Design for Manufacture and Assembly in the Australian Construction Industry
VerifiedAdded on 2023/06/03
|4
|1223
|240
AI Summary
This article discusses the benefits and opportunities of Design for Manufacture and Assembly (DFMA) in the Australian construction industry. It also highlights the current applications and practices, barriers to widespread application, and avenues for further research.
Contribute Materials
Your contribution can guide someone’s learning journey. Share your
documents today.
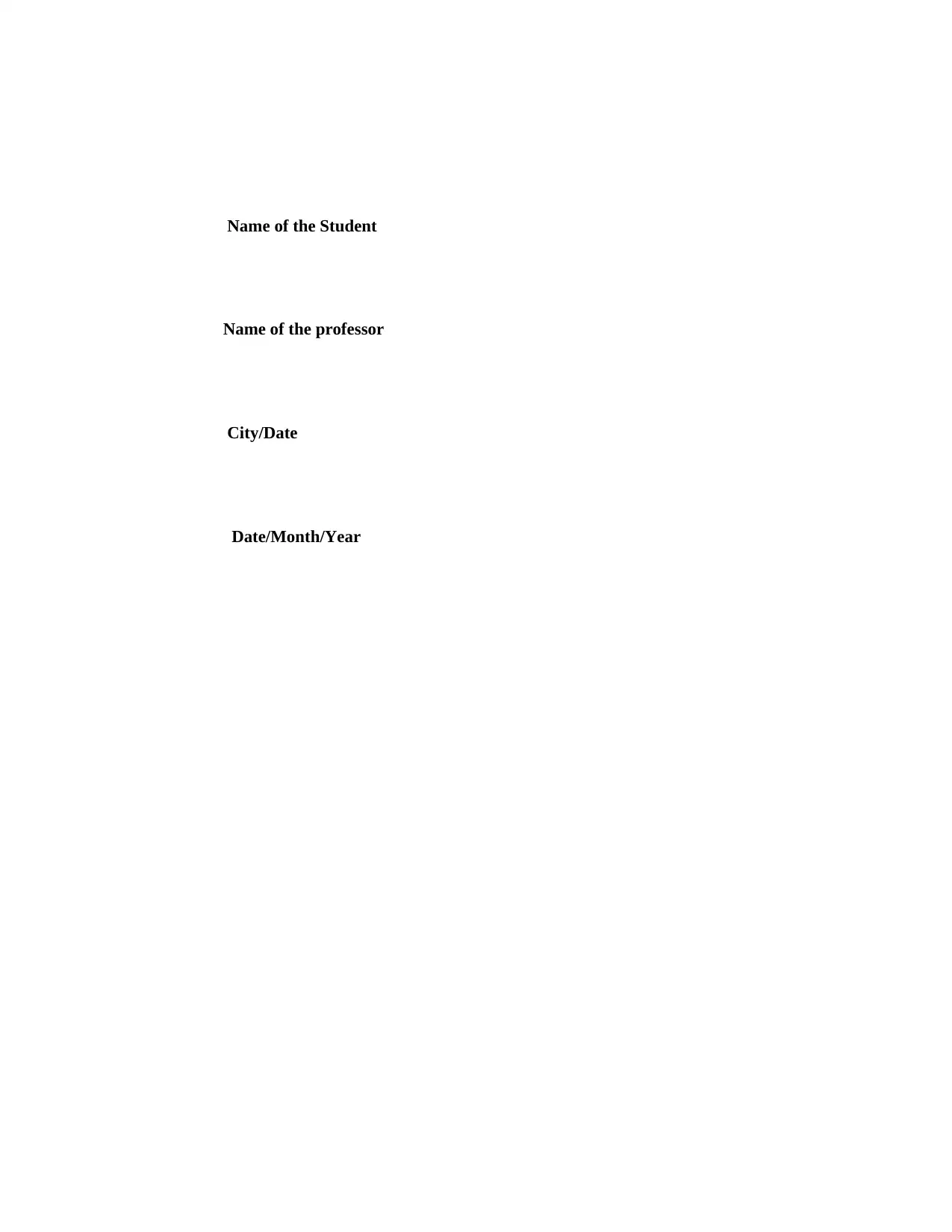
Name of the Student
Name of the professor
City/Date
Date/Month/Year
Name of the professor
City/Date
Date/Month/Year
Secure Best Marks with AI Grader
Need help grading? Try our AI Grader for instant feedback on your assignments.
