Detailed Analysis of Job Costing System for Turramurra Furniture
VerifiedAdded on 2020/06/05
|9
|2508
|64
Report
AI Summary
This report provides a comprehensive analysis of the job costing system at Turramurra Furniture. It begins with an introduction to accounting and the suitability of job costing for the company. The report then delves into specific calculations, including determining the work-in-progress (WIP) at the end of June 2017 and calculating the cost of chairs in the finished inventory. A significant portion of the report is dedicated to computing over or under-applied overhead for the year, with detailed calculations and interpretations. The report suggests corrective measures for over-applied overhead and discusses the appropriate approach for adjusting the over or under-application of overhead. Finally, it assesses the suitability of activity-based budgeting (ABB) for Turramurra Furniture, outlining the advantages and disadvantages of adopting this technique. The report concludes with a summary of the key findings and recommendations.
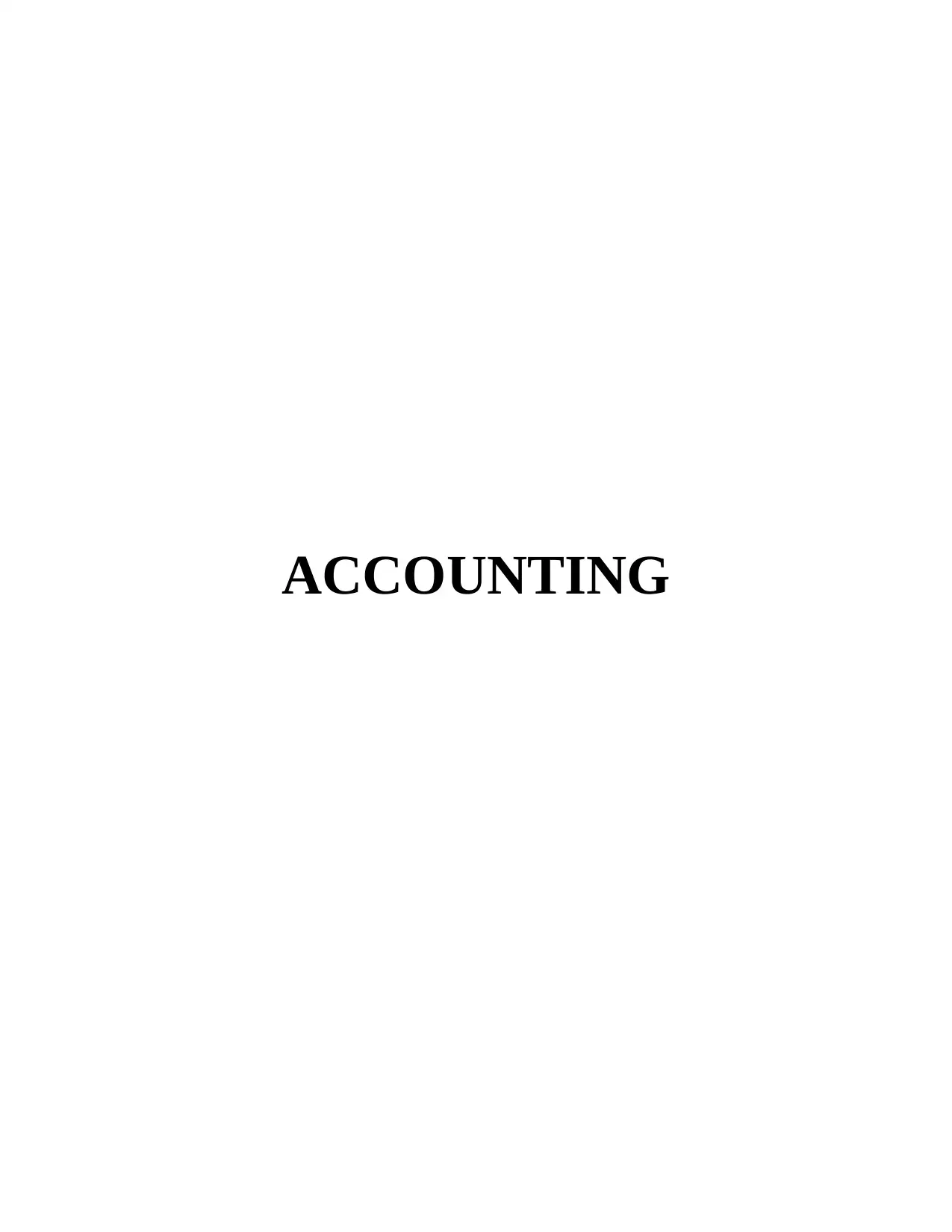
ACCOUNTING
Paraphrase This Document
Need a fresh take? Get an instant paraphrase of this document with our AI Paraphraser
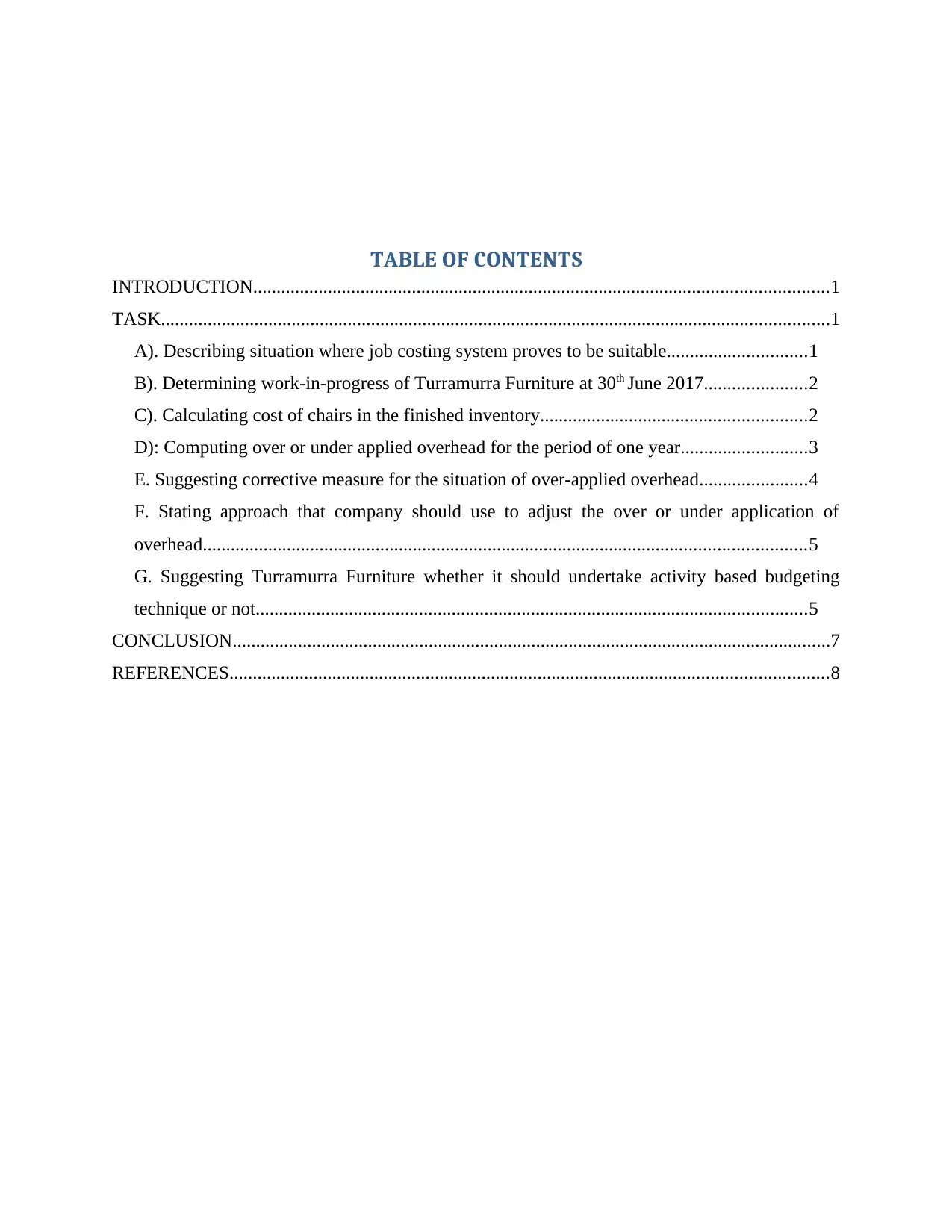
TABLE OF CONTENTS
INTRODUCTION...........................................................................................................................1
TASK...............................................................................................................................................1
A). Describing situation where job costing system proves to be suitable..............................1
B). Determining work-in-progress of Turramurra Furniture at 30th June 2017......................2
C). Calculating cost of chairs in the finished inventory.........................................................2
D): Computing over or under applied overhead for the period of one year...........................3
E. Suggesting corrective measure for the situation of over-applied overhead.......................4
F. Stating approach that company should use to adjust the over or under application of
overhead.................................................................................................................................5
G. Suggesting Turramurra Furniture whether it should undertake activity based budgeting
technique or not......................................................................................................................5
CONCLUSION................................................................................................................................7
REFERENCES................................................................................................................................8
INTRODUCTION...........................................................................................................................1
TASK...............................................................................................................................................1
A). Describing situation where job costing system proves to be suitable..............................1
B). Determining work-in-progress of Turramurra Furniture at 30th June 2017......................2
C). Calculating cost of chairs in the finished inventory.........................................................2
D): Computing over or under applied overhead for the period of one year...........................3
E. Suggesting corrective measure for the situation of over-applied overhead.......................4
F. Stating approach that company should use to adjust the over or under application of
overhead.................................................................................................................................5
G. Suggesting Turramurra Furniture whether it should undertake activity based budgeting
technique or not......................................................................................................................5
CONCLUSION................................................................................................................................7
REFERENCES................................................................................................................................8

INTRODUCTION
Accounting is the tool which is used by each and every company for having systematic
records of all transactions. There is a strong need to adopt the systematic accounting reporting
