MODERN CONSTRUCTION PROJECTS FABRICATION 2022
VerifiedAdded on  2022/09/26
|14
|2912
|23
AI Summary
Write a case study about the same topic featured in the Annotated Bibliography assessment. Citations used there should help students fully explore. assert and conclude major points about student’s chosen subject Students are encouraged to rewrite their first draft of annotation to correct errors such as grammatical mistakes, word choices, awkward flow, tautology, split infinitives, and run-on sentences. This will be marked in accordance with the grading matrix. It is best if students adhere to all ”High Distinction” column attributes and eliminate all in the ”Unsatisfactory” column. See the grading matrix for attributes encouraged and rewarded. I have attached the previous assignments bibliography report (completed by you guys). I have also attached the case study template we must follow. Please ensure that all answers are construction related.
Contribute Materials
Your contribution can guide someone’s learning journey. Share your
documents today.
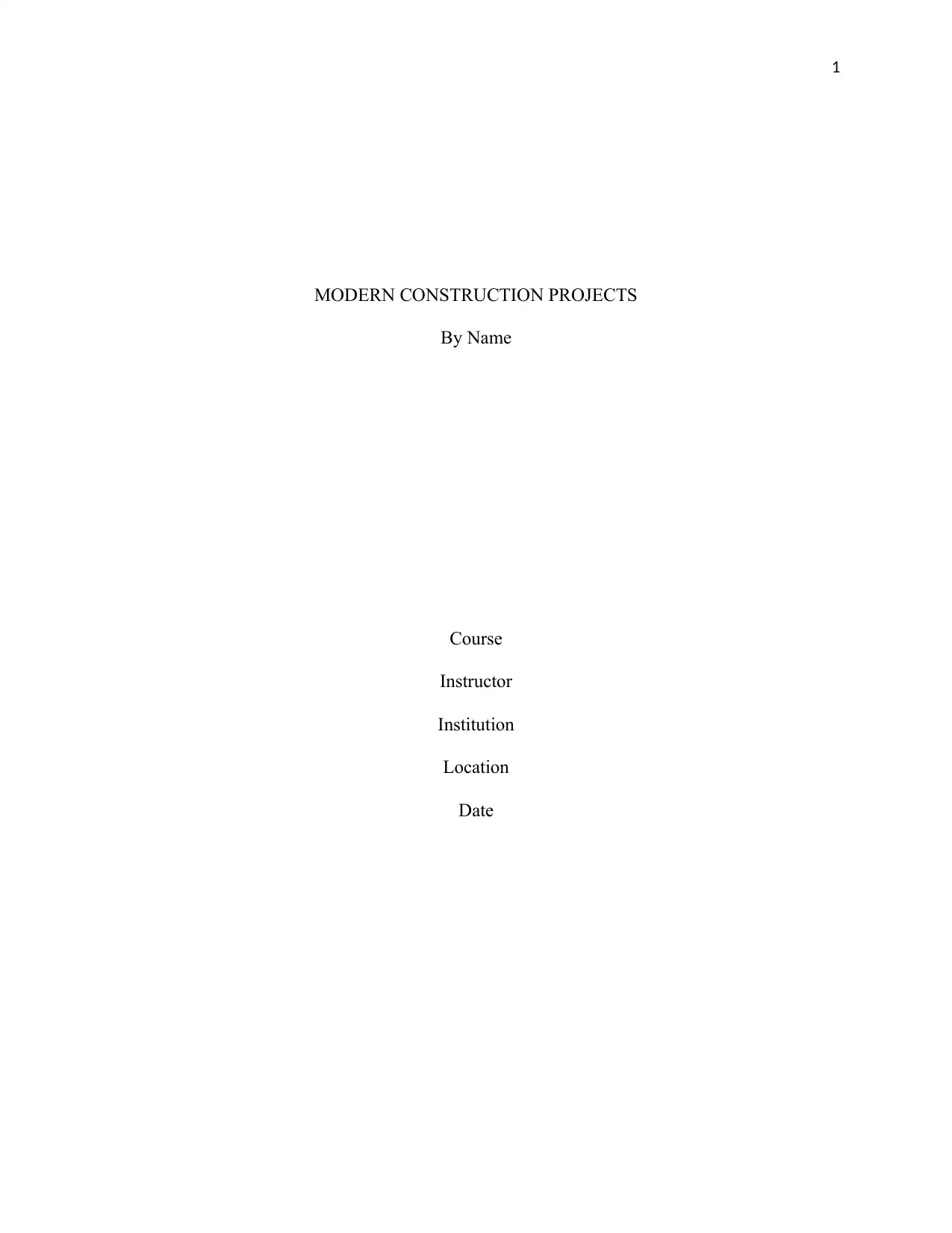
1
MODERN CONSTRUCTION PROJECTS
By Name
Course
Instructor
Institution
Location
Date
MODERN CONSTRUCTION PROJECTS
By Name
Course
Instructor
Institution
Location
Date
Secure Best Marks with AI Grader
Need help grading? Try our AI Grader for instant feedback on your assignments.
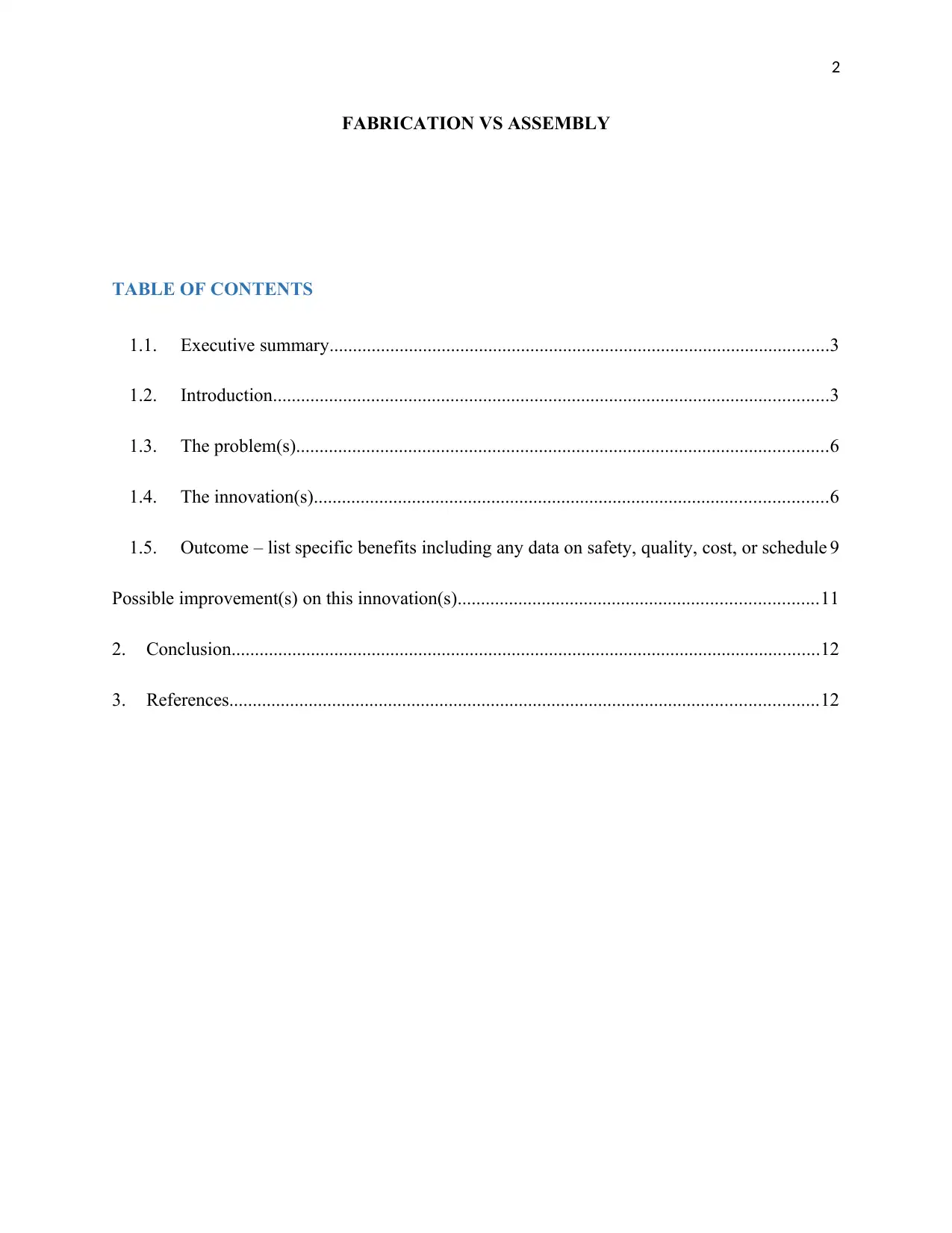
2
FABRICATION VS ASSEMBLY
TABLE OF CONTENTS
1.1. Executive summary...........................................................................................................3
1.2. Introduction.......................................................................................................................3
1.3. The problem(s)..................................................................................................................6
1.4. The innovation(s)..............................................................................................................6
1.5. Outcome – list specific benefits including any data on safety, quality, cost, or schedule 9
Possible improvement(s) on this innovation(s).............................................................................11
2. Conclusion..............................................................................................................................12
3. References..............................................................................................................................12
FABRICATION VS ASSEMBLY
TABLE OF CONTENTS
1.1. Executive summary...........................................................................................................3
1.2. Introduction.......................................................................................................................3
1.3. The problem(s)..................................................................................................................6
1.4. The innovation(s)..............................................................................................................6
1.5. Outcome – list specific benefits including any data on safety, quality, cost, or schedule 9
Possible improvement(s) on this innovation(s).............................................................................11
2. Conclusion..............................................................................................................................12
3. References..............................................................................................................................12
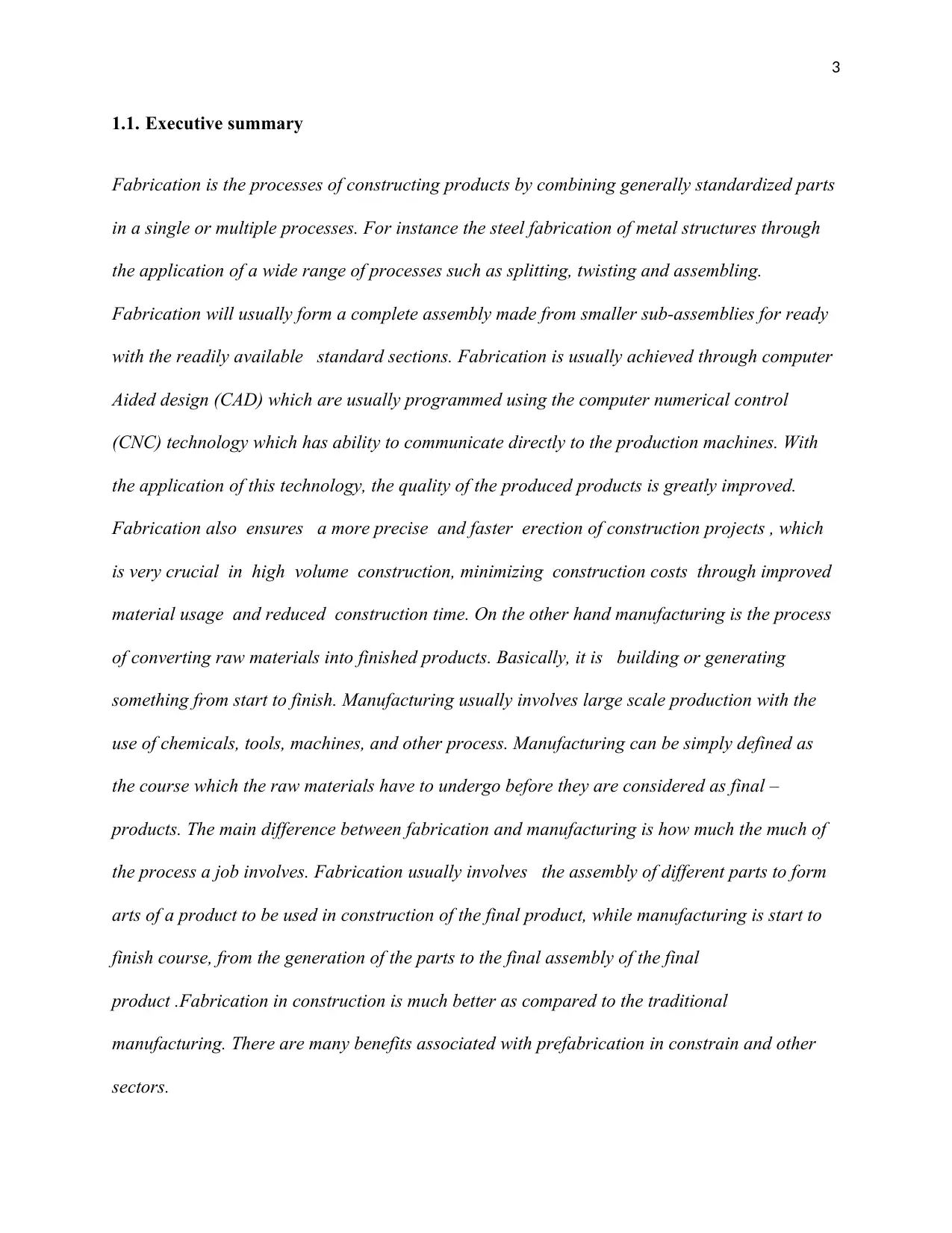
3
1.1. Executive summary
Fabrication is the processes of constructing products by combining generally standardized parts
in a single or multiple processes. For instance the steel fabrication of metal structures through
the application of a wide range of processes such as splitting, twisting and assembling.
Fabrication will usually form a complete assembly made from smaller sub-assemblies for ready
with the readily available standard sections. Fabrication is usually achieved through computer
Aided design (CAD) which are usually programmed using the computer numerical control
