Continuous Improvement for Business Success
VerifiedAdded on 2020/04/07
|13
|2659
|39
AI Summary
This assignment examines the principles and practices of continuous improvement in a business context. It discusses strategies for implementing continuous improvement programs, emphasizing regular meetings, employee recognition, and effective communication with stakeholders. The document highlights the positive impact of continuous improvement on performance management, workflow optimization, legislative compliance, and overall business sustainability.
Contribute Materials
Your contribution can guide someone’s learning journey. Share your
documents today.
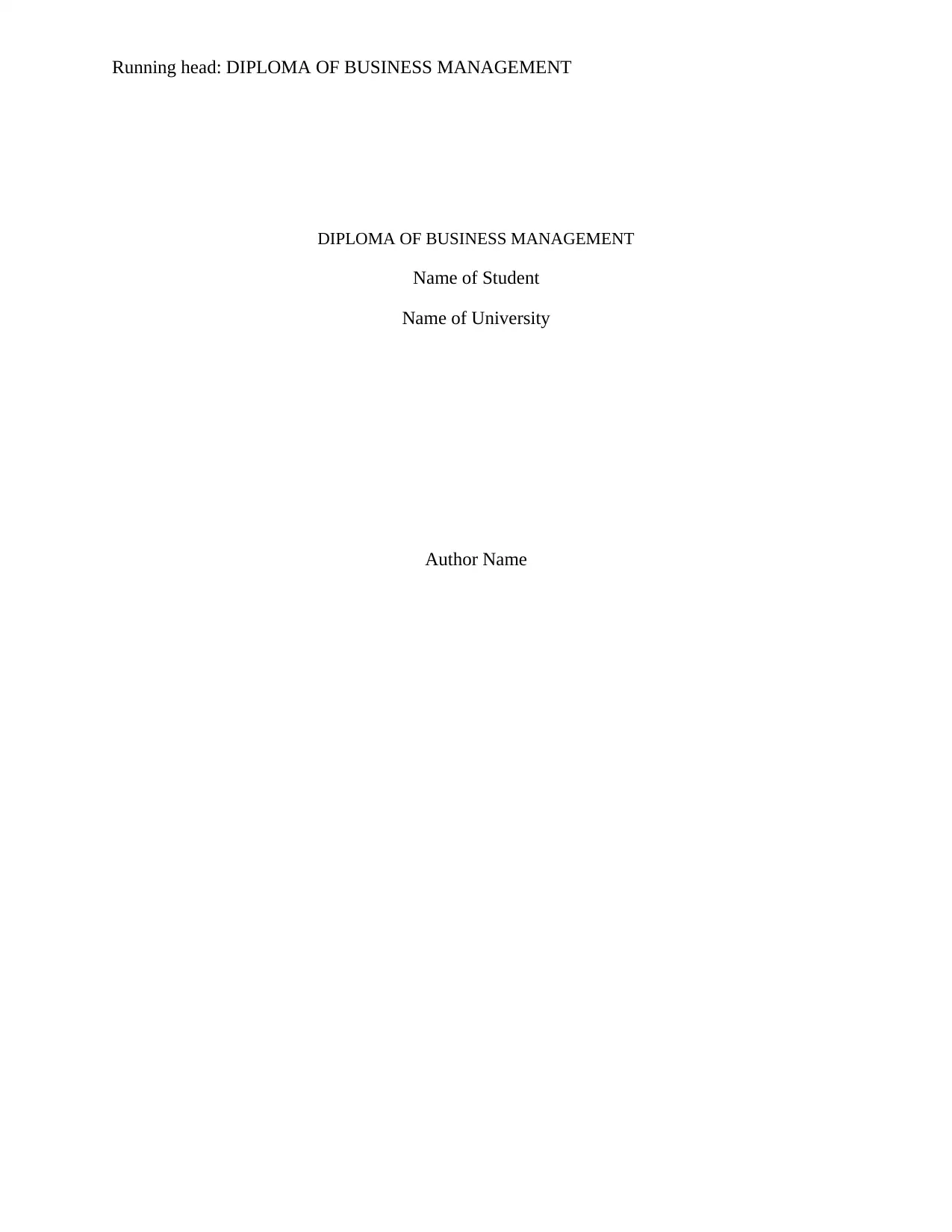
Running head: DIPLOMA OF BUSINESS MANAGEMENT
DIPLOMA OF BUSINESS MANAGEMENT
Name of Student
Name of University
Author Name
DIPLOMA OF BUSINESS MANAGEMENT
Name of Student
Name of University
Author Name
Secure Best Marks with AI Grader
Need help grading? Try our AI Grader for instant feedback on your assignments.
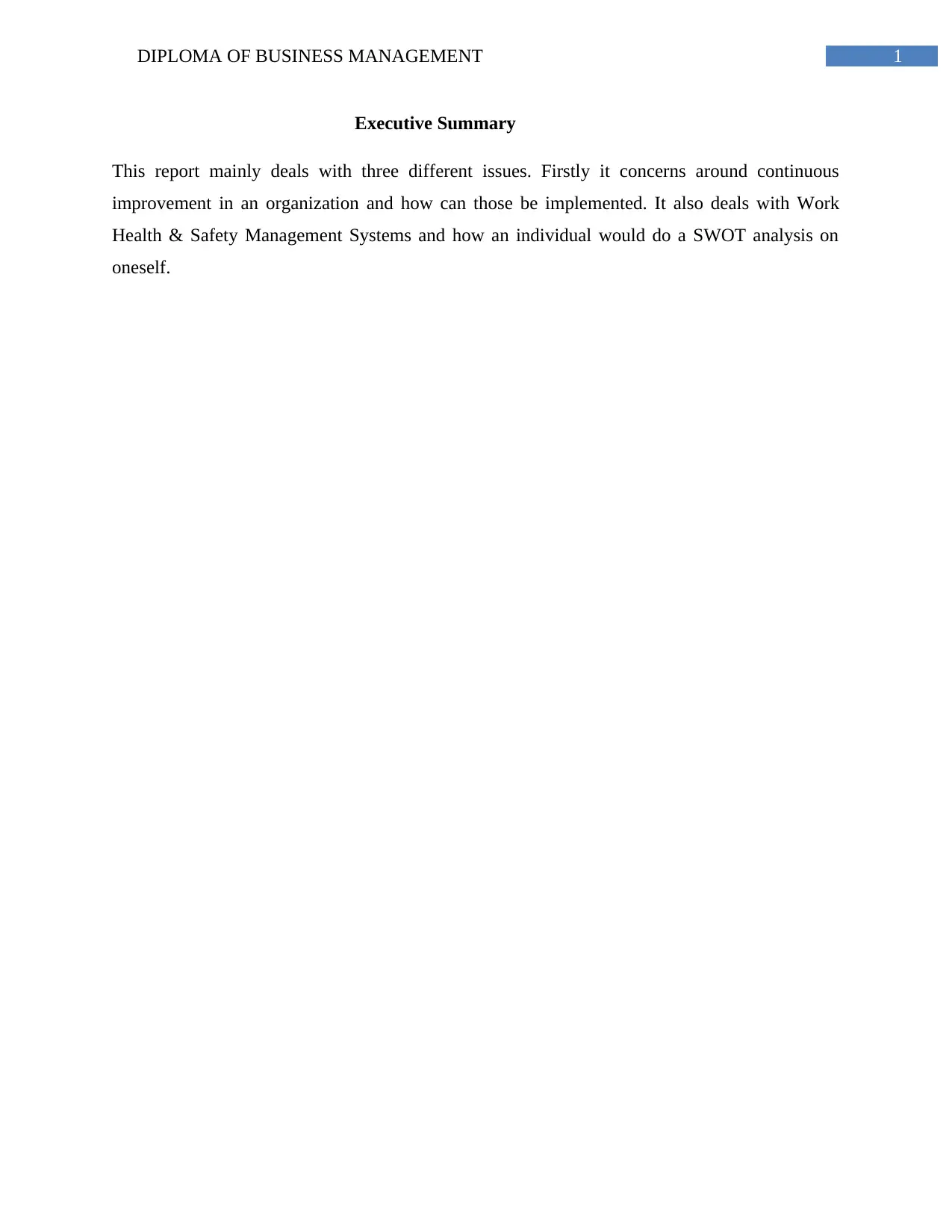
1DIPLOMA OF BUSINESS MANAGEMENT
Executive Summary
This report mainly deals with three different issues. Firstly it concerns around continuous
improvement in an organization and how can those be implemented. It also deals with Work
Health & Safety Management Systems and how an individual would do a SWOT analysis on
oneself.
Executive Summary
This report mainly deals with three different issues. Firstly it concerns around continuous
improvement in an organization and how can those be implemented. It also deals with Work
Health & Safety Management Systems and how an individual would do a SWOT analysis on
oneself.
