Charging Automation for Electric Vehicles: Is a larger Battery
VerifiedAdded on 2022/10/16
|3
|2222
|2
AI Summary
This assignment is an extension of 1069427
The assignment requirement and score sheet is attached. Please only say yes if you can guarantee a high grade. The research paper chosen is the same as 1069427.
Contribute Materials
Your contribution can guide someone’s learning journey. Share your
documents today.
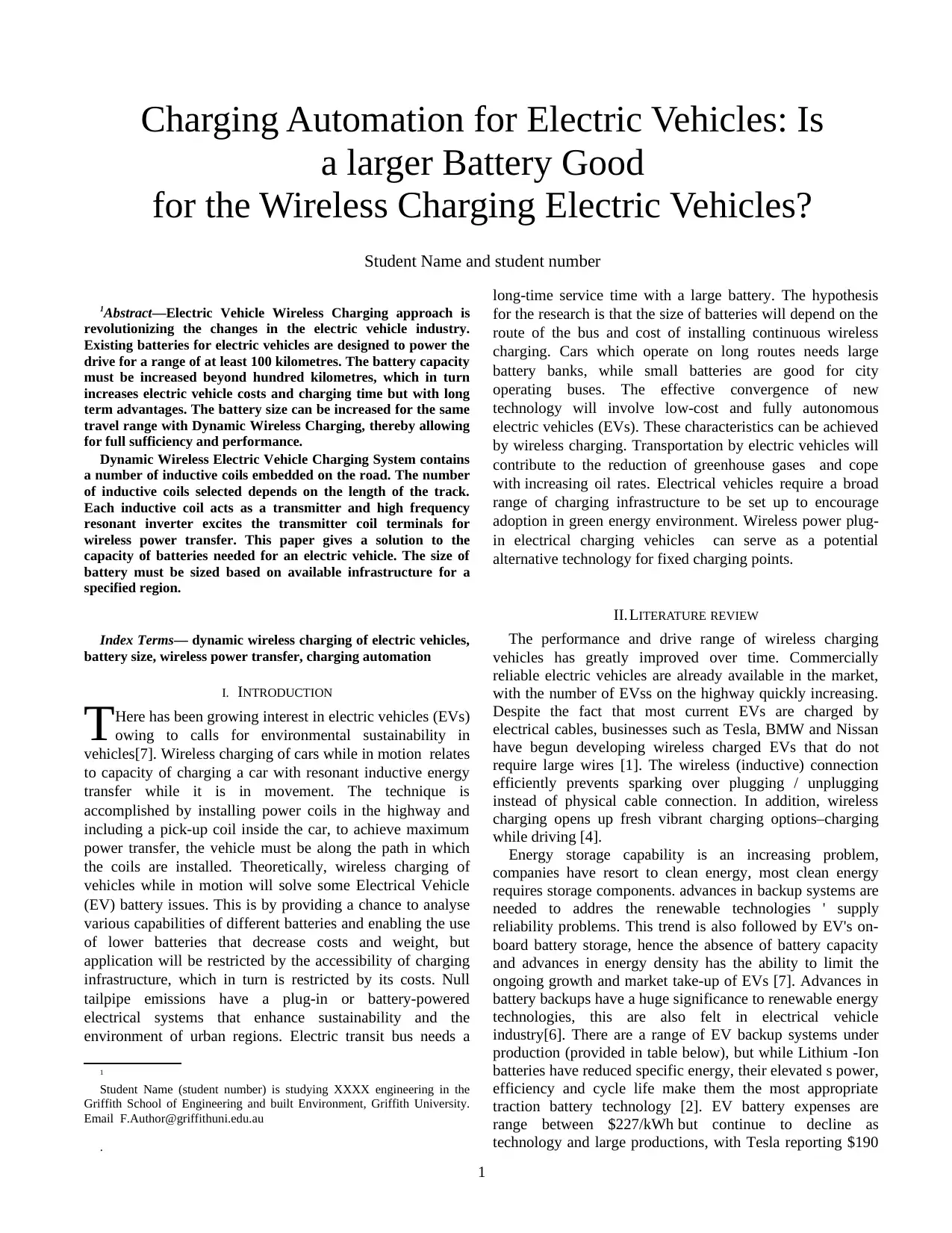
1Abstract—Electric Vehicle Wireless Charging approach is
revolutionizing the changes in the electric vehicle industry.
