49006 Risk Management: Comprehensive Engineering Risk Management Plan
VerifiedAdded on 2023/06/13
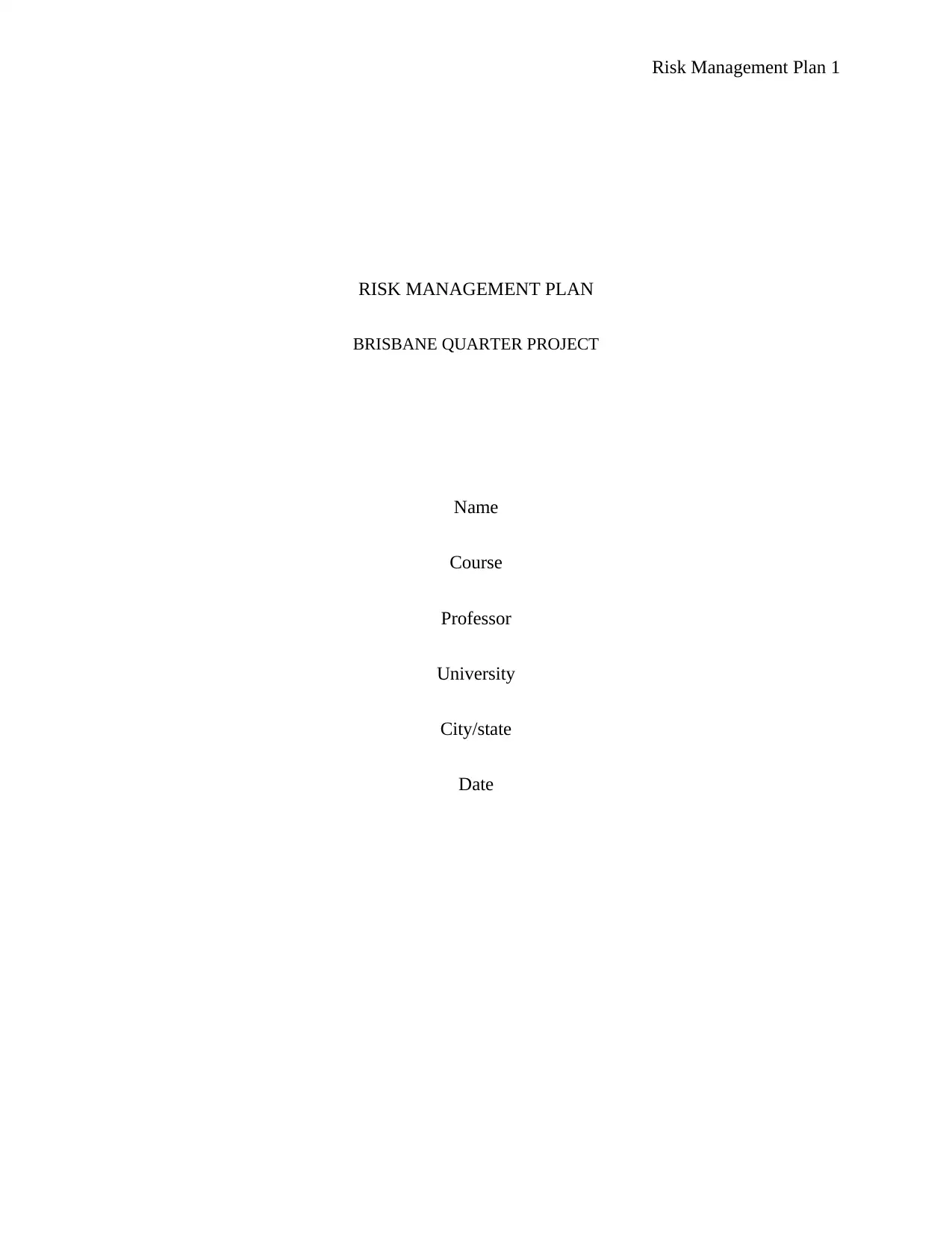
RISK MANAGEMENT PLAN
BRISBANE QUARTER PROJECT
Name
Course
Professor
University
City/state
Date
Paraphrase This Document
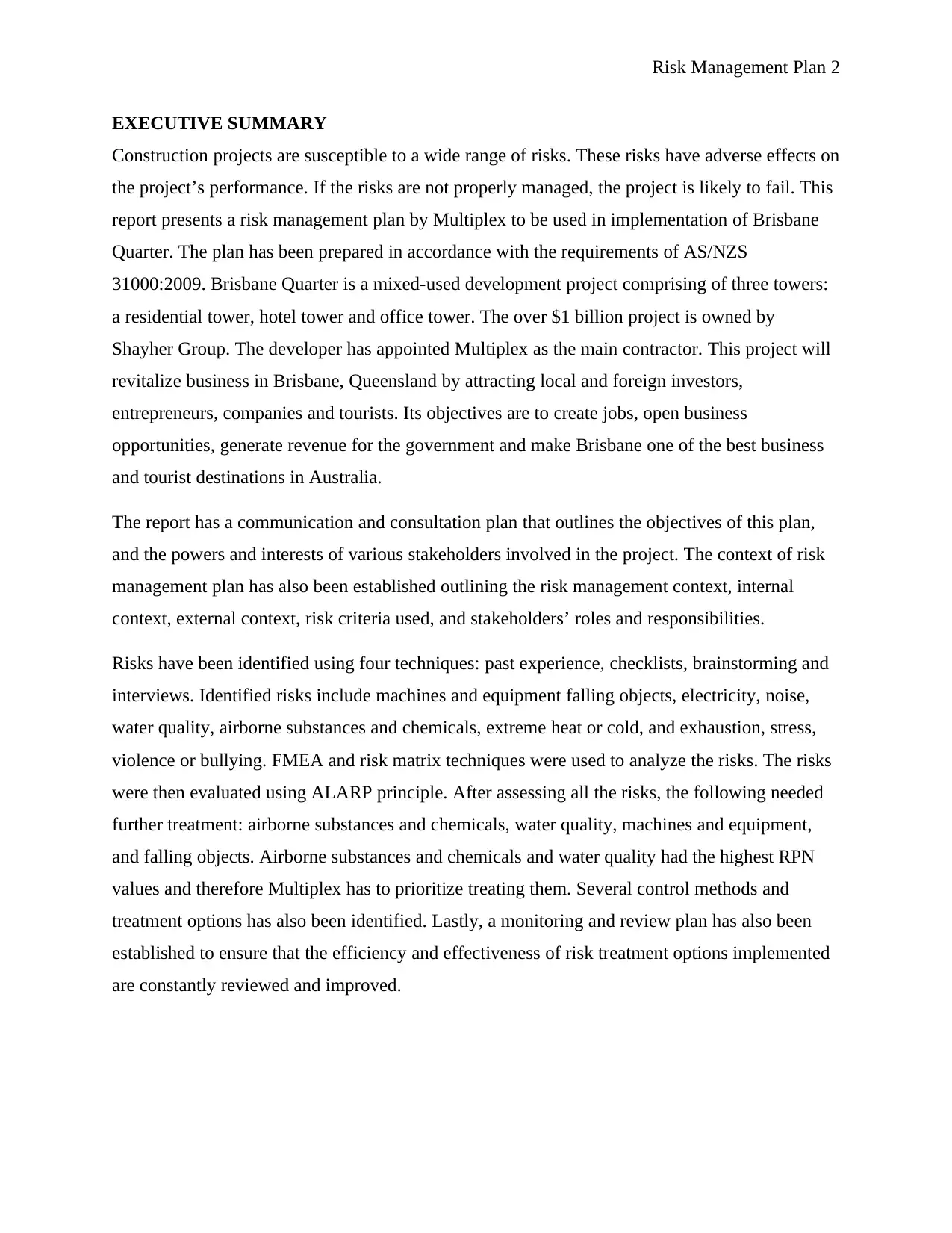
EXECUTIVE SUMMARY
Construction projects are susceptible to a wide range of risks. These risks have adverse effects on
the project’s performance. If the risks are not properly managed, the project is likely to fail. This
report presents a risk management plan by Multiplex to be used in implementation of Brisbane
Quarter. The plan has been prepared in accordance with the requirements of AS/NZS
31000:2009. Brisbane Quarter is a mixed-used development project comprising of three towers:
a residential tower, hotel tower and office tower. The over $1 billion project is owned by
Shayher Group. The developer has appointed Multiplex as the main contractor. This project will
revitalize business in Brisbane, Queensland by attracting local and foreign investors,
entrepreneurs, companies and tourists. Its objectives are to create jobs, open business
opportunities, generate revenue for the government and make Brisbane one of the best business
and tourist destinations in Australia.
The report has a communication and consultation plan that outlines the objectives of this plan,
and the powers and interests of various stakeholders involved in the project. The context of risk
management plan has also been established outlining the risk management context, internal
context, external context, risk criteria used, and stakeholders’ roles and responsibilities.
Risks have been identified using four techniques: past experience, checklists, brainstorming and
interviews. Identified risks include machines and equipment falling objects, electricity, noise,
water quality, airborne substances and chemicals, extreme heat or cold, and exhaustion, stress,
violence or bullying. FMEA and risk matrix techniques were used to analyze the risks. The risks
were then evaluated using ALARP principle. After assessing all the risks, the following needed
further treatment: airborne substances and chemicals, water quality, machines and equipment,
and falling objects. Airborne substances and chemicals and water quality had the highest RPN
values and therefore Multiplex has to prioritize treating them. Several control methods and
treatment options has also been identified. Lastly, a monitoring and review plan has also been
established to ensure that the efficiency and effectiveness of risk treatment options implemented
are constantly reviewed and improved.
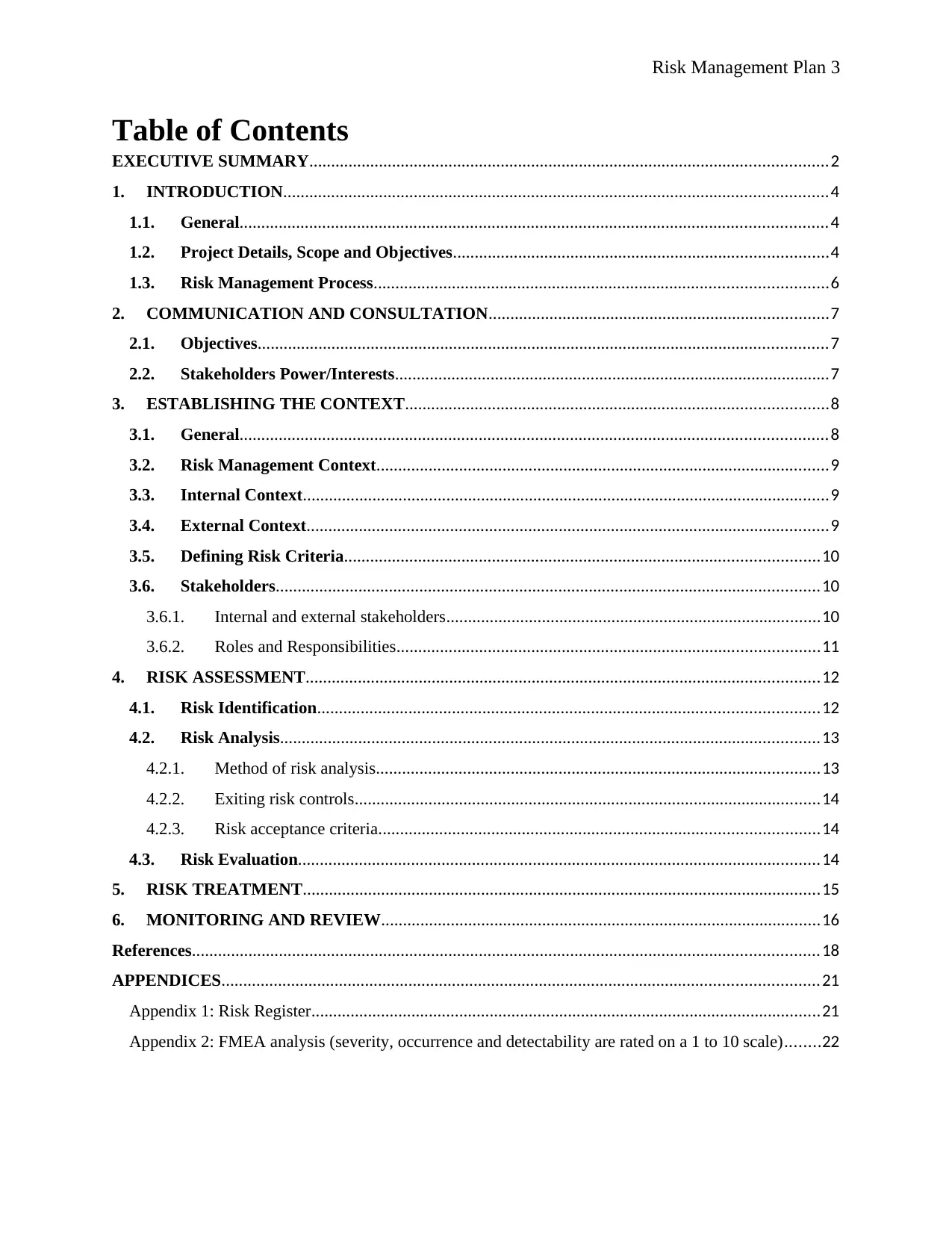
Table of Contents
EXECUTIVE SUMMARY.......................................................................................................................2
1. INTRODUCTION.............................................................................................................................4
1.1. General.......................................................................................................................................4
1.2. Project Details, Scope and Objectives......................................................................................4
1.3. Risk Management Process........................................................................................................6
2. COMMUNICATION AND CONSULTATION..............................................................................7
2.1. Objectives...................................................................................................................................7
2.2. Stakeholders Power/Interests....................................................................................................7
3. ESTABLISHING THE CONTEXT.................................................................................................8
3.1. General.......................................................................................................................................8
3.2. Risk Management Context........................................................................................................9
3.3. Internal Context.........................................................................................................................9
3.4. External Context........................................................................................................................9
3.5. Defining Risk Criteria.............................................................................................................10
3.6. Stakeholders.............................................................................................................................10
3.6.1. Internal and external stakeholders......................................................................................10
3.6.2. Roles and Responsibilities.................................................................................................11
4. RISK ASSESSMENT......................................................................................................................12
4.1. Risk Identification...................................................................................................................12
4.2. Risk Analysis............................................................................................................................13
4.2.1. Method of risk analysis......................................................................................................13
4.2.2. Exiting risk controls...........................................................................................................14
4.2.3. Risk acceptance criteria.....................................................................................................14
4.3. Risk Evaluation........................................................................................................................14
5. RISK TREATMENT.......................................................................................................................15
6. MONITORING AND REVIEW.....................................................................................................16
References................................................................................................................................................18
APPENDICES.........................................................................................................................................21
Appendix 1: Risk Register.....................................................................................................................21
Appendix 2: FMEA analysis (severity, occurrence and detectability are rated on a 1 to 10 scale)........22
⊘ This is a preview!⊘
Do you want full access?
