Kingston University: Exploring Automotive Aerodynamics History
VerifiedAdded on 2023/04/07
|26
|6371
|218
Report
AI Summary
This research paper provides a comprehensive overview of the general principles and history of automotive aerodynamics. It begins by outlining the early approaches and shapes used in automotive design, followed by a discussion of wind tunnels and their role in streamlining cars. The report exami...

Automotive Aerodynamics 1
GENERAL AND HISTORY OF AUTOMOTIVE AERODYNAMICS
A Research Paper on Aerodynamics By
Rikash Mohamed
Kingston University
GENERAL AND HISTORY OF AUTOMOTIVE AERODYNAMICS
A Research Paper on Aerodynamics By
Rikash Mohamed
Kingston University
Paraphrase This Document
Need a fresh take? Get an instant paraphrase of this document with our AI Paraphraser

Automotive Aerodynamics 2
Contents
INTRODUCTION...........................................................................................................................................3
OBJECTIVES..............................................................................................................................................4
HISTORY.......................................................................................................................................................4
Approaches in Early Stages and Shapes...................................................................................................4
Wind Tunnels...........................................................................................................................................8
Car Streamlining......................................................................................................................................9
Change in Drag Coefficient of Cars........................................................................................................10
FEATURES OF AERODYNAMIC VEHICLES....................................................................................................12
Flow Field..............................................................................................................................................13
Improvement of flow.............................................................................................................................15
Characteristics of Flow...........................................................................................................................16
Causes of Drag Force.............................................................................................................................16
Boundary Layer Separation...................................................................................................................17
COMPARISON WITH AIRCRAFT AERODYNAMICS.......................................................................................18
METHODS OF STUDYING AERODYNAMICS................................................................................................20
Wind Tunnel Testing..............................................................................................................................20
Computer Modelling..............................................................................................................................22
CONCLUSION.............................................................................................................................................23
BIBLIOGRAPHY...........................................................................................................................................24
Contents
INTRODUCTION...........................................................................................................................................3
OBJECTIVES..............................................................................................................................................4
HISTORY.......................................................................................................................................................4
Approaches in Early Stages and Shapes...................................................................................................4
Wind Tunnels...........................................................................................................................................8
Car Streamlining......................................................................................................................................9
Change in Drag Coefficient of Cars........................................................................................................10
FEATURES OF AERODYNAMIC VEHICLES....................................................................................................12
Flow Field..............................................................................................................................................13
Improvement of flow.............................................................................................................................15
Characteristics of Flow...........................................................................................................................16
Causes of Drag Force.............................................................................................................................16
Boundary Layer Separation...................................................................................................................17
COMPARISON WITH AIRCRAFT AERODYNAMICS.......................................................................................18
METHODS OF STUDYING AERODYNAMICS................................................................................................20
Wind Tunnel Testing..............................................................................................................................20
Computer Modelling..............................................................................................................................22
CONCLUSION.............................................................................................................................................23
BIBLIOGRAPHY...........................................................................................................................................24

Automotive Aerodynamics 3
INTRODUCTION
This research paper is about the general and history of automotive aerodynamics and majorly
focuses of the approaches in early stages and shapes, wind tunnels, car streamlining, change of
drag coefficient of cars, features of aerodynamic vehicle such as boundary layer separation,
causes of drag force, characteristics of flow, improvement of flow, as well as flow field and also
comparison with aircraft aerodynamics. Aerodynamics involves the study of air motion,
specifically as interaction with a solid object like automotive. Automotive aerodynamics can be
defined as the study of the road vehicles aerodynamic. The major objectives of studying
aerodynamics of vehicles are to prevent aerodynamic instability at high speed and undesired lift
forced, minimize noise emission, wind noise, and reduce drag.
It first began as a way to determine methods of reducing the required power to move the
automotive at a specific speed on the roadways. In the year 1920s, engineers started considering
the shape of automobiles as a way of minimizing aerodynamic drag at a high velocity. In the
1950s, British and German automotive engineers were examining the impacts of automotive
friction for vehicles of high performance. They became conscious of the substantial increase in
the levels of sound produced by automotive at high speed by the late 1960s. Soon the highway
engineers started designing roadways to contemplate the speed effect of aerodynamic friction
generated levels of sound and the manufactures of these automobiles considered the same factors
in the design of the vehicles. Currently, numerous automakers have their own facilities for
testing wind tunnel, using it in developing and studying the aerodynamic features of any new
automotive (Ainegren & Jonsson, 2018).
INTRODUCTION
This research paper is about the general and history of automotive aerodynamics and majorly
focuses of the approaches in early stages and shapes, wind tunnels, car streamlining, change of
drag coefficient of cars, features of aerodynamic vehicle such as boundary layer separation,
causes of drag force, characteristics of flow, improvement of flow, as well as flow field and also
comparison with aircraft aerodynamics. Aerodynamics involves the study of air motion,
specifically as interaction with a solid object like automotive. Automotive aerodynamics can be
defined as the study of the road vehicles aerodynamic. The major objectives of studying
aerodynamics of vehicles are to prevent aerodynamic instability at high speed and undesired lift
forced, minimize noise emission, wind noise, and reduce drag.
It first began as a way to determine methods of reducing the required power to move the
automotive at a specific speed on the roadways. In the year 1920s, engineers started considering
the shape of automobiles as a way of minimizing aerodynamic drag at a high velocity. In the
1950s, British and German automotive engineers were examining the impacts of automotive
friction for vehicles of high performance. They became conscious of the substantial increase in
the levels of sound produced by automotive at high speed by the late 1960s. Soon the highway
engineers started designing roadways to contemplate the speed effect of aerodynamic friction
generated levels of sound and the manufactures of these automobiles considered the same factors
in the design of the vehicles. Currently, numerous automakers have their own facilities for
testing wind tunnel, using it in developing and studying the aerodynamic features of any new
automotive (Ainegren & Jonsson, 2018).
You're viewing a preview
Unlock full access by subscribing today!

Automotive Aerodynamics 4
OBJECTIVES
The main objectives of this research paper on the general and history of automotive
aerodynamics are:
To analyze the approaches in the early stages and shapes of automotive
To evaluate the features of aerodynamics
To compare aerodynamics with aircraft aerodynamics
To determine the method of studying aerodynamics (Alam, et al., 2012)
HISTORY
The aerodynamic drag caused by the frictional force significantly increases with the speed of the
vehicle. In the early 1920s, engineers stated considering the shape of an automobile so as to
minimize aerodynamic friction at high velocity. By the year 1950s, British and German
automotive engineers were examining systematically the impacts of automotive friction for the
vehicles of higher performance. Engineers also became conscious of the substantial increase in
the levels of sound produced at high speed by the vehicles by the late 1960s (Antanaitis, 2012).
Approaches in Early Stages and Shapes
The air presented the greatest obstacle to the economy and automotive speed and this was
intuitively and scientifically understood before the dawn of automotive. Entrepreneurs, racers,
engineers, and dreamers were lured by the potential for the aerodynamic offered and profound
gains. The efforts to do resulted in more remarkable vehicles even if they challenged the
aesthetic assumptions of their moments. The origins of streamlining go back to 200 years ago
and the ideal form of streamline was illustrated by Sir George Cayley in 1865. Racers,
specifically those chasing the coveted and Speed Record were normally the first to apply the aids
OBJECTIVES
The main objectives of this research paper on the general and history of automotive
aerodynamics are:
To analyze the approaches in the early stages and shapes of automotive
To evaluate the features of aerodynamics
To compare aerodynamics with aircraft aerodynamics
To determine the method of studying aerodynamics (Alam, et al., 2012)
HISTORY
The aerodynamic drag caused by the frictional force significantly increases with the speed of the
vehicle. In the early 1920s, engineers stated considering the shape of an automobile so as to
minimize aerodynamic friction at high velocity. By the year 1950s, British and German
automotive engineers were examining systematically the impacts of automotive friction for the
vehicles of higher performance. Engineers also became conscious of the substantial increase in
the levels of sound produced at high speed by the vehicles by the late 1960s (Antanaitis, 2012).
Approaches in Early Stages and Shapes
The air presented the greatest obstacle to the economy and automotive speed and this was
intuitively and scientifically understood before the dawn of automotive. Entrepreneurs, racers,
engineers, and dreamers were lured by the potential for the aerodynamic offered and profound
gains. The efforts to do resulted in more remarkable vehicles even if they challenged the
aesthetic assumptions of their moments. The origins of streamlining go back to 200 years ago
and the ideal form of streamline was illustrated by Sir George Cayley in 1865. Racers,
specifically those chasing the coveted and Speed Record were normally the first to apply the aids
Paraphrase This Document
Need a fresh take? Get an instant paraphrase of this document with our AI Paraphraser

Automotive Aerodynamics 5
of aerodynamics (Antanaitis, 2016). The first automobile to break the 100km record in 1899 was
Jamais Contente shown in the figure below:
Figure 1: Jamais Contente of 1899 (Bansal & Sharma, 2014)
The position of the driver seems to reduce the aids of aerodynamics. The aerodynamic evolution
for the land speed record cars was rapidly remarkable as evidently shown in 1906 by Stanley
Rocket. The increased velocity was also even dramatic since the Rocket broke the barrier if
200km with a run of 205.44 kmh.
Figure 2: Stanley Rocket of 1906 (Buljac & Džijan, 2016)
of aerodynamics (Antanaitis, 2016). The first automobile to break the 100km record in 1899 was
Jamais Contente shown in the figure below:
Figure 1: Jamais Contente of 1899 (Bansal & Sharma, 2014)
The position of the driver seems to reduce the aids of aerodynamics. The aerodynamic evolution
for the land speed record cars was rapidly remarkable as evidently shown in 1906 by Stanley
Rocket. The increased velocity was also even dramatic since the Rocket broke the barrier if
200km with a run of 205.44 kmh.
Figure 2: Stanley Rocket of 1906 (Buljac & Džijan, 2016)

