ASME Division 2 Rules for Pressure Vessel Design: Local and Global Failure Analysis
24 Pages6152 Words407 Views
Added on 2023-06-10
About This Document
This article discusses the ASME Division 2 rules for pressure vessel design and analysis of local and global failure. It covers the procedures for buckling load, collapse load, limit of strain, ultimate strength, and yield strength. It also talks about the design of pressure vessels, types of failure, stress-strain analysis, and more. The article includes literature review, background of the code, local and global failure analysis, elastic-plastic analysis, types of failure, and more.
ASME Division 2 Rules for Pressure Vessel Design: Local and Global Failure Analysis
Added on 2023-06-10
ShareRelated Documents
Name of the Student
Name of the Professor
City/State
Date/Month/Year
Name of the Professor
City/State
Date/Month/Year
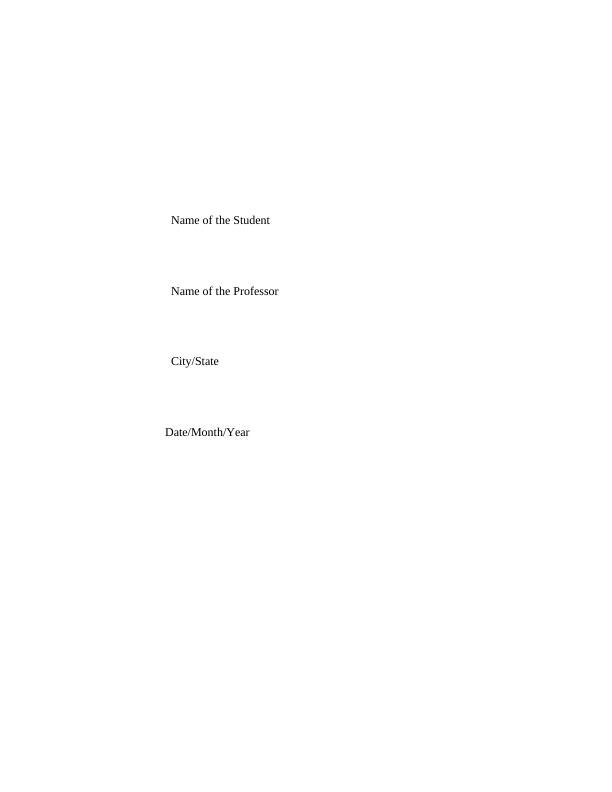
Introduction
The procedures and defines the allowable for buckling load, collapse load, the limit of the strain,
ultimate strength and yield strength are articulated in the ASME Division 2 rules. These
procedures are based on protection against failure models for example protection against collapse
from bulking and also safeguard contrary to local failure.
The requirement for local failure procedure is articulated in ASME division, and also it defines
the allowable yield strength, ultimate strength, strain limit, collapse load and buckling load that
needs to be satisfied. These procedures are based on protection against failure modes which are
guarded alongside local failure modes, plastic downfall, and protection against failure of
buckling. The procedure called out may be applied if the stress evaluated at the design
temperature is governed by time-independent properties unless it is allowed by specific design
procedure. The difference in material properties and variations in loading is accounted for by
load factors account. In the case of defense in contradiction of plastic failure, three alternate
approaches are allowed to be used. Aiming at determining an inferior guaranteed to the limit
weight of a component then the limit load method is preferred.
The limit load analysis articulates the manner in which the failing of rapture in malleable and the
commencement of plastic distortion of a building. The ASME also requires that in addition to
evaluating defense from plastic failure or from buckling, it shall be pleased to evade buckling of
constituents with a compressive stress field under applied design loads.
The procedures and defines the allowable for buckling load, collapse load, the limit of the strain,
ultimate strength and yield strength are articulated in the ASME Division 2 rules. These
procedures are based on protection against failure models for example protection against collapse
from bulking and also safeguard contrary to local failure.
