Application of Structural Principles to Medium Rise Projects
VerifiedAdded on 2022/08/18
|16
|3608
|18
AI Summary
Task 1: Preventive applications of structural principles to the construction process for medium rise projects The site is located at the Port Philip Council The planning scheme is in Port Melbourne In zone 2 The planning compliance requirements The planning of demolition works carried out is done to assess risks, identify hazards and finding out appropriate control measures which is done when the relevant persons who will be working are consulted. Apart from the neighbouring building near the site, the name of the authority that were approached for this work was Green demolition and earth
Contribute Materials
Your contribution can guide someone’s learning journey. Share your
documents today.
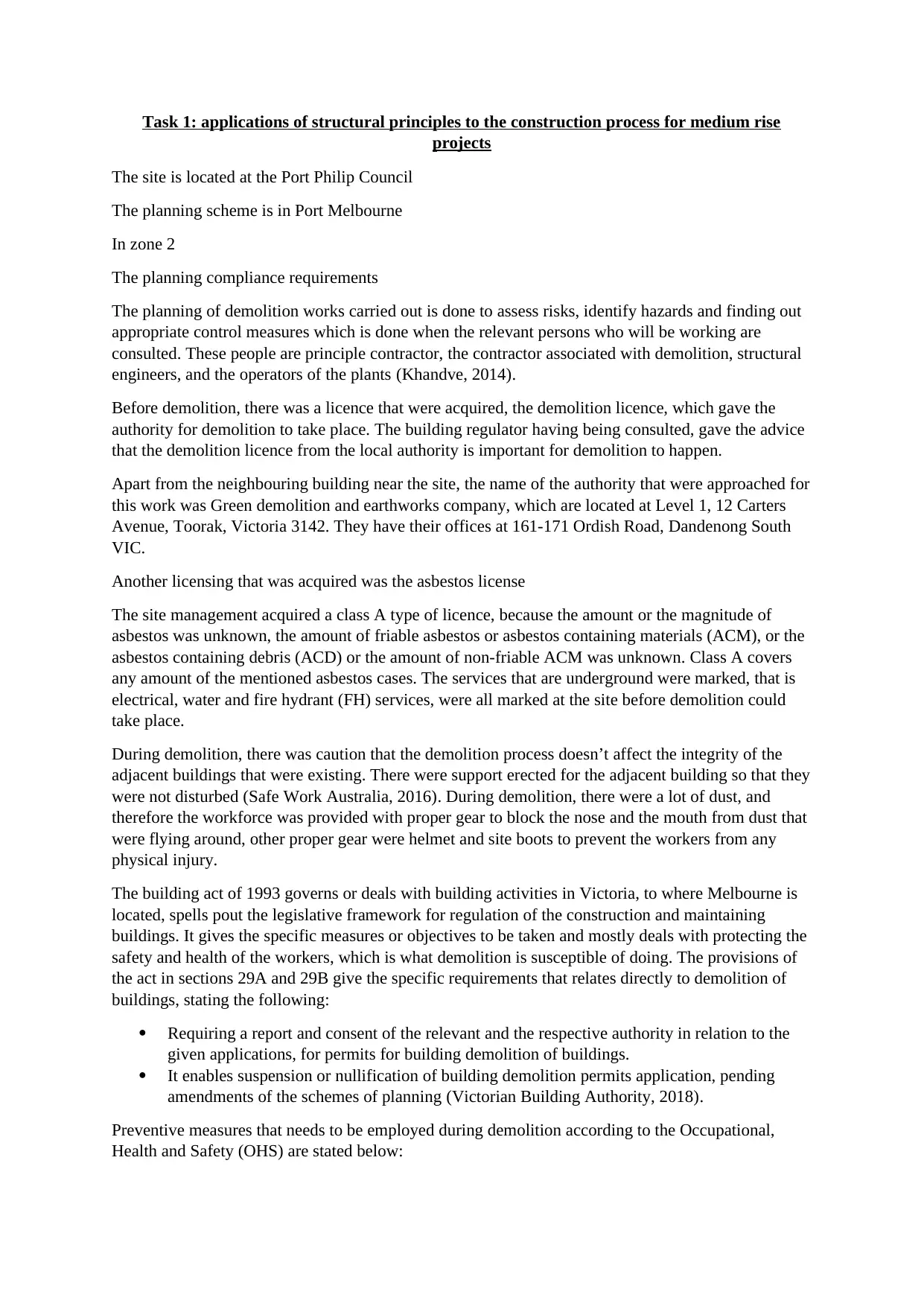
Task 1: applications of structural principles to the construction process for medium rise
projects
The site is located at the Port Philip Council
The planning scheme is in Port Melbourne
In zone 2
The planning compliance requirements
The planning of demolition works carried out is done to assess risks, identify hazards and finding out
appropriate control measures which is done when the relevant persons who will be working are
consulted. These people are principle contractor, the contractor associated with demolition, structural
engineers, and the operators of the plants (Khandve, 2014).
Before demolition, there was a licence that were acquired, the demolition licence, which gave the
authority for demolition to take place. The building regulator having being consulted, gave the advice
that the demolition licence from the local authority is important for demolition to happen.
Apart from the neighbouring building near the site, the name of the authority that were approached for
this work was Green demolition and earthworks company, which are located at Level 1, 12 Carters
Avenue, Toorak, Victoria 3142. They have their offices at 161-171 Ordish Road, Dandenong South
VIC.
Another licensing that was acquired was the asbestos license
The site management acquired a class A type of licence, because the amount or the magnitude of
asbestos was unknown, the amount of friable asbestos or asbestos containing materials (ACM), or the
asbestos containing debris (ACD) or the amount of non-friable ACM was unknown. Class A covers
any amount of the mentioned asbestos cases. The services that are underground were marked, that is
electrical, water and fire hydrant (FH) services, were all marked at the site before demolition could
take place.
During demolition, there was caution that the demolition process doesn’t affect the integrity of the
adjacent buildings that were existing. There were support erected for the adjacent building so that they
were not disturbed (Safe Work Australia, 2016). During demolition, there were a lot of dust, and
therefore the workforce was provided with proper gear to block the nose and the mouth from dust that
were flying around, other proper gear were helmet and site boots to prevent the workers from any
physical injury.
The building act of 1993 governs or deals with building activities in Victoria, to where Melbourne is
located, spells pout the legislative framework for regulation of the construction and maintaining
buildings. It gives the specific measures or objectives to be taken and mostly deals with protecting the
safety and health of the workers, which is what demolition is susceptible of doing. The provisions of
the act in sections 29A and 29B give the specific requirements that relates directly to demolition of
buildings, stating the following:
Requiring a report and consent of the relevant and the respective authority in relation to the
given applications, for permits for building demolition of buildings.
It enables suspension or nullification of building demolition permits application, pending
amendments of the schemes of planning (Victorian Building Authority, 2018).
Preventive measures that needs to be employed during demolition according to the Occupational,
Health and Safety (OHS) are stated below:
projects
The site is located at the Port Philip Council
The planning scheme is in Port Melbourne
In zone 2
The planning compliance requirements
The planning of demolition works carried out is done to assess risks, identify hazards and finding out
appropriate control measures which is done when the relevant persons who will be working are
consulted. These people are principle contractor, the contractor associated with demolition, structural
engineers, and the operators of the plants (Khandve, 2014).
Before demolition, there was a licence that were acquired, the demolition licence, which gave the
authority for demolition to take place. The building regulator having being consulted, gave the advice
that the demolition licence from the local authority is important for demolition to happen.
Apart from the neighbouring building near the site, the name of the authority that were approached for
this work was Green demolition and earthworks company, which are located at Level 1, 12 Carters
Avenue, Toorak, Victoria 3142. They have their offices at 161-171 Ordish Road, Dandenong South
VIC.
Another licensing that was acquired was the asbestos license
The site management acquired a class A type of licence, because the amount or the magnitude of
asbestos was unknown, the amount of friable asbestos or asbestos containing materials (ACM), or the
asbestos containing debris (ACD) or the amount of non-friable ACM was unknown. Class A covers
any amount of the mentioned asbestos cases. The services that are underground were marked, that is
electrical, water and fire hydrant (FH) services, were all marked at the site before demolition could
take place.
During demolition, there was caution that the demolition process doesn’t affect the integrity of the
adjacent buildings that were existing. There were support erected for the adjacent building so that they
were not disturbed (Safe Work Australia, 2016). During demolition, there were a lot of dust, and
therefore the workforce was provided with proper gear to block the nose and the mouth from dust that
were flying around, other proper gear were helmet and site boots to prevent the workers from any
physical injury.
The building act of 1993 governs or deals with building activities in Victoria, to where Melbourne is
located, spells pout the legislative framework for regulation of the construction and maintaining
buildings. It gives the specific measures or objectives to be taken and mostly deals with protecting the
safety and health of the workers, which is what demolition is susceptible of doing. The provisions of
the act in sections 29A and 29B give the specific requirements that relates directly to demolition of
buildings, stating the following:
Requiring a report and consent of the relevant and the respective authority in relation to the
given applications, for permits for building demolition of buildings.
It enables suspension or nullification of building demolition permits application, pending
amendments of the schemes of planning (Victorian Building Authority, 2018).
Preventive measures that needs to be employed during demolition according to the Occupational,
Health and Safety (OHS) are stated below:
Secure Best Marks with AI Grader
Need help grading? Try our AI Grader for instant feedback on your assignments.
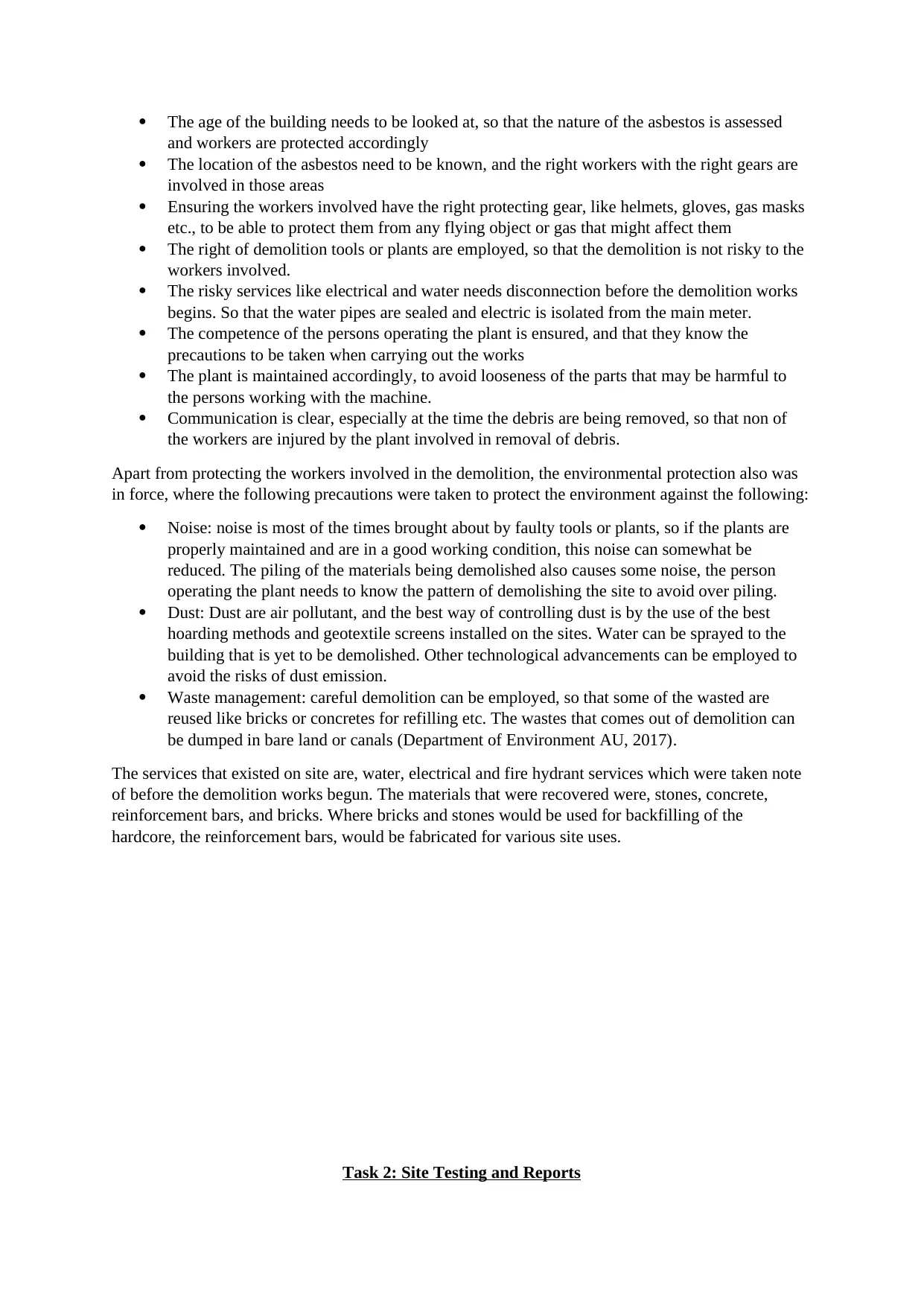
The age of the building needs to be looked at, so that the nature of the asbestos is assessed
and workers are protected accordingly
The location of the asbestos need to be known, and the right workers with the right gears are
involved in those areas
Ensuring the workers involved have the right protecting gear, like helmets, gloves, gas masks
etc., to be able to protect them from any flying object or gas that might affect them
The right of demolition tools or plants are employed, so that the demolition is not risky to the
workers involved.