Automotive Aerodynamics 6
The first known attempt at streamlining a passenger vehicle was in 1914 in the Alfa Romeo
which was built for the Italian Count Ricotti by the coachbuilder Castagna. This vehicle turned
out not to improve the maximum velocity of the open Alfa due to the very heavy bodywork it
possessed (Chandar & Damodaran, 2010).
Figure 3: Alfa streamliner of 1941 (Chen, 2014)
The actual success of aerodynamic passenger vehicle was the German Rumpler of 1921. Unlike
the heavy and impractical Castagna Alfa, this vehicle was influential and different dynamically
due to its complete integration and original engineering and design. This car had numerous
features such as a four-wheel independently suspended by the use of swing axles and also a mid-
engined W6 engine. The German Rumpler was tested in a wind tunnel of VW in 1979 and
attained a Coefficient of drag of .28 remarkably. This degree of Coefficient of drag was later
attained by the Passat in 1988. The Coefficient of drag of a body denotes the relative
aerodynamic slipperiness of the vehicle irrespective of its entire size. The cross-section of the
vehicle looking straight on is multiplied by the Coefficient of drag to attain the critical total
aerodynamic drag which determines efficiency and the power required. The German Rumpler
was very aerodynamic relatively, however, it was quite boxy and tall, which led to numerous of
such designs to be used basically as taxis (Dalessio & Duncan, 2017).
The first known attempt at streamlining a passenger vehicle was in 1914 in the Alfa Romeo
which was built for the Italian Count Ricotti by the coachbuilder Castagna. This vehicle turned
out not to improve the maximum velocity of the open Alfa due to the very heavy bodywork it
possessed (Chandar & Damodaran, 2010).
Figure 3: Alfa streamliner of 1941 (Chen, 2014)
The actual success of aerodynamic passenger vehicle was the German Rumpler of 1921. Unlike
the heavy and impractical Castagna Alfa, this vehicle was influential and different dynamically
due to its complete integration and original engineering and design. This car had numerous
features such as a four-wheel independently suspended by the use of swing axles and also a mid-
engined W6 engine. The German Rumpler was tested in a wind tunnel of VW in 1979 and
attained a Coefficient of drag of .28 remarkably. This degree of Coefficient of drag was later
attained by the Passat in 1988. The Coefficient of drag of a body denotes the relative
aerodynamic slipperiness of the vehicle irrespective of its entire size. The cross-section of the
vehicle looking straight on is multiplied by the Coefficient of drag to attain the critical total
aerodynamic drag which determines efficiency and the power required. The German Rumpler
was very aerodynamic relatively, however, it was quite boxy and tall, which led to numerous of
such designs to be used basically as taxis (Dalessio & Duncan, 2017).
You're viewing a preview
Unlock full access by subscribing today!

Automotive Aerodynamics 7
One of the most lasting and influential designers of this entire period was Hans Ledwinka of
Australia. After taking over the position of the chief design engineer in 1921 at Czech firm, he
came up with the primary series in 1921 of outstanding Tatra and ultimately streamliners with
frame platforms, rear air-cooled engines, and independent suspensions.
Figure 4: Tatra v570 of 1933 (Dong, et al., 2009)
The later series of Volkswagen after 1934 showed a very strong resemblance to the Tatra v570.
The introduction if streamlining in America had come in 1934, two years earlier with the
stunning Chrysler Airflow.
Wind Tunnels
Wind tunnels are huge tubes with air moving inside and this movement of air around the
automotive will make it seem like the vehicle is actually flying. The first enclosed wind tunnel
for the purposes of aerodynamics was operated and designed by Francis Herbert in 1871 from
the Aeronautical Society of Great Britain. Despite this early research, the testing of wind tunnel
was applied only to automobiles approximately one century later, after years of using simulations
by computer instead of the actual real-life. This delay was as a result of the fact that aircraft
aerodynamics differs from the automotive aerodynamics in numerous ways. This difference is
One of the most lasting and influential designers of this entire period was Hans Ledwinka of
Australia. After taking over the position of the chief design engineer in 1921 at Czech firm, he
came up with the primary series in 1921 of outstanding Tatra and ultimately streamliners with
frame platforms, rear air-cooled engines, and independent suspensions.
Figure 4: Tatra v570 of 1933 (Dong, et al., 2009)
The later series of Volkswagen after 1934 showed a very strong resemblance to the Tatra v570.
The introduction if streamlining in America had come in 1934, two years earlier with the
stunning Chrysler Airflow.
Wind Tunnels
Wind tunnels are huge tubes with air moving inside and this movement of air around the
automotive will make it seem like the vehicle is actually flying. The first enclosed wind tunnel
for the purposes of aerodynamics was operated and designed by Francis Herbert in 1871 from
the Aeronautical Society of Great Britain. Despite this early research, the testing of wind tunnel
was applied only to automobiles approximately one century later, after years of using simulations
by computer instead of the actual real-life. This delay was as a result of the fact that aircraft
aerodynamics differs from the automotive aerodynamics in numerous ways. This difference is
Paraphrase This Document
Need a fresh take? Get an instant paraphrase of this document with our AI Paraphraser

Automotive Aerodynamics 8
because vehicles do not run in free air and their motion is less affected by the forces of
aerodynamics while operating speed is also lower (Gatto, et al., 2010).
English mathematician and engineer Benjamin Robins first invented a whirling arm apparatus
which was used in determining drag and then used this apparatus to perform the first
experimentations on the theory of aviation. The whirling arm was also used by Sir George
Cayley to determine the lift and drag of numerous airfoils. His whirling arm attained top speed
between 20 and 10 feet per second and was 1.5m long. Nevertheless, the whirling arm does not
generate air flow that is reliable affecting the test shape at normal incidence. An Aeronautical
Society of Great Britain Council Member by the name Francis Herbert (1824-1908), addressed
this issue by operating, inventing, designing in 1871 the first enclosed wind tunnel. In 1897,
Konstantin Tsiolkovsky designed wind tunnel with an open-section as well as a centrifugal
blower and also determined spheres, cylinders, and flat plate’s coefficient of drag (Geyman, et
al., 2014).
In 1901, the Wright brothers used a sample wind tunnel to determine the impacts of airflow over
numerous shapes while establishing their Wright Flyer. In France 1909, Gustave Eiffel
constructed the first open-return wind tunnel at the base of the tower with his name written on it
which was powered by a 50kW electric motor. He performed wind tunnel tests equivalent to a
total of approximately 4000 tests, and his research set new aeronautical research standards
(Ghoreyshi, 2019).
Car Streamlining
While engineers have less or more conscious of what it takes to build aerodynamic designs for a
long duration, it took time for the principles of aerodynamics to be implemented in the designs of
because vehicles do not run in free air and their motion is less affected by the forces of
aerodynamics while operating speed is also lower (Gatto, et al., 2010).
English mathematician and engineer Benjamin Robins first invented a whirling arm apparatus
which was used in determining drag and then used this apparatus to perform the first
experimentations on the theory of aviation. The whirling arm was also used by Sir George
Cayley to determine the lift and drag of numerous airfoils. His whirling arm attained top speed
between 20 and 10 feet per second and was 1.5m long. Nevertheless, the whirling arm does not
generate air flow that is reliable affecting the test shape at normal incidence. An Aeronautical
Society of Great Britain Council Member by the name Francis Herbert (1824-1908), addressed
this issue by operating, inventing, designing in 1871 the first enclosed wind tunnel. In 1897,
Konstantin Tsiolkovsky designed wind tunnel with an open-section as well as a centrifugal
blower and also determined spheres, cylinders, and flat plate’s coefficient of drag (Geyman, et
al., 2014).
In 1901, the Wright brothers used a sample wind tunnel to determine the impacts of airflow over
numerous shapes while establishing their Wright Flyer. In France 1909, Gustave Eiffel
constructed the first open-return wind tunnel at the base of the tower with his name written on it
which was powered by a 50kW electric motor. He performed wind tunnel tests equivalent to a
total of approximately 4000 tests, and his research set new aeronautical research standards
(Ghoreyshi, 2019).
Car Streamlining
While engineers have less or more conscious of what it takes to build aerodynamic designs for a
long duration, it took time for the principles of aerodynamics to be implemented in the designs of

Automotive Aerodynamics 9
automotive. Previously, there was no concept of aerodynamic in these vehicles such as Ford
Model T which resembled more like a carriage of horse and was characterized by boxy design.
In the early 1900s, some racing cars incorporated aerodynamic and tapering features to one
degree or another. Edmund Rumpler who was a German inventor built the Rumper-Tropfenauto
in 1921 with a Coefficient of drag of .27. One of the biggest leaps on the American side ahead in
aerodynamic design came in 1930 with the Chrysler Airflow. Chrysler Airflow was one of the
initial vehicles designed with the mindset of aerodynamics and was inspired by the birds in
flight. This car design used some unique techniques in construction and had a nearly had an
equal distribution of weight (Gnemmi, et al., 2012).
Between 1960s and 1950s, there were some of the major developments in automotive
aerodynamics, especially in racing cars. Initially, automotive engineers investigated with
different designs having known that shapes that are streamlined could assist their vehicle to
handle between higher speeds and go faster. This ultimately evolved the racing cars into a very
precise crafting science that majority of aerodynamic. On the side of consumers, companies such
as Porsche, Lotus, and Citroen established vehicle designs that are very streamlined, however,
these were majorly implemented in sports cars of high-performance and not in daily automotive
for ordinary drivers. The development vehicle streamlined design of ordinary vehicles started in
the 1980s with the Audi 100 which had a Cd of .30 (Han & Cai, 2013).
automotive. Previously, there was no concept of aerodynamic in these vehicles such as Ford
Model T which resembled more like a carriage of horse and was characterized by boxy design.
In the early 1900s, some racing cars incorporated aerodynamic and tapering features to one
degree or another. Edmund Rumpler who was a German inventor built the Rumper-Tropfenauto
in 1921 with a Coefficient of drag of .27. One of the biggest leaps on the American side ahead in
aerodynamic design came in 1930 with the Chrysler Airflow. Chrysler Airflow was one of the
initial vehicles designed with the mindset of aerodynamics and was inspired by the birds in
flight. This car design used some unique techniques in construction and had a nearly had an
equal distribution of weight (Gnemmi, et al., 2012).
Between 1960s and 1950s, there were some of the major developments in automotive
aerodynamics, especially in racing cars. Initially, automotive engineers investigated with
different designs having known that shapes that are streamlined could assist their vehicle to
handle between higher speeds and go faster. This ultimately evolved the racing cars into a very
precise crafting science that majority of aerodynamic. On the side of consumers, companies such
as Porsche, Lotus, and Citroen established vehicle designs that are very streamlined, however,
these were majorly implemented in sports cars of high-performance and not in daily automotive
for ordinary drivers. The development vehicle streamlined design of ordinary vehicles started in
the 1980s with the Audi 100 which had a Cd of .30 (Han & Cai, 2013).
You're viewing a preview
Unlock full access by subscribing today!

