Design and Analysis of Piston for 4 Stroke Petrol Engine for Hero Splendor-Pro Bike
VerifiedAdded on 2023/05/28
|23
|3636
|230
AI Summary
This report discusses the design and analysis of a piston for a 4 stroke petrol engine used in Hero Splendor-Pro Bike. It covers the major forces acting over the piston, its functions, and factors considered for proper functioning. The report also delves into the design considerations, structural design requirements, and material used for pistons. It explores the failure modes of piston and provides insights into the modeling and analysis of the piston using CATIA and ANSYS software.
Contribute Materials
Your contribution can guide someone’s learning journey. Share your
documents today.
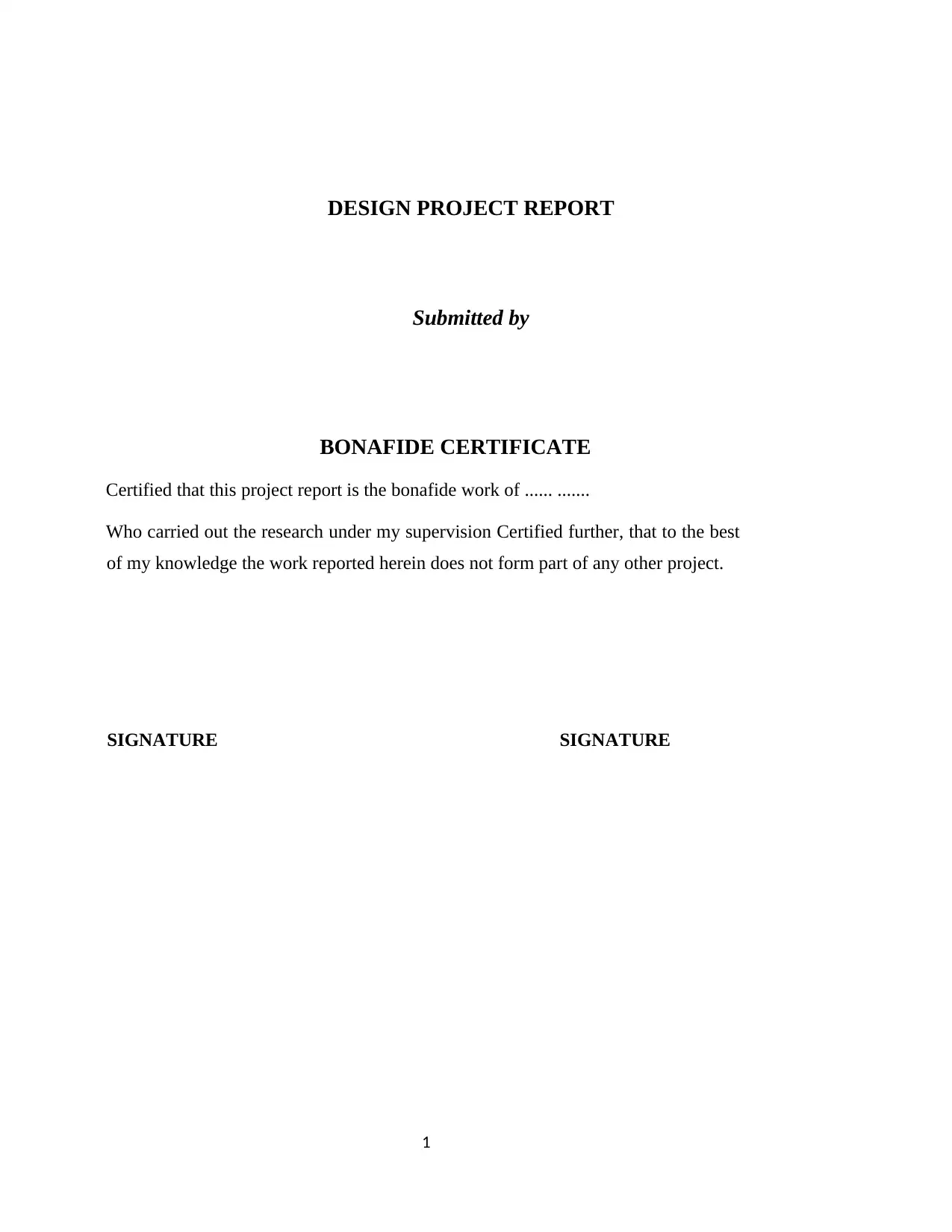
DESIGN PROJECT REPORT
Submitted by
BONAFIDE CERTIFICATE
Certified that this project report is the bonafide work of ...... .......
Who carried out the research under my supervision Certified further, that to the best
of my knowledge the work reported herein does not form part of any other project.
SIGNATURE SIGNATURE
1
Submitted by
BONAFIDE CERTIFICATE
Certified that this project report is the bonafide work of ...... .......
Who carried out the research under my supervision Certified further, that to the best
of my knowledge the work reported herein does not form part of any other project.
SIGNATURE SIGNATURE
1
Secure Best Marks with AI Grader
Need help grading? Try our AI Grader for instant feedback on your assignments.
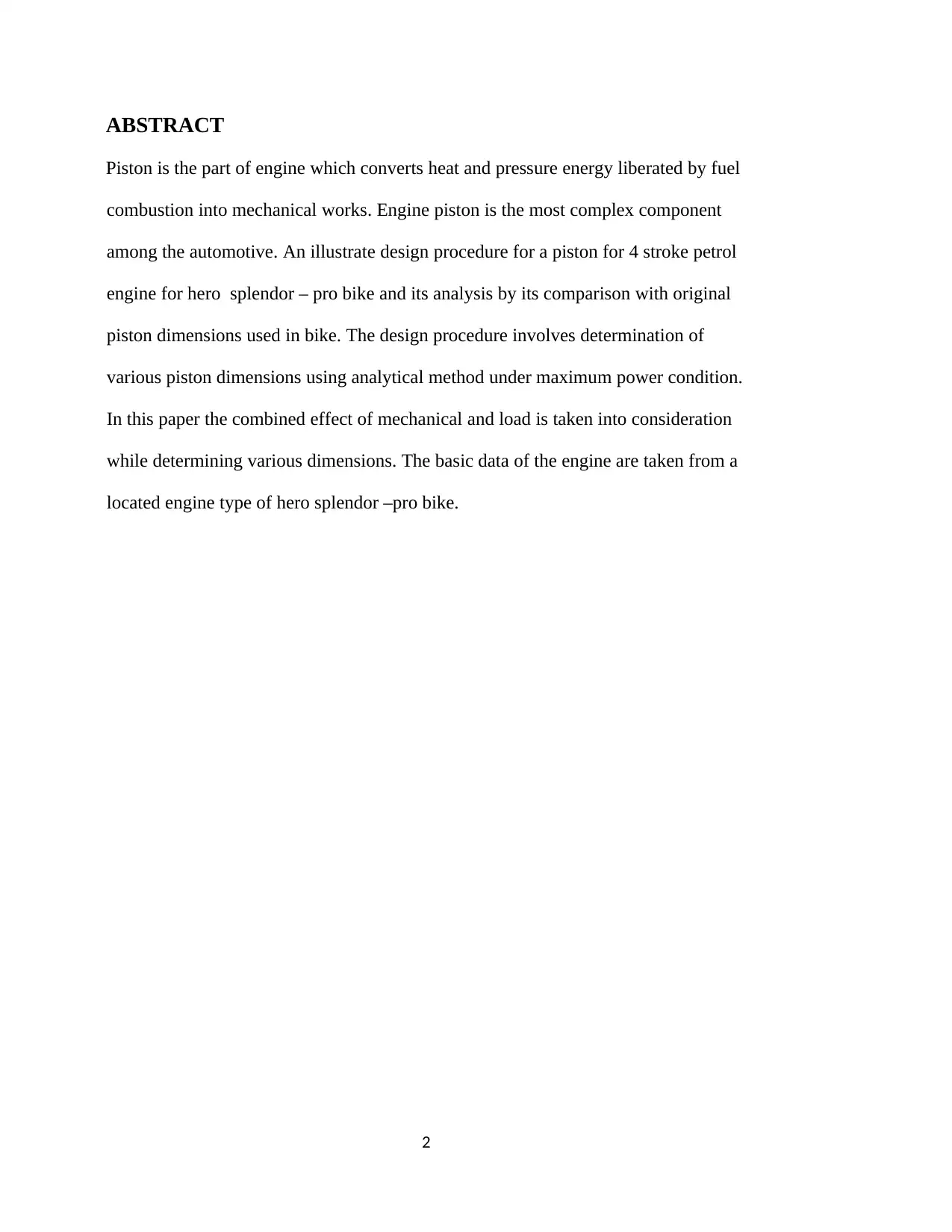
ABSTRACT
Piston is the part of engine which converts heat and pressure energy liberated by fuel
combustion into mechanical works. Engine piston is the most complex component
among the automotive. An illustrate design procedure for a piston for 4 stroke petrol
engine for hero splendor – pro bike and its analysis by its comparison with original
piston dimensions used in bike. The design procedure involves determination of
various piston dimensions using analytical method under maximum power condition.
In this paper the combined effect of mechanical and load is taken into consideration
while determining various dimensions. The basic data of the engine are taken from a
located engine type of hero splendor –pro bike.
2
Piston is the part of engine which converts heat and pressure energy liberated by fuel
combustion into mechanical works. Engine piston is the most complex component
among the automotive. An illustrate design procedure for a piston for 4 stroke petrol
engine for hero splendor – pro bike and its analysis by its comparison with original
piston dimensions used in bike. The design procedure involves determination of
various piston dimensions using analytical method under maximum power condition.
In this paper the combined effect of mechanical and load is taken into consideration
while determining various dimensions. The basic data of the engine are taken from a
located engine type of hero splendor –pro bike.
2
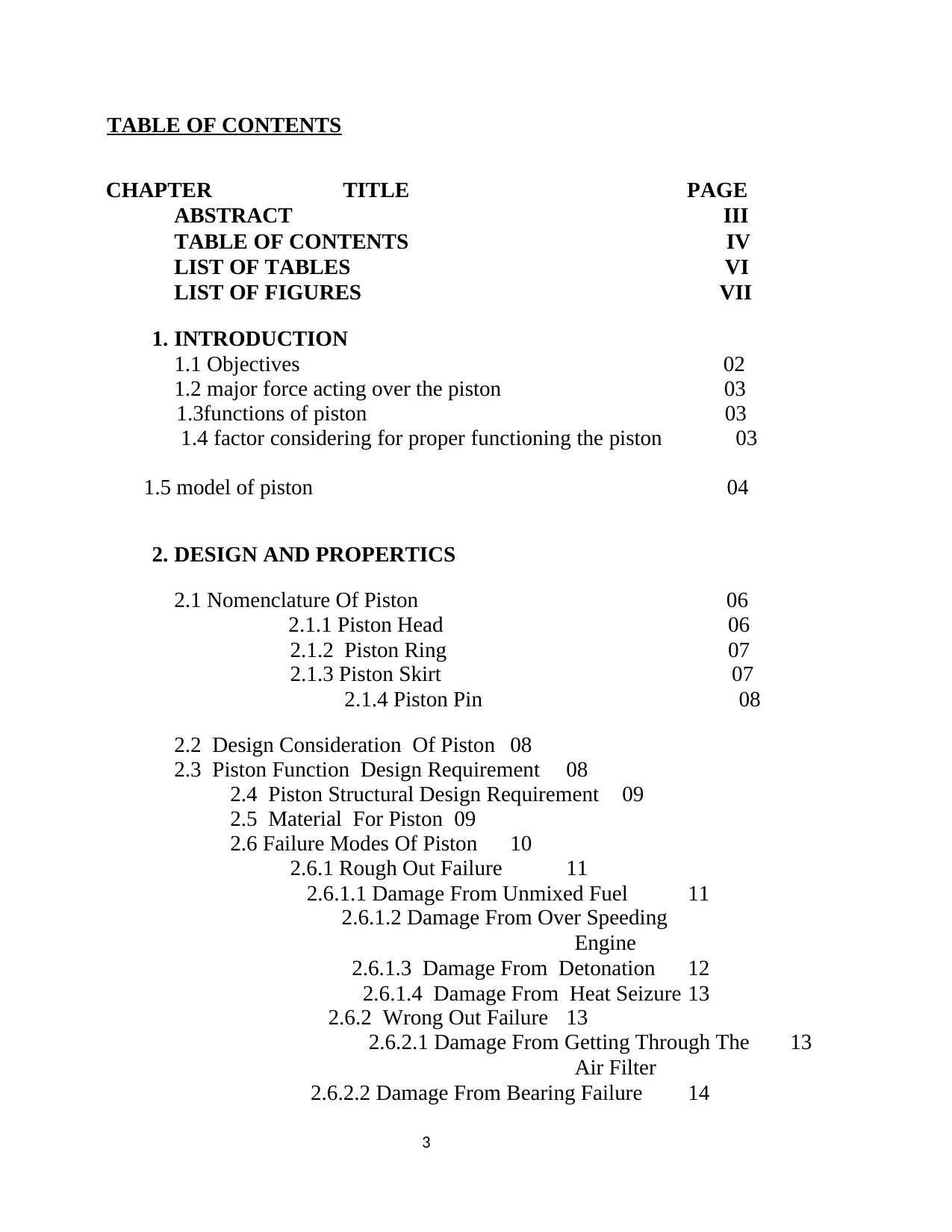
TABLE OF CONTENTS
CHAPTER TITLE PAGE
ABSTRACT III
TABLE OF CONTENTS IV
LIST OF TABLES VI
LIST OF FIGURES VII
1. INTRODUCTION
1.1 Objectives 02
1.2 major force acting over the piston 03
