Cleanroom Validation: Design, Certification, and Maintenance
VerifiedAdded on 2023/06/04
|34
|7315
|299
AI Summary
This article discusses the design, certification, and maintenance of cleanrooms for various industries, including biotechnology, pharmaceuticals, defense, microelectronics, and nanotechnology. It covers the steps for validating cleanrooms, the process required in maintaining the validated state of the cleanroom, and the importance of cleanroom clothing and cleaning instructions.
Contribute Materials
Your contribution can guide someone’s learning journey. Share your
documents today.
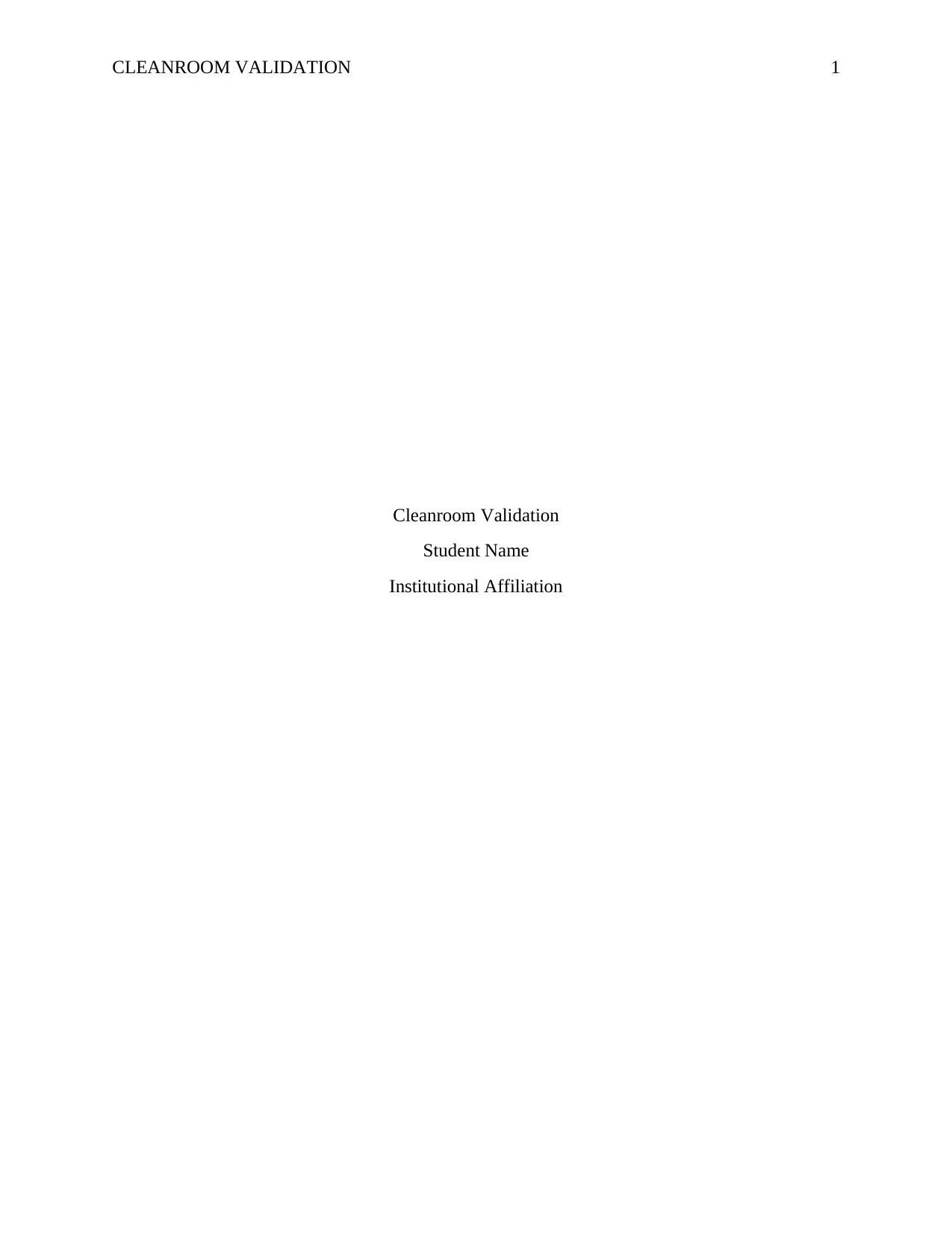
CLEANROOM VALIDATION 1
Cleanroom Validation
Student Name
Institutional Affiliation
Cleanroom Validation
Student Name
Institutional Affiliation
Secure Best Marks with AI Grader
Need help grading? Try our AI Grader for instant feedback on your assignments.
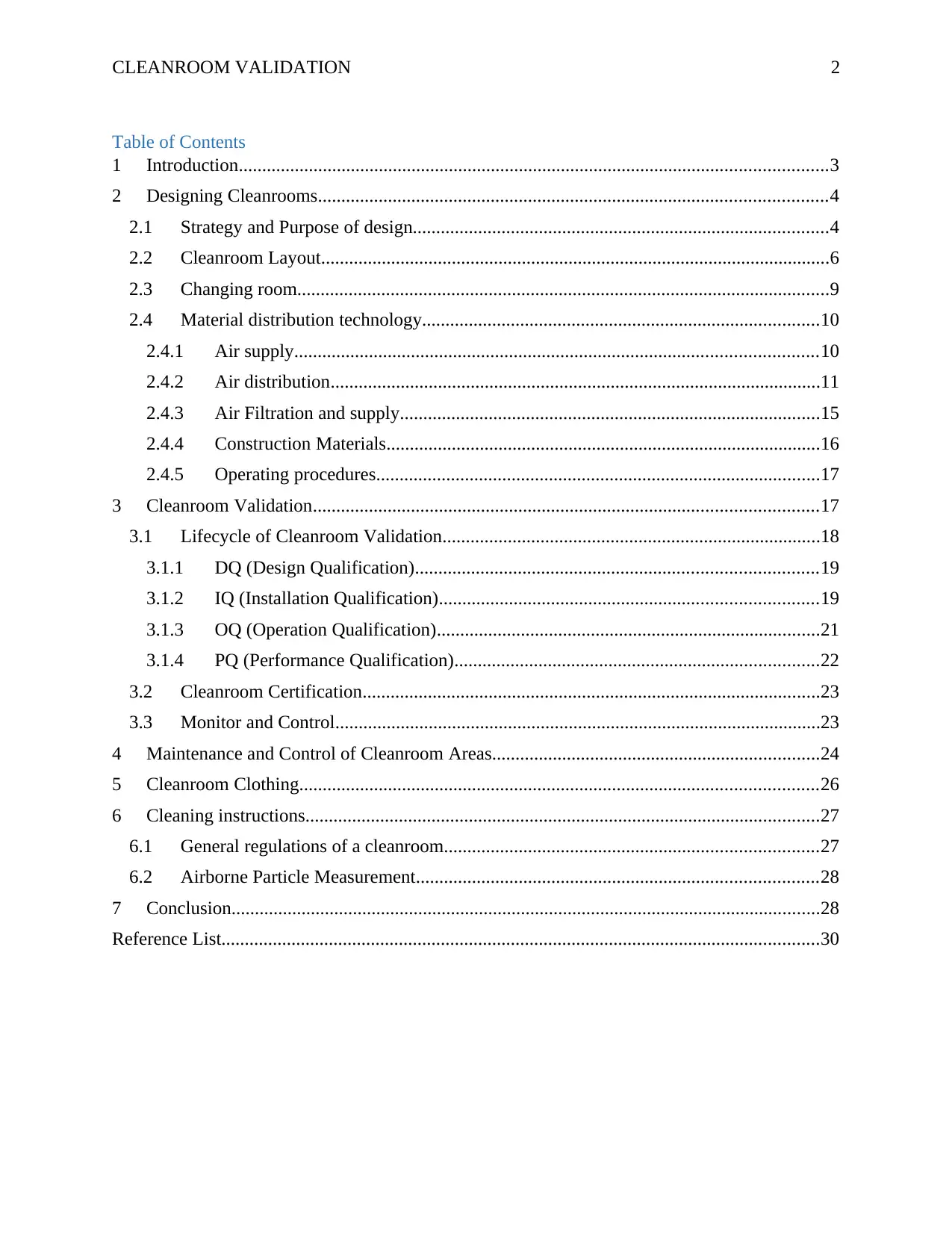
CLEANROOM VALIDATION 2
Table of Contents
1 Introduction..............................................................................................................................3
2 Designing Cleanrooms.............................................................................................................4
2.1 Strategy and Purpose of design.........................................................................................4
2.2 Cleanroom Layout.............................................................................................................6
2.3 Changing room..................................................................................................................9
2.4 Material distribution technology.....................................................................................10
2.4.1 Air supply................................................................................................................10
2.4.2 Air distribution.........................................................................................................11
2.4.3 Air Filtration and supply..........................................................................................15
2.4.4 Construction Materials.............................................................................................16
2.4.5 Operating procedures...............................................................................................17
3 Cleanroom Validation............................................................................................................17
3.1 Lifecycle of Cleanroom Validation.................................................................................18
3.1.1 DQ (Design Qualification)......................................................................................19
3.1.2 IQ (Installation Qualification).................................................................................19
3.1.3 OQ (Operation Qualification)..................................................................................21
3.1.4 PQ (Performance Qualification)..............................................................................22
3.2 Cleanroom Certification..................................................................................................23
3.3 Monitor and Control........................................................................................................23
4 Maintenance and Control of Cleanroom Areas......................................................................24
5 Cleanroom Clothing...............................................................................................................26
6 Cleaning instructions..............................................................................................................27
6.1 General regulations of a cleanroom................................................................................27
6.2 Airborne Particle Measurement......................................................................................28
7 Conclusion..............................................................................................................................28
Reference List................................................................................................................................30
Table of Contents
1 Introduction..............................................................................................................................3
2 Designing Cleanrooms.............................................................................................................4
2.1 Strategy and Purpose of design.........................................................................................4
2.2 Cleanroom Layout.............................................................................................................6
2.3 Changing room..................................................................................................................9
2.4 Material distribution technology.....................................................................................10
2.4.1 Air supply................................................................................................................10
2.4.2 Air distribution.........................................................................................................11
2.4.3 Air Filtration and supply..........................................................................................15
2.4.4 Construction Materials.............................................................................................16
2.4.5 Operating procedures...............................................................................................17
3 Cleanroom Validation............................................................................................................17
3.1 Lifecycle of Cleanroom Validation.................................................................................18
3.1.1 DQ (Design Qualification)......................................................................................19
3.1.2 IQ (Installation Qualification).................................................................................19
3.1.3 OQ (Operation Qualification)..................................................................................21
3.1.4 PQ (Performance Qualification)..............................................................................22
3.2 Cleanroom Certification..................................................................................................23
3.3 Monitor and Control........................................................................................................23
4 Maintenance and Control of Cleanroom Areas......................................................................24
5 Cleanroom Clothing...............................................................................................................26
6 Cleaning instructions..............................................................................................................27
6.1 General regulations of a cleanroom................................................................................27
6.2 Airborne Particle Measurement......................................................................................28
7 Conclusion..............................................................................................................................28
Reference List................................................................................................................................30
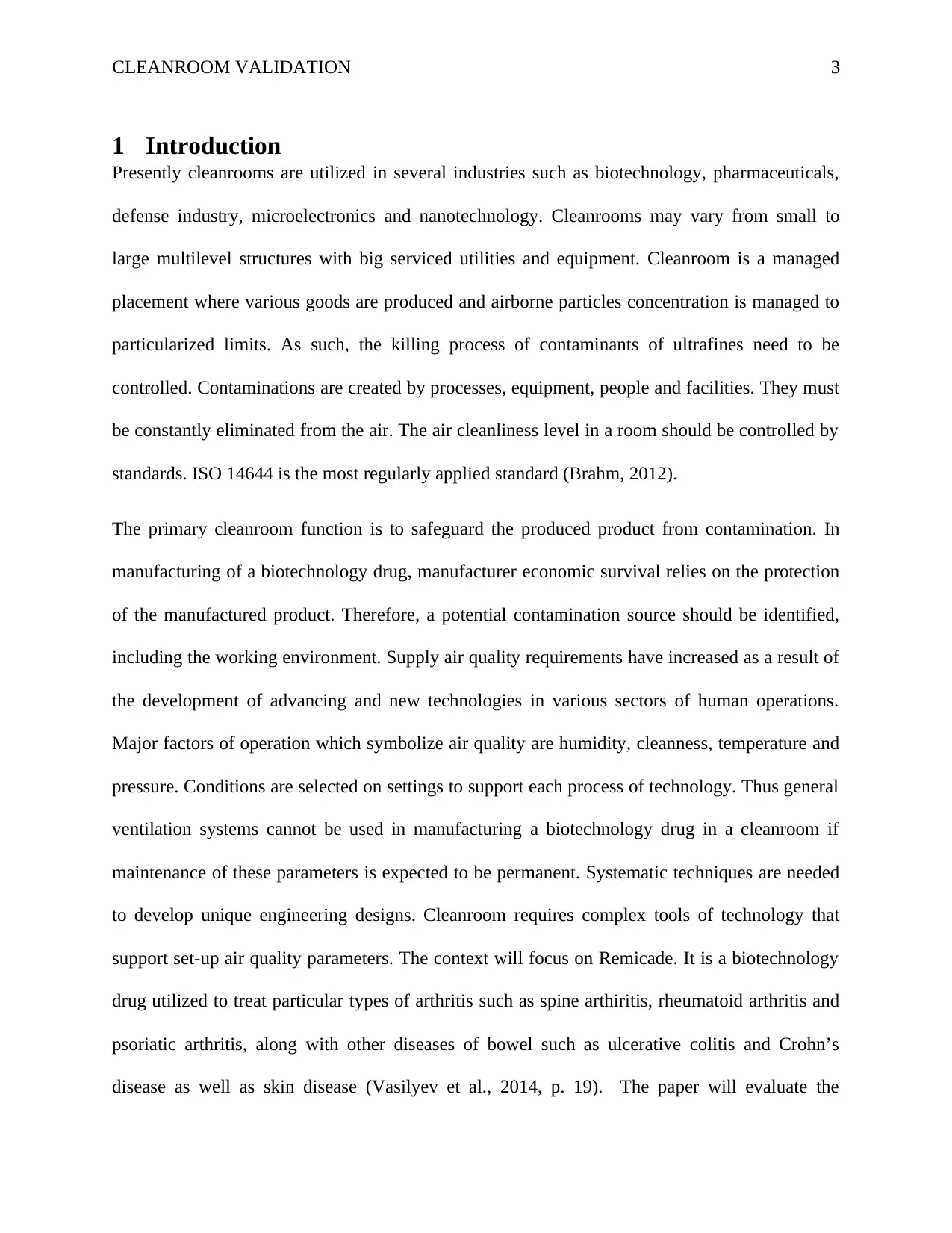
CLEANROOM VALIDATION 3
1 Introduction
Presently cleanrooms are utilized in several industries such as biotechnology, pharmaceuticals,
defense industry, microelectronics and nanotechnology. Cleanrooms may vary from small to
large multilevel structures with big serviced utilities and equipment. Cleanroom is a managed
placement where various goods are produced and airborne particles concentration is managed to
particularized limits. As such, the killing process of contaminants of ultrafines need to be
controlled. Contaminations are created by processes, equipment, people and facilities. They must
be constantly eliminated from the air. The air cleanliness level in a room should be controlled by
standards. ISO 14644 is the most regularly applied standard (Brahm, 2012).
The primary cleanroom function is to safeguard the produced product from contamination. In
manufacturing of a biotechnology drug, manufacturer economic survival relies on the protection
of the manufactured product. Therefore, a potential contamination source should be identified,
including the working environment. Supply air quality requirements have increased as a result of
the development of advancing and new technologies in various sectors of human operations.
Major factors of operation which symbolize air quality are humidity, cleanness, temperature and
pressure. Conditions are selected on settings to support each process of technology. Thus general
ventilation systems cannot be used in manufacturing a biotechnology drug in a cleanroom if
maintenance of these parameters is expected to be permanent. Systematic techniques are needed
to develop unique engineering designs. Cleanroom requires complex tools of technology that
support set-up air quality parameters. The context will focus on Remicade. It is a biotechnology
drug utilized to treat particular types of arthritis such as spine arthiritis, rheumatoid arthritis and
psoriatic arthritis, along with other diseases of bowel such as ulcerative colitis and Crohn’s
disease as well as skin disease (Vasilyev et al., 2014, p. 19). The paper will evaluate the
1 Introduction
Presently cleanrooms are utilized in several industries such as biotechnology, pharmaceuticals,
defense industry, microelectronics and nanotechnology. Cleanrooms may vary from small to
large multilevel structures with big serviced utilities and equipment. Cleanroom is a managed
placement where various goods are produced and airborne particles concentration is managed to
particularized limits. As such, the killing process of contaminants of ultrafines need to be
controlled. Contaminations are created by processes, equipment, people and facilities. They must
be constantly eliminated from the air. The air cleanliness level in a room should be controlled by
standards. ISO 14644 is the most regularly applied standard (Brahm, 2012).
The primary cleanroom function is to safeguard the produced product from contamination. In
manufacturing of a biotechnology drug, manufacturer economic survival relies on the protection
of the manufactured product. Therefore, a potential contamination source should be identified,
including the working environment. Supply air quality requirements have increased as a result of
the development of advancing and new technologies in various sectors of human operations.
Major factors of operation which symbolize air quality are humidity, cleanness, temperature and
pressure. Conditions are selected on settings to support each process of technology. Thus general
ventilation systems cannot be used in manufacturing a biotechnology drug in a cleanroom if
maintenance of these parameters is expected to be permanent. Systematic techniques are needed
to develop unique engineering designs. Cleanroom requires complex tools of technology that
support set-up air quality parameters. The context will focus on Remicade. It is a biotechnology
drug utilized to treat particular types of arthritis such as spine arthiritis, rheumatoid arthritis and
psoriatic arthritis, along with other diseases of bowel such as ulcerative colitis and Crohn’s
disease as well as skin disease (Vasilyev et al., 2014, p. 19). The paper will evaluate the
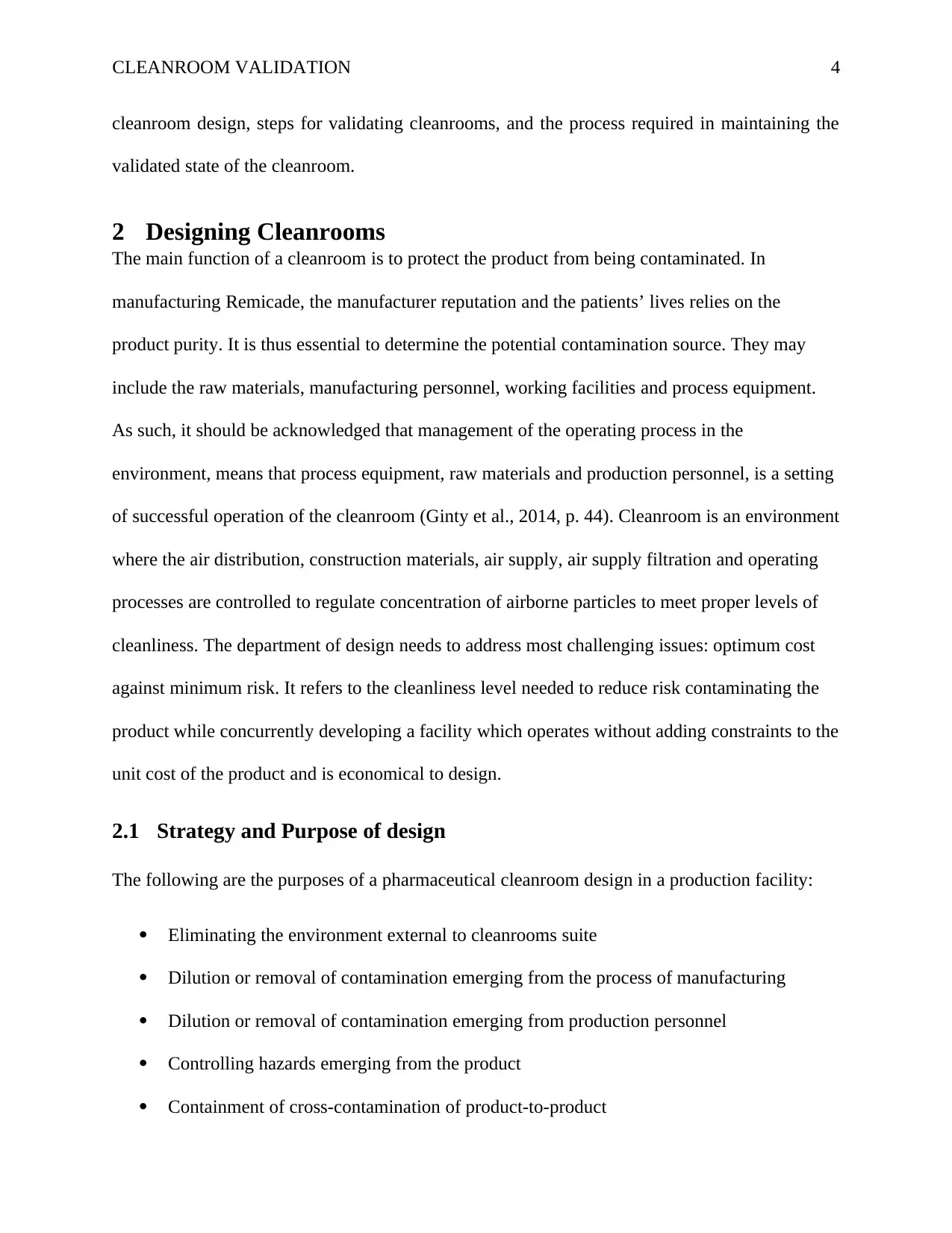
CLEANROOM VALIDATION 4
cleanroom design, steps for validating cleanrooms, and the process required in maintaining the
validated state of the cleanroom.
2 Designing Cleanrooms
The main function of a cleanroom is to protect the product from being contaminated. In
manufacturing Remicade, the manufacturer reputation and the patients’ lives relies on the
product purity. It is thus essential to determine the potential contamination source. They may
include the raw materials, manufacturing personnel, working facilities and process equipment.
As such, it should be acknowledged that management of the operating process in the
environment, means that process equipment, raw materials and production personnel, is a setting
of successful operation of the cleanroom (Ginty et al., 2014, p. 44). Cleanroom is an environment
where the air distribution, construction materials, air supply, air supply filtration and operating
processes are controlled to regulate concentration of airborne particles to meet proper levels of
cleanliness. The department of design needs to address most challenging issues: optimum cost
against minimum risk. It refers to the cleanliness level needed to reduce risk contaminating the
product while concurrently developing a facility which operates without adding constraints to the
unit cost of the product and is economical to design.
2.1 Strategy and Purpose of design
The following are the purposes of a pharmaceutical cleanroom design in a production facility:
Eliminating the environment external to cleanrooms suite
Dilution or removal of contamination emerging from the process of manufacturing
Dilution or removal of contamination emerging from production personnel
Controlling hazards emerging from the product
Containment of cross-contamination of product-to-product
cleanroom design, steps for validating cleanrooms, and the process required in maintaining the
validated state of the cleanroom.
2 Designing Cleanrooms
The main function of a cleanroom is to protect the product from being contaminated. In
manufacturing Remicade, the manufacturer reputation and the patients’ lives relies on the
product purity. It is thus essential to determine the potential contamination source. They may
include the raw materials, manufacturing personnel, working facilities and process equipment.
As such, it should be acknowledged that management of the operating process in the
environment, means that process equipment, raw materials and production personnel, is a setting
of successful operation of the cleanroom (Ginty et al., 2014, p. 44). Cleanroom is an environment
where the air distribution, construction materials, air supply, air supply filtration and operating
processes are controlled to regulate concentration of airborne particles to meet proper levels of
cleanliness. The department of design needs to address most challenging issues: optimum cost
against minimum risk. It refers to the cleanliness level needed to reduce risk contaminating the
product while concurrently developing a facility which operates without adding constraints to the
unit cost of the product and is economical to design.
2.1 Strategy and Purpose of design
The following are the purposes of a pharmaceutical cleanroom design in a production facility:
Eliminating the environment external to cleanrooms suite
Dilution or removal of contamination emerging from the process of manufacturing
Dilution or removal of contamination emerging from production personnel
Controlling hazards emerging from the product
Containment of cross-contamination of product-to-product
Secure Best Marks with AI Grader
Need help grading? Try our AI Grader for instant feedback on your assignments.