Subscribe today to unlock all pages.

Trusted by 1+ million students worldwide
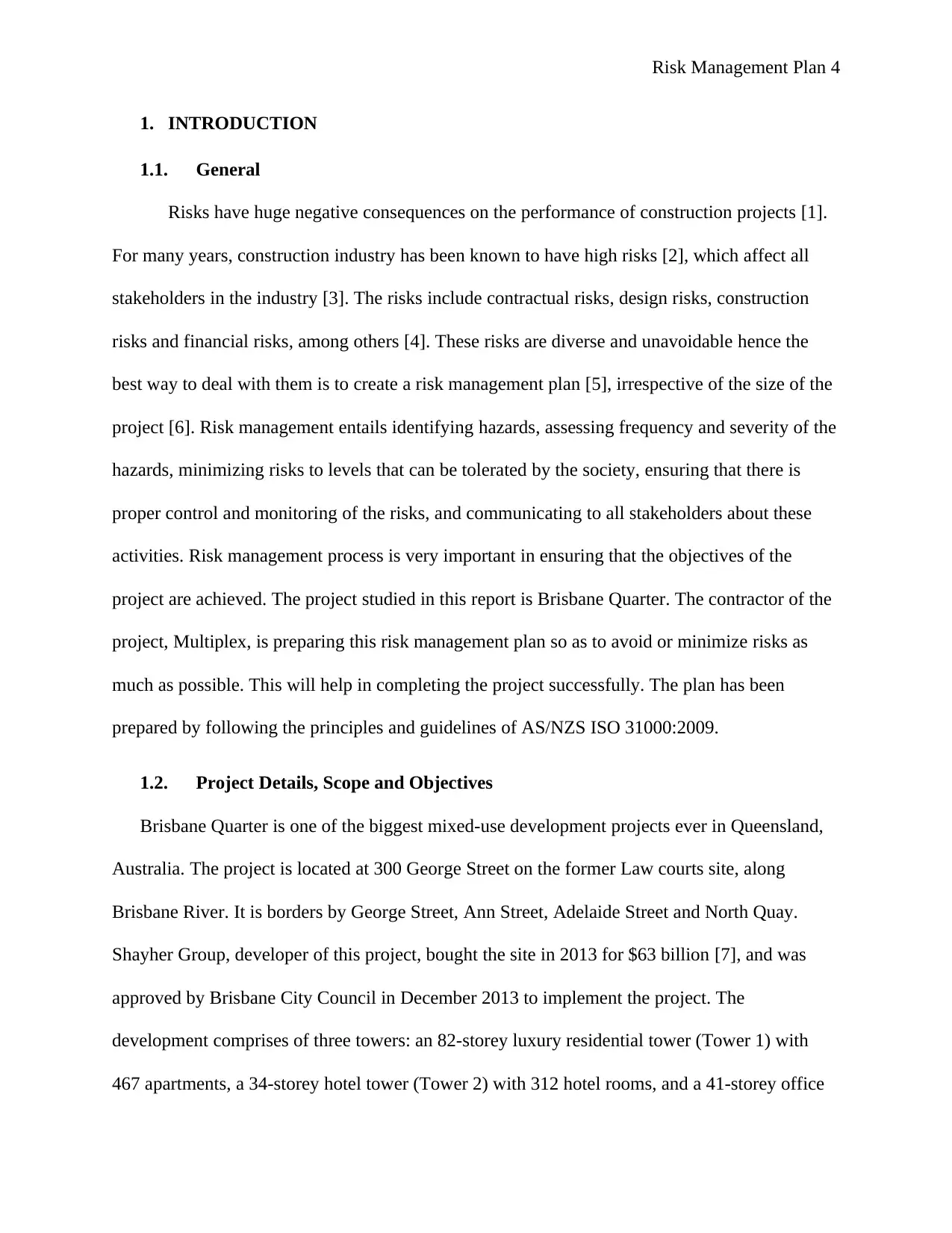
1. INTRODUCTION
1.1. General
Risks have huge negative consequences on the performance of construction projects [1].
For many years, construction industry has been known to have high risks [2], which affect all
stakeholders in the industry [3]. The risks include contractual risks, design risks, construction
risks and financial risks, among others [4]. These risks are diverse and unavoidable hence the
best way to deal with them is to create a risk management plan [5], irrespective of the size of the
project [6]. Risk management entails identifying hazards, assessing frequency and severity of the
hazards, minimizing risks to levels that can be tolerated by the society, ensuring that there is
proper control and monitoring of the risks, and communicating to all stakeholders about these
activities. Risk management process is very important in ensuring that the objectives of the
project are achieved. The project studied in this report is Brisbane Quarter. The contractor of the
project, Multiplex, is preparing this risk management plan so as to avoid or minimize risks as
much as possible. This will help in completing the project successfully. The plan has been
prepared by following the principles and guidelines of AS/NZS ISO 31000:2009.
1.2. Project Details, Scope and Objectives
Brisbane Quarter is one of the biggest mixed-use development projects ever in Queensland,
Australia. The project is located at 300 George Street on the former Law courts site, along
Brisbane River. It is borders by George Street, Ann Street, Adelaide Street and North Quay.
Shayher Group, developer of this project, bought the site in 2013 for $63 billion [7], and was
approved by Brisbane City Council in December 2013 to implement the project. The
development comprises of three towers: an 82-storey luxury residential tower (Tower 1) with
467 apartments, a 34-storey hotel tower (Tower 2) with 312 hotel rooms, and a 41-storey office
Paraphrase This Document
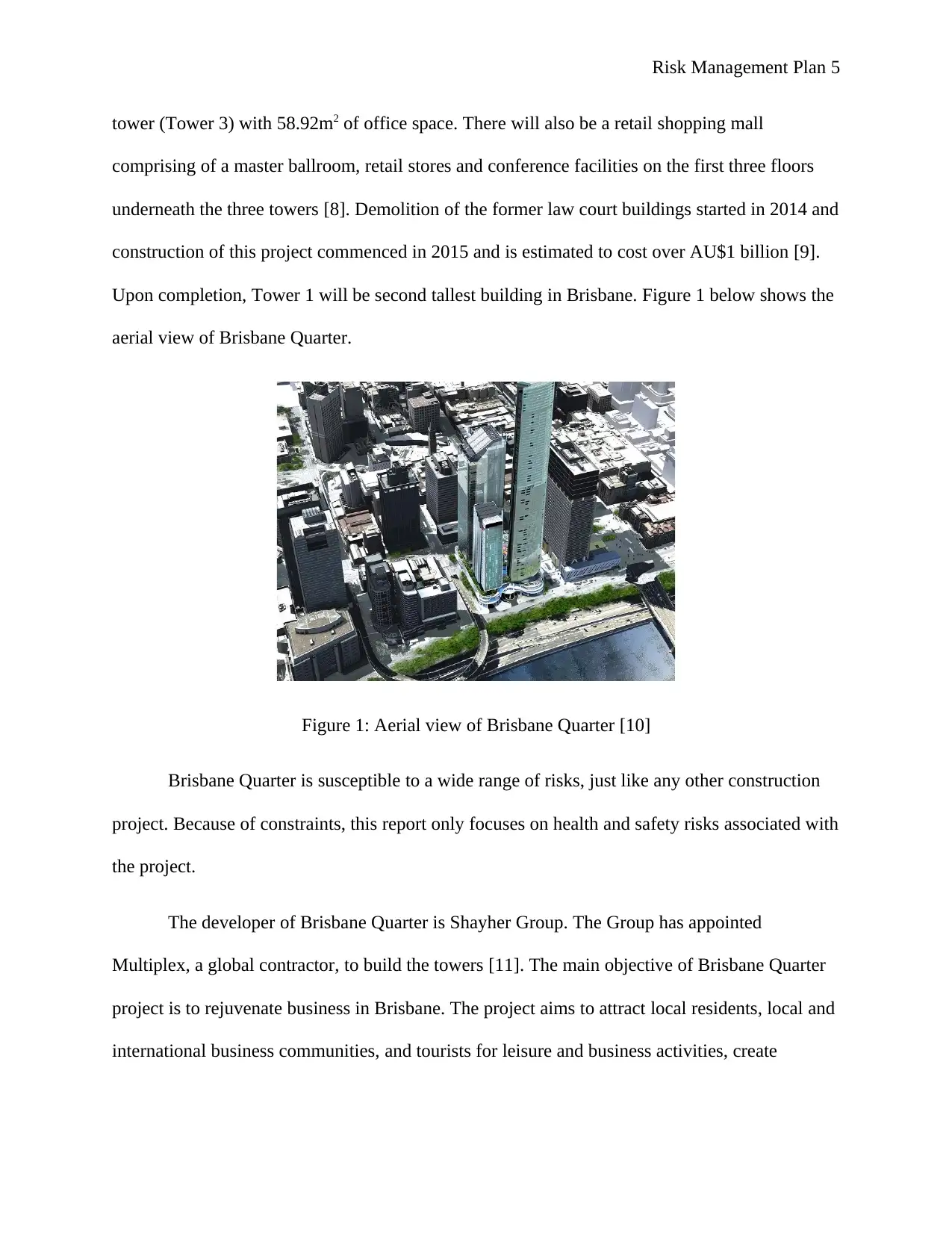
tower (Tower 3) with 58.92m2 of office space. There will also be a retail shopping mall
comprising of a master ballroom, retail stores and conference facilities on the first three floors
underneath the three towers [8]. Demolition of the former law court buildings started in 2014 and
construction of this project commenced in 2015 and is estimated to cost over AU$1 billion [9].
Upon completion, Tower 1 will be second tallest building in Brisbane. Figure 1 below shows the
aerial view of Brisbane Quarter.
Figure 1: Aerial view of Brisbane Quarter [10]
Brisbane Quarter is susceptible to a wide range of risks, just like any other construction
project. Because of constraints, this report only focuses on health and safety risks associated with
the project.
The developer of Brisbane Quarter is Shayher Group. The Group has appointed
Multiplex, a global contractor, to build the towers [11]. The main objective of Brisbane Quarter
project is to rejuvenate business in Brisbane. The project aims to attract local residents, local and
international business communities, and tourists for leisure and business activities, create
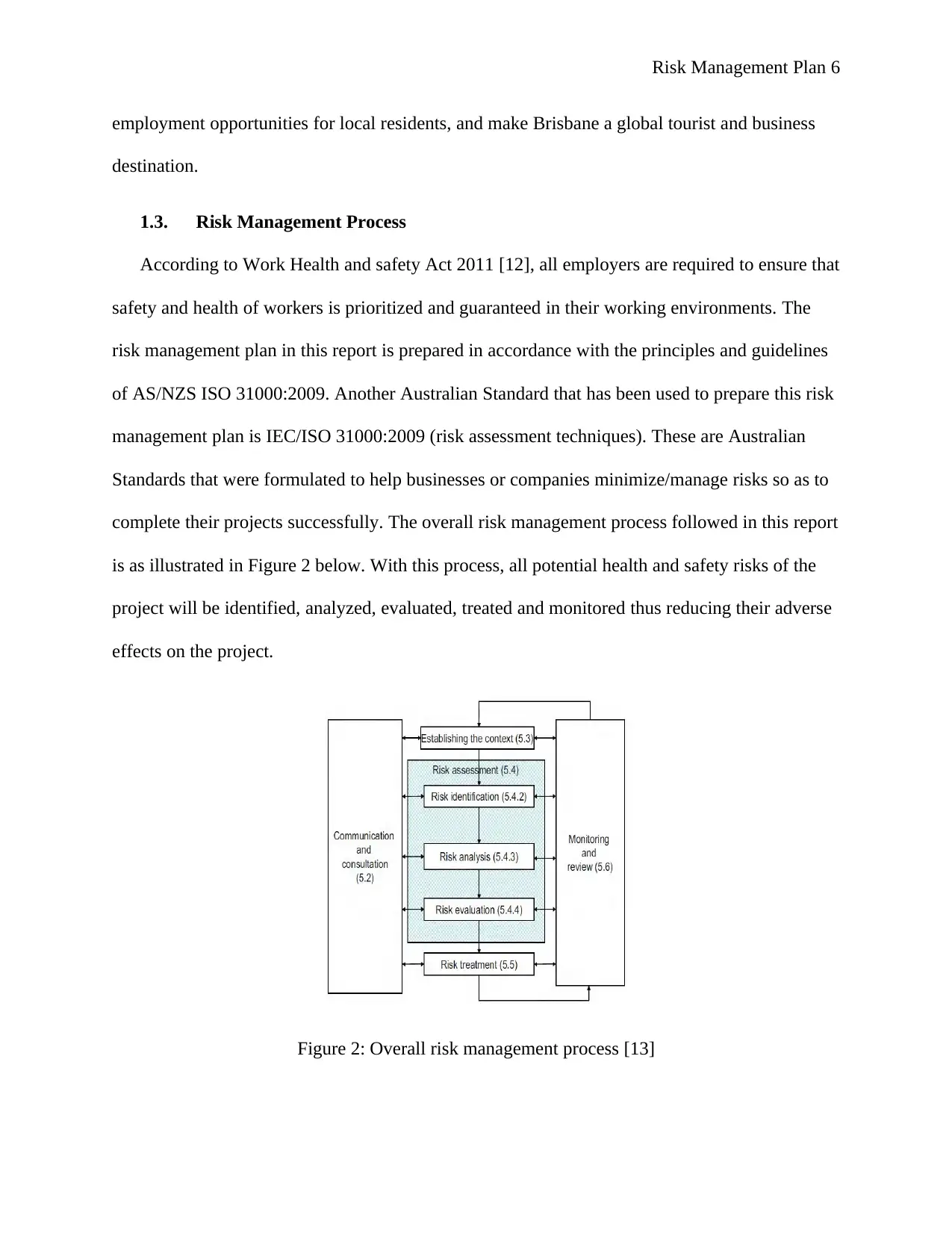
employment opportunities for local residents, and make Brisbane a global tourist and business
destination.
