Building Construction: Footing, Roofing, Flooring, Cladding, Walling, Demolition
VerifiedAdded on 2023/01/13
|14
|2666
|1
AI Summary
This document provides an overview of various aspects of building construction, including footing systems, roofing systems, flooring systems, cladding systems, walling systems, and demolition processes. It discusses the importance of engineering safety in building construction and provides recommendations for different types of building elements. The document also includes information on the materials and techniques used in each aspect of construction. The content is relevant for students studying building construction or anyone interested in learning about the different components of a building.
Contribute Materials
Your contribution can guide someone’s learning journey. Share your
documents today.
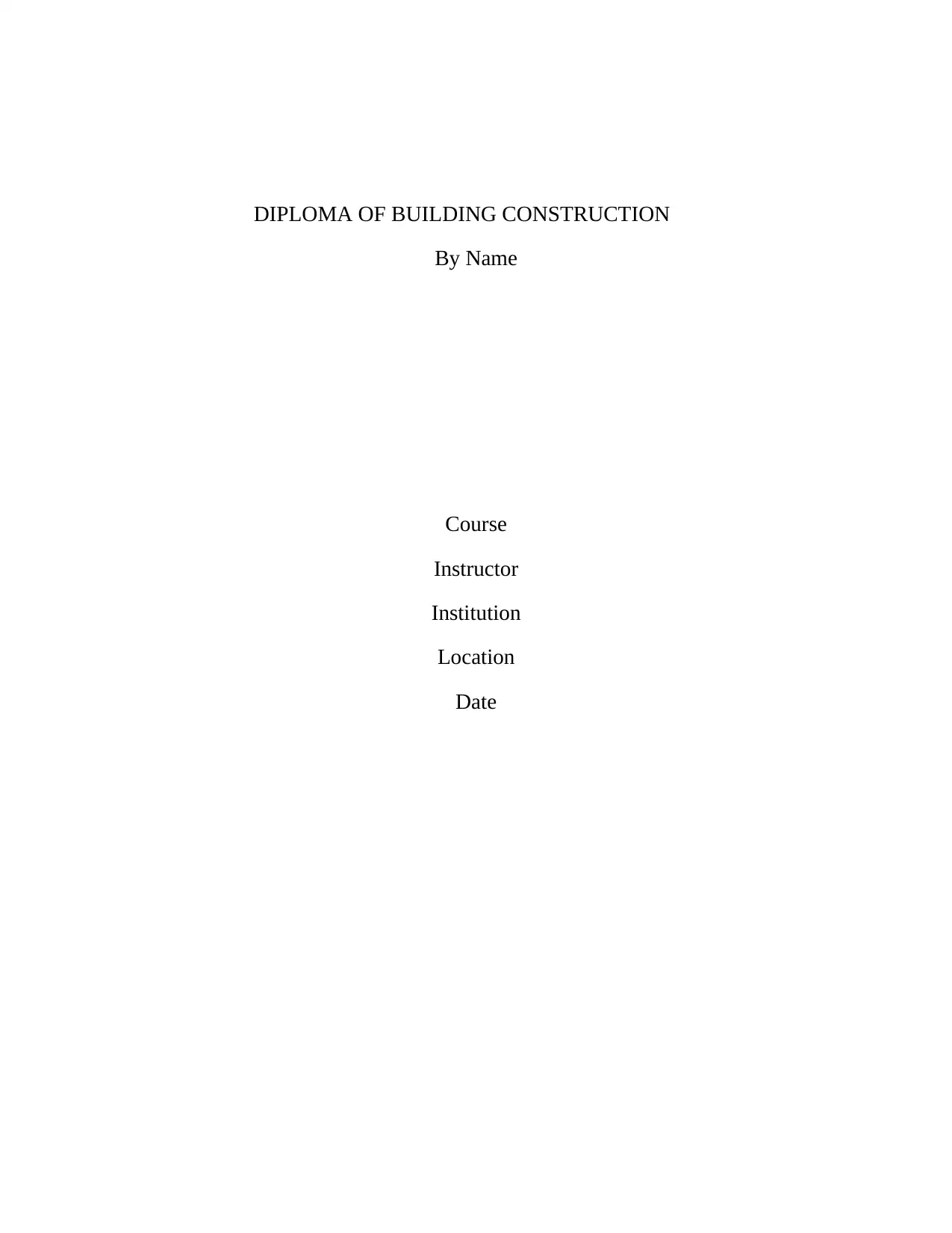
DIPLOMA OF BUILDING CONSTRUCTION
By Name
Course
Instructor
Institution
Location
Date
By Name
Course
Instructor
Institution
Location
Date
Secure Best Marks with AI Grader
Need help grading? Try our AI Grader for instant feedback on your assignments.
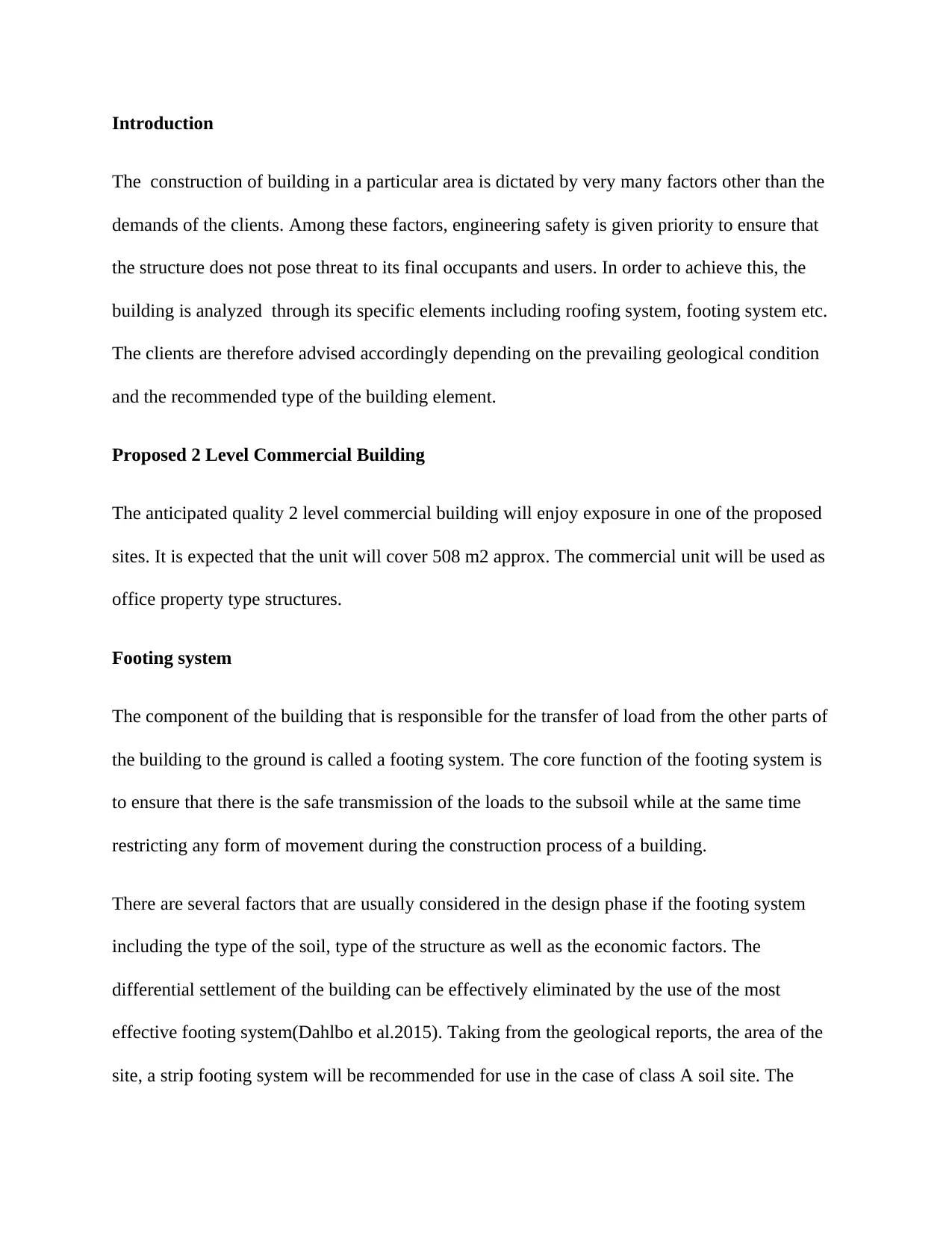
Introduction
The construction of building in a particular area is dictated by very many factors other than the
demands of the clients. Among these factors, engineering safety is given priority to ensure that
the structure does not pose threat to its final occupants and users. In order to achieve this, the
building is analyzed through its specific elements including roofing system, footing system etc.
The clients are therefore advised accordingly depending on the prevailing geological condition
and the recommended type of the building element.
Proposed 2 Level Commercial Building
The anticipated quality 2 level commercial building will enjoy exposure in one of the proposed
sites. It is expected that the unit will cover 508 m2 approx. The commercial unit will be used as
office property type structures.
Footing system
The component of the building that is responsible for the transfer of load from the other parts of
the building to the ground is called a footing system. The core function of the footing system is
to ensure that there is the safe transmission of the loads to the subsoil while at the same time
restricting any form of movement during the construction process of a building.
There are several factors that are usually considered in the design phase if the footing system
including the type of the soil, type of the structure as well as the economic factors. The
differential settlement of the building can be effectively eliminated by the use of the most
effective footing system(Dahlbo et al.2015). Taking from the geological reports, the area of the
site, a strip footing system will be recommended for use in the case of class A soil site. The
The construction of building in a particular area is dictated by very many factors other than the
demands of the clients. Among these factors, engineering safety is given priority to ensure that
the structure does not pose threat to its final occupants and users. In order to achieve this, the
building is analyzed through its specific elements including roofing system, footing system etc.
