Deep Water Horizon Project for Learning
VerifiedAdded on  2023/01/18
|7
|2452
|84
AI Summary
This report explores the Deep Water Horizon project for learning approach and analyzes the project risks and management strategies. It provides valuable insights for students to gain from this project-based exercise.
Contribute Materials
Your contribution can guide someone’s learning journey. Share your
documents today.
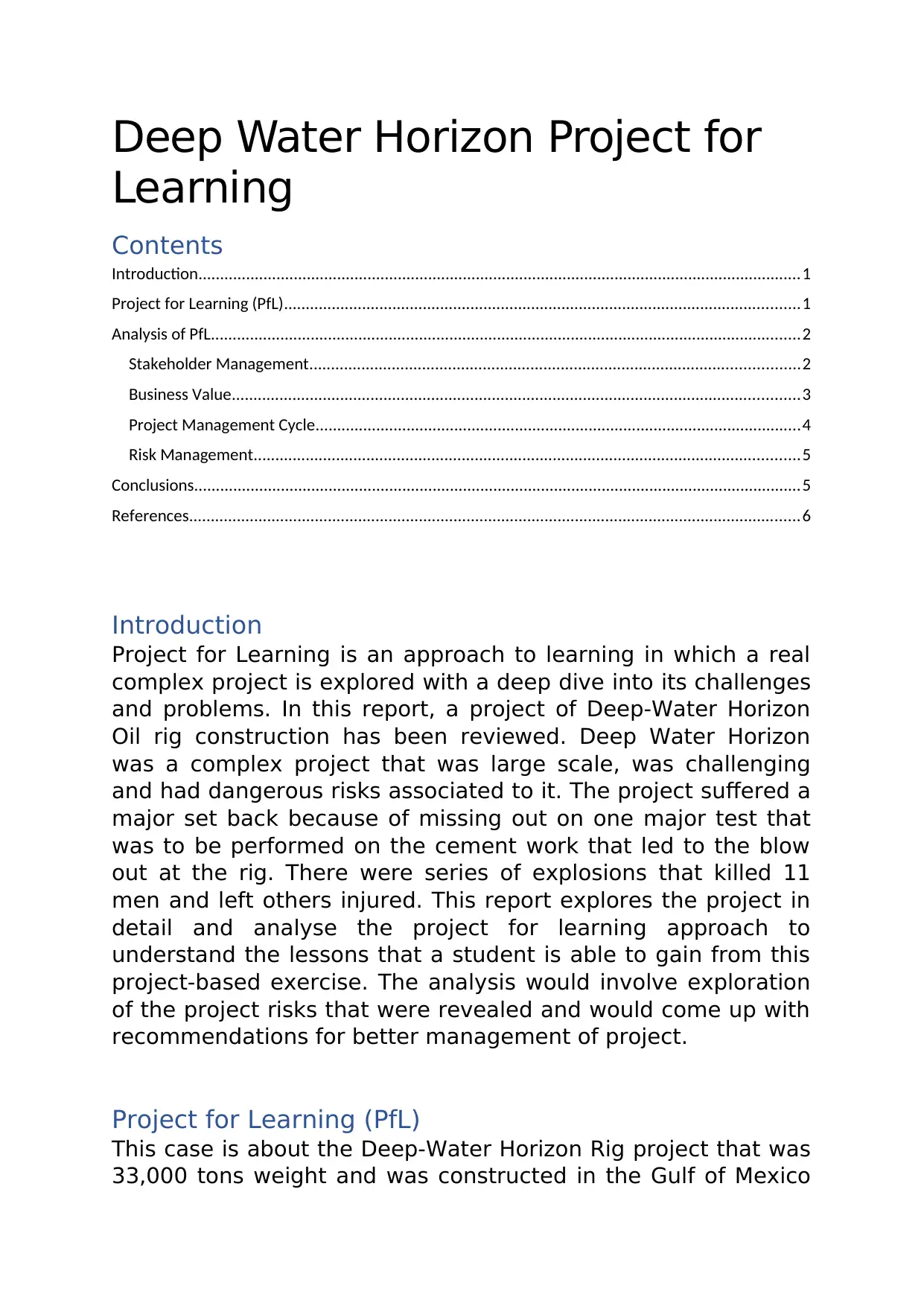
Deep Water Horizon Project for
Learning
Contents
Introduction...........................................................................................................................................1
Project for Learning (PfL).......................................................................................................................1
Analysis of PfL........................................................................................................................................2
Stakeholder Management.................................................................................................................2
Business Value...................................................................................................................................3
Project Management Cycle................................................................................................................4
Risk Management..............................................................................................................................5
Conclusions............................................................................................................................................5
References.............................................................................................................................................6
Introduction
Project for Learning is an approach to learning in which a real
complex project is explored with a deep dive into its challenges
and problems. In this report, a project of Deep-Water Horizon
Oil rig construction has been reviewed. Deep Water Horizon
was a complex project that was large scale, was challenging
and had dangerous risks associated to it. The project suffered a
major set back because of missing out on one major test that
was to be performed on the cement work that led to the blow
out at the rig. There were series of explosions that killed 11
men and left others injured. This report explores the project in
detail and analyse the project for learning approach to
understand the lessons that a student is able to gain from this
project-based exercise. The analysis would involve exploration
of the project risks that were revealed and would come up with
recommendations for better management of project.
Project for Learning (PfL)
This case is about the Deep-Water Horizon Rig project that was
33,000 tons weight and was constructed in the Gulf of Mexico
Learning
Contents
Introduction...........................................................................................................................................1
Project for Learning (PfL).......................................................................................................................1
Analysis of PfL........................................................................................................................................2
Stakeholder Management.................................................................................................................2
Business Value...................................................................................................................................3
Project Management Cycle................................................................................................................4
Risk Management..............................................................................................................................5
Conclusions............................................................................................................................................5
References.............................................................................................................................................6
Introduction
Project for Learning is an approach to learning in which a real
complex project is explored with a deep dive into its challenges
and problems. In this report, a project of Deep-Water Horizon
Oil rig construction has been reviewed. Deep Water Horizon
was a complex project that was large scale, was challenging
and had dangerous risks associated to it. The project suffered a
major set back because of missing out on one major test that
was to be performed on the cement work that led to the blow
out at the rig. There were series of explosions that killed 11
men and left others injured. This report explores the project in
detail and analyse the project for learning approach to
understand the lessons that a student is able to gain from this
project-based exercise. The analysis would involve exploration
of the project risks that were revealed and would come up with
recommendations for better management of project.
