Automation in Construction: FM-enabled BIM Implementation Case Study
VerifiedAdded on 2022/08/12
|17
|13303
|14
Report
AI Summary
This report presents a case study on the implementation of FM-enabled Building Information Modeling (BIM) for facility management (FM). The research focuses on defining FM-enabled BIM, examining its pilot implementation, and discussing encountered challenges and lessons learned. The study explores the process of developing and delivering FM-enabled BIM models, identifies required information, and investigates strategies for capturing and transmitting FM data, including the BIM-enabled handover process. The research highlights the potential of BIM in transforming the FM phase, which can lead to significant cost savings and improved efficiency. It also addresses the need for a systematic process of capturing and exchanging project information in an open data format, and proposes a roadmap for future research to build the knowledge foundation of BIM for FM. The study further examines the strategies for capturing FM data during design and construction phases and includes a summary of previous case studies. The overall goal is to bridge the gap between theoretical research and real-world projects, providing valuable insights into the successful implementation of FM-enabled BIM.
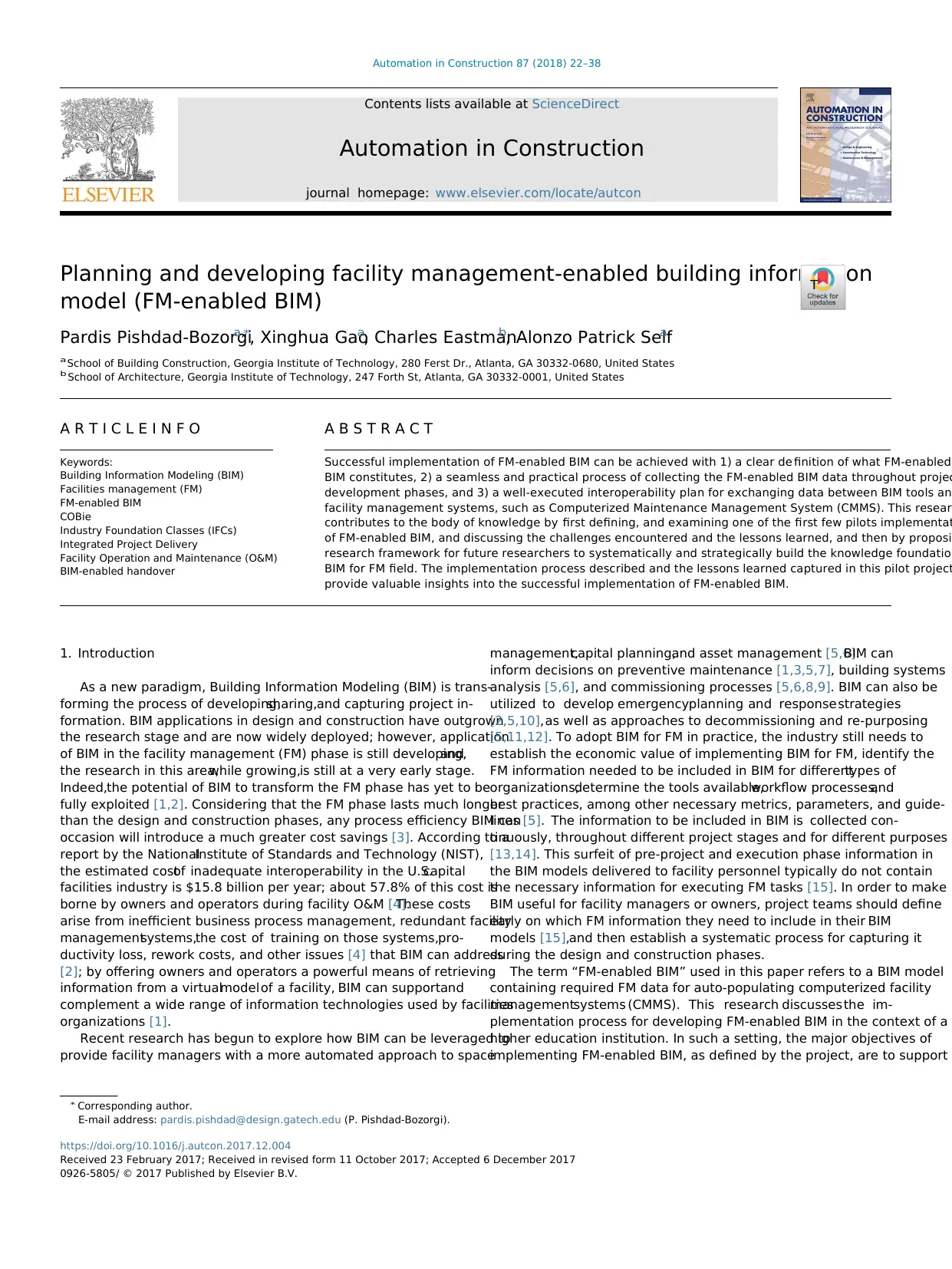
Contents lists available at ScienceDirect
Automation in Construction
journal homepage: www.elsevier.com/locate/autcon
Planning and developing facility management-enabled building information
model (FM-enabled BIM)
Pardis Pishdad-Bozorgia,⁎, Xinghua Gaoa, Charles Eastmanb, Alonzo Patrick Selfa
aSchool of Building Construction, Georgia Institute of Technology, 280 Ferst Dr., Atlanta, GA 30332-0680, United States
b School of Architecture, Georgia Institute of Technology, 247 Forth St, Atlanta, GA 30332-0001, United States
A R T I C L E I N F O
Keywords:
Building Information Modeling (BIM)
Facilities management (FM)
FM-enabled BIM
COBie
Industry Foundation Classes (IFCs)
Integrated Project Delivery
Facility Operation and Maintenance (O&M)
BIM-enabled handover
A B S T R A C T
Successful implementation of FM-enabled BIM can be achieved with 1) a clear de finition of what FM-enabled
BIM constitutes, 2) a seamless and practical process of collecting the FM-enabled BIM data throughout projec
development phases, and 3) a well-executed interoperability plan for exchanging data between BIM tools an
facility management systems, such as Computerized Maintenance Management System (CMMS). This resear
contributes to the body of knowledge by first defining, and examining one of the first few pilots implementat
of FM-enabled BIM, and discussing the challenges encountered and the lessons learned, and then by proposi
research framework for future researchers to systematically and strategically build the knowledge foundation
BIM for FM field. The implementation process described and the lessons learned captured in this pilot project
provide valuable insights into the successful implementation of FM-enabled BIM.
1. Introduction
As a new paradigm, Building Information Modeling (BIM) is trans-
forming the process of developing,sharing,and capturing project in-
formation. BIM applications in design and construction have outgrown
the research stage and are now widely deployed; however, application
of BIM in the facility management (FM) phase is still developing,and
the research in this area,while growing,is still at a very early stage.
Indeed,the potential of BIM to transform the FM phase has yet to be
fully exploited [1,2]. Considering that the FM phase lasts much longer
than the design and construction phases, any process efficiency BIM can
occasion will introduce a much greater cost savings [3]. According to a
report by the NationalInstitute of Standards and Technology (NIST),
the estimated costof inadequate interoperability in the U.S.capital
facilities industry is $15.8 billion per year; about 57.8% of this cost is
borne by owners and operators during facility O&M [4].These costs
arise from inefficient business process management, redundant facility
managementsystems,the cost of training on those systems,pro-
ductivity loss, rework costs, and other issues [4] that BIM can address
[2]; by offering owners and operators a powerful means of retrieving
information from a virtualmodelof a facility, BIM can supportand
complement a wide range of information technologies used by facilities
organizations [1].
Recent research has begun to explore how BIM can be leveraged to
provide facility managers with a more automated approach to space
management,capital planning,and asset management [5,6].BIM can
inform decisions on preventive maintenance [1,3,5,7], building systems
analysis [5,6], and commissioning processes [5,6,8,9]. BIM can also be
utilized to develop emergencyplanning and responsestrategies
[2,5,10],as well as approaches to decommissioning and re-purposing
[5,11,12]. To adopt BIM for FM in practice, the industry still needs to
establish the economic value of implementing BIM for FM, identify the
FM information needed to be included in BIM for differenttypes of
organizations,determine the tools available,workflow processes,and
best practices, among other necessary metrics, parameters, and guide-
lines [5]. The information to be included in BIM is collected con-
tinuously, throughout different project stages and for different purposes
[13,14]. This surfeit of pre-project and execution phase information in
the BIM models delivered to facility personnel typically do not contain
the necessary information for executing FM tasks [15]. In order to make
BIM useful for facility managers or owners, project teams should define
early on which FM information they need to include in their BIM
models [15],and then establish a systematic process for capturing it
during the design and construction phases.
The term “FM-enabled BIM” used in this paper refers to a BIM model
containing required FM data for auto-populating computerized facility
managementsystems (CMMS). This research discussesthe im-
plementation process for developing FM-enabled BIM in the context of a
higher education institution. In such a setting, the major objectives of
implementing FM-enabled BIM, as defined by the project, are to support
https://doi.org/10.1016/j.autcon.2017.12.004
Received 23 February 2017; Received in revised form 11 October 2017; Accepted 6 December 2017
⁎ Corresponding author.
E-mail address: pardis.pishdad@design.gatech.edu (P. Pishdad-Bozorgi).
Automation in Construction 87 (2018) 22–38
0926-5805/ © 2017 Published by Elsevier B.V.
T
Automation in Construction
journal homepage: www.elsevier.com/locate/autcon
Planning and developing facility management-enabled building information
model (FM-enabled BIM)
Pardis Pishdad-Bozorgia,⁎, Xinghua Gaoa, Charles Eastmanb, Alonzo Patrick Selfa
aSchool of Building Construction, Georgia Institute of Technology, 280 Ferst Dr., Atlanta, GA 30332-0680, United States
b School of Architecture, Georgia Institute of Technology, 247 Forth St, Atlanta, GA 30332-0001, United States
A R T I C L E I N F O
Keywords:
Building Information Modeling (BIM)
Facilities management (FM)
FM-enabled BIM
COBie
Industry Foundation Classes (IFCs)
Integrated Project Delivery
Facility Operation and Maintenance (O&M)
BIM-enabled handover
A B S T R A C T
Successful implementation of FM-enabled BIM can be achieved with 1) a clear de finition of what FM-enabled
BIM constitutes, 2) a seamless and practical process of collecting the FM-enabled BIM data throughout projec
development phases, and 3) a well-executed interoperability plan for exchanging data between BIM tools an
facility management systems, such as Computerized Maintenance Management System (CMMS). This resear
contributes to the body of knowledge by first defining, and examining one of the first few pilots implementat
of FM-enabled BIM, and discussing the challenges encountered and the lessons learned, and then by proposi
research framework for future researchers to systematically and strategically build the knowledge foundation
BIM for FM field. The implementation process described and the lessons learned captured in this pilot project
provide valuable insights into the successful implementation of FM-enabled BIM.
1. Introduction
As a new paradigm, Building Information Modeling (BIM) is trans-
forming the process of developing,sharing,and capturing project in-
formation. BIM applications in design and construction have outgrown
the research stage and are now widely deployed; however, application
of BIM in the facility management (FM) phase is still developing,and
the research in this area,while growing,is still at a very early stage.
Indeed,the potential of BIM to transform the FM phase has yet to be
fully exploited [1,2]. Considering that the FM phase lasts much longer
than the design and construction phases, any process efficiency BIM can
occasion will introduce a much greater cost savings [3]. According to a
report by the NationalInstitute of Standards and Technology (NIST),
the estimated costof inadequate interoperability in the U.S.capital
facilities industry is $15.8 billion per year; about 57.8% of this cost is
borne by owners and operators during facility O&M [4].These costs
arise from inefficient business process management, redundant facility
managementsystems,the cost of training on those systems,pro-
ductivity loss, rework costs, and other issues [4] that BIM can address
[2]; by offering owners and operators a powerful means of retrieving
information from a virtualmodelof a facility, BIM can supportand
complement a wide range of information technologies used by facilities
organizations [1].
Recent research has begun to explore how BIM can be leveraged to
provide facility managers with a more automated approach to space
management,capital planning,and asset management [5,6].BIM can
inform decisions on preventive maintenance [1,3,5,7], building systems
analysis [5,6], and commissioning processes [5,6,8,9]. BIM can also be
utilized to develop emergencyplanning and responsestrategies
[2,5,10],as well as approaches to decommissioning and re-purposing
[5,11,12]. To adopt BIM for FM in practice, the industry still needs to
establish the economic value of implementing BIM for FM, identify the
FM information needed to be included in BIM for differenttypes of
organizations,determine the tools available,workflow processes,and
best practices, among other necessary metrics, parameters, and guide-
lines [5]. The information to be included in BIM is collected con-
tinuously, throughout different project stages and for different purposes
[13,14]. This surfeit of pre-project and execution phase information in
the BIM models delivered to facility personnel typically do not contain
the necessary information for executing FM tasks [15]. In order to make
BIM useful for facility managers or owners, project teams should define
early on which FM information they need to include in their BIM
models [15],and then establish a systematic process for capturing it
during the design and construction phases.
The term “FM-enabled BIM” used in this paper refers to a BIM model
containing required FM data for auto-populating computerized facility
managementsystems (CMMS). This research discussesthe im-
plementation process for developing FM-enabled BIM in the context of a
higher education institution. In such a setting, the major objectives of
implementing FM-enabled BIM, as defined by the project, are to support
https://doi.org/10.1016/j.autcon.2017.12.004
Received 23 February 2017; Received in revised form 11 October 2017; Accepted 6 December 2017
⁎ Corresponding author.
E-mail address: pardis.pishdad@design.gatech.edu (P. Pishdad-Bozorgi).
Automation in Construction 87 (2018) 22–38
0926-5805/ © 2017 Published by Elsevier B.V.
T
Paraphrase This Document
Need a fresh take? Get an instant paraphrase of this document with our AI Paraphraser
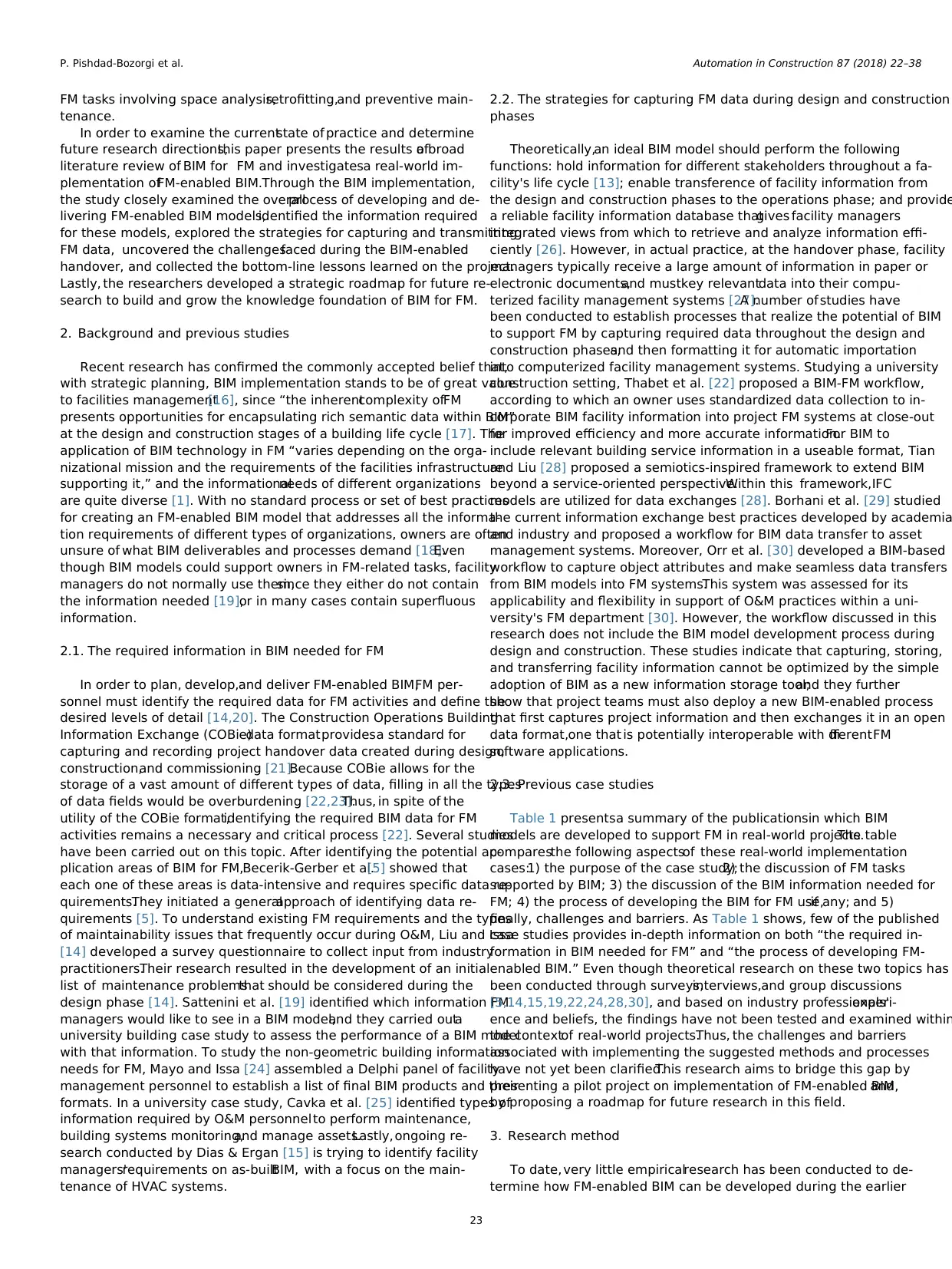
FM tasks involving space analysis,retrofitting,and preventive main-
tenance.
In order to examine the currentstate of practice and determine
future research directions,this paper presents the results ofa broad
literature review of BIM for FM and investigatesa real-world im-
plementation ofFM-enabled BIM.Through the BIM implementation,
the study closely examined the overallprocess of developing and de-
livering FM-enabled BIM models,identified the information required
for these models, explored the strategies for capturing and transmitting
FM data, uncovered the challengesfaced during the BIM-enabled
handover, and collected the bottom-line lessons learned on the project.
Lastly, the researchers developed a strategic roadmap for future re-
search to build and grow the knowledge foundation of BIM for FM.
2. Background and previous studies
Recent research has confirmed the commonly accepted belief that,
with strategic planning, BIM implementation stands to be of great value
to facilities management[16], since “the inherentcomplexity ofFM
presents opportunities for encapsulating rich semantic data within BIM”
at the design and construction stages of a building life cycle [17]. The
application of BIM technology in FM “varies depending on the orga-
nizational mission and the requirements of the facilities infrastructure
supporting it,” and the informationalneeds of different organizations
are quite diverse [1]. With no standard process or set of best practices
for creating an FM-enabled BIM model that addresses all the informa-
tion requirements of different types of organizations, owners are often
unsure of what BIM deliverables and processes demand [18].Even
though BIM models could support owners in FM-related tasks, facility
managers do not normally use them,since they either do not contain
the information needed [19],or in many cases contain superfluous
information.
2.1. The required information in BIM needed for FM
In order to plan, develop,and deliver FM-enabled BIM,FM per-
sonnel must identify the required data for FM activities and define the
desired levels of detail [14,20]. The Construction Operations Building
Information Exchange (COBie)data formatprovidesa standard for
capturing and recording project handover data created during design,
construction,and commissioning [21].Because COBie allows for the
storage of a vast amount of different types of data, filling in all the types
of data fields would be overburdening [22,23].Thus, in spite of the
utility of the COBie format,identifying the required BIM data for FM
activities remains a necessary and critical process [22]. Several studies
have been carried out on this topic. After identifying the potential ap-
plication areas of BIM for FM,Becerik-Gerber et al.[5] showed that
each one of these areas is data-intensive and requires specific data re-
quirements.They initiated a generalapproach of identifying data re-
quirements [5]. To understand existing FM requirements and the types
of maintainability issues that frequently occur during O&M, Liu and Issa
[14] developed a survey questionnaire to collect input from industry
practitioners.Their research resulted in the development of an initial
list of maintenance problemsthat should be considered during the
design phase [14]. Sattenini et al. [19] identified which information FM
managers would like to see in a BIM model,and they carried outa
university building case study to assess the performance of a BIM model
with that information. To study the non-geometric building information
needs for FM, Mayo and Issa [24] assembled a Delphi panel of facility
management personnel to establish a list of final BIM products and their
formats. In a university case study, Cavka et al. [25] identified types of
information required by O&M personnel to perform maintenance,
building systems monitoring,and manage assets.Lastly,ongoing re-
search conducted by Dias & Ergan [15] is trying to identify facility
managers'requirements on as-builtBIM, with a focus on the main-
tenance of HVAC systems.
2.2. The strategies for capturing FM data during design and construction
phases
Theoretically,an ideal BIM model should perform the following
functions: hold information for different stakeholders throughout a fa-
cility's life cycle [13]; enable transference of facility information from
the design and construction phases to the operations phase; and provide
a reliable facility information database thatgives facility managers
integrated views from which to retrieve and analyze information effi-
ciently [26]. However, in actual practice, at the handover phase, facility
managers typically receive a large amount of information in paper or
electronic documents,and mustkey relevantdata into their compu-
terized facility management systems [27].A number of studies have
been conducted to establish processes that realize the potential of BIM
to support FM by capturing required data throughout the design and
construction phases,and then formatting it for automatic importation
into computerized facility management systems. Studying a university
construction setting, Thabet et al. [22] proposed a BIM-FM workflow,
according to which an owner uses standardized data collection to in-
corporate BIM facility information into project FM systems at close-out
for improved efficiency and more accurate information.For BIM to
include relevant building service information in a useable format, Tian
and Liu [28] proposed a semiotics-inspired framework to extend BIM
beyond a service-oriented perspective.Within this framework,IFC
models are utilized for data exchanges [28]. Borhani et al. [29] studied
the current information exchange best practices developed by academia
and industry and proposed a workflow for BIM data transfer to asset
management systems. Moreover, Orr et al. [30] developed a BIM-based
workflow to capture object attributes and make seamless data transfers
from BIM models into FM systems.This system was assessed for its
applicability and flexibility in support of O&M practices within a uni-
versity's FM department [30]. However, the workflow discussed in this
research does not include the BIM model development process during
design and construction. These studies indicate that capturing, storing,
and transferring facility information cannot be optimized by the simple
adoption of BIM as a new information storage tool;and they further
show that project teams must also deploy a new BIM-enabled process
that first captures project information and then exchanges it in an open
data format,one that is potentially interoperable with differentFM
software applications.
2.3. Previous case studies
Table 1 presentsa summary of the publicationsin which BIM
models are developed to support FM in real-world projects.The table
comparesthe following aspectsof these real-world implementation
cases:1) the purpose of the case study;2) the discussion of FM tasks
supported by BIM; 3) the discussion of the BIM information needed for
FM; 4) the process of developing the BIM for FM use,if any; and 5)
finally, challenges and barriers. As Table 1 shows, few of the published
case studies provides in-depth information on both “the required in-
formation in BIM needed for FM” and “the process of developing FM-
enabled BIM.” Even though theoretical research on these two topics has
been conducted through surveys,interviews,and group discussions
[5,14,15,19,22,24,28,30], and based on industry professionals'experi-
ence and beliefs, the findings have not been tested and examined within
the contextof real-world projects.Thus, the challenges and barriers
associated with implementing the suggested methods and processes
have not yet been clarified.This research aims to bridge this gap by
presenting a pilot project on implementation of FM-enabled BIM,and
by proposing a roadmap for future research in this field.
3. Research method
To date, very little empiricalresearch has been conducted to de-
termine how FM-enabled BIM can be developed during the earlier
P. Pishdad-Bozorgi et al. Automation in Construction 87 (2018) 22–38
23
tenance.