The clients are therefore advised accordingly depending on the prevailing geological condition
and the recommended type of the building element.
Proposed 2 Level Commercial Building
The anticipated quality 2 level commercial building will enjoy exposure in one of the proposed
sites. It is expected that the unit will cover 508 m2 approx. The commercial unit will be used as
office property type structures.
Footing system
The component of the building that is responsible for the transfer of load from the other parts of
the building to the ground is called a footing system. The core function of the footing system is
to ensure that there is the safe transmission of the loads to the subsoil while at the same time
restricting any form of movement during the construction process of a building.
There are several factors that are usually considered in the design phase if the footing system
including the type of the soil, type of the structure as well as the economic factors. The
differential settlement of the building can be effectively eliminated by the use of the most
effective footing system(Dahlbo et al.2015). Taking from the geological reports, the area of the
site, a strip footing system will be recommended for use in the case of class A soil site. The
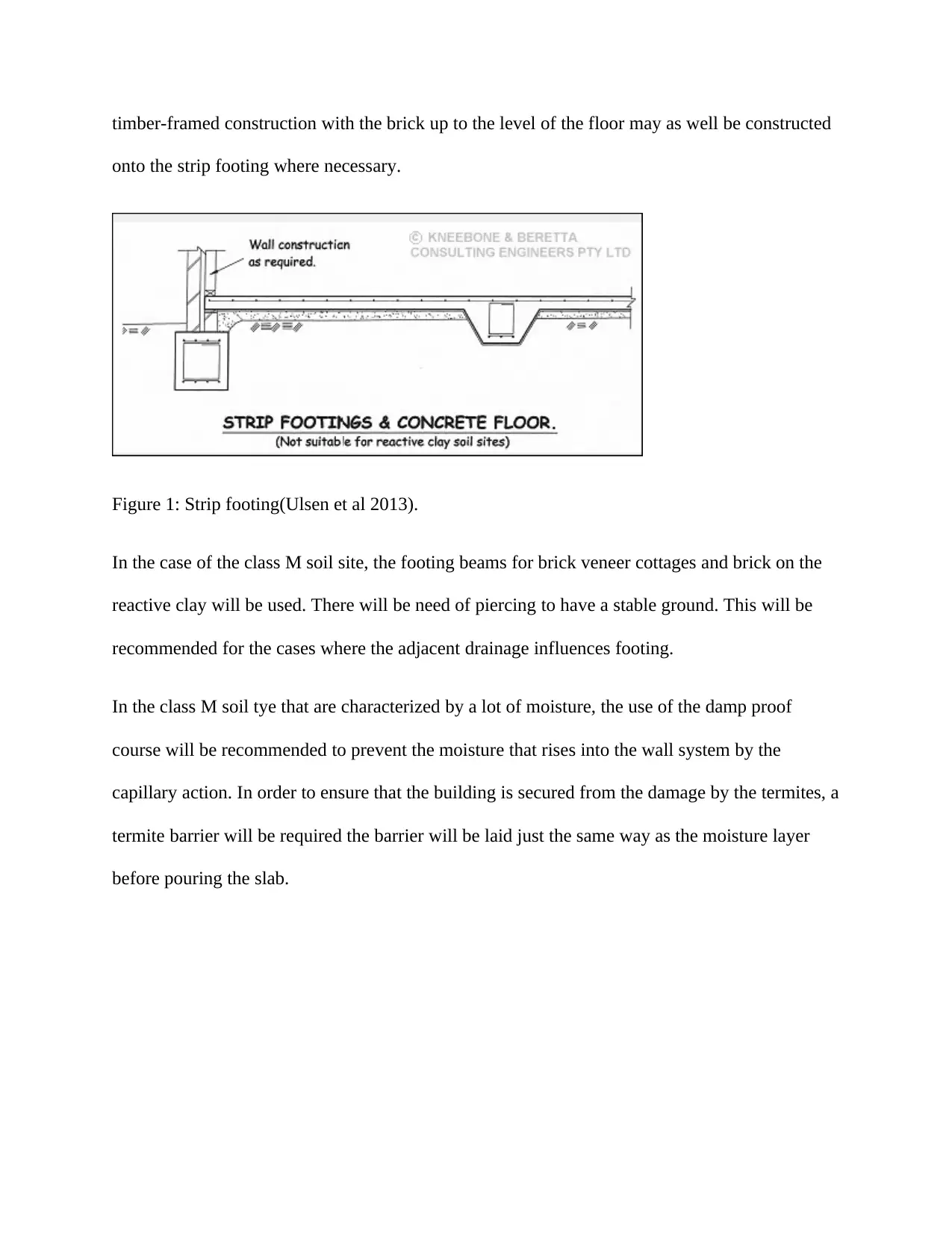
timber-framed construction with the brick up to the level of the floor may as well be constructed
onto the strip footing where necessary.
Figure 1: Strip footing(Ulsen et al 2013).
In the case of the class M soil site, the footing beams for brick veneer cottages and brick on the
reactive clay will be used. There will be need of piercing to have a stable ground. This will be
recommended for the cases where the adjacent drainage influences footing.
In the class M soil tye that are characterized by a lot of moisture, the use of the damp proof
course will be recommended to prevent the moisture that rises into the wall system by the
capillary action. In order to ensure that the building is secured from the damage by the termites, a
termite barrier will be required the barrier will be laid just the same way as the moisture layer
before pouring the slab.
onto the strip footing where necessary.
Figure 1: Strip footing(Ulsen et al 2013).
In the case of the class M soil site, the footing beams for brick veneer cottages and brick on the
reactive clay will be used. There will be need of piercing to have a stable ground. This will be
recommended for the cases where the adjacent drainage influences footing.
In the class M soil tye that are characterized by a lot of moisture, the use of the damp proof
course will be recommended to prevent the moisture that rises into the wall system by the
capillary action. In order to ensure that the building is secured from the damage by the termites, a
termite barrier will be required the barrier will be laid just the same way as the moisture layer
before pouring the slab.
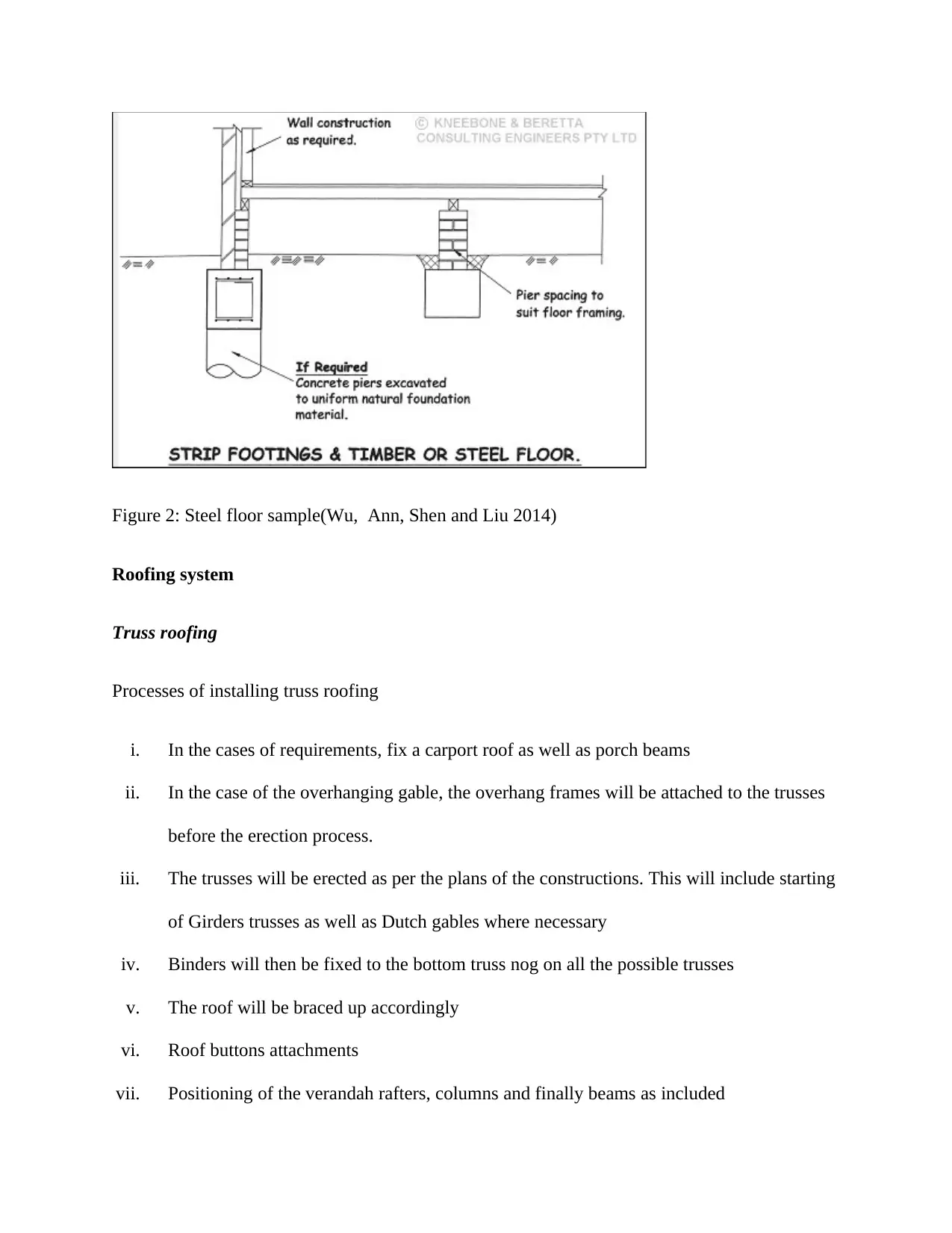
Figure 2: Steel floor sample(Wu, Ann, Shen and Liu 2014)
Roofing system
Truss roofing
Processes of installing truss roofing
i. In the cases of requirements, fix a carport roof as well as porch beams
ii. In the case of the overhanging gable, the overhang frames will be attached to the trusses
before the erection process.