The requirement for local failure procedure is articulated in ASME division, and also it defines
the allowable yield strength, ultimate strength, strain limit, collapse load and buckling load that
needs to be satisfied. These procedures are based on protection against failure modes which are
guarded alongside local failure modes, plastic downfall, and protection against failure of
buckling. The procedure called out may be applied if the stress evaluated at the design
temperature is governed by time-independent properties unless it is allowed by specific design
procedure. The difference in material properties and variations in loading is accounted for by
load factors account. In the case of defense in contradiction of plastic failure, three alternate
approaches are allowed to be used. Aiming at determining an inferior guaranteed to the limit
weight of a component then the limit load method is preferred.
The limit load analysis articulates the manner in which the failing of rapture in malleable and the
commencement of plastic distortion of a building. The ASME also requires that in addition to
evaluating defense from plastic failure or from buckling, it shall be pleased to evade buckling of
constituents with a compressive stress field under applied design loads.
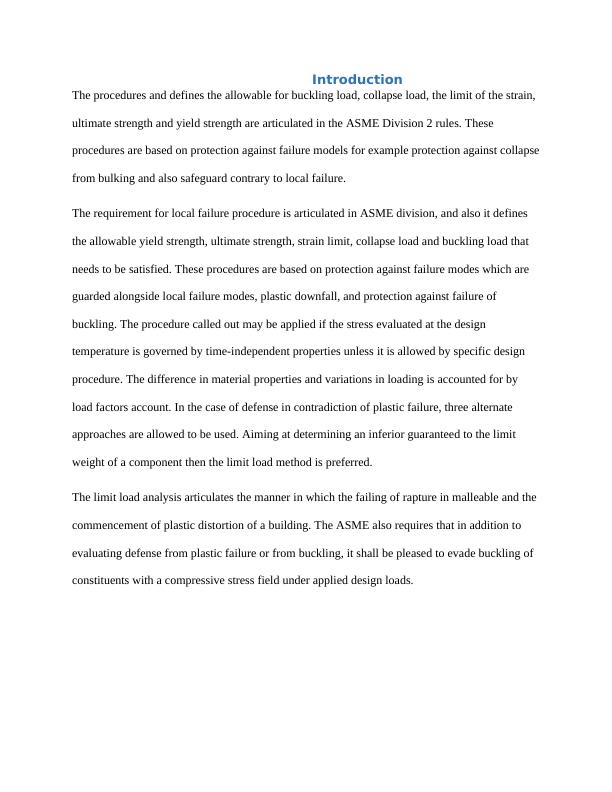
Literature Review
According to the research conducted by the International Journal of Research in Science and
Engineering, the fatigue analysis of a reactor pressure vessels is performed using heat transfer
coefficient based on operating environment. The overall stress intensity range is investigated to
determine the adequacy of design. The material of a pressure vessel may be brittle for example
ductile or cast iron. The failure behavior of pressure vessels during high pressure has been
investigated experimentally and the result showed that the pressurization rate and acoustic
emission response to the vessels to the pressure loading.
A practical analysis method was conducted by Hoyt et al (2003) for the power, toughness and
damage easiness assessment of compound. Strength-of-materials failure criteria assist in
predicting serious injury instigation weights and situations. A fracture mechanics technique is
applied in predicting destruction development and failure based on motionless and cyclic loads
based on test data for static fracture hardiness and crack rate of growth.
Instigation and development of matrix cracks produced AE events having low duration and low
energy as investigated by Surgeon et al (1997). The smaller period events could be accredited to
micro-cracks, a procedure by which was accompanied by deboning of matrix/fiber-matrix
interface. The formation of macro and micro-cracks could be resolved in the case of
unidirectional material.
Background of the code
The ASME Boiler and Pressure vessel code were created to regulate the design and construction
of pressure vessels and boilers. It was formed after numerous serious explosions in the state of
Massachusetts. The first edition of this code was in 1914 after which the verification that the
manufacturer was to the code was performed by independent inspectors causing numerous
According to the research conducted by the International Journal of Research in Science and
Engineering, the fatigue analysis of a reactor pressure vessels is performed using heat transfer
coefficient based on operating environment. The overall stress intensity range is investigated to
determine the adequacy of design. The material of a pressure vessel may be brittle for example
ductile or cast iron. The failure behavior of pressure vessels during high pressure has been
investigated experimentally and the result showed that the pressurization rate and acoustic
emission response to the vessels to the pressure loading.
