Evaluating Precast Concrete for Sustainable Engineering Practices
VerifiedAdded on 2020/02/24
|10
|3006
|51
Report
AI Summary
This report critically analyzes the viability of modular construction, specifically using precast concrete, for waste mitigation in the construction industry. It begins by highlighting the significant waste generated in the construction sector and the environmental and economic impacts of improper disposal. The report then explores the benefits of modular construction, particularly precast concrete systems, in reducing waste and promoting sustainability. It examines the fully and partially precast systems, detailing their advantages, such as reduced construction time, lower costs, and improved durability, as well as their disadvantages, including potential transportation costs and seismic performance concerns. Technical performance measures, including construction costs, waste generation, and project duration, are evaluated, with theoretical values and priority indexes provided. The report also identifies research gaps, such as the need for complementary sustainable materials and alternatives to concrete aggregates. Ultimately, the report concludes that precast concrete offers a promising approach to sustainable engineering by minimizing waste and promoting environmental friendliness, while also emphasizing the need for further research to enhance the building life cycle and sustainability of construction practices.
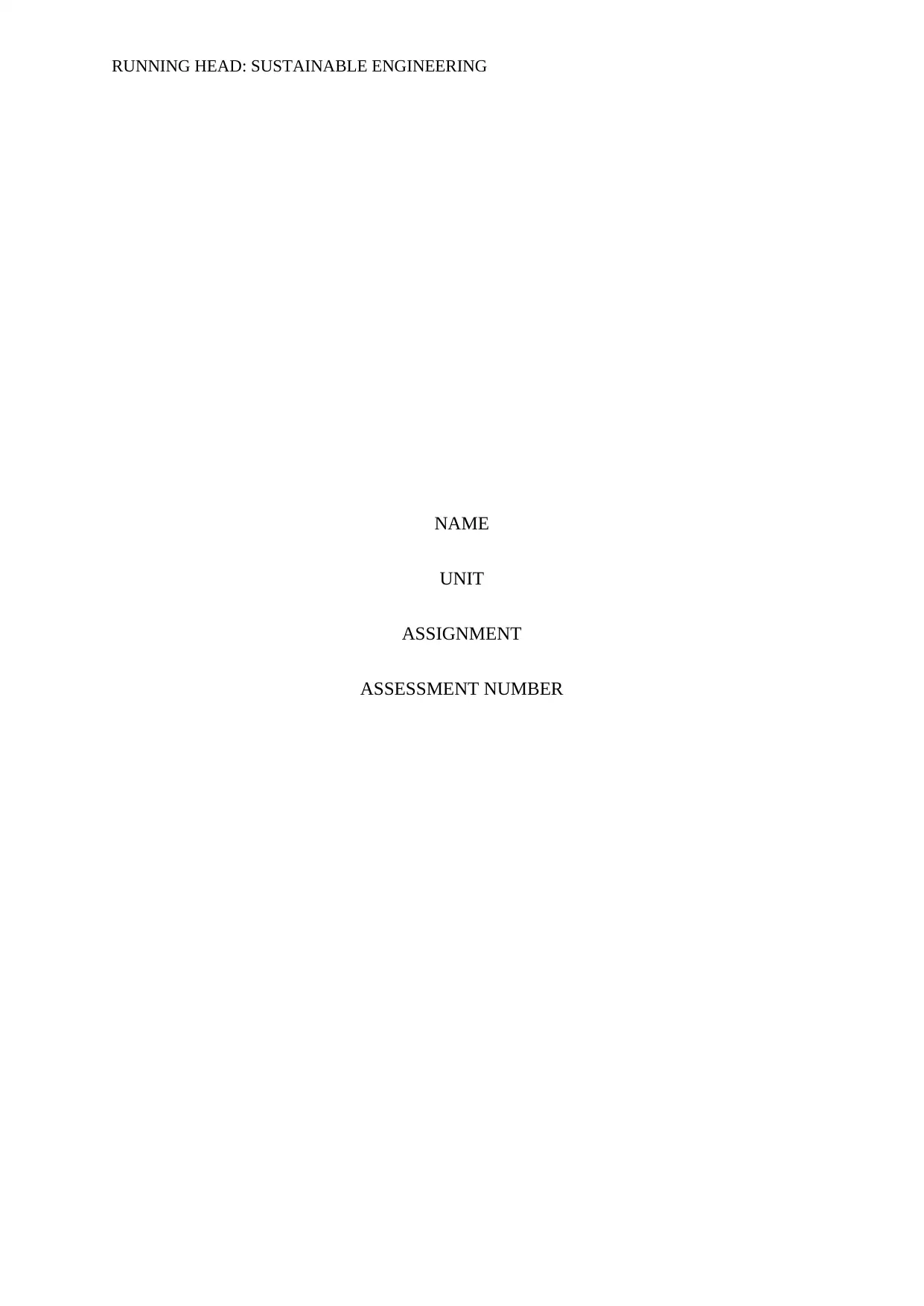
RUNNING HEAD: SUSTAINABLE ENGINEERING
NAME
UNIT
ASSIGNMENT
ASSESSMENT NUMBER
NAME
UNIT
ASSIGNMENT
ASSESSMENT NUMBER
Paraphrase This Document
Need a fresh take? Get an instant paraphrase of this document with our AI Paraphraser
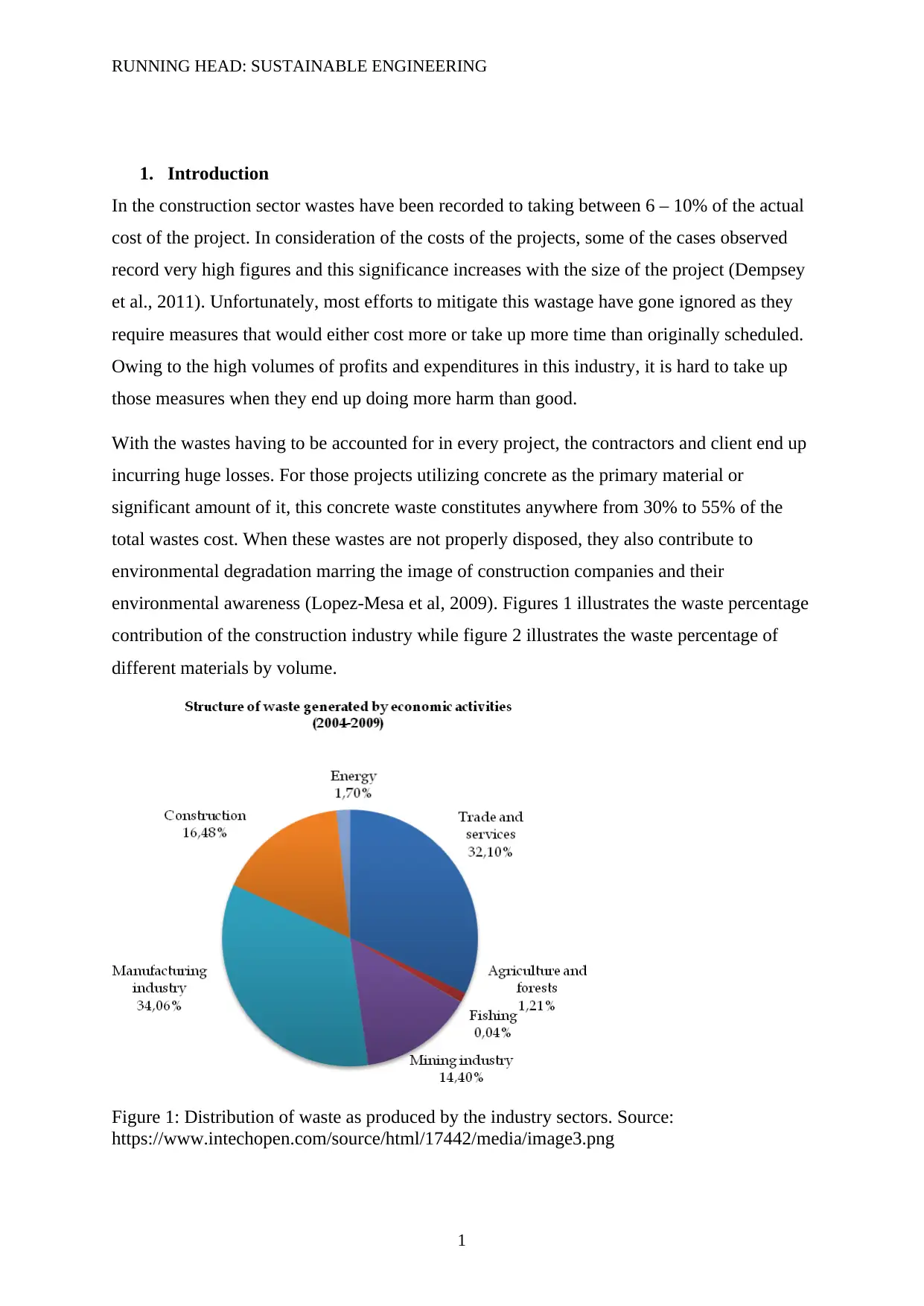
RUNNING HEAD: SUSTAINABLE ENGINEERING
1. Introduction
In the construction sector wastes have been recorded to taking between 6 – 10% of the actual
cost of the project. In consideration of the costs of the projects, some of the cases observed
record very high figures and this significance increases with the size of the project (Dempsey
et al., 2011). Unfortunately, most efforts to mitigate this wastage have gone ignored as they
require measures that would either cost more or take up more time than originally scheduled.
