Diploma of Building & Construction Study Material with Solved Assignments
VerifiedAdded on  2023/06/12
|15
|3438
|415
AI Summary
This study material covers various aspects of Diploma of Building & Construction including managing ordering of supplies, OHS legislation, safe use of plant and equipment, managing on-site construction problems, and more.
Contribute Materials
Your contribution can guide someone’s learning journey. Share your
documents today.
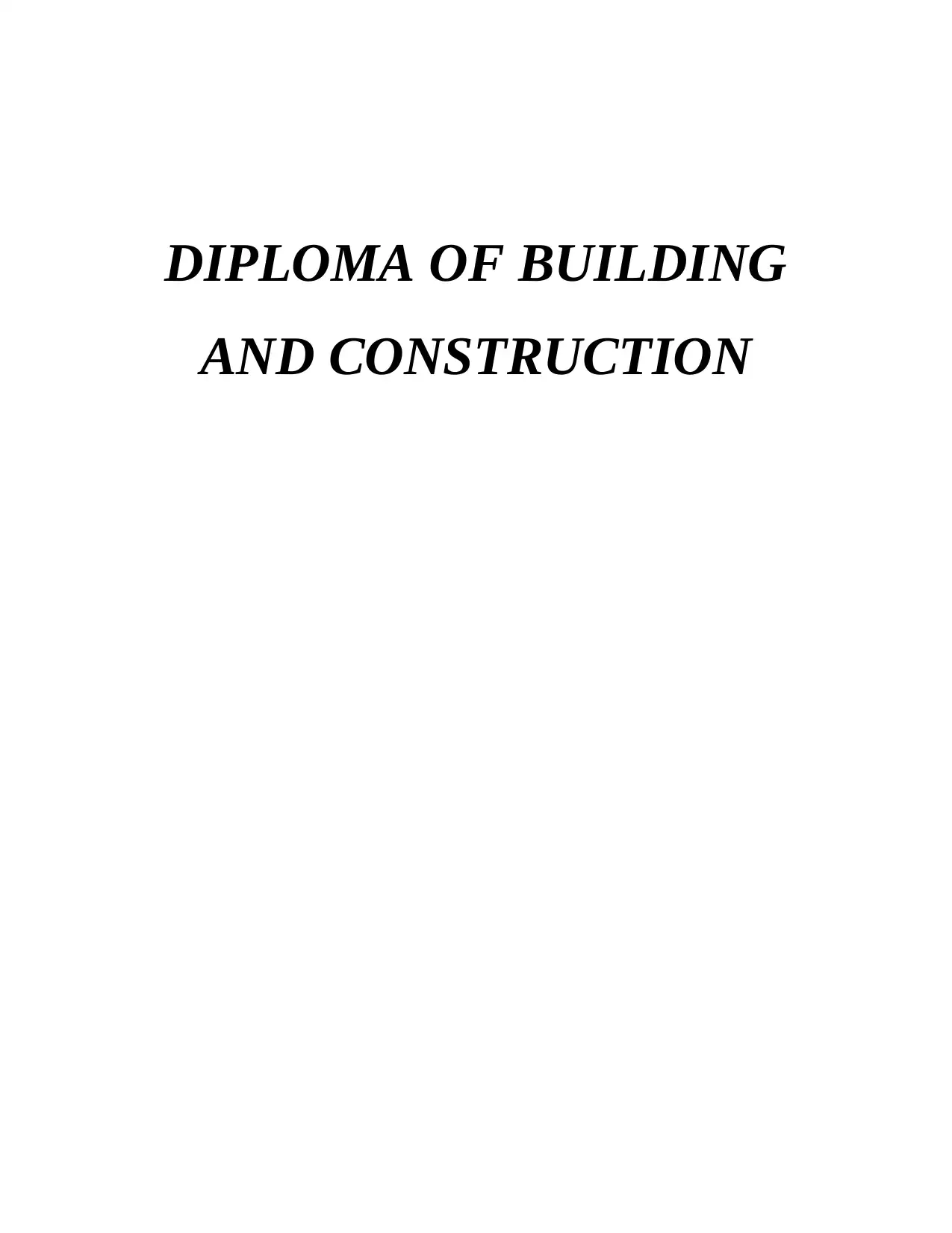
DIPLOMA OF BUILDING
AND CONSTRUCTION
AND CONSTRUCTION
Secure Best Marks with AI Grader
Need help grading? Try our AI Grader for instant feedback on your assignments.
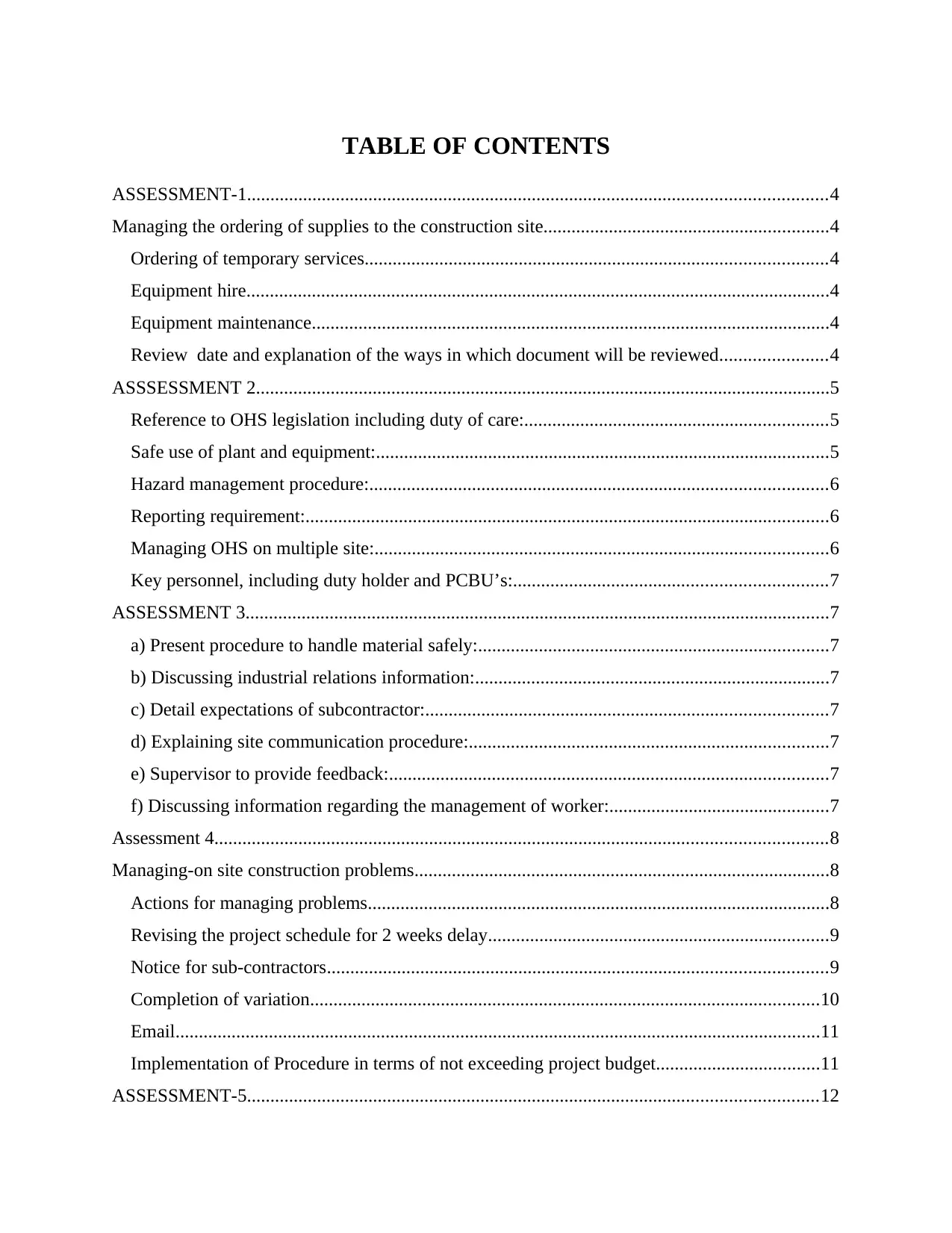
TABLE OF CONTENTS
ASSESSMENT-1............................................................................................................................4
Managing the ordering of supplies to the construction site.............................................................4
Ordering of temporary services...................................................................................................4
Equipment hire.............................................................................................................................4
Equipment maintenance...............................................................................................................4
Review date and explanation of the ways in which document will be reviewed.......................4
ASSSESSMENT 2...........................................................................................................................5
Reference to OHS legislation including duty of care:.................................................................5
Safe use of plant and equipment:.................................................................................................5
Hazard management procedure:..................................................................................................6
Reporting requirement:................................................................................................................6
Managing OHS on multiple site:.................................................................................................6
Key personnel, including duty holder and PCBU’s:...................................................................7
ASSESSMENT 3.............................................................................................................................7
a) Present procedure to handle material safely:...........................................................................7
b) Discussing industrial relations information:............................................................................7
c) Detail expectations of subcontractor:......................................................................................7
d) Explaining site communication procedure:.............................................................................7
e) Supervisor to provide feedback:..............................................................................................7
f) Discussing information regarding the management of worker:...............................................7
Assessment 4...................................................................................................................................8
Managing-on site construction problems.........................................................................................8
Actions for managing problems...................................................................................................8
Revising the project schedule for 2 weeks delay.........................................................................9
Notice for sub-contractors...........................................................................................................9
Completion of variation.............................................................................................................10
Email..........................................................................................................................................11
Implementation of Procedure in terms of not exceeding project budget...................................11
ASSESSMENT-5..........................................................................................................................12
ASSESSMENT-1............................................................................................................................4
Managing the ordering of supplies to the construction site.............................................................4
Ordering of temporary services...................................................................................................4
Equipment hire.............................................................................................................................4
Equipment maintenance...............................................................................................................4
Review date and explanation of the ways in which document will be reviewed.......................4
ASSSESSMENT 2...........................................................................................................................5
Reference to OHS legislation including duty of care:.................................................................5
Safe use of plant and equipment:.................................................................................................5
Hazard management procedure:..................................................................................................6
Reporting requirement:................................................................................................................6
Managing OHS on multiple site:.................................................................................................6
Key personnel, including duty holder and PCBU’s:...................................................................7
ASSESSMENT 3.............................................................................................................................7
a) Present procedure to handle material safely:...........................................................................7
b) Discussing industrial relations information:............................................................................7
c) Detail expectations of subcontractor:......................................................................................7
