Measurement of Conveyor Belt for Cut and Gouge Depth
VerifiedAdded on 2023/01/19
|11
|3963
|24
AI Summary
This document discusses the measurement of conveyor belts for cut and gouge depth. It provides an introduction to conveyor systems and their importance in various industries. The document also explores the factors to consider when selecting a conveyor system and the benefits and applications of conveyor chains. Additionally, it discusses the causes of conveyor failure and provides a methodology for measuring conveyor belts.
Contribute Materials
Your contribution can guide someone’s learning journey. Share your
documents today.
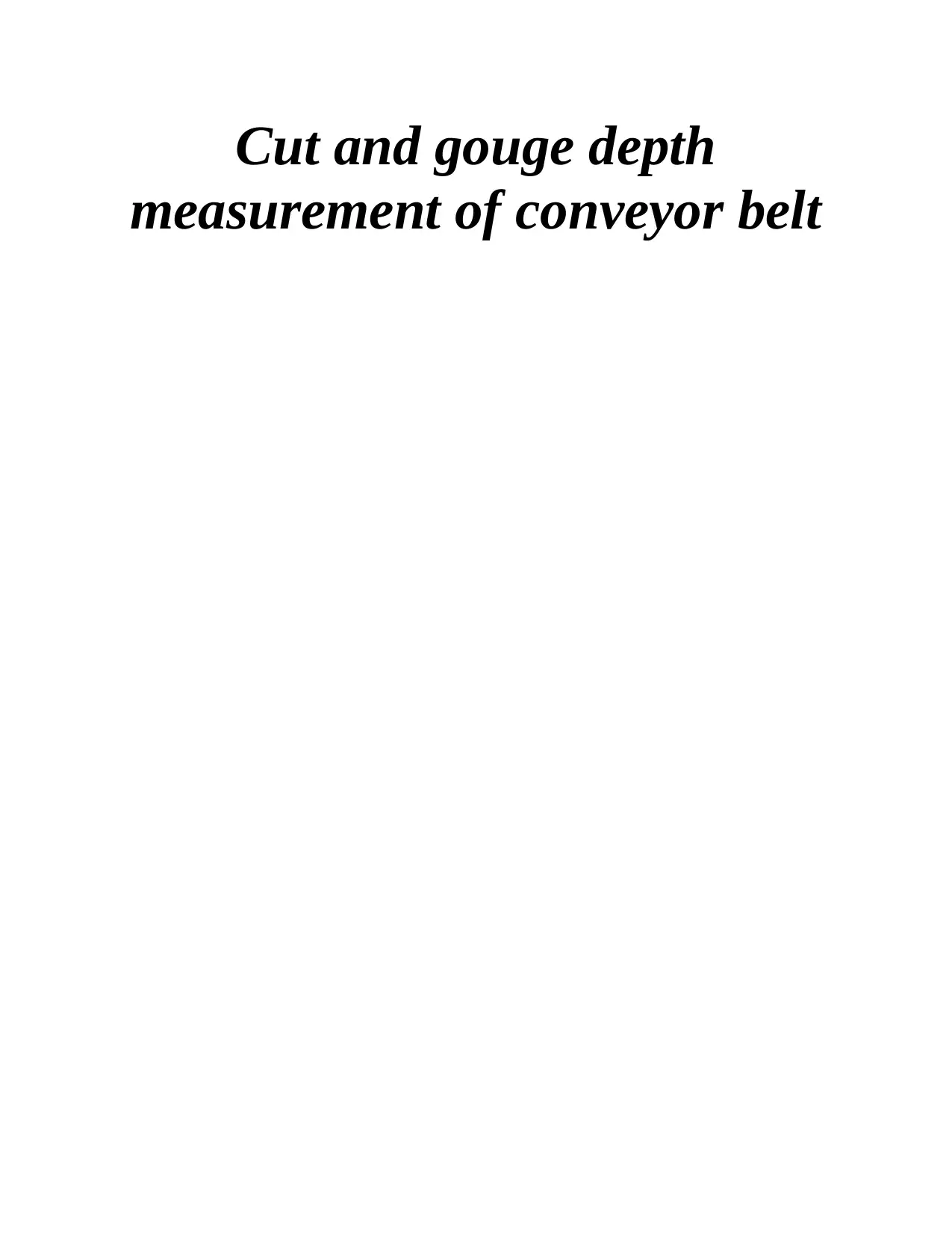
Cut and gouge depth
measurement of conveyor belt
measurement of conveyor belt
Secure Best Marks with AI Grader
Need help grading? Try our AI Grader for instant feedback on your assignments.
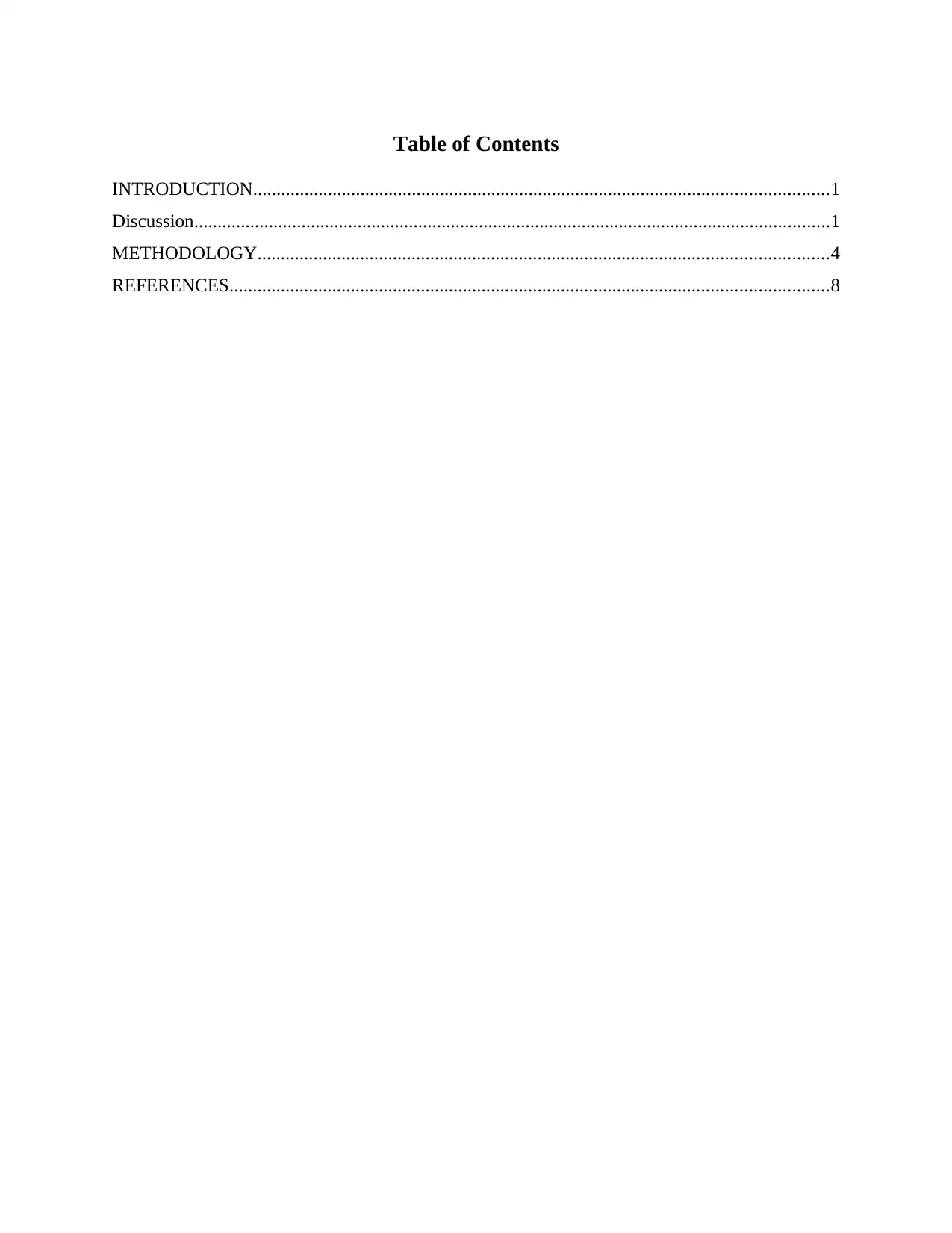
Table of Contents
INTRODUCTION...........................................................................................................................1
Discussion........................................................................................................................................1
METHODOLOGY..........................................................................................................................4
REFERENCES................................................................................................................................8
INTRODUCTION...........................................................................................................................1
Discussion........................................................................................................................................1
METHODOLOGY..........................................................................................................................4
REFERENCES................................................................................................................................8
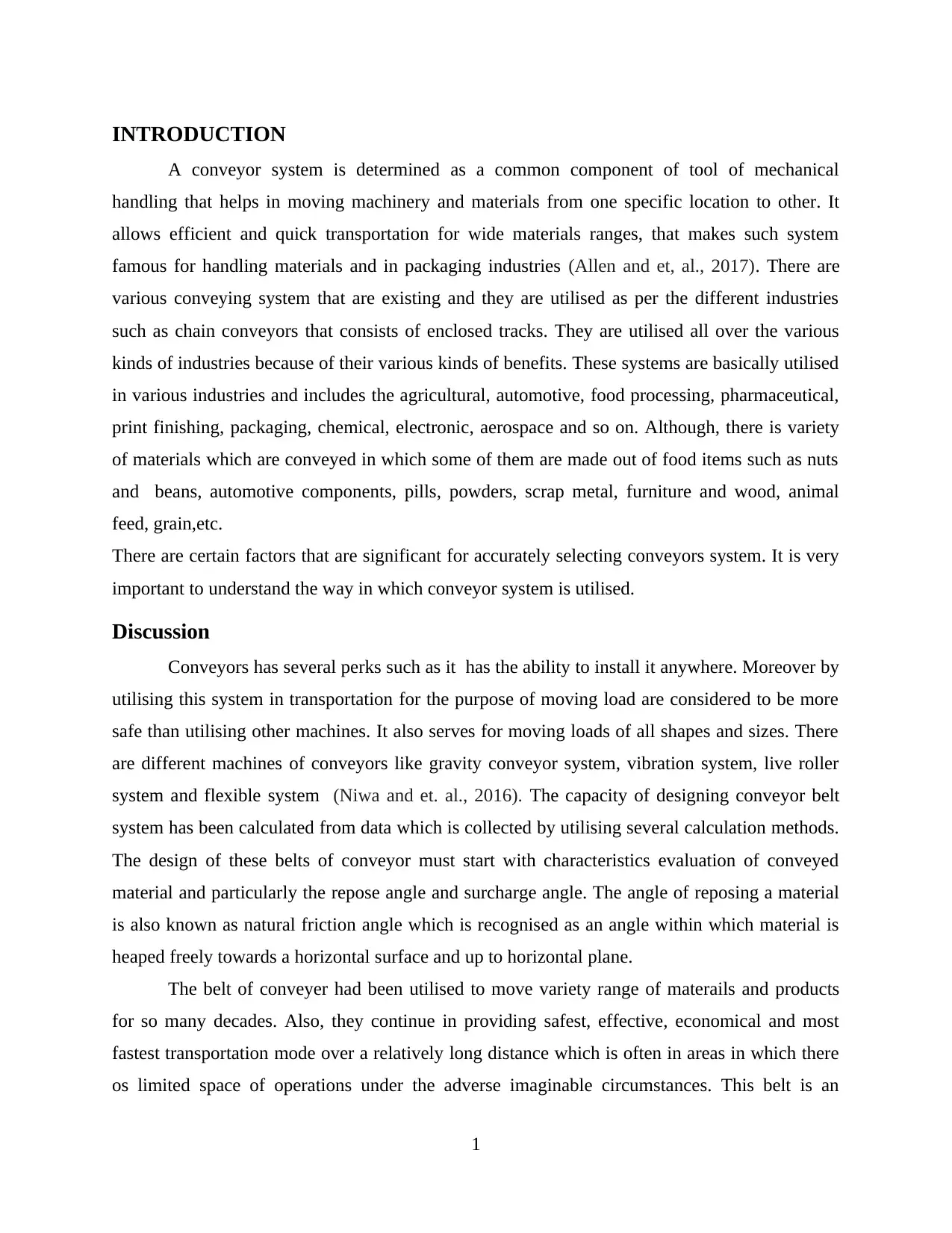
INTRODUCTION
A conveyor system is determined as a common component of tool of mechanical
handling that helps in moving machinery and materials from one specific location to other. It
allows efficient and quick transportation for wide materials ranges, that makes such system
famous for handling materials and in packaging industries (Allen and et, al., 2017). There are
various conveying system that are existing and they are utilised as per the different industries
such as chain conveyors that consists of enclosed tracks. They are utilised all over the various
kinds of industries because of their various kinds of benefits. These systems are basically utilised
in various industries and includes the agricultural, automotive, food processing, pharmaceutical,
print finishing, packaging, chemical, electronic, aerospace and so on. Although, there is variety
of materials which are conveyed in which some of them are made out of food items such as nuts
and beans, automotive components, pills, powders, scrap metal, furniture and wood, animal
feed, grain,etc.
There are certain factors that are significant for accurately selecting conveyors system. It is very
important to understand the way in which conveyor system is utilised.
Discussion
Conveyors has several perks such as it has the ability to install it anywhere. Moreover by
utilising this system in transportation for the purpose of moving load are considered to be more
safe than utilising other machines. It also serves for moving loads of all shapes and sizes. There
are different machines of conveyors like gravity conveyor system, vibration system, live roller
system and flexible system (Niwa and et. al., 2016). The capacity of designing conveyor belt
system has been calculated from data which is collected by utilising several calculation methods.
The design of these belts of conveyor must start with characteristics evaluation of conveyed
