Automation for Manufacturing: Comparison of Temperature Sensors and Infrared Temperature Sensor
Added on 2022-10-14
14 Pages5102 Words185 Views
Automation for manufacturing.1
AUTOMATION FOR MANUFACTURING
by (Name)
The Name of the Class (Course)
Professor (Tutor)
The Name of the School (University)
The City and State where it is located
The Date
AUTOMATION FOR MANUFACTURING
by (Name)
The Name of the Class (Course)
Professor (Tutor)
The Name of the School (University)
The City and State where it is located
The Date
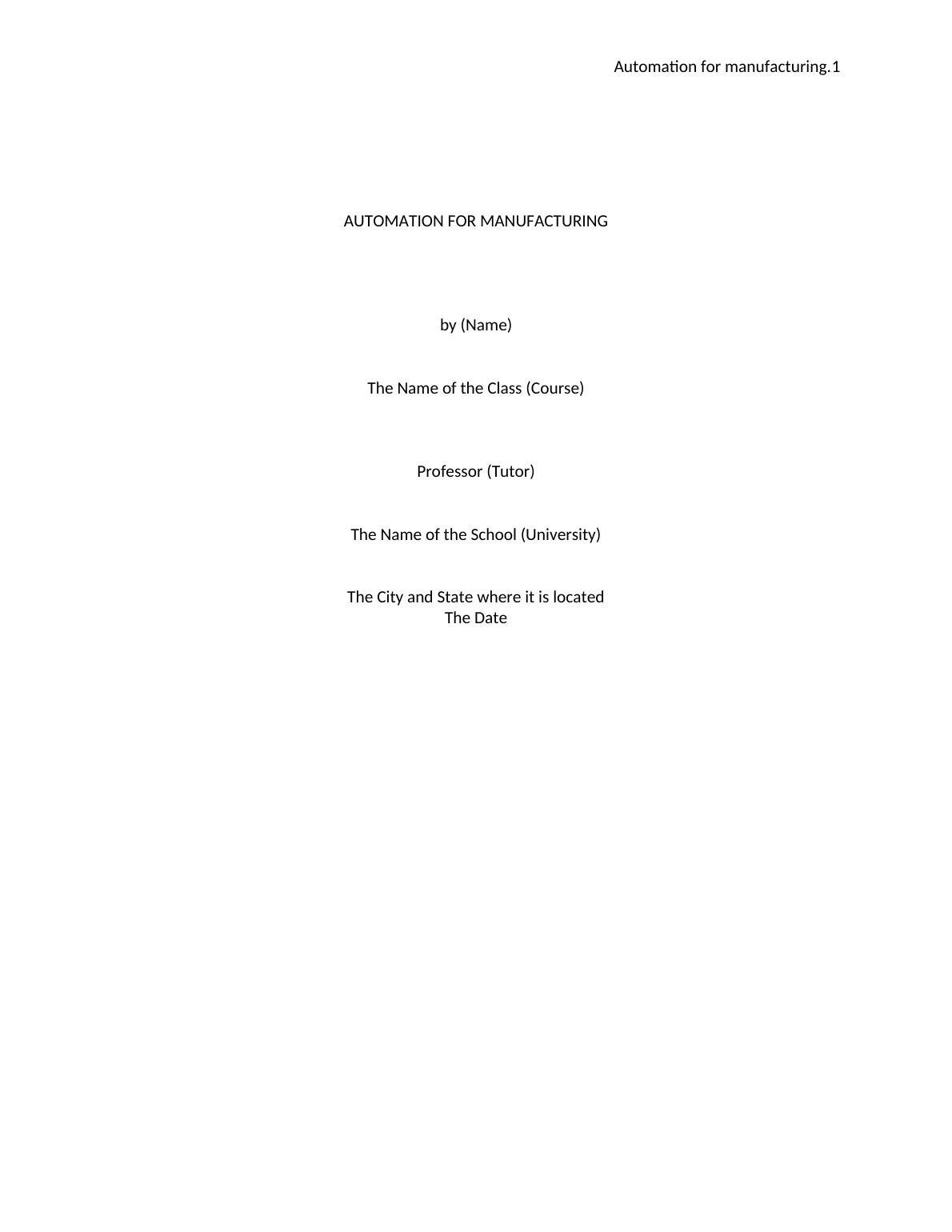
Automation for manufacturing.2
Settling on the right temperature sensor, for a particular application, requires a lot
of discernment. The broad variety of alternative temperature sensors makes such a
process time consuming and error-prone, particularly if one lacks the required
calibration expertise. Temperature sensors are generally grouped into non-contact
and contact temperature sensors. Furthermore, three are three popular contact
sensors in use today including thermistors, resistance temperature devices (RTDs)
and thermocouples. Additionally, non-contact temperature sensors include infrared
temperature sensors. Before selecting the appropriate sensor for this project, we
need to understand the demerits and merits of every sensor category, so that we
can select the relevant temperature sensor for this project.
