Uses of Chemical Vapor Deposition (CVD) Process for Growing Graphene
VerifiedAdded on 2023/06/12
|3
|2064
|479
AI Summary
This research paper focuses on the uses of chemical vapor deposition (CVD) process for growing graphene, etching copper foil, and making graphene-polymer composite. The experiment was conducted using the Moorfield NanoVCD system. The resulting graphene was combined with polymers to create composites like fullerenes. The mass of the graphene produced was 0.1647g, with a production efficiency of 12%. The paper also discusses the production of fullerenes, carbon nanotubes, and graphene using Molymod kits.
Contribute Materials
Your contribution can guide someone’s learning journey. Share your
documents today.
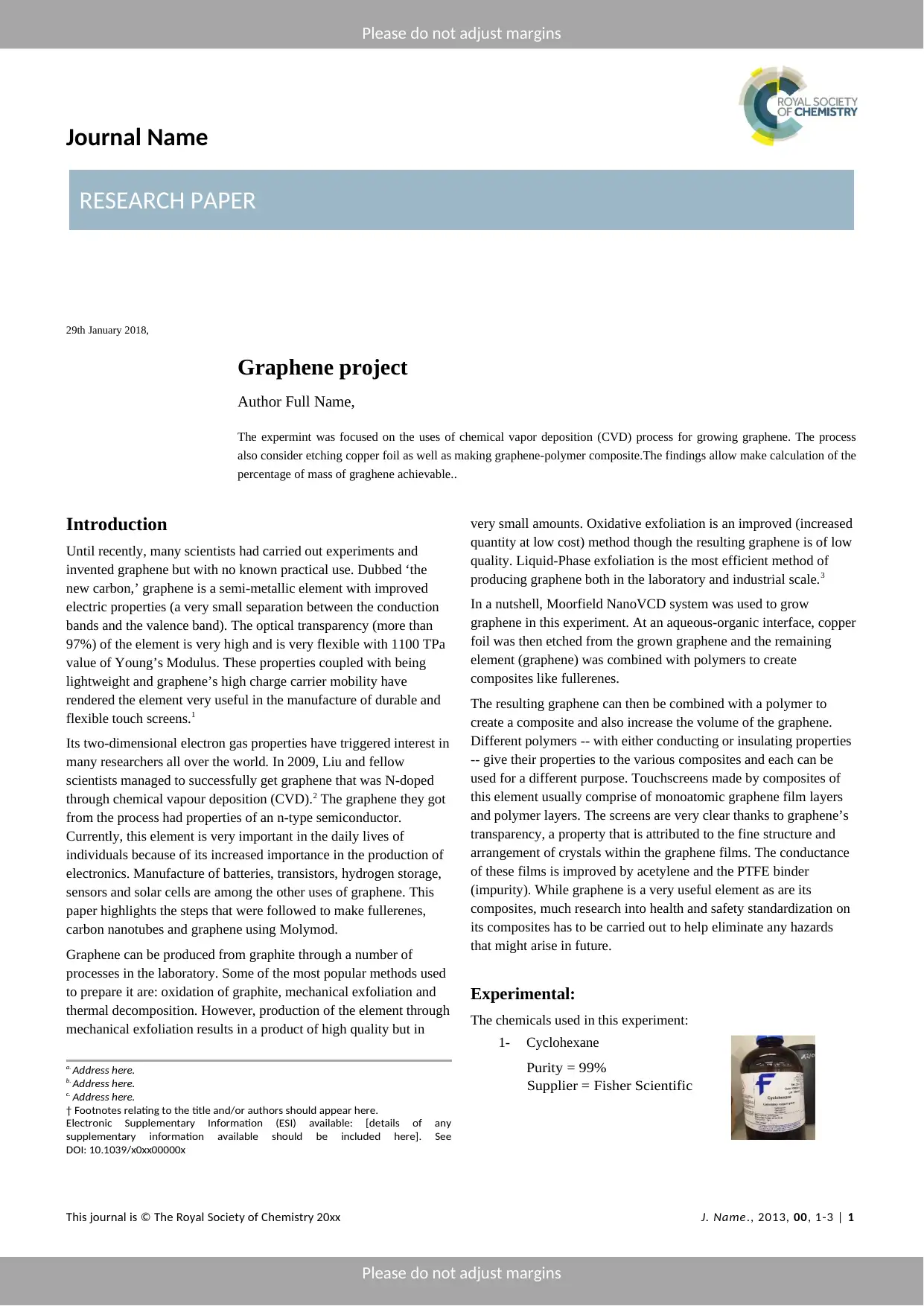
a. Address here.
b. Address here.
c. Address here.
