UiTM CMT 610: Bulk Polymerization of PMMA - Lab Report 2023/2024
VerifiedAdded on 2024/01/16
|10
|1882
|460
Practical Assignment
AI Summary
This report details an experiment on the bulk polymerization of methyl methacrylate (MMA) to polymethyl methacrylate (PMMA) using benzoyl peroxide as an initiator. The experiment investigated the effects of initiator weight, polymerization temperature, and polymerization time on the polymerization yield. The procedure involved dissolving benzoyl peroxide in MMA, heating the mixture in a water bath, and then drying the resulting polymer. The results showed that increasing the initiator concentration, temperature, and polymerization time generally increased the yield, up to a certain point. The highest polymerization yield was achieved with 1.0g of benzoyl peroxide, at 80Β°C, and with a polymerization time of 60 minutes. Potential sources of error, such as human error in measurements and contamination, were also discussed, along with suggestions for improvement. The experiment successfully demonstrated the bulk polymerization of MMA to PMMA and determined the optimal conditions for this process, providing valuable insights into polymer chemistry.
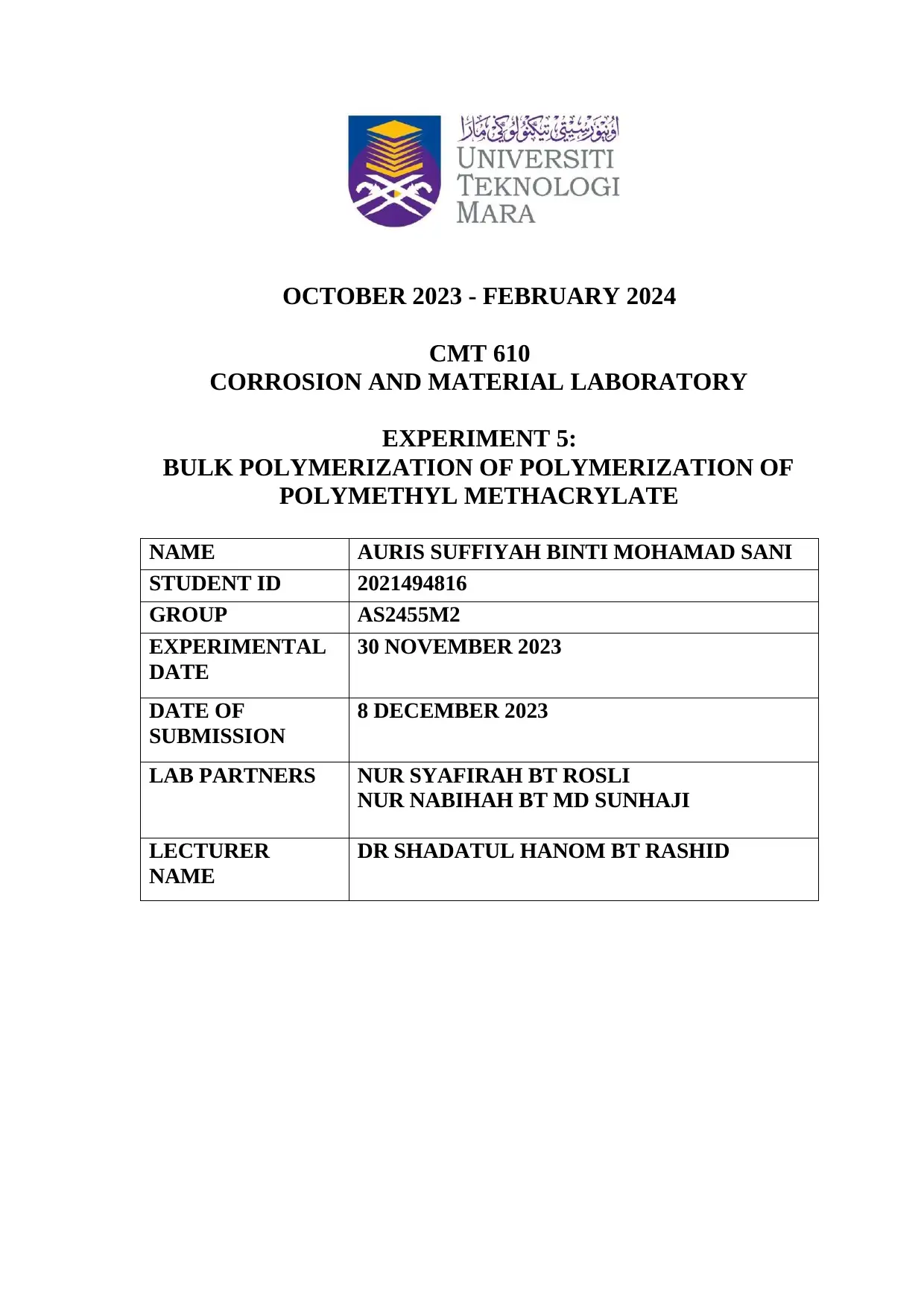
OCTOBER 2023 - FEBRUARY 2024
CMT 610
CORROSION AND MATERIAL LABORATORY
EXPERIMENT 5:
BULK POLYMERIZATION OF POLYMERIZATION OF
POLYMETHYL METHACRYLATE
NAME AURIS SUFFIYAH BINTI MOHAMAD SANI
STUDENT ID 2021494816
GROUP AS2455M2
EXPERIMENTAL
DATE
30 NOVEMBER 2023
DATE OF
SUBMISSION
8 DECEMBER 2023
LAB PARTNERS NUR SYAFIRAH BT ROSLI
NUR NABIHAH BT MD SUNHAJI
LECTURER
NAME
DR SHADATUL HANOM BT RASHID
CMT 610
CORROSION AND MATERIAL LABORATORY
EXPERIMENT 5:
BULK POLYMERIZATION OF POLYMERIZATION OF
POLYMETHYL METHACRYLATE
NAME AURIS SUFFIYAH BINTI MOHAMAD SANI
STUDENT ID 2021494816
GROUP AS2455M2
EXPERIMENTAL
DATE
30 NOVEMBER 2023
DATE OF
SUBMISSION
8 DECEMBER 2023
LAB PARTNERS NUR SYAFIRAH BT ROSLI
NUR NABIHAH BT MD SUNHAJI
LECTURER
NAME
DR SHADATUL HANOM BT RASHID
Paraphrase This Document
Need a fresh take? Get an instant paraphrase of this document with our AI Paraphraser
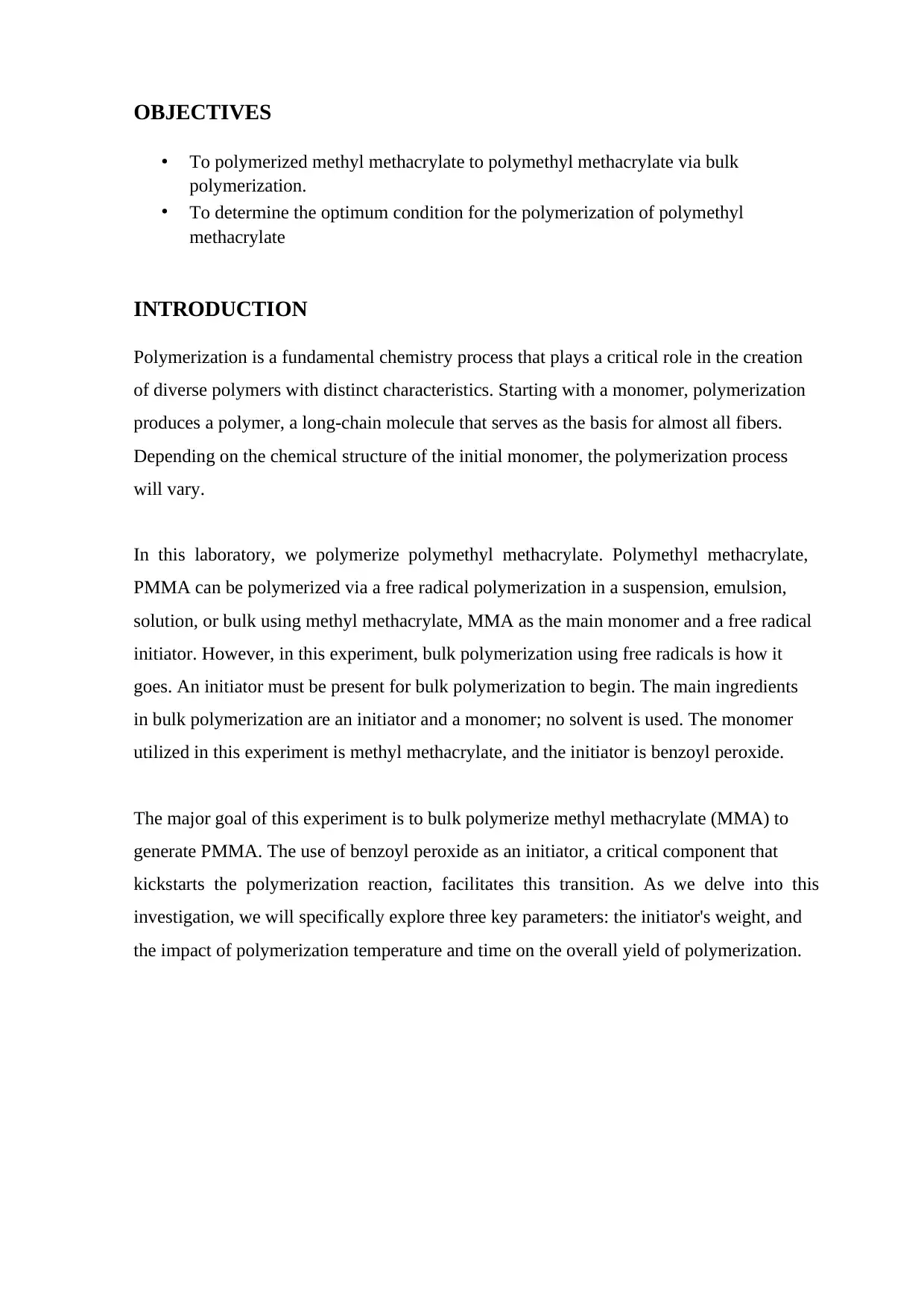
OBJECTIVES
β’ To polymerized methyl methacrylate to polymethyl methacrylate via bulk
polymerization.
β’ To determine the optimum condition for the polymerization of polymethyl
methacrylate
INTRODUCTION
Polymerization is a fundamental chemistry process that plays a critical role in the creation
of diverse polymers with distinct characteristics. Starting with a monomer, polymerization
produces a polymer, a long-chain molecule that serves as the basis for almost all fibers.
Depending on the chemical structure of the initial monomer, the polymerization process
will vary.
In this laboratory, we polymerize polymethyl methacrylate. Polymethyl methacrylate,