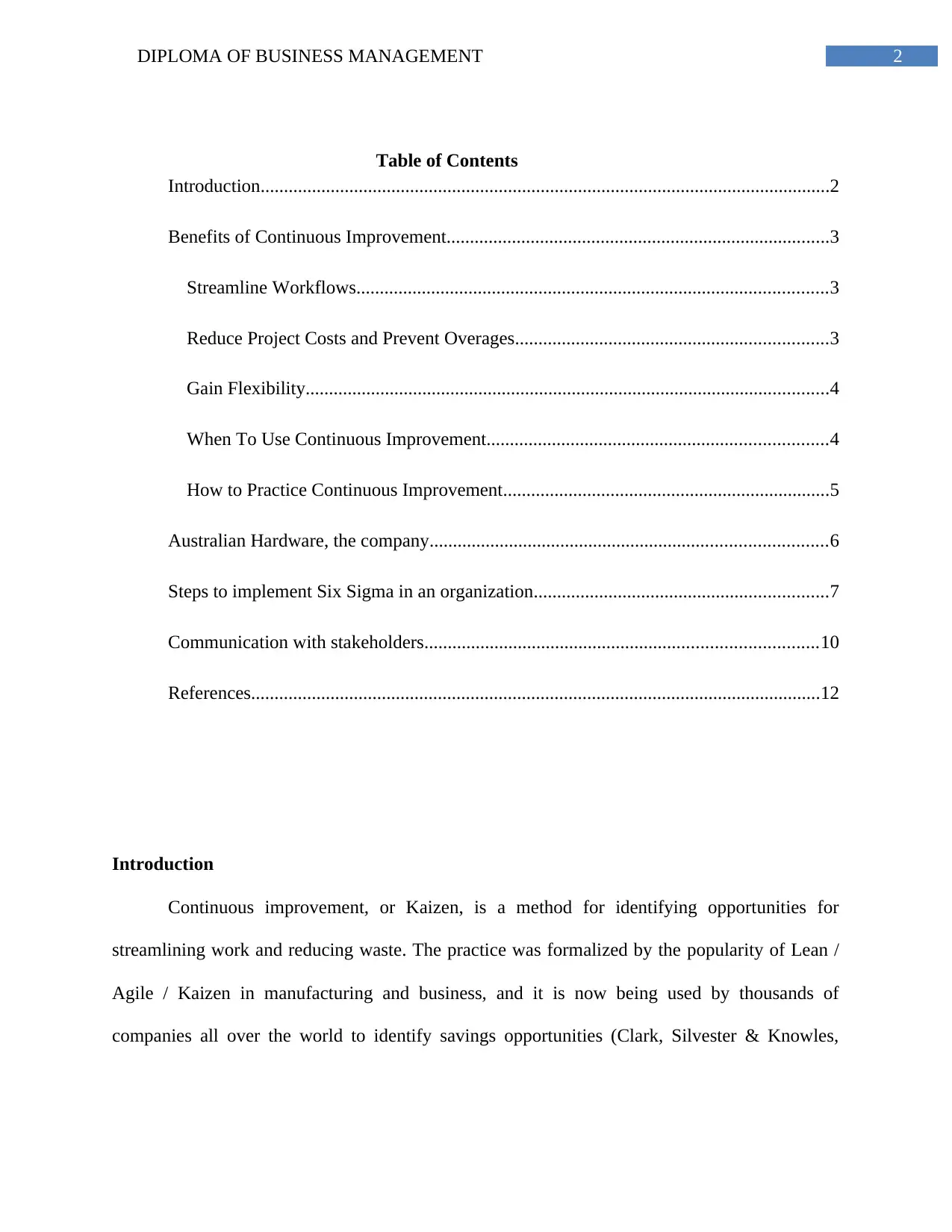
2DIPLOMA OF BUSINESS MANAGEMENT
Table of Contents
Introduction..........................................................................................................................2
Benefits of Continuous Improvement..................................................................................3
Streamline Workflows.....................................................................................................3
Reduce Project Costs and Prevent Overages...................................................................3
Gain Flexibility................................................................................................................4
When To Use Continuous Improvement.........................................................................4
How to Practice Continuous Improvement......................................................................5
Australian Hardware, the company.....................................................................................6
Steps to implement Six Sigma in an organization...............................................................7
Communication with stakeholders....................................................................................10
References..........................................................................................................................12
Introduction
Continuous improvement, or Kaizen, is a method for identifying opportunities for
streamlining work and reducing waste. The practice was formalized by the popularity of Lean /
Agile / Kaizen in manufacturing and business, and it is now being used by thousands of
companies all over the world to identify savings opportunities (Clark, Silvester & Knowles,
Table of Contents
Introduction..........................................................................................................................2
Benefits of Continuous Improvement..................................................................................3
Streamline Workflows.....................................................................................................3
Reduce Project Costs and Prevent Overages...................................................................3
Gain Flexibility................................................................................................................4
When To Use Continuous Improvement.........................................................................4
How to Practice Continuous Improvement......................................................................5
Australian Hardware, the company.....................................................................................6
Steps to implement Six Sigma in an organization...............................................................7
Communication with stakeholders....................................................................................10
References..........................................................................................................................12
Introduction
Continuous improvement, or Kaizen, is a method for identifying opportunities for
streamlining work and reducing waste. The practice was formalized by the popularity of Lean /
Agile / Kaizen in manufacturing and business, and it is now being used by thousands of
companies all over the world to identify savings opportunities (Clark, Silvester & Knowles,
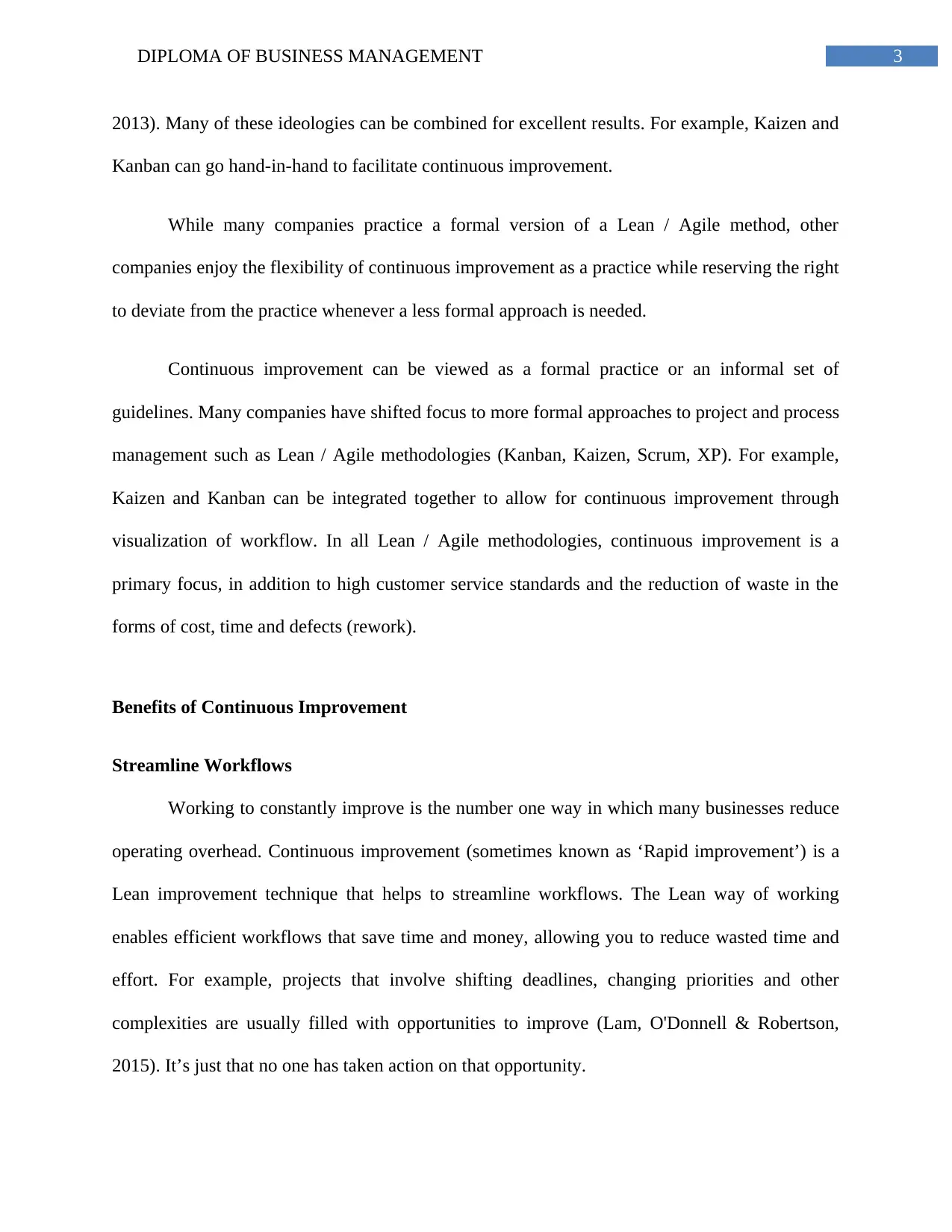
3DIPLOMA OF BUSINESS MANAGEMENT
2013). Many of these ideologies can be combined for excellent results. For example, Kaizen and
Kanban can go hand-in-hand to facilitate continuous improvement.
While many companies practice a formal version of a Lean / Agile method, other
companies enjoy the flexibility of continuous improvement as a practice while reserving the right
to deviate from the practice whenever a less formal approach is needed.
