Comparison of Additive Manufacturing and Subtractive Manufacturing
VerifiedAdded on 2023/06/07
|10
|2803
|184
AI Summary
This paper discusses the effective usage of additive (3D Printing) and subtractive (CNC machining) manufacturing process machines over various fields. The comparison of these manufacturing processes has also been made and described in our paper. The paper also discusses the industrial applications of both the processes and the similarities and differences between them. The parameters for comparison have also been discussed in detail. Subject: Manufacturing, Course Code: NA, Course Name: NA, College/University: NA.
Contribute Materials
Your contribution can guide someone’s learning journey. Share your
documents today.
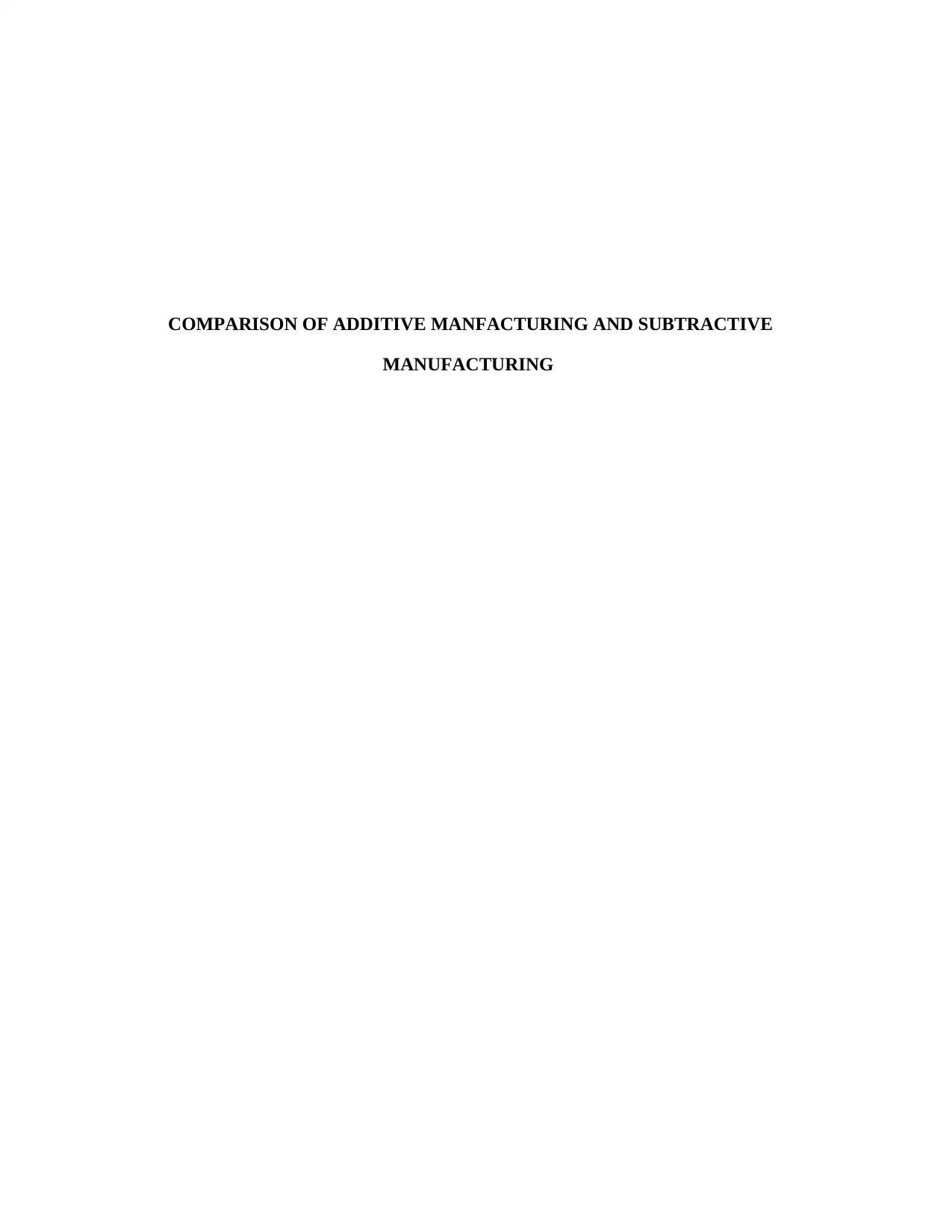
COMPARISON OF ADDITIVE MANFACTURING AND SUBTRACTIVE
MANUFACTURING
MANUFACTURING
Secure Best Marks with AI Grader
Need help grading? Try our AI Grader for instant feedback on your assignments.
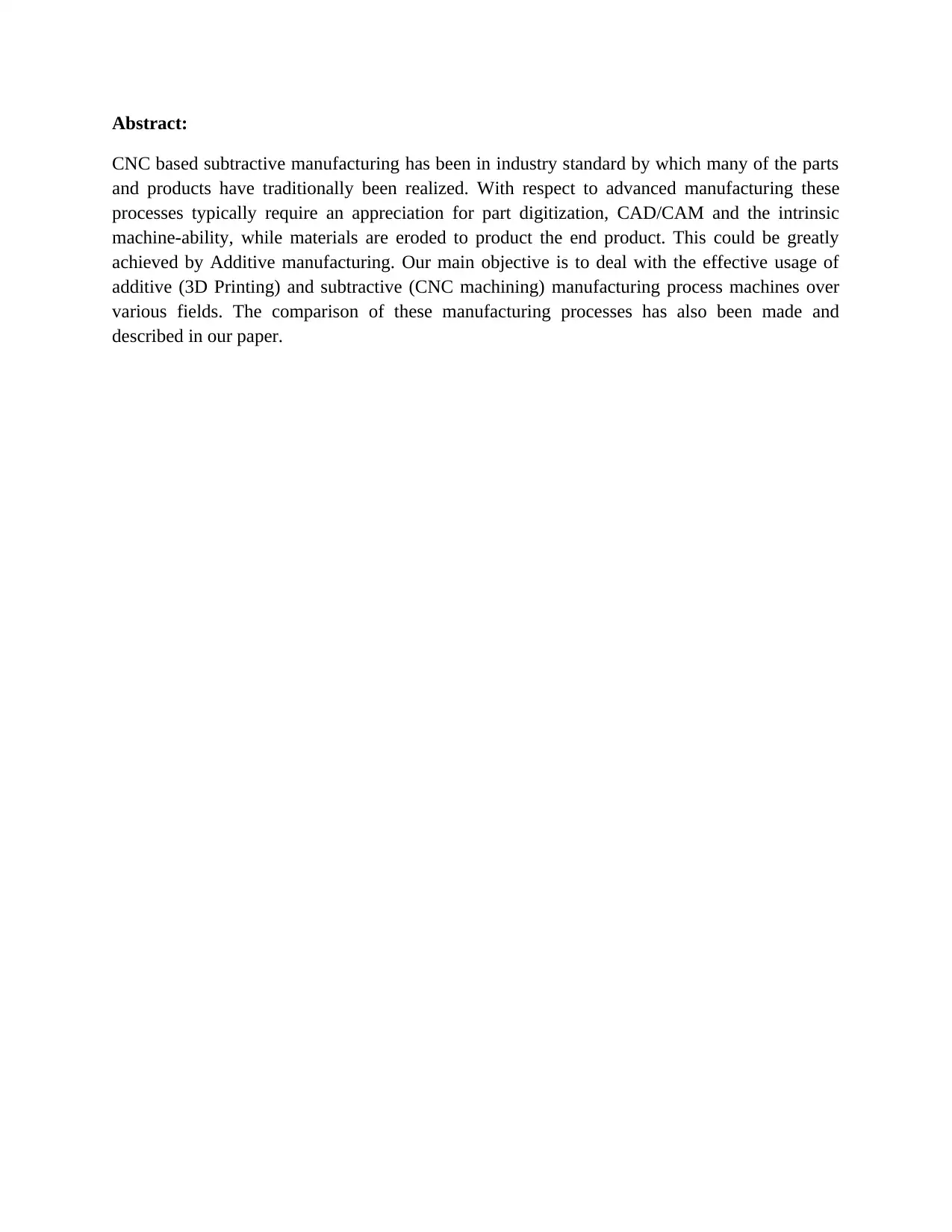
Abstract:
CNC based subtractive manufacturing has been in industry standard by which many of the parts
and products have traditionally been realized. With respect to advanced manufacturing these
processes typically require an appreciation for part digitization, CAD/CAM and the intrinsic
machine-ability, while materials are eroded to product the end product. This could be greatly
achieved by Additive manufacturing. Our main objective is to deal with the effective usage of
additive (3D Printing) and subtractive (CNC machining) manufacturing process machines over
various fields. The comparison of these manufacturing processes has also been made and
described in our paper.