Project for Learning (PfL)
This case is about the Deep-Water Horizon Rig project that was
33,000 tons weight and was constructed in the Gulf of Mexico
Secure Best Marks with AI Grader
Need help grading? Try our AI Grader for instant feedback on your assignments.
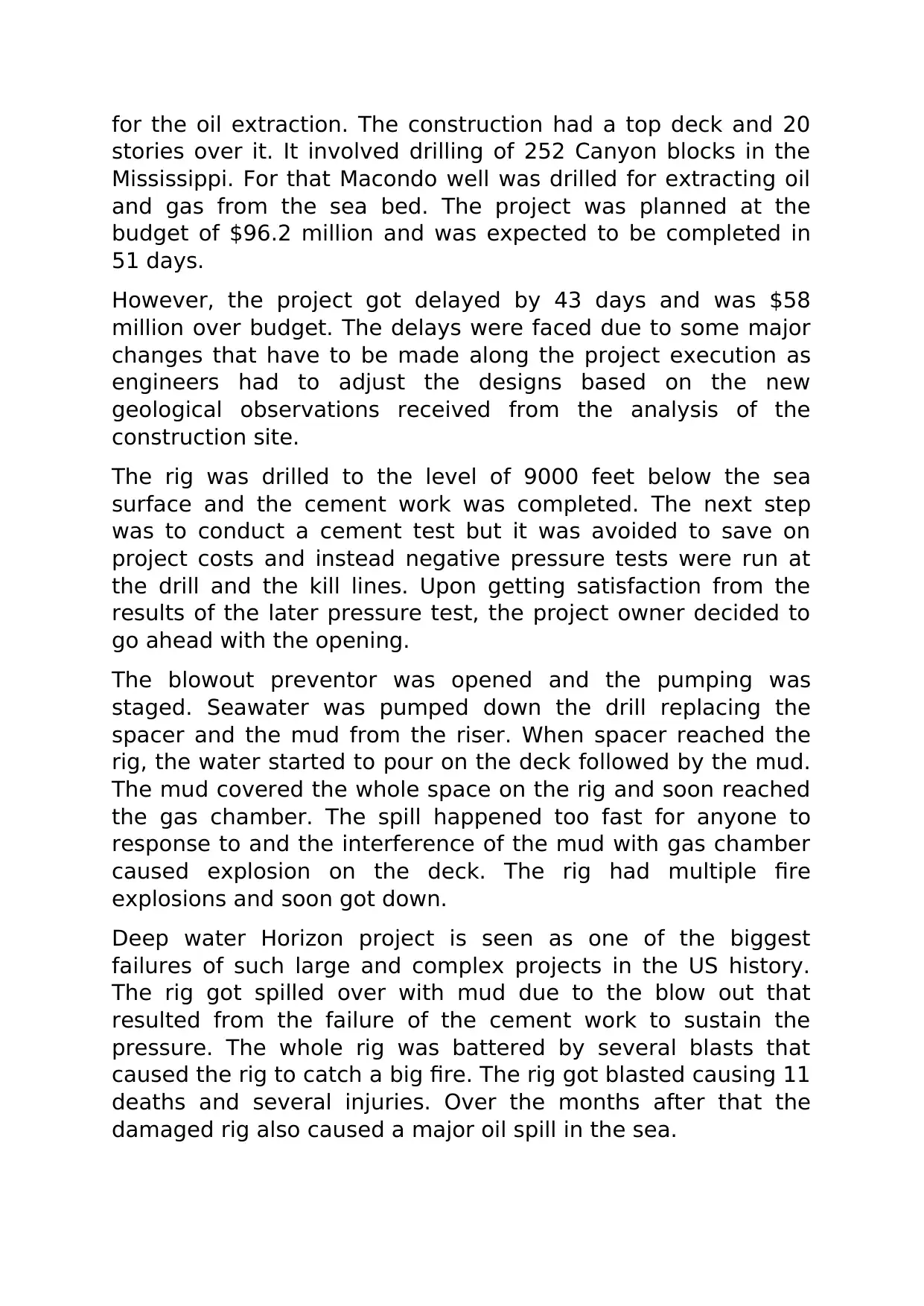
for the oil extraction. The construction had a top deck and 20
stories over it. It involved drilling of 252 Canyon blocks in the
Mississippi. For that Macondo well was drilled for extracting oil
and gas from the sea bed. The project was planned at the
budget of $96.2 million and was expected to be completed in
51 days.
However, the project got delayed by 43 days and was $58
million over budget. The delays were faced due to some major
changes that have to be made along the project execution as
engineers had to adjust the designs based on the new
geological observations received from the analysis of the
construction site.
The rig was drilled to the level of 9000 feet below the sea
surface and the cement work was completed. The next step
was to conduct a cement test but it was avoided to save on
project costs and instead negative pressure tests were run at
the drill and the kill lines. Upon getting satisfaction from the
results of the later pressure test, the project owner decided to
go ahead with the opening.
The blowout preventor was opened and the pumping was
staged. Seawater was pumped down the drill replacing the
spacer and the mud from the riser. When spacer reached the
rig, the water started to pour on the deck followed by the mud.
The mud covered the whole space on the rig and soon reached
the gas chamber. The spill happened too fast for anyone to
response to and the interference of the mud with gas chamber
caused explosion on the deck. The rig had multiple fire
explosions and soon got down.
Deep water Horizon project is seen as one of the biggest
failures of such large and complex projects in the US history.