standards by organisations so that they can be safeguard from prosecution. This is the only tool
by which a company could get sustainable development. The present report is based on
Turramurra Furniture which will provide deeper insight about the situations in which the system
of job costing needs to be undertaken. Besides this, it will shed light on the concept or aspects
under and over applied overhead. Further, report also depicts the manner in which activity based
costing technique helps in taking suitable decision regarding cost.
TASK
A). Describing situation where job costing system proves to be suitable
Job order costing is a normal way that been used by company producing diverse range of
products. This is one among mostly implemented system of costing in production area and is also
used in service industry. Mostly, production organisation implementes job order costing with a
motive to achieve orders for customised goods and services. These customized orders are also
known as jobs or batches. For example, A clothing company might attain an order for men shirts
with specific size, colour, and design.
When Turramurra Furniture Company accept jobs for diverse goods, the assignment of cost
to goods become a complicated task. Under these situations, cost record for every individual job
is kept as each job has a diverse good and henceforth, diverse costs is linked to it.
Per unit cost of a specific job is calculated by dividing the total cost allocated by number of
units under. Per unit cost formula is provided as below:
Per unit cost= Total cost applicable to job/ Number of units in the job
Job order costing is mostly implemented by organisations all around the globe. A job cost
sheet segregate production projects into three types of costs. These are direct material, direct
labour and manufacturing overheads. Direct material is related to the material required to
produce the project. Direct labour is the amount of the manpower cost which is implemented to
fulfil the project (Mu, Jiang and Leng, 2017). Manufacturing overheads are the third one which
is the indirect costs connected to manufacturing of goods.
1
Accounting is the tool which is used by each and every company for having systematic
records of all transactions. There is a strong need to adopt the systematic accounting reporting
standards by organisations so that they can be safeguard from prosecution. This is the only tool
by which a company could get sustainable development. The present report is based on
Turramurra Furniture which will provide deeper insight about the situations in which the system
of job costing needs to be undertaken. Besides this, it will shed light on the concept or aspects
under and over applied overhead. Further, report also depicts the manner in which activity based
costing technique helps in taking suitable decision regarding cost.
TASK
A). Describing situation where job costing system proves to be suitable
Job order costing is a normal way that been used by company producing diverse range of
products. This is one among mostly implemented system of costing in production area and is also
used in service industry. Mostly, production organisation implementes job order costing with a
motive to achieve orders for customised goods and services. These customized orders are also
known as jobs or batches. For example, A clothing company might attain an order for men shirts
with specific size, colour, and design.
When Turramurra Furniture Company accept jobs for diverse goods, the assignment of cost
to goods become a complicated task. Under these situations, cost record for every individual job
is kept as each job has a diverse good and henceforth, diverse costs is linked to it.
Per unit cost of a specific job is calculated by dividing the total cost allocated by number of
units under. Per unit cost formula is provided as below:
Per unit cost= Total cost applicable to job/ Number of units in the job
Job order costing is mostly implemented by organisations all around the globe. A job cost
sheet segregate production projects into three types of costs. These are direct material, direct
labour and manufacturing overheads. Direct material is related to the material required to
produce the project. Direct labour is the amount of the manpower cost which is implemented to
fulfil the project (Mu, Jiang and Leng, 2017). Manufacturing overheads are the third one which
is the indirect costs connected to manufacturing of goods.
