Resilient Modulus and Unconfined Compressive Strength
VerifiedAdded on 2020/05/11
|29
|5869
|120
AI Summary
This assignment delves into the evaluation of pavement materials through resilient modulus (Mr) and unconfined compressive strength (UCS) tests. It outlines the RLT test procedure for determining Mr, emphasizing loading conditions, specimen preparation, and data analysis using Puppala et al. (1996) and AASHTO (2002) models. The assignment further explains the UCS test, its application in assessing material solidity, and the determination of Young's modulus (E), secant modulus (E50), and Poisson's ratio (ν). The importance of these tests in evaluating pavement performance is highlighted.
Contribute Materials
Your contribution can guide someone’s learning journey. Share your
documents today.
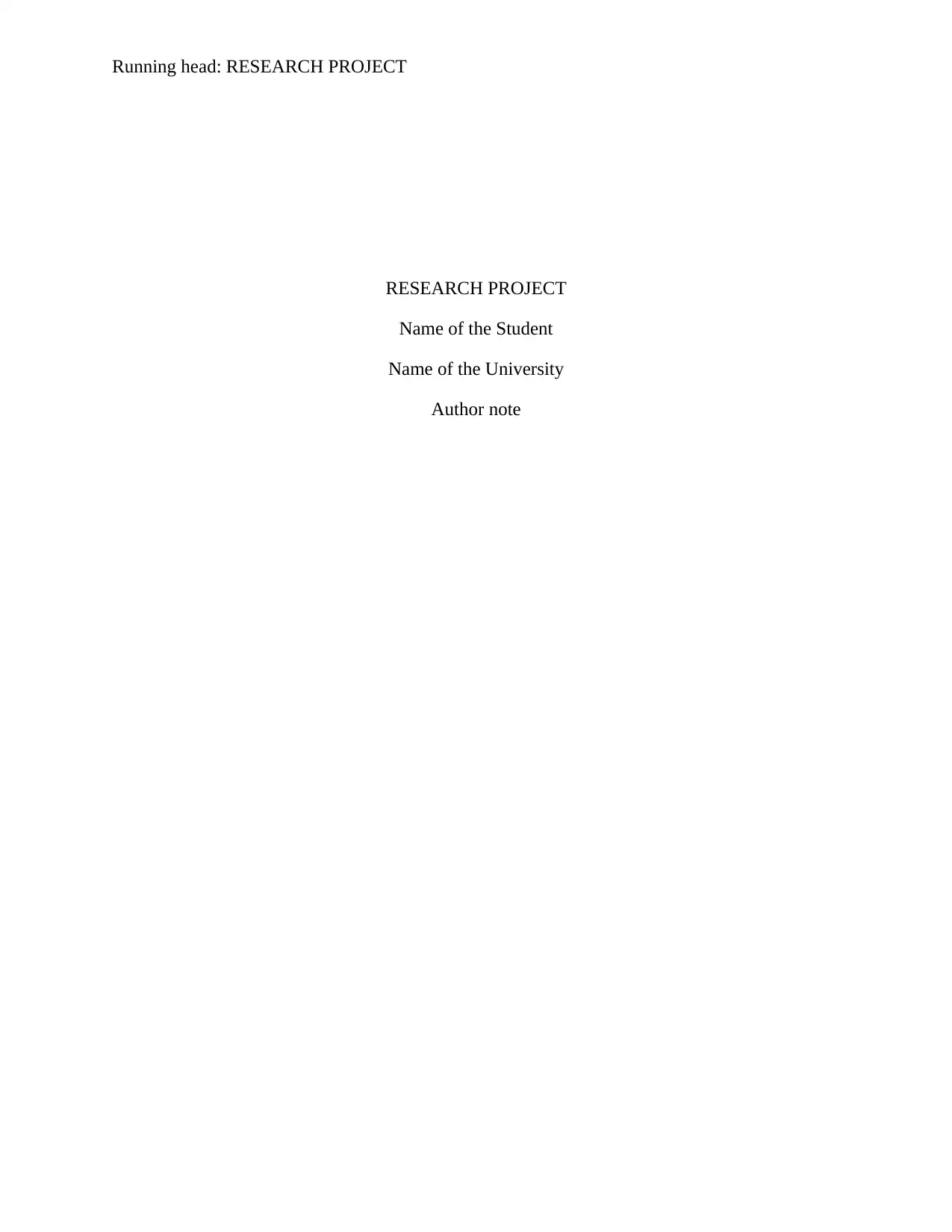
Running head: RESEARCH PROJECT
RESEARCH PROJECT
Name of the Student
Name of the University
Author note
RESEARCH PROJECT
Name of the Student
Name of the University
Author note
Secure Best Marks with AI Grader
Need help grading? Try our AI Grader for instant feedback on your assignments.
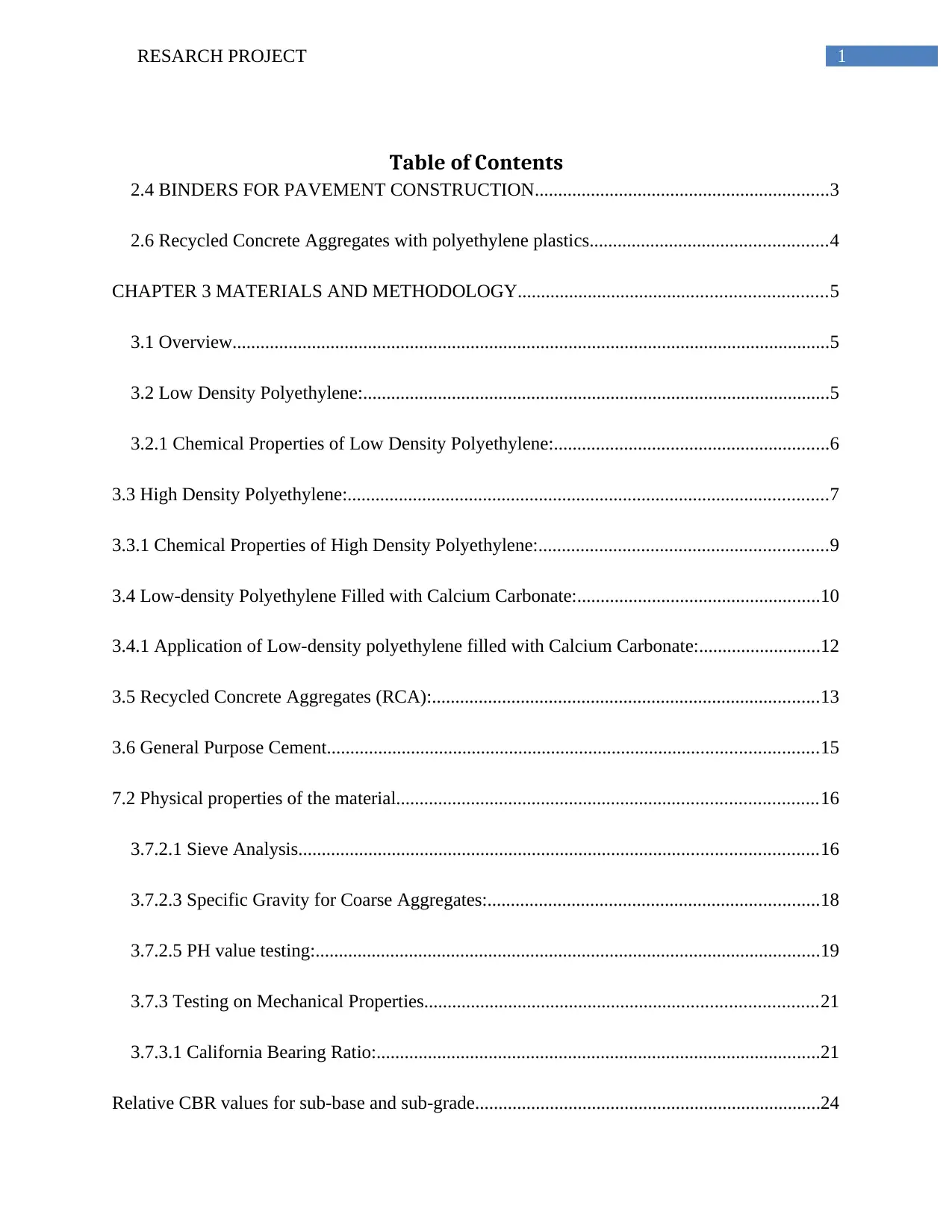
1RESARCH PROJECT
Table of Contents
2.4 BINDERS FOR PAVEMENT CONSTRUCTION...............................................................3
2.6 Recycled Concrete Aggregates with polyethylene plastics...................................................4
CHAPTER 3 MATERIALS AND METHODOLOGY..................................................................5
3.1 Overview................................................................................................................................5
3.2 Low Density Polyethylene:....................................................................................................5
3.2.1 Chemical Properties of Low Density Polyethylene:...........................................................6
3.3 High Density Polyethylene:.......................................................................................................7
3.3.1 Chemical Properties of High Density Polyethylene:..............................................................9
3.4 Low-density Polyethylene Filled with Calcium Carbonate:....................................................10
3.4.1 Application of Low-density polyethylene filled with Calcium Carbonate:..........................12
3.5 Recycled Concrete Aggregates (RCA):...................................................................................13
3.6 General Purpose Cement.........................................................................................................15
7.2 Physical properties of the material..........................................................................................16
3.7.2.1 Sieve Analysis...............................................................................................................16
3.7.2.3 Specific Gravity for Coarse Aggregates:.......................................................................18
3.7.2.5 PH value testing:............................................................................................................19
3.7.3 Testing on Mechanical Properties....................................................................................21
3.7.3.1 California Bearing Ratio:...............................................................................................21
Relative CBR values for sub-base and sub-grade..........................................................................24
Table of Contents
2.4 BINDERS FOR PAVEMENT CONSTRUCTION...............................................................3
2.6 Recycled Concrete Aggregates with polyethylene plastics...................................................4
CHAPTER 3 MATERIALS AND METHODOLOGY..................................................................5
3.1 Overview................................................................................................................................5
3.2 Low Density Polyethylene:....................................................................................................5
3.2.1 Chemical Properties of Low Density Polyethylene:...........................................................6
3.3 High Density Polyethylene:.......................................................................................................7
3.3.1 Chemical Properties of High Density Polyethylene:..............................................................9
3.4 Low-density Polyethylene Filled with Calcium Carbonate:....................................................10
3.4.1 Application of Low-density polyethylene filled with Calcium Carbonate:..........................12
3.5 Recycled Concrete Aggregates (RCA):...................................................................................13
3.6 General Purpose Cement.........................................................................................................15
7.2 Physical properties of the material..........................................................................................16
3.7.2.1 Sieve Analysis...............................................................................................................16
3.7.2.3 Specific Gravity for Coarse Aggregates:.......................................................................18
3.7.2.5 PH value testing:............................................................................................................19
3.7.3 Testing on Mechanical Properties....................................................................................21
3.7.3.1 California Bearing Ratio:...............................................................................................21
Relative CBR values for sub-base and sub-grade..........................................................................24
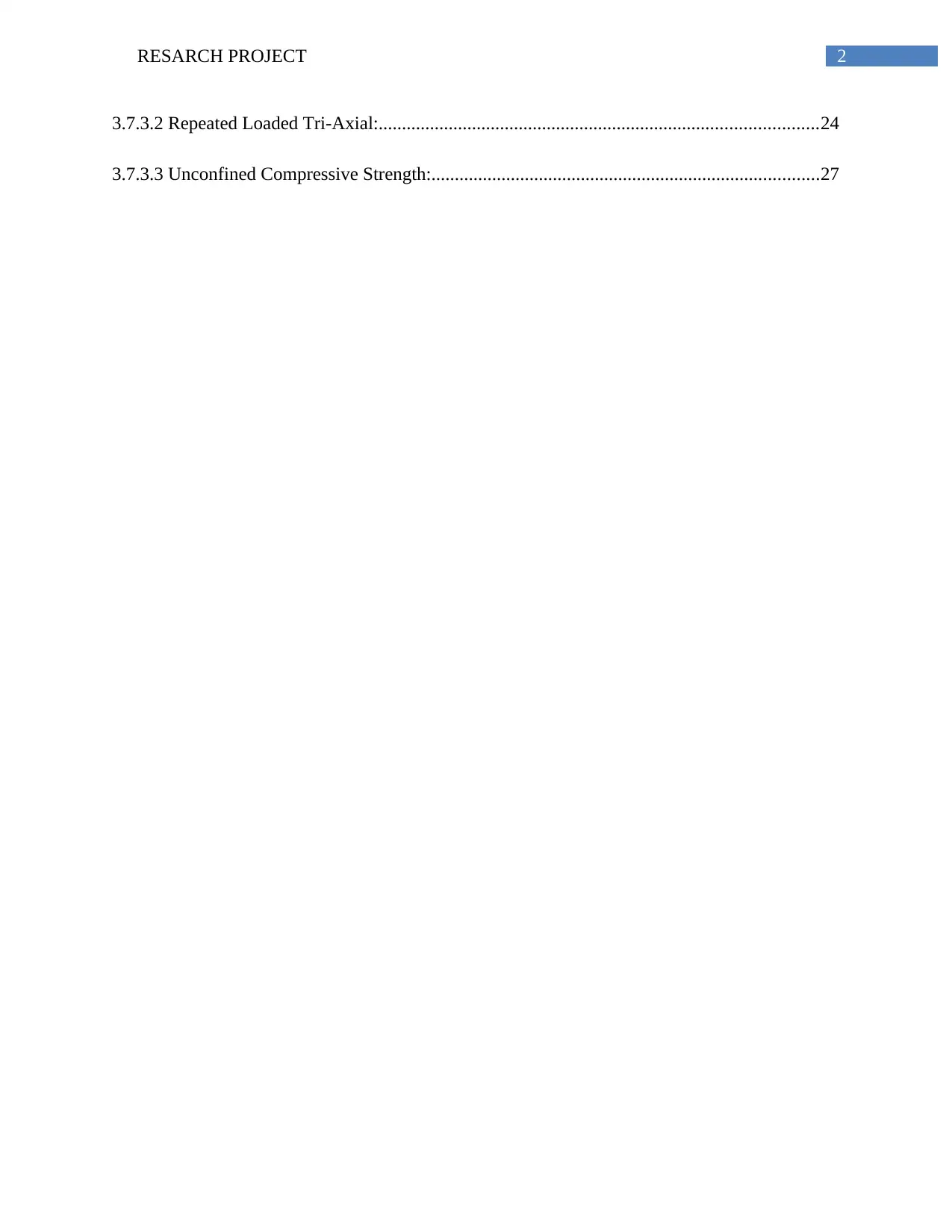
2RESARCH PROJECT
3.7.3.2 Repeated Loaded Tri-Axial:..............................................................................................24
3.7.3.3 Unconfined Compressive Strength:...................................................................................27
3.7.3.2 Repeated Loaded Tri-Axial:..............................................................................................24
3.7.3.3 Unconfined Compressive Strength:...................................................................................27
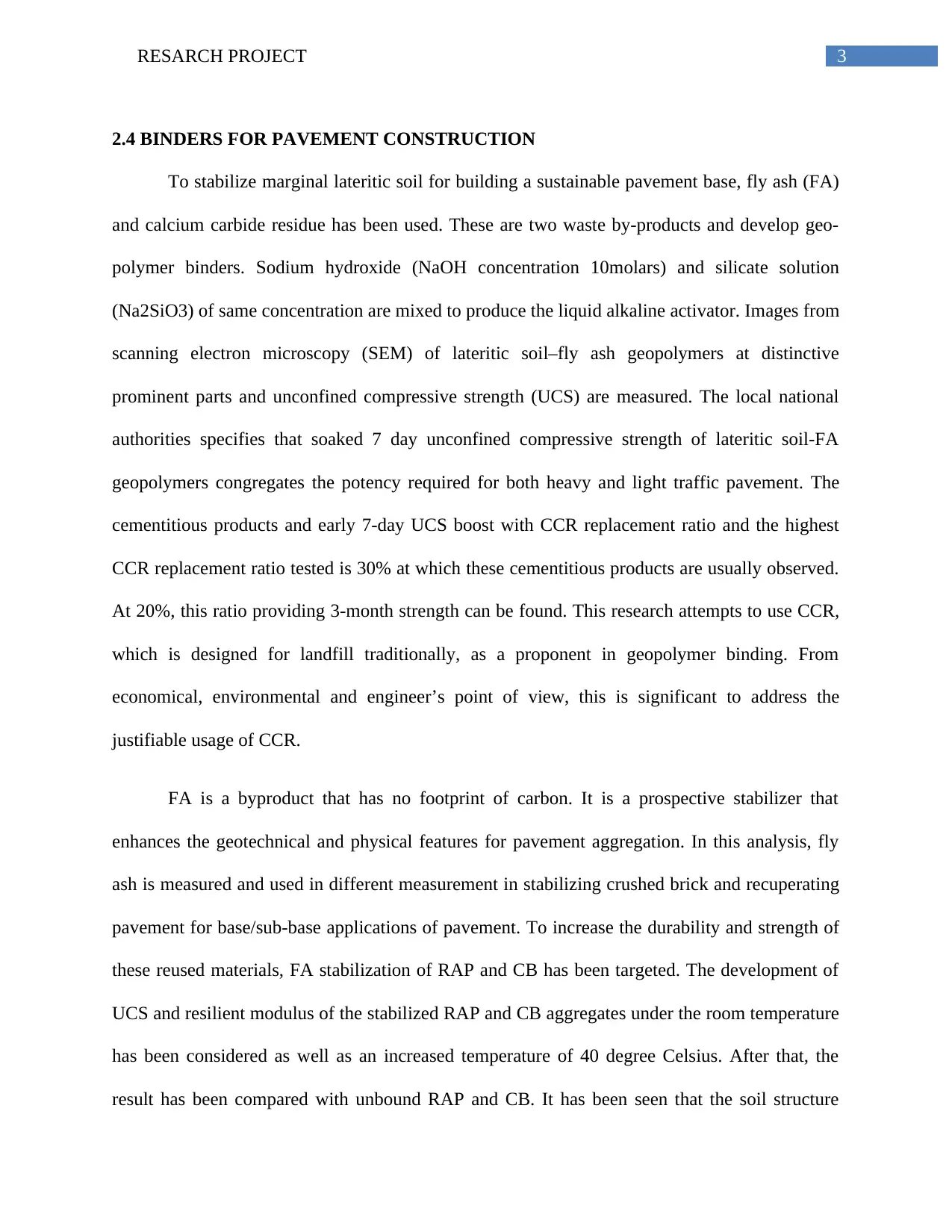
3RESARCH PROJECT
2.4 BINDERS FOR PAVEMENT CONSTRUCTION
To stabilize marginal lateritic soil for building a sustainable pavement base, fly ash (FA)
and calcium carbide residue has been used. These are two waste by-products and develop geo-
polymer binders. Sodium hydroxide (NaOH concentration 10molars) and silicate solution
(Na2SiO3) of same concentration are mixed to produce the liquid alkaline activator. Images from
scanning electron microscopy (SEM) of lateritic soil–fly ash geopolymers at distinctive
prominent parts and unconfined compressive strength (UCS) are measured. The local national
authorities specifies that soaked 7 day unconfined compressive strength of lateritic soil-FA
geopolymers congregates the potency required for both heavy and light traffic pavement. The
cementitious products and early 7-day UCS boost with CCR replacement ratio and the highest
CCR replacement ratio tested is 30% at which these cementitious products are usually observed.
At 20%, this ratio providing 3-month strength can be found. This research attempts to use CCR,
which is designed for landfill traditionally, as a proponent in geopolymer binding. From
economical, environmental and engineer’s point of view, this is significant to address the
justifiable usage of CCR.
FA is a byproduct that has no footprint of carbon. It is a prospective stabilizer that
enhances the geotechnical and physical features for pavement aggregation. In this analysis, fly
ash is measured and used in different measurement in stabilizing crushed brick and recuperating
pavement for base/sub-base applications of pavement. To increase the durability and strength of
these reused materials, FA stabilization of RAP and CB has been targeted. The development of
UCS and resilient modulus of the stabilized RAP and CB aggregates under the room temperature
has been considered as well as an increased temperature of 40 degree Celsius. After that, the
result has been compared with unbound RAP and CB. It has been seen that the soil structure
2.4 BINDERS FOR PAVEMENT CONSTRUCTION
To stabilize marginal lateritic soil for building a sustainable pavement base, fly ash (FA)
and calcium carbide residue has been used. These are two waste by-products and develop geo-
polymer binders. Sodium hydroxide (NaOH concentration 10molars) and silicate solution
(Na2SiO3) of same concentration are mixed to produce the liquid alkaline activator. Images from
scanning electron microscopy (SEM) of lateritic soil–fly ash geopolymers at distinctive
prominent parts and unconfined compressive strength (UCS) are measured. The local national
authorities specifies that soaked 7 day unconfined compressive strength of lateritic soil-FA
geopolymers congregates the potency required for both heavy and light traffic pavement. The
cementitious products and early 7-day UCS boost with CCR replacement ratio and the highest
CCR replacement ratio tested is 30% at which these cementitious products are usually observed.