The rig got spilled over with mud due to the blow out that
resulted from the failure of the cement work to sustain the
pressure. The whole rig was battered by several blasts that
caused the rig to catch a big fire. The rig got blasted causing 11
deaths and several injuries. Over the months after that the
damaged rig also caused a major oil spill in the sea.
stories over it. It involved drilling of 252 Canyon blocks in the
Mississippi. For that Macondo well was drilled for extracting oil
and gas from the sea bed. The project was planned at the
budget of $96.2 million and was expected to be completed in
51 days.
However, the project got delayed by 43 days and was $58
million over budget. The delays were faced due to some major
changes that have to be made along the project execution as
engineers had to adjust the designs based on the new
geological observations received from the analysis of the
construction site.
The rig was drilled to the level of 9000 feet below the sea
surface and the cement work was completed. The next step
was to conduct a cement test but it was avoided to save on
project costs and instead negative pressure tests were run at
the drill and the kill lines. Upon getting satisfaction from the
results of the later pressure test, the project owner decided to
go ahead with the opening.
The blowout preventor was opened and the pumping was
staged. Seawater was pumped down the drill replacing the
spacer and the mud from the riser. When spacer reached the
rig, the water started to pour on the deck followed by the mud.
The mud covered the whole space on the rig and soon reached
the gas chamber. The spill happened too fast for anyone to
response to and the interference of the mud with gas chamber
caused explosion on the deck. The rig had multiple fire
explosions and soon got down.
Deep water Horizon project is seen as one of the biggest
failures of such large and complex projects in the US history.
The rig got spilled over with mud due to the blow out that
resulted from the failure of the cement work to sustain the
pressure. The whole rig was battered by several blasts that
caused the rig to catch a big fire. The rig got blasted causing 11
deaths and several injuries. Over the months after that the
damaged rig also caused a major oil spill in the sea.
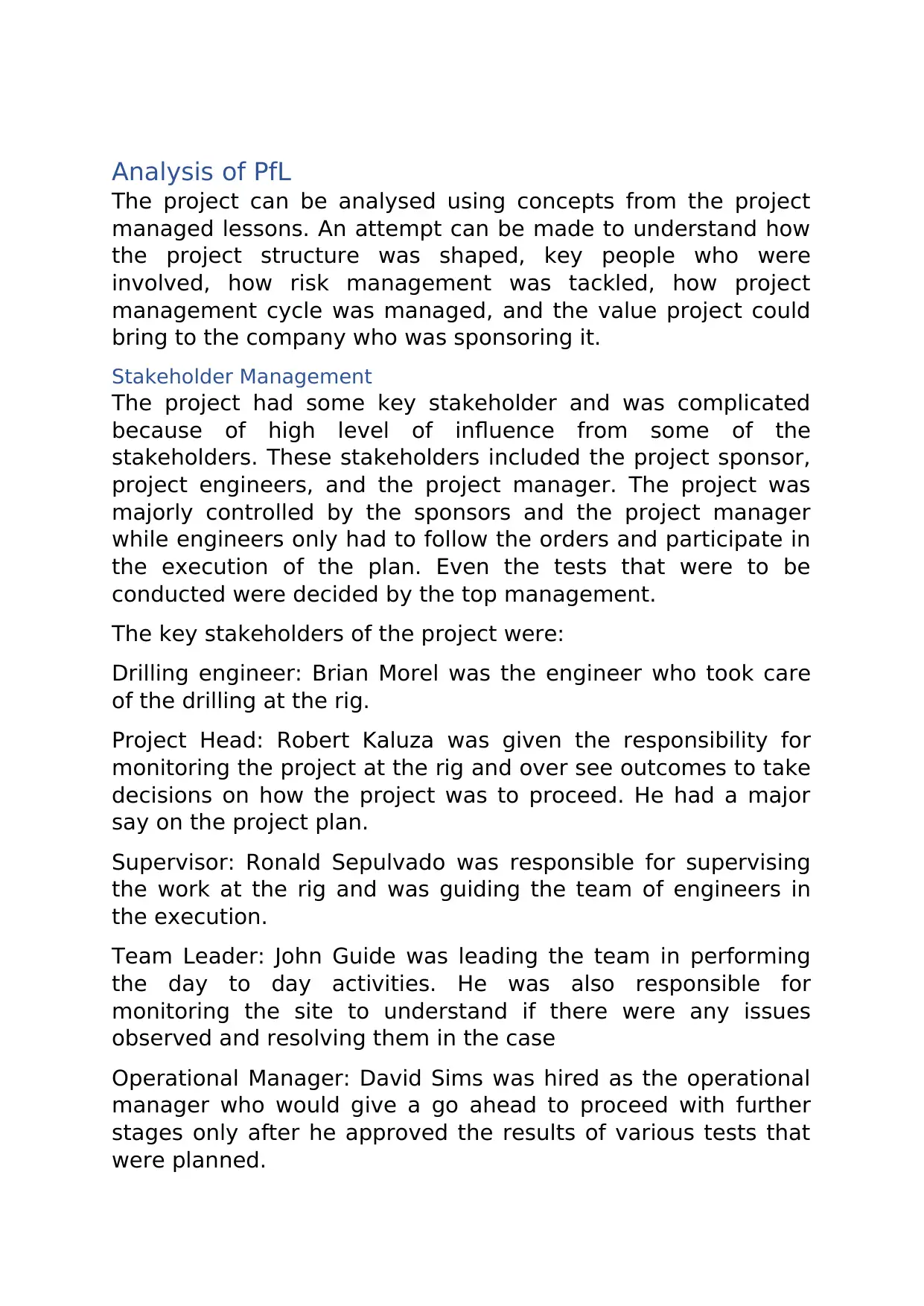
Analysis of PfL
The project can be analysed using concepts from the project
managed lessons. An attempt can be made to understand how
the project structure was shaped, key people who were
involved, how risk management was tackled, how project
management cycle was managed, and the value project could
bring to the company who was sponsoring it.