1.3. Risk Management Process
According to Work Health and safety Act 2011 [12], all employers are required to ensure that
safety and health of workers is prioritized and guaranteed in their working environments. The
risk management plan in this report is prepared in accordance with the principles and guidelines
of AS/NZS ISO 31000:2009. Another Australian Standard that has been used to prepare this risk
management plan is IEC/ISO 31000:2009 (risk assessment techniques). These are Australian
Standards that were formulated to help businesses or companies minimize/manage risks so as to
complete their projects successfully. The overall risk management process followed in this report
is as illustrated in Figure 2 below. With this process, all potential health and safety risks of the
project will be identified, analyzed, evaluated, treated and monitored thus reducing their adverse
effects on the project.
Figure 2: Overall risk management process [13]
⊘ This is a preview!⊘
Do you want full access?
Subscribe today to unlock all pages.

Trusted by 1+ million students worldwide
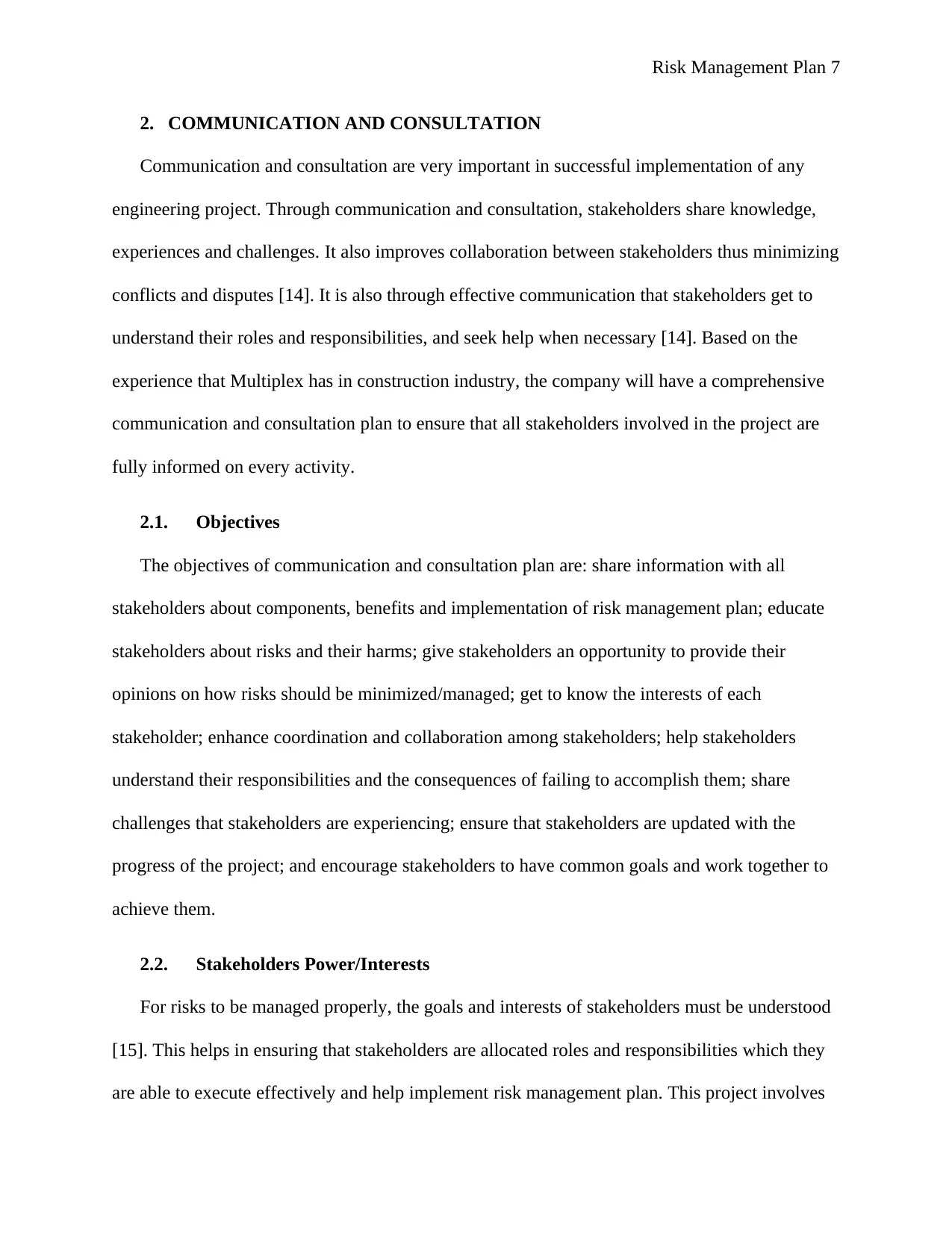
2. COMMUNICATION AND CONSULTATION
Communication and consultation are very important in successful implementation of any
engineering project. Through communication and consultation, stakeholders share knowledge,
experiences and challenges. It also improves collaboration between stakeholders thus minimizing
conflicts and disputes [14]. It is also through effective communication that stakeholders get to
understand their roles and responsibilities, and seek help when necessary [14]. Based on the
experience that Multiplex has in construction industry, the company will have a comprehensive
communication and consultation plan to ensure that all stakeholders involved in the project are
fully informed on every activity.
2.1. Objectives
The objectives of communication and consultation plan are: share information with all
stakeholders about components, benefits and implementation of risk management plan; educate
stakeholders about risks and their harms; give stakeholders an opportunity to provide their
opinions on how risks should be minimized/managed; get to know the interests of each
stakeholder; enhance coordination and collaboration among stakeholders; help stakeholders
understand their responsibilities and the consequences of failing to accomplish them; share
challenges that stakeholders are experiencing; ensure that stakeholders are updated with the
progress of the project; and encourage stakeholders to have common goals and work together to
achieve them.
2.2. Stakeholders Power/Interests
For risks to be managed properly, the goals and interests of stakeholders must be understood
[15]. This helps in ensuring that stakeholders are allocated roles and responsibilities which they
are able to execute effectively and help implement risk management plan. This project involves
Paraphrase This Document
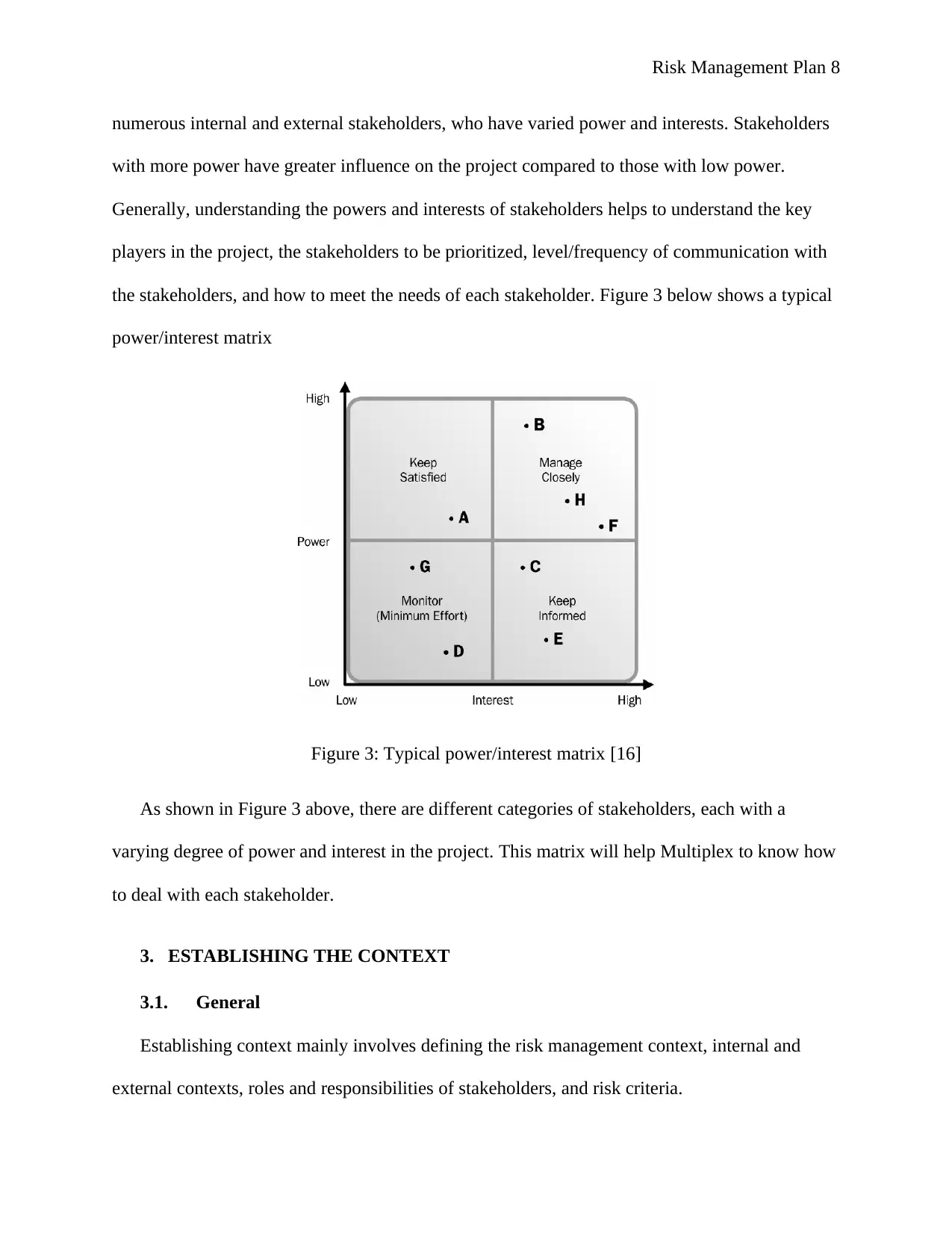
numerous internal and external stakeholders, who have varied power and interests. Stakeholders
with more power have greater influence on the project compared to those with low power.
Generally, understanding the powers and interests of stakeholders helps to understand the key
players in the project, the stakeholders to be prioritized, level/frequency of communication with
the stakeholders, and how to meet the needs of each stakeholder. Figure 3 below shows a typical
power/interest matrix
Figure 3: Typical power/interest matrix [16]
As shown in Figure 3 above, there are different categories of stakeholders, each with a
varying degree of power and interest in the project. This matrix will help Multiplex to know how
to deal with each stakeholder.
3. ESTABLISHING THE CONTEXT
3.1. General
Establishing context mainly involves defining the risk management context, internal and
external contexts, roles and responsibilities of stakeholders, and risk criteria.
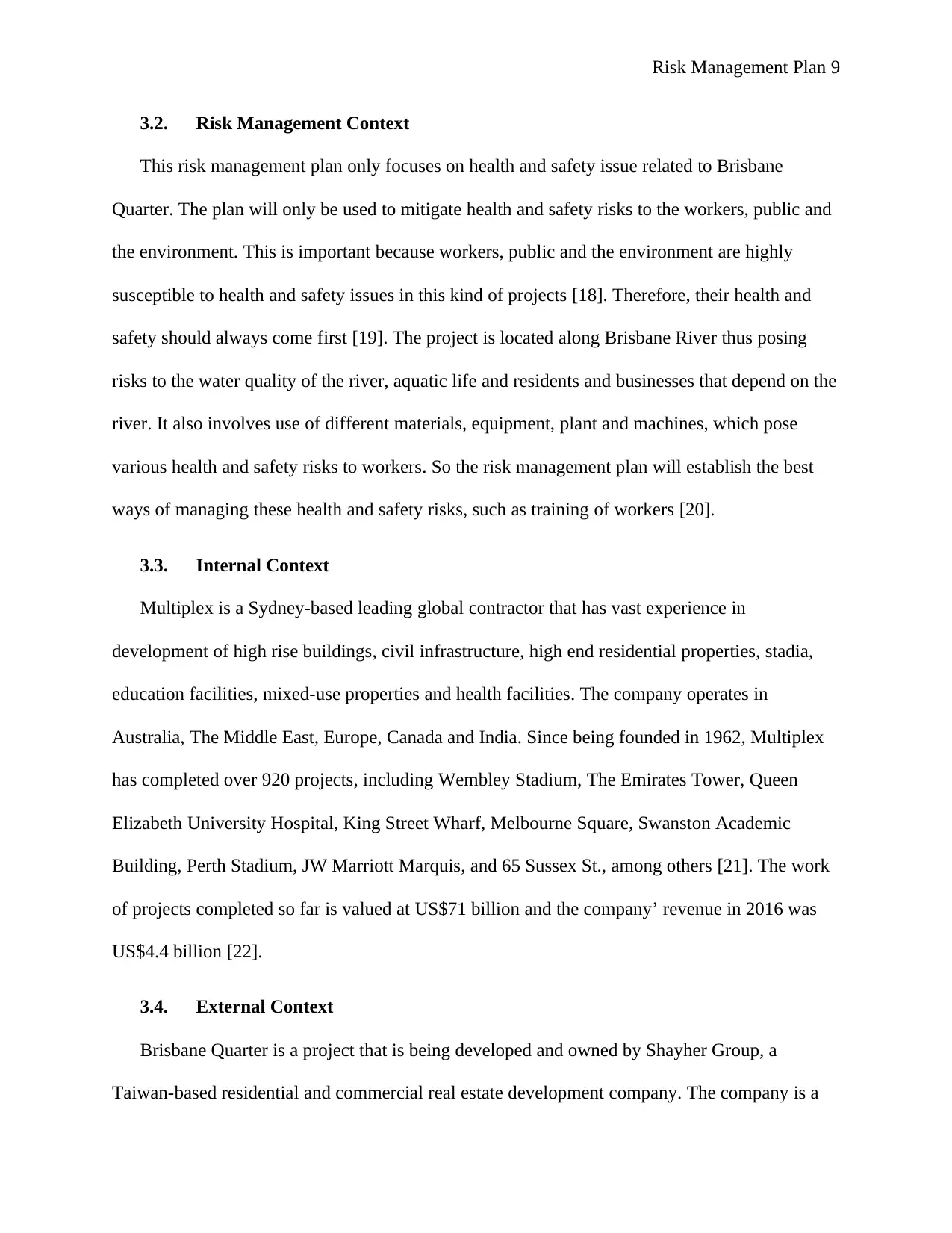
3.2. Risk Management Context
This risk management plan only focuses on health and safety issue related to Brisbane
Quarter. The plan will only be used to mitigate health and safety risks to the workers, public and
the environment. This is important because workers, public and the environment are highly
susceptible to health and safety issues in this kind of projects [18]. Therefore, their health and
safety should always come first [19]. The project is located along Brisbane River thus posing
risks to the water quality of the river, aquatic life and residents and businesses that depend on the
river. It also involves use of different materials, equipment, plant and machines, which pose
various health and safety risks to workers. So the risk management plan will establish the best
ways of managing these health and safety risks, such as training of workers [20].