The risky services like electrical and water needs disconnection before the demolition works
begins. So that the water pipes are sealed and electric is isolated from the main meter.
The competence of the persons operating the plant is ensured, and that they know the
precautions to be taken when carrying out the works
The plant is maintained accordingly, to avoid looseness of the parts that may be harmful to
the persons working with the machine.
Communication is clear, especially at the time the debris are being removed, so that non of
the workers are injured by the plant involved in removal of debris.
Apart from protecting the workers involved in the demolition, the environmental protection also was
in force, where the following precautions were taken to protect the environment against the following:
Noise: noise is most of the times brought about by faulty tools or plants, so if the plants are
properly maintained and are in a good working condition, this noise can somewhat be
reduced. The piling of the materials being demolished also causes some noise, the person
operating the plant needs to know the pattern of demolishing the site to avoid over piling.
Dust: Dust are air pollutant, and the best way of controlling dust is by the use of the best
hoarding methods and geotextile screens installed on the sites. Water can be sprayed to the
building that is yet to be demolished. Other technological advancements can be employed to
avoid the risks of dust emission.
Waste management: careful demolition can be employed, so that some of the wasted are
reused like bricks or concretes for refilling etc. The wastes that comes out of demolition can
be dumped in bare land or canals (Department of Environment AU, 2017).
The services that existed on site are, water, electrical and fire hydrant services which were taken note
of before the demolition works begun. The materials that were recovered were, stones, concrete,
reinforcement bars, and bricks. Where bricks and stones would be used for backfilling of the
hardcore, the reinforcement bars, would be fabricated for various site uses.
Task 2: Site Testing and Reports
and workers are protected accordingly
The location of the asbestos need to be known, and the right workers with the right gears are
involved in those areas
Ensuring the workers involved have the right protecting gear, like helmets, gloves, gas masks
etc., to be able to protect them from any flying object or gas that might affect them
The right of demolition tools or plants are employed, so that the demolition is not risky to the
workers involved.
The risky services like electrical and water needs disconnection before the demolition works
begins. So that the water pipes are sealed and electric is isolated from the main meter.
The competence of the persons operating the plant is ensured, and that they know the
precautions to be taken when carrying out the works
The plant is maintained accordingly, to avoid looseness of the parts that may be harmful to
the persons working with the machine.
Communication is clear, especially at the time the debris are being removed, so that non of
the workers are injured by the plant involved in removal of debris.
Apart from protecting the workers involved in the demolition, the environmental protection also was
in force, where the following precautions were taken to protect the environment against the following:
Noise: noise is most of the times brought about by faulty tools or plants, so if the plants are
properly maintained and are in a good working condition, this noise can somewhat be
reduced. The piling of the materials being demolished also causes some noise, the person
operating the plant needs to know the pattern of demolishing the site to avoid over piling.
Dust: Dust are air pollutant, and the best way of controlling dust is by the use of the best
hoarding methods and geotextile screens installed on the sites. Water can be sprayed to the
building that is yet to be demolished. Other technological advancements can be employed to
avoid the risks of dust emission.
Waste management: careful demolition can be employed, so that some of the wasted are
reused like bricks or concretes for refilling etc. The wastes that comes out of demolition can
be dumped in bare land or canals (Department of Environment AU, 2017).
The services that existed on site are, water, electrical and fire hydrant services which were taken note
of before the demolition works begun. The materials that were recovered were, stones, concrete,
reinforcement bars, and bricks. Where bricks and stones would be used for backfilling of the
hardcore, the reinforcement bars, would be fabricated for various site uses.
Task 2: Site Testing and Reports
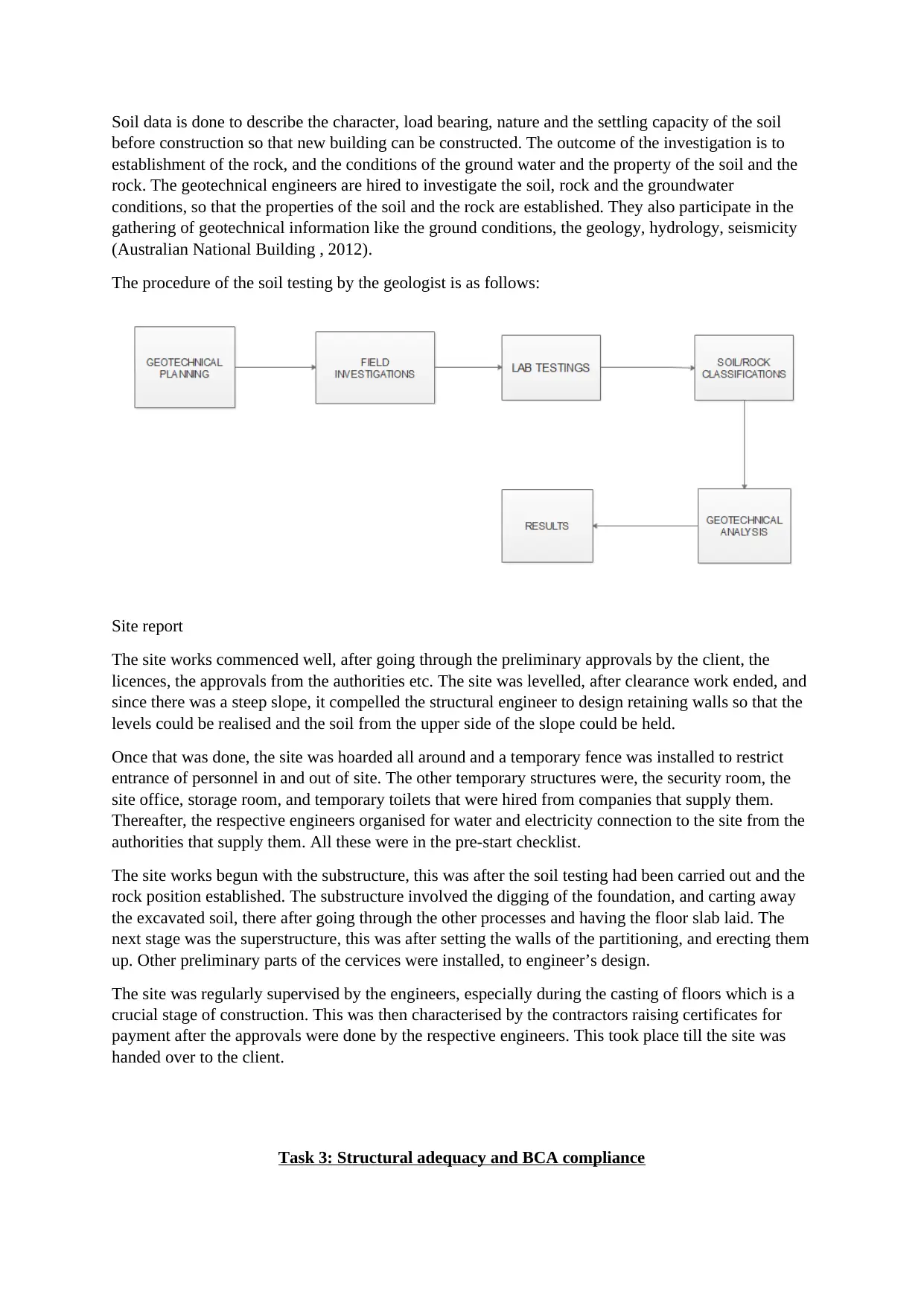
Soil data is done to describe the character, load bearing, nature and the settling capacity of the soil
before construction so that new building can be constructed. The outcome of the investigation is to
establishment of the rock, and the conditions of the ground water and the property of the soil and the
rock. The geotechnical engineers are hired to investigate the soil, rock and the groundwater
conditions, so that the properties of the soil and the rock are established. They also participate in the
gathering of geotechnical information like the ground conditions, the geology, hydrology, seismicity
(Australian National Building , 2012).
The procedure of the soil testing by the geologist is as follows:
Site report
The site works commenced well, after going through the preliminary approvals by the client, the
licences, the approvals from the authorities etc. The site was levelled, after clearance work ended, and
since there was a steep slope, it compelled the structural engineer to design retaining walls so that the
levels could be realised and the soil from the upper side of the slope could be held.
Once that was done, the site was hoarded all around and a temporary fence was installed to restrict
entrance of personnel in and out of site. The other temporary structures were, the security room, the
site office, storage room, and temporary toilets that were hired from companies that supply them.
Thereafter, the respective engineers organised for water and electricity connection to the site from the
authorities that supply them. All these were in the pre-start checklist.
The site works begun with the substructure, this was after the soil testing had been carried out and the
rock position established. The substructure involved the digging of the foundation, and carting away
the excavated soil, there after going through the other processes and having the floor slab laid. The
next stage was the superstructure, this was after setting the walls of the partitioning, and erecting them
up. Other preliminary parts of the cervices were installed, to engineer’s design.
The site was regularly supervised by the engineers, especially during the casting of floors which is a
crucial stage of construction. This was then characterised by the contractors raising certificates for
payment after the approvals were done by the respective engineers. This took place till the site was
handed over to the client.
Task 3: Structural adequacy and BCA compliance
before construction so that new building can be constructed. The outcome of the investigation is to
establishment of the rock, and the conditions of the ground water and the property of the soil and the
rock. The geotechnical engineers are hired to investigate the soil, rock and the groundwater
conditions, so that the properties of the soil and the rock are established. They also participate in the
gathering of geotechnical information like the ground conditions, the geology, hydrology, seismicity
(Australian National Building , 2012).
The procedure of the soil testing by the geologist is as follows:
Site report
The site works commenced well, after going through the preliminary approvals by the client, the
licences, the approvals from the authorities etc. The site was levelled, after clearance work ended, and
since there was a steep slope, it compelled the structural engineer to design retaining walls so that the
levels could be realised and the soil from the upper side of the slope could be held.