Owing to the high volumes of profits and expenditures in this industry, it is hard to take up
those measures when they end up doing more harm than good.
With the wastes having to be accounted for in every project, the contractors and client end up
incurring huge losses. For those projects utilizing concrete as the primary material or
significant amount of it, this concrete waste constitutes anywhere from 30% to 55% of the
total wastes cost. When these wastes are not properly disposed, they also contribute to
environmental degradation marring the image of construction companies and their
environmental awareness (Lopez-Mesa et al, 2009). Figures 1 illustrates the waste percentage
contribution of the construction industry while figure 2 illustrates the waste percentage of
different materials by volume.
Figure 1: Distribution of waste as produced by the industry sectors. Source:
https://www.intechopen.com/source/html/17442/media/image3.png
1
1. Introduction
In the construction sector wastes have been recorded to taking between 6 – 10% of the actual
cost of the project. In consideration of the costs of the projects, some of the cases observed
record very high figures and this significance increases with the size of the project (Dempsey
et al., 2011). Unfortunately, most efforts to mitigate this wastage have gone ignored as they
require measures that would either cost more or take up more time than originally scheduled.
Owing to the high volumes of profits and expenditures in this industry, it is hard to take up
those measures when they end up doing more harm than good.
With the wastes having to be accounted for in every project, the contractors and client end up
incurring huge losses. For those projects utilizing concrete as the primary material or
significant amount of it, this concrete waste constitutes anywhere from 30% to 55% of the
total wastes cost. When these wastes are not properly disposed, they also contribute to
environmental degradation marring the image of construction companies and their
environmental awareness (Lopez-Mesa et al, 2009). Figures 1 illustrates the waste percentage
contribution of the construction industry while figure 2 illustrates the waste percentage of
different materials by volume.
Figure 1: Distribution of waste as produced by the industry sectors. Source:
https://www.intechopen.com/source/html/17442/media/image3.png
1
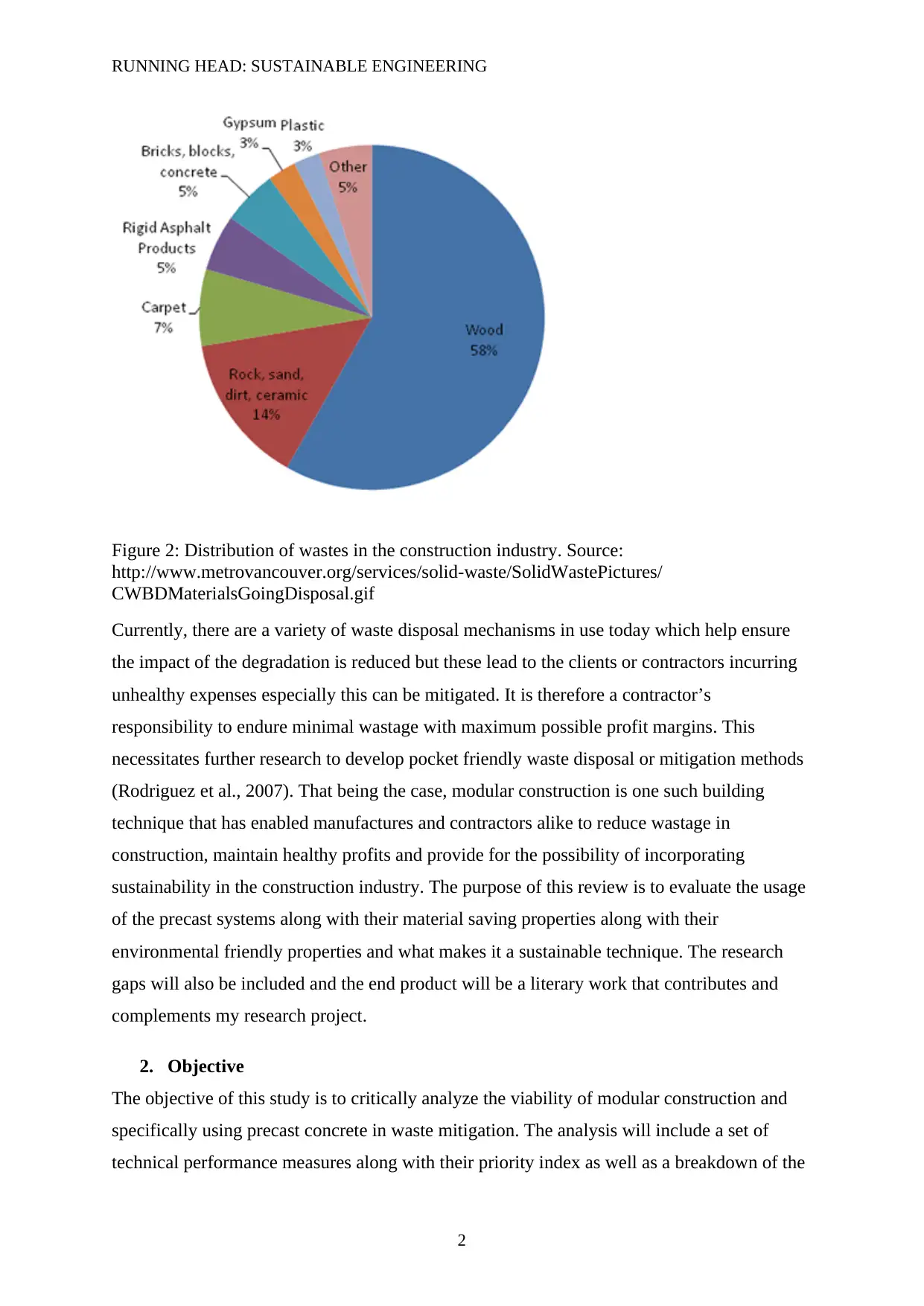
RUNNING HEAD: SUSTAINABLE ENGINEERING
Figure 2: Distribution of wastes in the construction industry. Source:
http://www.metrovancouver.org/services/solid-waste/SolidWastePictures/
CWBDMaterialsGoingDisposal.gif
Currently, there are a variety of waste disposal mechanisms in use today which help ensure
the impact of the degradation is reduced but these lead to the clients or contractors incurring
unhealthy expenses especially this can be mitigated. It is therefore a contractor’s
responsibility to endure minimal wastage with maximum possible profit margins. This
necessitates further research to develop pocket friendly waste disposal or mitigation methods
(Rodriguez et al., 2007). That being the case, modular construction is one such building
technique that has enabled manufactures and contractors alike to reduce wastage in
construction, maintain healthy profits and provide for the possibility of incorporating
sustainability in the construction industry. The purpose of this review is to evaluate the usage
of the precast systems along with their material saving properties along with their
environmental friendly properties and what makes it a sustainable technique. The research
gaps will also be included and the end product will be a literary work that contributes and
complements my research project.