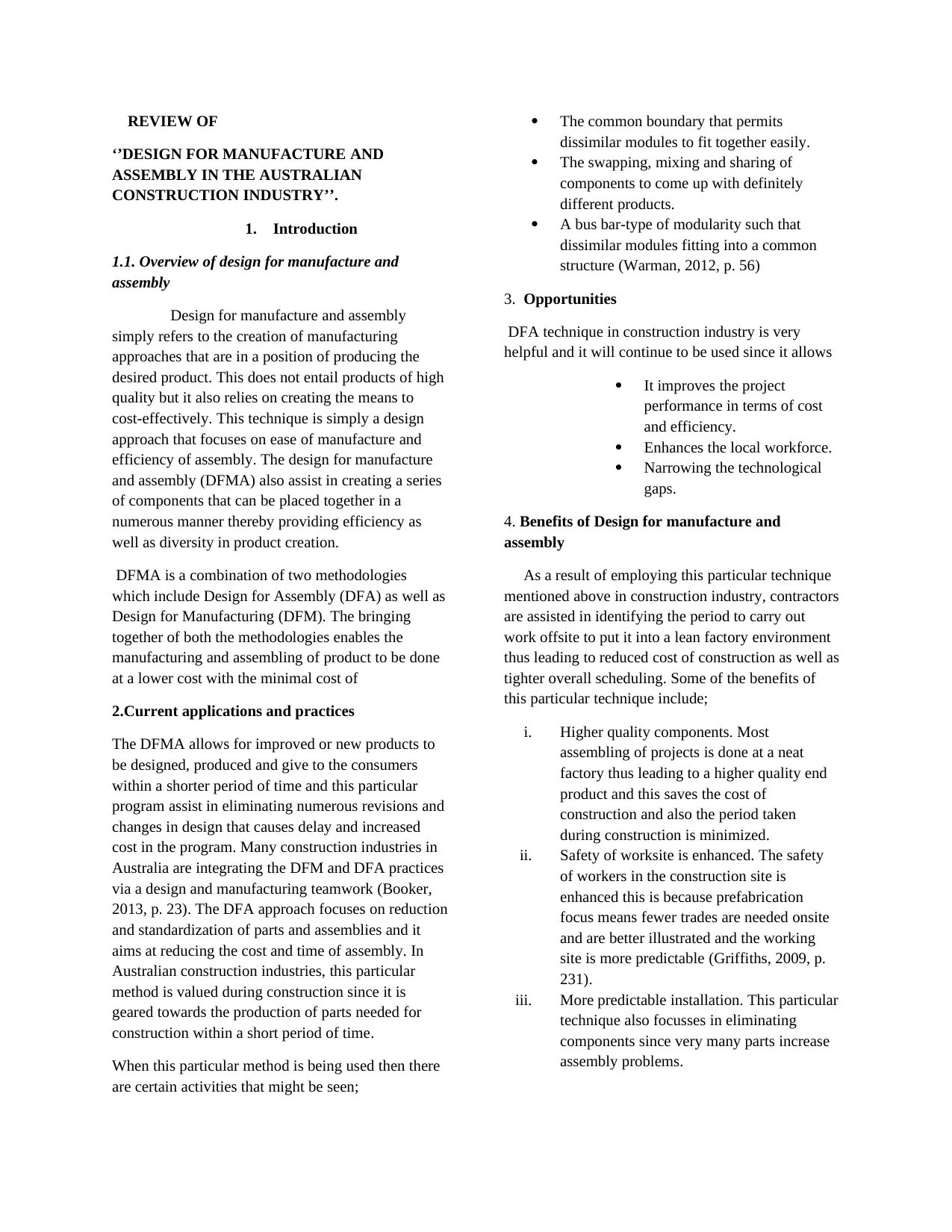
REVIEW OF
‘’DESIGN FOR MANUFACTURE AND
ASSEMBLY IN THE AUSTRALIAN
CONSTRUCTION INDUSTRY’’.
