Construction Management Plan: Industrial Estate Project in Melbourne
VerifiedAdded on 2023/06/07
|59
|14001
|216
Report
AI Summary
This report presents a comprehensive construction management plan for a small industrial estate project located in the Eastern suburbs of Melbourne, involving the construction of 12 warehouses, a common driveway, and parking facilities. The plan outlines the construction sequence, program, site layout, and bulk excavation strategy, emphasizing the importance of managing time, cost, and scope constraints. It details resource management, cash flow forecasting, and cost control strategies to ensure the project stays within budget and timeline. Furthermore, the plan addresses external factors such as health and safety, environmental impact (noise, dust, vibration), and trade overlaps, while also recommending quality management procedures based on ISO 9001 standards. The report concludes with recommendations for future projects to enhance management efficiency and achieve optimal outcomes by effectively balancing the triple constraints.
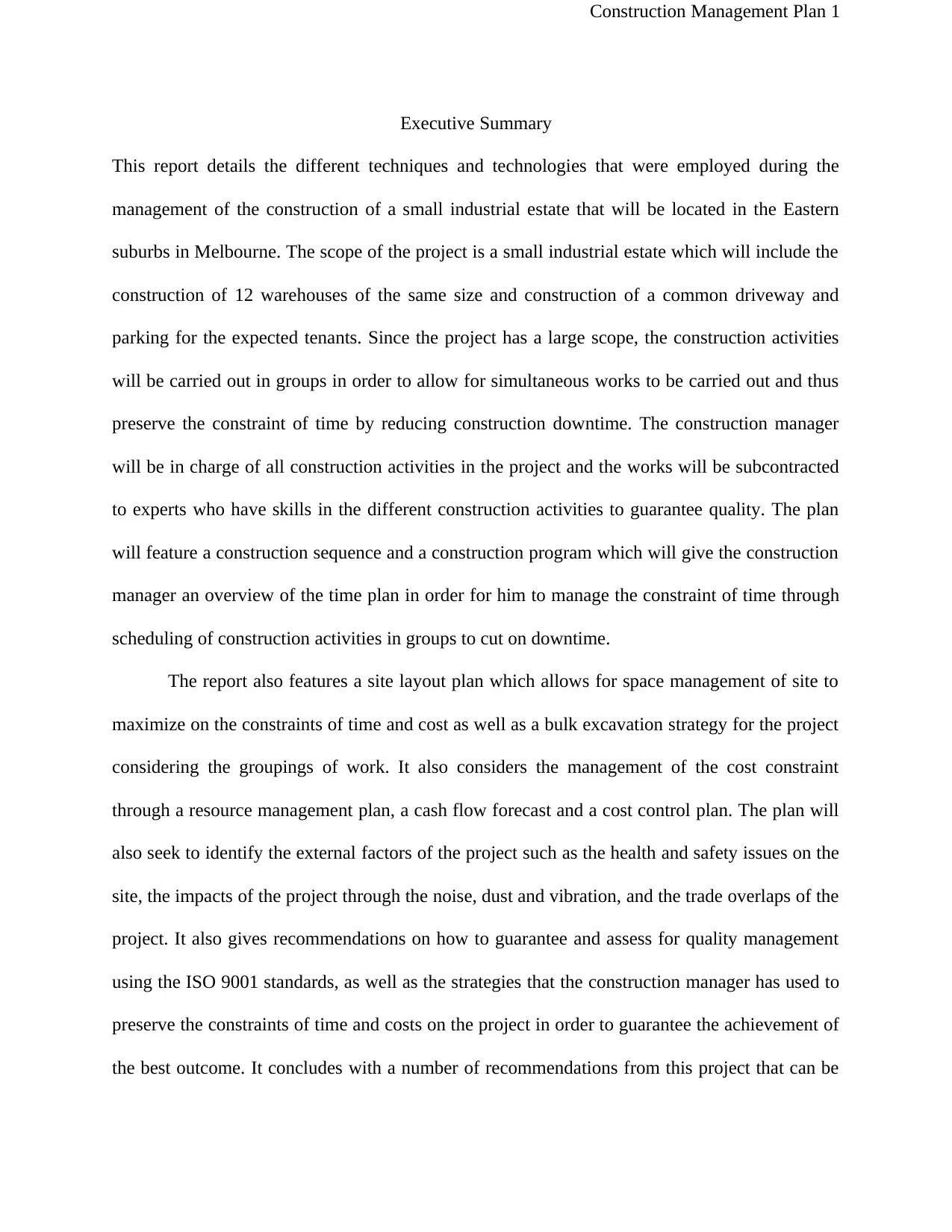
Construction Management Plan 1
Executive Summary
This report details the different techniques and technologies that were employed during the
management of the construction of a small industrial estate that will be located in the Eastern
suburbs in Melbourne. The scope of the project is a small industrial estate which will include the
construction of 12 warehouses of the same size and construction of a common driveway and
parking for the expected tenants. Since the project has a large scope, the construction activities
will be carried out in groups in order to allow for simultaneous works to be carried out and thus
preserve the constraint of time by reducing construction downtime. The construction manager
will be in charge of all construction activities in the project and the works will be subcontracted
to experts who have skills in the different construction activities to guarantee quality. The plan
will feature a construction sequence and a construction program which will give the construction
manager an overview of the time plan in order for him to manage the constraint of time through
scheduling of construction activities in groups to cut on downtime.
The report also features a site layout plan which allows for space management of site to
maximize on the constraints of time and cost as well as a bulk excavation strategy for the project
considering the groupings of work. It also considers the management of the cost constraint
through a resource management plan, a cash flow forecast and a cost control plan. The plan will
also seek to identify the external factors of the project such as the health and safety issues on the
site, the impacts of the project through the noise, dust and vibration, and the trade overlaps of the
project. It also gives recommendations on how to guarantee and assess for quality management
using the ISO 9001 standards, as well as the strategies that the construction manager has used to
preserve the constraints of time and costs on the project in order to guarantee the achievement of
the best outcome. It concludes with a number of recommendations from this project that can be
Executive Summary
This report details the different techniques and technologies that were employed during the
management of the construction of a small industrial estate that will be located in the Eastern
suburbs in Melbourne. The scope of the project is a small industrial estate which will include the
construction of 12 warehouses of the same size and construction of a common driveway and
parking for the expected tenants. Since the project has a large scope, the construction activities
will be carried out in groups in order to allow for simultaneous works to be carried out and thus
preserve the constraint of time by reducing construction downtime. The construction manager
will be in charge of all construction activities in the project and the works will be subcontracted
to experts who have skills in the different construction activities to guarantee quality. The plan
will feature a construction sequence and a construction program which will give the construction
manager an overview of the time plan in order for him to manage the constraint of time through
scheduling of construction activities in groups to cut on downtime.
