Brunel University ME551 Building Management Control Systems Assignment
VerifiedAdded on 2023/06/03
|11
|2174
|414
Project
AI Summary
This assignment, for the MSc in Building Services Engineering module ME551 at Brunel University, focuses on the control of a room's heating system. It begins with an analysis of an open-loop system, modeling the radiator's heat output and its effect on room temperature using a first-order syste...
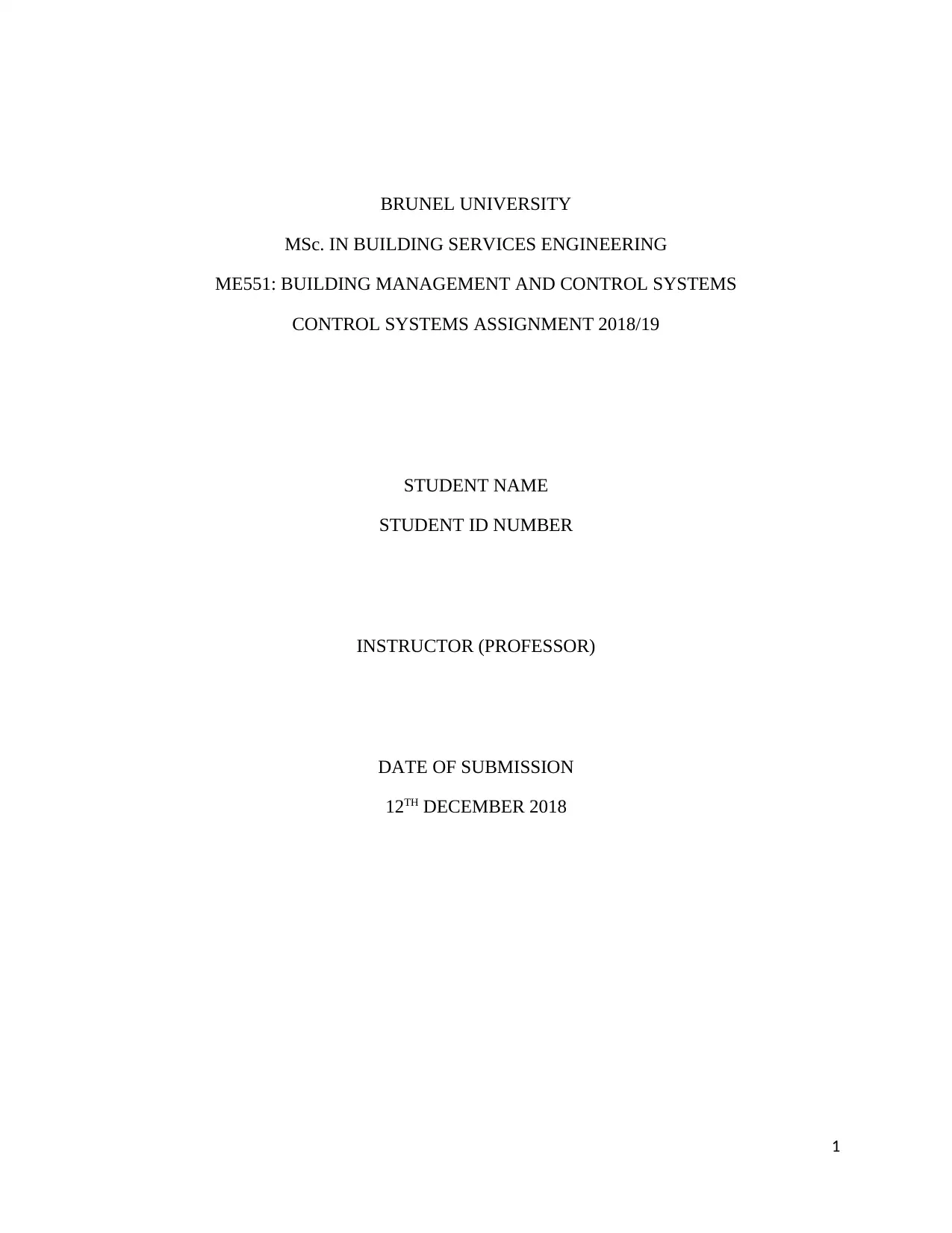
BRUNEL UNIVERSITY
MSc. IN BUILDING SERVICES ENGINEERING
ME551: BUILDING MANAGEMENT AND CONTROL SYSTEMS
CONTROL SYSTEMS ASSIGNMENT 2018/19
STUDENT NAME
STUDENT ID NUMBER
INSTRUCTOR (PROFESSOR)
DATE OF SUBMISSION
12TH DECEMBER 2018
1
MSc. IN BUILDING SERVICES ENGINEERING
ME551: BUILDING MANAGEMENT AND CONTROL SYSTEMS
CONTROL SYSTEMS ASSIGNMENT 2018/19
STUDENT NAME
STUDENT ID NUMBER
INSTRUCTOR (PROFESSOR)
DATE OF SUBMISSION
12TH DECEMBER 2018
1
Paraphrase This Document
Need a fresh take? Get an instant paraphrase of this document with our AI Paraphraser