material and particularly the repose angle and surcharge angle. The angle of reposing a material
is also known as natural friction angle which is recognised as an angle within which material is
heaped freely towards a horizontal surface and up to horizontal plane.
The belt of conveyer had been utilised to move variety range of materails and products
for so many decades. Also, they continue in providing safest, effective, economical and most
fastest transportation mode over a relatively long distance which is often in areas in which there
os limited space of operations under the adverse imaginable circumstances. This belt is an
1
A conveyor system is determined as a common component of tool of mechanical
handling that helps in moving machinery and materials from one specific location to other. It
allows efficient and quick transportation for wide materials ranges, that makes such system
famous for handling materials and in packaging industries (Allen and et, al., 2017). There are
various conveying system that are existing and they are utilised as per the different industries
such as chain conveyors that consists of enclosed tracks. They are utilised all over the various
kinds of industries because of their various kinds of benefits. These systems are basically utilised
in various industries and includes the agricultural, automotive, food processing, pharmaceutical,
print finishing, packaging, chemical, electronic, aerospace and so on. Although, there is variety
of materials which are conveyed in which some of them are made out of food items such as nuts
and beans, automotive components, pills, powders, scrap metal, furniture and wood, animal
feed, grain,etc.
There are certain factors that are significant for accurately selecting conveyors system. It is very
important to understand the way in which conveyor system is utilised.
Discussion
Conveyors has several perks such as it has the ability to install it anywhere. Moreover by
utilising this system in transportation for the purpose of moving load are considered to be more
safe than utilising other machines. It also serves for moving loads of all shapes and sizes. There
are different machines of conveyors like gravity conveyor system, vibration system, live roller
system and flexible system (Niwa and et. al., 2016). The capacity of designing conveyor belt
system has been calculated from data which is collected by utilising several calculation methods.
The design of these belts of conveyor must start with characteristics evaluation of conveyed
material and particularly the repose angle and surcharge angle. The angle of reposing a material
is also known as natural friction angle which is recognised as an angle within which material is
heaped freely towards a horizontal surface and up to horizontal plane.
The belt of conveyer had been utilised to move variety range of materails and products
for so many decades. Also, they continue in providing safest, effective, economical and most
fastest transportation mode over a relatively long distance which is often in areas in which there
os limited space of operations under the adverse imaginable circumstances. This belt is an
1
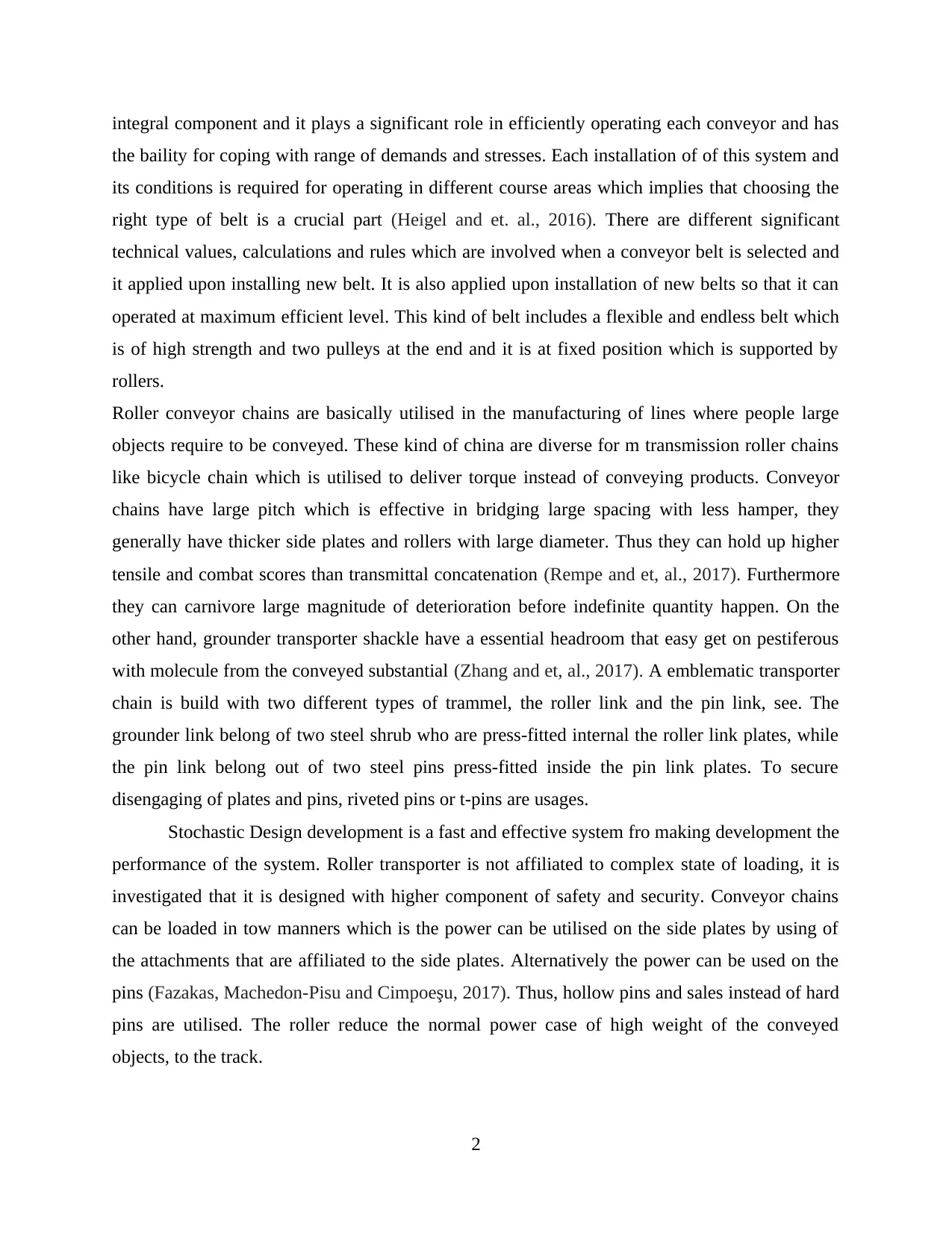
integral component and it plays a significant role in efficiently operating each conveyor and has
the baility for coping with range of demands and stresses. Each installation of of this system and
its conditions is required for operating in different course areas which implies that choosing the
right type of belt is a crucial part (Heigel and et. al., 2016). There are different significant
technical values, calculations and rules which are involved when a conveyor belt is selected and
it applied upon installing new belt. It is also applied upon installation of new belts so that it can
operated at maximum efficient level. This kind of belt includes a flexible and endless belt which
is of high strength and two pulleys at the end and it is at fixed position which is supported by
rollers.