The report also features a site layout plan which allows for space management of site to
maximize on the constraints of time and cost as well as a bulk excavation strategy for the project
considering the groupings of work. It also considers the management of the cost constraint
through a resource management plan, a cash flow forecast and a cost control plan. The plan will
also seek to identify the external factors of the project such as the health and safety issues on the
site, the impacts of the project through the noise, dust and vibration, and the trade overlaps of the
project. It also gives recommendations on how to guarantee and assess for quality management
using the ISO 9001 standards, as well as the strategies that the construction manager has used to
preserve the constraints of time and costs on the project in order to guarantee the achievement of
the best outcome. It concludes with a number of recommendations from this project that can be
Paraphrase This Document
Need a fresh take? Get an instant paraphrase of this document with our AI Paraphraser
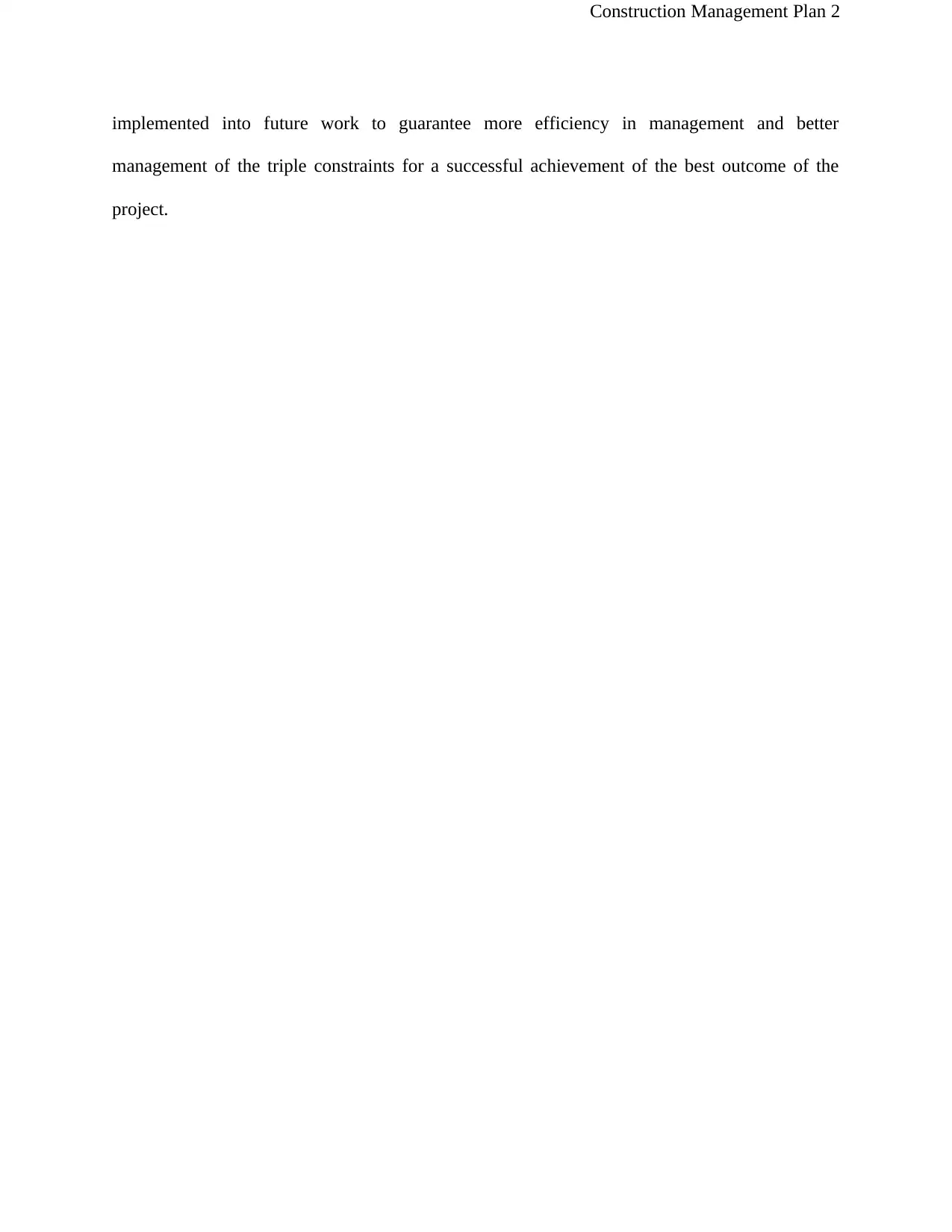
Construction Management Plan 2
implemented into future work to guarantee more efficiency in management and better
management of the triple constraints for a successful achievement of the best outcome of the
project.
implemented into future work to guarantee more efficiency in management and better
management of the triple constraints for a successful achievement of the best outcome of the
project.
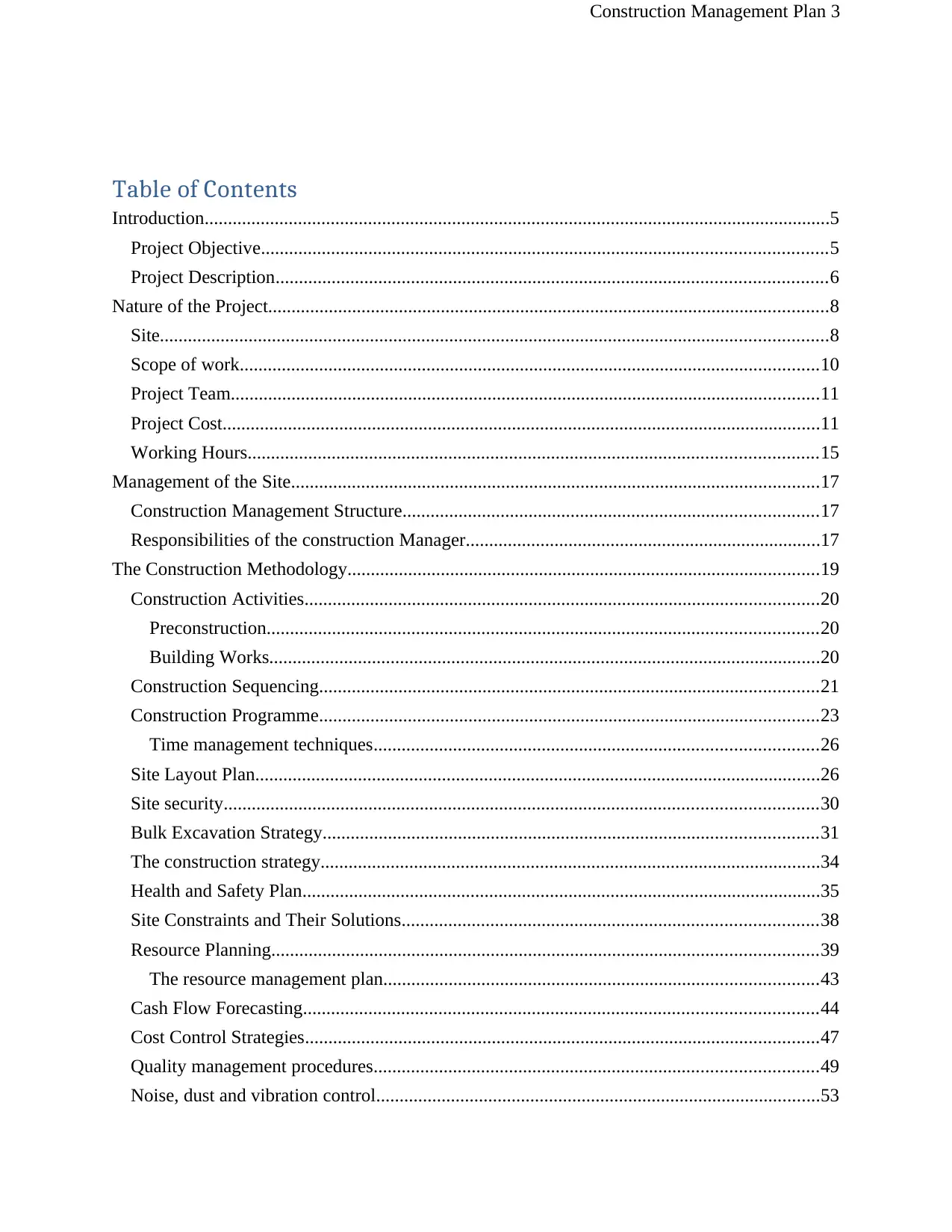
Construction Management Plan 3
Table of Contents
Introduction......................................................................................................................................5
Project Objective.........................................................................................................................5
Project Description......................................................................................................................6
Nature of the Project........................................................................................................................8
Site...............................................................................................................................................8
Scope of work............................................................................................................................10
Project Team..............................................................................................................................11
Project Cost................................................................................................................................11
Working Hours..........................................................................................................................15
Management of the Site.................................................................................................................17
Construction Management Structure.........................................................................................17
Responsibilities of the construction Manager............................................................................17
The Construction Methodology.....................................................................................................19
Construction Activities..............................................................................................................20
Preconstruction......................................................................................................................20
Building Works......................................................................................................................20
Construction Sequencing...........................................................................................................21
Construction Programme...........................................................................................................23
Time management techniques...............................................................................................26
Site Layout Plan.........................................................................................................................26
Site security...............................................................................................................................30
Bulk Excavation Strategy..........................................................................................................31
The construction strategy...........................................................................................................34
Health and Safety Plan...............................................................................................................35
Site Constraints and Their Solutions.........................................................................................38
Resource Planning.....................................................................................................................39
The resource management plan.............................................................................................43
Cash Flow Forecasting..............................................................................................................44
Cost Control Strategies..............................................................................................................47
Quality management procedures...............................................................................................49
Noise, dust and vibration control...............................................................................................53
Table of Contents
Introduction......................................................................................................................................5
Project Objective.........................................................................................................................5
Project Description......................................................................................................................6
Nature of the Project........................................................................................................................8
Site...............................................................................................................................................8
Scope of work............................................................................................................................10
Project Team..............................................................................................................................11
Project Cost................................................................................................................................11
Working Hours..........................................................................................................................15
Management of the Site.................................................................................................................17
Construction Management Structure.........................................................................................17
Responsibilities of the construction Manager............................................................................17
The Construction Methodology.....................................................................................................19
Construction Activities..............................................................................................................20
Preconstruction......................................................................................................................20
Building Works......................................................................................................................20
Construction Sequencing...........................................................................................................21
Construction Programme...........................................................................................................23
Time management techniques...............................................................................................26
Site Layout Plan.........................................................................................................................26
Site security...............................................................................................................................30
Bulk Excavation Strategy..........................................................................................................31
The construction strategy...........................................................................................................34
Health and Safety Plan...............................................................................................................35
Site Constraints and Their Solutions.........................................................................................38
Resource Planning.....................................................................................................................39
The resource management plan.............................................................................................43
Cash Flow Forecasting..............................................................................................................44
Cost Control Strategies..............................................................................................................47
Quality management procedures...............................................................................................49
Noise, dust and vibration control...............................................................................................53
⊘ This is a preview!⊘
Do you want full access?