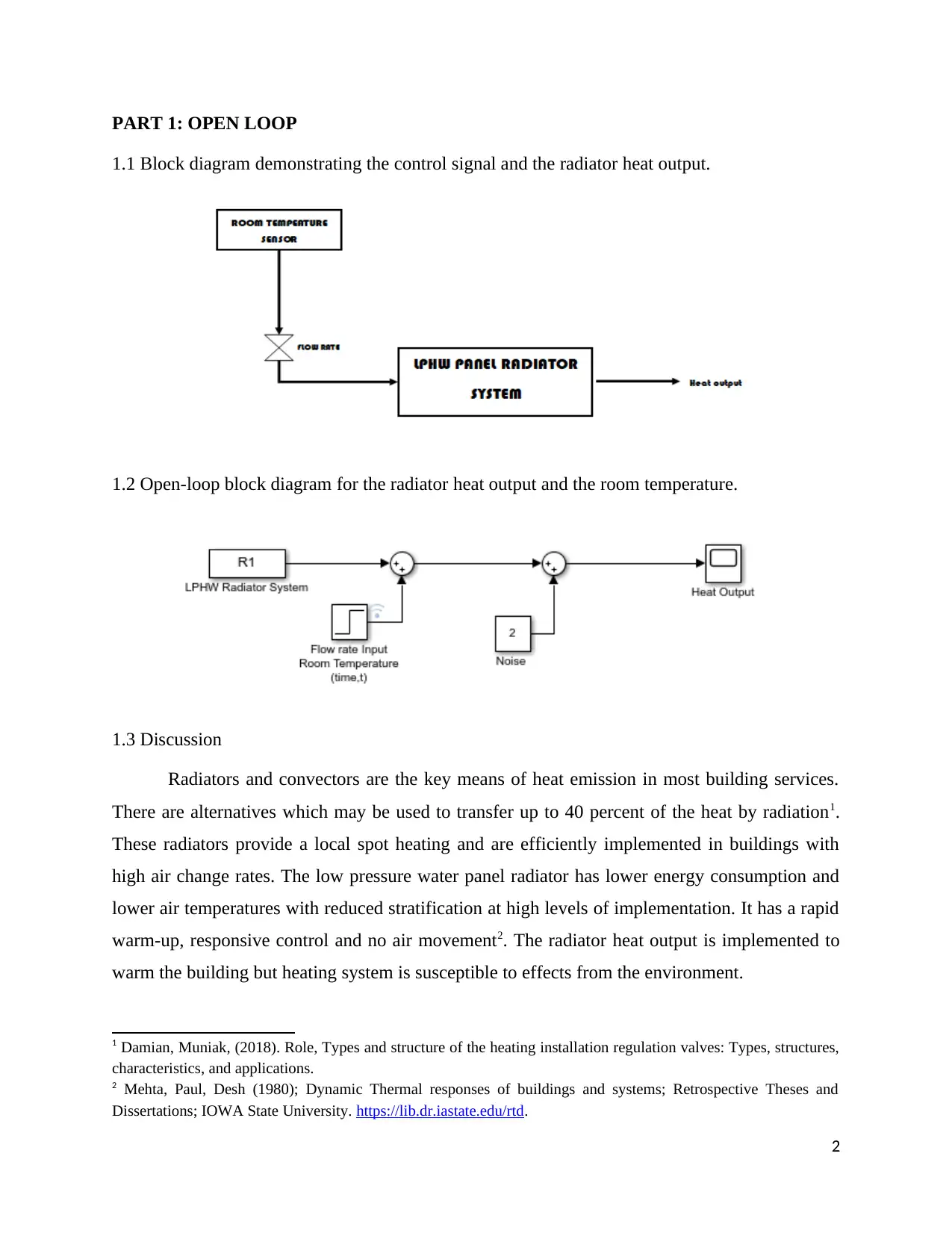
PART 1: OPEN LOOP
1.1 Block diagram demonstrating the control signal and the radiator heat output.
1.2 Open-loop block diagram for the radiator heat output and the room temperature.
1.3 Discussion
Radiators and convectors are the key means of heat emission in most building services.
There are alternatives which may be used to transfer up to 40 percent of the heat by radiation1.
These radiators provide a local spot heating and are efficiently implemented in buildings with
high air change rates. The low pressure water panel radiator has lower energy consumption and
lower air temperatures with reduced stratification at high levels of implementation. It has a rapid
warm-up, responsive control and no air movement2. The radiator heat output is implemented to
warm the building but heating system is susceptible to effects from the environment.
1 Damian, Muniak, (2018). Role, Types and structure of the heating installation regulation valves: Types, structures,
characteristics, and applications.
2 Mehta, Paul, Desh (1980); Dynamic Thermal responses of buildings and systems; Retrospective Theses and
Dissertations; IOWA State University. https://lib.dr.iastate.edu/rtd.
2
1.1 Block diagram demonstrating the control signal and the radiator heat output.
1.2 Open-loop block diagram for the radiator heat output and the room temperature.
1.3 Discussion
Radiators and convectors are the key means of heat emission in most building services.
There are alternatives which may be used to transfer up to 40 percent of the heat by radiation1.
These radiators provide a local spot heating and are efficiently implemented in buildings with
high air change rates. The low pressure water panel radiator has lower energy consumption and
lower air temperatures with reduced stratification at high levels of implementation. It has a rapid
warm-up, responsive control and no air movement2. The radiator heat output is implemented to
warm the building but heating system is susceptible to effects from the environment.
1 Damian, Muniak, (2018). Role, Types and structure of the heating installation regulation valves: Types, structures,
characteristics, and applications.
2 Mehta, Paul, Desh (1980); Dynamic Thermal responses of buildings and systems; Retrospective Theses and
Dissertations; IOWA State University. https://lib.dr.iastate.edu/rtd.
2
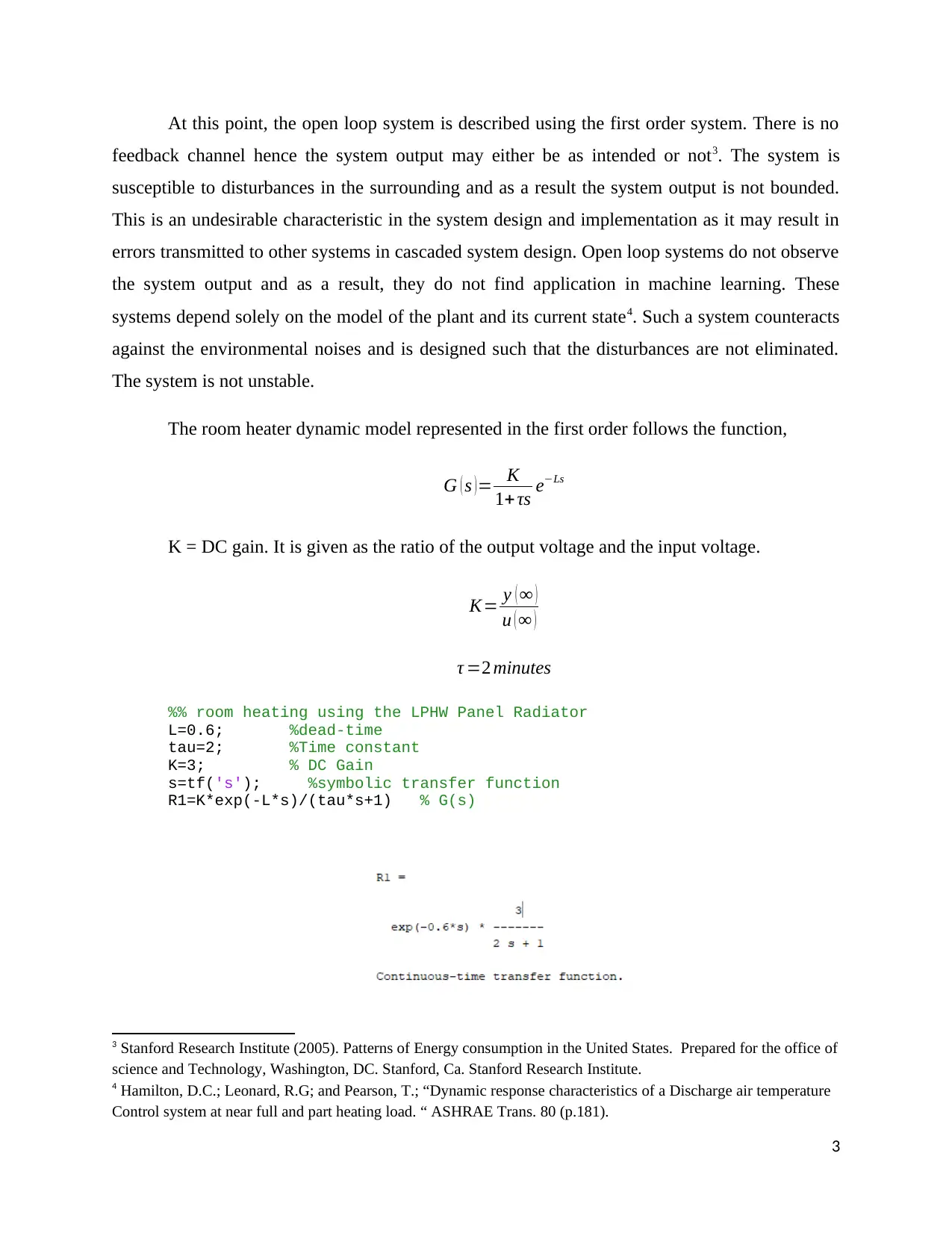
At this point, the open loop system is described using the first order system. There is no
feedback channel hence the system output may either be as intended or not3. The system is
susceptible to disturbances in the surrounding and as a result the system output is not bounded.
This is an undesirable characteristic in the system design and implementation as it may result in
errors transmitted to other systems in cascaded system design. Open loop systems do not observe
the system output and as a result, they do not find application in machine learning. These
systems depend solely on the model of the plant and its current state4. Such a system counteracts
against the environmental noises and is designed such that the disturbances are not eliminated.
The system is not unstable.
The room heater dynamic model represented in the first order follows the function,
G ( s ) = K
1+ τs e−Ls
K = DC gain. It is given as the ratio of the output voltage and the input voltage.
K= y ( ∞ )
u ( ∞ )
τ =2 minutes
%% room heating using the LPHW Panel Radiator
L=0.6; %dead-time
tau=2; %Time constant
K=3; % DC Gain
s=tf('s'); %symbolic transfer function
R1=K*exp(-L*s)/(tau*s+1) % G(s)
3 Stanford Research Institute (2005). Patterns of Energy consumption in the United States. Prepared for the office of
science and Technology, Washington, DC. Stanford, Ca. Stanford Research Institute.
