Design and Analysis of Pressure Vessel
VerifiedAdded on 2023/04/06
|13
|2076
|423
AI Summary
This document provides an overview of the design and analysis of pressure vessels. It covers topics such as construction, material selection, and FEA analysis. The document also discusses the importance of proper design and manufacturing processes to ensure the safety and integrity of pressure vessels. The content includes information on the design procedure, material selection, and FEA analysis results. The document concludes with a summary of the findings and the safety of the pressure vessel design.
Contribute Materials
Your contribution can guide someone’s learning journey. Share your
documents today.
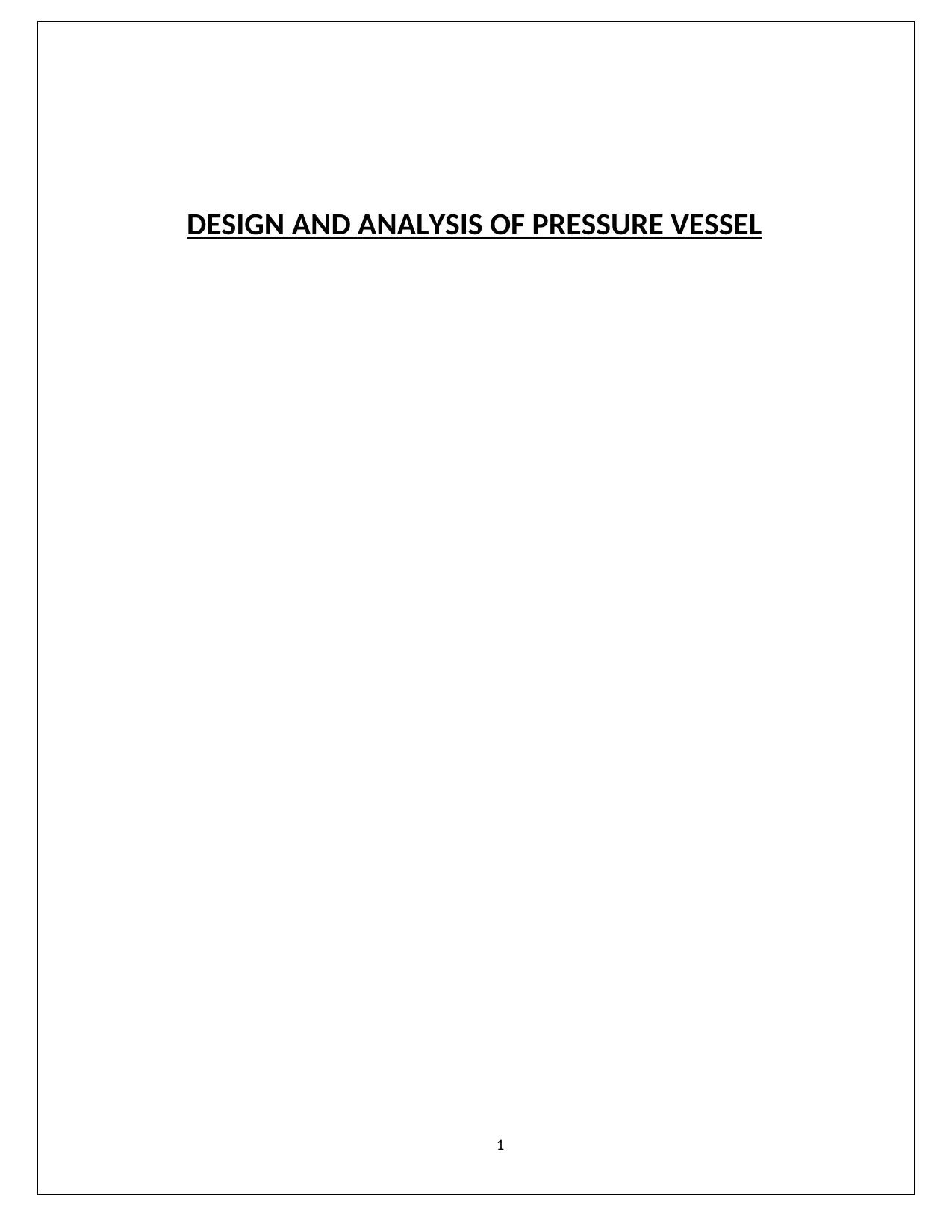
1
DESIGN AND ANALYSIS OF PRESSURE VESSEL
DESIGN AND ANALYSIS OF PRESSURE VESSEL
Secure Best Marks with AI Grader
Need help grading? Try our AI Grader for instant feedback on your assignments.
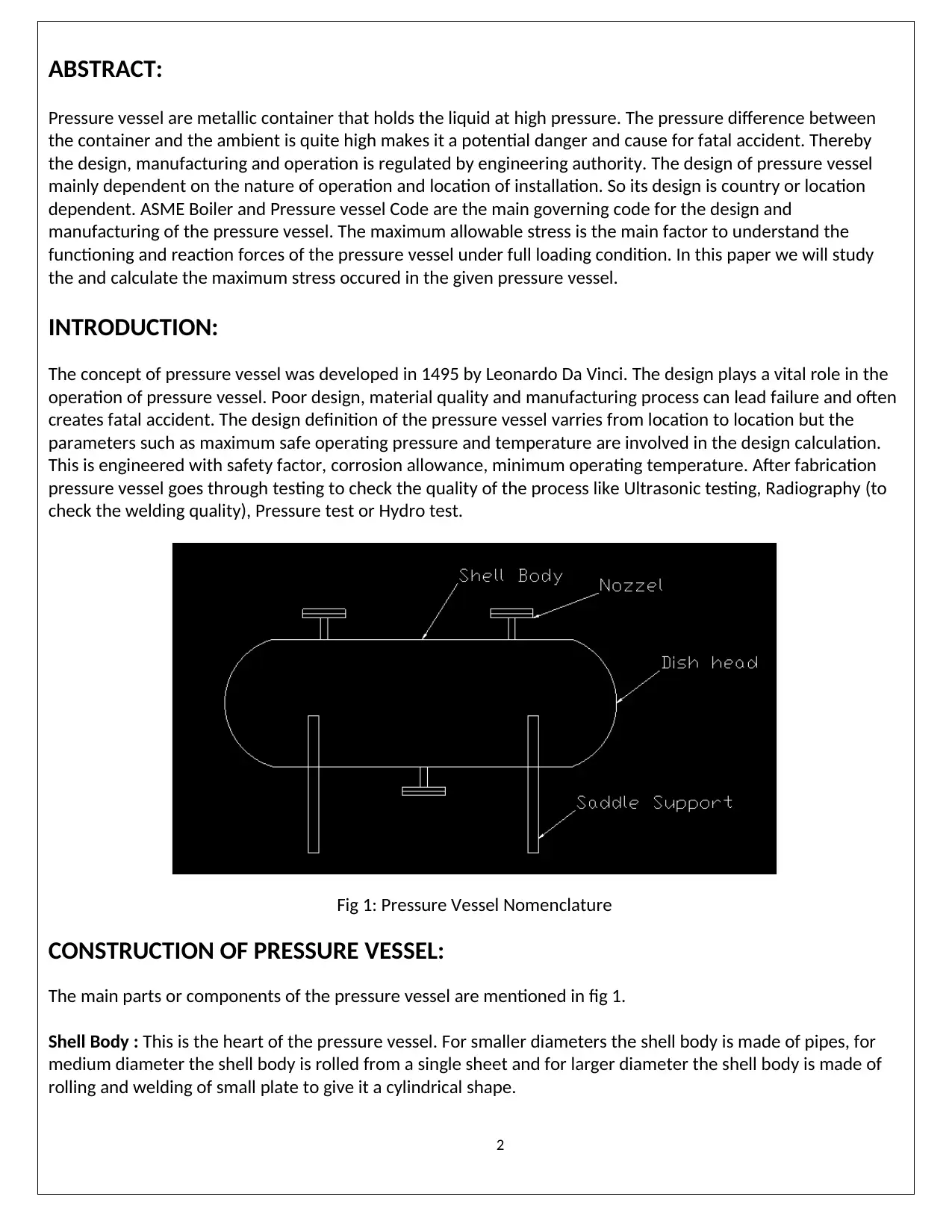
2
ABSTRACT:
Pressure vessel are metallic container that holds the liquid at high pressure. The pressure difference between
the container and the ambient is quite high makes it a potential danger and cause for fatal accident. Thereby
the design, manufacturing and operation is regulated by engineering authority. The design of pressure vessel
mainly dependent on the nature of operation and location of installation. So its design is country or location
dependent. ASME Boiler and Pressure vessel Code are the main governing code for the design and
manufacturing of the pressure vessel. The maximum allowable stress is the main factor to understand the
functioning and reaction forces of the pressure vessel under full loading condition. In this paper we will study
the and calculate the maximum stress occured in the given pressure vessel.
