Building Management Systems Design and Implementation
VerifiedAdded on 2020/03/01
|33
|12905
|33
AI Summary
This assignment delves into the crucial aspects of Building Management Systems (BMS). It examines the fundamental design principles behind BMS, outlining their various components and functionalities. The assignment explores the tangible benefits that BMS bring to buildings, including enhanced energy efficiency, improved occupant comfort, and reduced operational costs. Additionally, it discusses key considerations for successful BMS implementation, emphasizing the importance of factors like system integration, user training, and ongoing maintenance.
Contribute Materials
Your contribution can guide someone’s learning journey. Share your
documents today.
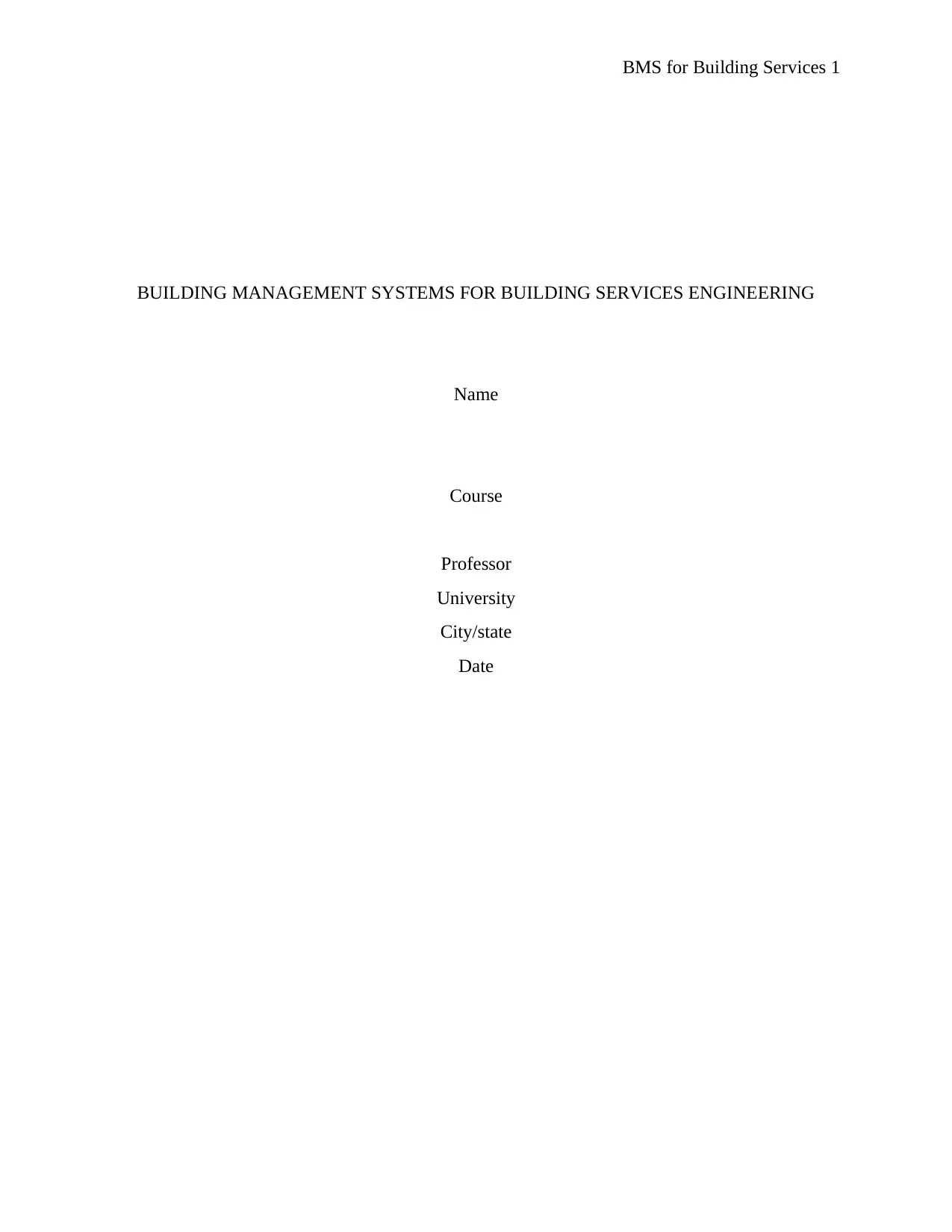
BMS for Building Services 1
BUILDING MANAGEMENT SYSTEMS FOR BUILDING SERVICES ENGINEERING
Name
Course
Professor
University
City/state
Date
BUILDING MANAGEMENT SYSTEMS FOR BUILDING SERVICES ENGINEERING
Name
Course
Professor
University
City/state
Date
Secure Best Marks with AI Grader
Need help grading? Try our AI Grader for instant feedback on your assignments.
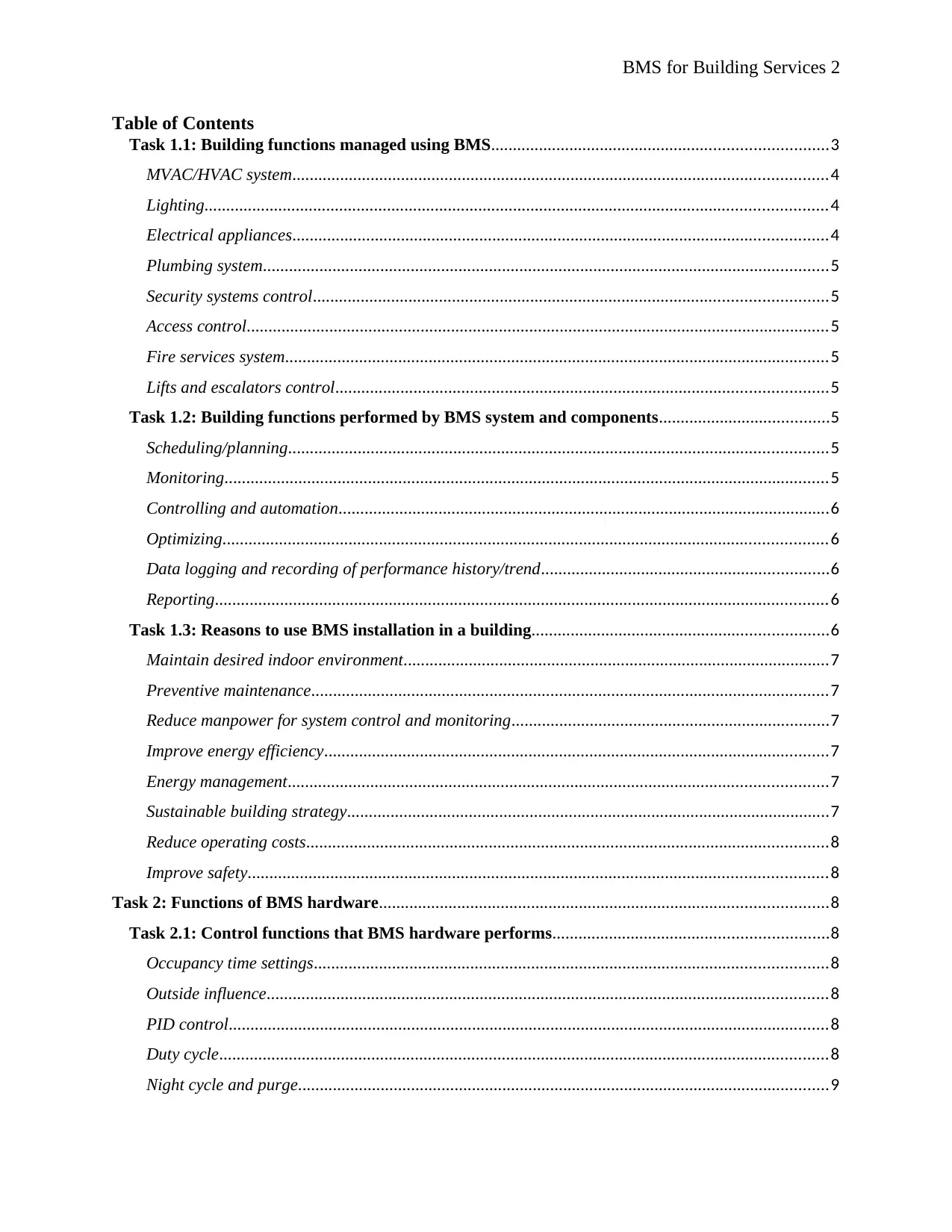
BMS for Building Services 2
Table of Contents
Task 1.1: Building functions managed using BMS.............................................................................3
MVAC/HVAC system...........................................................................................................................4
Lighting...............................................................................................................................................4
Electrical appliances...........................................................................................................................4
Plumbing system..................................................................................................................................5
Security systems control......................................................................................................................5
Access control......................................................................................................................................5
Fire services system.............................................................................................................................5
Lifts and escalators control.................................................................................................................5
Task 1.2: Building functions performed by BMS system and components.......................................5
Scheduling/planning............................................................................................................................5
Monitoring...........................................................................................................................................5
Controlling and automation.................................................................................................................6
Optimizing...........................................................................................................................................6
Data logging and recording of performance history/trend..................................................................6
Reporting.............................................................................................................................................6
Task 1.3: Reasons to use BMS installation in a building....................................................................6
Maintain desired indoor environment..................................................................................................7
Preventive maintenance.......................................................................................................................7
Reduce manpower for system control and monitoring.........................................................................7
Improve energy efficiency....................................................................................................................7
Energy management............................................................................................................................7
Sustainable building strategy...............................................................................................................7
Reduce operating costs........................................................................................................................8
Improve safety.....................................................................................................................................8
Task 2: Functions of BMS hardware.......................................................................................................8
Task 2.1: Control functions that BMS hardware performs...............................................................8
Occupancy time settings......................................................................................................................8
Outside influence.................................................................................................................................8
PID control..........................................................................................................................................8
Duty cycle............................................................................................................................................8
Night cycle and purge..........................................................................................................................9
Table of Contents
Task 1.1: Building functions managed using BMS.............................................................................3
MVAC/HVAC system...........................................................................................................................4
Lighting...............................................................................................................................................4
Electrical appliances...........................................................................................................................4
Plumbing system..................................................................................................................................5
Security systems control......................................................................................................................5
Access control......................................................................................................................................5
Fire services system.............................................................................................................................5
Lifts and escalators control.................................................................................................................5
Task 1.2: Building functions performed by BMS system and components.......................................5
Scheduling/planning............................................................................................................................5
Monitoring...........................................................................................................................................5
Controlling and automation.................................................................................................................6
Optimizing...........................................................................................................................................6
Data logging and recording of performance history/trend..................................................................6
Reporting.............................................................................................................................................6
Task 1.3: Reasons to use BMS installation in a building....................................................................6
Maintain desired indoor environment..................................................................................................7
Preventive maintenance.......................................................................................................................7
Reduce manpower for system control and monitoring.........................................................................7
Improve energy efficiency....................................................................................................................7
Energy management............................................................................................................................7
Sustainable building strategy...............................................................................................................7
Reduce operating costs........................................................................................................................8
Improve safety.....................................................................................................................................8
Task 2: Functions of BMS hardware.......................................................................................................8
Task 2.1: Control functions that BMS hardware performs...............................................................8
Occupancy time settings......................................................................................................................8
Outside influence.................................................................................................................................8
PID control..........................................................................................................................................8
Duty cycle............................................................................................................................................8
Night cycle and purge..........................................................................................................................9
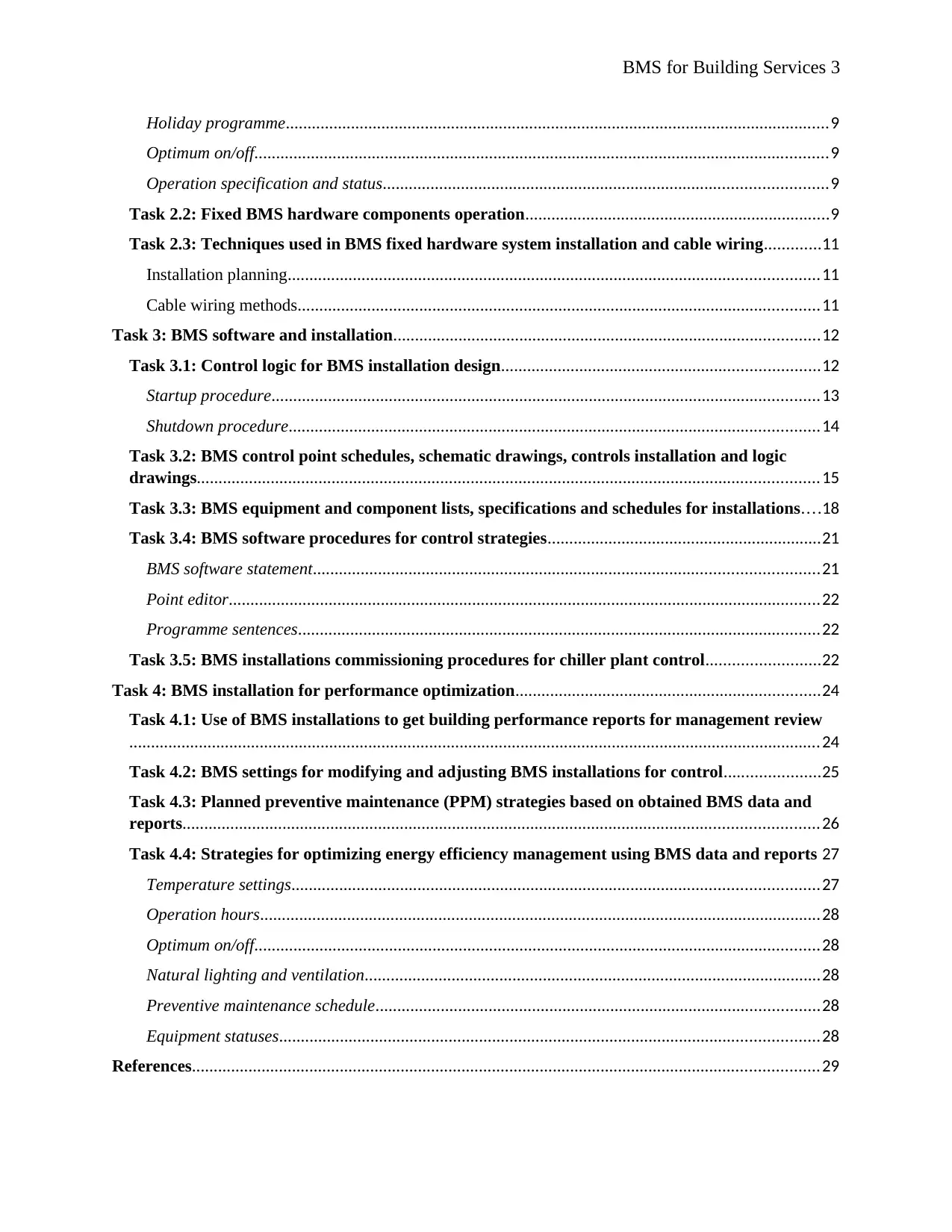
BMS for Building Services 3
Holiday programme.............................................................................................................................9
Optimum on/off....................................................................................................................................9
Operation specification and status......................................................................................................9
Task 2.2: Fixed BMS hardware components operation......................................................................9
Task 2.3: Techniques used in BMS fixed hardware system installation and cable wiring.............11
Installation planning..........................................................................................................................11
Cable wiring methods........................................................................................................................11
Task 3: BMS software and installation..................................................................................................12
Task 3.1: Control logic for BMS installation design.........................................................................12
Startup procedure..............................................................................................................................13
Shutdown procedure..........................................................................................................................14
Task 3.2: BMS control point schedules, schematic drawings, controls installation and logic
drawings...............................................................................................................................................15
Task 3.3: BMS equipment and component lists, specifications and schedules for installations....18
Task 3.4: BMS software procedures for control strategies...............................................................21
BMS software statement....................................................................................................................21
Point editor........................................................................................................................................22
Programme sentences........................................................................................................................22
Task 3.5: BMS installations commissioning procedures for chiller plant control..........................22
Task 4: BMS installation for performance optimization......................................................................24
Task 4.1: Use of BMS installations to get building performance reports for management review
...............................................................................................................................................................24
Task 4.2: BMS settings for modifying and adjusting BMS installations for control......................25
Task 4.3: Planned preventive maintenance (PPM) strategies based on obtained BMS data and
reports..................................................................................................................................................26
Task 4.4: Strategies for optimizing energy efficiency management using BMS data and reports 27
Temperature settings.........................................................................................................................27
Operation hours.................................................................................................................................28
Optimum on/off..................................................................................................................................28
Natural lighting and ventilation.........................................................................................................28
Preventive maintenance schedule......................................................................................................28
Equipment statuses............................................................................................................................28
References................................................................................................................................................29
Holiday programme.............................................................................................................................9
Optimum on/off....................................................................................................................................9
Operation specification and status......................................................................................................9
Task 2.2: Fixed BMS hardware components operation......................................................................9
Task 2.3: Techniques used in BMS fixed hardware system installation and cable wiring.............11
Installation planning..........................................................................................................................11
Cable wiring methods........................................................................................................................11
Task 3: BMS software and installation..................................................................................................12
Task 3.1: Control logic for BMS installation design.........................................................................12
Startup procedure..............................................................................................................................13
Shutdown procedure..........................................................................................................................14
Task 3.2: BMS control point schedules, schematic drawings, controls installation and logic
drawings...............................................................................................................................................15
Task 3.3: BMS equipment and component lists, specifications and schedules for installations....18
Task 3.4: BMS software procedures for control strategies...............................................................21
BMS software statement....................................................................................................................21
Point editor........................................................................................................................................22
Programme sentences........................................................................................................................22
Task 3.5: BMS installations commissioning procedures for chiller plant control..........................22
Task 4: BMS installation for performance optimization......................................................................24
Task 4.1: Use of BMS installations to get building performance reports for management review
...............................................................................................................................................................24
Task 4.2: BMS settings for modifying and adjusting BMS installations for control......................25
Task 4.3: Planned preventive maintenance (PPM) strategies based on obtained BMS data and
reports..................................................................................................................................................26
Task 4.4: Strategies for optimizing energy efficiency management using BMS data and reports 27
Temperature settings.........................................................................................................................27
Operation hours.................................................................................................................................28
Optimum on/off..................................................................................................................................28
Natural lighting and ventilation.........................................................................................................28
Preventive maintenance schedule......................................................................................................28
Equipment statuses............................................................................................................................28
References................................................................................................................................................29
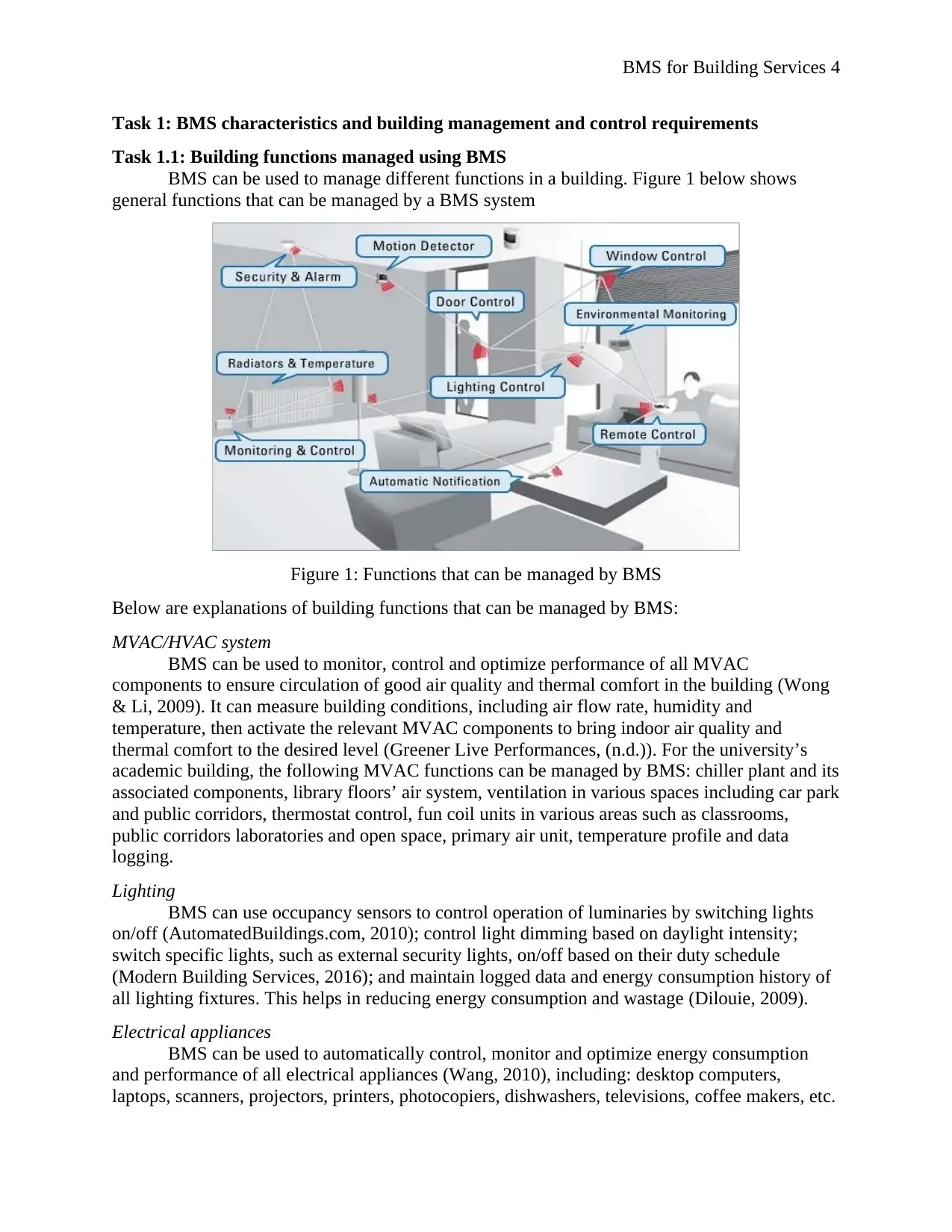
BMS for Building Services 4
Task 1: BMS characteristics and building management and control requirements
Task 1.1: Building functions managed using BMS
BMS can be used to manage different functions in a building. Figure 1 below shows
general functions that can be managed by a BMS system
Figure 1: Functions that can be managed by BMS
Below are explanations of building functions that can be managed by BMS:
MVAC/HVAC system
BMS can be used to monitor, control and optimize performance of all MVAC
components to ensure circulation of good air quality and thermal comfort in the building (Wong
& Li, 2009). It can measure building conditions, including air flow rate, humidity and
temperature, then activate the relevant MVAC components to bring indoor air quality and
thermal comfort to the desired level (Greener Live Performances, (n.d.)). For the university’s
academic building, the following MVAC functions can be managed by BMS: chiller plant and its
associated components, library floors’ air system, ventilation in various spaces including car park
and public corridors, thermostat control, fun coil units in various areas such as classrooms,
public corridors laboratories and open space, primary air unit, temperature profile and data
logging.
Lighting
BMS can use occupancy sensors to control operation of luminaries by switching lights
on/off (AutomatedBuildings.com, 2010); control light dimming based on daylight intensity;
switch specific lights, such as external security lights, on/off based on their duty schedule
(Modern Building Services, 2016); and maintain logged data and energy consumption history of
all lighting fixtures. This helps in reducing energy consumption and wastage (Dilouie, 2009).
Electrical appliances
BMS can be used to automatically control, monitor and optimize energy consumption
and performance of all electrical appliances (Wang, 2010), including: desktop computers,
laptops, scanners, projectors, printers, photocopiers, dishwashers, televisions, coffee makers, etc.
Task 1: BMS characteristics and building management and control requirements
Task 1.1: Building functions managed using BMS
BMS can be used to manage different functions in a building. Figure 1 below shows
general functions that can be managed by a BMS system
Figure 1: Functions that can be managed by BMS
Below are explanations of building functions that can be managed by BMS:
MVAC/HVAC system
BMS can be used to monitor, control and optimize performance of all MVAC
components to ensure circulation of good air quality and thermal comfort in the building (Wong
& Li, 2009). It can measure building conditions, including air flow rate, humidity and
temperature, then activate the relevant MVAC components to bring indoor air quality and
thermal comfort to the desired level (Greener Live Performances, (n.d.)). For the university’s
academic building, the following MVAC functions can be managed by BMS: chiller plant and its
associated components, library floors’ air system, ventilation in various spaces including car park
and public corridors, thermostat control, fun coil units in various areas such as classrooms,
public corridors laboratories and open space, primary air unit, temperature profile and data
logging.
Lighting
BMS can use occupancy sensors to control operation of luminaries by switching lights
on/off (AutomatedBuildings.com, 2010); control light dimming based on daylight intensity;
switch specific lights, such as external security lights, on/off based on their duty schedule
(Modern Building Services, 2016); and maintain logged data and energy consumption history of
all lighting fixtures. This helps in reducing energy consumption and wastage (Dilouie, 2009).
Electrical appliances
BMS can be used to automatically control, monitor and optimize energy consumption
and performance of all electrical appliances (Wang, 2010), including: desktop computers,
laptops, scanners, projectors, printers, photocopiers, dishwashers, televisions, coffee makers, etc.
Secure Best Marks with AI Grader
Need help grading? Try our AI Grader for instant feedback on your assignments.
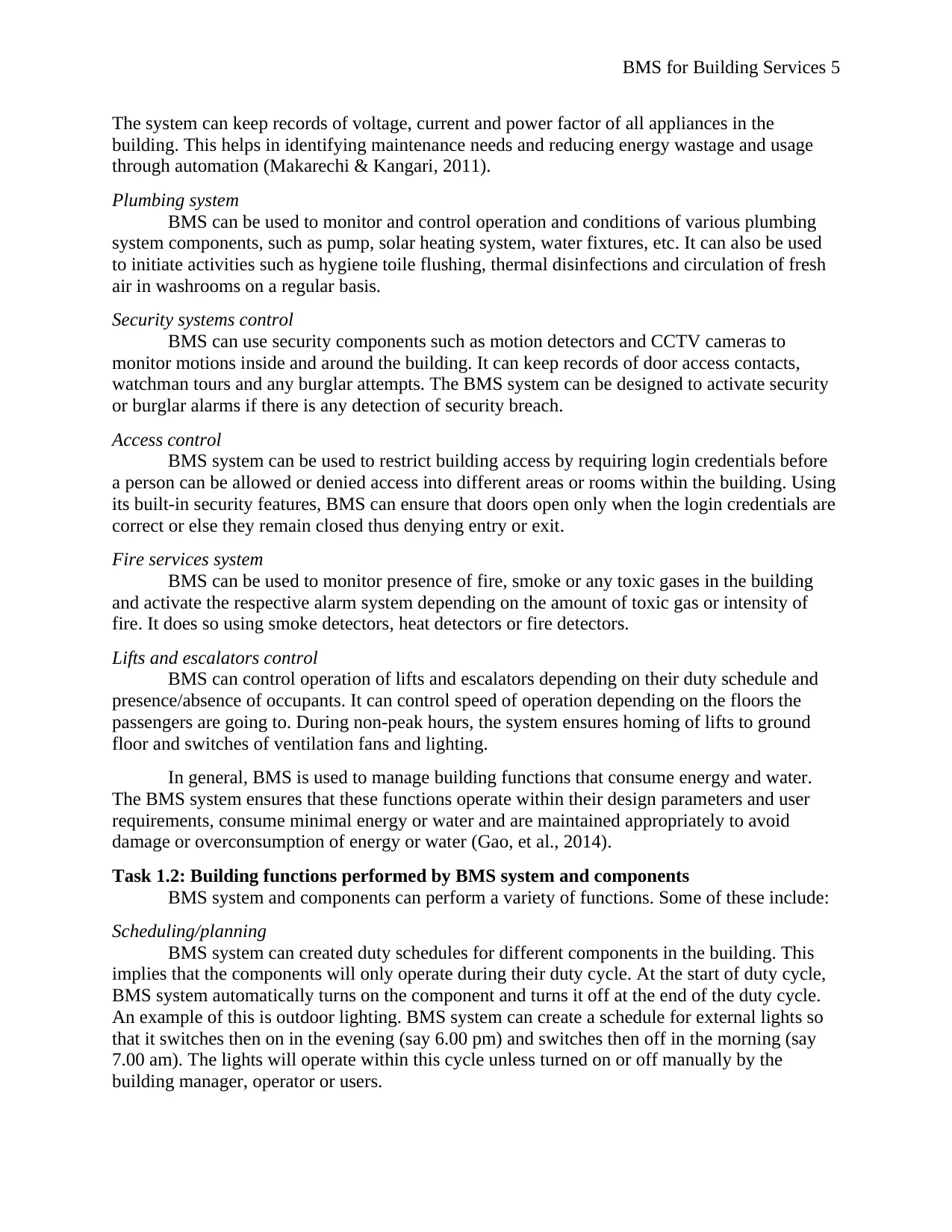
BMS for Building Services 5
The system can keep records of voltage, current and power factor of all appliances in the
building. This helps in identifying maintenance needs and reducing energy wastage and usage
through automation (Makarechi & Kangari, 2011).
Plumbing system
BMS can be used to monitor and control operation and conditions of various plumbing
system components, such as pump, solar heating system, water fixtures, etc. It can also be used
to initiate activities such as hygiene toile flushing, thermal disinfections and circulation of fresh
air in washrooms on a regular basis.
Security systems control
BMS can use security components such as motion detectors and CCTV cameras to
monitor motions inside and around the building. It can keep records of door access contacts,
watchman tours and any burglar attempts. The BMS system can be designed to activate security
or burglar alarms if there is any detection of security breach.
Access control
BMS system can be used to restrict building access by requiring login credentials before
a person can be allowed or denied access into different areas or rooms within the building. Using
its built-in security features, BMS can ensure that doors open only when the login credentials are
correct or else they remain closed thus denying entry or exit.
Fire services system
BMS can be used to monitor presence of fire, smoke or any toxic gases in the building
and activate the respective alarm system depending on the amount of toxic gas or intensity of
fire. It does so using smoke detectors, heat detectors or fire detectors.