3.3. Internal Context
Multiplex is a Sydney-based leading global contractor that has vast experience in
development of high rise buildings, civil infrastructure, high end residential properties, stadia,
education facilities, mixed-use properties and health facilities. The company operates in
Australia, The Middle East, Europe, Canada and India. Since being founded in 1962, Multiplex
has completed over 920 projects, including Wembley Stadium, The Emirates Tower, Queen
Elizabeth University Hospital, King Street Wharf, Melbourne Square, Swanston Academic
Building, Perth Stadium, JW Marriott Marquis, and 65 Sussex St., among others [21]. The work
of projects completed so far is valued at US$71 billion and the company’ revenue in 2016 was
US$4.4 billion [22].
3.4. External Context
Brisbane Quarter is a project that is being developed and owned by Shayher Group, a
Taiwan-based residential and commercial real estate development company. The company is a
⊘ This is a preview!⊘
Do you want full access?
Subscribe today to unlock all pages.

Trusted by 1+ million students worldwide
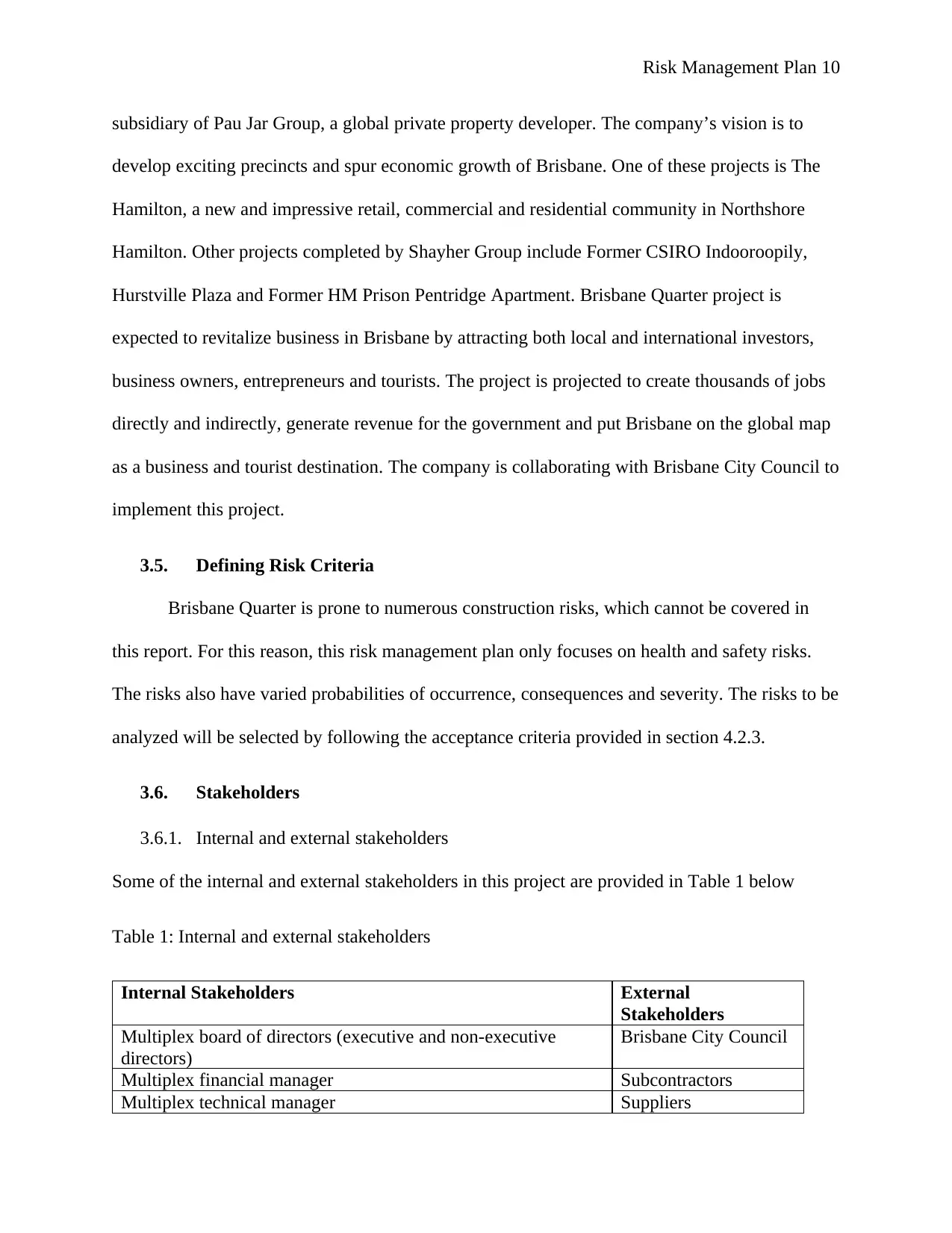
subsidiary of Pau Jar Group, a global private property developer. The company’s vision is to
develop exciting precincts and spur economic growth of Brisbane. One of these projects is The
Hamilton, a new and impressive retail, commercial and residential community in Northshore
Hamilton. Other projects completed by Shayher Group include Former CSIRO Indooroopily,
Hurstville Plaza and Former HM Prison Pentridge Apartment. Brisbane Quarter project is
expected to revitalize business in Brisbane by attracting both local and international investors,
business owners, entrepreneurs and tourists. The project is projected to create thousands of jobs
directly and indirectly, generate revenue for the government and put Brisbane on the global map
as a business and tourist destination. The company is collaborating with Brisbane City Council to
implement this project.
3.5. Defining Risk Criteria
Brisbane Quarter is prone to numerous construction risks, which cannot be covered in
this report. For this reason, this risk management plan only focuses on health and safety risks.
The risks also have varied probabilities of occurrence, consequences and severity. The risks to be
analyzed will be selected by following the acceptance criteria provided in section 4.2.3.
3.6. Stakeholders
3.6.1. Internal and external stakeholders
Some of the internal and external stakeholders in this project are provided in Table 1 below
Table 1: Internal and external stakeholders
Internal Stakeholders External
Stakeholders
Multiplex board of directors (executive and non-executive
directors)
Brisbane City Council
Multiplex financial manager Subcontractors
Multiplex technical manager Suppliers
Paraphrase This Document
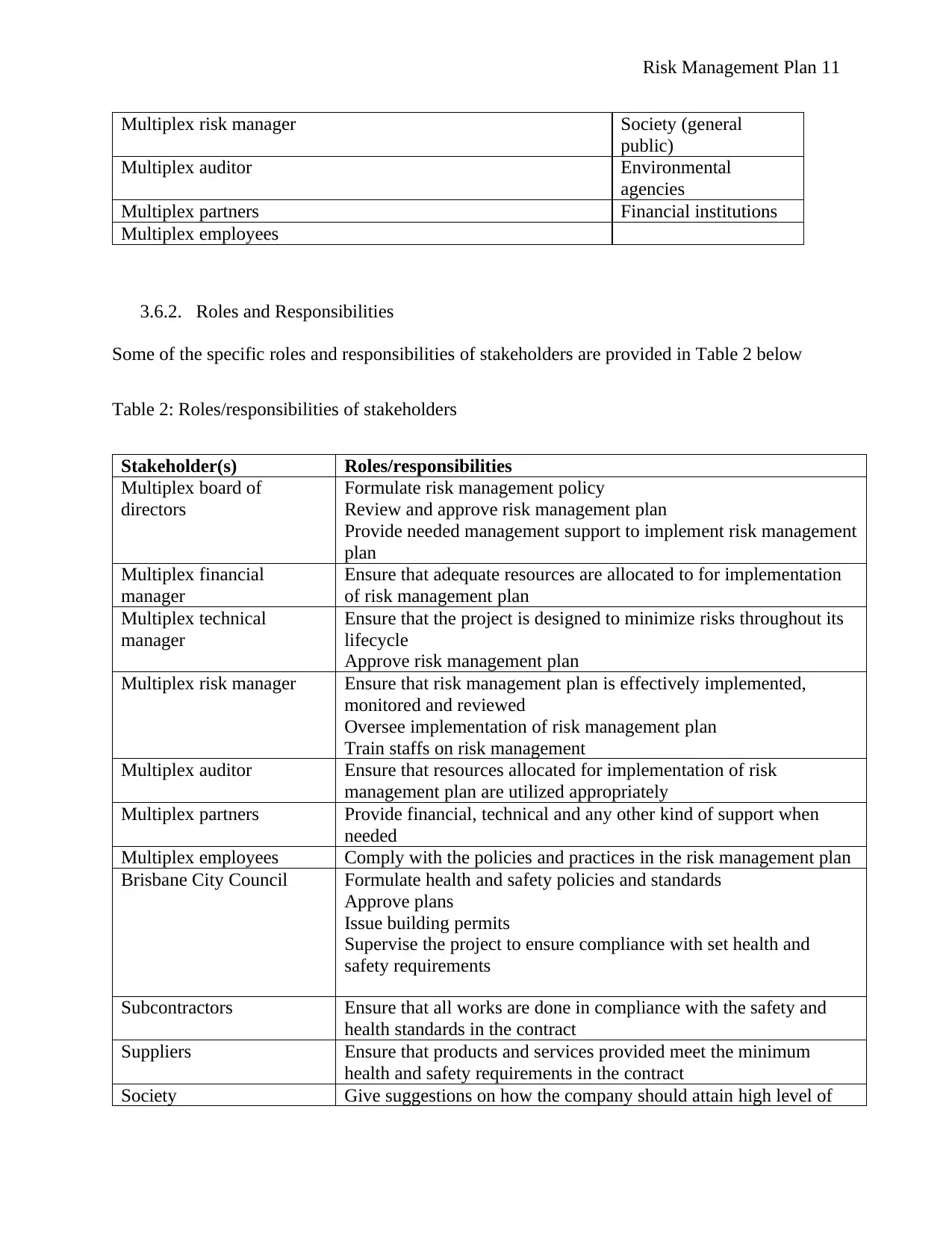
Multiplex risk manager Society (general
public)
Multiplex auditor Environmental
agencies
Multiplex partners Financial institutions
Multiplex employees
3.6.2. Roles and Responsibilities
Some of the specific roles and responsibilities of stakeholders are provided in Table 2 below
Table 2: Roles/responsibilities of stakeholders
Stakeholder(s) Roles/responsibilities
Multiplex board of
directors
Formulate risk management policy
Review and approve risk management plan
Provide needed management support to implement risk management
plan
Multiplex financial
manager
Ensure that adequate resources are allocated to for implementation
of risk management plan
Multiplex technical
manager
Ensure that the project is designed to minimize risks throughout its
lifecycle
Approve risk management plan
Multiplex risk manager Ensure that risk management plan is effectively implemented,
monitored and reviewed
Oversee implementation of risk management plan
Train staffs on risk management
Multiplex auditor Ensure that resources allocated for implementation of risk
management plan are utilized appropriately
Multiplex partners Provide financial, technical and any other kind of support when
needed
Multiplex employees Comply with the policies and practices in the risk management plan
Brisbane City Council Formulate health and safety policies and standards
Approve plans
Issue building permits
Supervise the project to ensure compliance with set health and
safety requirements
Subcontractors Ensure that all works are done in compliance with the safety and
health standards in the contract
Suppliers Ensure that products and services provided meet the minimum
health and safety requirements in the contract
Society Give suggestions on how the company should attain high level of
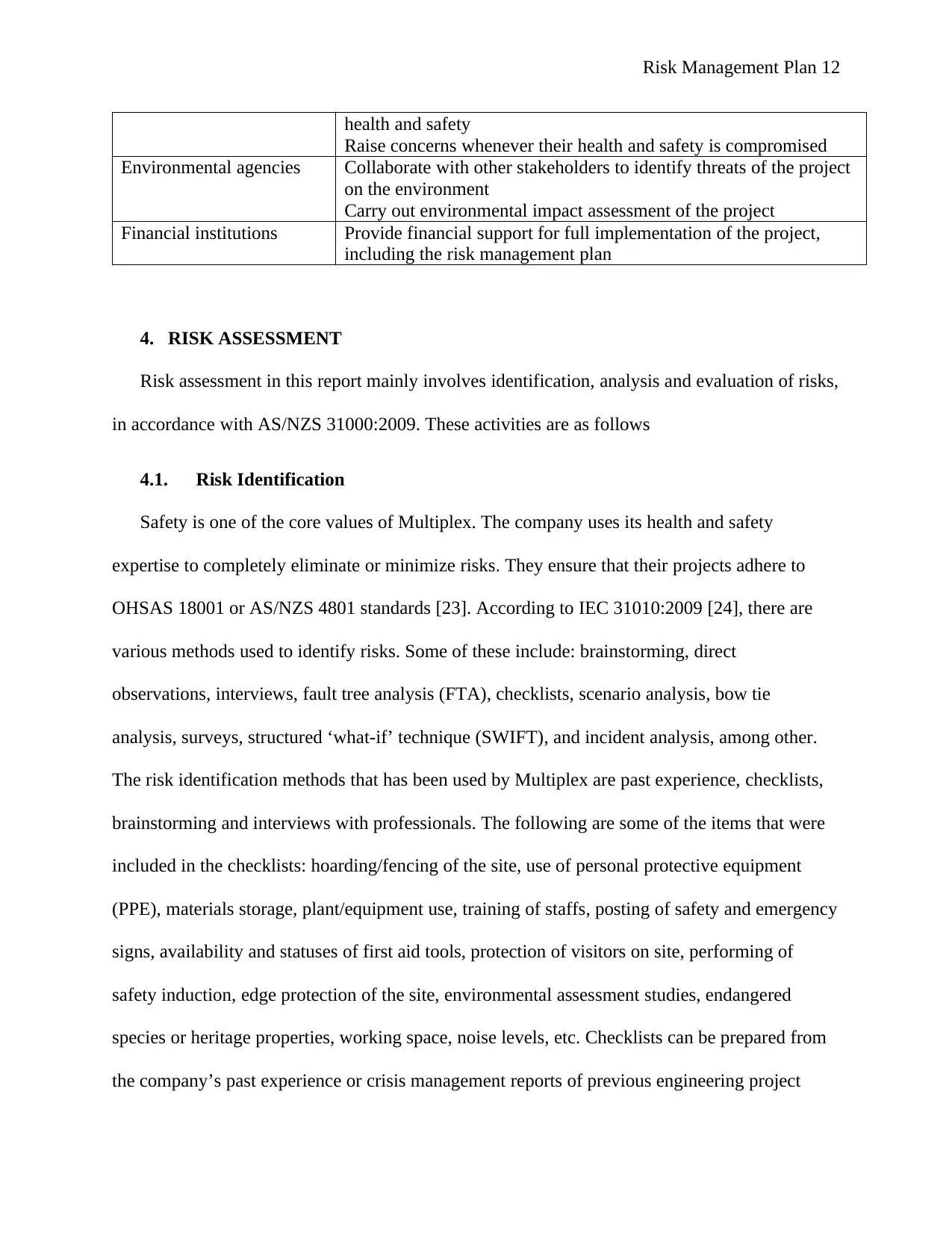
health and safety
Raise concerns whenever their health and safety is compromised
Environmental agencies Collaborate with other stakeholders to identify threats of the project
on the environment
Carry out environmental impact assessment of the project
Financial institutions Provide financial support for full implementation of the project,
including the risk management plan
4. RISK ASSESSMENT
Risk assessment in this report mainly involves identification, analysis and evaluation of risks,
in accordance with AS/NZS 31000:2009. These activities are as follows
4.1. Risk Identification
Safety is one of the core values of Multiplex. The company uses its health and safety
expertise to completely eliminate or minimize risks. They ensure that their projects adhere to
OHSAS 18001 or AS/NZS 4801 standards [23]. According to IEC 31010:2009 [24], there are
various methods used to identify risks. Some of these include: brainstorming, direct
observations, interviews, fault tree analysis (FTA), checklists, scenario analysis, bow tie
analysis, surveys, structured ‘what-if’ technique (SWIFT), and incident analysis, among other.