4 Hamilton, D.C.; Leonard, R.G; and Pearson, T.; “Dynamic response characteristics of a Discharge air temperature
Control system at near full and part heating load. “ ASHRAE Trans. 80 (p.181).
3
feedback channel hence the system output may either be as intended or not3. The system is
susceptible to disturbances in the surrounding and as a result the system output is not bounded.
This is an undesirable characteristic in the system design and implementation as it may result in
errors transmitted to other systems in cascaded system design. Open loop systems do not observe
the system output and as a result, they do not find application in machine learning. These
systems depend solely on the model of the plant and its current state4. Such a system counteracts
against the environmental noises and is designed such that the disturbances are not eliminated.
The system is not unstable.
The room heater dynamic model represented in the first order follows the function,
G ( s ) = K
1+ τs e−Ls
K = DC gain. It is given as the ratio of the output voltage and the input voltage.
K= y ( ∞ )
u ( ∞ )
τ =2 minutes
%% room heating using the LPHW Panel Radiator
L=0.6; %dead-time
tau=2; %Time constant
K=3; % DC Gain
s=tf('s'); %symbolic transfer function
R1=K*exp(-L*s)/(tau*s+1) % G(s)
3 Stanford Research Institute (2005). Patterns of Energy consumption in the United States. Prepared for the office of
science and Technology, Washington, DC. Stanford, Ca. Stanford Research Institute.
4 Hamilton, D.C.; Leonard, R.G; and Pearson, T.; “Dynamic response characteristics of a Discharge air temperature
Control system at near full and part heating load. “ ASHRAE Trans. 80 (p.181).
3
⊘ This is a preview!⊘
Do you want full access?
Subscribe today to unlock all pages.

Trusted by 1+ million students worldwide
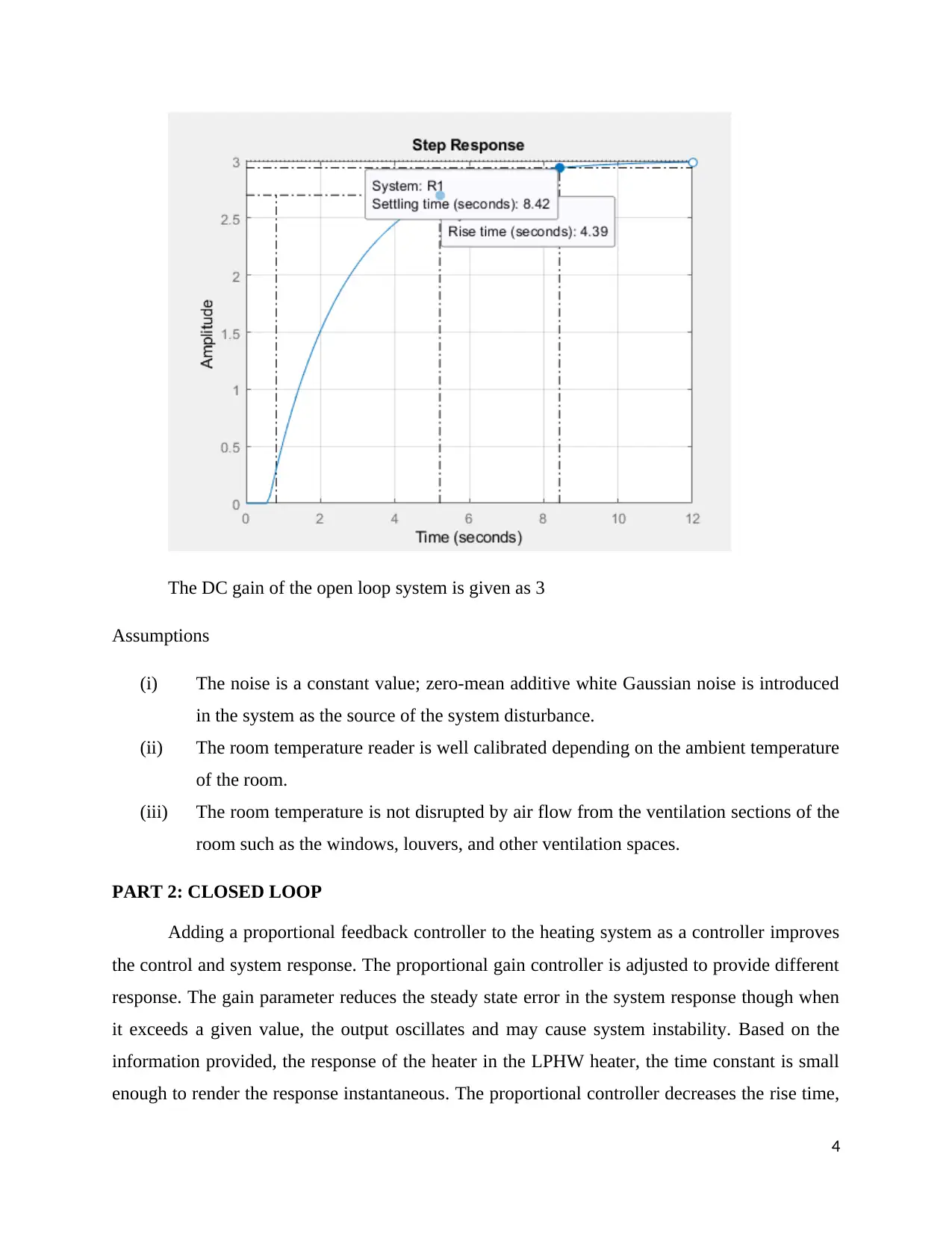
The DC gain of the open loop system is given as 3
Assumptions
(i) The noise is a constant value; zero-mean additive white Gaussian noise is introduced
in the system as the source of the system disturbance.
(ii) The room temperature reader is well calibrated depending on the ambient temperature
of the room.
(iii) The room temperature is not disrupted by air flow from the ventilation sections of the
room such as the windows, louvers, and other ventilation spaces.
PART 2: CLOSED LOOP
Adding a proportional feedback controller to the heating system as a controller improves
the control and system response. The proportional gain controller is adjusted to provide different
response. The gain parameter reduces the steady state error in the system response though when
it exceeds a given value, the output oscillates and may cause system instability. Based on the
information provided, the response of the heater in the LPHW heater, the time constant is small
enough to render the response instantaneous. The proportional controller decreases the rise time,
4
Assumptions
(i) The noise is a constant value; zero-mean additive white Gaussian noise is introduced
in the system as the source of the system disturbance.
(ii) The room temperature reader is well calibrated depending on the ambient temperature
of the room.
(iii) The room temperature is not disrupted by air flow from the ventilation sections of the
room such as the windows, louvers, and other ventilation spaces.