PMMA can be polymerized via a free radical polymerization in a suspension, emulsion,
solution, or bulk using methyl methacrylate, MMA as the main monomer and a free radical
initiator. However, in this experiment, bulk polymerization using free radicals is how it
goes. An initiator must be present for bulk polymerization to begin. The main ingredients
in bulk polymerization are an initiator and a monomer; no solvent is used. The monomer
utilized in this experiment is methyl methacrylate, and the initiator is benzoyl peroxide.
The major goal of this experiment is to bulk polymerize methyl methacrylate (MMA) to
generate PMMA. The use of benzoyl peroxide as an initiator, a critical component that
kickstarts the polymerization reaction, facilitates this transition. As we delve into this
investigation, we will specifically explore three key parameters: the initiator's weight, and
the impact of polymerization temperature and time on the overall yield of polymerization.
β’ To polymerized methyl methacrylate to polymethyl methacrylate via bulk
polymerization.
β’ To determine the optimum condition for the polymerization of polymethyl
methacrylate
INTRODUCTION
Polymerization is a fundamental chemistry process that plays a critical role in the creation
of diverse polymers with distinct characteristics. Starting with a monomer, polymerization
produces a polymer, a long-chain molecule that serves as the basis for almost all fibers.
Depending on the chemical structure of the initial monomer, the polymerization process
will vary.
In this laboratory, we polymerize polymethyl methacrylate. Polymethyl methacrylate,
PMMA can be polymerized via a free radical polymerization in a suspension, emulsion,
solution, or bulk using methyl methacrylate, MMA as the main monomer and a free radical
initiator. However, in this experiment, bulk polymerization using free radicals is how it
goes. An initiator must be present for bulk polymerization to begin. The main ingredients
in bulk polymerization are an initiator and a monomer; no solvent is used. The monomer
utilized in this experiment is methyl methacrylate, and the initiator is benzoyl peroxide.
The major goal of this experiment is to bulk polymerize methyl methacrylate (MMA) to
generate PMMA. The use of benzoyl peroxide as an initiator, a critical component that
kickstarts the polymerization reaction, facilitates this transition. As we delve into this
investigation, we will specifically explore three key parameters: the initiator's weight, and
the impact of polymerization temperature and time on the overall yield of polymerization.
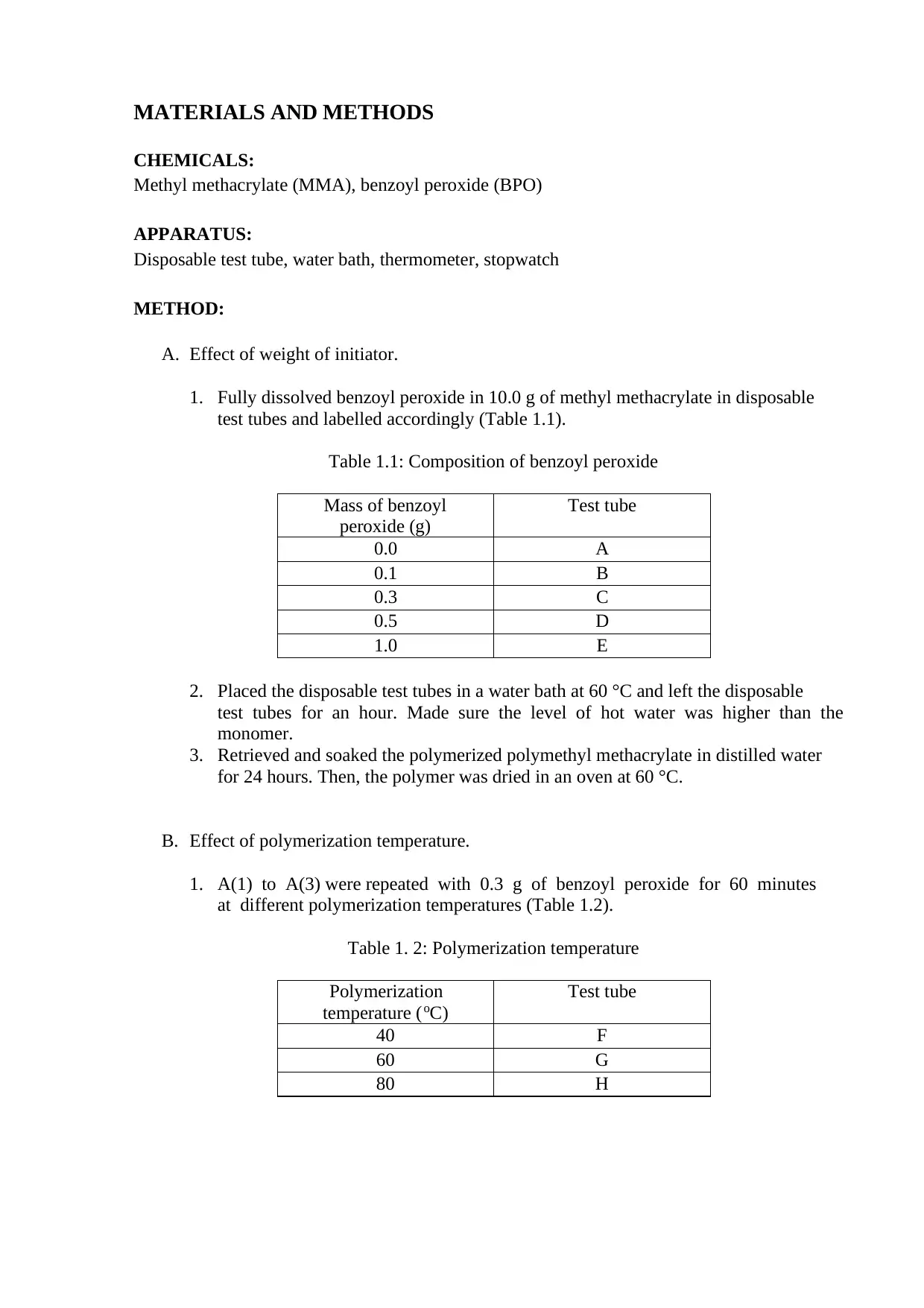
MATERIALS AND METHODS
CHEMICALS:
Methyl methacrylate (MMA), benzoyl peroxide (BPO)
APPARATUS:
Disposable test tube, water bath, thermometer, stopwatch
METHOD:
A. Effect of weight of initiator.
1. Fully dissolved benzoyl peroxide in 10.0 g of methyl methacrylate in disposable
test tubes and labelled accordingly (Table 1.1).
Table 1.1: Composition of benzoyl peroxide
Mass of benzoyl
peroxide (g)
Test tube
0.0 A
0.1 B
0.3 C
0.5 D
1.0 E
2. Placed the disposable test tubes in a water bath at 60 Β°C and left the disposable
test tubes for an hour. Made sure the level of hot water was higher than the
monomer.
3. Retrieved and soaked the polymerized polymethyl methacrylate in distilled water
for 24 hours. Then, the polymer was dried in an oven at 60 Β°C.
B. Effect of polymerization temperature.
1. A(1) to A(3) were repeated with 0.3 g of benzoyl peroxide for 60 minutes
at different polymerization temperatures (Table 1.2).
Table 1. 2: Polymerization temperature
Polymerization
temperature (oC)
Test tube
40 F
60 G
80 H
CHEMICALS:
Methyl methacrylate (MMA), benzoyl peroxide (BPO)
APPARATUS:
Disposable test tube, water bath, thermometer, stopwatch
METHOD:
A. Effect of weight of initiator.
1. Fully dissolved benzoyl peroxide in 10.0 g of methyl methacrylate in disposable
test tubes and labelled accordingly (Table 1.1).
Table 1.1: Composition of benzoyl peroxide
Mass of benzoyl
peroxide (g)
Test tube
0.0 A
0.1 B
0.3 C
0.5 D
1.0 E
2. Placed the disposable test tubes in a water bath at 60 Β°C and left the disposable
test tubes for an hour. Made sure the level of hot water was higher than the
monomer.
3. Retrieved and soaked the polymerized polymethyl methacrylate in distilled water
for 24 hours. Then, the polymer was dried in an oven at 60 Β°C.
B. Effect of polymerization temperature.
1. A(1) to A(3) were repeated with 0.3 g of benzoyl peroxide for 60 minutes
at different polymerization temperatures (Table 1.2).
Table 1. 2: Polymerization temperature
Polymerization
temperature (oC)
Test tube
40 F
60 G
80 H
β This is a preview!β
Do you want full access?
Subscribe today to unlock all pages.

Trusted by 1+ million students worldwide
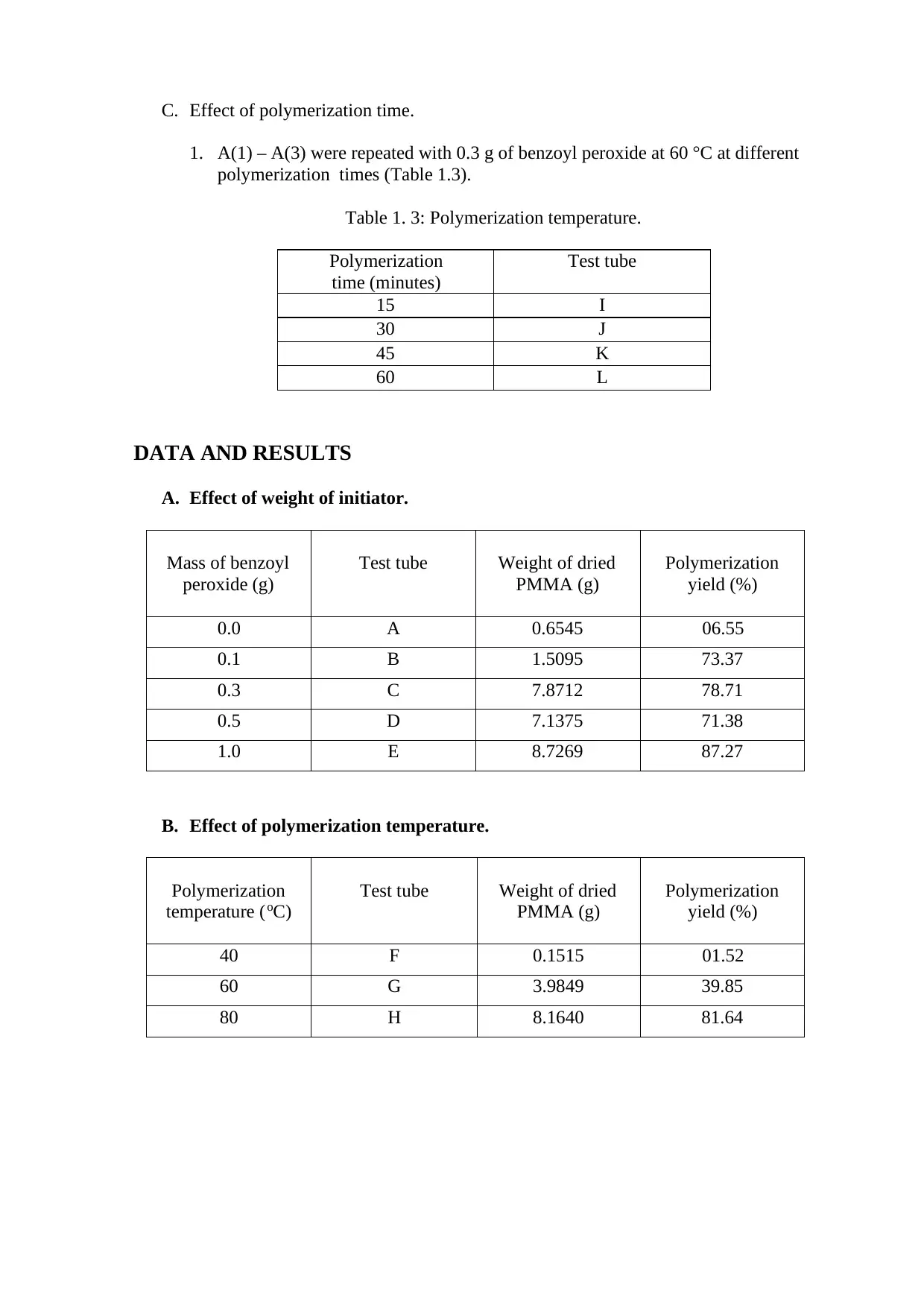
C. Effect of polymerization time.
1. A(1) β A(3) were repeated with 0.3 g of benzoyl peroxide at 60 Β°C at different
polymerization times (Table 1.3).
Table 1. 3: Polymerization temperature.