Thermocouples
According to Amin and Newnham (2015), a thermocouple gauges temperature by
generating a proportional voltage at the junction of two wires. There is a myriad of
thermocouples in industrial operation, and they utilize different metallic material to
quantify temperature in different applications. Conversely, resistance temperature
detectors apply the principle of resistance change, with fluctuations in the
temperature of metal components, to perform measurement tasks . Amin and
Newnham (2015) add that examples of typical RTDs include pt100 sensors, and
they incorporate platinum as their primary resistance material. Finally, thermistors
rely on the same principle of operation as RTDs, and the only difference between
them is the fact that thermistors use polymers and ceramic components as
resistance material (Amin and Newnham, 2015).
Comparison of RTD with thermocouples
It is possible to make a comparison of thermocouples and resistance temperature
devices, according to certain performance criteria. This will enable us to identify
which sensor is appropriate for our application.Per Amin and Newnham (2015), the
first performance factor is the temperature range. Thermocouples are the sensors
of choice in applications whereby the prevailing temperatures are very high. Amin
and Newnham (2015) argue that although recent technological Innovations have
attempted to improve the temperature measurement span of resistance
temperature devices, a vast majority of these devices are built to quantify
temperatures below 400 degrees. By contrast, thermocouples are capable of
recording temperatures approaching 2500 degrees centigrade.
The next comparison criterion is the cost of the devices. Arnolds (2013) states that
thermocouples are usually less expensive when compared to RTDs. The price of a
typical RTD is triple the price of a corresponding thermocouple with the same
measurement capabilities. However, it is more expensive to install a thermocouple,
because the installation of an RTD only requires simple copper wiring. Although
installing an RTD is less costly, the savings one would make from the installation of
an RTD are not enough to compensate for its high price .
Sensitivity is also an important factor to consider. Even though both devices
respond to temperature variations at a satisfactory pace, thermocouples respond
faster to temperature changes. In fact, a thermocouple that is grounded will
Settling on the right temperature sensor, for a particular application, requires a lot
of discernment. The broad variety of alternative temperature sensors makes such a
process time consuming and error-prone, particularly if one lacks the required
calibration expertise. Temperature sensors are generally grouped into non-contact
and contact temperature sensors. Furthermore, three are three popular contact
sensors in use today including thermistors, resistance temperature devices (RTDs)
and thermocouples. Additionally, non-contact temperature sensors include infrared
temperature sensors. Before selecting the appropriate sensor for this project, we
need to understand the demerits and merits of every sensor category, so that we
can select the relevant temperature sensor for this project.
Thermocouples
According to Amin and Newnham (2015), a thermocouple gauges temperature by
generating a proportional voltage at the junction of two wires. There is a myriad of
thermocouples in industrial operation, and they utilize different metallic material to
quantify temperature in different applications. Conversely, resistance temperature
detectors apply the principle of resistance change, with fluctuations in the
temperature of metal components, to perform measurement tasks . Amin and
Newnham (2015) add that examples of typical RTDs include pt100 sensors, and
they incorporate platinum as their primary resistance material. Finally, thermistors
rely on the same principle of operation as RTDs, and the only difference between
them is the fact that thermistors use polymers and ceramic components as
resistance material (Amin and Newnham, 2015).
Comparison of RTD with thermocouples
It is possible to make a comparison of thermocouples and resistance temperature
devices, according to certain performance criteria. This will enable us to identify
which sensor is appropriate for our application.Per Amin and Newnham (2015), the
first performance factor is the temperature range. Thermocouples are the sensors
of choice in applications whereby the prevailing temperatures are very high. Amin
and Newnham (2015) argue that although recent technological Innovations have
attempted to improve the temperature measurement span of resistance
temperature devices, a vast majority of these devices are built to quantify
temperatures below 400 degrees. By contrast, thermocouples are capable of
recording temperatures approaching 2500 degrees centigrade.
