Assembly Line Value Stream Mapping – Lean Manufacturing
VerifiedAdded on 2023/06/03
|6
|1285
|498
AI Summary
Career Episode 3 describes the experience of a Senior Engineering Consultant in Aspire for training and consulting for a period of 2 months from May 2013 to June 2013. The episode talks about the project of Assembly Line Value Stream Mapping – Lean Manufacturing for GB Auto, one of the largest manufacturers of vehicles in Egypt. The consultant led the value stream mapping session, acted as a middleman between the company and its customers, worked as a coach and technical leader of the team, led work to calculate savings, and communicated between different team members to share project updates. The episode also talks about the structure of the organization, activities involved in creating the project, and the proposed solutions that helped in increasing storage between two divisions, increasing body division throughput, and improving the total delivery cost of the plant.
Contribute Materials
Your contribution can guide someone’s learning journey. Share your
documents today.
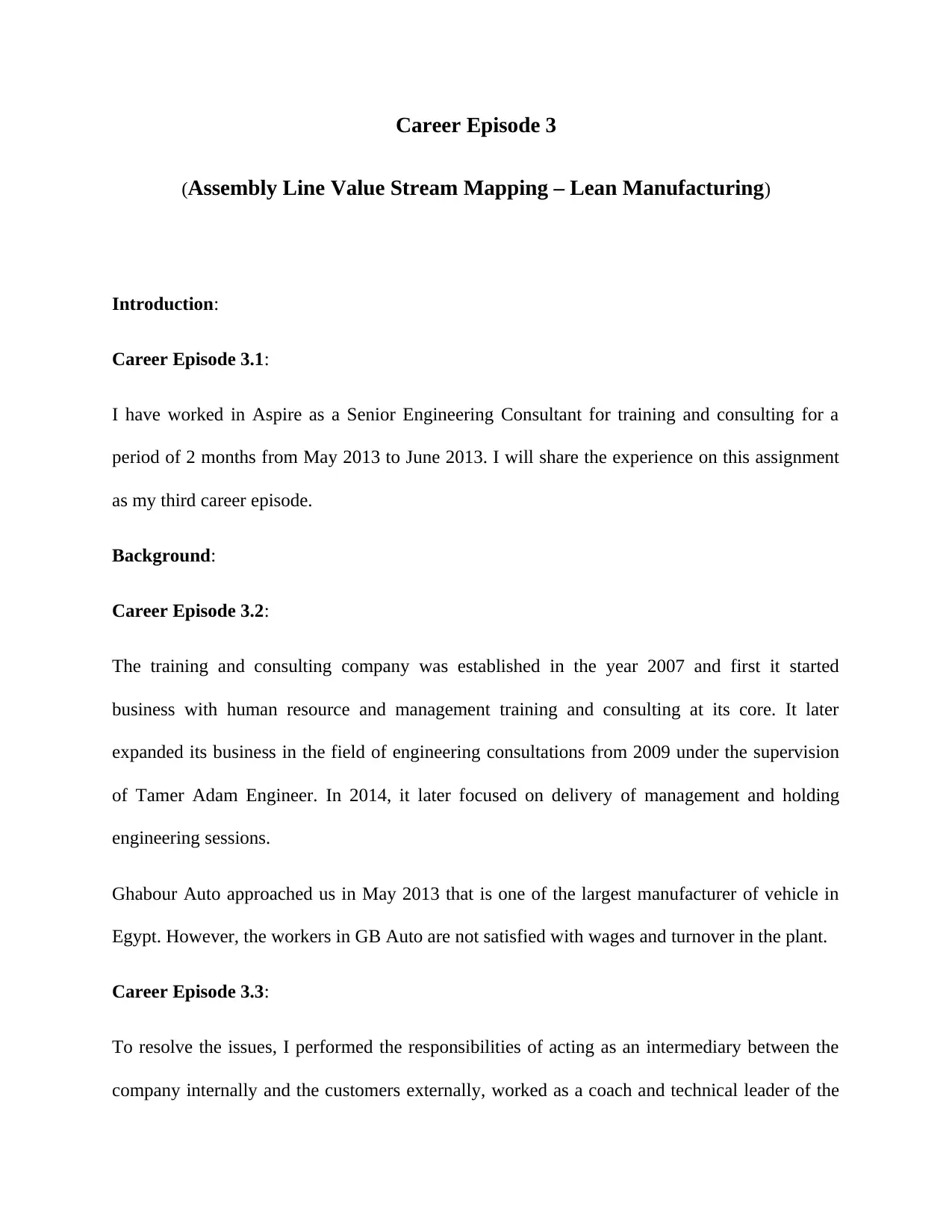
Career Episode 3
(Assembly Line Value Stream Mapping – Lean Manufacturing)
Introduction:
Career Episode 3.1:
I have worked in Aspire as a Senior Engineering Consultant for training and consulting for a
period of 2 months from May 2013 to June 2013. I will share the experience on this assignment
as my third career episode.