INTRODUCTION:
The concept of pressure vessel was developed in 1495 by Leonardo Da Vinci. The design plays a vital role in the
operation of pressure vessel. Poor design, material quality and manufacturing process can lead failure and often
creates fatal accident. The design definition of the pressure vessel varries from location to location but the
parameters such as maximum safe operating pressure and temperature are involved in the design calculation.
This is engineered with safety factor, corrosion allowance, minimum operating temperature. After fabrication
pressure vessel goes through testing to check the quality of the process like Ultrasonic testing, Radiography (to
check the welding quality), Pressure test or Hydro test.
Fig 1: Pressure Vessel Nomenclature
CONSTRUCTION OF PRESSURE VESSEL:
The main parts or components of the pressure vessel are mentioned in fig 1.
Shell Body : This is the heart of the pressure vessel. For smaller diameters the shell body is made of pipes, for
medium diameter the shell body is rolled from a single sheet and for larger diameter the shell body is made of
rolling and welding of small plate to give it a cylindrical shape.
ABSTRACT:
Pressure vessel are metallic container that holds the liquid at high pressure. The pressure difference between
the container and the ambient is quite high makes it a potential danger and cause for fatal accident. Thereby
the design, manufacturing and operation is regulated by engineering authority. The design of pressure vessel
mainly dependent on the nature of operation and location of installation. So its design is country or location
dependent. ASME Boiler and Pressure vessel Code are the main governing code for the design and
manufacturing of the pressure vessel. The maximum allowable stress is the main factor to understand the
functioning and reaction forces of the pressure vessel under full loading condition. In this paper we will study
the and calculate the maximum stress occured in the given pressure vessel.
INTRODUCTION:
The concept of pressure vessel was developed in 1495 by Leonardo Da Vinci. The design plays a vital role in the
operation of pressure vessel. Poor design, material quality and manufacturing process can lead failure and often
creates fatal accident. The design definition of the pressure vessel varries from location to location but the
parameters such as maximum safe operating pressure and temperature are involved in the design calculation.
This is engineered with safety factor, corrosion allowance, minimum operating temperature. After fabrication
pressure vessel goes through testing to check the quality of the process like Ultrasonic testing, Radiography (to
check the welding quality), Pressure test or Hydro test.
Fig 1: Pressure Vessel Nomenclature
CONSTRUCTION OF PRESSURE VESSEL:
The main parts or components of the pressure vessel are mentioned in fig 1.
Shell Body : This is the heart of the pressure vessel. For smaller diameters the shell body is made of pipes, for
medium diameter the shell body is rolled from a single sheet and for larger diameter the shell body is made of
rolling and welding of small plate to give it a cylindrical shape.

3
Dish End: This is can be considered as the closer plate for the shell. Dish end is manufactured by forging or
pressing.
Saddle Support: Where the pressure vessel rest. This is fabricated from plated and sometimes angle and
channels are used depending on the diameter of the pressure vessel.
Nozzle: This are mainly used for inlet and outlet purpose. Sometimes it is used for the fixing of the instruments
over the pressure vessel.
Problem Statement:
The failure of the pressure vessel can occur for the following reason
Design: Incorrect Design data, Incorrect design philosophy, incorrect testing procedure
Material: Wrong material selection, defective material
Fabrication: Poor manufacturing process, poor quality welding, defect in dimension
To design a pressure vessel it is important to select a proper reference guide. ASME VIII div 2 can be chosen as a
proper reference guide for the material selection. Standard material use are explained in this chapter. Also the
hand calculation and calculation obtained from the software are examined and compared.
Material Selection:
Several materials are used for the fabrication of the pressure vessel. Selection of material depends on the usage
type, design codes and working condition. Under same operating condition material varies if it is installed in hilly
area than the installed in sea shore. Also material selection depends on the fabrication capabilities of the
fabricator. For the case study the following material is taken into consideration
Element Composition
% (Grade B)
Carbon 0.3
Manganese 0.29-1.06
Phosphorus 0.035
Sulfur 0.035
Silicon 0.1
Chrome 0.4
Copper 0.4
Molybdenum 0.15
Nickel 0.4
Vanadium 0.08
Table 1: Chemical Properties
Dish End: This is can be considered as the closer plate for the shell. Dish end is manufactured by forging or
pressing.
Saddle Support: Where the pressure vessel rest. This is fabricated from plated and sometimes angle and
channels are used depending on the diameter of the pressure vessel.
Nozzle: This are mainly used for inlet and outlet purpose. Sometimes it is used for the fixing of the instruments
over the pressure vessel.
Problem Statement:
The failure of the pressure vessel can occur for the following reason
Design: Incorrect Design data, Incorrect design philosophy, incorrect testing procedure
Material: Wrong material selection, defective material
Fabrication: Poor manufacturing process, poor quality welding, defect in dimension
To design a pressure vessel it is important to select a proper reference guide. ASME VIII div 2 can be chosen as a
proper reference guide for the material selection. Standard material use are explained in this chapter. Also the
hand calculation and calculation obtained from the software are examined and compared.
