Tesco PLC: Internal Reporting, Costing Systems, and Decision Making
VerifiedAdded on 2020/10/23
|17
|4287
|104
Report
AI Summary
This report analyzes the costs and revenues of Tesco PLC, a major British multinational retailer. It explores the purpose of internal reporting, various costing systems (job, process, direct), and responsibility centers within an organization. The report details different cost classifications (direct, indirect, fixed, variable) and contrasts marginal and absorption costing methods. It covers recording and analyzing cost information for materials, labor, and expenses, including inventory valuation using FIFO, LIFO, and weighted average methods. The behavior of costs (fixed, variable, semi-variable, stepped) is examined, along with the application of different costing systems (job, batch, unit, process, service). Furthermore, the report discusses overhead cost allocation, absorption rates, variance analysis, and management reporting. Finally, it addresses the preparation of future income and cost estimates for decision-making, considering the effect of changing activity levels and factors influencing short-term and long-term decisions.
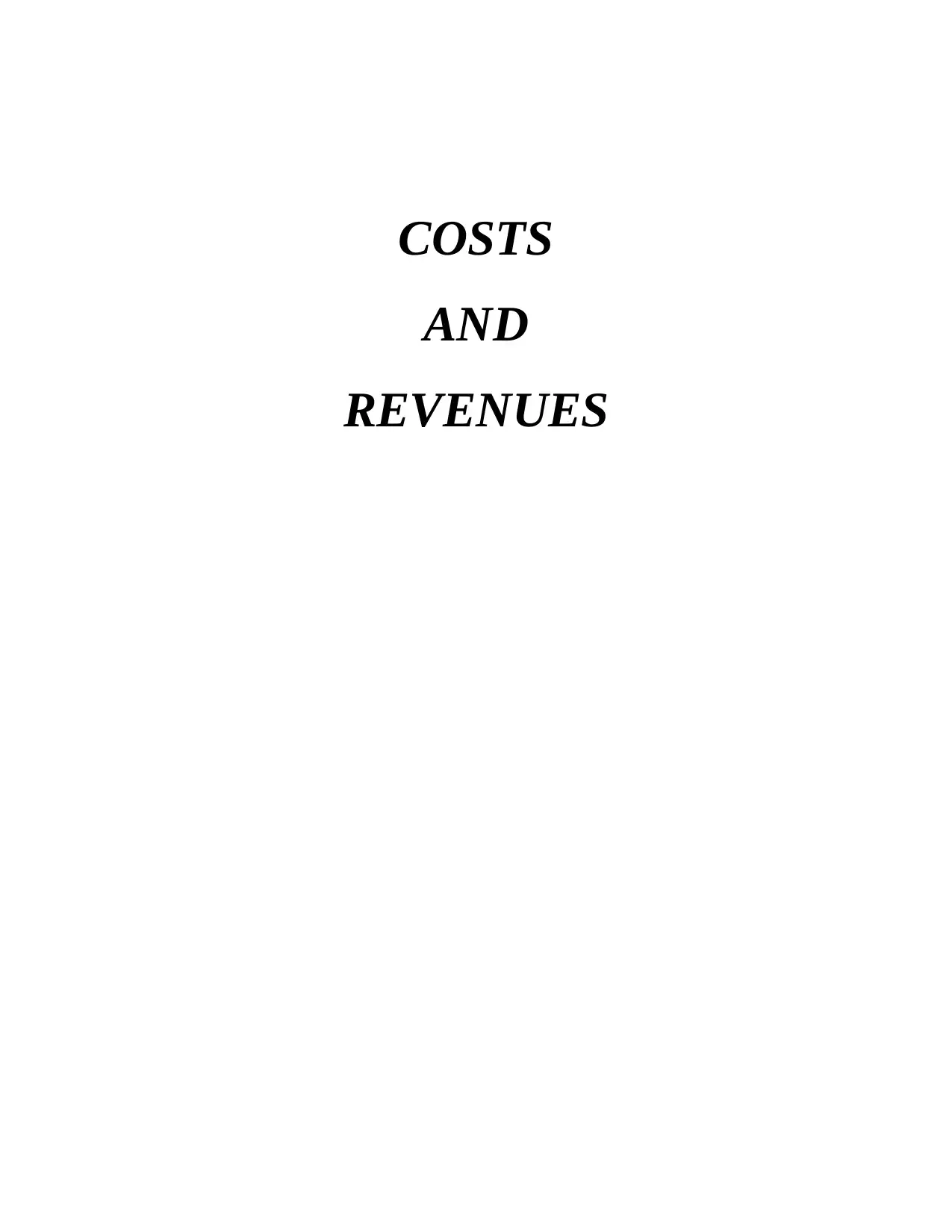
COSTS
AND
REVENUES
AND
REVENUES
Paraphrase This Document
Need a fresh take? Get an instant paraphrase of this document with our AI Paraphraser
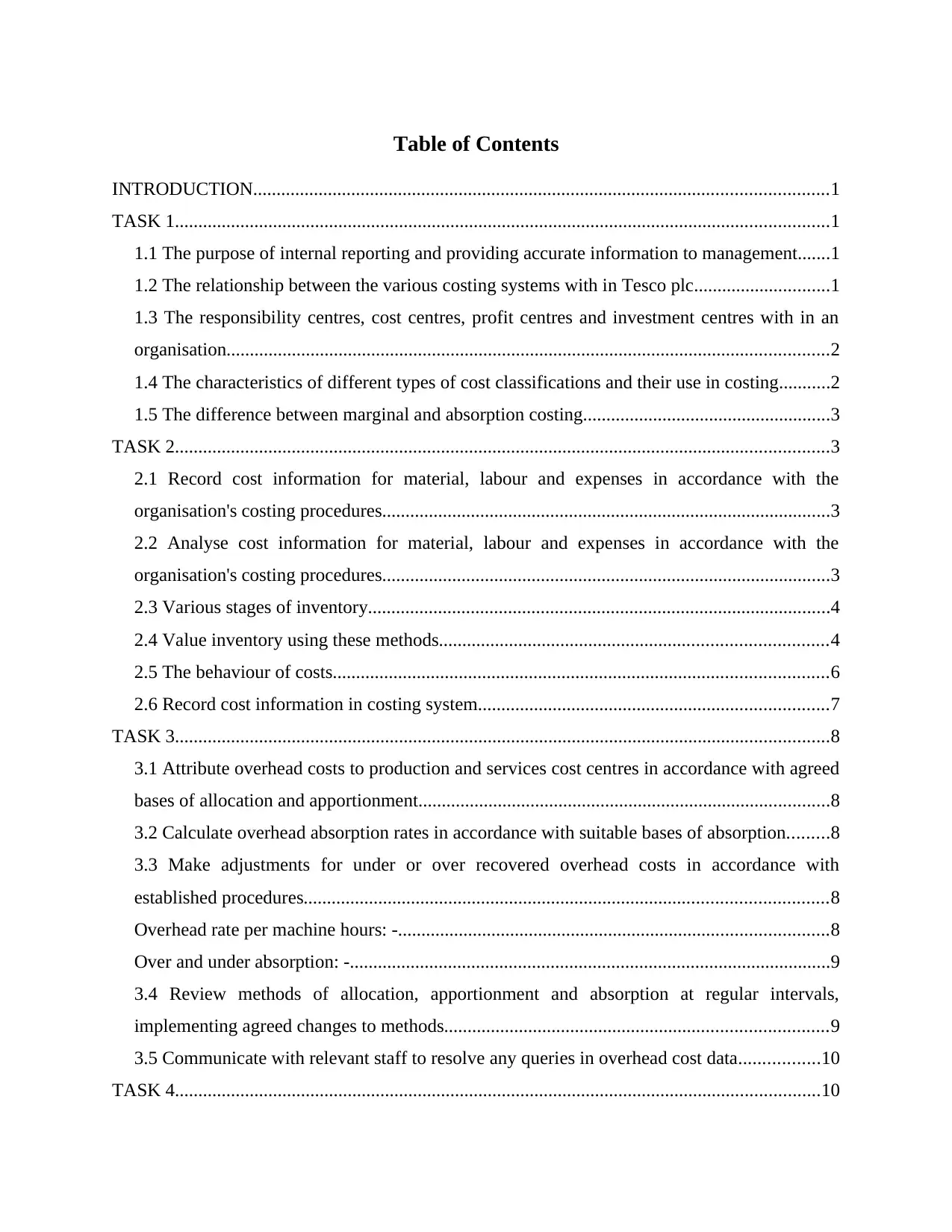
Table of Contents
INTRODUCTION...........................................................................................................................1
TASK 1............................................................................................................................................1
1.1 The purpose of internal reporting and providing accurate information to management.......1
1.2 The relationship between the various costing systems with in Tesco plc.............................1
1.3 The responsibility centres, cost centres, profit centres and investment centres with in an
organisation.................................................................................................................................2
1.4 The characteristics of different types of cost classifications and their use in costing...........2
1.5 The difference between marginal and absorption costing.....................................................3
TASK 2............................................................................................................................................3
2.1 Record cost information for material, labour and expenses in accordance with the
organisation's costing procedures................................................................................................3
2.2 Analyse cost information for material, labour and expenses in accordance with the
organisation's costing procedures................................................................................................3
2.3 Various stages of inventory...................................................................................................4
2.4 Value inventory using these methods...................................................................................4
2.5 The behaviour of costs..........................................................................................................6
2.6 Record cost information in costing system...........................................................................7
TASK 3............................................................................................................................................8
3.1 Attribute overhead costs to production and services cost centres in accordance with agreed
bases of allocation and apportionment........................................................................................8
3.2 Calculate overhead absorption rates in accordance with suitable bases of absorption.........8
3.3 Make adjustments for under or over recovered overhead costs in accordance with
established procedures................................................................................................................8
Overhead rate per machine hours: -............................................................................................8
Over and under absorption: -.......................................................................................................9
3.4 Review methods of allocation, apportionment and absorption at regular intervals,
implementing agreed changes to methods..................................................................................9
3.5 Communicate with relevant staff to resolve any queries in overhead cost data.................10
TASK 4..........................................................................................................................................10
INTRODUCTION...........................................................................................................................1
TASK 1............................................................................................................................................1
1.1 The purpose of internal reporting and providing accurate information to management.......1
1.2 The relationship between the various costing systems with in Tesco plc.............................1
1.3 The responsibility centres, cost centres, profit centres and investment centres with in an
organisation.................................................................................................................................2
1.4 The characteristics of different types of cost classifications and their use in costing...........2