Stakeholder Management
The project had some key stakeholder and was complicated
because of high level of influence from some of the
stakeholders. These stakeholders included the project sponsor,
project engineers, and the project manager. The project was
majorly controlled by the sponsors and the project manager
while engineers only had to follow the orders and participate in
the execution of the plan. Even the tests that were to be
conducted were decided by the top management.
The key stakeholders of the project were:
Drilling engineer: Brian Morel was the engineer who took care
of the drilling at the rig.
Project Head: Robert Kaluza was given the responsibility for
monitoring the project at the rig and over see outcomes to take
decisions on how the project was to proceed. He had a major
say on the project plan.
Supervisor: Ronald Sepulvado was responsible for supervising
the work at the rig and was guiding the team of engineers in
the execution.
Team Leader: John Guide was leading the team in performing
the day to day activities. He was also responsible for
monitoring the site to understand if there were any issues
observed and resolving them in the case
Operational Manager: David Sims was hired as the operational
manager who would give a go ahead to proceed with further
stages only after he approved the results of various tests that
were planned.
The project can be analysed using concepts from the project
managed lessons. An attempt can be made to understand how
the project structure was shaped, key people who were
involved, how risk management was tackled, how project
management cycle was managed, and the value project could
bring to the company who was sponsoring it.
Stakeholder Management
The project had some key stakeholder and was complicated
because of high level of influence from some of the
stakeholders. These stakeholders included the project sponsor,
project engineers, and the project manager. The project was
majorly controlled by the sponsors and the project manager
while engineers only had to follow the orders and participate in
the execution of the plan. Even the tests that were to be
conducted were decided by the top management.
The key stakeholders of the project were:
Drilling engineer: Brian Morel was the engineer who took care
of the drilling at the rig.
Project Head: Robert Kaluza was given the responsibility for
monitoring the project at the rig and over see outcomes to take
decisions on how the project was to proceed. He had a major
say on the project plan.
Supervisor: Ronald Sepulvado was responsible for supervising
the work at the rig and was guiding the team of engineers in
the execution.
Team Leader: John Guide was leading the team in performing
the day to day activities. He was also responsible for
monitoring the site to understand if there were any issues
observed and resolving them in the case
Operational Manager: David Sims was hired as the operational
manager who would give a go ahead to proceed with further
stages only after he approved the results of various tests that
were planned.
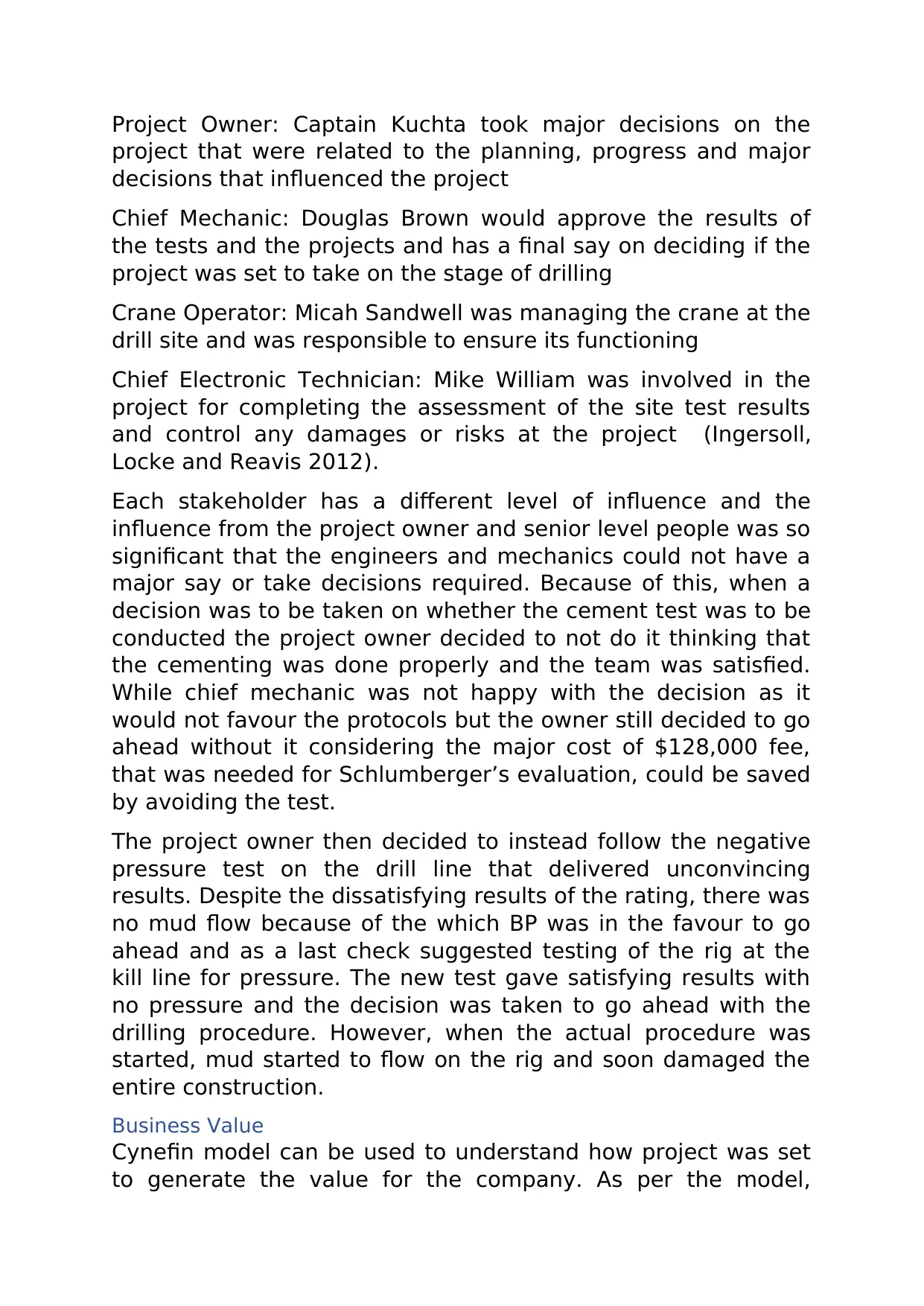
Project Owner: Captain Kuchta took major decisions on the
project that were related to the planning, progress and major
decisions that influenced the project
Chief Mechanic: Douglas Brown would approve the results of
the tests and the projects and has a final say on deciding if the
project was set to take on the stage of drilling
Crane Operator: Micah Sandwell was managing the crane at the
drill site and was responsible to ensure its functioning
Chief Electronic Technician: Mike William was involved in the
project for completing the assessment of the site test results
and control any damages or risks at the project (Ingersoll,
Locke and Reavis 2012).