Material Selection:
Several materials are used for the fabrication of the pressure vessel. Selection of material depends on the usage
type, design codes and working condition. Under same operating condition material varies if it is installed in hilly
area than the installed in sea shore. Also material selection depends on the fabrication capabilities of the
fabricator. For the case study the following material is taken into consideration
Element Composition
% (Grade B)
Carbon 0.3
Manganese 0.29-1.06
Phosphorus 0.035
Sulfur 0.035
Silicon 0.1
Chrome 0.4
Copper 0.4
Molybdenum 0.15
Nickel 0.4
Vanadium 0.08
Table 1: Chemical Properties
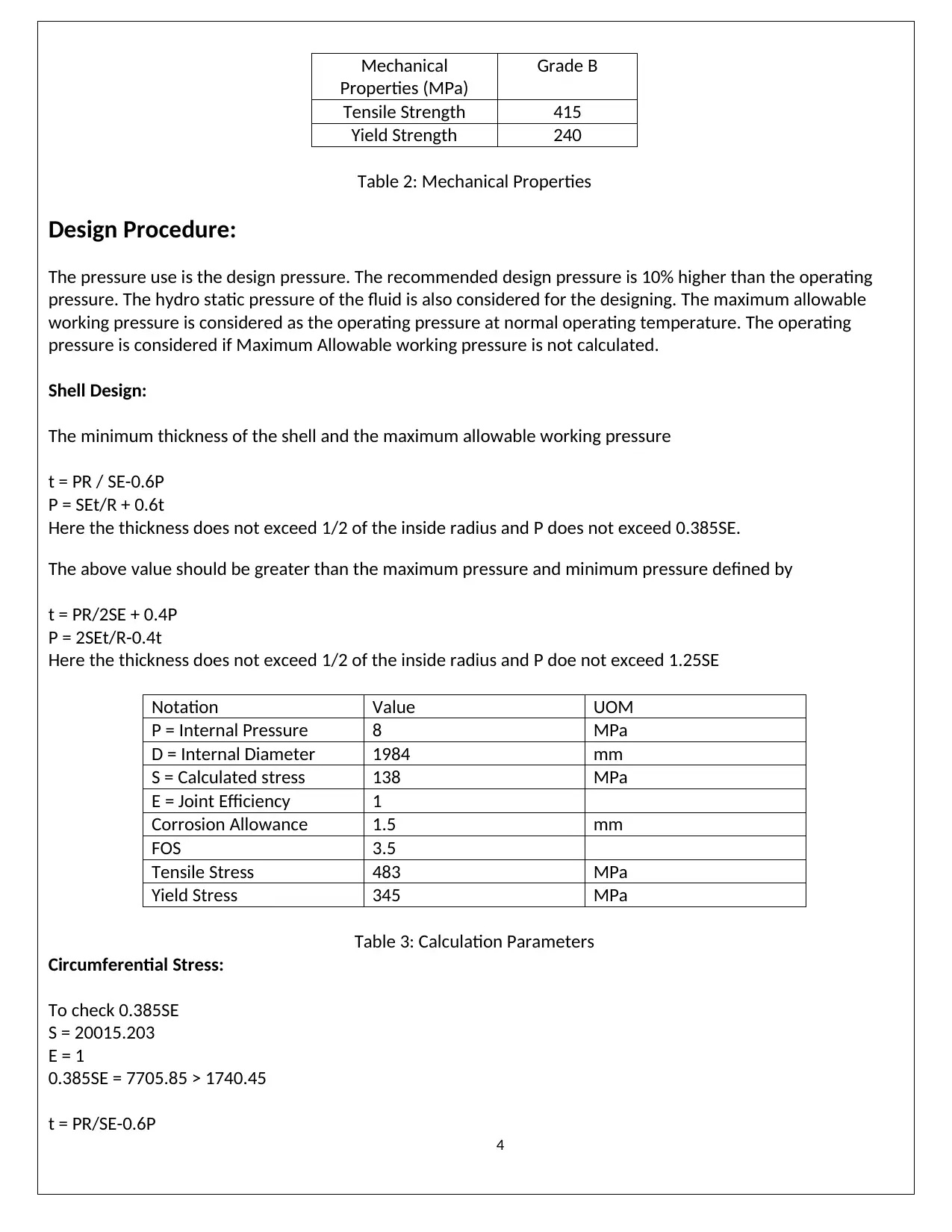
4
Mechanical
Properties (MPa)
Grade B
Tensile Strength 415
Yield Strength 240
Table 2: Mechanical Properties
Design Procedure:
The pressure use is the design pressure. The recommended design pressure is 10% higher than the operating
pressure. The hydro static pressure of the fluid is also considered for the designing. The maximum allowable
working pressure is considered as the operating pressure at normal operating temperature. The operating
pressure is considered if Maximum Allowable working pressure is not calculated.
Shell Design:
The minimum thickness of the shell and the maximum allowable working pressure
t = PR / SE-0.6P
P = SEt/R + 0.6t
Here the thickness does not exceed 1/2 of the inside radius and P does not exceed 0.385SE.
The above value should be greater than the maximum pressure and minimum pressure defined by
t = PR/2SE + 0.4P
P = 2SEt/R-0.4t
Here the thickness does not exceed 1/2 of the inside radius and P doe not exceed 1.25SE
Notation Value UOM
P = Internal Pressure 8 MPa
D = Internal Diameter 1984 mm
S = Calculated stress 138 MPa
E = Joint Efficiency 1
Corrosion Allowance 1.5 mm
FOS 3.5
Tensile Stress 483 MPa
Yield Stress 345 MPa
Table 3: Calculation Parameters
Circumferential Stress:
To check 0.385SE
S = 20015.203
E = 1
0.385SE = 7705.85 > 1740.45
t = PR/SE-0.6P
Mechanical
Properties (MPa)
Grade B
Tensile Strength 415
Yield Strength 240
Table 2: Mechanical Properties
Design Procedure:
The pressure use is the design pressure. The recommended design pressure is 10% higher than the operating
pressure. The hydro static pressure of the fluid is also considered for the designing. The maximum allowable
working pressure is considered as the operating pressure at normal operating temperature. The operating
pressure is considered if Maximum Allowable working pressure is not calculated.
Shell Design:
The minimum thickness of the shell and the maximum allowable working pressure
t = PR / SE-0.6P
P = SEt/R + 0.6t
Here the thickness does not exceed 1/2 of the inside radius and P does not exceed 0.385SE.
The above value should be greater than the maximum pressure and minimum pressure defined by
t = PR/2SE + 0.4P
P = 2SEt/R-0.4t
Here the thickness does not exceed 1/2 of the inside radius and P doe not exceed 1.25SE
Notation Value UOM
P = Internal Pressure 8 MPa
D = Internal Diameter 1984 mm
S = Calculated stress 138 MPa
E = Joint Efficiency 1
Corrosion Allowance 1.5 mm
FOS 3.5
Tensile Stress 483 MPa
Yield Stress 345 MPa
Table 3: Calculation Parameters
Circumferential Stress:
To check 0.385SE
S = 20015.203
E = 1
0.385SE = 7705.85 > 1740.45
t = PR/SE-0.6P
Secure Best Marks with AI Grader
Need help grading? Try our AI Grader for instant feedback on your assignments.
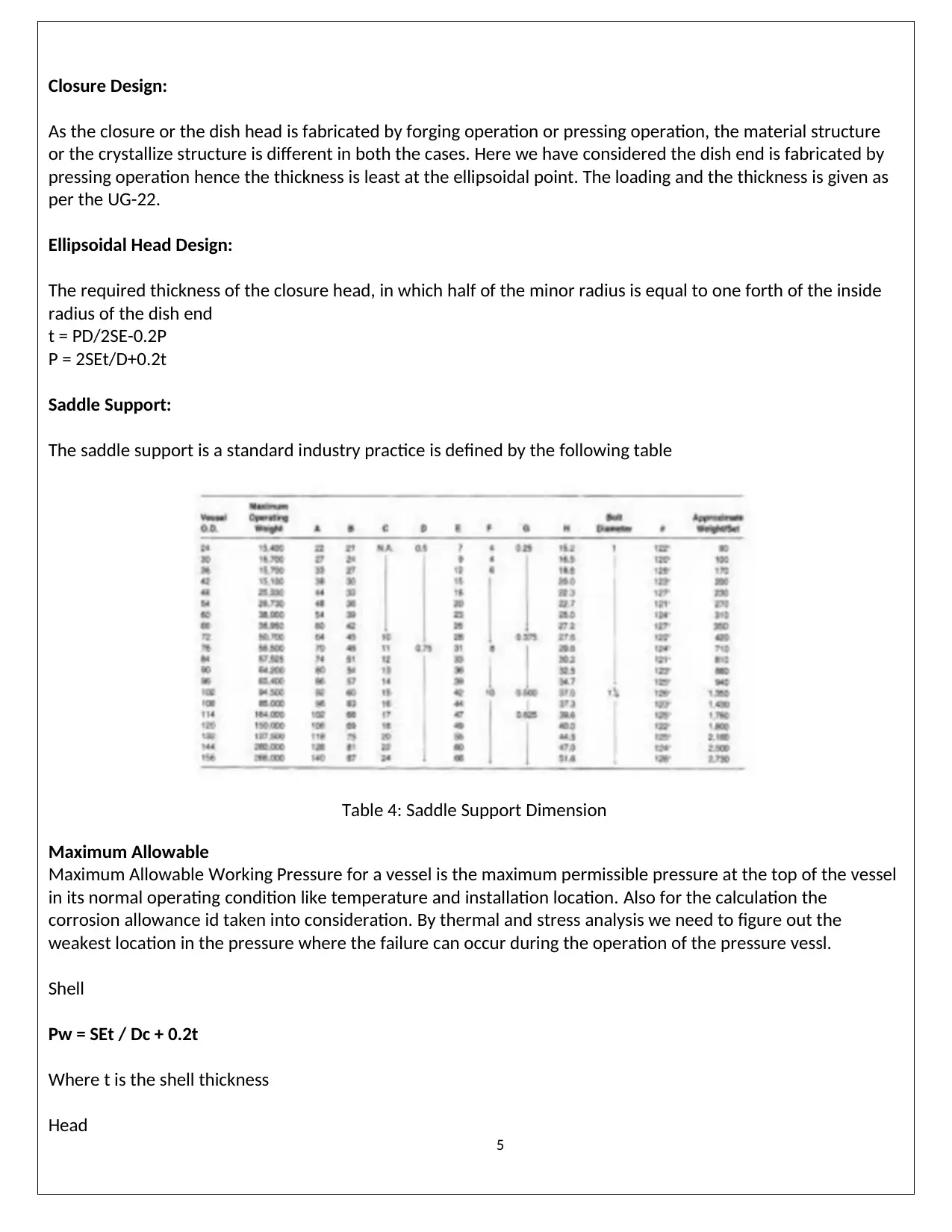
5
Closure Design:
As the closure or the dish head is fabricated by forging operation or pressing operation, the material structure
or the crystallize structure is different in both the cases. Here we have considered the dish end is fabricated by
pressing operation hence the thickness is least at the ellipsoidal point. The loading and the thickness is given as
per the UG-22.