1.5 The difference between marginal and absorption costing.....................................................3
TASK 2............................................................................................................................................3
2.1 Record cost information for material, labour and expenses in accordance with the
organisation's costing procedures................................................................................................3
2.2 Analyse cost information for material, labour and expenses in accordance with the
organisation's costing procedures................................................................................................3
2.3 Various stages of inventory...................................................................................................4
2.4 Value inventory using these methods...................................................................................4
2.5 The behaviour of costs..........................................................................................................6
2.6 Record cost information in costing system...........................................................................7
TASK 3............................................................................................................................................8
3.1 Attribute overhead costs to production and services cost centres in accordance with agreed
bases of allocation and apportionment........................................................................................8
3.2 Calculate overhead absorption rates in accordance with suitable bases of absorption.........8
3.3 Make adjustments for under or over recovered overhead costs in accordance with
established procedures................................................................................................................8
Overhead rate per machine hours: -............................................................................................8
Over and under absorption: -.......................................................................................................9
3.4 Review methods of allocation, apportionment and absorption at regular intervals,
implementing agreed changes to methods..................................................................................9
3.5 Communicate with relevant staff to resolve any queries in overhead cost data.................10
TASK 4..........................................................................................................................................10
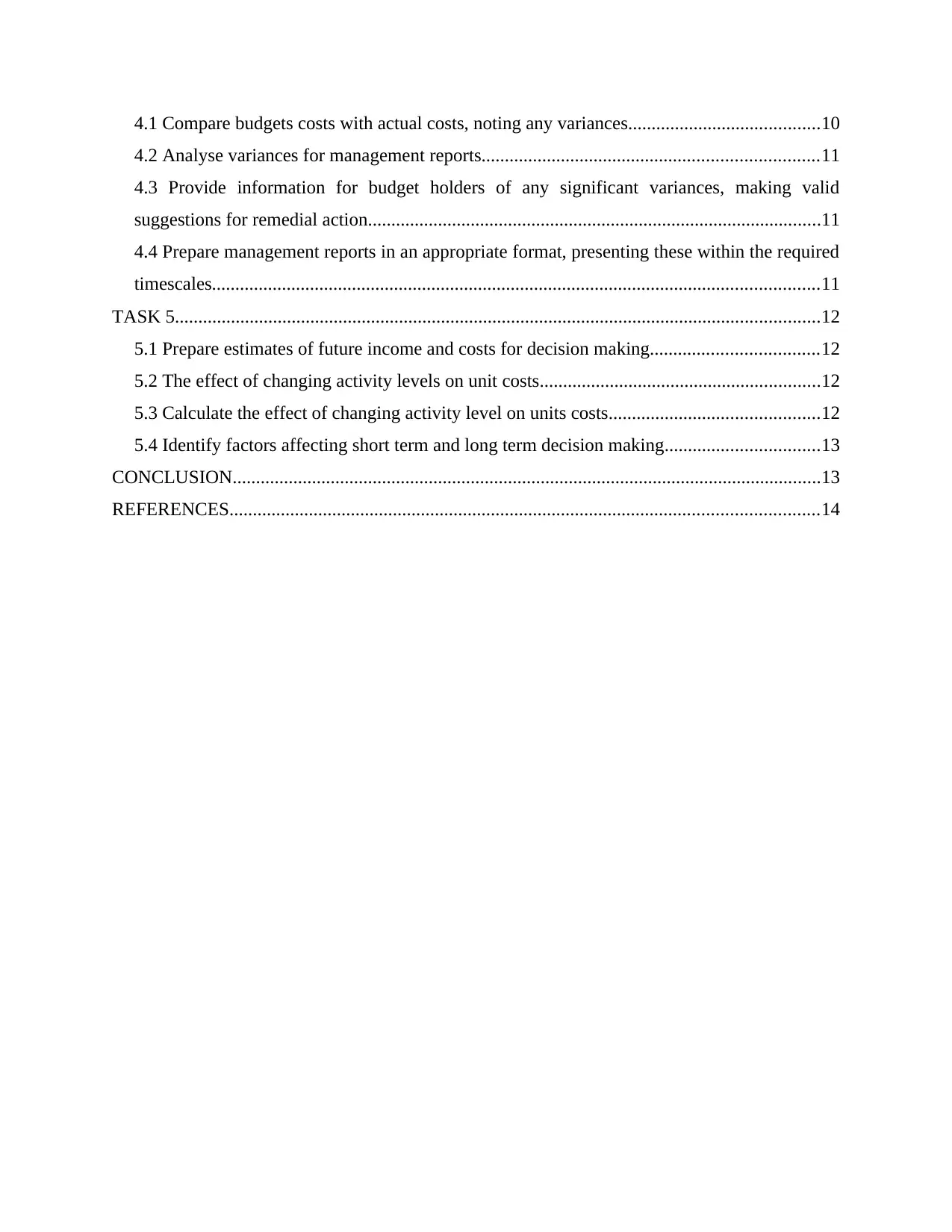
4.1 Compare budgets costs with actual costs, noting any variances.........................................10
4.2 Analyse variances for management reports........................................................................11
4.3 Provide information for budget holders of any significant variances, making valid
suggestions for remedial action.................................................................................................11
4.4 Prepare management reports in an appropriate format, presenting these within the required
timescales..................................................................................................................................11
TASK 5..........................................................................................................................................12
5.1 Prepare estimates of future income and costs for decision making....................................12
5.2 The effect of changing activity levels on unit costs............................................................12
5.3 Calculate the effect of changing activity level on units costs.............................................12
5.4 Identify factors affecting short term and long term decision making.................................13
CONCLUSION..............................................................................................................................13
REFERENCES..............................................................................................................................14
4.2 Analyse variances for management reports........................................................................11
4.3 Provide information for budget holders of any significant variances, making valid
suggestions for remedial action.................................................................................................11
4.4 Prepare management reports in an appropriate format, presenting these within the required
timescales..................................................................................................................................11
TASK 5..........................................................................................................................................12
5.1 Prepare estimates of future income and costs for decision making....................................12
5.2 The effect of changing activity levels on unit costs............................................................12
5.3 Calculate the effect of changing activity level on units costs.............................................12
5.4 Identify factors affecting short term and long term decision making.................................13
CONCLUSION..............................................................................................................................13
REFERENCES..............................................................................................................................14
⊘ This is a preview!⊘
Do you want full access?
Subscribe today to unlock all pages.