Subscribe today to unlock all pages.

Trusted by 1+ million students worldwide
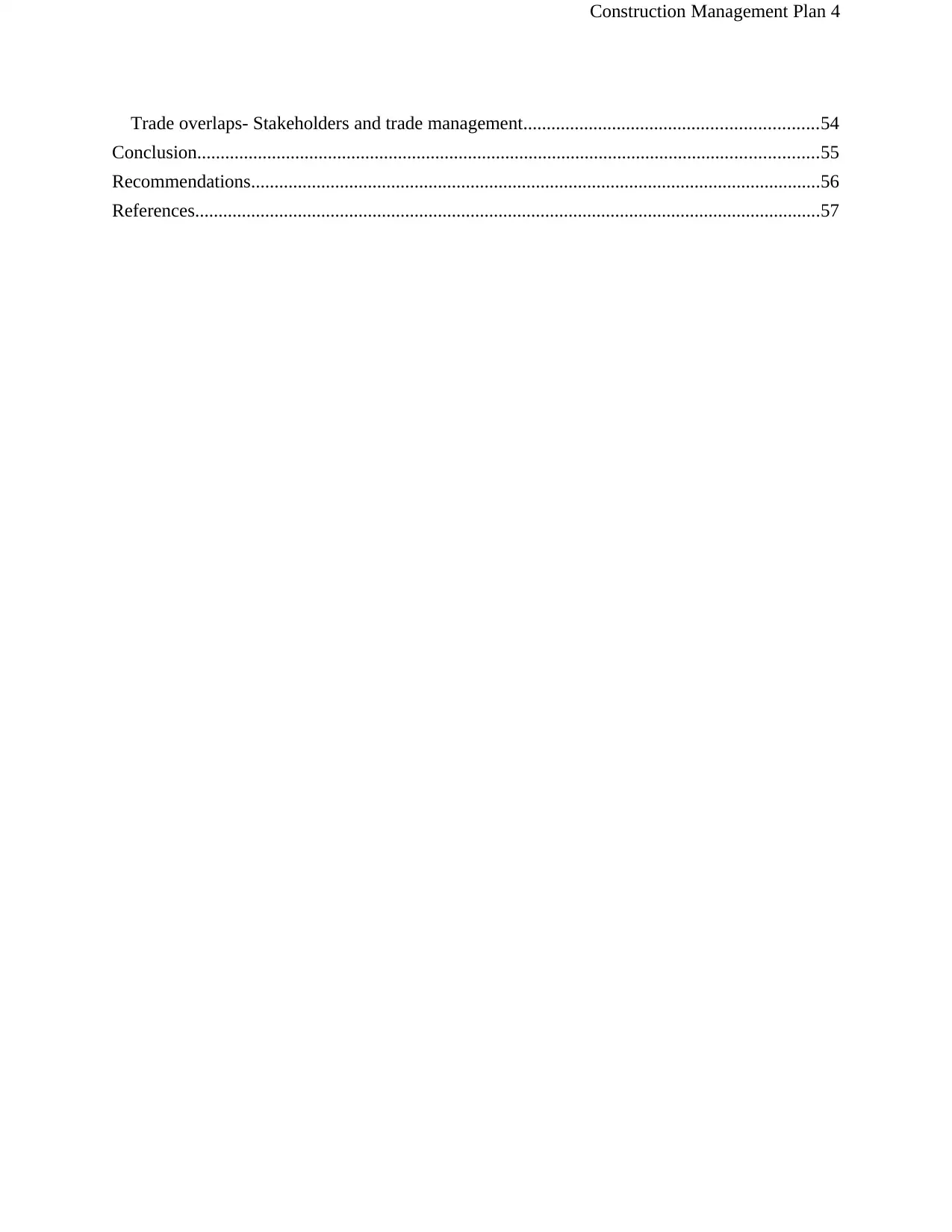
Construction Management Plan 4
Trade overlaps- Stakeholders and trade management...............................................................54
Conclusion.....................................................................................................................................55
Recommendations..........................................................................................................................56
References......................................................................................................................................57
Trade overlaps- Stakeholders and trade management...............................................................54
Conclusion.....................................................................................................................................55
Recommendations..........................................................................................................................56
References......................................................................................................................................57
Paraphrase This Document
Need a fresh take? Get an instant paraphrase of this document with our AI Paraphraser
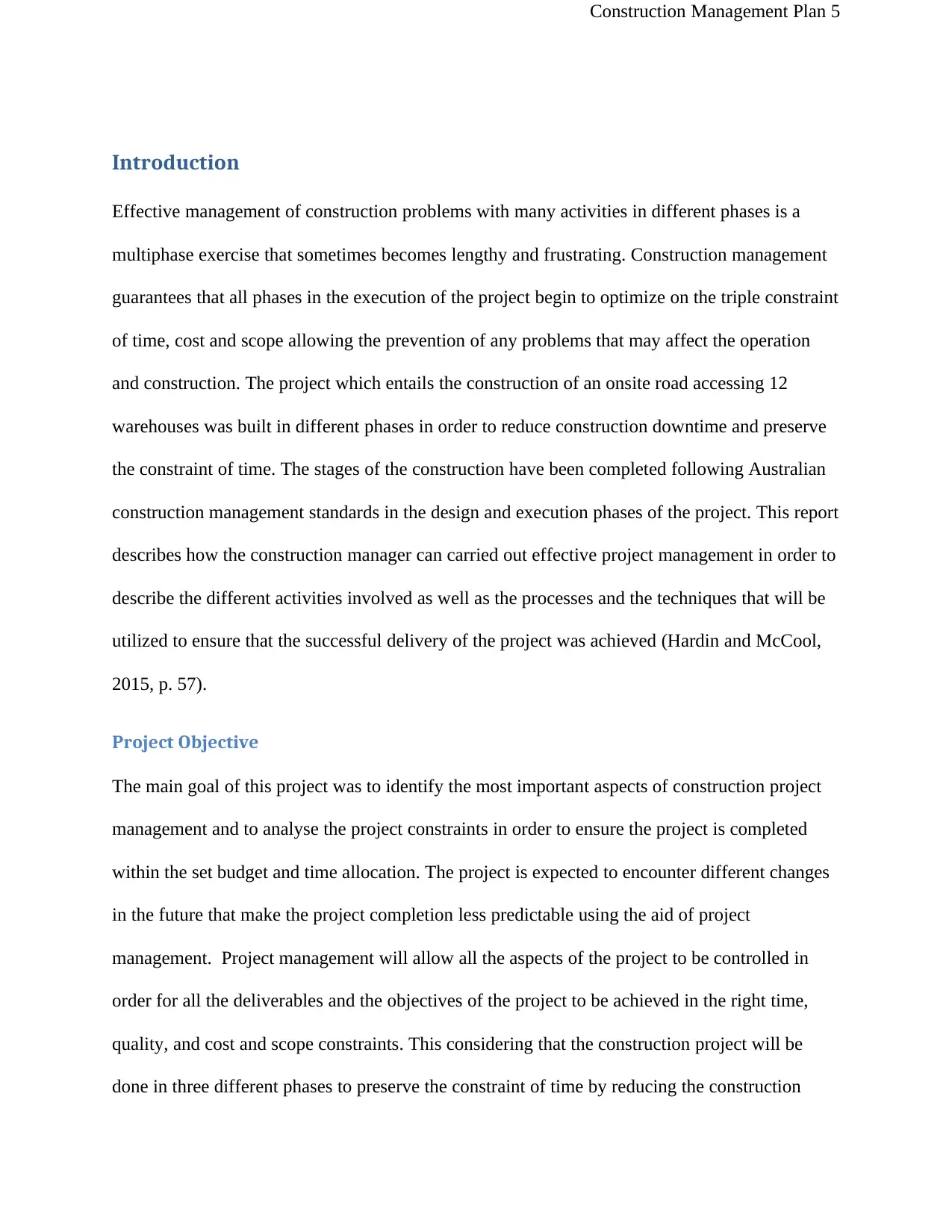
Construction Management Plan 5
Introduction
Effective management of construction problems with many activities in different phases is a
multiphase exercise that sometimes becomes lengthy and frustrating. Construction management
guarantees that all phases in the execution of the project begin to optimize on the triple constraint
of time, cost and scope allowing the prevention of any problems that may affect the operation
and construction. The project which entails the construction of an onsite road accessing 12
warehouses was built in different phases in order to reduce construction downtime and preserve
the constraint of time. The stages of the construction have been completed following Australian
construction management standards in the design and execution phases of the project. This report
describes how the construction manager can carried out effective project management in order to
describe the different activities involved as well as the processes and the techniques that will be
utilized to ensure that the successful delivery of the project was achieved (Hardin and McCool,
2015, p. 57).