The next comparison criterion is the cost of the devices. Arnolds (2013) states that
thermocouples are usually less expensive when compared to RTDs. The price of a
typical RTD is triple the price of a corresponding thermocouple with the same
measurement capabilities. However, it is more expensive to install a thermocouple,
because the installation of an RTD only requires simple copper wiring. Although
installing an RTD is less costly, the savings one would make from the installation of
an RTD are not enough to compensate for its high price .
Sensitivity is also an important factor to consider. Even though both devices
respond to temperature variations at a satisfactory pace, thermocouples respond
faster to temperature changes. In fact, a thermocouple that is grounded will
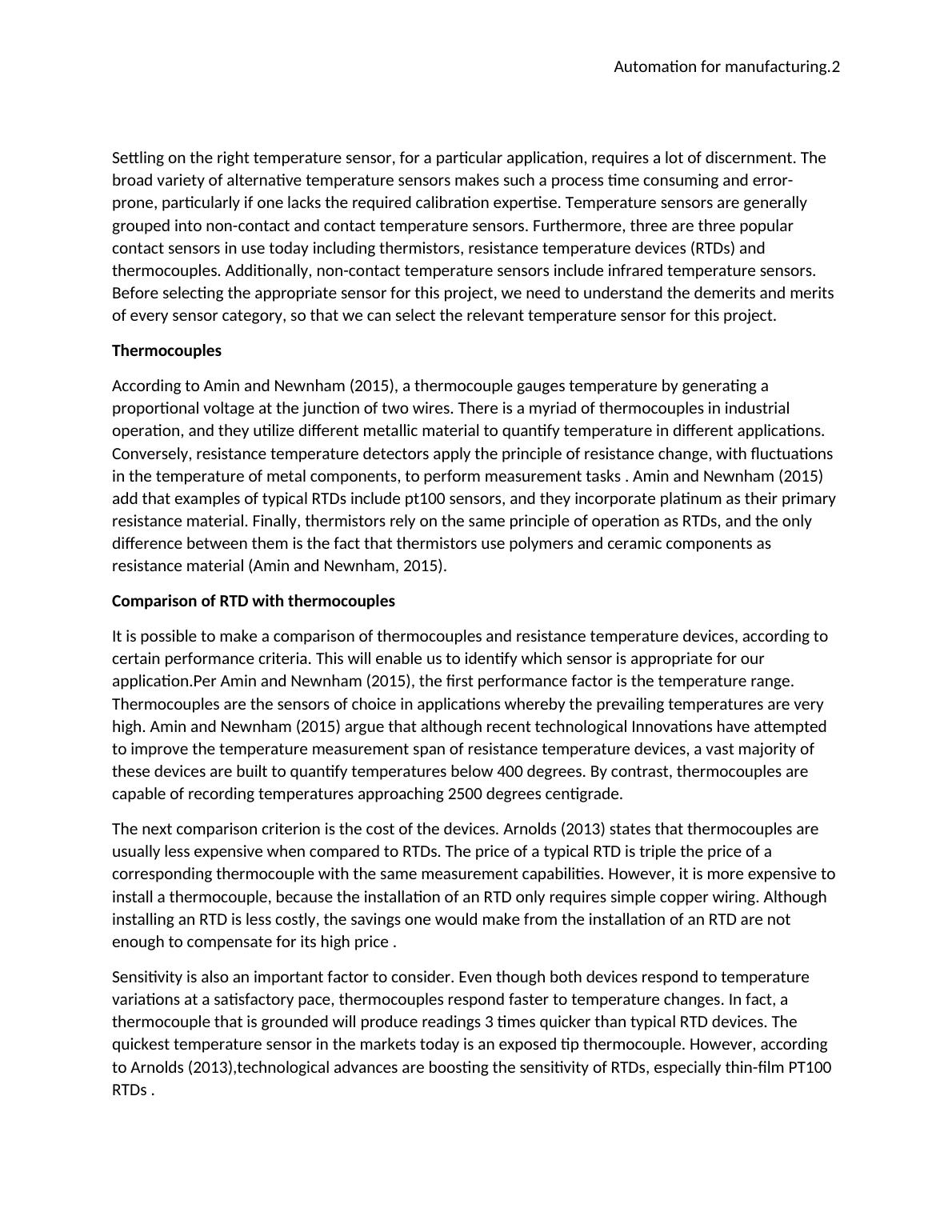
Automation for manufacturing.3
produce readings 3 times quicker than typical RTD devices. The quickest
temperature sensor in the markets today is an exposed tip thermocouple. However,
according to Arnolds (2013),technological advances are boosting the sensitivity of
RTDs, especially thin-film PT100 RTDs .