(CNC) technology which has ability to communicate directly to the production machines. With
the application of this technology, the quality of the produced products is greatly improved.
Fabrication also ensures a more precise and faster erection of construction projects , which
is very crucial in high volume construction, minimizing construction costs through improved
material usage and reduced construction time. On the other hand manufacturing is the process
of converting raw materials into finished products. Basically, it is building or generating
something from start to finish. Manufacturing usually involves large scale production with the
use of chemicals, tools, machines, and other process. Manufacturing can be simply defined as
the course which the raw materials have to undergo before they are considered as final –
products. The main difference between fabrication and manufacturing is how much the much of
the process a job involves. Fabrication usually involves the assembly of different parts to form
arts of a product to be used in construction of the final product, while manufacturing is start to
finish course, from the generation of the parts to the final assembly of the final
product .Fabrication in construction is much better as compared to the traditional
manufacturing. There are many benefits associated with prefabrication in constrain and other
sectors.
1.1. Executive summary
Fabrication is the processes of constructing products by combining generally standardized parts
in a single or multiple processes. For instance the steel fabrication of metal structures through
the application of a wide range of processes such as splitting, twisting and assembling.
Fabrication will usually form a complete assembly made from smaller sub-assemblies for ready
with the readily available standard sections. Fabrication is usually achieved through computer
Aided design (CAD) which are usually programmed using the computer numerical control
(CNC) technology which has ability to communicate directly to the production machines. With
the application of this technology, the quality of the produced products is greatly improved.
Fabrication also ensures a more precise and faster erection of construction projects , which
is very crucial in high volume construction, minimizing construction costs through improved
material usage and reduced construction time. On the other hand manufacturing is the process
of converting raw materials into finished products. Basically, it is building or generating
something from start to finish. Manufacturing usually involves large scale production with the
use of chemicals, tools, machines, and other process. Manufacturing can be simply defined as
the course which the raw materials have to undergo before they are considered as final –
products. The main difference between fabrication and manufacturing is how much the much of
the process a job involves. Fabrication usually involves the assembly of different parts to form
arts of a product to be used in construction of the final product, while manufacturing is start to
finish course, from the generation of the parts to the final assembly of the final
product .Fabrication in construction is much better as compared to the traditional
manufacturing. There are many benefits associated with prefabrication in constrain and other
sectors.
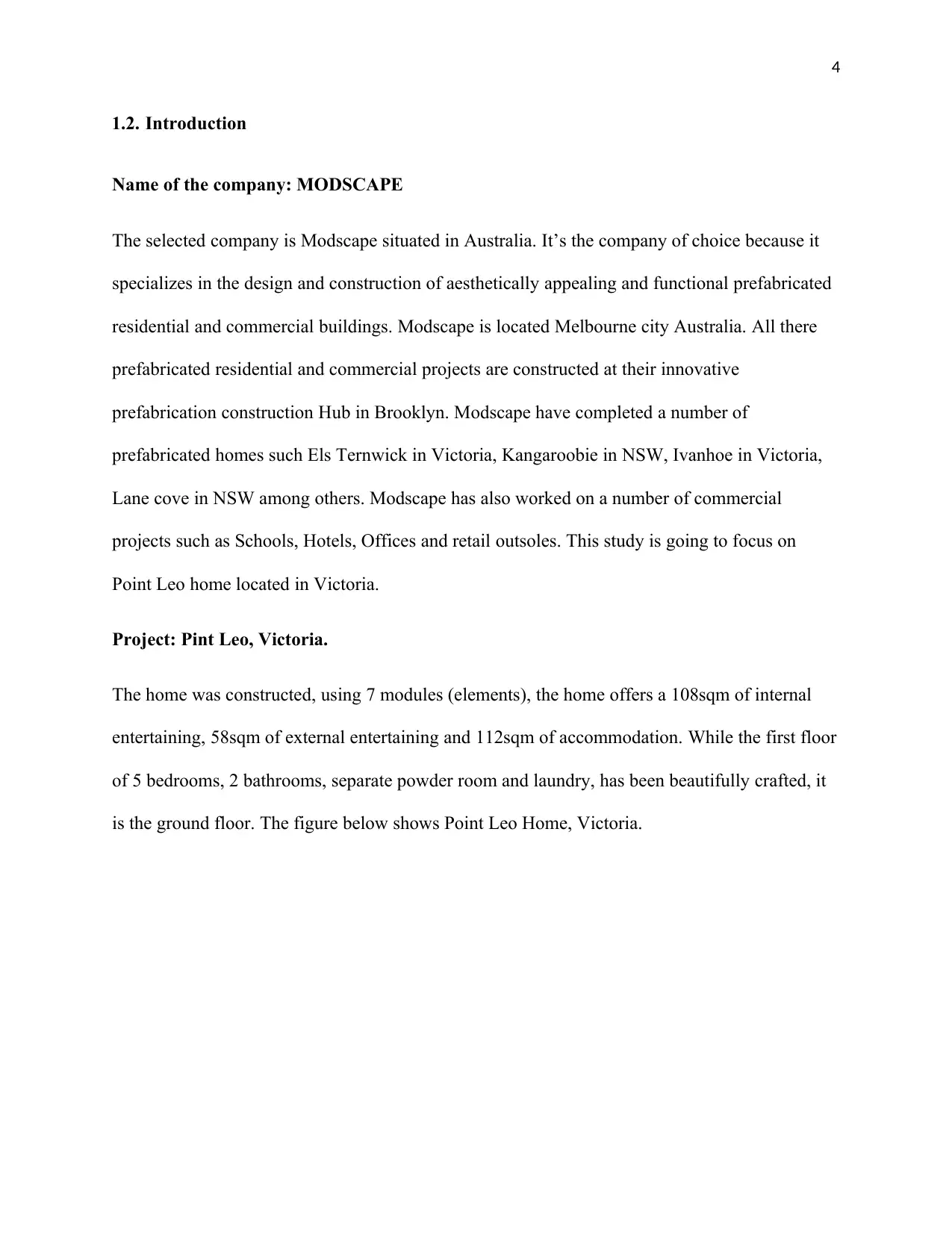
4
1.2. Introduction
Name of the company: MODSCAPE
The selected company is Modscape situated in Australia. It’s the company of choice because it
specializes in the design and construction of aesthetically appealing and functional prefabricated
residential and commercial buildings. Modscape is located Melbourne city Australia. All there
prefabricated residential and commercial projects are constructed at their innovative
prefabrication construction Hub in Brooklyn. Modscape have completed a number of
prefabricated homes such Els Ternwick in Victoria, Kangaroobie in NSW, Ivanhoe in Victoria,
Lane cove in NSW among others. Modscape has also worked on a number of commercial
projects such as Schools, Hotels, Offices and retail outsoles. This study is going to focus on
Point Leo home located in Victoria.