At 20%, this ratio providing 3-month strength can be found. This research attempts to use CCR,
which is designed for landfill traditionally, as a proponent in geopolymer binding. From
economical, environmental and engineer’s point of view, this is significant to address the
justifiable usage of CCR.
FA is a byproduct that has no footprint of carbon. It is a prospective stabilizer that
enhances the geotechnical and physical features for pavement aggregation. In this analysis, fly
ash is measured and used in different measurement in stabilizing crushed brick and recuperating
pavement for base/sub-base applications of pavement. To increase the durability and strength of
these reused materials, FA stabilization of RAP and CB has been targeted. The development of
UCS and resilient modulus of the stabilized RAP and CB aggregates under the room temperature
has been considered as well as an increased temperature of 40 degree Celsius. After that, the
result has been compared with unbound RAP and CB. It has been seen that the soil structure
Secure Best Marks with AI Grader
Need help grading? Try our AI Grader for instant feedback on your assignments.
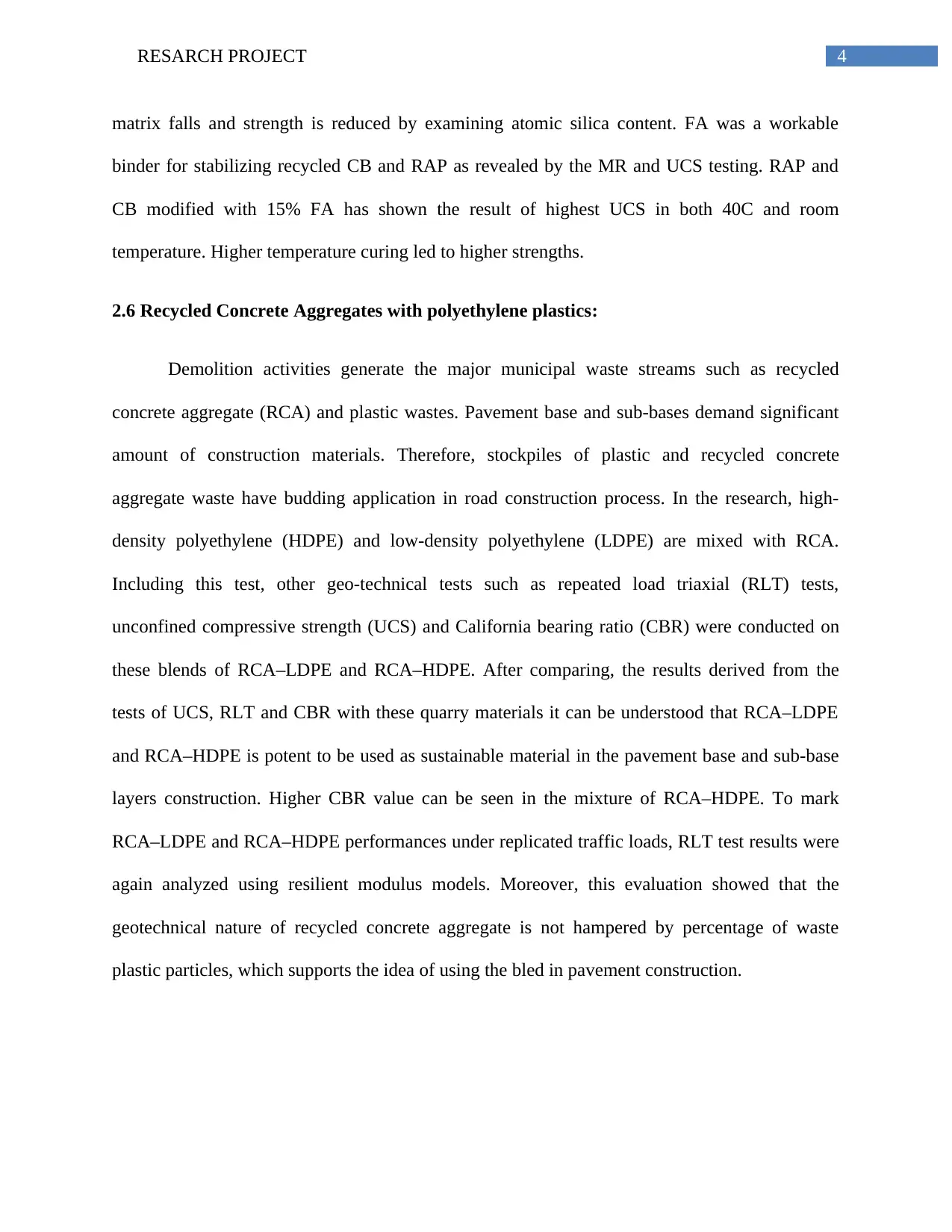
4RESARCH PROJECT
matrix falls and strength is reduced by examining atomic silica content. FA was a workable
binder for stabilizing recycled CB and RAP as revealed by the MR and UCS testing. RAP and
CB modified with 15% FA has shown the result of highest UCS in both 40C and room
temperature. Higher temperature curing led to higher strengths.
2.6 Recycled Concrete Aggregates with polyethylene plastics:
Demolition activities generate the major municipal waste streams such as recycled
concrete aggregate (RCA) and plastic wastes. Pavement base and sub-bases demand significant
amount of construction materials. Therefore, stockpiles of plastic and recycled concrete
aggregate waste have budding application in road construction process. In the research, high-
density polyethylene (HDPE) and low-density polyethylene (LDPE) are mixed with RCA.
Including this test, other geo-technical tests such as repeated load triaxial (RLT) tests,
unconfined compressive strength (UCS) and California bearing ratio (CBR) were conducted on
these blends of RCA–LDPE and RCA–HDPE. After comparing, the results derived from the
tests of UCS, RLT and CBR with these quarry materials it can be understood that RCA–LDPE
and RCA–HDPE is potent to be used as sustainable material in the pavement base and sub-base
layers construction. Higher CBR value can be seen in the mixture of RCA–HDPE. To mark
RCA–LDPE and RCA–HDPE performances under replicated traffic loads, RLT test results were
again analyzed using resilient modulus models. Moreover, this evaluation showed that the
geotechnical nature of recycled concrete aggregate is not hampered by percentage of waste
plastic particles, which supports the idea of using the bled in pavement construction.
matrix falls and strength is reduced by examining atomic silica content. FA was a workable
binder for stabilizing recycled CB and RAP as revealed by the MR and UCS testing. RAP and
CB modified with 15% FA has shown the result of highest UCS in both 40C and room
temperature. Higher temperature curing led to higher strengths.
2.6 Recycled Concrete Aggregates with polyethylene plastics:
Demolition activities generate the major municipal waste streams such as recycled
concrete aggregate (RCA) and plastic wastes. Pavement base and sub-bases demand significant
amount of construction materials. Therefore, stockpiles of plastic and recycled concrete
aggregate waste have budding application in road construction process. In the research, high-
density polyethylene (HDPE) and low-density polyethylene (LDPE) are mixed with RCA.
Including this test, other geo-technical tests such as repeated load triaxial (RLT) tests,
unconfined compressive strength (UCS) and California bearing ratio (CBR) were conducted on
these blends of RCA–LDPE and RCA–HDPE. After comparing, the results derived from the
tests of UCS, RLT and CBR with these quarry materials it can be understood that RCA–LDPE
and RCA–HDPE is potent to be used as sustainable material in the pavement base and sub-base
layers construction. Higher CBR value can be seen in the mixture of RCA–HDPE. To mark
RCA–LDPE and RCA–HDPE performances under replicated traffic loads, RLT test results were
again analyzed using resilient modulus models. Moreover, this evaluation showed that the
geotechnical nature of recycled concrete aggregate is not hampered by percentage of waste
plastic particles, which supports the idea of using the bled in pavement construction.
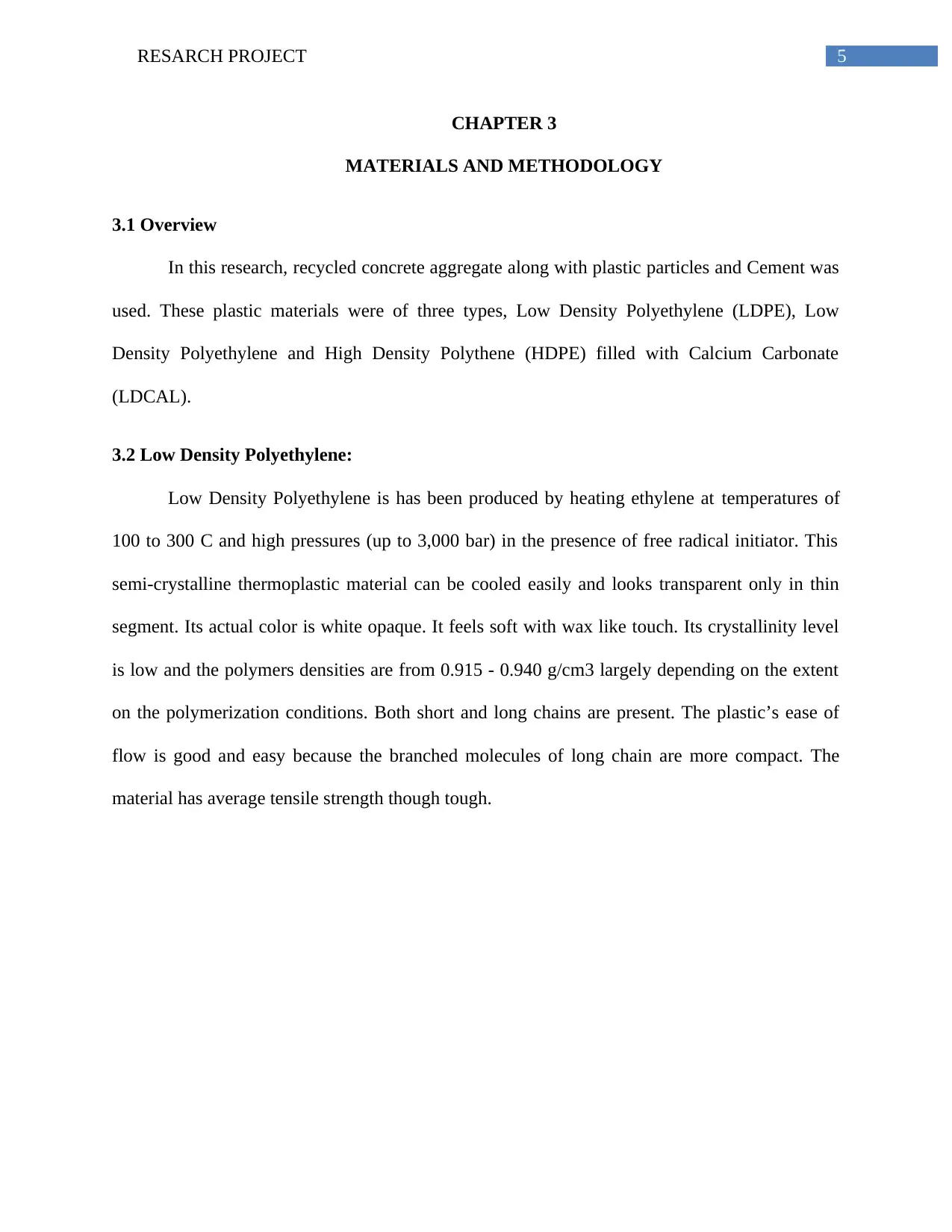
5RESARCH PROJECT
CHAPTER 3
MATERIALS AND METHODOLOGY
3.1 Overview
In this research, recycled concrete aggregate along with plastic particles and Cement was
used. These plastic materials were of three types, Low Density Polyethylene (LDPE), Low
Density Polyethylene and High Density Polythene (HDPE) filled with Calcium Carbonate
(LDCAL).
3.2 Low Density Polyethylene:
Low Density Polyethylene is has been produced by heating ethylene at temperatures of
100 to 300 C and high pressures (up to 3,000 bar) in the presence of free radical initiator. This
semi-crystalline thermoplastic material can be cooled easily and looks transparent only in thin
segment. Its actual color is white opaque. It feels soft with wax like touch. Its crystallinity level
is low and the polymers densities are from 0.915 - 0.940 g/cm3 largely depending on the extent
on the polymerization conditions. Both short and long chains are present. The plastic’s ease of
flow is good and easy because the branched molecules of long chain are more compact. The
material has average tensile strength though tough.
CHAPTER 3
MATERIALS AND METHODOLOGY
3.1 Overview
In this research, recycled concrete aggregate along with plastic particles and Cement was
used. These plastic materials were of three types, Low Density Polyethylene (LDPE), Low
Density Polyethylene and High Density Polythene (HDPE) filled with Calcium Carbonate
(LDCAL).
3.2 Low Density Polyethylene:
Low Density Polyethylene is has been produced by heating ethylene at temperatures of
100 to 300 C and high pressures (up to 3,000 bar) in the presence of free radical initiator. This
semi-crystalline thermoplastic material can be cooled easily and looks transparent only in thin
segment. Its actual color is white opaque. It feels soft with wax like touch. Its crystallinity level
is low and the polymers densities are from 0.915 - 0.940 g/cm3 largely depending on the extent
on the polymerization conditions. Both short and long chains are present. The plastic’s ease of
flow is good and easy because the branched molecules of long chain are more compact. The
material has average tensile strength though tough.
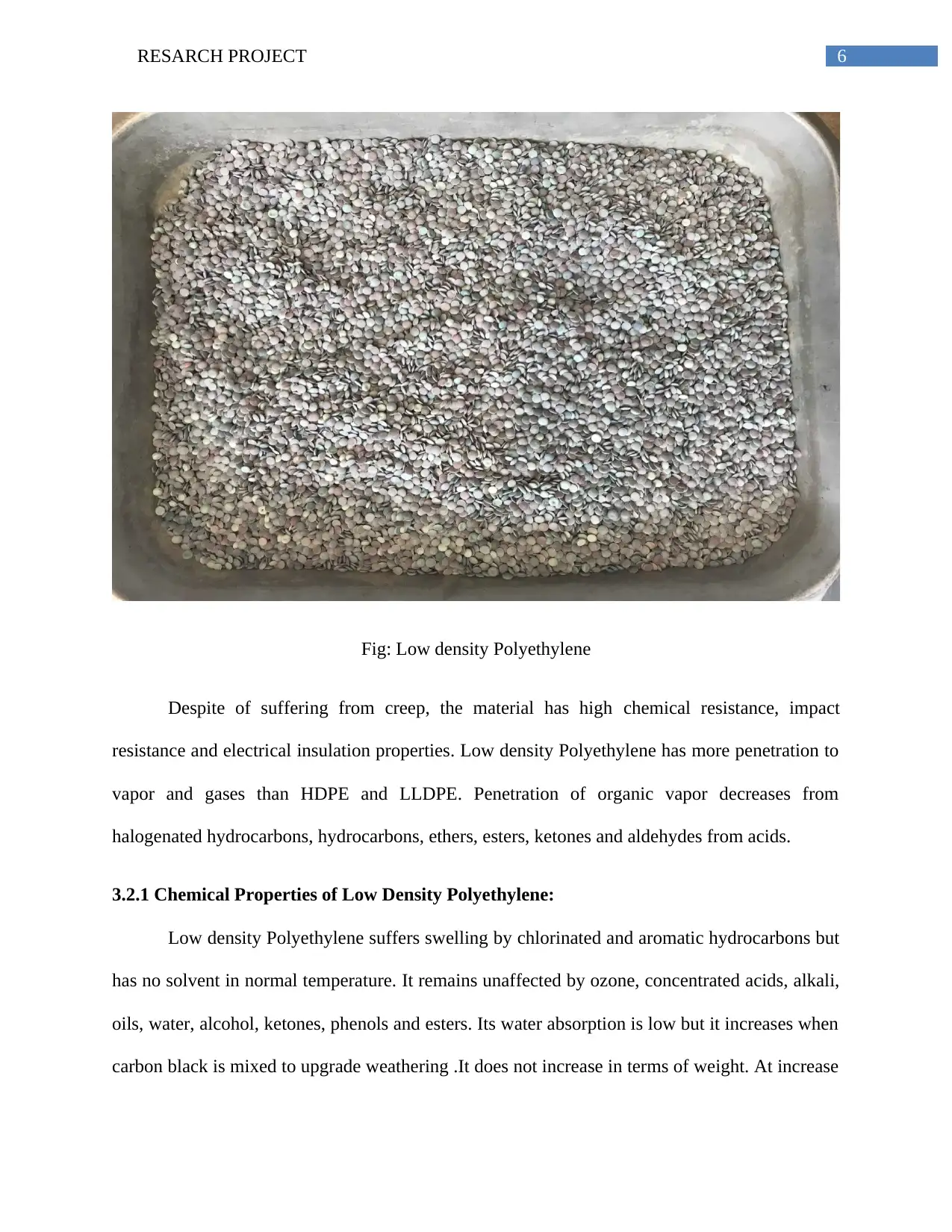
6RESARCH PROJECT
Fig: Low density Polyethylene
Despite of suffering from creep, the material has high chemical resistance, impact
resistance and electrical insulation properties. Low density Polyethylene has more penetration to
vapor and gases than HDPE and LLDPE. Penetration of organic vapor decreases from
halogenated hydrocarbons, hydrocarbons, ethers, esters, ketones and aldehydes from acids.
3.2.1 Chemical Properties of Low Density Polyethylene:
Low density Polyethylene suffers swelling by chlorinated and aromatic hydrocarbons but
has no solvent in normal temperature. It remains unaffected by ozone, concentrated acids, alkali,
oils, water, alcohol, ketones, phenols and esters. Its water absorption is low but it increases when
carbon black is mixed to upgrade weathering .It does not increase in terms of weight. At increase
Fig: Low density Polyethylene
Despite of suffering from creep, the material has high chemical resistance, impact
resistance and electrical insulation properties. Low density Polyethylene has more penetration to
vapor and gases than HDPE and LLDPE. Penetration of organic vapor decreases from
halogenated hydrocarbons, hydrocarbons, ethers, esters, ketones and aldehydes from acids.
3.2.1 Chemical Properties of Low Density Polyethylene:
Low density Polyethylene suffers swelling by chlorinated and aromatic hydrocarbons but
has no solvent in normal temperature. It remains unaffected by ozone, concentrated acids, alkali,
oils, water, alcohol, ketones, phenols and esters. Its water absorption is low but it increases when
carbon black is mixed to upgrade weathering .It does not increase in terms of weight. At increase
Paraphrase This Document
Need a fresh take? Get an instant paraphrase of this document with our AI Paraphraser
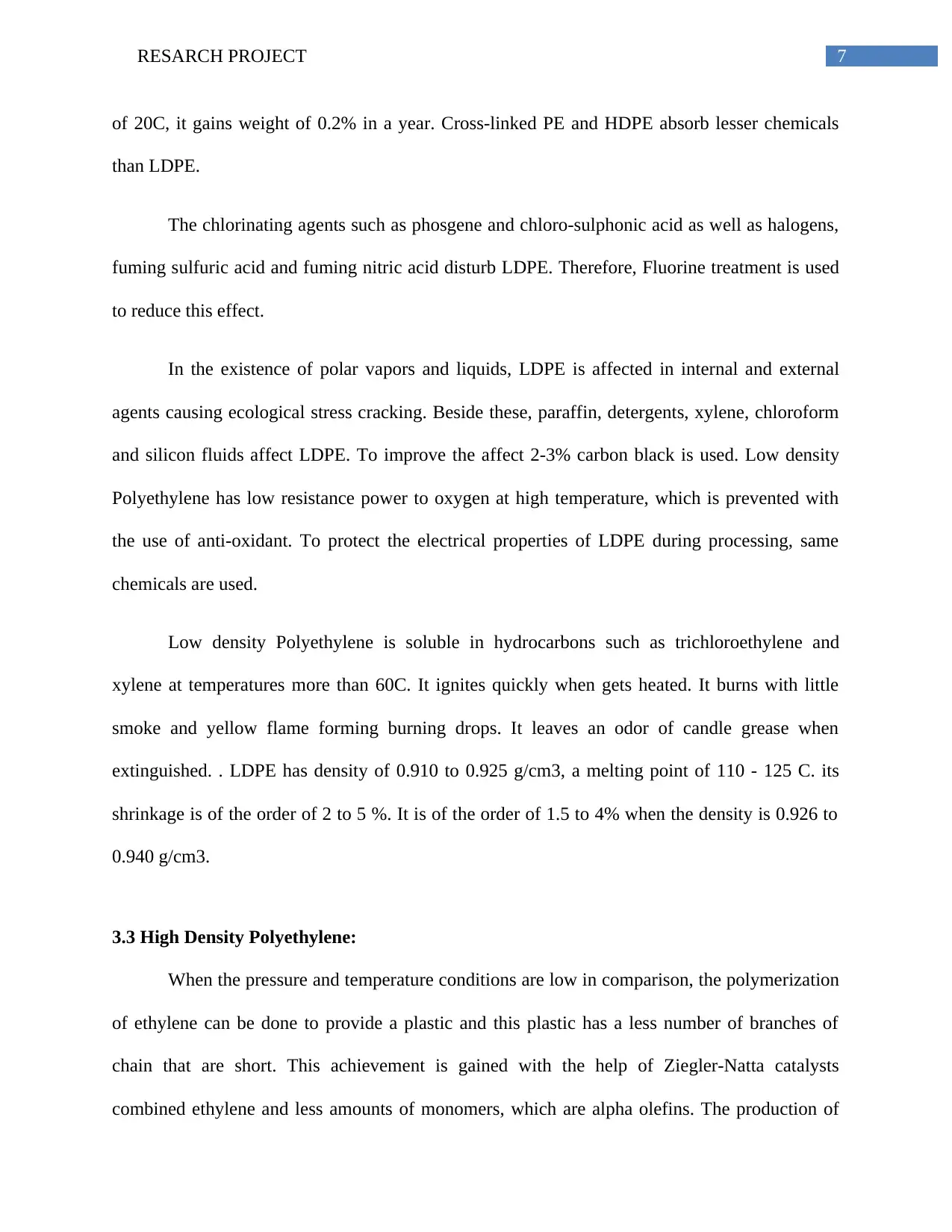
7RESARCH PROJECT
of 20C, it gains weight of 0.2% in a year. Cross-linked PE and HDPE absorb lesser chemicals
than LDPE.