Trusted by 1+ million students worldwide
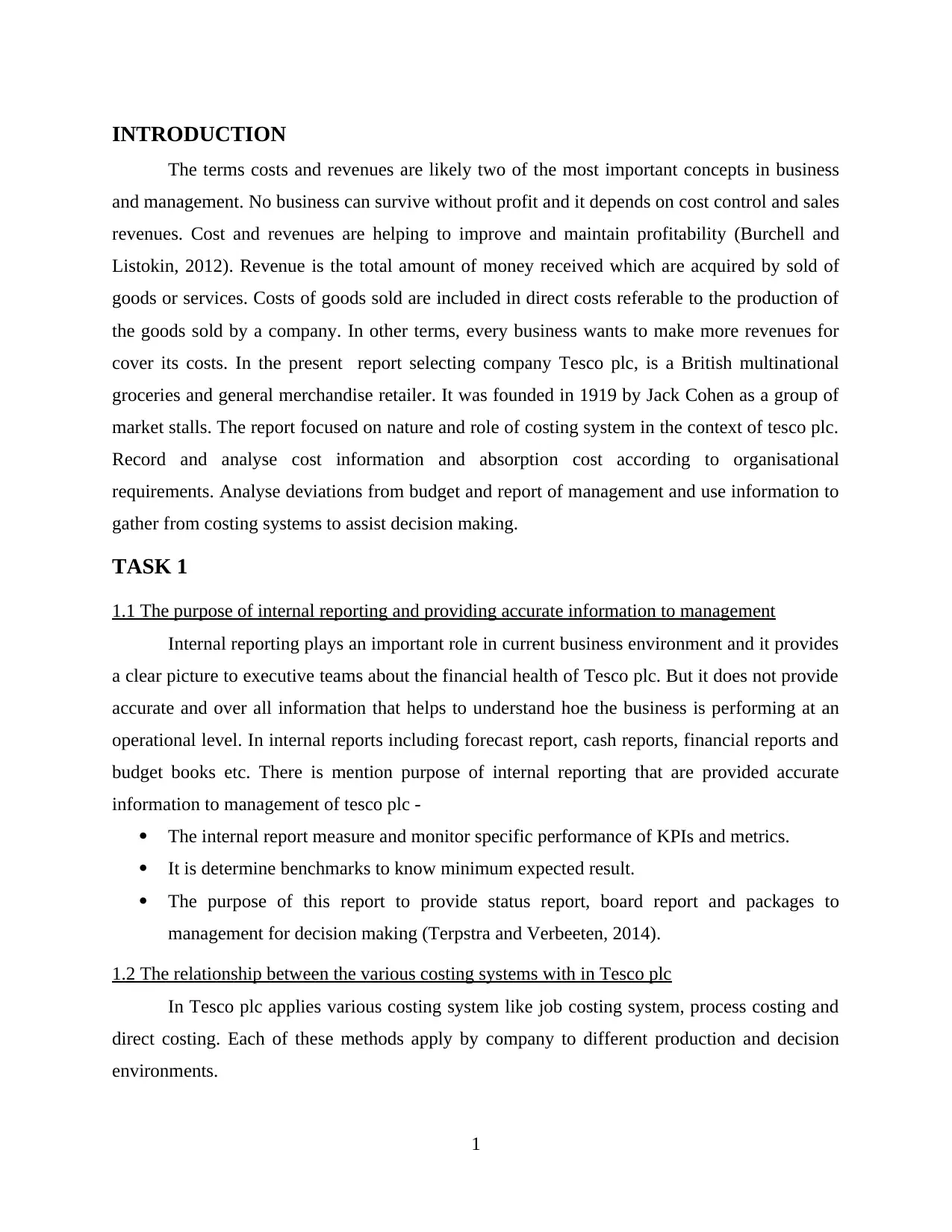
INTRODUCTION
The terms costs and revenues are likely two of the most important concepts in business
and management. No business can survive without profit and it depends on cost control and sales
revenues. Cost and revenues are helping to improve and maintain profitability (Burchell and
Listokin, 2012). Revenue is the total amount of money received which are acquired by sold of
goods or services. Costs of goods sold are included in direct costs referable to the production of
the goods sold by a company. In other terms, every business wants to make more revenues for
cover its costs. In the present report selecting company Tesco plc, is a British multinational
groceries and general merchandise retailer. It was founded in 1919 by Jack Cohen as a group of
market stalls. The report focused on nature and role of costing system in the context of tesco plc.
Record and analyse cost information and absorption cost according to organisational
requirements. Analyse deviations from budget and report of management and use information to
gather from costing systems to assist decision making.
TASK 1
1.1 The purpose of internal reporting and providing accurate information to management
Internal reporting plays an important role in current business environment and it provides
a clear picture to executive teams about the financial health of Tesco plc. But it does not provide
accurate and over all information that helps to understand hoe the business is performing at an
operational level. In internal reports including forecast report, cash reports, financial reports and
budget books etc. There is mention purpose of internal reporting that are provided accurate
information to management of tesco plc -
The internal report measure and monitor specific performance of KPIs and metrics.
It is determine benchmarks to know minimum expected result.
The purpose of this report to provide status report, board report and packages to
management for decision making (Terpstra and Verbeeten, 2014).
1.2 The relationship between the various costing systems with in Tesco plc
In Tesco plc applies various costing system like job costing system, process costing and
direct costing. Each of these methods apply by company to different production and decision
environments.
1
The terms costs and revenues are likely two of the most important concepts in business
and management. No business can survive without profit and it depends on cost control and sales
revenues. Cost and revenues are helping to improve and maintain profitability (Burchell and
Listokin, 2012). Revenue is the total amount of money received which are acquired by sold of
goods or services. Costs of goods sold are included in direct costs referable to the production of
the goods sold by a company. In other terms, every business wants to make more revenues for
cover its costs. In the present report selecting company Tesco plc, is a British multinational
groceries and general merchandise retailer. It was founded in 1919 by Jack Cohen as a group of
market stalls. The report focused on nature and role of costing system in the context of tesco plc.
Record and analyse cost information and absorption cost according to organisational
requirements. Analyse deviations from budget and report of management and use information to
gather from costing systems to assist decision making.
TASK 1
1.1 The purpose of internal reporting and providing accurate information to management
Internal reporting plays an important role in current business environment and it provides
a clear picture to executive teams about the financial health of Tesco plc. But it does not provide
accurate and over all information that helps to understand hoe the business is performing at an
operational level. In internal reports including forecast report, cash reports, financial reports and
budget books etc. There is mention purpose of internal reporting that are provided accurate
information to management of tesco plc -
The internal report measure and monitor specific performance of KPIs and metrics.
It is determine benchmarks to know minimum expected result.
The purpose of this report to provide status report, board report and packages to
management for decision making (Terpstra and Verbeeten, 2014).
1.2 The relationship between the various costing systems with in Tesco plc
In Tesco plc applies various costing system like job costing system, process costing and
direct costing. Each of these methods apply by company to different production and decision
environments.