Project: Pint Leo, Victoria.
The home was constructed, using 7 modules (elements), the home offers a 108sqm of internal
entertaining, 58sqm of external entertaining and 112sqm of accommodation. While the first floor
of 5 bedrooms, 2 bathrooms, separate powder room and laundry, has been beautifully crafted, it
is the ground floor. The figure below shows Point Leo Home, Victoria.
1.2. Introduction
Name of the company: MODSCAPE
The selected company is Modscape situated in Australia. It’s the company of choice because it
specializes in the design and construction of aesthetically appealing and functional prefabricated
residential and commercial buildings. Modscape is located Melbourne city Australia. All there
prefabricated residential and commercial projects are constructed at their innovative
prefabrication construction Hub in Brooklyn. Modscape have completed a number of
prefabricated homes such Els Ternwick in Victoria, Kangaroobie in NSW, Ivanhoe in Victoria,
Lane cove in NSW among others. Modscape has also worked on a number of commercial
projects such as Schools, Hotels, Offices and retail outsoles. This study is going to focus on
Point Leo home located in Victoria.
Project: Pint Leo, Victoria.
The home was constructed, using 7 modules (elements), the home offers a 108sqm of internal
entertaining, 58sqm of external entertaining and 112sqm of accommodation. While the first floor
of 5 bedrooms, 2 bathrooms, separate powder room and laundry, has been beautifully crafted, it
is the ground floor. The figure below shows Point Leo Home, Victoria.
Secure Best Marks with AI Grader
Need help grading? Try our AI Grader for instant feedback on your assignments.

5
Fig 1: Point Leo Home, Victoria
The living space located in the ground floor and orients towards the main street, while the rest
of the house is cranked towards the ocean creating a clear delineation of the spaces. The
home is clad in a combination of the dark stained pacific teak timber and rough saw shadow
clad and despite its contemporary nature, looks very much ease in its natural seaside
environment. The figure below shows the site plan for Point Leo Home Victoria.
Fig 1: Point Leo Home, Victoria
The living space located in the ground floor and orients towards the main street, while the rest
of the house is cranked towards the ocean creating a clear delineation of the spaces. The
home is clad in a combination of the dark stained pacific teak timber and rough saw shadow
clad and despite its contemporary nature, looks very much ease in its natural seaside
environment. The figure below shows the site plan for Point Leo Home Victoria.
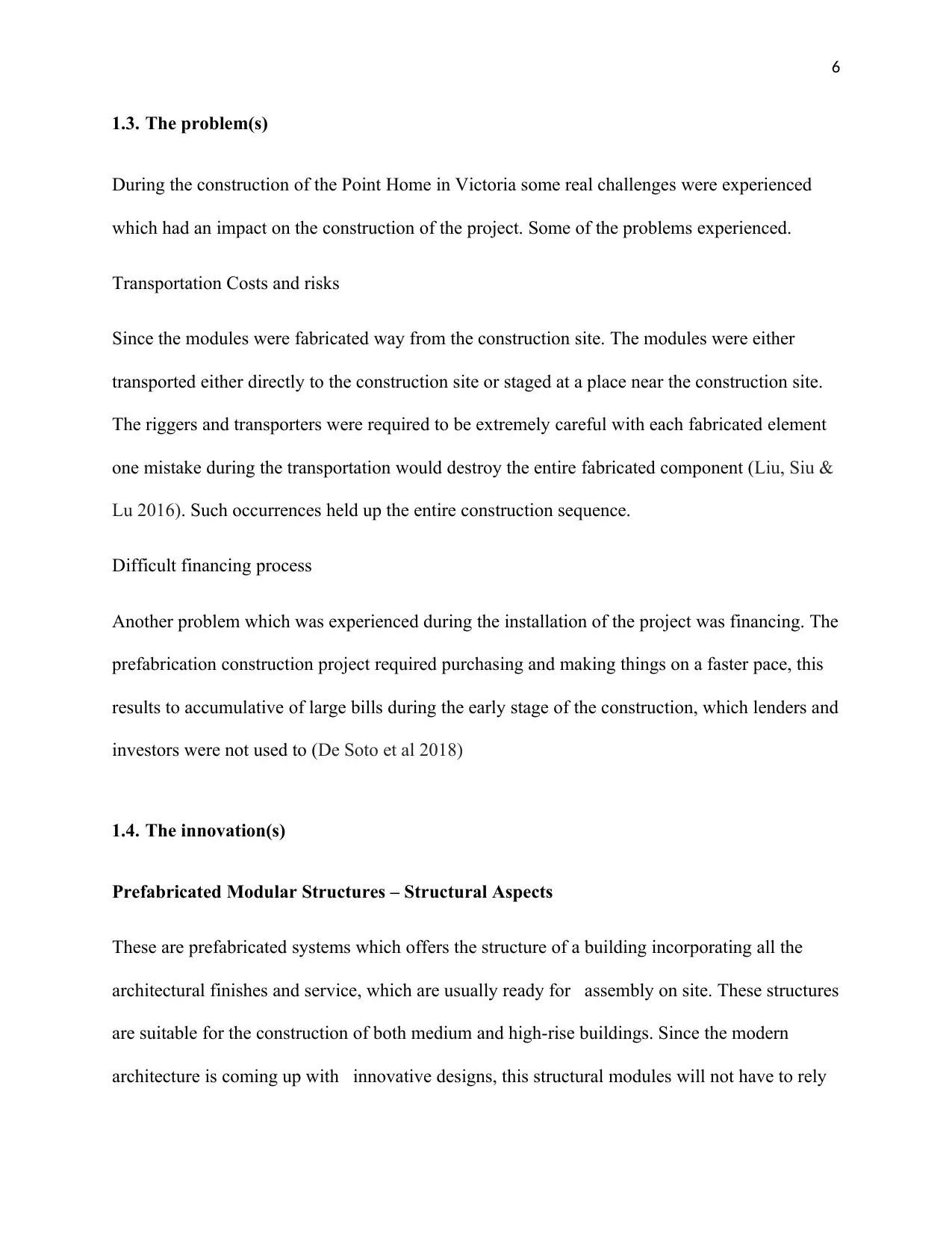
6
1.3. The problem(s)
During the construction of the Point Home in Victoria some real challenges were experienced
which had an impact on the construction of the project. Some of the problems experienced.
Transportation Costs and risks
Since the modules were fabricated way from the construction site. The modules were either
transported either directly to the construction site or staged at a place near the construction site.
The riggers and transporters were required to be extremely careful with each fabricated element
one mistake during the transportation would destroy the entire fabricated component (Liu, Siu &
Lu 2016). Such occurrences held up the entire construction sequence.
Difficult financing process
Another problem which was experienced during the installation of the project was financing. The
prefabrication construction project required purchasing and making things on a faster pace, this
results to accumulative of large bills during the early stage of the construction, which lenders and
investors were not used to (De Soto et al 2018)
1.4. The innovation(s)
Prefabricated Modular Structures – Structural Aspects
These are prefabricated systems which offers the structure of a building incorporating all the
architectural finishes and service, which are usually ready for assembly on site. These structures
are suitable for the construction of both medium and high-rise buildings. Since the modern
architecture is coming up with innovative designs, this structural modules will not have to rely
1.3. The problem(s)
During the construction of the Point Home in Victoria some real challenges were experienced
which had an impact on the construction of the project. Some of the problems experienced.