1. Introduction
1.1. Overview of design for manufacture and
assembly
Design for manufacture and assembly
simply refers to the creation of manufacturing
approaches that are in a position of producing the
desired product. This does not entail products of high
quality but it also relies on creating the means to
cost-effectively. This technique is simply a design
approach that focuses on ease of manufacture and
efficiency of assembly. The design for manufacture
and assembly (DFMA) also assist in creating a series
of components that can be placed together in a
numerous manner thereby providing efficiency as
well as diversity in product creation.
DFMA is a combination of two methodologies
which include Design for Assembly (DFA) as well as
Design for Manufacturing (DFM). The bringing
together of both the methodologies enables the
manufacturing and assembling of product to be done
at a lower cost with the minimal cost of
2.Current applications and practices
The DFMA allows for improved or new products to
be designed, produced and give to the consumers
within a shorter period of time and this particular
program assist in eliminating numerous revisions and
changes in design that causes delay and increased
cost in the program. Many construction industries in
Australia are integrating the DFM and DFA practices
via a design and manufacturing teamwork (Booker,
2013, p. 23). The DFA approach focuses on reduction
and standardization of parts and assemblies and it
aims at reducing the cost and time of assembly. In
Australian construction industries, this particular
method is valued during construction since it is
geared towards the production of parts needed for
construction within a short period of time.
When this particular method is being used then there
are certain activities that might be seen;
The common boundary that permits
dissimilar modules to fit together easily.
The swapping, mixing and sharing of
components to come up with definitely
different products.
A bus bar-type of modularity such that
dissimilar modules fitting into a common
structure (Warman, 2012, p. 56)
3. Opportunities
DFA technique in construction industry is very
helpful and it will continue to be used since it allows
It improves the project
performance in terms of cost
and efficiency.
Enhances the local workforce.
Narrowing the technological
gaps.
4. Benefits of Design for manufacture and
assembly
As a result of employing this particular technique
mentioned above in construction industry, contractors
are assisted in identifying the period to carry out
work offsite to put it into a lean factory environment
thus leading to reduced cost of construction as well as
tighter overall scheduling. Some of the benefits of
this particular technique include;
i. Higher quality components. Most
assembling of projects is done at a neat
factory thus leading to a higher quality end
product and this saves the cost of
construction and also the period taken
during construction is minimized.
ii. Safety of worksite is enhanced. The safety
of workers in the construction site is
enhanced this is because prefabrication
focus means fewer trades are needed onsite
and are better illustrated and the working
site is more predictable (Griffiths, 2009, p.
231).
iii. More predictable installation. This particular
technique also focusses in eliminating
components since very many parts increase
assembly problems.
‘’DESIGN FOR MANUFACTURE AND
ASSEMBLY IN THE AUSTRALIAN
CONSTRUCTION INDUSTRY’’.
1. Introduction
1.1. Overview of design for manufacture and
assembly
Design for manufacture and assembly
simply refers to the creation of manufacturing
approaches that are in a position of producing the
desired product. This does not entail products of high
quality but it also relies on creating the means to
cost-effectively. This technique is simply a design
approach that focuses on ease of manufacture and
efficiency of assembly. The design for manufacture
and assembly (DFMA) also assist in creating a series
of components that can be placed together in a
numerous manner thereby providing efficiency as
well as diversity in product creation.