Each stakeholder has a different level of influence and the
influence from the project owner and senior level people was so
significant that the engineers and mechanics could not have a
major say or take decisions required. Because of this, when a
decision was to be taken on whether the cement test was to be
conducted the project owner decided to not do it thinking that
the cementing was done properly and the team was satisfied.
While chief mechanic was not happy with the decision as it
would not favour the protocols but the owner still decided to go
ahead without it considering the major cost of $128,000 fee,
that was needed for Schlumberger’s evaluation, could be saved
by avoiding the test.
The project owner then decided to instead follow the negative
pressure test on the drill line that delivered unconvincing
results. Despite the dissatisfying results of the rating, there was
no mud flow because of the which BP was in the favour to go
ahead and as a last check suggested testing of the rig at the
kill line for pressure. The new test gave satisfying results with
no pressure and the decision was taken to go ahead with the
drilling procedure. However, when the actual procedure was
started, mud started to flow on the rig and soon damaged the
entire construction.
Business Value
Cynefin model can be used to understand how project was set
to generate the value for the company. As per the model,
project that were related to the planning, progress and major
decisions that influenced the project
Chief Mechanic: Douglas Brown would approve the results of
the tests and the projects and has a final say on deciding if the
project was set to take on the stage of drilling
Crane Operator: Micah Sandwell was managing the crane at the
drill site and was responsible to ensure its functioning
Chief Electronic Technician: Mike William was involved in the
project for completing the assessment of the site test results
and control any damages or risks at the project (Ingersoll,
Locke and Reavis 2012).
Each stakeholder has a different level of influence and the
influence from the project owner and senior level people was so
significant that the engineers and mechanics could not have a
major say or take decisions required. Because of this, when a
decision was to be taken on whether the cement test was to be
conducted the project owner decided to not do it thinking that
the cementing was done properly and the team was satisfied.
While chief mechanic was not happy with the decision as it
would not favour the protocols but the owner still decided to go
ahead without it considering the major cost of $128,000 fee,
that was needed for Schlumberger’s evaluation, could be saved
by avoiding the test.
The project owner then decided to instead follow the negative
pressure test on the drill line that delivered unconvincing
results. Despite the dissatisfying results of the rating, there was
no mud flow because of the which BP was in the favour to go
ahead and as a last check suggested testing of the rig at the
kill line for pressure. The new test gave satisfying results with
no pressure and the decision was taken to go ahead with the
drilling procedure. However, when the actual procedure was
started, mud started to flow on the rig and soon damaged the
entire construction.
Business Value
Cynefin model can be used to understand how project was set
to generate the value for the company. As per the model,
Secure Best Marks with AI Grader
Need help grading? Try our AI Grader for instant feedback on your assignments.
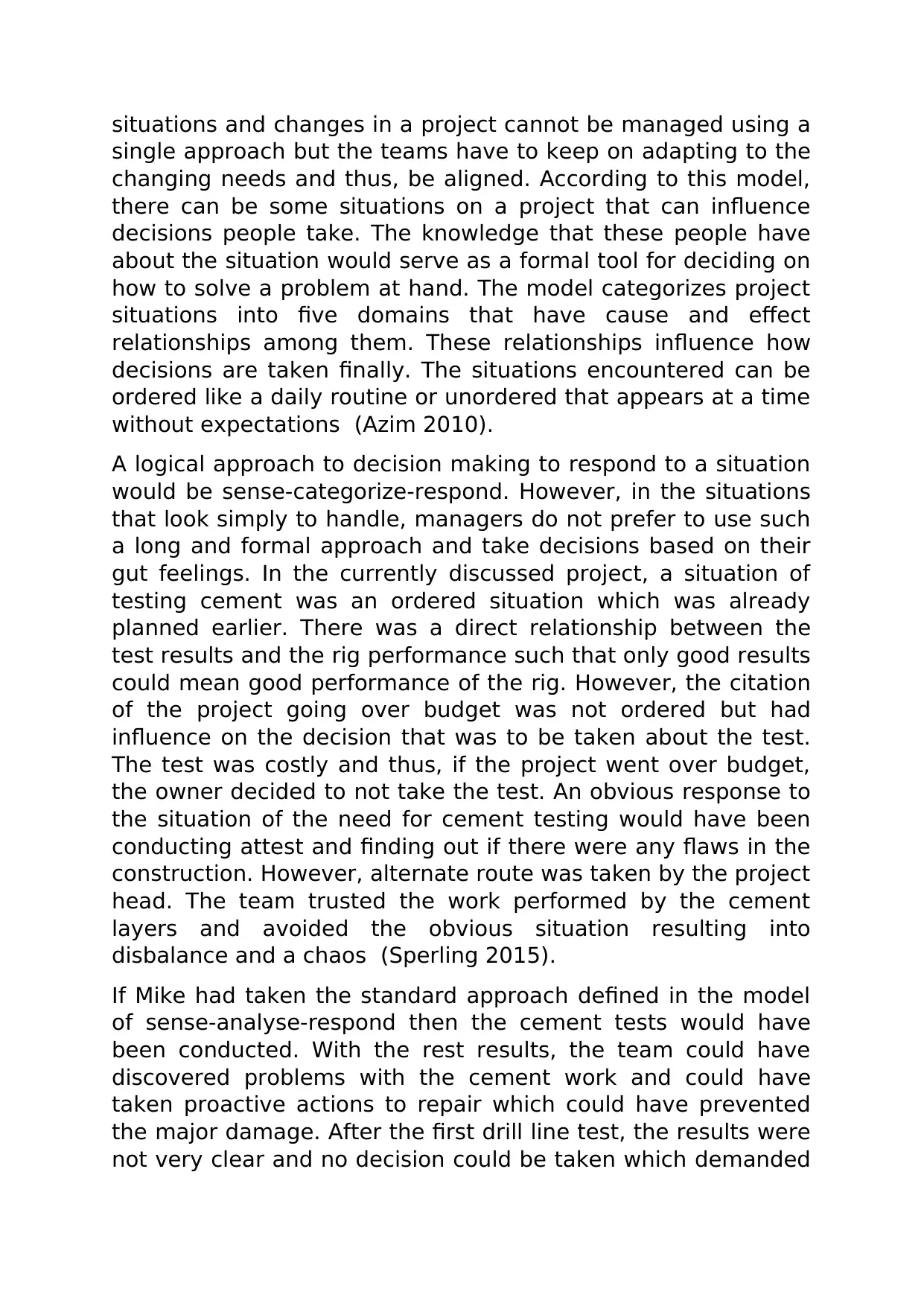
situations and changes in a project cannot be managed using a
single approach but the teams have to keep on adapting to the
changing needs and thus, be aligned. According to this model,
there can be some situations on a project that can influence
decisions people take. The knowledge that these people have
about the situation would serve as a formal tool for deciding on
how to solve a problem at hand. The model categorizes project
situations into five domains that have cause and effect
relationships among them. These relationships influence how
decisions are taken finally. The situations encountered can be
ordered like a daily routine or unordered that appears at a time
without expectations (Azim 2010).