CNC based subtractive manufacturing has been in industry standard by which many of the parts
and products have traditionally been realized. With respect to advanced manufacturing these
processes typically require an appreciation for part digitization, CAD/CAM and the intrinsic
machine-ability, while materials are eroded to product the end product. This could be greatly
achieved by Additive manufacturing. Our main objective is to deal with the effective usage of
additive (3D Printing) and subtractive (CNC machining) manufacturing process machines over
various fields. The comparison of these manufacturing processes has also been made and
described in our paper.
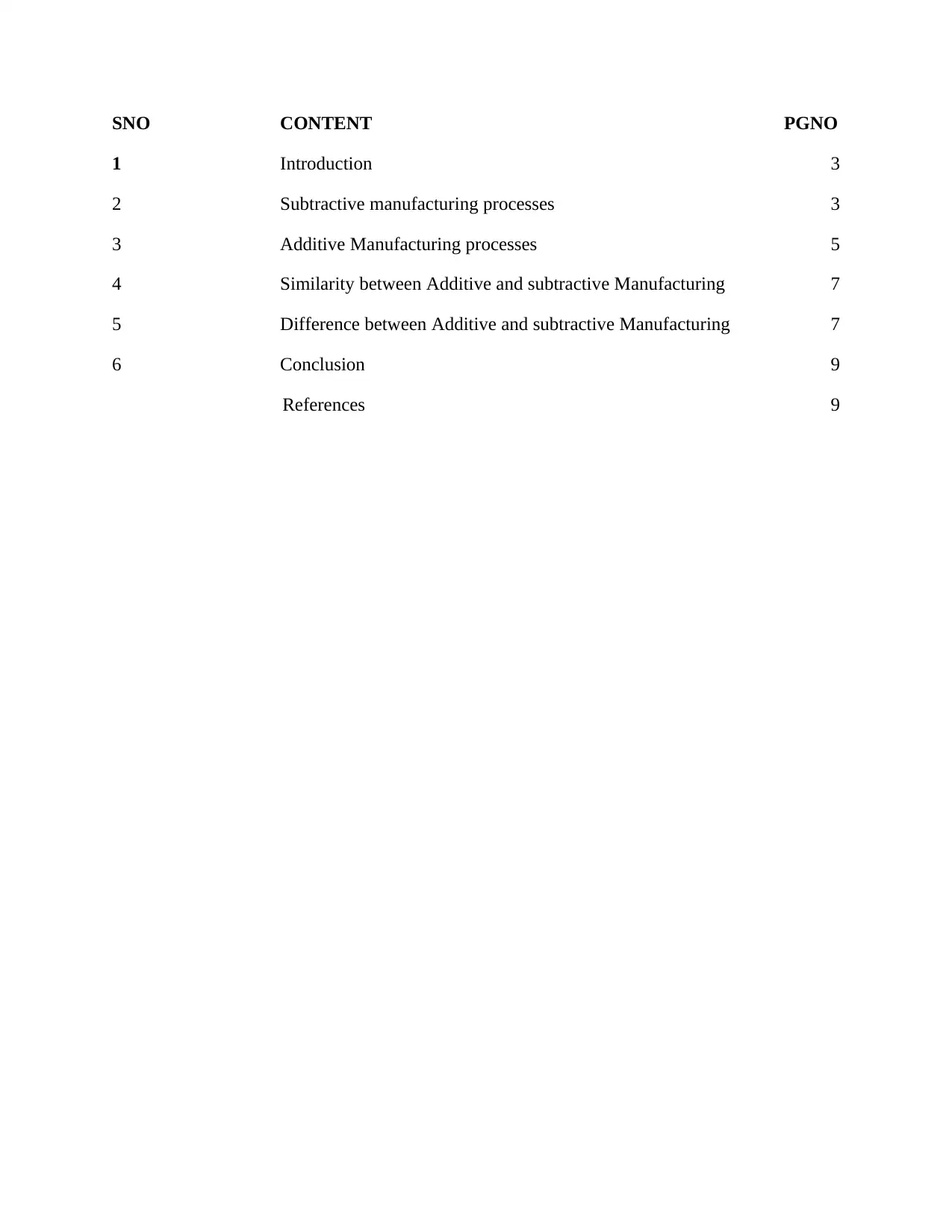
SNO CONTENT PGNO
1 Introduction 3
2 Subtractive manufacturing processes 3
3 Additive Manufacturing processes 5
4 Similarity between Additive and subtractive Manufacturing 7
5 Difference between Additive and subtractive Manufacturing 7
6 Conclusion 9
References 9
1 Introduction 3
2 Subtractive manufacturing processes 3
3 Additive Manufacturing processes 5
4 Similarity between Additive and subtractive Manufacturing 7
5 Difference between Additive and subtractive Manufacturing 7
6 Conclusion 9
References 9
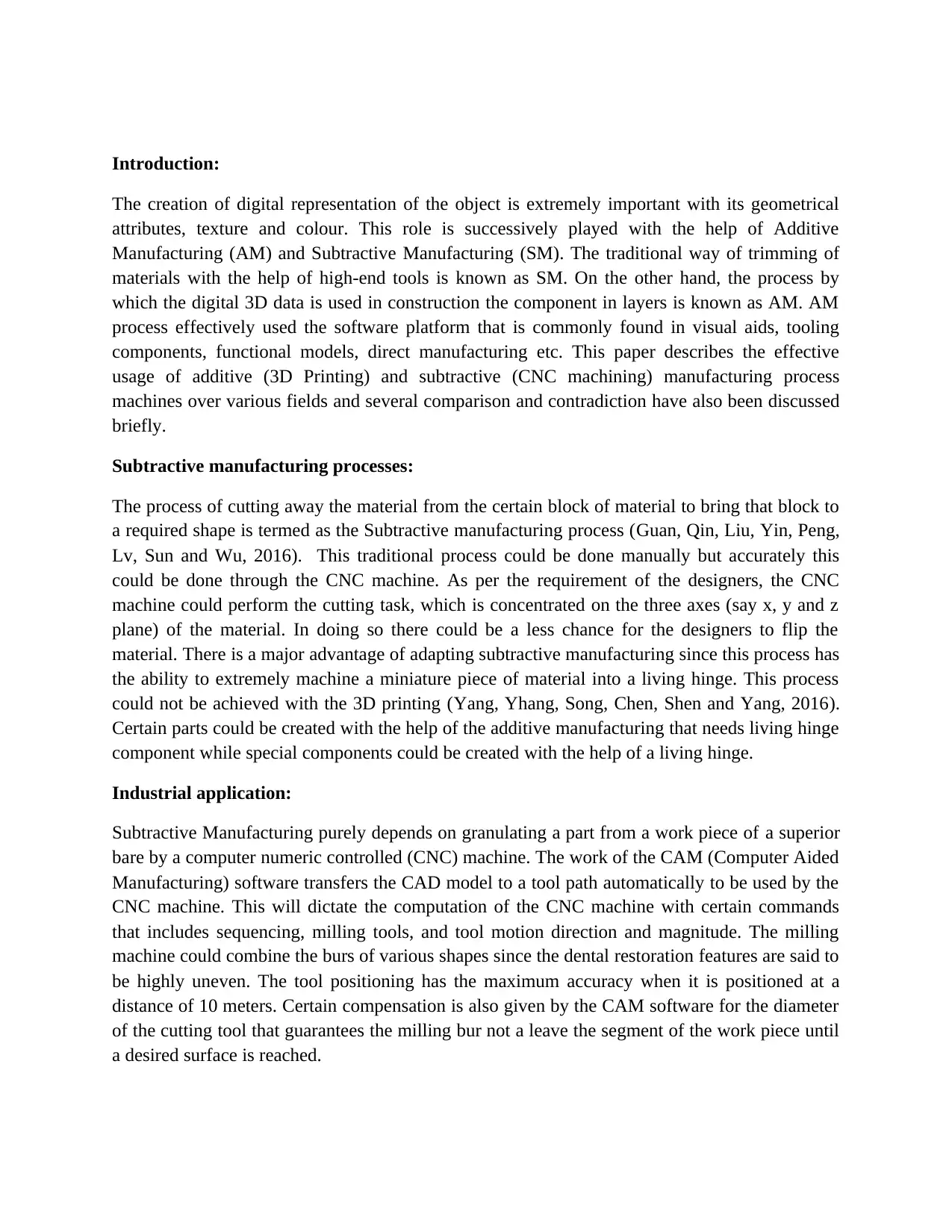
Introduction:
The creation of digital representation of the object is extremely important with its geometrical
attributes, texture and colour. This role is successively played with the help of Additive
Manufacturing (AM) and Subtractive Manufacturing (SM). The traditional way of trimming of
materials with the help of high-end tools is known as SM. On the other hand, the process by
which the digital 3D data is used in construction the component in layers is known as AM. AM
process effectively used the software platform that is commonly found in visual aids, tooling
components, functional models, direct manufacturing etc. This paper describes the effective
usage of additive (3D Printing) and subtractive (CNC machining) manufacturing process
machines over various fields and several comparison and contradiction have also been discussed
briefly.