2. Objective
The objective of this study is to critically analyze the viability of modular construction and
specifically using precast concrete in waste mitigation. The analysis will include a set of
technical performance measures along with their priority index as well as a breakdown of the
2
Figure 2: Distribution of wastes in the construction industry. Source:
http://www.metrovancouver.org/services/solid-waste/SolidWastePictures/
CWBDMaterialsGoingDisposal.gif
Currently, there are a variety of waste disposal mechanisms in use today which help ensure
the impact of the degradation is reduced but these lead to the clients or contractors incurring
unhealthy expenses especially this can be mitigated. It is therefore a contractor’s
responsibility to endure minimal wastage with maximum possible profit margins. This
necessitates further research to develop pocket friendly waste disposal or mitigation methods
(Rodriguez et al., 2007). That being the case, modular construction is one such building
technique that has enabled manufactures and contractors alike to reduce wastage in
construction, maintain healthy profits and provide for the possibility of incorporating
sustainability in the construction industry. The purpose of this review is to evaluate the usage
of the precast systems along with their material saving properties along with their
environmental friendly properties and what makes it a sustainable technique. The research
gaps will also be included and the end product will be a literary work that contributes and
complements my research project.
2. Objective
The objective of this study is to critically analyze the viability of modular construction and
specifically using precast concrete in waste mitigation. The analysis will include a set of
technical performance measures along with their priority index as well as a breakdown of the
2
⊘ This is a preview!⊘
Do you want full access?
Subscribe today to unlock all pages.

Trusted by 1+ million students worldwide
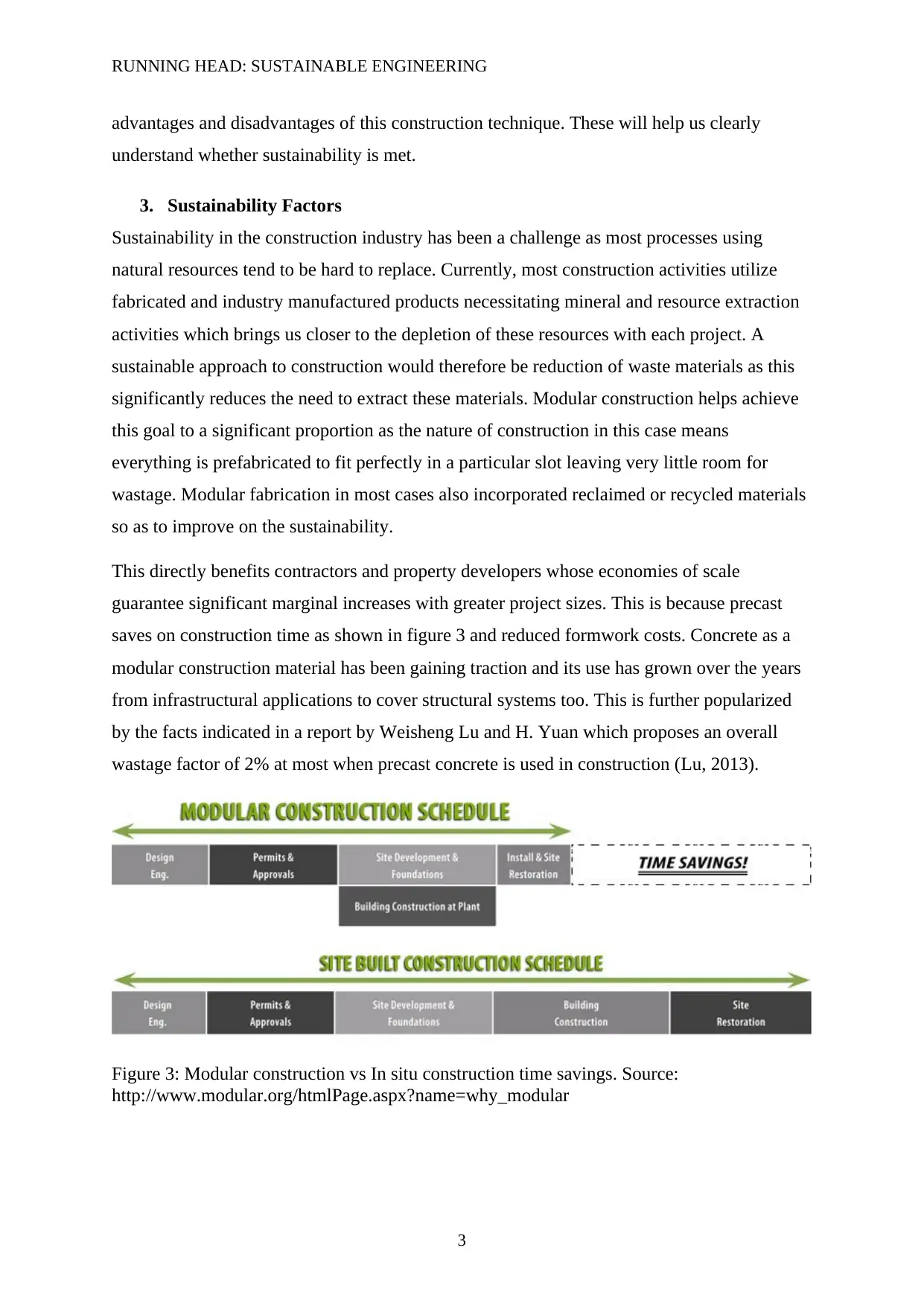
RUNNING HEAD: SUSTAINABLE ENGINEERING
advantages and disadvantages of this construction technique. These will help us clearly
understand whether sustainability is met.
3. Sustainability Factors
Sustainability in the construction industry has been a challenge as most processes using
natural resources tend to be hard to replace. Currently, most construction activities utilize
fabricated and industry manufactured products necessitating mineral and resource extraction
activities which brings us closer to the depletion of these resources with each project. A
sustainable approach to construction would therefore be reduction of waste materials as this
significantly reduces the need to extract these materials. Modular construction helps achieve
this goal to a significant proportion as the nature of construction in this case means
everything is prefabricated to fit perfectly in a particular slot leaving very little room for
wastage. Modular fabrication in most cases also incorporated reclaimed or recycled materials
so as to improve on the sustainability.
This directly benefits contractors and property developers whose economies of scale
guarantee significant marginal increases with greater project sizes. This is because precast
saves on construction time as shown in figure 3 and reduced formwork costs. Concrete as a
modular construction material has been gaining traction and its use has grown over the years
from infrastructural applications to cover structural systems too. This is further popularized
by the facts indicated in a report by Weisheng Lu and H. Yuan which proposes an overall
wastage factor of 2% at most when precast concrete is used in construction (Lu, 2013).
Figure 3: Modular construction vs In situ construction time savings. Source:
http://www.modular.org/htmlPage.aspx?name=why_modular
3
advantages and disadvantages of this construction technique. These will help us clearly
understand whether sustainability is met.
3. Sustainability Factors
Sustainability in the construction industry has been a challenge as most processes using
natural resources tend to be hard to replace. Currently, most construction activities utilize
fabricated and industry manufactured products necessitating mineral and resource extraction
activities which brings us closer to the depletion of these resources with each project. A
sustainable approach to construction would therefore be reduction of waste materials as this
significantly reduces the need to extract these materials. Modular construction helps achieve
this goal to a significant proportion as the nature of construction in this case means
everything is prefabricated to fit perfectly in a particular slot leaving very little room for
wastage. Modular fabrication in most cases also incorporated reclaimed or recycled materials
so as to improve on the sustainability.
This directly benefits contractors and property developers whose economies of scale
guarantee significant marginal increases with greater project sizes. This is because precast
saves on construction time as shown in figure 3 and reduced formwork costs. Concrete as a
modular construction material has been gaining traction and its use has grown over the years
from infrastructural applications to cover structural systems too. This is further popularized
by the facts indicated in a report by Weisheng Lu and H. Yuan which proposes an overall
wastage factor of 2% at most when precast concrete is used in construction (Lu, 2013).