A logical approach to decision making to respond to a situation
would be sense-categorize-respond. However, in the situations
that look simply to handle, managers do not prefer to use such
a long and formal approach and take decisions based on their
gut feelings. In the currently discussed project, a situation of
testing cement was an ordered situation which was already
planned earlier. There was a direct relationship between the
test results and the rig performance such that only good results
could mean good performance of the rig. However, the citation
of the project going over budget was not ordered but had
influence on the decision that was to be taken about the test.
The test was costly and thus, if the project went over budget,
the owner decided to not take the test. An obvious response to
the situation of the need for cement testing would have been
conducting attest and finding out if there were any flaws in the
construction. However, alternate route was taken by the project
head. The team trusted the work performed by the cement
layers and avoided the obvious situation resulting into
disbalance and a chaos (Sperling 2015).
If Mike had taken the standard approach defined in the model
of sense-analyse-respond then the cement tests would have
been conducted. With the rest results, the team could have
discovered problems with the cement work and could have
taken proactive actions to repair which could have prevented
the major damage. After the first drill line test, the results were
not very clear and no decision could be taken which demanded
single approach but the teams have to keep on adapting to the
changing needs and thus, be aligned. According to this model,
there can be some situations on a project that can influence
decisions people take. The knowledge that these people have
about the situation would serve as a formal tool for deciding on
how to solve a problem at hand. The model categorizes project
situations into five domains that have cause and effect
relationships among them. These relationships influence how
decisions are taken finally. The situations encountered can be
ordered like a daily routine or unordered that appears at a time
without expectations (Azim 2010).
A logical approach to decision making to respond to a situation
would be sense-categorize-respond. However, in the situations
that look simply to handle, managers do not prefer to use such
a long and formal approach and take decisions based on their
gut feelings. In the currently discussed project, a situation of
testing cement was an ordered situation which was already
planned earlier. There was a direct relationship between the
test results and the rig performance such that only good results
could mean good performance of the rig. However, the citation
of the project going over budget was not ordered but had
influence on the decision that was to be taken about the test.
The test was costly and thus, if the project went over budget,
the owner decided to not take the test. An obvious response to
the situation of the need for cement testing would have been
conducting attest and finding out if there were any flaws in the
construction. However, alternate route was taken by the project
head. The team trusted the work performed by the cement
layers and avoided the obvious situation resulting into
disbalance and a chaos (Sperling 2015).
If Mike had taken the standard approach defined in the model
of sense-analyse-respond then the cement tests would have
been conducted. With the rest results, the team could have
discovered problems with the cement work and could have
taken proactive actions to repair which could have prevented
the major damage. After the first drill line test, the results were
not very clear and no decision could be taken which demanded
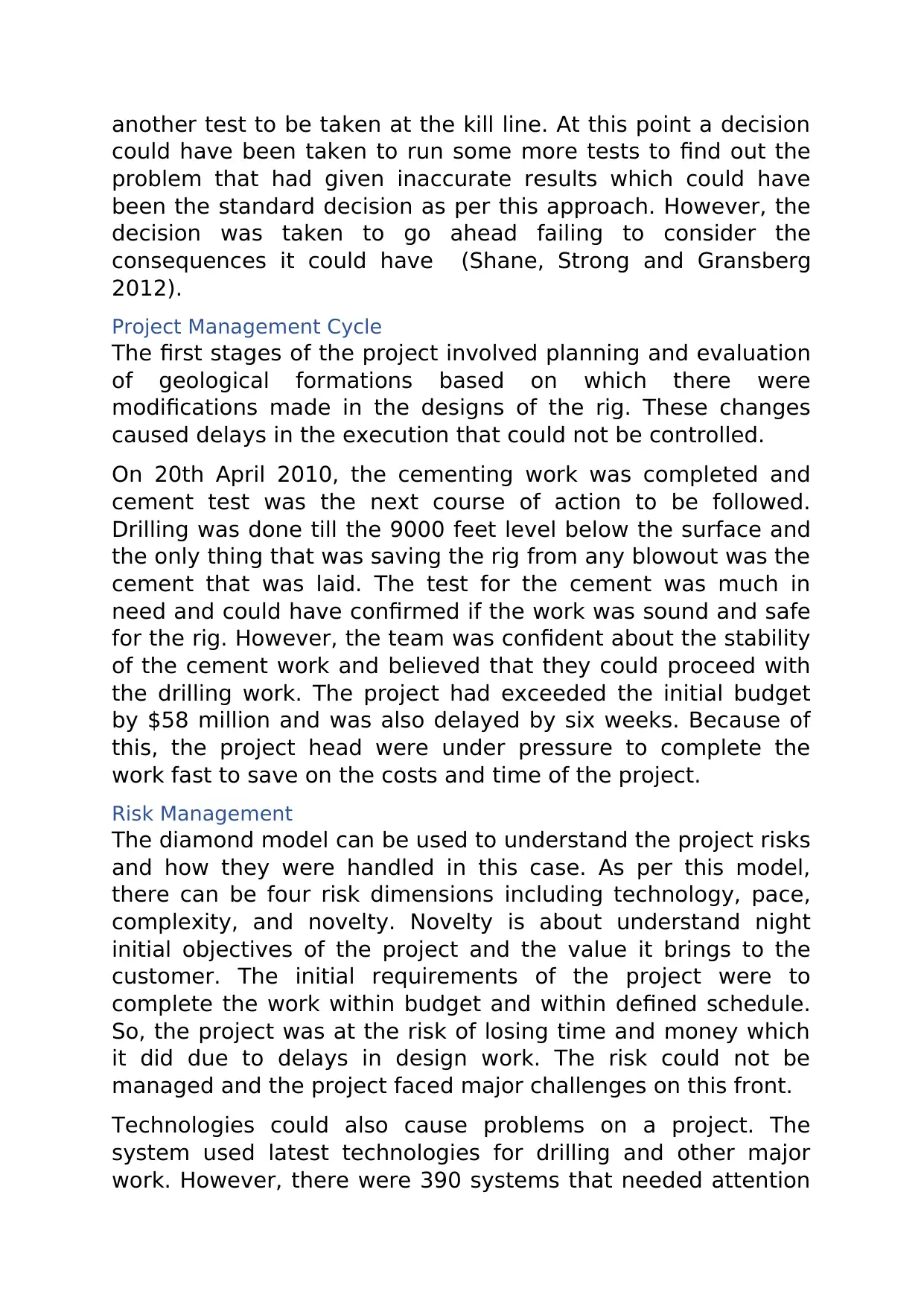
another test to be taken at the kill line. At this point a decision
could have been taken to run some more tests to find out the