Once that was done, the site was hoarded all around and a temporary fence was installed to restrict
entrance of personnel in and out of site. The other temporary structures were, the security room, the
site office, storage room, and temporary toilets that were hired from companies that supply them.
Thereafter, the respective engineers organised for water and electricity connection to the site from the
authorities that supply them. All these were in the pre-start checklist.
The site works begun with the substructure, this was after the soil testing had been carried out and the
rock position established. The substructure involved the digging of the foundation, and carting away
the excavated soil, there after going through the other processes and having the floor slab laid. The
next stage was the superstructure, this was after setting the walls of the partitioning, and erecting them
up. Other preliminary parts of the cervices were installed, to engineer’s design.
The site was regularly supervised by the engineers, especially during the casting of floors which is a
crucial stage of construction. This was then characterised by the contractors raising certificates for
payment after the approvals were done by the respective engineers. This took place till the site was
handed over to the client.
Task 3: Structural adequacy and BCA compliance
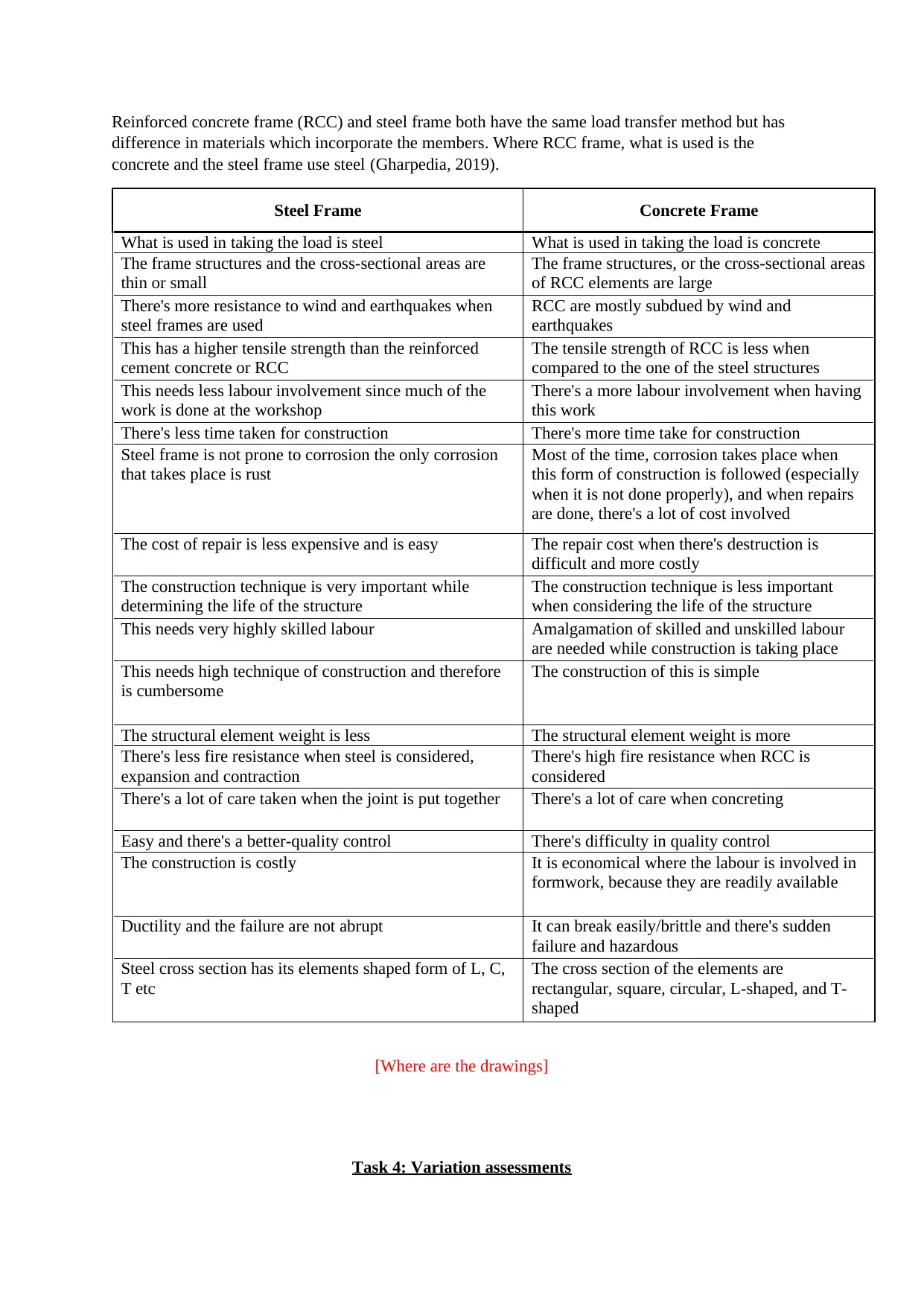
Reinforced concrete frame (RCC) and steel frame both have the same load transfer method but has
difference in materials which incorporate the members. Where RCC frame, what is used is the
concrete and the steel frame use steel (Gharpedia, 2019).
Steel Frame Concrete Frame
What is used in taking the load is steel What is used in taking the load is concrete
The frame structures and the cross-sectional areas are
thin or small
The frame structures, or the cross-sectional areas
of RCC elements are large
There's more resistance to wind and earthquakes when
steel frames are used
RCC are mostly subdued by wind and
earthquakes
This has a higher tensile strength than the reinforced
cement concrete or RCC
The tensile strength of RCC is less when
compared to the one of the steel structures
This needs less labour involvement since much of the
work is done at the workshop
There's a more labour involvement when having
this work
There's less time taken for construction There's more time take for construction
Steel frame is not prone to corrosion the only corrosion
that takes place is rust
Most of the time, corrosion takes place when
this form of construction is followed (especially
when it is not done properly), and when repairs
are done, there's a lot of cost involved
The cost of repair is less expensive and is easy The repair cost when there's destruction is
difficult and more costly
The construction technique is very important while
determining the life of the structure
The construction technique is less important
when considering the life of the structure
This needs very highly skilled labour Amalgamation of skilled and unskilled labour
are needed while construction is taking place
This needs high technique of construction and therefore
is cumbersome
The construction of this is simple
The structural element weight is less The structural element weight is more
There's less fire resistance when steel is considered,
expansion and contraction
There's high fire resistance when RCC is
considered
There's a lot of care taken when the joint is put together There's a lot of care when concreting
Easy and there's a better-quality control There's difficulty in quality control
The construction is costly It is economical where the labour is involved in
formwork, because they are readily available
Ductility and the failure are not abrupt It can break easily/brittle and there's sudden
failure and hazardous
Steel cross section has its elements shaped form of L, C,
T etc
The cross section of the elements are
rectangular, square, circular, L-shaped, and T-
shaped
[Where are the drawings]
Task 4: Variation assessments
difference in materials which incorporate the members. Where RCC frame, what is used is the
concrete and the steel frame use steel (Gharpedia, 2019).
Steel Frame Concrete Frame
What is used in taking the load is steel What is used in taking the load is concrete
The frame structures and the cross-sectional areas are
thin or small
The frame structures, or the cross-sectional areas
of RCC elements are large
There's more resistance to wind and earthquakes when
steel frames are used
RCC are mostly subdued by wind and
earthquakes
This has a higher tensile strength than the reinforced
cement concrete or RCC
The tensile strength of RCC is less when
compared to the one of the steel structures
This needs less labour involvement since much of the
work is done at the workshop
There's a more labour involvement when having
this work
There's less time taken for construction There's more time take for construction
Steel frame is not prone to corrosion the only corrosion
that takes place is rust
Most of the time, corrosion takes place when
this form of construction is followed (especially
when it is not done properly), and when repairs
are done, there's a lot of cost involved
The cost of repair is less expensive and is easy The repair cost when there's destruction is
difficult and more costly
The construction technique is very important while
determining the life of the structure
The construction technique is less important
when considering the life of the structure
This needs very highly skilled labour Amalgamation of skilled and unskilled labour
are needed while construction is taking place
This needs high technique of construction and therefore
is cumbersome
The construction of this is simple
The structural element weight is less The structural element weight is more
There's less fire resistance when steel is considered,
expansion and contraction
There's high fire resistance when RCC is
considered
There's a lot of care taken when the joint is put together There's a lot of care when concreting
Easy and there's a better-quality control There's difficulty in quality control
The construction is costly It is economical where the labour is involved in
formwork, because they are readily available
Ductility and the failure are not abrupt It can break easily/brittle and there's sudden
failure and hazardous
Steel cross section has its elements shaped form of L, C,
T etc
The cross section of the elements are
rectangular, square, circular, L-shaped, and T-
shaped
[Where are the drawings]
Task 4: Variation assessments
Secure Best Marks with AI Grader
Need help grading? Try our AI Grader for instant feedback on your assignments.
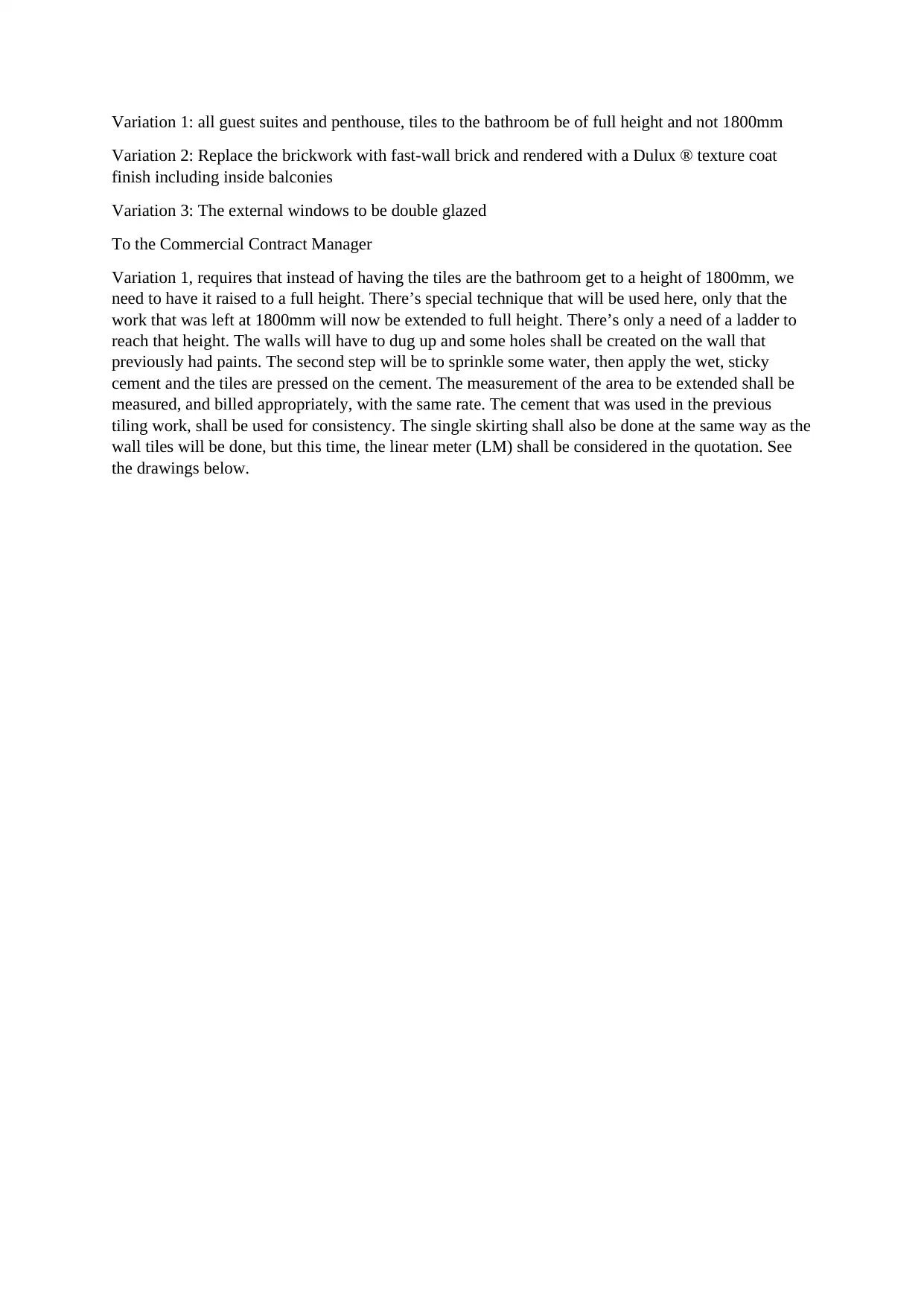
Variation 1: all guest suites and penthouse, tiles to the bathroom be of full height and not 1800mm
Variation 2: Replace the brickwork with fast-wall brick and rendered with a Dulux ® texture coat
finish including inside balconies
Variation 3: The external windows to be double glazed
To the Commercial Contract Manager
Variation 1, requires that instead of having the tiles are the bathroom get to a height of 1800mm, we
need to have it raised to a full height. There’s special technique that will be used here, only that the
work that was left at 1800mm will now be extended to full height. There’s only a need of a ladder to
reach that height. The walls will have to dug up and some holes shall be created on the wall that
previously had paints. The second step will be to sprinkle some water, then apply the wet, sticky
cement and the tiles are pressed on the cement. The measurement of the area to be extended shall be
measured, and billed appropriately, with the same rate. The cement that was used in the previous
tiling work, shall be used for consistency. The single skirting shall also be done at the same way as the
wall tiles will be done, but this time, the linear meter (LM) shall be considered in the quotation. See
the drawings below.
