Demolition Plan for Construction of Factory Units and Office Space in Banksia
VerifiedAdded on 2023/06/10
|17
|4021
|407
AI Summary
This article discusses the demolition plan for the construction of factory units and office space in Banksia, New South Wales. It covers the planning, preparation, demolition, and clean-up stages of the demolition process. The article also includes a sketch of the site, a preliminary site inspecti...
Read More
Contribute Materials
Your contribution can guide someone’s learning journey. Share your
documents today.
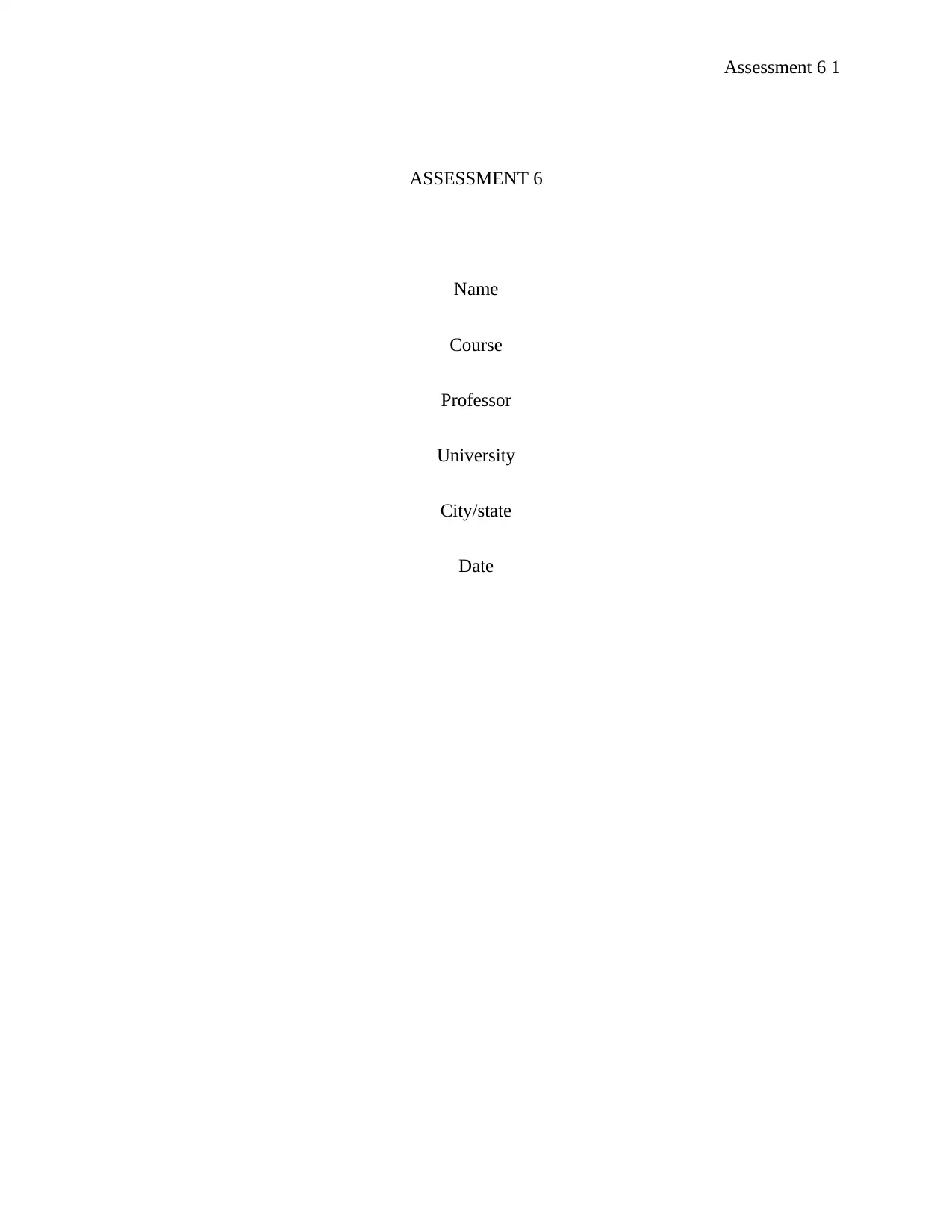
Assessment 6 1
ASSESSMENT 6
Name
Course
Professor
University
City/state
Date
ASSESSMENT 6
Name
Course
Professor
University
City/state
Date
Secure Best Marks with AI Grader
Need help grading? Try our AI Grader for instant feedback on your assignments.
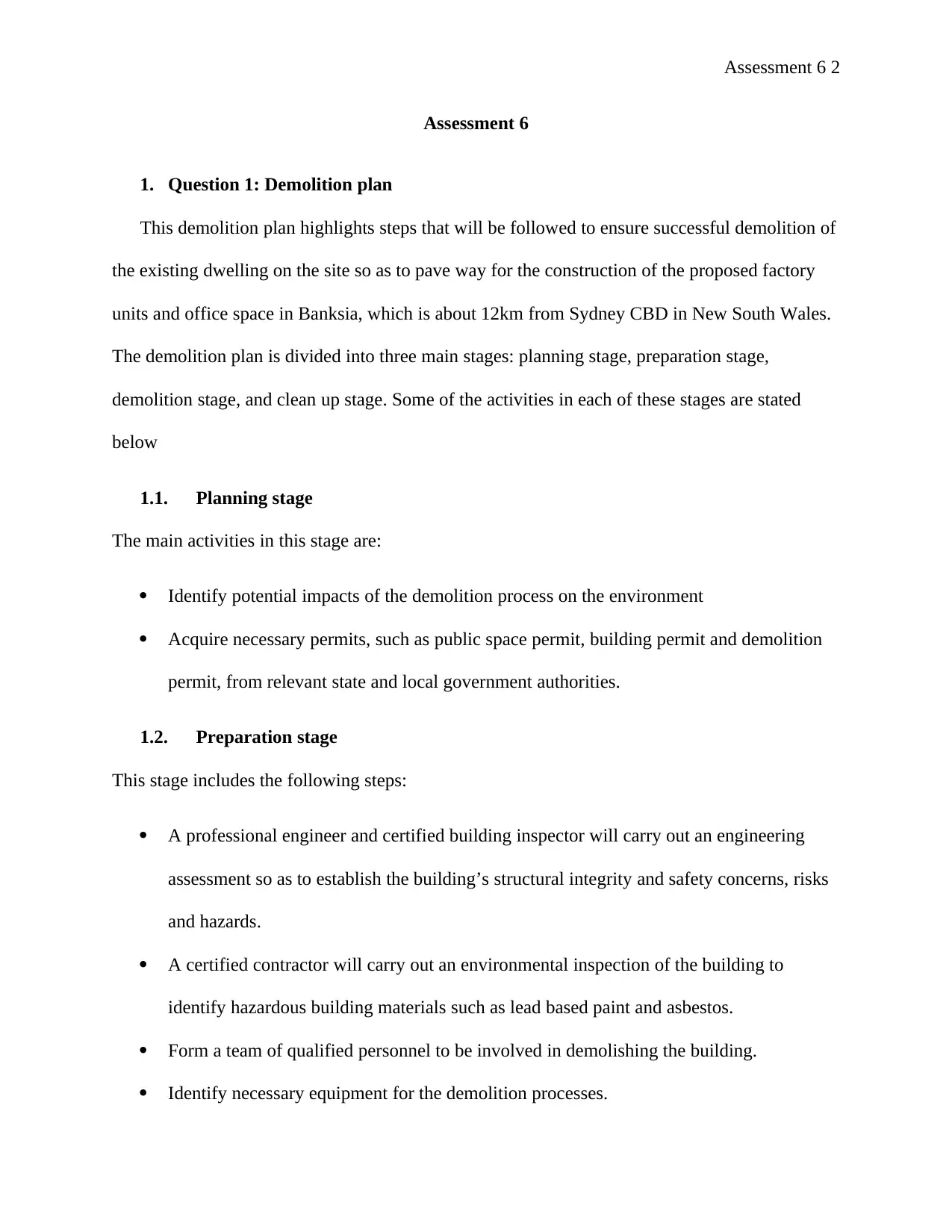
Assessment 6 2
Assessment 6
1. Question 1: Demolition plan
This demolition plan highlights steps that will be followed to ensure successful demolition of
the existing dwelling on the site so as to pave way for the construction of the proposed factory
units and office space in Banksia, which is about 12km from Sydney CBD in New South Wales.
The demolition plan is divided into three main stages: planning stage, preparation stage,
demolition stage, and clean up stage. Some of the activities in each of these stages are stated
below
1.1. Planning stage
The main activities in this stage are:
Identify potential impacts of the demolition process on the environment
Acquire necessary permits, such as public space permit, building permit and demolition
permit, from relevant state and local government authorities.
1.2. Preparation stage
This stage includes the following steps:
A professional engineer and certified building inspector will carry out an engineering
assessment so as to establish the building’s structural integrity and safety concerns, risks
and hazards.
A certified contractor will carry out an environmental inspection of the building to
identify hazardous building materials such as lead based paint and asbestos.
Form a team of qualified personnel to be involved in demolishing the building.
Identify necessary equipment for the demolition processes.
Assessment 6
1. Question 1: Demolition plan
This demolition plan highlights steps that will be followed to ensure successful demolition of
the existing dwelling on the site so as to pave way for the construction of the proposed factory
units and office space in Banksia, which is about 12km from Sydney CBD in New South Wales.
The demolition plan is divided into three main stages: planning stage, preparation stage,
demolition stage, and clean up stage. Some of the activities in each of these stages are stated
below
1.1. Planning stage
The main activities in this stage are:
Identify potential impacts of the demolition process on the environment
Acquire necessary permits, such as public space permit, building permit and demolition
permit, from relevant state and local government authorities.
1.2. Preparation stage
This stage includes the following steps:
A professional engineer and certified building inspector will carry out an engineering
assessment so as to establish the building’s structural integrity and safety concerns, risks
and hazards.
A certified contractor will carry out an environmental inspection of the building to
identify hazardous building materials such as lead based paint and asbestos.
Form a team of qualified personnel to be involved in demolishing the building.
Identify necessary equipment for the demolition processes.
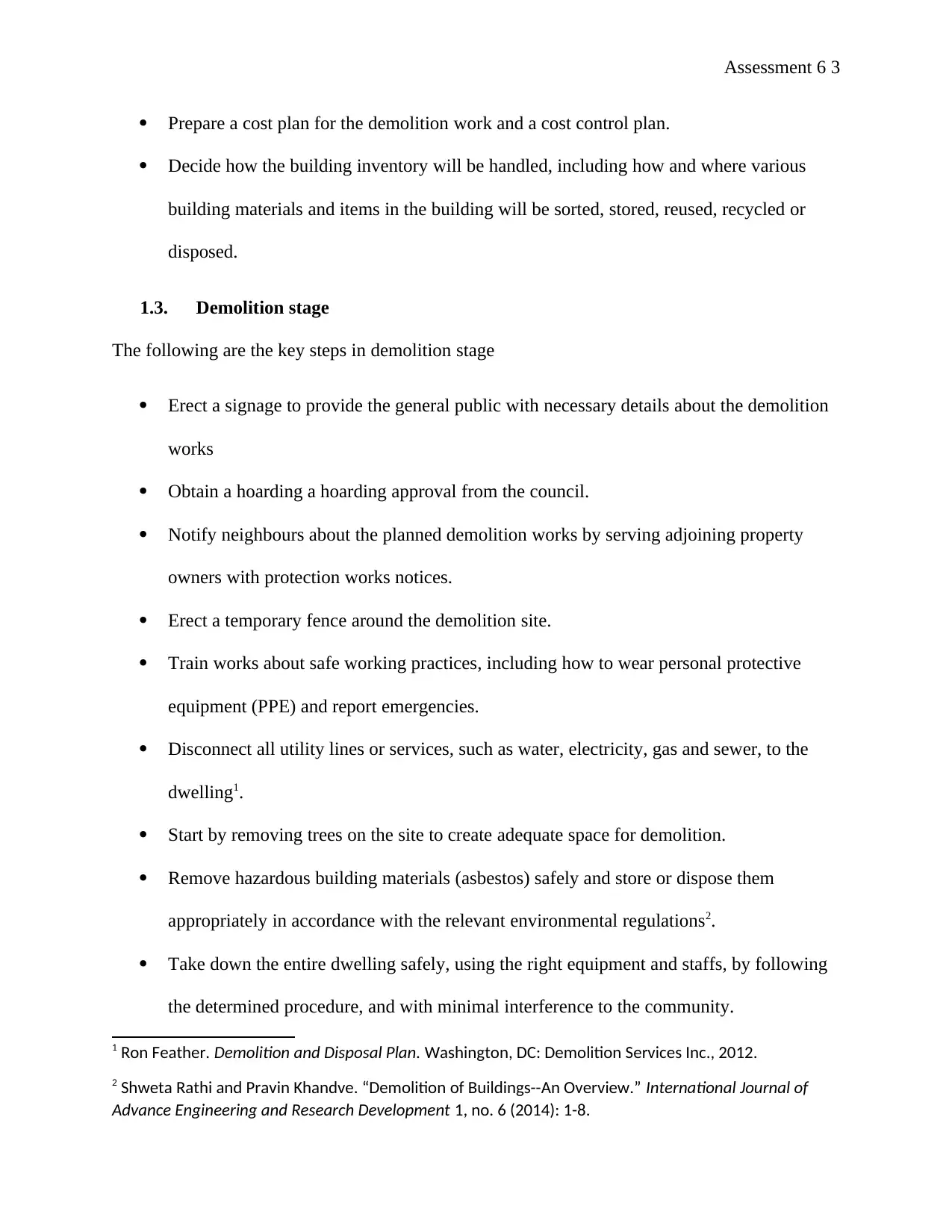
Assessment 6 3
Prepare a cost plan for the demolition work and a cost control plan.