Ellipsoidal Head Design:
The required thickness of the closure head, in which half of the minor radius is equal to one forth of the inside
radius of the dish end
t = PD/2SE-0.2P
P = 2SEt/D+0.2t
Saddle Support:
The saddle support is a standard industry practice is defined by the following table
Table 4: Saddle Support Dimension
Maximum Allowable
Maximum Allowable Working Pressure for a vessel is the maximum permissible pressure at the top of the vessel
in its normal operating condition like temperature and installation location. Also for the calculation the
corrosion allowance id taken into consideration. By thermal and stress analysis we need to figure out the
weakest location in the pressure where the failure can occur during the operation of the pressure vessl.
Shell
Pw = SEt / Dc + 0.2t
Where t is the shell thickness
Head
Closure Design:
As the closure or the dish head is fabricated by forging operation or pressing operation, the material structure
or the crystallize structure is different in both the cases. Here we have considered the dish end is fabricated by
pressing operation hence the thickness is least at the ellipsoidal point. The loading and the thickness is given as
per the UG-22.
Ellipsoidal Head Design:
The required thickness of the closure head, in which half of the minor radius is equal to one forth of the inside
radius of the dish end
t = PD/2SE-0.2P
P = 2SEt/D+0.2t
Saddle Support:
The saddle support is a standard industry practice is defined by the following table
Table 4: Saddle Support Dimension
Maximum Allowable
Maximum Allowable Working Pressure for a vessel is the maximum permissible pressure at the top of the vessel
in its normal operating condition like temperature and installation location. Also for the calculation the
corrosion allowance id taken into consideration. By thermal and stress analysis we need to figure out the
weakest location in the pressure where the failure can occur during the operation of the pressure vessl.
Shell
Pw = SEt / Dc + 0.2t
Where t is the shell thickness
Head
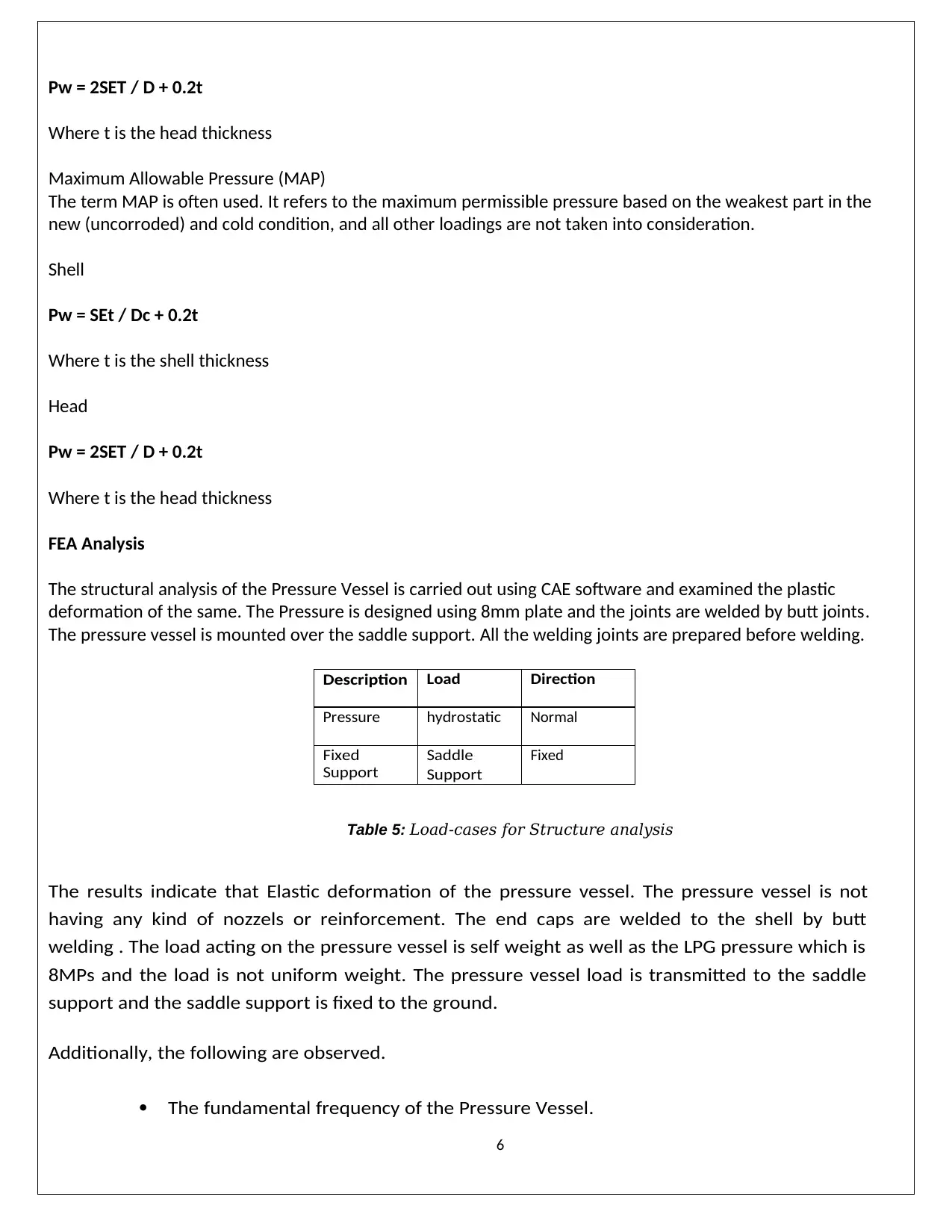
6
Pw = 2SET / D + 0.2t
Where t is the head thickness
Maximum Allowable Pressure (MAP)
The term MAP is often used. It refers to the maximum permissible pressure based on the weakest part in the
new (uncorroded) and cold condition, and all other loadings are not taken into consideration.
Shell
Pw = SEt / Dc + 0.2t
Where t is the shell thickness
Head
Pw = 2SET / D + 0.2t
Where t is the head thickness
FEA Analysis
The structural analysis of the Pressure Vessel is carried out using CAE software and examined the plastic
deformation of the same. The Pressure is designed using 8mm plate and the joints are welded by butt joints.
The pressure vessel is mounted over the saddle support. All the welding joints are prepared before welding.
Description Load Direction
Pressure hydrostatic Normal
Fixed
Support
Saddle
Support
Fixed
Table 5: Load-cases for Structure analysis
The results indicate that Elastic deformation of the pressure vessel. The pressure vessel is not
having any kind of nozzels or reinforcement. The end caps are welded to the shell by butt
welding . The load acting on the pressure vessel is self weight as well as the LPG pressure which is
8MPs and the load is not uniform weight. The pressure vessel load is transmitted to the saddle
support and the saddle support is fixed to the ground.
Additionally, the following are observed.
The fundamental frequency of the Pressure Vessel.
Pw = 2SET / D + 0.2t
Where t is the head thickness
Maximum Allowable Pressure (MAP)
The term MAP is often used. It refers to the maximum permissible pressure based on the weakest part in the
new (uncorroded) and cold condition, and all other loadings are not taken into consideration.