Variation 2: Replace the brickwork with fast-wall brick and rendered with a Dulux ® texture coat
finish including inside balconies
Variation 3: The external windows to be double glazed
To the Commercial Contract Manager
Variation 1, requires that instead of having the tiles are the bathroom get to a height of 1800mm, we
need to have it raised to a full height. There’s special technique that will be used here, only that the
work that was left at 1800mm will now be extended to full height. There’s only a need of a ladder to
reach that height. The walls will have to dug up and some holes shall be created on the wall that
previously had paints. The second step will be to sprinkle some water, then apply the wet, sticky
cement and the tiles are pressed on the cement. The measurement of the area to be extended shall be
measured, and billed appropriately, with the same rate. The cement that was used in the previous
tiling work, shall be used for consistency. The single skirting shall also be done at the same way as the
wall tiles will be done, but this time, the linear meter (LM) shall be considered in the quotation. See
the drawings below.
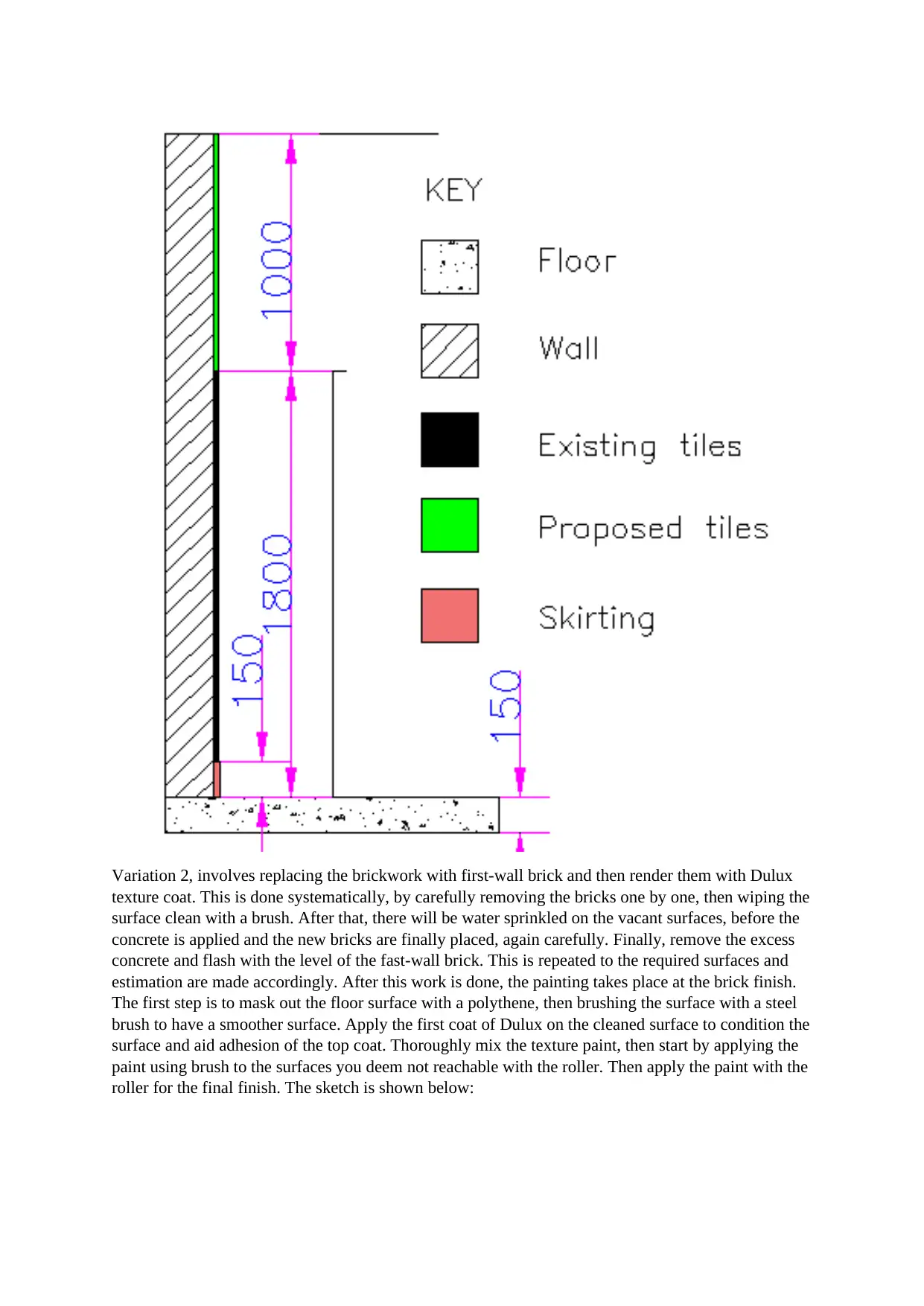
Variation 2, involves replacing the brickwork with first-wall brick and then render them with Dulux
texture coat. This is done systematically, by carefully removing the bricks one by one, then wiping the
surface clean with a brush. After that, there will be water sprinkled on the vacant surfaces, before the
concrete is applied and the new bricks are finally placed, again carefully. Finally, remove the excess
concrete and flash with the level of the fast-wall brick. This is repeated to the required surfaces and
estimation are made accordingly. After this work is done, the painting takes place at the brick finish.
The first step is to mask out the floor surface with a polythene, then brushing the surface with a steel
brush to have a smoother surface. Apply the first coat of Dulux on the cleaned surface to condition the
surface and aid adhesion of the top coat. Thoroughly mix the texture paint, then start by applying the
paint using brush to the surfaces you deem not reachable with the roller. Then apply the paint with the
roller for the final finish. The sketch is shown below:
texture coat. This is done systematically, by carefully removing the bricks one by one, then wiping the
surface clean with a brush. After that, there will be water sprinkled on the vacant surfaces, before the
concrete is applied and the new bricks are finally placed, again carefully. Finally, remove the excess
concrete and flash with the level of the fast-wall brick. This is repeated to the required surfaces and
estimation are made accordingly. After this work is done, the painting takes place at the brick finish.
The first step is to mask out the floor surface with a polythene, then brushing the surface with a steel
brush to have a smoother surface. Apply the first coat of Dulux on the cleaned surface to condition the
surface and aid adhesion of the top coat. Thoroughly mix the texture paint, then start by applying the
paint using brush to the surfaces you deem not reachable with the roller. Then apply the paint with the
roller for the final finish. The sketch is shown below:
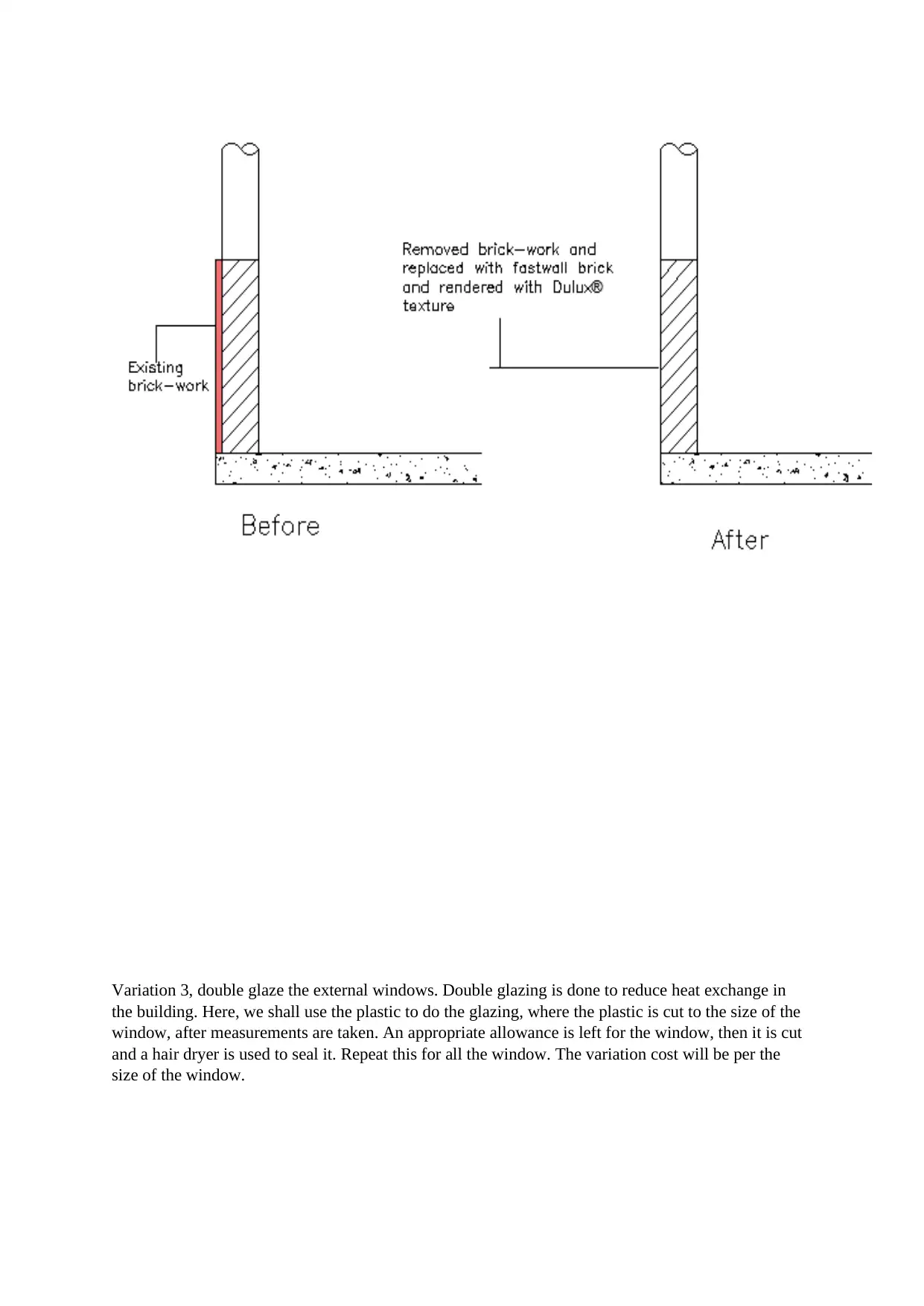
Variation 3, double glaze the external windows. Double glazing is done to reduce heat exchange in
the building. Here, we shall use the plastic to do the glazing, where the plastic is cut to the size of the
window, after measurements are taken. An appropriate allowance is left for the window, then it is cut
and a hair dryer is used to seal it. Repeat this for all the window. The variation cost will be per the
size of the window.
the building. Here, we shall use the plastic to do the glazing, where the plastic is cut to the size of the
window, after measurements are taken. An appropriate allowance is left for the window, then it is cut
and a hair dryer is used to seal it. Repeat this for all the window. The variation cost will be per the
size of the window.