Decide how the building inventory will be handled, including how and where various
building materials and items in the building will be sorted, stored, reused, recycled or
disposed.
1.3. Demolition stage
The following are the key steps in demolition stage
Erect a signage to provide the general public with necessary details about the demolition
works
Obtain a hoarding a hoarding approval from the council.
Notify neighbours about the planned demolition works by serving adjoining property
owners with protection works notices.
Erect a temporary fence around the demolition site.
Train works about safe working practices, including how to wear personal protective
equipment (PPE) and report emergencies.
Disconnect all utility lines or services, such as water, electricity, gas and sewer, to the
dwelling1.
Start by removing trees on the site to create adequate space for demolition.
Remove hazardous building materials (asbestos) safely and store or dispose them
appropriately in accordance with the relevant environmental regulations2.
Take down the entire dwelling safely, using the right equipment and staffs, by following
the determined procedure, and with minimal interference to the community.
1 Ron Feather. Demolition and Disposal Plan. Washington, DC: Demolition Services Inc., 2012.
2 Shweta Rathi and Pravin Khandve. “Demolition of Buildings--An Overview.” International Journal of
Advance Engineering and Research Development 1, no. 6 (2014): 1-8.
Prepare a cost plan for the demolition work and a cost control plan.
Decide how the building inventory will be handled, including how and where various
building materials and items in the building will be sorted, stored, reused, recycled or
disposed.
1.3. Demolition stage
The following are the key steps in demolition stage
Erect a signage to provide the general public with necessary details about the demolition
works
Obtain a hoarding a hoarding approval from the council.
Notify neighbours about the planned demolition works by serving adjoining property
owners with protection works notices.
Erect a temporary fence around the demolition site.
Train works about safe working practices, including how to wear personal protective
equipment (PPE) and report emergencies.
Disconnect all utility lines or services, such as water, electricity, gas and sewer, to the
dwelling1.
Start by removing trees on the site to create adequate space for demolition.
Remove hazardous building materials (asbestos) safely and store or dispose them
appropriately in accordance with the relevant environmental regulations2.
Take down the entire dwelling safely, using the right equipment and staffs, by following
the determined procedure, and with minimal interference to the community.
1 Ron Feather. Demolition and Disposal Plan. Washington, DC: Demolition Services Inc., 2012.
2 Shweta Rathi and Pravin Khandve. “Demolition of Buildings--An Overview.” International Journal of
Advance Engineering and Research Development 1, no. 6 (2014): 1-8.
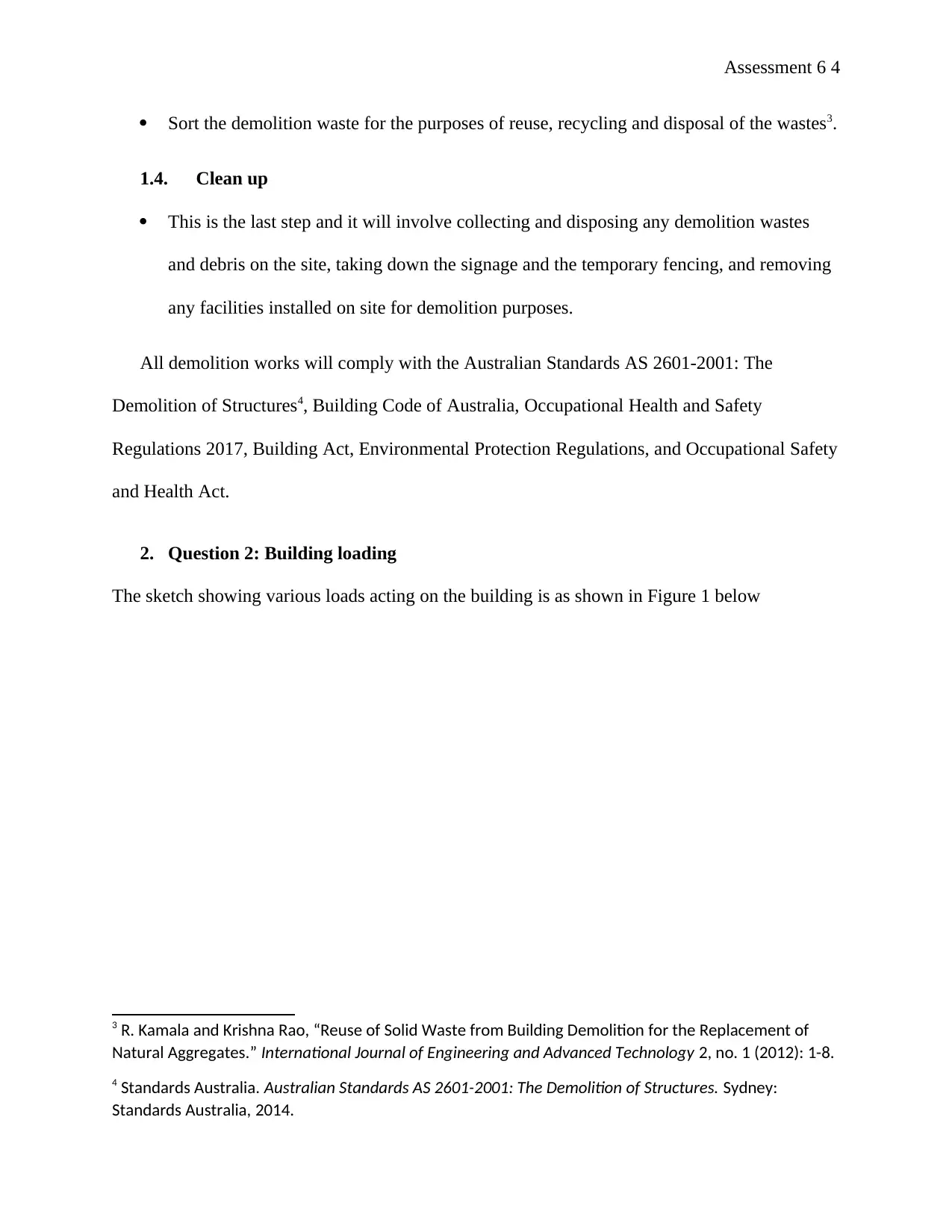
Assessment 6 4
Sort the demolition waste for the purposes of reuse, recycling and disposal of the wastes3.
1.4. Clean up
This is the last step and it will involve collecting and disposing any demolition wastes
and debris on the site, taking down the signage and the temporary fencing, and removing
any facilities installed on site for demolition purposes.
All demolition works will comply with the Australian Standards AS 2601-2001: The
Demolition of Structures4, Building Code of Australia, Occupational Health and Safety
Regulations 2017, Building Act, Environmental Protection Regulations, and Occupational Safety
and Health Act.
2. Question 2: Building loading
The sketch showing various loads acting on the building is as shown in Figure 1 below
3 R. Kamala and Krishna Rao, “Reuse of Solid Waste from Building Demolition for the Replacement of
Natural Aggregates.” International Journal of Engineering and Advanced Technology 2, no. 1 (2012): 1-8.
4 Standards Australia. Australian Standards AS 2601-2001: The Demolition of Structures. Sydney:
Standards Australia, 2014.
Sort the demolition waste for the purposes of reuse, recycling and disposal of the wastes3.
1.4. Clean up
This is the last step and it will involve collecting and disposing any demolition wastes
and debris on the site, taking down the signage and the temporary fencing, and removing
any facilities installed on site for demolition purposes.
All demolition works will comply with the Australian Standards AS 2601-2001: The
Demolition of Structures4, Building Code of Australia, Occupational Health and Safety
Regulations 2017, Building Act, Environmental Protection Regulations, and Occupational Safety
and Health Act.
2. Question 2: Building loading
The sketch showing various loads acting on the building is as shown in Figure 1 below
3 R. Kamala and Krishna Rao, “Reuse of Solid Waste from Building Demolition for the Replacement of
Natural Aggregates.” International Journal of Engineering and Advanced Technology 2, no. 1 (2012): 1-8.
4 Standards Australia. Australian Standards AS 2601-2001: The Demolition of Structures. Sydney:
Standards Australia, 2014.
Secure Best Marks with AI Grader
Need help grading? Try our AI Grader for instant feedback on your assignments.
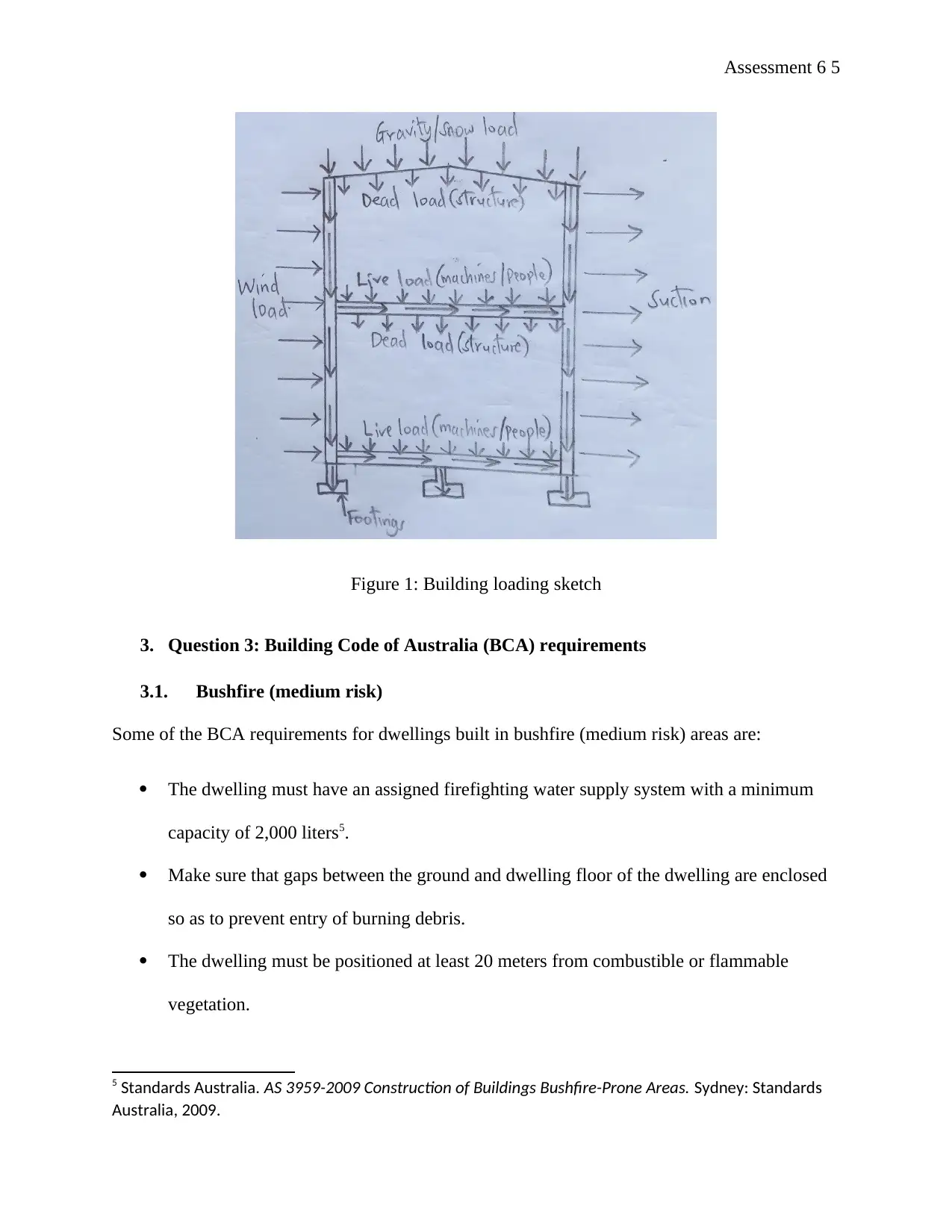
Assessment 6 5
Figure 1: Building loading sketch
3. Question 3: Building Code of Australia (BCA) requirements
3.1. Bushfire (medium risk)
Some of the BCA requirements for dwellings built in bushfire (medium risk) areas are:
The dwelling must have an assigned firefighting water supply system with a minimum
capacity of 2,000 liters5.