Polymerization
time (minutes)
Test tube
15 I
30 J
45 K
60 L
DATA AND RESULTS
A. Effect of weight of initiator.
Mass of benzoyl
peroxide (g)
Test tube Weight of dried
PMMA (g)
Polymerization
yield (%)
0.0 A 0.6545 06.55
0.1 B 1.5095 73.37
0.3 C 7.8712 78.71
0.5 D 7.1375 71.38
1.0 E 8.7269 87.27
B. Effect of polymerization temperature.
Polymerization
temperature (oC)
Test tube Weight of dried
PMMA (g)
Polymerization
yield (%)
40 F 0.1515 01.52
60 G 3.9849 39.85
80 H 8.1640 81.64
1. A(1) β A(3) were repeated with 0.3 g of benzoyl peroxide at 60 Β°C at different
polymerization times (Table 1.3).
Table 1. 3: Polymerization temperature.
Polymerization
time (minutes)
Test tube
15 I
30 J
45 K
60 L
DATA AND RESULTS
A. Effect of weight of initiator.
Mass of benzoyl
peroxide (g)
Test tube Weight of dried
PMMA (g)
Polymerization
yield (%)
0.0 A 0.6545 06.55
0.1 B 1.5095 73.37
0.3 C 7.8712 78.71
0.5 D 7.1375 71.38
1.0 E 8.7269 87.27
B. Effect of polymerization temperature.
Polymerization
temperature (oC)
Test tube Weight of dried
PMMA (g)
Polymerization
yield (%)
40 F 0.1515 01.52
60 G 3.9849 39.85
80 H 8.1640 81.64
Paraphrase This Document
Need a fresh take? Get an instant paraphrase of this document with our AI Paraphraser