1.3functions of piston 03
1.4 factor considering for proper functioning the piston 03
1.5 model of piston 04
2. DESIGN AND PROPERTICS
2.1 Nomenclature Of Piston 06
2.1.1 Piston Head 06
2.1.2 Piston Ring 07
2.1.3 Piston Skirt 07
2.1.4 Piston Pin 08
2.2 Design Consideration Of Piston 08
2.3 Piston Function Design Requirement 08
2.4 Piston Structural Design Requirement 09
2.5 Material For Piston 09
2.6 Failure Modes Of Piston 10
2.6.1 Rough Out Failure 11
2.6.1.1 Damage From Unmixed Fuel 11
2.6.1.2 Damage From Over Speeding
Engine
2.6.1.3 Damage From Detonation 12
2.6.1.4 Damage From Heat Seizure 13
2.6.2 Wrong Out Failure 13
2.6.2.1 Damage From Getting Through The 13
Air Filter
2.6.2.2 Damage From Bearing Failure 14
3
CHAPTER TITLE PAGE
ABSTRACT III
TABLE OF CONTENTS IV
LIST OF TABLES VI
LIST OF FIGURES VII
1. INTRODUCTION
1.1 Objectives 02
1.2 major force acting over the piston 03
1.3functions of piston 03
1.4 factor considering for proper functioning the piston 03
1.5 model of piston 04
2. DESIGN AND PROPERTICS
2.1 Nomenclature Of Piston 06
2.1.1 Piston Head 06
2.1.2 Piston Ring 07
2.1.3 Piston Skirt 07
2.1.4 Piston Pin 08
2.2 Design Consideration Of Piston 08
2.3 Piston Function Design Requirement 08
2.4 Piston Structural Design Requirement 09
2.5 Material For Piston 09
2.6 Failure Modes Of Piston 10
2.6.1 Rough Out Failure 11
2.6.1.1 Damage From Unmixed Fuel 11
2.6.1.2 Damage From Over Speeding
Engine
2.6.1.3 Damage From Detonation 12
2.6.1.4 Damage From Heat Seizure 13
2.6.2 Wrong Out Failure 13
2.6.2.1 Damage From Getting Through The 13
Air Filter
2.6.2.2 Damage From Bearing Failure 14
3
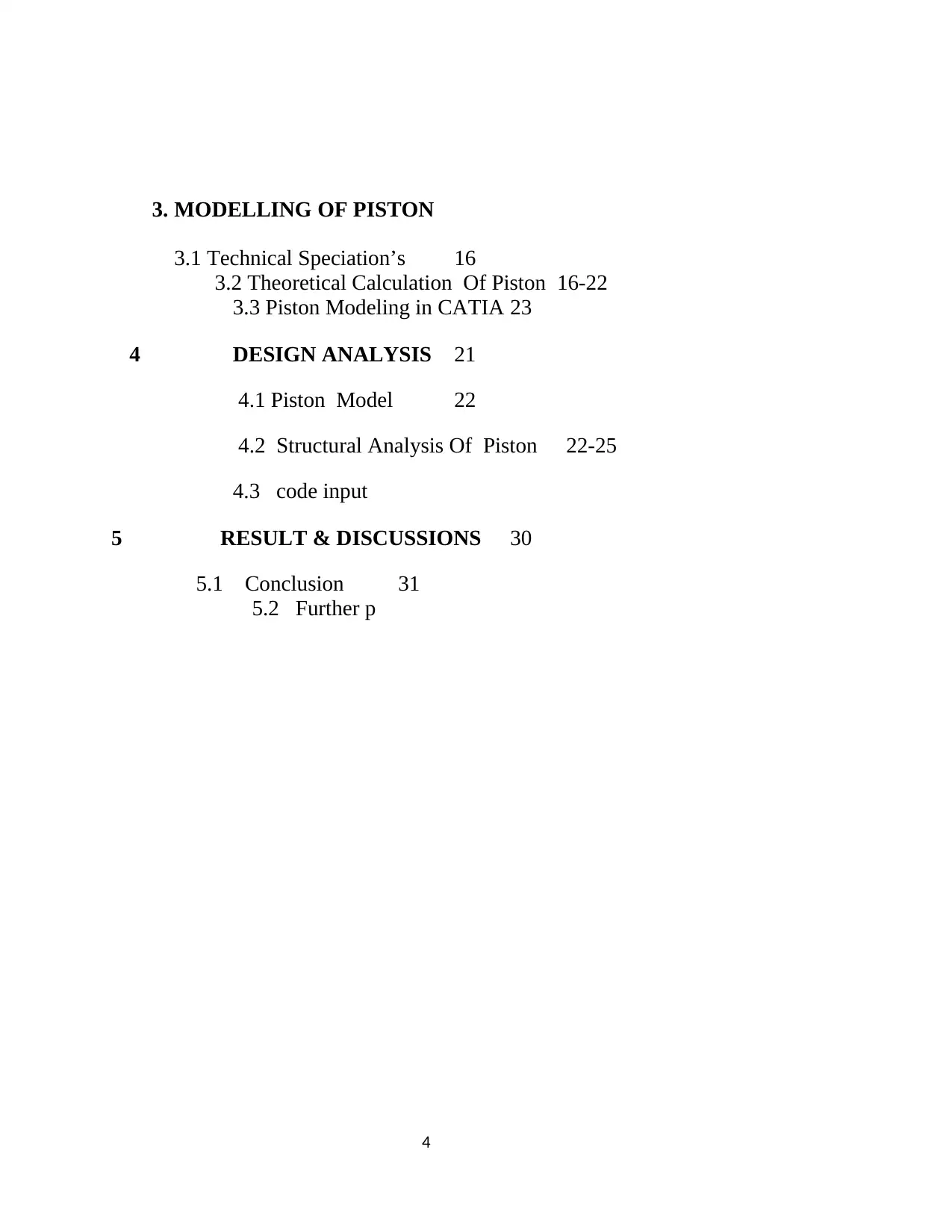
3. MODELLING OF PISTON
3.1 Technical Speciation’s 16
3.2 Theoretical Calculation Of Piston 16-22
3.3 Piston Modeling in CATIA 23
4 DESIGN ANALYSIS 21
4.1 Piston Model 22
4.2 Structural Analysis Of Piston 22-25
4.3 code input
5 RESULT & DISCUSSIONS 30
5.1 Conclusion 31
5.2 Further p
4
3.1 Technical Speciation’s 16
3.2 Theoretical Calculation Of Piston 16-22
3.3 Piston Modeling in CATIA 23
4 DESIGN ANALYSIS 21
4.1 Piston Model 22
4.2 Structural Analysis Of Piston 22-25
4.3 code input
5 RESULT & DISCUSSIONS 30
5.1 Conclusion 31
5.2 Further p
4
Secure Best Marks with AI Grader
Need help grading? Try our AI Grader for instant feedback on your assignments.
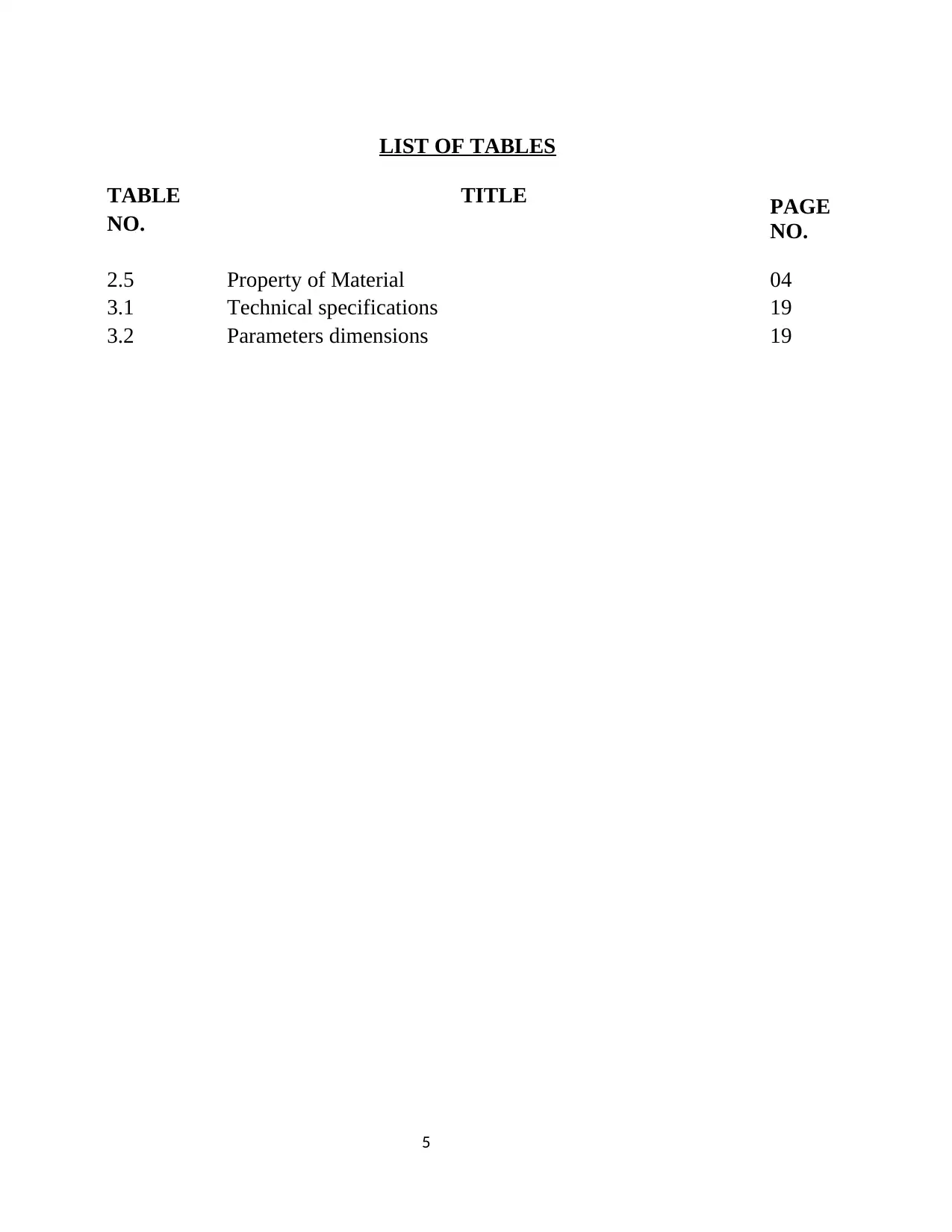
LIST OF TABLES
TABLE
NO.
TITLE PAGE
NO.
2.5 Property of Material 04
3.1 Technical specifications 19
3.2 Parameters dimensions 19
5
TABLE
NO.
TITLE PAGE
NO.
2.5 Property of Material 04
3.1 Technical specifications 19
3.2 Parameters dimensions 19
5
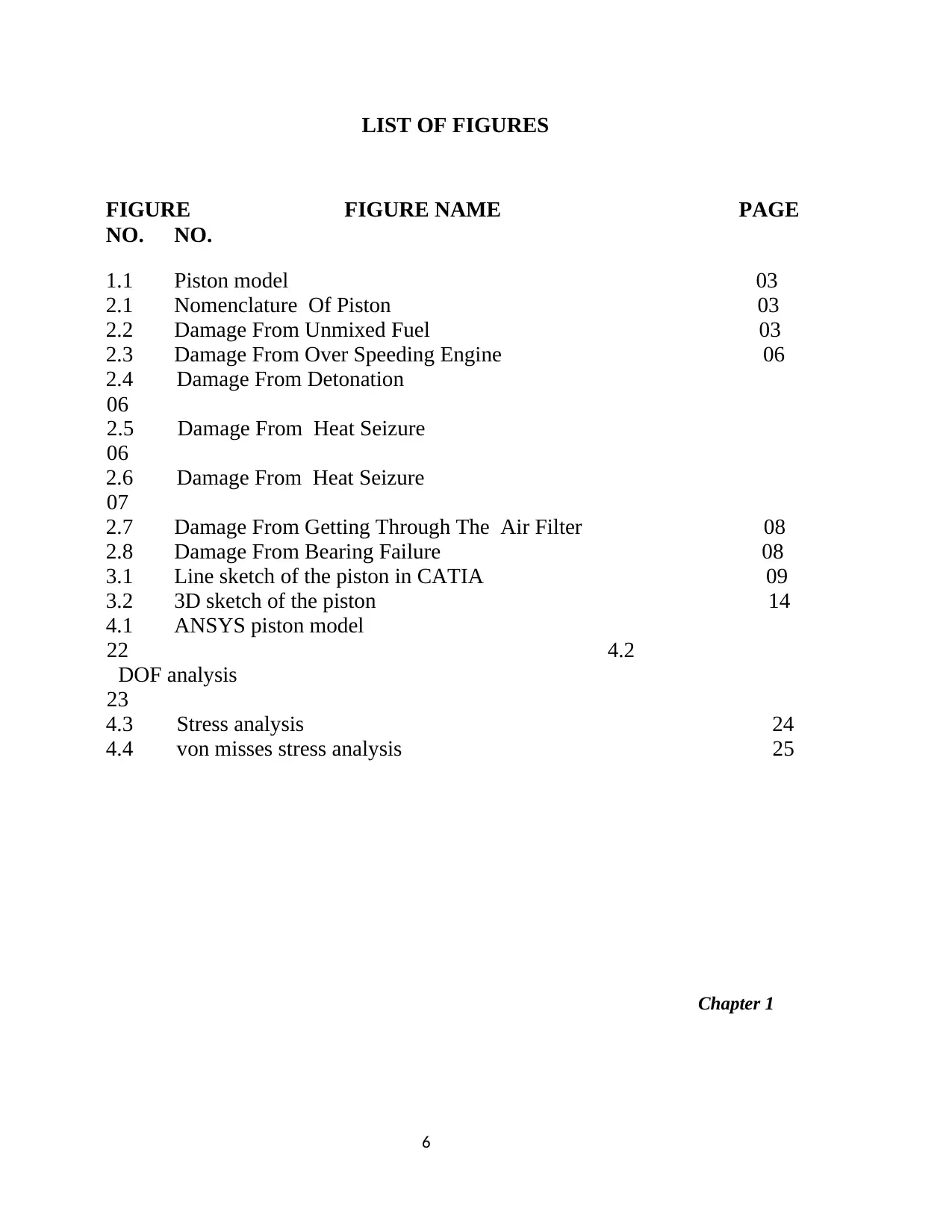
LIST OF FIGURES
FIGURE FIGURE NAME PAGE
NO. NO.
1.1 Piston model 03
2.1 Nomenclature Of Piston 03
2.2 Damage From Unmixed Fuel 03
2.3 Damage From Over Speeding Engine 06
2.4 Damage From Detonation
06
2.5 Damage From Heat Seizure
06
2.6 Damage From Heat Seizure
07
2.7 Damage From Getting Through The Air Filter 08
2.8 Damage From Bearing Failure 08
3.1 Line sketch of the piston in CATIA 09
3.2 3D sketch of the piston 14
4.1 ANSYS piston model
22 4.2
DOF analysis
23
4.3 Stress analysis 24
4.4 von misses stress analysis 25
Chapter 1
6
FIGURE FIGURE NAME PAGE
NO. NO.