Existing batteries for electric vehicles are designed to power the
drive for a range of at least 100 kilometres. The battery capacity
must be increased beyond hundred kilometres, which in turn
increases electric vehicle costs and charging time but with long
term advantages. The battery size can be increased for the same
travel range with Dynamic Wireless Charging, thereby allowing
for full sufficiency and performance.
Dynamic Wireless Electric Vehicle Charging System contains
a number of inductive coils embedded on the road. The number
of inductive coils selected depends on the length of the track.
Each inductive coil acts as a transmitter and high frequency
resonant inverter excites the transmitter coil terminals for
wireless power transfer. This paper gives a solution to the
capacity of batteries needed for an electric vehicle. The size of
battery must be sized based on available infrastructure for a
specified region.
Index Terms— dynamic wireless charging of electric vehicles,
battery size, wireless power transfer, charging automation
I. INTRODUCTION
Here has been growing interest in electric vehicles (EVs)
owing to calls for environmental sustainability in
vehicles[7]. Wireless charging of cars while in motion relates
to capacity of charging a car with resonant inductive energy
transfer while it is in movement. The technique is
accomplished by installing power coils in the highway and
including a pick-up coil inside the car, to achieve maximum
power transfer, the vehicle must be along the path in which
the coils are installed. Theoretically, wireless charging of
vehicles while in motion will solve some Electrical Vehicle
(EV) battery issues. This is by providing a chance to analyse
various capabilities of different batteries and enabling the use
of lower batteries that decrease costs and weight, but
application will be restricted by the accessibility of charging
infrastructure, which in turn is restricted by its costs. Null
tailpipe emissions have a plug-in or battery-powered
electrical systems that enhance sustainability and the
environment of urban regions. Electric transit bus needs a
T
1
Student Name (student number) is studying XXXX engineering in the
Griffith School of Engineering and built Environment, Griffith University.
Email F.Author@griffithuni.edu.au
.
long-time service time with a large battery. The hypothesis
for the research is that the size of batteries will depend on the
route of the bus and cost of installing continuous wireless
charging. Cars which operate on long routes needs large
battery banks, while small batteries are good for city
operating buses. The effective convergence of new
technology will involve low-cost and fully autonomous
electric vehicles (EVs). These characteristics can be achieved
by wireless charging. Transportation by electric vehicles will
contribute to the reduction of greenhouse gases and cope
with increasing oil rates. Electrical vehicles require a broad
range of charging infrastructure to be set up to encourage
adoption in green energy environment. Wireless power plug-
in electrical charging vehicles can serve as a potential
alternative technology for fixed charging points.
II.LITERATURE REVIEW
The performance and drive range of wireless charging
vehicles has greatly improved over time. Commercially
reliable electric vehicles are already available in the market,
with the number of EVss on the highway quickly increasing.
Despite the fact that most current EVs are charged by
electrical cables, businesses such as Tesla, BMW and Nissan
have begun developing wireless charged EVs that do not
require large wires [1]. The wireless (inductive) connection
efficiently prevents sparking over plugging / unplugging
instead of physical cable connection. In addition, wireless
charging opens up fresh vibrant charging options–charging
while driving [4].
Energy storage capability is an increasing problem,
companies have resort to clean energy, most clean energy
requires storage components. advances in backup systems are
needed to addres the renewable technologies ' supply
reliability problems. This trend is also followed by EV's on-
board battery storage, hence the absence of battery capacity
and advances in energy density has the ability to limit the
ongoing growth and market take-up of EVs [7]. Advances in
battery backups have a huge significance to renewable energy
technologies, this are also felt in electrical vehicle
industry[6]. There are a range of EV backup systems under
production (provided in table below), but while Lithium -Ion
batteries have reduced specific energy, their elevated s power,
efficiency and cycle life make them the most appropriate
traction battery technology [2]. EV battery expenses are
range between $227/kWh but continue to decline as
technology and large productions, with Tesla reporting $190
1
Charging Automation for Electric Vehicles: Is
a larger Battery Good
for the Wireless Charging Electric Vehicles?
Student Name and student number
revolutionizing the changes in the electric vehicle industry.
Existing batteries for electric vehicles are designed to power the
drive for a range of at least 100 kilometres. The battery capacity
must be increased beyond hundred kilometres, which in turn
increases electric vehicle costs and charging time but with long
term advantages. The battery size can be increased for the same
travel range with Dynamic Wireless Charging, thereby allowing
for full sufficiency and performance.