In order to examine the currentstate of practice and determine
future research directions,this paper presents the results ofa broad
literature review of BIM for FM and investigatesa real-world im-
plementation ofFM-enabled BIM.Through the BIM implementation,
the study closely examined the overallprocess of developing and de-
livering FM-enabled BIM models,identified the information required
for these models, explored the strategies for capturing and transmitting
FM data, uncovered the challengesfaced during the BIM-enabled
handover, and collected the bottom-line lessons learned on the project.
Lastly, the researchers developed a strategic roadmap for future re-
search to build and grow the knowledge foundation of BIM for FM.
2. Background and previous studies
Recent research has confirmed the commonly accepted belief that,
with strategic planning, BIM implementation stands to be of great value
to facilities management[16], since “the inherentcomplexity ofFM
presents opportunities for encapsulating rich semantic data within BIM”
at the design and construction stages of a building life cycle [17]. The
application of BIM technology in FM “varies depending on the orga-
nizational mission and the requirements of the facilities infrastructure
supporting it,” and the informationalneeds of different organizations
are quite diverse [1]. With no standard process or set of best practices
for creating an FM-enabled BIM model that addresses all the informa-
tion requirements of different types of organizations, owners are often
unsure of what BIM deliverables and processes demand [18].Even
though BIM models could support owners in FM-related tasks, facility
managers do not normally use them,since they either do not contain
the information needed [19],or in many cases contain superfluous
information.
2.1. The required information in BIM needed for FM
In order to plan, develop,and deliver FM-enabled BIM,FM per-
sonnel must identify the required data for FM activities and define the
desired levels of detail [14,20]. The Construction Operations Building
Information Exchange (COBie)data formatprovidesa standard for
capturing and recording project handover data created during design,
construction,and commissioning [21].Because COBie allows for the
storage of a vast amount of different types of data, filling in all the types
of data fields would be overburdening [22,23].Thus, in spite of the
utility of the COBie format,identifying the required BIM data for FM
activities remains a necessary and critical process [22]. Several studies
have been carried out on this topic. After identifying the potential ap-
plication areas of BIM for FM,Becerik-Gerber et al.[5] showed that
each one of these areas is data-intensive and requires specific data re-
quirements.They initiated a generalapproach of identifying data re-
quirements [5]. To understand existing FM requirements and the types
of maintainability issues that frequently occur during O&M, Liu and Issa
[14] developed a survey questionnaire to collect input from industry
practitioners.Their research resulted in the development of an initial
list of maintenance problemsthat should be considered during the
design phase [14]. Sattenini et al. [19] identified which information FM
managers would like to see in a BIM model,and they carried outa
university building case study to assess the performance of a BIM model
with that information. To study the non-geometric building information
needs for FM, Mayo and Issa [24] assembled a Delphi panel of facility
management personnel to establish a list of final BIM products and their
formats. In a university case study, Cavka et al. [25] identified types of
information required by O&M personnel to perform maintenance,
building systems monitoring,and manage assets.Lastly,ongoing re-
search conducted by Dias & Ergan [15] is trying to identify facility
managers'requirements on as-builtBIM, with a focus on the main-
tenance of HVAC systems.
2.2. The strategies for capturing FM data during design and construction
phases
Theoretically,an ideal BIM model should perform the following
functions: hold information for different stakeholders throughout a fa-
cility's life cycle [13]; enable transference of facility information from
the design and construction phases to the operations phase; and provide
a reliable facility information database thatgives facility managers
integrated views from which to retrieve and analyze information effi-
ciently [26]. However, in actual practice, at the handover phase, facility
managers typically receive a large amount of information in paper or
electronic documents,and mustkey relevantdata into their compu-
terized facility management systems [27].A number of studies have
been conducted to establish processes that realize the potential of BIM
to support FM by capturing required data throughout the design and
construction phases,and then formatting it for automatic importation
into computerized facility management systems. Studying a university
construction setting, Thabet et al. [22] proposed a BIM-FM workflow,
according to which an owner uses standardized data collection to in-
corporate BIM facility information into project FM systems at close-out
for improved efficiency and more accurate information.For BIM to
include relevant building service information in a useable format, Tian
and Liu [28] proposed a semiotics-inspired framework to extend BIM
beyond a service-oriented perspective.Within this framework,IFC
models are utilized for data exchanges [28]. Borhani et al. [29] studied
the current information exchange best practices developed by academia
and industry and proposed a workflow for BIM data transfer to asset
management systems. Moreover, Orr et al. [30] developed a BIM-based
workflow to capture object attributes and make seamless data transfers
from BIM models into FM systems.This system was assessed for its
applicability and flexibility in support of O&M practices within a uni-
versity's FM department [30]. However, the workflow discussed in this
research does not include the BIM model development process during
design and construction. These studies indicate that capturing, storing,
and transferring facility information cannot be optimized by the simple
adoption of BIM as a new information storage tool;and they further
show that project teams must also deploy a new BIM-enabled process
that first captures project information and then exchanges it in an open
data format,one that is potentially interoperable with differentFM
software applications.
2.3. Previous case studies
Table 1 presentsa summary of the publicationsin which BIM
models are developed to support FM in real-world projects.The table
comparesthe following aspectsof these real-world implementation
cases:1) the purpose of the case study;2) the discussion of FM tasks
supported by BIM; 3) the discussion of the BIM information needed for
FM; 4) the process of developing the BIM for FM use,if any; and 5)
finally, challenges and barriers. As Table 1 shows, few of the published
case studies provides in-depth information on both “the required in-
formation in BIM needed for FM” and “the process of developing FM-
enabled BIM.” Even though theoretical research on these two topics has
been conducted through surveys,interviews,and group discussions
[5,14,15,19,22,24,28,30], and based on industry professionals'experi-
ence and beliefs, the findings have not been tested and examined within
the contextof real-world projects.Thus, the challenges and barriers
associated with implementing the suggested methods and processes
have not yet been clarified.This research aims to bridge this gap by
presenting a pilot project on implementation of FM-enabled BIM,and
by proposing a roadmap for future research in this field.
3. Research method
To date, very little empiricalresearch has been conducted to de-
termine how FM-enabled BIM can be developed during the earlier
P. Pishdad-Bozorgi et al. Automation in Construction 87 (2018) 22–38
23
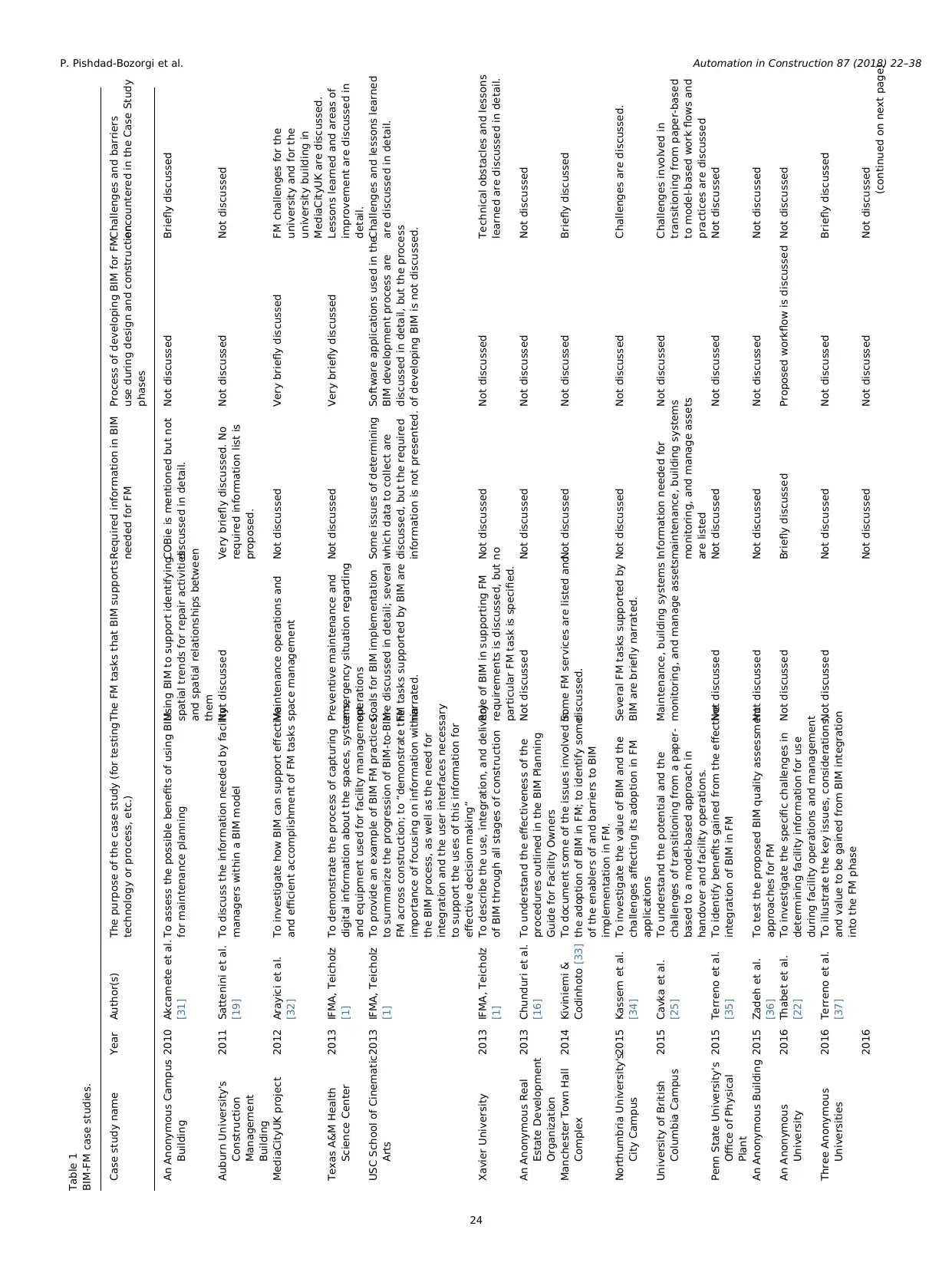
Table 1
BIM-FM case studies.
Case study name Year Author(s) The purpose of the case study (for testing
technology or process, etc.)
The FM tasks that BIM supportsRequired information in BIM
needed for FM
Process of developing BIM for FM
use during design and construction
phases
Challenges and barriers
encountered in the Case Study
An Anonymous Campus
Building
2010 Akcamete et al.
[31]
To assess the possible benefits of using BIM
for maintenance planning
Using BIM to support identifying
spatial trends for repair activities
and spatial relationships between
them
COBie is mentioned but not
discussed in detail.
Not discussed Briefly discussed
Auburn University's
Construction
Management
Building
2011 Sattenini et al.
[19]
To discuss the information needed by facility
managers within a BIM model
Not discussed Very briefly discussed. No
required information list is
proposed.
Not discussed Not discussed
MediaCityUK project 2012 Arayici et al.
[32]
To investigate how BIM can support effective
and efficient accomplishment of FM tasks
Maintenance operations and
space management
Not discussed Very briefly discussed FM challenges for the
university and for the
university building in
MediaCityUK are discussed.
Texas A&M Health
Science Center
2013 IFMA, Teicholz
[1]
To demonstrate the process of capturing
digital information about the spaces, systems,
and equipment used for facility management.
Preventive maintenance and
emergency situation regarding
operations
Not discussed Very briefly discussed Lessons learned and areas of
improvement are discussed in
detail.
USC School of Cinematic
Arts
2013 IFMA, Teicholz
[1]
To provide an example of BIM FM practices;
to summarize the progression of BIM-to-BIM-
FM across construction; to “demonstrate the
importance of focusing on information within
the BIM process, as well as the need for
integration and the user interfaces necessary
to support the uses of this information for
effective decision making”
Goals for BIM implementation
are discussed in detail; several
FM tasks supported by BIM are
narrated.
Some issues of determining
which data to collect are
discussed, but the required
information is not presented.
Software applications used in the
BIM development process are
discussed in detail, but the process
of developing BIM is not discussed.
Challenges and lessons learned
are discussed in detail.
Xavier University 2013 IFMA, Teicholz
[1]
To describe the use, integration, and delivery
of BIM through all stages of construction
Role of BIM in supporting FM
requirements is discussed, but no
particular FM task is specified.
Not discussed Not discussed Technical obstacles and lessons
learned are discussed in detail.
An Anonymous Real
Estate Development
Organization
2013 Chunduri et al.
[16]
To understand the effectiveness of the
procedures outlined in the BIM Planning
Guide for Facility Owners
Not discussed Not discussed Not discussed Not discussed
Manchester Town Hall
Complex
2014 Kiviniemi &
Codinhoto [33]
To document some of the issues involved in
the adoption of BIM in FM; to identify some
of the enablers of and barriers to BIM
implementation in FM.
Some FM services are listed and
discussed.
Not discussed Not discussed Briefly discussed
Northumbria University's
City Campus
2015 Kassem et al.
[34]
To investigate the value of BIM and the
challenges affecting its adoption in FM
applications
Several FM tasks supported by
BIM are briefly narrated.
Not discussed Not discussed Challenges are discussed.
University of British
Columbia Campus
2015 Cavka et al.
[25]
To understand the potential and the
challenges of transitioning from a paper-
based to a model-based approach in
handover and facility operations.
Maintenance, building systems
monitoring, and manage assets
Information needed for
maintenance, building systems
monitoring, and manage assets
are listed
Not discussed Challenges involved in
transitioning from paper-based
to model-based work flows and
practices are discussed
Penn State University's
Office of Physical
Plant
2015 Terreno et al.
[35]
To identify benefits gained from the effective
integration of BIM in FM
Not discussed Not discussed Not discussed Not discussed
An Anonymous Building 2015 Zadeh et al.
[36]
To test the proposed BIM quality assessment
approaches for FM
Not discussed Not discussed Not discussed Not discussed
An Anonymous
University
2016 Thabet et al.
[22]
To investigate the specific challenges in
determining facility information for use
during facility operations and management
Not discussed Briefly discussed Proposed workflow is discussed Not discussed
Three Anonymous
Universities
2016 Terreno et al.
[37]
To illustrate the key issues, considerations,
and value to be gained from BIM integration
into the FM phase
Not discussed Not discussed Not discussed Briefly discussed
2016 Not discussed Not discussed Not discussed
(continued on next page)P. Pishdad-Bozorgi et al. Automation in Construction 87 (2018) 22–38
24
BIM-FM case studies.
Case study name Year Author(s) The purpose of the case study (for testing
technology or process, etc.)
The FM tasks that BIM supportsRequired information in BIM
needed for FM
Process of developing BIM for FM
use during design and construction
phases
Challenges and barriers
encountered in the Case Study
An Anonymous Campus
Building
2010 Akcamete et al.
[31]
To assess the possible benefits of using BIM
for maintenance planning
Using BIM to support identifying
spatial trends for repair activities
and spatial relationships between
them
COBie is mentioned but not
discussed in detail.
Not discussed Briefly discussed
Auburn University's
Construction
Management
Building
2011 Sattenini et al.
[19]
To discuss the information needed by facility
managers within a BIM model
Not discussed Very briefly discussed. No
required information list is
proposed.
Not discussed Not discussed
MediaCityUK project 2012 Arayici et al.
[32]
To investigate how BIM can support effective
and efficient accomplishment of FM tasks
Maintenance operations and
space management
Not discussed Very briefly discussed FM challenges for the
university and for the
university building in
MediaCityUK are discussed.
Texas A&M Health
Science Center
2013 IFMA, Teicholz
[1]
To demonstrate the process of capturing
digital information about the spaces, systems,
and equipment used for facility management.
Preventive maintenance and
emergency situation regarding
operations
Not discussed Very briefly discussed Lessons learned and areas of
improvement are discussed in
detail.
USC School of Cinematic
Arts
2013 IFMA, Teicholz
[1]
To provide an example of BIM FM practices;
to summarize the progression of BIM-to-BIM-
FM across construction; to “demonstrate the
importance of focusing on information within
the BIM process, as well as the need for
integration and the user interfaces necessary
to support the uses of this information for
effective decision making”
Goals for BIM implementation
are discussed in detail; several
FM tasks supported by BIM are
narrated.
Some issues of determining
which data to collect are
discussed, but the required
information is not presented.
Software applications used in the
BIM development process are
discussed in detail, but the process
of developing BIM is not discussed.
Challenges and lessons learned
are discussed in detail.
Xavier University 2013 IFMA, Teicholz
[1]
To describe the use, integration, and delivery
of BIM through all stages of construction
Role of BIM in supporting FM
requirements is discussed, but no
particular FM task is specified.
Not discussed Not discussed Technical obstacles and lessons
learned are discussed in detail.
An Anonymous Real
Estate Development
Organization
2013 Chunduri et al.
[16]
To understand the effectiveness of the
procedures outlined in the BIM Planning
Guide for Facility Owners
Not discussed Not discussed Not discussed Not discussed
Manchester Town Hall
Complex
2014 Kiviniemi &
Codinhoto [33]
To document some of the issues involved in
the adoption of BIM in FM; to identify some
of the enablers of and barriers to BIM
implementation in FM.
Some FM services are listed and
discussed.
Not discussed Not discussed Briefly discussed
Northumbria University's
City Campus
2015 Kassem et al.
[34]
To investigate the value of BIM and the
challenges affecting its adoption in FM
applications
Several FM tasks supported by
BIM are briefly narrated.
Not discussed Not discussed Challenges are discussed.
University of British
Columbia Campus
2015 Cavka et al.
[25]
To understand the potential and the
challenges of transitioning from a paper-
based to a model-based approach in
handover and facility operations.
Maintenance, building systems
monitoring, and manage assets
Information needed for
maintenance, building systems
monitoring, and manage assets
are listed
Not discussed Challenges involved in
transitioning from paper-based
to model-based work flows and
practices are discussed
Penn State University's
Office of Physical
Plant
2015 Terreno et al.
[35]
To identify benefits gained from the effective
integration of BIM in FM
Not discussed Not discussed Not discussed Not discussed
An Anonymous Building 2015 Zadeh et al.
[36]
To test the proposed BIM quality assessment
approaches for FM
Not discussed Not discussed Not discussed Not discussed
An Anonymous
University
2016 Thabet et al.
[22]
To investigate the specific challenges in
determining facility information for use
during facility operations and management
Not discussed Briefly discussed Proposed workflow is discussed Not discussed
Three Anonymous
Universities
2016 Terreno et al.
[37]
To illustrate the key issues, considerations,
and value to be gained from BIM integration
into the FM phase
Not discussed Not discussed Not discussed Briefly discussed
2016 Not discussed Not discussed Not discussed
(continued on next page)P. Pishdad-Bozorgi et al. Automation in Construction 87 (2018) 22–38
24
⊘ This is a preview!⊘
Do you want full access?
Subscribe today to unlock all pages.

Trusted by 1+ million students worldwide
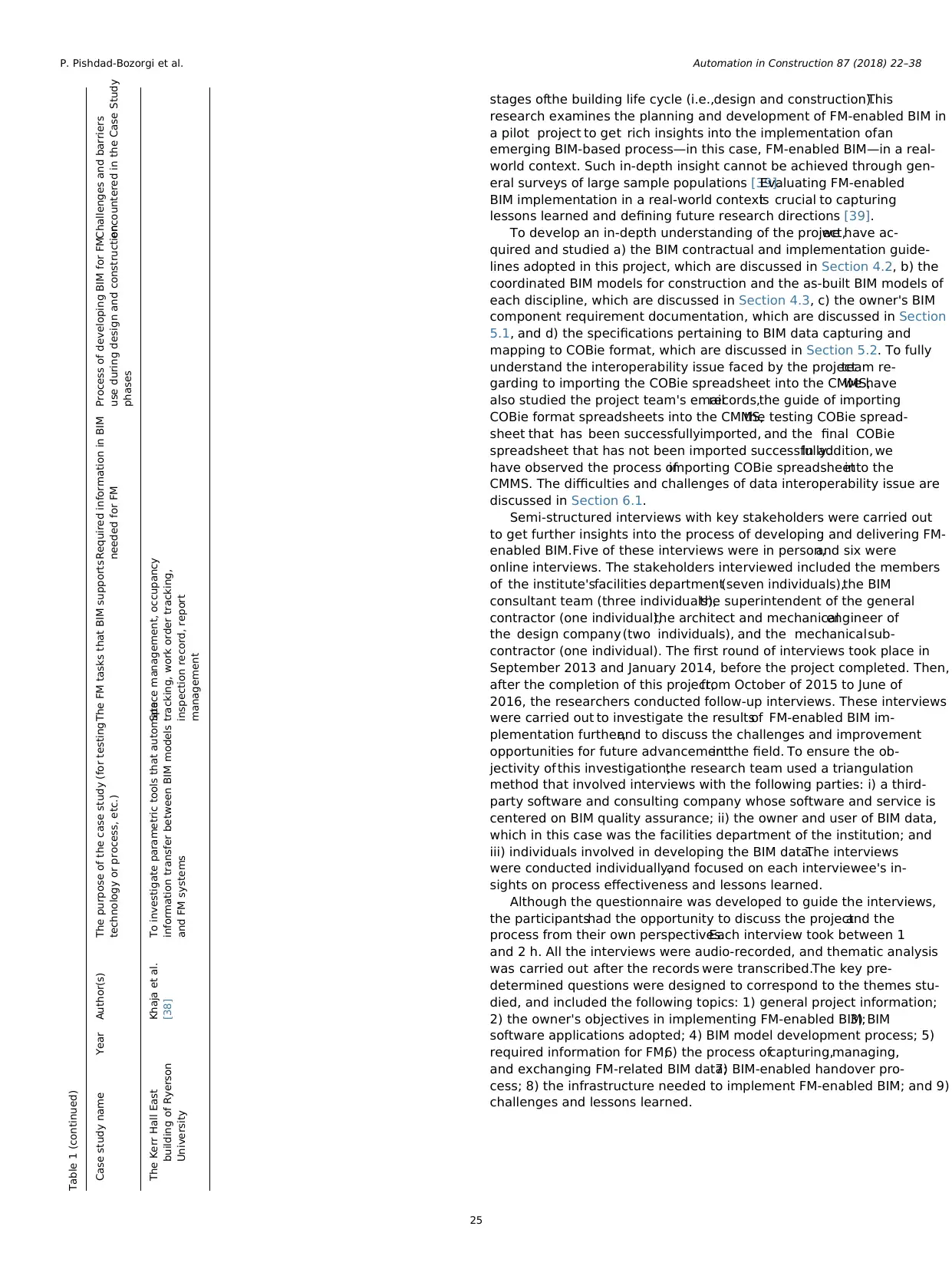
stages ofthe building life cycle (i.e.,design and construction).This
research examines the planning and development of FM-enabled BIM in
a pilot project to get rich insights into the implementation ofan
emerging BIM-based process—in this case, FM-enabled BIM—in a real-
world context. Such in-depth insight cannot be achieved through gen-
eral surveys of large sample populations [39].Evaluating FM-enabled
BIM implementation in a real-world contextis crucial to capturing
lessons learned and defining future research directions [39].
To develop an in-depth understanding of the project,we have ac-
quired and studied a) the BIM contractual and implementation guide-
lines adopted in this project, which are discussed in Section 4.2, b) the
coordinated BIM models for construction and the as-built BIM models of
each discipline, which are discussed in Section 4.3, c) the owner's BIM
component requirement documentation, which are discussed in Section
5.1, and d) the specifications pertaining to BIM data capturing and
mapping to COBie format, which are discussed in Section 5.2. To fully
understand the interoperability issue faced by the projectteam re-
garding to importing the COBie spreadsheet into the CMMS,we have
also studied the project team's emailrecords,the guide of importing
COBie format spreadsheets into the CMMS,the testing COBie spread-
sheet that has been successfullyimported, and the final COBie
spreadsheet that has not been imported successfully.In addition, we
have observed the process ofimporting COBie spreadsheetinto the
CMMS. The difficulties and challenges of data interoperability issue are
discussed in Section 6.1.