Background:
Career Episode 3.2:
The training and consulting company was established in the year 2007 and first it started
business with human resource and management training and consulting at its core. It later
expanded its business in the field of engineering consultations from 2009 under the supervision
of Tamer Adam Engineer. In 2014, it later focused on delivery of management and holding
engineering sessions.
Ghabour Auto approached us in May 2013 that is one of the largest manufacturer of vehicle in
Egypt. However, the workers in GB Auto are not satisfied with wages and turnover in the plant.
Career Episode 3.3:
To resolve the issues, I performed the responsibilities of acting as an intermediary between the
company internally and the customers externally, worked as a coach and technical leader of the
(Assembly Line Value Stream Mapping – Lean Manufacturing)
Introduction:
Career Episode 3.1:
I have worked in Aspire as a Senior Engineering Consultant for training and consulting for a
period of 2 months from May 2013 to June 2013. I will share the experience on this assignment
as my third career episode.
Background:
Career Episode 3.2:
The training and consulting company was established in the year 2007 and first it started
business with human resource and management training and consulting at its core. It later
expanded its business in the field of engineering consultations from 2009 under the supervision
of Tamer Adam Engineer. In 2014, it later focused on delivery of management and holding
engineering sessions.
Ghabour Auto approached us in May 2013 that is one of the largest manufacturer of vehicle in
Egypt. However, the workers in GB Auto are not satisfied with wages and turnover in the plant.
Career Episode 3.3:
To resolve the issues, I performed the responsibilities of acting as an intermediary between the
company internally and the customers externally, worked as a coach and technical leader of the
Secure Best Marks with AI Grader
Need help grading? Try our AI Grader for instant feedback on your assignments.