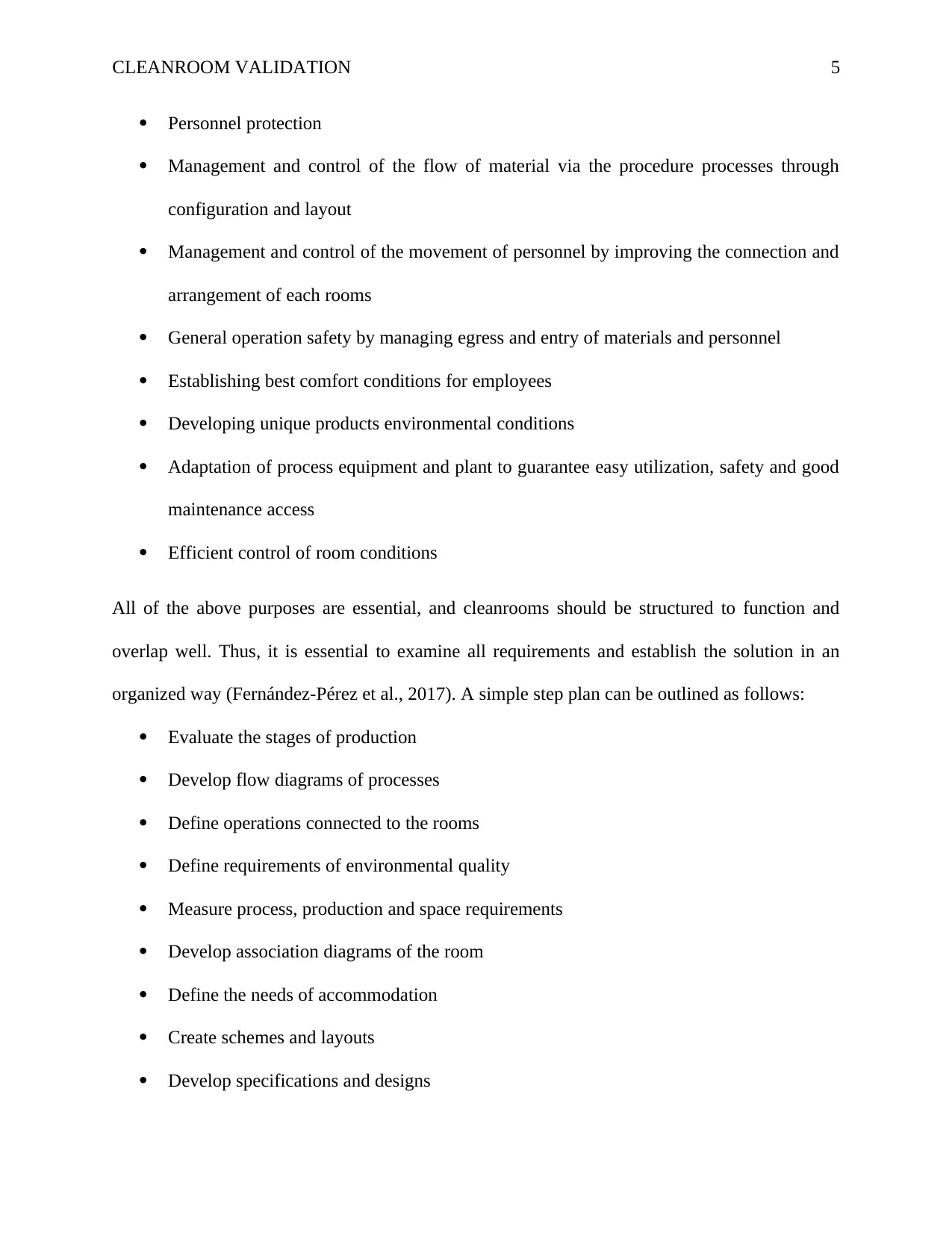
CLEANROOM VALIDATION 5
Personnel protection
Management and control of the flow of material via the procedure processes through
configuration and layout
Management and control of the movement of personnel by improving the connection and
arrangement of each rooms
General operation safety by managing egress and entry of materials and personnel
Establishing best comfort conditions for employees
Developing unique products environmental conditions
Adaptation of process equipment and plant to guarantee easy utilization, safety and good
maintenance access
Efficient control of room conditions
All of the above purposes are essential, and cleanrooms should be structured to function and
overlap well. Thus, it is essential to examine all requirements and establish the solution in an
organized way (Fernández-Pérez et al., 2017). A simple step plan can be outlined as follows:
Evaluate the stages of production
Develop flow diagrams of processes
Define operations connected to the rooms
Define requirements of environmental quality
Measure process, production and space requirements
Develop association diagrams of the room
Define the needs of accommodation
Create schemes and layouts
Develop specifications and designs
Personnel protection
Management and control of the flow of material via the procedure processes through
configuration and layout
Management and control of the movement of personnel by improving the connection and
arrangement of each rooms
General operation safety by managing egress and entry of materials and personnel
Establishing best comfort conditions for employees
Developing unique products environmental conditions
Adaptation of process equipment and plant to guarantee easy utilization, safety and good
maintenance access
Efficient control of room conditions
All of the above purposes are essential, and cleanrooms should be structured to function and
overlap well. Thus, it is essential to examine all requirements and establish the solution in an
organized way (Fernández-Pérez et al., 2017). A simple step plan can be outlined as follows:
Evaluate the stages of production
Develop flow diagrams of processes
Define operations connected to the rooms
Define requirements of environmental quality
Measure process, production and space requirements
Develop association diagrams of the room
Define the needs of accommodation
Create schemes and layouts
Develop specifications and designs
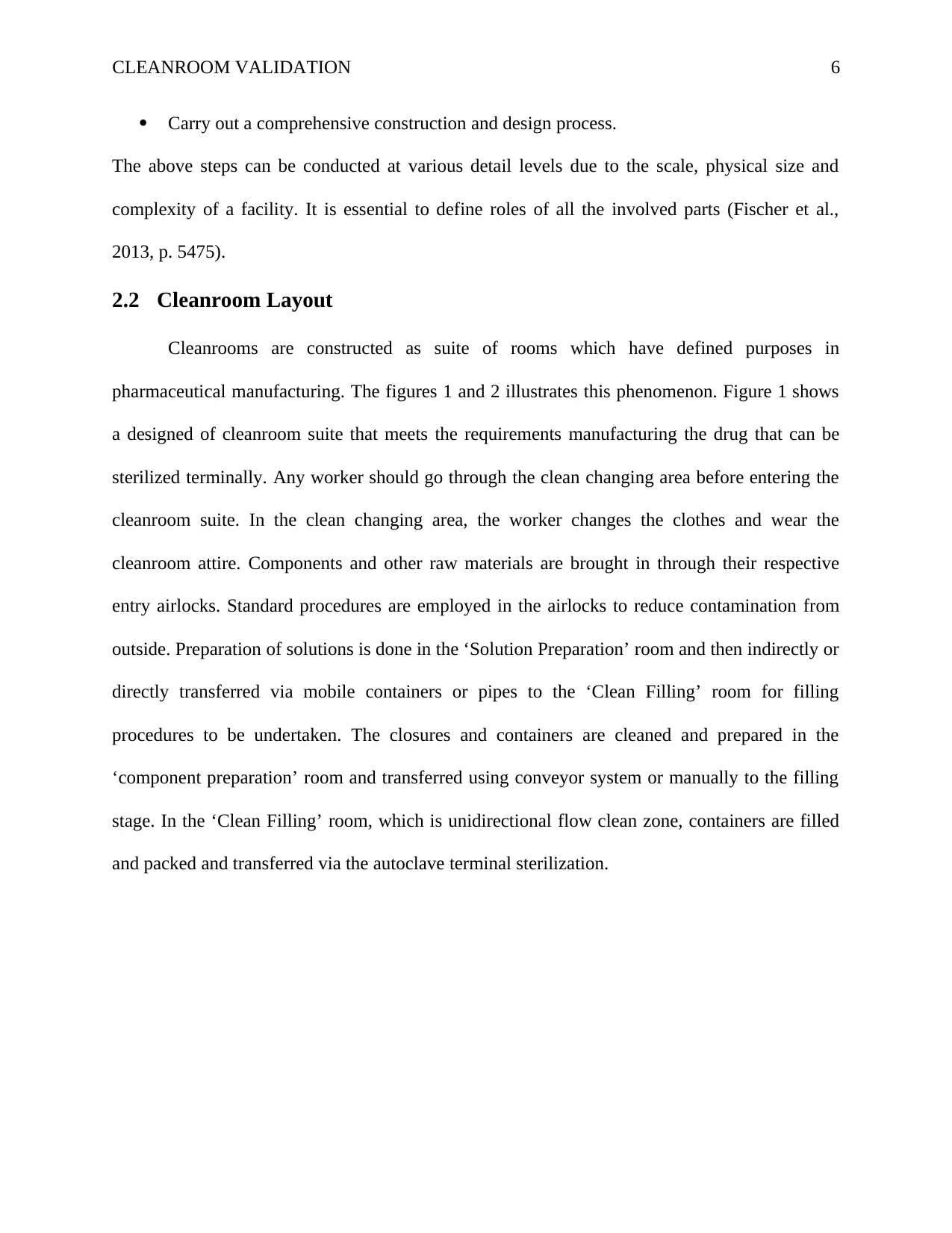
CLEANROOM VALIDATION 6
Carry out a comprehensive construction and design process.
The above steps can be conducted at various detail levels due to the scale, physical size and
complexity of a facility. It is essential to define roles of all the involved parts (Fischer et al.,
2013, p. 5475).
2.2 Cleanroom Layout
Cleanrooms are constructed as suite of rooms which have defined purposes in
pharmaceutical manufacturing. The figures 1 and 2 illustrates this phenomenon. Figure 1 shows
a designed of cleanroom suite that meets the requirements manufacturing the drug that can be
sterilized terminally. Any worker should go through the clean changing area before entering the
cleanroom suite. In the clean changing area, the worker changes the clothes and wear the
cleanroom attire. Components and other raw materials are brought in through their respective
entry airlocks. Standard procedures are employed in the airlocks to reduce contamination from
outside. Preparation of solutions is done in the ‘Solution Preparation’ room and then indirectly or
directly transferred via mobile containers or pipes to the ‘Clean Filling’ room for filling
procedures to be undertaken. The closures and containers are cleaned and prepared in the
‘component preparation’ room and transferred using conveyor system or manually to the filling
stage. In the ‘Clean Filling’ room, which is unidirectional flow clean zone, containers are filled
and packed and transferred via the autoclave terminal sterilization.
Carry out a comprehensive construction and design process.
The above steps can be conducted at various detail levels due to the scale, physical size and
complexity of a facility. It is essential to define roles of all the involved parts (Fischer et al.,
2013, p. 5475).
2.2 Cleanroom Layout
Cleanrooms are constructed as suite of rooms which have defined purposes in
pharmaceutical manufacturing. The figures 1 and 2 illustrates this phenomenon. Figure 1 shows
a designed of cleanroom suite that meets the requirements manufacturing the drug that can be
sterilized terminally. Any worker should go through the clean changing area before entering the
cleanroom suite. In the clean changing area, the worker changes the clothes and wear the
cleanroom attire. Components and other raw materials are brought in through their respective
entry airlocks. Standard procedures are employed in the airlocks to reduce contamination from
outside. Preparation of solutions is done in the ‘Solution Preparation’ room and then indirectly or
directly transferred via mobile containers or pipes to the ‘Clean Filling’ room for filling
procedures to be undertaken. The closures and containers are cleaned and prepared in the
‘component preparation’ room and transferred using conveyor system or manually to the filling
stage. In the ‘Clean Filling’ room, which is unidirectional flow clean zone, containers are filled
and packed and transferred via the autoclave terminal sterilization.
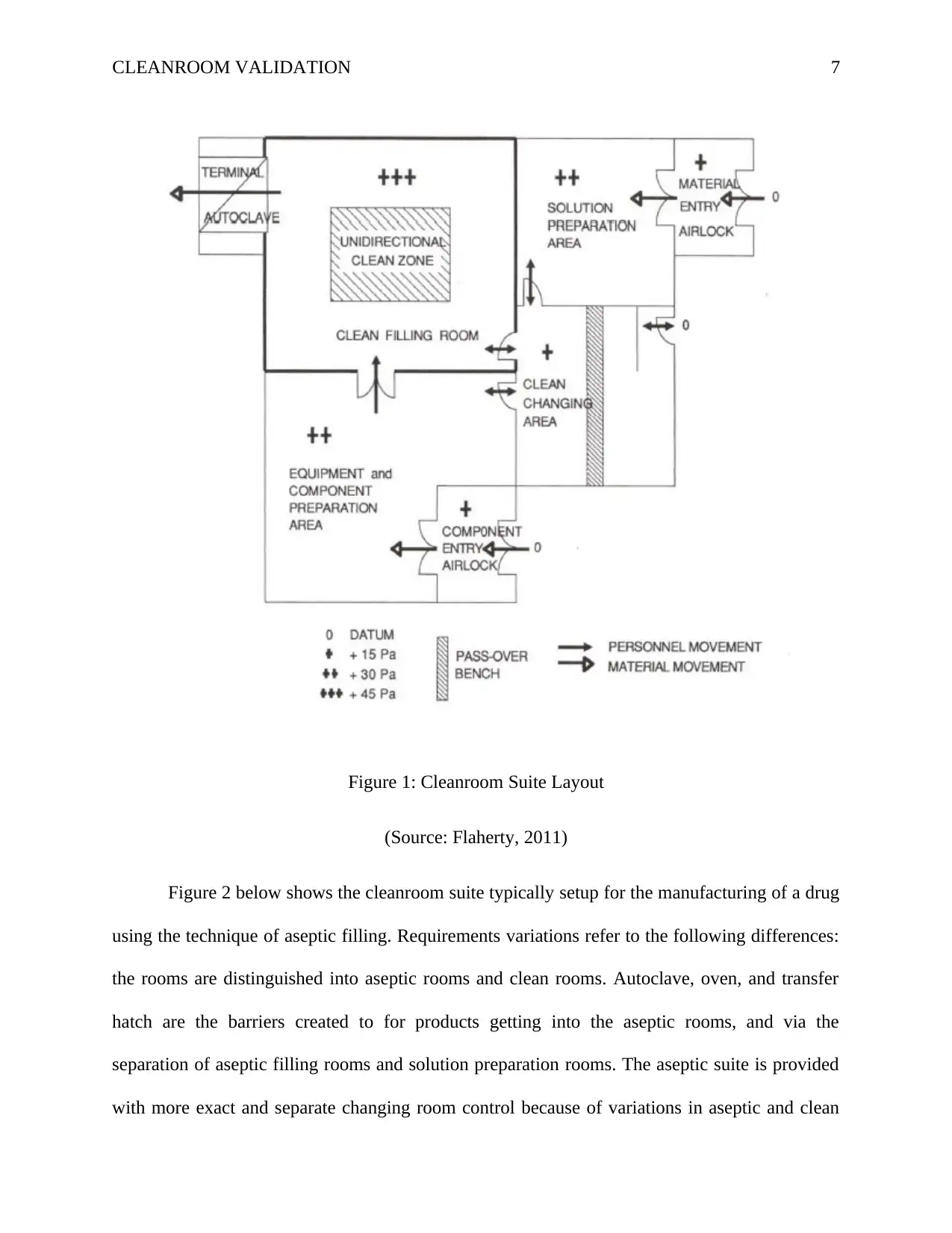
CLEANROOM VALIDATION 7
Figure 1: Cleanroom Suite Layout
(Source: Flaherty, 2011)
Figure 2 below shows the cleanroom suite typically setup for the manufacturing of a drug
using the technique of aseptic filling. Requirements variations refer to the following differences:
the rooms are distinguished into aseptic rooms and clean rooms. Autoclave, oven, and transfer
hatch are the barriers created to for products getting into the aseptic rooms, and via the
separation of aseptic filling rooms and solution preparation rooms. The aseptic suite is provided
with more exact and separate changing room control because of variations in aseptic and clean
Figure 1: Cleanroom Suite Layout
(Source: Flaherty, 2011)
Figure 2 below shows the cleanroom suite typically setup for the manufacturing of a drug
using the technique of aseptic filling. Requirements variations refer to the following differences:
the rooms are distinguished into aseptic rooms and clean rooms. Autoclave, oven, and transfer
hatch are the barriers created to for products getting into the aseptic rooms, and via the
separation of aseptic filling rooms and solution preparation rooms. The aseptic suite is provided
with more exact and separate changing room control because of variations in aseptic and clean
Paraphrase This Document
Need a fresh take? Get an instant paraphrase of this document with our AI Paraphraser
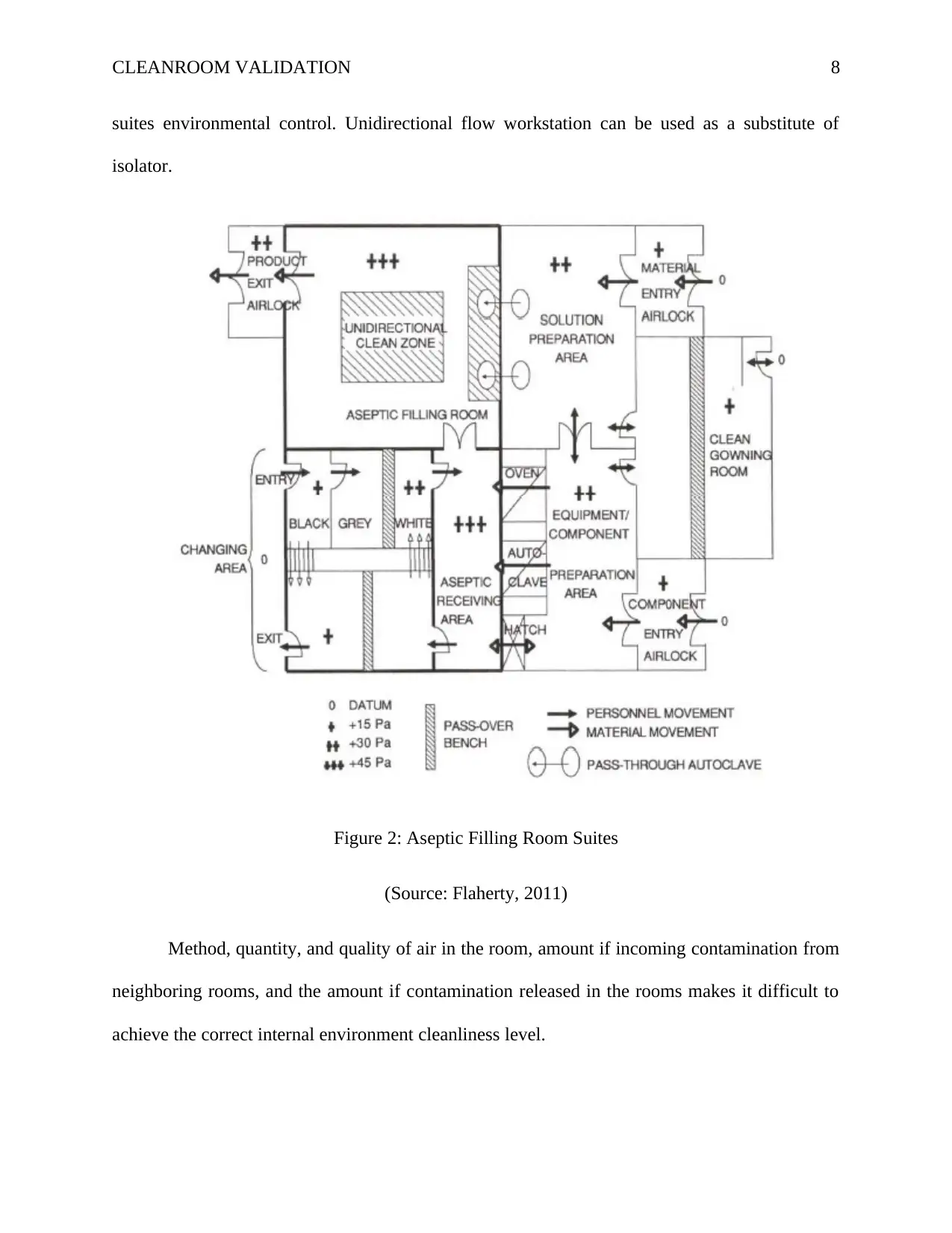
CLEANROOM VALIDATION 8
suites environmental control. Unidirectional flow workstation can be used as a substitute of
isolator.
Figure 2: Aseptic Filling Room Suites
(Source: Flaherty, 2011)
Method, quantity, and quality of air in the room, amount if incoming contamination from
neighboring rooms, and the amount if contamination released in the rooms makes it difficult to
achieve the correct internal environment cleanliness level.
suites environmental control. Unidirectional flow workstation can be used as a substitute of
isolator.
Figure 2: Aseptic Filling Room Suites
(Source: Flaherty, 2011)
Method, quantity, and quality of air in the room, amount if incoming contamination from
neighboring rooms, and the amount if contamination released in the rooms makes it difficult to
achieve the correct internal environment cleanliness level.
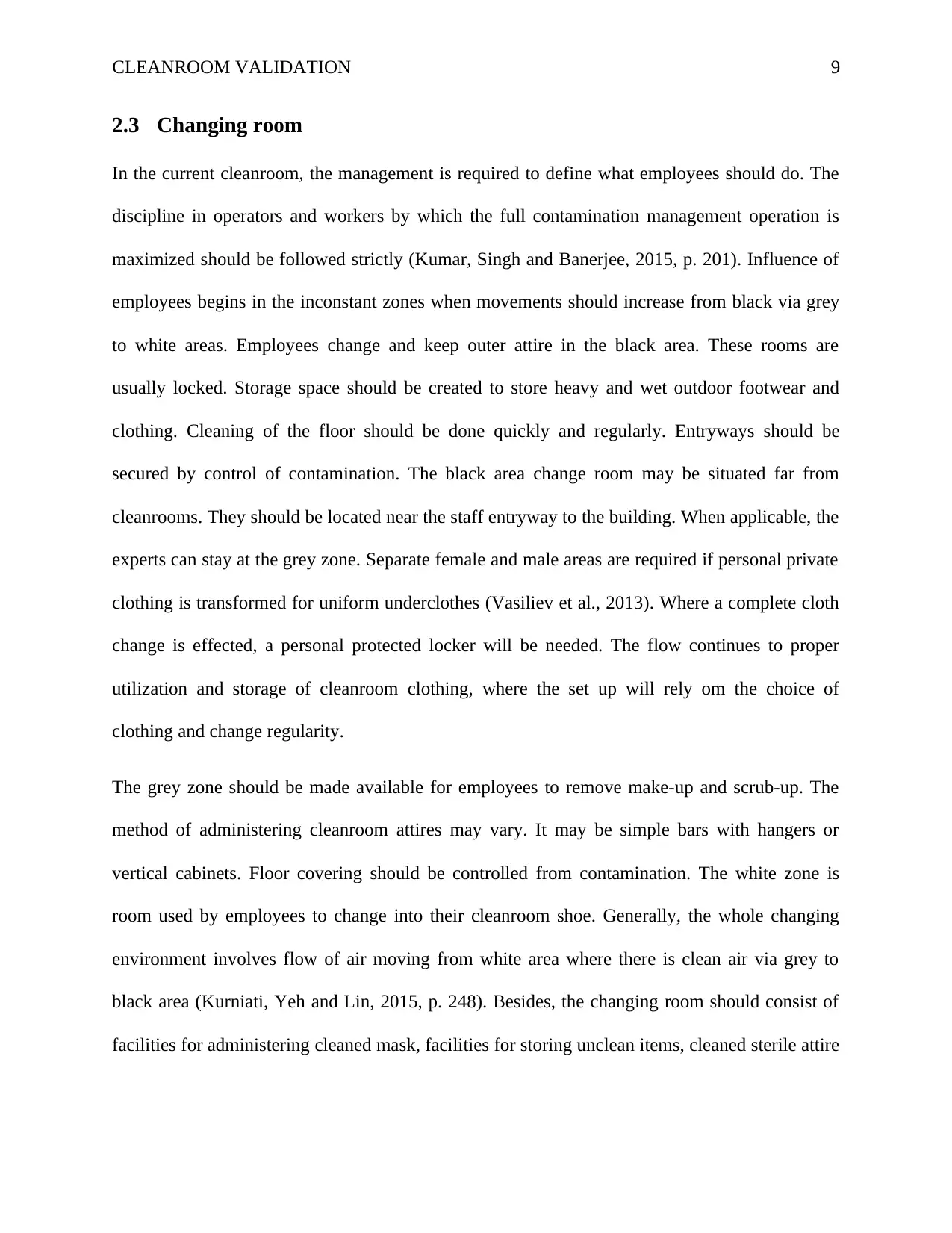
CLEANROOM VALIDATION 9
2.3 Changing room
In the current cleanroom, the management is required to define what employees should do. The
discipline in operators and workers by which the full contamination management operation is
maximized should be followed strictly (Kumar, Singh and Banerjee, 2015, p. 201). Influence of
employees begins in the inconstant zones when movements should increase from black via grey
to white areas. Employees change and keep outer attire in the black area. These rooms are
usually locked. Storage space should be created to store heavy and wet outdoor footwear and
clothing. Cleaning of the floor should be done quickly and regularly. Entryways should be
secured by control of contamination. The black area change room may be situated far from
cleanrooms. They should be located near the staff entryway to the building. When applicable, the
experts can stay at the grey zone. Separate female and male areas are required if personal private
clothing is transformed for uniform underclothes (Vasiliev et al., 2013). Where a complete cloth
change is effected, a personal protected locker will be needed. The flow continues to proper
utilization and storage of cleanroom clothing, where the set up will rely om the choice of
clothing and change regularity.