Paraphrase This Document
Need a fresh take? Get an instant paraphrase of this document with our AI Paraphraser
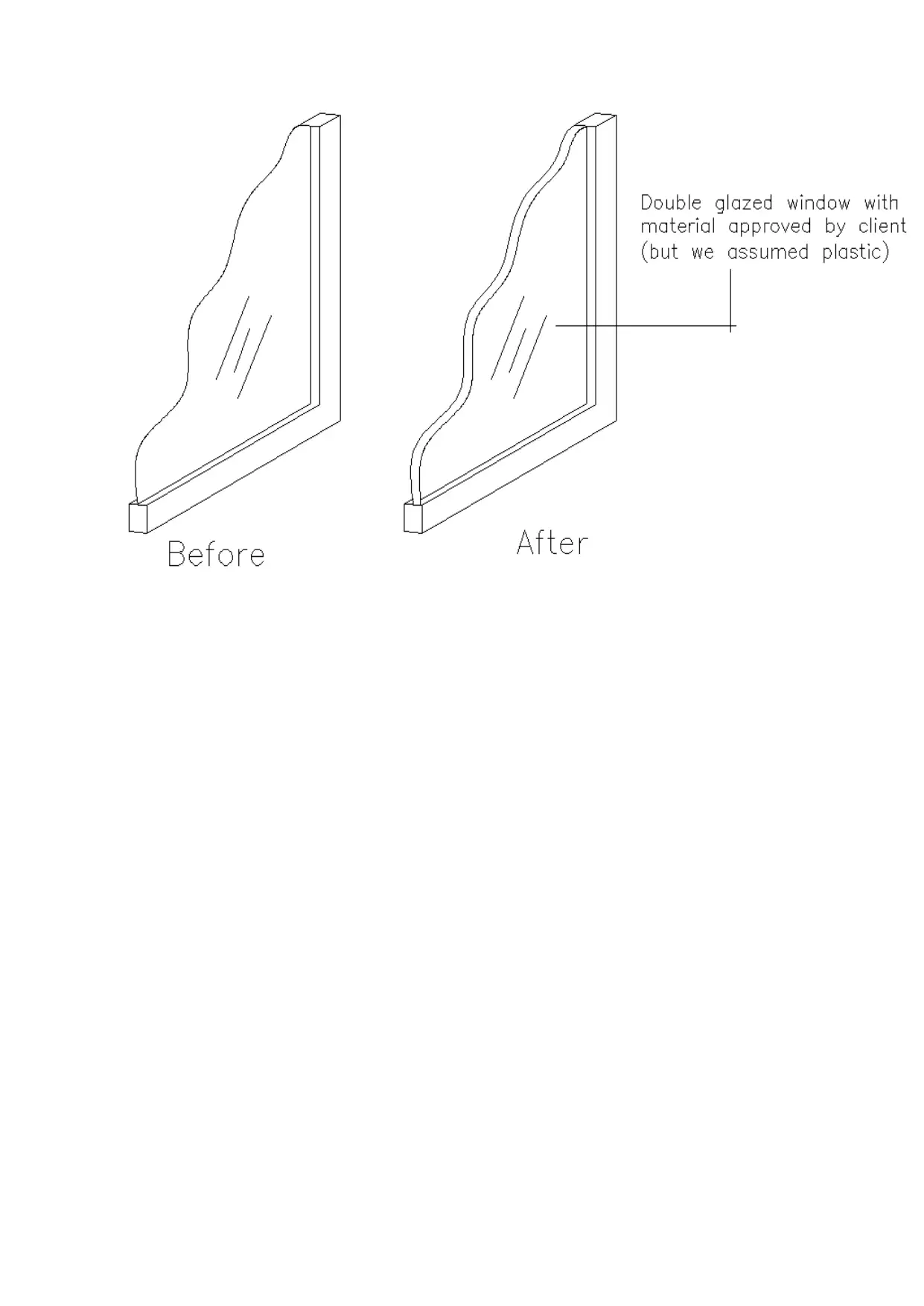
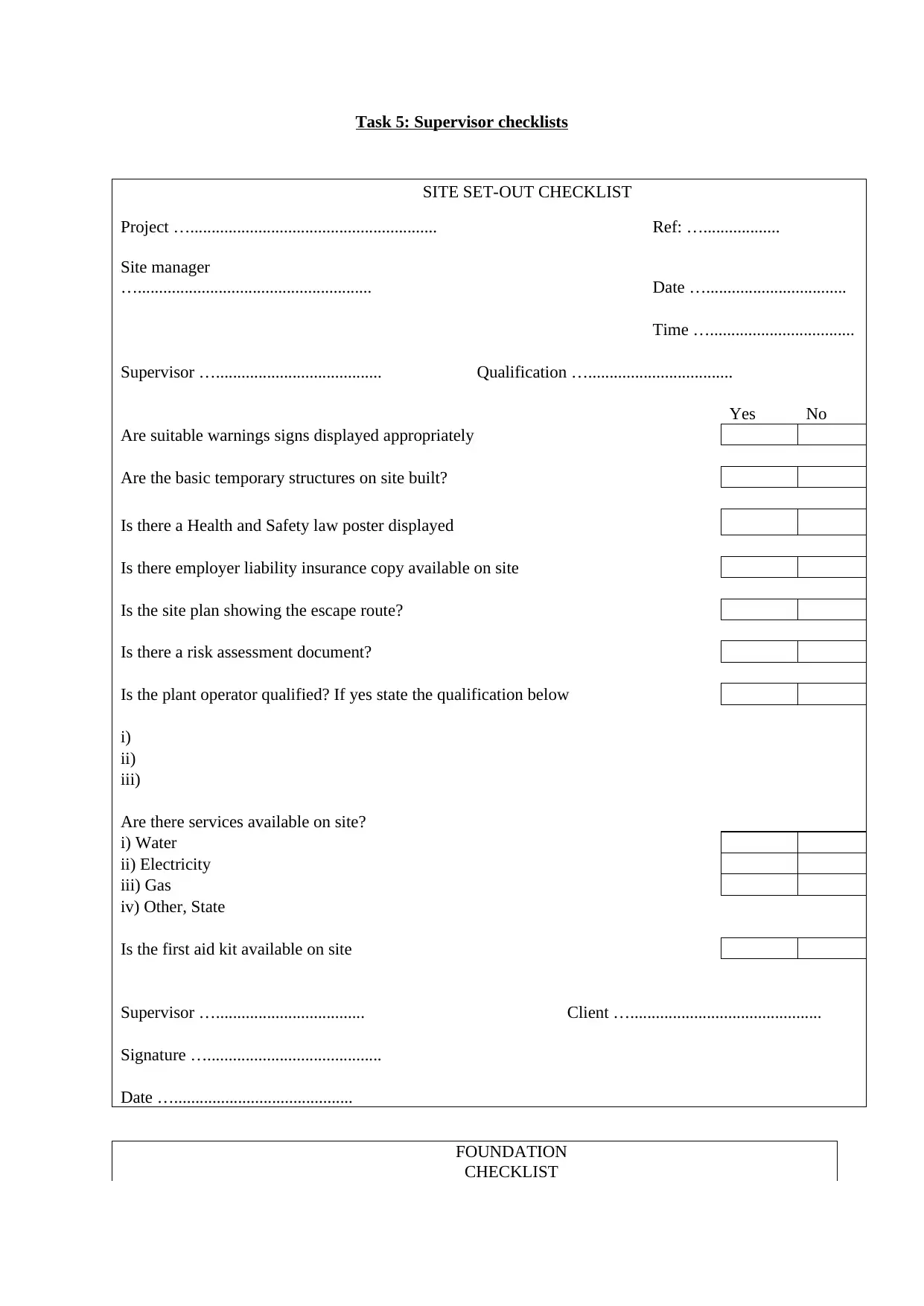
Task 5: Supervisor checklists
SITE SET-OUT CHECKLIST
Project ….......................................................... Ref: …..................
Site manager
…....................................................... Date ….................................
Time …..................................
Supervisor …....................................... Qualification …..................................
Yes No
Are suitable warnings signs displayed appropriately
Are the basic temporary structures on site built?
Is there a Health and Safety law poster displayed
Is there employer liability insurance copy available on site
Is the site plan showing the escape route?
Is there a risk assessment document?
Is the plant operator qualified? If yes state the qualification below
i)
ii)
iii)
Are there services available on site?
i) Water
ii) Electricity
iii) Gas
iv) Other, State
Is the first aid kit available on site
Supervisor …................................... Client ….............................................
Signature ….........................................
Date …..........................................
FOUNDATION
CHECKLIST
SITE SET-OUT CHECKLIST
Project ….......................................................... Ref: …..................
Site manager
…....................................................... Date ….................................
Time …..................................
Supervisor …....................................... Qualification …..................................
Yes No
Are suitable warnings signs displayed appropriately
Are the basic temporary structures on site built?
Is there a Health and Safety law poster displayed
Is there employer liability insurance copy available on site
Is the site plan showing the escape route?
Is there a risk assessment document?
Is the plant operator qualified? If yes state the qualification below
i)
ii)
iii)
Are there services available on site?
i) Water
ii) Electricity
iii) Gas
iv) Other, State
Is the first aid kit available on site
Supervisor …................................... Client ….............................................
Signature ….........................................
Date …..........................................