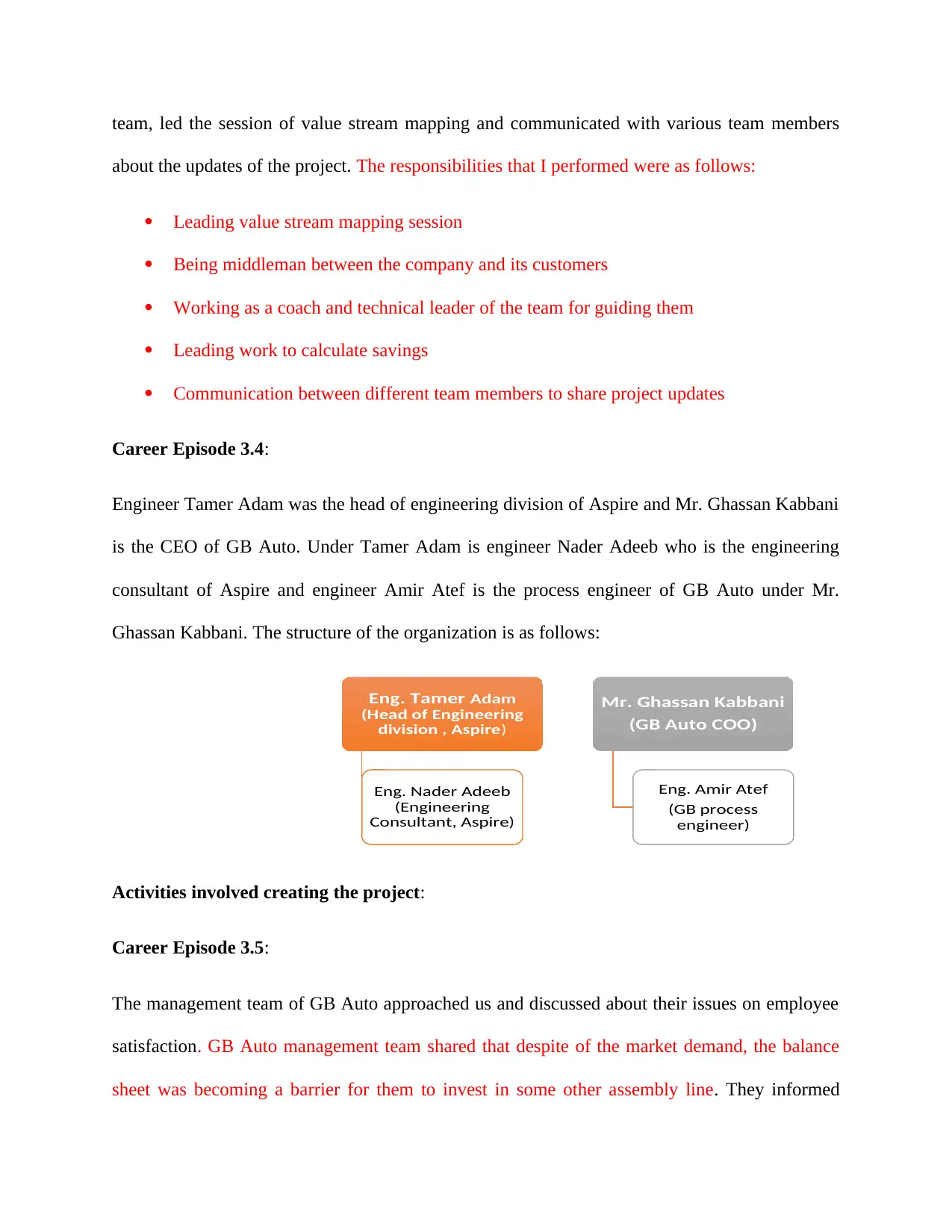
team, led the session of value stream mapping and communicated with various team members
about the updates of the project. The responsibilities that I performed were as follows:
Leading value stream mapping session
Being middleman between the company and its customers
Working as a coach and technical leader of the team for guiding them
Leading work to calculate savings
Communication between different team members to share project updates
Career Episode 3.4:
Engineer Tamer Adam was the head of engineering division of Aspire and Mr. Ghassan Kabbani
is the CEO of GB Auto. Under Tamer Adam is engineer Nader Adeeb who is the engineering
consultant of Aspire and engineer Amir Atef is the process engineer of GB Auto under Mr.
Ghassan Kabbani. The structure of the organization is as follows:
Activities involved creating the project:
Career Episode 3.5:
The management team of GB Auto approached us and discussed about their issues on employee
satisfaction. GB Auto management team shared that despite of the market demand, the balance
sheet was becoming a barrier for them to invest in some other assembly line. They informed
Eng. Tamer Adam
(Head of Engineering
division , Aspire)
Eng. Nader Adeeb
(Engineering
Consultant, Aspire)
Mr. Ghassan Kabbani
(GB Auto COO)
Eng. Amir Atef
(GB process
engineer)
about the updates of the project. The responsibilities that I performed were as follows:
Leading value stream mapping session
Being middleman between the company and its customers
Working as a coach and technical leader of the team for guiding them
Leading work to calculate savings
Communication between different team members to share project updates
Career Episode 3.4:
Engineer Tamer Adam was the head of engineering division of Aspire and Mr. Ghassan Kabbani
is the CEO of GB Auto. Under Tamer Adam is engineer Nader Adeeb who is the engineering
consultant of Aspire and engineer Amir Atef is the process engineer of GB Auto under Mr.
