Barriers to Warehouse Optimization: A Review of Challenges and Technical Optimization
VerifiedAdded on 2023/04/22
|6
|1345
|84
AI Summary
This research report is a review of the warehouse congestion which means the barriers to warehouse optimization. The major purpose of the review is to identify the barriers to warehouse optimization caused by space crunch. The review has been performed by considering eight journal articles performed on warehouse management.
Contribute Materials
Your contribution can guide someone’s learning journey. Share your
documents today.
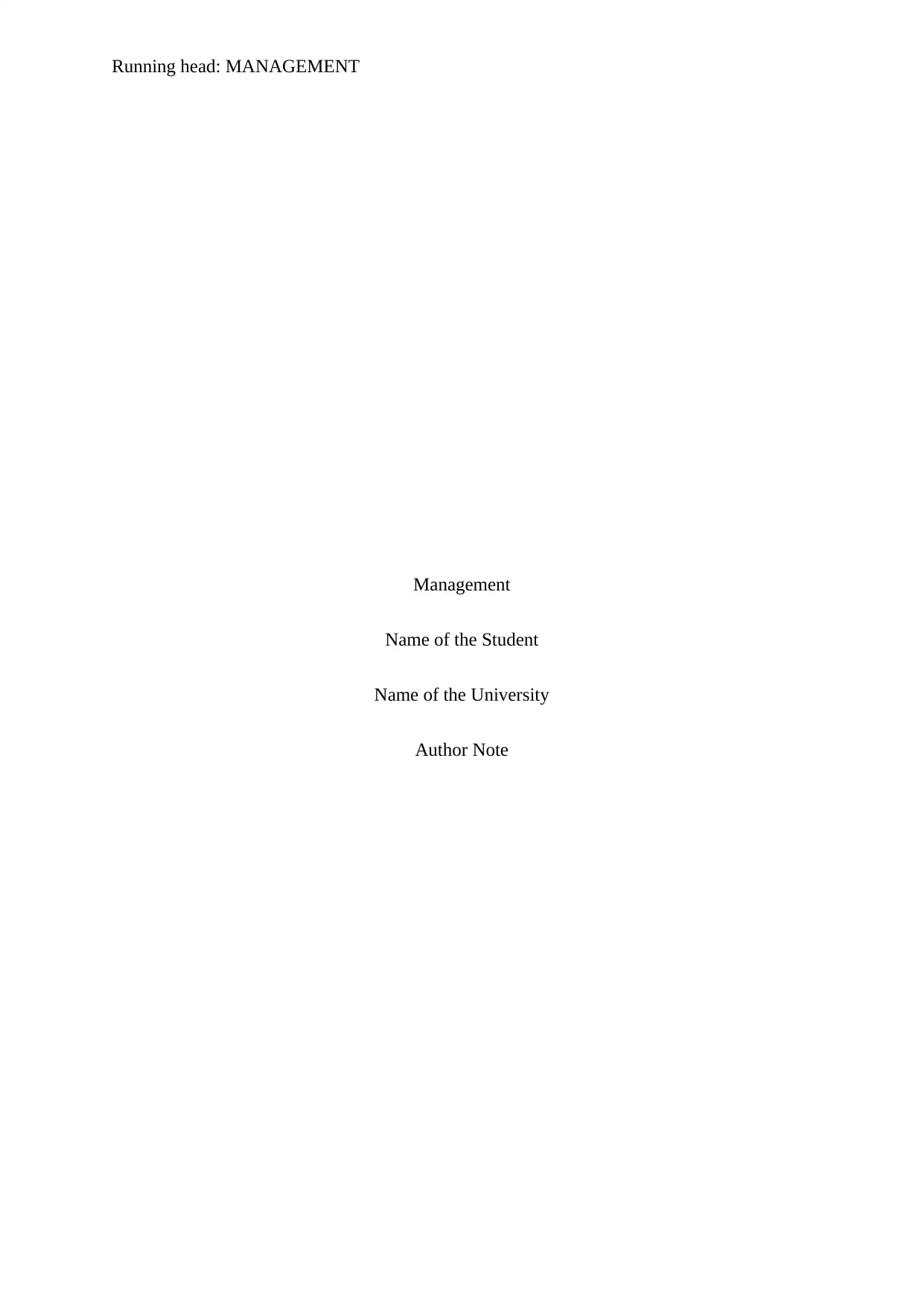
Running head: MANAGEMENT
Management
Name of the Student
Name of the University
Author Note
Management
Name of the Student
Name of the University
Author Note
Secure Best Marks with AI Grader
Need help grading? Try our AI Grader for instant feedback on your assignments.