iii. The trusses will be erected as per the plans of the constructions. This will include starting
of Girders trusses as well as Dutch gables where necessary
iv. Binders will then be fixed to the bottom truss nog on all the possible trusses
v. The roof will be braced up accordingly
vi. Roof buttons attachments
vii. Positioning of the verandah rafters, columns and finally beams as included
Roofing system
Truss roofing
Processes of installing truss roofing
i. In the cases of requirements, fix a carport roof as well as porch beams
ii. In the case of the overhanging gable, the overhang frames will be attached to the trusses
before the erection process.
iii. The trusses will be erected as per the plans of the constructions. This will include starting
of Girders trusses as well as Dutch gables where necessary
iv. Binders will then be fixed to the bottom truss nog on all the possible trusses
v. The roof will be braced up accordingly
vi. Roof buttons attachments
vii. Positioning of the verandah rafters, columns and finally beams as included
Paraphrase This Document
Need a fresh take? Get an instant paraphrase of this document with our AI Paraphraser
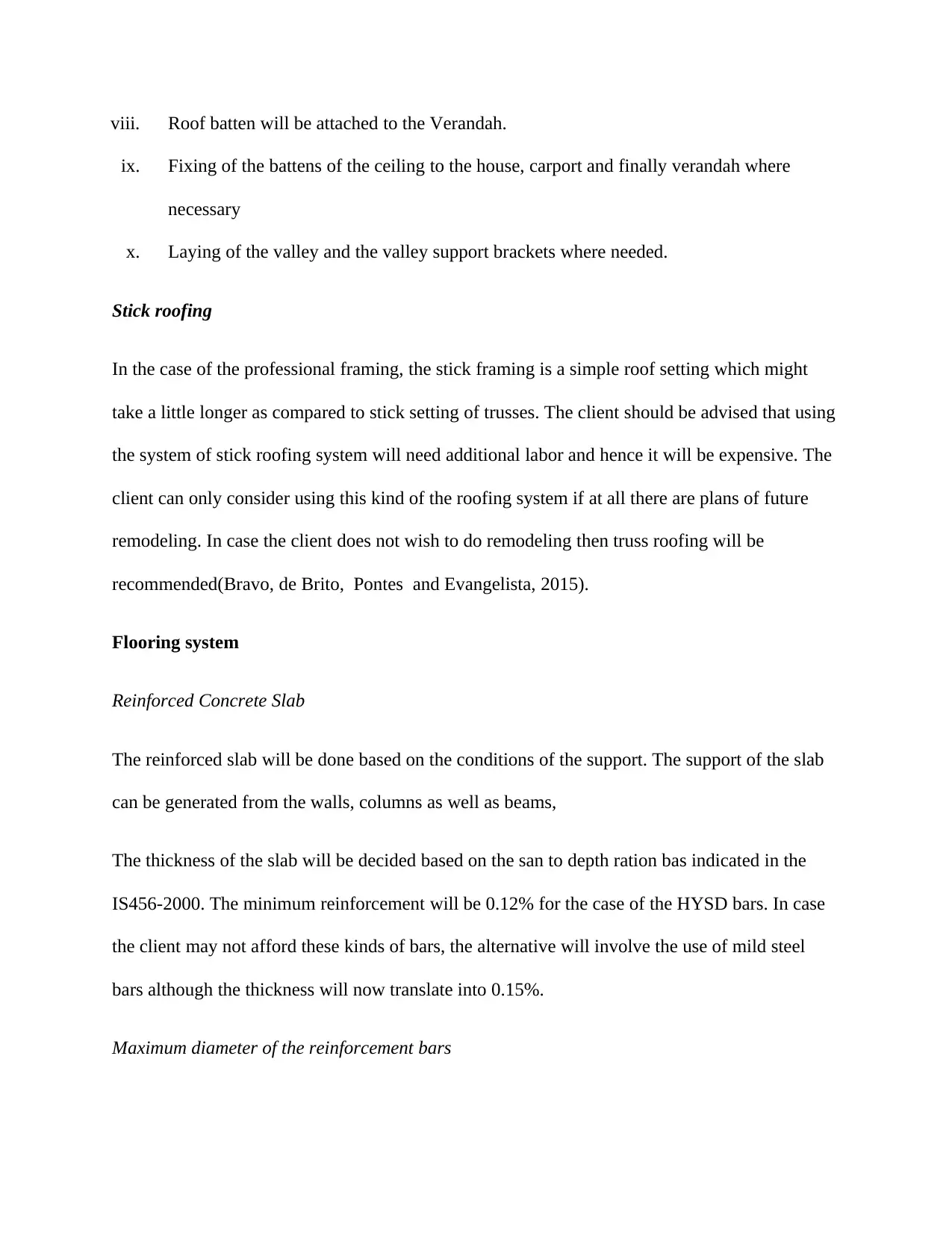
viii. Roof batten will be attached to the Verandah.
ix. Fixing of the battens of the ceiling to the house, carport and finally verandah where
necessary
x. Laying of the valley and the valley support brackets where needed.
Stick roofing
In the case of the professional framing, the stick framing is a simple roof setting which might
take a little longer as compared to stick setting of trusses. The client should be advised that using
the system of stick roofing system will need additional labor and hence it will be expensive. The
client can only consider using this kind of the roofing system if at all there are plans of future
remodeling. In case the client does not wish to do remodeling then truss roofing will be
recommended(Bravo, de Brito, Pontes and Evangelista, 2015).
Flooring system
Reinforced Concrete Slab
The reinforced slab will be done based on the conditions of the support. The support of the slab
can be generated from the walls, columns as well as beams,
The thickness of the slab will be decided based on the san to depth ration bas indicated in the
IS456-2000. The minimum reinforcement will be 0.12% for the case of the HYSD bars. In case
the client may not afford these kinds of bars, the alternative will involve the use of mild steel
bars although the thickness will now translate into 0.15%.
Maximum diameter of the reinforcement bars
ix. Fixing of the battens of the ceiling to the house, carport and finally verandah where
necessary
x. Laying of the valley and the valley support brackets where needed.
Stick roofing
In the case of the professional framing, the stick framing is a simple roof setting which might
take a little longer as compared to stick setting of trusses. The client should be advised that using
the system of stick roofing system will need additional labor and hence it will be expensive. The
client can only consider using this kind of the roofing system if at all there are plans of future
remodeling. In case the client does not wish to do remodeling then truss roofing will be
recommended(Bravo, de Brito, Pontes and Evangelista, 2015).
Flooring system
Reinforced Concrete Slab
The reinforced slab will be done based on the conditions of the support. The support of the slab
can be generated from the walls, columns as well as beams,
The thickness of the slab will be decided based on the san to depth ration bas indicated in the
IS456-2000. The minimum reinforcement will be 0.12% for the case of the HYSD bars. In case
the client may not afford these kinds of bars, the alternative will involve the use of mild steel
bars although the thickness will now translate into 0.15%.
Maximum diameter of the reinforcement bars
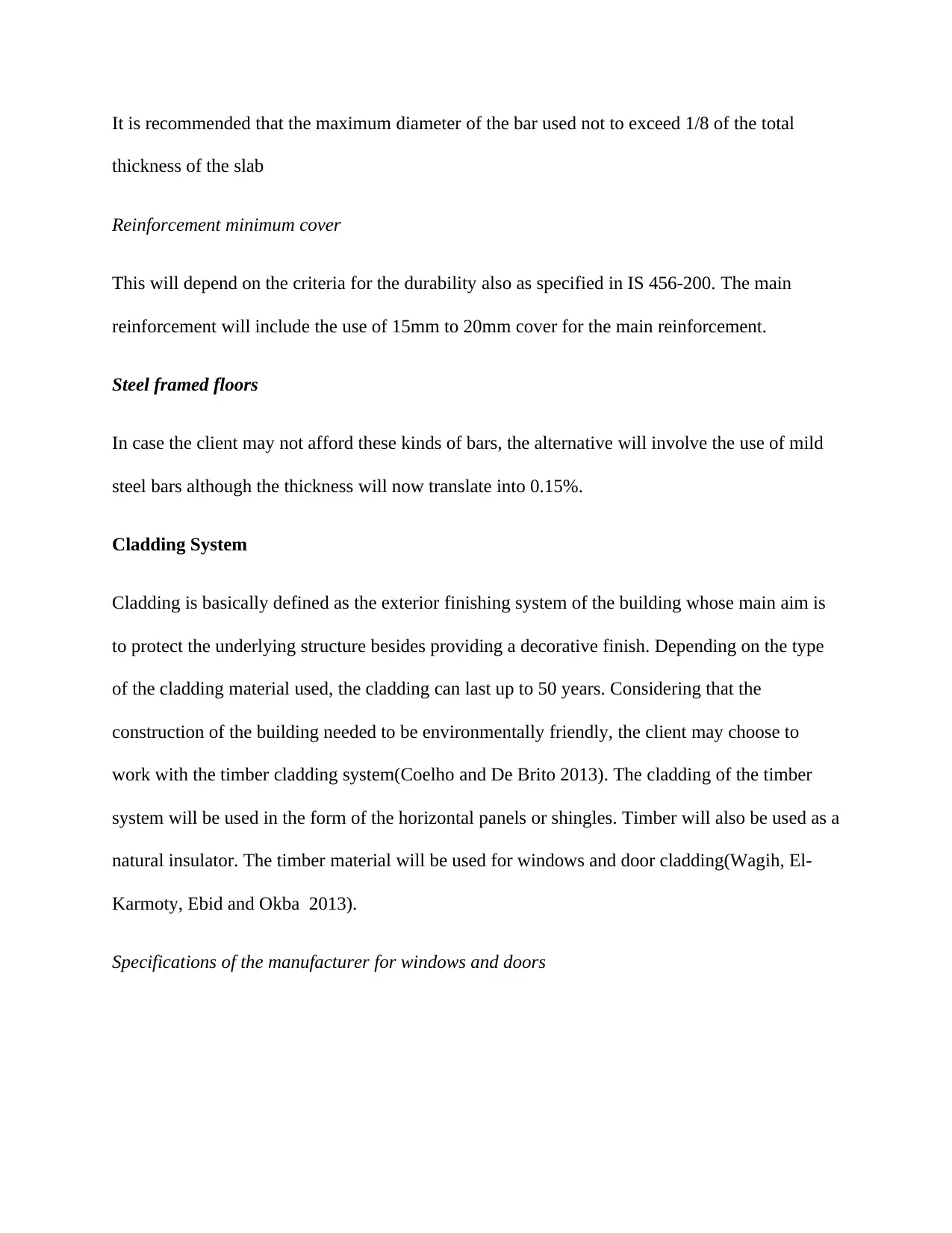
It is recommended that the maximum diameter of the bar used not to exceed 1/8 of the total
thickness of the slab
Reinforcement minimum cover
This will depend on the criteria for the durability also as specified in IS 456-200. The main
reinforcement will include the use of 15mm to 20mm cover for the main reinforcement.