Transportation Costs and risks
Since the modules were fabricated way from the construction site. The modules were either
transported either directly to the construction site or staged at a place near the construction site.
The riggers and transporters were required to be extremely careful with each fabricated element
one mistake during the transportation would destroy the entire fabricated component (Liu, Siu &
Lu 2016). Such occurrences held up the entire construction sequence.
Difficult financing process
Another problem which was experienced during the installation of the project was financing. The
prefabrication construction project required purchasing and making things on a faster pace, this
results to accumulative of large bills during the early stage of the construction, which lenders and
investors were not used to (De Soto et al 2018)
1.4. The innovation(s)
Prefabricated Modular Structures – Structural Aspects
These are prefabricated systems which offers the structure of a building incorporating all the
architectural finishes and service, which are usually ready for assembly on site. These structures
are suitable for the construction of both medium and high-rise buildings. Since the modern
architecture is coming up with innovative designs, this structural modules will not have to rely
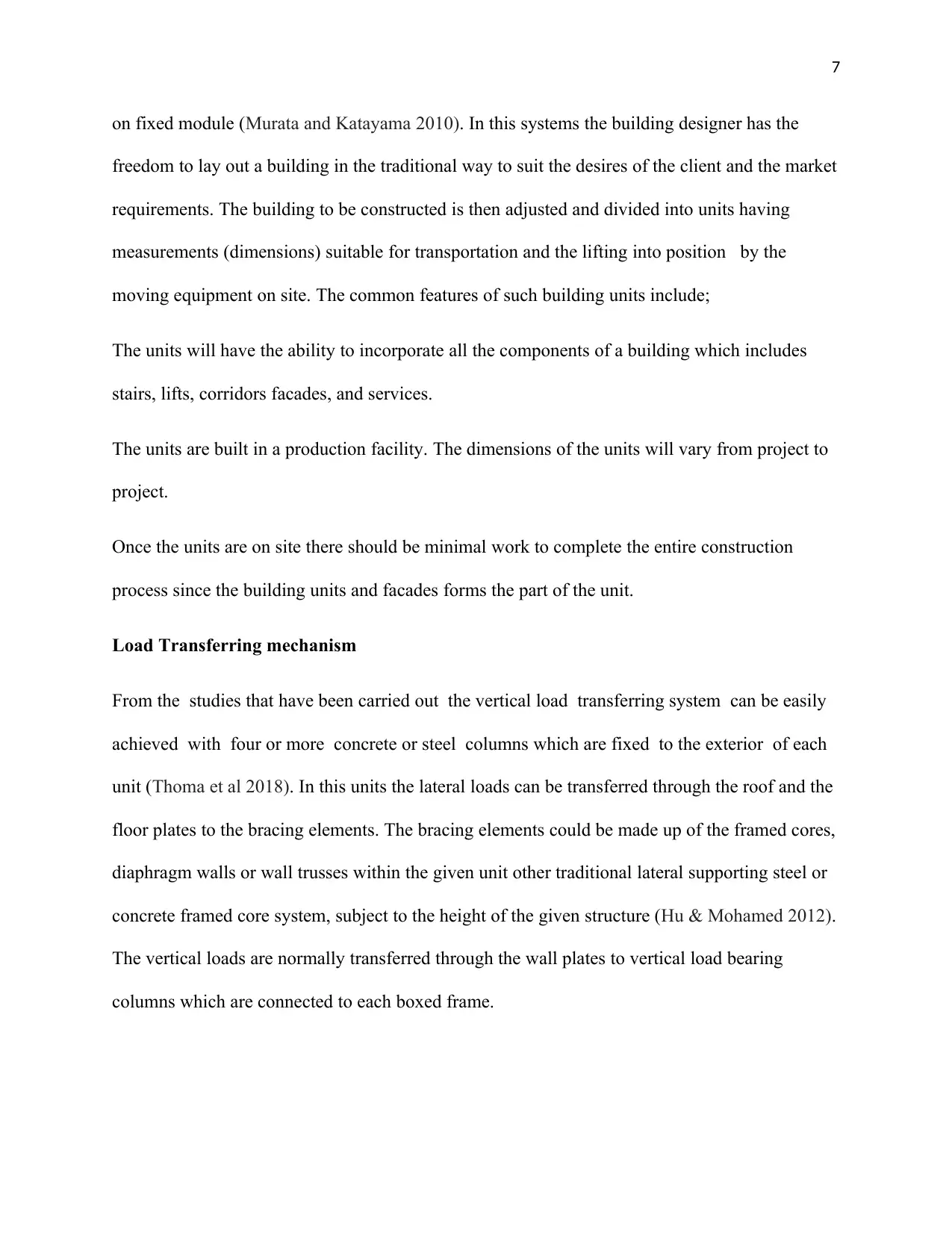
7
on fixed module (Murata and Katayama 2010). In this systems the building designer has the
freedom to lay out a building in the traditional way to suit the desires of the client and the market
requirements. The building to be constructed is then adjusted and divided into units having
measurements (dimensions) suitable for transportation and the lifting into position by the
moving equipment on site. The common features of such building units include;
The units will have the ability to incorporate all the components of a building which includes
stairs, lifts, corridors facades, and services.
The units are built in a production facility. The dimensions of the units will vary from project to
project.
Once the units are on site there should be minimal work to complete the entire construction
process since the building units and facades forms the part of the unit.
Load Transferring mechanism
From the studies that have been carried out the vertical load transferring system can be easily
achieved with four or more concrete or steel columns which are fixed to the exterior of each
unit (Thoma et al 2018). In this units the lateral loads can be transferred through the roof and the
floor plates to the bracing elements. The bracing elements could be made up of the framed cores,
diaphragm walls or wall trusses within the given unit other traditional lateral supporting steel or
concrete framed core system, subject to the height of the given structure (Hu & Mohamed 2012).
The vertical loads are normally transferred through the wall plates to vertical load bearing
columns which are connected to each boxed frame.
on fixed module (Murata and Katayama 2010). In this systems the building designer has the
freedom to lay out a building in the traditional way to suit the desires of the client and the market
requirements. The building to be constructed is then adjusted and divided into units having
measurements (dimensions) suitable for transportation and the lifting into position by the
moving equipment on site. The common features of such building units include;
The units will have the ability to incorporate all the components of a building which includes
stairs, lifts, corridors facades, and services.
The units are built in a production facility. The dimensions of the units will vary from project to
project.
Once the units are on site there should be minimal work to complete the entire construction
process since the building units and facades forms the part of the unit.
Load Transferring mechanism
From the studies that have been carried out the vertical load transferring system can be easily
achieved with four or more concrete or steel columns which are fixed to the exterior of each
unit (Thoma et al 2018). In this units the lateral loads can be transferred through the roof and the
floor plates to the bracing elements. The bracing elements could be made up of the framed cores,
diaphragm walls or wall trusses within the given unit other traditional lateral supporting steel or
concrete framed core system, subject to the height of the given structure (Hu & Mohamed 2012).
The vertical loads are normally transferred through the wall plates to vertical load bearing
columns which are connected to each boxed frame.
Paraphrase This Document
Need a fresh take? Get an instant paraphrase of this document with our AI Paraphraser
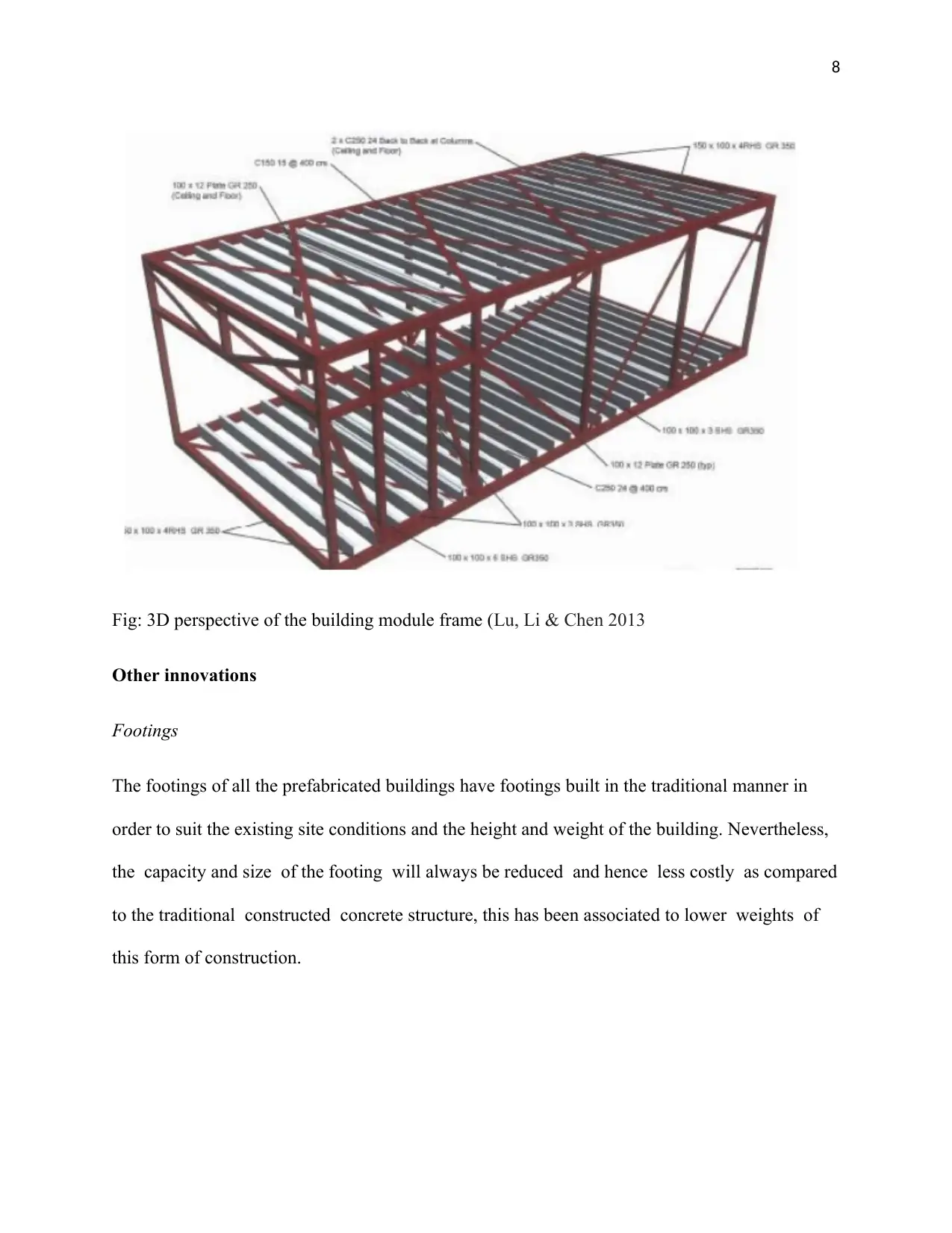
8
Fig: 3D perspective of the building module frame (Lu, Li & Chen 2013
Other innovations
Footings
The footings of all the prefabricated buildings have footings built in the traditional manner in
order to suit the existing site conditions and the height and weight of the building. Nevertheless,
the capacity and size of the footing will always be reduced and hence less costly as compared
to the traditional constructed concrete structure, this has been associated to lower weights of
this form of construction.