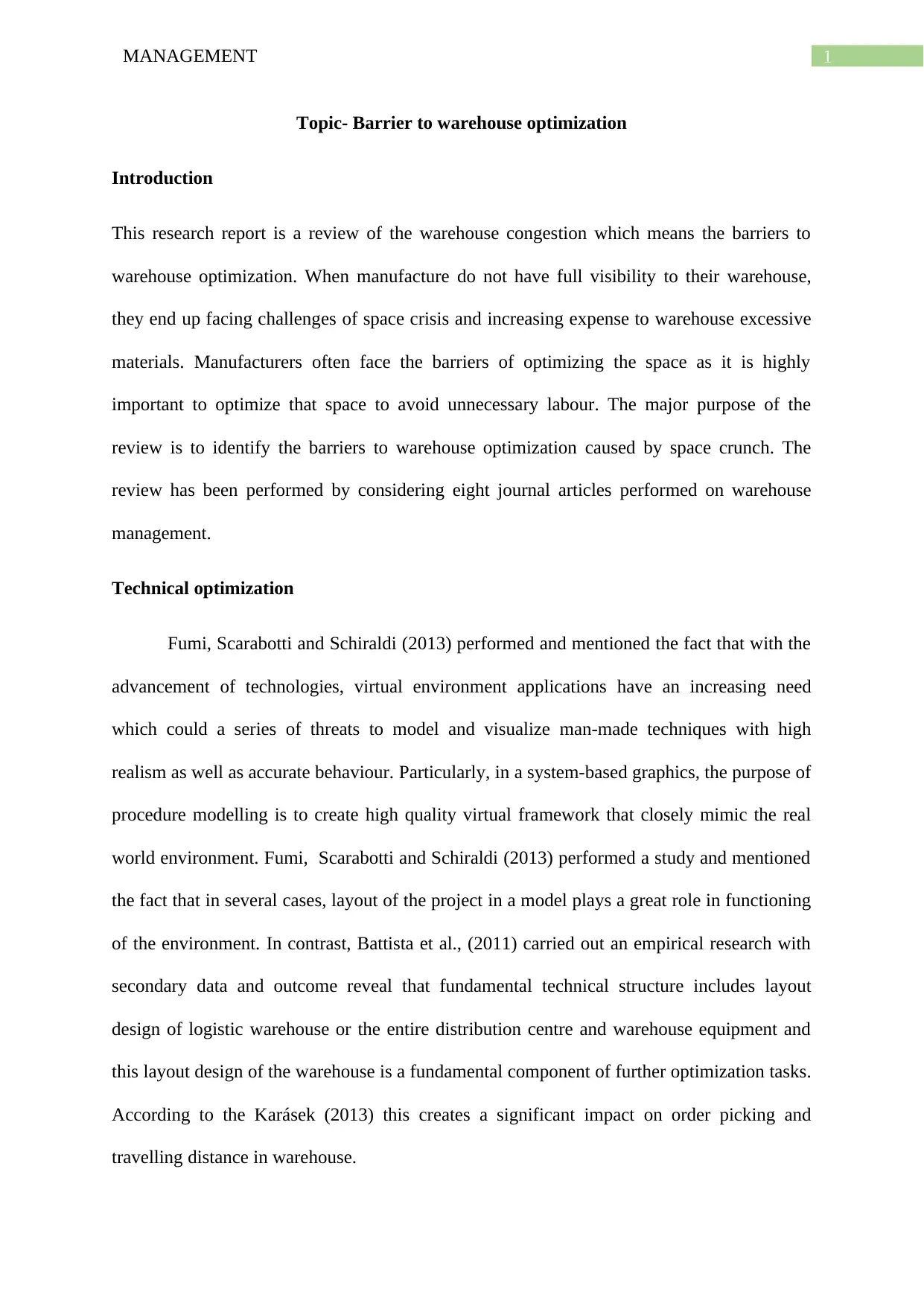
1MANAGEMENT
Topic- Barrier to warehouse optimization
Introduction
This research report is a review of the warehouse congestion which means the barriers to
warehouse optimization. When manufacture do not have full visibility to their warehouse,
they end up facing challenges of space crisis and increasing expense to warehouse excessive
materials. Manufacturers often face the barriers of optimizing the space as it is highly
important to optimize that space to avoid unnecessary labour. The major purpose of the
review is to identify the barriers to warehouse optimization caused by space crunch. The
review has been performed by considering eight journal articles performed on warehouse
management.