† Footnotes relating to the title and/or authors should appear here.
Electronic Supplementary Information (ESI) available: [details of any
supplementary information available should be included here]. See
DOI: 10.1039/x0xx00000x
Please do not adjust margins
Please do not adjust margins
Journal Name
RESEARCH PAPER
29th January 2018,
Graphene project
Author Full Name,
The expermint was focused on the uses of chemical vapor deposition (CVD) process for growing graphene. The process
also consider etching copper foil as well as making graphene-polymer composite.The findings allow make calculation of the
percentage of mass of graghene achievable..
Introduction
Until recently, many scientists had carried out experiments and
invented graphene but with no known practical use. Dubbed ‘the
new carbon,’ graphene is a semi-metallic element with improved
electric properties (a very small separation between the conduction
bands and the valence band). The optical transparency (more than
97%) of the element is very high and is very flexible with 1100 TPa
value of Young’s Modulus. These properties coupled with being
lightweight and graphene’s high charge carrier mobility have
rendered the element very useful in the manufacture of durable and
flexible touch screens.1
Its two-dimensional electron gas properties have triggered interest in
many researchers all over the world. In 2009, Liu and fellow
scientists managed to successfully get graphene that was N-doped
through chemical vapour deposition (CVD).2 The graphene they got
from the process had properties of an n-type semiconductor.
Currently, this element is very important in the daily lives of
individuals because of its increased importance in the production of
electronics. Manufacture of batteries, transistors, hydrogen storage,
sensors and solar cells are among the other uses of graphene. This
paper highlights the steps that were followed to make fullerenes,
carbon nanotubes and graphene using Molymod.
Graphene can be produced from graphite through a number of
processes in the laboratory. Some of the most popular methods used
to prepare it are: oxidation of graphite, mechanical exfoliation and
thermal decomposition. However, production of the element through
mechanical exfoliation results in a product of high quality but in
very small amounts. Oxidative exfoliation is an improved (increased
quantity at low cost) method though the resulting graphene is of low
quality. Liquid-Phase exfoliation is the most efficient method of
producing graphene both in the laboratory and industrial scale.3
In a nutshell, Moorfield NanoVCD system was used to grow
graphene in this experiment. At an aqueous-organic interface, copper
foil was then etched from the grown graphene and the remaining
element (graphene) was combined with polymers to create
composites like fullerenes.
The resulting graphene can then be combined with a polymer to
create a composite and also increase the volume of the graphene.
Different polymers -- with either conducting or insulating properties
-- give their properties to the various composites and each can be
used for a different purpose. Touchscreens made by composites of
this element usually comprise of monoatomic graphene film layers
and polymer layers. The screens are very clear thanks to graphene’s
transparency, a property that is attributed to the fine structure and
arrangement of crystals within the graphene films. The conductance
of these films is improved by acetylene and the PTFE binder
(impurity). While graphene is a very useful element as are its
composites, much research into health and safety standardization on
its composites has to be carried out to help eliminate any hazards
that might arise in future.
Experimental:
The chemicals used in this experiment:
1- Cyclohexane
Purity = 99%
Supplier = Fisher Scientific
This journal is © The Royal Society of Chemistry 20xx J. Name., 2013, 00, 1-3 | 1
b. Address here.
c. Address here.
† Footnotes relating to the title and/or authors should appear here.
Electronic Supplementary Information (ESI) available: [details of any
supplementary information available should be included here]. See
DOI: 10.1039/x0xx00000x
Please do not adjust margins
Please do not adjust margins
Journal Name
RESEARCH PAPER
29th January 2018,
Graphene project
Author Full Name,
The expermint was focused on the uses of chemical vapor deposition (CVD) process for growing graphene. The process
also consider etching copper foil as well as making graphene-polymer composite.The findings allow make calculation of the
percentage of mass of graghene achievable..