PART 2: CLOSED LOOP
Adding a proportional feedback controller to the heating system as a controller improves
the control and system response. The proportional gain controller is adjusted to provide different
response. The gain parameter reduces the steady state error in the system response though when
it exceeds a given value, the output oscillates and may cause system instability. Based on the
information provided, the response of the heater in the LPHW heater, the time constant is small
enough to render the response instantaneous. The proportional controller decreases the rise time,
4
Paraphrase This Document
Need a fresh take? Get an instant paraphrase of this document with our AI Paraphraser
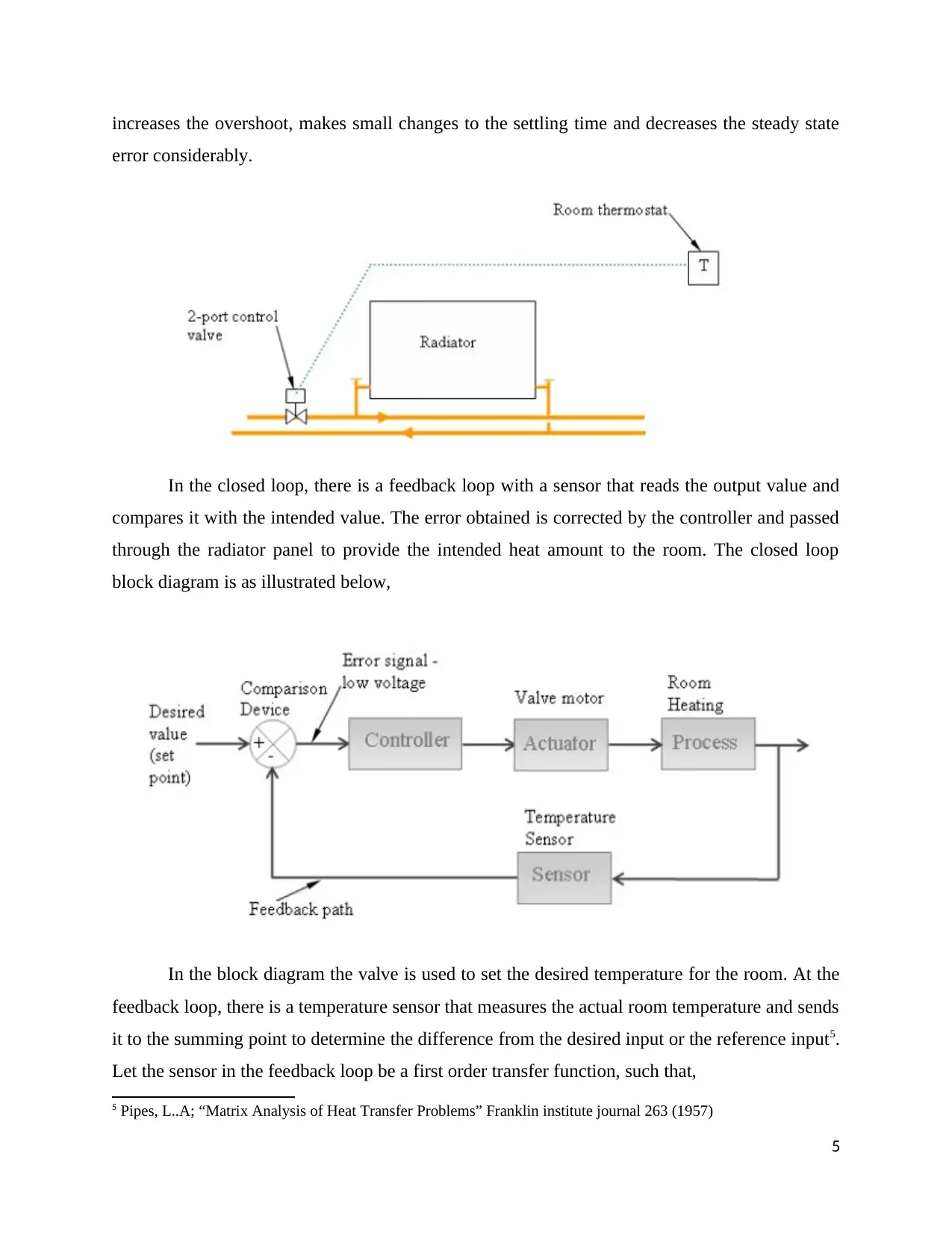
increases the overshoot, makes small changes to the settling time and decreases the steady state
error considerably.
In the closed loop, there is a feedback loop with a sensor that reads the output value and
compares it with the intended value. The error obtained is corrected by the controller and passed
through the radiator panel to provide the intended heat amount to the room. The closed loop
block diagram is as illustrated below,
In the block diagram the valve is used to set the desired temperature for the room. At the
feedback loop, there is a temperature sensor that measures the actual room temperature and sends
it to the summing point to determine the difference from the desired input or the reference input5.
Let the sensor in the feedback loop be a first order transfer function, such that,
5 Pipes, L..A; “Matrix Analysis of Heat Transfer Problems” Franklin institute journal 263 (1957)
5
error considerably.
In the closed loop, there is a feedback loop with a sensor that reads the output value and
compares it with the intended value. The error obtained is corrected by the controller and passed
through the radiator panel to provide the intended heat amount to the room. The closed loop
block diagram is as illustrated below,
In the block diagram the valve is used to set the desired temperature for the room. At the
feedback loop, there is a temperature sensor that measures the actual room temperature and sends
it to the summing point to determine the difference from the desired input or the reference input5.
Let the sensor in the feedback loop be a first order transfer function, such that,
5 Pipes, L..A; “Matrix Analysis of Heat Transfer Problems” Franklin institute journal 263 (1957)
5
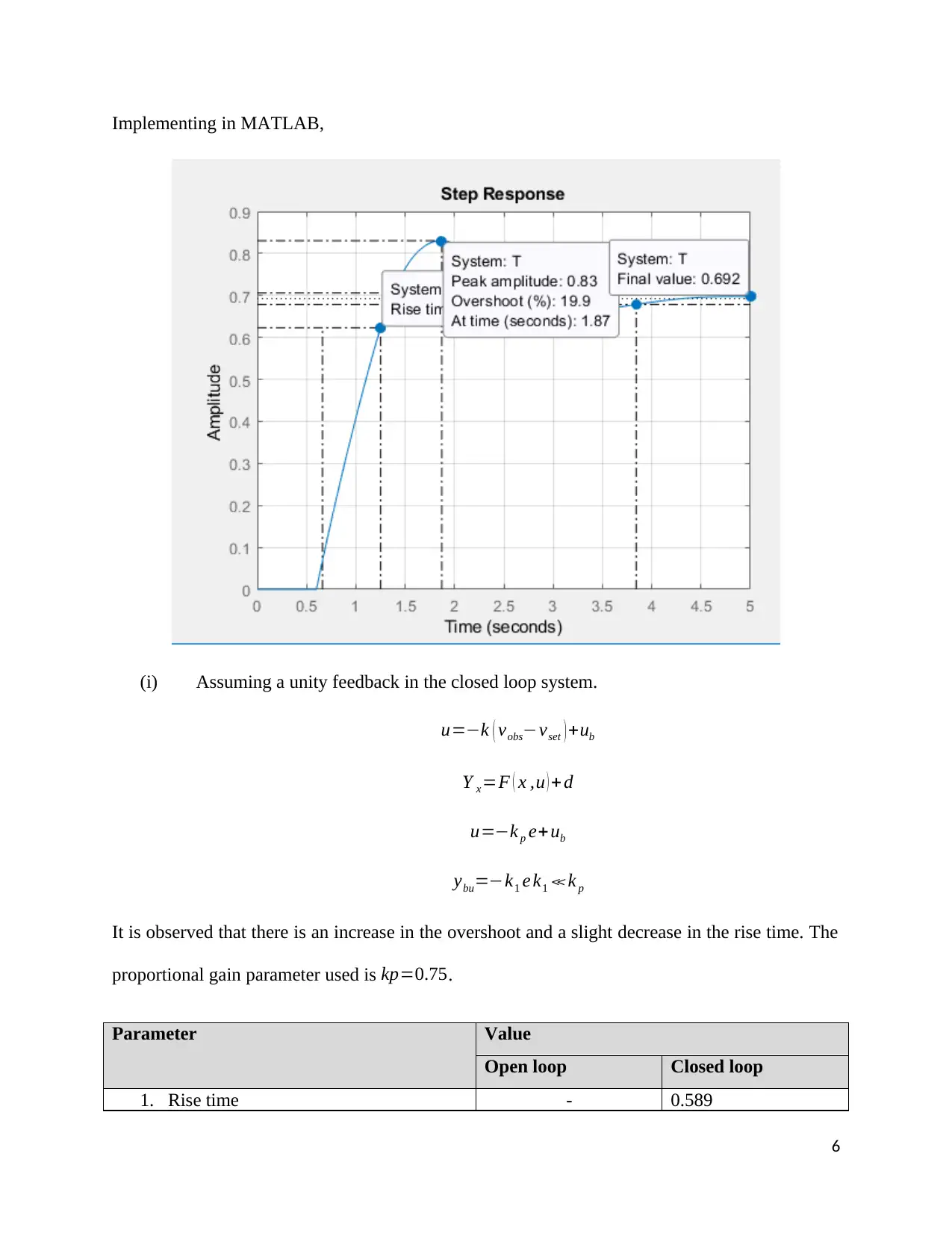
Implementing in MATLAB,
(i) Assuming a unity feedback in the closed loop system.
u=−k ( vobs−vset ) +ub
Y x=F ( x ,u ) + d
u=−k p e+ub
ybu=−k1 e k1 ≪ k p
It is observed that there is an increase in the overshoot and a slight decrease in the rise time. The
proportional gain parameter used is kp=0.75.