Make sure that gaps between the ground and dwelling floor of the dwelling are enclosed
so as to prevent entry of burning debris.
The dwelling must be positioned at least 20 meters from combustible or flammable
vegetation.
5 Standards Australia. AS 3959-2009 Construction of Buildings Bushfire-Prone Areas. Sydney: Standards
Australia, 2009.
Figure 1: Building loading sketch
3. Question 3: Building Code of Australia (BCA) requirements
3.1. Bushfire (medium risk)
Some of the BCA requirements for dwellings built in bushfire (medium risk) areas are:
The dwelling must have an assigned firefighting water supply system with a minimum
capacity of 2,000 liters5.
Make sure that gaps between the ground and dwelling floor of the dwelling are enclosed
so as to prevent entry of burning debris.
The dwelling must be positioned at least 20 meters from combustible or flammable
vegetation.
5 Standards Australia. AS 3959-2009 Construction of Buildings Bushfire-Prone Areas. Sydney: Standards
Australia, 2009.
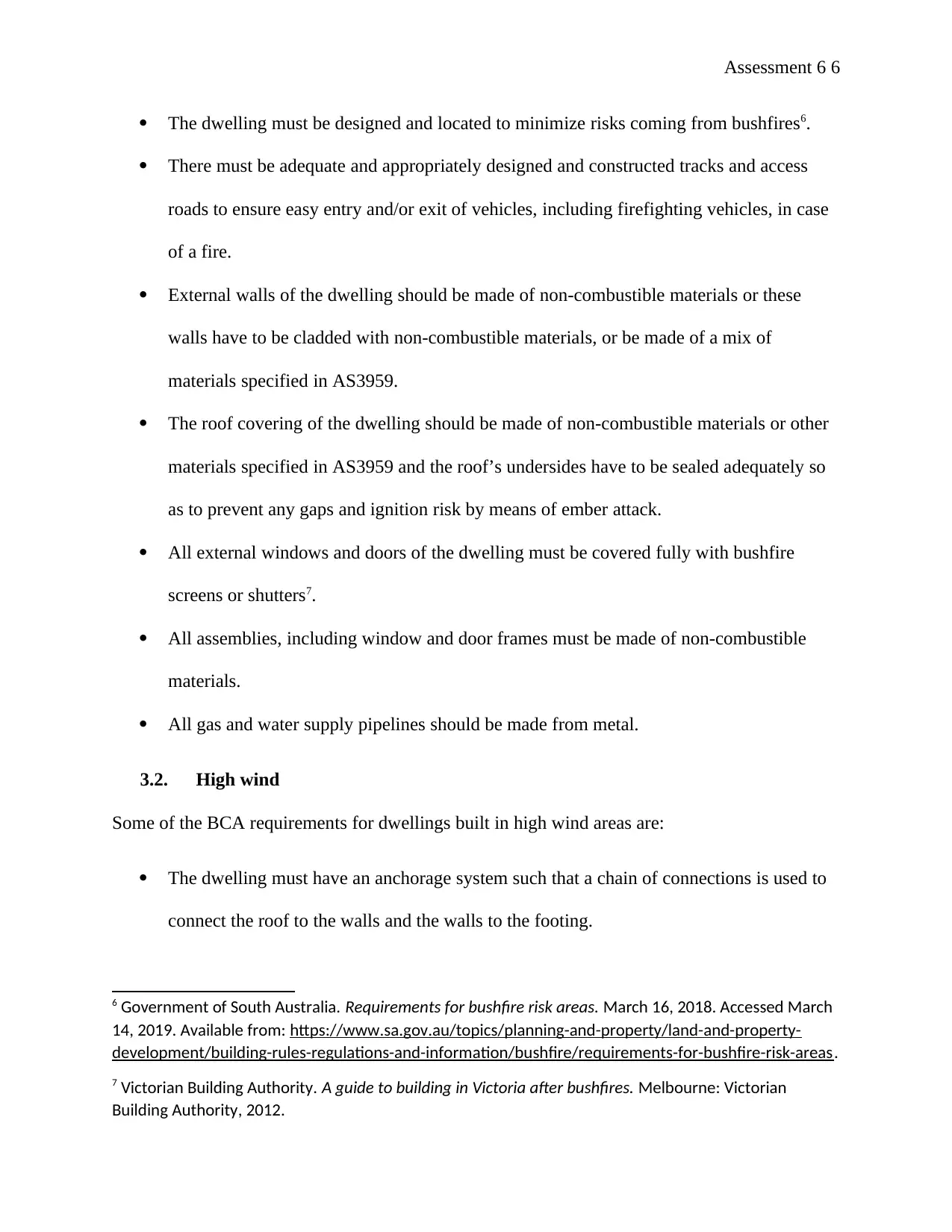
Assessment 6 6
The dwelling must be designed and located to minimize risks coming from bushfires6.
There must be adequate and appropriately designed and constructed tracks and access
roads to ensure easy entry and/or exit of vehicles, including firefighting vehicles, in case
of a fire.
External walls of the dwelling should be made of non-combustible materials or these
walls have to be cladded with non-combustible materials, or be made of a mix of
materials specified in AS3959.
The roof covering of the dwelling should be made of non-combustible materials or other
materials specified in AS3959 and the roof’s undersides have to be sealed adequately so
as to prevent any gaps and ignition risk by means of ember attack.
All external windows and doors of the dwelling must be covered fully with bushfire
screens or shutters7.
All assemblies, including window and door frames must be made of non-combustible
materials.
All gas and water supply pipelines should be made from metal.
3.2. High wind
Some of the BCA requirements for dwellings built in high wind areas are:
The dwelling must have an anchorage system such that a chain of connections is used to
connect the roof to the walls and the walls to the footing.
6 Government of South Australia. Requirements for bushfire risk areas. March 16, 2018. Accessed March
14, 2019. Available from: https://www.sa.gov.au/topics/planning-and-property/land-and-property-
development/building-rules-regulations-and-information/bushfire/requirements-for-bushfire-risk-areas.
7 Victorian Building Authority. A guide to building in Victoria after bushfires. Melbourne: Victorian
Building Authority, 2012.
The dwelling must be designed and located to minimize risks coming from bushfires6.
There must be adequate and appropriately designed and constructed tracks and access
roads to ensure easy entry and/or exit of vehicles, including firefighting vehicles, in case
of a fire.
External walls of the dwelling should be made of non-combustible materials or these
walls have to be cladded with non-combustible materials, or be made of a mix of
materials specified in AS3959.
The roof covering of the dwelling should be made of non-combustible materials or other
materials specified in AS3959 and the roof’s undersides have to be sealed adequately so
as to prevent any gaps and ignition risk by means of ember attack.
All external windows and doors of the dwelling must be covered fully with bushfire
screens or shutters7.
All assemblies, including window and door frames must be made of non-combustible
materials.
All gas and water supply pipelines should be made from metal.
3.2. High wind
Some of the BCA requirements for dwellings built in high wind areas are:
The dwelling must have an anchorage system such that a chain of connections is used to
connect the roof to the walls and the walls to the footing.
6 Government of South Australia. Requirements for bushfire risk areas. March 16, 2018. Accessed March
14, 2019. Available from: https://www.sa.gov.au/topics/planning-and-property/land-and-property-
development/building-rules-regulations-and-information/bushfire/requirements-for-bushfire-risk-areas.
7 Victorian Building Authority. A guide to building in Victoria after bushfires. Melbourne: Victorian
Building Authority, 2012.
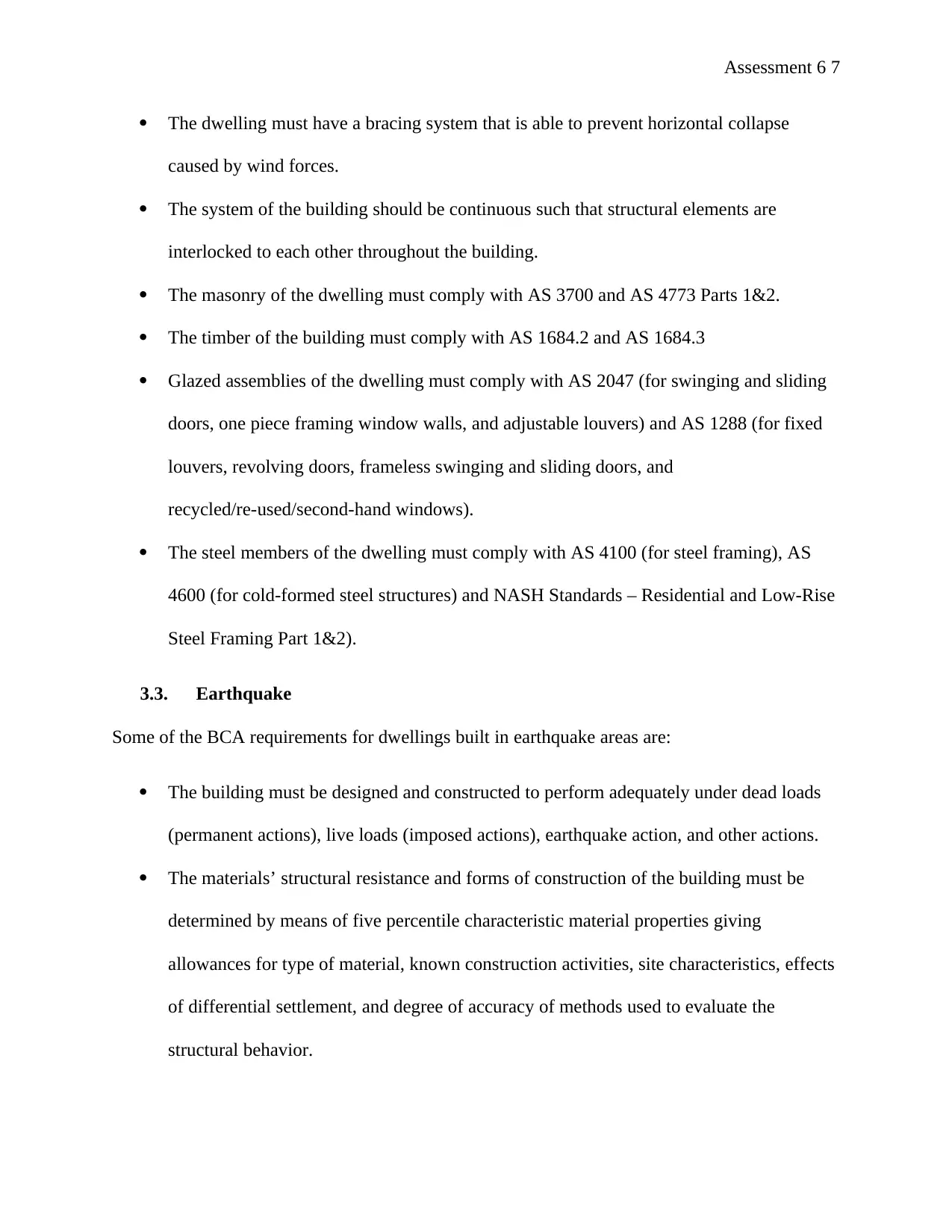
Assessment 6 7
The dwelling must have a bracing system that is able to prevent horizontal collapse
caused by wind forces.
The system of the building should be continuous such that structural elements are
interlocked to each other throughout the building.
The masonry of the dwelling must comply with AS 3700 and AS 4773 Parts 1&2.
The timber of the building must comply with AS 1684.2 and AS 1684.3
Glazed assemblies of the dwelling must comply with AS 2047 (for swinging and sliding
doors, one piece framing window walls, and adjustable louvers) and AS 1288 (for fixed
louvers, revolving doors, frameless swinging and sliding doors, and
recycled/re-used/second-hand windows).
The steel members of the dwelling must comply with AS 4100 (for steel framing), AS
4600 (for cold-formed steel structures) and NASH Standards – Residential and Low-Rise
Steel Framing Part 1&2).
3.3. Earthquake
Some of the BCA requirements for dwellings built in earthquake areas are:
The building must be designed and constructed to perform adequately under dead loads
(permanent actions), live loads (imposed actions), earthquake action, and other actions.
The materials’ structural resistance and forms of construction of the building must be
determined by means of five percentile characteristic material properties giving
allowances for type of material, known construction activities, site characteristics, effects
of differential settlement, and degree of accuracy of methods used to evaluate the
structural behavior.
The dwelling must have a bracing system that is able to prevent horizontal collapse
caused by wind forces.
The system of the building should be continuous such that structural elements are
interlocked to each other throughout the building.