The sensors can also be compared according to their accuracy. Accordingly, RTDs
are typically more accurate when their performance is compared with
thermocouples in this regard. While RTDs usually have an accuracy of 0.1 degrees,
the accuracy of most thermocouples is estimated to be at least 1 degree. However,
certain rare varieties of thermocouples have accuracies that are equal to those of
RTDs. Arnolds (2013) opines that In terms of linearity, the resistance temperature
relation in RTDs approaches perfectly linearity while thermocouples have an S-
shaped plot . Finally, in terms of stability, Arnolds (2013) asserts that the readings
that are generated from an RTD maintain their repeatability and stability for longer
spans of time. Conversely, the readings generated from thermocouples have a
tendency to drift due to the impact of the chemical reactions that occur within the
sensor. This implies that RTDs have long-term stability due to their linearity and
absence of drift .
A comparison of thermistors with RTDs
The popularity of thermistor sensors has risen in recent years as a result of the
technological advancement of controllers and meters. According to Asakawa et al.,
(2003), this is because current meters possess the flexibility that can allow a
technician to assemble a wider range of thermistors, and to manipulate their probes
with impressive ease . However, contrary to RTDs, which provide known standards,
the curve of a thermistor varies according to the manufacturer. This implies that the
system electronics of a thermistor needs to be in harmony with the curve of the
sensor. Asakawa et al. (2003) adds that the main difference between an RTD and a
thermistor results from the materials used in building this device. While thermistors
are manufactured out of ceramic or polymer materials, RTD sensors are fashioned
from the pure metal. Moreover, there are certain general factors that need to be
highlighted in order to understand the suitability of the sensors for different
applications.
Asakawa et al., (2003) suggest that the first factor to be considered is the
temperature range. Contrary to RTDs, Thermistors can monitor a limited range of
temperatures. Although RTDs capable of detecting temperatures as high as 600
degrees, thermistors are constrained to measure a maximum of 130°.In terms of
cost, thermistors are cheaper than RTDs. This implies that thermistors are suitable
for measuring lower temperatures. Furthermore, thermistors with brother
temperature ranges exist but are costlier than typical RTDs .
Chen, Gregory and Amani, (2010) state that the two sensors are can be compared
according to their sensitivity. Although both sensors produce readings due to the
resistance change, that is occasioned by a rise or drop in temperature, the
thermistor is more sensitive than the RTD. Accordingly, the resistance in a
produce readings 3 times quicker than typical RTD devices. The quickest
temperature sensor in the markets today is an exposed tip thermocouple. However,
according to Arnolds (2013),technological advances are boosting the sensitivity of
RTDs, especially thin-film PT100 RTDs .
The sensors can also be compared according to their accuracy. Accordingly, RTDs
are typically more accurate when their performance is compared with
thermocouples in this regard. While RTDs usually have an accuracy of 0.1 degrees,
the accuracy of most thermocouples is estimated to be at least 1 degree. However,
certain rare varieties of thermocouples have accuracies that are equal to those of
RTDs. Arnolds (2013) opines that In terms of linearity, the resistance temperature
relation in RTDs approaches perfectly linearity while thermocouples have an S-
shaped plot . Finally, in terms of stability, Arnolds (2013) asserts that the readings
that are generated from an RTD maintain their repeatability and stability for longer
spans of time. Conversely, the readings generated from thermocouples have a
tendency to drift due to the impact of the chemical reactions that occur within the
sensor. This implies that RTDs have long-term stability due to their linearity and
absence of drift .
A comparison of thermistors with RTDs
The popularity of thermistor sensors has risen in recent years as a result of the
technological advancement of controllers and meters. According to Asakawa et al.,
(2003), this is because current meters possess the flexibility that can allow a
technician to assemble a wider range of thermistors, and to manipulate their probes
with impressive ease . However, contrary to RTDs, which provide known standards,
the curve of a thermistor varies according to the manufacturer. This implies that the
system electronics of a thermistor needs to be in harmony with the curve of the
sensor. Asakawa et al. (2003) adds that the main difference between an RTD and a
thermistor results from the materials used in building this device. While thermistors
are manufactured out of ceramic or polymer materials, RTD sensors are fashioned
from the pure metal. Moreover, there are certain general factors that need to be
highlighted in order to understand the suitability of the sensors for different
applications.