Semi-structured interviews with key stakeholders were carried out
to get further insights into the process of developing and delivering FM-
enabled BIM.Five of these interviews were in person,and six were
online interviews. The stakeholders interviewed included the members
of the institute'sfacilities department(seven individuals),the BIM
consultant team (three individuals),the superintendent of the general
contractor (one individual),the architect and mechanicalengineer of
the design company (two individuals), and the mechanicalsub-
contractor (one individual). The first round of interviews took place in
September 2013 and January 2014, before the project completed. Then,
after the completion of this project,from October of 2015 to June of
2016, the researchers conducted follow-up interviews. These interviews
were carried out to investigate the resultsof FM-enabled BIM im-
plementation further,and to discuss the challenges and improvement
opportunities for future advancementin the field. To ensure the ob-
jectivity of this investigation,the research team used a triangulation
method that involved interviews with the following parties: i) a third-
party software and consulting company whose software and service is
centered on BIM quality assurance; ii) the owner and user of BIM data,
which in this case was the facilities department of the institution; and
iii) individuals involved in developing the BIM data.The interviews
were conducted individually,and focused on each interviewee's in-
sights on process effectiveness and lessons learned.
Although the questionnaire was developed to guide the interviews,
the participantshad the opportunity to discuss the projectand the
process from their own perspectives.Each interview took between 1
and 2 h. All the interviews were audio-recorded, and thematic analysis
was carried out after the records were transcribed.The key pre-
determined questions were designed to correspond to the themes stu-
died, and included the following topics: 1) general project information;
2) the owner's objectives in implementing FM-enabled BIM;3) BIM
software applications adopted; 4) BIM model development process; 5)
required information for FM;6) the process ofcapturing,managing,
and exchanging FM-related BIM data;7) BIM-enabled handover pro-
cess; 8) the infrastructure needed to implement FM-enabled BIM; and 9)
challenges and lessons learned.
Table 1 (continued)
Case study name Year Author(s) The purpose of the case study (for testing
technology or process, etc.)
The FM tasks that BIM supportsRequired information in BIM
needed for FM
Process of developing BIM for FM
use during design and construction
phases
Challenges and barriers
encountered in the Case Study
The Kerr Hall East
building of Ryerson
University
Khaja et al.
[38]
To investigate parametric tools that automate
information transfer between BIM models
and FM systems
Space management, occupancy
tracking, work order tracking,
inspection record, report
management
P. Pishdad-Bozorgi et al. Automation in Construction 87 (2018) 22–38
25
research examines the planning and development of FM-enabled BIM in
a pilot project to get rich insights into the implementation ofan
emerging BIM-based process—in this case, FM-enabled BIM—in a real-
world context. Such in-depth insight cannot be achieved through gen-
eral surveys of large sample populations [39].Evaluating FM-enabled
BIM implementation in a real-world contextis crucial to capturing
lessons learned and defining future research directions [39].
To develop an in-depth understanding of the project,we have ac-
quired and studied a) the BIM contractual and implementation guide-
lines adopted in this project, which are discussed in Section 4.2, b) the
coordinated BIM models for construction and the as-built BIM models of
each discipline, which are discussed in Section 4.3, c) the owner's BIM
component requirement documentation, which are discussed in Section
5.1, and d) the specifications pertaining to BIM data capturing and
mapping to COBie format, which are discussed in Section 5.2. To fully
understand the interoperability issue faced by the projectteam re-
garding to importing the COBie spreadsheet into the CMMS,we have
also studied the project team's emailrecords,the guide of importing
COBie format spreadsheets into the CMMS,the testing COBie spread-
sheet that has been successfullyimported, and the final COBie
spreadsheet that has not been imported successfully.In addition, we
have observed the process ofimporting COBie spreadsheetinto the
CMMS. The difficulties and challenges of data interoperability issue are
discussed in Section 6.1.
Semi-structured interviews with key stakeholders were carried out
to get further insights into the process of developing and delivering FM-
enabled BIM.Five of these interviews were in person,and six were
online interviews. The stakeholders interviewed included the members
of the institute'sfacilities department(seven individuals),the BIM
consultant team (three individuals),the superintendent of the general
contractor (one individual),the architect and mechanicalengineer of
the design company (two individuals), and the mechanicalsub-
contractor (one individual). The first round of interviews took place in
September 2013 and January 2014, before the project completed. Then,
after the completion of this project,from October of 2015 to June of
2016, the researchers conducted follow-up interviews. These interviews
were carried out to investigate the resultsof FM-enabled BIM im-
plementation further,and to discuss the challenges and improvement
opportunities for future advancementin the field. To ensure the ob-
jectivity of this investigation,the research team used a triangulation
method that involved interviews with the following parties: i) a third-
party software and consulting company whose software and service is
centered on BIM quality assurance; ii) the owner and user of BIM data,
which in this case was the facilities department of the institution; and
iii) individuals involved in developing the BIM data.The interviews
were conducted individually,and focused on each interviewee's in-
sights on process effectiveness and lessons learned.
Although the questionnaire was developed to guide the interviews,
the participantshad the opportunity to discuss the projectand the
process from their own perspectives.Each interview took between 1
and 2 h. All the interviews were audio-recorded, and thematic analysis
was carried out after the records were transcribed.The key pre-
determined questions were designed to correspond to the themes stu-
died, and included the following topics: 1) general project information;
2) the owner's objectives in implementing FM-enabled BIM;3) BIM
software applications adopted; 4) BIM model development process; 5)
required information for FM;6) the process ofcapturing,managing,
and exchanging FM-related BIM data;7) BIM-enabled handover pro-
cess; 8) the infrastructure needed to implement FM-enabled BIM; and 9)
challenges and lessons learned.
Table 1 (continued)
Case study name Year Author(s) The purpose of the case study (for testing
technology or process, etc.)
The FM tasks that BIM supportsRequired information in BIM
needed for FM
Process of developing BIM for FM
use during design and construction
phases
Challenges and barriers
encountered in the Case Study
The Kerr Hall East
building of Ryerson
University
Khaja et al.
[38]
To investigate parametric tools that automate
information transfer between BIM models
and FM systems
Space management, occupancy
tracking, work order tracking,
inspection record, report
management
P. Pishdad-Bozorgi et al. Automation in Construction 87 (2018) 22–38
25
Paraphrase This Document
Need a fresh take? Get an instant paraphrase of this document with our AI Paraphraser
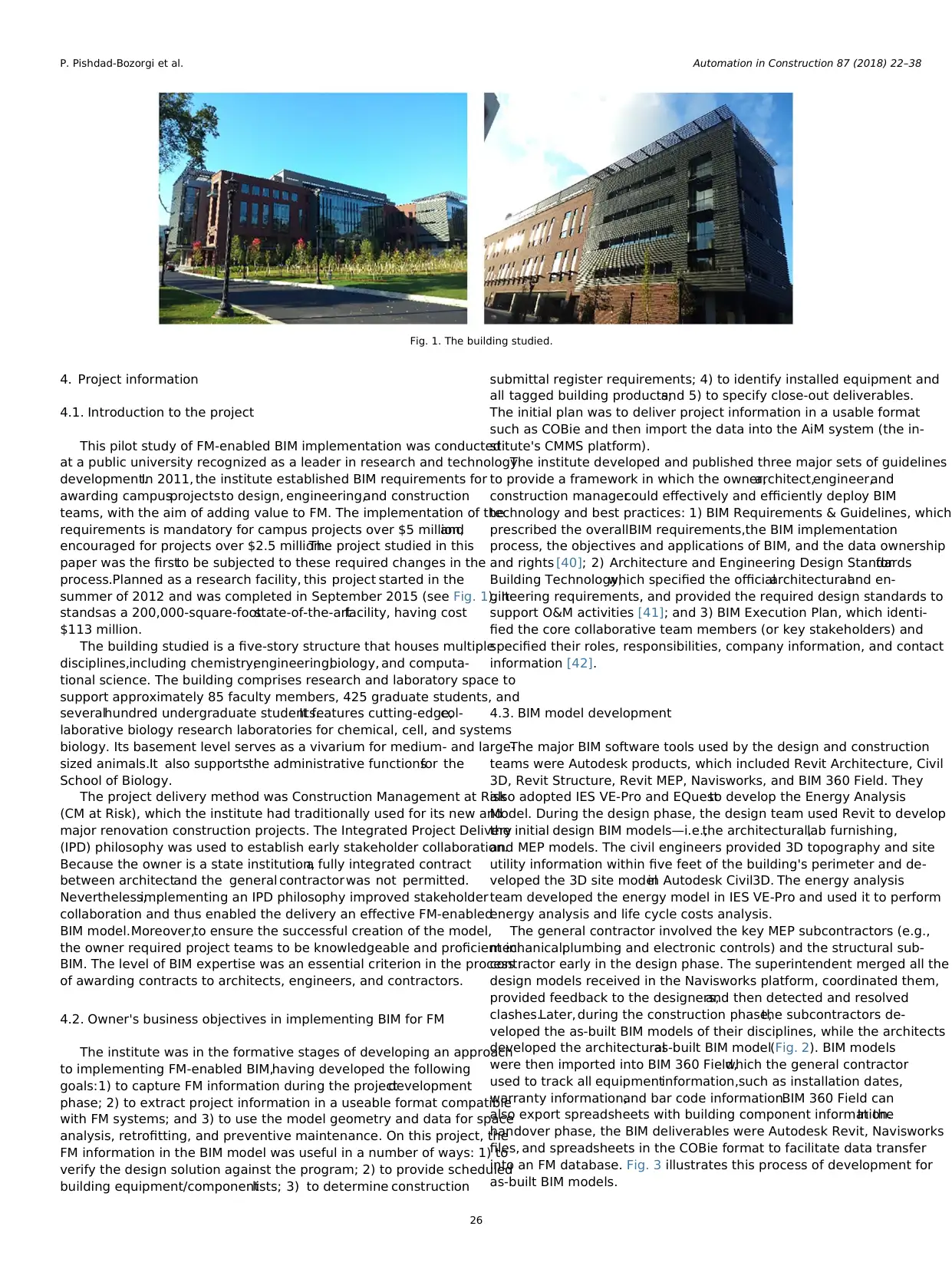
4. Project information
4.1. Introduction to the project
This pilot study of FM-enabled BIM implementation was conducted
at a public university recognized as a leader in research and technology
development.In 2011, the institute established BIM requirements for
awarding campusprojectsto design, engineering,and construction
teams, with the aim of adding value to FM. The implementation of the
requirements is mandatory for campus projects over $5 million,and
encouraged for projects over $2.5 million.The project studied in this
paper was the firstto be subjected to these required changes in the
process.Planned as a research facility, this project started in the
summer of 2012 and was completed in September 2015 (see Fig. 1). It
standsas a 200,000-square-footstate-of-the-artfacility, having cost
$113 million.
The building studied is a five-story structure that houses multiple
disciplines,including chemistry,engineering,biology, and computa-
tional science. The building comprises research and laboratory space to
support approximately 85 faculty members, 425 graduate students, and
severalhundred undergraduate students.It features cutting-edge,col-
laborative biology research laboratories for chemical, cell, and systems
biology. Its basement level serves as a vivarium for medium- and large-
sized animals.It also supportsthe administrative functionsfor the
School of Biology.
The project delivery method was Construction Management at Risk
(CM at Risk), which the institute had traditionally used for its new and
major renovation construction projects. The Integrated Project Delivery
(IPD) philosophy was used to establish early stakeholder collaboration.
Because the owner is a state institution,a fully integrated contract
between architectand the general contractorwas not permitted.
Nevertheless,implementing an IPD philosophy improved stakeholder
collaboration and thus enabled the delivery an effective FM-enabled
BIM model.Moreover,to ensure the successful creation of the model,
the owner required project teams to be knowledgeable and proficient in
BIM. The level of BIM expertise was an essential criterion in the process
of awarding contracts to architects, engineers, and contractors.
4.2. Owner's business objectives in implementing BIM for FM
The institute was in the formative stages of developing an approach
to implementing FM-enabled BIM,having developed the following
goals:1) to capture FM information during the projectdevelopment
phase; 2) to extract project information in a useable format compatible
with FM systems; and 3) to use the model geometry and data for space
analysis, retrofitting, and preventive maintenance. On this project, the
FM information in the BIM model was useful in a number of ways: 1) to
verify the design solution against the program; 2) to provide scheduled
building equipment/componentlists; 3) to determine construction
submittal register requirements; 4) to identify installed equipment and
all tagged building products;and 5) to specify close-out deliverables.
The initial plan was to deliver project information in a usable format
such as COBie and then import the data into the AiM system (the in-
stitute's CMMS platform).
The institute developed and published three major sets of guidelines
to provide a framework in which the owner,architect,engineer,and
construction managercould effectively and efficiently deploy BIM
technology and best practices: 1) BIM Requirements & Guidelines, which
prescribed the overallBIM requirements,the BIM implementation
process, the objectives and applications of BIM, and the data ownership
and rights [40]; 2) Architecture and Engineering Design Standardsfor
Building Technology,which specified the officialarchitecturaland en-
gineering requirements, and provided the required design standards to
support O&M activities [41]; and 3) BIM Execution Plan, which identi-
fied the core collaborative team members (or key stakeholders) and
specified their roles, responsibilities, company information, and contact
information [42].
4.3. BIM model development
The major BIM software tools used by the design and construction
teams were Autodesk products, which included Revit Architecture, Civil
3D, Revit Structure, Revit MEP, Navisworks, and BIM 360 Field. They
also adopted IES VE-Pro and EQuestto develop the Energy Analysis
Model. During the design phase, the design team used Revit to develop
the initial design BIM models—i.e.,the architectural,lab furnishing,
and MEP models. The civil engineers provided 3D topography and site
utility information within five feet of the building's perimeter and de-
veloped the 3D site modelin Autodesk Civil3D. The energy analysis
team developed the energy model in IES VE-Pro and used it to perform
energy analysis and life cycle costs analysis.
The general contractor involved the key MEP subcontractors (e.g.,
mechanical,plumbing and electronic controls) and the structural sub-
contractor early in the design phase. The superintendent merged all the
design models received in the Navisworks platform, coordinated them,
provided feedback to the designers,and then detected and resolved
clashes.Later, during the construction phase,the subcontractors de-
veloped the as-built BIM models of their disciplines, while the architects
developed the architecturalas-built BIM model(Fig. 2). BIM models
were then imported into BIM 360 Field,which the general contractor
used to track all equipmentinformation,such as installation dates,
warranty information,and bar code information.BIM 360 Field can
also export spreadsheets with building component information.In the
handover phase, the BIM deliverables were Autodesk Revit, Navisworks
files, and spreadsheets in the COBie format to facilitate data transfer
into an FM database. Fig. 3 illustrates this process of development for
as-built BIM models.
Fig. 1. The building studied.
P. Pishdad-Bozorgi et al. Automation in Construction 87 (2018) 22–38
26
4.1. Introduction to the project
This pilot study of FM-enabled BIM implementation was conducted
at a public university recognized as a leader in research and technology
development.In 2011, the institute established BIM requirements for
awarding campusprojectsto design, engineering,and construction
teams, with the aim of adding value to FM. The implementation of the
requirements is mandatory for campus projects over $5 million,and
encouraged for projects over $2.5 million.The project studied in this
paper was the firstto be subjected to these required changes in the
process.Planned as a research facility, this project started in the
summer of 2012 and was completed in September 2015 (see Fig. 1). It
standsas a 200,000-square-footstate-of-the-artfacility, having cost
$113 million.
The building studied is a five-story structure that houses multiple
disciplines,including chemistry,engineering,biology, and computa-
tional science. The building comprises research and laboratory space to
support approximately 85 faculty members, 425 graduate students, and
severalhundred undergraduate students.It features cutting-edge,col-
laborative biology research laboratories for chemical, cell, and systems
biology. Its basement level serves as a vivarium for medium- and large-
sized animals.It also supportsthe administrative functionsfor the
School of Biology.
The project delivery method was Construction Management at Risk
(CM at Risk), which the institute had traditionally used for its new and
major renovation construction projects. The Integrated Project Delivery
(IPD) philosophy was used to establish early stakeholder collaboration.
Because the owner is a state institution,a fully integrated contract
between architectand the general contractorwas not permitted.
Nevertheless,implementing an IPD philosophy improved stakeholder
collaboration and thus enabled the delivery an effective FM-enabled
BIM model.Moreover,to ensure the successful creation of the model,
the owner required project teams to be knowledgeable and proficient in
BIM. The level of BIM expertise was an essential criterion in the process
of awarding contracts to architects, engineers, and contractors.
4.2. Owner's business objectives in implementing BIM for FM
The institute was in the formative stages of developing an approach
to implementing FM-enabled BIM,having developed the following
goals:1) to capture FM information during the projectdevelopment
phase; 2) to extract project information in a useable format compatible
with FM systems; and 3) to use the model geometry and data for space
analysis, retrofitting, and preventive maintenance. On this project, the
FM information in the BIM model was useful in a number of ways: 1) to
verify the design solution against the program; 2) to provide scheduled
building equipment/componentlists; 3) to determine construction
submittal register requirements; 4) to identify installed equipment and
all tagged building products;and 5) to specify close-out deliverables.
The initial plan was to deliver project information in a usable format
such as COBie and then import the data into the AiM system (the in-
stitute's CMMS platform).
The institute developed and published three major sets of guidelines
to provide a framework in which the owner,architect,engineer,and
construction managercould effectively and efficiently deploy BIM
technology and best practices: 1) BIM Requirements & Guidelines, which
prescribed the overallBIM requirements,the BIM implementation
process, the objectives and applications of BIM, and the data ownership
and rights [40]; 2) Architecture and Engineering Design Standardsfor
Building Technology,which specified the officialarchitecturaland en-
gineering requirements, and provided the required design standards to
support O&M activities [41]; and 3) BIM Execution Plan, which identi-
fied the core collaborative team members (or key stakeholders) and
specified their roles, responsibilities, company information, and contact
information [42].
4.3. BIM model development
The major BIM software tools used by the design and construction
teams were Autodesk products, which included Revit Architecture, Civil
3D, Revit Structure, Revit MEP, Navisworks, and BIM 360 Field. They
also adopted IES VE-Pro and EQuestto develop the Energy Analysis
Model. During the design phase, the design team used Revit to develop
the initial design BIM models—i.e.,the architectural,lab furnishing,
and MEP models. The civil engineers provided 3D topography and site
utility information within five feet of the building's perimeter and de-
veloped the 3D site modelin Autodesk Civil3D. The energy analysis
team developed the energy model in IES VE-Pro and used it to perform
energy analysis and life cycle costs analysis.
The general contractor involved the key MEP subcontractors (e.g.,
mechanical,plumbing and electronic controls) and the structural sub-
contractor early in the design phase. The superintendent merged all the
design models received in the Navisworks platform, coordinated them,
provided feedback to the designers,and then detected and resolved
clashes.Later, during the construction phase,the subcontractors de-
veloped the as-built BIM models of their disciplines, while the architects
developed the architecturalas-built BIM model(Fig. 2). BIM models
were then imported into BIM 360 Field,which the general contractor
used to track all equipmentinformation,such as installation dates,
warranty information,and bar code information.BIM 360 Field can
also export spreadsheets with building component information.In the
handover phase, the BIM deliverables were Autodesk Revit, Navisworks
files, and spreadsheets in the COBie format to facilitate data transfer
into an FM database. Fig. 3 illustrates this process of development for
as-built BIM models.
Fig. 1. The building studied.
P. Pishdad-Bozorgi et al. Automation in Construction 87 (2018) 22–38
26
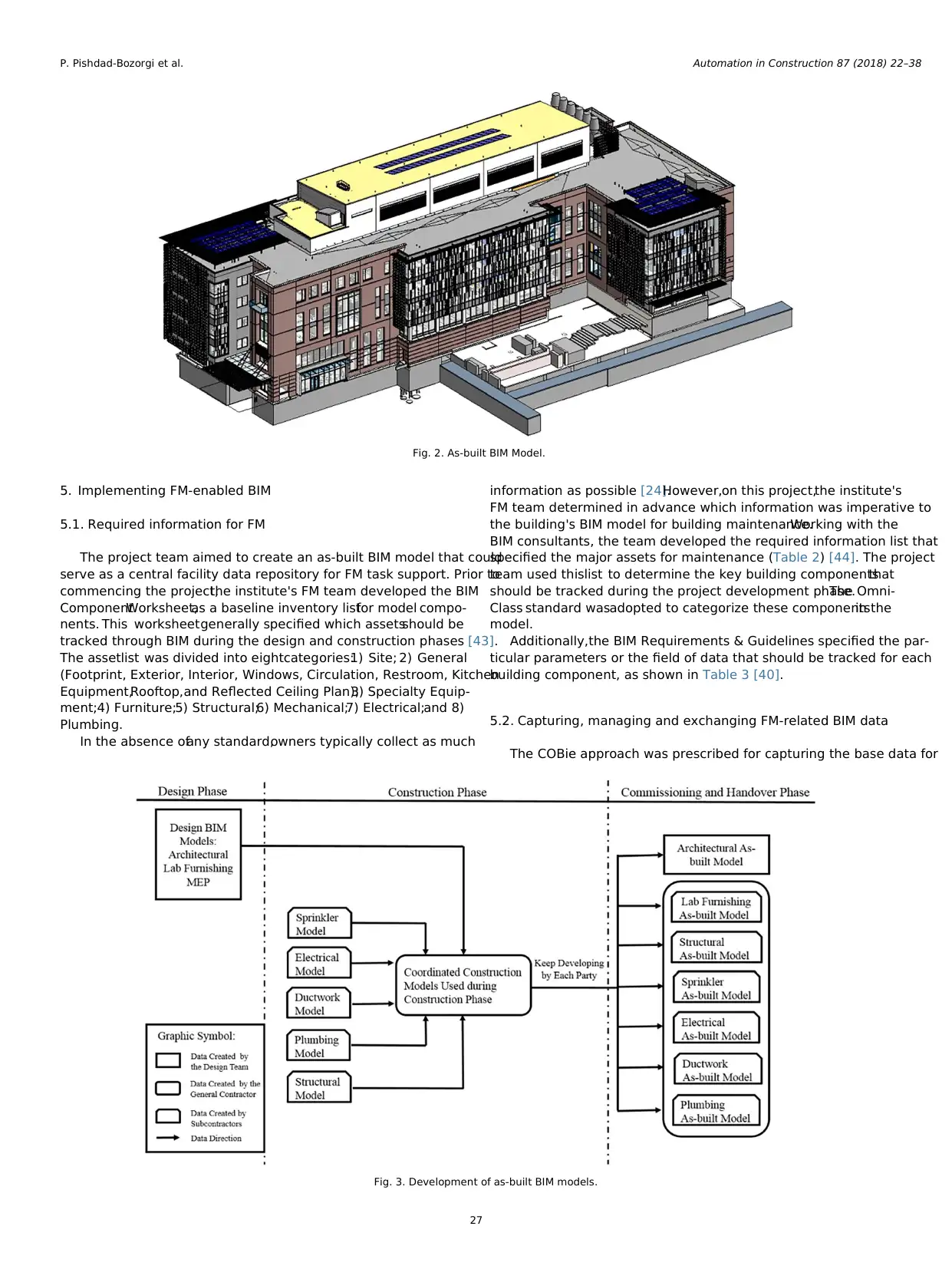
5. Implementing FM-enabled BIM
5.1. Required information for FM
The project team aimed to create an as-built BIM model that could
serve as a central facility data repository for FM task support. Prior to
commencing the project,the institute's FM team developed the BIM
ComponentWorksheet,as a baseline inventory listfor model compo-
nents. This worksheetgenerally specified which assetsshould be
tracked through BIM during the design and construction phases [43].
The assetlist was divided into eightcategories:1) Site; 2) General
(Footprint, Exterior, Interior, Windows, Circulation, Restroom, Kitchen
Equipment,Rooftop,and Reflected Ceiling Plan);3) Specialty Equip-
ment;4) Furniture;5) Structural;6) Mechanical;7) Electrical;and 8)
Plumbing.
In the absence ofany standard,owners typically collect as much
information as possible [24].However,on this project,the institute's
FM team determined in advance which information was imperative to
the building's BIM model for building maintenance.Working with the
BIM consultants, the team developed the required information list that
specified the major assets for maintenance (Table 2) [44]. The project
team used thislist to determine the key building componentsthat
should be tracked during the project development phase.The Omni-
Class standard wasadopted to categorize these componentsin the
model.