A practical analysis method was conducted by Hoyt et al (2003) for the power, toughness and
damage easiness assessment of compound. Strength-of-materials failure criteria assist in
predicting serious injury instigation weights and situations. A fracture mechanics technique is
applied in predicting destruction development and failure based on motionless and cyclic loads
based on test data for static fracture hardiness and crack rate of growth.
Instigation and development of matrix cracks produced AE events having low duration and low
energy as investigated by Surgeon et al (1997). The smaller period events could be accredited to
micro-cracks, a procedure by which was accompanied by deboning of matrix/fiber-matrix
interface. The formation of macro and micro-cracks could be resolved in the case of
unidirectional material.
Background of the code
The ASME Boiler and Pressure vessel code were created to regulate the design and construction
of pressure vessels and boilers. It was formed after numerous serious explosions in the state of
Massachusetts. The first edition of this code was in 1914 after which the verification that the
manufacturer was to the code was performed by independent inspectors causing numerous
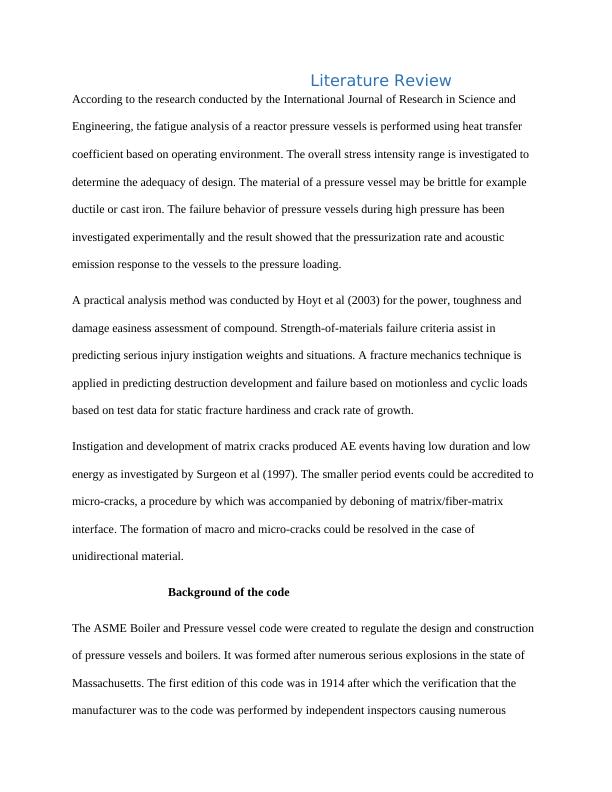
interpretations. The rules are provided by the code cases allowing the material use and
alternative methods of constructions.
Design of pressure vessels
The ASME governs the design of pressure vessels and the designing of pressure vessels is
carried out so that to contain pressure and withstand operating mechanically. Pressure vessels
maybe lined with numerous ceramics, polymers, and metals to prevent leakage and materials
needed for the construction, and should have properties such as heat resistant, high tensile
strength and resisting maximum stress.
Designing of spherical pressure vessel design is typically stronger compared to cylindrical shape,
with the same wall thickness through the spherical ones which are very expensive when it comes
to manufacturing and pressure vessels are typically made of steel and according to ASME
Section VIII, Division 1, design-by-rule approach is the most commonly used by engineers to
size the pressure vessels. In division 2 consist design-by-analysis approach while the third
decision entails pressure vessels that need internal or external operating pressure above 10,000
PSI. In order to size a pressure vessel then the following data is required by the engineer which
include;
Vessels function, operating conditions, materials of construction and operating conditions.
LOCAL FAILURE
The description against local failure is articulated in section 5.3 of the ASME. The chosen
method uses the elastic-plastic analysis and compares the total equivalent plastic strain to a
limiting strain (Wadsworth, 2009, p. 156). The material model requires that the effect of non-
linear geometry is included. The local failure requires the use of non-linear geometry with a load
alternative methods of constructions.