Introduction
Until recently, many scientists had carried out experiments and
invented graphene but with no known practical use. Dubbed ‘the
new carbon,’ graphene is a semi-metallic element with improved
electric properties (a very small separation between the conduction
bands and the valence band). The optical transparency (more than
97%) of the element is very high and is very flexible with 1100 TPa
value of Young’s Modulus. These properties coupled with being
lightweight and graphene’s high charge carrier mobility have
rendered the element very useful in the manufacture of durable and
flexible touch screens.1
Its two-dimensional electron gas properties have triggered interest in
many researchers all over the world. In 2009, Liu and fellow
scientists managed to successfully get graphene that was N-doped
through chemical vapour deposition (CVD).2 The graphene they got
from the process had properties of an n-type semiconductor.
Currently, this element is very important in the daily lives of
individuals because of its increased importance in the production of
electronics. Manufacture of batteries, transistors, hydrogen storage,
sensors and solar cells are among the other uses of graphene. This
paper highlights the steps that were followed to make fullerenes,
carbon nanotubes and graphene using Molymod.
Graphene can be produced from graphite through a number of
processes in the laboratory. Some of the most popular methods used
to prepare it are: oxidation of graphite, mechanical exfoliation and
thermal decomposition. However, production of the element through
mechanical exfoliation results in a product of high quality but in
very small amounts. Oxidative exfoliation is an improved (increased
quantity at low cost) method though the resulting graphene is of low
quality. Liquid-Phase exfoliation is the most efficient method of
producing graphene both in the laboratory and industrial scale.3
In a nutshell, Moorfield NanoVCD system was used to grow
graphene in this experiment. At an aqueous-organic interface, copper
foil was then etched from the grown graphene and the remaining
element (graphene) was combined with polymers to create
composites like fullerenes.
The resulting graphene can then be combined with a polymer to
create a composite and also increase the volume of the graphene.
Different polymers -- with either conducting or insulating properties
-- give their properties to the various composites and each can be
used for a different purpose. Touchscreens made by composites of
this element usually comprise of monoatomic graphene film layers
and polymer layers. The screens are very clear thanks to graphene’s
transparency, a property that is attributed to the fine structure and
