ENEM14016 Fluid Machinery: Excavator Design Optimization & Simulation
VerifiedAdded on 2023/03/31

Paraphrase This Document

Introduction......................................................................................................................................3
Literature Review............................................................................................................................5
Basic Concepts of Hydraulic Excavators........................................................................................9
Excavator Selection.......................................................................................................................13
Design & Calculations...................................................................................................................15
Position of joint 1.......................................................................................................................16
Finding of θ1...............................................................................................................................16
Position of joint 2.......................................................................................................................16
Finding of θ2...............................................................................................................................17
Position of joint 3.......................................................................................................................17
Position of B...............................................................................................................................18
Position of C...............................................................................................................................18
Position of D..............................................................................................................................19
Position of F...............................................................................................................................20
Position of H..............................................................................................................................20
1

Position of G..............................................................................................................................21
Position of M..............................................................................................................................21
Denavit Hartenberg parameters.................................................................................................22
Analysis & Comparison of Results................................................................................................23
Parametric Study........................................................................................................................23
Geotechnical Applications.........................................................................................................26
Conclusions....................................................................................................................................29
References......................................................................................................................................30
2
⊘ This is a preview!⊘
Do you want full access?
Subscribe today to unlock all pages.

Trusted by 1+ million students worldwide

Uses of hydraulic excavators: construction for multiple purposes and also for making
instruments. A boom, a bucket, and two hydraulic cylinders are the parts of the hydraulic
excavator's arm. Boom is the upper part of the arm. These arms will move like a human arm
which consists of a wrist and elbow. Oil is used to move the arm. A piston and rod in the
hydraulic cylinder empower the arm to move. In the end portion of the piston, oil is pumped and
hits the rod through the cylinder. This causes movement of the arm. We can simply manipulate
the accuracy of the arm by preventing the amount of oil which is pumped through the valve. The
digging motion of an excavator can be divided into 3 mechanisms; penetration, separation, and
secondary separation, which constantly put different contributions to the generation of soil
resistance in the digging process. The digging motion and force applied by the end bucket is
determined by the mixture of these 3 main mechanisms at different stages of digging process.
The hydraulic cylinders in the excavator arms are limited to linear actuation. Hence, their mode
of operation is fundamentally different from cable-operated excavators which use winches and
steel ropes. The boom (upper arm) and bucket attached to the body work in conjunction to move
materials, but are controlled independently. Hence, the optimal position for maximum efficiency
regarding digging needs to be assessed. The movement of the excavators arms can be modelled
as a manipulator and the movement/position of the end bucket can be computed using the body
and space Jacobians associated with the excavator. Using these techniques, our aim is to model
the excavator motion and behavior with MATLAB and to estimate the optimum orientation and
lengths of the excavator arms that maximizes the efficiency (power usage) of force applied
during excavation.
3
Paraphrase This Document

In this venture, we demonstrated a nonexclusive excavator arm as a 3 DOF controller and
determined its DH and screw parameters. The Jacobian determined from the made model of the
excavator in MATLAB was utilized to lead parametric investigations with respect to the joint
edges and connection length proportions. The geo mechanical properties of the uncovered soils
were considered to give a semi-ideal answer for the information joint plots for compelling
exhuming.
To exhibit and move extensive product, an excavator is used. It is a development vehicle.
It has major two sections: an improbable blast arm which is related to a driving base. It has a
connection planned for uncovering. A small taxi is related with the base. In this small taxi, the
administrator will sit and guides the arm. To create a Hydraulic power, the excavator uses a
hydraulic framework which is used to control the mechanical arm. It also uses a chain wheel for
its improvement.
There are 3 techniques on the best way to work an excavator 1.Power and Drive. An
excavator keeps running on diesel control since it creates a higher torque and is increasingly
hearty for substantial work. The motor powers the tracks which are like tank tracks, and the
water powered engines which raises and broadens the excavator arm. All power is provided by
the diesel motor, and the controls for development in forward and invert are worked from the
control lodge. An administrator will utilize pedals and switches to push the machine ahead and in
reverse, and to control the vehicle. 2. Excavator Arm. The excavator arm is attached to the
bottom of the edge case. There are three water powered cylinders. These cylinders are covered
with steel cylinder arms. This arm must consists of a loader and two parts. The two parts are
attached with a pivot. One cylinder is attached to the bottom side of the first part. The other
cylinder is situated upwards to the next part. When the first cylinder broadens the poll pushes in
opposition to the arm, moves upwards and the area had expanded. The other arm shrinks and
expands, take upwards and downwards the part. There is a cylinder which gives more pressure. It
pushes the container loader ahead and conversely.3.Track steering (Using fem we can analyze
4

located near a progression of apparatuses. It transfers the energy from a drive shafting
accordance with the motor. When in rigging the track moves the machine towards front or back
in a straight line. For turning machine, one track is fully ceased and the next track is used for
moving towards the front or back. This takes the machine turn in a curve. To make the device in
a total circle shape an administrator is used to put one track to move forward and the next track
to move backward.This requires two separate drive frameworks, and a progressively confused
transmission. It isn't accessible on all vehicles. What's more, a few excavators have a rotating
taxi that can swivel 360 degrees. This is fueled by another pressure driven engine that gets drive
from the principle motor.
Excavators are utilized for numerous reasons and is presumably the most regularly
utilized machine in the development business. A few applications are recorded underneath:
Digging of channels, gaps, establishments, material taking care of, general evaluating/finishing,
brush cutting with water powered connections, ranger service work, obliteration, lifting and
setting of funnels, mining yet not constrained to open-pit mining and waterway digging.
Exhibitions of excavators are constrained by the point and directivity of the controllers.
Power that given by excavators isn't show 100%. There are numerous elements that influence the
kinematic manipulability of the excavator arms. This report plans to give understanding into the
development of excavators and their association with the ground. There are two sorts of heading
that one can be work enormous power and other can be work little power, on the grounds that the
opportunity of bucket (end of excavator) is controlled by the turn hub and area of each
connection. This can be express utilizing the information from a Jacobian circle and
communicated as function (=length of oval hub as indicated by/the real pivot of the oval) as per
(about among basin and ground). The subsequent esteem, named the 'viable vulnerability',
communicates proportion about excavator’s development. (Yuan, 2014)
To show the excavator movement and conduct utilizing kinematics. This report will
demonstrate Jacobian-circle by utilizing DH parameter in light of the fact that we need to
contrast the directional pattern about power with locate the ideal direction and lengths of the
excavator arms that amplifies the productivity (control utilization) of vertical power connected
5
⊘ This is a preview!⊘
Do you want full access?
Subscribe today to unlock all pages.

