Electrolux Inventory Management Improvement
VerifiedAdded on 2020/04/07
|14
|2875
|87
AI Summary
This assignment examines inventory management practices at Electrolux and proposes improvements leveraging logistics principles. The report delves into current strategies and identifies areas for enhancement, focusing on optimizing inventory levels and supply chain efficiency.
Contribute Materials
Your contribution can guide someone’s learning journey. Share your
documents today.
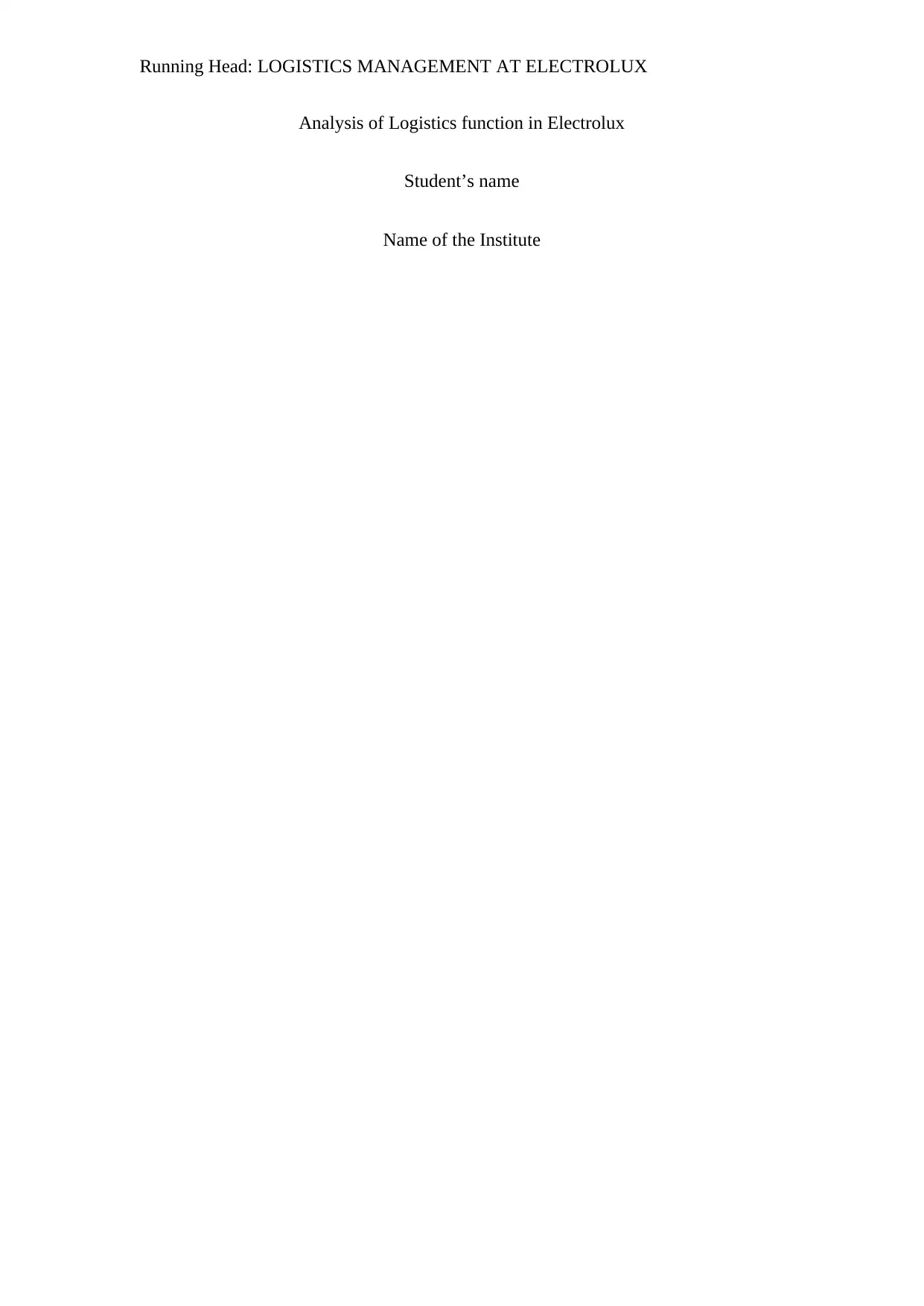
Running Head: LOGISTICS MANAGEMENT AT ELECTROLUX
Analysis of Logistics function in Electrolux
Student’s name
Name of the Institute
Analysis of Logistics function in Electrolux
Student’s name
Name of the Institute
Secure Best Marks with AI Grader
Need help grading? Try our AI Grader for instant feedback on your assignments.
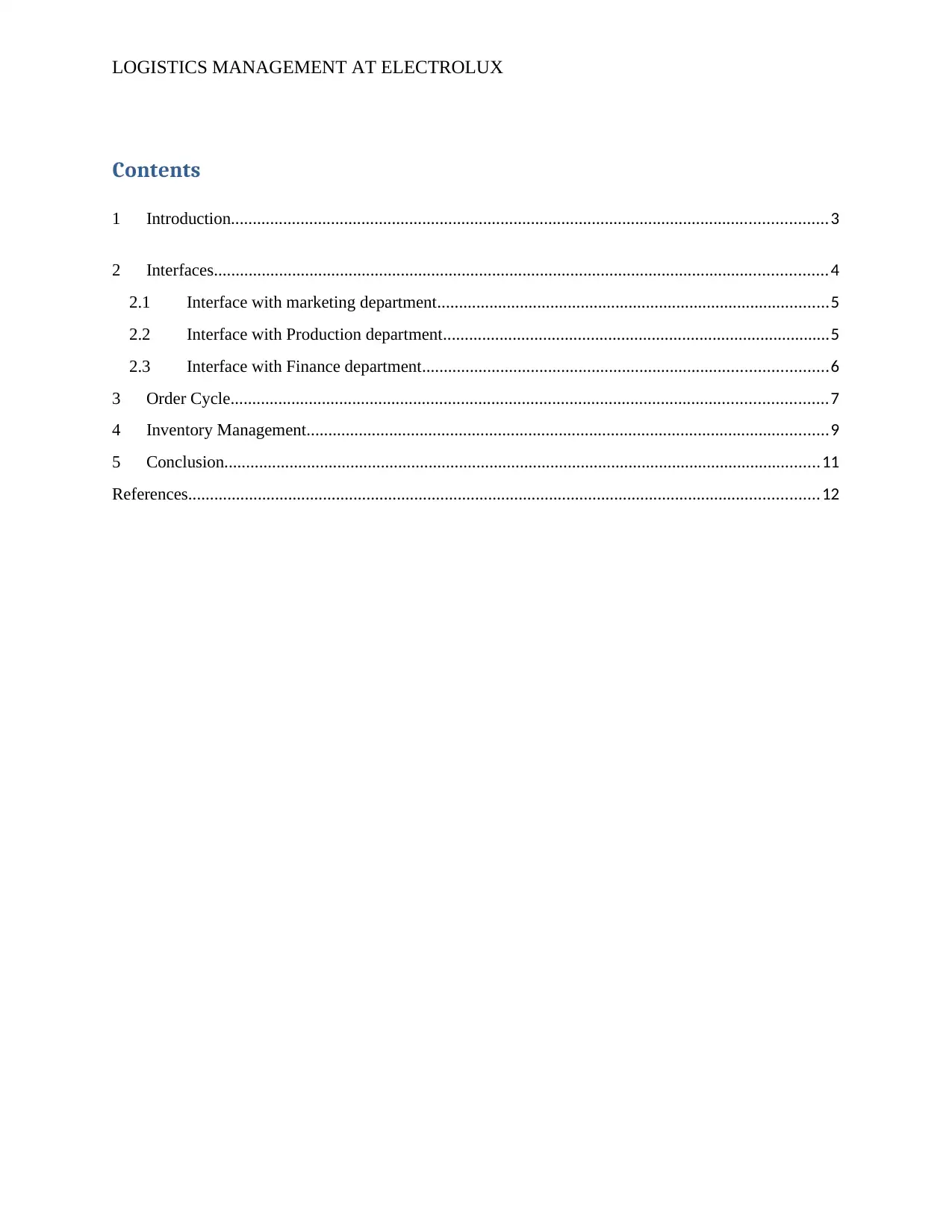
LOGISTICS MANAGEMENT AT ELECTROLUX
Contents
1 Introduction.........................................................................................................................................3
2 Interfaces.............................................................................................................................................4
2.1 Interface with marketing department..........................................................................................5
2.2 Interface with Production department.........................................................................................5
2.3 Interface with Finance department.............................................................................................6
3 Order Cycle.........................................................................................................................................7
4 Inventory Management........................................................................................................................9
5 Conclusion.........................................................................................................................................11
References.................................................................................................................................................12
Contents
1 Introduction.........................................................................................................................................3
2 Interfaces.............................................................................................................................................4
2.1 Interface with marketing department..........................................................................................5
2.2 Interface with Production department.........................................................................................5
2.3 Interface with Finance department.............................................................................................6
3 Order Cycle.........................................................................................................................................7
4 Inventory Management........................................................................................................................9
5 Conclusion.........................................................................................................................................11
References.................................................................................................................................................12
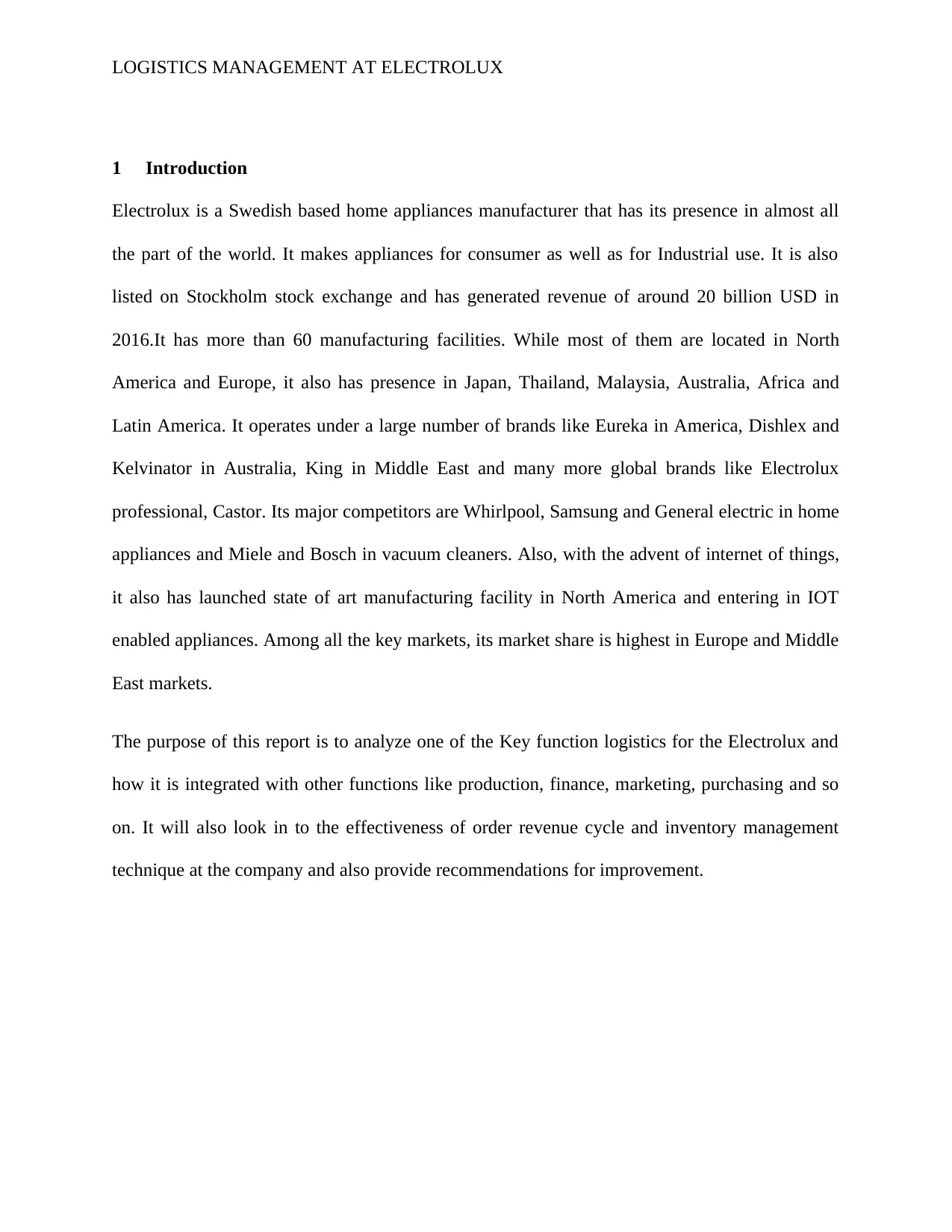
LOGISTICS MANAGEMENT AT ELECTROLUX
1 Introduction
Electrolux is a Swedish based home appliances manufacturer that has its presence in almost all
the part of the world. It makes appliances for consumer as well as for Industrial use. It is also
listed on Stockholm stock exchange and has generated revenue of around 20 billion USD in
2016.It has more than 60 manufacturing facilities. While most of them are located in North