1
Paraphrase This Document
Need a fresh take? Get an instant paraphrase of this document with our AI Paraphraser
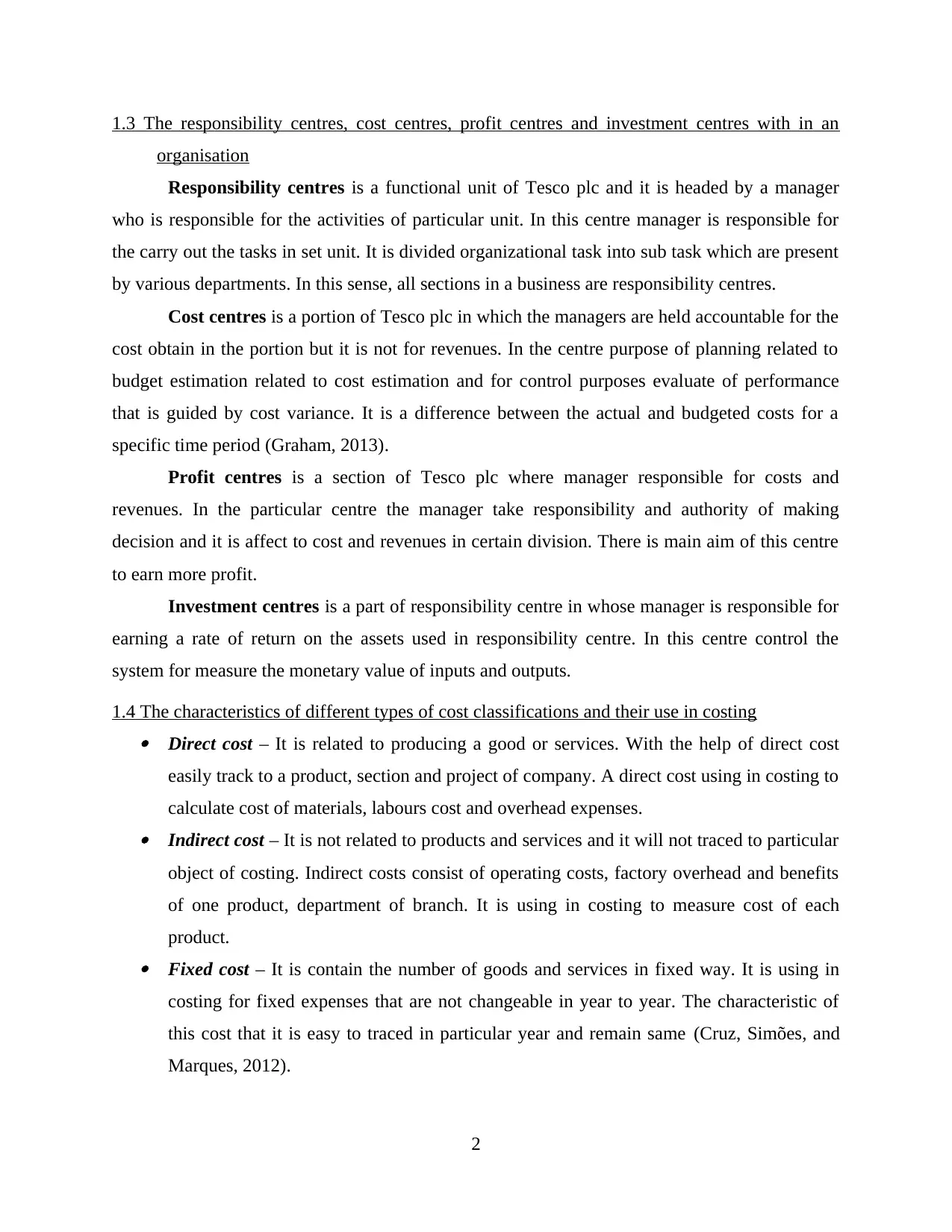
1.3 The responsibility centres, cost centres, profit centres and investment centres with in an
organisation
Responsibility centres is a functional unit of Tesco plc and it is headed by a manager
who is responsible for the activities of particular unit. In this centre manager is responsible for
the carry out the tasks in set unit. It is divided organizational task into sub task which are present
by various departments. In this sense, all sections in a business are responsibility centres.
Cost centres is a portion of Tesco plc in which the managers are held accountable for the
cost obtain in the portion but it is not for revenues. In the centre purpose of planning related to
budget estimation related to cost estimation and for control purposes evaluate of performance
that is guided by cost variance. It is a difference between the actual and budgeted costs for a
specific time period (Graham, 2013).
Profit centres is a section of Tesco plc where manager responsible for costs and
revenues. In the particular centre the manager take responsibility and authority of making
decision and it is affect to cost and revenues in certain division. There is main aim of this centre
to earn more profit.
Investment centres is a part of responsibility centre in whose manager is responsible for
earning a rate of return on the assets used in responsibility centre. In this centre control the
system for measure the monetary value of inputs and outputs.
1.4 The characteristics of different types of cost classifications and their use in costing Direct cost – It is related to producing a good or services. With the help of direct cost
easily track to a product, section and project of company. A direct cost using in costing to
calculate cost of materials, labours cost and overhead expenses. Indirect cost – It is not related to products and services and it will not traced to particular
object of costing. Indirect costs consist of operating costs, factory overhead and benefits
of one product, department of branch. It is using in costing to measure cost of each
product. Fixed cost – It is contain the number of goods and services in fixed way. It is using in
costing for fixed expenses that are not changeable in year to year. The characteristic of
this cost that it is easy to traced in particular year and remain same (Cruz, Simões, and
Marques, 2012).
2
organisation
Responsibility centres is a functional unit of Tesco plc and it is headed by a manager
who is responsible for the activities of particular unit. In this centre manager is responsible for
the carry out the tasks in set unit. It is divided organizational task into sub task which are present
by various departments. In this sense, all sections in a business are responsibility centres.
Cost centres is a portion of Tesco plc in which the managers are held accountable for the
cost obtain in the portion but it is not for revenues. In the centre purpose of planning related to
budget estimation related to cost estimation and for control purposes evaluate of performance
that is guided by cost variance. It is a difference between the actual and budgeted costs for a
specific time period (Graham, 2013).
Profit centres is a section of Tesco plc where manager responsible for costs and
revenues. In the particular centre the manager take responsibility and authority of making
decision and it is affect to cost and revenues in certain division. There is main aim of this centre
to earn more profit.
Investment centres is a part of responsibility centre in whose manager is responsible for
earning a rate of return on the assets used in responsibility centre. In this centre control the
system for measure the monetary value of inputs and outputs.
1.4 The characteristics of different types of cost classifications and their use in costing Direct cost – It is related to producing a good or services. With the help of direct cost
easily track to a product, section and project of company. A direct cost using in costing to
calculate cost of materials, labours cost and overhead expenses. Indirect cost – It is not related to products and services and it will not traced to particular
object of costing. Indirect costs consist of operating costs, factory overhead and benefits
of one product, department of branch. It is using in costing to measure cost of each
product. Fixed cost – It is contain the number of goods and services in fixed way. It is using in
costing for fixed expenses that are not changeable in year to year. The characteristic of
this cost that it is easy to traced in particular year and remain same (Cruz, Simões, and
Marques, 2012).
2

Variable cost – It is fluctuate the level of production to change output and it was
depended on the number products. It is helping to increases of volume production and
using in costing to calculate cost of products on various stages.
1.5 The difference between marginal and absorption costing
Basis Marginal costing Absorption costing
Meaning Marginal costing is a technique that
estimate of variable cost as product
cost.
Absorption costing is a technique
that anticipate of fixed and variable
cost as a product cost.
Nature of
overhead
In this method included fixed cost
and variable cost.
In the case of absorption costing
have different selling &
administration, production and
distribution.
Profit calculation In this method profit calculated by
using profit volume ratio (p/v ratio)
In absorption costing method fixed
cost are reasoned in product cost so
profit gets decreased.
TASK 2
2.1 Record cost information for material, labour and expenses in accordance with the
organisation's costing procedures
Costing procedure is the activity of recording cost in appropriate accounts and expenses
determined in manufacturing process. There are various types of costs these are -
Material – It is divided in two parts direct and indirect materials.
Labour – They are working in an organisation to manufacture products.
Expenses – It is related to revenues generation process and non operating business execution
process (Raisman, 2013).
2.2 Analyse cost information for material, labour and expenses in accordance with the
organisation's costing procedures
Material cost is a variable expenses that are changes according to demand in the market.
It is depended on market activities because in the market demand is high so need of material
3
depended on the number products. It is helping to increases of volume production and
using in costing to calculate cost of products on various stages.
1.5 The difference between marginal and absorption costing
Basis Marginal costing Absorption costing
Meaning Marginal costing is a technique that
estimate of variable cost as product
cost.
Absorption costing is a technique
that anticipate of fixed and variable
cost as a product cost.
Nature of
overhead
In this method included fixed cost
and variable cost.
In the case of absorption costing
have different selling &
administration, production and
distribution.
Profit calculation In this method profit calculated by
using profit volume ratio (p/v ratio)
In absorption costing method fixed
cost are reasoned in product cost so
profit gets decreased.
TASK 2
2.1 Record cost information for material, labour and expenses in accordance with the
organisation's costing procedures
Costing procedure is the activity of recording cost in appropriate accounts and expenses
determined in manufacturing process. There are various types of costs these are -
Material – It is divided in two parts direct and indirect materials.
Labour – They are working in an organisation to manufacture products.
Expenses – It is related to revenues generation process and non operating business execution
process (Raisman, 2013).
2.2 Analyse cost information for material, labour and expenses in accordance with the
organisation's costing procedures
Material cost is a variable expenses that are changes according to demand in the market.
It is depended on market activities because in the market demand is high so need of material
3
⊘ This is a preview!⊘
Do you want full access?
Subscribe today to unlock all pages.