1.1 Piston model 03
2.1 Nomenclature Of Piston 03
2.2 Damage From Unmixed Fuel 03
2.3 Damage From Over Speeding Engine 06
2.4 Damage From Detonation
06
2.5 Damage From Heat Seizure
06
2.6 Damage From Heat Seizure
07
2.7 Damage From Getting Through The Air Filter 08
2.8 Damage From Bearing Failure 08
3.1 Line sketch of the piston in CATIA 09
3.2 3D sketch of the piston 14
4.1 ANSYS piston model
22 4.2
DOF analysis
23
4.3 Stress analysis 24
4.4 von misses stress analysis 25
Chapter 1
6
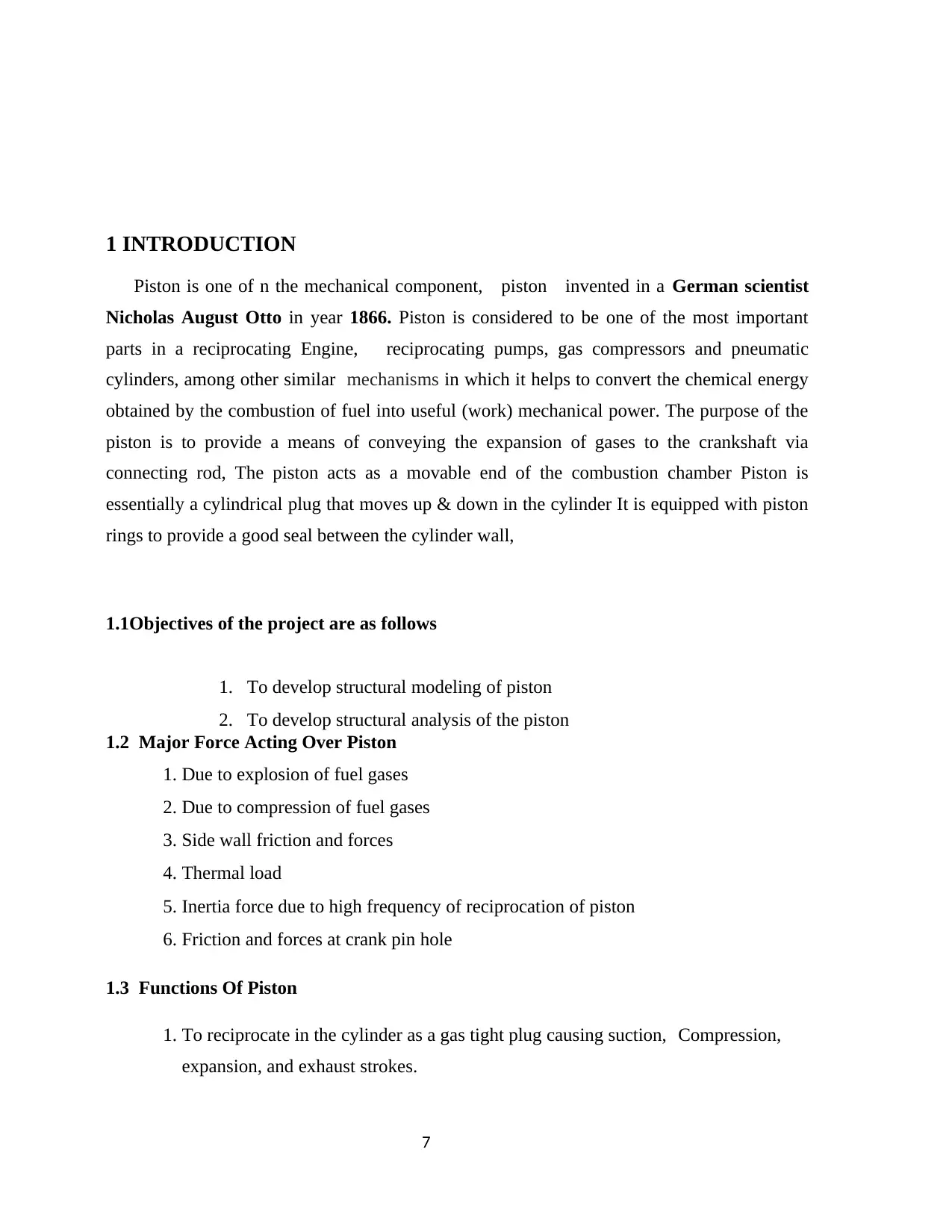
1 INTRODUCTION
Piston is one of n the mechanical component, piston invented in a German scientist
Nicholas August Otto in year 1866. Piston is considered to be one of the most important
parts in a reciprocating Engine, reciprocating pumps, gas compressors and pneumatic
cylinders, among other similar mechanisms in which it helps to convert the chemical energy
obtained by the combustion of fuel into useful (work) mechanical power. The purpose of the
piston is to provide a means of conveying the expansion of gases to the crankshaft via
connecting rod, The piston acts as a movable end of the combustion chamber Piston is
essentially a cylindrical plug that moves up & down in the cylinder It is equipped with piston
rings to provide a good seal between the cylinder wall,
1.1Objectives of the project are as follows
1. To develop structural modeling of piston
2. To develop structural analysis of the piston
1.2 Major Force Acting Over Piston
1. Due to explosion of fuel gases
2. Due to compression of fuel gases
3. Side wall friction and forces
4. Thermal load
5. Inertia force due to high frequency of reciprocation of piston
6. Friction and forces at crank pin hole
1.3 Functions Of Piston
1. To reciprocate in the cylinder as a gas tight plug causing suction, Compression,
expansion, and exhaust strokes.
7
Piston is one of n the mechanical component, piston invented in a German scientist
Nicholas August Otto in year 1866. Piston is considered to be one of the most important
parts in a reciprocating Engine, reciprocating pumps, gas compressors and pneumatic
cylinders, among other similar mechanisms in which it helps to convert the chemical energy
obtained by the combustion of fuel into useful (work) mechanical power. The purpose of the
piston is to provide a means of conveying the expansion of gases to the crankshaft via
connecting rod, The piston acts as a movable end of the combustion chamber Piston is
essentially a cylindrical plug that moves up & down in the cylinder It is equipped with piston
rings to provide a good seal between the cylinder wall,
1.1Objectives of the project are as follows
1. To develop structural modeling of piston
2. To develop structural analysis of the piston
1.2 Major Force Acting Over Piston
1. Due to explosion of fuel gases
2. Due to compression of fuel gases
3. Side wall friction and forces
4. Thermal load
5. Inertia force due to high frequency of reciprocation of piston
6. Friction and forces at crank pin hole
1.3 Functions Of Piston
1. To reciprocate in the cylinder as a gas tight plug causing suction, Compression,
expansion, and exhaust strokes.
7
Paraphrase This Document
Need a fresh take? Get an instant paraphrase of this document with our AI Paraphraser

2. To receive the thrust generated by the explosion of the gas in the cylinder and
transmit it to the connecting rod.
3.To form a guide and bearing to the small end of the connecting rod and to take
the side thrust due to obliquity of the rod.
1.4 Factors Considered For Proper Functioning Of Piston
1. The piston should have enormous strength and heat resistance properties to
withstand gas pressure and inertia forces. They should have minimum weight to
minimize the inertia forces.
2. The material of the piston should have good and quick dissipation of heat from the
crown to the rings and bearing area to the cylinder walls. It should form an
effective gas and oil seal.
3. Material of the piston must possess good wearing qualities, so that the piston is
able to maintain sufficient surface-hardness unto the operating temperatures.
4. Piston should have rigid construction to withstand thermal, mechanical distortion
and sufficient area to prevent undue wear. It has even expansion under thermal
loads so should be free as possible from discontinuities
1.5 Piston Assemble Model
DESIGN AND PROPERTIES
2.1 Nomenclature of Piston
2.1.1 Piston Head or Crown
The piston head or crown is designed keeping in view the following two main considerations, i.e.
1. It should have adequate strength to withstand the straining action due to
pressure of explosion inside the engine cylinder, and
8
transmit it to the connecting rod.
3.To form a guide and bearing to the small end of the connecting rod and to take
the side thrust due to obliquity of the rod.
1.4 Factors Considered For Proper Functioning Of Piston
1. The piston should have enormous strength and heat resistance properties to
withstand gas pressure and inertia forces. They should have minimum weight to
minimize the inertia forces.
2. The material of the piston should have good and quick dissipation of heat from the
crown to the rings and bearing area to the cylinder walls. It should form an
effective gas and oil seal.
3. Material of the piston must possess good wearing qualities, so that the piston is
able to maintain sufficient surface-hardness unto the operating temperatures.
4. Piston should have rigid construction to withstand thermal, mechanical distortion
and sufficient area to prevent undue wear. It has even expansion under thermal
loads so should be free as possible from discontinuities
1.5 Piston Assemble Model
DESIGN AND PROPERTIES
2.1 Nomenclature of Piston
2.1.1 Piston Head or Crown
The piston head or crown is designed keeping in view the following two main considerations, i.e.
1. It should have adequate strength to withstand the straining action due to
pressure of explosion inside the engine cylinder, and
8
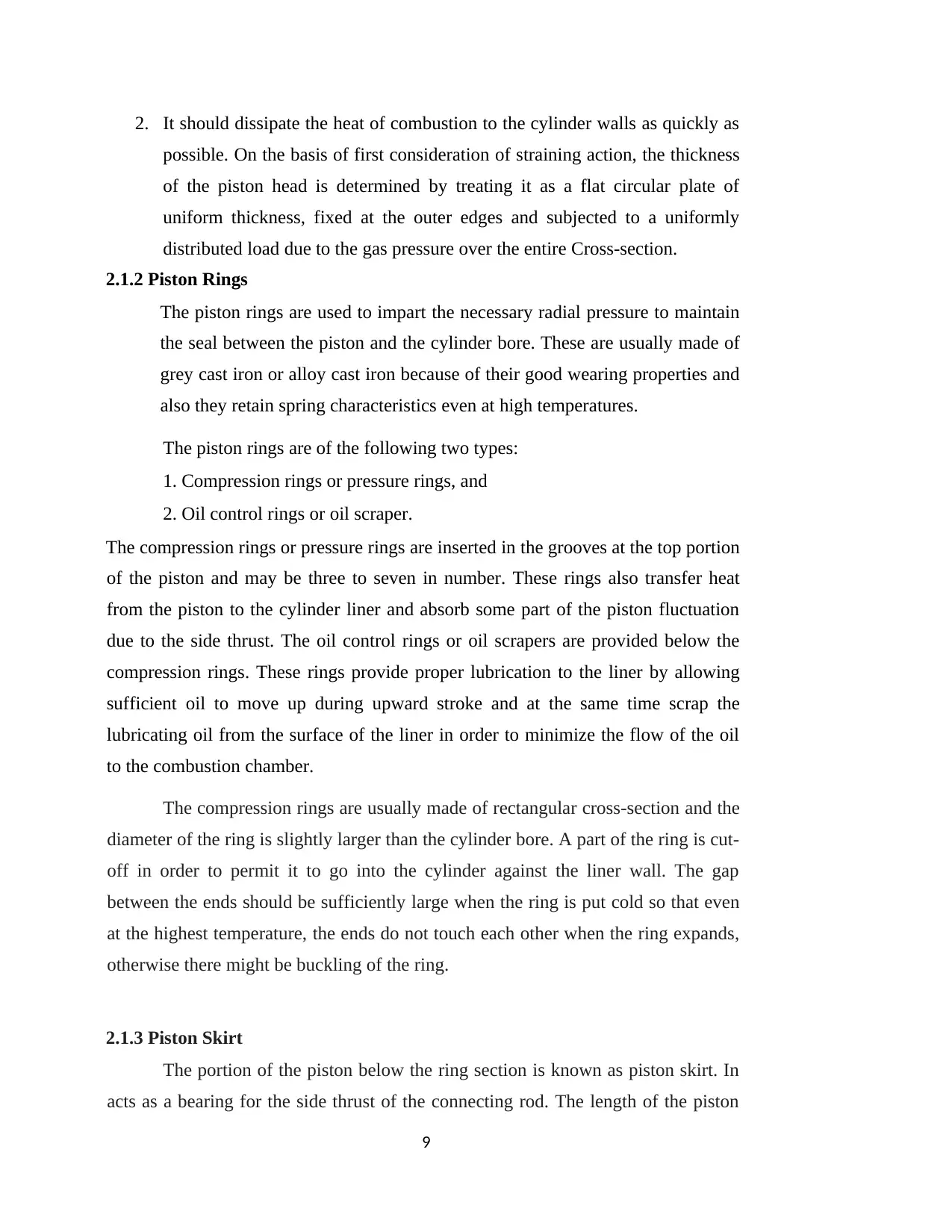
2. It should dissipate the heat of combustion to the cylinder walls as quickly as
possible. On the basis of first consideration of straining action, the thickness
of the piston head is determined by treating it as a flat circular plate of
uniform thickness, fixed at the outer edges and subjected to a uniformly
distributed load due to the gas pressure over the entire Cross-section.
2.1.2 Piston Rings
The piston rings are used to impart the necessary radial pressure to maintain
the seal between the piston and the cylinder bore. These are usually made of
grey cast iron or alloy cast iron because of their good wearing properties and
also they retain spring characteristics even at high temperatures.
The piston rings are of the following two types:
1. Compression rings or pressure rings, and
2. Oil control rings or oil scraper.
The compression rings or pressure rings are inserted in the grooves at the top portion
of the piston and may be three to seven in number. These rings also transfer heat
from the piston to the cylinder liner and absorb some part of the piston fluctuation
due to the side thrust. The oil control rings or oil scrapers are provided below the
compression rings. These rings provide proper lubrication to the liner by allowing
sufficient oil to move up during upward stroke and at the same time scrap the
lubricating oil from the surface of the liner in order to minimize the flow of the oil
to the combustion chamber.
The compression rings are usually made of rectangular cross-section and the
diameter of the ring is slightly larger than the cylinder bore. A part of the ring is cut-
off in order to permit it to go into the cylinder against the liner wall. The gap
between the ends should be sufficiently large when the ring is put cold so that even
at the highest temperature, the ends do not touch each other when the ring expands,
otherwise there might be buckling of the ring.
2.1.3 Piston Skirt
The portion of the piston below the ring section is known as piston skirt. In
acts as a bearing for the side thrust of the connecting rod. The length of the piston
9
possible. On the basis of first consideration of straining action, the thickness
of the piston head is determined by treating it as a flat circular plate of
uniform thickness, fixed at the outer edges and subjected to a uniformly
distributed load due to the gas pressure over the entire Cross-section.
2.1.2 Piston Rings
The piston rings are used to impart the necessary radial pressure to maintain
the seal between the piston and the cylinder bore. These are usually made of
grey cast iron or alloy cast iron because of their good wearing properties and
also they retain spring characteristics even at high temperatures.