Trusted by 1+ million students worldwide

procedure, and discover area of link1, link2 and link3 so as to guarantee most extreme execution
when the excavator burrows ground. That area can be improved proficiency about power (Chen
& Chen, 2011).
Literature Review
Infrastructure development relies a lot on hydraulic excavators and are considered to be
‘Earth Movers’. They play a vital role in excavation, construction of roads and building, mining
of granite, coal, or and many more. Equipped with work implement or attachment which include
buckets for digging and carrying materials, hydraulic hammers and drills, excavators help
perform important, heavy-weight tasks . For Multi Body Simulation analysis, computational
simulation method is used which aims to reduce the number of repetitions during the
development phase. A precise restricted code such as Altair Radios is used in the simulation
process. Furthermore, to improve the Lower Arm Excavator model, it is optimized for it to get
less weight and tense component. In this paper, FE analysis of Excavator of Lower Arm is
explained. To reduce the time required and the expenses for the development process, the results
obtained from CAE analysis are evaluated, keeping in mind the requirements. The project aims
to design and conduct Multi Body Simulation analysis for excavator and execute Topology
Optimization so the weight of the lower arm of the excavator can be reduced. To view the results
in hyper view, Catia V5 R19 for the modeling of the excavator and preprocessing in hyper mesh
and radios can be utilized. For reduction in weight,, Altair Optistruct is recommended and a
revision in lower arm of the excavator’s design is urged. The paper hopes to shed light on the
topology optimization approach which can be used to create a unique design of the lower arm of
the excavator. Along with this, the paper aims propose techniques that are effective to design and
develop high quality products at minimum expense. After looking at both the designs, the author
came to eh conclusion that the second design is more relevant to the aims of the paper
("DESIGN AND ANALYSIS OF EXCAVATOR BUCKET TOOTH", 2018).
An example of heavy equipment is an excavator which consists of jointed arm, which
known as a backhoe, a bucket and a rotating platform on which the cabins mounted, an
6
Paraphrase This Document

available material to improve the design of excavators and pinpoint the problems faced by them
when performing tasks like digging and lifting. Generally, mini hydraulic backhoe excavators are
used for light construction jobs and are mostly used when soil needs to be excavated. In
operations like digging, the design of backhoe excavator is very important which is developed
through actuators. For the developed design to be safe, the resistive forces of the surface that
needs to be excavated needs to be lesser than the forces produced by actuators. Consumption of
fuel and the productivity of the excavator are two vital factors that need to be considered when
the arm of the excavator is designed. During operations like digging and lifting, current
mechanism which is used in the arm of the excavator is exposed to torsional and stress caused by
bending. To get past this problem, the need of a new mechanism of excavator was realized and a
3D model of the excavator arm linkage was designed using the Pro-e software. A static analysis
of all the arms of the excavator’s components was done, keeping in mind the existing force
produced by the components as well as the new force calculated for digging with the help of
ANSYS workbench software. To deal with the loss in production which is caused by the
reduction in the digging force, an increase in the bucket volume is recommended. ("DESIGN
AND OPTIMIZATION OF EXCAVATOR", 2017) This paper aims to achieve positive analysis
results which prove that the new design of the excavator is safe for the digging force that has
been calculated.
Design and analysis of hydraulic excavator are one of the complicated processes. It involves the
CFD analysis such as FEA analysis. When talking about accuracy that makes the process more
complicated. Especially in practical problems, the explicit mathematical formula won't bring 100
% correct answers all times. Because some of the design variables are very difficult to formulate.
In some cases, it is impossible to develop a mathematical model. So that in modern process
scientists and researcher use surrogate model. In this paper also author used different surrogate
models to optimize the performance of the system. Here the author selected a number of
surrogate models suitable for excavator performance analysis. And the different methods
compared in this paper are surface methodology, support vector machine, and radial basis
function etc. After comparing all the methods the author selected the most suitable method for
the optimization process. And the author also developed the new concept. Here author used the
7

brings the optimum results (Xu and Yoon, 2019). Also, the magnitude of the stress calculated by
using the FEA technique is similar to the value founded by this algorithm. In the case of
efficiency, the present model has higher efficiency than the developed or proposed model in this
article. The new concept proposed in this paper mainly based on the length of the joints, the
angle between the hinges etc. Here the author successfully applied this concept on the design
process. And also the author simulated the concept using Matlab. Using the simulation author
measured the effectiveness of the sample points. In all the measured sample points the author
founded the improvement of effectiveness. Also expressing the different variables in terms of
length is not practically feasible. Because this method creates some errors & conflicts. This
method uses trigonometric functions. Usage of trigonometric functions instead of computational
variables and formula brings higher flexibility and advantages. Also, the proposed method is far
simpler than the conventional method. Also, the author considered different variables and their
influence on the final accuracy. In the optimization process, the author used the BIOA technique.
Here the author iterated the maximum stress values in terms of boom, arm and bucket. Here we
can't find any convergent violations, but the convergence velocity for the different points are
different. And the magnitude of the maximum stress in the bucket is 290.63 MPa, and maximum
stress in the boom is 248.09 MPa, and the maximum stress in the bucket is 221.91 MPa. These
are the founded values from this method. As per the results of this study the magnitude of the
maximum stress founded by both FEA technique and this technique has the same value (Qiu, Li
and Feng, 2016). Although the author verified the RSM model and its functionality and proved
this method is one of the most viable methods for conducting the design process for improving
the performance of the hydraulic excavator.
Tackles, pulleys, levers, and block were used for lifting the weight in early times.
Mechanical linkages gained movements for a ship’s rudder and steering a vehicle. These
mechanical linkages were gears, couplings, levers, and cams. This made the system more
complex. There were several drawbacks occurred in manual and mechanical methods. Big man
power should involve in them for a different job (Usman, Lawal and Shehu, 2014). Overtime
working was also involved. When the technology and population developed, the need for faster
and simpler apparatus also developed. Because of these needs, hydraulic machines were
8
⊘ This is a preview!⊘
Do you want full access?
Subscribe today to unlock all pages.

Trusted by 1+ million students worldwide

rams, accumulator or oil reservoir, safety device and a complete working mechanism. In a
medium, these hydraulic system are able to control a wide variety of apparatus which can
transfer force. This is carried by hydraulic fluid. Engineering and transportation fields uses
modern hydraulics. These system transmit high force quickly and correctly. They can transfer
even in small pipes of less weight, any shape, and over a small distance (FAN, 2017). These
system can play an important role in the field of small steering of car to manipulated devices of
the supersonic aircraft. In big ships, more strong and efficient system are used. The most famous
scientist Blaise Pascal proposed the law which is known as Pascal’s law. It implies that pressure
at a point has infinite direction and thus a pressure change at any point in a confined
incompressible fluid is transmitted throughout the fluid such that same change occurs
everywhere. (Khan, Islam & Hossain, 2016) This is the major principle of hydraulic system.
Blaise Pascal is a French mathematician. The force acting per unit area is known as Pressure.
The force applied perpendicular to the surface of an object per unit area over which that force is
distributed. Hydraulic pressure is the pressure of the hydraulic fluid which it exerts in all
direction of a vessel, hose or anything in which it is supposed to exert the force per unit area.
This pressure is responsible to create flow in a hydraulic system as fluid flows from high
pressure to low pressure.
Example of simple hydraulic system is a closed toothpaste. Consider the toothpaste as a
hydraulic fluid which is inside the system. Put four or five holes on the tube. By keeping the cap,
apply force at a particular point on the tube. Then we can see that the paste will come out from
the hole that we made. This is one of the example of Pascal’s law. The force on the particular
point of the tube is equal to the force on all other parts of the tube. That is, the force is
perpendicular to the walls of the restricted area (Usman, Lawal and Shehu, 2014). Brakes used in
automobile is another example of the hydraulic. When the driver applies brake to the vehicles,
the brake pedal acquires force and transmitted it to the hydraulic fluid under the piston. This is
same as the force applied to the brake shoes. This causes the vehicles to stop. Hydraulics are
applied in hydraulic cranes, petrol pumps, automobile garage, automobile brake, and robotics
and so on.
9
Paraphrase This Document