Fig: 3D perspective of the building module frame (Lu, Li & Chen 2013
Other innovations
Footings
The footings of all the prefabricated buildings have footings built in the traditional manner in
order to suit the existing site conditions and the height and weight of the building. Nevertheless,
the capacity and size of the footing will always be reduced and hence less costly as compared
to the traditional constructed concrete structure, this has been associated to lower weights of
this form of construction.
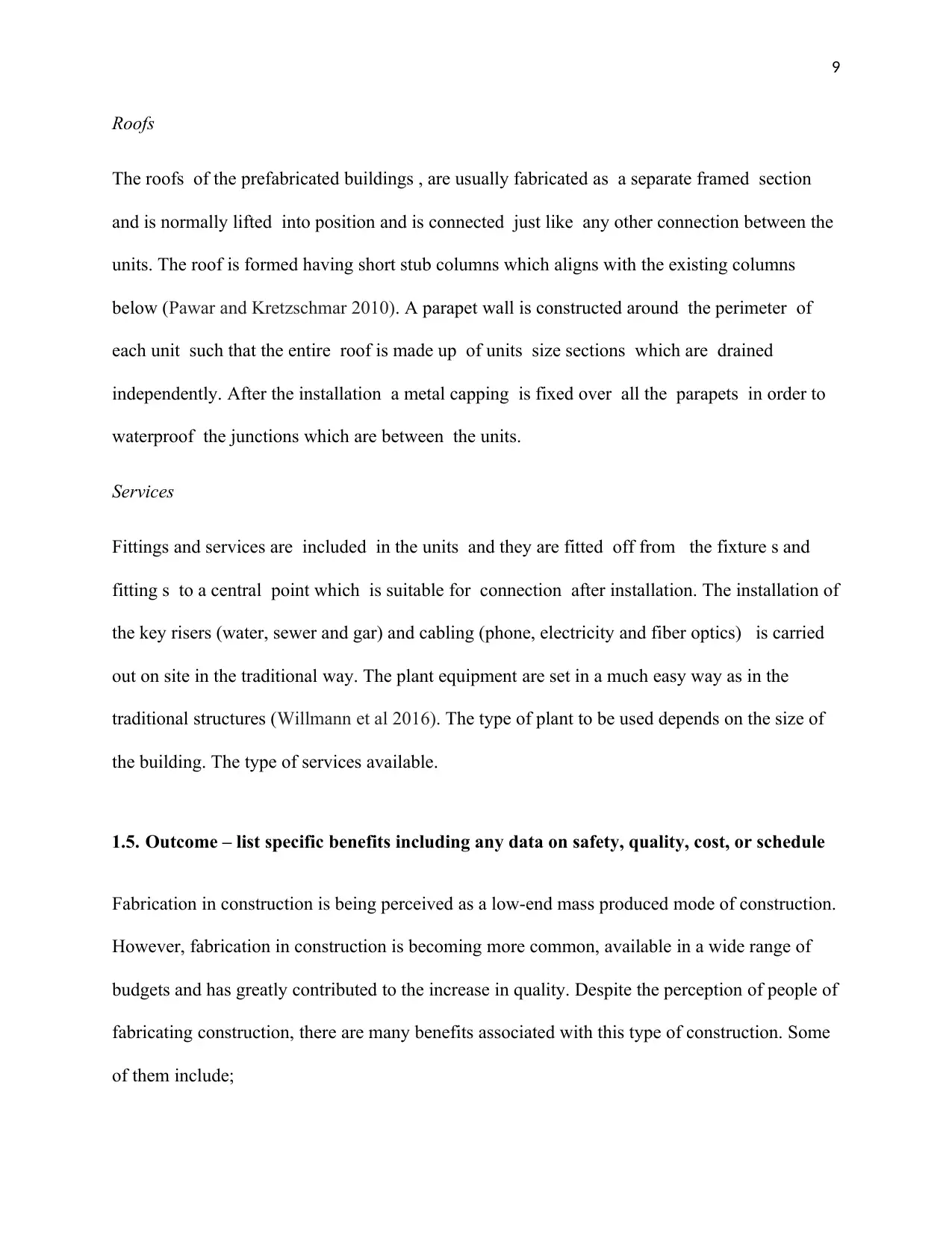
9
Roofs
The roofs of the prefabricated buildings , are usually fabricated as a separate framed section
and is normally lifted into position and is connected just like any other connection between the
units. The roof is formed having short stub columns which aligns with the existing columns
below (Pawar and Kretzschmar 2010). A parapet wall is constructed around the perimeter of
each unit such that the entire roof is made up of units size sections which are drained
independently. After the installation a metal capping is fixed over all the parapets in order to
waterproof the junctions which are between the units.
Services
Fittings and services are included in the units and they are fitted off from the fixture s and
fitting s to a central point which is suitable for connection after installation. The installation of
the key risers (water, sewer and gar) and cabling (phone, electricity and fiber optics) is carried
out on site in the traditional way. The plant equipment are set in a much easy way as in the
traditional structures (Willmann et al 2016). The type of plant to be used depends on the size of
the building. The type of services available.
1.5. Outcome – list specific benefits including any data on safety, quality, cost, or schedule
Fabrication in construction is being perceived as a low-end mass produced mode of construction.
However, fabrication in construction is becoming more common, available in a wide range of
budgets and has greatly contributed to the increase in quality. Despite the perception of people of
fabricating construction, there are many benefits associated with this type of construction. Some
of them include;
Roofs
The roofs of the prefabricated buildings , are usually fabricated as a separate framed section
and is normally lifted into position and is connected just like any other connection between the
units. The roof is formed having short stub columns which aligns with the existing columns
below (Pawar and Kretzschmar 2010). A parapet wall is constructed around the perimeter of
each unit such that the entire roof is made up of units size sections which are drained
independently. After the installation a metal capping is fixed over all the parapets in order to
waterproof the junctions which are between the units.
Services
Fittings and services are included in the units and they are fitted off from the fixture s and
fitting s to a central point which is suitable for connection after installation. The installation of
the key risers (water, sewer and gar) and cabling (phone, electricity and fiber optics) is carried
out on site in the traditional way. The plant equipment are set in a much easy way as in the
traditional structures (Willmann et al 2016). The type of plant to be used depends on the size of
the building. The type of services available.
1.5. Outcome – list specific benefits including any data on safety, quality, cost, or schedule
Fabrication in construction is being perceived as a low-end mass produced mode of construction.
However, fabrication in construction is becoming more common, available in a wide range of
budgets and has greatly contributed to the increase in quality. Despite the perception of people of
fabricating construction, there are many benefits associated with this type of construction. Some
of them include;

10
Improved safety
Since the sub-assemblies are produced in a factory-controlled settings, there is usually a less risk
for issues associated with environmental hazards. This normally ensures that those in the
construction sites are less exposed to risks and hazards. Also, an indoor production environment
presents significantly reduced risks for accidents and other serious liabilities (Sridhar et al 2013).
In most cases there are strict factory procedures which protects workers from the on-the-job
injury, as compared to the outdoor environment in the construction sites , where workers are
exposed to weather-related conditions and other hazards.