Roller conveyor chains are basically utilised in the manufacturing of lines where people large
objects require to be conveyed. These kind of china are diverse for m transmission roller chains
like bicycle chain which is utilised to deliver torque instead of conveying products. Conveyor
chains have large pitch which is effective in bridging large spacing with less hamper, they
generally have thicker side plates and rollers with large diameter. Thus they can hold up higher
tensile and combat scores than transmittal concatenation (Rempe and et, al., 2017). Furthermore
they can carnivore large magnitude of deterioration before indefinite quantity happen. On the
other hand, grounder transporter shackle have a essential headroom that easy get on pestiferous
with molecule from the conveyed substantial (Zhang and et, al., 2017). A emblematic transporter
chain is build with two different types of trammel, the roller link and the pin link, see. The
grounder link belong of two steel shrub who are press-fitted internal the roller link plates, while
the pin link belong out of two steel pins press-fitted inside the pin link plates. To secure
disengaging of plates and pins, riveted pins or t-pins are usages.
Stochastic Design development is a fast and effective system fro making development the
performance of the system. Roller transporter is not affiliated to complex state of loading, it is
investigated that it is designed with higher component of safety and security. Conveyor chains
can be loaded in tow manners which is the power can be utilised on the side plates by using of
the attachments that are affiliated to the side plates. Alternatively the power can be used on the
pins (Fazakas, Machedon-Pisu and Cimpoeşu, 2017). Thus, hollow pins and sales instead of hard
pins are utilised. The roller reduce the normal power case of high weight of the conveyed
objects, to the track.
2
the baility for coping with range of demands and stresses. Each installation of of this system and
its conditions is required for operating in different course areas which implies that choosing the
right type of belt is a crucial part (Heigel and et. al., 2016). There are different significant
technical values, calculations and rules which are involved when a conveyor belt is selected and
it applied upon installing new belt. It is also applied upon installation of new belts so that it can
operated at maximum efficient level. This kind of belt includes a flexible and endless belt which
is of high strength and two pulleys at the end and it is at fixed position which is supported by
rollers.
Roller conveyor chains are basically utilised in the manufacturing of lines where people large
objects require to be conveyed. These kind of china are diverse for m transmission roller chains
like bicycle chain which is utilised to deliver torque instead of conveying products. Conveyor
chains have large pitch which is effective in bridging large spacing with less hamper, they
generally have thicker side plates and rollers with large diameter. Thus they can hold up higher
tensile and combat scores than transmittal concatenation (Rempe and et, al., 2017). Furthermore
they can carnivore large magnitude of deterioration before indefinite quantity happen. On the
other hand, grounder transporter shackle have a essential headroom that easy get on pestiferous
with molecule from the conveyed substantial (Zhang and et, al., 2017). A emblematic transporter
chain is build with two different types of trammel, the roller link and the pin link, see. The
grounder link belong of two steel shrub who are press-fitted internal the roller link plates, while
the pin link belong out of two steel pins press-fitted inside the pin link plates. To secure
disengaging of plates and pins, riveted pins or t-pins are usages.
Stochastic Design development is a fast and effective system fro making development the
performance of the system. Roller transporter is not affiliated to complex state of loading, it is
investigated that it is designed with higher component of safety and security. Conveyor chains
can be loaded in tow manners which is the power can be utilised on the side plates by using of
the attachments that are affiliated to the side plates. Alternatively the power can be used on the
pins (Fazakas, Machedon-Pisu and Cimpoeşu, 2017). Thus, hollow pins and sales instead of hard
pins are utilised. The roller reduce the normal power case of high weight of the conveyed
objects, to the track.
2
Secure Best Marks with AI Grader
Need help grading? Try our AI Grader for instant feedback on your assignments.
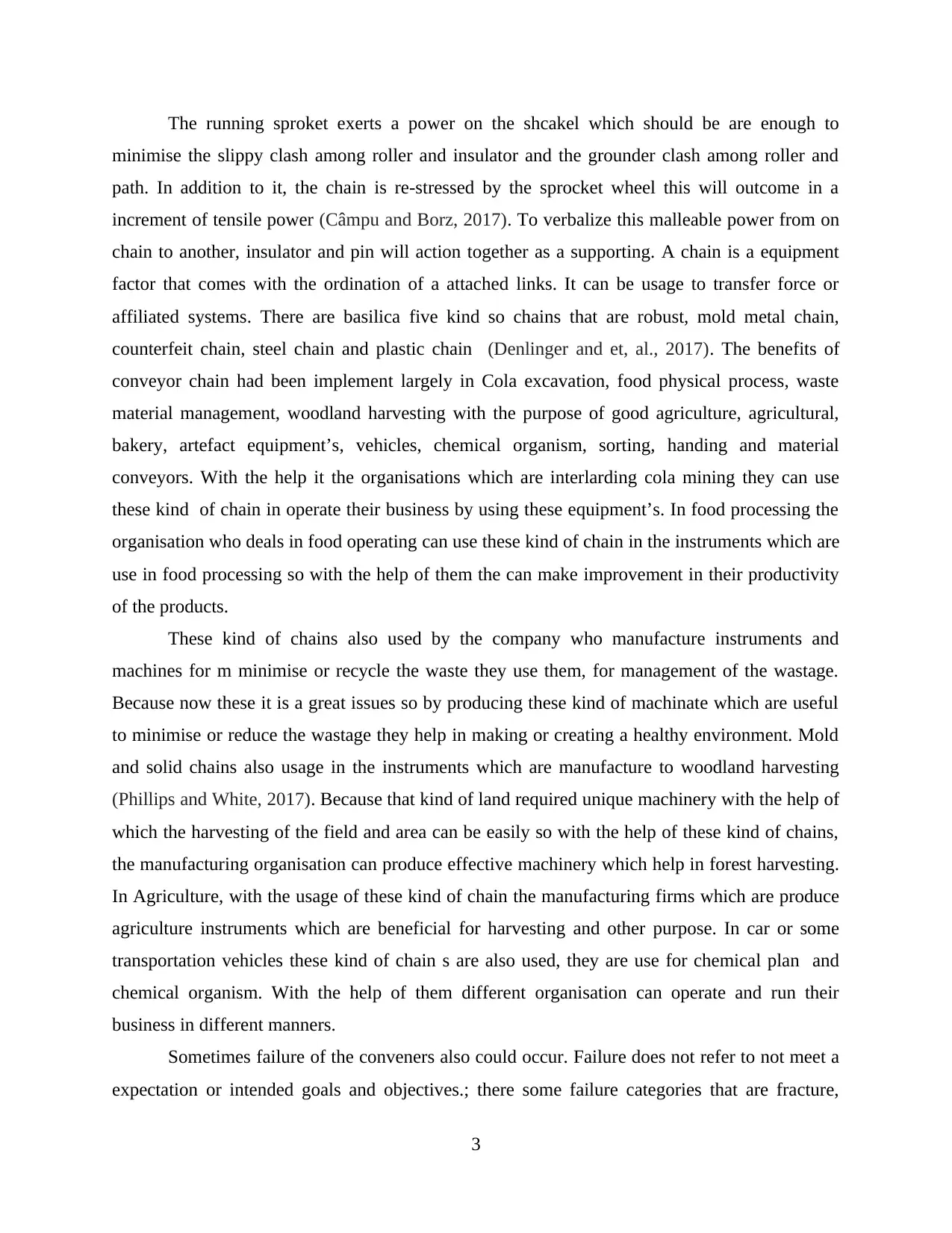
The running sproket exerts a power on the shcakel which should be are enough to
minimise the slippy clash among roller and insulator and the grounder clash among roller and
path. In addition to it, the chain is re-stressed by the sprocket wheel this will outcome in a
increment of tensile power (Câmpu and Borz, 2017). To verbalize this malleable power from on
chain to another, insulator and pin will action together as a supporting. A chain is a equipment
factor that comes with the ordination of a attached links. It can be usage to transfer force or
affiliated systems. There are basilica five kind so chains that are robust, mold metal chain,
counterfeit chain, steel chain and plastic chain (Denlinger and et, al., 2017). The benefits of
conveyor chain had been implement largely in Cola excavation, food physical process, waste
material management, woodland harvesting with the purpose of good agriculture, agricultural,
bakery, artefact equipment’s, vehicles, chemical organism, sorting, handing and material
conveyors. With the help it the organisations which are interlarding cola mining they can use
these kind of chain in operate their business by using these equipment’s. In food processing the
organisation who deals in food operating can use these kind of chain in the instruments which are
use in food processing so with the help of them the can make improvement in their productivity
of the products.