The grey zone should be made available for employees to remove make-up and scrub-up. The
method of administering cleanroom attires may vary. It may be simple bars with hangers or
vertical cabinets. Floor covering should be controlled from contamination. The white zone is
room used by employees to change into their cleanroom shoe. Generally, the whole changing
environment involves flow of air moving from white area where there is clean air via grey to
black area (Kurniati, Yeh and Lin, 2015, p. 248). Besides, the changing room should consist of
facilities for administering cleaned mask, facilities for storing unclean items, cleaned sterile attire
2.3 Changing room
In the current cleanroom, the management is required to define what employees should do. The
discipline in operators and workers by which the full contamination management operation is
maximized should be followed strictly (Kumar, Singh and Banerjee, 2015, p. 201). Influence of
employees begins in the inconstant zones when movements should increase from black via grey
to white areas. Employees change and keep outer attire in the black area. These rooms are
usually locked. Storage space should be created to store heavy and wet outdoor footwear and
clothing. Cleaning of the floor should be done quickly and regularly. Entryways should be
secured by control of contamination. The black area change room may be situated far from
cleanrooms. They should be located near the staff entryway to the building. When applicable, the
experts can stay at the grey zone. Separate female and male areas are required if personal private
clothing is transformed for uniform underclothes (Vasiliev et al., 2013). Where a complete cloth
change is effected, a personal protected locker will be needed. The flow continues to proper
utilization and storage of cleanroom clothing, where the set up will rely om the choice of
clothing and change regularity.
The grey zone should be made available for employees to remove make-up and scrub-up. The
method of administering cleanroom attires may vary. It may be simple bars with hangers or
vertical cabinets. Floor covering should be controlled from contamination. The white zone is
room used by employees to change into their cleanroom shoe. Generally, the whole changing
environment involves flow of air moving from white area where there is clean air via grey to
black area (Kurniati, Yeh and Lin, 2015, p. 248). Besides, the changing room should consist of
facilities for administering cleaned mask, facilities for storing unclean items, cleaned sterile attire
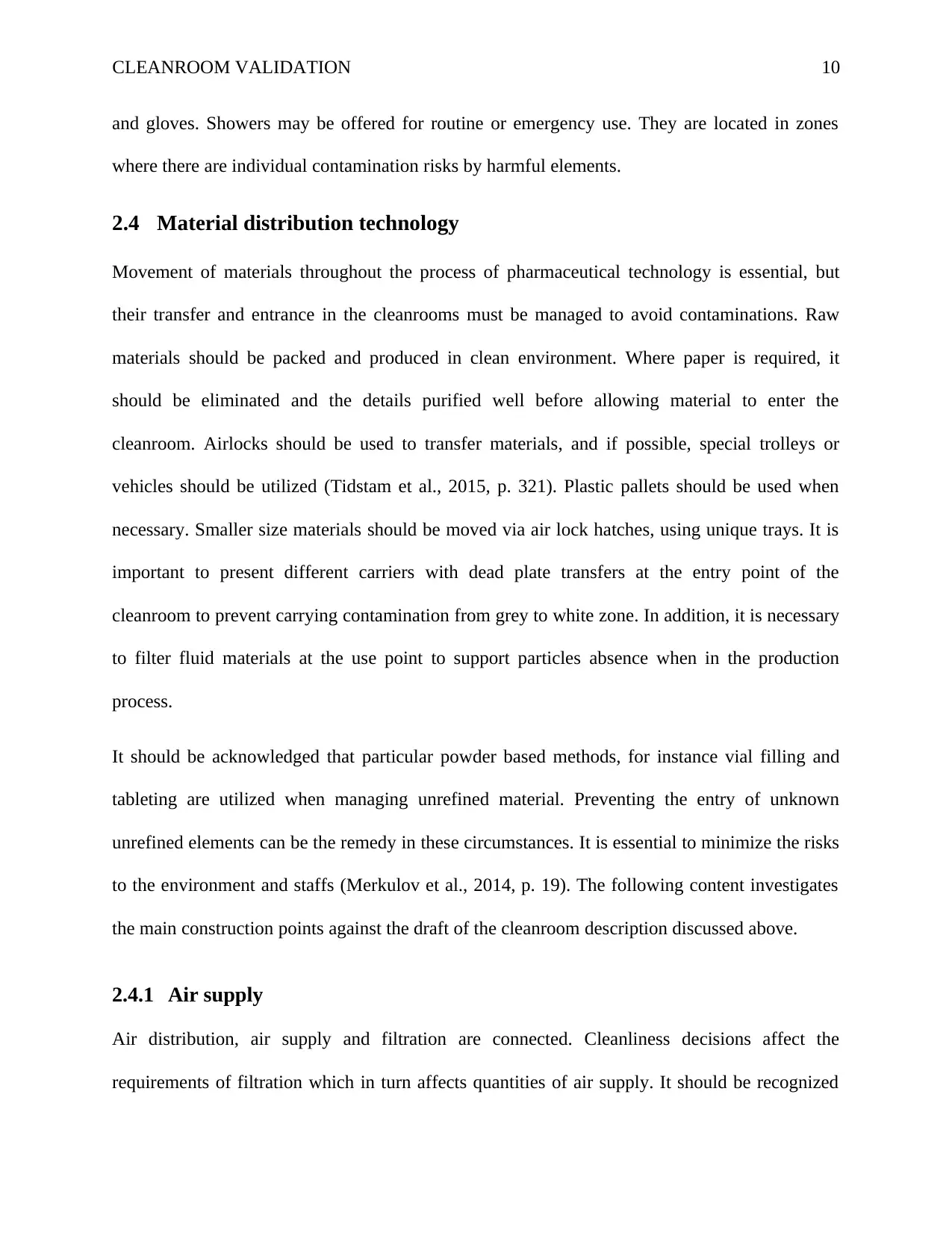
CLEANROOM VALIDATION 10
and gloves. Showers may be offered for routine or emergency use. They are located in zones
where there are individual contamination risks by harmful elements.
2.4 Material distribution technology
Movement of materials throughout the process of pharmaceutical technology is essential, but
their transfer and entrance in the cleanrooms must be managed to avoid contaminations. Raw
materials should be packed and produced in clean environment. Where paper is required, it
should be eliminated and the details purified well before allowing material to enter the
cleanroom. Airlocks should be used to transfer materials, and if possible, special trolleys or
vehicles should be utilized (Tidstam et al., 2015, p. 321). Plastic pallets should be used when
necessary. Smaller size materials should be moved via air lock hatches, using unique trays. It is
important to present different carriers with dead plate transfers at the entry point of the
cleanroom to prevent carrying contamination from grey to white zone. In addition, it is necessary
to filter fluid materials at the use point to support particles absence when in the production
process.
It should be acknowledged that particular powder based methods, for instance vial filling and
tableting are utilized when managing unrefined material. Preventing the entry of unknown
unrefined elements can be the remedy in these circumstances. It is essential to minimize the risks
to the environment and staffs (Merkulov et al., 2014, p. 19). The following content investigates
the main construction points against the draft of the cleanroom description discussed above.
2.4.1 Air supply
Air distribution, air supply and filtration are connected. Cleanliness decisions affect the
requirements of filtration which in turn affects quantities of air supply. It should be recognized
and gloves. Showers may be offered for routine or emergency use. They are located in zones
where there are individual contamination risks by harmful elements.
2.4 Material distribution technology
Movement of materials throughout the process of pharmaceutical technology is essential, but
their transfer and entrance in the cleanrooms must be managed to avoid contaminations. Raw
materials should be packed and produced in clean environment. Where paper is required, it
should be eliminated and the details purified well before allowing material to enter the
cleanroom. Airlocks should be used to transfer materials, and if possible, special trolleys or
vehicles should be utilized (Tidstam et al., 2015, p. 321). Plastic pallets should be used when
necessary. Smaller size materials should be moved via air lock hatches, using unique trays. It is
important to present different carriers with dead plate transfers at the entry point of the
cleanroom to prevent carrying contamination from grey to white zone. In addition, it is necessary
to filter fluid materials at the use point to support particles absence when in the production
process.
It should be acknowledged that particular powder based methods, for instance vial filling and
tableting are utilized when managing unrefined material. Preventing the entry of unknown
unrefined elements can be the remedy in these circumstances. It is essential to minimize the risks
to the environment and staffs (Merkulov et al., 2014, p. 19). The following content investigates
the main construction points against the draft of the cleanroom description discussed above.
2.4.1 Air supply
Air distribution, air supply and filtration are connected. Cleanliness decisions affect the
requirements of filtration which in turn affects quantities of air supply. It should be recognized
Secure Best Marks with AI Grader
Need help grading? Try our AI Grader for instant feedback on your assignments.
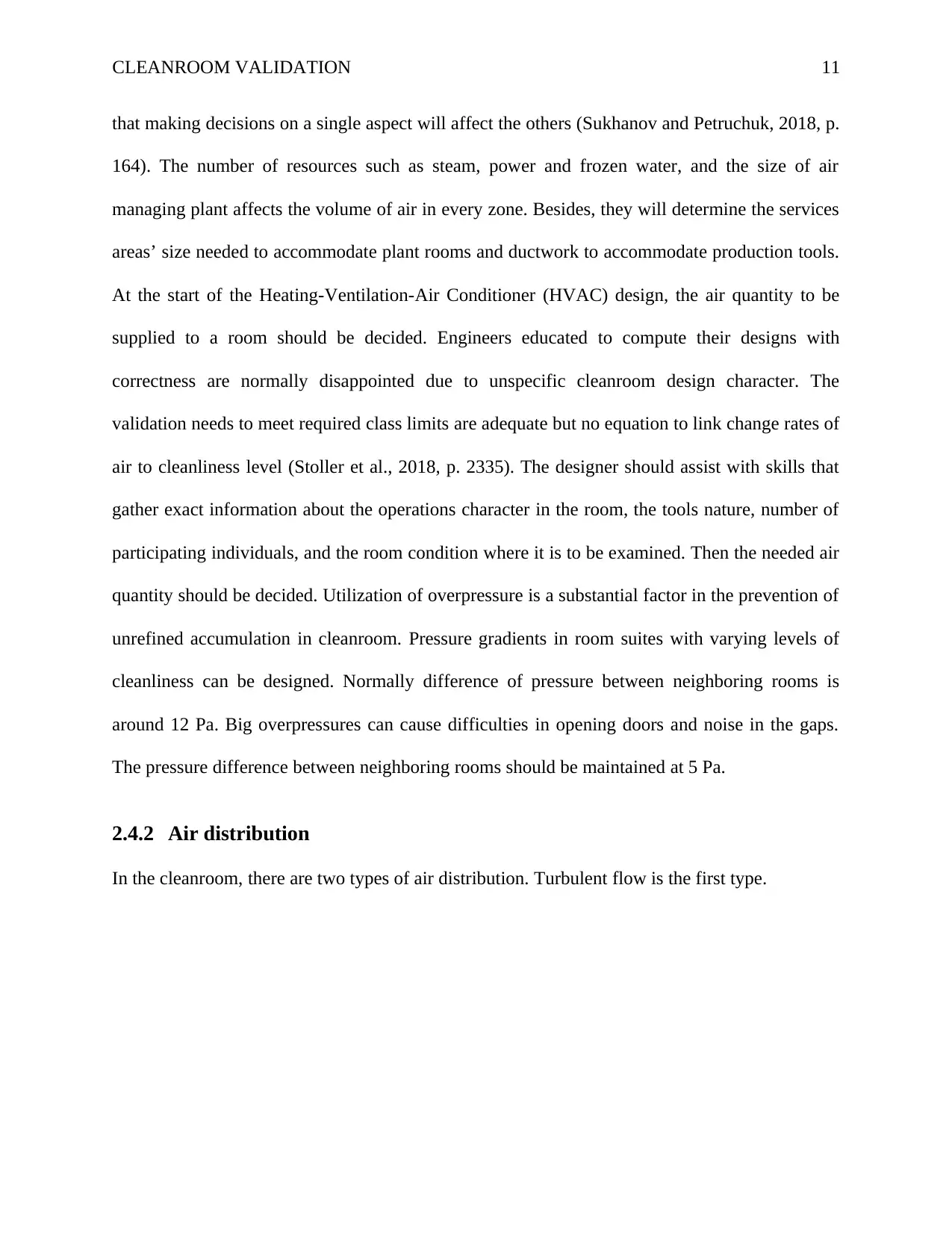
CLEANROOM VALIDATION 11
that making decisions on a single aspect will affect the others (Sukhanov and Petruchuk, 2018, p.
164). The number of resources such as steam, power and frozen water, and the size of air
managing plant affects the volume of air in every zone. Besides, they will determine the services
areas’ size needed to accommodate plant rooms and ductwork to accommodate production tools.
At the start of the Heating-Ventilation-Air Conditioner (HVAC) design, the air quantity to be
supplied to a room should be decided. Engineers educated to compute their designs with
correctness are normally disappointed due to unspecific cleanroom design character. The
validation needs to meet required class limits are adequate but no equation to link change rates of
air to cleanliness level (Stoller et al., 2018, p. 2335). The designer should assist with skills that
gather exact information about the operations character in the room, the tools nature, number of
participating individuals, and the room condition where it is to be examined. Then the needed air
quantity should be decided. Utilization of overpressure is a substantial factor in the prevention of
unrefined accumulation in cleanroom. Pressure gradients in room suites with varying levels of
cleanliness can be designed. Normally difference of pressure between neighboring rooms is
around 12 Pa. Big overpressures can cause difficulties in opening doors and noise in the gaps.
The pressure difference between neighboring rooms should be maintained at 5 Pa.
2.4.2 Air distribution
In the cleanroom, there are two types of air distribution. Turbulent flow is the first type.
that making decisions on a single aspect will affect the others (Sukhanov and Petruchuk, 2018, p.
164). The number of resources such as steam, power and frozen water, and the size of air
managing plant affects the volume of air in every zone. Besides, they will determine the services
areas’ size needed to accommodate plant rooms and ductwork to accommodate production tools.
At the start of the Heating-Ventilation-Air Conditioner (HVAC) design, the air quantity to be
supplied to a room should be decided. Engineers educated to compute their designs with
correctness are normally disappointed due to unspecific cleanroom design character. The
validation needs to meet required class limits are adequate but no equation to link change rates of
air to cleanliness level (Stoller et al., 2018, p. 2335). The designer should assist with skills that
gather exact information about the operations character in the room, the tools nature, number of
participating individuals, and the room condition where it is to be examined. Then the needed air
quantity should be decided. Utilization of overpressure is a substantial factor in the prevention of
unrefined accumulation in cleanroom. Pressure gradients in room suites with varying levels of
cleanliness can be designed. Normally difference of pressure between neighboring rooms is
around 12 Pa. Big overpressures can cause difficulties in opening doors and noise in the gaps.
The pressure difference between neighboring rooms should be maintained at 5 Pa.
2.4.2 Air distribution
In the cleanroom, there are two types of air distribution. Turbulent flow is the first type.
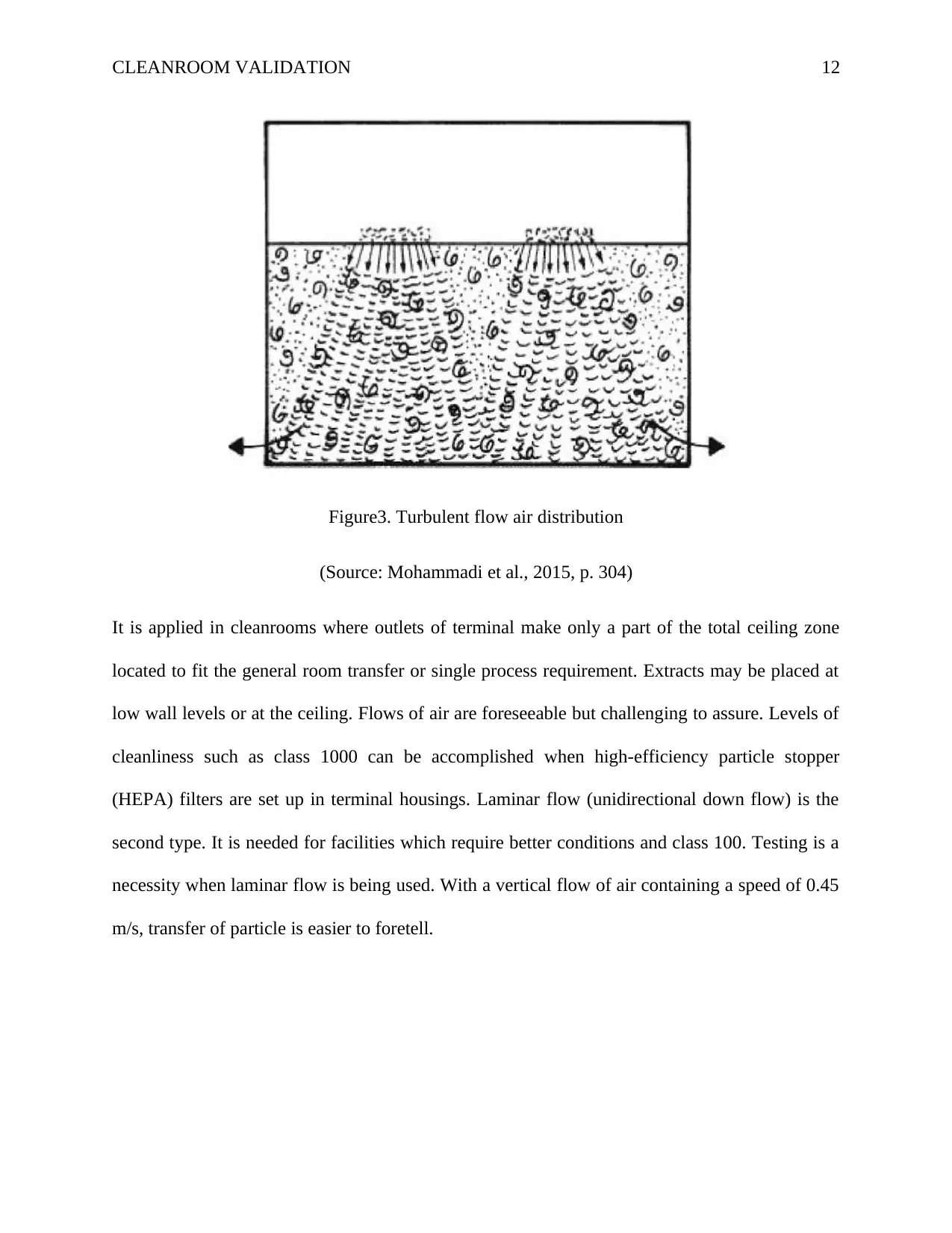
CLEANROOM VALIDATION 12
Figure3. Turbulent flow air distribution
(Source: Mohammadi et al., 2015, p. 304)
It is applied in cleanrooms where outlets of terminal make only a part of the total ceiling zone
located to fit the general room transfer or single process requirement. Extracts may be placed at
low wall levels or at the ceiling. Flows of air are foreseeable but challenging to assure. Levels of
cleanliness such as class 1000 can be accomplished when high-efficiency particle stopper
(HEPA) filters are set up in terminal housings. Laminar flow (unidirectional down flow) is the
second type. It is needed for facilities which require better conditions and class 100. Testing is a
necessity when laminar flow is being used. With a vertical flow of air containing a speed of 0.45
m/s, transfer of particle is easier to foretell.
Figure3. Turbulent flow air distribution
(Source: Mohammadi et al., 2015, p. 304)
It is applied in cleanrooms where outlets of terminal make only a part of the total ceiling zone
located to fit the general room transfer or single process requirement. Extracts may be placed at
low wall levels or at the ceiling. Flows of air are foreseeable but challenging to assure. Levels of
cleanliness such as class 1000 can be accomplished when high-efficiency particle stopper
(HEPA) filters are set up in terminal housings. Laminar flow (unidirectional down flow) is the
second type. It is needed for facilities which require better conditions and class 100. Testing is a
necessity when laminar flow is being used. With a vertical flow of air containing a speed of 0.45
m/s, transfer of particle is easier to foretell.
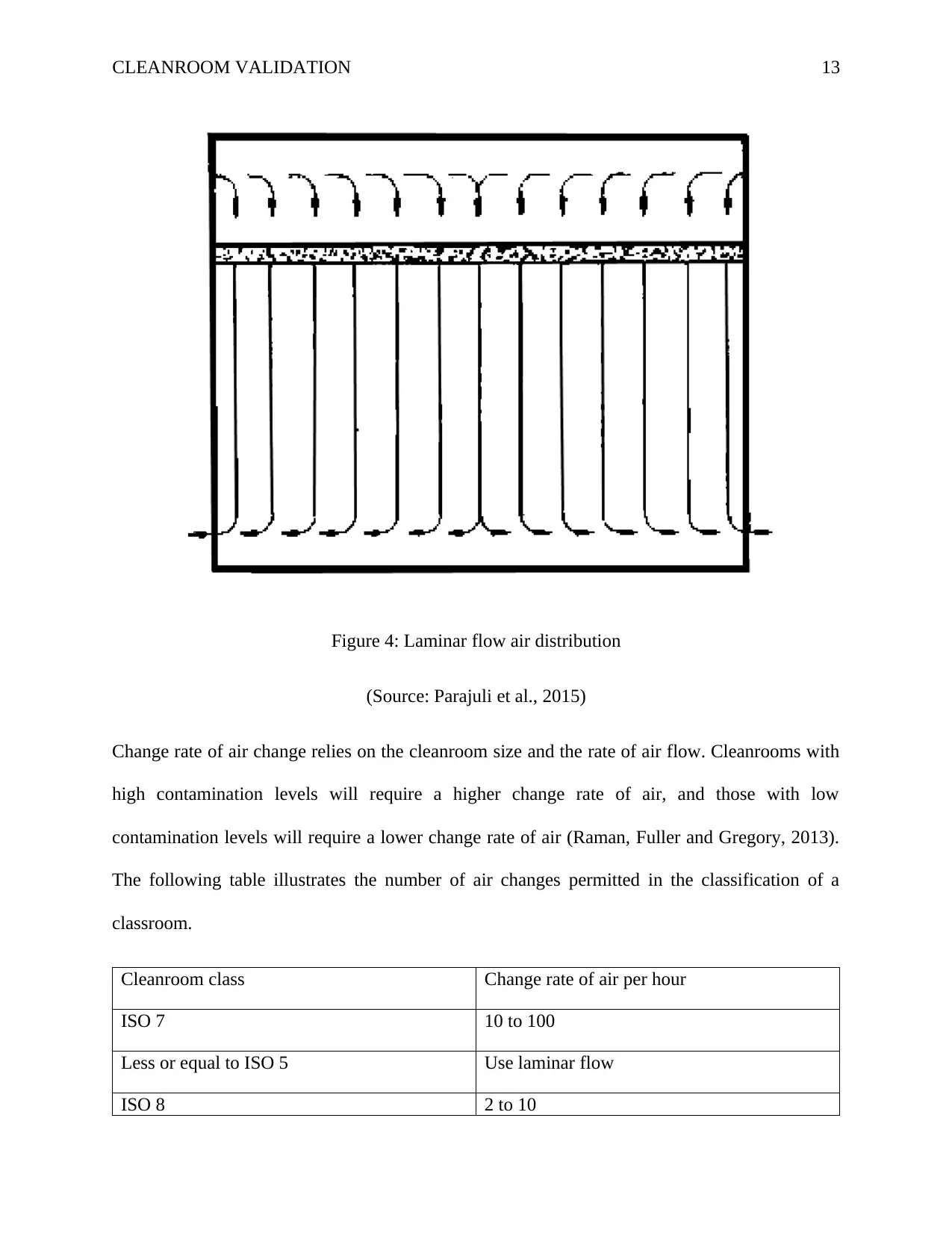
CLEANROOM VALIDATION 13
Figure 4: Laminar flow air distribution
(Source: Parajuli et al., 2015)
Change rate of air change relies on the cleanroom size and the rate of air flow. Cleanrooms with
high contamination levels will require a higher change rate of air, and those with low
contamination levels will require a lower change rate of air (Raman, Fuller and Gregory, 2013).