Additionally,the BIM Requirements & Guidelines specified the par-
ticular parameters or the field of data that should be tracked for each
building component, as shown in Table 3 [40].
5.2. Capturing, managing and exchanging FM-related BIM data
The COBie approach was prescribed for capturing the base data for
Fig. 2. As-built BIM Model.
Fig. 3. Development of as-built BIM models.
P. Pishdad-Bozorgi et al. Automation in Construction 87 (2018) 22–38
27
5.1. Required information for FM
The project team aimed to create an as-built BIM model that could
serve as a central facility data repository for FM task support. Prior to
commencing the project,the institute's FM team developed the BIM
ComponentWorksheet,as a baseline inventory listfor model compo-
nents. This worksheetgenerally specified which assetsshould be
tracked through BIM during the design and construction phases [43].
The assetlist was divided into eightcategories:1) Site; 2) General
(Footprint, Exterior, Interior, Windows, Circulation, Restroom, Kitchen
Equipment,Rooftop,and Reflected Ceiling Plan);3) Specialty Equip-
ment;4) Furniture;5) Structural;6) Mechanical;7) Electrical;and 8)
Plumbing.
In the absence ofany standard,owners typically collect as much
information as possible [24].However,on this project,the institute's
FM team determined in advance which information was imperative to
the building's BIM model for building maintenance.Working with the
BIM consultants, the team developed the required information list that
specified the major assets for maintenance (Table 2) [44]. The project
team used thislist to determine the key building componentsthat
should be tracked during the project development phase.The Omni-
Class standard wasadopted to categorize these componentsin the
model.
Additionally,the BIM Requirements & Guidelines specified the par-
ticular parameters or the field of data that should be tracked for each
building component, as shown in Table 3 [40].
5.2. Capturing, managing and exchanging FM-related BIM data
The COBie approach was prescribed for capturing the base data for
Fig. 2. As-built BIM Model.
Fig. 3. Development of as-built BIM models.
P. Pishdad-Bozorgi et al. Automation in Construction 87 (2018) 22–38
27
⊘ This is a preview!⊘
Do you want full access?
Subscribe today to unlock all pages.

Trusted by 1+ million students worldwide
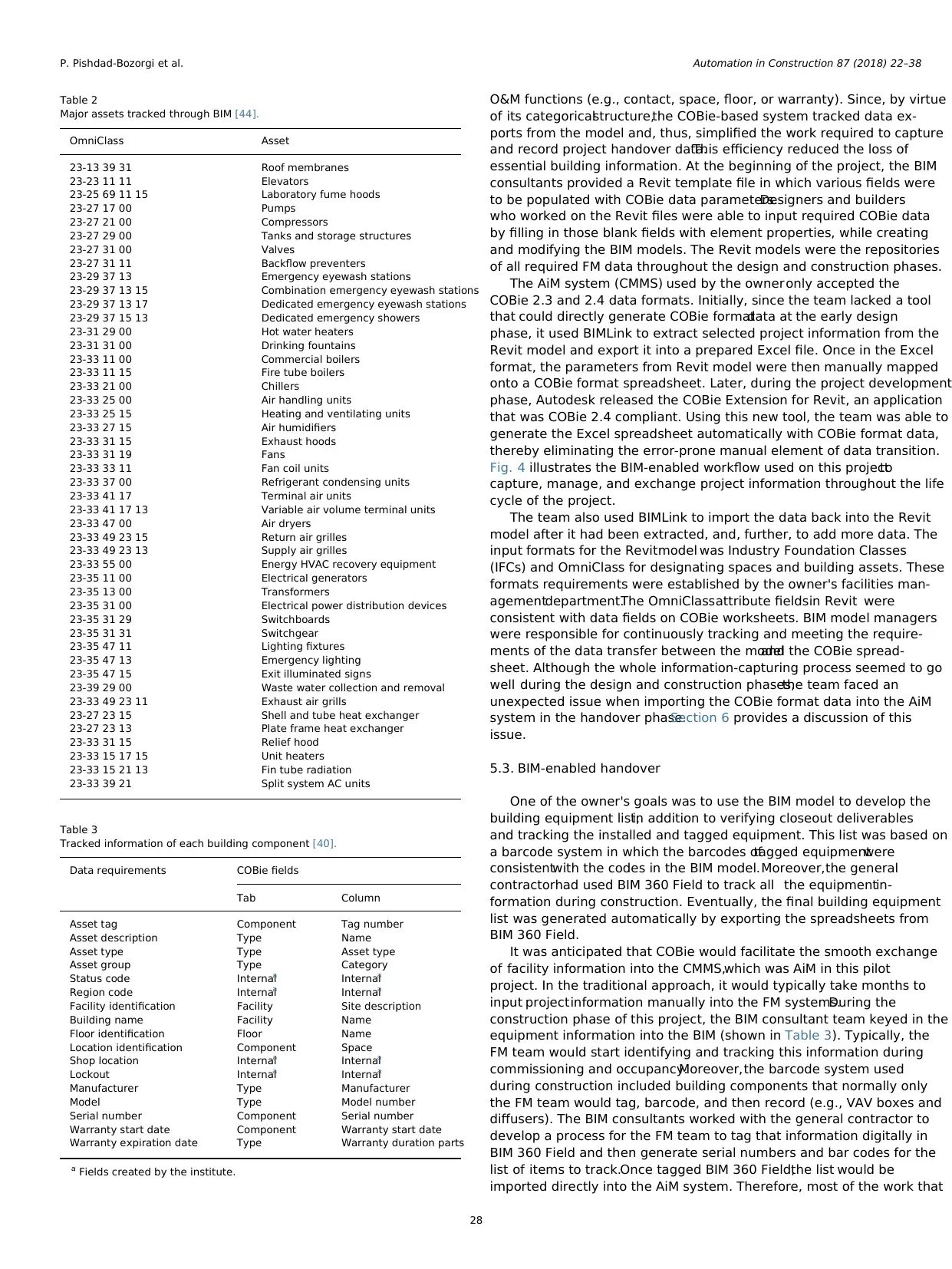
O&M functions (e.g., contact, space, floor, or warranty). Since, by virtue
of its categoricalstructure,the COBie-based system tracked data ex-
ports from the model and, thus, simplified the work required to capture
and record project handover data.This efficiency reduced the loss of
essential building information. At the beginning of the project, the BIM
consultants provided a Revit template file in which various fields were
to be populated with COBie data parameters.Designers and builders
who worked on the Revit files were able to input required COBie data
by filling in those blank fields with element properties, while creating
and modifying the BIM models. The Revit models were the repositories
of all required FM data throughout the design and construction phases.
The AiM system (CMMS) used by the owner only accepted the
COBie 2.3 and 2.4 data formats. Initially, since the team lacked a tool
that could directly generate COBie formatdata at the early design
phase, it used BIMLink to extract selected project information from the
Revit model and export it into a prepared Excel file. Once in the Excel
format, the parameters from Revit model were then manually mapped
onto a COBie format spreadsheet. Later, during the project development
phase, Autodesk released the COBie Extension for Revit, an application
that was COBie 2.4 compliant. Using this new tool, the team was able to
generate the Excel spreadsheet automatically with COBie format data,
thereby eliminating the error-prone manual element of data transition.
Fig. 4 illustrates the BIM-enabled workflow used on this projectto
capture, manage, and exchange project information throughout the life
cycle of the project.
The team also used BIMLink to import the data back into the Revit
model after it had been extracted, and, further, to add more data. The
input formats for the Revitmodel was Industry Foundation Classes
(IFCs) and OmniClass for designating spaces and building assets. These
formats requirements were established by the owner's facilities man-
agementdepartment.The OmniClassattribute fieldsin Revit were
consistent with data fields on COBie worksheets. BIM model managers
were responsible for continuously tracking and meeting the require-
ments of the data transfer between the modeland the COBie spread-
sheet. Although the whole information-capturing process seemed to go
well during the design and construction phases,the team faced an
unexpected issue when importing the COBie format data into the AiM
system in the handover phase.Section 6 provides a discussion of this
issue.
5.3. BIM-enabled handover
One of the owner's goals was to use the BIM model to develop the
building equipment list,in addition to verifying closeout deliverables
and tracking the installed and tagged equipment. This list was based on
a barcode system in which the barcodes oftagged equipmentwere
consistentwith the codes in the BIM model.Moreover,the general
contractorhad used BIM 360 Field to track all the equipmentin-
formation during construction. Eventually, the final building equipment
list was generated automatically by exporting the spreadsheets from
BIM 360 Field.
It was anticipated that COBie would facilitate the smooth exchange
of facility information into the CMMS,which was AiM in this pilot
project. In the traditional approach, it would typically take months to
input projectinformation manually into the FM systems.During the
construction phase of this project, the BIM consultant team keyed in the
equipment information into the BIM (shown in Table 3). Typically, the
FM team would start identifying and tracking this information during
commissioning and occupancy.Moreover,the barcode system used
during construction included building components that normally only
the FM team would tag, barcode, and then record (e.g., VAV boxes and
diffusers). The BIM consultants worked with the general contractor to
develop a process for the FM team to tag that information digitally in
BIM 360 Field and then generate serial numbers and bar codes for the
list of items to track.Once tagged BIM 360 Field,the list would be
imported directly into the AiM system. Therefore, most of the work that
Table 2
Major assets tracked through BIM [44].
OmniClass Asset
23-13 39 31 Roof membranes
23-23 11 11 Elevators
23-25 69 11 15 Laboratory fume hoods
23-27 17 00 Pumps
23-27 21 00 Compressors
23-27 29 00 Tanks and storage structures
23-27 31 00 Valves
23-27 31 11 Backflow preventers
23-29 37 13 Emergency eyewash stations
23-29 37 13 15 Combination emergency eyewash stations
23-29 37 13 17 Dedicated emergency eyewash stations
23-29 37 15 13 Dedicated emergency showers
23-31 29 00 Hot water heaters
23-31 31 00 Drinking fountains
23-33 11 00 Commercial boilers
23-33 11 15 Fire tube boilers
23-33 21 00 Chillers
23-33 25 00 Air handling units
23-33 25 15 Heating and ventilating units
23-33 27 15 Air humidifiers
23-33 31 15 Exhaust hoods
23-33 31 19 Fans
23-33 33 11 Fan coil units
23-33 37 00 Refrigerant condensing units
23-33 41 17 Terminal air units
23-33 41 17 13 Variable air volume terminal units
23-33 47 00 Air dryers
23-33 49 23 15 Return air grilles
23-33 49 23 13 Supply air grilles
23-33 55 00 Energy HVAC recovery equipment
23-35 11 00 Electrical generators
23-35 13 00 Transformers
23-35 31 00 Electrical power distribution devices
23-35 31 29 Switchboards
23-35 31 31 Switchgear
23-35 47 11 Lighting fixtures
23-35 47 13 Emergency lighting
23-35 47 15 Exit illuminated signs
23-39 29 00 Waste water collection and removal
23-33 49 23 11 Exhaust air grills
23-27 23 15 Shell and tube heat exchanger
23-27 23 13 Plate frame heat exchanger
23-33 31 15 Relief hood
23-33 15 17 15 Unit heaters
23-33 15 21 13 Fin tube radiation
23-33 39 21 Split system AC units
Table 3
Tracked information of each building component [40].
Data requirements COBie fields
Tab Column
Asset tag Component Tag number
Asset description Type Name
Asset type Type Asset type
Asset group Type Category
Status code Internala Internala
Region code Internala Internala
Facility identification Facility Site description
Building name Facility Name
Floor identification Floor Name
Location identification Component Space
Shop location Internala Internala
Lockout Internala Internala
Manufacturer Type Manufacturer
Model Type Model number
Serial number Component Serial number
Warranty start date Component Warranty start date
Warranty expiration date Type Warranty duration parts
a Fields created by the institute.
P. Pishdad-Bozorgi et al. Automation in Construction 87 (2018) 22–38
28
of its categoricalstructure,the COBie-based system tracked data ex-
ports from the model and, thus, simplified the work required to capture
and record project handover data.This efficiency reduced the loss of
essential building information. At the beginning of the project, the BIM
consultants provided a Revit template file in which various fields were
to be populated with COBie data parameters.Designers and builders
who worked on the Revit files were able to input required COBie data
by filling in those blank fields with element properties, while creating
and modifying the BIM models. The Revit models were the repositories
of all required FM data throughout the design and construction phases.
The AiM system (CMMS) used by the owner only accepted the
COBie 2.3 and 2.4 data formats. Initially, since the team lacked a tool
that could directly generate COBie formatdata at the early design
phase, it used BIMLink to extract selected project information from the
Revit model and export it into a prepared Excel file. Once in the Excel
format, the parameters from Revit model were then manually mapped
onto a COBie format spreadsheet. Later, during the project development
phase, Autodesk released the COBie Extension for Revit, an application
that was COBie 2.4 compliant. Using this new tool, the team was able to
generate the Excel spreadsheet automatically with COBie format data,
thereby eliminating the error-prone manual element of data transition.
Fig. 4 illustrates the BIM-enabled workflow used on this projectto
capture, manage, and exchange project information throughout the life
cycle of the project.
The team also used BIMLink to import the data back into the Revit
model after it had been extracted, and, further, to add more data. The
input formats for the Revitmodel was Industry Foundation Classes
(IFCs) and OmniClass for designating spaces and building assets. These
formats requirements were established by the owner's facilities man-
agementdepartment.The OmniClassattribute fieldsin Revit were
consistent with data fields on COBie worksheets. BIM model managers
were responsible for continuously tracking and meeting the require-
ments of the data transfer between the modeland the COBie spread-
sheet. Although the whole information-capturing process seemed to go
well during the design and construction phases,the team faced an
unexpected issue when importing the COBie format data into the AiM
system in the handover phase.Section 6 provides a discussion of this
issue.
5.3. BIM-enabled handover
One of the owner's goals was to use the BIM model to develop the
building equipment list,in addition to verifying closeout deliverables
and tracking the installed and tagged equipment. This list was based on
a barcode system in which the barcodes oftagged equipmentwere
consistentwith the codes in the BIM model.Moreover,the general
contractorhad used BIM 360 Field to track all the equipmentin-
formation during construction. Eventually, the final building equipment
list was generated automatically by exporting the spreadsheets from
BIM 360 Field.
It was anticipated that COBie would facilitate the smooth exchange
of facility information into the CMMS,which was AiM in this pilot
project. In the traditional approach, it would typically take months to
input projectinformation manually into the FM systems.During the
construction phase of this project, the BIM consultant team keyed in the
equipment information into the BIM (shown in Table 3). Typically, the
FM team would start identifying and tracking this information during
commissioning and occupancy.Moreover,the barcode system used
during construction included building components that normally only
the FM team would tag, barcode, and then record (e.g., VAV boxes and
diffusers). The BIM consultants worked with the general contractor to
develop a process for the FM team to tag that information digitally in
BIM 360 Field and then generate serial numbers and bar codes for the
list of items to track.Once tagged BIM 360 Field,the list would be
imported directly into the AiM system. Therefore, most of the work that
Table 2
Major assets tracked through BIM [44].
OmniClass Asset
23-13 39 31 Roof membranes
23-23 11 11 Elevators
23-25 69 11 15 Laboratory fume hoods
23-27 17 00 Pumps
23-27 21 00 Compressors
23-27 29 00 Tanks and storage structures
23-27 31 00 Valves
23-27 31 11 Backflow preventers
23-29 37 13 Emergency eyewash stations
23-29 37 13 15 Combination emergency eyewash stations
23-29 37 13 17 Dedicated emergency eyewash stations
23-29 37 15 13 Dedicated emergency showers
23-31 29 00 Hot water heaters
23-31 31 00 Drinking fountains
23-33 11 00 Commercial boilers
23-33 11 15 Fire tube boilers
23-33 21 00 Chillers
23-33 25 00 Air handling units
23-33 25 15 Heating and ventilating units
23-33 27 15 Air humidifiers
23-33 31 15 Exhaust hoods
23-33 31 19 Fans
23-33 33 11 Fan coil units
23-33 37 00 Refrigerant condensing units
23-33 41 17 Terminal air units
23-33 41 17 13 Variable air volume terminal units
23-33 47 00 Air dryers
23-33 49 23 15 Return air grilles
23-33 49 23 13 Supply air grilles
23-33 55 00 Energy HVAC recovery equipment
23-35 11 00 Electrical generators
23-35 13 00 Transformers
23-35 31 00 Electrical power distribution devices
23-35 31 29 Switchboards
23-35 31 31 Switchgear
23-35 47 11 Lighting fixtures
23-35 47 13 Emergency lighting
23-35 47 15 Exit illuminated signs
23-39 29 00 Waste water collection and removal
23-33 49 23 11 Exhaust air grills
23-27 23 15 Shell and tube heat exchanger
23-27 23 13 Plate frame heat exchanger
23-33 31 15 Relief hood
23-33 15 17 15 Unit heaters
23-33 15 21 13 Fin tube radiation
23-33 39 21 Split system AC units
Table 3
Tracked information of each building component [40].
Data requirements COBie fields
Tab Column
Asset tag Component Tag number
Asset description Type Name
Asset type Type Asset type
Asset group Type Category
Status code Internala Internala
Region code Internala Internala
Facility identification Facility Site description
Building name Facility Name
Floor identification Floor Name
Location identification Component Space
Shop location Internala Internala
Lockout Internala Internala
Manufacturer Type Manufacturer
Model Type Model number
Serial number Component Serial number
Warranty start date Component Warranty start date
Warranty expiration date Type Warranty duration parts
a Fields created by the institute.
P. Pishdad-Bozorgi et al. Automation in Construction 87 (2018) 22–38
28
Paraphrase This Document
Need a fresh take? Get an instant paraphrase of this document with our AI Paraphraser
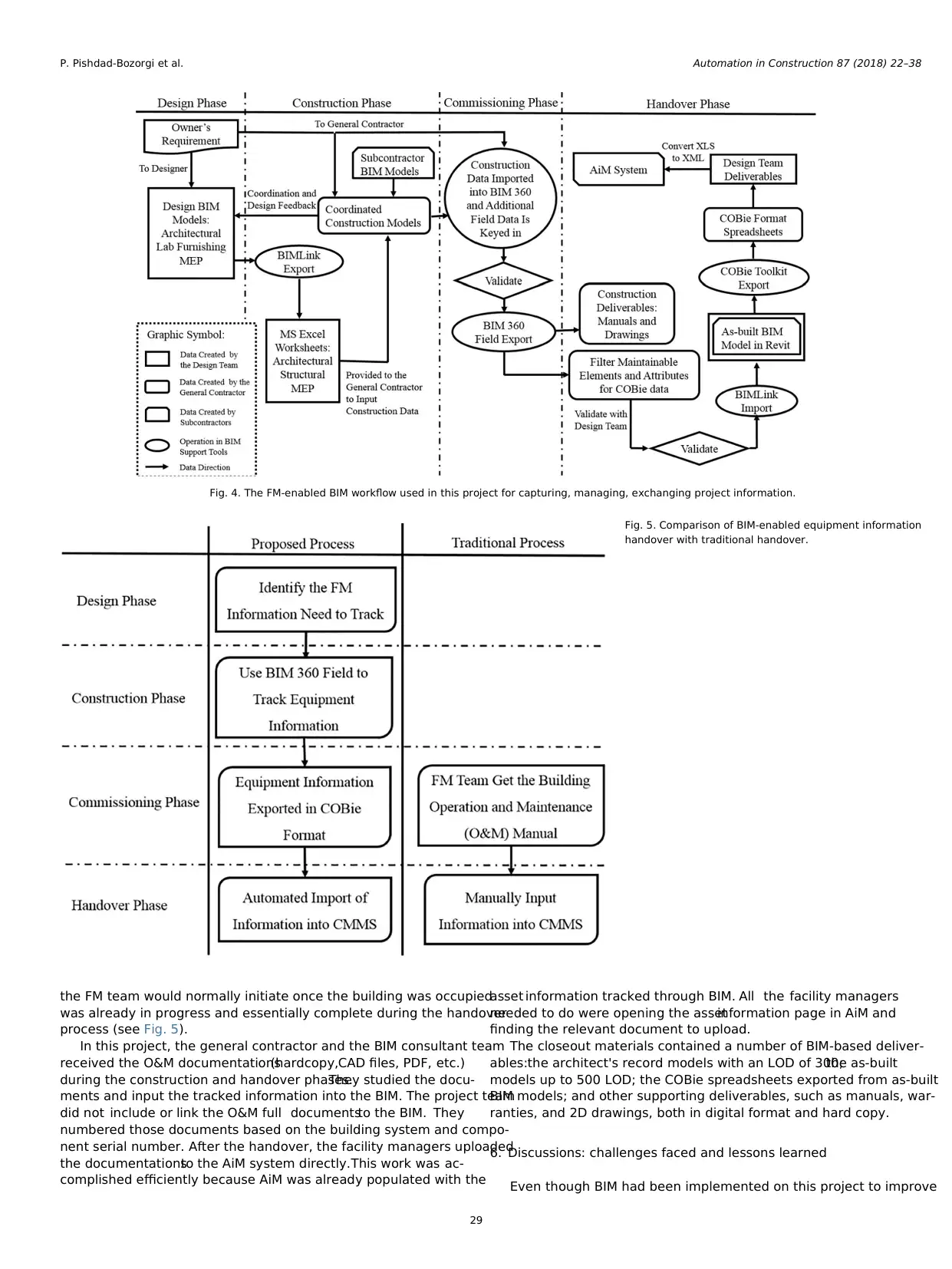
the FM team would normally initiate once the building was occupied
was already in progress and essentially complete during the handover
process (see Fig. 5).
In this project, the general contractor and the BIM consultant team
received the O&M documentations(hardcopy,CAD files, PDF, etc.)
during the construction and handover phases.They studied the docu-
ments and input the tracked information into the BIM. The project team
did not include or link the O&M full documentsto the BIM. They
numbered those documents based on the building system and compo-
nent serial number. After the handover, the facility managers uploaded
the documentationsto the AiM system directly.This work was ac-
complished efficiently because AiM was already populated with the
asset information tracked through BIM. All the facility managers
needed to do were opening the assetinformation page in AiM and
finding the relevant document to upload.
The closeout materials contained a number of BIM-based deliver-
ables:the architect's record models with an LOD of 300;the as-built
models up to 500 LOD; the COBie spreadsheets exported from as-built
BIM models; and other supporting deliverables, such as manuals, war-
ranties, and 2D drawings, both in digital format and hard copy.
6. Discussions: challenges faced and lessons learned
Even though BIM had been implemented on this project to improve
Fig. 4. The FM-enabled BIM workflow used in this project for capturing, managing, exchanging project information.
Fig. 5. Comparison of BIM-enabled equipment information
handover with traditional handover.
P. Pishdad-Bozorgi et al. Automation in Construction 87 (2018) 22–38
29
was already in progress and essentially complete during the handover
process (see Fig. 5).
In this project, the general contractor and the BIM consultant team
received the O&M documentations(hardcopy,CAD files, PDF, etc.)
during the construction and handover phases.They studied the docu-
ments and input the tracked information into the BIM. The project team
did not include or link the O&M full documentsto the BIM. They
numbered those documents based on the building system and compo-
nent serial number. After the handover, the facility managers uploaded
the documentationsto the AiM system directly.This work was ac-
complished efficiently because AiM was already populated with the
asset information tracked through BIM. All the facility managers
needed to do were opening the assetinformation page in AiM and
finding the relevant document to upload.
The closeout materials contained a number of BIM-based deliver-
ables:the architect's record models with an LOD of 300;the as-built
models up to 500 LOD; the COBie spreadsheets exported from as-built
BIM models; and other supporting deliverables, such as manuals, war-
ranties, and 2D drawings, both in digital format and hard copy.
6. Discussions: challenges faced and lessons learned
Even though BIM had been implemented on this project to improve
Fig. 4. The FM-enabled BIM workflow used in this project for capturing, managing, exchanging project information.