Trusted by 1+ million students worldwide
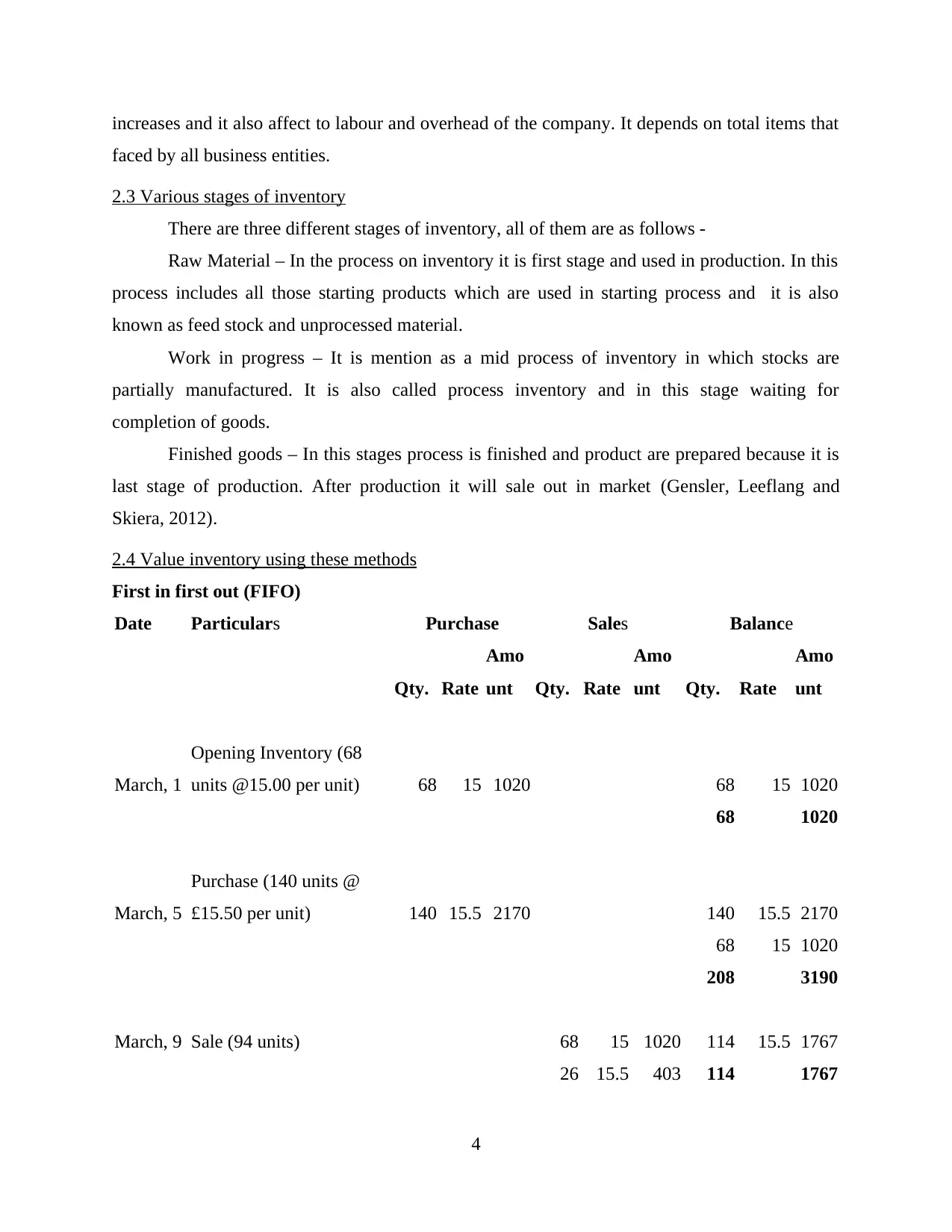
increases and it also affect to labour and overhead of the company. It depends on total items that
faced by all business entities.
2.3 Various stages of inventory
There are three different stages of inventory, all of them are as follows -
Raw Material – In the process on inventory it is first stage and used in production. In this
process includes all those starting products which are used in starting process and it is also
known as feed stock and unprocessed material.
Work in progress – It is mention as a mid process of inventory in which stocks are
partially manufactured. It is also called process inventory and in this stage waiting for
completion of goods.
Finished goods – In this stages process is finished and product are prepared because it is
last stage of production. After production it will sale out in market (Gensler, Leeflang and
Skiera, 2012).
2.4 Value inventory using these methods
First in first out (FIFO)
Date Particulars Purchase Sales Balance
Qty. Rate
Amo
unt Qty. Rate
Amo
unt Qty. Rate
Amo
unt
March, 1
Opening Inventory (68
units @15.00 per unit) 68 15 1020 68 15 1020
68 1020
March, 5
Purchase (140 units @
£15.50 per unit) 140 15.5 2170 140 15.5 2170
68 15 1020
208 3190
March, 9 Sale (94 units) 68 15 1020 114 15.5 1767
26 15.5 403 114 1767
4
faced by all business entities.
2.3 Various stages of inventory
There are three different stages of inventory, all of them are as follows -
Raw Material – In the process on inventory it is first stage and used in production. In this
process includes all those starting products which are used in starting process and it is also
known as feed stock and unprocessed material.
Work in progress – It is mention as a mid process of inventory in which stocks are
partially manufactured. It is also called process inventory and in this stage waiting for
completion of goods.
Finished goods – In this stages process is finished and product are prepared because it is
last stage of production. After production it will sale out in market (Gensler, Leeflang and
Skiera, 2012).
2.4 Value inventory using these methods
First in first out (FIFO)
Date Particulars Purchase Sales Balance
Qty. Rate
Amo
unt Qty. Rate
Amo
unt Qty. Rate
Amo
unt
March, 1
Opening Inventory (68
units @15.00 per unit) 68 15 1020 68 15 1020
68 1020
March, 5
Purchase (140 units @
£15.50 per unit) 140 15.5 2170 140 15.5 2170
68 15 1020
208 3190
March, 9 Sale (94 units) 68 15 1020 114 15.5 1767
26 15.5 403 114 1767
4
Paraphrase This Document
Need a fresh take? Get an instant paraphrase of this document with our AI Paraphraser
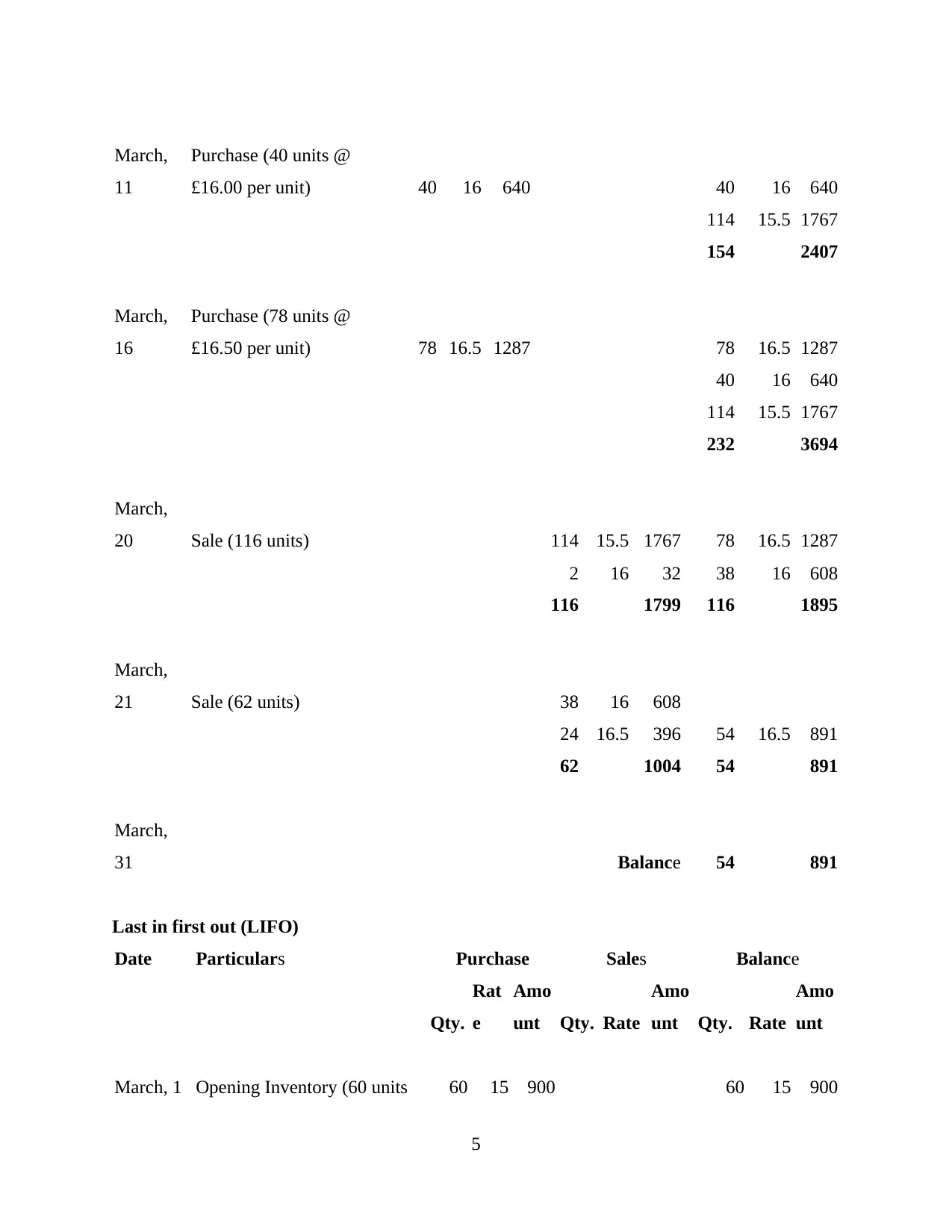
March,
11
Purchase (40 units @
£16.00 per unit) 40 16 640 40 16 640
114 15.5 1767
154 2407
March,
16
Purchase (78 units @
£16.50 per unit) 78 16.5 1287 78 16.5 1287
40 16 640
114 15.5 1767
232 3694
March,
20 Sale (116 units) 114 15.5 1767 78 16.5 1287
2 16 32 38 16 608
116 1799 116 1895
March,
21 Sale (62 units) 38 16 608
24 16.5 396 54 16.5 891
62 1004 54 891
March,
31 Balance 54 891
Last in first out (LIFO)
Date Particulars Purchase Sales Balance
Qty.