Ghassan Kabbani. The structure of the organization is as follows:
Activities involved creating the project:
Career Episode 3.5:
The management team of GB Auto approached us and discussed about their issues on employee
satisfaction. GB Auto management team shared that despite of the market demand, the balance
sheet was becoming a barrier for them to invest in some other assembly line. They informed
Eng. Tamer Adam
(Head of Engineering
division , Aspire)
Eng. Nader Adeeb
(Engineering
Consultant, Aspire)
Mr. Ghassan Kabbani
(GB Auto COO)
Eng. Amir Atef
(GB process
engineer)
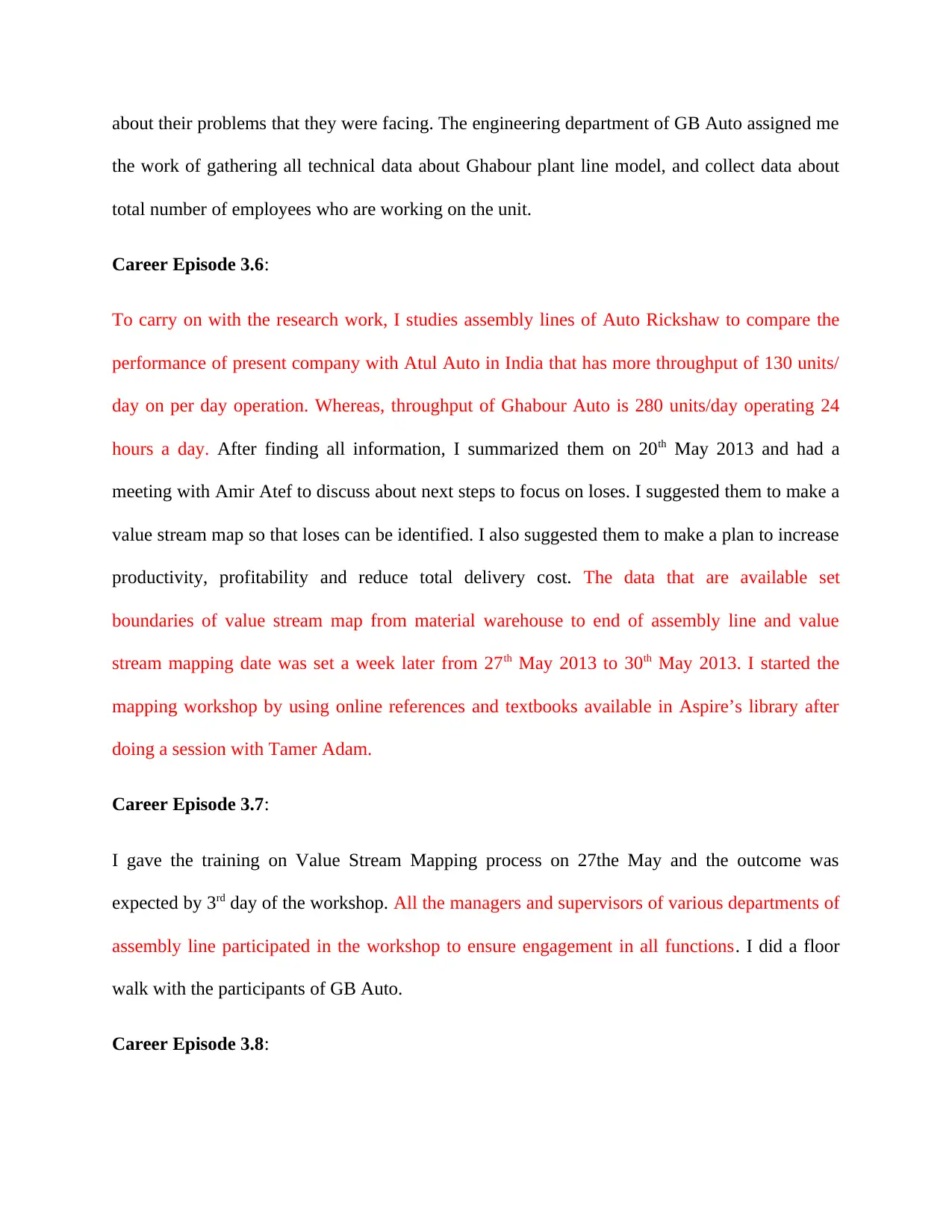
about their problems that they were facing. The engineering department of GB Auto assigned me
the work of gathering all technical data about Ghabour plant line model, and collect data about
total number of employees who are working on the unit.
Career Episode 3.6:
To carry on with the research work, I studies assembly lines of Auto Rickshaw to compare the
performance of present company with Atul Auto in India that has more throughput of 130 units/
day on per day operation. Whereas, throughput of Ghabour Auto is 280 units/day operating 24
hours a day. After finding all information, I summarized them on 20th May 2013 and had a
meeting with Amir Atef to discuss about next steps to focus on loses. I suggested them to make a
value stream map so that loses can be identified. I also suggested them to make a plan to increase
productivity, profitability and reduce total delivery cost. The data that are available set
boundaries of value stream map from material warehouse to end of assembly line and value
stream mapping date was set a week later from 27th May 2013 to 30th May 2013. I started the
mapping workshop by using online references and textbooks available in Aspire’s library after
doing a session with Tamer Adam.
Career Episode 3.7:
I gave the training on Value Stream Mapping process on 27the May and the outcome was
expected by 3rd day of the workshop. All the managers and supervisors of various departments of
assembly line participated in the workshop to ensure engagement in all functions. I did a floor
walk with the participants of GB Auto.
Career Episode 3.8:
the work of gathering all technical data about Ghabour plant line model, and collect data about
total number of employees who are working on the unit.