Continuous improvement can be viewed as a formal practice or an informal set of
guidelines. Many companies have shifted focus to more formal approaches to project and process
management such as Lean / Agile methodologies (Kanban, Kaizen, Scrum, XP). For example,
Kaizen and Kanban can be integrated together to allow for continuous improvement through
visualization of workflow. In all Lean / Agile methodologies, continuous improvement is a
primary focus, in addition to high customer service standards and the reduction of waste in the
forms of cost, time and defects (rework).
Benefits of Continuous Improvement
Streamline Workflows
Working to constantly improve is the number one way in which many businesses reduce
operating overhead. Continuous improvement (sometimes known as ‘Rapid improvement’) is a
Lean improvement technique that helps to streamline workflows. The Lean way of working
enables efficient workflows that save time and money, allowing you to reduce wasted time and
effort. For example, projects that involve shifting deadlines, changing priorities and other
complexities are usually filled with opportunities to improve (Lam, O'Donnell & Robertson,
2015). It’s just that no one has taken action on that opportunity.
2013). Many of these ideologies can be combined for excellent results. For example, Kaizen and
Kanban can go hand-in-hand to facilitate continuous improvement.
While many companies practice a formal version of a Lean / Agile method, other
companies enjoy the flexibility of continuous improvement as a practice while reserving the right
to deviate from the practice whenever a less formal approach is needed.
Continuous improvement can be viewed as a formal practice or an informal set of
guidelines. Many companies have shifted focus to more formal approaches to project and process
management such as Lean / Agile methodologies (Kanban, Kaizen, Scrum, XP). For example,
Kaizen and Kanban can be integrated together to allow for continuous improvement through
visualization of workflow. In all Lean / Agile methodologies, continuous improvement is a
primary focus, in addition to high customer service standards and the reduction of waste in the
forms of cost, time and defects (rework).
Benefits of Continuous Improvement
Streamline Workflows
Working to constantly improve is the number one way in which many businesses reduce
operating overhead. Continuous improvement (sometimes known as ‘Rapid improvement’) is a
Lean improvement technique that helps to streamline workflows. The Lean way of working
enables efficient workflows that save time and money, allowing you to reduce wasted time and
effort. For example, projects that involve shifting deadlines, changing priorities and other
complexities are usually filled with opportunities to improve (Lam, O'Donnell & Robertson,
2015). It’s just that no one has taken action on that opportunity.
Secure Best Marks with AI Grader
Need help grading? Try our AI Grader for instant feedback on your assignments.
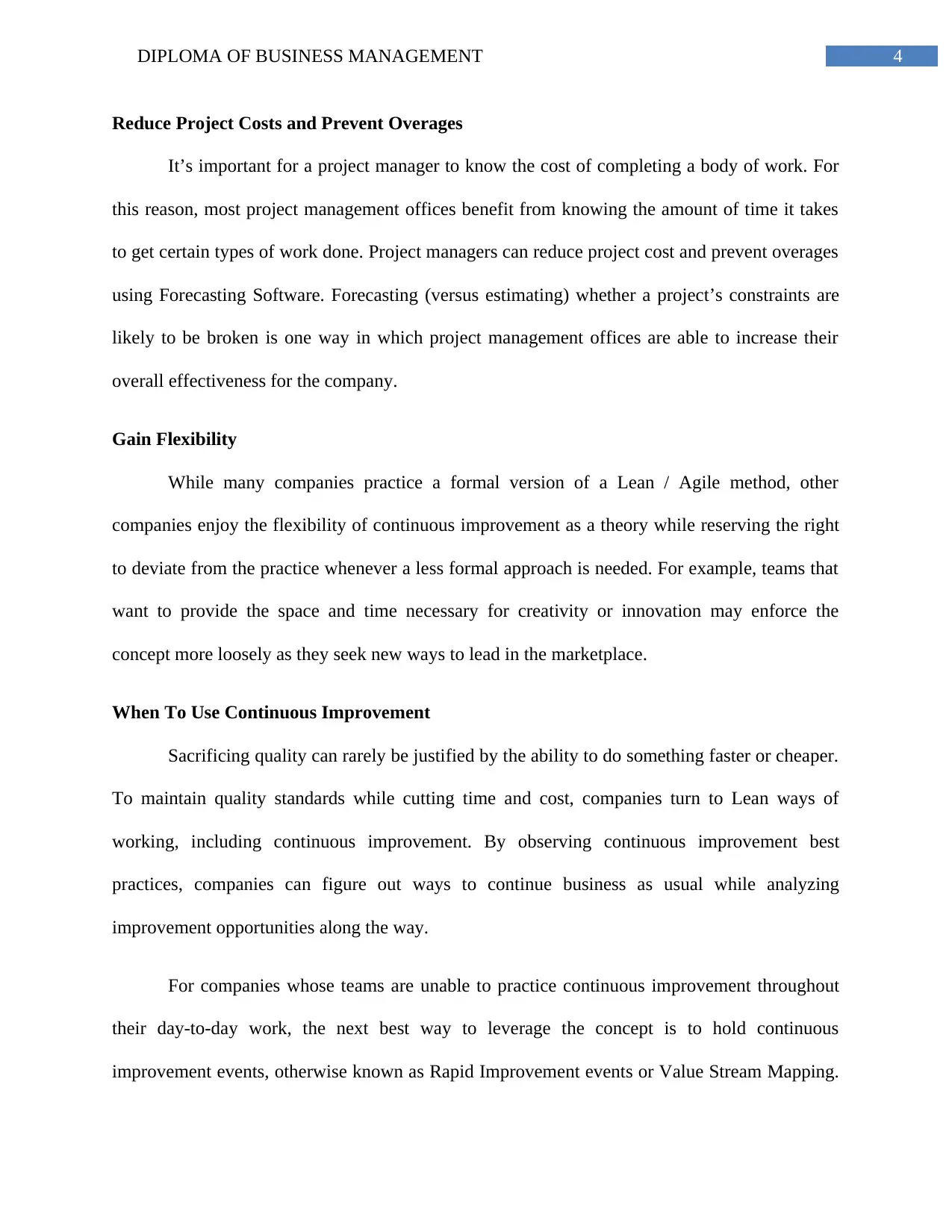
4DIPLOMA OF BUSINESS MANAGEMENT
Reduce Project Costs and Prevent Overages
It’s important for a project manager to know the cost of completing a body of work. For
this reason, most project management offices benefit from knowing the amount of time it takes
to get certain types of work done. Project managers can reduce project cost and prevent overages
using Forecasting Software. Forecasting (versus estimating) whether a project’s constraints are
likely to be broken is one way in which project management offices are able to increase their
overall effectiveness for the company.
Gain Flexibility
While many companies practice a formal version of a Lean / Agile method, other
companies enjoy the flexibility of continuous improvement as a theory while reserving the right
to deviate from the practice whenever a less formal approach is needed. For example, teams that
want to provide the space and time necessary for creativity or innovation may enforce the
concept more loosely as they seek new ways to lead in the marketplace.
When To Use Continuous Improvement
Sacrificing quality can rarely be justified by the ability to do something faster or cheaper.
To maintain quality standards while cutting time and cost, companies turn to Lean ways of
working, including continuous improvement. By observing continuous improvement best
practices, companies can figure out ways to continue business as usual while analyzing
improvement opportunities along the way.
For companies whose teams are unable to practice continuous improvement throughout
their day-to-day work, the next best way to leverage the concept is to hold continuous
improvement events, otherwise known as Rapid Improvement events or Value Stream Mapping.
Reduce Project Costs and Prevent Overages
It’s important for a project manager to know the cost of completing a body of work. For
this reason, most project management offices benefit from knowing the amount of time it takes
to get certain types of work done. Project managers can reduce project cost and prevent overages
using Forecasting Software. Forecasting (versus estimating) whether a project’s constraints are
likely to be broken is one way in which project management offices are able to increase their
overall effectiveness for the company.
Gain Flexibility
While many companies practice a formal version of a Lean / Agile method, other
companies enjoy the flexibility of continuous improvement as a theory while reserving the right
to deviate from the practice whenever a less formal approach is needed. For example, teams that
want to provide the space and time necessary for creativity or innovation may enforce the
concept more loosely as they seek new ways to lead in the marketplace.
When To Use Continuous Improvement
Sacrificing quality can rarely be justified by the ability to do something faster or cheaper.
To maintain quality standards while cutting time and cost, companies turn to Lean ways of
working, including continuous improvement. By observing continuous improvement best
practices, companies can figure out ways to continue business as usual while analyzing
improvement opportunities along the way.
For companies whose teams are unable to practice continuous improvement throughout
their day-to-day work, the next best way to leverage the concept is to hold continuous
improvement events, otherwise known as Rapid Improvement events or Value Stream Mapping.