The following table illustrates the number of air changes permitted in the classification of a
classroom.
Cleanroom class Change rate of air per hour
ISO 7 10 to 100
Less or equal to ISO 5 Use laminar flow
ISO 8 2 to 10
Figure 4: Laminar flow air distribution
(Source: Parajuli et al., 2015)
Change rate of air change relies on the cleanroom size and the rate of air flow. Cleanrooms with
high contamination levels will require a higher change rate of air, and those with low
contamination levels will require a lower change rate of air (Raman, Fuller and Gregory, 2013).
The following table illustrates the number of air changes permitted in the classification of a
classroom.
Cleanroom class Change rate of air per hour
ISO 7 10 to 100
Less or equal to ISO 5 Use laminar flow
ISO 8 2 to 10
Paraphrase This Document
Need a fresh take? Get an instant paraphrase of this document with our AI Paraphraser
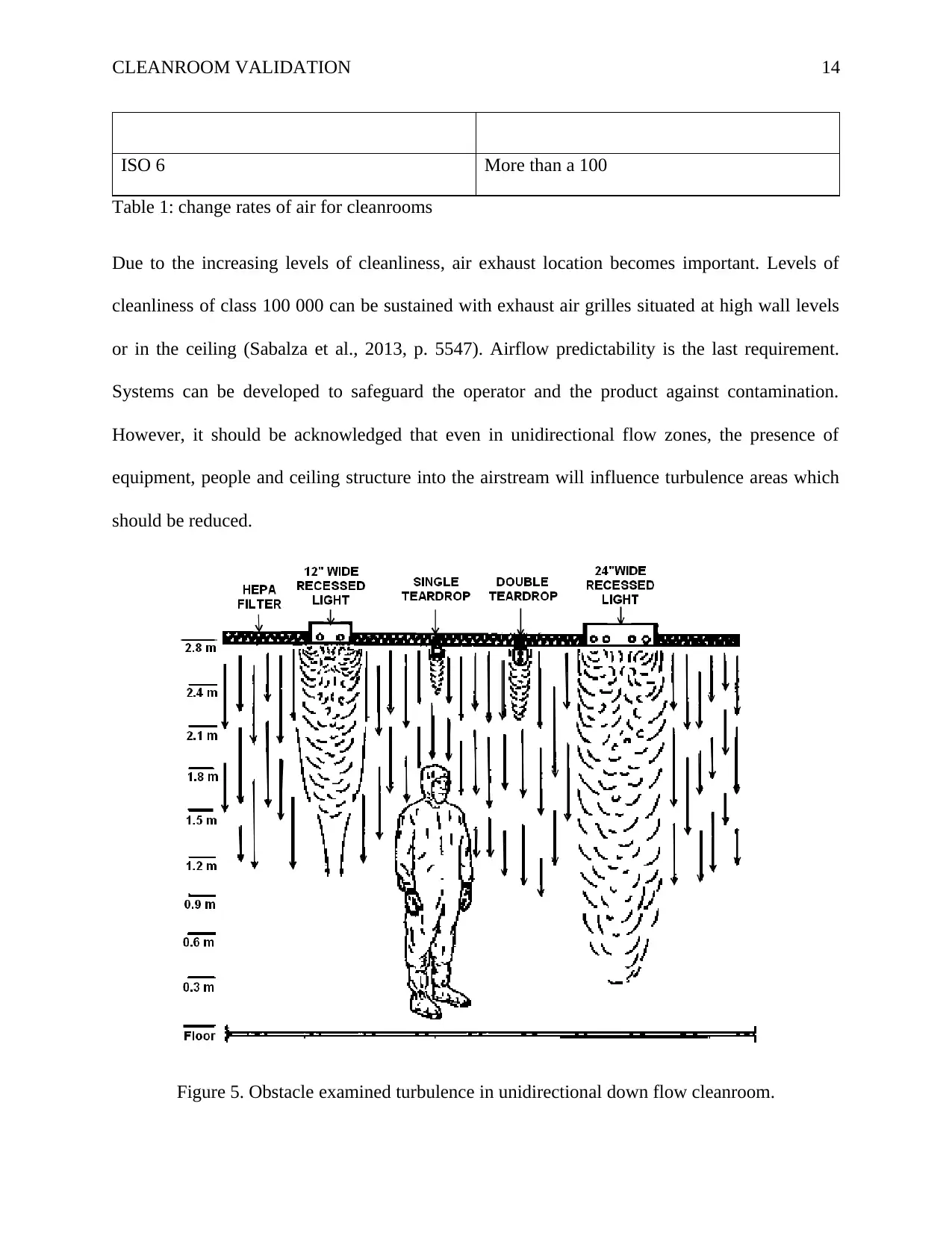
CLEANROOM VALIDATION 14
ISO 6 More than a 100
Table 1: change rates of air for cleanrooms
Due to the increasing levels of cleanliness, air exhaust location becomes important. Levels of
cleanliness of class 100 000 can be sustained with exhaust air grilles situated at high wall levels
or in the ceiling (Sabalza et al., 2013, p. 5547). Airflow predictability is the last requirement.
Systems can be developed to safeguard the operator and the product against contamination.
However, it should be acknowledged that even in unidirectional flow zones, the presence of
equipment, people and ceiling structure into the airstream will influence turbulence areas which
should be reduced.
Figure 5. Obstacle examined turbulence in unidirectional down flow cleanroom.
ISO 6 More than a 100
Table 1: change rates of air for cleanrooms
Due to the increasing levels of cleanliness, air exhaust location becomes important. Levels of
cleanliness of class 100 000 can be sustained with exhaust air grilles situated at high wall levels
or in the ceiling (Sabalza et al., 2013, p. 5547). Airflow predictability is the last requirement.
Systems can be developed to safeguard the operator and the product against contamination.
However, it should be acknowledged that even in unidirectional flow zones, the presence of
equipment, people and ceiling structure into the airstream will influence turbulence areas which
should be reduced.
Figure 5. Obstacle examined turbulence in unidirectional down flow cleanroom.
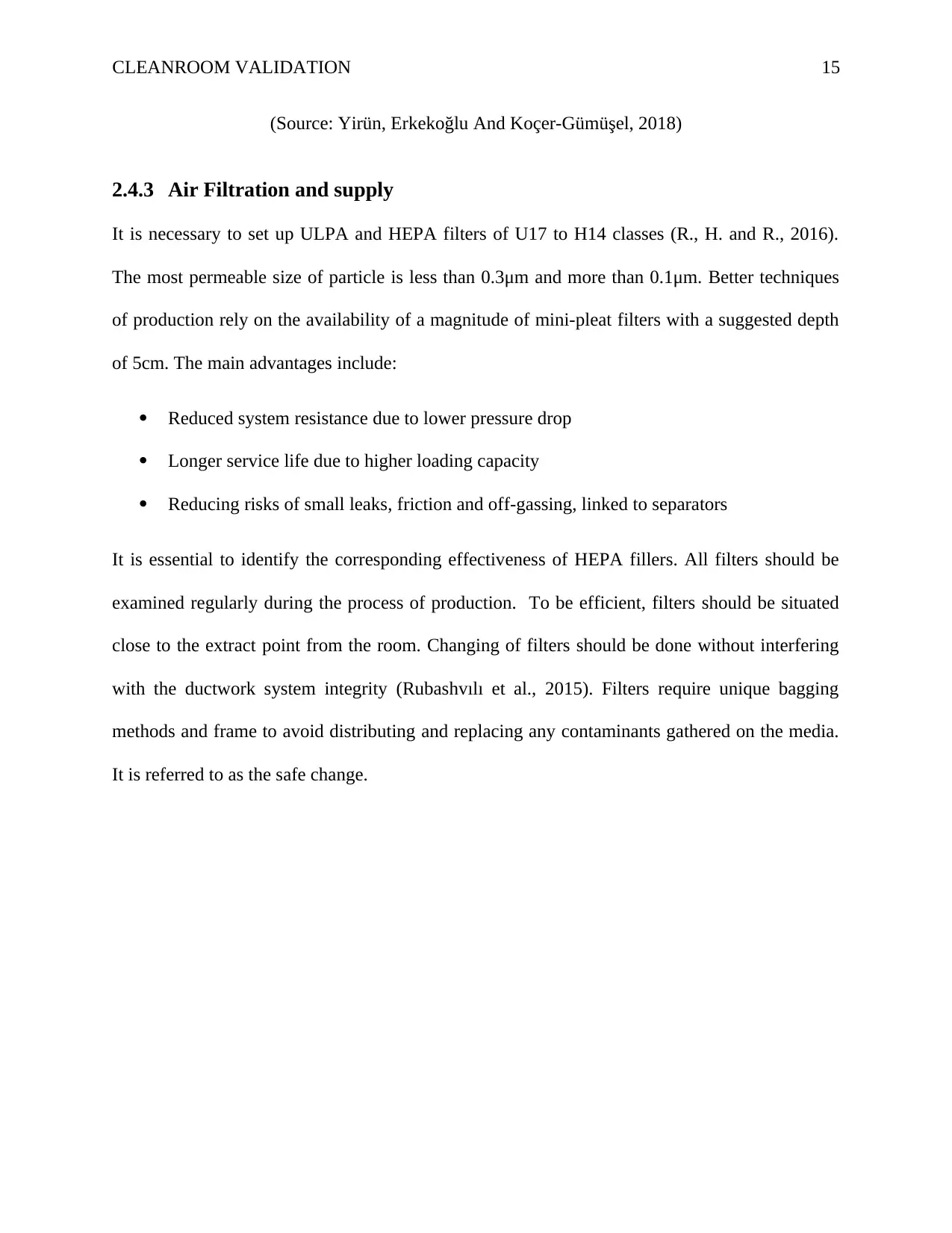
CLEANROOM VALIDATION 15
(Source: Yirün, Erkekoğlu And Koçer-Gümüşel, 2018)
2.4.3 Air Filtration and supply
It is necessary to set up ULPA and HEPA filters of U17 to H14 classes (R., H. and R., 2016).
The most permeable size of particle is less than 0.3μm and more than 0.1μm. Better techniques
of production rely on the availability of a magnitude of mini-pleat filters with a suggested depth
of 5cm. The main advantages include:
Reduced system resistance due to lower pressure drop
Longer service life due to higher loading capacity
Reducing risks of small leaks, friction and off-gassing, linked to separators
It is essential to identify the corresponding effectiveness of HEPA fillers. All filters should be
examined regularly during the process of production. To be efficient, filters should be situated
close to the extract point from the room. Changing of filters should be done without interfering
with the ductwork system integrity (Rubashvılı et al., 2015). Filters require unique bagging
methods and frame to avoid distributing and replacing any contaminants gathered on the media.
It is referred to as the safe change.
(Source: Yirün, Erkekoğlu And Koçer-Gümüşel, 2018)
2.4.3 Air Filtration and supply
It is necessary to set up ULPA and HEPA filters of U17 to H14 classes (R., H. and R., 2016).
The most permeable size of particle is less than 0.3μm and more than 0.1μm. Better techniques
of production rely on the availability of a magnitude of mini-pleat filters with a suggested depth
of 5cm. The main advantages include:
Reduced system resistance due to lower pressure drop
Longer service life due to higher loading capacity
Reducing risks of small leaks, friction and off-gassing, linked to separators
It is essential to identify the corresponding effectiveness of HEPA fillers. All filters should be
examined regularly during the process of production. To be efficient, filters should be situated
close to the extract point from the room. Changing of filters should be done without interfering
with the ductwork system integrity (Rubashvılı et al., 2015). Filters require unique bagging
methods and frame to avoid distributing and replacing any contaminants gathered on the media.
It is referred to as the safe change.
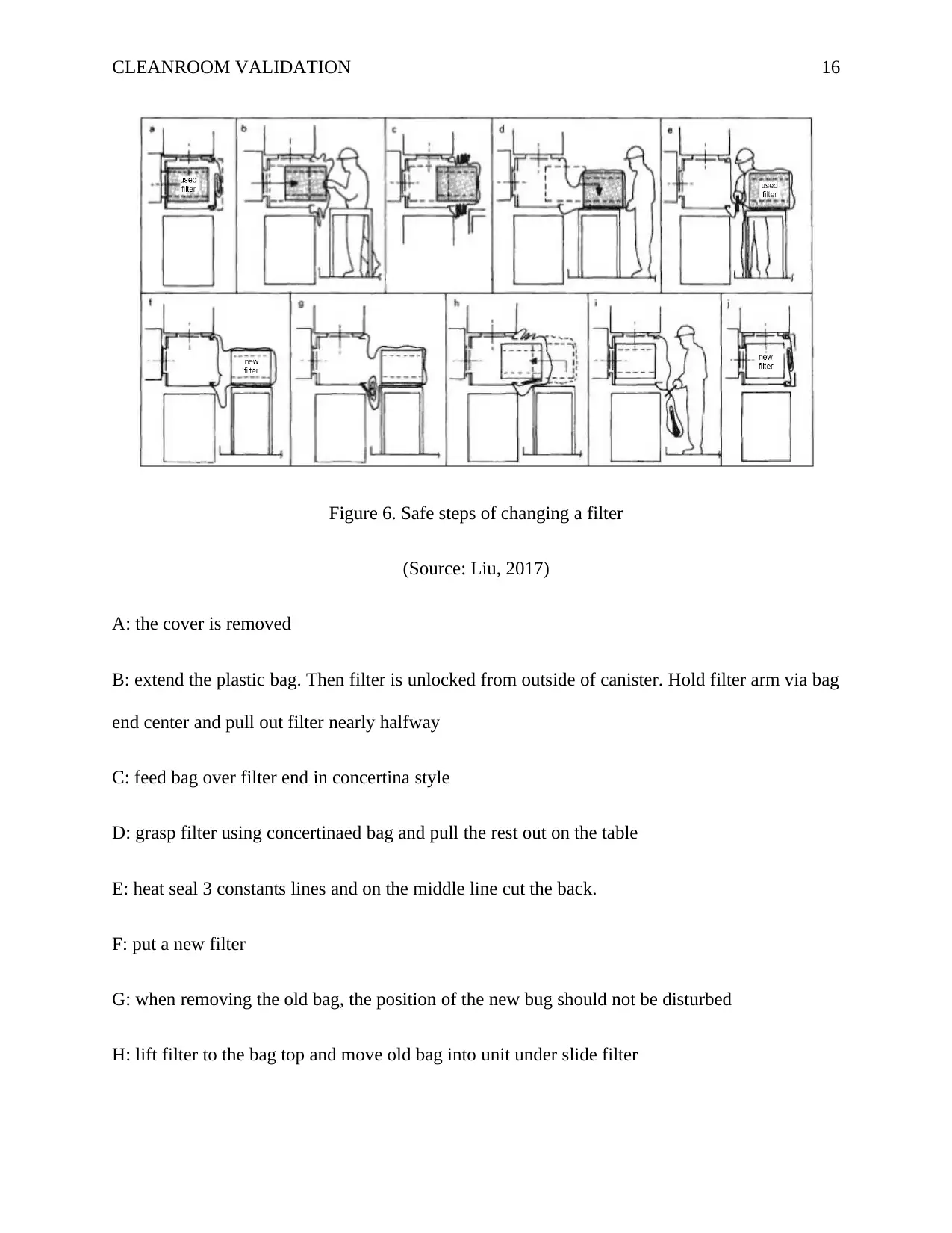
CLEANROOM VALIDATION 16
Figure 6. Safe steps of changing a filter
(Source: Liu, 2017)
A: the cover is removed
B: extend the plastic bag. Then filter is unlocked from outside of canister. Hold filter arm via bag
end center and pull out filter nearly halfway
C: feed bag over filter end in concertina style
D: grasp filter using concertinaed bag and pull the rest out on the table
E: heat seal 3 constants lines and on the middle line cut the back.
F: put a new filter
G: when removing the old bag, the position of the new bug should not be disturbed
H: lift filter to the bag top and move old bag into unit under slide filter
Figure 6. Safe steps of changing a filter
(Source: Liu, 2017)
A: the cover is removed
B: extend the plastic bag. Then filter is unlocked from outside of canister. Hold filter arm via bag
end center and pull out filter nearly halfway
C: feed bag over filter end in concertina style
D: grasp filter using concertinaed bag and pull the rest out on the table
E: heat seal 3 constants lines and on the middle line cut the back.
F: put a new filter
G: when removing the old bag, the position of the new bug should not be disturbed
H: lift filter to the bag top and move old bag into unit under slide filter
Secure Best Marks with AI Grader
Need help grading? Try our AI Grader for instant feedback on your assignments.
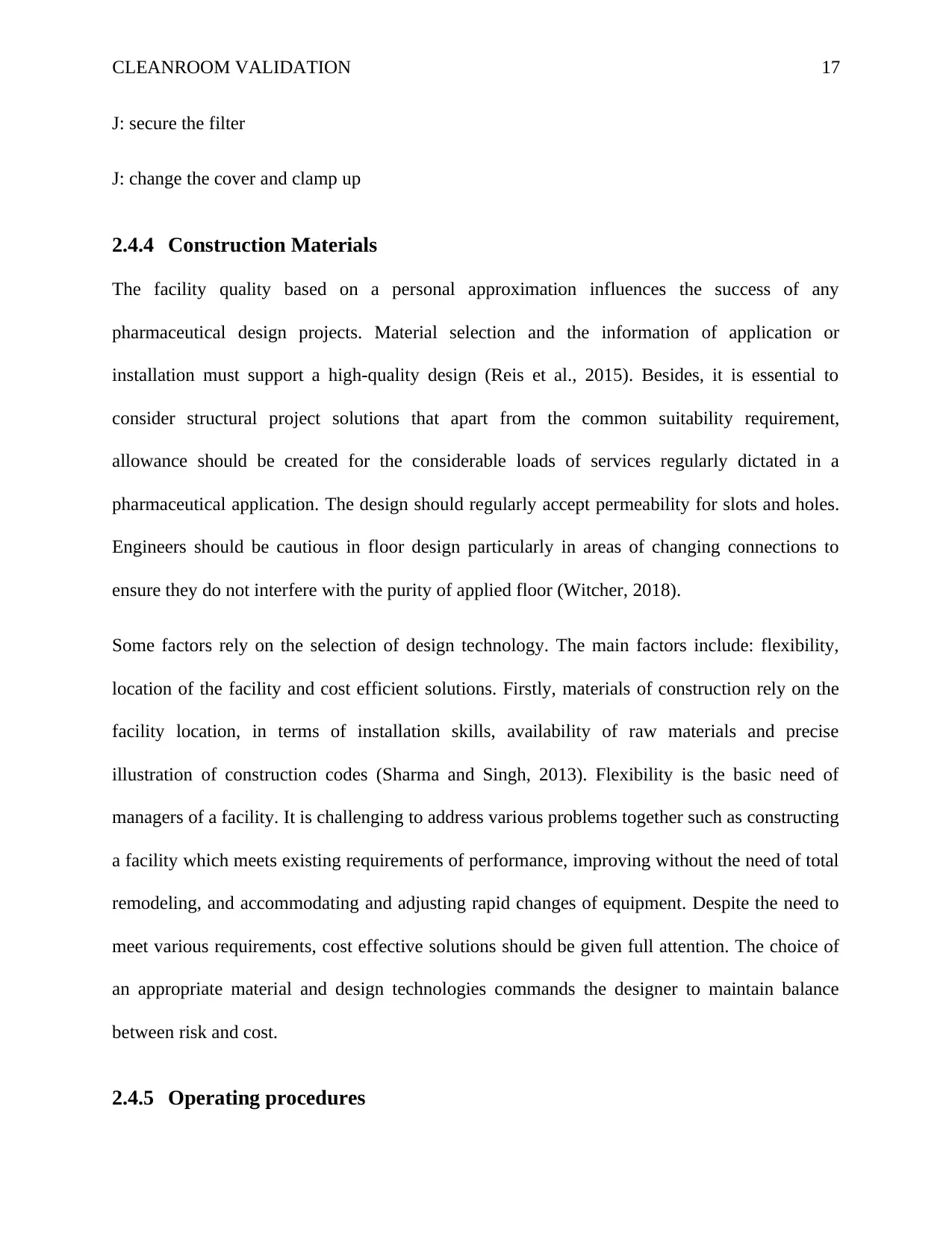
CLEANROOM VALIDATION 17
J: secure the filter
J: change the cover and clamp up
2.4.4 Construction Materials
The facility quality based on a personal approximation influences the success of any
pharmaceutical design projects. Material selection and the information of application or
installation must support a high-quality design (Reis et al., 2015). Besides, it is essential to
consider structural project solutions that apart from the common suitability requirement,
allowance should be created for the considerable loads of services regularly dictated in a
pharmaceutical application. The design should regularly accept permeability for slots and holes.
Engineers should be cautious in floor design particularly in areas of changing connections to
ensure they do not interfere with the purity of applied floor (Witcher, 2018).
Some factors rely on the selection of design technology. The main factors include: flexibility,
location of the facility and cost efficient solutions. Firstly, materials of construction rely on the
facility location, in terms of installation skills, availability of raw materials and precise
illustration of construction codes (Sharma and Singh, 2013). Flexibility is the basic need of
managers of a facility. It is challenging to address various problems together such as constructing
a facility which meets existing requirements of performance, improving without the need of total
remodeling, and accommodating and adjusting rapid changes of equipment. Despite the need to
meet various requirements, cost effective solutions should be given full attention. The choice of
an appropriate material and design technologies commands the designer to maintain balance
between risk and cost.
2.4.5 Operating procedures
J: secure the filter
J: change the cover and clamp up
2.4.4 Construction Materials
The facility quality based on a personal approximation influences the success of any
pharmaceutical design projects. Material selection and the information of application or
installation must support a high-quality design (Reis et al., 2015). Besides, it is essential to
consider structural project solutions that apart from the common suitability requirement,
allowance should be created for the considerable loads of services regularly dictated in a
pharmaceutical application. The design should regularly accept permeability for slots and holes.
Engineers should be cautious in floor design particularly in areas of changing connections to
ensure they do not interfere with the purity of applied floor (Witcher, 2018).
Some factors rely on the selection of design technology. The main factors include: flexibility,
location of the facility and cost efficient solutions. Firstly, materials of construction rely on the
facility location, in terms of installation skills, availability of raw materials and precise
illustration of construction codes (Sharma and Singh, 2013). Flexibility is the basic need of
managers of a facility. It is challenging to address various problems together such as constructing
a facility which meets existing requirements of performance, improving without the need of total
remodeling, and accommodating and adjusting rapid changes of equipment. Despite the need to
meet various requirements, cost effective solutions should be given full attention. The choice of
an appropriate material and design technologies commands the designer to maintain balance
between risk and cost.