The chlorinating agents such as phosgene and chloro-sulphonic acid as well as halogens,
fuming sulfuric acid and fuming nitric acid disturb LDPE. Therefore, Fluorine treatment is used
to reduce this effect.
In the existence of polar vapors and liquids, LDPE is affected in internal and external
agents causing ecological stress cracking. Beside these, paraffin, detergents, xylene, chloroform
and silicon fluids affect LDPE. To improve the affect 2-3% carbon black is used. Low density
Polyethylene has low resistance power to oxygen at high temperature, which is prevented with
the use of anti-oxidant. To protect the electrical properties of LDPE during processing, same
chemicals are used.
Low density Polyethylene is soluble in hydrocarbons such as trichloroethylene and
xylene at temperatures more than 60C. It ignites quickly when gets heated. It burns with little
smoke and yellow flame forming burning drops. It leaves an odor of candle grease when
extinguished. . LDPE has density of 0.910 to 0.925 g/cm3, a melting point of 110 - 125 C. its
shrinkage is of the order of 2 to 5 %. It is of the order of 1.5 to 4% when the density is 0.926 to
0.940 g/cm3.
3.3 High Density Polyethylene:
When the pressure and temperature conditions are low in comparison, the polymerization
of ethylene can be done to provide a plastic and this plastic has a less number of branches of
chain that are short. This achievement is gained with the help of Ziegler-Natta catalysts
combined ethylene and less amounts of monomers, which are alpha olefins. The production of
of 20C, it gains weight of 0.2% in a year. Cross-linked PE and HDPE absorb lesser chemicals
than LDPE.
The chlorinating agents such as phosgene and chloro-sulphonic acid as well as halogens,
fuming sulfuric acid and fuming nitric acid disturb LDPE. Therefore, Fluorine treatment is used
to reduce this effect.
In the existence of polar vapors and liquids, LDPE is affected in internal and external
agents causing ecological stress cracking. Beside these, paraffin, detergents, xylene, chloroform
and silicon fluids affect LDPE. To improve the affect 2-3% carbon black is used. Low density
Polyethylene has low resistance power to oxygen at high temperature, which is prevented with
the use of anti-oxidant. To protect the electrical properties of LDPE during processing, same
chemicals are used.
Low density Polyethylene is soluble in hydrocarbons such as trichloroethylene and
xylene at temperatures more than 60C. It ignites quickly when gets heated. It burns with little
smoke and yellow flame forming burning drops. It leaves an odor of candle grease when
extinguished. . LDPE has density of 0.910 to 0.925 g/cm3, a melting point of 110 - 125 C. its
shrinkage is of the order of 2 to 5 %. It is of the order of 1.5 to 4% when the density is 0.926 to
0.940 g/cm3.
3.3 High Density Polyethylene:
When the pressure and temperature conditions are low in comparison, the polymerization
of ethylene can be done to provide a plastic and this plastic has a less number of branches of
chain that are short. This achievement is gained with the help of Ziegler-Natta catalysts
combined ethylene and less amounts of monomers, which are alpha olefins. The production of
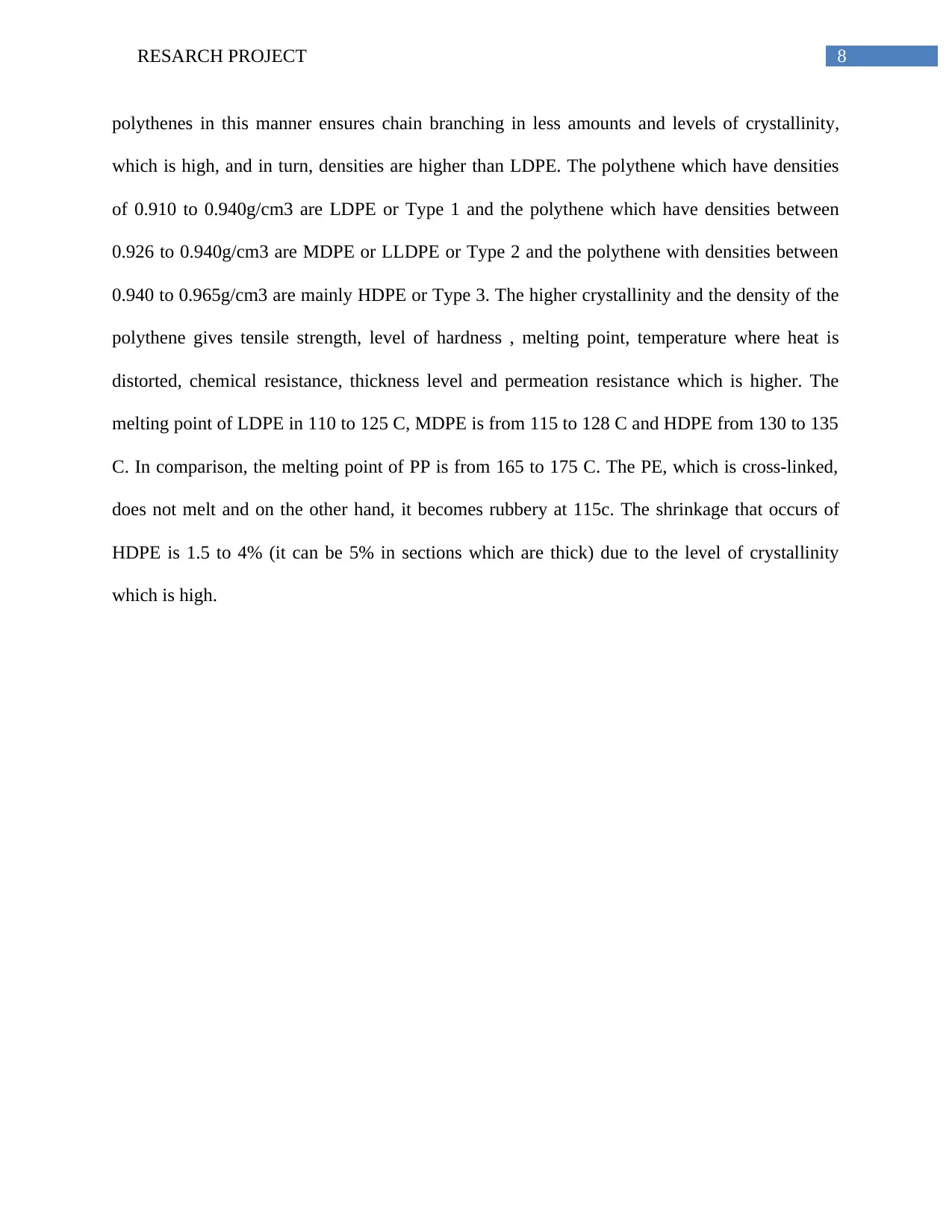
8RESARCH PROJECT
polythenes in this manner ensures chain branching in less amounts and levels of crystallinity,
which is high, and in turn, densities are higher than LDPE. The polythene which have densities
of 0.910 to 0.940g/cm3 are LDPE or Type 1 and the polythene which have densities between
0.926 to 0.940g/cm3 are MDPE or LLDPE or Type 2 and the polythene with densities between
0.940 to 0.965g/cm3 are mainly HDPE or Type 3. The higher crystallinity and the density of the
polythene gives tensile strength, level of hardness , melting point, temperature where heat is
distorted, chemical resistance, thickness level and permeation resistance which is higher. The
melting point of LDPE in 110 to 125 C, MDPE is from 115 to 128 C and HDPE from 130 to 135
C. In comparison, the melting point of PP is from 165 to 175 C. The PE, which is cross-linked,
does not melt and on the other hand, it becomes rubbery at 115c. The shrinkage that occurs of
HDPE is 1.5 to 4% (it can be 5% in sections which are thick) due to the level of crystallinity
which is high.
polythenes in this manner ensures chain branching in less amounts and levels of crystallinity,
which is high, and in turn, densities are higher than LDPE. The polythene which have densities
of 0.910 to 0.940g/cm3 are LDPE or Type 1 and the polythene which have densities between
0.926 to 0.940g/cm3 are MDPE or LLDPE or Type 2 and the polythene with densities between
0.940 to 0.965g/cm3 are mainly HDPE or Type 3. The higher crystallinity and the density of the
polythene gives tensile strength, level of hardness , melting point, temperature where heat is
distorted, chemical resistance, thickness level and permeation resistance which is higher. The
melting point of LDPE in 110 to 125 C, MDPE is from 115 to 128 C and HDPE from 130 to 135
C. In comparison, the melting point of PP is from 165 to 175 C. The PE, which is cross-linked,
does not melt and on the other hand, it becomes rubbery at 115c. The shrinkage that occurs of
HDPE is 1.5 to 4% (it can be 5% in sections which are thick) due to the level of crystallinity
which is high.
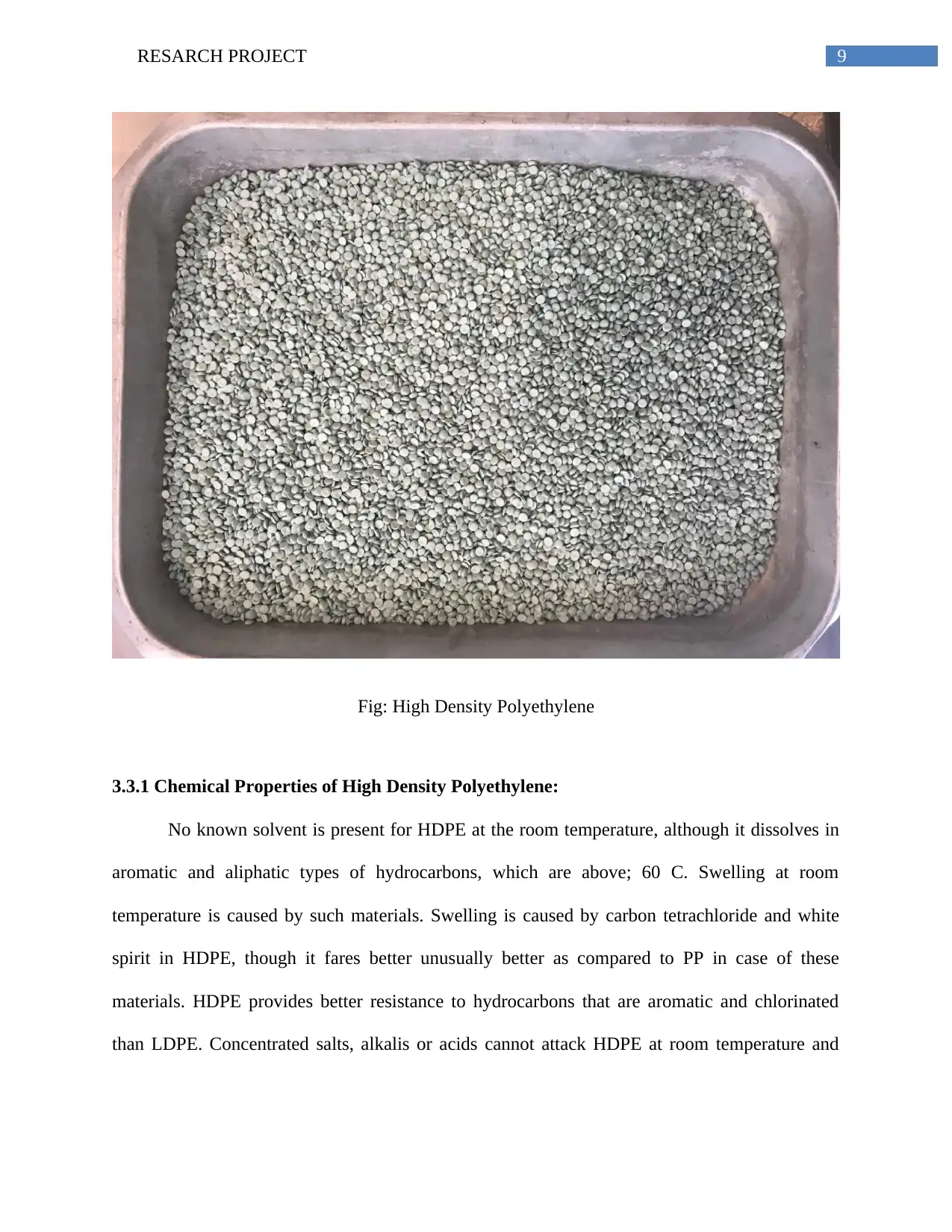
9RESARCH PROJECT
Fig: High Density Polyethylene
3.3.1 Chemical Properties of High Density Polyethylene:
No known solvent is present for HDPE at the room temperature, although it dissolves in
aromatic and aliphatic types of hydrocarbons, which are above; 60 C. Swelling at room
temperature is caused by such materials. Swelling is caused by carbon tetrachloride and white
spirit in HDPE, though it fares better unusually better as compared to PP in case of these
materials. HDPE provides better resistance to hydrocarbons that are aromatic and chlorinated
than LDPE. Concentrated salts, alkalis or acids cannot attack HDPE at room temperature and
Fig: High Density Polyethylene
3.3.1 Chemical Properties of High Density Polyethylene:
No known solvent is present for HDPE at the room temperature, although it dissolves in
aromatic and aliphatic types of hydrocarbons, which are above; 60 C. Swelling at room
temperature is caused by such materials. Swelling is caused by carbon tetrachloride and white
spirit in HDPE, though it fares better unusually better as compared to PP in case of these
materials. HDPE provides better resistance to hydrocarbons that are aromatic and chlorinated
than LDPE. Concentrated salts, alkalis or acids cannot attack HDPE at room temperature and
Secure Best Marks with AI Grader
Need help grading? Try our AI Grader for instant feedback on your assignments.
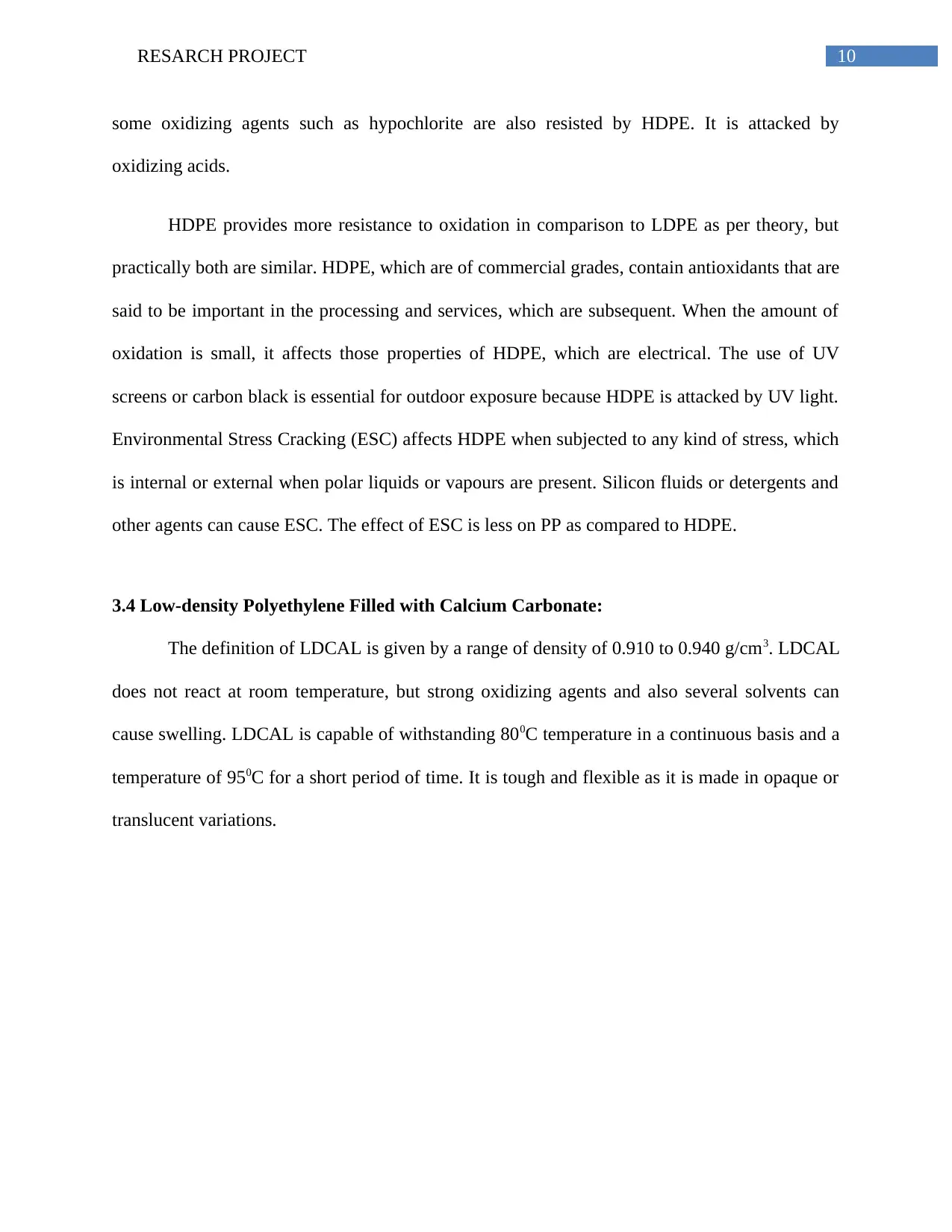
10RESARCH PROJECT
some oxidizing agents such as hypochlorite are also resisted by HDPE. It is attacked by
oxidizing acids.
HDPE provides more resistance to oxidation in comparison to LDPE as per theory, but
practically both are similar. HDPE, which are of commercial grades, contain antioxidants that are
said to be important in the processing and services, which are subsequent. When the amount of
oxidation is small, it affects those properties of HDPE, which are electrical. The use of UV
screens or carbon black is essential for outdoor exposure because HDPE is attacked by UV light.
Environmental Stress Cracking (ESC) affects HDPE when subjected to any kind of stress, which
is internal or external when polar liquids or vapours are present. Silicon fluids or detergents and
other agents can cause ESC. The effect of ESC is less on PP as compared to HDPE.
3.4 Low-density Polyethylene Filled with Calcium Carbonate:
The definition of LDCAL is given by a range of density of 0.910 to 0.940 g/cm3. LDCAL
does not react at room temperature, but strong oxidizing agents and also several solvents can
cause swelling. LDCAL is capable of withstanding 800C temperature in a continuous basis and a
temperature of 950C for a short period of time. It is tough and flexible as it is made in opaque or
translucent variations.
some oxidizing agents such as hypochlorite are also resisted by HDPE. It is attacked by
oxidizing acids.