d) Explaining site communication procedure:.............................................................................7
e) Supervisor to provide feedback:..............................................................................................7
f) Discussing information regarding the management of worker:...............................................7
Assessment 4...................................................................................................................................8
Managing-on site construction problems.........................................................................................8
Actions for managing problems...................................................................................................8
Revising the project schedule for 2 weeks delay.........................................................................9
Notice for sub-contractors...........................................................................................................9
Completion of variation.............................................................................................................10
Email..........................................................................................................................................11
Implementation of Procedure in terms of not exceeding project budget...................................11
ASSESSMENT-5..........................................................................................................................12
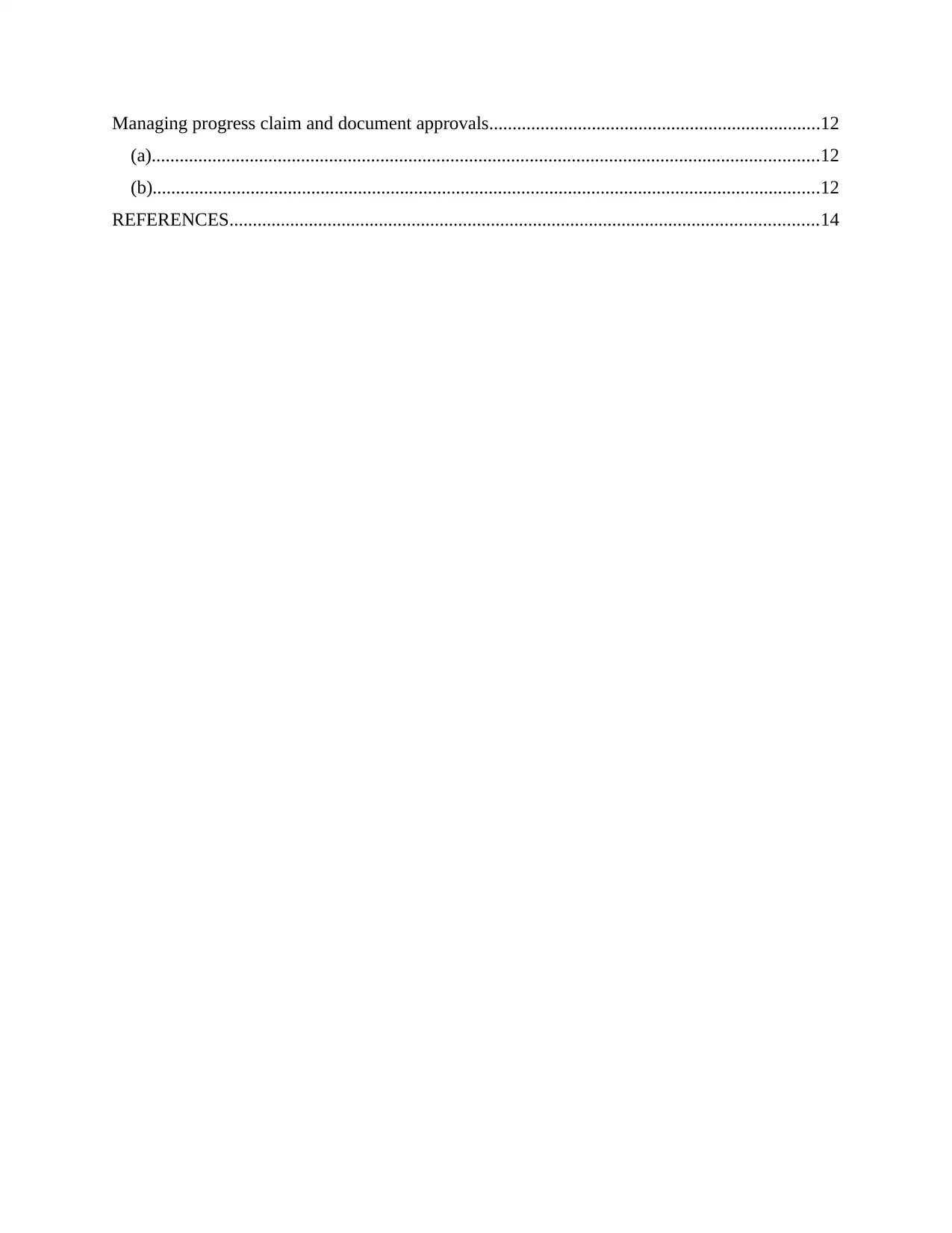
Managing progress claim and document approvals.......................................................................12
(a)...............................................................................................................................................12
(b)...............................................................................................................................................12
REFERENCES..............................................................................................................................14
(a)...............................................................................................................................................12
(b)...............................................................................................................................................12
REFERENCES..............................................................................................................................14

ASSESSMENT-1
Managing the ordering of supplies to the construction site
Ordering of temporary services
It refers to acquiring of temporary services at the construction site in order to completion
of construction project. Thus, the major Metharom construction needs to make focus over
ordering of temporary services that is concerned with the resources such as, temporary lighting,
temporary power and water (Hasmori and et.al., 2020). These are the temporary services that are
highly required in terms of managing construction process. The major motive is to make sure
that these services are supplied a consistent form at construction site.
Equipment hire
The requirement of the project has to be known by the company afterwards, the
mandatory machines that are needed has to be identified. The current condition of the machine
has to be evaluated and then, the cost has to be measure. Moreover, transportation of machines
needs to be decided and then it has to be installed.
Equipment maintenance
The major steps of equipment maintenance that needs to be performed by Metharom
construction are:
ï‚· Managing operational records
ï‚· Ensuring regular cleaning
ï‚· Recording the fluid level
ï‚· Performance of daily lubrication
ï‚· Protection over electrical Wiring
ï‚· Reviewing the tire and excel conditions
ï‚· Inspecting the leakages
The above mentioned steps helps in management of the equipments at the site. Furthermore, it
provides the assurance of keeping equipments updates (Li and et.al., 2018).
Review date and explanation of the ways in which document will be reviewed
Project quality management in construction has been comprised with the policies and
procedures that has been taken in consideration by the company in terms of delivering effective
outcomes to the customers. Also, it helps in performing the monitoring at the site that assures
Managing the ordering of supplies to the construction site
Ordering of temporary services
It refers to acquiring of temporary services at the construction site in order to completion
of construction project. Thus, the major Metharom construction needs to make focus over
ordering of temporary services that is concerned with the resources such as, temporary lighting,
temporary power and water (Hasmori and et.al., 2020). These are the temporary services that are
highly required in terms of managing construction process. The major motive is to make sure
that these services are supplied a consistent form at construction site.
Equipment hire
The requirement of the project has to be known by the company afterwards, the
mandatory machines that are needed has to be identified. The current condition of the machine
has to be evaluated and then, the cost has to be measure. Moreover, transportation of machines
needs to be decided and then it has to be installed.
Equipment maintenance
The major steps of equipment maintenance that needs to be performed by Metharom
construction are:
ï‚· Managing operational records
ï‚· Ensuring regular cleaning
ï‚· Recording the fluid level
ï‚· Performance of daily lubrication
ï‚· Protection over electrical Wiring
ï‚· Reviewing the tire and excel conditions
ï‚· Inspecting the leakages
The above mentioned steps helps in management of the equipments at the site. Furthermore, it
provides the assurance of keeping equipments updates (Li and et.al., 2018).
Review date and explanation of the ways in which document will be reviewed
Project quality management in construction has been comprised with the policies and
procedures that has been taken in consideration by the company in terms of delivering effective
outcomes to the customers. Also, it helps in performing the monitoring at the site that assures
Secure Best Marks with AI Grader
Need help grading? Try our AI Grader for instant feedback on your assignments.
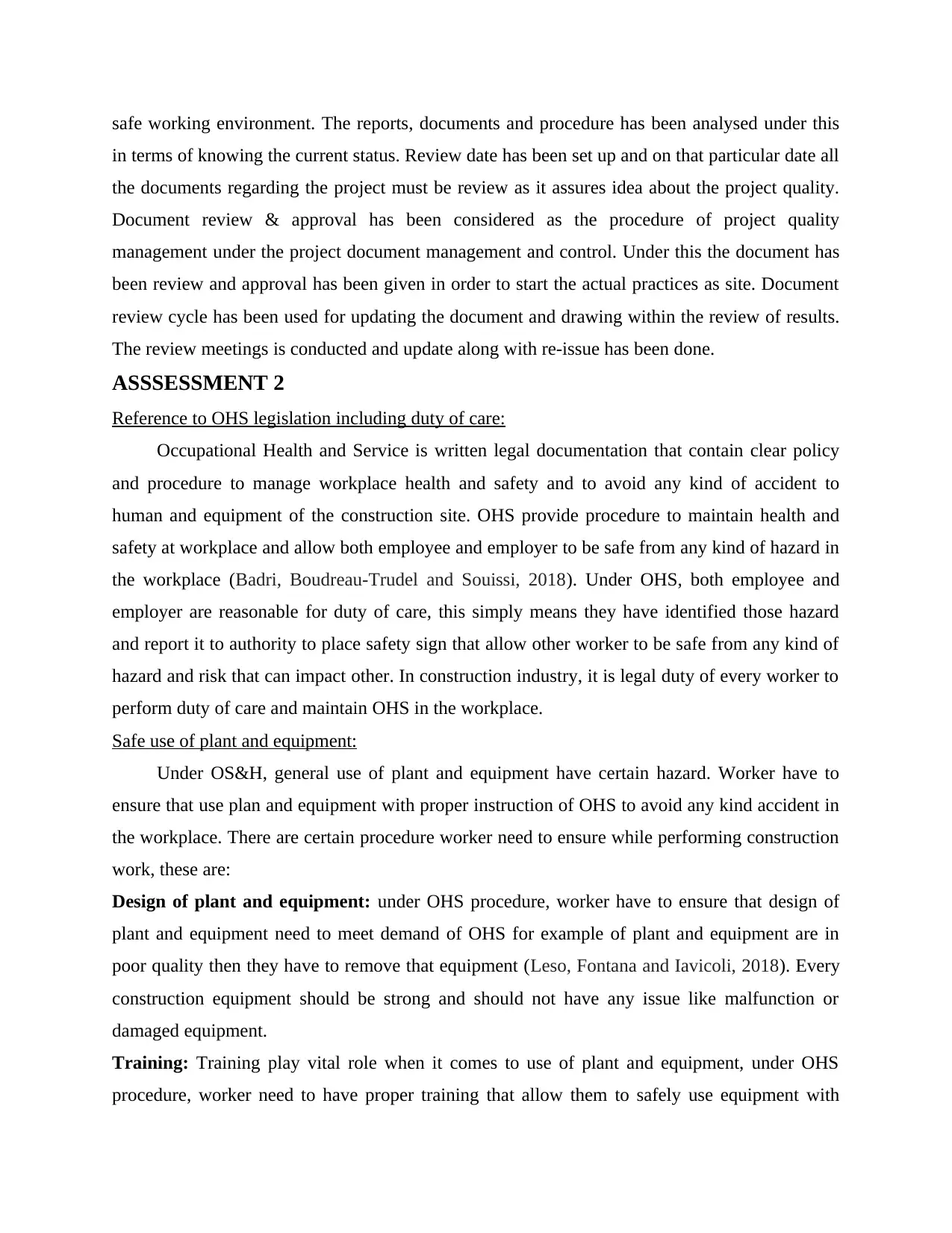
safe working environment. The reports, documents and procedure has been analysed under this
in terms of knowing the current status. Review date has been set up and on that particular date all
the documents regarding the project must be review as it assures idea about the project quality.