Dynamic Wireless Electric Vehicle Charging System contains
a number of inductive coils embedded on the road. The number
of inductive coils selected depends on the length of the track.
Each inductive coil acts as a transmitter and high frequency
resonant inverter excites the transmitter coil terminals for
wireless power transfer. This paper gives a solution to the
capacity of batteries needed for an electric vehicle. The size of
battery must be sized based on available infrastructure for a
specified region.
Index Terms— dynamic wireless charging of electric vehicles,
battery size, wireless power transfer, charging automation
I. INTRODUCTION
Here has been growing interest in electric vehicles (EVs)
owing to calls for environmental sustainability in
vehicles[7]. Wireless charging of cars while in motion relates
to capacity of charging a car with resonant inductive energy
transfer while it is in movement. The technique is
accomplished by installing power coils in the highway and
including a pick-up coil inside the car, to achieve maximum
power transfer, the vehicle must be along the path in which
the coils are installed. Theoretically, wireless charging of
vehicles while in motion will solve some Electrical Vehicle
(EV) battery issues. This is by providing a chance to analyse
various capabilities of different batteries and enabling the use
of lower batteries that decrease costs and weight, but
application will be restricted by the accessibility of charging
infrastructure, which in turn is restricted by its costs. Null
tailpipe emissions have a plug-in or battery-powered
electrical systems that enhance sustainability and the
environment of urban regions. Electric transit bus needs a
T
1
Student Name (student number) is studying XXXX engineering in the
Griffith School of Engineering and built Environment, Griffith University.
Email F.Author@griffithuni.edu.au
.
long-time service time with a large battery. The hypothesis
for the research is that the size of batteries will depend on the
route of the bus and cost of installing continuous wireless
charging. Cars which operate on long routes needs large
battery banks, while small batteries are good for city
operating buses. The effective convergence of new
technology will involve low-cost and fully autonomous
electric vehicles (EVs). These characteristics can be achieved
by wireless charging. Transportation by electric vehicles will
contribute to the reduction of greenhouse gases and cope
with increasing oil rates. Electrical vehicles require a broad
range of charging infrastructure to be set up to encourage
adoption in green energy environment. Wireless power plug-
in electrical charging vehicles can serve as a potential
alternative technology for fixed charging points.
II.LITERATURE REVIEW
The performance and drive range of wireless charging
vehicles has greatly improved over time. Commercially
reliable electric vehicles are already available in the market,
with the number of EVss on the highway quickly increasing.
Despite the fact that most current EVs are charged by
electrical cables, businesses such as Tesla, BMW and Nissan
have begun developing wireless charged EVs that do not
require large wires [1]. The wireless (inductive) connection
efficiently prevents sparking over plugging / unplugging
instead of physical cable connection. In addition, wireless
charging opens up fresh vibrant charging options–charging
while driving [4].
Energy storage capability is an increasing problem,
companies have resort to clean energy, most clean energy
requires storage components. advances in backup systems are
needed to addres the renewable technologies ' supply
reliability problems. This trend is also followed by EV's on-
board battery storage, hence the absence of battery capacity
and advances in energy density has the ability to limit the
ongoing growth and market take-up of EVs [7]. Advances in
battery backups have a huge significance to renewable energy
technologies, this are also felt in electrical vehicle
industry[6]. There are a range of EV backup systems under
production (provided in table below), but while Lithium -Ion
batteries have reduced specific energy, their elevated s power,
efficiency and cycle life make them the most appropriate
traction battery technology [2]. EV battery expenses are
range between $227/kWh but continue to decline as
technology and large productions, with Tesla reporting $190
1
Charging Automation for Electric Vehicles: Is
a larger Battery Good
for the Wireless Charging Electric Vehicles?
Student Name and student number
Secure Best Marks with AI Grader
Need help grading? Try our AI Grader for instant feedback on your assignments.