The piston rings are of the following two types:
1. Compression rings or pressure rings, and
2. Oil control rings or oil scraper.
The compression rings or pressure rings are inserted in the grooves at the top portion
of the piston and may be three to seven in number. These rings also transfer heat
from the piston to the cylinder liner and absorb some part of the piston fluctuation
due to the side thrust. The oil control rings or oil scrapers are provided below the
compression rings. These rings provide proper lubrication to the liner by allowing
sufficient oil to move up during upward stroke and at the same time scrap the
lubricating oil from the surface of the liner in order to minimize the flow of the oil
to the combustion chamber.
The compression rings are usually made of rectangular cross-section and the
diameter of the ring is slightly larger than the cylinder bore. A part of the ring is cut-
off in order to permit it to go into the cylinder against the liner wall. The gap
between the ends should be sufficiently large when the ring is put cold so that even
at the highest temperature, the ends do not touch each other when the ring expands,
otherwise there might be buckling of the ring.
2.1.3 Piston Skirt
The portion of the piston below the ring section is known as piston skirt. In
acts as a bearing for the side thrust of the connecting rod. The length of the piston
9
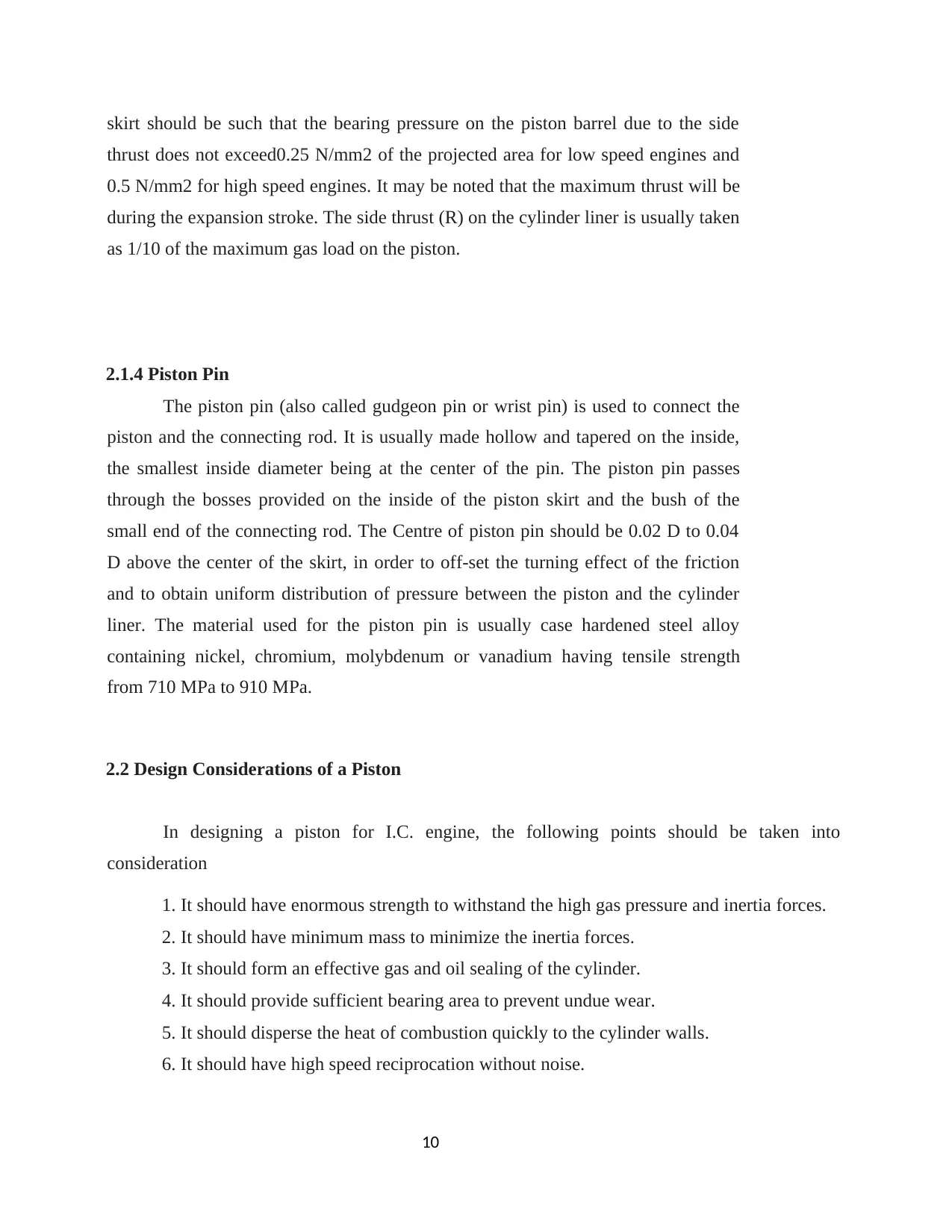
skirt should be such that the bearing pressure on the piston barrel due to the side
thrust does not exceed0.25 N/mm2 of the projected area for low speed engines and
0.5 N/mm2 for high speed engines. It may be noted that the maximum thrust will be
during the expansion stroke. The side thrust (R) on the cylinder liner is usually taken
as 1/10 of the maximum gas load on the piston.
2.1.4 Piston Pin
The piston pin (also called gudgeon pin or wrist pin) is used to connect the
piston and the connecting rod. It is usually made hollow and tapered on the inside,
the smallest inside diameter being at the center of the pin. The piston pin passes
through the bosses provided on the inside of the piston skirt and the bush of the
small end of the connecting rod. The Centre of piston pin should be 0.02 D to 0.04
D above the center of the skirt, in order to off-set the turning effect of the friction
and to obtain uniform distribution of pressure between the piston and the cylinder
liner. The material used for the piston pin is usually case hardened steel alloy
containing nickel, chromium, molybdenum or vanadium having tensile strength
from 710 MPa to 910 MPa.
2.2 Design Considerations of a Piston
In designing a piston for I.C. engine, the following points should be taken into
consideration
1. It should have enormous strength to withstand the high gas pressure and inertia forces.
2. It should have minimum mass to minimize the inertia forces.
3. It should form an effective gas and oil sealing of the cylinder.
4. It should provide sufficient bearing area to prevent undue wear.
5. It should disperse the heat of combustion quickly to the cylinder walls.
6. It should have high speed reciprocation without noise.
10
thrust does not exceed0.25 N/mm2 of the projected area for low speed engines and
0.5 N/mm2 for high speed engines. It may be noted that the maximum thrust will be
during the expansion stroke. The side thrust (R) on the cylinder liner is usually taken
as 1/10 of the maximum gas load on the piston.
2.1.4 Piston Pin
The piston pin (also called gudgeon pin or wrist pin) is used to connect the
piston and the connecting rod. It is usually made hollow and tapered on the inside,
the smallest inside diameter being at the center of the pin. The piston pin passes
through the bosses provided on the inside of the piston skirt and the bush of the
small end of the connecting rod. The Centre of piston pin should be 0.02 D to 0.04
D above the center of the skirt, in order to off-set the turning effect of the friction
and to obtain uniform distribution of pressure between the piston and the cylinder
liner. The material used for the piston pin is usually case hardened steel alloy
containing nickel, chromium, molybdenum or vanadium having tensile strength
from 710 MPa to 910 MPa.
2.2 Design Considerations of a Piston
In designing a piston for I.C. engine, the following points should be taken into
consideration
1. It should have enormous strength to withstand the high gas pressure and inertia forces.
2. It should have minimum mass to minimize the inertia forces.
3. It should form an effective gas and oil sealing of the cylinder.
4. It should provide sufficient bearing area to prevent undue wear.
5. It should disperse the heat of combustion quickly to the cylinder walls.
6. It should have high speed reciprocation without noise.
10
Secure Best Marks with AI Grader
Need help grading? Try our AI Grader for instant feedback on your assignments.
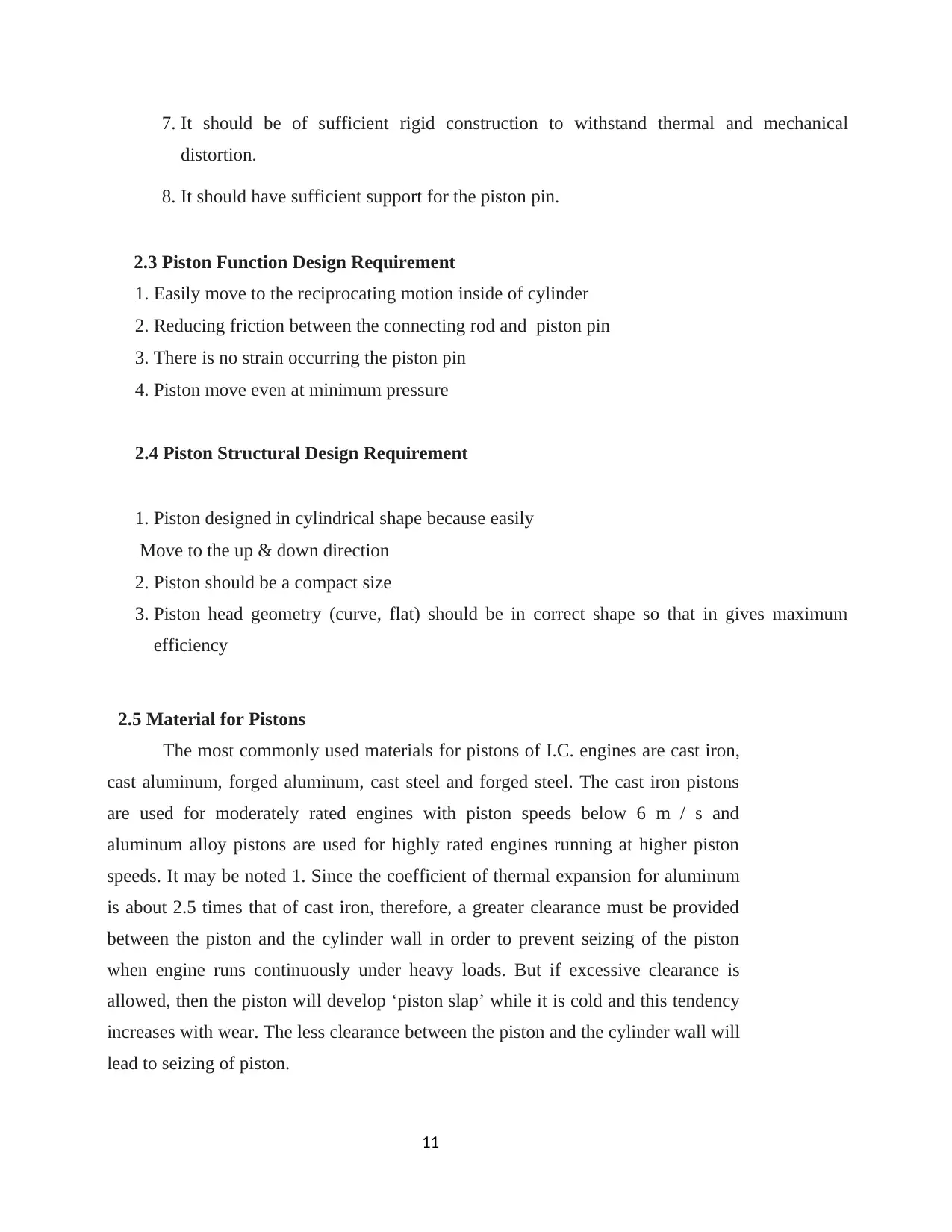
7. It should be of sufficient rigid construction to withstand thermal and mechanical
distortion.
8. It should have sufficient support for the piston pin.
2.3 Piston Function Design Requirement
1. Easily move to the reciprocating motion inside of cylinder
2. Reducing friction between the connecting rod and piston pin
3. There is no strain occurring the piston pin
4. Piston move even at minimum pressure
2.4 Piston Structural Design Requirement
1. Piston designed in cylindrical shape because easily
Move to the up & down direction
2. Piston should be a compact size
3. Piston head geometry (curve, flat) should be in correct shape so that in gives maximum
efficiency
2.5 Material for Pistons
The most commonly used materials for pistons of I.C. engines are cast iron,
cast aluminum, forged aluminum, cast steel and forged steel. The cast iron pistons
are used for moderately rated engines with piston speeds below 6 m / s and
aluminum alloy pistons are used for highly rated engines running at higher piston
speeds. It may be noted 1. Since the coefficient of thermal expansion for aluminum
is about 2.5 times that of cast iron, therefore, a greater clearance must be provided
between the piston and the cylinder wall in order to prevent seizing of the piston
when engine runs continuously under heavy loads. But if excessive clearance is
allowed, then the piston will develop ‘piston slap’ while it is cold and this tendency
increases with wear. The less clearance between the piston and the cylinder wall will
lead to seizing of piston.
11
distortion.
8. It should have sufficient support for the piston pin.
2.3 Piston Function Design Requirement
1. Easily move to the reciprocating motion inside of cylinder
2. Reducing friction between the connecting rod and piston pin
3. There is no strain occurring the piston pin
4. Piston move even at minimum pressure
2.4 Piston Structural Design Requirement
1. Piston designed in cylindrical shape because easily
Move to the up & down direction
2. Piston should be a compact size
3. Piston head geometry (curve, flat) should be in correct shape so that in gives maximum
efficiency
2.5 Material for Pistons
The most commonly used materials for pistons of I.C. engines are cast iron,
cast aluminum, forged aluminum, cast steel and forged steel. The cast iron pistons
are used for moderately rated engines with piston speeds below 6 m / s and
aluminum alloy pistons are used for highly rated engines running at higher piston
speeds. It may be noted 1. Since the coefficient of thermal expansion for aluminum
is about 2.5 times that of cast iron, therefore, a greater clearance must be provided
between the piston and the cylinder wall in order to prevent seizing of the piston
when engine runs continuously under heavy loads. But if excessive clearance is
allowed, then the piston will develop ‘piston slap’ while it is cold and this tendency
increases with wear. The less clearance between the piston and the cylinder wall will
lead to seizing of piston.