and analysis all component of an excavator. 'Bucket teeth' is the important part of the excavator.
It has various substances with impact load. These substances are differentiated to strain energies,
von mises stresses and deformations. The optimum component is weightless, strong and
sustainable. Therefore, the bucket has minimum weight and maximum strength. The cost of
manufacture and material saving are available. CATIA is used for its assembly and ANSYS for
analysis. Excavator bucket is manufactured with steel. Cast iron, steel and wrought iron are
materials used for analysis. Comparisons are seen in the strain energy, deformations and von
mises stresses. The weight of the steel is 7840 kg. The weight of the cast iron is 7300 kg and that
of wrought iron is 7550 kg. Deformation of the steel is less. But the deformation of wrought iron
and cast iron is greater than that of the steel. In the case of wrought iron, it can resist the load
with least deformation. Von mises stresses of cast iron is greater than that of wrought iron and
steel. The strain energy of wrought iron is more than that of steel and cast iron. The weight of
wrought iron is less but its strain energy is high (Solazzi, 2010). Stresses are low in it and
displays formal deformation. When we replace steel with wrought iron, wrought iron become
hard, tensile and flexible. It reduces its weight because of the same strength. Therefore, we can
save time and cost. Wrought iron is very strong. So we cannot break or destroy it. To avoid rust
in wrought iron, we must keep an efficient paint job. It has no need of maintenance and it can
resist with the weather. Due to these advantages, we can replace steel with wrought iron.
Wrought iron is an alloy of iron. It has low carbon content compared to cast iron. Mild steel is
produced from wrought iron. It includes nuts, chain, bolts, rails and wire. Cast iron is a ferrous
alloy. When it is heated, it will be liquefied. It is made from pig iron. Steel is also an alloy of
iron and includes carbon. We know that CATIA is used to design every component of an
excavator. Assembly is also done in CATIA. It is used by aerospace industries (Qi & Zhang,
2014). Most of the industries are architecture, construction, electronics, medical, automotive,
machinery, mold and die and so on. It is found in all over the world. In ANSYS, analysis and
meshing are accomplished through it. Universally, steel is used in excavator bucket. It provides
the means to balance the requirements and occur right mesh. In engineering simulation, mesh
generation is one of the major aspects. Excavator is used for digging holes, handling the
materials, forest work, mining, dredging the river, landscaping, and clearance .Bucket is used for
10

excavator boom and bucket can be handled by the operator’s cabin machine.
There is a method for doubling force by a fluid that is not compressible is named as
hydraulics. Basically: oil. Hydraulic machines use liquid fluid power. The basic example is a
heavy equipment.so liquid is the main medium in it. Control valves are used to control fluids
directly and it also distributes by using tubes and hoses. Hydraulic power was mainly used in
Bessemer steel productions. Hydraulic fluid is passed to the machine to different motors and
cylinders. Air is more compressible than hydraulic oil (Shetiye and Kungwani, 2018). The force
at the first stage is kept at one end and a stable pressure at another end. At one end of the system
a force of 10 pounds is applied. It consists of 1 square foot cross section. The final output is an
applied pressure of 10 pounds of cross section. It finalizes a force of 100 pounds. The piping
connections between two pistons are of any type. There is one base cylinder which gives force to
the sub cylinder. This is a very good mechanism. Scientific principles are used by hydraulic
equipment. There is a pump used for operating engines and motors. These pumps generates
pressure to the hydraulic fluid. The fluid passes through tubes to actuators. The arm or bucket in
excavation is done by the actuators. Hydraulic system mainly consists of valves, pumps, filters
check valves, hydraulic cylinders etc. Hydraulic multiplication is defined as the tradeoff within
the base and sub cylinder. It is within the movement and current force. Mechanical hydraulic
systems used by vehicles are joined by a group of valves and piping it. (Khan, Islam and
Hossain, 2016) This gives oil with heavy pressure. It is essential that these joining recollects the
tight seals.
Seal integrity is not essential. It is essential that the entry of air bubbles are not allowed.
The force produced by the system takes care of compression of air. It normally decreases the
force and goodness of system when they are not safe. The mobile based machines with six
hydraulic actuators. It is named as crawler excavators. The six hydraulic actuators are boom,
bucket, lift arm, travel left, and travel right and swing. These union gives certain orders to the
hydraulic system. The movements in crawler excavator’s hydraulic system must be sensitive,
smooth and it is not dependent. The engine output must be hydraulically must be translated
100% clearly by an excavator's drive system. In comparison with engine output the hydrostatic
11
⊘ This is a preview!⊘
Do you want full access?
Subscribe today to unlock all pages.

Trusted by 1+ million students worldwide

reasons. This movement must be gained by joining or separating pump circuits. For that reason
the newer systems uses the technique of censoring and software. Electronics and electric systems
are used by advanced hydraulic control systems (Heidari, 2017). Hydraulics are also used by
front end loaders and skid loaders. The front end bucket consists of three pairs of hydraulic
pistons. One pair is used to move buckets up and down. The other pair is used for rotation. The
last pair splits the bucket to some objects such as steel I-beams and logs. Hydraulics are also
used by dump trucks. Dump trucks consists of two hydraulic cylinders. It helps the truck bed for
moving up and down. The design features must be equal. Telescope in two parts helps for long
movements and it is more efficient.
In ancient times, man himself had to rely on his own physical strength to lift and move
heavy objects however with due time and increased intelligence, he utilized tools and apparatus
to help him in this regard and history has shown that with each progressive iteration. One such
machine is the hydraulic accumulator.This machine works on the principal of pressure
differential and fluid movement. There are basically 4 types of hydraulic accumulates which all
are different yet fundamentally similar. They are:
1. The bladder
2. Spring-loaded
3. Piston-type
4. Metal Bellows Accumulators.
Lifts are used to move heavy loads and its two major applications are
Fork lifts
Cranes
However the machines that are available in the market are either too inefficient or
expensive so the lifting work itself has to be done manually. This paper will present a solution in
the form of an integrated hydraulic accumulator and its design. When designing the lift two
things must be taken into consideration (Chen and Chen, 2011)
The allowable load must not exceed 250 kg
12
Paraphrase This Document
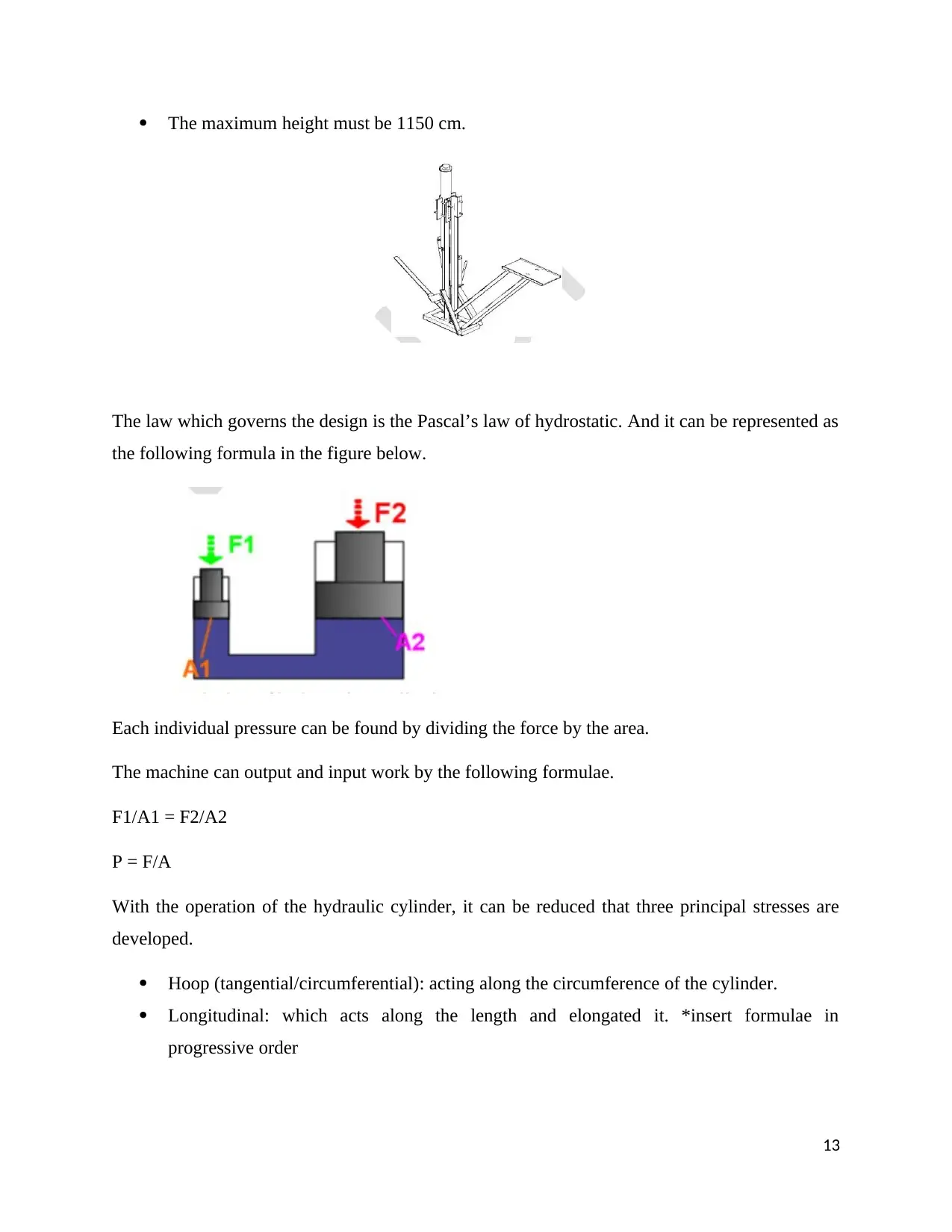
The law which governs the design is the Pascal’s law of hydrostatic. And it can be represented as
the following formula in the figure below.
Each individual pressure can be found by dividing the force by the area.
The machine can output and input work by the following formulae.
F1/A1 = F2/A2
P = F/A
With the operation of the hydraulic cylinder, it can be reduced that three principal stresses are
developed.
Hoop (tangential/circumferential): acting along the circumference of the cylinder.
Longitudinal: which acts along the length and elongated it. *insert formulae in
progressive order
13