Fig. 5. Comparison of BIM-enabled equipment information
handover with traditional handover.
P. Pishdad-Bozorgi et al. Automation in Construction 87 (2018) 22–38
29
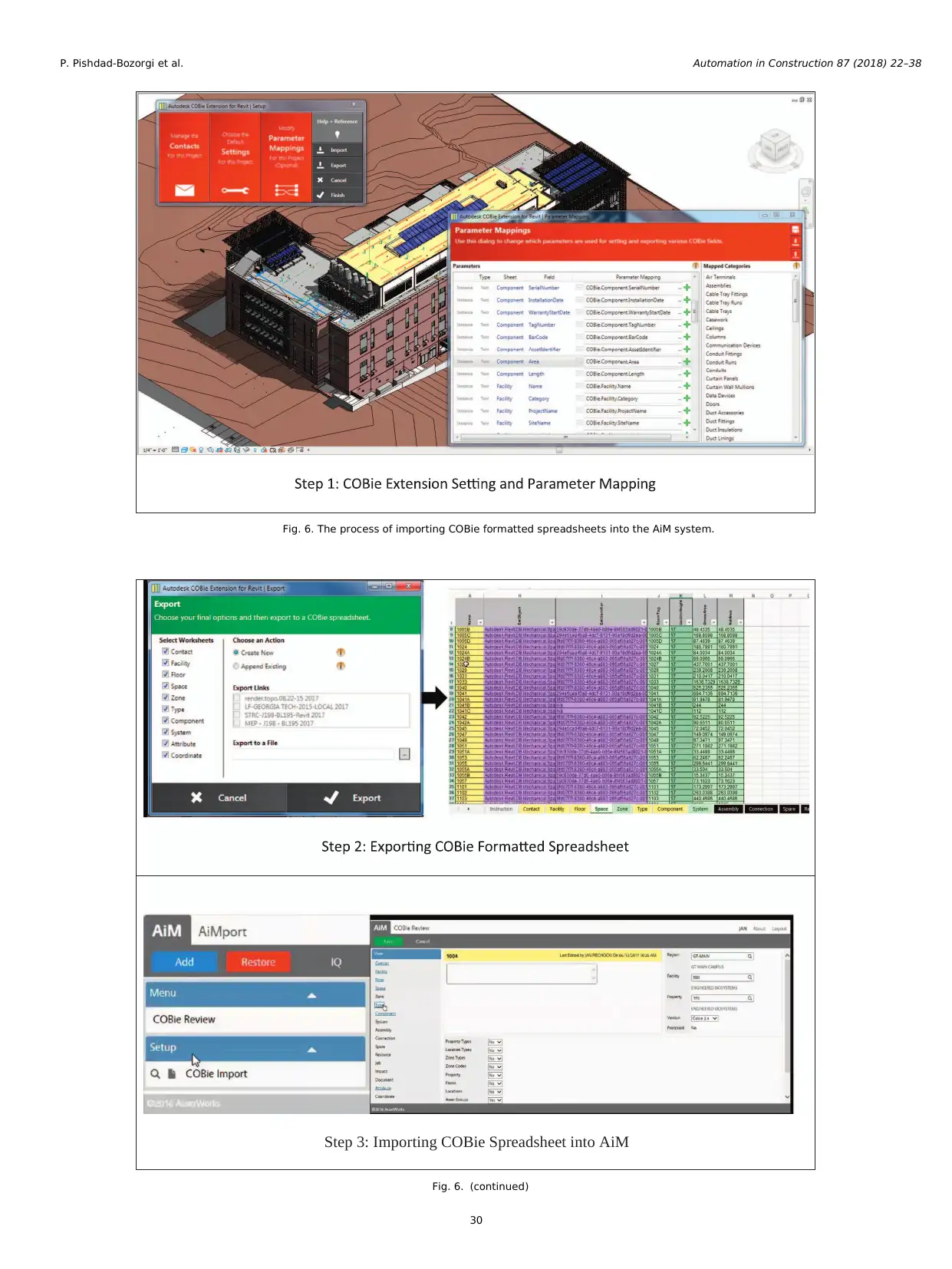
Fig. 6. The process of importing COBie formatted spreadsheets into the AiM system.
Step 3: Importing COBie Spreadsheet into AiM
Fig. 6. (continued)
P. Pishdad-Bozorgi et al. Automation in Construction 87 (2018) 22–38
30
Step 3: Importing COBie Spreadsheet into AiM
Fig. 6. (continued)
P. Pishdad-Bozorgi et al. Automation in Construction 87 (2018) 22–38
30
⊘ This is a preview!⊘
Do you want full access?
Subscribe today to unlock all pages.

Trusted by 1+ million students worldwide
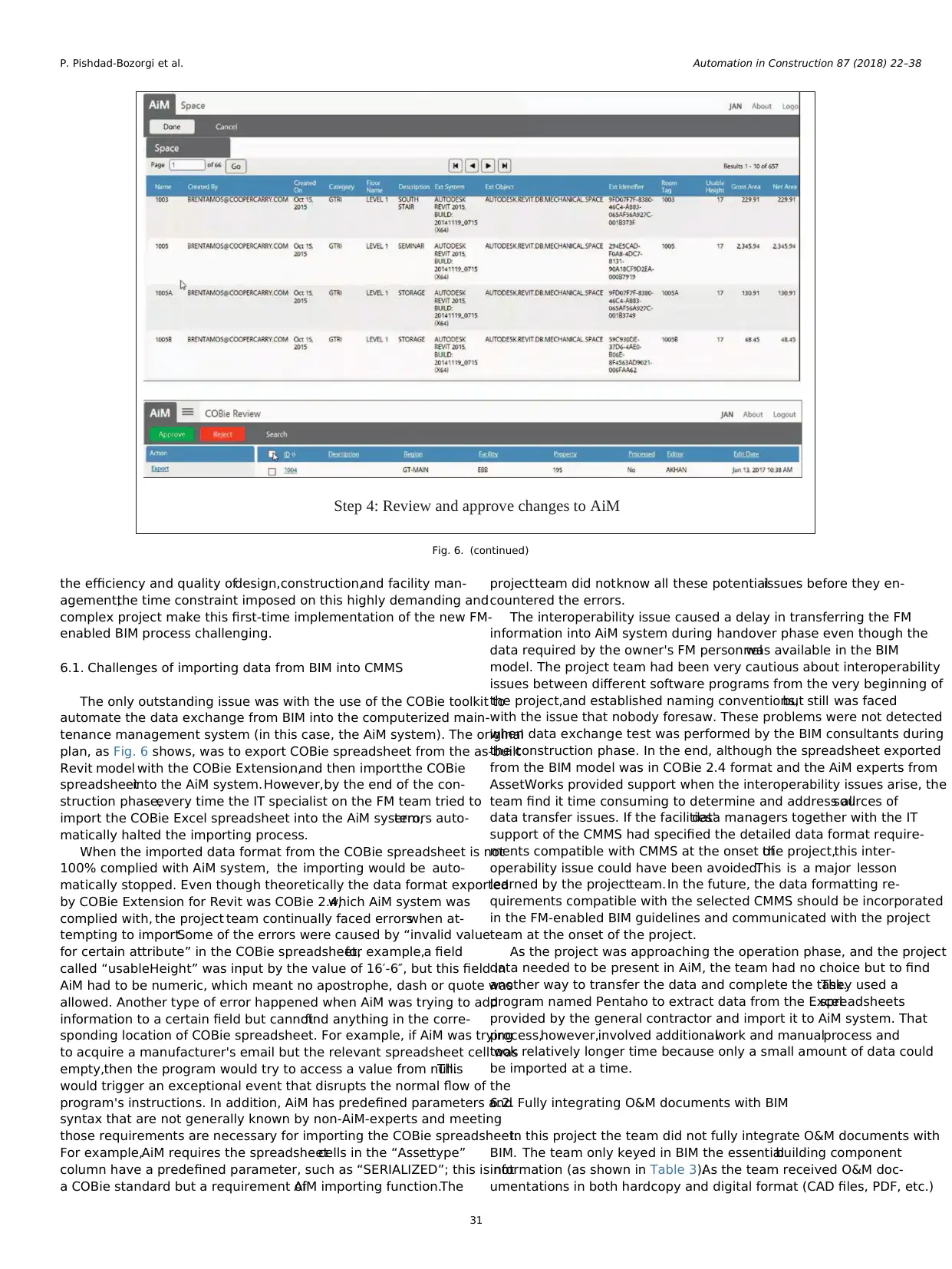
the efficiency and quality ofdesign,construction,and facility man-
agement,the time constraint imposed on this highly demanding and
complex project make this first-time implementation of the new FM-
enabled BIM process challenging.
6.1. Challenges of importing data from BIM into CMMS
The only outstanding issue was with the use of the COBie toolkit to
automate the data exchange from BIM into the computerized main-
tenance management system (in this case, the AiM system). The original
plan, as Fig. 6 shows, was to export COBie spreadsheet from the as-built
Revit model with the COBie Extension,and then importthe COBie
spreadsheetinto the AiM system.However,by the end of the con-
struction phase,every time the IT specialist on the FM team tried to
import the COBie Excel spreadsheet into the AiM system,errors auto-
matically halted the importing process.
When the imported data format from the COBie spreadsheet is not
100% complied with AiM system, the importing would be auto-
matically stopped. Even though theoretically the data format exported
by COBie Extension for Revit was COBie 2.4,which AiM system was
complied with, the project team continually faced errorswhen at-
tempting to import.Some of the errors were caused by “invalid value
for certain attribute” in the COBie spreadsheet,for example,a field
called “usableHeight” was input by the value of 16′-6″, but this field in
AiM had to be numeric, which meant no apostrophe, dash or quote was
allowed. Another type of error happened when AiM was trying to add
information to a certain field but cannotfind anything in the corre-
sponding location of COBie spreadsheet. For example, if AiM was trying
to acquire a manufacturer's email but the relevant spreadsheet cell was
empty,then the program would try to access a value from null.This
would trigger an exceptional event that disrupts the normal flow of the
program's instructions. In addition, AiM has predefined parameters and
syntax that are not generally known by non-AiM-experts and meeting
those requirements are necessary for importing the COBie spreadsheet.
For example,AiM requires the spreadsheetcells in the “Assettype”
column have a predefined parameter, such as “SERIALIZED”; this is not
a COBie standard but a requirement ofAiM importing function.The
projectteam did notknow all these potentialissues before they en-
countered the errors.
The interoperability issue caused a delay in transferring the FM
information into AiM system during handover phase even though the
data required by the owner's FM personnelwas available in the BIM
model. The project team had been very cautious about interoperability
issues between different software programs from the very beginning of
the project,and established naming conventions,but still was faced
with the issue that nobody foresaw. These problems were not detected
when data exchange test was performed by the BIM consultants during
the construction phase. In the end, although the spreadsheet exported
from the BIM model was in COBie 2.4 format and the AiM experts from
AssetWorks provided support when the interoperability issues arise, the
team find it time consuming to determine and address allsources of
data transfer issues. If the facilities'data managers together with the IT
support of the CMMS had specified the detailed data format require-
ments compatible with CMMS at the onset ofthe project,this inter-
operability issue could have been avoided.This is a major lesson
learned by the projectteam.In the future, the data formatting re-
quirements compatible with the selected CMMS should be incorporated
in the FM-enabled BIM guidelines and communicated with the project
team at the onset of the project.
As the project was approaching the operation phase, and the project
data needed to be present in AiM, the team had no choice but to find
another way to transfer the data and complete the task.They used a
program named Pentaho to extract data from the Excelspreadsheets
provided by the general contractor and import it to AiM system. That
process,however,involved additionalwork and manualprocess and
took relatively longer time because only a small amount of data could
be imported at a time.
6.2. Fully integrating O&M documents with BIM
In this project the team did not fully integrate O&M documents with
BIM. The team only keyed in BIM the essentialbuilding component
information (as shown in Table 3).As the team received O&M doc-
umentations in both hardcopy and digital format (CAD files, PDF, etc.)
Step 4: Review and approve changes to AiM
Fig. 6. (continued)
P. Pishdad-Bozorgi et al. Automation in Construction 87 (2018) 22–38
31
agement,the time constraint imposed on this highly demanding and
complex project make this first-time implementation of the new FM-
enabled BIM process challenging.
6.1. Challenges of importing data from BIM into CMMS
The only outstanding issue was with the use of the COBie toolkit to
automate the data exchange from BIM into the computerized main-
tenance management system (in this case, the AiM system). The original
plan, as Fig. 6 shows, was to export COBie spreadsheet from the as-built
Revit model with the COBie Extension,and then importthe COBie
spreadsheetinto the AiM system.However,by the end of the con-
struction phase,every time the IT specialist on the FM team tried to
import the COBie Excel spreadsheet into the AiM system,errors auto-
matically halted the importing process.
When the imported data format from the COBie spreadsheet is not
100% complied with AiM system, the importing would be auto-
matically stopped. Even though theoretically the data format exported
by COBie Extension for Revit was COBie 2.4,which AiM system was
complied with, the project team continually faced errorswhen at-
tempting to import.Some of the errors were caused by “invalid value
for certain attribute” in the COBie spreadsheet,for example,a field
called “usableHeight” was input by the value of 16′-6″, but this field in
AiM had to be numeric, which meant no apostrophe, dash or quote was
allowed. Another type of error happened when AiM was trying to add
information to a certain field but cannotfind anything in the corre-
sponding location of COBie spreadsheet. For example, if AiM was trying
to acquire a manufacturer's email but the relevant spreadsheet cell was
empty,then the program would try to access a value from null.This
would trigger an exceptional event that disrupts the normal flow of the
program's instructions. In addition, AiM has predefined parameters and
syntax that are not generally known by non-AiM-experts and meeting
those requirements are necessary for importing the COBie spreadsheet.
For example,AiM requires the spreadsheetcells in the “Assettype”
column have a predefined parameter, such as “SERIALIZED”; this is not
a COBie standard but a requirement ofAiM importing function.The
projectteam did notknow all these potentialissues before they en-
countered the errors.
The interoperability issue caused a delay in transferring the FM
information into AiM system during handover phase even though the
data required by the owner's FM personnelwas available in the BIM
model. The project team had been very cautious about interoperability
issues between different software programs from the very beginning of
the project,and established naming conventions,but still was faced
with the issue that nobody foresaw. These problems were not detected
when data exchange test was performed by the BIM consultants during
the construction phase. In the end, although the spreadsheet exported
from the BIM model was in COBie 2.4 format and the AiM experts from
AssetWorks provided support when the interoperability issues arise, the
team find it time consuming to determine and address allsources of
data transfer issues. If the facilities'data managers together with the IT
support of the CMMS had specified the detailed data format require-
ments compatible with CMMS at the onset ofthe project,this inter-
operability issue could have been avoided.This is a major lesson
learned by the projectteam.In the future, the data formatting re-
quirements compatible with the selected CMMS should be incorporated
in the FM-enabled BIM guidelines and communicated with the project
team at the onset of the project.
As the project was approaching the operation phase, and the project
data needed to be present in AiM, the team had no choice but to find
another way to transfer the data and complete the task.They used a
program named Pentaho to extract data from the Excelspreadsheets
provided by the general contractor and import it to AiM system. That
process,however,involved additionalwork and manualprocess and
took relatively longer time because only a small amount of data could
be imported at a time.
6.2. Fully integrating O&M documents with BIM
In this project the team did not fully integrate O&M documents with
BIM. The team only keyed in BIM the essentialbuilding component
information (as shown in Table 3).As the team received O&M doc-
umentations in both hardcopy and digital format (CAD files, PDF, etc.)
Step 4: Review and approve changes to AiM
Fig. 6. (continued)
P. Pishdad-Bozorgi et al. Automation in Construction 87 (2018) 22–38
31
Paraphrase This Document
Need a fresh take? Get an instant paraphrase of this document with our AI Paraphraser
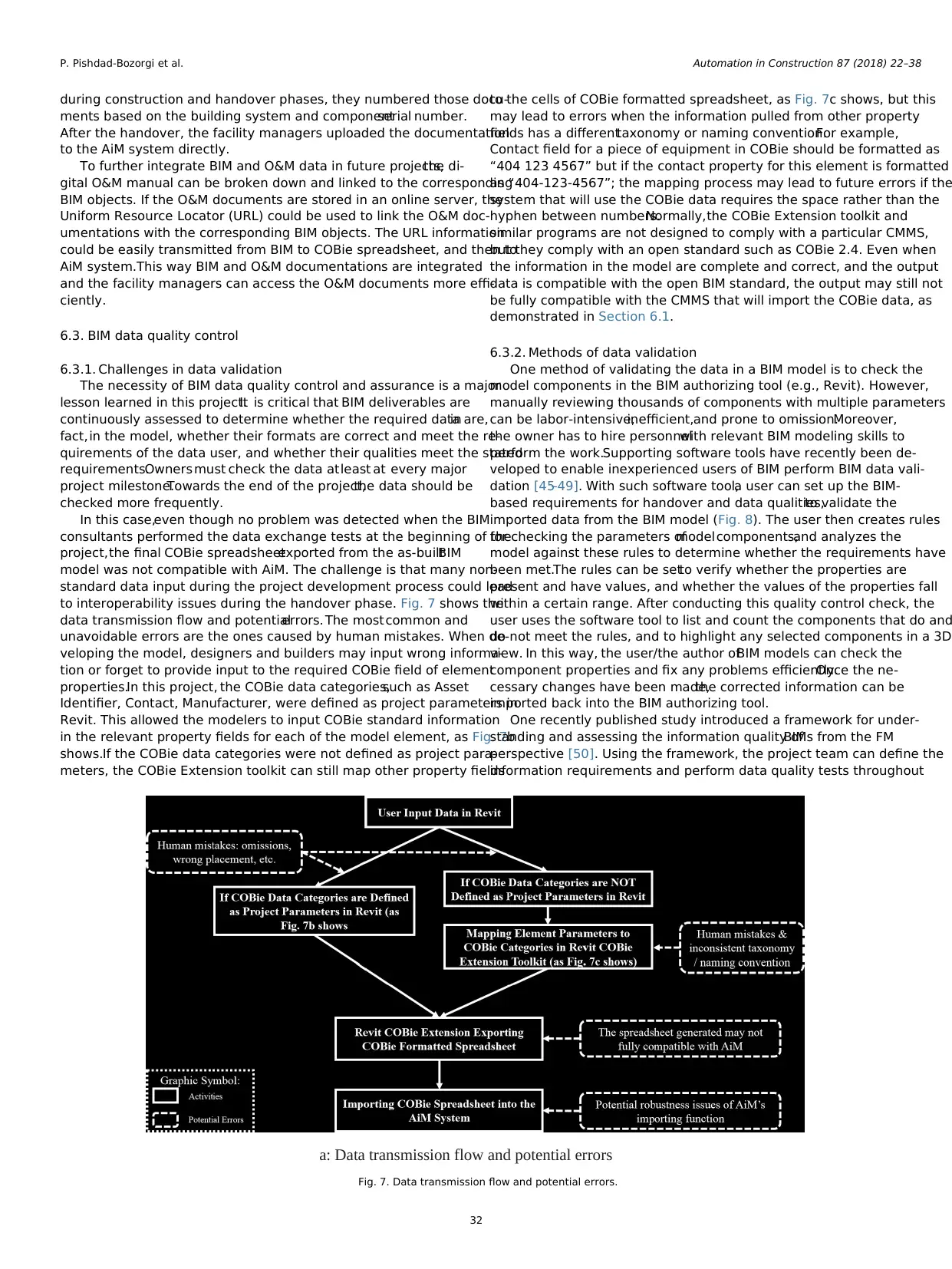
during construction and handover phases, they numbered those docu-
ments based on the building system and componentserial number.
After the handover, the facility managers uploaded the documentation
to the AiM system directly.
To further integrate BIM and O&M data in future projects,the di-
gital O&M manual can be broken down and linked to the corresponding
BIM objects. If the O&M documents are stored in an online server, the
Uniform Resource Locator (URL) could be used to link the O&M doc-
umentations with the corresponding BIM objects. The URL information
could be easily transmitted from BIM to COBie spreadsheet, and then to
AiM system.This way BIM and O&M documentations are integrated
and the facility managers can access the O&M documents more effi-
ciently.
6.3. BIM data quality control
6.3.1. Challenges in data validation
The necessity of BIM data quality control and assurance is a major
lesson learned in this project.It is critical that BIM deliverables are
continuously assessed to determine whether the required data are,in
fact,in the model, whether their formats are correct and meet the re-
quirements of the data user, and whether their qualities meet the stated
requirements.Owners must check the data atleast at every major
project milestone.Towards the end of the project,the data should be
checked more frequently.
In this case,even though no problem was detected when the BIM
consultants performed the data exchange tests at the beginning of the
project,the final COBie spreadsheetexported from the as-builtBIM
model was not compatible with AiM. The challenge is that many non-
standard data input during the project development process could lead
to interoperability issues during the handover phase. Fig. 7 shows the
data transmission flow and potentialerrors. The most common and
unavoidable errors are the ones caused by human mistakes. When de-
veloping the model, designers and builders may input wrong informa-
tion or forget to provide input to the required COBie field of element
properties.In this project, the COBie data categories,such as Asset
Identifier, Contact, Manufacturer, were defined as project parameters in
Revit. This allowed the modelers to input COBie standard information
in the relevant property fields for each of the model element, as Fig. 7b
shows.If the COBie data categories were not defined as project para-
meters, the COBie Extension toolkit can still map other property fields
to the cells of COBie formatted spreadsheet, as Fig. 7c shows, but this
may lead to errors when the information pulled from other property
fields has a differenttaxonomy or naming convention.For example,
Contact field for a piece of equipment in COBie should be formatted as
“404 123 4567” but if the contact property for this element is formatted
as “404-123-4567”; the mapping process may lead to future errors if the
system that will use the COBie data requires the space rather than the
hyphen between numbers.Normally,the COBie Extension toolkit and
similar programs are not designed to comply with a particular CMMS,
but they comply with an open standard such as COBie 2.4. Even when
the information in the model are complete and correct, and the output
data is compatible with the open BIM standard, the output may still not
be fully compatible with the CMMS that will import the COBie data, as
demonstrated in Section 6.1.
6.3.2. Methods of data validation
One method of validating the data in a BIM model is to check the
model components in the BIM authorizing tool (e.g., Revit). However,
manually reviewing thousands of components with multiple parameters
can be labor-intensive,inefficient,and prone to omission.Moreover,
the owner has to hire personnelwith relevant BIM modeling skills to
perform the work.Supporting software tools have recently been de-
veloped to enable inexperienced users of BIM perform BIM data vali-
dation [45–49]. With such software tool,a user can set up the BIM-
based requirements for handover and data qualities,to validate the
imported data from the BIM model (Fig. 8). The user then creates rules
for checking the parameters ofmodelcomponents,and analyzes the
model against these rules to determine whether the requirements have
been met.The rules can be setto verify whether the properties are
present and have values, and whether the values of the properties fall
within a certain range. After conducting this quality control check, the
user uses the software tool to list and count the components that do and
do not meet the rules, and to highlight any selected components in a 3D
view. In this way, the user/the author ofBIM models can check the
component properties and fix any problems efficiently.Once the ne-
cessary changes have been made,the corrected information can be
imported back into the BIM authorizing tool.
One recently published study introduced a framework for under-
standing and assessing the information quality ofBIMs from the FM
perspective [50]. Using the framework, the project team can define the
information requirements and perform data quality tests throughout
a: Data transmission flow and potential errors
Fig. 7. Data transmission flow and potential errors.
P. Pishdad-Bozorgi et al. Automation in Construction 87 (2018) 22–38
32
ments based on the building system and componentserial number.
After the handover, the facility managers uploaded the documentation
to the AiM system directly.