Career Episode 3.6:
To carry on with the research work, I studies assembly lines of Auto Rickshaw to compare the
performance of present company with Atul Auto in India that has more throughput of 130 units/
day on per day operation. Whereas, throughput of Ghabour Auto is 280 units/day operating 24
hours a day. After finding all information, I summarized them on 20th May 2013 and had a
meeting with Amir Atef to discuss about next steps to focus on loses. I suggested them to make a
value stream map so that loses can be identified. I also suggested them to make a plan to increase
productivity, profitability and reduce total delivery cost. The data that are available set
boundaries of value stream map from material warehouse to end of assembly line and value
stream mapping date was set a week later from 27th May 2013 to 30th May 2013. I started the
mapping workshop by using online references and textbooks available in Aspire’s library after
doing a session with Tamer Adam.
Career Episode 3.7:
I gave the training on Value Stream Mapping process on 27the May and the outcome was
expected by 3rd day of the workshop. All the managers and supervisors of various departments of
assembly line participated in the workshop to ensure engagement in all functions. I did a floor
walk with the participants of GB Auto.
Career Episode 3.8:
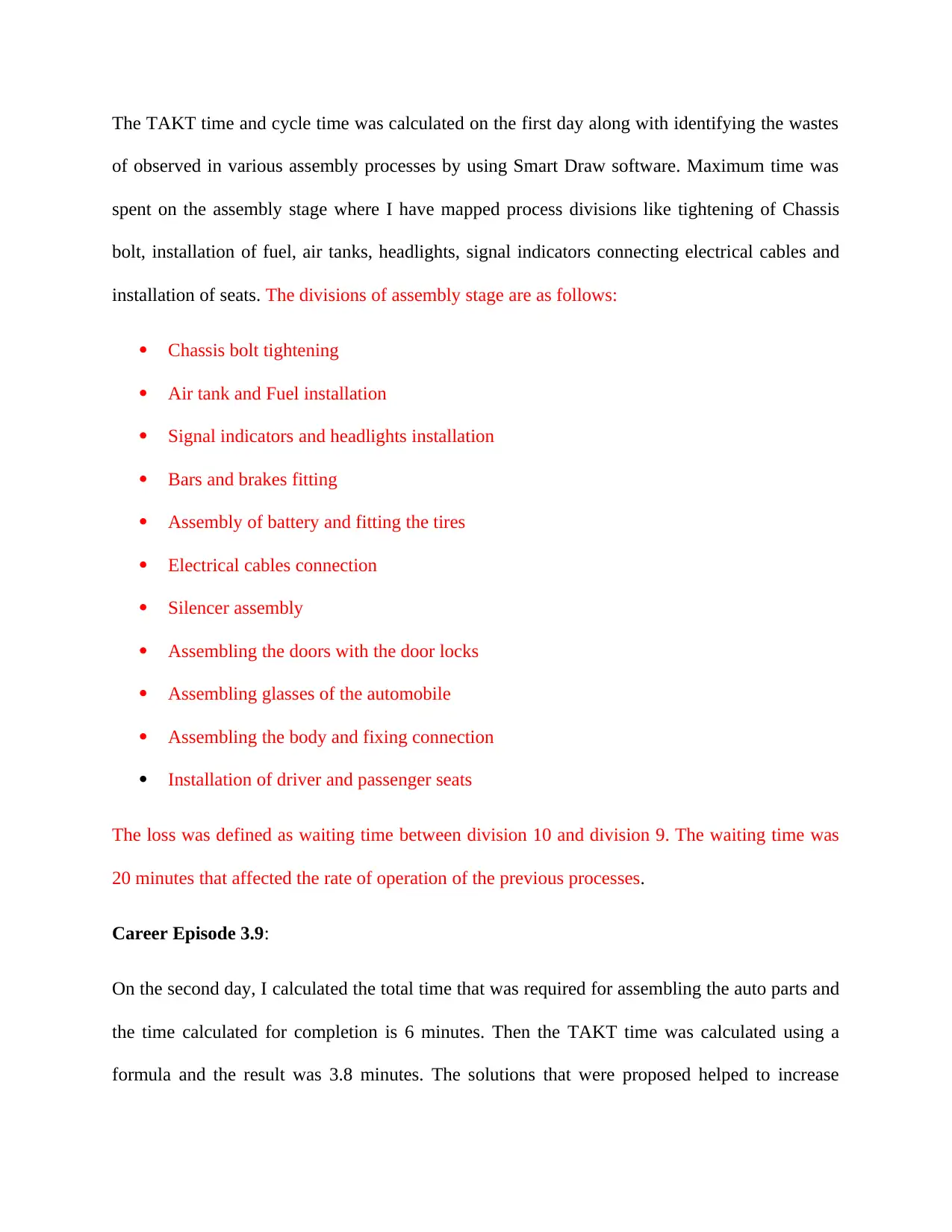
The TAKT time and cycle time was calculated on the first day along with identifying the wastes
of observed in various assembly processes by using Smart Draw software. Maximum time was
spent on the assembly stage where I have mapped process divisions like tightening of Chassis
bolt, installation of fuel, air tanks, headlights, signal indicators connecting electrical cables and
installation of seats. The divisions of assembly stage are as follows:
Chassis bolt tightening
Air tank and Fuel installation
Signal indicators and headlights installation
Bars and brakes fitting
Assembly of battery and fitting the tires
Electrical cables connection
Silencer assembly
Assembling the doors with the door locks
Assembling glasses of the automobile
Assembling the body and fixing connection
Installation of driver and passenger seats
The loss was defined as waiting time between division 10 and division 9. The waiting time was
20 minutes that affected the rate of operation of the previous processes.