Technical optimization
Fumi, Scarabotti and Schiraldi (2013) performed and mentioned the fact that with the
advancement of technologies, virtual environment applications have an increasing need
which could a series of threats to model and visualize man-made techniques with high
realism as well as accurate behaviour. Particularly, in a system-based graphics, the purpose of
procedure modelling is to create high quality virtual framework that closely mimic the real
world environment. Fumi, Scarabotti and Schiraldi (2013) performed a study and mentioned
the fact that in several cases, layout of the project in a model plays a great role in functioning
of the environment. In contrast, Battista et al., (2011) carried out an empirical research with
secondary data and outcome reveal that fundamental technical structure includes layout
design of logistic warehouse or the entire distribution centre and warehouse equipment and
this layout design of the warehouse is a fundamental component of further optimization tasks.
According to the Karásek (2013) this creates a significant impact on order picking and
travelling distance in warehouse.
Topic- Barrier to warehouse optimization
Introduction
This research report is a review of the warehouse congestion which means the barriers to
warehouse optimization. When manufacture do not have full visibility to their warehouse,
they end up facing challenges of space crisis and increasing expense to warehouse excessive
materials. Manufacturers often face the barriers of optimizing the space as it is highly
important to optimize that space to avoid unnecessary labour. The major purpose of the
review is to identify the barriers to warehouse optimization caused by space crunch. The
review has been performed by considering eight journal articles performed on warehouse
management.
Technical optimization
Fumi, Scarabotti and Schiraldi (2013) performed and mentioned the fact that with the
advancement of technologies, virtual environment applications have an increasing need
which could a series of threats to model and visualize man-made techniques with high
realism as well as accurate behaviour. Particularly, in a system-based graphics, the purpose of
procedure modelling is to create high quality virtual framework that closely mimic the real
world environment. Fumi, Scarabotti and Schiraldi (2013) performed a study and mentioned
the fact that in several cases, layout of the project in a model plays a great role in functioning
of the environment. In contrast, Battista et al., (2011) carried out an empirical research with
secondary data and outcome reveal that fundamental technical structure includes layout
design of logistic warehouse or the entire distribution centre and warehouse equipment and
this layout design of the warehouse is a fundamental component of further optimization tasks.
According to the Karásek (2013) this creates a significant impact on order picking and
travelling distance in warehouse.
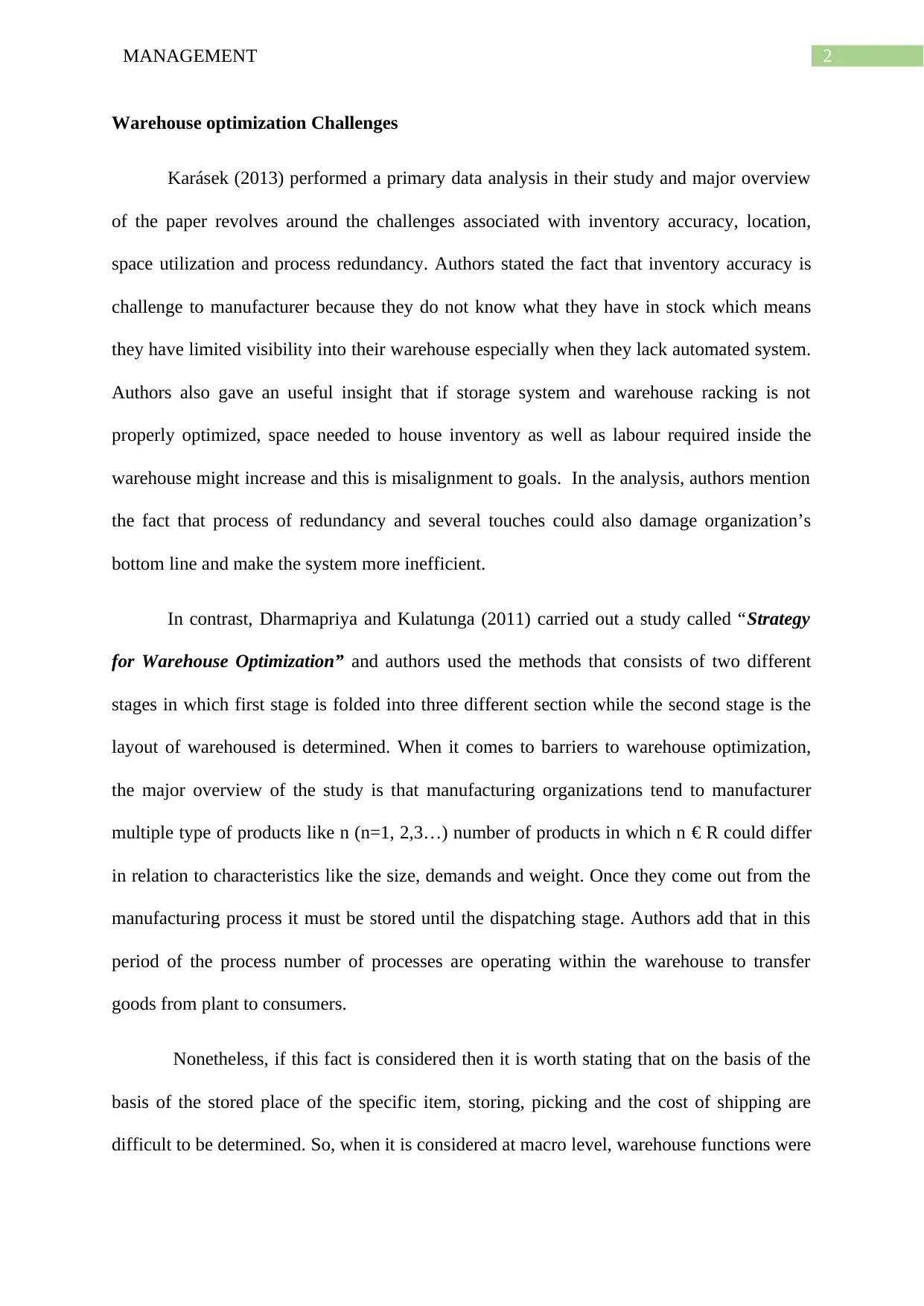
2MANAGEMENT
Warehouse optimization Challenges
Karásek (2013) performed a primary data analysis in their study and major overview
of the paper revolves around the challenges associated with inventory accuracy, location,
space utilization and process redundancy. Authors stated the fact that inventory accuracy is
challenge to manufacturer because they do not know what they have in stock which means