The masonry of the dwelling must comply with AS 3700 and AS 4773 Parts 1&2.
The timber of the building must comply with AS 1684.2 and AS 1684.3
Glazed assemblies of the dwelling must comply with AS 2047 (for swinging and sliding
doors, one piece framing window walls, and adjustable louvers) and AS 1288 (for fixed
louvers, revolving doors, frameless swinging and sliding doors, and
recycled/re-used/second-hand windows).
The steel members of the dwelling must comply with AS 4100 (for steel framing), AS
4600 (for cold-formed steel structures) and NASH Standards – Residential and Low-Rise
Steel Framing Part 1&2).
3.3. Earthquake
Some of the BCA requirements for dwellings built in earthquake areas are:
The building must be designed and constructed to perform adequately under dead loads
(permanent actions), live loads (imposed actions), earthquake action, and other actions.
The materials’ structural resistance and forms of construction of the building must be
determined by means of five percentile characteristic material properties giving
allowances for type of material, known construction activities, site characteristics, effects
of differential settlement, and degree of accuracy of methods used to evaluate the
structural behavior.
Paraphrase This Document
Need a fresh take? Get an instant paraphrase of this document with our AI Paraphraser
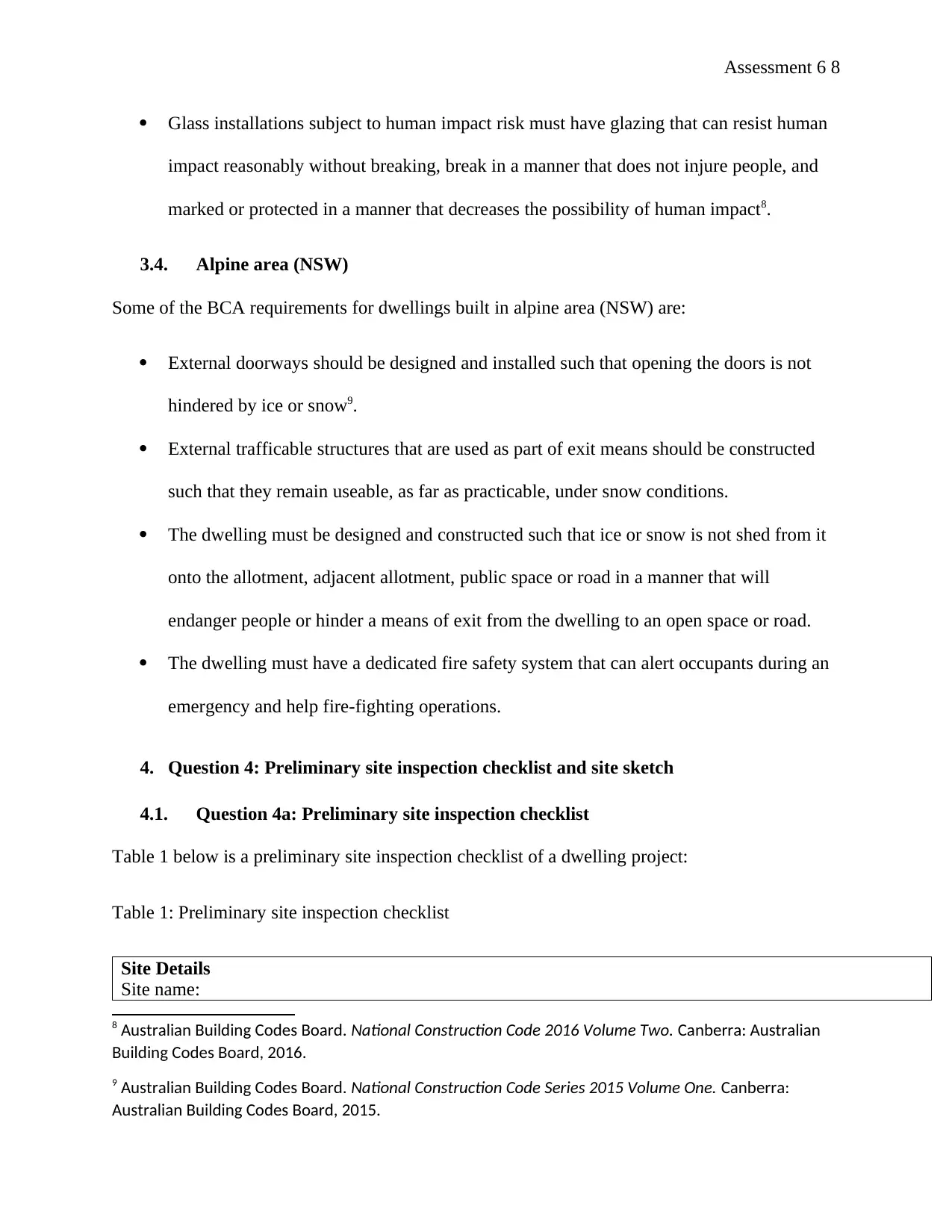
Assessment 6 8
Glass installations subject to human impact risk must have glazing that can resist human
impact reasonably without breaking, break in a manner that does not injure people, and
marked or protected in a manner that decreases the possibility of human impact8.
3.4. Alpine area (NSW)
Some of the BCA requirements for dwellings built in alpine area (NSW) are:
External doorways should be designed and installed such that opening the doors is not
hindered by ice or snow9.
External trafficable structures that are used as part of exit means should be constructed
such that they remain useable, as far as practicable, under snow conditions.
The dwelling must be designed and constructed such that ice or snow is not shed from it
onto the allotment, adjacent allotment, public space or road in a manner that will
endanger people or hinder a means of exit from the dwelling to an open space or road.
The dwelling must have a dedicated fire safety system that can alert occupants during an
emergency and help fire-fighting operations.
4. Question 4: Preliminary site inspection checklist and site sketch
4.1. Question 4a: Preliminary site inspection checklist
Table 1 below is a preliminary site inspection checklist of a dwelling project:
Table 1: Preliminary site inspection checklist
Site Details
Site name:
8 Australian Building Codes Board. National Construction Code 2016 Volume Two. Canberra: Australian
Building Codes Board, 2016.
9 Australian Building Codes Board. National Construction Code Series 2015 Volume One. Canberra:
Australian Building Codes Board, 2015.
Glass installations subject to human impact risk must have glazing that can resist human
impact reasonably without breaking, break in a manner that does not injure people, and
marked or protected in a manner that decreases the possibility of human impact8.
3.4. Alpine area (NSW)
Some of the BCA requirements for dwellings built in alpine area (NSW) are:
External doorways should be designed and installed such that opening the doors is not
hindered by ice or snow9.
External trafficable structures that are used as part of exit means should be constructed
such that they remain useable, as far as practicable, under snow conditions.
The dwelling must be designed and constructed such that ice or snow is not shed from it
onto the allotment, adjacent allotment, public space or road in a manner that will
endanger people or hinder a means of exit from the dwelling to an open space or road.
The dwelling must have a dedicated fire safety system that can alert occupants during an
emergency and help fire-fighting operations.
4. Question 4: Preliminary site inspection checklist and site sketch
4.1. Question 4a: Preliminary site inspection checklist
Table 1 below is a preliminary site inspection checklist of a dwelling project:
Table 1: Preliminary site inspection checklist
Site Details
Site name:
8 Australian Building Codes Board. National Construction Code 2016 Volume Two. Canberra: Australian
Building Codes Board, 2016.
9 Australian Building Codes Board. National Construction Code Series 2015 Volume One. Canberra:
Australian Building Codes Board, 2015.
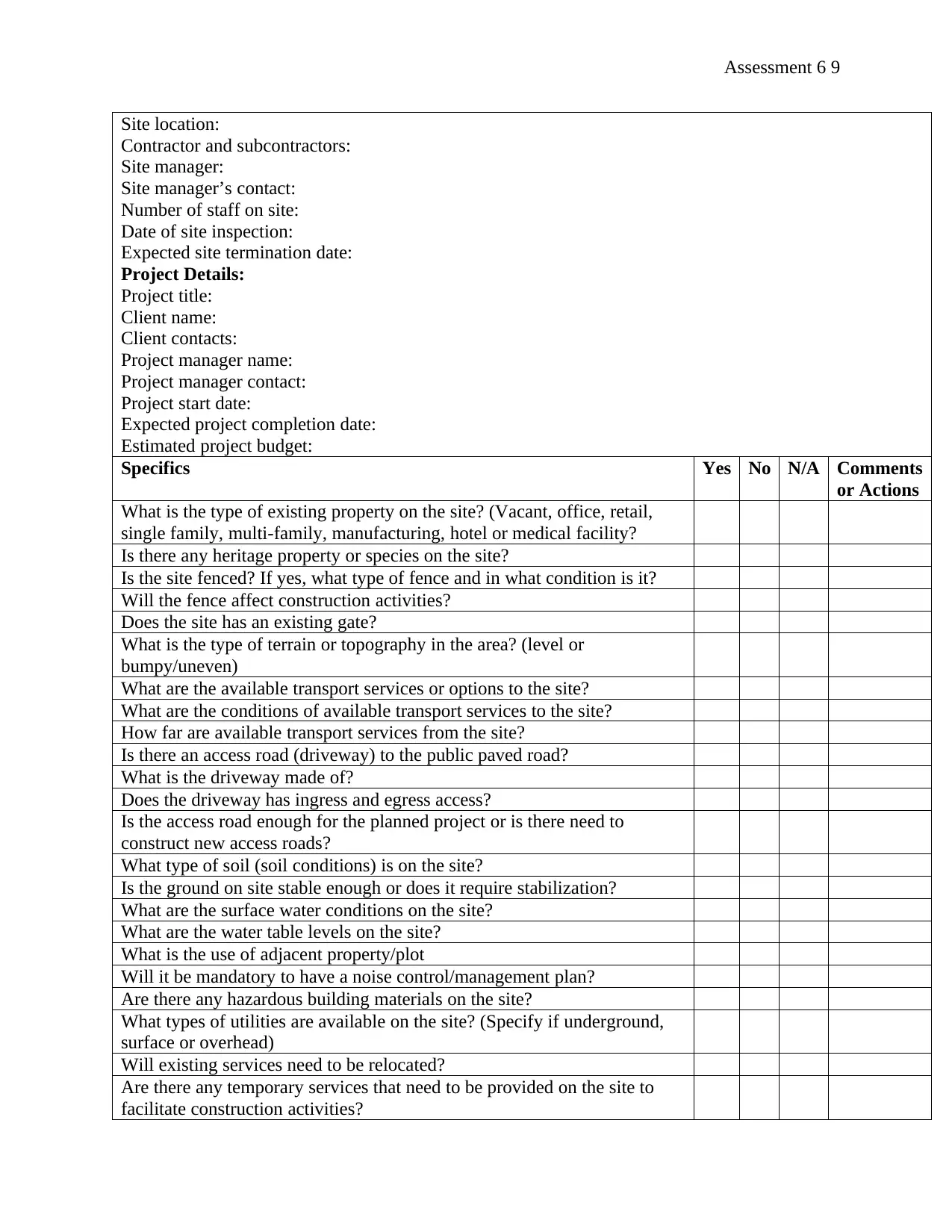
Assessment 6 9
Site location:
Contractor and subcontractors:
Site manager:
Site manager’s contact:
Number of staff on site:
Date of site inspection:
Expected site termination date:
Project Details:
Project title:
Client name:
Client contacts:
Project manager name:
Project manager contact:
Project start date:
Expected project completion date:
Estimated project budget:
Specifics Yes No N/A Comments
or Actions
What is the type of existing property on the site? (Vacant, office, retail,
single family, multi-family, manufacturing, hotel or medical facility?
Is there any heritage property or species on the site?
Is the site fenced? If yes, what type of fence and in what condition is it?
Will the fence affect construction activities?
Does the site has an existing gate?
What is the type of terrain or topography in the area? (level or
bumpy/uneven)
What are the available transport services or options to the site?
What are the conditions of available transport services to the site?
How far are available transport services from the site?
Is there an access road (driveway) to the public paved road?
What is the driveway made of?
Does the driveway has ingress and egress access?
Is the access road enough for the planned project or is there need to
construct new access roads?
What type of soil (soil conditions) is on the site?
Is the ground on site stable enough or does it require stabilization?
What are the surface water conditions on the site?
What are the water table levels on the site?
What is the use of adjacent property/plot
Will it be mandatory to have a noise control/management plan?
Are there any hazardous building materials on the site?
What types of utilities are available on the site? (Specify if underground,
surface or overhead)
Will existing services need to be relocated?
Are there any temporary services that need to be provided on the site to
facilitate construction activities?
Site location:
Contractor and subcontractors:
Site manager:
Site manager’s contact:
Number of staff on site:
Date of site inspection:
Expected site termination date:
Project Details:
Project title:
Client name:
Client contacts:
Project manager name:
Project manager contact:
Project start date:
Expected project completion date:
Estimated project budget:
Specifics Yes No N/A Comments
or Actions
What is the type of existing property on the site? (Vacant, office, retail,
single family, multi-family, manufacturing, hotel or medical facility?