Automotive Aerodynamics 10
Figure 5: Ley racing car of 1923 (Hart, et al., 2016).
Change in Drag Coefficient of Cars
Automobile drag coefficient is a parameter used in automotive design to measure its
aerodynamics and also other performance characteristics. Cd is a quantity that is dimensionless
and is used to determine the resistance or drag of a body in an environment made of fluid, like
water or air. This quantity is applied in the equation of drag in which a lower coefficient of drag
shows that the object will have a hydrodynamic drag or aerodynamic (Hirz & Stadler, 2013).
Figure 6: Measure of Coefficient of drag (Hodson, 2014)
Figure 5: Ley racing car of 1923 (Hart, et al., 2016).
Change in Drag Coefficient of Cars
Automobile drag coefficient is a parameter used in automotive design to measure its
aerodynamics and also other performance characteristics. Cd is a quantity that is dimensionless
and is used to determine the resistance or drag of a body in an environment made of fluid, like
water or air. This quantity is applied in the equation of drag in which a lower coefficient of drag
shows that the object will have a hydrodynamic drag or aerodynamic (Hirz & Stadler, 2013).
Figure 6: Measure of Coefficient of drag (Hodson, 2014)
Paraphrase This Document
Need a fresh take? Get an instant paraphrase of this document with our AI Paraphraser

Automotive Aerodynamics 11
The drag coefficient affects the way in which the vehicle passes through the air surrounding
since it increases with the square of speed. The first cars were manufactured before the invention
of wind tunnel tests and before Wright brother's era. The wind tunnels were used extensively in
the design of aircraft, however, the designers of cars notice slowly the effect of aerodynamics in
the performance of cars (Howell, 2015).
The beginning of drag reduction was between 1890 and 1920 and was started by the first car ever
to cross 100 kmh barrier in 1899. This car was made by racer Camille Jenatzy and was known as
La Jamais Content shown in figure 1 above. The shape of the vehicle was like torpedo so the
body of the vehicle was streamlined but the wheels and driver lost some of the benefits of the
body shape of the vehicle. However, this was the first attempt at designing a vehicle to be
advantageous aerodynamically. The next vehicle that was designed was the Alpha Romea Ricotti
which was designs in 1914 as an aerodynamic prototype with a shape like a teardrop and a hap
impressive high speed of 140 kmph. As shown in figure 3 above. As the aerodynamic principles
were becoming available to the engineers, they started to experiment and design with the
vehicles. The water drop falling was considered to be a perfect aerodynamic, and after the First
World War, numerous aeronautical engineers from Germany began designing vehicles (Islam &
Gaylard, 2017).
Edmund Rumpler was one of the engineers who in 1922 designed Rumpler Tropfenwagen. He
was the first person to perform wind tunnel experiments on cars and this car had drag three times
compared to the previously manufactured cars. One of the influential designers during this period
was Paul Jaray who was initially a designer of Zeppelin fenders. He designed cars with cambered
windshields, integrated headlights and fenders, and smooth body surfaces as well as other
innovations. This design was later copied by VW, Audi, and BMW. Jaray car design reduced Cd
The drag coefficient affects the way in which the vehicle passes through the air surrounding
since it increases with the square of speed. The first cars were manufactured before the invention
of wind tunnel tests and before Wright brother's era. The wind tunnels were used extensively in
the design of aircraft, however, the designers of cars notice slowly the effect of aerodynamics in
the performance of cars (Howell, 2015).
The beginning of drag reduction was between 1890 and 1920 and was started by the first car ever
to cross 100 kmh barrier in 1899. This car was made by racer Camille Jenatzy and was known as
La Jamais Content shown in figure 1 above. The shape of the vehicle was like torpedo so the
body of the vehicle was streamlined but the wheels and driver lost some of the benefits of the
body shape of the vehicle. However, this was the first attempt at designing a vehicle to be
advantageous aerodynamically. The next vehicle that was designed was the Alpha Romea Ricotti
which was designs in 1914 as an aerodynamic prototype with a shape like a teardrop and a hap
impressive high speed of 140 kmph. As shown in figure 3 above. As the aerodynamic principles
were becoming available to the engineers, they started to experiment and design with the
vehicles. The water drop falling was considered to be a perfect aerodynamic, and after the First
World War, numerous aeronautical engineers from Germany began designing vehicles (Islam &
Gaylard, 2017).
Edmund Rumpler was one of the engineers who in 1922 designed Rumpler Tropfenwagen. He
was the first person to perform wind tunnel experiments on cars and this car had drag three times
compared to the previously manufactured cars. One of the influential designers during this period
was Paul Jaray who was initially a designer of Zeppelin fenders. He designed cars with cambered
windshields, integrated headlights and fenders, and smooth body surfaces as well as other
innovations. This design was later copied by VW, Audi, and BMW. Jaray car design reduced Cd

Automotive Aerodynamics 12
to 0.29 from the prevailing 0.64. The wind tunnel experiments by Klempered showed that the
lowest Cd with wheels close to earth for half body was just 0.15 and therefore the succeeding
streamlined vehicles were designed while keeping in mind the half body design (Islam &
Gaylard, 2017).
This trend changed however after the crisis of petrol of 1970 which made oil to be unaffordable.
The result is that detailed optimized car such as VW Scirocco of 1974 has a Cd of 0.41 compared
to 1969 Open GT streamlined design of Cd 0.42. After late 1970, the work of aerodynamic
design continued from where it had previously stopped due to lack of petrol which led to the
introduction of shape optimization. The first design car to apply the shape optimization was Audi
C3100 which had Cd of 0.3 and was made in 1983. Modern cars have Cd which ranges between
0.25 and 0.30 and the future target is expected o be lower than 0.25 (Jiang & Liu, 2011).
FEATURES OF AERODYNAMIC VEHICLES
An aerodynamic automotive integrates the lights and wheel arcs into the entire shape so as to
minimize resistance caused by friction in fluid. The vehicle will be streamlined such that there
are no sharp edges above the windshield crossing the wind stream and also possess a kind of tail
known as liftback or fastback or Kammback. Vehicles such as Volkswagen 1-litre, Lomero, and
Aotra 2s tend to minimize the back area. They have a smooth and flat floor to produce desirable
downwards aerodynamic forces and support the venturi effect. It is used for passengers, cooling
and combustion, then accelerated by a nozzle and then removed beneath the floor. For mid
engines and rear of the vehicle, air is pressurized and decelerated in a diffuser, depressurizes
when passing the engine bay, and then finally filling the slipstream. These vehicles require seals
amid the high pressure around the gearbox and low-pressure region around the wheels. The
to 0.29 from the prevailing 0.64. The wind tunnel experiments by Klempered showed that the
lowest Cd with wheels close to earth for half body was just 0.15 and therefore the succeeding
streamlined vehicles were designed while keeping in mind the half body design (Islam &
Gaylard, 2017).
This trend changed however after the crisis of petrol of 1970 which made oil to be unaffordable.
The result is that detailed optimized car such as VW Scirocco of 1974 has a Cd of 0.41 compared
to 1969 Open GT streamlined design of Cd 0.42. After late 1970, the work of aerodynamic
design continued from where it had previously stopped due to lack of petrol which led to the
introduction of shape optimization. The first design car to apply the shape optimization was Audi
C3100 which had Cd of 0.3 and was made in 1983. Modern cars have Cd which ranges between
0.25 and 0.30 and the future target is expected o be lower than 0.25 (Jiang & Liu, 2011).
FEATURES OF AERODYNAMIC VEHICLES
An aerodynamic automotive integrates the lights and wheel arcs into the entire shape so as to
minimize resistance caused by friction in fluid. The vehicle will be streamlined such that there
are no sharp edges above the windshield crossing the wind stream and also possess a kind of tail
known as liftback or fastback or Kammback. Vehicles such as Volkswagen 1-litre, Lomero, and
Aotra 2s tend to minimize the back area. They have a smooth and flat floor to produce desirable
downwards aerodynamic forces and support the venturi effect. It is used for passengers, cooling
and combustion, then accelerated by a nozzle and then removed beneath the floor. For mid
engines and rear of the vehicle, air is pressurized and decelerated in a diffuser, depressurizes
when passing the engine bay, and then finally filling the slipstream. These vehicles require seals
amid the high pressure around the gearbox and low-pressure region around the wheels. The
You're viewing a preview
Unlock full access by subscribing today!

Automotive Aerodynamics 13
suspensions are either retracted or streamlined. The roof rails, the antenna, and door handle
normally have streamlined shape (Kabanovs & Garmory, 2017).
Flow Field
The centerline flow field around a passenger vehicle is defined by the reattachments and
separations. The flow character can be related directly to the pressure gradients, advanced in red
and favourable in blue.
Figure 7: Centerline flow field (Kajiwara, 2017)
Where h is unsteady attachment, g is separation at end of the roofline, f is reattachment
downstream on the roof, e is separation at roof corner, d is reattachment to top of the windshield,
c is separation in front of windshield, d is reattachment on hood, and a is separation above the
grille.
The nature of the counter-rotating structure of vortex is controlled majorly by the geometry at the
rear end while the condition of upstream flow plays a secondary role. The transverse plane
velocity vector shows the strong vortex moving and developing towards the ground with
suspensions are either retracted or streamlined. The roof rails, the antenna, and door handle
normally have streamlined shape (Kabanovs & Garmory, 2017).
Flow Field
The centerline flow field around a passenger vehicle is defined by the reattachments and
separations. The flow character can be related directly to the pressure gradients, advanced in red
and favourable in blue.
Figure 7: Centerline flow field (Kajiwara, 2017)
Where h is unsteady attachment, g is separation at end of the roofline, f is reattachment
downstream on the roof, e is separation at roof corner, d is reattachment to top of the windshield,
c is separation in front of windshield, d is reattachment on hood, and a is separation above the
grille.
The nature of the counter-rotating structure of vortex is controlled majorly by the geometry at the
rear end while the condition of upstream flow plays a secondary role. The transverse plane
velocity vector shows the strong vortex moving and developing towards the ground with
Paraphrase This Document
Need a fresh take? Get an instant paraphrase of this document with our AI Paraphraser