DFMA is a combination of two methodologies
which include Design for Assembly (DFA) as well as
Design for Manufacturing (DFM). The bringing
together of both the methodologies enables the
manufacturing and assembling of product to be done
at a lower cost with the minimal cost of
2.Current applications and practices
The DFMA allows for improved or new products to
be designed, produced and give to the consumers
within a shorter period of time and this particular
program assist in eliminating numerous revisions and
changes in design that causes delay and increased
cost in the program. Many construction industries in
Australia are integrating the DFM and DFA practices
via a design and manufacturing teamwork (Booker,
2013, p. 23). The DFA approach focuses on reduction
and standardization of parts and assemblies and it
aims at reducing the cost and time of assembly. In
Australian construction industries, this particular
method is valued during construction since it is
geared towards the production of parts needed for
construction within a short period of time.
When this particular method is being used then there
are certain activities that might be seen;
The common boundary that permits
dissimilar modules to fit together easily.
The swapping, mixing and sharing of
components to come up with definitely
different products.
A bus bar-type of modularity such that
dissimilar modules fitting into a common
structure (Warman, 2012, p. 56)
3. Opportunities
DFA technique in construction industry is very
helpful and it will continue to be used since it allows
It improves the project
performance in terms of cost
and efficiency.
Enhances the local workforce.
Narrowing the technological
gaps.
4. Benefits of Design for manufacture and
assembly
As a result of employing this particular technique
mentioned above in construction industry, contractors
are assisted in identifying the period to carry out
work offsite to put it into a lean factory environment
thus leading to reduced cost of construction as well as
tighter overall scheduling. Some of the benefits of
this particular technique include;
i. Higher quality components. Most
assembling of projects is done at a neat
factory thus leading to a higher quality end
product and this saves the cost of
construction and also the period taken
during construction is minimized.
ii. Safety of worksite is enhanced. The safety
of workers in the construction site is
enhanced this is because prefabrication
focus means fewer trades are needed onsite
and are better illustrated and the working
site is more predictable (Griffiths, 2009, p.
231).
iii. More predictable installation. This particular