Is there any heritage property or species on the site?
Is the site fenced? If yes, what type of fence and in what condition is it?
Will the fence affect construction activities?
Does the site has an existing gate?
What is the type of terrain or topography in the area? (level or
bumpy/uneven)
What are the available transport services or options to the site?
What are the conditions of available transport services to the site?
How far are available transport services from the site?
Is there an access road (driveway) to the public paved road?
What is the driveway made of?
Does the driveway has ingress and egress access?
Is the access road enough for the planned project or is there need to
construct new access roads?
What type of soil (soil conditions) is on the site?
Is the ground on site stable enough or does it require stabilization?
What are the surface water conditions on the site?
What are the water table levels on the site?
What is the use of adjacent property/plot
Will it be mandatory to have a noise control/management plan?
Are there any hazardous building materials on the site?
What types of utilities are available on the site? (Specify if underground,
surface or overhead)
Will existing services need to be relocated?
Are there any temporary services that need to be provided on the site to
facilitate construction activities?
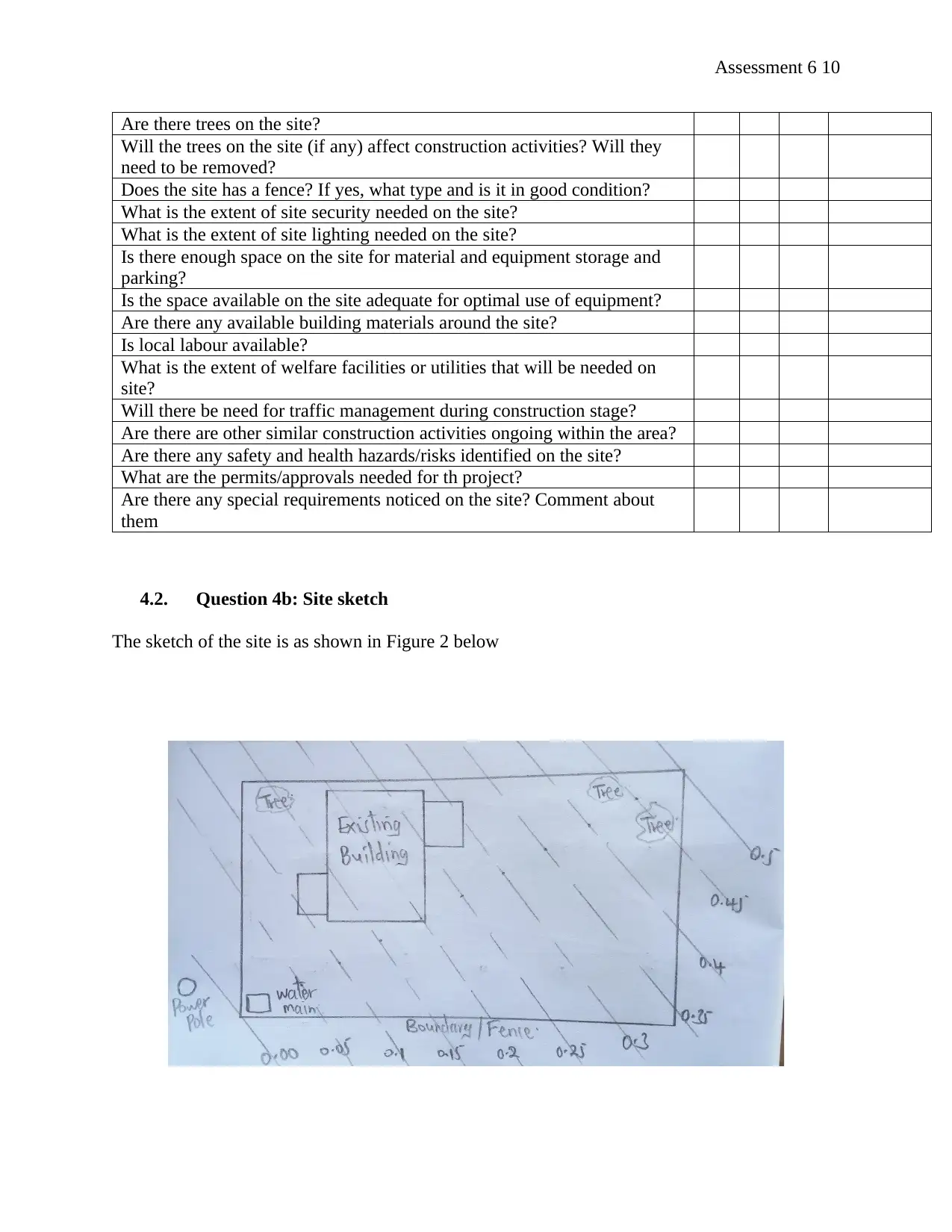
Assessment 6 10
Are there trees on the site?
Will the trees on the site (if any) affect construction activities? Will they
need to be removed?
Does the site has a fence? If yes, what type and is it in good condition?
What is the extent of site security needed on the site?
What is the extent of site lighting needed on the site?
Is there enough space on the site for material and equipment storage and
parking?
Is the space available on the site adequate for optimal use of equipment?
Are there any available building materials around the site?
Is local labour available?
What is the extent of welfare facilities or utilities that will be needed on
site?
Will there be need for traffic management during construction stage?
Are there are other similar construction activities ongoing within the area?
Are there any safety and health hazards/risks identified on the site?
What are the permits/approvals needed for th project?
Are there any special requirements noticed on the site? Comment about
them
4.2. Question 4b: Site sketch
The sketch of the site is as shown in Figure 2 below
Are there trees on the site?
Will the trees on the site (if any) affect construction activities? Will they
need to be removed?
Does the site has a fence? If yes, what type and is it in good condition?
What is the extent of site security needed on the site?
What is the extent of site lighting needed on the site?
Is there enough space on the site for material and equipment storage and
parking?
Is the space available on the site adequate for optimal use of equipment?
Are there any available building materials around the site?
Is local labour available?
What is the extent of welfare facilities or utilities that will be needed on
site?
Will there be need for traffic management during construction stage?
Are there are other similar construction activities ongoing within the area?
Are there any safety and health hazards/risks identified on the site?
What are the permits/approvals needed for th project?
Are there any special requirements noticed on the site? Comment about
them
4.2. Question 4b: Site sketch
The sketch of the site is as shown in Figure 2 below
Secure Best Marks with AI Grader
Need help grading? Try our AI Grader for instant feedback on your assignments.
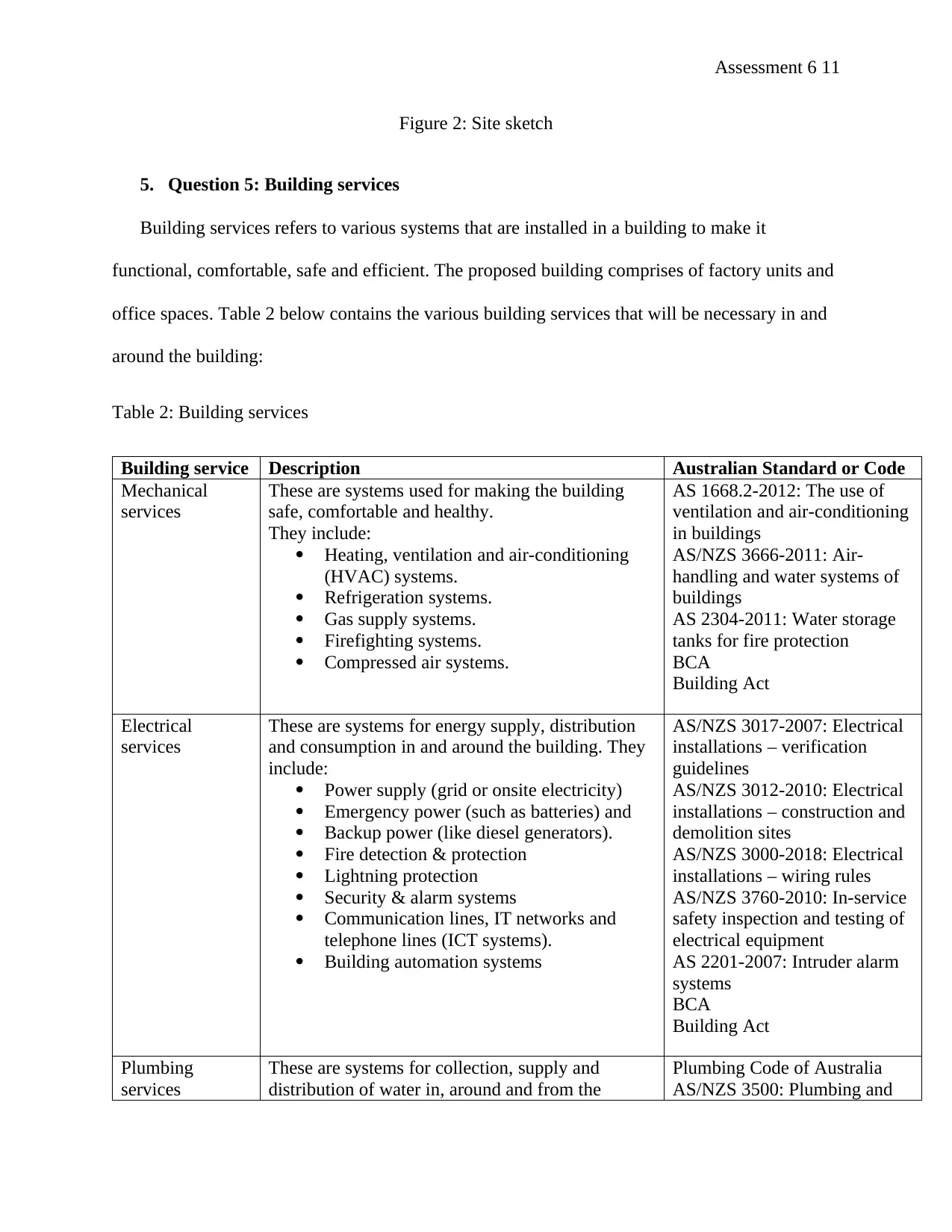
Assessment 6 11
Figure 2: Site sketch
5. Question 5: Building services
Building services refers to various systems that are installed in a building to make it
functional, comfortable, safe and efficient. The proposed building comprises of factory units and
office spaces. Table 2 below contains the various building services that will be necessary in and
around the building:
Table 2: Building services
Building service Description Australian Standard or Code
Mechanical
services
These are systems used for making the building
safe, comfortable and healthy.
They include:
Heating, ventilation and air-conditioning
(HVAC) systems.
Refrigeration systems.
Gas supply systems.
Firefighting systems.
Compressed air systems.
AS 1668.2-2012: The use of
ventilation and air-conditioning
in buildings
AS/NZS 3666-2011: Air-
handling and water systems of
buildings
AS 2304-2011: Water storage
tanks for fire protection
BCA
Building Act
Electrical
services
These are systems for energy supply, distribution
and consumption in and around the building. They
include:
Power supply (grid or onsite electricity)
Emergency power (such as batteries) and
Backup power (like diesel generators).
Fire detection & protection
Lightning protection
Security & alarm systems
Communication lines, IT networks and
telephone lines (ICT systems).
Building automation systems
AS/NZS 3017-2007: Electrical
installations – verification
guidelines
AS/NZS 3012-2010: Electrical
installations – construction and
demolition sites
AS/NZS 3000-2018: Electrical
installations – wiring rules
AS/NZS 3760-2010: In-service
safety inspection and testing of
electrical equipment
AS 2201-2007: Intruder alarm
systems
BCA
Building Act
Plumbing
services
These are systems for collection, supply and
distribution of water in, around and from the
Plumbing Code of Australia
AS/NZS 3500: Plumbing and
Figure 2: Site sketch
5. Question 5: Building services
Building services refers to various systems that are installed in a building to make it
functional, comfortable, safe and efficient. The proposed building comprises of factory units and
office spaces. Table 2 below contains the various building services that will be necessary in and
around the building:
Table 2: Building services
Building service Description Australian Standard or Code
Mechanical
services
These are systems used for making the building
safe, comfortable and healthy.
They include:
Heating, ventilation and air-conditioning
(HVAC) systems.
Refrigeration systems.
Gas supply systems.
Firefighting systems.
Compressed air systems.
AS 1668.2-2012: The use of
ventilation and air-conditioning
in buildings
AS/NZS 3666-2011: Air-
handling and water systems of
buildings
AS 2304-2011: Water storage
tanks for fire protection
BCA
Building Act
Electrical
services
These are systems for energy supply, distribution
and consumption in and around the building. They
include:
Power supply (grid or onsite electricity)
Emergency power (such as batteries) and
Backup power (like diesel generators).