Automotive Aerodynamics 14
increasing distance. The slant angle of the region of backlight determines the strength of vortex.
Downwash is induced between the down rear window and vortex pair pulling flow off the roof.
The angle of the rear window with the horizontal is referred to as a backlight angle. The
inclination angle affects the strength and location of the trailing vortex (Karásek & Preumont,
2012).
An airdam is a panel which minimizes ground clearance at the front of the car beneath the
bumper. The smaller gap forces flow to accelerate locally under the airdam hence minimizing the
pressure under the vehicle and result in the formation of downforce. The flow of lower air
volume to underbody minimizes drag because of the roughness of the underbody.
Figure 8: Airdams (Knight & Lucey, 2010)
The hood angle determines the pressure gradient and plays a role of maintenance of attached
flow. The angle of windshield plays a significant role by controlling the point of attachment of
roof flow. Boat-tailing provides the highest static base pressure possible and to reduce the area
over which it acts (Kumar & Shkarayev, 2015).
Improvement of flow
Removing the rack: Anything that might increase wind drag is likely to affect the flow of wind
and there is a need of removing anything that might disturb the flow of air over the surface of the
increasing distance. The slant angle of the region of backlight determines the strength of vortex.
Downwash is induced between the down rear window and vortex pair pulling flow off the roof.
The angle of the rear window with the horizontal is referred to as a backlight angle. The
inclination angle affects the strength and location of the trailing vortex (Karásek & Preumont,
2012).
An airdam is a panel which minimizes ground clearance at the front of the car beneath the
bumper. The smaller gap forces flow to accelerate locally under the airdam hence minimizing the
pressure under the vehicle and result in the formation of downforce. The flow of lower air
volume to underbody minimizes drag because of the roughness of the underbody.
Figure 8: Airdams (Knight & Lucey, 2010)
The hood angle determines the pressure gradient and plays a role of maintenance of attached
flow. The angle of windshield plays a significant role by controlling the point of attachment of
roof flow. Boat-tailing provides the highest static base pressure possible and to reduce the area
over which it acts (Kumar & Shkarayev, 2015).
Improvement of flow
Removing the rack: Anything that might increase wind drag is likely to affect the flow of wind
and there is a need of removing anything that might disturb the flow of air over the surface of the

Automotive Aerodynamics 15
vehicle. Majority of the roof racks have cross members that can easily be removed and also there
are some racks that can entirely be removed. The rack should be removed where there is nothing
that needs to be carried on the roof so as to keep the vehicle small and light to avoid weight
imbalance. The running boards and grille bar which makes SUV look rugged and also add extra
drag and weight should be removed (Lynge, et al., 2015).
Retaining tailgate: There are some beliefs that removing the tailgates on pickups or truck is a
way of saving fuel and this makes some of the operators to replace them with a metal gate or
mesh fabric or remove them permanently. Research shows that pickup trucks are majorly fuel
efficient when its tailgate is up. This is because when the upright tailgate results in air flowing
over the roof of the vehicle to collect as a dome that is stagnant in the cargo bed.
Proper External mirror design: The design of the external mirror will either promote the smooth
flow of air around the vehicle or block the air flow. A properly well-designed mirror on a
passenger vehicle will add approximately 0.01 to the overall coefficient of drag. Poorly designed
mirrors on huge trucks may result in an increase in drag by about 10% because of their
interference effects, shape, and size (Matouk & Christophe, 2015).
Windshield and hood: The angle of windshield plays a significant role in regulating the point of
attachment of the flow of the roof. It has been proved that no minimum in drag over a 30o range.
The angle of hood determines the pressure gradient and plays a role in attached flow
maintenance. Only a small angle is required as a hood angle (McAndrew & Moran, 2013).
Characteristics of Flow
The flow over automotive aerodynamics has been exposed to thorough research for a long
duration. A vehicle generates a large drag because of the difference in pressure between the
downstream and upstream flow direction. The pressure difference results in the interrupted flow
vehicle. Majority of the roof racks have cross members that can easily be removed and also there
are some racks that can entirely be removed. The rack should be removed where there is nothing
that needs to be carried on the roof so as to keep the vehicle small and light to avoid weight
imbalance. The running boards and grille bar which makes SUV look rugged and also add extra
drag and weight should be removed (Lynge, et al., 2015).
Retaining tailgate: There are some beliefs that removing the tailgates on pickups or truck is a
way of saving fuel and this makes some of the operators to replace them with a metal gate or
mesh fabric or remove them permanently. Research shows that pickup trucks are majorly fuel
efficient when its tailgate is up. This is because when the upright tailgate results in air flowing
over the roof of the vehicle to collect as a dome that is stagnant in the cargo bed.
Proper External mirror design: The design of the external mirror will either promote the smooth
flow of air around the vehicle or block the air flow. A properly well-designed mirror on a
passenger vehicle will add approximately 0.01 to the overall coefficient of drag. Poorly designed
mirrors on huge trucks may result in an increase in drag by about 10% because of their
interference effects, shape, and size (Matouk & Christophe, 2015).
Windshield and hood: The angle of windshield plays a significant role in regulating the point of
attachment of the flow of the roof. It has been proved that no minimum in drag over a 30o range.
The angle of hood determines the pressure gradient and plays a role in attached flow
maintenance. Only a small angle is required as a hood angle (McAndrew & Moran, 2013).
Characteristics of Flow
The flow over automotive aerodynamics has been exposed to thorough research for a long
duration. A vehicle generates a large drag because of the difference in pressure between the
downstream and upstream flow direction. The pressure difference results in the interrupted flow
You're viewing a preview
Unlock full access by subscribing today!

Automotive Aerodynamics 16
separation over the vehicle surface. As a body moves through the atmosphere, it moves the
surrounding air. The body is exposed to drag and gravity. Drag is produced when a solid body
moves through a fluid environment like air and water. Drag escalates with velocity, the faster the
velocity of the object, the more drag it will be experiencing. The velocity of flow is used in the
classification of flows according to the regime of speed. Supersonic flows can be defined as
flows in which the speed of flow is greater than the sound speed everywhere. Transonic flow is
those sections of subsonic flows and sections in which the local sped of flow is greater compared
to local sound speed. Subsonic flows are those flows in which the field of airspeed is always less
than the local sound speed (Miralbes, 2012).
An incompressible flow is a flow in which there is a constant density in both space and time and
also the changes in the density result in only small variations to the results calculated. The
compressibility effects are more significant at velocities above or close to sound speed. A flow is
considered to be compressible is there are changes in density along a streamline according to the
theory of aerodynamics. This means that the variations in the density are considered unlike in
incompressible flow (Ostermeyer & Graf, 2010).
Causes of Drag Force
Aerodynamics involves the study of flow of air over the object and the forces exerted by other
air and the body on each other. Drag is the air resistance or wind force pushing the moving
object in the opposite direction to the motion of the object. There are two different types of drag
that act against a moving automotive, namely pressure drag and skin friction drag. The pressure
drag is as a result of the particles of air being spaced out more on the back surfaces and
compressed more on the front-facing surfaces. This is as a result of the separation of air layers
from the surface and starts swirling hence resulting in turbulent flow. The difference in the
separation over the vehicle surface. As a body moves through the atmosphere, it moves the
surrounding air. The body is exposed to drag and gravity. Drag is produced when a solid body
moves through a fluid environment like air and water. Drag escalates with velocity, the faster the
velocity of the object, the more drag it will be experiencing. The velocity of flow is used in the
classification of flows according to the regime of speed. Supersonic flows can be defined as
flows in which the speed of flow is greater than the sound speed everywhere. Transonic flow is
those sections of subsonic flows and sections in which the local sped of flow is greater compared
to local sound speed. Subsonic flows are those flows in which the field of airspeed is always less
than the local sound speed (Miralbes, 2012).
An incompressible flow is a flow in which there is a constant density in both space and time and
also the changes in the density result in only small variations to the results calculated. The
compressibility effects are more significant at velocities above or close to sound speed. A flow is
considered to be compressible is there are changes in density along a streamline according to the
theory of aerodynamics. This means that the variations in the density are considered unlike in
incompressible flow (Ostermeyer & Graf, 2010).
Causes of Drag Force
Aerodynamics involves the study of flow of air over the object and the forces exerted by other
air and the body on each other. Drag is the air resistance or wind force pushing the moving
object in the opposite direction to the motion of the object. There are two different types of drag
that act against a moving automotive, namely pressure drag and skin friction drag. The pressure
drag is as a result of the particles of air being spaced out more on the back surfaces and
compressed more on the front-facing surfaces. This is as a result of the separation of air layers
from the surface and starts swirling hence resulting in turbulent flow. The difference in the
Paraphrase This Document
Need a fresh take? Get an instant paraphrase of this document with our AI Paraphraser
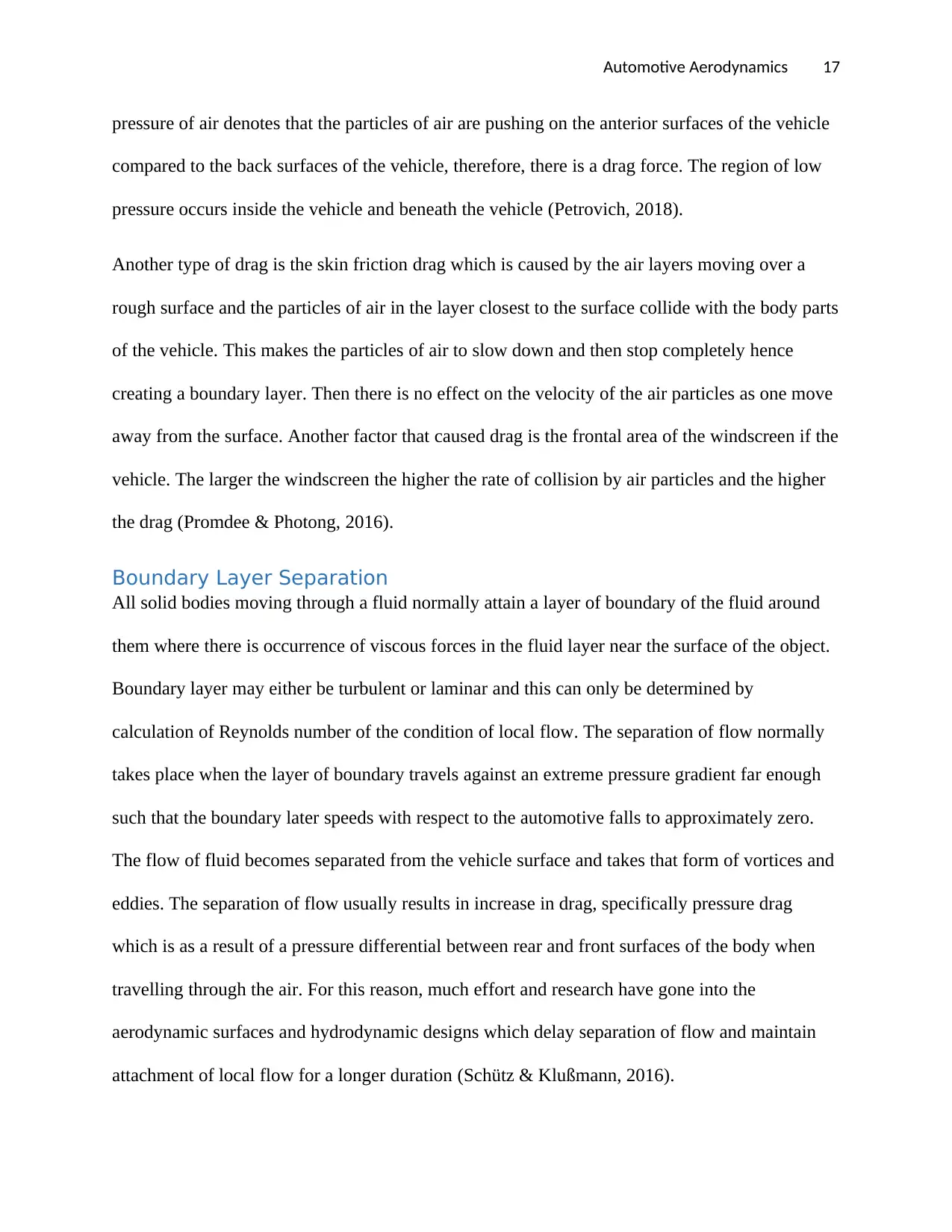
Automotive Aerodynamics 17
pressure of air denotes that the particles of air are pushing on the anterior surfaces of the vehicle
compared to the back surfaces of the vehicle, therefore, there is a drag force. The region of low
pressure occurs inside the vehicle and beneath the vehicle (Petrovich, 2018).
Another type of drag is the skin friction drag which is caused by the air layers moving over a
rough surface and the particles of air in the layer closest to the surface collide with the body parts
of the vehicle. This makes the particles of air to slow down and then stop completely hence
creating a boundary layer. Then there is no effect on the velocity of the air particles as one move
away from the surface. Another factor that caused drag is the frontal area of the windscreen if the
vehicle. The larger the windscreen the higher the rate of collision by air particles and the higher
the drag (Promdee & Photong, 2016).
Boundary Layer Separation
All solid bodies moving through a fluid normally attain a layer of boundary of the fluid around
them where there is occurrence of viscous forces in the fluid layer near the surface of the object.
Boundary layer may either be turbulent or laminar and this can only be determined by
calculation of Reynolds number of the condition of local flow. The separation of flow normally
takes place when the layer of boundary travels against an extreme pressure gradient far enough
such that the boundary later speeds with respect to the automotive falls to approximately zero.
The flow of fluid becomes separated from the vehicle surface and takes that form of vortices and
eddies. The separation of flow usually results in increase in drag, specifically pressure drag
which is as a result of a pressure differential between rear and front surfaces of the body when
travelling through the air. For this reason, much effort and research have gone into the
aerodynamic surfaces and hydrodynamic designs which delay separation of flow and maintain
attachment of local flow for a longer duration (Schütz & Klußmann, 2016).
pressure of air denotes that the particles of air are pushing on the anterior surfaces of the vehicle
compared to the back surfaces of the vehicle, therefore, there is a drag force. The region of low
pressure occurs inside the vehicle and beneath the vehicle (Petrovich, 2018).
Another type of drag is the skin friction drag which is caused by the air layers moving over a
rough surface and the particles of air in the layer closest to the surface collide with the body parts
of the vehicle. This makes the particles of air to slow down and then stop completely hence
creating a boundary layer. Then there is no effect on the velocity of the air particles as one move
away from the surface. Another factor that caused drag is the frontal area of the windscreen if the
vehicle. The larger the windscreen the higher the rate of collision by air particles and the higher
the drag (Promdee & Photong, 2016).
Boundary Layer Separation
All solid bodies moving through a fluid normally attain a layer of boundary of the fluid around
them where there is occurrence of viscous forces in the fluid layer near the surface of the object.
Boundary layer may either be turbulent or laminar and this can only be determined by
calculation of Reynolds number of the condition of local flow. The separation of flow normally
takes place when the layer of boundary travels against an extreme pressure gradient far enough
such that the boundary later speeds with respect to the automotive falls to approximately zero.
The flow of fluid becomes separated from the vehicle surface and takes that form of vortices and
eddies. The separation of flow usually results in increase in drag, specifically pressure drag
which is as a result of a pressure differential between rear and front surfaces of the body when
travelling through the air. For this reason, much effort and research have gone into the
aerodynamic surfaces and hydrodynamic designs which delay separation of flow and maintain
attachment of local flow for a longer duration (Schütz & Klußmann, 2016).