Rat
e
Amo
unt Qty. Rate
Amo
unt Qty. Rate
Amo
unt
March, 1 Opening Inventory (60 units 60 15 900 60 15 900
5
11
Purchase (40 units @
£16.00 per unit) 40 16 640 40 16 640
114 15.5 1767
154 2407
March,
16
Purchase (78 units @
£16.50 per unit) 78 16.5 1287 78 16.5 1287
40 16 640
114 15.5 1767
232 3694
March,
20 Sale (116 units) 114 15.5 1767 78 16.5 1287
2 16 32 38 16 608
116 1799 116 1895
March,
21 Sale (62 units) 38 16 608
24 16.5 396 54 16.5 891
62 1004 54 891
March,
31 Balance 54 891
Last in first out (LIFO)
Date Particulars Purchase Sales Balance
Qty.
Rat
e
Amo
unt Qty. Rate
Amo
unt Qty. Rate
Amo
unt
March, 1 Opening Inventory (60 units 60 15 900 60 15 900
5
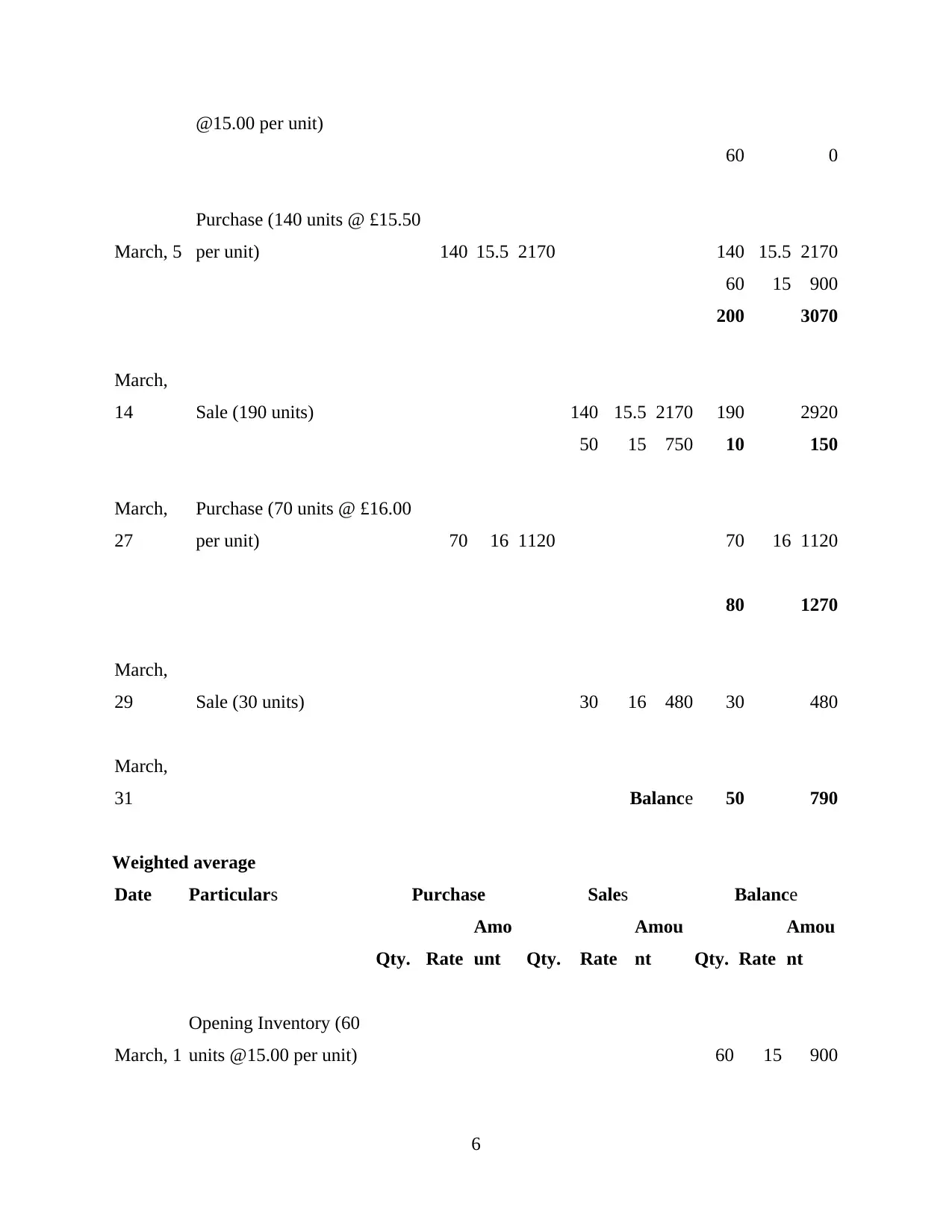
@15.00 per unit)
60 0
March, 5
Purchase (140 units @ £15.50
per unit) 140 15.5 2170 140 15.5 2170
60 15 900
200 3070
March,
14 Sale (190 units) 140 15.5 2170 190 2920
50 15 750 10 150
March,
27
Purchase (70 units @ £16.00
per unit) 70 16 1120 70 16 1120
80 1270
March,
29 Sale (30 units) 30 16 480 30 480
March,
31 Balance 50 790
Weighted average
Date Particulars Purchase Sales Balance
Qty. Rate
Amo
unt Qty. Rate
Amou
nt Qty. Rate
Amou
nt
March, 1
Opening Inventory (60
units @15.00 per unit) 60 15 900
6
60 0
March, 5
Purchase (140 units @ £15.50
per unit) 140 15.5 2170 140 15.5 2170
60 15 900
200 3070
March,
14 Sale (190 units) 140 15.5 2170 190 2920
50 15 750 10 150
March,
27
Purchase (70 units @ £16.00
per unit) 70 16 1120 70 16 1120
80 1270
March,
29 Sale (30 units) 30 16 480 30 480
March,
31 Balance 50 790
Weighted average
Date Particulars Purchase Sales Balance
Qty. Rate
Amo
unt Qty. Rate
Amou
nt Qty. Rate
Amou
nt
March, 1
Opening Inventory (60
units @15.00 per unit) 60 15 900
6
⊘ This is a preview!⊘
Do you want full access?
Subscribe today to unlock all pages.

