Demolition Plan, Building Services Checklist & Australian Standards
VerifiedAdded on 2023/06/15
|16
|1794
|289
Practical Assignment
AI Summary
This assignment provides a comprehensive overview of demolition planning, including assessing needs, creating a demolition plan, and obtaining necessary permits while adhering to regulations like the Planning and Development Regulation 2008 and Australian Standards. It details essential building services such as energy supply, water supply, heating, ventilation, lighting, communications, security, fire protection, air conditioning, and refrigeration, categorizing them into mechanical and electrical systems with relevant Australian codes. Additionally, the assignment includes a site inspection checklist covering erosion and sediment control, site management, material and waste management, soil management, erosion controls, and site stabilization/revegetation. Finally, it offers inspection checklists for footings, timber floors, concrete floors, timber frame walls, masonry walls, truss roofs, and framed roofs, ensuring thorough quality control and compliance.
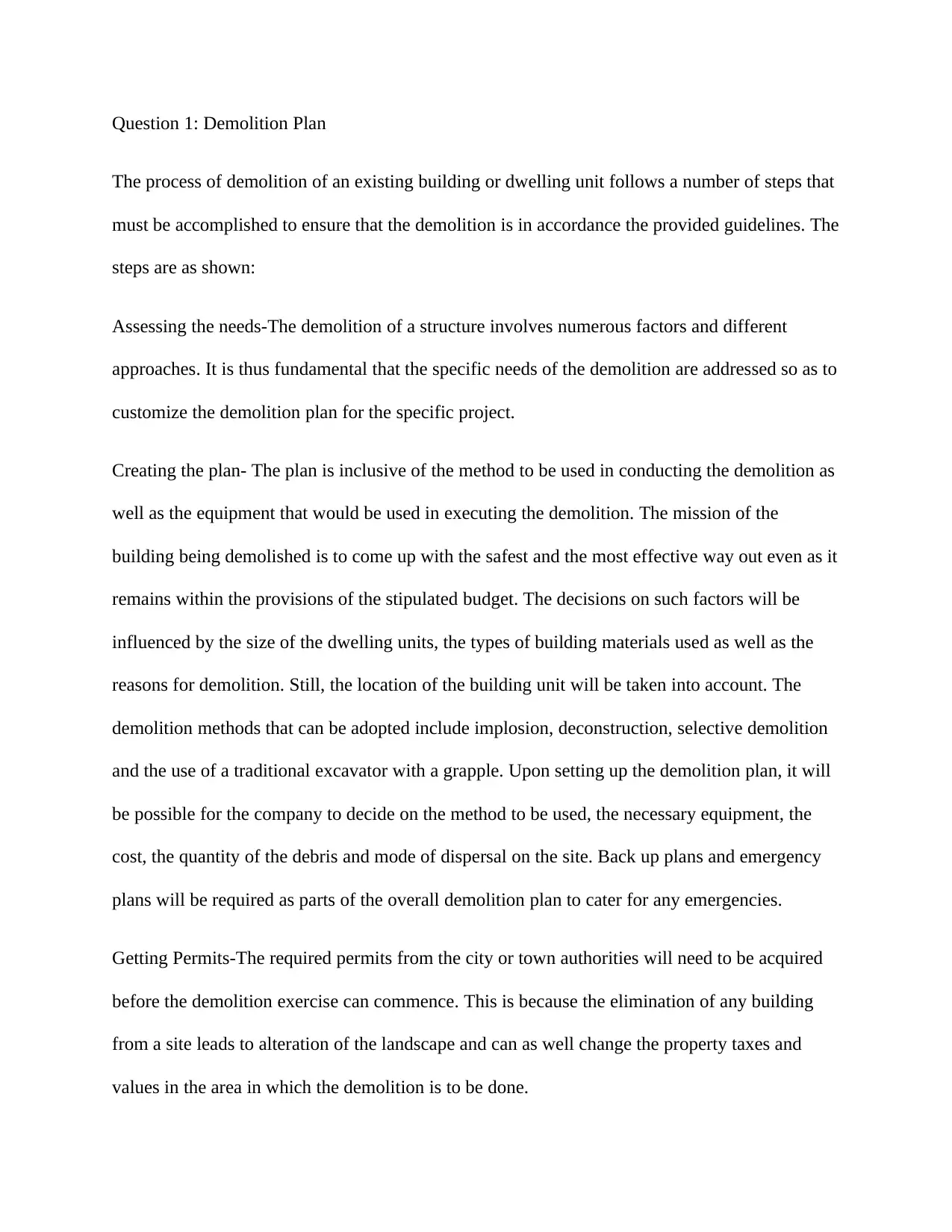
Question 1: Demolition Plan
The process of demolition of an existing building or dwelling unit follows a number of steps that
must be accomplished to ensure that the demolition is in accordance the provided guidelines. The
steps are as shown:
Assessing the needs-The demolition of a structure involves numerous factors and different
approaches. It is thus fundamental that the specific needs of the demolition are addressed so as to
customize the demolition plan for the specific project.
Creating the plan- The plan is inclusive of the method to be used in conducting the demolition as
well as the equipment that would be used in executing the demolition. The mission of the
building being demolished is to come up with the safest and the most effective way out even as it
remains within the provisions of the stipulated budget. The decisions on such factors will be
influenced by the size of the dwelling units, the types of building materials used as well as the
reasons for demolition. Still, the location of the building unit will be taken into account. The
demolition methods that can be adopted include implosion, deconstruction, selective demolition
and the use of a traditional excavator with a grapple. Upon setting up the demolition plan, it will
be possible for the company to decide on the method to be used, the necessary equipment, the
cost, the quantity of the debris and mode of dispersal on the site. Back up plans and emergency
plans will be required as parts of the overall demolition plan to cater for any emergencies.
Getting Permits-The required permits from the city or town authorities will need to be acquired
before the demolition exercise can commence. This is because the elimination of any building
from a site leads to alteration of the landscape and can as well change the property taxes and
values in the area in which the demolition is to be done.
The process of demolition of an existing building or dwelling unit follows a number of steps that
must be accomplished to ensure that the demolition is in accordance the provided guidelines. The
steps are as shown:
Assessing the needs-The demolition of a structure involves numerous factors and different
approaches. It is thus fundamental that the specific needs of the demolition are addressed so as to
customize the demolition plan for the specific project.
Creating the plan- The plan is inclusive of the method to be used in conducting the demolition as
well as the equipment that would be used in executing the demolition. The mission of the
building being demolished is to come up with the safest and the most effective way out even as it
remains within the provisions of the stipulated budget. The decisions on such factors will be
influenced by the size of the dwelling units, the types of building materials used as well as the
reasons for demolition. Still, the location of the building unit will be taken into account. The
demolition methods that can be adopted include implosion, deconstruction, selective demolition
and the use of a traditional excavator with a grapple. Upon setting up the demolition plan, it will
be possible for the company to decide on the method to be used, the necessary equipment, the
cost, the quantity of the debris and mode of dispersal on the site. Back up plans and emergency
plans will be required as parts of the overall demolition plan to cater for any emergencies.
Getting Permits-The required permits from the city or town authorities will need to be acquired
before the demolition exercise can commence. This is because the elimination of any building
from a site leads to alteration of the landscape and can as well change the property taxes and
values in the area in which the demolition is to be done.
Secure Best Marks with AI Grader
Need help grading? Try our AI Grader for instant feedback on your assignments.
