Resource Cost Categories and Resource Drivers
VerifiedAdded on 2022/11/25
|15
|2601
|102
AI Summary
This document provides information about resource cost categories and resource drivers. It includes details about wages, building costs, depreciation, consumables, energy, and other costs. The document also lists the activities and resource drivers used in baking and packing. The cost categories and resource drivers consumed by activity centers are also mentioned. The document concludes with a comparison of absorption costing and activity-based costing.
Contribute Materials
Your contribution can guide someone’s learning journey. Share your
documents today.
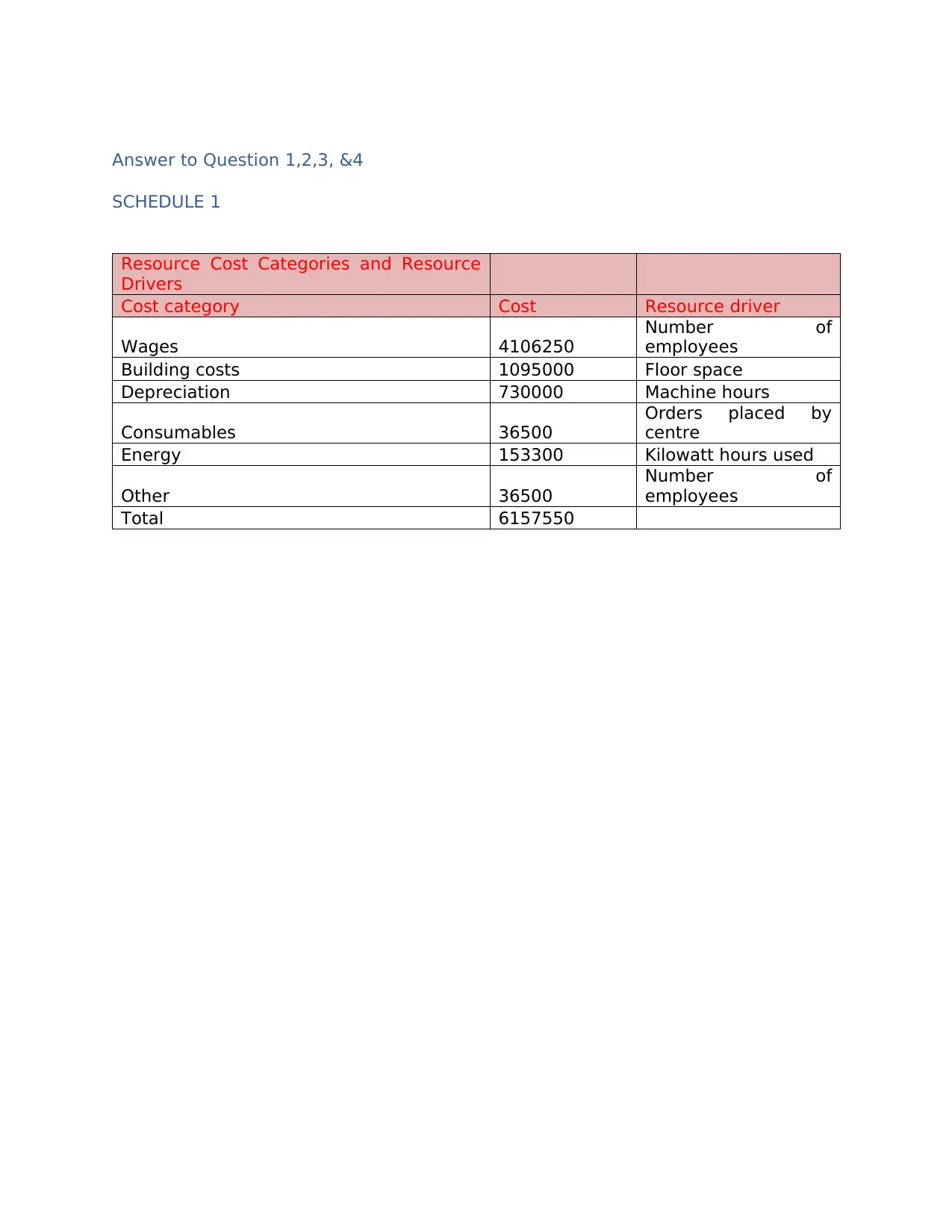
Answer to Question 1,2,3, &4
SCHEDULE 1
Resource Cost Categories and Resource
Drivers
Cost category Cost Resource driver
Wages 4106250
Number of
employees
Building costs 1095000 Floor space
Depreciation 730000 Machine hours
Consumables 36500
Orders placed by
centre
Energy 153300 Kilowatt hours used
Other 36500
Number of
employees
Total 6157550
SCHEDULE 1
Resource Cost Categories and Resource
Drivers
Cost category Cost Resource driver
Wages 4106250
Number of
employees
Building costs 1095000 Floor space
Depreciation 730000 Machine hours
Consumables 36500
Orders placed by
centre
Energy 153300 Kilowatt hours used
Other 36500
Number of
employees
Total 6157550
Secure Best Marks with AI Grader
Need help grading? Try our AI Grader for instant feedback on your assignments.
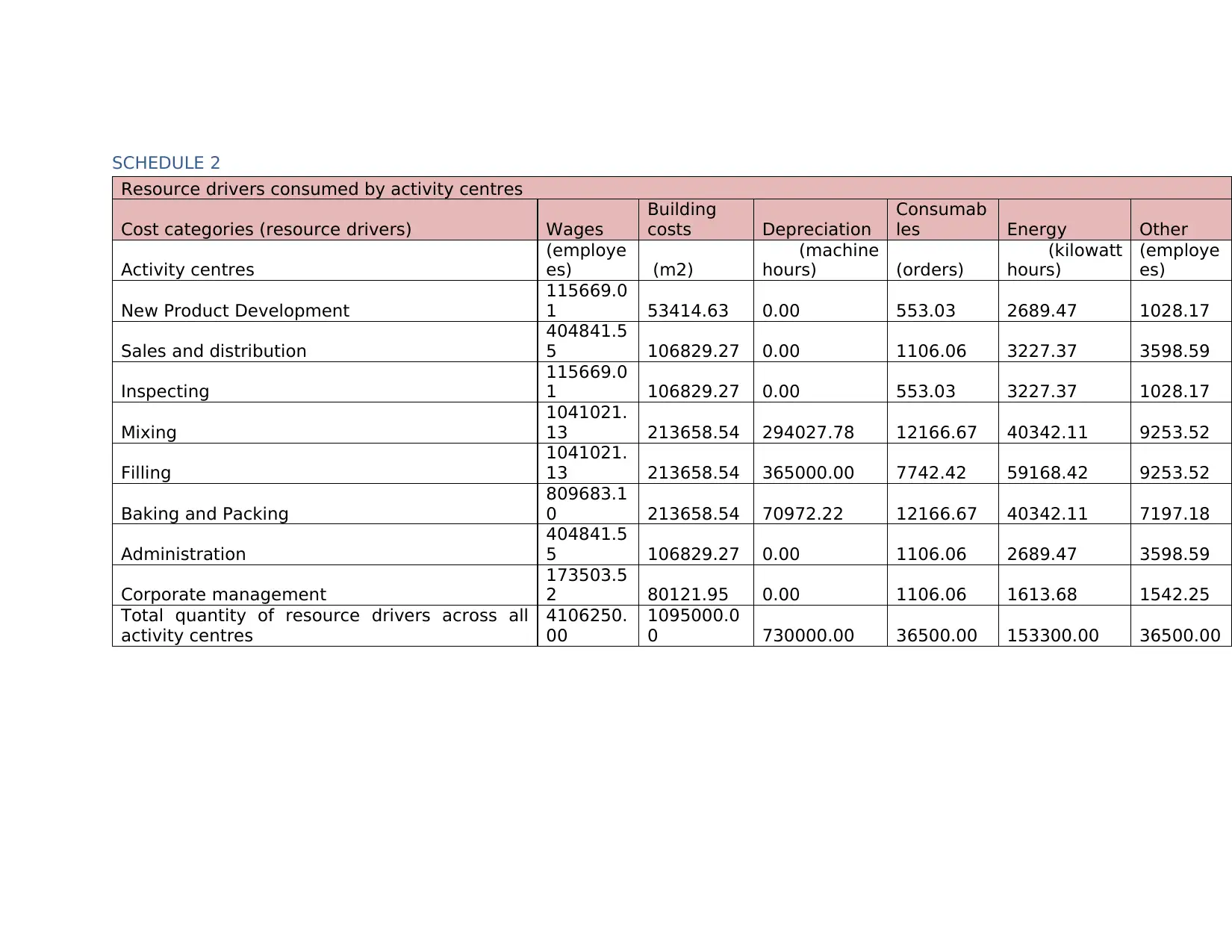
SCHEDULE 2
Resource drivers consumed by activity centres
Cost categories (resource drivers) Wages
Building
costs Depreciation
Consumab
les Energy Other
Activity centres
(employe
es) (m2)
(machine
hours) (orders)
(kilowatt
hours)
(employe
es)
New Product Development
115669.0
1 53414.63 0.00 553.03 2689.47 1028.17
Sales and distribution
404841.5
5 106829.27 0.00 1106.06 3227.37 3598.59
Inspecting
115669.0
1 106829.27 0.00 553.03 3227.37 1028.17
Mixing
1041021.
13 213658.54 294027.78 12166.67 40342.11 9253.52
Filling
1041021.
13 213658.54 365000.00 7742.42 59168.42 9253.52
Baking and Packing
809683.1
0 213658.54 70972.22 12166.67 40342.11 7197.18
Administration
404841.5
5 106829.27 0.00 1106.06 2689.47 3598.59
Corporate management
173503.5
2 80121.95 0.00 1106.06 1613.68 1542.25
Total quantity of resource drivers across all
activity centres
4106250.
00
1095000.0
0 730000.00 36500.00 153300.00 36500.00
Resource drivers consumed by activity centres
Cost categories (resource drivers) Wages
Building
costs Depreciation
Consumab
les Energy Other
Activity centres
(employe
es) (m2)
(machine
hours) (orders)
(kilowatt
hours)
(employe
es)
New Product Development
115669.0
1 53414.63 0.00 553.03 2689.47 1028.17
Sales and distribution
404841.5
5 106829.27 0.00 1106.06 3227.37 3598.59
Inspecting
115669.0
1 106829.27 0.00 553.03 3227.37 1028.17
Mixing
1041021.
13 213658.54 294027.78 12166.67 40342.11 9253.52
Filling
1041021.
13 213658.54 365000.00 7742.42 59168.42 9253.52
Baking and Packing
809683.1
0 213658.54 70972.22 12166.67 40342.11 7197.18
Administration
404841.5
5 106829.27 0.00 1106.06 2689.47 3598.59
Corporate management
173503.5
2 80121.95 0.00 1106.06 1613.68 1542.25
Total quantity of resource drivers across all
activity centres
4106250.