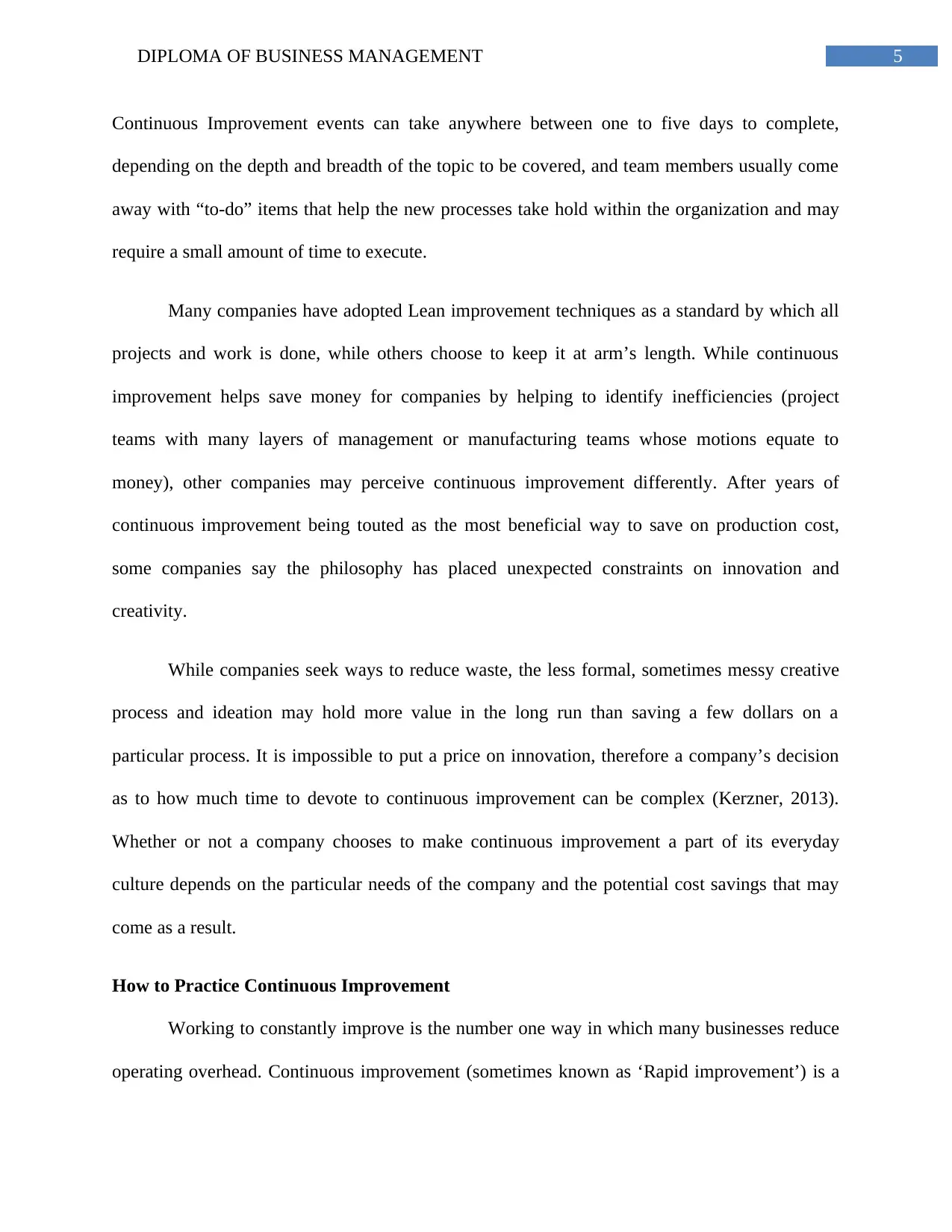
5DIPLOMA OF BUSINESS MANAGEMENT
Continuous Improvement events can take anywhere between one to five days to complete,
depending on the depth and breadth of the topic to be covered, and team members usually come
away with “to-do” items that help the new processes take hold within the organization and may
require a small amount of time to execute.
Many companies have adopted Lean improvement techniques as a standard by which all
projects and work is done, while others choose to keep it at arm’s length. While continuous
improvement helps save money for companies by helping to identify inefficiencies (project
teams with many layers of management or manufacturing teams whose motions equate to
money), other companies may perceive continuous improvement differently. After years of
continuous improvement being touted as the most beneficial way to save on production cost,
some companies say the philosophy has placed unexpected constraints on innovation and
creativity.
While companies seek ways to reduce waste, the less formal, sometimes messy creative
process and ideation may hold more value in the long run than saving a few dollars on a
particular process. It is impossible to put a price on innovation, therefore a company’s decision
as to how much time to devote to continuous improvement can be complex (Kerzner, 2013).
Whether or not a company chooses to make continuous improvement a part of its everyday
culture depends on the particular needs of the company and the potential cost savings that may
come as a result.
How to Practice Continuous Improvement
Working to constantly improve is the number one way in which many businesses reduce
operating overhead. Continuous improvement (sometimes known as ‘Rapid improvement’) is a
Continuous Improvement events can take anywhere between one to five days to complete,
depending on the depth and breadth of the topic to be covered, and team members usually come
away with “to-do” items that help the new processes take hold within the organization and may
require a small amount of time to execute.
Many companies have adopted Lean improvement techniques as a standard by which all
projects and work is done, while others choose to keep it at arm’s length. While continuous
improvement helps save money for companies by helping to identify inefficiencies (project
teams with many layers of management or manufacturing teams whose motions equate to
money), other companies may perceive continuous improvement differently. After years of
continuous improvement being touted as the most beneficial way to save on production cost,
some companies say the philosophy has placed unexpected constraints on innovation and
creativity.
While companies seek ways to reduce waste, the less formal, sometimes messy creative
process and ideation may hold more value in the long run than saving a few dollars on a
particular process. It is impossible to put a price on innovation, therefore a company’s decision
as to how much time to devote to continuous improvement can be complex (Kerzner, 2013).
Whether or not a company chooses to make continuous improvement a part of its everyday
culture depends on the particular needs of the company and the potential cost savings that may
come as a result.
How to Practice Continuous Improvement
Working to constantly improve is the number one way in which many businesses reduce
operating overhead. Continuous improvement (sometimes known as ‘Rapid improvement’) is a
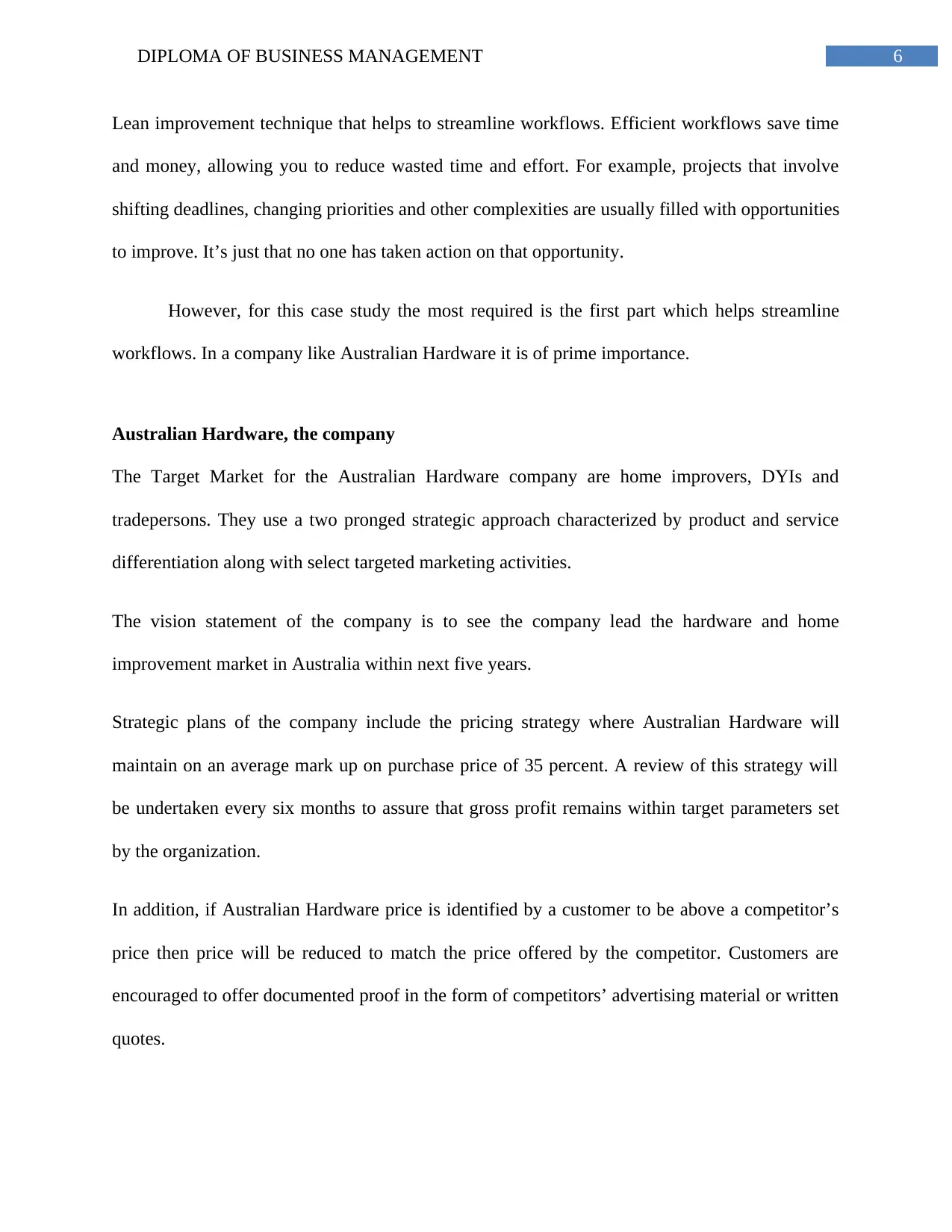
6DIPLOMA OF BUSINESS MANAGEMENT
Lean improvement technique that helps to streamline workflows. Efficient workflows save time
and money, allowing you to reduce wasted time and effort. For example, projects that involve
shifting deadlines, changing priorities and other complexities are usually filled with opportunities
to improve. It’s just that no one has taken action on that opportunity.