walled cylinders.
The hydraulic ram shaft is connected to the piston inside the cylinder and extends
outward from the lower end of the hydraulic cylinder. Only compressive forces will be
experienced. To find the allowable load we use the.
𝐸 = 𝜎/𝜀
Pa = Pcr/N
The arrangement of the frame is such that a pair of the angle bars holds the upper part of
the machine which contains the accumulator, the lower part which contains the base stand and
the lift linkage. The angle bars themselves are under the maximum load. For a centralized load
distribution, use. (Bright Hub Engineering, 2019)
Sy = Pa/A x N
In order to find load the centroids at X and Y arises must be found.
The spring in the hydraulic accumulator stores compression energy when the piston
moves upwards. The pressure can be found by the principal of hooks law and the following
formula.
P = B x Vchange/Vinitial
Machine Performance or efficiency can be found by
𝜂 = 𝑊/𝑊h × 100.
The stresses obtained are below the material strength of the cylinder and piston so it will
not be stresses beyond capacity. The bending moment indicates that it is within operational
limits. The machine when made is capable of storing energy in its accumulator therefore making
it highly effective.
The model based system design approach allows for an efficient way of designing and
developing complex engineering systems in a virtual environment. Four steps are followed.
1. Modelling a plant
14
⊘ This is a preview!⊘
Do you want full access?
Subscribe today to unlock all pages.

Trusted by 1+ million students worldwide

3. Simulating the plant and controller together
4. Integrating the system.
By using this product development cost and time can be significantly reduced. Hydraulic
excavators are the most widely used earth moving equipment in the construction and mining
Industry. However due to the high skill required operating it is difficult. So by the use of the
model based system, an automated excavation system can be made which will output nearly the
same or more than the manually operated one and can also work in hazardous conditions.
Cinematic equations describe the motion of an excavator manipulator without
consideration of the driving forces and torques. First the geometric components are defined. The
boom, arm and bucket are assumed to be straight joint links with each having a Cartesian
coordinate system. Forward cinematic equations are derived to find the positions and orientations
of the manipulator links. Also inverse kinematic relations can be used to determine the joint
angles and cylinder lengths. In the majority of this, the Denavit-Hatenberg convention is used.
(DESIGN AND ANALYSIS OF EXCAVATOR BUCKET TOOTH, 2018)
In a study, mathematical models can be derived by Newton-Euler's or Euler-Lagrange's
method. These two are different but lead to the same dynamic equations. In addition to this
various other methods can be used,
Dynamic response model based on transfer function by Gu et al.
Method for gravitational parameter estimation by Tafazoli et al.
For more accurate simulations three types of software are widely used
MATLAB/Simulink
Amesim
Adams
In excavator manipulators the torques are produced by hydraulic pumps, valves and
cylinders. And as modelling and simulation of hydraulic systems is as vital as the system itself is
so complex to fully comprehend. The conventional modelling approach is to use Newton’s law.
In a separate research by Casoli and Anthony, a variable displacement pump was simulated. In
15
Paraphrase This Document

is done so that the system can be easily understood by the user. In most cases, the governing
equations are derived first followed by a graphical diagram. By using these parameters and
graphs one can develop a relatively accurate hydraulic system.
To simplify the complexity of a hydraulic pump system, various laws, conventions and
equations are used as well as the use of design software. This makes it easier to understand and
individually manipulate each component of the system so that a highly accurate model can be
derived. By using the model based system design approach highly complex system architecture
can be processed as well. As the current models focus significantly on the performance of the
pump so the next step in the research should be towards developing more energy efficient
systems. So in the future highly performance heavy and energy efficient hydraulic pumps can be
used everywhere.
Excavator is a heavy construction equipment consisting of a boom, dipper, bucket and a
cab. It is mounted on a rotating platform known as the house. The whole setup sits atop a wheel
for linear movements. All the operations of excavators are carried out through hydraulic systems.
The determination of mining loading, mechanical movement and performance of excavators
largely dependent upon their size design.
Size designed and mechanism of the excavators can be optimized as per requirement of the
performance objective. General optimization design contains two levels
Overall design optimization which is optimization of whole structure
Parameter optimization which is optimization of a few parameters of genetic algorithms
Due to the multivariable and multiparameter complicated structure, excavators must meet
different performance needs which aids in setting the multiple optimization objectives. We know
that increasing boom hydraulic cylinder increase the torque.
The resistance torque can be expressed as
Where F1 is hydraulic cylinder thrust and e1 is the linear function of movable arm
hydraulic cylinder arm. At certain arm swing angle range, in the process of lifting boom arm
16

improvement. The objective function is:
The boom cylinder optimization target can be achieved by increasing the bucket rod
hydraulic cylinder arm. The optimization goal can be expressed as Eq. (4)
17
⊘ This is a preview!⊘
Do you want full access?
Subscribe today to unlock all pages.