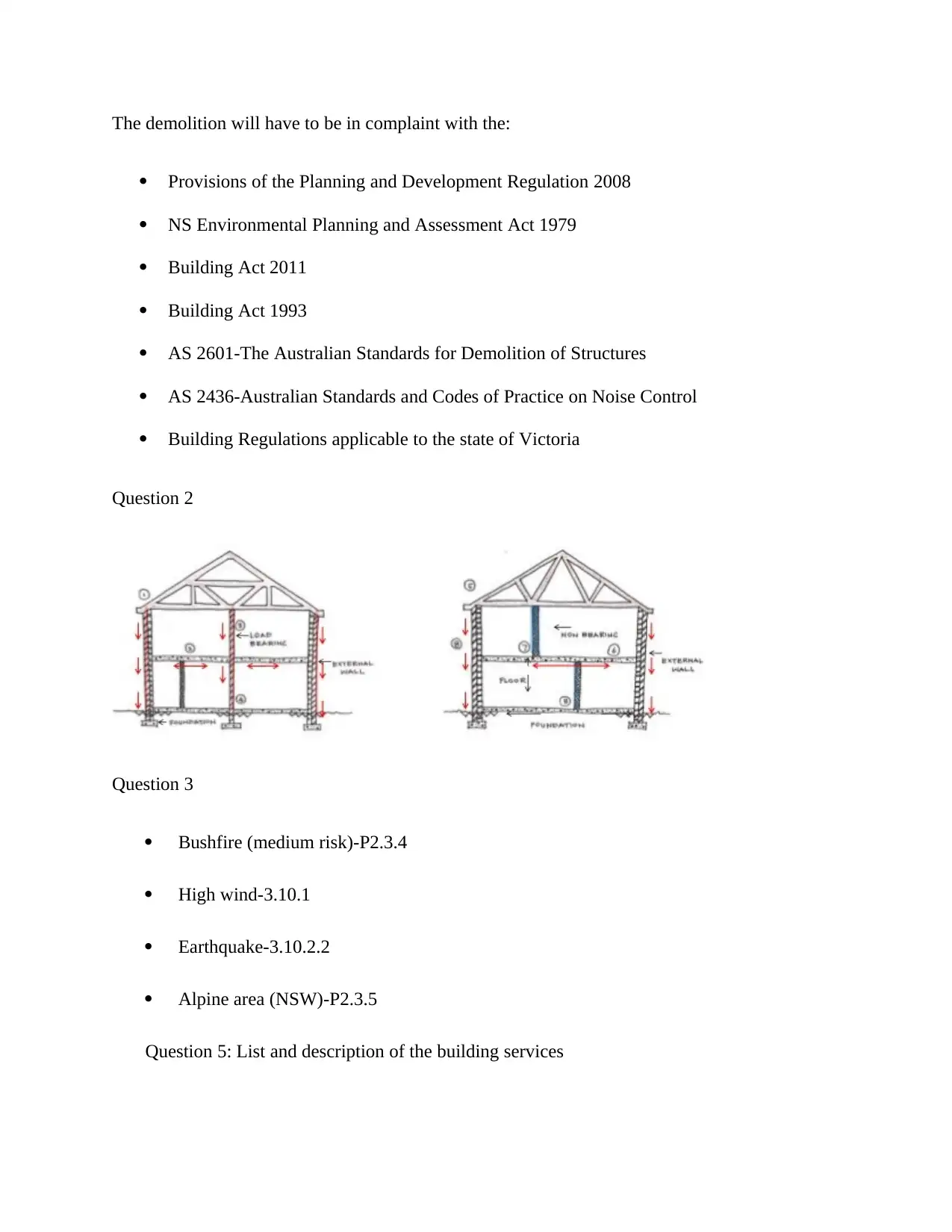
The demolition will have to be in complaint with the:
Provisions of the Planning and Development Regulation 2008
NS Environmental Planning and Assessment Act 1979
Building Act 2011
Building Act 1993
AS 2601-The Australian Standards for Demolition of Structures
AS 2436-Australian Standards and Codes of Practice on Noise Control
Building Regulations applicable to the state of Victoria
Question 2
Question 3
Bushfire (medium risk)-P2.3.4
High wind-3.10.1
Earthquake-3.10.2.2
Alpine area (NSW)-P2.3.5
Question 5: List and description of the building services
Provisions of the Planning and Development Regulation 2008
NS Environmental Planning and Assessment Act 1979
Building Act 2011
Building Act 1993
AS 2601-The Australian Standards for Demolition of Structures
AS 2436-Australian Standards and Codes of Practice on Noise Control
Building Regulations applicable to the state of Victoria
Question 2
Question 3
Bushfire (medium risk)-P2.3.4
High wind-3.10.1
Earthquake-3.10.2.2
Alpine area (NSW)-P2.3.5
Question 5: List and description of the building services

Energy supply-include the supplies for gas and electricity. The Australian code for
the service is AS 4564
Water supply-Encompasses the services of supply, drainage and plumbing-The
Australian code for the service is WSA 03-2011
Heating and ventilation-The Australian code for the service is AS 1668.2
Lighting-includes both day lighting and natural lighting services. The Australian
code for the service is AS 1680.
Communications and telephonic services-The Australian code for the service is AS
S009:2013
Security and alarm systems-The Australian code for the service is AS 2201.1
Fire detection and protection services-The Australian code for the service is AS
1670.1
Air conditioning and refrigeration services-The Australian code for the service is AS
1668.2
The above services are classified into either mechanical or electrical systems. Mechanical
systems include:
HVAC systems, which is an abbreviation for heating, ventilating and air-conditioning and
include such services as active mechanical/ electrical services
Site Drainage which include drainage, water, sanitary disposal and removal of waste water
from the various disposal points
the service is AS 4564
Water supply-Encompasses the services of supply, drainage and plumbing-The
Australian code for the service is WSA 03-2011
Heating and ventilation-The Australian code for the service is AS 1668.2
Lighting-includes both day lighting and natural lighting services. The Australian
code for the service is AS 1680.
Communications and telephonic services-The Australian code for the service is AS
S009:2013
Security and alarm systems-The Australian code for the service is AS 2201.1
Fire detection and protection services-The Australian code for the service is AS
1670.1
Air conditioning and refrigeration services-The Australian code for the service is AS
1668.2
The above services are classified into either mechanical or electrical systems. Mechanical
systems include:
HVAC systems, which is an abbreviation for heating, ventilating and air-conditioning and
include such services as active mechanical/ electrical services
Site Drainage which include drainage, water, sanitary disposal and removal of waste water
from the various disposal points
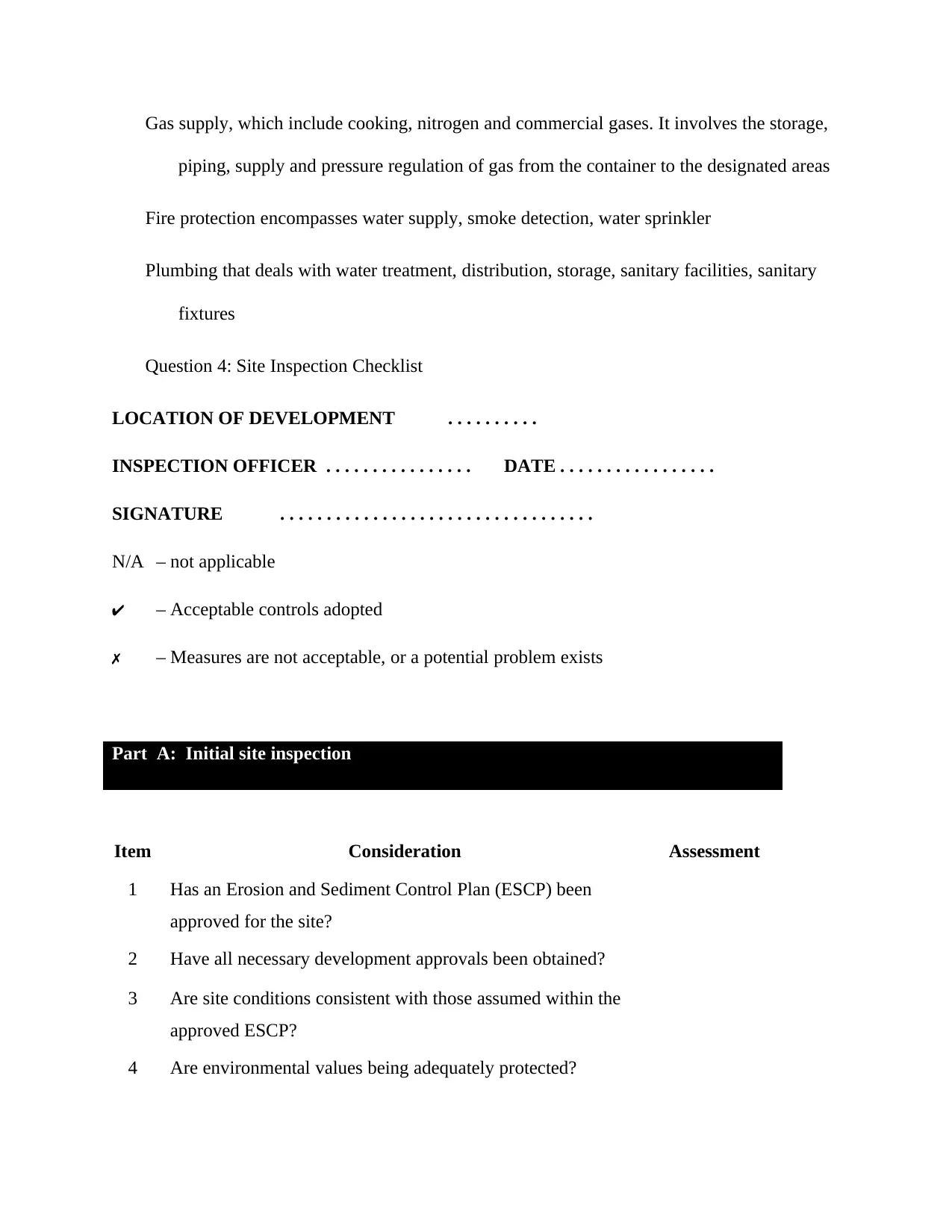
Gas supply, which include cooking, nitrogen and commercial gases. It involves the storage,
piping, supply and pressure regulation of gas from the container to the designated areas
Fire protection encompasses water supply, smoke detection, water sprinkler
Plumbing that deals with water treatment, distribution, storage, sanitary facilities, sanitary
fixtures
Question 4: Site Inspection Checklist
LOCATION OF DEVELOPMENT . . . . . . . . . .