These kind of chains also used by the company who manufacture instruments and
machines for m minimise or recycle the waste they use them, for management of the wastage.
Because now these it is a great issues so by producing these kind of machinate which are useful
to minimise or reduce the wastage they help in making or creating a healthy environment. Mold
and solid chains also usage in the instruments which are manufacture to woodland harvesting
(Phillips and White, 2017). Because that kind of land required unique machinery with the help of
which the harvesting of the field and area can be easily so with the help of these kind of chains,
the manufacturing organisation can produce effective machinery which help in forest harvesting.
In Agriculture, with the usage of these kind of chain the manufacturing firms which are produce
agriculture instruments which are beneficial for harvesting and other purpose. In car or some
transportation vehicles these kind of chain s are also used, they are use for chemical plan and
chemical organism. With the help of them different organisation can operate and run their
business in different manners.
Sometimes failure of the conveners also could occur. Failure does not refer to not meet a
expectation or intended goals and objectives.; there some failure categories that are fracture,
3
minimise the slippy clash among roller and insulator and the grounder clash among roller and
path. In addition to it, the chain is re-stressed by the sprocket wheel this will outcome in a
increment of tensile power (Câmpu and Borz, 2017). To verbalize this malleable power from on
chain to another, insulator and pin will action together as a supporting. A chain is a equipment
factor that comes with the ordination of a attached links. It can be usage to transfer force or
affiliated systems. There are basilica five kind so chains that are robust, mold metal chain,
counterfeit chain, steel chain and plastic chain (Denlinger and et, al., 2017). The benefits of
conveyor chain had been implement largely in Cola excavation, food physical process, waste
material management, woodland harvesting with the purpose of good agriculture, agricultural,
bakery, artefact equipment’s, vehicles, chemical organism, sorting, handing and material
conveyors. With the help it the organisations which are interlarding cola mining they can use
these kind of chain in operate their business by using these equipment’s. In food processing the
organisation who deals in food operating can use these kind of chain in the instruments which are
use in food processing so with the help of them the can make improvement in their productivity
of the products.
These kind of chains also used by the company who manufacture instruments and
machines for m minimise or recycle the waste they use them, for management of the wastage.
Because now these it is a great issues so by producing these kind of machinate which are useful
to minimise or reduce the wastage they help in making or creating a healthy environment. Mold
and solid chains also usage in the instruments which are manufacture to woodland harvesting
(Phillips and White, 2017). Because that kind of land required unique machinery with the help of
which the harvesting of the field and area can be easily so with the help of these kind of chains,
the manufacturing organisation can produce effective machinery which help in forest harvesting.
In Agriculture, with the usage of these kind of chain the manufacturing firms which are produce
agriculture instruments which are beneficial for harvesting and other purpose. In car or some
transportation vehicles these kind of chain s are also used, they are use for chemical plan and
chemical organism. With the help of them different organisation can operate and run their
business in different manners.
Sometimes failure of the conveners also could occur. Failure does not refer to not meet a
expectation or intended goals and objectives.; there some failure categories that are fracture,
3
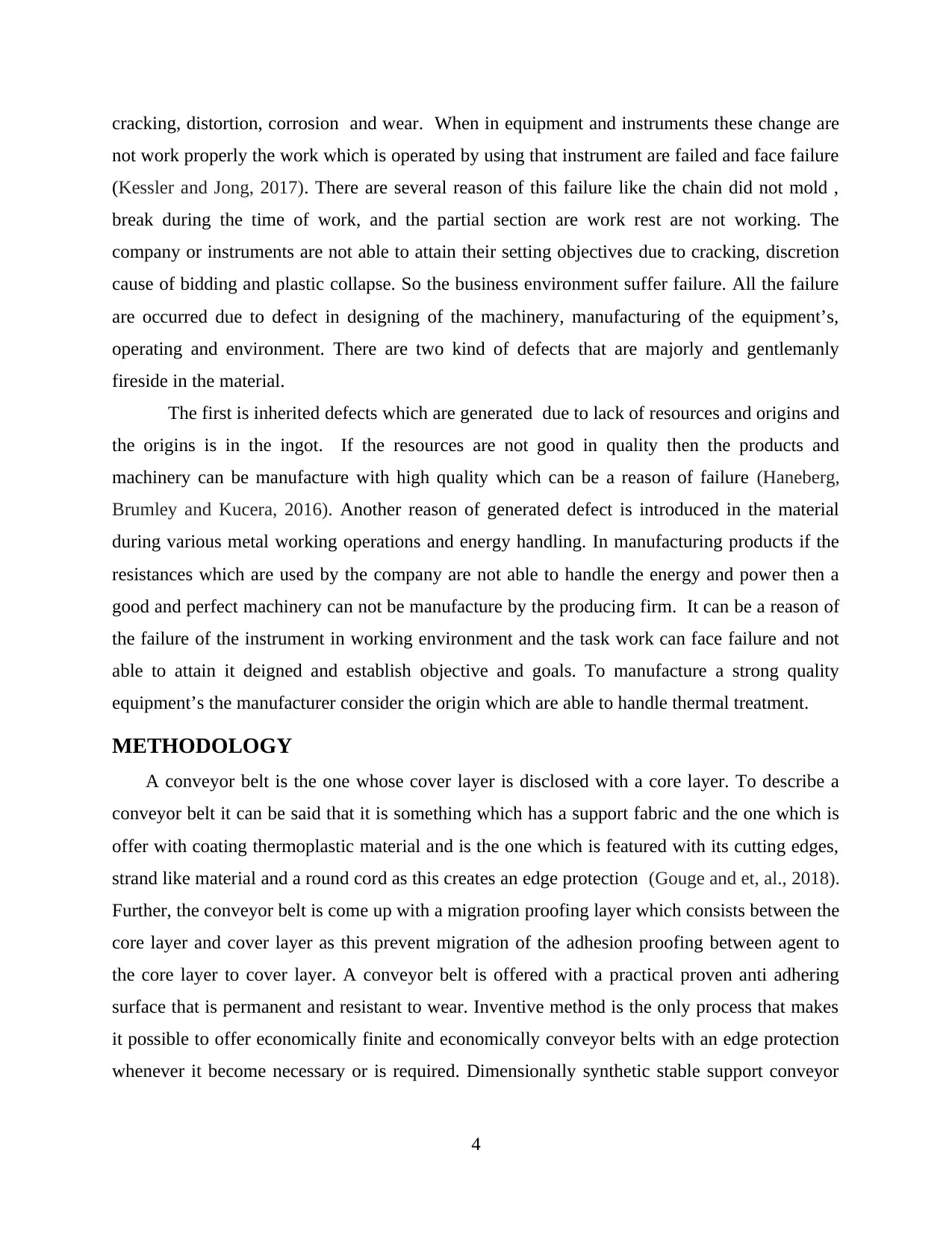
cracking, distortion, corrosion and wear. When in equipment and instruments these change are
not work properly the work which is operated by using that instrument are failed and face failure
(Kessler and Jong, 2017). There are several reason of this failure like the chain did not mold ,
break during the time of work, and the partial section are work rest are not working. The
company or instruments are not able to attain their setting objectives due to cracking, discretion
cause of bidding and plastic collapse. So the business environment suffer failure. All the failure
are occurred due to defect in designing of the machinery, manufacturing of the equipment’s,
operating and environment. There are two kind of defects that are majorly and gentlemanly
fireside in the material.
The first is inherited defects which are generated due to lack of resources and origins and
the origins is in the ingot. If the resources are not good in quality then the products and
machinery can be manufacture with high quality which can be a reason of failure (Haneberg,
Brumley and Kucera, 2016). Another reason of generated defect is introduced in the material
during various metal working operations and energy handling. In manufacturing products if the
resistances which are used by the company are not able to handle the energy and power then a
good and perfect machinery can not be manufacture by the producing firm. It can be a reason of
the failure of the instrument in working environment and the task work can face failure and not
able to attain it deigned and establish objective and goals. To manufacture a strong quality
equipment’s the manufacturer consider the origin which are able to handle thermal treatment.
METHODOLOGY
A conveyor belt is the one whose cover layer is disclosed with a core layer. To describe a
conveyor belt it can be said that it is something which has a support fabric and the one which is
offer with coating thermoplastic material and is the one which is featured with its cutting edges,
strand like material and a round cord as this creates an edge protection (Gouge and et, al., 2018).
Further, the conveyor belt is come up with a migration proofing layer which consists between the
core layer and cover layer as this prevent migration of the adhesion proofing between agent to
the core layer to cover layer. A conveyor belt is offered with a practical proven anti adhering
surface that is permanent and resistant to wear. Inventive method is the only process that makes
it possible to offer economically finite and economically conveyor belts with an edge protection
whenever it become necessary or is required. Dimensionally synthetic stable support conveyor
4
not work properly the work which is operated by using that instrument are failed and face failure
(Kessler and Jong, 2017). There are several reason of this failure like the chain did not mold ,
break during the time of work, and the partial section are work rest are not working. The
company or instruments are not able to attain their setting objectives due to cracking, discretion
cause of bidding and plastic collapse. So the business environment suffer failure. All the failure
are occurred due to defect in designing of the machinery, manufacturing of the equipment’s,
operating and environment. There are two kind of defects that are majorly and gentlemanly
fireside in the material.