Subtractive manufacturing processes:
The process of cutting away the material from the certain block of material to bring that block to
a required shape is termed as the Subtractive manufacturing process (Guan, Qin, Liu, Yin, Peng,
Lv, Sun and Wu, 2016). This traditional process could be done manually but accurately this
could be done through the CNC machine. As per the requirement of the designers, the CNC
machine could perform the cutting task, which is concentrated on the three axes (say x, y and z
plane) of the material. In doing so there could be a less chance for the designers to flip the
material. There is a major advantage of adapting subtractive manufacturing since this process has
the ability to extremely machine a miniature piece of material into a living hinge. This process
could not be achieved with the 3D printing (Yang, Yhang, Song, Chen, Shen and Yang, 2016).
Certain parts could be created with the help of the additive manufacturing that needs living hinge
component while special components could be created with the help of a living hinge.
Industrial application:
Subtractive Manufacturing purely depends on granulating a part from a work piece of a superior
bare by a computer numeric controlled (CNC) machine. The work of the CAM (Computer Aided
Manufacturing) software transfers the CAD model to a tool path automatically to be used by the
CNC machine. This will dictate the computation of the CNC machine with certain commands
that includes sequencing, milling tools, and tool motion direction and magnitude. The milling
machine could combine the burs of various shapes since the dental restoration features are said to
be highly uneven. The tool positioning has the maximum accuracy when it is positioned at a
distance of 10 meters. Certain compensation is also given by the CAM software for the diameter
of the cutting tool that guarantees the milling bur not a leave the segment of the work piece until
a desired surface is reached.
The creation of digital representation of the object is extremely important with its geometrical
attributes, texture and colour. This role is successively played with the help of Additive
Manufacturing (AM) and Subtractive Manufacturing (SM). The traditional way of trimming of
materials with the help of high-end tools is known as SM. On the other hand, the process by
which the digital 3D data is used in construction the component in layers is known as AM. AM
process effectively used the software platform that is commonly found in visual aids, tooling
components, functional models, direct manufacturing etc. This paper describes the effective
usage of additive (3D Printing) and subtractive (CNC machining) manufacturing process
machines over various fields and several comparison and contradiction have also been discussed
briefly.
Subtractive manufacturing processes:
The process of cutting away the material from the certain block of material to bring that block to
a required shape is termed as the Subtractive manufacturing process (Guan, Qin, Liu, Yin, Peng,
Lv, Sun and Wu, 2016). This traditional process could be done manually but accurately this
could be done through the CNC machine. As per the requirement of the designers, the CNC
machine could perform the cutting task, which is concentrated on the three axes (say x, y and z
plane) of the material. In doing so there could be a less chance for the designers to flip the
material. There is a major advantage of adapting subtractive manufacturing since this process has
the ability to extremely machine a miniature piece of material into a living hinge. This process
could not be achieved with the 3D printing (Yang, Yhang, Song, Chen, Shen and Yang, 2016).
Certain parts could be created with the help of the additive manufacturing that needs living hinge
component while special components could be created with the help of a living hinge.
Industrial application:
Subtractive Manufacturing purely depends on granulating a part from a work piece of a superior
bare by a computer numeric controlled (CNC) machine. The work of the CAM (Computer Aided
Manufacturing) software transfers the CAD model to a tool path automatically to be used by the
CNC machine. This will dictate the computation of the CNC machine with certain commands
that includes sequencing, milling tools, and tool motion direction and magnitude. The milling
machine could combine the burs of various shapes since the dental restoration features are said to
be highly uneven. The tool positioning has the maximum accuracy when it is positioned at a
distance of 10 meters. Certain compensation is also given by the CAM software for the diameter
of the cutting tool that guarantees the milling bur not a leave the segment of the work piece until
a desired surface is reached.
Secure Best Marks with AI Grader
Need help grading? Try our AI Grader for instant feedback on your assignments.