1
⊘ This is a preview!⊘
Do you want full access?
Subscribe today to unlock all pages.

Trusted by 1+ million students worldwide
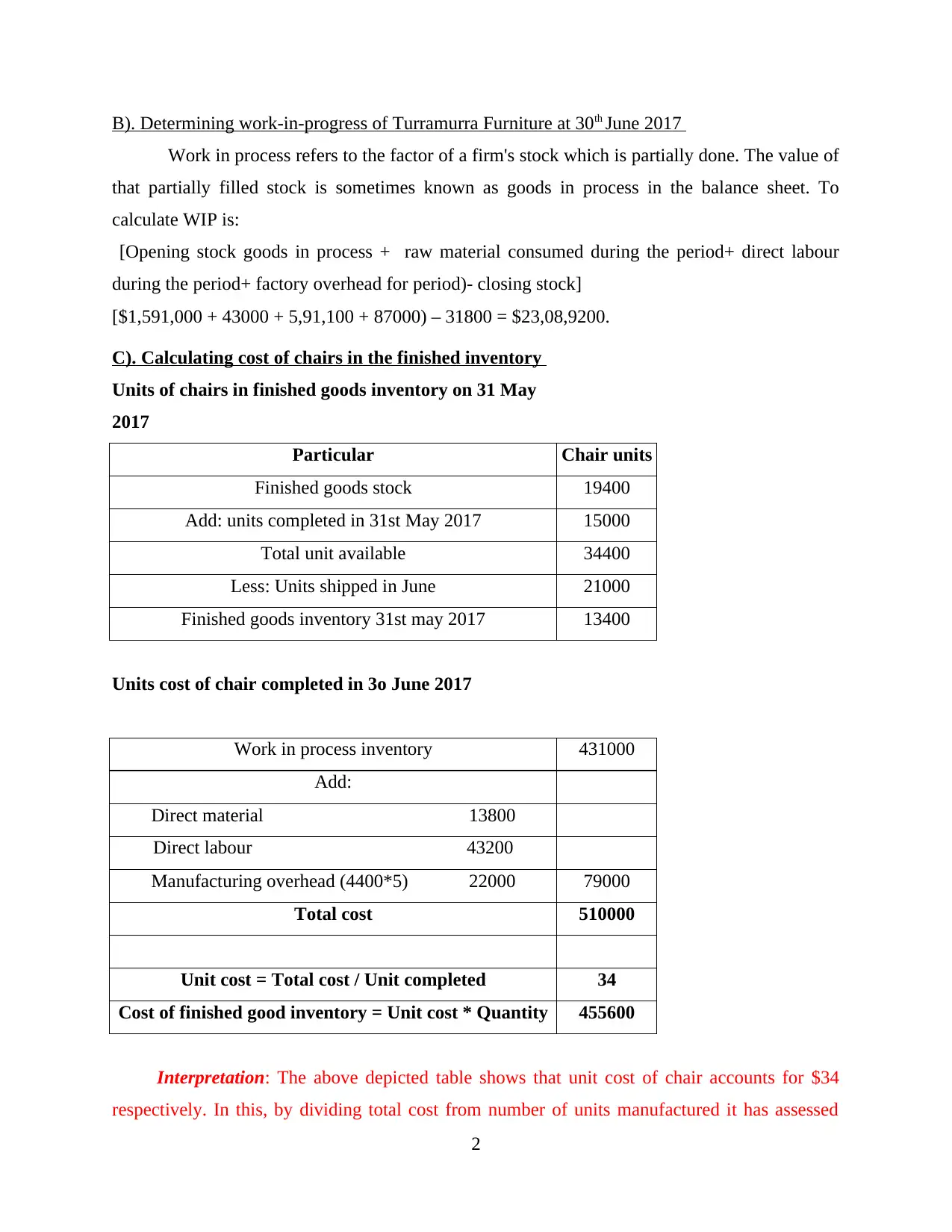
B). Determining work-in-progress of Turramurra Furniture at 30th June 2017
Work in process refers to the factor of a firm's stock which is partially done. The value of
that partially filled stock is sometimes known as goods in process in the balance sheet. To
calculate WIP is:
[Opening stock goods in process + raw material consumed during the period+ direct labour
during the period+ factory overhead for period)- closing stock]
[$1,591,000 + 43000 + 5,91,100 + 87000) – 31800 = $23,08,9200.
C). Calculating cost of chairs in the finished inventory
Units of chairs in finished goods inventory on 31 May
2017
Particular Chair units
Finished goods stock 19400
Add: units completed in 31st May 2017 15000
Total unit available 34400
Less: Units shipped in June 21000
Finished goods inventory 31st may 2017 13400
Units cost of chair completed in 3o June 2017
Work in process inventory 431000
Add:
Direct material 13800
Direct labour 43200
Manufacturing overhead (4400*5) 22000 79000
Total cost 510000
Unit cost = Total cost / Unit completed 34
Cost of finished good inventory = Unit cost * Quantity 455600
Interpretation: The above depicted table shows that unit cost of chair accounts for $34
respectively. In this, by dividing total cost from number of units manufactured it has assessed
2
Work in process refers to the factor of a firm's stock which is partially done. The value of
that partially filled stock is sometimes known as goods in process in the balance sheet. To
calculate WIP is:
[Opening stock goods in process + raw material consumed during the period+ direct labour
during the period+ factory overhead for period)- closing stock]
[$1,591,000 + 43000 + 5,91,100 + 87000) – 31800 = $23,08,9200.