The first is inherited defects which are generated due to lack of resources and origins and
the origins is in the ingot. If the resources are not good in quality then the products and
machinery can be manufacture with high quality which can be a reason of failure (Haneberg,
Brumley and Kucera, 2016). Another reason of generated defect is introduced in the material
during various metal working operations and energy handling. In manufacturing products if the
resistances which are used by the company are not able to handle the energy and power then a
good and perfect machinery can not be manufacture by the producing firm. It can be a reason of
the failure of the instrument in working environment and the task work can face failure and not
able to attain it deigned and establish objective and goals. To manufacture a strong quality
equipment’s the manufacturer consider the origin which are able to handle thermal treatment.
METHODOLOGY
A conveyor belt is the one whose cover layer is disclosed with a core layer. To describe a
conveyor belt it can be said that it is something which has a support fabric and the one which is
offer with coating thermoplastic material and is the one which is featured with its cutting edges,
strand like material and a round cord as this creates an edge protection (Gouge and et, al., 2018).
Further, the conveyor belt is come up with a migration proofing layer which consists between the
core layer and cover layer as this prevent migration of the adhesion proofing between agent to
the core layer to cover layer. A conveyor belt is offered with a practical proven anti adhering
surface that is permanent and resistant to wear. Inventive method is the only process that makes
it possible to offer economically finite and economically conveyor belts with an edge protection
whenever it become necessary or is required. Dimensionally synthetic stable support conveyor
4
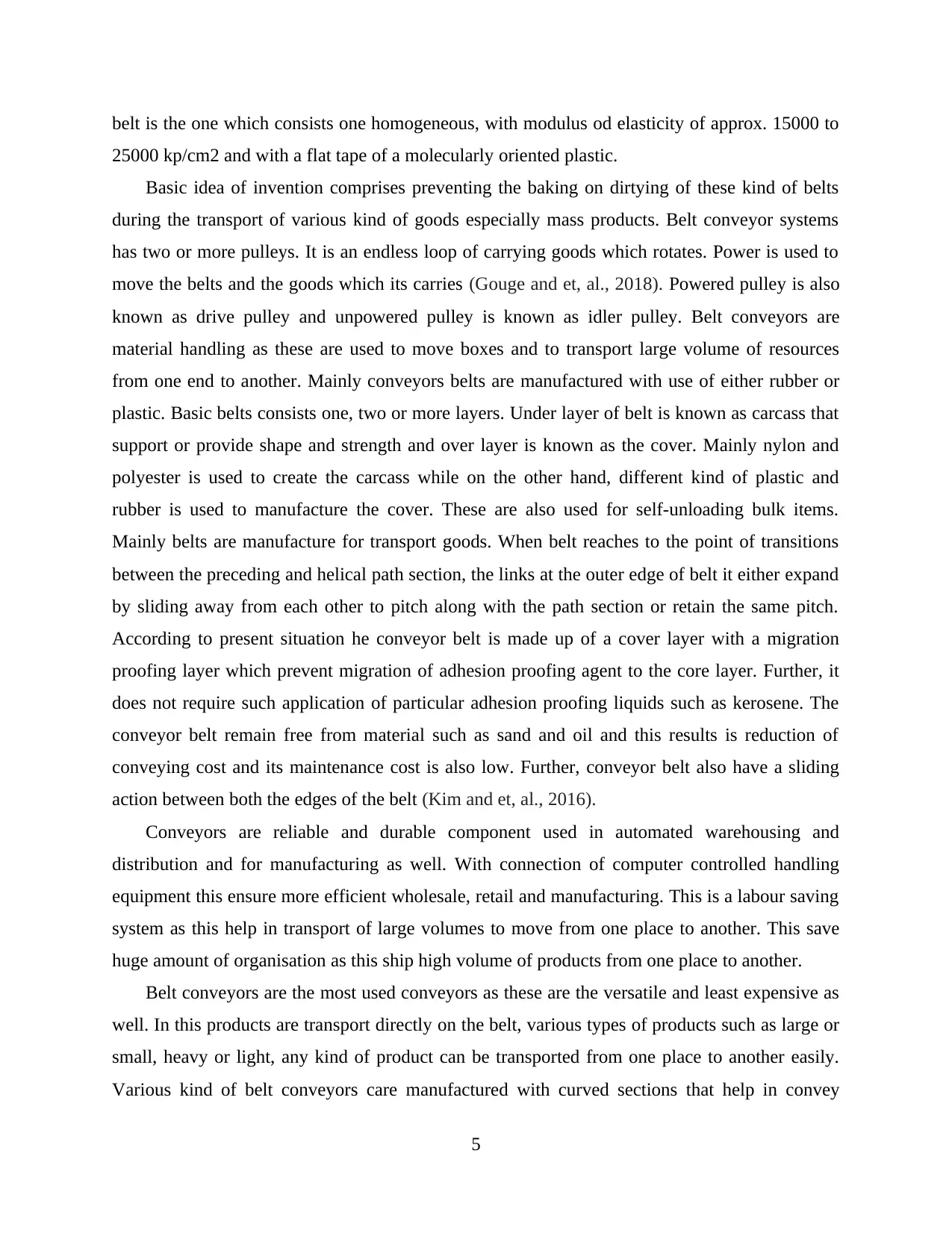
belt is the one which consists one homogeneous, with modulus od elasticity of approx. 15000 to
25000 kp/cm2 and with a flat tape of a molecularly oriented plastic.
Basic idea of invention comprises preventing the baking on dirtying of these kind of belts
during the transport of various kind of goods especially mass products. Belt conveyor systems
has two or more pulleys. It is an endless loop of carrying goods which rotates. Power is used to
move the belts and the goods which its carries (Gouge and et, al., 2018). Powered pulley is also
known as drive pulley and unpowered pulley is known as idler pulley. Belt conveyors are
material handling as these are used to move boxes and to transport large volume of resources
from one end to another. Mainly conveyors belts are manufactured with use of either rubber or
plastic. Basic belts consists one, two or more layers. Under layer of belt is known as carcass that
support or provide shape and strength and over layer is known as the cover. Mainly nylon and
polyester is used to create the carcass while on the other hand, different kind of plastic and
rubber is used to manufacture the cover. These are also used for self-unloading bulk items.
Mainly belts are manufacture for transport goods. When belt reaches to the point of transitions
between the preceding and helical path section, the links at the outer edge of belt it either expand
by sliding away from each other to pitch along with the path section or retain the same pitch.
According to present situation he conveyor belt is made up of a cover layer with a migration
proofing layer which prevent migration of adhesion proofing agent to the core layer. Further, it
does not require such application of particular adhesion proofing liquids such as kerosene. The
conveyor belt remain free from material such as sand and oil and this results is reduction of
conveying cost and its maintenance cost is also low. Further, conveyor belt also have a sliding
action between both the edges of the belt (Kim and et, al., 2016).
Conveyors are reliable and durable component used in automated warehousing and
distribution and for manufacturing as well. With connection of computer controlled handling
equipment this ensure more efficient wholesale, retail and manufacturing. This is a labour saving
system as this help in transport of large volumes to move from one place to another. This save
huge amount of organisation as this ship high volume of products from one place to another.
Belt conveyors are the most used conveyors as these are the versatile and least expensive as
well. In this products are transport directly on the belt, various types of products such as large or
small, heavy or light, any kind of product can be transported from one place to another easily.
Various kind of belt conveyors care manufactured with curved sections that help in convey
5
25000 kp/cm2 and with a flat tape of a molecularly oriented plastic.
Basic idea of invention comprises preventing the baking on dirtying of these kind of belts
during the transport of various kind of goods especially mass products. Belt conveyor systems
has two or more pulleys. It is an endless loop of carrying goods which rotates. Power is used to
move the belts and the goods which its carries (Gouge and et, al., 2018). Powered pulley is also
known as drive pulley and unpowered pulley is known as idler pulley. Belt conveyors are
material handling as these are used to move boxes and to transport large volume of resources
from one end to another. Mainly conveyors belts are manufactured with use of either rubber or
plastic. Basic belts consists one, two or more layers. Under layer of belt is known as carcass that
support or provide shape and strength and over layer is known as the cover. Mainly nylon and
polyester is used to create the carcass while on the other hand, different kind of plastic and
rubber is used to manufacture the cover. These are also used for self-unloading bulk items.
Mainly belts are manufacture for transport goods. When belt reaches to the point of transitions
between the preceding and helical path section, the links at the outer edge of belt it either expand
by sliding away from each other to pitch along with the path section or retain the same pitch.
According to present situation he conveyor belt is made up of a cover layer with a migration
proofing layer which prevent migration of adhesion proofing agent to the core layer. Further, it
does not require such application of particular adhesion proofing liquids such as kerosene. The
conveyor belt remain free from material such as sand and oil and this results is reduction of
conveying cost and its maintenance cost is also low. Further, conveyor belt also have a sliding
action between both the edges of the belt (Kim and et, al., 2016).
Conveyors are reliable and durable component used in automated warehousing and
distribution and for manufacturing as well. With connection of computer controlled handling
equipment this ensure more efficient wholesale, retail and manufacturing. This is a labour saving
system as this help in transport of large volumes to move from one place to another. This save
huge amount of organisation as this ship high volume of products from one place to another.
Belt conveyors are the most used conveyors as these are the versatile and least expensive as
well. In this products are transport directly on the belt, various types of products such as large or
small, heavy or light, any kind of product can be transported from one place to another easily.