To further integrate BIM and O&M data in future projects,the di-
gital O&M manual can be broken down and linked to the corresponding
BIM objects. If the O&M documents are stored in an online server, the
Uniform Resource Locator (URL) could be used to link the O&M doc-
umentations with the corresponding BIM objects. The URL information
could be easily transmitted from BIM to COBie spreadsheet, and then to
AiM system.This way BIM and O&M documentations are integrated
and the facility managers can access the O&M documents more effi-
ciently.
6.3. BIM data quality control
6.3.1. Challenges in data validation
The necessity of BIM data quality control and assurance is a major
lesson learned in this project.It is critical that BIM deliverables are
continuously assessed to determine whether the required data are,in
fact,in the model, whether their formats are correct and meet the re-
quirements of the data user, and whether their qualities meet the stated
requirements.Owners must check the data atleast at every major
project milestone.Towards the end of the project,the data should be
checked more frequently.
In this case,even though no problem was detected when the BIM
consultants performed the data exchange tests at the beginning of the
project,the final COBie spreadsheetexported from the as-builtBIM
model was not compatible with AiM. The challenge is that many non-
standard data input during the project development process could lead
to interoperability issues during the handover phase. Fig. 7 shows the
data transmission flow and potentialerrors. The most common and
unavoidable errors are the ones caused by human mistakes. When de-
veloping the model, designers and builders may input wrong informa-
tion or forget to provide input to the required COBie field of element
properties.In this project, the COBie data categories,such as Asset
Identifier, Contact, Manufacturer, were defined as project parameters in
Revit. This allowed the modelers to input COBie standard information
in the relevant property fields for each of the model element, as Fig. 7b
shows.If the COBie data categories were not defined as project para-
meters, the COBie Extension toolkit can still map other property fields
to the cells of COBie formatted spreadsheet, as Fig. 7c shows, but this
may lead to errors when the information pulled from other property
fields has a differenttaxonomy or naming convention.For example,
Contact field for a piece of equipment in COBie should be formatted as
“404 123 4567” but if the contact property for this element is formatted
as “404-123-4567”; the mapping process may lead to future errors if the
system that will use the COBie data requires the space rather than the
hyphen between numbers.Normally,the COBie Extension toolkit and
similar programs are not designed to comply with a particular CMMS,
but they comply with an open standard such as COBie 2.4. Even when
the information in the model are complete and correct, and the output
data is compatible with the open BIM standard, the output may still not
be fully compatible with the CMMS that will import the COBie data, as
demonstrated in Section 6.1.
6.3.2. Methods of data validation
One method of validating the data in a BIM model is to check the
model components in the BIM authorizing tool (e.g., Revit). However,
manually reviewing thousands of components with multiple parameters
can be labor-intensive,inefficient,and prone to omission.Moreover,
the owner has to hire personnelwith relevant BIM modeling skills to
perform the work.Supporting software tools have recently been de-
veloped to enable inexperienced users of BIM perform BIM data vali-
dation [45–49]. With such software tool,a user can set up the BIM-
based requirements for handover and data qualities,to validate the
imported data from the BIM model (Fig. 8). The user then creates rules
for checking the parameters ofmodelcomponents,and analyzes the
model against these rules to determine whether the requirements have
been met.The rules can be setto verify whether the properties are
present and have values, and whether the values of the properties fall
within a certain range. After conducting this quality control check, the
user uses the software tool to list and count the components that do and
do not meet the rules, and to highlight any selected components in a 3D
view. In this way, the user/the author ofBIM models can check the
component properties and fix any problems efficiently.Once the ne-
cessary changes have been made,the corrected information can be
imported back into the BIM authorizing tool.
One recently published study introduced a framework for under-
standing and assessing the information quality ofBIMs from the FM
perspective [50]. Using the framework, the project team can define the
information requirements and perform data quality tests throughout
a: Data transmission flow and potential errors
Fig. 7. Data transmission flow and potential errors.
P. Pishdad-Bozorgi et al. Automation in Construction 87 (2018) 22–38
32
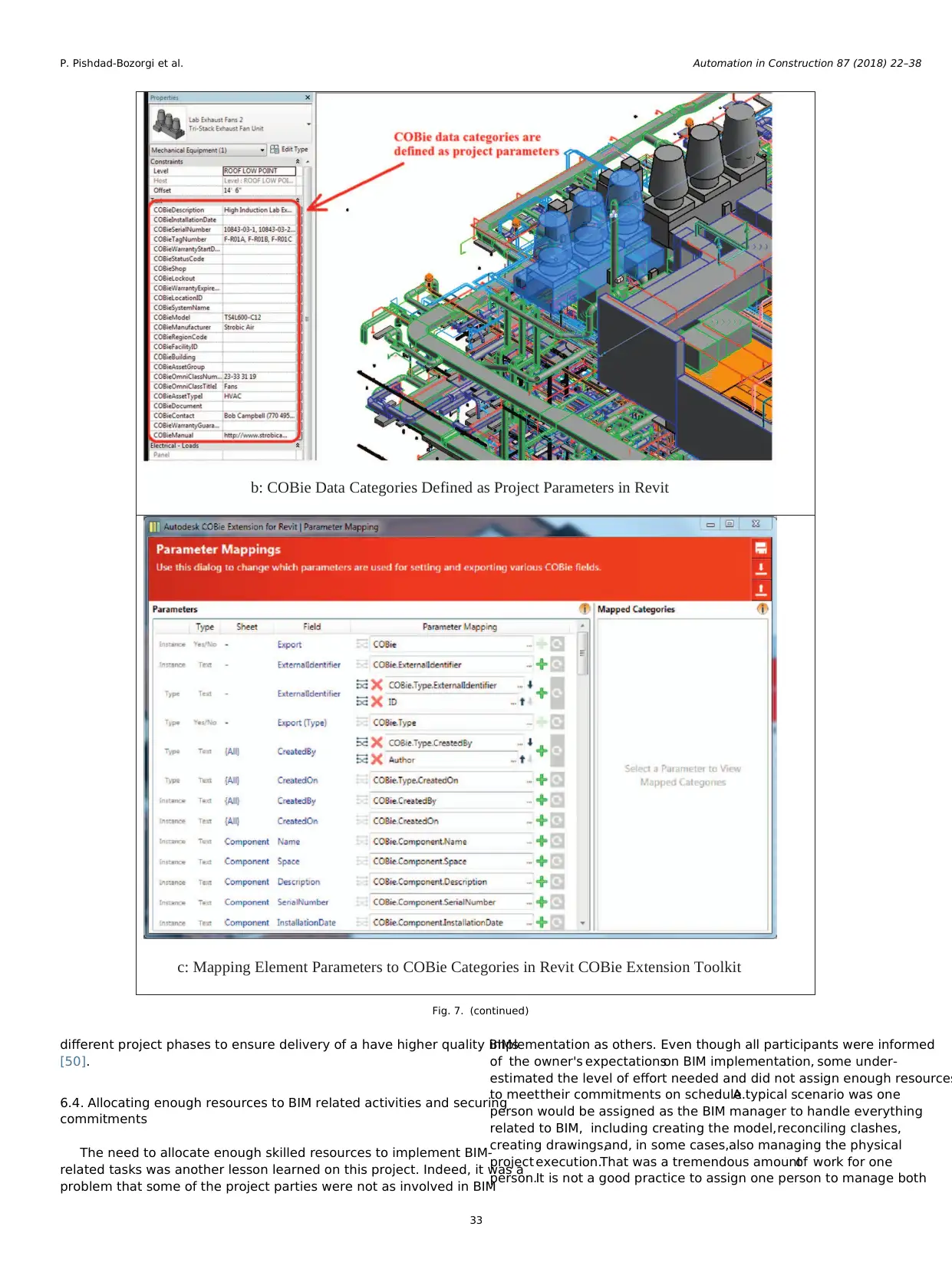
different project phases to ensure delivery of a have higher quality BIMs
[50].
6.4. Allocating enough resources to BIM related activities and securing
commitments
The need to allocate enough skilled resources to implement BIM-
related tasks was another lesson learned on this project. Indeed, it was a
problem that some of the project parties were not as involved in BIM
implementation as others. Even though all participants were informed
of the owner's expectationson BIM implementation, some under-
estimated the level of effort needed and did not assign enough resources
to meettheir commitments on schedule.A typical scenario was one
person would be assigned as the BIM manager to handle everything
related to BIM, including creating the model,reconciling clashes,
creating drawings,and, in some cases,also managing the physical
project execution.That was a tremendous amountof work for one
person.It is not a good practice to assign one person to manage both
b: COBie Data Categories Defined as Project Parameters in Revit
c: Mapping Element Parameters to COBie Categories in Revit COBie Extension Toolkit
Fig. 7. (continued)
P. Pishdad-Bozorgi et al. Automation in Construction 87 (2018) 22–38
33
[50].
6.4. Allocating enough resources to BIM related activities and securing
commitments
The need to allocate enough skilled resources to implement BIM-
related tasks was another lesson learned on this project. Indeed, it was a
problem that some of the project parties were not as involved in BIM
implementation as others. Even though all participants were informed
of the owner's expectationson BIM implementation, some under-
estimated the level of effort needed and did not assign enough resources
to meettheir commitments on schedule.A typical scenario was one
person would be assigned as the BIM manager to handle everything
related to BIM, including creating the model,reconciling clashes,
creating drawings,and, in some cases,also managing the physical
project execution.That was a tremendous amountof work for one
person.It is not a good practice to assign one person to manage both
b: COBie Data Categories Defined as Project Parameters in Revit
c: Mapping Element Parameters to COBie Categories in Revit COBie Extension Toolkit
Fig. 7. (continued)
P. Pishdad-Bozorgi et al. Automation in Construction 87 (2018) 22–38
33
⊘ This is a preview!⊘
Do you want full access?
Subscribe today to unlock all pages.

Trusted by 1+ million students worldwide
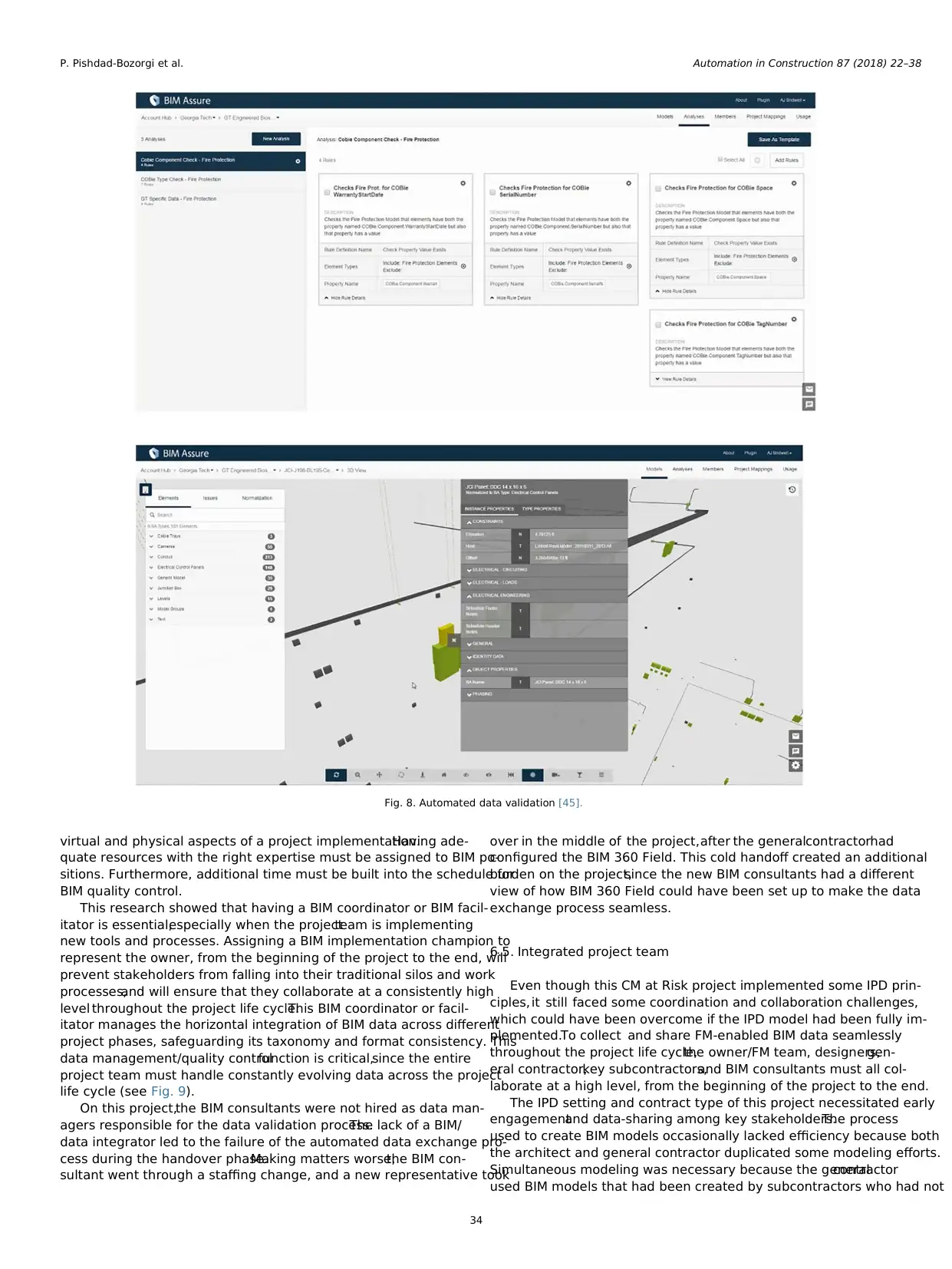
virtual and physical aspects of a project implementation.Having ade-
quate resources with the right expertise must be assigned to BIM po-
sitions. Furthermore, additional time must be built into the schedule for
BIM quality control.
This research showed that having a BIM coordinator or BIM facil-
itator is essential,especially when the projectteam is implementing
new tools and processes. Assigning a BIM implementation champion to
represent the owner, from the beginning of the project to the end, will
prevent stakeholders from falling into their traditional silos and work
processes,and will ensure that they collaborate at a consistently high
level throughout the project life cycle.This BIM coordinator or facil-
itator manages the horizontal integration of BIM data across different
project phases, safeguarding its taxonomy and format consistency. This
data management/quality controlfunction is critical,since the entire
project team must handle constantly evolving data across the project
life cycle (see Fig. 9).
On this project,the BIM consultants were not hired as data man-
agers responsible for the data validation process.The lack of a BIM/
data integrator led to the failure of the automated data exchange pro-
cess during the handover phase.Making matters worse,the BIM con-
sultant went through a staffing change, and a new representative took
over in the middle of the project,after the generalcontractorhad
configured the BIM 360 Field. This cold handoff created an additional
burden on the project,since the new BIM consultants had a different
view of how BIM 360 Field could have been set up to make the data
exchange process seamless.
6.5. Integrated project team
Even though this CM at Risk project implemented some IPD prin-
ciples, it still faced some coordination and collaboration challenges,
which could have been overcome if the IPD model had been fully im-
plemented.To collect and share FM-enabled BIM data seamlessly
throughout the project life cycle,the owner/FM team, designers,gen-
eral contractor,key subcontractors,and BIM consultants must all col-
laborate at a high level, from the beginning of the project to the end.
The IPD setting and contract type of this project necessitated early
engagementand data-sharing among key stakeholders.The process
used to create BIM models occasionally lacked efficiency because both
the architect and general contractor duplicated some modeling efforts.
Simultaneous modeling was necessary because the generalcontractor
used BIM models that had been created by subcontractors who had not
Fig. 8. Automated data validation [45].
P. Pishdad-Bozorgi et al. Automation in Construction 87 (2018) 22–38
34
quate resources with the right expertise must be assigned to BIM po-
sitions. Furthermore, additional time must be built into the schedule for
BIM quality control.
This research showed that having a BIM coordinator or BIM facil-
itator is essential,especially when the projectteam is implementing
new tools and processes. Assigning a BIM implementation champion to
represent the owner, from the beginning of the project to the end, will
prevent stakeholders from falling into their traditional silos and work
processes,and will ensure that they collaborate at a consistently high
level throughout the project life cycle.This BIM coordinator or facil-
itator manages the horizontal integration of BIM data across different
project phases, safeguarding its taxonomy and format consistency. This
data management/quality controlfunction is critical,since the entire
project team must handle constantly evolving data across the project
life cycle (see Fig. 9).
On this project,the BIM consultants were not hired as data man-
agers responsible for the data validation process.The lack of a BIM/
data integrator led to the failure of the automated data exchange pro-
cess during the handover phase.Making matters worse,the BIM con-
sultant went through a staffing change, and a new representative took
over in the middle of the project,after the generalcontractorhad
configured the BIM 360 Field. This cold handoff created an additional
burden on the project,since the new BIM consultants had a different
view of how BIM 360 Field could have been set up to make the data
exchange process seamless.
6.5. Integrated project team
Even though this CM at Risk project implemented some IPD prin-
ciples, it still faced some coordination and collaboration challenges,
which could have been overcome if the IPD model had been fully im-
plemented.To collect and share FM-enabled BIM data seamlessly
throughout the project life cycle,the owner/FM team, designers,gen-
eral contractor,key subcontractors,and BIM consultants must all col-
laborate at a high level, from the beginning of the project to the end.
The IPD setting and contract type of this project necessitated early
engagementand data-sharing among key stakeholders.The process
used to create BIM models occasionally lacked efficiency because both
the architect and general contractor duplicated some modeling efforts.
Simultaneous modeling was necessary because the generalcontractor
used BIM models that had been created by subcontractors who had not
Fig. 8. Automated data validation [45].
P. Pishdad-Bozorgi et al. Automation in Construction 87 (2018) 22–38
34
Paraphrase This Document
Need a fresh take? Get an instant paraphrase of this document with our AI Paraphraser

contracted with the design companies. Since they lacked a direct con-
tractual relationship,the data-sharing between them was unavoidably
delayed. Had the project been based on a multi-party IPD contract, its
fully integrated team would not have had such contractualsilos and,
thus, would have maximized the efficiency of the data-sharing process.
In addition, an IPD delivery modelwould have facilitated the es-
tablishment of a more realistic schedule by ensuring input and buy-in
from all key stakeholders,including tradesand suppliers.The IPD
modelwould also have mitigated the occurrence of change orders by
establishing early involvementof key stakeholders,since early en-
gagement enhances understanding of the project and increases colla-
boration from the beginning of the project. The challenges faced in this
project,resulting from unrealistic initialschedule and change orders,
could have been significantly mitigated if the IPD model had been fully
in place.
7. Conclusion
Successful implementation of FM-enabled BIM can be achieved with
1) a clear definition of what FM-enabled BIM constitutes, 2) a seamless
and practical process of collecting the FM-enabled BIM data throughout
projectdevelopmentphases,and 3) a well-executed interoperability
plan for exchanging data between BIM tools and facility management
systems,such as CMMS.This research examined a real-world FM-en-
abled BIM implementation on a university research building project, to
determine the information required for FM-enabled BIM,to articulate
the process ofgathering,managing,and exchanging FM-related BIM
data, to identify the challenges faced during the BIM enabled handover,
and to capture lessons learned.
FM-enabled BIM implementation is the process through which es-
sential facility information is captured, maintained, and shared digitally
in a set of integrated BIM models. At the handover phase, this process
ensures that important project information is readily available to auto-
input into the relevant CMMS. Through FM-enabled BIM, maintenance
personnelhave accessnot only to FM information, but also to the
geometrical BIM model, which provides information such as equipment
location, accessibility, and maintainability.
This research examines a proposed BIM-enabled workflow to cap-
ture, manage,and exchange projectinformation throughoutthe life
cycle of a project. Some of the BIM-enabled practices implemented on
this pilot project have also been suggested by previous research. These
practices include the following:the need to identify BIM Information
needs for FM [5,24];the importance ofusing COBie as the data ex-
change format[27,51–53];the usefulnessof BIM 360 Field during
construction [54]; the efficiency of a barcode system that gives tagged
equipmentBIM model codes [55,56];and the value ofBIM-enabled
handover [53,57]. Even though the data transfer during the handover
phase of this project was not fully automated, it provided an invaluable
insights and learning experience to all the participants.
The major lessons learned on this project include the following: 1)
involving the facilities data manager and the CMMS IT specialist at the
onset of the project to specify the data formatting requirements com-
patible with the selected CMMS, incorporating such requirements in the
FM-enabled BIM guidelines and communicating it with the project team
at the onset of the project; 2) creating models in BIM authoring appli-
cations,rather than importing models from non-BIM applications into
BIM applications that use IFC formats;3) conducting continuous BIM
data quality control and assurance throughout the project; 4) allocating
enough resources to BIM-related activities;5) establishing a fully in-
tegrated projectteam,consisting ofrepresentatives from the design,
construction, owner organizations, as well as the data facility manager;
6) avoiding projects with tightschedule when implementing a new
technology and workflow process,a team should build enough time
into the project schedule to overcome any unexpected issues.
These lessons learned are the unique contribution of this study and
are widely generalizable to all variety of projects.Some of the details
presented in this pilot project (e.g., FM tasks, BIM authorizing tool, and
FM System) may be limited in how much they apply to a specific project
type,and may only be applicable to projects with similar attributes.
Future research is needed to tackle each of these aspects and variations
of FM-enabled BIM workflows; it must define and establish the appro-
priate data requirements and interoperability needs and procedures for
each project type, FM task, BIM authoring tool, and FM system.
Different data and interoperability needs and procedures must be de-
fined and established. Based on the insights gained from this research,
the authors developed a framework for future research in BIM for FM
(see Fig. 10).
The proposed road map in Fig.8 provides a framework for future
researchersto carry out in-depth single case studiesto collect in-
formation and provide insightinto the new field of BIM for FM, by
addressing the following objectives:1) Define and prioritize BIM data
need for each FM task in each building type; 2) Identify the
Fig. 9. Virtual versus physical managers and the need for project life cycle integration.
P. Pishdad-Bozorgi et al. Automation in Construction 87 (2018) 22–38
35
tractual relationship,the data-sharing between them was unavoidably
delayed. Had the project been based on a multi-party IPD contract, its
fully integrated team would not have had such contractualsilos and,
thus, would have maximized the efficiency of the data-sharing process.
In addition, an IPD delivery modelwould have facilitated the es-
tablishment of a more realistic schedule by ensuring input and buy-in
from all key stakeholders,including tradesand suppliers.The IPD
modelwould also have mitigated the occurrence of change orders by
establishing early involvementof key stakeholders,since early en-
gagement enhances understanding of the project and increases colla-
boration from the beginning of the project. The challenges faced in this
project,resulting from unrealistic initialschedule and change orders,
could have been significantly mitigated if the IPD model had been fully
in place.
7. Conclusion
Successful implementation of FM-enabled BIM can be achieved with
1) a clear definition of what FM-enabled BIM constitutes, 2) a seamless
and practical process of collecting the FM-enabled BIM data throughout
projectdevelopmentphases,and 3) a well-executed interoperability
plan for exchanging data between BIM tools and facility management
systems,such as CMMS.This research examined a real-world FM-en-
abled BIM implementation on a university research building project, to
determine the information required for FM-enabled BIM,to articulate
the process ofgathering,managing,and exchanging FM-related BIM
data, to identify the challenges faced during the BIM enabled handover,
and to capture lessons learned.
FM-enabled BIM implementation is the process through which es-
sential facility information is captured, maintained, and shared digitally
in a set of integrated BIM models. At the handover phase, this process
ensures that important project information is readily available to auto-
input into the relevant CMMS. Through FM-enabled BIM, maintenance
personnelhave accessnot only to FM information, but also to the
geometrical BIM model, which provides information such as equipment
location, accessibility, and maintainability.
This research examines a proposed BIM-enabled workflow to cap-
ture, manage,and exchange projectinformation throughoutthe life
cycle of a project. Some of the BIM-enabled practices implemented on
this pilot project have also been suggested by previous research. These
practices include the following:the need to identify BIM Information
needs for FM [5,24];the importance ofusing COBie as the data ex-
change format[27,51–53];the usefulnessof BIM 360 Field during
construction [54]; the efficiency of a barcode system that gives tagged
equipmentBIM model codes [55,56];and the value ofBIM-enabled
handover [53,57]. Even though the data transfer during the handover
phase of this project was not fully automated, it provided an invaluable
insights and learning experience to all the participants.