11
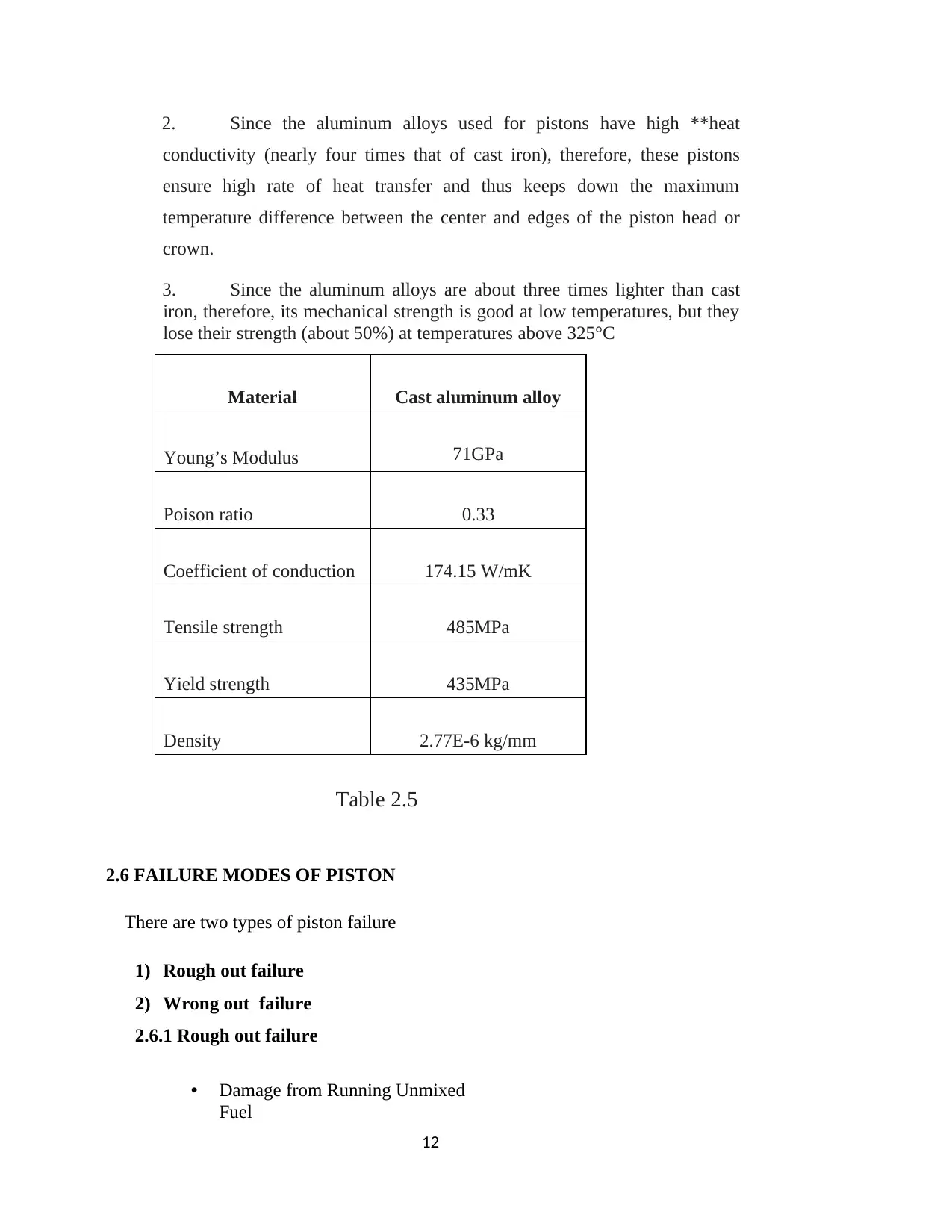
2. Since the aluminum alloys used for pistons have high **heat
conductivity (nearly four times that of cast iron), therefore, these pistons
ensure high rate of heat transfer and thus keeps down the maximum
temperature difference between the center and edges of the piston head or
crown.
3. Since the aluminum alloys are about three times lighter than cast
iron, therefore, its mechanical strength is good at low temperatures, but they
lose their strength (about 50%) at temperatures above 325°C
Material Cast aluminum alloy
Young’s Modulus 71GPa
Poison ratio 0.33
Coefficient of conduction 174.15 W/mK
Tensile strength 485MPa
Yield strength 435MPa
Density 2.77E-6 kg/mm
Table 2.5
2.6 FAILURE MODES OF PISTON
There are two types of piston failure
1) Rough out failure
2) Wrong out failure
2.6.1 Rough out failure
• Damage from Running Unmixed
Fuel
12
conductivity (nearly four times that of cast iron), therefore, these pistons
ensure high rate of heat transfer and thus keeps down the maximum
temperature difference between the center and edges of the piston head or
crown.
3. Since the aluminum alloys are about three times lighter than cast
iron, therefore, its mechanical strength is good at low temperatures, but they
lose their strength (about 50%) at temperatures above 325°C
Material Cast aluminum alloy
Young’s Modulus 71GPa
Poison ratio 0.33
Coefficient of conduction 174.15 W/mK
Tensile strength 485MPa
Yield strength 435MPa
Density 2.77E-6 kg/mm
Table 2.5
2.6 FAILURE MODES OF PISTON
There are two types of piston failure
1) Rough out failure
2) Wrong out failure
2.6.1 Rough out failure
• Damage from Running Unmixed
Fuel
12

• Damage from Over-Speeding the
Engine
• Damage from Detonation
• Damage from Heat Seizure
1) Wrong out failure
• Damage from Debris Getting Through the Air Filter
• Damage From Bearing Failure
• Rough out failure
2.6.1.1 Damage from Running Unmixed Fuel
The piston above has severe scouring on the exhaust skirt with the heaviest damage on the
clutch side of the piston. All of this damage was caused from running straight fuel. The
lack of lubrication on the piston has caused it to seize to the cylinder wall. The damage
you see was caused in the moments before the piston "stuck," which seized the engine.
This kind of piston damage can also be found on a saw that was run with the carburetor set too
lean or one that was run with an air leak. If you didn't know this saw had been run with no oil in
the fuel, how would you know it wasn't a heat seizure to fully understand the cause of this failure,
it is important to look at the rest of the piston. The photo below is of the same piston. It shows
additional damage that's usually only found on a saw engine that had been run with unmixed
2.6.1.2 Damage from Over-Speeding the Engine
The piston above has been damaged by over-speeding. Look at the piston material
between the ring-lands. You can see a big chunk of it is missing and some has been
"squished" thinner, creating a super-wide ring-land. Look at the top ring (bottom of
photo). You can see the edge is rounded-over, a sure sign the rings were catching in
the exhaust port. When this occurs, this sets off a high frequency vibration, eventually
breaking the ring-land.
13
Engine
• Damage from Detonation
• Damage from Heat Seizure
1) Wrong out failure
• Damage from Debris Getting Through the Air Filter
• Damage From Bearing Failure
• Rough out failure
2.6.1.1 Damage from Running Unmixed Fuel
The piston above has severe scouring on the exhaust skirt with the heaviest damage on the
clutch side of the piston. All of this damage was caused from running straight fuel. The
lack of lubrication on the piston has caused it to seize to the cylinder wall. The damage
you see was caused in the moments before the piston "stuck," which seized the engine.
This kind of piston damage can also be found on a saw that was run with the carburetor set too
lean or one that was run with an air leak. If you didn't know this saw had been run with no oil in
the fuel, how would you know it wasn't a heat seizure to fully understand the cause of this failure,
it is important to look at the rest of the piston. The photo below is of the same piston. It shows
additional damage that's usually only found on a saw engine that had been run with unmixed
2.6.1.2 Damage from Over-Speeding the Engine
The piston above has been damaged by over-speeding. Look at the piston material
between the ring-lands. You can see a big chunk of it is missing and some has been
"squished" thinner, creating a super-wide ring-land. Look at the top ring (bottom of
photo). You can see the edge is rounded-over, a sure sign the rings were catching in
the exhaust port. When this occurs, this sets off a high frequency vibration, eventually
breaking the ring-land.
13
Paraphrase This Document
Need a fresh take? Get an instant paraphrase of this document with our AI Paraphraser
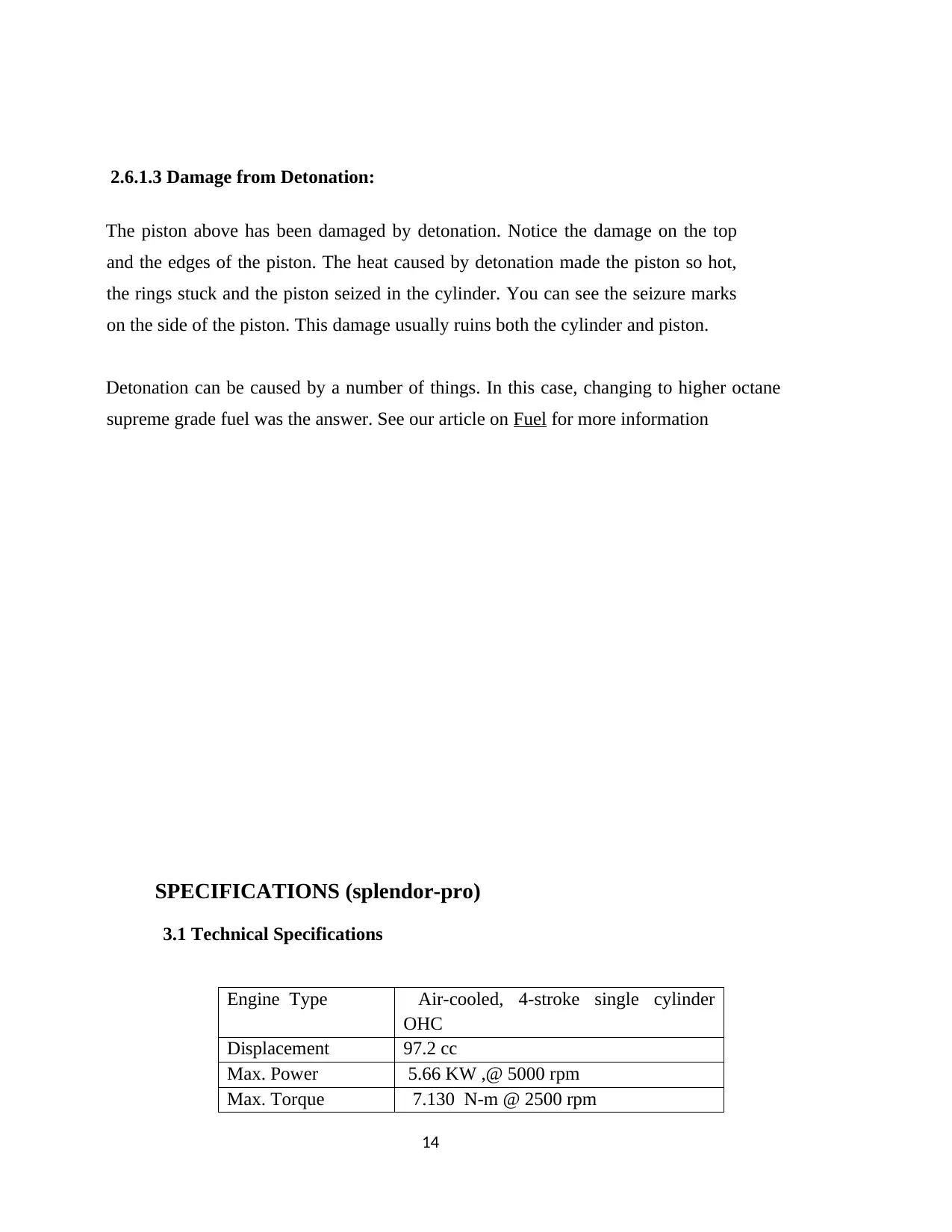
2.6.1.3 Damage from Detonation:
The piston above has been damaged by detonation. Notice the damage on the top
and the edges of the piston. The heat caused by detonation made the piston so hot,
the rings stuck and the piston seized in the cylinder. You can see the seizure marks
on the side of the piston. This damage usually ruins both the cylinder and piston.
Detonation can be caused by a number of things. In this case, changing to higher octane
supreme grade fuel was the answer. See our article on Fuel for more information
SPECIFICATIONS (splendor-pro)
3.1 Technical Specifications
Engine Type Air-cooled, 4-stroke single cylinder
OHC
Displacement 97.2 cc
Max. Power 5.66 KW ,@ 5000 rpm
Max. Torque 7.130 N-m @ 2500 rpm
14
The piston above has been damaged by detonation. Notice the damage on the top
and the edges of the piston. The heat caused by detonation made the piston so hot,
the rings stuck and the piston seized in the cylinder. You can see the seizure marks
on the side of the piston. This damage usually ruins both the cylinder and piston.