Parameter Value
Open loop Closed loop
1. Rise time - 0.589
6
(i) Assuming a unity feedback in the closed loop system.
u=−k ( vobs−vset ) +ub
Y x=F ( x ,u ) + d
u=−k p e+ub
ybu=−k1 e k1 ≪ k p
It is observed that there is an increase in the overshoot and a slight decrease in the rise time. The
proportional gain parameter used is kp=0.75.
Parameter Value
Open loop Closed loop
1. Rise time - 0.589
6
⊘ This is a preview!⊘
Do you want full access?
Subscribe today to unlock all pages.

Trusted by 1+ million students worldwide
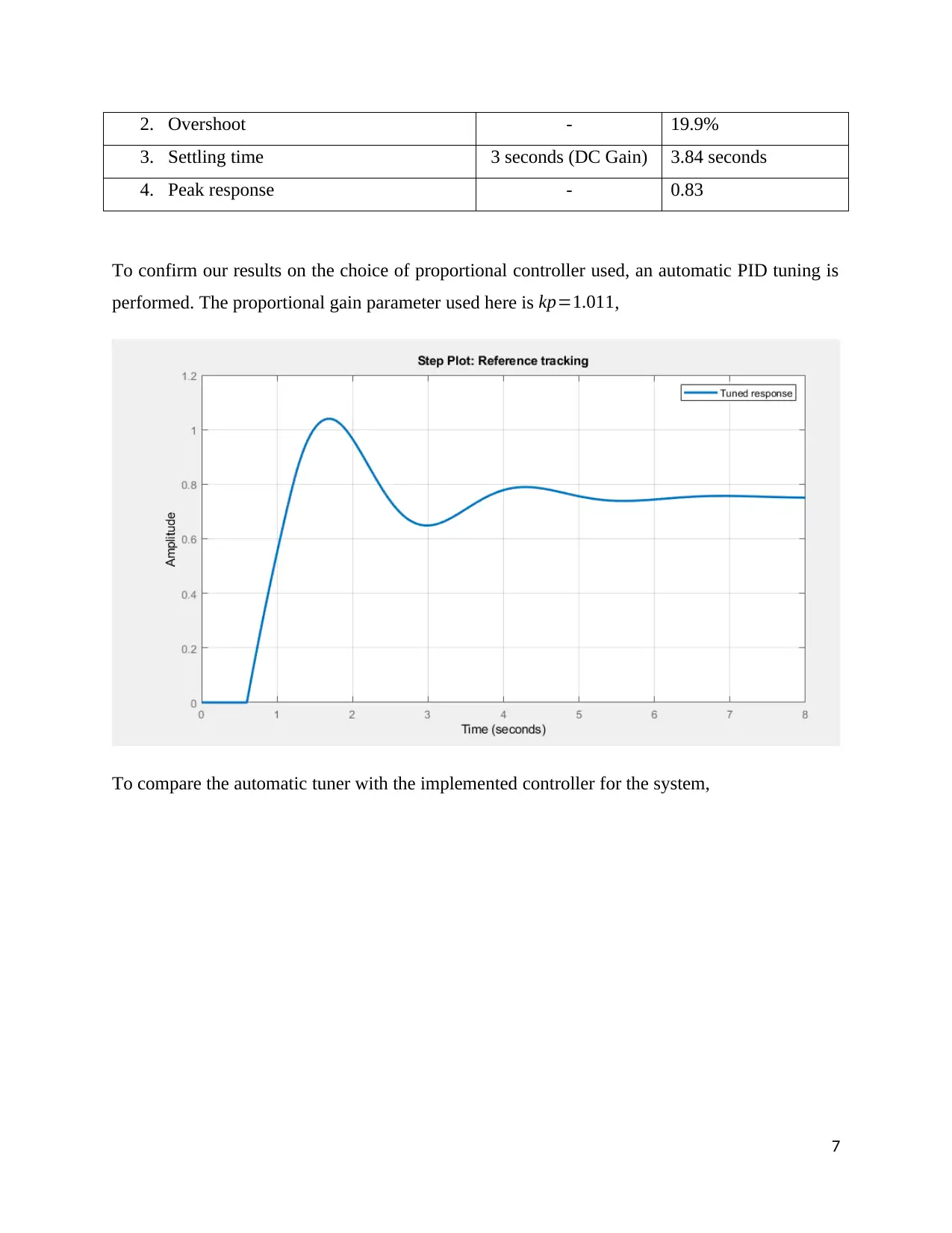
2. Overshoot - 19.9%
3. Settling time 3 seconds (DC Gain) 3.84 seconds
4. Peak response - 0.83
To confirm our results on the choice of proportional controller used, an automatic PID tuning is
performed. The proportional gain parameter used here is kp=1.011,
To compare the automatic tuner with the implemented controller for the system,
7
3. Settling time 3 seconds (DC Gain) 3.84 seconds
4. Peak response - 0.83
To confirm our results on the choice of proportional controller used, an automatic PID tuning is
performed. The proportional gain parameter used here is kp=1.011,
To compare the automatic tuner with the implemented controller for the system,
7
Paraphrase This Document
Need a fresh take? Get an instant paraphrase of this document with our AI Paraphraser
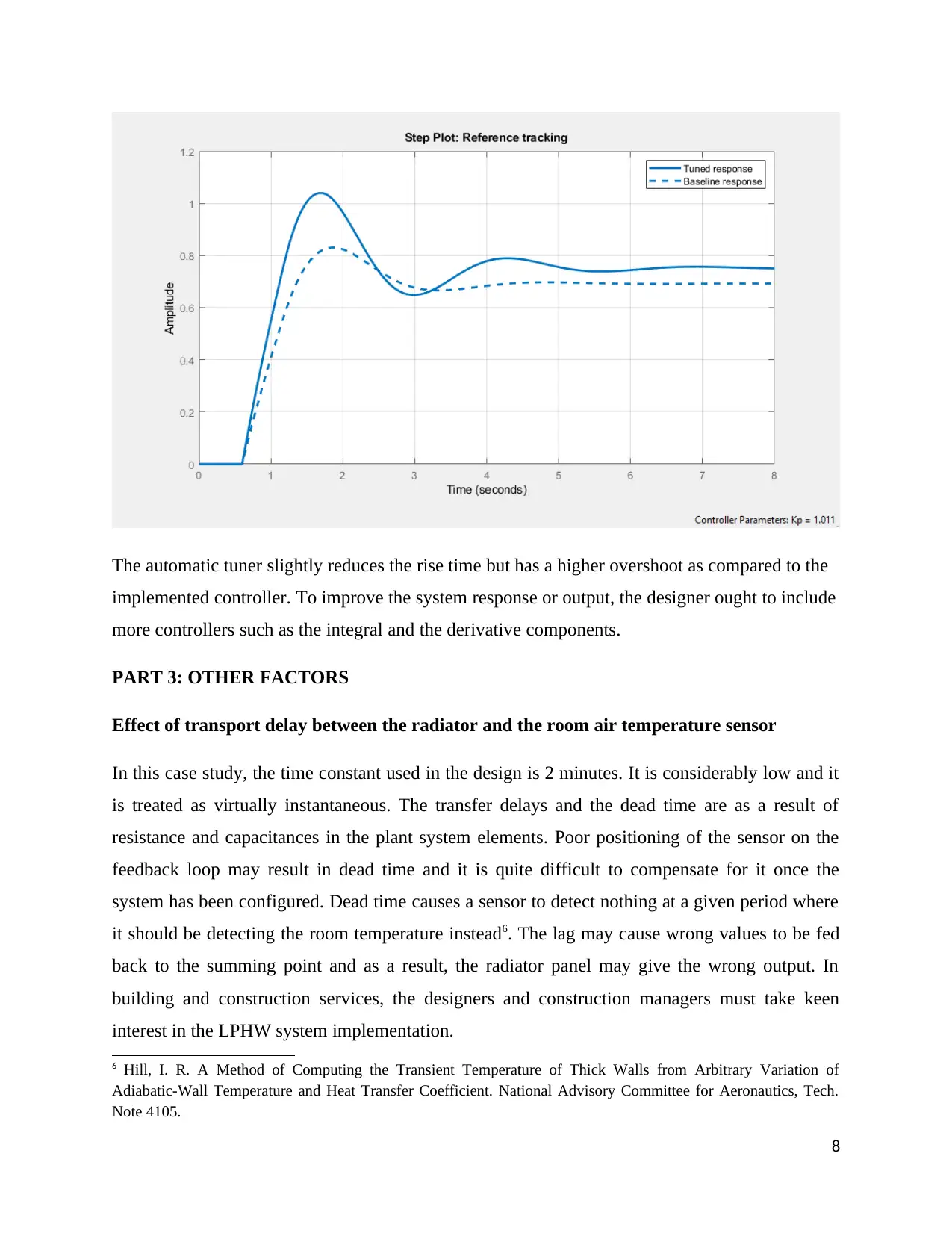
The automatic tuner slightly reduces the rise time but has a higher overshoot as compared to the
implemented controller. To improve the system response or output, the designer ought to include
more controllers such as the integral and the derivative components.