C). Calculating cost of chairs in the finished inventory
Units of chairs in finished goods inventory on 31 May
2017
Particular Chair units
Finished goods stock 19400
Add: units completed in 31st May 2017 15000
Total unit available 34400
Less: Units shipped in June 21000
Finished goods inventory 31st may 2017 13400
Units cost of chair completed in 3o June 2017
Work in process inventory 431000
Add:
Direct material 13800
Direct labour 43200
Manufacturing overhead (4400*5) 22000 79000
Total cost 510000
Unit cost = Total cost / Unit completed 34
Cost of finished good inventory = Unit cost * Quantity 455600
Interpretation: The above depicted table shows that unit cost of chair accounts for $34
respectively. In this, by dividing total cost from number of units manufactured it has assessed
2
Paraphrase This Document
Need a fresh take? Get an instant paraphrase of this document with our AI Paraphraser
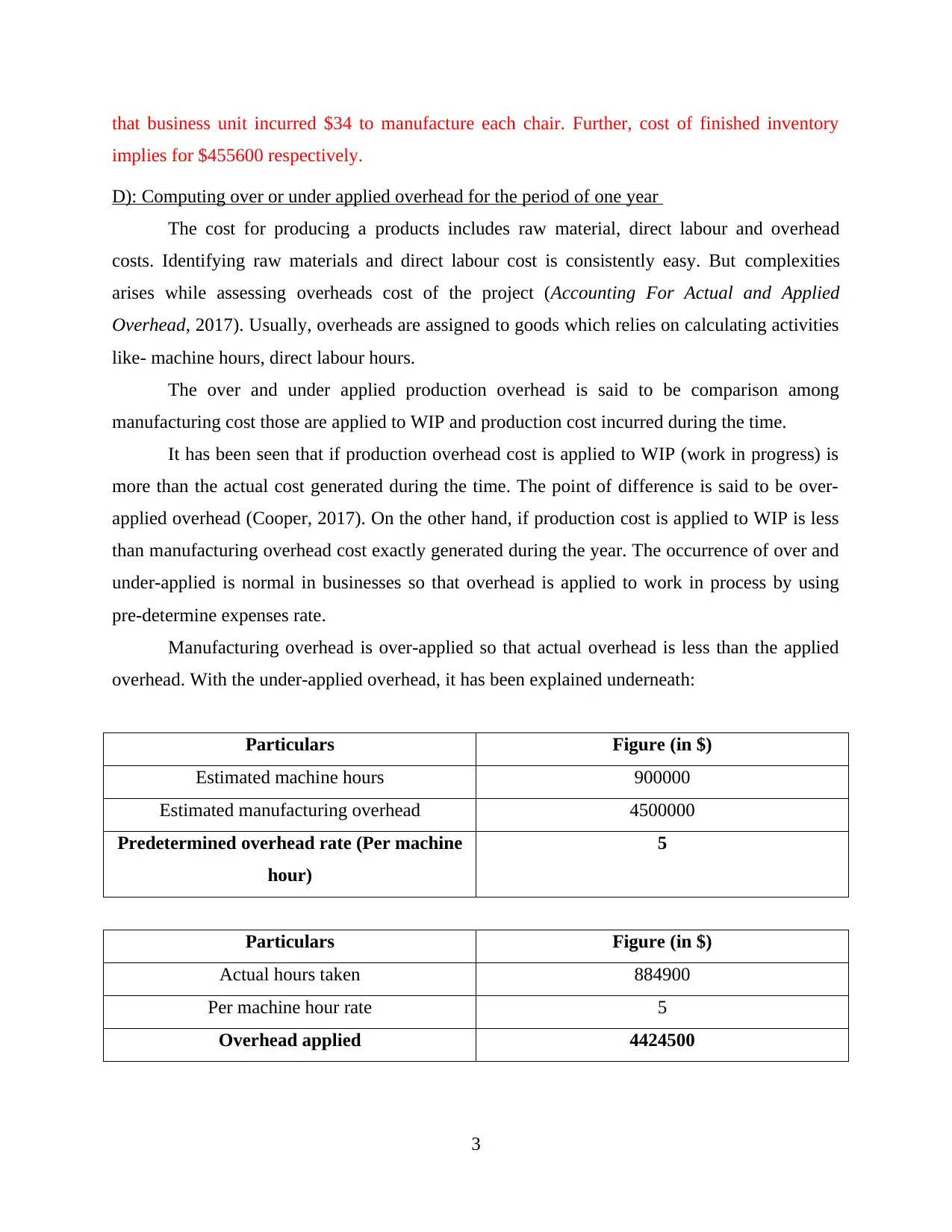
that business unit incurred $34 to manufacture each chair. Further, cost of finished inventory
implies for $455600 respectively.
D): Computing over or under applied overhead for the period of one year
The cost for producing a products includes raw material, direct labour and overhead
costs. Identifying raw materials and direct labour cost is consistently easy. But complexities
arises while assessing overheads cost of the project (Accounting For Actual and Applied
Overhead, 2017). Usually, overheads are assigned to goods which relies on calculating activities
like- machine hours, direct labour hours.
The over and under applied production overhead is said to be comparison among
manufacturing cost those are applied to WIP and production cost incurred during the time.
It has been seen that if production overhead cost is applied to WIP (work in progress) is
more than the actual cost generated during the time. The point of difference is said to be over-
applied overhead (Cooper, 2017). On the other hand, if production cost is applied to WIP is less
than manufacturing overhead cost exactly generated during the year. The occurrence of over and
under-applied is normal in businesses so that overhead is applied to work in process by using
pre-determine expenses rate.
Manufacturing overhead is over-applied so that actual overhead is less than the applied
overhead. With the under-applied overhead, it has been explained underneath:
Particulars Figure (in $)
Estimated machine hours 900000
Estimated manufacturing overhead 4500000
Predetermined overhead rate (Per machine
hour)
5
Particulars Figure (in $)
Actual hours taken 884900
Per machine hour rate 5
Overhead applied 4424500
3
implies for $455600 respectively.
D): Computing over or under applied overhead for the period of one year
The cost for producing a products includes raw material, direct labour and overhead
costs. Identifying raw materials and direct labour cost is consistently easy. But complexities
arises while assessing overheads cost of the project (Accounting For Actual and Applied
Overhead, 2017). Usually, overheads are assigned to goods which relies on calculating activities
like- machine hours, direct labour hours.
The over and under applied production overhead is said to be comparison among
manufacturing cost those are applied to WIP and production cost incurred during the time.
It has been seen that if production overhead cost is applied to WIP (work in progress) is
more than the actual cost generated during the time. The point of difference is said to be over-
applied overhead (Cooper, 2017). On the other hand, if production cost is applied to WIP is less
than manufacturing overhead cost exactly generated during the year. The occurrence of over and
under-applied is normal in businesses so that overhead is applied to work in process by using
pre-determine expenses rate.