Figure 3: Modular construction vs In situ construction time savings. Source:
http://www.modular.org/htmlPage.aspx?name=why_modular
3
Paraphrase This Document
Need a fresh take? Get an instant paraphrase of this document with our AI Paraphraser

RUNNING HEAD: SUSTAINABLE ENGINEERING
The various approaches to precast systems in use today are the fully modular approach and
the partially modular approach which sees to the precast concrete being combined with in situ
concrete in a project. Using fully precast systems means prefabricating every structural
element beforehand before transportation to the site. When these members are used, they
provide for easy demolition in case of a renovation or upgrade, good insulation, lower
construction costs and higher frame strength. These members are manufactured in a factory
and assembled either there and transported whole or on site. Figures 4 and 5 show modular
unit assembly on site.
Figure 4: Construction team lowering modular unit on to a structure. Source:
https://www.flickr.com/photos/rotondoweirich/sets/72157626682929934/
Figure 5: A model of a precast concrete modular building. Source: http://modulecon.com/
2 main approaches to using modular precast stand and are further explained below.
4
The various approaches to precast systems in use today are the fully modular approach and
the partially modular approach which sees to the precast concrete being combined with in situ
concrete in a project. Using fully precast systems means prefabricating every structural
element beforehand before transportation to the site. When these members are used, they
provide for easy demolition in case of a renovation or upgrade, good insulation, lower
construction costs and higher frame strength. These members are manufactured in a factory
and assembled either there and transported whole or on site. Figures 4 and 5 show modular
unit assembly on site.
Figure 4: Construction team lowering modular unit on to a structure. Source:
https://www.flickr.com/photos/rotondoweirich/sets/72157626682929934/
Figure 5: A model of a precast concrete modular building. Source: http://modulecon.com/
2 main approaches to using modular precast stand and are further explained below.
4
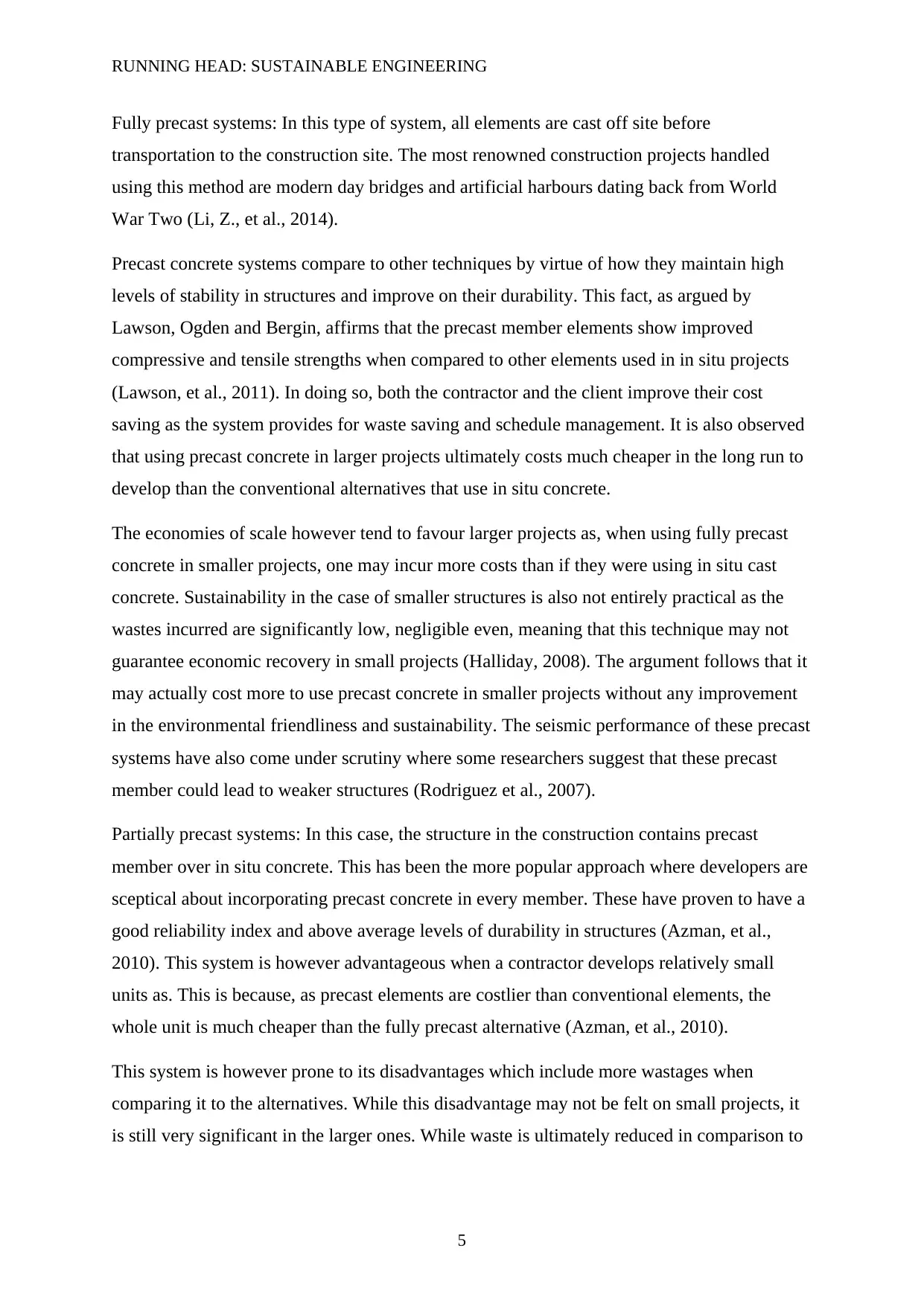
RUNNING HEAD: SUSTAINABLE ENGINEERING
Fully precast systems: In this type of system, all elements are cast off site before
transportation to the construction site. The most renowned construction projects handled
using this method are modern day bridges and artificial harbours dating back from World
War Two (Li, Z., et al., 2014).
Precast concrete systems compare to other techniques by virtue of how they maintain high
levels of stability in structures and improve on their durability. This fact, as argued by
Lawson, Ogden and Bergin, affirms that the precast member elements show improved
compressive and tensile strengths when compared to other elements used in in situ projects
(Lawson, et al., 2011). In doing so, both the contractor and the client improve their cost
saving as the system provides for waste saving and schedule management. It is also observed
that using precast concrete in larger projects ultimately costs much cheaper in the long run to
develop than the conventional alternatives that use in situ concrete.
The economies of scale however tend to favour larger projects as, when using fully precast
concrete in smaller projects, one may incur more costs than if they were using in situ cast
concrete. Sustainability in the case of smaller structures is also not entirely practical as the
wastes incurred are significantly low, negligible even, meaning that this technique may not
guarantee economic recovery in small projects (Halliday, 2008). The argument follows that it
may actually cost more to use precast concrete in smaller projects without any improvement
in the environmental friendliness and sustainability. The seismic performance of these precast
systems have also come under scrutiny where some researchers suggest that these precast
member could lead to weaker structures (Rodriguez et al., 2007).
Partially precast systems: In this case, the structure in the construction contains precast
member over in situ concrete. This has been the more popular approach where developers are
sceptical about incorporating precast concrete in every member. These have proven to have a
good reliability index and above average levels of durability in structures (Azman, et al.,
2010). This system is however advantageous when a contractor develops relatively small
units as. This is because, as precast elements are costlier than conventional elements, the
whole unit is much cheaper than the fully precast alternative (Azman, et al., 2010).
This system is however prone to its disadvantages which include more wastages when
comparing it to the alternatives. While this disadvantage may not be felt on small projects, it
is still very significant in the larger ones. While waste is ultimately reduced in comparison to
5
Fully precast systems: In this type of system, all elements are cast off site before
transportation to the construction site. The most renowned construction projects handled
using this method are modern day bridges and artificial harbours dating back from World
War Two (Li, Z., et al., 2014).
Precast concrete systems compare to other techniques by virtue of how they maintain high
levels of stability in structures and improve on their durability. This fact, as argued by
Lawson, Ogden and Bergin, affirms that the precast member elements show improved
compressive and tensile strengths when compared to other elements used in in situ projects
(Lawson, et al., 2011). In doing so, both the contractor and the client improve their cost
saving as the system provides for waste saving and schedule management. It is also observed
that using precast concrete in larger projects ultimately costs much cheaper in the long run to
develop than the conventional alternatives that use in situ concrete.