Automotive Aerodynamics 18
Figure 9: Separation of Boundary Layer (Sheng & Srigrarom, 2010)
Boundary layer separation is the boundary layer detachment from the surface into a broader
wake. The separation of boundary layer takes place when the section of the boundary layer
nearer the leading edges or wall reverses in flow direction. The point of separation is the point
between forward or backward flow, where there is zero shear stress. When there is a separation
of the boundary layer, its thickness of displacement sharply increases, which changes the
pressure field and exterior potential flow. The modification of pressure field results in an
increase in pressure drag in the case of airfoils, and if extreme will lead to undesirable stall and
loss of life (Sorbjan, 2013).
COMPARISON WITH AIRCRAFT AERODYNAMICS
Aircraft aerodynamics differs from automotive aerodynamics in numerous ways. The first
difference is the distinctive road vehicle shape which is not as streamlined as an aircraft. The
major reason why aircraft are more streamlined is because of the high velocity in which these
aircraft move so as to attain the required thrust to take off and also while in the air. In flights, the
engine thrust must be greater than the air resistance and drag. Drag is dependent on the area of
the front and also the shape of the automotive. The drag is minimize by streamlining the plane
Figure 9: Separation of Boundary Layer (Sheng & Srigrarom, 2010)
Boundary layer separation is the boundary layer detachment from the surface into a broader
wake. The separation of boundary layer takes place when the section of the boundary layer
nearer the leading edges or wall reverses in flow direction. The point of separation is the point
between forward or backward flow, where there is zero shear stress. When there is a separation
of the boundary layer, its thickness of displacement sharply increases, which changes the
pressure field and exterior potential flow. The modification of pressure field results in an
increase in pressure drag in the case of airfoils, and if extreme will lead to undesirable stall and
loss of life (Sorbjan, 2013).
COMPARISON WITH AIRCRAFT AERODYNAMICS
Aircraft aerodynamics differs from automotive aerodynamics in numerous ways. The first
difference is the distinctive road vehicle shape which is not as streamlined as an aircraft. The
major reason why aircraft are more streamlined is because of the high velocity in which these
aircraft move so as to attain the required thrust to take off and also while in the air. In flights, the
engine thrust must be greater than the air resistance and drag. Drag is dependent on the area of
the front and also the shape of the automotive. The drag is minimize by streamlining the plane
You're viewing a preview
Unlock full access by subscribing today!

Automotive Aerodynamics 19
leading to low consumption of fuel and high speed for a given power. The vehicles also operate
closer to the ground and not free air like aircraft. The vehicles are always in contact with the
ground and at no particular time will they operate without a surface. However, aircraft only use
the ground surface to attain the required momentum before take-off and also during landing
(Stoll, et al., 2016).
The third difference between aircraft and automotive is that the speed of operation is lower in the
case of automotive while in aircraft, the operating speed is higher and the drag varies as the
square of speed. The major reason why the aircraft have higher speeds is because of the
momentum they need to take off while in vehicles, they can operate at any speed. The ground
vehicles also have a fewer degree of freedom compared to aircraft, and its motion is not entirely
affected forces of aerodynamics. This means that the aircraft are more flexible and can turn at an
angle of 360o at a short distance without the risk of toppling. The last difference is that
commercial and passenger ground vehicles have specific constraints in design like high safety
standards and their intended purposes and also some regulations. This basically does not apply to
aircraft (Swanson & Isaac, 2010).
METHODS OF STUDYING AERODYNAMICS
Aerodynamics can be studied by the use of both wind tunnel testing and computer modelling.
There two methods of studying aerodynamics are discussed below:
leading to low consumption of fuel and high speed for a given power. The vehicles also operate
closer to the ground and not free air like aircraft. The vehicles are always in contact with the
ground and at no particular time will they operate without a surface. However, aircraft only use
the ground surface to attain the required momentum before take-off and also during landing
(Stoll, et al., 2016).
The third difference between aircraft and automotive is that the speed of operation is lower in the
case of automotive while in aircraft, the operating speed is higher and the drag varies as the
square of speed. The major reason why the aircraft have higher speeds is because of the
momentum they need to take off while in vehicles, they can operate at any speed. The ground
vehicles also have a fewer degree of freedom compared to aircraft, and its motion is not entirely
affected forces of aerodynamics. This means that the aircraft are more flexible and can turn at an
angle of 360o at a short distance without the risk of toppling. The last difference is that
commercial and passenger ground vehicles have specific constraints in design like high safety
standards and their intended purposes and also some regulations. This basically does not apply to
aircraft (Swanson & Isaac, 2010).
METHODS OF STUDYING AERODYNAMICS
Aerodynamics can be studied by the use of both wind tunnel testing and computer modelling.
There two methods of studying aerodynamics are discussed below:
Paraphrase This Document
Need a fresh take? Get an instant paraphrase of this document with our AI Paraphraser