INSPECTION OFFICER . . . . . . . . . . . . . . . . DATE . . . . . . . . . . . . . . . . .
SIGNATURE . . . . . . . . . . . . . . . . . . . . . . . . . . . . . . . . . .
N/A – not applicable
– Acceptable controls adopted
– Measures are not acceptable, or a potential problem exists
Part A: Initial site inspection
Item Consideration Assessment
1 Has an Erosion and Sediment Control Plan (ESCP) been
approved for the site?
2 Have all necessary development approvals been obtained?
3 Are site conditions consistent with those assumed within the
approved ESCP?
4 Are environmental values being adequately protected?
piping, supply and pressure regulation of gas from the container to the designated areas
Fire protection encompasses water supply, smoke detection, water sprinkler
Plumbing that deals with water treatment, distribution, storage, sanitary facilities, sanitary
fixtures
Question 4: Site Inspection Checklist
LOCATION OF DEVELOPMENT . . . . . . . . . .
INSPECTION OFFICER . . . . . . . . . . . . . . . . DATE . . . . . . . . . . . . . . . . .
SIGNATURE . . . . . . . . . . . . . . . . . . . . . . . . . . . . . . . . . .
N/A – not applicable
– Acceptable controls adopted
– Measures are not acceptable, or a potential problem exists
Part A: Initial site inspection
Item Consideration Assessment
1 Has an Erosion and Sediment Control Plan (ESCP) been
approved for the site?
2 Have all necessary development approvals been obtained?
3 Are site conditions consistent with those assumed within the
approved ESCP?
4 Are environmental values being adequately protected?
Secure Best Marks with AI Grader
Need help grading? Try our AI Grader for instant feedback on your assignments.
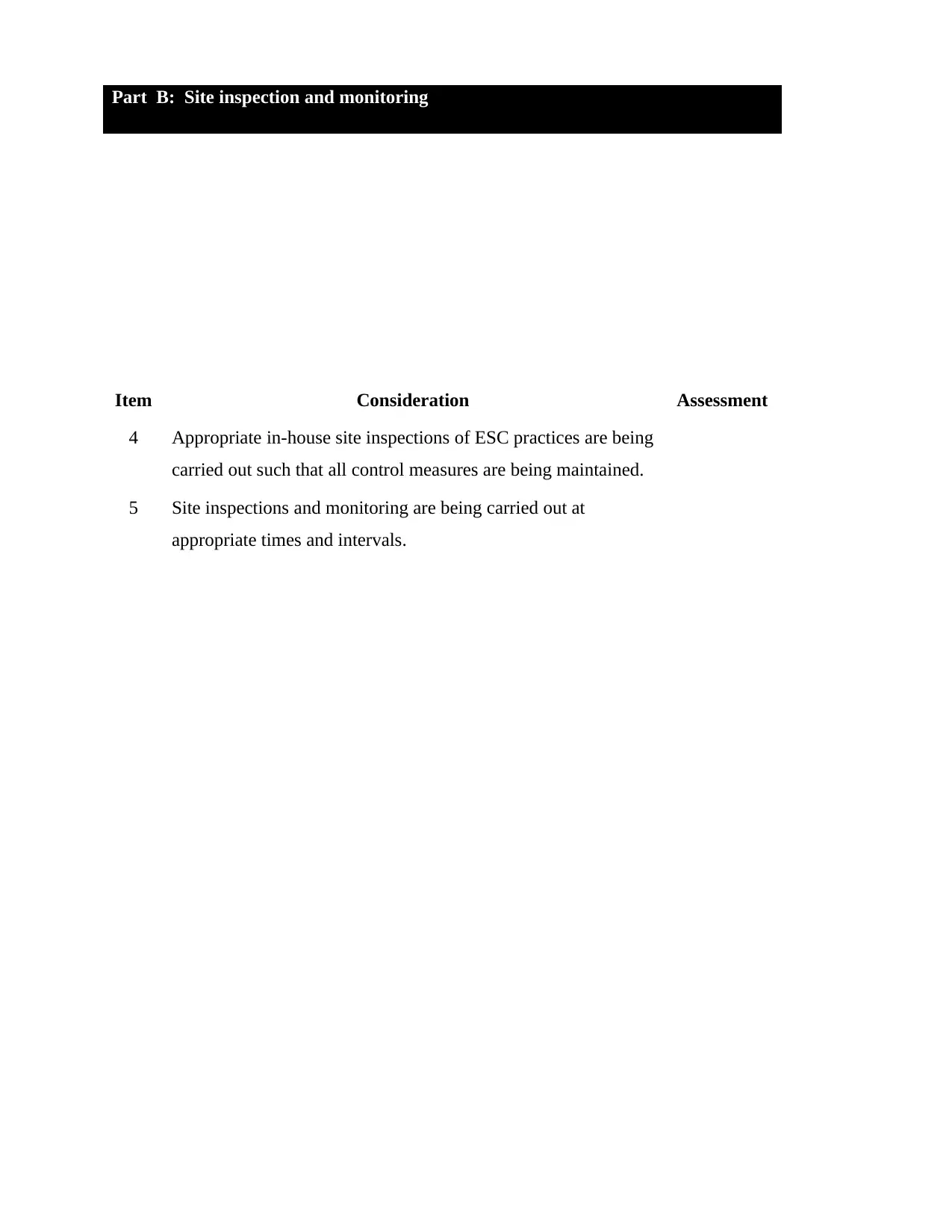
Item Consideration Assessment
4 Appropriate in-house site inspections of ESC practices are being
carried out such that all control measures are being maintained.
5 Site inspections and monitoring are being carried out at
appropriate times and intervals.
Part B: Site inspection and monitoring
4 Appropriate in-house site inspections of ESC practices are being
carried out such that all control measures are being maintained.
5 Site inspections and monitoring are being carried out at
appropriate times and intervals.
Part B: Site inspection and monitoring

Part C: Site establishment
Item Consideration Assessment
6 Site access is controlled and the number of access points
minimized.
7 Adequate drainage and sediment controls exist at site entry/exit
points.
8 Adequate drainage, erosion and sediment controls have been
placed around the site compound.
Part D: Site and vegetation management
Item Consideration Assessment
9 Vegetation Management Plan (VMP) and/or landscape plan has
been prepared.
10 VMP and/or landscape plan is being appropriately implemented.
11 Site personnel appear to be aware of ESC requirements and
have ready access to the Erosion and Sediment Control Plan.
12 ESC measures are being installed in accordance with the
approved Installation Sequence.
13 Adequate supplies of ESC materials stored on-site: such as
straw bales, wire, stakes, sediment fence fabric, filter cloth,
clean aggregate.
Item Consideration Assessment
6 Site access is controlled and the number of access points
minimized.
7 Adequate drainage and sediment controls exist at site entry/exit
points.
8 Adequate drainage, erosion and sediment controls have been
placed around the site compound.
Part D: Site and vegetation management
Item Consideration Assessment
9 Vegetation Management Plan (VMP) and/or landscape plan has
been prepared.
10 VMP and/or landscape plan is being appropriately implemented.
11 Site personnel appear to be aware of ESC requirements and
have ready access to the Erosion and Sediment Control Plan.
12 ESC measures are being installed in accordance with the
approved Installation Sequence.
13 Adequate supplies of ESC materials stored on-site: such as
straw bales, wire, stakes, sediment fence fabric, filter cloth,
clean aggregate.