Reduced construction time
Fabrication construction takes much less time to erect a structure as compared to onsite
construction. It has been witnessed in many occasions that, fabrication construction usually takes
almost half the time taken by on-site construction. This has been attributed to better upfront
planning, elimination of the on-site weather factors, delays by subcontractors and the quick
fabrication since multiple elements can be fabricated simultaneously (Nawari 2012). Reduced
construction time usually allows construction companies to implement many projects at the same
time. Hence allowing the companies to grow rather than putting all their resources and focuses
on one or a few projects at ago.
Flexibility in construction
Prefabricated construction can be easily dissembled and relocated to different sites. This greatly
reduces the demand or raw materials, reduced time and reduced the amount of labour required.
Also, prefabrication creates rooms or flexibility in the designs, this brings about many
opportunities (Newcombe., Pampanin & Buchanan 2010). Due to the fact that the fabricated
Improved safety
Since the sub-assemblies are produced in a factory-controlled settings, there is usually a less risk
for issues associated with environmental hazards. This normally ensures that those in the
construction sites are less exposed to risks and hazards. Also, an indoor production environment
presents significantly reduced risks for accidents and other serious liabilities (Sridhar et al 2013).
In most cases there are strict factory procedures which protects workers from the on-the-job
injury, as compared to the outdoor environment in the construction sites , where workers are
exposed to weather-related conditions and other hazards.
Reduced construction time
Fabrication construction takes much less time to erect a structure as compared to onsite
construction. It has been witnessed in many occasions that, fabrication construction usually takes
almost half the time taken by on-site construction. This has been attributed to better upfront
planning, elimination of the on-site weather factors, delays by subcontractors and the quick
fabrication since multiple elements can be fabricated simultaneously (Nawari 2012). Reduced
construction time usually allows construction companies to implement many projects at the same
time. Hence allowing the companies to grow rather than putting all their resources and focuses
on one or a few projects at ago.
Flexibility in construction
Prefabricated construction can be easily dissembled and relocated to different sites. This greatly
reduces the demand or raw materials, reduced time and reduced the amount of labour required.
Also, prefabrication creates rooms or flexibility in the designs, this brings about many
opportunities (Newcombe., Pampanin & Buchanan 2010). Due to the fact that the fabricated
Secure Best Marks with AI Grader
Need help grading? Try our AI Grader for instant feedback on your assignments.
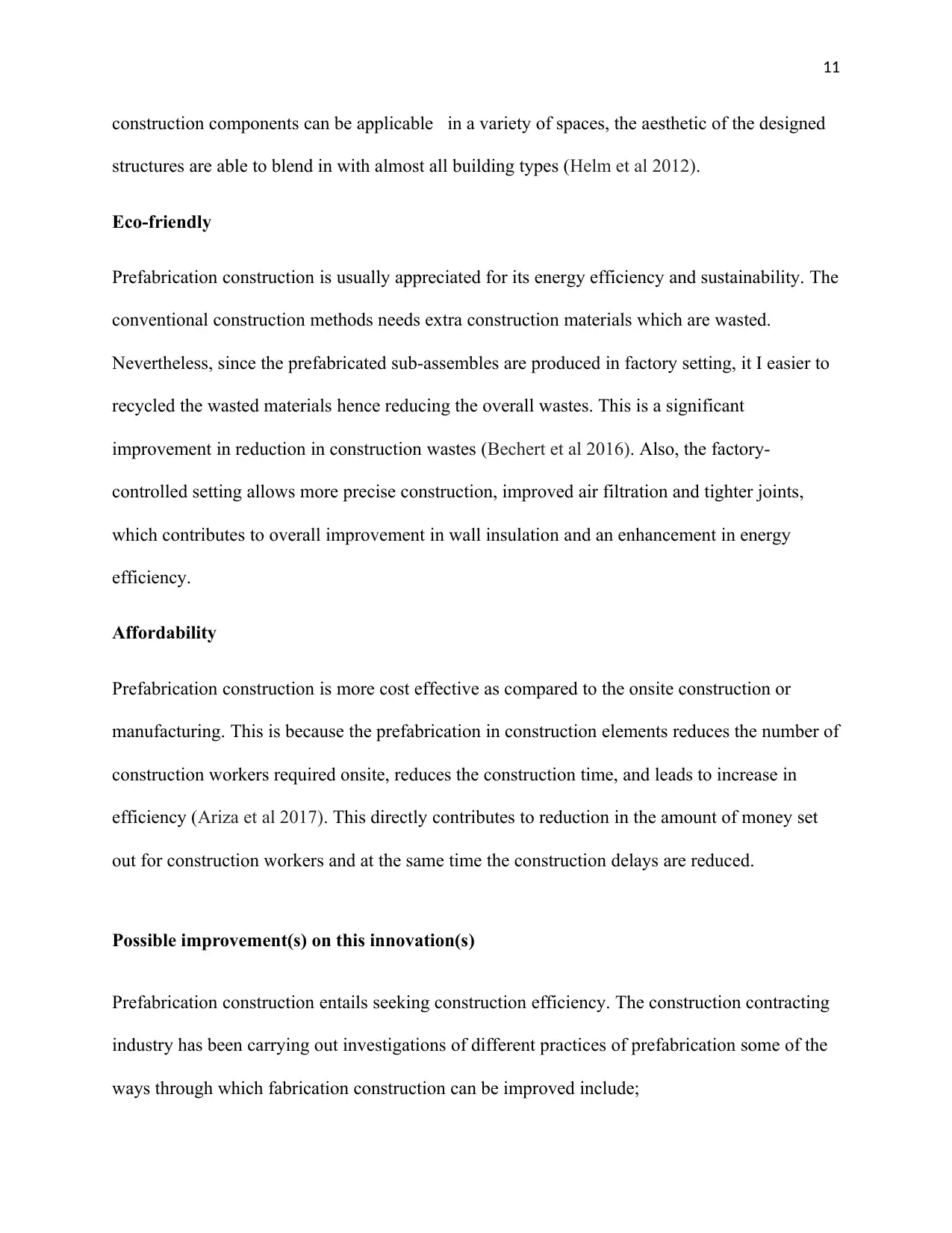
11
construction components can be applicable in a variety of spaces, the aesthetic of the designed
structures are able to blend in with almost all building types (Helm et al 2012).
Eco-friendly
Prefabrication construction is usually appreciated for its energy efficiency and sustainability. The
conventional construction methods needs extra construction materials which are wasted.
Nevertheless, since the prefabricated sub-assembles are produced in factory setting, it I easier to
recycled the wasted materials hence reducing the overall wastes. This is a significant
improvement in reduction in construction wastes (Bechert et al 2016). Also, the factory-
controlled setting allows more precise construction, improved air filtration and tighter joints,
which contributes to overall improvement in wall insulation and an enhancement in energy
efficiency.
Affordability
Prefabrication construction is more cost effective as compared to the onsite construction or
manufacturing. This is because the prefabrication in construction elements reduces the number of
construction workers required onsite, reduces the construction time, and leads to increase in
efficiency (Ariza et al 2017). This directly contributes to reduction in the amount of money set
out for construction workers and at the same time the construction delays are reduced.
Possible improvement(s) on this innovation(s)
Prefabrication construction entails seeking construction efficiency. The construction contracting
industry has been carrying out investigations of different practices of prefabrication some of the
ways through which fabrication construction can be improved include;
construction components can be applicable in a variety of spaces, the aesthetic of the designed
structures are able to blend in with almost all building types (Helm et al 2012).
Eco-friendly
Prefabrication construction is usually appreciated for its energy efficiency and sustainability. The
conventional construction methods needs extra construction materials which are wasted.
Nevertheless, since the prefabricated sub-assembles are produced in factory setting, it I easier to
recycled the wasted materials hence reducing the overall wastes. This is a significant
improvement in reduction in construction wastes (Bechert et al 2016). Also, the factory-
controlled setting allows more precise construction, improved air filtration and tighter joints,
which contributes to overall improvement in wall insulation and an enhancement in energy
efficiency.
Affordability
Prefabrication construction is more cost effective as compared to the onsite construction or
manufacturing. This is because the prefabrication in construction elements reduces the number of
construction workers required onsite, reduces the construction time, and leads to increase in
efficiency (Ariza et al 2017). This directly contributes to reduction in the amount of money set
out for construction workers and at the same time the construction delays are reduced.