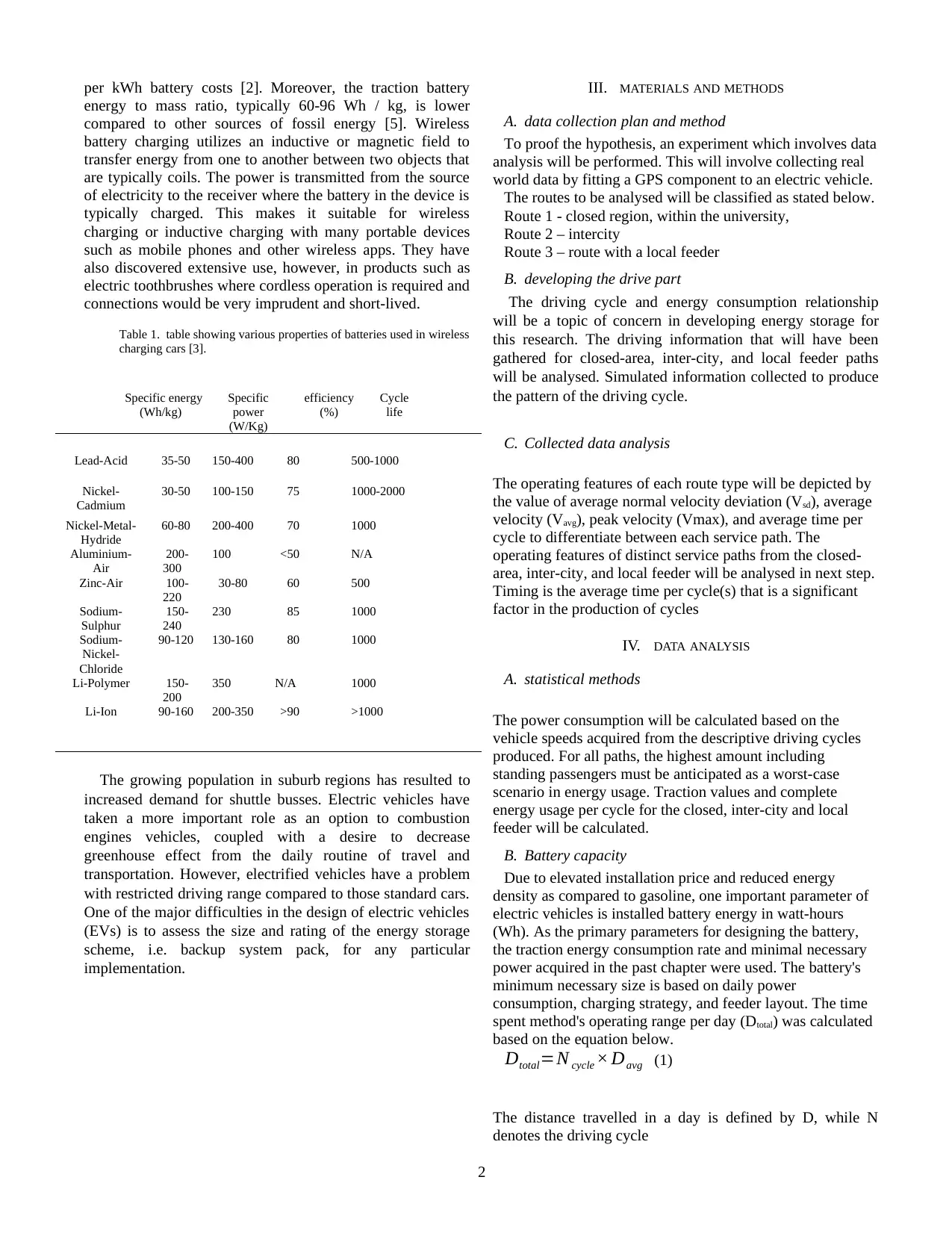
per kWh battery costs [2]. Moreover, the traction battery
energy to mass ratio, typically 60-96 Wh / kg, is lower
compared to other sources of fossil energy [5]. Wireless
battery charging utilizes an inductive or magnetic field to
transfer energy from one to another between two objects that
are typically coils. The power is transmitted from the source
of electricity to the receiver where the battery in the device is
typically charged. This makes it suitable for wireless
charging or inductive charging with many portable devices
such as mobile phones and other wireless apps. They have
also discovered extensive use, however, in products such as
electric toothbrushes where cordless operation is required and
connections would be very imprudent and short-lived.
Table 1. table showing various properties of batteries used in wireless
charging cars [3].
Specific energy
(Wh/kg)
Specific
power
(W/Kg)
efficiency
(%)
Cycle
life
Lead-Acid 35-50 150-400 80 500-1000
Nickel-
Cadmium
30-50 100-150 75 1000-2000
Nickel-Metal-
Hydride
60-80 200-400 70 1000
Aluminium-
Air
200-
300
100 <50 N/A
Zinc-Air 100-
220
30-80 60 500
Sodium-
Sulphur
150-
240
230 85 1000
Sodium-
Nickel-
Chloride
90-120 130-160 80 1000
Li-Polymer 150-
200
350 N/A 1000
Li-Ion 90-160 200-350 >90 >1000
The growing population in suburb regions has resulted to
increased demand for shuttle busses. Electric vehicles have
taken a more important role as an option to combustion
engines vehicles, coupled with a desire to decrease
greenhouse effect from the daily routine of travel and
transportation. However, electrified vehicles have a problem
with restricted driving range compared to those standard cars.