Project Objective
The main goal of this project was to identify the most important aspects of construction project
management and to analyse the project constraints in order to ensure the project is completed
within the set budget and time allocation. The project is expected to encounter different changes
in the future that make the project completion less predictable using the aid of project
management. Project management will allow all the aspects of the project to be controlled in
order for all the deliverables and the objectives of the project to be achieved in the right time,
quality, and cost and scope constraints. This considering that the construction project will be
done in three different phases to preserve the constraint of time by reducing the construction
Introduction
Effective management of construction problems with many activities in different phases is a
multiphase exercise that sometimes becomes lengthy and frustrating. Construction management
guarantees that all phases in the execution of the project begin to optimize on the triple constraint
of time, cost and scope allowing the prevention of any problems that may affect the operation
and construction. The project which entails the construction of an onsite road accessing 12
warehouses was built in different phases in order to reduce construction downtime and preserve
the constraint of time. The stages of the construction have been completed following Australian
construction management standards in the design and execution phases of the project. This report
describes how the construction manager can carried out effective project management in order to
describe the different activities involved as well as the processes and the techniques that will be
utilized to ensure that the successful delivery of the project was achieved (Hardin and McCool,
2015, p. 57).
Project Objective
The main goal of this project was to identify the most important aspects of construction project
management and to analyse the project constraints in order to ensure the project is completed
within the set budget and time allocation. The project is expected to encounter different changes
in the future that make the project completion less predictable using the aid of project
management. Project management will allow all the aspects of the project to be controlled in
order for all the deliverables and the objectives of the project to be achieved in the right time,
quality, and cost and scope constraints. This considering that the construction project will be
done in three different phases to preserve the constraint of time by reducing the construction
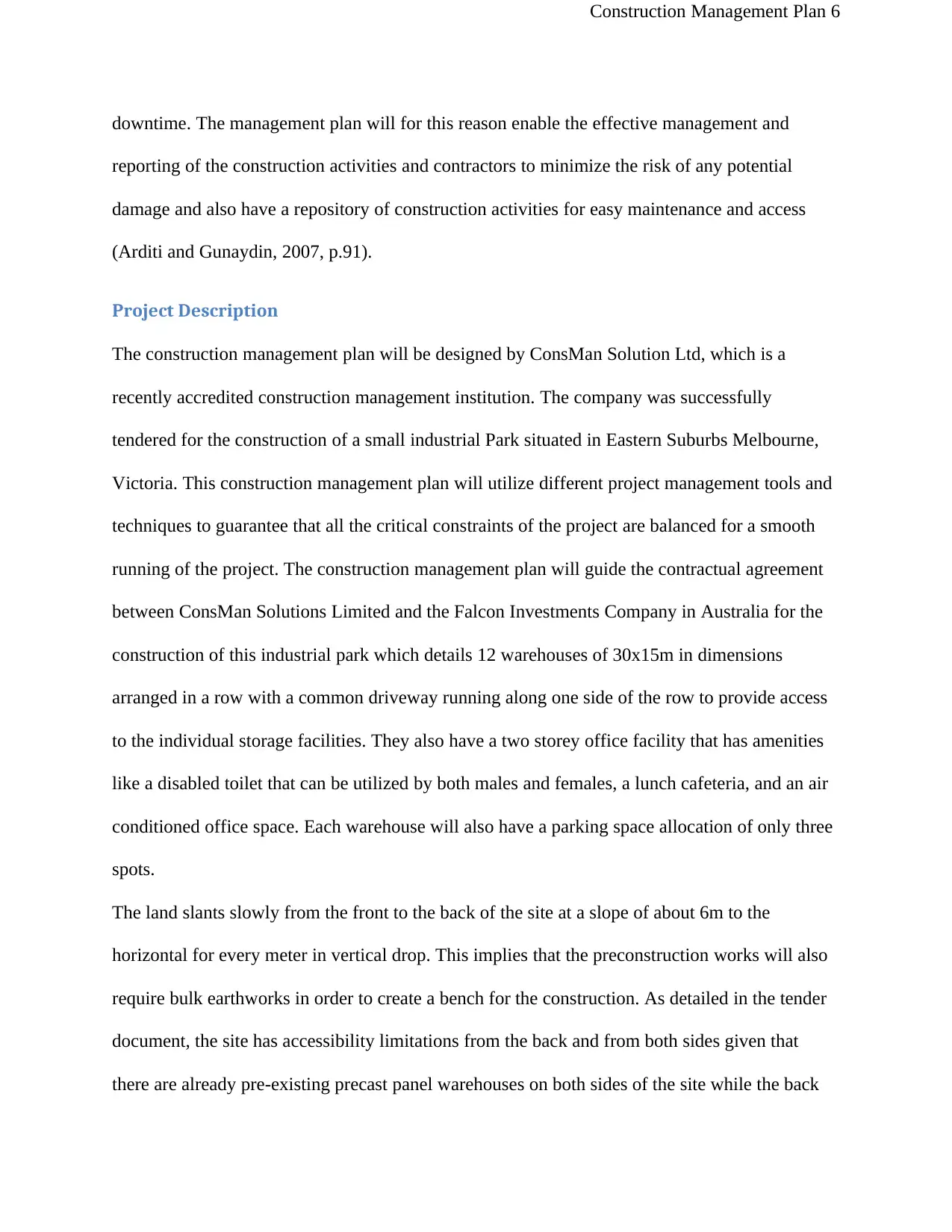
Construction Management Plan 6
downtime. The management plan will for this reason enable the effective management and
reporting of the construction activities and contractors to minimize the risk of any potential
damage and also have a repository of construction activities for easy maintenance and access
(Arditi and Gunaydin, 2007, p.91).
Project Description
The construction management plan will be designed by ConsMan Solution Ltd, which is a
recently accredited construction management institution. The company was successfully
tendered for the construction of a small industrial Park situated in Eastern Suburbs Melbourne,
Victoria. This construction management plan will utilize different project management tools and
techniques to guarantee that all the critical constraints of the project are balanced for a smooth
running of the project. The construction management plan will guide the contractual agreement
between ConsMan Solutions Limited and the Falcon Investments Company in Australia for the
construction of this industrial park which details 12 warehouses of 30x15m in dimensions
arranged in a row with a common driveway running along one side of the row to provide access
to the individual storage facilities. They also have a two storey office facility that has amenities
like a disabled toilet that can be utilized by both males and females, a lunch cafeteria, and an air
conditioned office space. Each warehouse will also have a parking space allocation of only three
spots.
The land slants slowly from the front to the back of the site at a slope of about 6m to the
horizontal for every meter in vertical drop. This implies that the preconstruction works will also
require bulk earthworks in order to create a bench for the construction. As detailed in the tender
document, the site has accessibility limitations from the back and from both sides given that
there are already pre-existing precast panel warehouses on both sides of the site while the back
downtime. The management plan will for this reason enable the effective management and
reporting of the construction activities and contractors to minimize the risk of any potential
damage and also have a repository of construction activities for easy maintenance and access
(Arditi and Gunaydin, 2007, p.91).
Project Description
The construction management plan will be designed by ConsMan Solution Ltd, which is a
recently accredited construction management institution. The company was successfully
tendered for the construction of a small industrial Park situated in Eastern Suburbs Melbourne,
Victoria. This construction management plan will utilize different project management tools and
techniques to guarantee that all the critical constraints of the project are balanced for a smooth
running of the project. The construction management plan will guide the contractual agreement
between ConsMan Solutions Limited and the Falcon Investments Company in Australia for the
construction of this industrial park which details 12 warehouses of 30x15m in dimensions
arranged in a row with a common driveway running along one side of the row to provide access
to the individual storage facilities. They also have a two storey office facility that has amenities
like a disabled toilet that can be utilized by both males and females, a lunch cafeteria, and an air
conditioned office space. Each warehouse will also have a parking space allocation of only three
spots.
