As per the estimation the Institute of Medicine
8 Pages1417 Words21 Views
Added on 2022-09-09
As per the estimation the Institute of Medicine
Added on 2022-09-09
ShareRelated Documents
As per the estimation the Institute of Medicine (IOM) is of the view that on average
hospitalized patient are prone to atleast one mediaction error per day (Radley et. Al, 2013).
Medication error are harmful for patient, it cost much to the patient and contradicts the most
basic element in healthcare i.e. ‘safe practices’ (Grout and Toussaint, 2009). Safety of patient
and quality of services ensures barrier to medical flaws. To mitigate such flaws the ideas that
are followed is through improving the process through relentless waste reduction also known
by the name ‘Lean’.
The origination of the concept of ‘Lean’ was coined in Japan, during the era of 70’s when the
automobile sector in USA struggled with the high maintenance cost levied on the consumer
front. Japanese giant ‘Toyota’ excelled in reducing the maintenance of thier cars by relying
on the less expensive models in comparision to American manufacturer (Ohno, 1988). The
manufacturer and academics from USA visited Japan to learn the new concept ‘Lean’. The
concept of Lean incorporates the combined concept taken from TQM and Friedrick W.
Taylor’s “Principle of scientific management”. Through the concept of TQM, Lean
deliberated the company culture of satisfying customer needs through relentless
improvisation in which all the employee are onboarded. Since then the concept of Lean has
been practiced in the service industries such as ‘healthcare’.
The first intervention in reducing waste is to identify steps in every process, as has been
discussed in the below given flowchart. For example, the customer would not hesitate to pay
for the gadget to be assembled and painted blue but not for the storage of items and for
overproduction. These are considered waste as illustrated in the chart below.
hospitalized patient are prone to atleast one mediaction error per day (Radley et. Al, 2013).
Medication error are harmful for patient, it cost much to the patient and contradicts the most
basic element in healthcare i.e. ‘safe practices’ (Grout and Toussaint, 2009). Safety of patient
and quality of services ensures barrier to medical flaws. To mitigate such flaws the ideas that
are followed is through improving the process through relentless waste reduction also known
by the name ‘Lean’.
The origination of the concept of ‘Lean’ was coined in Japan, during the era of 70’s when the
automobile sector in USA struggled with the high maintenance cost levied on the consumer
front. Japanese giant ‘Toyota’ excelled in reducing the maintenance of thier cars by relying
on the less expensive models in comparision to American manufacturer (Ohno, 1988). The
manufacturer and academics from USA visited Japan to learn the new concept ‘Lean’. The
concept of Lean incorporates the combined concept taken from TQM and Friedrick W.
Taylor’s “Principle of scientific management”. Through the concept of TQM, Lean
deliberated the company culture of satisfying customer needs through relentless
improvisation in which all the employee are onboarded. Since then the concept of Lean has
been practiced in the service industries such as ‘healthcare’.
The first intervention in reducing waste is to identify steps in every process, as has been
discussed in the below given flowchart. For example, the customer would not hesitate to pay
for the gadget to be assembled and painted blue but not for the storage of items and for
overproduction. These are considered waste as illustrated in the chart below.

The Seven Waste:
Ohnos seven waste Defination Healthcare example from
reviewed studies
Waste of time Unnecessary queues and wait
for the material, resources
and services that is just in
opposite to JIT delivery
In Canada through the
application of visual
reminders and worksheet
quality control team ensures
reduction in the time taken
for reassessment by the
physician. Such improvement
does not require additional
resources with minimal cost
Waste of movement Unnecessary movement of
patient or misaligned
movement as required to the
service demand. Too quick or
too slow.
Reduction in the movement
of people by 44% in Virginia
mason centre
Waste of inventory High inventory increases
waste that also includes
patient
Keeping patient on the roll
which should otherwise be
sent home or ordering too
high to compensate for
misalignment in supply
Waste of processing Unwanted processing Reprocessing diagnostic test
of patient because of error in
the readings, fulfillment of
Ohnos seven waste Defination Healthcare example from
reviewed studies
Waste of time Unnecessary queues and wait
for the material, resources
and services that is just in
opposite to JIT delivery
In Canada through the
application of visual
reminders and worksheet
quality control team ensures
reduction in the time taken
for reassessment by the
physician. Such improvement
does not require additional
resources with minimal cost
Waste of movement Unnecessary movement of
patient or misaligned
movement as required to the
service demand. Too quick or
too slow.