The risk identification methods that has been used by Multiplex are past experience, checklists,
brainstorming and interviews with professionals. The following are some of the items that were
included in the checklists: hoarding/fencing of the site, use of personal protective equipment
(PPE), materials storage, plant/equipment use, training of staffs, posting of safety and emergency
signs, availability and statuses of first aid tools, protection of visitors on site, performing of
safety induction, edge protection of the site, environmental assessment studies, endangered
species or heritage properties, working space, noise levels, etc. Checklists can be prepared from
the company’s past experience or crisis management reports of previous engineering project
⊘ This is a preview!⊘
Do you want full access?
Subscribe today to unlock all pages.

Trusted by 1+ million students worldwide
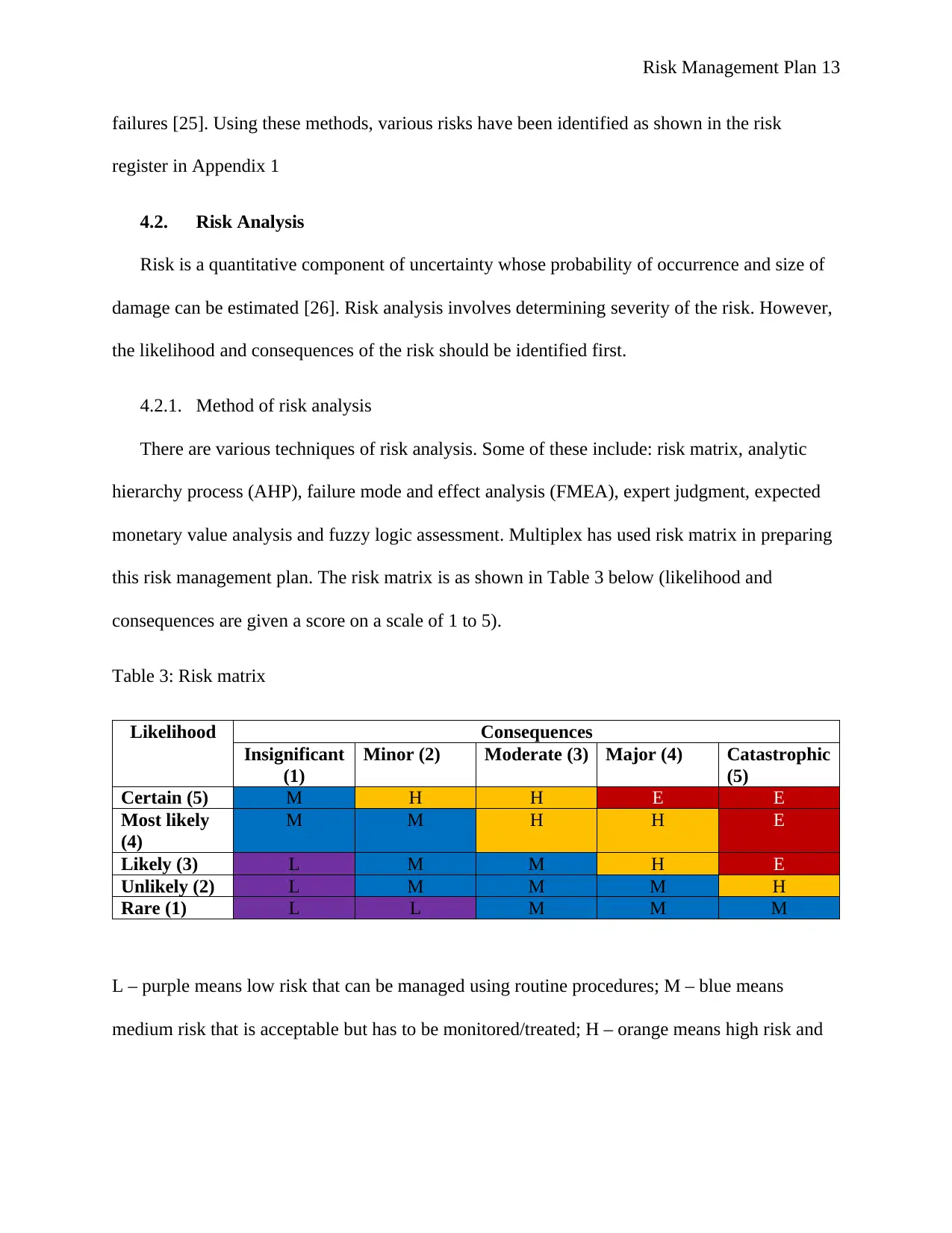
failures [25]. Using these methods, various risks have been identified as shown in the risk
register in Appendix 1
4.2. Risk Analysis
Risk is a quantitative component of uncertainty whose probability of occurrence and size of
damage can be estimated [26]. Risk analysis involves determining severity of the risk. However,
the likelihood and consequences of the risk should be identified first.
4.2.1. Method of risk analysis
There are various techniques of risk analysis. Some of these include: risk matrix, analytic
hierarchy process (AHP), failure mode and effect analysis (FMEA), expert judgment, expected
monetary value analysis and fuzzy logic assessment. Multiplex has used risk matrix in preparing
this risk management plan. The risk matrix is as shown in Table 3 below (likelihood and
consequences are given a score on a scale of 1 to 5).
Table 3: Risk matrix
Likelihood Consequences
Insignificant
(1)
Minor (2) Moderate (3) Major (4) Catastrophic
(5)
Certain (5) M H H E E
Most likely
(4)
M M H H E
Likely (3) L M M H E
Unlikely (2) L M M M H
Rare (1) L L M M M
L – purple means low risk that can be managed using routine procedures; M – blue means
medium risk that is acceptable but has to be monitored/treated; H – orange means high risk and
Paraphrase This Document
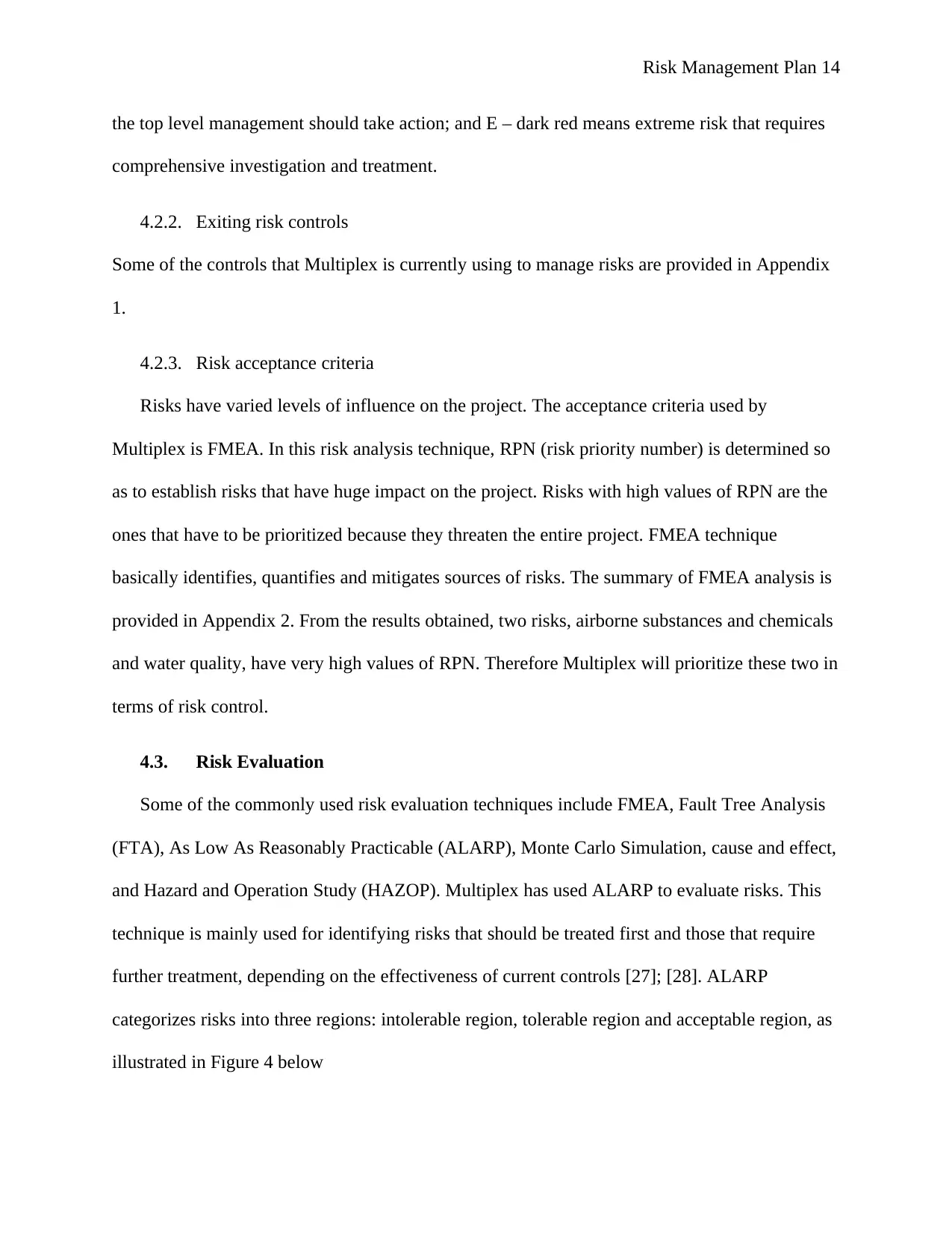
the top level management should take action; and E – dark red means extreme risk that requires
comprehensive investigation and treatment.
4.2.2. Exiting risk controls
Some of the controls that Multiplex is currently using to manage risks are provided in Appendix
1.
4.2.3. Risk acceptance criteria
Risks have varied levels of influence on the project. The acceptance criteria used by
Multiplex is FMEA. In this risk analysis technique, RPN (risk priority number) is determined so
as to establish risks that have huge impact on the project. Risks with high values of RPN are the
ones that have to be prioritized because they threaten the entire project. FMEA technique
basically identifies, quantifies and mitigates sources of risks. The summary of FMEA analysis is
provided in Appendix 2. From the results obtained, two risks, airborne substances and chemicals
and water quality, have very high values of RPN. Therefore Multiplex will prioritize these two in
terms of risk control.