The land slants slowly from the front to the back of the site at a slope of about 6m to the
horizontal for every meter in vertical drop. This implies that the preconstruction works will also
require bulk earthworks in order to create a bench for the construction. As detailed in the tender
document, the site has accessibility limitations from the back and from both sides given that
there are already pre-existing precast panel warehouses on both sides of the site while the back
⊘ This is a preview!⊘
Do you want full access?
Subscribe today to unlock all pages.

Trusted by 1+ million students worldwide
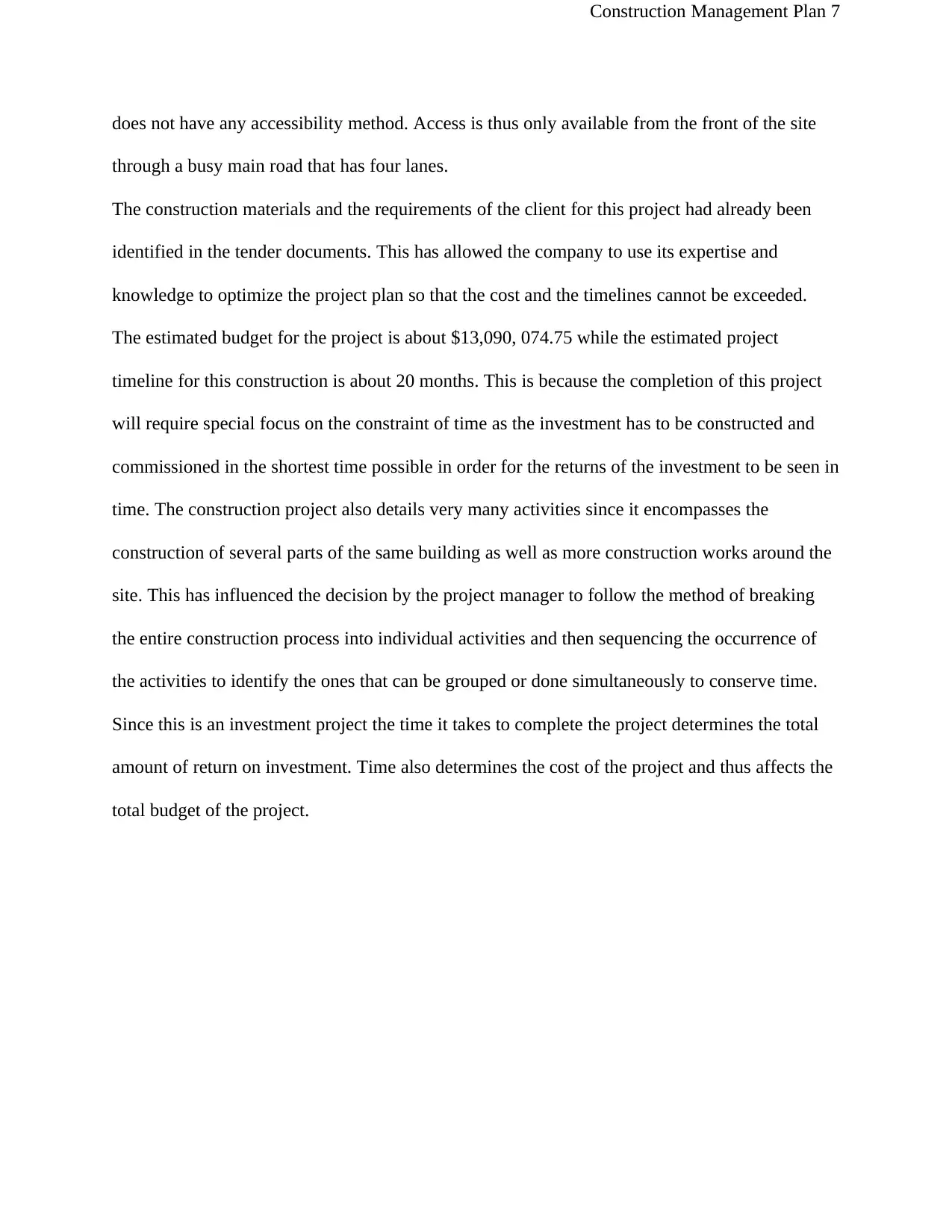
Construction Management Plan 7
does not have any accessibility method. Access is thus only available from the front of the site
through a busy main road that has four lanes.
The construction materials and the requirements of the client for this project had already been
identified in the tender documents. This has allowed the company to use its expertise and
knowledge to optimize the project plan so that the cost and the timelines cannot be exceeded.
The estimated budget for the project is about $13,090, 074.75 while the estimated project
timeline for this construction is about 20 months. This is because the completion of this project
will require special focus on the constraint of time as the investment has to be constructed and
commissioned in the shortest time possible in order for the returns of the investment to be seen in
time. The construction project also details very many activities since it encompasses the
construction of several parts of the same building as well as more construction works around the
site. This has influenced the decision by the project manager to follow the method of breaking
the entire construction process into individual activities and then sequencing the occurrence of
the activities to identify the ones that can be grouped or done simultaneously to conserve time.
Since this is an investment project the time it takes to complete the project determines the total
amount of return on investment. Time also determines the cost of the project and thus affects the
total budget of the project.
does not have any accessibility method. Access is thus only available from the front of the site
through a busy main road that has four lanes.
The construction materials and the requirements of the client for this project had already been
identified in the tender documents. This has allowed the company to use its expertise and
knowledge to optimize the project plan so that the cost and the timelines cannot be exceeded.
The estimated budget for the project is about $13,090, 074.75 while the estimated project
timeline for this construction is about 20 months. This is because the completion of this project
will require special focus on the constraint of time as the investment has to be constructed and
commissioned in the shortest time possible in order for the returns of the investment to be seen in
time. The construction project also details very many activities since it encompasses the
construction of several parts of the same building as well as more construction works around the
site. This has influenced the decision by the project manager to follow the method of breaking
the entire construction process into individual activities and then sequencing the occurrence of
the activities to identify the ones that can be grouped or done simultaneously to conserve time.
Since this is an investment project the time it takes to complete the project determines the total
amount of return on investment. Time also determines the cost of the project and thus affects the
total budget of the project.