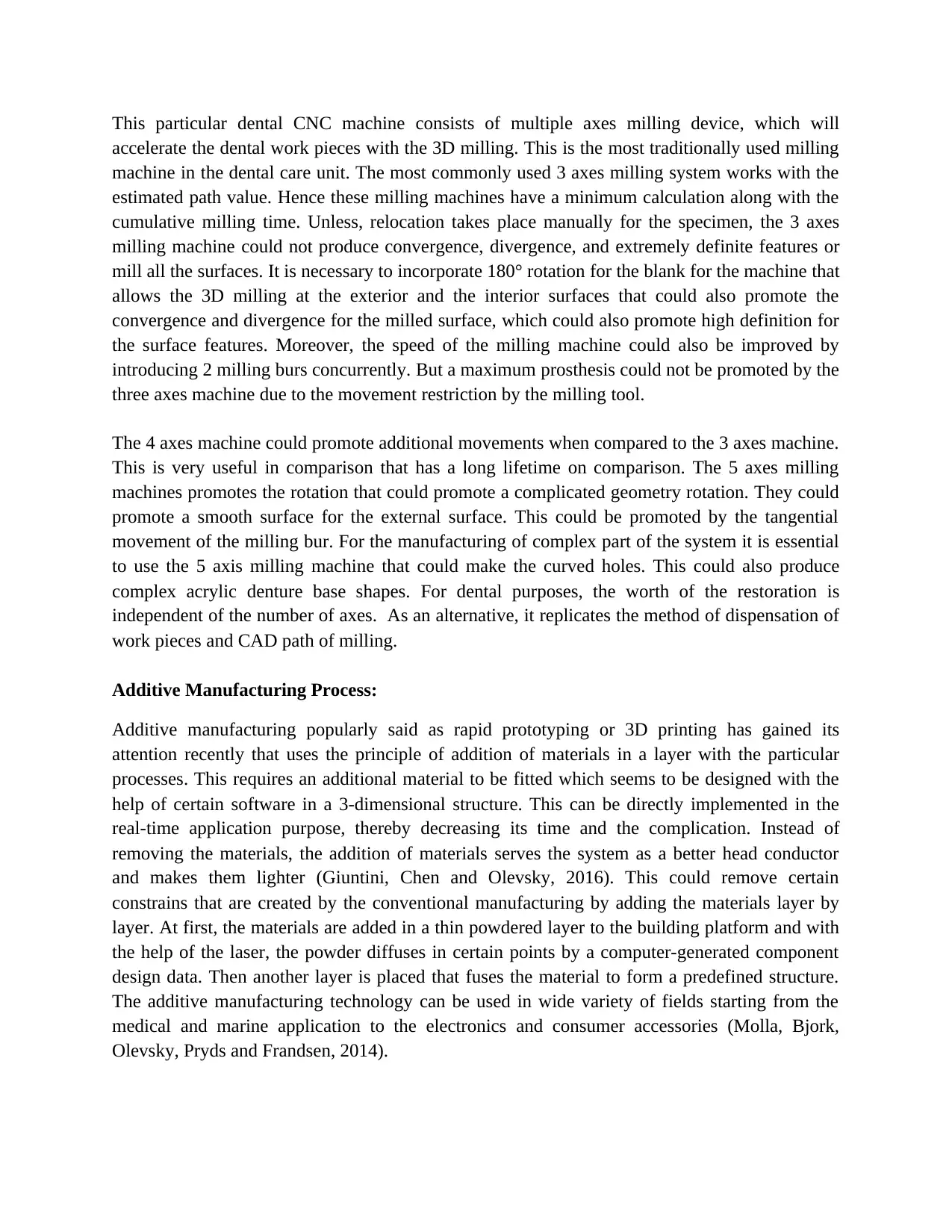
This particular dental CNC machine consists of multiple axes milling device, which will
accelerate the dental work pieces with the 3D milling. This is the most traditionally used milling
machine in the dental care unit. The most commonly used 3 axes milling system works with the
estimated path value. Hence these milling machines have a minimum calculation along with the
cumulative milling time. Unless, relocation takes place manually for the specimen, the 3 axes
milling machine could not produce convergence, divergence, and extremely definite features or
mill all the surfaces. It is necessary to incorporate 180° rotation for the blank for the machine that
allows the 3D milling at the exterior and the interior surfaces that could also promote the
convergence and divergence for the milled surface, which could also promote high definition for
the surface features. Moreover, the speed of the milling machine could also be improved by
introducing 2 milling burs concurrently. But a maximum prosthesis could not be promoted by the
three axes machine due to the movement restriction by the milling tool.
The 4 axes machine could promote additional movements when compared to the 3 axes machine.
This is very useful in comparison that has a long lifetime on comparison. The 5 axes milling
machines promotes the rotation that could promote a complicated geometry rotation. They could
promote a smooth surface for the external surface. This could be promoted by the tangential
movement of the milling bur. For the manufacturing of complex part of the system it is essential
to use the 5 axis milling machine that could make the curved holes. This could also produce
complex acrylic denture base shapes. For dental purposes, the worth of the restoration is
independent of the number of axes. As an alternative, it replicates the method of dispensation of
work pieces and CAD path of milling.
Additive Manufacturing Process:
Additive manufacturing popularly said as rapid prototyping or 3D printing has gained its
attention recently that uses the principle of addition of materials in a layer with the particular
processes. This requires an additional material to be fitted which seems to be designed with the
help of certain software in a 3-dimensional structure. This can be directly implemented in the
real-time application purpose, thereby decreasing its time and the complication. Instead of
removing the materials, the addition of materials serves the system as a better head conductor
and makes them lighter (Giuntini, Chen and Olevsky, 2016). This could remove certain
constrains that are created by the conventional manufacturing by adding the materials layer by
layer. At first, the materials are added in a thin powdered layer to the building platform and with
the help of the laser, the powder diffuses in certain points by a computer-generated component
design data. Then another layer is placed that fuses the material to form a predefined structure.
The additive manufacturing technology can be used in wide variety of fields starting from the
medical and marine application to the electronics and consumer accessories (Molla, Bjork,
Olevsky, Pryds and Frandsen, 2014).
accelerate the dental work pieces with the 3D milling. This is the most traditionally used milling
machine in the dental care unit. The most commonly used 3 axes milling system works with the
estimated path value. Hence these milling machines have a minimum calculation along with the
cumulative milling time. Unless, relocation takes place manually for the specimen, the 3 axes
milling machine could not produce convergence, divergence, and extremely definite features or
mill all the surfaces. It is necessary to incorporate 180° rotation for the blank for the machine that
allows the 3D milling at the exterior and the interior surfaces that could also promote the
convergence and divergence for the milled surface, which could also promote high definition for
the surface features. Moreover, the speed of the milling machine could also be improved by
introducing 2 milling burs concurrently. But a maximum prosthesis could not be promoted by the
three axes machine due to the movement restriction by the milling tool.
The 4 axes machine could promote additional movements when compared to the 3 axes machine.
This is very useful in comparison that has a long lifetime on comparison. The 5 axes milling
machines promotes the rotation that could promote a complicated geometry rotation. They could
promote a smooth surface for the external surface. This could be promoted by the tangential
movement of the milling bur. For the manufacturing of complex part of the system it is essential
to use the 5 axis milling machine that could make the curved holes. This could also produce
complex acrylic denture base shapes. For dental purposes, the worth of the restoration is
independent of the number of axes. As an alternative, it replicates the method of dispensation of
work pieces and CAD path of milling.
Additive Manufacturing Process:
Additive manufacturing popularly said as rapid prototyping or 3D printing has gained its
attention recently that uses the principle of addition of materials in a layer with the particular
processes. This requires an additional material to be fitted which seems to be designed with the
help of certain software in a 3-dimensional structure. This can be directly implemented in the
real-time application purpose, thereby decreasing its time and the complication. Instead of
removing the materials, the addition of materials serves the system as a better head conductor
and makes them lighter (Giuntini, Chen and Olevsky, 2016). This could remove certain
constrains that are created by the conventional manufacturing by adding the materials layer by
layer. At first, the materials are added in a thin powdered layer to the building platform and with
the help of the laser, the powder diffuses in certain points by a computer-generated component
design data. Then another layer is placed that fuses the material to form a predefined structure.
The additive manufacturing technology can be used in wide variety of fields starting from the
medical and marine application to the electronics and consumer accessories (Molla, Bjork,
Olevsky, Pryds and Frandsen, 2014).