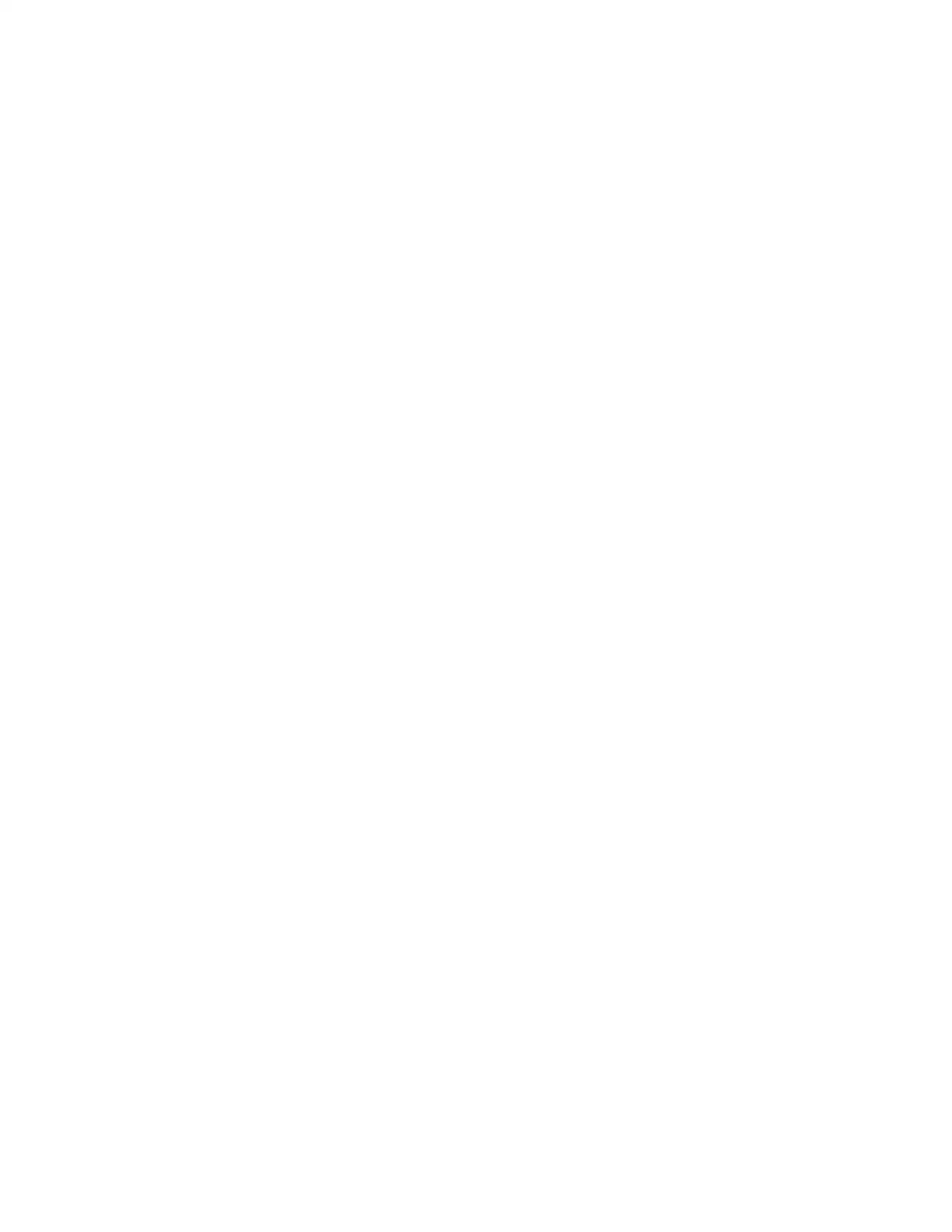
Paraphrase This Document
Need a fresh take? Get an instant paraphrase of this document with our AI Paraphraser
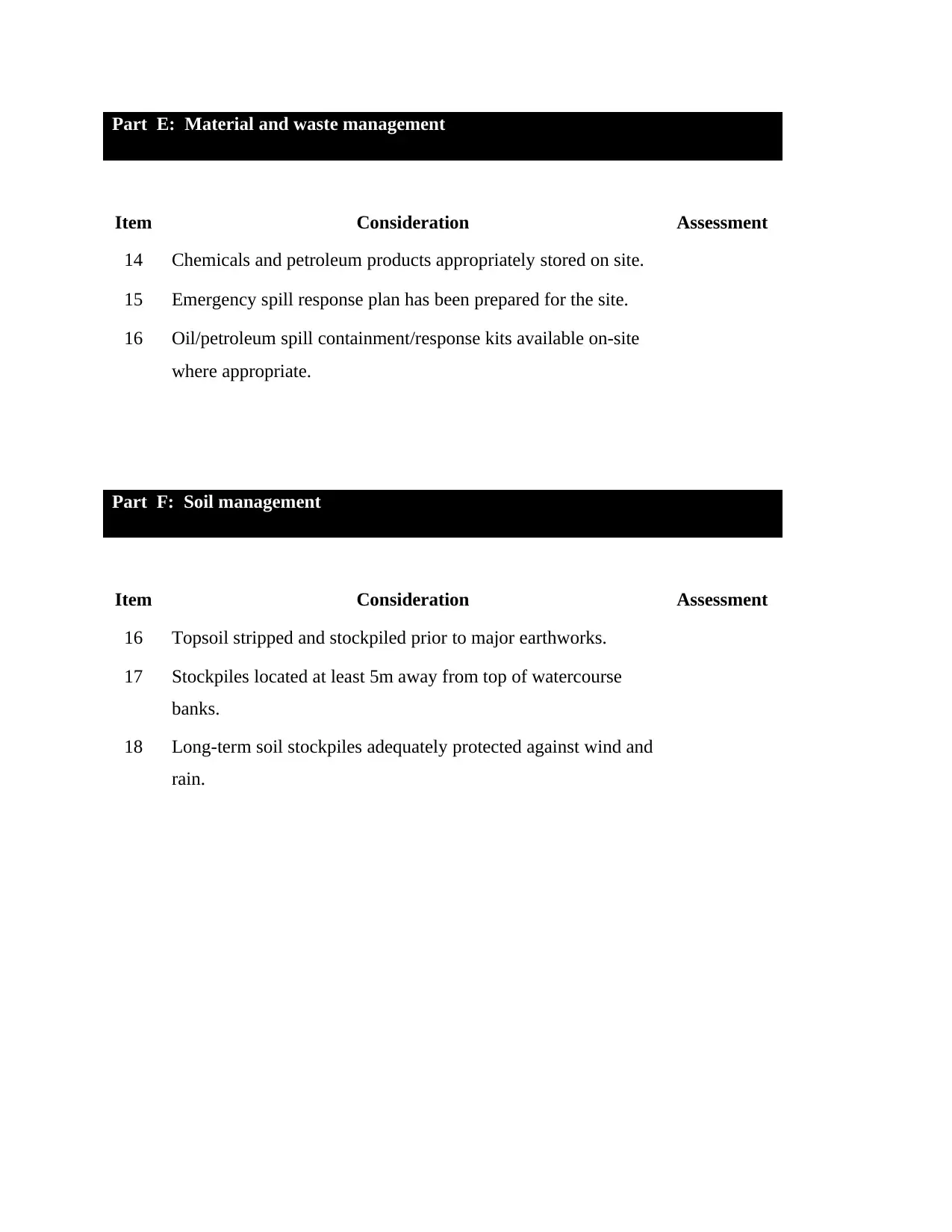
Part E: Material and waste management
Item Consideration Assessment
14 Chemicals and petroleum products appropriately stored on site.
15 Emergency spill response plan has been prepared for the site.
16 Oil/petroleum spill containment/response kits available on-site
where appropriate.
Part F: Soil management
Item Consideration Assessment
16 Topsoil stripped and stockpiled prior to major earthworks.
17 Stockpiles located at least 5m away from top of watercourse
banks.
18 Long-term soil stockpiles adequately protected against wind and
rain.
Item Consideration Assessment
14 Chemicals and petroleum products appropriately stored on site.
15 Emergency spill response plan has been prepared for the site.
16 Oil/petroleum spill containment/response kits available on-site
where appropriate.
Part F: Soil management
Item Consideration Assessment
16 Topsoil stripped and stockpiled prior to major earthworks.
17 Stockpiles located at least 5m away from top of watercourse
banks.
18 Long-term soil stockpiles adequately protected against wind and
rain.