America and Europe, it also has presence in Japan, Thailand, Malaysia, Australia, Africa and
Latin America. It operates under a large number of brands like Eureka in America, Dishlex and
Kelvinator in Australia, King in Middle East and many more global brands like Electrolux
professional, Castor. Its major competitors are Whirlpool, Samsung and General electric in home
appliances and Miele and Bosch in vacuum cleaners. Also, with the advent of internet of things,
it also has launched state of art manufacturing facility in North America and entering in IOT
enabled appliances. Among all the key markets, its market share is highest in Europe and Middle
East markets.
The purpose of this report is to analyze one of the Key function logistics for the Electrolux and
how it is integrated with other functions like production, finance, marketing, purchasing and so
on. It will also look in to the effectiveness of order revenue cycle and inventory management
technique at the company and also provide recommendations for improvement.
1 Introduction
Electrolux is a Swedish based home appliances manufacturer that has its presence in almost all
the part of the world. It makes appliances for consumer as well as for Industrial use. It is also
listed on Stockholm stock exchange and has generated revenue of around 20 billion USD in
2016.It has more than 60 manufacturing facilities. While most of them are located in North
America and Europe, it also has presence in Japan, Thailand, Malaysia, Australia, Africa and
Latin America. It operates under a large number of brands like Eureka in America, Dishlex and
Kelvinator in Australia, King in Middle East and many more global brands like Electrolux
professional, Castor. Its major competitors are Whirlpool, Samsung and General electric in home
appliances and Miele and Bosch in vacuum cleaners. Also, with the advent of internet of things,
it also has launched state of art manufacturing facility in North America and entering in IOT
enabled appliances. Among all the key markets, its market share is highest in Europe and Middle
East markets.
The purpose of this report is to analyze one of the Key function logistics for the Electrolux and
how it is integrated with other functions like production, finance, marketing, purchasing and so
on. It will also look in to the effectiveness of order revenue cycle and inventory management
technique at the company and also provide recommendations for improvement.
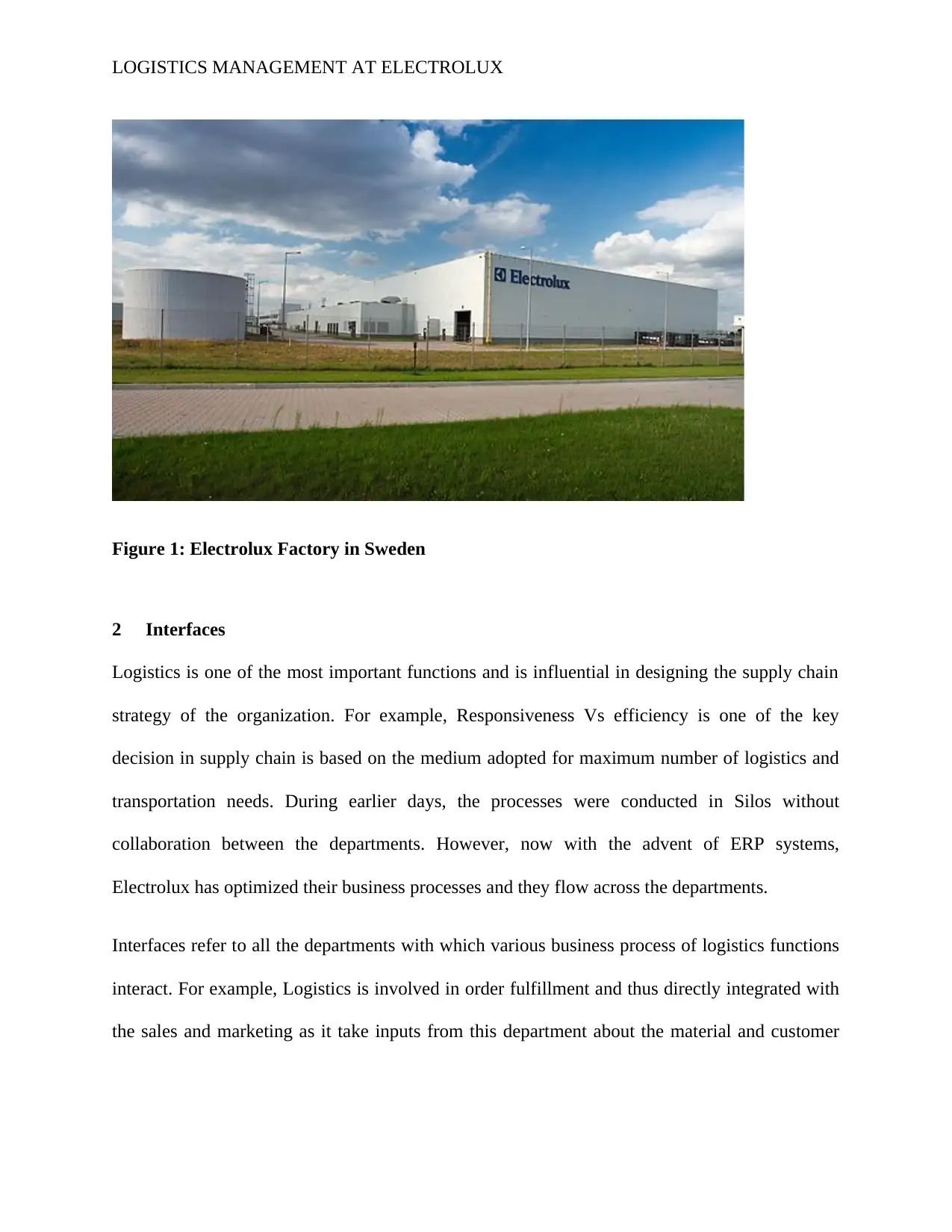
LOGISTICS MANAGEMENT AT ELECTROLUX
Figure 1: Electrolux Factory in Sweden
2 Interfaces
Logistics is one of the most important functions and is influential in designing the supply chain
strategy of the organization. For example, Responsiveness Vs efficiency is one of the key
decision in supply chain is based on the medium adopted for maximum number of logistics and
transportation needs. During earlier days, the processes were conducted in Silos without
collaboration between the departments. However, now with the advent of ERP systems,
Electrolux has optimized their business processes and they flow across the departments.
Interfaces refer to all the departments with which various business process of logistics functions
interact. For example, Logistics is involved in order fulfillment and thus directly integrated with
the sales and marketing as it take inputs from this department about the material and customer
Figure 1: Electrolux Factory in Sweden
2 Interfaces
Logistics is one of the most important functions and is influential in designing the supply chain
strategy of the organization. For example, Responsiveness Vs efficiency is one of the key
decision in supply chain is based on the medium adopted for maximum number of logistics and
transportation needs. During earlier days, the processes were conducted in Silos without
collaboration between the departments. However, now with the advent of ERP systems,
Electrolux has optimized their business processes and they flow across the departments.