Lifts and escalators control
BMS can control operation of lifts and escalators depending on their duty schedule and
presence/absence of occupants. It can control speed of operation depending on the floors the
passengers are going to. During non-peak hours, the system ensures homing of lifts to ground
floor and switches of ventilation fans and lighting.
In general, BMS is used to manage building functions that consume energy and water.
The BMS system ensures that these functions operate within their design parameters and user
requirements, consume minimal energy or water and are maintained appropriately to avoid
damage or overconsumption of energy or water (Gao, et al., 2014).
Task 1.2: Building functions performed by BMS system and components
BMS system and components can perform a variety of functions. Some of these include:
Scheduling/planning
BMS system can created duty schedules for different components in the building. This
implies that the components will only operate during their duty cycle. At the start of duty cycle,
BMS system automatically turns on the component and turns it off at the end of the duty cycle.
An example of this is outdoor lighting. BMS system can create a schedule for external lights so
that it switches then on in the evening (say 6.00 pm) and switches then off in the morning (say
7.00 am). The lights will operate within this cycle unless turned on or off manually by the
building manager, operator or users.
The system can keep records of voltage, current and power factor of all appliances in the
building. This helps in identifying maintenance needs and reducing energy wastage and usage
through automation (Makarechi & Kangari, 2011).
Plumbing system
BMS can be used to monitor and control operation and conditions of various plumbing
system components, such as pump, solar heating system, water fixtures, etc. It can also be used
to initiate activities such as hygiene toile flushing, thermal disinfections and circulation of fresh
air in washrooms on a regular basis.
Security systems control
BMS can use security components such as motion detectors and CCTV cameras to
monitor motions inside and around the building. It can keep records of door access contacts,
watchman tours and any burglar attempts. The BMS system can be designed to activate security
or burglar alarms if there is any detection of security breach.
Access control
BMS system can be used to restrict building access by requiring login credentials before
a person can be allowed or denied access into different areas or rooms within the building. Using
its built-in security features, BMS can ensure that doors open only when the login credentials are
correct or else they remain closed thus denying entry or exit.
Fire services system
BMS can be used to monitor presence of fire, smoke or any toxic gases in the building
and activate the respective alarm system depending on the amount of toxic gas or intensity of
fire. It does so using smoke detectors, heat detectors or fire detectors.
Lifts and escalators control
BMS can control operation of lifts and escalators depending on their duty schedule and
presence/absence of occupants. It can control speed of operation depending on the floors the
passengers are going to. During non-peak hours, the system ensures homing of lifts to ground
floor and switches of ventilation fans and lighting.
In general, BMS is used to manage building functions that consume energy and water.
The BMS system ensures that these functions operate within their design parameters and user
requirements, consume minimal energy or water and are maintained appropriately to avoid
damage or overconsumption of energy or water (Gao, et al., 2014).
Task 1.2: Building functions performed by BMS system and components
BMS system and components can perform a variety of functions. Some of these include:
Scheduling/planning
BMS system can created duty schedules for different components in the building. This
implies that the components will only operate during their duty cycle. At the start of duty cycle,
BMS system automatically turns on the component and turns it off at the end of the duty cycle.
An example of this is outdoor lighting. BMS system can create a schedule for external lights so
that it switches then on in the evening (say 6.00 pm) and switches then off in the morning (say
7.00 am). The lights will operate within this cycle unless turned on or off manually by the
building manager, operator or users.
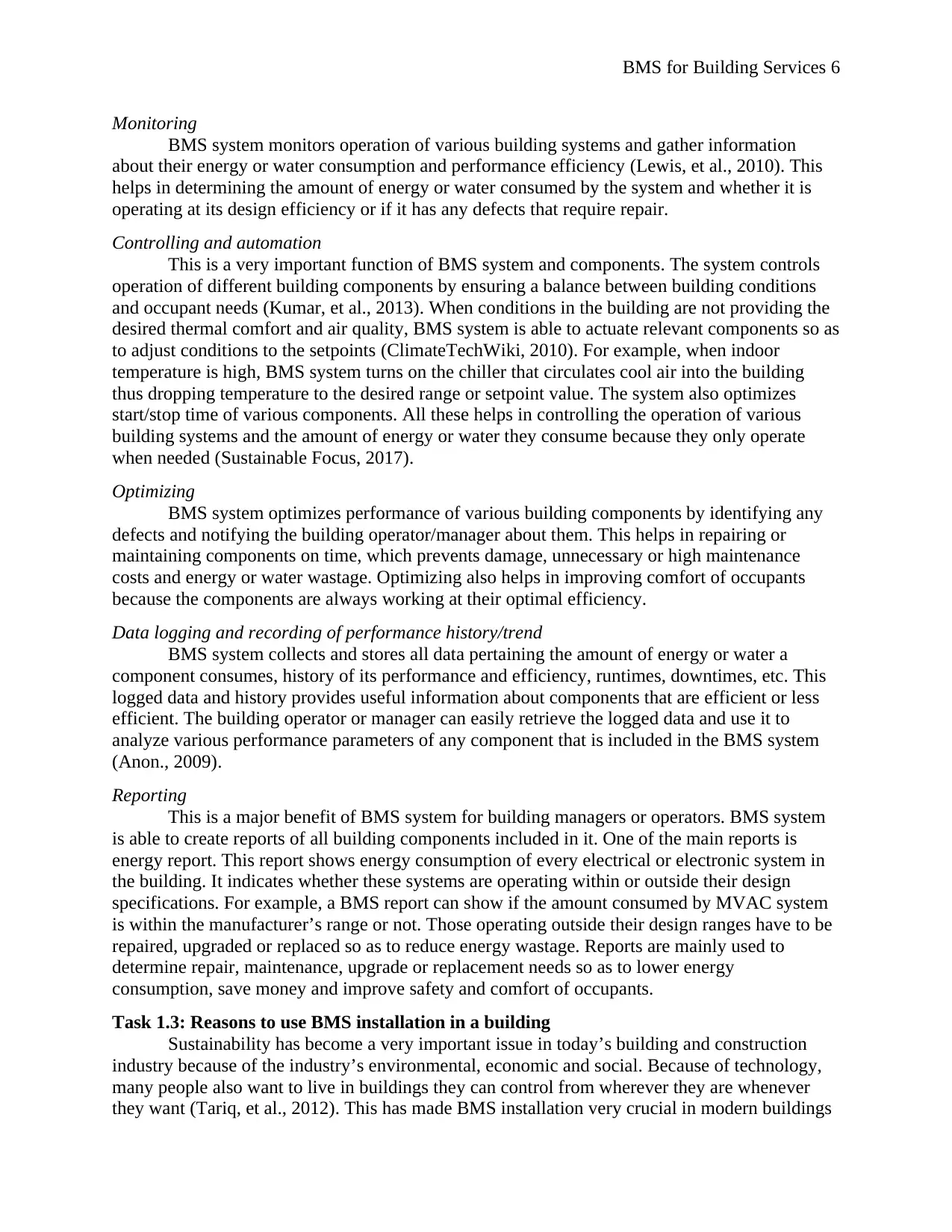
BMS for Building Services 6
Monitoring
BMS system monitors operation of various building systems and gather information
about their energy or water consumption and performance efficiency (Lewis, et al., 2010). This
helps in determining the amount of energy or water consumed by the system and whether it is
operating at its design efficiency or if it has any defects that require repair.
Controlling and automation
This is a very important function of BMS system and components. The system controls
operation of different building components by ensuring a balance between building conditions
and occupant needs (Kumar, et al., 2013). When conditions in the building are not providing the
desired thermal comfort and air quality, BMS system is able to actuate relevant components so as
to adjust conditions to the setpoints (ClimateTechWiki, 2010). For example, when indoor
temperature is high, BMS system turns on the chiller that circulates cool air into the building
thus dropping temperature to the desired range or setpoint value. The system also optimizes
start/stop time of various components. All these helps in controlling the operation of various
building systems and the amount of energy or water they consume because they only operate
when needed (Sustainable Focus, 2017).
Optimizing
BMS system optimizes performance of various building components by identifying any
defects and notifying the building operator/manager about them. This helps in repairing or
maintaining components on time, which prevents damage, unnecessary or high maintenance
costs and energy or water wastage. Optimizing also helps in improving comfort of occupants
because the components are always working at their optimal efficiency.
Data logging and recording of performance history/trend
BMS system collects and stores all data pertaining the amount of energy or water a
component consumes, history of its performance and efficiency, runtimes, downtimes, etc. This
logged data and history provides useful information about components that are efficient or less
efficient. The building operator or manager can easily retrieve the logged data and use it to
analyze various performance parameters of any component that is included in the BMS system
(Anon., 2009).
Reporting
This is a major benefit of BMS system for building managers or operators. BMS system
is able to create reports of all building components included in it. One of the main reports is
energy report. This report shows energy consumption of every electrical or electronic system in
the building. It indicates whether these systems are operating within or outside their design
specifications. For example, a BMS report can show if the amount consumed by MVAC system
is within the manufacturer’s range or not. Those operating outside their design ranges have to be
repaired, upgraded or replaced so as to reduce energy wastage. Reports are mainly used to
determine repair, maintenance, upgrade or replacement needs so as to lower energy
consumption, save money and improve safety and comfort of occupants.
Task 1.3: Reasons to use BMS installation in a building
Sustainability has become a very important issue in today’s building and construction
industry because of the industry’s environmental, economic and social. Because of technology,
many people also want to live in buildings they can control from wherever they are whenever
they want (Tariq, et al., 2012). This has made BMS installation very crucial in modern buildings
Monitoring
BMS system monitors operation of various building systems and gather information
about their energy or water consumption and performance efficiency (Lewis, et al., 2010). This
helps in determining the amount of energy or water consumed by the system and whether it is
operating at its design efficiency or if it has any defects that require repair.
Controlling and automation
This is a very important function of BMS system and components. The system controls
operation of different building components by ensuring a balance between building conditions
and occupant needs (Kumar, et al., 2013). When conditions in the building are not providing the
desired thermal comfort and air quality, BMS system is able to actuate relevant components so as
to adjust conditions to the setpoints (ClimateTechWiki, 2010). For example, when indoor
temperature is high, BMS system turns on the chiller that circulates cool air into the building
thus dropping temperature to the desired range or setpoint value. The system also optimizes
start/stop time of various components. All these helps in controlling the operation of various
building systems and the amount of energy or water they consume because they only operate
when needed (Sustainable Focus, 2017).
Optimizing
BMS system optimizes performance of various building components by identifying any
defects and notifying the building operator/manager about them. This helps in repairing or
maintaining components on time, which prevents damage, unnecessary or high maintenance
costs and energy or water wastage. Optimizing also helps in improving comfort of occupants
because the components are always working at their optimal efficiency.
Data logging and recording of performance history/trend
BMS system collects and stores all data pertaining the amount of energy or water a
component consumes, history of its performance and efficiency, runtimes, downtimes, etc. This
logged data and history provides useful information about components that are efficient or less
efficient. The building operator or manager can easily retrieve the logged data and use it to
analyze various performance parameters of any component that is included in the BMS system
(Anon., 2009).
Reporting
This is a major benefit of BMS system for building managers or operators. BMS system
is able to create reports of all building components included in it. One of the main reports is
energy report. This report shows energy consumption of every electrical or electronic system in
the building. It indicates whether these systems are operating within or outside their design
specifications. For example, a BMS report can show if the amount consumed by MVAC system
is within the manufacturer’s range or not. Those operating outside their design ranges have to be
repaired, upgraded or replaced so as to reduce energy wastage. Reports are mainly used to
determine repair, maintenance, upgrade or replacement needs so as to lower energy
consumption, save money and improve safety and comfort of occupants.
Task 1.3: Reasons to use BMS installation in a building
Sustainability has become a very important issue in today’s building and construction
industry because of the industry’s environmental, economic and social. Because of technology,
many people also want to live in buildings they can control from wherever they are whenever
they want (Tariq, et al., 2012). This has made BMS installation very crucial in modern buildings
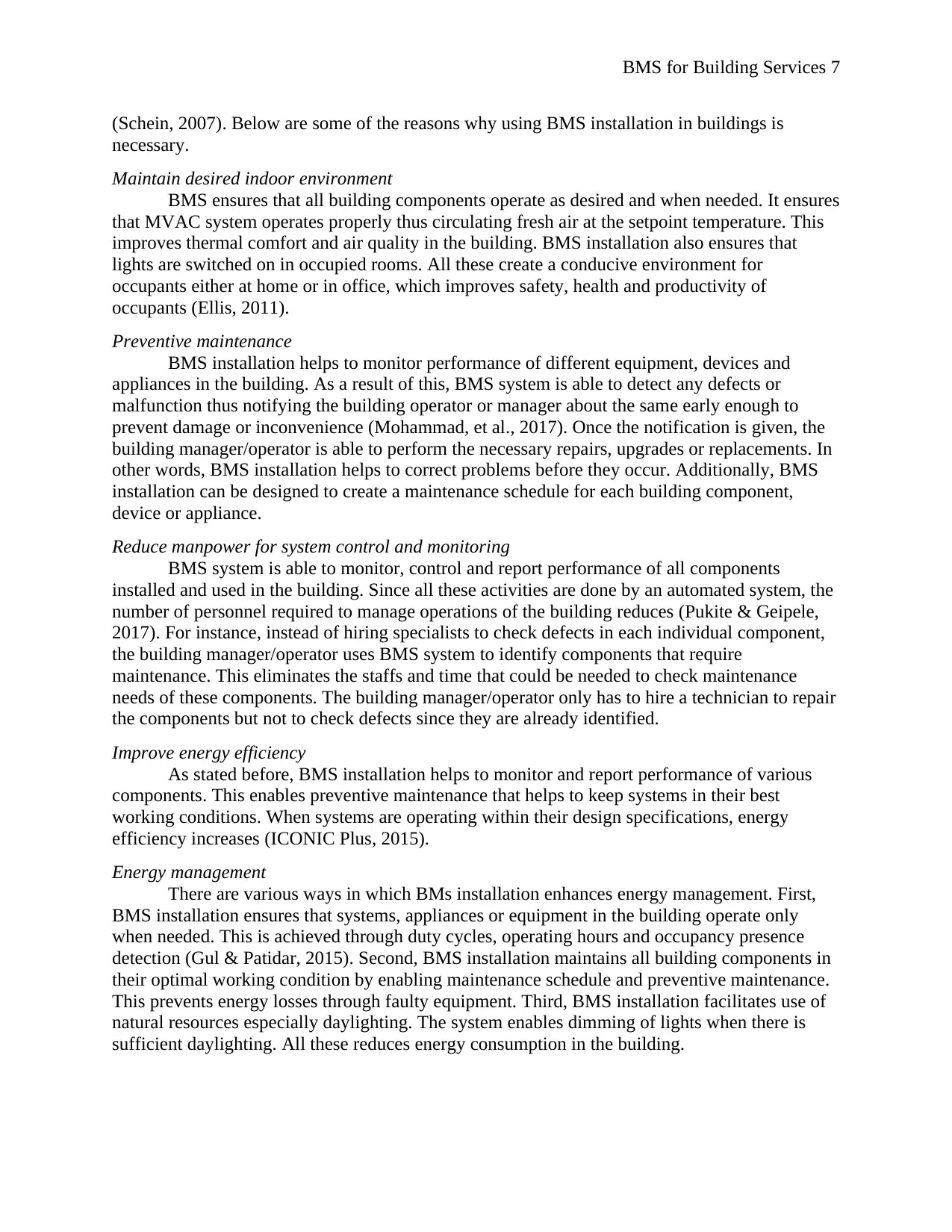
BMS for Building Services 7
(Schein, 2007). Below are some of the reasons why using BMS installation in buildings is
necessary.
Maintain desired indoor environment
BMS ensures that all building components operate as desired and when needed. It ensures
that MVAC system operates properly thus circulating fresh air at the setpoint temperature. This
improves thermal comfort and air quality in the building. BMS installation also ensures that
lights are switched on in occupied rooms. All these create a conducive environment for
occupants either at home or in office, which improves safety, health and productivity of
occupants (Ellis, 2011).
Preventive maintenance
BMS installation helps to monitor performance of different equipment, devices and
appliances in the building. As a result of this, BMS system is able to detect any defects or
malfunction thus notifying the building operator or manager about the same early enough to
prevent damage or inconvenience (Mohammad, et al., 2017). Once the notification is given, the
building manager/operator is able to perform the necessary repairs, upgrades or replacements. In
other words, BMS installation helps to correct problems before they occur. Additionally, BMS
installation can be designed to create a maintenance schedule for each building component,
device or appliance.
Reduce manpower for system control and monitoring
BMS system is able to monitor, control and report performance of all components
installed and used in the building. Since all these activities are done by an automated system, the
number of personnel required to manage operations of the building reduces (Pukite & Geipele,
2017). For instance, instead of hiring specialists to check defects in each individual component,
the building manager/operator uses BMS system to identify components that require
maintenance. This eliminates the staffs and time that could be needed to check maintenance
needs of these components. The building manager/operator only has to hire a technician to repair
the components but not to check defects since they are already identified.
Improve energy efficiency
As stated before, BMS installation helps to monitor and report performance of various
components. This enables preventive maintenance that helps to keep systems in their best
working conditions. When systems are operating within their design specifications, energy
efficiency increases (ICONIC Plus, 2015).
Energy management
There are various ways in which BMs installation enhances energy management. First,
BMS installation ensures that systems, appliances or equipment in the building operate only
when needed. This is achieved through duty cycles, operating hours and occupancy presence
detection (Gul & Patidar, 2015). Second, BMS installation maintains all building components in
their optimal working condition by enabling maintenance schedule and preventive maintenance.
This prevents energy losses through faulty equipment. Third, BMS installation facilitates use of
natural resources especially daylighting. The system enables dimming of lights when there is
sufficient daylighting. All these reduces energy consumption in the building.
(Schein, 2007). Below are some of the reasons why using BMS installation in buildings is
necessary.
Maintain desired indoor environment
BMS ensures that all building components operate as desired and when needed. It ensures
that MVAC system operates properly thus circulating fresh air at the setpoint temperature. This
improves thermal comfort and air quality in the building. BMS installation also ensures that
lights are switched on in occupied rooms. All these create a conducive environment for
occupants either at home or in office, which improves safety, health and productivity of
occupants (Ellis, 2011).
Preventive maintenance
BMS installation helps to monitor performance of different equipment, devices and
appliances in the building. As a result of this, BMS system is able to detect any defects or
malfunction thus notifying the building operator or manager about the same early enough to
prevent damage or inconvenience (Mohammad, et al., 2017). Once the notification is given, the
building manager/operator is able to perform the necessary repairs, upgrades or replacements. In
other words, BMS installation helps to correct problems before they occur. Additionally, BMS
installation can be designed to create a maintenance schedule for each building component,
device or appliance.
Reduce manpower for system control and monitoring
BMS system is able to monitor, control and report performance of all components
installed and used in the building. Since all these activities are done by an automated system, the
number of personnel required to manage operations of the building reduces (Pukite & Geipele,
2017). For instance, instead of hiring specialists to check defects in each individual component,
the building manager/operator uses BMS system to identify components that require
maintenance. This eliminates the staffs and time that could be needed to check maintenance
needs of these components. The building manager/operator only has to hire a technician to repair
the components but not to check defects since they are already identified.
Improve energy efficiency
As stated before, BMS installation helps to monitor and report performance of various
components. This enables preventive maintenance that helps to keep systems in their best
working conditions. When systems are operating within their design specifications, energy
efficiency increases (ICONIC Plus, 2015).
Energy management
There are various ways in which BMs installation enhances energy management. First,
BMS installation ensures that systems, appliances or equipment in the building operate only
when needed. This is achieved through duty cycles, operating hours and occupancy presence
detection (Gul & Patidar, 2015). Second, BMS installation maintains all building components in
their optimal working condition by enabling maintenance schedule and preventive maintenance.
This prevents energy losses through faulty equipment. Third, BMS installation facilitates use of
natural resources especially daylighting. The system enables dimming of lights when there is
sufficient daylighting. All these reduces energy consumption in the building.
Paraphrase This Document
Need a fresh take? Get an instant paraphrase of this document with our AI Paraphraser
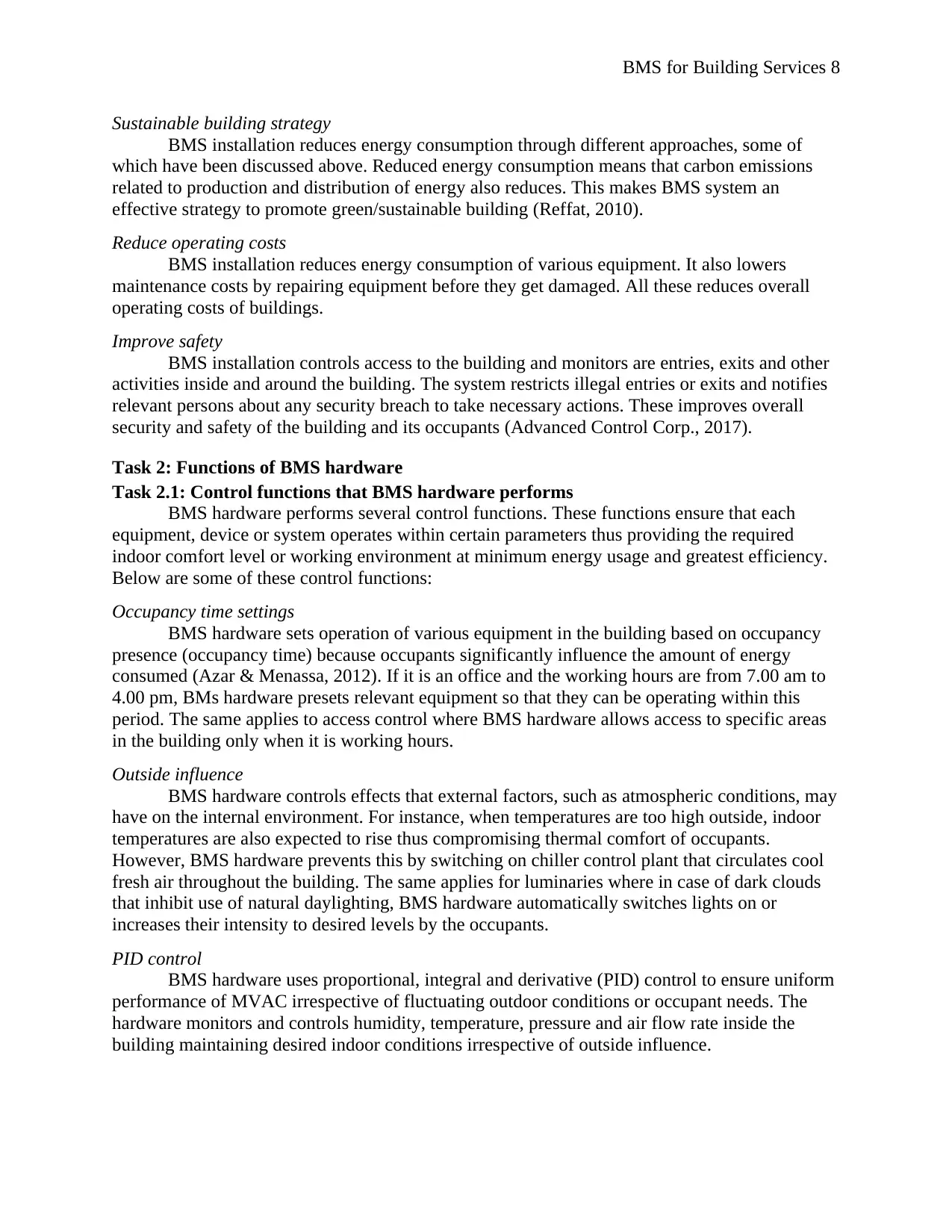
BMS for Building Services 8
Sustainable building strategy
BMS installation reduces energy consumption through different approaches, some of
which have been discussed above. Reduced energy consumption means that carbon emissions
related to production and distribution of energy also reduces. This makes BMS system an
effective strategy to promote green/sustainable building (Reffat, 2010).
Reduce operating costs
BMS installation reduces energy consumption of various equipment. It also lowers
maintenance costs by repairing equipment before they get damaged. All these reduces overall
operating costs of buildings.
Improve safety
BMS installation controls access to the building and monitors are entries, exits and other
activities inside and around the building. The system restricts illegal entries or exits and notifies
relevant persons about any security breach to take necessary actions. These improves overall
security and safety of the building and its occupants (Advanced Control Corp., 2017).
Task 2: Functions of BMS hardware
Task 2.1: Control functions that BMS hardware performs
BMS hardware performs several control functions. These functions ensure that each
equipment, device or system operates within certain parameters thus providing the required
indoor comfort level or working environment at minimum energy usage and greatest efficiency.
Below are some of these control functions:
Occupancy time settings
BMS hardware sets operation of various equipment in the building based on occupancy
presence (occupancy time) because occupants significantly influence the amount of energy
consumed (Azar & Menassa, 2012). If it is an office and the working hours are from 7.00 am to
4.00 pm, BMs hardware presets relevant equipment so that they can be operating within this
period. The same applies to access control where BMS hardware allows access to specific areas
in the building only when it is working hours.
Outside influence
BMS hardware controls effects that external factors, such as atmospheric conditions, may
have on the internal environment. For instance, when temperatures are too high outside, indoor
temperatures are also expected to rise thus compromising thermal comfort of occupants.
However, BMS hardware prevents this by switching on chiller control plant that circulates cool
fresh air throughout the building. The same applies for luminaries where in case of dark clouds
that inhibit use of natural daylighting, BMS hardware automatically switches lights on or
increases their intensity to desired levels by the occupants.
PID control
BMS hardware uses proportional, integral and derivative (PID) control to ensure uniform
performance of MVAC irrespective of fluctuating outdoor conditions or occupant needs. The
hardware monitors and controls humidity, temperature, pressure and air flow rate inside the
building maintaining desired indoor conditions irrespective of outside influence.
Sustainable building strategy
BMS installation reduces energy consumption through different approaches, some of
which have been discussed above. Reduced energy consumption means that carbon emissions
related to production and distribution of energy also reduces. This makes BMS system an
effective strategy to promote green/sustainable building (Reffat, 2010).
Reduce operating costs
BMS installation reduces energy consumption of various equipment. It also lowers
maintenance costs by repairing equipment before they get damaged. All these reduces overall
operating costs of buildings.
Improve safety
BMS installation controls access to the building and monitors are entries, exits and other
activities inside and around the building. The system restricts illegal entries or exits and notifies
relevant persons about any security breach to take necessary actions. These improves overall
security and safety of the building and its occupants (Advanced Control Corp., 2017).
Task 2: Functions of BMS hardware
Task 2.1: Control functions that BMS hardware performs
BMS hardware performs several control functions. These functions ensure that each
equipment, device or system operates within certain parameters thus providing the required
indoor comfort level or working environment at minimum energy usage and greatest efficiency.
Below are some of these control functions:
Occupancy time settings
BMS hardware sets operation of various equipment in the building based on occupancy
presence (occupancy time) because occupants significantly influence the amount of energy
consumed (Azar & Menassa, 2012). If it is an office and the working hours are from 7.00 am to
4.00 pm, BMs hardware presets relevant equipment so that they can be operating within this
period. The same applies to access control where BMS hardware allows access to specific areas
in the building only when it is working hours.
Outside influence
BMS hardware controls effects that external factors, such as atmospheric conditions, may
have on the internal environment. For instance, when temperatures are too high outside, indoor
temperatures are also expected to rise thus compromising thermal comfort of occupants.
However, BMS hardware prevents this by switching on chiller control plant that circulates cool
fresh air throughout the building. The same applies for luminaries where in case of dark clouds
that inhibit use of natural daylighting, BMS hardware automatically switches lights on or
increases their intensity to desired levels by the occupants.
PID control
BMS hardware uses proportional, integral and derivative (PID) control to ensure uniform
performance of MVAC irrespective of fluctuating outdoor conditions or occupant needs. The
hardware monitors and controls humidity, temperature, pressure and air flow rate inside the
building maintaining desired indoor conditions irrespective of outside influence.
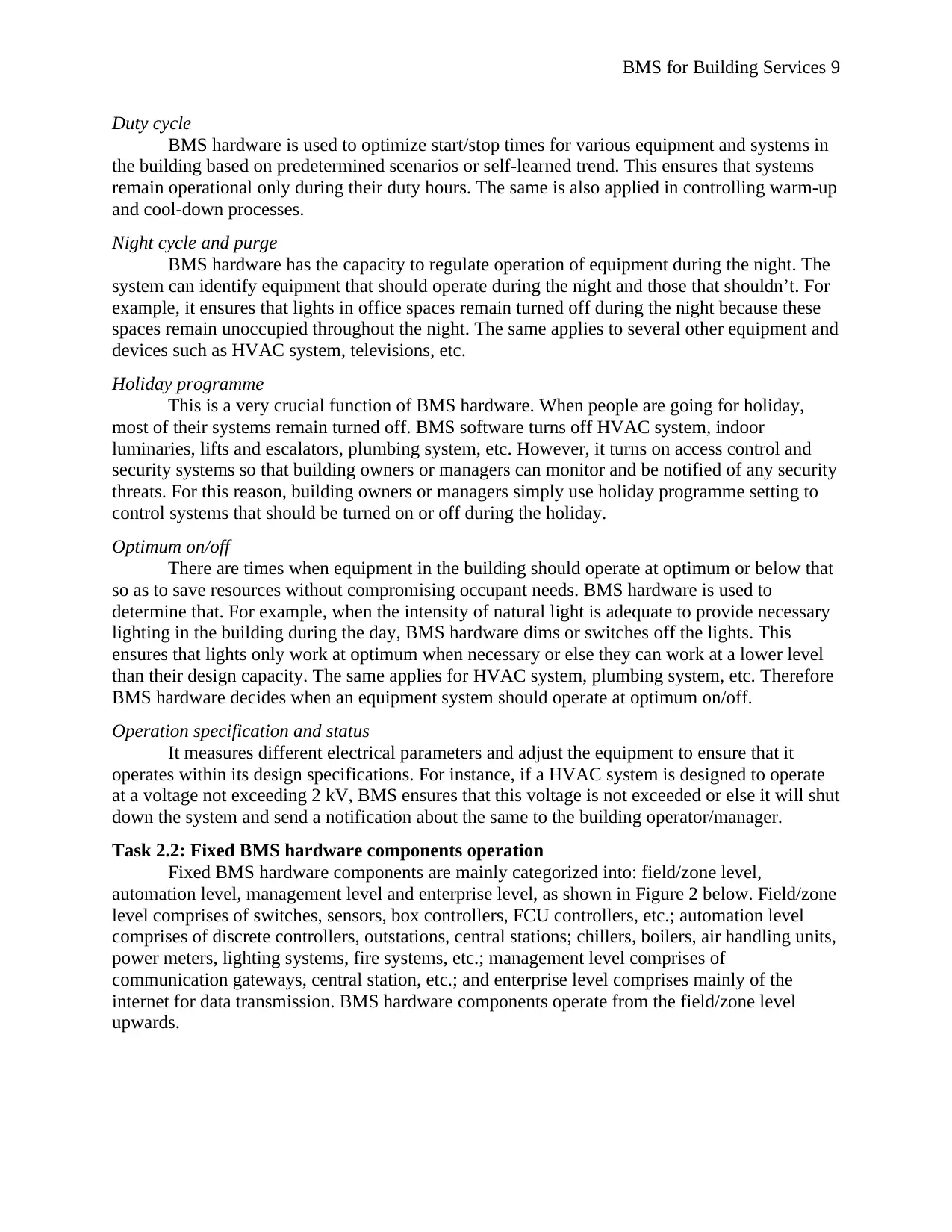
BMS for Building Services 9
Duty cycle
BMS hardware is used to optimize start/stop times for various equipment and systems in
the building based on predetermined scenarios or self-learned trend. This ensures that systems
remain operational only during their duty hours. The same is also applied in controlling warm-up
and cool-down processes.