HDPE provides more resistance to oxidation in comparison to LDPE as per theory, but
practically both are similar. HDPE, which are of commercial grades, contain antioxidants that are
said to be important in the processing and services, which are subsequent. When the amount of
oxidation is small, it affects those properties of HDPE, which are electrical. The use of UV
screens or carbon black is essential for outdoor exposure because HDPE is attacked by UV light.
Environmental Stress Cracking (ESC) affects HDPE when subjected to any kind of stress, which
is internal or external when polar liquids or vapours are present. Silicon fluids or detergents and
other agents can cause ESC. The effect of ESC is less on PP as compared to HDPE.
3.4 Low-density Polyethylene Filled with Calcium Carbonate:
The definition of LDCAL is given by a range of density of 0.910 to 0.940 g/cm3. LDCAL
does not react at room temperature, but strong oxidizing agents and also several solvents can
cause swelling. LDCAL is capable of withstanding 800C temperature in a continuous basis and a
temperature of 950C for a short period of time. It is tough and flexible as it is made in opaque or
translucent variations.
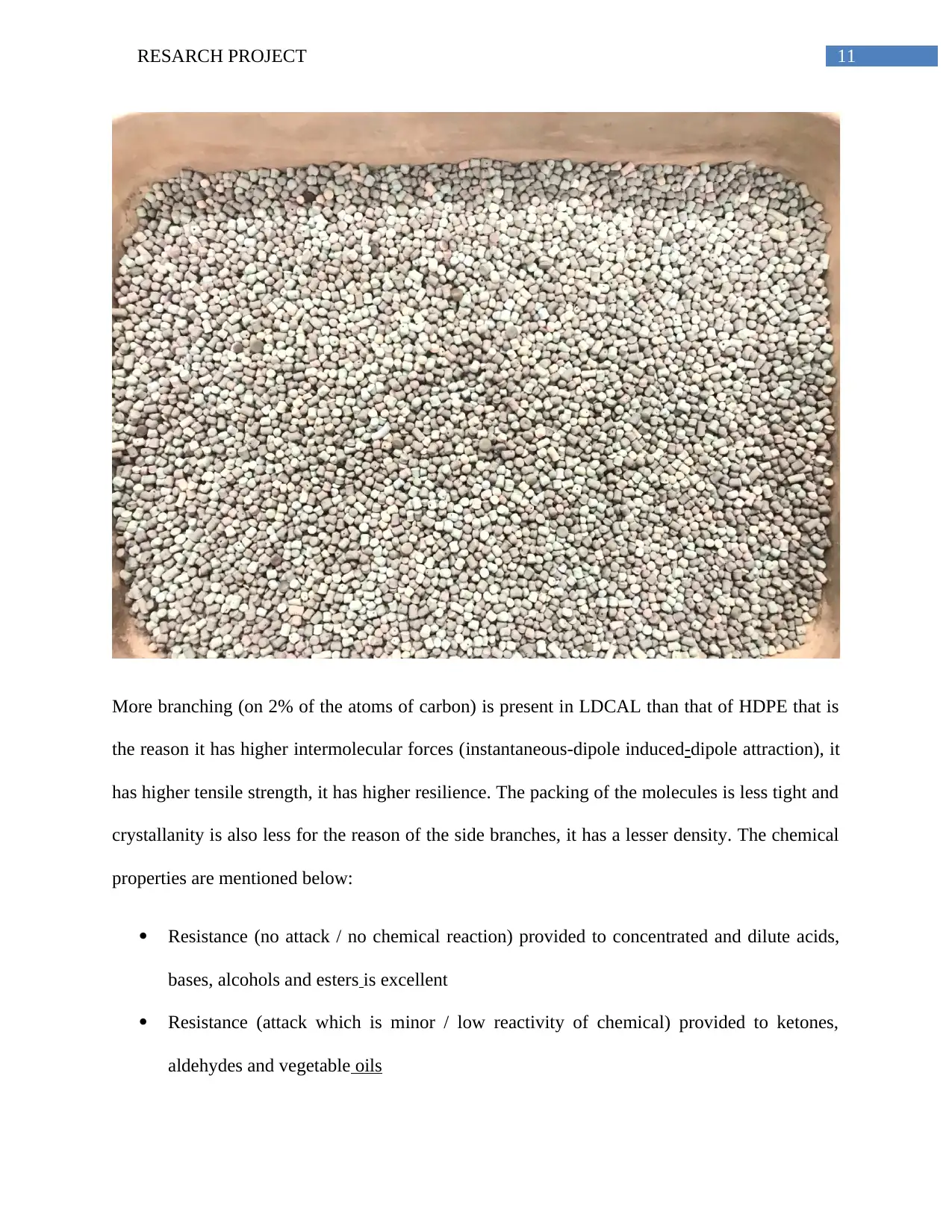
11RESARCH PROJECT
More branching (on 2% of the atoms of carbon) is present in LDCAL than that of HDPE that is
the reason it has higher intermolecular forces (instantaneous-dipole induced-dipole attraction), it
has higher tensile strength, it has higher resilience. The packing of the molecules is less tight and
crystallanity is also less for the reason of the side branches, it has a lesser density. The chemical
properties are mentioned below:
Resistance (no attack / no chemical reaction) provided to concentrated and dilute acids,
bases, alcohols and esters is excellent
Resistance (attack which is minor / low reactivity of chemical) provided to ketones,
aldehydes and vegetable oils
More branching (on 2% of the atoms of carbon) is present in LDCAL than that of HDPE that is
the reason it has higher intermolecular forces (instantaneous-dipole induced-dipole attraction), it
has higher tensile strength, it has higher resilience. The packing of the molecules is less tight and
crystallanity is also less for the reason of the side branches, it has a lesser density. The chemical
properties are mentioned below:
Resistance (no attack / no chemical reaction) provided to concentrated and dilute acids,
bases, alcohols and esters is excellent
Resistance (attack which is minor / low reactivity of chemical) provided to ketones,
aldehydes and vegetable oils
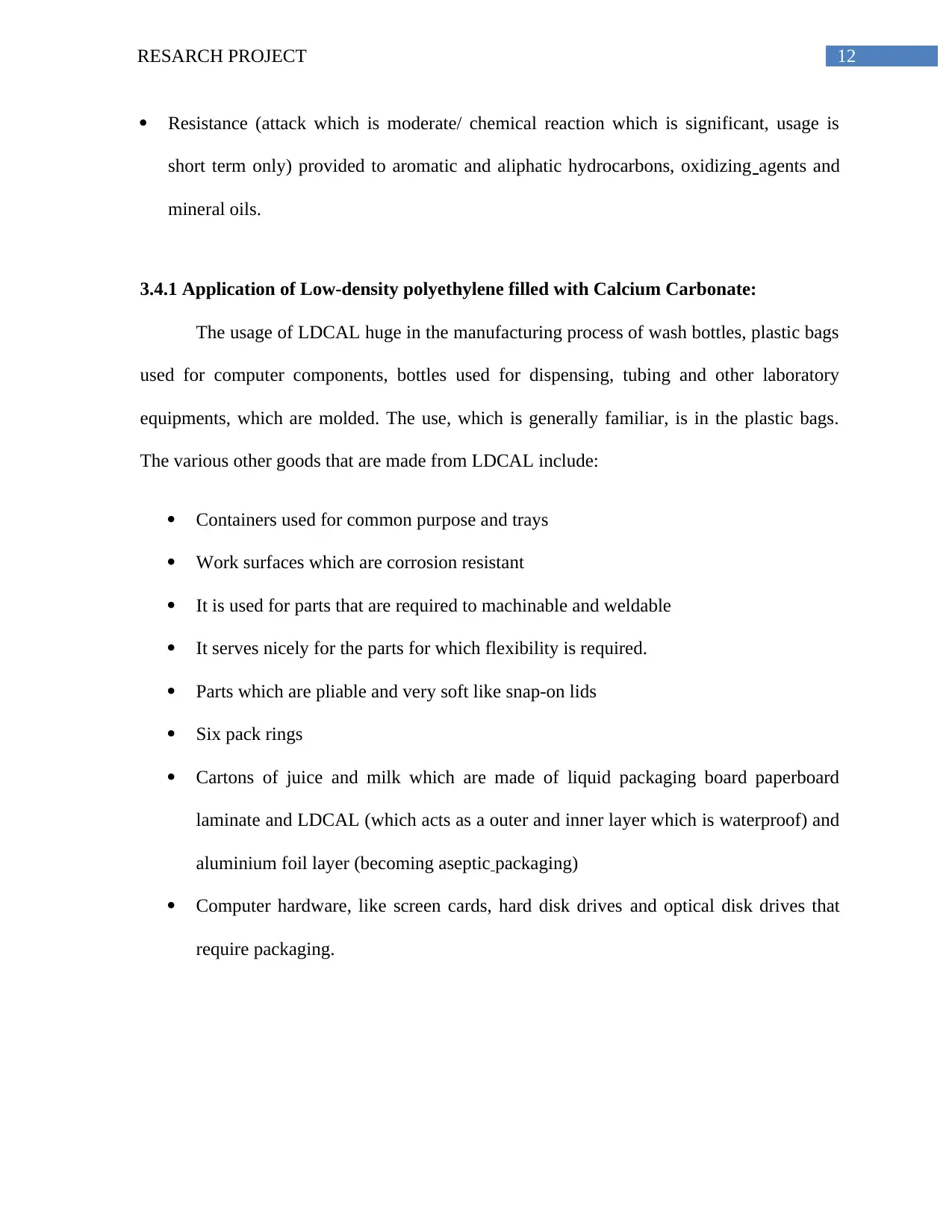
12RESARCH PROJECT
Resistance (attack which is moderate/ chemical reaction which is significant, usage is
short term only) provided to aromatic and aliphatic hydrocarbons, oxidizing agents and
mineral oils.
3.4.1 Application of Low-density polyethylene filled with Calcium Carbonate:
The usage of LDCAL huge in the manufacturing process of wash bottles, plastic bags
used for computer components, bottles used for dispensing, tubing and other laboratory
equipments, which are molded. The use, which is generally familiar, is in the plastic bags.
The various other goods that are made from LDCAL include:
Containers used for common purpose and trays
Work surfaces which are corrosion resistant
It is used for parts that are required to machinable and weldable
It serves nicely for the parts for which flexibility is required.
Parts which are pliable and very soft like snap-on lids
Six pack rings
Cartons of juice and milk which are made of liquid packaging board paperboard
laminate and LDCAL (which acts as a outer and inner layer which is waterproof) and
aluminium foil layer (becoming aseptic packaging)
Computer hardware, like screen cards, hard disk drives and optical disk drives that
require packaging.
Resistance (attack which is moderate/ chemical reaction which is significant, usage is
short term only) provided to aromatic and aliphatic hydrocarbons, oxidizing agents and
mineral oils.
3.4.1 Application of Low-density polyethylene filled with Calcium Carbonate:
The usage of LDCAL huge in the manufacturing process of wash bottles, plastic bags
used for computer components, bottles used for dispensing, tubing and other laboratory
equipments, which are molded. The use, which is generally familiar, is in the plastic bags.
The various other goods that are made from LDCAL include:
Containers used for common purpose and trays
Work surfaces which are corrosion resistant
It is used for parts that are required to machinable and weldable
It serves nicely for the parts for which flexibility is required.
Parts which are pliable and very soft like snap-on lids
Six pack rings
Cartons of juice and milk which are made of liquid packaging board paperboard
laminate and LDCAL (which acts as a outer and inner layer which is waterproof) and
aluminium foil layer (becoming aseptic packaging)
Computer hardware, like screen cards, hard disk drives and optical disk drives that
require packaging.
Paraphrase This Document
Need a fresh take? Get an instant paraphrase of this document with our AI Paraphraser
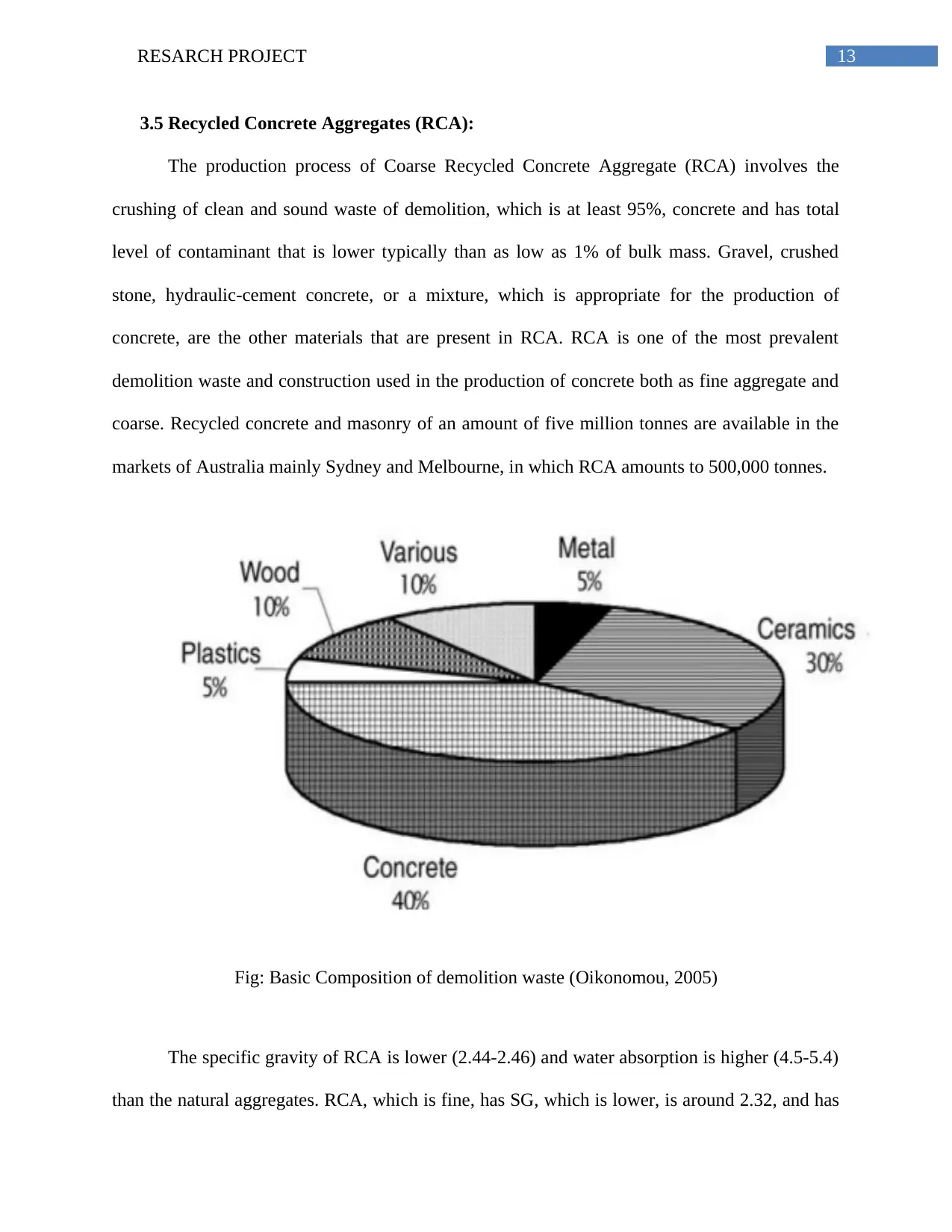
13RESARCH PROJECT
3.5 Recycled Concrete Aggregates (RCA):
The production process of Coarse Recycled Concrete Aggregate (RCA) involves the
crushing of clean and sound waste of demolition, which is at least 95%, concrete and has total
level of contaminant that is lower typically than as low as 1% of bulk mass. Gravel, crushed
stone, hydraulic-cement concrete, or a mixture, which is appropriate for the production of
concrete, are the other materials that are present in RCA. RCA is one of the most prevalent
demolition waste and construction used in the production of concrete both as fine aggregate and
coarse. Recycled concrete and masonry of an amount of five million tonnes are available in the
markets of Australia mainly Sydney and Melbourne, in which RCA amounts to 500,000 tonnes.
Fig: Basic Composition of demolition waste (Oikonomou, 2005)
The specific gravity of RCA is lower (2.44-2.46) and water absorption is higher (4.5-5.4)
than the natural aggregates. RCA, which is fine, has SG, which is lower, is around 2.32, and has
3.5 Recycled Concrete Aggregates (RCA):
The production process of Coarse Recycled Concrete Aggregate (RCA) involves the
crushing of clean and sound waste of demolition, which is at least 95%, concrete and has total
level of contaminant that is lower typically than as low as 1% of bulk mass. Gravel, crushed
stone, hydraulic-cement concrete, or a mixture, which is appropriate for the production of
concrete, are the other materials that are present in RCA. RCA is one of the most prevalent
demolition waste and construction used in the production of concrete both as fine aggregate and
coarse. Recycled concrete and masonry of an amount of five million tonnes are available in the
markets of Australia mainly Sydney and Melbourne, in which RCA amounts to 500,000 tonnes.
Fig: Basic Composition of demolition waste (Oikonomou, 2005)
The specific gravity of RCA is lower (2.44-2.46) and water absorption is higher (4.5-5.4)
than the natural aggregates. RCA, which is fine, has SG, which is lower, is around 2.32, and has
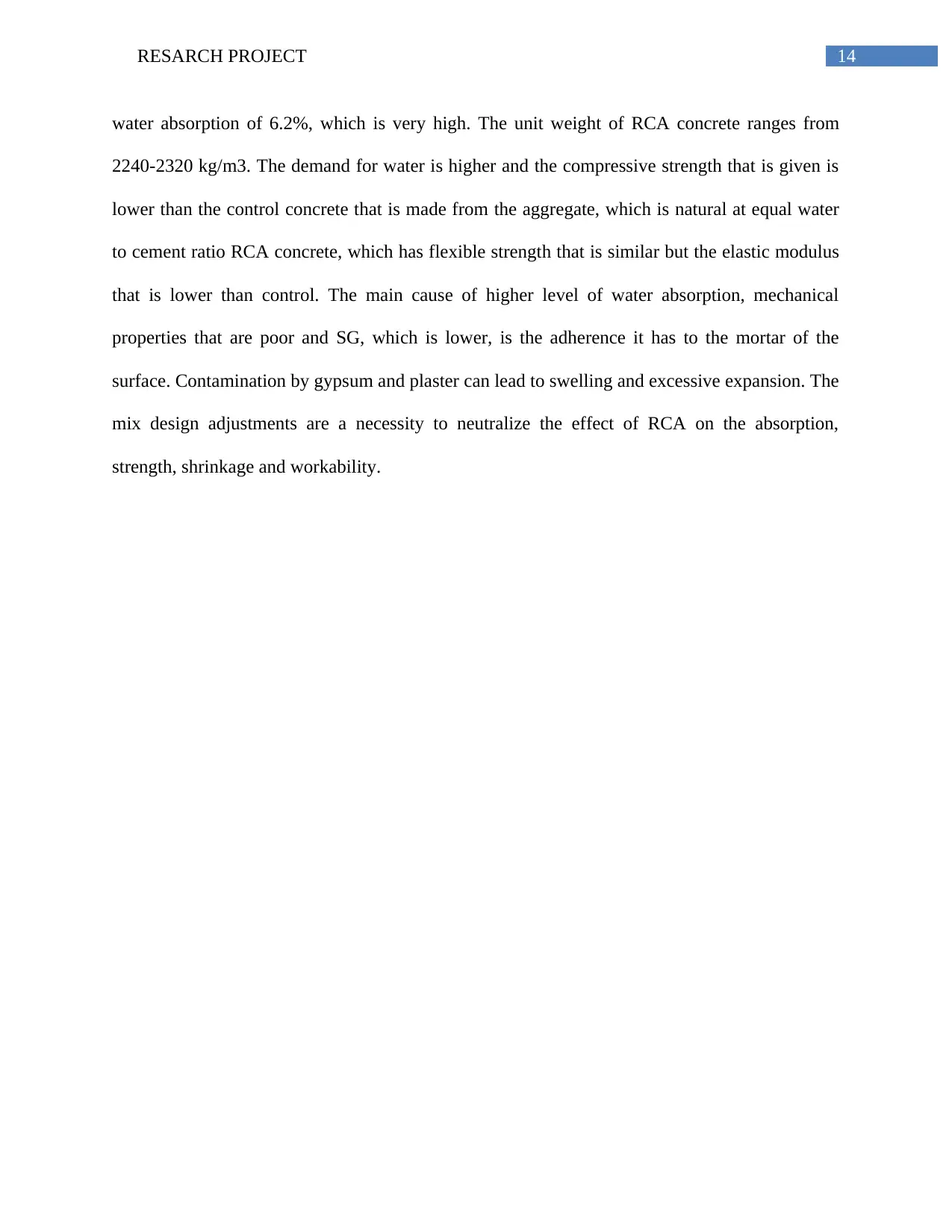
14RESARCH PROJECT
water absorption of 6.2%, which is very high. The unit weight of RCA concrete ranges from
2240-2320 kg/m3. The demand for water is higher and the compressive strength that is given is
lower than the control concrete that is made from the aggregate, which is natural at equal water
to cement ratio RCA concrete, which has flexible strength that is similar but the elastic modulus
that is lower than control. The main cause of higher level of water absorption, mechanical
properties that are poor and SG, which is lower, is the adherence it has to the mortar of the
surface. Contamination by gypsum and plaster can lead to swelling and excessive expansion. The
mix design adjustments are a necessity to neutralize the effect of RCA on the absorption,
strength, shrinkage and workability.
water absorption of 6.2%, which is very high. The unit weight of RCA concrete ranges from
2240-2320 kg/m3. The demand for water is higher and the compressive strength that is given is
lower than the control concrete that is made from the aggregate, which is natural at equal water
to cement ratio RCA concrete, which has flexible strength that is similar but the elastic modulus
that is lower than control. The main cause of higher level of water absorption, mechanical
properties that are poor and SG, which is lower, is the adherence it has to the mortar of the
surface. Contamination by gypsum and plaster can lead to swelling and excessive expansion. The
mix design adjustments are a necessity to neutralize the effect of RCA on the absorption,
strength, shrinkage and workability.