Manufacturing overhead is over-applied so that actual overhead is less than the applied
overhead. With the under-applied overhead, it has been explained underneath:
Particulars Figure (in $)
Estimated machine hours 900000
Estimated manufacturing overhead 4500000
Predetermined overhead rate (Per machine
hour)
5
Particulars Figure (in $)
Actual hours taken 884900
Per machine hour rate 5
Overhead applied 4424500
3
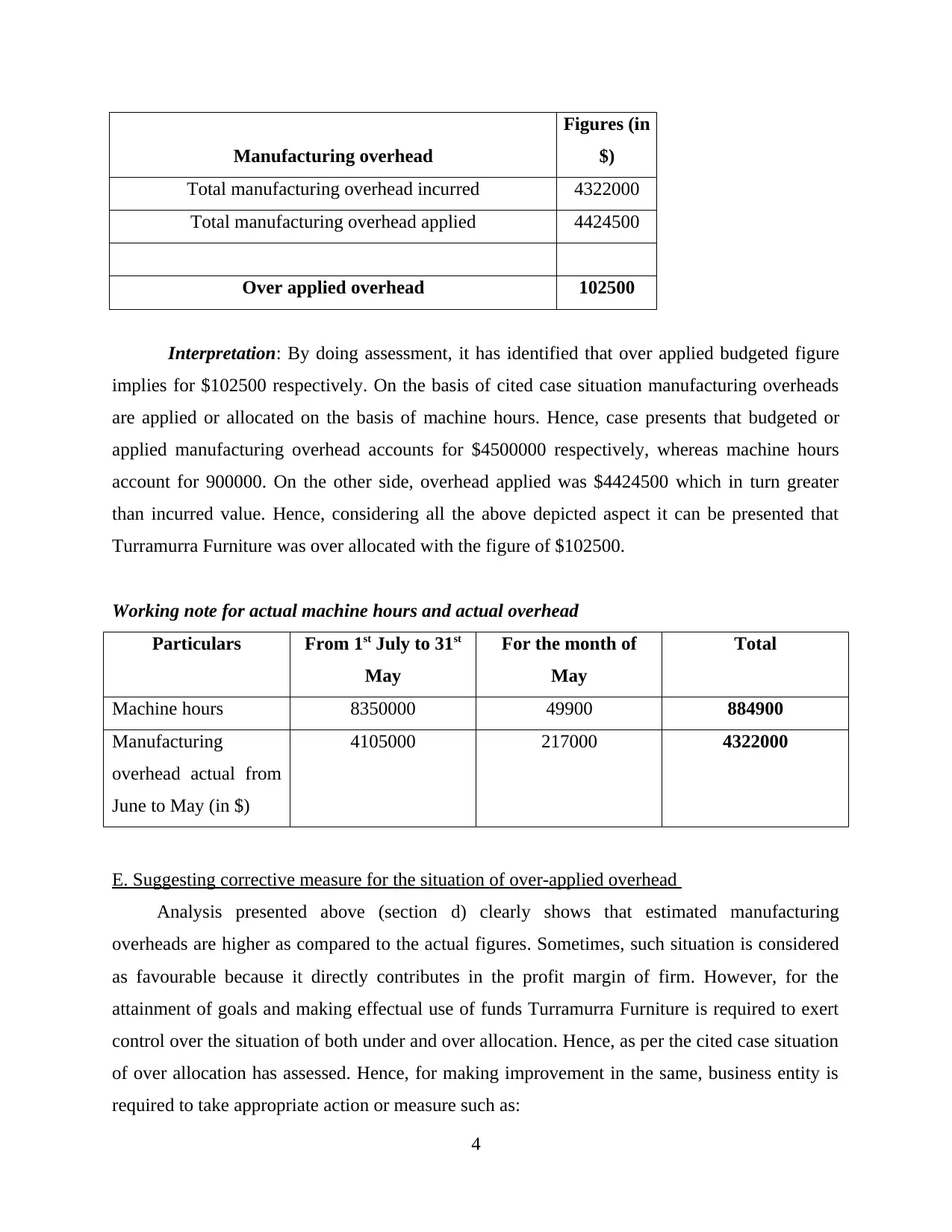
Manufacturing overhead
Figures (in
$)
Total manufacturing overhead incurred 4322000
Total manufacturing overhead applied 4424500
Over applied overhead 102500
Interpretation: By doing assessment, it has identified that over applied budgeted figure
implies for $102500 respectively. On the basis of cited case situation manufacturing overheads
are applied or allocated on the basis of machine hours. Hence, case presents that budgeted or
applied manufacturing overhead accounts for $4500000 respectively, whereas machine hours
account for 900000. On the other side, overhead applied was $4424500 which in turn greater
than incurred value. Hence, considering all the above depicted aspect it can be presented that
Turramurra Furniture was over allocated with the figure of $102500.
Working note for actual machine hours and actual overhead
Particulars From 1st July to 31st
May
For the month of
May
Total
Machine hours 8350000 49900 884900
Manufacturing
overhead actual from
June to May (in $)
4105000 217000 4322000
E. Suggesting corrective measure for the situation of over-applied overhead
Analysis presented above (section d) clearly shows that estimated manufacturing
overheads are higher as compared to the actual figures. Sometimes, such situation is considered
as favourable because it directly contributes in the profit margin of firm. However, for the
attainment of goals and making effectual use of funds Turramurra Furniture is required to exert
control over the situation of both under and over allocation. Hence, as per the cited case situation
of over allocation has assessed. Hence, for making improvement in the same, business entity is
required to take appropriate action or measure such as:
4
Figures (in
$)
Total manufacturing overhead incurred 4322000
Total manufacturing overhead applied 4424500
Over applied overhead 102500
Interpretation: By doing assessment, it has identified that over applied budgeted figure
implies for $102500 respectively. On the basis of cited case situation manufacturing overheads
are applied or allocated on the basis of machine hours. Hence, case presents that budgeted or
applied manufacturing overhead accounts for $4500000 respectively, whereas machine hours
account for 900000. On the other side, overhead applied was $4424500 which in turn greater
than incurred value. Hence, considering all the above depicted aspect it can be presented that
Turramurra Furniture was over allocated with the figure of $102500.
Working note for actual machine hours and actual overhead
Particulars From 1st July to 31st
May
For the month of
May
Total
Machine hours 8350000 49900 884900
Manufacturing
overhead actual from
June to May (in $)
4105000 217000 4322000
E. Suggesting corrective measure for the situation of over-applied overhead
Analysis presented above (section d) clearly shows that estimated manufacturing
overheads are higher as compared to the actual figures. Sometimes, such situation is considered
as favourable because it directly contributes in the profit margin of firm. However, for the
attainment of goals and making effectual use of funds Turramurra Furniture is required to exert
control over the situation of both under and over allocation. Hence, as per the cited case situation
of over allocation has assessed. Hence, for making improvement in the same, business entity is
required to take appropriate action or measure such as:
4
⊘ This is a preview!⊘
Do you want full access?
Subscribe today to unlock all pages.