Interfaces refer to all the departments with which various business process of logistics functions
interact. For example, Logistics is involved in order fulfillment and thus directly integrated with
the sales and marketing as it take inputs from this department about the material and customer
Secure Best Marks with AI Grader
Need help grading? Try our AI Grader for instant feedback on your assignments.
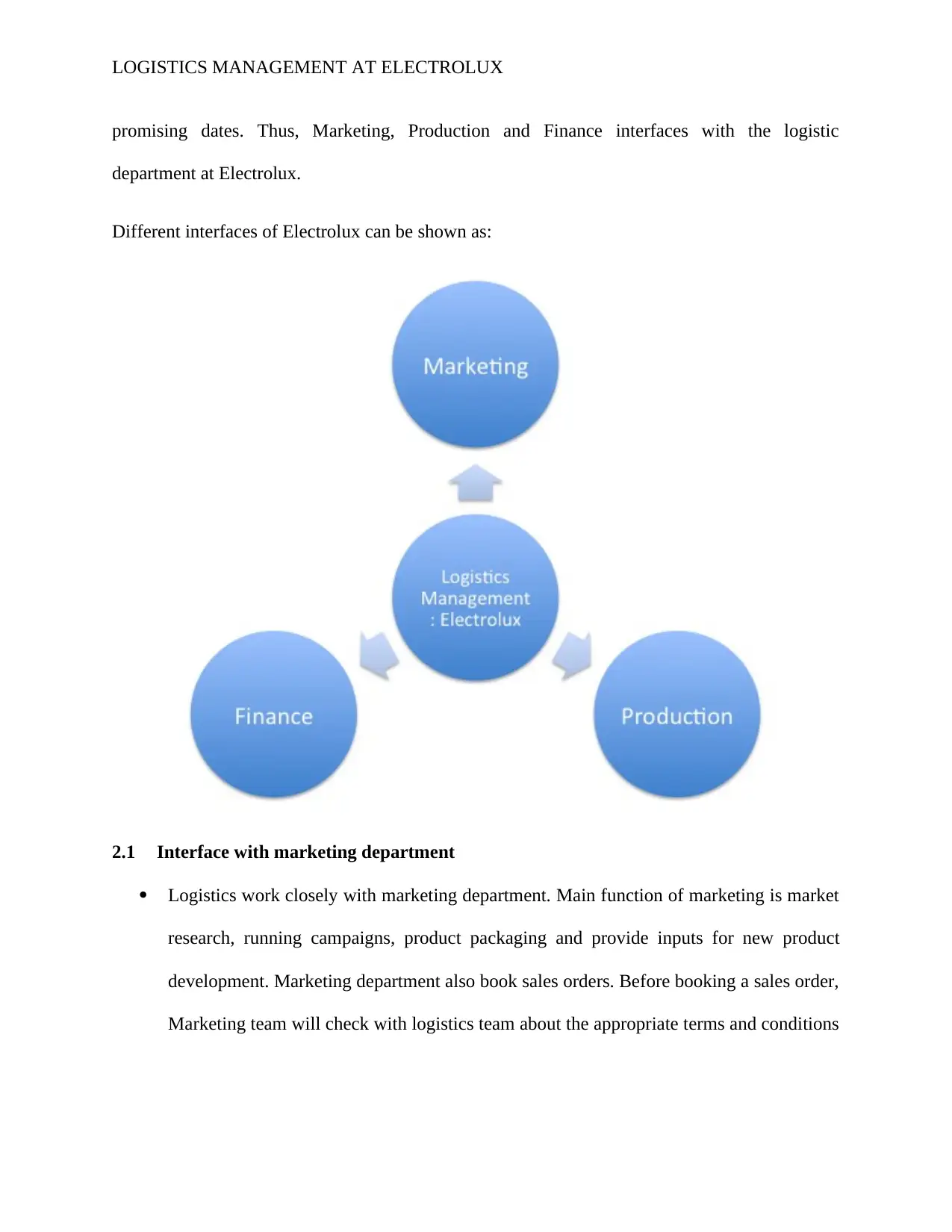
LOGISTICS MANAGEMENT AT ELECTROLUX
promising dates. Thus, Marketing, Production and Finance interfaces with the logistic
department at Electrolux.
Different interfaces of Electrolux can be shown as:
2.1 Interface with marketing department
Logistics work closely with marketing department. Main function of marketing is market
research, running campaigns, product packaging and provide inputs for new product
development. Marketing department also book sales orders. Before booking a sales order,
Marketing team will check with logistics team about the appropriate terms and conditions
promising dates. Thus, Marketing, Production and Finance interfaces with the logistic
department at Electrolux.
Different interfaces of Electrolux can be shown as:
2.1 Interface with marketing department
Logistics work closely with marketing department. Main function of marketing is market
research, running campaigns, product packaging and provide inputs for new product
development. Marketing department also book sales orders. Before booking a sales order,
Marketing team will check with logistics team about the appropriate terms and conditions
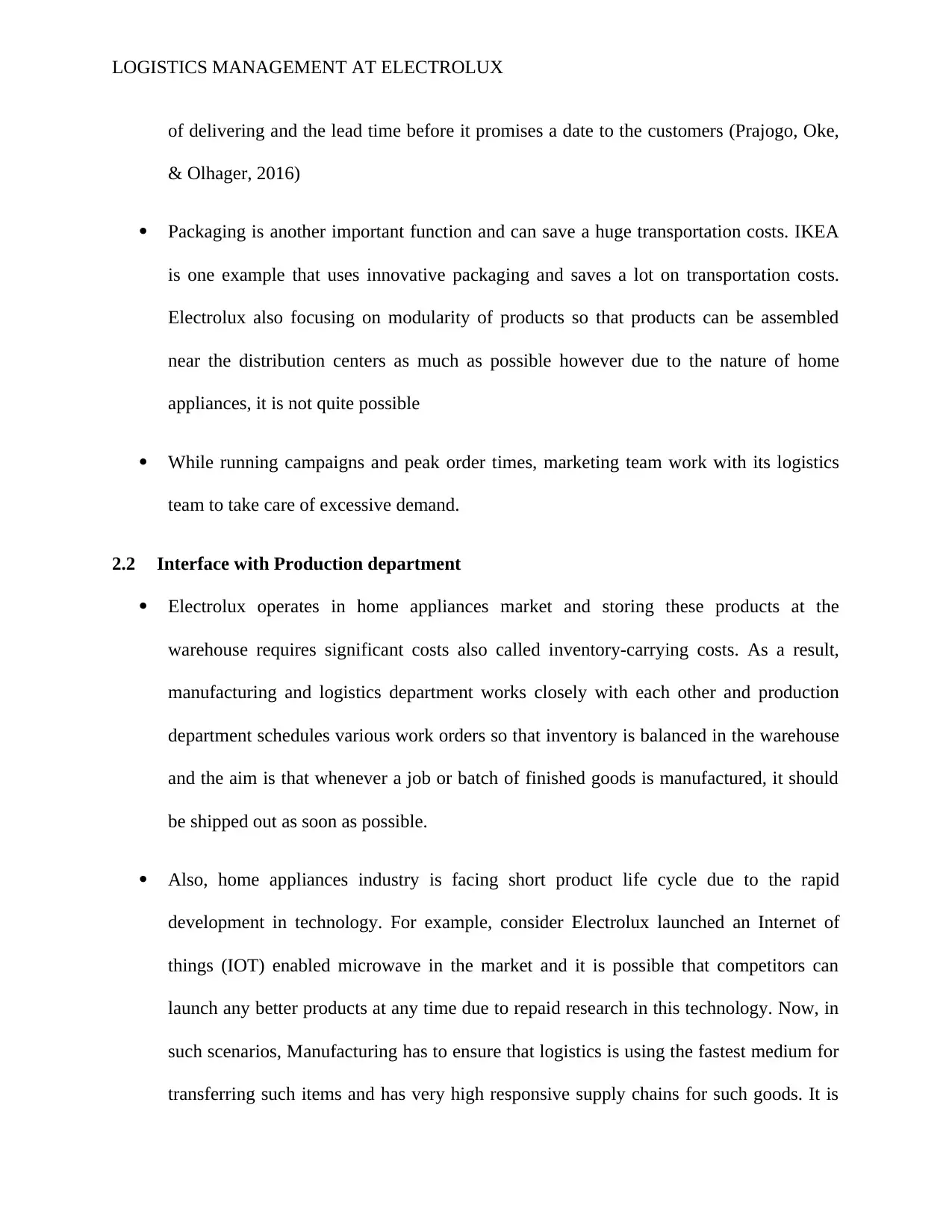
LOGISTICS MANAGEMENT AT ELECTROLUX
of delivering and the lead time before it promises a date to the customers (Prajogo, Oke,
& Olhager, 2016)
Packaging is another important function and can save a huge transportation costs. IKEA
is one example that uses innovative packaging and saves a lot on transportation costs.
Electrolux also focusing on modularity of products so that products can be assembled
near the distribution centers as much as possible however due to the nature of home
appliances, it is not quite possible
While running campaigns and peak order times, marketing team work with its logistics
team to take care of excessive demand.
2.2 Interface with Production department
Electrolux operates in home appliances market and storing these products at the
warehouse requires significant costs also called inventory-carrying costs. As a result,
manufacturing and logistics department works closely with each other and production
department schedules various work orders so that inventory is balanced in the warehouse
and the aim is that whenever a job or batch of finished goods is manufactured, it should
be shipped out as soon as possible.