Shell
Pw = SEt / Dc + 0.2t
Where t is the shell thickness
Head
Pw = 2SET / D + 0.2t
Where t is the head thickness
FEA Analysis
The structural analysis of the Pressure Vessel is carried out using CAE software and examined the plastic
deformation of the same. The Pressure is designed using 8mm plate and the joints are welded by butt joints.
The pressure vessel is mounted over the saddle support. All the welding joints are prepared before welding.
Description Load Direction
Pressure hydrostatic Normal
Fixed
Support
Saddle
Support
Fixed
Table 5: Load-cases for Structure analysis
The results indicate that Elastic deformation of the pressure vessel. The pressure vessel is not
having any kind of nozzels or reinforcement. The end caps are welded to the shell by butt
welding . The load acting on the pressure vessel is self weight as well as the LPG pressure which is
8MPs and the load is not uniform weight. The pressure vessel load is transmitted to the saddle
support and the saddle support is fixed to the ground.
Additionally, the following are observed.
The fundamental frequency of the Pressure Vessel.
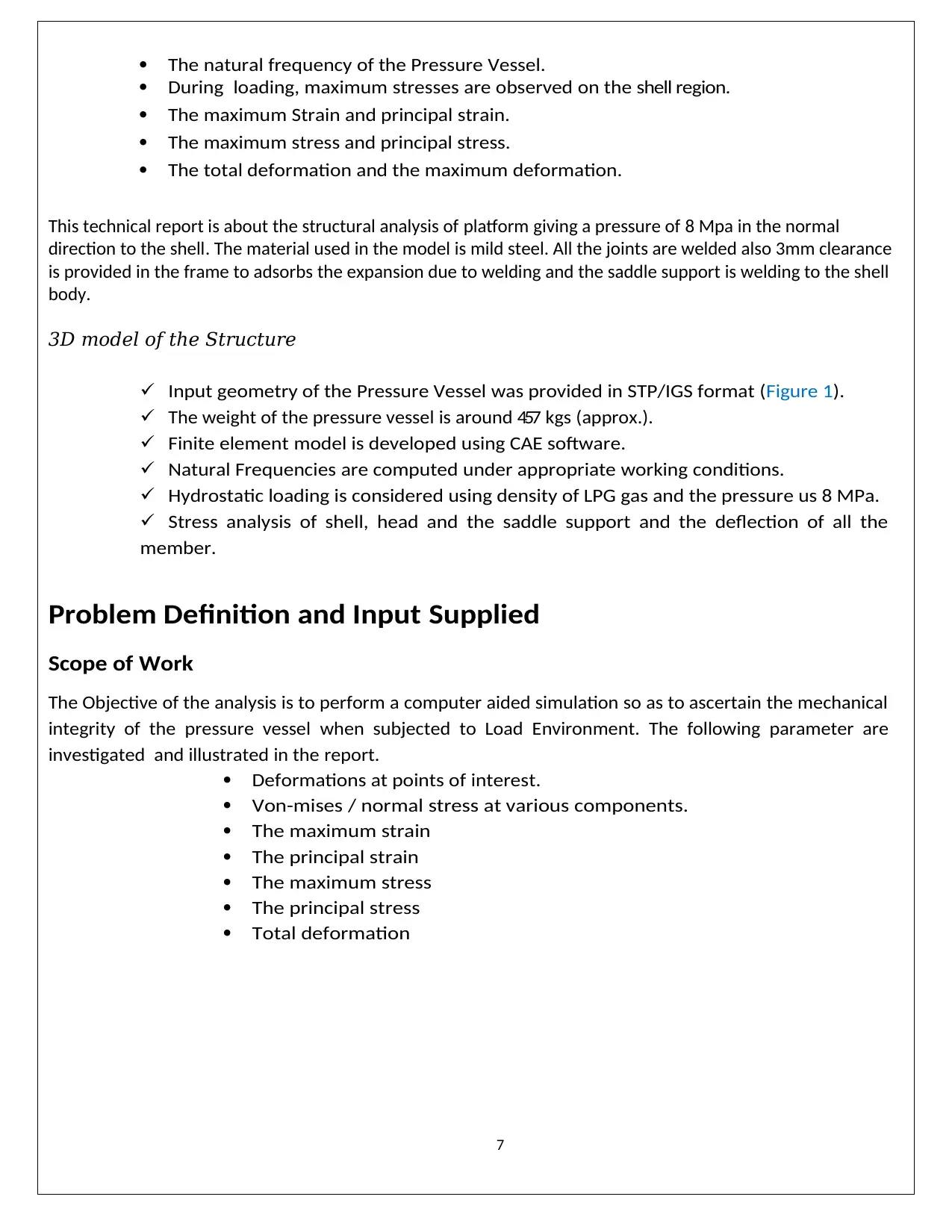
7
The natural frequency of the Pressure Vessel.
During loading, maximum stresses are observed on the shell region.
The maximum Strain and principal strain.
The maximum stress and principal stress.
The total deformation and the maximum deformation.
This technical report is about the structural analysis of platform giving a pressure of 8 Mpa in the normal
direction to the shell. The material used in the model is mild steel. All the joints are welded also 3mm clearance
is provided in the frame to adsorbs the expansion due to welding and the saddle support is welding to the shell
body.
3D model of the Structure
Input geometry of the Pressure Vessel was provided in STP/IGS format (Figure 1).
The weight of the pressure vessel is around 457 kgs (approx.).
Finite element model is developed using CAE software.
Natural Frequencies are computed under appropriate working conditions.
Hydrostatic loading is considered using density of LPG gas and the pressure us 8 MPa.
Stress analysis of shell, head and the saddle support and the deflection of all the
member.
Problem Definition and Input Supplied
Scope of Work
The Objective of the analysis is to perform a computer aided simulation so as to ascertain the mechanical
integrity of the pressure vessel when subjected to Load Environment. The following parameter are
investigated and illustrated in the report.
Deformations at points of interest.
Von-mises / normal stress at various components.
The maximum strain
The principal strain
The maximum stress
The principal stress
Total deformation
The natural frequency of the Pressure Vessel.
During loading, maximum stresses are observed on the shell region.
The maximum Strain and principal strain.
The maximum stress and principal stress.
The total deformation and the maximum deformation.
This technical report is about the structural analysis of platform giving a pressure of 8 Mpa in the normal
direction to the shell. The material used in the model is mild steel. All the joints are welded also 3mm clearance
is provided in the frame to adsorbs the expansion due to welding and the saddle support is welding to the shell
body.
3D model of the Structure
Input geometry of the Pressure Vessel was provided in STP/IGS format (Figure 1).
The weight of the pressure vessel is around 457 kgs (approx.).
Finite element model is developed using CAE software.
Natural Frequencies are computed under appropriate working conditions.
Hydrostatic loading is considered using density of LPG gas and the pressure us 8 MPa.
Stress analysis of shell, head and the saddle support and the deflection of all the
member.
Problem Definition and Input Supplied
Scope of Work
The Objective of the analysis is to perform a computer aided simulation so as to ascertain the mechanical
integrity of the pressure vessel when subjected to Load Environment. The following parameter are
investigated and illustrated in the report.
Deformations at points of interest.
Von-mises / normal stress at various components.