00
1095000.0
0 730000.00 36500.00 153300.00 36500.00
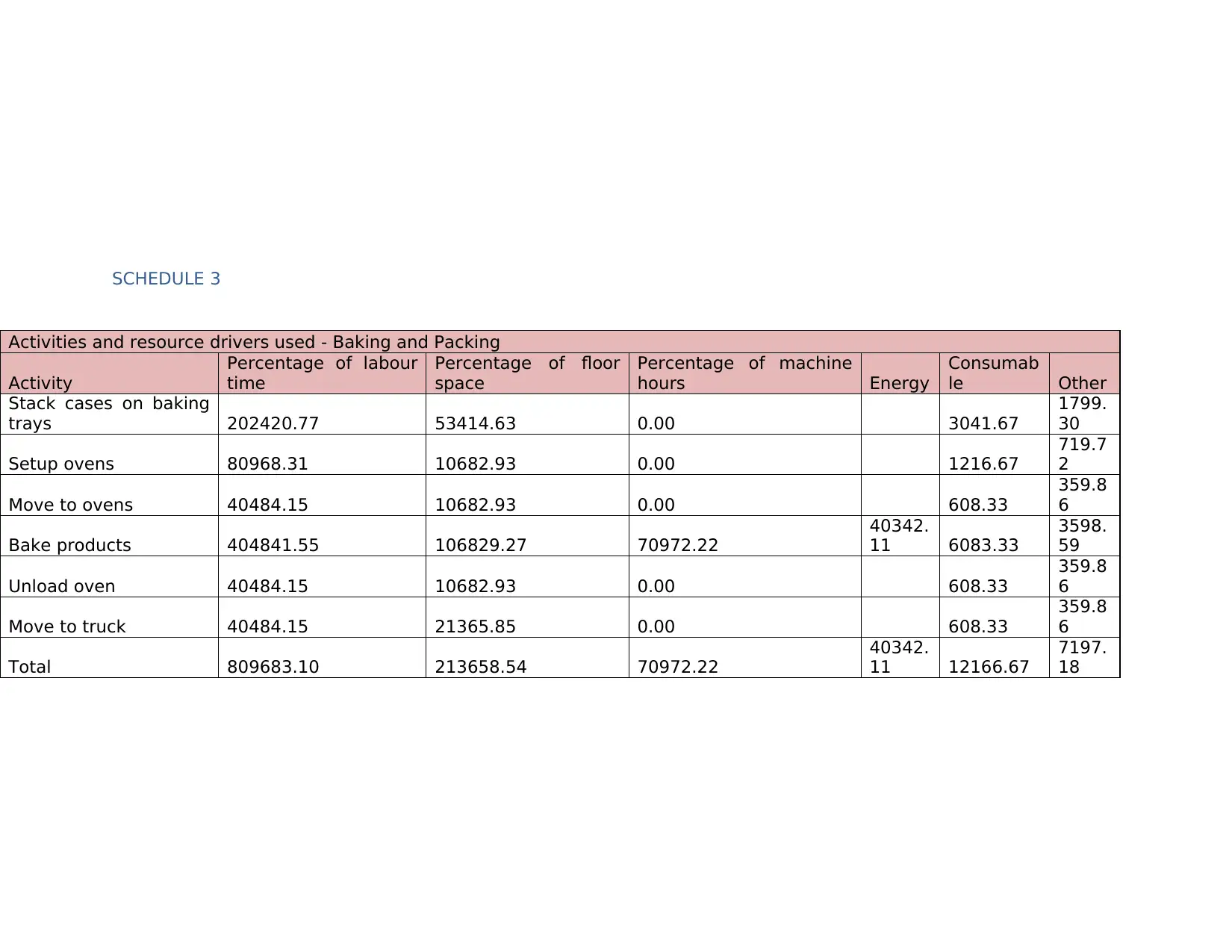
SCHEDULE 3
Activities and resource drivers used - Baking and Packing
Activity
Percentage of labour
time
Percentage of floor
space
Percentage of machine
hours Energy
Consumab
le Other
Stack cases on baking
trays 202420.77 53414.63 0.00 3041.67
1799.
30
Setup ovens 80968.31 10682.93 0.00 1216.67
719.7
2
Move to ovens 40484.15 10682.93 0.00 608.33
359.8
6
Bake products 404841.55 106829.27 70972.22
40342.
11 6083.33
3598.
59
Unload oven 40484.15 10682.93 0.00 608.33
359.8
6
Move to truck 40484.15 21365.85 0.00 608.33
359.8
6
Total 809683.10 213658.54 70972.22
40342.
11 12166.67
7197.
18
Activities and resource drivers used - Baking and Packing
Activity
Percentage of labour
time
Percentage of floor
space
Percentage of machine
hours Energy
Consumab
le Other
Stack cases on baking
trays 202420.77 53414.63 0.00 3041.67
1799.
30
Setup ovens 80968.31 10682.93 0.00 1216.67
719.7
2
Move to ovens 40484.15 10682.93 0.00 608.33
359.8
6
Bake products 404841.55 106829.27 70972.22
40342.
11 6083.33
3598.
59
Unload oven 40484.15 10682.93 0.00 608.33
359.8
6
Move to truck 40484.15 21365.85 0.00 608.33
359.8
6
Total 809683.10 213658.54 70972.22
40342.
11 12166.67
7197.
18
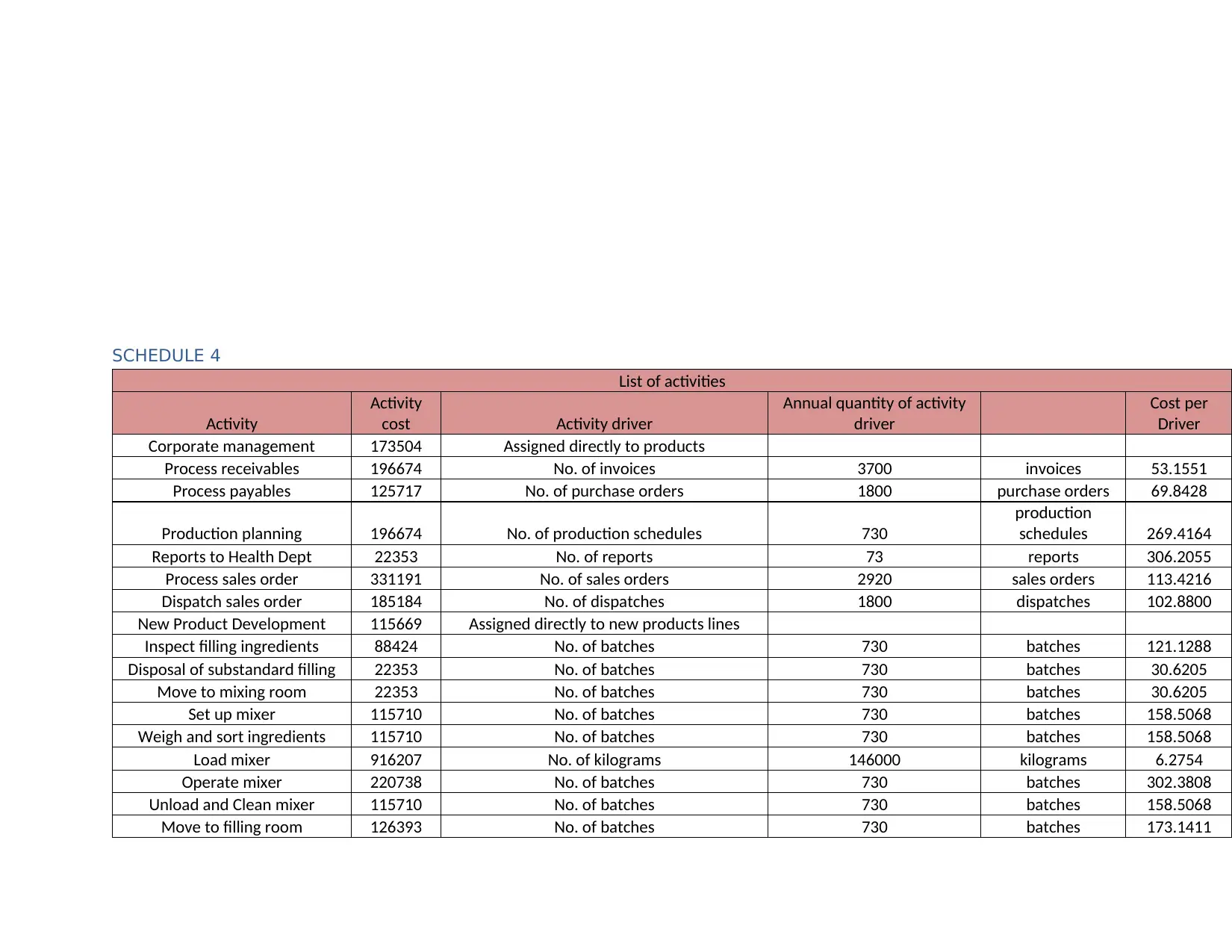
SCHEDULE 4
List of activities
Activity
Activity
cost Activity driver
Annual quantity of activity
driver
Cost per
Driver
Corporate management 173504 Assigned directly to products
Process receivables 196674 No. of invoices 3700 invoices 53.1551
Process payables 125717 No. of purchase orders 1800 purchase orders 69.8428
Production planning 196674 No. of production schedules 730
production
schedules 269.4164
Reports to Health Dept 22353 No. of reports 73 reports 306.2055
Process sales order 331191 No. of sales orders 2920 sales orders 113.4216
Dispatch sales order 185184 No. of dispatches 1800 dispatches 102.8800
New Product Development 115669 Assigned directly to new products lines
Inspect filling ingredients 88424 No. of batches 730 batches 121.1288
Disposal of substandard filling 22353 No. of batches 730 batches 30.6205
Move to mixing room 22353 No. of batches 730 batches 30.6205
Set up mixer 115710 No. of batches 730 batches 158.5068
Weigh and sort ingredients 115710 No. of batches 730 batches 158.5068
Load mixer 916207 No. of kilograms 146000 kilograms 6.2754
Operate mixer 220738 No. of batches 730 batches 302.3808
Unload and Clean mixer 115710 No. of batches 730 batches 158.5068
Move to filling room 126393 No. of batches 730 batches 173.1411
List of activities
Activity
Activity
cost Activity driver
Annual quantity of activity
driver
Cost per
Driver
Corporate management 173504 Assigned directly to products
Process receivables 196674 No. of invoices 3700 invoices 53.1551
Process payables 125717 No. of purchase orders 1800 purchase orders 69.8428
Production planning 196674 No. of production schedules 730
production
schedules 269.4164
Reports to Health Dept 22353 No. of reports 73 reports 306.2055
Process sales order 331191 No. of sales orders 2920 sales orders 113.4216
Dispatch sales order 185184 No. of dispatches 1800 dispatches 102.8800
New Product Development 115669 Assigned directly to new products lines
Inspect filling ingredients 88424 No. of batches 730 batches 121.1288
Disposal of substandard filling 22353 No. of batches 730 batches 30.6205
Move to mixing room 22353 No. of batches 730 batches 30.6205
Set up mixer 115710 No. of batches 730 batches 158.5068
Weigh and sort ingredients 115710 No. of batches 730 batches 158.5068
Load mixer 916207 No. of kilograms 146000 kilograms 6.2754
Operate mixer 220738 No. of batches 730 batches 302.3808
Unload and Clean mixer 115710 No. of batches 730 batches 158.5068
Move to filling room 126393 No. of batches 730 batches 173.1411
Secure Best Marks with AI Grader
Need help grading? Try our AI Grader for instant feedback on your assignments.