Also, home appliances industry is facing short product life cycle due to the rapid
development in technology. For example, consider Electrolux launched an Internet of
things (IOT) enabled microwave in the market and it is possible that competitors can
launch any better products at any time due to repaid research in this technology. Now, in
such scenarios, Manufacturing has to ensure that logistics is using the fastest medium for
transferring such items and has very high responsive supply chains for such goods. It is
of delivering and the lead time before it promises a date to the customers (Prajogo, Oke,
& Olhager, 2016)
Packaging is another important function and can save a huge transportation costs. IKEA
is one example that uses innovative packaging and saves a lot on transportation costs.
Electrolux also focusing on modularity of products so that products can be assembled
near the distribution centers as much as possible however due to the nature of home
appliances, it is not quite possible
While running campaigns and peak order times, marketing team work with its logistics
team to take care of excessive demand.
2.2 Interface with Production department
Electrolux operates in home appliances market and storing these products at the
warehouse requires significant costs also called inventory-carrying costs. As a result,
manufacturing and logistics department works closely with each other and production
department schedules various work orders so that inventory is balanced in the warehouse
and the aim is that whenever a job or batch of finished goods is manufactured, it should
be shipped out as soon as possible.
Also, home appliances industry is facing short product life cycle due to the rapid
development in technology. For example, consider Electrolux launched an Internet of
things (IOT) enabled microwave in the market and it is possible that competitors can
launch any better products at any time due to repaid research in this technology. Now, in
such scenarios, Manufacturing has to ensure that logistics is using the fastest medium for
transferring such items and has very high responsive supply chains for such goods. It is
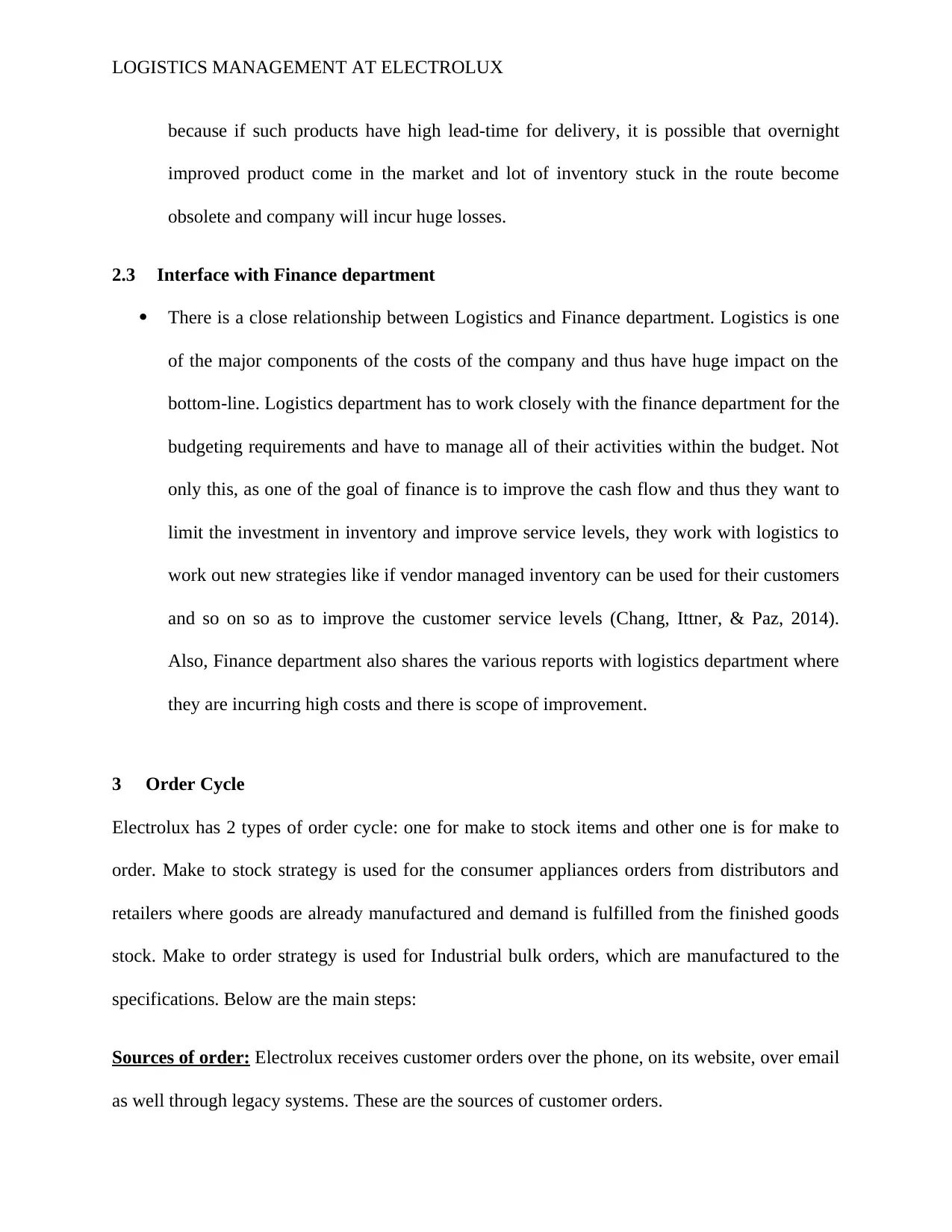
LOGISTICS MANAGEMENT AT ELECTROLUX
because if such products have high lead-time for delivery, it is possible that overnight
improved product come in the market and lot of inventory stuck in the route become
obsolete and company will incur huge losses.
2.3 Interface with Finance department
There is a close relationship between Logistics and Finance department. Logistics is one
of the major components of the costs of the company and thus have huge impact on the
bottom-line. Logistics department has to work closely with the finance department for the
budgeting requirements and have to manage all of their activities within the budget. Not
only this, as one of the goal of finance is to improve the cash flow and thus they want to
limit the investment in inventory and improve service levels, they work with logistics to
work out new strategies like if vendor managed inventory can be used for their customers
and so on so as to improve the customer service levels (Chang, Ittner, & Paz, 2014).
Also, Finance department also shares the various reports with logistics department where
they are incurring high costs and there is scope of improvement.
3 Order Cycle
Electrolux has 2 types of order cycle: one for make to stock items and other one is for make to
order. Make to stock strategy is used for the consumer appliances orders from distributors and
retailers where goods are already manufactured and demand is fulfilled from the finished goods
stock. Make to order strategy is used for Industrial bulk orders, which are manufactured to the
specifications. Below are the main steps:
Sources of order: Electrolux receives customer orders over the phone, on its website, over email
as well through legacy systems. These are the sources of customer orders.
because if such products have high lead-time for delivery, it is possible that overnight
improved product come in the market and lot of inventory stuck in the route become
obsolete and company will incur huge losses.
2.3 Interface with Finance department
There is a close relationship between Logistics and Finance department. Logistics is one
of the major components of the costs of the company and thus have huge impact on the
bottom-line. Logistics department has to work closely with the finance department for the
budgeting requirements and have to manage all of their activities within the budget. Not
only this, as one of the goal of finance is to improve the cash flow and thus they want to
limit the investment in inventory and improve service levels, they work with logistics to
work out new strategies like if vendor managed inventory can be used for their customers
and so on so as to improve the customer service levels (Chang, Ittner, & Paz, 2014).
Also, Finance department also shares the various reports with logistics department where
they are incurring high costs and there is scope of improvement.
3 Order Cycle
Electrolux has 2 types of order cycle: one for make to stock items and other one is for make to
order. Make to stock strategy is used for the consumer appliances orders from distributors and
retailers where goods are already manufactured and demand is fulfilled from the finished goods
stock. Make to order strategy is used for Industrial bulk orders, which are manufactured to the
specifications. Below are the main steps:
Sources of order: Electrolux receives customer orders over the phone, on its website, over email
as well through legacy systems. These are the sources of customer orders.
Paraphrase This Document
Need a fresh take? Get an instant paraphrase of this document with our AI Paraphraser
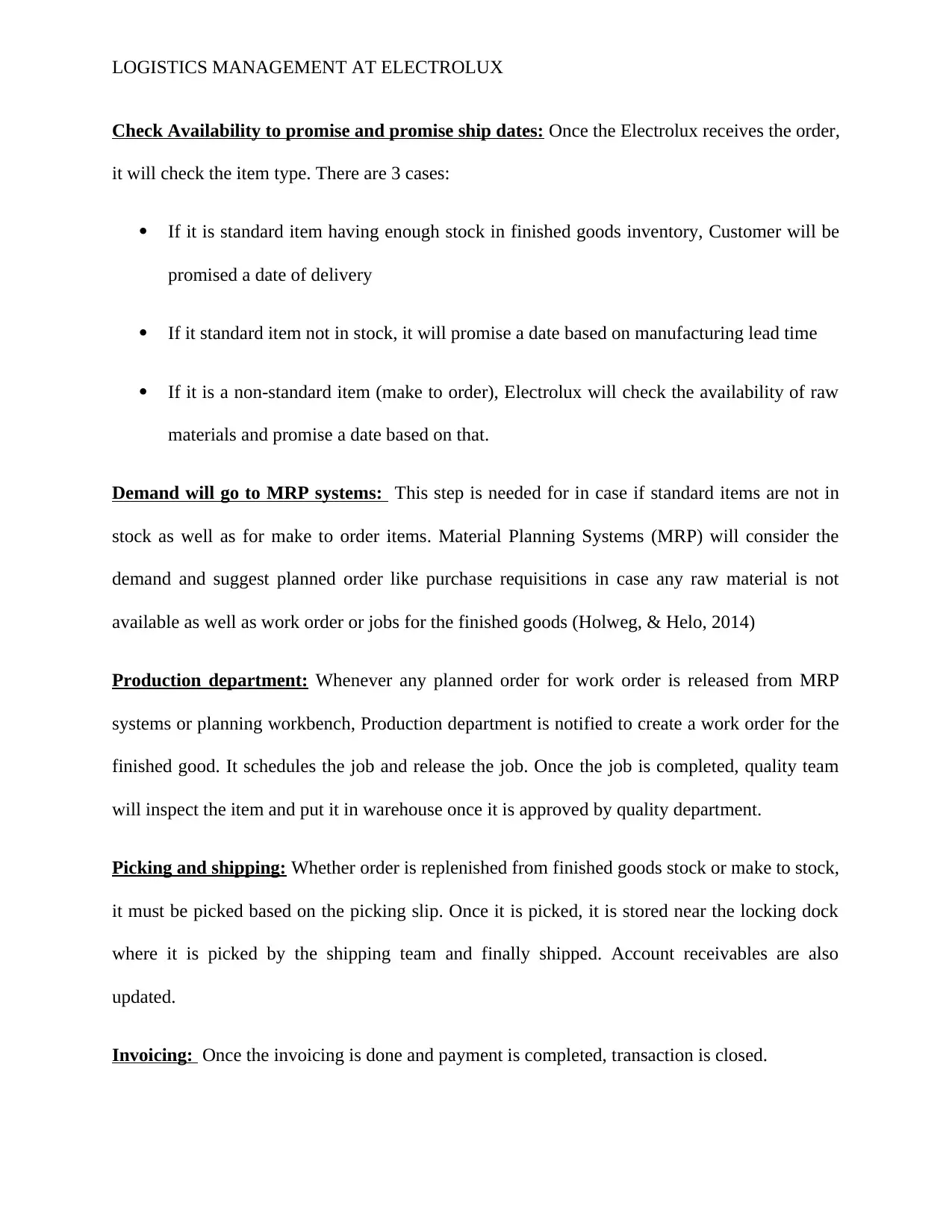
LOGISTICS MANAGEMENT AT ELECTROLUX
Check Availability to promise and promise ship dates: Once the Electrolux receives the order,
it will check the item type. There are 3 cases:
If it is standard item having enough stock in finished goods inventory, Customer will be
promised a date of delivery
If it standard item not in stock, it will promise a date based on manufacturing lead time
If it is a non-standard item (make to order), Electrolux will check the availability of raw
materials and promise a date based on that.