Fire detection & protection
Lightning protection
Security & alarm systems
Communication lines, IT networks and
telephone lines (ICT systems).
Building automation systems
AS/NZS 3017-2007: Electrical
installations – verification
guidelines
AS/NZS 3012-2010: Electrical
installations – construction and
demolition sites
AS/NZS 3000-2018: Electrical
installations – wiring rules
AS/NZS 3760-2010: In-service
safety inspection and testing of
electrical equipment
AS 2201-2007: Intruder alarm
systems
BCA
Building Act
Plumbing
services
These are systems for collection, supply and
distribution of water in, around and from the
Plumbing Code of Australia
AS/NZS 3500: Plumbing and
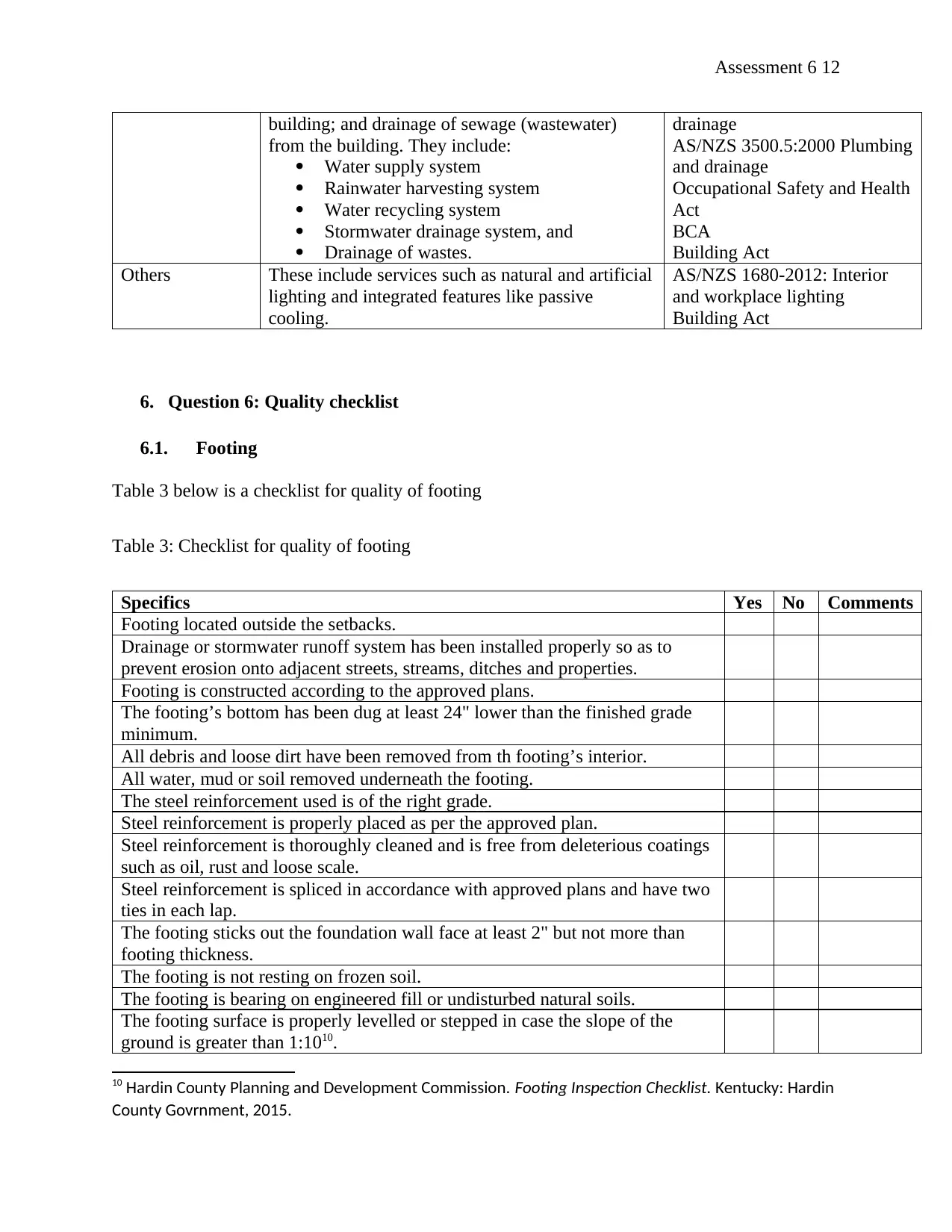
Assessment 6 12
building; and drainage of sewage (wastewater)
from the building. They include:
Water supply system
Rainwater harvesting system
Water recycling system
Stormwater drainage system, and
Drainage of wastes.
drainage
AS/NZS 3500.5:2000 Plumbing
and drainage
Occupational Safety and Health
Act
BCA
Building Act
Others These include services such as natural and artificial
lighting and integrated features like passive
cooling.
AS/NZS 1680-2012: Interior
and workplace lighting
Building Act
6. Question 6: Quality checklist
6.1. Footing
Table 3 below is a checklist for quality of footing
Table 3: Checklist for quality of footing
Specifics Yes No Comments
Footing located outside the setbacks.
Drainage or stormwater runoff system has been installed properly so as to
prevent erosion onto adjacent streets, streams, ditches and properties.
Footing is constructed according to the approved plans.
The footing’s bottom has been dug at least 24" lower than the finished grade
minimum.
All debris and loose dirt have been removed from th footing’s interior.
All water, mud or soil removed underneath the footing.
The steel reinforcement used is of the right grade.
Steel reinforcement is properly placed as per the approved plan.
Steel reinforcement is thoroughly cleaned and is free from deleterious coatings
such as oil, rust and loose scale.
Steel reinforcement is spliced in accordance with approved plans and have two
ties in each lap.
The footing sticks out the foundation wall face at least 2" but not more than
footing thickness.
The footing is not resting on frozen soil.
The footing is bearing on engineered fill or undisturbed natural soils.
The footing surface is properly levelled or stepped in case the slope of the
ground is greater than 1:1010.
10 Hardin County Planning and Development Commission. Footing Inspection Checklist. Kentucky: Hardin
County Govrnment, 2015.
building; and drainage of sewage (wastewater)
from the building. They include:
Water supply system
Rainwater harvesting system
Water recycling system
Stormwater drainage system, and
Drainage of wastes.
drainage
AS/NZS 3500.5:2000 Plumbing
and drainage
Occupational Safety and Health
Act
BCA
Building Act
Others These include services such as natural and artificial
lighting and integrated features like passive
cooling.
AS/NZS 1680-2012: Interior
and workplace lighting
Building Act
6. Question 6: Quality checklist
6.1. Footing
Table 3 below is a checklist for quality of footing
Table 3: Checklist for quality of footing
Specifics Yes No Comments
Footing located outside the setbacks.
Drainage or stormwater runoff system has been installed properly so as to
prevent erosion onto adjacent streets, streams, ditches and properties.
Footing is constructed according to the approved plans.
The footing’s bottom has been dug at least 24" lower than the finished grade
minimum.
All debris and loose dirt have been removed from th footing’s interior.
All water, mud or soil removed underneath the footing.
The steel reinforcement used is of the right grade.
Steel reinforcement is properly placed as per the approved plan.
Steel reinforcement is thoroughly cleaned and is free from deleterious coatings
such as oil, rust and loose scale.
Steel reinforcement is spliced in accordance with approved plans and have two
ties in each lap.
The footing sticks out the foundation wall face at least 2" but not more than
footing thickness.
The footing is not resting on frozen soil.
The footing is bearing on engineered fill or undisturbed natural soils.
The footing surface is properly levelled or stepped in case the slope of the
ground is greater than 1:1010.
10 Hardin County Planning and Development Commission. Footing Inspection Checklist. Kentucky: Hardin
County Govrnment, 2015.
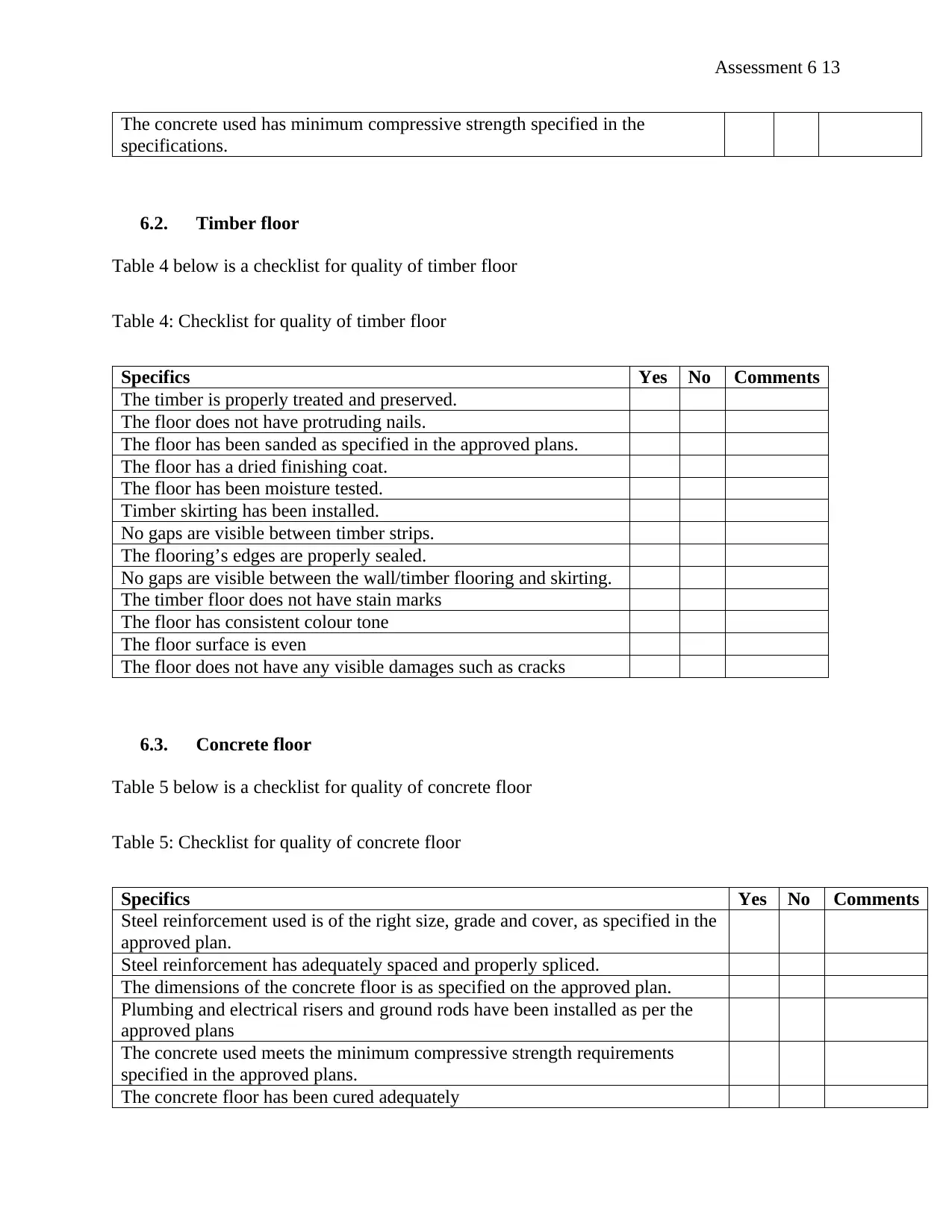
Assessment 6 13
The concrete used has minimum compressive strength specified in the
specifications.
6.2. Timber floor
Table 4 below is a checklist for quality of timber floor
Table 4: Checklist for quality of timber floor
Specifics Yes No Comments
The timber is properly treated and preserved.
The floor does not have protruding nails.
The floor has been sanded as specified in the approved plans.
The floor has a dried finishing coat.
The floor has been moisture tested.
Timber skirting has been installed.
No gaps are visible between timber strips.
The flooring’s edges are properly sealed.
No gaps are visible between the wall/timber flooring and skirting.
The timber floor does not have stain marks
The floor has consistent colour tone
The floor surface is even
The floor does not have any visible damages such as cracks
6.3. Concrete floor
Table 5 below is a checklist for quality of concrete floor
Table 5: Checklist for quality of concrete floor
Specifics Yes No Comments
Steel reinforcement used is of the right size, grade and cover, as specified in the
approved plan.
Steel reinforcement has adequately spaced and properly spliced.
The dimensions of the concrete floor is as specified on the approved plan.
Plumbing and electrical risers and ground rods have been installed as per the
approved plans
The concrete used meets the minimum compressive strength requirements
specified in the approved plans.
The concrete floor has been cured adequately
The concrete used has minimum compressive strength specified in the
specifications.
6.2. Timber floor
Table 4 below is a checklist for quality of timber floor
Table 4: Checklist for quality of timber floor
Specifics Yes No Comments
The timber is properly treated and preserved.
The floor does not have protruding nails.
The floor has been sanded as specified in the approved plans.
