism
clear all
close all
clc
36
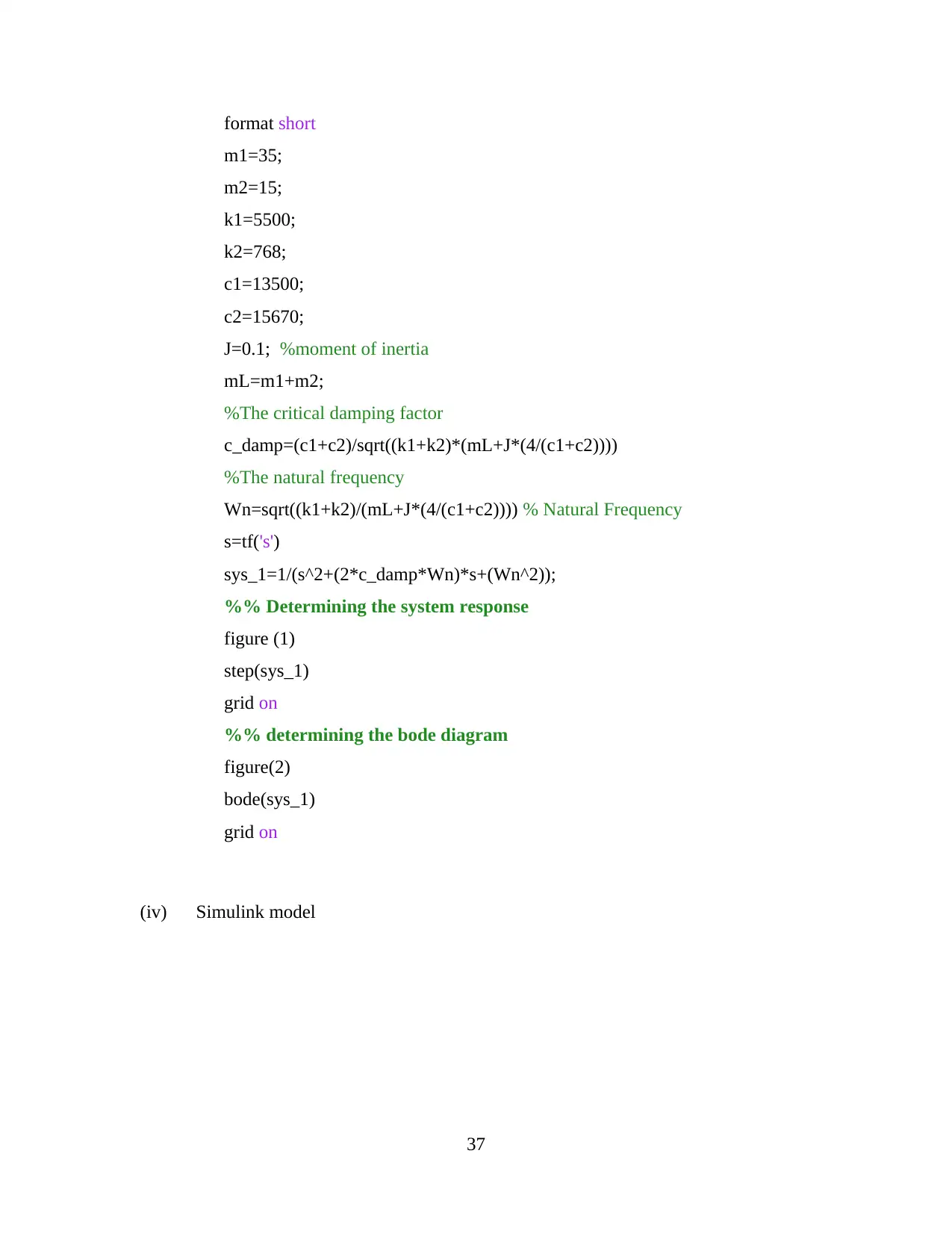
format short
m1=35;
m2=15;
k1=5500;
k2=768;
c1=13500;
c2=15670;
J=0.1; %moment of inertia
mL=m1+m2;
%The critical damping factor
c_damp=(c1+c2)/sqrt((k1+k2)*(mL+J*(4/(c1+c2))))
%The natural frequency
Wn=sqrt((k1+k2)/(mL+J*(4/(c1+c2)))) % Natural Frequency
s=tf('s')
sys_1=1/(s^2+(2*c_damp*Wn)*s+(Wn^2));
%% Determining the system response
figure (1)