Demand will go to MRP systems: This step is needed for in case if standard items are not in
stock as well as for make to order items. Material Planning Systems (MRP) will consider the
demand and suggest planned order like purchase requisitions in case any raw material is not
available as well as work order or jobs for the finished goods (Holweg, & Helo, 2014)
Production department: Whenever any planned order for work order is released from MRP
systems or planning workbench, Production department is notified to create a work order for the
finished good. It schedules the job and release the job. Once the job is completed, quality team
will inspect the item and put it in warehouse once it is approved by quality department.
Picking and shipping: Whether order is replenished from finished goods stock or make to stock,
it must be picked based on the picking slip. Once it is picked, it is stored near the locking dock
where it is picked by the shipping team and finally shipped. Account receivables are also
updated.
Invoicing: Once the invoicing is done and payment is completed, transaction is closed.
Check Availability to promise and promise ship dates: Once the Electrolux receives the order,
it will check the item type. There are 3 cases:
If it is standard item having enough stock in finished goods inventory, Customer will be
promised a date of delivery
If it standard item not in stock, it will promise a date based on manufacturing lead time
If it is a non-standard item (make to order), Electrolux will check the availability of raw
materials and promise a date based on that.
Demand will go to MRP systems: This step is needed for in case if standard items are not in
stock as well as for make to order items. Material Planning Systems (MRP) will consider the
demand and suggest planned order like purchase requisitions in case any raw material is not
available as well as work order or jobs for the finished goods (Holweg, & Helo, 2014)
Production department: Whenever any planned order for work order is released from MRP
systems or planning workbench, Production department is notified to create a work order for the
finished good. It schedules the job and release the job. Once the job is completed, quality team
will inspect the item and put it in warehouse once it is approved by quality department.
Picking and shipping: Whether order is replenished from finished goods stock or make to stock,
it must be picked based on the picking slip. Once it is picked, it is stored near the locking dock
where it is picked by the shipping team and finally shipped. Account receivables are also
updated.
Invoicing: Once the invoicing is done and payment is completed, transaction is closed.
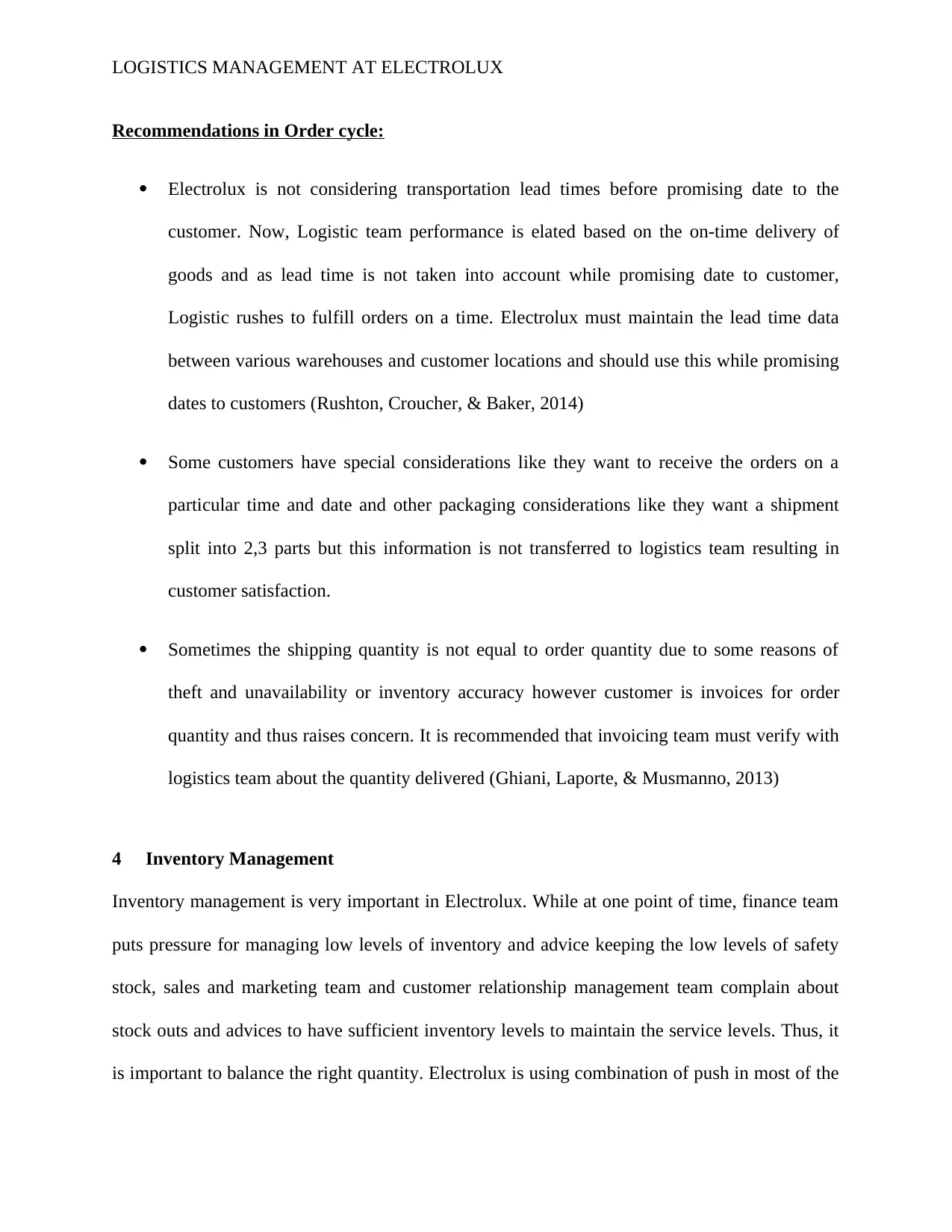
LOGISTICS MANAGEMENT AT ELECTROLUX
Recommendations in Order cycle:
Electrolux is not considering transportation lead times before promising date to the
customer. Now, Logistic team performance is elated based on the on-time delivery of
goods and as lead time is not taken into account while promising date to customer,
Logistic rushes to fulfill orders on a time. Electrolux must maintain the lead time data
between various warehouses and customer locations and should use this while promising
dates to customers (Rushton, Croucher, & Baker, 2014)
Some customers have special considerations like they want to receive the orders on a
particular time and date and other packaging considerations like they want a shipment
split into 2,3 parts but this information is not transferred to logistics team resulting in
customer satisfaction.
Sometimes the shipping quantity is not equal to order quantity due to some reasons of
theft and unavailability or inventory accuracy however customer is invoices for order
quantity and thus raises concern. It is recommended that invoicing team must verify with
logistics team about the quantity delivered (Ghiani, Laporte, & Musmanno, 2013)
4 Inventory Management
Inventory management is very important in Electrolux. While at one point of time, finance team
puts pressure for managing low levels of inventory and advice keeping the low levels of safety
stock, sales and marketing team and customer relationship management team complain about
stock outs and advices to have sufficient inventory levels to maintain the service levels. Thus, it
is important to balance the right quantity. Electrolux is using combination of push in most of the
Recommendations in Order cycle:
Electrolux is not considering transportation lead times before promising date to the
customer. Now, Logistic team performance is elated based on the on-time delivery of
goods and as lead time is not taken into account while promising date to customer,
Logistic rushes to fulfill orders on a time. Electrolux must maintain the lead time data
between various warehouses and customer locations and should use this while promising
dates to customers (Rushton, Croucher, & Baker, 2014)
Some customers have special considerations like they want to receive the orders on a
particular time and date and other packaging considerations like they want a shipment
split into 2,3 parts but this information is not transferred to logistics team resulting in
customer satisfaction.