they have limited visibility into their warehouse especially when they lack automated system.
Authors also gave an useful insight that if storage system and warehouse racking is not
properly optimized, space needed to house inventory as well as labour required inside the
warehouse might increase and this is misalignment to goals. In the analysis, authors mention
the fact that process of redundancy and several touches could also damage organization’s
bottom line and make the system more inefficient.
In contrast, Dharmapriya and Kulatunga (2011) carried out a study called “Strategy
for Warehouse Optimization” and authors used the methods that consists of two different
stages in which first stage is folded into three different section while the second stage is the
layout of warehoused is determined. When it comes to barriers to warehouse optimization,
the major overview of the study is that manufacturing organizations tend to manufacturer
multiple type of products like n (n=1, 2,3…) number of products in which n € R could differ
in relation to characteristics like the size, demands and weight. Once they come out from the
manufacturing process it must be stored until the dispatching stage. Authors add that in this
period of the process number of processes are operating within the warehouse to transfer
goods from plant to consumers.
Nonetheless, if this fact is considered then it is worth stating that on the basis of the
basis of the stored place of the specific item, storing, picking and the cost of shipping are
difficult to be determined. So, when it is considered at macro level, warehouse functions were
Warehouse optimization Challenges
Karásek (2013) performed a primary data analysis in their study and major overview
of the paper revolves around the challenges associated with inventory accuracy, location,
space utilization and process redundancy. Authors stated the fact that inventory accuracy is
challenge to manufacturer because they do not know what they have in stock which means
they have limited visibility into their warehouse especially when they lack automated system.
Authors also gave an useful insight that if storage system and warehouse racking is not
properly optimized, space needed to house inventory as well as labour required inside the
warehouse might increase and this is misalignment to goals. In the analysis, authors mention
the fact that process of redundancy and several touches could also damage organization’s
bottom line and make the system more inefficient.
In contrast, Dharmapriya and Kulatunga (2011) carried out a study called “Strategy
for Warehouse Optimization” and authors used the methods that consists of two different
stages in which first stage is folded into three different section while the second stage is the
layout of warehoused is determined. When it comes to barriers to warehouse optimization,
the major overview of the study is that manufacturing organizations tend to manufacturer
multiple type of products like n (n=1, 2,3…) number of products in which n € R could differ
in relation to characteristics like the size, demands and weight. Once they come out from the
manufacturing process it must be stored until the dispatching stage. Authors add that in this
period of the process number of processes are operating within the warehouse to transfer
goods from plant to consumers.