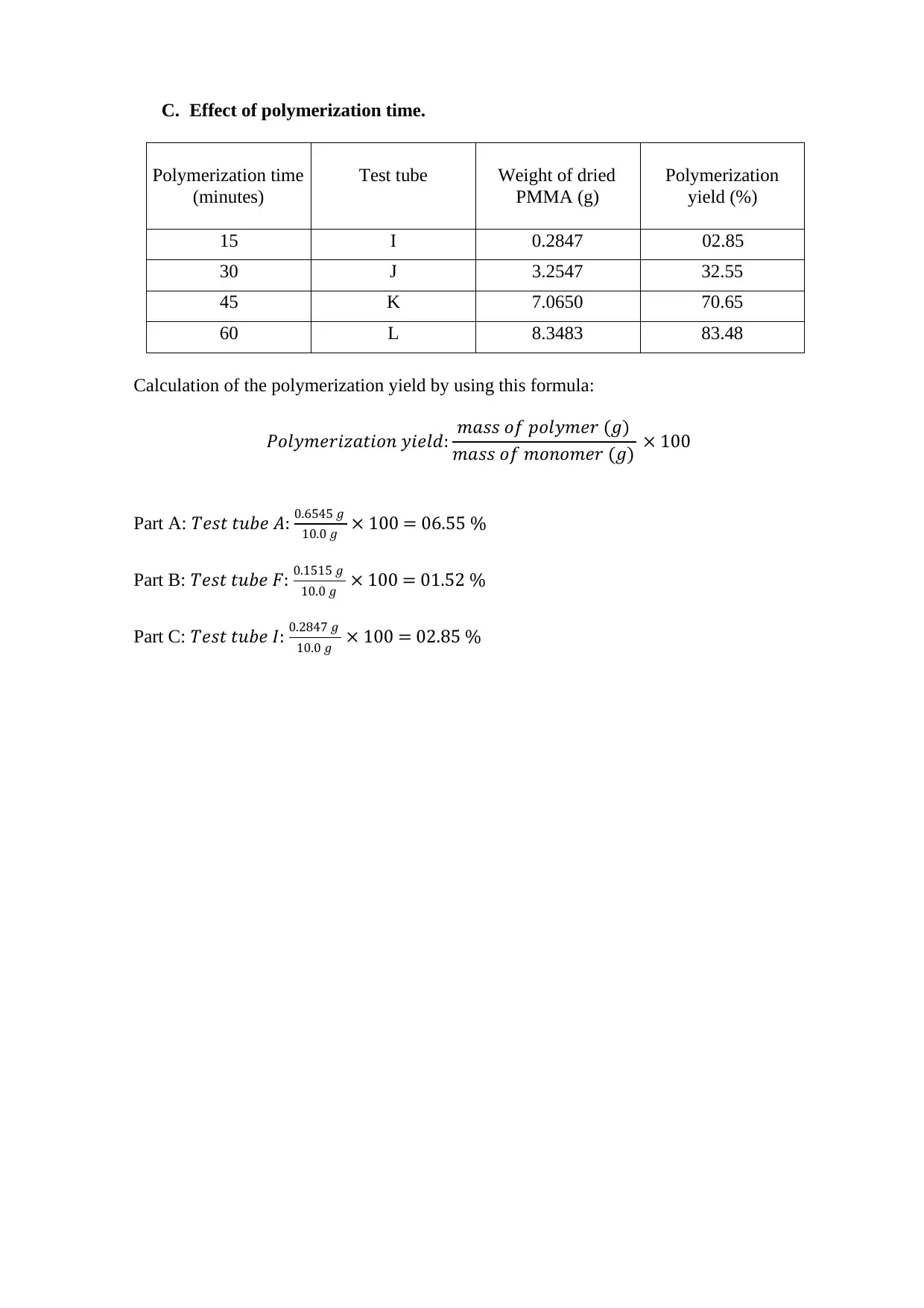
C. Effect of polymerization time.
Polymerization time
(minutes)
Test tube Weight of dried
PMMA (g)
Polymerization
yield (%)
15 I 0.2847 02.85
30 J 3.2547 32.55
45 K 7.0650 70.65
60 L 8.3483 83.48
Calculation of the polymerization yield by using this formula:
ππππ¦πππππ§ππ‘πππ π¦ππππ: πππ π ππ ππππ¦πππ (π)
πππ π ππ πππππππ (π) Γ 100
Part A: πππ π‘ π‘π’ππ π΄: 0.6545 π
10.0 π Γ 100 = 06.55 %
Part B: πππ π‘ π‘π’ππ πΉ: 0.1515 π
10.0 π Γ 100 = 01.52 %
Part C: πππ π‘ π‘π’ππ πΌ: 0.2847 π
10.0 π Γ 100 = 02.85 %
Polymerization time
(minutes)
Test tube Weight of dried
PMMA (g)
Polymerization
yield (%)
15 I 0.2847 02.85
30 J 3.2547 32.55
45 K 7.0650 70.65
60 L 8.3483 83.48
Calculation of the polymerization yield by using this formula:
ππππ¦πππππ§ππ‘πππ π¦ππππ: πππ π ππ ππππ¦πππ (π)
πππ π ππ πππππππ (π) Γ 100
Part A: πππ π‘ π‘π’ππ π΄: 0.6545 π
10.0 π Γ 100 = 06.55 %
Part B: πππ π‘ π‘π’ππ πΉ: 0.1515 π
10.0 π Γ 100 = 01.52 %
Part C: πππ π‘ π‘π’ππ πΌ: 0.2847 π
10.0 π Γ 100 = 02.85 %
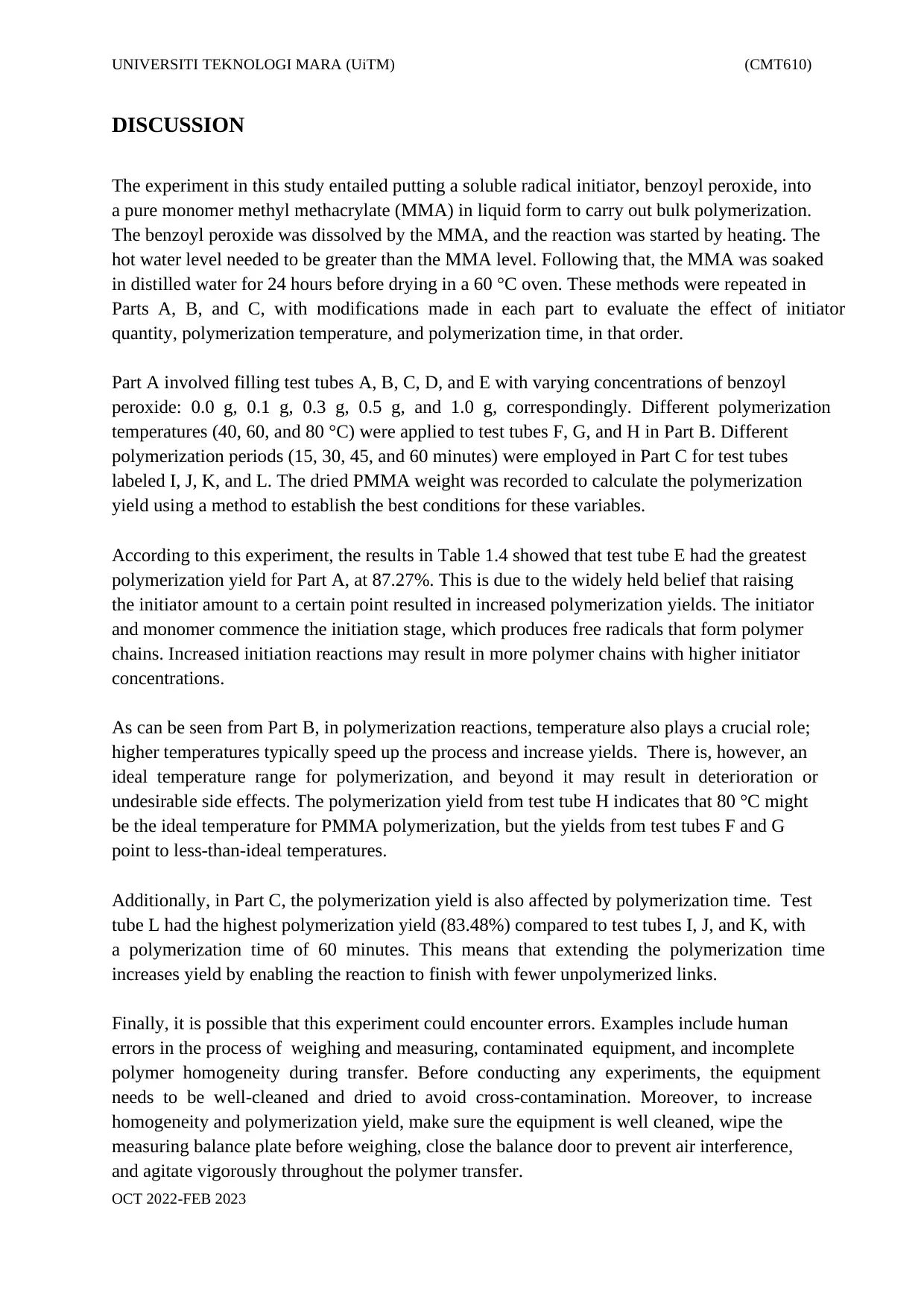
UNIVERSITI TEKNOLOGI MARA (UiTM) (CMT610)
OCT 2022-FEB 2023
DISCUSSION
The experiment in this study entailed putting a soluble radical initiator, benzoyl peroxide, into
a pure monomer methyl methacrylate (MMA) in liquid form to carry out bulk polymerization.
The benzoyl peroxide was dissolved by the MMA, and the reaction was started by heating. The
hot water level needed to be greater than the MMA level. Following that, the MMA was soaked
in distilled water for 24 hours before drying in a 60 Β°C oven. These methods were repeated in
Parts A, B, and C, with modifications made in each part to evaluate the effect of initiator
quantity, polymerization temperature, and polymerization time, in that order.
Part A involved filling test tubes A, B, C, D, and E with varying concentrations of benzoyl
peroxide: 0.0 g, 0.1 g, 0.3 g, 0.5 g, and 1.0 g, correspondingly. Different polymerization
temperatures (40, 60, and 80 Β°C) were applied to test tubes F, G, and H in Part B. Different
polymerization periods (15, 30, 45, and 60 minutes) were employed in Part C for test tubes
labeled I, J, K, and L. The dried PMMA weight was recorded to calculate the polymerization
yield using a method to establish the best conditions for these variables.
According to this experiment, the results in Table 1.4 showed that test tube E had the greatest
polymerization yield for Part A, at 87.27%. This is due to the widely held belief that raising
the initiator amount to a certain point resulted in increased polymerization yields. The initiator
and monomer commence the initiation stage, which produces free radicals that form polymer
chains. Increased initiation reactions may result in more polymer chains with higher initiator
concentrations.
As can be seen from Part B, in polymerization reactions, temperature also plays a crucial role;
higher temperatures typically speed up the process and increase yields. There is, however, an
ideal temperature range for polymerization, and beyond it may result in deterioration or
undesirable side effects. The polymerization yield from test tube H indicates that 80 Β°C might
be the ideal temperature for PMMA polymerization, but the yields from test tubes F and G
point to less-than-ideal temperatures.
Additionally, in Part C, the polymerization yield is also affected by polymerization time. Test
tube L had the highest polymerization yield (83.48%) compared to test tubes I, J, and K, with
a polymerization time of 60 minutes. This means that extending the polymerization time
increases yield by enabling the reaction to finish with fewer unpolymerized links.
Finally, it is possible that this experiment could encounter errors. Examples include human
errors in the process of weighing and measuring, contaminated equipment, and incomplete
polymer homogeneity during transfer. Before conducting any experiments, the equipment
needs to be well-cleaned and dried to avoid cross-contamination. Moreover, to increase
homogeneity and polymerization yield, make sure the equipment is well cleaned, wipe the
measuring balance plate before weighing, close the balance door to prevent air interference,
and agitate vigorously throughout the polymer transfer.
OCT 2022-FEB 2023
DISCUSSION
The experiment in this study entailed putting a soluble radical initiator, benzoyl peroxide, into
a pure monomer methyl methacrylate (MMA) in liquid form to carry out bulk polymerization.
The benzoyl peroxide was dissolved by the MMA, and the reaction was started by heating. The
hot water level needed to be greater than the MMA level. Following that, the MMA was soaked
in distilled water for 24 hours before drying in a 60 Β°C oven. These methods were repeated in
Parts A, B, and C, with modifications made in each part to evaluate the effect of initiator
quantity, polymerization temperature, and polymerization time, in that order.
Part A involved filling test tubes A, B, C, D, and E with varying concentrations of benzoyl
peroxide: 0.0 g, 0.1 g, 0.3 g, 0.5 g, and 1.0 g, correspondingly. Different polymerization
temperatures (40, 60, and 80 Β°C) were applied to test tubes F, G, and H in Part B. Different
polymerization periods (15, 30, 45, and 60 minutes) were employed in Part C for test tubes
labeled I, J, K, and L. The dried PMMA weight was recorded to calculate the polymerization
yield using a method to establish the best conditions for these variables.
According to this experiment, the results in Table 1.4 showed that test tube E had the greatest
polymerization yield for Part A, at 87.27%. This is due to the widely held belief that raising
the initiator amount to a certain point resulted in increased polymerization yields. The initiator
and monomer commence the initiation stage, which produces free radicals that form polymer
chains. Increased initiation reactions may result in more polymer chains with higher initiator
concentrations.
As can be seen from Part B, in polymerization reactions, temperature also plays a crucial role;
higher temperatures typically speed up the process and increase yields. There is, however, an
ideal temperature range for polymerization, and beyond it may result in deterioration or
undesirable side effects. The polymerization yield from test tube H indicates that 80 Β°C might
be the ideal temperature for PMMA polymerization, but the yields from test tubes F and G
point to less-than-ideal temperatures.