step(sys_1)
grid on
%% determining the bode diagram
figure(2)
bode(sys_1)
grid on
(iv) Simulink model
37
m1=35;
m2=15;
k1=5500;
k2=768;
c1=13500;
c2=15670;
J=0.1; %moment of inertia
mL=m1+m2;
%The critical damping factor
c_damp=(c1+c2)/sqrt((k1+k2)*(mL+J*(4/(c1+c2))))
%The natural frequency
Wn=sqrt((k1+k2)/(mL+J*(4/(c1+c2)))) % Natural Frequency
s=tf('s')
sys_1=1/(s^2+(2*c_damp*Wn)*s+(Wn^2));
%% Determining the system response
figure (1)
step(sys_1)
grid on
%% determining the bode diagram
figure(2)
bode(sys_1)
grid on
(iv) Simulink model
37
Paraphrase This Document
Need a fresh take? Get an instant paraphrase of this document with our AI Paraphraser
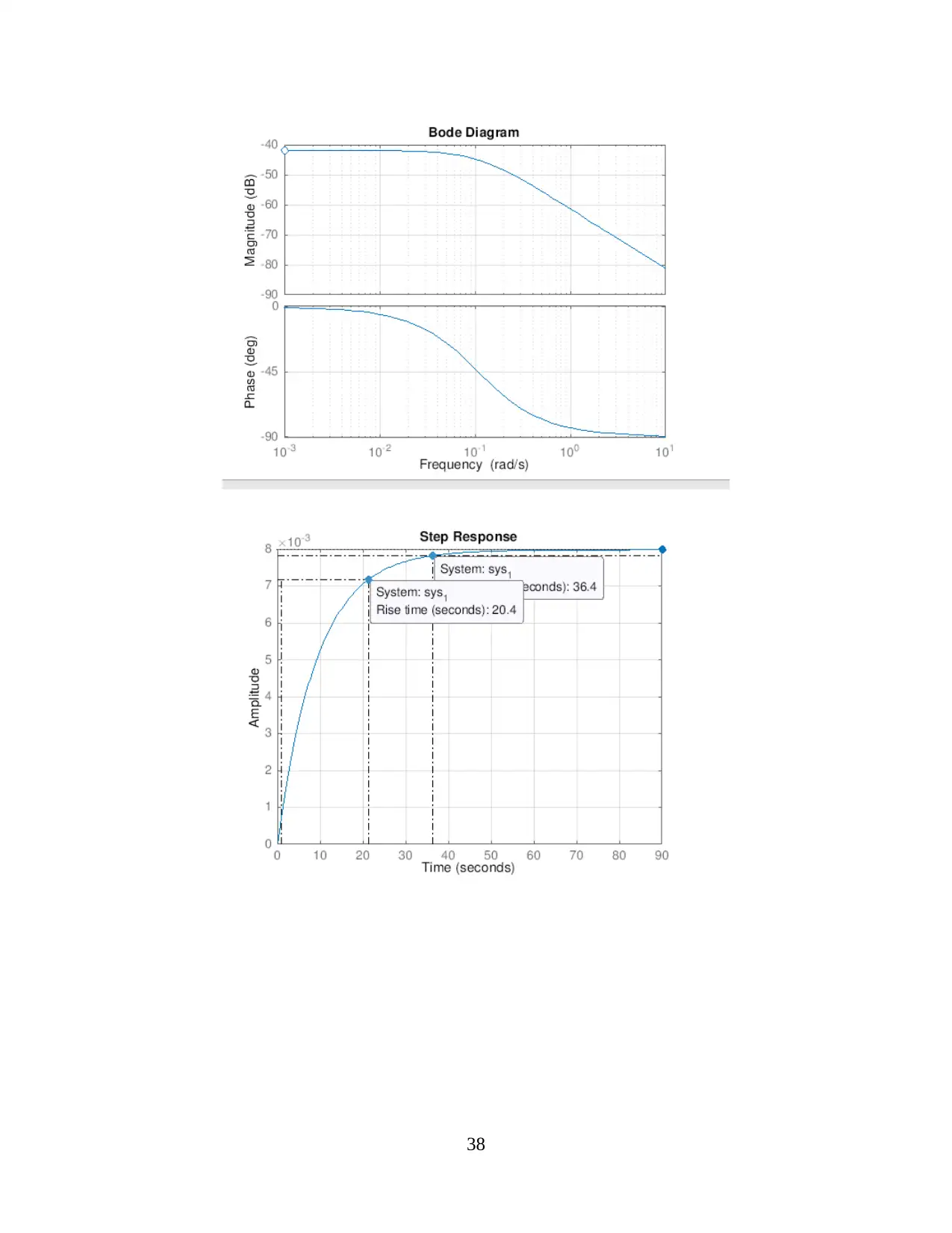
38
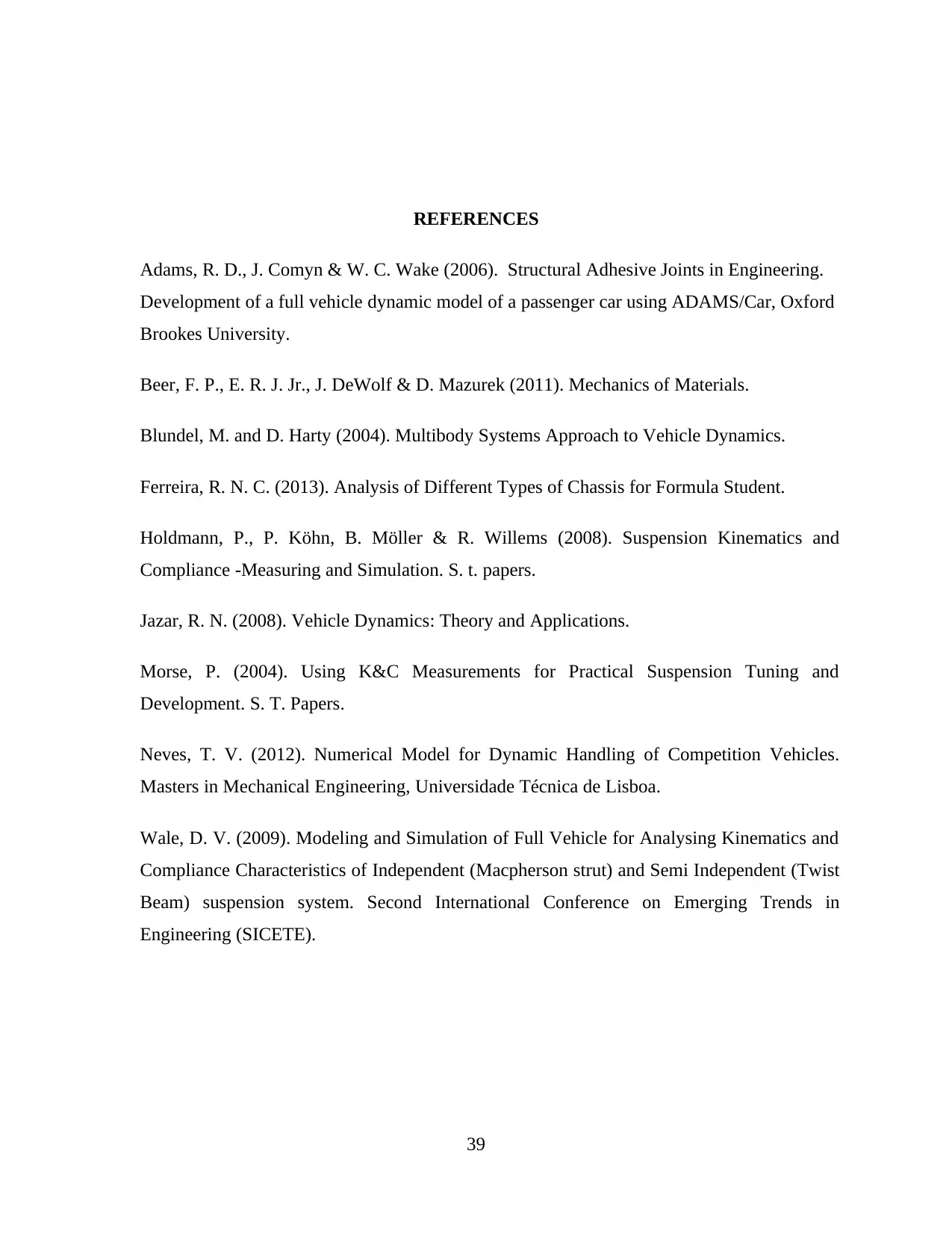
REFERENCES
Adams, R. D., J. Comyn & W. C. Wake (2006). Structural Adhesive Joints in Engineering.