The economies of scale however tend to favour larger projects as, when using fully precast
concrete in smaller projects, one may incur more costs than if they were using in situ cast
concrete. Sustainability in the case of smaller structures is also not entirely practical as the
wastes incurred are significantly low, negligible even, meaning that this technique may not
guarantee economic recovery in small projects (Halliday, 2008). The argument follows that it
may actually cost more to use precast concrete in smaller projects without any improvement
in the environmental friendliness and sustainability. The seismic performance of these precast
systems have also come under scrutiny where some researchers suggest that these precast
member could lead to weaker structures (Rodriguez et al., 2007).
Partially precast systems: In this case, the structure in the construction contains precast
member over in situ concrete. This has been the more popular approach where developers are
sceptical about incorporating precast concrete in every member. These have proven to have a
good reliability index and above average levels of durability in structures (Azman, et al.,
2010). This system is however advantageous when a contractor develops relatively small
units as. This is because, as precast elements are costlier than conventional elements, the
whole unit is much cheaper than the fully precast alternative (Azman, et al., 2010).
This system is however prone to its disadvantages which include more wastages when
comparing it to the alternatives. While this disadvantage may not be felt on small projects, it
is still very significant in the larger ones. While waste is ultimately reduced in comparison to
5
⊘ This is a preview!⊘
Do you want full access?
Subscribe today to unlock all pages.

Trusted by 1+ million students worldwide
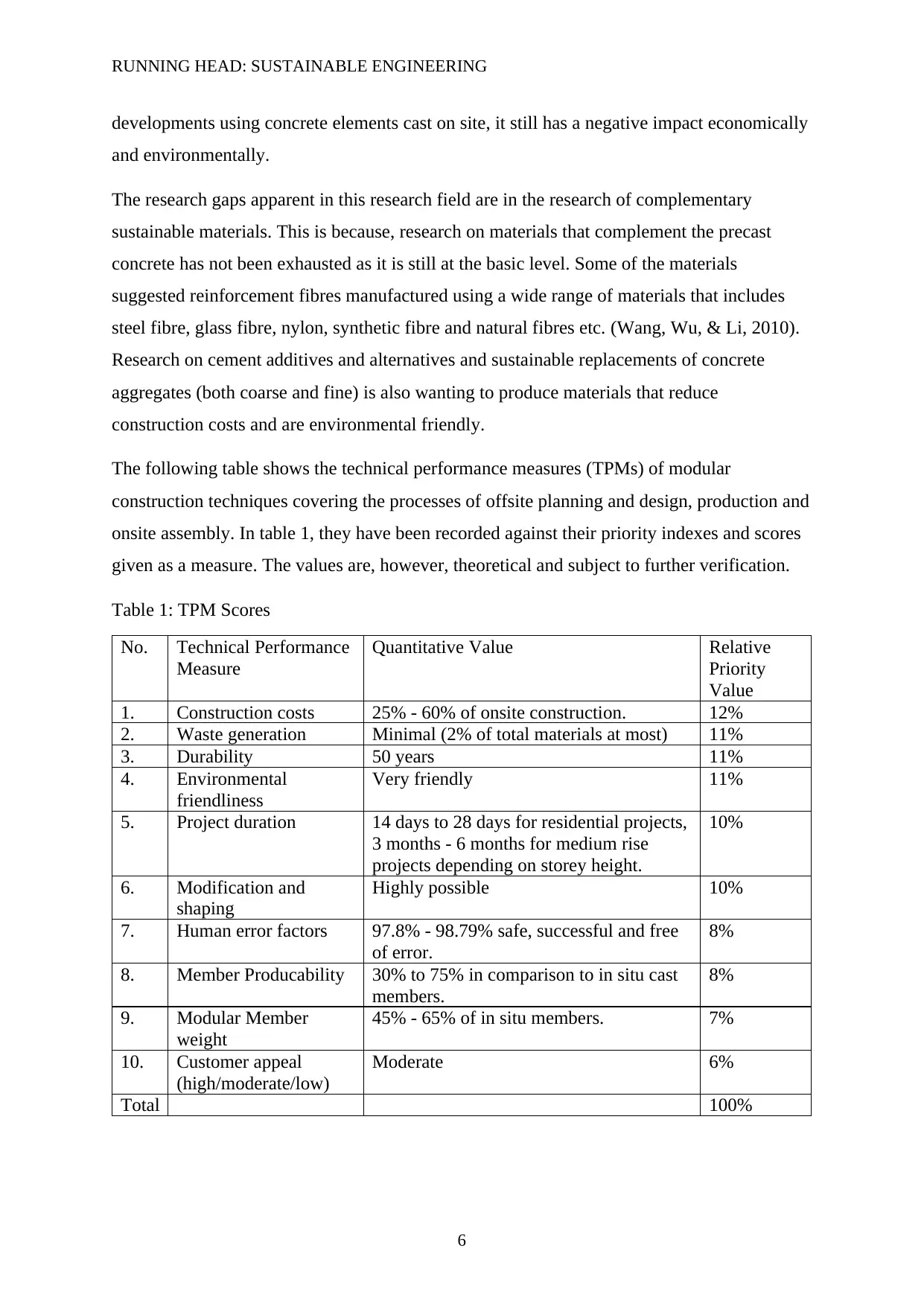
RUNNING HEAD: SUSTAINABLE ENGINEERING
developments using concrete elements cast on site, it still has a negative impact economically
and environmentally.
The research gaps apparent in this research field are in the research of complementary
sustainable materials. This is because, research on materials that complement the precast
concrete has not been exhausted as it is still at the basic level. Some of the materials
suggested reinforcement fibres manufactured using a wide range of materials that includes
steel fibre, glass fibre, nylon, synthetic fibre and natural fibres etc. (Wang, Wu, & Li, 2010).
Research on cement additives and alternatives and sustainable replacements of concrete
aggregates (both coarse and fine) is also wanting to produce materials that reduce
construction costs and are environmental friendly.
The following table shows the technical performance measures (TPMs) of modular
construction techniques covering the processes of offsite planning and design, production and
onsite assembly. In table 1, they have been recorded against their priority indexes and scores
given as a measure. The values are, however, theoretical and subject to further verification.
Table 1: TPM Scores
No. Technical Performance
Measure
Quantitative Value Relative
Priority
Value
1. Construction costs 25% - 60% of onsite construction. 12%
2. Waste generation Minimal (2% of total materials at most) 11%
3. Durability 50 years 11%
4. Environmental
friendliness
Very friendly 11%
5. Project duration 14 days to 28 days for residential projects,
3 months - 6 months for medium rise
projects depending on storey height.
10%
6. Modification and
shaping
Highly possible 10%
7. Human error factors 97.8% - 98.79% safe, successful and free
of error.
8%
8. Member Producability 30% to 75% in comparison to in situ cast
members.
8%
9. Modular Member
weight
45% - 65% of in situ members. 7%
10. Customer appeal
(high/moderate/low)
Moderate 6%
Total 100%
6
developments using concrete elements cast on site, it still has a negative impact economically
and environmentally.
The research gaps apparent in this research field are in the research of complementary
sustainable materials. This is because, research on materials that complement the precast
concrete has not been exhausted as it is still at the basic level. Some of the materials
suggested reinforcement fibres manufactured using a wide range of materials that includes
steel fibre, glass fibre, nylon, synthetic fibre and natural fibres etc. (Wang, Wu, & Li, 2010).
Research on cement additives and alternatives and sustainable replacements of concrete
aggregates (both coarse and fine) is also wanting to produce materials that reduce
construction costs and are environmental friendly.
The following table shows the technical performance measures (TPMs) of modular
construction techniques covering the processes of offsite planning and design, production and
onsite assembly. In table 1, they have been recorded against their priority indexes and scores
given as a measure. The values are, however, theoretical and subject to further verification.
Table 1: TPM Scores
No. Technical Performance
Measure
Quantitative Value Relative
Priority
Value
1. Construction costs 25% - 60% of onsite construction. 12%
2. Waste generation Minimal (2% of total materials at most) 11%
3. Durability 50 years 11%
4. Environmental
friendliness
Very friendly 11%
5. Project duration 14 days to 28 days for residential projects,
3 months - 6 months for medium rise
projects depending on storey height.