Career Episode 3.9:
On the second day, I calculated the total time that was required for assembling the auto parts and
the time calculated for completion is 6 minutes. Then the TAKT time was calculated using a
formula and the result was 3.8 minutes. The solutions that were proposed helped to increase
of observed in various assembly processes by using Smart Draw software. Maximum time was
spent on the assembly stage where I have mapped process divisions like tightening of Chassis
bolt, installation of fuel, air tanks, headlights, signal indicators connecting electrical cables and
installation of seats. The divisions of assembly stage are as follows:
Chassis bolt tightening
Air tank and Fuel installation
Signal indicators and headlights installation
Bars and brakes fitting
Assembly of battery and fitting the tires
Electrical cables connection
Silencer assembly
Assembling the doors with the door locks
Assembling glasses of the automobile
Assembling the body and fixing connection
Installation of driver and passenger seats
The loss was defined as waiting time between division 10 and division 9. The waiting time was
20 minutes that affected the rate of operation of the previous processes.
Career Episode 3.9:
On the second day, I calculated the total time that was required for assembling the auto parts and
the time calculated for completion is 6 minutes. Then the TAKT time was calculated using a
formula and the result was 3.8 minutes. The solutions that were proposed helped to increase
Secure Best Marks with AI Grader
Need help grading? Try our AI Grader for instant feedback on your assignments.
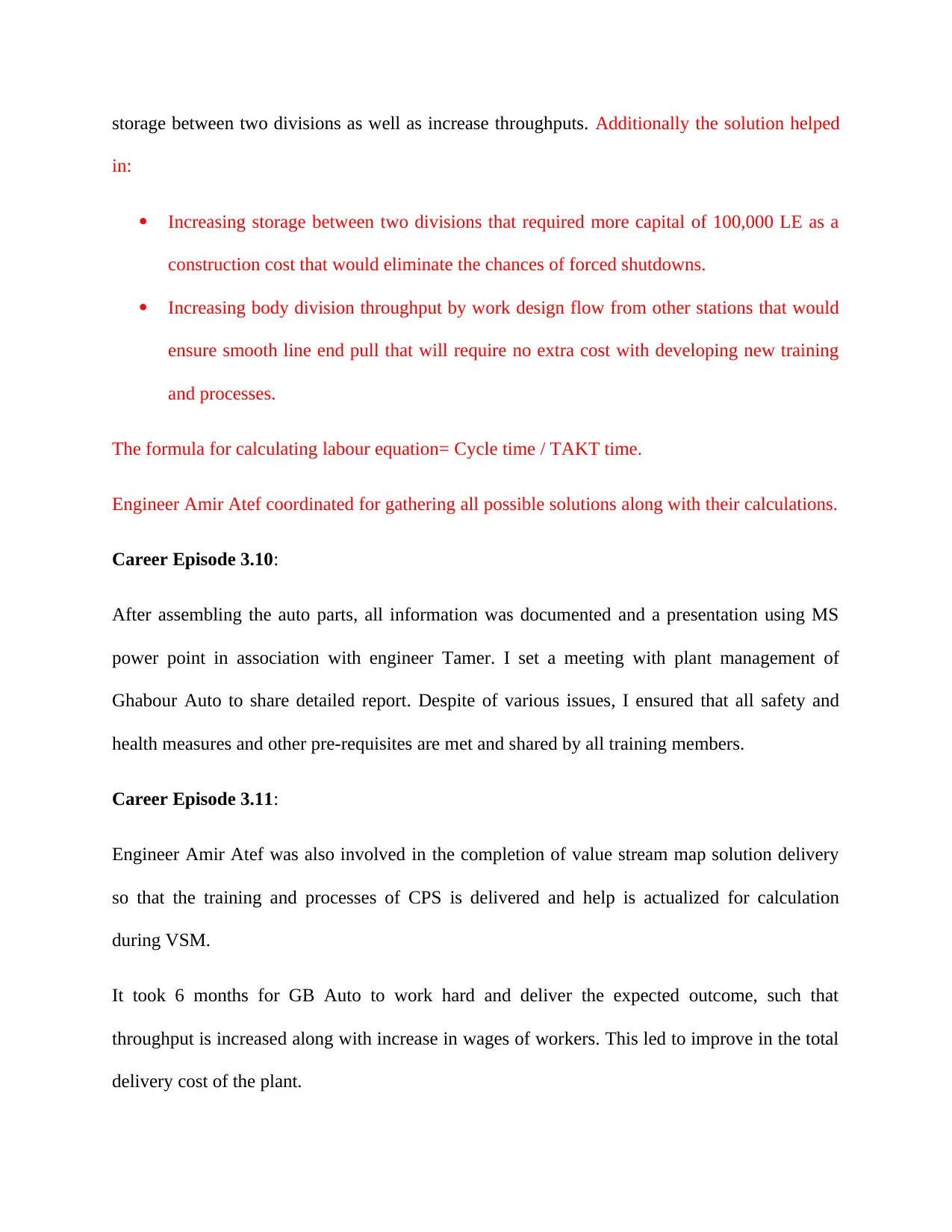
storage between two divisions as well as increase throughputs. Additionally the solution helped
in:
Increasing storage between two divisions that required more capital of 100,000 LE as a
construction cost that would eliminate the chances of forced shutdowns.
Increasing body division throughput by work design flow from other stations that would
ensure smooth line end pull that will require no extra cost with developing new training
and processes.
The formula for calculating labour equation= Cycle time / TAKT time.