Trusted by 1+ million students worldwide
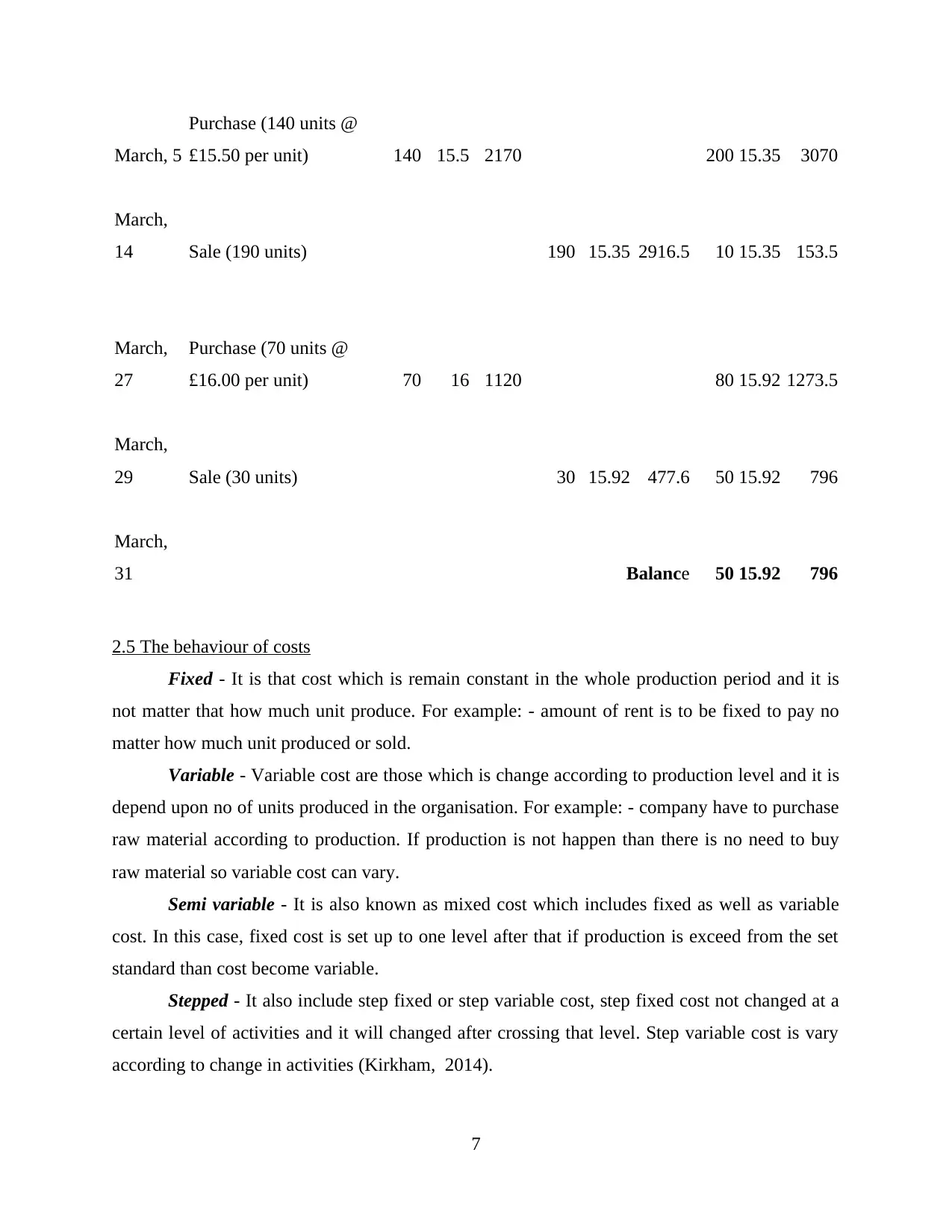
March, 5
Purchase (140 units @
£15.50 per unit) 140 15.5 2170 200 15.35 3070
March,
14 Sale (190 units) 190 15.35 2916.5 10 15.35 153.5
March,
27
Purchase (70 units @
£16.00 per unit) 70 16 1120 80 15.92 1273.5
March,
29 Sale (30 units) 30 15.92 477.6 50 15.92 796
March,
31 Balance 50 15.92 796
2.5 The behaviour of costs
Fixed - It is that cost which is remain constant in the whole production period and it is
not matter that how much unit produce. For example: - amount of rent is to be fixed to pay no
matter how much unit produced or sold.
Variable - Variable cost are those which is change according to production level and it is
depend upon no of units produced in the organisation. For example: - company have to purchase
raw material according to production. If production is not happen than there is no need to buy
raw material so variable cost can vary.
Semi variable - It is also known as mixed cost which includes fixed as well as variable
cost. In this case, fixed cost is set up to one level after that if production is exceed from the set
standard than cost become variable.
Stepped - It also include step fixed or step variable cost, step fixed cost not changed at a
certain level of activities and it will changed after crossing that level. Step variable cost is vary
according to change in activities (Kirkham, 2014).
7
Purchase (140 units @
£15.50 per unit) 140 15.5 2170 200 15.35 3070
March,
14 Sale (190 units) 190 15.35 2916.5 10 15.35 153.5
March,
27
Purchase (70 units @
£16.00 per unit) 70 16 1120 80 15.92 1273.5
March,
29 Sale (30 units) 30 15.92 477.6 50 15.92 796
March,
31 Balance 50 15.92 796
2.5 The behaviour of costs
Fixed - It is that cost which is remain constant in the whole production period and it is
not matter that how much unit produce. For example: - amount of rent is to be fixed to pay no
matter how much unit produced or sold.
Variable - Variable cost are those which is change according to production level and it is
depend upon no of units produced in the organisation. For example: - company have to purchase
raw material according to production. If production is not happen than there is no need to buy
raw material so variable cost can vary.
Semi variable - It is also known as mixed cost which includes fixed as well as variable
cost. In this case, fixed cost is set up to one level after that if production is exceed from the set
standard than cost become variable.
Stepped - It also include step fixed or step variable cost, step fixed cost not changed at a
certain level of activities and it will changed after crossing that level. Step variable cost is vary
according to change in activities (Kirkham, 2014).
7
Paraphrase This Document
Need a fresh take? Get an instant paraphrase of this document with our AI Paraphraser
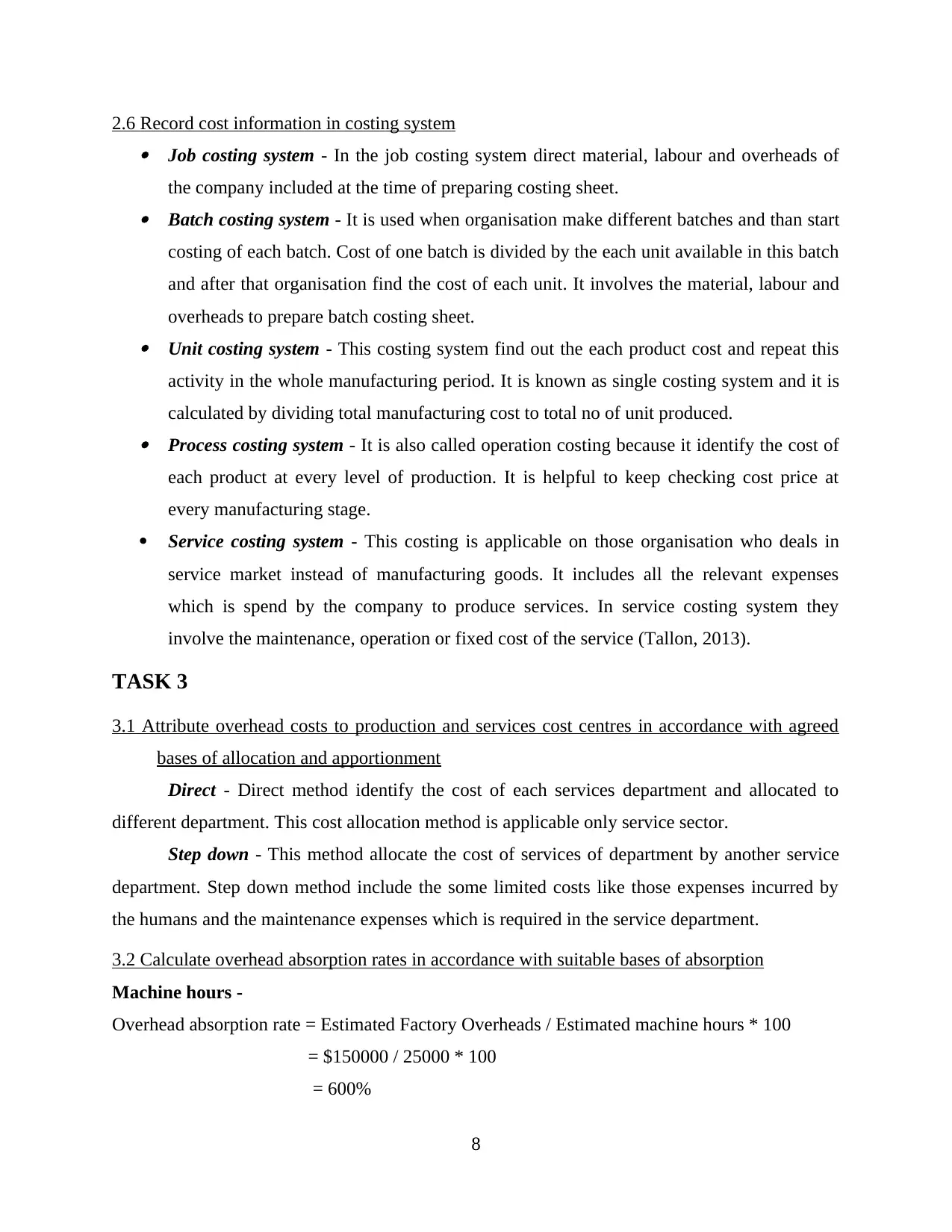
2.6 Record cost information in costing system Job costing system - In the job costing system direct material, labour and overheads of
the company included at the time of preparing costing sheet. Batch costing system - It is used when organisation make different batches and than start
costing of each batch. Cost of one batch is divided by the each unit available in this batch
and after that organisation find the cost of each unit. It involves the material, labour and
overheads to prepare batch costing sheet. Unit costing system - This costing system find out the each product cost and repeat this
activity in the whole manufacturing period. It is known as single costing system and it is
calculated by dividing total manufacturing cost to total no of unit produced. Process costing system - It is also called operation costing because it identify the cost of
each product at every level of production. It is helpful to keep checking cost price at
every manufacturing stage.