10%
6. Modification and
shaping
Highly possible 10%
7. Human error factors 97.8% - 98.79% safe, successful and free
of error.
8%
8. Member Producability 30% to 75% in comparison to in situ cast
members.
8%
9. Modular Member
weight
45% - 65% of in situ members. 7%
10. Customer appeal
(high/moderate/low)
Moderate 6%
Total 100%
6
Paraphrase This Document
Need a fresh take? Get an instant paraphrase of this document with our AI Paraphraser
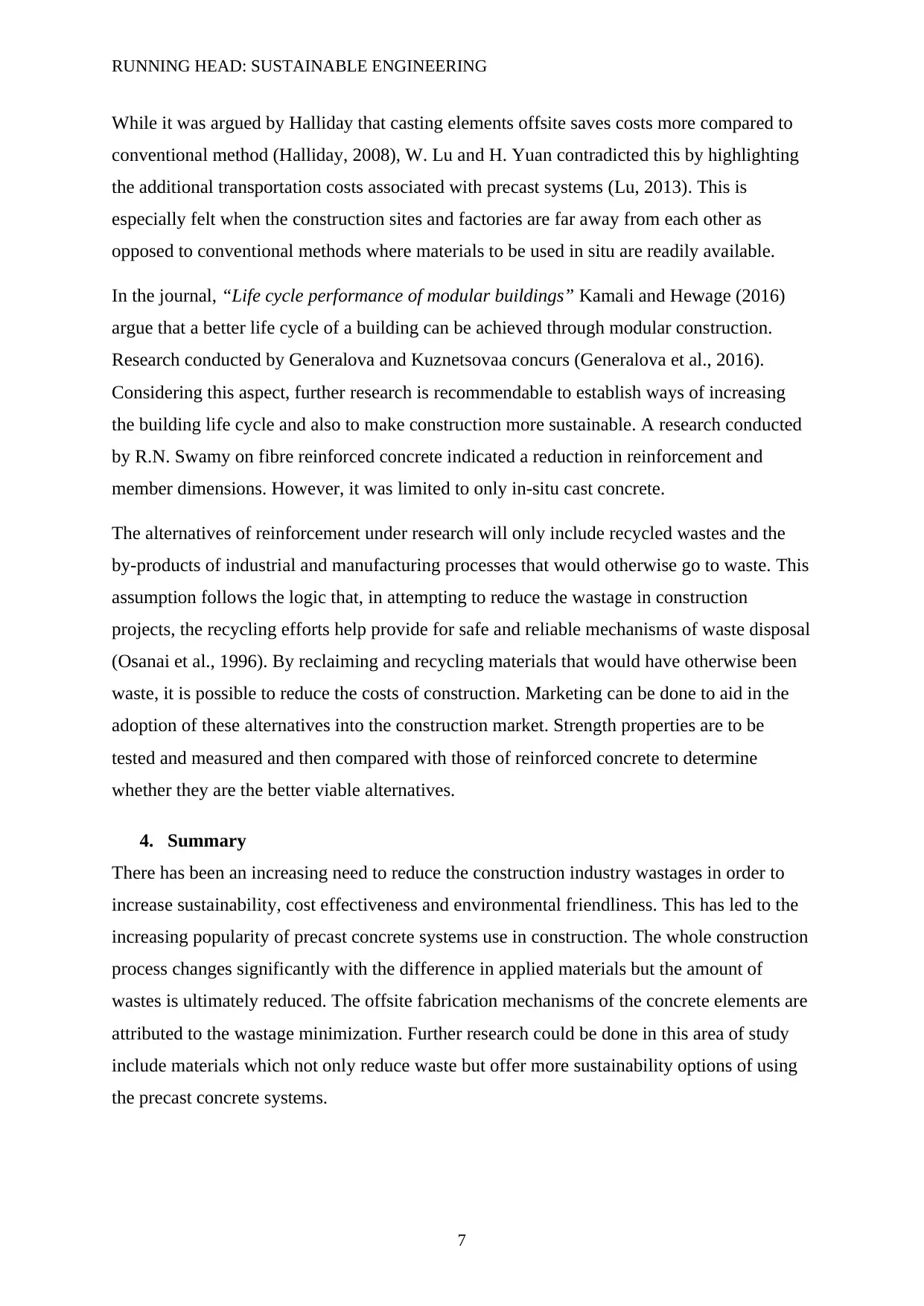
RUNNING HEAD: SUSTAINABLE ENGINEERING
While it was argued by Halliday that casting elements offsite saves costs more compared to
conventional method (Halliday, 2008), W. Lu and H. Yuan contradicted this by highlighting
the additional transportation costs associated with precast systems (Lu, 2013). This is
especially felt when the construction sites and factories are far away from each other as
opposed to conventional methods where materials to be used in situ are readily available.
In the journal, “Life cycle performance of modular buildings” Kamali and Hewage (2016)
argue that a better life cycle of a building can be achieved through modular construction.
Research conducted by Generalova and Kuznetsovaa concurs (Generalova et al., 2016).
Considering this aspect, further research is recommendable to establish ways of increasing
the building life cycle and also to make construction more sustainable. A research conducted
by R.N. Swamy on fibre reinforced concrete indicated a reduction in reinforcement and
member dimensions. However, it was limited to only in-situ cast concrete.
The alternatives of reinforcement under research will only include recycled wastes and the
by-products of industrial and manufacturing processes that would otherwise go to waste. This
assumption follows the logic that, in attempting to reduce the wastage in construction
projects, the recycling efforts help provide for safe and reliable mechanisms of waste disposal
(Osanai et al., 1996). By reclaiming and recycling materials that would have otherwise been
waste, it is possible to reduce the costs of construction. Marketing can be done to aid in the
adoption of these alternatives into the construction market. Strength properties are to be
tested and measured and then compared with those of reinforced concrete to determine
whether they are the better viable alternatives.
4. Summary
There has been an increasing need to reduce the construction industry wastages in order to
increase sustainability, cost effectiveness and environmental friendliness. This has led to the
increasing popularity of precast concrete systems use in construction. The whole construction
process changes significantly with the difference in applied materials but the amount of
wastes is ultimately reduced. The offsite fabrication mechanisms of the concrete elements are
attributed to the wastage minimization. Further research could be done in this area of study
include materials which not only reduce waste but offer more sustainability options of using
the precast concrete systems.
7
While it was argued by Halliday that casting elements offsite saves costs more compared to
conventional method (Halliday, 2008), W. Lu and H. Yuan contradicted this by highlighting
the additional transportation costs associated with precast systems (Lu, 2013). This is
especially felt when the construction sites and factories are far away from each other as
opposed to conventional methods where materials to be used in situ are readily available.
In the journal, “Life cycle performance of modular buildings” Kamali and Hewage (2016)
argue that a better life cycle of a building can be achieved through modular construction.
Research conducted by Generalova and Kuznetsovaa concurs (Generalova et al., 2016).
Considering this aspect, further research is recommendable to establish ways of increasing
the building life cycle and also to make construction more sustainable. A research conducted
by R.N. Swamy on fibre reinforced concrete indicated a reduction in reinforcement and
member dimensions. However, it was limited to only in-situ cast concrete.
The alternatives of reinforcement under research will only include recycled wastes and the
by-products of industrial and manufacturing processes that would otherwise go to waste. This
assumption follows the logic that, in attempting to reduce the wastage in construction
projects, the recycling efforts help provide for safe and reliable mechanisms of waste disposal
(Osanai et al., 1996). By reclaiming and recycling materials that would have otherwise been
waste, it is possible to reduce the costs of construction. Marketing can be done to aid in the
adoption of these alternatives into the construction market. Strength properties are to be
tested and measured and then compared with those of reinforced concrete to determine
whether they are the better viable alternatives.