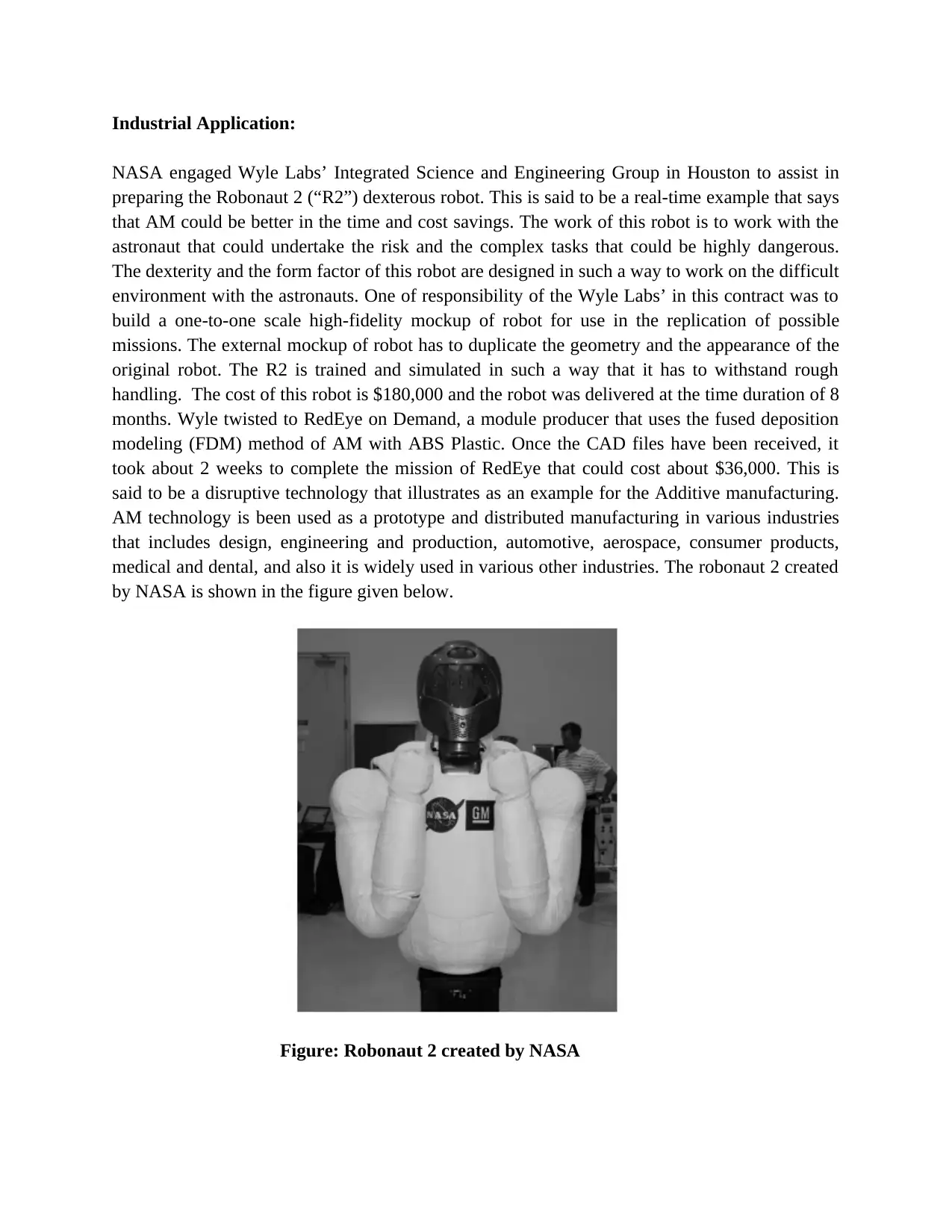
Industrial Application:
NASA engaged Wyle Labs’ Integrated Science and Engineering Group in Houston to assist in
preparing the Robonaut 2 (“R2”) dexterous robot. This is said to be a real-time example that says
that AM could be better in the time and cost savings. The work of this robot is to work with the
astronaut that could undertake the risk and the complex tasks that could be highly dangerous.
The dexterity and the form factor of this robot are designed in such a way to work on the difficult
environment with the astronauts. One of responsibility of the Wyle Labs’ in this contract was to
build a one-to-one scale high-fidelity mockup of robot for use in the replication of possible
missions. The external mockup of robot has to duplicate the geometry and the appearance of the
original robot. The R2 is trained and simulated in such a way that it has to withstand rough
handling. The cost of this robot is $180,000 and the robot was delivered at the time duration of 8
months. Wyle twisted to RedEye on Demand, a module producer that uses the fused deposition
modeling (FDM) method of AM with ABS Plastic. Once the CAD files have been received, it
took about 2 weeks to complete the mission of RedEye that could cost about $36,000. This is
said to be a disruptive technology that illustrates as an example for the Additive manufacturing.
AM technology is been used as a prototype and distributed manufacturing in various industries
that includes design, engineering and production, automotive, aerospace, consumer products,
medical and dental, and also it is widely used in various other industries. The robonaut 2 created
by NASA is shown in the figure given below.
Figure: Robonaut 2 created by NASA
NASA engaged Wyle Labs’ Integrated Science and Engineering Group in Houston to assist in
preparing the Robonaut 2 (“R2”) dexterous robot. This is said to be a real-time example that says
that AM could be better in the time and cost savings. The work of this robot is to work with the
astronaut that could undertake the risk and the complex tasks that could be highly dangerous.
The dexterity and the form factor of this robot are designed in such a way to work on the difficult
environment with the astronauts. One of responsibility of the Wyle Labs’ in this contract was to
build a one-to-one scale high-fidelity mockup of robot for use in the replication of possible
missions. The external mockup of robot has to duplicate the geometry and the appearance of the
original robot. The R2 is trained and simulated in such a way that it has to withstand rough
handling. The cost of this robot is $180,000 and the robot was delivered at the time duration of 8
months. Wyle twisted to RedEye on Demand, a module producer that uses the fused deposition
modeling (FDM) method of AM with ABS Plastic. Once the CAD files have been received, it
took about 2 weeks to complete the mission of RedEye that could cost about $36,000. This is
said to be a disruptive technology that illustrates as an example for the Additive manufacturing.
AM technology is been used as a prototype and distributed manufacturing in various industries
that includes design, engineering and production, automotive, aerospace, consumer products,
medical and dental, and also it is widely used in various other industries. The robonaut 2 created
by NASA is shown in the figure given below.
Figure: Robonaut 2 created by NASA
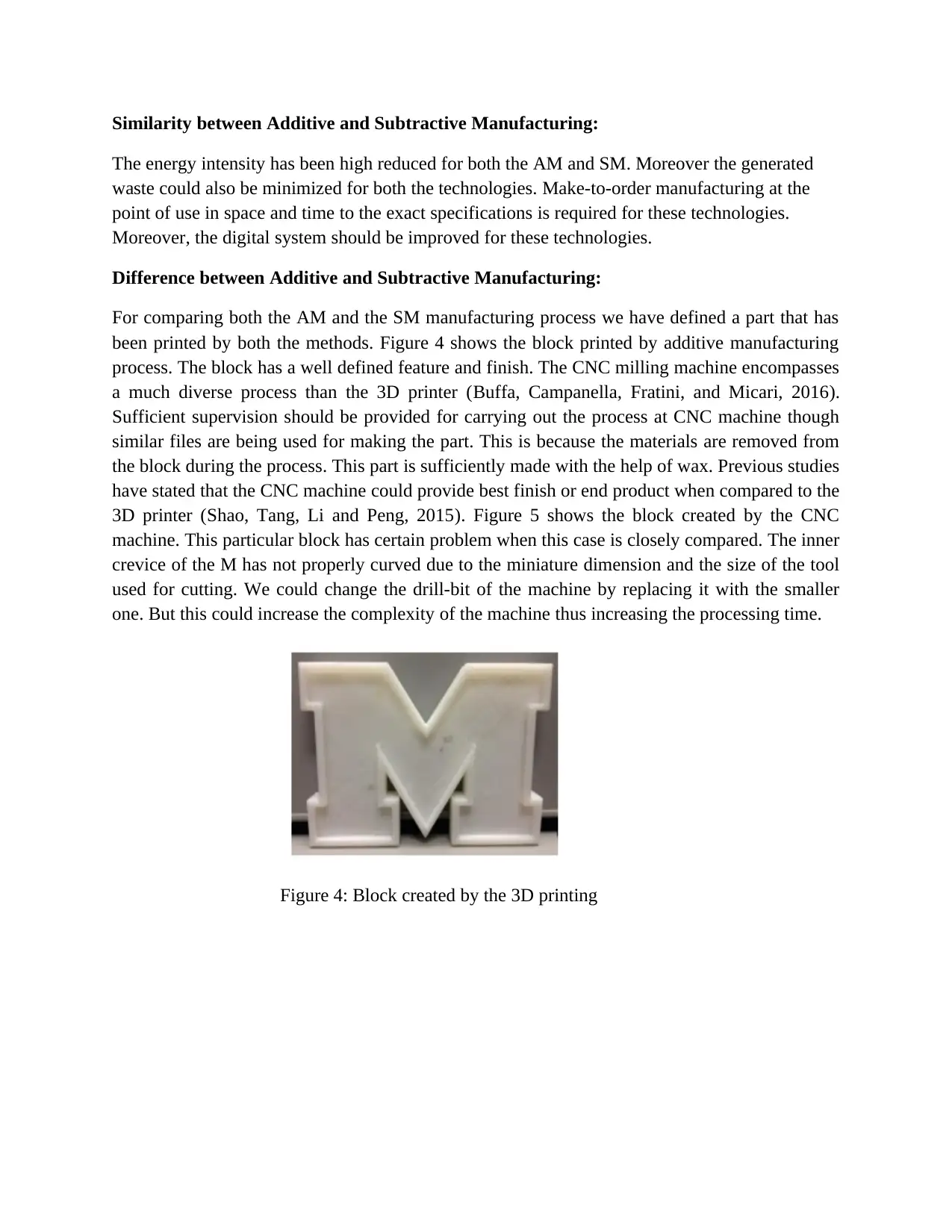
Similarity between Additive and Subtractive Manufacturing:
The energy intensity has been high reduced for both the AM and SM. Moreover the generated
waste could also be minimized for both the technologies. Make-to-order manufacturing at the
point of use in space and time to the exact specifications is required for these technologies.