Steel framed floors
In case the client may not afford these kinds of bars, the alternative will involve the use of mild
steel bars although the thickness will now translate into 0.15%.
Cladding System
Cladding is basically defined as the exterior finishing system of the building whose main aim is
to protect the underlying structure besides providing a decorative finish. Depending on the type
of the cladding material used, the cladding can last up to 50 years. Considering that the
construction of the building needed to be environmentally friendly, the client may choose to
work with the timber cladding system(Coelho and De Brito 2013). The cladding of the timber
system will be used in the form of the horizontal panels or shingles. Timber will also be used as a
natural insulator. The timber material will be used for windows and door cladding(Wagih, El-
Karmoty, Ebid and Okba 2013).
Specifications of the manufacturer for windows and doors
thickness of the slab
Reinforcement minimum cover
This will depend on the criteria for the durability also as specified in IS 456-200. The main
reinforcement will include the use of 15mm to 20mm cover for the main reinforcement.
Steel framed floors
In case the client may not afford these kinds of bars, the alternative will involve the use of mild
steel bars although the thickness will now translate into 0.15%.
Cladding System
Cladding is basically defined as the exterior finishing system of the building whose main aim is
to protect the underlying structure besides providing a decorative finish. Depending on the type
of the cladding material used, the cladding can last up to 50 years. Considering that the
construction of the building needed to be environmentally friendly, the client may choose to
work with the timber cladding system(Coelho and De Brito 2013). The cladding of the timber
system will be used in the form of the horizontal panels or shingles. Timber will also be used as a
natural insulator. The timber material will be used for windows and door cladding(Wagih, El-
Karmoty, Ebid and Okba 2013).
Specifications of the manufacturer for windows and doors
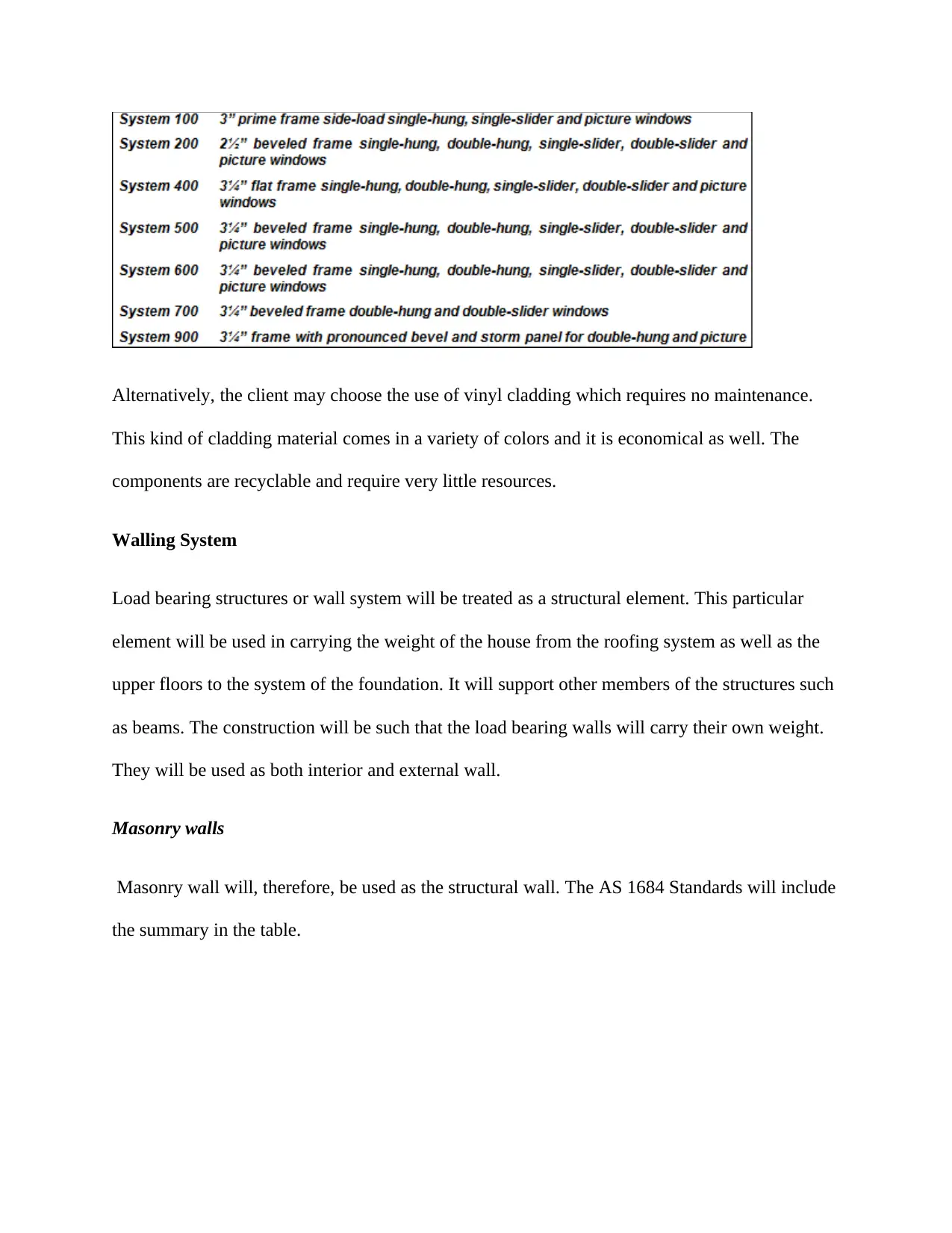
Alternatively, the client may choose the use of vinyl cladding which requires no maintenance.
This kind of cladding material comes in a variety of colors and it is economical as well. The
components are recyclable and require very little resources.
Walling System
Load bearing structures or wall system will be treated as a structural element. This particular
element will be used in carrying the weight of the house from the roofing system as well as the
upper floors to the system of the foundation. It will support other members of the structures such
as beams. The construction will be such that the load bearing walls will carry their own weight.
They will be used as both interior and external wall.
Masonry walls
Masonry wall will, therefore, be used as the structural wall. The AS 1684 Standards will include
the summary in the table.
This kind of cladding material comes in a variety of colors and it is economical as well. The
components are recyclable and require very little resources.
Walling System
Load bearing structures or wall system will be treated as a structural element. This particular
element will be used in carrying the weight of the house from the roofing system as well as the
upper floors to the system of the foundation. It will support other members of the structures such
as beams. The construction will be such that the load bearing walls will carry their own weight.
They will be used as both interior and external wall.
Masonry walls
Masonry wall will, therefore, be used as the structural wall. The AS 1684 Standards will include
the summary in the table.
Secure Best Marks with AI Grader
Need help grading? Try our AI Grader for instant feedback on your assignments.