arrangement of crystals within the graphene films. The conductance
of these films is improved by acetylene and the PTFE binder
(impurity). While graphene is a very useful element as are its
composites, much research into health and safety standardization on
its composites has to be carried out to help eliminate any hazards
that might arise in future.
Experimental:
The chemicals used in this experiment:
1- Cyclohexane
Purity = 99%
Supplier = Fisher Scientific
This journal is © The Royal Society of Chemistry 20xx J. Name., 2013, 00, 1-3 | 1
Secure Best Marks with AI Grader
Need help grading? Try our AI Grader for instant feedback on your assignments.
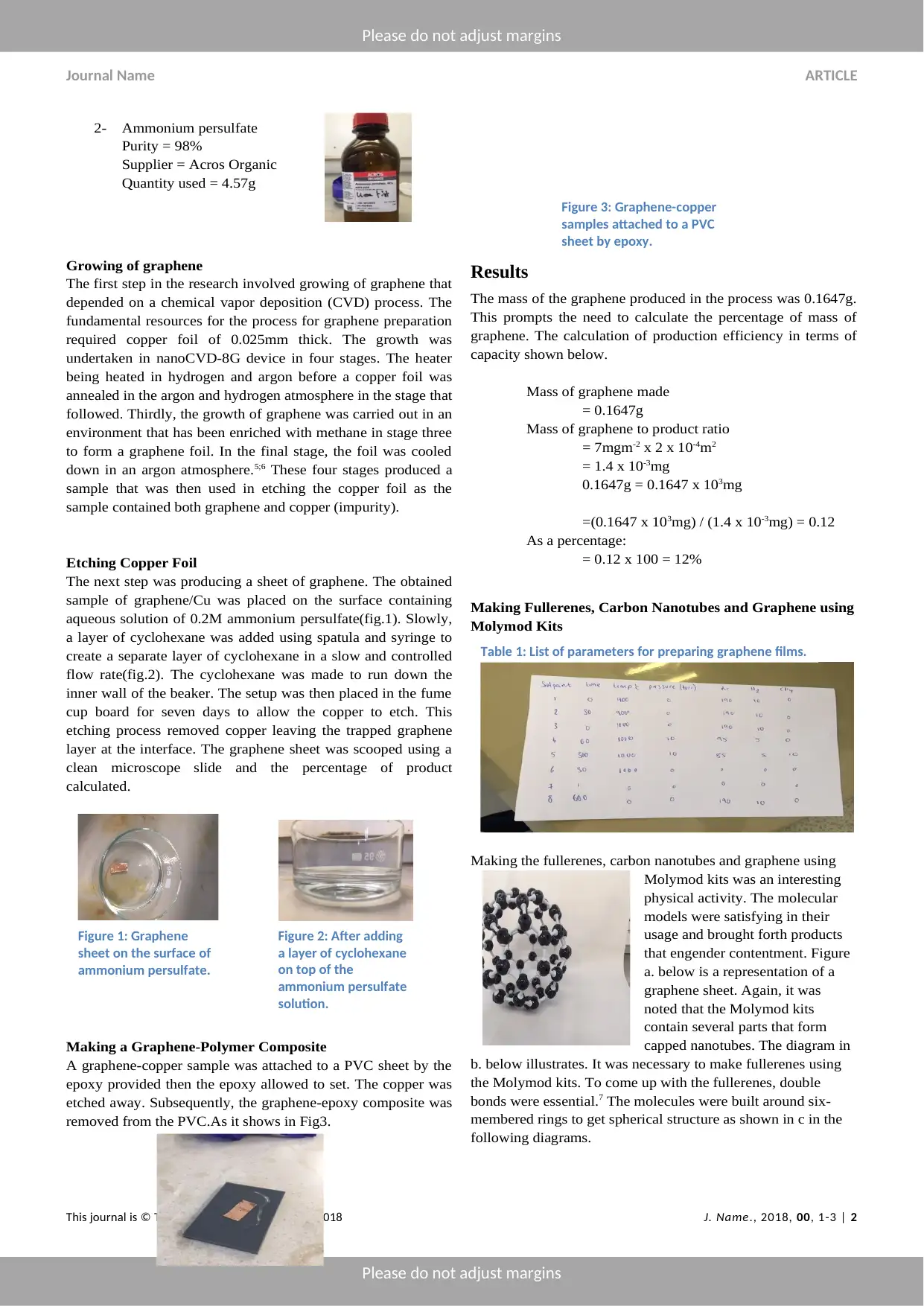
Please do not adjust margins
Please do not adjust margins
Journal Name ARTICLE
2- Ammonium persulfate
Purity = 98%
Supplier = Acros Organic
Quantity used = 4.57g
Growing of graphene
The first step in the research involved growing of graphene that
depended on a chemical vapor deposition (CVD) process. The
fundamental resources for the process for graphene preparation
required copper foil of 0.025mm thick. The growth was
undertaken in nanoCVD-8G device in four stages. The heater
being heated in hydrogen and argon before a copper foil was
annealed in the argon and hydrogen atmosphere in the stage that
followed. Thirdly, the growth of graphene was carried out in an
environment that has been enriched with methane in stage three
to form a graphene foil. In the final stage, the foil was cooled
down in an argon atmosphere. 5;6 These four stages produced a
sample that was then used in etching the copper foil as the
sample contained both graphene and copper (impurity).
Etching Copper Foil
The next step was producing a sheet of graphene. The obtained
sample of graphene/Cu was placed on the surface containing
aqueous solution of 0.2M ammonium persulfate(fig.1). Slowly,
a layer of cyclohexane was added using spatula and syringe to
create a separate layer of cyclohexane in a slow and controlled
flow rate(fig.2). The cyclohexane was made to run down the
inner wall of the beaker. The setup was then placed in the fume
cup board for seven days to allow the copper to etch. This
etching process removed copper leaving the trapped graphene
layer at the interface. The graphene sheet was scooped using a
clean microscope slide and the percentage of product
calculated.
Making a Graphene-Polymer Composite
A graphene-copper sample was attached to a PVC sheet by the
epoxy provided then the epoxy allowed to set. The copper was
etched away. Subsequently, the graphene-epoxy composite was
removed from the PVC.As it shows in Fig3.
Results
The mass of the graphene produced in the process was 0.1647g.