Trusted by 1+ million students worldwide
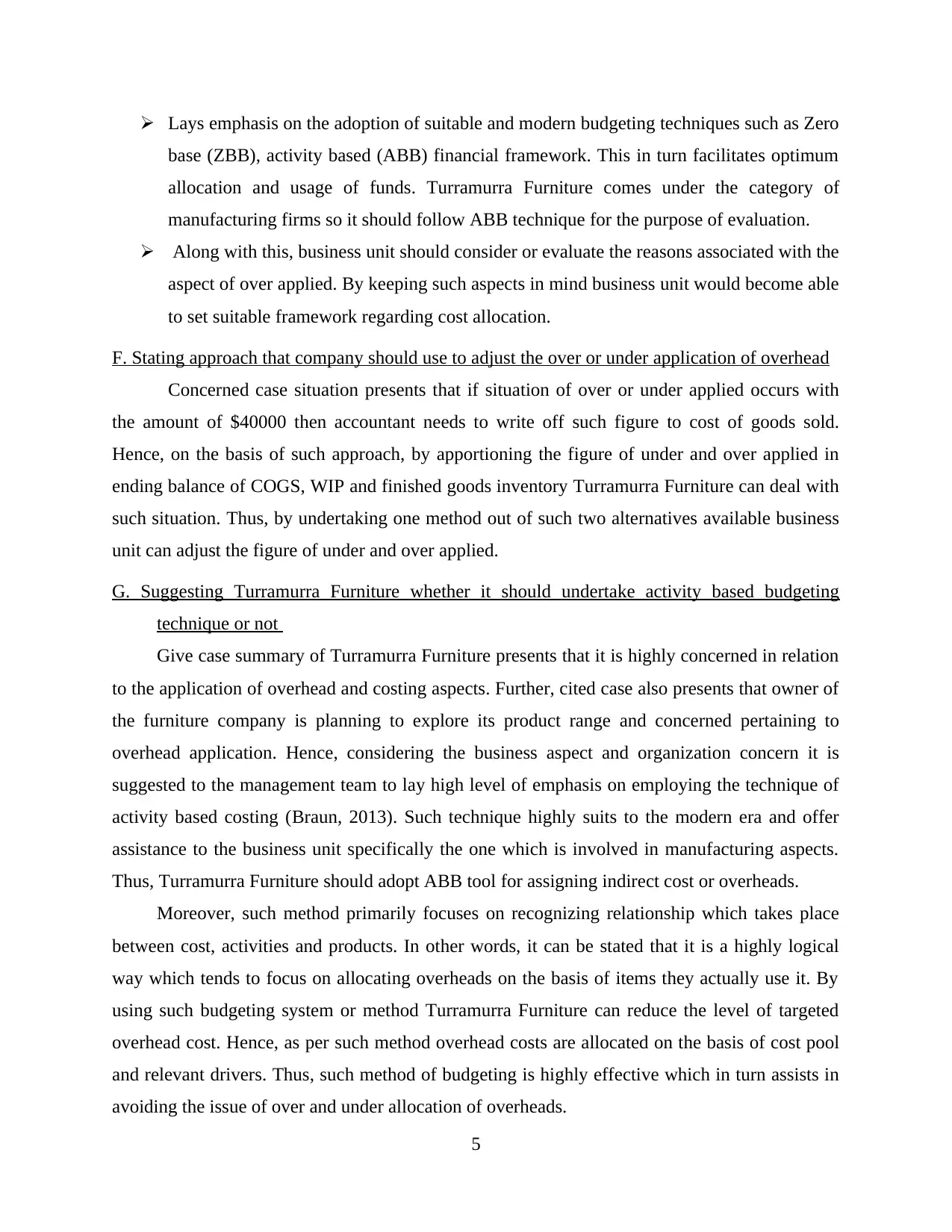
Lays emphasis on the adoption of suitable and modern budgeting techniques such as Zero
base (ZBB), activity based (ABB) financial framework. This in turn facilitates optimum
allocation and usage of funds. Turramurra Furniture comes under the category of
manufacturing firms so it should follow ABB technique for the purpose of evaluation.
Along with this, business unit should consider or evaluate the reasons associated with the
aspect of over applied. By keeping such aspects in mind business unit would become able
to set suitable framework regarding cost allocation.
F. Stating approach that company should use to adjust the over or under application of overhead
Concerned case situation presents that if situation of over or under applied occurs with
the amount of $40000 then accountant needs to write off such figure to cost of goods sold.
Hence, on the basis of such approach, by apportioning the figure of under and over applied in
ending balance of COGS, WIP and finished goods inventory Turramurra Furniture can deal with
such situation. Thus, by undertaking one method out of such two alternatives available business
unit can adjust the figure of under and over applied.
G. Suggesting Turramurra Furniture whether it should undertake activity based budgeting
technique or not
Give case summary of Turramurra Furniture presents that it is highly concerned in relation
to the application of overhead and costing aspects. Further, cited case also presents that owner of
the furniture company is planning to explore its product range and concerned pertaining to
overhead application. Hence, considering the business aspect and organization concern it is
suggested to the management team to lay high level of emphasis on employing the technique of
activity based costing (Braun, 2013). Such technique highly suits to the modern era and offer
assistance to the business unit specifically the one which is involved in manufacturing aspects.
Thus, Turramurra Furniture should adopt ABB tool for assigning indirect cost or overheads.
Moreover, such method primarily focuses on recognizing relationship which takes place
between cost, activities and products. In other words, it can be stated that it is a highly logical
way which tends to focus on allocating overheads on the basis of items they actually use it. By
using such budgeting system or method Turramurra Furniture can reduce the level of targeted
overhead cost. Hence, as per such method overhead costs are allocated on the basis of cost pool
and relevant drivers. Thus, such method of budgeting is highly effective which in turn assists in
avoiding the issue of over and under allocation of overheads.
5
base (ZBB), activity based (ABB) financial framework. This in turn facilitates optimum
allocation and usage of funds. Turramurra Furniture comes under the category of
manufacturing firms so it should follow ABB technique for the purpose of evaluation.
Along with this, business unit should consider or evaluate the reasons associated with the
aspect of over applied. By keeping such aspects in mind business unit would become able
to set suitable framework regarding cost allocation.
F. Stating approach that company should use to adjust the over or under application of overhead
Concerned case situation presents that if situation of over or under applied occurs with
the amount of $40000 then accountant needs to write off such figure to cost of goods sold.
Hence, on the basis of such approach, by apportioning the figure of under and over applied in
ending balance of COGS, WIP and finished goods inventory Turramurra Furniture can deal with
such situation. Thus, by undertaking one method out of such two alternatives available business
unit can adjust the figure of under and over applied.