PART 3: OTHER FACTORS
Effect of transport delay between the radiator and the room air temperature sensor
In this case study, the time constant used in the design is 2 minutes. It is considerably low and it
is treated as virtually instantaneous. The transfer delays and the dead time are as a result of
resistance and capacitances in the plant system elements. Poor positioning of the sensor on the
feedback loop may result in dead time and it is quite difficult to compensate for it once the
system has been configured. Dead time causes a sensor to detect nothing at a given period where
it should be detecting the room temperature instead6. The lag may cause wrong values to be fed
back to the summing point and as a result, the radiator panel may give the wrong output. In
building and construction services, the designers and construction managers must take keen
interest in the LPHW system implementation.
6 Hill, I. R. A Method of Computing the Transient Temperature of Thick Walls from Arbitrary Variation of
Adiabatic-Wall Temperature and Heat Transfer Coefficient. National Advisory Committee for Aeronautics, Tech.
Note 4105.
8
implemented controller. To improve the system response or output, the designer ought to include
more controllers such as the integral and the derivative components.
PART 3: OTHER FACTORS
Effect of transport delay between the radiator and the room air temperature sensor
In this case study, the time constant used in the design is 2 minutes. It is considerably low and it
is treated as virtually instantaneous. The transfer delays and the dead time are as a result of
resistance and capacitances in the plant system elements. Poor positioning of the sensor on the
feedback loop may result in dead time and it is quite difficult to compensate for it once the
system has been configured. Dead time causes a sensor to detect nothing at a given period where
it should be detecting the room temperature instead6. The lag may cause wrong values to be fed
back to the summing point and as a result, the radiator panel may give the wrong output. In
building and construction services, the designers and construction managers must take keen
interest in the LPHW system implementation.
6 Hill, I. R. A Method of Computing the Transient Temperature of Thick Walls from Arbitrary Variation of
Adiabatic-Wall Temperature and Heat Transfer Coefficient. National Advisory Committee for Aeronautics, Tech.
Note 4105.
8
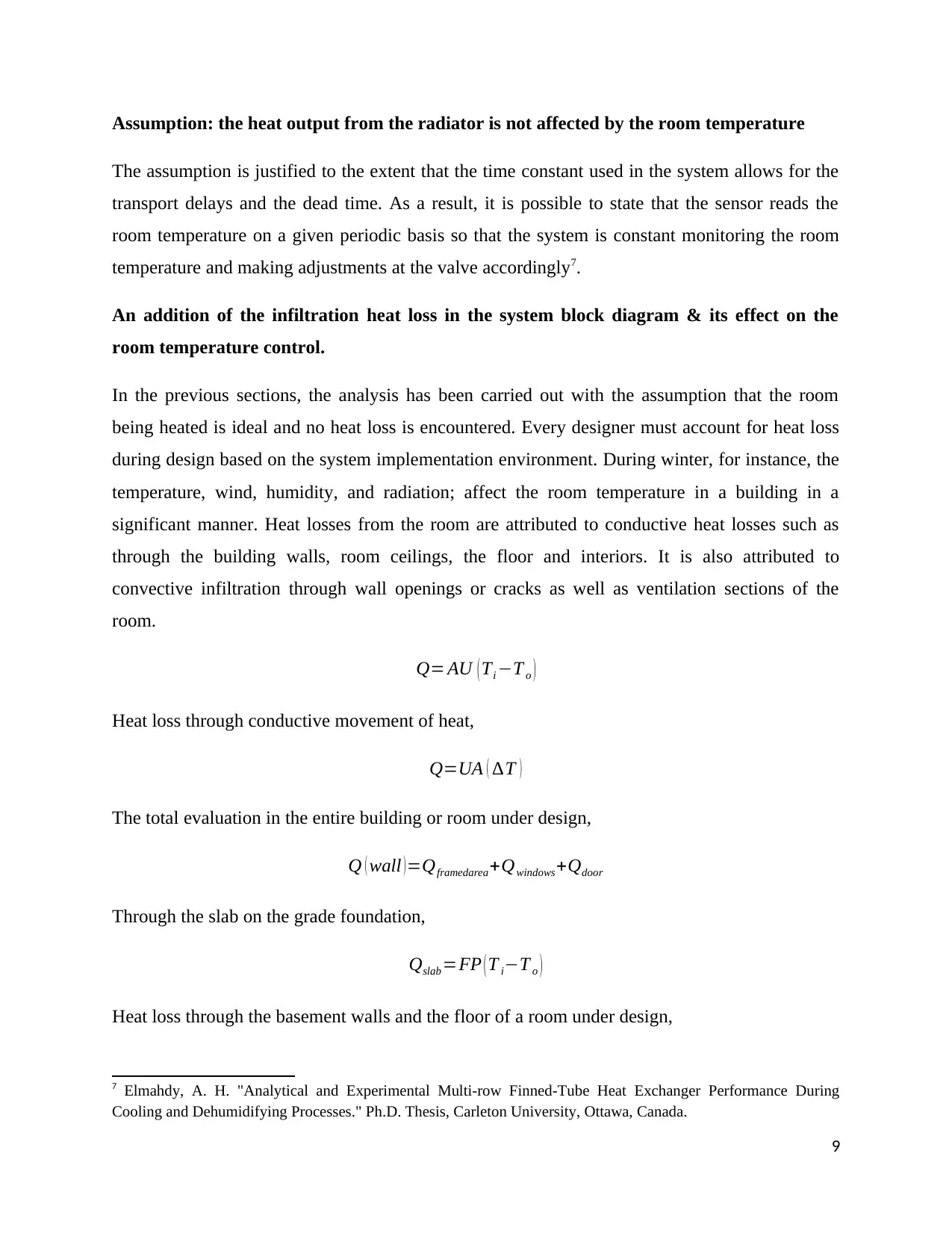
Assumption: the heat output from the radiator is not affected by the room temperature
The assumption is justified to the extent that the time constant used in the system allows for the
transport delays and the dead time. As a result, it is possible to state that the sensor reads the
room temperature on a given periodic basis so that the system is constant monitoring the room
temperature and making adjustments at the valve accordingly7.