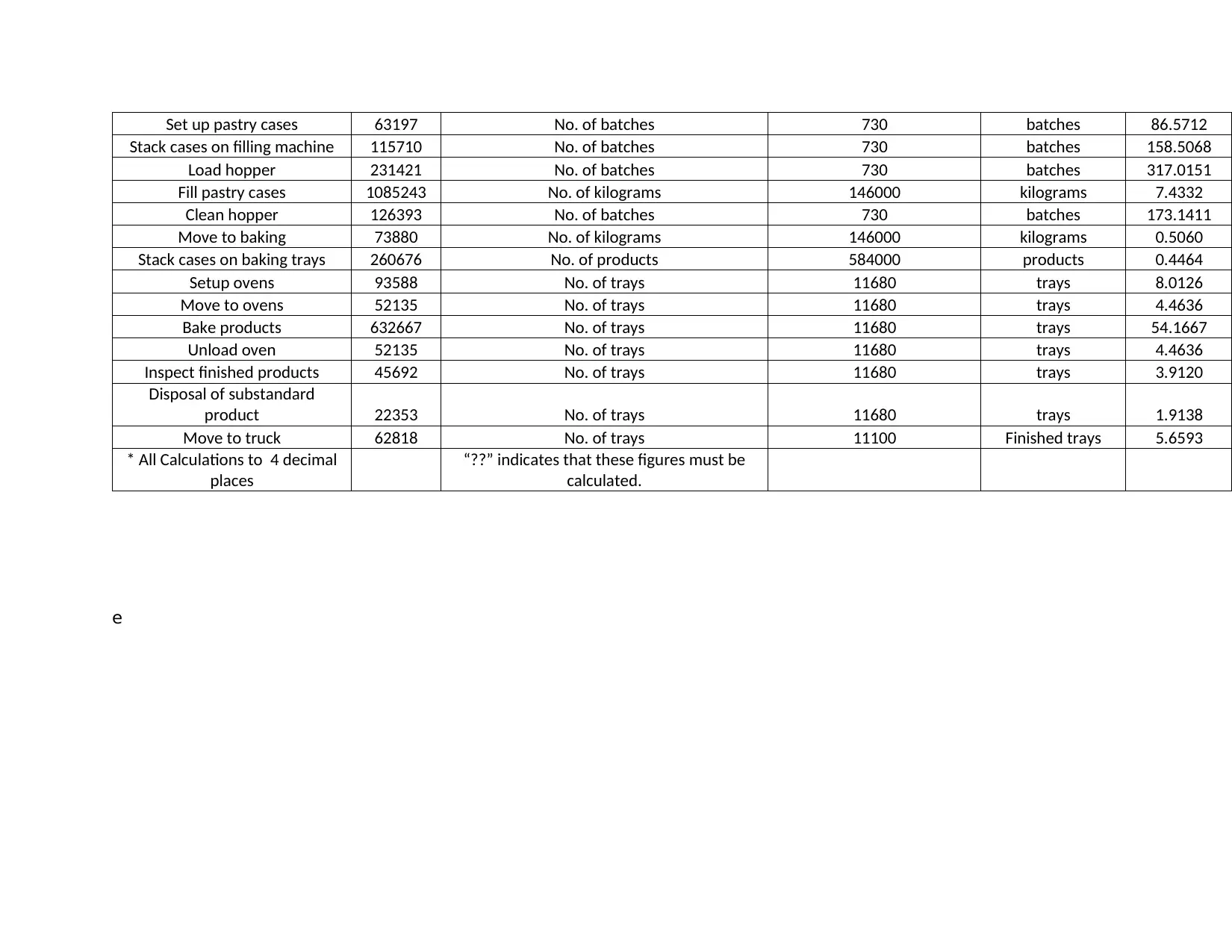
Set up pastry cases 63197 No. of batches 730 batches 86.5712
Stack cases on filling machine 115710 No. of batches 730 batches 158.5068
Load hopper 231421 No. of batches 730 batches 317.0151
Fill pastry cases 1085243 No. of kilograms 146000 kilograms 7.4332
Clean hopper 126393 No. of batches 730 batches 173.1411
Move to baking 73880 No. of kilograms 146000 kilograms 0.5060
Stack cases on baking trays 260676 No. of products 584000 products 0.4464
Setup ovens 93588 No. of trays 11680 trays 8.0126
Move to ovens 52135 No. of trays 11680 trays 4.4636
Bake products 632667 No. of trays 11680 trays 54.1667
Unload oven 52135 No. of trays 11680 trays 4.4636
Inspect finished products 45692 No. of trays 11680 trays 3.9120
Disposal of substandard
product 22353 No. of trays 11680 trays 1.9138
Move to truck 62818 No. of trays 11100 Finished trays 5.6593
* All Calculations to 4 decimal
places
“??” indicates that these figures must be
calculated.
e
Stack cases on filling machine 115710 No. of batches 730 batches 158.5068
Load hopper 231421 No. of batches 730 batches 317.0151
Fill pastry cases 1085243 No. of kilograms 146000 kilograms 7.4332
Clean hopper 126393 No. of batches 730 batches 173.1411
Move to baking 73880 No. of kilograms 146000 kilograms 0.5060
Stack cases on baking trays 260676 No. of products 584000 products 0.4464
Setup ovens 93588 No. of trays 11680 trays 8.0126
Move to ovens 52135 No. of trays 11680 trays 4.4636
Bake products 632667 No. of trays 11680 trays 54.1667
Unload oven 52135 No. of trays 11680 trays 4.4636
Inspect finished products 45692 No. of trays 11680 trays 3.9120
Disposal of substandard
product 22353 No. of trays 11680 trays 1.9138
Move to truck 62818 No. of trays 11100 Finished trays 5.6593
* All Calculations to 4 decimal
places
“??” indicates that these figures must be
calculated.
e
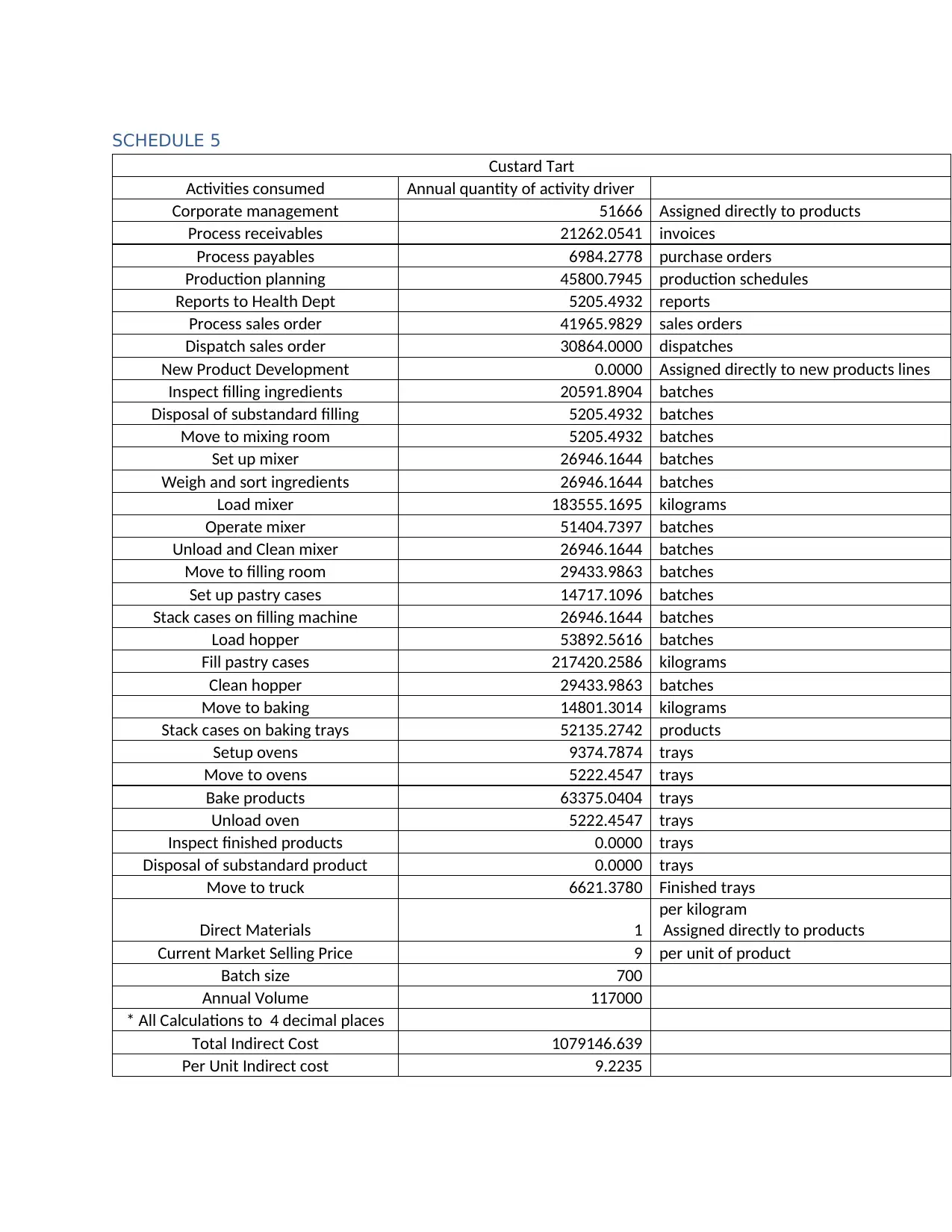
SCHEDULE 5
Custard Tart
Activities consumed Annual quantity of activity driver
Corporate management 51666 Assigned directly to products
Process receivables 21262.0541 invoices
Process payables 6984.2778 purchase orders
Production planning 45800.7945 production schedules
Reports to Health Dept 5205.4932 reports
Process sales order 41965.9829 sales orders
Dispatch sales order 30864.0000 dispatches
New Product Development 0.0000 Assigned directly to new products lines
Inspect filling ingredients 20591.8904 batches
Disposal of substandard filling 5205.4932 batches
Move to mixing room 5205.4932 batches
Set up mixer 26946.1644 batches
Weigh and sort ingredients 26946.1644 batches
Load mixer 183555.1695 kilograms
Operate mixer 51404.7397 batches
Unload and Clean mixer 26946.1644 batches
Move to filling room 29433.9863 batches
Set up pastry cases 14717.1096 batches
Stack cases on filling machine 26946.1644 batches
Load hopper 53892.5616 batches
Fill pastry cases 217420.2586 kilograms
Clean hopper 29433.9863 batches
Move to baking 14801.3014 kilograms
Stack cases on baking trays 52135.2742 products
Setup ovens 9374.7874 trays
Move to ovens 5222.4547 trays
Bake products 63375.0404 trays
Unload oven 5222.4547 trays
Inspect finished products 0.0000 trays
Disposal of substandard product 0.0000 trays
Move to truck 6621.3780 Finished trays
Direct Materials 1
per kilogram
Assigned directly to products
Current Market Selling Price 9 per unit of product
Batch size 700
Annual Volume 117000
* All Calculations to 4 decimal places
Total Indirect Cost 1079146.639
Per Unit Indirect cost 9.2235
Custard Tart