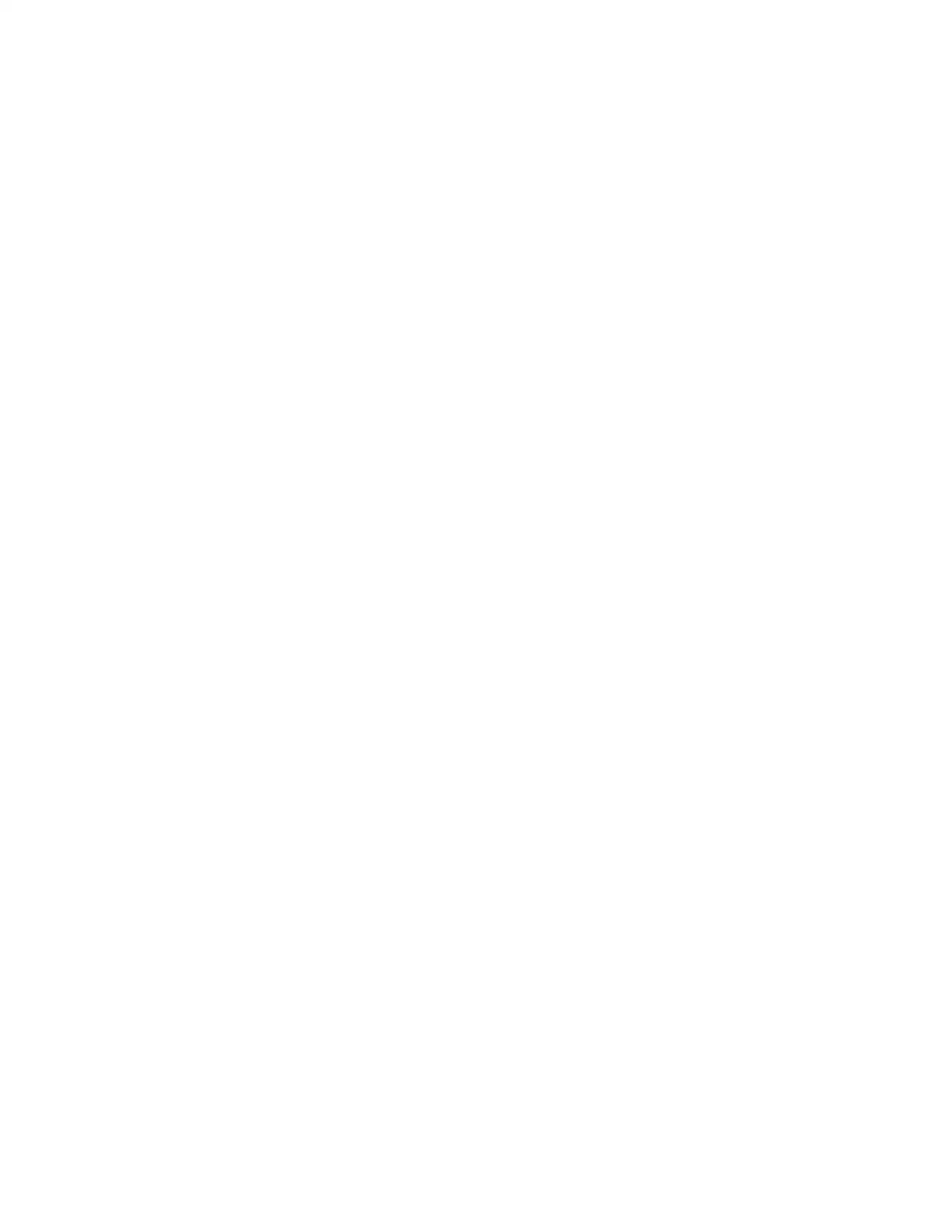
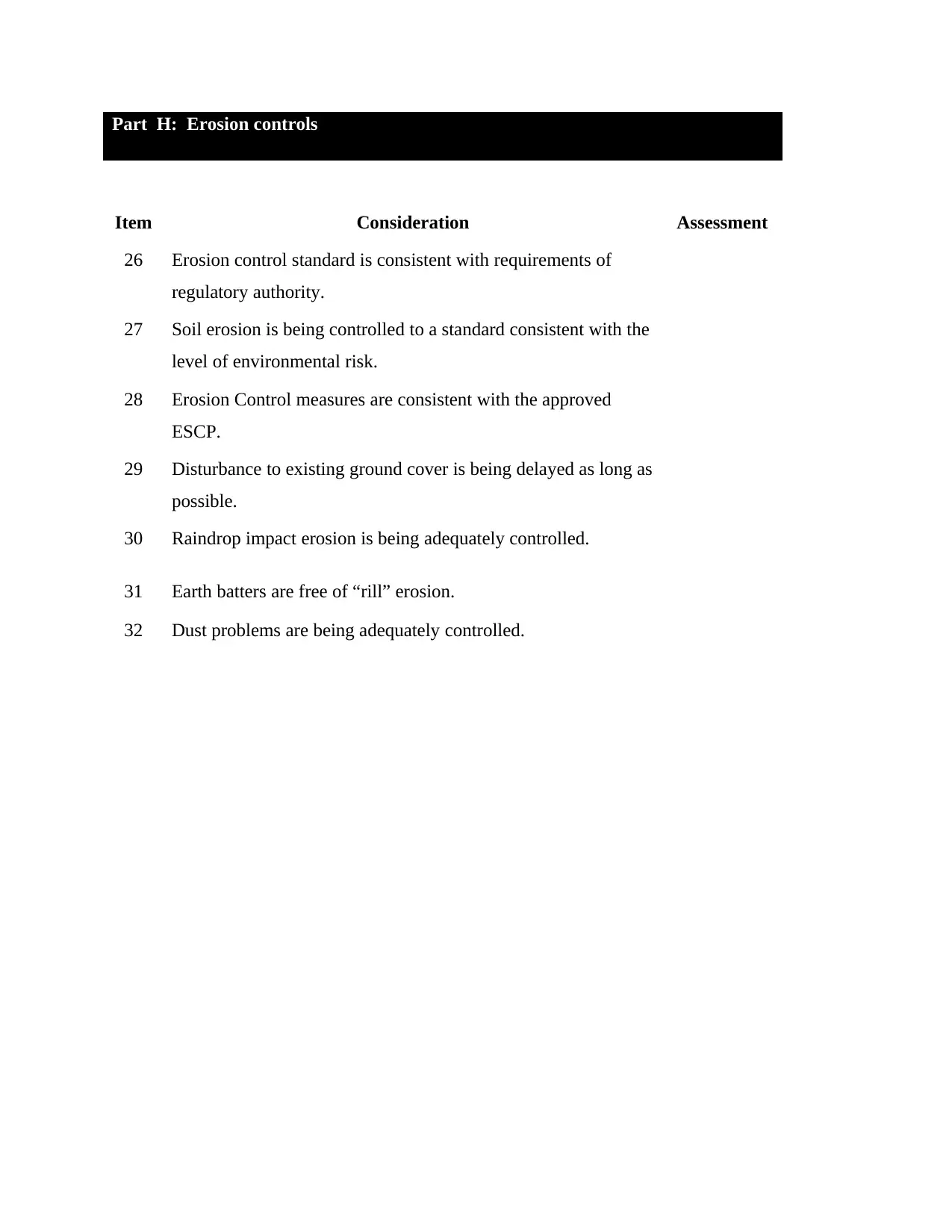
Part H: Erosion controls
Item Consideration Assessment
26 Erosion control standard is consistent with requirements of
regulatory authority.
27 Soil erosion is being controlled to a standard consistent with the
level of environmental risk.
28 Erosion Control measures are consistent with the approved
ESCP.
29 Disturbance to existing ground cover is being delayed as long as
possible.
30 Raindrop impact erosion is being adequately controlled.
31 Earth batters are free of “rill” erosion.
32 Dust problems are being adequately controlled.
Item Consideration Assessment
26 Erosion control standard is consistent with requirements of
regulatory authority.
27 Soil erosion is being controlled to a standard consistent with the
level of environmental risk.
28 Erosion Control measures are consistent with the approved
ESCP.
29 Disturbance to existing ground cover is being delayed as long as
possible.
30 Raindrop impact erosion is being adequately controlled.
31 Earth batters are free of “rill” erosion.
32 Dust problems are being adequately controlled.
Secure Best Marks with AI Grader
Need help grading? Try our AI Grader for instant feedback on your assignments.