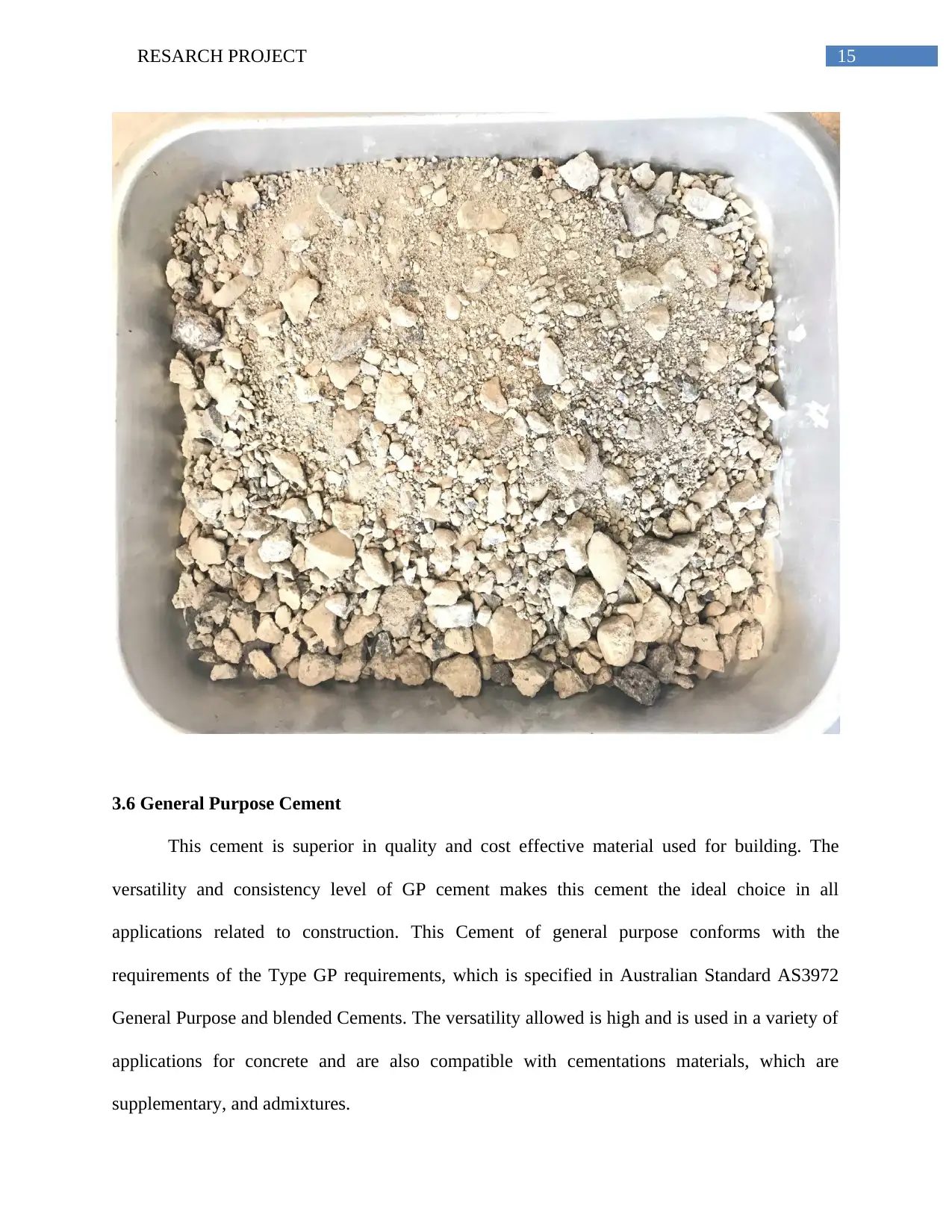
15RESARCH PROJECT
3.6 General Purpose Cement
This cement is superior in quality and cost effective material used for building. The
versatility and consistency level of GP cement makes this cement the ideal choice in all
applications related to construction. This Cement of general purpose conforms with the
requirements of the Type GP requirements, which is specified in Australian Standard AS3972
General Purpose and blended Cements. The versatility allowed is high and is used in a variety of
applications for concrete and are also compatible with cementations materials, which are
supplementary, and admixtures.
3.6 General Purpose Cement
This cement is superior in quality and cost effective material used for building. The
versatility and consistency level of GP cement makes this cement the ideal choice in all
applications related to construction. This Cement of general purpose conforms with the
requirements of the Type GP requirements, which is specified in Australian Standard AS3972
General Purpose and blended Cements. The versatility allowed is high and is used in a variety of
applications for concrete and are also compatible with cementations materials, which are
supplementary, and admixtures.
Secure Best Marks with AI Grader
Need help grading? Try our AI Grader for instant feedback on your assignments.
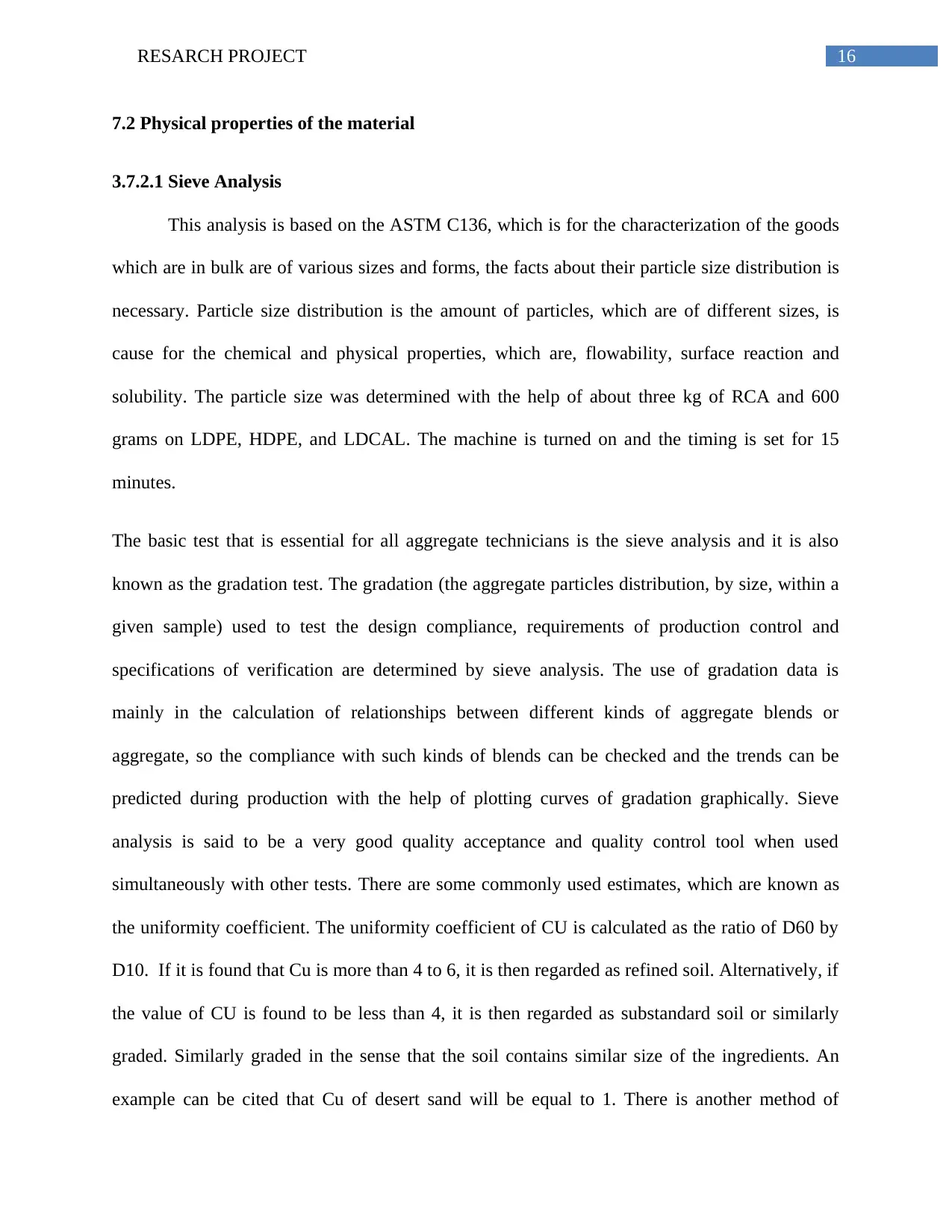
16RESARCH PROJECT
7.2 Physical properties of the material
3.7.2.1 Sieve Analysis
This analysis is based on the ASTM C136, which is for the characterization of the goods
which are in bulk are of various sizes and forms, the facts about their particle size distribution is
necessary. Particle size distribution is the amount of particles, which are of different sizes, is
cause for the chemical and physical properties, which are, flowability, surface reaction and
solubility. The particle size was determined with the help of about three kg of RCA and 600
grams on LDPE, HDPE, and LDCAL. The machine is turned on and the timing is set for 15
minutes.
The basic test that is essential for all aggregate technicians is the sieve analysis and it is also
known as the gradation test. The gradation (the aggregate particles distribution, by size, within a
given sample) used to test the design compliance, requirements of production control and
specifications of verification are determined by sieve analysis. The use of gradation data is
mainly in the calculation of relationships between different kinds of aggregate blends or
aggregate, so the compliance with such kinds of blends can be checked and the trends can be
predicted during production with the help of plotting curves of gradation graphically. Sieve
analysis is said to be a very good quality acceptance and quality control tool when used
simultaneously with other tests. There are some commonly used estimates, which are known as
the uniformity coefficient. The uniformity coefficient of CU is calculated as the ratio of D60 by
D10. If it is found that Cu is more than 4 to 6, it is then regarded as refined soil. Alternatively, if
the value of CU is found to be less than 4, it is then regarded as substandard soil or similarly
graded. Similarly graded in the sense that the soil contains similar size of the ingredients. An
example can be cited that Cu of desert sand will be equal to 1. There is another method of
7.2 Physical properties of the material
3.7.2.1 Sieve Analysis
This analysis is based on the ASTM C136, which is for the characterization of the goods
which are in bulk are of various sizes and forms, the facts about their particle size distribution is
necessary. Particle size distribution is the amount of particles, which are of different sizes, is
cause for the chemical and physical properties, which are, flowability, surface reaction and
solubility. The particle size was determined with the help of about three kg of RCA and 600
grams on LDPE, HDPE, and LDCAL. The machine is turned on and the timing is set for 15
minutes.
The basic test that is essential for all aggregate technicians is the sieve analysis and it is also
known as the gradation test. The gradation (the aggregate particles distribution, by size, within a
given sample) used to test the design compliance, requirements of production control and
specifications of verification are determined by sieve analysis. The use of gradation data is
mainly in the calculation of relationships between different kinds of aggregate blends or
aggregate, so the compliance with such kinds of blends can be checked and the trends can be
predicted during production with the help of plotting curves of gradation graphically. Sieve
analysis is said to be a very good quality acceptance and quality control tool when used
simultaneously with other tests. There are some commonly used estimates, which are known as
the uniformity coefficient. The uniformity coefficient of CU is calculated as the ratio of D60 by
D10. If it is found that Cu is more than 4 to 6, it is then regarded as refined soil. Alternatively, if
the value of CU is found to be less than 4, it is then regarded as substandard soil or similarly
graded. Similarly graded in the sense that the soil contains similar size of the ingredients. An
example can be cited that Cu of desert sand will be equal to 1. There is another method of
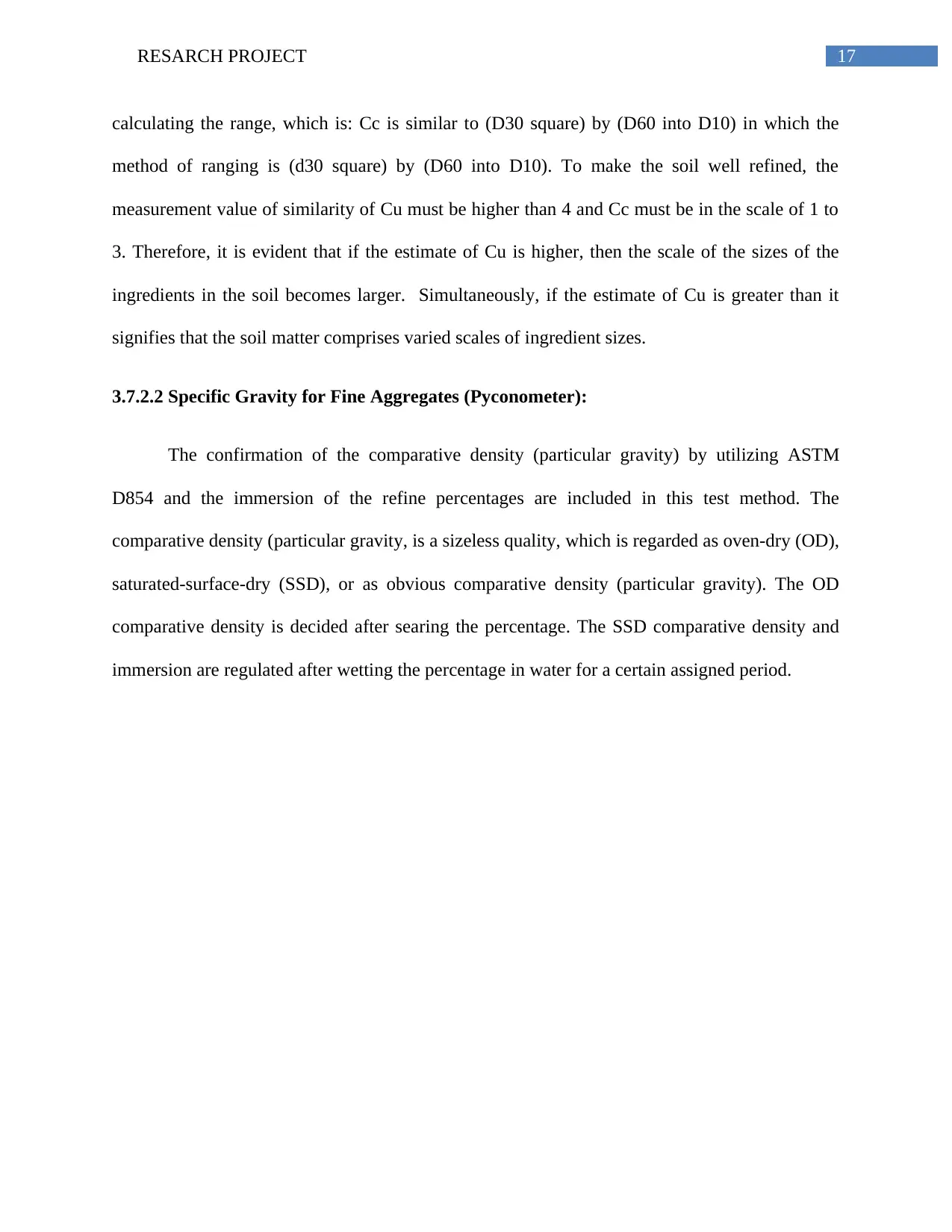
17RESARCH PROJECT
calculating the range, which is: Cc is similar to (D30 square) by (D60 into D10) in which the
method of ranging is (d30 square) by (D60 into D10). To make the soil well refined, the
measurement value of similarity of Cu must be higher than 4 and Cc must be in the scale of 1 to
3. Therefore, it is evident that if the estimate of Cu is higher, then the scale of the sizes of the
ingredients in the soil becomes larger. Simultaneously, if the estimate of Cu is greater than it
signifies that the soil matter comprises varied scales of ingredient sizes.
3.7.2.2 Specific Gravity for Fine Aggregates (Pyconometer):
The confirmation of the comparative density (particular gravity) by utilizing ASTM
D854 and the immersion of the refine percentages are included in this test method. The
comparative density (particular gravity, is a sizeless quality, which is regarded as oven-dry (OD),
saturated-surface-dry (SSD), or as obvious comparative density (particular gravity). The OD
comparative density is decided after searing the percentage. The SSD comparative density and
immersion are regulated after wetting the percentage in water for a certain assigned period.
calculating the range, which is: Cc is similar to (D30 square) by (D60 into D10) in which the
method of ranging is (d30 square) by (D60 into D10). To make the soil well refined, the
measurement value of similarity of Cu must be higher than 4 and Cc must be in the scale of 1 to
3. Therefore, it is evident that if the estimate of Cu is higher, then the scale of the sizes of the
ingredients in the soil becomes larger. Simultaneously, if the estimate of Cu is greater than it
signifies that the soil matter comprises varied scales of ingredient sizes.
3.7.2.2 Specific Gravity for Fine Aggregates (Pyconometer):
The confirmation of the comparative density (particular gravity) by utilizing ASTM
D854 and the immersion of the refine percentages are included in this test method. The
comparative density (particular gravity, is a sizeless quality, which is regarded as oven-dry (OD),
saturated-surface-dry (SSD), or as obvious comparative density (particular gravity). The OD
comparative density is decided after searing the percentage. The SSD comparative density and
immersion are regulated after wetting the percentage in water for a certain assigned period.
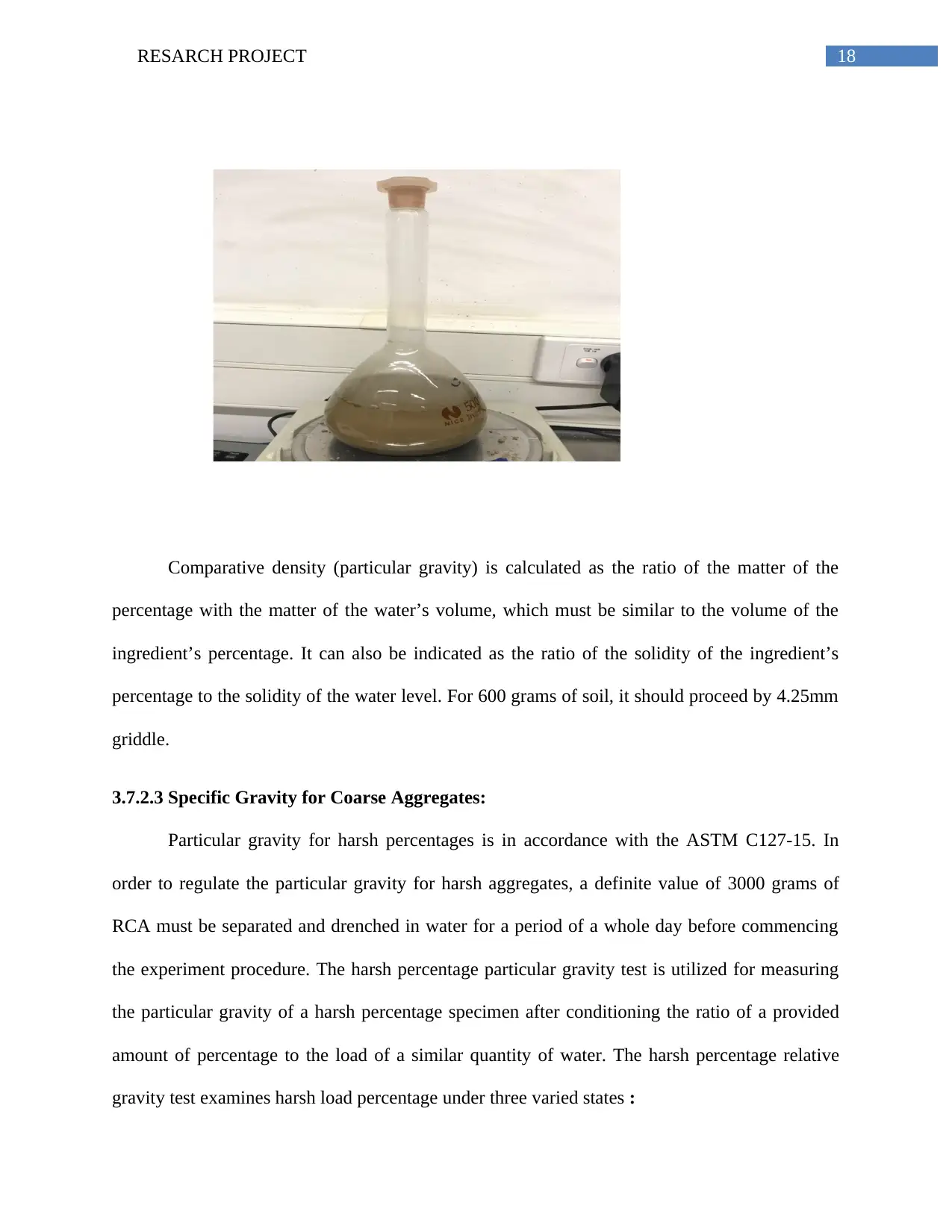
18RESARCH PROJECT
Comparative density (particular gravity) is calculated as the ratio of the matter of the
percentage with the matter of the water’s volume, which must be similar to the volume of the
ingredient’s percentage. It can also be indicated as the ratio of the solidity of the ingredient’s
percentage to the solidity of the water level. For 600 grams of soil, it should proceed by 4.25mm
griddle.