Activities consumed Annual quantity of activity driver
Corporate management 51666 Assigned directly to products
Process receivables 21262.0541 invoices
Process payables 6984.2778 purchase orders
Production planning 45800.7945 production schedules
Reports to Health Dept 5205.4932 reports
Process sales order 41965.9829 sales orders
Dispatch sales order 30864.0000 dispatches
New Product Development 0.0000 Assigned directly to new products lines
Inspect filling ingredients 20591.8904 batches
Disposal of substandard filling 5205.4932 batches
Move to mixing room 5205.4932 batches
Set up mixer 26946.1644 batches
Weigh and sort ingredients 26946.1644 batches
Load mixer 183555.1695 kilograms
Operate mixer 51404.7397 batches
Unload and Clean mixer 26946.1644 batches
Move to filling room 29433.9863 batches
Set up pastry cases 14717.1096 batches
Stack cases on filling machine 26946.1644 batches
Load hopper 53892.5616 batches
Fill pastry cases 217420.2586 kilograms
Clean hopper 29433.9863 batches
Move to baking 14801.3014 kilograms
Stack cases on baking trays 52135.2742 products
Setup ovens 9374.7874 trays
Move to ovens 5222.4547 trays
Bake products 63375.0404 trays
Unload oven 5222.4547 trays
Inspect finished products 0.0000 trays
Disposal of substandard product 0.0000 trays
Move to truck 6621.3780 Finished trays
Direct Materials 1
per kilogram
Assigned directly to products
Current Market Selling Price 9 per unit of product
Batch size 700
Annual Volume 117000
* All Calculations to 4 decimal places
Total Indirect Cost 1079146.639
Per Unit Indirect cost 9.2235
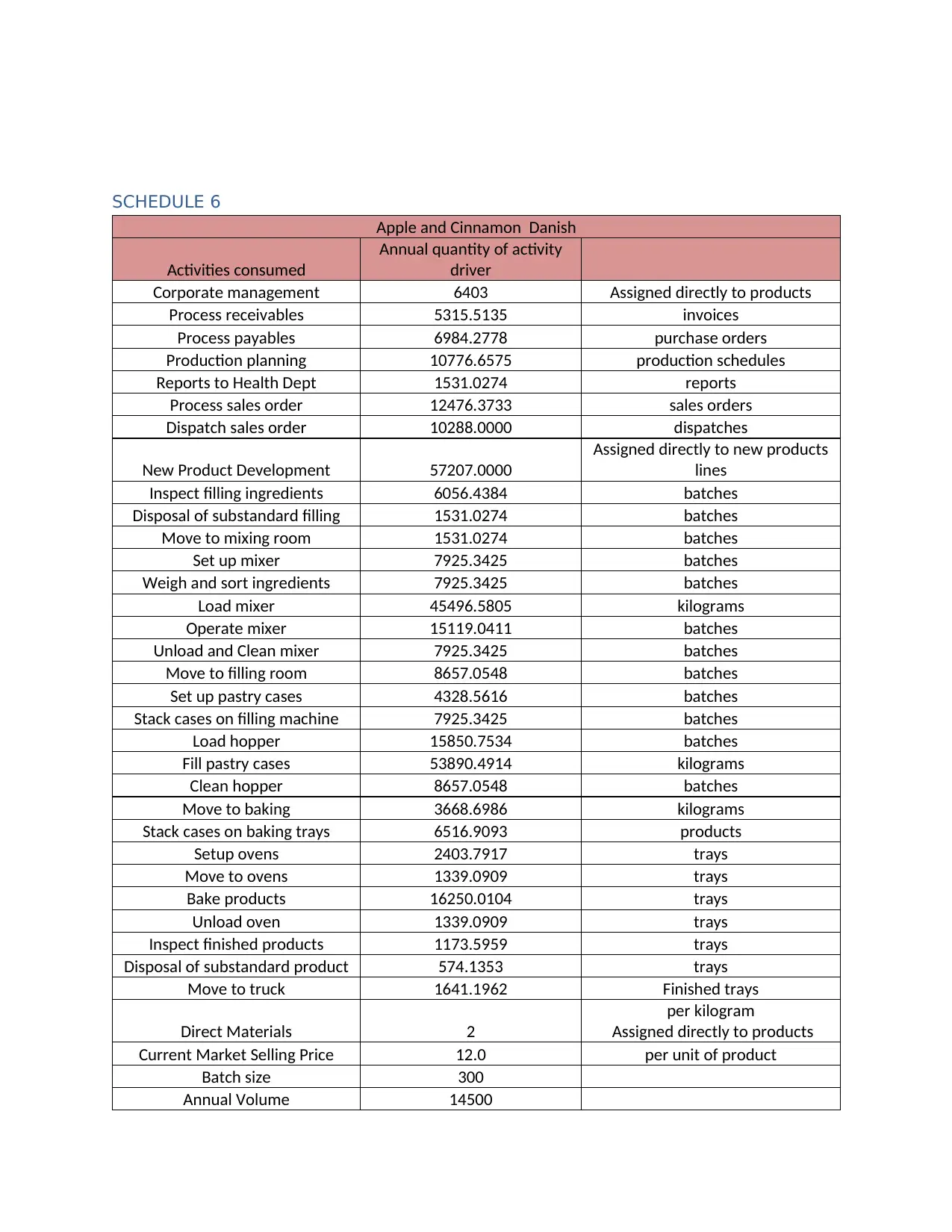
SCHEDULE 6
Apple and Cinnamon Danish
Activities consumed
Annual quantity of activity
driver
Corporate management 6403 Assigned directly to products
Process receivables 5315.5135 invoices
Process payables 6984.2778 purchase orders
Production planning 10776.6575 production schedules
Reports to Health Dept 1531.0274 reports
Process sales order 12476.3733 sales orders
Dispatch sales order 10288.0000 dispatches
New Product Development 57207.0000
Assigned directly to new products
lines
Inspect filling ingredients 6056.4384 batches
Disposal of substandard filling 1531.0274 batches
Move to mixing room 1531.0274 batches
Set up mixer 7925.3425 batches
Weigh and sort ingredients 7925.3425 batches
Load mixer 45496.5805 kilograms
Operate mixer 15119.0411 batches
Unload and Clean mixer 7925.3425 batches
Move to filling room 8657.0548 batches
Set up pastry cases 4328.5616 batches
Stack cases on filling machine 7925.3425 batches
Load hopper 15850.7534 batches
Fill pastry cases 53890.4914 kilograms
Clean hopper 8657.0548 batches
Move to baking 3668.6986 kilograms
Stack cases on baking trays 6516.9093 products
Setup ovens 2403.7917 trays
Move to ovens 1339.0909 trays
Bake products 16250.0104 trays
Unload oven 1339.0909 trays
Inspect finished products 1173.5959 trays
Disposal of substandard product 574.1353 trays
Move to truck 1641.1962 Finished trays
Direct Materials 2
per kilogram
Assigned directly to products
Current Market Selling Price 12.0 per unit of product
Batch size 300
Annual Volume 14500
Apple and Cinnamon Danish
Activities consumed
Annual quantity of activity
driver
Corporate management 6403 Assigned directly to products
Process receivables 5315.5135 invoices
Process payables 6984.2778 purchase orders
Production planning 10776.6575 production schedules
Reports to Health Dept 1531.0274 reports
Process sales order 12476.3733 sales orders
Dispatch sales order 10288.0000 dispatches
New Product Development 57207.0000
Assigned directly to new products