Automotive Aerodynamics 20
Wind Tunnel Testing
A wind tunnel is a tool in the aircraft industry that can be used to determine real time
effectiveness of aerodynamics of a vehicle. Wind tunnels are huge tube with fast which generate
flow of air over a vehicle inside. The object may be an aeroplane or vehicle that is supposed to
be measured for resistance of air. From the room opposite the wind tunnel, engineer analyzes the
manner in which the air currents flow over the various surfaces and the manner air interacts with
the object. The plane or car in the wind tunnel does not move, however, the fast produces wind at
different velocities to simulate the conditions of real-life. Computers are used to determine the
coefficient of drag (Cd) during the movement of wind over the automotive in the tunnel. Air
pressures and velocity are measured in numerous ways during wind tunnel testing (Tesch, et al.,
2010).
The velocity of air through the test section is noted through Bernoulli’s principle. The
temperature rise, static pressure, and dynamic pressure measurements in the airflow can also be
determined. The airflow direction around the object can be measured through yarn tufts coupled
to the surfaces of aerodynamic. The direction airflow approaching a surface can be imagined by
mounting threads in the airflow in front of the test object. A bubble of liquid or smoke can be
subjected into the upstream airflow of the test object. Aerodynamic forces on the test object are
normally determined with beam balances coupled to the test object with cables, strings, or beams
(Venkata, et al., 2014).
The distribution of pressure across the test object has always been measured historically through
drilling numerous minute holes along the path of airflow and using manometers to determine the
pressure in every hole. The distribution of pressure can also be measured appropriately by the
Wind Tunnel Testing
A wind tunnel is a tool in the aircraft industry that can be used to determine real time
effectiveness of aerodynamics of a vehicle. Wind tunnels are huge tube with fast which generate
flow of air over a vehicle inside. The object may be an aeroplane or vehicle that is supposed to
be measured for resistance of air. From the room opposite the wind tunnel, engineer analyzes the
manner in which the air currents flow over the various surfaces and the manner air interacts with
the object. The plane or car in the wind tunnel does not move, however, the fast produces wind at
different velocities to simulate the conditions of real-life. Computers are used to determine the
coefficient of drag (Cd) during the movement of wind over the automotive in the tunnel. Air
pressures and velocity are measured in numerous ways during wind tunnel testing (Tesch, et al.,
2010).
The velocity of air through the test section is noted through Bernoulli’s principle. The
temperature rise, static pressure, and dynamic pressure measurements in the airflow can also be
determined. The airflow direction around the object can be measured through yarn tufts coupled
to the surfaces of aerodynamic. The direction airflow approaching a surface can be imagined by
mounting threads in the airflow in front of the test object. A bubble of liquid or smoke can be
subjected into the upstream airflow of the test object. Aerodynamic forces on the test object are
normally determined with beam balances coupled to the test object with cables, strings, or beams
(Venkata, et al., 2014).
The distribution of pressure across the test object has always been measured historically through
drilling numerous minute holes along the path of airflow and using manometers to determine the
pressure in every hole. The distribution of pressure can also be measured appropriately by the

Automotive Aerodynamics 21
application of pressure belts that are pressure sensitive. The pitching moments, roll, yaw, lateral
forces, drag, and lift can be measured with the object mounted on a force balance over a variety
of attack angle. This enables one to generate mutual curves like angle of attack versus lift
coefficient (Vergne & Herpe, 2011).
During the wind tunnel testing, air is sucked or blown through a duct coupled with
instrumentation and port of viewing where geometrical or objects are mounted for research. The
air is typically pushed through the tunnel by the use of numerous fans. Due to the velocity of air
movement and sheer volume needed, static turbofan engines is used in powering the fans and not
electric motors. The airflow produced by the fans that are getting in the tunnel are highly
turbulent because of the motion of a fan blade and is not substantial directly for precise
determination. The moving air through the tunnel should be laminar and turbulence-free
relatively. The cross-section of the wind tunnel is normally circular and not squire due to the
effects of viscosity since there will be greater constriction flow in the square tunnel corners
which can make the airflow to be turbulent. Numerous methods can be used to determine the real
airflow around geometry and compare the result with theoretical outcomes which must also
consider Mach number and Reynolds number for operation (Xia & Wang, 2017).
Computer Modelling
The major area of computer simulation in fluid mechanics is referred to as Computation Fluid
Dynamics which is normally taken as involving the solution of complete equations controlling
energy, momentum, and mass of fluid. The turbulence modelling has limited accuracy of
Computation Fluid Dynamics, rendering the need for comparison with the data from tests.
Computation Fluid Dynamics is not purely used for what it is assumed traditionally as design,
application of pressure belts that are pressure sensitive. The pitching moments, roll, yaw, lateral
forces, drag, and lift can be measured with the object mounted on a force balance over a variety
of attack angle. This enables one to generate mutual curves like angle of attack versus lift
coefficient (Vergne & Herpe, 2011).
During the wind tunnel testing, air is sucked or blown through a duct coupled with
instrumentation and port of viewing where geometrical or objects are mounted for research. The
air is typically pushed through the tunnel by the use of numerous fans. Due to the velocity of air
movement and sheer volume needed, static turbofan engines is used in powering the fans and not
electric motors. The airflow produced by the fans that are getting in the tunnel are highly
turbulent because of the motion of a fan blade and is not substantial directly for precise
determination. The moving air through the tunnel should be laminar and turbulence-free
relatively. The cross-section of the wind tunnel is normally circular and not squire due to the
effects of viscosity since there will be greater constriction flow in the square tunnel corners
which can make the airflow to be turbulent. Numerous methods can be used to determine the real
airflow around geometry and compare the result with theoretical outcomes which must also
consider Mach number and Reynolds number for operation (Xia & Wang, 2017).
Computer Modelling
The major area of computer simulation in fluid mechanics is referred to as Computation Fluid
Dynamics which is normally taken as involving the solution of complete equations controlling
energy, momentum, and mass of fluid. The turbulence modelling has limited accuracy of
Computation Fluid Dynamics, rendering the need for comparison with the data from tests.
Computation Fluid Dynamics is not purely used for what it is assumed traditionally as design,
You're viewing a preview
Unlock full access by subscribing today!

Automotive Aerodynamics 22
but also provides suggestions in the current deficient designs through their analysis. The use of
CFD, as with other tools of modelling, should promote understanding of the problem in design
by rigorous requirements imposed by mathematical modelling (Zhang, 2017).
Figure 10: Computation Fluid Dynamics (Venkata, et al., 2014)
The manufacturers of aircraft use CFD for numerous range of design aspects. These include flow
control design like vortex generators, spoiler control surfaces, power plant integration, fuselage
design, wing design, tail design, belly fairing design, aerodynamic loads data, thrust reverser
design, ice prediction, cockpit ventilation, cabin ventilation, fuel system, and flutter (Ghoreyshi,
2019).
CONCLUSION
Aerodynamics involves the study of air motion, specifically as interaction with a solid object like
automotive. The major objectives of studying automotive aerodynamics are to prevent
aerodynamic instability at high speed and undesired lift forced, minimize noise emission, wind
noise, and reduce drag. Aircraft aerodynamics differs from automotive aerodynamics in
numerous ways, the major difference is that the distinctive shape of a road automotive which is
but also provides suggestions in the current deficient designs through their analysis. The use of
CFD, as with other tools of modelling, should promote understanding of the problem in design
by rigorous requirements imposed by mathematical modelling (Zhang, 2017).
Figure 10: Computation Fluid Dynamics (Venkata, et al., 2014)
The manufacturers of aircraft use CFD for numerous range of design aspects. These include flow
control design like vortex generators, spoiler control surfaces, power plant integration, fuselage
design, wing design, tail design, belly fairing design, aerodynamic loads data, thrust reverser
design, ice prediction, cockpit ventilation, cabin ventilation, fuel system, and flutter (Ghoreyshi,
2019).
CONCLUSION
Aerodynamics involves the study of air motion, specifically as interaction with a solid object like
automotive. The major objectives of studying automotive aerodynamics are to prevent
aerodynamic instability at high speed and undesired lift forced, minimize noise emission, wind
noise, and reduce drag. Aircraft aerodynamics differs from automotive aerodynamics in
numerous ways, the major difference is that the distinctive shape of a road automotive which is
Paraphrase This Document
Need a fresh take? Get an instant paraphrase of this document with our AI Paraphraser

Automotive Aerodynamics 23
not as streamlined as an aircraft. Drag is the force of wind or air resistance pushing the moving
body in the opposite direction to the motion of the object. There are two different categories of
drag that act against a moving automotive, namely skin friction drag and pressure drag.
Aerodynamics can be studied by the use of both wind tunnel testing and computer modelling. A
wind tunnel is a tool in the aircraft industry that can be used to measure the effectiveness of
aerodynamics of a car in real time.
not as streamlined as an aircraft. Drag is the force of wind or air resistance pushing the moving
body in the opposite direction to the motion of the object. There are two different categories of
drag that act against a moving automotive, namely skin friction drag and pressure drag.
Aerodynamics can be studied by the use of both wind tunnel testing and computer modelling. A
wind tunnel is a tool in the aircraft industry that can be used to measure the effectiveness of
aerodynamics of a car in real time.