Additionally, in Part C, the polymerization yield is also affected by polymerization time. Test
tube L had the highest polymerization yield (83.48%) compared to test tubes I, J, and K, with
a polymerization time of 60 minutes. This means that extending the polymerization time
increases yield by enabling the reaction to finish with fewer unpolymerized links.
Finally, it is possible that this experiment could encounter errors. Examples include human
errors in the process of weighing and measuring, contaminated equipment, and incomplete
polymer homogeneity during transfer. Before conducting any experiments, the equipment
needs to be well-cleaned and dried to avoid cross-contamination. Moreover, to increase
homogeneity and polymerization yield, make sure the equipment is well cleaned, wipe the
measuring balance plate before weighing, close the balance door to prevent air interference,
and agitate vigorously throughout the polymer transfer.
β This is a preview!β
Do you want full access?
Subscribe today to unlock all pages.

Trusted by 1+ million students worldwide
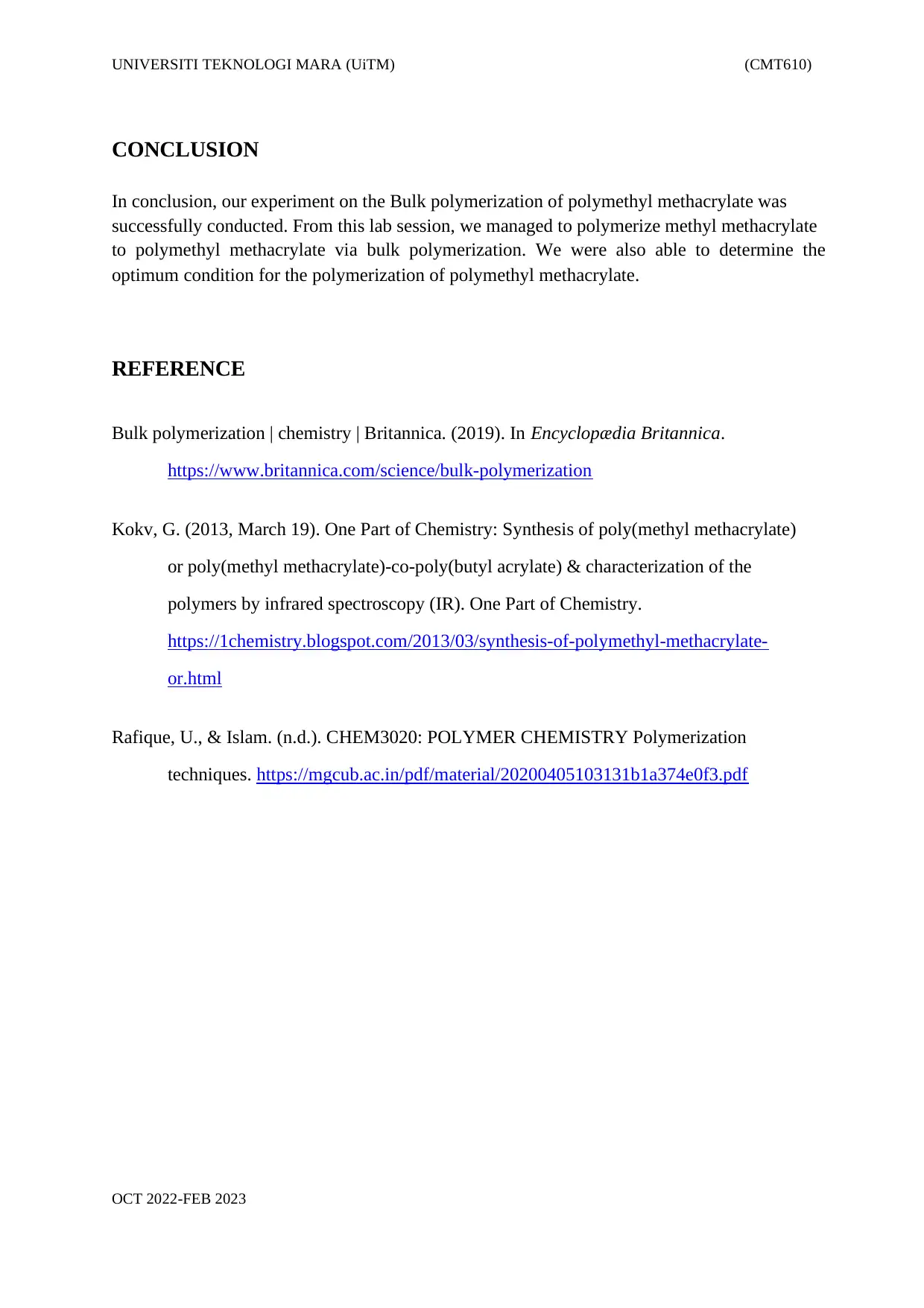
UNIVERSITI TEKNOLOGI MARA (UiTM) (CMT610)
OCT 2022-FEB 2023
CONCLUSION
In conclusion, our experiment on the Bulk polymerization of polymethyl methacrylate was
successfully conducted. From this lab session, we managed to polymerize methyl methacrylate
to polymethyl methacrylate via bulk polymerization. We were also able to determine the
optimum condition for the polymerization of polymethyl methacrylate.
REFERENCE
Bulk polymerization | chemistry | Britannica. (2019). In Encyclopædia Britannica.
https://www.britannica.com/science/bulk-polymerization
Kokv, G. (2013, March 19). One Part of Chemistry: Synthesis of poly(methyl methacrylate)
or poly(methyl methacrylate)-co-poly(butyl acrylate) & characterization of the
polymers by infrared spectroscopy (IR). One Part of Chemistry.
https://1chemistry.blogspot.com/2013/03/synthesis-of-polymethyl-methacrylate-
or.html
Rafique, U., & Islam. (n.d.). CHEM3020: POLYMER CHEMISTRY Polymerization
techniques. https://mgcub.ac.in/pdf/material/20200405103131b1a374e0f3.pdf
OCT 2022-FEB 2023
CONCLUSION
In conclusion, our experiment on the Bulk polymerization of polymethyl methacrylate was
successfully conducted. From this lab session, we managed to polymerize methyl methacrylate
to polymethyl methacrylate via bulk polymerization. We were also able to determine the
optimum condition for the polymerization of polymethyl methacrylate.
REFERENCE
Bulk polymerization | chemistry | Britannica. (2019). In Encyclopædia Britannica.
https://www.britannica.com/science/bulk-polymerization
Kokv, G. (2013, March 19). One Part of Chemistry: Synthesis of poly(methyl methacrylate)
or poly(methyl methacrylate)-co-poly(butyl acrylate) & characterization of the
polymers by infrared spectroscopy (IR). One Part of Chemistry.