The floor has a dried finishing coat.
The floor has been moisture tested.
Timber skirting has been installed.
No gaps are visible between timber strips.
The flooring’s edges are properly sealed.
No gaps are visible between the wall/timber flooring and skirting.
The timber floor does not have stain marks
The floor has consistent colour tone
The floor surface is even
The floor does not have any visible damages such as cracks
6.3. Concrete floor
Table 5 below is a checklist for quality of concrete floor
Table 5: Checklist for quality of concrete floor
Specifics Yes No Comments
Steel reinforcement used is of the right size, grade and cover, as specified in the
approved plan.
Steel reinforcement has adequately spaced and properly spliced.
The dimensions of the concrete floor is as specified on the approved plan.
Plumbing and electrical risers and ground rods have been installed as per the
approved plans
The concrete used meets the minimum compressive strength requirements
specified in the approved plans.
The concrete floor has been cured adequately
Paraphrase This Document
Need a fresh take? Get an instant paraphrase of this document with our AI Paraphraser
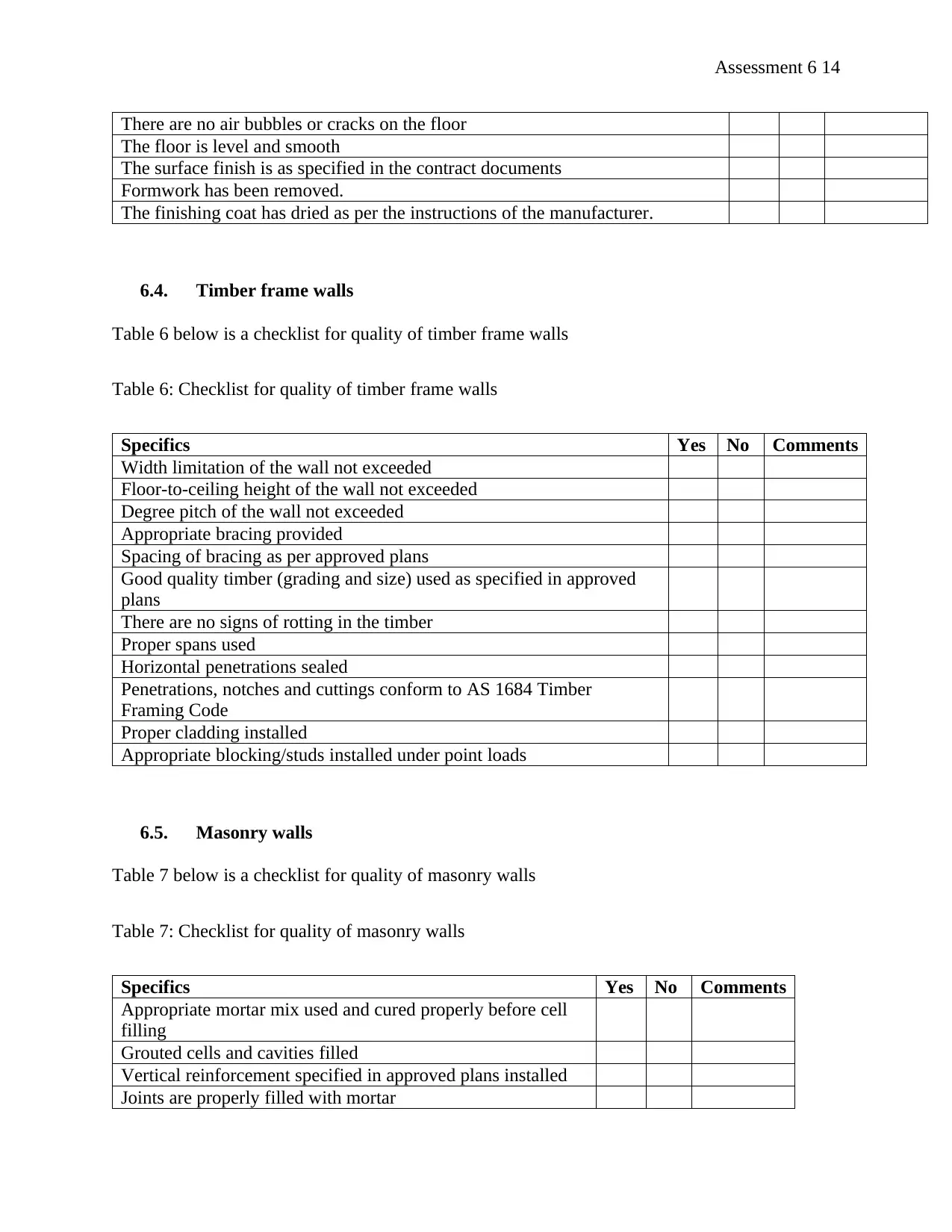
Assessment 6 14
There are no air bubbles or cracks on the floor
The floor is level and smooth
The surface finish is as specified in the contract documents
Formwork has been removed.
The finishing coat has dried as per the instructions of the manufacturer.
6.4. Timber frame walls
Table 6 below is a checklist for quality of timber frame walls
Table 6: Checklist for quality of timber frame walls
Specifics Yes No Comments
Width limitation of the wall not exceeded
Floor-to-ceiling height of the wall not exceeded
Degree pitch of the wall not exceeded
Appropriate bracing provided
Spacing of bracing as per approved plans
Good quality timber (grading and size) used as specified in approved
plans
There are no signs of rotting in the timber
Proper spans used
Horizontal penetrations sealed
Penetrations, notches and cuttings conform to AS 1684 Timber
Framing Code
Proper cladding installed
Appropriate blocking/studs installed under point loads
6.5. Masonry walls
Table 7 below is a checklist for quality of masonry walls
Table 7: Checklist for quality of masonry walls
Specifics Yes No Comments
Appropriate mortar mix used and cured properly before cell
filling
Grouted cells and cavities filled
Vertical reinforcement specified in approved plans installed
Joints are properly filled with mortar
There are no air bubbles or cracks on the floor
The floor is level and smooth
The surface finish is as specified in the contract documents
Formwork has been removed.
The finishing coat has dried as per the instructions of the manufacturer.
6.4. Timber frame walls
Table 6 below is a checklist for quality of timber frame walls
Table 6: Checklist for quality of timber frame walls
Specifics Yes No Comments
Width limitation of the wall not exceeded
Floor-to-ceiling height of the wall not exceeded
Degree pitch of the wall not exceeded
Appropriate bracing provided
Spacing of bracing as per approved plans
Good quality timber (grading and size) used as specified in approved
plans
There are no signs of rotting in the timber
Proper spans used
Horizontal penetrations sealed
Penetrations, notches and cuttings conform to AS 1684 Timber
Framing Code
Proper cladding installed
Appropriate blocking/studs installed under point loads
6.5. Masonry walls
Table 7 below is a checklist for quality of masonry walls
Table 7: Checklist for quality of masonry walls
Specifics Yes No Comments
Appropriate mortar mix used and cured properly before cell
filling
Grouted cells and cavities filled
Vertical reinforcement specified in approved plans installed
Joints are properly filled with mortar
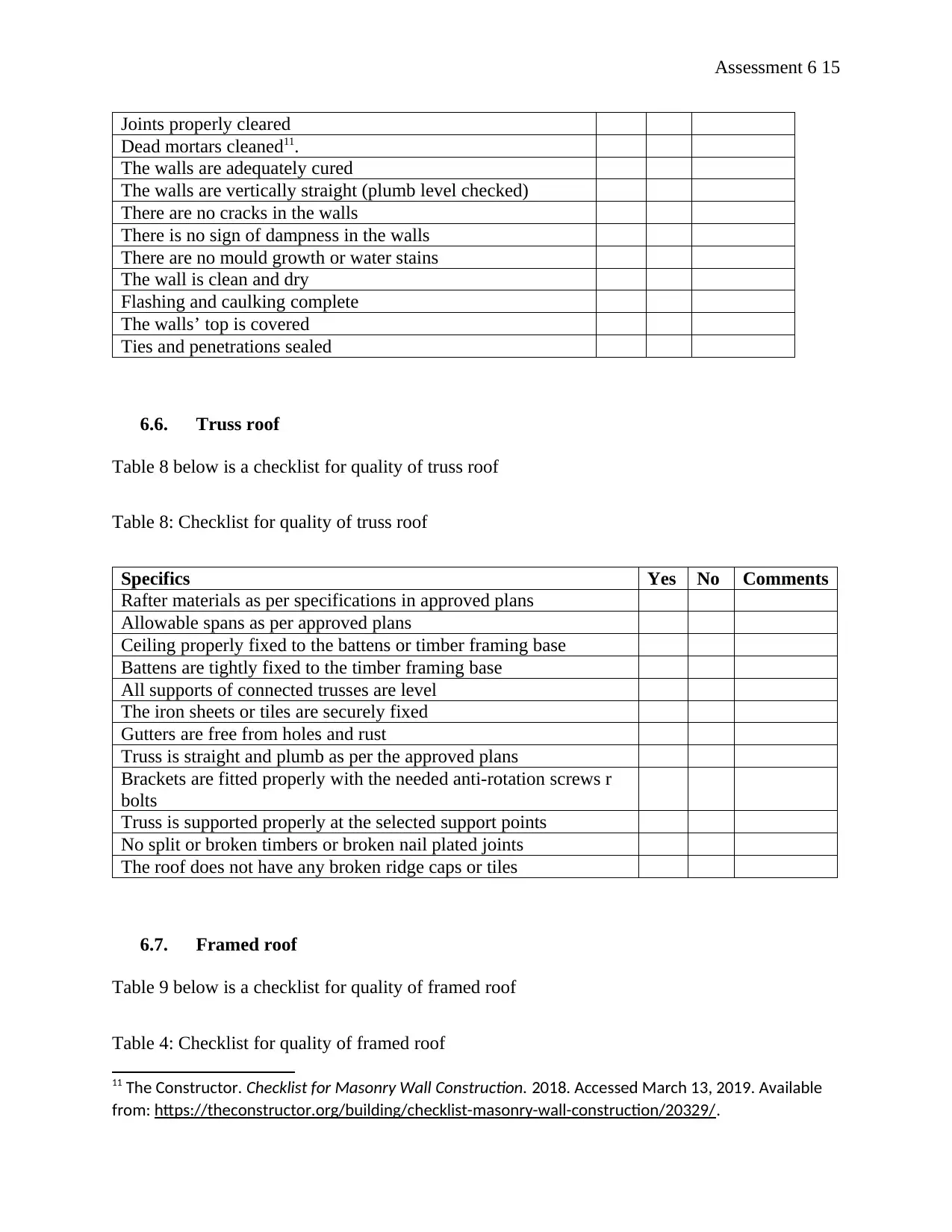
Assessment 6 15
Joints properly cleared
Dead mortars cleaned11.
The walls are adequately cured
The walls are vertically straight (plumb level checked)
There are no cracks in the walls
There is no sign of dampness in the walls
There are no mould growth or water stains
The wall is clean and dry
Flashing and caulking complete
The walls’ top is covered
Ties and penetrations sealed
6.6. Truss roof
Table 8 below is a checklist for quality of truss roof
Table 8: Checklist for quality of truss roof
Specifics Yes No Comments
Rafter materials as per specifications in approved plans
Allowable spans as per approved plans
Ceiling properly fixed to the battens or timber framing base
Battens are tightly fixed to the timber framing base
All supports of connected trusses are level
The iron sheets or tiles are securely fixed
Gutters are free from holes and rust
Truss is straight and plumb as per the approved plans
Brackets are fitted properly with the needed anti-rotation screws r
bolts
Truss is supported properly at the selected support points
No split or broken timbers or broken nail plated joints
The roof does not have any broken ridge caps or tiles
6.7. Framed roof
Table 9 below is a checklist for quality of framed roof
Table 4: Checklist for quality of framed roof
11 The Constructor. Checklist for Masonry Wall Construction. 2018. Accessed March 13, 2019. Available
from: https://theconstructor.org/building/checklist-masonry-wall-construction/20329/.
Joints properly cleared
Dead mortars cleaned11.
The walls are adequately cured
The walls are vertically straight (plumb level checked)
There are no cracks in the walls
There is no sign of dampness in the walls
There are no mould growth or water stains
The wall is clean and dry
Flashing and caulking complete
The walls’ top is covered
Ties and penetrations sealed
6.6. Truss roof
Table 8 below is a checklist for quality of truss roof
Table 8: Checklist for quality of truss roof
Specifics Yes No Comments
Rafter materials as per specifications in approved plans
Allowable spans as per approved plans
Ceiling properly fixed to the battens or timber framing base
Battens are tightly fixed to the timber framing base
All supports of connected trusses are level
The iron sheets or tiles are securely fixed
Gutters are free from holes and rust
Truss is straight and plumb as per the approved plans
Brackets are fitted properly with the needed anti-rotation screws r
bolts
Truss is supported properly at the selected support points
No split or broken timbers or broken nail plated joints
The roof does not have any broken ridge caps or tiles
6.7. Framed roof
Table 9 below is a checklist for quality of framed roof
Table 4: Checklist for quality of framed roof
11 The Constructor. Checklist for Masonry Wall Construction. 2018. Accessed March 13, 2019. Available
from: https://theconstructor.org/building/checklist-masonry-wall-construction/20329/.