Development of a full vehicle dynamic model of a passenger car using ADAMS/Car, Oxford
Brookes University.
Beer, F. P., E. R. J. Jr., J. DeWolf & D. Mazurek (2011). Mechanics of Materials.
Blundel, M. and D. Harty (2004). Multibody Systems Approach to Vehicle Dynamics.
Ferreira, R. N. C. (2013). Analysis of Different Types of Chassis for Formula Student.
Holdmann, P., P. Köhn, B. Möller & R. Willems (2008). Suspension Kinematics and
Compliance -Measuring and Simulation. S. t. papers.
Jazar, R. N. (2008). Vehicle Dynamics: Theory and Applications.
Morse, P. (2004). Using K&C Measurements for Practical Suspension Tuning and
Development. S. T. Papers.
Neves, T. V. (2012). Numerical Model for Dynamic Handling of Competition Vehicles.
Masters in Mechanical Engineering, Universidade Técnica de Lisboa.
Wale, D. V. (2009). Modeling and Simulation of Full Vehicle for Analysing Kinematics and
Compliance Characteristics of Independent (Macpherson strut) and Semi Independent (Twist
Beam) suspension system. Second International Conference on Emerging Trends in
Engineering (SICETE).
39
Adams, R. D., J. Comyn & W. C. Wake (2006). Structural Adhesive Joints in Engineering.
Development of a full vehicle dynamic model of a passenger car using ADAMS/Car, Oxford
Brookes University.
Beer, F. P., E. R. J. Jr., J. DeWolf & D. Mazurek (2011). Mechanics of Materials.
Blundel, M. and D. Harty (2004). Multibody Systems Approach to Vehicle Dynamics.
Ferreira, R. N. C. (2013). Analysis of Different Types of Chassis for Formula Student.
Holdmann, P., P. Köhn, B. Möller & R. Willems (2008). Suspension Kinematics and
Compliance -Measuring and Simulation. S. t. papers.
Jazar, R. N. (2008). Vehicle Dynamics: Theory and Applications.
Morse, P. (2004). Using K&C Measurements for Practical Suspension Tuning and
Development. S. T. Papers.
Neves, T. V. (2012). Numerical Model for Dynamic Handling of Competition Vehicles.
Masters in Mechanical Engineering, Universidade Técnica de Lisboa.
Wale, D. V. (2009). Modeling and Simulation of Full Vehicle for Analysing Kinematics and
Compliance Characteristics of Independent (Macpherson strut) and Semi Independent (Twist
Beam) suspension system. Second International Conference on Emerging Trends in
Engineering (SICETE).