https://1chemistry.blogspot.com/2013/03/synthesis-of-polymethyl-methacrylate-
or.html
Rafique, U., & Islam. (n.d.). CHEM3020: POLYMER CHEMISTRY Polymerization
techniques. https://mgcub.ac.in/pdf/material/20200405103131b1a374e0f3.pdf
Paraphrase This Document
Need a fresh take? Get an instant paraphrase of this document with our AI Paraphraser
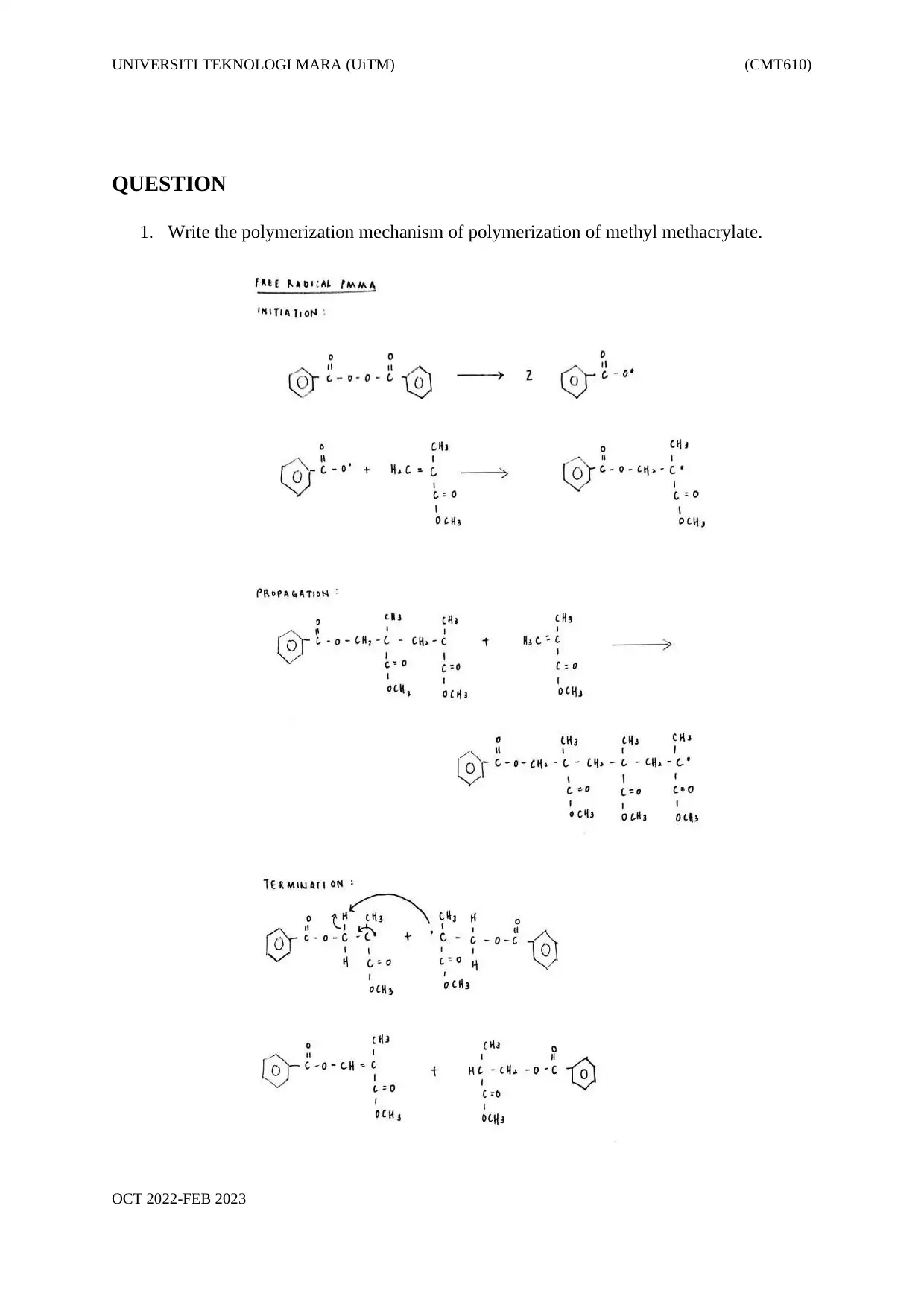
UNIVERSITI TEKNOLOGI MARA (UiTM) (CMT610)
OCT 2022-FEB 2023
QUESTION
1. Write the polymerization mechanism of polymerization of methyl methacrylate.
OCT 2022-FEB 2023
QUESTION
1. Write the polymerization mechanism of polymerization of methyl methacrylate.
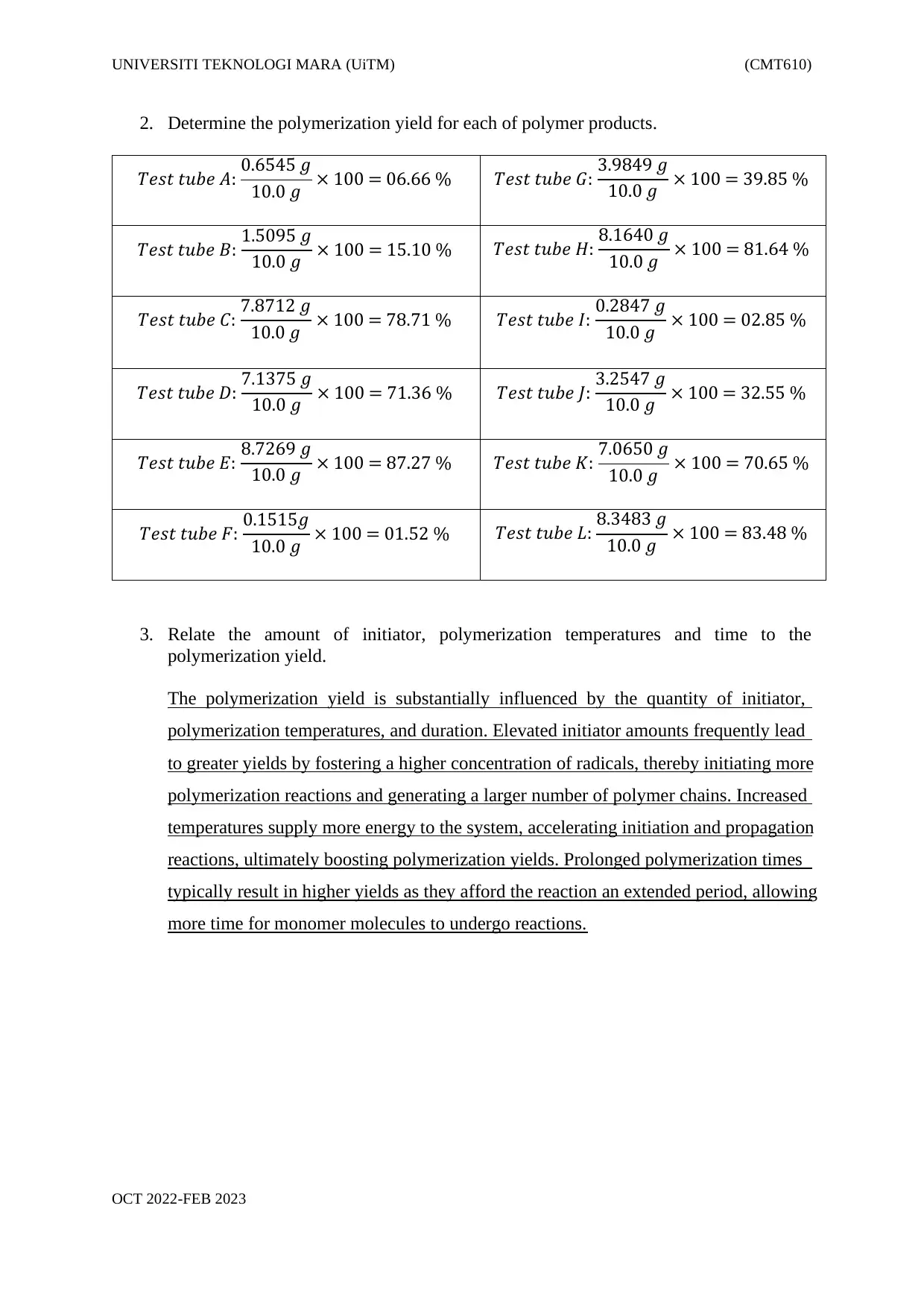
UNIVERSITI TEKNOLOGI MARA (UiTM) (CMT610)
OCT 2022-FEB 2023
2. Determine the polymerization yield for each of polymer products.
πππ π‘ π‘π’ππ π΄: 0.6545 π
10.0 π Γ 100 = 06.66 % πππ π‘ π‘π’ππ πΊ: 3.9849 π
10.0 π Γ 100 = 39.85 %
πππ π‘ π‘π’ππ π΅: 1.5095 π
10.0 π Γ 100 = 15.10 % πππ π‘ π‘π’ππ π»: 8.1640 π
10.0 π Γ 100 = 81.64 %
πππ π‘ π‘π’ππ πΆ: 7.8712 π
10.0 π Γ 100 = 78.71 % πππ π‘ π‘π’ππ πΌ: 0.2847 π
10.0 π Γ 100 = 02.85 %
πππ π‘ π‘π’ππ π·: 7.1375 π
10.0 π Γ 100 = 71.36 % πππ π‘ π‘π’ππ π½: 3.2547 π
10.0 π Γ 100 = 32.55 %
πππ π‘ π‘π’ππ πΈ: 8.7269 π
10.0 π Γ 100 = 87.27 % πππ π‘ π‘π’ππ πΎ: 7.0650 π
10.0 π Γ 100 = 70.65 %
πππ π‘ π‘π’ππ πΉ: 0.1515π
10.0 π Γ 100 = 01.52 % πππ π‘ π‘π’ππ πΏ: 8.3483 π
10.0 π Γ 100 = 83.48 %
3. Relate the amount of initiator, polymerization temperatures and time to the
polymerization yield.