One of the major difficulties in the design of electric vehicles
(EVs) is to assess the size and rating of the energy storage
scheme, i.e. backup system pack, for any particular
implementation.
III. MATERIALS AND METHODS
A. data collection plan and method
To proof the hypothesis, an experiment which involves data
analysis will be performed. This will involve collecting real
world data by fitting a GPS component to an electric vehicle.
The routes to be analysed will be classified as stated below.
Route 1 - closed region, within the university,
Route 2 – intercity
Route 3 – route with a local feeder
B. developing the drive part
The driving cycle and energy consumption relationship
will be a topic of concern in developing energy storage for
this research. The driving information that will have been
gathered for closed-area, inter-city, and local feeder paths
will be analysed. Simulated information collected to produce
the pattern of the driving cycle.
C. Collected data analysis
The operating features of each route type will be depicted by
the value of average normal velocity deviation (Vsd), average
velocity (Vavg), peak velocity (Vmax), and average time per
cycle to differentiate between each service path. The
operating features of distinct service paths from the closed-
area, inter-city, and local feeder will be analysed in next step.
Timing is the average time per cycle(s) that is a significant
factor in the production of cycles
IV. DATA ANALYSIS
A. statistical methods
The power consumption will be calculated based on the
vehicle speeds acquired from the descriptive driving cycles
produced. For all paths, the highest amount including
standing passengers must be anticipated as a worst-case
scenario in energy usage. Traction values and complete
energy usage per cycle for the closed, inter-city and local
feeder will be calculated.
B. Battery capacity
Due to elevated installation price and reduced energy
density as compared to gasoline, one important parameter of
electric vehicles is installed battery energy in watt-hours
(Wh). As the primary parameters for designing the battery,
the traction energy consumption rate and minimal necessary
power acquired in the past chapter were used. The battery's
minimum necessary size is based on daily power
consumption, charging strategy, and feeder layout. The time
spent method's operating range per day (Dtotal) was calculated
based on the equation below.
Dtotal=N cycle × Davg (1)
The distance travelled in a day is defined by D, while N
denotes the driving cycle
2
energy to mass ratio, typically 60-96 Wh / kg, is lower
compared to other sources of fossil energy [5]. Wireless
battery charging utilizes an inductive or magnetic field to
transfer energy from one to another between two objects that
are typically coils. The power is transmitted from the source
of electricity to the receiver where the battery in the device is
typically charged. This makes it suitable for wireless
charging or inductive charging with many portable devices
such as mobile phones and other wireless apps. They have
also discovered extensive use, however, in products such as
electric toothbrushes where cordless operation is required and
connections would be very imprudent and short-lived.
Table 1. table showing various properties of batteries used in wireless
charging cars [3].
Specific energy
(Wh/kg)
Specific
power
(W/Kg)
efficiency
(%)
Cycle
life
Lead-Acid 35-50 150-400 80 500-1000
Nickel-
Cadmium
30-50 100-150 75 1000-2000
Nickel-Metal-
Hydride
60-80 200-400 70 1000
Aluminium-
Air
200-
300
100 <50 N/A
Zinc-Air 100-
220
30-80 60 500
Sodium-
Sulphur
150-
240
230 85 1000
Sodium-
Nickel-
Chloride
90-120 130-160 80 1000
Li-Polymer 150-
200
350 N/A 1000
Li-Ion 90-160 200-350 >90 >1000
The growing population in suburb regions has resulted to
increased demand for shuttle busses. Electric vehicles have
taken a more important role as an option to combustion
engines vehicles, coupled with a desire to decrease
greenhouse effect from the daily routine of travel and
transportation. However, electrified vehicles have a problem
with restricted driving range compared to those standard cars.
One of the major difficulties in the design of electric vehicles
(EVs) is to assess the size and rating of the energy storage
scheme, i.e. backup system pack, for any particular
implementation.
III. MATERIALS AND METHODS
A. data collection plan and method
To proof the hypothesis, an experiment which involves data
analysis will be performed. This will involve collecting real
world data by fitting a GPS component to an electric vehicle.