FOUNDATION
CHECKLIST
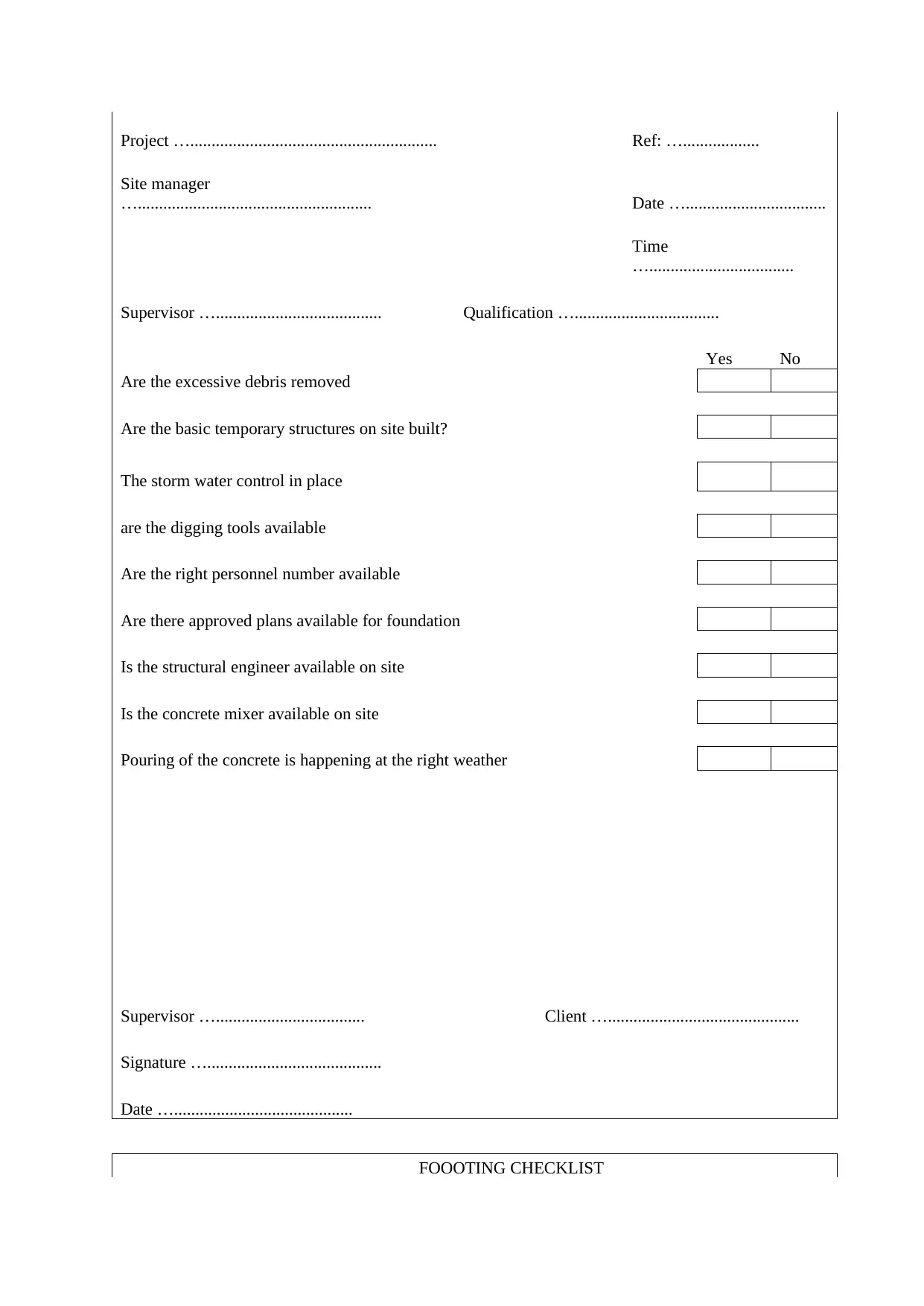
Project ….......................................................... Ref: …..................
Site manager
…....................................................... Date ….................................
Time
…..................................
Supervisor …....................................... Qualification …..................................
Yes No
Are the excessive debris removed
Are the basic temporary structures on site built?
The storm water control in place
are the digging tools available
Are the right personnel number available
Are there approved plans available for foundation
Is the structural engineer available on site
Is the concrete mixer available on site
Pouring of the concrete is happening at the right weather
Supervisor …................................... Client ….............................................
Signature ….........................................
Date …..........................................
FOOOTING CHECKLIST
Site manager
…....................................................... Date ….................................
Time
…..................................
Supervisor …....................................... Qualification …..................................
Yes No
Are the excessive debris removed
Are the basic temporary structures on site built?
The storm water control in place
are the digging tools available
Are the right personnel number available
Are there approved plans available for foundation
Is the structural engineer available on site
Is the concrete mixer available on site
Pouring of the concrete is happening at the right weather
Supervisor …................................... Client ….............................................
Signature ….........................................
Date …..........................................
FOOOTING CHECKLIST
Secure Best Marks with AI Grader
Need help grading? Try our AI Grader for instant feedback on your assignments.
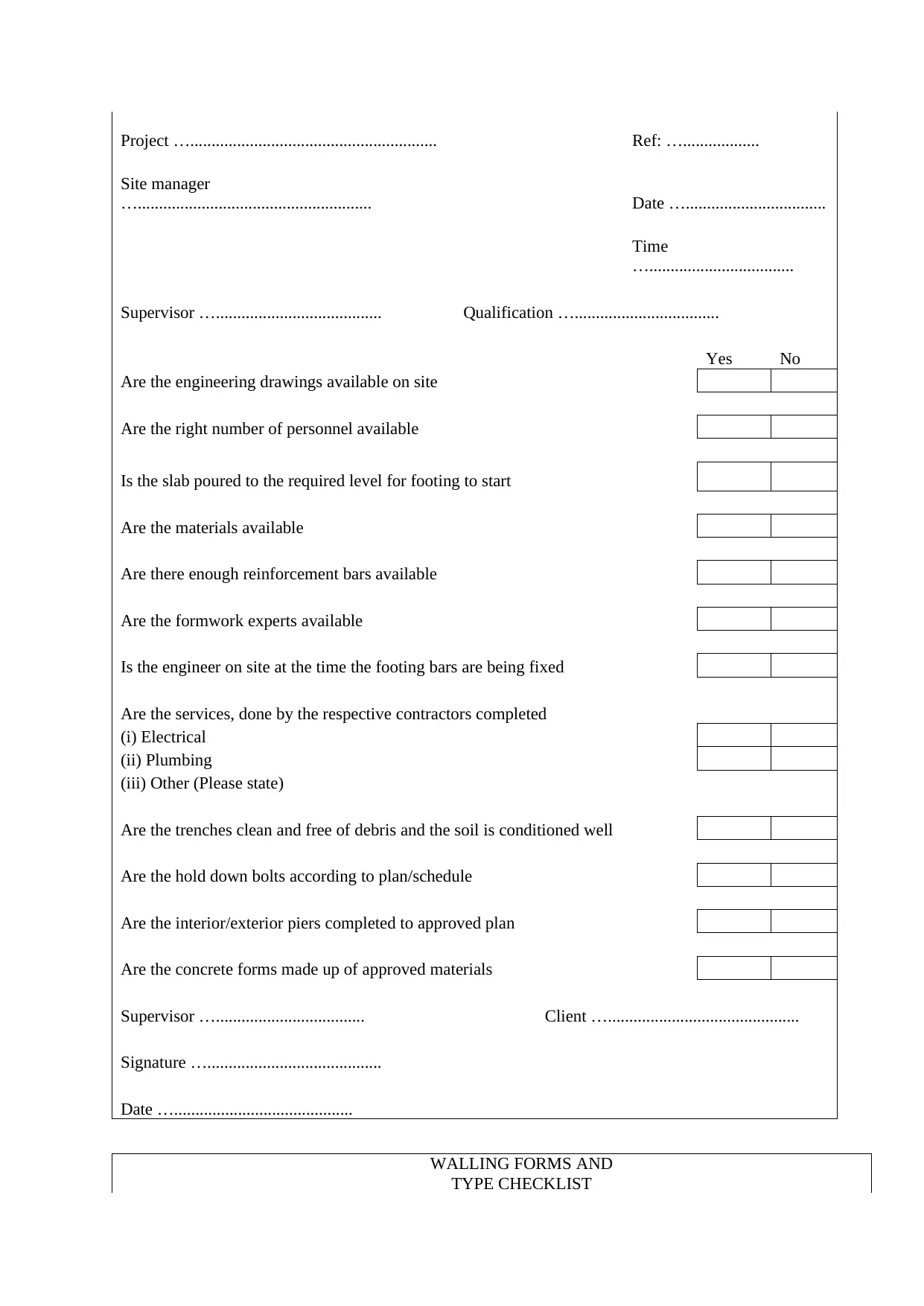
Project ….......................................................... Ref: …..................
Site manager
…....................................................... Date ….................................
Time
…..................................
Supervisor …....................................... Qualification …..................................
Yes No
Are the engineering drawings available on site
Are the right number of personnel available
Is the slab poured to the required level for footing to start
Are the materials available
Are there enough reinforcement bars available
Are the formwork experts available
Is the engineer on site at the time the footing bars are being fixed
Are the services, done by the respective contractors completed
(i) Electrical
(ii) Plumbing
(iii) Other (Please state)
Are the trenches clean and free of debris and the soil is conditioned well
Are the hold down bolts according to plan/schedule
Are the interior/exterior piers completed to approved plan
Are the concrete forms made up of approved materials
Supervisor …................................... Client ….............................................
Signature ….........................................
Date …..........................................
WALLING FORMS AND
TYPE CHECKLIST
Site manager
…....................................................... Date ….................................
Time
…..................................
Supervisor …....................................... Qualification …..................................
Yes No
Are the engineering drawings available on site
Are the right number of personnel available
Is the slab poured to the required level for footing to start
Are the materials available
Are there enough reinforcement bars available
Are the formwork experts available
Is the engineer on site at the time the footing bars are being fixed
Are the services, done by the respective contractors completed
(i) Electrical
(ii) Plumbing
(iii) Other (Please state)
Are the trenches clean and free of debris and the soil is conditioned well
Are the hold down bolts according to plan/schedule
Are the interior/exterior piers completed to approved plan
Are the concrete forms made up of approved materials
Supervisor …................................... Client ….............................................
Signature ….........................................
Date …..........................................
WALLING FORMS AND
TYPE CHECKLIST
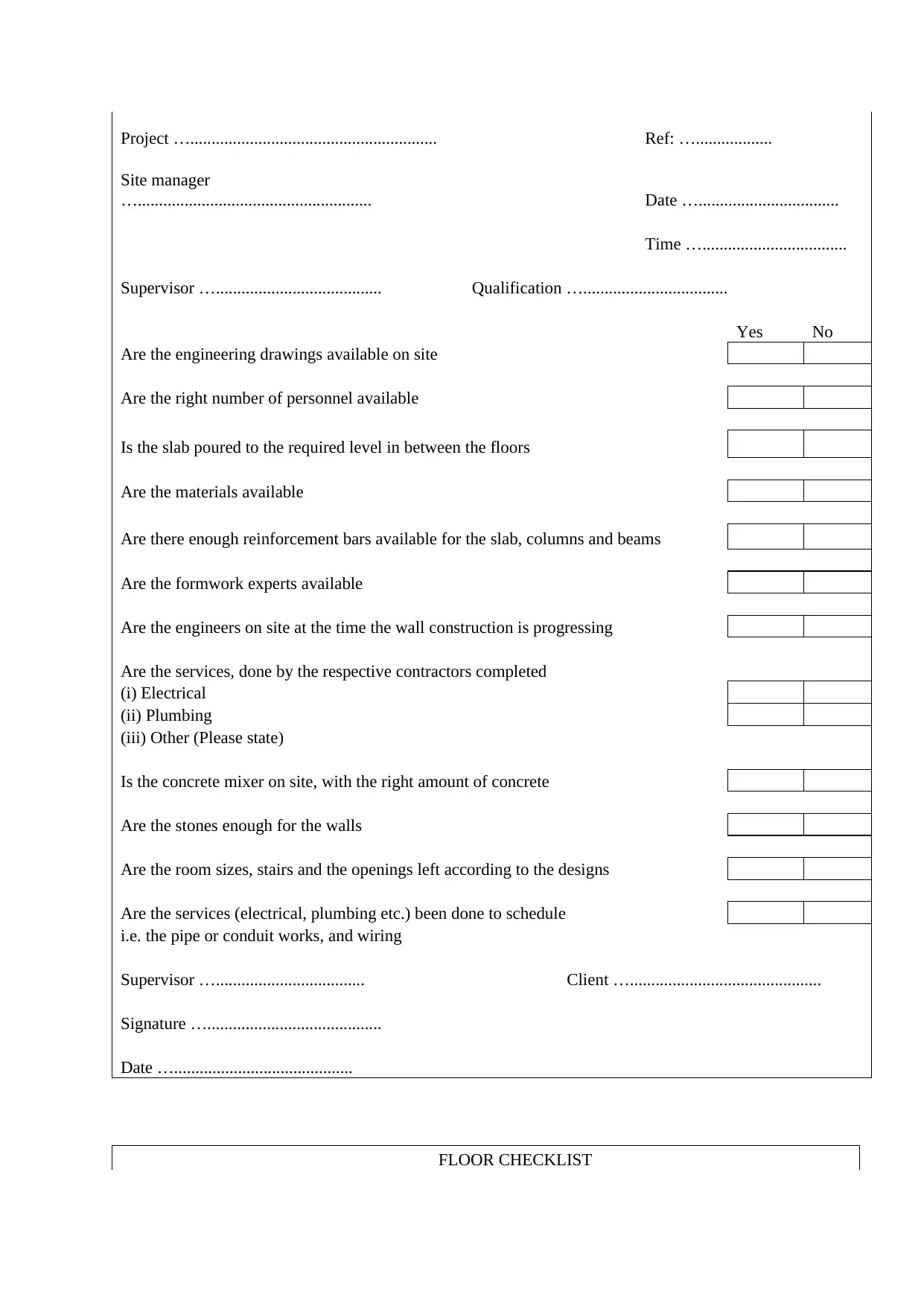
Project ….......................................................... Ref: …..................