4. Summary
There has been an increasing need to reduce the construction industry wastages in order to
increase sustainability, cost effectiveness and environmental friendliness. This has led to the
increasing popularity of precast concrete systems use in construction. The whole construction
process changes significantly with the difference in applied materials but the amount of
wastes is ultimately reduced. The offsite fabrication mechanisms of the concrete elements are
attributed to the wastage minimization. Further research could be done in this area of study
include materials which not only reduce waste but offer more sustainability options of using
the precast concrete systems.
7
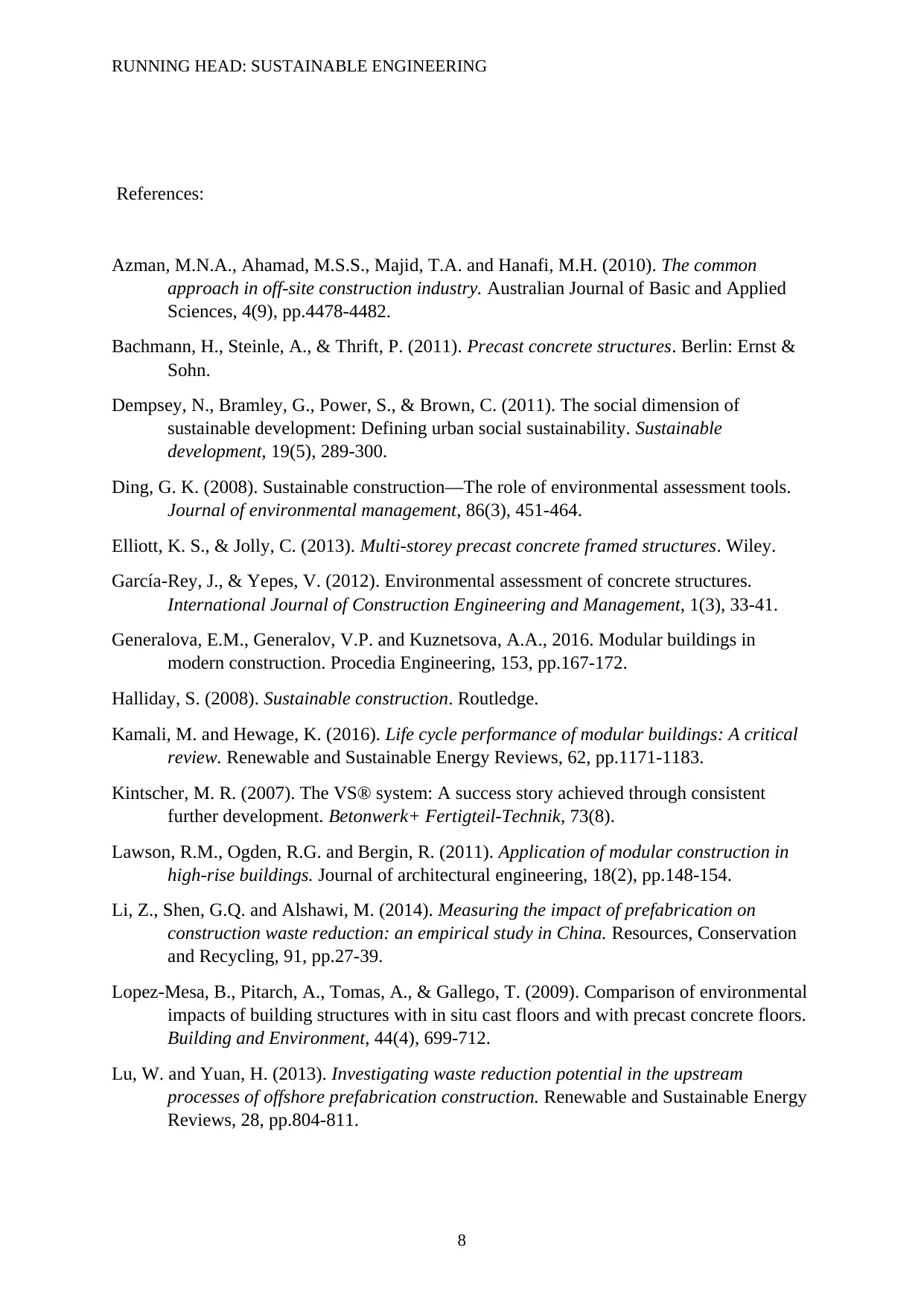
RUNNING HEAD: SUSTAINABLE ENGINEERING
References:
Azman, M.N.A., Ahamad, M.S.S., Majid, T.A. and Hanafi, M.H. (2010). The common
approach in off-site construction industry. Australian Journal of Basic and Applied
Sciences, 4(9), pp.4478-4482.
Bachmann, H., Steinle, A., & Thrift, P. (2011). Precast concrete structures. Berlin: Ernst &
Sohn.
Dempsey, N., Bramley, G., Power, S., & Brown, C. (2011). The social dimension of
sustainable development: Defining urban social sustainability. Sustainable
development, 19(5), 289-300.
Ding, G. K. (2008). Sustainable construction—The role of environmental assessment tools.
Journal of environmental management, 86(3), 451-464.
Elliott, K. S., & Jolly, C. (2013). Multi-storey precast concrete framed structures. Wiley.
García-Rey, J., & Yepes, V. (2012). Environmental assessment of concrete structures.
International Journal of Construction Engineering and Management, 1(3), 33-41.
Generalova, E.M., Generalov, V.P. and Kuznetsova, A.A., 2016. Modular buildings in
modern construction. Procedia Engineering, 153, pp.167-172.
Halliday, S. (2008). Sustainable construction. Routledge.
Kamali, M. and Hewage, K. (2016). Life cycle performance of modular buildings: A critical
review. Renewable and Sustainable Energy Reviews, 62, pp.1171-1183.
Kintscher, M. R. (2007). The VS® system: A success story achieved through consistent
further development. Betonwerk+ Fertigteil-Technik, 73(8).
Lawson, R.M., Ogden, R.G. and Bergin, R. (2011). Application of modular construction in
high-rise buildings. Journal of architectural engineering, 18(2), pp.148-154.
Li, Z., Shen, G.Q. and Alshawi, M. (2014). Measuring the impact of prefabrication on
construction waste reduction: an empirical study in China. Resources, Conservation
and Recycling, 91, pp.27-39.
Lopez-Mesa, B., Pitarch, A., Tomas, A., & Gallego, T. (2009). Comparison of environmental
impacts of building structures with in situ cast floors and with precast concrete floors.
Building and Environment, 44(4), 699-712.
Lu, W. and Yuan, H. (2013). Investigating waste reduction potential in the upstream
processes of offshore prefabrication construction. Renewable and Sustainable Energy
Reviews, 28, pp.804-811.
8
References:
Azman, M.N.A., Ahamad, M.S.S., Majid, T.A. and Hanafi, M.H. (2010). The common
approach in off-site construction industry. Australian Journal of Basic and Applied
Sciences, 4(9), pp.4478-4482.
Bachmann, H., Steinle, A., & Thrift, P. (2011). Precast concrete structures. Berlin: Ernst &
Sohn.
Dempsey, N., Bramley, G., Power, S., & Brown, C. (2011). The social dimension of
sustainable development: Defining urban social sustainability. Sustainable
development, 19(5), 289-300.
Ding, G. K. (2008). Sustainable construction—The role of environmental assessment tools.
Journal of environmental management, 86(3), 451-464.
Elliott, K. S., & Jolly, C. (2013). Multi-storey precast concrete framed structures. Wiley.
García-Rey, J., & Yepes, V. (2012). Environmental assessment of concrete structures.
International Journal of Construction Engineering and Management, 1(3), 33-41.
Generalova, E.M., Generalov, V.P. and Kuznetsova, A.A., 2016. Modular buildings in
modern construction. Procedia Engineering, 153, pp.167-172.
Halliday, S. (2008). Sustainable construction. Routledge.
Kamali, M. and Hewage, K. (2016). Life cycle performance of modular buildings: A critical
review. Renewable and Sustainable Energy Reviews, 62, pp.1171-1183.
Kintscher, M. R. (2007). The VS® system: A success story achieved through consistent
further development. Betonwerk+ Fertigteil-Technik, 73(8).
Lawson, R.M., Ogden, R.G. and Bergin, R. (2011). Application of modular construction in
high-rise buildings. Journal of architectural engineering, 18(2), pp.148-154.