Reduction in the movement
of people by 44% in Virginia
mason centre
Waste of inventory High inventory increases
waste that also includes
patient
Keeping patient on the roll
which should otherwise be
sent home or ordering too
high to compensate for
misalignment in supply
Waste of processing Unwanted processing Reprocessing diagnostic test
of patient because of error in
the readings, fulfillment of
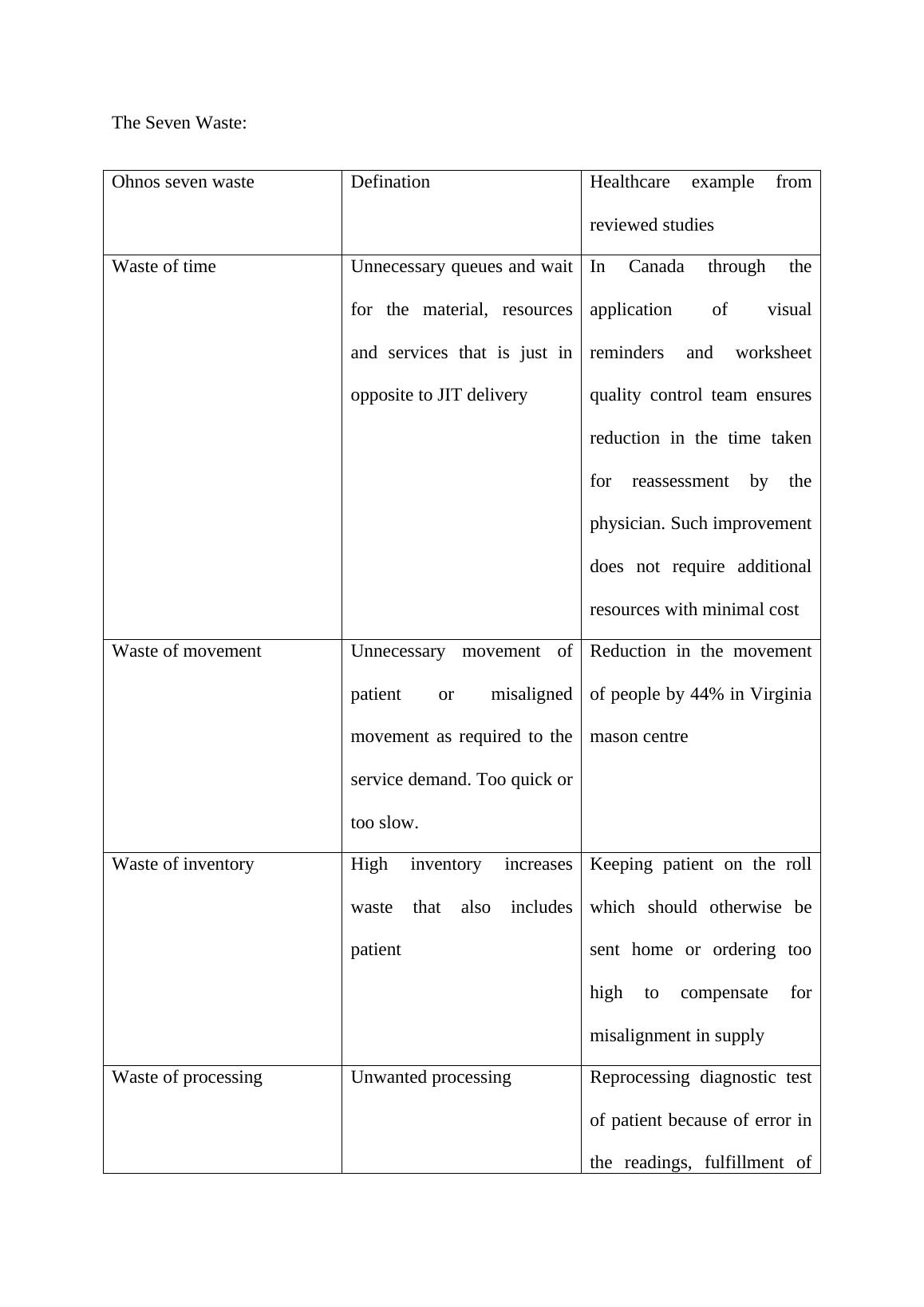
similar form in different
department for the same
patient and rescheduling the
missed appointment
Waste of making defective
product
Defective process and
services
Recieving complaints about
the service quality and
hospitality that does not meet
the customer expectation
(lack of value for customer)
Waste in transportation Unnecessary movement of
staff and material
The lean implementation in
the Virginia mason centre
helped to bring reduction in
72% of product travel
distance within 2 years
Waste of overproduction Production must match to
time and amount of requested
order
Unnecessary referral test,
hospitalization, acquiring
material in access
These waste can be identified and reduced using Lean principle and tools as described in the
table below (Virtue and Chaussalet, 2013). There is a several case stories on Lean thinking
intervention in the healthcare that demonstrate positive outcome on productivity, cost, quality
and JIT delivery services due to Lean principle applied throughout the organization. The
patient comes to the hospitals for either relief or cure and this is what value is in healthcare.