Night cycle and purge
BMS hardware has the capacity to regulate operation of equipment during the night. The
system can identify equipment that should operate during the night and those that shouldn’t. For
example, it ensures that lights in office spaces remain turned off during the night because these
spaces remain unoccupied throughout the night. The same applies to several other equipment and
devices such as HVAC system, televisions, etc.
Holiday programme
This is a very crucial function of BMS hardware. When people are going for holiday,
most of their systems remain turned off. BMS software turns off HVAC system, indoor
luminaries, lifts and escalators, plumbing system, etc. However, it turns on access control and
security systems so that building owners or managers can monitor and be notified of any security
threats. For this reason, building owners or managers simply use holiday programme setting to
control systems that should be turned on or off during the holiday.
Optimum on/off
There are times when equipment in the building should operate at optimum or below that
so as to save resources without compromising occupant needs. BMS hardware is used to
determine that. For example, when the intensity of natural light is adequate to provide necessary
lighting in the building during the day, BMS hardware dims or switches off the lights. This
ensures that lights only work at optimum when necessary or else they can work at a lower level
than their design capacity. The same applies for HVAC system, plumbing system, etc. Therefore
BMS hardware decides when an equipment system should operate at optimum on/off.
Operation specification and status
It measures different electrical parameters and adjust the equipment to ensure that it
operates within its design specifications. For instance, if a HVAC system is designed to operate
at a voltage not exceeding 2 kV, BMS ensures that this voltage is not exceeded or else it will shut
down the system and send a notification about the same to the building operator/manager.
Task 2.2: Fixed BMS hardware components operation
Fixed BMS hardware components are mainly categorized into: field/zone level,
automation level, management level and enterprise level, as shown in Figure 2 below. Field/zone
level comprises of switches, sensors, box controllers, FCU controllers, etc.; automation level
comprises of discrete controllers, outstations, central stations; chillers, boilers, air handling units,
power meters, lighting systems, fire systems, etc.; management level comprises of
communication gateways, central station, etc.; and enterprise level comprises mainly of the
internet for data transmission. BMS hardware components operate from the field/zone level
upwards.
Duty cycle
BMS hardware is used to optimize start/stop times for various equipment and systems in
the building based on predetermined scenarios or self-learned trend. This ensures that systems
remain operational only during their duty hours. The same is also applied in controlling warm-up
and cool-down processes.
Night cycle and purge
BMS hardware has the capacity to regulate operation of equipment during the night. The
system can identify equipment that should operate during the night and those that shouldn’t. For
example, it ensures that lights in office spaces remain turned off during the night because these
spaces remain unoccupied throughout the night. The same applies to several other equipment and
devices such as HVAC system, televisions, etc.
Holiday programme
This is a very crucial function of BMS hardware. When people are going for holiday,
most of their systems remain turned off. BMS software turns off HVAC system, indoor
luminaries, lifts and escalators, plumbing system, etc. However, it turns on access control and
security systems so that building owners or managers can monitor and be notified of any security
threats. For this reason, building owners or managers simply use holiday programme setting to
control systems that should be turned on or off during the holiday.
Optimum on/off
There are times when equipment in the building should operate at optimum or below that
so as to save resources without compromising occupant needs. BMS hardware is used to
determine that. For example, when the intensity of natural light is adequate to provide necessary
lighting in the building during the day, BMS hardware dims or switches off the lights. This
ensures that lights only work at optimum when necessary or else they can work at a lower level
than their design capacity. The same applies for HVAC system, plumbing system, etc. Therefore
BMS hardware decides when an equipment system should operate at optimum on/off.
Operation specification and status
It measures different electrical parameters and adjust the equipment to ensure that it
operates within its design specifications. For instance, if a HVAC system is designed to operate
at a voltage not exceeding 2 kV, BMS ensures that this voltage is not exceeded or else it will shut
down the system and send a notification about the same to the building operator/manager.
Task 2.2: Fixed BMS hardware components operation
Fixed BMS hardware components are mainly categorized into: field/zone level,
automation level, management level and enterprise level, as shown in Figure 2 below. Field/zone
level comprises of switches, sensors, box controllers, FCU controllers, etc.; automation level
comprises of discrete controllers, outstations, central stations; chillers, boilers, air handling units,
power meters, lighting systems, fire systems, etc.; management level comprises of
communication gateways, central station, etc.; and enterprise level comprises mainly of the
internet for data transmission. BMS hardware components operate from the field/zone level
upwards.
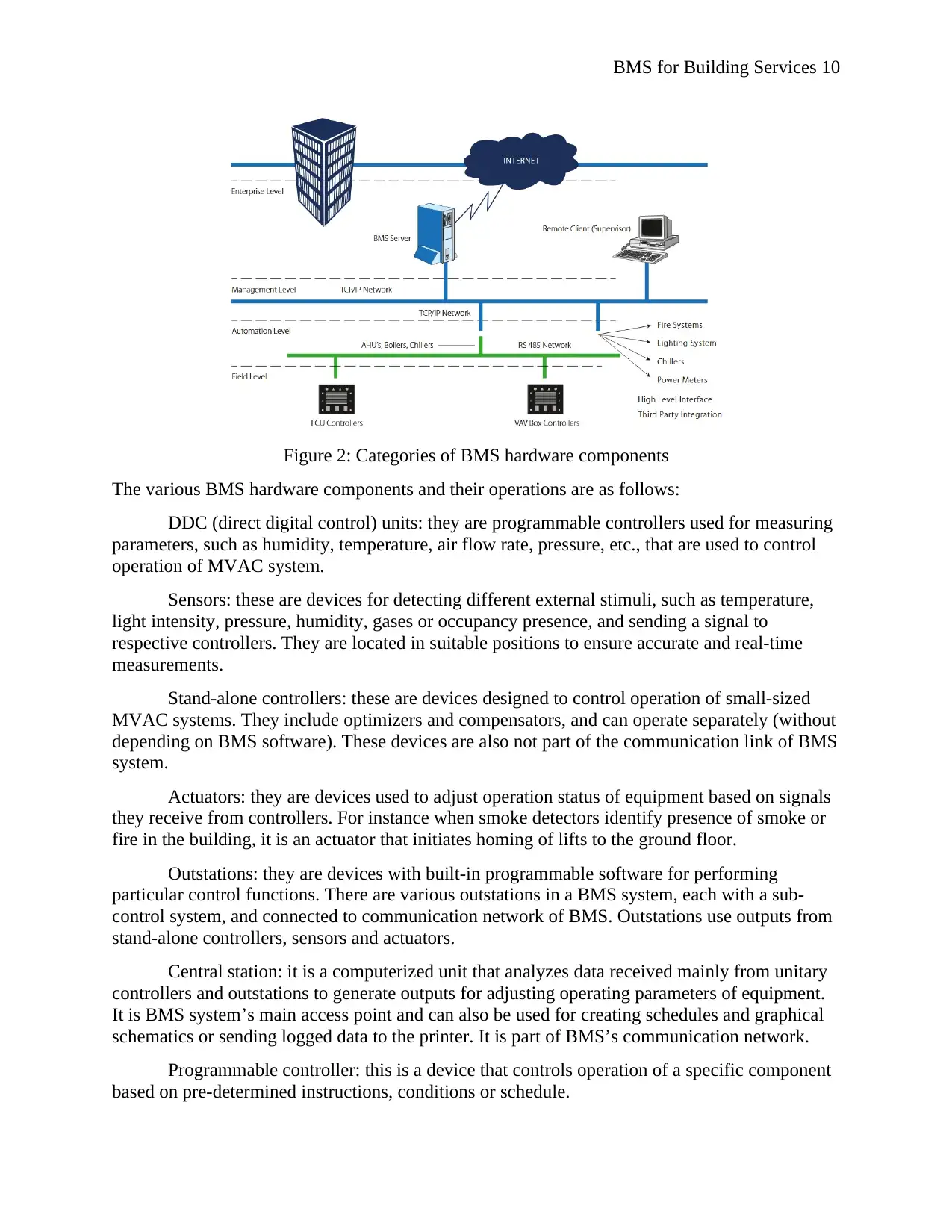
BMS for Building Services 10
Figure 2: Categories of BMS hardware components
The various BMS hardware components and their operations are as follows:
DDC (direct digital control) units: they are programmable controllers used for measuring
parameters, such as humidity, temperature, air flow rate, pressure, etc., that are used to control
operation of MVAC system.
Sensors: these are devices for detecting different external stimuli, such as temperature,
light intensity, pressure, humidity, gases or occupancy presence, and sending a signal to
respective controllers. They are located in suitable positions to ensure accurate and real-time
measurements.
Stand-alone controllers: these are devices designed to control operation of small-sized
MVAC systems. They include optimizers and compensators, and can operate separately (without
depending on BMS software). These devices are also not part of the communication link of BMS
system.
Actuators: they are devices used to adjust operation status of equipment based on signals
they receive from controllers. For instance when smoke detectors identify presence of smoke or
fire in the building, it is an actuator that initiates homing of lifts to the ground floor.
Outstations: they are devices with built-in programmable software for performing
particular control functions. There are various outstations in a BMS system, each with a sub-
control system, and connected to communication network of BMS. Outstations use outputs from
stand-alone controllers, sensors and actuators.
Central station: it is a computerized unit that analyzes data received mainly from unitary
controllers and outstations to generate outputs for adjusting operating parameters of equipment.
It is BMS system’s main access point and can also be used for creating schedules and graphical
schematics or sending logged data to the printer. It is part of BMS’s communication network.
Programmable controller: this is a device that controls operation of a specific component
based on pre-determined instructions, conditions or schedule.
Figure 2: Categories of BMS hardware components
The various BMS hardware components and their operations are as follows:
DDC (direct digital control) units: they are programmable controllers used for measuring
parameters, such as humidity, temperature, air flow rate, pressure, etc., that are used to control
operation of MVAC system.
Sensors: these are devices for detecting different external stimuli, such as temperature,
light intensity, pressure, humidity, gases or occupancy presence, and sending a signal to
respective controllers. They are located in suitable positions to ensure accurate and real-time
measurements.
Stand-alone controllers: these are devices designed to control operation of small-sized
MVAC systems. They include optimizers and compensators, and can operate separately (without
depending on BMS software). These devices are also not part of the communication link of BMS
system.
Actuators: they are devices used to adjust operation status of equipment based on signals
they receive from controllers. For instance when smoke detectors identify presence of smoke or
fire in the building, it is an actuator that initiates homing of lifts to the ground floor.
Outstations: they are devices with built-in programmable software for performing
particular control functions. There are various outstations in a BMS system, each with a sub-
control system, and connected to communication network of BMS. Outstations use outputs from
stand-alone controllers, sensors and actuators.
Central station: it is a computerized unit that analyzes data received mainly from unitary
controllers and outstations to generate outputs for adjusting operating parameters of equipment.
It is BMS system’s main access point and can also be used for creating schedules and graphical
schematics or sending logged data to the printer. It is part of BMS’s communication network.
Programmable controller: this is a device that controls operation of a specific component
based on pre-determined instructions, conditions or schedule.
Secure Best Marks with AI Grader
Need help grading? Try our AI Grader for instant feedback on your assignments.
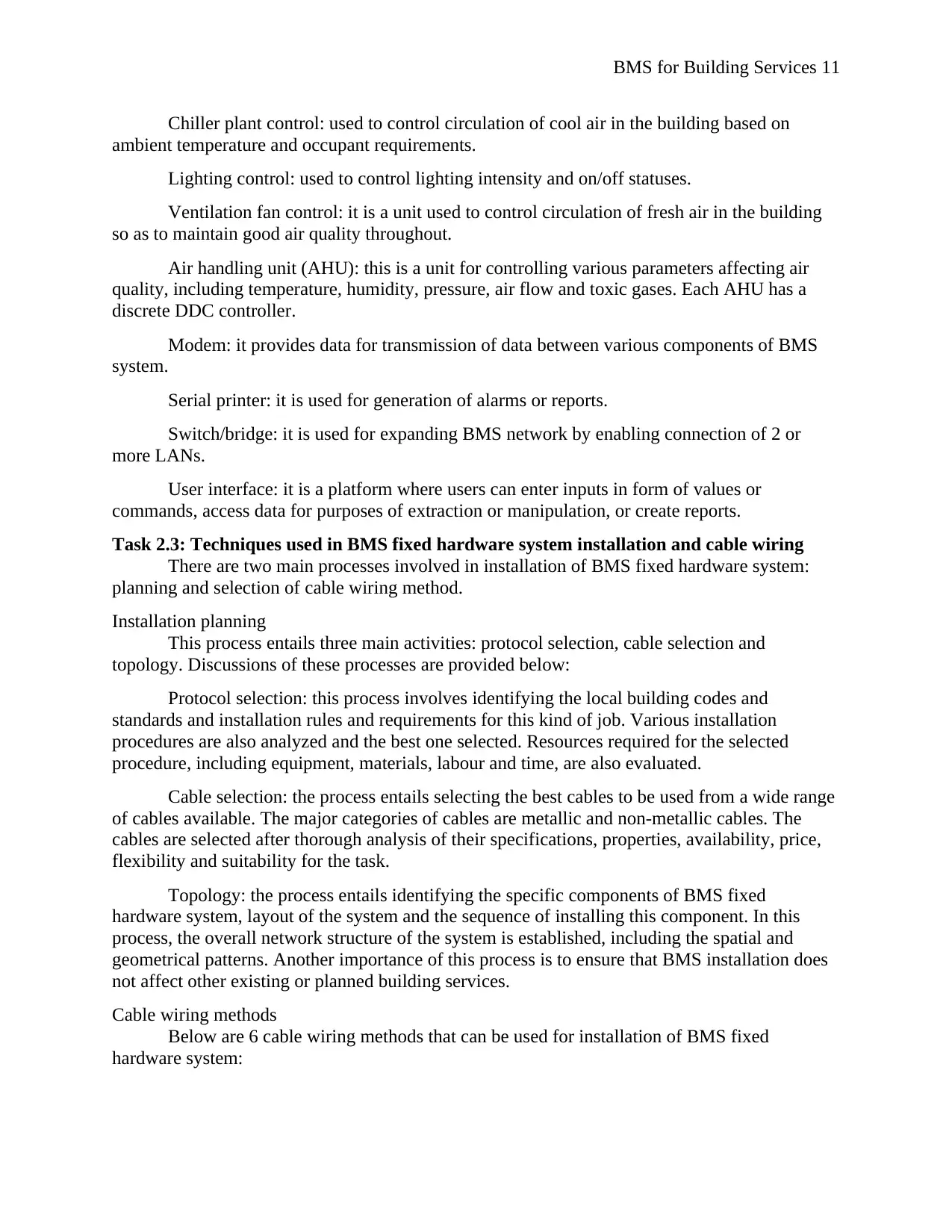
BMS for Building Services 11
Chiller plant control: used to control circulation of cool air in the building based on
ambient temperature and occupant requirements.
Lighting control: used to control lighting intensity and on/off statuses.
Ventilation fan control: it is a unit used to control circulation of fresh air in the building
so as to maintain good air quality throughout.
Air handling unit (AHU): this is a unit for controlling various parameters affecting air
quality, including temperature, humidity, pressure, air flow and toxic gases. Each AHU has a
discrete DDC controller.
Modem: it provides data for transmission of data between various components of BMS
system.
Serial printer: it is used for generation of alarms or reports.
Switch/bridge: it is used for expanding BMS network by enabling connection of 2 or
more LANs.
User interface: it is a platform where users can enter inputs in form of values or
commands, access data for purposes of extraction or manipulation, or create reports.
Task 2.3: Techniques used in BMS fixed hardware system installation and cable wiring
There are two main processes involved in installation of BMS fixed hardware system:
planning and selection of cable wiring method.
Installation planning
This process entails three main activities: protocol selection, cable selection and
topology. Discussions of these processes are provided below:
Protocol selection: this process involves identifying the local building codes and
standards and installation rules and requirements for this kind of job. Various installation
procedures are also analyzed and the best one selected. Resources required for the selected
procedure, including equipment, materials, labour and time, are also evaluated.
Cable selection: the process entails selecting the best cables to be used from a wide range
of cables available. The major categories of cables are metallic and non-metallic cables. The
cables are selected after thorough analysis of their specifications, properties, availability, price,
flexibility and suitability for the task.
Topology: the process entails identifying the specific components of BMS fixed
hardware system, layout of the system and the sequence of installing this component. In this
process, the overall network structure of the system is established, including the spatial and
geometrical patterns. Another importance of this process is to ensure that BMS installation does
not affect other existing or planned building services.
Cable wiring methods
Below are 6 cable wiring methods that can be used for installation of BMS fixed
hardware system:
Chiller plant control: used to control circulation of cool air in the building based on
ambient temperature and occupant requirements.
Lighting control: used to control lighting intensity and on/off statuses.
Ventilation fan control: it is a unit used to control circulation of fresh air in the building
so as to maintain good air quality throughout.
Air handling unit (AHU): this is a unit for controlling various parameters affecting air
quality, including temperature, humidity, pressure, air flow and toxic gases. Each AHU has a
discrete DDC controller.
Modem: it provides data for transmission of data between various components of BMS
system.
Serial printer: it is used for generation of alarms or reports.
Switch/bridge: it is used for expanding BMS network by enabling connection of 2 or
more LANs.
User interface: it is a platform where users can enter inputs in form of values or
commands, access data for purposes of extraction or manipulation, or create reports.
Task 2.3: Techniques used in BMS fixed hardware system installation and cable wiring
There are two main processes involved in installation of BMS fixed hardware system:
planning and selection of cable wiring method.
Installation planning
This process entails three main activities: protocol selection, cable selection and
topology. Discussions of these processes are provided below:
Protocol selection: this process involves identifying the local building codes and
standards and installation rules and requirements for this kind of job. Various installation
procedures are also analyzed and the best one selected. Resources required for the selected
procedure, including equipment, materials, labour and time, are also evaluated.
Cable selection: the process entails selecting the best cables to be used from a wide range
of cables available. The major categories of cables are metallic and non-metallic cables. The
cables are selected after thorough analysis of their specifications, properties, availability, price,
flexibility and suitability for the task.
Topology: the process entails identifying the specific components of BMS fixed
hardware system, layout of the system and the sequence of installing this component. In this
process, the overall network structure of the system is established, including the spatial and
geometrical patterns. Another importance of this process is to ensure that BMS installation does
not affect other existing or planned building services.
Cable wiring methods
Below are 6 cable wiring methods that can be used for installation of BMS fixed
hardware system:
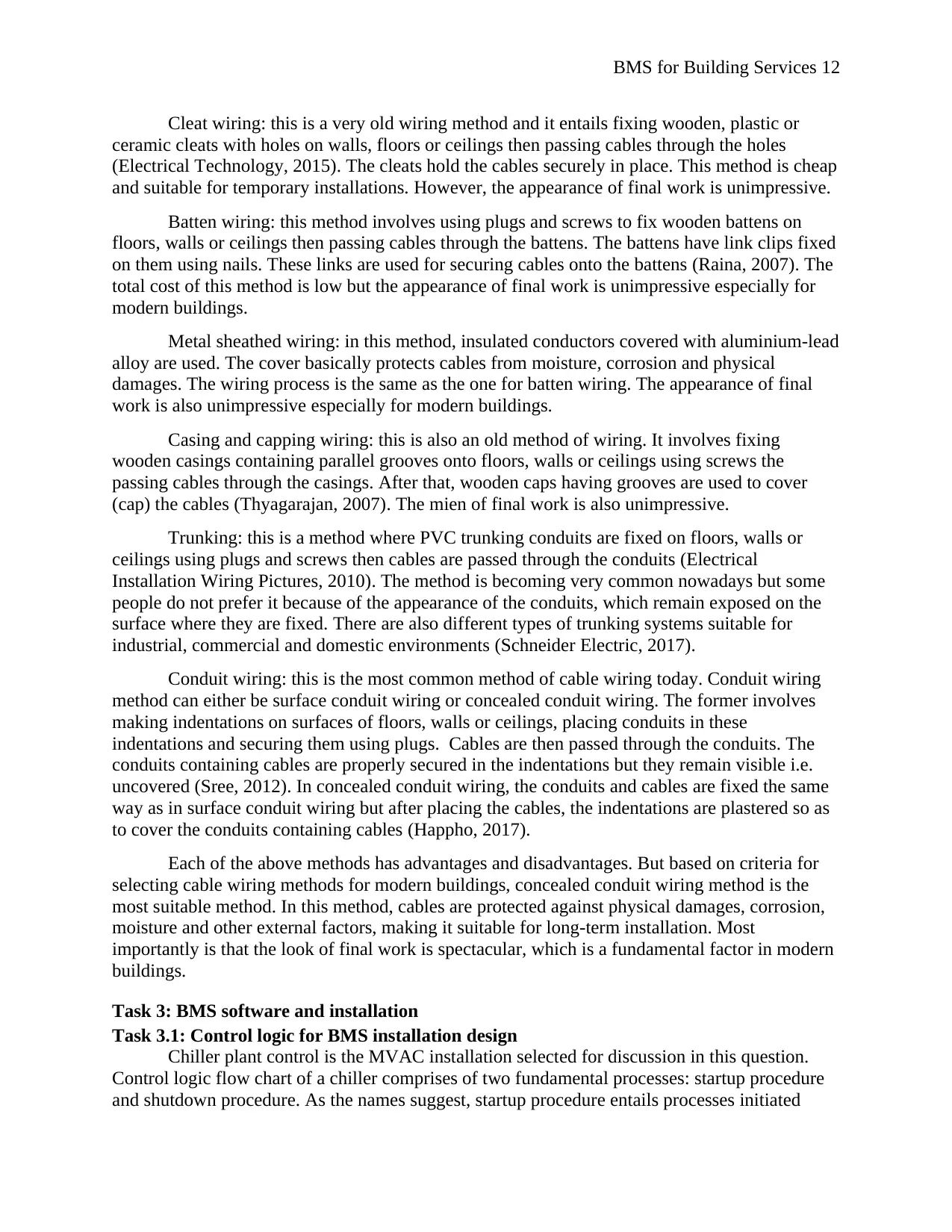
BMS for Building Services 12
Cleat wiring: this is a very old wiring method and it entails fixing wooden, plastic or
ceramic cleats with holes on walls, floors or ceilings then passing cables through the holes
(Electrical Technology, 2015). The cleats hold the cables securely in place. This method is cheap
and suitable for temporary installations. However, the appearance of final work is unimpressive.
Batten wiring: this method involves using plugs and screws to fix wooden battens on
floors, walls or ceilings then passing cables through the battens. The battens have link clips fixed
on them using nails. These links are used for securing cables onto the battens (Raina, 2007). The
total cost of this method is low but the appearance of final work is unimpressive especially for
modern buildings.
Metal sheathed wiring: in this method, insulated conductors covered with aluminium-lead
alloy are used. The cover basically protects cables from moisture, corrosion and physical
damages. The wiring process is the same as the one for batten wiring. The appearance of final
work is also unimpressive especially for modern buildings.
Casing and capping wiring: this is also an old method of wiring. It involves fixing
wooden casings containing parallel grooves onto floors, walls or ceilings using screws the
passing cables through the casings. After that, wooden caps having grooves are used to cover
(cap) the cables (Thyagarajan, 2007). The mien of final work is also unimpressive.
Trunking: this is a method where PVC trunking conduits are fixed on floors, walls or
ceilings using plugs and screws then cables are passed through the conduits (Electrical
Installation Wiring Pictures, 2010). The method is becoming very common nowadays but some
people do not prefer it because of the appearance of the conduits, which remain exposed on the
surface where they are fixed. There are also different types of trunking systems suitable for
industrial, commercial and domestic environments (Schneider Electric, 2017).
Conduit wiring: this is the most common method of cable wiring today. Conduit wiring
method can either be surface conduit wiring or concealed conduit wiring. The former involves
making indentations on surfaces of floors, walls or ceilings, placing conduits in these
indentations and securing them using plugs. Cables are then passed through the conduits. The
conduits containing cables are properly secured in the indentations but they remain visible i.e.
uncovered (Sree, 2012). In concealed conduit wiring, the conduits and cables are fixed the same
way as in surface conduit wiring but after placing the cables, the indentations are plastered so as
to cover the conduits containing cables (Happho, 2017).
Each of the above methods has advantages and disadvantages. But based on criteria for
selecting cable wiring methods for modern buildings, concealed conduit wiring method is the
most suitable method. In this method, cables are protected against physical damages, corrosion,
moisture and other external factors, making it suitable for long-term installation. Most
importantly is that the look of final work is spectacular, which is a fundamental factor in modern
buildings.
Task 3: BMS software and installation
Task 3.1: Control logic for BMS installation design
Chiller plant control is the MVAC installation selected for discussion in this question.
Control logic flow chart of a chiller comprises of two fundamental processes: startup procedure
and shutdown procedure. As the names suggest, startup procedure entails processes initiated
Cleat wiring: this is a very old wiring method and it entails fixing wooden, plastic or
ceramic cleats with holes on walls, floors or ceilings then passing cables through the holes
(Electrical Technology, 2015). The cleats hold the cables securely in place. This method is cheap
and suitable for temporary installations. However, the appearance of final work is unimpressive.
Batten wiring: this method involves using plugs and screws to fix wooden battens on
floors, walls or ceilings then passing cables through the battens. The battens have link clips fixed
on them using nails. These links are used for securing cables onto the battens (Raina, 2007). The
total cost of this method is low but the appearance of final work is unimpressive especially for
modern buildings.
Metal sheathed wiring: in this method, insulated conductors covered with aluminium-lead
alloy are used. The cover basically protects cables from moisture, corrosion and physical
damages. The wiring process is the same as the one for batten wiring. The appearance of final
work is also unimpressive especially for modern buildings.
Casing and capping wiring: this is also an old method of wiring. It involves fixing
wooden casings containing parallel grooves onto floors, walls or ceilings using screws the
passing cables through the casings. After that, wooden caps having grooves are used to cover
(cap) the cables (Thyagarajan, 2007). The mien of final work is also unimpressive.
Trunking: this is a method where PVC trunking conduits are fixed on floors, walls or
ceilings using plugs and screws then cables are passed through the conduits (Electrical
Installation Wiring Pictures, 2010). The method is becoming very common nowadays but some
people do not prefer it because of the appearance of the conduits, which remain exposed on the
surface where they are fixed. There are also different types of trunking systems suitable for
industrial, commercial and domestic environments (Schneider Electric, 2017).
Conduit wiring: this is the most common method of cable wiring today. Conduit wiring
method can either be surface conduit wiring or concealed conduit wiring. The former involves
making indentations on surfaces of floors, walls or ceilings, placing conduits in these
indentations and securing them using plugs. Cables are then passed through the conduits. The
conduits containing cables are properly secured in the indentations but they remain visible i.e.
uncovered (Sree, 2012). In concealed conduit wiring, the conduits and cables are fixed the same
way as in surface conduit wiring but after placing the cables, the indentations are plastered so as
to cover the conduits containing cables (Happho, 2017).
Each of the above methods has advantages and disadvantages. But based on criteria for
selecting cable wiring methods for modern buildings, concealed conduit wiring method is the
most suitable method. In this method, cables are protected against physical damages, corrosion,
moisture and other external factors, making it suitable for long-term installation. Most
importantly is that the look of final work is spectacular, which is a fundamental factor in modern
buildings.
Task 3: BMS software and installation
Task 3.1: Control logic for BMS installation design
Chiller plant control is the MVAC installation selected for discussion in this question.