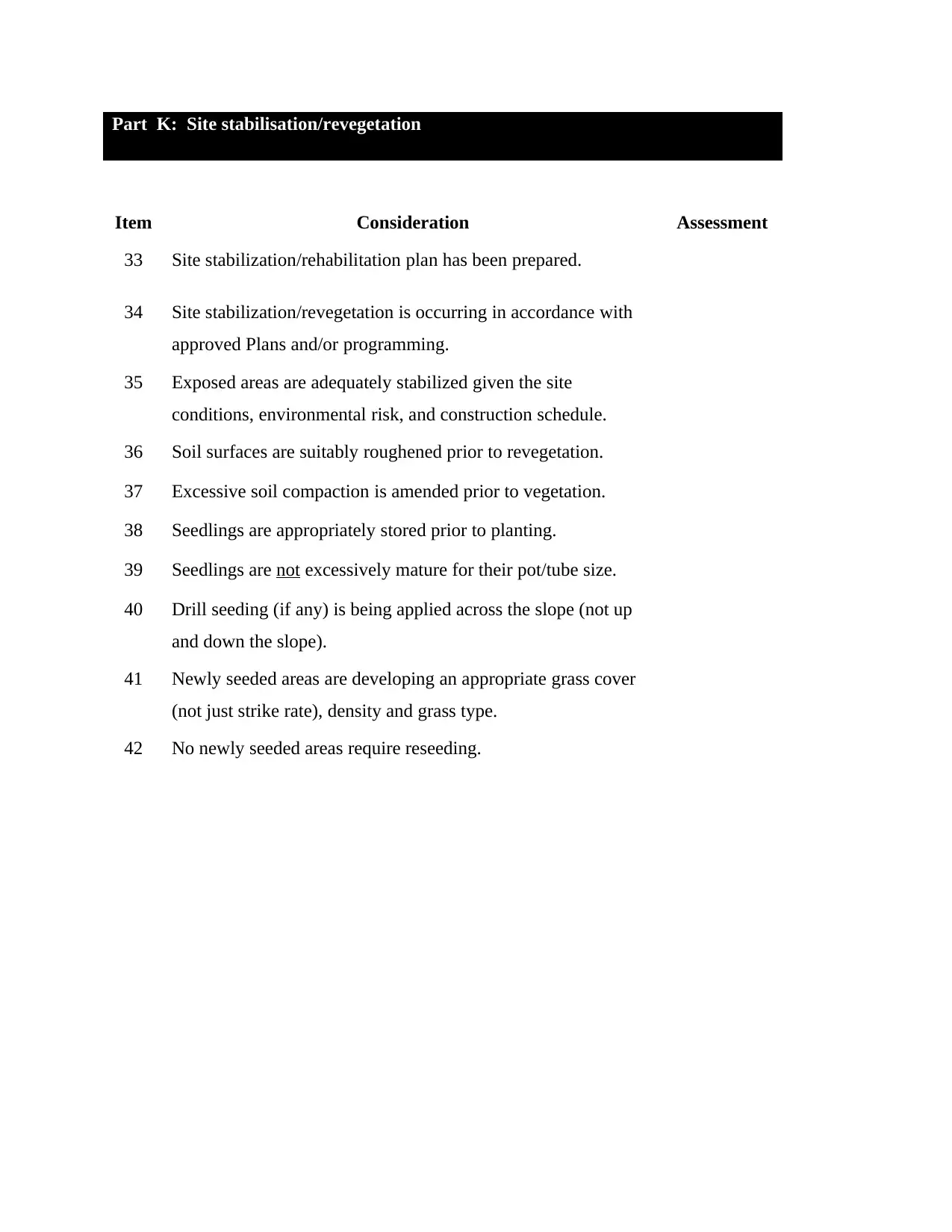
Part K: Site stabilisation/revegetation
Item Consideration Assessment
33 Site stabilization/rehabilitation plan has been prepared.
34 Site stabilization/revegetation is occurring in accordance with
approved Plans and/or programming.
35 Exposed areas are adequately stabilized given the site
conditions, environmental risk, and construction schedule.
36 Soil surfaces are suitably roughened prior to revegetation.
37 Excessive soil compaction is amended prior to vegetation.
38 Seedlings are appropriately stored prior to planting.
39 Seedlings are not excessively mature for their pot/tube size.
40 Drill seeding (if any) is being applied across the slope (not up
and down the slope).
41 Newly seeded areas are developing an appropriate grass cover
(not just strike rate), density and grass type.
42 No newly seeded areas require reseeding.
Item Consideration Assessment
33 Site stabilization/rehabilitation plan has been prepared.
34 Site stabilization/revegetation is occurring in accordance with
approved Plans and/or programming.
35 Exposed areas are adequately stabilized given the site
conditions, environmental risk, and construction schedule.
36 Soil surfaces are suitably roughened prior to revegetation.
37 Excessive soil compaction is amended prior to vegetation.
38 Seedlings are appropriately stored prior to planting.
39 Seedlings are not excessively mature for their pot/tube size.
40 Drill seeding (if any) is being applied across the slope (not up
and down the slope).
41 Newly seeded areas are developing an appropriate grass cover
(not just strike rate), density and grass type.
42 No newly seeded areas require reseeding.
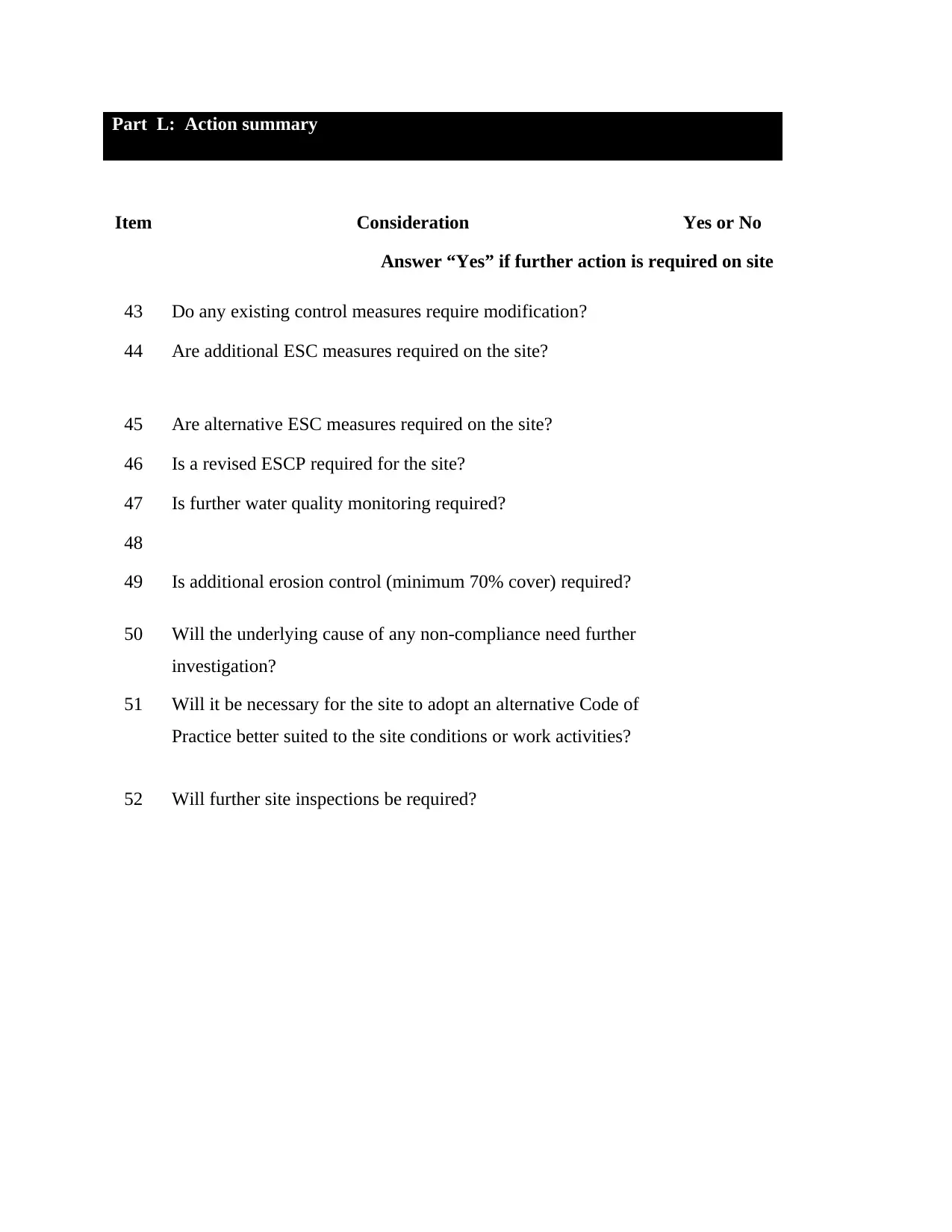
Part L: Action summary
Item Consideration Yes or No
Answer “Yes” if further action is required on site
43 Do any existing control measures require modification?
44 Are additional ESC measures required on the site?
45 Are alternative ESC measures required on the site?
46 Is a revised ESCP required for the site?
47 Is further water quality monitoring required?
48
49 Is additional erosion control (minimum 70% cover) required?
50 Will the underlying cause of any non-compliance need further
investigation?
51 Will it be necessary for the site to adopt an alternative Code of
Practice better suited to the site conditions or work activities?
52 Will further site inspections be required?
Item Consideration Yes or No
Answer “Yes” if further action is required on site
43 Do any existing control measures require modification?
44 Are additional ESC measures required on the site?
45 Are alternative ESC measures required on the site?
46 Is a revised ESCP required for the site?
47 Is further water quality monitoring required?
48
49 Is additional erosion control (minimum 70% cover) required?
50 Will the underlying cause of any non-compliance need further
investigation?
51 Will it be necessary for the site to adopt an alternative Code of
Practice better suited to the site conditions or work activities?