problem that had given inaccurate results which could have
been the standard decision as per this approach. However, the
decision was taken to go ahead failing to consider the
consequences it could have (Shane, Strong and Gransberg
2012).
Project Management Cycle
The first stages of the project involved planning and evaluation
of geological formations based on which there were
modifications made in the designs of the rig. These changes
caused delays in the execution that could not be controlled.
On 20th April 2010, the cementing work was completed and
cement test was the next course of action to be followed.
Drilling was done till the 9000 feet level below the surface and
the only thing that was saving the rig from any blowout was the
cement that was laid. The test for the cement was much in
need and could have confirmed if the work was sound and safe
for the rig. However, the team was confident about the stability
of the cement work and believed that they could proceed with
the drilling work. The project had exceeded the initial budget
by $58 million and was also delayed by six weeks. Because of
this, the project head were under pressure to complete the
work fast to save on the costs and time of the project.
Risk Management
The diamond model can be used to understand the project risks
and how they were handled in this case. As per this model,
there can be four risk dimensions including technology, pace,
complexity, and novelty. Novelty is about understand night
initial objectives of the project and the value it brings to the
customer. The initial requirements of the project were to
complete the work within budget and within defined schedule.
So, the project was at the risk of losing time and money which
it did due to delays in design work. The risk could not be
managed and the project faced major challenges on this front.
Technologies could also cause problems on a project. The
system used latest technologies for drilling and other major
work. However, there were 390 systems that needed attention
could have been taken to run some more tests to find out the
problem that had given inaccurate results which could have
been the standard decision as per this approach. However, the
decision was taken to go ahead failing to consider the
consequences it could have (Shane, Strong and Gransberg
2012).
Project Management Cycle
The first stages of the project involved planning and evaluation
of geological formations based on which there were
modifications made in the designs of the rig. These changes
caused delays in the execution that could not be controlled.
On 20th April 2010, the cementing work was completed and
cement test was the next course of action to be followed.
Drilling was done till the 9000 feet level below the surface and
the only thing that was saving the rig from any blowout was the
cement that was laid. The test for the cement was much in
need and could have confirmed if the work was sound and safe
for the rig. However, the team was confident about the stability
of the cement work and believed that they could proceed with
the drilling work. The project had exceeded the initial budget
by $58 million and was also delayed by six weeks. Because of
this, the project head were under pressure to complete the
work fast to save on the costs and time of the project.
Risk Management
The diamond model can be used to understand the project risks
and how they were handled in this case. As per this model,
there can be four risk dimensions including technology, pace,
complexity, and novelty. Novelty is about understand night
initial objectives of the project and the value it brings to the
customer. The initial requirements of the project were to
complete the work within budget and within defined schedule.
So, the project was at the risk of losing time and money which
it did due to delays in design work. The risk could not be
managed and the project faced major challenges on this front.