The process to achieve this final goal is known as patient flow in healthcare. It not only
department for the same
patient and rescheduling the
missed appointment
Waste of making defective
product
Defective process and
services
Recieving complaints about
the service quality and
hospitality that does not meet
the customer expectation
(lack of value for customer)
Waste in transportation Unnecessary movement of
staff and material
The lean implementation in
the Virginia mason centre
helped to bring reduction in
72% of product travel
distance within 2 years
Waste of overproduction Production must match to
time and amount of requested
order
Unnecessary referral test,
hospitalization, acquiring
material in access
These waste can be identified and reduced using Lean principle and tools as described in the
table below (Virtue and Chaussalet, 2013). There is a several case stories on Lean thinking
intervention in the healthcare that demonstrate positive outcome on productivity, cost, quality
and JIT delivery services due to Lean principle applied throughout the organization. The
patient comes to the hospitals for either relief or cure and this is what value is in healthcare.
The process to achieve this final goal is known as patient flow in healthcare. It not only
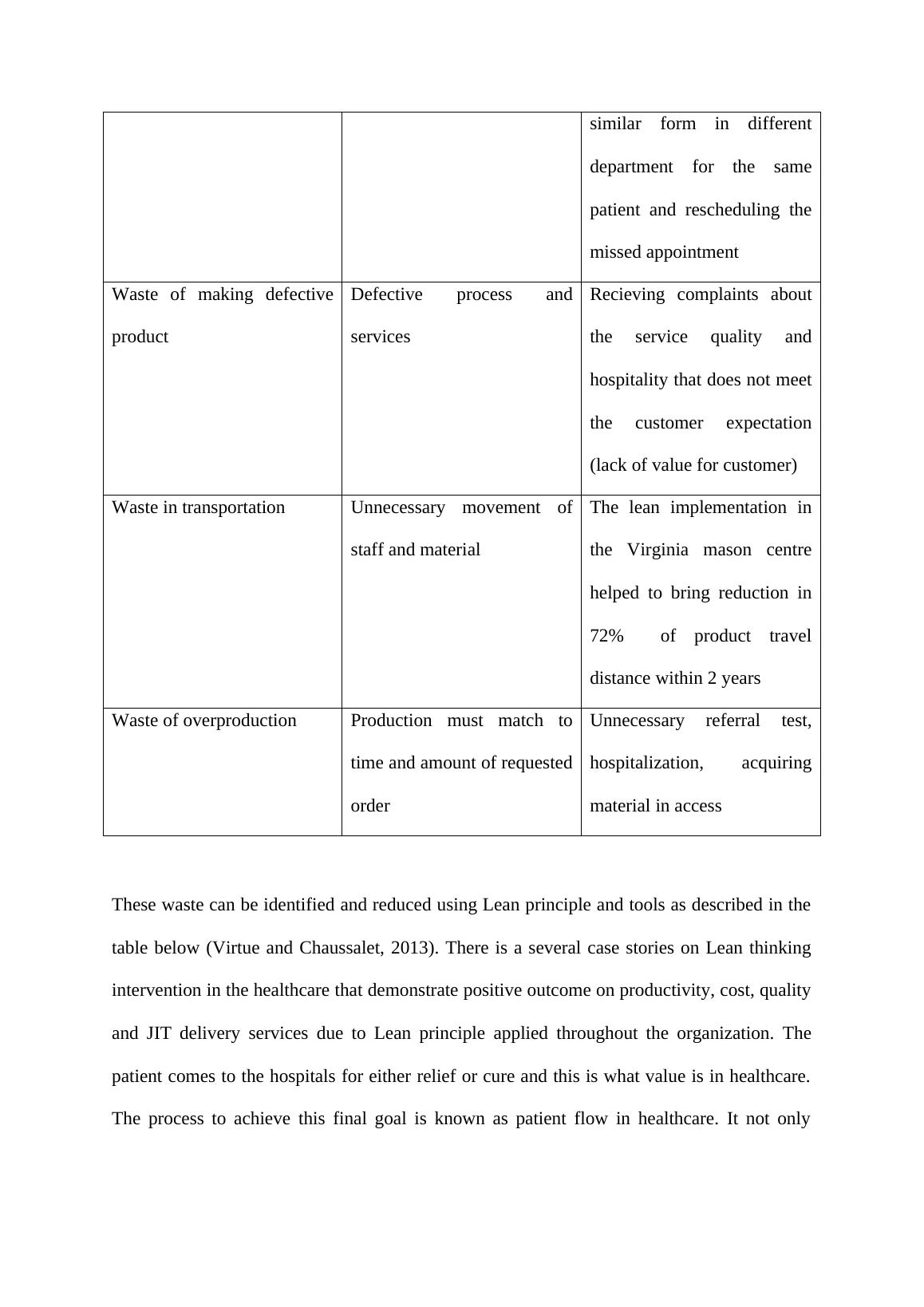
End of preview
Want to access all the pages? Upload your documents or become a member.