technique also focusses in eliminating
components since very many parts increase
assembly problems.
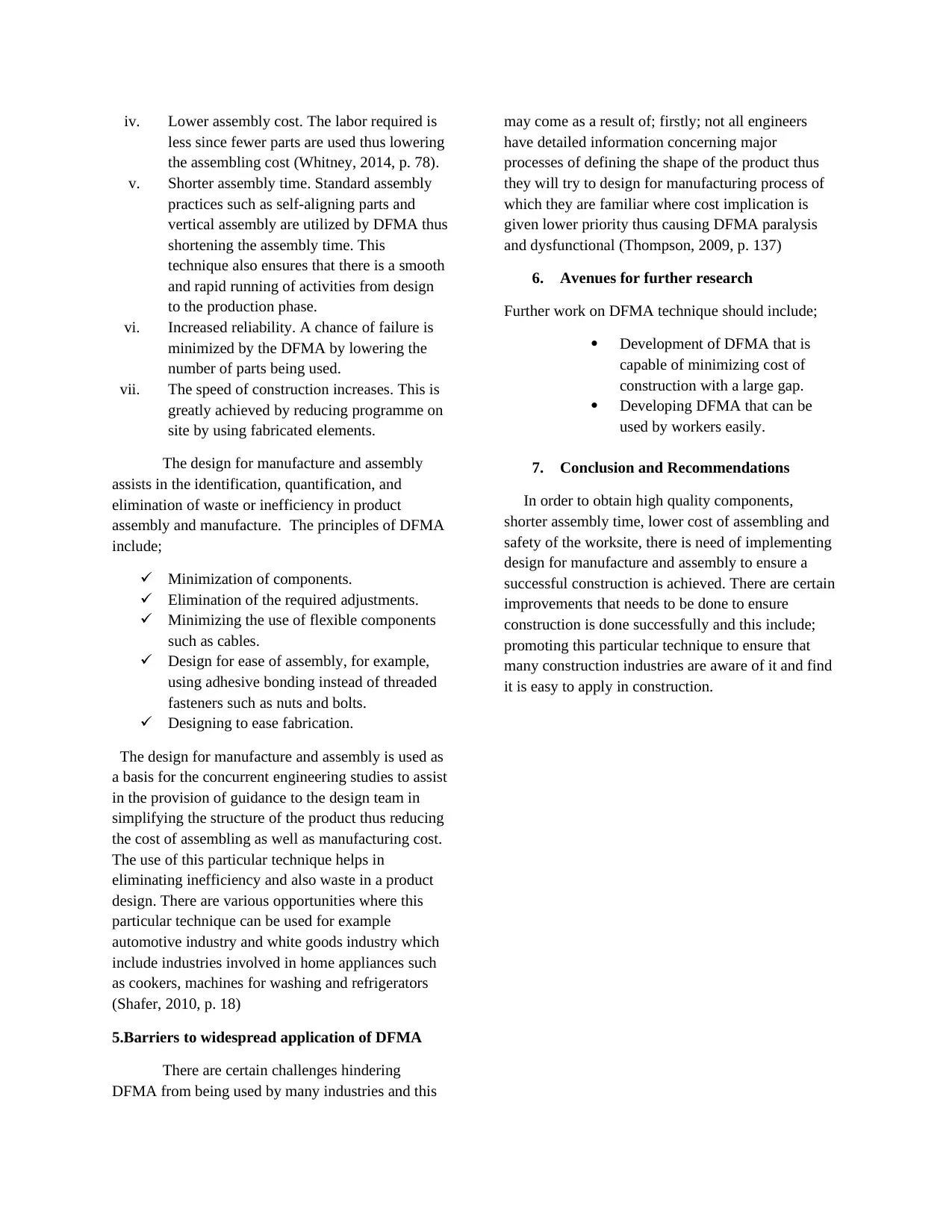
iv. Lower assembly cost. The labor required is
less since fewer parts are used thus lowering
the assembling cost (Whitney, 2014, p. 78).
v. Shorter assembly time. Standard assembly
practices such as self-aligning parts and
vertical assembly are utilized by DFMA thus
shortening the assembly time. This
technique also ensures that there is a smooth
and rapid running of activities from design
to the production phase.
vi. Increased reliability. A chance of failure is
minimized by the DFMA by lowering the
number of parts being used.
vii. The speed of construction increases. This is
greatly achieved by reducing programme on
site by using fabricated elements.
The design for manufacture and assembly
assists in the identification, quantification, and
elimination of waste or inefficiency in product
assembly and manufacture. The principles of DFMA
include;
Minimization of components.
Elimination of the required adjustments.
Minimizing the use of flexible components
such as cables.
Design for ease of assembly, for example,
using adhesive bonding instead of threaded
fasteners such as nuts and bolts.
Designing to ease fabrication.
The design for manufacture and assembly is used as
a basis for the concurrent engineering studies to assist
in the provision of guidance to the design team in
simplifying the structure of the product thus reducing
the cost of assembling as well as manufacturing cost.
The use of this particular technique helps in
eliminating inefficiency and also waste in a product
design. There are various opportunities where this
particular technique can be used for example
automotive industry and white goods industry which
include industries involved in home appliances such
as cookers, machines for washing and refrigerators
(Shafer, 2010, p. 18)
5.Barriers to widespread application of DFMA
There are certain challenges hindering
DFMA from being used by many industries and this
may come as a result of; firstly; not all engineers
have detailed information concerning major
processes of defining the shape of the product thus
they will try to design for manufacturing process of
which they are familiar where cost implication is
given lower priority thus causing DFMA paralysis
and dysfunctional (Thompson, 2009, p. 137)
6. Avenues for further research
Further work on DFMA technique should include;
Development of DFMA that is
capable of minimizing cost of
construction with a large gap.
Developing DFMA that can be
used by workers easily.