3.7.2.3 Specific Gravity for Coarse Aggregates:
Particular gravity for harsh percentages is in accordance with the ASTM C127-15. In
order to regulate the particular gravity for harsh aggregates, a definite value of 3000 grams of
RCA must be separated and drenched in water for a period of a whole day before commencing
the experiment procedure. The harsh percentage particular gravity test is utilized for measuring
the particular gravity of a harsh percentage specimen after conditioning the ratio of a provided
amount of percentage to the load of a similar quantity of water. The harsh percentage relative
gravity test examines harsh load percentage under three varied states :
Comparative density (particular gravity) is calculated as the ratio of the matter of the
percentage with the matter of the water’s volume, which must be similar to the volume of the
ingredient’s percentage. It can also be indicated as the ratio of the solidity of the ingredient’s
percentage to the solidity of the water level. For 600 grams of soil, it should proceed by 4.25mm
griddle.
3.7.2.3 Specific Gravity for Coarse Aggregates:
Particular gravity for harsh percentages is in accordance with the ASTM C127-15. In
order to regulate the particular gravity for harsh aggregates, a definite value of 3000 grams of
RCA must be separated and drenched in water for a period of a whole day before commencing
the experiment procedure. The harsh percentage particular gravity test is utilized for measuring
the particular gravity of a harsh percentage specimen after conditioning the ratio of a provided
amount of percentage to the load of a similar quantity of water. The harsh percentage relative
gravity test examines harsh load percentage under three varied states :
Paraphrase This Document
Need a fresh take? Get an instant paraphrase of this document with our AI Paraphraser
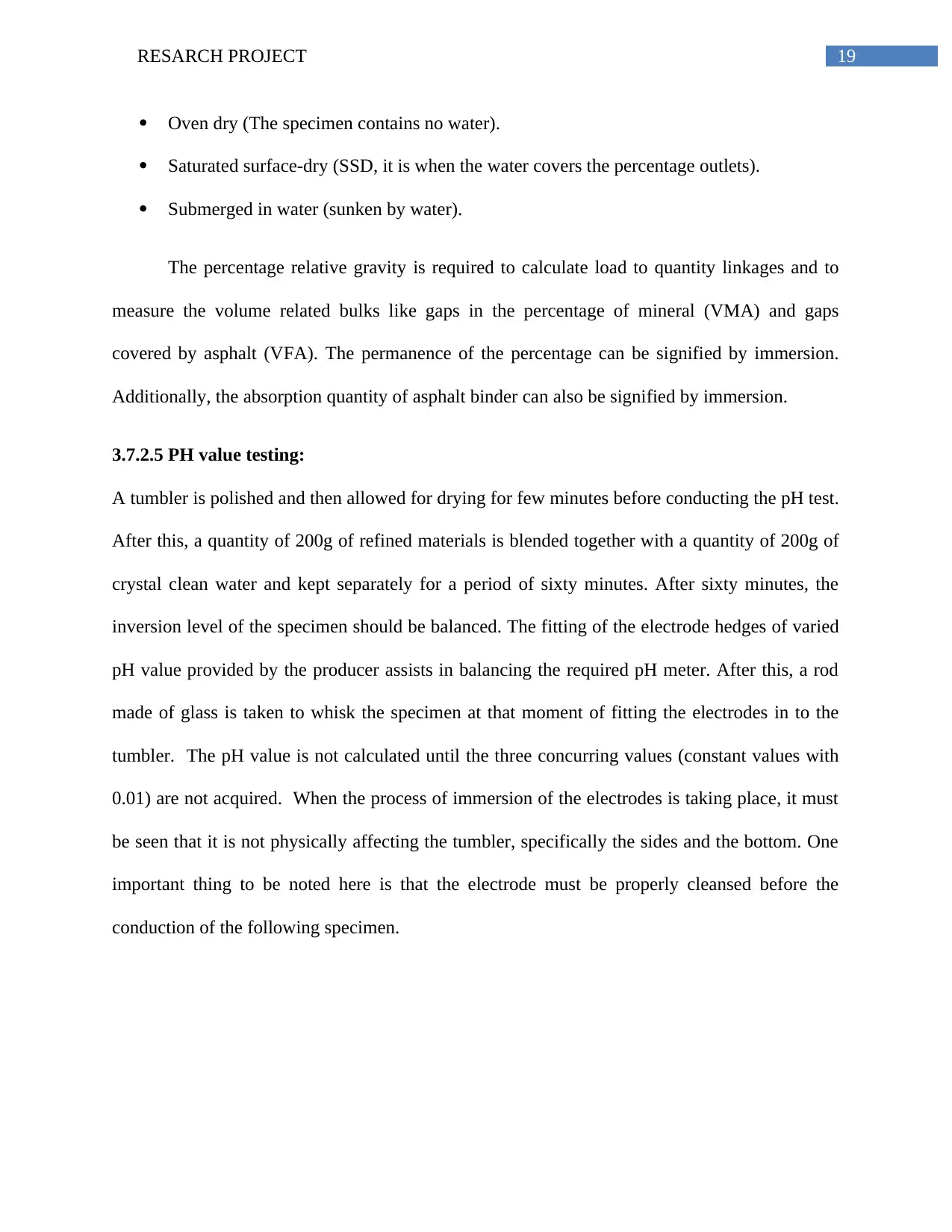
19RESARCH PROJECT
Oven dry (The specimen contains no water).
Saturated surface-dry (SSD, it is when the water covers the percentage outlets).
Submerged in water (sunken by water).
The percentage relative gravity is required to calculate load to quantity linkages and to
measure the volume related bulks like gaps in the percentage of mineral (VMA) and gaps
covered by asphalt (VFA). The permanence of the percentage can be signified by immersion.
Additionally, the absorption quantity of asphalt binder can also be signified by immersion.
3.7.2.5 PH value testing:
A tumbler is polished and then allowed for drying for few minutes before conducting the pH test.
After this, a quantity of 200g of refined materials is blended together with a quantity of 200g of
crystal clean water and kept separately for a period of sixty minutes. After sixty minutes, the
inversion level of the specimen should be balanced. The fitting of the electrode hedges of varied
pH value provided by the producer assists in balancing the required pH meter. After this, a rod
made of glass is taken to whisk the specimen at that moment of fitting the electrodes in to the
tumbler. The pH value is not calculated until the three concurring values (constant values with
0.01) are not acquired. When the process of immersion of the electrodes is taking place, it must
be seen that it is not physically affecting the tumbler, specifically the sides and the bottom. One
important thing to be noted here is that the electrode must be properly cleansed before the
conduction of the following specimen.
Oven dry (The specimen contains no water).
Saturated surface-dry (SSD, it is when the water covers the percentage outlets).
Submerged in water (sunken by water).
The percentage relative gravity is required to calculate load to quantity linkages and to
measure the volume related bulks like gaps in the percentage of mineral (VMA) and gaps
covered by asphalt (VFA). The permanence of the percentage can be signified by immersion.
Additionally, the absorption quantity of asphalt binder can also be signified by immersion.
3.7.2.5 PH value testing:
A tumbler is polished and then allowed for drying for few minutes before conducting the pH test.
After this, a quantity of 200g of refined materials is blended together with a quantity of 200g of
crystal clean water and kept separately for a period of sixty minutes. After sixty minutes, the
inversion level of the specimen should be balanced. The fitting of the electrode hedges of varied
pH value provided by the producer assists in balancing the required pH meter. After this, a rod
made of glass is taken to whisk the specimen at that moment of fitting the electrodes in to the
tumbler. The pH value is not calculated until the three concurring values (constant values with
0.01) are not acquired. When the process of immersion of the electrodes is taking place, it must
be seen that it is not physically affecting the tumbler, specifically the sides and the bottom. One
important thing to be noted here is that the electrode must be properly cleansed before the
conduction of the following specimen.
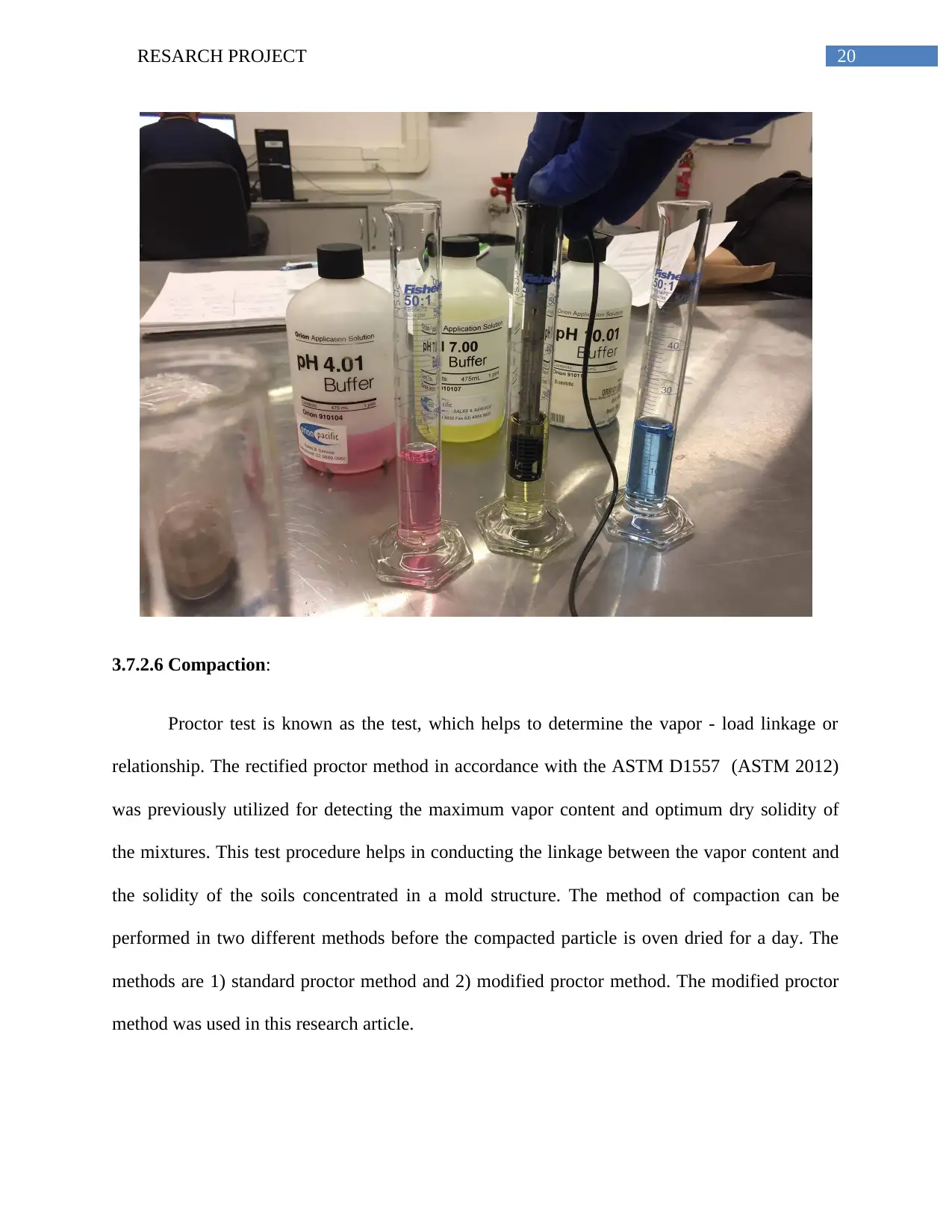
20RESARCH PROJECT
3.7.2.6 Compaction:
Proctor test is known as the test, which helps to determine the vapor - load linkage or
relationship. The rectified proctor method in accordance with the ASTM D1557 (ASTM 2012)
was previously utilized for detecting the maximum vapor content and optimum dry solidity of
the mixtures. This test procedure helps in conducting the linkage between the vapor content and
the solidity of the soils concentrated in a mold structure. The method of compaction can be
performed in two different methods before the compacted particle is oven dried for a day. The
methods are 1) standard proctor method and 2) modified proctor method. The modified proctor
method was used in this research article.
3.7.2.6 Compaction:
Proctor test is known as the test, which helps to determine the vapor - load linkage or
relationship. The rectified proctor method in accordance with the ASTM D1557 (ASTM 2012)
was previously utilized for detecting the maximum vapor content and optimum dry solidity of
the mixtures. This test procedure helps in conducting the linkage between the vapor content and
the solidity of the soils concentrated in a mold structure. The method of compaction can be
performed in two different methods before the compacted particle is oven dried for a day. The
methods are 1) standard proctor method and 2) modified proctor method. The modified proctor
method was used in this research article.
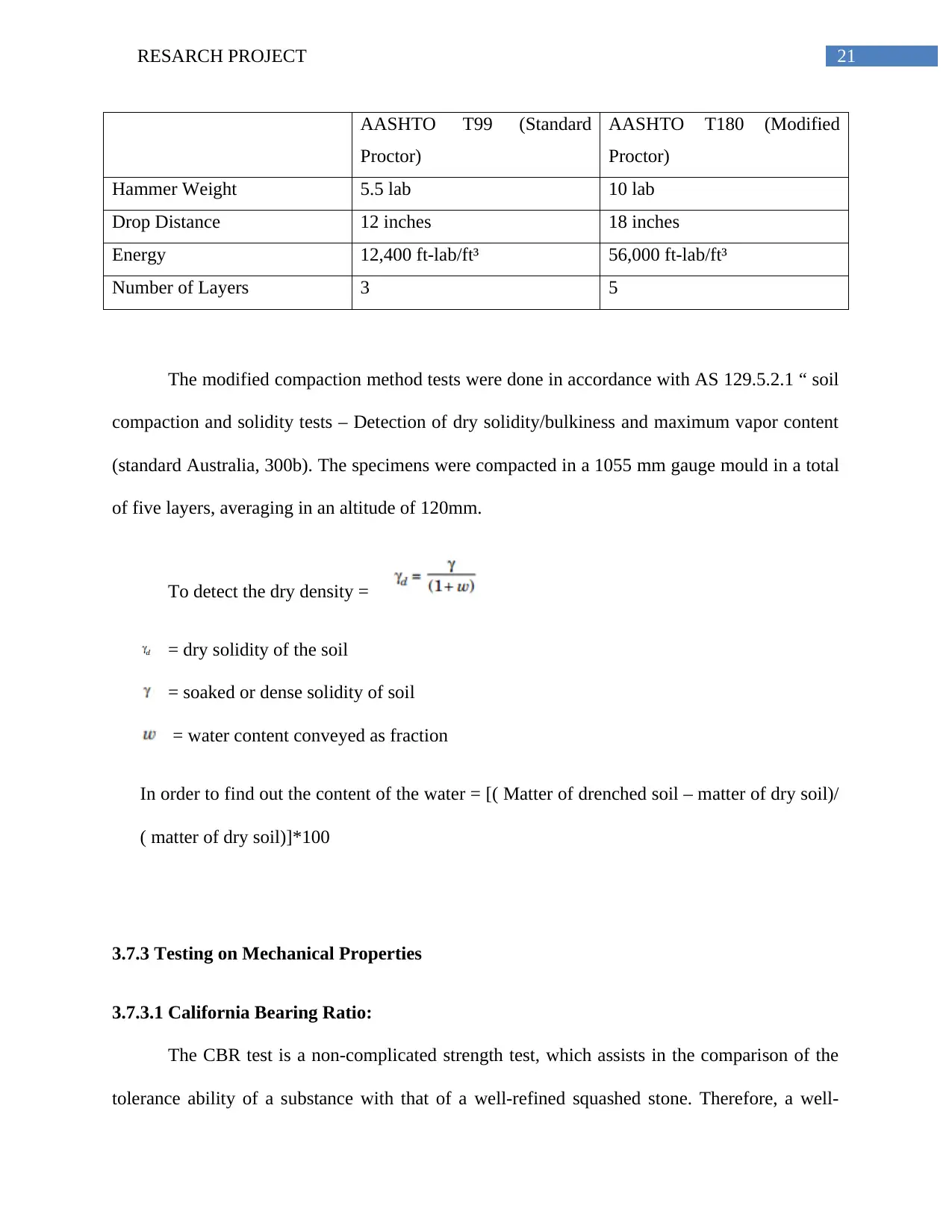
21RESARCH PROJECT
AASHTO T99 (Standard
Proctor)
AASHTO T180 (Modified
Proctor)
Hammer Weight 5.5 lab 10 lab
Drop Distance 12 inches 18 inches
Energy 12,400 ft-lab/ft³ 56,000 ft-lab/ft³
Number of Layers 3 5
The modified compaction method tests were done in accordance with AS 129.5.2.1 “ soil
compaction and solidity tests – Detection of dry solidity/bulkiness and maximum vapor content
(standard Australia, 300b). The specimens were compacted in a 1055 mm gauge mould in a total
of five layers, averaging in an altitude of 120mm.
To detect the dry density =
= dry solidity of the soil
= soaked or dense solidity of soil
= water content conveyed as fraction
In order to find out the content of the water = [( Matter of drenched soil – matter of dry soil)/
( matter of dry soil)]*100
3.7.3 Testing on Mechanical Properties
3.7.3.1 California Bearing Ratio:
The CBR test is a non-complicated strength test, which assists in the comparison of the
tolerance ability of a substance with that of a well-refined squashed stone. Therefore, a well-
AASHTO T99 (Standard
Proctor)
AASHTO T180 (Modified
Proctor)
Hammer Weight 5.5 lab 10 lab
Drop Distance 12 inches 18 inches
Energy 12,400 ft-lab/ft³ 56,000 ft-lab/ft³
Number of Layers 3 5
The modified compaction method tests were done in accordance with AS 129.5.2.1 “ soil
compaction and solidity tests – Detection of dry solidity/bulkiness and maximum vapor content
(standard Australia, 300b). The specimens were compacted in a 1055 mm gauge mould in a total
of five layers, averaging in an altitude of 120mm.
To detect the dry density =
= dry solidity of the soil
= soaked or dense solidity of soil
= water content conveyed as fraction
In order to find out the content of the water = [( Matter of drenched soil – matter of dry soil)/
( matter of dry soil)]*100
3.7.3 Testing on Mechanical Properties
3.7.3.1 California Bearing Ratio:
The CBR test is a non-complicated strength test, which assists in the comparison of the
tolerance ability of a substance with that of a well-refined squashed stone. Therefore, a well-
Secure Best Marks with AI Grader
Need help grading? Try our AI Grader for instant feedback on your assignments.