Document review & approval has been considered as the procedure of project quality
management under the project document management and control. Under this the document has
been review and approval has been given in order to start the actual practices as site. Document
review cycle has been used for updating the document and drawing within the review of results.
The review meetings is conducted and update along with re-issue has been done.
ASSSESSMENT 2
Reference to OHS legislation including duty of care:
Occupational Health and Service is written legal documentation that contain clear policy
and procedure to manage workplace health and safety and to avoid any kind of accident to
human and equipment of the construction site. OHS provide procedure to maintain health and
safety at workplace and allow both employee and employer to be safe from any kind of hazard in
the workplace (Badri, Boudreau-Trudel and Souissi, 2018). Under OHS, both employee and
employer are reasonable for duty of care, this simply means they have identified those hazard
and report it to authority to place safety sign that allow other worker to be safe from any kind of
hazard and risk that can impact other. In construction industry, it is legal duty of every worker to
perform duty of care and maintain OHS in the workplace.
Safe use of plant and equipment:
Under OS&H, general use of plant and equipment have certain hazard. Worker have to
ensure that use plan and equipment with proper instruction of OHS to avoid any kind accident in
the workplace. There are certain procedure worker need to ensure while performing construction
work, these are:
Design of plant and equipment: under OHS procedure, worker have to ensure that design of
plant and equipment need to meet demand of OHS for example of plant and equipment are in
poor quality then they have to remove that equipment (Leso, Fontana and Iavicoli, 2018). Every
construction equipment should be strong and should not have any issue like malfunction or
damaged equipment.
Training: Training play vital role when it comes to use of plant and equipment, under OHS
procedure, worker need to have proper training that allow them to safely use equipment with
in terms of knowing the current status. Review date has been set up and on that particular date all
the documents regarding the project must be review as it assures idea about the project quality.
Document review & approval has been considered as the procedure of project quality
management under the project document management and control. Under this the document has
been review and approval has been given in order to start the actual practices as site. Document
review cycle has been used for updating the document and drawing within the review of results.
The review meetings is conducted and update along with re-issue has been done.
ASSSESSMENT 2
Reference to OHS legislation including duty of care:
Occupational Health and Service is written legal documentation that contain clear policy
and procedure to manage workplace health and safety and to avoid any kind of accident to
human and equipment of the construction site. OHS provide procedure to maintain health and
safety at workplace and allow both employee and employer to be safe from any kind of hazard in
the workplace (Badri, Boudreau-Trudel and Souissi, 2018). Under OHS, both employee and
employer are reasonable for duty of care, this simply means they have identified those hazard
and report it to authority to place safety sign that allow other worker to be safe from any kind of
hazard and risk that can impact other. In construction industry, it is legal duty of every worker to
perform duty of care and maintain OHS in the workplace.
Safe use of plant and equipment:
Under OS&H, general use of plant and equipment have certain hazard. Worker have to
ensure that use plan and equipment with proper instruction of OHS to avoid any kind accident in
the workplace. There are certain procedure worker need to ensure while performing construction
work, these are:
Design of plant and equipment: under OHS procedure, worker have to ensure that design of
plant and equipment need to meet demand of OHS for example of plant and equipment are in
poor quality then they have to remove that equipment (Leso, Fontana and Iavicoli, 2018). Every
construction equipment should be strong and should not have any issue like malfunction or
damaged equipment.
Training: Training play vital role when it comes to use of plant and equipment, under OHS
procedure, worker need to have proper training that allow them to safely use equipment with
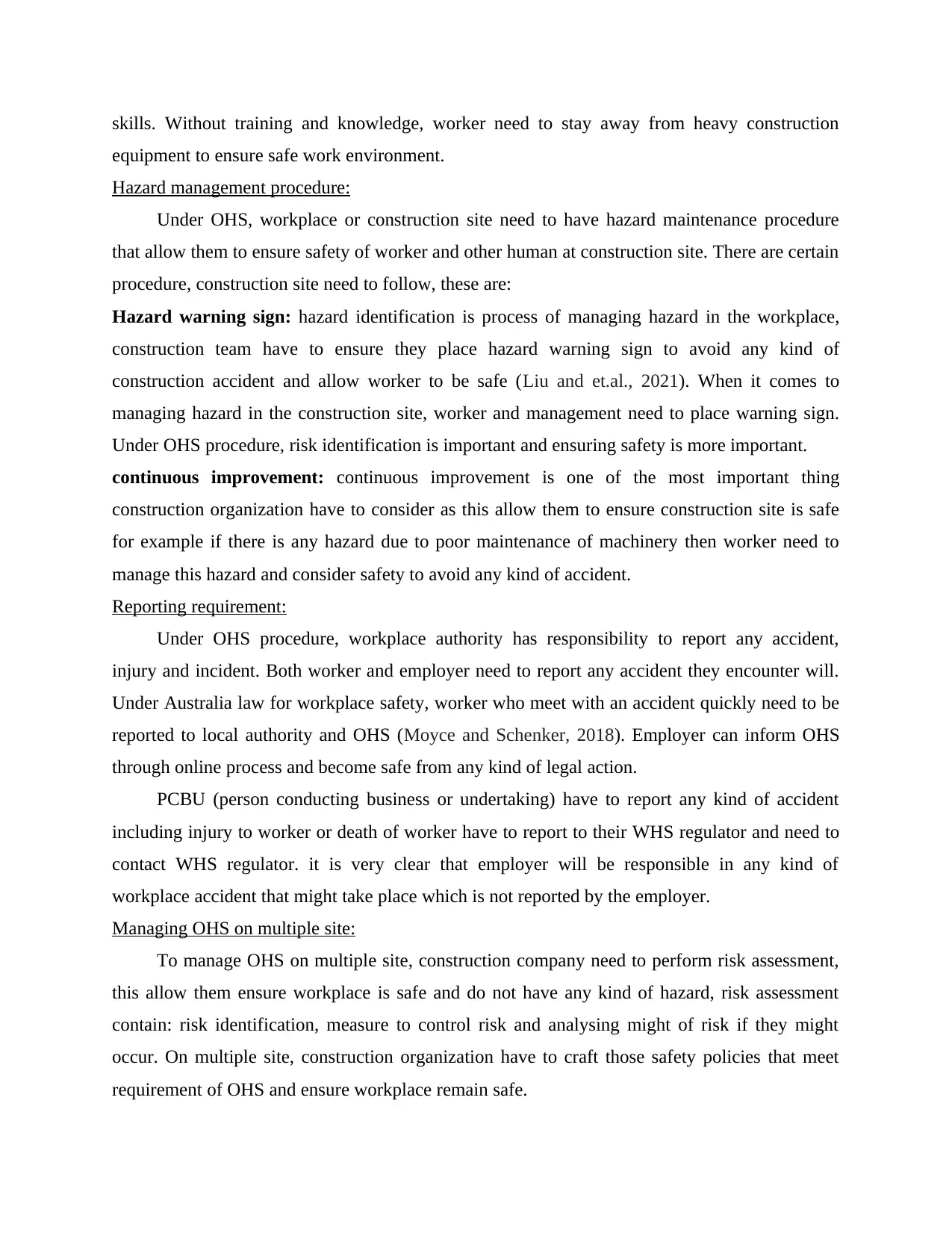
skills. Without training and knowledge, worker need to stay away from heavy construction
equipment to ensure safe work environment.
Hazard management procedure:
Under OHS, workplace or construction site need to have hazard maintenance procedure
that allow them to ensure safety of worker and other human at construction site. There are certain
procedure, construction site need to follow, these are:
Hazard warning sign: hazard identification is process of managing hazard in the workplace,
construction team have to ensure they place hazard warning sign to avoid any kind of
construction accident and allow worker to be safe (Liu and et.al., 2021). When it comes to
managing hazard in the construction site, worker and management need to place warning sign.
Under OHS procedure, risk identification is important and ensuring safety is more important.
continuous improvement: continuous improvement is one of the most important thing
construction organization have to consider as this allow them to ensure construction site is safe
for example if there is any hazard due to poor maintenance of machinery then worker need to
manage this hazard and consider safety to avoid any kind of accident.
Reporting requirement:
Under OHS procedure, workplace authority has responsibility to report any accident,
injury and incident. Both worker and employer need to report any accident they encounter will.
Under Australia law for workplace safety, worker who meet with an accident quickly need to be
reported to local authority and OHS (Moyce and Schenker, 2018). Employer can inform OHS
through online process and become safe from any kind of legal action.
PCBU (person conducting business or undertaking) have to report any kind of accident
including injury to worker or death of worker have to report to their WHS regulator and need to
contact WHS regulator. it is very clear that employer will be responsible in any kind of
workplace accident that might take place which is not reported by the employer.
Managing OHS on multiple site:
To manage OHS on multiple site, construction company need to perform risk assessment,
this allow them ensure workplace is safe and do not have any kind of hazard, risk assessment
contain: risk identification, measure to control risk and analysing might of risk if they might
occur. On multiple site, construction organization have to craft those safety policies that meet
requirement of OHS and ensure workplace remain safe.
equipment to ensure safe work environment.
Hazard management procedure:
Under OHS, workplace or construction site need to have hazard maintenance procedure
that allow them to ensure safety of worker and other human at construction site. There are certain
procedure, construction site need to follow, these are:
Hazard warning sign: hazard identification is process of managing hazard in the workplace,
construction team have to ensure they place hazard warning sign to avoid any kind of
construction accident and allow worker to be safe (Liu and et.al., 2021). When it comes to
managing hazard in the construction site, worker and management need to place warning sign.
Under OHS procedure, risk identification is important and ensuring safety is more important.
continuous improvement: continuous improvement is one of the most important thing
construction organization have to consider as this allow them to ensure construction site is safe
for example if there is any hazard due to poor maintenance of machinery then worker need to
manage this hazard and consider safety to avoid any kind of accident.
Reporting requirement:
Under OHS procedure, workplace authority has responsibility to report any accident,
injury and incident. Both worker and employer need to report any accident they encounter will.