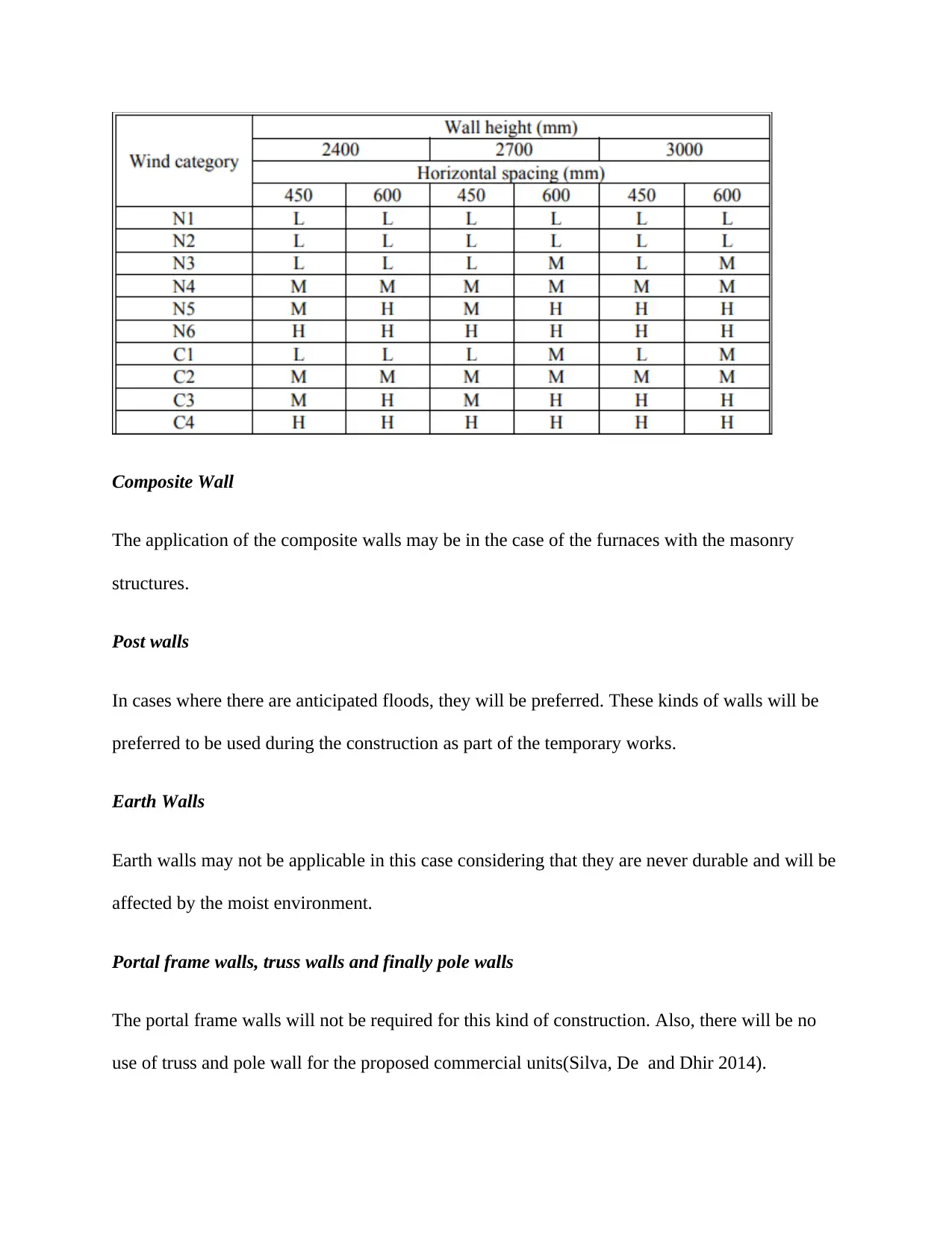
Composite Wall
The application of the composite walls may be in the case of the furnaces with the masonry
structures.
Post walls
In cases where there are anticipated floods, they will be preferred. These kinds of walls will be
preferred to be used during the construction as part of the temporary works.
Earth Walls
Earth walls may not be applicable in this case considering that they are never durable and will be
affected by the moist environment.
Portal frame walls, truss walls and finally pole walls
The portal frame walls will not be required for this kind of construction. Also, there will be no
use of truss and pole wall for the proposed commercial units(Silva, De and Dhir 2014).
The application of the composite walls may be in the case of the furnaces with the masonry
structures.
Post walls
In cases where there are anticipated floods, they will be preferred. These kinds of walls will be
preferred to be used during the construction as part of the temporary works.
Earth Walls
Earth walls may not be applicable in this case considering that they are never durable and will be
affected by the moist environment.
Portal frame walls, truss walls and finally pole walls
The portal frame walls will not be required for this kind of construction. Also, there will be no
use of truss and pole wall for the proposed commercial units(Silva, De and Dhir 2014).
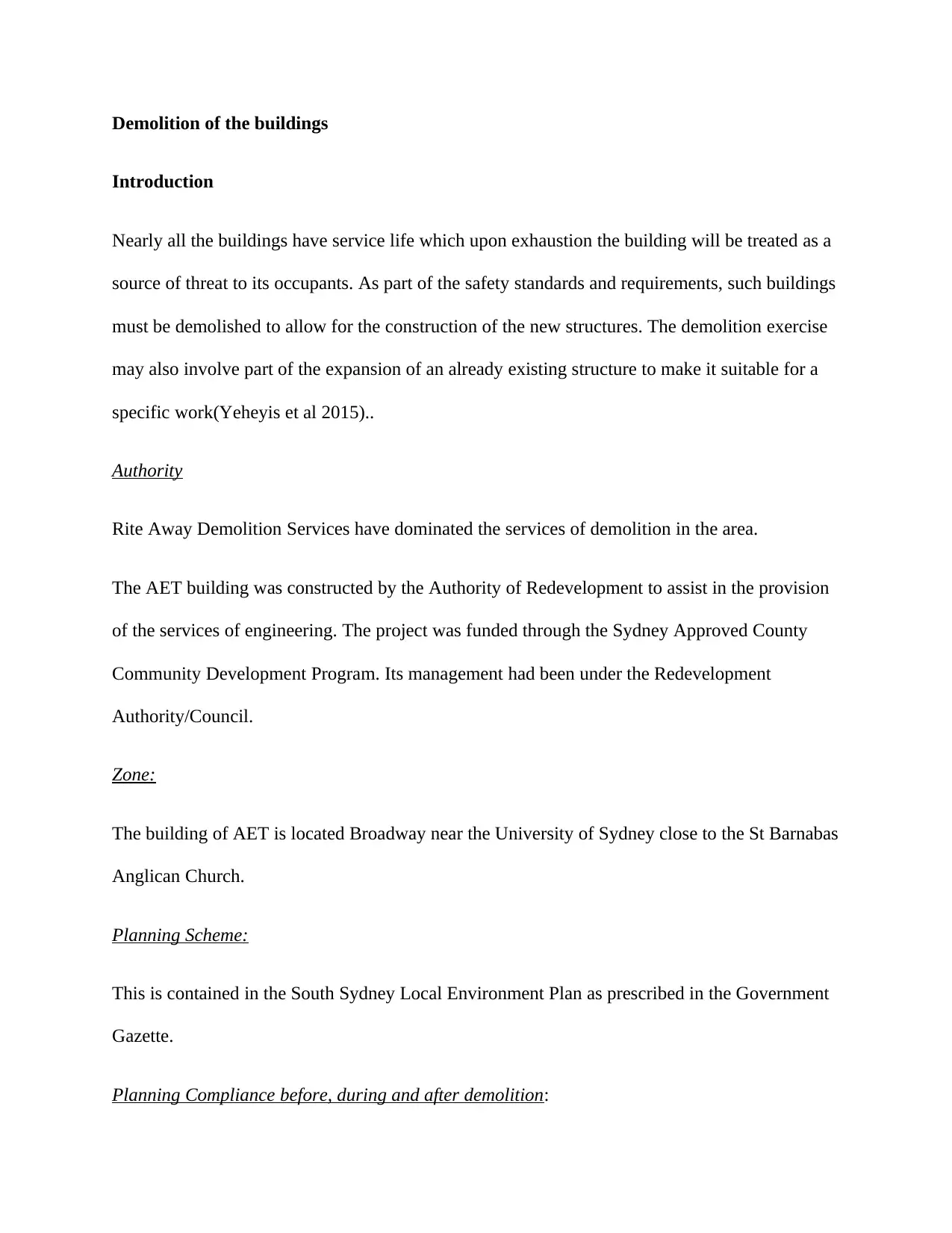
Demolition of the buildings
Introduction
Nearly all the buildings have service life which upon exhaustion the building will be treated as a
source of threat to its occupants. As part of the safety standards and requirements, such buildings
must be demolished to allow for the construction of the new structures. The demolition exercise
may also involve part of the expansion of an already existing structure to make it suitable for a
specific work(Yeheyis et al 2015)..
Authority
Rite Away Demolition Services have dominated the services of demolition in the area.
The AET building was constructed by the Authority of Redevelopment to assist in the provision
of the services of engineering. The project was funded through the Sydney Approved County
Community Development Program. Its management had been under the Redevelopment
Authority/Council.
Zone:
The building of AET is located Broadway near the University of Sydney close to the St Barnabas
Anglican Church.
Planning Scheme:
This is contained in the South Sydney Local Environment Plan as prescribed in the Government
Gazette.
Planning Compliance before, during and after demolition:
Introduction
Nearly all the buildings have service life which upon exhaustion the building will be treated as a
source of threat to its occupants. As part of the safety standards and requirements, such buildings
must be demolished to allow for the construction of the new structures. The demolition exercise
may also involve part of the expansion of an already existing structure to make it suitable for a
specific work(Yeheyis et al 2015)..
Authority
Rite Away Demolition Services have dominated the services of demolition in the area.
The AET building was constructed by the Authority of Redevelopment to assist in the provision
of the services of engineering. The project was funded through the Sydney Approved County
Community Development Program. Its management had been under the Redevelopment
Authority/Council.
Zone:
The building of AET is located Broadway near the University of Sydney close to the St Barnabas
Anglican Church.
Planning Scheme:
This is contained in the South Sydney Local Environment Plan as prescribed in the Government
Gazette.