Detonation can be caused by a number of things. In this case, changing to higher octane
supreme grade fuel was the answer. See our article on Fuel for more information
SPECIFICATIONS (splendor-pro)
3.1 Technical Specifications
Engine Type Air-cooled, 4-stroke single cylinder
OHC
Displacement 97.2 cc
Max. Power 5.66 KW ,@ 5000 rpm
Max. Torque 7.130 N-m @ 2500 rpm
14
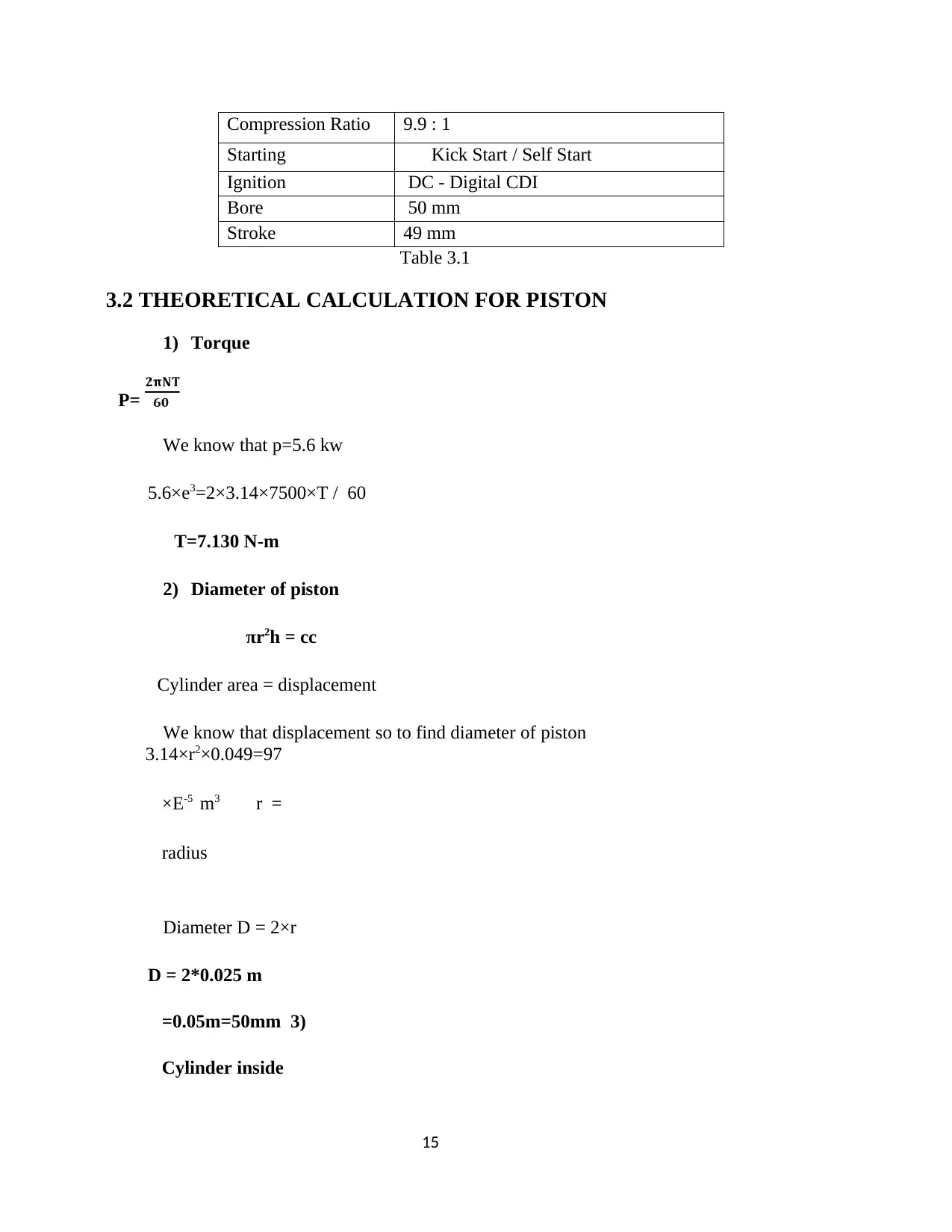
Compression Ratio 9.9 : 1
Starting Kick Start / Self Start
Ignition DC - Digital CDI
Bore 50 mm
Stroke 49 mm
Table 3.1
3.2 THEORETICAL CALCULATION FOR PISTON
1) Torque
P=
We know that p=5.6 kw
5.6×e3=2×3.14×7500×T / 60
T=7.130 N-m
2) Diameter of piston
πr2h = cc
Cylinder area = displacement
We know that displacement so to find diameter of piston
3.14×r2×0.049=97
×E-5 m3 r =
radius
Diameter D = 2×r
D = 2*0.025 m
=0.05m=50mm 3)
Cylinder inside
15
Starting Kick Start / Self Start
Ignition DC - Digital CDI
Bore 50 mm
Stroke 49 mm
Table 3.1
3.2 THEORETICAL CALCULATION FOR PISTON
1) Torque
P=
We know that p=5.6 kw
5.6×e3=2×3.14×7500×T / 60
T=7.130 N-m
2) Diameter of piston
πr2h = cc
Cylinder area = displacement
We know that displacement so to find diameter of piston
3.14×r2×0.049=97
×E-5 m3 r =
radius
Diameter D = 2×r
D = 2*0.025 m
=0.05m=50mm 3)
Cylinder inside
15
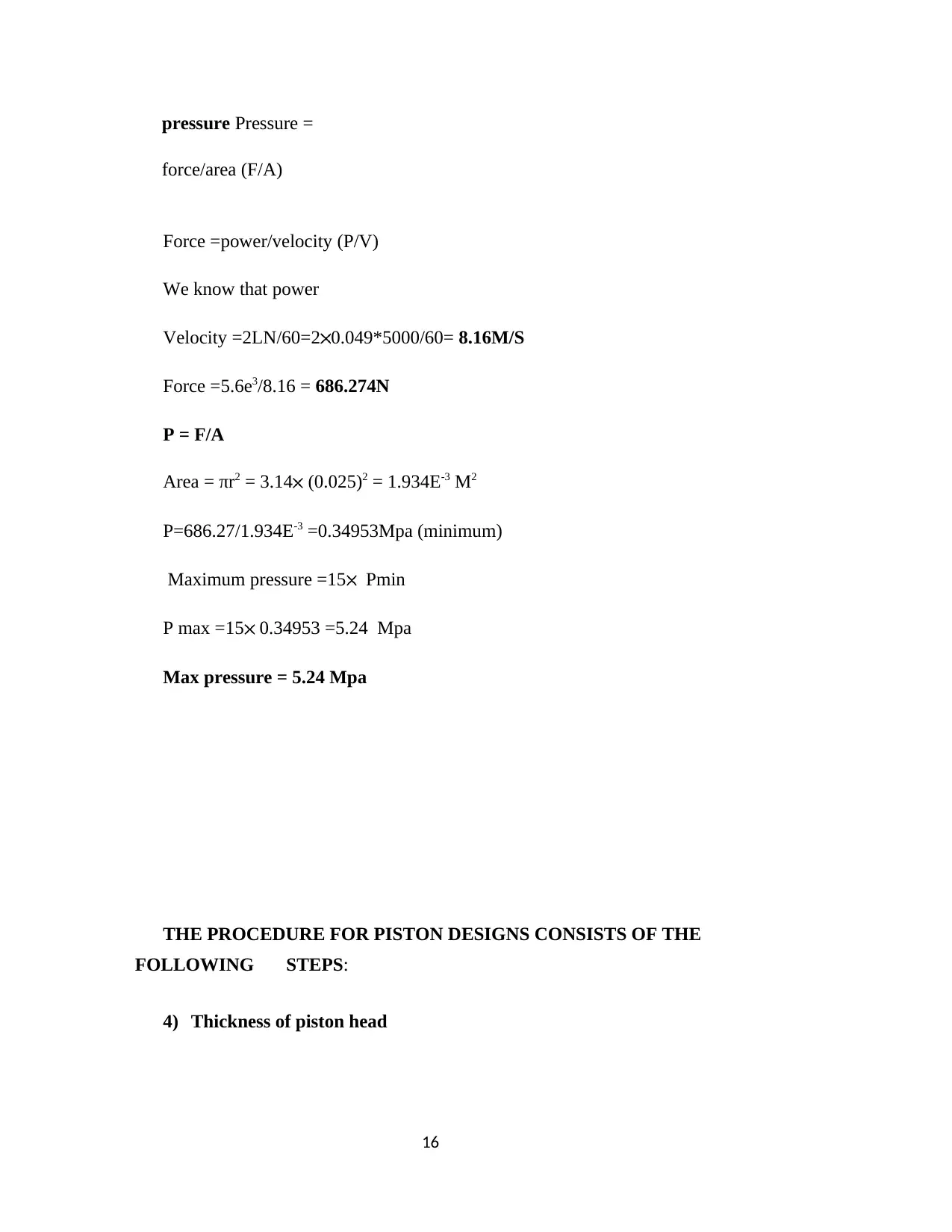
pressure Pressure =
force/area (F/A)
Force =power/velocity (P/V)
We know that power
Velocity =2LN/60=2 0.049*5000/60= 8.16M/S
Force =5.6e3/8.16 = 686.274N
P = F/A
Area = πr2 = 3.14 (0.025)2 = 1.934E-3 M2
P=686.27/1.934E-3 =0.34953Mpa (minimum)
Maximum pressure =15 Pmin
P max =15 0.34953 =5.24 Mpa
Max pressure = 5.24 Mpa
THE PROCEDURE FOR PISTON DESIGNS CONSISTS OF THE
FOLLOWING STEPS:
4) Thickness of piston head
16
force/area (F/A)
Force =power/velocity (P/V)
We know that power
Velocity =2LN/60=2 0.049*5000/60= 8.16M/S
Force =5.6e3/8.16 = 686.274N
P = F/A
Area = πr2 = 3.14 (0.025)2 = 1.934E-3 M2
P=686.27/1.934E-3 =0.34953Mpa (minimum)
Maximum pressure =15 Pmin
P max =15 0.34953 =5.24 Mpa
Max pressure = 5.24 Mpa
THE PROCEDURE FOR PISTON DESIGNS CONSISTS OF THE
FOLLOWING STEPS:
4) Thickness of piston head
16
Secure Best Marks with AI Grader
Need help grading? Try our AI Grader for instant feedback on your assignments.
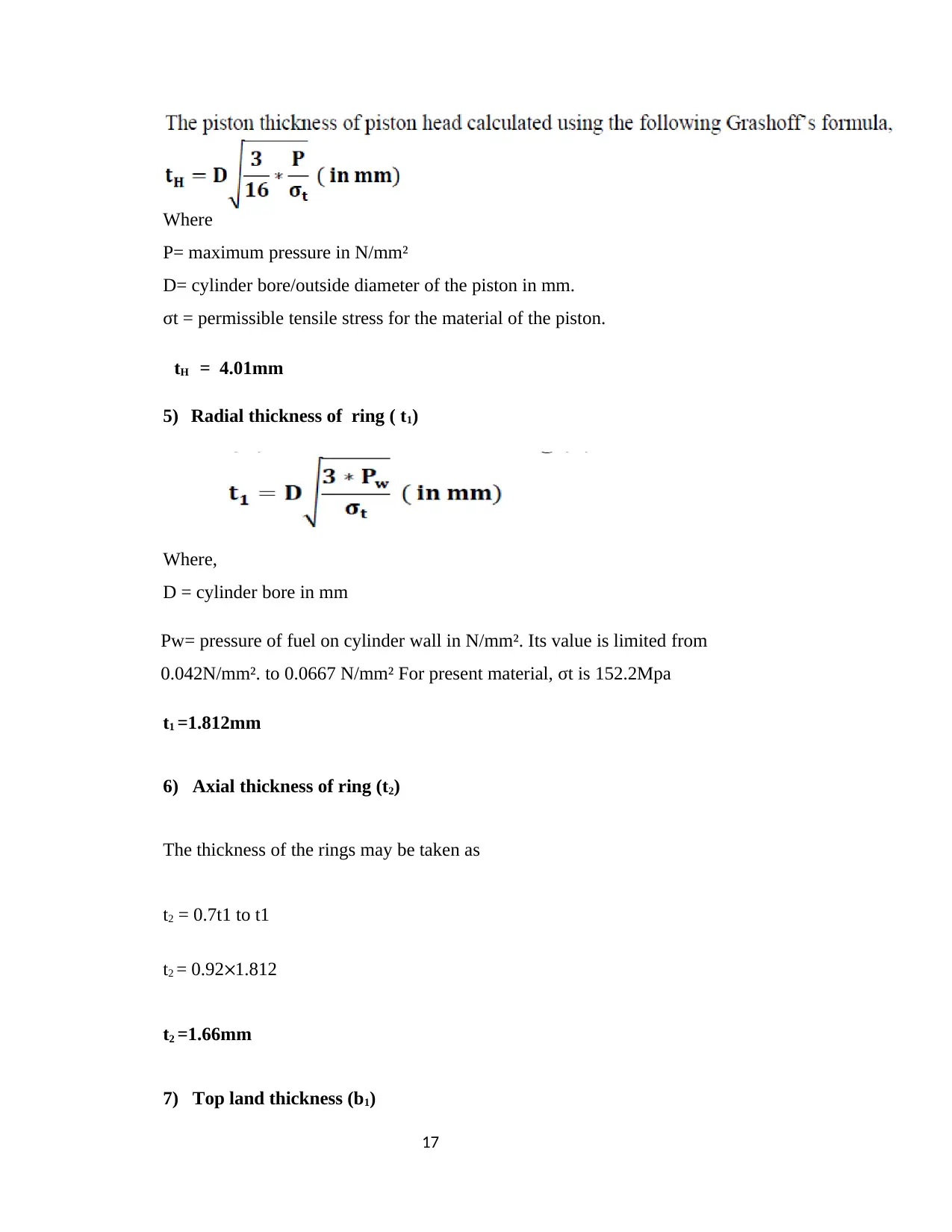
Where
P= maximum pressure in N/mm²
D= cylinder bore/outside diameter of the piston in mm.
σt = permissible tensile stress for the material of the piston.
tH = 4.01mm
5) Radial thickness of ring ( t1)
Where,
D = cylinder bore in mm
Pw= pressure of fuel on cylinder wall in N/mm². Its value is limited from
0.042N/mm². to 0.0667 N/mm² For present material, σt is 152.2Mpa
t1 =1.812mm
6) Axial thickness of ring (t2)
The thickness of the rings may be taken as
t2 = 0.7t1 to t1
t2 = 0.92 1.812
t2 =1.66mm
7) Top land thickness (b1)
17
P= maximum pressure in N/mm²
D= cylinder bore/outside diameter of the piston in mm.