Asakawa et al., (2003) suggest that the first factor to be considered is the
temperature range. Contrary to RTDs, Thermistors can monitor a limited range of
temperatures. Although RTDs capable of detecting temperatures as high as 600
degrees, thermistors are constrained to measure a maximum of 130°.In terms of
cost, thermistors are cheaper than RTDs. This implies that thermistors are suitable
for measuring lower temperatures. Furthermore, thermistors with brother
temperature ranges exist but are costlier than typical RTDs .
Chen, Gregory and Amani, (2010) state that the two sensors are can be compared
according to their sensitivity. Although both sensors produce readings due to the
resistance change, that is occasioned by a rise or drop in temperature, the
thermistor is more sensitive than the RTD. Accordingly, the resistance in a
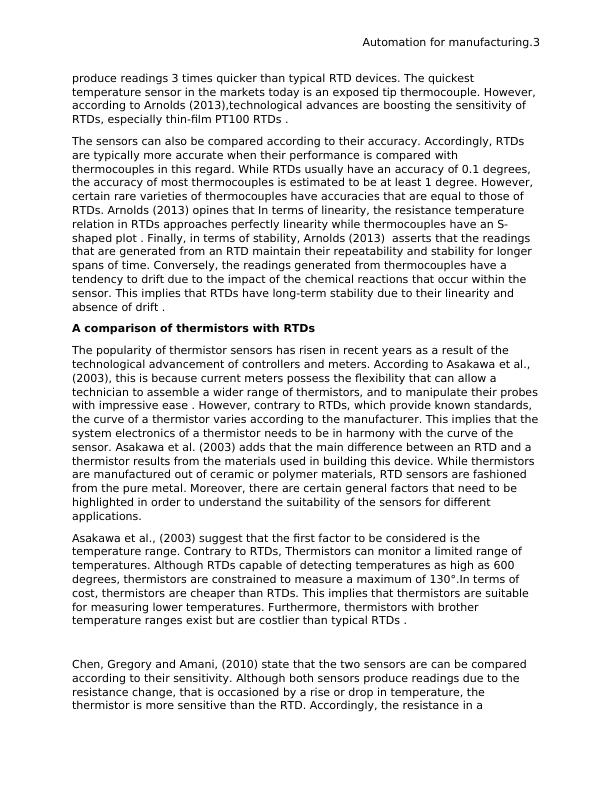
Automation for manufacturing.4
thermistor will vary by 10 ohms for every degree change in temperature, while the
resistance in an RTD will only vary by one ohm for every degree rise in temperature.
Moreover, the response time of thermistors is much higher than that of RTDs. Chen,
Gregory and Amani, (2010) add that this implies that a thermostat detects
temperature changes faster than RTDs. Moreover, the sensing region of thermistors
can be a small as possible to deliver the fastest feedback .
Chen, Gregory and Amani, (2010) emphasize the essence of contrasting the two
sensors in terms of accuracy. Even though the most efficient RTDs possess
accuracies that are equal to those of thermistors, an unwanted consequence of the
principle of operation of an RTD is the addition of resistance to the measurement
system. Consequently, the accuracy of the readings diminishes especially when
longer cables are employed, thus producing erroneous readings. Although larger
thermistors can experience similar unwanted effects of resistance, the addition of a
transmitter will ensure that such errors remain negligible. Therefore, the thermistor
surpasses the RTD in terms of accuracy .
Conclusion
Thermocouples are less costly than RTDs since the production processes that yields
thermocouples are cheaper. Moreover, they are most suitable for measuring
extremely high temperatures. On the other hand, RTDs, produce more trustworthy
readings when compared to the output from thermocouples. The major difference
between an RTD arises from the range of temperatures since the RTD is usable in
situations where the temperatures exceed 130°. However, if the temperature range
is below 130 degrees, the thermistor will be the most suitable temperature sensor
as it has higher accuracy. Conversely, RTDs are more preferable for applications
whereby tolerance is more important than accuracy. This means that RTDs are
selected in cases where pressure compensation is vital, while thermistors Provide
more precise temperature measurements. Since our application involves
temperatures below 130 degrees, then the thermistor would be the best choice.
However, our application involves the measurement of temperatures from canisters
that are in perpetual motion on a conveyor belt system. Therefore, we need a
temperature sensor that can take readings without being in physical contact with
the objects, unlike the aforementioned sensors which are all contact sensors. The
best alternative for our application is an infrared temperature sensor.