Design of pressure vessels
The ASME governs the design of pressure vessels and the designing of pressure vessels is
carried out so that to contain pressure and withstand operating mechanically. Pressure vessels
maybe lined with numerous ceramics, polymers, and metals to prevent leakage and materials
needed for the construction, and should have properties such as heat resistant, high tensile
strength and resisting maximum stress.
Designing of spherical pressure vessel design is typically stronger compared to cylindrical shape,
with the same wall thickness through the spherical ones which are very expensive when it comes
to manufacturing and pressure vessels are typically made of steel and according to ASME
Section VIII, Division 1, design-by-rule approach is the most commonly used by engineers to
size the pressure vessels. In division 2 consist design-by-analysis approach while the third
decision entails pressure vessels that need internal or external operating pressure above 10,000
PSI. In order to size a pressure vessel then the following data is required by the engineer which
include;
Vessels function, operating conditions, materials of construction and operating conditions.
LOCAL FAILURE
The description against local failure is articulated in section 5.3 of the ASME. The chosen
method uses the elastic-plastic analysis and compares the total equivalent plastic strain to a
limiting strain (Wadsworth, 2009, p. 156). The material model requires that the effect of non-
linear geometry is included. The local failure requires the use of non-linear geometry with a load
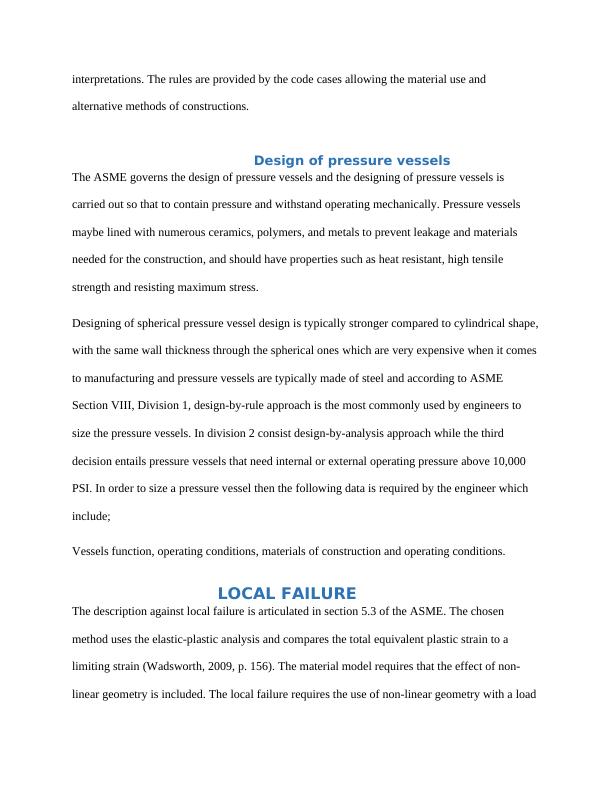
factor. The arc length procedure and gradually applied procedure are used in the local criteria so
that non-linear geometry and plastic effects would be accounted for properly (Dieter, 2014, p.
347).
The yield condition currently available and it is suitable for ductile materials for example metals
like aluminum and steel. The plastic behavior of materials may be combined with other types of
non-linearity (Kotelyanskii, 2008, p. 341). The von Mises yield criterion proposes that the
materials yielding begin when the critical value is attained by the additional deviatory stress
invariant. The von Mises criterion is appropriate for examination of plastic distortion for
materials which are ductile such as metals because it is independent of the primary stress
invariant (Chirag, 2015, p. 67).
In nonlinear properties of materials, the selected material will behave elastically during a non-
linear analysis, and plasticity can be enabled by selecting a type of plastic behavior (Hertzberg,
2012, p. 459). It corresponds to the bilinear stress-strain relationship, identical in tightness and
compression. The stress-strain relationship is automatically generated by three parameters which
are elastic part or young modulus, yield stress and slope of the elastic branch (Li, 2008, p. 500).
Plasticity simply defines the distortion of a material in solid form going through changes in
shape which cannot be reversed as a result of forces applied. In case of a metal solid in the state
being pounded or bent forming a fresh outline, shows plasticity as lasting variations arise in the
interior the material itself (Goh, 2016, p. 200). Plasticity is mostly observed in materials for
example soils, rocks, metals and many others and in metals, plastic deformation always comes as
a result of dislocations which is rare in crystalline materials (Li, 2007, p. 456).
that non-linear geometry and plastic effects would be accounted for properly (Dieter, 2014, p.