This prompts the need to calculate the percentage of mass of
graphene. The calculation of production efficiency in terms of
capacity shown below.
Mass of graphene made
= 0.1647g
Mass of graphene to product ratio
= 7mgm -2 x 2 x 10-4 m2
= 1.4 x 10 -3 mg
0.1647g = 0.1647 x 10 3 mg
=(0.1647 x 10 3 mg) / (1.4 x 10 -3 mg) = 0.12
As a percentage:
= 0.12 x 100 = 12%
Making Fullerenes, Carbon Nanotubes and Graphene using
Molymod Kits
Making the fullerenes, carbon nanotubes and graphene using
Molymod kits was an interesting
physical activity. The molecular
models were satisfying in their
usage and brought forth products
that engender contentment. Figure
a. below is a representation of a
graphene sheet. Again, it was
noted that the Molymod kits
contain several parts that form
capped nanotubes. The diagram in
b. below illustrates. It was necessary to make fullerenes using
the Molymod kits. To come up with the fullerenes, double
bonds were essential. 7 The molecules were built around six-
membered rings to get spherical structure as shown in c in the
following diagrams.
This journal is © The Royal Society of Chemistry 2018 J. Name., 2018, 00, 1-3 | 2
Figure 1: Graphene
sheet on the surface of
ammonium persulfate.
Figure 2: After adding
a layer of cyclohexane
on top of the
ammonium persulfate
solution.
Figure 3: Graphene-copper
samples attached to a PVC
sheet by epoxy.
Table 1: List of parameters for preparing graphene films.
Please do not adjust margins
Journal Name ARTICLE
2- Ammonium persulfate
Purity = 98%
Supplier = Acros Organic
Quantity used = 4.57g
Growing of graphene
The first step in the research involved growing of graphene that
depended on a chemical vapor deposition (CVD) process. The
fundamental resources for the process for graphene preparation
required copper foil of 0.025mm thick. The growth was
undertaken in nanoCVD-8G device in four stages. The heater
being heated in hydrogen and argon before a copper foil was
annealed in the argon and hydrogen atmosphere in the stage that
followed. Thirdly, the growth of graphene was carried out in an
environment that has been enriched with methane in stage three
to form a graphene foil. In the final stage, the foil was cooled
down in an argon atmosphere. 5;6 These four stages produced a
sample that was then used in etching the copper foil as the
sample contained both graphene and copper (impurity).
Etching Copper Foil
The next step was producing a sheet of graphene. The obtained
sample of graphene/Cu was placed on the surface containing
aqueous solution of 0.2M ammonium persulfate(fig.1). Slowly,
a layer of cyclohexane was added using spatula and syringe to
create a separate layer of cyclohexane in a slow and controlled
flow rate(fig.2). The cyclohexane was made to run down the
inner wall of the beaker. The setup was then placed in the fume
cup board for seven days to allow the copper to etch. This
etching process removed copper leaving the trapped graphene
layer at the interface. The graphene sheet was scooped using a
clean microscope slide and the percentage of product
calculated.
Making a Graphene-Polymer Composite
A graphene-copper sample was attached to a PVC sheet by the
epoxy provided then the epoxy allowed to set. The copper was
etched away. Subsequently, the graphene-epoxy composite was
removed from the PVC.As it shows in Fig3.
Results
The mass of the graphene produced in the process was 0.1647g.
This prompts the need to calculate the percentage of mass of
graphene. The calculation of production efficiency in terms of
capacity shown below.
Mass of graphene made
= 0.1647g
Mass of graphene to product ratio
= 7mgm -2 x 2 x 10-4 m2
= 1.4 x 10 -3 mg
0.1647g = 0.1647 x 10 3 mg
=(0.1647 x 10 3 mg) / (1.4 x 10 -3 mg) = 0.12
As a percentage:
= 0.12 x 100 = 12%
Making Fullerenes, Carbon Nanotubes and Graphene using
Molymod Kits
Making the fullerenes, carbon nanotubes and graphene using
Molymod kits was an interesting
physical activity. The molecular
models were satisfying in their
usage and brought forth products
that engender contentment. Figure
a. below is a representation of a
graphene sheet. Again, it was
noted that the Molymod kits
contain several parts that form
capped nanotubes. The diagram in
b. below illustrates. It was necessary to make fullerenes using
the Molymod kits. To come up with the fullerenes, double
bonds were essential. 7 The molecules were built around six-
membered rings to get spherical structure as shown in c in the
following diagrams.