Various kind of belt conveyors care manufactured with curved sections that help in convey
5
Paraphrase This Document
Need a fresh take? Get an instant paraphrase of this document with our AI Paraphraser
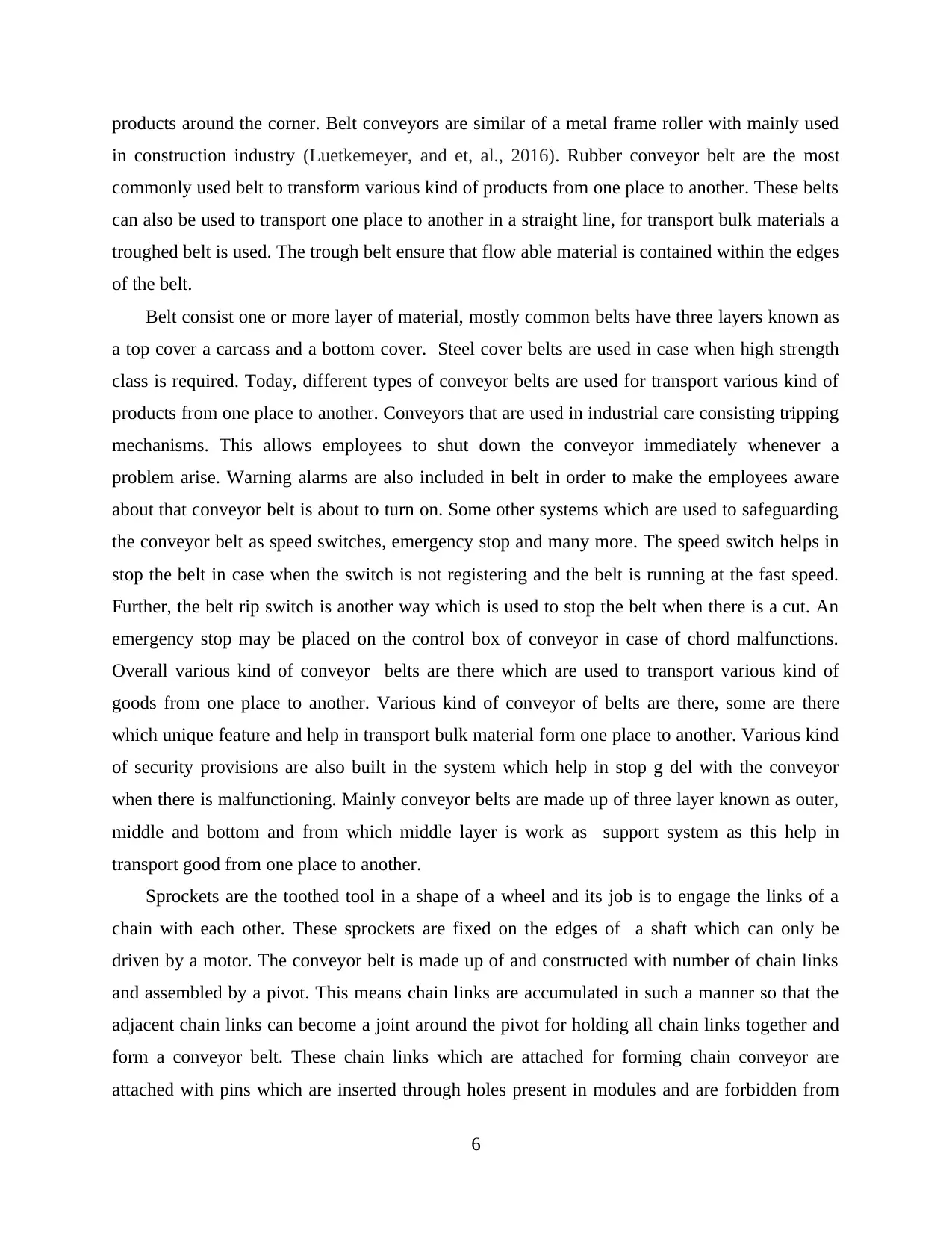
products around the corner. Belt conveyors are similar of a metal frame roller with mainly used
in construction industry (Luetkemeyer, and et, al., 2016). Rubber conveyor belt are the most
commonly used belt to transform various kind of products from one place to another. These belts
can also be used to transport one place to another in a straight line, for transport bulk materials a
troughed belt is used. The trough belt ensure that flow able material is contained within the edges
of the belt.
Belt consist one or more layer of material, mostly common belts have three layers known as
a top cover a carcass and a bottom cover. Steel cover belts are used in case when high strength
class is required. Today, different types of conveyor belts are used for transport various kind of
products from one place to another. Conveyors that are used in industrial care consisting tripping
mechanisms. This allows employees to shut down the conveyor immediately whenever a
problem arise. Warning alarms are also included in belt in order to make the employees aware
about that conveyor belt is about to turn on. Some other systems which are used to safeguarding
the conveyor belt as speed switches, emergency stop and many more. The speed switch helps in
stop the belt in case when the switch is not registering and the belt is running at the fast speed.
Further, the belt rip switch is another way which is used to stop the belt when there is a cut. An
emergency stop may be placed on the control box of conveyor in case of chord malfunctions.
Overall various kind of conveyor belts are there which are used to transport various kind of
goods from one place to another. Various kind of conveyor of belts are there, some are there
which unique feature and help in transport bulk material form one place to another. Various kind
of security provisions are also built in the system which help in stop g del with the conveyor
when there is malfunctioning. Mainly conveyor belts are made up of three layer known as outer,
middle and bottom and from which middle layer is work as support system as this help in
transport good from one place to another.
Sprockets are the toothed tool in a shape of a wheel and its job is to engage the links of a
chain with each other. These sprockets are fixed on the edges of a shaft which can only be
driven by a motor. The conveyor belt is made up of and constructed with number of chain links
and assembled by a pivot. This means chain links are accumulated in such a manner so that the
adjacent chain links can become a joint around the pivot for holding all chain links together and
form a conveyor belt. These chain links which are attached for forming chain conveyor are
attached with pins which are inserted through holes present in modules and are forbidden from
6
in construction industry (Luetkemeyer, and et, al., 2016). Rubber conveyor belt are the most
commonly used belt to transform various kind of products from one place to another. These belts
can also be used to transport one place to another in a straight line, for transport bulk materials a
troughed belt is used. The trough belt ensure that flow able material is contained within the edges
of the belt.
Belt consist one or more layer of material, mostly common belts have three layers known as
a top cover a carcass and a bottom cover. Steel cover belts are used in case when high strength
class is required. Today, different types of conveyor belts are used for transport various kind of
products from one place to another. Conveyors that are used in industrial care consisting tripping
mechanisms. This allows employees to shut down the conveyor immediately whenever a
problem arise. Warning alarms are also included in belt in order to make the employees aware
about that conveyor belt is about to turn on. Some other systems which are used to safeguarding
the conveyor belt as speed switches, emergency stop and many more. The speed switch helps in
stop the belt in case when the switch is not registering and the belt is running at the fast speed.
Further, the belt rip switch is another way which is used to stop the belt when there is a cut. An
emergency stop may be placed on the control box of conveyor in case of chord malfunctions.
Overall various kind of conveyor belts are there which are used to transport various kind of
goods from one place to another. Various kind of conveyor of belts are there, some are there
which unique feature and help in transport bulk material form one place to another. Various kind
of security provisions are also built in the system which help in stop g del with the conveyor
when there is malfunctioning. Mainly conveyor belts are made up of three layer known as outer,
middle and bottom and from which middle layer is work as support system as this help in
transport good from one place to another.
Sprockets are the toothed tool in a shape of a wheel and its job is to engage the links of a
chain with each other. These sprockets are fixed on the edges of a shaft which can only be
driven by a motor. The conveyor belt is made up of and constructed with number of chain links
and assembled by a pivot. This means chain links are accumulated in such a manner so that the
adjacent chain links can become a joint around the pivot for holding all chain links together and
form a conveyor belt. These chain links which are attached for forming chain conveyor are
attached with pins which are inserted through holes present in modules and are forbidden from
6
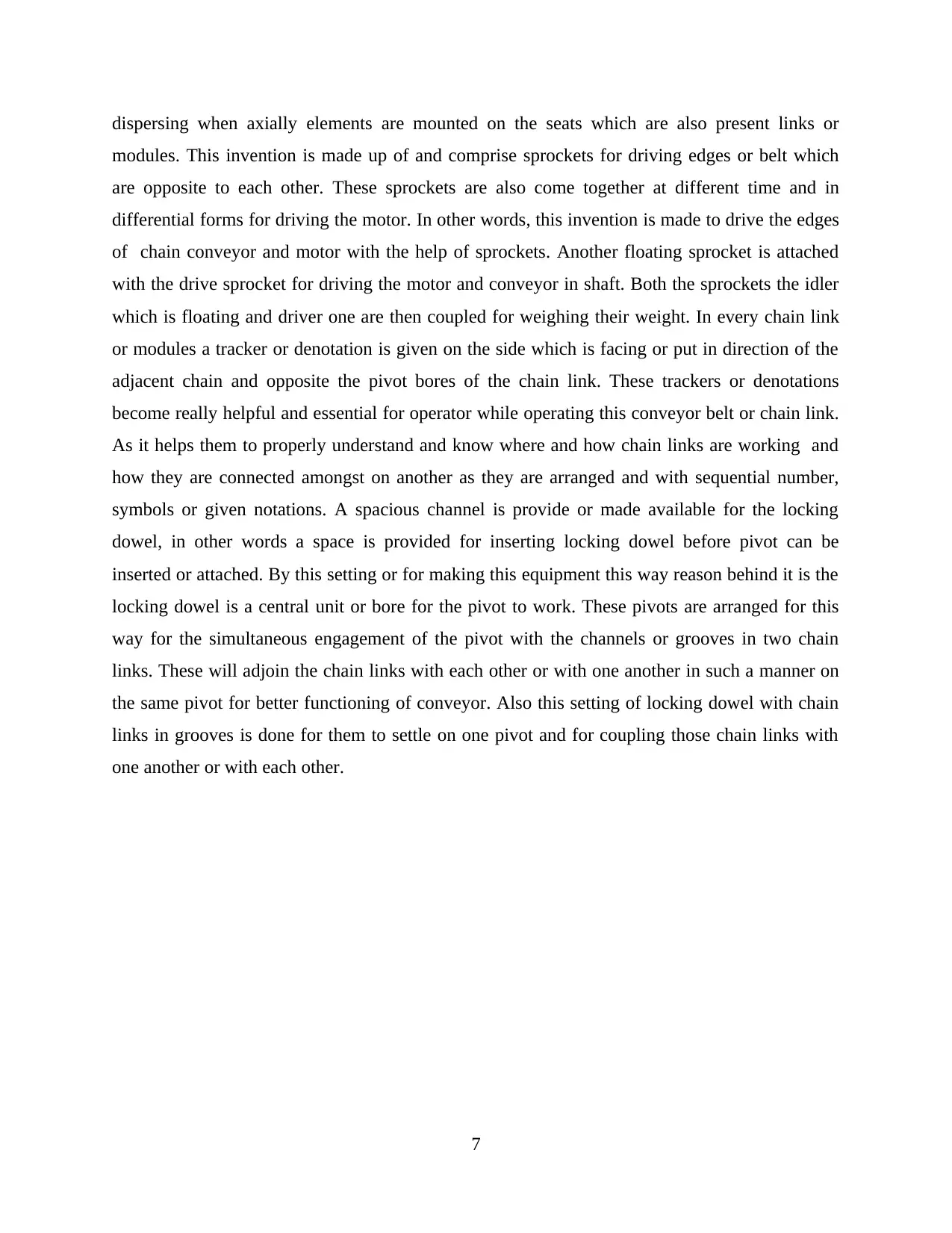
dispersing when axially elements are mounted on the seats which are also present links or
modules. This invention is made up of and comprise sprockets for driving edges or belt which
are opposite to each other. These sprockets are also come together at different time and in
differential forms for driving the motor. In other words, this invention is made to drive the edges
of chain conveyor and motor with the help of sprockets. Another floating sprocket is attached
with the drive sprocket for driving the motor and conveyor in shaft. Both the sprockets the idler
which is floating and driver one are then coupled for weighing their weight. In every chain link
or modules a tracker or denotation is given on the side which is facing or put in direction of the
adjacent chain and opposite the pivot bores of the chain link. These trackers or denotations
become really helpful and essential for operator while operating this conveyor belt or chain link.