Moreover, the digital system should be improved for these technologies.
Difference between Additive and Subtractive Manufacturing:
For comparing both the AM and the SM manufacturing process we have defined a part that has
been printed by both the methods. Figure 4 shows the block printed by additive manufacturing
process. The block has a well defined feature and finish. The CNC milling machine encompasses
a much diverse process than the 3D printer (Buffa, Campanella, Fratini, and Micari, 2016).
Sufficient supervision should be provided for carrying out the process at CNC machine though
similar files are being used for making the part. This is because the materials are removed from
the block during the process. This part is sufficiently made with the help of wax. Previous studies
have stated that the CNC machine could provide best finish or end product when compared to the
3D printer (Shao, Tang, Li and Peng, 2015). Figure 5 shows the block created by the CNC
machine. This particular block has certain problem when this case is closely compared. The inner
crevice of the M has not properly curved due to the miniature dimension and the size of the tool
used for cutting. We could change the drill-bit of the machine by replacing it with the smaller
one. But this could increase the complexity of the machine thus increasing the processing time.
Figure 4: Block created by the 3D printing
The energy intensity has been high reduced for both the AM and SM. Moreover the generated
waste could also be minimized for both the technologies. Make-to-order manufacturing at the
point of use in space and time to the exact specifications is required for these technologies.
Moreover, the digital system should be improved for these technologies.
Difference between Additive and Subtractive Manufacturing:
For comparing both the AM and the SM manufacturing process we have defined a part that has
been printed by both the methods. Figure 4 shows the block printed by additive manufacturing
process. The block has a well defined feature and finish. The CNC milling machine encompasses
a much diverse process than the 3D printer (Buffa, Campanella, Fratini, and Micari, 2016).
Sufficient supervision should be provided for carrying out the process at CNC machine though
similar files are being used for making the part. This is because the materials are removed from
the block during the process. This part is sufficiently made with the help of wax. Previous studies
have stated that the CNC machine could provide best finish or end product when compared to the
3D printer (Shao, Tang, Li and Peng, 2015). Figure 5 shows the block created by the CNC
machine. This particular block has certain problem when this case is closely compared. The inner
crevice of the M has not properly curved due to the miniature dimension and the size of the tool
used for cutting. We could change the drill-bit of the machine by replacing it with the smaller
one. But this could increase the complexity of the machine thus increasing the processing time.
Figure 4: Block created by the 3D printing
Paraphrase This Document
Need a fresh take? Get an instant paraphrase of this document with our AI Paraphraser
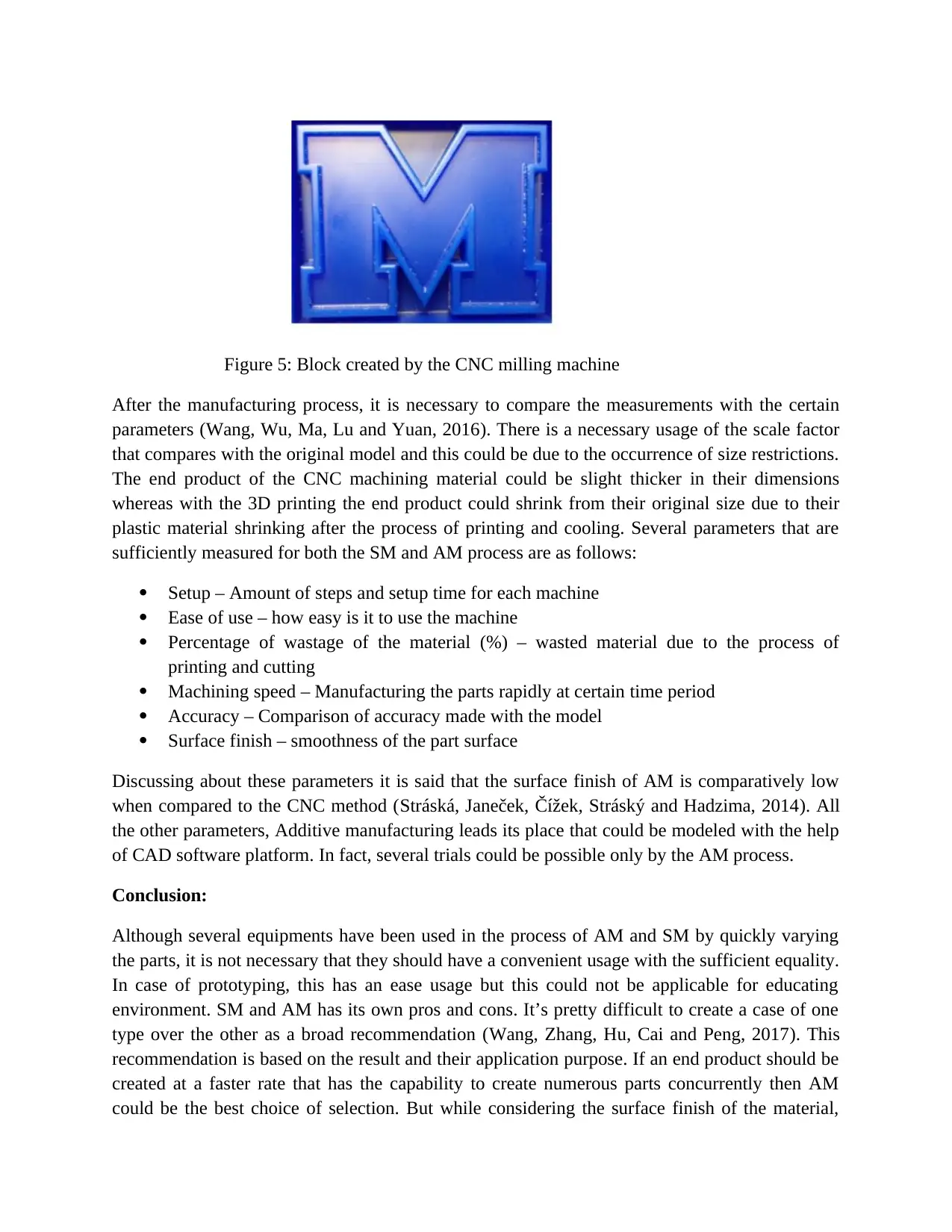
Figure 5: Block created by the CNC milling machine
After the manufacturing process, it is necessary to compare the measurements with the certain
parameters (Wang, Wu, Ma, Lu and Yuan, 2016). There is a necessary usage of the scale factor
that compares with the original model and this could be due to the occurrence of size restrictions.