Possible improvement(s) on this innovation(s)
Prefabrication construction entails seeking construction efficiency. The construction contracting
industry has been carrying out investigations of different practices of prefabrication some of the
ways through which fabrication construction can be improved include;
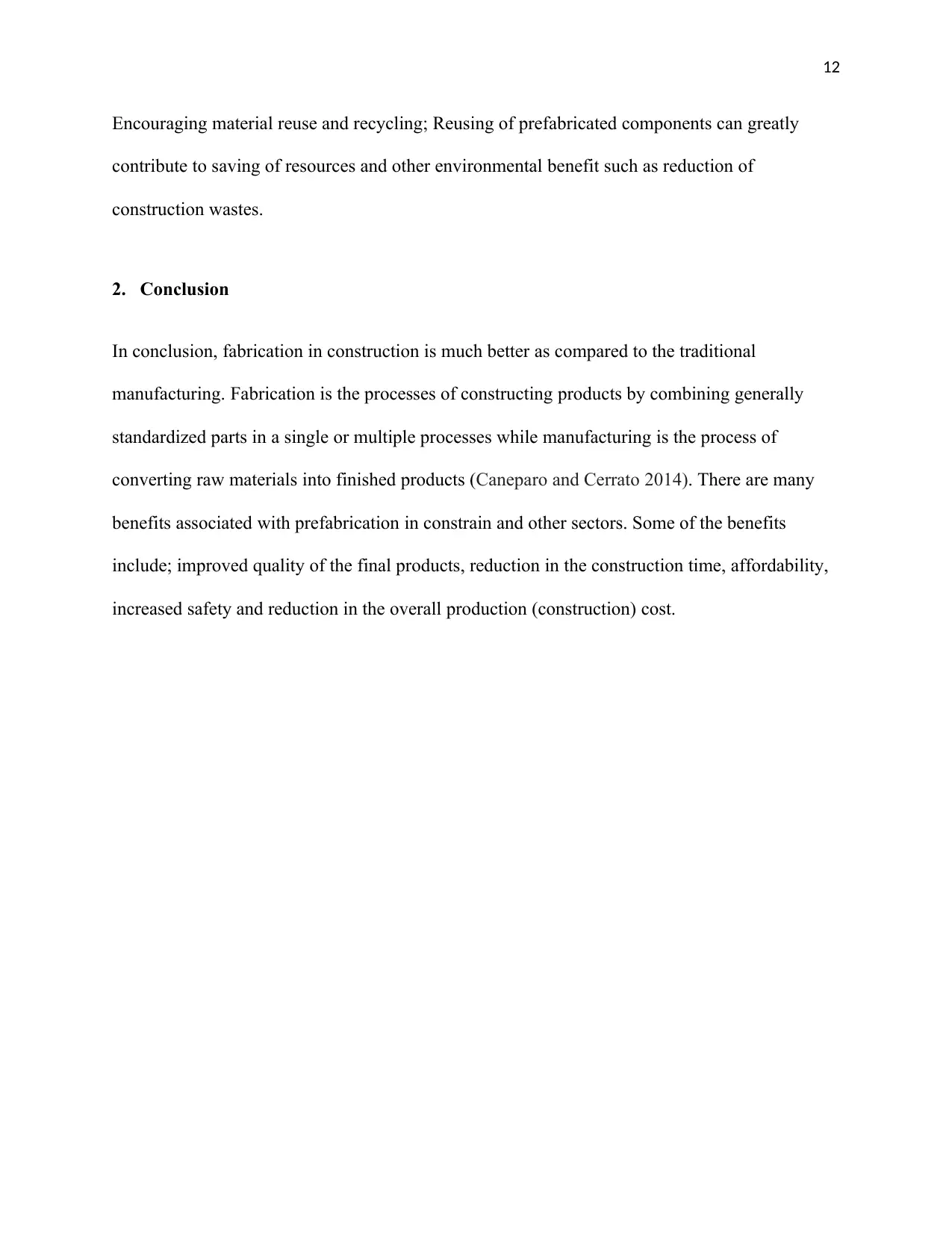
12
Encouraging material reuse and recycling; Reusing of prefabricated components can greatly
contribute to saving of resources and other environmental benefit such as reduction of
construction wastes.
2. Conclusion
In conclusion, fabrication in construction is much better as compared to the traditional
manufacturing. Fabrication is the processes of constructing products by combining generally
standardized parts in a single or multiple processes while manufacturing is the process of
converting raw materials into finished products (Caneparo and Cerrato 2014). There are many
benefits associated with prefabrication in constrain and other sectors. Some of the benefits
include; improved quality of the final products, reduction in the construction time, affordability,
increased safety and reduction in the overall production (construction) cost.
Encouraging material reuse and recycling; Reusing of prefabricated components can greatly
contribute to saving of resources and other environmental benefit such as reduction of
construction wastes.
2. Conclusion
In conclusion, fabrication in construction is much better as compared to the traditional
manufacturing. Fabrication is the processes of constructing products by combining generally
standardized parts in a single or multiple processes while manufacturing is the process of
converting raw materials into finished products (Caneparo and Cerrato 2014). There are many
benefits associated with prefabrication in constrain and other sectors. Some of the benefits
include; improved quality of the final products, reduction in the construction time, affordability,
increased safety and reduction in the overall production (construction) cost.
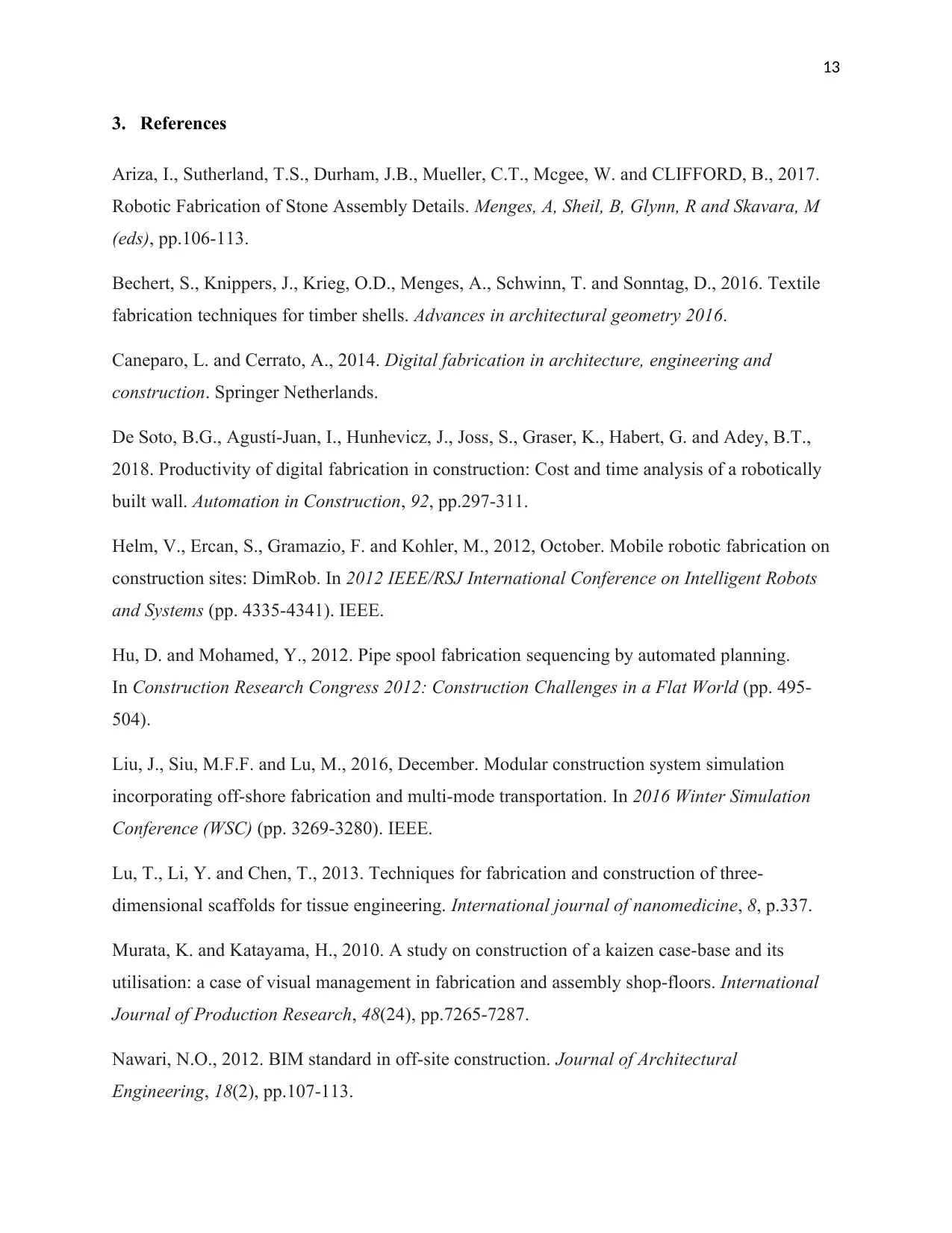
13
3. References
Ariza, I., Sutherland, T.S., Durham, J.B., Mueller, C.T., Mcgee, W. and CLIFFORD, B., 2017.
Robotic Fabrication of Stone Assembly Details. Menges, A, Sheil, B, Glynn, R and Skavara, M
(eds), pp.106-113.
Bechert, S., Knippers, J., Krieg, O.D., Menges, A., Schwinn, T. and Sonntag, D., 2016. Textile
fabrication techniques for timber shells. Advances in architectural geometry 2016.
Caneparo, L. and Cerrato, A., 2014. Digital fabrication in architecture, engineering and
construction. Springer Netherlands.
De Soto, B.G., AgustĂ-Juan, I., Hunhevicz, J., Joss, S., Graser, K., Habert, G. and Adey, B.T.,
2018. Productivity of digital fabrication in construction: Cost and time analysis of a robotically
built wall. Automation in Construction, 92, pp.297-311.
Helm, V., Ercan, S., Gramazio, F. and Kohler, M., 2012, October. Mobile robotic fabrication on
construction sites: DimRob. In 2012 IEEE/RSJ International Conference on Intelligent Robots
and Systems (pp. 4335-4341). IEEE.
Hu, D. and Mohamed, Y., 2012. Pipe spool fabrication sequencing by automated planning.
In Construction Research Congress 2012: Construction Challenges in a Flat World (pp. 495-
504).
Liu, J., Siu, M.F.F. and Lu, M., 2016, December. Modular construction system simulation
incorporating off-shore fabrication and multi-mode transportation. In 2016 Winter Simulation
Conference (WSC) (pp. 3269-3280). IEEE.