Control logic flow chart of a chiller comprises of two fundamental processes: startup procedure
and shutdown procedure. As the names suggest, startup procedure entails processes initiated
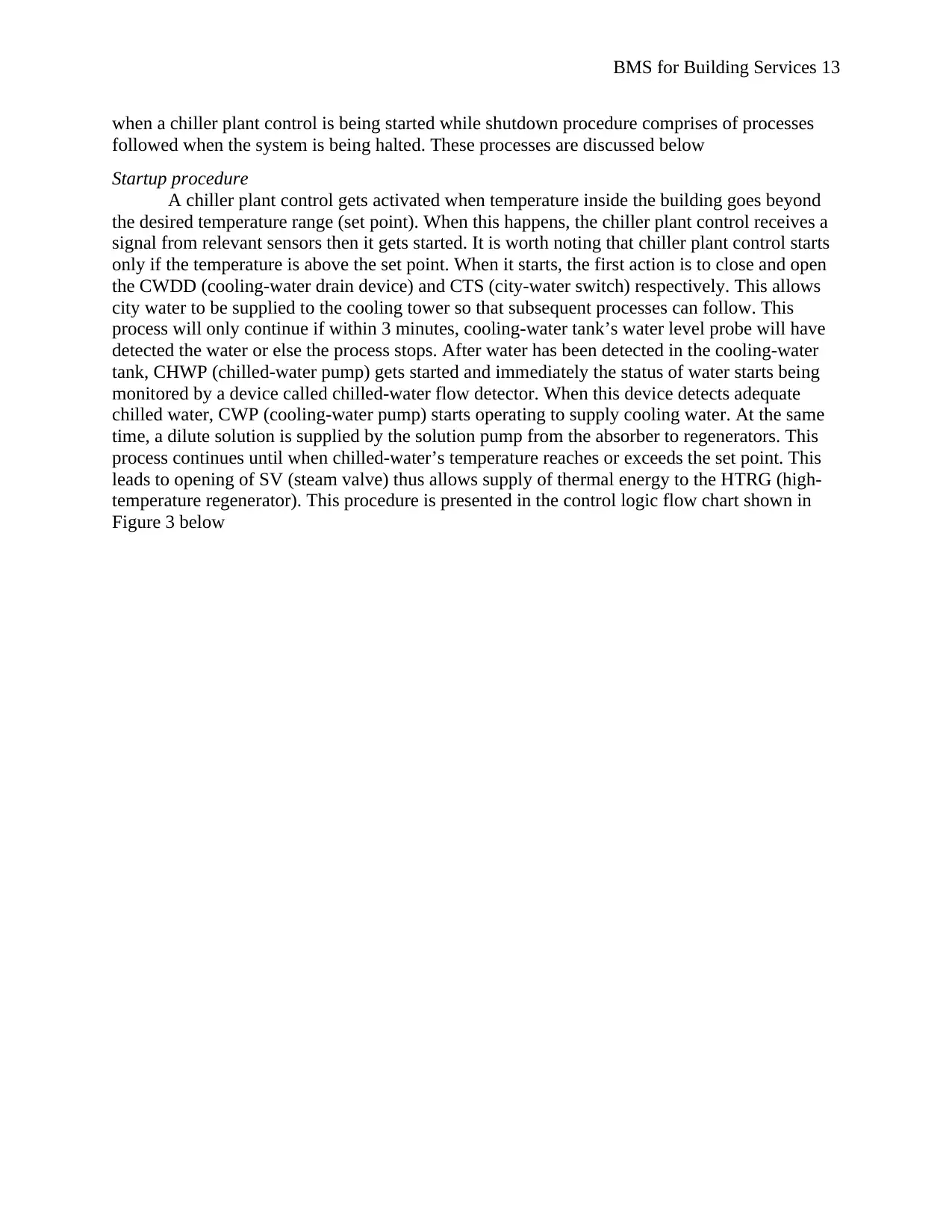
BMS for Building Services 13
when a chiller plant control is being started while shutdown procedure comprises of processes
followed when the system is being halted. These processes are discussed below
Startup procedure
A chiller plant control gets activated when temperature inside the building goes beyond
the desired temperature range (set point). When this happens, the chiller plant control receives a
signal from relevant sensors then it gets started. It is worth noting that chiller plant control starts
only if the temperature is above the set point. When it starts, the first action is to close and open
the CWDD (cooling-water drain device) and CTS (city-water switch) respectively. This allows
city water to be supplied to the cooling tower so that subsequent processes can follow. This
process will only continue if within 3 minutes, cooling-water tank’s water level probe will have
detected the water or else the process stops. After water has been detected in the cooling-water
tank, CHWP (chilled-water pump) gets started and immediately the status of water starts being
monitored by a device called chilled-water flow detector. When this device detects adequate
chilled water, CWP (cooling-water pump) starts operating to supply cooling water. At the same
time, a dilute solution is supplied by the solution pump from the absorber to regenerators. This
process continues until when chilled-water’s temperature reaches or exceeds the set point. This
leads to opening of SV (steam valve) thus allows supply of thermal energy to the HTRG (high-
temperature regenerator). This procedure is presented in the control logic flow chart shown in
Figure 3 below
when a chiller plant control is being started while shutdown procedure comprises of processes
followed when the system is being halted. These processes are discussed below
Startup procedure
A chiller plant control gets activated when temperature inside the building goes beyond
the desired temperature range (set point). When this happens, the chiller plant control receives a
signal from relevant sensors then it gets started. It is worth noting that chiller plant control starts
only if the temperature is above the set point. When it starts, the first action is to close and open
the CWDD (cooling-water drain device) and CTS (city-water switch) respectively. This allows
city water to be supplied to the cooling tower so that subsequent processes can follow. This
process will only continue if within 3 minutes, cooling-water tank’s water level probe will have
detected the water or else the process stops. After water has been detected in the cooling-water
tank, CHWP (chilled-water pump) gets started and immediately the status of water starts being
monitored by a device called chilled-water flow detector. When this device detects adequate
chilled water, CWP (cooling-water pump) starts operating to supply cooling water. At the same
time, a dilute solution is supplied by the solution pump from the absorber to regenerators. This
process continues until when chilled-water’s temperature reaches or exceeds the set point. This
leads to opening of SV (steam valve) thus allows supply of thermal energy to the HTRG (high-
temperature regenerator). This procedure is presented in the control logic flow chart shown in
Figure 3 below
Paraphrase This Document
Need a fresh take? Get an instant paraphrase of this document with our AI Paraphraser
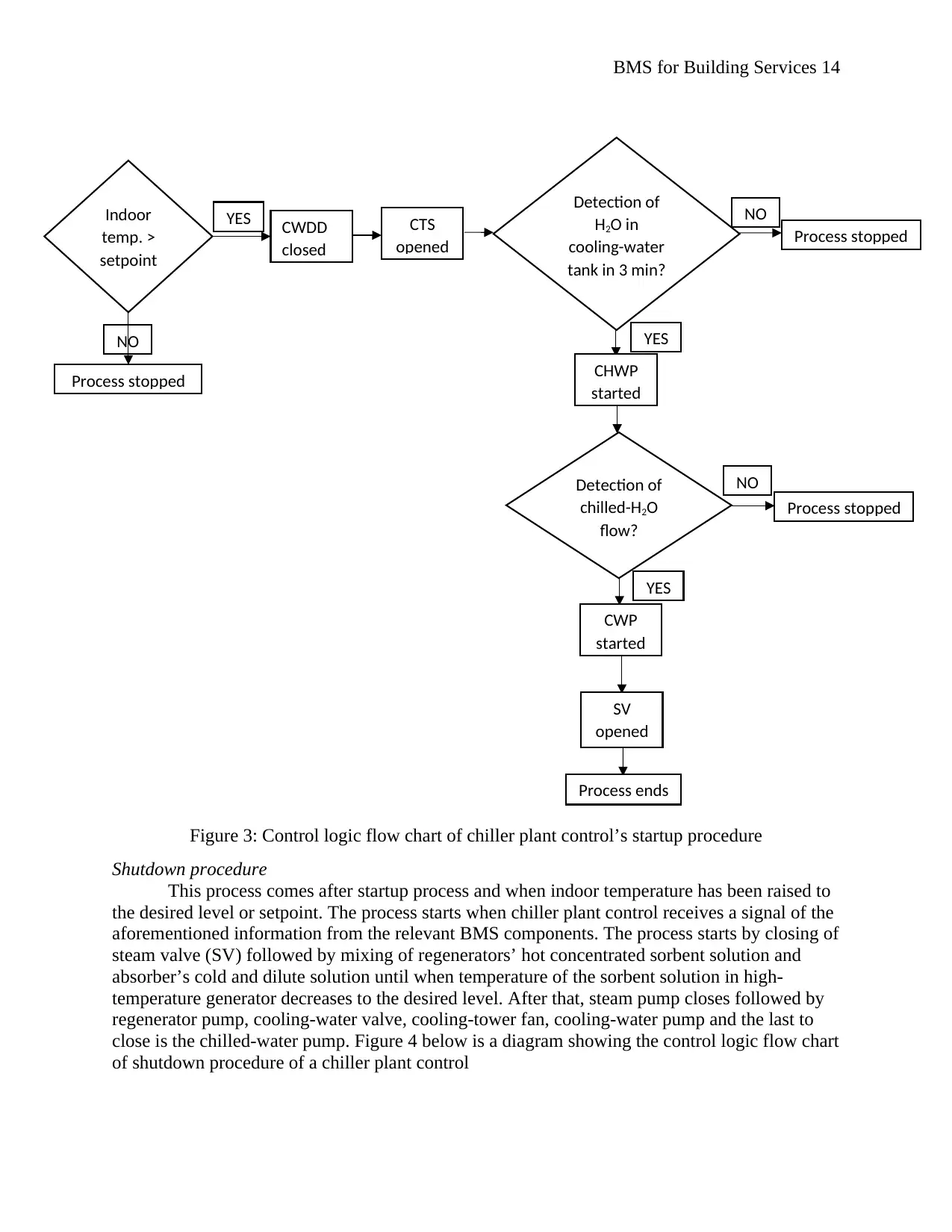
BMS for Building Services 14
Figure 3: Control logic flow chart of chiller plant control’s startup procedure
Shutdown procedure
This process comes after startup process and when indoor temperature has been raised to
the desired level or setpoint. The process starts when chiller plant control receives a signal of the
aforementioned information from the relevant BMS components. The process starts by closing of
steam valve (SV) followed by mixing of regenerators’ hot concentrated sorbent solution and
absorber’s cold and dilute solution until when temperature of the sorbent solution in high-
temperature generator decreases to the desired level. After that, steam pump closes followed by
regenerator pump, cooling-water valve, cooling-tower fan, cooling-water pump and the last to
close is the chilled-water pump. Figure 4 below is a diagram showing the control logic flow chart
of shutdown procedure of a chiller plant control
Indoor
temp. >
setpoint
NO
YES
Process stopped
CWDD
closed
CTS
opened
Detection of
H2O in
cooling-water
tank in 3 min?
NO
Process stopped
CHWP
started
Detection of
chilled-H2O
flow?
NO
Process stopped
CWP
started
YES
YES
SV
opened
Process ends
Figure 3: Control logic flow chart of chiller plant control’s startup procedure
Shutdown procedure
This process comes after startup process and when indoor temperature has been raised to
the desired level or setpoint. The process starts when chiller plant control receives a signal of the
aforementioned information from the relevant BMS components. The process starts by closing of
steam valve (SV) followed by mixing of regenerators’ hot concentrated sorbent solution and
absorber’s cold and dilute solution until when temperature of the sorbent solution in high-
temperature generator decreases to the desired level. After that, steam pump closes followed by
regenerator pump, cooling-water valve, cooling-tower fan, cooling-water pump and the last to
close is the chilled-water pump. Figure 4 below is a diagram showing the control logic flow chart
of shutdown procedure of a chiller plant control
Indoor
temp. >
setpoint
NO
YES
Process stopped
CWDD
closed
CTS
opened
Detection of
H2O in
cooling-water
tank in 3 min?
NO
Process stopped
CHWP
started
Detection of
chilled-H2O
flow?
NO
Process stopped
CWP
started
YES
YES
SV
opened
Process ends
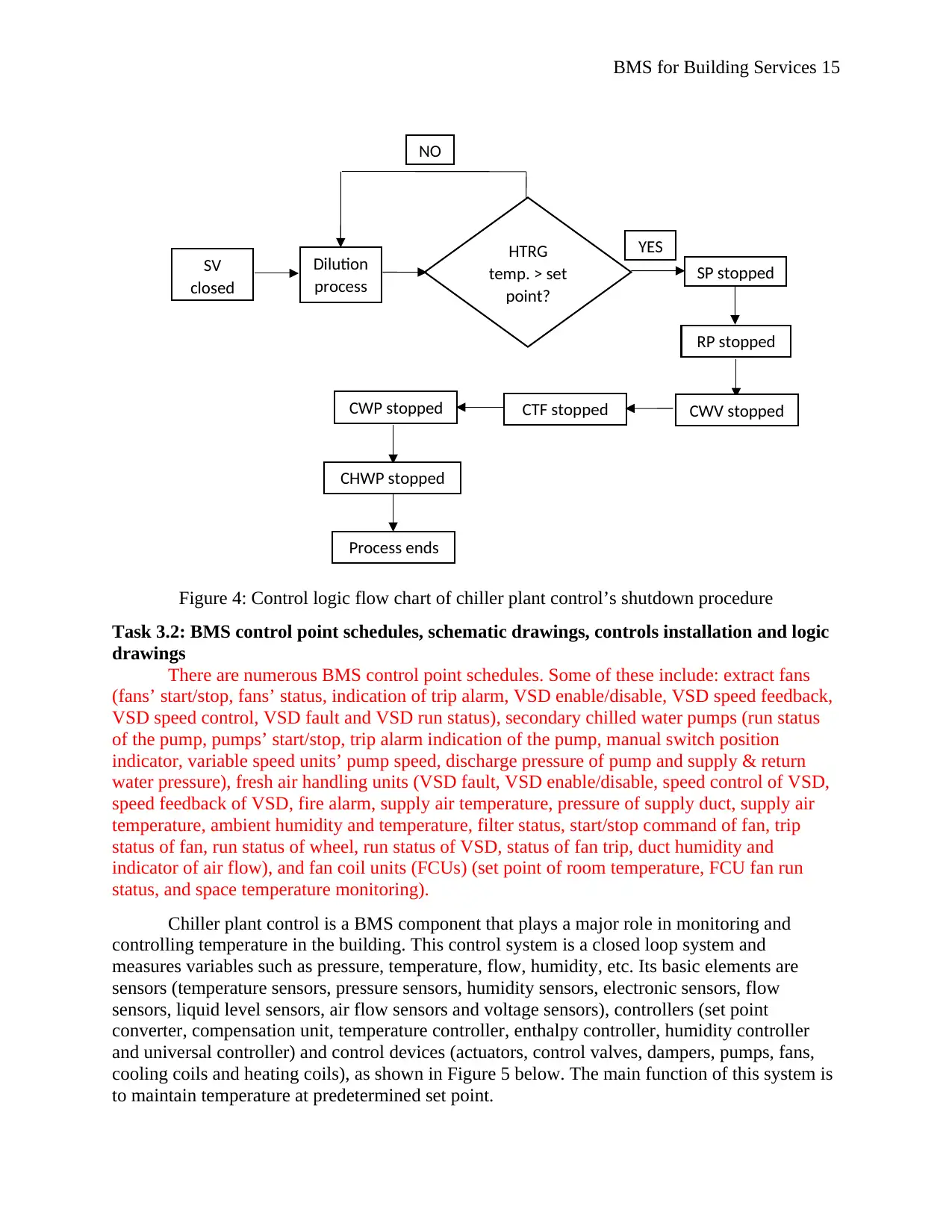
BMS for Building Services 15
Figure 4: Control logic flow chart of chiller plant control’s shutdown procedure
Task 3.2: BMS control point schedules, schematic drawings, controls installation and logic
drawings
There are numerous BMS control point schedules. Some of these include: extract fans
(fans’ start/stop, fans’ status, indication of trip alarm, VSD enable/disable, VSD speed feedback,
VSD speed control, VSD fault and VSD run status), secondary chilled water pumps (run status
of the pump, pumps’ start/stop, trip alarm indication of the pump, manual switch position
indicator, variable speed units’ pump speed, discharge pressure of pump and supply & return
water pressure), fresh air handling units (VSD fault, VSD enable/disable, speed control of VSD,
speed feedback of VSD, fire alarm, supply air temperature, pressure of supply duct, supply air
temperature, ambient humidity and temperature, filter status, start/stop command of fan, trip
status of fan, run status of wheel, run status of VSD, status of fan trip, duct humidity and
indicator of air flow), and fan coil units (FCUs) (set point of room temperature, FCU fan run
status, and space temperature monitoring).
Chiller plant control is a BMS component that plays a major role in monitoring and
controlling temperature in the building. This control system is a closed loop system and
measures variables such as pressure, temperature, flow, humidity, etc. Its basic elements are
sensors (temperature sensors, pressure sensors, humidity sensors, electronic sensors, flow
sensors, liquid level sensors, air flow sensors and voltage sensors), controllers (set point
converter, compensation unit, temperature controller, enthalpy controller, humidity controller
and universal controller) and control devices (actuators, control valves, dampers, pumps, fans,
cooling coils and heating coils), as shown in Figure 5 below. The main function of this system is
to maintain temperature at predetermined set point.
SV
closed
Dilution
process
HTRG
temp. > set
point?
YES
NO
SP stopped
RP stopped
CWV stoppedCTF stoppedCWP stopped
CHWP stopped
Process ends
Figure 4: Control logic flow chart of chiller plant control’s shutdown procedure
Task 3.2: BMS control point schedules, schematic drawings, controls installation and logic
drawings
There are numerous BMS control point schedules. Some of these include: extract fans
(fans’ start/stop, fans’ status, indication of trip alarm, VSD enable/disable, VSD speed feedback,
VSD speed control, VSD fault and VSD run status), secondary chilled water pumps (run status
of the pump, pumps’ start/stop, trip alarm indication of the pump, manual switch position
indicator, variable speed units’ pump speed, discharge pressure of pump and supply & return
water pressure), fresh air handling units (VSD fault, VSD enable/disable, speed control of VSD,
speed feedback of VSD, fire alarm, supply air temperature, pressure of supply duct, supply air
temperature, ambient humidity and temperature, filter status, start/stop command of fan, trip
status of fan, run status of wheel, run status of VSD, status of fan trip, duct humidity and
indicator of air flow), and fan coil units (FCUs) (set point of room temperature, FCU fan run
status, and space temperature monitoring).
Chiller plant control is a BMS component that plays a major role in monitoring and
controlling temperature in the building. This control system is a closed loop system and
measures variables such as pressure, temperature, flow, humidity, etc. Its basic elements are
sensors (temperature sensors, pressure sensors, humidity sensors, electronic sensors, flow
sensors, liquid level sensors, air flow sensors and voltage sensors), controllers (set point
converter, compensation unit, temperature controller, enthalpy controller, humidity controller
and universal controller) and control devices (actuators, control valves, dampers, pumps, fans,
cooling coils and heating coils), as shown in Figure 5 below. The main function of this system is
to maintain temperature at predetermined set point.
SV
closed
Dilution
process
HTRG
temp. > set
point?
YES
NO
SP stopped
RP stopped
CWV stoppedCTF stoppedCWP stopped
CHWP stopped
Process ends
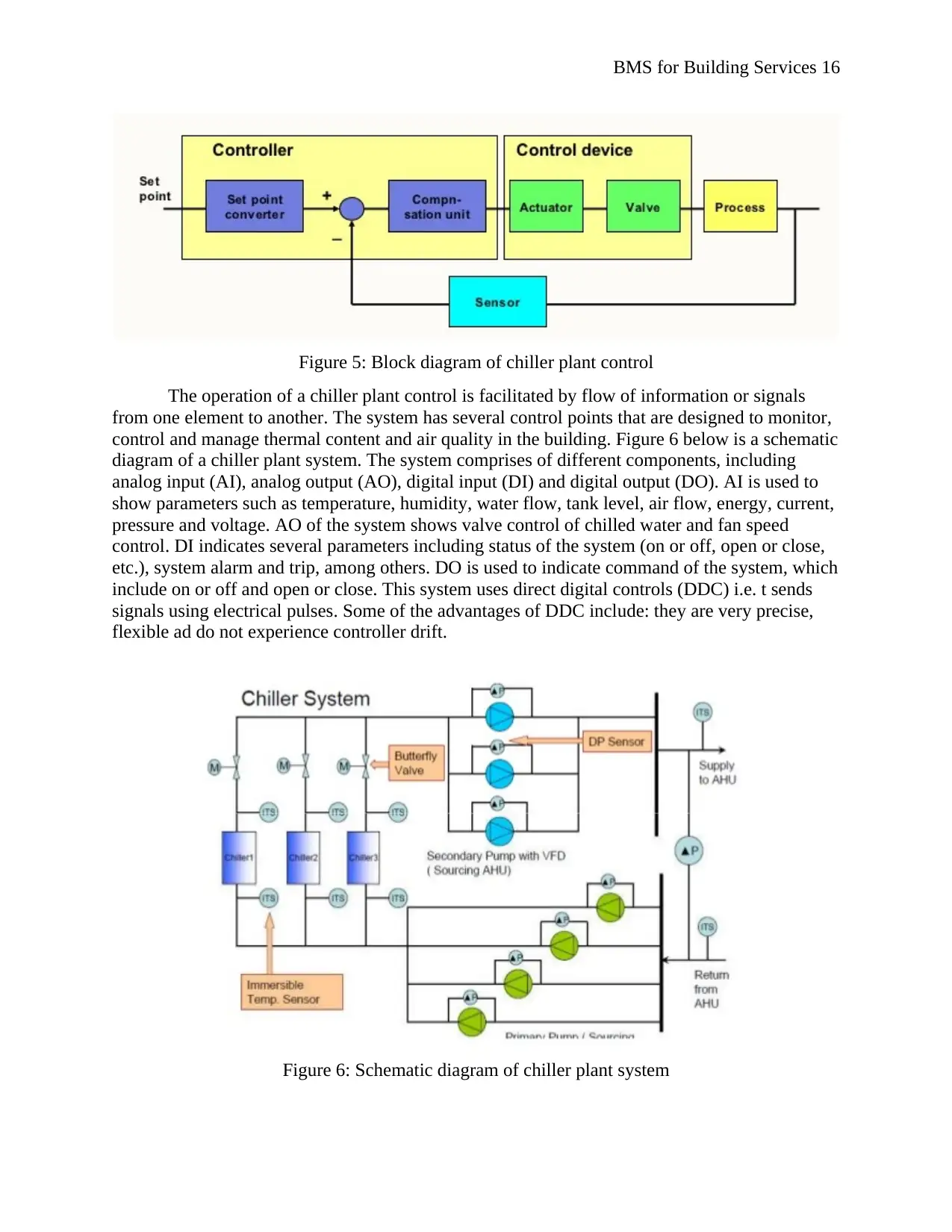
BMS for Building Services 16
Figure 5: Block diagram of chiller plant control
The operation of a chiller plant control is facilitated by flow of information or signals
from one element to another. The system has several control points that are designed to monitor,
control and manage thermal content and air quality in the building. Figure 6 below is a schematic
diagram of a chiller plant system. The system comprises of different components, including
analog input (AI), analog output (AO), digital input (DI) and digital output (DO). AI is used to
show parameters such as temperature, humidity, water flow, tank level, air flow, energy, current,
pressure and voltage. AO of the system shows valve control of chilled water and fan speed
control. DI indicates several parameters including status of the system (on or off, open or close,
etc.), system alarm and trip, among others. DO is used to indicate command of the system, which
include on or off and open or close. This system uses direct digital controls (DDC) i.e. t sends
signals using electrical pulses. Some of the advantages of DDC include: they are very precise,
flexible ad do not experience controller drift.
Figure 6: Schematic diagram of chiller plant system
Figure 5: Block diagram of chiller plant control
The operation of a chiller plant control is facilitated by flow of information or signals
from one element to another. The system has several control points that are designed to monitor,
control and manage thermal content and air quality in the building. Figure 6 below is a schematic
diagram of a chiller plant system. The system comprises of different components, including
analog input (AI), analog output (AO), digital input (DI) and digital output (DO). AI is used to
show parameters such as temperature, humidity, water flow, tank level, air flow, energy, current,
pressure and voltage. AO of the system shows valve control of chilled water and fan speed
control. DI indicates several parameters including status of the system (on or off, open or close,
etc.), system alarm and trip, among others. DO is used to indicate command of the system, which
include on or off and open or close. This system uses direct digital controls (DDC) i.e. t sends
signals using electrical pulses. Some of the advantages of DDC include: they are very precise,
flexible ad do not experience controller drift.
Figure 6: Schematic diagram of chiller plant system
Secure Best Marks with AI Grader
Need help grading? Try our AI Grader for instant feedback on your assignments.
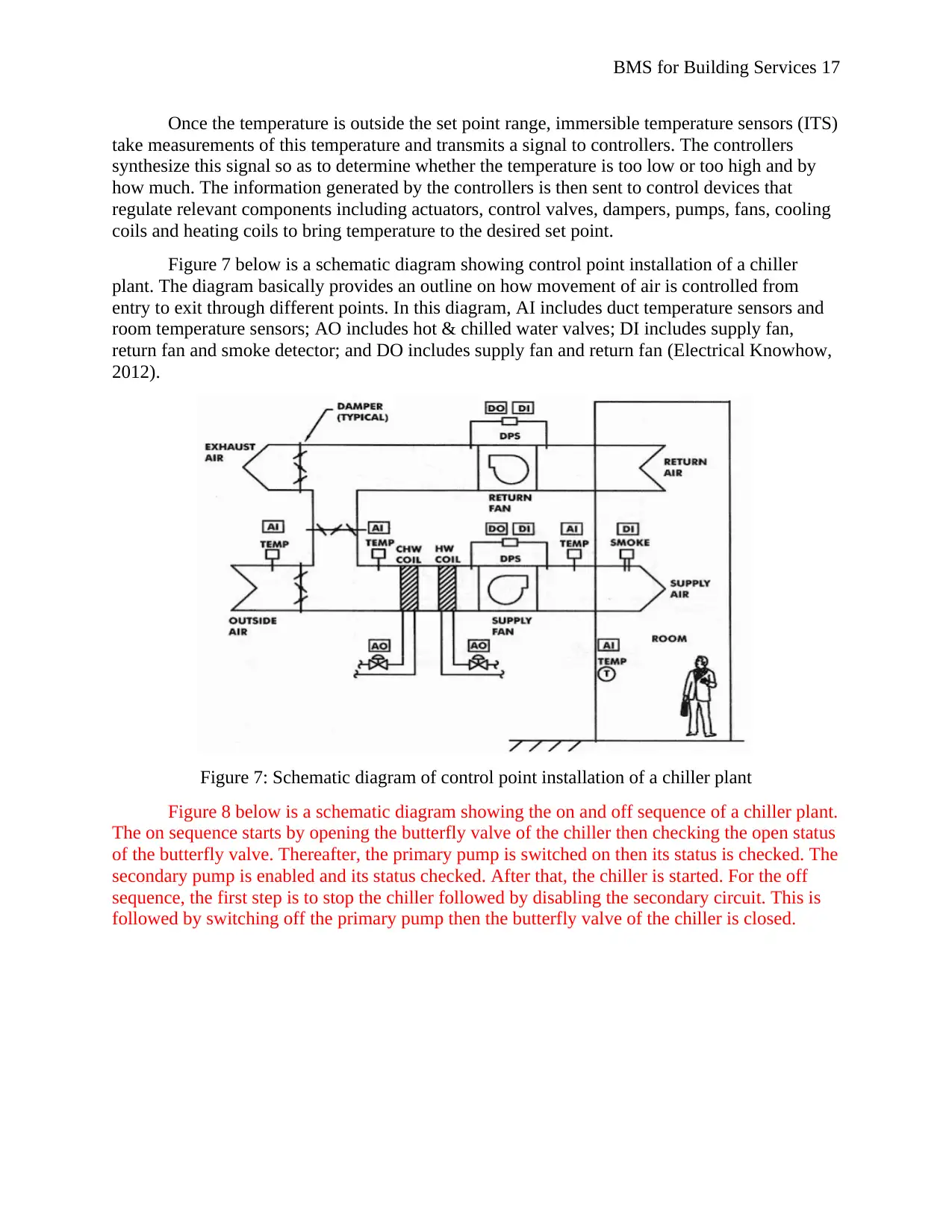
BMS for Building Services 17
Once the temperature is outside the set point range, immersible temperature sensors (ITS)
take measurements of this temperature and transmits a signal to controllers. The controllers
synthesize this signal so as to determine whether the temperature is too low or too high and by
how much. The information generated by the controllers is then sent to control devices that
regulate relevant components including actuators, control valves, dampers, pumps, fans, cooling
coils and heating coils to bring temperature to the desired set point.
Figure 7 below is a schematic diagram showing control point installation of a chiller
plant. The diagram basically provides an outline on how movement of air is controlled from
entry to exit through different points. In this diagram, AI includes duct temperature sensors and
room temperature sensors; AO includes hot & chilled water valves; DI includes supply fan,
return fan and smoke detector; and DO includes supply fan and return fan (Electrical Knowhow,
2012).
Figure 7: Schematic diagram of control point installation of a chiller plant
Figure 8 below is a schematic diagram showing the on and off sequence of a chiller plant.
The on sequence starts by opening the butterfly valve of the chiller then checking the open status
of the butterfly valve. Thereafter, the primary pump is switched on then its status is checked. The
secondary pump is enabled and its status checked. After that, the chiller is started. For the off
sequence, the first step is to stop the chiller followed by disabling the secondary circuit. This is
followed by switching off the primary pump then the butterfly valve of the chiller is closed.
Once the temperature is outside the set point range, immersible temperature sensors (ITS)
take measurements of this temperature and transmits a signal to controllers. The controllers
synthesize this signal so as to determine whether the temperature is too low or too high and by
how much. The information generated by the controllers is then sent to control devices that
regulate relevant components including actuators, control valves, dampers, pumps, fans, cooling
coils and heating coils to bring temperature to the desired set point.
Figure 7 below is a schematic diagram showing control point installation of a chiller
plant. The diagram basically provides an outline on how movement of air is controlled from
entry to exit through different points. In this diagram, AI includes duct temperature sensors and
room temperature sensors; AO includes hot & chilled water valves; DI includes supply fan,
return fan and smoke detector; and DO includes supply fan and return fan (Electrical Knowhow,
2012).
Figure 7: Schematic diagram of control point installation of a chiller plant
Figure 8 below is a schematic diagram showing the on and off sequence of a chiller plant.
The on sequence starts by opening the butterfly valve of the chiller then checking the open status
of the butterfly valve. Thereafter, the primary pump is switched on then its status is checked. The
secondary pump is enabled and its status checked. After that, the chiller is started. For the off
sequence, the first step is to stop the chiller followed by disabling the secondary circuit. This is
followed by switching off the primary pump then the butterfly valve of the chiller is closed.