Trusted by 1+ million students worldwide

point is the levelling shovel distance and the vertical coordinate is the height of the levelling
shovel. So, h is a negative number by
And the geometric equation yields
18
Paraphrase This Document
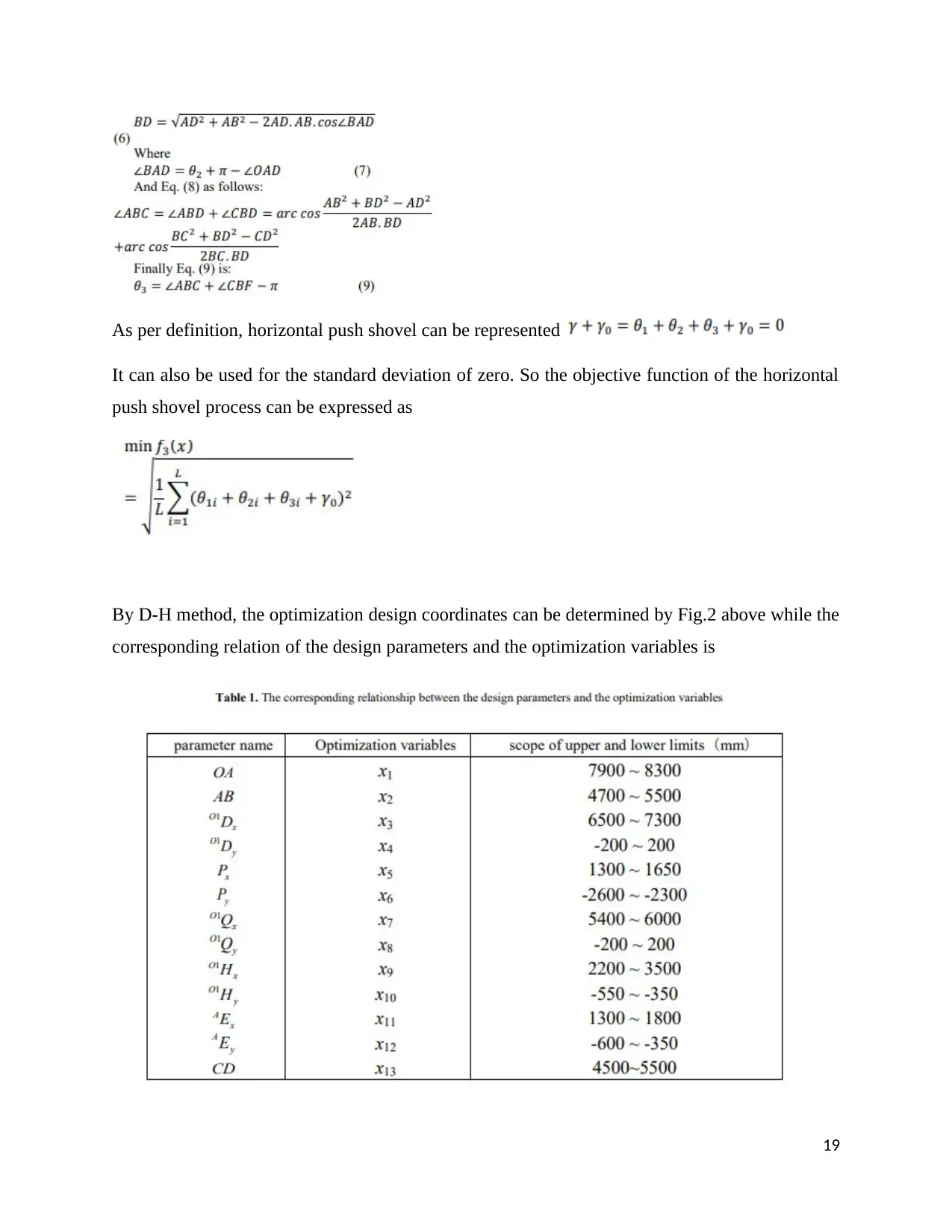
It can also be used for the standard deviation of zero. So the objective function of the horizontal
push shovel process can be expressed as
By D-H method, the optimization design coordinates can be determined by Fig.2 above while the
corresponding relation of the design parameters and the optimization variables is
19

range of shovel excavator working device there are several optimizations constrains such as
Using MATLAB for optimization the genetic algorithm toolbox. Three objective function
of the horizontal push shovel, hydraulic cylinder moving arm and hydraulic cylinder bucket rod
arm is respectively programmed by MATLAB. The MATLAB genetic algorithm toolbox is used
to obtain the optimal data of horizontal push shovel and the population fitness. As shown below,
the following function took place
20
⊘ This is a preview!⊘
Do you want full access?
Subscribe today to unlock all pages.

Trusted by 1+ million students worldwide

Paraphrase This Document

push shovel function. Comparison results can be seen in the image below
By optimizing the type of mining and lifting process using genetic algorithms, the
working device, boom, bucket rod and bucket mechanism transmission angle increased while the
stroke of hydraulic cylinders is shortening. Arm hydraulic cylinder lifting force more in line with
the full bucket by any mining location to ascend to the unloading point place needs power
changes, the bucket rod hydraulic cylinder of the digging force and bucket hydraulic cylinder of
the digging force optimization than before more in line.
22

Pascal’s law
Pascal law or Pascal’s principle is one of the most important principles used for different applications.
This principle mainly discusses the transmission of pressure on the fluid. This principle states that the
pressure of fluid throughout the fluid system is the same (Solazzi, 2010). A change in pressure at any
point in an enclosed fluid at rest is transmitted undiminished to all points in the fluid. He also
discovered that the pressure at any point for a fluid is equal to all planes passing through the
point.
P=F/A, where P is the pressure, F is the force and A is the area. This is the formula of Pascal’s
law.
Applications
Most of the hydraulic systems works based on the Pascal’s law.It is an enclosed fluid
system used to exert forces. Equal pressure transmitted throughout a fluid is the principle
of hydraulic lift.
23
⊘ This is a preview!⊘
Do you want full access?
Subscribe today to unlock all pages.

Trusted by 1+ million students worldwide
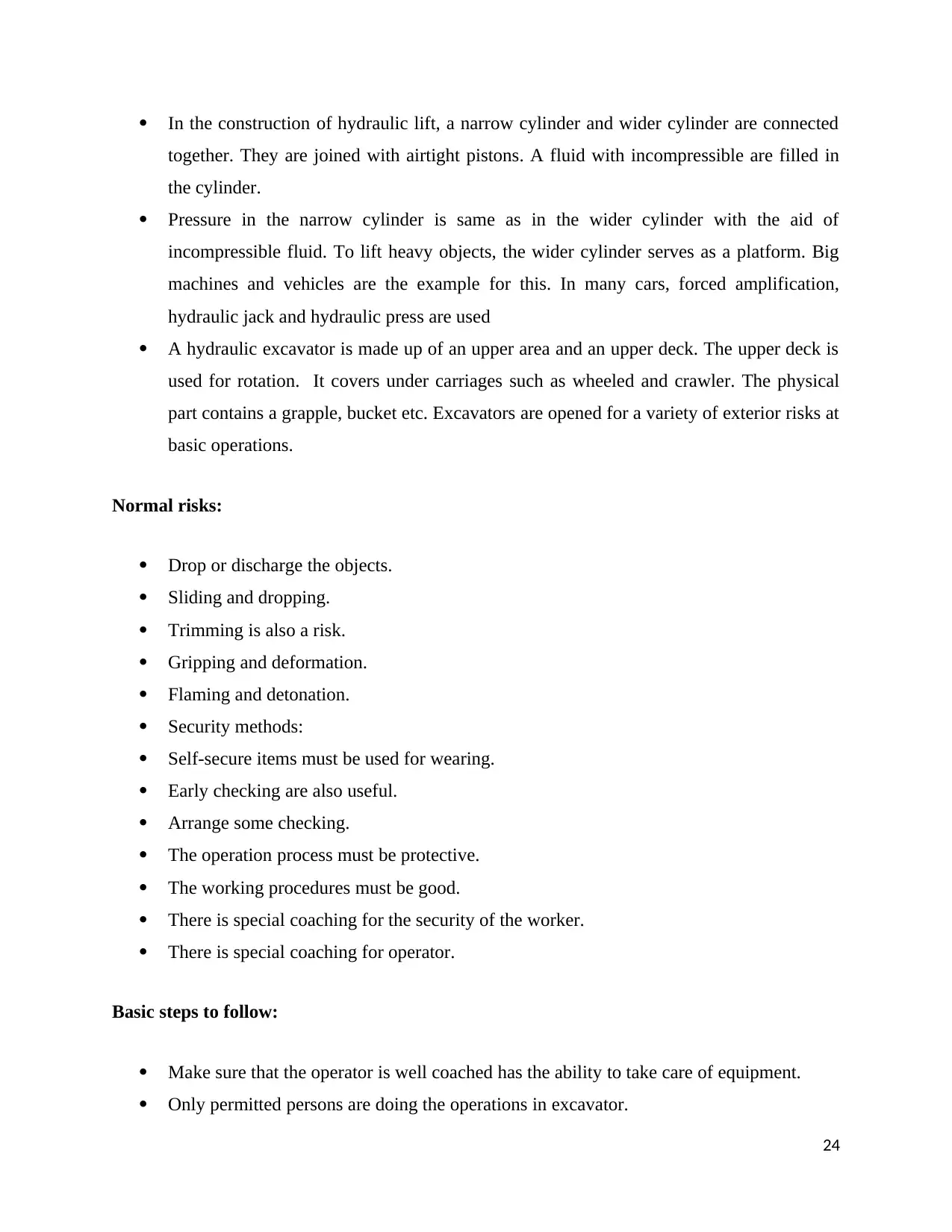
together. They are joined with airtight pistons. A fluid with incompressible are filled in
the cylinder.
Pressure in the narrow cylinder is same as in the wider cylinder with the aid of
incompressible fluid. To lift heavy objects, the wider cylinder serves as a platform. Big
machines and vehicles are the example for this. In many cars, forced amplification,
hydraulic jack and hydraulic press are used
A hydraulic excavator is made up of an upper area and an upper deck. The upper deck is
used for rotation. It covers under carriages such as wheeled and crawler. The physical
part contains a grapple, bucket etc. Excavators are opened for a variety of exterior risks at
basic operations.
Normal risks:
Drop or discharge the objects.
Sliding and dropping.
Trimming is also a risk.
Gripping and deformation.
Flaming and detonation.
Security methods:
Self-secure items must be used for wearing.
Early checking are also useful.
Arrange some checking.
The operation process must be protective.
The working procedures must be good.
There is special coaching for the security of the worker.
There is special coaching for operator.
Basic steps to follow:
Make sure that the operator is well coached has the ability to take care of equipment.
Only permitted persons are doing the operations in excavator.
24
Paraphrase This Document