Li, Z., Shen, G.Q. and Alshawi, M. (2014). Measuring the impact of prefabrication on
construction waste reduction: an empirical study in China. Resources, Conservation
and Recycling, 91, pp.27-39.
Lopez-Mesa, B., Pitarch, A., Tomas, A., & Gallego, T. (2009). Comparison of environmental
impacts of building structures with in situ cast floors and with precast concrete floors.
Building and Environment, 44(4), 699-712.
Lu, W. and Yuan, H. (2013). Investigating waste reduction potential in the upstream
processes of offshore prefabrication construction. Renewable and Sustainable Energy
Reviews, 28, pp.804-811.
8
⊘ This is a preview!⊘
Do you want full access?
Subscribe today to unlock all pages.

Trusted by 1+ million students worldwide
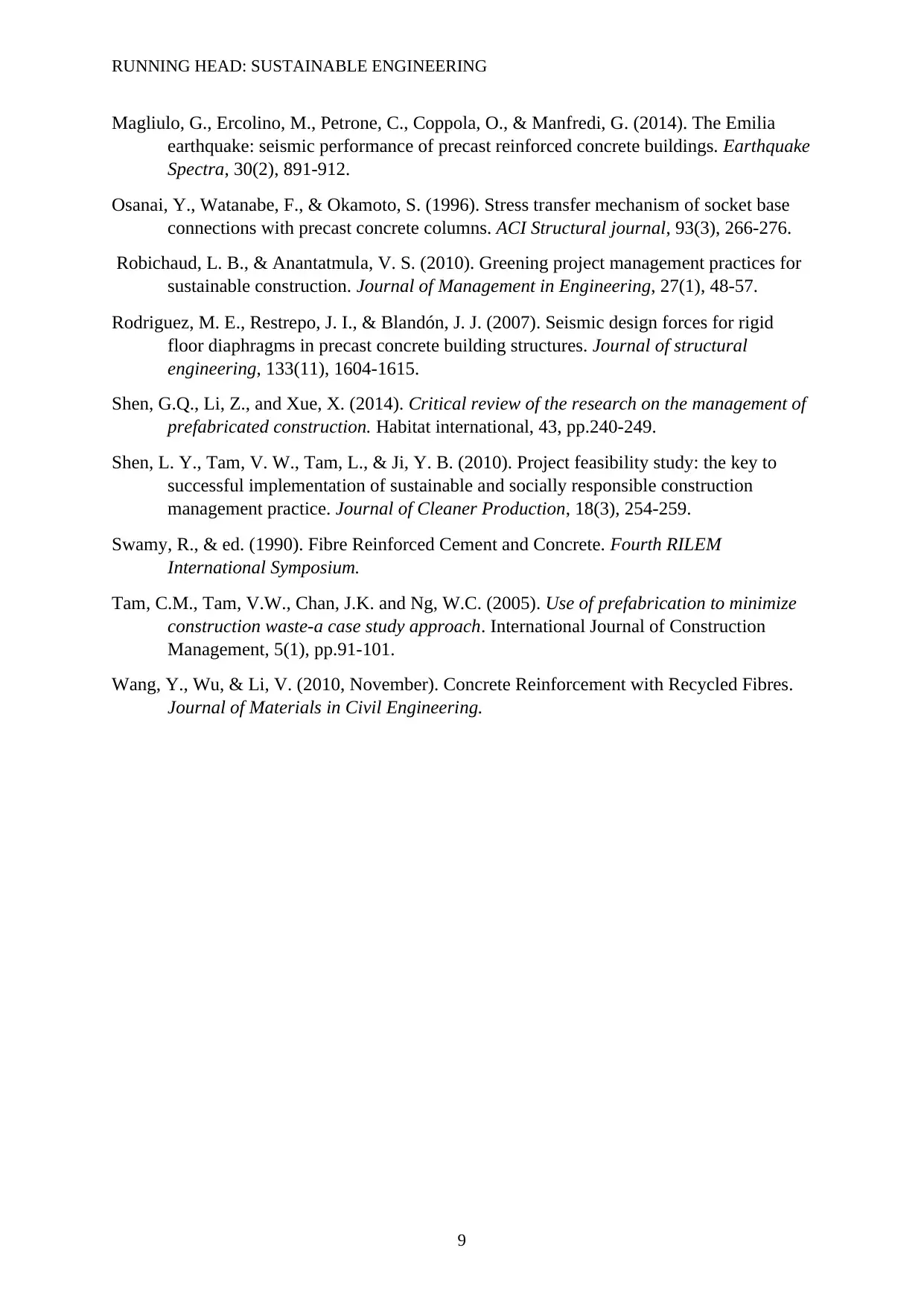
RUNNING HEAD: SUSTAINABLE ENGINEERING
Magliulo, G., Ercolino, M., Petrone, C., Coppola, O., & Manfredi, G. (2014). The Emilia
earthquake: seismic performance of precast reinforced concrete buildings. Earthquake
Spectra, 30(2), 891-912.
Osanai, Y., Watanabe, F., & Okamoto, S. (1996). Stress transfer mechanism of socket base
connections with precast concrete columns. ACI Structural journal, 93(3), 266-276.
Robichaud, L. B., & Anantatmula, V. S. (2010). Greening project management practices for
sustainable construction. Journal of Management in Engineering, 27(1), 48-57.
Rodriguez, M. E., Restrepo, J. I., & Blandón, J. J. (2007). Seismic design forces for rigid
floor diaphragms in precast concrete building structures. Journal of structural
engineering, 133(11), 1604-1615.
Shen, G.Q., Li, Z., and Xue, X. (2014). Critical review of the research on the management of
prefabricated construction. Habitat international, 43, pp.240-249.
Shen, L. Y., Tam, V. W., Tam, L., & Ji, Y. B. (2010). Project feasibility study: the key to
successful implementation of sustainable and socially responsible construction
management practice. Journal of Cleaner Production, 18(3), 254-259.
Swamy, R., & ed. (1990). Fibre Reinforced Cement and Concrete. Fourth RILEM
International Symposium.
Tam, C.M., Tam, V.W., Chan, J.K. and Ng, W.C. (2005). Use of prefabrication to minimize
construction waste-a case study approach. International Journal of Construction
Management, 5(1), pp.91-101.
Wang, Y., Wu, & Li, V. (2010, November). Concrete Reinforcement with Recycled Fibres.
Journal of Materials in Civil Engineering.
9
Magliulo, G., Ercolino, M., Petrone, C., Coppola, O., & Manfredi, G. (2014). The Emilia
earthquake: seismic performance of precast reinforced concrete buildings. Earthquake
Spectra, 30(2), 891-912.
Osanai, Y., Watanabe, F., & Okamoto, S. (1996). Stress transfer mechanism of socket base
connections with precast concrete columns. ACI Structural journal, 93(3), 266-276.
Robichaud, L. B., & Anantatmula, V. S. (2010). Greening project management practices for
sustainable construction. Journal of Management in Engineering, 27(1), 48-57.
Rodriguez, M. E., Restrepo, J. I., & Blandón, J. J. (2007). Seismic design forces for rigid
floor diaphragms in precast concrete building structures. Journal of structural
engineering, 133(11), 1604-1615.
Shen, G.Q., Li, Z., and Xue, X. (2014). Critical review of the research on the management of
prefabricated construction. Habitat international, 43, pp.240-249.
Shen, L. Y., Tam, V. W., Tam, L., & Ji, Y. B. (2010). Project feasibility study: the key to
successful implementation of sustainable and socially responsible construction
management practice. Journal of Cleaner Production, 18(3), 254-259.
Swamy, R., & ed. (1990). Fibre Reinforced Cement and Concrete. Fourth RILEM
International Symposium.
Tam, C.M., Tam, V.W., Chan, J.K. and Ng, W.C. (2005). Use of prefabrication to minimize
construction waste-a case study approach. International Journal of Construction
Management, 5(1), pp.91-101.
Wang, Y., Wu, & Li, V. (2010, November). Concrete Reinforcement with Recycled Fibres.
Journal of Materials in Civil Engineering.
9
1 out of 10