The routes to be analysed will be classified as stated below.
Route 1 - closed region, within the university,
Route 2 – intercity
Route 3 – route with a local feeder
B. developing the drive part
The driving cycle and energy consumption relationship
will be a topic of concern in developing energy storage for
this research. The driving information that will have been
gathered for closed-area, inter-city, and local feeder paths
will be analysed. Simulated information collected to produce
the pattern of the driving cycle.
C. Collected data analysis
The operating features of each route type will be depicted by
the value of average normal velocity deviation (Vsd), average
velocity (Vavg), peak velocity (Vmax), and average time per
cycle to differentiate between each service path. The
operating features of distinct service paths from the closed-
area, inter-city, and local feeder will be analysed in next step.
Timing is the average time per cycle(s) that is a significant
factor in the production of cycles
IV. DATA ANALYSIS
A. statistical methods
The power consumption will be calculated based on the
vehicle speeds acquired from the descriptive driving cycles
produced. For all paths, the highest amount including
standing passengers must be anticipated as a worst-case
scenario in energy usage. Traction values and complete
energy usage per cycle for the closed, inter-city and local
feeder will be calculated.
B. Battery capacity
Due to elevated installation price and reduced energy
density as compared to gasoline, one important parameter of
electric vehicles is installed battery energy in watt-hours
(Wh). As the primary parameters for designing the battery,
the traction energy consumption rate and minimal necessary
power acquired in the past chapter were used. The battery's
minimum necessary size is based on daily power
consumption, charging strategy, and feeder layout. The time
spent method's operating range per day (Dtotal) was calculated
based on the equation below.
Dtotal=N cycle × Davg (1)
The distance travelled in a day is defined by D, while N
denotes the driving cycle
2
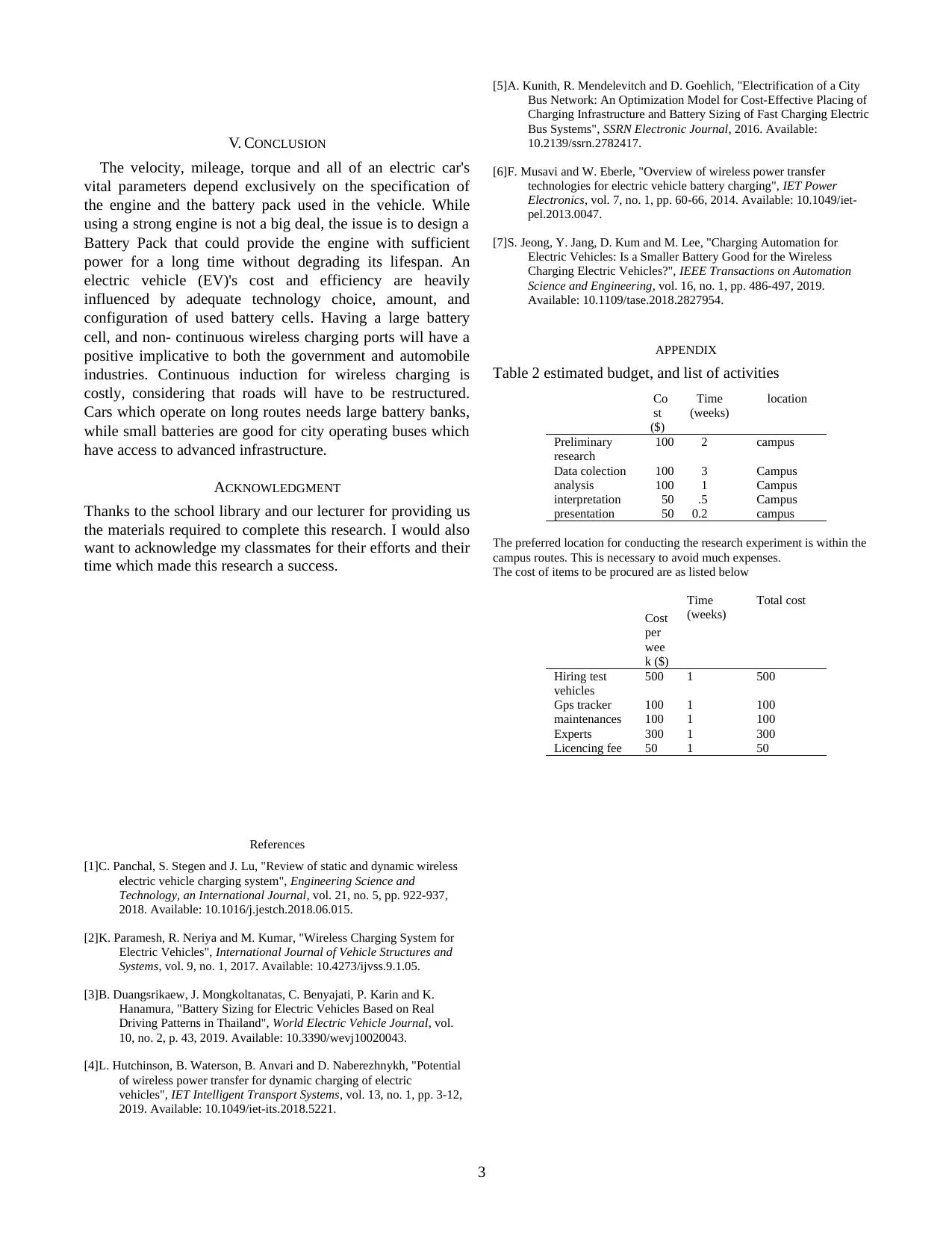
V. CONCLUSION
The velocity, mileage, torque and all of an electric car's
vital parameters depend exclusively on the specification of
the engine and the battery pack used in the vehicle. While
using a strong engine is not a big deal, the issue is to design a
Battery Pack that could provide the engine with sufficient
power for a long time without degrading its lifespan. An