The operator must have well creativity, spatial understanding, hearing power and
A spontaneous time needed for reaction.
The operator must have complete idea about the working of excavator.
Find pure and secure approaches to the machine.
All the perfections and imperfections of hydraulic excavator must be understand by the
operator.
Before each shifting the operator must perform a routine checking for excavator and its
environment.
Make sure that if there is any loose pin or any bolt connections.
Make sure that it must be problem free.
Create all security measures.
Not works on a problematic machine.
Finish all maintenance works.
Make sure that side doors are open but it must be kept safe.
Make sure that mirrors are tidy and it must be fixed for appropriate position.
Seat and armrests must be adjusted at suitable directions.
The working area must be clear.
Initiation and working of an excavator
Make sure that the machine had been initiated and what work it is doing.
Make good talking skills with other workers and have good sight of vision.
Make signals for warning by a horn or by using a beacon light or a flasher.
During high temperatures the systems such as engine coolant or oil must be used.
The devices functionality must be tested.
Fix excavator at the correct position.
When we are working we must understand that the device clears all power lines.
Power-off steps:
Fix excavator at the ground level.
25

The attachment must at the bottom or at ground.
The parking must be engaged.
The level of secureness must be disengaged.
Normally then decrease the engine speed.
To get free of system pressure the joysticks must be worked in a circle pattern.
Make sure that it is switched off then lock the window.
Then using a three point stance.
Switch off battery.
Steps for maintenance
Man-lifts, ladders and scaffolds, etc. are used for maintenance.
Above eight feet from ground level we must use fall protection.
Accurate tools are used to service the excavator.
Steps for security
It is important to give a coaching for every worker about alarm or a warning signal.
Find places where emission of debris will start.
Trip and fall hazards are not take during drive.
Give instructions for each worker about safety signs.
Excavator Selection
For this undertaking, we expected to choose a particular model for the water powered
excavator as it would manage the important measurements and geometry. The excavator we
chose for our undertaking is the Liebherr crawler excavator 974C model as appeared in the
figure beneath.
26
⊘ This is a preview!⊘
Do you want full access?
Subscribe today to unlock all pages.

Trusted by 1+ million students worldwide

the parameters required for the joint position were resolved. The underlying posture of the
excavator arm is set by the boxing conditions when the excavator is first transported out from
Liebherr. The fixed lengths and edges of the blast (arm) framework were estimated.
27
Paraphrase This Document

Simplification of the model
There are three actuators in the excavator and they have three degrees of motion. To make
simple model and to calculate the Matlab script, there are few new variables to be defined. We
can calculate every joint’s position.
28

In the case of Li, where i=letter, the length are fixed by the inventers.
In the case of di, they are the parameters of the system .They mention to the hydraulic cylinders.
The angles used in the Matlab simple model is θi.
The angles fixed by the inventers are αi, βi, γi, and φi. They mention to the point where angle is
from.
Abstract angles to the horizontal axis is δi.
To improve the model, we should modify the fixed parameters.
Position of joint 1
From the above diagram that is clear the joint one is situated in the origin. So that coordinates for the joint
is given as,
Finding of θ1
29
⊘ This is a preview!⊘
Do you want full access?
Subscribe today to unlock all pages.

Trusted by 1+ million students worldwide

Finding of θ2
30
Paraphrase This Document
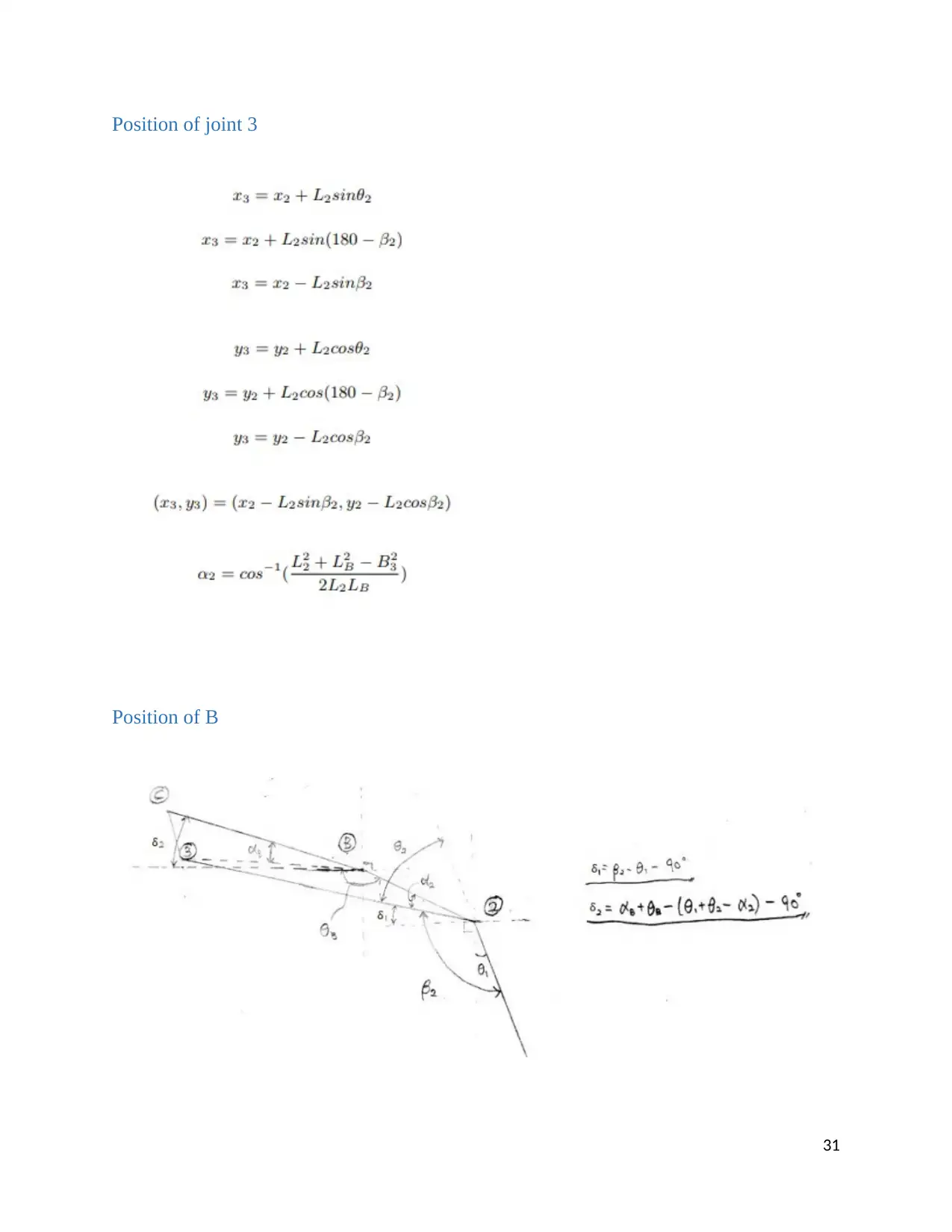
Position of B
31