An addition of the infiltration heat loss in the system block diagram & its effect on the
room temperature control.
In the previous sections, the analysis has been carried out with the assumption that the room
being heated is ideal and no heat loss is encountered. Every designer must account for heat loss
during design based on the system implementation environment. During winter, for instance, the
temperature, wind, humidity, and radiation; affect the room temperature in a building in a
significant manner. Heat losses from the room are attributed to conductive heat losses such as
through the building walls, room ceilings, the floor and interiors. It is also attributed to
convective infiltration through wall openings or cracks as well as ventilation sections of the
room.
Q= AU ( Ti −T o )
Heat loss through conductive movement of heat,
Q=UA ( ∆T )
The total evaluation in the entire building or room under design,
Q ( wall ) =Qframedarea+Qwindows+Qdoor
Through the slab on the grade foundation,
Qslab =FP ( T i−T o )
Heat loss through the basement walls and the floor of a room under design,
7 Elmahdy, A. H. "Analytical and Experimental Multi-row Finned-Tube Heat Exchanger Performance During
Cooling and Dehumidifying Processes." Ph.D. Thesis, Carleton University, Ottawa, Canada.
9
The assumption is justified to the extent that the time constant used in the system allows for the
transport delays and the dead time. As a result, it is possible to state that the sensor reads the
room temperature on a given periodic basis so that the system is constant monitoring the room
temperature and making adjustments at the valve accordingly7.
An addition of the infiltration heat loss in the system block diagram & its effect on the
room temperature control.
In the previous sections, the analysis has been carried out with the assumption that the room
being heated is ideal and no heat loss is encountered. Every designer must account for heat loss
during design based on the system implementation environment. During winter, for instance, the
temperature, wind, humidity, and radiation; affect the room temperature in a building in a
significant manner. Heat losses from the room are attributed to conductive heat losses such as
through the building walls, room ceilings, the floor and interiors. It is also attributed to
convective infiltration through wall openings or cracks as well as ventilation sections of the
room.
Q= AU ( Ti −T o )
Heat loss through conductive movement of heat,
Q=UA ( ∆T )
The total evaluation in the entire building or room under design,
Q ( wall ) =Qframedarea+Qwindows+Qdoor
Through the slab on the grade foundation,
Qslab =FP ( T i−T o )
Heat loss through the basement walls and the floor of a room under design,
7 Elmahdy, A. H. "Analytical and Experimental Multi-row Finned-Tube Heat Exchanger Performance During
Cooling and Dehumidifying Processes." Ph.D. Thesis, Carleton University, Ottawa, Canada.
9
⊘ This is a preview!⊘
Do you want full access?
Subscribe today to unlock all pages.

Trusted by 1+ million students worldwide
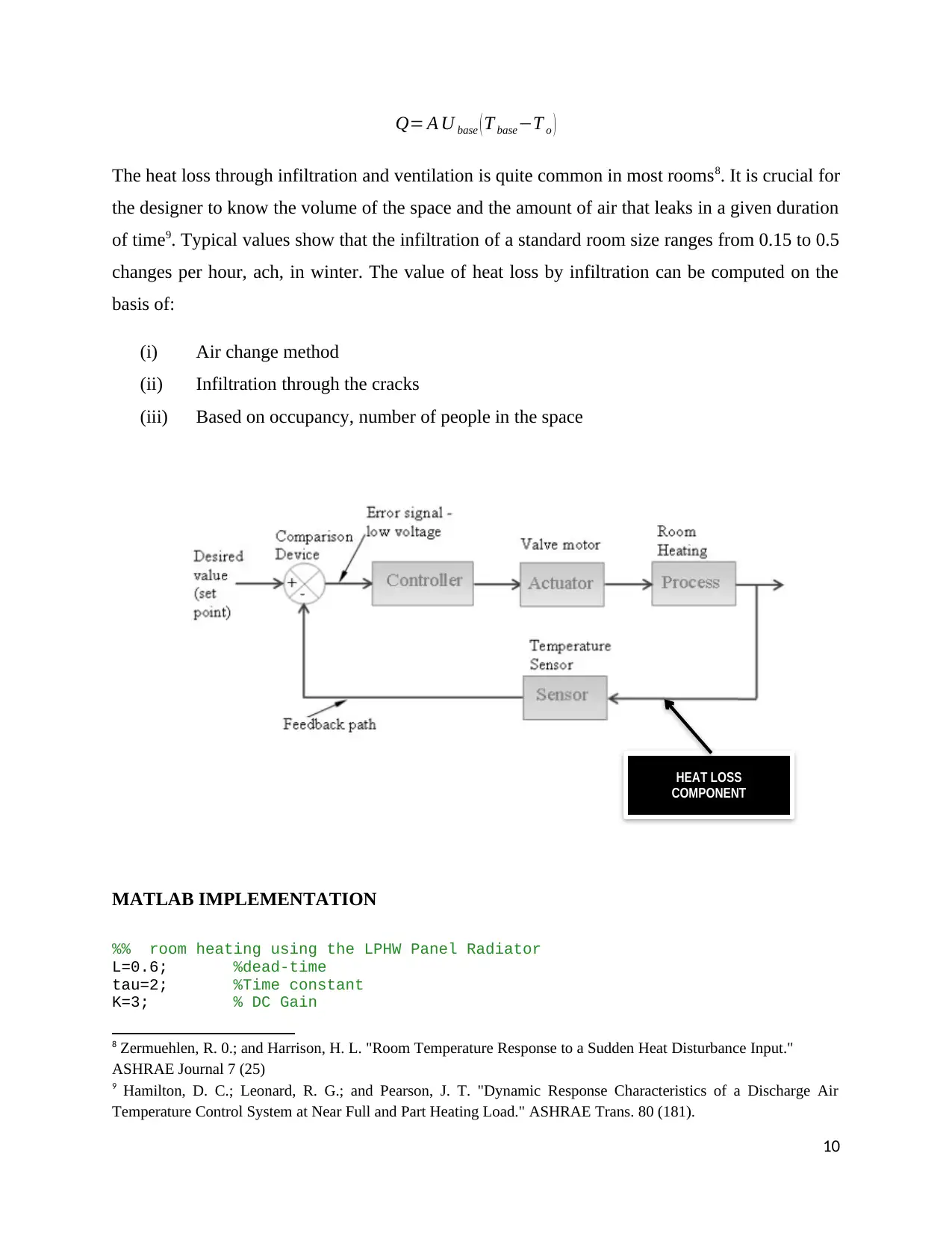
Q= A U base ( T base−T o )
The heat loss through infiltration and ventilation is quite common in most rooms8. It is crucial for
the designer to know the volume of the space and the amount of air that leaks in a given duration
of time9. Typical values show that the infiltration of a standard room size ranges from 0.15 to 0.5
changes per hour, ach, in winter. The value of heat loss by infiltration can be computed on the
basis of:
(i) Air change method
(ii) Infiltration through the cracks
(iii) Based on occupancy, number of people in the space
MATLAB IMPLEMENTATION
%% room heating using the LPHW Panel Radiator
L=0.6; %dead-time
tau=2; %Time constant
K=3; % DC Gain
8 Zermuehlen, R. 0.; and Harrison, H. L. "Room Temperature Response to a Sudden Heat Disturbance Input."
ASHRAE Journal 7 (25)
9 Hamilton, D. C.; Leonard, R. G.; and Pearson, J. T. "Dynamic Response Characteristics of a Discharge Air
Temperature Control System at Near Full and Part Heating Load." ASHRAE Trans. 80 (181).