electric vehicle (EV)'s cost and efficiency are heavily
influenced by adequate technology choice, amount, and
configuration of used battery cells. Having a large battery
cell, and non- continuous wireless charging ports will have a
positive implicative to both the government and automobile
industries. Continuous induction for wireless charging is
costly, considering that roads will have to be restructured.
Cars which operate on long routes needs large battery banks,
while small batteries are good for city operating buses which
have access to advanced infrastructure.
ACKNOWLEDGMENT
Thanks to the school library and our lecturer for providing us
the materials required to complete this research. I would also
want to acknowledge my classmates for their efforts and their
time which made this research a success.
References
[1]C. Panchal, S. Stegen and J. Lu, "Review of static and dynamic wireless
electric vehicle charging system", Engineering Science and
Technology, an International Journal, vol. 21, no. 5, pp. 922-937,
2018. Available: 10.1016/j.jestch.2018.06.015.
[2]K. Paramesh, R. Neriya and M. Kumar, "Wireless Charging System for
Electric Vehicles", International Journal of Vehicle Structures and
Systems, vol. 9, no. 1, 2017. Available: 10.4273/ijvss.9.1.05.
[3]B. Duangsrikaew, J. Mongkoltanatas, C. Benyajati, P. Karin and K.
Hanamura, "Battery Sizing for Electric Vehicles Based on Real
Driving Patterns in Thailand", World Electric Vehicle Journal, vol.
10, no. 2, p. 43, 2019. Available: 10.3390/wevj10020043.
[4]L. Hutchinson, B. Waterson, B. Anvari and D. Naberezhnykh, "Potential
of wireless power transfer for dynamic charging of electric
vehicles", IET Intelligent Transport Systems, vol. 13, no. 1, pp. 3-12,
2019. Available: 10.1049/iet-its.2018.5221.
[5]A. Kunith, R. Mendelevitch and D. Goehlich, "Electrification of a City
Bus Network: An Optimization Model for Cost-Effective Placing of
Charging Infrastructure and Battery Sizing of Fast Charging Electric
Bus Systems", SSRN Electronic Journal, 2016. Available:
10.2139/ssrn.2782417.
[6]F. Musavi and W. Eberle, "Overview of wireless power transfer
technologies for electric vehicle battery charging", IET Power
Electronics, vol. 7, no. 1, pp. 60-66, 2014. Available: 10.1049/iet-
pel.2013.0047.
[7]S. Jeong, Y. Jang, D. Kum and M. Lee, "Charging Automation for
Electric Vehicles: Is a Smaller Battery Good for the Wireless
Charging Electric Vehicles?", IEEE Transactions on Automation
Science and Engineering, vol. 16, no. 1, pp. 486-497, 2019.
Available: 10.1109/tase.2018.2827954.