7. Conclusion and Recommendations
In order to obtain high quality components,
shorter assembly time, lower cost of assembling and
safety of the worksite, there is need of implementing
design for manufacture and assembly to ensure a
successful construction is achieved. There are certain
improvements that needs to be done to ensure
construction is done successfully and this include;
promoting this particular technique to ensure that
many construction industries are aware of it and find
it is easy to apply in construction.
less since fewer parts are used thus lowering
the assembling cost (Whitney, 2014, p. 78).
v. Shorter assembly time. Standard assembly
practices such as self-aligning parts and
vertical assembly are utilized by DFMA thus
shortening the assembly time. This
technique also ensures that there is a smooth
and rapid running of activities from design
to the production phase.
vi. Increased reliability. A chance of failure is
minimized by the DFMA by lowering the
number of parts being used.
vii. The speed of construction increases. This is
greatly achieved by reducing programme on
site by using fabricated elements.
The design for manufacture and assembly
assists in the identification, quantification, and
elimination of waste or inefficiency in product
assembly and manufacture. The principles of DFMA
include;
Minimization of components.
Elimination of the required adjustments.
Minimizing the use of flexible components
such as cables.
Design for ease of assembly, for example,
using adhesive bonding instead of threaded
fasteners such as nuts and bolts.
Designing to ease fabrication.
The design for manufacture and assembly is used as
a basis for the concurrent engineering studies to assist
in the provision of guidance to the design team in
simplifying the structure of the product thus reducing
the cost of assembling as well as manufacturing cost.
The use of this particular technique helps in
eliminating inefficiency and also waste in a product
design. There are various opportunities where this
particular technique can be used for example
automotive industry and white goods industry which
include industries involved in home appliances such
as cookers, machines for washing and refrigerators
(Shafer, 2010, p. 18)
5.Barriers to widespread application of DFMA
There are certain challenges hindering
DFMA from being used by many industries and this
may come as a result of; firstly; not all engineers
have detailed information concerning major
processes of defining the shape of the product thus
they will try to design for manufacturing process of
which they are familiar where cost implication is
given lower priority thus causing DFMA paralysis
and dysfunctional (Thompson, 2009, p. 137)
6. Avenues for further research
Further work on DFMA technique should include;
Development of DFMA that is
capable of minimizing cost of
construction with a large gap.
Developing DFMA that can be
used by workers easily.
7. Conclusion and Recommendations
In order to obtain high quality components,
shorter assembly time, lower cost of assembling and
safety of the worksite, there is need of implementing
design for manufacture and assembly to ensure a
successful construction is achieved. There are certain
improvements that needs to be done to ensure
construction is done successfully and this include;
promoting this particular technique to ensure that
many construction industries are aware of it and find
it is easy to apply in construction.