Automotive Aerodynamics 24
BIBLIOGRAPHY
Ainegren, M. & Jonsson, P., 2018. Drag Area, Frontal Area and Drag Coefficient in Cross-Country Skiing
Techniques. s.l.:Proceedings. Vol 2. pp. 313.
Alam, F., Silva, P. & Zimmer, G., 2012. Aerodynamic study of Human Powered Vehicles. s.l.:Procedia
Engineering. Vol 34. pp. 9-14.
Antanaitis, D., 2012. Vehicle Integration Factors Affecting Brake Caliper Drag. s.l.:SAE International
Journal of Passenger Cars - Mechanical Systems. Vol 5. pp. 1244-1258.
Antanaitis, D., 2016. Vehicle Level Brake Drag Target Setting for EPA Fuel Economy Certification. s.l.:SAE
International Journal of Passenger Cars - Mechanical Systems. Vol 9. pp. 1157-1171.
Bansal, R. & Sharma, R., 2014. Drag Reduction of Passenger Car Using Add-On Devices. s.l.:Journal of
Aerodynamics. Vol 2014. pp. 1-13.
Buljac, A. & Džijan, I., 2016. Automobile aerodynamics influenced by airfoil-shaped rear wing.
s.l.:International Journal of Automotive Technology. Vol 17. pp. 377-385.
Chandar, D. & Damodaran, C., 2010. Computation of Unsteady Low Reynolds Number Free-Flight
Aerodynamics of Flapping Wings. s.l.:Journal of Aircraft. Vol 47. pp. 141-150.
Chen, Z., 2014. Application of Aerodynamics in the Automotive Repair. s.l.:Applied Mechanics and
Materials. Vol 556. pp. 991-995.
Dalessio, L. & Duncan, B., 2017. Accurate Fuel Economy Prediction via a Realistic Wind Averaged Drag
Coefficient. s.l.:SAE International Journal of Passenger Cars - Mechanical Systems. Vol 10. pp. 265-277.
Dong, H., Liang, Z. & Harff, M., 2009. Optimal Settings of Aerodynamic Performance Parameters in
Hovering Flight. s.l.:International Journal of Micro Air Vehicles. Vol 1. pp. 173-181.
Gatto, A., Bourdin, P. & Friswell, M., 2010. Experimental Investigation into Articulated Winglet Effects on
Flying Wing Surface Pressure Aerodynamics. s.l.:Journal of Aircraft. Vol 47. pp. 1811-1815.
Geyman, M., Altman, A. & Parker, G., 2014. Wing/Wall Aerodynamic Interactions in Free Flying,
Maneuvering MAVS. s.l.:nternational Journal of Micro Air Vehicles. Vol 6. pp. 89-103.
Ghoreyshi, M., 2019. Special Issue “Computational Aerodynamic Modeling of Aerospace Vehicles”.
s.l.:Aerospace. Vol 6. pp. 5.
Gnemmi, P., Meder, K. & Rey, C., 2012. Aerodynamic Performance of a Gun Launched Micro Air Vehicle.
s.l.:International Journal of Micro Air Vehicles. Vol 4. pp. 251-272.
Han, Y. & Cai, S., 2013. Aerodynamic Forces of Vehicles on the Bridge under Crosswinds. s.l.:Advanced
Materials Research. Vol 639. pp. 1206-1209.
Hart, A., Sytsma, M. & Ukeiley, L., 2016. An aerodynamic characterization facility for micro air vehicle
research. s.l.:International Journal of Micro Air Vehicles. Vol 8. pp. 79-91.
Hirz, M. & Stadler, S., 2013. A New Approach for the Reduction of Aerodynamic Drag of Long-Distance
Transportation Vehicles. s.l.:SAE International Journal of Commercial Vehicles. Vol 6. pp. 453-458.
BIBLIOGRAPHY
Ainegren, M. & Jonsson, P., 2018. Drag Area, Frontal Area and Drag Coefficient in Cross-Country Skiing
Techniques. s.l.:Proceedings. Vol 2. pp. 313.
Alam, F., Silva, P. & Zimmer, G., 2012. Aerodynamic study of Human Powered Vehicles. s.l.:Procedia
Engineering. Vol 34. pp. 9-14.
Antanaitis, D., 2012. Vehicle Integration Factors Affecting Brake Caliper Drag. s.l.:SAE International
Journal of Passenger Cars - Mechanical Systems. Vol 5. pp. 1244-1258.
Antanaitis, D., 2016. Vehicle Level Brake Drag Target Setting for EPA Fuel Economy Certification. s.l.:SAE
International Journal of Passenger Cars - Mechanical Systems. Vol 9. pp. 1157-1171.
Bansal, R. & Sharma, R., 2014. Drag Reduction of Passenger Car Using Add-On Devices. s.l.:Journal of
Aerodynamics. Vol 2014. pp. 1-13.
Buljac, A. & Džijan, I., 2016. Automobile aerodynamics influenced by airfoil-shaped rear wing.
s.l.:International Journal of Automotive Technology. Vol 17. pp. 377-385.
Chandar, D. & Damodaran, C., 2010. Computation of Unsteady Low Reynolds Number Free-Flight
Aerodynamics of Flapping Wings. s.l.:Journal of Aircraft. Vol 47. pp. 141-150.
Chen, Z., 2014. Application of Aerodynamics in the Automotive Repair. s.l.:Applied Mechanics and
Materials. Vol 556. pp. 991-995.
Dalessio, L. & Duncan, B., 2017. Accurate Fuel Economy Prediction via a Realistic Wind Averaged Drag
Coefficient. s.l.:SAE International Journal of Passenger Cars - Mechanical Systems. Vol 10. pp. 265-277.
Dong, H., Liang, Z. & Harff, M., 2009. Optimal Settings of Aerodynamic Performance Parameters in
Hovering Flight. s.l.:International Journal of Micro Air Vehicles. Vol 1. pp. 173-181.
Gatto, A., Bourdin, P. & Friswell, M., 2010. Experimental Investigation into Articulated Winglet Effects on
Flying Wing Surface Pressure Aerodynamics. s.l.:Journal of Aircraft. Vol 47. pp. 1811-1815.
Geyman, M., Altman, A. & Parker, G., 2014. Wing/Wall Aerodynamic Interactions in Free Flying,
Maneuvering MAVS. s.l.:nternational Journal of Micro Air Vehicles. Vol 6. pp. 89-103.
Ghoreyshi, M., 2019. Special Issue “Computational Aerodynamic Modeling of Aerospace Vehicles”.
s.l.:Aerospace. Vol 6. pp. 5.
Gnemmi, P., Meder, K. & Rey, C., 2012. Aerodynamic Performance of a Gun Launched Micro Air Vehicle.
s.l.:International Journal of Micro Air Vehicles. Vol 4. pp. 251-272.
Han, Y. & Cai, S., 2013. Aerodynamic Forces of Vehicles on the Bridge under Crosswinds. s.l.:Advanced
Materials Research. Vol 639. pp. 1206-1209.
Hart, A., Sytsma, M. & Ukeiley, L., 2016. An aerodynamic characterization facility for micro air vehicle
research. s.l.:International Journal of Micro Air Vehicles. Vol 8. pp. 79-91.
Hirz, M. & Stadler, S., 2013. A New Approach for the Reduction of Aerodynamic Drag of Long-Distance
Transportation Vehicles. s.l.:SAE International Journal of Commercial Vehicles. Vol 6. pp. 453-458.
You're viewing a preview
Unlock full access by subscribing today!