Paraphrase This Document
Need a fresh take? Get an instant paraphrase of this document with our AI Paraphraser
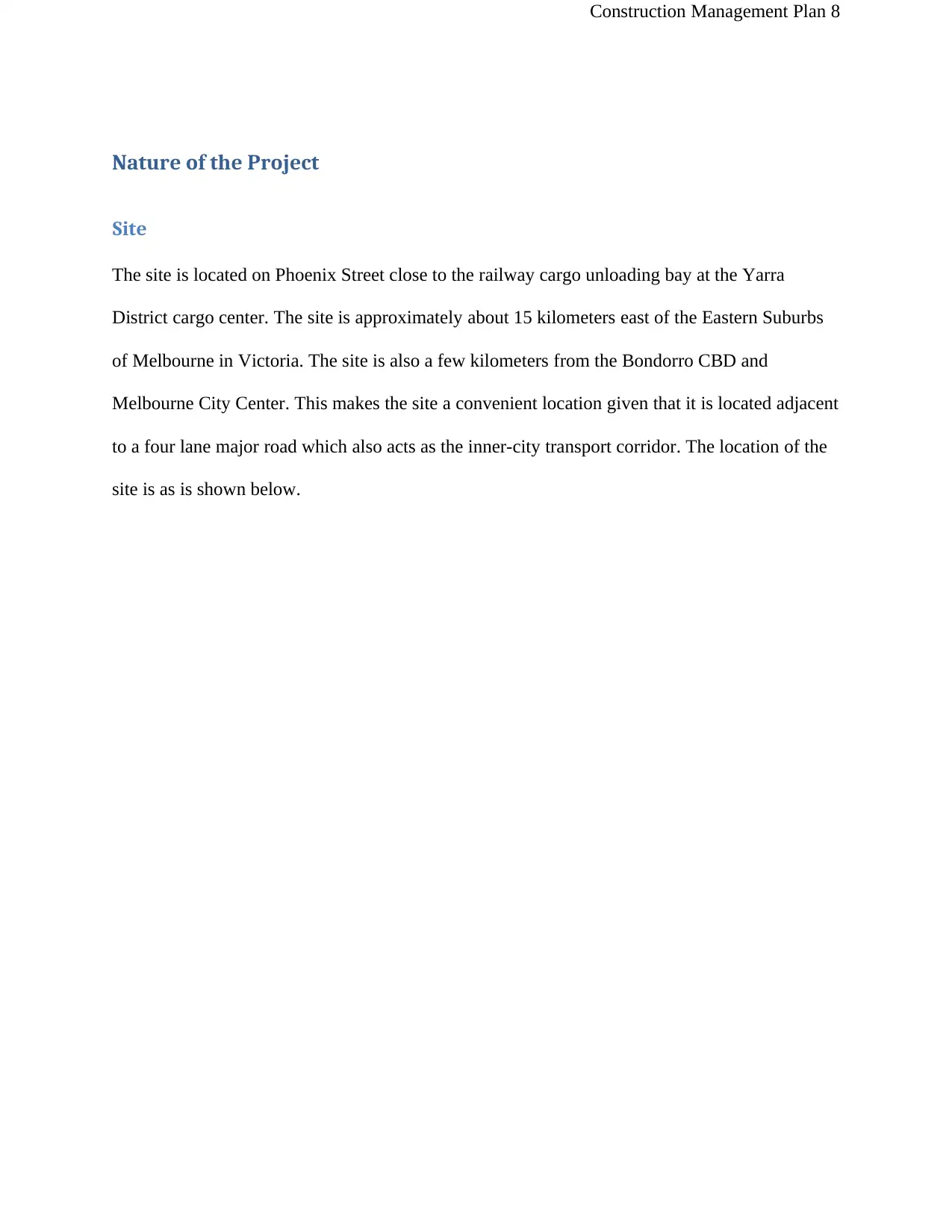
Construction Management Plan 8
Nature of the Project
Site
The site is located on Phoenix Street close to the railway cargo unloading bay at the Yarra
District cargo center. The site is approximately about 15 kilometers east of the Eastern Suburbs
of Melbourne in Victoria. The site is also a few kilometers from the Bondorro CBD and
Melbourne City Center. This makes the site a convenient location given that it is located adjacent
to a four lane major road which also acts as the inner-city transport corridor. The location of the
site is as is shown below.
Nature of the Project
Site
The site is located on Phoenix Street close to the railway cargo unloading bay at the Yarra
District cargo center. The site is approximately about 15 kilometers east of the Eastern Suburbs
of Melbourne in Victoria. The site is also a few kilometers from the Bondorro CBD and
Melbourne City Center. This makes the site a convenient location given that it is located adjacent
to a four lane major road which also acts as the inner-city transport corridor. The location of the
site is as is shown below.
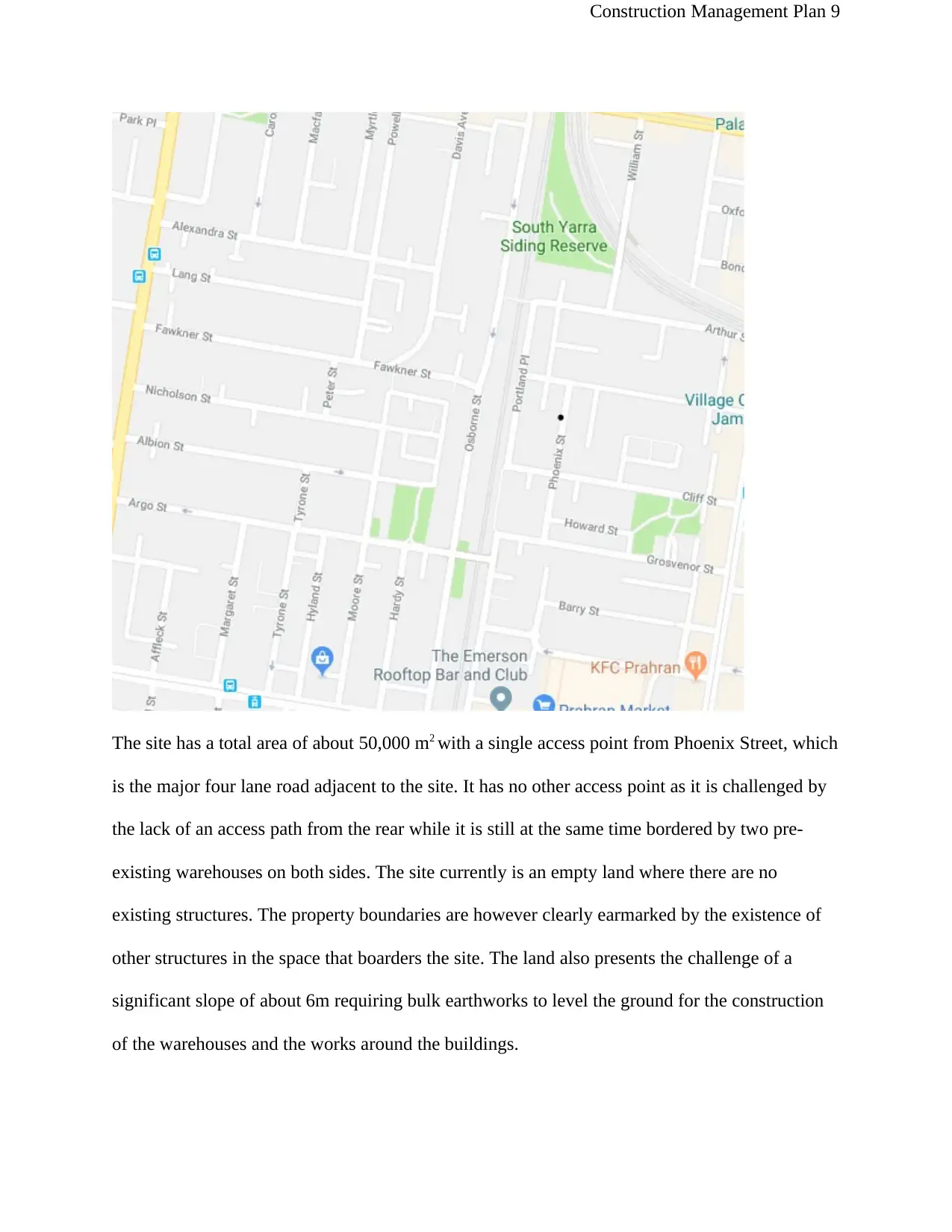
Construction Management Plan 9
The site has a total area of about 50,000 m2 with a single access point from Phoenix Street, which
is the major four lane road adjacent to the site. It has no other access point as it is challenged by
the lack of an access path from the rear while it is still at the same time bordered by two pre-
existing warehouses on both sides. The site currently is an empty land where there are no
existing structures. The property boundaries are however clearly earmarked by the existence of
other structures in the space that boarders the site. The land also presents the challenge of a
significant slope of about 6m requiring bulk earthworks to level the ground for the construction
of the warehouses and the works around the buildings.
The site has a total area of about 50,000 m2 with a single access point from Phoenix Street, which
is the major four lane road adjacent to the site. It has no other access point as it is challenged by
the lack of an access path from the rear while it is still at the same time bordered by two pre-
existing warehouses on both sides. The site currently is an empty land where there are no
existing structures. The property boundaries are however clearly earmarked by the existence of
other structures in the space that boarders the site. The land also presents the challenge of a
significant slope of about 6m requiring bulk earthworks to level the ground for the construction
of the warehouses and the works around the buildings.
⊘ This is a preview!⊘
Do you want full access?
Subscribe today to unlock all pages.