2.4.5 Operating procedures
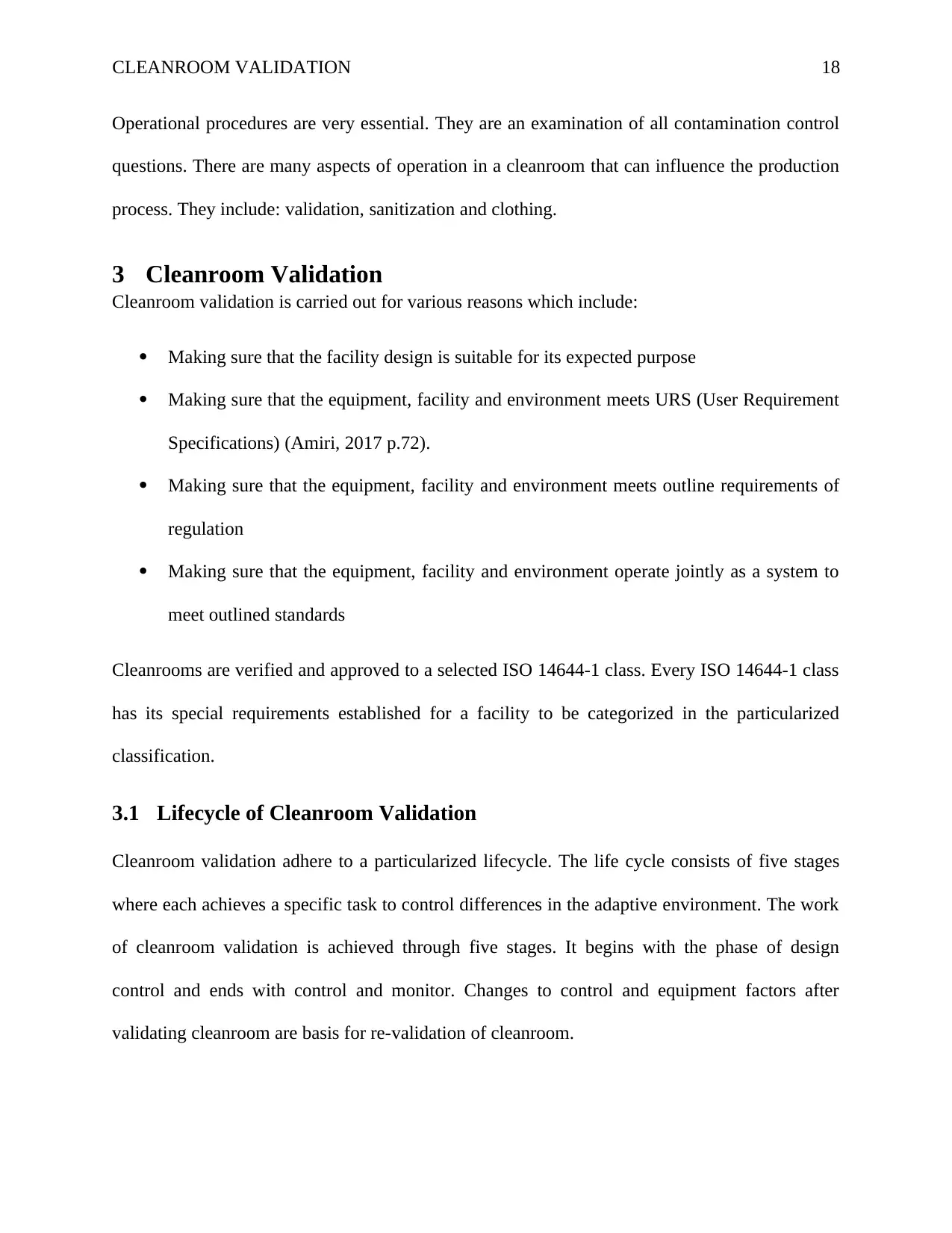
CLEANROOM VALIDATION 18
Operational procedures are very essential. They are an examination of all contamination control
questions. There are many aspects of operation in a cleanroom that can influence the production
process. They include: validation, sanitization and clothing.
3 Cleanroom Validation
Cleanroom validation is carried out for various reasons which include:
Making sure that the facility design is suitable for its expected purpose
Making sure that the equipment, facility and environment meets URS (User Requirement
Specifications) (Amiri, 2017 p.72).
Making sure that the equipment, facility and environment meets outline requirements of
regulation
Making sure that the equipment, facility and environment operate jointly as a system to
meet outlined standards
Cleanrooms are verified and approved to a selected ISO 14644-1 class. Every ISO 14644-1 class
has its special requirements established for a facility to be categorized in the particularized
classification.
3.1 Lifecycle of Cleanroom Validation
Cleanroom validation adhere to a particularized lifecycle. The life cycle consists of five stages
where each achieves a specific task to control differences in the adaptive environment. The work
of cleanroom validation is achieved through five stages. It begins with the phase of design
control and ends with control and monitor. Changes to control and equipment factors after
validating cleanroom are basis for re-validation of cleanroom.
Operational procedures are very essential. They are an examination of all contamination control
questions. There are many aspects of operation in a cleanroom that can influence the production
process. They include: validation, sanitization and clothing.
3 Cleanroom Validation
Cleanroom validation is carried out for various reasons which include:
Making sure that the facility design is suitable for its expected purpose
Making sure that the equipment, facility and environment meets URS (User Requirement
Specifications) (Amiri, 2017 p.72).
Making sure that the equipment, facility and environment meets outline requirements of
regulation
Making sure that the equipment, facility and environment operate jointly as a system to
meet outlined standards
Cleanrooms are verified and approved to a selected ISO 14644-1 class. Every ISO 14644-1 class
has its special requirements established for a facility to be categorized in the particularized
classification.
3.1 Lifecycle of Cleanroom Validation
Cleanroom validation adhere to a particularized lifecycle. The life cycle consists of five stages
where each achieves a specific task to control differences in the adaptive environment. The work
of cleanroom validation is achieved through five stages. It begins with the phase of design
control and ends with control and monitor. Changes to control and equipment factors after
validating cleanroom are basis for re-validation of cleanroom.
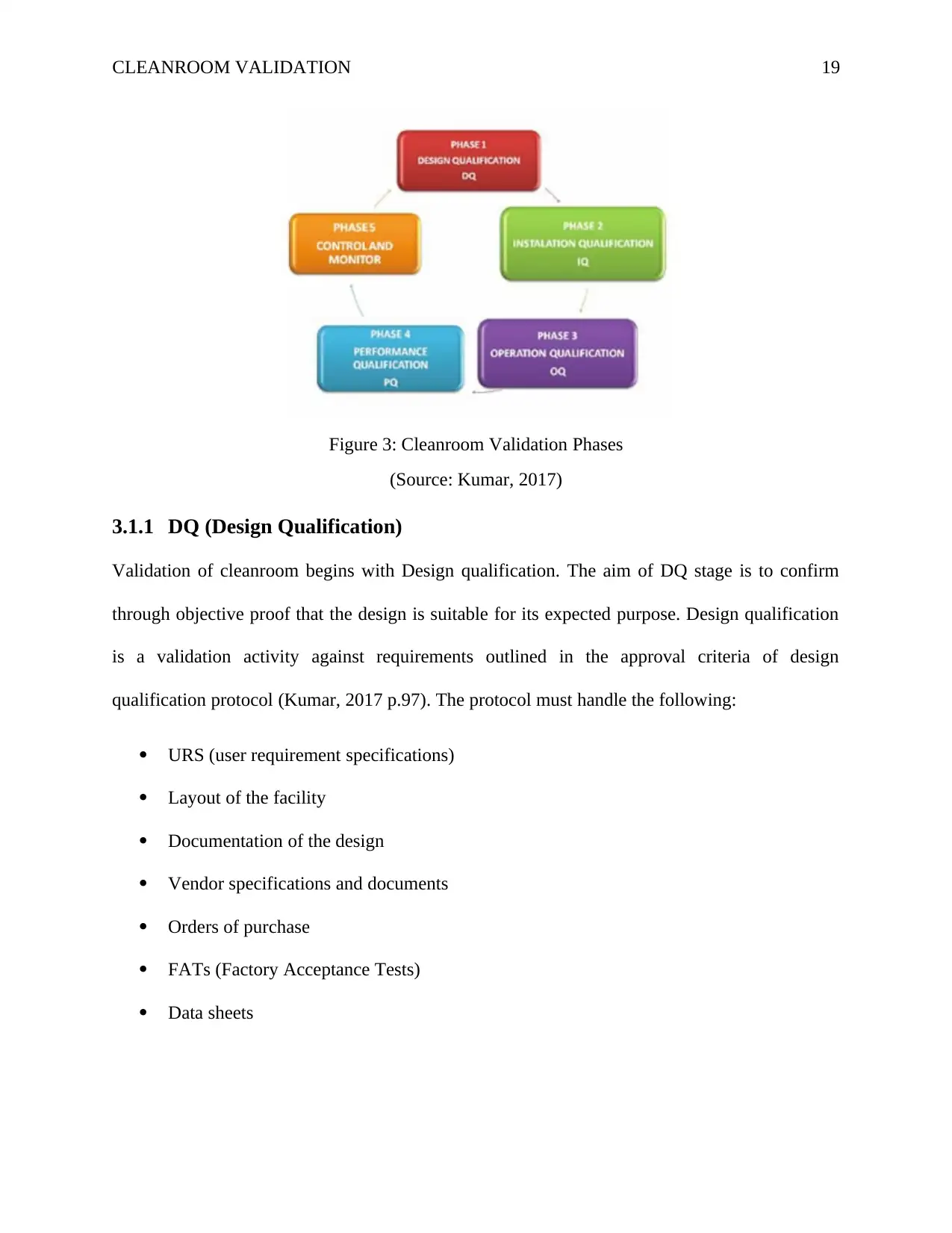
CLEANROOM VALIDATION 19
Figure 3: Cleanroom Validation Phases
(Source: Kumar, 2017)
3.1.1 DQ (Design Qualification)
Validation of cleanroom begins with Design qualification. The aim of DQ stage is to confirm
through objective proof that the design is suitable for its expected purpose. Design qualification
is a validation activity against requirements outlined in the approval criteria of design
qualification protocol (Kumar, 2017 p.97). The protocol must handle the following:
URS (user requirement specifications)
Layout of the facility
Documentation of the design
Vendor specifications and documents
Orders of purchase
FATs (Factory Acceptance Tests)
Data sheets
Figure 3: Cleanroom Validation Phases
(Source: Kumar, 2017)
3.1.1 DQ (Design Qualification)
Validation of cleanroom begins with Design qualification. The aim of DQ stage is to confirm
through objective proof that the design is suitable for its expected purpose. Design qualification
is a validation activity against requirements outlined in the approval criteria of design
qualification protocol (Kumar, 2017 p.97). The protocol must handle the following:
URS (user requirement specifications)
Layout of the facility
Documentation of the design
Vendor specifications and documents
Orders of purchase
FATs (Factory Acceptance Tests)
Data sheets
Paraphrase This Document
Need a fresh take? Get an instant paraphrase of this document with our AI Paraphraser
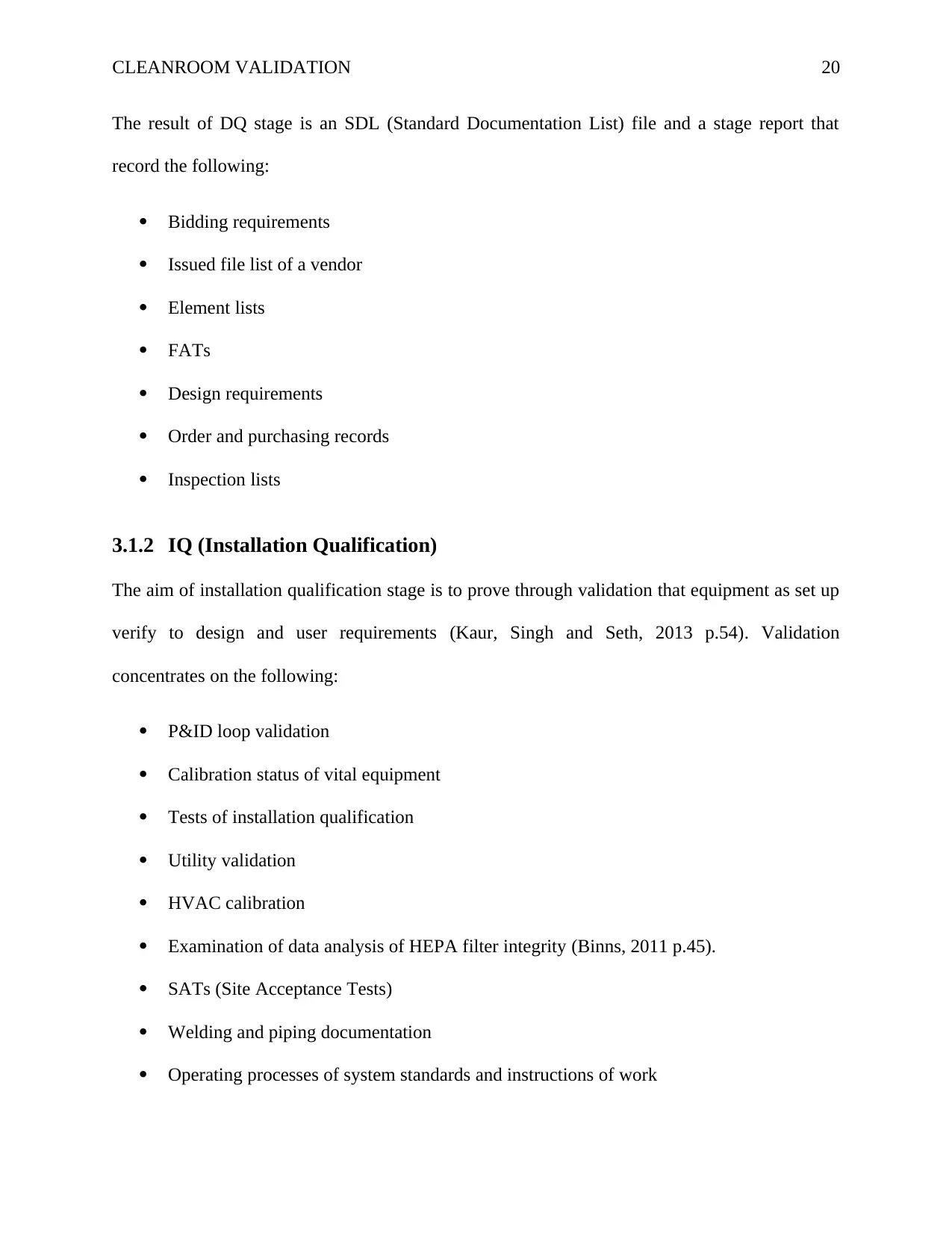
CLEANROOM VALIDATION 20
The result of DQ stage is an SDL (Standard Documentation List) file and a stage report that
record the following:
Bidding requirements
Issued file list of a vendor
Element lists
FATs
Design requirements
Order and purchasing records
Inspection lists
3.1.2 IQ (Installation Qualification)
The aim of installation qualification stage is to prove through validation that equipment as set up
verify to design and user requirements (Kaur, Singh and Seth, 2013 p.54). Validation
concentrates on the following:
P&ID loop validation
Calibration status of vital equipment
Tests of installation qualification
Utility validation
HVAC calibration
Examination of data analysis of HEPA filter integrity (Binns, 2011 p.45).
SATs (Site Acceptance Tests)
Welding and piping documentation
Operating processes of system standards and instructions of work
The result of DQ stage is an SDL (Standard Documentation List) file and a stage report that
record the following:
Bidding requirements
Issued file list of a vendor
Element lists
FATs
Design requirements
Order and purchasing records
Inspection lists
3.1.2 IQ (Installation Qualification)
The aim of installation qualification stage is to prove through validation that equipment as set up
verify to design and user requirements (Kaur, Singh and Seth, 2013 p.54). Validation
concentrates on the following:
P&ID loop validation
Calibration status of vital equipment
Tests of installation qualification
Utility validation
HVAC calibration
Examination of data analysis of HEPA filter integrity (Binns, 2011 p.45).
SATs (Site Acceptance Tests)
Welding and piping documentation
Operating processes of system standards and instructions of work
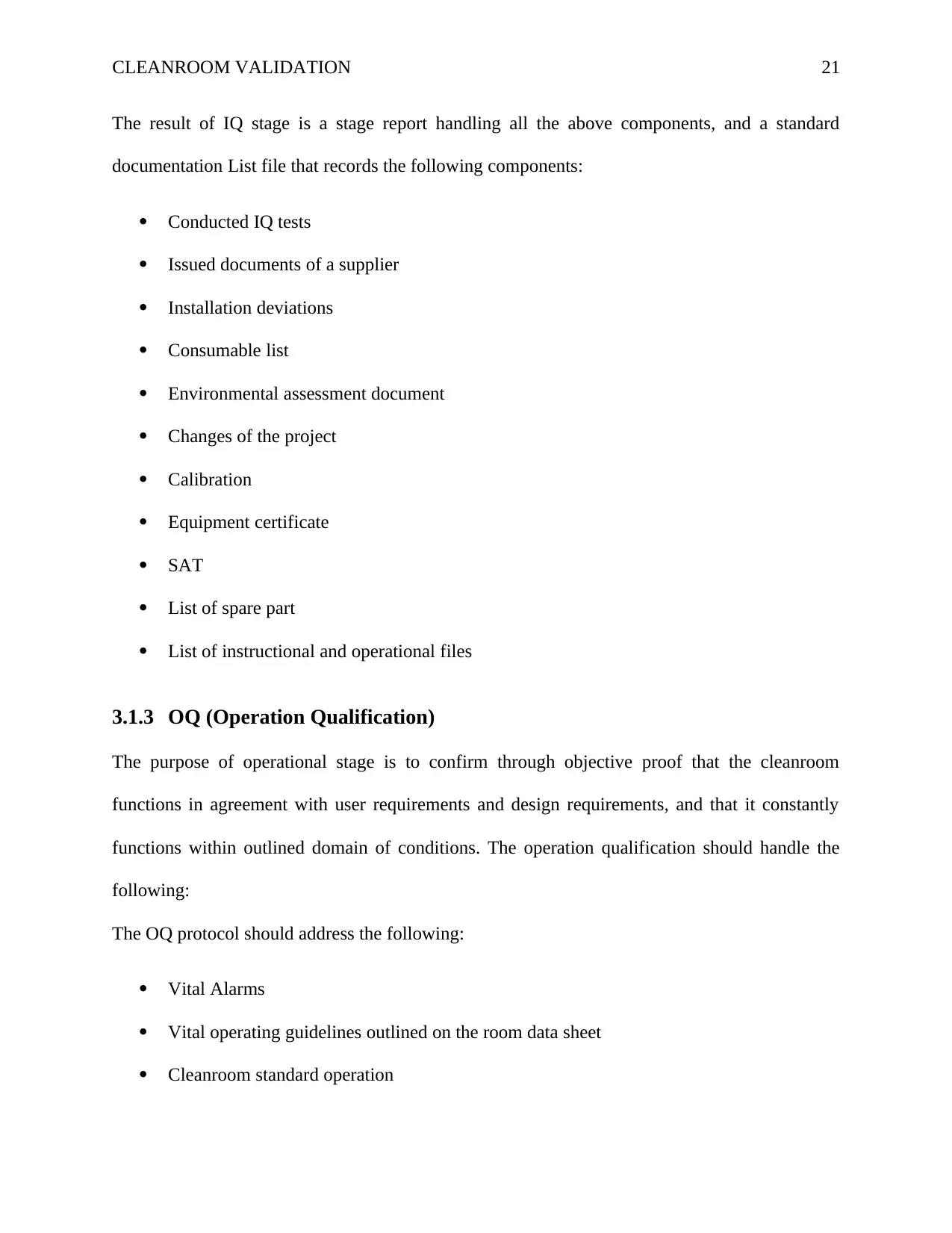
CLEANROOM VALIDATION 21
The result of IQ stage is a stage report handling all the above components, and a standard
documentation List file that records the following components:
Conducted IQ tests
Issued documents of a supplier
Installation deviations
Consumable list
Environmental assessment document
Changes of the project
Calibration
Equipment certificate
SAT
List of spare part
List of instructional and operational files
3.1.3 OQ (Operation Qualification)
The purpose of operational stage is to confirm through objective proof that the cleanroom
functions in agreement with user requirements and design requirements, and that it constantly
functions within outlined domain of conditions. The operation qualification should handle the
following:
The OQ protocol should address the following:
Vital Alarms
Vital operating guidelines outlined on the room data sheet
Cleanroom standard operation
The result of IQ stage is a stage report handling all the above components, and a standard
documentation List file that records the following components:
Conducted IQ tests
Issued documents of a supplier
Installation deviations
Consumable list
Environmental assessment document
Changes of the project
Calibration
Equipment certificate
SAT
List of spare part
List of instructional and operational files
3.1.3 OQ (Operation Qualification)
The purpose of operational stage is to confirm through objective proof that the cleanroom
functions in agreement with user requirements and design requirements, and that it constantly
functions within outlined domain of conditions. The operation qualification should handle the
following:
The OQ protocol should address the following:
Vital Alarms
Vital operating guidelines outlined on the room data sheet
Cleanroom standard operation
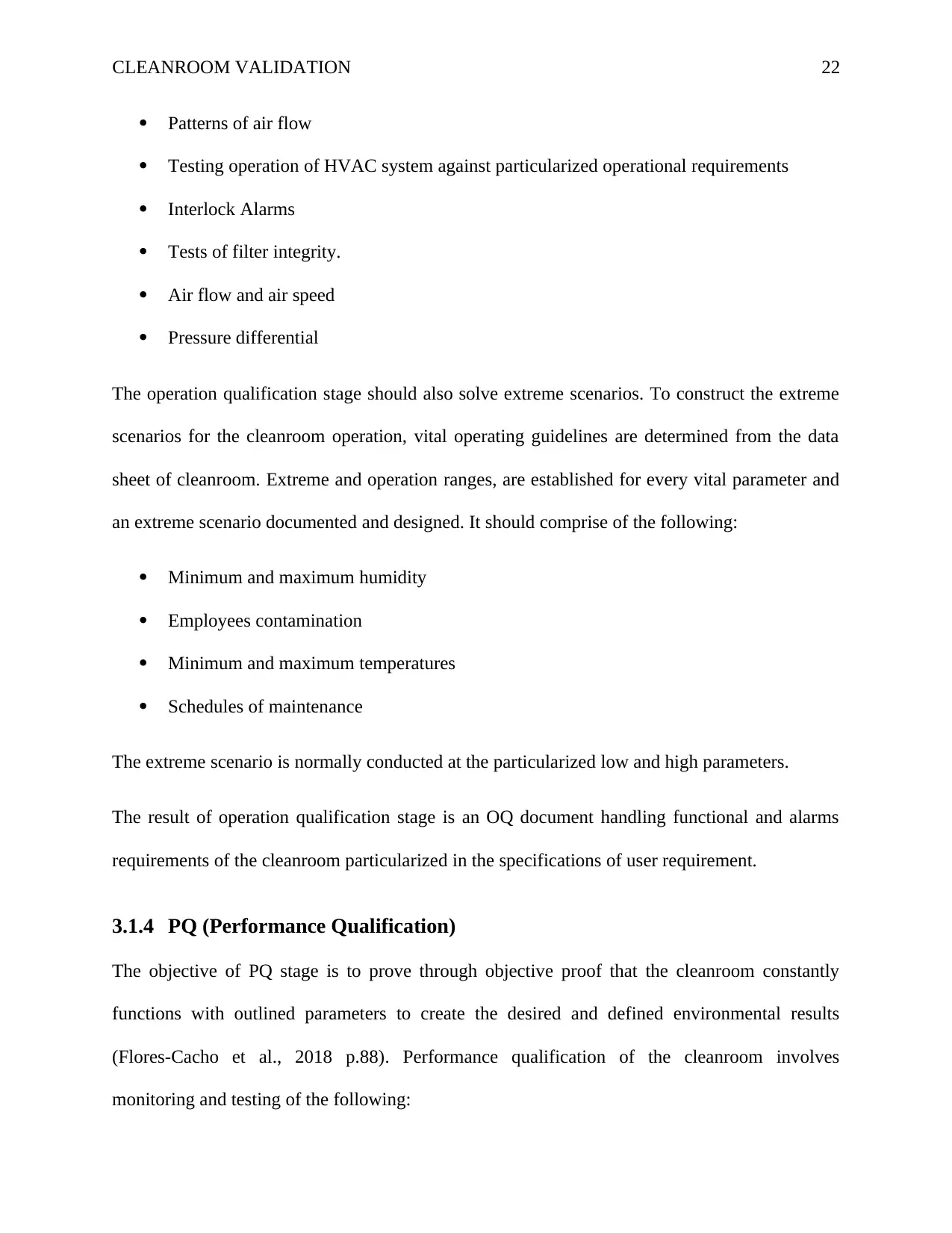
CLEANROOM VALIDATION 22
Patterns of air flow
Testing operation of HVAC system against particularized operational requirements
Interlock Alarms
Tests of filter integrity.
Air flow and air speed
Pressure differential
The operation qualification stage should also solve extreme scenarios. To construct the extreme
scenarios for the cleanroom operation, vital operating guidelines are determined from the data
sheet of cleanroom. Extreme and operation ranges, are established for every vital parameter and
an extreme scenario documented and designed. It should comprise of the following:
Minimum and maximum humidity
Employees contamination
Minimum and maximum temperatures
Schedules of maintenance
The extreme scenario is normally conducted at the particularized low and high parameters.
The result of operation qualification stage is an OQ document handling functional and alarms
requirements of the cleanroom particularized in the specifications of user requirement.