10
HEAT LOSS
COMPONENT
The heat loss through infiltration and ventilation is quite common in most rooms8. It is crucial for
the designer to know the volume of the space and the amount of air that leaks in a given duration
of time9. Typical values show that the infiltration of a standard room size ranges from 0.15 to 0.5
changes per hour, ach, in winter. The value of heat loss by infiltration can be computed on the
basis of:
(i) Air change method
(ii) Infiltration through the cracks
(iii) Based on occupancy, number of people in the space
MATLAB IMPLEMENTATION
%% room heating using the LPHW Panel Radiator
L=0.6; %dead-time
tau=2; %Time constant
K=3; % DC Gain
8 Zermuehlen, R. 0.; and Harrison, H. L. "Room Temperature Response to a Sudden Heat Disturbance Input."
ASHRAE Journal 7 (25)
9 Hamilton, D. C.; Leonard, R. G.; and Pearson, J. T. "Dynamic Response Characteristics of a Discharge Air
Temperature Control System at Near Full and Part Heating Load." ASHRAE Trans. 80 (181).
10
HEAT LOSS
COMPONENT
Paraphrase This Document
Need a fresh take? Get an instant paraphrase of this document with our AI Paraphraser
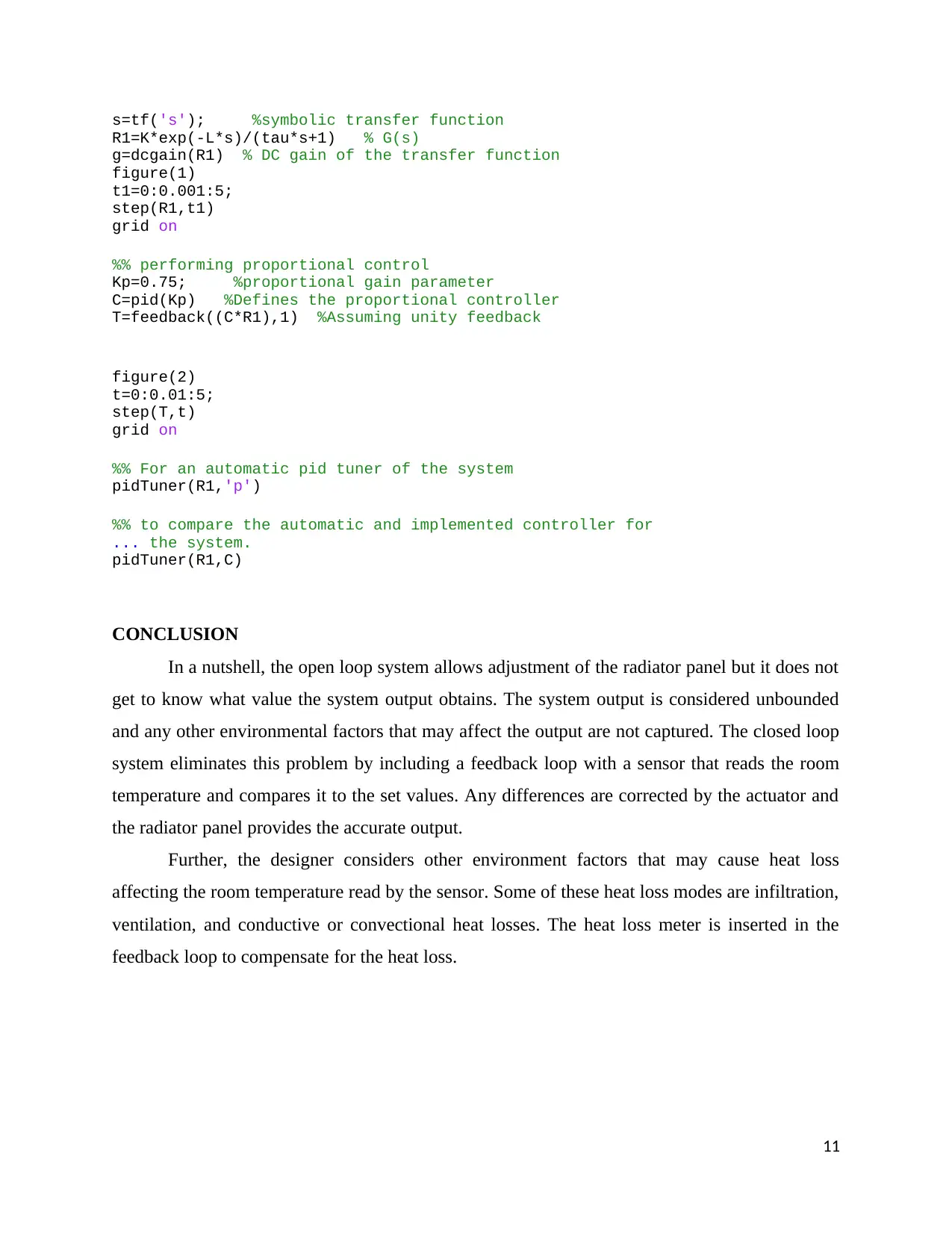
s=tf('s'); %symbolic transfer function
R1=K*exp(-L*s)/(tau*s+1) % G(s)
g=dcgain(R1) % DC gain of the transfer function
figure(1)
t1=0:0.001:5;
step(R1,t1)
grid on
%% performing proportional control
Kp=0.75; %proportional gain parameter
C=pid(Kp) %Defines the proportional controller
T=feedback((C*R1),1) %Assuming unity feedback
figure(2)
t=0:0.01:5;
step(T,t)
grid on
%% For an automatic pid tuner of the system
pidTuner(R1,'p')
%% to compare the automatic and implemented controller for
... the system.
pidTuner(R1,C)
CONCLUSION
In a nutshell, the open loop system allows adjustment of the radiator panel but it does not
get to know what value the system output obtains. The system output is considered unbounded
and any other environmental factors that may affect the output are not captured. The closed loop
system eliminates this problem by including a feedback loop with a sensor that reads the room
temperature and compares it to the set values. Any differences are corrected by the actuator and
the radiator panel provides the accurate output.
Further, the designer considers other environment factors that may cause heat loss
affecting the room temperature read by the sensor. Some of these heat loss modes are infiltration,
ventilation, and conductive or convectional heat losses. The heat loss meter is inserted in the
feedback loop to compensate for the heat loss.
11
R1=K*exp(-L*s)/(tau*s+1) % G(s)
g=dcgain(R1) % DC gain of the transfer function
figure(1)
t1=0:0.001:5;
step(R1,t1)
grid on
%% performing proportional control
Kp=0.75; %proportional gain parameter
C=pid(Kp) %Defines the proportional controller
T=feedback((C*R1),1) %Assuming unity feedback
figure(2)
t=0:0.01:5;
step(T,t)
grid on
%% For an automatic pid tuner of the system
pidTuner(R1,'p')
%% to compare the automatic and implemented controller for
... the system.
pidTuner(R1,C)
CONCLUSION
In a nutshell, the open loop system allows adjustment of the radiator panel but it does not
get to know what value the system output obtains. The system output is considered unbounded
and any other environmental factors that may affect the output are not captured. The closed loop
system eliminates this problem by including a feedback loop with a sensor that reads the room
temperature and compares it to the set values. Any differences are corrected by the actuator and
the radiator panel provides the accurate output.
Further, the designer considers other environment factors that may cause heat loss
affecting the room temperature read by the sensor. Some of these heat loss modes are infiltration,
ventilation, and conductive or convectional heat losses. The heat loss meter is inserted in the
feedback loop to compensate for the heat loss.
11
1 out of 11

Your All-in-One AI-Powered Toolkit for Academic Success.
+13062052269
info@desklib.com
Available 24*7 on WhatsApp / Email
Unlock your academic potential
© 2024 | Zucol Services PVT LTD | All rights reserved.