52 Will further site inspections be required?
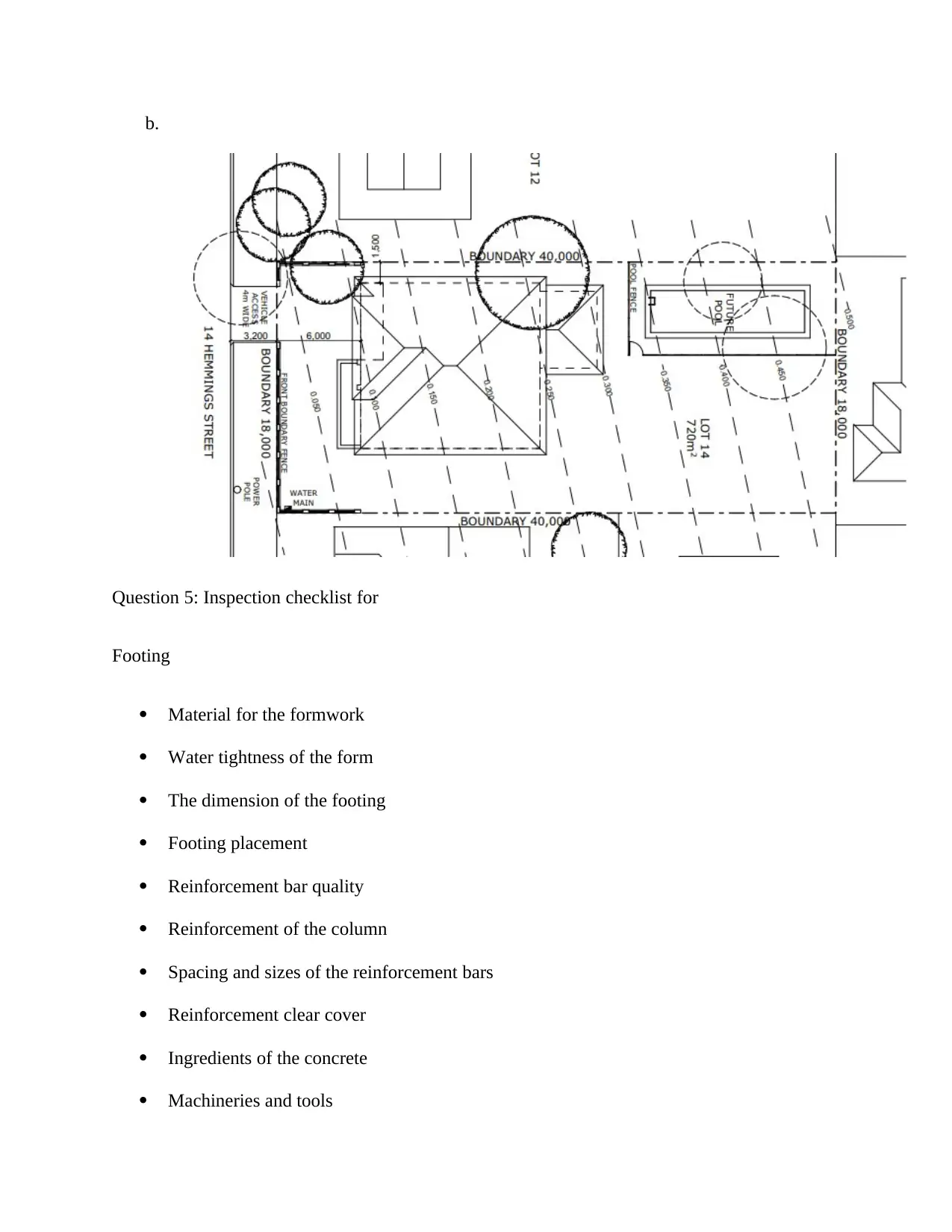
b.
Question 5: Inspection checklist for
Footing
Material for the formwork
Water tightness of the form
The dimension of the footing
Footing placement
Reinforcement bar quality
Reinforcement of the column
Spacing and sizes of the reinforcement bars
Reinforcement clear cover
Ingredients of the concrete
Machineries and tools
Question 5: Inspection checklist for
Footing
Material for the formwork
Water tightness of the form
The dimension of the footing
Footing placement
Reinforcement bar quality
Reinforcement of the column
Spacing and sizes of the reinforcement bars
Reinforcement clear cover
Ingredients of the concrete
Machineries and tools
Paraphrase This Document
Need a fresh take? Get an instant paraphrase of this document with our AI Paraphraser
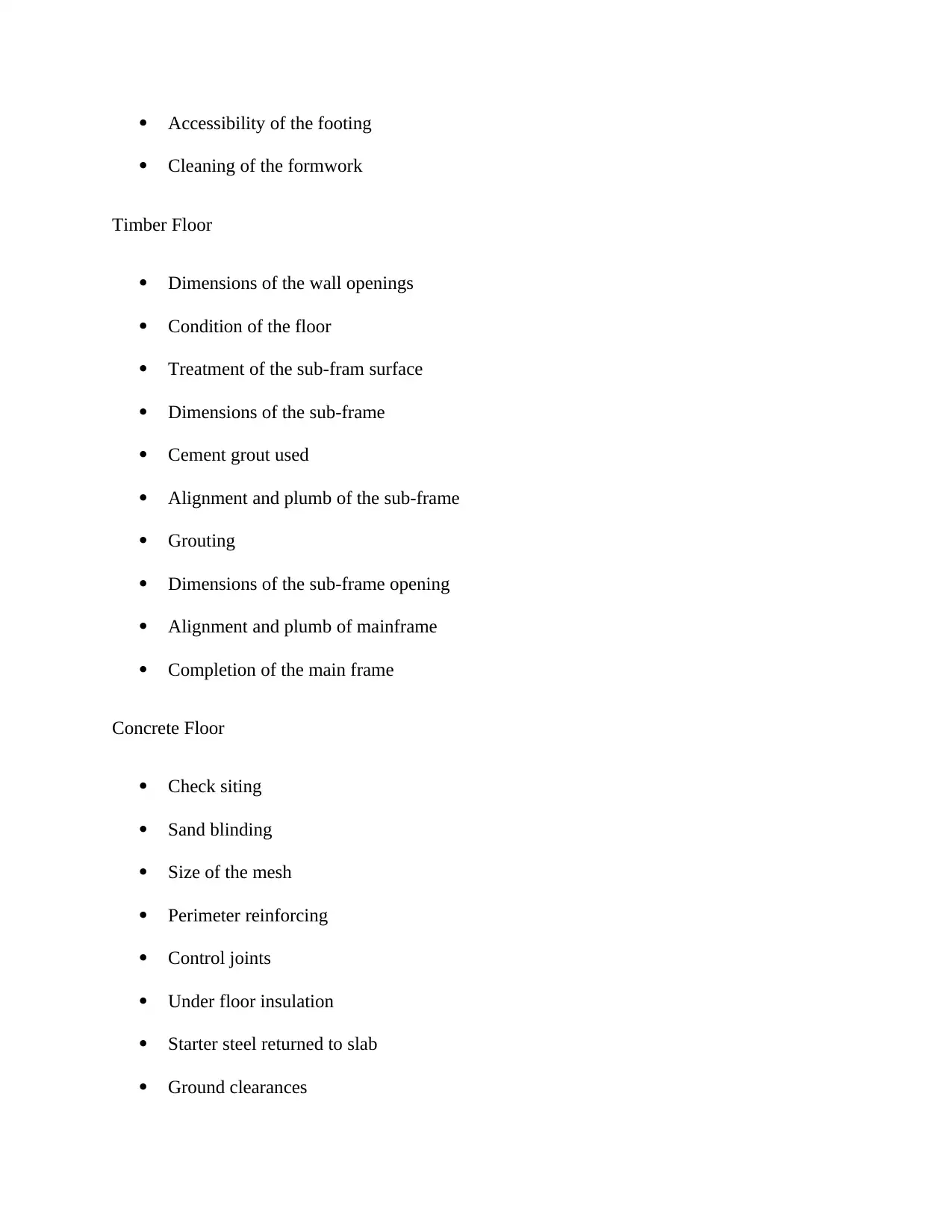
Accessibility of the footing
Cleaning of the formwork
Timber Floor
Dimensions of the wall openings
Condition of the floor
Treatment of the sub-fram surface
Dimensions of the sub-frame
Cement grout used
Alignment and plumb of the sub-frame
Grouting
Dimensions of the sub-frame opening
Alignment and plumb of mainframe
Completion of the main frame
Concrete Floor
Check siting
Sand blinding
Size of the mesh
Perimeter reinforcing
Control joints
Under floor insulation
Starter steel returned to slab
Ground clearances
Cleaning of the formwork
Timber Floor
Dimensions of the wall openings
Condition of the floor
Treatment of the sub-fram surface
Dimensions of the sub-frame
Cement grout used
Alignment and plumb of the sub-frame
Grouting
Dimensions of the sub-frame opening
Alignment and plumb of mainframe
Completion of the main frame
Concrete Floor
Check siting
Sand blinding
Size of the mesh
Perimeter reinforcing
Control joints
Under floor insulation
Starter steel returned to slab
Ground clearances
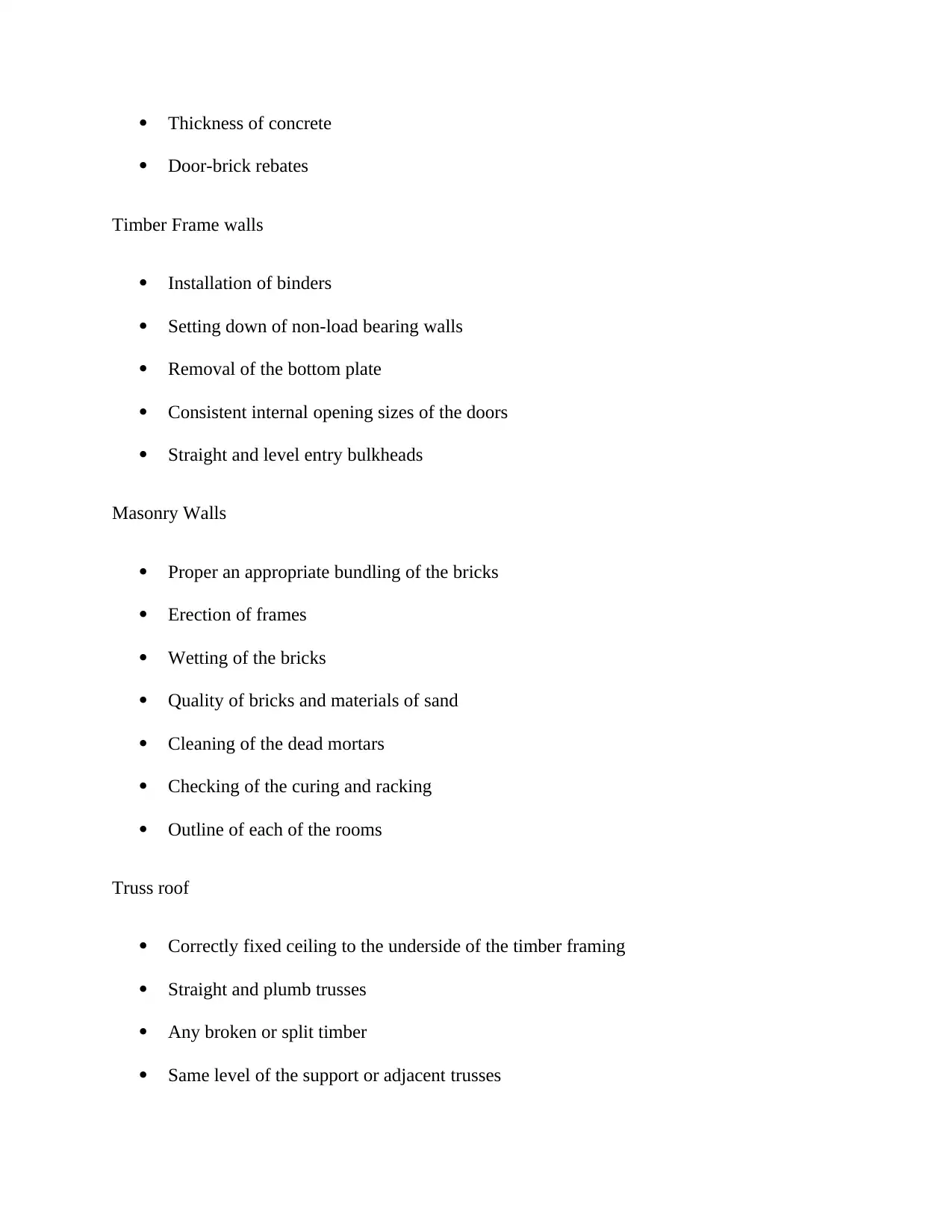
Thickness of concrete
Door-brick rebates
Timber Frame walls
Installation of binders
Setting down of non-load bearing walls
Removal of the bottom plate
Consistent internal opening sizes of the doors