Position of D
32
⊘ This is a preview!⊘
Do you want full access?
Subscribe today to unlock all pages.

Trusted by 1+ million students worldwide

33
Paraphrase This Document

Position of Joint 4
34

Position of M
35
⊘ This is a preview!⊘
Do you want full access?
Subscribe today to unlock all pages.

Trusted by 1+ million students worldwide

Parameters of Denavit Hartenberg
DH parameters are seen in the table (Usman, Lawal & Shehu, 2014). The figure shows the
matrixes of the joint’s position.
Screw parameters
To model the system with Matlab, we derive the screw parameters.
Jacobian
For the manipulator arm, the Jacobian was calculated by using the values computed above.
36
Paraphrase This Document

Matlab was implemented by using Jacobians and screw parameters. This was used to organize
parametric studies on the link lengths and joints angles. (Usman, Lawal & Shehu, 2014)
Analysis & Comparison of Results
Parametric Study
From the parametric studies, we can manipulate the joint angles by using the MATLAB
model. We can compute joint angles from 0 to 90 degrees. The kinetic manipulability was
described from the radius of the short and long axes of the manipulability ellipse. There is no
effect on the first joint angle because of the manipulability ellipse. The position of the end bucket
and its kinetic manipulability is related to this. There is a big change occur in the second joint
angle. 41% is seen for the short axis. The third angle also has kinetic manipulability. But its
37

the bucket with the manipulator arms. From this we can conclude that the second joint angle has
more effect.
38
⊘ This is a preview!⊘
Do you want full access?
Subscribe today to unlock all pages.

Trusted by 1+ million students worldwide

The manipulator arms must have ratio of lengths within arms 1-2 and arms2-3 .The
kinetic manipulation is more in second joint. The starting lengths of arm are L1, L2 and L3.The
values are 10, 5 and 1.The starting joint angles are θ1, θ2 and θ3 at 45◦ , 0◦ and 0◦ .The
proportions are 1:10,1:5,1:2,1:1,2:1,5:1 and 10:1.Some ratios are infeasible for an actual
excavator. It is not feasible for the bucket is longer than the Boom length. We also wanted to
check its consequences. The ratios are provided according to the second link. In fig 16 the
outputs must be seen. There are a lot of changes that are surveillance for the longer axis. The
smallest ellipse must be surveillance the length ratios L1/L2 and L3/L2 .The values of L1/L2 and
L3/L2 are 1 and 2.L1/L2 must provide a pure relationship that is not asymmetric. It is symmetric
and the value is L1/L2=1.The relationship of L3/L2 shows low clearance. The long axis had a
high ratio of more than 5:1.L3 is used to denote the Total length of the end bucket. In
comparison with the manipulator arms, the length of end bucket is shorter. The L3/L2
proportions are not feasible. Only the ratios must be considered.
39
Paraphrase This Document

Surface of failure
Using perumpral failure shape and McKye’s failure shapes park (2002) designed the
separation, movements and sub separation of soils because of the excavator bucket. We must
simplifies the Excavation model as a source. It is situated at the teeth of the bucket. The bucket
was designed as 90 degree to end bucket. This architecture was used in geotechnical apps. The
shear stresses with failure must be reached at the shear strength of soils during failure.
The soil grains slip along with the failure surface. Imagine that there is no crushing for
each grains. The failure surface of soils can be confirmed by failure envelope and Mohr circle.
The Mohr –Coulomb failure criteria must be equal to the maximal shear stress of soil with no
failure, τf below the normal stress 0 with soil parenthesis cohesion c and the internal friction
angle φ. It is denoted by the equation τf=c+tan (φ). (Yuan, 2014)
40

optimized only when the entry angle of the excavator must be same as the internal friction angle.
We can change the MATLAB code for deciding the entry angle and manipulator positions. The
radius of the kinetic manipulation ellipse at the position of interior friction angle conforms the
Maximal optimization. Imagine that the level of ground is zero.
Effective penetrability of the end bucket describes the deformation of efficiency
according to the entry angle. It was confirmed by a half-sine curve. It is used as the main factor.
Doubling the entry angle of the manipulator with good movement capacity of the ground
provides ‘manipulability index’ for every joint angles and length.
First in-situ soil conditions
The in-situ soil conditions in our study must be considered as sandy-loose gravel with an
interior friction angle of 45◦ .The limit of friction angle of soils are 20 to 35 degrees. Consider
our penetrability as a half sine curve then the maximal value must be at 45◦.We considers our
internal friction angle as a high value. We can redesign the penetrability method by Gaussian or
statistical distribution for actual applications. The mean value must be positioned at the interior
angle of friction. The elevation of ground must be imagined at the end of the bucket tip.
The excavator was fixed at the origin (0, 0).The values for excavator arms L1, L2, L3
was 10, 5 and 1.Imagine that the bucket was normal to the second link. The value of θ3=0. The
41
⊘ This is a preview!⊘
Do you want full access?
Subscribe today to unlock all pages.

Trusted by 1+ million students worldwide

range of 0◦ to 90◦.It increases by 5◦ .The first joint angle θ1 was inspected for 0◦, 15◦, 30◦ and
45◦.
In the above fig.the change in manipulability index with θ2 must be represented for
inspecting θ1.
A parabolic bond must been seen in θ2.The position of the maximal point of parabola changes to
negative values and it is not considered. For a particular position the optimal excavation angle
must be confirmed. The entry angle at a fixed position must be confirmed by various θ1 values.
It must be demonstrated in the above fig.
42
Paraphrase This Document

0◦ .It is because of the changes in negative x direction in parabolic bond with incrementing θ1
values. The maximal value surpassed the x=0 axis. The maximal value must be unseen in the
positive limit as in our outputs. Figure 20 denotes the index values at accurate positions for
various joint angle values. This bond denotes a decrement in maximal index and incrementing
θ1and maximal value exists when θ1=0. (Usman, Lawal & Shehu, 2014)
The output gives an idea about the soil parameters application when deciding the actual
position of an excavator. There are limitations in our design. The optimal pose must be seen as
θ1=0, it doesn’t bound the first arm. It lies parallel to the ground level. The ground must be fixed
at the penetrating teeth of the end bucket. Make changes by taking the actual position of ground
to a stable node, then take care of the pose of manipulators. By positioning a node limits link
lengths and joint angles. A good way is that fixing a stable level i.e. y=0.
43

This project described about the kinematic manipulability of a mechanical excavator.
This is used for construction purposes. Using MATLAB, we can pretend a simplified model of
the excavator. Hence the kinematic manipulability ellipses were proposed. A parametric study
was used for the effects of joint angles. From this we can conclude that the second joint angle
has more effect. To signify the optimization process, the model was referred to a case study.
Effective penetrability focuses the geomechanical parameter internal friction angle. This was
introduced for different θ1 and θ1 angles. When θ1=0, the maximum value will exist. We can
improve the model by using the actual location of the ground.
44
⊘ This is a preview!⊘
Do you want full access?
Subscribe today to unlock all pages.