347).
The yield condition currently available and it is suitable for ductile materials for example metals
like aluminum and steel. The plastic behavior of materials may be combined with other types of
non-linearity (Kotelyanskii, 2008, p. 341). The von Mises yield criterion proposes that the
materials yielding begin when the critical value is attained by the additional deviatory stress
invariant. The von Mises criterion is appropriate for examination of plastic distortion for
materials which are ductile such as metals because it is independent of the primary stress
invariant (Chirag, 2015, p. 67).
In nonlinear properties of materials, the selected material will behave elastically during a non-
linear analysis, and plasticity can be enabled by selecting a type of plastic behavior (Hertzberg,
2012, p. 459). It corresponds to the bilinear stress-strain relationship, identical in tightness and
compression. The stress-strain relationship is automatically generated by three parameters which
are elastic part or young modulus, yield stress and slope of the elastic branch (Li, 2008, p. 500).
Plasticity simply defines the distortion of a material in solid form going through changes in
shape which cannot be reversed as a result of forces applied. In case of a metal solid in the state
being pounded or bent forming a fresh outline, shows plasticity as lasting variations arise in the
interior the material itself (Goh, 2016, p. 200). Plasticity is mostly observed in materials for
example soils, rocks, metals and many others and in metals, plastic deformation always comes as
a result of dislocations which is rare in crystalline materials (Li, 2007, p. 456).
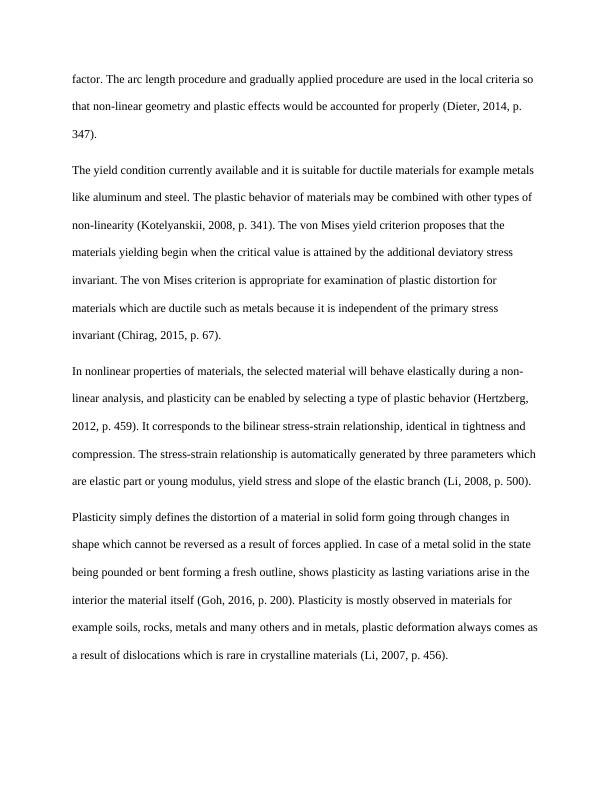
In ductile materials, stretchable loading used in a sample will make the material in a mutable
way. For each increase of load is escorted by a relative increase in extension and in case of
removing the load, the part goes back to its original size (Hiermairer, 2007, p. 652). In case the
weight surpasses the threshold, the yield strength, the allowance upsurges more quickly than
inelastic area and removal of the load, a certain grade of allowance will remain (Pullan, 2007, p.
67).
Global failure
Distortion of elastic is an estimation and its superiority rely on the time deliberated and the speed
of loading. Plasticity or malleability is a property of materials to go through irreparable distortion
deprived of any increase in loads and stresses (Kohser, 2013, p. 54). Plastic hardening involving
hardening which requires progressively advanced stresses to cause in extra plastic distortion. The
material plasticity relative to the material ductility, malleability and most plasticity in metals is
chiefly triggered by two nodes of distortion, which assist in atoms movement over many
interatomic spaces comparative to their original locations. Most plasticity is shown in metals
mostly when they are hot than when they are cold (Moavenzadeh, 2016, p. 531).