APPENDIX
Table 2 estimated budget, and list of activities
Co
st
($)
Time
(weeks)
location
Preliminary
research
100 2 campus
Data colection 100 3 Campus
analysis 100 1 Campus
interpretation 50 .5 Campus
presentation 50 0.2 campus
The preferred location for conducting the research experiment is within the
campus routes. This is necessary to avoid much expenses.
The cost of items to be procured are as listed below
Cost
per
wee
k ($)
Time
(weeks)
Total cost
Hiring test
vehicles
500 1 500
Gps tracker 100 1 100
maintenances 100 1 100
Experts 300 1 300
Licencing fee 50 1 50
3
The velocity, mileage, torque and all of an electric car's
vital parameters depend exclusively on the specification of
the engine and the battery pack used in the vehicle. While
using a strong engine is not a big deal, the issue is to design a
Battery Pack that could provide the engine with sufficient
power for a long time without degrading its lifespan. An
electric vehicle (EV)'s cost and efficiency are heavily
influenced by adequate technology choice, amount, and
configuration of used battery cells. Having a large battery
cell, and non- continuous wireless charging ports will have a
positive implicative to both the government and automobile
industries. Continuous induction for wireless charging is
costly, considering that roads will have to be restructured.
Cars which operate on long routes needs large battery banks,
while small batteries are good for city operating buses which
have access to advanced infrastructure.
ACKNOWLEDGMENT
Thanks to the school library and our lecturer for providing us
the materials required to complete this research. I would also
want to acknowledge my classmates for their efforts and their
time which made this research a success.
References
[1]C. Panchal, S. Stegen and J. Lu, "Review of static and dynamic wireless
electric vehicle charging system", Engineering Science and
Technology, an International Journal, vol. 21, no. 5, pp. 922-937,
2018. Available: 10.1016/j.jestch.2018.06.015.
[2]K. Paramesh, R. Neriya and M. Kumar, "Wireless Charging System for
Electric Vehicles", International Journal of Vehicle Structures and
Systems, vol. 9, no. 1, 2017. Available: 10.4273/ijvss.9.1.05.
[3]B. Duangsrikaew, J. Mongkoltanatas, C. Benyajati, P. Karin and K.
Hanamura, "Battery Sizing for Electric Vehicles Based on Real
Driving Patterns in Thailand", World Electric Vehicle Journal, vol.
10, no. 2, p. 43, 2019. Available: 10.3390/wevj10020043.
[4]L. Hutchinson, B. Waterson, B. Anvari and D. Naberezhnykh, "Potential
of wireless power transfer for dynamic charging of electric
vehicles", IET Intelligent Transport Systems, vol. 13, no. 1, pp. 3-12,
2019. Available: 10.1049/iet-its.2018.5221.
[5]A. Kunith, R. Mendelevitch and D. Goehlich, "Electrification of a City
Bus Network: An Optimization Model for Cost-Effective Placing of
Charging Infrastructure and Battery Sizing of Fast Charging Electric
Bus Systems", SSRN Electronic Journal, 2016. Available:
10.2139/ssrn.2782417.
[6]F. Musavi and W. Eberle, "Overview of wireless power transfer
technologies for electric vehicle battery charging", IET Power
Electronics, vol. 7, no. 1, pp. 60-66, 2014. Available: 10.1049/iet-
pel.2013.0047.
[7]S. Jeong, Y. Jang, D. Kum and M. Lee, "Charging Automation for
Electric Vehicles: Is a Smaller Battery Good for the Wireless
Charging Electric Vehicles?", IEEE Transactions on Automation
Science and Engineering, vol. 16, no. 1, pp. 486-497, 2019.
Available: 10.1109/tase.2018.2827954.
APPENDIX
Table 2 estimated budget, and list of activities
Co
st
($)
Time
(weeks)
location
Preliminary
research
100 2 campus
Data colection 100 3 Campus
analysis 100 1 Campus
interpretation 50 .5 Campus
presentation 50 0.2 campus
The preferred location for conducting the research experiment is within the
campus routes. This is necessary to avoid much expenses.
The cost of items to be procured are as listed below
Cost
per
wee
k ($)
Time
(weeks)
Total cost
Hiring test
vehicles
500 1 500
Gps tracker 100 1 100
maintenances 100 1 100
Experts 300 1 300
Licencing fee 50 1 50
3
1 out of 3

Your All-in-One AI-Powered Toolkit for Academic Success.
+13062052269
info@desklib.com
Available 24*7 on WhatsApp / Email
Unlock your academic potential
© 2024 | Zucol Services PVT LTD | All rights reserved.