Sometimes the shipping quantity is not equal to order quantity due to some reasons of
theft and unavailability or inventory accuracy however customer is invoices for order
quantity and thus raises concern. It is recommended that invoicing team must verify with
logistics team about the quantity delivered (Ghiani, Laporte, & Musmanno, 2013)
4 Inventory Management
Inventory management is very important in Electrolux. While at one point of time, finance team
puts pressure for managing low levels of inventory and advice keeping the low levels of safety
stock, sales and marketing team and customer relationship management team complain about
stock outs and advices to have sufficient inventory levels to maintain the service levels. Thus, it
is important to balance the right quantity. Electrolux is using combination of push in most of the
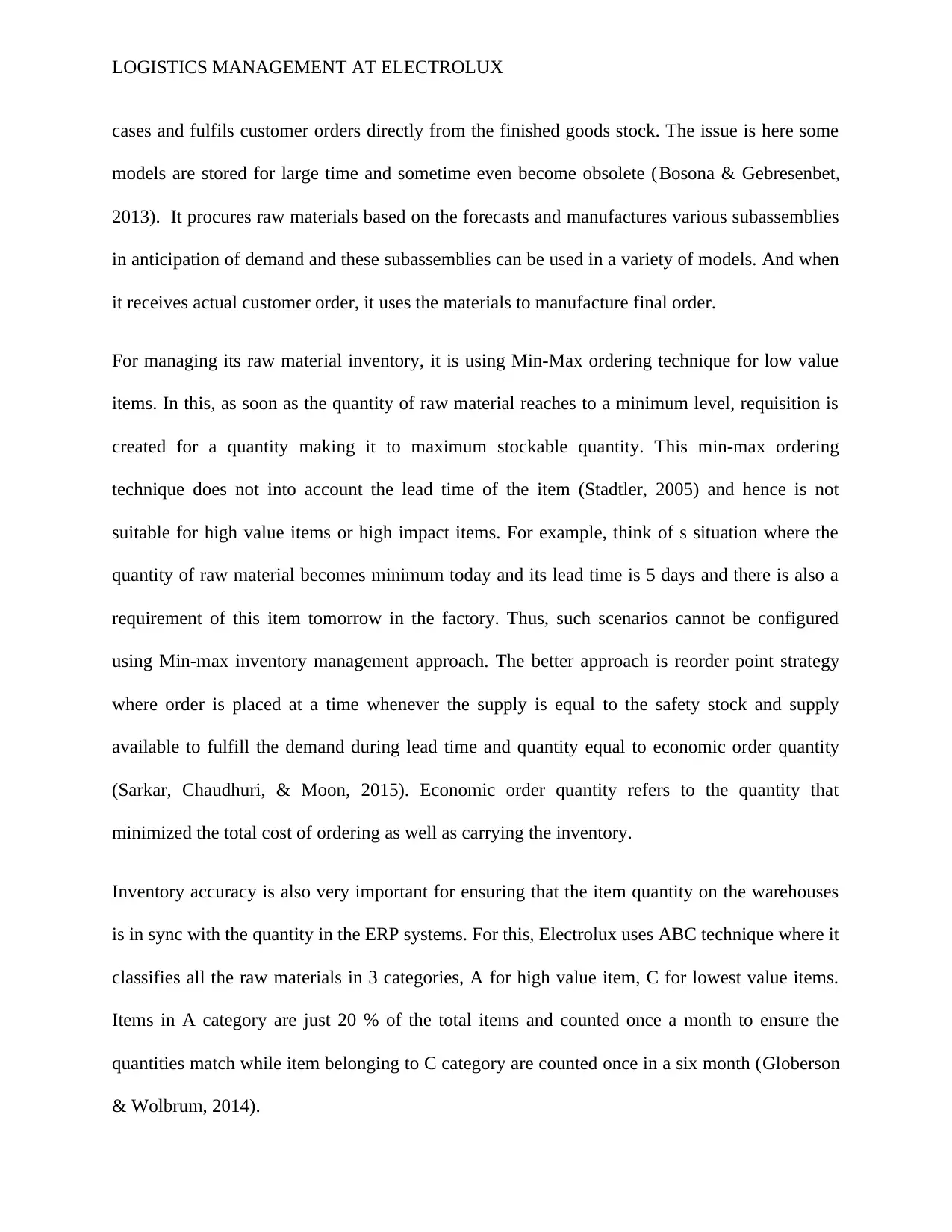
LOGISTICS MANAGEMENT AT ELECTROLUX
cases and fulfils customer orders directly from the finished goods stock. The issue is here some
models are stored for large time and sometime even become obsolete (Bosona & Gebresenbet,
2013). It procures raw materials based on the forecasts and manufactures various subassemblies
in anticipation of demand and these subassemblies can be used in a variety of models. And when
it receives actual customer order, it uses the materials to manufacture final order.
For managing its raw material inventory, it is using Min-Max ordering technique for low value
items. In this, as soon as the quantity of raw material reaches to a minimum level, requisition is
created for a quantity making it to maximum stockable quantity. This min-max ordering
technique does not into account the lead time of the item (Stadtler, 2005) and hence is not
suitable for high value items or high impact items. For example, think of s situation where the
quantity of raw material becomes minimum today and its lead time is 5 days and there is also a
requirement of this item tomorrow in the factory. Thus, such scenarios cannot be configured
using Min-max inventory management approach. The better approach is reorder point strategy
where order is placed at a time whenever the supply is equal to the safety stock and supply
available to fulfill the demand during lead time and quantity equal to economic order quantity
(Sarkar, Chaudhuri, & Moon, 2015). Economic order quantity refers to the quantity that
minimized the total cost of ordering as well as carrying the inventory.
Inventory accuracy is also very important for ensuring that the item quantity on the warehouses
is in sync with the quantity in the ERP systems. For this, Electrolux uses ABC technique where it
classifies all the raw materials in 3 categories, A for high value item, C for lowest value items.
Items in A category are just 20 % of the total items and counted once a month to ensure the
quantities match while item belonging to C category are counted once in a six month (Globerson
& Wolbrum, 2014).
cases and fulfils customer orders directly from the finished goods stock. The issue is here some
models are stored for large time and sometime even become obsolete (Bosona & Gebresenbet,
2013). It procures raw materials based on the forecasts and manufactures various subassemblies
in anticipation of demand and these subassemblies can be used in a variety of models. And when
it receives actual customer order, it uses the materials to manufacture final order.
For managing its raw material inventory, it is using Min-Max ordering technique for low value
items. In this, as soon as the quantity of raw material reaches to a minimum level, requisition is
created for a quantity making it to maximum stockable quantity. This min-max ordering
technique does not into account the lead time of the item (Stadtler, 2005) and hence is not
suitable for high value items or high impact items. For example, think of s situation where the
quantity of raw material becomes minimum today and its lead time is 5 days and there is also a
requirement of this item tomorrow in the factory. Thus, such scenarios cannot be configured
using Min-max inventory management approach. The better approach is reorder point strategy
where order is placed at a time whenever the supply is equal to the safety stock and supply
available to fulfill the demand during lead time and quantity equal to economic order quantity
(Sarkar, Chaudhuri, & Moon, 2015). Economic order quantity refers to the quantity that
minimized the total cost of ordering as well as carrying the inventory.
Inventory accuracy is also very important for ensuring that the item quantity on the warehouses
is in sync with the quantity in the ERP systems. For this, Electrolux uses ABC technique where it
classifies all the raw materials in 3 categories, A for high value item, C for lowest value items.
Items in A category are just 20 % of the total items and counted once a month to ensure the
quantities match while item belonging to C category are counted once in a six month (Globerson
& Wolbrum, 2014).
Secure Best Marks with AI Grader
Need help grading? Try our AI Grader for instant feedback on your assignments.