lines
Inspect filling ingredients 6056.4384 batches
Disposal of substandard filling 1531.0274 batches
Move to mixing room 1531.0274 batches
Set up mixer 7925.3425 batches
Weigh and sort ingredients 7925.3425 batches
Load mixer 45496.5805 kilograms
Operate mixer 15119.0411 batches
Unload and Clean mixer 7925.3425 batches
Move to filling room 8657.0548 batches
Set up pastry cases 4328.5616 batches
Stack cases on filling machine 7925.3425 batches
Load hopper 15850.7534 batches
Fill pastry cases 53890.4914 kilograms
Clean hopper 8657.0548 batches
Move to baking 3668.6986 kilograms
Stack cases on baking trays 6516.9093 products
Setup ovens 2403.7917 trays
Move to ovens 1339.0909 trays
Bake products 16250.0104 trays
Unload oven 1339.0909 trays
Inspect finished products 1173.5959 trays
Disposal of substandard product 574.1353 trays
Move to truck 1641.1962 Finished trays
Direct Materials 2
per kilogram
Assigned directly to products
Current Market Selling Price 12.0 per unit of product
Batch size 300
Annual Volume 14500
Paraphrase This Document
Need a fresh take? Get an instant paraphrase of this document with our AI Paraphraser
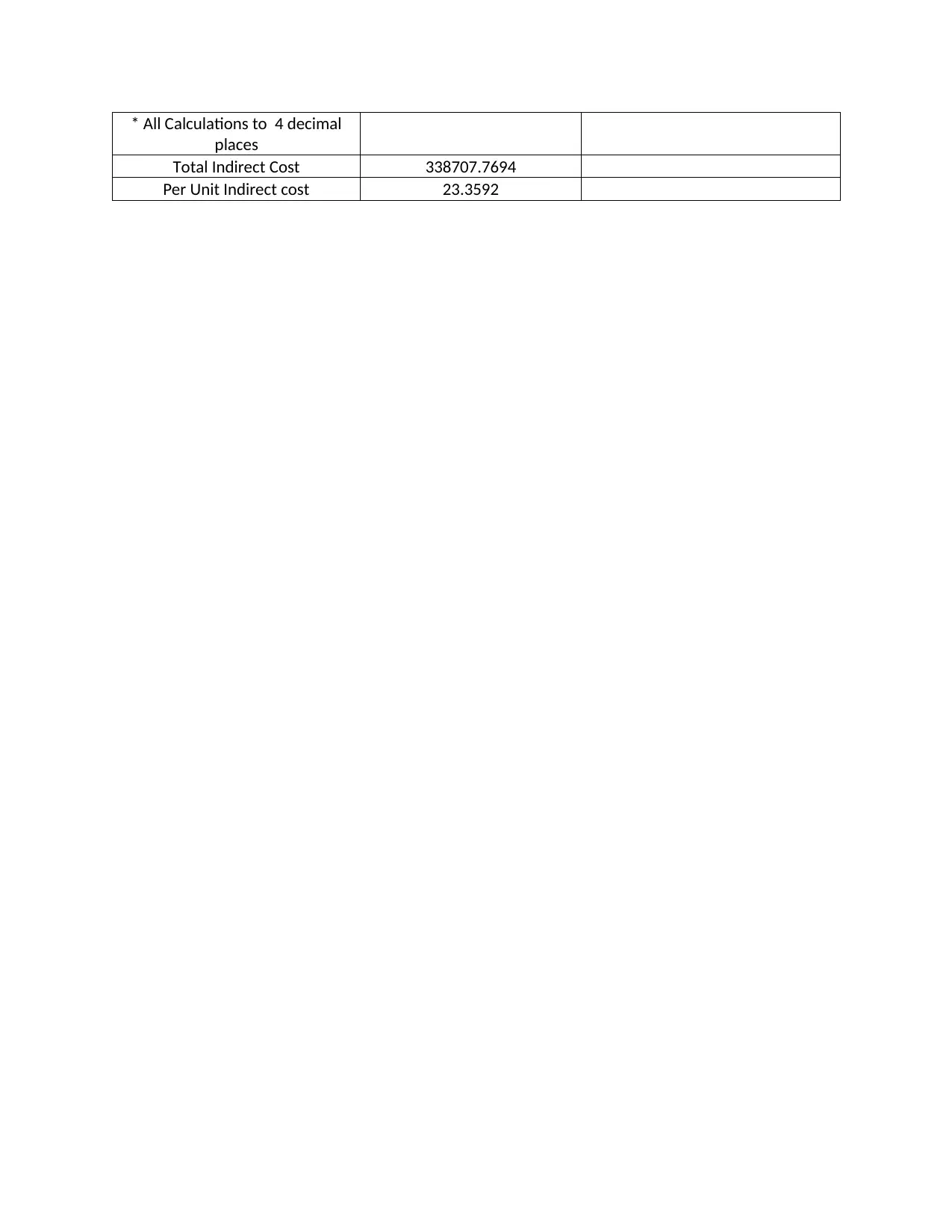
* All Calculations to 4 decimal
places
Total Indirect Cost 338707.7694
Per Unit Indirect cost 23.3592
places
Total Indirect Cost 338707.7694
Per Unit Indirect cost 23.3592
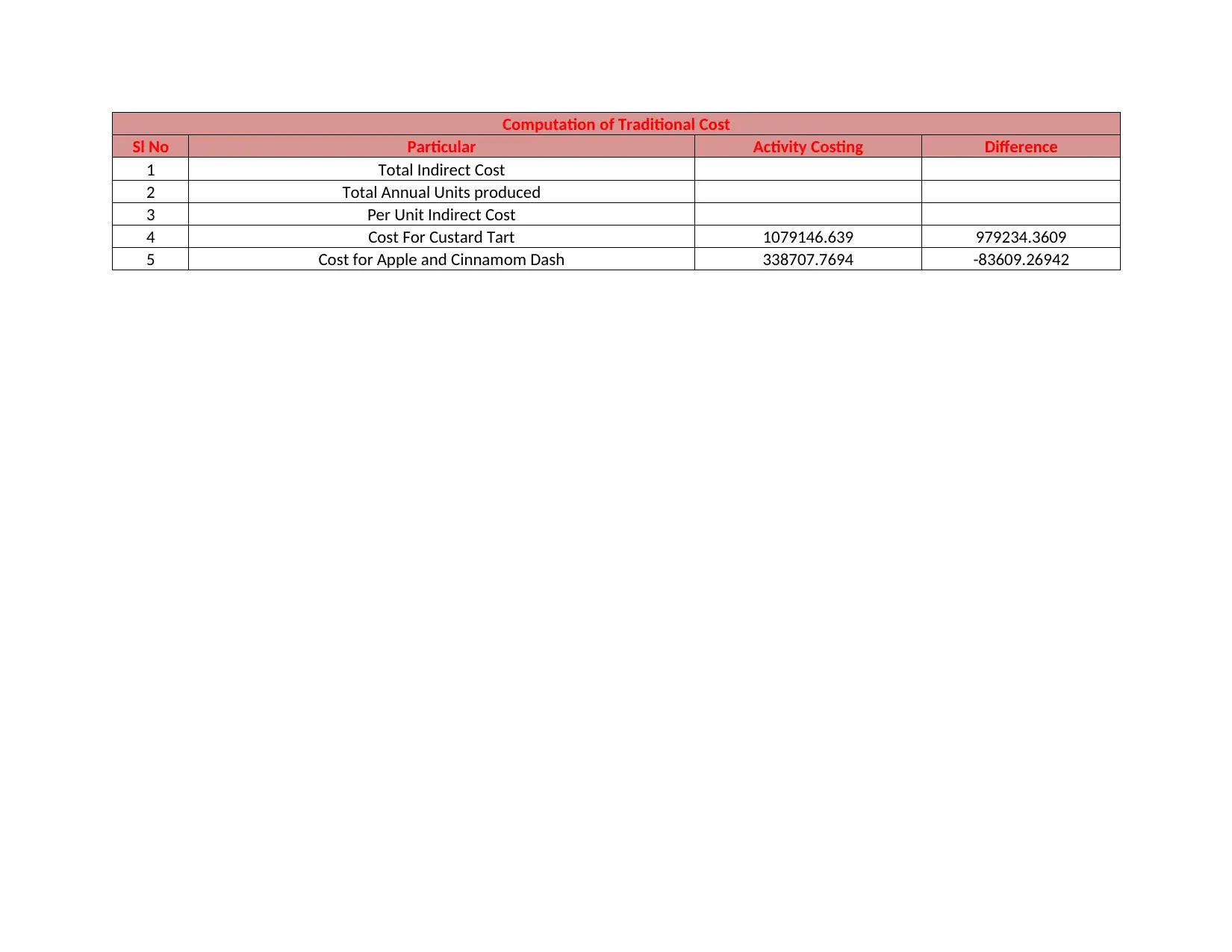
Computation of Traditional Cost
Sl No Particular Activity Costing Difference
1 Total Indirect Cost
2 Total Annual Units produced
3 Per Unit Indirect Cost
4 Cost For Custard Tart 1079146.639 979234.3609
5 Cost for Apple and Cinnamom Dash 338707.7694 -83609.26942
Sl No Particular Activity Costing Difference
1 Total Indirect Cost
2 Total Annual Units produced
3 Per Unit Indirect Cost
4 Cost For Custard Tart 1079146.639 979234.3609
5 Cost for Apple and Cinnamom Dash 338707.7694 -83609.26942
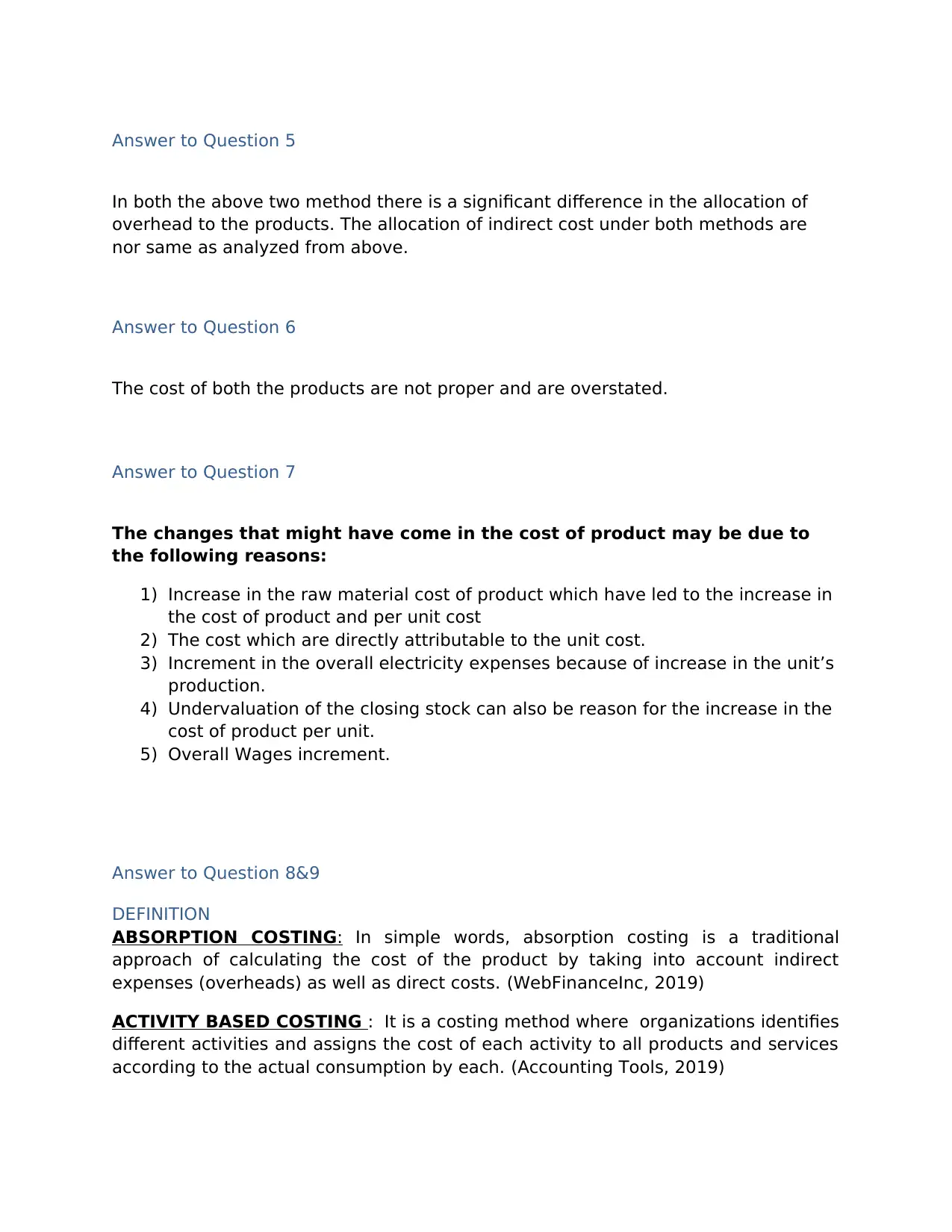
Answer to Question 5
In both the above two method there is a significant difference in the allocation of
overhead to the products. The allocation of indirect cost under both methods are
nor same as analyzed from above.
Answer to Question 6
The cost of both the products are not proper and are overstated.
Answer to Question 7
The changes that might have come in the cost of product may be due to
the following reasons:
1) Increase in the raw material cost of product which have led to the increase in
the cost of product and per unit cost
2) The cost which are directly attributable to the unit cost.
3) Increment in the overall electricity expenses because of increase in the unit’s
production.
4) Undervaluation of the closing stock can also be reason for the increase in the
cost of product per unit.
5) Overall Wages increment.
Answer to Question 8&9
DEFINITION
ABSORPTION COSTING: In simple words, absorption costing is a traditional
approach of calculating the cost of the product by taking into account indirect
expenses (overheads) as well as direct costs. (WebFinanceInc, 2019)
ACTIVITY BASED COSTING : It is a costing method where organizations identifies
different activities and assigns the cost of each activity to all products and services
according to the actual consumption by each. (Accounting Tools, 2019)
In both the above two method there is a significant difference in the allocation of
overhead to the products. The allocation of indirect cost under both methods are
nor same as analyzed from above.
Answer to Question 6
The cost of both the products are not proper and are overstated.