Under Australia law for workplace safety, worker who meet with an accident quickly need to be
reported to local authority and OHS (Moyce and Schenker, 2018). Employer can inform OHS
through online process and become safe from any kind of legal action.
PCBU (person conducting business or undertaking) have to report any kind of accident
including injury to worker or death of worker have to report to their WHS regulator and need to
contact WHS regulator. it is very clear that employer will be responsible in any kind of
workplace accident that might take place which is not reported by the employer.
Managing OHS on multiple site:
To manage OHS on multiple site, construction company need to perform risk assessment,
this allow them ensure workplace is safe and do not have any kind of hazard, risk assessment
contain: risk identification, measure to control risk and analysing might of risk if they might
occur. On multiple site, construction organization have to craft those safety policies that meet
requirement of OHS and ensure workplace remain safe.
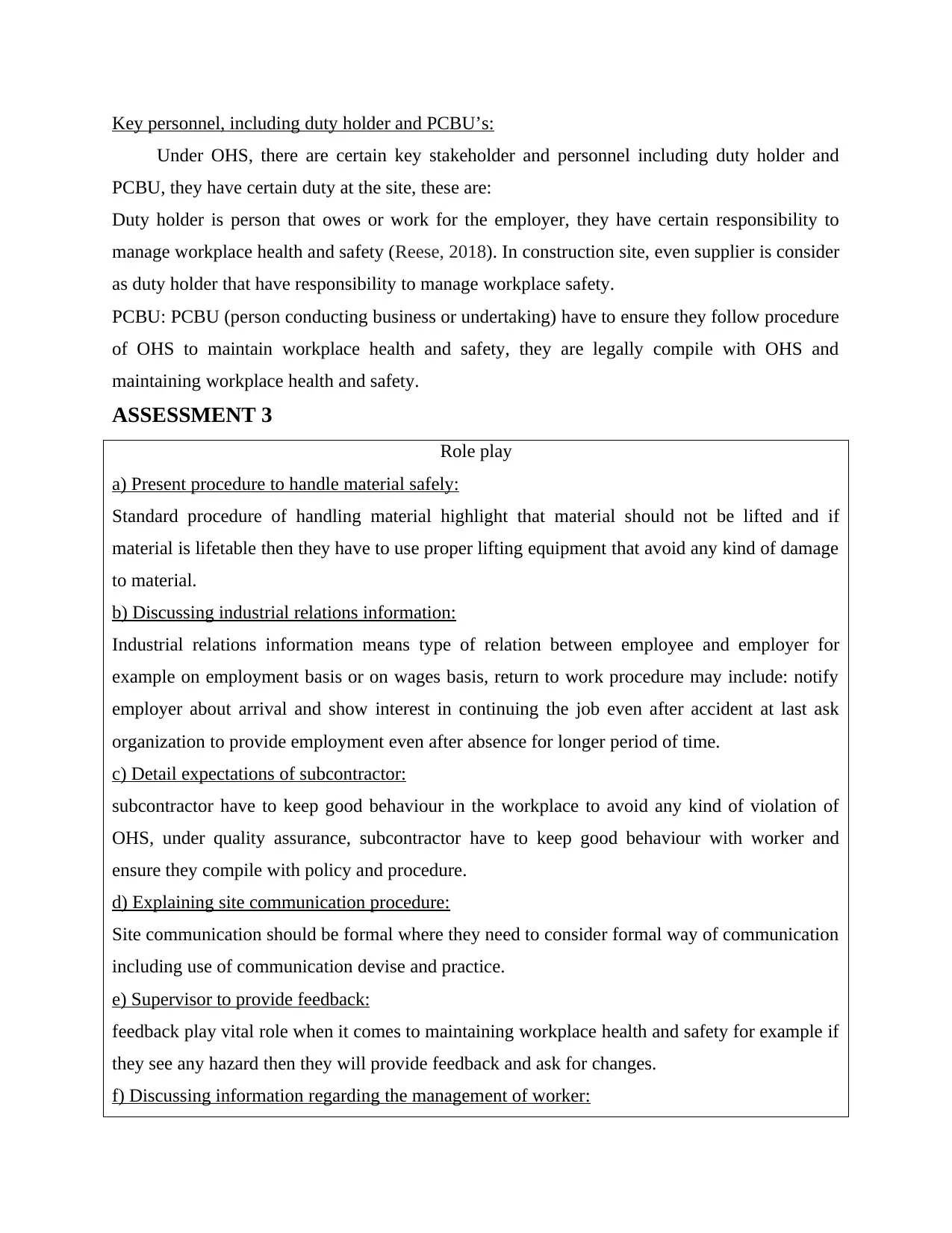
Key personnel, including duty holder and PCBU’s:
Under OHS, there are certain key stakeholder and personnel including duty holder and
PCBU, they have certain duty at the site, these are:
Duty holder is person that owes or work for the employer, they have certain responsibility to
manage workplace health and safety (Reese, 2018). In construction site, even supplier is consider
as duty holder that have responsibility to manage workplace safety.
PCBU: PCBU (person conducting business or undertaking) have to ensure they follow procedure
of OHS to maintain workplace health and safety, they are legally compile with OHS and
maintaining workplace health and safety.
ASSESSMENT 3
Role play
a) Present procedure to handle material safely:
Standard procedure of handling material highlight that material should not be lifted and if
material is lifetable then they have to use proper lifting equipment that avoid any kind of damage
to material.
b) Discussing industrial relations information:
Industrial relations information means type of relation between employee and employer for
example on employment basis or on wages basis, return to work procedure may include: notify
employer about arrival and show interest in continuing the job even after accident at last ask
organization to provide employment even after absence for longer period of time.
c) Detail expectations of subcontractor:
subcontractor have to keep good behaviour in the workplace to avoid any kind of violation of
OHS, under quality assurance, subcontractor have to keep good behaviour with worker and
ensure they compile with policy and procedure.
d) Explaining site communication procedure:
Site communication should be formal where they need to consider formal way of communication
including use of communication devise and practice.
e) Supervisor to provide feedback:
feedback play vital role when it comes to maintaining workplace health and safety for example if
they see any hazard then they will provide feedback and ask for changes.
f) Discussing information regarding the management of worker:
Under OHS, there are certain key stakeholder and personnel including duty holder and
PCBU, they have certain duty at the site, these are:
Duty holder is person that owes or work for the employer, they have certain responsibility to
manage workplace health and safety (Reese, 2018). In construction site, even supplier is consider
as duty holder that have responsibility to manage workplace safety.
PCBU: PCBU (person conducting business or undertaking) have to ensure they follow procedure
of OHS to maintain workplace health and safety, they are legally compile with OHS and
maintaining workplace health and safety.
ASSESSMENT 3
Role play
a) Present procedure to handle material safely:
Standard procedure of handling material highlight that material should not be lifted and if
material is lifetable then they have to use proper lifting equipment that avoid any kind of damage
to material.
b) Discussing industrial relations information:
Industrial relations information means type of relation between employee and employer for
example on employment basis or on wages basis, return to work procedure may include: notify
employer about arrival and show interest in continuing the job even after accident at last ask
organization to provide employment even after absence for longer period of time.
c) Detail expectations of subcontractor:
subcontractor have to keep good behaviour in the workplace to avoid any kind of violation of
OHS, under quality assurance, subcontractor have to keep good behaviour with worker and
ensure they compile with policy and procedure.
d) Explaining site communication procedure:
Site communication should be formal where they need to consider formal way of communication
including use of communication devise and practice.
e) Supervisor to provide feedback:
feedback play vital role when it comes to maintaining workplace health and safety for example if
they see any hazard then they will provide feedback and ask for changes.
f) Discussing information regarding the management of worker:
Paraphrase This Document
Need a fresh take? Get an instant paraphrase of this document with our AI Paraphraser
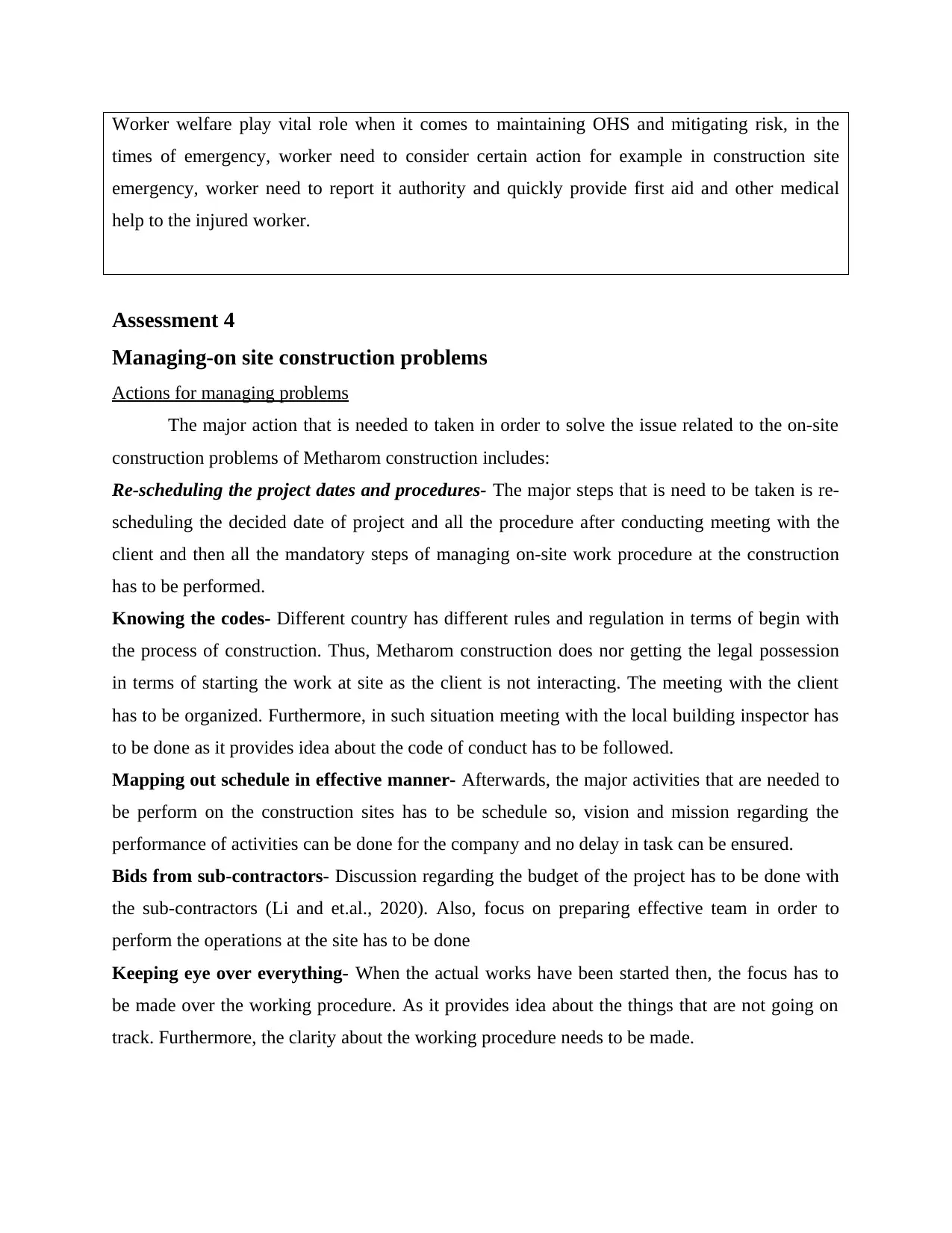
Worker welfare play vital role when it comes to maintaining OHS and mitigating risk, in the
times of emergency, worker need to consider certain action for example in construction site
emergency, worker need to report it authority and quickly provide first aid and other medical
help to the injured worker.