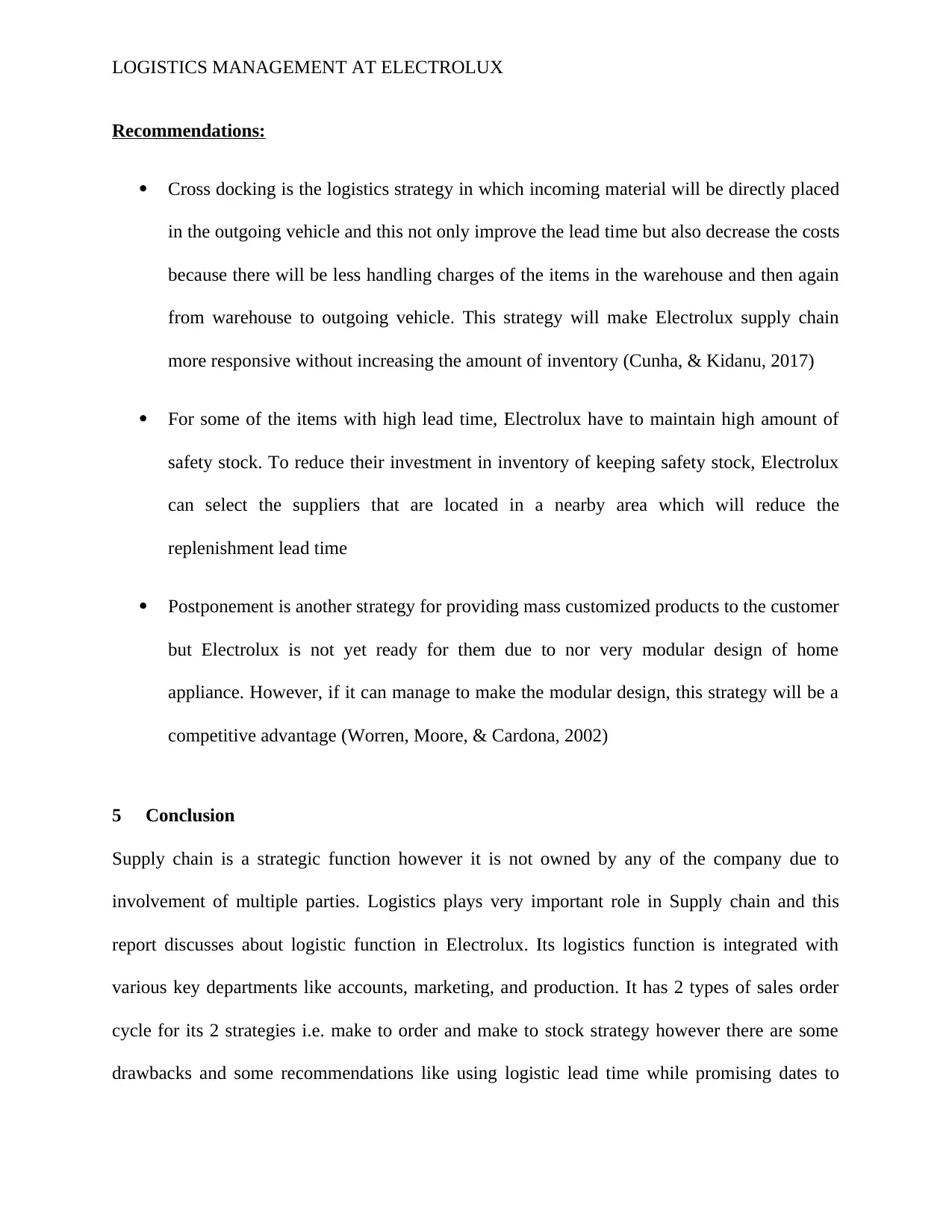
LOGISTICS MANAGEMENT AT ELECTROLUX
Recommendations:
Cross docking is the logistics strategy in which incoming material will be directly placed
in the outgoing vehicle and this not only improve the lead time but also decrease the costs
because there will be less handling charges of the items in the warehouse and then again
from warehouse to outgoing vehicle. This strategy will make Electrolux supply chain
more responsive without increasing the amount of inventory (Cunha, & Kidanu, 2017)
For some of the items with high lead time, Electrolux have to maintain high amount of
safety stock. To reduce their investment in inventory of keeping safety stock, Electrolux
can select the suppliers that are located in a nearby area which will reduce the
replenishment lead time
Postponement is another strategy for providing mass customized products to the customer
but Electrolux is not yet ready for them due to nor very modular design of home
appliance. However, if it can manage to make the modular design, this strategy will be a
competitive advantage (Worren, Moore, & Cardona, 2002)
5 Conclusion
Supply chain is a strategic function however it is not owned by any of the company due to
involvement of multiple parties. Logistics plays very important role in Supply chain and this
report discusses about logistic function in Electrolux. Its logistics function is integrated with
various key departments like accounts, marketing, and production. It has 2 types of sales order
cycle for its 2 strategies i.e. make to order and make to stock strategy however there are some
drawbacks and some recommendations like using logistic lead time while promising dates to
Recommendations:
Cross docking is the logistics strategy in which incoming material will be directly placed
in the outgoing vehicle and this not only improve the lead time but also decrease the costs
because there will be less handling charges of the items in the warehouse and then again
from warehouse to outgoing vehicle. This strategy will make Electrolux supply chain
more responsive without increasing the amount of inventory (Cunha, & Kidanu, 2017)
For some of the items with high lead time, Electrolux have to maintain high amount of
safety stock. To reduce their investment in inventory of keeping safety stock, Electrolux
can select the suppliers that are located in a nearby area which will reduce the
replenishment lead time
Postponement is another strategy for providing mass customized products to the customer
but Electrolux is not yet ready for them due to nor very modular design of home
appliance. However, if it can manage to make the modular design, this strategy will be a
competitive advantage (Worren, Moore, & Cardona, 2002)
5 Conclusion
Supply chain is a strategic function however it is not owned by any of the company due to
involvement of multiple parties. Logistics plays very important role in Supply chain and this
report discusses about logistic function in Electrolux. Its logistics function is integrated with
various key departments like accounts, marketing, and production. It has 2 types of sales order
cycle for its 2 strategies i.e. make to order and make to stock strategy however there are some
drawbacks and some recommendations like using logistic lead time while promising dates to
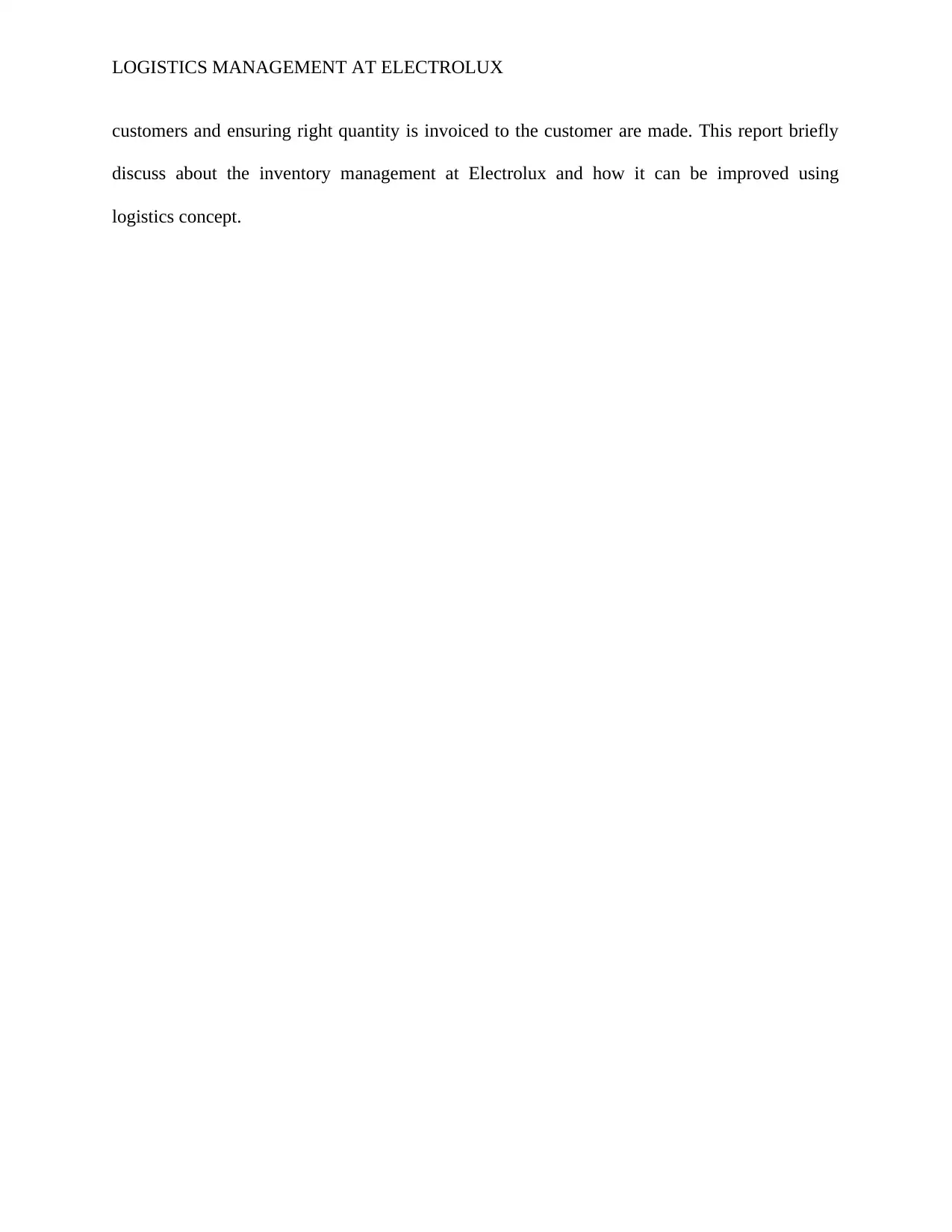
LOGISTICS MANAGEMENT AT ELECTROLUX
customers and ensuring right quantity is invoiced to the customer are made. This report briefly
discuss about the inventory management at Electrolux and how it can be improved using
logistics concept.
customers and ensuring right quantity is invoiced to the customer are made. This report briefly
discuss about the inventory management at Electrolux and how it can be improved using
logistics concept.
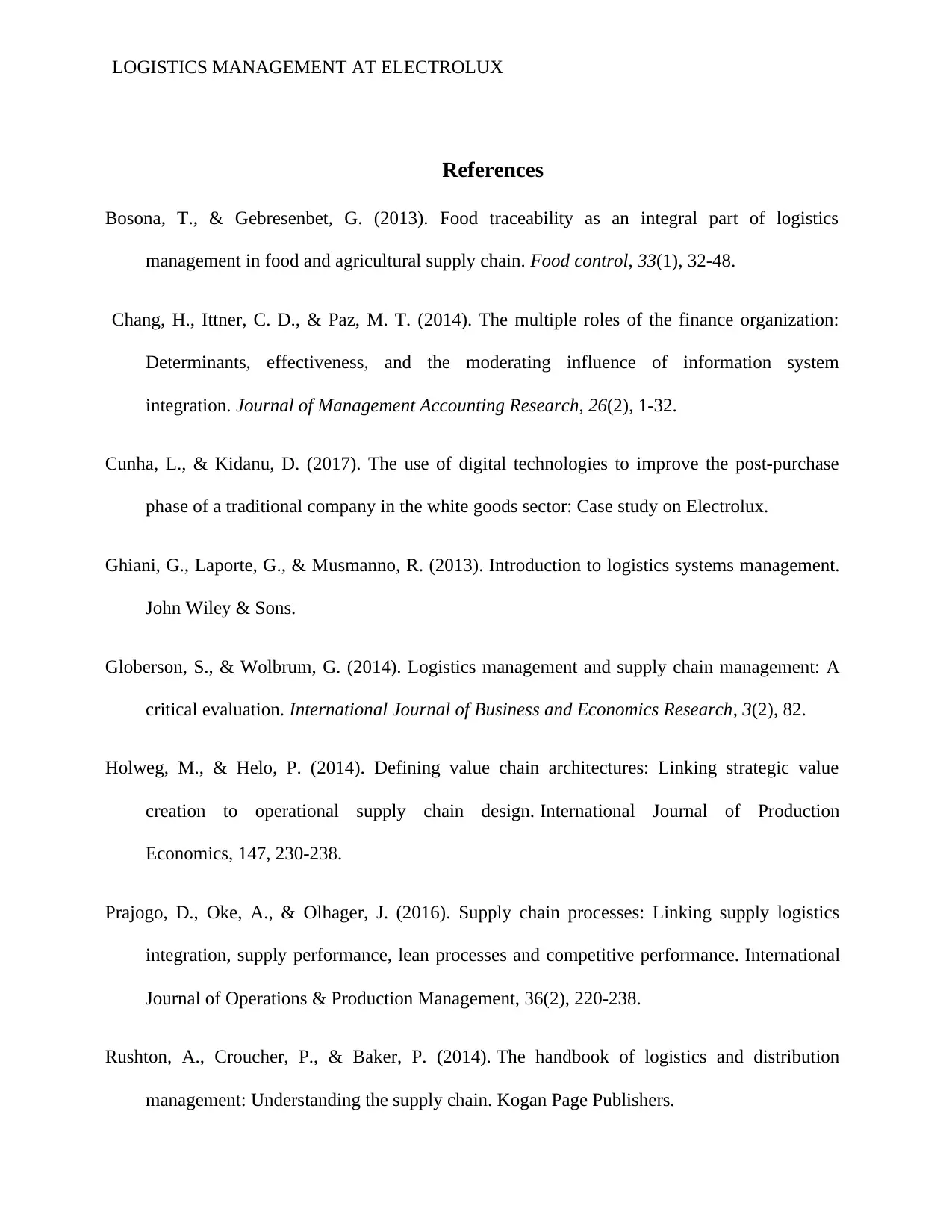
LOGISTICS MANAGEMENT AT ELECTROLUX
References
Bosona, T., & Gebresenbet, G. (2013). Food traceability as an integral part of logistics
management in food and agricultural supply chain. Food control, 33(1), 32-48.