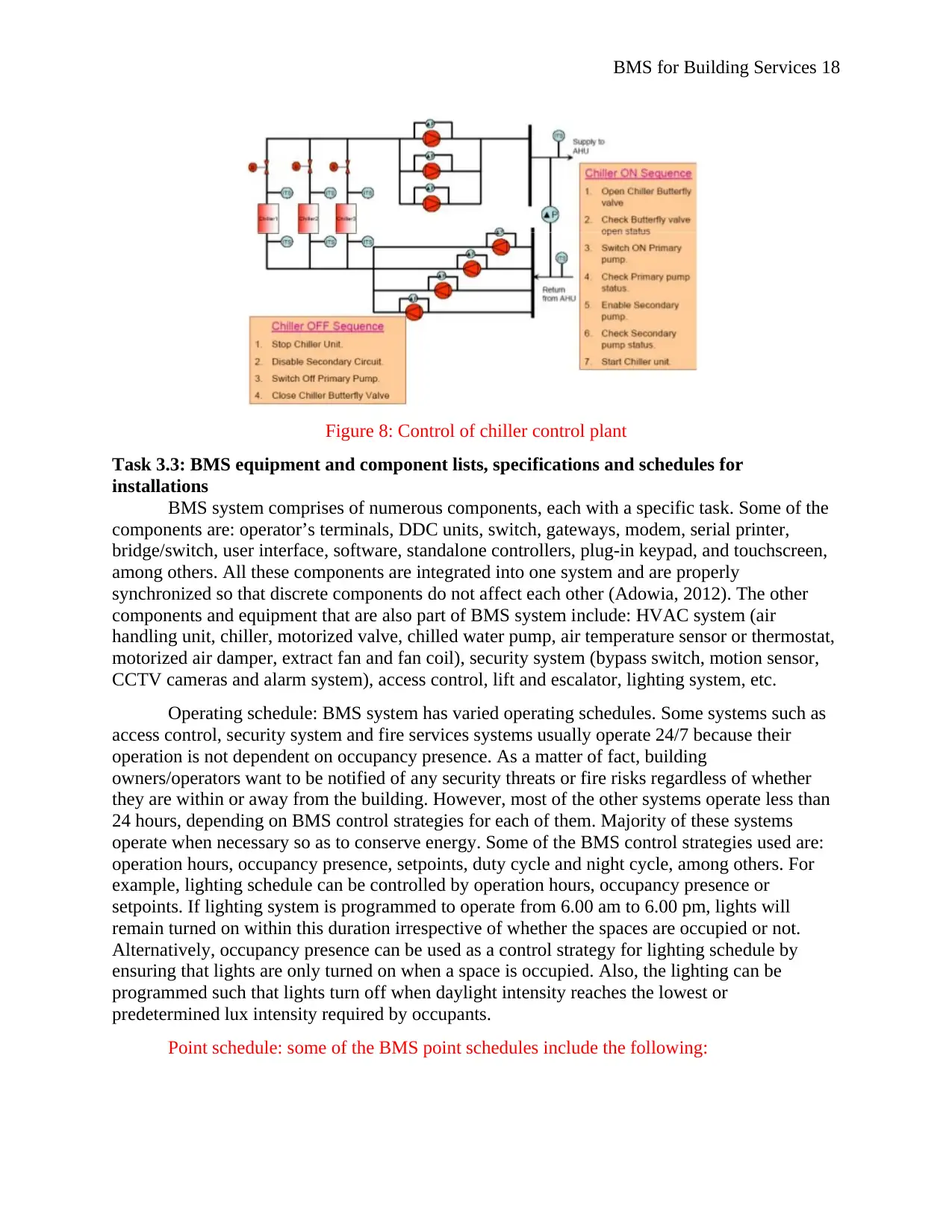
BMS for Building Services 18
Figure 8: Control of chiller control plant
Task 3.3: BMS equipment and component lists, specifications and schedules for
installations
BMS system comprises of numerous components, each with a specific task. Some of the
components are: operator’s terminals, DDC units, switch, gateways, modem, serial printer,
bridge/switch, user interface, software, standalone controllers, plug-in keypad, and touchscreen,
among others. All these components are integrated into one system and are properly
synchronized so that discrete components do not affect each other (Adowia, 2012). The other
components and equipment that are also part of BMS system include: HVAC system (air
handling unit, chiller, motorized valve, chilled water pump, air temperature sensor or thermostat,
motorized air damper, extract fan and fan coil), security system (bypass switch, motion sensor,
CCTV cameras and alarm system), access control, lift and escalator, lighting system, etc.
Operating schedule: BMS system has varied operating schedules. Some systems such as
access control, security system and fire services systems usually operate 24/7 because their
operation is not dependent on occupancy presence. As a matter of fact, building
owners/operators want to be notified of any security threats or fire risks regardless of whether
they are within or away from the building. However, most of the other systems operate less than
24 hours, depending on BMS control strategies for each of them. Majority of these systems
operate when necessary so as to conserve energy. Some of the BMS control strategies used are:
operation hours, occupancy presence, setpoints, duty cycle and night cycle, among others. For
example, lighting schedule can be controlled by operation hours, occupancy presence or
setpoints. If lighting system is programmed to operate from 6.00 am to 6.00 pm, lights will
remain turned on within this duration irrespective of whether the spaces are occupied or not.
Alternatively, occupancy presence can be used as a control strategy for lighting schedule by
ensuring that lights are only turned on when a space is occupied. Also, the lighting can be
programmed such that lights turn off when daylight intensity reaches the lowest or
predetermined lux intensity required by occupants.
Point schedule: some of the BMS point schedules include the following:
Figure 8: Control of chiller control plant
Task 3.3: BMS equipment and component lists, specifications and schedules for
installations
BMS system comprises of numerous components, each with a specific task. Some of the
components are: operator’s terminals, DDC units, switch, gateways, modem, serial printer,
bridge/switch, user interface, software, standalone controllers, plug-in keypad, and touchscreen,
among others. All these components are integrated into one system and are properly
synchronized so that discrete components do not affect each other (Adowia, 2012). The other
components and equipment that are also part of BMS system include: HVAC system (air
handling unit, chiller, motorized valve, chilled water pump, air temperature sensor or thermostat,
motorized air damper, extract fan and fan coil), security system (bypass switch, motion sensor,
CCTV cameras and alarm system), access control, lift and escalator, lighting system, etc.
Operating schedule: BMS system has varied operating schedules. Some systems such as
access control, security system and fire services systems usually operate 24/7 because their
operation is not dependent on occupancy presence. As a matter of fact, building
owners/operators want to be notified of any security threats or fire risks regardless of whether
they are within or away from the building. However, most of the other systems operate less than
24 hours, depending on BMS control strategies for each of them. Majority of these systems
operate when necessary so as to conserve energy. Some of the BMS control strategies used are:
operation hours, occupancy presence, setpoints, duty cycle and night cycle, among others. For
example, lighting schedule can be controlled by operation hours, occupancy presence or
setpoints. If lighting system is programmed to operate from 6.00 am to 6.00 pm, lights will
remain turned on within this duration irrespective of whether the spaces are occupied or not.
Alternatively, occupancy presence can be used as a control strategy for lighting schedule by
ensuring that lights are only turned on when a space is occupied. Also, the lighting can be
programmed such that lights turn off when daylight intensity reaches the lowest or
predetermined lux intensity required by occupants.
Point schedule: some of the BMS point schedules include the following:
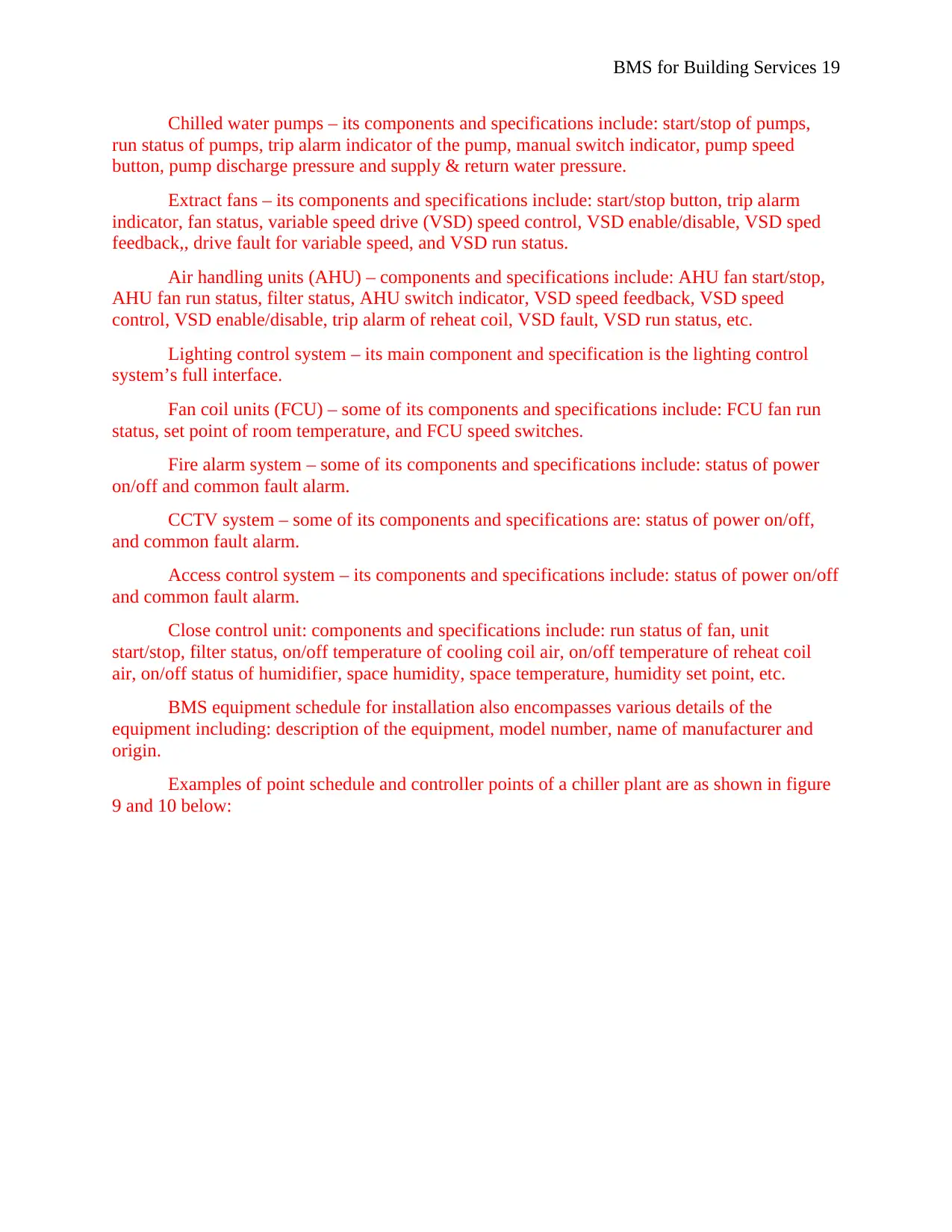
BMS for Building Services 19
Chilled water pumps – its components and specifications include: start/stop of pumps,
run status of pumps, trip alarm indicator of the pump, manual switch indicator, pump speed
button, pump discharge pressure and supply & return water pressure.
Extract fans – its components and specifications include: start/stop button, trip alarm
indicator, fan status, variable speed drive (VSD) speed control, VSD enable/disable, VSD sped
feedback,, drive fault for variable speed, and VSD run status.
Air handling units (AHU) – components and specifications include: AHU fan start/stop,
AHU fan run status, filter status, AHU switch indicator, VSD speed feedback, VSD speed
control, VSD enable/disable, trip alarm of reheat coil, VSD fault, VSD run status, etc.
Lighting control system – its main component and specification is the lighting control
system’s full interface.
Fan coil units (FCU) – some of its components and specifications include: FCU fan run
status, set point of room temperature, and FCU speed switches.
Fire alarm system – some of its components and specifications include: status of power
on/off and common fault alarm.
CCTV system – some of its components and specifications are: status of power on/off,
and common fault alarm.
Access control system – its components and specifications include: status of power on/off
and common fault alarm.
Close control unit: components and specifications include: run status of fan, unit
start/stop, filter status, on/off temperature of cooling coil air, on/off temperature of reheat coil
air, on/off status of humidifier, space humidity, space temperature, humidity set point, etc.
BMS equipment schedule for installation also encompasses various details of the
equipment including: description of the equipment, model number, name of manufacturer and
origin.
Examples of point schedule and controller points of a chiller plant are as shown in figure
9 and 10 below:
Chilled water pumps – its components and specifications include: start/stop of pumps,
run status of pumps, trip alarm indicator of the pump, manual switch indicator, pump speed
button, pump discharge pressure and supply & return water pressure.
Extract fans – its components and specifications include: start/stop button, trip alarm
indicator, fan status, variable speed drive (VSD) speed control, VSD enable/disable, VSD sped
feedback,, drive fault for variable speed, and VSD run status.
Air handling units (AHU) – components and specifications include: AHU fan start/stop,
AHU fan run status, filter status, AHU switch indicator, VSD speed feedback, VSD speed
control, VSD enable/disable, trip alarm of reheat coil, VSD fault, VSD run status, etc.
Lighting control system – its main component and specification is the lighting control
system’s full interface.
Fan coil units (FCU) – some of its components and specifications include: FCU fan run
status, set point of room temperature, and FCU speed switches.
Fire alarm system – some of its components and specifications include: status of power
on/off and common fault alarm.
CCTV system – some of its components and specifications are: status of power on/off,
and common fault alarm.
Access control system – its components and specifications include: status of power on/off
and common fault alarm.
Close control unit: components and specifications include: run status of fan, unit
start/stop, filter status, on/off temperature of cooling coil air, on/off temperature of reheat coil
air, on/off status of humidifier, space humidity, space temperature, humidity set point, etc.
BMS equipment schedule for installation also encompasses various details of the
equipment including: description of the equipment, model number, name of manufacturer and
origin.
Examples of point schedule and controller points of a chiller plant are as shown in figure
9 and 10 below:
Paraphrase This Document
Need a fresh take? Get an instant paraphrase of this document with our AI Paraphraser
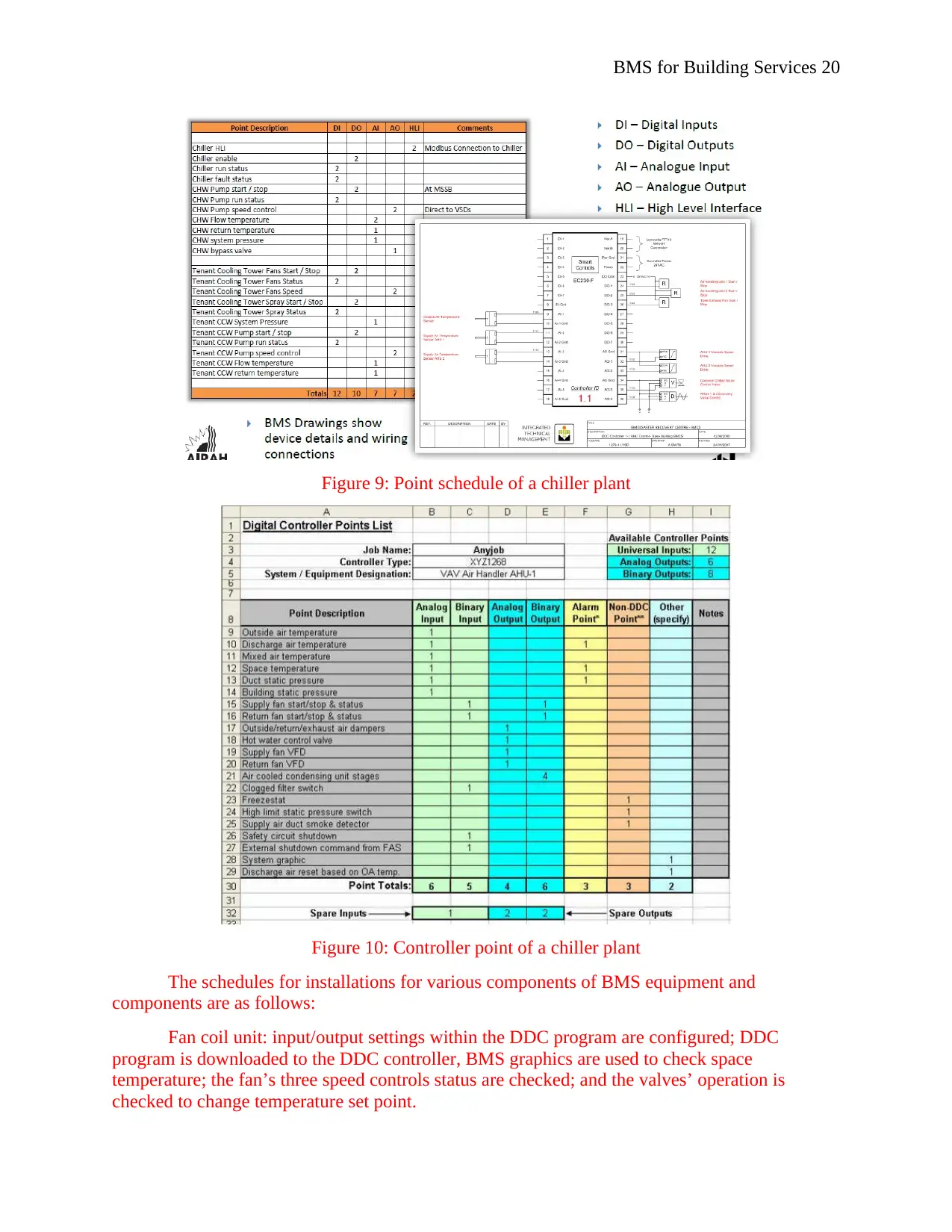
BMS for Building Services 20
Figure 9: Point schedule of a chiller plant
Figure 10: Controller point of a chiller plant
The schedules for installations for various components of BMS equipment and
components are as follows:
Fan coil unit: input/output settings within the DDC program are configured; DDC
program is downloaded to the DDC controller, BMS graphics are used to check space
temperature; the fan’s three speed controls status are checked; and the valves’ operation is
checked to change temperature set point.
Figure 9: Point schedule of a chiller plant
Figure 10: Controller point of a chiller plant
The schedules for installations for various components of BMS equipment and
components are as follows:
Fan coil unit: input/output settings within the DDC program are configured; DDC
program is downloaded to the DDC controller, BMS graphics are used to check space
temperature; the fan’s three speed controls status are checked; and the valves’ operation is
checked to change temperature set point.
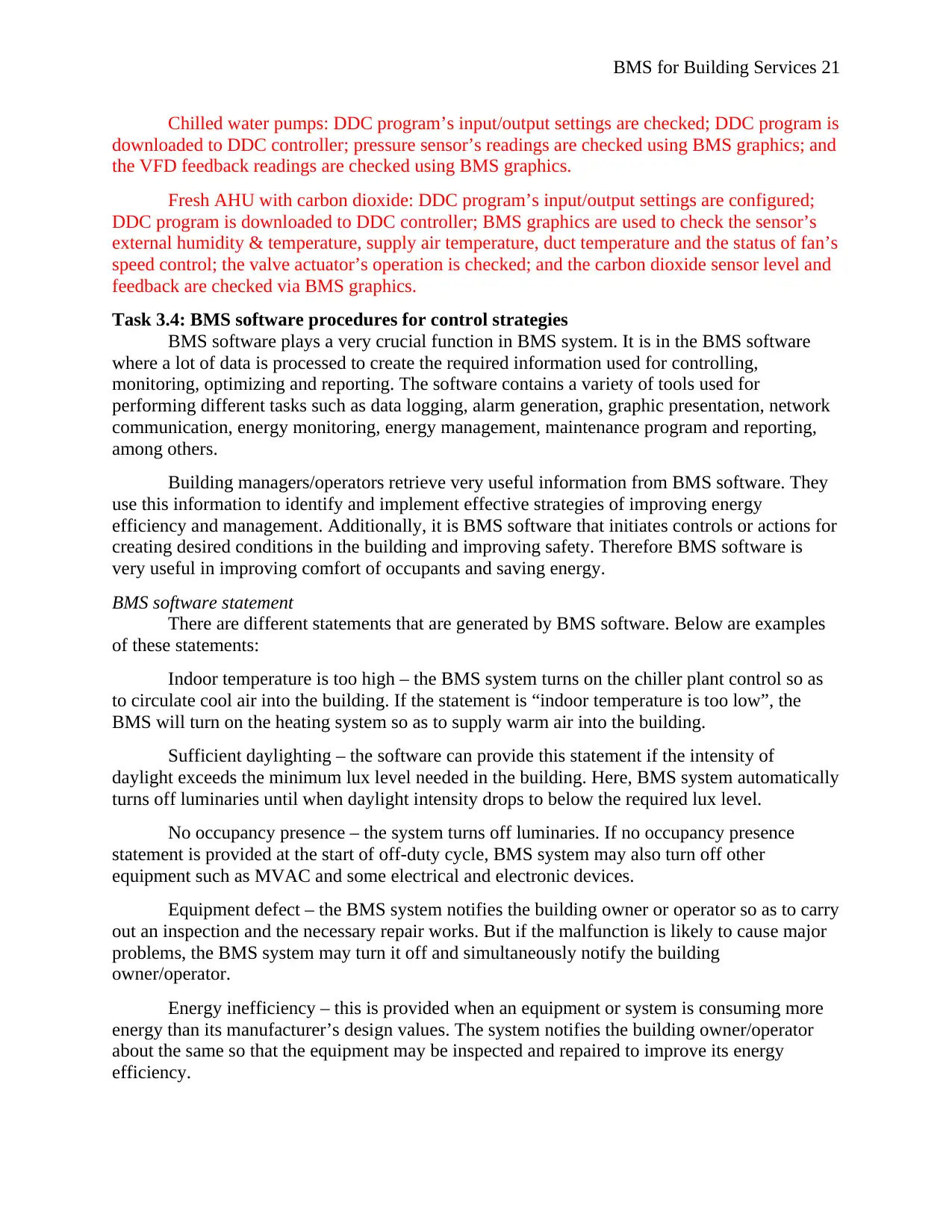
BMS for Building Services 21
Chilled water pumps: DDC program’s input/output settings are checked; DDC program is
downloaded to DDC controller; pressure sensor’s readings are checked using BMS graphics; and
the VFD feedback readings are checked using BMS graphics.
Fresh AHU with carbon dioxide: DDC program’s input/output settings are configured;
DDC program is downloaded to DDC controller; BMS graphics are used to check the sensor’s
external humidity & temperature, supply air temperature, duct temperature and the status of fan’s
speed control; the valve actuator’s operation is checked; and the carbon dioxide sensor level and
feedback are checked via BMS graphics.
Task 3.4: BMS software procedures for control strategies
BMS software plays a very crucial function in BMS system. It is in the BMS software
where a lot of data is processed to create the required information used for controlling,
monitoring, optimizing and reporting. The software contains a variety of tools used for
performing different tasks such as data logging, alarm generation, graphic presentation, network
communication, energy monitoring, energy management, maintenance program and reporting,
among others.
Building managers/operators retrieve very useful information from BMS software. They
use this information to identify and implement effective strategies of improving energy
efficiency and management. Additionally, it is BMS software that initiates controls or actions for
creating desired conditions in the building and improving safety. Therefore BMS software is
very useful in improving comfort of occupants and saving energy.
BMS software statement
There are different statements that are generated by BMS software. Below are examples
of these statements:
Indoor temperature is too high – the BMS system turns on the chiller plant control so as
to circulate cool air into the building. If the statement is “indoor temperature is too low”, the
BMS will turn on the heating system so as to supply warm air into the building.
Sufficient daylighting – the software can provide this statement if the intensity of
daylight exceeds the minimum lux level needed in the building. Here, BMS system automatically
turns off luminaries until when daylight intensity drops to below the required lux level.
No occupancy presence – the system turns off luminaries. If no occupancy presence
statement is provided at the start of off-duty cycle, BMS system may also turn off other
equipment such as MVAC and some electrical and electronic devices.
Equipment defect – the BMS system notifies the building owner or operator so as to carry
out an inspection and the necessary repair works. But if the malfunction is likely to cause major
problems, the BMS system may turn it off and simultaneously notify the building
owner/operator.
Energy inefficiency – this is provided when an equipment or system is consuming more
energy than its manufacturer’s design values. The system notifies the building owner/operator
about the same so that the equipment may be inspected and repaired to improve its energy
efficiency.
Chilled water pumps: DDC program’s input/output settings are checked; DDC program is
downloaded to DDC controller; pressure sensor’s readings are checked using BMS graphics; and
the VFD feedback readings are checked using BMS graphics.
Fresh AHU with carbon dioxide: DDC program’s input/output settings are configured;
DDC program is downloaded to DDC controller; BMS graphics are used to check the sensor’s
external humidity & temperature, supply air temperature, duct temperature and the status of fan’s
speed control; the valve actuator’s operation is checked; and the carbon dioxide sensor level and
feedback are checked via BMS graphics.
Task 3.4: BMS software procedures for control strategies
BMS software plays a very crucial function in BMS system. It is in the BMS software
where a lot of data is processed to create the required information used for controlling,
monitoring, optimizing and reporting. The software contains a variety of tools used for
performing different tasks such as data logging, alarm generation, graphic presentation, network
communication, energy monitoring, energy management, maintenance program and reporting,
among others.
Building managers/operators retrieve very useful information from BMS software. They
use this information to identify and implement effective strategies of improving energy
efficiency and management. Additionally, it is BMS software that initiates controls or actions for
creating desired conditions in the building and improving safety. Therefore BMS software is
very useful in improving comfort of occupants and saving energy.
BMS software statement
There are different statements that are generated by BMS software. Below are examples
of these statements:
Indoor temperature is too high – the BMS system turns on the chiller plant control so as
to circulate cool air into the building. If the statement is “indoor temperature is too low”, the
BMS will turn on the heating system so as to supply warm air into the building.
Sufficient daylighting – the software can provide this statement if the intensity of
daylight exceeds the minimum lux level needed in the building. Here, BMS system automatically
turns off luminaries until when daylight intensity drops to below the required lux level.
No occupancy presence – the system turns off luminaries. If no occupancy presence
statement is provided at the start of off-duty cycle, BMS system may also turn off other
equipment such as MVAC and some electrical and electronic devices.
Equipment defect – the BMS system notifies the building owner or operator so as to carry
out an inspection and the necessary repair works. But if the malfunction is likely to cause major
problems, the BMS system may turn it off and simultaneously notify the building
owner/operator.
Energy inefficiency – this is provided when an equipment or system is consuming more
energy than its manufacturer’s design values. The system notifies the building owner/operator
about the same so that the equipment may be inspected and repaired to improve its energy
efficiency.
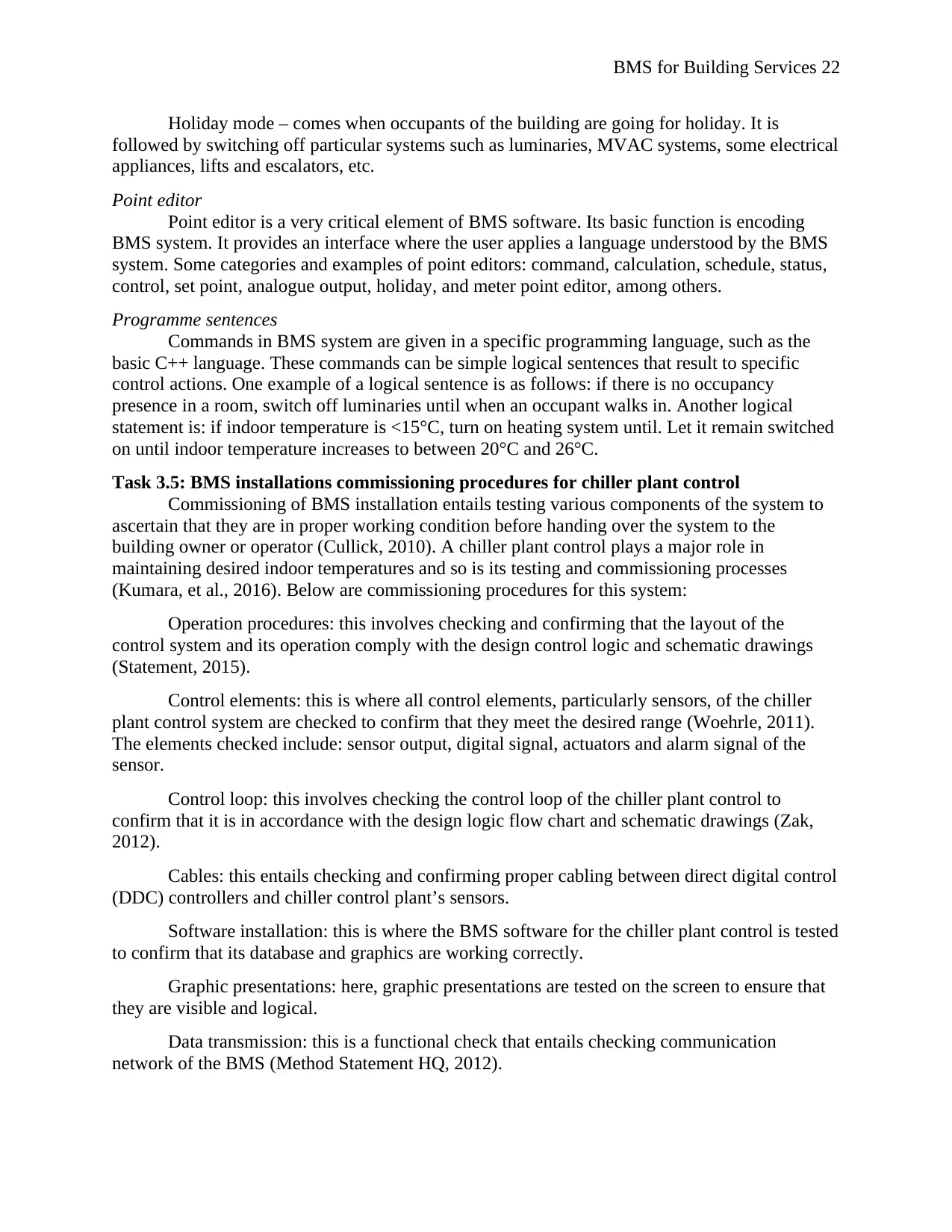
BMS for Building Services 22
Holiday mode – comes when occupants of the building are going for holiday. It is
followed by switching off particular systems such as luminaries, MVAC systems, some electrical
appliances, lifts and escalators, etc.