However, for this case study the most required is the first part which helps streamline
workflows. In a company like Australian Hardware it is of prime importance.
Australian Hardware, the company
The Target Market for the Australian Hardware company are home improvers, DYIs and
tradepersons. They use a two pronged strategic approach characterized by product and service
differentiation along with select targeted marketing activities.
The vision statement of the company is to see the company lead the hardware and home
improvement market in Australia within next five years.
Strategic plans of the company include the pricing strategy where Australian Hardware will
maintain on an average mark up on purchase price of 35 percent. A review of this strategy will
be undertaken every six months to assure that gross profit remains within target parameters set
by the organization.
In addition, if Australian Hardware price is identified by a customer to be above a competitor’s
price then price will be reduced to match the price offered by the competitor. Customers are
encouraged to offer documented proof in the form of competitors’ advertising material or written
quotes.
Lean improvement technique that helps to streamline workflows. Efficient workflows save time
and money, allowing you to reduce wasted time and effort. For example, projects that involve
shifting deadlines, changing priorities and other complexities are usually filled with opportunities
to improve. It’s just that no one has taken action on that opportunity.
However, for this case study the most required is the first part which helps streamline
workflows. In a company like Australian Hardware it is of prime importance.
Australian Hardware, the company
The Target Market for the Australian Hardware company are home improvers, DYIs and
tradepersons. They use a two pronged strategic approach characterized by product and service
differentiation along with select targeted marketing activities.
The vision statement of the company is to see the company lead the hardware and home
improvement market in Australia within next five years.
Strategic plans of the company include the pricing strategy where Australian Hardware will
maintain on an average mark up on purchase price of 35 percent. A review of this strategy will
be undertaken every six months to assure that gross profit remains within target parameters set
by the organization.
In addition, if Australian Hardware price is identified by a customer to be above a competitor’s
price then price will be reduced to match the price offered by the competitor. Customers are
encouraged to offer documented proof in the form of competitors’ advertising material or written
quotes.
Paraphrase This Document
Need a fresh take? Get an instant paraphrase of this document with our AI Paraphraser
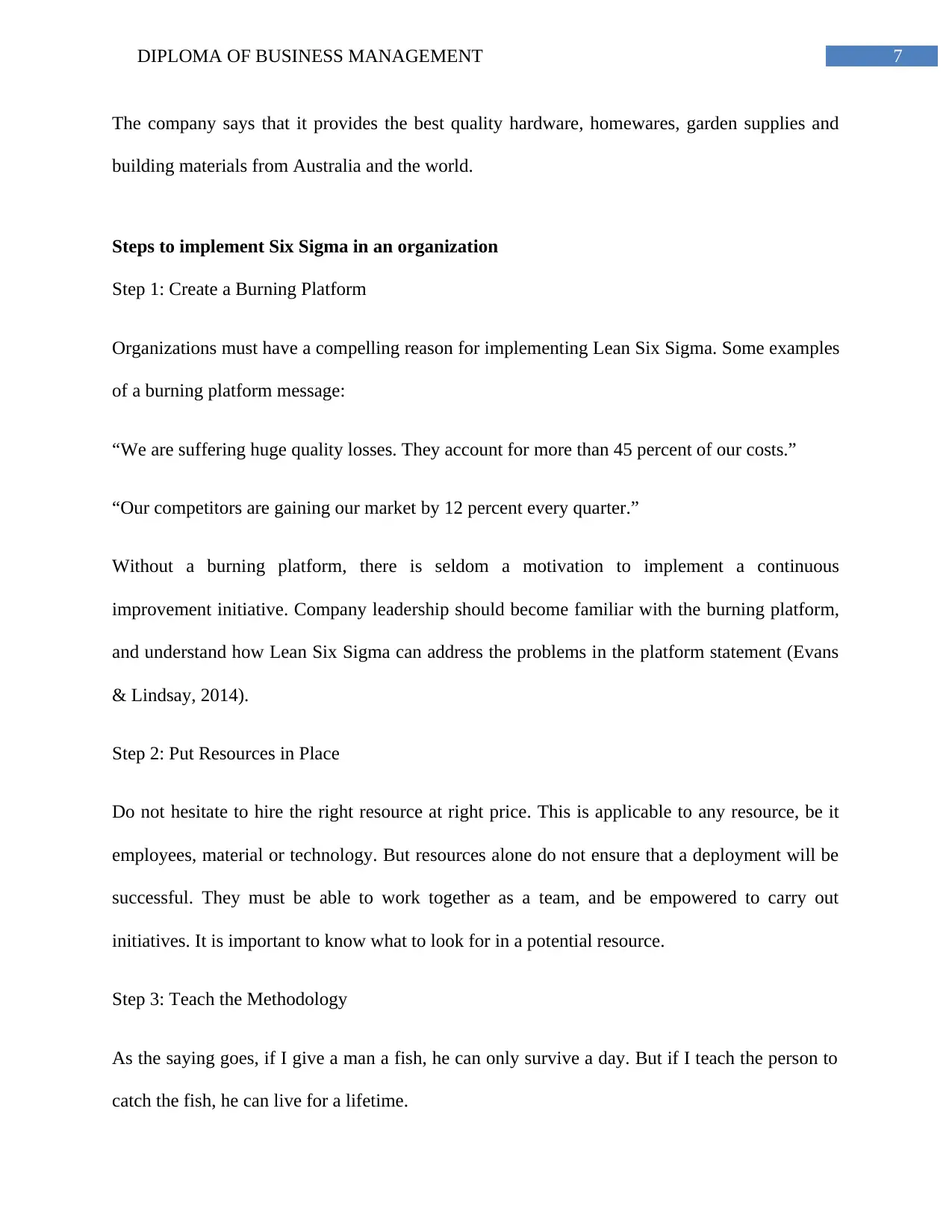
7DIPLOMA OF BUSINESS MANAGEMENT
The company says that it provides the best quality hardware, homewares, garden supplies and
building materials from Australia and the world.
Steps to implement Six Sigma in an organization
Step 1: Create a Burning Platform
Organizations must have a compelling reason for implementing Lean Six Sigma. Some examples
of a burning platform message:
“We are suffering huge quality losses. They account for more than 45 percent of our costs.”
“Our competitors are gaining our market by 12 percent every quarter.”
Without a burning platform, there is seldom a motivation to implement a continuous
improvement initiative. Company leadership should become familiar with the burning platform,
and understand how Lean Six Sigma can address the problems in the platform statement (Evans
& Lindsay, 2014).
Step 2: Put Resources in Place
Do not hesitate to hire the right resource at right price. This is applicable to any resource, be it
employees, material or technology. But resources alone do not ensure that a deployment will be
successful. They must be able to work together as a team, and be empowered to carry out
initiatives. It is important to know what to look for in a potential resource.
Step 3: Teach the Methodology
As the saying goes, if I give a man a fish, he can only survive a day. But if I teach the person to
catch the fish, he can live for a lifetime.
The company says that it provides the best quality hardware, homewares, garden supplies and
building materials from Australia and the world.
Steps to implement Six Sigma in an organization
Step 1: Create a Burning Platform
Organizations must have a compelling reason for implementing Lean Six Sigma. Some examples
of a burning platform message:
“We are suffering huge quality losses. They account for more than 45 percent of our costs.”
“Our competitors are gaining our market by 12 percent every quarter.”
Without a burning platform, there is seldom a motivation to implement a continuous
improvement initiative. Company leadership should become familiar with the burning platform,
and understand how Lean Six Sigma can address the problems in the platform statement (Evans
& Lindsay, 2014).
Step 2: Put Resources in Place
Do not hesitate to hire the right resource at right price. This is applicable to any resource, be it
employees, material or technology. But resources alone do not ensure that a deployment will be
successful. They must be able to work together as a team, and be empowered to carry out
initiatives. It is important to know what to look for in a potential resource.
Step 3: Teach the Methodology
As the saying goes, if I give a man a fish, he can only survive a day. But if I teach the person to
catch the fish, he can live for a lifetime.