Planning Compliance before, during and after demolition:
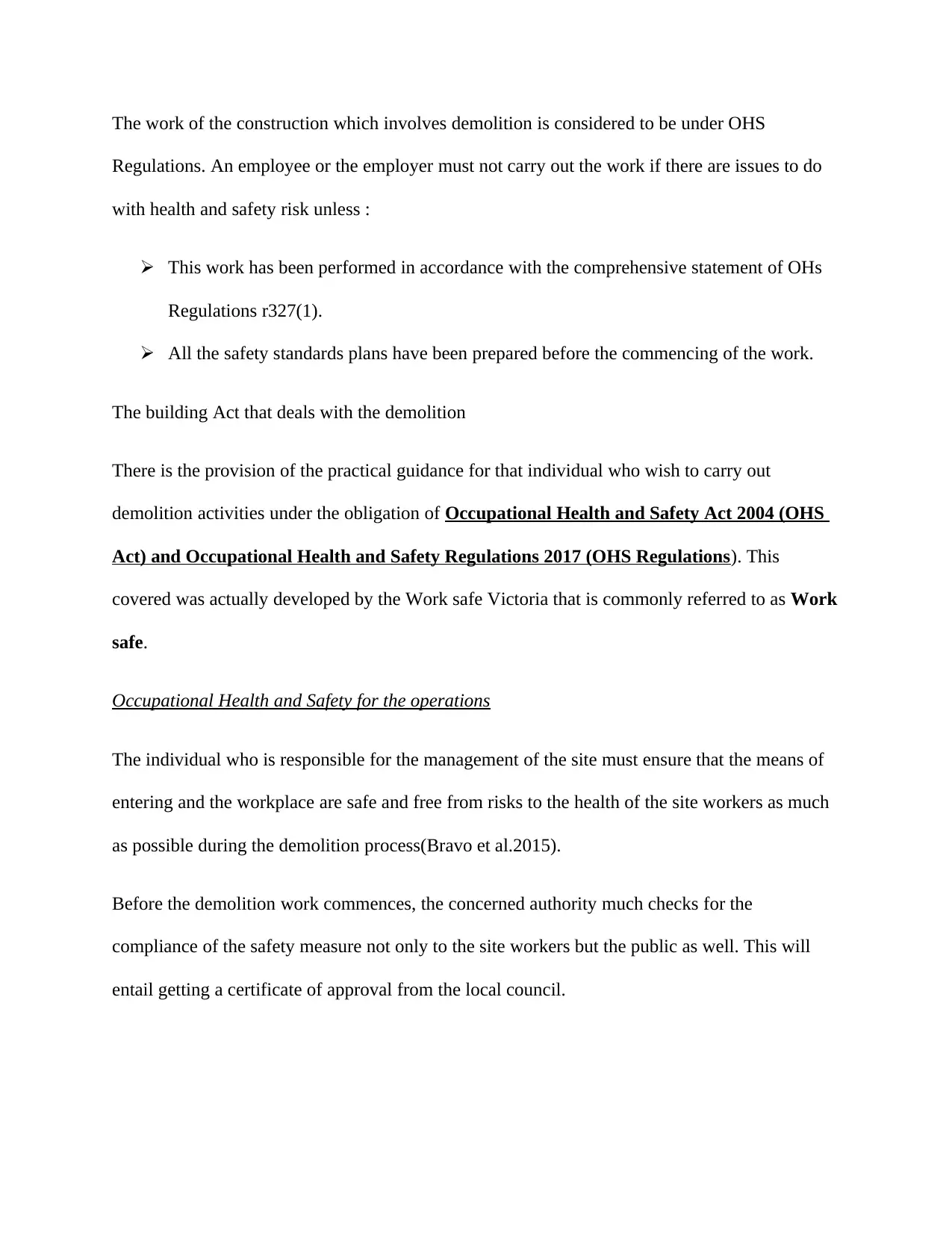
The work of the construction which involves demolition is considered to be under OHS
Regulations. An employee or the employer must not carry out the work if there are issues to do
with health and safety risk unless :
This work has been performed in accordance with the comprehensive statement of OHs
Regulations r327(1).
All the safety standards plans have been prepared before the commencing of the work.
The building Act that deals with the demolition
There is the provision of the practical guidance for that individual who wish to carry out
demolition activities under the obligation of Occupational Health and Safety Act 2004 (OHS
Act) and Occupational Health and Safety Regulations 2017 (OHS Regulations). This
covered was actually developed by the Work safe Victoria that is commonly referred to as Work
safe.
Occupational Health and Safety for the operations
The individual who is responsible for the management of the site must ensure that the means of
entering and the workplace are safe and free from risks to the health of the site workers as much
as possible during the demolition process(Bravo et al.2015).
Before the demolition work commences, the concerned authority much checks for the
compliance of the safety measure not only to the site workers but the public as well. This will
entail getting a certificate of approval from the local council.
Regulations. An employee or the employer must not carry out the work if there are issues to do
with health and safety risk unless :
This work has been performed in accordance with the comprehensive statement of OHs
Regulations r327(1).
All the safety standards plans have been prepared before the commencing of the work.
The building Act that deals with the demolition
There is the provision of the practical guidance for that individual who wish to carry out
demolition activities under the obligation of Occupational Health and Safety Act 2004 (OHS
Act) and Occupational Health and Safety Regulations 2017 (OHS Regulations). This
covered was actually developed by the Work safe Victoria that is commonly referred to as Work
safe.
Occupational Health and Safety for the operations
The individual who is responsible for the management of the site must ensure that the means of
entering and the workplace are safe and free from risks to the health of the site workers as much
as possible during the demolition process(Bravo et al.2015).
Before the demolition work commences, the concerned authority much checks for the
compliance of the safety measure not only to the site workers but the public as well. This will
entail getting a certificate of approval from the local council.
Paraphrase This Document
Need a fresh take? Get an instant paraphrase of this document with our AI Paraphraser
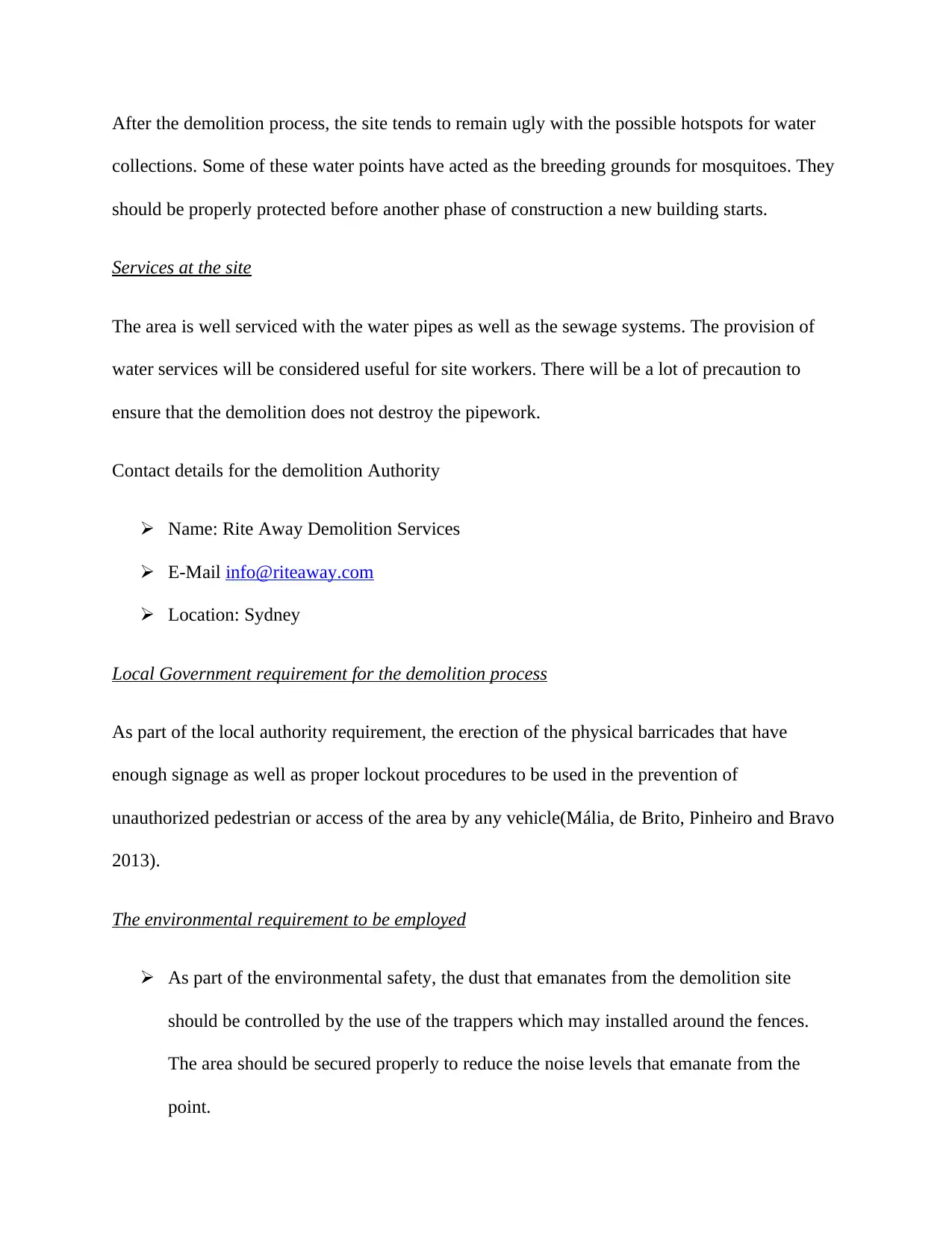
After the demolition process, the site tends to remain ugly with the possible hotspots for water
collections. Some of these water points have acted as the breeding grounds for mosquitoes. They
should be properly protected before another phase of construction a new building starts.