G. Suggesting Turramurra Furniture whether it should undertake activity based budgeting
technique or not
Give case summary of Turramurra Furniture presents that it is highly concerned in relation
to the application of overhead and costing aspects. Further, cited case also presents that owner of
the furniture company is planning to explore its product range and concerned pertaining to
overhead application. Hence, considering the business aspect and organization concern it is
suggested to the management team to lay high level of emphasis on employing the technique of
activity based costing (Braun, 2013). Such technique highly suits to the modern era and offer
assistance to the business unit specifically the one which is involved in manufacturing aspects.
Thus, Turramurra Furniture should adopt ABB tool for assigning indirect cost or overheads.
Moreover, such method primarily focuses on recognizing relationship which takes place
between cost, activities and products. In other words, it can be stated that it is a highly logical
way which tends to focus on allocating overheads on the basis of items they actually use it. By
using such budgeting system or method Turramurra Furniture can reduce the level of targeted
overhead cost. Hence, as per such method overhead costs are allocated on the basis of cost pool
and relevant drivers. Thus, such method of budgeting is highly effective which in turn assists in
avoiding the issue of over and under allocation of overheads.
5
Paraphrase This Document
Need a fresh take? Get an instant paraphrase of this document with our AI Paraphraser
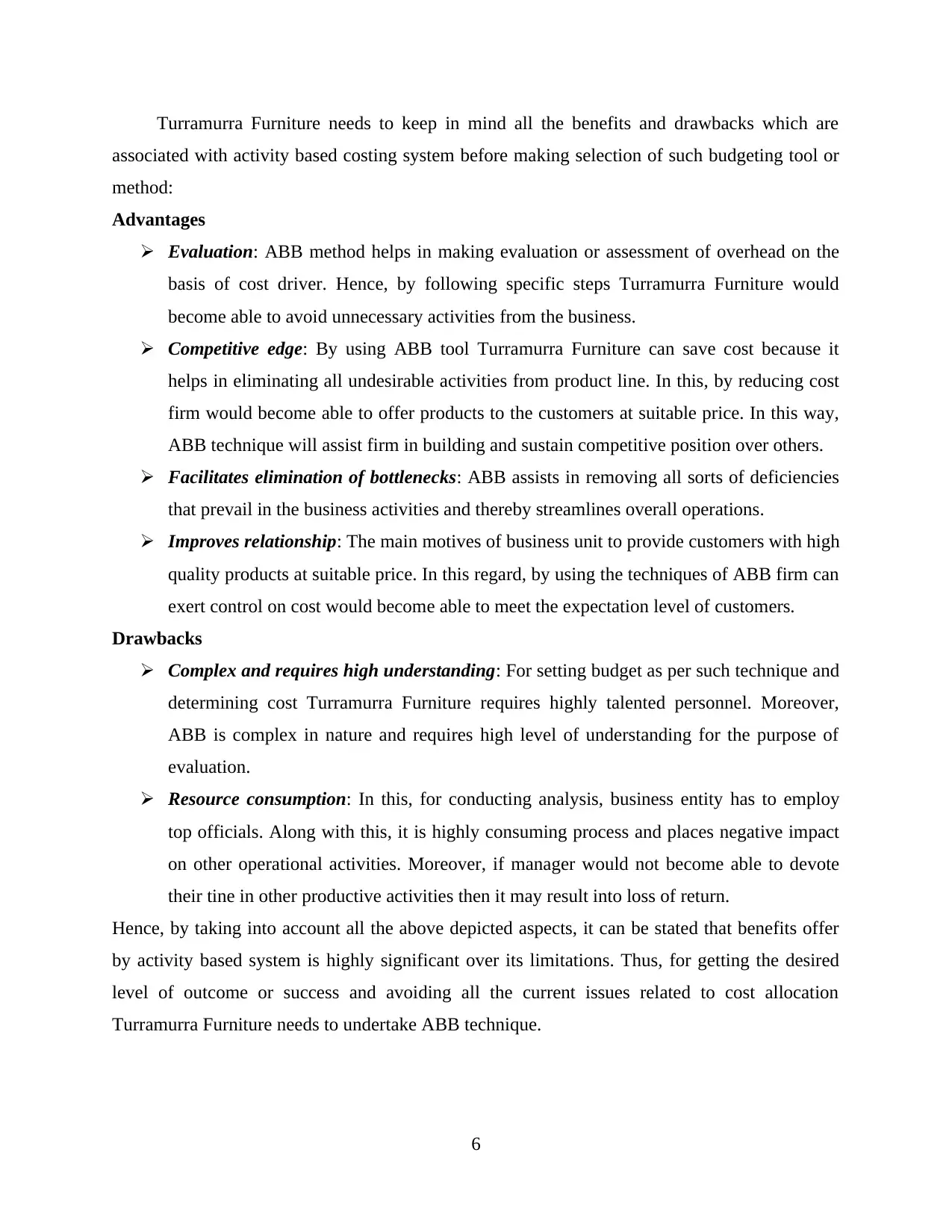
Turramurra Furniture needs to keep in mind all the benefits and drawbacks which are
associated with activity based costing system before making selection of such budgeting tool or
method:
Advantages
Evaluation: ABB method helps in making evaluation or assessment of overhead on the
basis of cost driver. Hence, by following specific steps Turramurra Furniture would
become able to avoid unnecessary activities from the business.
Competitive edge: By using ABB tool Turramurra Furniture can save cost because it
helps in eliminating all undesirable activities from product line. In this, by reducing cost
firm would become able to offer products to the customers at suitable price. In this way,
ABB technique will assist firm in building and sustain competitive position over others.
Facilitates elimination of bottlenecks: ABB assists in removing all sorts of deficiencies
that prevail in the business activities and thereby streamlines overall operations.
Improves relationship: The main motives of business unit to provide customers with high
quality products at suitable price. In this regard, by using the techniques of ABB firm can
exert control on cost would become able to meet the expectation level of customers.
Drawbacks
Complex and requires high understanding: For setting budget as per such technique and
determining cost Turramurra Furniture requires highly talented personnel. Moreover,
ABB is complex in nature and requires high level of understanding for the purpose of
evaluation.
Resource consumption: In this, for conducting analysis, business entity has to employ
top officials. Along with this, it is highly consuming process and places negative impact
on other operational activities. Moreover, if manager would not become able to devote
their tine in other productive activities then it may result into loss of return.
Hence, by taking into account all the above depicted aspects, it can be stated that benefits offer
by activity based system is highly significant over its limitations. Thus, for getting the desired
level of outcome or success and avoiding all the current issues related to cost allocation
Turramurra Furniture needs to undertake ABB technique.