The major lessons learned on this project include the following: 1)
involving the facilities data manager and the CMMS IT specialist at the
onset of the project to specify the data formatting requirements com-
patible with the selected CMMS, incorporating such requirements in the
FM-enabled BIM guidelines and communicating it with the project team
at the onset of the project; 2) creating models in BIM authoring appli-
cations,rather than importing models from non-BIM applications into
BIM applications that use IFC formats;3) conducting continuous BIM
data quality control and assurance throughout the project; 4) allocating
enough resources to BIM-related activities;5) establishing a fully in-
tegrated projectteam,consisting ofrepresentatives from the design,
construction, owner organizations, as well as the data facility manager;
6) avoiding projects with tightschedule when implementing a new
technology and workflow process,a team should build enough time
into the project schedule to overcome any unexpected issues.
These lessons learned are the unique contribution of this study and
are widely generalizable to all variety of projects.Some of the details
presented in this pilot project (e.g., FM tasks, BIM authorizing tool, and
FM System) may be limited in how much they apply to a specific project
type,and may only be applicable to projects with similar attributes.
Future research is needed to tackle each of these aspects and variations
of FM-enabled BIM workflows; it must define and establish the appro-
priate data requirements and interoperability needs and procedures for
each project type, FM task, BIM authoring tool, and FM system.
Different data and interoperability needs and procedures must be de-
fined and established. Based on the insights gained from this research,
the authors developed a framework for future research in BIM for FM
(see Fig. 10).
The proposed road map in Fig.8 provides a framework for future
researchersto carry out in-depth single case studiesto collect in-
formation and provide insightinto the new field of BIM for FM, by
addressing the following objectives:1) Define and prioritize BIM data
need for each FM task in each building type; 2) Identify the
Fig. 9. Virtual versus physical managers and the need for project life cycle integration.
P. Pishdad-Bozorgi et al. Automation in Construction 87 (2018) 22–38
35
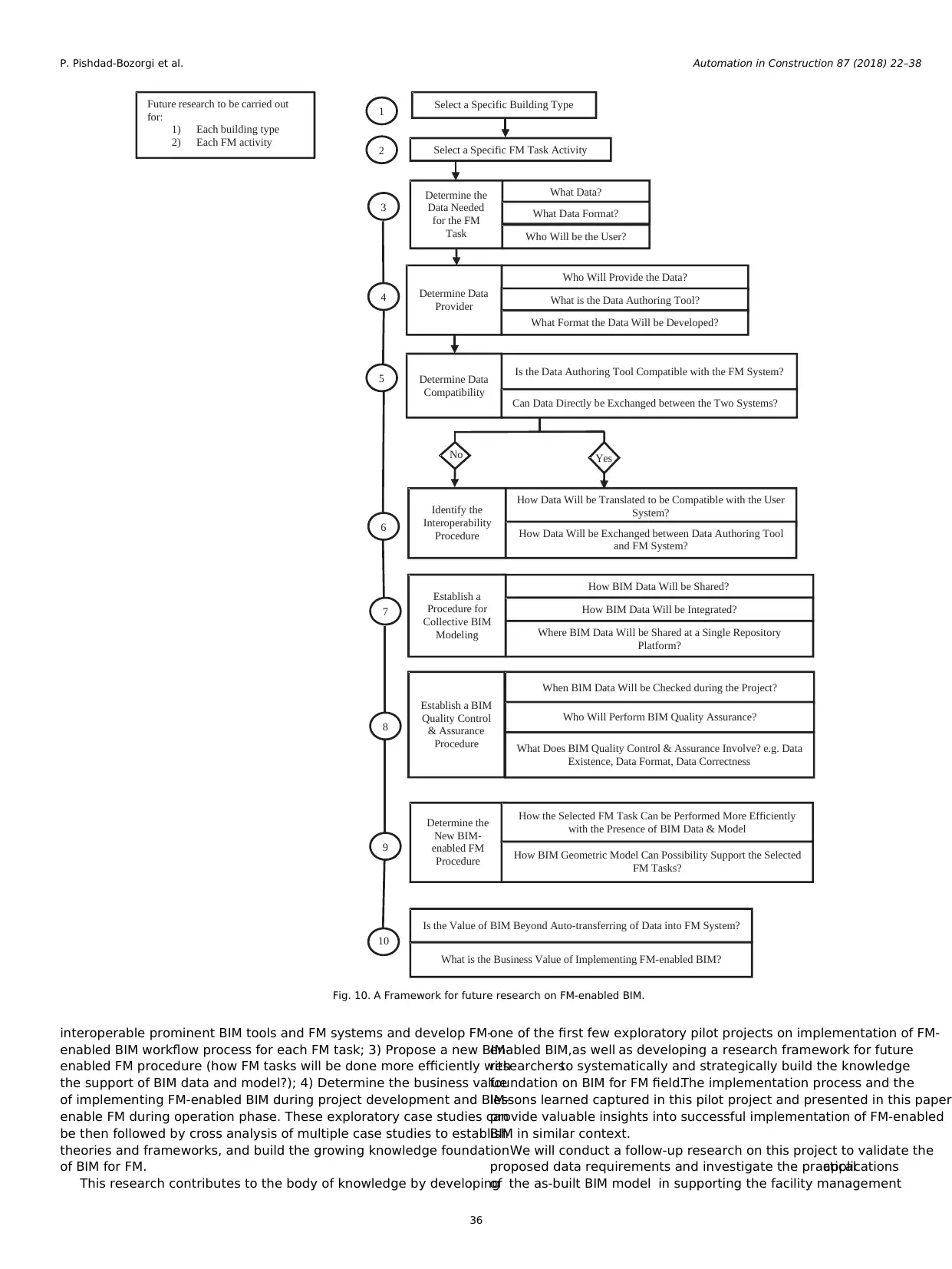
interoperable prominent BIM tools and FM systems and develop FM-
enabled BIM workflow process for each FM task; 3) Propose a new BIM-
enabled FM procedure (how FM tasks will be done more efficiently with
the support of BIM data and model?); 4) Determine the business value
of implementing FM-enabled BIM during project development and BIM-
enable FM during operation phase. These exploratory case studies can
be then followed by cross analysis of multiple case studies to establish
theories and frameworks, and build the growing knowledge foundation
of BIM for FM.
This research contributes to the body of knowledge by developing
one of the first few exploratory pilot projects on implementation of FM-
enabled BIM,as well as developing a research framework for future
researchersto systematically and strategically build the knowledge
foundation on BIM for FM field.The implementation process and the
lessons learned captured in this pilot project and presented in this paper
provide valuable insights into successful implementation of FM-enabled
BIM in similar context.
We will conduct a follow-up research on this project to validate the
proposed data requirements and investigate the practicalapplications
of the as-built BIM model in supporting the facility management
Future research to be carried out
for:
1) Each building type
2) Each FM activity
Select a Specific Building Type
Select a Specific FM Task Activity
What Data?Determine the
Data Needed
for the FM
Task
What Data Format?
Who Will be the User?
Who Will Provide the Data?
Determine Data
Provider What is the Data Authoring Tool?
What Format the Data Will be Developed?
Is the Data Authoring Tool Compatible with the FM System?
Determine Data
Compatibility
Can Data Directly be Exchanged between the Two Systems?
How Data Will be Translated to be Compatible with the User
System?Identify the
Interoperability
Procedure How Data Will be Exchanged between Data Authoring Tool
and FM System?
How BIM Data Will be Shared?
Establish a
Procedure for
Collective BIM
Modeling Where BIM Data Will be Shared at a Single Repository
Platform?
How BIM Data Will be Integrated?
When BIM Data Will be Checked during the Project?
Establish a BIM
Quality Control
& Assurance
Procedure What Does BIM Quality Control & Assurance Involve? e.g. Data
Existence, Data Format, Data Correctness
Who Will Perform BIM Quality Assurance?
Determine the
New BIM-
enabled FM
Procedure
How the Selected FM Task Can be Performed More Efficiently
with the Presence of BIM Data & Model
How BIM Geometric Model Can Possibility Support the Selected
FM Tasks?
9
8
7
6
5
4
3
2
1
Is the Value of BIM Beyond Auto-transferring of Data into FM System?
What is the Business Value of Implementing FM-enabled BIM?
No Yes
10
Fig. 10. A Framework for future research on FM-enabled BIM.
P. Pishdad-Bozorgi et al. Automation in Construction 87 (2018) 22–38
36
enabled BIM workflow process for each FM task; 3) Propose a new BIM-
enabled FM procedure (how FM tasks will be done more efficiently with
the support of BIM data and model?); 4) Determine the business value
of implementing FM-enabled BIM during project development and BIM-
enable FM during operation phase. These exploratory case studies can
be then followed by cross analysis of multiple case studies to establish
theories and frameworks, and build the growing knowledge foundation
of BIM for FM.
This research contributes to the body of knowledge by developing
one of the first few exploratory pilot projects on implementation of FM-
enabled BIM,as well as developing a research framework for future
researchersto systematically and strategically build the knowledge
foundation on BIM for FM field.The implementation process and the
lessons learned captured in this pilot project and presented in this paper
provide valuable insights into successful implementation of FM-enabled
BIM in similar context.
We will conduct a follow-up research on this project to validate the
proposed data requirements and investigate the practicalapplications
of the as-built BIM model in supporting the facility management
Future research to be carried out
for:
1) Each building type
2) Each FM activity
Select a Specific Building Type
Select a Specific FM Task Activity
What Data?Determine the
Data Needed
for the FM
Task
What Data Format?
Who Will be the User?
Who Will Provide the Data?
Determine Data
Provider What is the Data Authoring Tool?
What Format the Data Will be Developed?
Is the Data Authoring Tool Compatible with the FM System?
Determine Data
Compatibility
Can Data Directly be Exchanged between the Two Systems?
How Data Will be Translated to be Compatible with the User
System?Identify the
Interoperability
Procedure How Data Will be Exchanged between Data Authoring Tool
and FM System?
How BIM Data Will be Shared?
Establish a
Procedure for
Collective BIM
Modeling Where BIM Data Will be Shared at a Single Repository
Platform?
How BIM Data Will be Integrated?
When BIM Data Will be Checked during the Project?
Establish a BIM
Quality Control
& Assurance
Procedure What Does BIM Quality Control & Assurance Involve? e.g. Data
Existence, Data Format, Data Correctness
Who Will Perform BIM Quality Assurance?
Determine the
New BIM-
enabled FM
Procedure
How the Selected FM Task Can be Performed More Efficiently
with the Presence of BIM Data & Model
How BIM Geometric Model Can Possibility Support the Selected
FM Tasks?
9
8
7
6
5
4
3
2
1
Is the Value of BIM Beyond Auto-transferring of Data into FM System?
What is the Business Value of Implementing FM-enabled BIM?
No Yes
10
Fig. 10. A Framework for future research on FM-enabled BIM.
P. Pishdad-Bozorgi et al. Automation in Construction 87 (2018) 22–38
36
⊘ This is a preview!⊘
Do you want full access?
Subscribe today to unlock all pages.

Trusted by 1+ million students worldwide
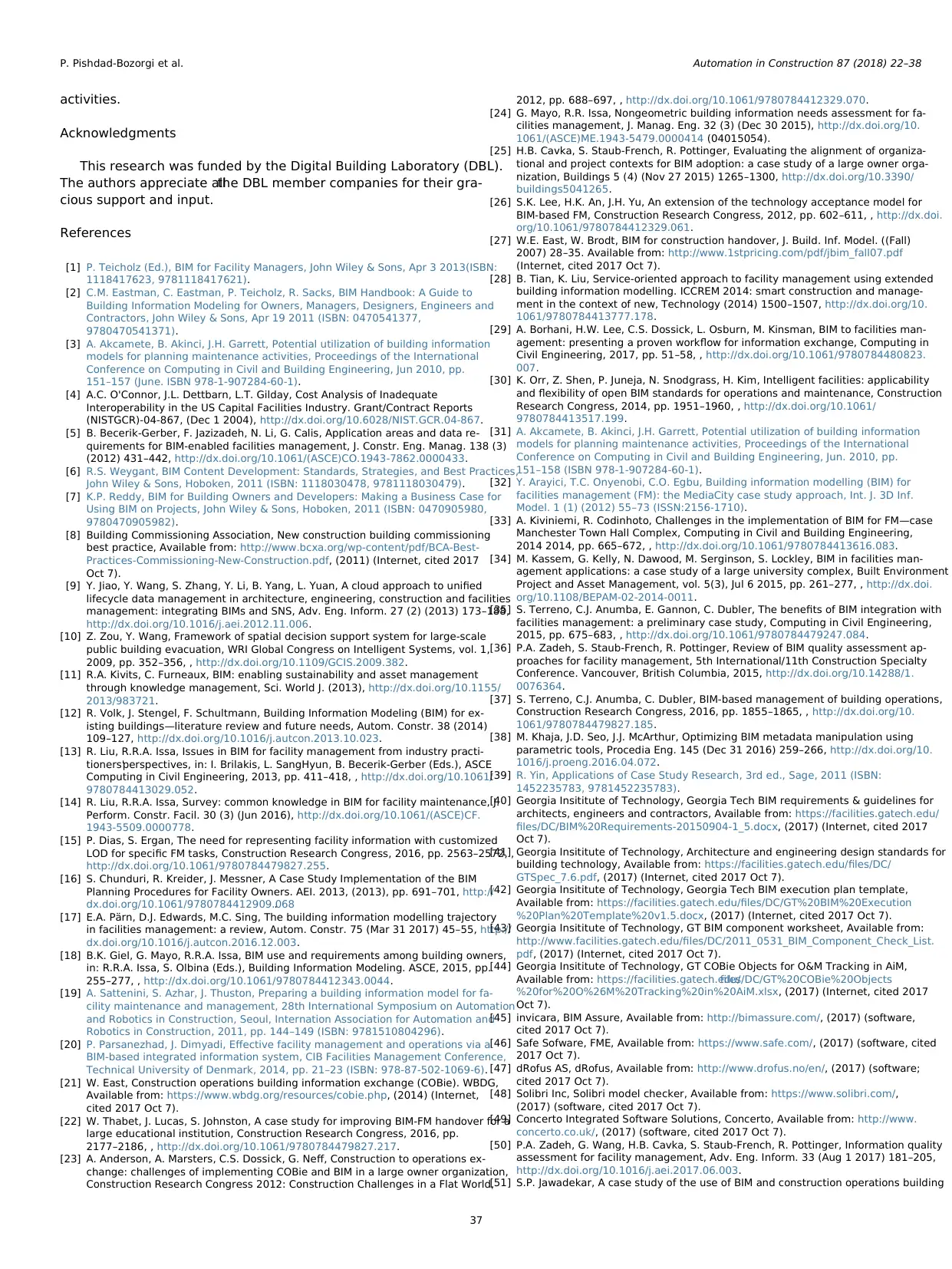
activities.
Acknowledgments
This research was funded by the Digital Building Laboratory (DBL).
The authors appreciate allthe DBL member companies for their gra-
cious support and input.
References
[1] P. Teicholz (Ed.), BIM for Facility Managers, John Wiley & Sons, Apr 3 2013(ISBN:
1118417623, 9781118417621).
[2] C.M. Eastman, C. Eastman, P. Teicholz, R. Sacks, BIM Handbook: A Guide to
Building Information Modeling for Owners, Managers, Designers, Engineers and
Contractors, John Wiley & Sons, Apr 19 2011 (ISBN: 0470541377,
9780470541371).
[3] A. Akcamete, B. Akinci, J.H. Garrett, Potential utilization of building information
models for planning maintenance activities, Proceedings of the International
Conference on Computing in Civil and Building Engineering, Jun 2010, pp.
151–157 (June. ISBN 978-1-907284-60-1).
[4] A.C. O'Connor, J.L. Dettbarn, L.T. Gilday, Cost Analysis of Inadequate
Interoperability in the US Capital Facilities Industry. Grant/Contract Reports
(NISTGCR)-04-867, (Dec 1 2004), http://dx.doi.org/10.6028/NIST.GCR.04-867.
[5] B. Becerik-Gerber, F. Jazizadeh, N. Li, G. Calis, Application areas and data re-
quirements for BIM-enabled facilities management, J. Constr. Eng. Manag. 138 (3)
(2012) 431–442, http://dx.doi.org/10.1061/(ASCE)CO.1943-7862.0000433.
[6] R.S. Weygant, BIM Content Development: Standards, Strategies, and Best Practices,
John Wiley & Sons, Hoboken, 2011 (ISBN: 1118030478, 9781118030479).
[7] K.P. Reddy, BIM for Building Owners and Developers: Making a Business Case for
Using BIM on Projects, John Wiley & Sons, Hoboken, 2011 (ISBN: 0470905980,
9780470905982).
[8] Building Commissioning Association, New construction building commissioning
best practice, Available from: http://www.bcxa.org/wp-content/pdf/BCA-Best-
Practices-Commissioning-New-Construction.pdf, (2011) (Internet, cited 2017
Oct 7).
[9] Y. Jiao, Y. Wang, S. Zhang, Y. Li, B. Yang, L. Yuan, A cloud approach to unified
lifecycle data management in architecture, engineering, construction and facilities
management: integrating BIMs and SNS, Adv. Eng. Inform. 27 (2) (2013) 173–188,
http://dx.doi.org/10.1016/j.aei.2012.11.006.
[10] Z. Zou, Y. Wang, Framework of spatial decision support system for large-scale
public building evacuation, WRI Global Congress on Intelligent Systems, vol. 1,
2009, pp. 352–356, , http://dx.doi.org/10.1109/GCIS.2009.382.
[11] R.A. Kivits, C. Furneaux, BIM: enabling sustainability and asset management
through knowledge management, Sci. World J. (2013), http://dx.doi.org/10.1155/
2013/983721.
[12] R. Volk, J. Stengel, F. Schultmann, Building Information Modeling (BIM) for ex-
isting buildings—literature review and future needs, Autom. Constr. 38 (2014)
109–127, http://dx.doi.org/10.1016/j.autcon.2013.10.023.
[13] R. Liu, R.R.A. Issa, Issues in BIM for facility management from industry practi-
tioners'perspectives, in: I. Brilakis, L. SangHyun, B. Becerik-Gerber (Eds.), ASCE
Computing in Civil Engineering, 2013, pp. 411–418, , http://dx.doi.org/10.1061/
9780784413029.052.
[14] R. Liu, R.R.A. Issa, Survey: common knowledge in BIM for facility maintenance, J.
Perform. Constr. Facil. 30 (3) (Jun 2016), http://dx.doi.org/10.1061/(ASCE)CF.
1943-5509.0000778.
[15] P. Dias, S. Ergan, The need for representing facility information with customized
LOD for specific FM tasks, Construction Research Congress, 2016, pp. 2563–2572, ,
http://dx.doi.org/10.1061/9780784479827.255.
[16] S. Chunduri, R. Kreider, J. Messner, A Case Study Implementation of the BIM
Planning Procedures for Facility Owners. AEI. 2013, (2013), pp. 691–701, http://
dx.doi.org/10.1061/9780784412909.068.
[17] E.A. Pärn, D.J. Edwards, M.C. Sing, The building information modelling trajectory
in facilities management: a review, Autom. Constr. 75 (Mar 31 2017) 45–55, http://
dx.doi.org/10.1016/j.autcon.2016.12.003.
[18] B.K. Giel, G. Mayo, R.R.A. Issa, BIM use and requirements among building owners,
in: R.R.A. Issa, S. Olbina (Eds.), Building Information Modeling. ASCE, 2015, pp.
255–277, , http://dx.doi.org/10.1061/9780784412343.0044.
[19] A. Sattenini, S. Azhar, J. Thuston, Preparing a building information model for fa-
cility maintenance and management, 28th International Symposium on Automation
and Robotics in Construction, Seoul, Internation Association for Automation and
Robotics in Construction, 2011, pp. 144–149 (ISBN: 9781510804296).
[20] P. Parsanezhad, J. Dimyadi, Effective facility management and operations via a
BIM-based integrated information system, CIB Facilities Management Conference,
Technical University of Denmark, 2014, pp. 21–23 (ISBN: 978-87-502-1069-6).
[21] W. East, Construction operations building information exchange (COBie). WBDG,
Available from: https://www.wbdg.org/resources/cobie.php, (2014) (Internet,
cited 2017 Oct 7).
[22] W. Thabet, J. Lucas, S. Johnston, A case study for improving BIM-FM handover for a
large educational institution, Construction Research Congress, 2016, pp.
2177–2186, , http://dx.doi.org/10.1061/9780784479827.217.
[23] A. Anderson, A. Marsters, C.S. Dossick, G. Neff, Construction to operations ex-
change: challenges of implementing COBie and BIM in a large owner organization,
Construction Research Congress 2012: Construction Challenges in a Flat World,
2012, pp. 688–697, , http://dx.doi.org/10.1061/9780784412329.070.
[24] G. Mayo, R.R. Issa, Nongeometric building information needs assessment for fa-
cilities management, J. Manag. Eng. 32 (3) (Dec 30 2015), http://dx.doi.org/10.
1061/(ASCE)ME.1943-5479.0000414 (04015054).
[25] H.B. Cavka, S. Staub-French, R. Pottinger, Evaluating the alignment of organiza-
tional and project contexts for BIM adoption: a case study of a large owner orga-
nization, Buildings 5 (4) (Nov 27 2015) 1265–1300, http://dx.doi.org/10.3390/
buildings5041265.
[26] S.K. Lee, H.K. An, J.H. Yu, An extension of the technology acceptance model for
BIM-based FM, Construction Research Congress, 2012, pp. 602–611, , http://dx.doi.
org/10.1061/9780784412329.061.
[27] W.E. East, W. Brodt, BIM for construction handover, J. Build. Inf. Model. ((Fall)
2007) 28–35. Available from: http://www.1stpricing.com/pdf/jbim_fall07.pdf
(Internet, cited 2017 Oct 7).
[28] B. Tian, K. Liu, Service-oriented approach to facility management using extended
building information modelling. ICCREM 2014: smart construction and manage-
ment in the context of new, Technology (2014) 1500–1507, http://dx.doi.org/10.
1061/9780784413777.178.
[29] A. Borhani, H.W. Lee, C.S. Dossick, L. Osburn, M. Kinsman, BIM to facilities man-
agement: presenting a proven workflow for information exchange, Computing in
Civil Engineering, 2017, pp. 51–58, , http://dx.doi.org/10.1061/9780784480823.
007.
[30] K. Orr, Z. Shen, P. Juneja, N. Snodgrass, H. Kim, Intelligent facilities: applicability
and flexibility of open BIM standards for operations and maintenance, Construction
Research Congress, 2014, pp. 1951–1960, , http://dx.doi.org/10.1061/
9780784413517.199.
[31] A. Akcamete, B. Akinci, J.H. Garrett, Potential utilization of building information
models for planning maintenance activities, Proceedings of the International
Conference on Computing in Civil and Building Engineering, Jun. 2010, pp.
151–158 (ISBN 978-1-907284-60-1).
[32] Y. Arayici, T.C. Onyenobi, C.O. Egbu, Building information modelling (BIM) for
facilities management (FM): the MediaCity case study approach, Int. J. 3D Inf.
Model. 1 (1) (2012) 55–73 (ISSN:2156-1710).
[33] A. Kiviniemi, R. Codinhoto, Challenges in the implementation of BIM for FM—case
Manchester Town Hall Complex, Computing in Civil and Building Engineering,
2014 2014, pp. 665–672, , http://dx.doi.org/10.1061/9780784413616.083.
[34] M. Kassem, G. Kelly, N. Dawood, M. Serginson, S. Lockley, BIM in facilities man-
agement applications: a case study of a large university complex, Built Environment
Project and Asset Management, vol. 5(3), Jul 6 2015, pp. 261–277, , http://dx.doi.
org/10.1108/BEPAM-02-2014-0011.