Automotive Aerodynamics 25
Hodson, H., 2014. Morphing dimpled skin could help cars reduce drag. s.l.:New Scientist. Vol 223. pp. 20.
Howell, J., 2015. Aerodynamic Drag of Passenger Cars at Yaw. s.l.:SAE International Journal of Passenger
Cars - Mechanical Systems. Vol 8.
Islam, A. & Gaylard, A., 2017. A detailed statistical study of unsteady wake dynamics from automotive
bluff bodies. s.l.:Journal of Wind Engineering and Industrial Aerodynamics. Vol 171. pp. 161-177.
Jiang, F. & Liu, H., 2011. Experimental Study of Automotive Aerodynamics in Headlamp Effect.
s.l.:Advanced Materials Research. Vol 279. pp. 339-344.
Kabanovs, A. & Garmory, A., 2017. Computational simulations of unsteady flow field and spray
impingement on a simplified automotive geometry. s.l.:Journal of Wind Engineering and Industrial
Aerodynamics. Vol 171. pp. 178-195.
Kajiwara, S., 2017. Passive variable rear-wing aerodynamics of an open-wheel racing car. s.l.:Automotive
and Engine Technology. Vol 2. pp. 107-117.
Karásek, M. & Preumont, A., 2012. Flapping Flight Stability in Hover: A Comparison of Various
Aerodynamic Models. s.l.:International Journal of Micro Air Vehicles. Vol 4. pp. 203-226.
Knight, J. & Lucey, A., 2010. Fluid–structure interaction of a two-dimensional membrane in a flow with a
pressure gradient with application to convertible car roofs. s.l.:Journal of Wind Engineering and
Industrial Aerodynamics. Vol 98. pp. 65-72.
Kumar, R. & Shkarayev, S., 2015. Kinematic and Aerodynamic Response of Locusts in Sideslip.
s.l.:International Journal of Micro Air Vehicles. Vol 7. pp. 159-180.
Lynge, K., Blanke, M. & Johansen, A., 2015. Diagnosis of Wing Icing Through Lift and Drag Coefficient
Change Detection for Small. s.l.:IFAC-PapersOnLine. Vol 48. pp. 541-546.
Matouk, R. & Christophe, J., 2015. Aerodynamics and Aeroacoustics Study of the Flow Around an
Automotive Fan Airfoil. s.l.:International Journal of Aeroacoustics. Vol 14. pp. 1049-1070.
McAndrew, I. & Moran, K., 2013. Aerodynamic Design Considerations for In-Flight Refueling of
Unmanned Vehicles. s.l.:Applied Mechanics and Materials. Vol 390. pp. 43-47.
Miralbes, R., 2012. Aerodynamic analysis of some vortex generator improvements for heavy vehicles.
s.l.:International Journal of Heavy Vehicle Systems. Vol 19. pp. 355.
Ostermeyer, G. & Graf, M., 2010. Mode Coupling Instabilities Induced by a Periodic Coefficient of
Friction. s.l.:SAE International Journal of Passenger Cars - Mechanical Systems. Vol 3. pp. 31-37.
Petrovich, A., 2018. HYPERSONIC WIND TUNNELS BASED ON PRESSURE MULTIPLIERS PART I, PRACTICAL
REQUIREMENTS: SCHEMES OF HYPERSONIC WIND TUNNELS. s.l.:TsAGI Science Journal. Vol 49. pp. 527-
541.
Promdee, C. & Photong, C., 2016. Effects of Wind Angles and Wind Speeds on Voltage Generation of
Savonius Wind Turbine with Double Wind Tunnels. s.l.:Procedia Computer Science. Vol 86. pp. 401-404.
Hodson, H., 2014. Morphing dimpled skin could help cars reduce drag. s.l.:New Scientist. Vol 223. pp. 20.
Howell, J., 2015. Aerodynamic Drag of Passenger Cars at Yaw. s.l.:SAE International Journal of Passenger
Cars - Mechanical Systems. Vol 8.
Islam, A. & Gaylard, A., 2017. A detailed statistical study of unsteady wake dynamics from automotive
bluff bodies. s.l.:Journal of Wind Engineering and Industrial Aerodynamics. Vol 171. pp. 161-177.
Jiang, F. & Liu, H., 2011. Experimental Study of Automotive Aerodynamics in Headlamp Effect.
s.l.:Advanced Materials Research. Vol 279. pp. 339-344.
Kabanovs, A. & Garmory, A., 2017. Computational simulations of unsteady flow field and spray
impingement on a simplified automotive geometry. s.l.:Journal of Wind Engineering and Industrial
Aerodynamics. Vol 171. pp. 178-195.
Kajiwara, S., 2017. Passive variable rear-wing aerodynamics of an open-wheel racing car. s.l.:Automotive
and Engine Technology. Vol 2. pp. 107-117.
Karásek, M. & Preumont, A., 2012. Flapping Flight Stability in Hover: A Comparison of Various
Aerodynamic Models. s.l.:International Journal of Micro Air Vehicles. Vol 4. pp. 203-226.
Knight, J. & Lucey, A., 2010. Fluid–structure interaction of a two-dimensional membrane in a flow with a
pressure gradient with application to convertible car roofs. s.l.:Journal of Wind Engineering and
Industrial Aerodynamics. Vol 98. pp. 65-72.
Kumar, R. & Shkarayev, S., 2015. Kinematic and Aerodynamic Response of Locusts in Sideslip.
s.l.:International Journal of Micro Air Vehicles. Vol 7. pp. 159-180.
Lynge, K., Blanke, M. & Johansen, A., 2015. Diagnosis of Wing Icing Through Lift and Drag Coefficient
Change Detection for Small. s.l.:IFAC-PapersOnLine. Vol 48. pp. 541-546.
Matouk, R. & Christophe, J., 2015. Aerodynamics and Aeroacoustics Study of the Flow Around an
Automotive Fan Airfoil. s.l.:International Journal of Aeroacoustics. Vol 14. pp. 1049-1070.
McAndrew, I. & Moran, K., 2013. Aerodynamic Design Considerations for In-Flight Refueling of
Unmanned Vehicles. s.l.:Applied Mechanics and Materials. Vol 390. pp. 43-47.
Miralbes, R., 2012. Aerodynamic analysis of some vortex generator improvements for heavy vehicles.
s.l.:International Journal of Heavy Vehicle Systems. Vol 19. pp. 355.
Ostermeyer, G. & Graf, M., 2010. Mode Coupling Instabilities Induced by a Periodic Coefficient of
Friction. s.l.:SAE International Journal of Passenger Cars - Mechanical Systems. Vol 3. pp. 31-37.
Petrovich, A., 2018. HYPERSONIC WIND TUNNELS BASED ON PRESSURE MULTIPLIERS PART I, PRACTICAL
REQUIREMENTS: SCHEMES OF HYPERSONIC WIND TUNNELS. s.l.:TsAGI Science Journal. Vol 49. pp. 527-
541.
Promdee, C. & Photong, C., 2016. Effects of Wind Angles and Wind Speeds on Voltage Generation of
Savonius Wind Turbine with Double Wind Tunnels. s.l.:Procedia Computer Science. Vol 86. pp. 401-404.
Paraphrase This Document
Need a fresh take? Get an instant paraphrase of this document with our AI Paraphraser
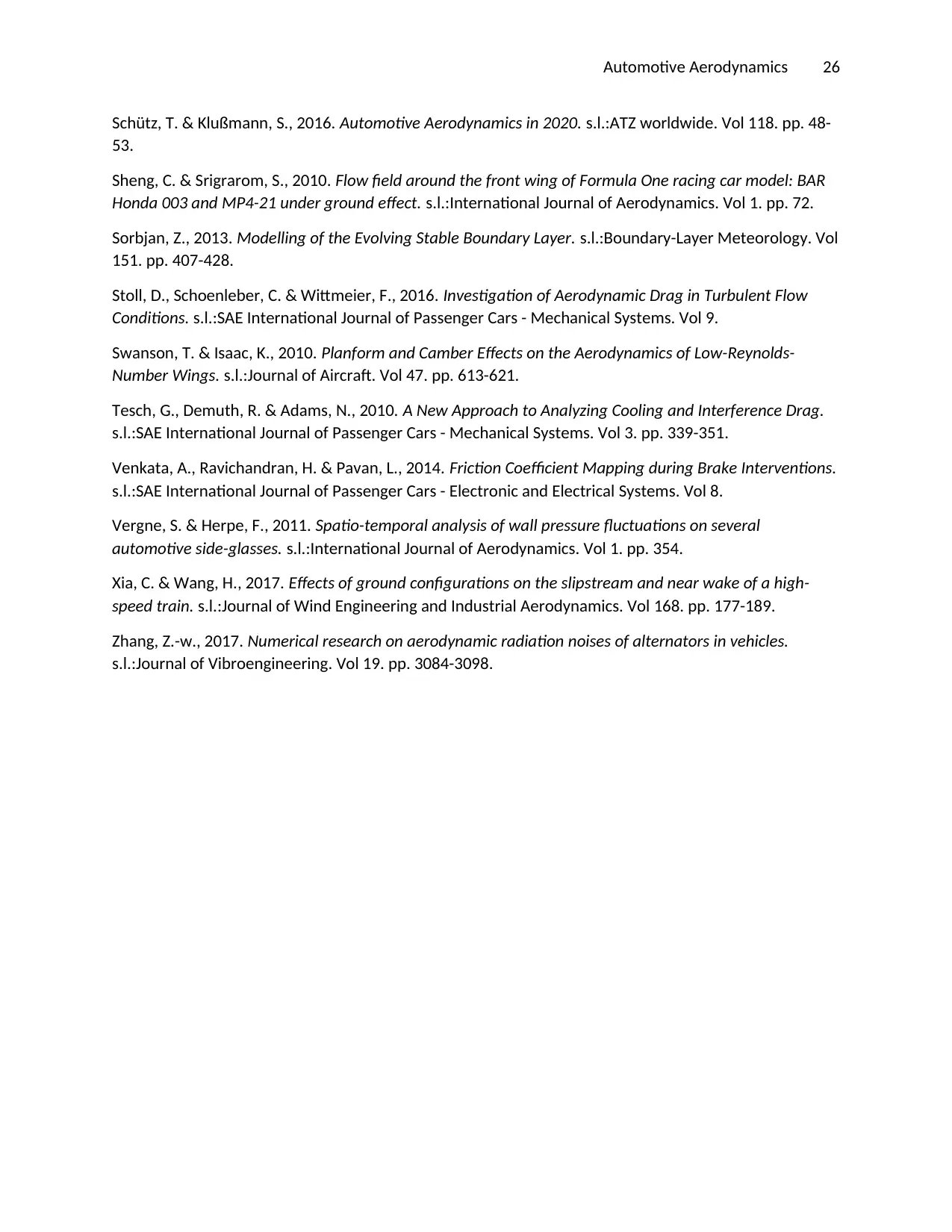
Automotive Aerodynamics 26
Schütz, T. & Klußmann, S., 2016. Automotive Aerodynamics in 2020. s.l.:ATZ worldwide. Vol 118. pp. 48-
53.
Sheng, C. & Srigrarom, S., 2010. Flow field around the front wing of Formula One racing car model: BAR
Honda 003 and MP4-21 under ground effect. s.l.:International Journal of Aerodynamics. Vol 1. pp. 72.
Sorbjan, Z., 2013. Modelling of the Evolving Stable Boundary Layer. s.l.:Boundary-Layer Meteorology. Vol
151. pp. 407-428.
Stoll, D., Schoenleber, C. & Wittmeier, F., 2016. Investigation of Aerodynamic Drag in Turbulent Flow
Conditions. s.l.:SAE International Journal of Passenger Cars - Mechanical Systems. Vol 9.
Swanson, T. & Isaac, K., 2010. Planform and Camber Effects on the Aerodynamics of Low-Reynolds-
Number Wings. s.l.:Journal of Aircraft. Vol 47. pp. 613-621.
Tesch, G., Demuth, R. & Adams, N., 2010. A New Approach to Analyzing Cooling and Interference Drag.
s.l.:SAE International Journal of Passenger Cars - Mechanical Systems. Vol 3. pp. 339-351.
Venkata, A., Ravichandran, H. & Pavan, L., 2014. Friction Coefficient Mapping during Brake Interventions.
s.l.:SAE International Journal of Passenger Cars - Electronic and Electrical Systems. Vol 8.
Vergne, S. & Herpe, F., 2011. Spatio-temporal analysis of wall pressure fluctuations on several
automotive side-glasses. s.l.:International Journal of Aerodynamics. Vol 1. pp. 354.
Xia, C. & Wang, H., 2017. Effects of ground configurations on the slipstream and near wake of a high-
speed train. s.l.:Journal of Wind Engineering and Industrial Aerodynamics. Vol 168. pp. 177-189.
Zhang, Z.-w., 2017. Numerical research on aerodynamic radiation noises of alternators in vehicles.
s.l.:Journal of Vibroengineering. Vol 19. pp. 3084-3098.
Schütz, T. & Klußmann, S., 2016. Automotive Aerodynamics in 2020. s.l.:ATZ worldwide. Vol 118. pp. 48-
53.
Sheng, C. & Srigrarom, S., 2010. Flow field around the front wing of Formula One racing car model: BAR
Honda 003 and MP4-21 under ground effect. s.l.:International Journal of Aerodynamics. Vol 1. pp. 72.
Sorbjan, Z., 2013. Modelling of the Evolving Stable Boundary Layer. s.l.:Boundary-Layer Meteorology. Vol
151. pp. 407-428.
Stoll, D., Schoenleber, C. & Wittmeier, F., 2016. Investigation of Aerodynamic Drag in Turbulent Flow
Conditions. s.l.:SAE International Journal of Passenger Cars - Mechanical Systems. Vol 9.
Swanson, T. & Isaac, K., 2010. Planform and Camber Effects on the Aerodynamics of Low-Reynolds-
Number Wings. s.l.:Journal of Aircraft. Vol 47. pp. 613-621.
Tesch, G., Demuth, R. & Adams, N., 2010. A New Approach to Analyzing Cooling and Interference Drag.
s.l.:SAE International Journal of Passenger Cars - Mechanical Systems. Vol 3. pp. 339-351.
Venkata, A., Ravichandran, H. & Pavan, L., 2014. Friction Coefficient Mapping during Brake Interventions.
s.l.:SAE International Journal of Passenger Cars - Electronic and Electrical Systems. Vol 8.
Vergne, S. & Herpe, F., 2011. Spatio-temporal analysis of wall pressure fluctuations on several
automotive side-glasses. s.l.:International Journal of Aerodynamics. Vol 1. pp. 354.
Xia, C. & Wang, H., 2017. Effects of ground configurations on the slipstream and near wake of a high-
speed train. s.l.:Journal of Wind Engineering and Industrial Aerodynamics. Vol 168. pp. 177-189.
Zhang, Z.-w., 2017. Numerical research on aerodynamic radiation noises of alternators in vehicles.
s.l.:Journal of Vibroengineering. Vol 19. pp. 3084-3098.
1 out of 26
Related Documents

Your All-in-One AI-Powered Toolkit for Academic Success.
+13062052269
info@desklib.com
Available 24*7 on WhatsApp / Email
Unlock your academic potential
© 2024 | Zucol Services PVT LTD | All rights reserved.