4.3. Risk Evaluation
Some of the commonly used risk evaluation techniques include FMEA, Fault Tree Analysis
(FTA), As Low As Reasonably Practicable (ALARP), Monte Carlo Simulation, cause and effect,
and Hazard and Operation Study (HAZOP). Multiplex has used ALARP to evaluate risks. This
technique is mainly used for identifying risks that should be treated first and those that require
further treatment, depending on the effectiveness of current controls [27]; [28]. ALARP
categorizes risks into three regions: intolerable region, tolerable region and acceptable region, as
illustrated in Figure 4 below
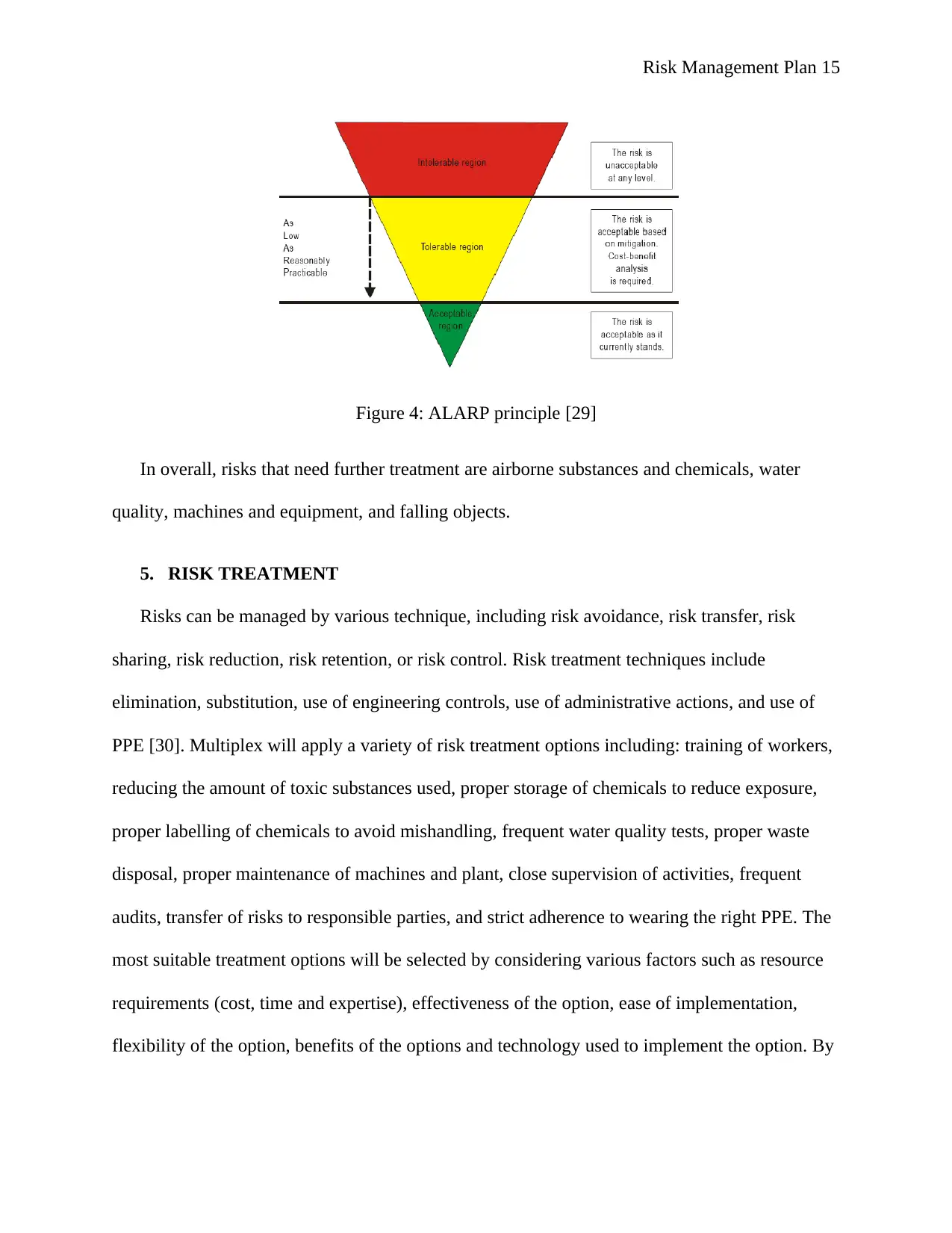
Figure 4: ALARP principle [29]
In overall, risks that need further treatment are airborne substances and chemicals, water
quality, machines and equipment, and falling objects.
5. RISK TREATMENT
Risks can be managed by various technique, including risk avoidance, risk transfer, risk
sharing, risk reduction, risk retention, or risk control. Risk treatment techniques include
elimination, substitution, use of engineering controls, use of administrative actions, and use of
PPE [30]. Multiplex will apply a variety of risk treatment options including: training of workers,
reducing the amount of toxic substances used, proper storage of chemicals to reduce exposure,
proper labelling of chemicals to avoid mishandling, frequent water quality tests, proper waste
disposal, proper maintenance of machines and plant, close supervision of activities, frequent
audits, transfer of risks to responsible parties, and strict adherence to wearing the right PPE. The
most suitable treatment options will be selected by considering various factors such as resource
requirements (cost, time and expertise), effectiveness of the option, ease of implementation,
flexibility of the option, benefits of the options and technology used to implement the option. By
⊘ This is a preview!⊘
Do you want full access?
Subscribe today to unlock all pages.

Trusted by 1+ million students worldwide
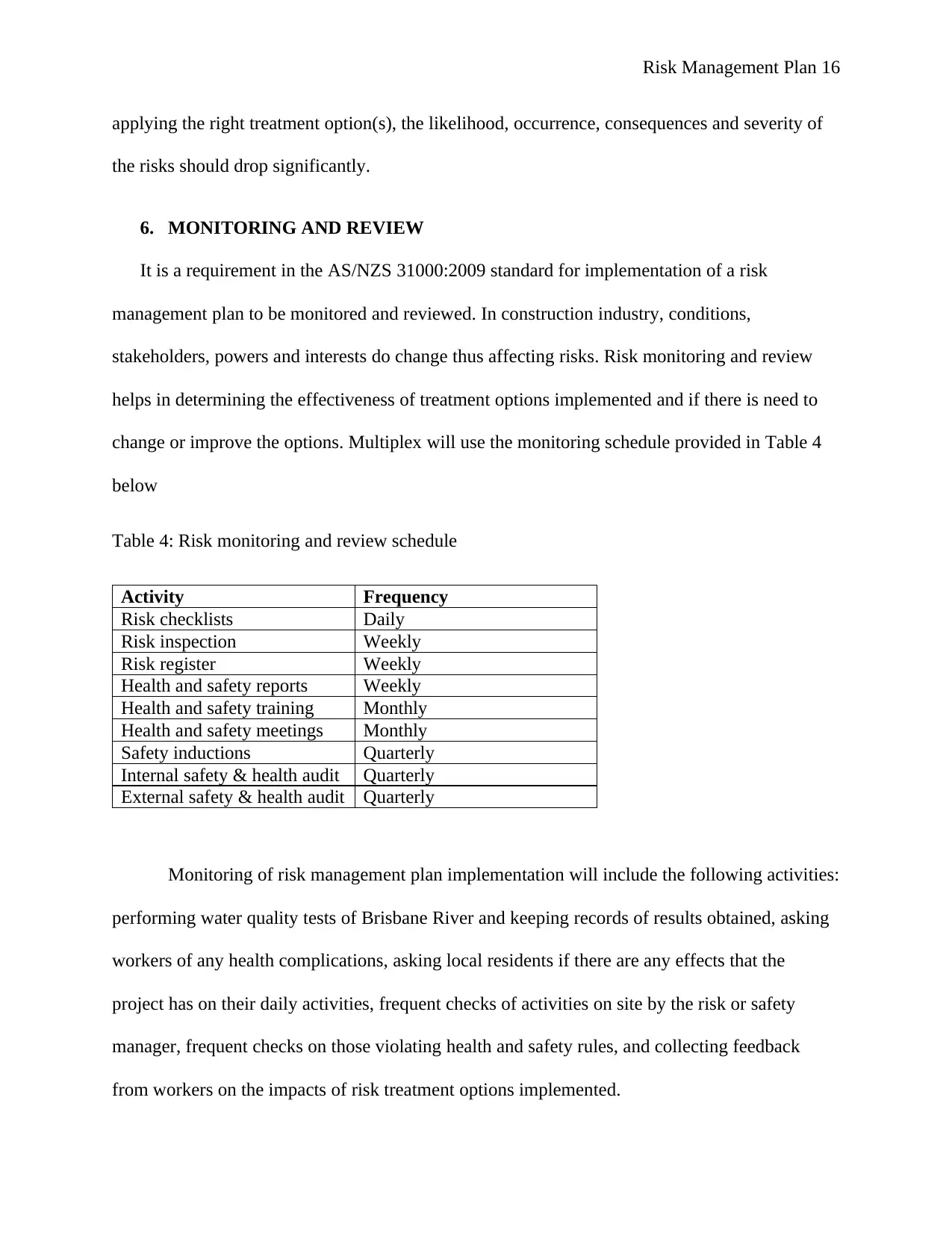
applying the right treatment option(s), the likelihood, occurrence, consequences and severity of
the risks should drop significantly.
6. MONITORING AND REVIEW
It is a requirement in the AS/NZS 31000:2009 standard for implementation of a risk
management plan to be monitored and reviewed. In construction industry, conditions,
stakeholders, powers and interests do change thus affecting risks. Risk monitoring and review
helps in determining the effectiveness of treatment options implemented and if there is need to
change or improve the options. Multiplex will use the monitoring schedule provided in Table 4
below
Table 4: Risk monitoring and review schedule
Activity Frequency
Risk checklists Daily
Risk inspection Weekly
Risk register Weekly
Health and safety reports Weekly
Health and safety training Monthly
Health and safety meetings Monthly
Safety inductions Quarterly
Internal safety & health audit Quarterly
External safety & health audit Quarterly
Monitoring of risk management plan implementation will include the following activities:
performing water quality tests of Brisbane River and keeping records of results obtained, asking
workers of any health complications, asking local residents if there are any effects that the
project has on their daily activities, frequent checks of activities on site by the risk or safety
manager, frequent checks on those violating health and safety rules, and collecting feedback
from workers on the impacts of risk treatment options implemented.
Paraphrase This Document
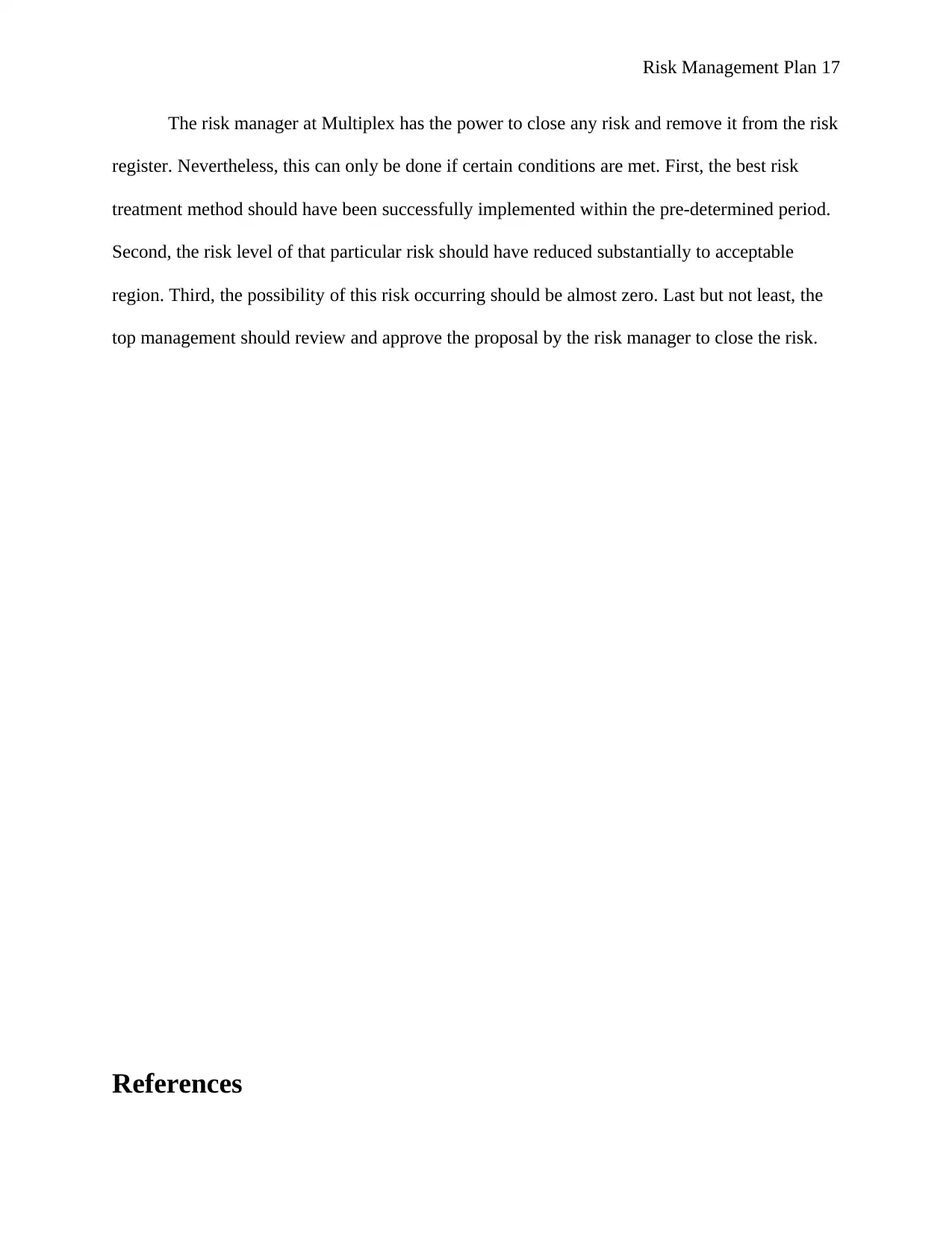
The risk manager at Multiplex has the power to close any risk and remove it from the risk
register. Nevertheless, this can only be done if certain conditions are met. First, the best risk
treatment method should have been successfully implemented within the pre-determined period.
Second, the risk level of that particular risk should have reduced substantially to acceptable
region. Third, the possibility of this risk occurring should be almost zero. Last but not least, the
top management should review and approve the proposal by the risk manager to close the risk.