The maximum strain
The principal strain
The maximum stress
The principal stress
Total deformation
Paraphrase This Document
Need a fresh take? Get an instant paraphrase of this document with our AI Paraphraser
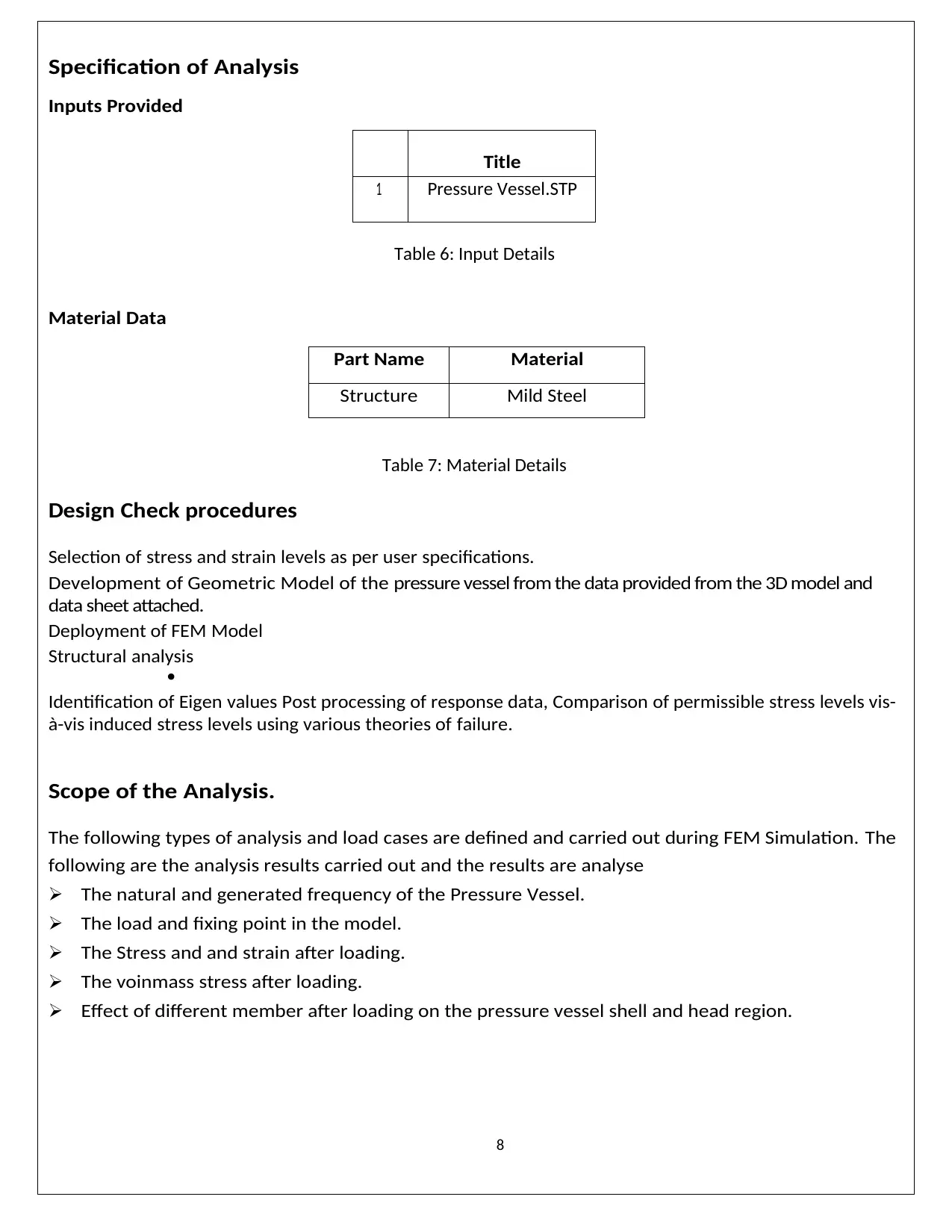
8
Specification of Analysis
Inputs Provided
Title
1 Pressure Vessel.STP
Table 6: Input Details
Material Data
Table 7: Material Details
Design Check procedures
Selection of stress and strain levels as per user specifications.
Development of Geometric Model of the pressure vessel from the data provided from the 3D model and
data sheet attached.
Deployment of FEM Model
Structural analysis
Identification of Eigen values Post processing of response data, Comparison of permissible stress levels vis-
à-vis induced stress levels using various theories of failure.
Scope of the Analysis.
The following types of analysis and load cases are defined and carried out during FEM Simulation. The
following are the analysis results carried out and the results are analyse
The natural and generated frequency of the Pressure Vessel.
The load and fixing point in the model.
The Stress and and strain after loading.
The voinmass stress after loading.
Effect of different member after loading on the pressure vessel shell and head region.
Part Name Material
Structure Mild Steel
Specification of Analysis
Inputs Provided
Title
1 Pressure Vessel.STP
Table 6: Input Details
Material Data
Table 7: Material Details
Design Check procedures
Selection of stress and strain levels as per user specifications.
Development of Geometric Model of the pressure vessel from the data provided from the 3D model and
data sheet attached.
Deployment of FEM Model
Structural analysis
Identification of Eigen values Post processing of response data, Comparison of permissible stress levels vis-
à-vis induced stress levels using various theories of failure.
Scope of the Analysis.
The following types of analysis and load cases are defined and carried out during FEM Simulation. The
following are the analysis results carried out and the results are analyse
The natural and generated frequency of the Pressure Vessel.
The load and fixing point in the model.
The Stress and and strain after loading.
The voinmass stress after loading.
Effect of different member after loading on the pressure vessel shell and head region.
Part Name Material
Structure Mild Steel
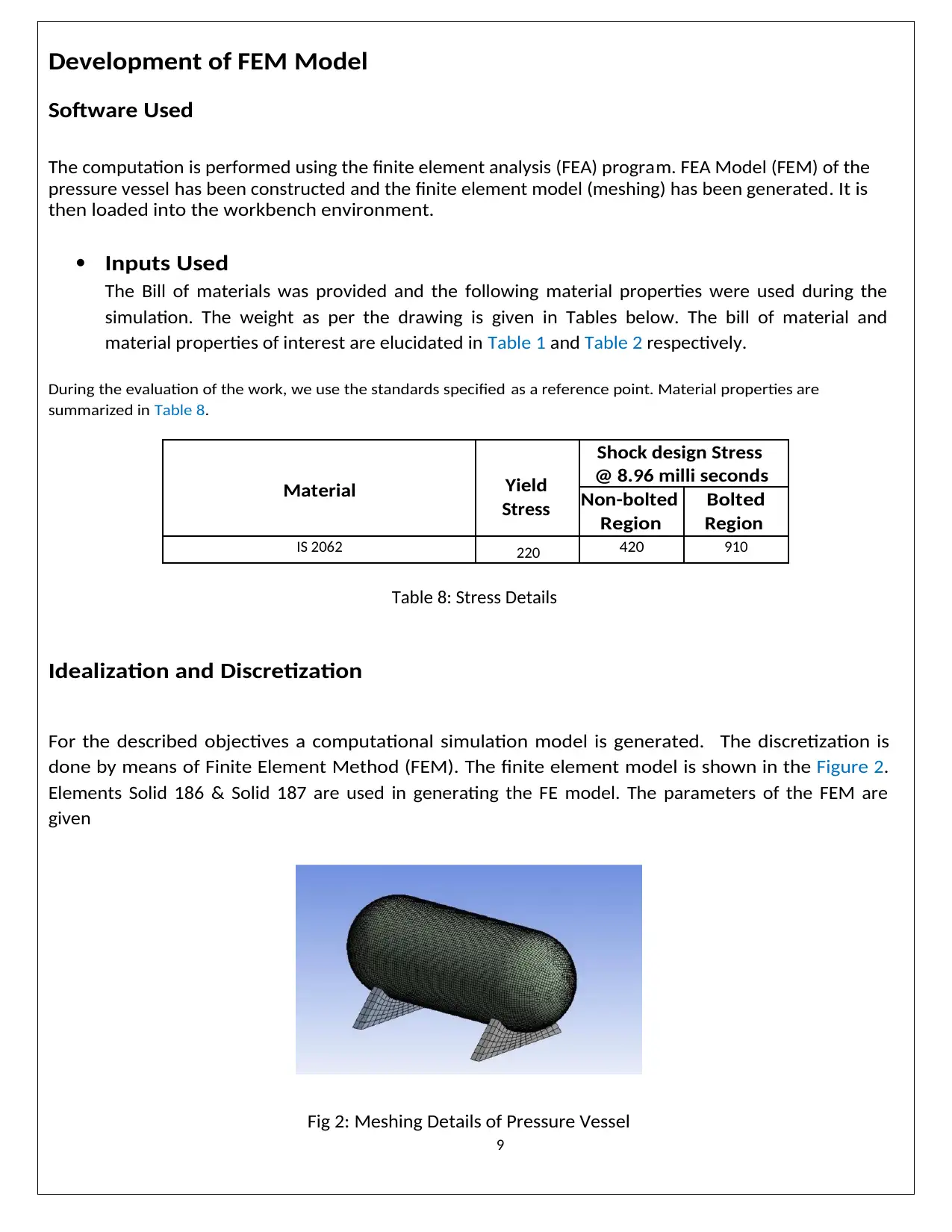
9
Development of FEM Model
Software Used
The computation is performed using the finite element analysis (FEA) program. FEA Model (FEM) of the
pressure vessel has been constructed and the finite element model (meshing) has been generated. It is
then loaded into the workbench environment.