Assessment 4
Managing-on site construction problems
Actions for managing problems
The major action that is needed to taken in order to solve the issue related to the on-site
construction problems of Metharom construction includes:
Re-scheduling the project dates and procedures- The major steps that is need to be taken is re-
scheduling the decided date of project and all the procedure after conducting meeting with the
client and then all the mandatory steps of managing on-site work procedure at the construction
has to be performed.
Knowing the codes- Different country has different rules and regulation in terms of begin with
the process of construction. Thus, Metharom construction does nor getting the legal possession
in terms of starting the work at site as the client is not interacting. The meeting with the client
has to be organized. Furthermore, in such situation meeting with the local building inspector has
to be done as it provides idea about the code of conduct has to be followed.
Mapping out schedule in effective manner- Afterwards, the major activities that are needed to
be perform on the construction sites has to be schedule so, vision and mission regarding the
performance of activities can be done for the company and no delay in task can be ensured.
Bids from sub-contractors- Discussion regarding the budget of the project has to be done with
the sub-contractors (Li and et.al., 2020). Also, focus on preparing effective team in order to
perform the operations at the site has to be done
Keeping eye over everything- When the actual works have been started then, the focus has to
be made over the working procedure. As it provides idea about the things that are not going on
track. Furthermore, the clarity about the working procedure needs to be made.
times of emergency, worker need to consider certain action for example in construction site
emergency, worker need to report it authority and quickly provide first aid and other medical
help to the injured worker.
Assessment 4
Managing-on site construction problems
Actions for managing problems
The major action that is needed to taken in order to solve the issue related to the on-site
construction problems of Metharom construction includes:
Re-scheduling the project dates and procedures- The major steps that is need to be taken is re-
scheduling the decided date of project and all the procedure after conducting meeting with the
client and then all the mandatory steps of managing on-site work procedure at the construction
has to be performed.
Knowing the codes- Different country has different rules and regulation in terms of begin with
the process of construction. Thus, Metharom construction does nor getting the legal possession
in terms of starting the work at site as the client is not interacting. The meeting with the client
has to be organized. Furthermore, in such situation meeting with the local building inspector has
to be done as it provides idea about the code of conduct has to be followed.
Mapping out schedule in effective manner- Afterwards, the major activities that are needed to
be perform on the construction sites has to be schedule so, vision and mission regarding the
performance of activities can be done for the company and no delay in task can be ensured.
Bids from sub-contractors- Discussion regarding the budget of the project has to be done with
the sub-contractors (Li and et.al., 2020). Also, focus on preparing effective team in order to
perform the operations at the site has to be done
Keeping eye over everything- When the actual works have been started then, the focus has to
be made over the working procedure. As it provides idea about the things that are not going on
track. Furthermore, the clarity about the working procedure needs to be made.
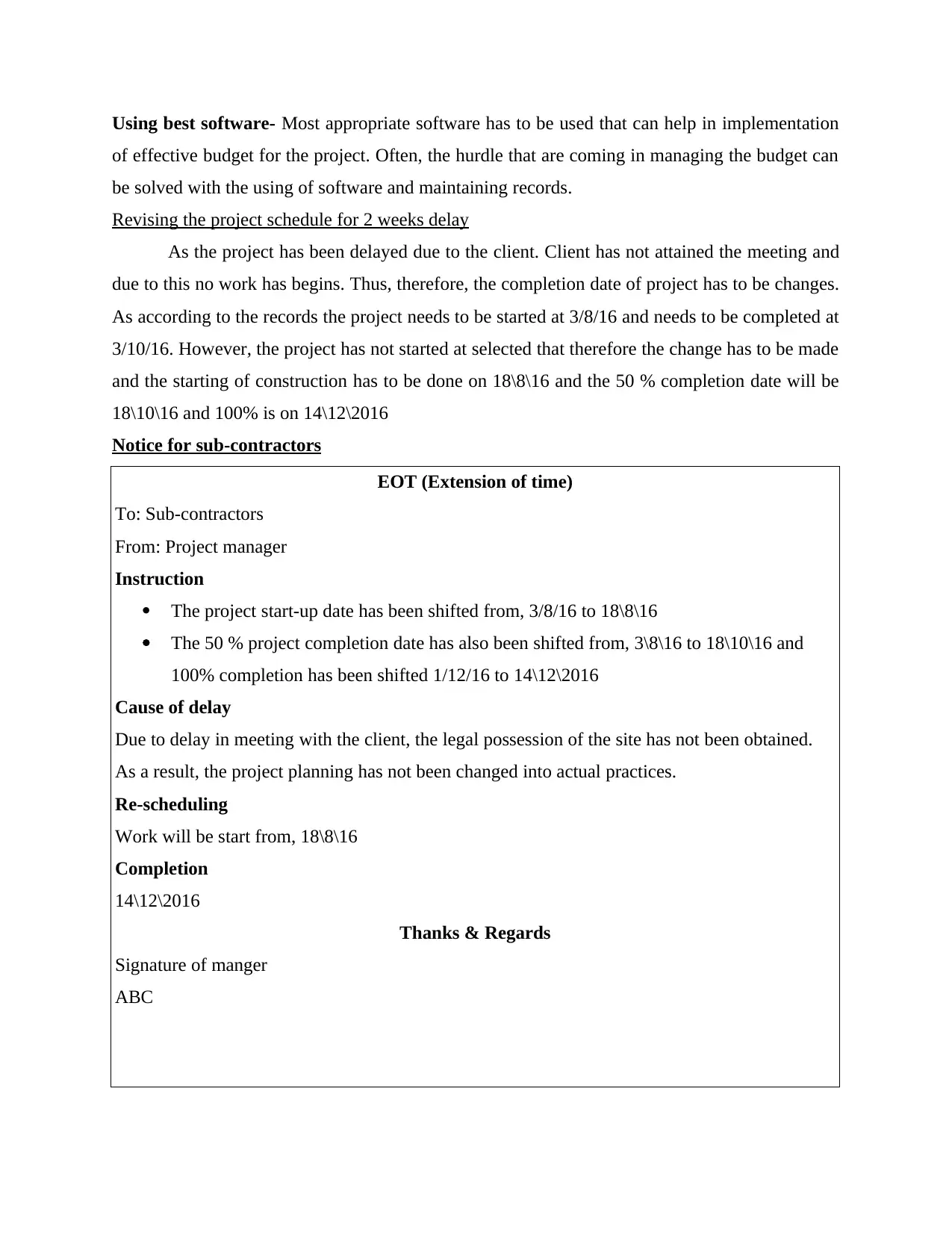
Using best software- Most appropriate software has to be used that can help in implementation
of effective budget for the project. Often, the hurdle that are coming in managing the budget can
be solved with the using of software and maintaining records.
Revising the project schedule for 2 weeks delay
As the project has been delayed due to the client. Client has not attained the meeting and
due to this no work has begins. Thus, therefore, the completion date of project has to be changes.
As according to the records the project needs to be started at 3/8/16 and needs to be completed at
3/10/16. However, the project has not started at selected that therefore the change has to be made
and the starting of construction has to be done on 18\8\16 and the 50 % completion date will be
18\10\16 and 100% is on 14\12\2016
Notice for sub-contractors
EOT (Extension of time)
To: Sub-contractors
From: Project manager
Instruction
ï‚· The project start-up date has been shifted from, 3/8/16 to 18\8\16
ï‚· The 50 % project completion date has also been shifted from, 3\8\16 to 18\10\16 and
100% completion has been shifted 1/12/16 to 14\12\2016
Cause of delay
Due to delay in meeting with the client, the legal possession of the site has not been obtained.
As a result, the project planning has not been changed into actual practices.
Re-scheduling
Work will be start from, 18\8\16
Completion
14\12\2016
Thanks & Regards
Signature of manger
ABC
of effective budget for the project. Often, the hurdle that are coming in managing the budget can
be solved with the using of software and maintaining records.
Revising the project schedule for 2 weeks delay
As the project has been delayed due to the client. Client has not attained the meeting and
due to this no work has begins. Thus, therefore, the completion date of project has to be changes.
As according to the records the project needs to be started at 3/8/16 and needs to be completed at
3/10/16. However, the project has not started at selected that therefore the change has to be made
and the starting of construction has to be done on 18\8\16 and the 50 % completion date will be
18\10\16 and 100% is on 14\12\2016
Notice for sub-contractors
EOT (Extension of time)
To: Sub-contractors
From: Project manager
Instruction
ï‚· The project start-up date has been shifted from, 3/8/16 to 18\8\16
ï‚· The 50 % project completion date has also been shifted from, 3\8\16 to 18\10\16 and
100% completion has been shifted 1/12/16 to 14\12\2016
Cause of delay
Due to delay in meeting with the client, the legal possession of the site has not been obtained.
As a result, the project planning has not been changed into actual practices.