[35] S. Terreno, C.J. Anumba, E. Gannon, C. Dubler, The benefits of BIM integration with
facilities management: a preliminary case study, Computing in Civil Engineering,
2015, pp. 675–683, , http://dx.doi.org/10.1061/9780784479247.084.
[36] P.A. Zadeh, S. Staub-French, R. Pottinger, Review of BIM quality assessment ap-
proaches for facility management, 5th International/11th Construction Specialty
Conference. Vancouver, British Columbia, 2015, http://dx.doi.org/10.14288/1.
0076364.
[37] S. Terreno, C.J. Anumba, C. Dubler, BIM-based management of building operations,
Construction Research Congress, 2016, pp. 1855–1865, , http://dx.doi.org/10.
1061/9780784479827.185.
[38] M. Khaja, J.D. Seo, J.J. McArthur, Optimizing BIM metadata manipulation using
parametric tools, Procedia Eng. 145 (Dec 31 2016) 259–266, http://dx.doi.org/10.
1016/j.proeng.2016.04.072.
[39] R. Yin, Applications of Case Study Research, 3rd ed., Sage, 2011 (ISBN:
1452235783, 9781452235783).
[40] Georgia Insititute of Technology, Georgia Tech BIM requirements & guidelines for
architects, engineers and contractors, Available from: https://facilities.gatech.edu/
files/DC/BIM%20Requirements-20150904-1_5.docx, (2017) (Internet, cited 2017
Oct 7).
[41] Georgia Insititute of Technology, Architecture and engineering design standards for
building technology, Available from: https://facilities.gatech.edu/files/DC/
GTSpec_7.6.pdf, (2017) (Internet, cited 2017 Oct 7).
[42] Georgia Insititute of Technology, Georgia Tech BIM execution plan template,
Available from: https://facilities.gatech.edu/files/DC/GT%20BIM%20Execution
%20Plan%20Template%20v1.5.docx, (2017) (Internet, cited 2017 Oct 7).
[43] Georgia Insititute of Technology, GT BIM component worksheet, Available from:
http://www.facilities.gatech.edu/files/DC/2011_0531_BIM_Component_Check_List.
pdf, (2017) (Internet, cited 2017 Oct 7).
[44] Georgia Insititute of Technology, GT COBie Objects for O&M Tracking in AiM,
Available from: https://facilities.gatech.edu/files/DC/GT%20COBie%20Objects
%20for%20O%26M%20Tracking%20in%20AiM.xlsx, (2017) (Internet, cited 2017
Oct 7).
[45] invicara, BIM Assure, Available from: http://bimassure.com/, (2017) (software,
cited 2017 Oct 7).
[46] Safe Sofware, FME, Available from: https://www.safe.com/, (2017) (software, cited
2017 Oct 7).
[47] dRofus AS, dRofus, Available from: http://www.drofus.no/en/, (2017) (software;
cited 2017 Oct 7).
[48] Solibri Inc, Solibri model checker, Available from: https://www.solibri.com/,
(2017) (software, cited 2017 Oct 7).
[49] Concerto Integrated Software Solutions, Concerto, Available from: http://www.
concerto.co.uk/, (2017) (software, cited 2017 Oct 7).
[50] P.A. Zadeh, G. Wang, H.B. Cavka, S. Staub-French, R. Pottinger, Information quality
assessment for facility management, Adv. Eng. Inform. 33 (Aug 1 2017) 181–205,
http://dx.doi.org/10.1016/j.aei.2017.06.003.
[51] S.P. Jawadekar, A case study of the use of BIM and construction operations building
P. Pishdad-Bozorgi et al. Automation in Construction 87 (2018) 22–38
37
Acknowledgments
This research was funded by the Digital Building Laboratory (DBL).
The authors appreciate allthe DBL member companies for their gra-
cious support and input.
References
[1] P. Teicholz (Ed.), BIM for Facility Managers, John Wiley & Sons, Apr 3 2013(ISBN:
1118417623, 9781118417621).
[2] C.M. Eastman, C. Eastman, P. Teicholz, R. Sacks, BIM Handbook: A Guide to
Building Information Modeling for Owners, Managers, Designers, Engineers and
Contractors, John Wiley & Sons, Apr 19 2011 (ISBN: 0470541377,
9780470541371).
[3] A. Akcamete, B. Akinci, J.H. Garrett, Potential utilization of building information
models for planning maintenance activities, Proceedings of the International
Conference on Computing in Civil and Building Engineering, Jun 2010, pp.
151–157 (June. ISBN 978-1-907284-60-1).
[4] A.C. O'Connor, J.L. Dettbarn, L.T. Gilday, Cost Analysis of Inadequate
Interoperability in the US Capital Facilities Industry. Grant/Contract Reports
(NISTGCR)-04-867, (Dec 1 2004), http://dx.doi.org/10.6028/NIST.GCR.04-867.
[5] B. Becerik-Gerber, F. Jazizadeh, N. Li, G. Calis, Application areas and data re-
quirements for BIM-enabled facilities management, J. Constr. Eng. Manag. 138 (3)
(2012) 431–442, http://dx.doi.org/10.1061/(ASCE)CO.1943-7862.0000433.
[6] R.S. Weygant, BIM Content Development: Standards, Strategies, and Best Practices,
John Wiley & Sons, Hoboken, 2011 (ISBN: 1118030478, 9781118030479).
[7] K.P. Reddy, BIM for Building Owners and Developers: Making a Business Case for
Using BIM on Projects, John Wiley & Sons, Hoboken, 2011 (ISBN: 0470905980,
9780470905982).
[8] Building Commissioning Association, New construction building commissioning
best practice, Available from: http://www.bcxa.org/wp-content/pdf/BCA-Best-
Practices-Commissioning-New-Construction.pdf, (2011) (Internet, cited 2017
Oct 7).
[9] Y. Jiao, Y. Wang, S. Zhang, Y. Li, B. Yang, L. Yuan, A cloud approach to unified
lifecycle data management in architecture, engineering, construction and facilities
management: integrating BIMs and SNS, Adv. Eng. Inform. 27 (2) (2013) 173–188,
http://dx.doi.org/10.1016/j.aei.2012.11.006.
[10] Z. Zou, Y. Wang, Framework of spatial decision support system for large-scale
public building evacuation, WRI Global Congress on Intelligent Systems, vol. 1,
2009, pp. 352–356, , http://dx.doi.org/10.1109/GCIS.2009.382.
[11] R.A. Kivits, C. Furneaux, BIM: enabling sustainability and asset management
through knowledge management, Sci. World J. (2013), http://dx.doi.org/10.1155/
2013/983721.
[12] R. Volk, J. Stengel, F. Schultmann, Building Information Modeling (BIM) for ex-
isting buildings—literature review and future needs, Autom. Constr. 38 (2014)
109–127, http://dx.doi.org/10.1016/j.autcon.2013.10.023.
[13] R. Liu, R.R.A. Issa, Issues in BIM for facility management from industry practi-
tioners'perspectives, in: I. Brilakis, L. SangHyun, B. Becerik-Gerber (Eds.), ASCE
Computing in Civil Engineering, 2013, pp. 411–418, , http://dx.doi.org/10.1061/
9780784413029.052.
[14] R. Liu, R.R.A. Issa, Survey: common knowledge in BIM for facility maintenance, J.
Perform. Constr. Facil. 30 (3) (Jun 2016), http://dx.doi.org/10.1061/(ASCE)CF.
1943-5509.0000778.
[15] P. Dias, S. Ergan, The need for representing facility information with customized
LOD for specific FM tasks, Construction Research Congress, 2016, pp. 2563–2572, ,
http://dx.doi.org/10.1061/9780784479827.255.
[16] S. Chunduri, R. Kreider, J. Messner, A Case Study Implementation of the BIM
Planning Procedures for Facility Owners. AEI. 2013, (2013), pp. 691–701, http://
dx.doi.org/10.1061/9780784412909.068.
[17] E.A. Pärn, D.J. Edwards, M.C. Sing, The building information modelling trajectory
in facilities management: a review, Autom. Constr. 75 (Mar 31 2017) 45–55, http://
dx.doi.org/10.1016/j.autcon.2016.12.003.
[18] B.K. Giel, G. Mayo, R.R.A. Issa, BIM use and requirements among building owners,
in: R.R.A. Issa, S. Olbina (Eds.), Building Information Modeling. ASCE, 2015, pp.
255–277, , http://dx.doi.org/10.1061/9780784412343.0044.
[19] A. Sattenini, S. Azhar, J. Thuston, Preparing a building information model for fa-
cility maintenance and management, 28th International Symposium on Automation
and Robotics in Construction, Seoul, Internation Association for Automation and
Robotics in Construction, 2011, pp. 144–149 (ISBN: 9781510804296).
[20] P. Parsanezhad, J. Dimyadi, Effective facility management and operations via a
BIM-based integrated information system, CIB Facilities Management Conference,
Technical University of Denmark, 2014, pp. 21–23 (ISBN: 978-87-502-1069-6).
[21] W. East, Construction operations building information exchange (COBie). WBDG,
Available from: https://www.wbdg.org/resources/cobie.php, (2014) (Internet,
cited 2017 Oct 7).
[22] W. Thabet, J. Lucas, S. Johnston, A case study for improving BIM-FM handover for a
large educational institution, Construction Research Congress, 2016, pp.
2177–2186, , http://dx.doi.org/10.1061/9780784479827.217.
[23] A. Anderson, A. Marsters, C.S. Dossick, G. Neff, Construction to operations ex-
change: challenges of implementing COBie and BIM in a large owner organization,
Construction Research Congress 2012: Construction Challenges in a Flat World,
2012, pp. 688–697, , http://dx.doi.org/10.1061/9780784412329.070.
[24] G. Mayo, R.R. Issa, Nongeometric building information needs assessment for fa-
cilities management, J. Manag. Eng. 32 (3) (Dec 30 2015), http://dx.doi.org/10.
1061/(ASCE)ME.1943-5479.0000414 (04015054).
[25] H.B. Cavka, S. Staub-French, R. Pottinger, Evaluating the alignment of organiza-
tional and project contexts for BIM adoption: a case study of a large owner orga-
nization, Buildings 5 (4) (Nov 27 2015) 1265–1300, http://dx.doi.org/10.3390/
buildings5041265.
[26] S.K. Lee, H.K. An, J.H. Yu, An extension of the technology acceptance model for
BIM-based FM, Construction Research Congress, 2012, pp. 602–611, , http://dx.doi.
org/10.1061/9780784412329.061.
[27] W.E. East, W. Brodt, BIM for construction handover, J. Build. Inf. Model. ((Fall)
2007) 28–35. Available from: http://www.1stpricing.com/pdf/jbim_fall07.pdf
(Internet, cited 2017 Oct 7).
[28] B. Tian, K. Liu, Service-oriented approach to facility management using extended
building information modelling. ICCREM 2014: smart construction and manage-
ment in the context of new, Technology (2014) 1500–1507, http://dx.doi.org/10.
1061/9780784413777.178.
[29] A. Borhani, H.W. Lee, C.S. Dossick, L. Osburn, M. Kinsman, BIM to facilities man-
agement: presenting a proven workflow for information exchange, Computing in
Civil Engineering, 2017, pp. 51–58, , http://dx.doi.org/10.1061/9780784480823.
007.
[30] K. Orr, Z. Shen, P. Juneja, N. Snodgrass, H. Kim, Intelligent facilities: applicability
and flexibility of open BIM standards for operations and maintenance, Construction
Research Congress, 2014, pp. 1951–1960, , http://dx.doi.org/10.1061/
9780784413517.199.
[31] A. Akcamete, B. Akinci, J.H. Garrett, Potential utilization of building information
models for planning maintenance activities, Proceedings of the International
Conference on Computing in Civil and Building Engineering, Jun. 2010, pp.
151–158 (ISBN 978-1-907284-60-1).
[32] Y. Arayici, T.C. Onyenobi, C.O. Egbu, Building information modelling (BIM) for
facilities management (FM): the MediaCity case study approach, Int. J. 3D Inf.
Model. 1 (1) (2012) 55–73 (ISSN:2156-1710).
[33] A. Kiviniemi, R. Codinhoto, Challenges in the implementation of BIM for FM—case
Manchester Town Hall Complex, Computing in Civil and Building Engineering,
2014 2014, pp. 665–672, , http://dx.doi.org/10.1061/9780784413616.083.
[34] M. Kassem, G. Kelly, N. Dawood, M. Serginson, S. Lockley, BIM in facilities man-
agement applications: a case study of a large university complex, Built Environment
Project and Asset Management, vol. 5(3), Jul 6 2015, pp. 261–277, , http://dx.doi.
org/10.1108/BEPAM-02-2014-0011.
[35] S. Terreno, C.J. Anumba, E. Gannon, C. Dubler, The benefits of BIM integration with
facilities management: a preliminary case study, Computing in Civil Engineering,
2015, pp. 675–683, , http://dx.doi.org/10.1061/9780784479247.084.
[36] P.A. Zadeh, S. Staub-French, R. Pottinger, Review of BIM quality assessment ap-
proaches for facility management, 5th International/11th Construction Specialty
Conference. Vancouver, British Columbia, 2015, http://dx.doi.org/10.14288/1.
0076364.
[37] S. Terreno, C.J. Anumba, C. Dubler, BIM-based management of building operations,
Construction Research Congress, 2016, pp. 1855–1865, , http://dx.doi.org/10.
1061/9780784479827.185.
[38] M. Khaja, J.D. Seo, J.J. McArthur, Optimizing BIM metadata manipulation using
parametric tools, Procedia Eng. 145 (Dec 31 2016) 259–266, http://dx.doi.org/10.
1016/j.proeng.2016.04.072.
[39] R. Yin, Applications of Case Study Research, 3rd ed., Sage, 2011 (ISBN:
1452235783, 9781452235783).
[40] Georgia Insititute of Technology, Georgia Tech BIM requirements & guidelines for
architects, engineers and contractors, Available from: https://facilities.gatech.edu/
files/DC/BIM%20Requirements-20150904-1_5.docx, (2017) (Internet, cited 2017
Oct 7).
[41] Georgia Insititute of Technology, Architecture and engineering design standards for
building technology, Available from: https://facilities.gatech.edu/files/DC/
GTSpec_7.6.pdf, (2017) (Internet, cited 2017 Oct 7).
[42] Georgia Insititute of Technology, Georgia Tech BIM execution plan template,
Available from: https://facilities.gatech.edu/files/DC/GT%20BIM%20Execution
%20Plan%20Template%20v1.5.docx, (2017) (Internet, cited 2017 Oct 7).
[43] Georgia Insititute of Technology, GT BIM component worksheet, Available from:
http://www.facilities.gatech.edu/files/DC/2011_0531_BIM_Component_Check_List.
pdf, (2017) (Internet, cited 2017 Oct 7).
[44] Georgia Insititute of Technology, GT COBie Objects for O&M Tracking in AiM,
Available from: https://facilities.gatech.edu/files/DC/GT%20COBie%20Objects
%20for%20O%26M%20Tracking%20in%20AiM.xlsx, (2017) (Internet, cited 2017
Oct 7).
[45] invicara, BIM Assure, Available from: http://bimassure.com/, (2017) (software,
cited 2017 Oct 7).
[46] Safe Sofware, FME, Available from: https://www.safe.com/, (2017) (software, cited
2017 Oct 7).
[47] dRofus AS, dRofus, Available from: http://www.drofus.no/en/, (2017) (software;
cited 2017 Oct 7).
[48] Solibri Inc, Solibri model checker, Available from: https://www.solibri.com/,
(2017) (software, cited 2017 Oct 7).
[49] Concerto Integrated Software Solutions, Concerto, Available from: http://www.
concerto.co.uk/, (2017) (software, cited 2017 Oct 7).
[50] P.A. Zadeh, G. Wang, H.B. Cavka, S. Staub-French, R. Pottinger, Information quality
assessment for facility management, Adv. Eng. Inform. 33 (Aug 1 2017) 181–205,
http://dx.doi.org/10.1016/j.aei.2017.06.003.
[51] S.P. Jawadekar, A case study of the use of BIM and construction operations building
P. Pishdad-Bozorgi et al. Automation in Construction 87 (2018) 22–38
37
Paraphrase This Document
Need a fresh take? Get an instant paraphrase of this document with our AI Paraphraser
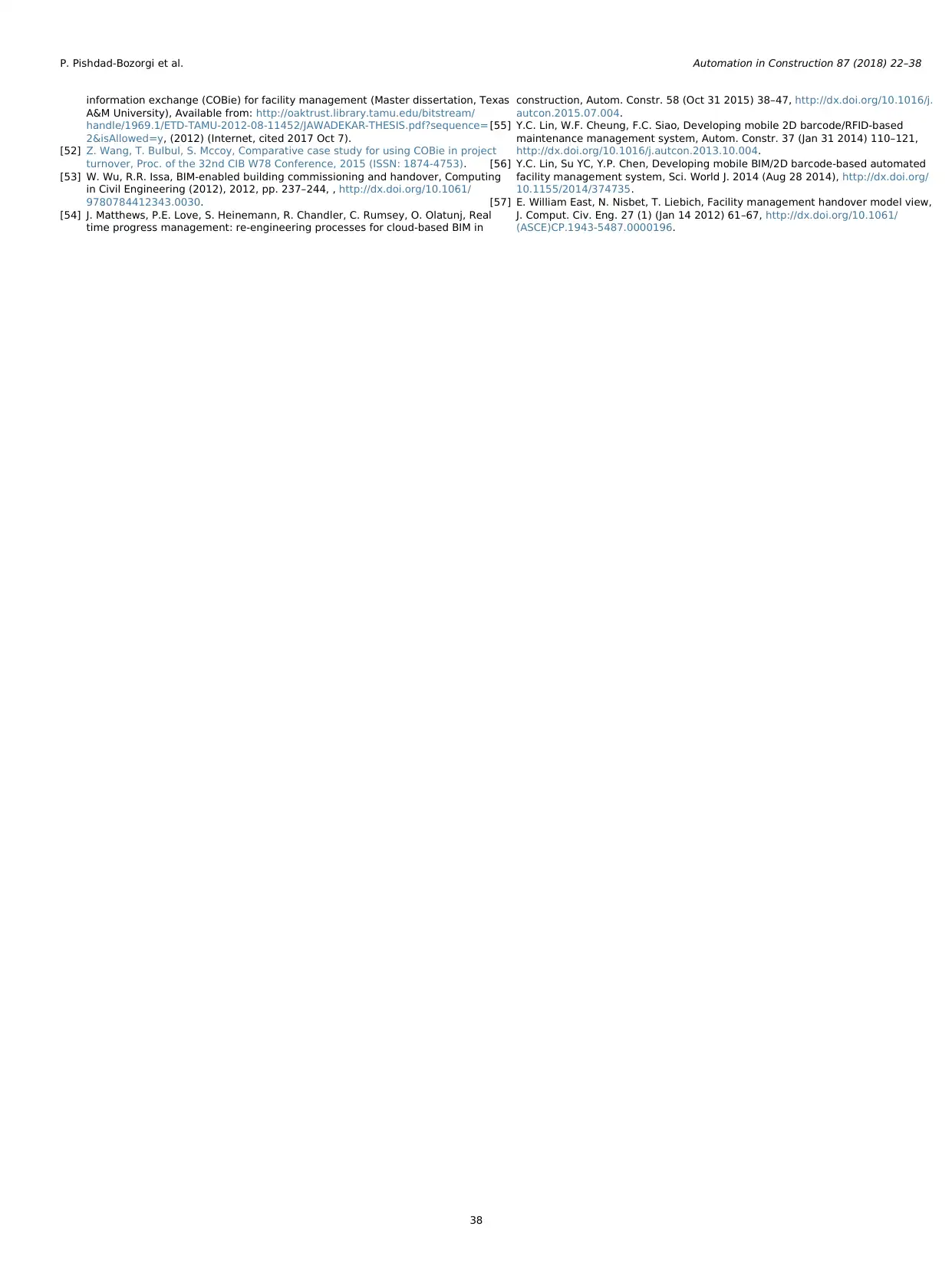
information exchange (COBie) for facility management (Master dissertation, Texas
A&M University), Available from: http://oaktrust.library.tamu.edu/bitstream/
handle/1969.1/ETD-TAMU-2012-08-11452/JAWADEKAR-THESIS.pdf?sequence=
2&isAllowed=y, (2012) (Internet, cited 2017 Oct 7).
[52] Z. Wang, T. Bulbul, S. Mccoy, Comparative case study for using COBie in project
turnover, Proc. of the 32nd CIB W78 Conference, 2015 (ISSN: 1874-4753).
[53] W. Wu, R.R. Issa, BIM-enabled building commissioning and handover, Computing
in Civil Engineering (2012), 2012, pp. 237–244, , http://dx.doi.org/10.1061/
9780784412343.0030.
[54] J. Matthews, P.E. Love, S. Heinemann, R. Chandler, C. Rumsey, O. Olatunj, Real
time progress management: re-engineering processes for cloud-based BIM in
construction, Autom. Constr. 58 (Oct 31 2015) 38–47, http://dx.doi.org/10.1016/j.
autcon.2015.07.004.
[55] Y.C. Lin, W.F. Cheung, F.C. Siao, Developing mobile 2D barcode/RFID-based
maintenance management system, Autom. Constr. 37 (Jan 31 2014) 110–121,
http://dx.doi.org/10.1016/j.autcon.2013.10.004.
[56] Y.C. Lin, Su YC, Y.P. Chen, Developing mobile BIM/2D barcode-based automated
facility management system, Sci. World J. 2014 (Aug 28 2014), http://dx.doi.org/
10.1155/2014/374735.
[57] E. William East, N. Nisbet, T. Liebich, Facility management handover model view,
J. Comput. Civ. Eng. 27 (1) (Jan 14 2012) 61–67, http://dx.doi.org/10.1061/
(ASCE)CP.1943-5487.0000196.
P. Pishdad-Bozorgi et al. Automation in Construction 87 (2018) 22–38
38
A&M University), Available from: http://oaktrust.library.tamu.edu/bitstream/
handle/1969.1/ETD-TAMU-2012-08-11452/JAWADEKAR-THESIS.pdf?sequence=
2&isAllowed=y, (2012) (Internet, cited 2017 Oct 7).
[52] Z. Wang, T. Bulbul, S. Mccoy, Comparative case study for using COBie in project
turnover, Proc. of the 32nd CIB W78 Conference, 2015 (ISSN: 1874-4753).
[53] W. Wu, R.R. Issa, BIM-enabled building commissioning and handover, Computing
in Civil Engineering (2012), 2012, pp. 237–244, , http://dx.doi.org/10.1061/
9780784412343.0030.
[54] J. Matthews, P.E. Love, S. Heinemann, R. Chandler, C. Rumsey, O. Olatunj, Real
time progress management: re-engineering processes for cloud-based BIM in
construction, Autom. Constr. 58 (Oct 31 2015) 38–47, http://dx.doi.org/10.1016/j.
autcon.2015.07.004.
[55] Y.C. Lin, W.F. Cheung, F.C. Siao, Developing mobile 2D barcode/RFID-based
maintenance management system, Autom. Constr. 37 (Jan 31 2014) 110–121,
http://dx.doi.org/10.1016/j.autcon.2013.10.004.
[56] Y.C. Lin, Su YC, Y.P. Chen, Developing mobile BIM/2D barcode-based automated
facility management system, Sci. World J. 2014 (Aug 28 2014), http://dx.doi.org/
10.1155/2014/374735.
[57] E. William East, N. Nisbet, T. Liebich, Facility management handover model view,
J. Comput. Civ. Eng. 27 (1) (Jan 14 2012) 61–67, http://dx.doi.org/10.1061/
(ASCE)CP.1943-5487.0000196.
P. Pishdad-Bozorgi et al. Automation in Construction 87 (2018) 22–38
38
1 out of 17
Related Documents

Your All-in-One AI-Powered Toolkit for Academic Success.
+13062052269
info@desklib.com
Available 24*7 on WhatsApp / Email
Unlock your academic potential
© 2024 | Zucol Services PVT LTD | All rights reserved.