Trusted by 1+ million students worldwide
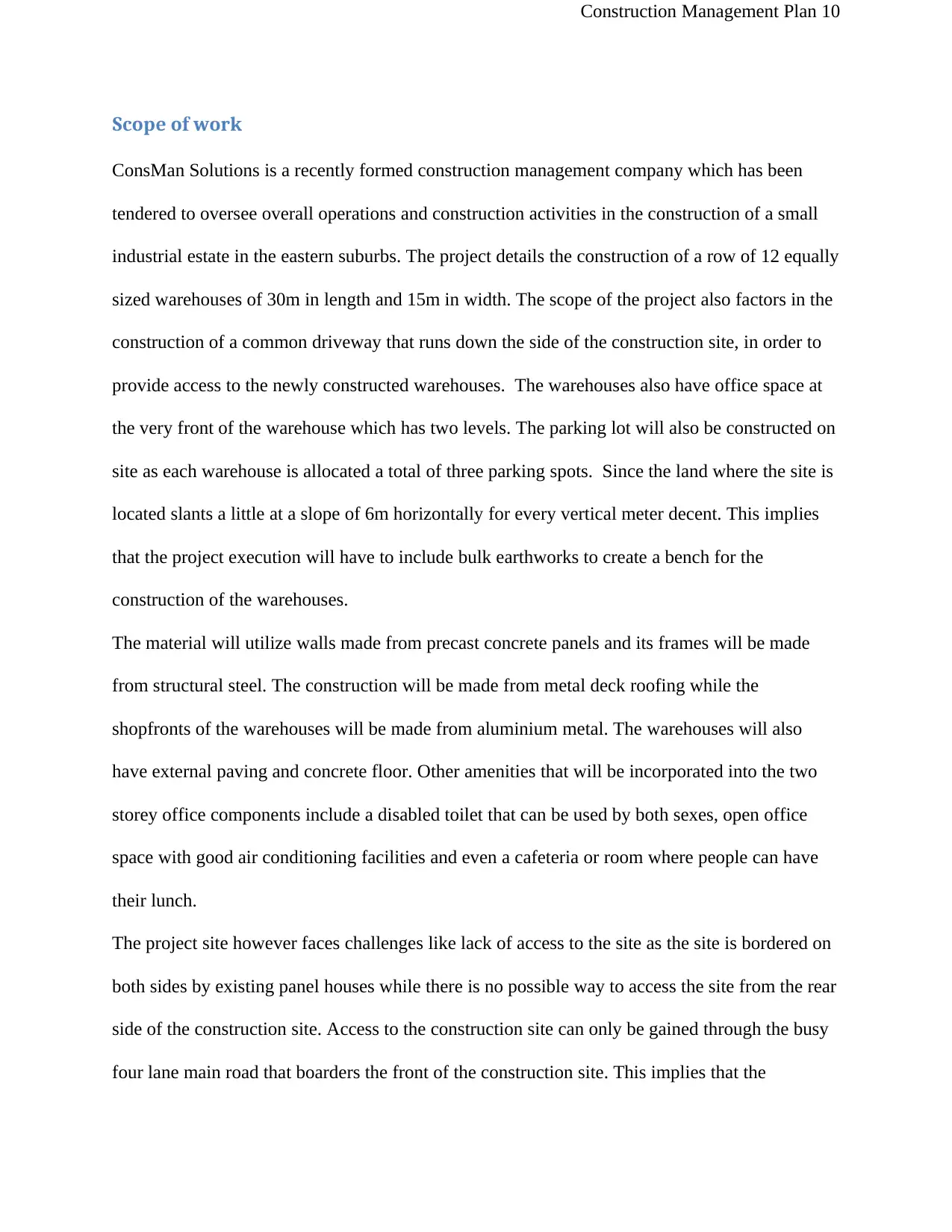
Construction Management Plan 10
Scope of work
ConsMan Solutions is a recently formed construction management company which has been
tendered to oversee overall operations and construction activities in the construction of a small
industrial estate in the eastern suburbs. The project details the construction of a row of 12 equally
sized warehouses of 30m in length and 15m in width. The scope of the project also factors in the
construction of a common driveway that runs down the side of the construction site, in order to
provide access to the newly constructed warehouses. The warehouses also have office space at
the very front of the warehouse which has two levels. The parking lot will also be constructed on
site as each warehouse is allocated a total of three parking spots. Since the land where the site is
located slants a little at a slope of 6m horizontally for every vertical meter decent. This implies
that the project execution will have to include bulk earthworks to create a bench for the
construction of the warehouses.
The material will utilize walls made from precast concrete panels and its frames will be made
from structural steel. The construction will be made from metal deck roofing while the
shopfronts of the warehouses will be made from aluminium metal. The warehouses will also
have external paving and concrete floor. Other amenities that will be incorporated into the two
storey office components include a disabled toilet that can be used by both sexes, open office
space with good air conditioning facilities and even a cafeteria or room where people can have
their lunch.
The project site however faces challenges like lack of access to the site as the site is bordered on
both sides by existing panel houses while there is no possible way to access the site from the rear
side of the construction site. Access to the construction site can only be gained through the busy
four lane main road that boarders the front of the construction site. This implies that the
Scope of work
ConsMan Solutions is a recently formed construction management company which has been
tendered to oversee overall operations and construction activities in the construction of a small
industrial estate in the eastern suburbs. The project details the construction of a row of 12 equally
sized warehouses of 30m in length and 15m in width. The scope of the project also factors in the
construction of a common driveway that runs down the side of the construction site, in order to
provide access to the newly constructed warehouses. The warehouses also have office space at
the very front of the warehouse which has two levels. The parking lot will also be constructed on
site as each warehouse is allocated a total of three parking spots. Since the land where the site is
located slants a little at a slope of 6m horizontally for every vertical meter decent. This implies
that the project execution will have to include bulk earthworks to create a bench for the
construction of the warehouses.
The material will utilize walls made from precast concrete panels and its frames will be made
from structural steel. The construction will be made from metal deck roofing while the
shopfronts of the warehouses will be made from aluminium metal. The warehouses will also
have external paving and concrete floor. Other amenities that will be incorporated into the two
storey office components include a disabled toilet that can be used by both sexes, open office
space with good air conditioning facilities and even a cafeteria or room where people can have
their lunch.
The project site however faces challenges like lack of access to the site as the site is bordered on
both sides by existing panel houses while there is no possible way to access the site from the rear
side of the construction site. Access to the construction site can only be gained through the busy
four lane main road that boarders the front of the construction site. This implies that the
Paraphrase This Document
Need a fresh take? Get an instant paraphrase of this document with our AI Paraphraser
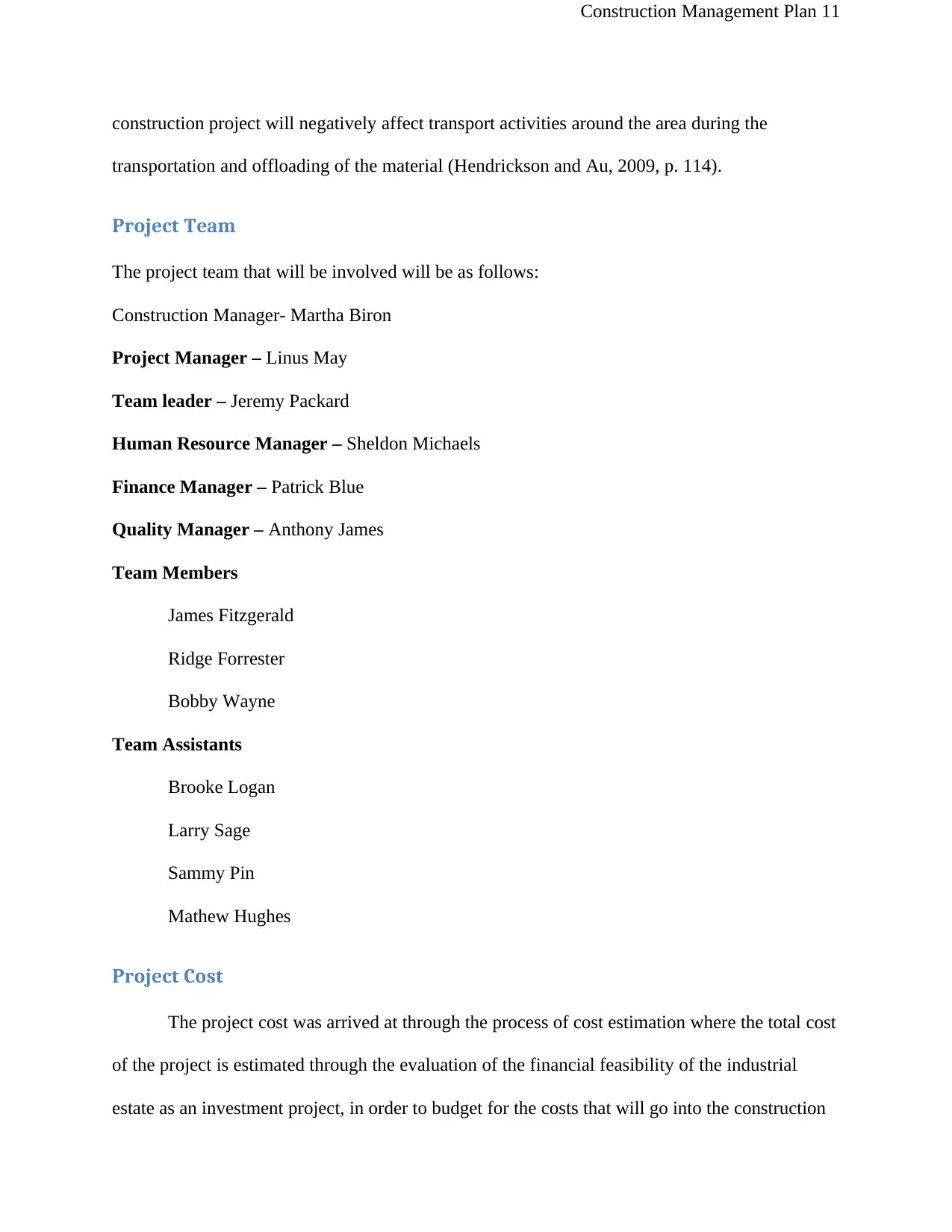
Construction Management Plan 11
construction project will negatively affect transport activities around the area during the
transportation and offloading of the material (Hendrickson and Au, 2009, p. 114).