Point editor
Point editor is a very critical element of BMS software. Its basic function is encoding
BMS system. It provides an interface where the user applies a language understood by the BMS
system. Some categories and examples of point editors: command, calculation, schedule, status,
control, set point, analogue output, holiday, and meter point editor, among others.
Programme sentences
Commands in BMS system are given in a specific programming language, such as the
basic C++ language. These commands can be simple logical sentences that result to specific
control actions. One example of a logical sentence is as follows: if there is no occupancy
presence in a room, switch off luminaries until when an occupant walks in. Another logical
statement is: if indoor temperature is <15°C, turn on heating system until. Let it remain switched
on until indoor temperature increases to between 20°C and 26°C.
Task 3.5: BMS installations commissioning procedures for chiller plant control
Commissioning of BMS installation entails testing various components of the system to
ascertain that they are in proper working condition before handing over the system to the
building owner or operator (Cullick, 2010). A chiller plant control plays a major role in
maintaining desired indoor temperatures and so is its testing and commissioning processes
(Kumara, et al., 2016). Below are commissioning procedures for this system:
Operation procedures: this involves checking and confirming that the layout of the
control system and its operation comply with the design control logic and schematic drawings
(Statement, 2015).
Control elements: this is where all control elements, particularly sensors, of the chiller
plant control system are checked to confirm that they meet the desired range (Woehrle, 2011).
The elements checked include: sensor output, digital signal, actuators and alarm signal of the
sensor.
Control loop: this involves checking the control loop of the chiller plant control to
confirm that it is in accordance with the design logic flow chart and schematic drawings (Zak,
2012).
Cables: this entails checking and confirming proper cabling between direct digital control
(DDC) controllers and chiller control plant’s sensors.
Software installation: this is where the BMS software for the chiller plant control is tested
to confirm that its database and graphics are working correctly.
Graphic presentations: here, graphic presentations are tested on the screen to ensure that
they are visible and logical.
Data transmission: this is a functional check that entails checking communication
network of the BMS (Method Statement HQ, 2012).
Holiday mode – comes when occupants of the building are going for holiday. It is
followed by switching off particular systems such as luminaries, MVAC systems, some electrical
appliances, lifts and escalators, etc.
Point editor
Point editor is a very critical element of BMS software. Its basic function is encoding
BMS system. It provides an interface where the user applies a language understood by the BMS
system. Some categories and examples of point editors: command, calculation, schedule, status,
control, set point, analogue output, holiday, and meter point editor, among others.
Programme sentences
Commands in BMS system are given in a specific programming language, such as the
basic C++ language. These commands can be simple logical sentences that result to specific
control actions. One example of a logical sentence is as follows: if there is no occupancy
presence in a room, switch off luminaries until when an occupant walks in. Another logical
statement is: if indoor temperature is <15°C, turn on heating system until. Let it remain switched
on until indoor temperature increases to between 20°C and 26°C.
Task 3.5: BMS installations commissioning procedures for chiller plant control
Commissioning of BMS installation entails testing various components of the system to
ascertain that they are in proper working condition before handing over the system to the
building owner or operator (Cullick, 2010). A chiller plant control plays a major role in
maintaining desired indoor temperatures and so is its testing and commissioning processes
(Kumara, et al., 2016). Below are commissioning procedures for this system:
Operation procedures: this involves checking and confirming that the layout of the
control system and its operation comply with the design control logic and schematic drawings
(Statement, 2015).
Control elements: this is where all control elements, particularly sensors, of the chiller
plant control system are checked to confirm that they meet the desired range (Woehrle, 2011).
The elements checked include: sensor output, digital signal, actuators and alarm signal of the
sensor.
Control loop: this involves checking the control loop of the chiller plant control to
confirm that it is in accordance with the design logic flow chart and schematic drawings (Zak,
2012).
Cables: this entails checking and confirming proper cabling between direct digital control
(DDC) controllers and chiller control plant’s sensors.
Software installation: this is where the BMS software for the chiller plant control is tested
to confirm that its database and graphics are working correctly.
Graphic presentations: here, graphic presentations are tested on the screen to ensure that
they are visible and logical.
Data transmission: this is a functional check that entails checking communication
network of the BMS (Method Statement HQ, 2012).
Secure Best Marks with AI Grader
Need help grading? Try our AI Grader for instant feedback on your assignments.
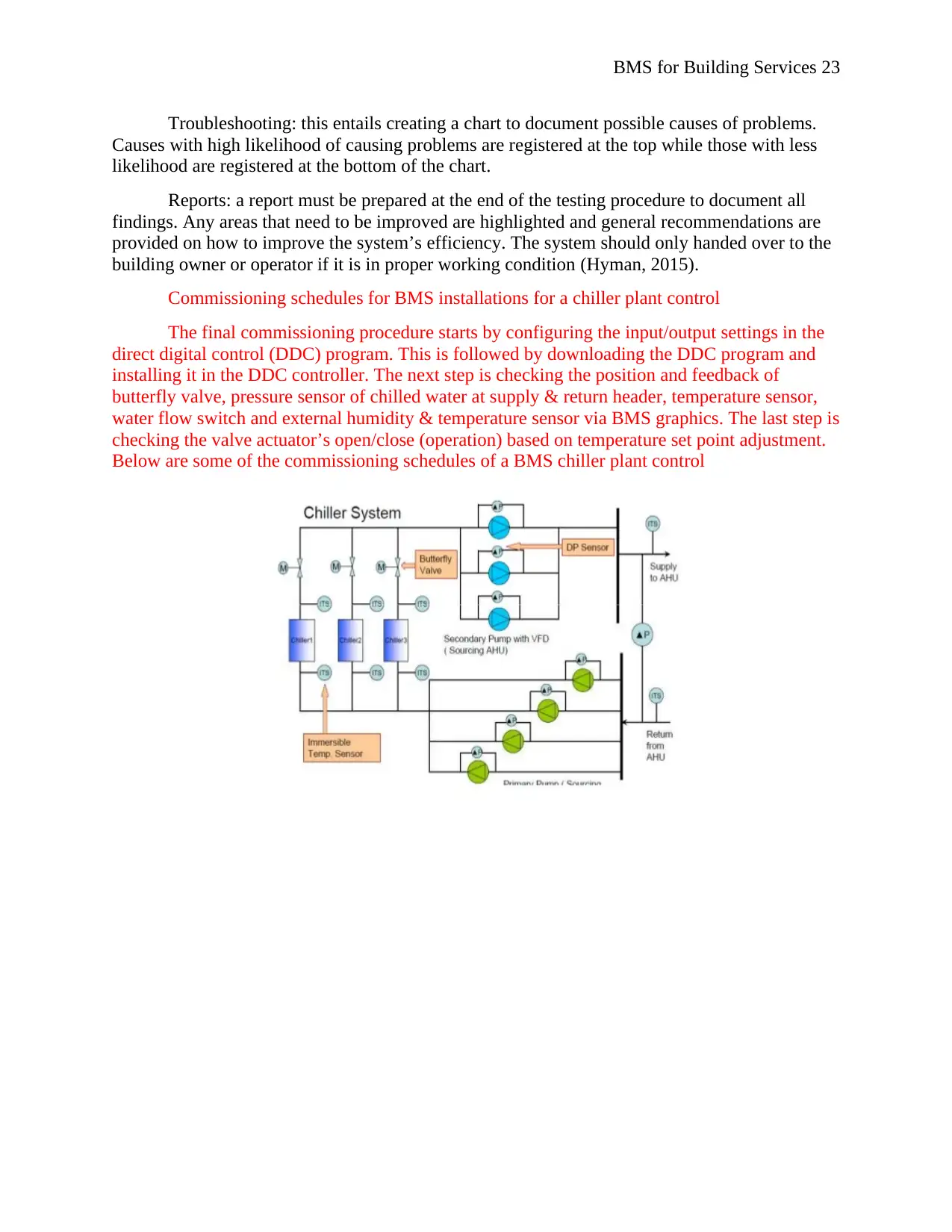
BMS for Building Services 23
Troubleshooting: this entails creating a chart to document possible causes of problems.
Causes with high likelihood of causing problems are registered at the top while those with less
likelihood are registered at the bottom of the chart.
Reports: a report must be prepared at the end of the testing procedure to document all
findings. Any areas that need to be improved are highlighted and general recommendations are
provided on how to improve the system’s efficiency. The system should only handed over to the
building owner or operator if it is in proper working condition (Hyman, 2015).
Commissioning schedules for BMS installations for a chiller plant control
The final commissioning procedure starts by configuring the input/output settings in the
direct digital control (DDC) program. This is followed by downloading the DDC program and
installing it in the DDC controller. The next step is checking the position and feedback of
butterfly valve, pressure sensor of chilled water at supply & return header, temperature sensor,
water flow switch and external humidity & temperature sensor via BMS graphics. The last step is
checking the valve actuator’s open/close (operation) based on temperature set point adjustment.
Below are some of the commissioning schedules of a BMS chiller plant control
Troubleshooting: this entails creating a chart to document possible causes of problems.
Causes with high likelihood of causing problems are registered at the top while those with less
likelihood are registered at the bottom of the chart.
Reports: a report must be prepared at the end of the testing procedure to document all
findings. Any areas that need to be improved are highlighted and general recommendations are
provided on how to improve the system’s efficiency. The system should only handed over to the
building owner or operator if it is in proper working condition (Hyman, 2015).
Commissioning schedules for BMS installations for a chiller plant control
The final commissioning procedure starts by configuring the input/output settings in the
direct digital control (DDC) program. This is followed by downloading the DDC program and
installing it in the DDC controller. The next step is checking the position and feedback of
butterfly valve, pressure sensor of chilled water at supply & return header, temperature sensor,
water flow switch and external humidity & temperature sensor via BMS graphics. The last step is
checking the valve actuator’s open/close (operation) based on temperature set point adjustment.
Below are some of the commissioning schedules of a BMS chiller plant control
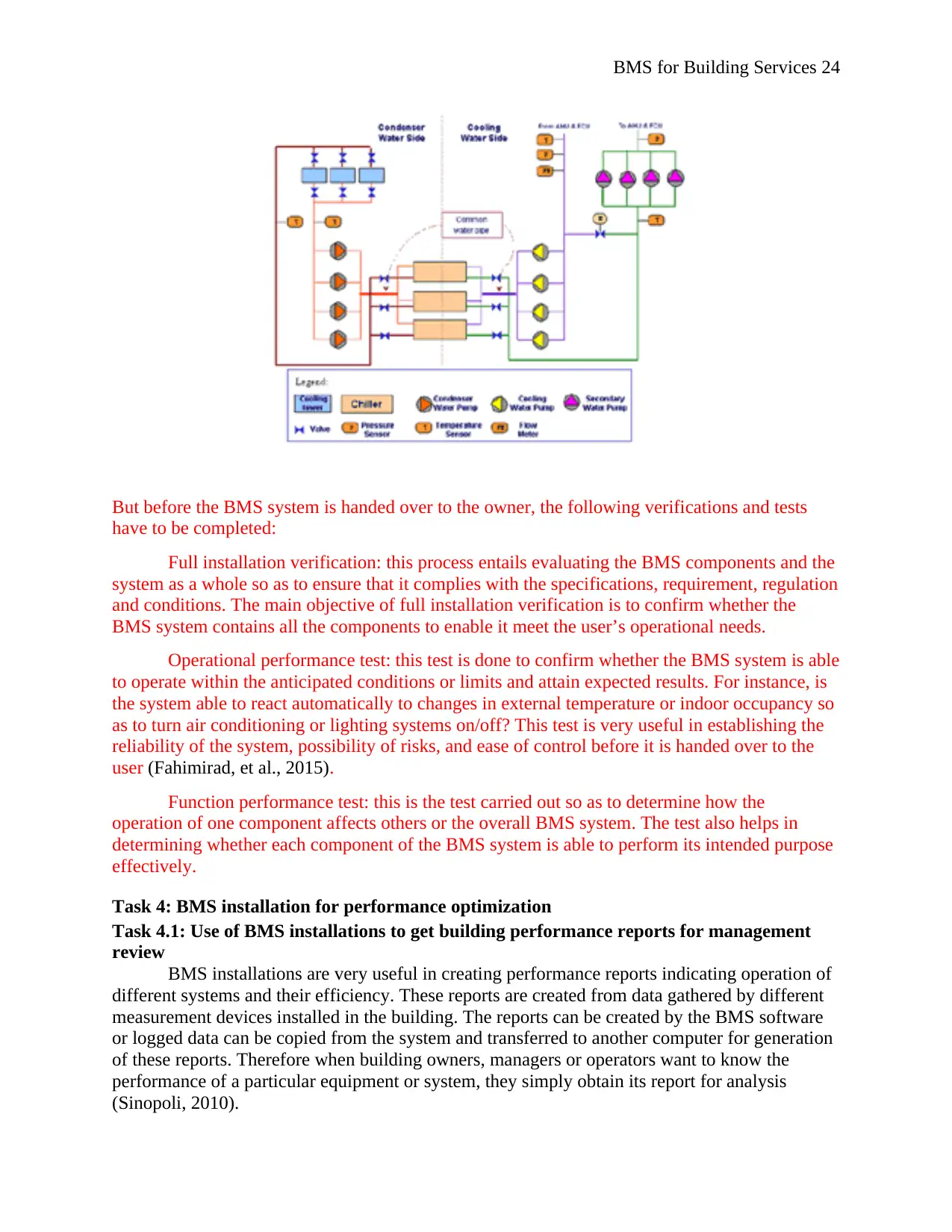
BMS for Building Services 24
But before the BMS system is handed over to the owner, the following verifications and tests
have to be completed:
Full installation verification: this process entails evaluating the BMS components and the
system as a whole so as to ensure that it complies with the specifications, requirement, regulation
and conditions. The main objective of full installation verification is to confirm whether the
BMS system contains all the components to enable it meet the user’s operational needs.
Operational performance test: this test is done to confirm whether the BMS system is able
to operate within the anticipated conditions or limits and attain expected results. For instance, is
the system able to react automatically to changes in external temperature or indoor occupancy so
as to turn air conditioning or lighting systems on/off? This test is very useful in establishing the
reliability of the system, possibility of risks, and ease of control before it is handed over to the
user (Fahimirad, et al., 2015).
Function performance test: this is the test carried out so as to determine how the
operation of one component affects others or the overall BMS system. The test also helps in
determining whether each component of the BMS system is able to perform its intended purpose
effectively.
Task 4: BMS installation for performance optimization
Task 4.1: Use of BMS installations to get building performance reports for management
review
BMS installations are very useful in creating performance reports indicating operation of
different systems and their efficiency. These reports are created from data gathered by different
measurement devices installed in the building. The reports can be created by the BMS software
or logged data can be copied from the system and transferred to another computer for generation
of these reports. Therefore when building owners, managers or operators want to know the
performance of a particular equipment or system, they simply obtain its report for analysis
(Sinopoli, 2010).
But before the BMS system is handed over to the owner, the following verifications and tests
have to be completed:
Full installation verification: this process entails evaluating the BMS components and the
system as a whole so as to ensure that it complies with the specifications, requirement, regulation
and conditions. The main objective of full installation verification is to confirm whether the
BMS system contains all the components to enable it meet the user’s operational needs.
Operational performance test: this test is done to confirm whether the BMS system is able
to operate within the anticipated conditions or limits and attain expected results. For instance, is
the system able to react automatically to changes in external temperature or indoor occupancy so
as to turn air conditioning or lighting systems on/off? This test is very useful in establishing the
reliability of the system, possibility of risks, and ease of control before it is handed over to the
user (Fahimirad, et al., 2015).
Function performance test: this is the test carried out so as to determine how the
operation of one component affects others or the overall BMS system. The test also helps in
determining whether each component of the BMS system is able to perform its intended purpose
effectively.
Task 4: BMS installation for performance optimization
Task 4.1: Use of BMS installations to get building performance reports for management
review
BMS installations are very useful in creating performance reports indicating operation of
different systems and their efficiency. These reports are created from data gathered by different
measurement devices installed in the building. The reports can be created by the BMS software
or logged data can be copied from the system and transferred to another computer for generation
of these reports. Therefore when building owners, managers or operators want to know the
performance of a particular equipment or system, they simply obtain its report for analysis
(Sinopoli, 2010).
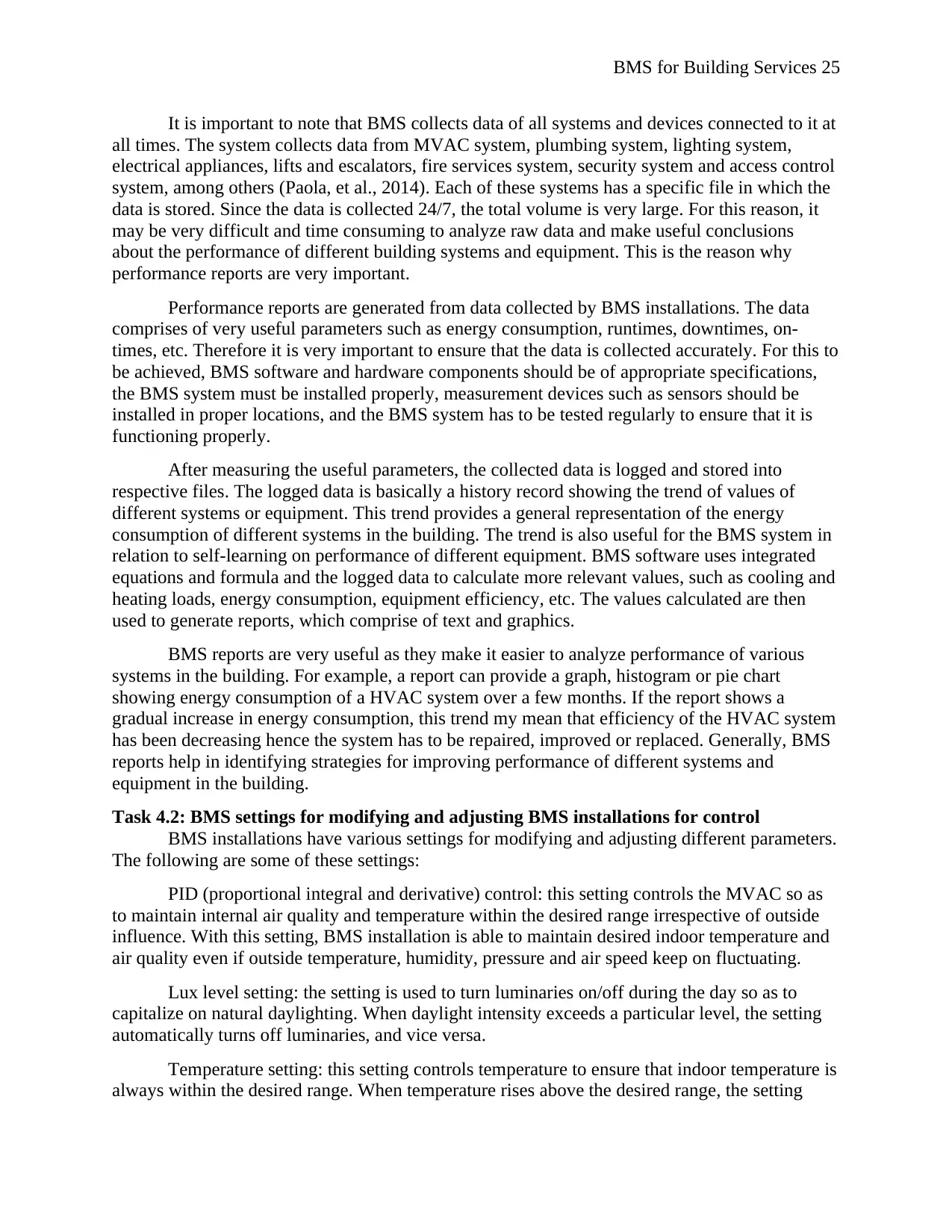
BMS for Building Services 25
It is important to note that BMS collects data of all systems and devices connected to it at
all times. The system collects data from MVAC system, plumbing system, lighting system,
electrical appliances, lifts and escalators, fire services system, security system and access control
system, among others (Paola, et al., 2014). Each of these systems has a specific file in which the
data is stored. Since the data is collected 24/7, the total volume is very large. For this reason, it
may be very difficult and time consuming to analyze raw data and make useful conclusions
about the performance of different building systems and equipment. This is the reason why
performance reports are very important.
Performance reports are generated from data collected by BMS installations. The data
comprises of very useful parameters such as energy consumption, runtimes, downtimes, on-
times, etc. Therefore it is very important to ensure that the data is collected accurately. For this to
be achieved, BMS software and hardware components should be of appropriate specifications,
the BMS system must be installed properly, measurement devices such as sensors should be
installed in proper locations, and the BMS system has to be tested regularly to ensure that it is
functioning properly.
After measuring the useful parameters, the collected data is logged and stored into
respective files. The logged data is basically a history record showing the trend of values of
different systems or equipment. This trend provides a general representation of the energy
consumption of different systems in the building. The trend is also useful for the BMS system in
relation to self-learning on performance of different equipment. BMS software uses integrated
equations and formula and the logged data to calculate more relevant values, such as cooling and
heating loads, energy consumption, equipment efficiency, etc. The values calculated are then
used to generate reports, which comprise of text and graphics.
BMS reports are very useful as they make it easier to analyze performance of various
systems in the building. For example, a report can provide a graph, histogram or pie chart
showing energy consumption of a HVAC system over a few months. If the report shows a
gradual increase in energy consumption, this trend my mean that efficiency of the HVAC system
has been decreasing hence the system has to be repaired, improved or replaced. Generally, BMS
reports help in identifying strategies for improving performance of different systems and
equipment in the building.
Task 4.2: BMS settings for modifying and adjusting BMS installations for control
BMS installations have various settings for modifying and adjusting different parameters.
The following are some of these settings:
PID (proportional integral and derivative) control: this setting controls the MVAC so as
to maintain internal air quality and temperature within the desired range irrespective of outside
influence. With this setting, BMS installation is able to maintain desired indoor temperature and
air quality even if outside temperature, humidity, pressure and air speed keep on fluctuating.
Lux level setting: the setting is used to turn luminaries on/off during the day so as to
capitalize on natural daylighting. When daylight intensity exceeds a particular level, the setting
automatically turns off luminaries, and vice versa.
Temperature setting: this setting controls temperature to ensure that indoor temperature is
always within the desired range. When temperature rises above the desired range, the setting
It is important to note that BMS collects data of all systems and devices connected to it at
all times. The system collects data from MVAC system, plumbing system, lighting system,
electrical appliances, lifts and escalators, fire services system, security system and access control
system, among others (Paola, et al., 2014). Each of these systems has a specific file in which the
data is stored. Since the data is collected 24/7, the total volume is very large. For this reason, it
may be very difficult and time consuming to analyze raw data and make useful conclusions
about the performance of different building systems and equipment. This is the reason why
performance reports are very important.
Performance reports are generated from data collected by BMS installations. The data
comprises of very useful parameters such as energy consumption, runtimes, downtimes, on-
times, etc. Therefore it is very important to ensure that the data is collected accurately. For this to
be achieved, BMS software and hardware components should be of appropriate specifications,
the BMS system must be installed properly, measurement devices such as sensors should be
installed in proper locations, and the BMS system has to be tested regularly to ensure that it is
functioning properly.
After measuring the useful parameters, the collected data is logged and stored into
respective files. The logged data is basically a history record showing the trend of values of
different systems or equipment. This trend provides a general representation of the energy
consumption of different systems in the building. The trend is also useful for the BMS system in
relation to self-learning on performance of different equipment. BMS software uses integrated
equations and formula and the logged data to calculate more relevant values, such as cooling and
heating loads, energy consumption, equipment efficiency, etc. The values calculated are then
used to generate reports, which comprise of text and graphics.
BMS reports are very useful as they make it easier to analyze performance of various
systems in the building. For example, a report can provide a graph, histogram or pie chart
showing energy consumption of a HVAC system over a few months. If the report shows a
gradual increase in energy consumption, this trend my mean that efficiency of the HVAC system
has been decreasing hence the system has to be repaired, improved or replaced. Generally, BMS
reports help in identifying strategies for improving performance of different systems and
equipment in the building.
Task 4.2: BMS settings for modifying and adjusting BMS installations for control
BMS installations have various settings for modifying and adjusting different parameters.
The following are some of these settings:
PID (proportional integral and derivative) control: this setting controls the MVAC so as
to maintain internal air quality and temperature within the desired range irrespective of outside
influence. With this setting, BMS installation is able to maintain desired indoor temperature and
air quality even if outside temperature, humidity, pressure and air speed keep on fluctuating.
Lux level setting: the setting is used to turn luminaries on/off during the day so as to
capitalize on natural daylighting. When daylight intensity exceeds a particular level, the setting
automatically turns off luminaries, and vice versa.
Temperature setting: this setting controls temperature to ensure that indoor temperature is
always within the desired range. When temperature rises above the desired range, the setting
Paraphrase This Document
Need a fresh take? Get an instant paraphrase of this document with our AI Paraphraser
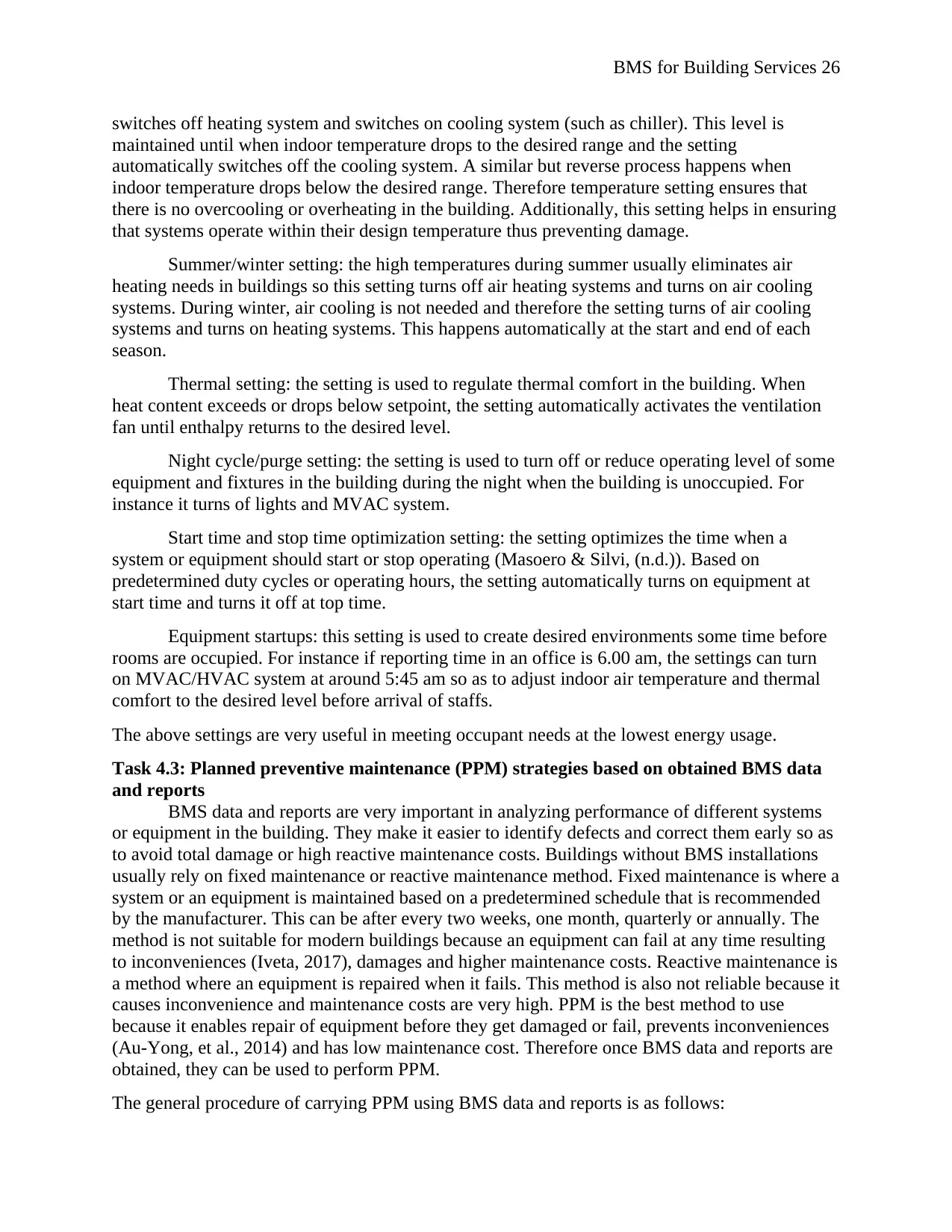
BMS for Building Services 26
switches off heating system and switches on cooling system (such as chiller). This level is
maintained until when indoor temperature drops to the desired range and the setting
automatically switches off the cooling system. A similar but reverse process happens when
indoor temperature drops below the desired range. Therefore temperature setting ensures that
there is no overcooling or overheating in the building. Additionally, this setting helps in ensuring
that systems operate within their design temperature thus preventing damage.
Summer/winter setting: the high temperatures during summer usually eliminates air
heating needs in buildings so this setting turns off air heating systems and turns on air cooling
systems. During winter, air cooling is not needed and therefore the setting turns of air cooling
systems and turns on heating systems. This happens automatically at the start and end of each
season.
Thermal setting: the setting is used to regulate thermal comfort in the building. When
heat content exceeds or drops below setpoint, the setting automatically activates the ventilation
fan until enthalpy returns to the desired level.
Night cycle/purge setting: the setting is used to turn off or reduce operating level of some
equipment and fixtures in the building during the night when the building is unoccupied. For
instance it turns of lights and MVAC system.
Start time and stop time optimization setting: the setting optimizes the time when a
system or equipment should start or stop operating (Masoero & Silvi, (n.d.)). Based on
predetermined duty cycles or operating hours, the setting automatically turns on equipment at
start time and turns it off at top time.
Equipment startups: this setting is used to create desired environments some time before
rooms are occupied. For instance if reporting time in an office is 6.00 am, the settings can turn
on MVAC/HVAC system at around 5:45 am so as to adjust indoor air temperature and thermal
comfort to the desired level before arrival of staffs.