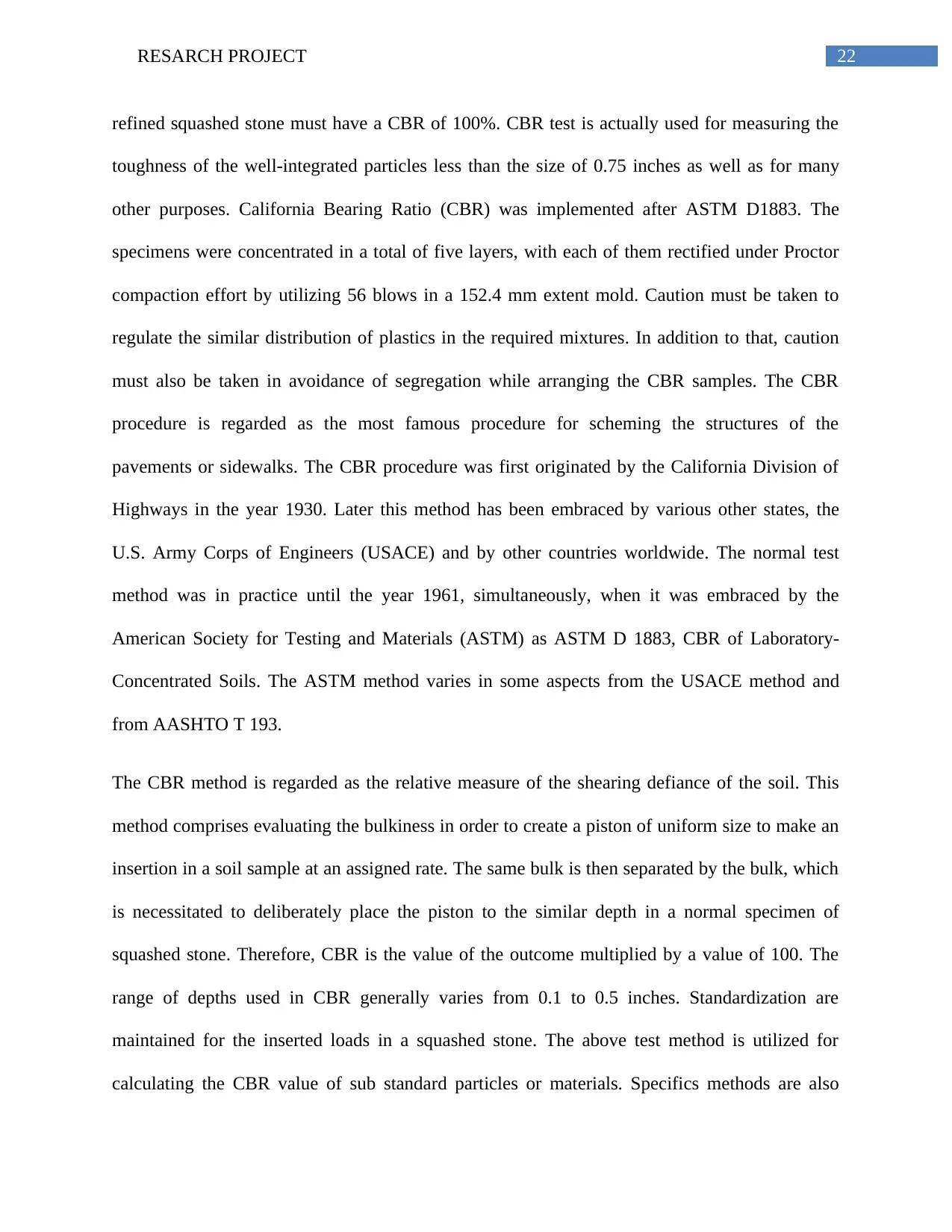
22RESARCH PROJECT
refined squashed stone must have a CBR of 100%. CBR test is actually used for measuring the
toughness of the well-integrated particles less than the size of 0.75 inches as well as for many
other purposes. California Bearing Ratio (CBR) was implemented after ASTM D1883. The
specimens were concentrated in a total of five layers, with each of them rectified under Proctor
compaction effort by utilizing 56 blows in a 152.4 mm extent mold. Caution must be taken to
regulate the similar distribution of plastics in the required mixtures. In addition to that, caution
must also be taken in avoidance of segregation while arranging the CBR samples. The CBR
procedure is regarded as the most famous procedure for scheming the structures of the
pavements or sidewalks. The CBR procedure was first originated by the California Division of
Highways in the year 1930. Later this method has been embraced by various other states, the
U.S. Army Corps of Engineers (USACE) and by other countries worldwide. The normal test
method was in practice until the year 1961, simultaneously, when it was embraced by the
American Society for Testing and Materials (ASTM) as ASTM D 1883, CBR of Laboratory-
Concentrated Soils. The ASTM method varies in some aspects from the USACE method and
from AASHTO T 193.
The CBR method is regarded as the relative measure of the shearing defiance of the soil. This
method comprises evaluating the bulkiness in order to create a piston of uniform size to make an
insertion in a soil sample at an assigned rate. The same bulk is then separated by the bulk, which
is necessitated to deliberately place the piston to the similar depth in a normal specimen of
squashed stone. Therefore, CBR is the value of the outcome multiplied by a value of 100. The
range of depths used in CBR generally varies from 0.1 to 0.5 inches. Standardization are
maintained for the inserted loads in a squashed stone. The above test method is utilized for
calculating the CBR value of sub standard particles or materials. Specifics methods are also
refined squashed stone must have a CBR of 100%. CBR test is actually used for measuring the
toughness of the well-integrated particles less than the size of 0.75 inches as well as for many
other purposes. California Bearing Ratio (CBR) was implemented after ASTM D1883. The
specimens were concentrated in a total of five layers, with each of them rectified under Proctor
compaction effort by utilizing 56 blows in a 152.4 mm extent mold. Caution must be taken to
regulate the similar distribution of plastics in the required mixtures. In addition to that, caution
must also be taken in avoidance of segregation while arranging the CBR samples. The CBR
procedure is regarded as the most famous procedure for scheming the structures of the
pavements or sidewalks. The CBR procedure was first originated by the California Division of
Highways in the year 1930. Later this method has been embraced by various other states, the
U.S. Army Corps of Engineers (USACE) and by other countries worldwide. The normal test
method was in practice until the year 1961, simultaneously, when it was embraced by the
American Society for Testing and Materials (ASTM) as ASTM D 1883, CBR of Laboratory-
Concentrated Soils. The ASTM method varies in some aspects from the USACE method and
from AASHTO T 193.
The CBR method is regarded as the relative measure of the shearing defiance of the soil. This
method comprises evaluating the bulkiness in order to create a piston of uniform size to make an
insertion in a soil sample at an assigned rate. The same bulk is then separated by the bulk, which
is necessitated to deliberately place the piston to the similar depth in a normal specimen of
squashed stone. Therefore, CBR is the value of the outcome multiplied by a value of 100. The
range of depths used in CBR generally varies from 0.1 to 0.5 inches. Standardization are
maintained for the inserted loads in a squashed stone. The above test method is utilized for
calculating the CBR value of sub standard particles or materials. Specifics methods are also
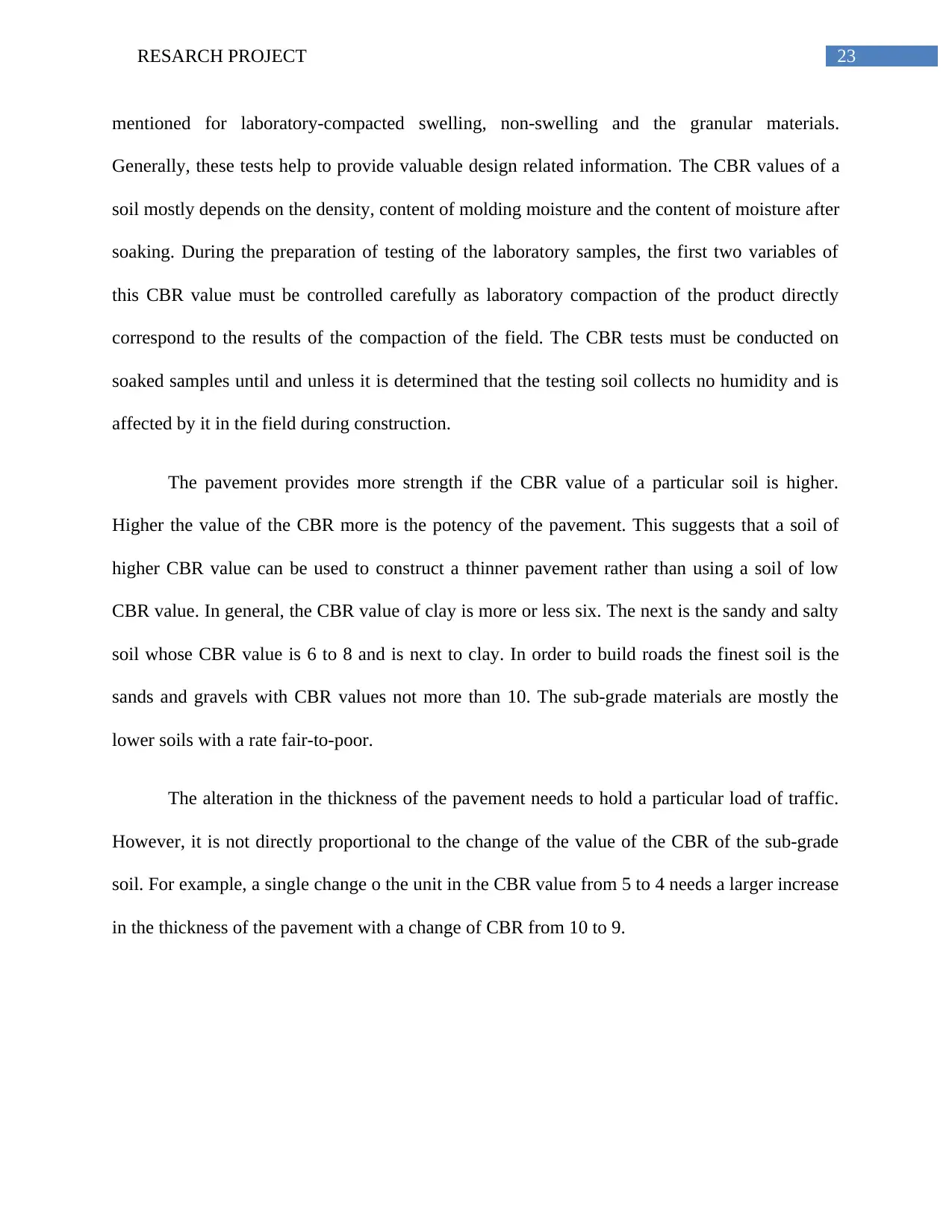
23RESARCH PROJECT
mentioned for laboratory-compacted swelling, non-swelling and the granular materials.
Generally, these tests help to provide valuable design related information. The CBR values of a
soil mostly depends on the density, content of molding moisture and the content of moisture after
soaking. During the preparation of testing of the laboratory samples, the first two variables of
this CBR value must be controlled carefully as laboratory compaction of the product directly
correspond to the results of the compaction of the field. The CBR tests must be conducted on
soaked samples until and unless it is determined that the testing soil collects no humidity and is
affected by it in the field during construction.
The pavement provides more strength if the CBR value of a particular soil is higher.
Higher the value of the CBR more is the potency of the pavement. This suggests that a soil of
higher CBR value can be used to construct a thinner pavement rather than using a soil of low
CBR value. In general, the CBR value of clay is more or less six. The next is the sandy and salty
soil whose CBR value is 6 to 8 and is next to clay. In order to build roads the finest soil is the
sands and gravels with CBR values not more than 10. The sub-grade materials are mostly the
lower soils with a rate fair-to-poor.
The alteration in the thickness of the pavement needs to hold a particular load of traffic.
However, it is not directly proportional to the change of the value of the CBR of the sub-grade
soil. For example, a single change o the unit in the CBR value from 5 to 4 needs a larger increase
in the thickness of the pavement with a change of CBR from 10 to 9.
mentioned for laboratory-compacted swelling, non-swelling and the granular materials.
Generally, these tests help to provide valuable design related information. The CBR values of a
soil mostly depends on the density, content of molding moisture and the content of moisture after
soaking. During the preparation of testing of the laboratory samples, the first two variables of
this CBR value must be controlled carefully as laboratory compaction of the product directly
correspond to the results of the compaction of the field. The CBR tests must be conducted on
soaked samples until and unless it is determined that the testing soil collects no humidity and is
affected by it in the field during construction.
The pavement provides more strength if the CBR value of a particular soil is higher.
Higher the value of the CBR more is the potency of the pavement. This suggests that a soil of
higher CBR value can be used to construct a thinner pavement rather than using a soil of low
CBR value. In general, the CBR value of clay is more or less six. The next is the sandy and salty
soil whose CBR value is 6 to 8 and is next to clay. In order to build roads the finest soil is the
sands and gravels with CBR values not more than 10. The sub-grade materials are mostly the
lower soils with a rate fair-to-poor.
The alteration in the thickness of the pavement needs to hold a particular load of traffic.
However, it is not directly proportional to the change of the value of the CBR of the sub-grade
soil. For example, a single change o the unit in the CBR value from 5 to 4 needs a larger increase
in the thickness of the pavement with a change of CBR from 10 to 9.
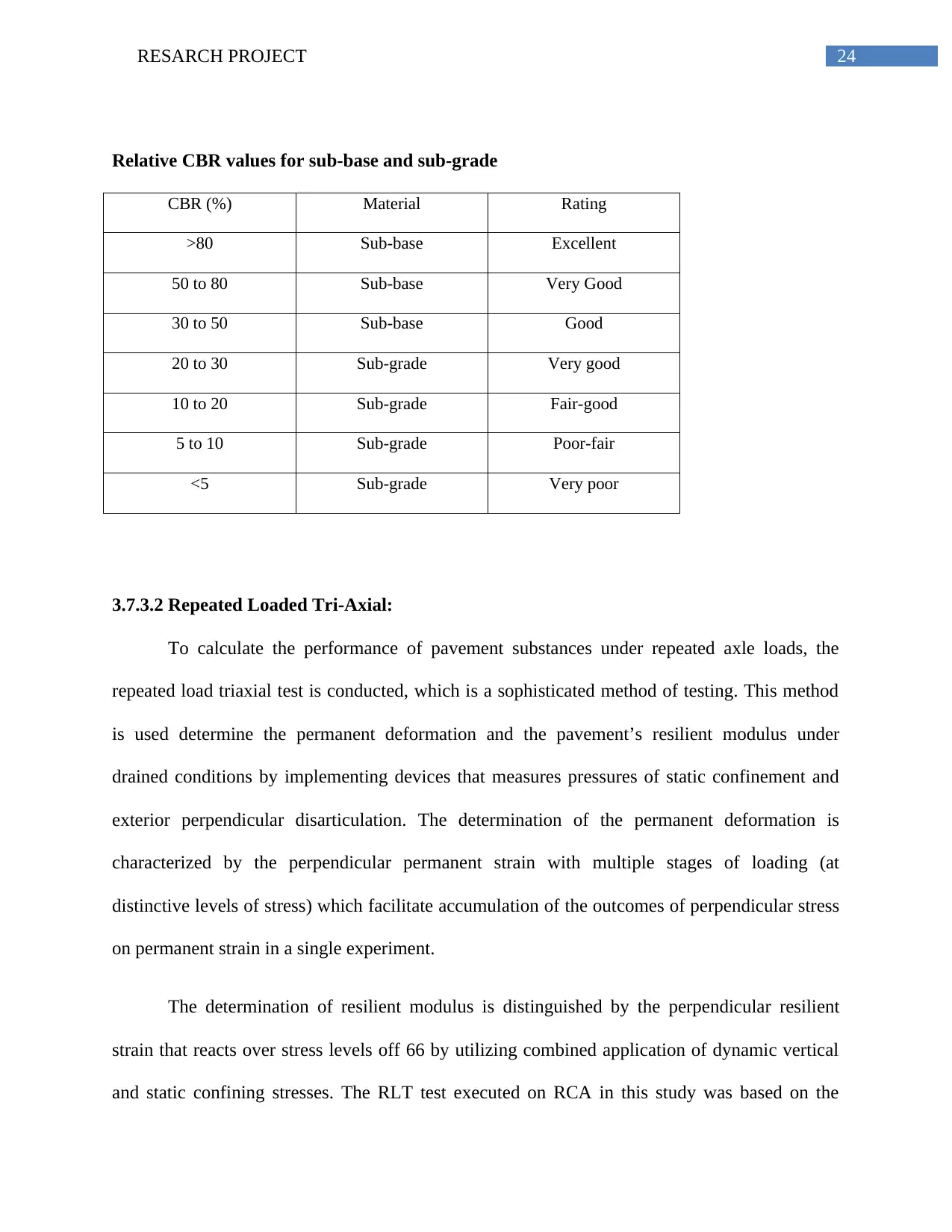
24RESARCH PROJECT
Relative CBR values for sub-base and sub-grade
CBR (%) Material Rating
>80 Sub-base Excellent
50 to 80 Sub-base Very Good
30 to 50 Sub-base Good
20 to 30 Sub-grade Very good
10 to 20 Sub-grade Fair-good
5 to 10 Sub-grade Poor-fair
<5 Sub-grade Very poor
3.7.3.2 Repeated Loaded Tri-Axial:
To calculate the performance of pavement substances under repeated axle loads, the
repeated load triaxial test is conducted, which is a sophisticated method of testing. This method
is used determine the permanent deformation and the pavement’s resilient modulus under
drained conditions by implementing devices that measures pressures of static confinement and
exterior perpendicular disarticulation. The determination of the permanent deformation is
characterized by the perpendicular permanent strain with multiple stages of loading (at
distinctive levels of stress) which facilitate accumulation of the outcomes of perpendicular stress
on permanent strain in a single experiment.
The determination of resilient modulus is distinguished by the perpendicular resilient
strain that reacts over stress levels off 66 by utilizing combined application of dynamic vertical
and static confining stresses. The RLT test executed on RCA in this study was based on the
Relative CBR values for sub-base and sub-grade
CBR (%) Material Rating
>80 Sub-base Excellent
50 to 80 Sub-base Very Good
30 to 50 Sub-base Good
20 to 30 Sub-grade Very good
10 to 20 Sub-grade Fair-good
5 to 10 Sub-grade Poor-fair
<5 Sub-grade Very poor
3.7.3.2 Repeated Loaded Tri-Axial:
To calculate the performance of pavement substances under repeated axle loads, the
repeated load triaxial test is conducted, which is a sophisticated method of testing. This method
is used determine the permanent deformation and the pavement’s resilient modulus under
drained conditions by implementing devices that measures pressures of static confinement and
exterior perpendicular disarticulation. The determination of the permanent deformation is
characterized by the perpendicular permanent strain with multiple stages of loading (at
distinctive levels of stress) which facilitate accumulation of the outcomes of perpendicular stress
on permanent strain in a single experiment.