Answer to Question 7
The changes that might have come in the cost of product may be due to
the following reasons:
1) Increase in the raw material cost of product which have led to the increase in
the cost of product and per unit cost
2) The cost which are directly attributable to the unit cost.
3) Increment in the overall electricity expenses because of increase in the unit’s
production.
4) Undervaluation of the closing stock can also be reason for the increase in the
cost of product per unit.
5) Overall Wages increment.
Answer to Question 8&9
DEFINITION
ABSORPTION COSTING: In simple words, absorption costing is a traditional
approach of calculating the cost of the product by taking into account indirect
expenses (overheads) as well as direct costs. (WebFinanceInc, 2019)
ACTIVITY BASED COSTING : It is a costing method where organizations identifies
different activities and assigns the cost of each activity to all products and services
according to the actual consumption by each. (Accounting Tools, 2019)
Secure Best Marks with AI Grader
Need help grading? Try our AI Grader for instant feedback on your assignments.
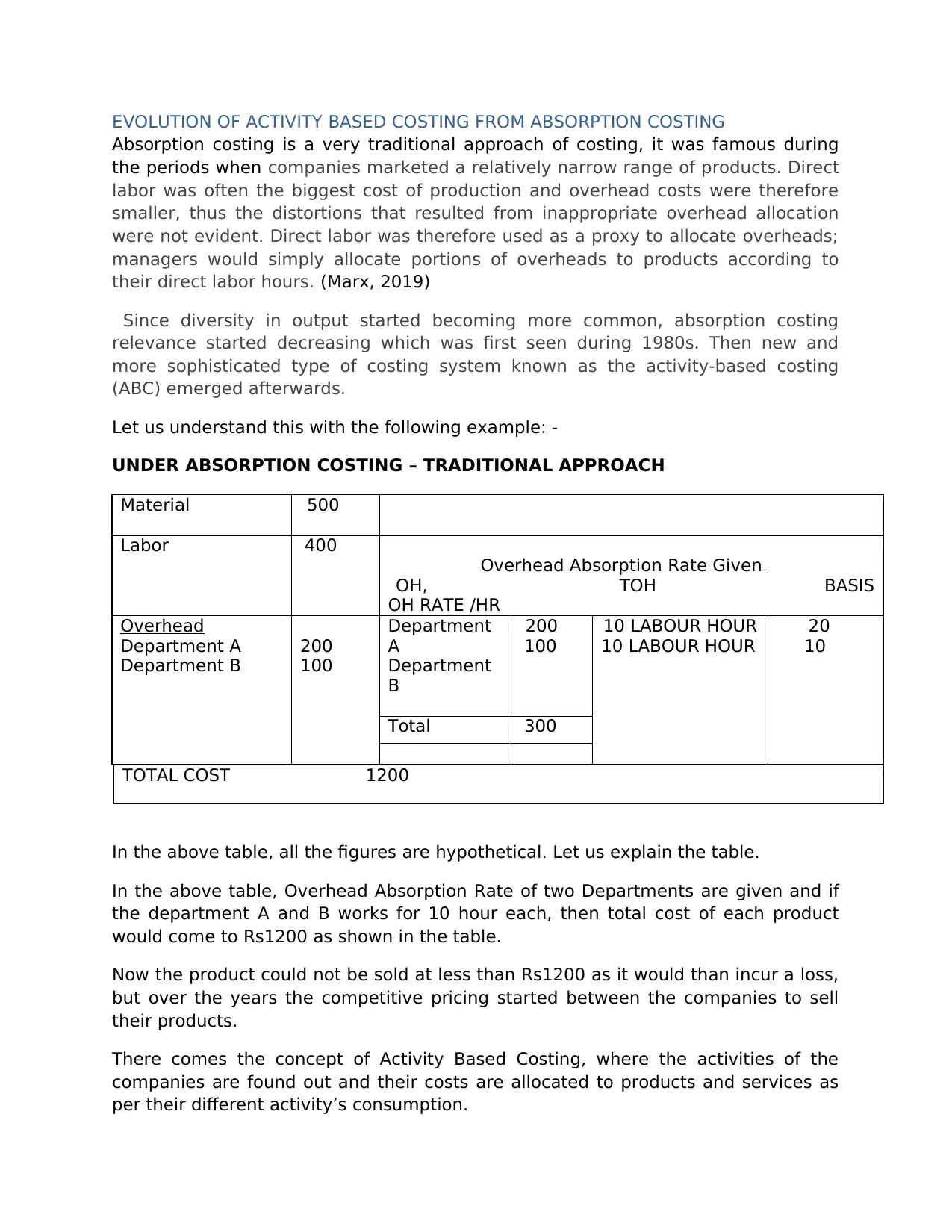
EVOLUTION OF ACTIVITY BASED COSTING FROM ABSORPTION COSTING
Absorption costing is a very traditional approach of costing, it was famous during
the periods when companies marketed a relatively narrow range of products. Direct
labor was often the biggest cost of production and overhead costs were therefore
smaller, thus the distortions that resulted from inappropriate overhead allocation
were not evident. Direct labor was therefore used as a proxy to allocate overheads;
managers would simply allocate portions of overheads to products according to
their direct labor hours. (Marx, 2019)
Since diversity in output started becoming more common, absorption costing
relevance started decreasing which was first seen during 1980s. Then new and
more sophisticated type of costing system known as the activity-based costing
(ABC) emerged afterwards.
Let us understand this with the following example: -
UNDER ABSORPTION COSTING – TRADITIONAL APPROACH
Material 500
Labor 400
Overhead Absorption Rate Given
OH, TOH BASIS
OH RATE /HR
Overhead
Department A
Department B
200
100
Department
A
Department
B
200
100
10 LABOUR HOUR
10 LABOUR HOUR
20
10
Total 300
TOTAL COST 1200
In the above table, all the figures are hypothetical. Let us explain the table.
In the above table, Overhead Absorption Rate of two Departments are given and if
the department A and B works for 10 hour each, then total cost of each product
would come to Rs1200 as shown in the table.
Now the product could not be sold at less than Rs1200 as it would than incur a loss,
but over the years the competitive pricing started between the companies to sell
their products.
There comes the concept of Activity Based Costing, where the activities of the
companies are found out and their costs are allocated to products and services as
per their different activity’s consumption.
Absorption costing is a very traditional approach of costing, it was famous during
the periods when companies marketed a relatively narrow range of products. Direct
labor was often the biggest cost of production and overhead costs were therefore
smaller, thus the distortions that resulted from inappropriate overhead allocation
were not evident. Direct labor was therefore used as a proxy to allocate overheads;
managers would simply allocate portions of overheads to products according to
their direct labor hours. (Marx, 2019)
Since diversity in output started becoming more common, absorption costing
relevance started decreasing which was first seen during 1980s. Then new and
more sophisticated type of costing system known as the activity-based costing
(ABC) emerged afterwards.
Let us understand this with the following example: -
UNDER ABSORPTION COSTING – TRADITIONAL APPROACH
Material 500
Labor 400
Overhead Absorption Rate Given
OH, TOH BASIS
OH RATE /HR
Overhead
Department A
Department B
200
100
Department
A
Department
B
200
100
10 LABOUR HOUR
10 LABOUR HOUR
20
10
Total 300
TOTAL COST 1200
In the above table, all the figures are hypothetical. Let us explain the table.
In the above table, Overhead Absorption Rate of two Departments are given and if
the department A and B works for 10 hour each, then total cost of each product
would come to Rs1200 as shown in the table.
Now the product could not be sold at less than Rs1200 as it would than incur a loss,
but over the years the competitive pricing started between the companies to sell
their products.
There comes the concept of Activity Based Costing, where the activities of the
companies are found out and their costs are allocated to products and services as
per their different activity’s consumption.
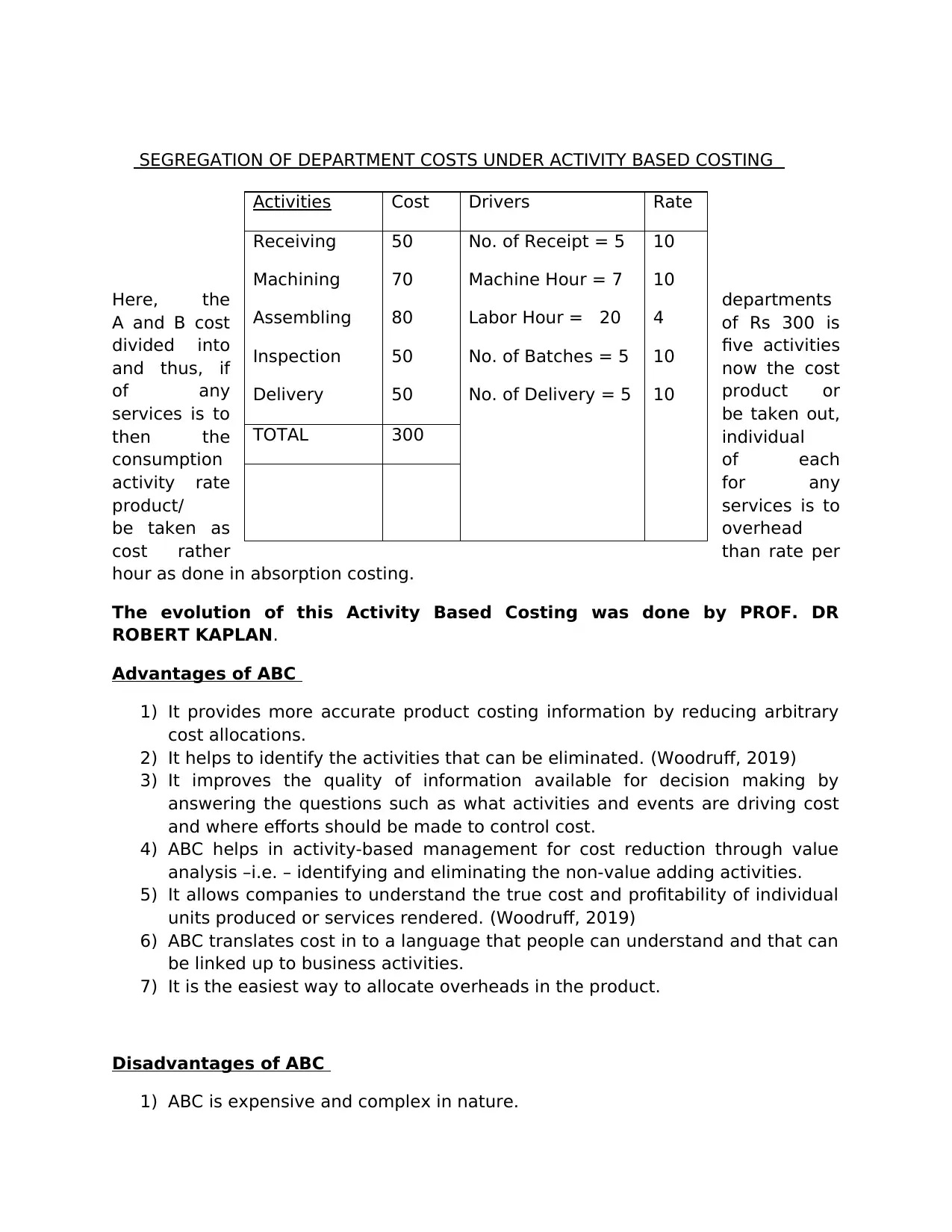
SEGREGATION OF DEPARTMENT COSTS UNDER ACTIVITY BASED COSTING
Here, the departments
A and B cost of Rs 300 is
divided into five activities
and thus, if now the cost
of any product or
services is to be taken out,
then the individual
consumption of each
activity rate for any
product/ services is to
be taken as overhead
cost rather than rate per
hour as done in absorption costing.