Lu, T., Li, Y. and Chen, T., 2013. Techniques for fabrication and construction of three-
dimensional scaffolds for tissue engineering. International journal of nanomedicine, 8, p.337.
Murata, K. and Katayama, H., 2010. A study on construction of a kaizen case-base and its
utilisation: a case of visual management in fabrication and assembly shop-floors. International
Journal of Production Research, 48(24), pp.7265-7287.
Nawari, N.O., 2012. BIM standard in off-site construction. Journal of Architectural
Engineering, 18(2), pp.107-113.
3. References
Ariza, I., Sutherland, T.S., Durham, J.B., Mueller, C.T., Mcgee, W. and CLIFFORD, B., 2017.
Robotic Fabrication of Stone Assembly Details. Menges, A, Sheil, B, Glynn, R and Skavara, M
(eds), pp.106-113.
Bechert, S., Knippers, J., Krieg, O.D., Menges, A., Schwinn, T. and Sonntag, D., 2016. Textile
fabrication techniques for timber shells. Advances in architectural geometry 2016.
Caneparo, L. and Cerrato, A., 2014. Digital fabrication in architecture, engineering and
construction. Springer Netherlands.
De Soto, B.G., AgustĂ-Juan, I., Hunhevicz, J., Joss, S., Graser, K., Habert, G. and Adey, B.T.,
2018. Productivity of digital fabrication in construction: Cost and time analysis of a robotically
built wall. Automation in Construction, 92, pp.297-311.
Helm, V., Ercan, S., Gramazio, F. and Kohler, M., 2012, October. Mobile robotic fabrication on
construction sites: DimRob. In 2012 IEEE/RSJ International Conference on Intelligent Robots
and Systems (pp. 4335-4341). IEEE.
Hu, D. and Mohamed, Y., 2012. Pipe spool fabrication sequencing by automated planning.
In Construction Research Congress 2012: Construction Challenges in a Flat World (pp. 495-
504).
Liu, J., Siu, M.F.F. and Lu, M., 2016, December. Modular construction system simulation
incorporating off-shore fabrication and multi-mode transportation. In 2016 Winter Simulation
Conference (WSC) (pp. 3269-3280). IEEE.
Lu, T., Li, Y. and Chen, T., 2013. Techniques for fabrication and construction of three-
dimensional scaffolds for tissue engineering. International journal of nanomedicine, 8, p.337.
Murata, K. and Katayama, H., 2010. A study on construction of a kaizen case-base and its
utilisation: a case of visual management in fabrication and assembly shop-floors. International
Journal of Production Research, 48(24), pp.7265-7287.
Nawari, N.O., 2012. BIM standard in off-site construction. Journal of Architectural
Engineering, 18(2), pp.107-113.
Paraphrase This Document
Need a fresh take? Get an instant paraphrase of this document with our AI Paraphraser
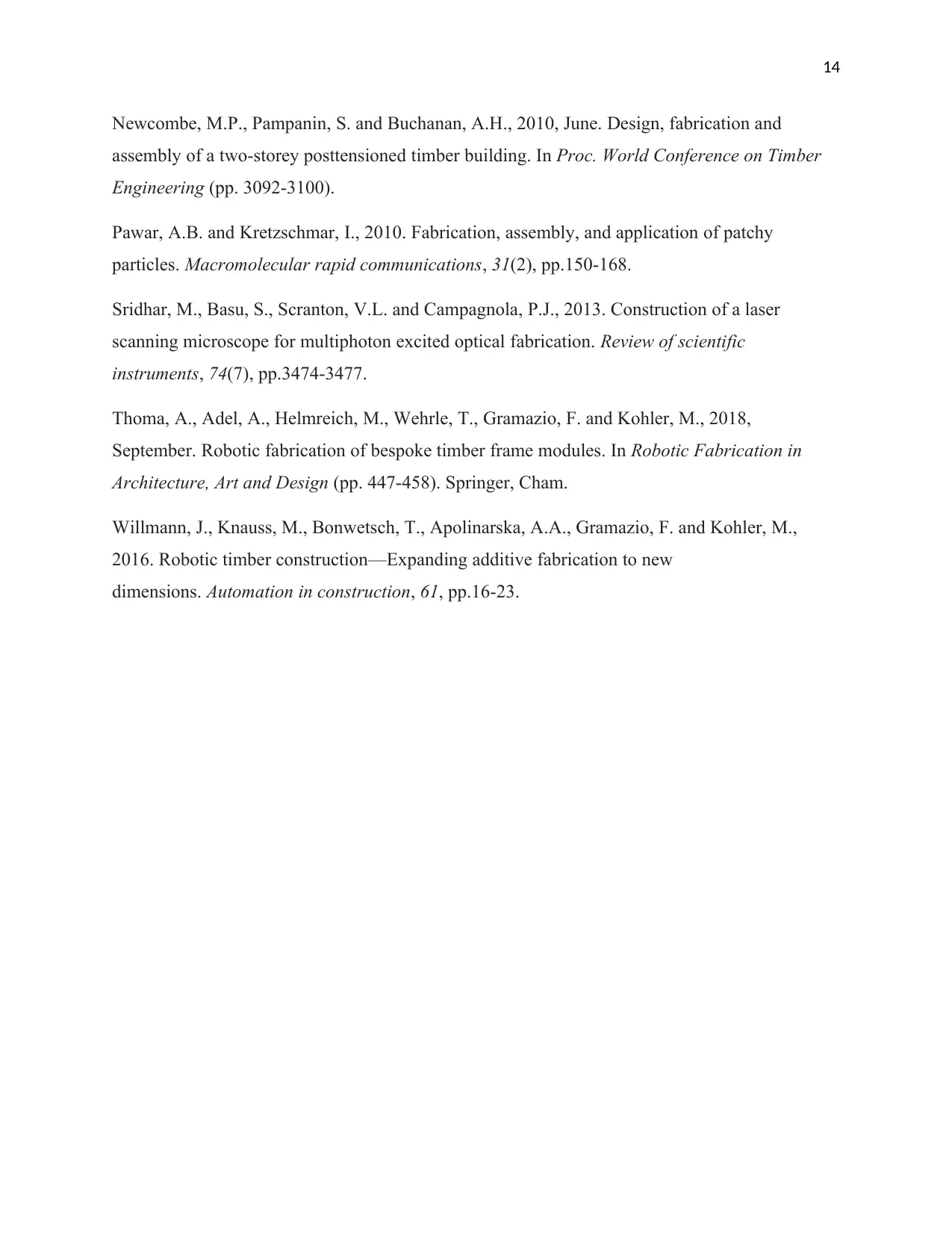
14
Newcombe, M.P., Pampanin, S. and Buchanan, A.H., 2010, June. Design, fabrication and
assembly of a two-storey posttensioned timber building. In Proc. World Conference on Timber
Engineering (pp. 3092-3100).
Pawar, A.B. and Kretzschmar, I., 2010. Fabrication, assembly, and application of patchy
particles. Macromolecular rapid communications, 31(2), pp.150-168.
Sridhar, M., Basu, S., Scranton, V.L. and Campagnola, P.J., 2013. Construction of a laser
scanning microscope for multiphoton excited optical fabrication. Review of scientific
instruments, 74(7), pp.3474-3477.
Thoma, A., Adel, A., Helmreich, M., Wehrle, T., Gramazio, F. and Kohler, M., 2018,
September. Robotic fabrication of bespoke timber frame modules. In Robotic Fabrication in
Architecture, Art and Design (pp. 447-458). Springer, Cham.
Willmann, J., Knauss, M., Bonwetsch, T., Apolinarska, A.A., Gramazio, F. and Kohler, M.,
2016. Robotic timber construction—Expanding additive fabrication to new
dimensions. Automation in construction, 61, pp.16-23.
Newcombe, M.P., Pampanin, S. and Buchanan, A.H., 2010, June. Design, fabrication and
assembly of a two-storey posttensioned timber building. In Proc. World Conference on Timber
Engineering (pp. 3092-3100).
Pawar, A.B. and Kretzschmar, I., 2010. Fabrication, assembly, and application of patchy
particles. Macromolecular rapid communications, 31(2), pp.150-168.
Sridhar, M., Basu, S., Scranton, V.L. and Campagnola, P.J., 2013. Construction of a laser
scanning microscope for multiphoton excited optical fabrication. Review of scientific
instruments, 74(7), pp.3474-3477.
Thoma, A., Adel, A., Helmreich, M., Wehrle, T., Gramazio, F. and Kohler, M., 2018,
September. Robotic fabrication of bespoke timber frame modules. In Robotic Fabrication in
Architecture, Art and Design (pp. 447-458). Springer, Cham.
Willmann, J., Knauss, M., Bonwetsch, T., Apolinarska, A.A., Gramazio, F. and Kohler, M.,
2016. Robotic timber construction—Expanding additive fabrication to new
dimensions. Automation in construction, 61, pp.16-23.
1 out of 14
Related Documents
![[object Object]](/_next/image/?url=%2F_next%2Fstatic%2Fmedia%2Flogo.6d15ce61.png&w=640&q=75)
Your All-in-One AI-Powered Toolkit for Academic Success.
 +13062052269
info@desklib.com
Available 24*7 on WhatsApp / Email
Unlock your academic potential
© 2024  |  Zucol Services PVT LTD  |  All rights reserved.