The end product of the CNC machining material could be slight thicker in their dimensions
whereas with the 3D printing the end product could shrink from their original size due to their
plastic material shrinking after the process of printing and cooling. Several parameters that are
sufficiently measured for both the SM and AM process are as follows:
Setup – Amount of steps and setup time for each machine
Ease of use – how easy is it to use the machine
Percentage of wastage of the material (%) – wasted material due to the process of
printing and cutting
Machining speed – Manufacturing the parts rapidly at certain time period
Accuracy – Comparison of accuracy made with the model
Surface finish – smoothness of the part surface
Discussing about these parameters it is said that the surface finish of AM is comparatively low
when compared to the CNC method (Stráská, Janeček, Čížek, Stráský and Hadzima, 2014). All
the other parameters, Additive manufacturing leads its place that could be modeled with the help
of CAD software platform. In fact, several trials could be possible only by the AM process.
Conclusion:
Although several equipments have been used in the process of AM and SM by quickly varying
the parts, it is not necessary that they should have a convenient usage with the sufficient equality.
In case of prototyping, this has an ease usage but this could not be applicable for educating
environment. SM and AM has its own pros and cons. It’s pretty difficult to create a case of one
type over the other as a broad recommendation (Wang, Zhang, Hu, Cai and Peng, 2017). This
recommendation is based on the result and their application purpose. If an end product should be
created at a faster rate that has the capability to create numerous parts concurrently then AM
could be the best choice of selection. But while considering the surface finish of the material,
After the manufacturing process, it is necessary to compare the measurements with the certain
parameters (Wang, Wu, Ma, Lu and Yuan, 2016). There is a necessary usage of the scale factor
that compares with the original model and this could be due to the occurrence of size restrictions.
The end product of the CNC machining material could be slight thicker in their dimensions
whereas with the 3D printing the end product could shrink from their original size due to their
plastic material shrinking after the process of printing and cooling. Several parameters that are
sufficiently measured for both the SM and AM process are as follows:
Setup – Amount of steps and setup time for each machine
Ease of use – how easy is it to use the machine
Percentage of wastage of the material (%) – wasted material due to the process of
printing and cutting
Machining speed – Manufacturing the parts rapidly at certain time period
Accuracy – Comparison of accuracy made with the model
Surface finish – smoothness of the part surface
Discussing about these parameters it is said that the surface finish of AM is comparatively low
when compared to the CNC method (Stráská, Janeček, Čížek, Stráský and Hadzima, 2014). All
the other parameters, Additive manufacturing leads its place that could be modeled with the help
of CAD software platform. In fact, several trials could be possible only by the AM process.
Conclusion:
Although several equipments have been used in the process of AM and SM by quickly varying
the parts, it is not necessary that they should have a convenient usage with the sufficient equality.
In case of prototyping, this has an ease usage but this could not be applicable for educating
environment. SM and AM has its own pros and cons. It’s pretty difficult to create a case of one
type over the other as a broad recommendation (Wang, Zhang, Hu, Cai and Peng, 2017). This
recommendation is based on the result and their application purpose. If an end product should be
created at a faster rate that has the capability to create numerous parts concurrently then AM
could be the best choice of selection. But while considering the surface finish of the material,
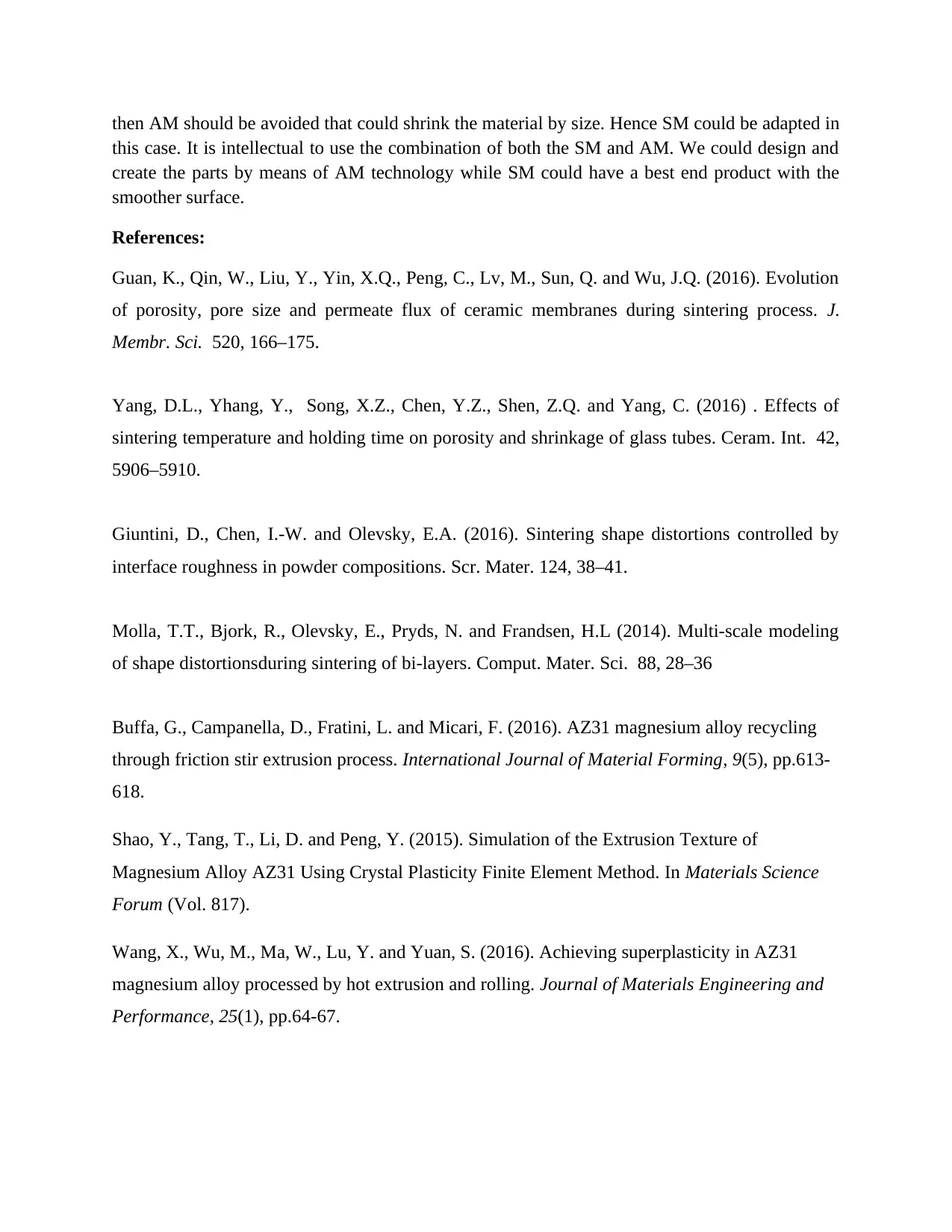
then AM should be avoided that could shrink the material by size. Hence SM could be adapted in
this case. It is intellectual to use the combination of both the SM and AM. We could design and
create the parts by means of AM technology while SM could have a best end product with the
smoother surface.
References:
Guan, K., Qin, W., Liu, Y., Yin, X.Q., Peng, C., Lv, M., Sun, Q. and Wu, J.Q. (2016). Evolution
of porosity, pore size and permeate flux of ceramic membranes during sintering process. J.
Membr. Sci. 520, 166–175.
Yang, D.L., Yhang, Y., Song, X.Z., Chen, Y.Z., Shen, Z.Q. and Yang, C. (2016) . Effects of
sintering temperature and holding time on porosity and shrinkage of glass tubes. Ceram. Int. 42,
5906–5910.
Giuntini, D., Chen, I.-W. and Olevsky, E.A. (2016). Sintering shape distortions controlled by
interface roughness in powder compositions. Scr. Mater. 124, 38–41.
Molla, T.T., Bjork, R., Olevsky, E., Pryds, N. and Frandsen, H.L (2014). Multi-scale modeling
of shape distortionsduring sintering of bi-layers. Comput. Mater. Sci. 88, 28–36
Buffa, G., Campanella, D., Fratini, L. and Micari, F. (2016). AZ31 magnesium alloy recycling
through friction stir extrusion process. International Journal of Material Forming, 9(5), pp.613-
618.