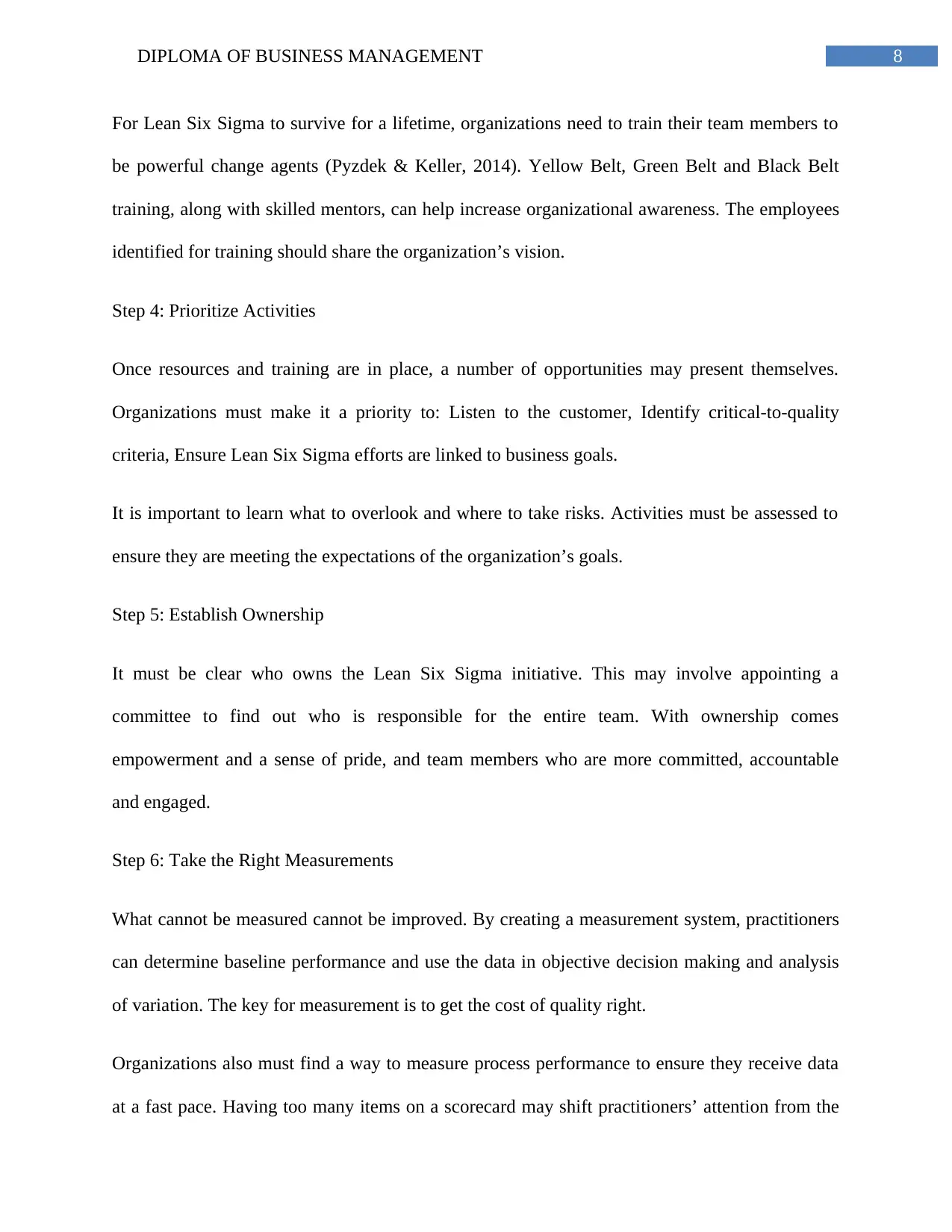
8DIPLOMA OF BUSINESS MANAGEMENT
For Lean Six Sigma to survive for a lifetime, organizations need to train their team members to
be powerful change agents (Pyzdek & Keller, 2014). Yellow Belt, Green Belt and Black Belt
training, along with skilled mentors, can help increase organizational awareness. The employees
identified for training should share the organization’s vision.
Step 4: Prioritize Activities
Once resources and training are in place, a number of opportunities may present themselves.
Organizations must make it a priority to: Listen to the customer, Identify critical-to-quality
criteria, Ensure Lean Six Sigma efforts are linked to business goals.
It is important to learn what to overlook and where to take risks. Activities must be assessed to
ensure they are meeting the expectations of the organization’s goals.
Step 5: Establish Ownership
It must be clear who owns the Lean Six Sigma initiative. This may involve appointing a
committee to find out who is responsible for the entire team. With ownership comes
empowerment and a sense of pride, and team members who are more committed, accountable
and engaged.
Step 6: Take the Right Measurements
What cannot be measured cannot be improved. By creating a measurement system, practitioners
can determine baseline performance and use the data in objective decision making and analysis
of variation. The key for measurement is to get the cost of quality right.
Organizations also must find a way to measure process performance to ensure they receive data
at a fast pace. Having too many items on a scorecard may shift practitioners’ attention from the
For Lean Six Sigma to survive for a lifetime, organizations need to train their team members to
be powerful change agents (Pyzdek & Keller, 2014). Yellow Belt, Green Belt and Black Belt
training, along with skilled mentors, can help increase organizational awareness. The employees
identified for training should share the organization’s vision.
Step 4: Prioritize Activities
Once resources and training are in place, a number of opportunities may present themselves.
Organizations must make it a priority to: Listen to the customer, Identify critical-to-quality
criteria, Ensure Lean Six Sigma efforts are linked to business goals.
It is important to learn what to overlook and where to take risks. Activities must be assessed to
ensure they are meeting the expectations of the organization’s goals.
Step 5: Establish Ownership
It must be clear who owns the Lean Six Sigma initiative. This may involve appointing a
committee to find out who is responsible for the entire team. With ownership comes
empowerment and a sense of pride, and team members who are more committed, accountable
and engaged.
Step 6: Take the Right Measurements
What cannot be measured cannot be improved. By creating a measurement system, practitioners
can determine baseline performance and use the data in objective decision making and analysis
of variation. The key for measurement is to get the cost of quality right.
Organizations also must find a way to measure process performance to ensure they receive data
at a fast pace. Having too many items on a scorecard may shift practitioners’ attention from the
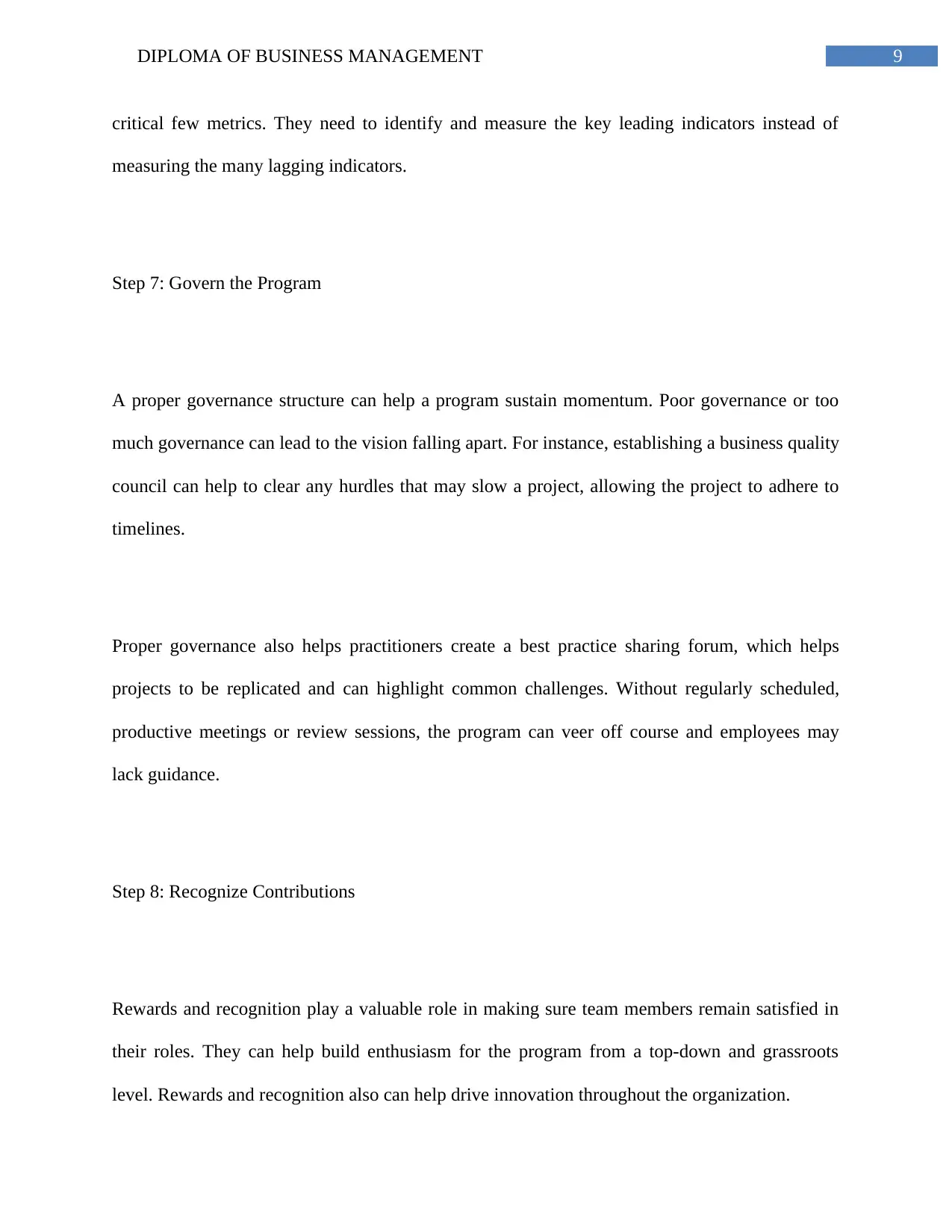
9DIPLOMA OF BUSINESS MANAGEMENT
critical few metrics. They need to identify and measure the key leading indicators instead of
measuring the many lagging indicators.