6
associated with activity based costing system before making selection of such budgeting tool or
method:
Advantages
Evaluation: ABB method helps in making evaluation or assessment of overhead on the
basis of cost driver. Hence, by following specific steps Turramurra Furniture would
become able to avoid unnecessary activities from the business.
Competitive edge: By using ABB tool Turramurra Furniture can save cost because it
helps in eliminating all undesirable activities from product line. In this, by reducing cost
firm would become able to offer products to the customers at suitable price. In this way,
ABB technique will assist firm in building and sustain competitive position over others.
Facilitates elimination of bottlenecks: ABB assists in removing all sorts of deficiencies
that prevail in the business activities and thereby streamlines overall operations.
Improves relationship: The main motives of business unit to provide customers with high
quality products at suitable price. In this regard, by using the techniques of ABB firm can
exert control on cost would become able to meet the expectation level of customers.
Drawbacks
Complex and requires high understanding: For setting budget as per such technique and
determining cost Turramurra Furniture requires highly talented personnel. Moreover,
ABB is complex in nature and requires high level of understanding for the purpose of
evaluation.
Resource consumption: In this, for conducting analysis, business entity has to employ
top officials. Along with this, it is highly consuming process and places negative impact
on other operational activities. Moreover, if manager would not become able to devote
their tine in other productive activities then it may result into loss of return.
Hence, by taking into account all the above depicted aspects, it can be stated that benefits offer
by activity based system is highly significant over its limitations. Thus, for getting the desired
level of outcome or success and avoiding all the current issues related to cost allocation
Turramurra Furniture needs to undertake ABB technique.
6
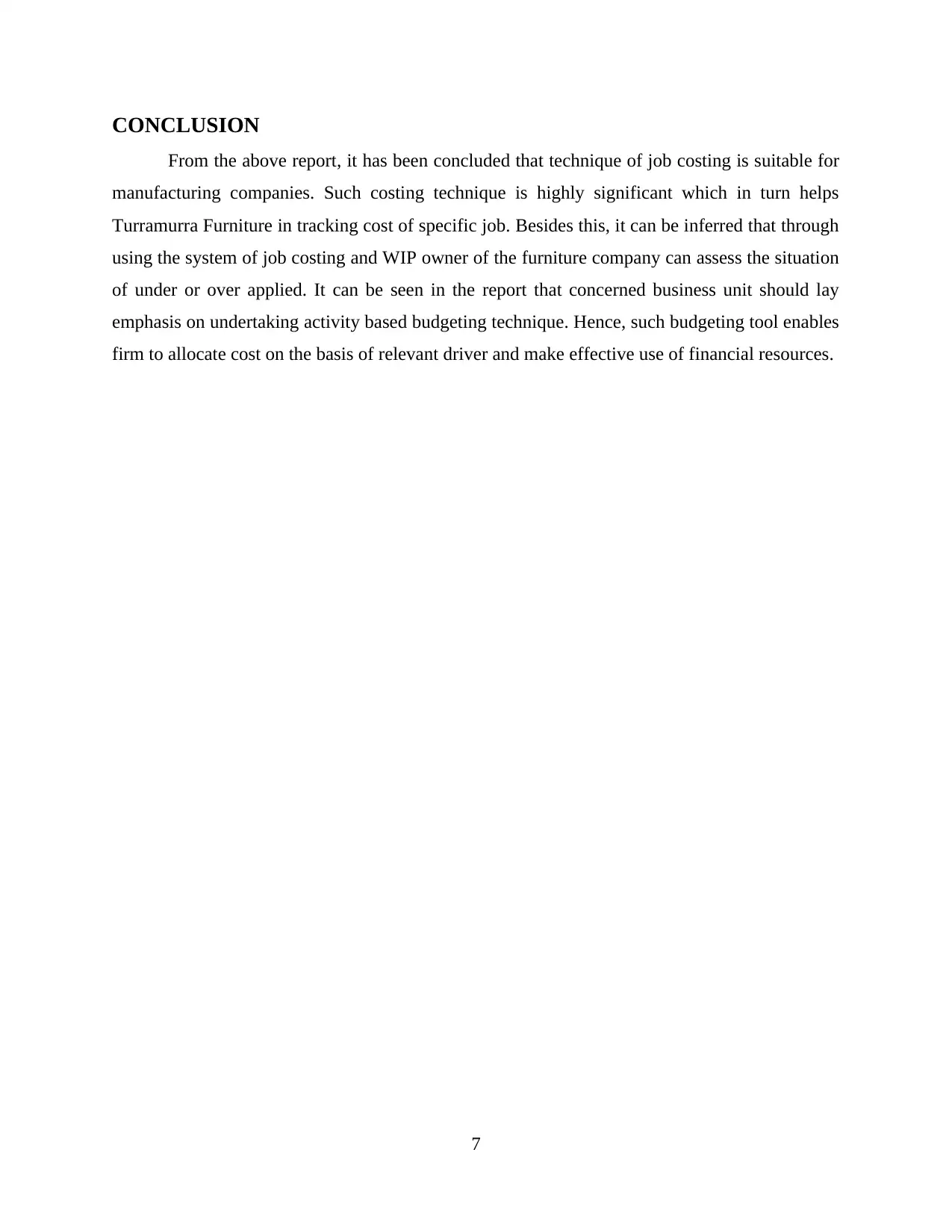
CONCLUSION
From the above report, it has been concluded that technique of job costing is suitable for
manufacturing companies. Such costing technique is highly significant which in turn helps
Turramurra Furniture in tracking cost of specific job. Besides this, it can be inferred that through
using the system of job costing and WIP owner of the furniture company can assess the situation
of under or over applied. It can be seen in the report that concerned business unit should lay
emphasis on undertaking activity based budgeting technique. Hence, such budgeting tool enables
firm to allocate cost on the basis of relevant driver and make effective use of financial resources.
7
From the above report, it has been concluded that technique of job costing is suitable for
manufacturing companies. Such costing technique is highly significant which in turn helps
Turramurra Furniture in tracking cost of specific job. Besides this, it can be inferred that through
using the system of job costing and WIP owner of the furniture company can assess the situation
of under or over applied. It can be seen in the report that concerned business unit should lay
emphasis on undertaking activity based budgeting technique. Hence, such budgeting tool enables
firm to allocate cost on the basis of relevant driver and make effective use of financial resources.
7
⊘ This is a preview!⊘
Do you want full access?
Subscribe today to unlock all pages.

Trusted by 1+ million students worldwide
1 out of 9