The determination of resilient modulus is distinguished by the perpendicular resilient
strain that reacts over stress levels off 66 by utilizing combined application of dynamic vertical
and static confining stresses. The RLT test executed on RCA in this study was based on the
Paraphrase This Document
Need a fresh take? Get an instant paraphrase of this document with our AI Paraphraser
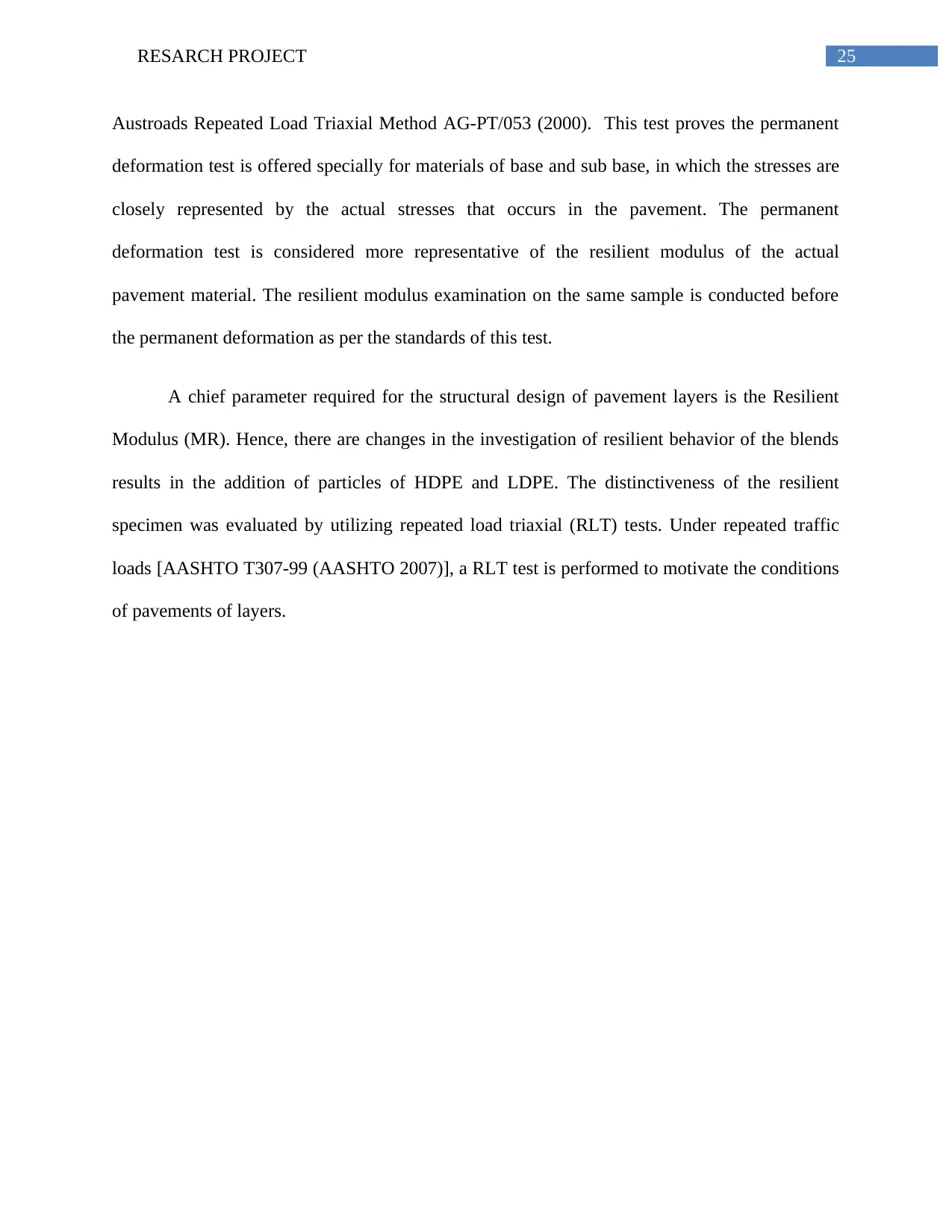
25RESARCH PROJECT
Austroads Repeated Load Triaxial Method AG-PT/053 (2000). This test proves the permanent
deformation test is offered specially for materials of base and sub base, in which the stresses are
closely represented by the actual stresses that occurs in the pavement. The permanent
deformation test is considered more representative of the resilient modulus of the actual
pavement material. The resilient modulus examination on the same sample is conducted before
the permanent deformation as per the standards of this test.
A chief parameter required for the structural design of pavement layers is the Resilient
Modulus (MR). Hence, there are changes in the investigation of resilient behavior of the blends
results in the addition of particles of HDPE and LDPE. The distinctiveness of the resilient
specimen was evaluated by utilizing repeated load triaxial (RLT) tests. Under repeated traffic
loads [AASHTO T307-99 (AASHTO 2007)], a RLT test is performed to motivate the conditions
of pavements of layers.
Austroads Repeated Load Triaxial Method AG-PT/053 (2000). This test proves the permanent
deformation test is offered specially for materials of base and sub base, in which the stresses are
closely represented by the actual stresses that occurs in the pavement. The permanent
deformation test is considered more representative of the resilient modulus of the actual
pavement material. The resilient modulus examination on the same sample is conducted before
the permanent deformation as per the standards of this test.
A chief parameter required for the structural design of pavement layers is the Resilient
Modulus (MR). Hence, there are changes in the investigation of resilient behavior of the blends
results in the addition of particles of HDPE and LDPE. The distinctiveness of the resilient
specimen was evaluated by utilizing repeated load triaxial (RLT) tests. Under repeated traffic
loads [AASHTO T307-99 (AASHTO 2007)], a RLT test is performed to motivate the conditions
of pavements of layers.
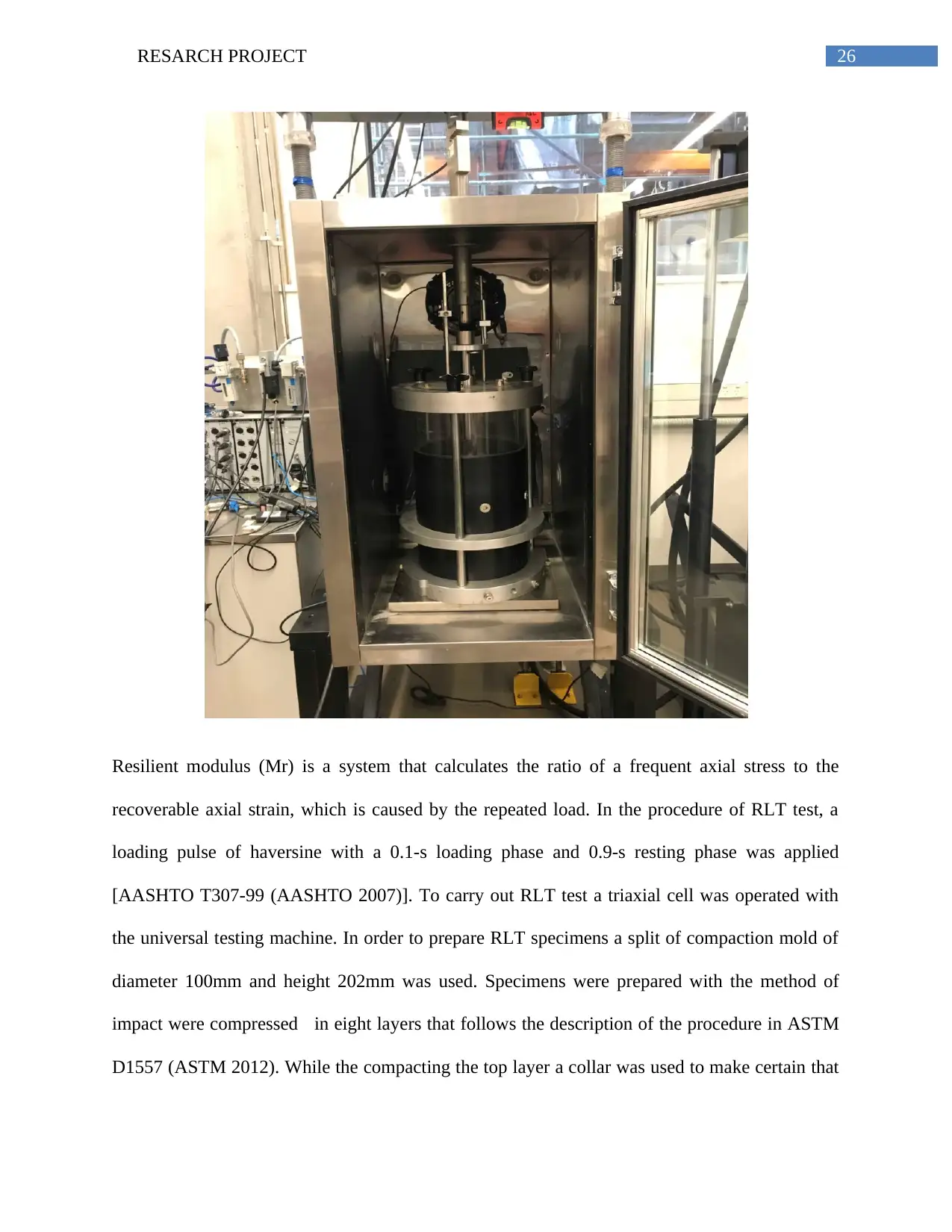
26RESARCH PROJECT
Resilient modulus (Mr) is a system that calculates the ratio of a frequent axial stress to the
recoverable axial strain, which is caused by the repeated load. In the procedure of RLT test, a
loading pulse of haversine with a 0.1-s loading phase and 0.9-s resting phase was applied
[AASHTO T307-99 (AASHTO 2007)]. To carry out RLT test a triaxial cell was operated with
the universal testing machine. In order to prepare RLT specimens a split of compaction mold of
diameter 100mm and height 202mm was used. Specimens were prepared with the method of
impact were compressed in eight layers that follows the description of the procedure in ASTM
D1557 (ASTM 2012). While the compacting the top layer a collar was used to make certain that
Resilient modulus (Mr) is a system that calculates the ratio of a frequent axial stress to the
recoverable axial strain, which is caused by the repeated load. In the procedure of RLT test, a
loading pulse of haversine with a 0.1-s loading phase and 0.9-s resting phase was applied
[AASHTO T307-99 (AASHTO 2007)]. To carry out RLT test a triaxial cell was operated with
the universal testing machine. In order to prepare RLT specimens a split of compaction mold of
diameter 100mm and height 202mm was used. Specimens were prepared with the method of
impact were compressed in eight layers that follows the description of the procedure in ASTM
D1557 (ASTM 2012). While the compacting the top layer a collar was used to make certain that
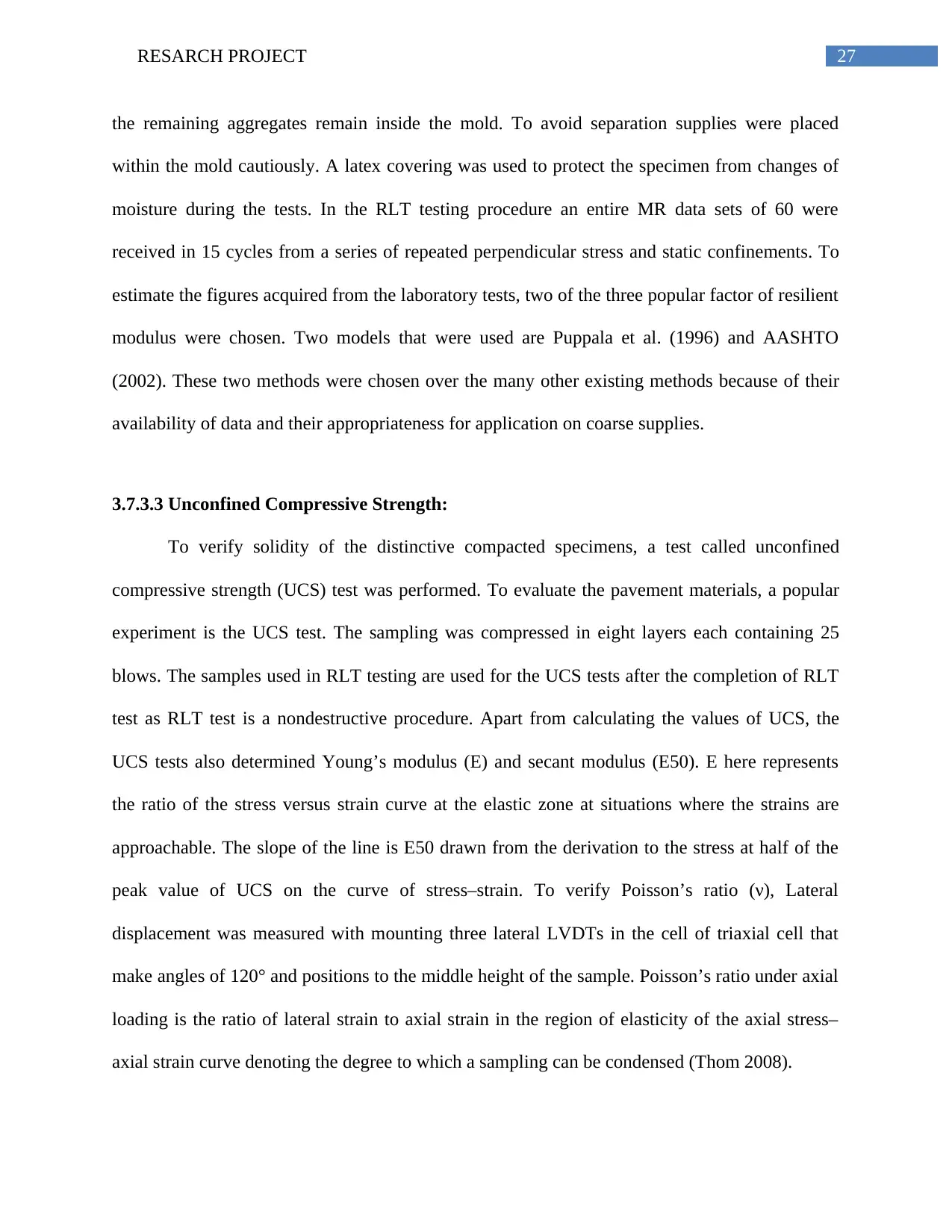
27RESARCH PROJECT
the remaining aggregates remain inside the mold. To avoid separation supplies were placed
within the mold cautiously. A latex covering was used to protect the specimen from changes of
moisture during the tests. In the RLT testing procedure an entire MR data sets of 60 were
received in 15 cycles from a series of repeated perpendicular stress and static confinements. To
estimate the figures acquired from the laboratory tests, two of the three popular factor of resilient
modulus were chosen. Two models that were used are Puppala et al. (1996) and AASHTO
(2002). These two methods were chosen over the many other existing methods because of their
availability of data and their appropriateness for application on coarse supplies.
3.7.3.3 Unconfined Compressive Strength:
To verify solidity of the distinctive compacted specimens, a test called unconfined
compressive strength (UCS) test was performed. To evaluate the pavement materials, a popular
experiment is the UCS test. The sampling was compressed in eight layers each containing 25
blows. The samples used in RLT testing are used for the UCS tests after the completion of RLT
test as RLT test is a nondestructive procedure. Apart from calculating the values of UCS, the
UCS tests also determined Young’s modulus (E) and secant modulus (E50). E here represents
the ratio of the stress versus strain curve at the elastic zone at situations where the strains are
approachable. The slope of the line is E50 drawn from the derivation to the stress at half of the
peak value of UCS on the curve of stress–strain. To verify Poisson’s ratio (ν), Lateral
displacement was measured with mounting three lateral LVDTs in the cell of triaxial cell that
make angles of 120° and positions to the middle height of the sample. Poisson’s ratio under axial
loading is the ratio of lateral strain to axial strain in the region of elasticity of the axial stress–
axial strain curve denoting the degree to which a sampling can be condensed (Thom 2008).
the remaining aggregates remain inside the mold. To avoid separation supplies were placed
within the mold cautiously. A latex covering was used to protect the specimen from changes of
moisture during the tests. In the RLT testing procedure an entire MR data sets of 60 were
received in 15 cycles from a series of repeated perpendicular stress and static confinements. To
estimate the figures acquired from the laboratory tests, two of the three popular factor of resilient
modulus were chosen. Two models that were used are Puppala et al. (1996) and AASHTO
(2002). These two methods were chosen over the many other existing methods because of their
availability of data and their appropriateness for application on coarse supplies.
3.7.3.3 Unconfined Compressive Strength:
To verify solidity of the distinctive compacted specimens, a test called unconfined
compressive strength (UCS) test was performed. To evaluate the pavement materials, a popular
experiment is the UCS test. The sampling was compressed in eight layers each containing 25
blows. The samples used in RLT testing are used for the UCS tests after the completion of RLT
test as RLT test is a nondestructive procedure. Apart from calculating the values of UCS, the
UCS tests also determined Young’s modulus (E) and secant modulus (E50). E here represents
the ratio of the stress versus strain curve at the elastic zone at situations where the strains are
approachable. The slope of the line is E50 drawn from the derivation to the stress at half of the
peak value of UCS on the curve of stress–strain. To verify Poisson’s ratio (ν), Lateral
displacement was measured with mounting three lateral LVDTs in the cell of triaxial cell that
make angles of 120° and positions to the middle height of the sample. Poisson’s ratio under axial
loading is the ratio of lateral strain to axial strain in the region of elasticity of the axial stress–
axial strain curve denoting the degree to which a sampling can be condensed (Thom 2008).
Secure Best Marks with AI Grader
Need help grading? Try our AI Grader for instant feedback on your assignments.
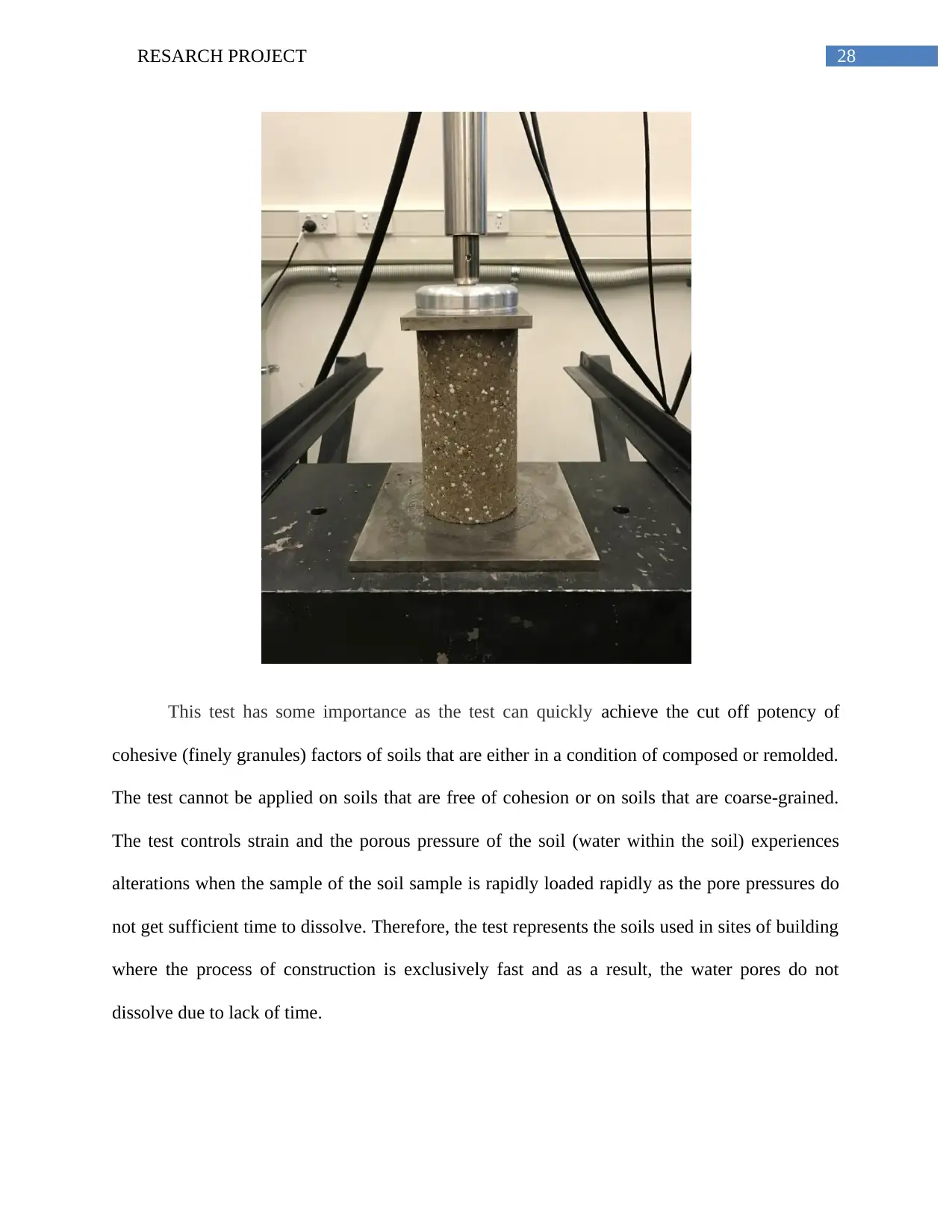
28RESARCH PROJECT
This test has some importance as the test can quickly achieve the cut off potency of
cohesive (finely granules) factors of soils that are either in a condition of composed or remolded.
The test cannot be applied on soils that are free of cohesion or on soils that are coarse-grained.
The test controls strain and the porous pressure of the soil (water within the soil) experiences
alterations when the sample of the soil sample is rapidly loaded rapidly as the pore pressures do
not get sufficient time to dissolve. Therefore, the test represents the soils used in sites of building
where the process of construction is exclusively fast and as a result, the water pores do not
dissolve due to lack of time.
This test has some importance as the test can quickly achieve the cut off potency of
cohesive (finely granules) factors of soils that are either in a condition of composed or remolded.
The test cannot be applied on soils that are free of cohesion or on soils that are coarse-grained.
The test controls strain and the porous pressure of the soil (water within the soil) experiences
alterations when the sample of the soil sample is rapidly loaded rapidly as the pore pressures do
not get sufficient time to dissolve. Therefore, the test represents the soils used in sites of building
where the process of construction is exclusively fast and as a result, the water pores do not
dissolve due to lack of time.
1 out of 29
![[object Object]](/_next/image/?url=%2F_next%2Fstatic%2Fmedia%2Flogo.6d15ce61.png&w=640&q=75)
Your All-in-One AI-Powered Toolkit for Academic Success.
+13062052269
info@desklib.com
Available 24*7 on WhatsApp / Email
Unlock your academic potential
© 2024 | Zucol Services PVT LTD | All rights reserved.