Engineer Amir Atef coordinated for gathering all possible solutions along with their calculations.
Career Episode 3.10:
After assembling the auto parts, all information was documented and a presentation using MS
power point in association with engineer Tamer. I set a meeting with plant management of
Ghabour Auto to share detailed report. Despite of various issues, I ensured that all safety and
health measures and other pre-requisites are met and shared by all training members.
Career Episode 3.11:
Engineer Amir Atef was also involved in the completion of value stream map solution delivery
so that the training and processes of CPS is delivered and help is actualized for calculation
during VSM.
It took 6 months for GB Auto to work hard and deliver the expected outcome, such that
throughput is increased along with increase in wages of workers. This led to improve in the total
delivery cost of the plant.
in:
Increasing storage between two divisions that required more capital of 100,000 LE as a
construction cost that would eliminate the chances of forced shutdowns.
Increasing body division throughput by work design flow from other stations that would
ensure smooth line end pull that will require no extra cost with developing new training
and processes.
The formula for calculating labour equation= Cycle time / TAKT time.
Engineer Amir Atef coordinated for gathering all possible solutions along with their calculations.
Career Episode 3.10:
After assembling the auto parts, all information was documented and a presentation using MS
power point in association with engineer Tamer. I set a meeting with plant management of
Ghabour Auto to share detailed report. Despite of various issues, I ensured that all safety and
health measures and other pre-requisites are met and shared by all training members.
Career Episode 3.11:
Engineer Amir Atef was also involved in the completion of value stream map solution delivery
so that the training and processes of CPS is delivered and help is actualized for calculation
during VSM.
It took 6 months for GB Auto to work hard and deliver the expected outcome, such that
throughput is increased along with increase in wages of workers. This led to improve in the total
delivery cost of the plant.