σt = permissible tensile stress for the material of the piston.
tH = 4.01mm
5) Radial thickness of ring ( t1)
Where,
D = cylinder bore in mm
Pw= pressure of fuel on cylinder wall in N/mm². Its value is limited from
0.042N/mm². to 0.0667 N/mm² For present material, σt is 152.2Mpa
t1 =1.812mm
6) Axial thickness of ring (t2)
The thickness of the rings may be taken as
t2 = 0.7t1 to t1
t2 = 0.92 1.812
t2 =1.66mm
7) Top land thickness (b1)
17
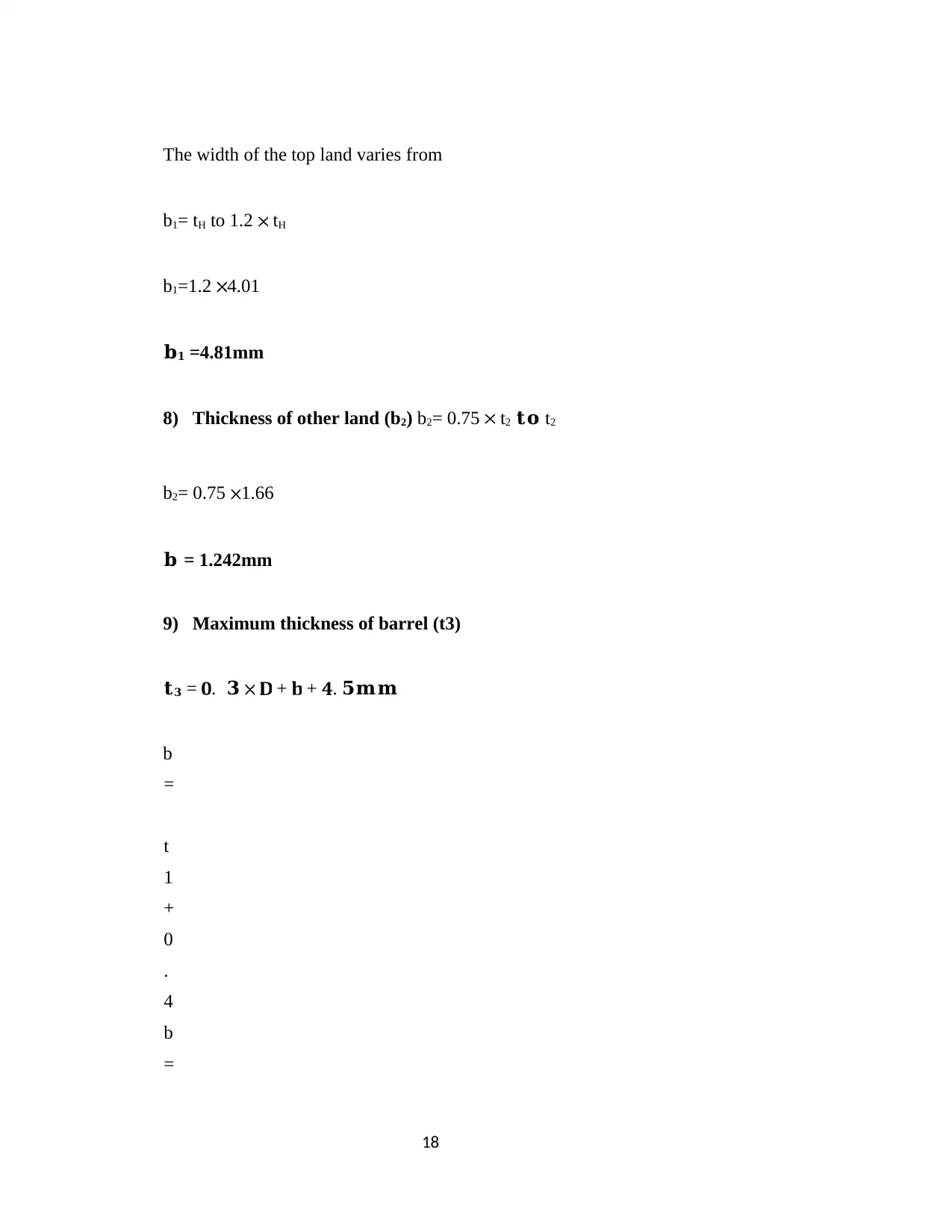
The width of the top land varies from
b1= tH to 1.2 tH
b1=1.2 4.01
𝐛𝟏 =4.81mm
8) Thickness of other land (b2) b2= 0.75 t2 𝐭𝐨 t2
b2= 0.75 1.66
𝐛 = 1.242mm
9) Maximum thickness of barrel (t3)
𝐭𝟑 = . 𝟑 + + . 𝟓𝐦𝐦
b
=
t
1
+
0
.
4
b
=
18
b1= tH to 1.2 tH
b1=1.2 4.01
𝐛𝟏 =4.81mm
8) Thickness of other land (b2) b2= 0.75 t2 𝐭𝐨 t2
b2= 0.75 1.66
𝐛 = 1.242mm
9) Maximum thickness of barrel (t3)
𝐭𝟑 = . 𝟑 + + . 𝟓𝐦𝐦
b
=
t
1
+
0
.
4
b
=
18
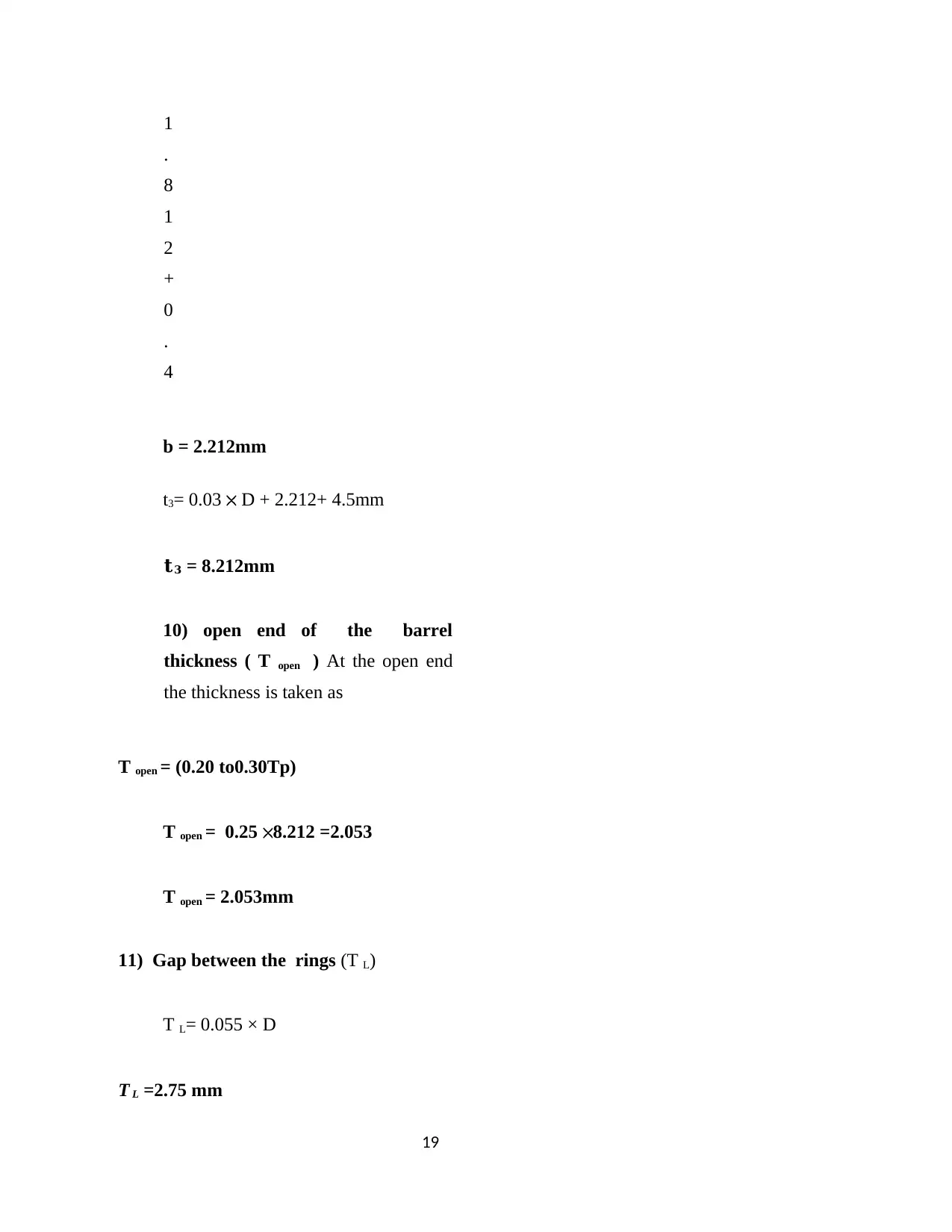
1
.
8
1
2
+
0
.
4
b = 2.212mm
t3= 0.03 D + 2.212+ 4.5mm
𝐭𝟑 = 8.212mm
10) open end of the barrel
thickness ( T open ) At the open end
the thickness is taken as
T open = (0.20 to0.30Tp)
T open = 0.25 8.212 =2.053
T open = 2.053mm
11) Gap between the rings (T L)
T L= 0.055 × D
T L =2.75 mm
19
.
8
1
2
+
0
.
4
b = 2.212mm
t3= 0.03 D + 2.212+ 4.5mm
𝐭𝟑 = 8.212mm
10) open end of the barrel
thickness ( T open ) At the open end
the thickness is taken as
T open = (0.20 to0.30Tp)
T open = 0.25 8.212 =2.053
T open = 2.053mm
11) Gap between the rings (T L)
T L= 0.055 × D
T L =2.75 mm
19
Paraphrase This Document
Need a fresh take? Get an instant paraphrase of this document with our AI Paraphraser
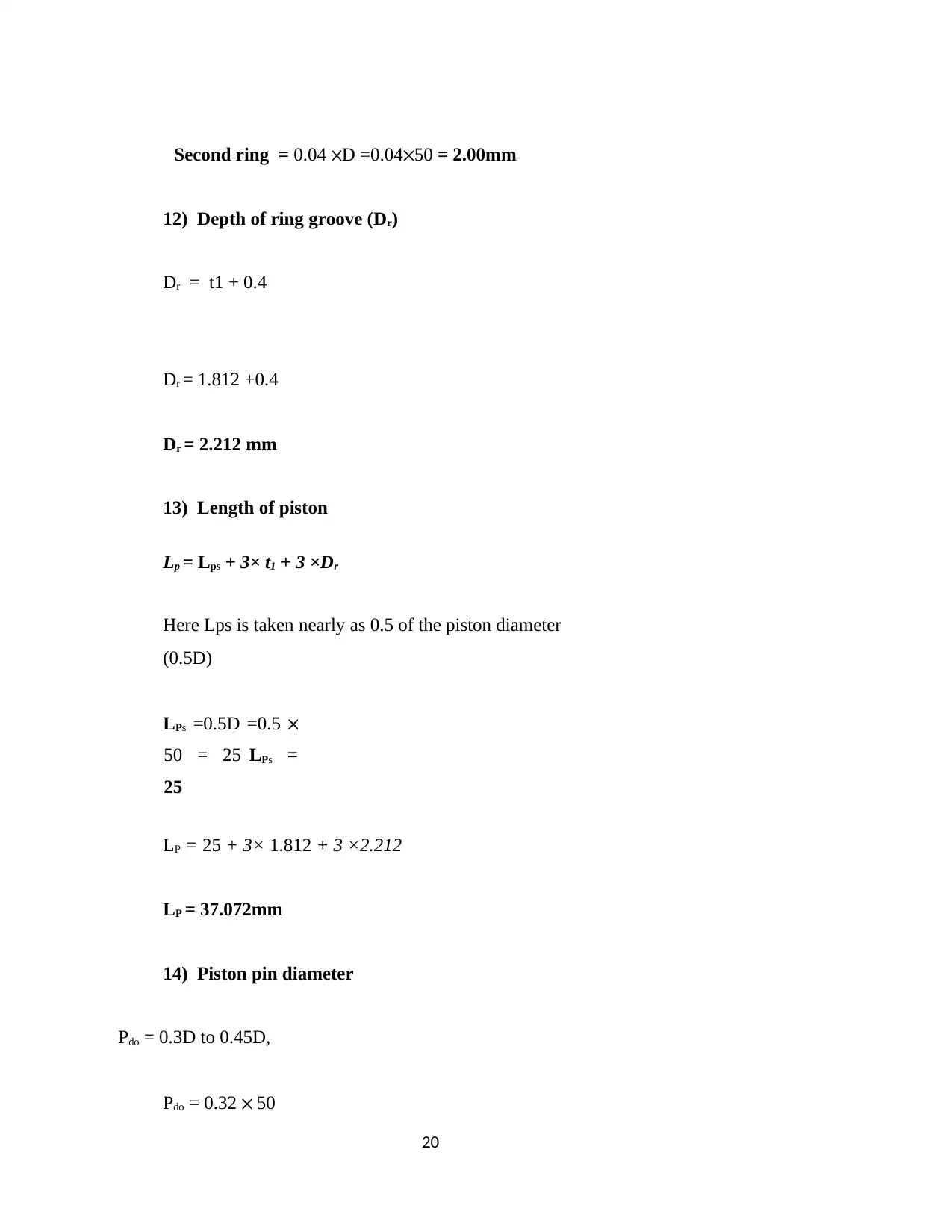
Second ring = 0.04 D =0.04 50 = 2.00mm
12) Depth of ring groove (Dr)
Dr = t1 + 0.4
Dr = 1.812 +0.4
Dr = 2.212 mm
13) Length of piston
Lp = Lps + 3× t1 + 3 ×Dr
Here Lps is taken nearly as 0.5 of the piston diameter
(0.5D)
LPs =0.5D =0.5
50 = 25 LPs =
25
LP = 25 + 3× 1.812 + 3 ×2.212
LP = 37.072mm
14) Piston pin diameter
Pdo = 0.3D to 0.45D,
Pdo = 0.32 50
20
12) Depth of ring groove (Dr)
Dr = t1 + 0.4
Dr = 1.812 +0.4
Dr = 2.212 mm
13) Length of piston
Lp = Lps + 3× t1 + 3 ×Dr
Here Lps is taken nearly as 0.5 of the piston diameter
(0.5D)
LPs =0.5D =0.5
50 = 25 LPs =
25
LP = 25 + 3× 1.812 + 3 ×2.212
LP = 37.072mm
14) Piston pin diameter
Pdo = 0.3D to 0.45D,
Pdo = 0.32 50
20
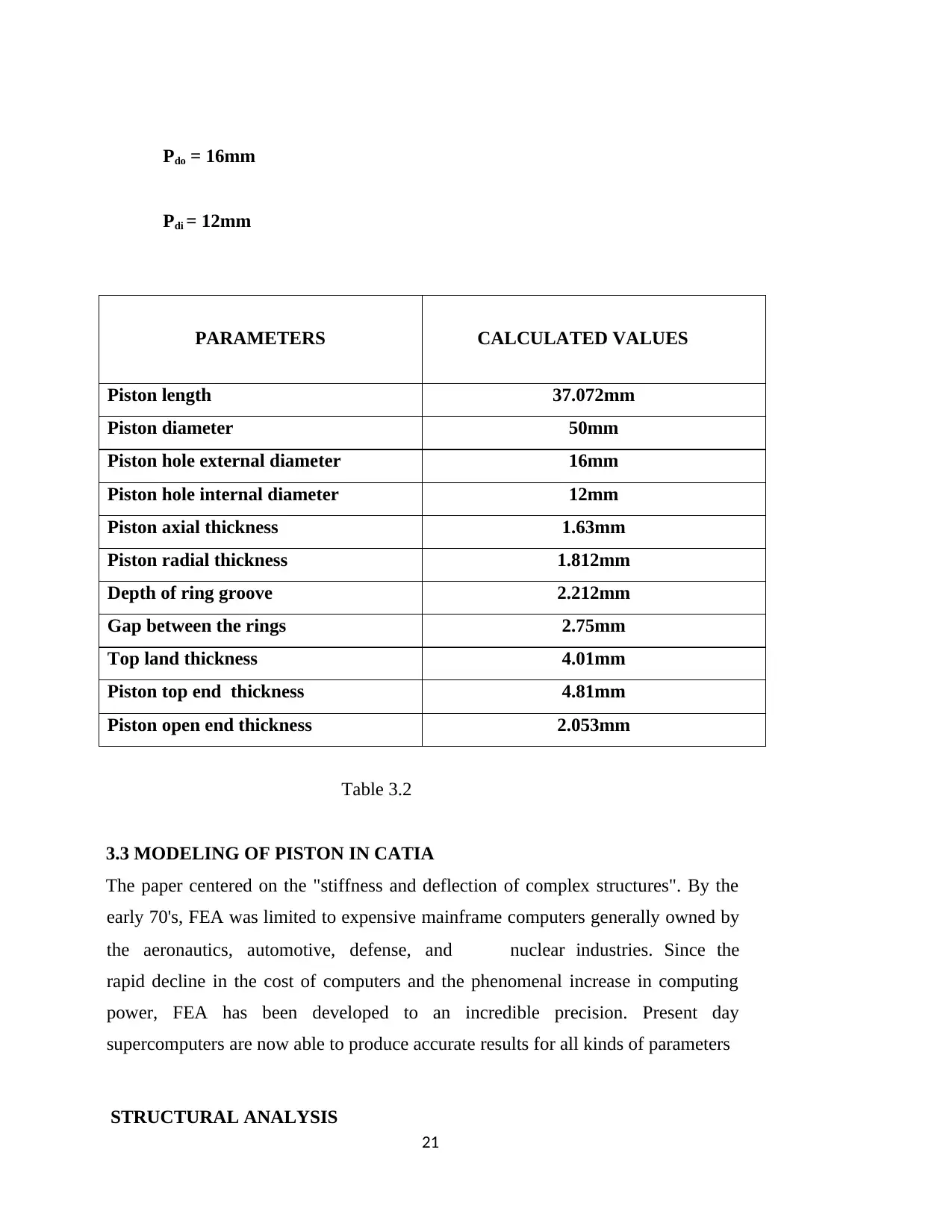
Pdo = 16mm
Pdi = 12mm
PARAMETERS CALCULATED VALUES
Piston length 37.072mm
Piston diameter 50mm
Piston hole external diameter 16mm
Piston hole internal diameter 12mm
Piston axial thickness 1.63mm
Piston radial thickness 1.812mm
Depth of ring groove 2.212mm
Gap between the rings 2.75mm
Top land thickness 4.01mm
Piston top end thickness 4.81mm
Piston open end thickness 2.053mm
Table 3.2
3.3 MODELING OF PISTON IN CATIA
The paper centered on the "stiffness and deflection of complex structures". By the
early 70's, FEA was limited to expensive mainframe computers generally owned by
the aeronautics, automotive, defense, and nuclear industries. Since the
rapid decline in the cost of computers and the phenomenal increase in computing
power, FEA has been developed to an incredible precision. Present day
supercomputers are now able to produce accurate results for all kinds of parameters
STRUCTURAL ANALYSIS
21
Pdi = 12mm
PARAMETERS CALCULATED VALUES
Piston length 37.072mm
Piston diameter 50mm
Piston hole external diameter 16mm
Piston hole internal diameter 12mm
Piston axial thickness 1.63mm
Piston radial thickness 1.812mm
Depth of ring groove 2.212mm
Gap between the rings 2.75mm
Top land thickness 4.01mm
Piston top end thickness 4.81mm
Piston open end thickness 2.053mm
Table 3.2
3.3 MODELING OF PISTON IN CATIA
The paper centered on the "stiffness and deflection of complex structures". By the
early 70's, FEA was limited to expensive mainframe computers generally owned by
the aeronautics, automotive, defense, and nuclear industries. Since the
rapid decline in the cost of computers and the phenomenal increase in computing
power, FEA has been developed to an incredible precision. Present day
supercomputers are now able to produce accurate results for all kinds of parameters
STRUCTURAL ANALYSIS