The polymerization yield is substantially influenced by the quantity of initiator,
polymerization temperatures, and duration. Elevated initiator amounts frequently lead
to greater yields by fostering a higher concentration of radicals, thereby initiating more
polymerization reactions and generating a larger number of polymer chains. Increased
temperatures supply more energy to the system, accelerating initiation and propagation
reactions, ultimately boosting polymerization yields. Prolonged polymerization times
typically result in higher yields as they afford the reaction an extended period, allowing
more time for monomer molecules to undergo reactions.
OCT 2022-FEB 2023
2. Determine the polymerization yield for each of polymer products.
πππ π‘ π‘π’ππ π΄: 0.6545 π
10.0 π Γ 100 = 06.66 % πππ π‘ π‘π’ππ πΊ: 3.9849 π
10.0 π Γ 100 = 39.85 %
πππ π‘ π‘π’ππ π΅: 1.5095 π
10.0 π Γ 100 = 15.10 % πππ π‘ π‘π’ππ π»: 8.1640 π
10.0 π Γ 100 = 81.64 %
πππ π‘ π‘π’ππ πΆ: 7.8712 π
10.0 π Γ 100 = 78.71 % πππ π‘ π‘π’ππ πΌ: 0.2847 π
10.0 π Γ 100 = 02.85 %
πππ π‘ π‘π’ππ π·: 7.1375 π
10.0 π Γ 100 = 71.36 % πππ π‘ π‘π’ππ π½: 3.2547 π
10.0 π Γ 100 = 32.55 %
πππ π‘ π‘π’ππ πΈ: 8.7269 π
10.0 π Γ 100 = 87.27 % πππ π‘ π‘π’ππ πΎ: 7.0650 π
10.0 π Γ 100 = 70.65 %
πππ π‘ π‘π’ππ πΉ: 0.1515π
10.0 π Γ 100 = 01.52 % πππ π‘ π‘π’ππ πΏ: 8.3483 π
10.0 π Γ 100 = 83.48 %
3. Relate the amount of initiator, polymerization temperatures and time to the
polymerization yield.
The polymerization yield is substantially influenced by the quantity of initiator,
polymerization temperatures, and duration. Elevated initiator amounts frequently lead
to greater yields by fostering a higher concentration of radicals, thereby initiating more
polymerization reactions and generating a larger number of polymer chains. Increased
temperatures supply more energy to the system, accelerating initiation and propagation
reactions, ultimately boosting polymerization yields. Prolonged polymerization times
typically result in higher yields as they afford the reaction an extended period, allowing
more time for monomer molecules to undergo reactions.
β This is a preview!β
Do you want full access?
Subscribe today to unlock all pages.

Trusted by 1+ million students worldwide
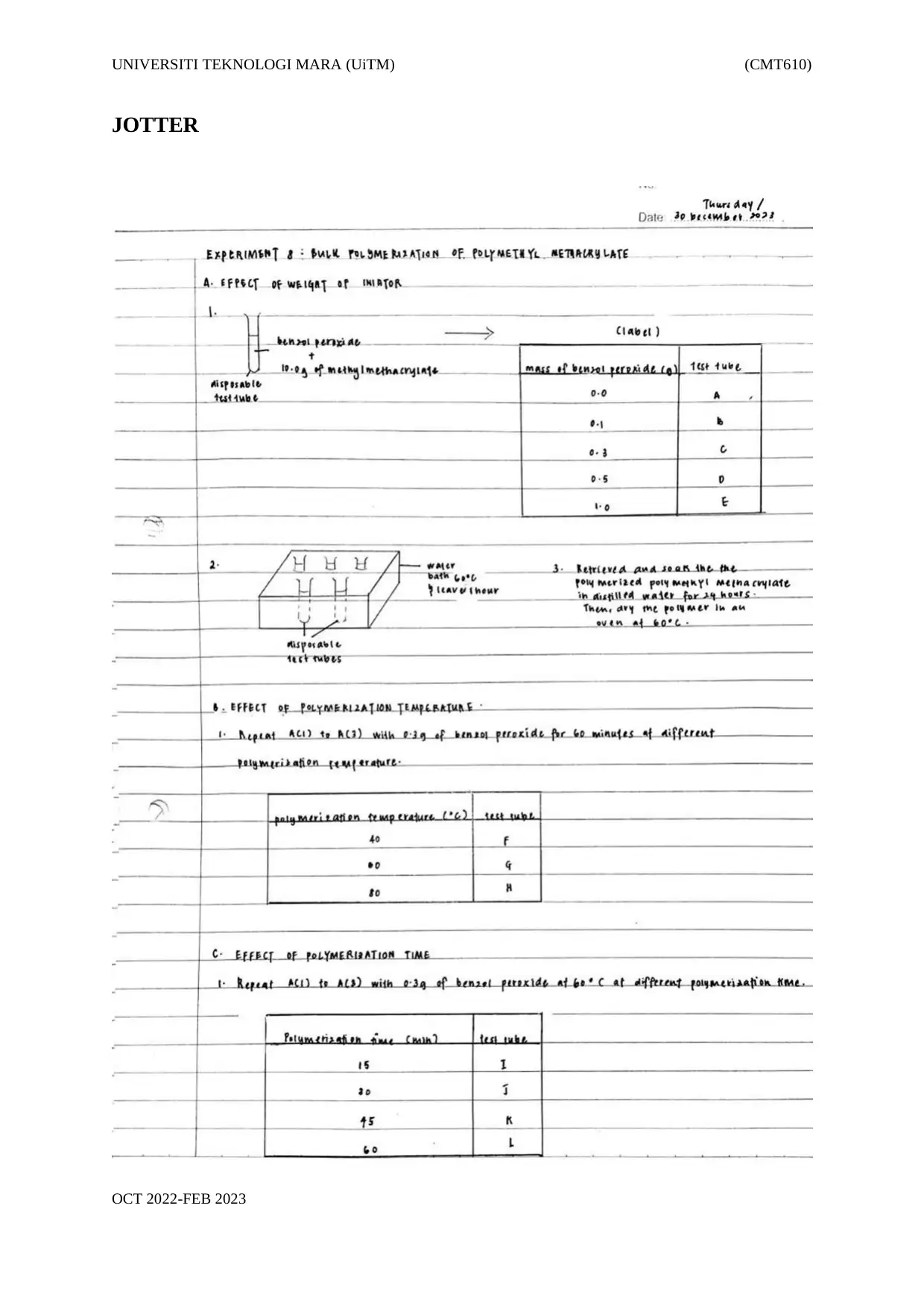
UNIVERSITI TEKNOLOGI MARA (UiTM) (CMT610)
OCT 2022-FEB 2023
JOTTER
OCT 2022-FEB 2023
JOTTER
1 out of 10