References
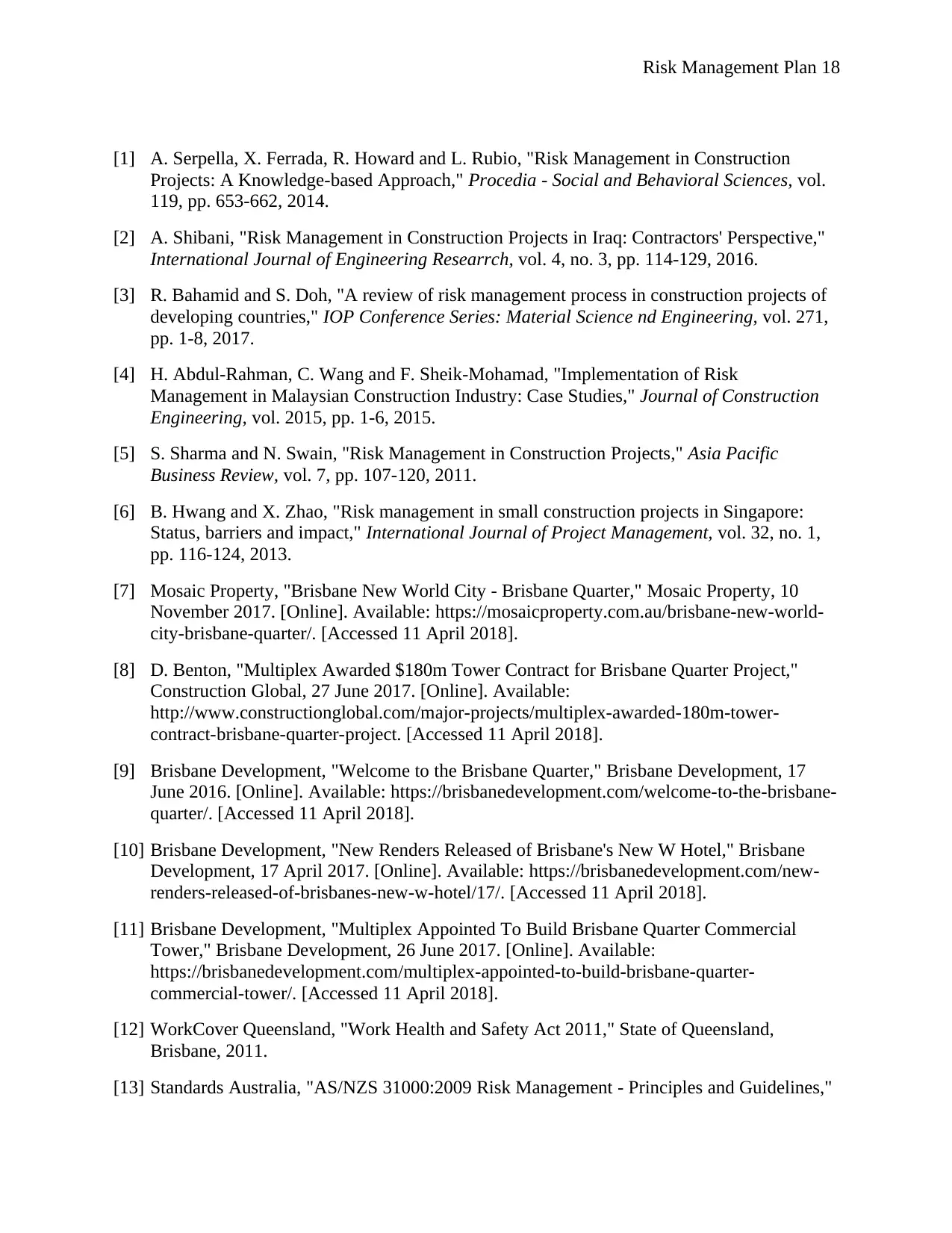
[1] A. Serpella, X. Ferrada, R. Howard and L. Rubio, "Risk Management in Construction
Projects: A Knowledge-based Approach," Procedia - Social and Behavioral Sciences, vol.
119, pp. 653-662, 2014.
[2] A. Shibani, "Risk Management in Construction Projects in Iraq: Contractors' Perspective,"
International Journal of Engineering Researrch, vol. 4, no. 3, pp. 114-129, 2016.
[3] R. Bahamid and S. Doh, "A review of risk management process in construction projects of
developing countries," IOP Conference Series: Material Science nd Engineering, vol. 271,
pp. 1-8, 2017.
[4] H. Abdul-Rahman, C. Wang and F. Sheik-Mohamad, "Implementation of Risk
Management in Malaysian Construction Industry: Case Studies," Journal of Construction
Engineering, vol. 2015, pp. 1-6, 2015.
[5] S. Sharma and N. Swain, "Risk Management in Construction Projects," Asia Pacific
Business Review, vol. 7, pp. 107-120, 2011.
[6] B. Hwang and X. Zhao, "Risk management in small construction projects in Singapore:
Status, barriers and impact," International Journal of Project Management, vol. 32, no. 1,
pp. 116-124, 2013.
[7] Mosaic Property, "Brisbane New World City - Brisbane Quarter," Mosaic Property, 10
November 2017. [Online]. Available: https://mosaicproperty.com.au/brisbane-new-world-
city-brisbane-quarter/. [Accessed 11 April 2018].
[8] D. Benton, "Multiplex Awarded $180m Tower Contract for Brisbane Quarter Project,"
Construction Global, 27 June 2017. [Online]. Available:
http://www.constructionglobal.com/major-projects/multiplex-awarded-180m-tower-
contract-brisbane-quarter-project. [Accessed 11 April 2018].
[9] Brisbane Development, "Welcome to the Brisbane Quarter," Brisbane Development, 17
June 2016. [Online]. Available: https://brisbanedevelopment.com/welcome-to-the-brisbane-
quarter/. [Accessed 11 April 2018].
[10] Brisbane Development, "New Renders Released of Brisbane's New W Hotel," Brisbane
Development, 17 April 2017. [Online]. Available: https://brisbanedevelopment.com/new-
renders-released-of-brisbanes-new-w-hotel/17/. [Accessed 11 April 2018].
[11] Brisbane Development, "Multiplex Appointed To Build Brisbane Quarter Commercial
Tower," Brisbane Development, 26 June 2017. [Online]. Available:
https://brisbanedevelopment.com/multiplex-appointed-to-build-brisbane-quarter-
commercial-tower/. [Accessed 11 April 2018].
[12] WorkCover Queensland, "Work Health and Safety Act 2011," State of Queensland,
Brisbane, 2011.
[13] Standards Australia, "AS/NZS 31000:2009 Risk Management - Principles and Guidelines,"
⊘ This is a preview!⊘
Do you want full access?
Subscribe today to unlock all pages.

Trusted by 1+ million students worldwide
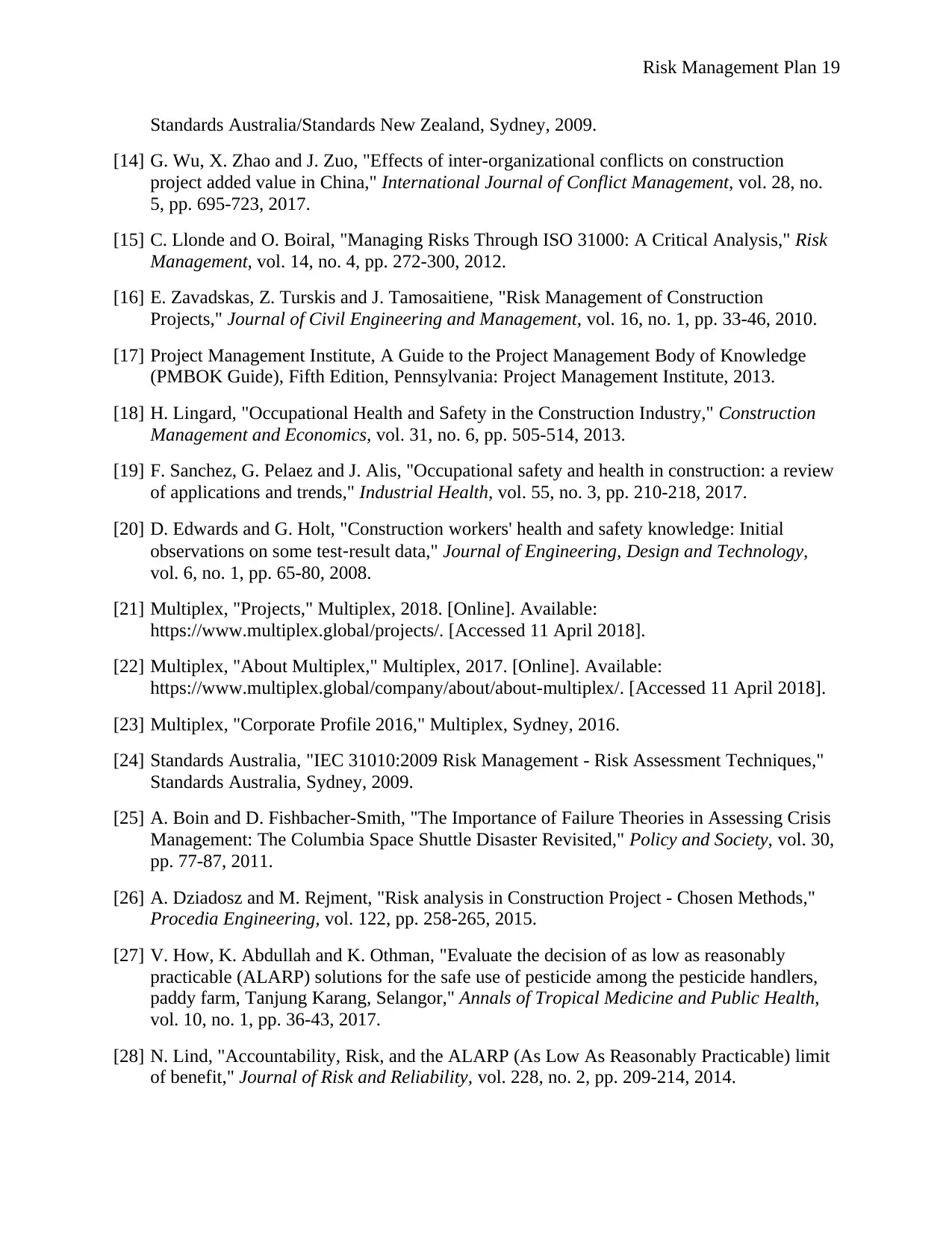
Standards Australia/Standards New Zealand, Sydney, 2009.
[14] G. Wu, X. Zhao and J. Zuo, "Effects of inter-organizational conflicts on construction
project added value in China," International Journal of Conflict Management, vol. 28, no.
5, pp. 695-723, 2017.
[15] C. Llonde and O. Boiral, "Managing Risks Through ISO 31000: A Critical Analysis," Risk
Management, vol. 14, no. 4, pp. 272-300, 2012.
[16] E. Zavadskas, Z. Turskis and J. Tamosaitiene, "Risk Management of Construction
Projects," Journal of Civil Engineering and Management, vol. 16, no. 1, pp. 33-46, 2010.
[17] Project Management Institute, A Guide to the Project Management Body of Knowledge
(PMBOK Guide), Fifth Edition, Pennsylvania: Project Management Institute, 2013.
[18] H. Lingard, "Occupational Health and Safety in the Construction Industry," Construction
Management and Economics, vol. 31, no. 6, pp. 505-514, 2013.
[19] F. Sanchez, G. Pelaez and J. Alis, "Occupational safety and health in construction: a review
of applications and trends," Industrial Health, vol. 55, no. 3, pp. 210-218, 2017.
[20] D. Edwards and G. Holt, "Construction workers' health and safety knowledge: Initial
observations on some test‐result data," Journal of Engineering, Design and Technology,
vol. 6, no. 1, pp. 65-80, 2008.
[21] Multiplex, "Projects," Multiplex, 2018. [Online]. Available:
https://www.multiplex.global/projects/. [Accessed 11 April 2018].
[22] Multiplex, "About Multiplex," Multiplex, 2017. [Online]. Available:
https://www.multiplex.global/company/about/about-multiplex/. [Accessed 11 April 2018].
[23] Multiplex, "Corporate Profile 2016," Multiplex, Sydney, 2016.
[24] Standards Australia, "IEC 31010:2009 Risk Management - Risk Assessment Techniques,"
Standards Australia, Sydney, 2009.
[25] A. Boin and D. Fishbacher-Smith, "The Importance of Failure Theories in Assessing Crisis
Management: The Columbia Space Shuttle Disaster Revisited," Policy and Society, vol. 30,
pp. 77-87, 2011.
[26] A. Dziadosz and M. Rejment, "Risk analysis in Construction Project - Chosen Methods,"
Procedia Engineering, vol. 122, pp. 258-265, 2015.
[27] V. How, K. Abdullah and K. Othman, "Evaluate the decision of as low as reasonably
practicable (ALARP) solutions for the safe use of pesticide among the pesticide handlers,
paddy farm, Tanjung Karang, Selangor," Annals of Tropical Medicine and Public Health,
vol. 10, no. 1, pp. 36-43, 2017.
[28] N. Lind, "Accountability, Risk, and the ALARP (As Low As Reasonably Practicable) limit
of benefit," Journal of Risk and Reliability, vol. 228, no. 2, pp. 209-214, 2014.
Paraphrase This Document

[29] O. Cokorilo, "Quantified risk assessment modelling of aircraft landing operations,"
Scientific Research and Essays, vol. 6, no. 20, pp. 4406-4413, 2011.
[30] Safe Work Australia, "How To Manage Work Health and Safety Risks," Safe Work
Australia, Sydney, 2011.
[31] C. Goh and H. Abdul-Rahman, "The Identification and Management of Major Risks in
Malaysian Construction Industry," Journal of Construction in Developing Countries, vol.
18, pp. 19-32, 2013.
[32] N. Smith, T. Mema and P. Jobling, Managing Risk in Construction Projects, Oxford: John
Wiley & Sons, 2009.