39
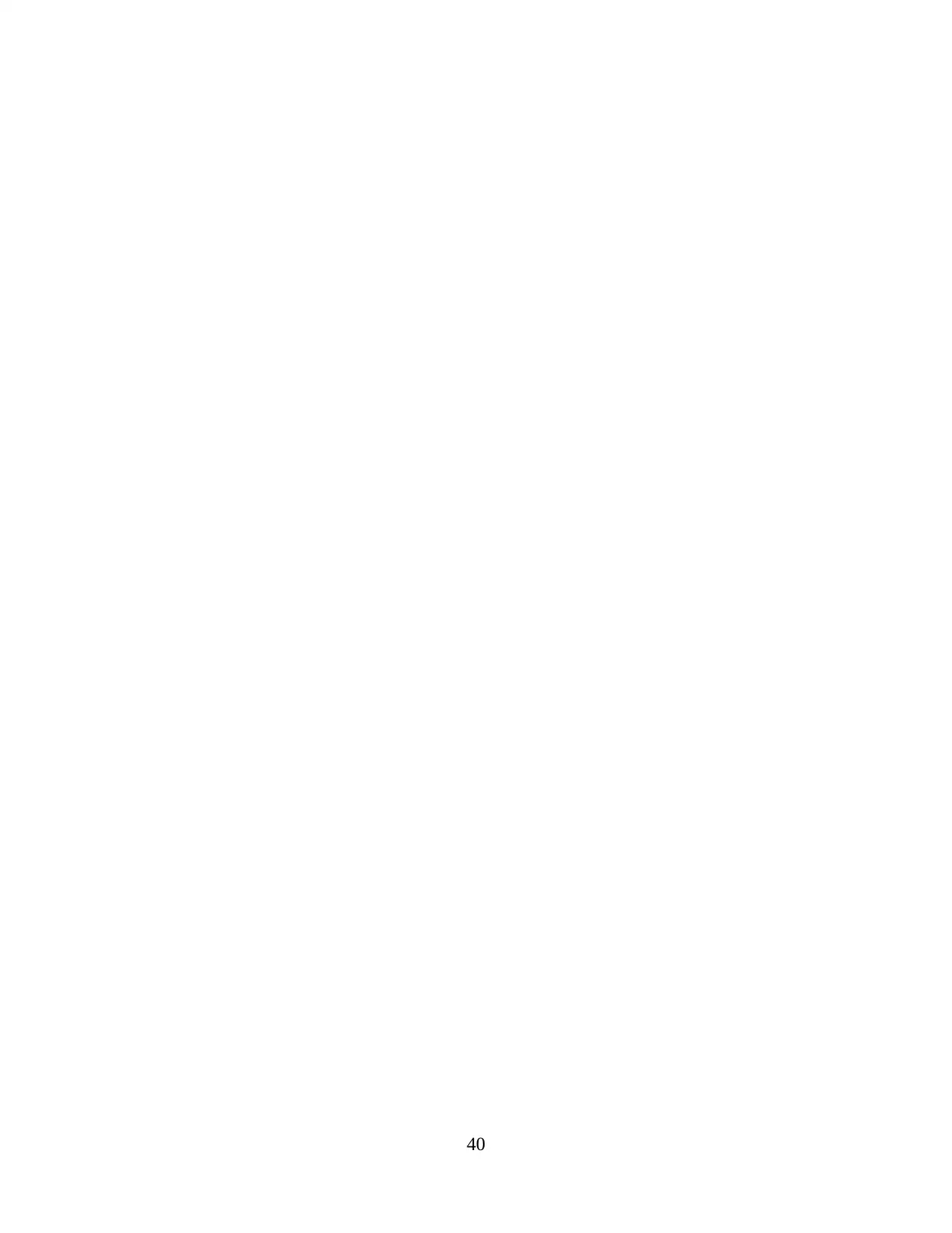
40
1 out of 40
![[object Object]](/_next/image/?url=%2F_next%2Fstatic%2Fmedia%2Flogo.6d15ce61.png&w=640&q=75)
Your All-in-One AI-Powered Toolkit for Academic Success.
+13062052269
info@desklib.com
Available 24*7 on WhatsApp / Email
Unlock your academic potential
© 2024 | Zucol Services PVT LTD | All rights reserved.