The above settings are very useful in meeting occupant needs at the lowest energy usage.
Task 4.3: Planned preventive maintenance (PPM) strategies based on obtained BMS data
and reports
BMS data and reports are very important in analyzing performance of different systems
or equipment in the building. They make it easier to identify defects and correct them early so as
to avoid total damage or high reactive maintenance costs. Buildings without BMS installations
usually rely on fixed maintenance or reactive maintenance method. Fixed maintenance is where a
system or an equipment is maintained based on a predetermined schedule that is recommended
by the manufacturer. This can be after every two weeks, one month, quarterly or annually. The
method is not suitable for modern buildings because an equipment can fail at any time resulting
to inconveniences (Iveta, 2017), damages and higher maintenance costs. Reactive maintenance is
a method where an equipment is repaired when it fails. This method is also not reliable because it
causes inconvenience and maintenance costs are very high. PPM is the best method to use
because it enables repair of equipment before they get damaged or fail, prevents inconveniences
(Au-Yong, et al., 2014) and has low maintenance cost. Therefore once BMS data and reports are
obtained, they can be used to perform PPM.
The general procedure of carrying PPM using BMS data and reports is as follows:
switches off heating system and switches on cooling system (such as chiller). This level is
maintained until when indoor temperature drops to the desired range and the setting
automatically switches off the cooling system. A similar but reverse process happens when
indoor temperature drops below the desired range. Therefore temperature setting ensures that
there is no overcooling or overheating in the building. Additionally, this setting helps in ensuring
that systems operate within their design temperature thus preventing damage.
Summer/winter setting: the high temperatures during summer usually eliminates air
heating needs in buildings so this setting turns off air heating systems and turns on air cooling
systems. During winter, air cooling is not needed and therefore the setting turns of air cooling
systems and turns on heating systems. This happens automatically at the start and end of each
season.
Thermal setting: the setting is used to regulate thermal comfort in the building. When
heat content exceeds or drops below setpoint, the setting automatically activates the ventilation
fan until enthalpy returns to the desired level.
Night cycle/purge setting: the setting is used to turn off or reduce operating level of some
equipment and fixtures in the building during the night when the building is unoccupied. For
instance it turns of lights and MVAC system.
Start time and stop time optimization setting: the setting optimizes the time when a
system or equipment should start or stop operating (Masoero & Silvi, (n.d.)). Based on
predetermined duty cycles or operating hours, the setting automatically turns on equipment at
start time and turns it off at top time.
Equipment startups: this setting is used to create desired environments some time before
rooms are occupied. For instance if reporting time in an office is 6.00 am, the settings can turn
on MVAC/HVAC system at around 5:45 am so as to adjust indoor air temperature and thermal
comfort to the desired level before arrival of staffs.
The above settings are very useful in meeting occupant needs at the lowest energy usage.
Task 4.3: Planned preventive maintenance (PPM) strategies based on obtained BMS data
and reports
BMS data and reports are very important in analyzing performance of different systems
or equipment in the building. They make it easier to identify defects and correct them early so as
to avoid total damage or high reactive maintenance costs. Buildings without BMS installations
usually rely on fixed maintenance or reactive maintenance method. Fixed maintenance is where a
system or an equipment is maintained based on a predetermined schedule that is recommended
by the manufacturer. This can be after every two weeks, one month, quarterly or annually. The
method is not suitable for modern buildings because an equipment can fail at any time resulting
to inconveniences (Iveta, 2017), damages and higher maintenance costs. Reactive maintenance is
a method where an equipment is repaired when it fails. This method is also not reliable because it
causes inconvenience and maintenance costs are very high. PPM is the best method to use
because it enables repair of equipment before they get damaged or fail, prevents inconveniences
(Au-Yong, et al., 2014) and has low maintenance cost. Therefore once BMS data and reports are
obtained, they can be used to perform PPM.
The general procedure of carrying PPM using BMS data and reports is as follows:
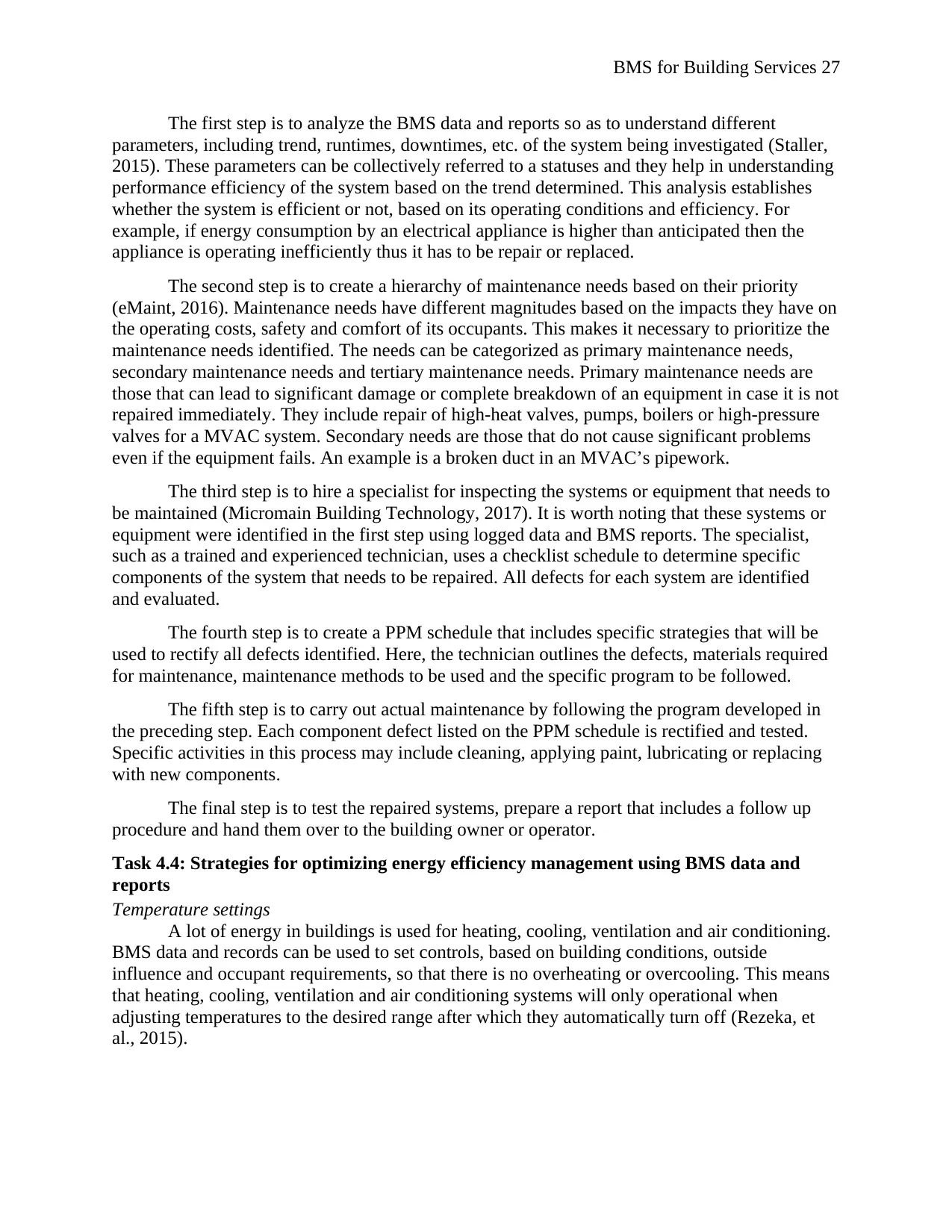
BMS for Building Services 27
The first step is to analyze the BMS data and reports so as to understand different
parameters, including trend, runtimes, downtimes, etc. of the system being investigated (Staller,
2015). These parameters can be collectively referred to a statuses and they help in understanding
performance efficiency of the system based on the trend determined. This analysis establishes
whether the system is efficient or not, based on its operating conditions and efficiency. For
example, if energy consumption by an electrical appliance is higher than anticipated then the
appliance is operating inefficiently thus it has to be repair or replaced.
The second step is to create a hierarchy of maintenance needs based on their priority
(eMaint, 2016). Maintenance needs have different magnitudes based on the impacts they have on
the operating costs, safety and comfort of its occupants. This makes it necessary to prioritize the
maintenance needs identified. The needs can be categorized as primary maintenance needs,
secondary maintenance needs and tertiary maintenance needs. Primary maintenance needs are
those that can lead to significant damage or complete breakdown of an equipment in case it is not
repaired immediately. They include repair of high-heat valves, pumps, boilers or high-pressure
valves for a MVAC system. Secondary needs are those that do not cause significant problems
even if the equipment fails. An example is a broken duct in an MVAC’s pipework.
The third step is to hire a specialist for inspecting the systems or equipment that needs to
be maintained (Micromain Building Technology, 2017). It is worth noting that these systems or
equipment were identified in the first step using logged data and BMS reports. The specialist,
such as a trained and experienced technician, uses a checklist schedule to determine specific
components of the system that needs to be repaired. All defects for each system are identified
and evaluated.
The fourth step is to create a PPM schedule that includes specific strategies that will be
used to rectify all defects identified. Here, the technician outlines the defects, materials required
for maintenance, maintenance methods to be used and the specific program to be followed.
The fifth step is to carry out actual maintenance by following the program developed in
the preceding step. Each component defect listed on the PPM schedule is rectified and tested.
Specific activities in this process may include cleaning, applying paint, lubricating or replacing
with new components.
The final step is to test the repaired systems, prepare a report that includes a follow up
procedure and hand them over to the building owner or operator.
Task 4.4: Strategies for optimizing energy efficiency management using BMS data and
reports
Temperature settings
A lot of energy in buildings is used for heating, cooling, ventilation and air conditioning.
BMS data and records can be used to set controls, based on building conditions, outside
influence and occupant requirements, so that there is no overheating or overcooling. This means
that heating, cooling, ventilation and air conditioning systems will only operational when
adjusting temperatures to the desired range after which they automatically turn off (Rezeka, et
al., 2015).
The first step is to analyze the BMS data and reports so as to understand different
parameters, including trend, runtimes, downtimes, etc. of the system being investigated (Staller,
2015). These parameters can be collectively referred to a statuses and they help in understanding
performance efficiency of the system based on the trend determined. This analysis establishes
whether the system is efficient or not, based on its operating conditions and efficiency. For
example, if energy consumption by an electrical appliance is higher than anticipated then the
appliance is operating inefficiently thus it has to be repair or replaced.
The second step is to create a hierarchy of maintenance needs based on their priority
(eMaint, 2016). Maintenance needs have different magnitudes based on the impacts they have on
the operating costs, safety and comfort of its occupants. This makes it necessary to prioritize the
maintenance needs identified. The needs can be categorized as primary maintenance needs,
secondary maintenance needs and tertiary maintenance needs. Primary maintenance needs are
those that can lead to significant damage or complete breakdown of an equipment in case it is not
repaired immediately. They include repair of high-heat valves, pumps, boilers or high-pressure
valves for a MVAC system. Secondary needs are those that do not cause significant problems
even if the equipment fails. An example is a broken duct in an MVAC’s pipework.
The third step is to hire a specialist for inspecting the systems or equipment that needs to
be maintained (Micromain Building Technology, 2017). It is worth noting that these systems or
equipment were identified in the first step using logged data and BMS reports. The specialist,
such as a trained and experienced technician, uses a checklist schedule to determine specific
components of the system that needs to be repaired. All defects for each system are identified
and evaluated.
The fourth step is to create a PPM schedule that includes specific strategies that will be
used to rectify all defects identified. Here, the technician outlines the defects, materials required
for maintenance, maintenance methods to be used and the specific program to be followed.
The fifth step is to carry out actual maintenance by following the program developed in
the preceding step. Each component defect listed on the PPM schedule is rectified and tested.
Specific activities in this process may include cleaning, applying paint, lubricating or replacing
with new components.
The final step is to test the repaired systems, prepare a report that includes a follow up
procedure and hand them over to the building owner or operator.
Task 4.4: Strategies for optimizing energy efficiency management using BMS data and
reports
Temperature settings
A lot of energy in buildings is used for heating, cooling, ventilation and air conditioning.
BMS data and records can be used to set controls, based on building conditions, outside
influence and occupant requirements, so that there is no overheating or overcooling. This means
that heating, cooling, ventilation and air conditioning systems will only operational when
adjusting temperatures to the desired range after which they automatically turn off (Rezeka, et
al., 2015).
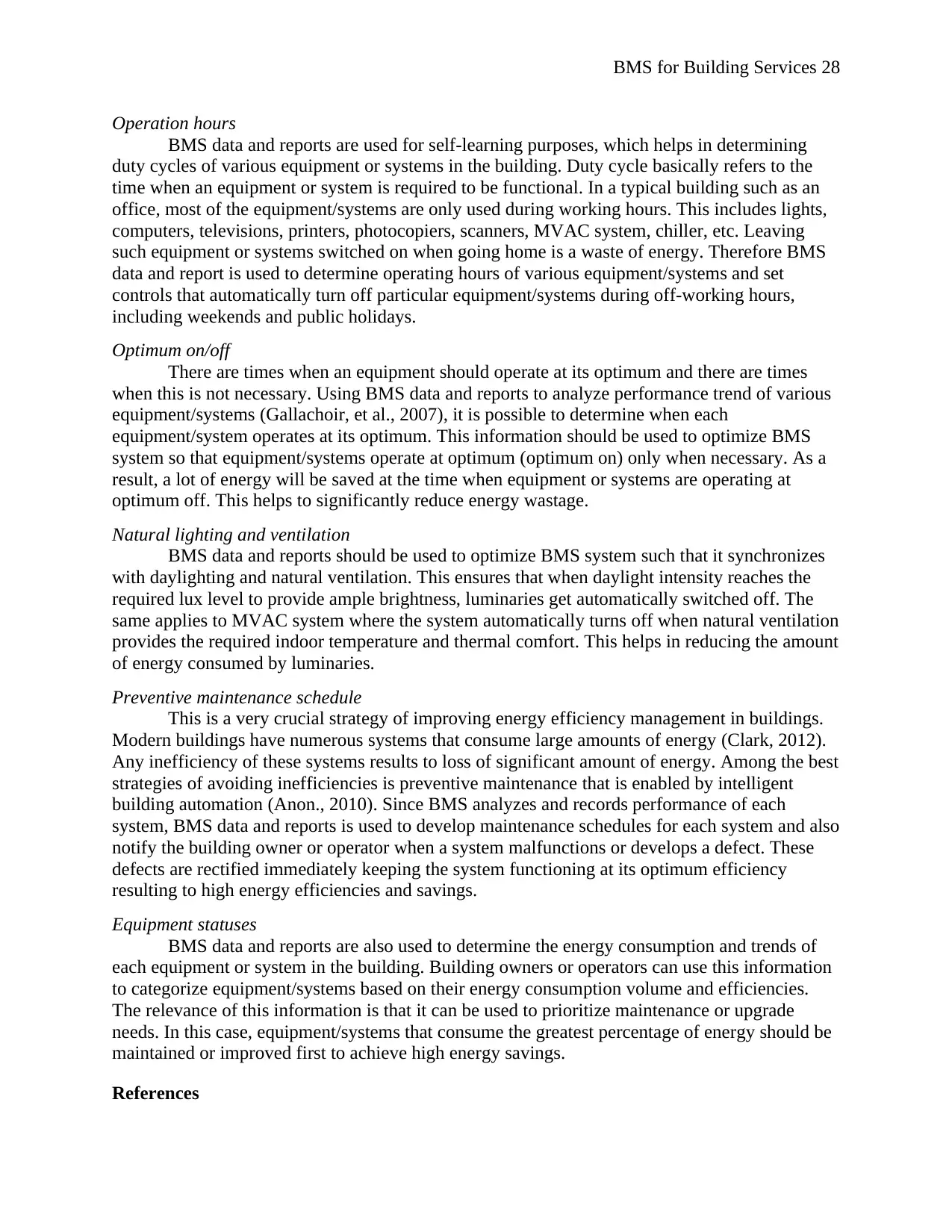
BMS for Building Services 28
Operation hours
BMS data and reports are used for self-learning purposes, which helps in determining
duty cycles of various equipment or systems in the building. Duty cycle basically refers to the
time when an equipment or system is required to be functional. In a typical building such as an
office, most of the equipment/systems are only used during working hours. This includes lights,
computers, televisions, printers, photocopiers, scanners, MVAC system, chiller, etc. Leaving
such equipment or systems switched on when going home is a waste of energy. Therefore BMS
data and report is used to determine operating hours of various equipment/systems and set
controls that automatically turn off particular equipment/systems during off-working hours,
including weekends and public holidays.
Optimum on/off
There are times when an equipment should operate at its optimum and there are times
when this is not necessary. Using BMS data and reports to analyze performance trend of various
equipment/systems (Gallachoir, et al., 2007), it is possible to determine when each
equipment/system operates at its optimum. This information should be used to optimize BMS
system so that equipment/systems operate at optimum (optimum on) only when necessary. As a
result, a lot of energy will be saved at the time when equipment or systems are operating at
optimum off. This helps to significantly reduce energy wastage.
Natural lighting and ventilation
BMS data and reports should be used to optimize BMS system such that it synchronizes
with daylighting and natural ventilation. This ensures that when daylight intensity reaches the
required lux level to provide ample brightness, luminaries get automatically switched off. The
same applies to MVAC system where the system automatically turns off when natural ventilation
provides the required indoor temperature and thermal comfort. This helps in reducing the amount
of energy consumed by luminaries.
Preventive maintenance schedule
This is a very crucial strategy of improving energy efficiency management in buildings.
Modern buildings have numerous systems that consume large amounts of energy (Clark, 2012).
Any inefficiency of these systems results to loss of significant amount of energy. Among the best
strategies of avoiding inefficiencies is preventive maintenance that is enabled by intelligent
building automation (Anon., 2010). Since BMS analyzes and records performance of each
system, BMS data and reports is used to develop maintenance schedules for each system and also
notify the building owner or operator when a system malfunctions or develops a defect. These
defects are rectified immediately keeping the system functioning at its optimum efficiency
resulting to high energy efficiencies and savings.
Equipment statuses
BMS data and reports are also used to determine the energy consumption and trends of
each equipment or system in the building. Building owners or operators can use this information
to categorize equipment/systems based on their energy consumption volume and efficiencies.
The relevance of this information is that it can be used to prioritize maintenance or upgrade
needs. In this case, equipment/systems that consume the greatest percentage of energy should be
maintained or improved first to achieve high energy savings.
References
Operation hours
BMS data and reports are used for self-learning purposes, which helps in determining
duty cycles of various equipment or systems in the building. Duty cycle basically refers to the
time when an equipment or system is required to be functional. In a typical building such as an
office, most of the equipment/systems are only used during working hours. This includes lights,
computers, televisions, printers, photocopiers, scanners, MVAC system, chiller, etc. Leaving
such equipment or systems switched on when going home is a waste of energy. Therefore BMS
data and report is used to determine operating hours of various equipment/systems and set
controls that automatically turn off particular equipment/systems during off-working hours,
including weekends and public holidays.
Optimum on/off
There are times when an equipment should operate at its optimum and there are times
when this is not necessary. Using BMS data and reports to analyze performance trend of various
equipment/systems (Gallachoir, et al., 2007), it is possible to determine when each
equipment/system operates at its optimum. This information should be used to optimize BMS
system so that equipment/systems operate at optimum (optimum on) only when necessary. As a
result, a lot of energy will be saved at the time when equipment or systems are operating at
optimum off. This helps to significantly reduce energy wastage.
Natural lighting and ventilation
BMS data and reports should be used to optimize BMS system such that it synchronizes
with daylighting and natural ventilation. This ensures that when daylight intensity reaches the
required lux level to provide ample brightness, luminaries get automatically switched off. The
same applies to MVAC system where the system automatically turns off when natural ventilation
provides the required indoor temperature and thermal comfort. This helps in reducing the amount
of energy consumed by luminaries.
Preventive maintenance schedule
This is a very crucial strategy of improving energy efficiency management in buildings.
Modern buildings have numerous systems that consume large amounts of energy (Clark, 2012).
Any inefficiency of these systems results to loss of significant amount of energy. Among the best
strategies of avoiding inefficiencies is preventive maintenance that is enabled by intelligent
building automation (Anon., 2010). Since BMS analyzes and records performance of each
system, BMS data and reports is used to develop maintenance schedules for each system and also
notify the building owner or operator when a system malfunctions or develops a defect. These
defects are rectified immediately keeping the system functioning at its optimum efficiency
resulting to high energy efficiencies and savings.
Equipment statuses
BMS data and reports are also used to determine the energy consumption and trends of
each equipment or system in the building. Building owners or operators can use this information
to categorize equipment/systems based on their energy consumption volume and efficiencies.
The relevance of this information is that it can be used to prioritize maintenance or upgrade
needs. In this case, equipment/systems that consume the greatest percentage of energy should be
maintained or improved first to achieve high energy savings.
References
Secure Best Marks with AI Grader
Need help grading? Try our AI Grader for instant feedback on your assignments.
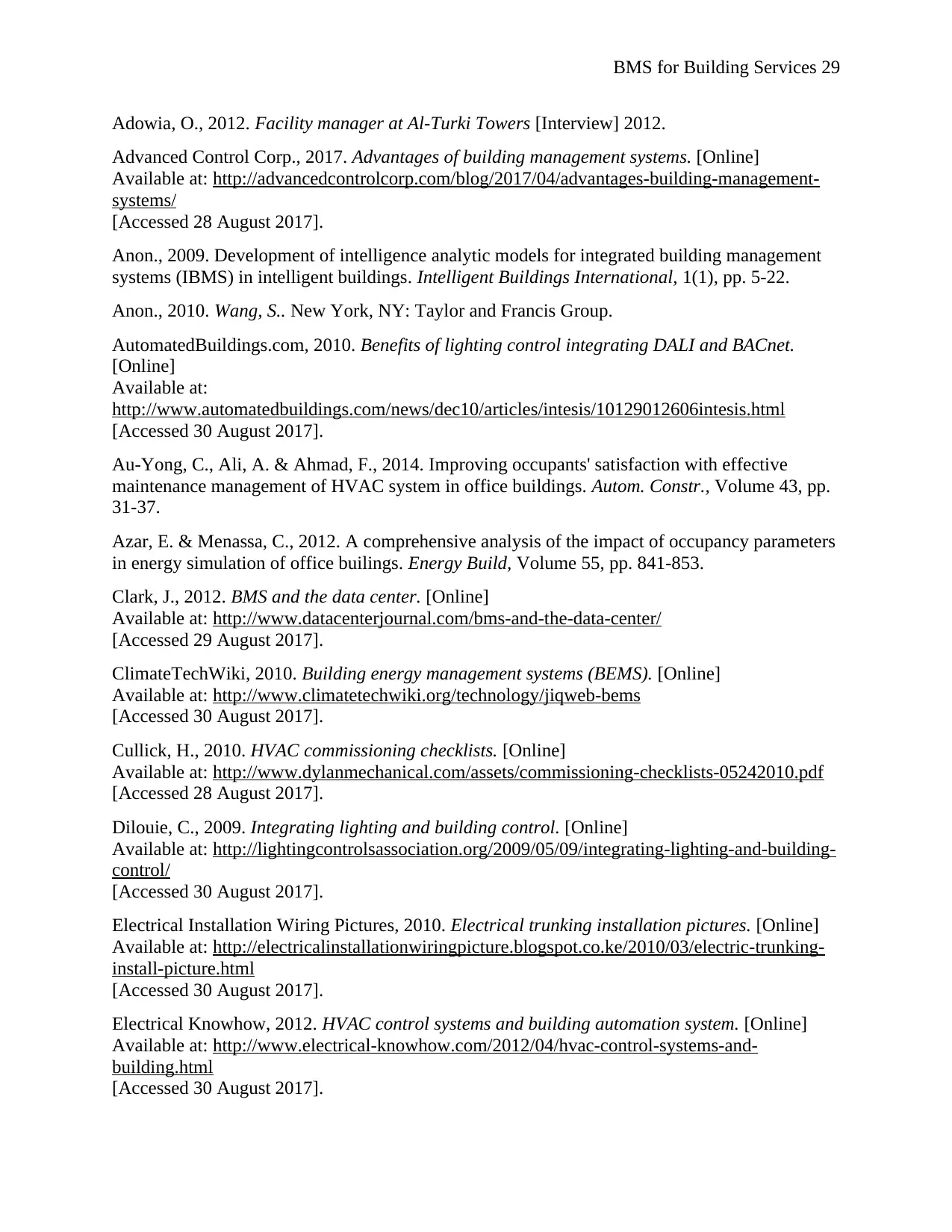
BMS for Building Services 29
Adowia, O., 2012. Facility manager at Al-Turki Towers [Interview] 2012.
Advanced Control Corp., 2017. Advantages of building management systems. [Online]
Available at: http://advancedcontrolcorp.com/blog/2017/04/advantages-building-management-
systems/
[Accessed 28 August 2017].
Anon., 2009. Development of intelligence analytic models for integrated building management
systems (IBMS) in intelligent buildings. Intelligent Buildings International, 1(1), pp. 5-22.
Anon., 2010. Wang, S.. New York, NY: Taylor and Francis Group.
AutomatedBuildings.com, 2010. Benefits of lighting control integrating DALI and BACnet.
[Online]
Available at:
http://www.automatedbuildings.com/news/dec10/articles/intesis/10129012606intesis.html
[Accessed 30 August 2017].
Au-Yong, C., Ali, A. & Ahmad, F., 2014. Improving occupants' satisfaction with effective
maintenance management of HVAC system in office buildings. Autom. Constr., Volume 43, pp.
31-37.
Azar, E. & Menassa, C., 2012. A comprehensive analysis of the impact of occupancy parameters
in energy simulation of office builings. Energy Build, Volume 55, pp. 841-853.
Clark, J., 2012. BMS and the data center. [Online]
Available at: http://www.datacenterjournal.com/bms-and-the-data-center/
[Accessed 29 August 2017].
ClimateTechWiki, 2010. Building energy management systems (BEMS). [Online]
Available at: http://www.climatetechwiki.org/technology/jiqweb-bems
[Accessed 30 August 2017].
Cullick, H., 2010. HVAC commissioning checklists. [Online]
Available at: http://www.dylanmechanical.com/assets/commissioning-checklists-05242010.pdf
[Accessed 28 August 2017].
Dilouie, C., 2009. Integrating lighting and building control. [Online]
Available at: http://lightingcontrolsassociation.org/2009/05/09/integrating-lighting-and-building-
control/
[Accessed 30 August 2017].
Electrical Installation Wiring Pictures, 2010. Electrical trunking installation pictures. [Online]
Available at: http://electricalinstallationwiringpicture.blogspot.co.ke/2010/03/electric-trunking-
install-picture.html
[Accessed 30 August 2017].
Electrical Knowhow, 2012. HVAC control systems and building automation system. [Online]
Available at: http://www.electrical-knowhow.com/2012/04/hvac-control-systems-and-
building.html
[Accessed 30 August 2017].
Adowia, O., 2012. Facility manager at Al-Turki Towers [Interview] 2012.
Advanced Control Corp., 2017. Advantages of building management systems. [Online]
Available at: http://advancedcontrolcorp.com/blog/2017/04/advantages-building-management-
systems/
[Accessed 28 August 2017].
Anon., 2009. Development of intelligence analytic models for integrated building management
systems (IBMS) in intelligent buildings. Intelligent Buildings International, 1(1), pp. 5-22.
Anon., 2010. Wang, S.. New York, NY: Taylor and Francis Group.
AutomatedBuildings.com, 2010. Benefits of lighting control integrating DALI and BACnet.
[Online]
Available at:
http://www.automatedbuildings.com/news/dec10/articles/intesis/10129012606intesis.html
[Accessed 30 August 2017].
Au-Yong, C., Ali, A. & Ahmad, F., 2014. Improving occupants' satisfaction with effective
maintenance management of HVAC system in office buildings. Autom. Constr., Volume 43, pp.
31-37.
Azar, E. & Menassa, C., 2012. A comprehensive analysis of the impact of occupancy parameters
in energy simulation of office builings. Energy Build, Volume 55, pp. 841-853.
Clark, J., 2012. BMS and the data center. [Online]
Available at: http://www.datacenterjournal.com/bms-and-the-data-center/
[Accessed 29 August 2017].
ClimateTechWiki, 2010. Building energy management systems (BEMS). [Online]
Available at: http://www.climatetechwiki.org/technology/jiqweb-bems
[Accessed 30 August 2017].
Cullick, H., 2010. HVAC commissioning checklists. [Online]
Available at: http://www.dylanmechanical.com/assets/commissioning-checklists-05242010.pdf
[Accessed 28 August 2017].
Dilouie, C., 2009. Integrating lighting and building control. [Online]
Available at: http://lightingcontrolsassociation.org/2009/05/09/integrating-lighting-and-building-
control/
[Accessed 30 August 2017].
Electrical Installation Wiring Pictures, 2010. Electrical trunking installation pictures. [Online]
Available at: http://electricalinstallationwiringpicture.blogspot.co.ke/2010/03/electric-trunking-
install-picture.html
[Accessed 30 August 2017].
Electrical Knowhow, 2012. HVAC control systems and building automation system. [Online]
Available at: http://www.electrical-knowhow.com/2012/04/hvac-control-systems-and-
building.html
[Accessed 30 August 2017].