Re-scheduling
Work will be start from, 18\8\16
Completion
14\12\2016
Thanks & Regards
Signature of manger
ABC
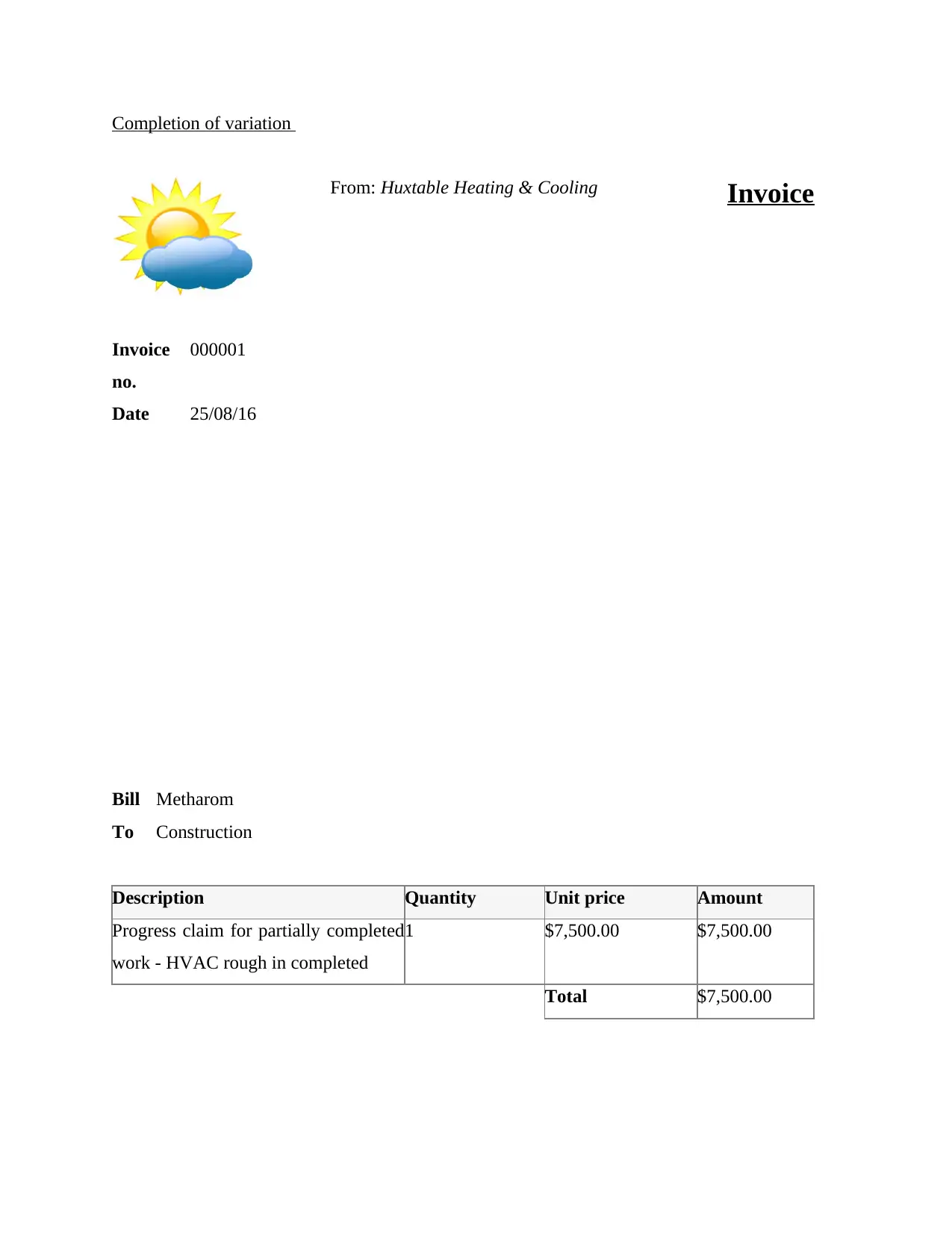
Completion of variation
From: Huxtable Heating & Cooling Invoice
Invoice
no.
000001
Date 25/08/16
Bill
To
Metharom
Construction
Description Quantity Unit price Amount
Progress claim for partially completed
work - HVAC rough in completed
1 $7,500.00 $7,500.00
Total $7,500.00
From: Huxtable Heating & Cooling Invoice
Invoice
no.
000001
Date 25/08/16
Bill
To
Metharom
Construction
Description Quantity Unit price Amount
Progress claim for partially completed
work - HVAC rough in completed
1 $7,500.00 $7,500.00
Total $7,500.00
Secure Best Marks with AI Grader
Need help grading? Try our AI Grader for instant feedback on your assignments.
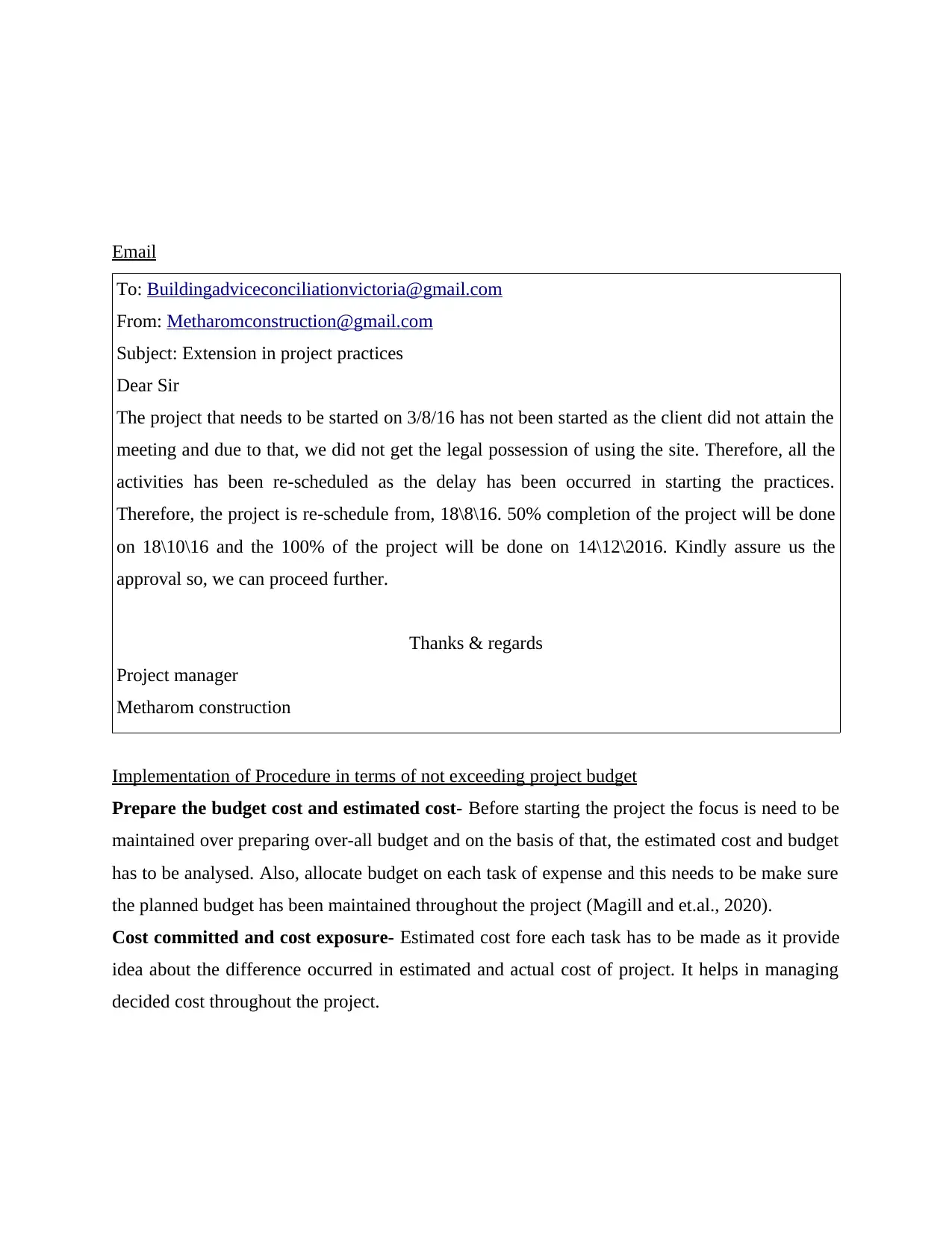
Email
To: Buildingadviceconciliationvictoria@gmail.com
From: Metharomconstruction@gmail.com
Subject: Extension in project practices
Dear Sir
The project that needs to be started on 3/8/16 has not been started as the client did not attain the
meeting and due to that, we did not get the legal possession of using the site. Therefore, all the
activities has been re-scheduled as the delay has been occurred in starting the practices.
Therefore, the project is re-schedule from, 18\8\16. 50% completion of the project will be done
on 18\10\16 and the 100% of the project will be done on 14\12\2016. Kindly assure us the
approval so, we can proceed further.
Thanks & regards
Project manager
Metharom construction
Implementation of Procedure in terms of not exceeding project budget
Prepare the budget cost and estimated cost- Before starting the project the focus is need to be
maintained over preparing over-all budget and on the basis of that, the estimated cost and budget
has to be analysed. Also, allocate budget on each task of expense and this needs to be make sure
the planned budget has been maintained throughout the project (Magill and et.al., 2020).
Cost committed and cost exposure- Estimated cost fore each task has to be made as it provide
idea about the difference occurred in estimated and actual cost of project. It helps in managing
decided cost throughout the project.
To: Buildingadviceconciliationvictoria@gmail.com
From: Metharomconstruction@gmail.com
Subject: Extension in project practices
Dear Sir
The project that needs to be started on 3/8/16 has not been started as the client did not attain the
meeting and due to that, we did not get the legal possession of using the site. Therefore, all the
activities has been re-scheduled as the delay has been occurred in starting the practices.
Therefore, the project is re-schedule from, 18\8\16. 50% completion of the project will be done
on 18\10\16 and the 100% of the project will be done on 14\12\2016. Kindly assure us the
approval so, we can proceed further.
Thanks & regards
Project manager
Metharom construction
Implementation of Procedure in terms of not exceeding project budget
Prepare the budget cost and estimated cost- Before starting the project the focus is need to be
maintained over preparing over-all budget and on the basis of that, the estimated cost and budget
has to be analysed. Also, allocate budget on each task of expense and this needs to be make sure
the planned budget has been maintained throughout the project (Magill and et.al., 2020).
Cost committed and cost exposure- Estimated cost fore each task has to be made as it provide
idea about the difference occurred in estimated and actual cost of project. It helps in managing
decided cost throughout the project.