APPENDICES
Appendix 1: Risk Register
Risk What may happen Co
ns
eq
ue
nc
e
Lik
elih
ood
Ris
k
leve
l
Current controls Further
controls
needed
Responsib
le person
Machi Bruises, fractures, cuts, 3 3 M Proper Training of Safety
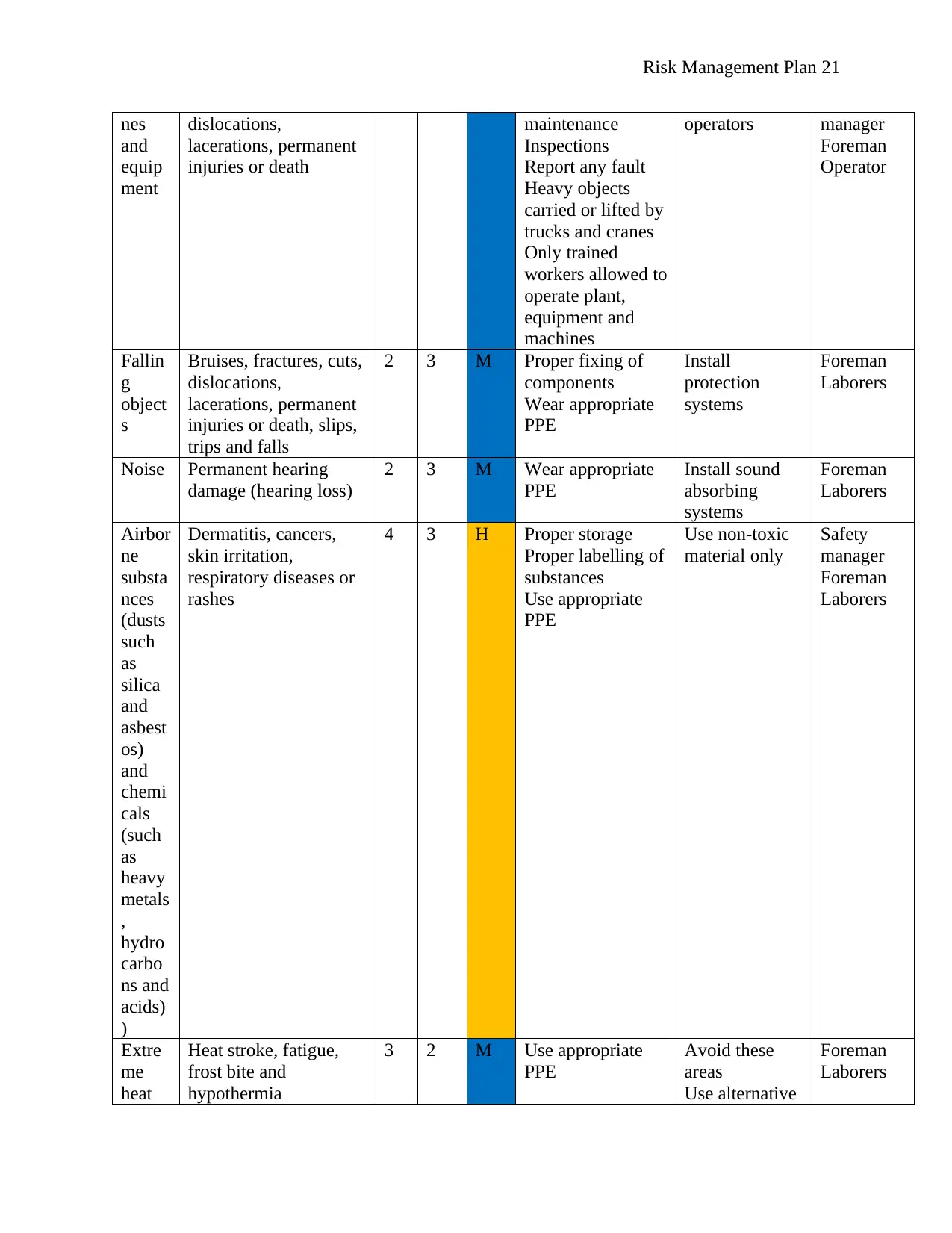
nes
and
equip
ment
dislocations,
lacerations, permanent
injuries or death
maintenance
Inspections
Report any fault
Heavy objects
carried or lifted by
trucks and cranes
Only trained
workers allowed to
operate plant,
equipment and
machines
operators manager
Foreman
Operator
Fallin
g
object
s
Bruises, fractures, cuts,
dislocations,
lacerations, permanent
injuries or death, slips,
trips and falls
2 3 M Proper fixing of
components
Wear appropriate
PPE
Install
protection
systems
Foreman
Laborers
Noise Permanent hearing
damage (hearing loss)
2 3 M Wear appropriate
PPE
Install sound
absorbing
systems
Foreman
Laborers
Airbor
ne
substa
nces
(dusts
such
as
silica
and
asbest
os)
and
chemi
cals
(such
as
heavy
metals
,
hydro
carbo
ns and
acids)
)
Dermatitis, cancers,
skin irritation,
respiratory diseases or
rashes
4 3 H Proper storage
Proper labelling of
substances
Use appropriate
PPE
Use non-toxic
material only
Safety
manager
Foreman
Laborers
Extre
me
heat
Heat stroke, fatigue,
frost bite and
hypothermia
3 2 M Use appropriate
PPE
Avoid these
areas
Use alternative
Foreman
Laborers
⊘ This is a preview!⊘
Do you want full access?
Subscribe today to unlock all pages.

Trusted by 1+ million students worldwide
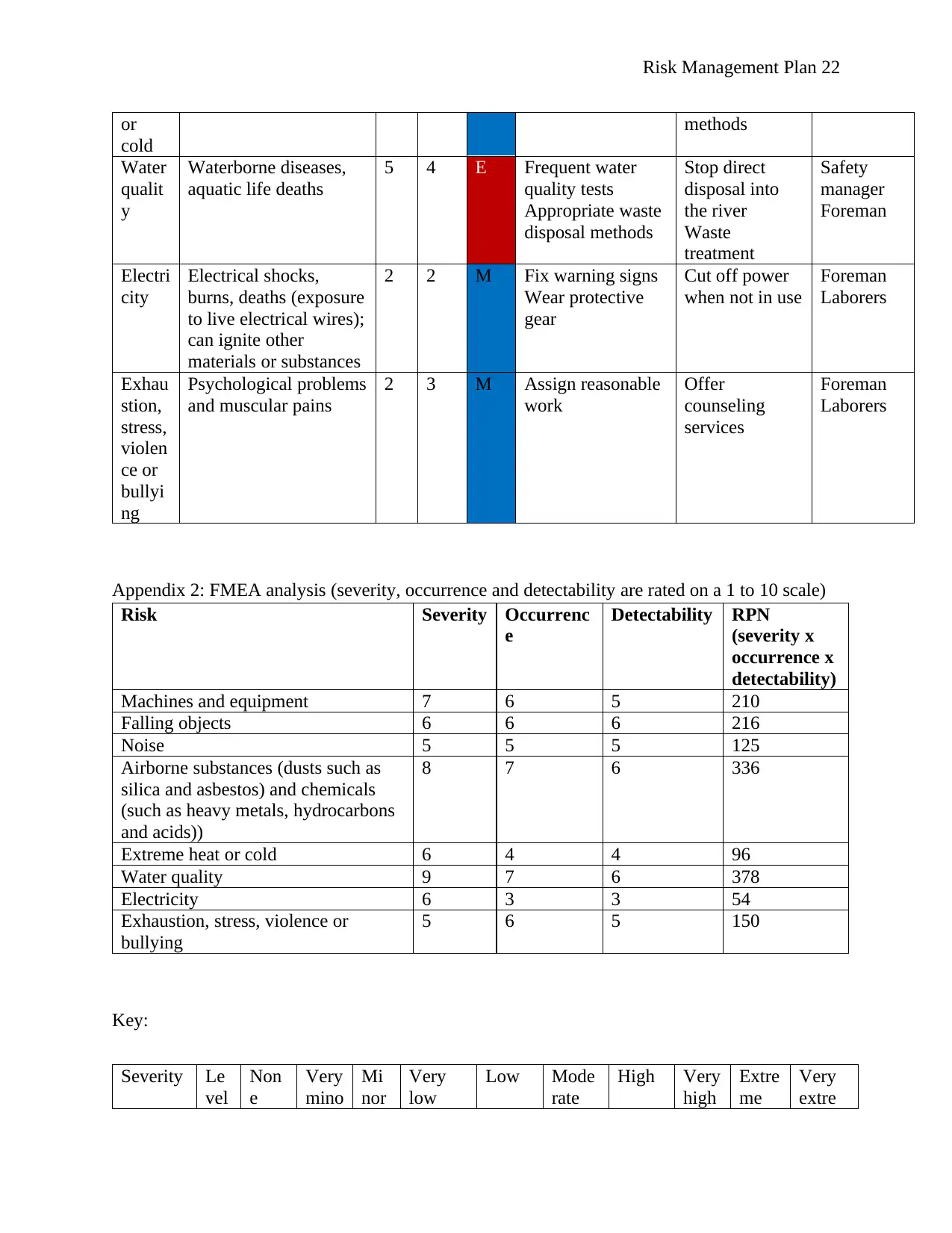
or
cold
methods
Water
qualit
y
Waterborne diseases,
aquatic life deaths
5 4 E Frequent water
quality tests
Appropriate waste
disposal methods
Stop direct
disposal into
the river
Waste
treatment
Safety
manager
Foreman
Electri
city
Electrical shocks,
burns, deaths (exposure
to live electrical wires);
can ignite other
materials or substances
2 2 M Fix warning signs
Wear protective
gear
Cut off power
when not in use
Foreman
Laborers
Exhau
stion,
stress,
violen
ce or
bullyi
ng
Psychological problems
and muscular pains
2 3 M Assign reasonable
work
Offer
counseling
services
Foreman
Laborers
Appendix 2: FMEA analysis (severity, occurrence and detectability are rated on a 1 to 10 scale)
Risk Severity Occurrenc
e
Detectability RPN
(severity x
occurrence x
detectability)
Machines and equipment 7 6 5 210
Falling objects 6 6 6 216
Noise 5 5 5 125
Airborne substances (dusts such as
silica and asbestos) and chemicals
(such as heavy metals, hydrocarbons
and acids))
8 7 6 336
Extreme heat or cold 6 4 4 96
Water quality 9 7 6 378
Electricity 6 3 3 54
Exhaustion, stress, violence or
bullying
5 6 5 150
Key:
Severity Le
vel
Non
e
Very
mino
Mi
nor
Very
low
Low Mode
rate
High Very
high
Extre
me
Very
extre
Paraphrase This Document
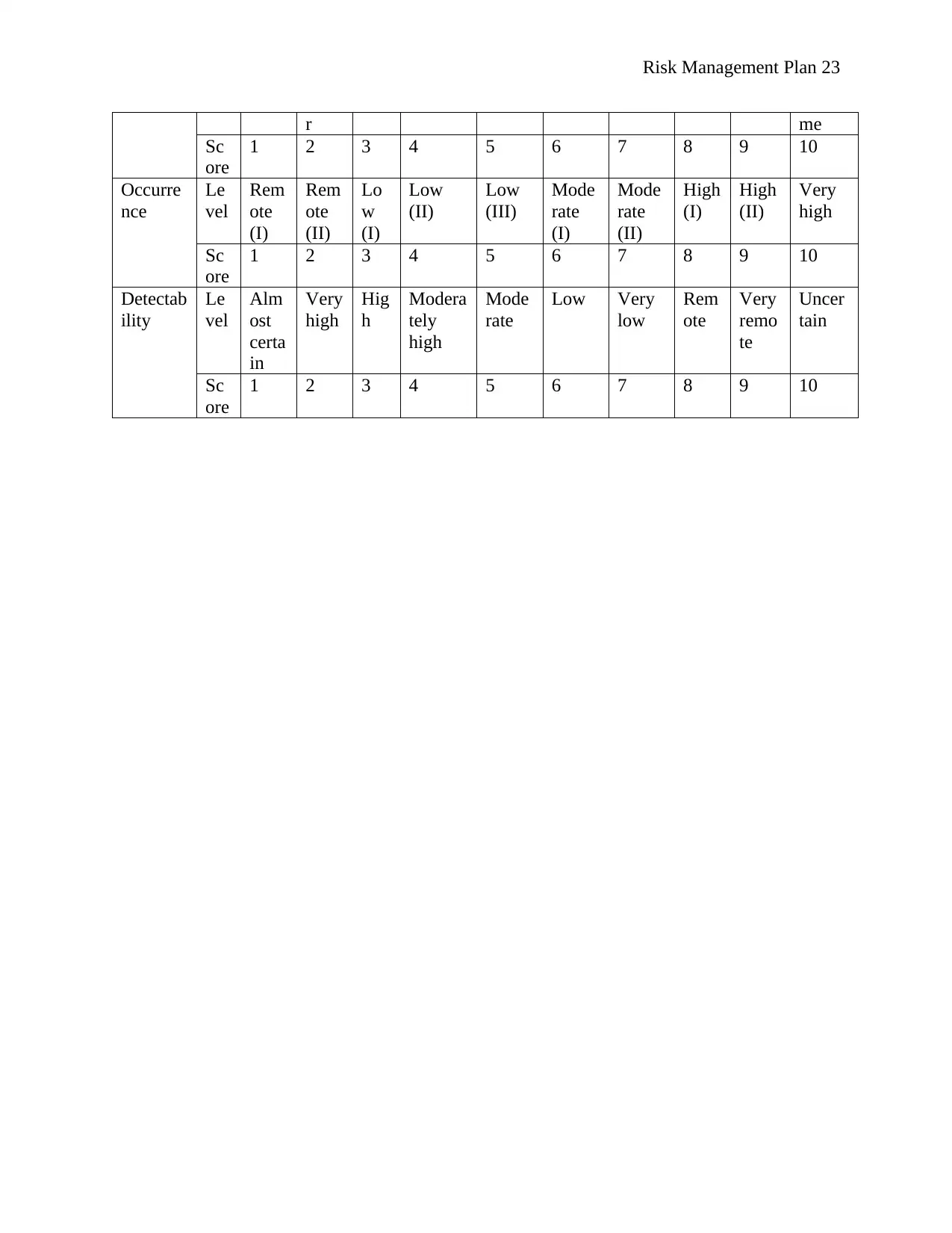
r me
Sc
ore
1 2 3 4 5 6 7 8 9 10
Occurre
nce
Le
vel
Rem
ote
(I)
Rem
ote
(II)
Lo
w
(I)
Low
(II)
Low
(III)
Mode
rate
(I)
Mode
rate
(II)
High
(I)
High
(II)
Very
high
Sc
ore
1 2 3 4 5 6 7 8 9 10
Detectab
ility
Le
vel
Alm
ost
certa
in
Very
high
Hig
h
Modera
tely
high
Mode
rate
Low Very
low
Rem
ote
Very
remo
te
Uncer
tain
Sc
ore
1 2 3 4 5 6 7 8 9 10
Related Documents

Your All-in-One AI-Powered Toolkit for Academic Success.
+13062052269
info@desklib.com
Available 24*7 on WhatsApp / Email
© 2024 | Zucol Services PVT LTD | All rights reserved.