Site manager
…....................................................... Date ….................................
Time …..................................
Supervisor …....................................... Qualification …..................................
Yes No
Are the engineering drawings available on site
Are the right number of personnel available
Is the slab poured to the required level in between the floors
Are the materials available
Are there enough reinforcement bars available for the slab, columns and beams
Are the formwork experts available
Are the engineers on site at the time the wall construction is progressing
Are the services, done by the respective contractors completed
(i) Electrical
(ii) Plumbing
(iii) Other (Please state)
Is the concrete mixer on site, with the right amount of concrete
Are the stones enough for the walls
Are the room sizes, stairs and the openings left according to the designs
Are the services (electrical, plumbing etc.) been done to schedule
i.e. the pipe or conduit works, and wiring
Supervisor …................................... Client ….............................................
Signature ….........................................
Date …..........................................
FLOOR CHECKLIST
Site manager
…....................................................... Date ….................................
Time …..................................
Supervisor …....................................... Qualification …..................................
Yes No
Are the engineering drawings available on site
Are the right number of personnel available
Is the slab poured to the required level in between the floors
Are the materials available
Are there enough reinforcement bars available for the slab, columns and beams
Are the formwork experts available
Are the engineers on site at the time the wall construction is progressing
Are the services, done by the respective contractors completed
(i) Electrical
(ii) Plumbing
(iii) Other (Please state)
Is the concrete mixer on site, with the right amount of concrete
Are the stones enough for the walls
Are the room sizes, stairs and the openings left according to the designs
Are the services (electrical, plumbing etc.) been done to schedule
i.e. the pipe or conduit works, and wiring
Supervisor …................................... Client ….............................................
Signature ….........................................
Date …..........................................
FLOOR CHECKLIST
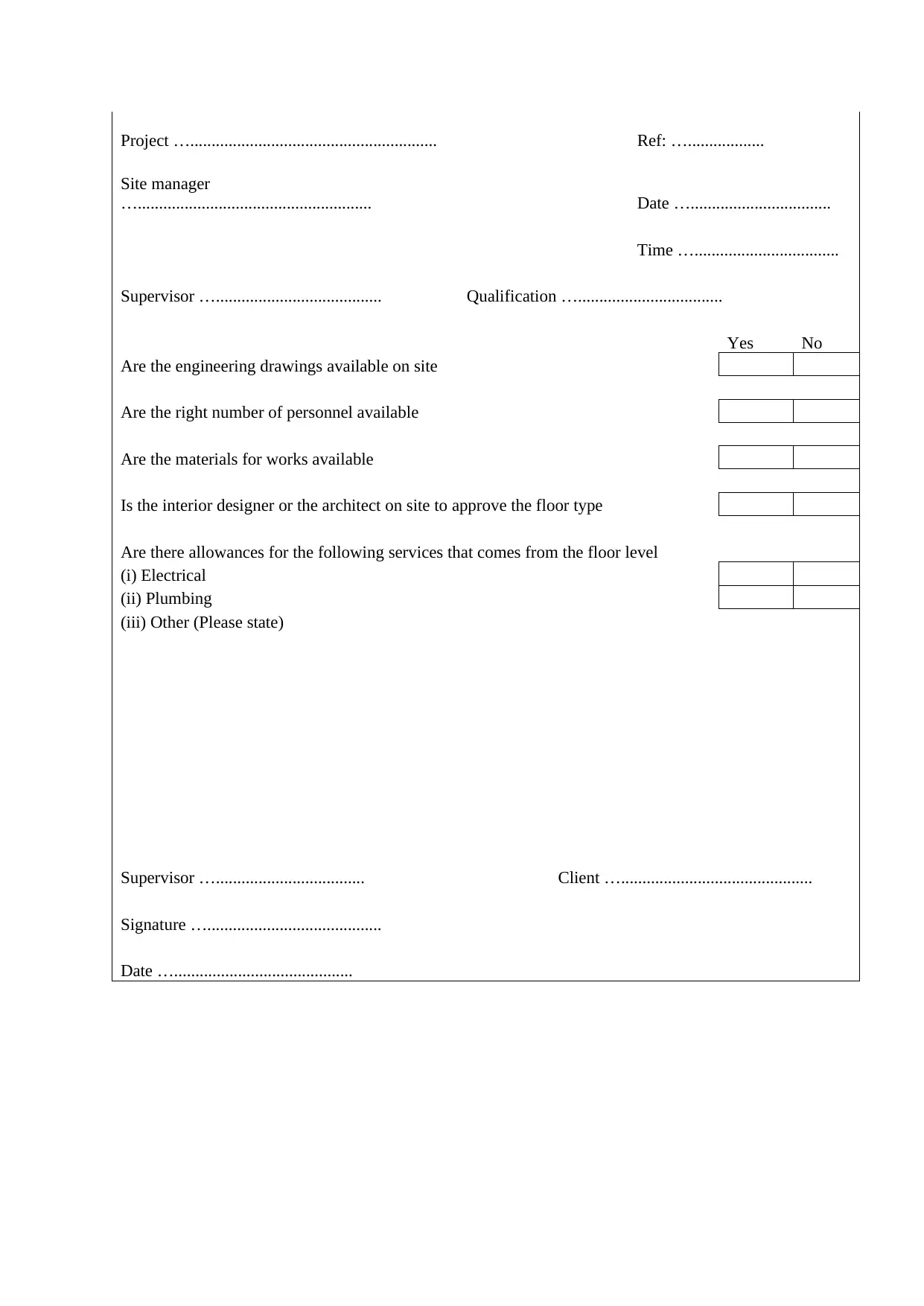
Project ….......................................................... Ref: …..................
Site manager
…....................................................... Date ….................................
Time …..................................
Supervisor …....................................... Qualification …..................................
Yes No
Are the engineering drawings available on site
Are the right number of personnel available
Are the materials for works available
Is the interior designer or the architect on site to approve the floor type
Are there allowances for the following services that comes from the floor level
(i) Electrical
(ii) Plumbing
(iii) Other (Please state)
Supervisor …................................... Client ….............................................
Signature ….........................................
Date …..........................................
Site manager
…....................................................... Date ….................................
Time …..................................
Supervisor …....................................... Qualification …..................................
Yes No
Are the engineering drawings available on site
Are the right number of personnel available
Are the materials for works available
Is the interior designer or the architect on site to approve the floor type
Are there allowances for the following services that comes from the floor level
(i) Electrical
(ii) Plumbing
(iii) Other (Please state)
Supervisor …................................... Client ….............................................
Signature ….........................................
Date …..........................................
Paraphrase This Document
Need a fresh take? Get an instant paraphrase of this document with our AI Paraphraser
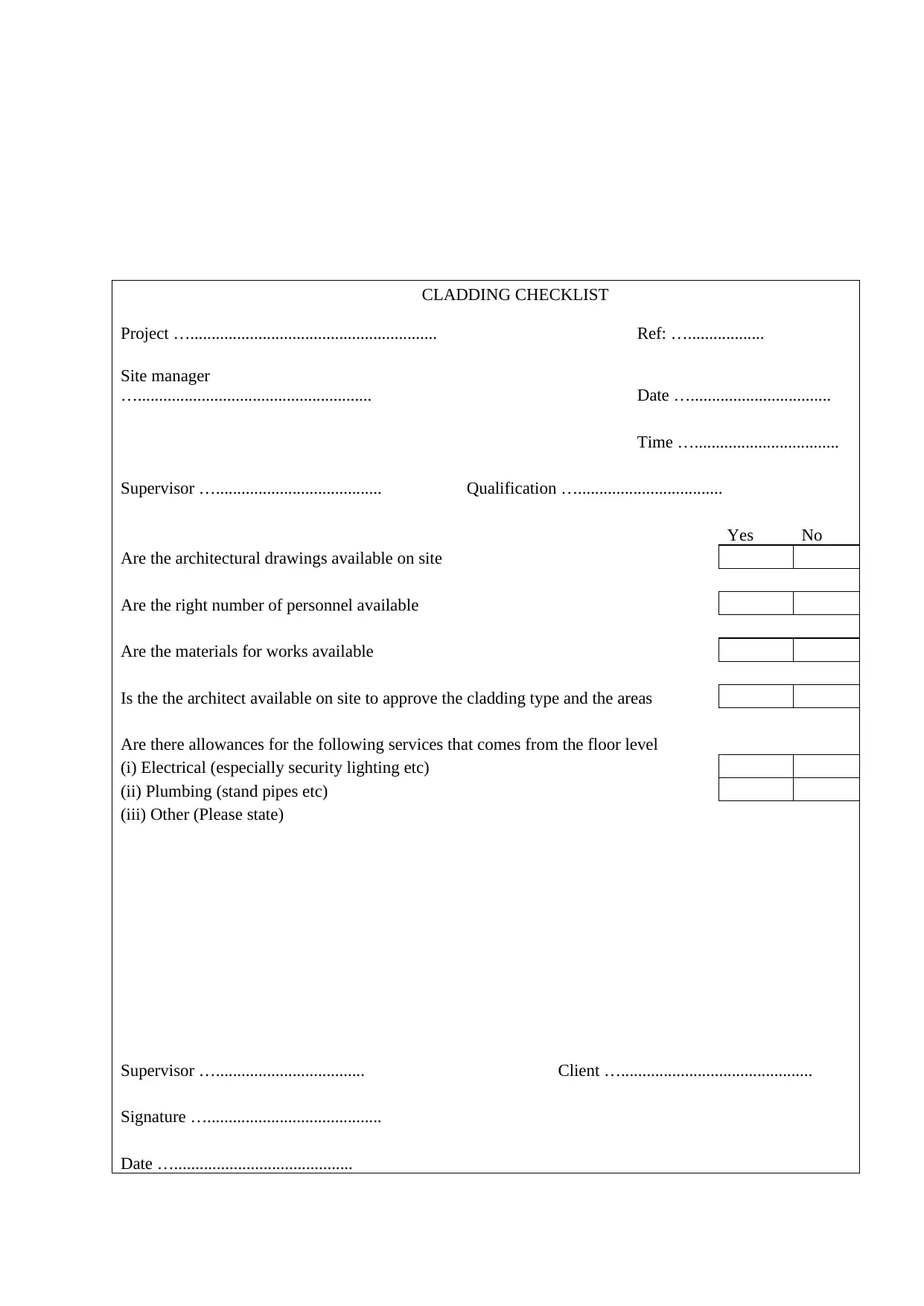
CLADDING CHECKLIST
Project ….......................................................... Ref: …..................
Site manager
…....................................................... Date ….................................
Time …..................................
Supervisor …....................................... Qualification …..................................