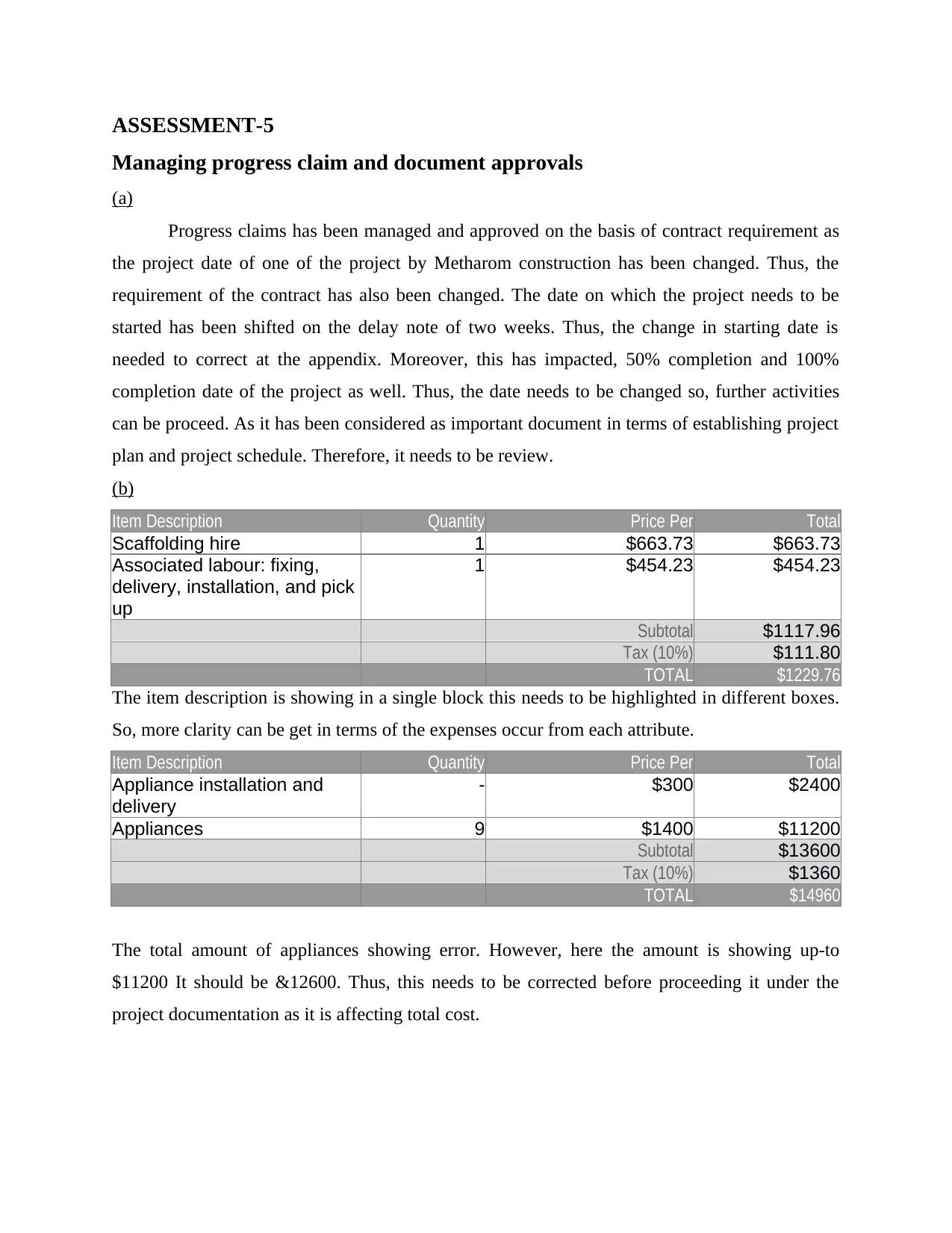
ASSESSMENT-5
Managing progress claim and document approvals
(a)
Progress claims has been managed and approved on the basis of contract requirement as
the project date of one of the project by Metharom construction has been changed. Thus, the
requirement of the contract has also been changed. The date on which the project needs to be
started has been shifted on the delay note of two weeks. Thus, the change in starting date is
needed to correct at the appendix. Moreover, this has impacted, 50% completion and 100%
completion date of the project as well. Thus, the date needs to be changed so, further activities
can be proceed. As it has been considered as important document in terms of establishing project
plan and project schedule. Therefore, it needs to be review.
(b)
Item Description Quantity Price Per Total
Scaffolding hire 1 $663.73 $663.73
Associated labour: fixing,
delivery, installation, and pick
up
1 $454.23 $454.23
Subtotal $1117.96
Tax (10%) $111.80
TOTAL $1229.76
The item description is showing in a single block this needs to be highlighted in different boxes.
So, more clarity can be get in terms of the expenses occur from each attribute.
Item Description Quantity Price Per Total
Appliance installation and
delivery
- $300 $2400
Appliances 9 $1400 $11200
Subtotal $13600
Tax (10%) $1360
TOTAL $14960
The total amount of appliances showing error. However, here the amount is showing up-to
$11200 It should be &12600. Thus, this needs to be corrected before proceeding it under the
project documentation as it is affecting total cost.
Managing progress claim and document approvals
(a)
Progress claims has been managed and approved on the basis of contract requirement as
the project date of one of the project by Metharom construction has been changed. Thus, the
requirement of the contract has also been changed. The date on which the project needs to be
started has been shifted on the delay note of two weeks. Thus, the change in starting date is
needed to correct at the appendix. Moreover, this has impacted, 50% completion and 100%
completion date of the project as well. Thus, the date needs to be changed so, further activities
can be proceed. As it has been considered as important document in terms of establishing project
plan and project schedule. Therefore, it needs to be review.
(b)
Item Description Quantity Price Per Total
Scaffolding hire 1 $663.73 $663.73
Associated labour: fixing,
delivery, installation, and pick
up
1 $454.23 $454.23
Subtotal $1117.96
Tax (10%) $111.80
TOTAL $1229.76
The item description is showing in a single block this needs to be highlighted in different boxes.
So, more clarity can be get in terms of the expenses occur from each attribute.
Item Description Quantity Price Per Total
Appliance installation and
delivery
- $300 $2400
Appliances 9 $1400 $11200
Subtotal $13600
Tax (10%) $1360
TOTAL $14960
The total amount of appliances showing error. However, here the amount is showing up-to
$11200 It should be &12600. Thus, this needs to be corrected before proceeding it under the
project documentation as it is affecting total cost.
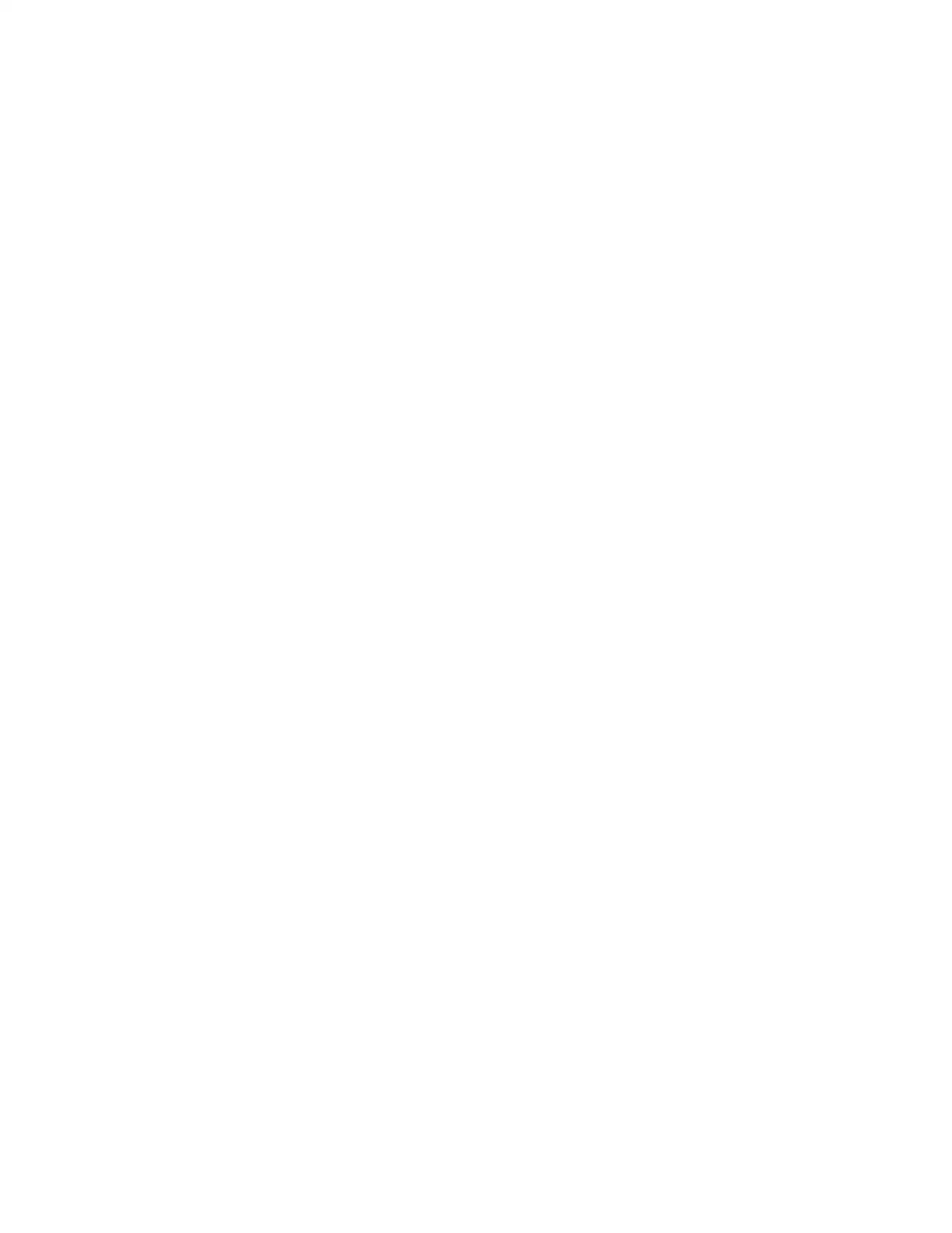
Paraphrase This Document
Need a fresh take? Get an instant paraphrase of this document with our AI Paraphraser
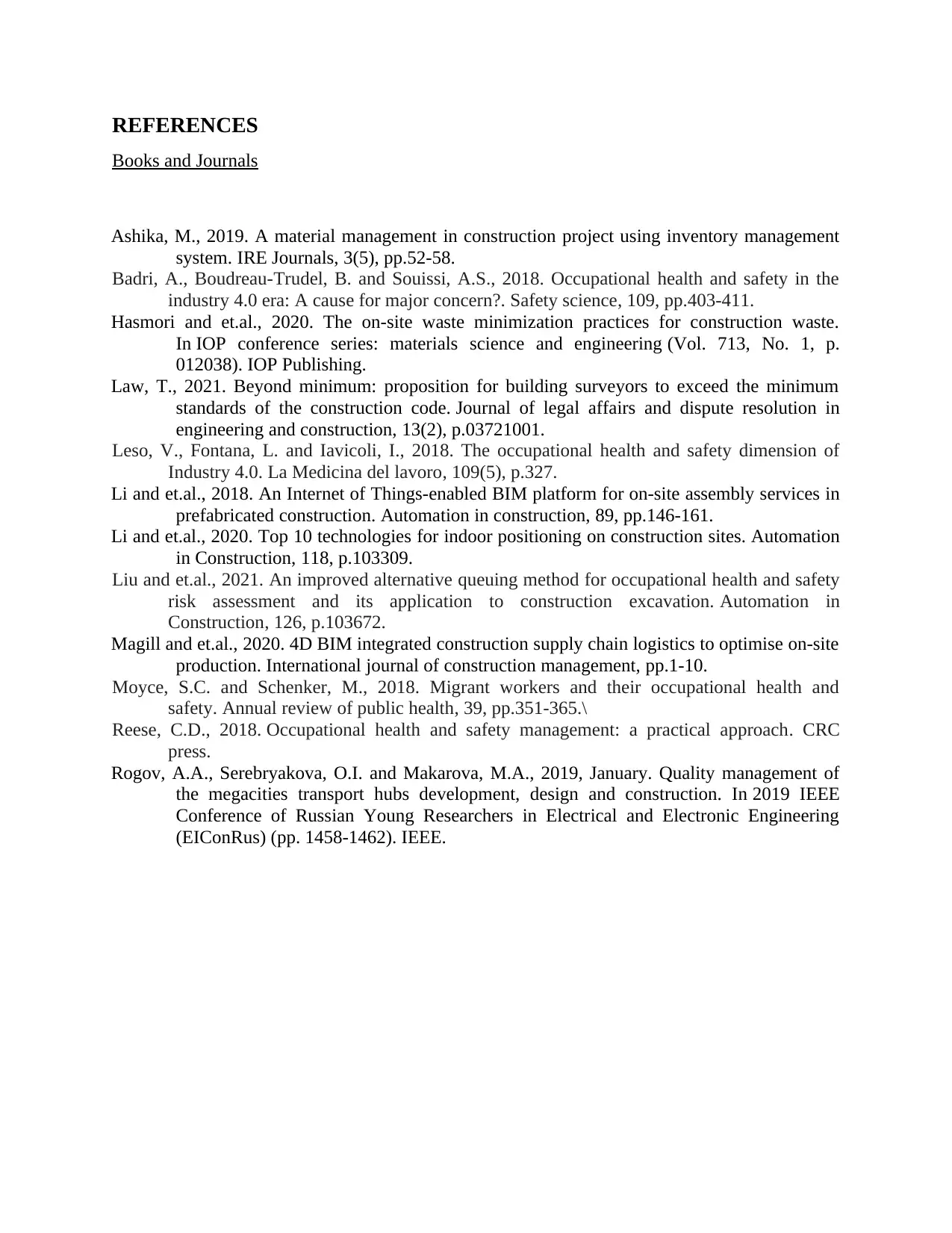
REFERENCES
Books and Journals
Ashika, M., 2019. A material management in construction project using inventory management
system. IRE Journals, 3(5), pp.52-58.