This journal is © The Royal Society of Chemistry 2018 J. Name., 2018, 00, 1-3 | 2
Figure 1: Graphene
sheet on the surface of
ammonium persulfate.
Figure 2: After adding
a layer of cyclohexane
on top of the
ammonium persulfate
solution.
Figure 3: Graphene-copper
samples attached to a PVC
sheet by epoxy.
Table 1: List of parameters for preparing graphene films.
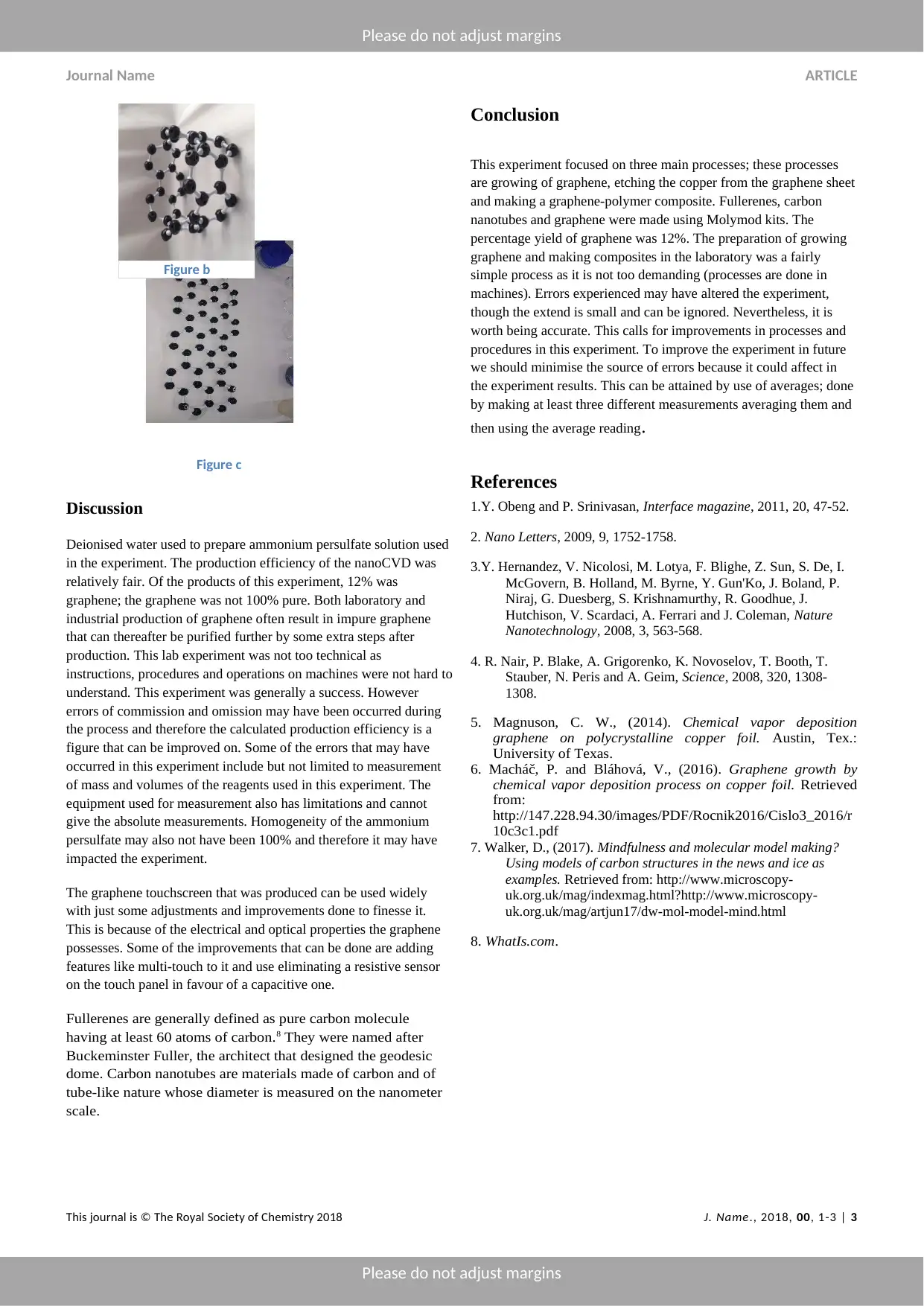
Please do not adjust margins
Please do not adjust margins
Journal Name ARTICLE
Discussion
Deionised water used to prepare ammonium persulfate solution used
in the experiment. The production efficiency of the nanoCVD was
relatively fair. Of the products of this experiment, 12% was
graphene; the graphene was not 100% pure. Both laboratory and
industrial production of graphene often result in impure graphene
that can thereafter be purified further by some extra steps after
production. This lab experiment was not too technical as
instructions, procedures and operations on machines were not hard to
understand. This experiment was generally a success. However
errors of commission and omission may have been occurred during
the process and therefore the calculated production efficiency is a
figure that can be improved on. Some of the errors that may have
occurred in this experiment include but not limited to measurement
of mass and volumes of the reagents used in this experiment. The
equipment used for measurement also has limitations and cannot
give the absolute measurements. Homogeneity of the ammonium
persulfate may also not have been 100% and therefore it may have
impacted the experiment.