Project Team
The project team that will be involved will be as follows:
Construction Manager- Martha Biron
Project Manager – Linus May
Team leader – Jeremy Packard
Human Resource Manager – Sheldon Michaels
Finance Manager – Patrick Blue
Quality Manager – Anthony James
Team Members
James Fitzgerald
Ridge Forrester
Bobby Wayne
Team Assistants
Brooke Logan
Larry Sage
Sammy Pin
Mathew Hughes
Project Cost
The project cost was arrived at through the process of cost estimation where the total cost
of the project is estimated through the evaluation of the financial feasibility of the industrial
estate as an investment project, in order to budget for the costs that will go into the construction
construction project will negatively affect transport activities around the area during the
transportation and offloading of the material (Hendrickson and Au, 2009, p. 114).
Project Team
The project team that will be involved will be as follows:
Construction Manager- Martha Biron
Project Manager – Linus May
Team leader – Jeremy Packard
Human Resource Manager – Sheldon Michaels
Finance Manager – Patrick Blue
Quality Manager – Anthony James
Team Members
James Fitzgerald
Ridge Forrester
Bobby Wayne
Team Assistants
Brooke Logan
Larry Sage
Sammy Pin
Mathew Hughes
Project Cost
The project cost was arrived at through the process of cost estimation where the total cost
of the project is estimated through the evaluation of the financial feasibility of the industrial
estate as an investment project, in order to budget for the costs that will go into the construction
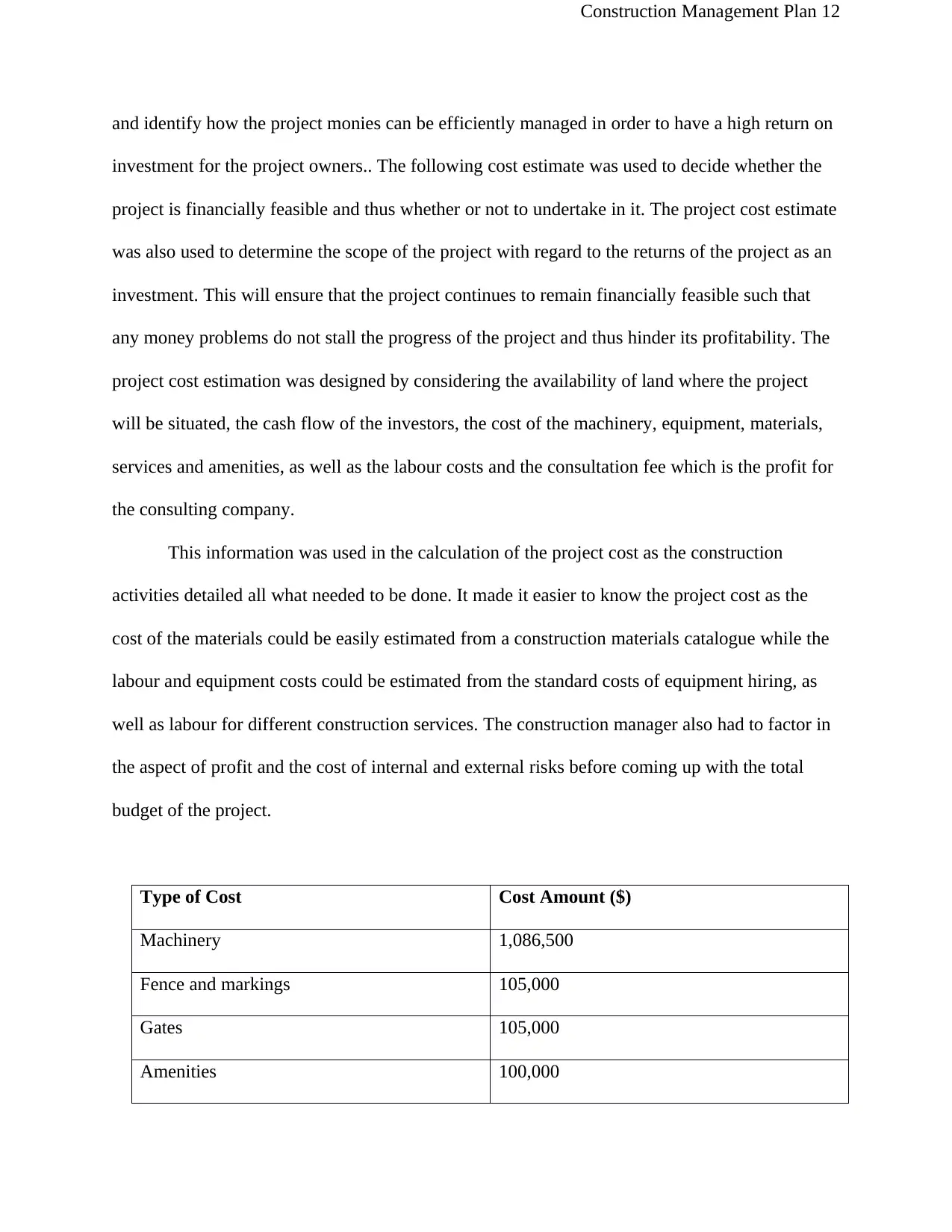
Construction Management Plan 12
and identify how the project monies can be efficiently managed in order to have a high return on
investment for the project owners.. The following cost estimate was used to decide whether the
project is financially feasible and thus whether or not to undertake in it. The project cost estimate
was also used to determine the scope of the project with regard to the returns of the project as an
investment. This will ensure that the project continues to remain financially feasible such that
any money problems do not stall the progress of the project and thus hinder its profitability. The
project cost estimation was designed by considering the availability of land where the project
will be situated, the cash flow of the investors, the cost of the machinery, equipment, materials,
services and amenities, as well as the labour costs and the consultation fee which is the profit for
the consulting company.
This information was used in the calculation of the project cost as the construction
activities detailed all what needed to be done. It made it easier to know the project cost as the
cost of the materials could be easily estimated from a construction materials catalogue while the
labour and equipment costs could be estimated from the standard costs of equipment hiring, as
well as labour for different construction services. The construction manager also had to factor in
the aspect of profit and the cost of internal and external risks before coming up with the total
budget of the project.
Type of Cost Cost Amount ($)
Machinery 1,086,500
Fence and markings 105,000
Gates 105,000
Amenities 100,000
and identify how the project monies can be efficiently managed in order to have a high return on
investment for the project owners.. The following cost estimate was used to decide whether the
project is financially feasible and thus whether or not to undertake in it. The project cost estimate
was also used to determine the scope of the project with regard to the returns of the project as an
investment. This will ensure that the project continues to remain financially feasible such that
any money problems do not stall the progress of the project and thus hinder its profitability. The
project cost estimation was designed by considering the availability of land where the project
will be situated, the cash flow of the investors, the cost of the machinery, equipment, materials,
services and amenities, as well as the labour costs and the consultation fee which is the profit for
the consulting company.
This information was used in the calculation of the project cost as the construction
activities detailed all what needed to be done. It made it easier to know the project cost as the
cost of the materials could be easily estimated from a construction materials catalogue while the
labour and equipment costs could be estimated from the standard costs of equipment hiring, as
well as labour for different construction services. The construction manager also had to factor in
the aspect of profit and the cost of internal and external risks before coming up with the total
budget of the project.
Type of Cost Cost Amount ($)
Machinery 1,086,500
Fence and markings 105,000
Gates 105,000
Amenities 100,000
⊘ This is a preview!⊘
Do you want full access?
Subscribe today to unlock all pages.

Trusted by 1+ million students worldwide
1 out of 59