Badri, A., Boudreau-Trudel, B. and Souissi, A.S., 2018. Occupational health and safety in the
industry 4.0 era: A cause for major concern?. Safety science, 109, pp.403-411.
Hasmori and et.al., 2020. The on-site waste minimization practices for construction waste.
In IOP conference series: materials science and engineering (Vol. 713, No. 1, p.
012038). IOP Publishing.
Law, T., 2021. Beyond minimum: proposition for building surveyors to exceed the minimum
standards of the construction code. Journal of legal affairs and dispute resolution in
engineering and construction, 13(2), p.03721001.
Leso, V., Fontana, L. and Iavicoli, I., 2018. The occupational health and safety dimension of
Industry 4.0. La Medicina del lavoro, 109(5), p.327.
Li and et.al., 2018. An Internet of Things-enabled BIM platform for on-site assembly services in
prefabricated construction. Automation in construction, 89, pp.146-161.
Li and et.al., 2020. Top 10 technologies for indoor positioning on construction sites. Automation
in Construction, 118, p.103309.
Liu and et.al., 2021. An improved alternative queuing method for occupational health and safety
risk assessment and its application to construction excavation. Automation in
Construction, 126, p.103672.
Magill and et.al., 2020. 4D BIM integrated construction supply chain logistics to optimise on-site
production. International journal of construction management, pp.1-10.
Moyce, S.C. and Schenker, M., 2018. Migrant workers and their occupational health and
safety. Annual review of public health, 39, pp.351-365.\
Reese, C.D., 2018. Occupational health and safety management: a practical approach. CRC
press.
Rogov, A.A., Serebryakova, O.I. and Makarova, M.A., 2019, January. Quality management of
the megacities transport hubs development, design and construction. In 2019 IEEE
Conference of Russian Young Researchers in Electrical and Electronic Engineering
(EIConRus) (pp. 1458-1462). IEEE.
Books and Journals
Ashika, M., 2019. A material management in construction project using inventory management
system. IRE Journals, 3(5), pp.52-58.
Badri, A., Boudreau-Trudel, B. and Souissi, A.S., 2018. Occupational health and safety in the
industry 4.0 era: A cause for major concern?. Safety science, 109, pp.403-411.
Hasmori and et.al., 2020. The on-site waste minimization practices for construction waste.
In IOP conference series: materials science and engineering (Vol. 713, No. 1, p.
012038). IOP Publishing.
Law, T., 2021. Beyond minimum: proposition for building surveyors to exceed the minimum
standards of the construction code. Journal of legal affairs and dispute resolution in
engineering and construction, 13(2), p.03721001.
Leso, V., Fontana, L. and Iavicoli, I., 2018. The occupational health and safety dimension of
Industry 4.0. La Medicina del lavoro, 109(5), p.327.
Li and et.al., 2018. An Internet of Things-enabled BIM platform for on-site assembly services in
prefabricated construction. Automation in construction, 89, pp.146-161.
Li and et.al., 2020. Top 10 technologies for indoor positioning on construction sites. Automation
in Construction, 118, p.103309.
Liu and et.al., 2021. An improved alternative queuing method for occupational health and safety
risk assessment and its application to construction excavation. Automation in
Construction, 126, p.103672.
Magill and et.al., 2020. 4D BIM integrated construction supply chain logistics to optimise on-site
production. International journal of construction management, pp.1-10.
Moyce, S.C. and Schenker, M., 2018. Migrant workers and their occupational health and
safety. Annual review of public health, 39, pp.351-365.\
Reese, C.D., 2018. Occupational health and safety management: a practical approach. CRC
press.
Rogov, A.A., Serebryakova, O.I. and Makarova, M.A., 2019, January. Quality management of
the megacities transport hubs development, design and construction. In 2019 IEEE
Conference of Russian Young Researchers in Electrical and Electronic Engineering
(EIConRus) (pp. 1458-1462). IEEE.
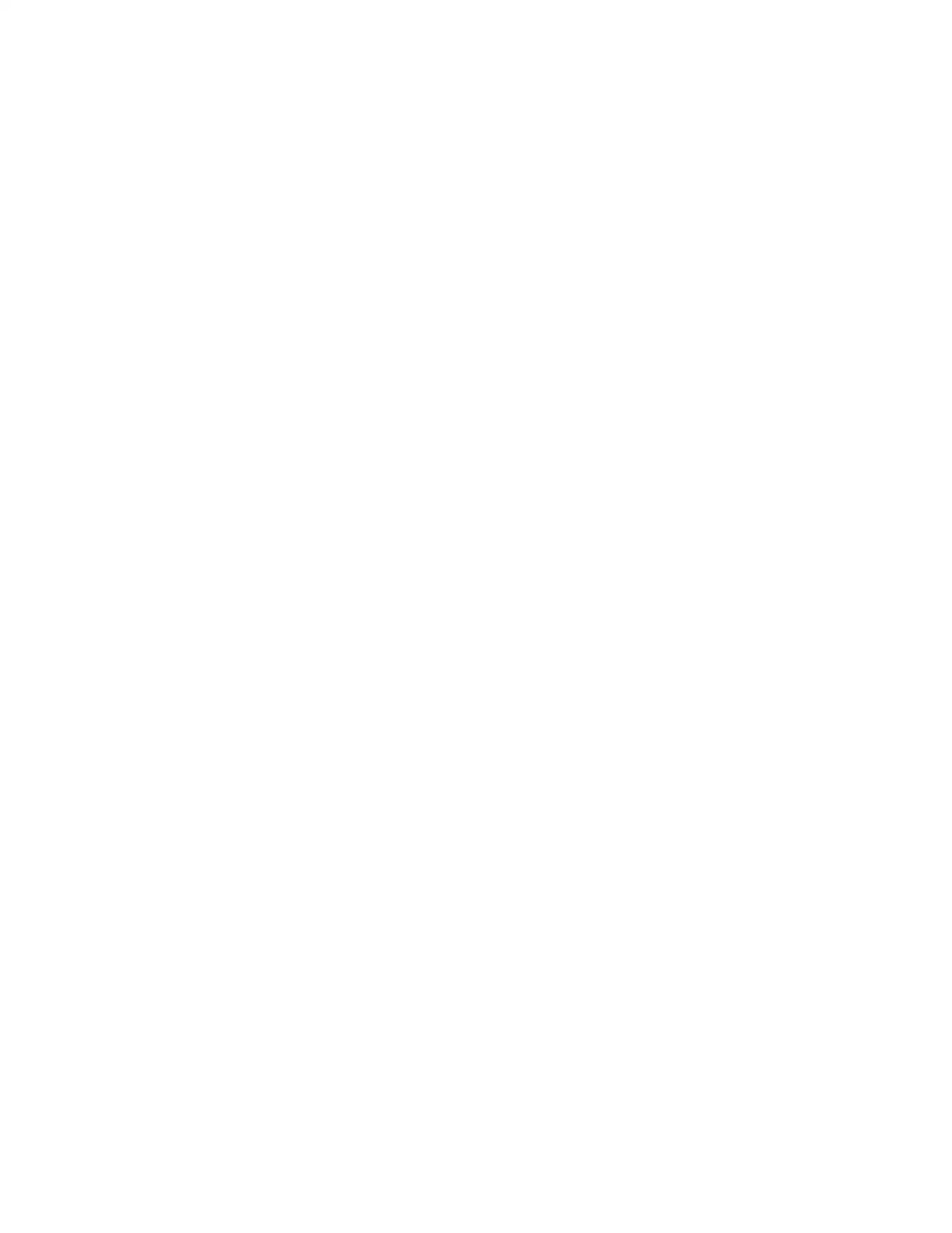
1 out of 15
![[object Object]](/_next/image/?url=%2F_next%2Fstatic%2Fmedia%2Flogo.6d15ce61.png&w=640&q=75)
Your All-in-One AI-Powered Toolkit for Academic Success.
 +13062052269
info@desklib.com
Available 24*7 on WhatsApp / Email
Unlock your academic potential
© 2024  |  Zucol Services PVT LTD  |  All rights reserved.