The graphene touchscreen that was produced can be used widely
with just some adjustments and improvements done to finesse it.
This is because of the electrical and optical properties the graphene
possesses. Some of the improvements that can be done are adding
features like multi-touch to it and use eliminating a resistive sensor
on the touch panel in favour of a capacitive one.
Fullerenes are generally defined as pure carbon molecule
having at least 60 atoms of carbon. 8 They were named after
Buckeminster Fuller, the architect that designed the geodesic
dome. Carbon nanotubes are materials made of carbon and of
tube-like nature whose diameter is measured on the nanometer
scale.
Conclusion
This experiment focused on three main processes; these processes
are growing of graphene, etching the copper from the graphene sheet
and making a graphene-polymer composite. Fullerenes, carbon
nanotubes and graphene were made using Molymod kits. The
percentage yield of graphene was 12%. The preparation of growing
graphene and making composites in the laboratory was a fairly
simple process as it is not too demanding (processes are done in
machines). Errors experienced may have altered the experiment,
though the extend is small and can be ignored. Nevertheless, it is
worth being accurate. This calls for improvements in processes and
procedures in this experiment. To improve the experiment in future
we should minimise the source of errors because it could affect in
the experiment results. This can be attained by use of averages; done
by making at least three different measurements averaging them and
then using the average reading.
References
1.Y. Obeng and P. Srinivasan, Interface magazine, 2011, 20, 47-52.
2. Nano Letters, 2009, 9, 1752-1758.
3.Y. Hernandez, V. Nicolosi, M. Lotya, F. Blighe, Z. Sun, S. De, I.
McGovern, B. Holland, M. Byrne, Y. Gun'Ko, J. Boland, P.
Niraj, G. Duesberg, S. Krishnamurthy, R. Goodhue, J.
Hutchison, V. Scardaci, A. Ferrari and J. Coleman, Nature
Nanotechnology, 2008, 3, 563-568.
4. R. Nair, P. Blake, A. Grigorenko, K. Novoselov, T. Booth, T.
Stauber, N. Peris and A. Geim, Science, 2008, 320, 1308-
1308.
5. Magnuson, C. W., (2014). Chemical vapor deposition
graphene on polycrystalline copper foil. Austin, Tex.:
University of Texas.
6. Macháč, P. and Bláhová, V., (2016). Graphene growth by
chemical vapor deposition process on copper foil. Retrieved
from:
http://147.228.94.30/images/PDF/Rocnik2016/Cislo3_2016/r
10c3c1.pdf
7. Walker, D., (2017). Mindfulness and molecular model making?
Using models of carbon structures in the news and ice as
examples. Retrieved from: http://www.microscopy-
uk.org.uk/mag/indexmag.html?http://www.microscopy-
uk.org.uk/mag/artjun17/dw-mol-model-mind.html
8. WhatIs.com.
This journal is © The Royal Society of Chemistry 2018 J. Name., 2018, 00, 1-3 | 3
Figure c
Figure ba
Please do not adjust margins
Journal Name ARTICLE
Discussion
Deionised water used to prepare ammonium persulfate solution used
in the experiment. The production efficiency of the nanoCVD was
relatively fair. Of the products of this experiment, 12% was
graphene; the graphene was not 100% pure. Both laboratory and
industrial production of graphene often result in impure graphene
that can thereafter be purified further by some extra steps after
production. This lab experiment was not too technical as
instructions, procedures and operations on machines were not hard to
understand. This experiment was generally a success. However
errors of commission and omission may have been occurred during
the process and therefore the calculated production efficiency is a
figure that can be improved on. Some of the errors that may have
occurred in this experiment include but not limited to measurement
of mass and volumes of the reagents used in this experiment. The
equipment used for measurement also has limitations and cannot
give the absolute measurements. Homogeneity of the ammonium
persulfate may also not have been 100% and therefore it may have
impacted the experiment.
The graphene touchscreen that was produced can be used widely
with just some adjustments and improvements done to finesse it.
This is because of the electrical and optical properties the graphene
possesses. Some of the improvements that can be done are adding
features like multi-touch to it and use eliminating a resistive sensor
on the touch panel in favour of a capacitive one.
Fullerenes are generally defined as pure carbon molecule
having at least 60 atoms of carbon. 8 They were named after
Buckeminster Fuller, the architect that designed the geodesic
dome. Carbon nanotubes are materials made of carbon and of
tube-like nature whose diameter is measured on the nanometer
scale.
Conclusion
This experiment focused on three main processes; these processes
are growing of graphene, etching the copper from the graphene sheet
and making a graphene-polymer composite. Fullerenes, carbon
nanotubes and graphene were made using Molymod kits. The
percentage yield of graphene was 12%. The preparation of growing
graphene and making composites in the laboratory was a fairly
simple process as it is not too demanding (processes are done in
machines). Errors experienced may have altered the experiment,
though the extend is small and can be ignored. Nevertheless, it is
worth being accurate. This calls for improvements in processes and
procedures in this experiment. To improve the experiment in future
we should minimise the source of errors because it could affect in
the experiment results. This can be attained by use of averages; done
by making at least three different measurements averaging them and
then using the average reading.
References
1.Y. Obeng and P. Srinivasan, Interface magazine, 2011, 20, 47-52.
2. Nano Letters, 2009, 9, 1752-1758.
3.Y. Hernandez, V. Nicolosi, M. Lotya, F. Blighe, Z. Sun, S. De, I.
McGovern, B. Holland, M. Byrne, Y. Gun'Ko, J. Boland, P.
Niraj, G. Duesberg, S. Krishnamurthy, R. Goodhue, J.
Hutchison, V. Scardaci, A. Ferrari and J. Coleman, Nature
Nanotechnology, 2008, 3, 563-568.
4. R. Nair, P. Blake, A. Grigorenko, K. Novoselov, T. Booth, T.
Stauber, N. Peris and A. Geim, Science, 2008, 320, 1308-
1308.
5. Magnuson, C. W., (2014). Chemical vapor deposition
graphene on polycrystalline copper foil. Austin, Tex.:
University of Texas.
6. Macháč, P. and Bláhová, V., (2016). Graphene growth by
chemical vapor deposition process on copper foil. Retrieved
from:
http://147.228.94.30/images/PDF/Rocnik2016/Cislo3_2016/r
10c3c1.pdf
7. Walker, D., (2017). Mindfulness and molecular model making?
Using models of carbon structures in the news and ice as
examples. Retrieved from: http://www.microscopy-
uk.org.uk/mag/indexmag.html?http://www.microscopy-
uk.org.uk/mag/artjun17/dw-mol-model-mind.html
8. WhatIs.com.
This journal is © The Royal Society of Chemistry 2018 J. Name., 2018, 00, 1-3 | 3
Figure c
Figure ba
1 out of 3
![[object Object]](/_next/image/?url=%2F_next%2Fstatic%2Fmedia%2Flogo.6d15ce61.png&w=640&q=75)
Your All-in-One AI-Powered Toolkit for Academic Success.
+13062052269
info@desklib.com
Available 24*7 on WhatsApp / Email
Unlock your academic potential
© 2024 | Zucol Services PVT LTD | All rights reserved.