Step 7: Govern the Program
A proper governance structure can help a program sustain momentum. Poor governance or too
much governance can lead to the vision falling apart. For instance, establishing a business quality
council can help to clear any hurdles that may slow a project, allowing the project to adhere to
timelines.
Proper governance also helps practitioners create a best practice sharing forum, which helps
projects to be replicated and can highlight common challenges. Without regularly scheduled,
productive meetings or review sessions, the program can veer off course and employees may
lack guidance.
Step 8: Recognize Contributions
Rewards and recognition play a valuable role in making sure team members remain satisfied in
their roles. They can help build enthusiasm for the program from a top-down and grassroots
level. Rewards and recognition also can help drive innovation throughout the organization.
critical few metrics. They need to identify and measure the key leading indicators instead of
measuring the many lagging indicators.
Step 7: Govern the Program
A proper governance structure can help a program sustain momentum. Poor governance or too
much governance can lead to the vision falling apart. For instance, establishing a business quality
council can help to clear any hurdles that may slow a project, allowing the project to adhere to
timelines.
Proper governance also helps practitioners create a best practice sharing forum, which helps
projects to be replicated and can highlight common challenges. Without regularly scheduled,
productive meetings or review sessions, the program can veer off course and employees may
lack guidance.
Step 8: Recognize Contributions
Rewards and recognition play a valuable role in making sure team members remain satisfied in
their roles. They can help build enthusiasm for the program from a top-down and grassroots
level. Rewards and recognition also can help drive innovation throughout the organization.
Secure Best Marks with AI Grader
Need help grading? Try our AI Grader for instant feedback on your assignments.
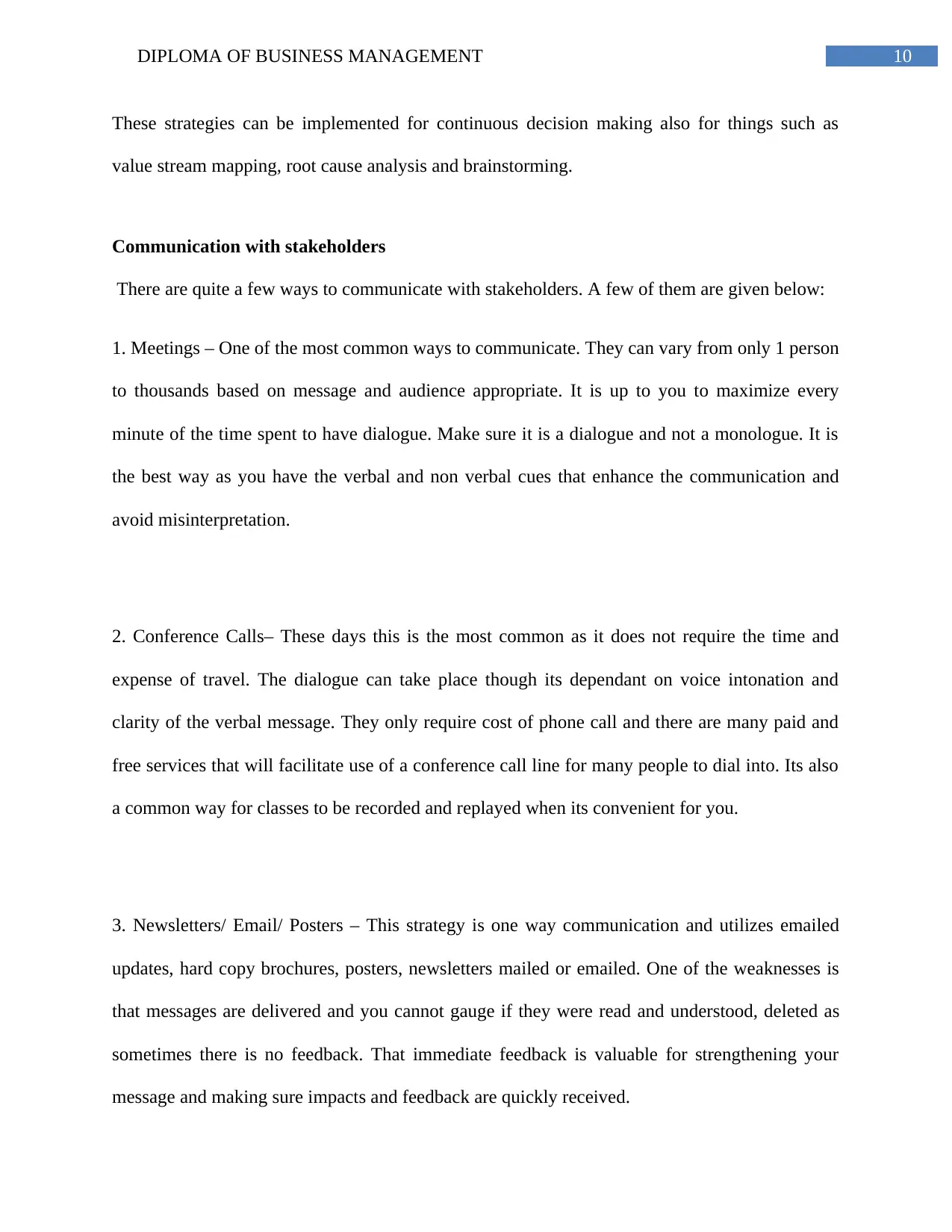
10DIPLOMA OF BUSINESS MANAGEMENT
These strategies can be implemented for continuous decision making also for things such as
value stream mapping, root cause analysis and brainstorming.
Communication with stakeholders
There are quite a few ways to communicate with stakeholders. A few of them are given below:
1. Meetings – One of the most common ways to communicate. They can vary from only 1 person
to thousands based on message and audience appropriate. It is up to you to maximize every
minute of the time spent to have dialogue. Make sure it is a dialogue and not a monologue. It is
the best way as you have the verbal and non verbal cues that enhance the communication and
avoid misinterpretation.
2. Conference Calls– These days this is the most common as it does not require the time and
expense of travel. The dialogue can take place though its dependant on voice intonation and
clarity of the verbal message. They only require cost of phone call and there are many paid and
free services that will facilitate use of a conference call line for many people to dial into. Its also
a common way for classes to be recorded and replayed when its convenient for you.
3. Newsletters/ Email/ Posters – This strategy is one way communication and utilizes emailed
updates, hard copy brochures, posters, newsletters mailed or emailed. One of the weaknesses is
that messages are delivered and you cannot gauge if they were read and understood, deleted as
sometimes there is no feedback. That immediate feedback is valuable for strengthening your
message and making sure impacts and feedback are quickly received.
These strategies can be implemented for continuous decision making also for things such as
value stream mapping, root cause analysis and brainstorming.
Communication with stakeholders
There are quite a few ways to communicate with stakeholders. A few of them are given below:
1. Meetings – One of the most common ways to communicate. They can vary from only 1 person
to thousands based on message and audience appropriate. It is up to you to maximize every
minute of the time spent to have dialogue. Make sure it is a dialogue and not a monologue. It is
the best way as you have the verbal and non verbal cues that enhance the communication and
avoid misinterpretation.
2. Conference Calls– These days this is the most common as it does not require the time and
expense of travel. The dialogue can take place though its dependant on voice intonation and
clarity of the verbal message. They only require cost of phone call and there are many paid and
free services that will facilitate use of a conference call line for many people to dial into. Its also
a common way for classes to be recorded and replayed when its convenient for you.
3. Newsletters/ Email/ Posters – This strategy is one way communication and utilizes emailed
updates, hard copy brochures, posters, newsletters mailed or emailed. One of the weaknesses is
that messages are delivered and you cannot gauge if they were read and understood, deleted as
sometimes there is no feedback. That immediate feedback is valuable for strengthening your
message and making sure impacts and feedback are quickly received.