3.1.4 PQ (Performance Qualification)
The objective of PQ stage is to prove through objective proof that the cleanroom constantly
functions with outlined parameters to create the desired and defined environmental results
(Flores-Cacho et al., 2018 p.88). Performance qualification of the cleanroom involves
monitoring and testing of the following:
Patterns of air flow
Testing operation of HVAC system against particularized operational requirements
Interlock Alarms
Tests of filter integrity.
Air flow and air speed
Pressure differential
The operation qualification stage should also solve extreme scenarios. To construct the extreme
scenarios for the cleanroom operation, vital operating guidelines are determined from the data
sheet of cleanroom. Extreme and operation ranges, are established for every vital parameter and
an extreme scenario documented and designed. It should comprise of the following:
Minimum and maximum humidity
Employees contamination
Minimum and maximum temperatures
Schedules of maintenance
The extreme scenario is normally conducted at the particularized low and high parameters.
The result of operation qualification stage is an OQ document handling functional and alarms
requirements of the cleanroom particularized in the specifications of user requirement.
3.1.4 PQ (Performance Qualification)
The objective of PQ stage is to prove through objective proof that the cleanroom constantly
functions with outlined parameters to create the desired and defined environmental results
(Flores-Cacho et al., 2018 p.88). Performance qualification of the cleanroom involves
monitoring and testing of the following:
Secure Best Marks with AI Grader
Need help grading? Try our AI Grader for instant feedback on your assignments.
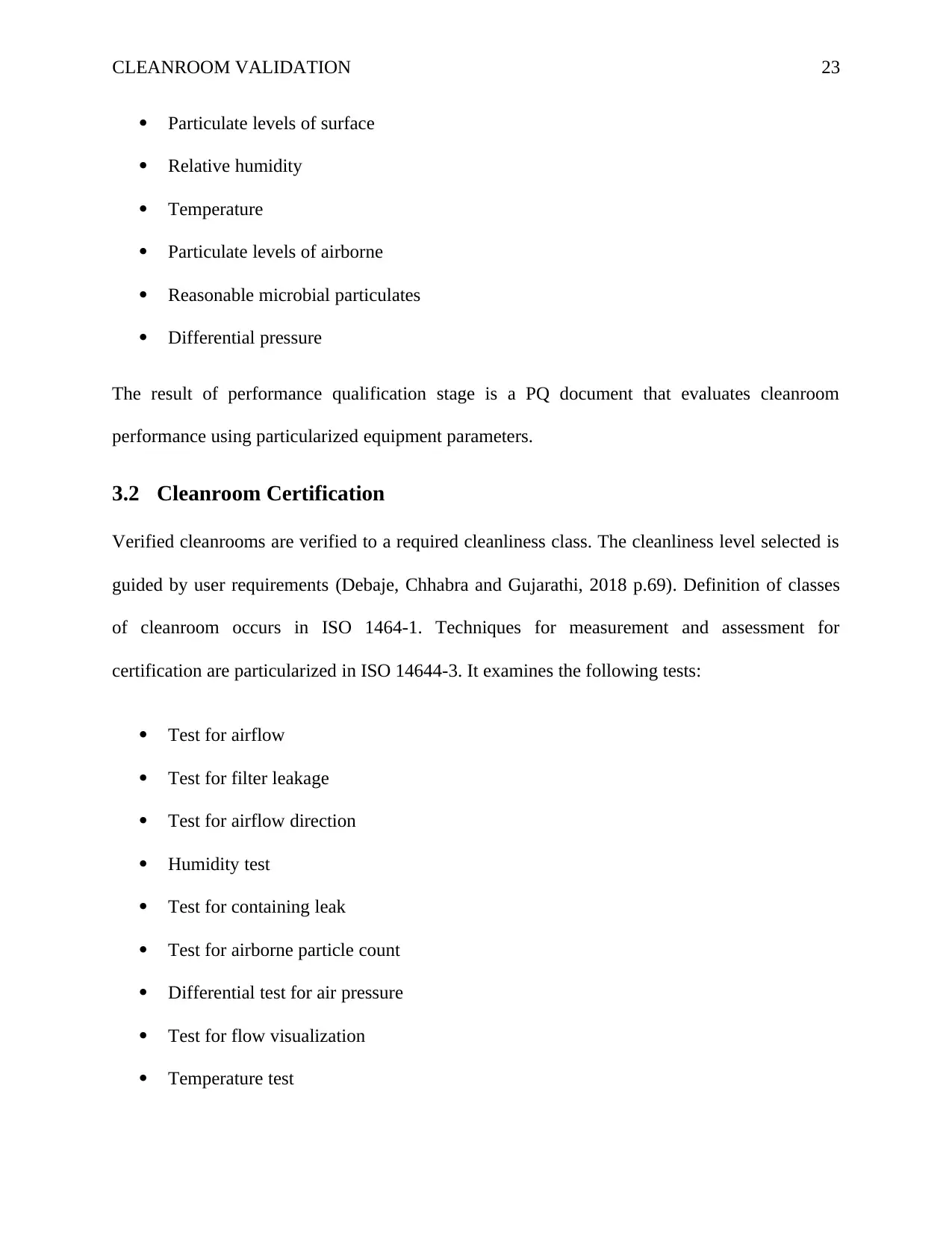
CLEANROOM VALIDATION 23
Particulate levels of surface
Relative humidity
Temperature
Particulate levels of airborne
Reasonable microbial particulates
Differential pressure
The result of performance qualification stage is a PQ document that evaluates cleanroom
performance using particularized equipment parameters.
3.2 Cleanroom Certification
Verified cleanrooms are verified to a required cleanliness class. The cleanliness level selected is
guided by user requirements (Debaje, Chhabra and Gujarathi, 2018 p.69). Definition of classes
of cleanroom occurs in ISO 1464-1. Techniques for measurement and assessment for
certification are particularized in ISO 14644-3. It examines the following tests:
Test for airflow
Test for filter leakage
Test for airflow direction
Humidity test
Test for containing leak
Test for airborne particle count
Differential test for air pressure
Test for flow visualization
Temperature test
Particulate levels of surface
Relative humidity
Temperature
Particulate levels of airborne
Reasonable microbial particulates
Differential pressure
The result of performance qualification stage is a PQ document that evaluates cleanroom
performance using particularized equipment parameters.
3.2 Cleanroom Certification
Verified cleanrooms are verified to a required cleanliness class. The cleanliness level selected is
guided by user requirements (Debaje, Chhabra and Gujarathi, 2018 p.69). Definition of classes
of cleanroom occurs in ISO 1464-1. Techniques for measurement and assessment for
certification are particularized in ISO 14644-3. It examines the following tests:
Test for airflow
Test for filter leakage
Test for airflow direction
Humidity test
Test for containing leak
Test for airborne particle count
Differential test for air pressure
Test for flow visualization
Temperature test
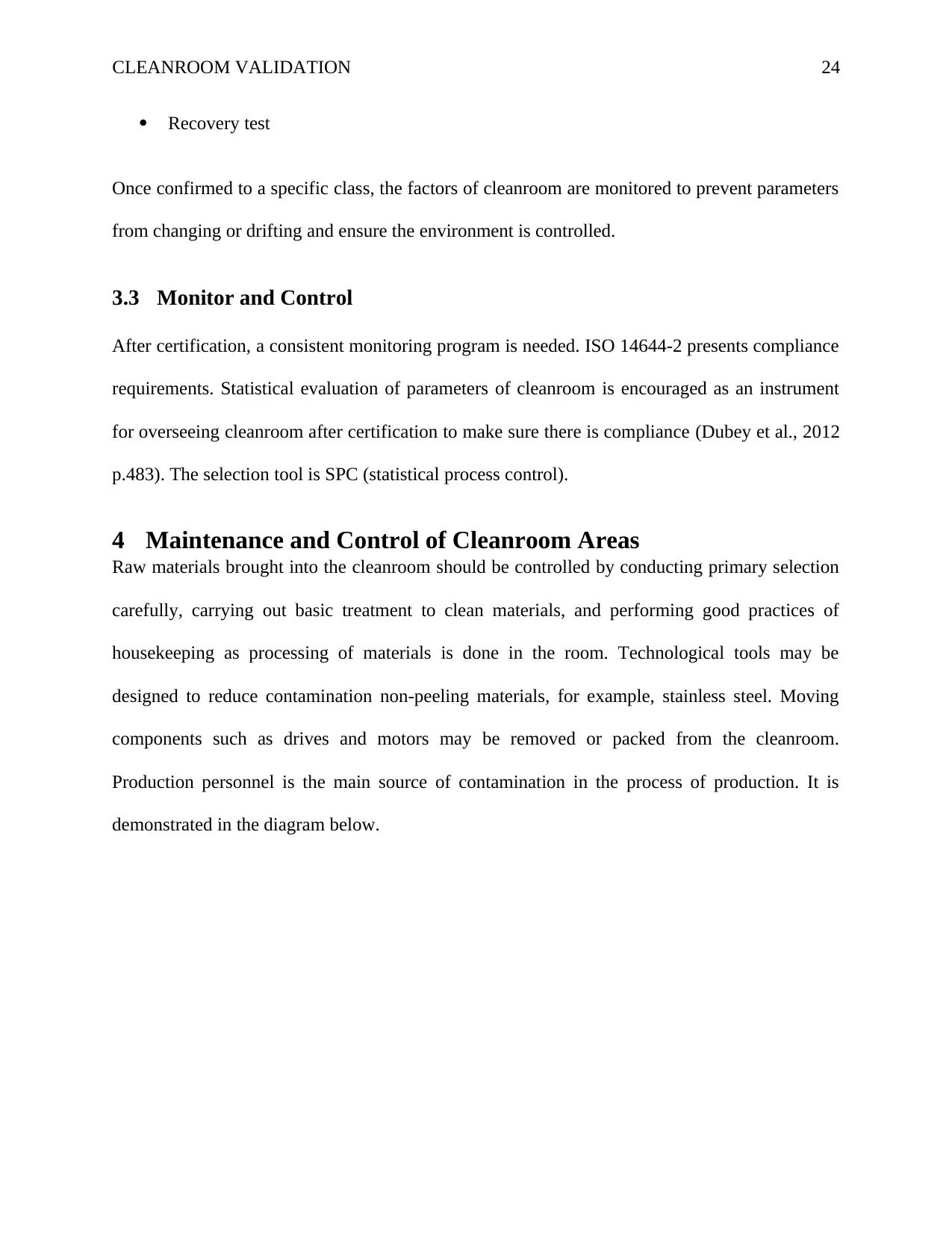
CLEANROOM VALIDATION 24
Recovery test
Once confirmed to a specific class, the factors of cleanroom are monitored to prevent parameters
from changing or drifting and ensure the environment is controlled.
3.3 Monitor and Control
After certification, a consistent monitoring program is needed. ISO 14644-2 presents compliance
requirements. Statistical evaluation of parameters of cleanroom is encouraged as an instrument
for overseeing cleanroom after certification to make sure there is compliance (Dubey et al., 2012
p.483). The selection tool is SPC (statistical process control).
4 Maintenance and Control of Cleanroom Areas
Raw materials brought into the cleanroom should be controlled by conducting primary selection
carefully, carrying out basic treatment to clean materials, and performing good practices of
housekeeping as processing of materials is done in the room. Technological tools may be
designed to reduce contamination non-peeling materials, for example, stainless steel. Moving
components such as drives and motors may be removed or packed from the cleanroom.
Production personnel is the main source of contamination in the process of production. It is
demonstrated in the diagram below.
Recovery test
Once confirmed to a specific class, the factors of cleanroom are monitored to prevent parameters
from changing or drifting and ensure the environment is controlled.
3.3 Monitor and Control
After certification, a consistent monitoring program is needed. ISO 14644-2 presents compliance
requirements. Statistical evaluation of parameters of cleanroom is encouraged as an instrument
for overseeing cleanroom after certification to make sure there is compliance (Dubey et al., 2012
p.483). The selection tool is SPC (statistical process control).
4 Maintenance and Control of Cleanroom Areas
Raw materials brought into the cleanroom should be controlled by conducting primary selection
carefully, carrying out basic treatment to clean materials, and performing good practices of
housekeeping as processing of materials is done in the room. Technological tools may be
designed to reduce contamination non-peeling materials, for example, stainless steel. Moving
components such as drives and motors may be removed or packed from the cleanroom.
Production personnel is the main source of contamination in the process of production. It is
demonstrated in the diagram below.
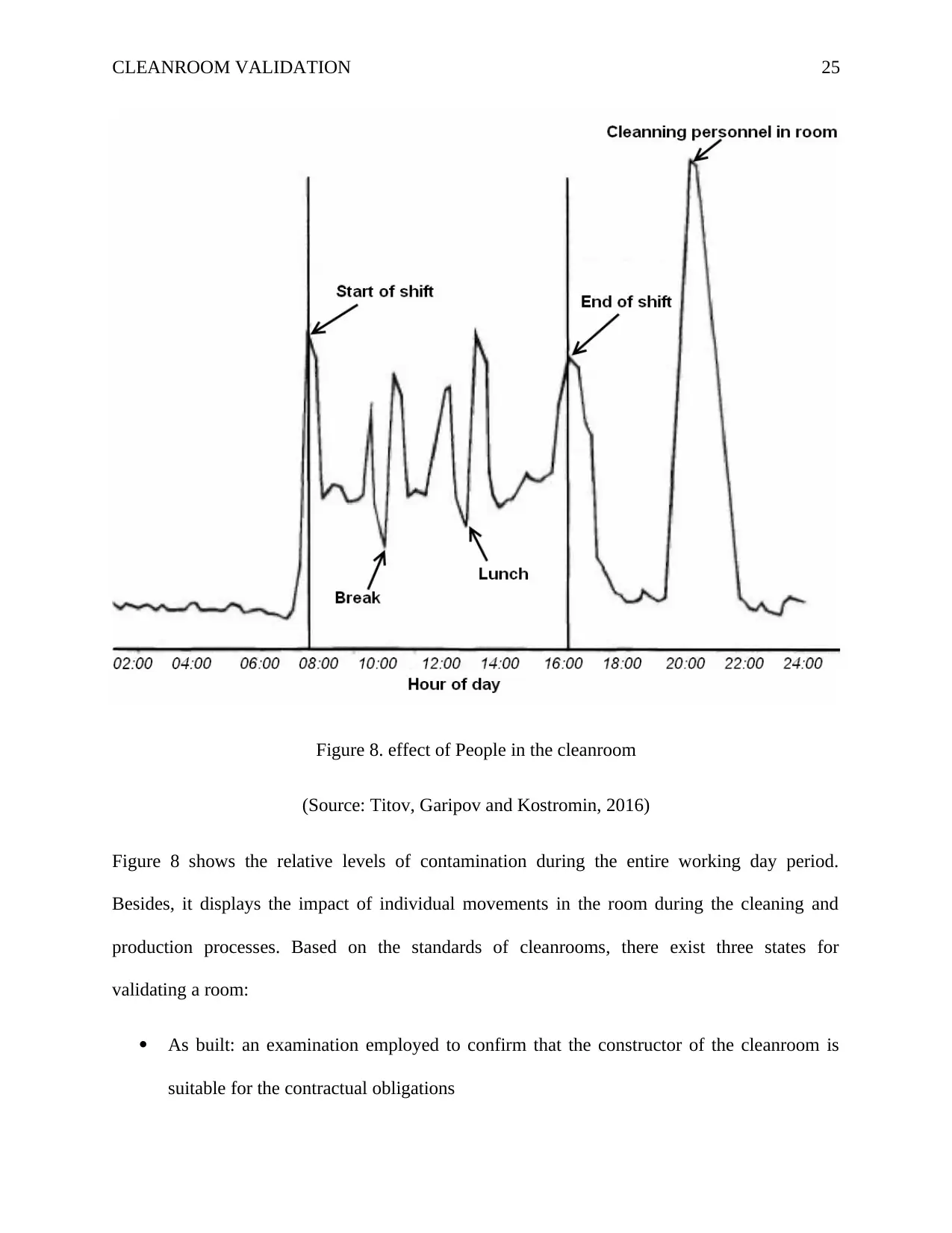
CLEANROOM VALIDATION 25
Figure 8. effect of People in the cleanroom
(Source: Titov, Garipov and Kostromin, 2016)
Figure 8 shows the relative levels of contamination during the entire working day period.
Besides, it displays the impact of individual movements in the room during the cleaning and
production processes. Based on the standards of cleanrooms, there exist three states for
validating a room:
As built: an examination employed to confirm that the constructor of the cleanroom is
suitable for the contractual obligations
Figure 8. effect of People in the cleanroom
(Source: Titov, Garipov and Kostromin, 2016)
Figure 8 shows the relative levels of contamination during the entire working day period.
Besides, it displays the impact of individual movements in the room during the cleaning and
production processes. Based on the standards of cleanrooms, there exist three states for
validating a room:
As built: an examination employed to confirm that the constructor of the cleanroom is
suitable for the contractual obligations
Paraphrase This Document
Need a fresh take? Get an instant paraphrase of this document with our AI Paraphraser
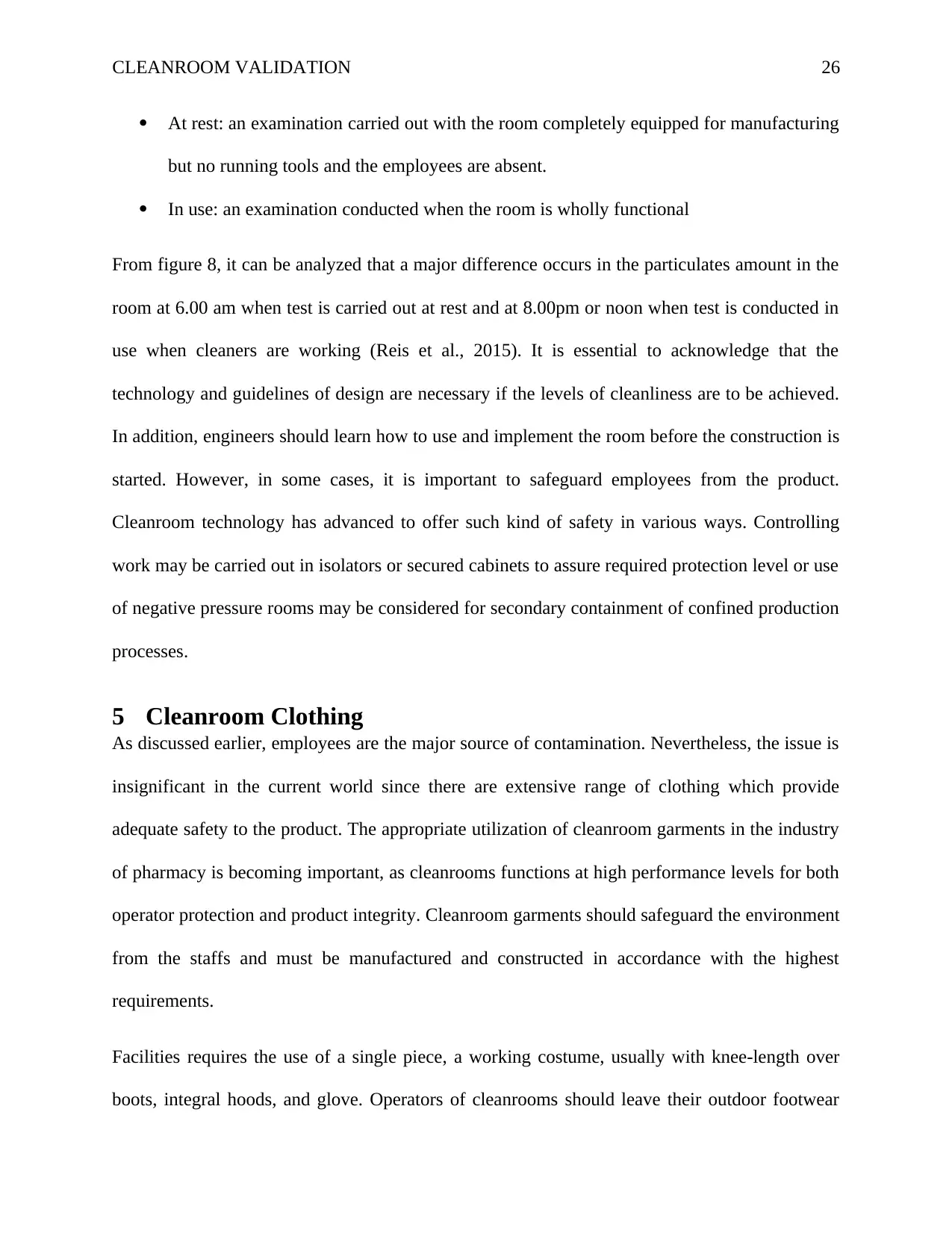
CLEANROOM VALIDATION 26
At rest: an examination carried out with the room completely equipped for manufacturing
but no running tools and the employees are absent.
In use: an examination conducted when the room is wholly functional
From figure 8, it can be analyzed that a major difference occurs in the particulates amount in the
room at 6.00 am when test is carried out at rest and at 8.00pm or noon when test is conducted in
use when cleaners are working (Reis et al., 2015). It is essential to acknowledge that the
technology and guidelines of design are necessary if the levels of cleanliness are to be achieved.
In addition, engineers should learn how to use and implement the room before the construction is
started. However, in some cases, it is important to safeguard employees from the product.
Cleanroom technology has advanced to offer such kind of safety in various ways. Controlling
work may be carried out in isolators or secured cabinets to assure required protection level or use
of negative pressure rooms may be considered for secondary containment of confined production
processes.
5 Cleanroom Clothing
As discussed earlier, employees are the major source of contamination. Nevertheless, the issue is
insignificant in the current world since there are extensive range of clothing which provide
adequate safety to the product. The appropriate utilization of cleanroom garments in the industry
of pharmacy is becoming important, as cleanrooms functions at high performance levels for both
operator protection and product integrity. Cleanroom garments should safeguard the environment
from the staffs and must be manufactured and constructed in accordance with the highest
requirements.
Facilities requires the use of a single piece, a working costume, usually with knee-length over
boots, integral hoods, and glove. Operators of cleanrooms should leave their outdoor footwear
At rest: an examination carried out with the room completely equipped for manufacturing
but no running tools and the employees are absent.
In use: an examination conducted when the room is wholly functional
From figure 8, it can be analyzed that a major difference occurs in the particulates amount in the
room at 6.00 am when test is carried out at rest and at 8.00pm or noon when test is conducted in
use when cleaners are working (Reis et al., 2015). It is essential to acknowledge that the
technology and guidelines of design are necessary if the levels of cleanliness are to be achieved.
In addition, engineers should learn how to use and implement the room before the construction is
started. However, in some cases, it is important to safeguard employees from the product.
Cleanroom technology has advanced to offer such kind of safety in various ways. Controlling
work may be carried out in isolators or secured cabinets to assure required protection level or use
of negative pressure rooms may be considered for secondary containment of confined production
processes.
5 Cleanroom Clothing
As discussed earlier, employees are the major source of contamination. Nevertheless, the issue is
insignificant in the current world since there are extensive range of clothing which provide
adequate safety to the product. The appropriate utilization of cleanroom garments in the industry
of pharmacy is becoming important, as cleanrooms functions at high performance levels for both
operator protection and product integrity. Cleanroom garments should safeguard the environment
from the staffs and must be manufactured and constructed in accordance with the highest
requirements.