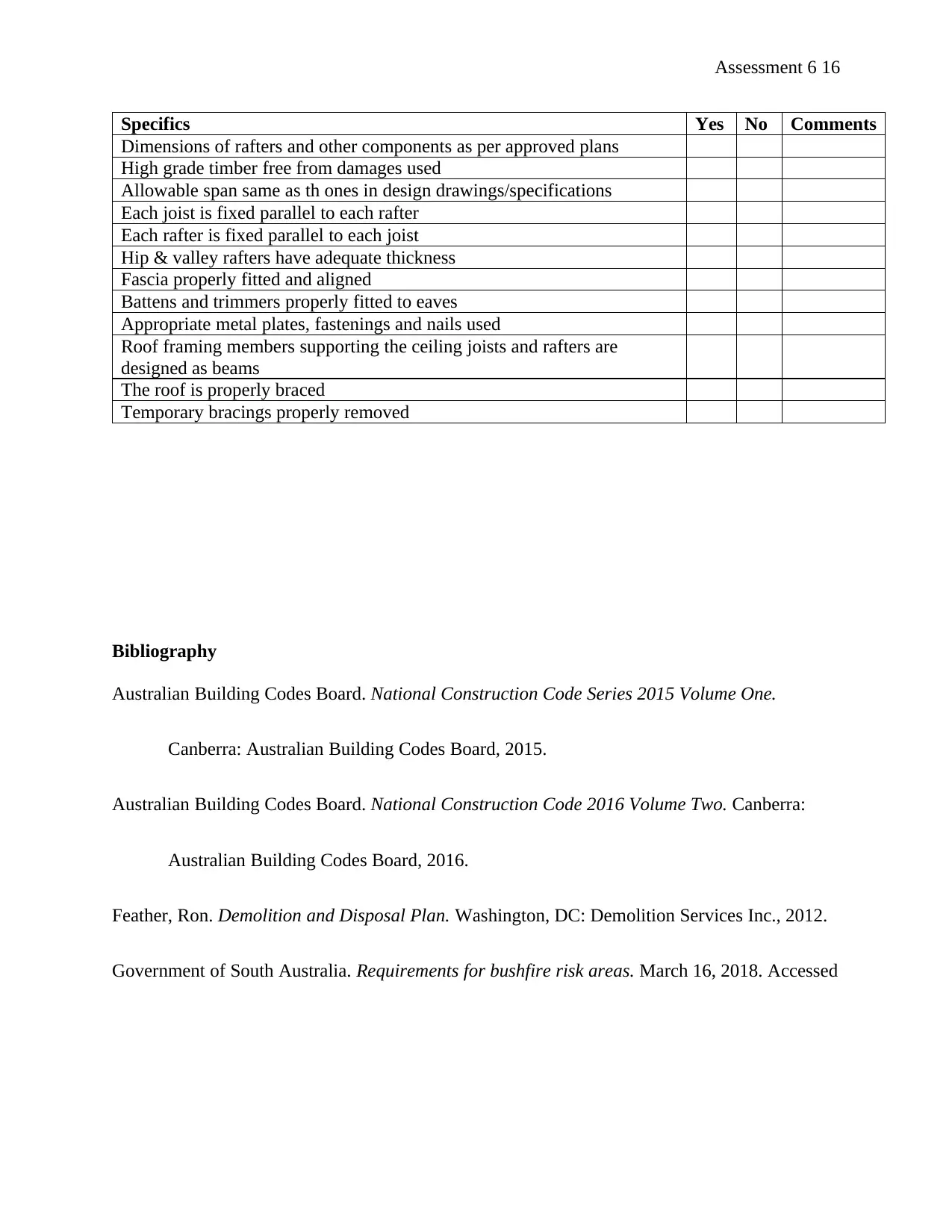
Assessment 6 16
Specifics Yes No Comments
Dimensions of rafters and other components as per approved plans
High grade timber free from damages used
Allowable span same as th ones in design drawings/specifications
Each joist is fixed parallel to each rafter
Each rafter is fixed parallel to each joist
Hip & valley rafters have adequate thickness
Fascia properly fitted and aligned
Battens and trimmers properly fitted to eaves
Appropriate metal plates, fastenings and nails used
Roof framing members supporting the ceiling joists and rafters are
designed as beams
The roof is properly braced
Temporary bracings properly removed
Bibliography
Australian Building Codes Board. National Construction Code Series 2015 Volume One.
Canberra: Australian Building Codes Board, 2015.
Australian Building Codes Board. National Construction Code 2016 Volume Two. Canberra:
Australian Building Codes Board, 2016.
Feather, Ron. Demolition and Disposal Plan. Washington, DC: Demolition Services Inc., 2012.
Government of South Australia. Requirements for bushfire risk areas. March 16, 2018. Accessed
Specifics Yes No Comments
Dimensions of rafters and other components as per approved plans
High grade timber free from damages used
Allowable span same as th ones in design drawings/specifications
Each joist is fixed parallel to each rafter
Each rafter is fixed parallel to each joist
Hip & valley rafters have adequate thickness
Fascia properly fitted and aligned
Battens and trimmers properly fitted to eaves
Appropriate metal plates, fastenings and nails used
Roof framing members supporting the ceiling joists and rafters are
designed as beams
The roof is properly braced
Temporary bracings properly removed
Bibliography
Australian Building Codes Board. National Construction Code Series 2015 Volume One.
Canberra: Australian Building Codes Board, 2015.
Australian Building Codes Board. National Construction Code 2016 Volume Two. Canberra:
Australian Building Codes Board, 2016.
Feather, Ron. Demolition and Disposal Plan. Washington, DC: Demolition Services Inc., 2012.
Government of South Australia. Requirements for bushfire risk areas. March 16, 2018. Accessed
Secure Best Marks with AI Grader
Need help grading? Try our AI Grader for instant feedback on your assignments.
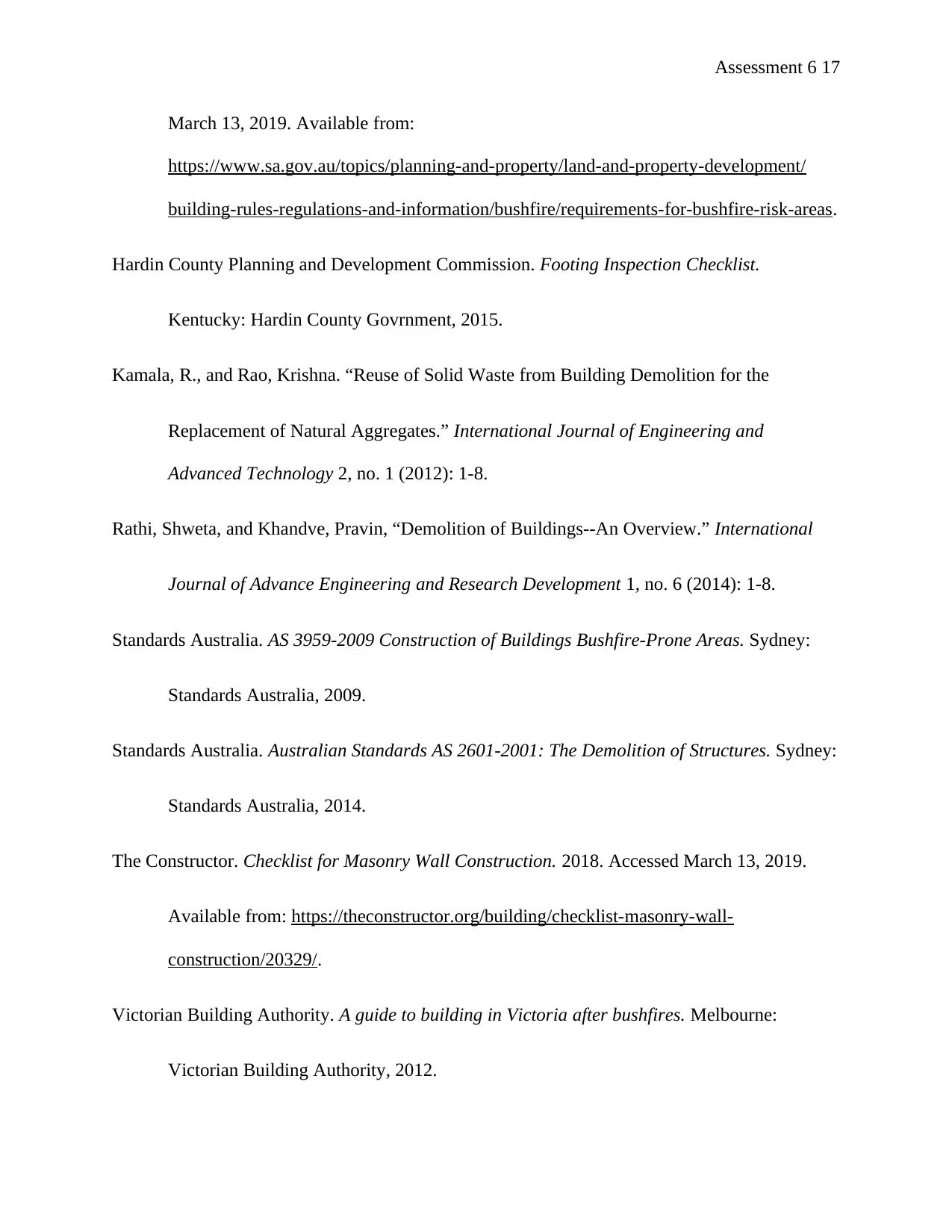
Assessment 6 17
March 13, 2019. Available from:
https://www.sa.gov.au/topics/planning-and-property/land-and-property-development/
building-rules-regulations-and-information/bushfire/requirements-for-bushfire-risk-areas.
Hardin County Planning and Development Commission. Footing Inspection Checklist.
Kentucky: Hardin County Govrnment, 2015.
Kamala, R., and Rao, Krishna. “Reuse of Solid Waste from Building Demolition for the
Replacement of Natural Aggregates.” International Journal of Engineering and
Advanced Technology 2, no. 1 (2012): 1-8.
Rathi, Shweta, and Khandve, Pravin, “Demolition of Buildings--An Overview.” International
Journal of Advance Engineering and Research Development 1, no. 6 (2014): 1-8.
Standards Australia. AS 3959-2009 Construction of Buildings Bushfire-Prone Areas. Sydney:
Standards Australia, 2009.
Standards Australia. Australian Standards AS 2601-2001: The Demolition of Structures. Sydney:
Standards Australia, 2014.
The Constructor. Checklist for Masonry Wall Construction. 2018. Accessed March 13, 2019.
Available from: https://theconstructor.org/building/checklist-masonry-wall-
construction/20329/.
Victorian Building Authority. A guide to building in Victoria after bushfires. Melbourne:
Victorian Building Authority, 2012.
March 13, 2019. Available from:
https://www.sa.gov.au/topics/planning-and-property/land-and-property-development/
building-rules-regulations-and-information/bushfire/requirements-for-bushfire-risk-areas.
Hardin County Planning and Development Commission. Footing Inspection Checklist.
Kentucky: Hardin County Govrnment, 2015.
Kamala, R., and Rao, Krishna. “Reuse of Solid Waste from Building Demolition for the
Replacement of Natural Aggregates.” International Journal of Engineering and
Advanced Technology 2, no. 1 (2012): 1-8.
Rathi, Shweta, and Khandve, Pravin, “Demolition of Buildings--An Overview.” International
Journal of Advance Engineering and Research Development 1, no. 6 (2014): 1-8.
Standards Australia. AS 3959-2009 Construction of Buildings Bushfire-Prone Areas. Sydney:
Standards Australia, 2009.
Standards Australia. Australian Standards AS 2601-2001: The Demolition of Structures. Sydney:
Standards Australia, 2014.
The Constructor. Checklist for Masonry Wall Construction. 2018. Accessed March 13, 2019.
Available from: https://theconstructor.org/building/checklist-masonry-wall-
construction/20329/.
Victorian Building Authority. A guide to building in Victoria after bushfires. Melbourne:
Victorian Building Authority, 2012.
1 out of 17
Related Documents
![[object Object]](/_next/image/?url=%2F_next%2Fstatic%2Fmedia%2Flogo.6d15ce61.png&w=640&q=75)
Your All-in-One AI-Powered Toolkit for Academic Success.
+13062052269
info@desklib.com
Available 24*7 on WhatsApp / Email
Unlock your academic potential
© 2024 | Zucol Services PVT LTD | All rights reserved.