As it helps them to properly understand and know where and how chain links are working and
how they are connected amongst on another as they are arranged and with sequential number,
symbols or given notations. A spacious channel is provide or made available for the locking
dowel, in other words a space is provided for inserting locking dowel before pivot can be
inserted or attached. By this setting or for making this equipment this way reason behind it is the
locking dowel is a central unit or bore for the pivot to work. These pivots are arranged for this
way for the simultaneous engagement of the pivot with the channels or grooves in two chain
links. These will adjoin the chain links with each other or with one another in such a manner on
the same pivot for better functioning of conveyor. Also this setting of locking dowel with chain
links in grooves is done for them to settle on one pivot and for coupling those chain links with
one another or with each other.
7
modules. This invention is made up of and comprise sprockets for driving edges or belt which
are opposite to each other. These sprockets are also come together at different time and in
differential forms for driving the motor. In other words, this invention is made to drive the edges
of chain conveyor and motor with the help of sprockets. Another floating sprocket is attached
with the drive sprocket for driving the motor and conveyor in shaft. Both the sprockets the idler
which is floating and driver one are then coupled for weighing their weight. In every chain link
or modules a tracker or denotation is given on the side which is facing or put in direction of the
adjacent chain and opposite the pivot bores of the chain link. These trackers or denotations
become really helpful and essential for operator while operating this conveyor belt or chain link.
As it helps them to properly understand and know where and how chain links are working and
how they are connected amongst on another as they are arranged and with sequential number,
symbols or given notations. A spacious channel is provide or made available for the locking
dowel, in other words a space is provided for inserting locking dowel before pivot can be
inserted or attached. By this setting or for making this equipment this way reason behind it is the
locking dowel is a central unit or bore for the pivot to work. These pivots are arranged for this
way for the simultaneous engagement of the pivot with the channels or grooves in two chain
links. These will adjoin the chain links with each other or with one another in such a manner on
the same pivot for better functioning of conveyor. Also this setting of locking dowel with chain
links in grooves is done for them to settle on one pivot and for coupling those chain links with
one another or with each other.
7
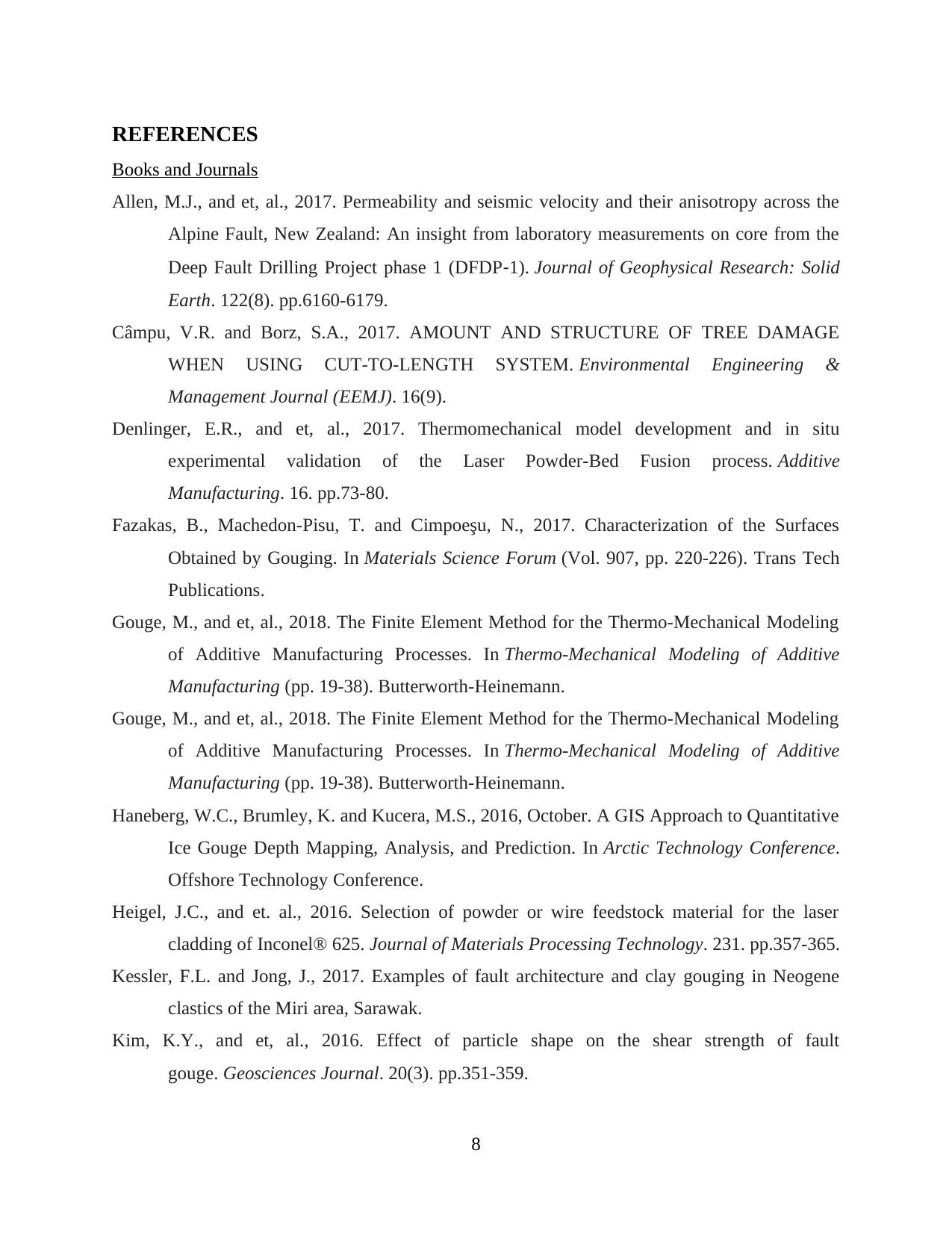
REFERENCES
Books and Journals
Allen, M.J., and et, al., 2017. Permeability and seismic velocity and their anisotropy across the
Alpine Fault, New Zealand: An insight from laboratory measurements on core from the
Deep Fault Drilling Project phase 1 (DFDP‐1). Journal of Geophysical Research: Solid
Earth. 122(8). pp.6160-6179.
Câmpu, V.R. and Borz, S.A., 2017. AMOUNT AND STRUCTURE OF TREE DAMAGE
WHEN USING CUT-TO-LENGTH SYSTEM. Environmental Engineering &
Management Journal (EEMJ). 16(9).
Denlinger, E.R., and et, al., 2017. Thermomechanical model development and in situ
experimental validation of the Laser Powder-Bed Fusion process. Additive
Manufacturing. 16. pp.73-80.
Fazakas, B., Machedon-Pisu, T. and Cimpoeşu, N., 2017. Characterization of the Surfaces
Obtained by Gouging. In Materials Science Forum (Vol. 907, pp. 220-226). Trans Tech
Publications.
Gouge, M., and et, al., 2018. The Finite Element Method for the Thermo-Mechanical Modeling
of Additive Manufacturing Processes. In Thermo-Mechanical Modeling of Additive
Manufacturing (pp. 19-38). Butterworth-Heinemann.
Gouge, M., and et, al., 2018. The Finite Element Method for the Thermo-Mechanical Modeling
of Additive Manufacturing Processes. In Thermo-Mechanical Modeling of Additive
Manufacturing (pp. 19-38). Butterworth-Heinemann.