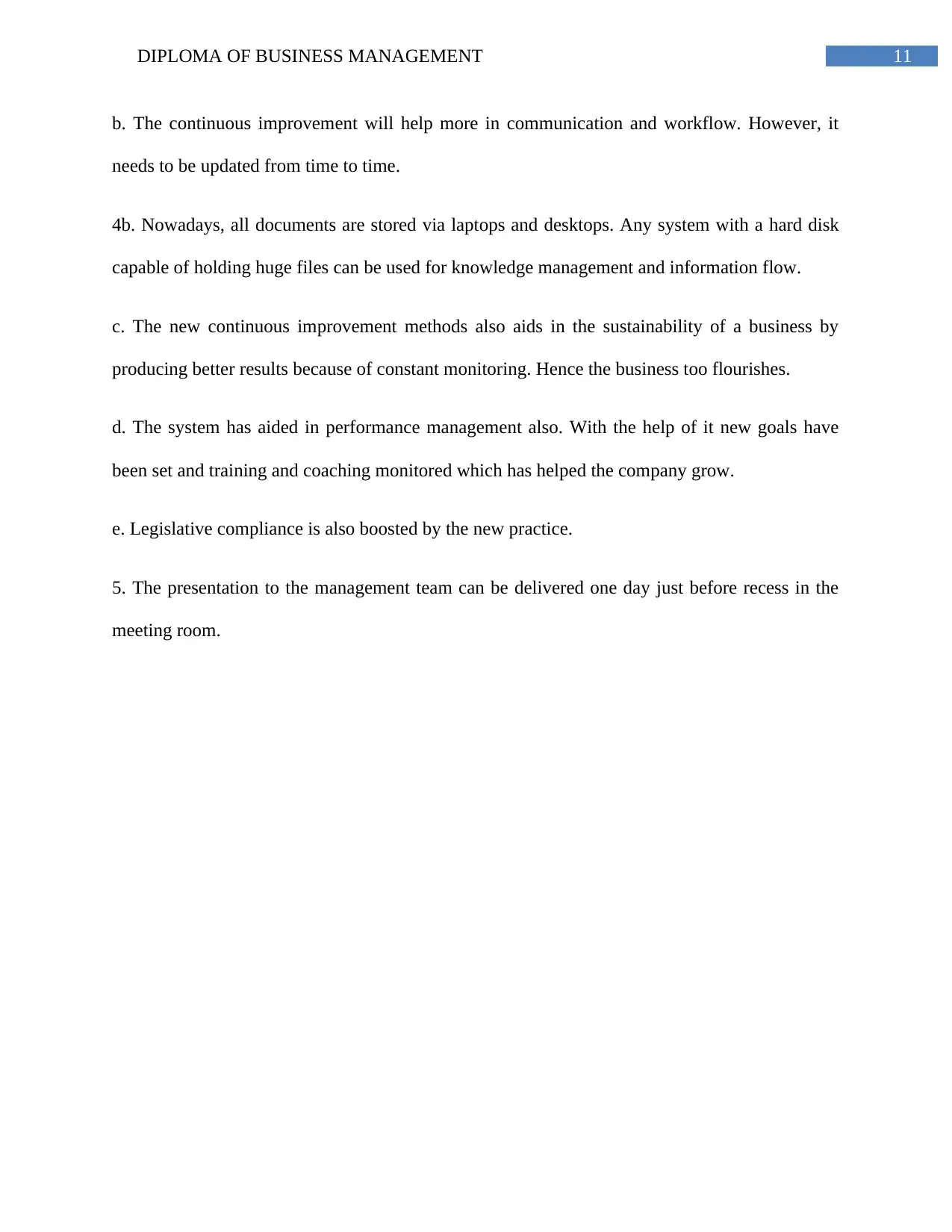
11DIPLOMA OF BUSINESS MANAGEMENT
b. The continuous improvement will help more in communication and workflow. However, it
needs to be updated from time to time.
4b. Nowadays, all documents are stored via laptops and desktops. Any system with a hard disk
capable of holding huge files can be used for knowledge management and information flow.
c. The new continuous improvement methods also aids in the sustainability of a business by
producing better results because of constant monitoring. Hence the business too flourishes.
d. The system has aided in performance management also. With the help of it new goals have
been set and training and coaching monitored which has helped the company grow.
e. Legislative compliance is also boosted by the new practice.
5. The presentation to the management team can be delivered one day just before recess in the
meeting room.
b. The continuous improvement will help more in communication and workflow. However, it
needs to be updated from time to time.
4b. Nowadays, all documents are stored via laptops and desktops. Any system with a hard disk
capable of holding huge files can be used for knowledge management and information flow.
c. The new continuous improvement methods also aids in the sustainability of a business by
producing better results because of constant monitoring. Hence the business too flourishes.
d. The system has aided in performance management also. With the help of it new goals have
been set and training and coaching monitored which has helped the company grow.
e. Legislative compliance is also boosted by the new practice.
5. The presentation to the management team can be delivered one day just before recess in the
meeting room.
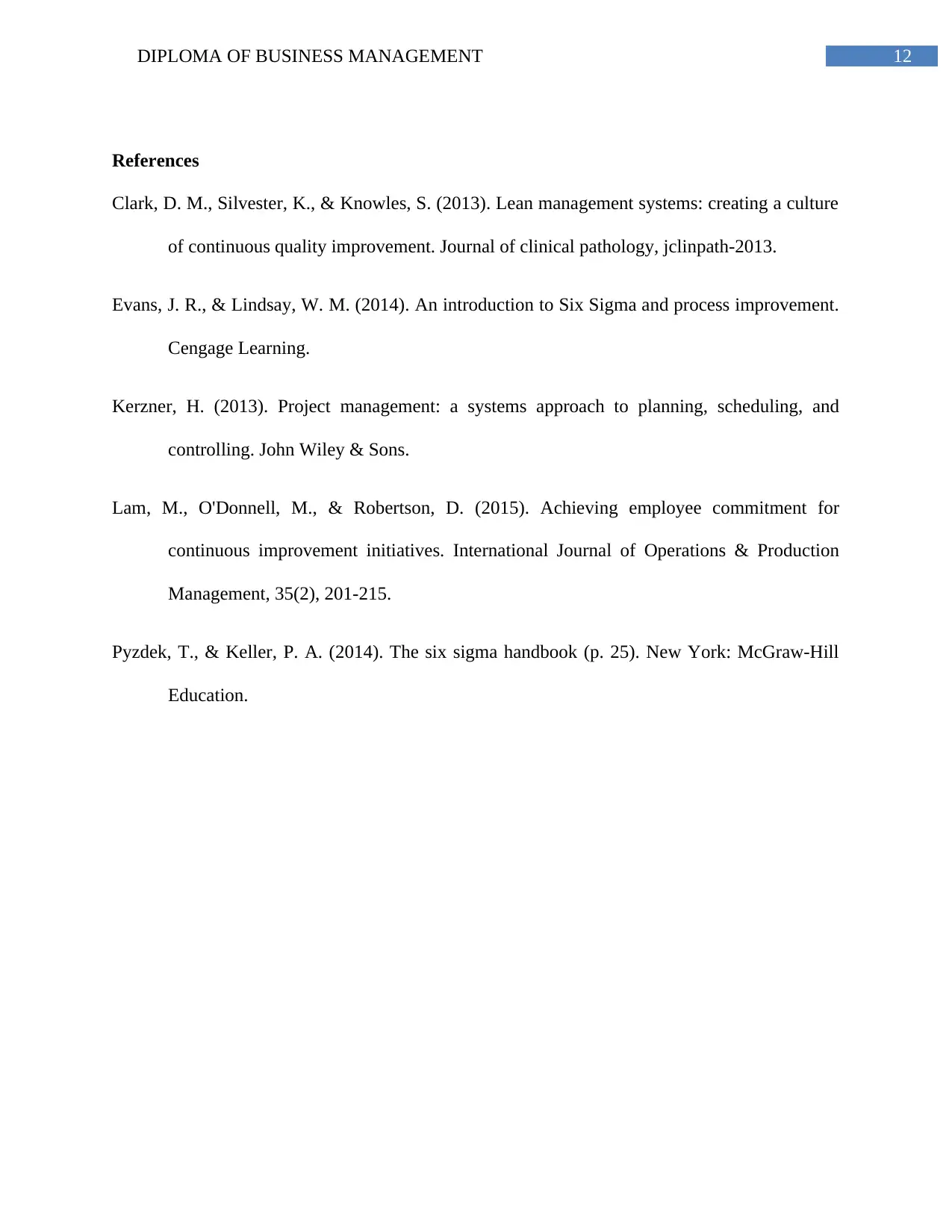
12DIPLOMA OF BUSINESS MANAGEMENT
References
Clark, D. M., Silvester, K., & Knowles, S. (2013). Lean management systems: creating a culture
of continuous quality improvement. Journal of clinical pathology, jclinpath-2013.
Evans, J. R., & Lindsay, W. M. (2014). An introduction to Six Sigma and process improvement.
Cengage Learning.
Kerzner, H. (2013). Project management: a systems approach to planning, scheduling, and
controlling. John Wiley & Sons.
Lam, M., O'Donnell, M., & Robertson, D. (2015). Achieving employee commitment for
continuous improvement initiatives. International Journal of Operations & Production
Management, 35(2), 201-215.
Pyzdek, T., & Keller, P. A. (2014). The six sigma handbook (p. 25). New York: McGraw-Hill
Education.
References
Clark, D. M., Silvester, K., & Knowles, S. (2013). Lean management systems: creating a culture
of continuous quality improvement. Journal of clinical pathology, jclinpath-2013.
Evans, J. R., & Lindsay, W. M. (2014). An introduction to Six Sigma and process improvement.
Cengage Learning.
Kerzner, H. (2013). Project management: a systems approach to planning, scheduling, and
controlling. John Wiley & Sons.
Lam, M., O'Donnell, M., & Robertson, D. (2015). Achieving employee commitment for
continuous improvement initiatives. International Journal of Operations & Production
Management, 35(2), 201-215.
Pyzdek, T., & Keller, P. A. (2014). The six sigma handbook (p. 25). New York: McGraw-Hill
Education.
1 out of 13
Related Documents
![[object Object]](/_next/image/?url=%2F_next%2Fstatic%2Fmedia%2Flogo.6d15ce61.png&w=640&q=75)
Your All-in-One AI-Powered Toolkit for Academic Success.
+13062052269
info@desklib.com
Available 24*7 on WhatsApp / Email
Unlock your academic potential
© 2024 | Zucol Services PVT LTD | All rights reserved.