Nonetheless, if this fact is considered then it is worth stating that on the basis of the
basis of the stored place of the specific item, storing, picking and the cost of shipping are
difficult to be determined. So, when it is considered at macro level, warehouse functions were
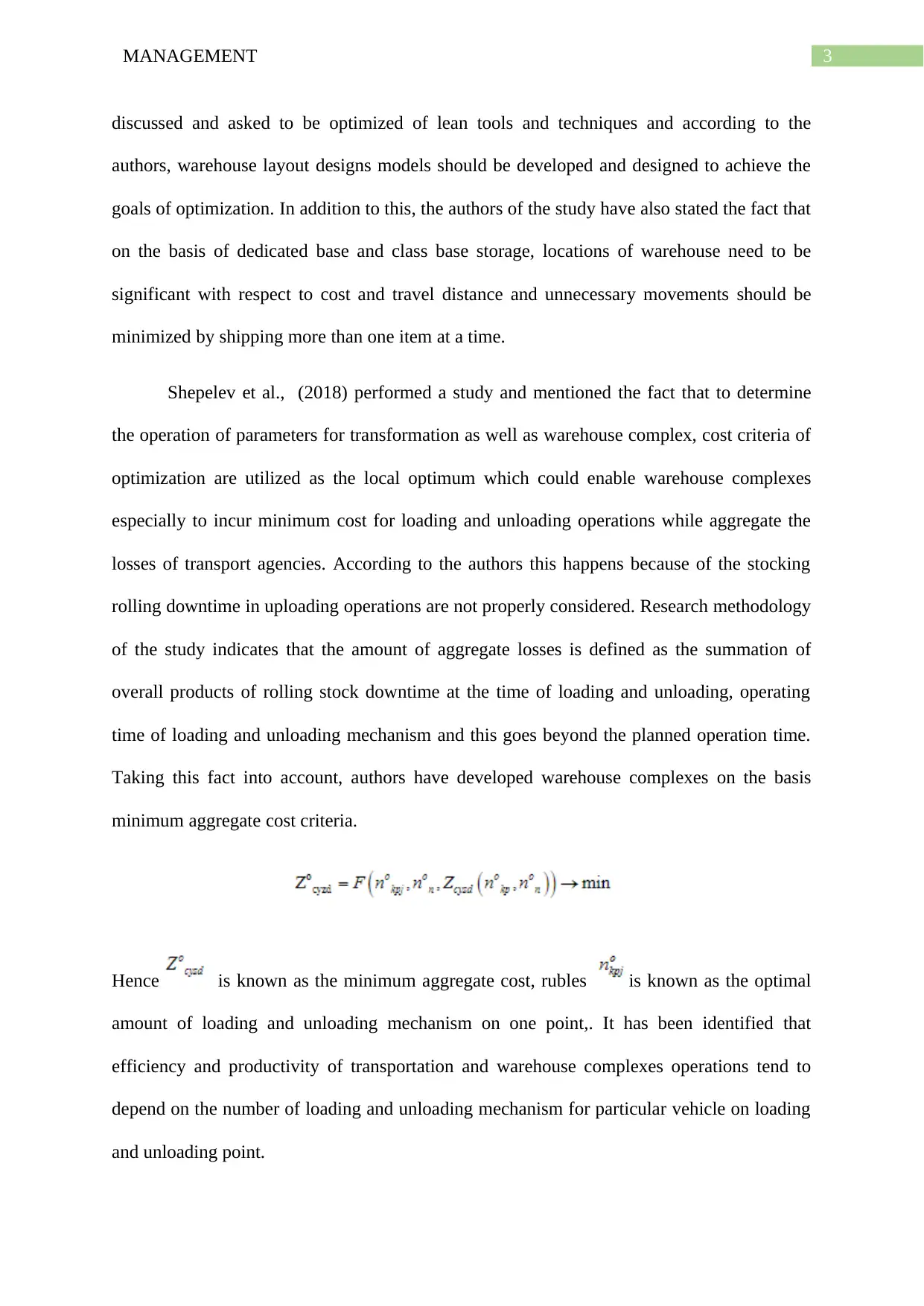
3MANAGEMENT
discussed and asked to be optimized of lean tools and techniques and according to the
authors, warehouse layout designs models should be developed and designed to achieve the
goals of optimization. In addition to this, the authors of the study have also stated the fact that
on the basis of dedicated base and class base storage, locations of warehouse need to be
significant with respect to cost and travel distance and unnecessary movements should be
minimized by shipping more than one item at a time.
Shepelev et al., (2018) performed a study and mentioned the fact that to determine
the operation of parameters for transformation as well as warehouse complex, cost criteria of
optimization are utilized as the local optimum which could enable warehouse complexes
especially to incur minimum cost for loading and unloading operations while aggregate the
losses of transport agencies. According to the authors this happens because of the stocking
rolling downtime in uploading operations are not properly considered. Research methodology
of the study indicates that the amount of aggregate losses is defined as the summation of
overall products of rolling stock downtime at the time of loading and unloading, operating
time of loading and unloading mechanism and this goes beyond the planned operation time.