The evolution of this Activity Based Costing was done by PROF. DR
ROBERT KAPLAN.
Advantages of ABC
1) It provides more accurate product costing information by reducing arbitrary
cost allocations.
2) It helps to identify the activities that can be eliminated. (Woodruff, 2019)
3) It improves the quality of information available for decision making by
answering the questions such as what activities and events are driving cost
and where efforts should be made to control cost.
4) ABC helps in activity-based management for cost reduction through value
analysis –i.e. – identifying and eliminating the non-value adding activities.
5) It allows companies to understand the true cost and profitability of individual
units produced or services rendered. (Woodruff, 2019)
6) ABC translates cost in to a language that people can understand and that can
be linked up to business activities.
7) It is the easiest way to allocate overheads in the product.
Disadvantages of ABC
1) ABC is expensive and complex in nature.
Activities Cost Drivers Rate
Receiving
Machining
Assembling
Inspection
Delivery
50
70
80
50
50
No. of Receipt = 5
Machine Hour = 7
Labor Hour = 20
No. of Batches = 5
No. of Delivery = 5
10
10
4
10
10
TOTAL 300
Here, the departments
A and B cost of Rs 300 is
divided into five activities
and thus, if now the cost
of any product or
services is to be taken out,
then the individual
consumption of each
activity rate for any
product/ services is to
be taken as overhead
cost rather than rate per
hour as done in absorption costing.
The evolution of this Activity Based Costing was done by PROF. DR
ROBERT KAPLAN.
Advantages of ABC
1) It provides more accurate product costing information by reducing arbitrary
cost allocations.
2) It helps to identify the activities that can be eliminated. (Woodruff, 2019)
3) It improves the quality of information available for decision making by
answering the questions such as what activities and events are driving cost
and where efforts should be made to control cost.
4) ABC helps in activity-based management for cost reduction through value
analysis –i.e. – identifying and eliminating the non-value adding activities.
5) It allows companies to understand the true cost and profitability of individual
units produced or services rendered. (Woodruff, 2019)
6) ABC translates cost in to a language that people can understand and that can
be linked up to business activities.
7) It is the easiest way to allocate overheads in the product.
Disadvantages of ABC
1) ABC is expensive and complex in nature.
Activities Cost Drivers Rate
Receiving
Machining
Assembling
Inspection
Delivery
50
70
80
50
50
No. of Receipt = 5
Machine Hour = 7
Labor Hour = 20
No. of Batches = 5
No. of Delivery = 5
10
10
4
10
10
TOTAL 300
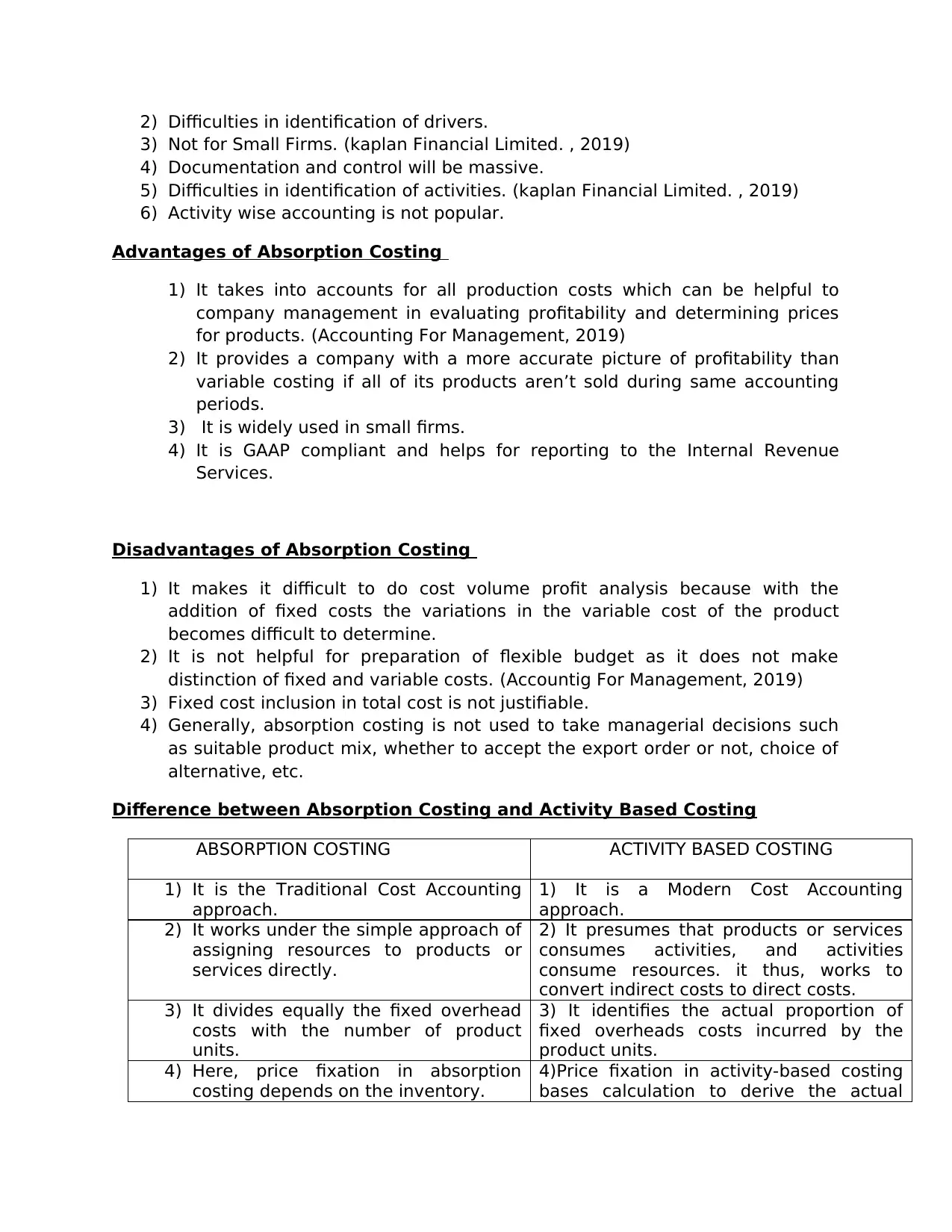
2) Difficulties in identification of drivers.
3) Not for Small Firms. (kaplan Financial Limited. , 2019)
4) Documentation and control will be massive.
5) Difficulties in identification of activities. (kaplan Financial Limited. , 2019)
6) Activity wise accounting is not popular.
Advantages of Absorption Costing
1) It takes into accounts for all production costs which can be helpful to
company management in evaluating profitability and determining prices
for products. (Accounting For Management, 2019)
2) It provides a company with a more accurate picture of profitability than
variable costing if all of its products aren’t sold during same accounting
periods.
3) It is widely used in small firms.
4) It is GAAP compliant and helps for reporting to the Internal Revenue
Services.
Disadvantages of Absorption Costing
1) It makes it difficult to do cost volume profit analysis because with the
addition of fixed costs the variations in the variable cost of the product
becomes difficult to determine.
2) It is not helpful for preparation of flexible budget as it does not make
distinction of fixed and variable costs. (Accountig For Management, 2019)
3) Fixed cost inclusion in total cost is not justifiable.
4) Generally, absorption costing is not used to take managerial decisions such
as suitable product mix, whether to accept the export order or not, choice of
alternative, etc.
Difference between Absorption Costing and Activity Based Costing
ABSORPTION COSTING ACTIVITY BASED COSTING
1) It is the Traditional Cost Accounting
approach.
1) It is a Modern Cost Accounting
approach.
2) It works under the simple approach of
assigning resources to products or
services directly.
2) It presumes that products or services
consumes activities, and activities
consume resources. it thus, works to
convert indirect costs to direct costs.
3) It divides equally the fixed overhead
costs with the number of product
units.
3) It identifies the actual proportion of
fixed overheads costs incurred by the
product units.
4) Here, price fixation in absorption
costing depends on the inventory.
4)Price fixation in activity-based costing
bases calculation to derive the actual
3) Not for Small Firms. (kaplan Financial Limited. , 2019)
4) Documentation and control will be massive.
5) Difficulties in identification of activities. (kaplan Financial Limited. , 2019)
6) Activity wise accounting is not popular.
Advantages of Absorption Costing
1) It takes into accounts for all production costs which can be helpful to
company management in evaluating profitability and determining prices
for products. (Accounting For Management, 2019)
2) It provides a company with a more accurate picture of profitability than
variable costing if all of its products aren’t sold during same accounting
periods.
3) It is widely used in small firms.
4) It is GAAP compliant and helps for reporting to the Internal Revenue
Services.
Disadvantages of Absorption Costing
1) It makes it difficult to do cost volume profit analysis because with the
addition of fixed costs the variations in the variable cost of the product
becomes difficult to determine.
2) It is not helpful for preparation of flexible budget as it does not make
distinction of fixed and variable costs. (Accountig For Management, 2019)
3) Fixed cost inclusion in total cost is not justifiable.
4) Generally, absorption costing is not used to take managerial decisions such
as suitable product mix, whether to accept the export order or not, choice of
alternative, etc.
Difference between Absorption Costing and Activity Based Costing
ABSORPTION COSTING ACTIVITY BASED COSTING
1) It is the Traditional Cost Accounting
approach.
1) It is a Modern Cost Accounting
approach.
2) It works under the simple approach of
assigning resources to products or
services directly.
2) It presumes that products or services
consumes activities, and activities
consume resources. it thus, works to
convert indirect costs to direct costs.
3) It divides equally the fixed overhead
costs with the number of product
units.
3) It identifies the actual proportion of
fixed overheads costs incurred by the
product units.
4) Here, price fixation in absorption
costing depends on the inventory.