Yes No
Are the architectural drawings available on site
Are the right number of personnel available
Are the materials for works available
Is the the architect available on site to approve the cladding type and the areas
Are there allowances for the following services that comes from the floor level
(i) Electrical (especially security lighting etc)
(ii) Plumbing (stand pipes etc)
(iii) Other (Please state)
Supervisor …................................... Client ….............................................
Signature ….........................................
Date …..........................................
Project ….......................................................... Ref: …..................
Site manager
…....................................................... Date ….................................
Time …..................................
Supervisor …....................................... Qualification …..................................
Yes No
Are the architectural drawings available on site
Are the right number of personnel available
Are the materials for works available
Is the the architect available on site to approve the cladding type and the areas
Are there allowances for the following services that comes from the floor level
(i) Electrical (especially security lighting etc)
(ii) Plumbing (stand pipes etc)
(iii) Other (Please state)
Supervisor …................................... Client ….............................................
Signature ….........................................
Date …..........................................
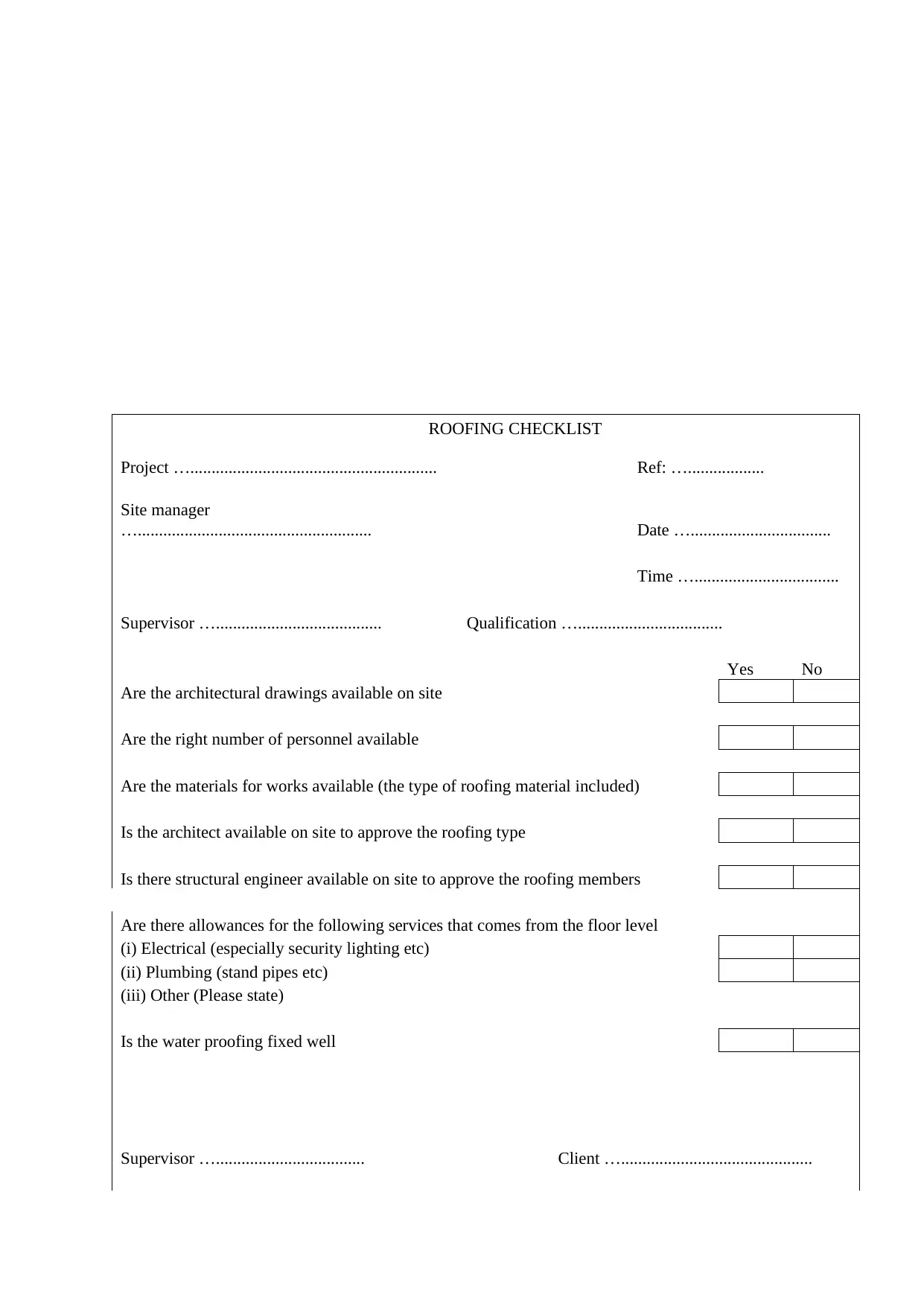
ROOFING CHECKLIST
Project ….......................................................... Ref: …..................
Site manager
…....................................................... Date ….................................
Time …..................................
Supervisor …....................................... Qualification …..................................
Yes No
Are the architectural drawings available on site
Are the right number of personnel available
Are the materials for works available (the type of roofing material included)
Is the architect available on site to approve the roofing type
Is there structural engineer available on site to approve the roofing members
Are there allowances for the following services that comes from the floor level
(i) Electrical (especially security lighting etc)
(ii) Plumbing (stand pipes etc)
(iii) Other (Please state)
Is the water proofing fixed well
Supervisor …................................... Client ….............................................
Project ….......................................................... Ref: …..................
Site manager
…....................................................... Date ….................................
Time …..................................
Supervisor …....................................... Qualification …..................................
Yes No
Are the architectural drawings available on site
Are the right number of personnel available
Are the materials for works available (the type of roofing material included)
Is the architect available on site to approve the roofing type
Is there structural engineer available on site to approve the roofing members
Are there allowances for the following services that comes from the floor level
(i) Electrical (especially security lighting etc)
(ii) Plumbing (stand pipes etc)
(iii) Other (Please state)
Is the water proofing fixed well
Supervisor …................................... Client ….............................................
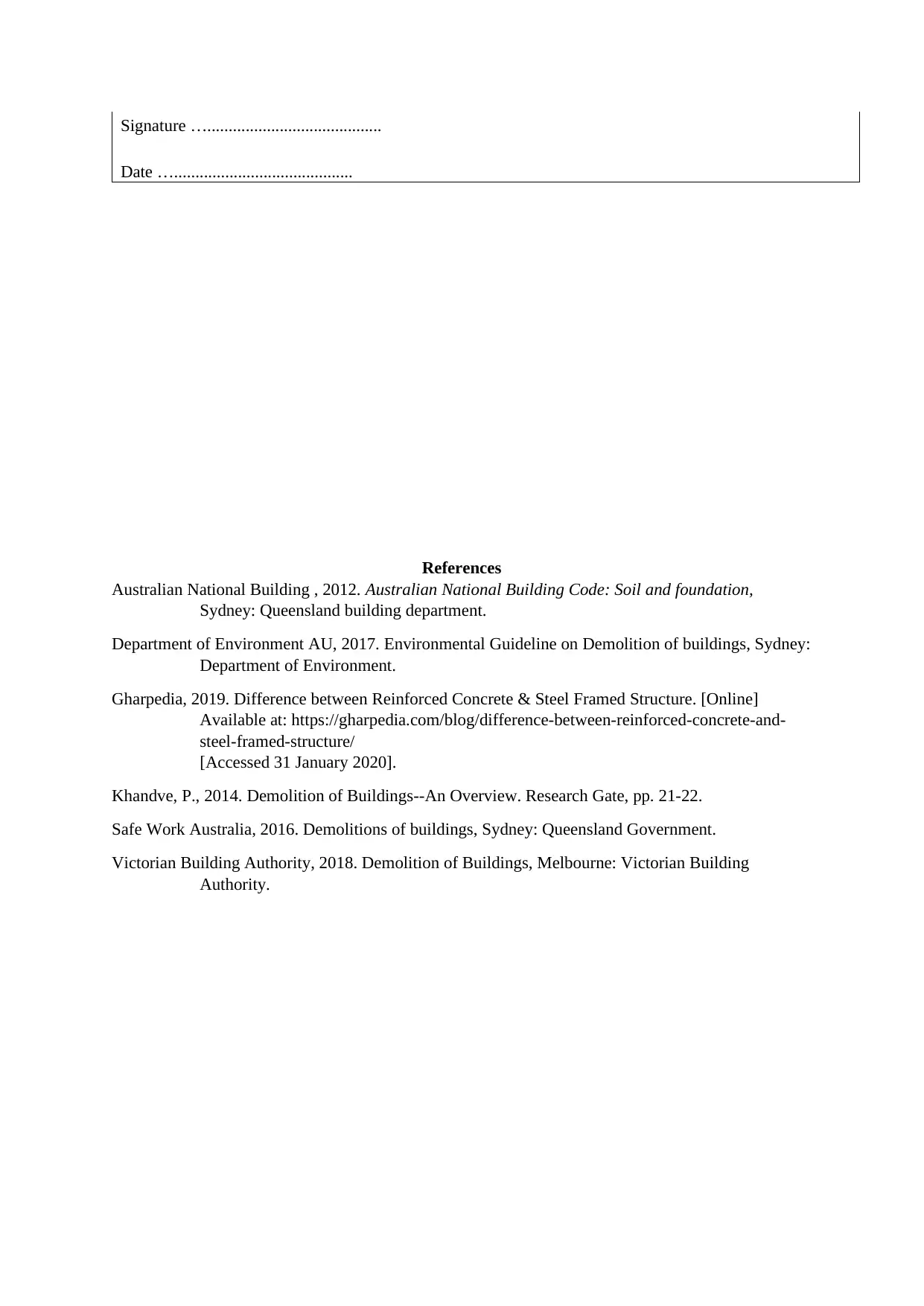
Signature ….........................................
Date …..........................................
References
Australian National Building , 2012. Australian National Building Code: Soil and foundation,
Sydney: Queensland building department.
Department of Environment AU, 2017. Environmental Guideline on Demolition of buildings, Sydney:
Department of Environment.
Gharpedia, 2019. Difference between Reinforced Concrete & Steel Framed Structure. [Online]
Available at: https://gharpedia.com/blog/difference-between-reinforced-concrete-and-
steel-framed-structure/
[Accessed 31 January 2020].
Khandve, P., 2014. Demolition of Buildings--An Overview. Research Gate, pp. 21-22.
Safe Work Australia, 2016. Demolitions of buildings, Sydney: Queensland Government.
Victorian Building Authority, 2018. Demolition of Buildings, Melbourne: Victorian Building
Authority.
Date …..........................................
References
Australian National Building , 2012. Australian National Building Code: Soil and foundation,
Sydney: Queensland building department.
Department of Environment AU, 2017. Environmental Guideline on Demolition of buildings, Sydney:
Department of Environment.
Gharpedia, 2019. Difference between Reinforced Concrete & Steel Framed Structure. [Online]
Available at: https://gharpedia.com/blog/difference-between-reinforced-concrete-and-
steel-framed-structure/
[Accessed 31 January 2020].
Khandve, P., 2014. Demolition of Buildings--An Overview. Research Gate, pp. 21-22.
Safe Work Australia, 2016. Demolitions of buildings, Sydney: Queensland Government.
Victorian Building Authority, 2018. Demolition of Buildings, Melbourne: Victorian Building
Authority.
1 out of 16
![[object Object]](/_next/image/?url=%2F_next%2Fstatic%2Fmedia%2Flogo.6d15ce61.png&w=640&q=75)
Your All-in-One AI-Powered Toolkit for Academic Success.
+13062052269
info@desklib.com
Available 24*7 on WhatsApp / Email
Unlock your academic potential
© 2024 | Zucol Services PVT LTD | All rights reserved.