Inputs Used
The Bill of materials was provided and the following material properties were used during the
simulation. The weight as per the drawing is given in Tables below. The bill of material and
material properties of interest are elucidated in Table 1 and Table 2 respectively.
During the evaluation of the work, we use the standards specified as a reference point. Material properties are
summarized in Table 8.
Table 8: Stress Details
Idealization and Discretization
For the described objectives a computational simulation model is generated. The discretization is
done by means of Finite Element Method (FEM). The finite element model is shown in the Figure 2.
Elements Solid 186 & Solid 187 are used in generating the FE model. The parameters of the FEM are
given
Fig 2: Meshing Details of Pressure Vessel
Material Yield
Stress
Shock design Stress
@ 8.96 milli seconds
Non-bolted
Region
Bolted
Region
IS 2062 220 420 910
Development of FEM Model
Software Used
The computation is performed using the finite element analysis (FEA) program. FEA Model (FEM) of the
pressure vessel has been constructed and the finite element model (meshing) has been generated. It is
then loaded into the workbench environment.
Inputs Used
The Bill of materials was provided and the following material properties were used during the
simulation. The weight as per the drawing is given in Tables below. The bill of material and
material properties of interest are elucidated in Table 1 and Table 2 respectively.
During the evaluation of the work, we use the standards specified as a reference point. Material properties are
summarized in Table 8.
Table 8: Stress Details
Idealization and Discretization
For the described objectives a computational simulation model is generated. The discretization is
done by means of Finite Element Method (FEM). The finite element model is shown in the Figure 2.
Elements Solid 186 & Solid 187 are used in generating the FE model. The parameters of the FEM are
given
Fig 2: Meshing Details of Pressure Vessel
Material Yield
Stress
Shock design Stress
@ 8.96 milli seconds
Non-bolted
Region
Bolted
Region
IS 2062 220 420 910

1
0
Boundary Conditions
The boundary, loading conditions and the material properties are correspondingly applied.
Fig 3: Boundary Condition
The load is given as LPG load on the shell and head of the body and the fixed load on the saddle support.
Fig 4: Stress Details
0
Boundary Conditions
The boundary, loading conditions and the material properties are correspondingly applied.
Fig 3: Boundary Condition
The load is given as LPG load on the shell and head of the body and the fixed load on the saddle support.
Fig 4: Stress Details
Secure Best Marks with AI Grader
Need help grading? Try our AI Grader for instant feedback on your assignments.
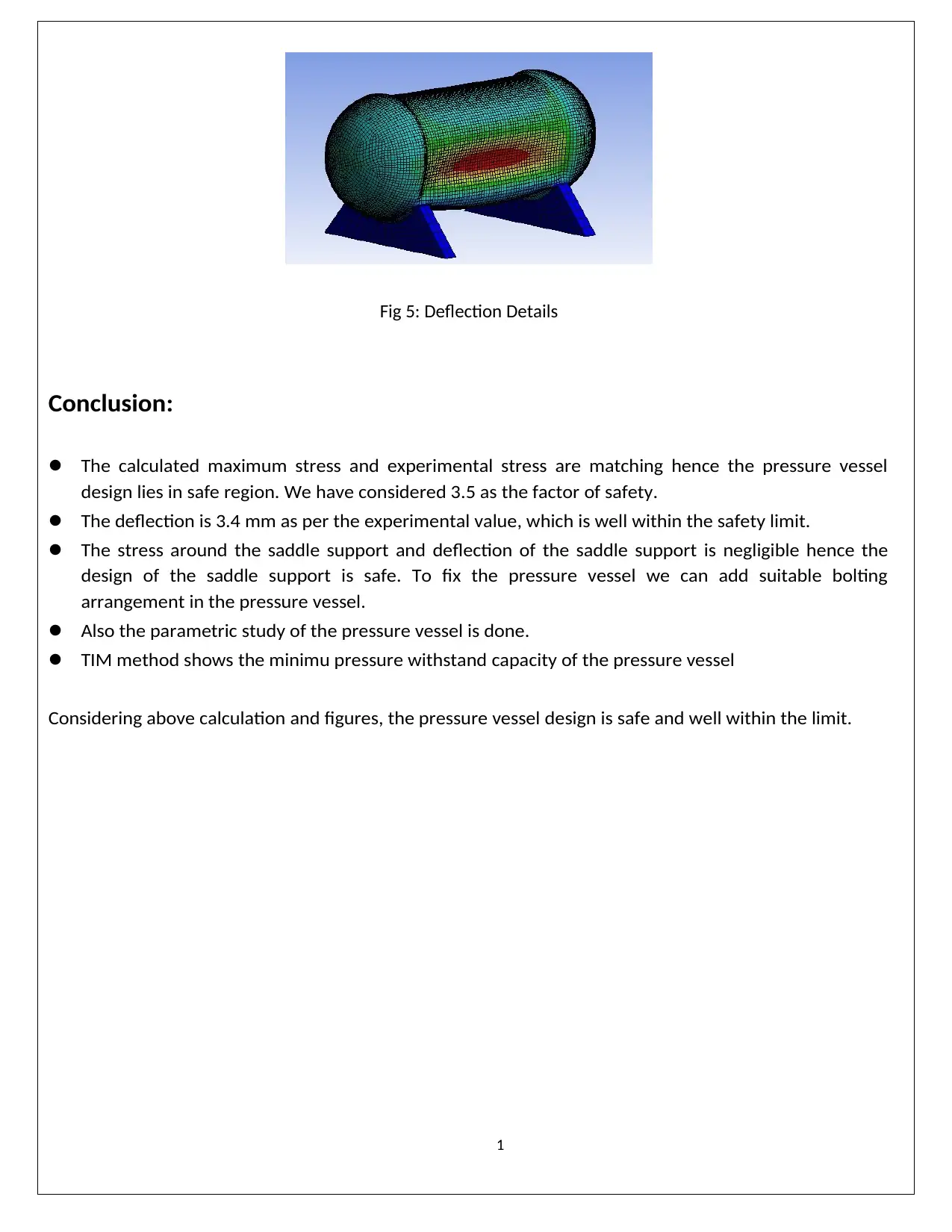
1
1
Fig 5: Deflection Details
Conclusion:
The calculated maximum stress and experimental stress are matching hence the pressure vessel
design lies in safe region. We have considered 3.5 as the factor of safety.
The deflection is 3.4 mm as per the experimental value, which is well within the safety limit.
The stress around the saddle support and deflection of the saddle support is negligible hence the
design of the saddle support is safe. To fix the pressure vessel we can add suitable bolting
arrangement in the pressure vessel.
Also the parametric study of the pressure vessel is done.
TIM method shows the minimu pressure withstand capacity of the pressure vessel
Considering above calculation and figures, the pressure vessel design is safe and well within the limit.
1
Fig 5: Deflection Details
Conclusion:
The calculated maximum stress and experimental stress are matching hence the pressure vessel
design lies in safe region. We have considered 3.5 as the factor of safety.
The deflection is 3.4 mm as per the experimental value, which is well within the safety limit.
The stress around the saddle support and deflection of the saddle support is negligible hence the
design of the saddle support is safe. To fix the pressure vessel we can add suitable bolting
arrangement in the pressure vessel.
Also the parametric study of the pressure vessel is done.
TIM method shows the minimu pressure withstand capacity of the pressure vessel
Considering above calculation and figures, the pressure vessel design is safe and well within the limit.