Chang, H., Ittner, C. D., & Paz, M. T. (2014). The multiple roles of the finance organization:
Determinants, effectiveness, and the moderating influence of information system
integration. Journal of Management Accounting Research, 26(2), 1-32.
Cunha, L., & Kidanu, D. (2017). The use of digital technologies to improve the post-purchase
phase of a traditional company in the white goods sector: Case study on Electrolux.
Ghiani, G., Laporte, G., & Musmanno, R. (2013). Introduction to logistics systems management.
John Wiley & Sons.
Globerson, S., & Wolbrum, G. (2014). Logistics management and supply chain management: A
critical evaluation. International Journal of Business and Economics Research, 3(2), 82.
Holweg, M., & Helo, P. (2014). Defining value chain architectures: Linking strategic value
creation to operational supply chain design. International Journal of Production
Economics, 147, 230-238.
Prajogo, D., Oke, A., & Olhager, J. (2016). Supply chain processes: Linking supply logistics
integration, supply performance, lean processes and competitive performance. International
Journal of Operations & Production Management, 36(2), 220-238.
Rushton, A., Croucher, P., & Baker, P. (2014). The handbook of logistics and distribution
management: Understanding the supply chain. Kogan Page Publishers.
References
Bosona, T., & Gebresenbet, G. (2013). Food traceability as an integral part of logistics
management in food and agricultural supply chain. Food control, 33(1), 32-48.
Chang, H., Ittner, C. D., & Paz, M. T. (2014). The multiple roles of the finance organization:
Determinants, effectiveness, and the moderating influence of information system
integration. Journal of Management Accounting Research, 26(2), 1-32.
Cunha, L., & Kidanu, D. (2017). The use of digital technologies to improve the post-purchase
phase of a traditional company in the white goods sector: Case study on Electrolux.
Ghiani, G., Laporte, G., & Musmanno, R. (2013). Introduction to logistics systems management.
John Wiley & Sons.
Globerson, S., & Wolbrum, G. (2014). Logistics management and supply chain management: A
critical evaluation. International Journal of Business and Economics Research, 3(2), 82.
Holweg, M., & Helo, P. (2014). Defining value chain architectures: Linking strategic value
creation to operational supply chain design. International Journal of Production
Economics, 147, 230-238.
Prajogo, D., Oke, A., & Olhager, J. (2016). Supply chain processes: Linking supply logistics
integration, supply performance, lean processes and competitive performance. International
Journal of Operations & Production Management, 36(2), 220-238.
Rushton, A., Croucher, P., & Baker, P. (2014). The handbook of logistics and distribution
management: Understanding the supply chain. Kogan Page Publishers.
Paraphrase This Document
Need a fresh take? Get an instant paraphrase of this document with our AI Paraphraser
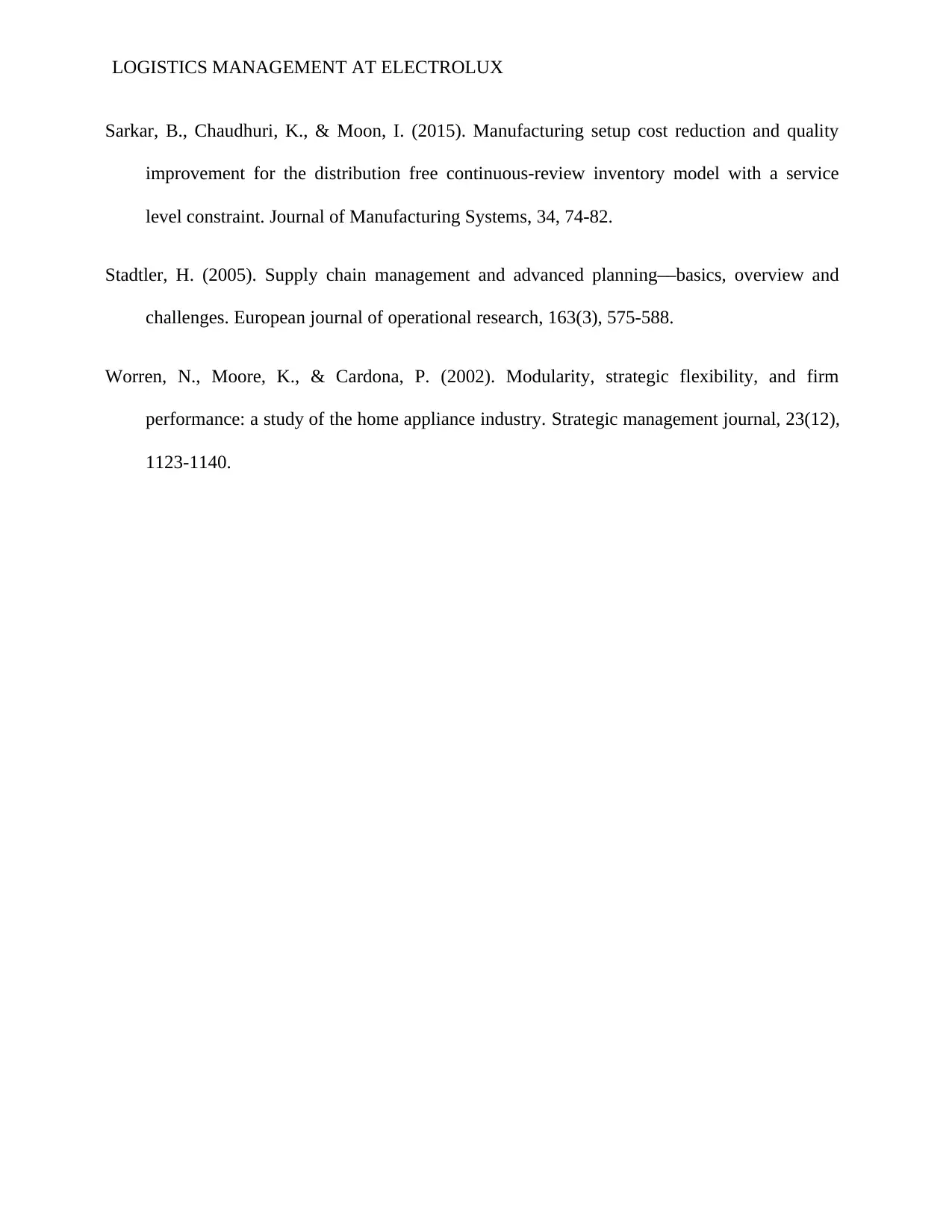
LOGISTICS MANAGEMENT AT ELECTROLUX
Sarkar, B., Chaudhuri, K., & Moon, I. (2015). Manufacturing setup cost reduction and quality
improvement for the distribution free continuous-review inventory model with a service
level constraint. Journal of Manufacturing Systems, 34, 74-82.
Stadtler, H. (2005). Supply chain management and advanced planning––basics, overview and
challenges. European journal of operational research, 163(3), 575-588.
Worren, N., Moore, K., & Cardona, P. (2002). Modularity, strategic flexibility, and firm
performance: a study of the home appliance industry. Strategic management journal, 23(12),
1123-1140.
Sarkar, B., Chaudhuri, K., & Moon, I. (2015). Manufacturing setup cost reduction and quality
improvement for the distribution free continuous-review inventory model with a service
level constraint. Journal of Manufacturing Systems, 34, 74-82.
Stadtler, H. (2005). Supply chain management and advanced planning––basics, overview and
challenges. European journal of operational research, 163(3), 575-588.
Worren, N., Moore, K., & Cardona, P. (2002). Modularity, strategic flexibility, and firm
performance: a study of the home appliance industry. Strategic management journal, 23(12),
1123-1140.
1 out of 14
Related Documents
![[object Object]](/_next/image/?url=%2F_next%2Fstatic%2Fmedia%2Flogo.6d15ce61.png&w=640&q=75)
Your All-in-One AI-Powered Toolkit for Academic Success.
+13062052269
info@desklib.com
Available 24*7 on WhatsApp / Email
Unlock your academic potential
© 2024 | Zucol Services PVT LTD | All rights reserved.