Services at the site
The area is well serviced with the water pipes as well as the sewage systems. The provision of
water services will be considered useful for site workers. There will be a lot of precaution to
ensure that the demolition does not destroy the pipework.
Contact details for the demolition Authority
Name: Rite Away Demolition Services
E-Mail info@riteaway.com
Location: Sydney
Local Government requirement for the demolition process
As part of the local authority requirement, the erection of the physical barricades that have
enough signage as well as proper lockout procedures to be used in the prevention of
unauthorized pedestrian or access of the area by any vehicle(Mália, de Brito, Pinheiro and Bravo
2013).
The environmental requirement to be employed
As part of the environmental safety, the dust that emanates from the demolition site
should be controlled by the use of the trappers which may installed around the fences.
The area should be secured properly to reduce the noise levels that emanate from the
point.
collections. Some of these water points have acted as the breeding grounds for mosquitoes. They
should be properly protected before another phase of construction a new building starts.
Services at the site
The area is well serviced with the water pipes as well as the sewage systems. The provision of
water services will be considered useful for site workers. There will be a lot of precaution to
ensure that the demolition does not destroy the pipework.
Contact details for the demolition Authority
Name: Rite Away Demolition Services
E-Mail info@riteaway.com
Location: Sydney
Local Government requirement for the demolition process
As part of the local authority requirement, the erection of the physical barricades that have
enough signage as well as proper lockout procedures to be used in the prevention of
unauthorized pedestrian or access of the area by any vehicle(Mália, de Brito, Pinheiro and Bravo
2013).
The environmental requirement to be employed
As part of the environmental safety, the dust that emanates from the demolition site
should be controlled by the use of the trappers which may installed around the fences.
The area should be secured properly to reduce the noise levels that emanate from the
point.
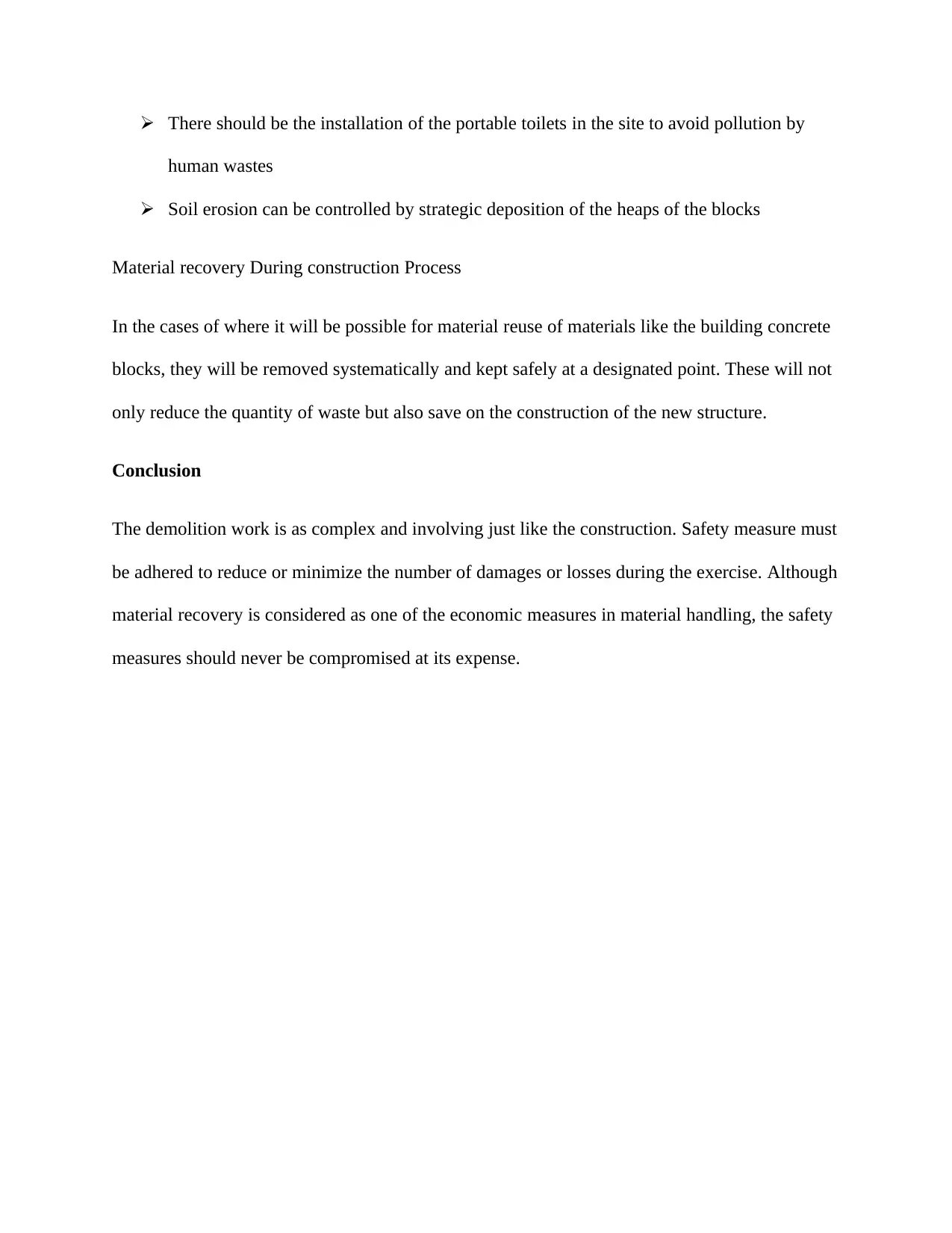
There should be the installation of the portable toilets in the site to avoid pollution by
human wastes
Soil erosion can be controlled by strategic deposition of the heaps of the blocks
Material recovery During construction Process
In the cases of where it will be possible for material reuse of materials like the building concrete
blocks, they will be removed systematically and kept safely at a designated point. These will not
only reduce the quantity of waste but also save on the construction of the new structure.
Conclusion
The demolition work is as complex and involving just like the construction. Safety measure must
be adhered to reduce or minimize the number of damages or losses during the exercise. Although
material recovery is considered as one of the economic measures in material handling, the safety
measures should never be compromised at its expense.
human wastes
Soil erosion can be controlled by strategic deposition of the heaps of the blocks
Material recovery During construction Process
In the cases of where it will be possible for material reuse of materials like the building concrete
blocks, they will be removed systematically and kept safely at a designated point. These will not
only reduce the quantity of waste but also save on the construction of the new structure.
Conclusion
The demolition work is as complex and involving just like the construction. Safety measure must
be adhered to reduce or minimize the number of damages or losses during the exercise. Although
material recovery is considered as one of the economic measures in material handling, the safety
measures should never be compromised at its expense.
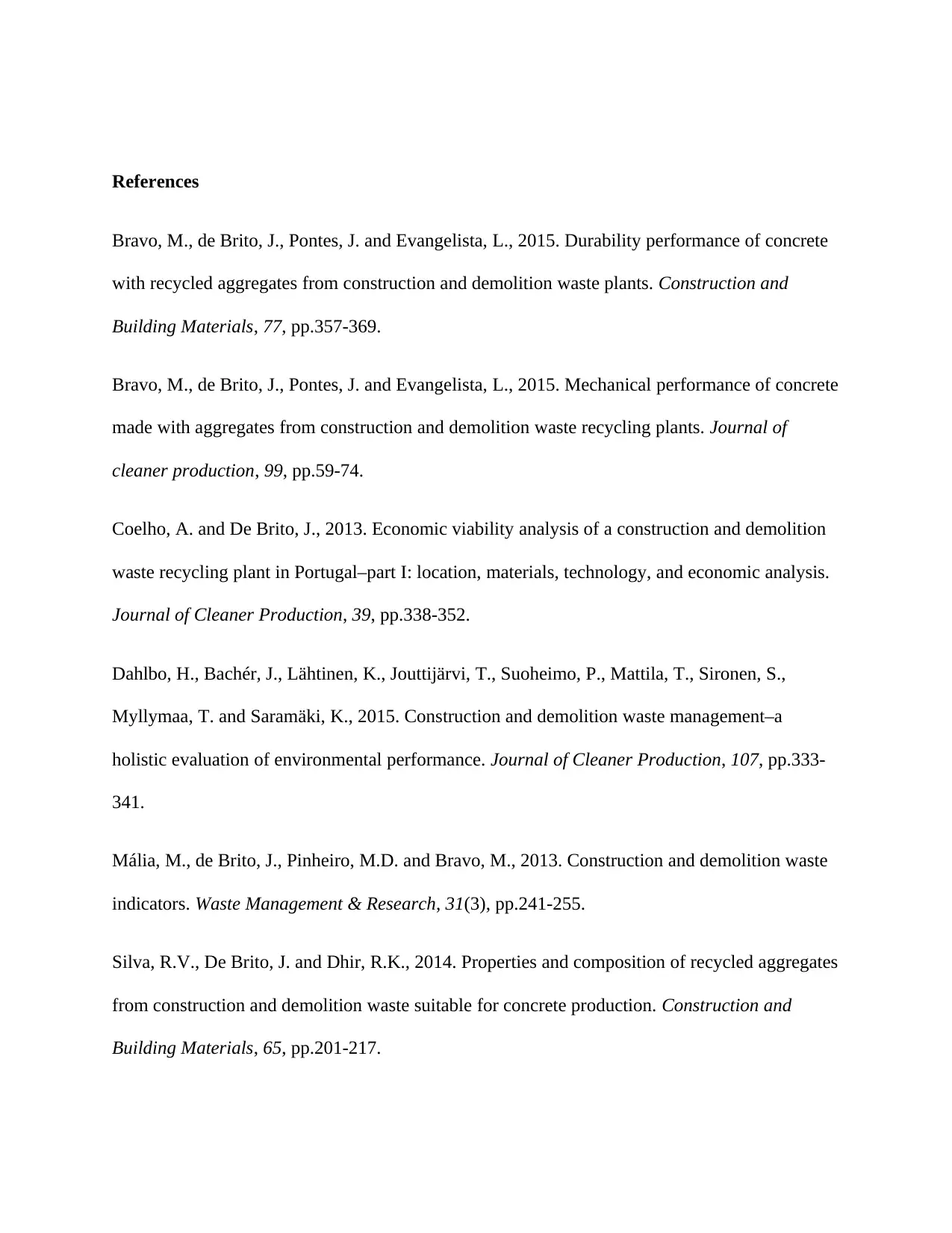
References
Bravo, M., de Brito, J., Pontes, J. and Evangelista, L., 2015. Durability performance of concrete
with recycled aggregates from construction and demolition waste plants. Construction and
Building Materials, 77, pp.357-369.