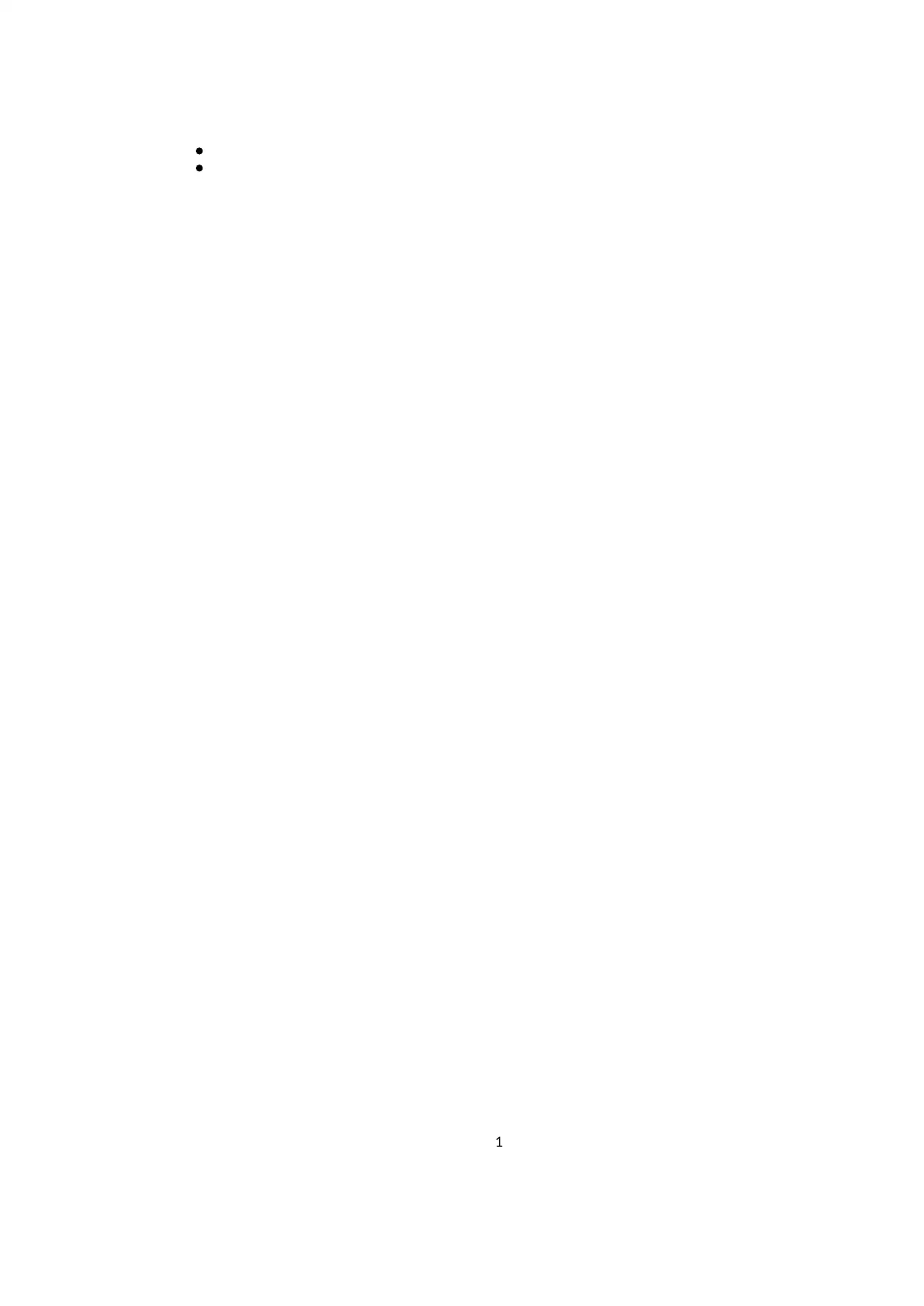
1
2
2
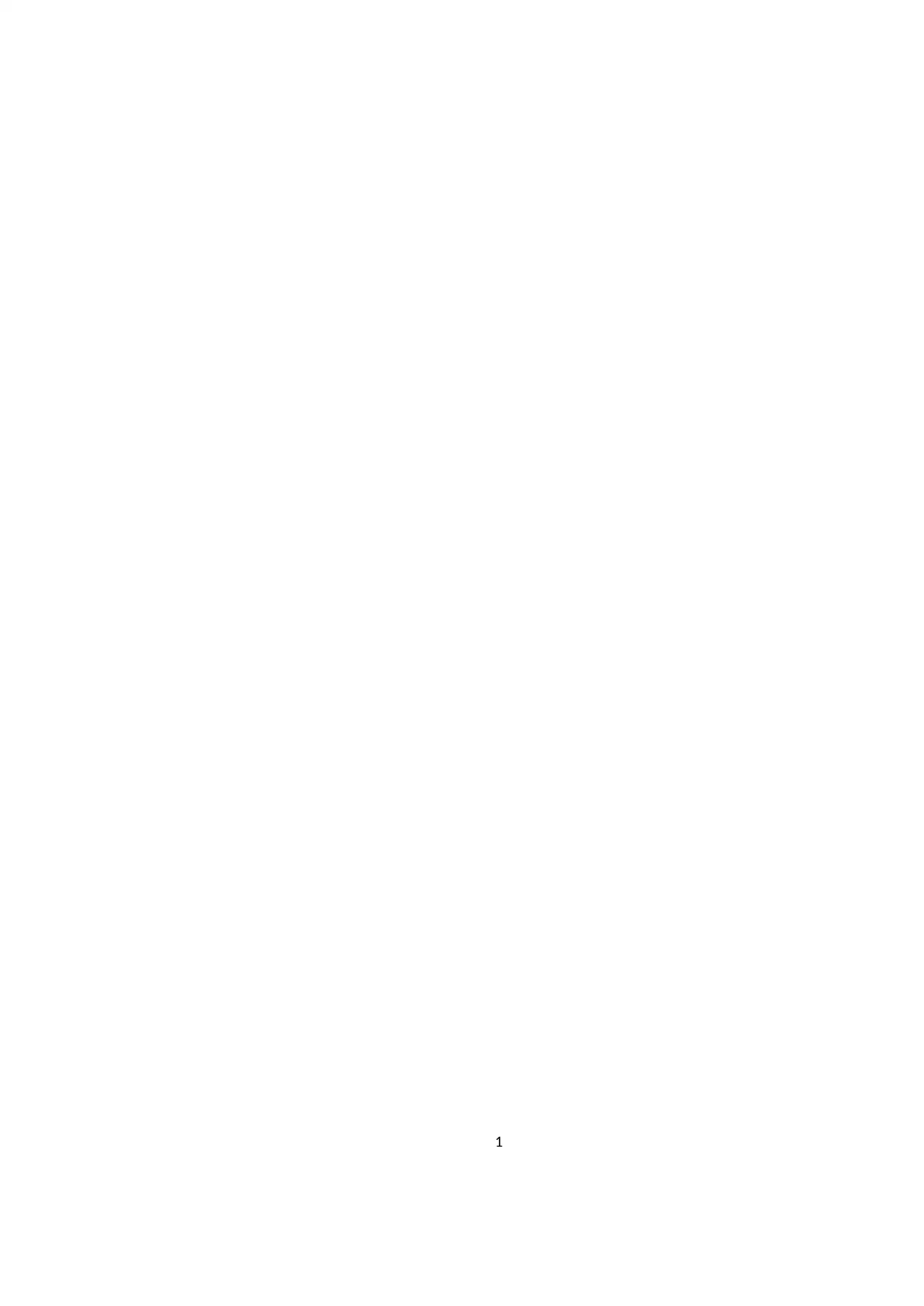
1
3
3
1 out of 13
![[object Object]](/_next/image/?url=%2F_next%2Fstatic%2Fmedia%2Flogo.6d15ce61.png&w=640&q=75)
Your All-in-One AI-Powered Toolkit for Academic Success.
+13062052269
info@desklib.com
Available 24*7 on WhatsApp / Email
Unlock your academic potential
© 2024 | Zucol Services PVT LTD | All rights reserved.