Technologies could also cause problems on a project. The
system used latest technologies for drilling and other major
work. However, there were 390 systems that needed attention
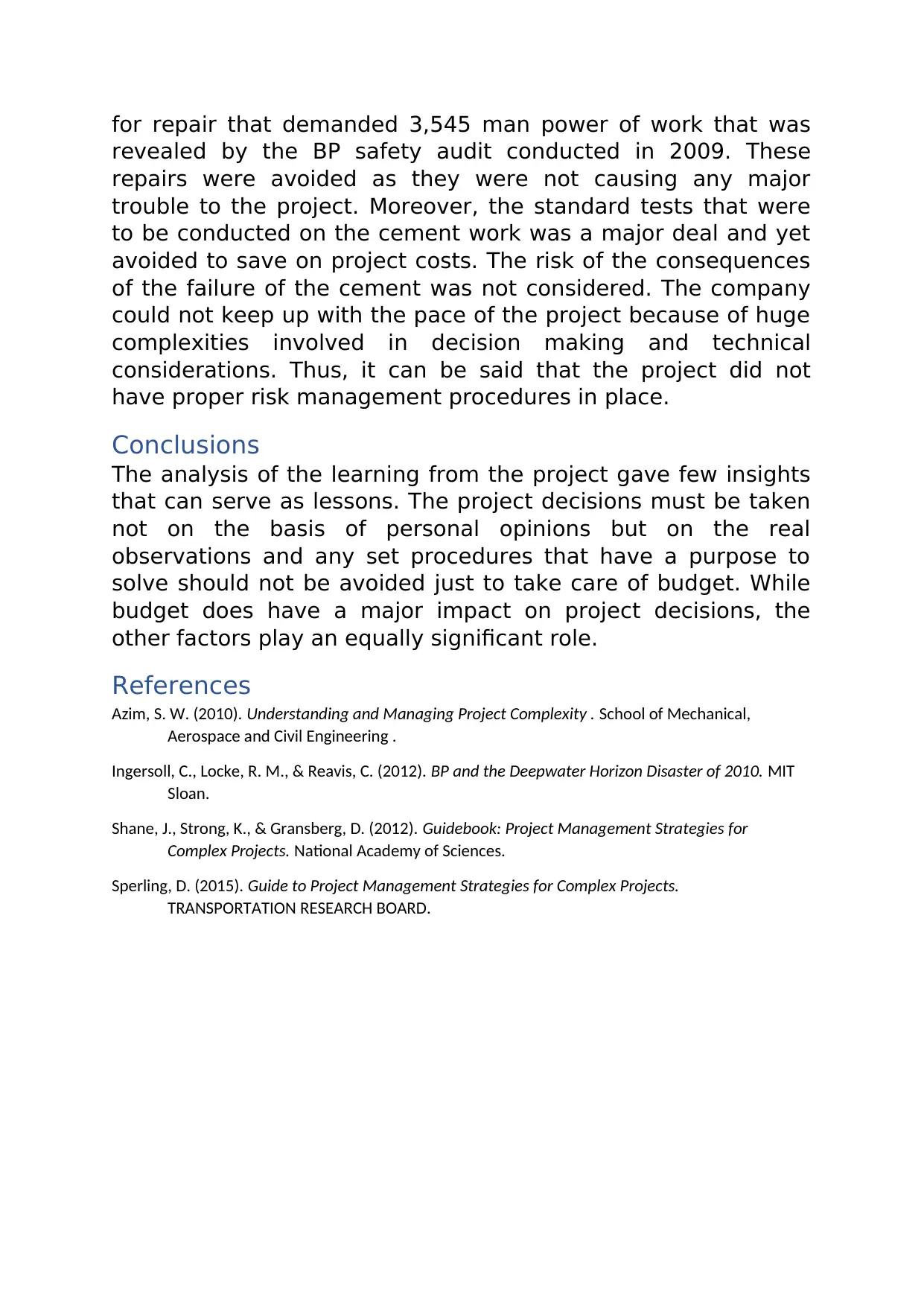
for repair that demanded 3,545 man power of work that was
revealed by the BP safety audit conducted in 2009. These
repairs were avoided as they were not causing any major
trouble to the project. Moreover, the standard tests that were
to be conducted on the cement work was a major deal and yet
avoided to save on project costs. The risk of the consequences
of the failure of the cement was not considered. The company
could not keep up with the pace of the project because of huge
complexities involved in decision making and technical
considerations. Thus, it can be said that the project did not
have proper risk management procedures in place.
Conclusions
The analysis of the learning from the project gave few insights
that can serve as lessons. The project decisions must be taken
not on the basis of personal opinions but on the real
observations and any set procedures that have a purpose to
solve should not be avoided just to take care of budget. While
budget does have a major impact on project decisions, the
other factors play an equally significant role.
References
Azim, S. W. (2010). Understanding and Managing Project Complexity . School of Mechanical,
Aerospace and Civil Engineering .
Ingersoll, C., Locke, R. M., & Reavis, C. (2012). BP and the Deepwater Horizon Disaster of 2010. MIT
Sloan.
Shane, J., Strong, K., & Gransberg, D. (2012). Guidebook: Project Management Strategies for
Complex Projects. National Academy of Sciences.
Sperling, D. (2015). Guide to Project Management Strategies for Complex Projects.
TRANSPORTATION RESEARCH BOARD.
revealed by the BP safety audit conducted in 2009. These
repairs were avoided as they were not causing any major
trouble to the project. Moreover, the standard tests that were
to be conducted on the cement work was a major deal and yet
avoided to save on project costs. The risk of the consequences
of the failure of the cement was not considered. The company
could not keep up with the pace of the project because of huge
complexities involved in decision making and technical
considerations. Thus, it can be said that the project did not
have proper risk management procedures in place.
Conclusions
The analysis of the learning from the project gave few insights
that can serve as lessons. The project decisions must be taken
not on the basis of personal opinions but on the real
observations and any set procedures that have a purpose to
solve should not be avoided just to take care of budget. While
budget does have a major impact on project decisions, the
other factors play an equally significant role.
References
Azim, S. W. (2010). Understanding and Managing Project Complexity . School of Mechanical,
Aerospace and Civil Engineering .
Ingersoll, C., Locke, R. M., & Reavis, C. (2012). BP and the Deepwater Horizon Disaster of 2010. MIT
Sloan.
Shane, J., Strong, K., & Gransberg, D. (2012). Guidebook: Project Management Strategies for
Complex Projects. National Academy of Sciences.
Sperling, D. (2015). Guide to Project Management Strategies for Complex Projects.
TRANSPORTATION RESEARCH BOARD.
1 out of 7
![[object Object]](/_next/image/?url=%2F_next%2Fstatic%2Fmedia%2Flogo.6d15ce61.png&w=640&q=75)
Your All-in-One AI-Powered Toolkit for Academic Success.
 +13062052269
info@desklib.com
Available 24*7 on WhatsApp / Email
Unlock your academic potential
© 2024  |  Zucol Services PVT LTD  |  All rights reserved.