Facilities requires the use of a single piece, a working costume, usually with knee-length over
boots, integral hoods, and glove. Operators of cleanrooms should leave their outdoor footwear
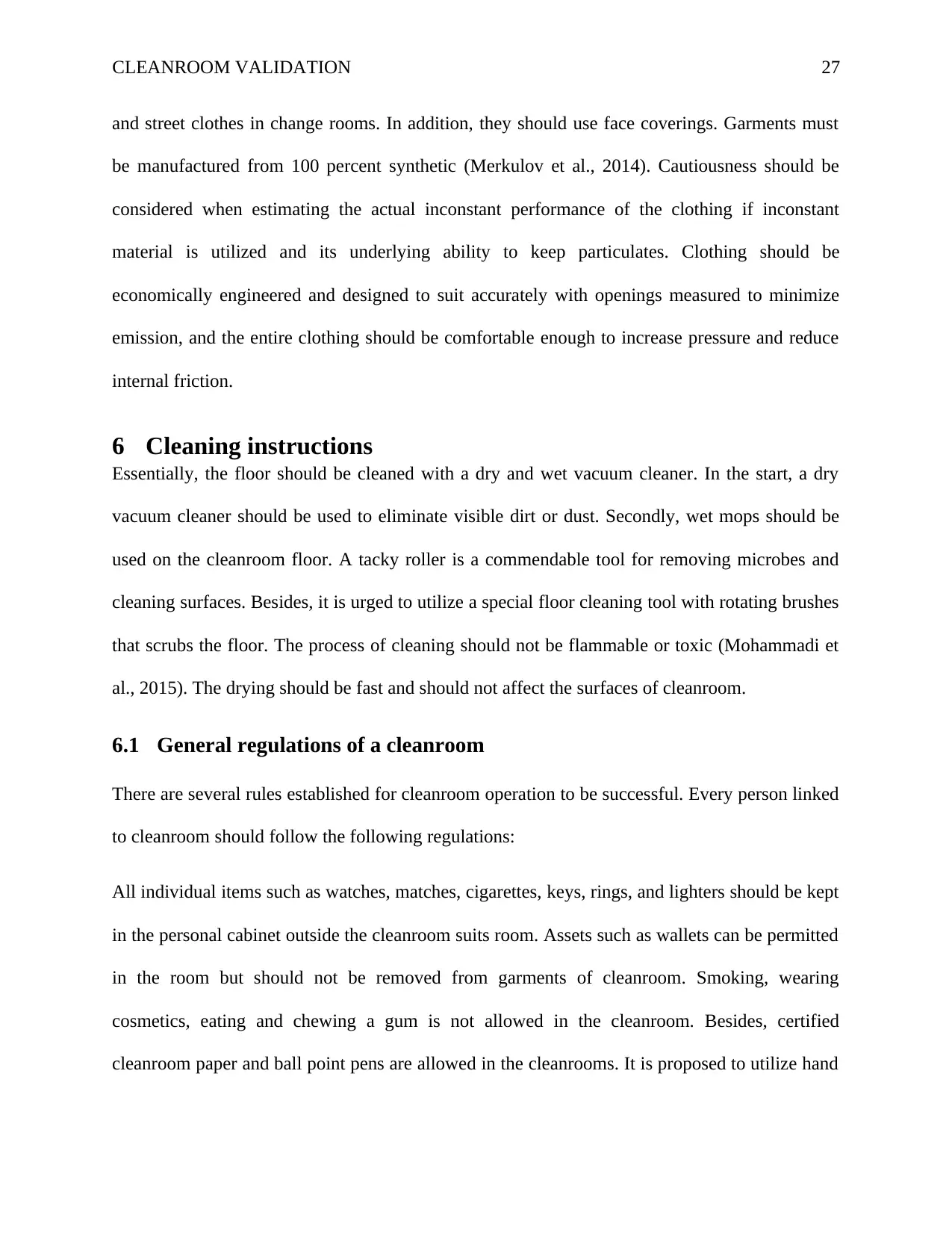
CLEANROOM VALIDATION 27
and street clothes in change rooms. In addition, they should use face coverings. Garments must
be manufactured from 100 percent synthetic (Merkulov et al., 2014). Cautiousness should be
considered when estimating the actual inconstant performance of the clothing if inconstant
material is utilized and its underlying ability to keep particulates. Clothing should be
economically engineered and designed to suit accurately with openings measured to minimize
emission, and the entire clothing should be comfortable enough to increase pressure and reduce
internal friction.
6 Cleaning instructions
Essentially, the floor should be cleaned with a dry and wet vacuum cleaner. In the start, a dry
vacuum cleaner should be used to eliminate visible dirt or dust. Secondly, wet mops should be
used on the cleanroom floor. A tacky roller is a commendable tool for removing microbes and
cleaning surfaces. Besides, it is urged to utilize a special floor cleaning tool with rotating brushes
that scrubs the floor. The process of cleaning should not be flammable or toxic (Mohammadi et
al., 2015). The drying should be fast and should not affect the surfaces of cleanroom.
6.1 General regulations of a cleanroom
There are several rules established for cleanroom operation to be successful. Every person linked
to cleanroom should follow the following regulations:
All individual items such as watches, matches, cigarettes, keys, rings, and lighters should be kept
in the personal cabinet outside the cleanroom suits room. Assets such as wallets can be permitted
in the room but should not be removed from garments of cleanroom. Smoking, wearing
cosmetics, eating and chewing a gum is not allowed in the cleanroom. Besides, certified
cleanroom paper and ball point pens are allowed in the cleanrooms. It is proposed to utilize hand
and street clothes in change rooms. In addition, they should use face coverings. Garments must
be manufactured from 100 percent synthetic (Merkulov et al., 2014). Cautiousness should be
considered when estimating the actual inconstant performance of the clothing if inconstant
material is utilized and its underlying ability to keep particulates. Clothing should be
economically engineered and designed to suit accurately with openings measured to minimize
emission, and the entire clothing should be comfortable enough to increase pressure and reduce
internal friction.
6 Cleaning instructions
Essentially, the floor should be cleaned with a dry and wet vacuum cleaner. In the start, a dry
vacuum cleaner should be used to eliminate visible dirt or dust. Secondly, wet mops should be
used on the cleanroom floor. A tacky roller is a commendable tool for removing microbes and
cleaning surfaces. Besides, it is urged to utilize a special floor cleaning tool with rotating brushes
that scrubs the floor. The process of cleaning should not be flammable or toxic (Mohammadi et
al., 2015). The drying should be fast and should not affect the surfaces of cleanroom.
6.1 General regulations of a cleanroom
There are several rules established for cleanroom operation to be successful. Every person linked
to cleanroom should follow the following regulations:
All individual items such as watches, matches, cigarettes, keys, rings, and lighters should be kept
in the personal cabinet outside the cleanroom suits room. Assets such as wallets can be permitted
in the room but should not be removed from garments of cleanroom. Smoking, wearing
cosmetics, eating and chewing a gum is not allowed in the cleanroom. Besides, certified
cleanroom paper and ball point pens are allowed in the cleanrooms. It is proposed to utilize hand
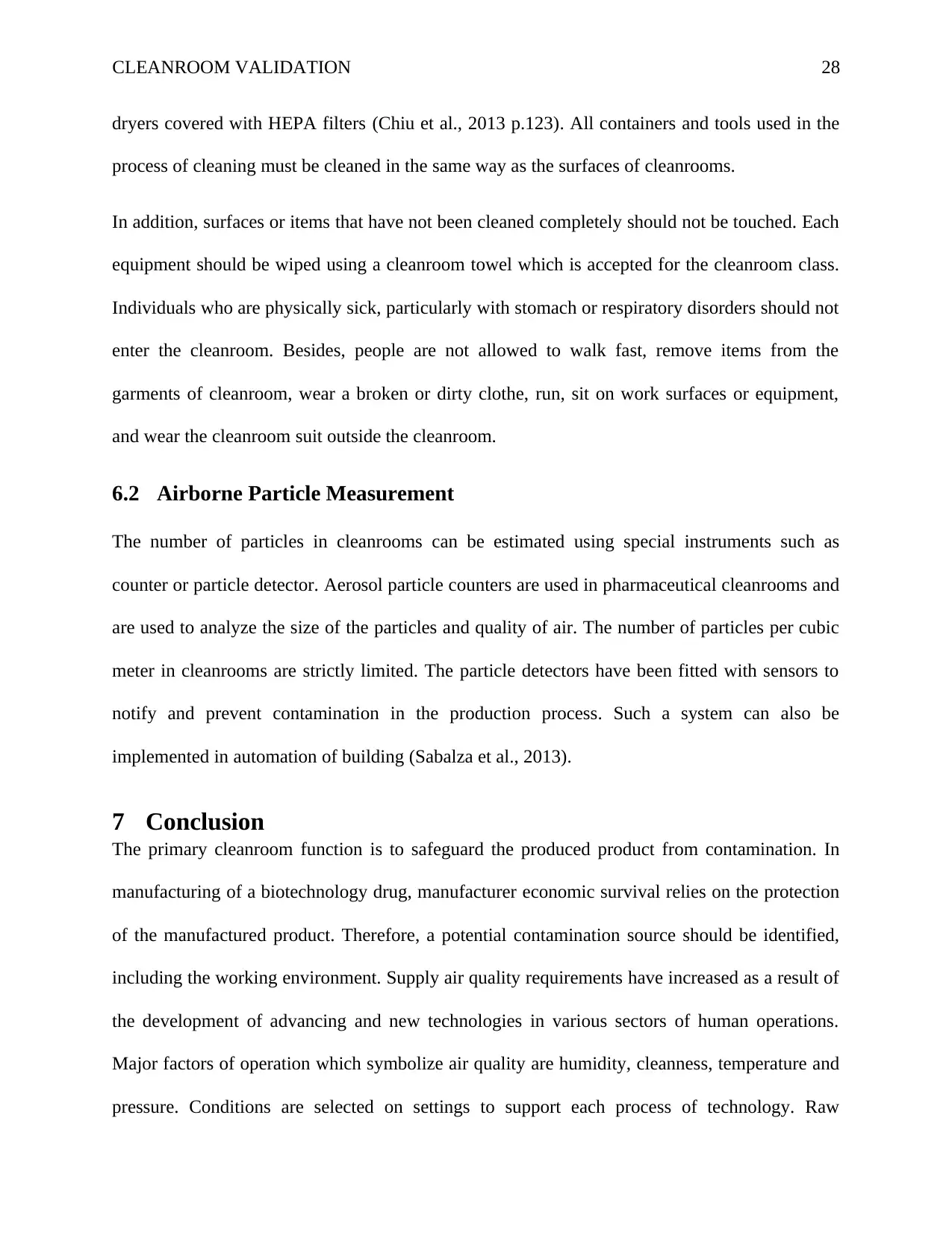
CLEANROOM VALIDATION 28
dryers covered with HEPA filters (Chiu et al., 2013 p.123). All containers and tools used in the
process of cleaning must be cleaned in the same way as the surfaces of cleanrooms.
In addition, surfaces or items that have not been cleaned completely should not be touched. Each
equipment should be wiped using a cleanroom towel which is accepted for the cleanroom class.
Individuals who are physically sick, particularly with stomach or respiratory disorders should not
enter the cleanroom. Besides, people are not allowed to walk fast, remove items from the
garments of cleanroom, wear a broken or dirty clothe, run, sit on work surfaces or equipment,
and wear the cleanroom suit outside the cleanroom.
6.2 Airborne Particle Measurement
The number of particles in cleanrooms can be estimated using special instruments such as
counter or particle detector. Aerosol particle counters are used in pharmaceutical cleanrooms and
are used to analyze the size of the particles and quality of air. The number of particles per cubic
meter in cleanrooms are strictly limited. The particle detectors have been fitted with sensors to
notify and prevent contamination in the production process. Such a system can also be
implemented in automation of building (Sabalza et al., 2013).
7 Conclusion
The primary cleanroom function is to safeguard the produced product from contamination. In
manufacturing of a biotechnology drug, manufacturer economic survival relies on the protection
of the manufactured product. Therefore, a potential contamination source should be identified,
including the working environment. Supply air quality requirements have increased as a result of
the development of advancing and new technologies in various sectors of human operations.
Major factors of operation which symbolize air quality are humidity, cleanness, temperature and
pressure. Conditions are selected on settings to support each process of technology. Raw
dryers covered with HEPA filters (Chiu et al., 2013 p.123). All containers and tools used in the
process of cleaning must be cleaned in the same way as the surfaces of cleanrooms.
In addition, surfaces or items that have not been cleaned completely should not be touched. Each
equipment should be wiped using a cleanroom towel which is accepted for the cleanroom class.
Individuals who are physically sick, particularly with stomach or respiratory disorders should not
enter the cleanroom. Besides, people are not allowed to walk fast, remove items from the
garments of cleanroom, wear a broken or dirty clothe, run, sit on work surfaces or equipment,
and wear the cleanroom suit outside the cleanroom.
6.2 Airborne Particle Measurement
The number of particles in cleanrooms can be estimated using special instruments such as
counter or particle detector. Aerosol particle counters are used in pharmaceutical cleanrooms and
are used to analyze the size of the particles and quality of air. The number of particles per cubic
meter in cleanrooms are strictly limited. The particle detectors have been fitted with sensors to
notify and prevent contamination in the production process. Such a system can also be
implemented in automation of building (Sabalza et al., 2013).
7 Conclusion
The primary cleanroom function is to safeguard the produced product from contamination. In
manufacturing of a biotechnology drug, manufacturer economic survival relies on the protection
of the manufactured product. Therefore, a potential contamination source should be identified,
including the working environment. Supply air quality requirements have increased as a result of
the development of advancing and new technologies in various sectors of human operations.
Major factors of operation which symbolize air quality are humidity, cleanness, temperature and
pressure. Conditions are selected on settings to support each process of technology. Raw
Secure Best Marks with AI Grader
Need help grading? Try our AI Grader for instant feedback on your assignments.
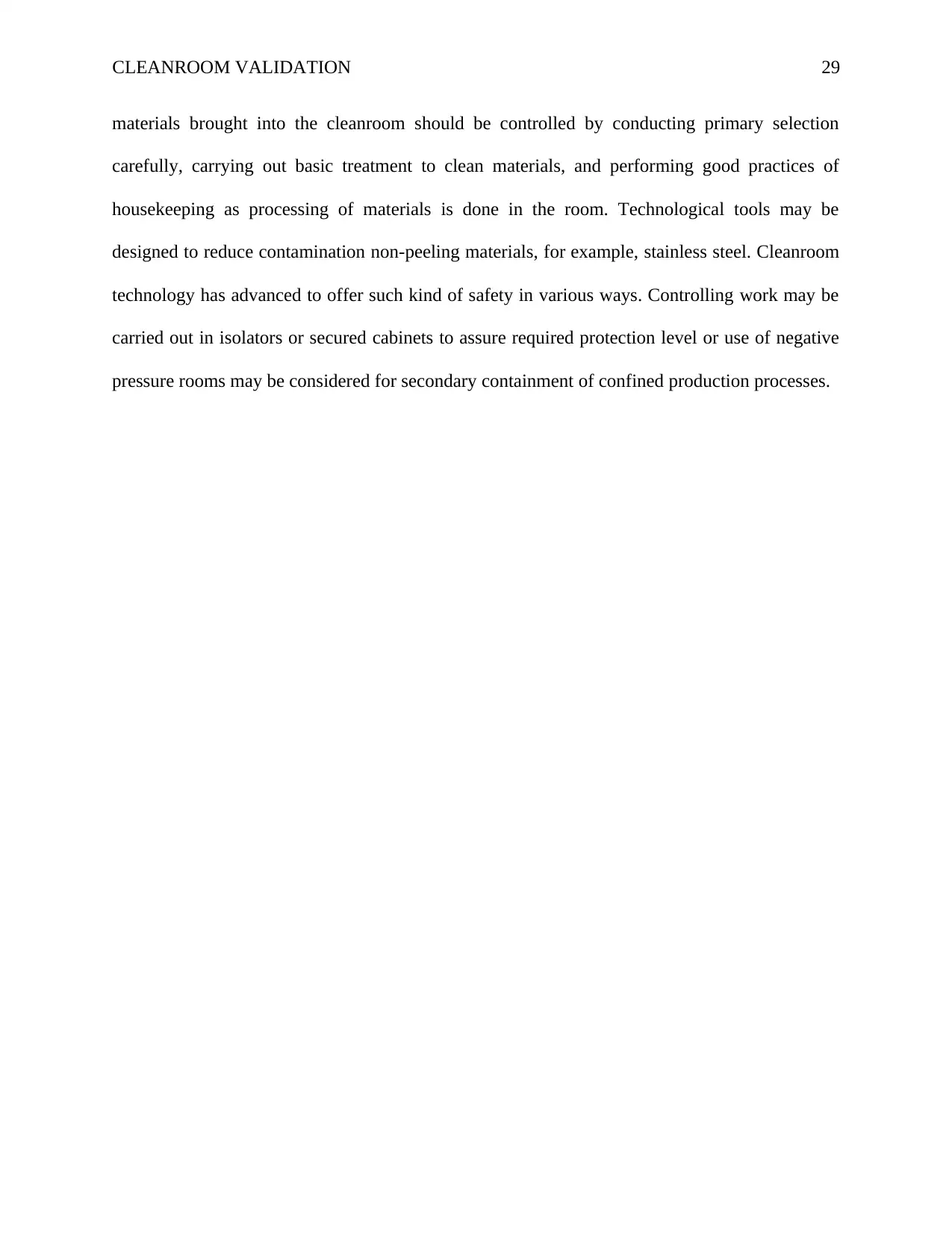
CLEANROOM VALIDATION 29
materials brought into the cleanroom should be controlled by conducting primary selection
carefully, carrying out basic treatment to clean materials, and performing good practices of
housekeeping as processing of materials is done in the room. Technological tools may be
designed to reduce contamination non-peeling materials, for example, stainless steel. Cleanroom
technology has advanced to offer such kind of safety in various ways. Controlling work may be
carried out in isolators or secured cabinets to assure required protection level or use of negative
pressure rooms may be considered for secondary containment of confined production processes.
materials brought into the cleanroom should be controlled by conducting primary selection
carefully, carrying out basic treatment to clean materials, and performing good practices of
housekeeping as processing of materials is done in the room. Technological tools may be
designed to reduce contamination non-peeling materials, for example, stainless steel. Cleanroom
technology has advanced to offer such kind of safety in various ways. Controlling work may be
carried out in isolators or secured cabinets to assure required protection level or use of negative
pressure rooms may be considered for secondary containment of confined production processes.
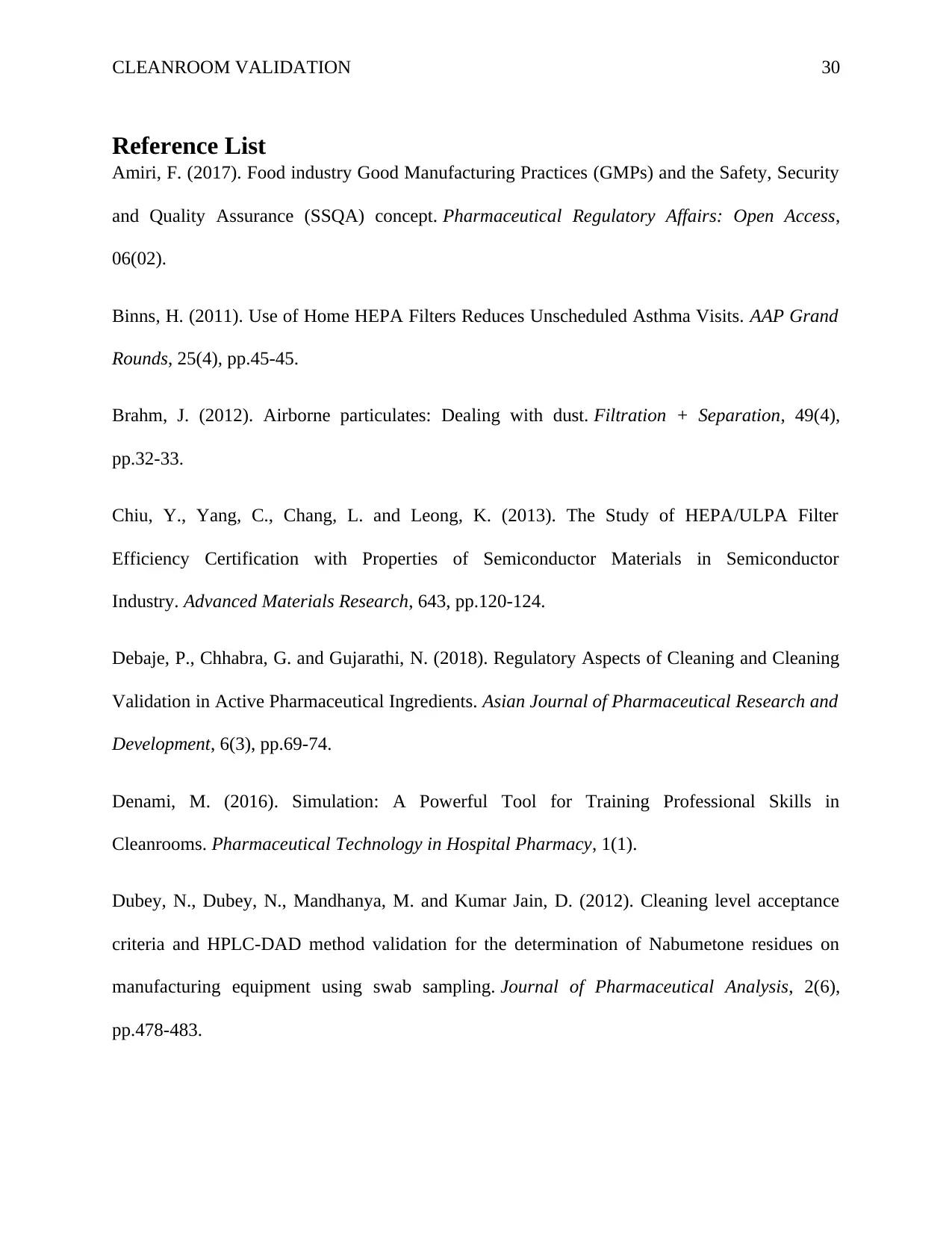
CLEANROOM VALIDATION 30
Reference List
Amiri, F. (2017). Food industry Good Manufacturing Practices (GMPs) and the Safety, Security
and Quality Assurance (SSQA) concept. Pharmaceutical Regulatory Affairs: Open Access,
06(02).
Binns, H. (2011). Use of Home HEPA Filters Reduces Unscheduled Asthma Visits. AAP Grand
Rounds, 25(4), pp.45-45.
Brahm, J. (2012). Airborne particulates: Dealing with dust. Filtration + Separation, 49(4),
pp.32-33.
Chiu, Y., Yang, C., Chang, L. and Leong, K. (2013). The Study of HEPA/ULPA Filter
Efficiency Certification with Properties of Semiconductor Materials in Semiconductor
Industry. Advanced Materials Research, 643, pp.120-124.
Debaje, P., Chhabra, G. and Gujarathi, N. (2018). Regulatory Aspects of Cleaning and Cleaning
Validation in Active Pharmaceutical Ingredients. Asian Journal of Pharmaceutical Research and
Development, 6(3), pp.69-74.
Denami, M. (2016). Simulation: A Powerful Tool for Training Professional Skills in
Cleanrooms. Pharmaceutical Technology in Hospital Pharmacy, 1(1).
Dubey, N., Dubey, N., Mandhanya, M. and Kumar Jain, D. (2012). Cleaning level acceptance
criteria and HPLC-DAD method validation for the determination of Nabumetone residues on
manufacturing equipment using swab sampling. Journal of Pharmaceutical Analysis, 2(6),
pp.478-483.
Reference List
Amiri, F. (2017). Food industry Good Manufacturing Practices (GMPs) and the Safety, Security
and Quality Assurance (SSQA) concept. Pharmaceutical Regulatory Affairs: Open Access,
06(02).
Binns, H. (2011). Use of Home HEPA Filters Reduces Unscheduled Asthma Visits. AAP Grand
Rounds, 25(4), pp.45-45.
Brahm, J. (2012). Airborne particulates: Dealing with dust. Filtration + Separation, 49(4),
pp.32-33.
Chiu, Y., Yang, C., Chang, L. and Leong, K. (2013). The Study of HEPA/ULPA Filter
Efficiency Certification with Properties of Semiconductor Materials in Semiconductor
Industry. Advanced Materials Research, 643, pp.120-124.
Debaje, P., Chhabra, G. and Gujarathi, N. (2018). Regulatory Aspects of Cleaning and Cleaning
Validation in Active Pharmaceutical Ingredients. Asian Journal of Pharmaceutical Research and
Development, 6(3), pp.69-74.
Denami, M. (2016). Simulation: A Powerful Tool for Training Professional Skills in
Cleanrooms. Pharmaceutical Technology in Hospital Pharmacy, 1(1).
Dubey, N., Dubey, N., Mandhanya, M. and Kumar Jain, D. (2012). Cleaning level acceptance
criteria and HPLC-DAD method validation for the determination of Nabumetone residues on
manufacturing equipment using swab sampling. Journal of Pharmaceutical Analysis, 2(6),
pp.478-483.