Taking this fact into account, authors have developed warehouse complexes on the basis
minimum aggregate cost criteria.
Hence is known as the minimum aggregate cost, rubles is known as the optimal
amount of loading and unloading mechanism on one point,. It has been identified that
efficiency and productivity of transportation and warehouse complexes operations tend to
depend on the number of loading and unloading mechanism for particular vehicle on loading
and unloading point.
discussed and asked to be optimized of lean tools and techniques and according to the
authors, warehouse layout designs models should be developed and designed to achieve the
goals of optimization. In addition to this, the authors of the study have also stated the fact that
on the basis of dedicated base and class base storage, locations of warehouse need to be
significant with respect to cost and travel distance and unnecessary movements should be
minimized by shipping more than one item at a time.
Shepelev et al., (2018) performed a study and mentioned the fact that to determine
the operation of parameters for transformation as well as warehouse complex, cost criteria of
optimization are utilized as the local optimum which could enable warehouse complexes
especially to incur minimum cost for loading and unloading operations while aggregate the
losses of transport agencies. According to the authors this happens because of the stocking
rolling downtime in uploading operations are not properly considered. Research methodology
of the study indicates that the amount of aggregate losses is defined as the summation of
overall products of rolling stock downtime at the time of loading and unloading, operating
time of loading and unloading mechanism and this goes beyond the planned operation time.
Taking this fact into account, authors have developed warehouse complexes on the basis
minimum aggregate cost criteria.
Hence is known as the minimum aggregate cost, rubles is known as the optimal
amount of loading and unloading mechanism on one point,. It has been identified that
efficiency and productivity of transportation and warehouse complexes operations tend to
depend on the number of loading and unloading mechanism for particular vehicle on loading