Bravo, M., de Brito, J., Pontes, J. and Evangelista, L., 2015. Mechanical performance of concrete
made with aggregates from construction and demolition waste recycling plants. Journal of
cleaner production, 99, pp.59-74.
Coelho, A. and De Brito, J., 2013. Economic viability analysis of a construction and demolition
waste recycling plant in Portugal–part I: location, materials, technology, and economic analysis.
Journal of Cleaner Production, 39, pp.338-352.
Dahlbo, H., Bachér, J., Lähtinen, K., Jouttijärvi, T., Suoheimo, P., Mattila, T., Sironen, S.,
Myllymaa, T. and Saramäki, K., 2015. Construction and demolition waste management–a
holistic evaluation of environmental performance. Journal of Cleaner Production, 107, pp.333-
341.
Mália, M., de Brito, J., Pinheiro, M.D. and Bravo, M., 2013. Construction and demolition waste
indicators. Waste Management & Research, 31(3), pp.241-255.
Silva, R.V., De Brito, J. and Dhir, R.K., 2014. Properties and composition of recycled aggregates
from construction and demolition waste suitable for concrete production. Construction and
Building Materials, 65, pp.201-217.
Bravo, M., de Brito, J., Pontes, J. and Evangelista, L., 2015. Durability performance of concrete
with recycled aggregates from construction and demolition waste plants. Construction and
Building Materials, 77, pp.357-369.
Bravo, M., de Brito, J., Pontes, J. and Evangelista, L., 2015. Mechanical performance of concrete
made with aggregates from construction and demolition waste recycling plants. Journal of
cleaner production, 99, pp.59-74.
Coelho, A. and De Brito, J., 2013. Economic viability analysis of a construction and demolition
waste recycling plant in Portugal–part I: location, materials, technology, and economic analysis.
Journal of Cleaner Production, 39, pp.338-352.
Dahlbo, H., Bachér, J., Lähtinen, K., Jouttijärvi, T., Suoheimo, P., Mattila, T., Sironen, S.,
Myllymaa, T. and Saramäki, K., 2015. Construction and demolition waste management–a
holistic evaluation of environmental performance. Journal of Cleaner Production, 107, pp.333-
341.
Mália, M., de Brito, J., Pinheiro, M.D. and Bravo, M., 2013. Construction and demolition waste
indicators. Waste Management & Research, 31(3), pp.241-255.
Silva, R.V., De Brito, J. and Dhir, R.K., 2014. Properties and composition of recycled aggregates
from construction and demolition waste suitable for concrete production. Construction and
Building Materials, 65, pp.201-217.
Secure Best Marks with AI Grader
Need help grading? Try our AI Grader for instant feedback on your assignments.
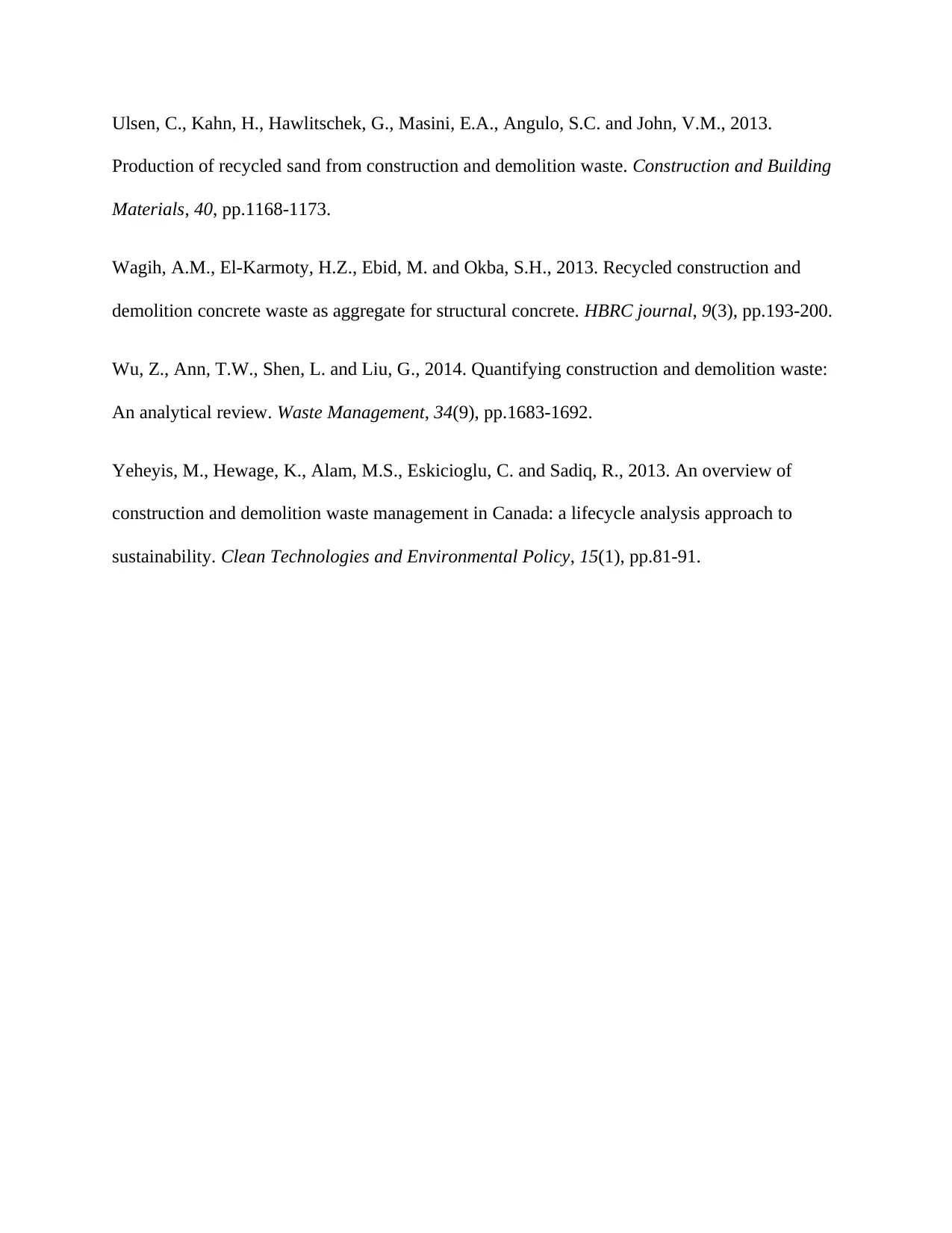
Ulsen, C., Kahn, H., Hawlitschek, G., Masini, E.A., Angulo, S.C. and John, V.M., 2013.
Production of recycled sand from construction and demolition waste. Construction and Building
Materials, 40, pp.1168-1173.
Wagih, A.M., El-Karmoty, H.Z., Ebid, M. and Okba, S.H., 2013. Recycled construction and
demolition concrete waste as aggregate for structural concrete. HBRC journal, 9(3), pp.193-200.
Wu, Z., Ann, T.W., Shen, L. and Liu, G., 2014. Quantifying construction and demolition waste:
An analytical review. Waste Management, 34(9), pp.1683-1692.
Yeheyis, M., Hewage, K., Alam, M.S., Eskicioglu, C. and Sadiq, R., 2013. An overview of
construction and demolition waste management in Canada: a lifecycle analysis approach to
sustainability. Clean Technologies and Environmental Policy, 15(1), pp.81-91.
Production of recycled sand from construction and demolition waste. Construction and Building
Materials, 40, pp.1168-1173.
Wagih, A.M., El-Karmoty, H.Z., Ebid, M. and Okba, S.H., 2013. Recycled construction and
demolition concrete waste as aggregate for structural concrete. HBRC journal, 9(3), pp.193-200.
Wu, Z., Ann, T.W., Shen, L. and Liu, G., 2014. Quantifying construction and demolition waste:
An analytical review. Waste Management, 34(9), pp.1683-1692.
Yeheyis, M., Hewage, K., Alam, M.S., Eskicioglu, C. and Sadiq, R., 2013. An overview of
construction and demolition waste management in Canada: a lifecycle analysis approach to
sustainability. Clean Technologies and Environmental Policy, 15(1), pp.81-91.
1 out of 14
Related Documents
![[object Object]](/_next/image/?url=%2F_next%2Fstatic%2Fmedia%2Flogo.6d15ce61.png&w=640&q=75)
Your All-in-One AI-Powered Toolkit for Academic Success.
+13062052269
info@desklib.com
Available 24*7 on WhatsApp / Email
Unlock your academic potential
© 2024 | Zucol Services PVT LTD | All rights reserved.