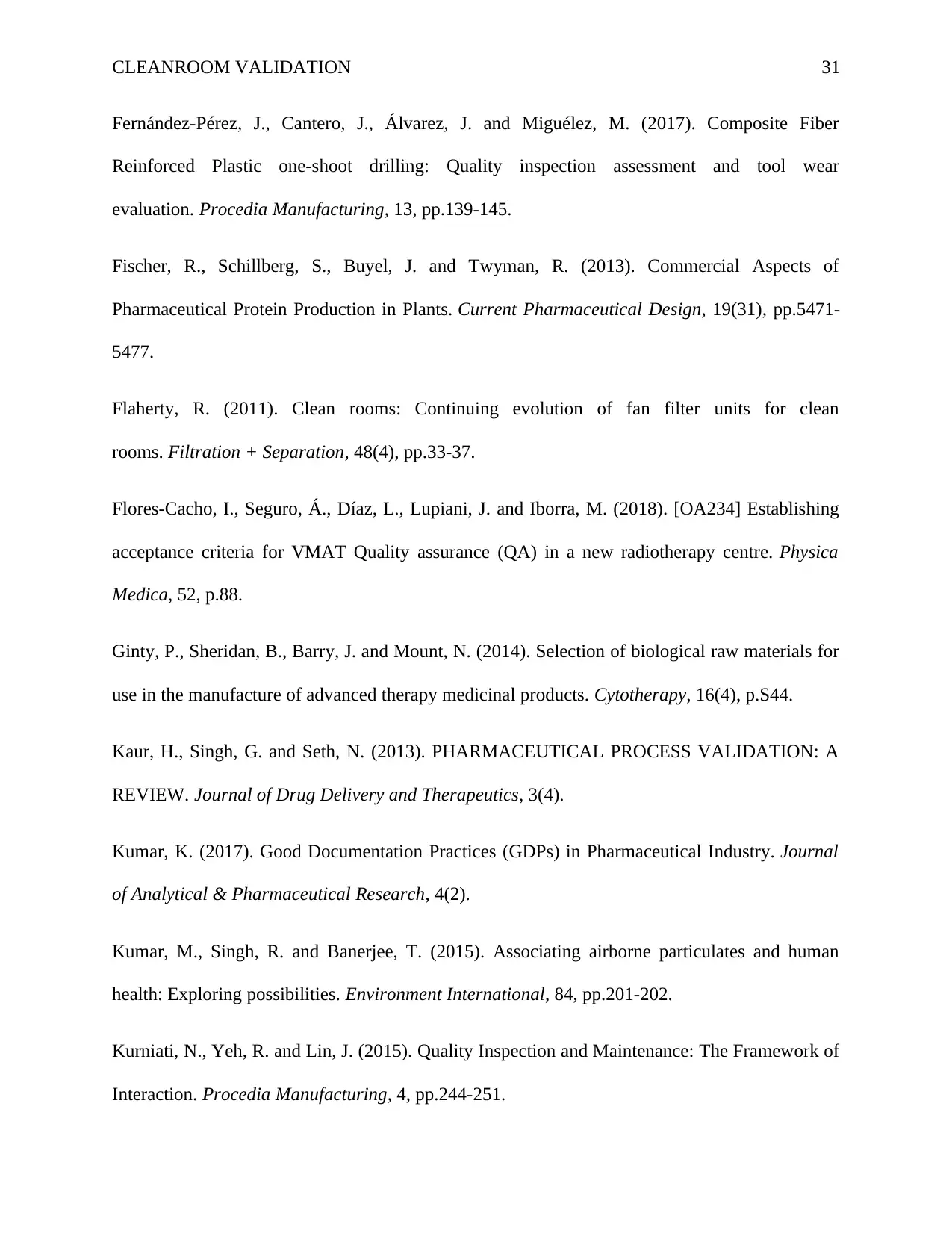
CLEANROOM VALIDATION 31
Fernández-Pérez, J., Cantero, J., Álvarez, J. and Miguélez, M. (2017). Composite Fiber
Reinforced Plastic one-shoot drilling: Quality inspection assessment and tool wear
evaluation. Procedia Manufacturing, 13, pp.139-145.
Fischer, R., Schillberg, S., Buyel, J. and Twyman, R. (2013). Commercial Aspects of
Pharmaceutical Protein Production in Plants. Current Pharmaceutical Design, 19(31), pp.5471-
5477.
Flaherty, R. (2011). Clean rooms: Continuing evolution of fan filter units for clean
rooms. Filtration + Separation, 48(4), pp.33-37.
Flores-Cacho, I., Seguro, Á., Díaz, L., Lupiani, J. and Iborra, M. (2018). [OA234] Establishing
acceptance criteria for VMAT Quality assurance (QA) in a new radiotherapy centre. Physica
Medica, 52, p.88.
Ginty, P., Sheridan, B., Barry, J. and Mount, N. (2014). Selection of biological raw materials for
use in the manufacture of advanced therapy medicinal products. Cytotherapy, 16(4), p.S44.
Kaur, H., Singh, G. and Seth, N. (2013). PHARMACEUTICAL PROCESS VALIDATION: A
REVIEW. Journal of Drug Delivery and Therapeutics, 3(4).
Kumar, K. (2017). Good Documentation Practices (GDPs) in Pharmaceutical Industry. Journal
of Analytical & Pharmaceutical Research, 4(2).
Kumar, M., Singh, R. and Banerjee, T. (2015). Associating airborne particulates and human
health: Exploring possibilities. Environment International, 84, pp.201-202.
Kurniati, N., Yeh, R. and Lin, J. (2015). Quality Inspection and Maintenance: The Framework of
Interaction. Procedia Manufacturing, 4, pp.244-251.
Fernández-Pérez, J., Cantero, J., Álvarez, J. and Miguélez, M. (2017). Composite Fiber
Reinforced Plastic one-shoot drilling: Quality inspection assessment and tool wear
evaluation. Procedia Manufacturing, 13, pp.139-145.
Fischer, R., Schillberg, S., Buyel, J. and Twyman, R. (2013). Commercial Aspects of
Pharmaceutical Protein Production in Plants. Current Pharmaceutical Design, 19(31), pp.5471-
5477.
Flaherty, R. (2011). Clean rooms: Continuing evolution of fan filter units for clean
rooms. Filtration + Separation, 48(4), pp.33-37.
Flores-Cacho, I., Seguro, Á., Díaz, L., Lupiani, J. and Iborra, M. (2018). [OA234] Establishing
acceptance criteria for VMAT Quality assurance (QA) in a new radiotherapy centre. Physica
Medica, 52, p.88.
Ginty, P., Sheridan, B., Barry, J. and Mount, N. (2014). Selection of biological raw materials for
use in the manufacture of advanced therapy medicinal products. Cytotherapy, 16(4), p.S44.
Kaur, H., Singh, G. and Seth, N. (2013). PHARMACEUTICAL PROCESS VALIDATION: A
REVIEW. Journal of Drug Delivery and Therapeutics, 3(4).
Kumar, K. (2017). Good Documentation Practices (GDPs) in Pharmaceutical Industry. Journal
of Analytical & Pharmaceutical Research, 4(2).
Kumar, M., Singh, R. and Banerjee, T. (2015). Associating airborne particulates and human
health: Exploring possibilities. Environment International, 84, pp.201-202.
Kurniati, N., Yeh, R. and Lin, J. (2015). Quality Inspection and Maintenance: The Framework of
Interaction. Procedia Manufacturing, 4, pp.244-251.
Paraphrase This Document
Need a fresh take? Get an instant paraphrase of this document with our AI Paraphraser

CLEANROOM VALIDATION 32
Li, H., Zou, Z. and Wang, F. (2013). The Effect of Air Change Rate and Cleanroom Garment on
Cleanliness in Grade B Cleanroom. Applied Mechanics and Materials, 441, pp.514-517.
Liu, D. (2017). Statistics in action: A case study for a pharmaceutical active ingredient (API)
manufacturing process in the USA. Journal of Biomedical Engineering and Medical Devices,
02(02).
Merkulov, V., Vasiliev, A., Goryachev, D., Gavrishina, E., Niyazov, R. and Korneeva, L. (2014).
Assessment of quality, safety, and efficacy of medicinal products as one of the fundamentals of
public health protection. Remedium. Journal about the Russian market of medicines and medical
equipment, (6), pp.14-23.
Mohammadi, B., Taleizadeh, A., Noorossana, R. and Samimi, H. (2015). Optimizing integrated
manufacturing and products inspection policy for deteriorating manufacturing system with
imperfect inspection. Journal of Manufacturing Systems, 37, pp.299-315.
Parajuli, R., Shrestha, S., Lamichane, S. and Pokhrel, P. (2015). A REVIEW ON
PHARMACEUTICAL PROCESS VALIDATION OF SOLID DOSAGE FORM
[TABLETS]. Journal of Drug Delivery and Therapeutics, 5(6).
R., N., H., N. and R., M. (2016). KNOWLEDGE, ATTITUDES AND PRACTICES (KAP) ON
GOOD MANUFACTURING PRACTICES (GMP) AMONG FOOD HANDLERS IN
TERENGGANU HOSPITALS. International Journal of Pharmacy and Pharmaceutical
Sciences, 8(11), p.53.
Raman, P., Fuller, K. and Gregory, D. (2013). Polarization signatures of airborne
particulates. Optical Engineering, 52(7), p.074106.
Li, H., Zou, Z. and Wang, F. (2013). The Effect of Air Change Rate and Cleanroom Garment on
Cleanliness in Grade B Cleanroom. Applied Mechanics and Materials, 441, pp.514-517.
Liu, D. (2017). Statistics in action: A case study for a pharmaceutical active ingredient (API)
manufacturing process in the USA. Journal of Biomedical Engineering and Medical Devices,
02(02).
Merkulov, V., Vasiliev, A., Goryachev, D., Gavrishina, E., Niyazov, R. and Korneeva, L. (2014).
Assessment of quality, safety, and efficacy of medicinal products as one of the fundamentals of
public health protection. Remedium. Journal about the Russian market of medicines and medical
equipment, (6), pp.14-23.
Mohammadi, B., Taleizadeh, A., Noorossana, R. and Samimi, H. (2015). Optimizing integrated
manufacturing and products inspection policy for deteriorating manufacturing system with
imperfect inspection. Journal of Manufacturing Systems, 37, pp.299-315.
Parajuli, R., Shrestha, S., Lamichane, S. and Pokhrel, P. (2015). A REVIEW ON
PHARMACEUTICAL PROCESS VALIDATION OF SOLID DOSAGE FORM
[TABLETS]. Journal of Drug Delivery and Therapeutics, 5(6).
R., N., H., N. and R., M. (2016). KNOWLEDGE, ATTITUDES AND PRACTICES (KAP) ON
GOOD MANUFACTURING PRACTICES (GMP) AMONG FOOD HANDLERS IN
TERENGGANU HOSPITALS. International Journal of Pharmacy and Pharmaceutical
Sciences, 8(11), p.53.
Raman, P., Fuller, K. and Gregory, D. (2013). Polarization signatures of airborne
particulates. Optical Engineering, 52(7), p.074106.
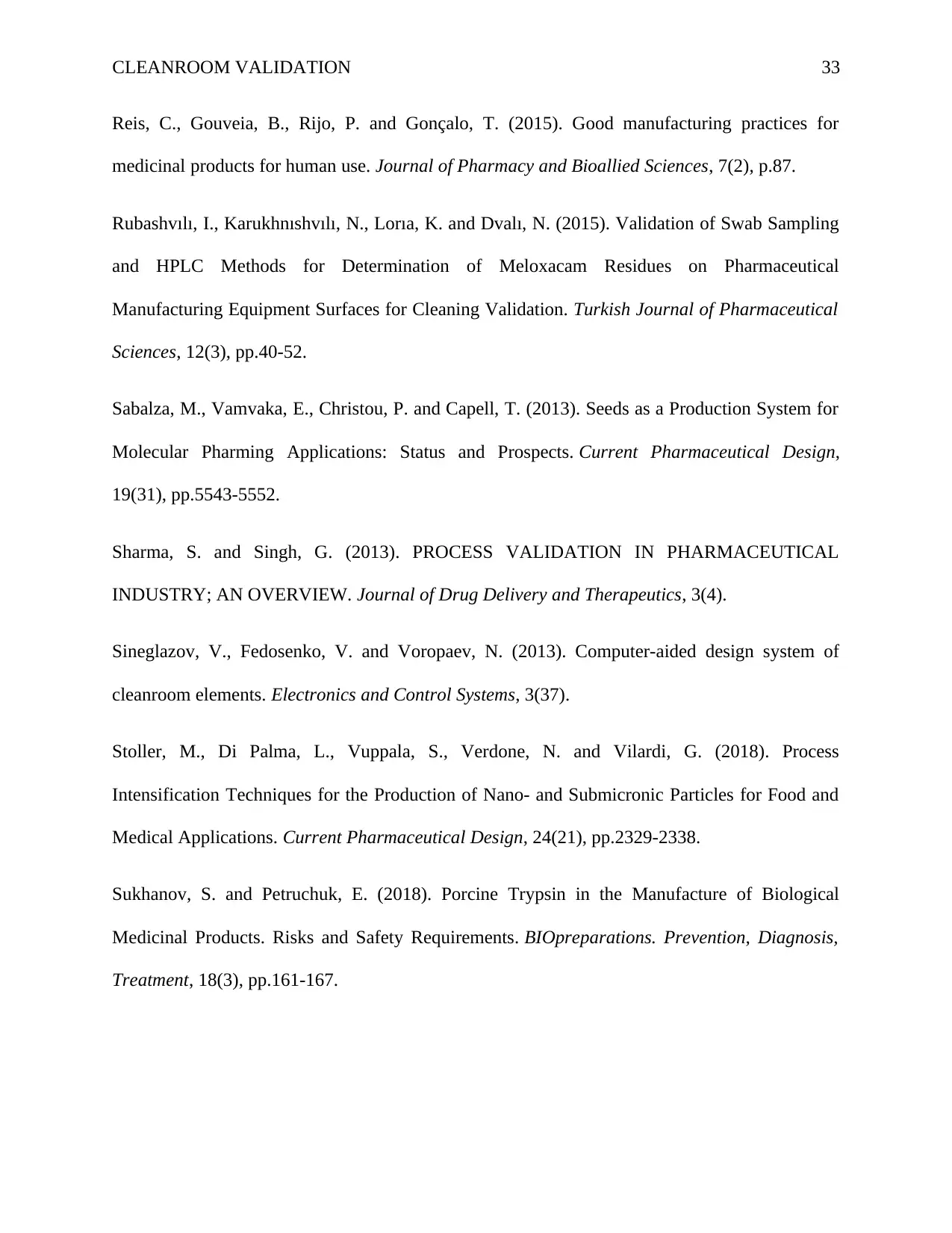
CLEANROOM VALIDATION 33
Reis, C., Gouveia, B., Rijo, P. and Gonçalo, T. (2015). Good manufacturing practices for
medicinal products for human use. Journal of Pharmacy and Bioallied Sciences, 7(2), p.87.
Rubashvılı, I., Karukhnıshvılı, N., Lorıa, K. and Dvalı, N. (2015). Validation of Swab Sampling
and HPLC Methods for Determination of Meloxacam Residues on Pharmaceutical
Manufacturing Equipment Surfaces for Cleaning Validation. Turkish Journal of Pharmaceutical
Sciences, 12(3), pp.40-52.
Sabalza, M., Vamvaka, E., Christou, P. and Capell, T. (2013). Seeds as a Production System for
Molecular Pharming Applications: Status and Prospects. Current Pharmaceutical Design,
19(31), pp.5543-5552.
Sharma, S. and Singh, G. (2013). PROCESS VALIDATION IN PHARMACEUTICAL
INDUSTRY; AN OVERVIEW. Journal of Drug Delivery and Therapeutics, 3(4).
Sineglazov, V., Fedosenko, V. and Voropaev, N. (2013). Computer-aided design system of
cleanroom elements. Electronics and Control Systems, 3(37).
Stoller, M., Di Palma, L., Vuppala, S., Verdone, N. and Vilardi, G. (2018). Process
Intensification Techniques for the Production of Nano- and Submicronic Particles for Food and
Medical Applications. Current Pharmaceutical Design, 24(21), pp.2329-2338.
Sukhanov, S. and Petruchuk, E. (2018). Porcine Trypsin in the Manufacture of Biological
Medicinal Products. Risks and Safety Requirements. BIOpreparations. Prevention, Diagnosis,
Treatment, 18(3), pp.161-167.
Reis, C., Gouveia, B., Rijo, P. and Gonçalo, T. (2015). Good manufacturing practices for
medicinal products for human use. Journal of Pharmacy and Bioallied Sciences, 7(2), p.87.
Rubashvılı, I., Karukhnıshvılı, N., Lorıa, K. and Dvalı, N. (2015). Validation of Swab Sampling
and HPLC Methods for Determination of Meloxacam Residues on Pharmaceutical
Manufacturing Equipment Surfaces for Cleaning Validation. Turkish Journal of Pharmaceutical
Sciences, 12(3), pp.40-52.
Sabalza, M., Vamvaka, E., Christou, P. and Capell, T. (2013). Seeds as a Production System for
Molecular Pharming Applications: Status and Prospects. Current Pharmaceutical Design,
19(31), pp.5543-5552.
Sharma, S. and Singh, G. (2013). PROCESS VALIDATION IN PHARMACEUTICAL
INDUSTRY; AN OVERVIEW. Journal of Drug Delivery and Therapeutics, 3(4).
Sineglazov, V., Fedosenko, V. and Voropaev, N. (2013). Computer-aided design system of
cleanroom elements. Electronics and Control Systems, 3(37).
Stoller, M., Di Palma, L., Vuppala, S., Verdone, N. and Vilardi, G. (2018). Process
Intensification Techniques for the Production of Nano- and Submicronic Particles for Food and
Medical Applications. Current Pharmaceutical Design, 24(21), pp.2329-2338.
Sukhanov, S. and Petruchuk, E. (2018). Porcine Trypsin in the Manufacture of Biological
Medicinal Products. Risks and Safety Requirements. BIOpreparations. Prevention, Diagnosis,
Treatment, 18(3), pp.161-167.
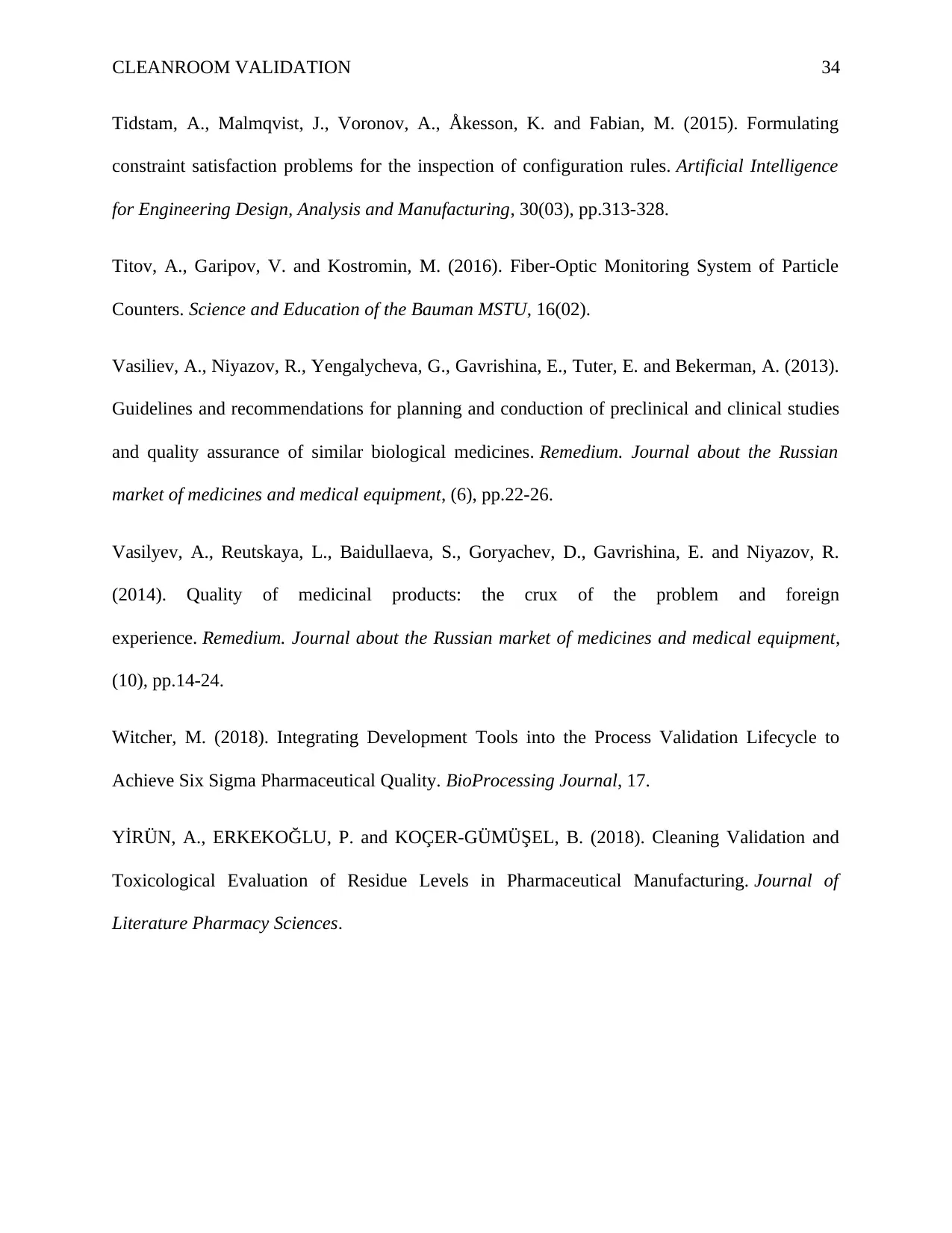
CLEANROOM VALIDATION 34
Tidstam, A., Malmqvist, J., Voronov, A., Åkesson, K. and Fabian, M. (2015). Formulating
constraint satisfaction problems for the inspection of configuration rules. Artificial Intelligence
for Engineering Design, Analysis and Manufacturing, 30(03), pp.313-328.
Titov, A., Garipov, V. and Kostromin, M. (2016). Fiber-Optic Monitoring System of Particle
Counters. Science and Education of the Bauman MSTU, 16(02).
Vasiliev, A., Niyazov, R., Yengalycheva, G., Gavrishina, E., Tuter, E. and Bekerman, A. (2013).
Guidelines and recommendations for planning and conduction of preclinical and clinical studies
and quality assurance of similar biological medicines. Remedium. Journal about the Russian
market of medicines and medical equipment, (6), pp.22-26.
Vasilyev, A., Reutskaya, L., Baidullaeva, S., Goryachev, D., Gavrishina, E. and Niyazov, R.
(2014). Quality of medicinal products: the crux of the problem and foreign
experience. Remedium. Journal about the Russian market of medicines and medical equipment,
(10), pp.14-24.
Witcher, M. (2018). Integrating Development Tools into the Process Validation Lifecycle to
Achieve Six Sigma Pharmaceutical Quality. BioProcessing Journal, 17.
YİRÜN, A., ERKEKOĞLU, P. and KOÇER-GÜMÜŞEL, B. (2018). Cleaning Validation and
Toxicological Evaluation of Residue Levels in Pharmaceutical Manufacturing. Journal of
Literature Pharmacy Sciences.
Tidstam, A., Malmqvist, J., Voronov, A., Åkesson, K. and Fabian, M. (2015). Formulating
constraint satisfaction problems for the inspection of configuration rules. Artificial Intelligence
for Engineering Design, Analysis and Manufacturing, 30(03), pp.313-328.
Titov, A., Garipov, V. and Kostromin, M. (2016). Fiber-Optic Monitoring System of Particle
Counters. Science and Education of the Bauman MSTU, 16(02).
Vasiliev, A., Niyazov, R., Yengalycheva, G., Gavrishina, E., Tuter, E. and Bekerman, A. (2013).
Guidelines and recommendations for planning and conduction of preclinical and clinical studies
and quality assurance of similar biological medicines. Remedium. Journal about the Russian
market of medicines and medical equipment, (6), pp.22-26.
Vasilyev, A., Reutskaya, L., Baidullaeva, S., Goryachev, D., Gavrishina, E. and Niyazov, R.
(2014). Quality of medicinal products: the crux of the problem and foreign
experience. Remedium. Journal about the Russian market of medicines and medical equipment,
(10), pp.14-24.
Witcher, M. (2018). Integrating Development Tools into the Process Validation Lifecycle to
Achieve Six Sigma Pharmaceutical Quality. BioProcessing Journal, 17.
YİRÜN, A., ERKEKOĞLU, P. and KOÇER-GÜMÜŞEL, B. (2018). Cleaning Validation and
Toxicological Evaluation of Residue Levels in Pharmaceutical Manufacturing. Journal of
Literature Pharmacy Sciences.
1 out of 34
![[object Object]](/_next/image/?url=%2F_next%2Fstatic%2Fmedia%2Flogo.6d15ce61.png&w=640&q=75)
Your All-in-One AI-Powered Toolkit for Academic Success.
+13062052269
info@desklib.com
Available 24*7 on WhatsApp / Email
Unlock your academic potential
© 2024 | Zucol Services PVT LTD | All rights reserved.