Straight and level entry bulkheads
Masonry Walls
Proper an appropriate bundling of the bricks
Erection of frames
Wetting of the bricks
Quality of bricks and materials of sand
Cleaning of the dead mortars
Checking of the curing and racking
Outline of each of the rooms
Truss roof
Correctly fixed ceiling to the underside of the timber framing
Straight and plumb trusses
Any broken or split timber
Same level of the support or adjacent trusses
Door-brick rebates
Timber Frame walls
Installation of binders
Setting down of non-load bearing walls
Removal of the bottom plate
Consistent internal opening sizes of the doors
Straight and level entry bulkheads
Masonry Walls
Proper an appropriate bundling of the bricks
Erection of frames
Wetting of the bricks
Quality of bricks and materials of sand
Cleaning of the dead mortars
Checking of the curing and racking
Outline of each of the rooms
Truss roof
Correctly fixed ceiling to the underside of the timber framing
Straight and plumb trusses
Any broken or split timber
Same level of the support or adjacent trusses
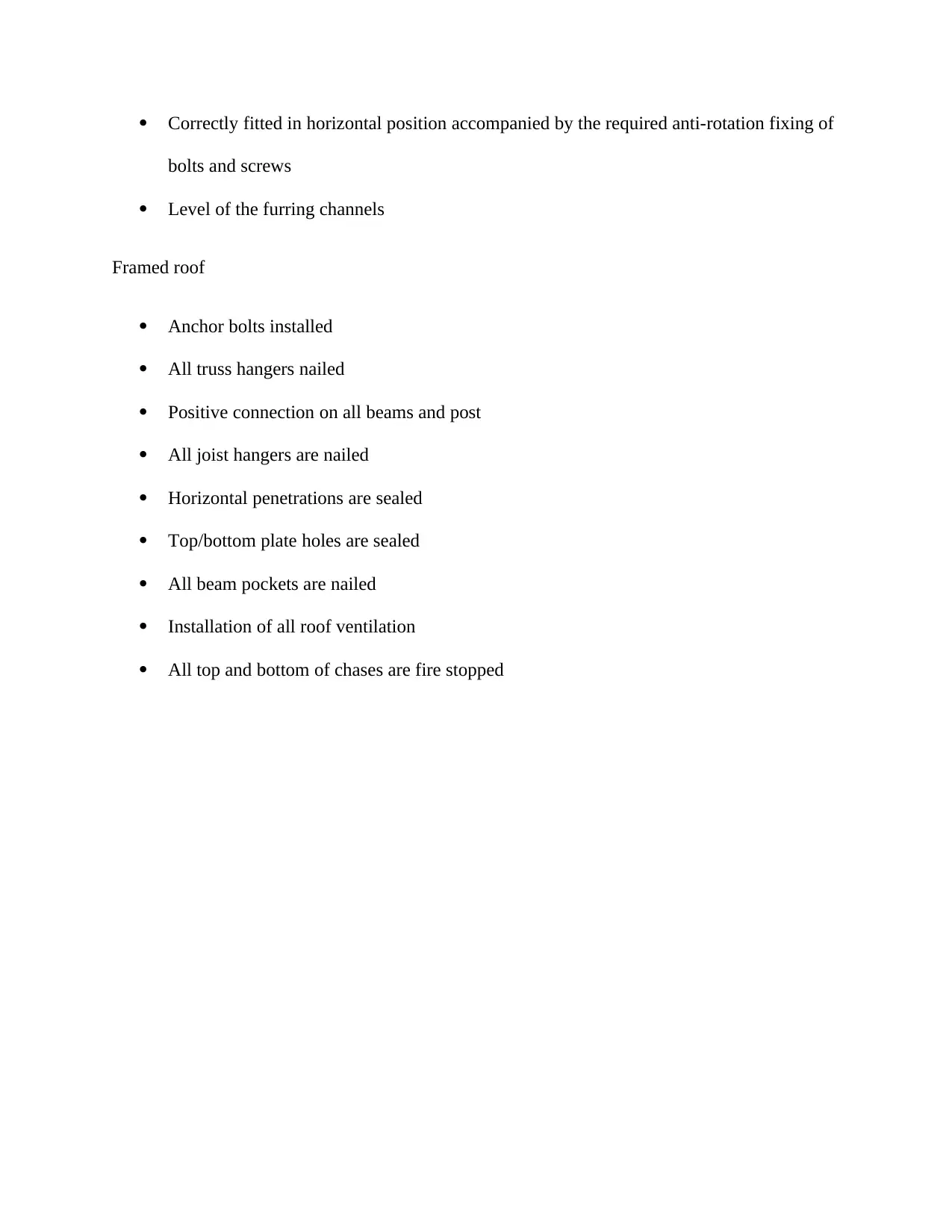
Correctly fitted in horizontal position accompanied by the required anti-rotation fixing of
bolts and screws
Level of the furring channels
Framed roof
Anchor bolts installed
All truss hangers nailed
Positive connection on all beams and post
All joist hangers are nailed
Horizontal penetrations are sealed
Top/bottom plate holes are sealed
All beam pockets are nailed
Installation of all roof ventilation
All top and bottom of chases are fire stopped
bolts and screws
Level of the furring channels
Framed roof
Anchor bolts installed
All truss hangers nailed
Positive connection on all beams and post
All joist hangers are nailed
Horizontal penetrations are sealed
Top/bottom plate holes are sealed
All beam pockets are nailed
Installation of all roof ventilation
All top and bottom of chases are fire stopped
1 out of 16
Related Documents

Your All-in-One AI-Powered Toolkit for Academic Success.
+13062052269
info@desklib.com
Available 24*7 on WhatsApp / Email
Unlock your academic potential
© 2024 | Zucol Services PVT LTD | All rights reserved.