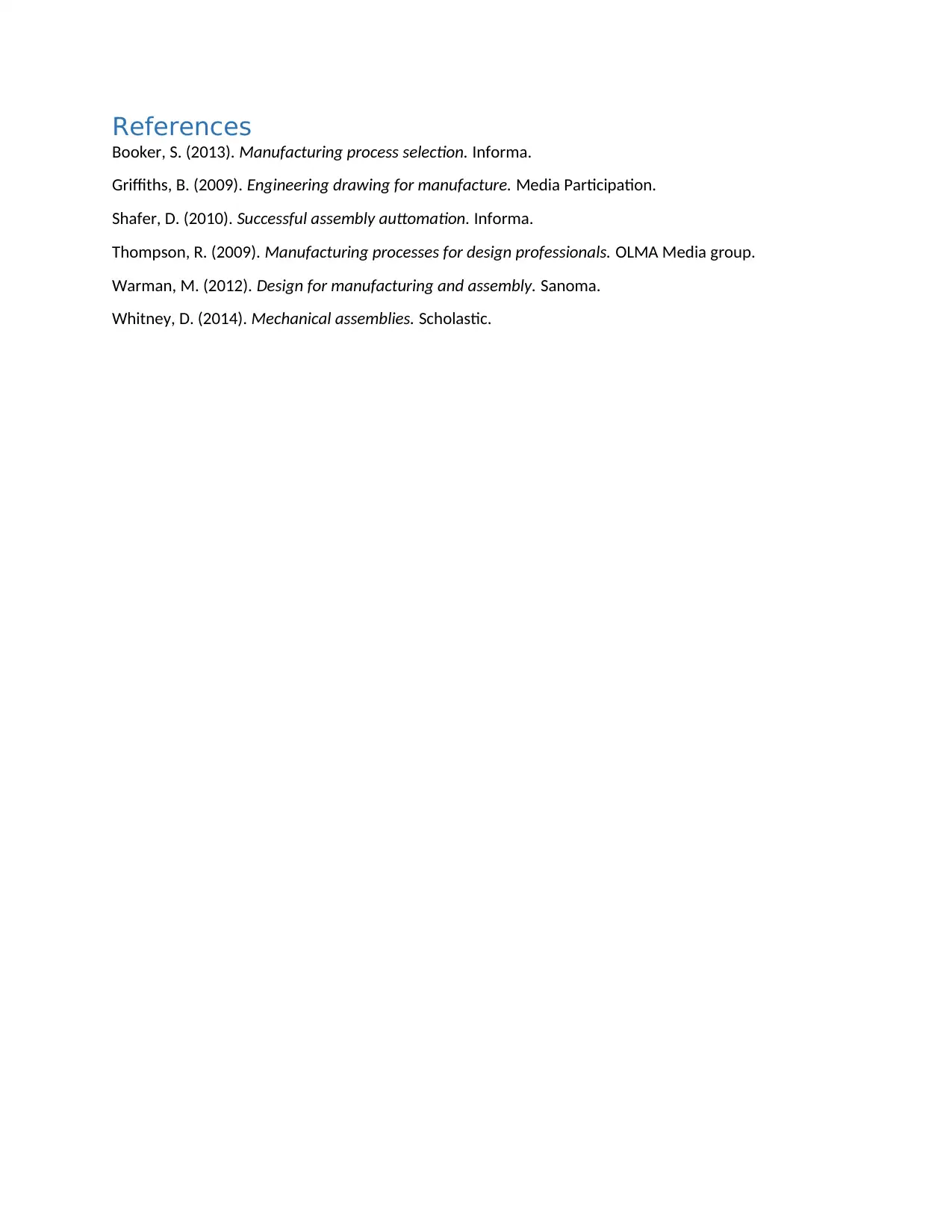
References
Booker, S. (2013). Manufacturing process selection. Informa.
Griffiths, B. (2009). Engineering drawing for manufacture. Media Participation.
Shafer, D. (2010). Successful assembly auttomation. Informa.
Thompson, R. (2009). Manufacturing processes for design professionals. OLMA Media group.
Warman, M. (2012). Design for manufacturing and assembly. Sanoma.
Whitney, D. (2014). Mechanical assemblies. Scholastic.
Booker, S. (2013). Manufacturing process selection. Informa.
Griffiths, B. (2009). Engineering drawing for manufacture. Media Participation.
Shafer, D. (2010). Successful assembly auttomation. Informa.
Thompson, R. (2009). Manufacturing processes for design professionals. OLMA Media group.
Warman, M. (2012). Design for manufacturing and assembly. Sanoma.
Whitney, D. (2014). Mechanical assemblies. Scholastic.
1 out of 4
Related Documents
![[object Object]](/_next/image/?url=%2F_next%2Fstatic%2Fmedia%2Flogo.6d15ce61.png&w=640&q=75)
Your All-in-One AI-Powered Toolkit for Academic Success.
+13062052269
info@desklib.com
Available 24*7 on WhatsApp / Email
Unlock your academic potential
© 2024 | Zucol Services PVT LTD | All rights reserved.