Trusted by 1+ million students worldwide

ANALYSYS & OPTIMIZATION OF HYDRAULIC EXCAVATOR BUCKET TEETH USING
FEM. (2017). International Journal of Recent Trends in Engineering and Research, 3(4),
pp.267-275.
Bright Hub Engineering. (2019). Basic Principles Of Hydraulics. [online] Available at:
https://www.brighthubengineering.com/hydraulics-civil-engineering/43171-what-are-the-basic-
principles-of-hydraulics/ [Accessed 5 Jun. 2019].
Chen, C. and Chen, X. (2011). Design of New Excavator with Telescopic Arm. Advanced
Materials Research, 228-229, pp.340-344.
DESIGN AND ANALYSIS OF EXCAVATOR BUCKET TOOTH. (2018). International
Journal of Modern Trends in Engineering & Research, 5(4), pp.79-86.
DESIGN AND OPTIMIZATION OF EXCAVATOR. (2017). International Journal of Recent
Trends in Engineering and Research, 3(4), pp.535-549.
FAN, Q. (2017). Leveling Theory and Experiment Study on High Strength Steel Plate of
Excavator Working Arm. Journal of Mechanical Engineering, 53(8), p.82.
Heidari, M. (2017). DESIGN AND OPTIMIZATION OF EXCAVATOR. International Journal
of Recent Trends in Engineering and Research, 3(4), pp.535-549.
Khan, F., Islam, M. and Hossain, M. (2016). Design Aspects of an Excavator Arm. International
Review of Mechanical Engineering (IREME), 10(6), p.437.
Qi, X. and Zhang, J. (2014). ANSYS Workbench for Static Analysis of Excavator
Arm. Advanced Materials Research, 926-930, pp.759-762.
Qiu, Q., Li, B. and Feng, P. (2016). Optimal design of hydraulic excavator working device based
on multiple surrogate models. Advances in Mechanical Engineering, 8(5), p.168781401664794.
Shetiye, G. and Kungwani, B. (2018). DESIGN OPTIMIZATION OF HYDRAULIC LIFT
CONNECTING ROD. Industrial Engineering Journal, 11(4).
45
Paraphrase This Document
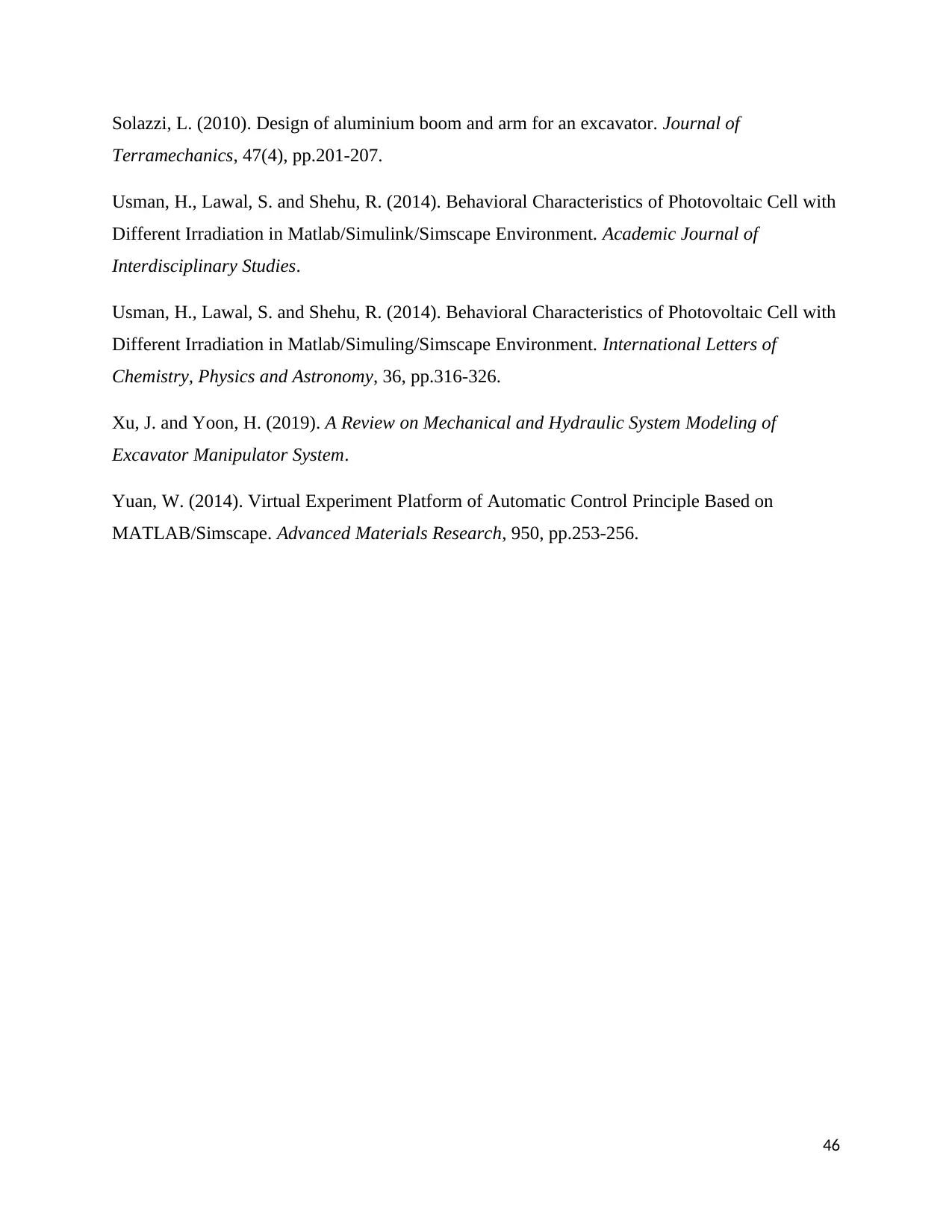
Terramechanics, 47(4), pp.201-207.
Usman, H., Lawal, S. and Shehu, R. (2014). Behavioral Characteristics of Photovoltaic Cell with
Different Irradiation in Matlab/Simulink/Simscape Environment. Academic Journal of
Interdisciplinary Studies.
Usman, H., Lawal, S. and Shehu, R. (2014). Behavioral Characteristics of Photovoltaic Cell with
Different Irradiation in Matlab/Simuling/Simscape Environment. International Letters of
Chemistry, Physics and Astronomy, 36, pp.316-326.
Xu, J. and Yoon, H. (2019). A Review on Mechanical and Hydraulic System Modeling of
Excavator Manipulator System.
Yuan, W. (2014). Virtual Experiment Platform of Automatic Control Principle Based on
MATLAB/Simscape. Advanced Materials Research, 950, pp.253-256.
46

Your All-in-One AI-Powered Toolkit for Academic Success.
+13062052269
info@desklib.com
Available 24*7 on WhatsApp / Email
© 2024 | Zucol Services PVT LTD | All rights reserved.