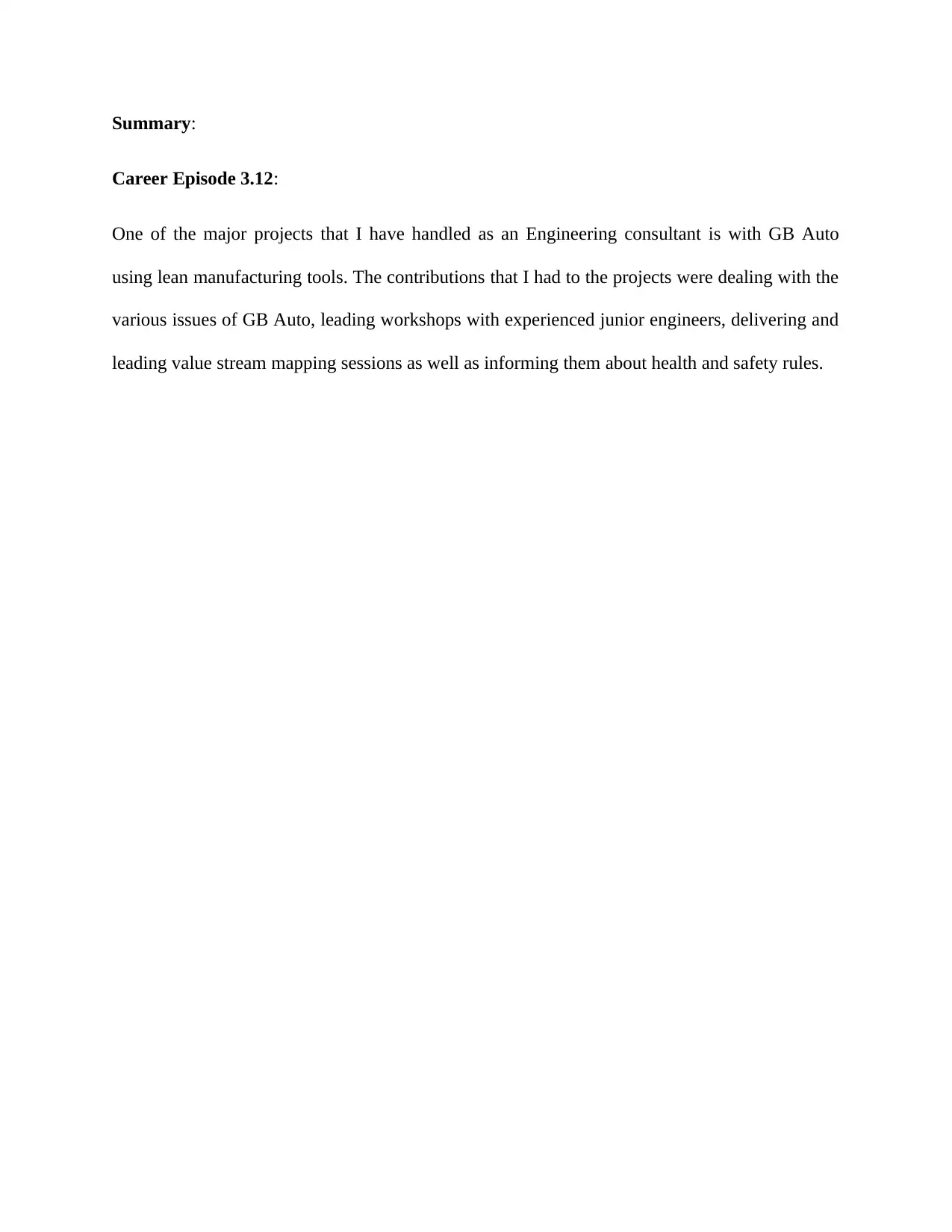
Summary:
Career Episode 3.12:
One of the major projects that I have handled as an Engineering consultant is with GB Auto
using lean manufacturing tools. The contributions that I had to the projects were dealing with the
various issues of GB Auto, leading workshops with experienced junior engineers, delivering and
leading value stream mapping sessions as well as informing them about health and safety rules.
Career Episode 3.12:
One of the major projects that I have handled as an Engineering consultant is with GB Auto
using lean manufacturing tools. The contributions that I had to the projects were dealing with the
various issues of GB Auto, leading workshops with experienced junior engineers, delivering and
leading value stream mapping sessions as well as informing them about health and safety rules.
1 out of 6
![[object Object]](/_next/image/?url=%2F_next%2Fstatic%2Fmedia%2Flogo.6d15ce61.png&w=640&q=75)
Your All-in-One AI-Powered Toolkit for Academic Success.
+13062052269
info@desklib.com
Available 24*7 on WhatsApp / Email
Unlock your academic potential
© 2024 | Zucol Services PVT LTD | All rights reserved.