Haneberg, W.C., Brumley, K. and Kucera, M.S., 2016, October. A GIS Approach to Quantitative
Ice Gouge Depth Mapping, Analysis, and Prediction. In Arctic Technology Conference.
Offshore Technology Conference.
Heigel, J.C., and et. al., 2016. Selection of powder or wire feedstock material for the laser
cladding of Inconel® 625. Journal of Materials Processing Technology. 231. pp.357-365.
Kessler, F.L. and Jong, J., 2017. Examples of fault architecture and clay gouging in Neogene
clastics of the Miri area, Sarawak.
Kim, K.Y., and et, al., 2016. Effect of particle shape on the shear strength of fault
gouge. Geosciences Journal. 20(3). pp.351-359.
8
Books and Journals
Allen, M.J., and et, al., 2017. Permeability and seismic velocity and their anisotropy across the
Alpine Fault, New Zealand: An insight from laboratory measurements on core from the
Deep Fault Drilling Project phase 1 (DFDP‐1). Journal of Geophysical Research: Solid
Earth. 122(8). pp.6160-6179.
Câmpu, V.R. and Borz, S.A., 2017. AMOUNT AND STRUCTURE OF TREE DAMAGE
WHEN USING CUT-TO-LENGTH SYSTEM. Environmental Engineering &
Management Journal (EEMJ). 16(9).
Denlinger, E.R., and et, al., 2017. Thermomechanical model development and in situ
experimental validation of the Laser Powder-Bed Fusion process. Additive
Manufacturing. 16. pp.73-80.
Fazakas, B., Machedon-Pisu, T. and Cimpoeşu, N., 2017. Characterization of the Surfaces
Obtained by Gouging. In Materials Science Forum (Vol. 907, pp. 220-226). Trans Tech
Publications.
Gouge, M., and et, al., 2018. The Finite Element Method for the Thermo-Mechanical Modeling
of Additive Manufacturing Processes. In Thermo-Mechanical Modeling of Additive
Manufacturing (pp. 19-38). Butterworth-Heinemann.
Gouge, M., and et, al., 2018. The Finite Element Method for the Thermo-Mechanical Modeling
of Additive Manufacturing Processes. In Thermo-Mechanical Modeling of Additive
Manufacturing (pp. 19-38). Butterworth-Heinemann.
Haneberg, W.C., Brumley, K. and Kucera, M.S., 2016, October. A GIS Approach to Quantitative
Ice Gouge Depth Mapping, Analysis, and Prediction. In Arctic Technology Conference.
Offshore Technology Conference.
Heigel, J.C., and et. al., 2016. Selection of powder or wire feedstock material for the laser
cladding of Inconel® 625. Journal of Materials Processing Technology. 231. pp.357-365.
Kessler, F.L. and Jong, J., 2017. Examples of fault architecture and clay gouging in Neogene
clastics of the Miri area, Sarawak.
Kim, K.Y., and et, al., 2016. Effect of particle shape on the shear strength of fault
gouge. Geosciences Journal. 20(3). pp.351-359.
8
Secure Best Marks with AI Grader
Need help grading? Try our AI Grader for instant feedback on your assignments.
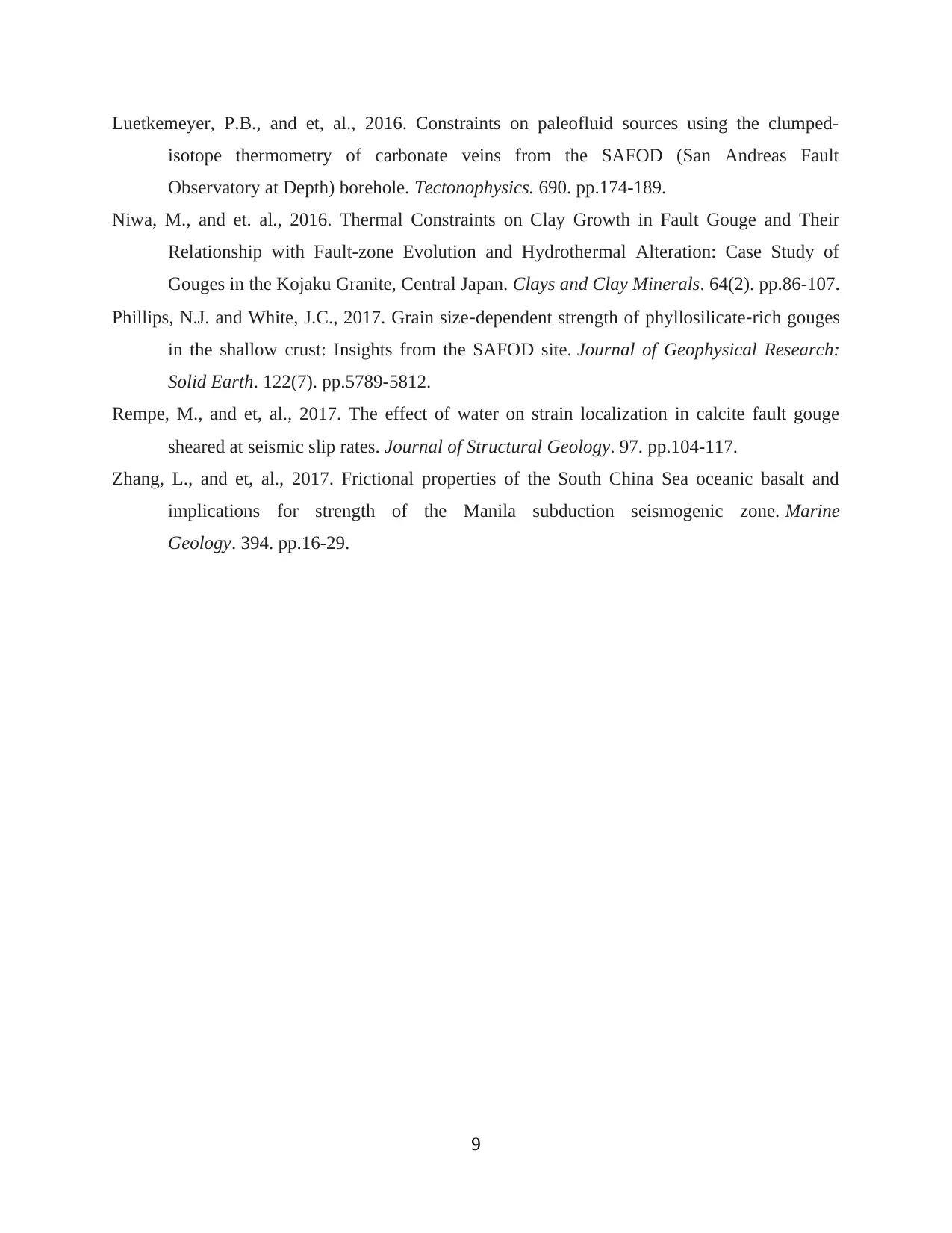
Luetkemeyer, P.B., and et, al., 2016. Constraints on paleofluid sources using the clumped-
isotope thermometry of carbonate veins from the SAFOD (San Andreas Fault
Observatory at Depth) borehole. Tectonophysics. 690. pp.174-189.
Niwa, M., and et. al., 2016. Thermal Constraints on Clay Growth in Fault Gouge and Their
Relationship with Fault-zone Evolution and Hydrothermal Alteration: Case Study of
Gouges in the Kojaku Granite, Central Japan. Clays and Clay Minerals. 64(2). pp.86-107.
Phillips, N.J. and White, J.C., 2017. Grain size‐dependent strength of phyllosilicate‐rich gouges
in the shallow crust: Insights from the SAFOD site. Journal of Geophysical Research:
Solid Earth. 122(7). pp.5789-5812.
Rempe, M., and et, al., 2017. The effect of water on strain localization in calcite fault gouge
sheared at seismic slip rates. Journal of Structural Geology. 97. pp.104-117.
Zhang, L., and et, al., 2017. Frictional properties of the South China Sea oceanic basalt and
implications for strength of the Manila subduction seismogenic zone. Marine
Geology. 394. pp.16-29.
9
isotope thermometry of carbonate veins from the SAFOD (San Andreas Fault
Observatory at Depth) borehole. Tectonophysics. 690. pp.174-189.
Niwa, M., and et. al., 2016. Thermal Constraints on Clay Growth in Fault Gouge and Their
Relationship with Fault-zone Evolution and Hydrothermal Alteration: Case Study of
Gouges in the Kojaku Granite, Central Japan. Clays and Clay Minerals. 64(2). pp.86-107.
Phillips, N.J. and White, J.C., 2017. Grain size‐dependent strength of phyllosilicate‐rich gouges
in the shallow crust: Insights from the SAFOD site. Journal of Geophysical Research:
Solid Earth. 122(7). pp.5789-5812.
Rempe, M., and et, al., 2017. The effect of water on strain localization in calcite fault gouge
sheared at seismic slip rates. Journal of Structural Geology. 97. pp.104-117.
Zhang, L., and et, al., 2017. Frictional properties of the South China Sea oceanic basalt and
implications for strength of the Manila subduction seismogenic zone. Marine
Geology. 394. pp.16-29.
9
1 out of 11
Related Documents
![[object Object]](/_next/image/?url=%2F_next%2Fstatic%2Fmedia%2Flogo.6d15ce61.png&w=640&q=75)
Your All-in-One AI-Powered Toolkit for Academic Success.
+13062052269
info@desklib.com
Available 24*7 on WhatsApp / Email
Unlock your academic potential
© 2024 | Zucol Services PVT LTD | All rights reserved.