and unloading point.
Secure Best Marks with AI Grader
Need help grading? Try our AI Grader for instant feedback on your assignments.
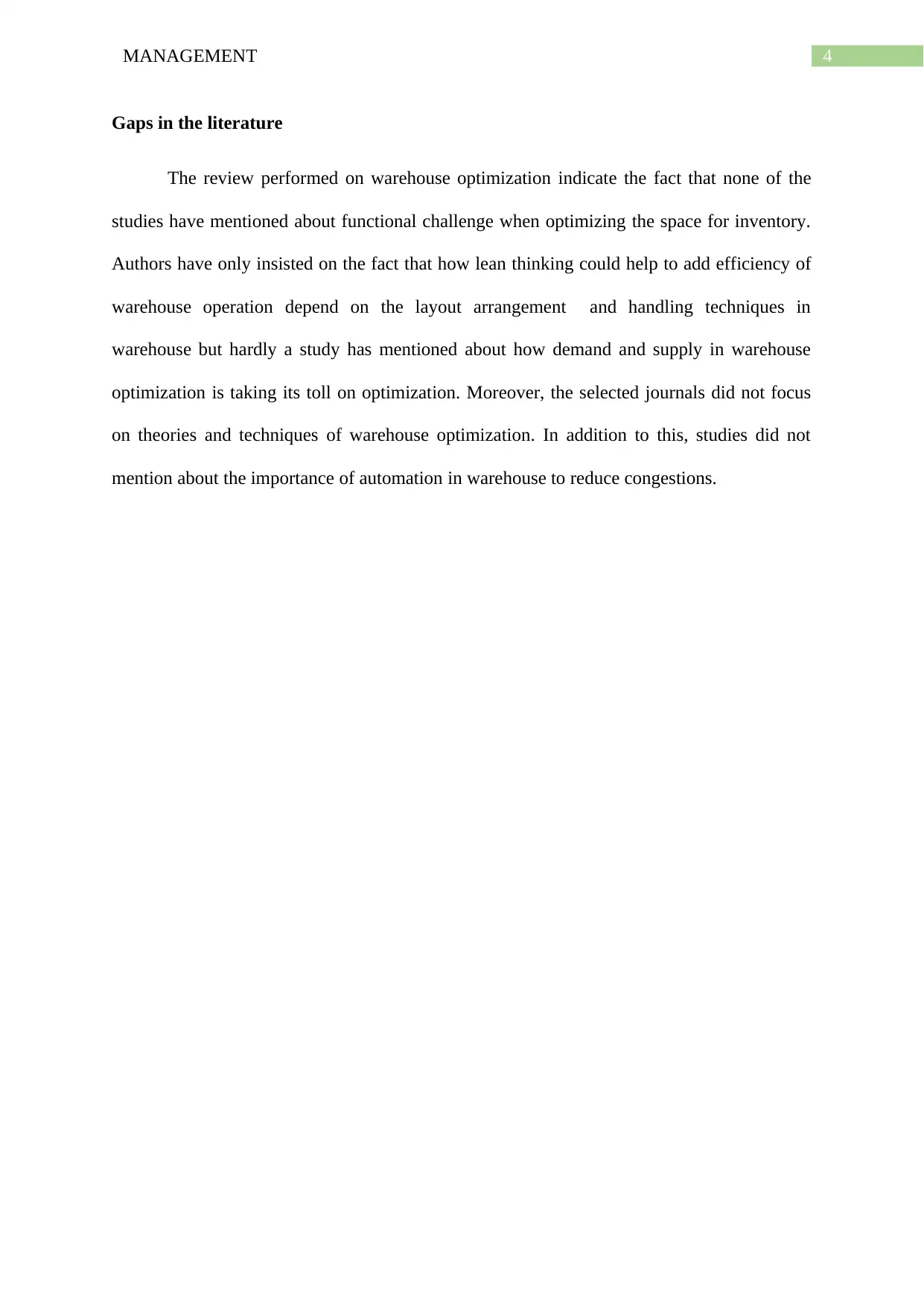
4MANAGEMENT
Gaps in the literature
The review performed on warehouse optimization indicate the fact that none of the
studies have mentioned about functional challenge when optimizing the space for inventory.
Authors have only insisted on the fact that how lean thinking could help to add efficiency of
warehouse operation depend on the layout arrangement and handling techniques in
warehouse but hardly a study has mentioned about how demand and supply in warehouse
optimization is taking its toll on optimization. Moreover, the selected journals did not focus
on theories and techniques of warehouse optimization. In addition to this, studies did not
mention about the importance of automation in warehouse to reduce congestions.
Gaps in the literature
The review performed on warehouse optimization indicate the fact that none of the
studies have mentioned about functional challenge when optimizing the space for inventory.
Authors have only insisted on the fact that how lean thinking could help to add efficiency of
warehouse operation depend on the layout arrangement and handling techniques in
warehouse but hardly a study has mentioned about how demand and supply in warehouse
optimization is taking its toll on optimization. Moreover, the selected journals did not focus
on theories and techniques of warehouse optimization. In addition to this, studies did not
mention about the importance of automation in warehouse to reduce congestions.
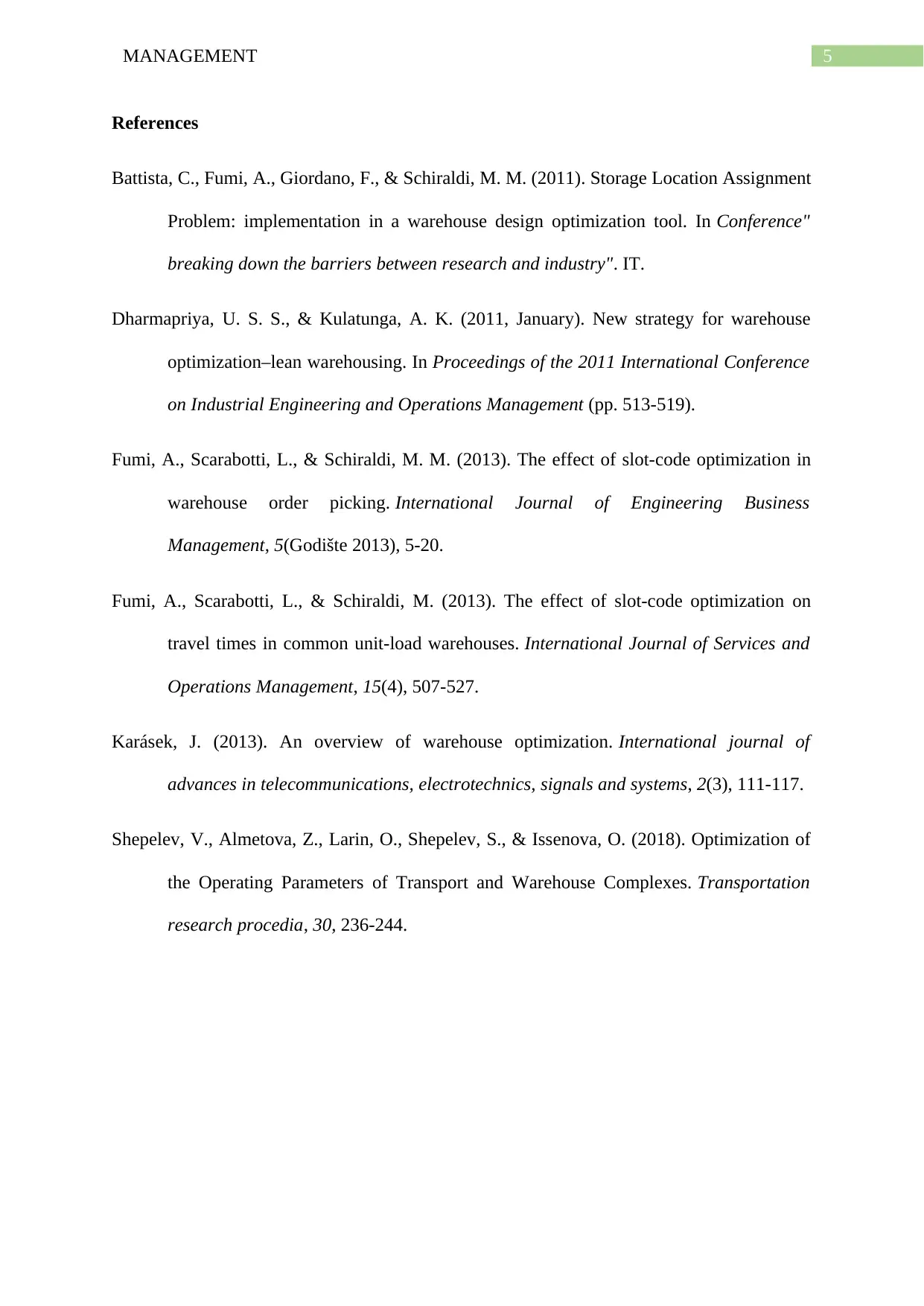
5MANAGEMENT
References
Battista, C., Fumi, A., Giordano, F., & Schiraldi, M. M. (2011). Storage Location Assignment
Problem: implementation in a warehouse design optimization tool. In Conference"
breaking down the barriers between research and industry". IT.
Dharmapriya, U. S. S., & Kulatunga, A. K. (2011, January). New strategy for warehouse
optimization–lean warehousing. In Proceedings of the 2011 International Conference
on Industrial Engineering and Operations Management (pp. 513-519).
Fumi, A., Scarabotti, L., & Schiraldi, M. M. (2013). The effect of slot-code optimization in