The origins of soil malleability are multifaceted fairly and powerfully relies on the
microstructure chemical conformation, and the gratified of water (Besson, 2009, p. 188).
Plasticity performance in soils is triggered mostly by reorganization of clusters of head-to-head
grains while inelastic deformations of rock are mostly instigated through the creation of minor
cracks and sliding motions comparative to these cracks (Mai, 2009, p. 319). There are three
alternative techniques which are used in evaluating the structure used in protecting material
against plastic collapse and they include elastic stress analysis approach and elastic-plastic stress
analysis.
way. For each increase of load is escorted by a relative increase in extension and in case of
removing the load, the part goes back to its original size (Hiermairer, 2007, p. 652). In case the
weight surpasses the threshold, the yield strength, the allowance upsurges more quickly than
inelastic area and removal of the load, a certain grade of allowance will remain (Pullan, 2007, p.
67).
Global failure
Distortion of elastic is an estimation and its superiority rely on the time deliberated and the speed
of loading. Plasticity or malleability is a property of materials to go through irreparable distortion
deprived of any increase in loads and stresses (Kohser, 2013, p. 54). Plastic hardening involving
hardening which requires progressively advanced stresses to cause in extra plastic distortion. The
material plasticity relative to the material ductility, malleability and most plasticity in metals is
chiefly triggered by two nodes of distortion, which assist in atoms movement over many
interatomic spaces comparative to their original locations. Most plasticity is shown in metals
mostly when they are hot than when they are cold (Moavenzadeh, 2016, p. 531).
The origins of soil malleability are multifaceted fairly and powerfully relies on the
microstructure chemical conformation, and the gratified of water (Besson, 2009, p. 188).
Plasticity performance in soils is triggered mostly by reorganization of clusters of head-to-head
grains while inelastic deformations of rock are mostly instigated through the creation of minor
cracks and sliding motions comparative to these cracks (Mai, 2009, p. 319). There are three
alternative techniques which are used in evaluating the structure used in protecting material
against plastic collapse and they include elastic stress analysis approach and elastic-plastic stress
analysis.
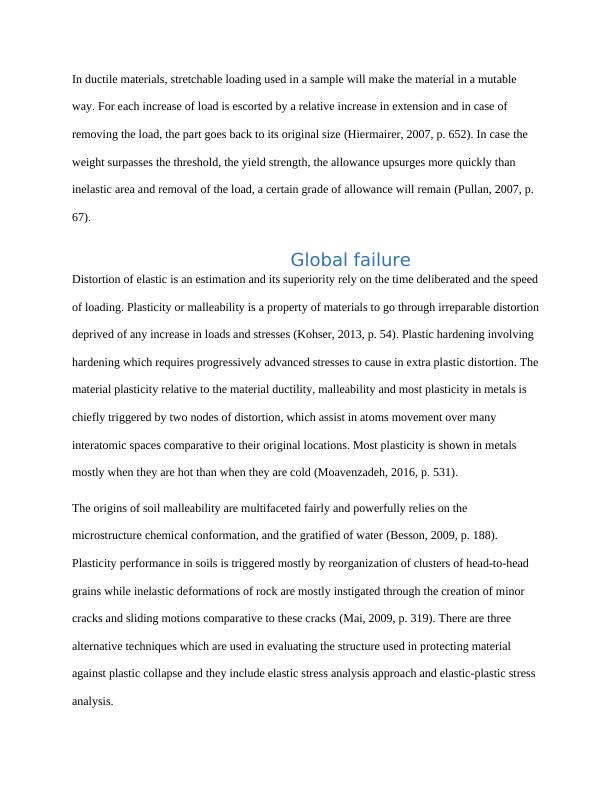
End of preview
Want to access all the pages? Upload your documents or become a member.
Related Documents
Materials Engineeringlg...
|17
|3437
|115
Life Assessment of Steam Headerlg...
|14
|2201
|13
Structural Design - Introductionlg...
|34
|19295
|480
Material Selection for Building a Pedestrian Bridge - A Tensile Testing and MATLAB Analysislg...
|13
|551
|76