Infrared temperature sensor
According to Peterson (2004) ,infra-red temperature sensors can detect
electromagnetic waves that exist in the 700nm to 14,000nm span. Although the
infrared spectrum reaches 1,000,000 nm, infrared temperature sensors are only
thermistor will vary by 10 ohms for every degree change in temperature, while the
resistance in an RTD will only vary by one ohm for every degree rise in temperature.
Moreover, the response time of thermistors is much higher than that of RTDs. Chen,
Gregory and Amani, (2010) add that this implies that a thermostat detects
temperature changes faster than RTDs. Moreover, the sensing region of thermistors
can be a small as possible to deliver the fastest feedback .
Chen, Gregory and Amani, (2010) emphasize the essence of contrasting the two
sensors in terms of accuracy. Even though the most efficient RTDs possess
accuracies that are equal to those of thermistors, an unwanted consequence of the
principle of operation of an RTD is the addition of resistance to the measurement
system. Consequently, the accuracy of the readings diminishes especially when
longer cables are employed, thus producing erroneous readings. Although larger
thermistors can experience similar unwanted effects of resistance, the addition of a
transmitter will ensure that such errors remain negligible. Therefore, the thermistor
surpasses the RTD in terms of accuracy .
Conclusion
Thermocouples are less costly than RTDs since the production processes that yields
thermocouples are cheaper. Moreover, they are most suitable for measuring
extremely high temperatures. On the other hand, RTDs, produce more trustworthy
readings when compared to the output from thermocouples. The major difference
between an RTD arises from the range of temperatures since the RTD is usable in
situations where the temperatures exceed 130°. However, if the temperature range
is below 130 degrees, the thermistor will be the most suitable temperature sensor
as it has higher accuracy. Conversely, RTDs are more preferable for applications
whereby tolerance is more important than accuracy. This means that RTDs are
selected in cases where pressure compensation is vital, while thermistors Provide
more precise temperature measurements. Since our application involves
temperatures below 130 degrees, then the thermistor would be the best choice.
However, our application involves the measurement of temperatures from canisters
that are in perpetual motion on a conveyor belt system. Therefore, we need a
temperature sensor that can take readings without being in physical contact with
the objects, unlike the aforementioned sensors which are all contact sensors. The
best alternative for our application is an infrared temperature sensor.
Infrared temperature sensor
According to Peterson (2004) ,infra-red temperature sensors can detect
electromagnetic waves that exist in the 700nm to 14,000nm span. Although the
infrared spectrum reaches 1,000,000 nm, infrared temperature sensors are only
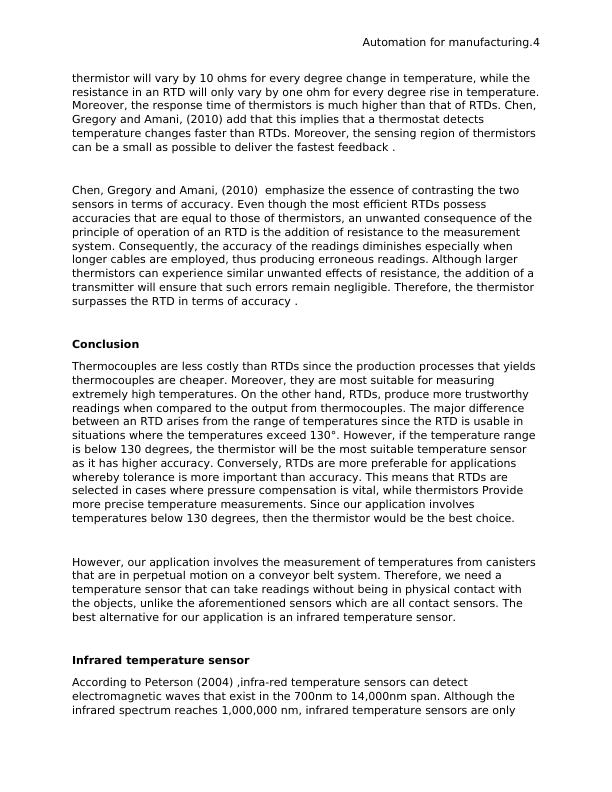
End of preview
Want to access all the pages? Upload your documents or become a member.
Related Documents
Automation for Manufacturing: Non-Contact Temperature Sensors and PIC Microcontroller Programminglg...
|24
|5927
|387
Organizational Structures and Design - Assignmentlg...
|16
|2518
|166
Automation for Manufacturing Research 2022lg...
|18
|5136
|13
4-20 mA Current Loop For a Temperature Sensorlg...
|70
|13620
|6