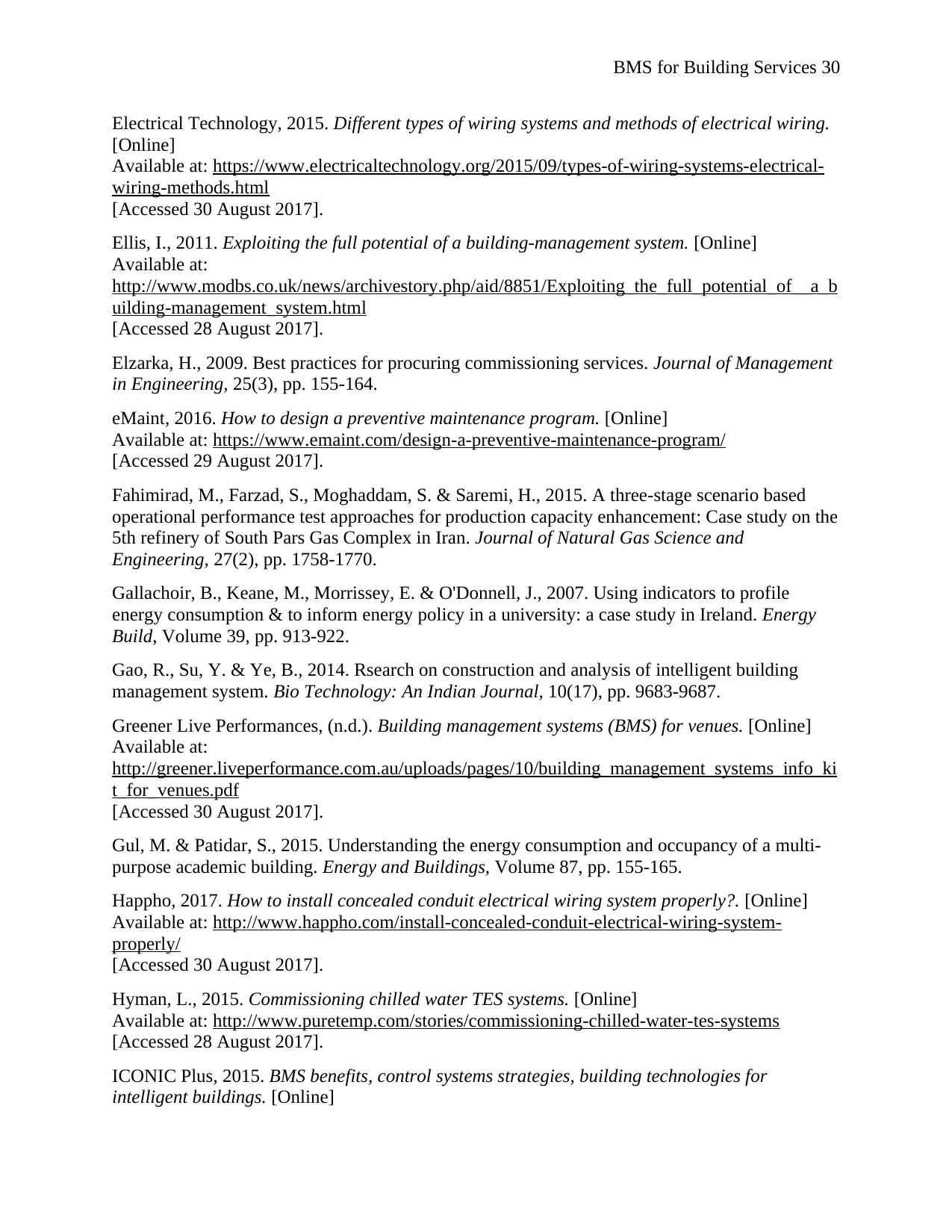
BMS for Building Services 30
Electrical Technology, 2015. Different types of wiring systems and methods of electrical wiring.
[Online]
Available at: https://www.electricaltechnology.org/2015/09/types-of-wiring-systems-electrical-
wiring-methods.html
[Accessed 30 August 2017].
Ellis, I., 2011. Exploiting the full potential of a building-management system. [Online]
Available at:
http://www.modbs.co.uk/news/archivestory.php/aid/8851/Exploiting_the_full_potential_of__a_b
uilding-management_system.html
[Accessed 28 August 2017].
Elzarka, H., 2009. Best practices for procuring commissioning services. Journal of Management
in Engineering, 25(3), pp. 155-164.
eMaint, 2016. How to design a preventive maintenance program. [Online]
Available at: https://www.emaint.com/design-a-preventive-maintenance-program/
[Accessed 29 August 2017].
Fahimirad, M., Farzad, S., Moghaddam, S. & Saremi, H., 2015. A three-stage scenario based
operational performance test approaches for production capacity enhancement: Case study on the
5th refinery of South Pars Gas Complex in Iran. Journal of Natural Gas Science and
Engineering, 27(2), pp. 1758-1770.
Gallachoir, B., Keane, M., Morrissey, E. & O'Donnell, J., 2007. Using indicators to profile
energy consumption & to inform energy policy in a university: a case study in Ireland. Energy
Build, Volume 39, pp. 913-922.
Gao, R., Su, Y. & Ye, B., 2014. Rsearch on construction and analysis of intelligent building
management system. Bio Technology: An Indian Journal, 10(17), pp. 9683-9687.
Greener Live Performances, (n.d.). Building management systems (BMS) for venues. [Online]
Available at:
http://greener.liveperformance.com.au/uploads/pages/10/building_management_systems_info_ki
t_for_venues.pdf
[Accessed 30 August 2017].
Gul, M. & Patidar, S., 2015. Understanding the energy consumption and occupancy of a multi-
purpose academic building. Energy and Buildings, Volume 87, pp. 155-165.
Happho, 2017. How to install concealed conduit electrical wiring system properly?. [Online]
Available at: http://www.happho.com/install-concealed-conduit-electrical-wiring-system-
properly/
[Accessed 30 August 2017].
Hyman, L., 2015. Commissioning chilled water TES systems. [Online]
Available at: http://www.puretemp.com/stories/commissioning-chilled-water-tes-systems
[Accessed 28 August 2017].
ICONIC Plus, 2015. BMS benefits, control systems strategies, building technologies for
intelligent buildings. [Online]
Electrical Technology, 2015. Different types of wiring systems and methods of electrical wiring.
[Online]
Available at: https://www.electricaltechnology.org/2015/09/types-of-wiring-systems-electrical-
wiring-methods.html
[Accessed 30 August 2017].
Ellis, I., 2011. Exploiting the full potential of a building-management system. [Online]
Available at:
http://www.modbs.co.uk/news/archivestory.php/aid/8851/Exploiting_the_full_potential_of__a_b
uilding-management_system.html
[Accessed 28 August 2017].
Elzarka, H., 2009. Best practices for procuring commissioning services. Journal of Management
in Engineering, 25(3), pp. 155-164.
eMaint, 2016. How to design a preventive maintenance program. [Online]
Available at: https://www.emaint.com/design-a-preventive-maintenance-program/
[Accessed 29 August 2017].
Fahimirad, M., Farzad, S., Moghaddam, S. & Saremi, H., 2015. A three-stage scenario based
operational performance test approaches for production capacity enhancement: Case study on the
5th refinery of South Pars Gas Complex in Iran. Journal of Natural Gas Science and
Engineering, 27(2), pp. 1758-1770.
Gallachoir, B., Keane, M., Morrissey, E. & O'Donnell, J., 2007. Using indicators to profile
energy consumption & to inform energy policy in a university: a case study in Ireland. Energy
Build, Volume 39, pp. 913-922.
Gao, R., Su, Y. & Ye, B., 2014. Rsearch on construction and analysis of intelligent building
management system. Bio Technology: An Indian Journal, 10(17), pp. 9683-9687.
Greener Live Performances, (n.d.). Building management systems (BMS) for venues. [Online]
Available at:
http://greener.liveperformance.com.au/uploads/pages/10/building_management_systems_info_ki
t_for_venues.pdf
[Accessed 30 August 2017].
Gul, M. & Patidar, S., 2015. Understanding the energy consumption and occupancy of a multi-
purpose academic building. Energy and Buildings, Volume 87, pp. 155-165.
Happho, 2017. How to install concealed conduit electrical wiring system properly?. [Online]
Available at: http://www.happho.com/install-concealed-conduit-electrical-wiring-system-
properly/
[Accessed 30 August 2017].
Hyman, L., 2015. Commissioning chilled water TES systems. [Online]
Available at: http://www.puretemp.com/stories/commissioning-chilled-water-tes-systems
[Accessed 28 August 2017].
ICONIC Plus, 2015. BMS benefits, control systems strategies, building technologies for
intelligent buildings. [Online]
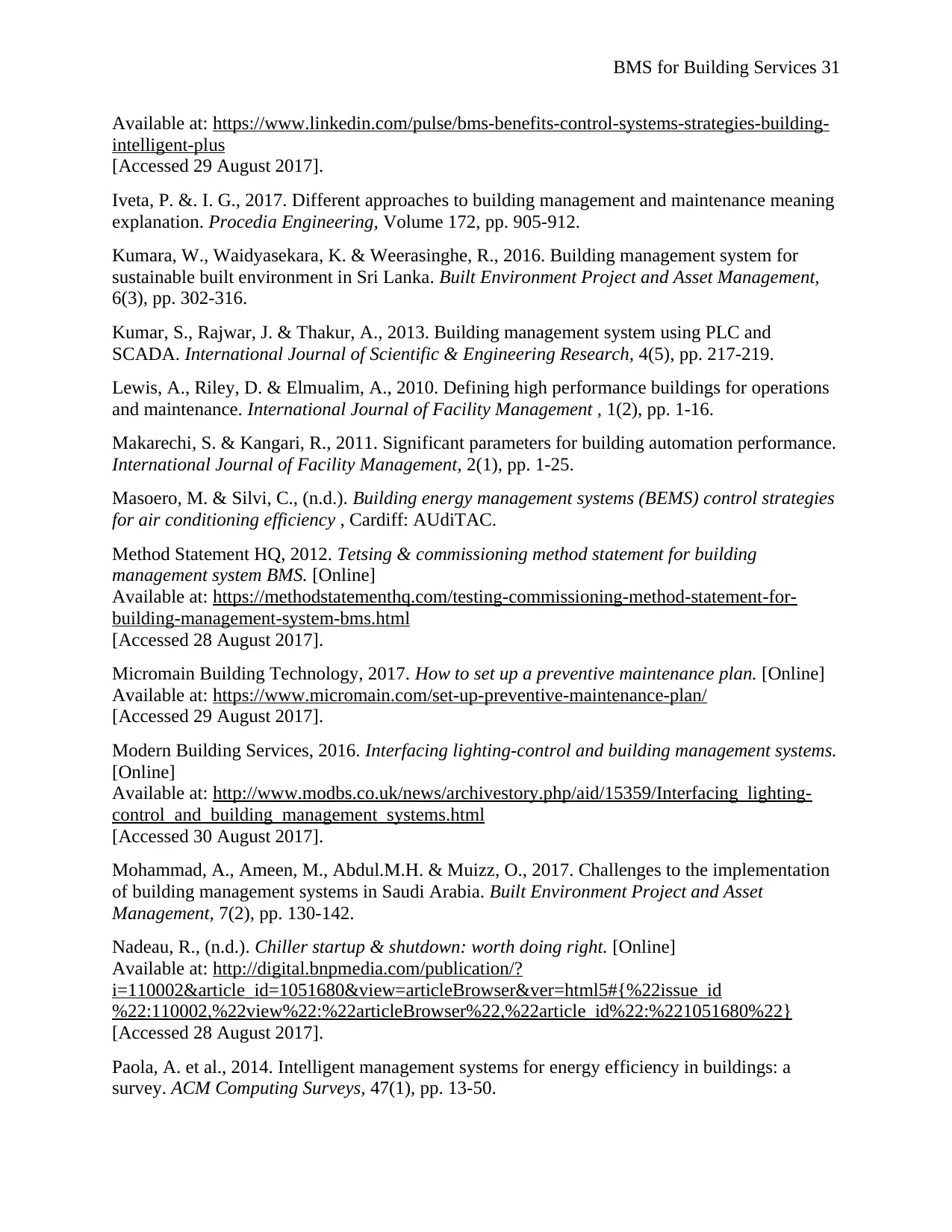
BMS for Building Services 31
Available at: https://www.linkedin.com/pulse/bms-benefits-control-systems-strategies-building-
intelligent-plus
[Accessed 29 August 2017].
Iveta, P. &. I. G., 2017. Different approaches to building management and maintenance meaning
explanation. Procedia Engineering, Volume 172, pp. 905-912.
Kumara, W., Waidyasekara, K. & Weerasinghe, R., 2016. Building management system for
sustainable built environment in Sri Lanka. Built Environment Project and Asset Management,
6(3), pp. 302-316.
Kumar, S., Rajwar, J. & Thakur, A., 2013. Building management system using PLC and
SCADA. International Journal of Scientific & Engineering Research, 4(5), pp. 217-219.
Lewis, A., Riley, D. & Elmualim, A., 2010. Defining high performance buildings for operations
and maintenance. International Journal of Facility Management , 1(2), pp. 1-16.
Makarechi, S. & Kangari, R., 2011. Significant parameters for building automation performance.
International Journal of Facility Management, 2(1), pp. 1-25.
Masoero, M. & Silvi, C., (n.d.). Building energy management systems (BEMS) control strategies
for air conditioning efficiency , Cardiff: AUdiTAC.
Method Statement HQ, 2012. Tetsing & commissioning method statement for building
management system BMS. [Online]
Available at: https://methodstatementhq.com/testing-commissioning-method-statement-for-
building-management-system-bms.html
[Accessed 28 August 2017].
Micromain Building Technology, 2017. How to set up a preventive maintenance plan. [Online]
Available at: https://www.micromain.com/set-up-preventive-maintenance-plan/
[Accessed 29 August 2017].
Modern Building Services, 2016. Interfacing lighting-control and building management systems.
[Online]
Available at: http://www.modbs.co.uk/news/archivestory.php/aid/15359/Interfacing_lighting-
control_and_building_management_systems.html
[Accessed 30 August 2017].
Mohammad, A., Ameen, M., Abdul.M.H. & Muizz, O., 2017. Challenges to the implementation
of building management systems in Saudi Arabia. Built Environment Project and Asset
Management, 7(2), pp. 130-142.
Nadeau, R., (n.d.). Chiller startup & shutdown: worth doing right. [Online]
Available at: http://digital.bnpmedia.com/publication/?
i=110002&article_id=1051680&view=articleBrowser&ver=html5#{%22issue_id
%22:110002,%22view%22:%22articleBrowser%22,%22article_id%22:%221051680%22}
[Accessed 28 August 2017].
Paola, A. et al., 2014. Intelligent management systems for energy efficiency in buildings: a
survey. ACM Computing Surveys, 47(1), pp. 13-50.
Available at: https://www.linkedin.com/pulse/bms-benefits-control-systems-strategies-building-
intelligent-plus
[Accessed 29 August 2017].
Iveta, P. &. I. G., 2017. Different approaches to building management and maintenance meaning
explanation. Procedia Engineering, Volume 172, pp. 905-912.
Kumara, W., Waidyasekara, K. & Weerasinghe, R., 2016. Building management system for
sustainable built environment in Sri Lanka. Built Environment Project and Asset Management,
6(3), pp. 302-316.
Kumar, S., Rajwar, J. & Thakur, A., 2013. Building management system using PLC and
SCADA. International Journal of Scientific & Engineering Research, 4(5), pp. 217-219.
Lewis, A., Riley, D. & Elmualim, A., 2010. Defining high performance buildings for operations
and maintenance. International Journal of Facility Management , 1(2), pp. 1-16.
Makarechi, S. & Kangari, R., 2011. Significant parameters for building automation performance.
International Journal of Facility Management, 2(1), pp. 1-25.
Masoero, M. & Silvi, C., (n.d.). Building energy management systems (BEMS) control strategies
for air conditioning efficiency , Cardiff: AUdiTAC.
Method Statement HQ, 2012. Tetsing & commissioning method statement for building
management system BMS. [Online]
Available at: https://methodstatementhq.com/testing-commissioning-method-statement-for-
building-management-system-bms.html
[Accessed 28 August 2017].
Micromain Building Technology, 2017. How to set up a preventive maintenance plan. [Online]
Available at: https://www.micromain.com/set-up-preventive-maintenance-plan/
[Accessed 29 August 2017].
Modern Building Services, 2016. Interfacing lighting-control and building management systems.
[Online]
Available at: http://www.modbs.co.uk/news/archivestory.php/aid/15359/Interfacing_lighting-
control_and_building_management_systems.html
[Accessed 30 August 2017].
Mohammad, A., Ameen, M., Abdul.M.H. & Muizz, O., 2017. Challenges to the implementation
of building management systems in Saudi Arabia. Built Environment Project and Asset
Management, 7(2), pp. 130-142.
Nadeau, R., (n.d.). Chiller startup & shutdown: worth doing right. [Online]
Available at: http://digital.bnpmedia.com/publication/?
i=110002&article_id=1051680&view=articleBrowser&ver=html5#{%22issue_id
%22:110002,%22view%22:%22articleBrowser%22,%22article_id%22:%221051680%22}
[Accessed 28 August 2017].
Paola, A. et al., 2014. Intelligent management systems for energy efficiency in buildings: a
survey. ACM Computing Surveys, 47(1), pp. 13-50.
Paraphrase This Document
Need a fresh take? Get an instant paraphrase of this document with our AI Paraphraser
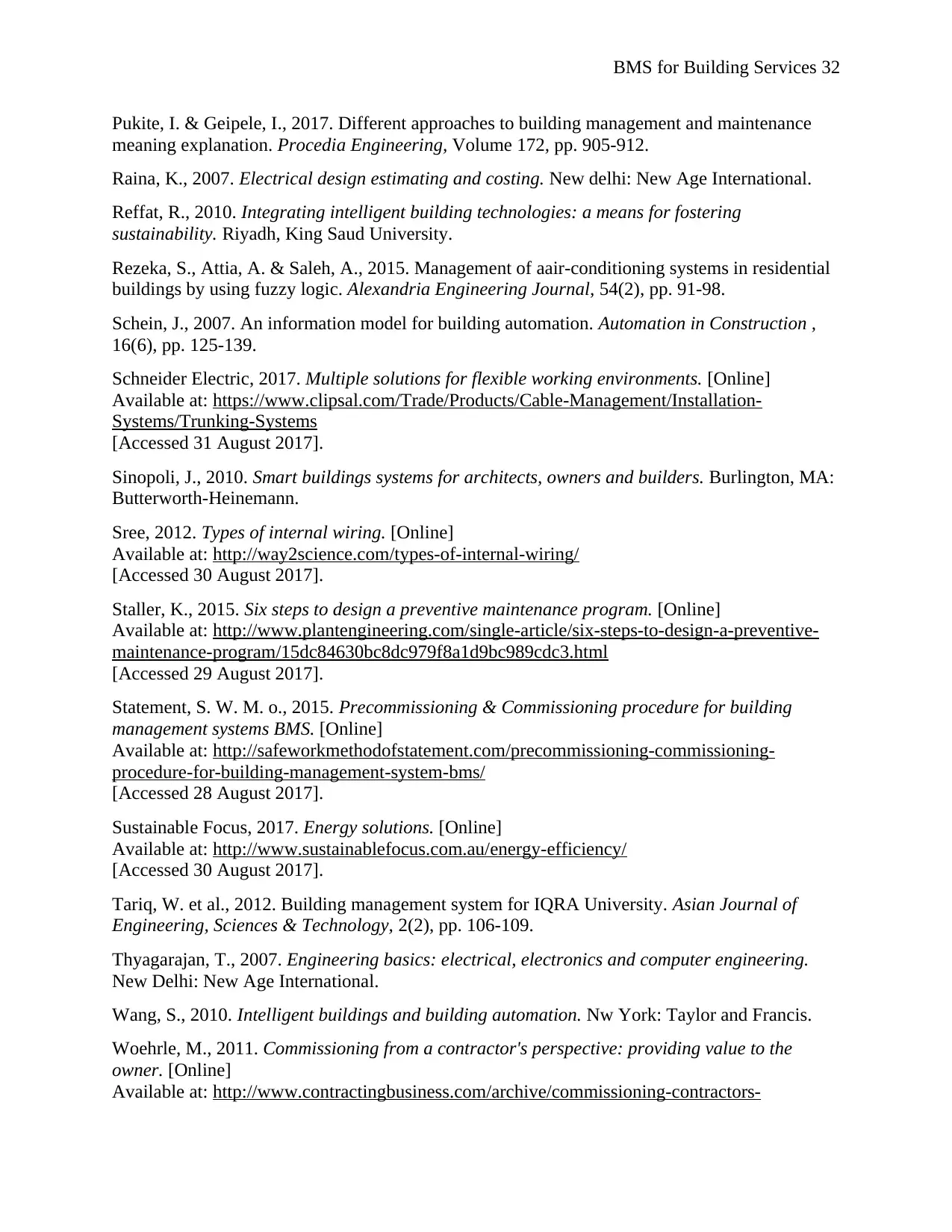
BMS for Building Services 32
Pukite, I. & Geipele, I., 2017. Different approaches to building management and maintenance
meaning explanation. Procedia Engineering, Volume 172, pp. 905-912.
Raina, K., 2007. Electrical design estimating and costing. New delhi: New Age International.
Reffat, R., 2010. Integrating intelligent building technologies: a means for fostering
sustainability. Riyadh, King Saud University.
Rezeka, S., Attia, A. & Saleh, A., 2015. Management of aair-conditioning systems in residential
buildings by using fuzzy logic. Alexandria Engineering Journal, 54(2), pp. 91-98.
Schein, J., 2007. An information model for building automation. Automation in Construction ,
16(6), pp. 125-139.
Schneider Electric, 2017. Multiple solutions for flexible working environments. [Online]
Available at: https://www.clipsal.com/Trade/Products/Cable-Management/Installation-
Systems/Trunking-Systems
[Accessed 31 August 2017].
Sinopoli, J., 2010. Smart buildings systems for architects, owners and builders. Burlington, MA:
Butterworth-Heinemann.
Sree, 2012. Types of internal wiring. [Online]
Available at: http://way2science.com/types-of-internal-wiring/
[Accessed 30 August 2017].
Staller, K., 2015. Six steps to design a preventive maintenance program. [Online]
Available at: http://www.plantengineering.com/single-article/six-steps-to-design-a-preventive-
maintenance-program/15dc84630bc8dc979f8a1d9bc989cdc3.html
[Accessed 29 August 2017].
Statement, S. W. M. o., 2015. Precommissioning & Commissioning procedure for building
management systems BMS. [Online]
Available at: http://safeworkmethodofstatement.com/precommissioning-commissioning-
procedure-for-building-management-system-bms/
[Accessed 28 August 2017].
Sustainable Focus, 2017. Energy solutions. [Online]
Available at: http://www.sustainablefocus.com.au/energy-efficiency/
[Accessed 30 August 2017].
Tariq, W. et al., 2012. Building management system for IQRA University. Asian Journal of
Engineering, Sciences & Technology, 2(2), pp. 106-109.
Thyagarajan, T., 2007. Engineering basics: electrical, electronics and computer engineering.
New Delhi: New Age International.
Wang, S., 2010. Intelligent buildings and building automation. Nw York: Taylor and Francis.
Woehrle, M., 2011. Commissioning from a contractor's perspective: providing value to the
owner. [Online]
Available at: http://www.contractingbusiness.com/archive/commissioning-contractors-
Pukite, I. & Geipele, I., 2017. Different approaches to building management and maintenance
meaning explanation. Procedia Engineering, Volume 172, pp. 905-912.
Raina, K., 2007. Electrical design estimating and costing. New delhi: New Age International.
Reffat, R., 2010. Integrating intelligent building technologies: a means for fostering
sustainability. Riyadh, King Saud University.
Rezeka, S., Attia, A. & Saleh, A., 2015. Management of aair-conditioning systems in residential
buildings by using fuzzy logic. Alexandria Engineering Journal, 54(2), pp. 91-98.
Schein, J., 2007. An information model for building automation. Automation in Construction ,
16(6), pp. 125-139.
Schneider Electric, 2017. Multiple solutions for flexible working environments. [Online]
Available at: https://www.clipsal.com/Trade/Products/Cable-Management/Installation-
Systems/Trunking-Systems
[Accessed 31 August 2017].
Sinopoli, J., 2010. Smart buildings systems for architects, owners and builders. Burlington, MA:
Butterworth-Heinemann.
Sree, 2012. Types of internal wiring. [Online]
Available at: http://way2science.com/types-of-internal-wiring/
[Accessed 30 August 2017].
Staller, K., 2015. Six steps to design a preventive maintenance program. [Online]
Available at: http://www.plantengineering.com/single-article/six-steps-to-design-a-preventive-
maintenance-program/15dc84630bc8dc979f8a1d9bc989cdc3.html
[Accessed 29 August 2017].
Statement, S. W. M. o., 2015. Precommissioning & Commissioning procedure for building
management systems BMS. [Online]
Available at: http://safeworkmethodofstatement.com/precommissioning-commissioning-
procedure-for-building-management-system-bms/
[Accessed 28 August 2017].
Sustainable Focus, 2017. Energy solutions. [Online]
Available at: http://www.sustainablefocus.com.au/energy-efficiency/
[Accessed 30 August 2017].
Tariq, W. et al., 2012. Building management system for IQRA University. Asian Journal of
Engineering, Sciences & Technology, 2(2), pp. 106-109.
Thyagarajan, T., 2007. Engineering basics: electrical, electronics and computer engineering.
New Delhi: New Age International.
Wang, S., 2010. Intelligent buildings and building automation. Nw York: Taylor and Francis.
Woehrle, M., 2011. Commissioning from a contractor's perspective: providing value to the
owner. [Online]
Available at: http://www.contractingbusiness.com/archive/commissioning-contractors-
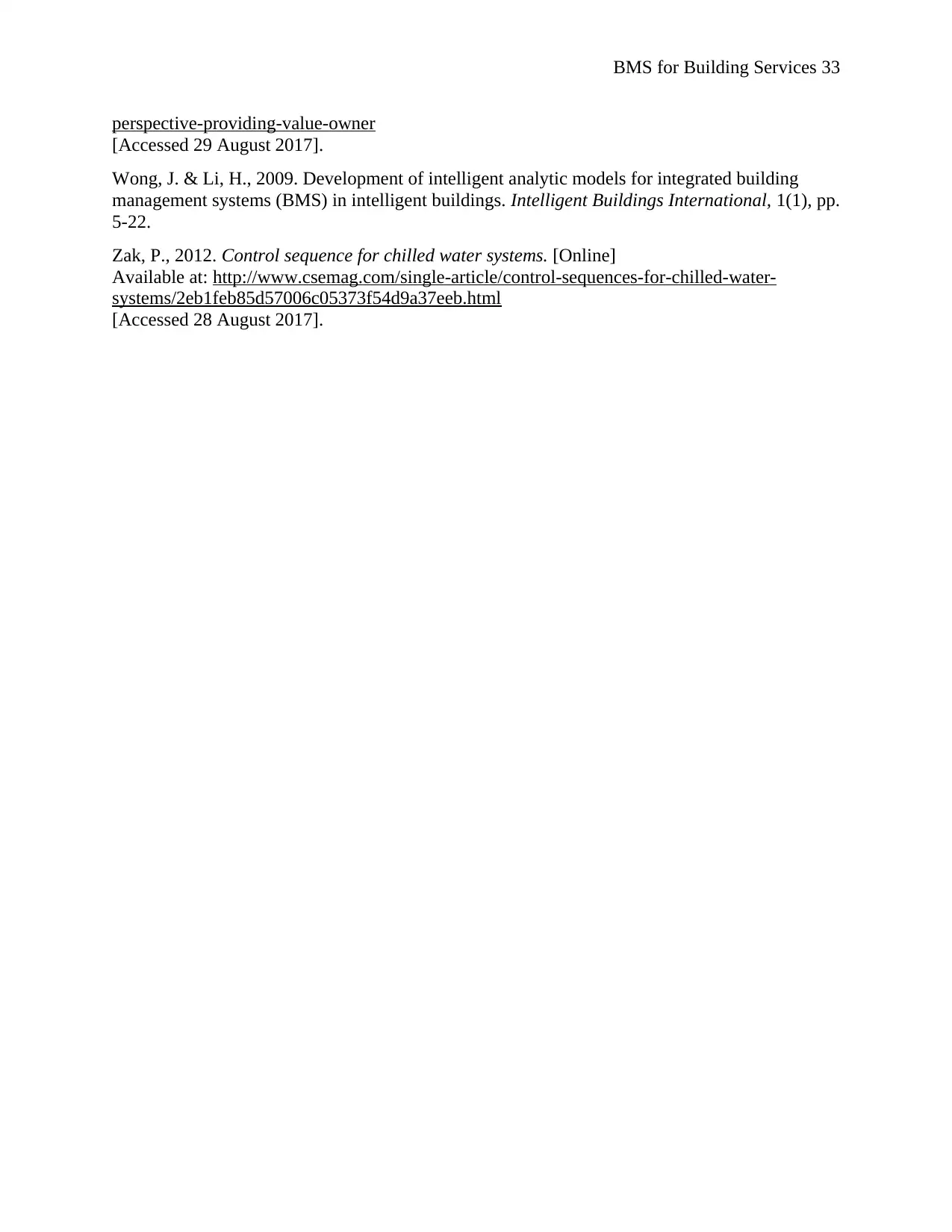
BMS for Building Services 33
perspective-providing-value-owner
[Accessed 29 August 2017].
Wong, J. & Li, H., 2009. Development of intelligent analytic models for integrated building
management systems (BMS) in intelligent buildings. Intelligent Buildings International, 1(1), pp.
5-22.
Zak, P., 2012. Control sequence for chilled water systems. [Online]
Available at: http://www.csemag.com/single-article/control-sequences-for-chilled-water-
systems/2eb1feb85d57006c05373f54d9a37eeb.html
[Accessed 28 August 2017].
perspective-providing-value-owner
[Accessed 29 August 2017].
Wong, J. & Li, H., 2009. Development of intelligent analytic models for integrated building
management systems (BMS) in intelligent buildings. Intelligent Buildings International, 1(1), pp.
5-22.
Zak, P., 2012. Control sequence for chilled water systems. [Online]
Available at: http://www.csemag.com/single-article/control-sequences-for-chilled-water-
systems/2eb1feb85d57006c05373f54d9a37eeb.html
[Accessed 28 August 2017].
1 out of 33
Related Documents
![[object Object]](/_next/image/?url=%2F_next%2Fstatic%2Fmedia%2Flogo.6d15ce61.png&w=640&q=75)
Your All-in-One AI-Powered Toolkit for Academic Success.
+13062052269
info@desklib.com
Available 24*7 on WhatsApp / Email
Unlock your academic potential
© 2024 | Zucol Services PVT LTD | All rights reserved.