4)Price fixation in activity-based costing
bases calculation to derive the actual
Paraphrase This Document
Need a fresh take? Get an instant paraphrase of this document with our AI Paraphraser
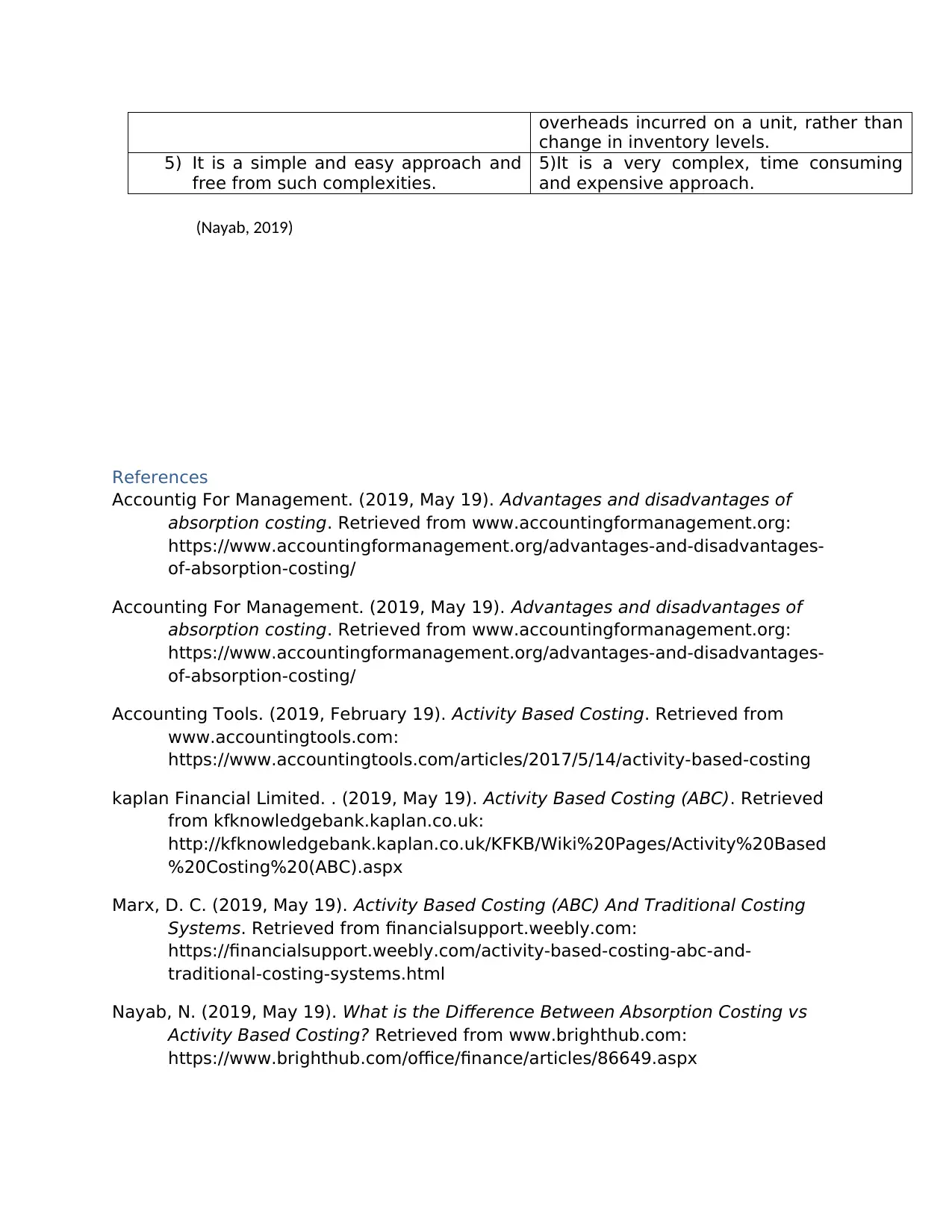
overheads incurred on a unit, rather than
change in inventory levels.
5) It is a simple and easy approach and
free from such complexities.
5)It is a very complex, time consuming
and expensive approach.
(Nayab, 2019)
References
Accountig For Management. (2019, May 19). Advantages and disadvantages of
absorption costing. Retrieved from www.accountingformanagement.org:
https://www.accountingformanagement.org/advantages-and-disadvantages-
of-absorption-costing/
Accounting For Management. (2019, May 19). Advantages and disadvantages of
absorption costing. Retrieved from www.accountingformanagement.org:
https://www.accountingformanagement.org/advantages-and-disadvantages-
of-absorption-costing/
Accounting Tools. (2019, February 19). Activity Based Costing. Retrieved from
www.accountingtools.com:
https://www.accountingtools.com/articles/2017/5/14/activity-based-costing
kaplan Financial Limited. . (2019, May 19). Activity Based Costing (ABC). Retrieved
from kfknowledgebank.kaplan.co.uk:
http://kfknowledgebank.kaplan.co.uk/KFKB/Wiki%20Pages/Activity%20Based
%20Costing%20(ABC).aspx
Marx, D. C. (2019, May 19). Activity Based Costing (ABC) And Traditional Costing
Systems. Retrieved from financialsupport.weebly.com:
https://financialsupport.weebly.com/activity-based-costing-abc-and-
traditional-costing-systems.html
Nayab, N. (2019, May 19). What is the Difference Between Absorption Costing vs
Activity Based Costing? Retrieved from www.brighthub.com:
https://www.brighthub.com/office/finance/articles/86649.aspx
change in inventory levels.
5) It is a simple and easy approach and
free from such complexities.
5)It is a very complex, time consuming
and expensive approach.
(Nayab, 2019)
References
Accountig For Management. (2019, May 19). Advantages and disadvantages of
absorption costing. Retrieved from www.accountingformanagement.org:
https://www.accountingformanagement.org/advantages-and-disadvantages-
of-absorption-costing/
Accounting For Management. (2019, May 19). Advantages and disadvantages of
absorption costing. Retrieved from www.accountingformanagement.org:
https://www.accountingformanagement.org/advantages-and-disadvantages-
of-absorption-costing/
Accounting Tools. (2019, February 19). Activity Based Costing. Retrieved from
www.accountingtools.com:
https://www.accountingtools.com/articles/2017/5/14/activity-based-costing
kaplan Financial Limited. . (2019, May 19). Activity Based Costing (ABC). Retrieved
from kfknowledgebank.kaplan.co.uk:
http://kfknowledgebank.kaplan.co.uk/KFKB/Wiki%20Pages/Activity%20Based
%20Costing%20(ABC).aspx
Marx, D. C. (2019, May 19). Activity Based Costing (ABC) And Traditional Costing
Systems. Retrieved from financialsupport.weebly.com:
https://financialsupport.weebly.com/activity-based-costing-abc-and-
traditional-costing-systems.html
Nayab, N. (2019, May 19). What is the Difference Between Absorption Costing vs
Activity Based Costing? Retrieved from www.brighthub.com:
https://www.brighthub.com/office/finance/articles/86649.aspx
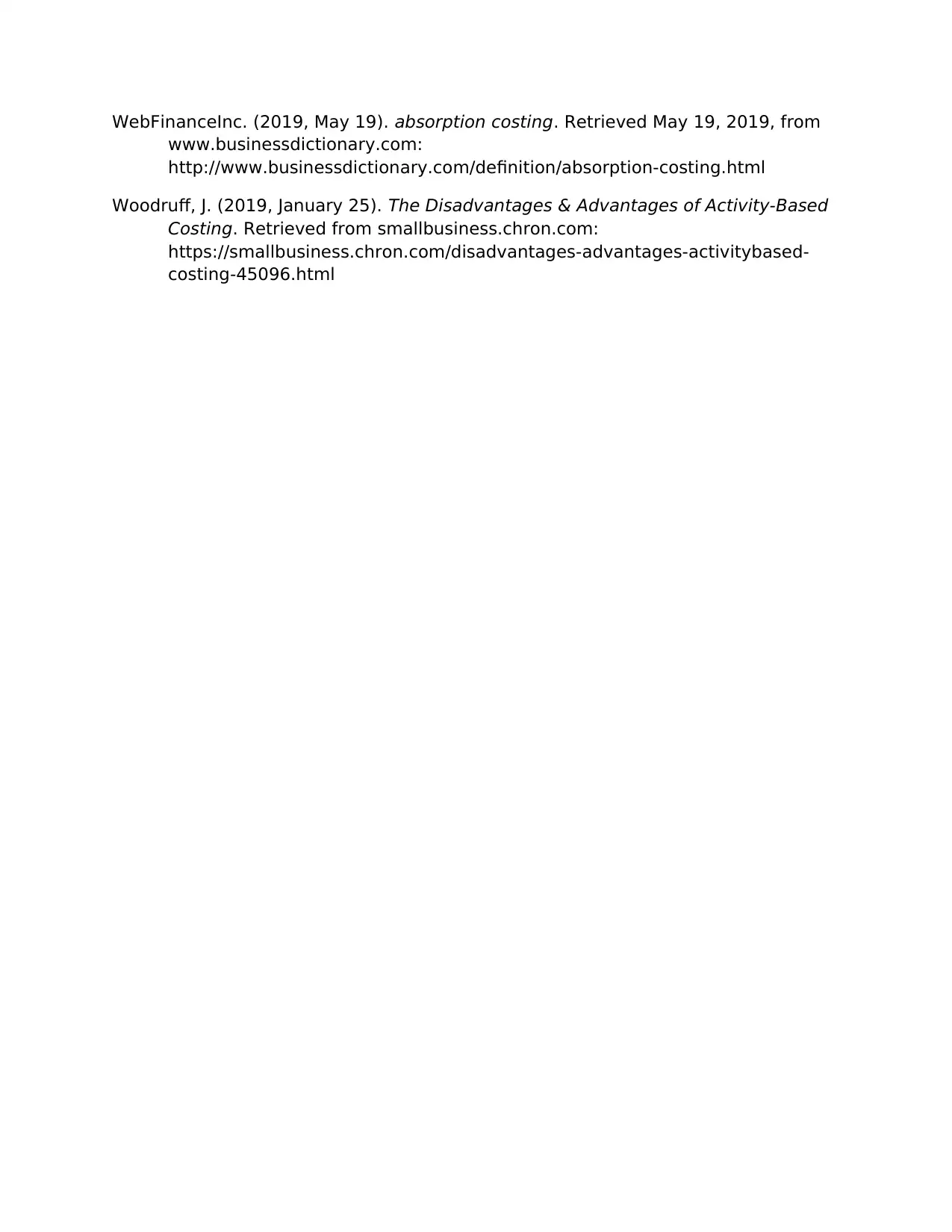
WebFinanceInc. (2019, May 19). absorption costing. Retrieved May 19, 2019, from
www.businessdictionary.com:
http://www.businessdictionary.com/definition/absorption-costing.html
Woodruff, J. (2019, January 25). The Disadvantages & Advantages of Activity-Based
Costing. Retrieved from smallbusiness.chron.com:
https://smallbusiness.chron.com/disadvantages-advantages-activitybased-
costing-45096.html
www.businessdictionary.com:
http://www.businessdictionary.com/definition/absorption-costing.html
Woodruff, J. (2019, January 25). The Disadvantages & Advantages of Activity-Based
Costing. Retrieved from smallbusiness.chron.com:
https://smallbusiness.chron.com/disadvantages-advantages-activitybased-
costing-45096.html
1 out of 15
Related Documents
![[object Object]](/_next/image/?url=%2F_next%2Fstatic%2Fmedia%2Flogo.6d15ce61.png&w=640&q=75)
Your All-in-One AI-Powered Toolkit for Academic Success.
+13062052269
info@desklib.com
Available 24*7 on WhatsApp / Email
Unlock your academic potential
© 2024 | Zucol Services PVT LTD | All rights reserved.