Service costing system - This costing is applicable on those organisation who deals in
service market instead of manufacturing goods. It includes all the relevant expenses
which is spend by the company to produce services. In service costing system they
involve the maintenance, operation or fixed cost of the service (Tallon, 2013).
TASK 3
3.1 Attribute overhead costs to production and services cost centres in accordance with agreed
bases of allocation and apportionment
Direct - Direct method identify the cost of each services department and allocated to
different department. This cost allocation method is applicable only service sector.
Step down - This method allocate the cost of services of department by another service
department. Step down method include the some limited costs like those expenses incurred by
the humans and the maintenance expenses which is required in the service department.
3.2 Calculate overhead absorption rates in accordance with suitable bases of absorption
Machine hours -
Overhead absorption rate = Estimated Factory Overheads / Estimated machine hours * 100
= $150000 / 25000 * 100
= 600%
8
the company included at the time of preparing costing sheet. Batch costing system - It is used when organisation make different batches and than start
costing of each batch. Cost of one batch is divided by the each unit available in this batch
and after that organisation find the cost of each unit. It involves the material, labour and
overheads to prepare batch costing sheet. Unit costing system - This costing system find out the each product cost and repeat this
activity in the whole manufacturing period. It is known as single costing system and it is
calculated by dividing total manufacturing cost to total no of unit produced. Process costing system - It is also called operation costing because it identify the cost of
each product at every level of production. It is helpful to keep checking cost price at
every manufacturing stage.
Service costing system - This costing is applicable on those organisation who deals in
service market instead of manufacturing goods. It includes all the relevant expenses
which is spend by the company to produce services. In service costing system they
involve the maintenance, operation or fixed cost of the service (Tallon, 2013).
TASK 3
3.1 Attribute overhead costs to production and services cost centres in accordance with agreed
bases of allocation and apportionment
Direct - Direct method identify the cost of each services department and allocated to
different department. This cost allocation method is applicable only service sector.
Step down - This method allocate the cost of services of department by another service
department. Step down method include the some limited costs like those expenses incurred by
the humans and the maintenance expenses which is required in the service department.
3.2 Calculate overhead absorption rates in accordance with suitable bases of absorption
Machine hours -
Overhead absorption rate = Estimated Factory Overheads / Estimated machine hours * 100
= $150000 / 25000 * 100
= 600%
8
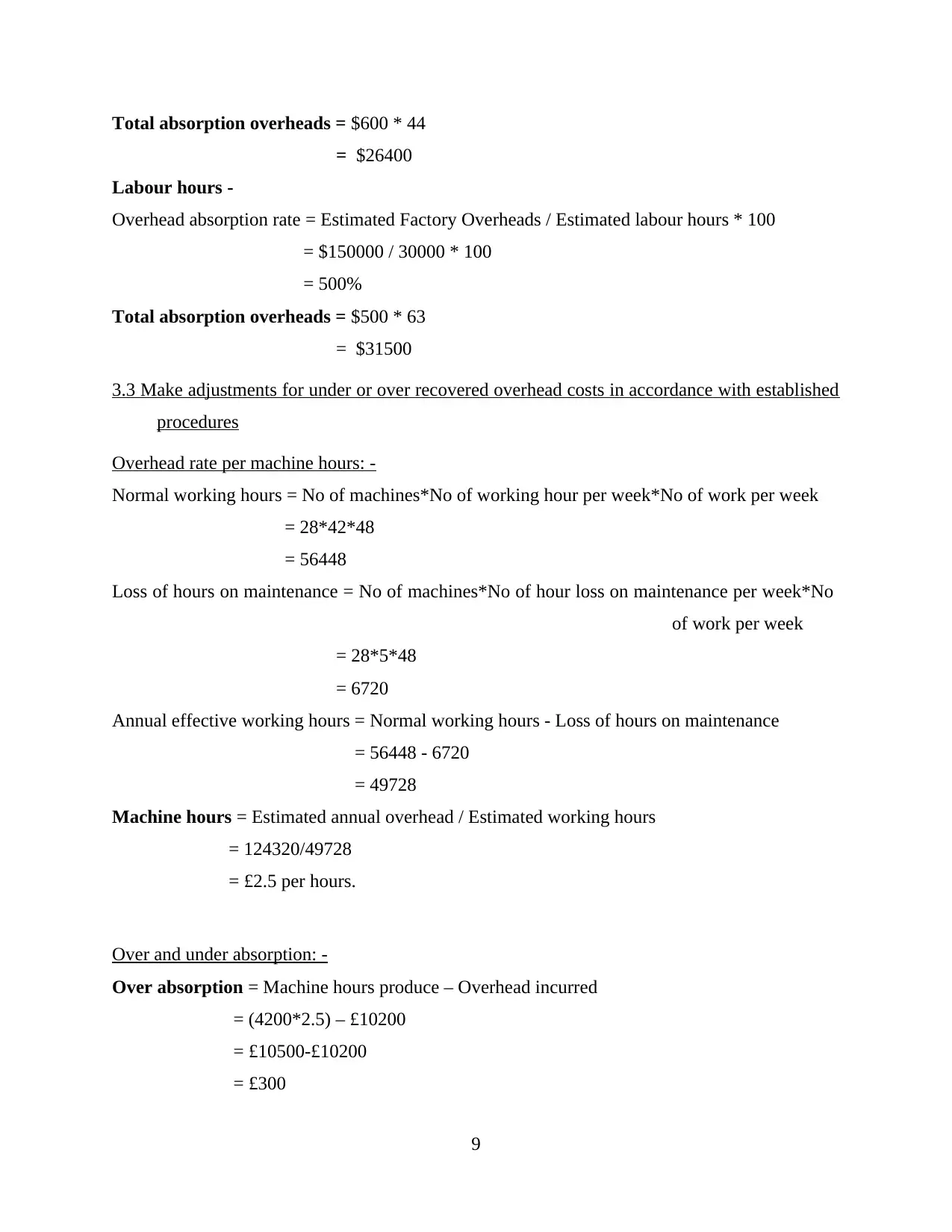
Total absorption overheads = $600 * 44
= $26400
Labour hours -
Overhead absorption rate = Estimated Factory Overheads / Estimated labour hours * 100
= $150000 / 30000 * 100
= 500%
Total absorption overheads = $500 * 63
= $31500
3.3 Make adjustments for under or over recovered overhead costs in accordance with established
procedures
Overhead rate per machine hours: -
Normal working hours = No of machines*No of working hour per week*No of work per week
= 28*42*48
= 56448
Loss of hours on maintenance = No of machines*No of hour loss on maintenance per week*No
of work per week
= 28*5*48
= 6720
Annual effective working hours = Normal working hours - Loss of hours on maintenance
= 56448 - 6720
= 49728
Machine hours = Estimated annual overhead / Estimated working hours
= 124320/49728
= £2.5 per hours.
Over and under absorption: -
Over absorption = Machine hours produce – Overhead incurred
= (4200*2.5) – £10200
= £10500-£10200
= £300
9
= $26400
Labour hours -
Overhead absorption rate = Estimated Factory Overheads / Estimated labour hours * 100
= $150000 / 30000 * 100
= 500%
Total absorption overheads = $500 * 63
= $31500
3.3 Make adjustments for under or over recovered overhead costs in accordance with established
procedures
Overhead rate per machine hours: -
Normal working hours = No of machines*No of working hour per week*No of work per week
= 28*42*48
= 56448
Loss of hours on maintenance = No of machines*No of hour loss on maintenance per week*No
of work per week
= 28*5*48
= 6720
Annual effective working hours = Normal working hours - Loss of hours on maintenance
= 56448 - 6720
= 49728
Machine hours = Estimated annual overhead / Estimated working hours
= 124320/49728
= £2.5 per hours.
Over and under absorption: -
Over absorption = Machine hours produce – Overhead incurred
= (4200*2.5) – £10200
= £10500-£10200
= £300
9
⊘ This is a preview!⊘
Do you want full access?
Subscribe today to unlock all pages.

Trusted by 1+ million students worldwide
1 out of 17