21
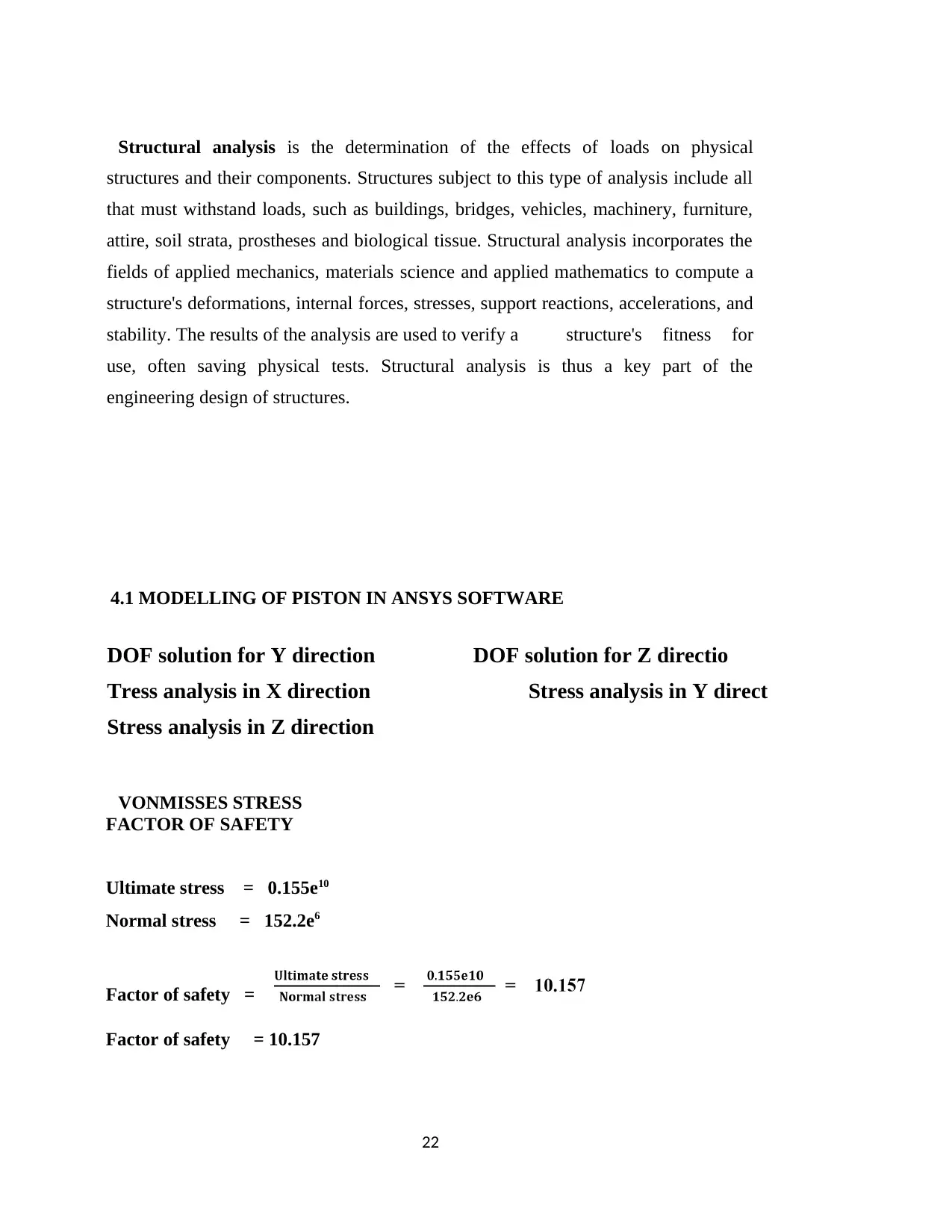
Structural analysis is the determination of the effects of loads on physical
structures and their components. Structures subject to this type of analysis include all
that must withstand loads, such as buildings, bridges, vehicles, machinery, furniture,
attire, soil strata, prostheses and biological tissue. Structural analysis incorporates the
fields of applied mechanics, materials science and applied mathematics to compute a
structure's deformations, internal forces, stresses, support reactions, accelerations, and
stability. The results of the analysis are used to verify a structure's fitness for
use, often saving physical tests. Structural analysis is thus a key part of the
engineering design of structures.
4.1 MODELLING OF PISTON IN ANSYS SOFTWARE
DOF solution for Y direction DOF solution for Z directio
Tress analysis in X direction Stress analysis in Y direct
Stress analysis in Z direction
VONMISSES STRESS
FACTOR OF SAFETY
Ultimate stress = 0.155e10
Normal stress = 152.2e6
Factor of safety =
Factor of safety = 10.157
22
structures and their components. Structures subject to this type of analysis include all
that must withstand loads, such as buildings, bridges, vehicles, machinery, furniture,
attire, soil strata, prostheses and biological tissue. Structural analysis incorporates the
fields of applied mechanics, materials science and applied mathematics to compute a
structure's deformations, internal forces, stresses, support reactions, accelerations, and
stability. The results of the analysis are used to verify a structure's fitness for
use, often saving physical tests. Structural analysis is thus a key part of the
engineering design of structures.
4.1 MODELLING OF PISTON IN ANSYS SOFTWARE
DOF solution for Y direction DOF solution for Z directio
Tress analysis in X direction Stress analysis in Y direct
Stress analysis in Z direction
VONMISSES STRESS
FACTOR OF SAFETY
Ultimate stress = 0.155e10
Normal stress = 152.2e6
Factor of safety =
Factor of safety = 10.157
22
Secure Best Marks with AI Grader
Need help grading? Try our AI Grader for instant feedback on your assignments.
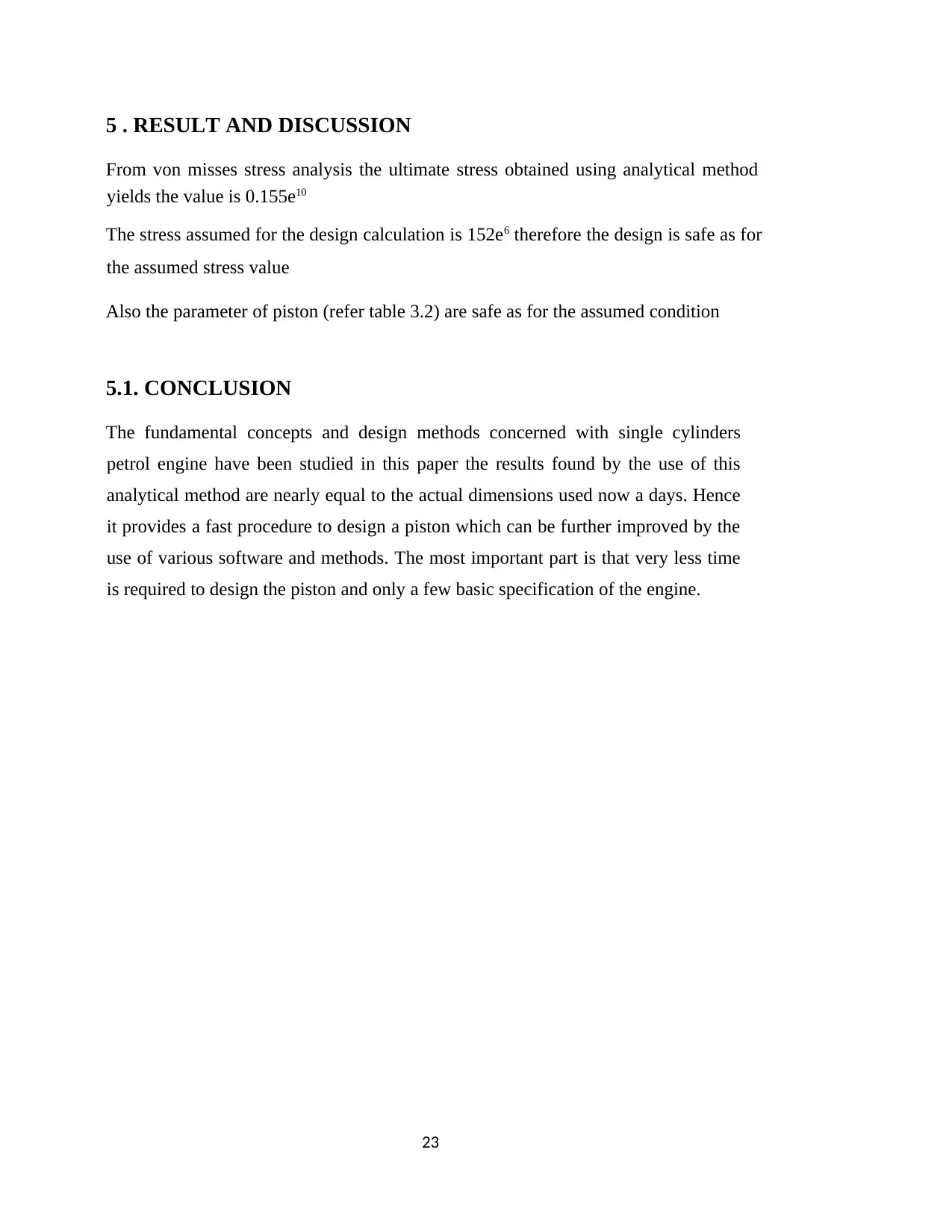
5 . RESULT AND DISCUSSION
From von misses stress analysis the ultimate stress obtained using analytical method
yields the value is 0.155e10
The stress assumed for the design calculation is 152e6 therefore the design is safe as for
the assumed stress value
Also the parameter of piston (refer table 3.2) are safe as for the assumed condition
5.1. CONCLUSION
The fundamental concepts and design methods concerned with single cylinders
petrol engine have been studied in this paper the results found by the use of this
analytical method are nearly equal to the actual dimensions used now a days. Hence
it provides a fast procedure to design a piston which can be further improved by the
use of various software and methods. The most important part is that very less time
is required to design the piston and only a few basic specification of the engine.
23
From von misses stress analysis the ultimate stress obtained using analytical method
yields the value is 0.155e10
The stress assumed for the design calculation is 152e6 therefore the design is safe as for
the assumed stress value
Also the parameter of piston (refer table 3.2) are safe as for the assumed condition
5.1. CONCLUSION
The fundamental concepts and design methods concerned with single cylinders
petrol engine have been studied in this paper the results found by the use of this
analytical method are nearly equal to the actual dimensions used now a days. Hence
it provides a fast procedure to design a piston which can be further improved by the
use of various software and methods. The most important part is that very less time
is required to design the piston and only a few basic specification of the engine.
23
1 out of 23
Related Documents
![[object Object]](/_next/image/?url=%2F_next%2Fstatic%2Fmedia%2Flogo.6d15ce61.png&w=640&q=75)
Your All-in-One AI-Powered Toolkit for Academic Success.
+13062052269
info@desklib.com
Available 24*7 on WhatsApp / Email
Unlock your academic potential
© 2024 | Zucol Services PVT LTD | All rights reserved.