Shao, Y., Tang, T., Li, D. and Peng, Y. (2015). Simulation of the Extrusion Texture of
Magnesium Alloy AZ31 Using Crystal Plasticity Finite Element Method. In Materials Science
Forum (Vol. 817).
Wang, X., Wu, M., Ma, W., Lu, Y. and Yuan, S. (2016). Achieving superplasticity in AZ31
magnesium alloy processed by hot extrusion and rolling. Journal of Materials Engineering and
Performance, 25(1), pp.64-67.
this case. It is intellectual to use the combination of both the SM and AM. We could design and
create the parts by means of AM technology while SM could have a best end product with the
smoother surface.
References:
Guan, K., Qin, W., Liu, Y., Yin, X.Q., Peng, C., Lv, M., Sun, Q. and Wu, J.Q. (2016). Evolution
of porosity, pore size and permeate flux of ceramic membranes during sintering process. J.
Membr. Sci. 520, 166–175.
Yang, D.L., Yhang, Y., Song, X.Z., Chen, Y.Z., Shen, Z.Q. and Yang, C. (2016) . Effects of
sintering temperature and holding time on porosity and shrinkage of glass tubes. Ceram. Int. 42,
5906–5910.
Giuntini, D., Chen, I.-W. and Olevsky, E.A. (2016). Sintering shape distortions controlled by
interface roughness in powder compositions. Scr. Mater. 124, 38–41.
Molla, T.T., Bjork, R., Olevsky, E., Pryds, N. and Frandsen, H.L (2014). Multi-scale modeling
of shape distortionsduring sintering of bi-layers. Comput. Mater. Sci. 88, 28–36
Buffa, G., Campanella, D., Fratini, L. and Micari, F. (2016). AZ31 magnesium alloy recycling
through friction stir extrusion process. International Journal of Material Forming, 9(5), pp.613-
618.
Shao, Y., Tang, T., Li, D. and Peng, Y. (2015). Simulation of the Extrusion Texture of
Magnesium Alloy AZ31 Using Crystal Plasticity Finite Element Method. In Materials Science
Forum (Vol. 817).
Wang, X., Wu, M., Ma, W., Lu, Y. and Yuan, S. (2016). Achieving superplasticity in AZ31
magnesium alloy processed by hot extrusion and rolling. Journal of Materials Engineering and
Performance, 25(1), pp.64-67.
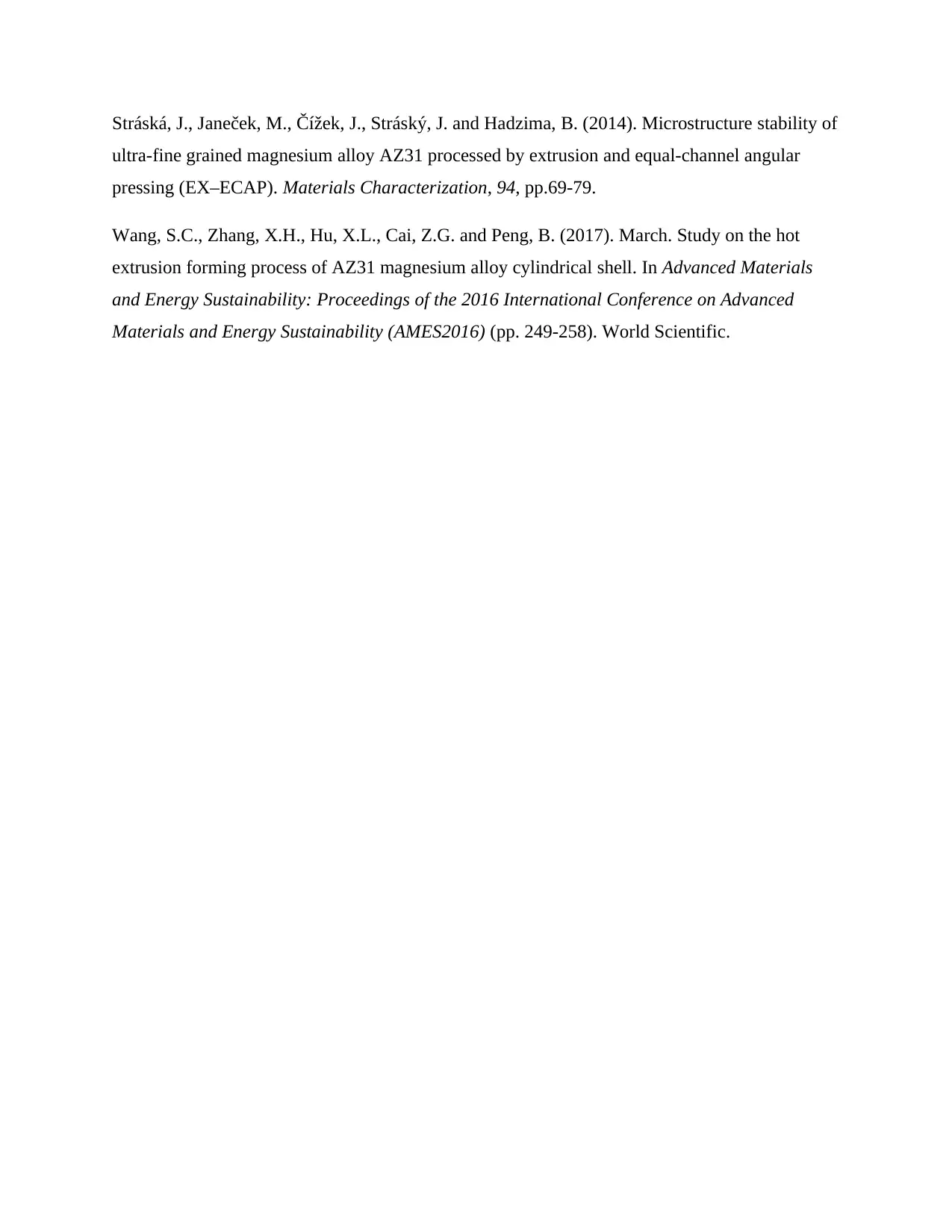
Stráská, J., Janeček, M., Čížek, J., Stráský, J. and Hadzima, B. (2014). Microstructure stability of
ultra-fine grained magnesium alloy AZ31 processed by extrusion and equal-channel angular
pressing (EX–ECAP). Materials Characterization, 94, pp.69-79.
Wang, S.C., Zhang, X.H., Hu, X.L., Cai, Z.G. and Peng, B. (2017). March. Study on the hot
extrusion forming process of AZ31 magnesium alloy cylindrical shell. In Advanced Materials
and Energy Sustainability: Proceedings of the 2016 International Conference on Advanced
Materials and Energy Sustainability (AMES2016) (pp. 249-258). World Scientific.
ultra-fine grained magnesium alloy AZ31 processed by extrusion and equal-channel angular
pressing (EX–ECAP). Materials Characterization, 94, pp.69-79.
Wang, S.C., Zhang, X.H., Hu, X.L., Cai, Z.G. and Peng, B. (2017). March. Study on the hot
extrusion forming process of AZ31 magnesium alloy cylindrical shell. In Advanced Materials
and Energy Sustainability: Proceedings of the 2016 International Conference on Advanced
Materials and Energy Sustainability (AMES2016) (pp. 249-258). World Scientific.
1 out of 10
Related Documents
![[object Object]](/_next/image/?url=%2F_next%2Fstatic%2Fmedia%2Flogo.6d15ce61.png&w=640&q=75)
Your All-in-One AI-Powered Toolkit for Academic Success.
+13062052269
info@desklib.com
Available 24*7 on WhatsApp / Email
Unlock your academic potential
© 2024 | Zucol Services PVT LTD | All rights reserved.