warehouse order picking. International Journal of Engineering Business
Management, 5(Godište 2013), 5-20.
Fumi, A., Scarabotti, L., & Schiraldi, M. (2013). The effect of slot-code optimization on
travel times in common unit-load warehouses. International Journal of Services and
Operations Management, 15(4), 507-527.
Karásek, J. (2013). An overview of warehouse optimization. International journal of
advances in telecommunications, electrotechnics, signals and systems, 2(3), 111-117.
Shepelev, V., Almetova, Z., Larin, O., Shepelev, S., & Issenova, O. (2018). Optimization of
the Operating Parameters of Transport and Warehouse Complexes. Transportation
research procedia, 30, 236-244.
References
Battista, C., Fumi, A., Giordano, F., & Schiraldi, M. M. (2011). Storage Location Assignment
Problem: implementation in a warehouse design optimization tool. In Conference"
breaking down the barriers between research and industry". IT.
Dharmapriya, U. S. S., & Kulatunga, A. K. (2011, January). New strategy for warehouse
optimization–lean warehousing. In Proceedings of the 2011 International Conference
on Industrial Engineering and Operations Management (pp. 513-519).
Fumi, A., Scarabotti, L., & Schiraldi, M. M. (2013). The effect of slot-code optimization in
warehouse order picking. International Journal of Engineering Business
Management, 5(Godište 2013), 5-20.
Fumi, A., Scarabotti, L., & Schiraldi, M. (2013). The effect of slot-code optimization on
travel times in common unit-load warehouses. International Journal of Services and
Operations Management, 15(4), 507-527.
Karásek, J. (2013). An overview of warehouse optimization. International journal of
advances in telecommunications, electrotechnics, signals and systems, 2(3), 111-117.
Shepelev, V., Almetova, Z., Larin, O., Shepelev, S., & Issenova, O. (2018). Optimization of
the Operating Parameters of Transport and Warehouse Complexes. Transportation
research procedia, 30, 236-244.
1 out of 6
![[object Object]](/_next/image/?url=%2F_next%2Fstatic%2Fmedia%2Flogo.6d15ce61.png&w=640&q=75)
Your All-in-One AI-Powered Toolkit for Academic Success.
+13062052269
info@desklib.com
Available 24*7 on WhatsApp / Email
Unlock your academic potential
© 2024 | Zucol Services PVT LTD | All rights reserved.